Проектирование гальванических производств
Состав работ по разделу проекта «Технологические решения»
В рамках разработки раздела проектной документации «Технологические решения» цехов и участков гальваники, а также очистных сооружений для них выполняются следующие работы:
- Расчет количества и номенклатуры производственного оборудования (автоматические/полуавтоматические гальванические линии; механизированные линии; технологические гальванические ванны, обслуживаемые вручную) и рабочих мест (столы для монтажа/демонтажа деталей, протирки деталей, изоляции поверхности изделий и т.п.). Расчет производительности гальванических линий. Расчет количества линий. Расчет неавтоматизированного оборудования, источников тока, оборудования для шлифования, полирования и т.д.
- Определение количества и номенклатуры вспомогательного оборудования (для приготовления, корректировки и фильтрации растворов, для сливания растворов из ванн с жестким единичным циклом и т.д.)
- Расчет численности рабочих (основные рабочие, вспомогательные рабочие, инженерно-технические работники, служащие, младший обслуживающий персонал)
- Распределение работающих по группам санитарной характеристики производственных процессов
- Объемно-планировочные решения (определение площадей цеха (участка) гальваники путем размещения технологического оборудования, рабочих мест, подъемно-транспортных средств и других устройств с учетом расстояний между оборудованием и строительными конструкциями, ширины проездов, установленных нормами технологического проектирования)
- Определение и расчет категорий производства по взрывной, взрывопожарной и пожарной опасности в соответствии с нормативными документами
- Определение средств механизации и автоматизации. Расчет удельного веса автоматизированного оборудования в общем количестве производственного оборудования. Определение степени охвата рабочих механизированным трудом
- Определение складского хозяйства (организация цеховых складов и кладовых, механизация и автоматизация транспортно-складских работ, состав цеховых складов и кладовых). Расчет площадей складов и кладовых
- Разработка материального баланса (расход химикатов, анодов, катодов, вспомогательных материалов)
- Расчет расхода воды на промывку деталей. Расчет расхода воды на составление растворов, восполнение испарения, промывку оборудования
- Расчет расхода сжатого воздуха для перемешивания электролитов, растворов и воды при промывных операциях
- Расчет расхода сжатого воздуха для обдувки и сушки деталей
- Расчет расхода пара для нагрева непроточных жидкостей, для промывных операций, для сушильных камер
- Расчет мощности электронагрева растворов, электролитов, промывной воды
- Расчет силы тока для подбора источников постоянного тока
- Расчет расхода воды для охлаждения оборудования (водяных выпрямителей, технологических гальванических ванн, требующих охлаждения)
- Расчет концентрации сточных вод от технологического оборудования
- Расчет количества выделений (выбросов) загрязняющих веществ при производстве металлических покрытий (по величинам удельных выделений)
- Разработка технологических заданий на проектирование:
- Архитектурно-строительной части помещений цехов и участков гальваники
- Антикоррозионной защиты полов, стен, металлических конструкций
- Станций нейтрализации (очистки) сточных вод
- Вентиляции и отопления
- Водоснабжения и канализации
- Внутреннего освещения (основного, местного, рабочего, аварийного)
- Охранной сигнализации (для помещений: хранения или применения драгоценных металлов, кладовых ядов, материальных ценностей и т.д.)
- Автоматизации технологического процесса нанесения металлопокрытий и диспетчеризации
- Сжатого воздуха
- Теплоснабжения
- Электроснабжения технологического и вспомогательного оборудования
- Источников тока
- Разработка задания на нестандартизированное оборудование (НСО)
- Разработка пояснительной записки (к соответствующей стадии проекта)
- Разработка необходимых технологических чертежей (компоновка, планировка размещения оборудования гальванического цеха или участка и очистных сооружений, схемы, разрезы)
- Составление спецификации (к соответствующей стадии проекта)
Содержание раздела проекта «Технологические решения»
при проектировании гальваники
Содержание раздела «Технологические решения» при проектировании цеха или участка гальванических покрытий и очистных сооружений для стадии Проект («П») следующий:
- Пояснительная записка:
- Данные о производственной программе гальванического цеха или участка
- Краткая характеристика и обоснование решений по технологии производства гальванических покрытий
- Данные о трудоемкости изготовления продукции, механизации и автоматизации технологических процессов
- Состав и обоснование применяемого оборудования, в том числе импортного
- Решения по применению малоотходных и безотходных технологических процессов и производств, повторному использованию тепла и уловленных химреагентов
- Число рабочих мест и их оснащенность
- Характеристика межцеховых и цеховых коммуникаций
- Предложения по организации контроля качества продукции
- Решения по организации ремонтного хозяйства
- Данные о количестве и составе вредных выбросов в атмосферу и сбросов в водные источники (по отдельным цехам, производствам, сооружениям)
- Технические решения по предотвращению (сокращению) выбросов и сбросов вредных веществ в окружающую среду; оценка возможности возникновения аварийных ситуаций и решения по их предотвращению
- Вид, состав и объем отходов производства, подлежащих утилизации и захоронению
- Потребность в основных видах ресурсов для технологических нужд
- Топливно-энергетический и материальный балансы технологических процессов
- Основные чертежи:
- Принципиальные схемы технологических процессов
- Технологические планировки по корпусам (цехам или участкам) с указанием размещения оборудования и транспортных средств
- Схемы грузопотоков
- Спецификация оборудования и материалов
vskproekt.ru
Проектирование гальванического участка — КиберПедия
Гальванический участок предназначен для восстановления деталей электролитическим осаждением металла на изношенные поверхности. На участке обычно выполняют следующие гальванические процессы: хромирование износостойкое и декоративное, железнение, меднение, цинкование, никелирование и фосфатирование. На участок детали поступают партиями со склада деталей, ожидающих ремонта, или с других производственных участков. Детали, требующие восстановления размеров, поступают после предварительного шлифования со слесарно—механического участка. Туда же они возвращаются после гальванического наращивания на окончательную механическую обработку. Детали, отдельные поверхности которых подлежат меднению для защиты от цементации, поступают также со слесарно-механического участка, а после меднения направляются на термический участок. Детали, проходящие восстановление декоративных покрытий, доставляются с участка дефектования или ремонта и после обработки транспортируются на участки комплектования и сборки.
