Основные технологические процессы топливного производства. Нефтепереработка кратко — Переработка
Процесс переработки нефти можно разделить на 3 основных технологических процесса:
Процесс переработки нефти можно разделить на 3 основных технологических процесса:
1. Первичная переработка — Разделение нефтяного сырья на фракции различных интервалов температур кипения;
2. Вторичная переработка — Переработка фракций первичной переработки путем химического превращения содержащихся в них углеводородов и выработка компонентов товарных нефтепродуктов;
3. Товарное производство — Смешение компонентов с использованием различных присадок, с получением товарных н/продуктов с заданными показателями качества.
Номенклатура продукции нефтеперерабатывающего завода (НПЗ) может включать до 40 позиций, в тч:
— моторное топливо,
— котельное топливо,
— сжиженные газы,
— сырье для нефтехимического производства,
— смазочное, гидравлическое и прочее масло,
— битум,
— нефтяной кокс,
— прочие н/продукты.
Номенклатура н/продуктов, получаемых на конкретных НПЗ, зависит от состава и свойств поставляемой сырой нефти и потребностей в н/продуктах.
Характеристики фракций:
Газы, растворенные в нефти в количестве 1,9 % масс на нефть, и полученные при первичной перегонке нефти, состоят в основном из пропана и бутана. Это — сырье газофракционирующих установок и топливо (бытовой сжиженный газ).
Фракции нк -62 и 62-85оС имеют небольшое октановое число, поэтому направляется на установку изомеризации для повышения октанового числа.
Фракция 85-120 оС — это сырье каталитического риформинга для получения бензола и толуола, компонентов высокооктанового бензина.
Фракции 85-120 и 120-180 оС — сырье каталитического риформинга для получения компонентов высокооктанового бензина, и компонента реактивного топлива.
Фракция 180-230 оС — компонент реактивного и дизельного топлива.
Фракции 230-280 оС и 280-350 оС — это фракции летнего и зимнего дизельного топлива. Цетановое число объединенной фракции 240 — 350 оС = 55 . Температура застывания -12 оС. Депарафинизация фракции 230 — 350 оС позволяет получить зимнее дизтопливо.
Фракция 350-500 оС — вакуумный газойль — сырье процессов каталитического крекинга и гидрокрекинга для получения высокооктанового бензина.
Фракция, выкипающая при температурах выше 500 оС — гудрон — используется как сырье установок термического крекинга, висбрекинга, коксования, производства битума.
Нефтепереработка — непрерывный технологический процесс, остановка которого предусмотрена только для проведения планово — предупредительного ремонта (ППР), ориентировочно каждые 3 года.
Одна из основных задач модернизации НПЗ, проводимой компаниями, — это увеличение межремонтного периода, который, к примеру, у Московского НПЗ составляет около 4,5 лет.
Основная техническая единица НПЗ — технологическая установка, комплекс оборудования которой позволяет выполнить все операции основных технологических процессов переработки.
Основные операции
1. Поставка и прием нефти.
Основные пути доставки сырья на НПЗ:
— магистральные нефтепроводы (МНП) — основной для РФ вариант доставки сырой нефти,
— по железной дороге с использованием вагонов — цистерн,
— нефтеналивными танкерами для прибрежных НПЗ
Нефть поступает на заводской нефтетерминал (рис 1) в нефтяные резервуары (обычно, типа Шухова), который связан нефтепроводами со всеми технологическими установками завода.
Учет принятой на нефтетерминал нефти производится по приборам или путем замеров в нефтяных резервуарах.
2. Первичная переработка
2. 1. Подготовка нефти к переработке (электрообессоливание).
Обессоливание служит для уменьшения коррозии технологического оборудования от сырой нефти.
Поступающую из нефтерезервуаров сырую нефть смешивают с водой для растворения солей и отправляют на ЭЛОУ — электрообессоливающую установку.
Электродегидраторы — цилиндрические аппараты со смонтированными внутри электродами — это основное оборудование ЭЛОУ.
Здесь под воздействием тока высокого напряжения (25 кВ и более), эмульсия (смесь воды и нефти) разрушается, вода собирается в низу аппарата и откачивается.
Для более эффективного разрушения эмульсии, в сырье вводятся специальные вещества — деэмульгаторы.
Температура процесса обессоливания — 100-120°С.
2.2.Перегонка нефти
Обессоленая и обезвоженная нефть с ЭЛОУ поступает на установку атмосферно-вакуумной перегонки нефти (АВТ — атмосферно-вакуумная трубчатка).
Нагрев нефти перед разделением на фракции производится в змеевиках трубчатых печей за счет тепла сжигания топлива и тепла дымовых газов.
