Как получают бензин? Присадки и добавки бензина.
Автомобильные бензины получают путем переработки нефти, газового конденсата, природного газа, угля, торфа и горючих сланцев, а также синтезом из окиси углерода и водорода.
Основным сырьем для производства автомобильных бензинов является нефть: около 25% нефти, добываемой в мире, перерабатывают в бензин.
В России все товарные бензины получают из нефти и газоконденсатов. На газоперерабатывающих заводах путем выделения из газов жидких углеводородов получают газовый бензин. Газовые бензины обладают хорошими пусковыми свойствами и при добавлении в небольших количествах в товарные бензины способны улучшать их эксплуатационные свойства.
Современные автобензины готовят смешением компонентов, получаемых путем прямой перегонки, каталитического риформинга и каталитического крекинга, изомеризации, алкилирования, полимеризации и других процессов переработки нефти и газа.
Качество компонентов, используемых для приготовления тех или иных марок товарных автомобильных бензинов, существенно различается и зависит от технологических возможностей предприятия. Товарные бензины одной и той же марки, но выработанные на различных нефтеперерабатывающих заводах (НПЗ), имеют неодинаковый компонентный и фракционный составы, что связано с различием технологических процессов и перерабатываемого на них сырья на каждом конкретном нефтеперерабатывающем предприятии. Даже бензины одной марки, выработанные конкретным заводом в разное время, могут отличаться по компонентному составу в связи с проведением регламентных работ на отдельных технологических установках, изменением состава сырья и программы завода по выпуску продукции.
Однако во всех случаях должна соблюдаться технология получения товарных бензинов на данном предприятии, что является обязательным требованием стандартов и технических условий на автомобильные бензины.
Основными технологическими процессами производства автомобильных бензинов является каталитический риформинг и каталитический крекинг. Несмотря на ограничения по содержанию ароматических углеводородов, процесс каталитического риформинга по-прежнему остается определяющим процессом производства бензинов, так как он является основным источником высокооктановых компонентов, а также водорода для установок гидроочистки.
Вследствие ужесточения норм на содержание серы в моторных топливах необходимо увеличение мощностей гидрообессеривания, что требует дополнительного водорода.
Снижение доли и роли бензина риформинга в производстве экологически чистых реформулированных бензинов обусловлено не только ограничением содержания ароматических углеводородов, но и неудовлетворительным распределением октановых характеристик по фракциям катализата, в особенности до 100 °С.
В связи с этим процесс бензинового риформинга целесообразно и необходимо сочетать с процессами удаления бензола и изомеризации бензина С5 — 1 00 °С.
В последние годы технология и коммерческая активность по созданию на НПЗ мира новых установок каталитического крекинга в псевдоожиженном слое микросферического катализатора приобрела рекордно высокий уровень за все время применения этого процесса.
Таким образом, если уже в настоящее время объем вырабатываемого в мире бензина каталитического крекинга практически сравнялся с суммарным объемом выработки бензинов риформинга и изомеризации, то в ближайшем будущем бензин каталитического крекинга плюс компоненты сопряженных с ним процессов (алки-лирование, получение оксигенатов, полимербензинов и др.) будут лидировать в производстве автобензинов на НПЗ в сравнении с процессами риформинга, требующими дополнительных ресурсов прямогонных бензинов и, соответственно, нефти.
В последние 10—15 лет процесс каталитического крекинга был значительно усовершенствован, главным образом с целью увеличения селективности при конверсии исходного вторичного сырья в бензин (каталитические реакции основные, термические — минимальны).
На отечественных НПЗ эксплуатируются установки каталитического крекинга с лифт-реактором с предварительной гидроочистки исходного сырья — вакуумного газойля мощностью 2 млн т/год по сырью. Эти установки обеспечивают выход бензина более 50% на сырье, который имеет октановое число по моторному методу 80—82 ед. и по исследовательскому методу 90—93 ед.
Улучшение октановых характеристик достигают выбором катализатора и ужесточением режима работы установок. Это сопровождается так же приростом выхода низкокипящих олефинов С3 — С4, что благоприятно для увеличения ресурсов сырья алки- лирования и получения высокооктановых оксигена- тов: метил-третбутилового эфира (МТБЭ), метилтретамилового эфира (МТАЭ), ди-изопропило- вого эфира (ДИПЭ) и др. Однако, когда при жестких режимах крекируют тяжелое сырье, это приводит к образованию диеновых углеводородов во фракциях С4 — С5. Диены отрицательно влияют на процесс алкилирования: увеличивается расход кислоты, снижается выход и качество алкилата. Меры по ужесточению режима крекирования, подбору сырья и катализатора позволяют улучшить (на 2—4 ед.) октановую характеристику по исследовательскому методу. Однако при этом, в связи с ростом содержания олефинов в бензине, увеличивается его чувствительность, то есть разность между октановыми числами по исследовательскому и моторному методам.
Широкое применение находят системы комплекса каталитического крекинга предварительно гидроочи- щен-ного вакуумного газойля в блоке с производством МТБЭ и алкилированием. Это решает проблему углубления переработки сырья по бензиновому варианту, частично — проблему снижения содержания сернистых соединений в бензине, увеличения производства высокооктановых компонентов бензина и собственного производства кислородсодержащей высокооктановой добавки. Однако состав непосредственно бензина каталитического крекинга С5 — 1 80 °С остается неудовлетворительным по содержанию олефиновых углеводородов, содержанию остаточной серы, разнице между ИОЧ и МОЧ, также по химической стабильности компонента.
Поэтому целесообразно использовать в этих комплексах каталитического крекинга следующие технологические решения: изоамилены, третичные гексены и гептены бензина каталитического крекинга превращать в высокооктановые эфиры метанола, что повышает октановое число топлива.
Если этерифицировать низкокипящий бензин каталитического крекинга, а не только фракцию С5, выработка эфиров возрастает на 40—50%.
На установках каталитического крекинга разделением бензина в процессе каталитической дистилляции можно получить бензин фракции С5 — 100 °С, пригодный для этерификации. Сырье этерификации нуждается в очистке от диенов и сернистых соединений. Содержание диолефинов снижают до 0,1 — 0,05% путем селективного гидрирования в реакторе-колонне.
В результате этерификации фракции С5 — 100 °С каталитического крекинга ее октановый индекс повышается на 2—3 ед. и значительно, на 25%, уменьшается содержание в ней олефинов.
Поскольку МТАЭ и сумму МТГЭ (метил-трет- гекси-ловый и метил-трет-гептиловый эфир) получают для нужд данного завода, их выделение в чистом виде не требуется. Технологически целесообразно оставить эфиры в бензине каталитического крекинга, как компоненты товарного бензина.
Важное значение для увеличения ресурсов реформулированных товарных бензинов приобретает пропилен каталитического крекинга. Вырабатываемый в увеличенном объеме при жестких режимах на новых катализаторах пропилен каталитического крекинга на заводах, не производящих полипропилен, наиболее целесообразно использовать для организации производства диизо-пропилового эфира (ДИПЭ).
ДИПЭ обладает свойствами конкурентными с МТБЭ, МТАЭ: содержит 15,7% кислорода (МТБЭ — 1 8,2%, МТАЭ — 1 5,7%), обладает высоким октановым числом 98 ед. по моторному методу и 112 ед. по исследовательскому, октановый индекс — 105 ед. (МТБЭ — 108 ед., МТАЭ — 104 ед.), имеет теплоту сгорания 9400 ккал/кг, температуру кипения 68 °С, давление насыщенных паров по Рейду — 30 кПа (МТБЭ — 60 кПа). Склонность ДИПЭ к образованию гидроперекисей является его недостатком.
В целом, технический прогресс в технологии каталитического крекинга позволяет существенно увеличить выход легких олефинов C3 — С7 и вырабатывать меньше высококипящих фракций бензина, обогащенных ароматическими углеводородами. При эффективном использовании этих возможностей суммарный эффект облагораживания бензинов каталитического крекинга (включая ДИПЭ + МТБЭ + ал- килат + этерификат С5 — С7) — значительно возрастает.