На АРП в зависимости от объема работ применяют различное оборудование гальванических участков. При малых объемах работ выполнение как подготовительных операций (обезжиривание, промывка и пр.), так и нанесение гальванических покрытий на детали производится в ваннах. При этом ванны для подготовительных работ используются для различных видов покрытий. Планировка оборудования таких участков должна выполняться с учетом этих особенностей использования подготовительного оборудования. Выпрямители в этом случае, как правило, устанавливают непосредственно у ванн на расстоянии 200… 300 мм. Поскольку процессы гальванических покрытий протекают при низком напряжении (6… 12 В), то удаление источников тока от ванн влечет за собой неоправданное увеличение расхода металла на шинопроводы (применение шинопроводов большего поперечного сечения), что необходимо для сохранения в допустимых пределах величины падения напряжения.
Периодическую смену электролита в ваннах и его фильтрацию следует производить при оснащении гальванических участков передвижными установками, на которых монтируются и насосные агрегаты.
На рис. 35.12 показаны схемы расстановки ванн с указанием расстояний, принимаемых согласно нормам технологического проектирования. При значительных объемах работ, связанных с нанесением гальванических покрытий, следует применять полуавтоматические или автоматические установки для нанесения каждого из видов гальванических покрытий.
Рис. 35.12. Схемы расположения гальванических ванн, мм:
а = 300…400; 5= 600…800; в = 2000…2500; г = 800… 1000; д = 1500…2000;
е = 1200… 1500; ж = 800… 1000; з = 500…600; и = 1500…2000
Рис. 35.13. Схемы расположения автомата для гальванопокрытий, мм: а = 500…3500; б = 1500…2000; в = 2000…2500 |
В зависимости от конструктивных особенностей эти установки имеют большей частью или прямоугольную, или овальную конфигурацию. Автоматическая (полуавтоматическая) установка включает весь комплекс ванн для подготовительных операций и нанесения покрытий. Выпрямители, обслуживающие соответствующие ванны автоматических установок, следует размещать вблизи установок на расстоянии от них 200… 300 мм до фронта выпрямителя или его боковой стороны и 800…900 мм до его тыльной стороны.
Гальванические участки, оснащенные автоматическими установками, целесообразно размещать таким образом, чтобы вспомогательное комплектующее оборудование этих установок (теплообменники, фильтры, резервуары для слива и приготовления растворов и пр.) располагалось в подвальном помещении.
На рис. 35.13 показана примерная схема размещения автомата для металлопокрытий кареточного типа. Габаритные размеры автоматов показаны с учетом площадок для их обслуживания, оборудованных специальным настилом.
Таблица 35.10
Ориентировочные площади поверхности покрытия для грузового автомобиля средней грузоподъемности, дм2
Наименование изделия | Вид покрытия | ||||
Износостойкое хромирование | Железнение | Меднение | Никелирование | Цинкование | |
Полнокомплектный автомобиль | 3,0 | 6,0 | 2,7 | 6,0 | 15,0 |
Двигатель с сцеплением | 0,8 | 1,0 | 0,6 | — | — |
Коробка передач | 0,5 | 1,2 | 0,5 | — | — |
Задний мост | 0,7 | 1,8 | 0,7 | — | |
Передний мост | 0,8 | 1,6 | 0,5 | — | |
Рулевое управление | 0,1 | 0,2 | 0,2 | — | |
Карданный вал | 0,1 | 0,2 | 0,2 | — | — |
Межцеховой проезд
Рис. 35.14. Планировка гальванического участка авторемонтного завода с программой 8500 приведенных капитальных ремонтов автомобилей ГАЗ-53А в год:
1, 9, 12 — выпрямительные устройства; 2 — ванна для отслаивания; 3 — ванна с холодной водой для промывки деталей после всех процессов, кроме хромирования; 4 — ванна с теплой водой для промывки деталей после всех процессов, кроме хромирования; 5 — ванна для нейтрализации; 6 — стол для навешивания деталей; 7— ванна для анодного травления; 8 — стол для вневанного железнения деталей; 10 — ванна для электролитического обезжиривания; 11 — стеллаж для деталей; 13 — ванна для никелирования; 14 — ванна для кислого меднения; 15 — ванна с холодной водой для промывки деталей в процессе хромирования; 16 — ванна с теплой водой для промывки деталей в процессе хромирования; 17 — бак для отстоя электролита; 18 — кислотостойкий насос; 19 — конторский стол; 20 — раковина; 21 — ванна для снятия старого хромового покрытия; 22 — ванна для хромирования; 23 — ванна для улавливания электролита; полировочная: 24 — полировочный станок; 25 — стеллаж для деталей; 26 — стол для накатки полировальных кругов; 27 — сушильный шкаф
