Чугун углерода — Энциклопедия по машиностроению XXL
В ковких чугунах углерод также находится в свободном со стоянии, но имеет хлопьевидную форму за счет длительного отжига (томления) при высокой температуре (20—25 ч при 950—1000°С). Маркируют ковкий чугун как высокопрочный. Например, КЧ 30—6 означает ковкий чугун с пределом прочности при растяжении 300 МПа и относительным удлинением 6%. [c.129]Чугун, как известно, — это сплав железа с углеродом при содержании углерода 2,14 % и более. В белом чугуне углерод входит в состав цементита химического соединения железа с углеродом. Такой чугун обладает высокой твердостью и хрупкостью, и его применяют сравнительно редко. В чугуне других видов путем графитизации углерод частично или полностью переводят в свободное состояние — графит. Применяют также отбеленный чугун белый снаружи и графитизированный во внутренней части изделия. [c.434]
Коррозионностойкие чугуны можно разделить на два класса серые чугуны с феррито-графитовой или аустенито-графитовой структурой и белые чугуны со структурой феррита. Важное значение имеет форма распределения углерода. В серых чугунах углерод находится в виде графита пластинчатого, чешуйчатого, глобулярного или шаровидного. Наибольшей коррозионной стойкостью в растворах электролитов обладают модифицированные чугуны с шаровидным графитом. В белых чугунах углерод находится в форме карбидов.
Углеродистая сталь представляет собой соединение железа с углеродом. Это такой же сплав, как и чугун, только в чугуне углерода больше, потому и его свойства иные, чем у стали. [c.140]
Согласно ГОСТу 5200—50 в сталях (углерода до 2%) марганец считается легирующим компонентом при содержании более 1 % и кремний — при его содержании более 0,8%. В чугунах (углерода более 2%) марганец считается легирующим элементом при содержании более 2% и кремний — при его содержании более 470- [c.25]
Влияние элементов химсостава. Влияние элементов сказывается на обрабатываемости через структуру однако влияние структуры недостаточно изучено и мало разработано. Известно, что наличие в чугуне углерода в виде графита улучшает обрабатываемость, феррит способствует хорошей обрабатываемости, перлит даёт удовлетворительную обрабатываемость. [c.30]
В белом чугуне углерод содержится только в химически связанном состоянии. В простом белом чугуне встречаются карбиды железа и марганца, в легированном могут быть карбиды хрома, молибдена, ванадия, вольфрама и других элементов. [c.57]
Важнейшим фактором, определяющим скорость распада цементита, является температура нагрева. Для чугуна данного химического состава с повышением температуры нагрева уменьшается время первой стадии графитизации (см. фиг. 74, 75 и 85). Однако при нагреве до температур, превышающих 1050—1100° С, в зависимости от химического состава чугуна углерод в чугуне может выделяться в виде пластинчатых включений, что недопустимо для ковкого чугуна.
Химический состав и основные механические свойства (табл. 3). Химический состав ковкого чугуна не регламентируется ГОСТом, а определяется требованиями к его механическим и технологическим свойствам. Основные элементы, с помощью которых регулируются свойства ковкого чугуна, — углерод и кремний, а в производстве перлитного чугуна, кроме того, марганец, хром и др. [c.112]
Ковкий чугун (углерод отжига) [c.194]
В результате протекающих в печи физико-химических процессов происходит угар примесей чугуна углерода 10—30%, кремния 20—50%, марганца 25—65%, серы 0—50%. Содержание железа повышается на I—2%. Угар примесей во вращающихся пламенных [c.44]
Важнейшим условием получения из вагранки малоуглеродистого чугуна является подбор ее конструкции и режима работы, обеспечивающий заданное содержание в чугуне углерода, интенсивное плавление и перегрев чугуна. [c.46]
МПа. Оптимальное положение фурмы устанавливают экспериментально. При этом необходима высокая скорость обезуглероживания и шлакообразования и ведение продувки без выбросов. Правильно организованный режим продувки обеспечивает хорошую циркуляцию металла и его перемешивание со шлаком. Последнее в свою очередь способствует повышению скорости окисления содержащихся в чугуне углерода, кремния, марганца, фосфора. На процесс шлакообразования и скорость окисления примесей влияет глубина проникновения кислородной струи в металл, которая зависит от давления и [c.126]
Чугун — железоуглеродистый сплав, содержащий более 2,14% углерода. По содержанию углерода и наличию структурных составляющих различают чугуны доэвтектические (углерода 2,14—4,3%), эвтектические (углерода 4,3%) и заэвтектические чугуны (углерода 4,3—6,67%). [c.216]
В ковком чугуне углерод полностью или частично входит в состав хлопьевидных включений углерода отжига. Получается путем термической обработки белого чугуна.
В высокопрочном чугуне углерод образует шаровидные включения графита. [c.91]
Эта диаграмма построена для обычного содержания кремния в сером чугуне (около 2,5%) и показывает, что чем больше в чугуне углерода, тем больше требуется магния для создания шаровидного графита. Кривая 3 характеризует полный отбел чугуна. [c.159]
Белый чугун очень тверд, не поддается механической обработке, применяется только в качестве материала для переработки в ковкий чугун. В белом чугуне углерод связан в виде карбидов железа (цемента). Сварщику в машиностроении не приходится иметь дела с изделиями из белого чугуна. Они встречаются только в литейном цехе, где литейный брак приходится заваривать до последующей его переработки. Излом светло-серый, почти белый. [c.94]
Другие сплавы Fe—С чугун (белый и серый) литейный чугун (углерод существует в виде графита) серый чугун с пластинчатым графитом серый чугун со сферическими графитовыми выделениями чугун, отлитый в специальные формы, с отбеленной поверхностью ковкий чугун, черносердечный ковкий чугун белосердечный ковкий чугун перлитный ковкий чугун. [c.29]
Таким образом, степень графитизации в чугунах возрастает с увеличением содержания углерода и кремния. Аналогичное, но более слабое влияние оказывают примеси (или легирующие элементы) меди и никеля. Элементами, затрудняющими графитизацию (отбеливающими), являются марганец, сера, хром. Основные элементы, которыми регулируют структуру металлической основы серых чугунов, — углерод и кремний. [c.293]
Чугун, углерод в котором находится полностью в связанном состоянии в виде карбида железа (цементита) , называется белым. По механическим свойствам он твердый и хрупкий, трудно обрабатывается резанием.
Анализируя зависимость модуля упругости (см. рис. 95, о) и потерь массы образца при микроударном воздействии (рис. 95, б) от содержания в чугуне углерода, можно убедиться в том, что сопротивление микроударному разрушению, как и модуль упру гости при растяжении, возрастает по мере уменьшения содержания углерода. Такая же закономерность свойственна и другим [c.149]
В обычном чугуне углерод в количестве до 0,8% может находиться, в связанном состоянии с железом, остальная часть — в свободном состоянии в виде графита. Графит придает излому чугуна серый оттенок, отчего такой чугун называют серым. [c.17]
Серый чугун является наиболее распространенным материалом для изготовления различных отливок. В сером чугуне углерод содержится в виде графита, который имеет пластинчатую форму. Серый чугун маркируют СЧЮ—СЧ25 и т. д. Буквы обозначают i p i-надлежность данного сплава к серым чугунам, цифры показывают временное сопротивление разрыву. [c.157]
В табл. 11-1 приведены некоторые данные о значениях коэффициента теплопроводности для разных веществ. Из нее видно, что наихудшими проводникам тепла являются газы, для которых Я = 0,006 -f— 0,6 вт1 м-град). Некоторые чистые металлы, наоборот, отличаются высокими значениями X и для них величина его колеблется от 12 до 420 втЦм -град). Примеси к металлам вызывают значительное уменьшение коэффициента теплопроводности. Так, у чугуна X тем меньше, чем больше содержится в чугуне углерода. Для строительных материалов Я = 0,164-1,4 вт/ (м-град). Пористые материалы, плохо проводящие тепло, называют теплоизоляционными и для, них значения X находятся в пределах от 0,02 до 0,23 вт1 м-град). К этим материалам относят шлаковату, минеральную шерсть, диатомит, ньювель, совелит, асбест и др. Чем более порист материал, т. е- чем больше содержится в нем пузырьков малотеплопроводного воздуха, чем меньше его плотность, тем менее он теплопроводен. Очень широкое применение получил теплоизоляционный материал диатомит в 1 см которого содержится до 2-10 скорлупок, заполненных внутри воздухом.