В последнее время актуальность приобрела задача перевода печей с жидкого на газообразное топливо, что повышает эффективность техпроцесса и существенно улучшает экологию.
АВТ разделена на 2 блока — атмосферной и вакуумной перегонки.
2.2.1. Атмосферная перегонка
Атмосферная перегонка обеспечивает отбор светлых нефтяных фракций — бензиновой, керосиновой и дизельных, выкипающих при температуре до 360°С, выход которых может составлять 45-60% на нефть.
Нагретая в печи нефть разделяются на отдельные фракции в ректификационной колонне — цилиндрическом вертикальном аппарате, внутри которого расположены контактные устройства (тарелки), через которые пары движутся вверх, а жидкость — вниз.
Различные по размеру и конфигурации ректификационные колонны используются на всех установках нефтеперерабатывающего производства, количество тарелок в них меняется в интервале 20 — 60.
Тепло подводится в нижнюю часть колонны и отводится с верхней части колонны, поэтому температура в колонне постепенно снижается от низа к верху.
В результате сверху колонны отводится бензиновая фракция в виде паров, пары керосиновой и дизельных фракций конденсируются в соответствующих частях колонны и выводятся, а жидкий мазут — остаток атмосферной перегонки , откачивается с низа колонны.
2.2.2. Вакуумная перегонка
Вакуумная перегонка обеспечивает отбор масляных дистиллятов или широкой масляной фракции (вакуумного газойля) от мазута.
На НПЗ топливно-масляного профиля — отбор масляных дистиллятов, на НПЗ топливного профиля — вакуумного газойля.
Термическое разложение углеводородов (крекинг) начинается при при температуре более 380°С , а конец кипения вакуумного газойля — при 520°С и более.
Перегонка при близком к вакууму остаточном давлении 40-60 мм рт ст позволяет снизить максимальную температуру в аппарате до 360-380°С, что позволяет отбирать масляные фракции.
Паровые или жидкостные эжекторы — основное оборудование для создания разряжения в колонне.
Остаток вакуумной перегонки — гудрон.
2.2.3. Стабилизация и вторичная перегонка бензина
Получаемая на блоке АВТ бензиновая фракция не может быть использована по следующим причинам:
— содержит газы, в основном пропан и бутан, в превышающем требования по качеству объеме, что не позволяет использовать их как компоненты автомобильного бензина или товарного прямогонного бензина,
— процессы нефтепереработки, направленные на повышение октанового числа бензина и производства ароматических углеводородов в качестве сырья используют узкие бензиновые фракции.
Поэтому используется техпроцесс, в результате которого от бензиновой фракции отгоняются сжиженные газы, и осуществляется ее разгонка на 2-5 узких фракций на соответствующем количестве колонн.
Продукты первичной переработки нефти, собственно, как и продукты в других техпроцессах переработки, охлаждаются:
— в теплообменниках, что обеспечивает экономию технологического топлива,
— в водяных и воздушных холодильниках.
Далее продукты первичной переработки идут на очередные переделы.
Установка первичной переработки — обычно комбинированные ЭЛОУ -АВТ — 6 мощностью переработки до 6 млн т/ год нефти, в составе:
— блока ЭЛОУ, предназначенного для подготовки нефти к переработке путем удаления из нее воды и солей,
— блока АТ, предназначенного для разгонки светлых нефтепродуктов на узкие фракции,
— блока ВТ, предназначен для разгонки мазута (>350оС) на фракции,
— блока стабилизации, предназначенного для удаления из бензина газообразных компонентов, в тч коррозийно-активного сероводорода и углеводородных газов,
— блока вторичной разгонки бензиновых фракций, предназначенного для разделения бензина на фракции.
В стандартной конфигурации установки, сырая нефть смешивается с деэмульгатором, нагревается в теплообменниках, 4мя параллельными потоками обессоливается в 2х ступенях горизонтальных электродегидраторов, дополнительно нагревается в теплообменниках и направляется в отбензинивающую колонну.
Тепло к нижнейчасти этой колонны подводится горячей струей, циркулирующей через печь.
Далее частично отбензиненная нефть из колонны после нагрева в печи направляется в основную колонну, где осуществляется ректификация с получением паров бензина в верхней части колонны, 3 боковых дистиллятов из отпарных колонн и мазута в нижней части колонны.
Отвод тепла в колонне осуществляется верхним испаряющим орошением и 2мя промежуточными циркуляционными орошениями.
Смесь бензиновых фракций из колонн и направляется на стабилизацию в колонну, где сверху отбираются легкие головные фракции (жидкая головка), а снизу- стабильный бензин.