Таблица 35.11
cyberpedia.su
Проектирование гальванического участка авторемонтного предприятия
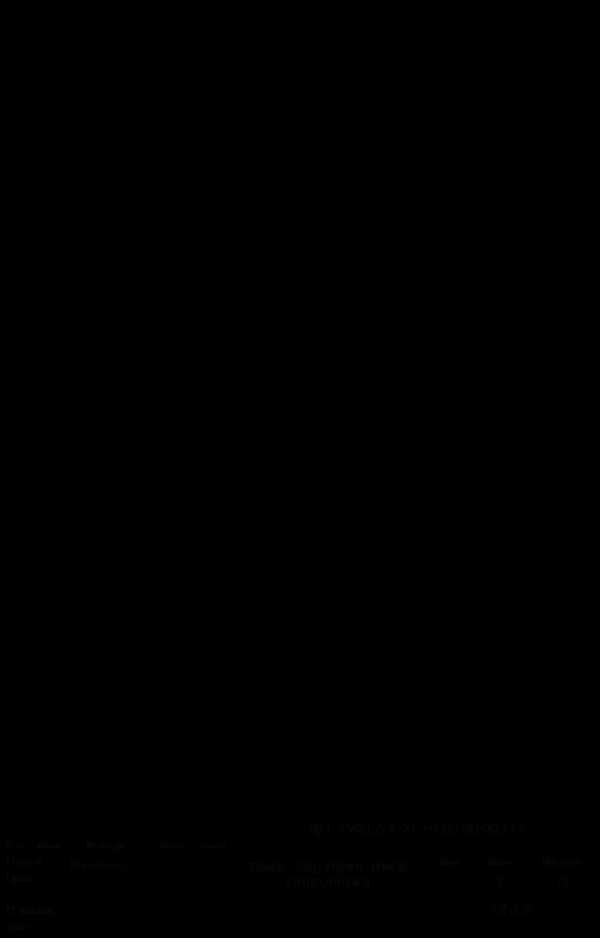
Введение. 3
1 Общая характеристика объекта проектирования. 5
1.1 Назначение объекта. 5
1.2 Краткий технологический процесс на объекте проектирования. 5
1.3 Перечень объектов ремонта. 5
2 РАСЧЕТНО-ТЕХНОЛОГИЧЕСКАЯ ЧАСТЬ. 6
2.1 Выбор исходных данных. 6
2.2. Расчет годовой производственной программы рассчитывается по формуле: 6
2.3 Определение годового фонда времени оборудования и рабочих мест. 7
3. ОРГАНИЗАЦИОННАЯ ЧАСТЬ. 8
3.1 Описание технологических процессов на объекте проектирования. 8
3.2 Расчет количества и состава работающих. 11
3.3 Определение количества технологического и подъемного оборудования. 11
3.4 Расчет производственной площади объекта проектирования. 12
3.5 Расчет потребности в энергоресурсах. 15
3.6 Охрана труда на объекте проектирования. 17
3.7 Техника безопасности на объекте проектирования. 17
3.8 Охрана окружающей среды.. 18
4. ЭКОНОМИЧЕСКИЙ РАЗДЕЛ.. 19
4.1 Обоснование выбора формы оплаты труда и условий премирования. 19
4.2 Смета затрат и калькуляция себестоимости. 19
4.2.1 Расчет фонда заработной платы с начислениями в социальные фонды.. 19
4.3 Расчет цеховых расходов. 20
4.4. Калькуляция себестоимости. 25
5. РЕМОНТНО-ТЕХНОЛОГИЧЕСКИЙ РАЗДЕЛ.. 26
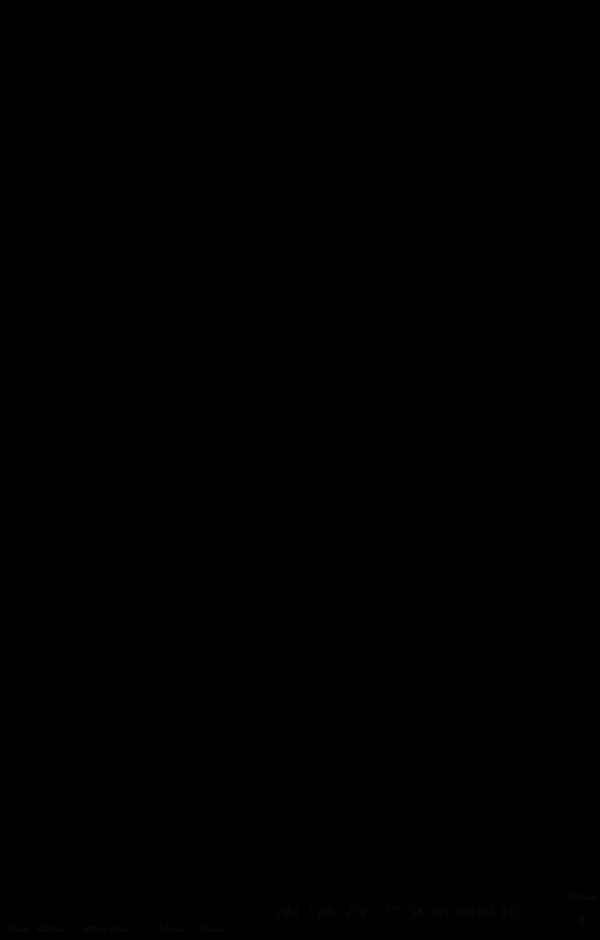
5.2.Технические условия на контроль и сортировку детали. 26
5.3. Дефекты и причины их возникновения. 28
5.4. Обоснование выбора рационального способа восстановления детали. 28
5.5. Обоснование схемы движения детали по цехам и участкам. 31
5.6 Выбор установочных баз. 34
5.7. Выбор оборудования. 35
5.8. Выбор рабочего измерительного инструмента и технологической оснастки 36
5.9 Выбор режима резания и обработки. 36
5.10 Определение партии деталей. 40
5.11. Определение технической нормы времени. 40
5.12. Определение квалификации рабочих по специальностям. 43
6. КОНСТРУКТИВНЫЙ РАЗДЕЛ.. 45
6.1. Назначение и обоснование выбора конструкции приспособления. 45
6.2. Описание конструкции приспособления и его работа. 45
6.3. Расчет деталей приспособления. 45
7 ОХРАНА ТРУДА НА ОБЪЕКТЕ ПРОЕКТИРОВАНИЯ. 48
7.1 Техника безопасности на объекте проектирования. 48
РЕКОМЕНДУЕМАЯ ЛИТЕРАТУРА.. 54
Ремонт автомобилей является объективной необходимостью, которая обусловлена техническими и экономическими причинами.
Во-первых, потребность народного хозяйства в автомобилях частично удовлетворяется путем эксплуатации отремонтированных автомобилей. Во-вторых, ремонт обеспечивает дальнейшее использование тех элементов автомобилей, которые не полностью изношены. В результате сохраняется значительный объем прошлого труда. В-третьих, ремонт способствует экономии материалов идущих на изготовление новых автомобилей. При восстановлении деталей расход материалов в 20…30 раз ниже, чем при их изготовлении.
Многочисленные исследования показали, что первый капитальный ремонт, как правило, по всем слагающим экономической эффективности затрат общественного труда выгоднее приобретения нового автомобиля. Это объясняется двумя возможными обстоятельствами:
— фактические затраты на первый капитальный ремонт большинства видов машин и оборудования не превышает 30-40% их балансовой стоимости, повторные же ремонты обходятся значительно дороже;
— большинство видов машин подвергаются первому капитальному ремонту, как правило, до наступления морального износа.
Общее число деталей в современных автомобилях составляет тысячи наименований. Однако число деталей, лимитирующих их срок службы до капитального ремонта, не превышает нескольких десятков наименований. Задача заключается в том, чтобы повысить долговечность этих деталей до уровня обеспечивающего наибольшую долговечность автомобиля.