Определение углерода. Углерод в стали находится главным образом в связанном состоянии в виде карбидов. В сером чугуне он присутствует преимущественно в свободном состоянии в виде графита, а такнщ в связанном состоянии в виде карбидов. Свободный углерод может находиться также в ковком чугуне углерод отжига). [c.93]
Термаобработанный ферритный ковкий чугун (класс VIII, № 13 и 14). Перлитный ковкий чугун может быть получен путём добавочной термообработки ферритного ковкого чугуна. При повторном нагреве отожжённого ковкого чугуна углерод отжига частично снова переходит в раствор. В зависимости от . температуры нагрева и времени выдержки количество растворённого углерода различно и в среднем составляет около 0,3—О.ЙИ/д. [c.86]
Общие потери материала в угар при плавке в пламенных печах составляют 4—7%. Плавка на жидкой завалке дает следующий угар элементов чугуна углерода 15—20%, марганца 5—10%. Содержание кремния, фосфора и серы п яктическн остается неизменным. [c.44]
В углеродистых сталях и чугунах углерод образует обычно карбид железа химическое соединение РезС, называемое в металловедении цементитом, которое содержит 6,67% углерода. Рассмотрим часть диаграммы железо—углерод от железа до цементита, который ввиду его стойкости можно считать самостоятельным компонентом. В этом случае часть диаграммы состояния сплавов железа с углеродом, содержащих до 6,67% углерода, превращается в диаграмму сплавов железо—цементит (рис. 2-1). [c.35]
В составе серого чугуна углерод частично или полностью находится в состоянии графита наличие его придает чугуну в изломе темный серый цвет, поэтому этот чугун и назван серым чугунум. Чем больше графита в сером чугуне, тем ниже механическая прочность его в серых чугунах углерода содержится 2,8—4%, из них в виде свободного графита находится 2—3%.
Кремний способствует процессу графитизации, действуя Б том же направлении, что и замедление скорости охлаждения. Изменяя, с одной стороны, содержание в чугуне углерода и кре.м-ния, а с другой — скорость охлаждения, можно голучить различную структуру металлической основы чугуна. г руктурная диаграмма для чугунов, показывающая, какой должна быть структура в отливке с толщиной стенки 50 мм, в зависимости от содер- [c.145]
При науглероживании расплава необходимо корректировать условия процесса в зависимости от химического состава жидкого металла. Поскольку скорость науглероживания обусловлена концентрацией углерода в расплаве (рис. 34), следует, разумеется, корректировать продол-жительность науглероживания. В расплаве высокомар-ганцовистого чугуна углерод усваивается полностью, в то же время угар углерода в расплаве с высоким содержанием кремния составляет 18% (рис. 35 [4]). Опыт производственных плавок показывает, что каждый процент присутствуюш,его в расплаве кремния снижает усвоение углерода на 4—5%. Науглероживание жидкого стального сплава целесообразно производит перед добавлением ферросилиция, который в жидком чугуне усваивается практически полностью. [c.78]
Марка чугуна Углерод Кремний Марганец Фосфор Сера Хром Медь Магний ZP3M [c.416]
ЧУГУН ковкий — пластичный чугун, получаемый путем отжига белого чугуна, значительно превосходящий по пластичности серый чугун с пластинчатым графитом в структуре. Пластичность Ч. к. обусловлена тем, что выделения графита — т. и. углерода отжига в его структуре имеют хлопьевидную форму и поэтому расчленяют металлич.основу чугуна в меньшей степени, чем пластинчатый графит — основу серого чугуна. Углерод отжига образуется в процессе отжига белого чугуна при разложении карбидной составляющей последнего. По микроструктуре Ч. к. подразделяются на более пластичные ферритные и менее пластичные, но более прочные перлитные или нерлито-ферритные. Хим. состав Ч. к. (табл. 1) отличается пониженным, по сравнению с серым чугуном, содержанием углерода и кремния. Пониж. содержание углерода (т, е. общее уд1еныпепие количества [c.442]
В чугунных отливках при прочих равных условиях легирован ный слой меньше насьщен марганцем, чем в стальных отливках Это объясняется высоким содержанием в чугуне углерода и дру гих примесей, тормозящих процесс диффузии марганца. Поверх ностный слой, легированный марганцем, состоит из твердых ра створов 7 = Fe и 7 = Мп. На участках, содержаш,их более 12% Мп, обнаружена е-фаза. Кроме того в структуре легированного слоя имеются карбиды типа МидС и Feg . В некоторых случаях концентрация легирующего элемента на поверхности легированного слоя значительно меньше концентрации его в более отдаленных от поверхности слоях. Но в большинстве случаев в поверхностном слое концентрация хрома и марганца значительно выше, чем в более глубоких слоях. Различный характер распределения легирующих элементов по глубине легированного слоя свидетельствует о возможности его образования различными путями. [c.278]
Рассмотрим процесс коррозии и графитизацин чугуна. В белом чугуне весь углерод находится в форме цементита. Степень графитизацин равна нулю. В сером чугуне имеется графит количество, формы и размеры которого изменяются в широких пределах. В высокопрочных чугунах углерод в значшельной степени или полностью находится в свободном состоянии в форме шаровидного графита. В ковком чугуне весь углерод или значительная часть его находятся в свободном состоянии в форме хлопьевидного графита (углерода отжига). [c.485]
Скорость коррозии чугунов в водных средах зависит от их состава и в значительной степени от содержания кислорода. В насыщенной воздухом неподвижной морской или пресной воде скорость коррозии составляет 0,05. .. 0,1 мм/год. В жесткой воде скорость коррозии ниже, нежели в смягченной воде. Крайне агрессивны по отношению к чугуну шахтные воды с высоким содержанием кислот, образующихся при гидролизе железных солей сильных кислот, в основном сульфатов. Ионы железа могут действовать как эффективные деполяризаторы. Б ряде случаев использование чугуна в шахтных водах недопустимо. Снижение концентрации кислорода в среде увеличивает стойкость чугунов. Однако в деаэрированных средах могут присутствовать сульфатовосстанавливающие бактерии, которые могут действовать как эффективные деполяризаторы. В такой ситуации скорость коррозии чугуна достигает 1,5 мм/год. При этом происходит интенсивное обогащение поверхности чугуна углеродом. Такой процесс иногда называют графитовой коррозией (графитизацией чугуна). Движение коррозионной среды интенсифицирует подвод кислорода к поверхности и тем самым способствует увеличению скорости коррозии. Турбулентный поток вызывает местную коррозию чугуна. Подземная коррозия чугунных труб зависит от электропроводности почв. Обычно считается, что почва с удельным сопротивлением более 3000 Ом. см не агрессивна. При уменьшении удельного сопротивления агрессивность почвы быстро повышается. В неагрессивных почвах влажность составляет менее 20 %. Скорость общей коррозии в почве близка к 0,1 г/(м .сут), скорость местной коррозии до 1,75 мм/год в песчаных грунтах с удельным электрическим сопротивлением НО Ом. см. Скорость коррозии серого чугуна в городской, промышленной и морской атмосфере близка к 1 г/(м .сут). [c.486]
mash-xxl.info
Виды чугуна, классификация, состав, свойства, маркировка и применение
Сегодня почти нет ни одной сферы жизни человека, где бы не применялся чугун. Этот материал известен человечеству уже достаточно давно и превосходно зарекомендовал себя с практической точки зрения. Чугунное литье – основа великого множества деталей, узлов и механизмов, а в некоторых случаях даже самодостаточное изделие, способное выполнять возложенные на него функции. Поэтому в данной статье мы уделим самое пристальное внимание данному железосодержащему соединению. Также выясним, какие бывают виды чугуна, их физические и химические особенности.
Определение
Чугун – это поистине уникальный сплав железа и углерода, в котором Fe более 90%, а C — не более 6,67%, но и не менее 2,14%. Также углерод может находиться в чугуне в виде цементита или же графита.
Углерод дает сплаву достаточно высокую твёрдость, однако, вместе с тем, понижает ковкость и пластичность. В связи с этим чугун является хрупким материалом. Также в определенные марки чугуна добавляют специальные присадки, которые способны придать соединению определенные свойства. В роли легирующих элементов могут выступать: никель, хром, ванадий, алюминий. Показатель плотности чугуна равен 7200 килограмм на метр кубический. Из чего можно сделать вывод, что вес чугуна – показатель, который никак нельзя назвать маленьким.
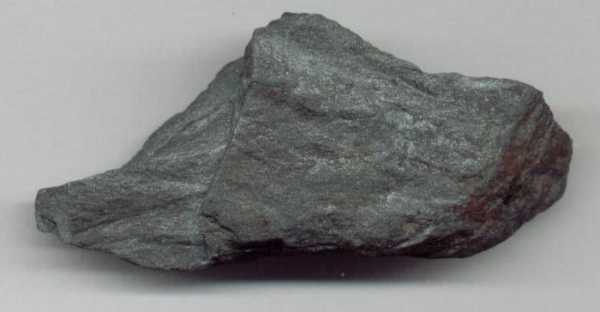
Историческая справка
Выплавка чугуна уже достаточно давно известна человеку. Первые упоминания о сплаве датируются шестым веком до нашей эры.
В Китае в древние времена получали чугун с довольно низкой температурой плавления. В Европе чугун стали получать примерно в 14 веке, когда впервые начали использовать доменные печи. На тот момент такое чугунное литье шло на производство оружия, снарядов, деталей для строительства.
На территории России производство чугуна активно началось в 16 столетии и далее быстро расширялось. Во времена Петра I Российская империя по объему производства чугуна смогла обойти все государства мира, однако уже через сто лет начала снова сдавать свои позиции на рынке черной металлургии.
Чугунное литье использовалось для создания разнообразных художественных произведений ещё в эпоху Средневековья. В частности, в 10 веке китайские мастера отлили поистине уникальную фигуру льва, вес которого превысил 100 тонн. Начиная с 15 века на территории Германии, а после и в других странах литье из чугуна получило широчайшее распространение. Из него делали оградки, решетки, парковые скульптуры, садовую мебель, надгробия.
