Сталь 20 (Сталь 20А) — Полный марочник сталей и сплавов
Общие данные
Заменитель |
Сталь 15, Сталь 25 |
Вид поставки |
Сортовой прокат, в том числе фасонный: ГОСТ 1050-74, ГОСТ 2590-71, ГОСТ 2591-71, ГОСТ 2879-69, ГОСТ 8509-86, ГОСТ 8510-86, ГОСТ 8240-72, ГОСТ 8239-72. Калиброванный пруток ГОСТ 7417-75, ГОСТ 8559-75, ГОСТ 8560-78, ГОСТ 10702-78. Шлифованный пруток и серебрянка ГОСТ 14955-77, ГОСТ 10702-78. Лист толстый ГОСТ 1577-81, ГОСТ 19903-74. Лист тонкий ГОСТ 16523-70. Лента ГОСТ 6009-74, ГОСТ 10234-77. Полоса ГОСТ 1577-81, ГОСТ 103-76, ГОСТ 82-70. Проволока ГОСТ 5663-79, ГОСТ 17305-71. Поковки и кованые заготовки ГОСТ 8479-70. Трубы ГОСТ 10704-76, ГОСТ 10705-80, ГОСТ 8731-87, ГОСТ 8732-78, ГОСТ 8733-87, ГОСТ 5654-76, ГОСТ 550-75. |
Назначение |
После нормализации или без термообработки крюки кранов, муфты, вкладыши подшипников и другие детали, работающие при температуре от -40 до 450°С под давлением, после ХТО — шестерни, червяки и другие детали, к которым предъявляются требования высокой поверхностной твердости при невысокой прочности сердцевины.![]() |
Химический состав (по ГОСТ 1050-2013)
Химический элемент | % |
Углерод (C) | 0.17-0.24 |
Кремний (Si) | 0.17-0.37 |
Медь (Cu), не более | 0.25 |
Мышьяк (As), не более | 0.08 |
Марганец (Mn) | 0.35-0.65 |
Никель (Ni), не более | 0.25 |
Фосфор (P), не более | 0.035 |
Хром (Cr), не более | 0.25 |
Сера (S), не более | 0.04 |
Основные отличия Стали 20 от Стали 20А
Добавление буквы «А» в конце обозначения Стали 20, указывает на то что Сталь 20А относиться к категории — сталь высококачественная. Основные отличия в химическом составе это более жёсткие требования по содержанию Серы (S) и более широкие по содержанию Углерода (С) (смотреть таблицу).
Химический элемент | % | |
Сталь 20 | Сталь 20А | |
Углерод (C) | 0.17-0.24 | 0.15-0.25 |
Сера (S), не более | 0.04 | 0.035 |
Следовательно Сталь 20А менее подвержено охрупчиванию.
Механические свойства
Механические свойства при повышенных температурах
t испытания, °C | σ0,2, МПа | σB, МПа | δ5, % | ψ, % | KCU, Дж/м2 |
410 | 25 | 55 | |||
490 | 7 | 40 | |||
390 | 21 | 50 | |||
390-490 | 50 | 163 | |||
340-440 | 50 | 163 | |||
490 | 7 | 40 | 207 | ||
410 | 25 | 55 | |||
340-490 | 28 | 127 | |||
20 | 280 | 430 | 34 | 67 | 218 |
200 | 230 | 405 | 28 | 67 | 186 |
300 | 170 | 415 | 29 | 64 | 188 |
400 | 150 | 340 | 39 | 81 | 100 |
500 | 140 | 245 | 40 | 86 | 88 |
700 | 130 | 39 | 94 | ||
800 | 89 | 51 | 96 | ||
900 | 75 | 55 | 100 | ||
1000 | 47 | 63 | 100 | ||
1100 | 30 | 59 | 100 | ||
1200 | 20 | 64 | 100 |
Механические свойства проката
Термообработка, состояние поставки | σB, МПа | δ5, % | ψ, % | KCU, Дж/м2 |
Сталь калиброванная горячекатаная, кованая и серебрянка 2-й категории после нормализации | 410 | 25 | 55 | |
Сталь калиброванная 5-й категории после нагартовки | 490 | 7 | 40 | |
Сталь калиброванная 5-й категории после отжига или высокого отпуска | 21 | 50 | ||
Сталь калиброванная и калиброванная со специальной отделкой после отпуска или отжига | 390-490 | 50 | 163 | |
Сталь калиброванная и калиброванная со специальной отделкой после сфероидизирующего отжига | 340-440 | 50 | 163 | |
Сталь калиброванная и калиброванная со специальной отделкой нагартованная без термообработки | 490 | 7 | 40 | 207 |
Полосы нормализованные или горячекатаные | 410 | 25 | 55 | |
Лист термообработанный 1-2-й категории | 340-490 | 28 | 127 | |
430 | 34 | 67 | 218 | |
405 | 28 | 67 | 186 | |
415 | 29 | 64 | 188 | |
340 | 39 | 81 | 100 | |
245 | 40 | 86 | 88 | |
130 | 39 | 94 | ||
89 | 51 | 96 | ||
75 | 55 | 100 | ||
47 | 63 | 100 | ||
30 | 59 | 100 | ||
20 | 64 | 100 |
Механические свойства поковок
Термообработка, состояние поставки | Сечение, мм | σ0,2, МПа | σB, МПа | δ5, % | ψ, % | KCU, Дж/м2 | HB |
Нормализация | |||||||
КП 175 | <100 | 175 | 350 | 28 | 55 | 64 | 101-143 |
КП 175 | 100-300 | 175 | 350 | 24 | 50 | 59 | 101-143 |
КП 175 | 300-500 | 175 | 350 | 22 | 45 | 54 | 101-143 |
КП 175 | 500-800 | 175 | 350 | 20 | 40 | 49 | 101-143 |
КП 195 | <100 | 195 | 390 | 26 | 55 | 59 | 111-156 |
КП 195 | 100-300 | 195 | 390 | 23 | 50 | 54 | 111-156 |
КП 215 | <100 | 215 | 430 | 24 | 53 | 54 | 123-167 |
КП 215 | 100-300 | 215 | 430 | 20 | 48 | 49 | 123-167 |
Закалка.![]() | |||||||
КП 245 | 100-300 | 245 | 470 | 19 | 42 | 39 | 143-179 |
Механические свойства стали после ХТО
Сечение, мм | σ0,2, МПа | σB, МПа | δ5, % | ψ, % | KCU, Дж/м2 | HB | HRCэ |
Цементация 920-950 °С, воздух. Закалка 800-820 °С, вода. Отпуск 180-200 °С, воздух. | |||||||
50 | 290-340 | 490-590 | 18 | 45 | 54 | 156 | 55-63 |
Технологические свойства
Температура ковки |
Начала 1280, конца 750. Охлаждение на воздухе. |
Свариваемость |
Сваривается без ограничений, кроме деталей после химико-термической обработки.![]() |
Обрабатываемость резанием |
В горячекатанном состоянии при НВ 126-131 и sB = 450-490 МПа, Ku тв.спл. = 1,7 и Ku б.ст. = 1,6. |
Склонность к отпускной способности |
Не склонна. |
Флокеночувствительность |
Не чувствительна. |
Температура критических точек
Критическая точка | °С |
Ac1 | 735 |
Ac3 | 850 |
Ar3 | 835 |
Ar1 | 680 |
Ударная вязкость
Ударная вязкость, KCU, Дж/см2
Состояние поставки, термообработка | +20 | -20 | -40 | -60 |
Отжиг | 110 | 68 | 47 | 10 |
Номализация | 157 | 109 | 86 | 15-38 |
Предел выносливости
σ-1, МПа | τ-1, МПа | n | σB, МПа | σ0,2, МПа | Термообработка, состояние стали |
206 | 1Е+7 | 500 | 320 | ||
245 | 520 | 310 | |||
225 | 490 | 280 | |||
205 | 127 | Нормализация 910 С, отпуск 620 С.![]() | |||
193 | 420 | 280 | |||
255 | 451 | Цементация 930 С, закалка 810 С, отпуск 190 С. |
Физические свойства
Температура испытания, °С | 20 | 100 | 200 | 300 | 400 | 500 | 600 | 700 | 800 | 900 |
Модуль нормальной упругости, Е, ГПа | 212 | 208 | 203 | 197 | 189 | 177 | 163 | 140 | ||
Модуль упругости при сдвиге кручением G, ГПа | 78 | 77 | 76 | 73 | 69 | 66 | 59 | |||
Плотность, pn, кг/см3 | 7859 | 7834 | 7803 | 7770 | 7736 | 7699 | 7659 | 7917 | 7624 | 7600 |
Коэффициент теплопроводности Вт/(м ·°С) | 51 | 49 | 44 | 43 | 39 | 36 | 32 | 26 | 26 | |
Уд.![]() | 219 | 292 | 381 | 487 | 601 | 758 | 925 | 1094 | 1135 | |
Температура испытания, °С | 20- 100 | 20- 200 | 20- 300 | 20- 400 | 20- 500 | 20- 600 | 20- 700 | 20- 800 | 20- 900 | 20- 1000 |
Коэффициент линейного расширения (a, 10-6 1/°С) | 12.3 | 13.1 | 13.8 | 14.3 | 14.8 | 15.1 | 15.2 | |||
Удельная теплоемкость (С, Дж/(кг · °С)) | 486 | 498 | 514 | 533 | 555 | 584 | 636 | 703 | 703 | 695 |
Зарубежные аналоги Стали 20
Страна | США | Германия | Япония | Франция | Англия | Евросоюз | Италия | Бельгия | Испания |
Стандарт | — | DIN,WNr | JIS | AFNOR | BS | EN | UNI | NBN | UNE |
Марка | 1020 | 1,0402 | S20C | 1C22 | 050A20 | 1,0402 | C18 | C25-1 | 1C22 |
1023 | 1,0405 | S20CK | 2C22 | 055M15 | 1,1151 | C20 | C25-2 | C22 | |
1024 | 1,1151 | S22C | AF42 | 070M20 | 1,1152 | C21 | C25k | ||
G10200 | C22 | STB410 | AF42C20 | 070M26 | 2C22 | C22 | F.![]() | ||
G10230 | C22E | STKM12A | C20 | 1449-22CS | C20E2C | C22E | F.1120 | ||
h20200 | C22R | STKM12A-S | C22 | 1449-22HS | C22 | C22R | |||
M1020 | Ck22 | STKM13B | C22E | 1C22 | C22E | C25 | |||
M1023 | Cm22 | STKM13B-W | C25E | 22HS | C25E | ||||
Cq22 | XC15 | 430 | |||||||
St35 | XC18 | C22 | |||||||
St45-8 | XC25 | C22E | |||||||
Страна | Китай | Швеция | Болгария | Венгрия | Польша | Румыния | Чехия | Швейцария | Юж.![]() |
Стандарт | GB | SS | BDS | MSZ | PN | STAS | CSN | SNV | KS |
Марка | 20 | 1450 | 20 | A45.47 | 20 | OLC20 | 12022 | Ck22 | SM20C |
20G | C22 | C22E | K18 | OLC20X | 12024 | SM20CK | |||
20R | C22E | SM22C | |||||||
20Z |
Условные обозначения
Механические свойства | |
σB | временное сопротивление разрыву (предел прочности при растяжении), МПа |
σ0,2 | предел текучести условный, МПа |
σсж | предел прочности при сжатии, МПа |
σсж0,2 | предел текучести при сжатии, МПа |
σ0,05 | предел упругости, МПа |
σизг | предел прочности при изгибе, МПа |
σ-1 | предел выносливости при испытании на изгиб с симметричным циклом нагружения, МПа |
δ5 , δ4 , δ10 | относительное удлинение после разрыва, % |
ψ | относительное сужение, % |
ν | относительный сдвиг, % |
ε | относительная осадка при появлении первой трещины, % |
τК | предел прочности при кручении, максимальное касательное напряжение, МПа |
τ-1 | предел выносливости при испытании на кручение с симметричным циклом нагружения, МПа |
KCU и KCV | ударная вязкость, определенная на образце с концентраторами вида U и V, Дж/см2 |
HRCэ и HRB | твёрдость по Роквеллу (шкала C и B соответственно) |
HB | твёрдость по Бринеллю |
HV | твёрдость по Виккерсу |
HSD | твёрдость по Шору |
Физические свойства | |
E | модуль упругости нормальный, ГПа |
G | модуль упругости при сдвиге кручением, ГПа |
ρn | плотность, кг/м3 |
λ | коэффициент теплопроводности, Вт/(м∙°C) |
ρ | удельное электросопротивление, Ом∙м |
α | коэффициент линейного теплового расширения, 10-61/°С |
с | удельная теплоёмкость, Дж/(кг∙°С) |
Поделиться:
Просмотров: 5 848
Сталь 20: характеристики, свойства, область применения
Основные характеристики и свойства
При выборе металла уделяется много внимания основным характеристикам. К ним отнесем:
- Показатель твердости. Он может варьировать в большом диапазоне и зависеть от того, была ли проведена термическая обработка. Твердость стали 20 выдерживается на уровне 163 МПа. Этого вполне достаточно для изготовления различных изделий, которые обладают высокой износостойкостью.
