Поршневой экструдер: конструкция, технология, нагреватели :: информационная статья компании Полимернагрев
В данной статье мы рассмотрим подробно такой тип экструзионного оборудования, как поршневый экструдер. Хотя данный тип экструдеров не является таким популярным, как шнековый, однако поршневые экструдеры имеют ряд особенностей, делающих их эффективными при производстве некоторых типов продукции.
Поршневые экструдеры используются при производстве стержней, профилей и трубок из таких материалов, как фторпласты, реактопласты и некоторые типы термопластов. Их широко применяют в цветной металлургии, при производстве керамики, полимеров и композитов, в фармацевтической отрасли и прочих областях промышленности.
Наиболее часто поршневые экструдеры применяются в тех случаях, когда сложно использовать шнековые экструдеры. К примеру, слаботекучие материалы высокофрикционные, намного лучше обрабатываются именно на поршневых типах экструдеров.
История использования поршневых экструдеров
Наибольшей популярностью поршневые экструдеры пользовались в 1960-1970-х годах при производстве древесностружечных материалов. Машины того времени имели производительность от 50 до 120 см в минуту. Позже им на замену пришли машины с применением плоского прессования, которые имели уже гораздо более высокую производительность. В России в то время (тогда еще СССР) использовалось порядка 20 установок поршневых экструдеров для древесностружечных плит.
Однако в Германии до сих пор сохранился крупный завод, который изготавливает пустотные древесностружечные плиты методом поршневой экструзии.
Также поршневые экструзионные установки используются для производства топливных брикетов и гранул из древесного материала.
Современные перспективы поршневых экструдеров
Если рассматривать в общем, то, конечно же, распространение поршневых экструдеров очень сильно уступает шнековым машинам. Производством поршневых экструдеров сейчас занимается всего несколько компаний по всему миру.
Для производства древеснополимерных композитов в литературных источниках довольно часто можно встретить упоминание о поршневых экструдерах, там они описаны как лабораторное оборудование. Но все же перспективы у поршневых экструдеров еще есть, рано их записывать в пережитки истории. Сейчас ведутся исследования в одной японской компании по поводу эффективности использования поршневых экструдеров при работе с ДПКТ, которые получены с применением сшитых полимеров.
Конструкция поршневого экструдера
В поршневом экструдере главными деталаями являются:
- Материальный цилиндр, который может быть с нагревом при помощи электронагревателей кольцевого типа или холодный без обогрева.
- Плунжер (поршень), который проталкивает материал, выполняя возвратно-поступательные движения.
- Фильера экструдера, которая должна иметь соответствующий дорн при изготовлении полых труб или профилей.
В некоторых конструкциях поршневого экструдера фильера с материальным цилиндром выполняется как одно целое, но чаще всего фильеру можно снимать отдельно.
При работе экструдера поданный материал из бункера (может быть холодное или горячее сырье, смесь, компаунд или полимер) поступает в цилиндр через специальное отверстие загрузки. Материал может продвигаться в цилиндр как принудительно, так и без дополнительного воздействия, просто самотеком. В цилиндре уже создается высокое давление при помощи движения поршня, таким образом сырье продвигается в сторону фильеры со значительным уплотнением в своей структуре. Когда поршень возвращается в исходное положение, загрузочное окно опять открывается и в цилиндр поступает следующая порция материала. Схему данного процесса вы можете посмотреть на рисунке.
Электронагреватели для горячей экструзии
Для многих материалов необходимо нагревание сырья, чтобы получить конечный продукт. К примеру, реактопласты при нагревании отвердевают, фторпласты спекаются, термопласты должны подогреваться для контроля текучести. Для этого фильера и цилиндр экструдера оснащаются определенным количеством электронагревателей. Так как форма цилиндра и фильеры часто бывает кольцевая, используются хомутовые нагреватели. Для фильеры экструдера также бывает необходимо использовать плоские рамочные нагреватели с миканитовой изоляцией. Компания Полимернагрев может предложить вам кольцевые миканитовые нагреватели для экструдера и керамические кольцевые нагреватели для экструдера, изготовленные по чертежам с индивидуальными характеристиками.
В горячей зоне экструдера сырье при воздействии высокой температуры принимает свою финальную форму. Очень важно подобрать нагреватели, которые будут выдавать оптимальную температуру для воздействия на материал.
Так же, как и в шнековых экструдерах, в поршневых могут использоваться не только нагреватели, но и охлаждающие зоны, калибровщики, отрезные механизмы и прочие элементы. Для различных материалов процессы, происходящие при нагреве материала, существенно различаются, ведь экструзия реактопластов, переработка термопластических материалов и спекание – это принципиально разные процессы. Также нужно иметь в виду, что поршневые экструдеры не смешивают сырье, как это делают шнековые машины, поэтому поданное сырье в экструдер должно быть уже смешанное.
На рисунке ниже вы можете посмотреть один из вариантов конструкций поршневого экструдера
Поршневые экструдеры можно разделить на вертикальные и горизонтальные. Поршневые экструдеры вертикальной компоновки применяют для обработки наиболее сложных материалов. Для смесей с большей пластичностью можно использовать горизонтальные экструдеры.
При работе поршня в современных экструдерах используется гидросистема для управления частотой и амплитудой работы. Данная гидросистема обычно включает в себя масляный циркуляционный насос с системой управления и двухходовый поршень.
Показатель производительности поршневого экструдера прямопропорционален частоте хода поршневого механизма и объему цилиндра. Также значительное влияние на производительность оказывают такие факторы, как мощность электронагревателей, гидросистемы, длина фильеры (которая может достигать нескольких метров в некоторых конструкциях) и прочие показатели.
