Термодерево: свойства и применение — Как сделать самому?
Подготовлено компанией Research. Techart
Что такое термодерево?
Термодревесина (термически обработанная древесина, термически модифицированная древесина, термодерево, ТМД, Thermally modified timber, TMT, Thermally modified wood, TMW) – древесина, прошедшая термическую обработку при высоких температурах (от 180°С). Главная особенность термодревесины как конечного продукта заключается в сочетании высоких физико-механических свойств, схожих со свойствами химически модифицированной древесины, и экологичности натуральной древесины.
Технологию термообработки древесины на научной основе начали исследовать в 30-е годы XX века в Германии, затем в 40-е – в США. Новейшие исследования были проведены в 90-е годы в Финляндии, Франции, Нидерландах, Италии, Германии. В результате было установлено, что при воздействии на древесину температуры 180-230°С в ее биологическом составе происходят необратимые изменения, влияющие на свойства конечного продукта.
Первые пилотные производства термодеревесины были организованы в Финляндии в начале 90-х годов прошлого века. Начиная с этого момента, Финляндия считается признанным лидером исследований в этой области, а также крупнейшим мировым производителем инновационного материала. Через некоторое время активность на рынке проявили деревообработчики из Германии, Франции, Нидерландов, России. Отсутствие тесного взаимодействия привело к тому, что в этих странах технологии производства развивались относительно независимо. На сегодняшний день в Европе, по некоторым оценкам, насчитывается около 10 патентованных процессов термообработки. Проникновение материала в Северную Америку осуществлялось путем покупки патентов у европейских производителей.
Наиболее распространенной в мире является финская технология ThermoWood, и иногда под термином «thermowood» (дословный перевод, англ. – «термодревесина») ошибочно понимают весь спектр технологий термической обработки древесины. Кроме того, процесс ThermoWood отличается методической поддержкой, которую оказывает Международная ассоциация ThermoWood (International ThermoWood Association, Финляндия, www. thermowood. fi).
Физико-механические свойства термодерева
При термообработке происходит изменение клеточного строения древесины, что приводит к модификации ее свойств. Для древесных материалов наиболее важными являются следующие характеристики:
- Долговечность. Тесты в лабораторных условиях показали, что термообработка существенно (в 15-25 раз) повышает биологическую долговечность материала (устойчивость к биологическим поражениям). За счет высоких температур обработки в древесине разлагаются полисахариды, что на фоне низкой равновесной влажности устраняет условия для возникновения и размножения грибка и микроорганизмов.
- Размерная стабильность. Тангенциальная и радиальная стабильность по окончании процесса обработки улучшается в 10-15 раз. Термодревесина обладает стабильностью размеров при перепадах влажности и температуры окружающей среды.
- Гигроскопичность. Термообработка приводит к уменьшению равновесной влажности материала в среднем на 40-50% по отношению к необработанному дереву и существенно уменьшает проникновение воды (в 3-5 раз). Сброс избыточной влажности у термообработанного дерева происходит в десятки раз быстрее, чем у обычного. При сверхдлительном воздействии влаги изменение геометрических размеров термообработанного дерева в 3-4 раза ниже, чем необработанного. Поверхность термодревесины не пористая, а плотная, что снижает его способность впитывать влагу из воздуха.
- Теплопроводность. У термодревесины этот показатель ниже на 20-25% по сравнению с необработанным деревом.
Термическая модификация негативно влияет на следующие свойства:
- Плотность. Испытания показывают, что термообработка древесины уменьшает плотность на 5-10% за счет уменьшения равновесной влажности древесины и высвобождения связанной на химическом уровне воды. Стоит отметить, что основным фактором, влияющим на прочность, является порода древесины; уменьшение этого показателя во время термической обработки не может иметь решающего значения.
- Прочность на изгиб. Прочность древесины в общем случае коррелирует с ее плотностью. В результате термической модификации заметно ухудшается прочность на изгиб, при этом потеря достигает 20-40%. Этот факт приводит к ограничению сфер применения термодревесины.
Независимые исследования, проведенные в шведском университете Lulea University of Technology (www. ltu. se), показали, что влияние процесса модификации (процесс Thermowood, T=200°C) на физико-механические характеристики зависит от породы древесины. В частности, результаты испытаний свидетельствуют о большей потери прочности у твердых пород древесины по сравнению с мягкими породами.
Преимущества и недостатки
Преимущества
1.Высокие физико-механические и эксплуатационные характеристики. С практической точки это означает:
- Расширение сфер применения древесины.
- Экономия защитных средств, которые используются совместно с необработанной древесиной.
- Возможность предоставления длительной гарантии на древесные изделия без каких-либо дополнительных условий (например, таких как необходимость правильного ухода и регулярной обработки химическими составами). Некоторые европейские и российские производители уже сегодня предлагают гарантию на свои продукты в течение 25-30 лет.
2.Эстетичный внешний вид. Процесс термообработки заметно улучшает эстетическую ценность дерева, придавая материалу вид древесины, подвергнувшейся долговременному старению (более 100 лет). После модификации проявляется древесная текстура. Оттенок, приобретаемый материалом, вызван не тонировкой, а изменением в самой структуре древесины. Цвет однороден по всему сечению. Основным результатом обработки с этой точки зрения является придание недорогим сортам древесины внешнего вида ценных пород.
