Продукция из древесины — что делают из сухой доски
Здравствуйте уважаемые читатели и подписчики блога Андрея Ноака! Сегодня я вам расскажу о том какая бывает продукция из древесины при переработки сухой доски. Влажность такого пиломатериала колеблется от 8 до 14%.
От чего зависит цена погонажа
Три самых главных критерия от которых зависит цена цельных погонажных изделий из древесины:
- Порода древесины. В одних случаях бывают дороже лиственные породы чем хвойные, в других наоборот, хорошая статья имеется на эту тему здесь.
- Наличие таких дефектов как синева, гниль, загнившие сучки, червоточины снижают стоимость погонажных изделий в разы. Поэтому хозяин желающий сэкономить покупает цельный погонаж более низкой категории и дорабатывает его сам, синева закрашивается, сучки и червоточины с легкостью замазываются.
- Длина погонажа. Чем короче изделие тем оно стоит дешевле. Связано это с тем, что более короткие изделия получают путем удаления дефектов из длиной продукции. Также дешевизна связана с тем, что получение более длинного изделия более затратна на производстве, так как увеличивается коэффициент выхода пиломатериала из бревна, увеличивается вероятность появления на изделии дефекта.
От чего зависит качество погонажа
- Качество пиловочника. С качеством пиловочника думаю все понятно, пиловочник не должен иметь синеву, червоточины, пиловочник не должен быть сухостойным.
- Порода древесины. Из ровной и прямой сосны качество цельного погонажа будет выше чем к примеру из свилеватой березы или осины. Длительность сохранения качества у сосновой панели будет больше чем у березовой.
- Место произростания. А этот показатель больше относится к качеству пиловочника. К примеру пиловочник с северных районов сибири имеет меньшее количество сучков, более плотный. А вот пиловочник из болотистых мест может иметь большее количество гнили, пиловочник из южных районов имеет меньшую плотность и соответственно прочность.
- Часть древесины из которой получена продукция. Верхняя часть дерева имеет гораздо меньшее количество гнилых, загнивших и черных сучков чем нижняя комлевая часть. Но с другой стороны количество здоровых сучков, снижающих прочность цельного погонажа, имеется больше из верхушечной части дерева.
Половая рейка, вагонка — самая востребованная продукция из цельного погонажа
К каждому виду продукции даются свои технологические рекомендации. Итак, вот собственно и список самой распространенной цельной продукции на Российском рынке, производя данную продукцию у предприятия всегда будет сбыт:
- Половая рейка. Половая рейка цельная в промышленных масштабах изготавливается как правило из пиломатериалов хвойных пород. Связано это с тем, что лиственные пиломатериалы не столь устойчивы к гниению с одной стороны, а с другой изготовление к примеру из дуба довольно дорого.
Особой ценностью из хвойных пород пользуется половая рейка из лиственницы, так как именно она меньше всего подвержена гниению и имеет достаточную твердость и износостойкость.
Применяется половая рейка из лиственницы в саунах, банях и местах с повышенной влажностью. Распиловка пиломатериала для половой рейки осуществляется из не слишком толстого леса, диаметром 18-22 см. Сегодня идет тенденция к снижению толщины половой рейки и увеличению количества лаг, связано это прежде всего с довольно высокой ценой рейки. К получению половой рейки класса экстра можно причислить древесину такой породы как дуб, красное дерево.
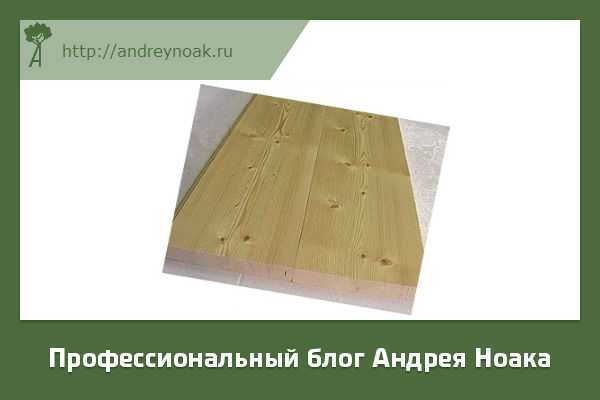
Половая рейка является одним из самых востребованных продуктов глубокой переработки древесины…
- Вагонка. Этот вид цельной продукции применяется для облицовки и придания эстетического вида как внутри помещения, так и снаружи. Облицовка вагонкой осуществляется вертикально. Получают вагонку из так называемых боковых пиломатериалов или при распиле тонких диаметров леса 12 — 16см. Опять же наблюдается снижение толщины вагонки, в связи с желанием снизить стоимость квадратного метра.
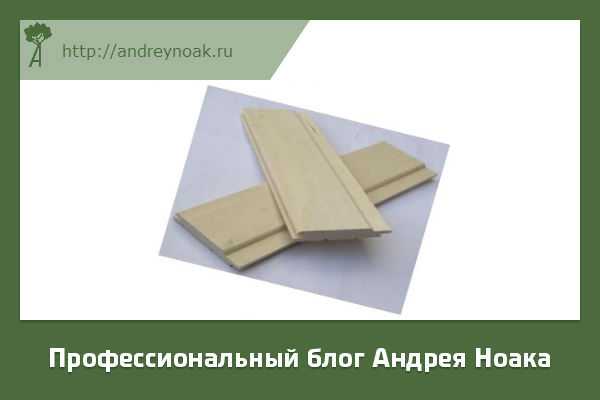
Вагонка уступает по объемам производства половой рейки, но упорно держит второе место…
- Блокхаус. Благодаря этому материалу можно сделать дизайн любой стены под дизайн из леса кругляка. Обшивка блок хаусом осуществляется горизонтально. Выглядит довольно эстетично. Изготавливается из центральной доски леса диаметром 16-22см или боковой доски при распиловке диаметров 26 и выше.
- Имитация бруса отлично подойдет если вы желаете отделать свой дом под деревянный брус.
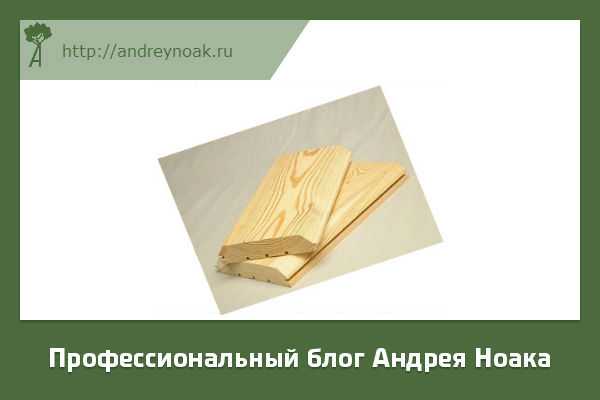
Данный материал с каждым годом все более активно выходит на рынок…
- Плинтус. Как правило идет как побочная продукция от основной и более дорогой. К примеру при производстве клееного бруса часто остаются отходы, которые можно выкинуть или получить из них плинтус небольшой длины.
