Сочетая преимущества стали и алюминия
Скачать PDF |
Получения новых сочетаний материалов с помощью дуговой сварки
При любом сравнении стали и алюминия, как конструкционных материалов, необходимо учитывать многочисленные технические и экономические критерии. К ним относятся: масса, прочность, жесткость, предел текучести или обрабатываемость, а также доступность ресурсов, стоимость сырья, производственные затраты и последующие расходы. В частности, в сфере производства легких конструкций предпочтительнее выбирать оптимальную комбинацию обоих материалов: твердую сталь для конструкций с тяжелыми условиями работы, в сочетании с легким алюминием для конструкций, испытывающих меньшие напряжения. До недавнего времени, тем не менее, использование дуговой сварки для таких соединений не представлялось возможным, несмотря на многочисленные технические и экономические достоинства технологии. Компании Fronius удалось решить эту проблему.
Легкие конструкции обеспечивают существенные преимущества при использовании в автомобилестроении, например, при создании эксклюзивных автомобилей, в кровельных конструкциях промышленных предприятий или на ветросиловых установках. В автомобилестроении легкие конструкции играют особенно важную роль. Масса кузова составляет большую часть от общей массы автомобиля (порядка 40%). Если транспортному сектору необходимо сократить выбросы CO2, снижение веса и внедрение новых идей — это первое, с чего можно начать. Снижение веса на 100 кг может обеспечить снижение расхода топлива до 0,3 л/100 км, что в свою очередь снизит выбросы CO2 на 700 г/100 км.
Учитывая необходимость обеспечивать приемлемую массу и ёмкость аккумулятора, масса кузова — критически значимый параметр для электромобилей. Значительное сокращение массы таким образом продолжает оставаться основной целью современного кузовостроения.
Это означает, что технология соединения материалов играет значимую роль в сфере производства легких конструкций, в частности в плане соединения стали и алюминия. Для решения данной задачи компания Fronius заключила партнерство с австрийской сталелитейной компанией Voestalpine. Цель проекта состояла в разработке заготовок из стали и алюминия с высокой способностью к формообразованию, причем заготовки из обоих металлов соединяются с использованием технологии термического соединения.
Рис. 1: Элементы, изготовленные из гибридных листов из металлов, способны систематически поглощать, например, энергию удара, возникающего в результате аварии.
Проблемы и ограничивающие условия
Долгое время считалось, что прочное соединение стали и алюминия невозможно обеспечить при использовании термических средств. Основную трудность представляет различие точек плавления, составляющих 1 500°C и 660°C соответственно, и, в частности, формирование интерметаллических фаз (IMP). Это происходит из-за ограниченной взаимной растворимости железа и алюминия при комнатной температуре. IMP образуется в процессе диффузии и, как правило, характеризуется высокой твердостью и чрезвычайно низкой ударной вязкостью. Для примера, твердость сплава Fe2Al5 по Виккерсу составляет около 1 050 HV, а сплава FeAl3 около 900 HV. Чем больше тепловложение в шов, тем меньше IMP — и тем хуже механические и конструкционные свойства шва. Слой IMP должен быть как можно более тонким, и не должен превышать 10 мкм. Дальнейшие сложности вызваны значительно отличающимися коэффициентами теплового расширения, составляющими около 1,2 мм/100°C для стали и 2,34 мм/100°C для алюминия. Еще одним фактором является изменение электрохимического потенциала, равного ок. 1,22 В при использовании стали/алюминия и ок. 0,9 В при использовании цинка/алюминия.
В свете этих физических факторов, специалисты в сфере металлургии и эксперты по сварке определили следующие необходимые условия для сварки алюминия и стали:
- Используемая технология должна обеспечивать наименьшее возможное тепловложение;
- Поверхность стального листа должна быть оцинкована;
- Величина интерметаллической фазы должна быть минимизирована, а ее свойства должны использоваться по максимуму.
Поиск технологии теплового соединения предопределил использование технологии CMT (холодный перенос металла). Данная технология дуговой сварки была выбрана во многом благодаря великолепным результатам, демонстрировавшимся на протяжении десяти лет ее использования экспертами по сварке из компании Fronius.
Рис. 2: Прочность паяно-сварного соединения настолько велика, что при проведении испытания на разрыв, разрыв происходит не в районе шва, а в алюминиевой части элемента.
Пути достижения инновационного соединения
Три основных фактора, обеспечивающих образование бездефектного соединения:
- две заготовки, которые необходимо соединить
- технология соединения присадочный металл
Помимо слоя цинка, толщина которого должна быть не менее 10 мкм, еще одним фактором, влияющим на качество и упругость соединения, является подготовка кромок стальных листов. Геометрические характеристики кромки, разработанные компанией «Voestalpine» для листов, подлежащих соединению, запатентованы.
