Физики определили самое тугоплавкое вещество
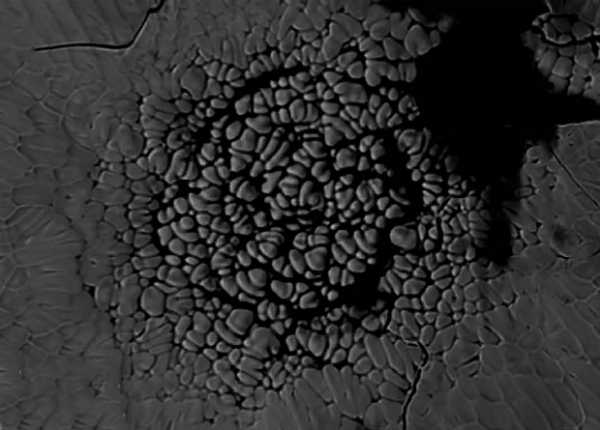
Дендритная структура, возникшая в месте плавления карбида тантала-гафния
Omar Cedillos-Barraza et al. / Scientific Reports, 2016
Физики из Имперского колледжа Лондона, Института трансурановых элементов (Карлсруэ) и Университета Лондона уточнили температуры плавления карбидов гафния и тантала. С помощью лазерных методов плавки ученые показали, что наибольшей температурой плавления обладает чистый карбид гафния — HfC
Исследования температуры плавления карбидов гафния и тантала датируются еще первой половиной XX века. Для этого использовался метод Пирани-Алтертума: с помощью электрического тока нагревалась пластинка материала с отверстием в центре. За пластинкой следили с помощью пирометра. В момент плавления отверстие оказывалось заполнено материалом и изменяло свое свечение. Разброс температур плавления, определенных этим методом для карбида гафния составил почти двести градусов, и по результатам измерений трудно было однозначно определить, какой из карбидов гафния и тантала является самым тугоплавким.
Образцы карбидов после плавления лазером. Слева-направо: кабрид тантала, карбид тантала-гафния, карбид гафния
Omar Cedillos-Barraza et al. / Scientific Reports, 2016
Авторы новой работы, отметив несовершенство ранних пирометров и методик, предложили использовать новый подход для определения температуры плавления. В ней образец керамики плавился под действием мощного 4,5-киловаттного лазера, после чего исследователи следили за его свечением. Момент плавления определялся по изменению отражения от поверхности. После этого лазер отключался, а температура плавления определялась по плато на графике остывания образца: в момент затвердевания отводимая от образца теплота не меняет его температуры.
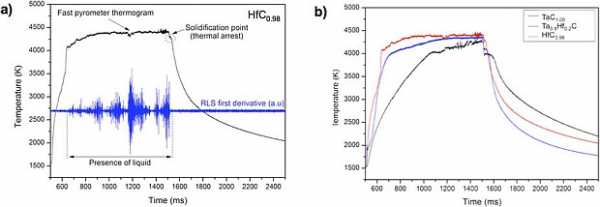
Слева: кривая температурной зависимости карбида гафния (черная) и производная сигнала отраженного света. Справа: температурные кривые для карбида тантала, гафния и тантала-гафния.
Omar Cedillos-Barraza et al. / Scientific Reports, 2016
В результате оказалось, что наименьшей температурой плавления обладает карбид тантала — она соответствует 3768 ± 77 градусам Цельсия. Интересно, что в некоторых ранних работах карбид тантала наоборот считался более тугоплавким, чем карбид гафния. Высокими температурами плавления обладал состав Ta0.8Hf0.2C, ранее считавшийся рекордсменом — порядка 3905 ± 82 градусов Цельсия. Остальные смешанные карбиды плавились при более низких температурах. Абсолютным рекордсменом, по данным новой работы, стал карбид гафния HfC 0,98, материал плавится при 3959 ±84 градусах Цельсия. Для сравнения, самым тугоплавким металлом является вольфрам, плавящийся при 3422 градусах Цельсия.
Считается, что карбидные керамики могут найти применение при строительстве гиперзвуковых самолетов. При движении в атмосфере на скорости свыше пяти чисел Маха теплозащита должна выдерживать температуры в 2200 кельвин и выше.
Ранее химики из Университета Брауна (Провиденс) теоретически предсказали существование фазы смешанного карбида-нитрида гафния с рекордно высокой температурой плавления — свыше 4400 кельвин. Ее состав отвечает формуле HfN0.38C0.51.
Владимир Королёв
Наиболее тугоплавкий металл. Характеристика металлов
Металлы — это самый распространенный материал (наряду с пластмассами и стеклом), который применяется людьми с древних времен. Уже тогда человеку была известна характеристика металлов, он с выгодой использовал все их свойства для создания прекрасных произведений искусства, посуды, предметов быта, сооружений.
Одной из главных черт при рассмотрении этих веществ является их твердость и тугоплавкость. Именно эти качества позволяют определять область использования того или иного металла. Поэтому рассмотрим все физические свойства и особое внимание уделим вопросам плавкости.
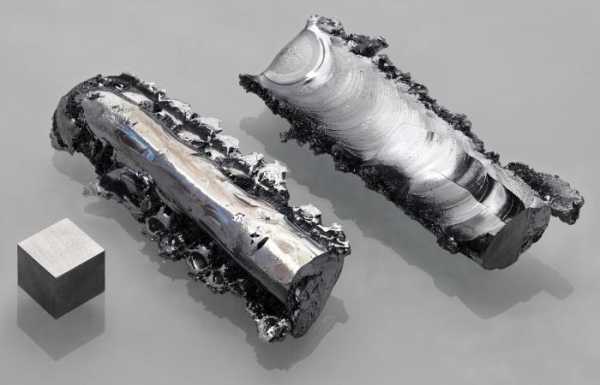
Физические свойства металлов
Характеристика металлов по физическим свойствам может быть выражена в виде четырех основных пунктов.
- Металлический блеск — все имеют примерно одинаковый серебристо-белый красивый характерный блеск, кроме меди и золота. Они имеют красноватый и желтый отлив соответственно. Кальций — серебристо-голубой.
- Агрегатное состояние — все твердые при обычных условиях, кроме ртути, которая находится в виде жидкости.
- Электро- и теплопроводность — характерна для всех металлов, однако выражена в разной степени.
- Ковкость и пластичность — также общий для всех металлов параметр, который способен варьироваться в зависимости от конкретного представителя.
- Температура плавления и кипения — определяет, какой металл тугоплавкий, а какой легкоплавкий. Этот параметр разный для всех элементов.
Все физические свойства объясняются особым строением металлической кристаллической решетки. Ее пространственным расположением, формой и прочностью.