В настоящее время алкилат становится важнейшим компонентом реформулированных экологически чистых бензинов.
Алкилат — идеальный компонент бензина, поскольку имеет высокие октановые числа по исследовательскому и моторному методам, низкое давление насыщенных паров, не содержит ароматических соединений олефинов и серы.
Алкилирование — это не только процесс повышения октановых характеристик бензина при снижении в нем ароматических углеводородов, но и процесс снижения его испаряемости.
Высокое давление насыщенных паров фракций С4 — С5 .исключает возможность увеличения их использования в товарном бензине, поэтому процесс аликилирования, позволяющий снижать давление насыщенных паров и одновременно увеличивать значение октанового числа продукта по моторному методу, имеет исключительно важное значение для производства современных автобензинов.
Получение товарного бензина с высоким моторным октановым числом путем замены бензола и других ароматических углеводородов в бензине на алкилат и эфиры (МТБЭ, МТАЭ) позволяет в более мягких условиях осуществлять процесс каталитического риформинга. При снижении жесткости процесса каталитического риформинга увеличивается срок службы катализатора и период работы установки между его регенерациями, повышается выход катализата с пониженным содержанием ароматических углеводородов, улучшается качество получаемого водорода для установок гидроочистки.
Лучшим сырьем (особенно сернокислотного алкилирования) являются бутилены нормального ряда, не содержащие в своем составе изобутилена. В связи с этим фракцию С4 каталитического крекинга для избирательного извлечения изобутилена предварительно этерифи-цируют метанолом, а рафинат направляют на алкилирование, обеспечивая двойной эффект: получение МТБЭ и алкилата в едином технологическом потоке.
Наряду с использованием диалкиловых эфиров С5 и выше в состав товарных автобензинов допускается в Европе вовлекать до 3% метанола, до 5% этанола (в США до 10%), до 7% третбутилового спирта и до 10% изопропилового или изобутилового спирта. При этом массовая доля кислорода не должна превышать 2,7%.
При введении в бензины метанола обязательно добавление стабилизирующих агентов. В случае введения этанола стабилизирующие агенты могут также добавляться. В бензин следует вводить антикоррозионные присадки, если может возникнуть опасность выделения воды.
На смену широко применяемому МТБЭ, мировое потребление которого в 2001 году превысило 25,7 млн тонн, приходит денатурированный этанол, так как его получают из возобновляемого сырья (биомасса, древесина и т. д.), и он не оказывает вредного влияния на источники водоснабжения, что является причиной запрещения применения МТБЭ в США (штат Калифорния).
В то же время, по оценке сторонников МТБЭ, эффект от его вклада в решение экологической проблемы значительно превосходит риск, связанный с его применением.
Вовлечение в состав автобензинов этанола до 10% позволяет уменьшить на то же количество содержание ароматических углеводородов без снижения детонационной стойкости товарного бензина.
Недостатками спиртовых добавок являются низкая гидролитическая устойчивость, низкие противоиз- нос-Л ные и антикоррозионные свойства. Спирты проникают в материал шдангов и уплотнений топливной системы автомобиля и АЗС, что выводит их из строя, нарушая герметичность. При использовании спиртов в 2—3 раза возрастает содержание альдегидов в составе отработавших газов.
Однако, как показывает зарубежный опыт, использование спиртовых компонентов в автобензинах является перспективным не только в плане сохранения нефтяных ресурсов, но и улучшения экологических свойств моторных топлив. Количество вводимых спиртов позволяет снизить на ту же величину концентрацию нежелательных ароматических углеводородов и содержание оксида углерода в отработавших газах автомобилей.
Ароматические углеводороды (толуол, ксилолы) обладают высокой детонационной стойко стью и применяются как высокооктановые компоненты бензинов, а азотсодержащие производные ароматических углеводородов можно использовать как октаноповы- шающие добавки.
Антидетонационные свойства N-метиланилина были обнаружены практически одновременно с открытием антидетонационных свойств тетраэтилсвинца.
В качестве добавки к авиационным бензинам N-метиланилин применялся в Германии и СССР, а в автомобильных бензинах более 1 0 лет используется в России в концентрации до 1,3 % масс. В настоящее время разработан ряд композиционных октаноповы- шающих добавок, содержащих N-метиланилин: АДА, АвтоВэм, БВД, Феррада и др.
Добавка АДА — это практически N-метиланилин.
Добавка АвтоВэм — смесь N-метиланилина с марга-нецсодержащим компонентом.
Добавка БВД — смесь N-метиланилин с МТБЭ.
При использовании сочетания N-метиланилина с соединениями марганца отмечается синергетический эффект, то есть прирост октанового числа бензина при совместном использовании этих антидетонаторов больше, чем суммарный прирост в случае раздельного их применения в тех же концентрациях.
Наряду с антидетонаторами на основе марганца в составе неэтилированных бензинов могут быть использованы железосодержащие антидетонаторы: карбинол-ферроцены, диалкилферроцены и ферроцены. На основании положительных испытаний автобензинов, содержащих ферроценовые соединения до 37 мг железа на 1 дм3 бензина, Государственная Межведомственная комиссия по испытанию топлив, масел, смазок и специальных жидкостей при Госстандарте РФ допустила их к производству и применению.
С целью улучшения эксплуатационных и экологических свойств автомобильных бензинов в их состав вводят моющие и многофункциональные присадки.
Необходимость применения моющих присадок для обеспечения чистоты карбюраторов и впускной системы двигателей впервые возникла в США. Причиной этому послужило ужесточение норм на выбросы вредных веществ с отработавшими газами. Как показала практика, многие автомашины, успешно прошедшие контроль по содержанию окиси углерода в отработавших газах на холостом ходу, после некоторого пробега не удовлетворяли нормам.
Было установлено, что причиной этого является образование осадков и отложений в системе всасывания и в результате окисления под влиянием воздуха и
полимеризации на подогретой поверхности нестабильных угле-водородов-олефинов, а также реакционно-способных соединений картерных газов, которые направляют в систему всасывания для уменьшения эмиссии углеводородов.
Эффективным способом борьбы с отложениями в карбюраторе и впускной системе является добавление к бензинам специальных моющих присадок. Впервые бензины с моющими присадками были разработаны фирмой «Шеврон» в 1954 г., но широкое распространение они получили с введением принудительной системы вентиляции картера. Требование по обязательному применению моющих присадок возникло после установки на двигателях инжекторных топливных систем нейтрализаторов ОГ, а также частичной рециркуляции ОГ, то есть возврата их во впускную систему двигателя.
Предотвращение загрязнения карбюратора с помощью моющих присадок позволяет сохранить заводские регулировки карбюратора и тем самым снизить расход бензина, уменьшить токсичность ОГ в процессе эксплуатации двигателя и сократить число ремонтов, связанных с регулировкой карбюратора.
При работе двигателей с принудительной системой вентиляции картера на бензинах без моющих присадок, нарушение работы карбюратора наблюдается через 12-15 тыс. км пробега, а при использовании бензина с моющими присадками длина пробега автомобиля возрастает до 32 тыс. км, то есть больше чем в 2 раза.
Необходимо отметить, что моющие присадки первого поколения, эффективно удаляя отложения из карбюратора, имеют существенный недостаток: они могут способствовать образованию отложений на впускных клапанах. Этим недостатком не обладают моюще-диспергирующие присадки для авиабензинов или присадки второго поколения.
Самыми совершенными являются присадки третьего и четвертого поколения или присадки, предотвращающие образование отложений в карбюраторе, на впускных клапанах, на форсунках и других критических деталях и узлах двигателя. Кроме того, присадки четвертого поколения уменьшают образование нагара в камере сгорания двигателя и тем самым — требования к антидетонационным свойствам бензина в процессе эксплуатации автомобиля.
