Пресс для древесной стружки | Пресс для щепок
Древесная стружка и щепки обычно обладают размером от 1 до 1,5 см. По сравнению с опилками они не такие мелкие, а чтобы их спрессовать требуется пресс с небольшим усилием, как например, 15 тонный паковочный пресс. В зависимости от размера кипы и веса, который вы хотите получить, вы можете выбрать для себя подходящую модель, которая будет полностью соответствовать вашим параметрам.
При выборе усилия прессования в 15 тонн, идеальным размером камеры прессования будет 550*250 мм, с размерами канала 400*250 мм. Если вы хотите получить кипу большего размера, то и усилие прессования должно быть больше – 25 тонн, 30 тонн, 40 тонн, или даже 60 тонн. Если выбрать 15 тонный пресс, с размеров камеры 400*250мм, то размер кипы будет меньше, а плотность её соответственно больше.
Плотные кипы более экономичны при транспортировки, и в тоже время конечный потребитель может легко раскрошить её. В большинстве случаев стружка и щепки используются в качестве подстилки для животных, поэтому и необходимо её предварительно измельчить. Однако, тюк из стружку может быть использован и по другому, например, для сжигания, в таком случае высокая плотность кипы – это преимущество.
Еще один важный момент нужно иметь в виду – некоторые щепки могут быть большего размеры, волнистые и объемные, более 3 см в длину. Такой материал обладает низкой начальной плотностью. Что бы получить плотную кипу нужного веса из того материала, необходимо дважды его прессовать. Для стружки размером до 1,5 см достаточно будет и одного цикла — необходимая кипа будет готова. Другими словами, стружка большего размера не обязательно будет давать большую производительность.
Чтобы подобрать подходящую комбинацию между усилием прессования и размером камеры прессования, мы настоятельно рекомендуем связаться с нашим отделом продаж.
Если вы планируете прессовать такие древесные отходы как опилки, которые размером в районе 1 мм, пожалуйста, перейдите в раздел «Опилки», для получения детальной информации по данному типу материала.
ru.sinobaler.com
Как выбрать оборудование для производства опилок :: BusinessMan.ru
Сегодняшний рынок буквально пестрит различными промышленными установками для мелкого и крупного бизнеса. Среди этого разнообразия даже у бывалых спецов иногда буквально разбегаются глаза. В этой статье мы рассмотрим оборудование для производства опилок и производных от них (пеллет, гранул).
Ведь сырье для этого бизнеса в нашей стране достать не проблема, можно договориться с любым лесничеством о сборе и вывозе валежника и сухостоя. Таким образом, вы будете очищать лес и зарабатывать на этом деньги.
Проблема выбора
Перед приобретением промышленной установки у большинства покупателей возникают естественные вопросы: «Какой тип лучше выбрать?» «Купить новое оборудование или бывшее в употреблении?» «Дешевое или дорогое?» Рассмотрим вкратце три основных варианта.
1. Новая установка «под ключ».
2. Линия, бывшая в употреблении.
3. Купить по частям у разных производителей и самостоятельно скомплектовать на месте.
Каждый из этих вариантов имеет свои плюсы и минусы, однако прежде чем рассматривать их, следует ознакомиться с теоретической частью.
Из чего состоит оборудование для производства опилок
По сути, данная установка является элементарной дереводробилкой, в ее комплектацию входят:
1. Рубительная машина, предназначенная для измельчения древесины в технологическую щепу.
2. Бункер-накопитель-дозатор.
3. Измельчитель щепы.
Как видите, такой станок для производства опилок элементарен.
Линия-гранулятор
Станок для производства прессованных опилок немного сложнее, он состоит из:
1. Участка измельчения.
2. Приемного бункера для опилок с подвижным дном.
3. Сушильного барабана.
4. Теплогенератора.
5. Циклона с вентилятором.
6. Приемного бункера сухого сырья.
7. Пресс-гранулятора (брикетировщика).
Оборудование для изготовления пеллет
Данная установка имеет несколько вариантов комплектации.
1. Линия для переработки древесины или ее кусковых отходов (включает в себя оборудование для производства опилок).
2. Линия, работающая на производственных отходах древесины (дополнительный станок для измельчения не нужен).
3. Линия пеллетирования для сырья с влажностью более 13% (дополнительно требуется сушильный комплекс).
4. Линия, работающая с материалом, влажность которого менее 13%.
Полный список комплектации такой установки: молотковая мельница, дисковая и барабанная дробилка, котел газовый (или на дровах), сушильный барабан, а также механизм для загрузки в него стружки, циклон, дымосос, ленточный или скребковый транспортер, подвижные полы, вентилятор, смеситель, бункер для сырья с транспортером, пресс-гранулятор, охладитель, сито, вентилятор для удаления пыли и отсева, бункер для готовых пеллет, весы, упаковочный станок.
Что нужно учитывать, приобретая оборудование для производства опилок и их производных? Рассмотрим плюсы и минусы трех вариантов.
Линия «под ключ»
К достоинствам такого варианта можно отнести:
- Минимальное количество затрачиваемых трудочасов на монтаж установки и высокое качество таких работ.