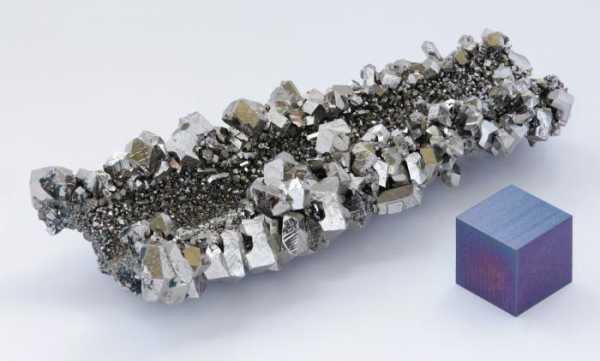
Легкоплавкие и тугоплавкие металлы
Данный параметр является очень важным, когда речь заходит об областях применения рассматриваемых веществ. Тугоплавкие металлы и сплавы — это основа машино- и кораблестроения, выплавки и литья многих важный изделий, получения качественного рабочего инструмента. Поэтому знание температур плавления и кипения играет основополагающую роль.
Характеризуя металлы по прочности, можно разделить их на твердые и хрупкие. Если же говорить о тугоплавкости, то здесь выделяют две основные группы:
- Легкоплавкие — это такие, которые способны менять агрегатное состояние при температурах ниже 1000 оС. Примерами могут служить: олово, свинец, ртуть, натрий, цезий, марганец, цинк, алюминий и другие.
- Тугоплавкими считаются те, чья температура плавления выше обозначенной величины. Их не так много, а на практике применяется еще меньше.
Таблица металлов, имеющих температуру плавления свыше 1000 оС, представлена ниже. Именно в ней и располагаются самые тугоплавкие представители.
Название металла | Температура плавления, оС | Температура кипения, оС |
Золото, Au | 1064.18 | 2856 |
Бериллий, Ве | 1287 | 2471 |
Кобальт, Со | 1495 | 2927 |
Хром, Cr | 1907 | 2671 |
Медь, Cu | 1084,62 | 2562 |
Железо, Fe | 1538 | 2861 |
Гафний, Hf | 2233 | 4603 |
Иридий, Ir | 2446 | 4428 |
Марганец, Mn | 1246 | 2061 |
Молибден, Мо | 2623 | 4639 |
Ниобий, Nb | 2477 | 4744 |
Никель, Ni | 1455 | 2913 |
Палладий, Pd | 1554,9 | 2963 |
Платина, Pt | 1768.4 | 3825 |
Рений, Re | 3186 | 5596 |
Родий, Rh | 1964 | 3695 |
Рутений, Ru | 2334 | 4150 |
Тантал, Та | 3017 | 5458 |
Технеций, Тс | 2157 | 4265 |
Торий, Th | 1750 | 4788 |
Титан, Ti | 1668 | 3287 |
Ванадий, V | 1910 | 3407 |
Вольфрам, W | 3422 | 5555 |
Цирконий, Zr | 1855 | 4409 |
Данная таблица металлов включает в себя всех представителей, чья температура плавления выше 1000 оС. Однако на практике многие из них не применяются по различным причинам. Например, из-за экономической выгоды или вследствие радиоактивности, слишком высокой степени хрупкости, подверженности коррозионному воздействию.
Также из данных таблицы очевидно, что самый тугоплавкий металл в мире — это вольфрам. Наименьший показатель у золота. При работе с металлами важное значение имеет мягкость. Поэтому многие из обозначенных выше также не используются в технических целях.
Наиболее тугоплавкий металл — вольфрам
В периодической системе располагается под порядковым номером 74. Название получил по фамилии известного физика Стивена Вольфрама. При обычных условиях представляет собой твердый тугоплавкий металл серебристо-белого цвета. Обладает ярко выраженным металлическим блеском. Химически практически инертен, в реакции вступает неохотно.
В природе содержится в виде минералов:
- вольфрамит;
- шеелит;
- гюбнерит;
- ферберит.
Учеными было доказано, что вольфрам — наиболее тугоплавкий металл из всех существующих. Однако существуют предположения о том, что сиборгий теоретически способен побить рекорд этого металла. Но он является радиоактивным элементом с очень коротким периодом существования. Поэтому доказать это пока невозможно.
При определенной температуре (свыше 1500 оС) вольфрам становится ковким и пластичным. Поэтому возможно изготовление тонкой проволоки на его основе. Это свойство используется для изготовления нитей накаливания в обычных бытовых электрических лампочках.
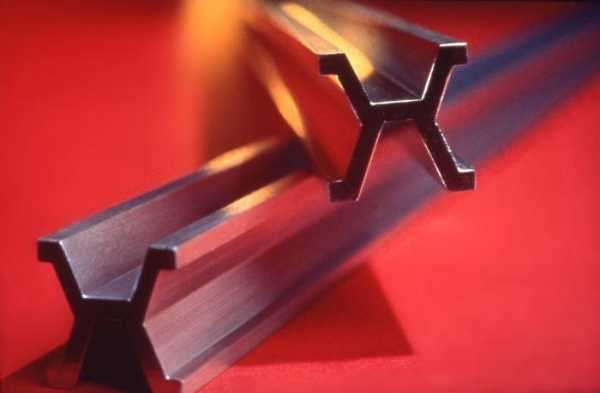
Как наиболее тугоплавкий металл, выдерживающий температуры больше 3400 оС, вольфрам применяется в следующих областях техники:
- как электрод при аргонной сварке;
- для получения кислотоустойчивых, износостойких и жаростойких сплавов;
- в качестве нагревательного элемента;
- в вакуумных трубках как нить накаливания и прочее.
Помимо металлического вольфрама, широко применяются в технике, науке и электронике его соединения. Как самый тугоплавкий металл в мире он и соединения формирует с очень высококачественными характеристиками: прочные, устойчивые практически ко всем видам химического воздействия, не подвергающиеся коррозии, выдерживающие низкие и высокие температуры (победит, сульфид вольфрама, его монокристаллы и другие вещества).
Ниобий и его сплавы
Nb, или ниобий, — при обычных условиях серебристо-белый блестящий металл. Он также является тугоплавким, поскольку температура перехода в жидкое состояние для него составляет 2477 оС. Именно это качество, а также сочетание низкой химической активности и сверхпроводимости позволяет ниобию становиться все более популярным в практической деятельности человека с каждым годом. Сегодня этот металл используется в таких отраслях, как:
- ракетостроение;
- авиационная и космическая промышленность;
- атомная энергетика;
- химическое аппаратостроение;
- радиотехника.
Этот металл сохраняет свои физические свойства даже при очень низких температурах. Изделия на его основе отличаются коррозионной устойчивостью, жаростойкостью, прочностью, отличной проводимостью.
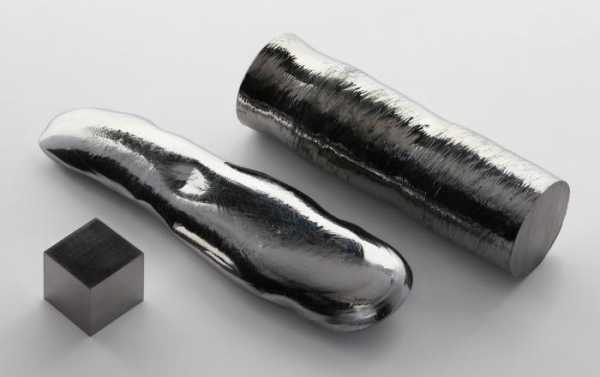
Этот металл добавляют к алюминиевым материалам для повышения химической стойкости. Из него изготовляют катоды и аноды, им легируют цветные сплавы. Даже монеты в некоторых странах делают с содержанием ниобия.
