Какая самая прочная сталь в мире? • Наука
Какая самая прочная сталь в мире?
Сталь — издавна применяемый для создания некоторых видов оружия и ряда других приспособлений сплав из железа, углерода и отдельных примесей и ценящийся за свою прочность. Особо прочные стали обычно использовались именитыми мастерами в штучном производстве особо крепких клинков, легко рассекавших не только ткани человеческого тела, но и значительно более твердые материалы, а также в изготовлении дорогостоящих и ценимых шеф-поварами кухонных ножей.
Разумеется, выше перечислены отнюдь не все варианты применения данного сплава в тех его вариантах, что имеют наилучшие характеристики, ведь для определения того, какая сталь прочнее, неизменно принимается в расчет несколько важных факторов. Прежде всего, это твердость, т.е. способность такого металла противостоять внешним деформациям и различным нагрузкам, воздействующим на него извне. Кроме того, нельзя не учитывать его износостойкость (т.е. то, насколько он поддается фактору времени), устойчивость к корродирующим агентам и способность при этом удерживать нанесенную заточку.
Прочность в широком понимании данного слова включает каждую из названных выше характеристик, высокую степень которых достигнуть невероятно сложно в силу того, что зачастую они противоречат друг другу. В частности, значительная коррозионная устойчивость какого-либо металла обычно достигается в ущерб прочим его свойствам, в том числе способности противостоять нагрузкам. Потому способность создать самую прочную сталь в мире, которая отличалась бы хорошо выверенным балансом между всеми характеристиками, доступна далеко не каждому квалифицированному металлургу. Соответственно, любой, кому удастся достичь подобной цели, может смело причислять себя к особо талантливым или даже гениальным личностям, творящим нечто поистине уникальное.
В этой связи стоит упомянуть сравнительно недавнее, датирующееся 2011 годом, достижение некоего американского металлурга-самоучки Гари Колы, уроженца Огайо, сделавшего в области прочности сталей новое открытие. Этому человеку удалось добавить к бесчисленному количеству уже имеющихся на планете марок данного металла еще одну, получившую название Flash Bainite и по своим прочностным свойствам примерно на 7 процентов превосходящую прежние достижения в данной сфере.
Изготовлена была новая сверхпрочная сталь в одной из специализированных лабораторий Детройта, где была собрана установка для получения таких металлических листов. Секрет прочности детища Колы — в особой технологии обработки стали: американец догадался повысить на две сотни градусов температуру нагрева подобного металла, с общепринятых 900 до 1100 по Цельсию. Благодаря этому значительно сокращается время пребывания стальных листов на стадии нагрева и, соответственно, фактически не разрушаются находящиеся в них углеродистые соединения, делающие сплав более гибким и прочным.
Изобретение Гари Колы, по утверждениям ученых и его самого, способно получить широкое применение в автомобильной индустрии и ряде других промышленных отраслей, где вообще используется сталь и ценится ее способность противостоять даже серьезным нагрузкам.
Последние опубликованные

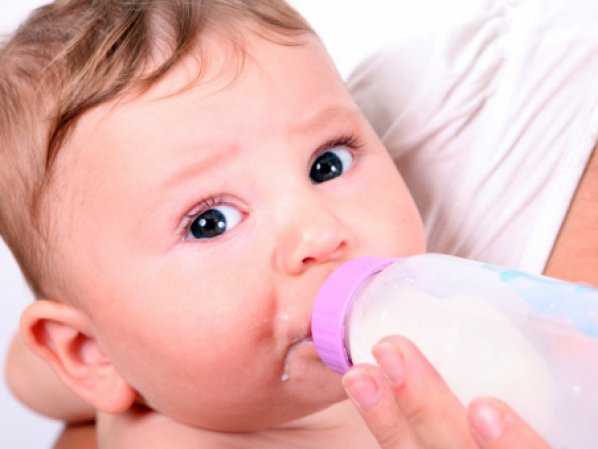
samogoo.net
Самый дорогой металл в мире
На сегодняшний день металлов огромное множество, они бывают легкими тяжелыми, мягкими и твердыми, дорогими и дешевыми. В наше время самый дорогой металл – это Калифорний, он оценивается в 10 миллионов долларов за один грамм. Во всем мире его около пяти грамм, именно поэтому он так отличается ценой от всех других металлов. Калифорний является радиоактивным металлом и его можно использовать в качестве заменителя атомного реактора и в других отраслях. В природе этот металл добыть невозможно, он был искусственно создан еще в 1950 году в университете Беркли в Калифорнии. Сегодня этот метал, чаще всего применяется в проведении экспериментов, связанных с проведением лучевой терапии и делением ядер.
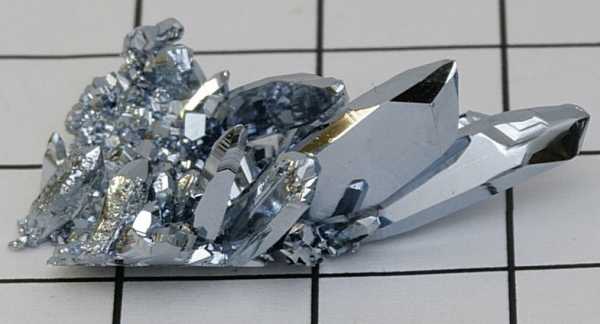
Калифорний
Самый легкий метал в мире, был искусственно создан китайскими учеными. Металл получил название графен, он настолько легкий, что может удержаться на лепестках цветка. Этот легчайший во всем мире материал был создан из лиофилизированного углерода и оксида графена. Если убрать добавленные примеси, то металл представляет собой двумерный кристалл, который был признан самым тонким рукотворным материалом на планете. Для того чтобы добиться стопки графена в один миллиметр, необходимо сложить три миллиона листов графена.
Помимо того что графен является самым легким, он еще и самый прочный металл в мире. Его свойства просто поражают, только представьте себе, что один лист графена толщиной в целлофановый пакет, способен выдержать гигантский вес слона. Металл обладает целой массой достоинств, среди которых также следует выделить гибкость. В это невозможно поверить, но графен можно растянуть без какого-либо вреда для него на целых двадцать процентов. И даже на этом его преимущества не заканчиваются, ученые выявили, что этот металл обладает уникальной способностью фильтровать воду и задерживать газы и различные жидкости.
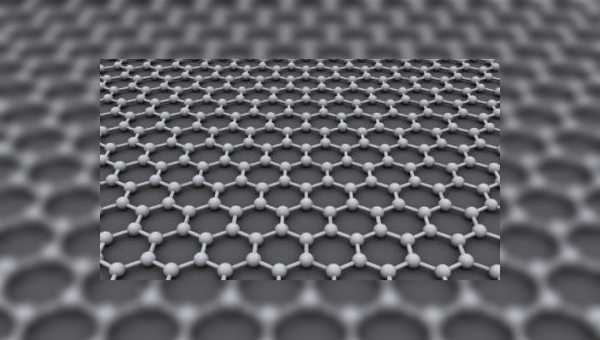
Графен
Статус самый твердый металл заслуженно был присвоен титану. Его открытие произошло еще в конце восемнадцатого века, и тогда же металл занял свое место в таблице Менделеева. Титан обладает очень высокой удельной прочностью при высоких температурах, хорошей стойкостью от коррозии и достаточно маленькой плотностью. Если, к примеру, при высоких температурах такие легкие сплавы, как магний и алюминий не выдерживают, титан придется в самую пору. Титановый сплав способен устоять даже при 300 градусов по Цельсию. Сегодня титан добывают во многих странах, в том числе и в России.