Специальная технология дуговой сварки в среде защитного газа CMT отвечает важнейшим требованиям к используемой здесь технологии соединения: низкое тепловложение и хорошая управляемость. Эта технология «холодной» сварки защищена несколькими патентами, выданными компании Fronius. При соединении стали и алюминия, присадочный металл и алюминий смачивают лист оцинкованной стали, а присадочный металл сплавляется с алюминием.
Рис. 3: Технология пайки-сварки CMT характеризуется сочетанием сварки на алюминиевой стороне и пайки на стальной стороне.
Третьим определяющим фактором является присадочный металл. Компания Fronius также является обладателем патента на особый сплав алюминия, используемый в процессе пайки-сварки. Для получения оптимального шва важно обеспечить правильное позиционирование присадочного металла в процессе пайки-сварки.
Рис. 4: Учет всех различных воздействующих факторов обеспечивает возможность для создания плотного металлургического соединения листов алюминия (справа) и стали (слева).
Рис. 5: Гибридные листы также отвечают практическим требованиям к дальнейшему изменению формы.
Практичные и проверенные — гибридные листы из стали и алюминия
Для выяснения и документирования пригодности продукта для фактического применения, как партнеры компании, так и внешние организации провели обширные испытания гибридных листов из стали и алюминия, соединенных методом пайки-сварки.
Основное исследование: Отправным пунктом здесь являются материалы AW5182-h211 и DX54D, а также присадочный материал Z200, изготовленный из сплава AlSi3Mn1. Институт исследований металлов им. Макса Планка (MPIE) определил размер зерен в околошовной зоне, а также оптимальный присадочный металл. Размер зерен в зоне плавления алюминиевого образца представлен на Рис. 12. Цвета иллюстрируют гранулометрический состав и рост зерен.
Предел прочности на разрыв: Два различных образца имитируют подходящую комбинацию материалов для крыш автомобилей и оконных рам. Ключевым результатом испытания на разрыв стал окончательный разрыв образца в области алюминиевого листа, при этом шов, созданный методом пайки-сварки, не получил никаких повреждений в ходе испытаний. Основные значения указаны в Таблице 1 и на соответствующих фотографиях.
Коррозионные свойства и испытания в солевой камере: Коррозионная стойкость незащищенного гибридного листа из стали и алюминия проверялась в солевой камере (SST). Даже после 300 часов пребывания, следов местной коррозии/коррозии под напряжением или межкристаллитной коррозии не было обнаружено. Легкие следы коррозии были заметны лишь на поверхности.
Способность к деформации: Способность листов к деформации играет ключевую роль в кузовостроении. Гибридные листы из стали и алюминия подходят для неоднократной обработки листового металла только в случае, если они могут удовлетворить данным требованиям. О пригодности листов свидетельствует возможность осуществления различных процессов деформации. Соответствующие данные представлены в Таблице 2. Пример «испытания на вытяжку» наглядно демонстрирует, что даже в пограничной зоне при глубокой вытяжке все равно достигаются положительные результаты.
Испытание на удар: Когда гибридные листы из материалов изначально проектируются как элементы, обеспечивающие безопасность, они могут систематически поглощать энергию удара. При использовании амортизатора ударной нагрузки из гибридных материалов, поглощение происходит практически полностью в алюминиевой части элемента. Как паяно-сварной шов, так и стальная часть элемента остаются нетронутыми. В противоположность этому, элемент, состоящий только из стали и поглощающий то же количество энергии, получает более серьезные повреждения. Надлежащим образом спроектированные элементы из гибридных материалов отвечают требованиям к поглощению энергии, когда это необходимо, обеспечивая при этом соответствие требованиям к геометрическим характеристикам и безопасным расстояниям. Подробная информация содержится в Таблице 3.
Рис. 6: «Испытание на вытяжку» ясно демонстрирует, что даже в пограничной зоне рассматриваемая технология обеспечивает хорошие результаты.
Рис. 7: Паяно-сварной шов остается неповрежденным даже в ходе испытания элемента на удар.
Рис. 8: Гибридные листы размером 300 × 220 мм, толщиной 1,2 / 1,5 мм подвергаются пайке-сварке на скорости 78 см/мин. перед формовкой по модели паяно-сварных несущих конструкций крыши.
Заключение
Компании Fronius и «Voestalpine» разработали технологический процесс, предназначенный для серийного производства гибридных листов из алюминия и стали. Длительные испытания доказали их практическую пригодность, а также позволили документально зафиксировать дополнительные конструкционные преимущества и возможности применения в некоторых отдельных случаях.