Стабильный бензин в колоннах подвергается вторичной перегонке с получением узких фракций, используемых в качестве сырья для каталитического риформинга.
Тепло к низу стабилизатора и колонн вторичной перегонки подводится циркулирующими флегмами, нагреваемыми в печи.
Мазут из основной колонны в атмосферной секции насосом подается в вакуумную печь, откуда с температурой 420 оС направляется в вакуумную колонну.
В нижнюю часть этой вакуумной колонны подается перегретый водяной пар.
С верха колонны водяной пар вместе с газообразными продуктами разложения поступает в поверхностные конденсаторы, откуда газы разложения отсасываются 3-ступенчатыми пароэжекторными вакуумными насосами.
Остаточное давление в колонне 50 мм рт cт.
Боковым погоном вакуумной колонны служат фракции , которые насосом через теплообменник и холодильник направляются в емкости.
В 3 сечениях вакуумной колонны организовано промежуточное циркуляционное орошение. Гудрон в низу вакуумной колонны откачивается насосом через теплообменник и холодильник в резервуары.
Аппаратура и оборудование АВТ-6 занимают площадку 265*130 м2, или 3.4 га.
Инфраструктура ЭЛОУ — АВТ — 6 включает:
— подстанцию, насосную станцию для перекачки воды и компрессорную станцию,
— блок ректификационной аппаратуры,
— конденсационно-холодильная аппаратура и промежуточные емкости, установленные на 1-ярусном ж/бетонном постаменте,
— насосы технологического назначения для перекачки н/продуктов,
— многосекционные печи общей тепловой мощностью порядка 160 млн ккал*ч, используемых в качестве огневых нагревателей мазута, нефти и циркулирующей флегмы.
Продукты первичной переработки нефти
Фотографии установок первичной переработки различной конфигурации
Рис. 3. Установка ЭЛОУ-АВТ-6 Саратовского НПЗ. В центре — атмосферная колонна (показаны точки отбора фракций), справа — вакуумная |
Рис. |
Рис. 5. Установка вакуумной перегонки мощностью 1,5 млн. тонн в год на Туркменбашинском НПЗ по проекту фирмы Uhde |
Рис. 6. Установка вакуумной перегонки мощностью 1,6 млн. тонн в год на НПЗ «ЛУКОЙЛ-ПНОС». На переднем плане — трубчатая печь (жёлтого цвета) |
Рис. 7. Вакуумсоздающая аппаратура фирмы Graham. Видны 3 эжектора, в которые поступают пары с верха колонны |
3. Вторичная переработка нефти
Продукты первичной переработки нефти, как правило, не являются товарными н/продуктами.
Например, октановое число бензиновой фракции составляет около 65 пунктов, содержание серы в дизельной фракции может достигать 1,0% и более, тогда как норматив составляет, в зависимости от марки, 0,005% — 0,2%.
Кроме того, темные нефтяные фракции могут быть подвергнуты дальнейшей квалифицированной переработке.
Поэтому, нефтяные фракции поступают на установки вторичных процессов, которые обеспечивают улучшение качества н/продуктов и углубление переработки нефти.
Каталитический крекинг (каткрекинг) — важнейший процесс нефтепереработки, существенно влияющий на эффективность НПЗ в целом.
Сущность процесса заключается в разложении углеводородов, входящих в состав сырья (вакуумного газойля) под воздействием температуры в присутствии цеолитсодержащего алюмосиликатного катализатора.
Целевой продукт установки КК — высокооктановый компонент бензина с октановым числом 90 п и более, его выход составляет 50 — 65% в зависимости от используемого сырья, применяемой технологии и режима.
Высокое октановое число обусловлено тем, что при каткрекинге происходит также изомеризация.
В ходе процесса образуются газы, содержащие пропилен и бутилены, используемые в качестве сырья для нефтехимии и производства высокооктановых компонентов бензина, легкий газойль — компонент дизельных и печных топлив, и тяжелый газойль — сырье для производства сажи, или компонент мазутов.
Мощность современных установок в среднем 1,5 — 2,5 млн т/год, но есть и 4,0 млн т/год.
Ключевым участком установки является реакторно-регенераторный блок.
В состав блока входит печь нагрева сырья, реактор, в котором непосредственно происходят реакции крекинга, и регенератор катализатора.
Назначение регенератора — выжиг кокса, образующегося в ходе крекинга и осаждающегося на поверхности катализатора. Реактор, регенератор и узел ввода сырья связаны трубопроводами (линиями пневмотранспорта), по которым циркулирует катализатор.
Мощностей каталитического крекинга на российских НПЗ в настоящее время недостаточно, и за счет ввода новых установок решается проблема с прогнозируемым дефицитом бензина.