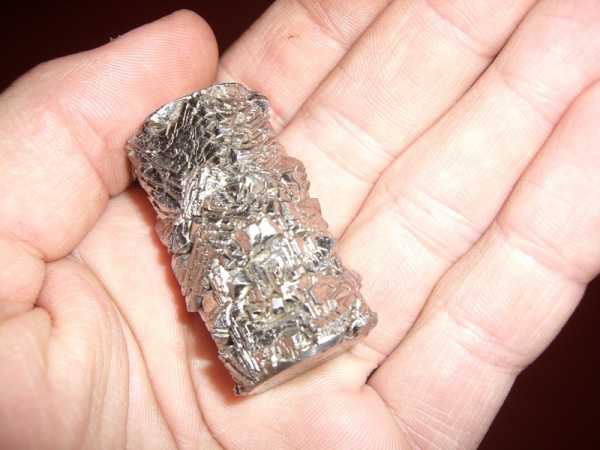
Титан
Самый мягкий металл – это галлий, который к тому же является и очень редким металлом. В чистом виде его не встретишь в природе, но в небольших количествах его можно обнаружить в цинковых рудах, а также в бокситах. Галлий имеет серебристый цвет, он очень мягкий и пластичный. Если его держать в низких температурах, то он будет сохранять свою твердую консистенцию, но только стоить переместить металл в помещение с комнатной температурой, и он тут же начнет плавиться. На сегодняшний день галлий не имеет какой-либо своей биологической роли, но он широко используется в микроэлектронике и даже в фармацевтике.
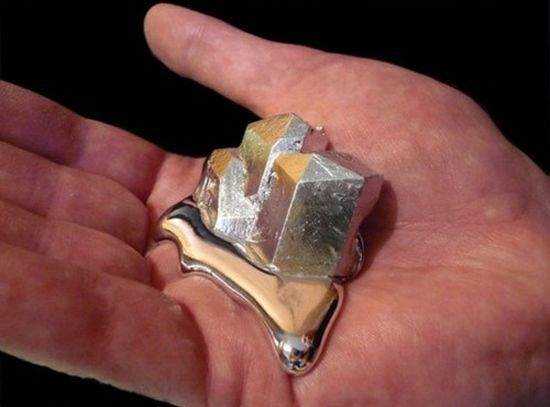
Галлий
Учеными доказано, что самый крепкий металл – это все тот же титан. Этот металл был открыт германским и английскими учеными, правда, их открытия были сделаны с разницей в шесть лет. Этот элемент занимает двадцать второй порядковый номер в таблице Менделеева. Если учитывать показатели прочности, то прочность титана в шесть раз превосходит прочность алюминия, именно, поэтому, возможности применения этого металла безграничны. Разработка этого металла стала настоящим прорывом в истории человечества и предоставила ему возможность использовать титан в самых различных сферах.
Самый дешевый металл на сегодняшний день – это медь. В чистом виде медь представляет собой тягучий красноватого цвета металл, имеющий удельный вес 8,9. Медь является одним из самых ранних металлов, которые были освоены человеком. Этот элемент таблицы Менделеева обладает хорошими техническими свойствами, поэтому очень широко используется во многих отраслях и сферах. Очень важно суметь распознать чистую медь от ее сплавов. Стоит отметить, что в чистом виде она сегодня встречается достаточно редко.
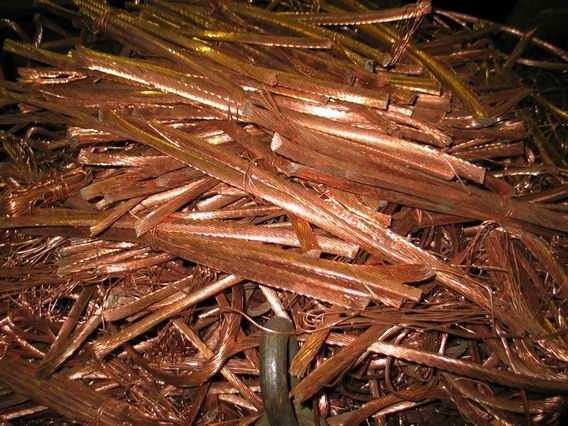
Медь
Самый редкий металл – рений, его первооткрывателем стал ученый из Германии Вальтер и Иде Ноддак, именно он открыл самый редкий устойчивый металл. Этот редкий металл был назван в честь реки Рейн. На сегодняшний день рений производится из медных и молибденовых руд путем обжига концентрата. Это довольно сложный процесс, где для получения одного килограмма этого метала необходимо переработать около двух тысяч тонн руды. Статистика говорит, что производство рения в год составляет около 40 тонн.
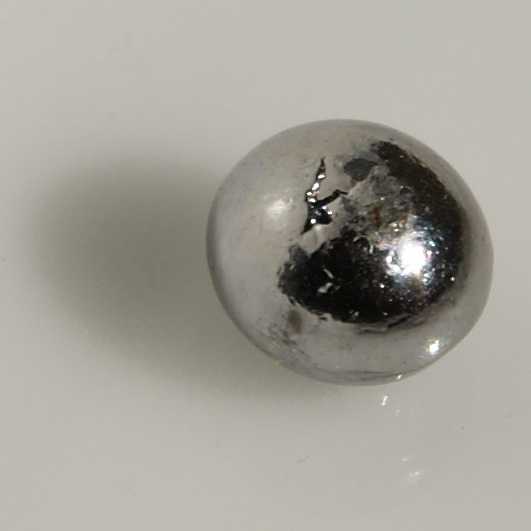
Рений
Еще один самый дорогой металл в мире – изотоп осмий-187. Его стоимость совсем немного уступает Калифорнию и составляет 200 тысяч долларов за один грамм. Этот металл очень редкий, для того чтобы его создать потребуется девять месяцев. Получить его можно путем деления изотопа, что представляет собой очень трудоемкий процесс. Изотоп имеет вид черного порошка с фиолетовым оттенком, при этом является самым плотным веществом на земле. Очень широко применяется в различных медицинских исследованиях, служит катализатором в химических реакциях.
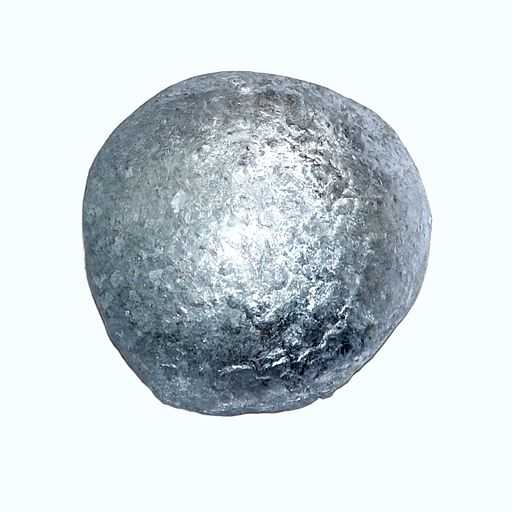
Изотоп
Предлагаем также посмотреть список самых красивых мест в мире.
24smi.org
Какой самый крепкий материал на земле
Знаете ли вы, какой материал на нашей планете считается самым крепким? Со школы нам всем известно, что алмаз — крепчайший минерал, но он далеко не самый крепкий. Твёрдость — не главное свойство, которым характеризуется материя. Одни свойства могут мешать появлению царапин, другие — способствовать эластичности. Хотите знать больше? Перед вами рейтинг материалов, которые будет очень сложно разрушить.
Алмаз
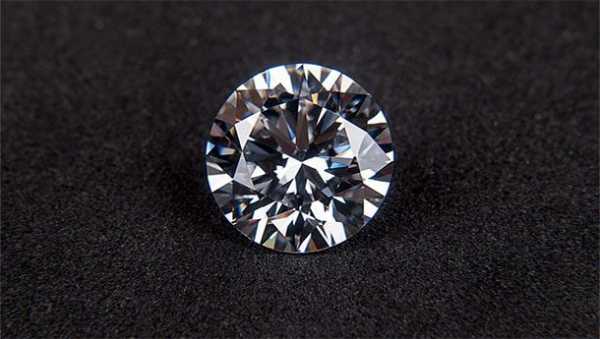
Классический пример прочности, засевший в учебниках и головах. Его твёрдость означает устойчивость к царапинам. В шкале Мооса (качественная шкала, которая измеряет сопротивление различных минералов) алмаз показывает результат в 10 (шкала идёт от 1 до 10, где 10 — самое твёрдое вещество). Алмаз настолько твёрдый, что другие алмазы должны быть использованы для его резки.