В последние годы 18 века чугунное литье максимально задействовано в архитектуре России. А 19 столетие так и вообще прозвали «чугунным веком», так как сплав очень активно использовался в зодчестве.
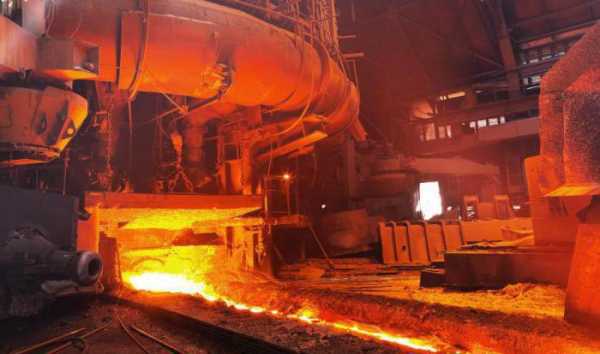
Особенности
Существуют различные виды чугуна, однако средняя температура плавления этого металлического соединения составляет порядка 1200 градусов Цельсия. Этот показатель на 250-300 градусов меньше, чем требуется для выплавления стали. Такая разница связана с достаточно высоким содержанием углерода, что приводит к его менее тесным связям с атомами железа на молекулярном уровне.
В момент выплавки и последующей кристаллизации углерод, содержащийся в чугуне, не успевает полностью проникнуть в молекулярную решётку железа, и потому чугун в итоге получается довольно хрупким. В связи с этим он не применяется там, где имеют место постоянные динамические нагрузки. Но при этом он отлично подходит для тех деталей, которые имеют повышенные требования к прочности.
Технология производства
Абсолютно все виды чугуна производятся в доменной печи. Собственно, сам процесс плавки – довольно трудоемкая деятельность, требующая серьёзных материальных вложений. Одна тонна чугуна требует примерно 550 килограмм кокса и почти тонну воды. Объем загружаемой в печь руды будет зависеть от содержания железа. Чаще всего применяют руду, в которой железа не менее 70%. Меньшая концентрация элемента нежелательна, поскольку ее будет невыгодно экономически использовать.
Первый этап производства
Выплавка чугуна происходит следующим образом. В первую очередь в печь засыпают руду, а также коксующиеся марки угля, которые служат для нагнетания и поддержания требуемой температуры внутри шахты печи. Помимо этого, эти продукты в процессе горения активно принимают участие в протекающих химических реакциях в роли восстановителей железа.
Параллельно в печь отгружается флюс, служащий в качестве катализатора. Он помогает породам быстрее расплавляться, что содействует скорейшему высвобождению железа.
Важно заметить, что руда перед загрузкой в печь подвергается специальной предварительной обработке. Ее измельчают на дробильной установке (мелкие частицы быстрее плавятся). После она промывается с целью удаления частиц, не содержащих металл. После чего сырье обжигают, за счет этого из него удаляется сера и прочие чужеродные элементы.
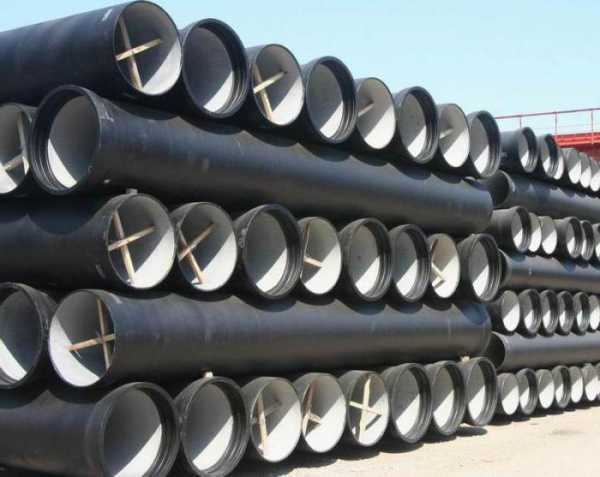
Второй этап производства
В загруженную и готовую к эксплуатации печь подают природный газ через специальные горелки. Кокс разогревает сырье. При этом выделяется углерод, который соединяется с кислородом и образует оксид. Этот оксид впоследствии принимает участие в восстановлении железа из руды. Отметим, что с увеличением количества газа в печи скорость протекания химической реакции снижается, а при достижении определённого соотношения и вовсе останавливается.
Избыток углерода проникает в расплав и входит в соединение с железом, формируя в конечном счете чугун. Все те элементы, которые не расплавились, оказываются на поверхности и в итоге удаляются. Эти отходы именуют шлаком. Его также можно использовать для производства других материалов. Виды чугуна, получаемые таким образом, называются литейным и передельным.
Дифференциация
Современная классификация чугунов предусматривает разделение данных сплавов на следующие типы:
- Белые.
- Половинчатые.
- Серые с пластинчатым графитом.
- Высокопрочные с шаровидным графитом.
- Ковкие.
Давайте рассмотрим каждый вид по отдельности.
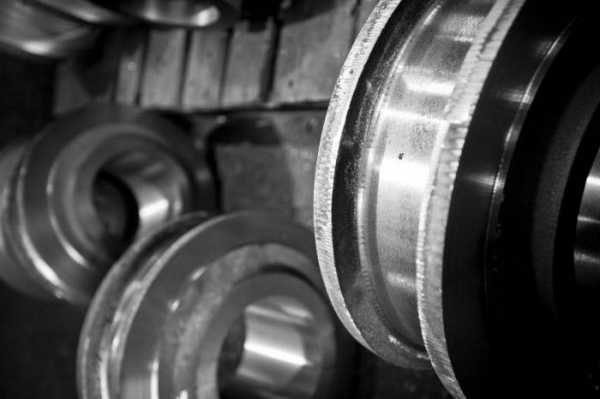
Белый чугун
Таким чугуном называется тот, у которого практически весь углерод химически связан. В машиностроении этот сплав применяется не очень часто, потому что он твёрдый, но очень хрупкий. Также он не поддается механической обработке различными режущими инструментами, а потому используется для отливания деталей, которые не требуют какой-либо обработки. Хотя этот вид чугуна допускает шлифование абразивными кругами. Белый чугун может быть как обыкновенным, так и легированным. При этом сварка его вызывает затруднения, поскольку сопровождается образованием различных трещин во время охлаждения или нагрева, а также по причине неоднородности структуры, формирующейся в точке сварки.
Белые износостойкие чугуны получают за счет первичной кристаллизации жидкого сплава при скоротечном охлаждении. Чаще всего они используются для работы в условиях сухого трения (например, тормозные колодки) или для производства деталей, обладающих повышенной износостойкостью и жаростойкостью (валки прокатных станов).
Кстати, белый чугун получил свое название благодаря тому, что внешний вид его излома – светло-кристаллическая, лучистая поверхность. Структура этого чугуна представляет собой совокупность ледебурита, перлита и вторичного цементита. Если же данный чугун подвергают легированию, то перлит трансформируется в троостит, аустенит или мартенсит.
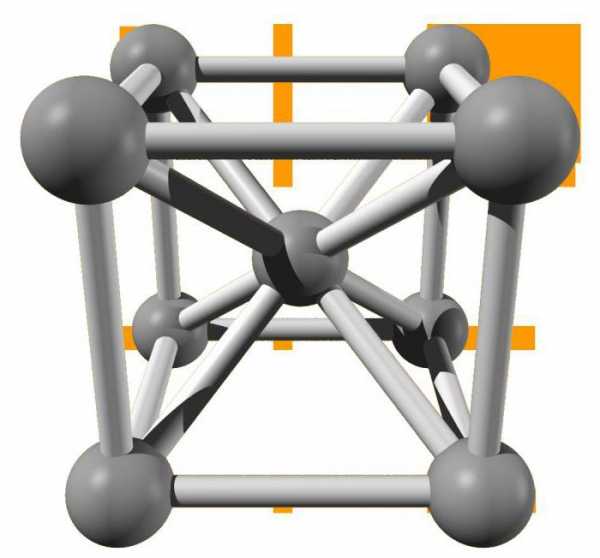
Половинчатый чугун
Классификация чугунов будет неполной, если не упомянуть об этой разновидности металлического сплава.
Для указанного чугуна характерно сочетание карбидной эвтектики и графита в его структуре. В целом же, полноценная структура имеет следующий вид: графит, перлит, ледебурит. Если же чугун подвергнуть термической обработке или легированию, то это приведет к образованию аустенита, мартенсита или игольчатого троостита.
Этот вид чугуна достаточно хрупок, поэтому его применение весьма ограничено. Само же название сплав получил потому, что его излом – сочетание темных и светлых участков кристаллического строения.
Самый распространенный машиностроительный материал
Серый чугун ГОСТ 1412-85 содержит в своем составе около 3,5% углерода, от 1,9 до 2,5% кремния, до 0,8% марганца, до 0,3% фосфора и менее 0,12% серы.
Графит в таком чугуне имеет пластинчатую форму. При этом не требуется специального модифицирования.
