Станы. Прокатные станы
Механическое оборудование
1.1 Входное оборудование
1.1.1 Стеллаж для рулонов разматывающего барабана
Описание
Этот стеллаж для рулонов располагается на стороне оператора и предназначается для получения рулона с мостового крана и хранения рулона перед разматывающим барабаном.
Технические данные
1.1.2 Тележка для подъема рулона на разматывающий барабан
Описание
Эта тележка для рулонов располагается перпендикулярно к линии прокатки около разматывающего барабана и предназначается для транспортировки рулонов от стеллажа для рулонов до разматывающего барабана.
Подвижная плита настила предназначается для закрытия открытого приямка, когда тележка для рулонов находится под оправкой разматывающего барабана. Она будет крепиться к каретке и двигаться на ней.
Будет состоять из каретки, подъемного устройства, подвижной плиты настила и трубопровода.
Технические данные
1.1.3 Разматывающий барабан
Описание
Мы предполагаем, что намотка рулона обычная, с натяжением, а не спиральная. Если намотка рулона спиральная, то мы предложим другую систему разматывателя.
Разматывающий барабан располагается перед входом на входной натяжной барабан и предназначается для подачи полосы в стан.
Материал подается на разматывающий барабан с помощью тележки разматывающего барабана, перемещающейся горизонтально.
Разматыватель будет подвесного типа с закрытым приводом.
Опорная плита представляет собой толстолистовую плиту. Она устанавливается на смазанных обработанных направляющих со сменными бронзовыми накладками.
Головка барабана состоит из четырех сегментов. Она разжимается с помощью гидроцилиндра, сегменты клиновидные. Оправка разжимается до номинального диаметра 600 мм.
Амортизирующий ролик будет опускаться посредством цилиндра, чтобы упростить процесс заправки полосы.
Технические данные
1) Собственно барабан
Технические данные
2) Амортизирующий ролик
1.1.4 Устройство для измерения рулона
Описание
Высота центрирующего устройства используется для измерения внешнего диаметра рулона, чтобы отцентрировать оправку разматывающего барабана и рулон, находящийся на тележке. Ширина центрирующего устройства используется для измерения ширины рулона, чтобы выровнять центр оправки разматывающего барабана с центром рулона, находящимся на тележке.
Оно состоит из сварной стальной рамы и фотоэлементов.
Технические данные
1.1.5 Подающее устройство рулонов с отгибателем для конца рулонов и заправочным столом
Описание
Устройство подачи полосы предназначается для отгибания и подачи переднего конца рулона на входную секцию стана.
Оно состоит из верхнего ролика, нижнего ролика, перегибного ролика, входного калибра и направляющей для заправки, и заправочного стола на выходе.
Входной калибр и направляющая для заправки поворотного типа, со специальным ножом из специальной инструментальной стали на гидроцилиндре.
Нижний ролик – свободно вращающийся стальной ролик, установлен на сварной металлоконструкции. Верхний ролик установлен на поворотном рычаге наверху основания, с гидроцилиндром. Приводится в движение мотором-редуктором перем. тока через универсальный шарнир.
Перегибной ролик подводится к передней кромке рулона. Это свободно вращающийся ролик, установленный на сварной металлоконструкции.
Заправочный стол на выходе представляет собой сварную металлоконструкцию.
Технические данные
1.1.6 Барабан на входе и натяжной барабан
Описание
Барабан и натяжной барабан располагаются на входной стороне стана и предназначаются для намотки и размотки полосы до или после прокатки.
Барабан и натяжной барабан подвесного типа с закрытым приводом.
Опорная плита представляет собой толстолистовую плиту. Она устанавливается на смазанных обработанных направляющих со сменными бронзовыми накладками.
Головка барабана и натяжного барабана представляет собой один барабан и четыре клиновидных сегмента. Головка барабана имеет зажим для конца рулона с гидроклапаном. Головка натяжного барабана разжимается вращающимся гидроцилиндром, установленном на приводной стороне оправки барабана. Оправка разжимается до номинального диаметра 500 мм.
Технические данные
Технические данные
2) Амортизирующий ролик для барабана и натяжного барабана
3) Наружный подшипник (Опора барабана)
1.7 Входная тележка для подъема рулона
Описание
Эта тележка для рулонов располагается перпендикулярно к линии прокатки на стороне оператора около натяжного барабана и предназначается для транспортировки рулонов от входного стеллажа для рулонов до входной натяжного барабана.
Подвижная плита настила предоставляется для закрытия открытого приямка, когда тележка для рулонов находится под оправкой барабана. Она будет крепиться к каретке и двигаться на ней.
Будет состоять из каретки, подъемного устройства, подвижной плиты настила и трубопровода.
Технические данные
1.1.8 Входной стеллаж для рулона
Описание
Этот стеллаж для рулона располагается на стороне оператора у входной натяжного барабана и предназначается для получения рулона из тележки для рулонов и хранения рулона до разгрузки.
Технические данные
1.2 Описание двухвалковый реверсивный стан
1.2.1 Клеть стана
Описание
2-валковый стан, станина цельная, изготавливается из литой или листовой стали.
Станина будет соединяться разделителем из сварной стали.
Линия прокатки будет регулироваться вручную, с использованием планки, или системы сдвигания клиновой пластины и клинового зажима, приводимого в движение гидроцилиндром.
Аспирационные колпаки установлены на станине стана для сбора дыма, образующегося во время прокатки.
Технические данные
1.2.2 Гидравлическое устройство позиционирования валка
Описание
Гидравлическое устройство позиционирования валка предоставляется для контроля рабочего зазора для уменьшения толщины полосы и получения указанной толщины вручную.
Рабочие гидроцилиндры в двух комплектах. Гидравлические механизмы сервоклапанов контролируют шаг гидроцилиндра.
Месдозы установлены наверху станины стана.
Технические данные
1.2.3 Узел валков
Описание
Два рабочих валка.
Технические данные
1) Рабочий валок
1.2.4 Направляющие клети на входе и выходе
Описание
Направляющая на входе предназначается для подачи верхнего конца полосы на валки стана. Она будет состоять из прижимного роликового захвата и боковой направляющей.
В прижимном захвате используется шарнирный параллелограмм. Предоставляется с верхними и нижними валками и с пневмоцилиндром. Извлекается через люк станина стана для смены валком и техобслуживания.
Боковая направляющая вертикального роликового типа. Открывается и закрывается с помощью гидравлического двигателя для регулировки ширины. Механизм быстрого открытия/закрытия с гидроцилиндром также предоставляется.
Направляющая на выходе расположена на выходной стороне клети стана и предназначается для подачи передней кромки полосы на отклоняющие ролики.
Защита от перекоса также предоставляется для предотвращения перекоса оборудования во время заправки и разрыва полосы на входной и выходной сторонах. Убирается через люк станина стана гидроцилиндром для смены валков и техобслуживания.
Технические данные
1.2.5 Вспомогательное оборудование стана
Описание
Стойки с контактным толщиномером располагаются на выходной стороне для измерения толщины полосы.
Ролик с трубчатым скребком располагается на входной и выходной сторонах клети стана и стойки с толщиномером.
Большое число охлаждающих коллекторов предназначено для подачи охлаждающего масла на валки и полосу. Охлаждающий коллектор для рабочего валка разделен на две секции. Точечные охлаждающие коллекторы также устанавливаются на выходной стороне нижнего рабочего валка. Они разделены на восемь секций.
Технические данные
1) Толщиномер и стойка
Спецификация
1.2.6 Отклоняющие и тянущие ролики на входе и выходе
Описание
Отклоняющие ролики на входе и выходе располагаются на входной и выходной сторонах прокатного стана и предназначаются для отклонения линии прокатки полосы и направления передней кромки полосы на оправку натяжного барабана на входе и выходе.