Шёлк паука Дарвина
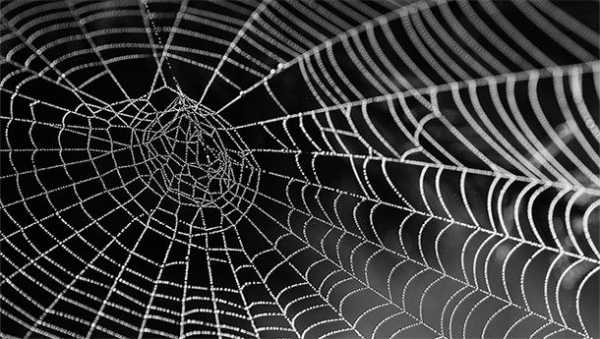
Этот материал часто упоминается как самое сложное биологическое вещество в мире (хотя это утверждение сейчас оспаривается изобретателями), сеть паука Дарвина сильнее, чем сталь и обладает большим запасом жёсткости, чем кевлар. Её вес не менее замечателен: нить, достаточно длинная, чтобы окружить Землю, весит всего 0,5 кг.
Аэрографит
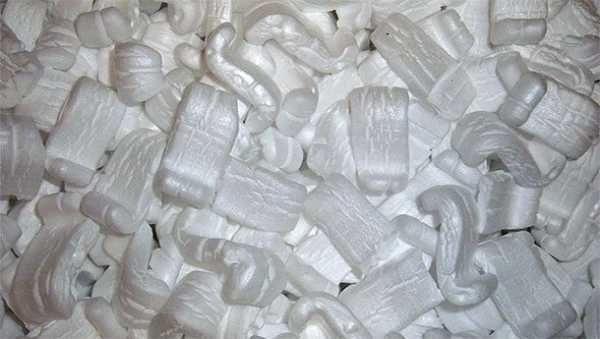
Эта синтетическая пена является одним из самых лёгких строительных материалов в мире. Аэрографит примерно в 75 раз легче пенополистирола (но намного сильнее!). Этот материал может быть спрессован в 30 раз от его первоначального размера без ущерба для его структуры. Ещё один интересный момент: аэрографит может выдержать массу в 40 000 раз больше собственного веса.
Палладиевое микролегированное стекло
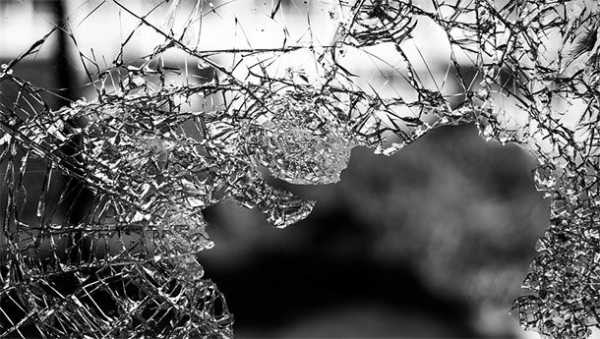
Это вещество разработано учёными в Калифорнии. Микролегированное стекло имеет почти совершенное сочетание жёсткости и прочности. Причиной этого является то, что его химическая структура снижает хрупкость стекла, но сохраняет жёсткость палладия.
Карбид вольфрама
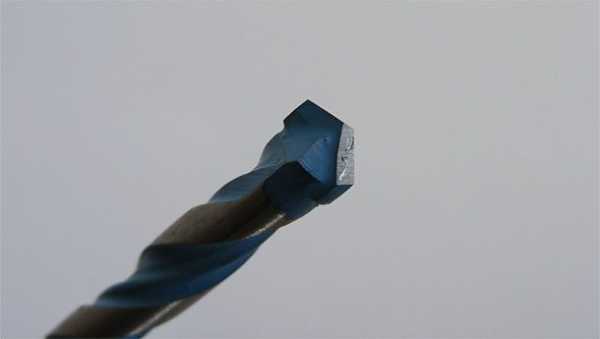
Карбид вольфрама невероятно твёрдый и имеет качественно высокую жёсткость, но он довольно хрупкий, его легко можно согнуть.
Карбид кремния
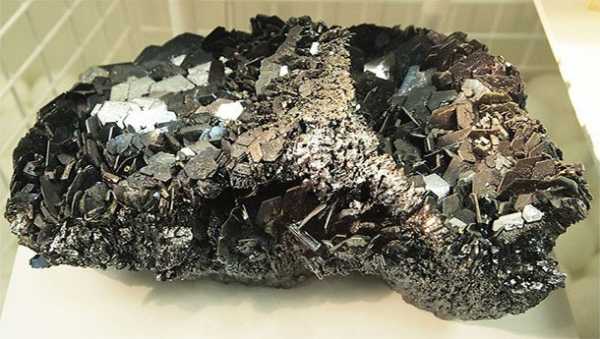
Этот материал используется в создании брони для боевых танков. Фактически он используется почти во всём, что может защищать от пуль. Он имеет рейтинг твёрдости Мооса 9, а также имеет низкий уровень теплового расширения.
Кубический нитрид бора
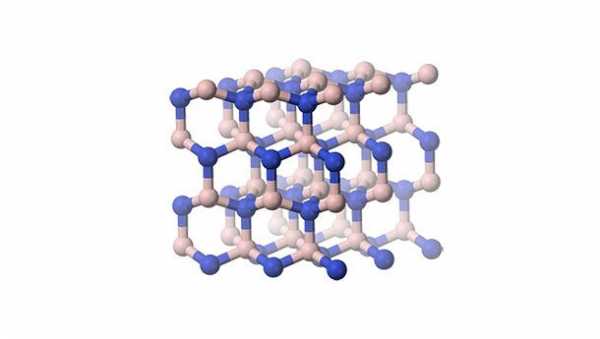
Примерно такой же сильный, как алмаз, кубический нитрид бора имеет одно важное преимущество: он нерастворим в никеле и железе при высоких температурах. По этой причине его можно использовать для обработки этих элементов (алмазные формы нитридов с железом и никелем при высоких температурах).
Dyneema
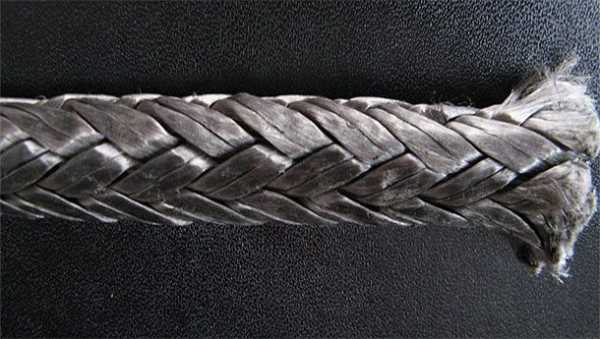
Считается самым сильным волокном в мире. Возможно, вас удивит факт: «дайнима» легче воды, но она может остановить пули!