Пластинки графита имеют сильно ослабляющее действие и потому серому чугуну характерны очень низкая ударная вязкость и практически полное отсутствие относительного удлинения (показатель составляет мене 0,5%).
Серый чугун хорошо подвергается обработке. Структура сплава может быть следующей:
- Феррито-графитовой.
- Феррито-перлито-графитовой.
- Перлито-графитовой.
На сжатие серый чугун работает гораздо лучше, нежели на растяжение. Также он довольно хорошо сваривается, но для этого требуется предварительный подогрев, а в качестве присадочного материала следует использовать специальные чугунные стержни с высоким содержанием кремния и углерода. Без предварительного разогрева сварка будет затруднена, поскольку будет происходить отбеливание чугуна в зоне шва.
Из серого чугуна производят детали, работающие при отсутствии ударной нагрузки (шкивы, крышки, станины).
Обозначение данного чугуна происходит по такому принципу: СЧ 25-52. Две буквы сигнализируют о том, что это именно серый чугун, число 25 – показатель предела прочности при растяжении (в Мпа или кгс/мм2), число 52 – предел прочности в момент изгиба.
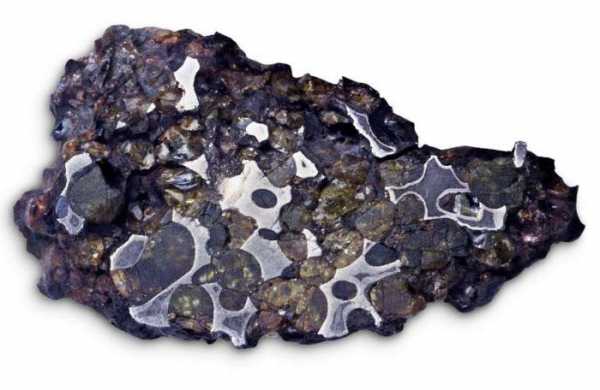
Высокопрочный чугун
Чугун с шаровидным графитом принципиально отличается от других своих «собратьев» тем, что в нем содержится графит шаровидной формы. Она получается за счет введения в жидкий сплав специальных модификаторов (Mg, Се). Количество графитных включений и их линейные размеры могут быть различными.
Чем хорош шаровидный графит? Тем, что такая форма минимально ослабляет металлическую основу, которая, в свою очередь, может быть перлитной, ферритной или перлитно-ферритной.
Благодаря применению термической обработки или легирования основа чугуна может быть игольчато-трооститной, мартенситной, аустенитной.
Марки высокопрочного чугуна бывают различны, но в общем виде обозначение его таково: ВЧ 40-5. Легко догадаться, что ВЧ – это высокопрочный чугун, число 40 – показатель предела прочности при растяжении (кгс/мм2), число 5 – относительно удлинение, выражаемое в процентах.
Ковкий чугун
Структура ковкого чугуна заключается в наличии в нем графита в хлопьевидной или шаровидной форме. При этом хлопьевидный графит может иметь различную дисперсность и компактность, что, в свою очередь, оказывает непосредственное влияние на механические свойства чугуна.
В промышленности ковкий чугун производится зачастую с ферритной основой, которая обеспечивает большую пластичность.
Внешний вид излома ферритного ковкого чугуна имеет черно-бархатистый вид. Чем выше количество перлита в структуре, тем светлее будет становиться излом.
В целом же, ковкий чугун получается из отливок белого чугуна благодаря длительному томлению в печах, нагретых до температуры 800–950 градусов Цельсия.
На сегодняшний день есть два способа изготовления ковкого чугуна: европейский и американский.
Американский метод заключается в томлении сплава в песке при температуре 800-850 градусов. В этом процессе графит располагается между зернами чистейшего железа. В итоге чугун приобретает вязкость.
В европейском методе отливки томятся в железной руде. Температура при этом составляет около 850-950 градусов Цельсия. Углерод переходит в железную руду, за счет чего поверхностный слой отливок обезуглероживается и становится мягким. Чугун становится ковким, а сердцевина сохраняет хрупкость.
Маркировка ковкого чугуна: КЧ 40-6, где КЧ — это, разумеется ковкий чугун; 40 – показатель прочности при растяжении; 6 – относительное удлинение, %.
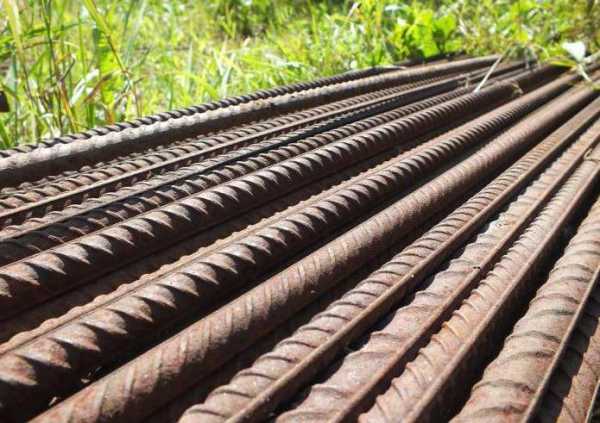
Прочие показатели
Что касается разделения чугунов по прочности, то здесь применяется следующая классификация:
- Обычная прочность: σв до 20 кг/мм2.
- Повышенная прочность: σв = 20 — 38 кг/мм2.
- Высокая прочность: σв = 40 кг/мм2 и выше.
По пластичности чугуны разделяются на:
- Непластичные – относительное удлинение менее 1%.
- Малопластичные – от 1% до 5%.
- Пластичные – от 5% до 10%.
- Повышенной пластичности – более 10%.
В заключение также хотелось бы обязательно отметить, что на свойства любого чугуна довольно существенное влияние оказывает даже форма и характер заливки.
fb.ru
Состояние углерода в чугуне — Энциклопедия по машиностроению XXL
В зависимости от состояния углерода в чугуне различают [c.203]Состояние углерода в чугуне [c.199]
В зависимости от состояния углерода в чугуне различают белы чугуны, в которых углерод находится в виде цементита серые чугуны, в которых углерод в значительной степени или полностью находится в свободном состоянии в форме пластинчатого графита [c.181]
Сплавы железа с углеродом, в которых содержание углерода больше 2,14%, называются чугунами. В зависимости от состояния углерода в чугуне различают [c.181]
Сплавы железа с углеродом, в которых содержание углерода больше 2,14%, называются чугунами. В зависимости от состояния углерода в чугуне различают белые чугуны, в которых весь углерод находится в связанном состоянии в виде цементита (структуры белых чугунов были рассмотрены в 8), излом чугуна матово-белый [c.166]
В зависимости от состояния углерода в чугуне различают белый чугун, в котором весь углерод связан в цементит (см. 2) серый чугун в котором весь углерод находится в свободном состоянии р виде графита или часть углерода (большая) находится в виде [c.62]
В зависимости от состояния углерода в чугуне различают два вида чугуна серый и белый. Серый чугун имеет в изломе серый цвет. Большинство отливок изготовляют из серого чугуна. Серый чугун хорошо обрабатывается резанием. В белом или отбеленном чугуне весь углерод находится в химическом соединении с железом в виде цементита (Ре С) Цементит очень тверд и хрупок, поэтому белый чугун обладает высокой твердостью и хрупкостью и не поддается обработке обычным режущим инструментом. В изломе белый чугун имеет белый цвет. Если белый чугун подвергать длительному отжигу (томлению), то цементит в чугуне распадается и углерод выделяется в свободном состоянии. [c.459]
Свариваемость и свойства сварных соединений зависят от структуры чугуна. Структура определяется составом чугуна и технологическими факторами, главным из которых является скорость охлаждения с высоких температур. Главный процесс, формирующий структуру,— это процесс графитизации, т. е. процесс выделения углерода в чугуне. Процесс графитизации при сварке является благоприятным, так как выделение углерода в свободном состоянии уменьшает хрупкость чугуна. Все элементы, содержащиеся в чугуне, делятся на две группы [c.129]
Графит — углерод в свободном состоянии, образующийся в чугунах в результате распада цементита при медленном охлаждении. Графит не магнитен, мягок и обладает низкой прочностью. [c.14]
Чугун — сплав на железной основе. Принципиальное отличие чугуна от стали заключается в более высоком содержании в нем углерода (более 2,14 %). Наибольшее распространение получили чугуны, содержаш ие 3-3,5 % углерода. В состав чугунов входят те же примеси, что и в сталь, т. е. кремний, марганец, сера и фосфор, но в несколько больших количествах. Углерод в чугуне может находиться в химическом соединении с железом либо в свободном состоянии в виде графита. Чугуны, у которых весь углерод находится в химическом соединении с железом, называют белыми (по виду излома), а чугуны, весь углерод которых или большая его часть представляет собой графит, получили название серых. В данной главе рассматривается строение белых чугунов. [c.58]
Углерод в чугуне может быть как в связанном с железом состоянии (цементит), так и в свободном (графит). Графит в чугуне имеет разнообразную форму 1) пластинчатого графита, [c.122]
Шихту подбирают так, чтобы получить нужный химический состав чугуна в зависимости от назначения отливок. При составлении шихты учитывают также возможные изменения состава чугуна при плавке. Они состоят в том, что в процессе плавки от соприкосновения с топливом изменяется количество углерода в чугуне, повышается содержание серы, а также происходит частичное окисление содержащихся в чугуне кремния и марганца. В результате понижения содержания кремния уменьшается выделение графита, и чугун отбеливается, т. е. в наружном слое отливок углерод остается в химически связанном с железом состоянии в виде очень твердого цементита (условия для образования отбеливания чугуна подробнее изложены в главе П1), [c.200]
После медленного охлаждения и затвердевания углерод в чугуне находите- в свободном состоянии в виде графита. Наличие графита приводит к снижению твердости и улучшению обрабатываемости чугуна. Такой чугун называется серым, он широко используется в промышленности. [c.11]
Углерод в чугуне находится либо в химически связанном состоянии (карбиды железа в виде ледебурита, первичного и вторичного цементита), либо в свободном состоянии, т. е. в виде графита. Поэтому структура чугуна зависит от количества углерода, находящегося в химически связанном состоянии и может быть перлито-графи-товая феррито-перЛито-графитовая феррито-графитовая. Чугуны различают по структуре, способам изготовления, химическому составу и назначению. [c.189]
