Механические свойства металлов и способы их определения Категория: Технология металлов Механические свойства металлов и способы их определения Большинство деталей машин находится в эксплуатации под воздействием внешних сил. При этом характер внешних сил может быть самым разнообразным. Иногда внешняя сила действует постоянно в течение длительного времени или статически. Могут быть другие условия работы, когда внешняя сила действует непродолжительное время и действие имеет ударный характер. В этом случае нагрузка имеет динамический характер. Наконец возможны случаи длительного воздействия многократно повторяющейся силы. Усилие носит пульсирующий, повторно-переменный, или, как называют иначе, циклический характер. Детали или конструкции в этом случае работают, как говорят, на выносливость (или усталость), Для того чтобы решить, какой материал может быть использован для изготовления той или иной детали или конструкции, необходимо знать механические свойства этого материала. Механическими свойствами материала называется совокупность свойств, характеризующих способность материала сопротивляться воздействию внешних усилий. Способность сопротивляться у всех материалов зависит, во-первых, от того, каким образом прикладывается усилие (статически, динамически или циклически), во-вторых, от того, какой характер имеет внешнее усилие — растягивающее, сжимающее, крутящее, изгибающее и т. п. Статические испытания на растяжение. Испытание на растяжение производится путем растяжения специально приготовленного для этой цели образца на испытательной машине. Механические свойства материала, определяемые при этих испытаниях, объединяют в две группы: При этом под прочностью понимают способ-кость металла сопротивляться разрушению под действием внешних нагрузок. Под пластичностью — способность под действием нагрузок принимать новую форму не разрушаясь. Стандартным образцом для испытания на растяжение является образец, показанный на рис. 20, а. Диаметр стандартного образца выбирается в зависимости от мощности машины и предполагаемой прочности материала. Расчетная длина цилиндрической части определяется соотношением l0= \Od0, где d0 — его начальный диаметр. Все остальные размеры образца определяются конструкцией захватных устройств испытательной машины. При испытании листового материала применяется образец, показанный на рис. 20, б. Толщина образца определяется толщиной листового материала, ширина — мощностью машины и предполагаемой прочностью материалу. Расчетная длина образца устанавливается из соотношения 10 — 11,3 VFa, где F0 — начальная площадь его поперечного сечения. Определение механических свойств производят обычно по диаграмме деформации, записываемой самой испытательной машиной. Диаграмма деформации показывает зависимость изменения длины образца при постепенном возрастании величины прилагаемого усилия. В первый момент испытания длина образца увеличивается пропорционально нагрузке — чем больше растягивающее усилие, тем больше увеличение длины. При этом образец деформируется упруго, т. е. при устранении нагрузки образец примет свою первоначальную длину. Такая деформация носит название упругой деформации. При достижении нагрузки Ps в металле возникает заметная пластическая деформация — сдвиги слоев металла относительно друг друга, и при устранении нагрузки образец не принимает своей первоначальной длины. Рис. 1. Эскизы стандартных образцов для испытания на растяжение: Нагрузка, отвечающая этому моменту Ps, называется нагрузкой предела текучести. Отношение этой нагрузки к площади поперечного сечения называют пределом текучести. Рис. 2. Диаграмма деформации при испытании металлов на растяжение Как видно из формулы, предел текучести измеряется в кг/мм2. Величины, выраженные в таких единицах, называют напряжением. Таким образом, пределом текучести называют напряжение, при котором начинает развиваться заметная пластическая деформация. При дальнейшем увеличении нагрузки за пределом текучести прямолинейной зависимости между нагрузкой и длиной образца уже нет. Наконец наступает такой момент, когда нагрузка начинает падать, а в образце намечается образование сужения поперечного сечения (образование шейки). Таким образом, пределом прочности называют максимальное напряжение, выдержанное образцом. Дальнейшее растяжение образца сопровождается образованием все более сужающейся шейки и падением нагрузки. Вслед за этим наступает разрушение образца. Пределы прочности и текучести характеризуют прочность материала. Другой, не менее важной характеристикой является пластичность. Рис. 3. Изменение образца в результате растяжения: При испытании на растяжение пластичность определяют двумя величинами: относительным удлинением и относительным сужением. Для того чтобы понять, как эти величины определяются, следует образец до испытания сопоставить с разрушенным образцом, как это сделано на рис. 22. После разрушения образец оказался длиннее, но он сузился, особенно в месте образования шейки. Испытательные машины, применяемые для определения механических свойств металлов при растяжении, очень разнообразны как по способу создания растягивающего усилия, так и по способу определения этого усилия и деформаций образца. Испытательные машины снабжены специальным нагружающим механизмом для создания усилий. Эти механизмы бывают механического и гидравлического действия. Для определения этих усилий и деформаций образца при растяжении машины снабжаются силоизме-рительными устройствами разных типов. Эти устройства в большинстве случаев имеют диаграммный аппарат, позволяющий автоматически записывать диаграмму деформации. По этой диаграмме и определяются прочностные и пластические свойства металла. На рис. 23 показан общий вид разрывной 4-тонной машины. Верхний захват связан с маятником, который, отклоняясь на определенный угол, уравнобешивает силу, тянущую образец вниз. Угол отклонения маятника соответствует нагрузке, прикладываемой к образцу. Эта нагрузка, а также растяжение образца отмечаются на диаграммном аппарате