Это оборудование состоит из сварной металлоконструкции, отклоняющих роликов, направляющей для заправки и тянущих роликов.
Технические данные
1.2.7 Трубопровод стана
Описание
Данный трубопровод будет поставляться для гидравлической жидкости для приводов или подшипников на клетях от мест присоединения со стороны стана межсоединительных трубопроводов до них.
Это касается следующих систем:
- гидравлическая система стана
- дополнительная гидравлическая система
- система смазки масляным туманом
- система охлаждения валков
- система регулирования подвода воздуха
Технические данные
- Количество: одна партия
4.1.2.8 Устройство перевалки валков
Описание
Устройство для перевалки рабочих валков будет предоставлено для одновременной смены верхних и нижних рабочих валков.
Оно будет состоять из тележки для перевалки валков с боковым передвижным столом, выталкивателем и рельсой. Тележка перемещается с помощью гидравлического выталкивателя и оборудована гидравлическим боковым передвижным столом.
Устройство для перевалки рабочих валков будет предоставлено для перевалки верхних и нижних валков. Оно с захватом и состоит из рельсы и проставки. Рельса для нижнего рабочего валка с гидроприводом типа колесо-рельс. Управляется вручную.
Технические данные
1) Устройство для перевалки рабочих валков
1.2.9 Рабочий шпиндель
Описание
Рабочий шпиндель будет располагаться между клетью стана и главным приводом стана на стороне привода стана, он передает крутящий момент от главного привода к двум рабочим валкам.
Технические данные
- Тип: шестеренный
- Вал: из стали
- Муфта: сделано из кованой стали
- Смазка муфты: шприцом для консистентной смазки
4.1.2.10 Рабочий привод стана
Описание
Рабочий привод будет располагаться между клетью стана и приводом стана, он будет приводить два рабочих валка прокатной клети через это оборудование приводным двигателем.
Технические данные
1.2.11 Передняя шторка стана
Описание
Защитная шторка со стороны оператора стана будет установлена для предотвращения разбрызгивания валкового охладителя со стороны прокатной клети. Более того, защитная шторка улучшит эффективность работы системы вытяжной вентиляции.
В случае перевалки валков шторка будет открываться и закрываться вручную.
Технические данные
- Количество : один комплект
4.1.3 Оборудование выходной секции
1.3.1 Барабан и натяжной барабан на выходе
Описание
Барабан и натяжной барабан располагаются перед входом в стан и предназначаются для наматывания/разматывания прокатываемой или уже прокатанной полосы.
Барабан и натяжной барабан будут подвесного типа с закрытым приводом.
Опорная плита представляет собой толстолистовую плиту. Она устанавливается на смазанных обработанных направляющих со сменными бронзовыми накладками.
Головка барабана и натяжного барабана представляет собой один барабан с четырьмя клиновидными сегментами. Головка барабана имеет зажим для конца рулона с гидроклапаном. Она разжимается с вращающимся гидроцилиндром, установленном на приводном конце оправки барабана. Оправка будет разжиматься до номинального диаметра 500 мм.
Технические данные
1) Барабан
Технические данные
1.3.2 Выходная тележка для подъема рулона
Описание
Эта тележка для рулонов располагается перпендикулярно к линии прокатки на стороне оператора около выходного натяжного барабана и предназначается для транспортировки рулонов от стеллажа для рулонов до натяжного барабана.
Подвижная плита настила предоставляется для закрытия открытого приямка, когда тележка для рулонов находится под оправкой натяжного барабана. Она будет крепиться к каретке и двигаться на ней.
Будет состоять из каретки, подъемного устройства, подвижной плиты настила и трубопровода.
Технические данные
1.3.3 Выходной стеллаж для рулонов
Описание
Этот стеллаж для рулонов располагается на стороне оператора на входе натяжного барабана и предназначается для получения рулона с тележки и хранения рулона для разгрузки рулонов.
Технические данные
1.4 Вспомогательное оборудование
1.4.1 Гидравлическая система стана
Описание
Данная система устанавливается в маслоподвал и необходима для подачи гидравлического масла для балансировки валка, прогиба рабочего и промежуточного валка, позиционирования валка и перемещения промежуточного валка.
Данная система состоит из резервуара, насосов, аккумуляторов, клапанов и масел.
Технические данные
1.4.1. Вспомогательная гидравлическая система
Описание
Данная система устанавливается в маслоподвал и необходима для подачи гидравлического масла для всех гидравлических усилителей стана и дополнительного оборудования.
Данная система состоит из резервуара, насосов, аккумуляторов, клапанов и масел.
1.4.3 Клапанная стойка
Описание
Данная клапанная стойка устанавливается в техническом подвале, маслоподвале и на станине. Она необходима для компактного размещения электромагнитных клапанов для гидравлической и пневматической систем. Некоторые из пневмораспределителей с электромагнитным управлением будут предоставлены на соответствующем оборудовании.
Технические данные:
1.4.4 Система смазки зубчатой передачи
Описание
Данная система устанавливается в маслоподвал, и необходима для подачи смазочного масла в подшипник и зубчатые колеса основного привода стана, моталок и их узла привода.
Она состоит из резервуара, насоса, фильтров, теплообменника, температурного регулятора, клапанов и трубной обвязки.
Технические данные
Комплектующие:
— фильтр
— обогрев с помощью нагревателя
— охлаждение с помощью водоохладителя
— реле давления, дифференциальные реле давления и поплавковые переключатели
1.4.5 Система смазки масляным туманом
Описание
Данная система необходима для подачи масляного тумана для смазки подшипника опорного валка стана и отклоняющих валок.
Она состоит из генератора масляного тумана, узла дозагрузочного клапана (refill valve) и узла дозагрузочного насоса
Технические данные
1.4.6 Система охлаждения валков
Описание
Данная система необходима для подачи охлаждающего масла на полосу и валки для смазки и охлаждения.
Она состоит из резервуара, насоса для орошения, охладителя, фильтра, фильтр-насоса, клапанов и трубной обвязки.
Резервуар для охлаждающего масла находится в маслоподвале и имеет смотровое окошко.
Технические данные
1.4.7 Система аспирации
Описание
Данная система необходима для отсоса паров вокруг стана с помощью колпака стана и выпуска пара из выхлопной трубы наружу .
Она состоит из всасывающего вентилятора (эксгаустера), очистителя, противопожарного клапана, трубок и выводной трубки.
Противопожарный клапан должен быть предоставлен в трубке на входе всасывающего вентилятора. Он управляется пневматическим цилиндром. Рабочий сигнал подается системой обнаружения огня и системой противопожарной безопасности.
Технические данные
1.4.8 Дренажный насос
Описание
Данная система устанавливается на слив (сливное отверстие) в маслоподвале и от очистителя в установку очистки сточных вод.
Система дренажного насоса состоит из насоса, клапанов и комплектующих.
Технические данные
1.4.9 Специальные инструменты
Описание
Партия специальных инструментов будет предоставлена для технического обслуживания оборудования.
Подробный список инструментов будет уточнен на этапе проектирования.
Технические данные
1.4.10 Анкерные болты, гайки и прокладки
Описание
Будет поставлена партия анкерных болтов, гаек, шайб и прокладок, необходимых для установки оборудования стана.
Технические данные
Комплектующие
- анкерный болт, гайка и шайба
- анкерная плита для вставленных болтов
- Прокладки и накладки для оконечного оборудование и оборудования стана
1.4.11 Соединительный трубопровод
Описание
Поставщик поставляет схематическую диаграмму и сборочные чертежи в качестве основного проектного решения.