Титановые сплавы
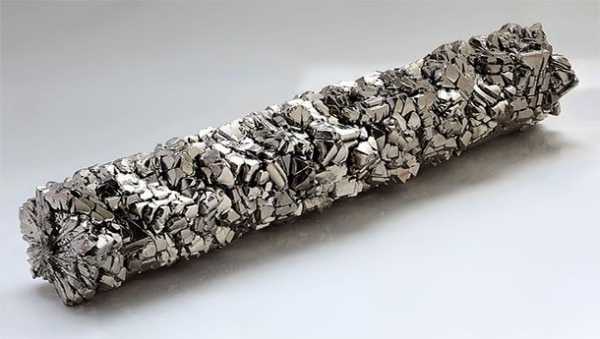
Титановые сплавы чрезвычайно гибкие и имеют очень высокую прочность на растяжение, но не имеют такой жёсткости, как стальные сплавы.
Аморфные сплавы
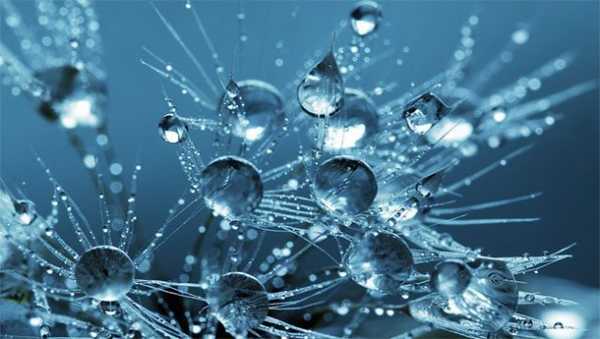
Liquidmetal разработан в компании Caltech. Несмотря на название, этот металл не является жидким и при комнатной температуре имеют высокий уровень прочности и износотойкости. При нагревании аморфные сплавы могут менять форму.
Наноцеллюлоза
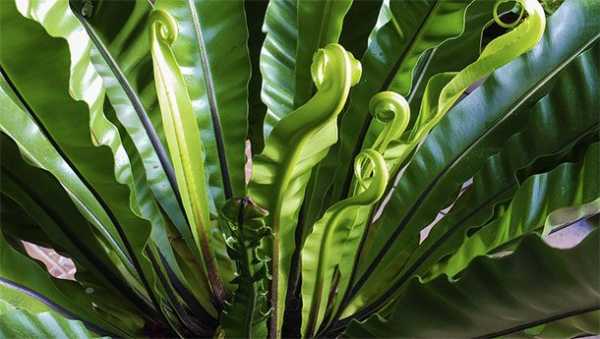
Это новейшее изобретение создаётся из древесной массы, при этом обладая большей степенью прочности, чем сталь! И гораздо дешевле. Многие учёные считают наноцеллюлозу дешёвой альтернативой палладиевому стеклу и углеродному волокну.
Зубы моллюсков
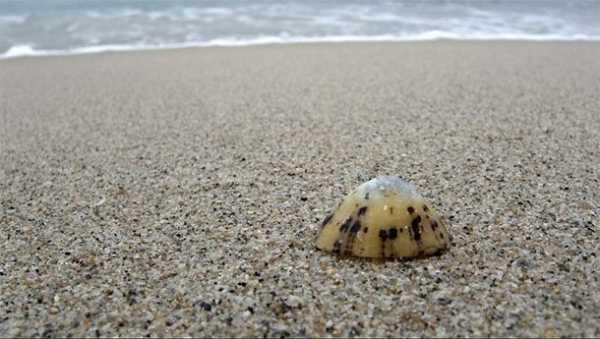
Ранее мы упоминали, что пауки Дарвина плетут нить одного из самых прочных органических материалов на Земле. Тем не менее зубы морского блюдечка оказались ещё сильнее, чем паутины. Зубы лимпетов чрезвычайно жёсткие. Причина этих удивительных характеристик в назначении: сбор водорослей с поверхности горных пород и кораллов. Учёные считают, что в будущем мы могли бы скопировать волокнистую структуру зубов лимпета и использовать её в автомобильной промышленности, кораблях и даже авиационной индустрии.
Мартенситностареющие стали
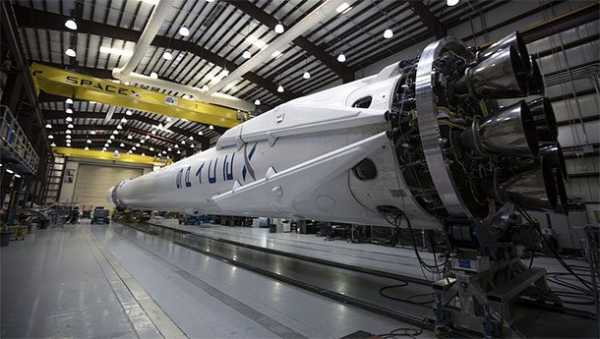
Это вещество сочетает в себе высокий уровень прочности и жёсткости без потери эластичности. Стальные сплавы этого типа находят применение в аэрокосмических и промышленно-производственных технологиях.
Осмий
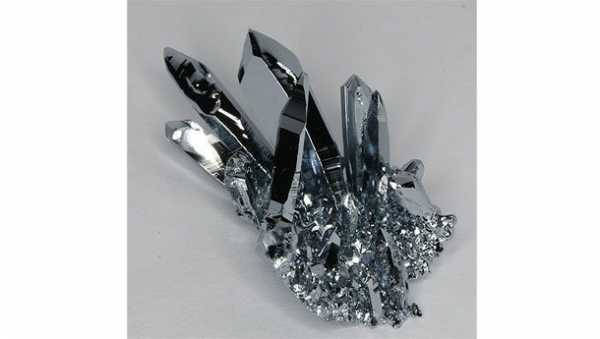
Осмий чрезвычайно плотен. Его используют при изготовлении вещей, требующих высокого уровня прочности и твёрдости (электрические контакты, ручки для наконечников и т.д.).
Кевлар
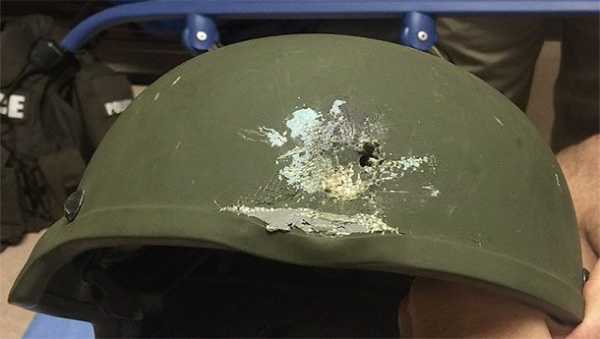
Используемый во всём, от барабанов до пуленепробиваемых жилетов, кевлар является синонимом твёрдости. Кевлар — это тип пластика, который обладает чрезвычайно высокой прочностью на растяжение. Фактически она примерно в 8 раз больше, чем у стальной проволоки! Он также может выдерживать температуры около 450 ℃.
Spectra

Высокоэффективный полиэтилен является действительно прочным пластиком. Эта лёгкая, прочная нить может выдерживать невероятное натяжение и в десять раз прочнее стали. Подобно кевлару, Spectra также используется для баллистических устойчивых жилетов, шлемов и бронетехники.
Графен
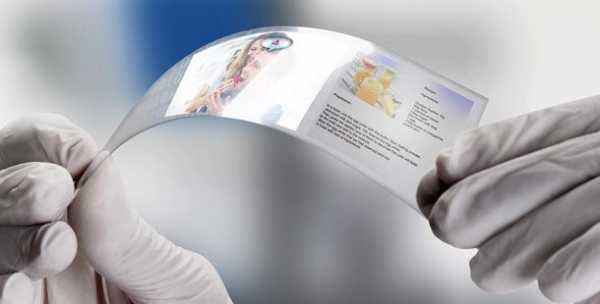
Лист графена (аллотроп углерода) толщиной в один атом в 200 раз сильнее, чем сталь. Хотя графен похож на целлофан, он действительно поражает. Понадобится школьный автобус, балансирующий на карандаше, чтобы проткнуть стандартный лист А1 из этого материала!