- Также учитывается и плотность. Менее плотные материалы применяются для изготовления изделий, которые будут обладать небольшим весом. В рассматриваемом случае показатель составляет 7,85 к/см3.
- Рассматривая основные характеристики учитывается предел текучести и предел прочности. Они рассматриваются при создании различных проектов. Металл Ст 20 может улучшаться для того, чтобы увеличить характеристики материала.
- Структура характеризуется тем, что не склонна к отпускной хрупкости и образованию флокенов.
- Проводимая термообработка стали 20 позволяет существенно увеличить срок службы изделия. Проводится она при определенных режимах. К примеру, для ковки структура нагревается до температуры 1 280 градусов Цельсия.
- При необходимости есть возможность проводить сваривание деталей.
- Ударная вязкость стали 20 определяет то, что металл часто применяется при изготовлении валов и других подобных изделий, которые могут использоваться при создании элементов, применяемых при создании различных механизмов. Модуль упругости также учитывается при рассмотрении основных свойств металла.
- Средний коэффициент теплопроводности определяет то, что структура может нагреваться достаточно быстро, но при этом тепло отводится с высокой эффективностью.
Свойства Ст 20
Механические свойства стали 20 определяют довольно широкое распространение этой марки в машиностроительной и других область промышленности. Как ранее было отмечено, технические характеристики могут улучшаться при проведении термической обработки или легировании. Перестроение структуры металла позволяет повысить твердость поверхностного слоя, при добавлении других химических веществ могут придаваться особые качества, к примеру, коррозионная стойкость.
Термическая обработка предусматривает изменение структуры за счет оказания воздействия определенной температуры. Критические точки выбираются в зависимости от особенностей химического состава. К особенностям подобной процедуры отнесем следующие моменты:
Для оказания требуемого воздействия применяется специальное оборудование. Примером можно назвать доменные и индукционные печи. На протяжении длительного периода использовали именно доменные печи, но они уступают индукционным. Второй вариант исполнения подходит для установки в небольших мастерских.
Критические точки учитываются при проведении рассматриваемой процедуры. Стоит учитывать, что они уже были выявлены для всех металлов, поэтому не нужно проводить исследования повторно.
Заготовка разогревается до требуемой температуры, после чего происходит первичное перестроение структуры
Время выдержки также является важным показателем, который должен учитываться, как и скорость нагрева.
Уделяется внимание и процессу охлаждения. Слишком большие заготовки охлаждаются на воздухе, так как возникают проблемы с созданием требующейся среды
На протяжении длительного периода охлаждение проводилось в воде, но это приводило к появлению окалины. Обеспечить более высокое качество термической обработки возможно за счет применения масла в качестве охлаждающей среды. Однако, при охлаждении в масле следует учитывать высокую вероятность образования токсичного дыма и воспламенения поверхности от высокой температуры.
Цвета закалки стали
Во многих случаях после термической обработки образуются поверхностные дефекты. Именно поэтому процедура применяется для заготовок или изделий, которые созданы с учетом припуска. После закалки часто проводится отпуск, который позволяет снять внутренние напряжения и снизить вероятность повреждения изделия при падении или возникновении ударной нагрузки.
Процесс производства закалки
Закалка представляет вид термообработки металлов и их сплавов, стекла, и заключается в нагревании до температурного уровня, превышающего критические значения, и проведением быстрого охлаждения. Выполнение закалки металла, позволяющей получить качественные характеристики, не следует приравнивать к обычному виду обработки, производимой для осуществления фазовых преобразований.
Охлаждение зачастую выполняют в водной или масляной среде, но имеются и иные методы: твёрдый теплоноситель псевдокипящего характера, поток сжатого воздуха, водяное облако, полимеры.
Существуют такие виды закалки:
- для сталей, обладающих полиморфическими преобразованиями;
- для преобладающей части цветных металлов без наличия полиморфического преобразования.
После закалочной операции возрастает твердость материала, но он приобретает хрупкость, наблюдается снижение уровня пластичности и вязкости при повторных процедурах нагрева и охлаждения. Применение отпуска металла после операции закаливания с полиморфным преобразованием позволяет добиться уменьшения хрупкости, повышая при этом характеристики пластичности и вязкости. При выполнении процедуры без структурных преобразований используют операцию старения. Отпуск способствует незначительному понижению твердости и прочностных характеристик металла.
Учитывая температурные режимы нагревания, выполняется разделение процедуры закаливания на полную и неполную. Полное закаливание выполняют нагреванием на 30…50 0С по уровню выше линии GS для сталей, обладающих доэвтектоидной и эвтектоидной структурой, для заэвтектоидной — по линии PSK (согласно диаграммы железоуглеродистых сплавов). При этом наблюдается образование структуры аустенита и аустенит + цементит. При производстве неполного закаливания выполняют нагрев выше линии PSK, что ведет к появлению излишних фаз.
Проведение отпуска позволяет снимать напряжения закаливания.
Для определенной категории изделий требуется проведение неполного или выборочного закаливания, к примеру, процесс производства катан (японских мечей) предполагает выполнение закаливания по режущей кромке.
Сталь 20 – конструкционная сталь
Продажа проката стали 20 со складов на Урале и в Москвской области. Всегда в наличии на складе более 200тн стали 20.
(351) 735-59-79
Сталь 20. Описание
В целом сталь 20 находит широкое применение в котлостроении, для труб и нагревательных трубопроводов различного назначения, кроме того промышленность выпускает пруток, лист. После цементации и цианирования из этой стали можно изготавливать детали, от которых требуется высокая твердость поверхности и допускается невысокая прочность сердцевины: кулачковые валики, оси, крепежные детали, шпиндели, пальцы, звездочки, шпильки, вилки тяг и валики переключения передач, толкатели клапанов, валики масляных насосов, пальцы рессор, малонагруженные шестерни и другие детали автотракторного и сельскохозяйственного машиностроения.
Из стали 20 изготавливается богатый ассортимент проката, конечно при этом учитываются оссобености стали этой марки. Так поковки из этой марки могут быть изготовлены категории прочности только 175, 195, 215, 245 при толщине поковок от 100 до 300 мм, для получения поковок с большей категорией прочностью необходимо уже использовать другую сталь. Для изготовления поковок используют блюмсы или слитки стали, ккатаные или кованые заготовки, либо заготовки отлитые на линии непрерывной разливки стали и какие-либо другие виды проката.
Труба прямошовная из марки 20 создается методом электросварки из листов или рулонов стали, при этом при обозначении такой трубы пишется ее диаметр, толщина стенки, длина, класс точности, ГОСТ, например: труба прямошовная толщиной 89 мм, стенкой 4 мм, мерной длины 6 метров II класса точности, которая была изготовлена по группе Б ГОСТ 10507-80 обозначается следующим образом:
89х4х6000 II ГОСТ 10704-91
Б-20 ГОСТ 10507-80
Методом горячего деформирования изготавливаются бесшовные трубы, при этом они должны обладать следующими свойствами: временное сопротивление разрыву 412 МПа, предел текучести 245 МПа, относительное удлинение 21%, твердость по Бринеллю 4,8.
Технологические свойства ст20
Температура начала ковки стали 20 составляет 1280° С, окончания – 750° С, охлаждение поковки – воздушное. Сталь 20 нефлокеночувствительна и не склонна к отпускной способности. Свариваемость стали 20 не ограничена, исключая детали, подвергавшиеся химико-термической обработке. Рекомендованы способы сварки АДС, КТС, РДС, под газовой защитой и флюсом.