Технические данные
1) Гидравлическая система
- резервуар ~ насосная установка
- насосная установка ~ клапанный стенд
- клапанный стенд ~ трубопровод установки
2) Система смазки
- резервуар ~ насосная установка
- насосная установка ~ фильтр или охладитель
- фильтр или охладитель ~ трубопровод установки
3) Система охлаждения валка
- стан ~ грязевик
- грязевик или резервуар с профильтрованной жидкостью ~ насос
- насос ~ фильтр или охладитель
- фильтр или охладитель ~ трубопровод установки
2 Электрическое оборудование
2.1 Оборудование для подачи электроэнергии
Описание
Мощность трансформатора будет определена на стадии детальной проработки
1) Пневматический прерыватель цепи и распределительный щит
Тип: устанавливаемый на полу и самоподдерживаемый, для внутреннего размещения
Выдвижного типа для ввода
Пневматический прерыватель цепи установленного типа
Для питателя магнитных выключателей
2) Центр управления двигателем
Двустороннего выдвижного типа
мягкий пуск для гидравлических двигателей
Напряжение основной цепи: 380 В перем. тока, 3 фазы, 50 Гц
Напряжение цепи управления: 220В перем. тока, 1 фаза, 50 Гц
2.2 Двигатели и пульт привода
2.2.1 Двигатели переменного тока
Двигатели с постоянной скоростью вращения переменного тока являются индукционными двигателями промышленного назначения.
Следующие технические спецификации применимы ко всем нерегулируемым двигателям переменного тока, если иначе не указано в перечне двигателей.
2.2.2 Редукторный двигатель переменного тока
Передача двигателя представляет собой промышленный редуктор. Следующие технические спецификации применимы ко всем редукторным двигателям, если иначе не указано в перечне двигателей.
Двигатель
- Спецификация та же, что и на нерегулируемый двигатель
Передача
- Тип подшипника : антифрикционный с уплотнениями
- Смазка : консистентная либо разбрызгиванием
- Монтаж : на лапах / горизонтальный
- Тип соединения : прямая муфта
- Эксплуатац. коэфф. : AGMA CLASS II (1.4 Основан на номинале двигателя)
2.2.3 Двигатель постоянного тока с постоянной мощностью
Двигатели постоянного тока являются индукционными двигателями промышленного назначения. Следующие технические спецификации применимы ко всем двигателям переменного тока, если иначе не указано в перечне двигателей.
1. Фаза : 3 фазы
2. Номинальное напряжение : 380В постоянного тока (устанавливается в соответствии с основным проектом)
3. Коэффициент мощности : 125% 1 минута
4. Класс защиты кожуха : IP 22, IP54
5. Класс изоляции : F
6. Охлаждение : принудительное или самоохлаждающий вентилятор
7. Комплектующие : основание, анкерные болты, гайки и втулка/гильза для двигателя
8. КПД : стандартный
9. Детектор скорости (генератор импульсов, если управление с замкнутым контуром)
10. Муфта для детектора скорости
11. Тормоз (в соответствии с проектом)
2.2.5 Двигатель постоянного тока с постоянной мощностью и управляющее устройство привода
2.3 Система ПЛК
Описание
Система программируемого логического контроля (ПЛК) будет поставляться для управления холодный станом и дополнительным оборудованием. Она будет управлять редуктором и дополнительным оборудованием холодного стана, используя рабочий стол и человеко-машинный интерфейс (ЧМИ).
Соединение холодного стана с главным ПЛК будет определено на стадии детальной проработки.
Технические данные
Функции стана
- Толчок вперед или назад; сигнал скорости регулируется программным обеспечением, диапазон сигналов – индивидуальный.
- Позиционирование шпинделя
Генерирует сигнал низкой скорости для клети с тем же диапазоном, как толчок.
Остановка позиционирования для шпинделя обеспечивается бесконтактным выключателем. - Управление привода
Необходимые блокировки отправляются к приводу. - Коэффициент скорости
Коэффициент линейной скорости намотки барабана и окружная скорость рабочих валков измеряется посредством генераторов импульсов, установленных на отклоняющих роликах и клети.
Коэффициент представляет сдавливание (уменьшение) для наматывающего (разматывающего) барабана; он используется при расчете исходной скорости и натяжения и при инерционном контроле на правом барабане или контроле левого барабана.
Функции барабана
Данная функция – при выборе “reel” (барабан): подсчет натяжения и скорости автоматический.
Толчок
Толчок вперед или назад; опорный сигнал скорости регулируется с помощью программного обеспечения, расчетная скорость индивидуальна.
Позиционирование зажима
Создает низкоскоростной опорный сигнал для барабана с той же скоростью, что толчок. Положение стоп для зажима обеспечивается бесконтактным выключателем.
Позиционирование конца полосы (только для разматывающего устройства)
Вырабатывает низкоскоростной сигнал для позиционирования конца полосы возле люльки. Позиционирование работает с кодирующим устройством барабана и останавливается, когда достигается рассчитанное расстояние (от механических размеров).
Управление приводом
Необходимые блокировочные устройства отправляются к приводу.
Диаметр рулона
Измеряется как соотношение между линейной и угловой скоростью барабана с помощью генераторов импульсов, установленных на отклоняющем ролике и барабане. Значение обновляется на постоянных углах поворота барабана. В случае проскальзывания рулона на отклоняющий ролик диаметр ограничен до примерного значения, рассчитанного на основе количества поворотов на барабане и толщины рулона.
Длина полосы
Длина полосы измеряется с помощью аналого-цифрового преобразователя отклоняющего устройства
Угловая скорость
От главного сигнала стана и фактического диаметра рулона рассчитывается и автоматически компенсируется расширением/сужением сигнал угловой скорости барабана. Рассчитанный сигнал увеличивается с величиной дополнительной скорости.
Компенсация момента инерции
Рассчитывается с использованием фактических значений ускорения рулона, диаметра рулона, расширения/сужения и ширины рулона.
Компенсация потерь на трение и двигателя
Данные по потерям хранятся в таблице в зависимости от реальной угловой скорости барабана.
Ток барабана
Заданное значение тока барабана рассчитывается на основе предварительной установки натяжения и компенсации момента инерции. Исходное значение корректируется, чтобы скомпенсировать механические и электрические потери.
Управление натяжением типа “Максимальный крутящий момент”, т.е. у поля всегда максимально возможная величина, тогда как ток в обмотке меняется в зависимости от требуемого натяжения , скорости и диаметра рулона.
Работа с максимальным крутящим моментом дает преимущество лучшего коэффициента мощности и меньшей нагрузки на двигатель (детали в «Управлении натяжением»).
rolling-mills.ru
Прокатный стан – откуда берется разнообразие изделий из металла? + видео
С развитием металлургии сильно возросли требования и к используемому в данной области оборудованию, так что современный высокопроизводительный прокатный стан отличается от своих предшественников.
1 Назначение и роль прокатного стана
Одной из самых важных областей промышленности является производство металла, и с этим поспорить довольно тяжело, ведь от того, насколько развита данная отрасль, зависит не только состояние народного хозяйства, но и экономика всего государства. При этом стоит учитывать, что потребность человечества в этом прочном материале постоянно растет. Поэтому сейчас практически невозможно представить себе промышленную область, где бы не участвовала металлургия. Она применяется и в машиностроении, и в строительстве, и в кораблестроении – в общем, список можно продолжать и продолжать. Завершающим же технологическим этапом производства столь нужного материала является получение проката.