Наряду с поиском путей и методов повышения надежности, которая закладывается в конструкцию автомобиля при проектировании и внедряется в сфере производства, необходимо изыскать пути и методы для решения этой же задачи в сфере эксплуатации и ремонта. От того, как разумно будет использоваться ресурс автомобилей в эксплуатации, зависит действительный
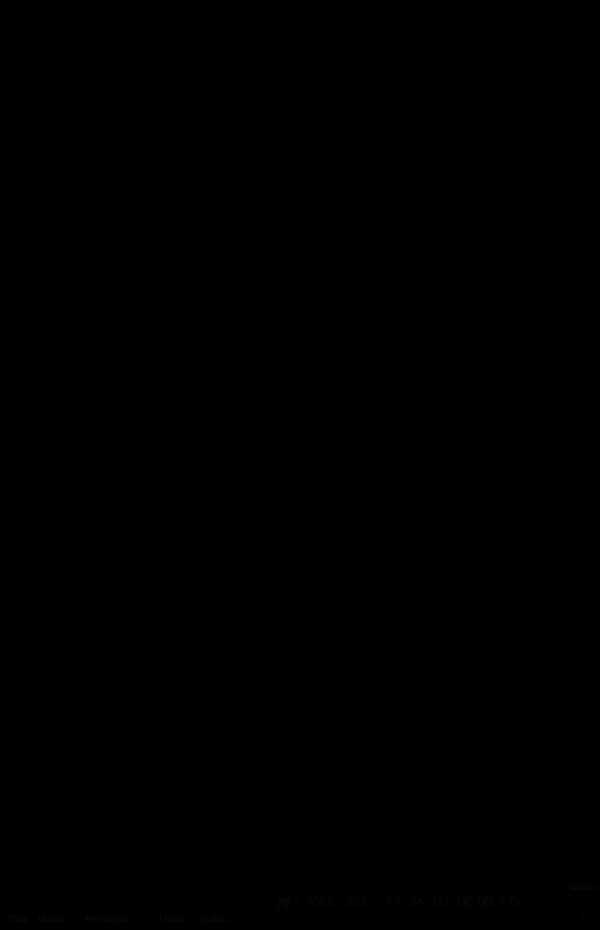
Авторемонтное производство, получив значительное развитие, еще не в полной мере, реализует свои потенциальны возможности. По своей эффективности, организационному и технологическому уровню оно еще отстает от основного производства автомобилестроения. Качество ремонта остается низким, стоимость высокой, уровень механизации достигает лишь 25…40%, вследствие чего производительность труда в два раза ниже, чем в автомобилестроении. Авторемонтное предприятие (АРП) оснащены в основном универсальным оборудованием большой степени изношенности и малой точностью. Это негативные стороны современного состояния авторемонтного производства и определяют пути его развития.
Целью данного дипломного проекта является проектирование гальванического участка авторемонтного предприятия.
Гальванический цех предназначен для восстановления деталей электролитическим осаждением металла на предварительно подготовленные поверхности. На участке проводятся износостойкие и защитно-декоративные хромирование, железнение, меднение, никерование и цинкование.
В цех детали поступают партиями. Детали, требующие восстановления размеров после предварительного шлифования , поступают с слесарно-механического участка. Туда же они поступают после гальванического наращивания на окончательную механическую обработку. Детали, отдельные поверхности которых подлежат омеднению для защиты от цементации, тоже поступают с слесарно-механического участка и после омеднения направляются на термический участок . Детали, нуждающиеся в восстановлении защитно-декоративного покрытия. Поступают с участка деффектаци или со склада деталей, ожидающих ремонта. После восстановления покрытий детали поступают на участок комплектования или поста сборки.
Базовые детали (осталивание):
— блок цилиндров (посадочные гнезда под подшипники),
— картер коробки передач (посадочные гнезда под подшипники).
Детали двигателя:
— цилиндры двигателя (хромирование),
— шатуны (осталивание),
— гнезда клапанов (осталивание),
— стержни шатунов (железнение).
Годовая производственная программа – 1110 капитальных ремонтов автомобилей ГАЗ-3302.
Вид строительства – новое.
Режим работы предприятия – 305 дней в году по 8 часов в 1 смену.
Природно-климатическая зона – холодная.
Т=tr*N, (1)
где tr — трудоемкост на 1 автомобиль гальванических работ, N – число капитальных ремонтов.
N = 1110 шт.
tr =
, (2)где ta – трудоемкость капитального ремонта всего автомобиля, Cr – процентная доля гальванических работ от всей трудоемкости автомобиля.
Принимаем
Cr=3,95% [1с.267]
ta = tom*Kn*Kc,
где: tom – нормативная трудоемкость капитального ремонта, Кс – коэффициент коррекции трудоемкости, учитывающий структуру годовой производственной программы предприятия, Кn – коэффициент коррекции трудоемкости, учитывающий годовую производственную программу.
Принимаем:
tom = 195 чел. час [1c. 240]
Кс = 1,03 [1c. 240]
Kn = 0,8 [1c. 268]
ta = 195*1,03*0,8=160чел. час
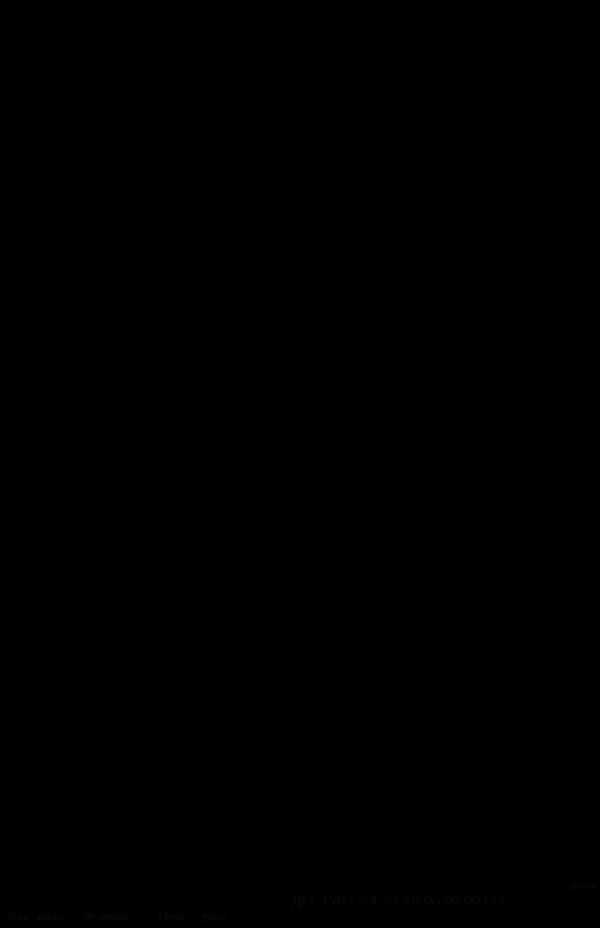
T = 5,6*1110=6216 чел. час
Годовая производственная программа равна 1110 капитальных ремонтов и трудоемкость 6993 чел. час.