Сталь 20 применяют для производства малонагруженных деталей ( пальцы, оси, копиры, упоры, шестерни), цементуемых деталей для длительной и весьма длительной службы (эксплуатация при температуре не выше 350° С), тонких деталей, работающих на истирание. Сталь 20 без термической обработки или после нормализации используется для производства крюков кранов, вкладышей подшипников и прочих деталей для эксплуатации под давлением в температурном диапазоне от -40 до 450°С . Сталь 20 после химико-термической обработки идет на производство деталей, которым требуется высокая поверхностная прочность ( червяки, червячные пары, шестерни). Широко применяют ст20 для производства трубопроводной арматуры, труб, предназначенных для паропроводов с критическими и сверхкритическими параметрами пара, бесшовных труб высокого давления, сварных профилей прямоугольного и квадратного сечения и т. д.
0.17 – 0.24 | 0.17 – 0.37 | 0.35 – 0.65 | до 0.3 | до 0.04 | до 0.035 | до 0.25 | до 0.3 |
Ac1 = 724 , Ar1 = 682 , Ac3(Acm) = 845 , Ar3(Arcm) = 815 |
Механические свойства при Т=20oС материала 20
Сортамент | Размер | Напр. | sв | sT | d5 | y | KCU | Термообр. |
– | мм | – | МПа | МПа | % | % | кДж / м2 | – |
Лист термообработ., ГОСТ 4041-71 | 4 – 14 | 340-490 | 28 | |||||
Трубы горячедеформир., ГОСТ 550-75 | 431 | 255 | 22 | 50 | 780 | |||
Трубы, ГОСТ 8731-87 | 412 | 245 | 21 | |||||
Трубы, ГОСТ 10705-80 | 372 | 225 | 22 | |||||
Прокат, ГОСТ 1050-88 | до 80 | 410 | 245 | 25 | 55 | Нормализация | ||
Прокат нагартован.![]() | 490 | 7 | 40 | |||||
Прокат отожжен., ГОСТ 1050-88 | 390 | 21 | 50 | |||||
Лента отожжен., ГОСТ 2284-79 | 310-540 | 18 | ||||||
Лента нагартован., ГОСТ 2284-79 | 490-830 |
Твердость 20 после отжига , ГОСТ 1050-88 | HB 10 -1 = 163 МПа |
Физические свойства материала 20
T | E 10- 5 | a 10 6 | l | r | C | R 10 9 |
Град | МПа | 1/Град | Вт/(м·град) | кг/м3 | Дж/(кг·град) | Ом·м |
20 | 2.13 | 52 | 7859 | |||
100 | 2.![]() | 11.6 | 50.6 | 7834 | 486 | 219 |
200 | 1.99 | 12.6 | 48.6 | 7803 | 498 | 292 |
300 | 1.9 | 13.1 | 46.2 | 7770 | 514 | 381 |
400 | 1.82 | 13.6 | 42.8 | 7736 | 533 | 487 |
500 | 1.72 | 14.1 | 39.1 | 7699 | 555 | 601 |
600 | 1.6 | 14.6 | 35.8 | 7659 | 584 | 758 |
700 | 14.8 | 32 | 7617 | 636 | 925 | |
800 | 12.9 | 7624 | 703 | 1094 | ||
900 | 7600 | 703 | 1135 | |||
1000 | 695 |
Сталь 20. Характеристики и аналоги – Все о стали
Сталь марки 20 используется на протяжении многих лет практически во всех областях промышленности. Широкой распространенностью она обязана своими механическими и физическими свойствами, относительной простотой и дешевизной получения.
Применение
Наибольшее распространение сталь марки 20 получила при изготовлении различного сечения труб, а также самую большую нишу занимает в машиностроении для изготовления деталей не сильного нагружения. Широко используется для конструкций, работающих при температуре или под давлением – котлов, коллекторов, трубопроводов.
Расширить границы использования стали 20 можно с помощью, так называемой, химико-термической термообработки. Чаще всего для данной стали применяется процесс цементации, нитроцементации или цианирования. Происходит упрочнение с помощью насыщения углеродом или смесью углерода и азота. После такой термообработки повышается поверхностная твердость и износостойкость стали на небольшую глубину, сердцевина материала остается по-прежнему относительно мягкой. В этом случае, детали из стали 20 работают в наиболее ответственных или ключевых узлах механизмов. Таким способом изготавливают шестерни, сателлиты, другие червячные передачи с высоким сроком службы и износостойкостью поверхностного слоя зубьев.
Количественный состав
В качественный и количественный состав стали 20 входят, как основополагающие элементы для всех сталей, так и примеси в небольших количествах и концентрации. Основные компоненты этой стали железо около 98%, углерод в содержании от 0,17 до 0,24 %, кремний от 0,17 до 0,37%, марганца содержится от 0,35 до 0,65%, никель и медь не более 0,25%. В данной стали может также присутствовать сера и фосфор в количестве не более 0,04%.
Аналоги
Аналоги стали 20 в химическом составе и физических свойствах, это стали 15 и 25. Они имеют подобную структуру и качество при использовании, отличаются только процентным содержанием углерода.
Согласно марочнику сталей, заменителями для стали 20 также могут быть марки 15ХФА, 20Ф, 09СФА.
Похожее количественное содержание углерода имеют марки стали 20Л и 20Х, они имеют немного другие области применения. Сталь 20Л используется для отливок, сталь 20Х это легированная хромом сталь (содержит до 1% хрома). Эти стали имеют подобные технологические свойства со ст 20.
Виды производства
Сталь 20 поставляется в виде листов, различных труб, калиброванных прутков, отливок и других профилей. Также изделия из данной стали могут быть без термообработки и нормализованные.
Характеристики
- Твердость материала стали 20 в термообработанном состоянии, после отжига, должна быть 167 НВ, калиброванного нагартованного материала 207НВ.
- Сталь хорошо поддается ковке и штамповке, температура ковки в начале должна быть 1280 С, в конце около 750 С, охлаждение на воздухе.
- Сталь не подвержена после термообработки такому явлению, как отпускная хрупкость.
- Не имеет данная сталь склонности к отпускной хрупкости.
- Сталь без термообработки и в нормализованном состоянии сваривается без каких-либо ограничений (только не после поверхностного упрочнения).
- Коррозионно-устойчивая сталь по сравнению с другими малоуглеродистыми конструкционными сталями.
Конструкции и детали из стали марки 20 имеют достаточно высокий срок эксплуатации, отличаются дешевизной материала, быстро окупается и имеет ряд других эксплуатационных свойств. Для производства необходимых деталей, заготовки их этой стали предоставляются в широкомасштабном выборе, для одних целей используются круги или проволока, для других важны именно трубы, третьи выбирают из поковок или листов.
Расшифровка
Сталь 20 относится к группе высококачественных конструкционных сталей. Высококачественная означает более строгие требования к химическому составу шихты, процессам выплавки и разливки.
Сталь 20 включает в себя следующие химические элементы:
- Углерод (0,2%). Цифра 20 в названии сплава отображает содержание данного компонента в сотых долях процента. Углерод ответственен за упрочнение. Увеличение его в составе приводит к повышению твердости и прочности.
Обратным эффектом является параллельное уменьшение пластичности.
- Кремний (0,17-0,35%). Основное назначение кремния – это удаление частиц водорода, кислорода и азота из состава сплава. Наличие данных газов в составе повышает пористость и количество газовых раковин, что сильно снижает прочность стали.
- Марганец (0,35-0,6%), как и кремний, – сильный раскислитель, но помимо этого активно способствует удалению серы. Он положительно влияет на качество поверхности сплава. Также снижает вероятность образования трещин во время горячей обработки давлением. Улучшает протекание процессов сварки и ковки.
- Никель (до 0,3%), хром (до 0,2%) и медь (до 0,3%) в целом положительно влияют как на механические, так и на коррозионностойкие характеристики стали. Но их содержание слишком мало, чтобы оказать какое-то серьезное воздействие на сплав.
- Фосфор (до 0,035%) и сера (до 0,04) относятся к вредным типам примесей. Их содержание является причиной повышенной хрупкости стали. Также сильно падает значение вязкости и, соответственно, устойчивости к ударным нагрузкам.
- Остальная часть химического состава приходится на железо.
По уровню раскисления сталь марки 20 делится на 3 категории: спокойная, полуспокойная и кипящая.
- Спокойная сталь 20 получается в результате полного удаления кислорода из состава сплава. Осуществляется это с помощью введения таких элементов как кремний и марганец. Данный тип стали включает минимальное количество оксидов железа, которое и способствует «спокойному» (без выделения газов) застыванию сплава в ковше. Сталь получается плотная и однородная по составу. Лишь в верхней части образуется газовая раковина, которая благополучно удаляется в процессе механической обработки.
- Кипящая сталь 20 раскисляется только марганцем. Как результат, это становится причиной повышенного содержания закиси железа. Данное соединение при взаимодействии с углеродом образует углекислый газ. Как следствие, на поверхности расплавленного сплава начинают появляться газовые пузыри, создавая впечатление, будто сплав кипит.
Данная сталь имеет высокую пористость. Ее химические компоненты неравномерно распределены по всему объему сплава. Все это приводит к резкому снижению механических характеристик, увеличению риска образования трещин и ухудшение свариваемости. Среди плюсов кипящей стали стоит отметить меньшую стоимость и безотходность производства.
Существует также полуспокойная сталь 20, которая по своим характеристикам представляет что-то среднее между двумя вышеописанными видами сталей.
Особенности и область применения
Область применения рассматриваемой стали весьма обширна. Примером можно назвать получение скоб и шаблонов большой длины. Для повышения жесткости и твердости поверхностного слоя дополнительно проводится цементирование в масле.
Чаще всего сталь 20х применяется для получения:
- Гильз;
- Втулок;
- Шестерен;
- Дисков;
- Рычагов;
- Обоймы.
При необходимости рассматриваемый металл заменяется аналогами 15Х или 18ХГТ. В других странах есть аналоги этой стали, которые маркируются по иным стандартам.
В качестве заготовки на заводы поставляют:
- Прокат после отжига;
- Горячекатаный прокат.
Относительно невысокая прочность структуры и другие физико-химические качества определяют нижеприведенные особенности применения металла:
- При изготовлении измерительного инструмента, который при финишной обработке не подвергается процессу шлифования, рекомендуется проводить термическую обработку, представленную сочетанием закалки и отпуска.
- Рекомендуется выполнять цементацию при изготовлении ответственных инструментов. В зависимости от толщины самого инструмента выбирается наиболее подходящая глубина цементации.