в виде диаграммы деформации, показанной на рис. 2. Методы определения твердости. Твердость — это способность металла сопротивляться проникновению в него другого, более твердого тела. Рис. 4. Испытательная 4-тонная машина ИМ-4р Твердость является весьма важной характеристикой, так как тесно связана с такими основными характеристиками металлов и сплавов, как прочность, износостойкость и др. В настоящее время имеется много способов определения твердости металлов. Рассмотрим некоторые из них, наиболее широко применяемые в промышленности. Определение твердости вдавливанием стального шарика (метод Бринелля). С помощью специальной лупы измеряется диаметр лунки. По таблицам, приложенным к прибору, определяется значение твердости Не. Для испытания применяют специальный пресс типа Бринелля, внешний вид которого показан на рис. 5. Стальной шарик крепится в оправке. Исследуемый образец ставится на предметный столик и поднимается к шарику штурвалом. При включения мотора грузы пресса опускаются и вдавливают стальной шарик в образец. Рис. 5. Пресс типа Бринелля Определение твердости по глубине вдавливания.алмазного конуса (метод Роквелла). Алмазный конус с углом при вершине 120° вдавливается в металл предварительной постоянной нагрузкой 10 кг, а затем полной нагрузкой 60 или 150 кг. Для испытания используют специальный пресс, внешний вид которого показан на рис. 6. Алмазный конус крепится в оправке. Образец устанавливается на столик и поднимается с помощью штурвала до нагрузки 10 кг. Значения твердости этим методом определяются по разности глубины вдавливания алмазного конуса под действием полной и предварительной нагрузок. Чем тверже металл, тем на меньшую глубину проникает алмаз при вдавливании, тем больше будет число твердости. Стандартной нагрузкой при этом методе является 150 кг. Обозначается твердость Hrc. В некоторых случаях, например при измерении твердости на тонком образце или при измерении твердости поверхностного слоя металла, нагрузку применяют до 60 кг. На этом же приборе можно производить измерение твердости мягких материалов (цветные металлы, отожженная сталь). Рис. 6. Прибор типа Роквелла Рис. 7. Прибор для определения твердости ударным вдавливанием шарика Определение твердости динамическим вдавливанием шарика. При изменении твердости массивных деталей и конструкций, когда нельзя использовать описанные выше приборы, применяют переносный прибор, показанный на рис. В прибор закладывают эталонный образец. При ударе по прибору молотком специальный шарик 2 наносит отпечатки на исследуемый предмет и эталонный образец, твердость которого известна. Сопоставляя значения диаметров лунок образца и детали по таблицам, определяют твердость детали. Определение твердости методом упругой отдачи. В тех случаях, когда нельзя применять методы вдавливания, чтобы не испортить поверхности изделия, используется прибор,.определяющий твердость методом упругой отдачи. На рис. 8 показан внешний вид прибора. С постоянной высоты на металл падает определенного веса боек и отскакивает. По величине отскока судят о твердости. Чем больше твердость, тем больше отскок бойка. Производительность этого метода испытаний очень велика (несколько сот измерений в час). Однако применять его можно только для сравнения между собой твердости изделий из одного и того же металла или из металлов, имеющих одинаковые упругие свойства. Испытание на удар. Весьма распространенным видом механических испытаний является испытание на удар. С помощью таких испытаний можно выявить склонность к хрупкости, появляющейся в некоторых материалах при низких температурах («хладноломкость»), а также к тепловой хрупкости, возникающей в процессе работы при повышенных температурах, проконтролировать качество обработки металла и т. д. Испытание чаше всего производится на маятниковых копрах; внешний вид одного из них показан на рис. 9. Копер представляет собой тяжелый маятник, подвешенный на легкой штанге. Перед испытанием маятник поднимается на определенную высоту, что сообщает ему определенный запас энергии. При падении маятник ударяется об образец, разрушает его и по инерции проходит вперед, поднимаясь уже на меньшую высоту. Работа, затраченная на деформирование образца Адеф, пропорциональна разности высот и определяется с помощью отсчетного приспособления, установленного на станине копра. Рис. 8. Прибор для определения твердости способом упругой отдачи Образец для этого вида испытания представляет собой призматический брусок размером 10X10X55 с прорезью посередине. При этом испытании устанавливается величина ударной вязкост и, которая определяется отношением работы, затраченной на деформацию образца, к площади поперечного сечения образца в надрезе. Технологические пробы. Технологическими пробами называют испытания материала с целью выявления пригодности его к тому или иному виду обработки. Технологические пробы весьма разнообразны. Они служат лишь для качественной или сравнительной оценки металла. Обычно проведение технологической пробы оговаривается техническими условиями. Как правило, размеры образцов и-условия испытания должны быть строго одинаковыми, лишь в этом случае результаты могут сравниваться. В качестве показателей пригодности металла для каждого вида пробы выбираются свои характеристики. Такими характеристиками могут служить угол загиба, степень обжатия, число перегибов проволоки до возникновения первых признаков разрушения, степень высадки и т. д. Рис. 9. Копер, для определения механических свойств при ударе Рис. Рис. 11. Технологическая проба еварных швов Рис. 12. Проба на осадку в холодном состоянии Рис. 13. Проба на загиб трубы Рис. 14. Проба на перегиб проволоки В качестве примеров приведем следующие технологические пробы: Реклама:Читать далее:Железоуглеродистые сплавы
Статьи по теме:
Главная → Справочник → Статьи → Блог → Форум |
Лабораторная работа № 2 механические свойства металлов и методы их определения
Цель работы:
изучить способы определения основных
механических свойств металлических
материалов.