Таблица 1: Предел прочности на разрыв
Заготовка | Несущая конструкция крыши | Оконная рама |
Материал | DX54 + AW6181 | DX54 + AW6016 |
Толщина [мм] | 1,2 + 1,5 | 1,0 + 1,2 |
Присадочный металл | Z140 | Z140 |
Предел текучести1) Rp0.![]() |
126 | 132 |
Предел прочности на разрыв1) Rm [МПа] | 210 | 239 |
1) с учетом поперечного сечения алюминия
Таблица 2: Деформируемость
Технологическая заготовка | Сгиб таврового профиля | Испытание на вытяжку |
Материал | DX54 + AW 5182 | DX54 + AW 5182 |
Толщина [мм] | 1,0 + 1,5 | 1,0 + 1,5 |
Радиус [мм] | 2×10; 2×11 | 5 |
Диаметр пуансона [мм] | 90 | |
Присадочный металл | Z255 |
Таблица 3: Испытание в имитаторе аварийных ситуаций
Заготовка | Амортизатор удара при аварии |
Условия испытаний | 6,4 кДж при комнатной температуре |
Материал | h440 + AW6181 |
Толщина [мм] | 1,0 + 2,0 |
Присадочный металл | ZE75/75 |
Молот, масса [кг] | 86 |
Скорость [км/ч] | 44 |
Начальная высота [мм] | 280 |
Конечная высота [мм] | 173 |
Поглощенная энергия [кДж] | 6 523 |
Сила, макс.![]() |
296 |
Рис. 9: Сравнение поведения при ударе амортизаторов продольных ударов показывает, что стальная часть гибридного элемента (слева) сохраняет форму и необходимое безопасное расстояние, в то время как элемент, состоящий только из стали (справа) деформируется по всей длине.
Рис. 10: Основные исследования, проведенные Институтом исследований металлов им. Макса Планка (MPIE), расположенном в Дюссельдорфе, указывают на образование гранул в зоне соединения в соответствии с типом материала и размером частиц.
Легче алюминия и прочнее стали. Загадка булатного узора
Легче алюминия и прочнее стали
Исследование свойств различных композиционных материалов показало, что не только по прочности, но и по другим физико-механическим свойствам они превосходят каждый компонент, входящий в их состав. Созданы композиционные материалы, выдерживающие большие нагрузки, подвергающиеся большому тепловому воздействию, выдерживающие частые и резкие смены температур. Например, введением волокон асбеста в керамику можно повысить в несколько раз ее способность выносить тепловые удары. Волокна асбеста, как стальная арматура железобетона, связывают зерна огнеупора и удерживают их при резких перепадах температур от распада. Если изготовить трубку из керамической массы шамота, добавив в качестве высокотемпературного связующего скелета волокна каолина, то термостойкость шамота возрастает в десятки и даже сотни раз, Без подобных материалов сегодня немыслимы атомоходы, сверхзвуковые самолеты и космическая аппаратура.
Волокнистые композиционные материалы конструируются из металлической или керамической основы и упрочняющего волокна различного строения. Для получения волокон в зависимости от необходимых свойств используют самые разнообразные материалы: проволоку из молибдена или вольфрама, жаропрочной и жаростойкой стали, окись алюминия, каолин, графит, различные бориды, карбиды и нитриды. Каждый из таких волокон обеспечивает материалу определенный комплекс свойств. Введение волокон в матрицу чаще всего осуществляется методом формования волокон и порошка материала для матрицы или пропиткой волокон жидким металлом матрицы.
Очень напоминают технологию приготовления сварочного булата методы производства волокнистых композиционных материалов, упрочненных проволокой. Такие материалы разделяются на армированные проволоками, армированные сетками и армированные проволочными волокнами ограниченной длины. В последнем случае отдельные проволочные волокна располагаются в матрице в виде включений.
Прочность кобальта, нихрома и других сплавов, армированных вольфрамовой или молибденовой проволокой при температурах 300–1100 °C, повышается в несколько раз. Армирование серебра волокнами окиси алюминия повышает его прочность в 5 раз. Алюминий, упрочненный волокнами окиси кремния, имеет прочностные свойства лучших алюминиевых сплавов. По данным ряда исследований, введение в вольфрам частиц тугоплавких окислов или карбидов и боридов повышает его длительную прочность и срок службы в 25–50 раз.
Все большее значение приобретают в технике композиционные материалы, армированные монокристаллами — усами или нитевидными кристаллами. Нитевидные кристаллы повышенной прочности встречаются и в природе. К таким кристаллам можно отнести нефрит — разновидность минерала актинолита (лучистого камня, от греч. «актис» — луч, «литое» — камень). Нефрит состоит из игольчато-лучистых, иногда волосовидных агрегатов. Его цвет может меняться в зависимости от содержания в нем закиси железа от светлых зеленовато-серых тонов до темно-зеленых. С древнейших времен нефрит ценят как необычайно прочный поделочный камень. В Самарканде в мавзолее Гур-Эмир выделяется строгой красотой темно-зеленое нефритовое надгробие Тимура.