Выше мы установили, что углерод в чугуне может быть в двух состояниях в виде графита (свободный углерод) и в виде цементита (углерод, химически связанный с железом) — структурно свободного или входящего в состав перлита. Таким образом можно написать [c.200]
В каком состоянии находится углерод в чугуне [c.209]
Чугун представляет собой железоуглеродистый сплав, содержание углерода в котором превышает 2,14%. Углерод в чугуне может находиться в свободном состоянии в виде графита (серый, ковкий, высокопрочный чугун) и в связанно.м состоянии в виде карбидов (белый чугун в приборостроении не используют). Наличие графита в чугунах определяет повышенную износостойкость и способность поглощать вибрацию. Чугуны в основном используют в качестве литейных сплавов, так как для них характерны малая усадка (1 % ) и высокая жидкотекучесть. [c.129]
Хром, переходя частично в твердый раствор с железом, способствует образованию сорбитообразного перлита. Будучи карбидообразующим элементом, хром тормозит графитизацию чугуна, уменьшая тем самым развитие выделений графита. Ввиду того что никель является сравнительно слабой графитизирующей примесью, а хром — сильной карбидообразующей, при присадке обоих этих элементов в чугун необходимо уравновесить влияние их на состояние углерода в структуре чугуна соотношением содержания их N1 Сг [c.304]
В зависимости от состояния углерода различают чугуны серые, белые и половинчатые. Наибольшее распространение получили серые чугуны, в которых большая часть углерода находится в свободном состоянии в виде графитовых включений. В зависимости от формы последних и степени легирования серые чугуны подразделяют на серые с пластинчатым графитом (серые), ковкие, высокопрочные, антифрикционные и легированные со специальными свойствами. [c.267]
Углерод в чугуне находится как в свободном состоянии, так и в виде соедине-н яя с железом. [c.101]
Как и в стали, углерод в чугуне является главной примесью. Он может быть в связанном состоянии в виде цементита или в свободном — в виде графита. Цементит — это вещество, которое представляет собой химическое соединение углерода и железа. Он очень тверд, но хрупок. Графит — это чистый углерод, оц очень мягок. [c.15]
Серые чугуны, обыкновенные и легированные, отличаются от сталей более высоким процентом содержания углерода, колеблющимся примерно от 2,6 до 3,6%. Углерод в чугунах находится либо полностью в свободном состоянии, либо частично в связанном. В свободном состоянии углерод имеет форму графитных включений различных размеров и конфигураций. В сталях весь углерод находится в связанном состоянии в виде химического соединения — цементита. [c.16]
Как указывалось выше, углерод в чугунах может находиться либо в свободном состоянии — в виде графитных включений, либо в связанном состоянии — в виде цементита. Количество связанного или свободного углерода в чугуне определяется наличием кремния, марганца и других легирующих элементов. Например, кремний является графитизирующим элементом. Его содержание в чугуне колеблется от 0,5 до 5%. Кремний не образует с углеродом карбидов, способствуя распаду цементита. Марганец, наоборот, является карбидообразующим элементом. Он уменьшает состав графита, способствуя образованию перлитной структуры. [c.52]
Чугунами называются сплавы железа с углеродом при содержании 2,14…6,3 % С. Наиболее распространены чугуны с 2,5…4 % С. Кроме углерода в чугунах имеется некоторое количество марганца и кремния, а также примесь серы и фосфора. Углерод в чугунах может находиться либо в свободном состоянии -в виде графита (серые чугуны), либо в связанном — в виде карбидов железа (белые чугуны). [c.582]
В зависимости от состояния углерода в сплаве различают белые, серые, ковкие и высокопрочные чугуны. [c.89]
Чугуны представляют собой железоуглеродистые сплавы с содержанием углерода более 1,7%. Углерод в чугуне может находиться или в связанном состоянии в виде карбидов железа, или в свободном состоянии в виде графита. В зависимости от этого чугуны подразделяются на белые и серые. В белых чу-гунах углерод находится только в связанном состоянии, в серых — главным образом в свободном. К особой группе серых чугунов относятся ковкие чугуны, получающиеся из белых путем длительного отжига (томления). Кроме железа и углерода, в чу-гунах содержатся кремний, марганец, сера и фосфор, а в легированных чугунах также могут содержаться никель, хром, ванадий и другие элементы. [c.199]
В зависимости от состояния углерода в чугуне различают два вида чугуна серый и белый. В сером чугуне углерод находится в свободном состоянии в виде пластинчатого графита. Серый чугун в изломе имеет серый цвет. Большинство отливок изготовляется из серого чугуна. Серый чугун хорошо обрабатывается режущим ин-струменто.м. В белом, или отбеленном, чугуне весь углерод находится в связанном состоянии а виде химического соединения с железом (РезС). Химическое соединение углерода с железом называется цементитом, или карбидом железа. Цементит очень тверд и хрупок, поэтому белый чугун обладает высокой твердостью и хрупкостью и не поддается обработке обычным режущим инструментом. В изломе белый чугун имеет белый цвет. Если белый чугун подвергать длительному отжигу (томлению), то в результате этой операции цементит в чугуне распадается и углерод выделяется 3 свободном состоянии. [c.555]
Чугун представляет собой сплав железа с углеродом, кремнием, марганцем, фосфором и серой, в котором содержание углерода колеблется от 1,7 до 6,67 /о. Углерод может находиться в чугуне в химически не связанном состоянии с железом, т. е. в виде свободного графита, располагающегося равномерно по всей массе чугуна блестящими черными чешуйками, либо в виде химического соединения с железом РезС, которое носит название цементита. Состояние углерода в чугуне оказывает большое влияние на его механические свойства. Выделению углерода в виде графита способствует кремний, а образованию цементита—марганец. Сера и фосфор являются вредными примесями, ухудшающими механические свойства чугуна. Сера придает чугуну красноломкость (хрупкость металла в нагретом состоянии) и ухудшает литейные качества. Фосфор придает ему хладноломкость (хрупкость металла в холодном состоянии). Сера вносится в чугун из кокса, а фосфор из руды при ее плавке. [c.14]
Капли железоуглеродистого расплава сливаются в струйки и стекают в горн печи. При движении вниз металл контактирует с кусками раскаленного кокса и путем прямого растворения углерода 3Fe-f = Fe3 дополнительно науглероживается. Благодаря науглероживанию в жидком состоянии концентрация углерода в металле повышается до 3,5—4,5 %. Конечное содержание углерода в чугуне будет определяться следующими факторами 1) химическим составом металла, т. е. содержанием в нем кремния, марганца и других элементов, влияющих на растворимость углерода в железе 2) температурой нагрева чугуна 3) длительностью пребывания чугуна в нижней части печи. Чугун тем больше насыщается углеродом, чем дольше он находится в контак те с раскаленным коксом и чем выше его температура. Высокий нагрев увеличивает растворимость углерода в железе. После выпуска чугуна из печи и некоторого его охлаждения углерод выделяется из сплава в виде твердого чешуйчатого графита или спели, которая при хранении чугуна в ковше или в миксере всплывает на поверхность. Кроме углерода, в железо переходят фосфор, кремний, марганец, сера. Содержание углерода в литейном чугуне составляет -4,0 %, а в передельном 4,5 % [c.76]
Чугун находит широкое применение в промышленности в качестве конструкционного материала, так как имеет невысокую стоимость, хорошие литейные свойства, износостойкость, стойкость при знакопеременных нагрузках и повышенных температурах. Чугун содержит свыше 2 % углерода, до 5 % кремния и некоторое количество марганца. Используются легированные чугуны с добавками хрома, никеля, молибдена. В зависимости от состава, условий кристаллизации и скорости охлаждения углерод в чугуне может находиться в химически связанном или свободном состоянии в виде графита. В первом случае чугун называется белым, так как на изломе он более светлый. Такой чугун имеет высокую твердость, изностойкость, чрезвычайно трудно обрабатывается, имеет ограниченное использование в конструкциях. Во втором случае чугун называется серым, он на изломе имеет серый цвет. Этот чугун имеет удовлетворительную прочность, достаточную твердость, хорошо обрабатывается на механическом оборудовании. Серый чугун более распространен в промышленности в качестве конструкционного материала. [c.127]
Чугун — сплав железа с углеродом (свыше 2 %), кремнием (до 5 %) и марганцем с примесями — серой и фосфором. В специальные чугуны дополнительно вводят хром, никель, молибден, титан, медь и др. Углерод в чугуне может находится в химическом соединении в виде цементита РезС или в структурно-свободном состоянии в виде графита. [c.337]