Buckypaper
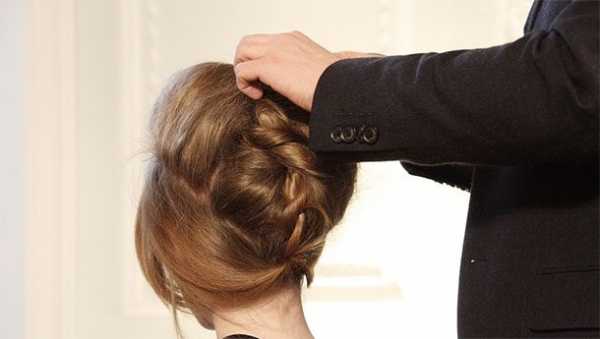
Эта нанотехнология изготовлена из углеродных труб, которые в 50 000 раз тоньше человеческих волос. Это объясняет, почему он в 10 раз легче, чем сталь, но в 500 раз сильнее.
Металлическая микрорешётка
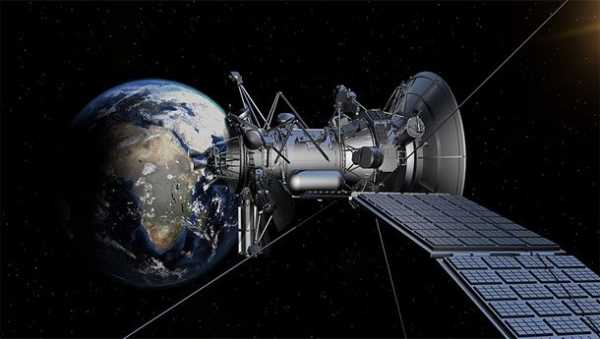
Самый лёгкий в мире металл, металлическая микрорешётка также является одним из самых лёгких конструкционных материалов на Земле. Некоторые учёные утверждают, что он в 100 раз легче пенополистирола! Пористый, но чрезвычайно сильный материал, он используется во многих областях техники. Boeing упомянул об использовании его при изготовлении самолётов, в основном в полах, сидениях и стенах.
Углеродные нанотрубки
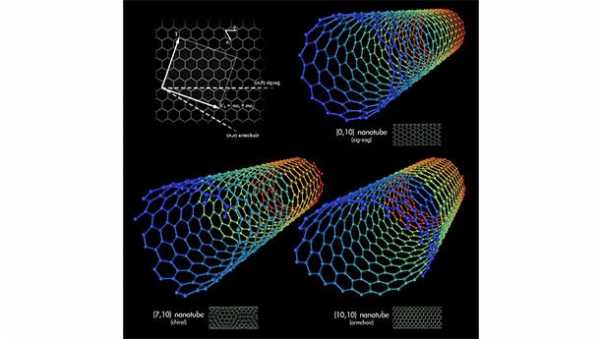
Углеродные нанотрубки (УНТ) можно описать как «бесшовные цилиндрические полые волокна», которые состоят из одного скатанного молекулярного листа чистого графита. В результате получается очень лёгкий материал. В наномасштабе углеродные нанотрубки имеют прочность в 200 раз больше, чем у стали.
Аэрографен
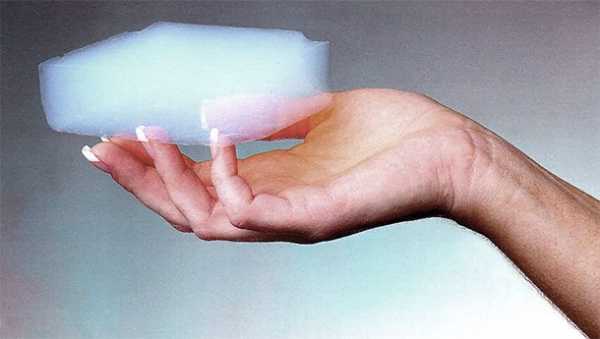
Также известен как графеновый аэрогель. Представьте себе прочность графена в сочетании с невообразимой лёгкостью. Аэрогель в 7 раз легче воздуха! Этот невероятный материал может полностью восстановиться после сжатия в более чем 90% и может поглощать до 900 раз больше собственного веса в масле. Есть надежда, что этот материал можно будет использовать для ликвидации разливов нефти.
Неназванное вещество, находящееся в разработке в Массачусетском технологическом институте

На момент написания этой статьи учёные из Массачусетского технологического института полагали, что они обнаружили секрет максимизации 2-мерной прочности графена в 3-х измерениях. Их пока ещё неназванное вещество может иметь примерно 5% плотности стали, но в 10 раз больше прочности.
Карбин
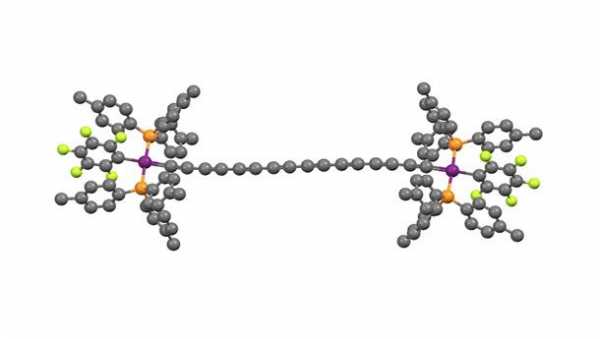
Несмотря на то что он является единой цепочкой атомов, карбин имеет удвоенную прочность на растяжение от графена и в три раза большую жёсткость, чем алмаз.
Вюрцит нитрид бора
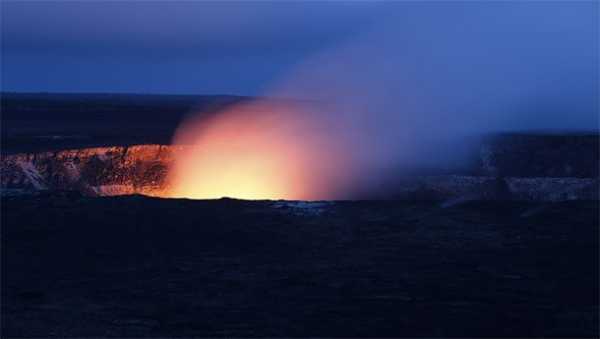
Это природное вещество производится в жерле действующих вулканов и на 18% прочнее, чем алмаз. Это одно из двух веществ, встречающихся в природе, которые, как было установлено, в настоящее время превосходят алмазы по твёрдости. Проблема в том, что там не так много этого вещества, и сейчас трудно сказать наверняка, является ли это утверждение на 100% верным.
Лонсдейлит
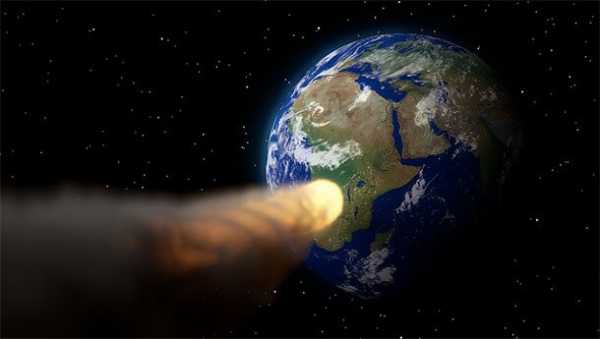
Также известный как гексагональный алмаз, это вещество состоит из атомов углерода, но они просто расположены по-другому. Наряду с вюрцитом нитридом бора это одно из двух природных веществ тверже алмаза. На самом деле Лондсдейлит 58% тверже! Однако, как и в случае с предыдущим веществом, он находится в относительно малых объёмах. Иногда он возникает, когда графитовые метеориты, сталкиваются с планетой Землёй.
Будущее не за горами, поэтому к концу XXI века можно ожидать появление сверхпрочных и сверхлёгких материалов, которые придут на смену кевлару и алмазам. А пока остаётся только удивляться развитию современных технологий.