На рисунках ниже представлены образцы термически обработанной сосны. Температура обработки составляла слева-направо 70°С, 100°С-240°С (с интервалом в 20°С). Рисунок слева представляет вид древесины непосредственно после проведенной обработки, а справа – по истечении шести месяцев эксплуатации материала на открытом воздухе.
Лучшего результата сохранности термически обработанной древесины можно добиться, если использовать специальные защитные составы.
3.Экологичность материалов. Термодревесина является экологически чистым и нейтральным по отношению к организму человека материалом. Этот факт играет большую роль для людей, подверженных различным аллергическим реакциям. Экологичность материалов позволяет утилизировать их по окончании процесса эксплуатации. В отличие от химически обработанной древесины, которую обычно сдают на свалку, термодревесина может быть использована в качестве топлива.
- Термодревесина обладает повышенной хрупкостью, поэтому требует внимательного отношения как в процессе производства, так и в процессе эксплуатации. Снижение прочности на изгиб ограничивает применение термодревесины в качестве материала несущих конструкций в строительстве.
- В настоящее время не разработаны технологии термообработки древесины для эффективного использования материалов в случаях контакта с землей. Термодревесину в большинстве случаев нельзя заглублять в грунт.
- Как и большинство природных материалов, термообработанная древесина подвержена влиянию ультрафиолетовых лучей. В результате продолжительного нахождения под воздействием прямых солнечных лучей цвет постепенно меняется от коричневого к коричневому с сероватым оттенком. Ультрафиолетовое излучение также может привести к появлению маленьких поверхностных трещин, если древесина не была покрыта лаком или краской. Чтобы избежать этого, рекомендуется использовать обычные пигментные поверхностные средства защиты от ультрафиолетовых лучей.
- Механическая обработка термически модифицированной древесины приводит к образованию древесной пыли, вредной для дыхания человека.
- Отдельным видам термодревесины (в том числе Thermowood) присущ запах горелого дерева. Его выветривание может занять несколько месяцев.
- Значительная стоимость термодревесины, которая относится к материалам премиум-класса. Производители стараются подчеркнуть, что высокая цена термодревесины оправдана последующей экономией при эксплуатации (не требуется нанесения покрытий, переборки фасадов и т. п.). Однако при текущих ценах на российском рынке термодревесины, особенно в сравнении со стоимостью товаров-заменителей, эти аргументы можно считать малообоснованными.
- С точки зрения маркетинга, недостаток термодревесины заключается в том, что даже профессионалам часто сложно отличить термодревесину от обычной древесины дорогих пород или древесины, пропитанной специальными составами. Этот факт является препятствием к распространению материала на строительных рынках и строительных магазинах формата DIY («сделай сам»).
- Отсутствие единых стандартов качества термодревесины.
Области применения
Обширность сферы применения термодревесины обусловлена тремя основными свойствами материала: долговечностью, низкой гигроскопичностью и размерной стабильностью. Важно отметить, что в некоторых областях уникальным становится сочетание нескольких или всех перечисленных свойств.
Рассмотрим отдельные области применения термодревесины:
1.Конструкционный материал для уличного применения.
Термообработанная древесина, благодаря устойчивости к атмосферным воздействиям, подходит для уличных конструкций, ландшафтного дизайна, строительства мостов, причалов, облицовки водных каналов.
2.Внешняя отделка фасадов.
Одна из наиболее популярных сфер применения термодревесины в Европе – облицовка фасадов зданий, в том числе в составе готовых панелей в деревянном домостроении.
3.Внутренняя отделка.
Вследствие эстетичности внешнего вида данный материал часто используется дизайнерами для внутренней отделки. Из термодревесины изготавливают деревянные плитки для санузлов и кухонь, которые могут стать хорошей альтернативой холодной кафельной плитке. Материал используется также для изготовления цельных ванных и раковин, для комплексной внутренней отделки саун.
4.Производство мебели.
Стабильность геометрических размеров и устойчивость ко внешней среде способствует использованию термодревесины в производстве мебели, оконных рам, дверей, паркетных полов, декинга.
Потенциальная сфера применения термодревесины так же обширна, как и сфера применения обычной древесины: из термодревесины могут изготавливаться комплектующие, музыкальные инструменты, домашние принадлежности, малые архитектурные формы, садово-парковые конструкции и т. п.
В настоящее время одной из приоритетных областей научных исследований является использование термодревесины в качестве материала несущих конструкций. В частности, решение найдено в виде композитного клееного бруса («клееный термобрус»), объединяющего ламели из модифицированной и обычной древесины. Функции термодревесины заключаются в поддержании стабильности размеров и противодействии внешней среде, а центральные ламели из необработанного материала служат для придания необходимой прочности. Помимо клееного бруса на рынке присутствует и другой конструкционный материал – термически обработанный массивный (профилированный) брус.
Статья подготовлена аналитическим агентством Research. Techart
с использованием данных обзора рынка термодревесины
remont-doma24.ru
Как сделать термообработку гранита? | CargoWork.ru
Гранит, как облицовочный материал, известен тысячи лет. Плиткой из полированного гранита облицовывают фасады зданий. Также, гранит укладывают на пол, в качестве тротуарного покрытия.