- Исключение покупки «кота в мешке» — качественное новое оборудование будет лучше и дольше функционировать без поломок.
- Кроме того, современная техника характеризуется более высоким ресурсом работы, она менее энергоемка, это снизит затраты на изготовление конечного продукта.
К недостаткам относятся:
- Высокая стоимость такого проекта.
- Отсутствие возможности самостоятельного обслуживания, что соответственно приведет к простоям оборудования даже при незначительных поломках. Происходит это, потому что установка находится на гарантийном и сервисном обслуживании. В результате, даже если порвется шланг, замена которого занимает около 20 минут, все равно необходимо вызывать специалистов фирмы, а это может затянуться на несколько дней.
Линия, бывшая в употреблении
Достоинством данного варианта является дешевизна. Если промониторить отечественный и импортный рынки подержанной техники, то вполне можно подобрать установку, бывшую в употреблении, в хорошем состоянии за низкую стоимость. Кроме того, можно найти вариант с гораздо большей производительностью, чем новая линия, за те же деньги.
Недостатками являются: покупка «кота в мешке», сложный монтаж с внесением собственных нововведений, не всегда полная комплектация оборудования, некомплект документации. Кроме того, исключается гарантийное и сервисное обслуживание, снижается вероятность использования оригинальных запчастей. Если установка очень старая, то запасные детали к ней уже не изготавливают.
При покупке ненового оборудования следует придерживаться следующих рекомендаций: проведите тщательный осмотр и прослушайте работу линии на отсутствие посторонних шумов, особое внимание необходимо уделять головной части (сушильный комплекс, дробилка, пресс). Кроме того, останавливайте свой выбор на работоспособных линиях более свежих годов.
Скомплектованная линия
Это довольно редкий вариант, но он также имеет право на существование. По сути, это наиболее дешевая схема, но при этом и самая сложная. Она больше подойдет для тех, кто имеет большой опыт работы в данном бизнесе. Зачастую при таком варианте покупки можно в придачу практически даром получить тот или иной узел.
Если вы решились установить скомплектованную линию, то наиболее важные узлы лучше приобретать новые, а второстепенного характера – бывшие в употреблении. В таком случае вам удастся сэкономить значительные средства, зато придется повозиться с монтажом оборудования.
Различные варианты реализации опилок
Подводя итоги, можно отметить, что данный бизнес будет весьма выгодным, если вы не станете зацикливаться только на одной сфере реализации своего продукта. Ведь он используется повсеместно – от удобрений и до строительства, а значит, спрос на него обязательно будет.
Например, вы можете начать производство опилок для копчения и топливных брикетов (сегодня такой продукт пользуется повышенным спросом, ведь брикеты горят в четыре раза дольше и жара дают больше, чем дрова). Для этого в качестве сырья лучше использовать фруктовые породы деревьев. Параллельно с этим начните производство опилок для животных, ведь подстилка необходима не только домашним питомцам, но и крупному скоту, для этого наладьте контакты с фермерами.
Для изготовления наполнителей кошачьего туалета вам потребуется использовать гранулятор. В качестве сырья, кроме опилок, понадобятся сорбционные компоненты: целлюлоза, мел, карбометилцеллюлозный клей, кроме того, для поглощения неприятного запаха следует добавлять цеолит.
Для производства подстилки в качестве сырья можно использовать любые породы деревьев, початки кукурузы и прочее. Обязательно займитесь изготовлением утеплителей на базе опилок, ведь строительная сфера в наши дни актуальна, как никогда. Если вы займете сразу несколько сфер, то прибыль вашему предприятию будет обеспечена.
В заключение
Дополнительным удобством такого бизнеса является тот факт, что линия не занимает много места и не требует большого количества квалифицированного персонала. Если вы проживаете в частном секторе, то можете даже организовать производство опилок в домашних условиях. Таким образом, вы сможете существенно сократить затратную часть своего дела, сэкономив на аренде производственных площадей и организации охраны.
businessman.ru
Топливо из древесины и виды
Отходы деревообрабатывающей отрасли, к примеру, опилки, щепа, являются прекрасным материалом для изготовления экологичного прессованного топлива. Популярность таких видов топлива на протяжении последнего десятилетия увеличилась в несколько раз.
Щепа древесины
Древесная щепа представляет собой остатки вырубки и обработки пиломатериалов. В прошлом веке их не использовали и тратили много денег на утилизацию. Сегодня щепа довольно популярна как горючее для котлов. Невозможно подсчитать, сколько же щепок остается каждый день, потому что вырубка лесных массивов и производство разных деревянных предметов, происходит круглый год каждую минуту. Кроме топлива древесная щепа используется для изготовления строительных материалов, предметов мебели, бумаги, и даже как удобрение в сельскохозяйственной отрасли. Для того, чтобы сделать из щепы топливо, прежде всего, ее сортируют по видам дерева. После этого она подвергается механической обработке, перемалыванию в особых аппаратах. Следующий этап — обработка паром, для удаления вредных соединений, которые могут быть в составе. Далее полученное сырье высушивают и прессуют. В результате таких мероприятий получаются плиты и брикеты, которые более удобны в использовании в различных сферах жизни. Созданные брикеты отличаются более высокой теплотворностью, чем простые пиломатериалы.