Мы уже рассказывали об огромной прочности металлических усов. Однако наиболее прочными из всех известных материалов являются графитовые нитевидные кристаллы — их прочность на растяжение достигает 20000 МПа, а модуль упругости составляет 106 МПа. И все это при относительной легкости материала. Известны два способа получения усов графита: в дуге с графитовыми электродами, горящей при высоком давлении, и при термическом разложении углеводородов.
Сапфир — одна из форм существования оксида алюминия. Нитевидные волокна сапфира получают из расплавленной окиси алюминия. Устройством для вытягивания волокон служит молибденовый капилляр, укрепленный на дне молибденового тигля. Расплав окиси алюминия при температуре плавления 2050 °C поднимается по капилляру, захватывается затравкой, с помощью которой вытягивается волокно. Вытягивание волокон диаметром 0,1–0,5 мм производится с достаточно большой скоростью. Прочность сапфировых волокон при растяжении достигает 2600 МПа.
К сожалению, до настоящего времени не разработаны эффективные методы введения нитевидных кристаллов в различные матрицы. Не изучены также в достаточной мере методы предотвращения взаимодействия и достижения необходимой степени сцепления нитевидных кристаллов с матрицей. Это в значительной мере препятствует достижению высокого уровня упрочнения и позволяет использовать только малую часть чрезвычайно высоких свойств нитевидных кристаллов. Кроме того, производство нитевидных кристаллов пока еще очень сложно, и они еще очень дороги.
Правда, в настоящее время освоено промышленное производство усов сапфира и карбида кремния. Цена за последнее время на них снизилась более чем в 200 раз. Волокна сапфира характеризуются высокой химической инертностью к металлам, что дает возможность использовать их в качестве упрочнителей никелевых, кобальтовых, титановых и других сплавов для работы при высоких температурах. Нитевидные кристаллы сапфира (прочность 7000 МПа) и карбида кремния (прочность — 12000 МПа) в будущем станут широко использоваться в качестве армирующих материалов.
Для эффективного использования волокон, как уже отмечалось, необходимо решить проблему хорошего сцепления твердых и прочных нитевидных кристаллов с мягкой и пластичной металлической матрицей. Разрешима ли эта проблема? Оказывается, да! Недавно было найдено, что покрытие из сплава железо — никель — кобальт, нанесенное на поверхность усов сапфира вакуумным напылением, обеспечивает достаточно прочное сцепление волокон этого материала со сплавом никель — палладий. Установлено также, что предварительная обработка поверхности углеродных волокон или нанесение на них барьерного слоя металлов, карбидов или нитридов значительно улучшает их смачиваемость металлом матрицы, а следовательно, и прочность сцепления с ней.
В связи с этим весьма перспективным становится композиционный материал на основе углеродного волокна. Хотя углеродное волокно известно более 70 лет, интерес к нему возник сравнительно недавно, после того как был разработан процесс получения высокопрочных и высокомодульных углеродистых волокон из полиакрил-нитрида. Этим методом при низкотемпературной графитизации получают углеграфитные волокна прочностью 3500 МПа. Углеграфитные волокна выпускаются в виде нитей, содержащих 1000–2000 элементарных волокон.
Давайте представим себе, что ученые и инженеры нашли метод получения дешевых углеграфитных волокон, а еще лучше — нитевидных кристаллов графита, и разработали эффективную технологию армирования такими кристаллами алюминия или пластмассы. Такой материал может быть в 2–6 раз прочнее легированных сталей и гораздо легче самого легкого металла — алюминия. Но этого мало, материал на основе алюминия должен легко подвергаться горячей деформации при 500–550 °C, а на основе пластмассы — 100–120 °C. Последний можно «ковать», например, нагревая в воде или паре.
Автомобиль из такого материала будет в 3–4 раза легче, его сумеет поднять один человек… Кроме того, в любых погодных условиях кузов автомобиля не будет подвержен атмосферной коррозии, а расход горючего сократится в несколько раз. Фантазия? Нет. Фирма «Форд» уже сделала опытный образец такого легкового автомобиля — его стоимость составила 3,5 миллиона долларов!
Появление сравнительно дешевых автомобилей из прочных и легких композитов — дело недалекого будущего. Получение и применение композиционных материалов в промышленности развивается быстрыми темпами. Так, первый высокопрочный композиционный материал, армированный нитевидными кристаллами, был получен в 1961 году, а в 1975 году такие композиции уже применялись в газотурбинных двигателях, корпусах глубоководных аппаратов в качестве пропитанных тканей, тросов, кабелей и других изделий. Есть все основания надеяться, что скоро композиты будут армировать волокнами с пределом прочности 7000–15000 МПа, а промышленность в достаточно большом количестве будет производить дешевые композиционные материалы на их основе. Итак, будущее за материалами со структурой типа булата.