- Для нагрева металла под закалку могут применяться камерные печи. Охлаждение выполняется в соляных или свинцовых ваннах. Если конфигурация детали сложная, то выполняется подогрев путем двукратного или трехкратного погружения с расплавленную соль. За счет этого обеспечивается равномерность разогрева структуры.
- Охлаждение можно проводить в масляной ванной или в расплавленной соли. За счет этого можно существенно уменьшить степень проявления дефектов.
- Целью проводимого отпуска становится снижение внутренних напряжений, которые могут возникать при проведении закалки. Подобные напряжения становятся причиной образования трещин и других дефектов на момент шлифования или выполнения чистовой обработки.
Вышеприведенная информация определяет то, что подобная сталь в большинстве случаев применима только при условии последующей химико-термической обработки. Поэтому в последнее время все чаще используют аналоги, которые обладают более высокими эксплуатационными качествами.
Сталь 20-КХС / Evek
Сталь 38 (38-ПВ)
Сталь 20-КС
Сталь 20-КХС
Сталь 20К
Сталь 20кп
Сталь 20пс
Сталь 20ЮА
Сталь 20ЮЧА (20ЮЧ)
Сталь 22ЖР
Сталь 22К
Сталь 25
Сталь 25пс
Сталь 30
Сталь 35
Сталь 20 (20А; 20В)
Сталь 40 (40А)
Сталь 43 (43-ПВ)
Сталь 45
Сталь 45Т (45СТ)
Сталь 50
Сталь 54 (54пп)
Сталь 55
Сталь 58 (55пп)
Сталь 60
Сталь 60пп (60пп-ПВ)
Сталь 90 (БП5)
Сталь Д
Сталь ДБ
Сталь Е55 (НИПРА)
Сталь 11кп
Сталь 0501
Сталь 05кп
Сталь 08
Сталь 08кп
Сталь 08пс
Сталь 08Фкп
Сталь 08Ю (08ЮА; 08Ю2 (08Ю2А))
Сталь 08ЮП
Сталь 08ЮПР
Сталь 10
Сталь 10кп
Сталь 10пс
Сталь 10ЮА (10Ю)
Сталь 18ЮА
Сталь 11МТЮА
Сталь 11ЮА
Сталь 12К
Сталь 15 (15А)
Сталь 15К
Сталь 15кп
Сталь 15пс
Сталь 15ФЮА
Сталь 15ЮА
Сталь 16ГНМА
Сталь 16К
Сталь 18К
Сталь 18кп
Обозначения
Название | Значение |
---|---|
Обозначение ГОСТ кирилица | 20-КХС |
Обозначение ГОСТ латиница | 20-KXC |
Транслит | 20-KHS |
По химическим элементам | 20-CoCrС |
Описание
Сталь 20-КХС применяется: для производства из листового проката электросварных прямошовных нефтепроводных труб повышенной стойкости против локальной коррозии на рабочее давление до 7,4 МПа класса прочности К52 диаметром 530 — 1020 мм и диаметром 114−530 мм классов прочности К48 и К52, применяемых для сооружения нефтесборных сетей (транспортирующих коррозионно-активные газ, нефть и пластовую воду) и нефтепродуктопроводов на давление не более 7,4 МПа (75 кгс/см2), для эксплуатации при минимальной температуре окружающей среды — минус 60 °C.
Стандарты
Название | Код | Стандарты |
---|---|---|
Трубы стальные и соединительные части к ним | В62 | TУ 14-1-5433-2005, TУ 14-1-5491-2004 |
Химический состав
Стандарт | C | S | P | Mn | Cr | Si | Ni | Fe | Cu | N | As | Al | Nb |
---|---|---|---|---|---|---|---|---|---|---|---|---|---|
TУ 14-1-5433-2005 | 0.14-0.2 | ≤0.009 | ≤0.02 | 0.4-0.8 | 0.1-0.3 | 0.17-0.37 | 0.1-0.3 | Остаток | ≤0.3 | ≤0.008 | ≤0.08 | 0.02-0.05 | 0.03-0.06 |
TУ 14-1-5491-2004 | 0.18-0.22 | ≤0.009 | ≤0.02 | 0.4-0.8 | ≤0.25 | 0.17-0.37 | ≤0.3 | Остаток | ≤0.3 | ≤0.008 | ≤0.08 | 0.02-0.05 | 0.![]() |
Fe — основа.
По ТУ 14-1-5491-2004 допустимы отклонения от химического состава: по углероду ±0,010 %, по марганцу ±0,050 %, по сере +0,0010%, по фосфору +0,0030 %, по азоту +0,0030 %, по кремнию ±0,020 %, по хрому +0,020 %, по ванадию +0,020 %, по алюминию +0,010 %, по ниобию +0,010 %.
Углеродный эквивалент Сэкв расчитывается по формуле и не должен превышать 0,43 %: Сэкв = С + Mn/6 + (Cr + Nb)/5 + (Ni + Cu)/15, где C, Mn, Cr, Nb, Ni, Cu — массовые доли основных элементов, входящих в состав стали.
По ТУ 14-1-5433-2005 допустимы отклонения от химического состава: по углероду ±0,010 %, по марганцу ±0,050 %, по сере +0,0010%, по фосфору +0,0030 %, по азоту +0,0030 %, по ниобию +0,010 %.
Механические свойства
Сечение, мм | sТ|s0,2, МПа | σB, МПа | d5, % | KCU, кДж/м2 |
---|---|---|---|---|
Основной металл труб: термообработанных, в состоянии поставки по ТУ 14-1-5433-2005.![]() | ||||
≥335 | ≥470 | ≥20 | ≥294/294 | |
≥355 | ≥510 | ≥20 | ≥294/294 | |
Основной металл труб: термообработанных, в состоянии поставки по ТУ 14-1-5491-2004 | ||||
≥350 | 510-630 | ≥20 | ≥392 |
Описание механических обозначений
Название | Описание |
---|---|
sТ|s0,2 | Предел текучести или предел пропорциональности с допуском на остаточную деформацию — 0,2% |
σB | Предел кратковременной прочности |
d5 | Относительное удлинение после разрыва |
KCU | Ударная вязкость |
Технологические свойства
Название | Значение |
---|---|
Ударная вязкость | В основном металле труб по ТУ 14-1-5491-2004 ударная вязкость KCU-60 при толщине стенки труб до 15 мм включительно должна быть ≥39,2 Дж/см2(392 кДж/м2), а при толщине стенки труб свыше 15 мм — 49,0 Дж/см2 (490 кДж/м2).![]() |
20NiCrMo2-2, AISI 8620, 805M20 — Цементируемая сталь
Цементируемая сталь 20NiCrMo2-2, 1.6523, AISI 8620, 805M20 для тяжелонагруженных деталей машин и транспортных средств по EN 10084.

4
4 Standards Steel Grades Chemical Composition % C: Mn: Si: P: S: Cr: Mo: Ni: V: Al: Ti: Cu: N: W: PN 20HNM 0.17 — 0.23 0.6 — 0.9 0.17 — 0.37 <0.035 <0.035 0.35 — 0.65 0.15 — 0.25 0.35 — 0.75 — — — — — — EN 20NiCrMo2-2 — 20 NiCrMo 2-2 — 21NiCrMo2 — 21 NiCrMo 2- 1.
6523 0.17 — 0.23 0.65 — 0.95 <0.4 <0.025 <0.035 0.35 — 0.70 0.15 — 0.25 0.4 — 0.7 — — — — — — ISO 20NiCrMo2F — 20NiCrMo2 — 20 NiCrMo 2 — 1.6522 0.17 — 0.23 0.60 — 0.95 <0.4 <0,025 <0,030 0,35 — 0,65 0,15 — 0,25 0,4 - 0,7 — <0,05 — <0,3 9004 <0,05 — 9004 <0,3 <0,05 — 9.0057 — — AFNOR 20NCD2 — 20 NCD 2 0.
17 — 0.23 0.65 — 0.95 0.10 — 0.35 <0.03 <0.025 0,40 — 0,65 0,15 — 0,25 0,4 - 0,7 — <0,02 — — — — — — — — — — — — — 0014 DIN 20NICRMOS2-2 — 20 NICRMOS 2-2 — 21NICRMOS2 — 21 NICRMOS 2 — 1,6526 0,17 — 0,23 0,17 — 0,23 . 0.02 — 0.04 0.35 — 0.70 0.15 — 0.25 0.4 — 0.7 — — — — — — GOST 20HGNM — 20ChGNM — 20KhGNM — 20ХГНМ 0.
18 — 0.23 0.7 — 1.1 0.17 — 0.37 <0.035 <0.035 0.4 — 0.7 0,15 — 0,25 0,4 - 0,7 <0,05 — <0,03 <0,3 <0,008 710 <0 SAE J1268 — AISI 8620H — 8620 H — UNS H86200 0.17 — 0.23 0.60 — 0.95 0.15 — 0.35 <0.035 <0.040 0.35 — 0.65 0,15 — 0,25 0,35 — 0,75 — — — — — — 69 9000 9000 9000 9000 9000 9000 9000 0350 20NiCrMo2-2, 1.6523 — технические характеристики и применение Сталь 20ХНМ — конструкционная легированная сталь из группы углеродистых материалов, применяемая в качестве полуфабриката для изготовления деталей, работающих в тяжелых условиях, подверженных различным нагрузкам, высоким давлениям и ударам, требует высокой прочности сердцевины и твердой поверхности.
Материалы 20ХНМ предназначены для деталей и узлов сельскохозяйственных машин, автомобилей и машин для таких узлов, как зубчатые колеса, болты, подшипники, валы, работающие на высоких скоростях, цапфы или дисковые колеса.
Продукция данной марки поставляется в виде горячекатаного проката, кованого проката, поковок, колец, проволоки. Сталь 20ХНМА согласно PN-H-93028, также используется для производства звеньев цепи.
Общие механические свойства 20NICRMO2-2 Стали и ее эквиваленты
- Прочность на растяжение, R M = 660 — 1160 МПа
- , r E = 470 -560 -560 -560 -560 -560 -560 -560 -560 -560 -566. 25 — 30 Дж
- Удлинение, А = 9- 11%
. при 650 — 700 ℃- Науглероживание при 880 950 ℃
- Нитроцементация при 860 — 930 ℃
- Первая закалка после науглероживания с охлаждением в воде или масле при 860 — 900 °С
6- Отжиг после науглероживания6
- 0365
- Второе затвердевание после карбинизации с охлаждением в масле или воде при 810 — 830 ℃
- Управление при 150 — 200 ℃
Virgamet в вышеупомянутых классах:
- Round -Hot -ROLLED HOT -ROLLEDEDEDEDEDEDEDMH.