- Дверная коробка.
Удачи и до новых встреч!
andreynoak.ru
Изделия из древесины
В зависимости от вида обработки к строительным деталям и изделиям относят строганные бруски, строганные и шпунтованные доски для настила чистых полов, столярные плиты, паркет, строганные погонажные изделия, профильные материалы, клееные столярные изделия и др.
Производство строганых погонажных изделий включает в себя несколько технологических этапов: заготовка древесины, распиловка, сушка, торцевое сращивание, строгание. Погонажные изделия выпускаются различных профилей – количество рисунков профилей практически неограниченно. К строганным погонажным изделиям относятся доски для настила полов, подоконные доски и перильные поручни, строганные бруски и брусья, плинтусы и наличники, кровельные плиты для временных зданий и т.д. Строганные и шпунтованные доски и бруски имеют на одной кромке шпунт, а на другой – гребень для плотного соединения элементов. Они могут иметь различную форму – прямоугольную, треугольную, трапецевидную и сегментную.
Паркет используется для лицевого покрытия полов. Выпускается паркет в виде паркетных досок, щитового паркета, наборного и штучного паркета с влажностью древесины 8+2%. Паркетные доски состоят из двух слоев: верхнего – лицевого покрытия и паркетных планок толщиной 6-8 мм и нижнего – в виде реечного основания толщиной 18-19 мм. Паркетные доски бывают различных размеров и имеют профилированные края для плотного соединения при укладке досок в паркетный пол. Щитовой паркет состоит из реечного основания хвойных пород, на которое наклеивается планочный паркет. Паркет изготавливается из древесины твердых пород: дуба, бука, ясеня, сосны, красное дерево и др. Наборный паркет представляет собой набор паркетных планок из твердых пород дерева, наклеенных лицевой стороной на бумагу в определенном порядке. Штучный паркет состоит из планок твердых пород дерева определенного размера и формы.
Столярные изделия – оконные и дверные блоки с вмонтированными в них оконными переплетами и дверными полотнами, столярные перегородки и панели для жилых и гражданских зданий. Оконные и дверные блоки поступают на строительство в полной готовности с навешенными полотнами и створками, окрашенными и застекленными. Клееные изделия и конструкции могут изготовляться в виде балок, ферм, арок. Склеиванием древесных заготовок из маломерного пиленого материала можно изготовить дверные полотна, оконные и дверные коробки, шиты для полов, а также крупные конструктивные элементы – балки, прогоны, фермы, сваи, шпунты, брус длиной до 12 метров. Клееные пиломатериалы – это продукт, уникальным образом сочетающий в себе достоинства дерева как традиционного природного материала и новейшие технологические достижения строительной индустрии.
studfiles.net
10.3. Лесоматериалы и изделия из древесины
Лесоматериалы получают механической обработкой древесины. Они подразделяются на круглые лесоматериалы, пиломатериалы, фрезерованные и строганые материалы, вторичные продукты: опилки, стружки, щепа, древесная мука.
Круглые лесоматериалы – стволы поваленного дерева, очищенные от сучьев. В зависимости от диаметра ствола в верхнем отрубе различают: бревна (диаметр более 12 см), подтоварник (диаметр 8 – 11 см) и жерди (диаметр 3 – 7 см). Бревна делят на строительные (из сосны, лиственницы, кедра, реже ели и дуба), предназначенные для несущих конструкций, и пиловочные, используемые для получения пиломатериалов.
Пиломатериалыполучают продольной распиловкой пиловочных бревен. Они подразделяются на доски (толщиной 100 мм и менее), бруски (имеющие толщину менее 100 мм, но ширину меньше трехкратной толщины), брусья (имеющие ширину и толщину более 100 мм).
Строганые и шпунтованные доски и бруски имеют на одной кромке шпунт, а на другой – гребень для плотного соединения элементов. Фрезерованные изделия – плинтус, поручни, наличники и т.п.
Изделия из древесины.К ним относятся паркет, мебельные щиты, столярные изделия – оконные и дверные блоки, двери и т.п., фанера, древесно-стружечные и древесно-волокнистые плиты, древесно-слоистые пластики, а также сборные дома, клееные деревянные конструкции и изделия из модифицированной древесины (обработанной синтетическими смолами, прессованной, пластифицированной аммиаком и др.).
11. Конструкционные материалы на основе органических вяжущих веществ
Конструкционные материалы на основе органических вяжущих веществ, как и предыдущие их группы на основе неорганических вяжущих, являются безобжиговыми композитами. К ним относятся асфальтовые бетоны и растворы, дегтебетоны, полимербетоны и другие композиции на основе битумных и дегтевых вяжущих, а также полимерных вяжущих. Связующее вещество (матрица) в этих материалах, как и в композитах на основе неорганических вяжущих, формируется путем взаимодействия между жидкой дисперсионной средой, в качестве которой выступает органическое вяжущее, и твердой дисперсной фазой – порошкообразным компонентом.
Органические вяжущие веществапредставляют собой природные или искусственные твердые, вязкопластичные или жидкие (при обычной температуре) вещества, состоящие из химических соединений с атомами углерода, обладающие способностью отвердевать и сцепляться (иметь достаточную адгезию) с минеральными или органическими наполнителями и заполнителями, растворяться в органических растворителях. К органическим вяжущим относят битумные и дегтевые вяжущие (битумы, дегти и композиции на их основе – битумно-резиновые, битумно-полимерные и др.), часто называемые «черными» вяжущими, и полимерные вяжущие (олигомеры, полимеры и сополимеры). Эти вяжущие придают материалам водоотталкивающие свойства (гидрофобность) и водостойкость, эластичность, малую пористость. Поэтому органические вяжущие широко используются в изоляционных и кровельных материалах. Определенное количество их применяется в конструкционных материалах типа бетонов, растворов и изделий из них.
studfiles.net
Пороки древесины
Пороками древесины
Пороки, зависящие от неправильного строения, образующиеся в период роста древесины:
косослой древесины выражается в винтообразном направлении волокон, что значительно ухудшает физико-механические свойства древесины;
крень однобокая и местная встречается у хвойных пород и представляет собой неравномерную по окружности толщину годовых слоев со смещением сердцевины;
кривизна представляет собой искривление ствола дерева по длине, причем ствол может быть искривлен в одной или нескольких плоскостях;
сбежистость
заключается в уменьшении диаметра ствола от комля в вершине, превышающем норму, т.е. более чем на 2 см на 1 м длины ствола;двойная сердцевина характеризуется наличием двух сердцевин в поперечном сечении ствола;
сучковатость выражается количеством сучков на 1 м длины ствола, величиной и видами самих сучков;
трещины образуются не только при высыхании срубленного дерева, но и у растущего от различных причин (усыхание ядра, раскачивание ветром, от мороза и т.д.).