Наиболее часто используются экструдеры с показателем производительности на уровне от 5 до 7 кг продукции в час. При этом в основном поршневые экструдеры в основном используют для изготовления профилей и стержней с небольшими размерами, но бывают и машины с большей мощностью для производства изделий большого диаметра.
Купить нагреватели для поршневых или шнековых экструдеров от компании Полимернагрев вы можете заполнив форму заказа или просто написав нам письмо на электронный ящик . Или просто оставьте свои данные в форме заказа обратного звонка, и мы перезвоним вам в ближайшее время. Также при возникновении вопросов оставляйте комментарии к данной статье, мы постараемся сразу же на них ответить.
Экструдеры
Категория: Оборудование для производства
Экструдер состоит из нескольких основных узлов — корпуса, оснащенного нагревательными элементами, рабочего органа (шнека, диска, поршня), размещенного в корпусе, узла загрузки перерабатываемого продукта, привода, системы задания и поддержания температурного режима и других контрольно-измерительных и регулирующих устройств.
Наибольшее распространение в промышленности получили шнековые экструдеры. Захватывая исходный продукт, шнек перемещает его от загрузочного устройства вдоль корпуса экструдера. При этом продукт сжимается, разогревается, пластифицируется и гомогенизируется. Давление в экструдере достигает 15… 100 МПа. По частоте вращения шнека экструдеры подразделяют на нормальные и быстроходные с окружной скоростью соответственно до 0,5 и 7 м/мин, а по конструктивному исполнению — на стационарные и с вращающимся корпусом, с горизонтальным и вертикальным расположением шнека.
Существуют экструдеры со шнеками, осуществляющими не только вращательное, но и возвратно-поступательное движение. Для эффективной гомогенизации продукта на шнеках устанавливают дополнительные устройства — зубья, шлицы, диски, кулачки и др. В последнее время получают распространение планетарно-вальцовые экструдеры, у которых вокруг центрального рабочего органа (шпинделя) вращается несколько дополнительных шнеков (от 4 до 12). Принцип действия дискового экструдера основан на использовании возникающих в упруговязком материале напряжений, нормальных к сдвиговым. Основу конструкций такого экструдера составляют два плоскопараллельных диска, один из которых вращается, создавая сдвиговые и нормальные напряжения, а другой неподвижен. В центре неподвижного диска имеется отверстие, через которое выдавливается размеченный материал. Поршневой экструдер из-за низкой производительности используют ограниченно, в основном для изготовления труб и профилей из реактопластов.
Конструкции экструдеров могут быть классифицированы также по геометрической форме, механическим, функциональным или термодинамическим характеристикам. Кроме того, экструдеры рекомендуется классифицировать по их физическим признакам, поскольку они оказывают влияние на химические структурные характеристики экструдированных продуктов. Особое значение имеют такие параметры, как уклон режущей кромки матрицы и количество тепловой энергии, образующейся в процессе экструдирования за счет механического преобразования энергии; температура во время ведения процесса; влажность экструдируемой массы.
При переработке пищевых продуктов наибольшее распространение получили экструдеры со шнеками полного зацепления, вращающимися в одном направлении, когда вершины одного шнека взаимодействуют с впадинами другого.
В двухшнековых самоочищающихся экструдерах обеспечиваются более быстрый пуск шнека и работа на повышенной скорости. В них реже возникают подъемы давления, так как не происходит накопление продукта. В одношнековых экструдерах, вследствие того, что продукт может оставаться в витках и накапливаться, создавая разрывы потока, подъемы давления бывают чаще. В результате продукт из экструдера выпускается неравномерно.
Однако предполагается, что в одношнековом экструдере износ шнека концентрируется по наружной кромке к торцу его витков, и это обеспечивает восстановление шнека.
Двухшнековый экструдер более подвержен износу. Изнашиваются шнеки в местах загрузки и выгрузки продукта. В этой связи свойства конечного продукта и эффективность процесса экструдирования в большой степени зависят от износа рабочих органов машины при обработке в двухшнековом экструдере. При использовании двухшнекового экструдера не требуется предварительной гидротермической обработки продукта, что упрощает производственный процесс. Гидролиз крахмала пшеничной муки протекает гораздо эффективнее в двухшнековом экструдере, чем в одношнековом. В двухшнековом экструдере зоны пластификации и повышения давления отделены друг от друга, что позволяет независимо осуществлять пластификацию и экструдирование продукта. Известно, что затраты, связанные с приобретением одношнековых экструдеров, ниже по сравнению с затратами на приобретение двухшнековых машин. Однако последние компенсируются меньшими эксплуатационными расходами. Высокие расходы по эксплуатации одношнековых машин связаны с длительными простоями при чистке, большими трудозатратами и объемом работ по обслуживанию.
Сравнение конструктивных и технологических достоинств одношнековых и двухшнековых экструдеров показывает значительное преимущество последних.
Материал для матриц должен быть коррозионно-стойким, обладать антиадгезионными свойствами и высокой прочностью. Чтобы снизить прилипаемость формуемого продукта, отверстия полируют и хромируют. Широко применяют в настоящее время матрицы, состоящие из металлической обоймы и сменных вставок. Вставки представляют собой сменные гильзы с формующими отверстиями, изготовляются из пластмасс с сильно выраженными антиадгезионными свойствами.
Форма и размер предматричной камеры зависят от свойств перерабатываемого продукта, типа и размеров нагнетающего механизма и должны способствовать выходу выпрессовываемой массы через каналы матрицы с возможно более равномерной скоростью, а также препятствовать образованию застойных зон. Формование экструзией имеет ряд преимуществ: непрерывность осуществления процесса с высокой скоростью, безотходность технологии и высокая культура производства.