Почему для сжигания более популярно прессованное топливо, а не обычная щепа? Это происходит по таким причинам:
- малая теплотворность. К примеру, во время сгорания 1 килограмма щепы мягких сортов пиломатериалов удельная теплота достигает примерно 2500, а твердыхсортов – 2700 ккал. А во время перегорания прессованных материалов тепла образуется на 35-40% больше
- неудобное применение. Даже при расфасовке древесных остатков в мешки, в условиях неправильного хранения, они будут занимать большую площадь, а при малейшем увеличении влажности активно поглощают ее
- быстрое сгорание и необходимость регулярно подсыпать щепу.
В строительной отрасли древесные щепки применяют на производстве ДСП – древесно-строительных плит, из которых делают различные предметы мебели. Из таких плит мебель получается более бюджетная, чем из массива дерева. Кроме того, ДСП подходит для создания перегородок, напольного покрытия, балконов и подоконников. Этим же материалом обшивают стены и потолки. Изготовление ДСП включает такие этапы:
- прессование в условиях повышенной температуры
- склеивание особым клеевым составом.
Древесная щепа применяется и для создания цементно-стружечных плит (ЦСП), которые популярны в строительной отрасли для реализации технологии «сухого монтажа». ЦСП делают из цемента и древесной щепы с добавлением незначительной части химических веществ. Из этих плит сооружают модульные здания, отличающиеся повышенной стойкостью к влажности, плесени, возгоранию, жукам и атмосферным явлениям. Эту технологию придумали канадские специалисты.
Еще одной областью использования древесной щепы является бумажно-картонное производство. В сельском хозяйстве остатки древесины применяют как удобрение почвы, в работах, которые связаны с садовым строительством. Именно это сырье помогает осуществить лесовозобновление покрова в местах вырубки древесины.
Вследствие незначительной стоимости древесная щепа столь популярна и с каждым годом привлекает все больше потенциальных покупателей.
Целлюлоза древесина
В составе лесоматериала 99 % органических соединений. Элементный химический состав сырья различных видов практически не отличается. Полностью высушенная древесина на 49% состоит из углерода, на 44% — из кислорода, на 6% — из водорода, а также содержит 0,1-0,3% азота. После сгорания дерева остается его неорганическая часть — зола, которая содержит много кальция, калия, натрия, магния.
Самыми важными составляющими древесины являются такие органические соединения:
- целлюлоза
- лигнин
- гемицеллюлоза.
Целлюлоза — это натуральный полимер, полисахарид в виде длинной цепочной молекулы. Данное соединение очень стойкое, оно не растворяется в воде и стандартных орграстворителях, к примеру, спирте, или эфире. Сплетения ее макромолекул – сверхтонкие волокна – микрофибриллы, из которых образован целлюлозный каркас клеточной стенки. Микрофибриллы расположены вдоль длинной оси клетки, промежутки заполнены лигнином, гемицеллюлозой, водой. Благодаря этому соединению происходит отвердевание клеточной стенки. Гемицеллюлоза — полисахариды, имеющие недлинные цепочки молекул и низкую стойкость в отличие от целлюлозы.
Помимо важных органических соединений, в лесоматериалах имеется незначительный объем экстрактивных веществ, к примеру, танин, смола, камедь.
В целлюлозно-бумажной отрасли получают целлюлозу для производства бумаги, картона, а также древесноволокнистых плит. Целлюлозу получают следующими методами:
- кислотный
- щёлочной
- нейтральный.
Стружка древесины
Древесную стружку делают из дробленой коры деревьев, к примеру, дуба, сосны, кедра и целого ряда мягких и твердых пород. Этот материал является отличным вариантом мульчи для плодово-ягодных насаждений. Питательные соединения, входящие в состав коры попадают в землю и помогают питать другие деревья и цветы. Древесная стружка имеет большое значение в садоводстве. К тому же она довольно дешевая и для ее применения не нужно оборудование или специальный опыт.
Купить этот материал можно в каждом магазине товаров для садоводства. Кроме этого, ее можно произвести собственноручно, купив аппарат – стружечный станок. Однако цена этого оборудования довольно высока, и покупать его целесообразно лишь тогда, когда вам нужно строгать большой объем.
Древесная стружка применяется разными методами. Зачастую ее рассыпают на участках под кустами и деревьями, где нельзя высадить газон. Такая процедура поможет избавиться от сорняков, уменьшит испарение жидкости. Ухоженного внешнего вида можно добиться, высыпав под деревьями стружку.
Сосновая стружка является прекрасным материалом для укладки и хранения овощей и фруктов.
Дровяная древесина
Дровяная древесина – это сырье низкого качества, которое подходит по размеру и качеству для изготовления древесных плит, стружки. Также ее используют в гидролизном производстве и создании различной тары.
Такая древесина остается после изготовления заготовок для поддонов соответствующих европейским нормам, а также европоддонов, европалет и поддонов СР. Она может быть разных сортов дерева, к примеру, кедр, береза, осина. После сортировки предприятия предлагают дровяные материалы разного качества и стоимости.
Характеристики дровяной древесины:
- толщина более 10 см на узком конце
- длина 2,5 м или 1,25 м;
- без мягкой гнили.