Рекомендуем ознакомиться
Безусловно, добиться результата можно, только используя специальное оборудование, которое путем пластической деформации осуществляет прокат. Вообще, на производстве слаженно работает целый комплекс машин, в их функции входит не только основная операция, но и ряд вспомогательных. Это, например, подача сырья, калибровка материала, кантовка, а также транспортировка уже готовой продукции. Кроме того, автоматизированы и такие процессы, как резка, маркировка, правка, упаковка и, конечно же, передача на склад. Но в этой статье мы разберем именно стадию проката и соответствующие агрегаты.
2 Какие могут быть виды прокатных станов?
Виды прокатных станов можно разделить по назначению в зависимости от типа выпускаемого продукта. Так существуют заготовочные и обжимные станы, к последним относятся слябинги и блюминги. Это своего рода черновое оборудование, в их функции входит переработка большого слитка металла в заготовку, поступающую в дальнейшем на прокатку в другие цеха, продукция на разных типах этих станков различается геометрической формой. После них материал идет на сортовые, трубные либо же проволочные машины, где происходит более специализированный прокат.
Сортовые станы имеют достаточно разнообразные возможности. Так, на них изготавливаются многие виды швеллеров, балки, уголки, разные типы профилей, рельсы и широкополосная сталь. Типы этих машин делятся в зависимости от заданной программы, так существуют крупносортные, среднесортные, рельсопрокатные, а также установка MPS для изготовления профилей. Листовые агрегаты могут быть как горячей, так и холодной прокатки. Выпускаемая продукция делится в зависимости от габаритов на плиты толщиной от 50 до 350 мм, 3–50 миллиметровые листы и полосы (1,2–20 мм). Последние, как правило, сматывают в рулоны весом до 50 тонн.
С трубопрокатным оборудованием все ясно уже из его названия, оно необходимо для получения бесшовных труб различного диаметра. Так производят следующие изделия:
- на непрерывно удлинительном стане выходит продукция сечением до 110 мм;
- на короткоправочном – 60–450 мм,
- трехвалковый стан выпускает толстостенные трубы с пониженной разностенностью, диаметр которых составляет 35–200 мм;
- для получения бесшовных труб довольно большого диаметра (400–700 мм) нашли свое применение пилигримовые агрегаты.
Последний тип прокатного оборудования – специальное (деталепрокатное), на котором осуществляется производство труб и профилей длиной не более трех метров, а также шаров, винтов, гнутых профилей, ребристых труб, зубчатых колес и т. д. Далее эти заготовки дорабатываются уже непосредственно в автомобильной, мебельной либо иной промышленности.
3 Устройство прокатного стана – особенности механизмов
Устройство прокатного стана включает три основных узла: рабочие клети, электродвигатели и передаточные устройства. В состав первых входят валки, установочные механизмы, станины плитовины и проводки. Электродвигатели же выполняют одну из самых важных функций – вращают валки посредством передаточных устройств, состоящих в большей степени из муфт, шестерен и шпинделей.
Главной характеристикой обжимных и заготовочных станков является диаметр рабочего валка, если же участвуют сразу несколько клетей, тогда руководствуются только численными показателями чистовой, именно значение ее параметра обычно упоминается в названии.
Сортовое оборудование обычно состоит из нескольких последовательно расположенных клетей, так, например, универсальные станы имеют 5 или 3 клети, из которых 3 или 2, соответственно, имеют горизонтальные валы диаметром приблизительно 1350 мм, а сечение валов у оставшихся – около 800 мм. Толстолистовые станы обычно имеют одну или две клети, дина же валков составляет 3500–5500 мм, очень часто с целью обжатия боковых кромок они оснащаются дополнительными клетями с вертикальными валками. Наиболее же распространенными среди агрегатов для прокатки полос являются широкополосные, количество клетей в них от десяти до пятнадцати, длина бочки валов колеблется в пределах 1500–2500 мм. Они также имеют и дополнительные клети с вертикальными валками.
Как видно, иногда эти агрегаты могут занимать очень много места. А вообще, трубопрокатное оборудование в основном состоит из 3 станов, так как сначала осуществляется прошивка отверстия в заготовке путем винтовой прокатки, затем данную заготовку следует вытянуть в трубу, и последней операцией является калибровка, т. е. достижение необходимого диаметра. Основой деталепрокатных механизмов является принцип винтовой и поперечной обработки.
4 Можно ли сделать прокатный станок своими руками?
Безусловно, если говорить о крупном промышленном производстве, то здесь ни о какой самодеятельности не может идти и речи, но для домашнего использования можно сделать прокатный станок своими руками. Однако не надо недооценивать подобное оборудование, так как с его помощью можно не только получать проволоку разного сечения, но и осуществлять рихтовочные работы или резать листовые материалы, толщина которых не будет превышать полмиллиметра. Итак, нам понадобятся две стойки, верхняя плита, 4 винта М10 и, соответственно, такие же болты, стальной прут диаметром 5 см, втулки и подшипники из бронзы, пружины и упоры, 2 шестеренки и зубчатое колесо.
Соединяем стойки с плитой винтами и болтами так, чтобы получился достаточно прочный остов-клеть. Из прутка вытачиваются 2 валика, с целью увеличения их твердости следует осуществить закалку. Нижний вал монтируется в стойки посредством бронзовых втулок-подшипников, а верхний крепится в ползунах, так он свободно сможет перемещаться по вертикали. Чтобы ограничить их ход вверх, в плите монтируются специальные упоры, ну а снизу устанавливаются пружины, которые стремятся раздвинуть валки.
Обеспечение синхронного поворота упоров происходит за счет зубчатой передачи, расположенной на верхней плите. В ее состав входит зубчатое колесо на оси, запрессованной в центре пластины, оно передает крутящий момент посредством шестеренок, находящихся на хвостовике упоров. Так можно регулировать величину зазора. На нижнем валике есть рукоятка, при ее вращении он прокручивается и передает крутящий момент посредством все той же зубчатой передаче верхнему.
Благодаря специальным насадкам, например дисковым ножам, можно осуществить резку листового металла, а цилиндрические валки с фасонными канавками позволят произвести проволоку нужного сечения. Если же необходимо накатать ребра жесткости, то тут понадобятся валики с симметричным расположением паза и гребня. В общем, возможности данного станка, учитывая то, что он делается в домашних условиях, просто впечатляют.
tutmet.ru
Классификация и типы прокатных станов :: Технология металлов
Все прокатные станы, работающие на металлургических предприятиях, несмотря на многообразие конструкций классифицируются по назначению, количеству и расположению рабочих клетей и валков в рабочих клетях. Прокатные станы в зависимости от назначения, т.е. от вида выпускаемой продукции, можно разделить на следующие три группы.
Станы горячей прокатки, к которым относятся обжимные, заготовочные, рельсобалочные, сортовые, проволочные, штрипсовые, листовые, широкополосные.
Станы холодной прокатки, к которым относятся листовые, жестепрокатные и станы для прокатки тонкой и тончайшей ленты.
Станы специального назначения — колесопрокатные, бандажепрокатные, для прокатки полос и профилей переменного сечения, шаров, шестерен, винтов, гнутых профилей и т.п.
Основным параметром обжимных, заготовочных и сортовых станов является диаметр валков или шестерен шестеренной клети в мм. При наличии в стане нескольких рабочих клетей параметром стана является диаметр валков чистовой клети. Так, название «мелкосортный стан 250» означает, что диаметр рабочих валков или шестерен чистовой клети равен 250 мм, а назначение его — производство мелкосортного проката.
Основным параметром листовых станов является длина бочки валка, мм, которая определяет наибольшую ширину прокатываемых на стане листов или полос. В этом случае название «толстолистовой стан 3000» означает, что длина бочки валков равна 3000 мм, при этом на стане прокатывают толстый лист шириной до 2700—2800 мм.