Изменения, внесенные в конструкцию двигателя с целью снижения содержания вредных компонентов в отработавших газах, усиливают тенденцию образования отложений на впускном клапане.
Поэтому значение этих присадок в последние годы заметно возросло. В США и ряде стран Европы применение моющих присадок становится обязательным.
Разработкой и производством моющих присадок занимаются такие фирмы, как «Shell», «BASF», «Лубри-зол», «Этил» и др.
В нашей стране разработаны и вырабатываются моющие присадки к автобензинам второго поколения «Афен» и «Автомаг». Проводятся работы по синтезу и отработке технологии получения моющих присадок третьего и четвертого поколения.
При наличии в товарных бензинах нестабильных компонентов для обеспечения требуемого качества в процессе длительного хранения (3—5 лет) в них вводят антиокислители и деактиваторы металлов. В качестве антиокислителей используют 2,6-ди-трет-бутил-4ме-тилфенол или парооксидифе- ниламин. Антиокислительные присадки вводят в нестабильные компоненты бензина непосредственно на технологических установках в концентрации до 0,10% массы для обеспечения требуемого индукционного периода
Деактиваторы металлов —это присадки, подавляющие каталитическое действие металлов на окисление топлива. Они усиливают стабилизирующее действие антиокислителя, что позволяет на 30—70% снизить его концентрацию в топливе. При этом концентрация деак-тиватора металлов в бензине составляет 0,005—0,01 % масс. Наиболее эффективны соединения, способные образовывать внутрикомплексные соли, главным образом хелатного (клешневидного) строения. К ним относятся салицилидены, например, дисалицилиденпропилендиамин (N^N-дисалицилаль-1,2-пропилендиамин).
В таких соединениях атом металла надежно экранирован и не способен вступать в реакции, катализирующие окисление.
В некоторых случаях возникает необходимость каким-либо образом маркировать то или иное топливо. Например, в этилированный бензин добавляют красители с целью обратить внимание на наличие в нем токсичного тетраэтилсвинца. Окрашивают дизельное топливо с минимальным (50—10 ррт) содержанием серы. Маркировка топлив может осуществляться не только при помощи красителей, для этой цели можно использовать одорирующие присадки и бесцветные специальные вещества. Маркирующие присадки вводят в бензин в столь малой концентрации, что они практически не влияют на физико-химические и эксплуатационные характеристики.
Присадки вводят в бензин различными способами при его производстве на НПЗ, терминалах, в автохозяйствах и непосредственно в топливный бак автомобиля.
Во всех случаях требуется обеспечить эффективное смешение присадки с бензином при наименьших энергетических и трудовых затратах.
Вне всякого сомнения, продолжающиеся совершенствования конструкции двигателей автомобилей будут приводить к постоянному изменению роли присадок к бензинам. Поскольку эффективность присадок зависит от топлива и конструкции двигателя, производители и поставщики присадок к бензинам должны работать вместе с конструкторами двигателей и автотранспортными компаниями для достижения оптимальной эксплуатации автомобилей по расходу топлива, обеспечивая экологические требования.
www.vseznaniya.ru
Основные способы получения автомобильных топлив из нефти
Строительные машины и оборудование, справочник
Категория:
Автомобильные эксплуатационные материалы
Публикация:
Основные способы получения автомобильных топлив из нефти
Читать далее:
Основные способы получения автомобильных топлив из нефти
Автомобильные топлива получают из нефти прямой перегонкой (первичный процесс) и деструктивными методами (вторичные процессы) ее переработки. Прямая перегонка всегда предшествует деструктивным методам переработки.
При деструктивных (химических) способах происходит изменение структуры и химического состава углеводородов, образующих нефть, а при прямой перегонке (физическом способе) нефть лишь разделяется на фракции (с определенными температурами кипения) без протекания химических реакций
Прямая перегонка нефти осуществляется в установке, представляющей собой комплекс сложных устройств, основными элементами которых являются трубчатая печь и ректификационная колонна.
В результате нагрева нефти до 330—350 °С образуется смесь паров нефти и неиспарившегося жидкого остатка, которая направляется в ректификационную колонну. В ректификационной колонне происходит разделение нефтяных паров на фракции-, составляющие тот или иной нефтепродукт; причем можно отобрать в одну группу фракции, у которых температура кипения отличается всего лишь на 5-8 °С.
Тяжелые фракции нефти, поступая в колонну в жидкой фазе,, Уже в нижней ее части отделяются от паров и отводятся из нее в в аде мазута, а пары конденсируются на тарелках колонны. Чем в иже температура кипения фракций, тем выше в колонне они конденсируются.
Прямая перегонка нефти позволяет получить лишь 10—15% бензина, и только отдельные сорта нефти дают выход бензина до 20—25%, т. е. столько, сколько составляют ее фракции, выкипающие в пределах от 35 до 195 °С. Поэтому, для того чтобы обеспечить, например, Работу одного грузового автомобиля на прямогонно.м бензине в течение года, нужно переработать около 75—100 тыс. л. нефти. Для Увеличения выхода бензина и других светлых нефтепродуктов применяют деструктивные (химические) методы переработки нефти, при помощи которых можно также улучшить качество нефтепродуктов, в частности детонационную стойкость бензина.
Рис. 1. Схема нефтеперегонной установки: 1 — трубчатая печь; 2 — испарительная колонна; 3 — ректификационная колонна; 4 — до. полнительная колонна; 5 — насос; в — теплообменник; 7 — нодогрлзеотделитель
Крекинг является основным методом деструктивной переработки нефти. При крекинге происходит расщепление высокомолекулярных углеводородов и превращение их в низкомолекулярные легкокипя-щие углеводороды, пз которых состоят бензин и другие светлые нефтепродукты.
Крекинг может происходить под действием повышенных температур (470 — 540 °С) и давлении (20—70 кгс/см2)— термический крекинг или же под действием повышенной температуры (450— 500 °С), незначительного давления (до 1,5 кгс/см2), но в присутствии катализатора — каталитический крекинг. В обоих случаях пары сырья направляются в ректификационную колонну для разделения на фракции, как и при прямой перегонке. При термическом крекинге они поступают из нагревательной печи, пройдя испаритель, а при каталитическом — еще н реактор.
Проект первой в мире промышленной установки для крекинга нефти был разработан в 1891 г. русским инженером В. Г. Шуховым.
Легко расщепляются молекулы нефти, содержащие серу и кислород. По этой причине в бензинах термического крекинга находятся нежелательные сернистые и кислородные соединения. У бензинов, получаемых термическим крекингом, недостаточно высокие оюано-е число (не более 66—74)— основной показатель качества бензина п большое содержание непредельных углеводородов (до 30—40%). Из-за непредельных углеводородов бензин термического крекинга обладает плохой стабильностью и при хранении интенсивно окисляется и осмоляется. Поэтому на современных нефтеперегонных заводах термический крекинг не применяют. Каталитический крекинг является основным деструктивным методом получения бензинов.
Катализатор, направляя процесс в нужную сторону, способствует образованию изомерных предельных углеводородов (парафинов, ароматических), а также превращению части образовавшихся непредельных углеводородов в предельные.
Каталитический крекинг позволяет получнть бензин с октановым числом до 95. Сырьем для каталитическго крекинга обычно служат керосиновые, соляровые и газойлевые фракции прямой перегонки нефти.
Качество прямогонных бензинов (особенно полученных из сернистых нефтей) улучшается при их последующем каталитическом риформинге, являющемся одним из основных процессов современного нефтеперерабатывающего завода. Каталитический риформинг протекает в атмосфере водорода при температуре 480— 520 °С, давлении примерно 30 кгс/см2 и в присутствии алюмомолибденового катализатора (гидроформинг-процесс) или алюмоплатинового катализатора (платформинг-процесс),
Бензиновые фракции получают также из углеводородных газов методами полимеризации и алкилирования. Полимерные бензины, получаемые из газов, богатых олефиновыми углеводородами, имеют высокое октановое число, но обладают недостаточной химической стабильностью
Автомобильные топлива, полученные одним из указанных способов, должны быть очищены от органических (нафтеновых) кислот, непредельных углеводородов, смолисто-асфальтеновых веществ, сернистых соединений, а также подвергнуты стабилизации для повышения их химической и физической стойкости во время транспортирования, хранения и потребления.