Годовой фонд рабочего времени оборудования и рабочих мест принимаем 2030 часов [1c. 269] и в последующих расчетах будем принимать это число для односменной работы.
Технологический процесс хромирования:
1. механическая обработка детали – шлифование, полирование мелким наждачным полотном, придание поверхности гладкой и правильной геометрической формы. Промывка в бензине.
2. Изоляция мест не подлежащих хромированию, целлулоидной лентой или цапон-лаком (целлулоид растворенный в ацетоне).
Имеющиеся отверстия закрываются свинцовыми пробками с тем, чтобы избежать искривления силовых линий и непокрытых участков вокруг отверстий.
3. Монтаж деталей на подвеску, что облегчает затеску деталей ванну и обеспечивает выдерживания более точного расстояния между анодами и деталями, что необходимо для более равного отложения хрома.
4. Электролитическое обеспечение в электролите следующего состава и режима: едкий натр NaOH 100 гр., жидкое стекло Na2 SiO3 2-3 гр., плотность тока 5 A/дм2 ., температура ванны – 800 .
mirznanii.com
Проектирование гальванического участка авторемонтного предприятия
Содержание
Введение3
1 Общая характеристика объекта проектирования5
1.1 Назначение объекта5
1.2 Краткий технологический процесс на объекте проектирования5
1.3 Перечень объектов ремонта5
2 РАСЧЕТНО-ТЕХНОЛОГИЧЕСКАЯ ЧАСТЬ6
2.1 Выбор исходных данных6
2.2. Расчет годовой производственной программы рассчитывается по формуле:6
2.3 Определение годового фонда времени оборудования и рабочих мест7
3. ОРГАНИЗАЦИОННАЯ ЧАСТЬ8
3.1 Описание технологических процессов на объекте проектирования8
3.2 Расчет количества и состава работающих11
3.3 Определение количества технологического и подъемного оборудования.11
3.4 Расчет производственной площади объекта проектирования12
3.5 Расчет потребности в энергоресурсах15
3.6 Охрана труда на объекте проектирования17
3.7 Техника безопасности на объекте проектирования17
3.8 Охрана окружающей среды18
4. ЭКОНОМИЧЕСКИЙ РАЗДЕЛ19
4.1 Обоснование выбора формы оплаты труда и условий премирования19
4.2 Смета затрат и калькуляция себестоимости19
4.2.1 Расчет фонда заработной платы с начислениями в социальные фонды19
4.3 Расчет цеховых расходов20
4.4. Калькуляция себестоимости25
5. РЕМОНТНО-ТЕХНОЛОГИЧЕСКИЙ РАЗДЕЛ26
5.1. Описание конструктивных особенностей и условий работы восстанавливаемой детали26
5.2.Технические условия на контроль и сортировку детали26
5.3. Дефекты и причины их возникновения28
5.4. Обоснование выбора рационального способа восстановления детали28
5.5. Обоснование схемы движения детали по цехам и участкам31
5.6 Выбор установочных баз34
5.7. Выбор оборудования35
5.8. Выбор рабочего измерительного инструмента и технологической оснастки36
5.9 Выбор режима резания и обработки36
5.10 Определение партии деталей40
5.11. Определение технической нормы времени40
5.12. Определение квалификации рабочих по специальностям43
6. КОНСТРУКТИВНЫЙ РАЗДЕЛ45
6.1. Назначение и обоснование выбора конструкции приспособления45
6.2. Описание конструкции приспособления и его работа45
6.3. Расчет деталей приспособления45
7 ОХРАНА ТРУДА НА ОБЪЕКТЕ ПРОЕКТИРОВАНИЯ.48
7.1 Техника безопасности на объекте проектирования48
РЕКОМЕНДУЕМАЯ ЛИТЕРАТУРА54
Введение
Ремонт автомобилей является объективной необходимостью, которая обусловлена техническими и экономическими причинами.
Во-первых, потребность народного хозяйства в автомобилях частично удовлетворяется путем эксплуатации отремонтированных автомобилей. Во-вторых, ремонт обеспечивает дальнейшее использование тех элементов автомобилей, которые не полностью изношены. В результате сохраняется значительный объем прошлого труда. В-третьих, ремонт способствует экономии материалов идущих на изготовление новых автомобилей. При восстановлении деталей расход материалов в 20…30 раз ниже, чем при их изготовлении.
Многочисленные исследования показали, что первый капитальный ремонт, как правило, по всем слагающим экономической эффективности затрат общественного труда выгоднее приобретения нового автомобиля. Это объясняется двумя возможными обстоятельствами:
— фактические затраты на первый капитальный ремонт большинства видов машин и оборудования не превышает 30-40% их балансовой стоимости, повторные же ремонты обходятся значительно дороже;
— большинство видов машин подвергаются первому капитальному ремонту, как правило, до наступления морального износа.
Общее число деталей в современных автомобилях составляет тысячи наименований. Однако число деталей, лимитирующих их срок службы до капитального ремонта, не превышает нескольких десятков наименований. Задача заключается в том, чтобы повысить долговечность этих деталей до уровня обеспечивающего наибольшую долговечность автомобиля.
Наряду с поиском путей и методов повышения надежности, которая закладывается в конструкцию автомобиля при проектировании и внедряется в сфере производства, необходимо изыскать пути и методы для решения этой же задачи в сфере эксплуатации и ремонта. От того, как разумно будет использоваться ресурс автомобилей в эксплуатации, зависит действительный
срок его службы до капитального ремонта.
Авторемонтное производство, получив значительное развитие, еще не в полной мере, реализует свои потенциальны возможности. По своей эффективности, организационному и технологическому уровню оно еще отстает от основного производства автомобилестроения. Качество ремонта остается низким, стоимость высокой, уровень механизации достигает лишь 25…40%, вследствие чего производительность труда в два раза ниже, чем в автомобилестроении. Авторемонтное предприятие (АРП) оснащены в основном универсальным оборудованием большой степени изношенности и малой точностью. Это негативные стороны современного состояния авторемонтного производства и определяют пути его развития.