Но полированный гранит имеет один серьезный недостаток – он становится очень скользким в зимний период, что может привести к серьезным травмам.
Для облицовки горизонтальных наружных поверхностей применяют термообработанный или обожженный гранит. Обработанный таким образом гранит, имеет сильно шероховатую поверхность и совсем не скользит. Его вполне можно применять для наружной облицовки тротуаров и ступеней. Такую обработку поверхности обычно производят на заводах, выпускающих гранитную плитку, но обжиг гранита вполне можно произвести и своими силами.
Для «огневания» гранита понадобится газовая горелка с соответствующими газовыми баллонами (кислород и пропан). Полежащая термообработке плита, закрепляется вертикально, в положении, обеспечивающим удобный подход к ее лицевой стороне. Очень важно наличие средств защиты у работника, выполняющего операцию. Обязательна защита глаз и всех поверхностей тела, поскольку, разлетающиеся при обжиге мельчайшие части гранита, могут серьезно повредить кожу.
Пламя горелки устанавливается более «длинным», чем при резке металла. Далее, работник, держа горелку на расстоянии не более 10 см от поверхности, начинает выполнять зигзагообразные движения. Под воздействием высокой температуры, вкрапления кварца, насыщающего гранит, начинают лопаться, придавая поверхности шероховатость.
Выполняя термообработку, следует избегать длительного воздействия пламени горелки на один участок гранита. Это может привести к растрескиванию материала.
_______
Теплый пол «Теплолюкс» относится к системам управления домашним комфортом. Нагревательный кабель применяется не только для обеспечения теплого пола в помещении, но и для обогрева кровель, трубопроводов, открытых стадионов, дорог. Гарантия на теплый пол наивысшего качества — 25 лет.
cargowork.ru
как сделать термошкаф для пчел, назначение, правила обработки от клеща варроа
Осень для пасечников — важный период подготовки пчел к зимовке. Наряду с утеплением ульев предстоит позаботиться и о здоровье насекомых. Термокамера и химические средства позволят защитить пчел от паразитов. После окончания сезона медосбора все пчелы должны пройти специальную обработку, чтобы избавиться от клещей Варроа. Более безопасным считается способ термической обработки. Готовый термошкаф можно приобрести в специализированных магазинах, но многие пчеловоды предпочитают изготовить его собственноручно.
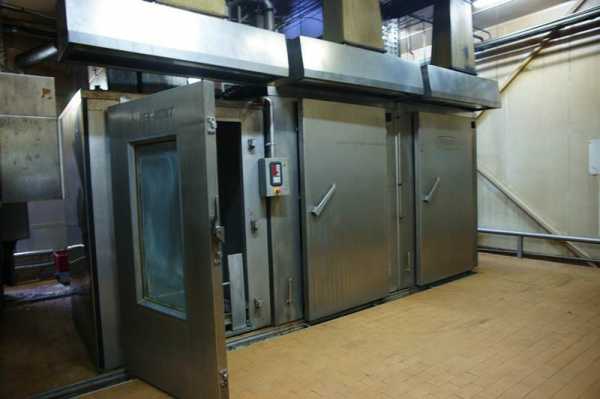
Для тех, кто немного знаком со столярными работами, соорудить термошкаф своими руками не составит труда. Но и любители успешно справятся с этой работой, если будут опираться на чертежи и советы специалистов.
Содержание материала
Подготовка к работе
Для выполнения работы потребуются следующие инструменты:
- рулетка;
- линейка;
- угольник;
- карандаш;
- ножовка;
- молоток;
- шуруповерт.
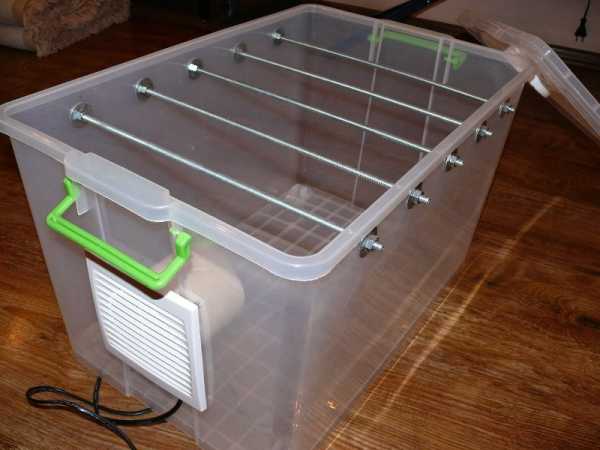
Строительные материалы и оборудование:
- пиломатериалы — бруски 3×3 см;
- фанера толщиной от 0,6 до 1 см;
- саморезы, гвозди;
- лампочки;
- электрокабель;
- стабилизатор напряжения;
- терморегулятор или ртутные термометры с делениями от 0,1 до 0,2°С;
- вентилятор;
- часы с секундной стрелкой;
- щетка с мягким ворсом;
- мелкоячеистые сетчатые кассеты;
- гладкостенная воронка для сбора пчел;
- подставка, позволяющая вращать кассету во время термообработки.
Лечение пчелосемей (видео)
Последовательность сборки
Термокамера для обработки конструируется в зависимости от размеров рамок ульев.
Также рекомендуем прочитать:
Этапы сборки:
- Нарезка бруса для каркаса в соответствии с заданными размерами.
- Сборка каркаса.