Механические свойства определяют способность металлов сопротивляться воздействию внешних сил (нагрузок). Они зависят от химического состава металлов, их структуры, характера технологической обработки и других факторов. Зная механические свойства металлов, можно судить о поведении металла при обработке и в процессе работы машин и механизмов.
К основным механическим свойствам металлов относятся прочность, пластичность, твердость и ударная вязкость.
Прочность – способность металла не разрушаться под действием приложенных к нему внешних сил.
Пластичность – способность металла получать остаточное изменение формы и размеров без разрушения.
Твердость – способность металла сопротивляться вдавливанию в него другого, более твердого тела.
Ударная вязкость – степень сопротивления металла разрушению при ударной нагрузке.
Механические свойства определяют путем проведения механических испытаний.
Испытания на
растяжение. Этими
испытаниями определяют такие
характеристики, как пределы
пропорциональности, упругости, прочности
и пластичность металлов. Для испытаний
на растяжение применяют круглые и
плоские образцы (рисунок 2.1, а, б),
форма и размеры которых установлены
стандартом. Цилиндрические образцы
диаметром d0 = 10 мм, имеющие расчетную длину l0 = 10d0,
называют нормальными, а образцы, у
которых длина l0 = 5d0,
– короткими.
При испытании на растяжение образец
растягивается под действием плавно
возрастающей нагрузки и доводится до
разрушения.
Разрывные
машины снабжены специальным самопишущим
прибором, который автоматически
вычерчивает кривую деформации, называемую
диаграммой растяжения. Диаграмма
растяжения в координатах «нагрузка Р – удлинение ∆l»
отражает характерные участки и точки,
позволяющие определить ряд свойств
металлов и сплавов (рисунок 2. 1). На участке
0 — Рпц удлинение образца увеличивается прямо
пропорционально возрастанию нагрузки.
При повышении нагрузки свыше Рпц,
на участке Рпц — Pупр прямая пропорциональность нарушается,
но деформация остается упругой
(обратимой). На участке выше точки Pvпр возникают заметные остаточные деформации,
и кривая растяжения значительно
отклоняется от прямой. При нагрузке Рт появляется горизонтальный участок
диаграммы — площадка текучести Т-Т1,
которая наблюдается, главным образом,
у деталей из низкоуглеродистой стали.
На кривых растяжения хрупких металлов
площадка текучести отсутствует. Выше
точки Рт нагрузка возрастает до точки А,
соответствующей максимальной нагрузке Рв,
после которой начинается ее падение,
связанное с образованием местного
утонения образца (шейки).
Затем нагрузка
падает до точки В,
где и происходит разрушение образца. С
образованием шейки разрушаются только
пластичные металлы.
а, б – стандартные образцы для испытания на растяжение;
в – диаграмма растяжения образца из пластичного материала
Рисунок 2.1 – Испытание на растяжение
Усилия, соответствующие основным точкам диаграммы растяжения, дают возможность определить характеристики прочности, выраженные в мегапаскалях, МПа, по формуле
, (2.1)
где σi – напряжение, МПа;
Pi – соответствующая точка диаграммы растяжения, Н;
F0 – площадь поперечного сечения образца до испытания, мм2.
Предел пропорциональности σпц – это наибольшее напряжение, до которого сохраняется прямая пропорциональность между напряжением и деформацией:
. (2.2)
где σпц – предел пропорциональности, МПа;
Pпц – напряжение, соответствующее пределу пропорциональности, Н;
F0 – площадь поперечного сечения образца до испытания, мм2.
Предел упругости σупр — напряжение, при котором пластические деформации впервые достигают некоторой малой величины, характеризуемой определенным допуском (обычно 0,05 % ):
. (2.3)
где σупр – предел упругости, МПа;
Pупр – напряжение, соответствующее пределу упругости, Н;
F0 – площадь поперечного сечения образца до испытания, мм2.
Предел текучести физический σт — напряжение, начиная с которого деформация образца происходит почти без дальнейшего увеличения нагрузки:
. (2.4)
где σт – предел текучести физический, МПа;
Pт – напряжение, соответствующее пределу текучести, Н;
F0 – площадь поперечного сечения образца до испытания, мм2.
Если площадка текучести на диаграмме растяжения данного материала отсутствует, то определяется условный предел текучести σ0,2 — напряжение, вызывающее пластическую деформацию, равную 0,2 %.
Предел прочности (временное сопротивление) σв — напряжение, равное отношению наибольшей нагрузки, предшествующей разрушению образца, к первоначальной площади его сечения:
. (2.5)
где σв – предел прочности, МПа;
Pв – напряжение, соответствующее пределу прочности, Н;
F0 – площадь поперечного сечения образца до испытания, мм2.
По
результатам испытания на растяжение
определяют характеристики пластичности металлов.
Показатели пластичности металлов — относительное удлинение и относительное сужение — рассчитывают по результатам замеров образца до и после испытания.
Относительное удлинение δ находится как отношение увеличения длины образца после разрыва к его первоначальной расчетной длине, выраженное в процентах:
, (2.6)
где lk — длина образца после разрыва, мм;
l0 — расчетная (начальная) длина образца, мм.