Пороки древесины, вызываемые жизнедеятельностью различных грибов:
плесени и гнили могут поражать древесину растущего дерева, однако большую опасность для долговечности лесных материалов представляют гнили, поражающие древесину в условиях ее службы в зданиях и сооружениях;
споры грибов, попадая в древесину, прорастают в виде тонких нитей (гиф), которые, проникая из одной клетки в другую, оставляют в их оболочках отверстия;
грибы, развивающиеся на древесине непосредственно в зданиях и сооружениях, называются домовыми.
Пороки древесины, вызываемые насекомыми:
червоточина появляется как на растущем, так и на срубленном дереве всех пород; это глубокое повреждение древесины насекомыми и их личинками;
поверхностное повреждение древесины в виде неглубоких извилистых борозд вызывают жучки-короеды, лубоеды и их личинки.
2. Основные виды материалов и изделий из древесины, защита древесины
Виды лесных материалов и изделий: круглые лесные материалы, пилопродукцию и заготовки, изделия строганые погонажные, материалы для полов, плиты столярные, фанеру и столярные изделия.
Круглые лесные материалы в зависимости от диаметра в верхнем отрубе подразделяют на мелкие (6-13 см), средние (14-24 см) и крупные (более 25 см), подтоварник и бревна. По назначению бревна делят на строительные (12-24 см) и пиловочные (более 24 см). Строительные бревна предназначены для применения в круглом виде, а пиловочные – для получения пилопродукции.
Пилопродукция подразделяется на пиломатериалы и заготовки.
Изделия строганые погонажные изготавливают из древесины хвойных и лиственных пород и выпускают длиной 2,1 м и более с градацией через 100 мм. К ним относятся наличники, раскладки, плинтусы, поручни, проступи, доски подоконные и др. Погонажные строганые изделия могут быть не только цельными, но и составными как по сечению, так и по длине. Влажность древесины не должна превышать 15%.
Материалы для полов выпускают следующих видов: штучный паркет, паркет, наклеенный на бумагу, щитовой паркет, паркетные доски, доски для настила чистых полов и шашка торцовая. Для их изготовления применяют различные хвойные и лиственные породы.
Фанеру изготавливают склеиванием тонких слоев (шпона) древесины. В строительстве применяют фанеру трех видов: клееную, бакелизированную и декоративную.
Столярные изделия производят следующих основных видов: элементы дверей, окон, ворот, перегородки и панели. Столярные изделия изготавливают в основном из древесины хвойных пород, а из лиственных пород делают только внутренние двери и фрамуги для помещений с относительной влажностью воздуха до 70%.
Деревянные конструкции поставляют на стройку в готовом виде. Комплекты деревянных изделий и деталей для домов изготавливают из различных хвойных и лиственных пород. Дома заводского изготовления производят одно- и двухэтажные. Их собирают на строительной площадке по различным конструктивным схемам: брусчатые (рубленые), каркасные и щитовые, что определяет конкретный набор деревянных конструкций. Элементы несущих и ограждающих конструкций выполняют из древесины хвойных пород.
Защита древесины
Защита древесины представляет собой совокупность мероприятий, повышающих ее стойкость к разрушающим факторам. Древесина разрушается под действием физических (температура, влажность воздуха), химических (кислоты, щелочи и другие агрессивные среды) и главным образом биологических (грибные гнили, насекомые) факторов.
Физическая защита включает мероприятия, создающие такое состояние древесины или окружающей среды, которое прекращает действие разрушающих факторов. К ним относят создание требуемого температурно-влажностного режима древесины (сушка, искусственное дождевание и др.), а также конструкционную защиту: предохранение от увлажнения с помощью гидроизоляционных, лакокрасочных и других покрытий, создание условий для естественной вентиляции и т.п.
Химическая защита древесины проводится с помощью химических препаратов и подразделяется на профилактическую и истребительную.
Комплексная защита включает мероприятия, останавливающие разрушение древесины от двух и более неблагоприятных факторов. Она проводится с использованием физических и химических принципов защиты. рассмотренных выше.
Антисептики – токсинные химические препараты, придающие древесины стойкость к поражению грибами, насекомыми, морскими древоточцами и т.п. Они должны хорошо проникать в древесину, не разрушать ее и не вымываться, не иметь неприятного запаха, быть относительно безвредными для человека и животных. Требования к антисептикам определяются условиями службы древесины в строительных конструкциях.
Антисептики по растворимости делят на три типа: водорастворимые (ВР), растворимые в легких органических растворителях (Л) и растворимые в маслах и тяжелых нефтепродуктах (М). По вымываемости различают четыре класса: легковымываемые (ЛВ), вымываемые (В), трудновымываемые (ТВ) и невымываемые (НВ).
Таблица 1
studfiles.net
Продукция из дерева
Наше предприятие предлагает широкий спектр разнообразной продукции из древесины. Это деревянные черенки, дранка, гонт, щепа для копчения, древесный наполнитель пеллеты и т.д. Дерево универсальный материал, его легко обрабатывать, пилить, склеивать, рубить, точить. Из него можно сделать все что угодно любых форм и размеров. Во всех сферах человеческой деятельности найдется место для деревянной продукции. Дерево используют как топливо, применяют в строительстве, из него делают бытовую продукцию. Деревянные изделия в быту – это всегда уютно, практично и безопасно.
Всю продукцию из дерева мы изготавливаем на оборудовании собственного производства. Деревообрабатывающие станки помогают ускорить и упростить процесс выпуска деревянных изделий. К примеру, если рассматривать бытовые изделия из древесины – черенки для инвентаря, деревянные ручки, то при станочной обработке поверхность изделий получается гладкая, качественная. Также с помощью станков можно перерабатывать отходы древесины и получать готовый продукт.
Изделия из древесины никогда не выйдут из моды, потому что они красивые, экологически чистые, приятные на ощупь, всегда теплые. К тому же материал древесина доступен в наших северных широтах, что позволяет делать недорогие товары для широких масс. Для производства продукции из дерева мы используем древесину осины и ольхи. Каждый вид древесины уникален по-своему, например древесина осины со временем становится прочней, ее не портят насекомые, ольха отлично подходит для копчения, и у нее приятный цвет.