Применяемые для очистки продукты обладают способностью взаимодействовать с нежелательными примесями (соединениями) и образовывать вещества удаляемне из топлива путем отстаивания или Другим способом.
Содержание серы в дизельном топливе может быть снижено путем ого гидрогенизации. Здесь происходит расщепление сернистых соединении и образование сероводорода, который удаляется промывкой щелочью.
Для снижения температуры застывания дизельное топливо подвергают депарафинизацин.
Повышение химической стабильности топлив осуществляется путем торможения процессов окисления непредельных углеводородов. К бензину добавляются специальные присадки, называемые антиокислителями (ингибиторами).
Такие ингибиторы, как параоксидифениламин, древестно-смоляной антиокислитель и другие, добавляются к бензину в сотых и тысячных его долях, но они увеличивают срок хранения бензина в несколько раз.
Повышение физической стабильности бензина достигается снижением содержания растворенных в нем газообразных и жидких углеводородов с высоким давлением паров, которые легко улетучиваются при его транспортировании и хранении. При этом изменяются фракционный состав, давление насыщенных паров, испаряемость и часто детонационная стойкость бензина.
Пары бензина пропускают через стабилизационные установки (ректификационные колонны), где происходит отделение газообразных углеводородов.
Для повышения детонационной стойкости бензинов к ним добавляют присадки.
Товарное топливо, т. е. то, которое поступает в автотранспортные предприятия, чаще всего представляет собой смесь из фракций, полученных несколькими способами переработки. В частности, бензин может представлять собой сложную смесь продуктов прямой перегонки, крекинга, каталитического риформинга, полимерных бензинов и высокооктановых изопарафиновых и ароматических компонентов.
Реклама:
Читать далее: Краткие сведения о производстве автомобильных масел
Категория: — Автомобильные эксплуатационные материалы
Главная → Справочник → Статьи → Форум
stroy-technics.ru
Все о бензине: Получение бензина
Один из способов получения бензина – прямая перегонка нефти. Проходя через ряд теплообменников, нефть подогревается, очищается и попадает в ректификационную колонку высотой 15-30 метров. Различные фракции выкипают в разных интервалах температур и конденсируются на разной высоте. Бензин выкипает при температурах 95 — 180 0С.Для получения высококачественного топлива и присадок проводят и вторичную перегонку нефти.
Основными методами деструктивной переработки нефти и получения высококачественного бензина(получение присадок) являются:
Термический крекинг – переработка сырья при температуре 450 — 5000С и давлении 2-5 МПа.
Каталитический крекинг – протекает при температуре 470-5300С и давлении 70-370 МПа в присутствии катализатора для получения желательных углеводородов.
Каталитический риформинг – это процесс облагораживания низкокачественного бензина путем его каталитической переработки под давлением водорода в присутствии катализатора. В результате каталитического риформинга получается высокооктановый компонент автомобильных бензинов в результате каталитических превращений низкооктановых фракций, вырабатываемых при прямой перегонке и крекинге.
Гидрокрекинг – это каталитическая переработка нефтяных фракций и остаточных продуктов дистилляции нефти (мазута, гудрона) под давлением водорода для получения бензина. Гидрокрекинг протекает при температуре 260-4500С и давлении 5-20 МПа на целиотсодержащих катализаторах.
Гидроочистка проводится для повышения качества и стабильности светлых дистиллятов при температуре 250-4200С и давлении 2-5МПа в присутствии катализаторов.[1]
Известны особые случаи, когда для производства бензинов применяется и иное углеводородное сырьё. Возможен отгон бензиновых фракций из смолполукоксования и коксования (утилизация тяжелых остатков крекинга с целью получения дистиллята широкого фракционного состава) с дополнительной их очисткой (например, в Эстонской ССР бензин производился из горючих сланцев). Производятся бензины и из синтез-газа (продукт газификации угля, конверсии метана) при помощи синтин-процесса (синтез Фишера — Тропша).
Синтезирование применяют для получения индивидуальных углеводородов, обладающих высокими антидетонационными свойствами и используемых в качестве добавок к бензинам. Процесс осуществляется в присутствии катализаторов.
Существуют и другие процессы получения высокооктановых компонентов бензина (алкилирование, изомеризация).
ben4in.blogspot.com
Бензин из угля в домашних условиях своими руками: технолошия производста
Далеко не каждая европейская, да и любая страна мира может похвастать большими запасами нефти. Зато углеводородное топливо в виде бензина или солярки активно используется во всех странах. В то же время залежи бурого и каменного угля встречаются куда чаще, отсюда и возникла идея получать дизельное топливо и бензин из угля. В этой статье мы рассмотрим, как это делается на производстве и можно ли что-то подобное организовать в условиях частного домашнего хозяйства.
Как происходит выделение бензина из угля?
Стоит отметить, что переработка угля с целью получить разные виды моторного топлива – вовсе не миф. Более, того существует две проверенных методики, реализованные на практике еще в начале прошлого века.
В те времена нацистская Германия, стремящаяся завоевать всю Европу, именно этими способами обеспечивала свою военную технику горючим, поскольку собственных месторождений нефти у нее нет. В то же время в распоряжении страны имелись залежи бурого угля, из которого на двух десятках заводов производился синтетический бензин и дизельное топливо.
Для справки. Обе методики были изобретены разными немецкими учеными в начале 20-го века, соответственно, получили их имена.
Как оказалось, уголь по своему химическому составу не слишком отличается от нефти. Основа у них общая – горючие соединения углерода с водородом, только доля водорода в нефти значительно больше. Если число водорода в углях удастся уравнять с нефтью, то и получение жидкого горючего станет реальностью. Вот способы решения проблемы:
- гидрогенизация, иначе – ожижение (процесс Бергиуса).
- газификация с последующим синтезом топлива (процесс Фишера – Тропша).
Чтобы понять, удастся ли наладить выделение бензина в домашних условиях, надо получить общее представление об этих химико-технологических процессах, о них будет рассказано ниже.
Процесс гидрогенизации
Для успешного проведения процесса и получения до 800 кг жидкого топлива из 1 т сырья берут бурый или каменный уголь. Главное условие эффективного достижения результата – наличие в углях 35% летучих веществ. Перед переработкой их перемалывают, измельчая до пылевидной фракции, а затем просушивают. После этого угольную фракцию смешивают с мазутом или тяжелыми маслами, чтобы получилось сырье в виде пасты.
Во время протекания процесса деструктивной гидрогенизации технология предусматривает прямое добавление недостающего водорода в уголь.
Для этого сырье помещают в специальный автоклав и производят его нагрев. При этом давление внутри сосуда достигает 200 Бар, а температура – 500 °С. Мало того, в зоне химической реакции должны находиться вещества — катализаторы и растворители. По данной методике получение бензина из угля проходит внутри автоклава в 2 стадии:
- жидкофазная;
- парофазная.
В сосуде под большим давлением и при высокой температуре протекает несколько сложных химических реакций. Чтобы не нагружать рассказ специфическими терминами, поясним простыми словами: в автоклаве происходит насыщение угля водородом и распад сложных органических соединений на простые. В результате после операций очистки на выходе получаем синтетическое дизтопливо или бензин. Это зависит от условий протекания процесса и степени трансформации угольно-масляной смеси. Но выходу горючего из установки предшествует еще ряд операций:
- центрифугирование;
- полукоксование;
- дистилляция.