По количеству и расположению рабочих клетей прокатные станы разделяют на следующие пять групп: одноклетевые, линейные многоклетевые, последовательные, полунепрерывные и непрерывные (рис. 1).
Одноклетевые станы являются простейшим типом прокатного стана. В состав оборудования стана входят одна рабочая клеть и линия привода рабочих валков, которая состоит из шпинделей, шестеренной клети, редуктора, муфт и главного электродвигателя. Входящее в линию привода валков оборудование в основном повторяется на прокатных станах с более сложным расположением рабочих клетей. К станам этой группы относятся станы для производства полупродукта (блюминги, слябинги, заготовочные) и готового проката (станы горячей и холодной прокатки).
Наиболее простыми являются линейные многоклетевые прокатные станы, на которых рабочие клети расположены в одну или более линий. При этом каждая линия приводится от одного электродвигателя. Одноклетевые станы могут быть реверсивными, когда рабочие валки могут попеременно вращаться в одну и другую сторону, или нереверсивными — рабочие валки вращаются только в одну сторону. Линейные многоклетевые станы используют главным образец как заготовочные, сортовые, рельсобалочные, проволочные и листовые.
Рис.1. Схема расположения рабочих клетей прокатных станов: а — одноклетевой; б — линейный многоклетевой в две линии; в— последовательный; г — полунепрерывный; д — непрерывный:
1 — двигатель; 2 — шестеренная клеть; 3 — рабочие клети; 4 — непрерывная черновая группа; 5 — непрерывная чистовая группа
Последовательные станыхарактеризуются расположением рабочих клетей, стоящих друг за другом таким образом, что прокатываемая полоса проходит в каждой клети один раз. Поэтому число клетей такого стана должно быть равно максимальному числу проходов, необходимых для получения готового профиля. На последовательных станах рабочие клети обычно размещают в несколько параллельных рядов» с тем чтобы сократить длину цеха и лучше использовать его площади. Причем на таких станах расстояние от клети к клети в направлении прокатки увеличивается соответственно увеличению длины прокатываемой полосы. Увеличивается и частота вращения валков.
К последовательным станам относятся станы с рабочими клетями, расположенными в шахматном порядке.
Последовательные станы используют в основном как сортовые.
Полунепрерывные станы состоят из двух групп рабочих клетей: непрерывной и линейной, или последовательной. В непрерывной группе клетей прокатываемая полоса может нахолиться одновременно в двух, трех и более клетях, т.е. прокатываться непрерывно. А во второй группе полоса прокатывается или на линейном, или на последовательном стане.
Полунепрерывные станы используются как сортовые, проволочные и полосовые.
Наиболее современными станами являются непрерывные станы. По сравнению с другими типами станов непрерывные характеризуются более высокими скоростями прокатки. При этом привод валков рабочих клетей может быть как индивидуальный, так и групповой.
Непрерывные станы характеризуются наибольшей производительностью по сравнению с другими типами станов. Эти станы используют в качестве заготовочных, широкополосных, средне- и мелкосортных, проволочных и др.
По расположению и количеству валков в рабочих клетях и их конструкции прокатные станы делятся на несколько групп: двух-, трех-, четырех- и многовалковые, универсальные специальной конструкции (рис.2).
Двухвалковые клети наиболее распространены, и бывают реверсивные и нереверсивные. В реверсивных клетях валки имеют переменное направление вращения.
Рис2. Схема расположения валков в рабочих клетях:
а — двухвалковая клеть; б — трехвалковая сортовая и листовая; в — четырехвалковая клеть; г — шестивалковая клеть; д — двенадцативалковая клеть; е — двадцативалковая клеть; ж — универсальная балочная клеть; з — универсальная клеть слябинга
Прокатываемый металл проходит между валками вперед и назад нужное количество раз, а валки соответственно изменяют направление вращения, реверсируются. Реверсивные двухвалковые клети применяют в обжимных, толстолистовых, сортовых и листовых станах.
В нереверсивных двухвалковых клетях валки имеют постоянное вращение в одну сторону. Прокатываемый металл проходит между валками такой клети только один раз и в одном направлении. Нереверсивные клети применяют в линейных многоклетевых, последовательных, полунепрерывных и непрерывных прокатных станах при производстве заготовок, сортового проката, катанки, листа.
В трехвалковых клетях оси валков расположены в одной вертикальной плоскости и имеют постоянное направление вращения. Трехвалковые клети нашли широкое применение при производстве сортового проката. Прокатываемый металл движется в одну сторону между нижним и средним валками и в обратную сторону — между средним и верхним. Для подъема металла на верхний уровень и его задачи между верхним и средним валками перед клетью или позади ее устанавливают подъемно-качающиеся столы.
При производстве листа также применяют трехвалковые клети, но со средним валком меньшего диаметра, чем нижний и верхний. Средний валок является неприводным и в процессе прокатки прижимается то к верхнему, то к нижнему валку.
Так же как и при производстве сортового проката, перед клетью и позади нее устанавливают подъемно-качающиеся столы. Поскольку трехвалковые клети обладают небольшой производительностью и малой жесткостью валковой системы, в последнее время их применяют все реже.
В четырехвалковых клетях, как и в трехвалковых, валки также расположены в одной вертикальной плоскости один над другим. В этих клетях два валка 1 являются рабочими, а два других 2 — опорными. Рабочие валки имеют меньший диаметр и размещены в середине клети, опорные валки имеют больший диаметр и расположены сверху и снизу. Опорные валки предназначены для уменьшения прогиба рабочих валков и для увеличения жесткости валковой системы. Приводными валками в клетях кварто являются рабочие валки. Станы с четырехвалковыми клетями получили широкое распространение для горячей и холодной прокатки толстых и тонких листов, широких полос и лент.
С использованием четырехвалковых клетей прокатка осуществляется на непрерывных многоклетевых и одноклетевых станах. Четырехвалковые нереверсивные клети используют на непрерывных станах. Реверсивные четырехвалковые клети используют в одноклетевых станах горячей и холодной прокатки.
К многовалковым клетям относятся шести-, двенадцати- и двадцативалковые клети.
Шестивалковые клети имеют два рабочих приводных валка 1 и четыре опорных 2. Эти клети отличаются повышенной жесткостью самой клети и меньшим прогибом опорных валков. Благодаря этому клети используют для холодной прокатки тонких полос и узких лент в рулонах с точными допусками по толщине. Однако поскольку преимущества этих клетей по сравнению с четырехвалковыми клетями невелики, а конструкция их сложнее, то значительного распространения они не получили.
Широко применяются в прокатном производстве двенадцати- и двадцативалковые клети. Такое усложнение конструкций рабочих клетей оправдывается рядом преимуществ, которые выражаются в жесткой конструкции валковой системы и всей рабочей клети. Это позволяет применять их для производства тонкой и тончайшей ленты. Диаметры рабочих валков в таких многовалковых клетях назначительны и лежат в пределах от 3 до 50 мм. Они являются неприводными и опираются на ряд приводных валков 2 с большим диаметром, а последние, в свою очередь, на ряд опорных валков.
Универсальные клети имеют горизонтальные 3 и вертикальные 4 валки, расположенные в одной вертикальной плоскости. Обжатие металла осуществляется горизонтальными и вертикальными валками одновременно.
Такие клети применяются в универсальных балочных клетях, где вертикальные валки неприводные. Эти клети применяют только для прокатки широполочных двутавровых балок (высота балок до 1000 мм, ширина полок до 400 мм). Но последнее время их начинают использовать и для прокатки других профилей (рельсов, универсальных листов и др.). Кроме того, универсальные (обычные) клети применяют как реверсивные двухвалковые (в слябингах) или четырехвалковые (в черновых широкополосных станах) клети. В этих клетях вертикальные плоскости, в которых размешены или горизонтальные, или вертикальные валки, находятся на некотором близком расстоянии друг от друга. В этих клетях обжатие прокатываемого металла осуществляется и горизонтальными и вертикальными валками. При этом вертикальные валки располагают с передней или задней стороны рабочей клети, в задачу которых входит получение ровных и гладких боковых граней прокатываемого металла.