- Крой фанеры.
- Обшивка каркаса. Стенки — тонкой фанерой, дно — толстой.
- Просверливание отверстий в верхней и нижней частях камеры для наблюдения за пчелами, количеством клещей, а также температурным режимом.
- Монтирование ламп накаливания как нагревательных элементов в верхних углах ящика. Электропроводка прокладывается по наружной поверхности термоящика.
- Установка маломощного вентилятора для циркуляции воздуха.
- Установка термометов или подключение терморегуляторов. Чаще всего пасечники устанавливают в термокамерах обычные термометры, однако при этом существует риск перегрева воздуха. Использование терморегулятора позволяет поддерживать заданную температуру в камере посредством установки датчика в середине шкафа.
Сегодня существует множество видов конструкций термокамер, отличающихся объемами, количеством кассет, типами строительных материалов, способами нагрева и вентилирования. Каждый пчеловод имеет возможность выбора более подходящей модели для своих пчел.
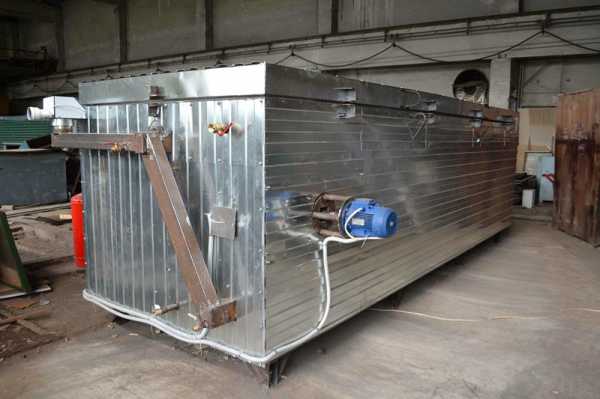
Термообработка семей пчел
Температура воздуха окружающей среды от 0 до +8°С считается оптимальной для процедуры оздоровления питомцев.
Этапы термической обработки пчел:
- Подача 10-ти клубов дыма в нижний леток с пчелами, подготовленными к обработке, на 5 минут. Пчелы набирают в зоб мед, брюхо увеличивается в размерах и клещи падают из мест между брюшными кольцами. Закрытые летки перемещают в какое-либо место с более высокой температурой воздуха, но не превышающей +12°С.
- Стряхивание особей с рамок в кассету через воронку. После 15 минут нахождения пчел и паразитов в закрытых кассетах можно начинать их обработку в камерах.
- Размещение кассет в камеру, прогретую до температуры +46…+48°С. Осторожно поворачивая и встряхивая кассету, выдержать ее нужное время. Для удобства сбора выпавших паразитов под кассетой расстилают бумагу, которую сжигают вместе с клещами после окончания работ.
- Определение температуры внутри камеры осуществляется на основании показаний 2-х термометров.
- Равномерное распределение семей на кассетах во избежание образования клубков.
- Выдержка обработанных пчел в помещении с нормальной температурой в течение 15 минут при красном свете.
- Возвращение пчел в ульи. Ответственный момент, травмоопасный. Как только особи успокоятся, улей выносят на свежий воздух. Для проветривания приоткрывают нижний леток на 5-7 см примерно на час.
Для пчел эта процедура совершенно безопасна, однако при повышении температуры до +50°С есть риск потери семейства.
Равномерный нагрев можно обеспечить вращающейся конструкцией. Это важно, так как даже несколько оставшихся зараженных пчел могут привести к повторному заражению всей семьи. Кроме того, широко применяется принудительная подача воздуха, что ускоряет процесс обработки и увеличивает его эффективность.
Термообработка пчел (видео)
Требования к безопасности
За день до обработки следует изолировать матку от семьи, так как ее присутствие в кассетах побуждает семью создавать вокруг нее клубки, в результате чего примерно 10% особей остаются зараженными. Кроме того, нужно соблюдать следующие условия:
- В случае весенней обработки или затяжных похолоданий в осенний период пчелам с переполненным задним отделом кишечника необходимо облететься.
- Термообработка противопоказана трутням.
- Термошкаф должен находиться в чистом состоянии, без обломков древесины, а также без посторонних запахов.
- Необходимо поддерживать одинаковую температуру с точностью до ±0,5°С, чтобы все семьи получили равную степень обработки.
- Время гибели паразитов — 12 минут при +47°С, 18 минут — при +46°С и 26 минут — при 45°С.
Клещи Варроа гибнут, так как у них затрудняется дыхание, происходит обезвоживание, и, как следствие, ослабевают присоски на лапках. Обездвиженные клещи падают на специальную подстилку.
Термообработка не только позволяет освободиться от паразитов, но и увеличивает сопротивляемость семей к инфекционным заболеваниям. Обрабатывать пчел таким образом можно не только перед началом зимы, но и весной.
Внимание, только СЕГОДНЯ!
fermok.ru
Строительный Комплекс Азиатско — Тихоокеанского региона. Термообработанная древесина
Термообработанная древесина. Что такое термообработка древесины и зачем она нужна — Как сделать самому?
С 16.01.2001 по 21.01.2001 в Мюнхене прошла международная строительная выставка BAU 2001, на которой была представлена новая разработка финскойдеревообрабатывающей промышленности — термообработанная древесина.