Как видите, наладить столь сложное производство своими руками не представляется возможным. Главная сложность – оборудование, вряд ли удастся такое изготовить самому. Взять хотя бы автоклав, где давление выше, чем в кислородных баллонах. Да и в целом подобное производство представляет взрывопожарную опасность.
Получение бензина путем газификации
Данный метод, изобретенный немецкими учеными Ф. Фишером и Г. Тропшем, предусматривает производство дизельного топлива и бензина путем предварительной газификации угольного сырья. Это происходит в большой емкости – реакторе при температуре до 350 °С и давлении не более 30 Бар. Хотя здесь условия и не настолько жесткие, как при гидрогенизации, но реализовать их ничуть не проще. Например, потому что сквозь слой угля надо под большим давлением продувать перегретый водяной пар, а значит, не обойтись без мощного парового котла.
После газификации на выходе из реактора образуется так называемый синтез-газ, состоящий из водорода и обычного угарного газа (СО). Кстати, сингаз можно прямо использовать в качестве газообразного топлива без последующей переработки.
Полученные газы поступают во второй реактор, где и происходит окончательная переработка угля в жидкое топливо. Там же располагаются вещества – катализаторы. В промышленности для этой цели могут использоваться разные соединения, но любое из них обязательно содержит железо, никель или кобальт. Не вдаваясь в тонкости химии, отметим, что на выходе из второго реактора получается горючее, которое должно еще пройти процедуру крекинга. То есть, разделение на бензин и дизельное топливо из угля.
Побочными продуктами реакции являются различные вещества и парафин. Среди выделяющихся летучих веществ наибольшая доля приходится на углекислый газ, что считается большой проблемой производства горючего подобным методом. Также достаточно быстро теряет активность катализатор, поэтому его постоянно требуется обновлять. Эти факторы, да еще ряд не столь значительных причин, приводят к высокой себестоимости продукта. При цене на нефть 50 долларов за баррель производство бензина из угля методом Фишера – Тропша считается нерентабельным.
Существует и другой метод газификации углей – термический. Он схож с явлением пиролиза, поскольку осуществляется нагревом сырья в емкости извне и при отсутствии кислорода. Другое дело, что разложение твердого топлива на газы происходит при температуре 1200 °С, а для этого требуется соответствующее оборудование. Позитивная сторона термического метода состоит в том, что часть пиролизных газов направляется на подогрев исходного сырья, а другая – на синтез бензина. За счет этого снижаются затраты на энергоносители, так как уголь во время разложения может подогревать себя сам.
Для справки. На просторах интернета можно найти описание разных установок, с помощью которых можно получить бензин из природного газа в домашних условиях. Вначале он конвертируется в синтез-газ, а затем перерабатывается в жидкое топливо. Даже если считать, что эти самодельные аппараты работоспособны, провести газификацию угля гораздо сложнее.
Выводы
Невзирая на то, что выделение моторного топлива из каменного и бурого угля вполне реально и давно проверено на производстве, организовать его в домашних условиях вряд ли возможно. Конечно, всегда найдется несколько умельцев – энтузиастов, что любят добиваться поставленной цели и смогут синтезировать бензин своими руками. Но для этого надо подробно изучить технологию и прилично повозиться с оборудованием, не говоря уже о пожарной опасности.
Для широкого круга домовладельцев и автолюбителей получение солярки и бензина из угля недоступно. А если подойти к вопросу с точки зрения экономики, то и нерентабельно. На данный момент, пока на эту тему не появилось новых изобретений и разработок, проще и надежнее пользоваться обычным, «нефтяным» бензином.
cotlix.com
Сами делайте дома бесплатный бензин
Руководство по изготовлению в домашних условиях 100% заменителя бензина любой марки из воды и бытового газа, поступающих в квартиру.
Общее описание
Получаемая при помощи данного описания жидкость – метанол или метиловый спирт.
В чистом виде метанол применяется в качестве растворителя, а так же как высокооктановая добавка к моторному топливу, а также как самый высокооктановый (с октановым числом равным 150) бензин. Это тот самый бензин, которым заправляют гоночные мотоциклы и автомобили. Зарубежные исследования показали, что двигатель, работающий на метаноле, служит во много раз дольше чем при использовании обычного автомобильного бензина. При неизменном рабочем объеме двигателя его мощность повышается на 20%. Выхлоп двигателя, работающего на этом топливе, экологически чист и при проверке его на токсичность вредные вещества практически отсутствуют.
Малогабаритный аппарат для получения этого топлива прост в изготовлении, не требует особых знаний и дефицитных деталей, безотказен в работе. Его производительность зависит от различных причин, в том числе и от габаритов. Аппарат, схему и описание сборки которого предлагаем вашему вниманию, при Д=75мм дает три литра готового топлива в час, имеет вес около 20 кг, и габариты приблизительно: 20 см в высоту, 50 см в длину и 30 см в ширину.
Внимание: метанол является сильным ядом. Он представляет собой бесцветную жидкость с температурой кипения 65оС, имеет запах, подобный запаху обычного питьевого спирта, и смешивается во всех отношениях с водой и многими органическими жидкостями. Помните о том, что 30 миллилитров выпитого метанола смертельны!
Принцип действия и работа аппарата
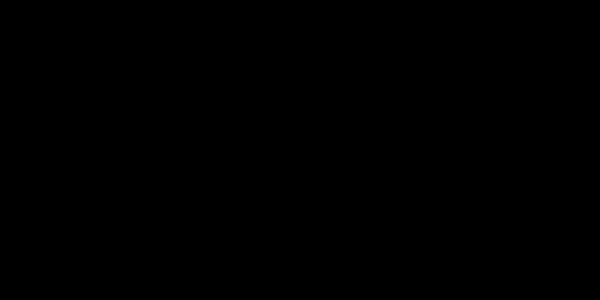
Рисунок 1 – Схема принципиальная аппарата
Водопроводная вода подключается к «входу воды» (15) и, проходя далее, разделяется на два потока: один поток через краник (14) и отверстие (С) входит в смеситель (1), а другой поток через краник (4) и отверстие (Ж) идет в холодильник (3), проходя через который вода, охлаждая синтез-газ и конденсат бензина, выходит через отверстие (Ю).

Рисунок 2 – Смеситель
Бытовой природный газ подключается к трубопроводу «Вход газа» (16). Далее газ входит в смеситель (1) через отверстие (Б), в котором перемешивается с паром воды, затем нагревается на горелке (12) до температуры 100 – 120оС. Далее из смесителя (1) через отверстие (Д) нагретая смесь газа и водяного пара поступает в реактор (2) через отверстие (В).
Реактор (2) наполнен катализатором №1, состоящим из 25% никеля и 75% алюминия (состоит из стружки или в зерен, промышленная марка ГИАЛ-16). В реакторе происходит образование синтез газа под воздействием температуры от 500оС и выше, получаемой за счет нагрева горелкой (13). Далее нагретый синтез-газ входит через отверстие (Е) в холодильник (З), где он должен охладиться до температуры 30-40оС или ниже. Затем охлажденный синтез-газ через отверстие (И) выходит из холодильника и через отверстие (М) входит в компрессор (5), в качестве которого можно использовать компрессор от любого бытового холодильника. Далее сжатый синтез-газ с давлением 5-50 через отверстие (Н) выходит из компрессора и через отверстие (О) поступает в реактор (6).
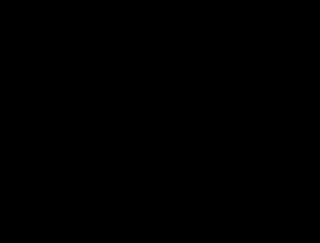
Рисунок 3 – Реактор
Реактор (6) заполнен катализатором №2, состоящим из стружки 80% меди и 20% цинка (состав фирмы «ICI», марка в России СНМ-1). В этом реакторе, который является самым главным узлом аппарата, образуется пар синтез-бензина. Температура в реакторе не должна превышать 270оС, что можно проконтролировать градусником (7) и регулировать краником (4). Желательно поддерживать температуру в пределах 200-250оС, можно и ниже.