Сырье с температурой 500-520°С в смеси с пылевидным катализатором движется по лифт-реактору вверх в течение 2-4 секунд и подвергается крекингу.
Продукты крекинга поступают в сепаратор, расположенный сверху лифт-реактора, где завершаются химические реакции и происходит отделение катализатора, который отводится из нижней части сепаратора и самотеком поступает в регенератор, в котором при температуре 700°С осуществляется выжиг кокса.
После этого восстановленный катализатор возвращается на узел ввода сырья.
Давление в реакторно-регенераторном блоке близко к атмосферному.
Общая высота реакторно-регенераторного блока составляет 30 — 55 м, диаметры сепаратора и регенератора — 8 и 11 м соответственно для установки мощностью 2,0 млн т/год.
Продукты крекинга уходят с верха сепаратора, охлаждаются и поступают на ректификацию.
Каткрекинг может входить в состав комбинированных установок, включающих предварительную гидроочистку или легкий гидрокрекинг сырья, очистку и фракционирование газов.
В правой части — реактор, слева от него — регенератор
Гидрокрекинг — процесс, направленный на получение высококачественных керосиновых и дизельных дистиллятов, а также вакуумного газойля путем крекинга углеводородов исходного сырья в присутствии водорода.
Одновременно с крекингом происходит очистка продуктов от серы, насыщение олефинов и ароматических соединений, что обуславливает высокие эксплуатационные и экологические характеристики получаемых топлив.
Например, содержание серы в дизельном дистилляте гидрокрекинга составляет миллионные доли %.
Получаемая бензиновая фракция имеет невысокое октановое число, ее тяжелая часть может служить сырьем риформинга.
Гидрокрекинг также используется в масляном производстве для получения высококачественных основ масел, близких по эксплуатационным характеристикам к синтетическим.
Линейка сырья гидрокрекинга довольно широкая — прямогонный вакуумный газойль, газойли каталитического крекинга и коксования, побочные продукты маслоблока, мазут, гудрон.
Установки гидрокрекинга, как правило, строятся большой единичной мощности переработки — 3-4 млн т/год.
Обычно объемов водорода, получаемых на установках риформинга, недостаточно для обеспечения гидрокрекинга, поэтому на НПЗ сооружаются отдельные установки по производству водорода путем паровой конверсии углеводородных газов.
Технологические схемы принципиально схожи с установками гидроочистки — сырье, смешанное с водородосодержащим газом (ВСГ), нагревается в печи, поступает в реактор со слоем катализатора, продукты из реактора отделяются от газов и поступают на ректификацию.
Однако, реакции гидрокрекинга протекают с выделением тепла, поэтому технологической схемой предусматривается ввод в зону реакции холодного ВСГ, расходом которого регулируется температура. Гидрокрекинг — один из самых опасных процессов нефтепереработки, при выходе температурного режима из-под контроля, происходит резкий рост температуры, приводящий к взрыву реакторного блока.
Аппаратурное оформление и технологический режим установок гидрокрекинга различаются в зависимости от задач, обусловленных технологической схемой конкретного НПЗ, и используемого сырья.
Например, для получения малосернистого вакуумного газойля и относительно небольшого количества светлых (легкий гидрокрекинг), процесс ведется при давлении до 80 атм на одном реакторе при температуре около 350°С.
Для максимального выхода светлых (до 90%, в том числе до 20% бензиновой фракции на сырье) процесс осуществляется на 2х реакторах.
При этом, продукты после 1го реактора поступают в ректификационную колонну, где отгоняются полученные в результате химических реакций светлые, а остаток поступает во 2й реактор, где повторно подвергается гидрокрекингу.
В данном случае, при гидрокрекинге вакуумного газойля давление составляет около 180 атм, а при гидрокрекинге мазута и гудрона — более 300.
Температура процесса, соответственно, варьируется в интервале 380 — 450°С и выше.
В России технология гидрокрекинга внедрена в 2000х гг на НПЗ в Перми, Ярославле и Уфе, на ряде заводов установки гидроочистки реконструированы под процесс легкого гидрокрекинга.
Совместное строительство установок гидрокрекинга и каталитического крекинга в рамках комплексов глубокой переработки нефти представляется наиболее эффективным для производства высокооктановых бензинов и высококачественных средних дистиллятов.
4. Товарное производство
В ходе вышеуказанных технологических процессов вырабатываются только компоненты моторных, авиационных и котельных топлив с различными показателями качества.
Например, октановое число прямогонного бензина составляет около 65, риформата — 95-100, бензина коксования — 60.
Другие показатели качества (например, фракционный состав, содержание серы) у компонентов также различаются.