Топливная древесина
Древесина — это наиболее старый тип горючего. Но, в процессе эволюции значение ее как топлива снижалось. Уменьшение удельного объема древесного топлива в топливном балансе государства можно объяснить несколькими причинами, основная из них – огромные нужды в топливе, в значительной степени превышающие возможности воспроизводства в лесных угодьях государства.
Топливную древесину добывает в лесных угодьях при помощи оборудования, которое имеет низкий показатель выбросов и потребляет мало энергии.
С помощью обработки сразу двух и более стволов можно существенно увеличить эффективность манипулятора. Все зависит от плотности и размера древесного материала. Так как настройки машины не позволяют осуществить замеры во время работы с двумя и более стволами, древесину измеряют по массе. Все обработанные стволы считаются в автоматическом режиме.
Топливо из древесины
Ученые РАН продемонстрировали, как при помощи радиолиза с высокой температурой из опилок выделяют высококачественное жидкое горючее. Они рассказали, что раствор, которую они получили из берёзовых опилок, по параметрам совпадает с горючим, октановое число которого выше 90.
Ученые получили топливо из лигнина и целлюлозы, которые являются важными составляющими древесины. Авторы разработки осуществили две стадии этого процесса:
сухая перегонка лесоматериалов в вакууме. В специальном аппарате нагревают сухие опилки до температуры 400—450С. Происходит распад лигнина и целлюлозы под действием энергии ионизирующего излучения
парообразные выработки радиолиза необходимо охладить и конденсировать в жидкостном холодильнике при 15С.
Состав конечного раствора зависит от сорта лесоматериалов, к примеру, при использовании сосновых опилок, массовый объем толуола составляет 10%. Но этот раствор отличается нестабильностью, и из него нужно получить стабильное топливо. Для преобразования необходима метановая или пропан-бутановая атмосфера.
Выход составляющих жидкого горючего регулируется, при помощи условий сухой перегонки, а также изменением соотношения паров и газовой смеси во время процесса стабилизации. Авторы проекта заявили, что могут получить горючее даже для реактивных двигателей.
wood-prom.ru
Применение щепы — 4 идеи получения из нее денег
Здравствуйте уважаемые читатели и подписчики Блога Андрея Ноака. Одним из самых распространенных видов отходов от деревообработки является древесная щепа. Сегодня мы рассмотрим применение щепы, а именно четыре самых распространенных варианта ее использования и получение от этого хорошей прибыли, и если вас заинтересует один из способов, то значит статья написана будет не зря!
Введение
Утилизация древесных отходов не дает спать многим владельцам предприятий. Кучи отходов не только занимают производственные площади, но и являются опасными для людей, к примеру известны случаи самовоспламенения и даже выделения вредных веществ от гниения древесины.
Особенно интересна статья тем, что в некоторых случаях на щепе можно неплохо заработать без особых вложений. И как обычно главное это не огромные инвестиции, а неординарный подход к делу!
Использование в дизайне
Несомненно самый неординарный способ использования щепы это конечно же в дизайне. В связи с появлением спроса, на декоративной щепе можно сделать прибыльный бизнес, что и делают производители разноцветной продукции, зарабатывая хорошие деньги.
Декоративная мульча пользуется спросом в гостиницах, санаториях, турбазах и просто у людей желающих придать красивый вид окружающей среде. Кроме того ее использование увеличивает качество произрастания посаженных растений и уменьшает вероятность появления сорняка.
Играя с оттенками и цветами можно сделать уникальный дизайн. Кроме крашеной мульчи неплохо в дело идут и натуральные цвета ценных пород древесины (стоимость такой продукции гораздо выше). Как правило продажа и отгрузка продукции осуществляется в мешках. Заказав и оплатив счет через несколько недель можно получить товар из другого города или даже региона.
Сам процесс окраски товара довольно прост. Его или окунают или обрызгивают пигментными красками на водной основе (коих можно найти в интернете огромное количество).
При этом влажность материала нужно чтобы была на уровне 20%. Расход краски от 1 кг на кг готового товара. Особое внимание стоит уделить качеству мульчи, желательно использовать ее из древесины с минимальным содержанием гнили и примесей коры, хотя некоторые дизайнеры наоборот приветствуют наличие коры.
Как мы уже с вами поняли затраты на оборудование не большие и поэтому данный вид бизнеса становится очень популярен.
Производство продукции на предприятиях
Из мульчи можно изготовить древесные плиты, пеллет или даже жидкое дерево о котором я уже писал на нашем блоге подробно. В данном случае роль будут играть начальные вложения в бизнес и объемы имеющегося сырья.
Если брать по себестоимости то конечно изделия из прессованной древесины (пеллеты, евродрова) конечно выгоднее чем древесные плиты на связующем или жидкое дерево. Если вы соберетесь вкладывать средства в оборудование для пеллет, то вам просто очень сильно поможет моя новая книжечка. Более подробно о ней в разделе «МОИ КНИГИ».
Использование в качестве энергии
Отопление на древесной мульчи актуально только в районах с наличием дешевого сырья. Почему я пишу что использование щепы для отопления это получение денег? Потому что тепло ценится и стоит денег.