Машина А1-КХП (рис.) предназначена для формования палочек из кукурузной крупы тепловой и механической обработкой.
Рис. Машина А1-КХП
Машина состоит из станины 1, бункера 7, корпуса подшипника 9, цилиндра 3, механизма резки 4, вариатора, щита управления с нагревателями. Машина имеет два индивидуальных привода: для шнека и механизма резки.
На верхней плите сварной станины установлен электродвигатель 8 привода шнека, соединенный через муфту с быстроходным валом редуктора 10. Последний, в свою очередь, с помощью муфты соединяется с валом корпуса подшипника. В литом корпусе подшипника установлен вал, вращающийся в радиальных подшипниках качения. Для восприятия осевой нагрузки от формующего шнека в корпусе установлен упорный шарикоподшипник.
К корпусу подшипника фланцем крепится сварной цилиндр с расположенным внутри него шнеком. С противоположной стороны цилиндр закрыт матрицей. Температура в рабочей зоне контролируется термопарами, введенными в зону через пробку 5. Для нагрева кукурузной массы в передней части цилиндра укреплен блок электронагревателей 6.
У переднего торца матрицы расположен механизм резки с вращающимися ножами, который приводится в движение от отдельного электродвигателя через бесступенчатый вариатор. Электродвигатель и вариатор находятся внутри станины. Частота вращения вариатора регулируется рукояткой 2, установленной в непосредственной близости от панели управления. Для удобства обслуживания механизм резки отводится в сторону.
Над цилиндром установлен бункер для приема кукурузной крупы. Кукурузная крупа из бункера машины через регулируемую заслонку поступает в приемное отверстие цилиндра, где происходит прессование продукта и нагрев до температуры 145 °С.
В результате воздействия тепла, влаги и давления крупа превращается в пластическую массу, которая выдавливается шнеком через отверстия матрицы. При выходе из отверстий матрицы масса под действием пара, образующегося из перегретой влаги, вспучивается, образуя пористую хрустящую жилу. Механизм резки делит выходящие жилы на палочки, которые уносятся конвейером.
Порция крупы (1,5… 2,0 кг при температуре в цилиндре 80… 145 °С) приготовляется за 30…60 мин до пуска машины.
Режим нагрева цилиндра подбирается для каждой машины индивидуально в зависимости от сорта, помола, влажности крупы и степени износа.
Техническая характеристика экструдера А1-КХП приведена в табл.
Машина Б8-КХ-ЗП (рис.) предназначена для производства палочек из кукурузной крупы посредством ее тепловой и механической обработки с последующей фасовкой на других автоматах.
Рис. Машина Б8-КХ-ЗП
Машина состоит из станины 1, формующего механизма 2, механизма 5 отрезки палочек по длине, ворошителя 3 кукурузной крупы, блока электронагревателей 4.
Формующий механизм состоит из охватываемого шнека с правой нарезкой, шнековой втулки с левой нарезкой, матрицы с двенадцатью отверстиями диаметром 3 мм, обоймы с четырьмя отрезными ножами, приводимой во вращение через цепную и клиноременную передачи от электродвигателя.
Ворошитель представляет собой корпус, внутри которого вращается вал с лопастями, перемешивающий поступающую из бункера крупу.
Блок электронагревателей предназначен для нагрева рабочей зоны машины в период пуска и автоматического под держания постоянной температуры от 160 до 180 °С. Во избежание перегрева машины в зоне загрузки предусматривается принудительное водяное циркуляционное охлаждение корпуса формующего механизма с подключением к сети водоснабжения.
Схемой машины предусмотрено ручное управление электроприводами шнека и ножа, а также ручное и автоматическое управление блоком нагревателей.
Перед пуском машины производится нагрев рабочей зоны формующего механизма в течение 30…35 мин до 160… 180 °С с помощью блока электронагревателей. За 25.. .30 мин до пуска машины готовится первая порция крупы влажностью 20.. .21 %. Подготовленная крупа по специальному лотку вручную засыпается небольшим потоком в отверстие зоны загрузки при включенной машине. После выхода палочек из формующей матрицы открывается заслонка, и в машину поступает крупа влажностью 13. .. 14 %.
Нагрев продукта в момент запуска происходит за счет теплопередачи, а в дальнейшем — за счет тепла, образующегося в результате трения между продуктом, шнеком и шнековой втулкой. Выпрессованная полужидкая масса за счет перепада давления при выходе из отверстия формующей матрицы взрывается с диаметра 3 мм до диаметра 8… 12 мм.
Таблица. Техническая характеристика экструдеров
Показатель |
А1-КХП |
Б8-КХ-ЗП |
Производительность, кг/ч |
75 |
90 |
Мощность, кВт: | ||
привода |
21 |
18,5 |
электронагревателя |
3,84 |
2,8 |
Число шнеков |
1 |
1 |
Частота вращения шнеков, мин»1 |
71 |
79,3 |
Диаметр шнеков, мм |
155 |
74 |
Максимальная температура в зоне нагрева, «С |
145 |
160. |
Максимально допустимое давление экструзии, МПа |
10 |
12 |
Габаритные размеры, мм |
1750x890x1635 |
1200x1200x1900 |
Масса, кг |
1300 |
950 |
Экструдер МФБ-1 (рис.) состоит из плиты 15, станины 1 с кронштейном 12, электродвигателя 14, червячного редуктора 13, корпуса 4 со шнеком 3 и формующей матрицей 2, головки 7 с парой конических шестерен 8 и загрузочной воронки 5 со спиралью 11.