Тантал
Металл, в свободном виде и при обычных условиях покрытый оксидной пленкой. Обладает набором физических свойств, которые позволяют ему быть широко распространенным и очень важным для человека. Его основные характеристики следующие:
- При температуре свыше 1000 оС становится сверхпроводником.
- Это наиболее тугоплавкий металл после вольфрама и рения. Температура плавления составляет 3017 оС.
- Прекрасно поглощает газы.
- С ним легко работать, так как он прокатывается в пласты, фольгу и проволоку без особого труда.
- Обладает хорошей твердостью и не хрупкий, сохраняет пластичность.
- Очень устойчив к воздействию химических агентов (не растворяется даже в царской водке).
Благодаря таким характеристикам сумел завоевать популярность как основа для многих жаропрочных и кислотоустойчивых, антикоррозионных сплавов. Его многочисленные соединения находят применение в ядерной физике, электронике, приборах вычислительного плана. Используются как сверхпроводники. Раньше тантал использовался как элемент в лампах накаливания. Сейчас его место занял вольфрам.
Хром и его сплавы
Один из самых твердых металлов, в естественном виде голубовато-белой окраски. Его температура плавления ниже, чем у рассмотренных до сих пор элементов, и составляет 1907 оС. Однако он все равно используется в технике и промышленности повсеместно, так как хорошо поддается механическим воздействиям, обрабатывается и формуется.
Особенно ценен хром в качестве напылителя. Его наносят на изделия для придания им красивого блеска, защиты от коррозии и повышения износостойкости. Процесс называется хромированием.
Сплавы хрома очень популярны. Ведь даже небольшое количество этого металла в сплаве значительно увеличивает твердость и устойчивость последнего к воздействиям.
Цирконий
Один из самых дорогих металлов, поэтому применение его в технических целях затруднено. Однако физические характеристики делают его просто незаменимым во многих других отраслях.
При обычных условиях это красивый серебристо-белый металл. Обладает достаточно высокой температурой плавления — 1855 оС. Имеет хорошую твердость, устойчивость к коррозии, так как химически не активен. Также отличается великолепной биологической совместимостью с кожей человека и всего организма в целом. Это делает его ценным металлом для использования в медицине (инструменты, протезы и так далее).
Основные области применения циркония и его соединений, в том числе сплавов, следующие:
- ядерная энергетика;
- пиротехника;
- легирование металлов;
- медицина;
- изготовление биопосуды;
- конструкционный материал;
- как сверхпроводник.
Из циркония и сплавов на его основе изготавливаются даже украшения, способные влиять на улучшение состояния здоровья человека.
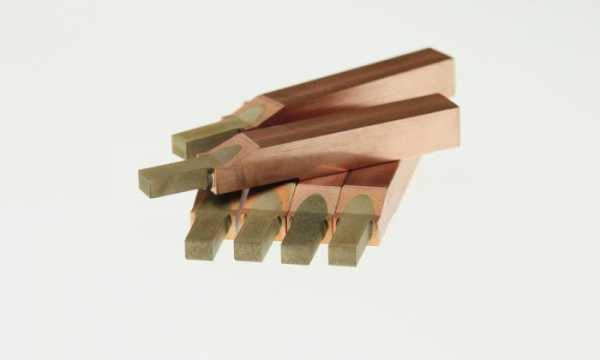
Молибден
Если выяснять, какой металл самый тугоплавкий, то, помимо обозначенного вольфрама, можно назвать и молибден. Его температура плавления составляет 2623 оС. При этом он достаточно твердый, пластичный и поддающийся обработке.
Используется он в основном не в чистом виде, а как составной компонент сплавов. Они, благодаря присутствию молибдена, значительно укрепляются в износостойкости, жаропрочности и антикоррозийности.
Некоторые соединения молибдена используют как технические смазки. Также этот металл является легирующим материалом, одновременно влияющим и на прочность, и на антикоррозийность, что встречается очень редко.
Ванадий
Серый металл с серебристым блеском. Обладает достаточно высоким показателем плавкости (1920 оС). Используется в основном как катализатор во многих процессах, благодаря своей инертности. Применяется в энергетике как химический источник тока, в производствах неорганических кислот. Основное значение имеет не чистый металл, а именно некоторые его соединения.
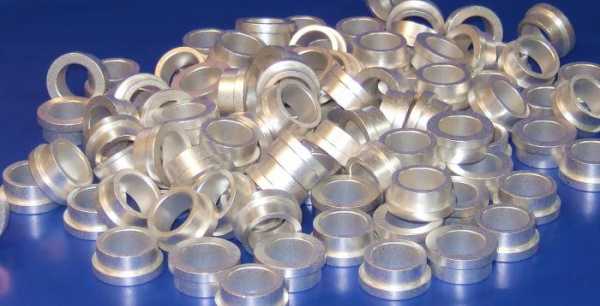
Рений и сплавы на его основе
Какой металл самый тугоплавкий после вольфрама? Это рений. Его показатель плавкости составляет 3186 оС. По прочности превосходит и вольфрам, и молибден. Пластичность его не слишком высока. Спрос на рений очень велик, а вот добыча составляет сложности. Вследствие этого он является самым дорогим металлом из существующих на сегодняшний день.
Применяется для изготовления:
- реактивных двигателей;
- термопар;
- нитей накаливания для спектрометров и прочих устройств;
- как катализатор при нефтепереработке.
Все области применения дорогостоящие, поэтому он используется только в случае крайней необходимости, когда заменить чем-либо другим возможности нет.
Титановые сплавы
Титан — это очень легкий металл серебристо-белого цвета, который находит широкое применение в металлургической промышленности и металлообработке. Может взорваться при нахождении в мелкодисперсном состоянии, поэтому является пожароопасным.
Применяется в авиа- и ракетостроении, при производстве кораблей. Широко используется в медицине благодаря биологической совместимости с организмом (протезы, пирсинги, имплантаты и прочее).
fb.ru
Россияне расплавили самый тугоплавкий материал в мире :: Hi-tech :: Дни.ру
Российские ученые всего за несколько минут расплавили самый тугоплавкий материал в мире. Ранее даже для менее качественной обработки карбида гафния требовались большие затраты энергии, времени и денег.
Соединение гафния и углерода – материал с самой высокой температурой плавления, передает пресс-служба Института ядерной физики им. Г.И. Будкера. На сайте организации подчеркивается, что при классической технологии производства на получение карбида уходит несколько часов. При этом предложенная учеными методика позволяет расплавить вещество всего за несколько минут.