Продукция из дерева отличный выбор, ведь натуральное, несмотря на некоторую внешнюю уязвимость, намного лучше синтетических аналогов, к тому многие изделия из дерева не уступают на самом деле по прочности и долговечности искусственным материалам, ведь многие постройки из древесины сохранились сотни лет, а деревянные вещи находят в раскопках в довольно хорошем состоянии. Вряд ли в ближайшее время появится другой похожий материал, который сможет конкурировать с деревом или заменить его совсем. Именно поэтому продукция из дерева всегда будет востребована на рынке.
www.bmpa.ru
Продукция переработки древесины. Пиломатериалы и продукты переработки древесины. Материалы из продуктов древесины. древесина
Древесина — сравнительно твердый и прочный волокнистый материал, скрытая корой основная часть стволов, ветвей и корней деревьев и кустарника. Состоит из бесчисленных трубковидных клеток с оболочками в основном из целлюлозы, прочно сцементированных пектатами кальция и магния в почти однородную массу. В природном виде используется в качестве строительного материала и топлива, а в размельченном и химически обработанном виде – как сырье для производства бумаги, древесноволокнистых плит, искусственного волокна.
Материалы из продуктов древесины.
При распиливании круглого дерева и последующей обработке пиломатериалов на станках получаются отходы (40-50% от количества поступающего на переработку круглого леса): кора, горбыль, обрезки пиломатериалов, опилки, стружки и т. д.
На базе древесных отходов, а также из неделового леса изготовляют древесностружечные плиты, клееные плиты, оргалит, ксилолит, фибролит, деревобетон и др.
Древесные отходы могут быть крупными (обапол, обрезки, неделовая древесина) и мелкими. Обаполы применяют для устройства временных заборов, временных складских закромов, для укрепления траншей и т. д. Обрезки пиленого леса применяют для производства клееных столярных щитов, дверных полотен, плит под паркетный набор и т. д. Из мелких отходов и неделовой древесины можно изготовлять древесную шерсть для фибролита, щепу для деревобетона и др.
Древесные опилки являются сырьем для гипсопилочных перегородок и подготовок под полы при изготовлении магнезиального ксилолита, битумно-опилочных плит; их используют также в качестве выгорающей добавки при производстве легковесных керамических изделий.
Станковую стружку (с короткими древесными волокнами) используют для получения древесно-цементных камней и изготовления теплоизоляционных плит и др.
Как видно из приведенных данных, на основе перечисленных отходов можно изготовлять целый ряд эффективных искусственных материалов на цементных, гипсовых (см. разд. X и XII) и смоляных (см. разд. XIV) вяжущих.
Из волокнистой древесной водной пульпы изготовляют древесноволокнистые плиты, которые называются оргалитом. Органическое сырье поступает в рубильную машину, а затем через магнитный сепаратор — на сортировку. Крупная щепа направляется на вторичное дробление, после чего вновь на сортировку. Отсортированная мелкая щепа попадает в пульперы, где ее размалывают и одновременно разжижают водой до 3-процентной концентрации волокна в пульпе. Из пульпера масса поступает в центробежную барабанную сортировку для отделения крупных волокон, а затем — в вакуум-сгуститель для смешивания со специальными добавками (антисептиками, красителями, коагулянтами, смоляными эмульсиями).
Эмульсии могут быть парафиновые, приготовленные на синтетических жирных кислотах, на олеиновой кислоте, фенолформаль-дегидные и другие, придающие изделиям водостойкость, устойчивость против дереворазрушающих грибов, а также повышающие степень огнестойкости и механическую прочность.
Обработанная эмульсиями и другими составами масса поступает в регулятор консистенции, а затем в отливочную машину, где масса обезвоживается способом вакуумирования, и слои массы откладываются на сетки барабана. Плиты с концентрацией органической массы до 20% снимают с барабана и отправляют на прессование. После прессования плиты обрезают и сушат.
Полутвердые и твердые плиты изготовляют из пористых плит прессованием на гидравлических прессах при температуре 230° С и давлении до 107 н/м2.
В зависимости от назначения древесноволокнистые плиты подразделяют на сверхтвердые, твердые, полутвердые, изоляционно-отделочные и изоляционные. По физико-механическим свойствам плиты должны удовлетворять требованиям.
Твердые и сверхтвердые отделочные плиты применяют для сто-лярно-мебельных работ, для покрытий пола. При горячем прессовании полутвердых или твердых плит, на поверхность которых нанесена смоляная пленка, можно получать облицовочные гладкие поверхности. При изготовлении сверхтвердых плит, предназначенных для полов, в массу вводят синтетические смолы и покрывают епециальным лаком.
Изоляционно-отделочные и изоляционные плиты, применяют для утепления и звукоизоляции ограждающих конструкций, полов и других элементов зданий, полутвердые — для обшивки стен и потолков (органическая сухая штукатурка), для изготовления дверных полотен (внутренней части).
Плиты с сеткой отверстий называют перфорированными и применяют для звукоизоляционных конструкций.
Плиты выпускают длиной до 3600, шириной до 1800, толщиной для твердых групп 3-8 и изоляционных 8-25 мм.
Продукты переработки древесины
Превосходные свойства LVL позволяют отнести его к наиболее перспективным материалам, используемым в строительстве. Слоистая структура шпоновых балок делает их прочными и долговечными. Снижающие прочность дефекты отдельных слоёв шпона, такие как сучки, распределяются в толще слоёв таким образом, что их влияние на прочность конечного продукта незначительно. Благодаря таким характеристикам, как постоянство качества, стабильность и точность размеров, прямолинейность, клееные шпоновые балки LVL значительно превосходят другие конструктивные материалы из древесины.
Эстетически шпоновые балки имеют вид массивной древесины, который может выигрышно использоваться архитекторами и дизайнерами в строительстве. При необходимости эстетические качества изделия могут быть в дальнейшем улучшены за счёт использования древесины лучшего качества в верхнем слое шпона. Технология производства LVL сходна с технологией производства фанеры. Она включает лущение шпона из хвойных пород древесины с последующим склеиванием нескольких слоев шпона. Несмотря на сходство технологий производства фанеры и LVL, эти процессы имеют существенные различия.
При производстве фанеры волокна соседних слоев шпона расположены перекрестно, а при производстве LVL — параллельно. При изготовлении LVL используется шпон большей толщины (до 3,2 мм), а готовое изделие может иметь толщину до 10 см. В результате получается однородный бездефектный материал. Технология LVL позволяет изготовлять балки для несущих конструкций (стены, перекрытия для крыш и полов, и пр.), несущие балки мостов, шпалы, брус для профилирования. Ориентированно-стружечные плиты OSB являются новым высокотехнологичным материалом, применяемым в деревянном каркасном домостроении, при изготовлении мебели, для упаковки. Плиты OSB производятся путем склейки крупноразмерной (3-8 см) тонкой стружки, причем в верхнем и нижнем слоях направление волокон расположено продольно, а в среднем слое — поперечно длине плиты
По физическим свойствам плиты OSB схожи с хвойной фанерой, однако гораздо более дешевы в изготовлении за счет низких требований к качеству древесного сырья. Из-за более низкой стоимости при одинаковых потребительских качествах ориентированно-стружечные плиты постепенно вытесняют фанеру во многих традиционных областях применения.
