Полимерное покрытие труб
Для стальных трубопроводов самая большая опасность — влажность. Металлические коммуникации не боятся трения и вибрации, выдерживают резкое повышение внутреннего и внешнего давления. Однако во влажной среде самые прочные и надежные стальные трубы могут быстро прийти в негодность. Коррозия и ржавчина очень быстро разрушают любой металл, из-за чего система теряет герметичность.
Особенно опасны такие повреждения для газопроводов. Даже небольшое нарушение герметичности коммуникаций может привести к утечке газа, которая очень опасна для людей и окружающей среды. Газопроводам при прокладке нужно обеспечить максимальную защиту от коррозии.
Полимерное покрытие труб — лучшая защита от влаги и преждевременного износа. Современные полимерные материалы отличаются уникальной водостойкостью. Они не впитывают и не пропускают влагу, даже если полностью погрузить их в жидкость на длительный срок.
На газовые стальные трубы обычно наносят многослойное полимерное защитное покрытие. Основной слой — экструдированный полиэтилен, дополнительные — адгезивы, праймеры или грунтовки. Этот полимерный материал обладает рядом преимуществ:
- выдерживает длительное нахождение в воде или влажной среде,
- биостоек, на нем не растут плесень, мох, грибки,
- имеет ровную гладкую поверхность, которая защищает от образования минеральных отложений,
- износостоек,
- устойчив к растяжению и разрыву,
- имеет небольшой вес, не утяжеляет трубы.
Покрытие на газовые трубы наносят на предприятии. Существуют также специальные ленты на битумной основе, с помощью которых можно обеспечить трубопроводу защиту от коррозии уже после монтажа, в полевых условиях. Однако созданная в заводских условиях изоляция считается более надежной и долговечной.
Срок службы газопроводов, на которые нанесено полимерное защитное покрытие, — более 30 лет. Антикоррозийную изоляцию после этого срока можно восстановить. Те участки, где покрытие повреждено, дополнительно защищают полимерными лентами. Эту операцию можно провести в полевых условиях, демонтировать трубы для этого не придется.
В нашем каталоге представлены стальные газовые трубы с уже нанесенным защитным полимерным покрытием. Всегда в наличии любые типоразмеры:
- диаметр — от 57 до 630 мм,
- толщина стенки — от 3,5 до 10 мм.
Для создания изоляции на предприятии используется современное оборудование. После окончания работ готовая продукция проходит многоступенчатую проверку, один из этапов которой — исследования в заводской лаборатории. Покупателям мы предлагаем только те трубы, которые прошли все испытания, полностью соответствуют требованиям стандартов. Чтобы узнать цены на выбранные наименования, оставьте заявку на сайте. Менеджер очень скоро свяжется с Вами и поможет оформить заказ.
antikorpolimer.ru
Полимерное покрытие труб – один из методов антикоррозионной защиты трубопровода
С самого начала использования металлических труб довольно остро стоит вопрос об их защите от коррозионных процессов. Наиболее остро, подобная проблема стоит в сети газовых и нефтяных трубопроводов, которые эксплуатируются над землей и под землей. Поскольку подобные системы находятся в довольно жестких климатических условиях, они нуждаются, как и любое металлическое изделие, в мерах антикоррозионной защиты. Наиболее эффективным средством, для защиты металлов от соприкосновения с окружающей средой, является полимерное покрытие труб.
Трубы с внутренней защитой
Подобные трубы используются в трубопроводах, которые предназначены для транспортировки агрессивных сред. Трубы, которые используются для транспортировки подобных сред, имеют внутреннее покрытие. Внутренние покрытие трубопроводов может быть нанесено при помощи порошковых полимеров и при помощи ЛКМ на полимерной основе. Современная промышленность выпускает достаточно много видов полимерных покрытий труб. Критерием выбора являются условия, в которых эксплуатируется трубопровод, степень агрессивности перекачиваемой жидкости и технические параметры самого полимерного покрытия.
Наружная защита труб
Такая защита может быть нанесена в заводских условиях и в условиях непосредственной прокладки трубопровода. Традиционно, в трассовых условиях, применяется битумно-мастичная изоляция. Однако, с появлением более прогрессивных и более эффективных полимерных материалов, подобная изоляция, применяется довольно редко. Наиболее эффективной защитой трубопроводов, в трассовых условиях, является ленточное покрытие. Такая лента клеится на трубу при помощи адгезионной грунтовки. Толщина защитного слоя составляет не менее 1,2мм. Полимерные покрытия для трубопроводов применяются достаточно давно. За время их эксплуатации они показали себя с самой лучшей стороны. А, перенос нанесения подобной изоляции из трассовых условий в заводские, может значительно ускорить монтаж наружных сетей.