Представители института отметили, что температура плавления этого материала – 3953 градуса, а максимально возможная температура разогрева печи – 2500 градусов. Из этого следует, что полностью расплавить этот материал невозможно. «Поэтому при традиционной технологии, сначала получают карбид гафния нагревом смеси порошков гафния и углерода, затем его размалывают как можно мельче, прессуют и спекают, как керамику, десятки часов, при максимально возможной температуре», – пояснила пресс-служба учреждения. Отметим, что производство в таком случае получается дорогим и энергозатратным, а конечный материал – пористым.
Представленная новосибирскими учеными методика предполагает обработку карбида гафния в три этапа – после прокрутки в специальной шаровой мельнице полученную смесь просвечивают жестким рентгеновским излучением на ускорителе ВЭПП-3, после чего полученное вещество нагревается на установке для электронно-лучевой сварки. По задумке ученых, жидкий материал при этом будет находится «в кольце» порошка до тех пор, пока форма не будет отлита полностью. Затем материал проходит контрольное просвечивание синхротронным излучением.
Старший научный сотрудник института Алексей Анчаров рассказал, что в будущем разработка может применять и в отношении других, более дешевых материалов с подобными свойствами. «В первую очередь, карбидов и боридов тугоплавких металлов – тантала, вольфрама, молибдена», – пояснили в пресс-службе.
Отметим, что карбид гафния используется при изготовлении оборудования для ядерных реакторов. По мнению ученых, этот материал также «с успехом может применяться в сфере ракетостроения, в качестве внешнего покрытия для теплозащитных оболочек возвращаемых космических аппаратов типа «Буран».
dni.ru
Тугоплавкие сплавы Википедия
Схема турбореактивного двигателя. Детали последних ступеней компрессора высокого давления и детали турбины изготавливаются из жаропрочных сплавов на никелевой основе.Жаропрочные сплавы — металлические материалы, обладающие высоким сопротивлением пластической деформации и разрушению при действии высоких температур и окислительных сред. Начало систематических исследований жаропрочных сплавов приходится на конец 1930-х годов — период нового этапа в развитии авиации, связанного с появлением реактивной авиации и газотурбинных двигателей (ГТД).
Жаропрочные сплавы могут быть на алюминиевой, титановой, железной, медной, кобальтовой и никелевой основах. Наиболее широкое применение в авиационных двигателях получили никелевые жаропрочные сплавы, из которых изготавливают рабочие и сопловые лопатки, диски ротора турбины, детали камеры сгорания и т. п. В зависимости от технологии изготовления никелевые жаропрочные сплавы могут быть литейными, деформируемыми и порошковыми. Наиболее жаропрочными являются литейные сложнолегированные сплавы на никелевой основе, способные работать до температур 1050—1100 °C в течение сотен и тысяч часов при высоких статических и динамических нагрузках[1].
История
Первые жаропрочные стали для газотурбинных двигателей были разработаны в Германии фирмой Krupp в 1936—1938 годах. Высоколегированная аустенитная сталь Тинидур создавалась как материал рабочих лопаток турбины на температуры 600—700°C. Тинидур — аустенитная сталь с дисперсионным твердением (Ni
Наименование | %C | %Mn | %Si | %Ni | %Co | %Cr | %Mo | %W | %Ti | %Al | % др. элементов |
---|---|---|---|---|---|---|---|---|---|---|---|
Тинидур | до 0,14 | 0,6-1,0 | 0,6-1,0 | 29,0-31,0 | 14,5-15,5 | 1,8-2,2 | 0,2 | Fe основа | |||
DVL42 | до 0,1 | 0,6-1,0 | 0,4-0,8 | 30-35 | 22-25 | 12-17 | 4-6 | 4-6 | 1,5-2,0 | Fe основа | |
DVL52 | до 0,1 | 0,6-1,0 | 0,4-0,8 | 30-35 | 22-25 | 12-17 | 4-6 | 4-6 | 4-5 %Ta | ||
Хромадур | 0,9-0,12 | 17,5-18,5 | 0,55-0,7 | 11,0-14,0 | 0,7-0,8 | V 0,60-0,70 0,18-0,23 N2 |
В Германии 1940-х годов среди разработчиков авиационных ГТД существовало стремление повысить температуру газа перед турбиной до 900°C. С этой целью институт DVL совместно с рядом фирм экспериментировал с аустенитными сложнолегированными сплавами. В ходе войны была признана невозможность подобного решения по причине острого дефицита в Германии легирующих элементов. В результате исследования приняли два направления: 1. создание полых охлаждаемых воздухом лопаток (рабочих и сопловых) при соответствующем снижении легирования используемых материалов; 2. исследование возможностей керамических материалов. Оба направления работ являлись пионерскими, по каждому из них были получены значимые результаты.
Первые серии реактивного двигателя Jumo-004A выпускались с 1942 года с монолитными рабочими и сопловыми лопатками из материала Тинидур фирмы Крупп. Позднее заменены полыми охлаждаемыми лопатками из того же материала, что позволило повысить температуру газа перед турбиной до 850°C (серия Jumo-004E). С 1944 года на серийных модификациях двигателя Jumo-004B применялись полые охлаждаемые рабочие лопатки из менее дефицитной стали Cromadur.
Лопатки турбины из сплава Нимоник 80A ТРД Роллс-Ройс «Нин», экспонируемого в Science Museum, Лондон.К 1942 году в Великобритании создан жаропрочный сплав нимоник-80 — первый в серии высокожаропрочных дисперсионно-твердеющих сплавов на никель-хромовой основе. Создатель сплава — сэр Уильям Гриффитс Griffiths W.T. Основа сплава нимоник-80 — нихром (80 %Ni — 20 %Cr), известный с начала XX века своей высокой жаростойкостью и высоким электрическим сопротивлением. Ключевыми легирующими элементами сплава нимоник-80 являлись титан (2,5 %) и алюминий (1,2 %), образующие упрочняющую фазу. Количество упрочняющей гамма-штрих фазы в сплаве составляло 25-35 об%[5]. Нимоник-80 использовался в деформированном состоянии для изготовления рабочих лопаток турбины одного из первых газотурбинных двигателей Роллс-Ройс «Нин», стендовые испытания которого начались в октябре 1944 г. Лопатки турбины из сплава нимоник-80 обладали высокой длительной прочностью при температурах 750—850 °C. В СССР аналогами сплава нимоник-80 являются никелевые жаропрочные сплавы ЭИ437, ЭИ437А (ХН77ТЮ) и ЭИ437Б (ХН77ТЮР), срочным порядком созданные к 1948 году сотрудниками ВИАМ, ЦНИИЧермет и завода «Электросталь» при участии Ф. Ф. Химушина[6].
Основу жаропрочных сплавов, как правило, составляют элементы VIII группы таблицы Менделеева. До 1940-х годов основу жаропрочных сплавов составляли железо или никель. Добавлялось значительное количество хрома для увеличения коррозионной стойкости. Добавки алюминия, титана или ниобия увеличивали сопротивление ползучести. В некоторых случаях образовывались хрупкие фазы, такие, например, как карбиды M23C6. В конце 40-х годов прекратилось, в основном, использование железа как основы жаропрочных сплавов, предпочтение начали отдавать сплавам на основе никеля и кобальта. Это позволило получить более прочную и стабильную гранецентрированную матрицу.