Целью данного дипломного проекта является проектирование гальванического участка авторемонтного предприятия.
1 Общая характеристика объекта проектирования
1.1 Назначение объекта
Гальванический цех предназначен для восстановления деталей электролитическим осаждением металла на предварительно подготовленные поверхности. На участке проводятся износостойкие и защитно-декор
www.studsell.com
Проектирование гальванического участка — часть 2
2.1.2 Для никелирования применяют следующие электролиты: борфторидный, сульфаматный, сульфатный
Борфторидный электролит является скоростным, но он дорог из-за бора, а так же агрессивен из-за фтора.
Сульфаматный электролит применяется для нанесения толстых слоёв никеля. Но этот электролит дорог. Требуется перемешивания, подогрева и непрерывная фильтрация.
Сульфатный электролит – это самый распространенный. Позволяет получить осадки с различными физическими и химическими свойствами.
Для данного проекта предлагается сульфатный электролит следующего состава [1]:
−сульфат никеля – основной компонент, источник ионов никеля;
−хлорид никеля – депассиватор;
– борная кислота – буферная добавка, для поддержания pH среды.
Механизм осаждения заключается в следующем:
На катоде происходит восстановление:
Ni 2+ ∙ mH 2 O + 2 e — → Ni 0 + mH 2 0,
2 H + + 2 e — → H 2 0
На аноде происходит окисление:
Ni 0 -2 e — → Ni 2+ .
Ионы никеля в электролите окружены оболочкой из дипольных молекул воды. В двойном электрическом слое часть молекул воды отрывается. Дегидратация последних молекул воды требует затрат энергии, что проявляется ростом перенапряжения, называемого химической поляризацией. При этом равновесный потенциал никеля даже при малых плотностях тока становятся отрицательным. При низких значениях рН, никель почти не осаждается и на катоде выделяется водород. По мере увеличения рН потенциал выделения водорода становится становится более отрицательным и на катоде создаются условия для совместного выделения водорода и никеля. При высоких значениях рН вести осаждение никеля нельзя, так как начинается гидролиз. Для процесса никелирования характерно явление, называемое питтингом. При низких значениях pH (ниже 1-2) никель почти не осаждается и на катоде выделяется водород. По мере увеличения pH потенциал выделения водорода становится более отрицательным и на катоде создаются условия совместного выделения водорода и никеля. Чем выше значение pH, тем меньше доля выделяемого водорода. Но при высоких значениях pH процесс осаждения никеля вести нельзя, так как начинается гидролиз. При высоких значениях pH невооруженным глазом можно заметить на деталях зеленый осадок нерастворимых солей никеля. При увеличении температуры выход по току возрастает, так как потенциал осаждения никеля становится более положительным.
2.2 Схема техпроцесса и его описание
Схема технологического процесса покрытия сплавом олово-висмут составлена в соответствии с ГОСТ 9.305-84 и представлена в картах техпроцесса согласно ГОСТ 3.1408-74. Описание операции техпроцесса приводится ниже.
2.2.1 Химическое обезжиривание применяется для удаления с поверхности деталей основной массы жировых загрязнений. Оно заключается в том, что под воздействием щелочи жиры омыляются и переходят в раствор, а минеральные масла в присутствии специальных поверхностно активных веществ – образуют эмульсию. К веществам входящим в состав обезжиривающих растворов предъявляются особые требования. Они должны хорошо удалять жировые пленки, не должны вызывать коррозию обрабатываемых деталей и должны хорошо смываться при промывке водой. Применение для очистки поверхности изделий растворов готовых моющих препаратов технологически и экологически весьма целесообразно, если они сочетают хорошую обезжиривающую способность по отношению к различным загрязнениям с отсутствием коррозионного воздействия на обрабатываемые металлы.
–МЛ-51 – готовое моющее средство, предназначено для удаления основной массы жировых загрязнений. Смывает минеральные масла, горюче-смазочные материалы, сложнее удаляет полировальные пасты. Механизм операции заключается в эмульгировании жиров, т.к. жиры, входящие в состав полировальных паст неомыляемы. Для улучшения качества обезжиривания повышают температуру раствора и время выдержки.
2.2.2 Промывка проводится с целью уменьшения концентрации химических соединений на поверхности обрабатываемых деталей до такой величины, когда они не будут оказывать неблагоприятного действия на качество выполнения последующих операций. От качества промывки после обезжиривания и травления зависит качество покрытия, работа всех электролитов и состав сточных вод. После операции обезжиривания (химического и электрохимического) применяется промывка в горячей воде т.к. в ней лучше растворяется мыло. Также промывка в горячей воде применяется перед сушкой для ускорения процесса сушки и снижения затрат тепла на неё. Холодная промывка после электрохимического обезжиривания проводится для контроля качества обезжиривания. Улавливание – промывка в ванне с непроточной дистилированой водой, осуществляется до операции покрытия, для предотвращения разбавления электролита, и после неё, для экономии химикатов и снижения затрат на нейтрализацию сточных вод. Вода из ванн улавливания используется для доливки в основные ванны покрытия.
2.2.3 Электрохимическое обезжиривание предназначено для удаления тонких, прочно сцепленных с металлом жировых плёнок, оставшихся после химического обезжиривания.
Операция производится в электролите следующего состава:
–гидроксид натрия – для повышения электропроводности раствора, для омыления омыляемых жиров по реакции:
(C17 H35 COO)3 C3 H5 + 3NaOH →3C17 H35 COONa + C3 H5 (OH)3
–кальцинированная сода – для поддержания щелочности раствора в результате гидролиза:
Na2 CO3 + H2 O → Na2 HCO3 + NaOH
Na2 HCO3 + H2 O → NaOH + H2 O + CO2 .
–тринатрийфосфат – смягчает воду, улучшает моющую способность, в результате гидролиза поддерживают щелочность. Обладая поверхностно-активными свойствами пептизируют загрязнения. Фосфаты хорошо смываются водой;
–синтанол ДС-10 – биологическая добавка, для эмульгирования неомыляемых жиров и улучшения.
2.2.4 Дозированное травление применяется для удаления оксидов с поверхности деталей с помощью кислых растворов
Дозированное травление заключается в последовательной обработке деталей в двух растворах: в растворе нитрата натрия и в растворе серной кислоты.