-2, 1,6523 - ковена, кованые стержни и кольца 20hnm, 20nicrmo2-2, 1,6523
- Нарисованные и вычитанные стержни 20HNM, 20NICRMO2-2, 1,6523
- .0004 Virgamet в вышеупомянутых оценках:
20nicrmo2-2, 20 HNM, 20 NICRMO 2-2, 21nicrmo2, 21 NICRMO 2, 1,6523, 6523, 20nicrmo2-1, 20nicrmo3, 20nicrmo2f, 1,6522222222, 20nico2, 20nco2, 20nco2, 20nco2, 20nco2, 20-й, 20nico2, 20nico2, 20nico2, 20nico2, 20nico2, 20nico2, 20nico2, 20nico2, 20nico2, 20nico2, 20nico2, 20nico2, 20nico2, 20nico3, 20nicrmo2f, 20-й. NCD 2, 20NICRMO7, 22NCD2, 22HNM, 20 NICRMO 7, SAE 8620, AISI 8620H, J1268, 8620 H, UNS H86200, 806M20, 806 M 20, 20NICRMOS2-2, 20 NICRMOS 2-2, 20NI2CR2MO2, 20NICRMOS2, 20, 20NI2MO2, 20NICRMO2HRMHRMHRMHRHRMHRMHRMHRMHRMOS2-2, 20, 20NI2CR2MO2, 20NICRMOS2-2, 20, 20ni2mo2mo2, 20nicrmos2-2, 20, 20ni2mo2mo2, 20nicrmos2-2, 20, 20ni2mo2mo2, 20nicrmos2-2. , 20nicrmo2hl, 20nicrmos2h, sncm 220, 22hnm, 20mocrni06, 20 Mocrni 06, 1,3576, 1,6526, 1,6522, 8617H, UNS H86170, 20crnimo, 20nicrmo2kd, 20hgnm, 20kgnmmmmhgnmmmmhgnmmmhgnmmmhgnmmm, 20, 20 -й.
0005
Руководство по прочности на растяжение | OneMonroe
Что такое прочность на растяжение? С точки зрения непрофессионала, это измерение силы, необходимой для растяжения материала до его разрыва. Тест проводится, чтобы увидеть, какое усилие натяжения может выдержать материал, прежде чем он достигнет предела прочности. Это чрезвычайно важно во многих областях, таких как машиностроение, материаловедение и, возможно, самое важное в проектировании конструкций.
Существует три различных способа измерения предела прочности при растяжении: предел текучести, предел прочности и предел прочности на разрыв. Предел текучести — это величина напряжения, которое вы можете приложить к материалу, не разрушая и не деформируя его. Предел текучести — это точка, в которой материал больше не будет возвращаться к своей первоначальной форме и станет необратимо деформированным. Предел прочности – это максимальное усилие, которое материал может выдержать при растяжении или растяжении.
Прочность на разрыв относится к точке на кривой напряжения-деформации, в которой материал больше не может выдерживать напряжение растяжения и ломается.
Ниже приведено руководство по прочности на растяжение нескольких распространенных материалов.
Типичная прочность на растяжение некоторых материалов Материал Предел текучести Предел прочности при растяжении Плотность (МПа) (МПа) (г/см³) Сталь, конструкционная сталь ASTM A36 250 400–550 7,8 Сталь, 1090 мягкая 247 841 7,58 Хромованадиевая сталь AISI 6150 620 940 7,8 Кожа человека 15 20 2 Сталь, мартенситностареющая сталь 2800 2617 2693 8 Сталь, AerMet 340 2160 2430 7,86 Сталь, каротажный кабель Sandvik Sanicro 36Mo прецизионная проволока 1758 2070 8 Сталь AISI 4130, закалка в воде 855 °C (1570 °F), отпуск 480 °C (900 °F) 951 1110 7,85 Сталь, API 5L X65 448 531 7,8 Сталь, высокопрочный сплав ASTM A514 690 760 7,8 Акрил, прозрачный литой лист (ПММА) 72 87 1,16 Полиэтилен высокой плотности (HDPE) 26–33 37 0,85 Полипропилен 12–43 19,7–80 0,91 Сталь нержавеющая AISI 302 – холоднокатаная 520 860 8.
19 Чугун 4,5% C, ASTM A-48 130 200 7,3 Сплав «жидкий металл» 1723 550–1600 6.1 Бериллий 99,9% Be 345 448 1,84 Алюминиевый сплав 2014-T6 414 483 2,8 Полиэфирная смола (неармированная) 55 55 Полиэстер и ламинат из рубленого волокна 30% Е-стекло 100 100 Эпоксидный композит S-Glass 2358 2358 Алюминиевый сплав 6061-T6 270 310 2,7 Медь 99,9% Cu 69 220 8,92 Мельхиор 10 % Ni, 1,6 % Fe, 1 % Mn, остальное Cu 130 350 8,94 Латунь 200 + 500 8,73 Вольфрам 941 1510 19,25 Стекло 33 2,53 Электронное стекло Н/Д 1500 для ламината, 2,57 3450 только для волокон S-стекло н/д 4710 2,48 Базальтовое волокно н/д 4840 2,7 Мрамор н/д 15 2,6 Бетон н/д 2–5 2,7 Углеродное волокно Н/Д 1600 для ламината, 1,75 4137 только для волокон Углеродное волокно (Toray T1000G) (самое прочное искусственное волокно) 6370 только оптоволокно 1,8 Человеческий волос 140–160 200–250 Бамбук 350–500 0,4 Шелк паука (см.
примечание ниже) 1000 1,3 Шелковый паук, паук Дарвина 1652 Шелк тутового шелкопряда 500 1,3 Арамид (кевлар или тварон) 3620 3757 1,44 СВМПЭ 24 52 0,97 Волокна СВМПЭ (Dyneema или Spectra) 2300–3500 0,97 Вектран 2850–3340 Полибензоксазол (Зилон) 2700 5800 1,56 Древесина сосна (параллельно волокнам) 40 Кость (конечность) 104–121 130 1,6 Нейлон, формованный, тип 6/6 450 750 1,15 Нейлоновое волокно, вытянутое 900 1,13 Эпоксидный клей – 12–30 – Резина – 16 Бор н/д 3100 2,46 Кремний монокристаллический (m-Si) н/д 7000 2,33 Волоконные нити из сверхчистого кварцевого стекла 4100 Сапфир (Al2O3) 400 при 25°C, 275 при 500°C, 345 при 1000°C 1900 3,9–4,1 Нанотрубка из нитрида бора н/д 33000 2,62 Алмаз 1600 2800 3,5 Графен н/д 130000 1 Первые канаты из углеродных нанотрубок ? 3600 1,3 Колоссальная карбоновая трубка н/д 7000 0,116 Углеродная нанотрубка (см.
примечание ниже) н/д 11000–63000 0,037–1,34 Композиты из углеродных нанотрубок н/д 1200 н/д Пленка из высокопрочных углеродных нанотрубок н/д 9600 н/д Железо (чистый монокристалл) 3 7,874 Зубы блюдца Patella vulgata (Goethite) 4900 3000–6500
Вы ищете
изготовление на заказ ? Отправьте запрос сейчас!
ремонт или замена? – Прочность материала на растяжение ключ к ремонтопригодности
20 лет разработки
В последние годы перед автопроизводителями стояла задача снизить вес автомобиля, сделать его более безопасным (дополнительный вес) и при этом обеспечить все развлечения (дополнительный вес).
) и информационные системы (дополнительный вес), которые требуют сегодняшние потребители. Эти противоборствующие силы потребовали от производителей автомобилей изменить свой подход к конструированию автомобилей. За последние два десятилетия большинство модифицированных подходов были связаны с различными типами сталей. В течение многих лет большинство транспортных средств изготавливались в основном из мягкой стали, иногда из высокопрочной стали (HSS) и сверхвысокопрочной стали (UHSS), используемой для ряда дверных балок и усилителей бамперов. Но это начало меняться 20 лет назад.
(В общих чертах, мягкие стали обычно находятся в диапазоне до 210 МПа; быстрорежущая сталь — в диапазоне от 210 до 600 МПа; и UHSS — все, что выше 600 МПа. (1 МПа равен 145 фунтам на кв. 87 020 фунтов на квадратный дюйм. Эти цифры варьируются от OEM к OEM, но, вообще говоря, это общие диапазоны.)
стальная конструкция кузова автомобиля, отвечающая широкому кругу требований безопасности и производительности».
Результатом этих совместных усилий стал автомобиль UltraLight Steel Auto Body (ULSAB) — конструкция автомобиля, которая весила на 36 % меньше, чем автомобиль аналогичного размера, но изготовлена из обычных (в то время) типов стали. Эта работа привела к созданию многих усовершенствованных высокопрочных сталей (AHSS), используемых в современных автомобилях.
ULSAB был построен с использованием более чем 90% HSS и UHSS, и это был рассвет автомобильной промышленности, где слышались такие термины, как:
- Двухфазный (DP)
- Индуцированная трансформацией пластичность (TRIP)
- Сложная фаза (CP)
- Бор
- Горячештампованные и горячеформованные
- Мартенситный
- Гидроформинг
- Заготовки на заказ
- Лазерная сварка
Хотя сегодня эти термины более широко известны, их значения не всегда ясны и часто добавляют дополнительный уровень сложности к решениям «ремонт или замена», которые ежедневно принимаются на предприятиях по ремонту после столкновений по всей стране.
Что важно знать с точки зрения ремонтопригодности, так это не обязательно тип стали (DP, TRIP, CP и т. д.) или производственный процесс (индивидуальные заготовки, гидроформовка и горячая штамповка), а прочность на растяжение. прочность материала (DP600, DP800, DP1000 и др.). Прочность материалов на растяжение — это то, что позволяет специалистам по ремонту после столкновений определять, можно ли выпрямить деталь или она требует замены; и если он требует замены, он часто диктует методы крепления, допустимые (иногда требуемые) для ремонта современных автомобилей последних моделей.