Сегодня большое количество деревообрабатывающих комбинатов с большими объемами производства мульчи устанавливают специализированные котельные установки и экономят колоссальные средства на отопление.
При этом у комбинатов имеются возможности продавать это тепло в жилые районы. А иногда даже на предприятии устанавливают генераторы и получают из измельченной древесины электроэнергию для собственных нужд и продажи.
Измельченная древесина для отопления очень ценна тем, что требования к ее качество ничтожны. Здесь может иметься какое то количество гнили, коры и даже минеральных примесей.
Продажа для копчения
Копченая пища один из любимых деликатесов человека. Продажа щепы для копчения получило огромное распространение среди гурманов. Теперь нужно просто зайти в магазин и купить мешочек щепы для копчения любимого блюда. Преимуществом для копчения обладает щепа ольхи, осины, бука и березы. Организация бизнеса по расфасовке и отправке щепы ну очень не сложная. Для этого необходимо запастись
Кстати недорого щепу можно купить тут!
Удачи и до новых встреч!
andreynoak.ru
Технология производства ДСП (древесностружечных плит)
Древесностружечные плиты за последние 10—15 лет стали, очевидно, одним из самых известных и распространенных древесных материалов. Они являются основным конструкционным материалом в производстве мебели, а в последнее время получают все большее признание и в строительстве, в частности в производстве малоэтажных домов.
Сырье для древесностружечных плит — различного вида отходы лесопиления, лесозаготовок, деревообработки (горбыли, рейки, откомлевки, сучья, срезки, стружка, опилки), а также низкокачественные круглые лесоматериалы. Становится понятным значимость этого производства: из отходов и низкокачественной древесины получается материал, из которого изготовляют высококачественные, долговечные изделия.
Все кусковые отходы измельчаются в щепу на рубительных машинах. Из щепы, а также из стружки, отходов и опилок на специальных роторных станках приготовляется стружка. Из круглых лесоматериалов стружка изготовляется или непосредственно из бревна на станках с ножевым валом, или по схеме щепа — стружка, когда сначала изготовляется щепа, а затем из щепы стружка. Перед подачей бревен на струженный станок их разрезают на мерные заготовки (обычно длиной 1 м).
Стружка должна иметь определенные, наперед заданные размеры (толщина 0,2—0,5 мм, ширина 1 — 10 мм, длина 5—40 мм). В наружные слои плиты направляется стружка наименьших размеров. Кроме соблюдения размеров необходимо также следить, чтобы стружка была плоской, равномерной толщины, с ровной поверхностью. Стружка для наружных слоев после стружечных станков проходит дополнительное измельчение на дробилках (здесь уменьшается ширина) или в мельницах, где изменяется толщина. Последняя операция имеет особое значение для плит, которые отделываются методом ламинирования, так как в этом случае предъявляются высокие требования к качеству их поверхности.
Изготовленная сырая стружка хранится в бункерах, куда подается системой пневмотранспорта или механическими транспортерами. Из бункеров сырая стружка подается в сушилки. Сушить стружку необходимо до влажности 4—6%, а для внутреннего слоя — до 2—4%. Поэтому стружку разных слоев сушат в отдельных сушилках. В производстве древесностружечных плит используются, как правило, конвективные сушилки, в большинстве случаев барабанного типа. В топке сушилки сжигается газ или мазут, температура в ней 900— 1000° С. На входе в барабан Температура сушильного агента достигает 450—550° С, на выходе она от 90 до 120° С. Барабан имеет диаметр 2,2 м и длину 10 м, устанавливается он с наклоном в 2—3° в сторону входа сырой стружки.
После сушки стружка сортируется или на механических (ситовых) агрегатах, или пневматически. На этих машинах происходит разделение стружки на фракции для наружных и внутренних слоев. На этом заканчивается изготовление стружки. Автор должен заметить, что эта часть технологического процесса во многом предопределяет успешное выполнение последующих операций, производительность процесса и особенно качество плит. Поэтому приготовлению стружки (работе оборудования на этом участке, квалификации операторов) уделяется большое внимание.
Стружка смешивается со связующим в специальных агрегатах, Называемых смесителями. Операция эта сложная, поскольку технология производства требует покрытия связующим каждой стружки. Неосмоленные стружки не склеиваются, а излишняя смола на стружке приводит к перерасходу связующего и плохому качеству плит. Связующее в смеситель подается в виде растворов. Их концентрация в потоке наружного слоя 53— 55%, внутреннего слоя несколько больше (60—61%). В настоящее время наиболее распространены смесители, в которых распыленное связующее (размеры частиц 30—100 мкм) факелом направляется на поток взвешенных в воздухе стружек. Эти два потока перемешиваются, связующее осаждается на поверхности стружек. Смесители, как правило, нуждаются в тонком регулировании, при котором соблюдаются строгие количественные соотношения между стружкой, смолой и отвердителем. После осмоления стружка ленточными или скребковыми транспортерами направляется в формирующие машины.