Согласно другим представлениям в расплаве могут находиться как отдельные ионы углерода, так и плоские макромолекулы (пинакоиды). Однако пинакоиды не являются обособленной фазой — они отдают четвертый валентный электрон в электронный газ металлического расплава, образуя таким образом макроионы. В результате получается истинный, а не коллоидный раствор [27]. Эти точки зрения не противоречат фактам. Для расплавов железо — углерод эффекты, связанные с появлением неоднородности, наблюдаются при концентрации углерода свыше 2% для системы железо — углерод — кремний (2% кремния) они имеют место уже при содержаниях углерода свыше 1,5%. Состояние углерода в расплаве сильно зависит от степени перегрева чугуна над линией ликвидуса. Предполагаются также области су-шествования различных агрегатных состояний углерода в жидких чугунах. В расплавах, имеющих температуру на 100° С и выше температуры ликвидуса углерод находится в растворе и частично в форме полиатомарного состояния. Ближе к температуре ликвидуса возможны дисперсные образования графита из гексагональных колеи (пинакоиды). [c.57]
Классификация чугунов. В зависимости от того, в какой форме содержится углерод в чугунах, различают следующие их виды. В белом чугуне весь углерод находится в связанном состоянии в виде цементита. Структура белого чугуна соответствует диаграмме Fe-Feg (рис. 2.9). В сером чугуне большая часть углерода находится в виде графита, включения которого имеют пластинчатую форму. В высокопрочном чугуне графитные включения имеют шаровидную форму, а в ковком — хлопьевидную. Содержание углерода в виде цементита в сером, высокопрочном и ковком чугунах может составлять не более 0,8 %. [c.78]
Углерод в чугунах может находиться в виде химического соединения — цементита (такие чугуны называют белыми) или в свободном состоянии в виде графита — частично или полностью (в этом случае чугуны называют серыми). Получение того или иного вида чугуна зависит в основном от его химического состава и скорости охлаждения. Такие элементы, как кремний, титан, никель, медь и алюминий, способствующие выделению графита, называют графитизирующими. При введении таких элементов, как марганец, молибден, сера, хром, ванадий, вольфрам, углерод входит в химическое соединение с железом, образуя цементит (Feg ). Эти элементы называют антиграфитизирующими, или тормозящими графитизацию. При одном и том же химическом составе структура чугуна может быть различной в зависимости от толщины отливки. Чтобы обеспечить необходимую структуру отливок разной толщины, надо знать их химический состав. Для определения химического состава отливок опытным путем строят структурные диаграммы. Например отливка имеет химический состав С + Si = 4 % (линия аа. на рис. 8.1). При таком составе в отливке толщиной до 10 мм получится белый чугун, толщиной до 20 мм — половинчатый, толщиной до 60 мм — серый перлитный и толщиной свыше 60 мм — серый ферритно-пер-литный. При толщине отливки свыше 120 мм и указанном химическом составе чугун будет серый ферритный. [c.133]
Углерод в чугуне бывает в двух видах в свободном состоянии — в виде графита в химическом соединеншт с железом РезС — в виде цементита. Если углерод в чугуне находится полностью или частично в виде графита то чугун имеет в изломе серый цвет и называется серым. Если углерод в чугуне находится в виде цементита, то-чугун имеет в изломе белый цвет и называется белым. Кремний способствует получению серого чугуна, а марганец — белого. Сера и фосфор — вредные примеси сера придает чугуну хрупкость, фосфор — хрупкость, но улучшает его литейные качества, жидкотекучесть. Серый и белый чугуны резко отличаются по свойствам. Белые чугуны очень твердые и хрупкие, плохо обрабатываются инструментом, в основном идут на переплавку в сталь и называются передельными чугунами. Часть белого чугуна используется для получения ковкого чугуна. Серые чугуны обладают хорошими литейными свойствами, мягкие, хорошо обрабатываются и сопротивляются износу, они называются литейными чугунами. Чугуны с содержанием фосфора 0,3—1,2% жидкотекучи и применяются для художественного литья. Серый чугун поступает в производство в виде отливок и характеризуется прочностью и твердостью. [c.46]
Углерод, входящий в состав чугуна, может находиться в свободном состоянии в виде отдельных частиц графита, вкрапленных между зернами железа, и в химически связанном состоянии — в виде карбида железа РезС (цементита). В зависимости от того, в какой форме присутствует углерод в чугуне, различают серый, белый, высокопрочный и ковкий чугун. [c.15]
Чугун — это сплав железа с углеродом (более 2% С) я другими элементами. Углерод в чугуне может находиться в химически связанном состоянии в виде цементита или в структурно-свободном состоянии в виде граф1па. Постоянными примесями в чугуне являются кремний, марганец, сера и фосфор. Наряду с этим в состав чугуна могут входить специальные примеси (легирующие элементы). [c.77]
Углерод в чугунной отливке может быть в двух формах а) в виде карбида железа РезС (цементит) б) графита в свободном состоянии, образующ,егося при охлаждении отливки в форме и при термической обработке. [c.36]
Углерод в чугуне может находиться в виде карбида железа РезС (первичный и вторичный цементит). Такой чугун, называемый белым чугуном , обладает повышенной твердостью и плохо поддается механической обработке. Б сером чугуне углерод находится в свободном состоянии в виде прослоек графита и только частично может быть в виде вторичных карбидов (перлит). Кремний способствует графитизации чугуна и увеличению размеров графитовых включений. Мар- [c.134]
Основными составляющими чугуна являются железо и углерод. Железо — элемент VIII группы системы Менделеева, принадлежащий к группе переходных металлов с недостроенной Зг -оболочкой с распределением электронов по энергетическим уровням . Энергетические уровни Зй и 45 очень близки, и между ними может легко осуществляться переход электронов, чем и обусловлены переменная валентность и полиморфизм железа. Углерод — элемент IV группы системы Менделеева с распределением электронов 18 28 2Р в нормальном состоянии и 15 252Р — в возбужденном (при этом наблюдается 5Р — гибридизация). Свойства железа и графита, который является наиболее характерной формой углерода в чугуне, приведены в табл. 1.1. [c.7]
mash-xxl.info
Количество углерода в стали и чугуне влияет на качественные характеристики этих сплавов
Количество углерода в стали и чугуне влияет на качественные характеристики этих сплавов. Он, наряду с железом, является основным компонентом чугуна и стали. От количества углерода зависят такие параметры как прочность, твердость, пластичность и др. В железоуглеродистых сплавах углерод находится в виде графита с гексагональной плотноупакованной кристаллической решеткой.
Чистое железо плавится при температуре 1539 °С. Оно обладает очень важной особенностью: в твердом состоянии имеет две полиморфные модификации — и .
Альфа-железо (Fe) существует в интервале температур до 911°С и от 1392 до 1539°С и имеет объемно-центрированную кристаллическую решетку, -железо существует в интервале температур от 911 до 1392°С и имеет кубическую гранецентрированную кристаллическую решетку. Часть -железа в интервале температур от 1392 до 1539 °С иногда называют δ-железом.
С металлическими элементами железо образует твердые растворы замещения, с неметаллическими (С, N2, H2 и другие) — твердые растворы внедрения.
При температуре 768 °С, называемой точкой Кюри, -железо испытывает магнитное превращение — выше этой температуры оно парамагнитное, ниже – ферромагнитное.
Углерод растворим в железе в жидком и твердом состоянии, а также образует с железом химическое соединение Fе3С, названное цементитом.
Альфа — и -железо обладают различной способностью растворять углерод; в -железе его растворяется мало — до 0,02 %, в - железе — до 2,14 %.
В зависимости от температуры и содержания углерода железоуглеродистые сплавы образуют ряд структурных составляющих (фаз).
Феррит (Ф) — твердый раствор внедрения углерода в -железа. Феррит имеет объемно-центрированную кристаллическую решетку. Максимальная растворимость углерода в феррите 0,02 % при температуре 727 °С. Феррит обладает низкой прочностью, твердостью и высокой пластичностью. Механические свойства зависят от величины зерна. Феррит обладает магнитными свойствами до температуры 768 °С.
Аустенит (А) — твердый раствор внедрения углерода в -железо. Предельная растворимость углерода в аустените 2,14% при 1147 °С. Аустенит немагнитная, твердая фаза.
Цементит (Ц) — химическое соединение железа с углеродом Fе3С. Цемент содержит 6,67 % углерода. Цементит имеет сложную ромбическую решетку с плотной упаковкой атомов. Температура плавления цементита точно не установлена – 1250…1260 °С. Цементит магнитный (до 227 0С) материал, имеющий высокую твердость. Цементит является неустойчивым соединением и при определенных условиях распадается с выделением свободного графита. В зависимости от условий образования различают цементит первичный (Ц), который образуется из жидкого раствора при затвердевании, вторичный (ЦII)- при распаде аустенита и третичный (ЦIII) — при выделении углерода из феррита.