Относительное сужение ψ определяется отношением уменьшения площади поперечного сечения образца после разрыва к первоначальной площади его поперечного сечения, выраженным в процентах:
, (2.7)
где F0 — начальная площадь поперечного сечения образца;
Fк — площадь поперечного сечения образца в месте разрушения.
Методы
определения твердости. Наиболее
распространенным методом определения
твердости металлических материалов
является метод вдавливания, при котором
в испытуемую поверхность под действием
постоянной статической нагрузки
вдавливается другое, более твердое тело
(наконечник). На поверхности материала
остается отпечаток, по величине которого
судят о твердости материала. Показатель
твердости характеризует сопротивление
материала пластической деформации, как
правило, большой, при местном контактном
приложении нагрузки.
Твердость определяют на специальных приборах — твердомерах, которые отличаются друг от друга формой, размером и материалом вдавливаемого наконечника, величиной приложенной нагрузки и способом определения числа твердости. Так как для измерения твердости испытывают поверхностные слои металла, то для получения правильного результата поверхность металла не должна иметь наружных дефектов (трещин, крупных царапин и т. д.).
Измерение
твердости по Бринеллю. Сущность
этого способа заключается в том, что в
поверхность испытуемого металла
вдавливается стальной закаленный шарик
диаметром 10, 5 или 2,5 мм в зависимости от
толщины образца под действием нагрузки,
которая выбирается в зависимости от
предполагаемой твердости испытуемого
материала и диаметра наконечника по
формулам: Р = 30D2; Р = 10D2; Р = 2,5D2 (таблица 2. 1).
Таблица 2.1 – Выбор диаметра шарика D и нагрузки Р
Материал образца | Твердость, кгс/мм2 | Толщина образца, мм | Диаметр шарика D, мм | P/D2, кгс/мм2 | Нагрузка Р, кгс | Выдержка под нагрузкой, с |
Черные металлы (сталь, чугун) | 450 — 140 | более 6 6 – 3 менее 3 | 10 5 2,5 | 30 | 3000 750 187,5 | 10 |
Черные металлы | Менее 140 | более 6 6 – 3 менее 3 | 10 5 2,5 | 30 | 3000 750 187,5 | 30 |
Твердые цветные металлы (латунь, бронза, медь) | 140 – 32 | более 6 6 – 3 менее 3 | 10 5 2,5 | 10 | 1000 250 62,5 | 30 |
Мягкие
цветные металлы (олово, алюминий и
др. | 35 — 8 | более 6 6 – 3 менее 3 | 10 5 2,5 | 2,5 | 250 62,5 15,6 | 60 |
На поверхности образца остается отпечаток (рисунок 2.2, а), по диаметру которого определяют твердость. Диаметр отпечатка измеряют специальной лупой с делениями.
Твердость рассчитывают по формуле
, (2.8)
где НВ – твердость по Бринеллю, кгс/мм2;
Р – нагрузка при испытании, кгс или Н;
F – площадь полученного отпечатка, мм2;
D – диаметр наконечника, мм;
d – диаметр отпечатка, мм.
Рисунок 2.2 – Измерение твердости методами Бринелля (а),
Роквелла (б), Виккерса (в)
На практике пользуются специальными таблицами, которые дают перевод диаметра отпечатка в число твердости, обозначаемое НВ. Например: 120 НВ, 350 НВ и т.д. (Н – твердость, В – по Бринеллю, 120, 350 – число твердости в кгс/мм2, что соответствует 1200 и 3500 МПа).
Этот способ применяют, главным образом, для измерения твердости незакаленных металлов и сплавов: проката, поковок, отливок и др.
Твердомер Бринелля можно использовать в том случае, если твердость материала не превышает 450 кгс/мм2. В противном случае произойдет деформация шарика, что приведет к погрешностям в измерении. Кроме того, твердомер Бринелля не применяется для испытания тонких поверхностных слоев и образцов тонкого сечения.
Измерение
твердости по Роквеллу. Измерение
осуществляют путем вдавливания в
испытуемый металл стального шарика
диаметром 1,588 мм или алмазного конуса
с углом при вершине 120° (см. рисунок 2.2, б). В
отличие от метода Бринелля твердость
по Роквеллу определяют не по диаметру
отпечатка, а по глубине вдавливания
наконечника.
Вдавливание производится под действием двух последовательно приложенных нагрузок — предварительной, равной ≈ 100 Н, и окончательной (общей) нагрузки, равной 1400, 500 и 900 Н. Твердость определяют по разности глубин вдавливания отпечатков. Для испытания твердых материалов (например, закаленной стали) необходима нагрузка 1500 Н, а вдавливание стальным шариком нагрузкой 1000 Н производят для определения твердости незакаленной стали, бронзы, латуни и других мягких материалов. Глубина вдавливания измеряется автоматически, а твердость после измерения отсчитывается по трем шкалам: А, В, С (таблица 2.2).
Таблица 2.2 – Наконечники и нагрузки для шкал А, В, С
Наконечник | Суммарная нагрузка Р, Н (кгс) | Отсчет по шкале | Обозначение твердости |
Стальной шарик | 1000 (100) | В (красная) | HRB |
Алмазный конус | 1500 (150) | С (черная) | HRC |
Алмазный конус | 600 (60) | А (черная) | HRA |
Твердость
(число твердости) по Роквеллу обозначается
следующим образом: 90 HRA,
80 HRB,
55 HRC
(Н – твердость, Р – Роквелл, А, В, С – шкала твердости, 90, 80, 55 – число
твердости в условных единицах).