Ориентированно-стружечная плита — это плотная спрессованная трехслойная древесная плита из крупной ориентированной щепы хвойных пород. Является заменителем фанеры и ДСП. Внешний вид ориентированно-стружечной плиты наглядно объясняет ее название. Плиту легко отличить по удлиненной щепе. Ориентированно-стружечная плита состоит из трех слоев. В наружных (верхнем и нижнем) слоях щепа расположена продольно, а во внутреннем слое поперечно. Каждый слой проклеен водостойкими смолами и спрессован под воздействием высокого давления и температур.
В результате этой технологической особенности плит OSB приобретает водостойкость, упругость и устойчивость к растяжению и строительным нагрузкам. Древесностружечные плиты с ориентированной структурой (OSB) изготавливаются методом горячего прессования древесной щепы, смешанной со связующим материалом. Плита средней плотности MDF (Medium density fiberboard) представляет собой древесноволокнистую плиту средней плотности, получаемую смешением в определенной пропорции древесноволокнистой фракции с заданными параметрами и связующим, с последующим прессованием высоким давлением.
От обычной ДВП МДФ отличается меньшей подверженностью воздействию влаги, большим диапазоном толщины (от 3 до 60 мм). На настоящий момент времени данный продукт имеет самое быстрое распространение в мире в сфере производства древесных плит, а так же расширяет свою популярность среди отечественных потребителей, использующих MDF как эффективный конструкционный материал для изготовления современной мебели и строительства (для изготовления полов и облицовки стен). При этом развитие МДФ, ранее происходившее с четкой ориентацией преимущественно на мебельное производство, постепенно расширяет сферы применения.
Распиловочный сортамент, используемый в столярном производстве, получается в результате распиловки ствола дерева. Сортамент пиломатериалов определяется наличием различных дефектов древесины и зависит от точности ее распиловки, чистоты обработки и степенипокоробленности. Приобретая или заготавливая материал, исходят из его размеров и необходимого объема. Материала заготавливают всегда чуть больше, чем необходимо, учитывая скрытый брак заготовок.Наиболее употребительные размеры пиломатериалов для работы в домашних условиях следующие: досок — толщина 13…45, ширина 80…250 мм; брусков — соответственно 50… 100 и 80…200 мм; брусьев — сечение 130…250Х130…250 мм. Длина пиломатериалов — не более 6,5 м.
Для столярной заготовки используют обычно необрезные доски, выпиленные ближе к центру ствола. Они в меньшей степени подвержены усадке и высыханию. Для небольших изделий используют и дефектные в целом доски: со сбежистостью, кривизной, трещинами, незначительным косослоем, сучковатостью.
Материал для столярных изделий покупают в магазинах. Но не следует забывать, что для их изготовления можно использовать старую мебель, тарную дощечку, отходы пиломатериалов, старый паркет, элементы разбираемых деревянных построек, балочных перекрытий и т. д.
Продуктами переработки древесины являются строганый и лущеный шпон, фанера, древесностружечные и древесноволокнистые плиты.
Строганый и лущеный шпон служит материалом для облицовочных и мозаичных работ. В магазины шпон поступает с деревообрабатывающих комбинатов или мебельных фабрик в пачках различной длины и ширины. Получают его при строгании или лущении древесины: лущеный—березы, ольхи, ели, сосны, бука, липы и других пород со слабовыраженной текстурой, строганый — грецкого ореха, ясеня, бука и т. д. Строганый шпон используют, как правило, для облицовывания мебели, а лущеный — столярных и древесностружечных плит. Для облицовывания в домашних условиях рекомендуется шпон толщиной 0,6…1,5 мм.
Кроме строганого и лущеного шпона, для облицовывания изделий в столярном деле используют еще пиленый шпон толщиной от 1 до 12 мм. В домашних условиях такой шпон получают, распиливая древесину обыкновенной одноручной пилой с соответствующим разводом зубьев. Пиленый шпон используют для облицовывания небольших изделий.
Фанера состоит из нескольких (три, пять и более) склеенных слоев лущеного шпона. Основными породами древесины, используемой для изготовления фанеры, являются ольха, береза, бук, сосна, липа и др. В продажу фанера поступает шлифованной и нешлифованной с маркировкой согласно применяемым клеевым составам. Фанеру применяют в качестве конструкционного и облицовочного материала. Оклеивают ее строганым шпоном ценных пород — дуба, ясеня, березы, бука, грецкого ореха, красного дерева, клена и т. д. Вместо шпона фанеру можно облицовывать декоративными пленками или декоративной бумагой. Толщина фанеры — от 3 до 18 мм.
Столярные плиты — это склеенные между собой рейки, облицованные лущеным шпоном или фанерой. Для облегчения конструкций изготовляют также плиты, в которых рейки размещены блоками с образованием пустот. Щиты, изготовленные таким образом, не гнутся и не трескаются. Толщина столярных плит — 16…50 мм. В домашних условиях мастер может изготовить столярную плиту сам, используя соответствующие материалы и инструмент. Столярные плиты используют для изготовления предметов мебели.
Древесностружечные плиты (ДСП) изготовляют из древесины и ее отходов, которые измельчают, сушат, сортируют, смешивают со связующим, формуют и при определенном давлении и температуре прессуют. Толщина плит—10… 20 мм. Плиты бывают водостойкие и неводостойкие, разной плотности, шлифованные и нешлифованные. ДСП применяют в основном для устройства перегородок, обшивки каркасов конструкций и изготовления отдельных предметов мебели.
Древесноволокнистые плиты (ДВП) также изготовляют из дробленой древесины, которая проходит дополнительную специальную обработку. Толщина ДВП — 2,5…25 мм. Плиты имеют различные плотность, водостойкость и степень звукопоглощения. ДВП повышенной твердости применяют для облицовывания каркасов мебели, щитовых конструкций раздвижных дверей, перегородок и т. д.
Использование коры.
В мозаичных работах используется кора некоторых деревьев (см. фото 9). Наиболее широко применяется кора березы (береста), сосны в возрасте 45… 60 лет, ивы, молодых побегов розового куста и т. д.