Оцените статью: Поделитесь с друзьями!www.publy.ru
Какая сталь для ножей самая лучшая
В ноже первостепенную роль играет клинок, который должен обладать необходимыми параметрами. Это может быть кухонная или охотничья модель, но главный показатель качества этих изделий – сталь. От нее зависят режущие, антикоррозийные свойства и многое другое. Если при выборе ножа вы будете внимательны к материалу лезвия, то покупка окажется удачной.
Какая сталь лучше для ножа
Характеристики стали определяют качество такого инструмента. Материал представляет собой сплав железа, углерода, в этот состав добавляют дополнительные элементы, чтобы обеспечить необходимые свойства для ножа. Конечный результат будет зависеть еще и от термической обработки, закалки (финишные процессы). При изготовлении ножевой стали благодаря химическому составу клинок обретает необходимые характеристики:
- Твердость в зарубежных странах обозначается «Hardness». Это значение указывает на способность изделия противостоять нагрузкам, деформации из-за внешних сил.
- Износостойкость. Лучшая сталь для ножа обладает способностью противостоять износу при обычном использовании (истирание).
- Прочность (в англ. – Toughness). Указывает на способность изделия противостоять сколам, трещинам при серьёзных нагрузках.
- Стойкость к коррозии. Хорошие изделия способны сопротивляться ржавчине и прочим коррозийным воздействиям со стороны окружающей среды. Это свойство часто достигается за счет уменьшения других, более полезных характеристик.
- Способность держать заточку.
Прочность стали
Все клинки обладают определенными характеристиками. Высокий показатель прочности указывает на способность изделия под большими нагрузками сохранять свою целостность. Такой инструмент надежно защищен от трещин, сколов. Этот же показатель говорит о способности клинка не ломаться под изгибом. Как правило, самая прочная сталь для ножа не обладает нужным значением твердости.
Твердость стали для ножей
Эта еще одна основная характеристика, которая влияет на выбор инструмента для применения в разных условиях. В некоторых ситуациях клинок должен выдерживать нагрузку под изгибом, и показатель твердости отвечает за это свойство. Достигается эта характеристика в ущерб прочности, поэтому самая твердая сталь для ножа может быть подвержена сколам или даже трескается под действием серьезных нагрузок.
Износостойкость
Самая крепкая сталь обладает хорошей сопротивляемостью к износу во время эксплуатации, истиранию. Сюда же можно отнести коррозийную стойкость, которая не дает агрессивным внешним факторам разрушать структуру материала. Часто износостойкостью жертвуют в пользу других более важных свойств изделия. Важно учитывать этот параметр в случаях, когда подбирается охотничий нож, который часто бывает во влажной среде.
Из какой стали делают ножи
Все ножевые стали являются сплавом углерода и железа в одинаковых пропорциях. Если добавить больше первого элемента, получается жесть, если второго – чугун. При добавлении в состав дополнительных химических элементов (примеси и легирование) материал получает особенные свойства. Как правило, для этого используют такие элементы:
- углерод;
- хром;
- марганец;
- молибден;
- кремний;
- никель;
- вольфрам;
- ванадий.
Виды стали для ножей
Когда человек определяется с тем, какая сталь для ножей самая лучшая, в голову приходят названия, которые были услышаны много раз в самых разных приключенческих фильмах – булатная и дамасская. Этим двум видам приписывают небывалые особенности, являющиеся, как правило, элементом фольклора. К примеру:
- Булатная. Очень часто упоминается в былинных рассказах про богатырей. Сплав имеет сложный состав из углерода и кристаллических фракций железа. Обладает специфическим узором на поверхности, волокнистой структурой металла. Булатный нож, изготовленный по всем требованиям, будет отличным режущим инструментом, но не лучше, чем варианты из других видов металла.
- Дамасская. Еще один окруженный мифами сплав с красивым узором на поверхности из-за послойного использования мало и сильно науглероженного железа. Композит за счет своей структуры обладает некоторой вязкостью, гибкостью, способностью долго удерживать заточку. Главным плюсом изделий из этого металла стал своеобразный рисунок, который мог появляться спонтанно при перемешивании слоев.
Современные изготовители часто используют порошковую композитную, японскую, углеродистую, нержавеющую, русскую или китайскую сталь. Каждый из этих вариантов обладает своими особенностями, которые определяют сферу применения изделия и его цену. Какой из видов материала самый лучший, сказать невозможно, потому что их характеристики используются в разных ситуациях для достижения необходимого эффекта.
Какую сталь выбрать для ножа
Каждый мастер или пользователь сам определяет, какая сталь для ножей самая лучшая. Это связано с особенностью работы над материалом, его свойствами, характеристиками или стоимостью. Можно выделить несколько фирм производителей и марок стали, которые среди покупателей признаны самыми удачными по совокупности свойств изделия. Изучите их рейтинг ниже, чтобы выбрать подходящее изделие.
Марка стали для ножей
Между мастерами, пользователями постоянно идет спор, какая сталь для ножей считается самой лучшей, но согласно потребительскому спросу и отзывам, популярными и надежными считаются такие марки:
- М390 – нержавеющая сталь из премиум сегмента. Обладает стойкостью к износу, ржавчине из-за наличия в составе хрома. Лучший показатель удержания заточки и вариант среди ножевых металлов. Пользуется высокой популярностью благодаря одной из самых дешевых моделей изделий с этой маркой – Benchmade Barrage.
- ZDP-189 – материал из того же сегмента. Обладает высокой твердостью и приемлемой пластичностью. Часто применяется для создания дорогих ножей от компании Spuderco, используют они его при изготовлении своих лучших «лимитных» моделей.
- СРМ S35VN – улучшенная версия известной S30V от Криса Рива. Для ее создания использовались более мелкая структура порошка и добавление ниобия. Это помогло улучшить способность принимать заточку, прочность.
- ATS-34 – японский металл, вариант марки 154СМ. Эти две разновидности схожи по свойствам. Высококачественный материал с хорошим показателем удержания заточки. К минусам можно отнести меньшую устойчивость к ржавчине, чем у других вариантов из этого сегмента.
- VG-10 – этот металл похож на описанный выше, но содержит большое количество хрома и ванадия, что делает его лучше. Часто используется для изделий дешевле 100$ у японской компании Spydreco.
- 440С – материал среднего ценового сегмента, очень популярен среди производителей. В составе много хрома, углерода. Изделия из него легко точатся, не склонны к износу, питтингу (коррозии).
- AUS-8 – японский сплав хорошего уровня, устойчив к ржавчине, но из-за более низкого количества углерода не очень хорошо держит заточку.
Видео: ножевые стали
Отзывы
Дмитрий, 38 лет
Не думал, что так сложно определиться с тем, какая сталь для ножей является самой лучшей. Подбирал себе нож для выезда на природу (иногда ездим на рыбалку или охоту). Искал вариант, который бы не был подвержен ржавлению. На мой взгляд, лучшим был вариант из M390, хоть и обошелся в кругленькую сумму. Покупкой полностью доволен.
Кирилл, 28 лет
Мы с друзьями часто выезжаем на пикники, где приходится много резать, ковырять, разделывать. Под это дело искал недорогой вариант ножа, который будет не жалко и не так-то просто испортить. Остановился на модели из стали AUS-8, прекрасное соотношение цена/качество. Долго не тупится, стальная часть без единой зазубрины (пока что).
Эксперт в областях
sovets.net
Самый прочный металл • Наука
апреля 07, 2012
Самый прочный металл
Титан
Прочный металл – эти слова чаще всего ассоциируются у нас с саблей из известной дамасской стали или какими-нибудь средневековыми доспехами. Материал, из которого издревле изготавливали доспехи, оружие, а в более поздний период корпус корабля – это сталь, а сталь, в общем-то, если сказать точнее, не чистый металл. Сталь – это сплав железа с углеродом и другими соединениями. С помощью различных добавок (ванадий, вольфрам, хром и др.) получают необходимые для сплава свойства. Чтобы получить наиболее прочный сплав, в сталь включают титан (Titanium).