Линии наружного покрытия труб
В промышленности существует четкое разграничение полимерных покрытий, которые наносятся на трубы. Для труб большого диаметра, которые используются в трубопроводах для транспортировки нефти и газа, применяется трехслойное покрытие на основе полимерных порошковых покрытий. В таком покрытии, порошковый полимер, играет двойную роль. Во-первых, он надежно защищает поверхность трубы от контакта с внешней средой и надежно склеивается со слоем экструдированного полимера, который выполняет функцию механической защиты трубы. Современные покрытия, вместо традиционного полиэтилена, содержат полипропиленовые композиции, которые позволяют эксплуатировать трубы при температурах в +100град.
Подобные покрытия, как внутренние, так и наружные, наносятся на трубы в заводских условиях. Для этого используются специальные производственные линии, которые полностью автоматизированы. Процесс нанесения покрытия состоит из двух основных этапов. На первом этапе труба подвергается тщательной обработке, которая заключается в подготовке поверхности. Механическая очистка позволяет удалить ненужные образования на поверхности трубы. Затем, на поверхность трубы наносят хроматирующий раствор, который обеспечивает лучшую адгезию покрытия к основанию металла. Далее следует нанесение основного слоя полимерного материала. Весь этот процесс происходит в условиях высокой температуры, что позволяет материалу растекаться и образовывать однородную равномерную пленку.
Основное преимущество заводских изолированных труб состоит не только в качестве наносимого покрытия, но и в возможности всесезонной прокладки трубопроводов.
Современные трубы и изделия для ремонта и строительства инженерных сетей
1. Оценка состояния коммунальных инженерных сетей
1.1. Общие сведения
По протяженности инженерных сетей Россия занимает одно из первых мест в мире. Общая протяженность наружных инженерных сетей составляет около 2 млн км, в том числе в системе ЖКХ эксплуатируется свыше 1 млн км трубопроводов. Кроме того, насчитывается около 3 млн км внутридомовых трубопроводов. Состояние инженерных коммуникаций определяется возрастом и материалом трубопроводов, условиями их эксплуатации, качеством строительства, степенью агрессивности грунтов и транспортируемой среды, другими местными условиями [1,2].
Основная часть инженерных коммуникаций в нашей стране выполнена из металлических труб (75%), из которых 70% — стальные и 5% — чугунные (рис. 1).
Возраст основной части трубопроводов Санкт – Петербурга превышает нормативный срок эксплуатации, а отдельные участки труб работают более 100 лет (рис. 2). Такая же картина наблюдается и во многих других городах России [5]. С подобными проблемами сталкиваются и некоторые зарубежные города, например Лондон.
По данным Росстроя РФ, количество аварий на подземных инженерных сетях страны за 10 лет выросло почти в 5 раз и составило на сетях водоснабжения – до 70 аварий на 100 км, теплоснабжения – до 200 аварий на 100 км. Планово-восстановительный ремонт сетей и оборудования систем водоснабжения и коммунальной энергетики практически полностью вытеснили аварийно-восстановительные работы, единичные затраты на проведение которых в 2,5-3 раза выше.
Рис.2. Характеристика водопроводных сетей Санкт — Петербурга (по годам ввода в эксплуатацию)
Средний уровень износа сетей в коммунальном хозяйстве составляет около 60 %, а в отдельных регионах превышает 70 %. В системе водоснабжения требуют полной замены 67 тыс. км стальных и 60 тыс. км чугунных трубопроводов, дополнительно к этому 120 тыс. км металлических трубопроводов нуждаются в срочном ремонте (рис. 3). В аналогичном состоянии находятся и канализационные трубопроводы, 30% которых требуют немедленной замены, а также тепловые сети (требуется заменить 62 тыс. км сетей) [1,2].
1. 2. Коррозия металлических трубопроводов и отложения в трубах
Отсутствие надежной наружной и внутренней гидроизоляции, агрессивность грунтовых вод, грунта и транспортируемой воды, наличие блуждающих токов, приводит к значительной коррозии металлических труб, и к снижению фактического срока их службы. Зарастание внутренней поверхности продуктами коррозии или карбонатными отложениями приводит к снижению пропускной способности трубопроводов, повышению затрат электроэнергии на транспортирование воды.
Рис. 3. Состояние чугунных и стальных трубопроводов системы водоснабжения: 1 – исправное состояние; 2 – требуют ремонта;
3 – требуют замены
Внутренняя поверхность металлических трубопроводов водоснабжения, как правило, не имеющая защитного покрытия в условиях агрессивности воды, подвергается коррозии. Коррозионной активностью обладают природные воды с малым содержанием минеральных солей и низким щелочным резервом. К ним, относятся воды многих поверхностных водоисточников Северо-Западного региона, в частности, Ладожского озера и р. Невы. Вода городского водопровода Санкт-Петербурга также является агрессивной – суммарное содержание в ней сульфатов и хлоридов не превышает 40 мг/л, кальция – не более 12 мг/л. Индекс насыщения водопроводной воды карбонатом кальция – отрицательный (– 2,5…– 3,0), что говорит о высокой агрессивности воды [5, 6, 10] .