AHSS Ремонтопригодность
Тот факт, что деталь изготовлена из AHSS, не обязательно означает, что ее нельзя выпрямить. Некоторые производители транспортных средств предлагают рекомендации по ремонтопригодности, основанные на типе и прочности стали на растяжение. В то время как стали с более низкой прочностью на растяжение, как правило, предлагают больше возможностей для правки, некоторые автопроизводители разрешают холодную правку до 700 мегапаскалей (МПа).
OEM-производители, включая GM, Ford, Chrysler, Toyota и Honda, предоставляют рекомендации по типам материалов, которые можно выпрямлять, а также о том, можно ли использовать тепло для выпрямления. Высокопрочные стали более склонны к потере прочности, чем низкоуглеродистые стали, когда для правки используется тепло. Сверхвысокопрочные стали чрезвычайно чувствительны к нагреву и теряют свою прочность при применении тепла для правки. Всегда следуйте рекомендациям производителя транспортного средства по использованию тепла.
Руководящим принципом, который исторически использовался для принятия решения о ремонте или замене, является правило I-CAR ® излома или изгиба. Проще говоря, погнутые детали часто можно было отремонтировать, а согнутые части требовали замены. Прежнее определение излома было «резким изгибом с малым радиусом на небольшом расстоянии. Деталь считается перекрученной, если после выпрямления остается участок постоянной деформации, который не вернется в исходное состояние и форму без применения избыточного тепла.
Согнутые детали также могут иметь видимые трещины или разрывы в металле». Важно восстановить как форму, так и состояние детали. Если какой-либо из них неполный, после выпрямления деталь следует считать перегнутой и ее следует заменить.
Правило излома и изгиба больше не так просто, как кажется. Деталь может не выглядеть перегнутой, но ее невозможно выпрямить без повреждения структуры зерна, если она уже не повреждена в результате столкновения. Повреждение может быть в виде микротрещин, которые нелегко увидеть. В более экстремальных случаях во время выпрямления может возникнуть трещина, которую легче увидеть, и потребуется замена детали.
Чем прочнее сталь, тем труднее ее ремонтировать. Например, попытка выпрямить небольшой изгиб детали UHSS может привести к ее растрескиванию, если ее вообще можно выпрямить. Когда необходимо выпрямить сталь в диапазоне 600–800 МПа, рекомендуется использовать проникающий краситель, чтобы гарантировать отсутствие микротрещин в стали. Некоторые производители транспортных средств не рекомендуют выпрямлять детали UHSS, выдерживающие нагрузку выше 600 МПа, из-за возможности растрескивания и разрыва детали, а также из-за возможного повреждения соседних панелей и других частей конструкции автомобиля.
Если деталь погнута, но толщина или прочность металла не позволяют выпрямить ее без остаточной деформации, то целесообразна замена частичная или полная.
Идентификация
Поскольку ремонтопригодность часто зависит от типа используемой стали, очень важно знать прочность детали при принятии решения о ремонте. Существует ряд параметров, которые можно использовать для определения прочности стали, используемой в современных автомобилях.
Первый и самый надежный способ — обратиться к руководству по кузовному ремонту производителя автомобиля. Многие OEM-производители проделывают большую работу по четкой идентификации конструкционных материалов, используемых в их автомобилях. Эта информация в сочетании с рекомендациями OEM по ремонтопригодности является наиболее эффективным способом определить, что можно отремонтировать, а что требует замены.
Другим надежным способом определения прочности детали является использование оборудования для определения прочности.
GYSTEEL VISION — это инструмент, который можно использовать для определения прочности стали. После очистки стали (требуется двусторонний доступ) VISION крепится к стальной детали и затягивается на месте. Затем измерительная ручка используется для измерения стали. Число на ручке сравнивается с таблицей, предоставленной производителем инструмента, для определения прочности стали.
Другим вариантом, хотя и значительно менее надежным, чем вышеупомянутые варианты, является попытка идентифицировать сталь по ее расположению на транспортном средстве. Все автомобили построены с учетом управления энергией столкновения. Передняя и задняя части автомобиля спроектированы таким образом, чтобы разрушаться при столкновении, а центральная часть вокруг пассажирского салона спроектирована так, чтобы оставаться неповрежденной, защищая пассажиров, поэтому она передает энергию столкновения, а не поглощает ее, как зоны разрушения. машина делаю. Используя эту «логику», разумно полагать, что те стали, которые находятся в передней и задней части, могут иметь меньшую прочность, чем те, что на боках автомобиля; особенно усиления в передних и средних стойках, порогах и рейлингах на крыше.
Однако эта логика не всегда точна, так как General Motors теперь использует материал с пределом прочности 700 МПа в передних и нижних направляющих некоторых своих автомобилей, например, Cadillac ATS. Учитывая, что тенденция проектирования состоит в том, чтобы стали становиться все тоньше для снижения веса, они также должны стать прочнее. В связи с этим, если сделать какое-либо предположение о том, что в боковой конструкции ремонтируемого автомобиля используется неизвестный тип стали, то следует предположить, что детали изготовлены из сверхпрочной стали. Внешние панели могут быть изготовлены из относительно более мягкой стали для облегчения формовки, но даже прочность наружных панелей увеличивается по мере уменьшения толщины панелей для снижения веса.
Частичная замена детали
Если деталь требует замены, не всегда требуется полная замена. Ряд производителей транспортных средств допускают частичную замену по заводским швам или разделение этих деталей на части.
Частичная замена сборки на заводе, по-видимому, является подходом, принятым производителями автомобилей, такими как Honda. Например, нижняя рейка Accord последней модели обслуживается как единый узел, включая часть рейки, которая крепится под пассажирским салоном. Если повреждение ограничено областью перед капотом, Honda разрешает демонтировать этот узел прямо перед капотом и установить его. Это делает ремонт менее инвазивным, поскольку точечные сварные швы OEM под салоном остаются нетронутыми, а защита от коррозии OEM остается нетронутой. Не все производители транспортных средств допускают этот тип процедуры, поэтому важно, как всегда, ссылаться на процедуры производителя транспортного средства. Если производитель транспортного средства не дает рекомендаций за или против этого типа процедуры, специалисты по ДТП должны тщательно взвесить все преимущества, прежде чем принимать решение о проведении такого вида ремонта.
Другие производители транспортных средств предлагают различные процедуры разрезания многих конструктивных элементов.
В отличие от частичной замены узла на заводском шве, разрезание позволяет техническому специалисту заменить часть детали путем маркировки и вырезания детали в месте, указанном производителем транспортного средства. Некоторые производители транспортных средств предлагают несколько мест в одной детали для разделения на секции; другие предлагают только одно местоположение. Разделение должно выполняться только в местах, указанных производителем транспортного средства. Совместная конфигурация места секционирования также должна быть определена на основе процедур производителя транспортного средства.
В конце 1980-х годов компания I-CAR разработала общие рекомендации по разделке, которые многие годы использовались профессионалами отрасли. Эти общие рекомендации по разделению больше не применимы к автомобилям последних моделей. Полный обзор этих общих рекомендаций по разделению см. на портале технической поддержки по ремонтопригодности I-CAR (RTS). Статью можно найти по адресу: Обновление: применимы ли общие рекомендации по разделам?
В следующей статье I‑CAR мы подробно рассмотрим способы крепления для установки деталей
Быстрые изменения требуют переосмысления
Мы находимся в эпицентре «технического цунами» с быстрым развитием транспортных средств, включая мир стали.
Специалисты по ремонту должны быть в курсе последних изменений в технологиях, материалах, процессах и обучении. Старый способ ремонта или замены не обязательно является правильным способом выполнения полного, безопасного и качественного ремонта современных сложных транспортных средств. Крайне важно точно определить материал автомобиля и определить, что подлежит ремонту, а что подлежит замене, а также знать возможные варианты.
Программа I-CAR ® Обучение и сертификация сварщиков ™ включает в себя обучение теории сварки, практическую оценку инструктором оборудования, оборудования и инфраструктуры объекта перед обучением в цеху, практикой, и признанный в отрасли сертификационный тест. Дополнительную информацию обо всех курсах I-CAR по сварке (сварка GMA (MIG) стали, сварка GMA (MIG) алюминия и резка стали) можно найти на сайте www.i-car.com. В рамках обязательств I-CAR перед отраслью цены на обучение сварке были снижены, чтобы каждый технический специалист мог пройти практическое обучение, необходимое для выполнения надлежащей сварки, более доступным.
Все большее число OEM-производителей используют обучение и сертификацию I-CAR по сварке в своих сетевых программах, включая Acura, Audi, Chrysler, Ford, GM, Honda, Infiniti, Jaguar, Land Rover, Lexus, Nissan, Porsche, Scion, Toyota, Вольво и Фольксваген. Кроме того, предприятия, получившие Золотой класс ® , отраслевой стандарт обучения ремонту после аварии, также включают обучение сварке в качестве обязательного требования программы.
Будь то сталь, алюминий, другие конструкционные материалы для транспортных средств или комбинация материалов, важно, чтобы вы оснастили свое предприятие соответствующими инструментами, оборудованием и прошли обучение, чтобы обеспечить полный, безопасный и качественный ремонт. Эти инвестиции могут привести к увеличению прибыльности, повышению операционной эффективности и производительности, а также к более высокому уровню удовлетворенности и удержания клиентов.
Джейсон Бартанен (Jason Bartanen) — директор I-CAR по техническим связям с промышленностью и отвечает за инициативу технической поддержки I-CAR по ремонтопригодности в Техническом центре I-CAR в Эпплтоне, штат Висконсин.
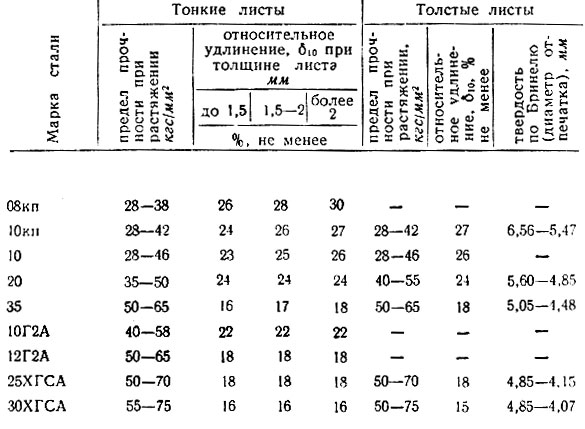


Сталь 20ХНМ — конструкционная легированная сталь из группы углеродистых материалов, применяемая в качестве полуфабриката для изготовления деталей, работающих в тяжелых условиях, подверженных различным нагрузкам, высоким давлениям и ударам, требует высокой прочности сердцевины и твердой поверхности.