Клети специальной конструкции имеют самое различное расположение валков. К этой группе относятся колесопрокатные, бандажепрокатные, кольцепрокатные, шаропрокатные станы, а также станы для прокатки профилей переменного и периодического сечения, шестерен и других изделий.
Источник:
Зотов В.Ф. Производство проката – М. : Интермет Инжиниринг, 2000
markmet.ru
Прокатный стан Википедия
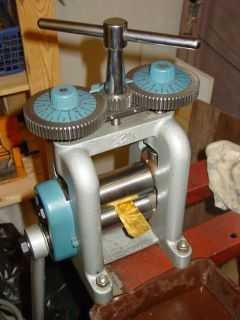
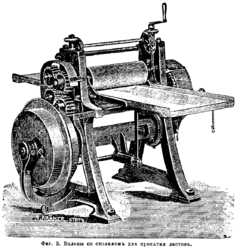
Прока́тный стан — комплекс оборудования, в котором происходит пластическая деформация металла между вращающимися валками. В более широком значении — система машин, выполняющая не только прокатку, но и вспомогательные операции:
- транспортирование исходной заготовки со склада к нагревательным печам и к валкам стана,
- передачу прокатываемого материала от одного калибра к другому,
- кантовку,
- транспортирование металла после прокатки,
- резку на части,
- маркировку или клеймение,
- правку,
- упаковку,
- передачу на склад готовой продукции и др.
История[ | ]
С развитием железнодорожного транспорта значительно увеличилась потребность в прокатной продукции. Первые рельсы были чугунными, однако в начале XIX века в Англии перешли на производство железных рельсов. В 1828 году появился первый прокатный стан для прокатки рельсов из пудлингового железа, а с 1825 года[источник не указан 262 дня] начали прокатывать рельсы из бессемеровской стали, впервые отлитой через 30 лет. Рельсы были главным продуктом прокатного производства. Помимо рельсов надо было производить различные детали паровозов, броня требовалась и для развития флота, в котором деревянные корабли заменялись металлическими бронированными. Первый броневой прокатный стан был сконструирован в 1859 году русским механиком В. С. Пятовым. До этого броневые листы получали сковывая между собой более тонкие листы. Все эти станы были довольно примитивными: валки станков приводились во вращение от водяного колеса, а позднее- паровой машины. Перемещение горячего металла к стану и от него осуществлялось вручную. В одном из музеев старого уральского завода имеется картина: по железному горячему настилу с помощью крючков бригада рабочих передает раскаленную болванку к стану. Труд прокатчика был самым тяжелым на заводе[1].
Первые станки[ | ]
Считается, что первый прокатный стан (с деревянными валками) был сконструирован ещё Леонардо да Винчи. Первые прокатные станы появились в конце XVI века По своему устройству они были весьма просты и представляли собой деревянные станки с двумя железными валками. Верхний валок насаживался на четырёхгранную ось. На один конец этой оси надевалась большая крестовина. Между двумя валками вставляли одним концом нагретую до высокой температуры металлическую болванку, а затем начинали вращать крестовиной верхний валок. Болванка проходила между валками и сплющивалась. На таких станах прокатывали сначала свинцовые листы, идущие на изготовление органных труб, а затем стали прокатывать серебро и золото для чеканки монет[2].
Долгое время было распространено мнение, будто железо прокатывать нельзя. Нагретое железо быстро остывало от соприкосновения с валками при медленной работе. Остывшее же железо не поддавалось раскатке, его можно было только сгибать и резать[2]. Первые прокатные станы для производства полосового железа и мелкого сорта были изготовлены в XVIII в. Они приводились во вращение от водяных колес.
Дуо и Трио-станы[ |
ru-wiki.ru
Прокатный стан — Википедия
Материал из Википедии — свободной энциклопедии

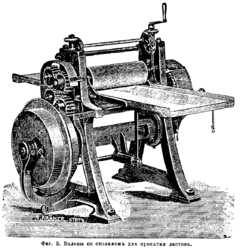
Прока́тный стан — комплекс оборудования, в котором происходит пластическая деформация металла между вращающимися валками. В более широком значении — система машин, выполняющая не только прокатку, но и вспомогательные операции:
- транспортирование исходной заготовки со склада к нагревательным печам и к валкам стана,
- передачу прокатываемого материала от одного калибра к другому,
- кантовку,
- транспортирование металла после прокатки,
- резку на части,
- маркировку или клеймение,
- правку,
- упаковку,
- передачу на склад готовой продукции и др.
История
С развитием железнодорожного транспорта значительно увеличилась потребность в прокатной продукции. Первые рельсы были чугунными, однако в начале XIX века в Англии перешли на производство железных рельсов. В 1828 году появился первый прокатный стан для прокатки рельсов из пудлингового железа, а с 1825 года[источник?] начали прокатывать рельсы из бессемеровской стали, впервые отлитой через 30 лет. Рельсы были главным продуктом прокатного производства. Помимо рельсов надо было производить различные детали паровозов, броня требовалась и для развития флота, в котором деревянные корабли заменялись металлическими бронированными. Первый броневой прокатный стан был сконструирован в 1859 году русским механиком В. С. Пятовым. До этого броневые листы получали сковывая между собой более тонкие листы. Все эти станы были довольно примитивными: валки станков приводились во вращение от водяного колеса, а позднее- паровой машины. Перемещение горячего металла к стану и от него осуществлялось вручную. В одном из музеев старого уральского завода имеется картина: по железному горячему настилу с помощью крючков бригада рабочих передает раскаленную болванку к стану. Труд прокатчика был самым тяжелым на заводе[1].
Первые станки
Считается, что первый прокатный стан (с деревянными валками) был сконструирован ещё Леонардо да Винчи. Первые прокатные станы появились в конце XVI века По своему устройству они были весьма просты и представляли собой деревянные станки с двумя железными валками. Верхний валок насаживался на четырёхгранную ось. На один конец этой оси надевалась большая крестовина. Между двумя валками вставляли одним концом нагретую до высокой температуры металлическую болванку, а затем начинали вращать крестовиной верхний валок. Болванка проходила между валками и сплющивалась. На таких станах прокатывали сначала свинцовые листы, идущие на изготовление органных труб, а затем стали прокатывать серебро и золото для чеканки монет[2].
Долгое время было распространено мнение, будто железо прокатывать нельзя. Нагретое железо быстро остывало от соприкосновения с валками при медленной работе. Остывшее же железо не поддавалось раскатке, его можно было только сгибать и резать[2]. Первые прокатные станы для производства полосового железа и мелкого сорта были изготовлены в XVIII в. Они приводились во вращение от водяных колес.
Дуо и Трио-станы
Дуо-станы
Прокатка в таких станках происходила следующим образом. Стальные слитки или болванки нагревались до высокой температуры в особых печах и затем подавались во вращающиеся валки. Теперь вращались уже оба валка: и верхний и нижний. Металл затягивался в щель силой трения. Это достигалось вращением валков в разные стороны. Прокатать толстую болванку в тонкий лист нельзя в один раз. Поэтому прошедшую через валик полосу передавали обратно «вхолостую» через верхний валок, поджимали тем временем друг к кругу валки и вновь пропускали полосу, но уж в более узкую щель. Повторяя эту операцию несколько раз, получали уже полосу необходимой толщины. Чтобы избежать необходимости прижимать верхний валок к нижнему, в некоторых прокатных станах на валках вытачивали борозды или ручьи (калибры). Слиток подавался сначала в больший калибр, затем в меньший и так далее. Благодаря этому не надо было каждый раз регулировать расстояние между валками[2].