Рис. Шнековый экструдер МФБ-1
Внутри головки 7 находятся горизонтальный вал 9 с конической шестерней и приводной звездочкой 10, вертикальный вал 6 с конической шестерней и спиралью. Спираль 11 подает конфетную массу в корпус 4 и непрерывно перемешивает ее в загрузочной воронке 5. Шнек 3 выпрессовывает массу через формующие каналы матрицы 2 в виде пяти бесконечных жгутов, которые после предварительного охлаждения разрезаются на конфеты.
Техническая характеристика экструдера МФБ-1 приведена в табл.
Двухшнековый экструдер поточных линий ШФК (рис.) отличается от экструдера МФБ-1 наличием двух горизонтальных шнеков, находящихся в самостоятельных камерах. Шнеки нагнетают массу в общую предматричную камеру 3. Масса выходит через шесть или восемь формующих каналов. Частота вращения спирали в загрузочной воронке 2 изменяется бесступенчатой рукояткой 1. Нагнетающие шнеки имеют постоянную частоту вращения. При переходе с формования жгутов круглого сечения на прямоугольные шнеки заменяют.
Рис. Шнековый экструдер ШФК
В шнековых экструдерах скорости выхода жгутов через формующие каналы неодинаковы. Для выравнивания скоростей увеличивают длину средних формующих каналов по сравнению с крайними, устанавливают дополнительные сопротивления перед средними каналами или в самих каналах либо устанавливают более высокую температуру стенок крайних формующих каналов. Добиться полного равенства скоростей во всех каналах весьма трудно.
Техническая характеристика экструдера приведена в табл.
Экструдер ШВФ-22 (рис.) предназначен для выдавливания конфетной массы при производстве пралиновых конфет.
Рис. Экструдер ШВФ-22
Он имеет в предматричной камере перегородки, образующие секции у каждого выходного отверстия. Это выравнивает скорости у выдавливаемых жгутов. Бункер 1 укреплен на корпусе питателя 2 с расположенными в нем рифлеными валками 3. В корпусе нагнетателя 4 вращаются нагнетающие шестеренные роторы 5, выполненные из набора шестерен. Предматричная камера 7 имеет вертикальные формующие каналы 8. В нижней части корпуса нагнетателя и предматричной камеры имеются вертикальные перегородки 6, которые делят корпус и камеру на отдельные секции.
Бункер, корпус нагнетателя и нагнетатель, а также предматричная камера имеют рубашки для обогрева.
Конфетная масса вытягивается из бункера рифлеными валками 3 и равномерно подается по всей длине шестеренных роторов 5. Они нагнетают массу в предматричную камеру 7 и из нее через формующие каналы 8 выдавливаются жгуты 9 пралиновой массы.
Техническая характеристика экструдера ШВФ-22 приведена в табл.
Таблица. Техническая характеристика экструдеров
Показатель |
МФБ-1 |
ШФК |
ШВФ-22 |
Производительность, кг/ч |
325 |
150…310 |
1000 |
Число отверстий в матрице |
5 |
6 |
22 |
Потребная мощность, кВт |
1,7 |
2,8 |
2,8 |
Габаритные размеры, мм |
1250x845x1640 |
1365x775x2100 |
1000x1160x2980 |
Масса, кг |
410 |
955 |
1220 |
DeltaBots представляет 3D-принтер 3D PotterBot с поршневым экструдером
Бизнес
Подпишитесь на автора
Подписаться
Не хочу
2
Компания DeltaBots решила произвести революцию в керамическом и гончарном производстве, и помогает ей в этом 3D-принтер 3D PotterBot и поршневой экструдер собственного производства. Этот 3D-принтер был разработан специально для изготовления гончарных и керамических изделий. 3D-принтер 3D PotterBot обладает чрезвычайно прочной конструкцией, позволяющей ему создавать красивые и аккуратные керамические сосуды.
Главным отличием 3D PotterBot можно считать стационарный поршневой экструдер. Еще ни один дельта 3D-принтер прежде не был снабжен таким экструдером. Разработчикам пришлось немало попотеть, чтобы создать его, однако это был единственный способ получить полный контроль над процессом экструзии пастообразных материалов.
DeltaBots использовала новаторский подход: вместо того чтобы закрепить экструдер на шарнирных руках дельта 3D-принтера, она перенесла управление платформой вниз. Сочетание поршневого экструдера и шагового двигателя стало таким выигрышным, потому что экструдер ведет себя как печатающая головка обычного настольного FFF/FDM 3D-принтера, только вместо пластика используется глина. Так как конструкция поршневого экструдера отличается от экструдеров с применением сжатого воздуха, у пользователя появилась возможность управлять скоростью экструзии во время печати, а также изменять направление потока, когда слой закончен. Если при экструзии пастообразных материалов используется сжатый воздух, то экструзия часто идет рывками. У 3D PotterBot таких проблем не бывает, и глина всегда выдавливается равномерно.
Второе отличие 3D PotterBot в чрезвычайно большом рабочем объеме: этому принтеру под силу напечатать керамический сосуд высотой 43 см.
3D PotterBot был создан специально для творческих студий, школ и институтов искусств, которые хотят расширить свои возможности и привлечь внимание дизайнеров к гончарному делу. DeltaBots предлагает приобрести 3D PotterBot с поршневым экструдером за 2950 долларов. Стоит упомянуть, что экструдер представлен в двух размерах: 2000 мл и 4000 мл.