Московская компания ЗАО уже начала поставлять на строительный рынок этот новый продукт.
В Финляндии еще в 1920-х годах начали изучать процессы, протекающие в дереве под действием высоких температур. Однако, только в 1990-х годах результаты исследований финских ученых нашли промышленное применение.
Что такое термообработка?
Для получения высококачественных пиломатериалов дерево необходимо высушить.
До середины 1990-х годов самой передовой технологией являлась высокотемпературная сушка при температуре 100 — 150 градусов Цельсия.
В 1997 году на одном из деревообрабатывающих заводов Финляндии в г. Миккели внедрили новую технологию, которая получила название . При данном технологическом процессе сушку ведут при температуре 150 — 230 градусов. Чем вышетемпература, тем больше потеря веса за счет испарения летучих соединений (инымисловами, дерево становится легче). Чем больше потеря веса, тем меньше в древесинеостается воды. В зависимости от условий термообработки и породы дерева остаточнаявлажность древесины на 40 — 60% меньше, чем у высушенной обычным способом.
Процесс термообработки обычно длится около 24 часов. Влажность древесины после термообработки уменьшается на 80 — 90%. Как следствие, существенно уменьшается ее теплоемкость: термообработанное дерево нагревается значительно слабеенеобработанного, приближаясь по этому показателю к абашу. Поверхностьтермообработанной древесины не пористая, а плотная, что значительно снижаетспособность дерева впитывать влагу из воздуха (на 30% — 90% в зависимости оттемпературы и времени сушки).
На практике это означает, что дерево способно отталкивать воду без дополнительной обработки специальными пропитками. При термической обработке разлагаютсядревесные сахара, являющиеся питательной средой для микроорганизмов, способствующих гниению дерева. Оно становится исключительно стойким к гниению, приближаясь по этому показателю к лиственнице, а, следовательно, и гигиеничнымматериалом.
Особо следует отметить, что хвойные породы дерева практически полностью теряют смолу, сохраняя замечательный аромат, усиливающийся при повышении влажности итемпературы воздуха.
При термообработке древесина меняет цвет, приобретая красивый коричневый оттенок. Следует отметить, что изменение цвета — сквозное, что хорошо видно на срезе. Царапины на такой поверхности практически незаметны. Изменяя температурутермообработки можно добиваться желаемого оттенка древесины и/или степениустойчивости к условиям окружающей среды.
Где используется термообработанная древесина?
Благодаря красивому внешнему виду и уникальным свойствам термообработанной древесины ее можно использовать во многих областях, в том числе для внутреннейотделки саун, для наружной обшивки строений, устройства полов, как паркетных, так идощатых, изготовления садовой мебели, лодок, музыкальных инструментов и т. п.
С точки зрения планетарной экологии в качестве материала для полоков в сауне и бане термообработанная древесина (в том числе, хвойных пород) является достойнойальтернативой традиционному абашу-самбо, которое растет только в экваториальных вечнозеленых, так называемых, лесах — основном источнике кислорода в атмосфере Земли, которые невозможно восстановить.»
Что происходит с деревом при термообработке?
- Смола высыхает или полностью испарается.
- Цвет становиться темным.
- Теплопроводность 0-30%
- Поверхностная прочность возрастает.
- Способность впитывать влагу уменьшается.
- Бактериостойкость увеличивается.
- Чувствительность к воздействию неблагопрятных условия окружающей среды уменьшается
- Склонность к деформации на 30-90% ниже по сравнени с необработанной.
- Балансовая влажность на 10-50% меньше по сравнению с необработанной.
- Меняется клеточная структура дерева, становясь такой, как если бы дерево сушили несколько сотен лет.
Предоставлено компанией ЗАО КЕСТРОЙ
remont-doma24.ru
Термообработанная древесина | RUUD
С 16.01.2001 по 21.01.2001 в Мюнхене прошла международная строительная выставка BAU 2001, на которой была представлена новая разработка финскойдеревообрабатывающей промышленности — термообработанная древесина.
Московская компания ЗАО уже начала поставлять на строительный рынок этот новый продукт.
В Финляндии еще в 1920-х годах начали изучать процессы, протекающие в дереве под действием высоких температур. Однако, только в 1990-х годах результаты исследований финских ученых нашли промышленное применение.
Что такое термообработка?
Для получения высококачественных пиломатериалов дерево необходимо высушить.
До середины 1990-х годов самой передовой технологией являлась высокотемпературная сушка при температуре 100 — 150 градусов Цельсия.
В 1997 году на одном из деревообрабатывающих заводов Финляндии в г. Миккели внедрили новую технологию, которая получила название . При данном технологическом процессе сушку ведут при температуре 150 — 230 градусов. Чем вышетемпература, тем больше потеря веса за счет испарения летучих соединений (инымисловами, дерево становится легче). Чем больше потеря веса, тем меньше в древесинеостается воды. В зависимости от условий термообработки и породы дерева остаточнаявлажность древесины на 40 — 60% меньше, чем у высушенной обычным способом.
Процесс термообработки обычно длится около 24 часов. Влажность древесины после термообработки уменьшается на 80 — 90%. Как следствие, существенно уменьшается ее теплоемкость: термообработанное дерево нагревается значительно слабеенеобработанного, приближаясь по этому показателю к абашу. Поверхностьтермообработанной древесины не пористая, а плотная, что значительно снижаетспособность дерева впитывать влагу из воздуха (на 30% — 90% в зависимости оттемпературы и времени сушки).