Бересту заготавливают в мае — июне, когда особенно сильное сокодвижение. Лучше других — кора с обычной березы, особенно с деревьев, растущих на умеренно-влажных грунтах: она чистая, без черных отметин и штрихов. Бересту отслаивают со срубленного дерева острым еловым или рябиновым клином по сделанным предварительно надрезам. После отделения от дерева ее тщательно протирают тканью; хранят в пачках под грузом в прохладном затененном месте. Перед работой бересту вымачивают в горячей воде, после чего она становится мягкой и податливой. Иногда береста бывает толще строганого шпона, и чтобы сделать ее тоньше, снимают несколько внутренних слоев. В процессе работы на бересту давить не рекомендуется, потому что она от этого уплотняется и темнеет. Под лаком береста также немного темнеет.
Кора сосны сверху имеет красно-оранжевую чешуйчатую структуру, под которой расположен зеленый подслой — молодая кора, легко снимаемая со ствола. Бить по коре не рекомендуется, так как в местах удара появляется почернение. После снятия с дерева кору сосны подсушивают до исчезновения излишков влаги. При высыхании она немного темнеет. После покрытия лаком цвет коры становится насыщеннее. Применяется кора сосны в основном для вставок, где необходим природный зеленый цвет, в растительных орнаментах и т. д.
Для определения влажности древесины на свежий скол отщепа от заготовки кисточкой наносят спиртовой раствор йода. Если дерево заготовлено зимой (менее сырое), то прожилки приобретут темно-фиолетовый оттенок, если летом (более сырое) — желтоватый. ф Если при ударе молотом или обухом топора по торцу заготовки получается глухой звук — древесина сырая, если звонкий — сухая. Однако определить таким образом влажность сучковатой заготовки трудно, так как наличие сучков будет усиливать «звучание» древесины.
Лучше всего влажность древесины определить по стружке, снимаемой фуганком с заготовки. Древесина будет сырая, если тонкую и длинную стружку можно завязать в узел, и сухая, если стружка ломается.
Плотность древесины можно определить по степени насыщения ее влагой. Так, чтобы отобрать дубовую доску высокого качества, одинаковые по размеру образцы нескольких досок помещают на несколько часов в воду, после чего их взвешивают. Самый тяжелый образец будет самого низкого качества, так как он впитал много воды, а это значит, что у него древесина менее плотная, чем у остальных.
В соках, которыми питается дерево во время своего роста, содержится много различных солей. При высыхании древесины они остаются в порах клетчатой структуры дерева, куда при определенных условиях поступает и влага с воздухом. Это способствует загниванию материала заготовок. Чтобы избавиться от солей, заготовки с грузом опускают на чистое речное дно комлем против течения. Через определенное время (обычно 7…8 месяцев) вода вымоет из древесины все соли. После сушки дерево становится очень прочным, почти не коробится и не трескается. Следует помнить, что не каждое дерево можно таким способом освобождать от солей, так как многие породы во влажной среде загнивают. Поэтому выщелачиванию подлежат лишь те породы, которые выносливы к пребыванию во влажной среде: дуб, сосна, ольха, тис и некоторые другие.
Глубокая переработка древесины — особенности
Древесина по объему использования занимает одно из передовых позиций среди существующих природных ресурсов.
В этой связи, широкое распространение получила глубокая переработка древесины. И преимуществом этого является переход к безотходной технологии.
Применение
Наряду с известными древесными материалами, имея в виду круглый лес, брусья, доски, шпалы и прочие, все большее распространение получают конструкции и изделия из отходов древесины. И это притом, что отходы переработки древесного сырья составляют до 60%.
Получаемые значительные отходы, а также неделовая древесина идет на переработку, в результате чего получаются, так называемые, ДСП — древесностружечные плиты и ДВП – древесноволокнистые плиты. И трудно представить себе какую-либо сферу человеческой деятельности без использования такой продукции.
Между тем, глубокая переработка древесины мягких лиственных пород имеет ряд превосходств и перед добычей нефти, газа, и другими отраслевыми гигантами.
Глубокая переработка древесины
Это, прежде всего:
Восстанавливаемость лесов;
Транспортная доступность к лесным массивам;
Наличие ЛЭП и построенных ранее дорог;
Простота технологии;
Избыток рабочей силы;
Относительно низкая стоимость перерабатывающего оборудования.
Следует отметить, что древесное сырье в виде сучьев, коры, ветвей, корневища, горбыля по сырьевым показателям, часто превосходит стволовую древесину.
Итак, после доставки древесины на территорию переработки, она сортируется по породам и диаметру. Далее производится штабелировка, и подача сырья на накопительную площадку для распила.
Производится:
распиловка круглого леса;
распиловка горбыля на 3-х кантовый брус;
распиловка 3-х кантового бруса;
боковая распиловка горбыля.
Далее идет технологический цикл переработки. На сегодняшний день, на основе нано технологий разрабатываются уникальные способы для резкого улучшения физико-механических свойств низкосортной древесины. Они пропитываются соответствующими растворами.
Для придания продукции качеств огнестойкости и надежности от грибков, также применяются различные варианты водных растворов. Эти нововведения позволяют получить и такие преимущества, как плотность и прочность, 2-х кратный срок службы, улучшение повторного лакокрасочного покрытия.
Переработка древесины считается экологичным и безотходным производством. Заключается это и в том, что утилизация древесных отходов происходит за счет использования остатков переработки.
Древесина — сравнительно твердый и прочный волокнистый материал, скрытая корой основная часть стволов, ветвей и корней деревьев и кустарника. Состоит из бесчисленных трубковидных клеток с оболочками в основном из целлюлозы, прочно сцементированных пектатами кальция и магния в почти однородную массу. В природном виде используется в качестве строительного материала и топлива, а в размельченном и химически обработанном виде – как сырье для производства бумаги, древесноволокнистых плит, искусственного волокна. Древесина была одним из главных факторов развития цивилизации и даже в наши дни остается одним из важнейших для человека видов сырья, без которого не могли бы обойтись многие отрасли промышленности.
Трудно назвать какую-нибудь отрасль народного хозяйства, где древесина не использовалась в том ли ином виде, и перечислить разнообразные изделия, в которые древесина входит составной частью. По объему использования и разнообразию применения в народном хозяйстве с древесиной не может сравниться никакой другой материал.
Древесину применяют для изготовления мебели, столярно-строительных изделий. Из неё делают элементы мостов, судов, кузовов, вагонов, тару, шпалы, спортивный инвентарь, музыкальные инструменты, спички, карандаши, бумагу, предметы обихода, игрушки, сувениры. Натуральную или модифицированную древесину применяют в машиностроении и горнорудной промышленности; она является исходным сырьём для целлюлозно-бумажной промышленности, производства древесных плит.