Определение твердости по Роквеллу имеет широкое применение, так как дает возможность испытывать мягкие и твердые металлы без дополнительных измерений; размер отпечатков очень незначителен, поэтому можно испытывать готовые детали без их порчи.
Измерение твердости по Виккерсу. Данный метод позволяет измерять твердость как мягких, так и очень твердых металлов и сплавов. Он пригоден для определения твердости очень тонких поверхностных слоев (толщиной до 0,3 мм). В этом случае в испытуемый образец вдавливается четырехгранная алмазная пирамида с углом при вершине 136о (см. рисунок 2.2, в). При таких испытаниях применяются нагрузки от 50 до 1200 Н. Измерение отпечатка производят по длине его диагонали, рассматривая отпечаток под микроскопом, входящим в твердомер. Число твердости по Виккерсу, обозначаемое НV, находят по формуле
, (2.9)
где Р — нагрузка, Н;
d — длина диагонали
отпечатка, мм.
На практике число твердости НV находят по специальным таблицам.
Определение ударной вязкости производят на специальном маятниковом копре (рисунок 2.3). Для испытаний применяется стандартный надрезанный образец, который устанавливается на опорах копра. Маятник определенной массой поднимают на установленную высоту Н и закрепляют, а затем освобожденный от защелки маятник падает, разрушает образец и снова поднимается на некоторую высоту h. Удар наносится по стороне образца, противоположной надрезу. Для испытаний используют призматические образцы с надрезами различных видов: U-образный, V-образный, T-образный (надрез с усталостной трещиной).
а – схема испытания, б – образцы для испытаний.
Рисунок 2.3 – Испытания на ударную вязкость
Ударная вязкость КС (Дж/см2) оценивается работой, затраченной маятником на разрушение стандартного надрезанного образца, отнесенной к сечению образца в месте надреза:
,
(2. 10)
где А – работа, затраченная на разрушение образца (определяется по разности энергий маятника до и после удара: А0 – А1), Дж;
F – площадь поперечного сечения образца в месте надреза, см2.
В зависимости от вида надреза в образце ударная вязкость обозначается KCU, KCV, KCТ (третья буква – вид надреза).
World Of NDT Механические свойства металлов
Распространяйте любовь
Механические свойства — это физические свойства, которые материал (металл) проявляет при приложении сил. Механические свойства металлов определяют диапазон полезности материала и определяют ожидаемый срок службы. Механические свойства также используются для классификации и идентификации материала. Механические свойства материала не являются постоянными и часто меняются в зависимости от температуры, скорости нагружения и других условий.
, чтобы узнать о инженерном материале. Прочитайте наш блог:
.
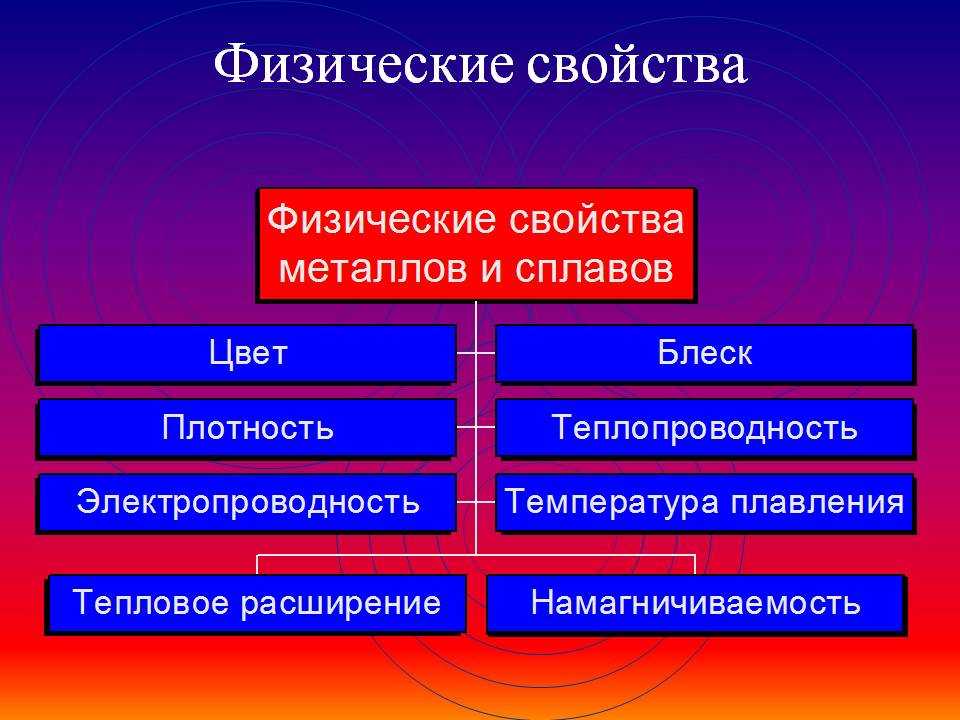
- Прочность на растяжение
- Прочность на сдвиг
- Прочность на кручение
- Прочность на удар
- Усталостная прочность
. Прочность на растяжение обычно определяется двумя разными способами: пределом прочности на растяжение и пределом текучести. Оба относятся к разным аспектам материального поведения.