В конце 1940-х годов была обнаружена возможность дополнительного упрочнения жаропрочных сплавов путём легирования молибденом. Позже для этой же цели начали применять добавки таких элементов, как вольфрам, ниобий, тантал, рений и гафний. (См. Карбид тантала-гафния, хотя в жаропрочных сплавах гафний не образует подобных карбидов, а повышает прочность и пластичность «механически», вызывая закручивание границ зёрен, т.н. «гафниевый эффект». Помимо этого, он участвует в образовании дополнительных количеств гамма-штрих фазы[7]).
Сплавы на основе никеля
Рабочая лопатка ротора турбины двигателя RB199, из литейного никелевого жаропрочного сплава, бывшая в эксплуатации.В 1950-х годах компаниями Pratt & Whitney и General Electric были разработаны сплавы Уаспалой (Waspaloy) и M-252, легированные молибденом и предназначенные для лопаток авиационных двигателей. Затем были разработаны такие сплавы, как Hastelloy alloy X, Rene 41, Инконель, в том числе Inco 718, Incoloy 901 и др.
Согласно оценкам экспертов, за период 1950-1980-х годов химические составы никелевых жаропрочных сплавов изменялись наиболее значительно за счет введения алюминия и замещающих его элементов в γ{\displaystyle \gamma }’ фазе. Указанное привело к увеличению объемной доли γ{\displaystyle \gamma }’ фазы от 25-35 об.% в сплавах нимоник 80 и U-700 до 65-70 об.% в современных лопаточных материалах[5].
Легирование
Жаропрочные сплавы на основе никеля, как правило, обладают сложным химсоставом. Он включает 12 — 13 компонентов, тщательно сбалансированных для получения необходимых свойств. Содержание таких примесей, как кремний (Si), фосфор (P), сера (S), кислород (O) и азот (N) также контролируется. Содержание таких элементов, как селен (Se), теллур (Te), свинец (Pb) и висмут (Bi) должно быть ничтожно малым, что обеспечивается подбором шихтовых материалов с низким содержанием этих элементов, т.к. избавиться от них в ходе плавки не представляется возможным. Эти сплавы обычно содержат 10—12 % хрома (Cr), до 8 % алюминия (Al) и титана (Ti), 5-10 % кобальта (Co), а также небольшие количества бора (B), циркония (Zr) и углерода (C). Иногда добавляются молибден (Mo), вольфрам (W), ниобий (Nb), тантал (Ta) и гафний (Hf).
Легирующие элементы в этих сплавах можно сгруппировать следующим образом:
- Элементы, образующие с Ni аустенитную γ{\displaystyle \gamma }-матрицу с гранецентрированной кристаллической решёткой — Co, Fe, Cr, Mo и W
- Элементы, образующие упрочняющую γ{\displaystyle \gamma }’ фазу (Ni3X) — Al, Ti, Nb, Ta, Hf. При этом Ti, Nb и Ta входят в состав фазы и упрочняют её.
- Элементы, образующие сегрегации по границам зёрен — B, C и Zr
К карбидообразующим элементам относятся Cr, Mo, W, Nb, Ta и Ti. Al и Cr образуют оксидные плёнки, защищающие изделия от коррозии.
Типичный химсостав деформируемых жаропрочных сплавов на никелевой основе[8]Сплав | %Ni | %Cr | %Co | %Mo | %Al | %Ti | %Nb | %C | %B | Zr | % др. элементов |
---|---|---|---|---|---|---|---|---|---|---|---|
Inconel X-750 | 73,0 | 18,0 | — | — | 0,8 | 2,5 | 0,9 | 0,04 | — | — | 6,8 % Fe |
Udimet 500 | 53,6 | 18,0 | 18,5 | 4,0 | 2,9 | 2,9 | — | 0,08 | 0,006 | 0,05 | |
Udimet 700 | 53,4 | 15,0 | 18,5 | 5,2 | 4,3 | 3,5 | — | 0,08 | 0,03 | — | |
Waspaloy | 58,3 | 19,5 | 13,5 | 4,3 | 1,3 | 3,0 | — | 0,08 | 0,006 | 0,06 | |
Astroloy | 55,1 | 15,0 | 17,0 | 5,2 | 4,0 | 3,5 | — | 0,06 | 0,03 | — | |
Rene 41 | 55,3 | 19,0 | 11,0 | 10,0 | 1,5 | 3,1 | — | 0,09 | 0,005 | — | |
Nimonic 80A | 74,7 | 19,5 | 1,1 | — | 1,3 | 2,5 | — | 0,06 | — | — | |
Nimonic 90 | 57,4 | 19,5 | 18,0 | — | 1,4 | 2,4 | — | 0,07 | — | — | |
Nimonic 105 | 53,3 | 14,5 | 20,0 | 5,0 | 1,2 | 4,5 | — | 0,2 | — | — | |
Nimonic 115 | 57,3 | 15,0 | 15,0 | 3,5 | 5,0 | 4,0 | — | 0,15 | — | — |
Сплав | %Ni | %Cr | %Co | %Mo | %Al | %Ti | %Nb | %C | %B | Zr | % др. элементов |
---|---|---|---|---|---|---|---|---|---|---|---|
B-1900 | 64,0 | 8,0 | 10,0 | 6,0 | 6,0 | 1,0 | — | 0,10 | 0,015 | 0,1 | 4,0 % Ta |
MAR-M200 | 60,0 | 9,0 | 10,0 | — | 5,0 | 2.0 | 1.0 | 0,13 | 0,015 | 0,05 | 12,0 % W |
Inconel 738 | 61,0 | 16,0 | 8,5 | 1,7 | 3,4 | 3,4 | 0,9 | 0,12 | 0,01 | 0,10 | 1,7 % Ta, 3,6 % W |
Rene 77 | 58,0 | 14,6 | 15,0 | 4,2 | 4,3 | 3,3 | — | 0,07 | 0,016 | 0,04 | |
Rene 80 | 60,0 | 14,0 | 9,5 | 4,0 | 3,0 | 5,0 | — | 0,17 | 0,015 | 0,03 | 4,0 %W |
Фазовый состав
К основным фазам жаропрочных сплавов относятся:
- Гамма-фаза (γ{\displaystyle \gamma }) является матрицей с г.ц.к. кристаллической решёткой. В твёрдом растворе этой фазы содержится большое количество Co, Cr, Mo, W
- Гамма-штрих (γ{\displaystyle \gamma }’) фаза образует частицы преципитата, имеющего также г.ц.к. кристаллическую решётку. В эту фазу входят такие элементы, как Al и Ti. Объёмная доля этой фазы, когерентной аустенитной матрице достаточно велика
- Карбиды. Содержание углерода в сплавах относительно невелико (0,05-0,2 %). Он соединяется с карбидообразующими элементами — Ti, Ta, Hf
- Зернограничная γ{\displaystyle \gamma }’-фаза. Эта фаза образуется в виде плёнки по границам зёрен в процессе термической обработки.