Установки электролиза алюминия
Установки электролиза алюминия Вопрос. Какие конструкции в корпусах установки электролиза должны иметь электрическую изоляцию?Ответ. Должны иметь металлические перекрытия поперечных каналов токопроводов, а на участках между смежными электролизерами эти перекрытия
Установки электролитического рафинирования алюминия
Установки электролитического рафинирования алюминия
Вопрос. Какие расстояния должны быть между торцами соседних в ряду электр олизер ов?Ответ. Должны быть не менее 1 м, а между выступающими частями – не менее 0,6 м. Если между торцами соседних в ряду электролизеров не
2. ВЕТЕР В СТАЛИ
2. ВЕТЕР В СТАЛИ 2.1. «Изо всех сил старайтесь стать образованными, воспитанными людьми и берегите себя» Тикубасё. 9 февраля 1383 года. Третий год Эйтоку Учиться в МИФИ было трудно. Неудовлетворительные оценки на первых курсах не миновали многих, а треть поступивших была
Виды летательных аппаратов легче воздуха
Виды летательных аппаратов легче воздуха Летательные аппараты легче воздуха составляют три категории: жесткие, полужесткие и нежесткие (с мягкой оболочкой). Оболочка жестких летательных аппаратов обычно сделана из легкого алюминия. Наиболее известными являются
2. Стали: классификация, автоматные стали
2. Стали: классификация, автоматные стали
Стали служат материальной основой машиностроения, строительства и других отраслей промышленности. Стали являются основным сырьем для производства листового и профильного проката.По способу производства стали разделяют на
3. Жаропрочные стали и сплавы
3. Жаропрочные стали и сплавы Жаропрочные стали и сплавы относятся к третьей группе высоколегированных сталей. Их микроструктура после термической обработки должна состоять из скрыто—и мелкоигольчатого мартенсита или мелкоигольчатого мартенсита и избыточных
Покрытия из драгоценных металлов, алюминия, люстровых красок
Покрытия из драгоценных металлов, алюминия, люстровых красок Существует несколько способов нанесения драгоценных металлов на стекло. Широко известен прием наклеивания на холодную поверхность стекла листочков сусального золота, но у него имеется существенный
8.
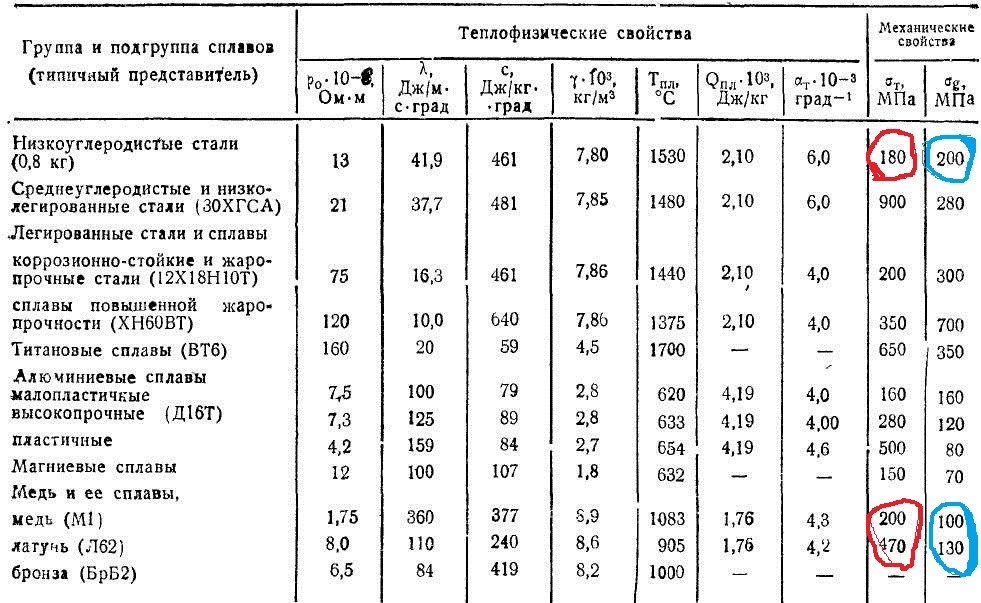
8. Сплавы на основе алюминия Алюминиевые сплавы классифицируют по технологии изготовления (деформируемые и литейные), способности к термической обработке (упрочняемые и неупрочнямые) и свойствам (рис. 8.1). Рис. 8.1. Диаграмма состояния алюминий – легирующий элемент
8.1. Деформируемые сплавы на основе алюминия
8.1. Деформируемые сплавы на основе алюминия К сплавам, не упрочняемым термической обработкой, относятся сплавы АМц и АМг (табл. 8.1).Сплавы отличаются высокой пластичностью, хорошей свариваемостью и высокой коррозионной стойкостью.Сплавы АМц относятся к системе Al – Мп
8. 2. Литейные сплавы на основе алюминия
8. 2. Литейные сплавы на основе алюминия Некоторые ювелирные изделия, такие как предметы быта, курительные наборы, столовые приборы, оружейные накладки, элементы перьевых и шариковых ручек, а также бижутерия, поверхность которых анодируется или обрабатывается
4.