Материалы 20ХНМ предназначены для деталей и узлов сельскохозяйственных машин, автомобилей и машин для таких узлов, как зубчатые колеса, болты, подшипники, валы, работающие на высоких скоростях, цапфы или дисковые колеса.
Продукция данной марки поставляется в виде горячекатаного проката, кованого проката, поковок, колец, проволоки. Сталь 20ХНМА согласно PN-H-93028, также используется для производства звеньев цепи.
Общие механические свойства 20NICRMO2-2 Стали и ее эквиваленты
- Прочность на растяжение, R M = 660 — 1160 МПа
- , r E = 470 -560 -560 -560 -560 -560 -560 -560 -560 -560 -566. 25 — 30 Дж
- Удлинение, А = 9- 11% . при 650 — 700 ℃
- Науглероживание при 880 950 ℃
- Нитроцементация при 860 — 930 ℃
- Первая закалка после науглероживания с охлаждением в воде или масле при 860 — 900 °С 6
- Отжиг после науглероживания6
- 0365
- Второе затвердевание после карбинизации с охлаждением в масле или воде при 810 — 830 ℃
- Управление при 150 — 200 ℃
Virgamet в вышеупомянутых классах:
- Round -Hot -ROLLED HOT -ROLLEDEDEDEDEDEDEDMH.
-2, 1,6523
- ковена, кованые стержни и кольца 20hnm, 20nicrmo2-2, 1,6523
- Нарисованные и вычитанные стержни 20HNM, 20NICRMO2-2, 1,6523
- .0004 Virgamet в вышеупомянутых оценках:
20nicrmo2-2, 20 HNM, 20 NICRMO 2-2, 21nicrmo2, 21 NICRMO 2, 1,6523, 6523, 20nicrmo2-1, 20nicrmo3, 20nicrmo2f, 1,6522222222, 20nico2, 20nco2, 20nco2, 20nco2, 20nco2, 20-й, 20nico2, 20nico2, 20nico2, 20nico2, 20nico2, 20nico2, 20nico2, 20nico2, 20nico2, 20nico2, 20nico2, 20nico2, 20nico2, 20nico3, 20nicrmo2f, 20-й. NCD 2, 20NICRMO7, 22NCD2, 22HNM, 20 NICRMO 7, SAE 8620, AISI 8620H, J1268, 8620 H, UNS H86200, 806M20, 806 M 20, 20NICRMOS2-2, 20 NICRMOS 2-2, 20NI2CR2MO2, 20NICRMOS2, 20, 20NI2MO2, 20NICRMO2HRMHRMHRMHRHRMHRMHRMHRMHRMOS2-2, 20, 20NI2CR2MO2, 20NICRMOS2-2, 20, 20ni2mo2mo2, 20nicrmos2-2, 20, 20ni2mo2mo2, 20nicrmos2-2, 20, 20ni2mo2mo2, 20nicrmos2-2. , 20nicrmo2hl, 20nicrmos2h, sncm 220, 22hnm, 20mocrni06, 20 Mocrni 06, 1,3576, 1,6526, 1,6522, 8617H, UNS H86170, 20crnimo, 20nicrmo2kd, 20hgnm, 20kgnmmmmhgnmmmmhgnmmmhgnmmmhgnmmm, 20, 20 -й.
0005
Руководство по прочности на растяжение | OneMonroe
Что такое прочность на растяжение? С точки зрения непрофессионала, это измерение силы, необходимой для растяжения материала до его разрыва. Тест проводится, чтобы увидеть, какое усилие натяжения может выдержать материал, прежде чем он достигнет предела прочности. Это чрезвычайно важно во многих областях, таких как машиностроение, материаловедение и, возможно, самое важное в проектировании конструкций.
Существует три различных способа измерения предела прочности при растяжении: предел текучести, предел прочности и предел прочности на разрыв. Предел текучести — это величина напряжения, которое вы можете приложить к материалу, не разрушая и не деформируя его. Предел текучести — это точка, в которой материал больше не будет возвращаться к своей первоначальной форме и станет необратимо деформированным. Предел прочности – это максимальное усилие, которое материал может выдержать при растяжении или растяжении.
Прочность на разрыв относится к точке на кривой напряжения-деформации, в которой материал больше не может выдерживать напряжение растяжения и ломается.
Ниже приведено руководство по прочности на растяжение нескольких распространенных материалов.
Типичная прочность на растяжение некоторых материалов Материал Предел текучести Предел прочности при растяжении Плотность (МПа) (МПа) (г/см³) Сталь, конструкционная сталь ASTM A36 250 400–550 7,8 Сталь, 1090 мягкая 247 841 7,58 Хромованадиевая сталь AISI 6150 620 940 7,8 Кожа человека 15 20 2 Сталь, мартенситностареющая сталь 2800 2617 2693 8 Сталь, AerMet 340 2160 2430 7,86 Сталь, каротажный кабель Sandvik Sanicro 36Mo прецизионная проволока 1758 2070 8 Сталь AISI 4130, закалка в воде 855 °C (1570 °F), отпуск 480 °C (900 °F) 951 1110 7,85 Сталь, API 5L X65 448 531 7,8 Сталь, высокопрочный сплав ASTM A514 690 760 7,8 Акрил, прозрачный литой лист (ПММА) 72 87 1,16 Полиэтилен высокой плотности (HDPE) 26–33 37 0,85 Полипропилен 12–43 19,7–80 0,91 Сталь нержавеющая AISI 302 – холоднокатаная 520 860 8. 19
Чугун 4,5% C, ASTM A-48 130 200 7,3 Сплав «жидкий металл» 1723 550–1600 6.1 Бериллий 99,9% Be 345 448 1,84 Алюминиевый сплав 2014-T6 414 483 2,8 Полиэфирная смола (неармированная) 55 55 Полиэстер и ламинат из рубленого волокна 30% Е-стекло 100 100 Эпоксидный композит S-Glass 2358 2358 Алюминиевый сплав 6061-T6 270 310 2,7 Медь 99,9% Cu 69 220 8,92 Мельхиор 10 % Ni, 1,6 % Fe, 1 % Mn, остальное Cu 130 350 8,94 Латунь 200 + 500 8,73 Вольфрам 941 1510 19,25 Стекло 33 2,53 Электронное стекло Н/Д 1500 для ламината, 2,57 3450 только для волокон S-стекло н/д 4710 2,48 Базальтовое волокно н/д 4840 2,7 Мрамор н/д 15 2,6 Бетон н/д 2–5 2,7 Углеродное волокно Н/Д 1600 для ламината, 1,75 4137 только для волокон Углеродное волокно (Toray T1000G) (самое прочное искусственное волокно) 6370 только оптоволокно 1,8 Человеческий волос 140–160 200–250 Бамбук 350–500 0,4 Шелк паука (см. примечание ниже)
1000 1,3 Шелковый паук, паук Дарвина 1652 Шелк тутового шелкопряда 500 1,3 Арамид (кевлар или тварон) 3620 3757 1,44 СВМПЭ 24 52 0,97 Волокна СВМПЭ (Dyneema или Spectra) 2300–3500 0,97 Вектран 2850–3340 Полибензоксазол (Зилон) 2700 5800 1,56 Древесина сосна (параллельно волокнам) 40 Кость (конечность) 104–121 130 1,6 Нейлон, формованный, тип 6/6 450 750 1,15 Нейлоновое волокно, вытянутое 900 1,13 Эпоксидный клей – 12–30 – Резина – 16 Бор н/д 3100 2,46 Кремний монокристаллический (m-Si) н/д 7000 2,33 Волоконные нити из сверхчистого кварцевого стекла 4100 Сапфир (Al2O3) 400 при 25°C, 275 при 500°C, 345 при 1000°C 1900 3,9–4,1 Нанотрубка из нитрида бора н/д 33000 2,62 Алмаз 1600 2800 3,5 Графен н/д 130000 1 Первые канаты из углеродных нанотрубок ? 3600 1,3 Колоссальная карбоновая трубка н/д 7000 0,116 Углеродная нанотрубка (см. примечание ниже)
н/д 11000–63000 0,037–1,34 Композиты из углеродных нанотрубок н/д 1200 н/д Пленка из высокопрочных углеродных нанотрубок н/д 9600 н/д Железо (чистый монокристалл) 3 7,874 Зубы блюдца Patella vulgata (Goethite) 4900 3000–6500 Вы ищете
изготовление на заказ ?Отправьте запрос сейчас!
ремонт или замена? – Прочность материала на растяжение ключ к ремонтопригодности
20 лет разработки
В последние годы перед автопроизводителями стояла задача снизить вес автомобиля, сделать его более безопасным (дополнительный вес) и при этом обеспечить все развлечения (дополнительный вес).
) и информационные системы (дополнительный вес), которые требуют сегодняшние потребители. Эти противоборствующие силы потребовали от производителей автомобилей изменить свой подход к конструированию автомобилей. За последние два десятилетия большинство модифицированных подходов были связаны с различными типами сталей. В течение многих лет большинство транспортных средств изготавливались в основном из мягкой стали, иногда из высокопрочной стали (HSS) и сверхвысокопрочной стали (UHSS), используемой для ряда дверных балок и усилителей бамперов. Но это начало меняться 20 лет назад.
(В общих чертах, мягкие стали обычно находятся в диапазоне до 210 МПа; быстрорежущая сталь — в диапазоне от 210 до 600 МПа; и UHSS — все, что выше 600 МПа. (1 МПа равен 145 фунтам на кв. 87 020 фунтов на квадратный дюйм. Эти цифры варьируются от OEM к OEM, но, вообще говоря, это общие диапазоны.)
стальная конструкция кузова автомобиля, отвечающая широкому кругу требований безопасности и производительности».
Результатом этих совместных усилий стал автомобиль UltraLight Steel Auto Body (ULSAB) — конструкция автомобиля, которая весила на 36 % меньше, чем автомобиль аналогичного размера, но изготовлена из обычных (в то время) типов стали. Эта работа привела к созданию многих усовершенствованных высокопрочных сталей (AHSS), используемых в современных автомобилях.
ULSAB был построен с использованием более чем 90% HSS и UHSS, и это был рассвет автомобильной промышленности, где слышались такие термины, как:
- Двухфазный (DP)
- Индуцированная трансформацией пластичность (TRIP)
- Сложная фаза (CP)
- Бор
- Горячештампованные и горячеформованные
- Мартенситный
- Гидроформинг
- Заготовки на заказ
- Лазерная сварка
Хотя сегодня эти термины более широко известны, их значения не всегда ясны и часто добавляют дополнительный уровень сложности к решениям «ремонт или замена», которые ежедневно принимаются на предприятиях по ремонту после столкновений по всей стране.