- Бориды Выделяются по границам зёрен в виде редких частиц
- Фазы т. п. у. (топологически плотно упакованные фазы) имеют пластинчатую морфологию. Пример: фазы σ{\displaystyle \sigma }, μ{\displaystyle \mu } и фаза Лавеса. Эти фазы приводят к охрупчиванию материала и являются нежелательными.
Термическая обработка
Деформируемые никелевые жаропрочные сплавы содержат в матрице дисперсные выделения карбидов типа MC. Гомогенизационный отжиг даёт возможность подготовить матрицу к получению равномерного распределения частиц упрочняющей фазы γ{\displaystyle \gamma }’ в процессе последующего старения. Для примера, для сплава Inco 718 гомогенизационный отжиг продлится в течение 1 часа при 768 °C, а старение проводится в два этапа: 8 часов при 718 °C и 8 часов при 621 °C. После гомогенизационного отжига важно выдержать скорость охлаждения, чтобы препятствовать выделению нежелательных фаз. Охлаждение между этапами старения проводится плавно в течение 2 часов.
Жаропрочность
Одним из факторов, определяющих жаропрочность, является высокое сопротивление ползучести. Жаропрочность сплавов оценивается пределами длительной прочности или ползучести при высоких температурах, и связана, в первую очередь, с их структурой и составом. По структуре жаропрочные сплавы должны быть многофазными с прочными границами зёрен и фаз[1]. В никелевых жаропрочных сплавах сказанное обеспечивается многокомпонентным легированием. При этом жаропрочность сплавов тем выше, чем больше объёмная доля упрочняющих фаз и чем выше их термическая стабильность, то есть устойчивость против растворения и коагуляции при повышении температуры.
Длительная прочность
Никелевые жаропрочные сплавы используются при температурах 760—980 °C. Литые жаропрочные сплавы имеют высокую длительную прочность при более высоких температурах. Например, сплав MAR-M246 имеет длительную прочность 124 МПа после 1000 часов выдержки при 982 °C.
Жаропрочные сплавы на никелево-железной основе используются при температурах 650—815 °C. Их длительная прочность намного ниже.
Длительная прочность жаропрочных сплавов при трёх температурах, МПа[9]Сплав | 650 °C 100 часов | 650 °C 1000 часов | 815 °C 100 часов | 815 °C 1000 часов | 982 °C 100 часов | 982 °C 1000 часов |
---|---|---|---|---|---|---|
Inconel X-750 | 552 | 469 | 179 | 110 | 24 | |
Udimet 700 | 703 | 400 | 296 | 117 | 55 | |
Astroloy | 772 | 407 | 290 | 103 | 55 | |
IN-100 | 503 | 379 | 172 | 103 | ||
MAR-M246 | 565 | 448 | 186 | 124 |
Монокристаллические жаропрочные сплавы
В 1970—1980 годы началось применение литых жаропрочных сплавов, полученных методами направленной кристаллизации и монокристаллических сплавов на никелевой основе. Применение этих материалов (на никелевой основе) позволило увеличить прочность и термическую долговечность лопаток газовых турбин.
Химический состав жаропрочных сплавов,полученных методами направленной кристаллизации[9]
Сплав | %Cr | %Co | %W | %Mo | %Ta | %Nb | %Ti | %Al | %Hf | %B | %Zr | %C |
---|---|---|---|---|---|---|---|---|---|---|---|---|
MAR-M200+Hf | 9,0 | 10,0 | 12,0 | — | — | 1,0 | 2,0 | 5,0 | 2,0 | 0,015 | 0,08 | 0,14 |
MAR-M246+Hf | 9,0 | 10,0 | 10,0 | 2,5 | 1,5 | — | 1,5 | 5,5 | 1,5 | 0,015 | 0,05 | 0,15 |
MAR-M247 | 8,4 | 10,0 | 10,0 | 0,6 | 3,0 | — | 1,0 | 5,5 | 1,4 | 0,015 | 0,05 | 0,15 |
RENE 80H | 14,0 | 9,5 | 4,0 | 4,0 | — | — | 4,8 | 3,0 | 0,75 | 0,015 | 0,02 | 0,08 |
Сплав | %Cr | %Co | %W | %Mo | %Ta | %Nb | %Ti | %Al | %Hf |
---|---|---|---|---|---|---|---|---|---|
Pratt & Whitney № 1 | 10,0 | 5,0 | 4,0 | — | 12,0 | — | 1,5 | 5,0 | — |
Pratt & Whitney № 2 (3 % Re) | 5,0 | 10,0 | 6,0 | 2,0 | 8,7 | — | — | 5,6 | 0,1 |
CMSX-2 | 8,0 | 5,0 | 8,0 | 0,6 | 6,0 | — | 1,0 | 5,5 | — |
SRR99 | 8,5 | 5,0 | 9,5 | — | 2,8 | — | 2,2 | 5,5 | — |
Уже ранний опыт эксплуатации лопаток газотурбинных двигателей Jumo-004 показал (исследования К. Гебхардт, фирма Крупп, Эссен), что на практике срок службы лопаток определяется усталостной прочностью, и подавляющее число разрушений лопаток являются усталостными[10].
Сплавы на основе кобальта
Ещё в начале XX века компанией Хэйнс (англ. Haynes) были получены патенты на сплавы системы Co — Cr и Co — Cr — W. Эти сплавы, именуемые «стеллитами» использовались вначале для производства режущего инструмента. и износостойких деталей. В 1930-х годах был разработан литейный Co — Cr — Mo сплав для зубного протезирования Vitallium. Аналогичный по составу сплав HS-21 начал использоваться десятилетие спустя в турбонагревателях и газовых турбинах. Тогда же начали использовать сплав системы Co — Ni — Cr для направляющих лопаток газотурбинных двигателей. В 1943 г. был разработан литейный сплав Co — Ni — Cr — W (X-40) также применяемый при изготовлении лопаток. В 1950—1970 годы были разработаны новые никелевые жаропрочные сплавы, изготовленные путём вакуумной выплавки и упрочняемые за счёт выделения фазы γ{\displaystyle \gamma }’. Это привело к уменьшению использования сплавов на основе кобальта.
Особенности жаропрочных сплавов на кобальтовой основе
- Температура плавления у сплавов на кобальтовой основе — более высокая. По этой причине повышены характеристики длительной прочности. Эти жаропрочные сплавы могут работать при более высоких температурах, по сравнению со сплавами на основе никеля и железа
- Высокое содержание хрома повышает сопротивление горячей коррозии
- Сплавы характеризуются повышенным сопротивлением термической усталости и имеют хорошую свариваемость.