UTS (предел прочности при растяжении) , иногда называемый просто пределом прочности при растяжении, относится к максимальной несущей способности этого металла или прочности этого металла в точном месте, когда происходит разрушение.
Для определения предела текучести необходимо понимать, что имеется в виду, когда металл ведет себя «упруго». Упругое поведение относится к деформации металла под нагрузкой, которая не вызывает остаточной деформации при снятии нагрузки. Например, резинка растягивается под нагрузкой, но возвращается к своей первоначальной форме, когда нагрузка снимается. Когда металл нагружается в области упругости, он реагирует некоторым растяжением или удлинением. В этом диапазоне растяжение прямо пропорционально приложенной нагрузке, поэтому упругое поведение называют линейным. Если металл подвергается напряжению за пределами своего предела упругости, он больше не ведет себя упруго, его поведение теперь называется пластичным, это также означает, что зависимость между напряжением и деформацией больше не является линейной. После того, как произойдет пластическая деформация, материал не вернется к исходной длине после снятия приложенной нагрузки. Точка, в которой поведение материала меняется с упругого на пластическое, называется пределом текучести.
Пластичность — это термин, который относится к способности материала деформироваться или растягиваться под нагрузкой без разрушения. Чем пластичнее металл, тем больше он будет растягиваться, прежде чем сломается. Пластичный материал будет изгибаться, прежде чем сломаться, что является хорошим показателем того, что предел текучести металла превышен. Металлы с низкой пластичностью внезапно разрушаются хрупким образом без какого-либо предупреждения. Пластичность металла напрямую связана с его температурой. С повышением температуры пластичность металла увеличивается, а с понижением температуры пластичность уменьшается. Металл с высокой пластичностью называют пластичным, а металл с низкой пластичностью – хрупким.
Это способность материала сопротивляться вдавливанию или проникновению. Термин твердость также упоминается как жесткость или характер или сопротивление изгибу, царапанью, истиранию или порезу. Это свойство материала, придающее ему способность противостоять постоянной деформации при приложении нагрузки. Чем больше твердость материала, тем больше сопротивление деформации. Твердость по-разному определяется как сопротивление локальному проникновению, царапанию, механической обработке, износу или истиранию, а также текучесть. Как правило, разные материалы различаются по своей твердости; например, твердые металлы, такие как титан и бериллий, тверже, чем мягкие металлы, такие как натрий и металлическое олово, или дерево и обычные пластмассы.
Прочность — это способность материала поглощать энергию. Другим распространенным термином является ударная вязкость. Он отличается от ударной вязкости тем, что относится к способности материала поглощать энергию при наличии поверхностных дефектов, тогда как ударная вязкость относится к способности поглощать энергию гладкого образца без надреза. Разница между металлами низкой и высокой ударной вязкости заключается в том, что низкие значения ударной вязкости определяют хрупкое поведение, а высокие значения ударной вязкости связаны с пластичным разрушением.
Прочность металла изменяется при изменении температуры. Как правило, при понижении температуры снижается и ударная вязкость металла. Если материал демонстрирует высокую вязкость надреза, это означает, что он будет работать хорошо независимо от того, есть надрез или нет. Однако, если материал чувствителен к надрезам, то есть обладает низкой ударной вязкостью, он может легко выйти из строя во время удара или повторяющихся нагрузок. Как правило, ударная вязкость металла с надрезом уменьшается по мере увеличения его твердости и снижения температуры.
Усталостная прочность металла определяется как прочность, необходимая для сопротивления разрушению при повторяющихся нагрузках. Предел выносливости — это максимальное напряжение, при котором не происходит разрушения, независимо от того, сколько циклов прикладывается нагрузка.
Усталость металла вызывается циклическим или повторяющимся механическим воздействием на элемент. То есть нагрузка попеременно изменяется между и некоторым более низким напряжением или реверсированием напряжения. Это действие может происходить быстро, как в случае вращения двигателя, или медленно, когда циклы могут измеряться днями. Примером усталостного разрушения может быть многократное изгибание вала двигателя с целью его поломки. Этот тип отказа обычно происходит ниже предела прочности вала на растяжение. Усталостная прочность углеродистой стали примерно равна половине ее прочности на растяжение.
Усталостная прочность, как и ударная вязкость, сильно зависит от геометрии поверхности элемента. Наличие любой выемки или концентраторов напряжения может увеличить напряжение в этой точке выше предела выносливости металла. После применения достаточного количества циклов произойдет усталостное разрушение.
Каталожные номера:
https://www.nde-ed.org/
AWS – Технология контроля сварки
функция Фото Павла Незнанова на Unsplash
Распространяйте любовь
Механические свойства металлов
Механические свойства металла определяют его пригодность для применения. Свойства помогают предсказывать поведение металлов при определенных условиях. Знание свойств металла также помогает в уточнении требований при закупке сырья для изготовления оборудования.
С точки зрения сварки важна количественная оценка поведения основного металла в цифрах. Выбор электрода для сварки основного металла важен, поскольку свойства металла шва должны быть совместимы со свойствами основного металла. Обычно определяемыми свойствами, которые помогают сделать правильный выбор электрода или сварки, являются: химический состав, предел прочности при растяжении, ударная вязкость, твердость и т. д.
Механические свойства металла можно определить, проведя различные тесты , помогающие установить поведение металла. В этой статье мы кратко обсудим различные механические свойства металлов и их важность.