Трио-станы
Чтобы увеличить производительность прокатных станов, начали делать не два валка, а три. Такой стан назывался трехвалковым или станом «трио». Теперь полосу не надо было передавать обратно «вхолостую». Её пропускали в обратную сторону между средним валком и третьим, верхним. Верхний валок вращается в ту же сторону, что и самый нижний, но в противоположную сторону по сравнению со средним валком. Для подачи металла между средним и верхним валком в прокатных цехах устанавливалось особое приспособление, называемое «подъемным столом». Подъемный стол представлял собой платформу, на которую попадала болванка, выходя между нижними и средним валками. Рабочий, управлявший подъемным столам, пускал воду или пар в цилиндры, на которых покоилась платформа. Воздух или пар двигали поршень в цилиндре и поднимали стол на уровень щели между средним и верхним валками[2].
Блюминг
Основная часть блюминга—это две станины, в которые вложены два стальных вала. Верхний вал может приподниматься и опускаться. Прокатные валы блюминга приводятся во вращение электромотором. Слиток подъезжает на роликах к валам. Как только он коснется поверхности валов, они захватывают его в зев, сжимают, вытягивают, делают тоньше и выталкивают на другую сторону. Далее разъем между валами делается меньше. Затем двигатель, вращающий валы, делает «реверс», то есть начинает вращаться в обратную сторону. Слиток на роликах снова подкатывается к валам, но уже с другой стороны, валы снова захватывают его, снова сжимают, делают ещё тоньше и ещё длиннее. Чтобы избежать получения длинного листа вместо болванки, после нескольких пропусков, слиток при помощи особого, так называемого кантовального аппарата, поворачивается на 90°. Кантовальный аппарат имеет рычаги с крючками на концах. Этими крючками слиток, вышедший из валков, подхватывается сбоку, под нижнюю сторону. Рычаги поворачиваются, как на шарнире, и переворачивают своими крючками слиток на 90°(кантуют)[2].
Классификация и устройство прокатных станов
Главный признак, определяющий устройство — его назначение в зависимости от ассортимента продукции или выполняемого технологического процесса.
По сортаменту продукции станы разделяют на:
- заготовочные, в том числе станы для прокатки слябов и блюмов,
- листовые и полосовые,
- сортовые, в том числе балочные и проволочные,
- трубопрокатные
- деталепрокатные (бандажи, колёса, оси и т. д.).
По технологическому процессу делят на следующие группы:
- литейно-прокатные (агрегаты),
- обжимные (для обжатия слитков), в том числе слябинги и блюминги,
- реверсивные одноклетевые,
- тандемы,
- многоклетевые,
- непрерывные,
- холодной прокатки.
См. также
Примечания
- ↑ Обработка металлов давлением В. А. Лунев,1975
- ↑ 1 2 3 4 5 Журавский А. Прокат // Техника молодежи : журнал. — 1934. — Май (№ 5). — С. 17—23.
wikipedia.green
Прокатный стан — WiKi
С развитием железнодорожного транспорта значительно увеличилась потребность в прокатной продукции. Первые рельсы были чугунными, однако в начале XIX века в Англии перешли на производство железных рельсов. В 1828 году появился первый прокатный стан для прокатки рельсов из пудлингового железа, а с 1825 года[источник не указан 185 дней] начали прокатывать рельсы из бессемеровской стали, впервые отлитой через 30 лет. Рельсы были главным продуктом прокатного производства. Помимо рельсов надо было производить различные детали паровозов, броня требовалась и для развития флота, в котором деревянные корабли заменялись металлическими бронированными. Первый броневой прокатный стан был сконструирован в 1859 году русским механиком В. С. Пятовым. До этого броневые листы получали сковывая между собой более тонкие листы. Все эти станы были довольно примитивными: валки станков приводились во вращение от водяного колеса, а позднее- паровой машины. Перемещение горячего металла к стану и от него осуществлялось вручную. В одном из музеев старого уральского завода имеется картина: по железному горячему настилу с помощью крючков бригада рабочих передает раскаленную болванку к стану. Труд прокатчика был самым тяжелым на заводе[1].
Первые станки
Считается, что первый прокатный стан (с деревянными валками) был сконструирован ещё Леонардо да Винчи. Первые прокатные станы появились в конце XVI века По своему устройству они были весьма просты и представляли собой деревянные станки с двумя железными валками. Верхний валок насаживался на четырёхгранную ось. На один конец этой оси надевалась большая крестовина. Между двумя валками вставляли одним концом нагретую до высокой температуры металлическую болванку, а затем начинали вращать крестовиной верхний валок. Болванка проходила между валками и сплющивалась. На таких станах прокатывали сначала свинцовые листы, идущие на изготовление органных труб, а затем стали прокатывать серебро и золото для чеканки монет[2].
Долгое время было распространено мнение, будто железо прокатывать нельзя. Нагретое железо быстро остывало от соприкосновения с валками при медленной работе. Остывшее же железо не поддавалось раскатке, его можно было только сгибать и резать[2]. Первые прокатные станы для производства полосового железа и мелкого сорта были изготовлены в XVIII в. Они приводились во вращение от водяных колес.
Дуо и Трио-станы
Дуо-станы
Прокатка в таких станках происходила следующим образом. Стальные слитки или болванки нагревались до высокой температуры в особых печах и затем подавались во вращающиеся валки. Теперь вращались уже оба валка: и верхний и нижний. Металл затягивался в щель силой трения. Это достигалось вращением валков в разные стороны. Прокатать толстую болванку в тонкий лист нельзя в один раз. Поэтому прошедшую через валик полосу передавали обратно «вхолостую» через верхний валок, поджимали тем временем друг к кругу валки и вновь пропускали полосу, но уж в более узкую щель. Повторяя эту операцию несколько раз, получали уже полосу необходимой толщины. Чтобы избежать необходимости прижимать верхний валок к нижнему, в некоторых прокатных станах на валках вытачивали борозды или ручьи (калибры). Слиток подавался сначала в больший калибр, затем в меньший и так далее. Благодаря этому не надо было каждый раз регулировать расстояние между валками[2].
Трио-станы
Чтобы увеличить производительность прокатных станов, начали делать не два валка, а три. Такой стан назывался трехвалковым или станом «трио». Теперь полосу не надо было передавать обратно «вхолостую». Её пропускали в обратную сторону между средним валком и третьим, верхним. Верхний валок вращается в ту же сторону, что и самый нижний, но в противоположную сторону по сравнению со средним валком. Для подачи металла между средним и верхним валком в прокатных цехах устанавливалось особое приспособление, называемое «подъемным столом». Подъемный стол представлял собой платформу, на которую попадала болванка, выходя между нижними и средним валками. Рабочий, управлявший подъемным столам, пускал воду или пар в цилиндры, на которых покоилась платформа. Воздух или пар двигали поршень в цилиндре и поднимали стол на уровень щели между средним и верхним валками[2].