Ниже перечислены основные характеристики 3D PotterBot:
- дельта 3D-принтер, созданный специально для изготовления керамических изделий
- высокомощный шаговый двигатель, совместимый с Arduino/Ramps и другими драйверами 3D-принтера
- четыре взаимозаменяемых сопла
- набор программ, чтобы облегчить вашу жизнь
Со слов представителя компании, экструдер сделан из авиационного алюминия и поликарбоната. 3D PotterBot способен выдерживать высокое давление, оказываемое на его конструкцию при экструзии глины. Пользователь может экспериментировать с разными пастообразными материалами и не беспокоиться о том, что экструдер сломается. Экструдер приводится в действие высокоточным шаговым двигателем NEMA-23, управляемым специальными программами для 3D-печати.
Подпишитесь на автора
Подписаться
Не хочу
2
Комментарии к статье
Еще больше интересных статей
daymon
Загрузка
02.04.2015
82723
150
Подпишитесь на автора
Подписаться
Не хочу
На сайте периодически задают вопросы куда можно применить свой принтер. Вот решил выложить немного а…
Читать дальше
daymon
Загрузка
16.08.2017
21559
84
Подпишитесь на автора
Подписаться
Не хочу
Всем привет!
Сегодня я познакомлю с очередной партией ошибок, которые оставят все в…
Читать дальше
el_mind
Загрузка
13.11.2018
12143
73
Подпишитесь на автора
Подписаться
Не хочу
Сей опус подразумевает, что вы уже приняли решение о том, что этому бизнесу быть и вы четко понимает…
Читать дальше
Экструзия материала на основе поршня из сырья Ti-6Al-4V для дополнительного использования в литье металлов под давлением
. 2022 4 января; 15 (1): 351.
дои: 10.3390/ma15010351.
Леннарт Ваалкс 1 , Ян Ленгерих 1 , Филипп Имгрунд 1 , Клаус Эммельманн 2
Принадлежности
- 1 Научно-исследовательский институт аддитивных технологий Фраунгофера IAPT, Am Schleusengraben 14, 21029 Гамбург, Германия.
- 2 Институт лазерных и системных технологий iLAS, Гамбургский технологический университет TUHH, Denickestr. 17, 21073 Гамбург, Германия.
- PMID: 35009497
- PMCID: PMC8746147
- DOI:
10.
3390/ма15010351
Бесплатная статья ЧВК
Леннарт Ваалкс и др. Материалы (Базель). .
Бесплатная статья ЧВК
. 2022 4 января; 15 (1): 351.
дои: 10.3390/ma15010351.
Авторы
Леннарт Ваалкс 1 , Ян Ленгерих 1 , Филипп Имгрунд 1 , Клаус Эммельманн 2
Принадлежности
- 1 Научно-исследовательский институт аддитивных технологий Фраунгофера IAPT, Am Schleusengraben 14, 21029 Гамбург, Германия.
- 2 Институт лазерных и системных технологий iLAS, Гамбургский технологический университет TUHH, Denickestr. 17, 21073 Гамбург, Германия.
- PMID: 35009497
- PMCID: PMC8746147
- DOI: 10.3390/ма15010351
Абстрактный
Экструзия материалов на основе поршней обеспечивает экономию средств для пользователей литья металлов под давлением, когда она используется в качестве дополнительного процесса формования сырых деталей небольшими партиями. Это, однако, требует использования серийного сырья и производства достаточно плотных неспеченных деталей, чтобы обеспечить свойства материала, подобные металлическому литью под давлением. В этой статье представлен методологический подход к определению параметров процесса, специфичных для материала, для промышленно используемого сырья для литья под давлением металла Ti-6Al-4V на основе усилия экструзии. Установлено, что при оптимальной температуре экструзии 95 °C и скорость печати 8 мм/с, усилие экструзии 1300 Н обеспечивает высокую плотность сырых деталей без недоэкструзии. Полученные свойства спеченных деталей демонстрируют значения, сравнимые с литьем металла под давлением с точки зрения плотности деталей (макс. 99,1%) и свойств при растяжении (макс. предел текучести: 933 МПа, макс. предел прочности на растяжение: 1000 МПа, макс. удлинение при разрыве: 18,5%) в зависимости от выбранной ориентации сборки. Таким образом, в принципе может быть продемонстрировано дополнительное использование исходного сырья Ti-6Al-4V.
Ключевые слова: Ти-6Ал-4В; производство добавок; сырье; зеленые детали; экструзия материала; литье металла под давлением.
Заявление о конфликте интересов
Авторы заявляют об отсутствии конфликта интересов.
Цифры
Рисунок 1
( а ) Макросъёмка…
Рисунок 1
( a ) Макросъемка гранулированного сырья Ti-6Al-4V; ( б ) СЭМ…
фигура 1( a ) Макроснимок гранулированного сырья Ti-6Al-4V; ( b ) СЭМ-изображение ингредиентов исходного сырья.
Рисунок 2
( a ) Изображение…
Рисунок 2
( a ) Изображение используемой системы PEX; ( б ) сечение…
фигура 2 ( a ) Изображение используемой системы PEX; ( b ) Поперечное сечение поршневого экструдера в формате САПР.
Рисунок 3
Экструзионная модель для поршневого материала…
Рисунок 3
Экструзионная модель для экструзии материала на основе поршня.
Рисунок 3Экструзионная модель для экструзии материала на основе поршня.
Рисунок 4
( a ) Уитстоун полный…
Рисунок 4
( a ) Полномостовая схема Уитстона с четырьмя активными тензодатчиками; (…
Рисунок 4 ( a ) Полномостовая схема Уитстона с четырьмя активными тензодатчиками; ( b ) экспериментальная установка для калибровки; ( c ) результаты калибровки.
Рисунок 5
Микроструктура использованного сырья Ti-6Al-4V…
Рисунок 5
Микроструктура использованного сырья Ti-6Al-4V после спекания.
Рисунок 5Микроструктура использованного сырья Ti-6Al-4V после спекания.