После обработки в первом растворе на поверхности латунных деталей остаются капли нитрата натрия. При погружении во второй раствор на поверхности деталей образуется азотная кислота по реакции:
2 NaNO 3 + H 2 SO 4 → 2 HNO 3 + Na 2 SO 4 .
Травление протекает по следующим реакциям:
CuO + 2HNO3 → Cu(NO3 )2 +H2 O;
CuO + H2 SO4 → CuSO4 + H2 O;
ZnO + 2HNO3 → Zn(NO3 )2 + H2 O;
ZnO + H 2 SO 4 → ZnSO 4 + H 2 O .
При таком способе травления азотной кислоты на поверхности деталей образуется мало, но достаточно для растворения окислов. Основа практически не подтравливается. Окислов азота при таком травлении выделяется в 50 раз меньше, чем при обычном травлении. Поэтому этот способ травления называется экологически чистым [3].
2.2.5 Активирование – процесс удаления с поверхности деталей тончайшего слоя окислов, которые могли образоваться в промежутке между операциями. При активировании одновременно происходит лёгкое протравливание верхнего слоя металла и выявление его кристаллической структуры, что благоприятствует прочному сцеплению покрытия с основой.
Активирование производится непосредственно перед загрузкой деталей в ванны для нанесения покрытия.
2.2.6 Никелирование – процесс осаждения никеля на поверхность деталей (состав и назначение компонентов см. 2.1).
2.2.7 Покрытие сплавом олово-висмут – осаждения сплава олова с висмутом на поверхность деталей (состав и назначение компонентов см. 2.1).
2.3 Приготовление электролитов для покрытия
2.3.1 Для приготовления электролита никелирования соли, входящие в состав электролита, растворяют отдельно в теплой деминерализованной воде, борную кислоту – в кипящей. Перед приготовлением ванну промывают 3-5% раствором серной кислоты в течение 2-4 часов при температуре 50-600 С. Затем ванну промывают водой и сливают в неё все растворы, перемешивают и проверяют pH. Для повышения pHдобавляют 0,3% раствор гидроксида натрия, а для понижения pH – 1н раствор серной кислоты и через 5-10 минут определяют pH.
2.3.2 Для приготовления электролита для нанесения сплава олово-висмут растворяют сульфат олова в тёплой воде при непрерывном перемешивании.
Воду подкисляют серной кислотой. После фильтрации раствора в рабочую ванну добавляют оставшуюся серную кислоту и растворенный в воде сульфат натрия. Препарат ОС-20 растворяют в небольшом количестве тёплой воды и вводят в электролит. Кроме того, в электролит вводят добавки ДДДМ. После проработки электролита током 0,5-1 А/дм2 вводят блескообразующую добавку – формалин.
2.4 Основные неполадки при работе ванн покрытия и их устранение
2.4.1 Основные неполадки в процессе никелирования представлены в таблице 2.1
Таблица 2.1 Основные неполадки в процессеникелирования, их причины и устранение
2.4.1.1 Удаление недоброкачественного покрытия никелем производится химическим способом в растворе следующего состава [ ]:
mirznanii.com
Проектирование гальванического участка — часть 6
4.5.1 Расчет расхода пара на разогрев ванны производится по формуле
, (4.9)где
— расход пара на разогрев ванны, кг; — норма расхода пара на разогрев 100 л электролита в течение 1 часа, кг; — объем ванны, л; — время разогрева ванны, = 1 час; — количество ванн.4.5.2 Расчет расхода пара на поддержание температуры производится по формуле
, (4.10)где
— расход пара на разогрев ванны, кг; — норма расхода пара на поддержание рабочей температуры в течение 1 часа, кг; — время работы ванны.4.5.3 Суточная потребность в паре определяется по формуле
, (4.12)где
— суточная потребность в паре, т.4.5.4 Годовой расход пара рассчитывается по формуле
, (4.13)где Т – число рабочих суток в году (260 суток).
Результаты расчета расхода пара представлены в таблице 4.4
Таблица 4.4 Ведомость расхода пара
4.6 Расчёт расхода воды
4.6.1 При промывке способом погружения удельный расход воды определяется по формулам
Для одноступенчатой промывки
Q уд = q ∙ K 0 , (4.14)
Для двухступенчатой
Q уд = q √ K 0 , (4.15)
Для двухступенчатой прямоточной промывки с равным расходом воды в ваннах и самостоятельной подачей воды в каждую ванну
Q уд = q 2√ K 0 , (4.16)
где Q уд – удельный расход воды на промывку 1 м2 поверхности, л/м2 ;
q – унос раствора поверхностью деталей, л ∙ м2 . q = 0, 2 л/м2 ;
K 0 – критерий промывки.
Критерий промывки определяется по формуле
K 0 = , (4.17)
где С0 – концентрация основного компонента в технологической ванне, предшествующей промывке, г/л;
С n –допустимая концентрация компонента в ванне промывки, г/л
Если после технологической ванны устанавливается ванна улавливания, то K 0 заменяется Кв.у . , который ориентировочно принимается равным
Кв.у. = (0,06 — 0,4) ∙ K 0 , (4.18)
4.6.2 Часовой расход воды определяется по формуле
, (4.17)где F – часовая производительность линии,
;4.6.3 Годовой расход воды определяется по формуле
, (4.19)Результаты расчетов расхода воды представлены в таблице 4.5.
Таблица 4.5 Ведомость расхода воды
5. Планировка участка
Гальванический цех в системе завода располагается вблизи цехов изготовителей и сборочных цехов исходя из грузопотока деталей. Поскольку нанесение металлопокрытий относится к категории вредных производств, гальванический цех размещают у наружной стены здания. По пожарной и взрывной опасности цех гальванопокрытий относится к категории Д – пожаро- и взрывобезопасные производства. Цех расположен на первом этаже здания и имеет подвал, что существенно упрощает разводку коммуникаций, располагаемых по потолку подвала, чем облегается их ремонт и обслуживание, а также повышается срок службы за счет меньшего воздействия коррозионных условий цеха.
В подвале располагается комната с выпрямителями, помещения ремонта и изоляции подвесок, изготовления и накатки полировальных кругов, помещения с емкостями для очистки и сбора сточных вод, а также комната для снятия брака. На первом этаже здания располагается основное отделения металлопокрытий, бюро технического контроля, склад продукции и помещения для приготовления и корректировки растворов. Промежуточный склад оборудован стеллажами для хранения изделий. В помещении для приготовления и корректировки растворов находится вытяжной шкаф, стол, весы, емкости для растворов, раковина для мытья рук, а также средства оказания первой помощи.