Блюминг
Основная часть блюминга—это две станины, в которые вложены два стальных вала. Верхний вал может приподниматься и опускаться. Прокатные валы блюминга приводятся во вращение электромотором. Слиток подъезжает на роликах к валам. Как только он коснется поверхности валов, они захватывают его в зев, сжимают, вытягивают, делают тоньше и выталкивают на другую сторону. Далее разъем между валами делается меньше. Затем двигатель, вращающий валы, делает «реверс», то есть начинает вращаться в обратную сторону. Слиток на роликах снова подкатывается к валам, но уже с другой стороны, валы снова захватывают его, снова сжимают, делают ещё тоньше и ещё длиннее. Чтобы избежать получения длинного листа вместо болванки, после нескольких пропусков, слиток при помощи особого, так называемого кантовального аппарата, поворачивается на 90°. Кантовальный аппарат имеет рычаги с крючками на концах. Этими крючками слиток, вышедший из валков, подхватывается сбоку, под нижнюю сторону. Рычаги поворачиваются, как на шарнире, и переворачивают своими крючками слиток на 90°(кантуют)[2].
ru-wiki.org
Прокатный стан Википедия
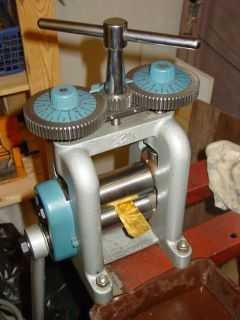
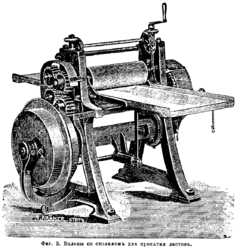
Прока́тный стан — комплекс оборудования, в котором происходит пластическая деформация металла между вращающимися валками. В более широком значении — система машин, выполняющая не только прокатку, но и вспомогательные операции:
- транспортирование исходной заготовки со склада к нагревательным печам и к валкам стана,
- передачу прокатываемого материала от одного калибра к другому,
- кантовку,
- транспортирование металла после прокатки,
- резку на части,
- маркировку или клеймение,
- правку,
- упаковку,
- передачу на склад готовой продукции и др.
История
С развитием железнодорожного транспорта значительно увеличилась потребность в прокатной продукции. Первые рельсы были чугунными, однако в начале XIX века в Англии перешли на производство железных рельсов. В 1828 году появился первый прокатный стан для прокатки рельсов из пудлингового железа, а с 1825 года[источник не указан 262 дня] начали прокатывать рельсы из бессемеровской стали, впервые отлитой через 30 лет. Рельсы были главным продуктом прокатного производства. Помимо рельсов надо было производить различные детали паровозов, броня требовалась и для развития флота, в котором деревянные корабли заменялись металлическими бронированными. Первый броневой прокатный стан был сконструирован в 1859 году русским механиком В. С. Пятовым. До этого броневые листы получали сковывая между собой более тонкие листы. Все эти станы были довольно примитивными: валки станков приводились во вращение от водяного колеса, а позднее- паровой машины. Перемещение горячего металла к стану и от него осуществлялось вручную. В одном из музеев старого уральского завода имеется картина: по железному горячему настилу с помощью крючков бригада рабочих передает раскаленную болванку к стану. Труд прокатчика был самым тяжелым на заводе[1].
Первые станки
Считается, что первый прокатный стан (с деревянными валками) был сконструирован ещё Леонардо да Винчи. Первые прокатные станы появились в конце XVI века По своему устройству они были весьма просты и представляли собой деревянные станки с двумя железными валками. Верхний валок насаживался на четырёхгранную ось. На один конец этой оси надевалась большая крестовина. Между двумя валками вставляли одним концом нагретую до высокой температуры металлическую болванку, а затем начинали вращать крестовиной верхний валок. Болванка проходила между валками и сплющивалась. На таких станах прокатывали сначала свинцовые листы, идущие на изготовление органных труб, а затем стали прокатывать серебро и золото для чеканки монет[2].
Долгое время было распространено мнение, будто железо прокатывать нельзя. Нагретое железо быстро остывало от соприкосновения с валками при медленной работе. Остывшее же железо не поддавалось раскатке, его можно было только сгибать и резать[2]. Первые прокатные станы для производства полосового железа и мелкого сорта были изготовлены в XVIII в. Они приводились во вращение от водяных колес.
Дуо и Трио-станы
Дуо-станы
Прокатка в таких станках происходила следующим образом. Стальные слитки или болванки нагревались до высокой температуры в особых печах и затем подавались во вращающиеся валки. Теперь вращались уже оба валка: и верхний и нижний. Металл затягивался в щель силой трения. Это достигалось вращением валков в разные стороны. Прокатать толстую болванку в тонкий лист нельзя в один раз. Поэтому прошедшую через валик полосу передавали обратно «вхолостую» через верхний валок, поджимали тем временем друг к кругу валки и вновь пропускали полосу, но уж в более узкую щель. Повторяя эту операцию несколько раз, получали уже полосу необходимой толщины. Чтобы избежать необходимости прижимать верхний валок к нижнему, в некоторых прокатных станах на валках вытачивали борозды или ручьи (калибры). Слиток подавался сначала в больший калибр, затем в меньший и так далее. Благодаря этому не надо было каждый раз регулировать расстояние между валками[2].
Трио-станы
Чтобы увеличить производительность прокатных станов, начали делать не два валка, а три. Такой стан назывался трехвалковым или станом «трио». Теперь полосу не надо было передавать обратно «вхолостую». Её пропускали в обратную сторону между средним валком и третьим, верхним. Верхний валок вращается в ту же сторону, что и самый нижний, но в противоположную сторону по сравнению со средним валком. Для подачи металла между средним и верхним валком в прокатных цехах устанавливалось особое приспособление, называемое «подъемным столом». Подъемный стол представлял собой платформу, на которую попадала болванка, выходя между нижними и средним валками. Рабочий, управлявший подъемным столам, пускал воду или пар в цилиндры, на которых покоилась платформа. Воздух или пар двигали поршень в цилиндре и поднимали стол на уровень щели между средним и верхним валками[2].
Блюминг
Основная часть блюминга—это две станины, в которые вложены два стальных вала. Верхний вал может приподниматься и опускаться. Прокатные валы блюминга приводятся во вращение электромотором. Слиток подъезжает на роликах к валам. Как только он коснется поверхности валов, они захватывают его в зев, сжимают, вытягивают, делают тоньше и выталкивают на другую сторону. Далее разъем между валами делается меньше. Затем двигатель, вращающий валы, делает «реверс», то есть начинает вращаться в обратную сторону. Слиток на роликах снова подкатывается к валам, но уже с другой стороны, валы снова захватывают его, снова сжимают, делают ещё тоньше и ещё длиннее. Чтобы избежать получения длинного листа вместо болванки, после нескольких пропусков, слиток при помощи особого, так называемого кантовального аппарата, поворачивается на 90°. Кантовальный аппарат имеет рычаги с крючками на концах. Этими крючками слиток, вышедший из валков, подхватывается сбоку, под нижнюю сторону. Рычаги поворачиваются, как на шарнире, и переворачивают своими крючками слиток на 90°(кантуют)[2].
Классификация и устройство прокатных станов
Главный признак, определяющий устройство — его назначение в зависимости от ассортимента продукции или выполняемого технологического процесса.
По сортаменту продукции станы разделяют на:
- заготовочные, в том числе станы для прокатки слябов и блюмов,
- листовые и полосовые,
- сортовые, в том числе балочные и проволочные,
- трубопрокатные
- деталепрокатные (бандажи, колёса, оси и т. д.).
По технологическому процессу делят на следующие группы:
- литейно-прокатные (агрегаты),
- обжимные (для обжатия слитков), в том числе слябинги и блюминги,
- реверсивные одноклетевые,
- тандемы,
- многоклетевые,
- непрерывные,
- холодной прокатки.
См. также
Примечания
- ↑ Обработка металлов давлением В. А. Лунев,1975
- ↑ 1 2 3 4 5 Журавский А. Прокат // Техника молодежи : журнал. — 1934. — Май (№ 5). — С. 17—23.
wikiredia.ru