Для получения товарных н/продуктов организуется смешение полученных компонентов в соответствующих емкостях НПЗ в соотношениях, которые обеспечивают нормируемые показатели качества.
Расчет рецептуры смешения (компаундирования) компонентов осуществляется при помощи модулей математических моделей, используемых для планирования производства по НПЗ в целом.
Исходными данными для моделирования являются прогнозные остатки сырья, компонентов и товарной продукции, план реализации н/продуктов в разрезе ассортимента, плановый объем поставок нефти. Таким образом возможно рассчитать наиболее эффективные соотношения между компонентами при смешении.
Зачастую на заводах используются устоявшиеся рецептуры смешения, которые корректируются при изменении технологической схемы.
Компоненты н/продуктов в заданном соотношении закачиваются в емкость для смешения, куда также могут подаваться присадки.
Полученные товарные н/продукты проходят контроль качества и откачиваются в резервуары товарно-сырьевой базы, откуда отгружаются потребителю.
5. Доставка нефтепродуктов
— перевозка ж/д транспортом — основной способ доставки н/продуктов в России. Для погрузки в вагоны-цистерны используются наливные эстакады.
— по магистральным нефтепродуктопроводам (МНПП) Транснефтепродукта,
— речными и морскими судами.
Первичная переработка нефти — PetroDigest.ru / Нефтегазовый портал
Термины / П
Тема:
Переработка нефти
Под первичной переработкой подразумевают процессы физического разделения нефти на фракции (фракционирование), как при нормальном, так и при пониженном давлении.
Первой стадией современной первичной переработки нефти является атмосферная перегонка. При этом получается ряд фракций, некоторые из которых используются как конечные продукты, другие отправляются на дальнейшую вторичную переработку и компаундирование.
Атмосферную перегонку проводят в ограниченном интервале температур — примерно до 350 °С. Это связано с тем, что при дальнейшем нагревании соединения входящие в состав нефти начинаю разрушатся, что на данной стадии переработки недопустимо.
Остаток атмосферной перегонки нефти называется мазут. Чтобы разделить мазут на фракции и при этом исключить деструкцию некоторых молекул, используют так называемую вакуумную дистилляцию. Этот процесс основан на том факте, что понижение давления уменьшает температуру начала кипения вещества. При этом принято оперировать мнимыми температурами кипения веществ, т.е. температурами, которые бы были при нормальном атмосферном давлении.
Однако, и здесь имеются свои температурные пределы. Вакуумную дистилляцию обычно проводят до мнимой температуры кипения 500 — 600 °С. Дальнейшее нагревание, даже при пониженном давлении, приведет к расщеплению молекул. Не выкипающий при данной температуре темный высоковязкий продукт называется остатком вакуумной перегонки, или гудроном.
Таким образом, первичная переработка нефти включает два основных процесса:
- атмосферная перегонка
- вакуумная дистилляция
На нефтеперерабатывающих предприятиях эти процессы обычно объединяют в одну установку, под названием АВТ (атмосферно-вакуумная трубчатка). Также, зачастую в комплекс включают электро-обессолевающую установку, в результате получается блок ЭЛОУ-АВТ.
Пиролиз
Гидроочистка
Алкилирование
Риформинг каталитический
Популярные статьи
Нефть
Термины
Сланцевая нефть …
Термины
Баррель нефти
Определение, перевод в литры, история …
Термины
ОПЕК
Страны-участники, цели, влияние. Организация Стран — Эксп …
Компании / Организации
Фьючерс на нефть …
Термины
Брент (Brent) — марка …
Термины
Природный газ
Состав, свойства, нахождение в природе …
Термины
Апстрим
Upstream в нефтяной индустрии
Термины
Добыча нефти
Термины
Путь нефти
Статьи
Тяжелая нефть
Термины
СПГ — сжиженный природ . ..
Технология сжижения, хранение, транспортировка…
Термины
Конечная продукция нефтеперерабатывающего завода – нефть и газ
Конечные продукты
Описание процесса
Основными продуктами нефтепереработки являются: сжиженный нефтяной газ, бензин, дизельное топливо, топливо для реактивных двигателей, мазут и керосин — смесь нескольких различных потоков, производимых различными процессами нефтепереработки для удовлетворения окончательных требований. Затем эти продукты хранятся в резервуарном парке на территории нефтеперерабатывающего завода перед поставкой на розничные рынки. Доставка может осуществляться по трубопроводу на районные распределительные терминалы или загружаться в автоцистерны для прямой доставки в торговые точки.