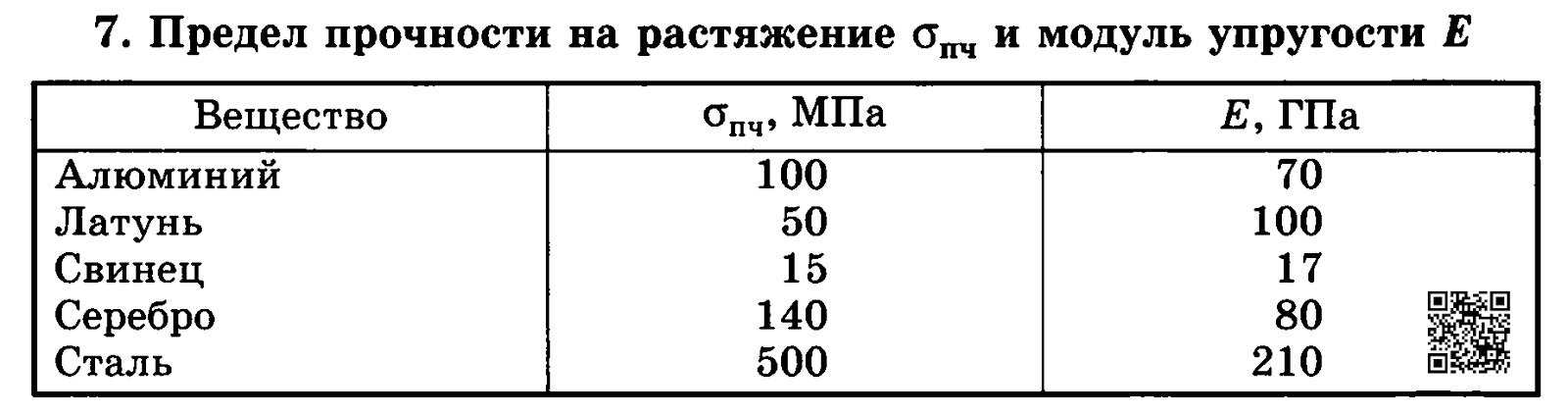
4.13.6. Отделка алюминия Этот металл обладает множеством достоинств, благодаря которым его охотно применяют мастера декоративного искусства. Он легок, мягок, пластичен, имеет красивый серебристый цвет. Но алюминий с трудом поддается химической обработке. Существующие ныне
41. Конструкционные стали: строительные, машиностроительные, высокопрочные. Инструментальные стали: стали для режущего инструмента, подшипниковые, штамповые
41. Конструкционные стали: строительные, машиностроительные, высокопрочные. Инструментальные стали: стали для режущего инструмента, подшипниковые, штамповые Углеродистые инструментальные стали У8, У10, У11,У12 вследствие малой устойчивости переохлажденного аустенита
44. Алюминий; влияние примесей на свойства алюминия; деформируемые и литейные алюминиевые сплавы
44. Алюминий; влияние примесей на свойства алюминия; деформируемые и литейные алюминиевые сплавы
Алюминий отличают низкая плотность, высокие тепло– и электропроводность, хорошая коррозийная стойкость во многих средах за счет образования на поверхности металла плотной
Когда использовать алюминий по сравнению с нержавеющей сталью
Нержавеющая сталь и алюминий являются двумя наиболее популярными металлами, используемыми в производстве. Широко используемые благодаря своей универсальности и коррозионной стойкости, алюминий и нержавеющая сталь являются основными продуктами металлургической промышленности. Чтобы понять, когда лучше использовать алюминий или нержавеющую сталь, мы должны сравнить такие факторы, как их состав, механические свойства и стоимость.
Основные характеристики нержавеющей стали по сравнению с алюминиемНержавеющая сталь
- Содержит не менее 11% хрома
- Является ферросплавом (содержит железо)
- Обычно магнитный
- Высокая прочность на растяжение
Нержавеющая сталь бывает различных марок. Сорта классифицируются по порядковому номеру и им присваивается числовой класс. Цифры классифицируют марки стали в зависимости от их состава, физических свойств и областей применения. Наиболее популярными марками являются нержавеющая сталь 304 и нержавеющая сталь 316.
Алюминий
- Немагнитный
- Низкая плотность
- Цветной сплав (не содержит железа)
Из-за низкой прочности на растяжение алюминий обычно сплавляют с другими металлами, чтобы придать ему ряд различных превосходных свойств. Одними из наиболее распространенных алюминиевых сплавов являются алюминий 3003 и алюминий 3004.
Алюминий или нержавеющая сталь: что выбрать?Оба металла обладают свойствами, необходимыми для производства различных продуктов. Однако различия в их свойствах являются ключевым фактором при выборе металла для использования.