Описание металла
Известно, что титан – самый прочный из всех чистых металлов на Земле. Даже название этого металла говорит уже о многом. В мифологии титаны – бесстрашные и могучие дети богини Геи. Существует и другая версия, согласно которой название этого металла пошло от имени королевы фей Титании, что вызвано уникальной легкостью металла.
Титан был открыт в конце 18- го века, но очень долгое время не находил применения из-за своей хрупкости.
Исследуя свойства этого материала, ученные получили чистый титан. Металл оказался очень полезным для конструкторов и инженеров. Среди физических свойств этого металла можно выделить высокую удельную прочность, малую плотность, прочность при высоких температурах и коррозийную стойкость. Если сравнивать титан с другими металлами, то по прочности он превосходит железо вдвое, а алюминий в шесть раз.
Титановые сплавы
Титановые сплавы используют в условиях повышенных температур, при которых легкие сплавы уже не справляются. Этот материал активно используют в сверхзвуковой авиации. Корпус самолета, который летит со скоростью, превышающей скорость звука в три раза, разогревается до 300 градусов. С такими нагрузками может справиться только титановый сплав.
Месторождения этого металла разбросаны по всему миру. Индия, Япония, Украина, Россия, Китай – это далеко не все страны, которые владеют таким ценным металлом.
Возможности применения титана практически неограниченны. Военная промышленность, медицина, авиастроение и многие другие отрасли уже никак не смогут обойтись без него.
Денис Малецкий, Samogo.Net
Последние опубликованные

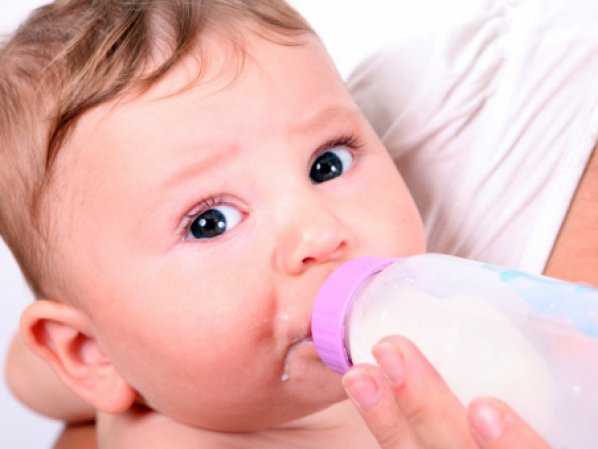
samogoo.net
В 15 раз прочнее стали: изобретены самые прочные в мире кремниевые нановолокна
Ученые из Университета исследовательского центра оптоэлектроники в Саутгемптоне первыми начали разработку самых крепких в мире нановолокон кремния
Главной задачей, стоящей перед учеными, было нахождение материала сверхвысокой прочности. Ход работы привел сотрудников исследовательского центра к созданию легкого и очень прочного нанопровода, исключительно устойчивого по отношению к разного рода нагрузкам. Исторически сложилось, что углеродные нанотрубки стали самым доступным из прочных материалов, однако их высокая прочность может быть измерена только на достаточно небольших образцах – размером буквально в несколько микрон, что говорит о малой возможности их практического применения.
Новый научный проект исследовательского центра, организованный профессором Дэвидом Пейном и старшим научным сотрудником доктором наук Джилберто Брамбиллой, завершился созданием самого прочного и легкого кремниевого нановолокна – «нанопровода», который оказался в 15 раз крепче стали и может производиться длиною в тысячи километров.
Их изобретение уже вызвало большой интерес у многих компаний по всему миру: ведь такие прочные и легкие волокна могут помочь модернизировать авиационную и судостроительную промышленность и отрасли, связанные с созданием средств безопасности. В настоящее время проводятся масштабные испытания волокон, чтобы определить возможности их дальнейшего практического применения.
«Очень важно, чтобы синтетические волокна обладали высокой прочностью, которую можно достичь с помощью производства волокон с очень низкой степенью повреждаемости и малым весом.
Обычно, если вам необходимо увеличить прочность волокна, вы вынуждены увеличивать его диаметр, а соответственно, и вес, однако наше исследование показало, что если вы уменьшите размеры кремниевого нановолокна, то его прочность, напротив, увеличится, а вес останется таким же малым. Мы являемся первыми исследователями, которые смогли оптимизировать прочность таких волокон.
Наше открытие способно усовершенствовать комбинированные материалы и материалы с высокой прочностью по всему миру и значительно повлиять на модернизацию авиационной и судостроительной промышленности и отрасли, связанной с созданием средств безопасности. Мы хотим исследовать потенциальные возможности использования волокон в комбинированных материалах и определить, могут ли они свободно использоваться при создании таких машин, как самолеты, катера и вертолеты», – рассказывает доктор Брамбилла.
Профессор Пейн добавляет: «Кремниевые нановолокна в 15 раз крепче высокопрочной стали и в 10 раз крепче обычного стеклопластика. Мы даже можем уменьшить количество затраченного материала, тем самым уменьшив вес объекта, не снизив его прочности.
Кремний и кислород, необходимые для производства нановолокон, – два наиболее распространенных вещества земной коры, что позволит сделать производство стабильным и недорогим. Более того, мы даже можем производить нановолокна тоннами, так, как мы это делаем сейчас в отношении оптических волокон для Интернета».
Новое изобретение стало результатом пятилетних исследований доктора Брамбиллы и профессора Пейна, проводимых за счет финансирования со стороны Королевского сообщества в размере 500 000 фунтов стерлингов. Доктор Брамбилла поделился результатами своих исследований с другими учеными на специальном семинаре, который он недавно организовал в Королевском общественном международном центре в Кавли (Чичели Холл, Бакингемшир).
«Это был вызов для нас – работа с волокнами, которые были настолько маленькими. Они почти в 1000 раз тоньше, чем человеческий волос, и я работал с ними почти голыми руками, – говорит доктор Брамбилла. – Мне потребовалось некоторое время, чтобы привыкнуть к материалу. Но в конце концов я смог обнаружить, что кварцевые нановолокна становятся тем более прочными, чем меньше их размер. Фактически, если очень уменьшить нановолокна, они начинают удивительно вести себя. Они перестают быть хрупкими и не ломаются как стекло, а становятся податливыми и гнутся как пластмасса. Это означает, что их можно растягивать».
«До настоящего времени мы проводили в основном теоретические научные исследования нановолокон, однако в ближайшем будущем мы заинтересованы непосредственно в изучении практического применения этих волокон в современных технологиях», – добавляет доктор Брамбилла.
www.km.ru
Дамасская сталь | www.samsmasteril.ru
Как ни крути, но в кузнечном (в частности — оружейном) ремесле самым большим ореолом тайны и романтики окружена легендарная дамасская сталь.
Процесс создания дамасской стали и ее свойства всегда были чем-то таинственным, почти сакральным. Считается, что секрет изготовления этой стали давно и навеки утерян.
На самом деле — все не так сокрыто и потеряно, как принято считать. Для начала давайте избавимся от самых устойчивых мифов о дамасской стали.
Развенчание мифов
Миф первый и самый устойчивый: «Секрет дамасской стали давно и безнадежно утерян».
Так утверждают все, кто не связан с производством клинков.
Дамасская сталь — композит как минимум из двух сортов сталей, что ни для кого не секрет. Приготовляют дамасскую сталь методом соединения пластинок из этих самых сталей путем кузнечной сварки (и это — тоже не тайна).