Механические свойства обычно используемых металлов
Предел прочности
Прочность на сдвиг
Предел выносливости
Прочность на сжатие
Эластичность
Модуль упругости
Пластичность
Пластичность
Пластичность
Уменьшение площади
Хрупкость
Прочность
Обрабатываемость и свариваемость
Стойкость к истиранию
твердость
Испытание на твердость по Бринеллю
Испытание на твердость по Роквеллу
Склероскопический тест на твердость
Изменяет ли термическая обработка свойства металла?
Механические свойства обычно используемых металлов
Различные металлы имеют разные свойства. Свойства определяют пригодность металла для применения. В следующей таблице показаны обычно указанные механические свойства металлов, обычно используемых в производстве.
Прочность на растяжение
Когда мы тянем металлический стержень, он реагирует, развивая противодействующую силу внутри своего тела, которая сопротивляется внешнему натяжению. Эта противодействующая сила равна по величине приложенной извне силе и возрастает по мере увеличения внешней силы. Однако она не может увеличиваться бесконечно. То, насколько металл может сопротивляться внешнему натяжению, прежде чем отдать, является его неотъемлемым свойством, которое также называется прочностью.
Внутренняя реакция, возникающая внутри металла, зависит от площади поперечного сечения металлической детали и приложенной внешней нагрузки. Эту реакцию чаще называют напряжение развивалось внутри металла. Другими словами, напряжение, возникающее внутри металлического образца, представляет собой нагрузку на единицу площади.
Максимальное напряжение, которому металлический образец стандартного размера может выдержать до разрушения, называется предельным растягивающим напряжением (UTS) и выражается в фунтах на квадратный дюйм (psi). В метрической системе это выражается в ньютонах на квадратный миллиметр. Напряжение, при котором металл начинает достигать предела текучести 90 152, 90 153, называется пределом текучести (YS). UTS и YS металла можно определить, выполнив простое испытание на растяжение на универсальной испытательной машине или UTM. Нахождение этих двух значений дает нам представление о поведении металла при одинаковых условиях нагрузки.
В ходе этого испытания мы также можем найти процентное удлинение образца (что является показателем пластичности металла), процентное уменьшение площади (что также является показателем пластичности металла). С практической точки зрения, прочность в фунтах на квадратный дюйм указывает на силу (в фунтах), необходимую для разрыва металлического куска с площадью поперечного сечения 1 дюйм (25,4 мм) на 1 дюйм (25,4 мм).
Прочность на сдвиг
Прочность на сдвиг указывает на способность металла сопротивляться сдвигу. Когда две силы действуют на металл, но не в одной плоскости (см. рисунок ниже), они пытаются вызвать сдвиг в металле. Металл пытается сопротивляться сдвигу. Степень его способности делать это называется прочностью на сдвиг. Его можно рассчитать по математическим формулам.
Усталостная прочность
Когда металл подвергается нагрузкам противоположного типа (например, растяжению и сжатию) большое количество раз, в металле возникает «усталость». Например, вращающийся вал, несущий груз, имеет сжимающую нагрузку в металлических волокнах, находящихся вверху в данный момент. В этот же момент на волокна, находящиеся внизу, действует растягивающая нагрузка.
В следующее мгновение волокна, которые были наверху, оказались внизу, а те, что раньше были внизу, теперь наверху. Теперь нагрузка на эти волокна обратная. Волокна, которые раньше находились под растягивающей нагрузкой, теперь находятся под сжимающей нагрузкой, а те, которые раньше подвергались сжимающей нагрузке, наоборот.
Это значение продолжает изменяться, пока вращается вал. Это повторяющееся изменение типа нагрузки на металлические волокна вызывает в них усталость. Свойство усталостной прочности металла является мерой того, сколько циклов (такой изменяющейся нагрузки) металл может выдержать без разрушения. Иногда это также выражается как нагрузка, которую металл может выдержать в течение заданного количества циклов без разрушения.
Усталостная прочность металла зависит от микроструктуры, твердости поверхности, нагартовки и т. д.
Прочность на сжатие
Прочность на сжатие — это максимальная сжимающая нагрузка, которую может выдержать металл до того, как произойдет заданная величина деформации. Другими словами, прочность на сжатие — это способность металла выдерживать сжимающие усилия (как показано на рисунке ниже) до деформации.
Для некоторых веществ их прочность на сжатие выше, чем их прочность на растяжение. Несколько примеров такого поведения — чугун и бетон. Однако для большинства материалов верно обратное.
Эластичность
Когда мы растягиваем резину, она немного деформируется. Тем не менее, он возвращается к своей первоначальной форме после снятия натяжения. Это связано с тем, что резина является очень эластичным материалом. Металлы на руке не такие эластичные.
Металлы крепкие. Они не подвергаются деформации при небольших нагрузках. Однако при увеличении нагрузок происходит небольшая деформация. Фактически, ровный металл возвращается к своему первоначальному размеру после снятия нагрузки. Другими словами, металл демонстрирует упругое поведение. Это называется эластичностью. Металл проявляет такое поведение только до определенной нагрузки, после которой деформация становится постоянной.
Когда нагрузка превышает предел упругости, металл проявляет пластическое поведение. То есть деформация постоянная. Эластичность выражается через предел текучести и представляет собой ту нагрузку, при которой начинается пластическое поведение.