Рисунок 6
Схематическое изображение влияния…
Рисунок 6
Схематическое изображение влияния силы выдавливания на зеленую часть…
Рисунок 6 Схематическое изображение влияния усилия экструзии на плотность сырца при заданной скорости печати, температуре экструзии и расходе 100%.
Рисунок 7
Методический подход к идентификации и…
Рисунок 7
Методический подход к идентификации и валидации специфических для материалов параметров процесса для дополнительной…
Рисунок 7Методический подход к идентификации и проверке параметров процесса для конкретных материалов для дополнительного использования PEX в уже установленных технологических цепочках MIM.
Рисунок 8
( и ) Тестовая установка…
Рисунок 8
( a ) Испытательная установка для определения массовых расходов; ( б )…
Рисунок 8 ( a ) Испытательная установка для определения массовых расходов; ( b ) примерный график усилия выдавливания в испытанном интервале усилия.
Рисунок 9
Представление образцов на растяжение в…
Рисунок 9
Представление образцов на растяжение в Slic3r: ( a ) плоский; ( б )…
Рисунок 9Представление образцов на растяжение в Slic3r: ( a ) плоский; ( b ) боковые; ( c ) вертикальный.
Рисунок 10
( a ) Определено экспериментально…
Рисунок 10
( a ) Массовые расходы, определенные экспериментальным путем для испытанного интервала усилий и температур;…
Рисунок 10 ( a ) Экспериментально определенные массовые расходы для испытанного интервала сил и температур; ( b ) кривые вязкости, показывающие поведение псевдопластического течения для испытанного температурного интервала экструзии.
Рисунок 11
Цифровые изображения теста…
Рисунок 11
Цифровые изображения края испытуемого образца в плоскости x-y: ( а ) Т…
Рисунок 11Цифровые изображения края испытуемого образца в плоскости x-y: ( a ) T = 95 °C, v c = 8 мм/с, F e = 1300 Н; ( b ) T = 95 °C, v c = 12 мм/с, F e = 1700 Н.
Рисунок 12
Цифровые изображения поверхности разрушения…
Рисунок 12
Цифровые изображения поверхности излома в плоскости z-x испытательного образца, напечатанные на…
Рисунок 12 Цифровые изображения поверхности излома в плоскости z-x испытательного образца, напечатанные при v = 8 мм/с и T = 95 °C: ( a ) F e = 1200 Н; ( b ) F e = 1300 Н; ( c ) кривые вязкости с выделенным серым цветом диапазоном скоростей сдвига для плотных зеленых частей при v = 4 мм/с и v = 8 мм/с.
Рисунок 13
СЭМ-изображения теста…
Рисунок 13
СЭМ-изображения образца для испытаний, напечатанные при v = 8 мм/с, T…
Рисунок 13РЭМ-изображений тестового образца, напечатанного при v = 8 мм/с, T = 95 °C и F e = 1300 Н с образцовым дефектом слоя в плоскости z-x при разных уровнях увеличения: ( и ) 100×; ( б ) 500×.
Рисунок 14
Средняя усадка PEX…
Рисунок 14
Средняя усадка распечатанных на растяжение образцов PEX из-за спекания; показано здесь…
Рисунок 14 Средняя усадка распечатанных на растяжение образцов PEX из-за спекания; здесь показана плоская ориентация.
Рисунок 15
Микрофотографии срезанного образца…
Рисунок 15
Микрофотографии вырезанных головок образцов из справочника MIM и исследуемых…
Рисунок 15Микрофотографии вырезанных головок образцов из справочника MIM и исследованных ориентаций сборки для анализа плотности; поры из-за спекания отмечены желтым цветом, а поры из-за PEX отмечены красным: ( a ) ссылка MIM; ( b ) плоская ориентация; ( c ) боковая ориентация; ( d ) вертикальная ориентация.
Рисунок 16
Поверхности излома испытанных на растяжение…
Рисунок 16
Поверхности излома испытанных образцов на растяжение ( a ) Справочник MIM; ( б…
Рисунок 16 Поверхности излома испытанных образцов на растяжение ( и ) ссылка MIM; ( b ) плоская ориентация; ( c ) боковая ориентация, желтые стрелки показывают плохо соединенные пути выдавливания в области опорной конструкции; ( d ) вертикальная ориентация, желтые стрелки указывают на видимые пути экструзии на поверхности трещины.
Рисунок 17
Схематическое изображение модели трещины…
Рисунок 17
Схематическое изображение модели трещины (см. [38]): ( a ) Плоская ориентация: трещина…
Рисунок 17Схематическое изображение модели разрушения (см. [38]): ( a ) Плоская ориентация: рост трещины в пределах путей выдавливания; ( b ) вертикальная ориентация: рост трещины между слоями склеивания.
См. это изображение и информацию об авторских правах в PMC
Похожие статьи
Структурная, механическая и in vitro характеристика индивидуально структурированного Ti-6Al-4V, полученного методом прямого лазерного формования.
Холландер Д.А., фон Вальтер М., Вирц Т., Селлеи Р., Шмидт-Рольфинг Б., Паар О., Эрли Х.Дж. Холландер Д.А. и соавт. Биоматериалы. 2006 март; 27 (7): 955-63. doi: 10.1016/j.biomaterials.2005.07.041. Epub 2005, 22 августа. Биоматериалы. 2006. PMID: 16115681
Механические свойства образцов Ti-6Al-4V, полученных фасонным напылением металла.
Бауфельд Б., ван дер Бист О. Бауфельд Б. и соавт. Sci Techn Adv Mater. 2009 18 мая; 10 (1): 015008. дои: 10.1088/1468-6996/10/1/015008. Электронная коллекция 2009, февраль. Sci Techn Adv Mater. 2009. PMID: 27877271 Бесплатная статья ЧВК.