На практике это означает, что дерево способно отталкивать воду без дополнительной обработки специальными пропитками. При термической обработке разлагаютсядревесные сахара, являющиеся питательной средой для микроорганизмов,способствующих гниению дерева. Оно становится исключительно стойким к гниению,приближаясь по этому показателю к лиственнице, а, следовательно, и гигиеничнымматериалом.
Особо следует отметить, что хвойные породы дерева практически полностью теряют смолу, сохраняя замечательный аромат, усиливающийся при повышении влажности итемпературы воздуха.
При термообработке древесина меняет цвет, приобретая красивый коричневый оттенок. Следует отметить, что изменение цвета — сквозное, что хорошо видно на срезе.Царапины на такой поверхности практически незаметны. Изменяя температурутермообработки можно добиваться желаемого оттенка древесины и/или степениустойчивости к условиям окружающей среды.
Где используется термообработанная древесина?
Благодаря красивому внешнему виду и уникальным свойствам термообработанной древесины ее можно использовать во многих областях, в том числе для внутреннейотделки саун, для наружной обшивки строений, устройства полов, как паркетных, так идощатых, изготовления садовой мебели, лодок, музыкальных инструментов
rinnipool.ru
Термообработка. — DRIVE2
В первую очередь спасибо kvas777 за совет написать о закалке.
Я много раз сталкивался с тем, что люди в наш век компьютерных технологий до сих пор считают закалку чем то таинственным, непонятным и не совсем (если вообще) понимают, как этот процесс происходит. Чтобы всем стало понятно, я напишу понятными словами, что да как.
Закалкой называют структурные изменения в стали происходящие за счет резкого охлаждения, как известно эти изменения делают сталь тверже. В большинстве случаев сталь закаливают на мартенсит – она получается твердой, есть еще тростит, и др. состояния но они нам не нужны. Нельзя сталь перекалить или не докалить, сталь или приняла закалку – стала твердой, или не приняла – осталась мягкой (не будем рассматривать закалку на тростит, когда сталь должна оставаться пластичной). Чем ниже температура закалки, при которой принимает закалку данная сталь и чем меньше время охлаждения тем тверже получиться сталь после закалки. Многие забывают, что не только твердость главное в изделии, но и зернистость металла, если сильно нагреть, возьмем для примера нож, то при закалке мы получим, крупное зерно и он хоть и будет твердым, резать не будет – режущая кромка выкрошиться. Со всего выше написанного делаем вывод — мы должны так закалить нож, чтобы он получился в своей структуре мелкозернистым (почти не видно зерно) и твердым.
С закалкой думаю, разобрались. Но если взять и уронить нож после закалки на пол, то скорее всего он разломается на несколько частей – он твердый но не пластичный, а хрупкий как стекло.
Отпуск стали. Выделил специально, потому, что если его не сделать любое изделие, которое подверглось закалке можно выкинуть, так как случится описанное выше. Отпуск – это процесс нагрева стали до определенной температуры с целью снижения хрупкости после закалки. Отпуск бывает полный или частичный, может быть еще самоотпуск, когда сталь закаливают в масле (его подогревают до 200 градусов перед закалкой) то опустив изделие в него не вытаскивают пока масло не перестанет дымить, получиться закалка и отпуск при температуре 200 градусов. Полный отпуск само по себе понятно, когда полностью изделие отпускается, а частичный когда только часть изделия (можно делать после закалки в масле или чтобы получить разную твердость на режущей кромке и обуху).
Запомните главное: всегда после закалки нужен отпуск и когда у вас ломается или крошиться нож его не перекалили, а сделали неправильно термообработку – это и закалка и отпуск.
Не люблю когда мне самому указывают как делать, но попрошу порекомендовать эту запись, а то обидно, что люди не имеют малейшего представления о таком процессе как термообработка. В дальнейшем распишу как я делаю термообработку.
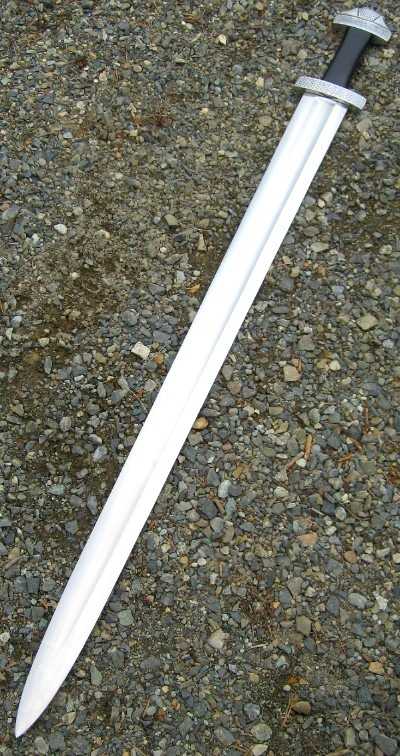
Когда то сделаю))) (точить не буду, чтобы не получилось ХО)
www.drive2.ru
В изделиях «хэнд мейд» (сделай сам по-нашему) часто используется обработка металлов и металлических изделий. Одним из способов обработки металлов является термическая обработка, которая применима как к металлам, так и к их сплавам. Примеры изделий, в которых может применяться термообработка, можно посмотреть, например здесь — http://sharovar.com/khend-mejjd-16/.Термическая обработка металлов и сплавов (термообработка), используемая в любительской практике, подразделяется на отжиг, закалку и отпуск.