Основные преимущества каждого металла
Алюминий | Нержавеющая сталь |
— Хорошая пластичность — Высокая пластичность — Хорошая проводимость -Легкий вес | — Высокая прочность на растяжение — Термостойкий -Очень прочный — Низкие эксплуатационные расходы |
Прочность
Нержавеющая сталь тяжелее и прочнее алюминия. На самом деле, алюминий составляет около 1/3 веса стали. Несмотря на то, что нержавеющая сталь прочнее, алюминий имеет гораздо лучшее соотношение прочности и веса, чем нержавеющая сталь.
Проводимость
Сталь плохо проводит электричество из-за плотного защитного оксидного слоя. С другой стороны, алюминий является очень хорошим электрическим и тепловым проводником.
Стоимость
Алюминий дороже нержавеющей стали, если смотреть на цену в зависимости от веса. Но если вы посмотрите на цену по объему, алюминий более эффективен с точки зрения затрат, потому что вы получаете больше продукта.
Теплостойкость
При сравнении нержавеющей стали с алюминием нержавеющая сталь имеет гораздо лучшую теплостойкость с температурой плавления 2500 ℉, в то время как алюминий становится очень мягким при температуре около 400 ℉ с температурой плавления 1220 ℉. Однако алюминий имеет преимущество перед сталью при низких температурах. При понижении температуры предел прочности алюминия увеличивается, а сталь при низких температурах становится хрупкой.
Коррозионная стойкость
Алюминий не ржавеет; однако он подвергается коррозии при воздействии соли. Нержавеющая сталь обладает высокой коррозионной стойкостью и не ржавеет. Кроме того, нержавеющая сталь непористая, что придает ей большую устойчивость к коррозии.
СоставСостав основных сплавов нержавеющей стали
Марки сплава | %С | %Mn | %Р | %S | %Si | %Cr | %Ni | % Мо |
SS304 | 0,040 | 1,580 | 0,024 | 0,040 | 0,400 | 18,35 | 8.040 | 0,070 |
SS304L | 0,010 | 1,638 | 0,023 | 0,002 | 0,412 | 18,56 | 8.138 | 0,364 |
Нержавеющая сталь 316 | 0,080 | 2.000 | 0,045 | 0,030 | 1.![]() | 16,80 | 11.20 | 2.500 |
SS316L | 0,020 | 1,390 | 0,024 | 0,080 | 0,480 | 16,80 | 10,22 | 2,080 |
Состав основных алюминиевых сплавов
Сплав | %Cu | %Mg | %Mn | %Si | %Zn |
2024 | 4,4 | 1,5 | 0,6 | 0 | 0 |
6061 | 0 | 1 | 0 | 0,6 | 0 |
7005 | 0 | 1,4 | 0 | 0 | 4,5 |
7075 | 1,6 | 2,5 | 0 | 0 | 5,6 |
356,0 | 0 | 0,3 | 0 | 7 | 0 |
Нержавеющая сталь известна своей пригодностью для вторичной переработки. По данным Napa Recycling, сталь является наиболее перерабатываемым материалом в мире. Он обладает особыми магнитными свойствами, что делает его легко извлекаемым из потока отходов для переработки. Кроме того, свойства стали остаются неизменными независимо от того, сколько раз сталь перерабатывается.
Несмотря на то, что сталь является наиболее перерабатываемым материалом, алюминий является наиболее пригодным для повторного использования из всех материалов. На самом деле выброшенный алюминий более ценен, чем любой другой материал в вашей мусорной корзине. Почти 75% всего алюминия, произведенного в США, все еще используется сегодня, потому что алюминий можно перерабатывать снова и снова в действительно замкнутом цикле. Чтобы узнать больше о переработке алюминия, посетите Алюминиевую ассоциацию.
Различное применение алюминия и стали Алюминий и сталь повсюду. Если вы осмотритесь в любом месте, скорее всего, вы увидите что-то, содержащее один из этих металлов. Ниже приведены некоторые распространенные области применения нержавеющей стали и алюминия.
Применение алюминия
- Алюминий широко используется в транспортной отрасли, поскольку он легкий и устойчив к коррозии.
- Автомобильная промышленность
- Железнодорожные рельсы
- Самолеты
- Космические корабли
Алюминий - широко используется в электротехнической промышленности из-за его проводимости, пластичности и низкой плотности.
- Линии электропередачи дальней связи
Алюминий - используется в архитектуре из-за его пластичности, высокого отношения прочности к весу и экономической эффективности.
- Оконные рамы
- Высотные здания (забавный факт: Эмпайр Стейт Билдинг был одним из первых зданий, в которых использовался алюминий)
Алюминий - широко используется в бытовой технике из-за его теплопроводности.
- Посудомоечные машины
- Шайбы
- Сушилки
- Холодильники
Применение нержавеющей стали
- Нержавеющая сталь широко используется в кухонном оборудовании из-за ее устойчивости к коррозии и нагреванию.