Перед тем, как покинуть предприятие, продукты обычно фильтруются и коалесцируются для удаления твердых загрязнителей и взвешенной воды. Загрязняющие вещества, такие как ржавчина и окалина, могут загрязнять и разрушать распределительное оборудование (например, насосы, форсунки, расходомеры), а также оборудование конечных пользователей (например, двигатели, котлы). Вода также может вызвать проблемы с обслуживанием двигателя. Вода в топливе часто выделяет высококоррозионные соединения серы и хлориды, усугубляющие коррозию и закупоривающие системы впрыска двигателя или сам двигатель.
Потребности НПЗ
- Достижение квот по добыче нефти за счет соответствия требованиям к качеству продукции по твердым частицам и воде
- Достижение спецификаций продукта без необходимости дорогостоящей переработки
- Защита от коррозии и загрязнения оборудования для транспортировки продукта
- Защита оборудования конечных пользователей от коррозии и засорения
Производственная задача / решение Pall
Проблема
СОБСТВЕННЫЕ Спецификации частиц для конечных продуктов
Решение
Улучшение работоспособности и обеспечение спецификации продукта путем удаления военнопленных водных оборудования.
- Доступен ряд фильтрующих элементов с абсолютной и номинальной номинальной мощностью для снижения содержания взвешенных твердых частиц до <5 ppmw, а также для уменьшения загрязнения и эрозии распределительного оборудования, а также оборудования конечных пользователей.
Задача
Защита от мутных конечных продуктов, ведущих к коррозии и закупорке оборудования конечных пользователей
Решение
- Высокоэффективные коалесцеры AquaSep® XS жидкость/жидкость надежно соответствуют спецификации продукта «прозрачность и яркость» и содержат 15 частей на миллион по массе на выходе согласно измерению Aqua-Glo1, обеспечивая превосходную защиту оборудования конечного пользователя от коррозии и закупоривания.
Ключевые рекомендации по применению/фильтра (другие не показаны приложения)
Применение
1.
Предварительная дофильтрация до жидкой коалсы 9000 9000
96696969696969696969696969669696966966969696696966966966966966966966966966966
. Низкие эксплуатационные расходы за счет увеличения срока службы коагулятора L/L
2.
Свободное удаление воды из топлива для отгрузки
Снижение затрат на соль при использовании нисходящих солевых сушилок используются
Устранение перерывов и затрат на изменение из -за замены смягченных CoaleScers
66. обработанный галлон
3.
После обработки солью, осушителем или глиной
Отсутствие поставок некондиционных материалов из-за высокого содержания твердых частиц
PDF-версия этой страницы
-
Готовые продукты
Скачать:
Английский
Мобильные салазки для аренды
Мобильные фильтрующие блоки Pall оснащены фильтрующими картриджами с абсолютным номиналом для высокой пропускной способности. Это надежное и экономичное решение, помогающее поддерживать непрерывную поставку чистого топлива конечным пользователям независимо от уровня загрязнения, накопленного при транспортировке по трубопроводам или из любого другого источника загрязнения.
Мобильные фильтрующие блоки Pall оснащены фильтрующими картриджами с абсолютным номиналом для высокой пропускной способности. Это надежное и экономичное решение, помогающее поддерживать непрерывную поставку чистого топлива конечным пользователям независимо от уровня загрязнения, накопленного при транспортировке по трубопроводам или из любого другого источника загрязнения.
Читать далее
Учить больше
Учить больше
Меньше
Давайте вместе найдем правильное решение.