Закалка дает стальной детали большую твердость и износоустойчивость. Деталь нагревают до определенной температуры, выдерживают некоторое время, необходимое дли прогрева всего объема материала, а затем быстро охлаждают. Обычно детали конструкционных сталей нагревают до 880—900, из инструментальных — до 750—760, из нержавеющей стали — до 1050—1100°С.
Ниже приведены рекомендуемые температуры отпуска для некоторых инструментов и деталей (в градусах Цельсия):
Дюралюминиевые детали при закалке нагревают до 360—400 °С, выдерживают некоторое время при этой температуре, а затем погружают в воду комнатной температуры и оставляют до полного охлаждения. После этого дюралюминий становится мягким и пластичным, легко гнется и куется. Повышенную же твердость он приобретает спустя 3—4 дня: твердость и хрупкость его увеличиваются настолько, что он не выдерживает изгиба даже на небольшой угол. При отжиге деталь разогревают до 360 °С, выдерживают некоторое время, после чего охлаждают на воздухе. Для отпуска деталь слегка нагревают и натирают хозяйственным мылом. Затем продолжают нагревать до тех пор, пока слой мыла не почернеет, после чего дают остыть на воздухе. (Почернение происходит при температуре отпуска.) |
hobbyhandmade.com
Термическая обработка углеродистых сталей
Термическая обработка – это технологический процесс, состоящий из нагрева и охлаждения материала изделия с целью изменения его структуры и свойств.
На стадии изготовления деталей необходимо, чтобы металл был пластичным, нетвердым, имел хорошую обрабатываемость резанием.
В готовых изделиях всегда желательно иметь материал максимально прочным, вязким, с необходимой твердостью.
Такие изменения в свойствах материала позволяет сделать термообработка. Любой процесс термообработки может быть описан графиком в координатах температура-время и включает нагрев, выдержку и охлаждение. При термообработке протекают фазовые превращения, которые определяют вид термической обработки. Температура нагрева стали зависит от положения ее критических точек и выбирается по диаграмме состояния Fe – Fe3С в зависимости от вида термической обработки (рис.9.1.).
Рис.9.1. Интервалы рекомендуемых температур нагрева при различных видах
Критические точки (температуры фазовых превращений) определяют: линия PSK – точку А1, GS – точку А3 и SE – точку Аm. Нижняя критическая точка А1 соответствует превращению А ® П при 727ОС. Верхняя критическая точка соответствует началу выделения феррита из аустенита (при охлаждении) или концу растворения феррита в аустените (при нагреве). Температура линии SE, соответствующая началу выделения вторичного цементита из аустенита, обозначается Аm.
Время нагрева до заданной температуры зависит, главным образом, от химического состава стали и толщины наиболее массивного сечения детали (в среднем 60 с на каждый миллиметр сечения).
Выдержка при температуре термообработки необходима для завершения фазовых превращений, происходящих в металле, выравнивания температуры по всему объему детали. Продолжительность выдержки зависит от химического состава стали и для нелегированных сплавов определяется из расчета 60 с. на один миллиметр сечения.
Скорость охлаждения зависит, главным образом, от химического состава стали, а также от твердости, которую необходимо получить.
Самыми распространенными видами термообработки сталей являются закалка и отпуск. Производятся с целью упрочнения изделий. Температура нагрева под закалку выбирается по диаграмме железо-углерод.
Закалка сталей
ЗАКАЛКОЙ называется фиксация при комнатной температуре высокотемпературного состояния сплава. Основная цель закалки – получение высокой твердости, прочности и износостойкости. Для достижения этой цели стали нагревают до температур на 30 – 50ОС выше линии GSK (рис. 9.1), выдерживают определенное время при этой температуре и затем быстро охлаждают. Для доэвтектоидных сталей температура нагрева под закалку определяется Ас3+(30-50)оС, для эвтектоидных и заэвтектоидных Ас1+(30-50)оС.
Процессы, происходящие в сплаве на различных стадиях закалки, можно рассмотреть на примере эвтектоидной стали У8. В исходном отожженном состоянии эта сталь имеет структуру перлита (эвтектоидная смесь феррита и цементита). При достижении температуры А1 (727 0С) произойдет полиморфное превращение, т.е. перестройка кристаллической решетки феррита (ОЦК) в решетку аустенита (ГЦК), вследствие чего растворимость углерода резко возрастает. В процессе выдержки весь цементит растворится в аустените и концентрация углерода в нем достигнет содержания углерода в стали, т.е. 0,8 %
Следующий этап – охлаждение стали из аустенитной области до комнатной температуры – является определяющим при закалке. При охлаждении стали ниже температуры А1 происходит обратное полиморфное превращение, т.е. решетка аустенита (ГЦК) перестраивается в решетку феррита (ОЦК) и при этом растворимость углерода уменьшается в 40 раз (с 0,8 до 0,02). Если охлаждение происходит медленно, то “лишний” углерод успевает выйти из решетки феррита и образовать цементит. В результате формируется структура феррито-цементитной смеси. Если же охлаждение производится быстро, то после полиморфного превращения углерод остается вследствие подавления диффузионных процессов в решетке ОЦК. Образуется пересыщенный твердый раствор углерода в a — железе, который называется МАРТЕНСИТОМТОМ. Перенасыщенность мартенсита углеродом создает в его решетке большие внутренние напряжения, которые приводят к искажению ее формы и превращению из кубической в тетрагональную. Уровень внутренних напряжений оценивается степенью тетрагональности.