Так в чем же этот самый «утерянный секрет»? В используемых сталях? Отчасти — верно. До технической революции очень остро стояла проблема получения качественной стали, которая использовалась в том числе и как сырье для производства дамаска. Поэтому у каждого мастера имелись свои проверенные методы испытания сталей. Именно их мастера и делали тем самым «секретом».
В современном мире все несравненно проще. Марки сталей имеют постоянный состав в соответствии с ГОСТом, и где бы вы ни находились, взяв сталь марки У10, или ШХ15, или 65 Г, получите каждый раз практически один и тот же рабочий материал, свойства которого более или менее стабильны.
Получается, что тот самый «сокровенный секрет» действительно утерян, но намеренно. Причина — в потери актуальности.
Миф второй: «Дамасская сталь — самая прочная сталь в мире».
Миф только отчасти. Говорящие так просто повторяют точку зрения наших далеких предков, которых действительно удивляли и впечатляли свойства и внешний вид дамасских клинков в сравнении с обычными сталями того периода. Ведь, как уже было отмечено, проблема получения качественной стали была очень трудноразрешима несколько веков назад.
В сравнении же с современным качеством сталей исторический дамаск в большинстве своем не дотягивает до привычных стандартов качества.
Хотя это можно проверить, если взять и попробовать самому сварить дамаск!
Выбор стали
Для получения качественного дамаска мы должны приобрести качественные стали, которые и будем сваривать в пакет. Чтобы обеспечить будущей стали хорошие свойства, среднее содержание углерода в пакете должно быть не менее 0,7 %. Поэтому в качестве сырья подходят инструментальные стали; кроме того, можно использовать конструкционные стали с содержанием углерода не менее 0,5 %.
Легирующие добавки в инструментальных и конструкционных сталях зачастую все усложняют. Однозначно непригодны для первых опытов со сваркой все нержавеющие стали. Следует воздержаться от использования обойм подшипников, так как их изготавливают из стали ШХ15, в которой содержится излишнее количество хрома.
Лучше всего остановить свой выбор на простых углеродистых сталях. В качестве источника материала можно использовать старые напильники, рессоры, пружины.
Предварительная подготовка
Давайте остановимся на варианте сборки пакета из напильника и рессоры. Напильники изготавливают из стали У10– У12 (т. е. содержание углерода — 1–1,2 %), на рессоры идет сталь с содержанием углерода примерно 0,5–0,6 %. Взяв эти стали в соотношении 1:1, получаем среднее содержание углерода в пакете 0,7–0,8 %.
Перед сборкой пакета нужно порезать напильник и рессору на пластинки одинакового размера. С напильника можно сточить насечку, а с рессоры следует удалить ржавчину и окалину. Зачистите пластинки, сложите их в стопку, чередуя напильник и рессору, и скрепите пакет по углам точками электросварки.
Для сварки и ковки вручную пакет должен быть невысоким и узким, шириной около 25 мм и высотой 25–30 мм. В длину пакет не должен превышать 200 мм.
Для кузнечной сварки необходим флюс, который растворяет образующуюся окалину и защищает сталь от окисления. Самым лучшим флюсом считается бура (тетраборат натрия), обладающая хорошей текучестью в расплавленном состоянии, прекрасно растворяющая окалину и окислы и легко удаляющаяся во время ковки. Для сварки небольшого пакета нам вполне хватит горсти флюса.
В качестве топлива для горна при кузнечной сварке древесный уголь практически не знает себе конкурентов. Годится литейный кокс. А вот каменный уголь для сварки не подходит.
Следует не забыть приготовить пару молотков: один — полегче, граммов 500–700 (для выдавливания расплавленного флюса и сварки сталей), второй — потяжелее (для протяжки проваренного пакета).
Нам пригодится стальная щетка-крацовка, чтобы смахивать с пакета окалину и излишки флюса. Щетка должна быть стальная, а не латунная, так как присутствие меди при кузнечной сварке сведет все попытки сварить пакет к неминуемому провалу.
Следует заранее позаботиться о емкости, в которой будет находиться бура при флюсовании пакета. Подойдет неглубокая металлическая ванночка или старая сковорода. Подготовьте также «ложку», чтобы наносить буру на раскаленный пакет стали.
Внимание! При работе обязательно используйте средства защиты! Плотная куртка с длинными рукавами, кожаный фартук, кожаные рукавицы, защитные очки или маска-щиток обязательны!
Прогрев пакета
Сначала нужно разжечь горн и как следует прокалить уголь. Загрузив пакет в среднюю (нейтральную) зону горна, его следует медленно прогреть при слабом дутье до желто-оранжевого цвета (примерно +850–900 °С), что займет минут 15–20 (для пакета среднего размера).
Как только пакет хорошенько прогрелся, достаем его из горна и быстро смахиваем с него образовавшуюся окалину металлической щеткой-крацовкой. При прогреве до светло-оранжевого цвета окалина легко отстает от стали. Сразу же обсыпаем пакет флюсом.
Снова загружаем пакет в горн и на этот раз быстро нагреваем его до сварочной температуры при достаточно сильном дутье. Как только языки пламени окрасились в желтый цвет, значит, сталь нагрелась до температуры +1 100 °С — достигнута нижняя граница сварочной температуры.
Продолжаем нагрев и внимательно наблюдаем за пламенем! Как только замечаем первые одиночные «пушистые» искорки, начинающие проскакивать в пламени, значит, нужная нам температура достигнута.
Прекращаем дутье в горн и достаем пакет. Не допускайте сильного перегрева стали — это будет уже пережог.
Выдавливание флюса
Теперь нужно выдавить флюс с растворенной окалиной из пространства между пластинами пакета и добиться плотного примыкания пластин стали между собой.
Вооружившись небольшим ручником, начинаем наносить не сильные, но точные удары, выдавливая флюс с одного конца пакета к другому. Работать следует, нанося только кистевые удары. Как только мы выдавили весь флюс между пластинами, необходимо зачистить пакет от остатков шлака щеткой и снова нанести порцию свежего флюса для защиты от окисления при следующем прогреве.
Два способа ковки
Нагреваем пакет до сварочной температуры и интенсивно проковываем. Повторяем эту процедуру столько раз, сколько будет необходимо для того, чтобы осадить пакет примерно в 2–3 раза от первоначальной высоты.
Далее можно действовать двумя способами. Первый — «одноходовая ковка». Прокованный пакет в горячем состоянии надрубается на две или три части и складывается вдвое или втрое. Надрубать следует на 2/3 или 3/4 толщины пакета со стороны, противоположной складыванию. Перед складыванием поверхности зачищаются щеткой и флюсуются.
Мы увеличиваем количество слоев в пакете соответственно способу надрубания. Предположим, изначальный пакет состоял из 6 слоев стали. Надрубая пополам и складывая вдвое, мы получаем соответственно 12 слоев, далее — 24, 48, 96 и т. д. Складывая втрое, мы получаем 18 слоев, затем — 54, 162, 486 и т. д. Набирая слои стали, следует остановиться в промежутке от 150 до 350 слоев.
Второй способ — «многоходовая ковка». При нем после сварки пакета он проковывается на полосу, которой нужно дать остыть и которая затем режется на пластинки, снова укладывающиеся в первоначальный пакет. Получается, мы каждый раз свариваем первоначальный пакет. Набор слоев стали при этом будет выглядеть так: изначальный пакет из 6 слоев; проковав на полосу и снова собрав пакет из 6 пластинок, получим пакет с 36 слоями стали; повторив процедуру, получим пакет с 216 слоями и т. д.
Каждый способ по-своему хорош и дает несколько различные рисунки полученной стали.
Чтобы увидеть результаты своего труда, нужно зачистить пакет и протравить сталь в слабом растворе кислоты или хлорного железа.
Антон Жуйков, руководитель регионального отделения Союза кузнецов России по Кировской области, фото автора
www.samsmasteril.ru