Продукты коррозии металлических трубопроводов, состоящие, в основном, из окислов железа, отлагаются на внутренней поверхности труб водопроводной сети. В большей степени отложения проявляются на удаленных от водопроводных станций и тупиковых участках сети, в частности на вводах. Слой отложений в трубах на отдельных участках достигает 10…15 мм. В результате сечение трубы уменьшается до 50%. Износ трубы из-за коррозии местами достигает 45%. Продукты коррозии представляют собой рыхлый пористый осадок, легко разрушающийся при механическом воздействии. Интенсивная коррозия стальных трубопроводов в результате появления в воде растворенных окислов железа приводит к ухудшению качества воды в системе.
На рис. 4 – 6 показаны фотографии участков стальных трубопроводов, разрушенных в результате коррозии, с образованием сквозных отверстий и появлений утечек воды [11].
Рис.4. Графитовая коррозия металлических труб
Рис.5. Язвенная коррозия
стальных водопроводных труб
Графитовая коррозия, возникающая в результате разрушения металлической стенки трубопровода, приводит к ухудшению прочности стенок и развитию язвенной и точечной (питинговой) коррозии. На рис. 7 даны фотографии внутренней поверхности участков металлических трубопроводов водопроводной сети Санкт-Петербурга разного возраста с различной степенью отложений продуктов коррозии.
А)
Б)
Рис. 7. Вид внутренней поверхности водопроводных труб: А – участок стального трубопровода после 10 лет эксплуатации; Б – то же после 20 лет эксплуатации
Классификация видов повреждений трубопроводов при авариях на водопроводной сети Санкт-Петербурга приведена на рис. 8 [11].
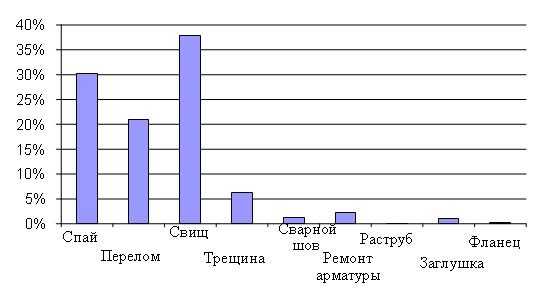
Рис.8 Характер повреждений при авариях на водопроводной сети Санкт-Петербурга
Из представленных данных (см. рис.8) видно, что основными причинами аварий являются коррозия металлических труб (свищи – 37%), а также значительный возраст аварийных участков трубопроводов (разрушение стыков – спай – 30%, переломы – 21%, трещины – 6%).
2. Защитные покрытия для металлических труб
Стальные трубопроводы получили преимущественное распространение в нашей стране (см.гл.1) благодаря высокой механической прочности, устойчивости к температурным воздействиям, низкому коэффициенту температурного расширения, простоте монтажа трубопроводов (сварка) и ремонтопригодности.
Основной недостаток стальных труб – низкая коррозионная стойкость. Стальные трубопроводы, не
teplo.kr-company.ru
Стальные трубы с полимерным покрытием
Стальные трубы с полимерным покрытием используют для подземной прокладки промысловых, магистральных и коммунальных трубопроводов с жидкостью и газом. Сталь хорошо сопротивляется механическим повреждениям и давлению грунта, а полимерная изоляция защищает металл от негативного влияния внешней среды. Нанесение защитного покрытия позволяет увеличить срок безремонтной службы газопровода до 30 лет. По истечении этого срока можно заменить износившиеся участки изоляции непосредственно в полевых условиях.
Полимерное покрытие защищает стальные трубы от:
- коррозии,
- блуждающих токов,
- перепадов температур,
- повышенной влажности,
- грибков и плесени.
На стальные трубы полимерное покрытие обычно наносят в несколько слоев. Самую надежную защиту от влаги и коррозии металлу обеспечивает трехслойная весьма усиленная изоляция. Для ее создания на сталь последовательно наносят:
- грунтовку,
- адгезив,
- экструдированный полиэтилен.
После изготовления каждая стальная труба с полимерным покрытием проходит проверку качества и испытания в лаборатории. Специалисты оценивают соответствие геометрических размеров заданным параметрам, измеряют уровень водопоглощения изоляции, ее способность сопротивляться другим негативным факторам. Только полностью соответствующие государственным и отраслевым стандартам стальные изолированные изделия поступают в продажу.