Проблемы аддитивного производства космических деталей: перекрестное загрязнение порошкового сырья и его влияние на конечные продукты.
Брандао А.Д., Джерард Р., Гампингер Дж., Беретта С., Макая А., Памбагуян Л., Гидини Т. Брандао А.Д. и др. Материалы (Базель). 2017 12 мая; 10 (5): 522. дои: 10.3390/ma10050522. Материалы (Базель). 2017. PMID: 28772882 Бесплатная статья ЧВК.
Формирование структуры и свойств двухфазного сплава Ti-6Al-4V при холодном напылении присадок с межпроходной ковкой.
Щицын Ю., Карташев М., Кривоносова Е., Ольшанская Т., Трушников Д. Щицын Ю. и соавт. Материалы (Базель). 2021 6 августа; 14 (16): 4415. дои: 10.3390/ma14164415. Материалы (Базель). 2021. PMID: 34442935 Бесплатная статья ЧВК.
Начальное исследование диффузионных связей между сверхпластичным Ti-6Al-4V для применения в имплантологии.
Элиас К.
Л., Даэн Г.С., Брантли В.А., МакГламфи Э.А. Элиас К.Л. и соавт. Джей Простет Дент. 2007 г., июнь; 97 (6): 357–65. doi: 10.1016/S0022-3913(07)60024-9. Джей Простет Дент. 2007. PMID: 17618918
Посмотреть все похожие статьи
Цитируется
Разработка технологии трехмерной оптической верификации без загрязнения окружающей среды металлических деталей с различными свойствами поверхности.
Куо CC, He ZY, Lee CX. Куо С.С. и др. Материалы (Базель). 2022 4 сентября; 15 (17): 6139. дои: 10.3390/ma15176139. Материалы (Базель). 2022. PMID: 36079520 Бесплатная статья ЧВК.
использованная литература
- немецкий Р.М. Справочник по литью металлов под давлением.
Эльзевир; Амстердам, Нидерланды: 2019. Литье металлических порошков под давлением (MIM): основные тенденции и рынки; стр. 1–21.
- немецкий Р.М. Справочник по литью металлов под давлением.
- Герман Р.М., Бозе А. Литье металлов и керамики под давлением. Федерация производителей металлических порошков; Принстон, Нью-Джерси, США: 1997.
- Хини Д.Ф. Справочник по литью металлов под давлением. Эльзевир; Амстердам, Нидерланды: 2019. Порошки для литья металлов под давлением (MIM), стр. 45–56.
- Эннети Р.К., Онбаттувелли В.П., Гульсой О., Кейт К.Х., Атре С.В. Справочник по литью металлов под давлением. Эльзевир; Амстердам, Нидерланды: 2019. Рецептура порошкового связующего и производство компаундов для литья металлов под давлением (MIM), стр.
57–88.
- Эннети Р.К., Онбаттувелли В.П., Гульсой О., Кейт К.Х., Атре С.В. Справочник по литью металлов под давлением. Эльзевир; Амстердам, Нидерланды: 2019. Рецептура порошкового связующего и производство компаундов для литья металлов под давлением (MIM), стр.
- Гонсалес-Гутьеррес Дж., Кано С., Шушниг С., Кукла С., Сапкота Дж., Хольцер С. Аддитивное производство металлических и керамических компонентов путем экструзии материалов из высоконаполненных полимеров: обзор и перспективы на будущее. Материалы. 2018;11:840. дои: 10.3390/ma11050840. — DOI — ЧВК — пабмед
Грантовая поддержка
- ZF4547817DE8/Федеральное министерство экономики и энергетики
деталей для JAWA, ČZ, JAWA-ČZ, Stadion, Babetta, Simson,.
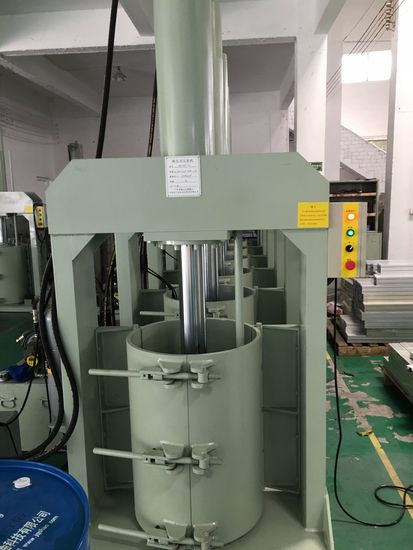
Уважаемые покупатели, на основании новых правил взимания НДС в странах ЕС с конечных клиентов (One Stop Shop) взимание НДС обязательно по ставке в зависимости от страны доставки. После заполнения всех данных о доставке и выставлении счета (без заполнения реквизитов компании) на следующем этапе оформления заказа ставка НДС переключится на национальную ставку покупателя. Этот шаг изменит цену в соответствии с начисленной ставкой НДС. Все цены в интернет-магазине указаны по умолчанию с чешским НДС 21%. Обратите внимание на правильность заполнения всех данных о доставке и выставлении счета, особенно выбор страны. Последующие изменения не могут быть изменены, и заказ будет отменен. Спасибо за Ваше понимание. Доставка в Великобританию невозможна с 01.01.2021. |