Формирующие машины принимают осмоленную стружку и высыпают ее ровным слоем (ковром) на проходящие под ними поддоны или ленточные транспортеры. Стружечный ковер — это непрерывная лента определенной ширины и толщины. Он разделяется на пакеты, из которых и образуются в последующем при горячем прессовании плиты. Естественно, что равномерность насыпки ковра прямым образом влияет на качество плит (равноплотность, равнотолщинность). Кроме того, формирующие машины должны насыпать во внешние слои мелкие стружки.
Конвейер перемещает пакеты, которые после прохождения пресса для подпрессовки становятся плотными, обладающими транспортной прочностью брикетами. В настоящее время в промышленности древесностружечных плит известно два принципиально различных типа главных конвейеров. Они различаются тем, что в одном случае пакеты (а затем брикеты) перемещаются на металлических поддонах, в другом типе главного конвейера — на ленточных транспортерах, когда прессование бесподдонное. Каждая схема главного конвейера имеет преимущества и недостатки. Поддонный способ более простой и надежный, но плиты получаются с большей разнотолщинностью, расход тепловой энергии больше. Бесподдонный способ обеспечивает некоторую экономию энергии, повышенное качество плит. Конструкции главных конвейеров достаточно подробно описаны в специальной литературе, и при необходимости читатель может с -ее помощью более детально изучить эту основную технологическую линию заводов древесностружечных плит.
Автор уже упоминал, что в состав главного конвейера входит пресс для подпрессовки. Подпрессовка необходима для уменьшения толщины пакета и повышения его транспортабельности. Толщина пакета уменьшается в 2,5—4 раза (больше при бесподдонном прессовании). Давление при этом составляет 1—1,5 МПа при прессовании на поддонах и 3—4 МПа при бесподдонном прессовании. Подпрессовка производится обычно в одноэтажных прессах, иногда это бывает подвижный пресс, чаще — стационарный.
После подпрессовки брикеты на поддонах поступают в многоэтажный гидравлический пресс для горячего прессования. При бесподдонном прессовании брикеты выкладываются лентой непосредственно на горячие плиты пресса; При прессовании на брикет воздействуют тепло и давление. Читателю, очевидно, понятно, что продолжительность горячего прессования предопределяет продолжительность цикла работы пресса и тем самым производительность всего завода. Поэтому уделяется большое внимание уменьшению цикла прессования. Стоимость пресса для горячего прессования, как и в производстве древесноволокнистых плит, составляет 20— 25% стоимости всего оборудования завода, и поэтому проблема его лучшего использования — постоянная забота работников заводов, а профессия оператора пресса — самая почитаемая.
Прессование производится при 180°С и удельном давлении 2,5—3,5 МПа. Продолжительность прессования 0,3—0,35 мин на 1 мм толщины плиты. Современные прессы имеют размеры горячих плит, достигающие 6×3 м, до 22 рабочих промежутков (одновременно прессуются 22 древесностружечные плиты). Высота пресса достигает 8 м.
Сокращение цикла прессования (увеличение производительности пресса) достигается за счет повышения температуры прессования, применения смол с меньшей продолжительностью отверждения, увеличения количества рабочих промежутков. Эти мероприятия реализованы на большинстве заводов, что позволило поднять производительность прессов с 35 до 80—85 тыс. м3 плит в год.
Автор считает необходимым информировать читателя о том, что имеются и одноэтажные прессы. У них длина горячих плит достигает 20 м, а общая длина главного конвейера —60—70 м. При его обслуживании оператор для перемещения вынужден использовать велосипед.
Готовые плиты пресса выгружаются на приемную (разгрузочную) этажерку, а с нее на линию, где они обрезаются с четырех сторон (линию форматной обрезки). В состав этой линии часто входит агрегат для охлаждения плит. Затем они укладываются в стопы, где выдерживаются не менее 5 суток. Далее плиты шлифуются на оборудований и инструментом, которые были описаны выше. В соответствии с требованиями стандарта плиты сортируются, а затем или раскраиваются на заготовки для мебельных щитов, или отправляются потребителям полноформатными.
В заключение укажем, что на 1 м3 древесностружечных плит расходуется 1,75—1,85 м3 древесины, 70— 80 кг смолы (в пересчете на сухое вещество), 1,4— 1,5 т пара, 160—170 кВт-ч электроэнергии. Затраты труда составляют 2,5—4 чел.-ч на 1 м3.
Необходимо отметить, что производство древесностружечных плит непрерывно совершенствуется: появляются новые виды плит, принципиально новые машины, более эффективные связующие. Представляют, в частности, интерес плиты из стружки, размеры которых по длине и ширине составляют десятки миллиметров; стружка располагается в плоскости плиты. Это обеспечивает высокую прочность плит на статический изгиб,
что важно при их применении в строительстве. Такие плиты (из ориентированной крупноформатной стружки) с успехом заменяют фанеру, которая становится все более дефицитной.
В последние годы стали использовать нетоксичные быстроотверждающиеся смолы, что увеличивает производительность прессов, а значит, и заводов, ликвидирует загазованность в цехах, позволяет использовать плиты внутри жилых помещений. Объем производства древесностружечных плит непрерывно растет, эта тенденция сохранится и в будущем. Для отрасли, оснащенной современным оборудованием, нужны высококвалифицированные рабочие, инженеры и техники, хорошо знающие технологию и механической и химической переработки древесины, электронику, гидравлику, теплотехнику.
www.stroitelstvo-new.ru
Производство древесной стружки — советы технолога
Приветствую всех читателей Блога Андрея Ноака. Сегодня рассмотрим производство древесной стружки на стружечных станках. И главное в изготовлении древесной стружки это объем и качество. На примере изготовления древесных плит мы и рассмотрим как делают там стружку.