Чем выше степень тетрагональности решетки мартенсита, тем выше его твердость. Степень тетрагональности, в свою очередь, будет зависеть от содержания углерода в стали.
Рис. 9.2. Кристаллическая решетка феррита (с/а=1) (а) и
кристаллическая решетка мартенсита (с/а1) (б)
Получить структуру мартенсита (или закалить сталь) можно только в том случае, если обеспечить скорость охлаждения больше или равную критической (Vкр) (рис 9.3),чтобы не успели пройти процессы распада аустенита в верхнем районе температур.
КРИТИЧЕСКАЯ СКОРОСТЬ закалки или минимальная скорость охлаждения (Vкр) – это скорость, при которой аустенит переходит в мартенсит. Если же скорости охлаждения будут меньше Vкр , при распаде аустенита получим феррито-цементитные смеси различной дисперсности ТРООСТИТ, СОРБИТ И ПЕРЛИТ.
Перлит (грубодисперсионная смесь феррита и цементита) может быть получен при очень медленных скоростях охлаждения (на рис. 10- это скорость V1). Такие скорости охлаждения характерны для отжига (охлаждение вместе с печью).
При охлаждении углеродистых сталей на воздухе (вид термообработки – нормализация) со скоростями V2 и V3 получаем структуры сорбита и троостита. Сорбит – механическая смесь феррита и цементита средней дисперсности. Троостит – мелкодисперсная феррито-цементитная смесь. Свойства сорбита и троостита занимают промежуточное положение между свойствами перлита (П) и мартенсита (М).
Практической целью закалки является получение максимальной прочности и твердости стали. Достигается эта цель при следующих режимах: нагрев стали на 30 – 50ОС выше линии GSK, выдержка при этой температуре и охлаждение со скоростью ³ Vкр.
Рис 9.3. Диаграмма изотермического распада аустенита эвтектоидной стали со схемами микроструктур и их примерной твердостью: I – кривая начала диффузионного распада аустенита; II – кривая конца диффузионного распада аустенита; Мн – линия начала мартенситного превращения; Vкр – критическая скорость охлаждения.
Отпуск сталей
К важнейшим механическим свойствам сталей наряду с твердостью относится и пластичность, которая после закалки очень мала. Структура резко-
неравновесная, возникают большие закалочные напряжения. Чтобы снять закалочные напряжения и получить оптимальное сочетание свойств для различных групп деталей, обычно после закалки проводят отпуск стали. Отпуском стали является термообработка, состоящая из нагрева закаленной стали до температуры ниже линии PSK (критическая точка А1), выдержки при этой температуре и дальнейшего произвольного охлаждения. Этот процесс связан с изменением строения и свойств закаленной стали. При отпуске происходит распад мартенсита (выделение углерода), переход к более устойчивому состоянию. При этом повышается пластичность, вязкость, снижается твердость и уменьшаются остаточные напряжения в стали. Механизм протекающих превращений при отпуске сталей – диффузионный, он определяется температурой и продолжительностью нагрева.
Первое превращение, протекающее в интервале 80 – 200ОС (низкий отпуск), соответствует выделению из мартенсита тонких пластин x – карбида Fe2С. Выделение углерода из решетки приводит к уменьшению степени ее тетрагональности. Полученный при этом мартенсит, имеющий степень тетрагональности, близкую к 1, называется отпущенным.
При нагреве закаленной стали до температур 300-450ОС (средний отпуск) происходит полное выделение углерода из раствора и снятие внутренних напряжений. Сталь состоит из мелкодисперсной смеси феррита и цементита (троостит отпуска).
При нагреве до температур 480- 600 о С (высокий отпуск) идет процесс коагуляции (укрупнения) карбидных частиц и максимальное снятие остаточных напряжений. Формируется структура сорбита отпуска.
В зависимости от температуры нагрева различают низкий, средний и высокий отпуск. Низкий отпуск проводят в интервале температур 80 – 250ОС для инструментов-изделий, которым необходимы высокая твердость и износостойкость. Получаемая структура МОТП или МОТП + ЦII (мартенсит отпуска + цементит вторичный).
Средний отпуск (350 – 500ОС) применяется для рессор, пружин, штампов и другого ударного инструмента, т.е. для тех изделий, где требуется достаточная твердость и высокая упругость. Получаемая структура – ТОТП (троостит отпуска).
Высокий отпуск (500 – 650ОС) полностью устраняет внутренние напряжения. Достигается наилучший комплекс механических свойств: повышенная прочность, вязкость и пластичность. Применяется для изделий из конструкционных сталей, подверженных воздействию высоких напряжений. Структура – СОТП (сорбит отпуска).
Термообработку, заключающуюся в закалке на мартенсит и последующем высоком отпуске, называют улучшением.
studfiles.net