Что важно знать с точки зрения ремонтопригодности, так это не обязательно тип стали (DP, TRIP, CP и т. д.) или производственный процесс (индивидуальные заготовки, гидроформовка и горячая штамповка), а прочность на растяжение. прочность материала (DP600, DP800, DP1000 и др.). Прочность материалов на растяжение — это то, что позволяет специалистам по ремонту после столкновений определять, можно ли выпрямить деталь или она требует замены; и если он требует замены, он часто диктует методы крепления, допустимые (иногда требуемые) для ремонта современных автомобилей последних моделей.
AHSS Ремонтопригодность
Тот факт, что деталь изготовлена из AHSS, не обязательно означает, что ее нельзя выпрямить. Некоторые производители транспортных средств предлагают рекомендации по ремонтопригодности, основанные на типе и прочности стали на растяжение. В то время как стали с более низкой прочностью на растяжение, как правило, предлагают больше возможностей для правки, некоторые автопроизводители разрешают холодную правку до 700 мегапаскалей (МПа).
OEM-производители, включая GM, Ford, Chrysler, Toyota и Honda, предоставляют рекомендации по типам материалов, которые можно выпрямлять, а также о том, можно ли использовать тепло для выпрямления. Высокопрочные стали более склонны к потере прочности, чем низкоуглеродистые стали, когда для правки используется тепло. Сверхвысокопрочные стали чрезвычайно чувствительны к нагреву и теряют свою прочность при применении тепла для правки. Всегда следуйте рекомендациям производителя транспортного средства по использованию тепла.
Руководящим принципом, который исторически использовался для принятия решения о ремонте или замене, является правило I-CAR ® излома или изгиба. Проще говоря, погнутые детали часто можно было отремонтировать, а согнутые части требовали замены. Прежнее определение излома было «резким изгибом с малым радиусом на небольшом расстоянии. Деталь считается перекрученной, если после выпрямления остается участок постоянной деформации, который не вернется в исходное состояние и форму без применения избыточного тепла.
Согнутые детали также могут иметь видимые трещины или разрывы в металле». Важно восстановить как форму, так и состояние детали. Если какой-либо из них неполный, после выпрямления деталь следует считать перегнутой и ее следует заменить.
Правило излома и изгиба больше не так просто, как кажется. Деталь может не выглядеть перегнутой, но ее невозможно выпрямить без повреждения структуры зерна, если она уже не повреждена в результате столкновения. Повреждение может быть в виде микротрещин, которые нелегко увидеть. В более экстремальных случаях во время выпрямления может возникнуть трещина, которую легче увидеть, и потребуется замена детали.
Чем прочнее сталь, тем труднее ее ремонтировать. Например, попытка выпрямить небольшой изгиб детали UHSS может привести к ее растрескиванию, если ее вообще можно выпрямить. Когда необходимо выпрямить сталь в диапазоне 600–800 МПа, рекомендуется использовать проникающий краситель, чтобы гарантировать отсутствие микротрещин в стали. Некоторые производители транспортных средств не рекомендуют выпрямлять детали UHSS, выдерживающие нагрузку выше 600 МПа, из-за возможности растрескивания и разрыва детали, а также из-за возможного повреждения соседних панелей и других частей конструкции автомобиля.
Если деталь погнута, но толщина или прочность металла не позволяют выпрямить ее без остаточной деформации, то целесообразна замена частичная или полная.
Идентификация
Поскольку ремонтопригодность часто зависит от типа используемой стали, очень важно знать прочность детали при принятии решения о ремонте. Существует ряд параметров, которые можно использовать для определения прочности стали, используемой в современных автомобилях.
Первый и самый надежный способ — обратиться к руководству по кузовному ремонту производителя автомобиля. Многие OEM-производители проделывают большую работу по четкой идентификации конструкционных материалов, используемых в их автомобилях. Эта информация в сочетании с рекомендациями OEM по ремонтопригодности является наиболее эффективным способом определить, что можно отремонтировать, а что требует замены.
Другим надежным способом определения прочности детали является использование оборудования для определения прочности.
GYSTEEL VISION — это инструмент, который можно использовать для определения прочности стали. После очистки стали (требуется двусторонний доступ) VISION крепится к стальной детали и затягивается на месте. Затем измерительная ручка используется для измерения стали. Число на ручке сравнивается с таблицей, предоставленной производителем инструмента, для определения прочности стали.
Другим вариантом, хотя и значительно менее надежным, чем вышеупомянутые варианты, является попытка идентифицировать сталь по ее расположению на транспортном средстве. Все автомобили построены с учетом управления энергией столкновения. Передняя и задняя части автомобиля спроектированы таким образом, чтобы разрушаться при столкновении, а центральная часть вокруг пассажирского салона спроектирована так, чтобы оставаться неповрежденной, защищая пассажиров, поэтому она передает энергию столкновения, а не поглощает ее, как зоны разрушения. машина делаю. Используя эту «логику», разумно полагать, что те стали, которые находятся в передней и задней части, могут иметь меньшую прочность, чем те, что на боках автомобиля; особенно усиления в передних и средних стойках, порогах и рейлингах на крыше.
Однако эта логика не всегда точна, так как General Motors теперь использует материал с пределом прочности 700 МПа в передних и нижних направляющих некоторых своих автомобилей, например, Cadillac ATS. Учитывая, что тенденция проектирования состоит в том, чтобы стали становиться все тоньше для снижения веса, они также должны стать прочнее. В связи с этим, если сделать какое-либо предположение о том, что в боковой конструкции ремонтируемого автомобиля используется неизвестный тип стали, то следует предположить, что детали изготовлены из сверхпрочной стали. Внешние панели могут быть изготовлены из относительно более мягкой стали для облегчения формовки, но даже прочность наружных панелей увеличивается по мере уменьшения толщины панелей для снижения веса.
Частичная замена детали
Если деталь требует замены, не всегда требуется полная замена. Ряд производителей транспортных средств допускают частичную замену по заводским швам или разделение этих деталей на части.
Частичная замена сборки на заводе, по-видимому, является подходом, принятым производителями автомобилей, такими как Honda. Например, нижняя рейка Accord последней модели обслуживается как единый узел, включая часть рейки, которая крепится под пассажирским салоном. Если повреждение ограничено областью перед капотом, Honda разрешает демонтировать этот узел прямо перед капотом и установить его. Это делает ремонт менее инвазивным, поскольку точечные сварные швы OEM под салоном остаются нетронутыми, а защита от коррозии OEM остается нетронутой. Не все производители транспортных средств допускают этот тип процедуры, поэтому важно, как всегда, ссылаться на процедуры производителя транспортного средства. Если производитель транспортного средства не дает рекомендаций за или против этого типа процедуры, специалисты по ДТП должны тщательно взвесить все преимущества, прежде чем принимать решение о проведении такого вида ремонта.
Другие производители транспортных средств предлагают различные процедуры разрезания многих конструктивных элементов.
В отличие от частичной замены узла на заводском шве, разрезание позволяет техническому специалисту заменить часть детали путем маркировки и вырезания детали в месте, указанном производителем транспортного средства. Некоторые производители транспортных средств предлагают несколько мест в одной детали для разделения на секции; другие предлагают только одно местоположение. Разделение должно выполняться только в местах, указанных производителем транспортного средства. Совместная конфигурация места секционирования также должна быть определена на основе процедур производителя транспортного средства.
В конце 1980-х годов компания I-CAR разработала общие рекомендации по разделке, которые многие годы использовались профессионалами отрасли. Эти общие рекомендации по разделению больше не применимы к автомобилям последних моделей. Полный обзор этих общих рекомендаций по разделению см. на портале технической поддержки по ремонтопригодности I-CAR (RTS). Статью можно найти по адресу: Обновление: применимы ли общие рекомендации по разделам?
В следующей статье I‑CAR мы подробно рассмотрим способы крепления для установки деталей
Быстрые изменения требуют переосмысления
Мы находимся в эпицентре «технического цунами» с быстрым развитием транспортных средств, включая мир стали.
Специалисты по ремонту должны быть в курсе последних изменений в технологиях, материалах, процессах и обучении. Старый способ ремонта или замены не обязательно является правильным способом выполнения полного, безопасного и качественного ремонта современных сложных транспортных средств. Крайне важно точно определить материал автомобиля и определить, что подлежит ремонту, а что подлежит замене, а также знать возможные варианты.
Программа I-CAR ® Обучение и сертификация сварщиков ™ включает в себя обучение теории сварки, практическую оценку инструктором оборудования, оборудования и инфраструктуры объекта перед обучением в цеху, практикой, и признанный в отрасли сертификационный тест. Дополнительную информацию обо всех курсах I-CAR по сварке (сварка GMA (MIG) стали, сварка GMA (MIG) алюминия и резка стали) можно найти на сайте www.i-car.com. В рамках обязательств I-CAR перед отраслью цены на обучение сварке были снижены, чтобы каждый технический специалист мог пройти практическое обучение, необходимое для выполнения надлежащей сварки, более доступным.
Все большее число OEM-производителей используют обучение и сертификацию I-CAR по сварке в своих сетевых программах, включая Acura, Audi, Chrysler, Ford, GM, Honda, Infiniti, Jaguar, Land Rover, Lexus, Nissan, Porsche, Scion, Toyota, Вольво и Фольксваген. Кроме того, предприятия, получившие Золотой класс ® , отраслевой стандарт обучения ремонту после аварии, также включают обучение сварке в качестве обязательного требования программы.
Будь то сталь, алюминий, другие конструкционные материалы для транспортных средств или комбинация материалов, важно, чтобы вы оснастили свое предприятие соответствующими инструментами, оборудованием и прошли обучение, чтобы обеспечить полный, безопасный и качественный ремонт. Эти инвестиции могут привести к увеличению прибыльности, повышению операционной эффективности и производительности, а также к более высокому уровню удовлетворенности и удержания клиентов.
Джейсон Бартанен (Jason Bartanen) — директор I-CAR по техническим связям с промышленностью и отвечает за инициативу технической поддержки I-CAR по ремонтопригодности в Техническом центре I-CAR в Эпплтоне, штат Висконсин.