Введение в тему
Довольно длительное время я работал в цехе по производству ДСП технологом, а затем и главным технологом. За это время я приобрел колоссальный опыт передовых предприятий по производству древесностружечной плиты. Я посещал различные выставки, другие передовые заводы и смотрел как работают предприятия. Придя на новое предприятие в Казахстане я понял что просто обязан поделиться своим опытом, чтобы другим людям было проще работать в данной отрасли. Ведь за время работы я понял что самое ценное в работе — это умение работать!
Стружечный станок
Ни для кого не открою секрет что станок для щепы это один из основных узлов в любой технологии переработки древесины, так как от качества выпускаемой им стружки зависит очень много факторов на производстве:
- Качество просушивания стружки в сушильном барабане.
- Производительность сушильного барабана.
- Время посадки пресса на планки, время прессования.
- Получение необходимых физико механических показателей.
- Расход сырья.
В общем качество стружки это основа основ в производстве древесностружечной плиты, влияющее на технологию производства в целом, поэтому станок для щепы это очень ответственный этап технологии, которым не следует пренебрегать. Состоит станок для стружки из:
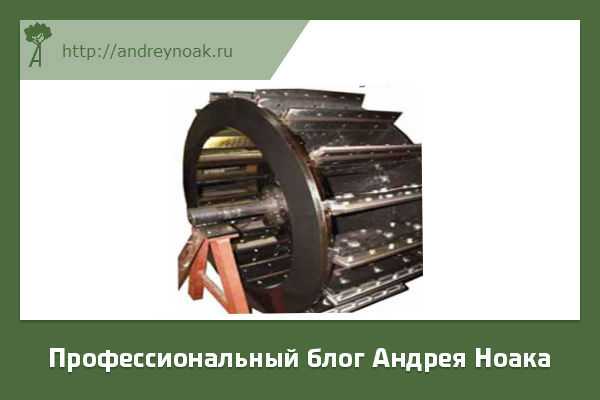
- Электродвигатель крыльчатки.
- Электродвигатель барабана.
- Корпус.
Режущий инструмент стружечного станка, как его заточить?
Весь режущий инструмент станка для щепы расположен на барабане и крыльчатке. Для того чтобы стружка выдерживала все технологические параметры, необходима очень точная выставка непосредственно режущего инструмента и защитных пластин. Точная выставка оборудования в свою очередь просто невозможна без идеальной работы механической части станков, а это исключение работы станка для стружки с вибрацией, разбитость подшипников крыльчатки и барабана, кривизна валов и др… Проверяется это довольно просто, в любом положении по кругу крыльчатки и барабана, расстояние между ними должно быть одинаковым. Для этого расстояние измеряется между билом и пластиной барабана, затем крыльчатка прокручивается по кругу и просматривается зазор.
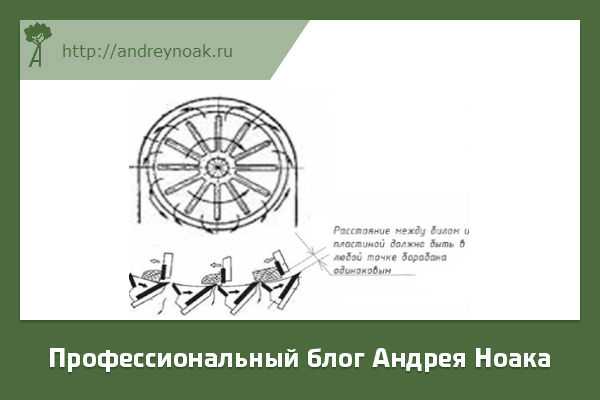
Своевременная замена ножей станка для щепы должна производиться в строго отведенное время для этого или после производства строго отведенного объема продукции, нагрузка на стружечных станках выводится на визуализацию, выводится в архив и служит основным параметром контролирующим качество заточки ножей.
Станок для стружки как и любой деревообрабатывающий станок изнашивается. Какие то детали меняются, что то выкидывается сразу, а что то подлежит заточке и дальнейшей эксплуатации. Давайте посмотрим что у нас подлежит заточке:
- Ножи на барабане. Хочу дополнить, что не всегда даже самое новое и современное оборудование может выдавать максимальные характеристики, необходимые для работы производства. Я очень часто встречал когда иностранные производители оборудования поставляют станки или узлы и хорошие технологи на этих узлах при минимальных вложениях увеличивают показатели в 1,5-2 раза. При этом сами иностранцы могут даже и не верить… Поэтому обращаю ваше внимание на то что высота ножей и толщина ножей зависит только от нас самих, этим нужно пользоваться и подбирать режущий инструмент необходимых нам, а не написанный в технических характеристиках станка.