Затем пары бензина и не прореагировавший синтез-газ через отверстие (П) выходят из реактора (6) и через отверстие (Л) входят в холодильник (З), где пары бензина конденсируют и через отверстие (К) выходят из холодильника. Далее конденсат и не прореагировавший синтез-газ входят через отверстие (У) в конденсатор (8), где накапливается готовый бензин, который выходит из конденсатора через отверстие (Р) и краник (9) в какую-либо емкость.
Рисунок 4 – Холодильник
Отверстие (Т) в конденсаторе (8) служит для установки манометра (10), который необходим для контроля давления в конденсаторе. Оно поддерживается в пределах 5-10 атмосфер или больше в основном с помощью краника (11) и частично краника (9). Отверстие (Х) и краник (11) необходимы для выхода из конденсатора не прореагировавшего синтез газа, который идет на рециркуляцию обратно в смеситель (1) через отверстие (А). Краник (9) регулируют так, чтобы постоянно выходил чистый жидкий бензин без газа. Лучше будет, если уровень бензина в конденсаторе будет увеличиваться, чем уменьшаться. Но самый оптимальный случай, когда уровень бензина будет постоянным (что можно проконтролировать путем встроенного стекла или какого-либо другого способа). Краник (14) регулируют так, чтобы в бензине не было /воды/ и в смесителе пара образовывалось лучше меньше, чем больше.

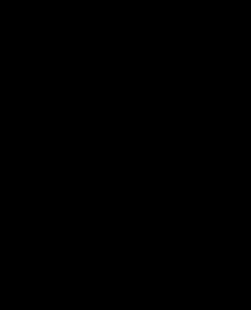
Рисунок 5 – Конденсатор и рисунок 6 – Реактор
Запуск аппарата
Открывают доступ газа, вода (14) пока закрыта, горелки (12), (13) работают. Краник (4) полностью открыт, компрессор (5) включен, краник (9) закрыт, краник (11) полностью открыт.
Затем приоткрывают краник (14) доступа воды, а краником (11) регулируют нужное давление в конденсаторе, контролируя его манометром (10). Но не в коем случае не закрывайте краник (11) полностью!!! Далее, минут через пять, клапаном (14) доводят температуру в реакторе (6) до 200-250оС. Затем чуть-чуть приоткрывают краник (9), из которого должна пойти струя бензина. Если она будет идти постоянно – приоткройте краник больше, если будет идти бензин в смеси с газом – приоткройте краник (14). Вообще, чем на большую производительность настроите аппарат, тем лучше. Содержание воды в бензине (метаноле) вы можете проверить с помощью спиртометра. Плотность метанола равна 793 кг/м3.
Данный аппарат желательно изготавливать из нержавеющей стали или железа. Все детали изготовлены из труб, в качестве тонких соединительных труб можно использовать медные трубки. В холодильнике необходимо сохранить соотношение X:Y=4, то есть, например, если X+Y=300 мм, то X должно быть равно 240 мм, а Y, соответственно, 60 мм. 240/60=4. Чем больше витков уместится в холодильнике с той и с другой стороны, тем лучше. Все краники применены от газосварочных горелок. Вместо краников (9) и (11) можно использовать редукционные клапана от бытовых газовых баллонов или капиллярные трубки от бытовых холодильников. Смеситель (1) и реактор (2) нагреваются в горизонтальном положении (смотрите чертеж).
Ну вот, и вся конструкция. В заключении следует добавить, что цикл статей по изготовлению этой конструкции в домашних условиях, било опубликовано в журналах “Приоритет” в 1991, 1992, 1993 гг., но полностью готовый проект опубликован так и не был (зажали обещанные правильные катализаторы для подписчиков). В данных номерах были чертежи реактора с электрической схемой управления и конструкция охладителя, после чего г-н Вакс (автор статьи) вежливо извинился и сообщил, что дальнейшая публикация прекращается по просьбе силовых структур СССР и тем кто хочет повторить данную установку поле творчества неограниченно.
Квасников Игорь, изготавлиавшый эту конструкцию сделал уточнение:
Категорически запрещается подавать воду прямо из крана в реактор так как водопроводная вода содержит хлор , который моментально отравит катализатор 2-го реактора. Тоже самое относится и к газу, который содержит примеси серы и активных органических веществ. В своей установке я применял дистиллированную воду и моноэтаноламинную очистку газа, все это даёт неплохой результат. После более детальной проработки оригинальной статьи всплывает множество неточностей которые следует уточнять и дорабатывать.
P.S.
На начало 2012 года стоимость готовой к использованию установки, производительностью 1 литр в час составляла более 2000 у. е.
P.S.2
В данный момент времени изготовление описанной в статье установки не представляется возможным, поскольку цеха, где происходило изготовление комплектующих и сборка, сейчас разрушены, так как находятся в зоне конфликта.
Комментарии:
Удельная теплота сгорания веществУ Николая Джуманчука во дворе есть самодельный газ, получаемый из коровьего навоза
www.altsyn.com
[Н3.5] Получение компонентов бензина | Нефтянка
Бензиновые фракции, получаемые с установки атмосферно-вакуумной перегонки, имеют октановое число около 60 единиц. Чтобы поднять октановое число топлива до уровня 92-98 единиц, на нефтеперерабатывающем заводе реализуется ряд технологических процессов, наиболее распространённые из которых будут рассмотрены в этой статье.
Углеводороды обладают интересным свойством — они могут менять пространственное строение молекулы, сохраняя число входящих в неё атомов. Это явление широко распространено среди органических веществ. Например, фруктоза и глюкоза отличаются только пространственным строением, а химические формулы у них одинаковы — C6H12O6.
Среди алканов только три самых простых (метан, этан, пропан) не могут образовывать изомеров. Чем сложнее устроена молекула, тем больше у неё возможностей для создания различных пространственных фигур. Бутан имеет один изомер, пентан — два, гексан — четыре. Изомеры отличаются не только плотностью и температурой кипения, но, что особенно важно при производстве бензина — октановым числом. К примеру, октановое число нормального пентана по исследовательскому методу равно 61,7, а у двух его изомеров этот показатель намного выше — 85,5 для 2,2-диметилпропана и 92,3 для 2-метилбутана.
В качестве сырья для установки изомеризации используется лёгкая прямогонная бензиновая фракция (C5-С6). В зависимости от применяемой технологии, процесс протекает при температуре от 180 до 410°С в присутствии платиносодержащего катализатора. На выходе из реактора стоит ректификационная колонна, на которой осуществляется отбор готового изомеризата, а непрореагировавшие вещества вновь возвращаются в реактор. Изомеризат имеет октановое число более 90 единиц. Он направляется на установку компаундирования для получения товарного топлива.
Тяжёлая бензиновая фракция с установки АВТ направляется на установку риформинга. Повышение октанового числа происходит за счёт превращения аренов и нафтенов в ароматические углеводороды. Процесс протекает в присутствии алюмо-платино-рениевого катализатора при температуре 500-530°С. Сырьё проходит через 3-4 реактора, в которых созданы условия для протекания конкретной реакции. Основные реакции риформинга идут с поглощением тепла, поэтому перед каждым реактором смесь углеводородов подвергается нагреву в трубчатых печах. В качестве побочного продукта получается водород, который нужен для установок гидроочистки и гидрокрекинга.
Риформат имеет очень высокое октановое число (100 и выше по исследовательскому методу) и является ценным компонентом бензина. Однако, ароматические углеводороды способствуют образованию нагара в двигателе, поэтому их содержание в готовом топливе не должно превышать 35%. Хуже обстоит дело с самым известным ароматическим веществом — бензолом. Он ядовит сам по себе, а при сгорании образует ещё более опасные для здоровья вещества. Техрегламент ограничивает содержание бензола в бензине на уровне 1%.