Предел текучести металла можно определить, выполнив простое испытание на растяжение. Как и UTS, YS также выражается в фунтах на квадратный дюйм (МПа или Н/мм2 в метрической системе).
Модуль упругости
Проще говоря, модуль упругости представляет собой отношение напряжения к деформации. Поскольку деформация является безразмерной величиной, модуль упругости имеет те же единицы измерения, что и напряжение.
Мера сопротивления металла упругой деформации при воздействии на него внешней нагрузки. Его можно рассчитать по наклону кривой напряжения-деформации в упругой области. Более жесткий металл будет иметь более высокий наклон на этой кривой.
Пластичность
Пластичность металла – это его способность растягиваться без остаточной деформации. Такие металлы, как медь и алюминий, довольно пластичны, в то время как металлы, такие как чугун, не такие пластичные и хрупкие.
Прямого теста для измерения пластичности не существует. Однако параметр «удлинение в процентах» при испытании на растяжение является показателем пластичности металла. Металл с высокой пластичностью будет иметь более высокий процент удлинения, в то время как металл с меньшей пластичностью будет иметь меньшее значение процентного удлинения.
Пластичность
Пластичность противоположна эластичности. Свойство металла постоянно деформироваться без разрыва и без возможности вернуться к своей первоначальной форме при снятии внешней нагрузки.
Пластичность
Пластичность аналогична пластичности. Проще говоря, это способность металла растягиваться в листы без разрыва. Это волочение в листы осуществляется посредством ковки или прокатки и представляет собой необратимую деформацию. Такие металлы, как золото, олово и серебро, обладают превосходной ковкостью. На самом деле, добро обладает такой исключительной податливостью, что его можно раскатать в листы, достаточно тонкие, чтобы пропускать свет.
Уменьшение площади
Когда испытуемый образец подвергается деформации при испытании на растяжение, площадь его поперечного сечения постоянно уменьшается, прежде чем произойдет окончательный разрыв. Для пластичных материалов это уменьшение площади настолько велико, что точка излома становится острой. Для хрупких материалов величина деформации, которая возникает перед разрушением, намного меньше. Следовательно, уменьшение площади также происходит не сильно.
Уменьшение площади в процентах можно рассчитать, измерив площадь поперечного сечения сломанного образца и сравнив ее с первоначальной площадью поперечного сечения. Мера этого значения указывает на пластичность металла.
Хрупкость
Противоположность пластичности. Когда металл является хрупким, он не подвергается деформации, как это происходит с пластичным материалом при испытании на растяжение. На самом деле, он внезапно ломается, как только внешняя нагрузка превышает его прочность. Другими словами, хрупкому материалу не хватает пластичности или эластичности.
Мел, которым пишут на школьной доске, является примером хрупкого материала. Среди металлов мартенситная микроструктура является примером хрупкости.
Прочность
Прочность – это способность материала поглощать энергию без разрушения. Это площадь под кривой напряжения-деформации. Для высокой ударной вязкости материал должен иметь сочетание высокой прочности и пластичности.
Обрабатываемость и свариваемость
Обрабатываемость – это легкость обработки металла.
Свариваемость – это способность металла поддаваться сварке без каких-либо дефектов.
Сопротивление истиранию
Это стойкость металла к эрозии поверхности в результате износа вследствие трения.
Твердость
Твердость – это способность материала сопротивляться вдавливанию. Металл обычно показывает высокие значения твердости, если он обладает высокой прочностью и ударной вязкостью. Твердый материал трудно обрабатывать и сваривать. Вообще говоря, изготовление твердого металла затруднено.
Твердость материала выражается по-разному. Одной из единиц является число твердости по Бринеллю. Другой часто используемой единицей измерения является число твердости по Роквеллу. Число твердости по Виккеру — еще одна широко используемая единица измерения.
В этом испытании шарик из твердой стали медленно вдавливается в металл с известной силой. За счет этого на поверхности металла образуется небольшая вмятина. Размер этого отступа измеряется и сравнивается со стандартными таблицами.
Испытание на твердость по РоквеллуВ этом испытании сначала прикладывается легкая нагрузка, а затем большая нагрузка. Разница в глубине вдавливания, вызванная двумя нагрузками, измеряется и используется в качестве показателя твердости материала. Значение твердости отображается на циферблате. Полученное таким образом значение называют числом твердости по Роквеллу.
Определение твердости с помощью склероскопа В ходе этого испытания молоток с алмазным наконечником падает на поверхность металла с фиксированной высоты и отскакивает. Вес молота фиксирован. Отскок измеряется по шкале. Величина отскока принимается за показатель твердости материала.
Этот тест подходит для поверхностей, на которых вмятины нежелательны по разным причинам.
Изменяет ли термическая обработка свойства металла?
Термическая обработка, если она выполнена правильно, приводит к желаемому изменению свойств металла. Он используется в промышленности для улучшения пластичности, увеличения твердости и прочности, а иногда и для его размягчения для улучшения обрабатываемости и свариваемости.
Термическая обработка может проводиться в одну или несколько стадий. Иногда это делается в виде серии операций для достижения желаемых свойств. Скорость нагревания, скорость охлаждения, температура выдержки и время, проведенное при температуре.
Закалка и размягчение углеродистой стали, содержащей более 0,35% углерода, могут осуществляться путем регулирования скорости нагрева и охлаждения. Для малоуглеродистых сталей с помощью этого метода невозможно получить заметное упрочнение.