- Кухонные мойки
- Столовые приборы
- Столы для приготовления пищи
- Нержавеющая сталь используется в хирургических инструментах и медицинском оборудовании благодаря ее коррозионной стойкости.
- Щипцы
- Хирургические имплантаты
- Ножницы
Нержавеющая сталь - также используется в архитектуре из-за ее прочности и долговечности, только в разных областях применения.
- Мосты
- Памятники и скульптуры
- Здания
Нержавеющая сталь - также используется в автомобильной промышленности благодаря своей прочности и термостойкости.
- Автомобильные кузова
- Железнодорожные вагоны
- Двигатели
Сравнивая нержавеющую сталь и алюминий, вы видите, что они оба обладают характеристиками, которые делают их популярными материалами для производства. Знание различий между ними поможет вам понять, когда использовать алюминий или нержавеющую сталь. Например, алюминий используется в электротехнике, поскольку он является проводящим и легким, а нержавеющая сталь — нет. С другой стороны, нержавеющая сталь используется для таких вещей, как двигатели и технологическое оборудование, из-за ее прочности, устойчивости к нагреву и коррозии.
Разница между сталью и алюминием
Как сталь, так и алюминий широко используются в различных отраслях промышленности и для различных проектов и продуктов. Сталь, например, используется для всего: от кухонной посуды и столовых приборов до строительства зданий и многих бытовых приборов, которыми мы пользуемся каждый день. Алюминий является неотъемлемой частью конструкции большинства автомобилей и мотоциклов, велосипедов и самолетов, а также архитектурной лепнины и отделки жилых домов и коммерческих зданий.
При таком разнообразии применений каждого материала вам может быть интересно узнать, в чем разница между ними и как определить, какой материал подходит для вашего конкретного применения. Когда вы сравните прочность, вес, коррозионную стойкость и стоимость алюминия и стали, вы быстро поймете, почему Eagle Moldings полагается на многочисленные преимущества использования алюминия для нестандартных профилей и профилей.
Алюминий и сталь: прочность
При сравнении общей прочности стали и алюминия нет четкого и простого ответа. Это связано с тем, что, хотя сталь технически прочнее алюминия, алюминий часто намного легче, поэтому вы должны учитывать соотношение веса и прочности. Однако, если сосредоточиться только на прочности на сдвиг, сталь имеет большое количество углерода, что способствует ее общему преимуществу в прочности.
При сравнении прочности стали и алюминия также важно учитывать пластичность. Алюминий гораздо более податлив, чем сталь, а это означает, что его можно успешно сгибать или экструдировать в различные нестандартные формы или профили без разрывов или трещин. Также известно, что алюминий очень пластичен, что позволяет растягивать его без разрушения. Алюминиевые профили могут быть сделаны настолько прочными, насколько это необходимо для большинства применений. Алюминий хорошо подходит для применения в холодную погоду, потому что при понижении температуры алюминий фактически становится прочнее.
Алюминий и сталь: вес
Учитывая тот факт, что алюминий считается легким, хорошо известно, что сталь тяжелее двух металлов. Как уже упоминалось, вес стали обусловлен высокой концентрацией углерода. Чем больше углерода содержится в сплаве, тем он тяжелее. Основное преимущество веса стали заключается в том, что она невероятно прочная. Его прочность означает, что он вряд ли согнется, деформируется или деформируется под действием веса, тепла или силы. В среднем сталь будет в 2,5 раза плотнее алюминия. Существуют более легкие формы стали, такие как мягкая сталь, которые весят меньше, чем углеродистые стали. Однако мягкие стали, которые весят так же, как алюминий, не такие прочные и более подвержены разрывам и трещинам. Поскольку алюминиевые профили весят меньше, чем большинство других металлов, это упрощает обращение и удешевляет доставку.
Алюминий против стали: коррозионная стойкость
Когда дело доходит до коррозионной стойкости, алюминий является явным победителем. Алюминий невероятно устойчив к коррозии, не требуя дополнительной обработки после экструзии. Кроме того, алюминий не ржавеет и не требует покрытия или краски, которые будут изнашиваться или царапаться. Алюминий защищен собственной природной оксидной пленкой. С другой стороны, сталь подвержена сопротивлению. Углеродистая сталь требует покрытия краской или другой отделкой для защиты от ржавчины или коррозии. Это особенно верно, если сталь будет находиться во влажной или влажной или особенно абразивной среде. Алюминий может быть дополнительно улучшен с помощью различных видов отделки, таких как анодирование, порошковое покрытие, матовая обработка, пескоструйная обработка, покраска, полировка или химическая промывка.
Алюминий и сталь: стоимость
При сравнении двух сплавов стоимость стали и алюминия является одним из наиболее важных факторов при выборе материалов для работы.