В ходе реакции крекинга образуется достаточно много газообразных углеводородов, в то время как наибольшая эффективность работы НПЗ достигается при максимальном выходе бензина. Для превращения легких углеводородов (С3-С4) в компонент бензина используется установка алкилирования. Катализатором реакции служит серная или фтороводородная кислота. Процесс проходит при пониженной температуре (0-10°С для сернокислотного алкилирования и 25-30°С для фтороводородного алкилирования), поэтому требуется охлаждение реактора. Октановое число получаемого продукта — около 95 единиц. В составе алкилата значительная доля приходится на изооктан (2,2,4-триметилпентан) — то самое вещество, которое было выбрано в качестве эталона для шкалы октановых чисел. Октановое число 2,2,4-триметилпентана всегда равно 100, вне зависимости от способа определения (исследовательский или моторный). Это полезное свойство используется для сокращения разницы между ОЧИ и ОЧМ производимого бензина, что повышает его потребительские свойства.
В качестве высокооктанового компонента бензина часто используется метил-трет-бутиловый эфир (МТБЭ). Его октановое число по исследовательскому методу — 117 единиц, а октановое число смешения может достигать 135 единиц. Благодаря таким высоким показателям увеличение октанового числа бензина может быть достигнуто путём небольшой добавки МТБЭ. Полезные свойства МТБЭ не исчерпываются высоким октановым числом — он малотоксичен, а за счёт содержания кислорода способствует более полному сгоранию топлива. Сырьём для МТБЭ служит бутан-бутиленовая фракция, получаемая в процессе каталитического крекинга. Эта же фракция же нужна для установки алкилирования. Выбор направления использования бутан-бутиленовой фракции зависит от технологической схемы НПЗ.
Полученные компоненты смешиваются таким образом, чтобы готовый бензин соответствовал всем нормам Технического регламента «О требованиях к автомобильному и авиационному бензину, дизельному и судовому топливу, топливу для реактивных двигателей и топочному мазуту».
ПРИЛОЖЕНИЕ №1
к техническому регламенту «О требованиях
к автомобильному и авиационному бензину,
дизельному и судовому топливу,
топливу для реактивных двигателей
и топочному мазуту»
Требования к характеристикам автомобильного бензина
Характеристики автомобильного бензина | Единица измерения | Нормы в отношении | |||
класса 2 | класса 3 | класса 4 | класса 5 | ||
Массовая доля серы, не более | мг/кг | 500 | 150 | 50 | 10 |
Объемная доля бензола, не более | процентов | 5 | 1 | 1 | 1 |
Концентрация железа, не более | мг/дм3 | отсутствие | отсутствие | отсутствие | отсутствие |
Концентрация марганца, не более | мг/дм3 | отсутствие | отсутствие | отсутствие | отсутствие |
Концентрация свинца, не более | мг/дм3 | отсутствие | отсутствие | отсутствие | отсутствие |
Массовая доля кислорода, не более | процентов | — | 2,7 | 2,7 | 2,7 |
Объемная доля углеводородов, не более: | процентов | ||||
ароматических | — | 42 | 35 | 35 | |
олефиновых | — | 18 | 18 | 18 | |
Давление паров, не более: | кПа | ||||
в летний период | — | 45-80 | 45-80 | 45-80 | |
в зимний период | — | 50-100 | 50-100 | 50-100 | |
Объемная доля оксигенатов, не более: | процентов | ||||
метанола | — | отсутствие | отсутствие | отсутствие | |
этанола | — | 5 | 5 | 5 | |
изопропанола | — | 10 | 10 | 10 | |
третбутанола | — | 7 | 7 | 7 | |
изобутанола | — | 10 | 10 | 10 | |
эфиров, содержащих 5 или более атомов углерода в молекуле | — | 15 | 15 | 15 | |
других оксигенатов (с температурой конца кипения не выше 210 градусов Цельсия) | — | 10 | 10 | 10 | |
Объемная доля монометиланилина, не более: | процентов | 1,3 | 1 | 1 | отсутствие |
* В оформлении использованы изображения технологических установок из компьютерной игры «ЛУКОЙЛ-Менеджер НПЗ».
Комментариев:neftianka.ru
Получение автомобильных топлив из нефти
Строительные машины и оборудование, справочник
Категория:
Автомобильные эксплуатационные материалы
Публикация:
Получение автомобильных топлив из нефти
Читать далее:
Получение автомобильных топлив из нефти
Если вода послужила источником жизни на земле, то о нефти можно сказать, что она стала основным источником «жизни» техники XX века.
Начало использования нефти человеком теряется в глубине веков. Установлено существование нефтяного промысла на берегах Евфрата за 4…6 тыс. лет до нашей эры. Около 700 лет назад Марко Поло при посещении Кавказа обратил внимание на «земляное масло», которое нельзя есть, но можно жечь или лечить с его помощью верблюдов.
Первым целевым продуктом, выработанным из нефти, стал керосин. В 1823 г. русские мастеровые братья Дубинины построили простейшую нефтеперегонную установку для получения керосина (рис. 4). Однако значение нефти в качестве источника энергии человечество впервые поняло в начале XX века, когда в качестве топлива для паровых котлов и двигателей внутреннего сгорания стали широко применять нефть и нефтепродукты. Во время Первой мировой войны 1914 г. бытовала крылатая фраза «Союзники пришл-и к победе на гребне нефтяной волны».
Нефть представляет собой вязкую, несколько маслянистую жидкость темно-коричневого, иногда зеленоватого цвета. Плотность нефтей колеблется от 820 до 900 кг/м3, хотя на отдельных месторождениях добывают более легкие или тяжелые нефти.
В состав нефти входят следующие химические элементы: углерод (82…87%), водород (11…14%), сера (0,1… 7%), азот (0,001… 1,8%), кислород (0,05… 1%). Основными компонентами нефти являются углеводороды — алка-ны, циклоалканы и арены. Алканы (парафиновые углеводороды) имеют общую эмпирическую формулу С,,Н2„+2. Они характеризуются предельным насыщением водородом, в связи с чем известны также под названием предельных углеводородов. Плотность и температура кипения парафинов повышаются с ростом молекулярной массы. Поэтому парафиновые углеводороды с числом атомов 16 и выше представляют собой твердые вещества и находятся в нефти в растворенном состоянии. Содержание парафинов в нефтях равно 30…35%, однако в некоторых случаях может доходить до 50%.
Рис. 1. Нефтеперегонная установка братьев Дубининых, 1823 г: 1 — нефть; 2 — вода; 3 — керосин
В среднем в нефтях содержится от 25 до 75% циклоалканов. Арены (ароматические углеводороды) отличаются наличием в молекуле группы атомов углерода, называемых бензольным кольцом. Нефти содержат 10… 20% аренов, которые обычно представлены бензолом, его гомологами и производными нафталина.
Наряду с углеводородами нефть содержит различные сернистые соединения, органические кислоты, азотистые соединения, а также асфальто-смолистые вещества. Ряд из них несмотря на незначительное содержание оказывают отрицательное влияние на свойства нефтяных топлив. Так, некоторые из сернистых соединений ведут к проявлению сильного коррозионного воздействия на металлы. Наличие органических кислот, получивших название нафтеновых, также способствует коррозии металлических изделий. Особенностью асфальто-смолистых веществ является склонность к отложениям и повышенным нагарам.
В процессах переработки нефти образуются непредельные соединения. Такими соединениями являются, например, олефиновые углеводороды. Для непредельных углеводородов характерна низкая химическая стойкость, в связи с чем их присутствие в нефтепродуктах нежелательно.
При разнообразии содержащихся углеводородов особенностью нефти является также широкий температурный диапазон выкипания. Уже при нагреве до 30…40 °С из нефти начинают испаряться наиболее легкие углеводороды. С повышением температуры состав выкипающих углеводородов становится тяжелее. Это позволяет разделить нефть на части или фракции, выкипающие в определенных температурных пределах. Получаемые продукты называют дистиллятами, а сам процесс — прямой перегонкой нефти.