Перлит (П) — механическая смесь (эвтектоид) феррита и цементита, содержащая 0,8% углерода. Перлит образуется при температуре 727 °С в результате распаде аустенита в процессе его охлаждения. Перлит имеет две модификации. Если цементит в перлите расположен в виде пластинок, то его называют пластинчатым, если в виде зерен -зернистым. Вид зерен перлита определяет его механические свойства.
Ледебурит (Л) — механическая смесь (эвтектика) аустенита и цементита, образующаяся из жидкого расплава при температуре 1147 °С. Содержание углерода в ледебурите 4,3%. Ледебурит — структура твердая и хрупкая.
Классификация и маркировка углеродистых сталей
Углеродистые стали принято классифицировать по химическому составу, назначению, структуре, качеству и раскисленности.
По структуре в равновесных условиях стали делятся на доэвтектоидные, эвтектоидные и заэвтектоидные.
По составу углеродистые, стали в зависимости от содержания углерода, делятся на 3 группы: низкоуглеродистые — с содержанием углерода до 0,3 %; среднеуглеродистые — с содержанием углерода до 0,7 %; высокоуглеродистые — с содержанием углерода более 0,7 %.
По назначению стали делятся на конструкционные, инструментальные и специальные — с особыми свойствами: автоматные и др.
По качеству стали классифицируют на стали обыкновенного качества, качественные, высококачественные и особо высококачественные в зависимости от вредных примесей (в основном это сера и фосфор). Под качеством стали понимают совокупность свойств, зависящих от способа ее производства. Чем выше качество стали, тем меньше она содержит вредные примеси. Марки углеродистых конструкционных сталей обыкновенного качества обозначаются буквами Ст и цифрами: СтО – Ст6, где цифры от 0 до 6 обозначают условный номер марки стали в зависимости от химического состава и механических свойств. Чем выше номер в марке стали, тем больше содержание углерода, выше прочность и ниже пластичность. Цифра в марке стали содержание углерода не показывает. В зависимости от химического состава и свойств углеродистые стали обыкновенного качества делят на три группы: А, Б, В (группа А в марке стали не указывается).
К группе А относят стали с гарантированными механическими свойствами. Поставляемая сталь не подвергается термической обработке.
К группе Б относят стали с гарантированным химическим составом. Стали этой группы подвергается термической обработке у потребителя.
К группе В относят стали с гарантированным химическим составом и механическими свойствами. Стали этой группы, в основном, используются в сварных конструкциях.
Группа стали ставится перед маркой стали: например, ВСтЗ.
По степени раскисления стали делят на кипящие, полуспокойные, спокойные.
Спокойная сталь раскисляется наиболее хорошо марганцем, кремнием и алюминием и ее затвердевание происходит спокойно, без выделения пузырьков газов.
Кипящая сталь раскисляется не полностью, только марганцем. В ней сохраняется много окислов железа. В процессе затвердевания выделяется окись углерода, что создает впечатление кипения стали. Кипящие стали дешевле спокойных, но обладают повышенной газонасыщенностью и имеют больше примесей.
Полуспокойные стали раскисляются марганцем и алюминием и занимают промежуточные положение между спокойными и кипящими. Степень раскисления обозначается индексами кп, сп, пс, стоящими справа от марки стали: например, ВСт6 кп.
Конструкционные качественные углеродистые стали обозначаются двумя цифрами 05…85, которые показывают содержание углерода в сотых долях процента.
В зависимости от содержания углерода их условно делят на четыре группы. После марки стали указывается степень раскисления: например, 30 сп.
Для высококачественных сталей после цифр, показывающих содержание углерода в сотых долях процента (05…85), ставится буква А (например, 55А), особо высококачественных — буква ПП, ШП, ЭП. (например, 40ШП).
Углеродистые инструментальные стали обозначают: буквой У, после которой следуют цифры, показывающие среднее содержание углерода в десятых долях процента: например, У12 (1,2 % С). В марках некоторых специальных сталей буква впереди обозначения указывает на назначение: А — автоматная (А30 — 0,3 % С), Р – быстрорежущая (Р9) и др.
Чугуны
Наиболее широко используемые чугуны в зависимости от состояния углерода делят на белые, серые, высокопрочные и ковкие.
В белых чугуне весь углерод находится в виде химического соединения Fе3С. Этот чугун для изготовления деталей машин не используется, так как имеет высокую твердость, хрупкость и практически не обрабатывается резанием. Белый доэвтектический чугун используется для получения ковкого чугуна, заэвтектический — для переплавки в сталь.
Серый чугун. В нем большая часть углерода или весь углерод находится в свободном состоянии в виде графита. В обычном сером чугуне графит образуется в виде пластинок. Этот чугун обозначается буквами СЧ, за которыми следуют цифры, показывающие значение предела прочности при растяжении в кгс/мм2. Например, СЧ15 (В = 150 МПа = 15 кгс/мм2). Серый чугун используется для изготовления деталей простой конфигурации: станин, корпусов, крышек, шкивов, стоек и др.
Высокопрочный чугун получают из серого чугуна, добавляя в жидкий серый чугун магний, церий и другие элементы, под влиянием которых образуется графит шаровидной формы. Высокопрочные чугуны имеют более высокие механические свойства, чем другие чугуны, и используются вместо поковок и отливок из углеродистой стали для деталей, работающих в тяжелых условиях. Высокопрочный чугун обозначают буквами ВЧ, после которых следуют две цифры, обозначающие предел прочности В в кгс/мм2 , a затем — цифры, показывающие относительное удлинение при растяжении δ в процентах. Например, ВЧ 45-1,5 (В = 45 кгс/мм2, δ = 1,5 %).
Ковкий чугун получают из белого доэвтектического чугуна путем длительного нагрева в твердом состоянии при высоких температурах. В результате образуется графит хлопьевидной формы. Ковкий чугун обозначают буквами КЧ и цифрами. Первые две цифры указывают предел прочности чугуна при растяжении, а вторые относительное удлинение при растяжении. Ковкий чугун используется для изготовления деталей, работающих при средних и высоких статических и динамических нагрузках (поршни, подшипники, ступицы и др.).
Графит в чугуне, уменьшая прочность и пластичность, по сравнению со сталью, дает чугуну и преимущества.
Включения графита облегчают обрабатываемость резанием, благодаря его смазывающему действию, улучшают его антифрикционные свойства, (т.е. уменьшает коэффициент трения), снижают вибраций.
Следует также отметить хорошие литейные свойства чугуна, дающие ему преимущества по сравнению со сталью.
Чугуны дешевле стали и имеют лучшую стойкость против коррозии.
По назначению, различают чугуны литейные — для изготовления отливок и передельные — для переплавки в сталь.
Виды термической диагностики. Превращения в стали
Термической обработкой (ТО) называются процессы, связанные с нагревом и охлаждением металла, находящегося в твердом состоянии, с целью изменения структуры и свойств металла без изменения его химического состава.
Термическую обработку характеризуют следующие основные параметры: температура нагрева, время выдержки при этой температуре, скорость нагрева и скорость охлаждения.
В зависимости от температурных режимов термическая обработка подразделяется на следующие виды: отжиг, нормализация, закалка, отпуск, химико-термическая обработка (ХТО), термомеханическая обработка (ТМО).
Возможность упрочнения сталей путем термической обработки обусловлена наличием полиморфных превращений в твердом состоянии. Ускоренное охлаждение стали, нагретой до состояния аустенита, ведет к ее переохлаждению, т.е. температура перлитных превращений смещается в область более низких температур. Переохлаждение характеризуется степенью переохлаждения ДТ, т.е. разностью между температурой 727 °С и температурой, при которой действительно идут перлитные превращения.
Отжиг и нормализация стали
Отжиг заключается в нагреве стали выше критических температур фазовых превращений (выше линий GS — АС3, РК – AС1, SE – АСm) (рис. 2), выдержке при данной температуре и медленном охлаждении (обычно вместе с печью). Цель отжига — устранение внутренних напряжений, измельчение зерна, придание стали пластичности перед последующей обработкой и приведение структуры в равновесное состояние.
В зависимости от требований, предъявляемых к свойствам стали, различают следующие основные виды отжига: диффузионный (гомогенизация), полный, неполный, изотермический и низкий отжиг (рис. 2).
Рис. 2. Схема различных видов отжига
Нормализация заключается в нагреве доэвтектоидных сталей выше линии GS (АС3), заэвтектоидных сталей выше линии SE (AСm) на 30…50 °С, непродолжительной выдержке при этой температуре для завершения фазовых превращений и последующим охлаждением на воздухе. Цель у нормализации та же, что и у полного отжига, однако твердость и прочность выше, чем после полного отжига.
Часто нормализация используется вместо более сложных операций закалки и отпуски, а также вместо полного отжига, как операция, обеспечивающая лучшее качество поверхности и облегчающая обрабатываемость резанием.