Широкому использованию продукция переработки древесины способствуют её высокие физико-механические качества. Хорошая обрабатываемость. А также эффективные способы изменения отдельных свойств древесины путем химической и механической обработки. Древесина легко обрабатывается, имеет малую теплопроводность, достаточно высокую прочность, при небольшой массе хорошую сопротивляемость ударным и вибрационным нагрузкам, в сухой среде долговечна. Древесина соединяется крепёжными изделиями, прочно склеивается, сохраняет красивый внешний вид, на неё хорошо наносятся защитно-декоративные покрытия. Вместе с тем она имеет недостатки, такие как горение древесины, ее загниванию, разрушение от воздействия насекомых и грибов, гигроскопична, вследствие чего древесина может разбухать и подвергаться усушке, короблению и растрескиванию. Кроме того, древесина имеет пороки биологического происхождения, которые снижают её качество. Чтобы использовать древесину, надо знать её свойства, строение и пороки.
sawwood.ru
Изготовление древесины. Изготовление и обработка древесины. Изделия из древесины. древесина
Древесина это материал, производящийся из кустарников и стволов деревьев. Ее используют для изготовления различных предметов. Древесина легко поддается обработке, но она тяжелая. Главным преимуществом древесины является то, что это возобновляемый ресурс и, заботясь о лесах люди, смогут вечно использовать его.
Деревянные двери
Вы хотите установить деревянные двери? У Вас в доме нестандартные проемы дверей? Тогда Вам нужна услуга деревянные двери на заказ.
Двери из массива дуба никогда не выйдут из моды. Дуб — благородное дерево, обладающее уникальными свойствами: потрясающая текстура дерева, и твердость древесины. Но, в тоже время, при своей твердости двери из дуба очень привередливы к перепадам температуры и влажности. К этим условиям нужно подготавливаться заранее.
Ясень относится к самым ценным породам дерева, поэтому двери из массива ясеня обладают удивительной красотой и очень ценятся. Текстура дверей из дуба и ясеня практически совпадает, но у дверей из ясеня она более выражена и благодаря текстуре дерева двери из ясеня выглядят намного красивее.
Двери из массива дуба и ясеня самые износоустойчивые в сравнении с дверями из массива другой древесины.
В народе говорят: «Ясень- материал королей и дизайнеров».
Изготовление дверей из дерева — это одна из главных специализаций нашей мастерской. Наша мастерская по изготовлению дверей из дерева находится в г. Днепрорудное Запорожской обл. Также мы успешно изготавливаем двери из дерева для заказчиков из других близлежащих областей, таких как Днепропетровская, Запорожская, Донецкая, Херсонская. Возможна отправка дверей перевозчиками в любую область Украины.
Высококачественное изготовление дверей из дерева достигается за счет использования правильно высушенной высококачественной древесины и материалов (лаки, краски, клей, фурнитура) импортного производства.
Изготовление мебели из дерева
Самая лучшая мебель — это мебель из массива ценных пород дерева, ведь это и есть вершина мебельной эстетики и аристократизма вкуса. Тут сразу вспоминаются виды королевских дворцов с замечательными интерьерами библиотек и домашних кабинетов, с удивительными по красоте лестницами и массивными деревянными дверями. Ну и, конечно же, в памяти всплывает деревянная отделка стеновыми панелями — буазери.
И действительно, ведь мебель из ценных пород дерева в интерьере вашего дома всегда подчеркивает солидный статус и благородный вкус хозяина дома. Такая мебель создает аристократическую красоту, которой никогда вам не надоест, домашний уют и комфорт от её использования. И не забудьте об особой атмосфере, создаваемой теплом и ароматом натурального дерева.
В создании такой мебели используют ценные породы деревьев, такие как дуб, бук, ясень, орех и другие. Их ценность заключается в твердости древесины, ив неповторимом рисунке узора дерева.
Дуб издревле — это один из наиболее популярных сортов ценных пород. Мебель из дуба ценят за прочность, долговечность и замечательный внешний вид — благородная структура с ярко выраженными крупными сосудами и оттенками цвета от светло-желто до красно-бурого, темнеющие со временем. Мебель из дуба всегда смотрится благородно и монументально.
Мебель из бука (дерево светло-розового оттенка) — это отличная альтернатива дубу, которая тоже обладает высокой прочностью, но не является таким дорогим материалом. Массив бука отлично подходит для производства высокоуровневой ценной мебели, так как замечательно обрабатывается, и хорошо тонируется в любой цвет. Его структура более мелкая, из-за чего мебель из бука смотрится более теплой, уютной. В ряды мебели из ценных пород древесины входит и мебель из ясеня, который даже более прочный, чем предыдущие сорта ценных деревьев. Обладая при этом большой гибкостью и пластичностью, он позволяет делать красивую мебель, при этом разную по цвету: от светло-розовой до темно-бурой.
Широко используется и знаменитое красное дерево — махагони, а также и другие породы, имеющие общий цвет и строение древесины. Так мебель из розово-коричневой вишни смотрится очень декоративно, обладает уютным теплым оттенком, который со временем будет темнеть. Вишня — это не очень твердая порода, и поэтому она замечательно поддается любому виду обработки. Её текстура отлично будет сочетаться с резной мебелью, витражами.
Перечень разнообразных ценных пород, использущихся в наше время, состоит из десятков наименований. Мебель из этих разнообразных пород дерева способна украсить не только дома (комнаты, прихожие и кухни), но и элитные деревянные кабинеты руководителей, клубы и рестораны, и любые другие статусные помещения. Наше производство находится на высоком уровне, с учетом всех последних достижений в технологии деревообработки, потому наши изделия высочайшего качества и стиля. А уж долговечность, прочность мебели из массива ценных пород древесины проверены веками, если не тысячелетиями. Современное оборудование позволяют делать мебель по актуальным технологиям, при этом сохраняя неизменно те же формы и содержание, что и века назад.
Магнезиальный фибролит
Изготавливают без специальной минерализации, так как каустический магнезит затворяется водными растворами магнезиальных солей, которые связывают содержащиеся в древесине водорастворимые вещества. Прочность его несколько выше, чем цементного. Это связано с тем, что кристаллизующиеся при сушке в клетках древесины соли препятствуют её усушке, а это положительно сказывается на сцеплении магнезиального камня с шерстью. Магнезиальный фибролит обладает, по сравнению с цементным, меньшей водостойкостью и большей гигроскопичностью.
Теплоизоляционно-конструктивный фибролит
Его применяют для утепления стен и покрытий, конструкционный — для перегородок, каркасных стен и перекрытий только в сухих условиях.
В настоящее время основное применение фибролита — установка несъемной опалубки в строительстве. Фибролитовые плиты не удаляются, как некоторые другие виды опалубки, а остаются конструктивной частью или стены, или любого перекрытия.