Список литературы
1. М.А. Дасоян, И.Я. Пальмская «Технология электрохимических покрытий» 1989
2. П.М. Вячеславов «Электрохимическое осаждение сплавов» 1986
3. С.Я. Грилихес «Обезжиривание, травление и полирование металлов» 1983
4. П.С. Мельников «Справочник по гальванопокрытиям в машиностроение» 1991
5. М.А. Шлугер, М.Д. Ток «Гальванические покрытия в машиностроении» справочник в двух томах, 1985
6. А.М. Ямпольский, В.А. Ильин «Краткий справочник гальванотехника» 1981
7. Методическое пособие
Размещено на http://www.
mirznanii.com
Проектирование гальванического участка — часть 5
w нар = w вн + 100 (3.14)
Для ванн с односторонним бортотсосом
w нар = w вн + 300 (3.15)
Для ванн с двусторонним бортотсосом
w нар = w вн + 500 (3.16)
Результаты расчета стандартного оборудования сводятся в таблицу 3.3.
Таблица 3.3 Ведомость стандартного оборудования
4. Расчётно-экономическая часть
4.1 Определение загрузки и тока для ванн электрохимических процессов, выбор источников тока
4.1.1 Расчёт поверхности и тока для ванн производится по формуле
Sy = ( S 1 + S 2 ) ∙ у, (4.1)
где S 1 – рабочая поверхность, т.е. поверхность деталей на подвеске, дм2 ;
S 2 – нерабочая поверхность, т.е. поверхность изолированной части подвески, дм2 . S 2 = 0,03 S 1 ;
у – количество подвесок в ванне.
Sy = (7, 56+7, 56·0, 03) ·8= 62, 29 дм2 .
4.1.2Ток на ванне рассчитывается по формуле
Yy = D к ∙ Sy , (4.2)
где D к – максимально допустимая плотность тока для данного процесса,
А/ дм2 ;
Для электрохимического обезжиривания
Yy = 62, 29 ∙ 10 = 623 А;
Для никелирования
Yy = 62, 29 ∙2 = 125 А;
Для нанесения сплава олово-висмут
Yy = 62, 29 ∙3 = 187 А.
В соответствии с рассчитанной силой тока и напряжением на ванне выбираются выпрямители для питания ванн, технические характеристики которых представлены в таблице 4.1
Таблица 4.1
4.2 Расчёт общего расхода электроэнергии на участке
4.2.1 Суточный расход технологической энергии на участке определяется по формуле
(4.3)где Z – число часов работы оборудования в сутки, ч;
N нагрев – мощность сушильной ванны;
Σ N эл дв – суммарная мощность электродвигателей, кВт;
Σ I – суммарная сила токов на ваннах, А;
N кач – мощность устройства для качания штанг, кВт;
U – среднее рабочее напряжение на ваннах, В;
η0 – КПД выпрямителя;
K 1 –коэффициент загрузки оборудования (K 1 = K з) ;
K 2 – коэффициент загрузки источника тока, равный отношению потреблённого для электролиза тока к току, указанному в паспорте выпрямителя.
W сут = 16 · (3, 6 + 2, 36+) · 0, 85 · 0, 39 = 85, 52 кВт·ч
4.2.2 Годовой расход технологической электроэнергии на участке определяется по формуле
(4.4)где T – число рабочих суток в году. T = 260 .
W год =85, 52 · 260 = 22235 кВт∙ч
4.3 Расчёт расхода анодов
4.3.1 Расчёт анодов на пуск участка, т.е. на первоначальную загрузку оборудования производится по формуле
кг (4.5)где Q п – расход анодов на пуск участка, кг;
l – длинна анодов, м. Принимается равной высоте столба электролита, т.е. около 80% высоты ванны;
b – суммарная ширина анодов, м. Составляет 60% длинны ванны;
c – толщина анодов, м. c = 0, 01 м ;
ρ – плотность металла анодов, кг/м3 ;
n 1 – количество анодных штанг в ванне;
n 2 – количество ванн.
Q п Ni = 0, 8 ·1 ·0, 6 · 2· 0, 01 · 8900 · 3 ·2 = 513 кг;
Q п Sn = 0, 8 · 1 · 0, 6 · 2· 0, 01 · 7280 · 3 ·2 = 420 кг;
Q п сталь = 0,8 · 1 · 0,6 · 2· 0,01 · 7800 · 3 ·2 = 450 кг.
4.3.2 Расчет анодов на выполнение программы
Расход растворимых анодов на выполнение годовой программы рассчитывается по формуле
Q год = N ∙ P год ∙ a ∙10-3 , (4.6)
где
— годовой расход растворимых анодов, кг; – норма расхода растворимых анодов, ;P год – производственная годовая программа с учетом брака, допускающего переделку, м2 ;
а – толщина покрытия, мкм.
Q год Ni = 9, 4 · 18360 · 3 · 10-3 = 517, 75 кг
Q год Sn = 7, 7 · 18360 · 6 · 10-3 = 848, 23 кг
Расход нерастворимых анодов выражают в процентах от первоначального расхода анодов, т.е. расхода анодов на пуск участка.
Расход стальных нерастворимых анодов в ванне электрохимического обезжиривания составляет 100%.
Результаты расчётов расхода анодов представлены в таблице 4.2
Таблица 4.2 Ведомость расхода анодов
4.4 Расчёт расхода химикатов
4.4.1 Расчёт расхода химикатов на пуск участка производится по формуле
, (4.7)
где Q п – расход химикатов на пуск участка, кг;
C – рецептурное содержание компонента, г/л;
V – объём ванны, л;
n – количество однотипных ванн;
K – массовая доля основного вещества в химикате.
4.4.2 Годовой расход химикатов определяется по формуле
Q год = N · P год · 10-3 ; (4.8)
где Q год – годовой расход химикатов, кг;
N – норма расхода химиката на покрытие 1м2 , г;
P год – годовая программа с учётом % брака, м2 .
Годовой расход химикатов для ванны снятия брака определяется исходя из её сменяемости (2-4 раза в год).
Результаты расчёта расхода химикатов предоставлены в таблице 4.3
Таблица 4.3 Ведомость расхода химикатов
4.5 Расчет расхода пара
mirznanii.com