Экструдер поршневого пальца (10-18 мм) — UNI
Наша цена 15,90 евро
Крышка лицевой маски (реплика) — JAWA 50 23 (Mustang)
Наша цена 71,15 евро
Щуп опережения
Наша цена 7,73 евро
Модель Škoda Fabia R5 (1:43), Ян КОПЕЦКИЙ #32 Ралли Монте-Карло 2018
Наша цена 25,05 евро
Каретка привода спидометра — Pionýr
Наша цена 52,17 евро
Улавливание реакции, АЛЮМИНИЙ — JAWA 50 05,20-23
Наша цена 7,78 евро
В НАЛИЧИИ
Сумка на раме (большая), КРАСНАЯ — JAWA 50 Pionýr
Наша цена 84,08 евро
В НАЛИЧИИ
Винт коробки — Pérák, ČZ 125/150
Наша цена 3,98 евро
Ступица колеса (TWN) — JAWA 50 05,20-23
Наша цена 57,32 евро
Руль, ХРОМ (Чехия) — Babetta
Наша цена 42,84 евро
Окончание выхлопной трубы — JAWA 350 634-640
Наша цена 5,79 евро
В НАЛИЧИИ
Модель JAWA 350 Automatic (1966) 1:18, ЧЕРНЫЙ
Наша цена 19,87 евро
Модель JAWA 50 тип 21 Масштаб 1:18, БИРЮЗОВЫЙ
Наша цена 24,98 евро
Колесо в сборе 19″ (новая ступица CZ), ZINC — Stadion, Jawetta
Наша цена 118,76 евро
Ступица колеса, НОВЫЙ ПРОДУКТ (Чехия) — Stadion, Jawetta
Наша цена 71,86 евро
Шестерня привода спидометра (CZ) — Babetta 210
Наша цена 29,54 евро
Подарочный набор косметики для мужчин — Яростный поршень
Наша цена 5,96 евро
Замок для планшета, комплект из 2 шт. — JAWA, ČZ
Наша цена 31,44 евро
Держатель подножек, сварной (поперечный) — JAWA 50 05
Наша цена 35,76 евро
Ручка переключения передач, ХРОМ — Stadion, Jawetta
Наша цена 39,20 евро
Ось колеса (ПЕРЕДНЯЯ), ЦИНК — JAWA 350 634
Наша цена 5,96 евро
Ось колеса (ЗАДНЯЯ), ЦИНК — JAWA-ČZ 355-356, ČZ 450-475
Наша цена 8,81 евро
Ручка газа (слайдер) BARE — JAWA, ČZ
Наша цена 10,78 евро
Сумка на раме (большая), ГОЛУБАЯ — JAWA 50 Pionýr
Наша цена 78,85 евро
В НАЛИЧИИ
Сумка на раме (большая), ТЕМНО-СИНИЙ — JAWA 50 Pionýr
Наша цена 78,85 евро
В НАЛИЧИИ
Ось колеса (ПЕРЕДНЯЯ), ЦИНК — JAWA 250/350 Pérák
Наша цена 9,08 евро
Ось колеса (ПЕРЕДНЯЯ), ЦИНК — JAWA-ČZ 355-356, ČZ 450-475
Наша цена 5,96 евро
Ось колеса (ПЕРЕДНЯЯ), ЦИНК — JAWA 250/350 Pérák
Наша цена 7,09 евро
Передняя крышка (реплика) — JAWA 50 05,20
Наша цена 79,21 евро
В НАЛИЧИИ
Тоннель передней крышки — JAWA 50 05-20
Общая цена 60,50 евро
Наша цена 32,04 евро
Коробка в сборе — JAWA 50 23 (Мустанг)
Наша цена 97,94 евро
Модель JAWA 350 OGAR (1948) 1:18, СЕРЫЙ ГОЛУБЬ
Наша цена 19,87 евро
Модель JAWA 500 OHC (1956) Масштаб 1:18, КРАСНЫЙ (ЧЕРНОЕ СИДЕНЬЕ)
Наша цена 19,87 евро
Модель JAWA 250 Perák (1948) 1:18, КРАСНЫЙ
Наша цена 19,87 евро
Модель JAWA 250 Perák (1948 г. ) Масштаб 1:18, ВОЕННО-ЗЕЛЕНЫЙ
Наша цена 19,87 евро
Модель JAWA 350 Perák (1948) Масштаб 1:18, КРАСНЫЙ
Наша цена 19,87 евро
Ароматизированная автомобильная карта ручной работы — JAWA 250
Наша цена 1,99 евро
В НАЛИЧИИ
Ароматизированная автомобильная открытка ручной работы — JAWA Kývačka
Наша цена 1,99 евро
АКЦИЯ
Подарочный набор косметики для мужчин — Моторные масла
Наша цена 6,65 евро
Головка блока цилиндров (CZ) — JAWA 50 550-555
Наша цена 36,58 евро
Ступица колеса, НОВЫЙ ПРОДУКТ (Чехия) — JAWA 50 05,20-23
Наша цена 93,28 евро
Держатель подножек, сварной (поперечный) — JAWA 50 20
Наша цена 37,73 EUR
Втулка ручки газа (слайдер) — JAWA, ČZ
Наша цена 3,98 евро
Горловина всасывания — JAWA 50 555
Наша цена 14,08 евро
Передняя крышка с дверью (правосторонний карбюратор) — JAWA 50 550-555
Наша цена 147,17 евро
В НАЛИЧИИ
Модель JAWA 350 Automatic (1966) 1:18, КРАСНЫЙ
Наша цена 19,87 евро
Модель JAWA 50 тип 20 1:18, ЗЕЛЕНЫЙ ВОЕННЫЙ
Наша цена 19,87 евро
Модель JAWA 50 тип 20 1:18, СВЕТЛО-КРАСНЫЙ
Наша цена 19,87 евро
Grover Heavy Transfer — экструзионные заливочные поршневые насосы
Grover Heavy Transfer — экструзионные заливочные поршневые насосыДом | О Нам | Гарантия | Контакт США |