Лучший строительный материал изготавливается из хвойных пород деревьев. Среди них особое место занимает ель, которая на мировом рынке котируется выше сосны. Лучшие срубы – срубы, изготовленные зимой, т.е. из зимнего леса. Это обуславливается состоянием самой древесины срубленной зимой. Сруб, изготовленный из зимнего леса, обладает рядом преимуществ, в частности, бревно за счет медленного высыхания менее подвержено появлению трещин, а учитывая современную тенденцию к отсутствию отделки внутри сруба — это существенно.
Дерево по-особому взаимодействует с окружающей средой, оно обеззараживает воздух, не допуская в дом вредные вещества. Только древесина, являясь экологически чистым материалом, не оказывает вредного воздействия на организм. Дерево создает уникальный микроклимат дома. В отличие от других строительных материалов дерево «дышит». Клеточное строение бревна обеспечивает постоянный воздухообмен. В то же время внутри дома постоянно поддерживается на оптимальном уровне влажность и кислородный баланс.
Деревянные стены не требуют внутренней отделки, регулируют влажность воздуха, поглощая и отдавая влагу по мере изменения атмосферных условий. Дерево обладает теплоизоляционными свойствами, в несколько раз превышающими аналогичные показатели кирпичных и бетонных стен. Бревенчатые стены накапливают тепло, равномерно распределяя его по всему дому.
Для изготовления срубов наше преприятие применяет только высококачественную древесину. На первом этапе производится заготовка бревен нужной длины и диаметра (комлевые стороны бревен отесываются до толщины верхнего диаметра). Технология изготовления углового сопряжения сруба — любая и выполняется в зависимости от желания заказчика или в соответствии с представленным проектом. Долговечность деревянного дома во многом зависит от правильной технологии изготовления и сборки сруба. При обработке древесины мы стараемся максимально сохранить наиболее прочный поверхностный слой бревна – оболонь. Осуществляется это благодаря использованию стволов деревьев только заданного диаметра. Перепад не превышает 2-2,5 см от радиуса по всей длине бревна.
Бревно, не подверженное калибровке, лучше сохраняет свои природные свойства, вследствие чего оно более долговечно и не требует дополнительной обработки антисептиком.Оцилиндрованное бревно изготавливается на финском оборудовании. В результате – поверхность готового материала идеально гладкая, не требует шлифовки, и дополнительной обработки. Дерево не гниёт, не теряет своих свойств. Брёвна стыкуются между собой не оставляя щелей и зазоров.
Дельта-древесина или бакелитовая фанера — конструкционный материал, получаемый пластификацией древесного шпона (обычно берёзового) путём пропитки его феноло- или крезоло-формальдегидной смолой под давлением порядка 6 атмосфер и температуре 270 °С, а затем склеивания или прессования.
Дельта-древесина имеет в два раза большую, чем обычная древесина, плотность, но значительно превосходит её по прочности. Изготовляется дельта-древесина авиационная согласно ГОСТ 226-41 и имеет два сорта — А и Б в зависимости от физико-механических свойств.
Иногда может применяться обозначение ДСП-10. Существует мнение, что дельта-древесина была разработана к 1940-му году во Всесоюзном институте авиационных материалов Я. Д. Аврасиным.
Технология производства была усовершенствована специалистами завода «Карболит». В те времена дюралюминий и другие алюминиевые сплавы всё ещё являлись дефицитными конструкционными материалами, не хватало металлических полуфабрикатов из стали хромансиль (использовались главным образом в ферменных конструкциях), также были проблемы с поставкой на заводы качественной древесины.
Всё это, учитывая значительный опыт по деревообработке на наших авиационных заводах, подстёгивало опытные работы по изготовлению различных древеснослоистых пластиков, или по терминологии второй половины 1930-х годов, «облагороженной древесины» (кроме дельта-древесины ещё бакелитовая фанера, далинит и пр.) Первоначально дельта-древесину изготавливали из шпона толщиной 0,5 мм, пропитывали бакелитовым лаком, прессовали при температуре 145—150 °С и давлении 1—1,1 кг/мм².
В итоге уплотнённая древесина имела временное сопротивление растяжению 27 кг/мм², тогда как у сосны этот параметр составлял 11 кг/мм², у алюминиевого сплава Д-16 — 43 кг/мм². Дельта-древесина применялась при изготовлении первого цельнодеревянного советского истребителя ЛаГГ-3 (в первых модификациях имел обозначение И-22 и ЛаГГ-1) конструкции ОКБ — 301 В. П. Горбунова, также из неё некоторое время делались части фюзеляжей и крыльев самолётов Ил и Як, некоторые детали машин (для экономии металлов).
В наши дни дельта-древесина применяется в мебельном производстве (для деревянных узлов, испытывающих повышенные нагрузки).
Из дельта-древесины изготовлены воздушные рули, устанавливаемые на блоки первой ступени ракет-носителей семейства Р7. Также из неё изготовляются опорные изоляторы, преимущественно троллейбусных, изредка трамвайных, контактных сетей. Из похожего есть балинит.
С каждым годом в стволе дерева откладывается все больше древесины. Этот прирост образует годичные кольца, которые придают волокнам неповторимый рисунок.
Для изготовления древесины лесорубы спиливают дерево, а мощные машины срезают со стволов все ветки, на эту процедуру уходят считанные секунды. После, бревна доставляют на лесопилку, где распиливают их на доски. Перед использованием, пиломатериалы надо просушить иначе они могут треснуть или будут скручиваться. Сушатся доски в специальных помещениях с определенной температурой воздуха для ускорения процесса. Помимо продукции лесопиления (досок и брусьев)) из древесины производят и тонкие пластины, так называемую фанеру. Бревна вращают, приставив к ним острые лезвия. Из фанеры делают клееную фанеру, она дешевле в производстве, чем цельные доски. Отходы древесины уходят на изготовление щитов из прессованных опилок. Также из дерева делают бумагу. Для этого подходят тонкие стволы, которые измельчают и делают бумажную массу. Некоторые страны специально выращивают леса для бумажных нужд. Бумажную массу используют для производства вискозы и фотопленки.
Лесоматериалы разделяются на две группы:
Мягкие лесоматериалы получают из хвойных пород деревьев, сосна, ель и кедр. Их искусственно высаживают, потому что они быстро растут. Такую древесину легко пилить, сверлить и гнуть. Без мягкой древесины нельзя обойтись в производстве упаковочных материалов.
Твердой древесиной является медленно растущие деревья, например, дуб, ясень и береза, а также тик и красное дерево. Их тяжело пилить, но твердая древесина почти не гниет и очень прочная. Из таких деревьев делают дорогую мебель, лодки и музыкальные инструменты. Тропические виды древесины становятся все более редкими, из-за массовой вырубки.
sawwood.ru