Дисперсноупрочненные жаропрочные сплавы
Важной проблемой в разработке конструкционных материалов с повышенной прочностью и пластичностью является обеспечение их стабильности и однородности физико-механических свойств во всем интервале температур эксплуатации от криогенных и вплоть до предплавильных температур. В настоящее время наиболее перспективным путем решения этой проблемы является упрочнение базового сплава дисперсными наночастицами тугоплавких оксидов[источник не указан 439 дней]. Такие материалы принято называть ODS (oxide dispersion strengthened) сплавами[11]. Базой для ODS-сплавов наиболее часто служат аустенитные жаропрочные сплавы на основе Ni, Cr и Fe. В качестве упрочняющих частиц, как правило, используют тугоплавкие оксиды Al2O3, TiO2, ThO2, La2O3, BeO и Y2O3. ODS- суперсплавы получают методом механического легирования, который включает следующие стадии: 1) совместное перемалывание в шаровых мельницах порошков исходных компонент суперсплава с добавлением мелкодисперсных конгломератов тугоплавкого оксида; 2) запайка дегазированного порошка в герметичный стальной контейнер; 3) компактирование экструзией; 4) горячая опрессовка; 5) зонная рекристаллизация. ODS- суперсплав (Inconel MA758) на основе оксида иттрия Y2O3 был разработан в 90-х годах прошлого века.
Диффузионные покрытия
Поскольку турбинные лопатки, изготовленные из литейных жаропрочных сплавов работают при высоких температурах и в агрессивной среде, возникает необходимость в их защите от горячей коррозии. С этой целью используют диффузионные покрытия двух типов, т. н. пакетная цементация и покрытия, наносимые в газовой фазе. В процессе покрытия происходит обогащение поверхностного слоя алюминием и образование алюминида никеля, как матрицы покрытия.
Процесс пакетной цементации
Процесс происходит при более низкой температуре (около 750 °C). Детали помещаются в коробки со смесью порошков: активный материал, содержащий алюминий и образующий покрытие, активатор (хлорид или фторид) и термический балласт, например, окись алюминия. При высокой температуре образуется газообразный хлорид (или фторид) алюминия, который переносится на поверхность изделия. Затем происходит распад хлорида алюминия и диффузия алюминия вглубь объема. Образуется т. н. «зелёное покрытие», очень хрупкое и тонкое. После этого проводится диффузионный отжиг (несколько часов при температурах около 1080 °C). При этом образуется окончательное покрытие.
Покрытие в газовой фазе
Процесс идёт при более высокой температуре около 1080 °C. Активный материал, содержащий алюминий, не находится в непосредственном контакте с изделием. Нет необходимости и в термическом балласте. Процесс отличается диффузией вовне. Также требуется диффузионный отжиг.
Плазменные покрытия
Более современной технологией защиты лопаток является плазменное напыление термобарьерных покрытий. Как правило, термобарьерное покрытие состоит из нескольких слоев — подслой, слой MeCrAlY, слой керамики (часто применяют оксид циркония, стабилизированный иттрием). Для разных двигателей аттестованы вакуумное или атмосферное плазменное напыление, однако все современные разработки выполняются на атмосферной плазме, как более дешевой в эксплуатации.
См. также
Примечания
- ↑ 1 2 Авиация. Энциклопедия. М.: Большая Российская энциклопедия, 1994, с. 201
- ↑ Luft.-Forschung, Bd 18(1941), N 8, S. 275—279
- ↑ Pomp A., Krisch A.: Zur Frage der Dauerstandfestigkeit warmfester Staehle bei 600, 700 und 800°C. Mitteilungen der KWI fuer Eisenforschung (Abhandl. 400), 1940
- ↑ Report on Visit to Germany and Austria to investigate Alloys for Use at High Temperature. BIOS Final Report N 396, London, 1946
- ↑ 1 2 Giamei A.F., Pearson D.D., Anton D.L. Materials Research Society Symposium Proc. 1985, v. 39, pp. 293-307
- ↑ Туманов А. Т., Шалин Р. Е., Старков Д. П. Авиационное материаловедение. — в кн.: Развитие авиационной науки и техники в СССР. Историко-технические очерки. М.: Наука, 1980, с. 332—334
- ↑ Суперсплавы II под ред. Симса, Столоффа, Хагеля. Перевод на русский язык. М., Металлургия, 1995, т 1, стр. 29
- ↑ http://www.msm.cam.ac.uk/phase-trans/2003/nickel.html
- ↑ 1 2 3 4 Superalloys
- ↑ Report on Visit to Germany and Austria to investigate Alloys for use at a High Temperatures/ — BIOS Final Report No 396. London 1946, p. 13.
- ↑ К.А. Ющенко, Ю.А. Семеренко, Е.Д. Табачникова, А.В. Подольский, Л.В. Скибина, С.Н. Смирнов, В.С. Савченко. Inconel MA758: новый наноструктурный суперсплав. Акустические и механические свойства в интервале температур 4,2—310 К // Металлофиз. новейшие технол. — 2013. — Т. 35, вып. 2. — С. 225-231.
Литература
- Суперсплавы II. Жаропрочные материалы для аэрокосмических и промышленных энергоустановок. — М.: «Металлургия», 1995.
- Строение и свойства авиационных материалов. — М.: «Металлургия», 1989.
- Лекции о суперсплавах на сайте университета Кембриджа.
- Химушин Ф. Ф. Жаропрочные стали и сплавы. — М.: «Металлургия», 1969.
wikiredia.ru
Самый тугоплавкий сплав на Земле ? Напишите химическую формулу, если можно.
предлагаю для разнообразия не «псевдонаучный» , а нормальный ответ: самый тугоплавкий металл — вольфрам. темп. плавление 3422 C, плотность 19,3 г/куб. см. для справки, любой сплав всегда имеет температуру плавления ниже чем у самого легкоплавкого компонента.
Телекилл — представляет собой вещество с металлическими свойствами, составленное из различных элементов, как известных, так и неизвестных ранее. Цвет сплава — серо-зелёный с голубоватым отливом, материал быстро окисляется в воде. Температура плавления сплава — приблизительно 4500 °С, температура кипения — приблизительно 9000 °С. Плотность телекилла составляет 6,20 г/см3 6,76 г/см3, твердость — 39 HRC по шкале твердости Роквелла. Материальные свойства сплава, такие как прочность, вязкость и обрабатываемость, сходны со свойствами платины. Телекилл состоит в основном из платины и иридия; эти элементы образут 62% и 20% массы сплава соответственно. Также в состав сплава входят ещё несколько металлов, в т. ч. железо, кобальт и медь, образующие 16,5% массы сплава. Остальные 1,5% приходятся на вещество или вещества, не определяемые с помощью спектроскопии или какими-либо другими методами. Изображения, снятые с помощью сканирующего туннельного микроскопа, показывают пробелы в кристаллической решётке, которые, при нормальных условиях, должны быть заполнены другими материалами. Телекилл может частично или полностью блокировать любые экстрасенсорные и/или телепатические свойства живых организмов, находящихся в непосредственной близости от него. Воздействие сложно просчитать, но, похоже, что оно ослабевает прямо пропорционально квадрату расстояния от объекта и усиливается прямо пропорционально количеству используемого материала. Эффект можно однозначно определить на расстоянии примерно 80 сантиметров на каждый килограмм сплава. Общий произведённый и имеющийся в распоряжении людей объем телекилла имеет массу приблизительно 1,1 — 1,2 тонны. Был обнаружен на месте крушения неопознанного летающего объекта недалеко от г. Монтеррей, Мексика. в 2008г.
touch.otvet.mail.ru
Самый тугоплавкий металл в мире
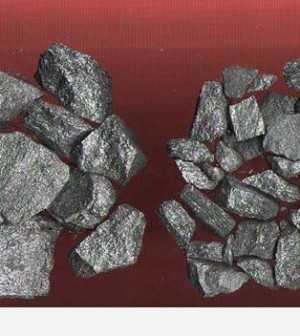
1783 год. Братья Элюар выделили из вольфрамита и с помощью углерода восстановили самый тугоплавкий материал – вольфрам (Wolframium). Тогда они и предположить не могли, что их открытие совершит революцию в промышленности, хотя долгое время ему не могли найти применение.