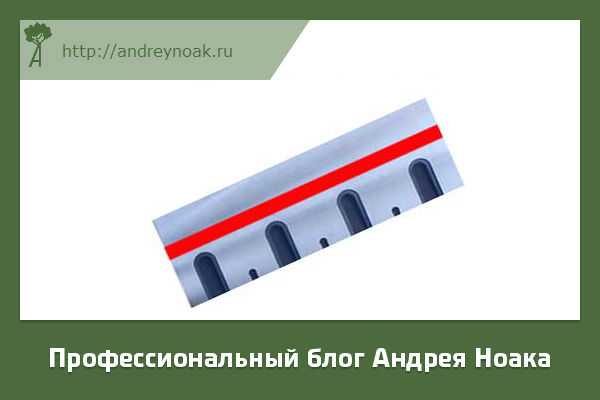
- Била. Било тупиться по кромкам, после затупления одной кромки, било можно перевернуть. Заточка может производиться как по кромке била, так и по плоскости. Била и ножи точатся на обычных станках для заточки плоских ножей.
- Износостойкие пластины. Заточка пластин производится на специальных станках, при установленных пластинах на барабане. Барабан устанавливают на заточной станок и протачивают по кругу, при этом наждак двигается от передней части барабана к задней. Многие задают вопрос: «Нужна ли нам эта заточка, ведь необходимо покупать дорогостоящий станок для заточки пластин, а какая будет выгода от этого?». Покупать или нет это дело каждого, после установки пластин на барабан, барабан выходит небольшим элипсом, пластины то выступают, то впадают. В результате при большой нагрузке на станок может происходить отрывание пластин и выход из строя барабана. Еще одним минусом является недополучение в качестве стружки. Отрыв пластин также может происходить и по причине большого износа этих самых пластин, они становятся тоньше, толщина резьбы где происходит крепление к барабану уменьшается, разброс по кругу барабана (выступ пластин) становится больше. Многие задают вопрос, а стоит ли производить вторичную заточку пластин на барабане, когда на пластинах барабана появляется выработка. Здесь нет однозначного ответа, некоторые точат, некоторые предпочитают устанавливать новые пластины и точить только с новыми элементами.
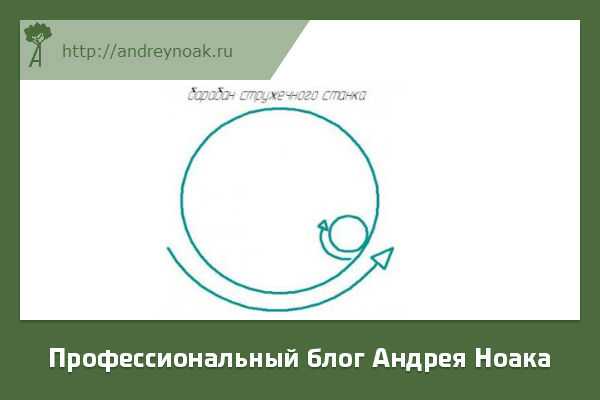
Схема заточки стружечного барабана.
Для более быстрой установки ножей в барабан используется шаблон. Ножи собираются по шаблону и только затем устанавливаются на стружечный барабан. Если кому то будет интересно, то выставлю схемку или фото.
Отдельным пунктом хочу добавить про заточку плоских ножей на заточных станках, так вот в статье описан станок с установкой ножей на держатель с механическим упором и затем крепление ножей планкой, я же рекомендую автору применять станки с магнитным держателем ножей. При этом практически все проблемы с высотой заточки ножей, с кривизной заточки ножей будут сняты. Жду ваших вопросов и предложений! С уважением Андрей Ноак.
andreynoak.ru
Оборудование для производства опилок. Как делают опилки
Опилки производятся на деревообрабатывающих предприятиях как отходы промышленности. Новые технологии позволяют не просто сжигать их, отравляя атмосферу, а использовать с помощью переработки — для изготовления различных материалов, необходимых в повседневной жизни и производстве.
Опилки можно изготавливать на специально предназначенном для этого оборудовании. Оно состоит из нескольких элементов:
- Машина для рубки дерева, которая измельчает дерево в техническую щепу,
- Дозатор-накопитель (бункер),
- Измельчитель для щепок.
Такое оборудование довольно простое и стоит относительно недорого. Для производства опилок можно использовать неликвидную древесину, которая не годится для изготовления мебели, строительных материалов и шпона. Можно использовать валежник и павшие деревья из леса. Таким образом, вы получите дешевый материал и способствуете очищению природы.
Для производства прессованных опилок необходимо более сложное и дорогостоящее оборудование, которое называется линия-гранулятор. Он состоит из следующих элементов:
- Измельчителя,
- Бункера-приемника и дозатора,
- Сушилки,
- Теплового генератора,
- Вентилятора типа циклон,
- Бункера для сухого продукта,
- Машины для производства брикетов.
Реализация опилок может вестись в нескольких направлениях. Большим спросом пользуются прессованные опилки в строительстве, где их применяют для производства утеплительных материалов. Также, можно делать прессованные опилки для животноводства, где их используют как подстилку для скота, кошачьих туалетов и брикетов для копчения. Из опилок делают топливные брикеты.
kudavlozitdengi.adne.info