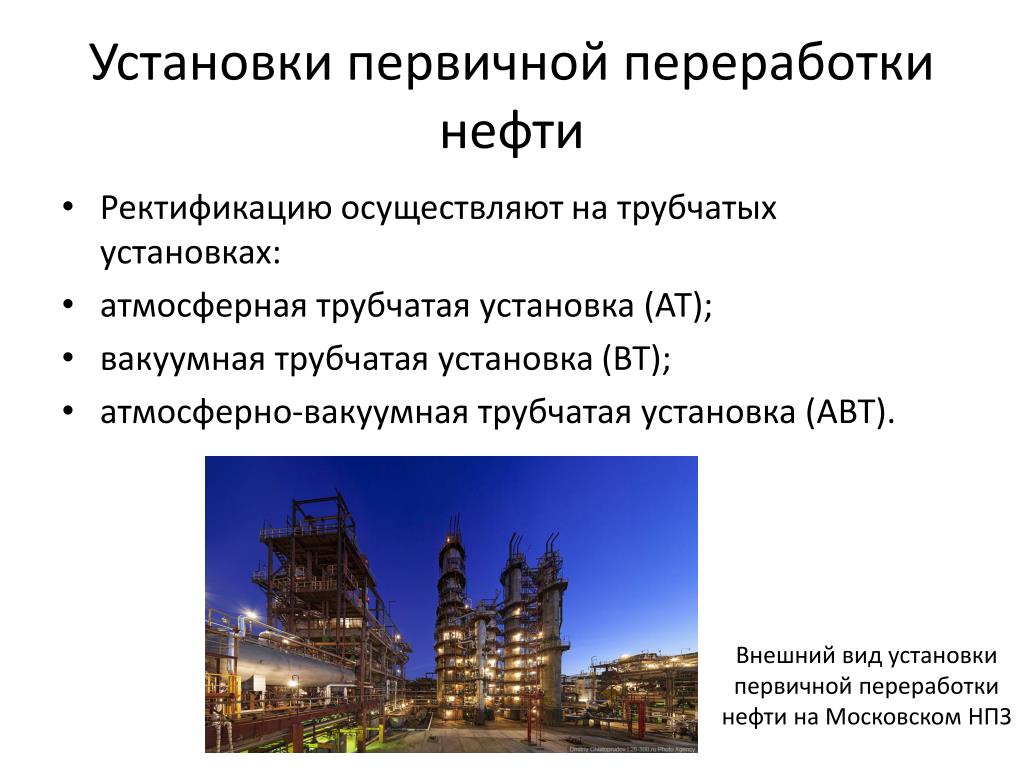
Подключаемся. Сегодня мы хотим поделиться с вами нашими инновационными решениями в области фильтрации. Свяжитесь с нашими опытными экспертами в предметной области для получения информации о том, как мы можем помочь. Спасибо, и мы с нетерпением ждем возможности помочь вам в ближайшее время.
Обзор продуктов и процессов нефтепереработки
Печать
Обзор продуктов и процессов нефтепереработки
Принимая во внимание только что рассмотренные движущие силы рынка, связанные с небольшой прибылью, которая часто обычно связана с продуктами нефтепереработки, нефтеперерабатывающие заводы должны тщательно выбирать сырую нефть и настраивать процессы нефтепереработки таким образом, чтобы они производили желаемые нефтепродукты с наименьшими затратами.
На нефтеперерабатывающих заводах США основное внимание уделяется производству бензина из-за высокого спроса. Дизельное топливо является основным продуктом нефтепереработки в большинстве других частей мира. На рис. 1.4 показано типичное распределение продуктов из барреля сырой нефти на нефтеперерабатывающем заводе в США. В процессе дистилляции сырая нефть разделяется на фракции с температурой кипения. Сжиженный нефтяной газ (LPG) представляет собой продукт нефтеперерабатывающего завода с самой низкой температурой кипения (наиболее летучий), а более высококипящие фракции приводят к наиболее желательным дистиллятным жидкостям, таким как бензин, топливо для реактивных двигателей, дизельное топливо и мазут в порядке возрастания кипения. точек, а асфальт производится из остаточной фракции, оставшейся после перегонки.
Рисунок 1.4: Типичное распределение продуктов, произведенных из сырой нефти на нефтеперерабатывающем заводе в США.
Щелкните здесь для просмотра текстового описания рисунка 1.4
Продукты, изготовленные из барреля сырой нефти
Источник: Министерство энергетики США
На следующей анимации показана блок-схема нефтеперерабатывающего завода, на которой показаны некоторые основные процессы нефтепереработки и продукты нефтепереработки. Обратите внимание, что процесс дистилляции (фракционирующая колонна) разделяет сырую нефть на ряд фракций дистиллята, которые отправляются в качестве сырья в разные процессы, некоторые из которых взаимосвязаны. Также важно признать, что нефтепереработка не только производит транспортное топливо и топливо для отопления помещений или промышленных печей, но также производит материалы, необходимые для работы двигателей внутреннего сгорания и мощения дорог для движения транспортных средств.
Видео: FSC 432 Технологическая схема нефтеперерабатывающего завода (4:12)
Технологическая схема нефтеперерабатывающего завода по переработке сырой нефти в топливо и материалы.
Щелкните здесь, чтобы просмотреть расшифровку FSC Блок-схемы нефтеперерабатывающего завода.
Здесь мы построим простую блок-схему нефтеперерабатывающего завода. Слева вы видите подачу сырой нефти на нефтеперерабатывающий завод. С правой стороны основные продукты нефтепереработки идут от самых легких к самым тяжелым. Начиная с бензина, топлива для реактивных двигателей и керосина, топлива для отопления и дизельного топлива, промышленного мазута, парафинов, смазочных масел, смазок, асфальта и нефтяного кокса будет самым тяжелым продуктом, который будет представлять собой твердое вещество, полученное на нефтеперерабатывающем заводе.