Вольфрам получают из концентратов вольфрамита и шеелита. Технология его получения довольно сложная. Вначале при температуре 700-850° С в электропечах получают вольфрамовый порошок. Затем из него методом прессования в стальных формах под давлением и термической обработке получают металлические заготовки. В заключении их нагревают до 3000°С, пропуская через них электрический ток.
В XIX промышленности потребовалась сталь с особыми свойствами. Исследования привели к тому, что получить эти свойства оказалось возможным после добавления в сталь вольфрама. Затем наступил золотой век вольфрама – изобретение электричества и из вольфрама стали изготовлять нити для лампочек. Температура в 2200°С оказалась переносимой только для вольфрама. На изготовление нити накаливания для 23 лампочек мощностью 60 ватт требуется всего 1 грамм вольфрама.
Вольфрам незаменим при литье титановых сплавов, кокиль с вольфрамовым напылением способен выдерживать большие температуры.
В настоящее время вольфрам применяется при изготовлении танковой брони, торпед и снарядов, в космической и авиационной промышленности. А изготовленные из вольфрамовой стали инструменты, благодаря своей тугоплавкости, тяжести и твердости практически не поддаются процессам металлообработки. Вольфрам начинает плавиться при температуре 3380°С, а кипит при температуре 5900°С. Это единственный металл, который может кипеть только на поверхности Солнце. Именно поэтому вольфрам особенно широкое применение получил в авиации, чтобы материал, из которого создают летательные аппараты, выдерживал трение воздуха и не плавился во время полета.
Читайте также:
topxlist.ru
Тугоплавкие металлы к сплавы — Справочник химика 21
Тугоплавкие металлы и сплавы, Металлургия , 1965, [c.297]Металлический алюминий служит в основном для производства сплавов. Сплавы алюминия менее устойчивы к коррозии из-за возникновения гальванических микроэлементов в местах включений примесей. Алюминий идет на производство кабелей, фольги, зеркал, серебристой краски. Способность алюминия восстанавливать металлы из оксидов при высоких температурах послужила основой метода алюмотермии, т. е. восстановления тугоплавких металлов, например хрома или марганца, из их оксидов [c.152]
Тугоплавкие металлы в чистом виде и в виде сплавов получили в последнее время исключительное значение в ряде отраслей новой техники. [c.652]
Метод порошковой технологии широко используется для получения большинства компактных тугоплавких металлов и ряда других тугоплавких материалов, к числу которых относятся карбидные твердые сплавы, керметы и пр. Керметы (металлокерамические материалы) получают спеканием смеси порошков металлов (чаще всего используются порошки Сг, Ре и их аналогов) и неметаллических компонентов — тугоплавких боридов, карбидов, оксидов и др. Керметы сочетают в себе тугоплавкость, твердость и жаростойкость керамики с проводимостью, пластичностью и прочими свойствами металлов. [c.321]
В настоящее время в основном металлический натрий применяется в производстве тетраэтилсвинца, как антидетонатора при получении высокооктанового моторного топлива, кроме того, его используют для производства чистых цианидов, синтетических моющих средств — детергентов, перекиси натрия, синтетического каучука, индиго, гидрида натрия, фармацевтических препаратов и других продуктов неорганического и органического синтеза. Натрий как восстановитель используется для получения металлического калия и различных тугоплавких металлов. Применяется натрий также для модификации в раскислении сплавов цветных металлов, специальных сталей и для производства безоловянистых антифрикционных сплавов. За последнее время появился повышенных интерес к натрию и его сплавам с калием как к эффективным теплоносителям для атомных реакторов. Табл. 44 дает представление о масштабах потребления натрия в различных производствах в США. [c.303]
ТУГОПЛАВКИЕ МЕТАЛЛЫ — металлы, имеющие высокую температуру плавления. Например, W — 3410° С, Та — 2850 С, Мо — 2620 С, Nb — 2500° С. Эти металлы и их сплавы широко применяются в технике. [c.254]
Кроме компактных тугоплавких металлов методами порошковой металлургии получают ряд других материалов. Важнейшими из них являются карбидные твердые сплавы, ферриты, пористые материалы, керметы. [c.659]
Амальгамным методом получают сплавы тугоплавких металлов, которые трудно приготовить сплавлением компонентов. Для [c.599]
Радиусы атомов ниобия и тантала, а также радиусы их ионов (Э «) очень близки из-за лантаноидного сжатия. Это объясняет большое сходство их физико-химических свойств. В свободном состоянии ванадий, ниобий и тантал весьма стойки к химическим воздействиям и обладают высокими температурами плавления. Эти металлы вместе с хромом, молибденом, вольфрамом, рением, а также рутением, родием, осмием и иридием (см. ниже) относятся к тугоплавким металлам. Тугоплавкими условно считают те металлы, температура плавления которых выше, чем хрома (1890°С). Тугоплавкие металлы и их сплавы играют большую роль в современной технике. [c.286]
Для технического получения тугоплавких металлов разработаны или разрабатываются методы термического восстановления их из соединений при помощи А1, Mg, Na, Si, СаСг, сплавов Al — Si, Si — Са в вакууме или в атмосфере инертного газа. [c.324]
Описан рентгенофлуоресцентный метод [1112] определения серебра в тугоплавких металлах, сплавах, в порошкообразном титане, в карбидах и других соединениях. [c.189]Из-за высокотемпературных переходов у некоторых тугоплавких металлов, в том числе титана, циркония, скандия, железа, марганца, они непригодны в качестве компонентов жаропрочных материалов. Никель не имеет высокотемпературного фазового перехода, и этот металл используется для создания жаропрочных сплавов. [c.229]
Как самый тугоплавкий металл, вольфрам входит в состав ряда жаропрочных сплавов. В частности, его сплавы с кобальтом н хр.о-мом — стеллиты — обладают высокими твердостью, износоустойчивостью, жаростойкостью. Сплавы вольфрама с медью и с серебром сочетают в себе высокие электро- и теплопроводность, и износоустойчивость. Они применяются для изготовления рабочих частей рубильников, выключателей, электродов для точечной сварки. [c.661]
Электролиз рас
www.chem21.info