Закалка и отпуск стали
После механической обработки изделие, как правило, подвергается упрочняющей термической обработке. Наиболее распространенным видом упрочняющей термической обработки является закалка. Закалка заключается в нагреве стали выше критических температур фазовых превращений (выше линии GS для доэвтектоидных сталей и выше линии SK для заэвтектоидных сталей) выдержке при этих температурах с последующим охлаждении со скоростью, превышающей критическую. Закалка не является окончательной операцией термической обработки. С целью уменьшения хрупкости и напряжений, вызванные закалкой, а также получения требуемых механических свойств, сталь после закалки подвергается отпуску. Стали подвергаются закалке для повышения твердости и получения требуемых физико-механических свойств. Способность стали принимать закалку возрастает с увеличением углерода. При содержании углерода меньше 0,2 % сталь практически не закаливается.
Охлаждение с высокой скоростью, выше критической, приводит к образованию мартенситной структуры. Чаще всего для закалки используют кипящие жидкости — воду, водные растворы щелочей и солей, масло, реже — расплавленные соли.
Отпуском называют нагрев стали до температуры ниже температуры перлитных превращений GS (АС1), выдержке при заданной температуре и последующим охлаждением с заданной скоростью. Отпуск является окончательной операцией термической обработки. Его цель — уменьшение закалочных напряжений, снижение твердости и получение необходимых механических свойств. Чем выше температура отпуска, тем полнее снимаются закалочные напряжения. Наиболее полно остаточные напряжения снимаются уже при нагреве до температуры 550 °С.
Основное превращение при отпуске — распад мартенсита, т.е. выделение углерода из пересыщенного твердого раствора в виде мельчайших кристалликов цементита. Распад мартенсита завершается при температуре около 400 °С.
При нагреве до 300…450 °С (500 °С) образуется смесь феррита и цементита, которую называют трооститом отпуска. При нагреве до 500…650 °С образуется более крупнозернистая феррито-цементная смесь, названная сорбитом отпуска. Кроме этих превращений в интервале температур 200…300 °С происходит распад остаточного аустенита с образованием отпущенного мартенсита. Скорость охлаждения после отпуска оказывает большое влияние на остаточные напряжения — чем она меньше, тем меньше остаточные напряжения. Особое влияние на окончательные свойства стали оказывает температура отпуска.
Поверхностная закалка
Для повышения твердости, предела выносливости и износостойкости детали машин подвергаются поверхностному упрочнению. Обычно для этих целей применяют поверхностную закалку, закалку с индукционным нагревом, закалку при нагреве лазером. При поверхностной закалке закаливается на некоторую (заданную) глубину только поверхностный слой. Сердцевина изделия остается вязкой и воспринимает ударные нагрузки. Нагрев поверхности детали производится до температуры выше линии GS (АС3) с последующим быстрым охлаждением.
Газоплазменная закалка применяется для крупных изделий. Поверхность нагревают, чаще всего, ацитиленкислородным пламенем, температура которого 2400…3150 °С. При этом поверхность изделия быстро нагревается до температуры закалки, а сердцевина не успевает нагреваться. Быстрое охлаждение обеспечивает закалку поверхностного слоя. Толщина закаленного слоя 2…4 мм, твердость для стали с 0,45…1,5 % С — HRC50…56.
Газопламенную закалку применяют в мелкосерийном и единичном производстве.
Недостатком этого способа закалки является неравномерность нагрева стали с поверхности и возникающая из-за этого структурная неоднородность, выгорание углерода с поверхности, возникновение значительной окалины. В тонком поверхностном слое образуется мартенсит, второй слой имеет структуру мартенсит и троостит, в третьем слое сохраняется исходная структура. Газопламенная закалка вызывает меньшие деформаций, чем объемная закалка.
Закалка с индукционным нагревом токами высокой частоты наиболее распространенный и прогрессивный метод поверхностного упрочнения. Его преимуществом является возможность автоматизации, отсутствие выгорания углерода с поверхности изделия, а также отсутствие окисления его поверхности. Сущность этого вида закалки состоит в том, что под действием переменного магнитного поля в изделии, находящемся в этом поле, возникают вихревые токи. Из-за поверхностного эффекта эти токи наводятся, в тонком поверхностном слое изделия. Протекание вихревых токов и вызывает нагрев поверхности изделия.
Твердость поверхностного слоя при нагреве токами высокой частоты несколько выше, чем твердость при обычной закалке (HRC50…60). Толщина упрочняющего слоя определяется условиями работы.
Этот вид закалки используется для закалки изделий из сталей, для получения заданной твердости, с содержанием углерода более 0,4 %. В качестве охлаждающей жидкости используют воду и водные растворы полимеров.
Поверхностная закалка при нагреве лазером. Под воздействием лазерного излучения за короткий промежуток времени (10-3 – 10-7 с) поверхность нагревается до очень высоких температур. Тепло в глубь металла распространяется путем теплопроводности. После прекращения действия лазерного излучения происходит закалка нагретых участков, благодаря интенсивному обводу тепла в глубь металла (самозакалка).
Глубина закаленного слоя регулируется плотностью мощности лазерного пучка и временем его взаимодействия с поверхностью изделия и изменяется в пределах 0,1…2 мм. Закалку при нагреве лазером применяют основном для отливок из стали и чугуна.
Преимуществом лазерного упрочнения является его высокая производительность, возможность автоматизации, обеспечение обработки строго определенных участков и контуров, а также деталей сложной формы. Поверхностная закалка при нагреве лазером значительно повышает твердость, износостойкость и предел выносливости при изгибе.
Химико-термическая обработка.
Химико-термической обработкой (ХТО) или поверхностным легированием, называют обработку, заключающуюся в сочетании термического и химического воздействия на металлы и их сплавы с целью изменения химического состава, структуры и свойств поверхностного слоя. Эти изменения происходят за счет диффузии в поверхностный слой элементов в атомарном состоянии в процессе выдержки при высоких температурах в активной твердой, жидкой или газообразной среде.
Основная цель химико-термической обработки — упрочнение поверхности, повышение твердости, износостойкости, усталостной прочности, а также повышение стойкости к воздействию агрессивных сред.
К процессам химико-термической обработки относится: цементация, азотирование, цианирование, нитроцементация, диффузионная металлизация и др.
Химико-термическая обработка характеризуется тремя одновременно протекающими процессами. Первый процесс — диссоциация — распад молекул и образование диффундирующего элемента в атомарном состоянии. Второй — абсорбция — взаимодействие атомов диффундирующего элемента с поверхностью изделия и поглощение (растворение) поверхностью свободных атомов. Третий — диффузия — проникновение атомов диффундирующего элемента в глубь металла.
Рассмотрим кратко некоторые вида химико-термической обработки.
Цементацией называют процесс насыщения поверхности изделия углеродом. Основное назначение цементации — придание поверхности металла твердости и износостойкости. Как правило, цементацию проводят при температуре выше линии Ас3 (930 — 950 °С), когда устойчив аустенит, растворяющий углерод в большом количестве. Цементацию проводят в твердых, жидких и газообразных средах, называемых карбюризаторами.
В качестве твердой среды, чаще всего, используется древесный уголь в смеси с другими компонентами.
Жидкие карбюризаторы — это, как правило, смеси цианистого калия с бурой, содой и другими компонентами. Они применяются для получения тонкого цементированного слоя с высоким содержанием углерода.
Газовую цементацию проводят в атмосфере метана, керосина, бензола и других средах.
Окончательные свойства цементированные изделия приобретают после закалки с температуры 820…850 °С и низкого отпуска.
Цементации подвергаются изделия из низкоуглеродистых сталей (до 0,25…0,3 % углерода), работающие в условиях ударных нагрузок и подвергающиеся износу (зубья зубчатых колес, шестерни, втулки). Толщина цементирующего слоя 0,1…4 см.
Азотирование — это процесс насыщения поверхностного слоя стали азотом. Цель азотирования — придать поверхности высокую твердость, износостойкость, усталостную прочность и сопротивляемость коррозии в таких средах, как влажная атмосфера, вода, газ и др. Твердость азотированного слоя заметно выше, чем цементированного, и сохраняется при нагреве до более высоких температур – 400…500 °С, тогда как твердость цементированного слоя сохраняется только при нагреве до 200…300 °С. Процесс азотирования, чаще всего, заключается в воздействии на сталь аммиака (газовое азотирование) при температуре 500…600 °С. Иногда проводят азотирование в жидких средах — в расплавленных цианистых солях при температуре 570 °С. Толщина азотированного слоя 0,25…0,75 мм. Азотированию подвергаются только легированные стали, т.к. азотирование железа и углеродистых сталей не приводит к значительному повышению твердости. Перед азотированием, с целью улучшения механических свойств, деталь подвергают закалке и высокому отпуску.
Достоинством азотирования, по сравнению с цементацией является незначительное изменение размеров и отсутствие коробления вследствие низкой температуры нагрева.
Нитроцементация представляет собой процесс насыщения поверхностного слоя стали одновременно углеродом и азотом при температуре 840…860 °С в газовой среде азота, водорода и окиси углерода. Назначение нитроцементации — повышение износостойкости предела выносливости при изгибе, твердости, коррозионной стойкости. Сразу после нитроцементации назначают закалку и низкий отпуск.
refdb.ru