Обычно выделяют дистилляты со следующими пределами выкипания:
Бензиновый……….28…180 °С
Лигроиновый …. 110…230 °С
Керосиновый …. 120…315 °С
Газойлевый……….230…330 °С
Соляровый……….280…380 °С
Масляный……….320…500 °С
Прямая перегонка является первичным и обязательным процессом переработки нефти в топлива и масла. Она осуществляется путем испарения нефти в трубчатых печах с последующим разделением фракций в ректификационных колоннах. В трубчатой печи нефть нагревается до температуры 330…350 °С и затем подается в среднюю часть ректификационной колонны. Жидкий остаток стекает вниз, а углеводородные пары поднимаются вверх и конденсируются по пути в виде дистиллятов на так называемых ректификационных тарелках. Эти тарелки установлены на различной высоте колонны. На первых тарелках конденсируются тяжелые углеводороды, несколько выше — более легкие. Наиболее легкие углеводороды отводятся с верха колонны в газообразном виде.
В атмосферной ректификационной колонне получают топливные дистилляты. После перегонки остается мазут, который может подвергаться дальнейшему разделению либо использоваться на установках крекинга или в качестве топлива (топочного мазута). Нефтяные смеси термически нестойкие, в связи с чем во избежание их разложения при перегонке мазутов применяют вакуум, снижающий температуру кипения. Испарение мазутов осуществляют в вакуумных трубчатых установках, а их разделение — в вакуумных ректификационных колоннах. В верхней части вакуумной колонны конденсируются соляровые фракции, ниже — масляные, идущие на приготовление товарных масел. Жидкий остаток наиболее, тяжелых фракций мазута — полугудрон или гудрон — собирается в нижней части вакуумной колонны.
Рис. 2. Получение автомобильных топлив и масел из нефти
Рис. 3. Принципиальная схема нефтеперегонной установки: 1 — трубчатая печь; 2 — испарительная колонна; 3 — ректификационная колонна; 4 — теплообменник; 5 — холодильник
Для улучшения эксплуатационных свойств нефтепродукты подвергаются специальной очистке. Например, для удаления сернистых, азотистых, кислородных, металло-органических и непредельных соединений используется гидроочистка. В процессе гидроочистки соединения, содержащие серу, азот или кислород, путем реакции с водородом переводятся в газообразные, легко удаляющиеся продукты. Гидроочистка проводится при температуре 350…420 °С и давлении 1,7…4,0 МПа в присутствии катализаторов. Гидроочистку применяют для обессеривания дизельных топлив, для очистки масел, а также при подготовке сырья для некоторых вторичных процессов переработки нефти.
Для удаления из топливных дистиллятов некоторых кислородных и сернистых соединений применение находит также очистка щелочью. Этот процесс заключается в добавлении щелочи в очищаемый нефтепродукт с последующим удалением водных растворов образующихся веществ совместно с остатками щелочи.
При разгонке ряда нефтей в получаемых высококипя-щих топливных и масляных дистиллятах содержится большое количество соединений, застывающих при сравнительно высоких температурах. К этим соединениям относятся главным образом парафиновые и некоторые циклические углеводороды. Их наличие ухудшает эксплуатационные свойства нефтепродуктов при пониженных температурах применения. Для удаления этих углеводородов используются различные методы депарафинизации. При производстве дизельных топлив зимних сортов распространение получила так называемая карбамидная депара-финизация. Этот метод основан на свойстве карбамида (мочевины) образовывать комплексные соединения с парафинами, которые достаточно просто отделяются от остальных углеводородов. Депарафинизация масляных дистиллятов осуществляется с помощью их охлаждения до низких температур с последующим отделением образующихся твердых кристаллов углеводородов на специальных фильтрах-прессах.
Прямая перегонка нефти обеспечивает лишь ограниченное количество топливных дистиллятов, не удовлетворяющих постоянно растущий спрос на моторное топливо. Большинство нефтей содержит 15…20% бензиновых дистиллятов и 45…55% фракций, перегоняющихся до 300…350 °С. Поэтому для получения большего количества (увеличения выхода) моторных топлив (в первую очередь бензинов) используются методы химической переработки нефти, получившие название вторичных процессов.
Наибольшую известность получил крекинг-процесс, заключающийся в расщеплении крупных молекул под действием высоких температур (термический крекинг) или в присутствии катализатора (каталитический крекинг). Из-за невысокого качества бензинов термического крекинга в настоящее время используются главным образом процессы каталитического крекинга. Каталитический крекинг проводится при температуре 450… 530 °С и давлении 0,07…0,3 МПа. В качестве катализатора обычно применяются алюмосиликаты (75…80% окиси кремния и 10…20% окиси алюминия). С помощью каталитического крекинга получают бензин с октановым числом до 85 ед. и керосино-газойлевые фракции, используемые в качестве реактивного и дизельного топлива.
Процесс, сочетающий крекирование и гидрирование (присоединение водорода), получил название гидрокрекинга. Гидрокрекинг проводится при температуре 360…440 °С под давлением 15…17 МПа в присутствии водородосодержащего газа. В зависимости от условий процесса и типа сырья гидрокрекинг позволяет получить из керосино-соляровых фракций, вакуумных дистиллятов и остаточных продуктов бензины, реактивные и дизельные топлива.
Для улучшения одного из важнейших эксплуатационных свойств бензина — стойкости к детонации — используются процессы риформинга. Различают два вида рифор-минга: термический и каталитический. Наиболее широкое-применение в промышленности нашел каталитический риформинг, позволяющий из прямогон-ного бензина получить риформинг-бензин. Этот бензин содержит значительное количество (65…75%) ценных ароматических углеводородов, что позволяет их использовать для повышения детонационной стойкости товарных бензинов.
Каталитический риформинг протекает в среде водорода при температуре 500…540 °С, давлении 1,5…4 МПа и в присутствии катализатора. В качестве катализатора промышленное применение получила платина на окиси алюминия, отчего такой процесс получил название платфор-минга.
Компоненты бензинов с высокой детонационной стойкостью получают также с помощью процессов алкилиро-вания и изомеризации. Алкилирование представляет собой реакцию введения алкильных радикалов в органическое соединение. Путем алкирования вырабатывают ценные компоненты бензинов, известные под названием алкилата и алкилбензола. Изомеризация ведет к перегруппировке атомов в молекуле с образованием молекулы с изоструктурой, которая обеспечивает необходимые свойства топлива.
Очистка и вторичные процессы существенно улучшают эксплуатационные свойства топлив, однако недостаточны для удовлетворения всех требований двигателей современных автомобилей. Поэтому на заключительном этапе производства топлива после смешения продуктов прямой перегонки и вторичных процессов осуществляется добавление различных присадок. Присадки это вещества, добавка которых в небольших количествах существенно улучшает один или ряд показателей эксплуатационных свойств нефтепродуктов.
Производство нефтепродуктов и нефтехимического сырья из нефти осуществляется на нефтеперерабатывающих заводах (НПЗ). При переработке нефти применяются различные технологические процессы, тип и режимные условия которых определяются специализацией завода и характеристиками используемого сырья — нефти.
До недавнего времени НПЗ топливной специализации строились по схеме неглубокой переработки, при которой из каждой тонны нефти производится в среднем 15% бензина, 22% дизельного топлива и свыше 40% топочного мазута. Для более рационального использования нефтяного сырья в настоящее время осуществляется строительство установок для углубленной переработки нефти с использованием различных вторичных процессов, что позволит довести выработку автомобильного топлива до 55…60%.
Реклама:
Читать далее: Особенности производства смазочных материалов
Категория: — Автомобильные эксплуатационные материалы
Главная → Справочник → Статьи → Форум
stroy-technics.ru