Сырая нефть подается в колонну фракционирования, которую мы называем дистилляционной колонной. Мы разделяем сырую нефть на различные кипящие фракции. И эти фракции подаются в процессы, расположенные ниже по течению, которые представляют собой установку улавливания паров, а также алкилирование, каталитический крекинг, экстракцию, коксование, депарафинизацию, производство жиров, очистку и смешивание, а также дополнительную переработку. Таким образом, мы, по сути, соединим сырую нефть через эти процессы с конечным продуктом.
Обратите внимание, что некоторые установки нефтеперерабатывающего завода подключены. Если вы посмотрите на установку улавливания паров, связанную с каталитическим крекингом, она также связана с коксованием. А наверху ультраформинг. Теперь все эти процессы производят бензин и легкие углеводороды, такие как СНГ, из различных связующих фракций сырой нефти, поступающих из дистилляционных колонн. Вот почему они связаны на этой диаграмме.
Проследим, что происходит с различными дистилляционными фракциями, поступающими из дистилляционной колонны. Во-первых, парообразный продукт сверху направляется в блок улавливания паров и разделяется на бензин и сжиженный нефтяной газ — это сжиженный нефтяной газ. Вы можете видеть процесс ультраформинга, который мы сейчас называем каталитическим риформингом для производства высокооктанового бензина.
Как видите, требуется дополнительная обработка для удаления серы из этих продуктов. ГБО так же как и бензин. Следует отметить, что каталитический крекинг также может производить реактивное топливо. Как вы можете видеть, стрелка от растрескивания кота касается точки реактивного топлива. Каталитический крекинг также дает сырье для установки алкилирования для производства дополнительного высокооктанового бензина.
Когда мы спускаемся к дистилляционной колонне, мы попадаем на территорию вакуумной дистилляции, и продукт вакуумной дистилляции проходит через экстракцию, депарафинизацию, а также различные виды обработки и смешивания для производства смазочных масел, а также парафинов и смазок.
Теперь мы находимся на дне колонны вакуумной перегонки, остаток после вакуумной перегонки может делать с этой фракцией разные вещи, а не коксоваться. Это очень тяжелый процесс термического крекинга, в результате которого в качестве побочного продукта образуется нефтяной кокс. Нефтеперерабатывающие заводы используют коксование для производства большего количества бензина для реактивных двигателей, а затем сжиженного нефтяного газа. Нефтяной кокс — это просто побочный продукт.
Остаток после вакуумной перегонки может быть переработан в процессе деасфальтизации для производства асфальта. Итак, опять же, в качестве побочного продукта основной продукт деасфальтизации, называемый деасфальтизированной нефтью, может быть использован для производства зажигалок, углеводородов, топлива и химикатов из этой фракции.
На этом очень простая блок-схема нефтеперерабатывающего завода почти завершена.
Источник: 1995 Amoco Corp.
На рис. 1.5 показано, что химический состав и физические свойства сырой нефти являются важными параметрами, определяющими конфигурацию нефтеперерабатывающего завода. Как указано, процессы рафинирования можно разделить на четыре группы. В то время как процессы разделения связаны только с физическими явлениями, процессы конверсии, окончательной обработки и поддержки требуют химических изменений, то есть разрыва химических связей для изменения молекулярной структуры исходного сырья. Эти изменения необходимы для производства топлива и материалов в соответствии с промышленными/коммерческими спецификациями.
Рисунок 1. 5. Классификация процессов нефтепереработки и видов продуктов нефтепереработки.
Щелкните здесь, чтобы открыть доступную версию изображения выше.
Это классификация процессов нефтепереработки и типов продуктов нефтепереработки, показанная на блок-схеме. Блок-схема начинается с сырой нефти. Сверху написан химический состав сырой нефти, а снизу написаны физические свойства. Сырая нефть проходит процесс переработки, включая сепарацию, конверсию, доводку и поддержку. Оттуда они идут на продукты, включая топливо, нефтехимию и материалы. Под ним написаны характеристики.
Авторы и права: д-р Семих Эсер. © Penn State имеет лицензию CC BY-NC-SA 4.0. топлива и материалов.
Рисунок 1.6. Блок-схема, объединяющая четыре типа процессов на нефтеперерабатывающем заводе (25 секунд).
Автор: д-р Семих Эсер © Penn State имеет лицензию CC BY-NC-SA 4.0
Процессы разделения, такие как дистилляция, депарафинизация и деасфальтизация, используют различия в физических свойствах компонентов сырой нефти для разделения групп углеводородных соединений или неорганических примесей, тогда как процессы конверсии вызывают химические изменения в углеводородном составе сырой нефти.