У нас Вы можете заказать стальные трубы, покрытые экструдированным полиэтиленом, а также материалы для защиты трубопроводов в полевых условиях. Всегда в наличии лента Лит , Пирма, Полилен, битумные грунтовки и другие наименования.
В нашем каталоге трубы:
- диаметр — от 57 до 630 мм,
- толщина стенки — от 3,5 до 10 мм.
Толщина антикоррозийной изоляции зависит от диаметра стальной трубы и типа покрытия, в среднем составляет 3-3,5 мм.
Мы также предоставляем услуги по нанесению антикоррозийной изоляции на трубы, предоставленные заказчиком. Создание защитного покрытия ведется в заводских условиях, на полностью автоматизированном оборудовании.
Чтобы получить подробную информацию об условиях сотрудничества, закажите обратный звонок на сайте. Наш менеджер перезвонит Вам в ближайшее время и подробно ответит на все вопросы.
antikorpolimer.ru
Способ нанесения полимерного покрытия на стальные трубопроводы
Изобретение относится к строительству трубопроводного транспорта и может быть использовано при горячем нанесении полимерного защитного покрытия на стальные трубы, а также в трассовых условиях при ремонте трубопроводов с заводским полимерным покрытием. Предварительно очищают и нагревают изолируемую поверхность, наносят на нее спиральной намоткой с одновременной прикаткой роликом ленту термоусаживающегося полимерного материала защитного покрытия с адгезионным термопластичным слоем из адгезионной композиции. Нагрев поверхности производят до температуры плавления адгезионной композиции, на изолируемую поверхность дополнительно наносят намоткой ленту адгезионного термопластичного материала, армированного сеткой. Для защитного покрытия используют двухслойную термоусаживающуюся ленту, которую наносят с натяжением перед прикатывающим роликом. После нанесения поверхность двухслойной термоусаживающейся ленты дополнительно нагревают до температуры усадки с помощью источника лучистого нагрева. Изобретение повышает стойкость защитного покрытия к сдвиговым нагрузкам.
Изобретение относится к области защиты металлов от коррозии и может быть использовано при горячем нанесении полимерного защитного покрытия на стальные трубы, а также при ремонте трубопроводов с заводским полимерным покрытием в трассовых условиях.
Известен способ нанесения защитного покрытия на стальные трубы на основе мастичных лент, например типа «ЛИАМ», с раздельным нанесением мастичного армированного слоя и полимерного защитного покрытия с мастичным слоем при холодном нанесении на трубы с предварительным нанесением праймера на поверхность (Рябов В.М. и др. Мастично-битумные и другие покрытия для защиты трубопроводов. Свойства покрытий, технология и оборудование для их нанесения. Сб. Разработка и внедрение технологий, оборудования и материалов по ремонту изоляционных покрытий и дефектных участков труб, включая дефекты КРН, на магистральных газопроводах ОАО «Газпром». Материалы Научно-технического совета ОАО «Газпром». Г.Ухта, ООО «Севергазпром», 28-30 октября 2003 г., в 2-х томах. Том 1. М.: ООО «ИРЦ Газпром», 2004, с.54-65).
Однако характеристики покрытия холодного нанесения и его долговечность ниже, чем покрытия горячего нанесения.
Известен способ нанесения полимерного защитного покрытия на изолируемую поверхность стальных труб в заводских условиях, включающий нагрев изолируемой поверхности и формирование на ней изоляции из полимерного термоусаживающегося материала с термопластичным адгезионным слоем. Контакт полимерного материала с изолируемой поверхностью создают намоткой одновременно с прикаткой по всей ширине изолируемого участка (а.с. СССР №1536154, F16L 58/00, опубл. 15.01.1990).
К недостатку способа относится то, что покрытие, получаемое по известному способу, не всегда обеспечивает когезионное отслаивание изоляционного материала по поверхности трубы.
Наиболее близким техническим решением, принятым за прототип, является способ нанесения полимерного защитного покрытия на изолируемую поверхность стальных трубопроводов (Халлыев Н.Х., Селиверстов В.Г. и др. Ремонт локальных участков трубопроводов. / Обз. информ. — Серия Ремонт трубопроводов. — М.: ООО «ИРЦ Газпром», 2001, с.24-28). Способ включает очистку поверхности трубы, нанесение аппликатора на околошовную зону, разогрев изолируемой поверхности в индукторе и намотку ленты из полимерного термоусаживающегося материала с адгезионным термопластичным слоем с одновременной прикаткой.
Однако данный способ не всегда обеспечивает надежную изоляцию поверхности трубы при наличии на ней каверн (коррозионных углублений), а также в области перехода от сварного шва к поверхности трубы, вследствие возможного образования околошовных «шатровых» зон, вызванных натяжением полимерной ленты после термической усадки. Кроме того, локальная изоляция околошовной зоны (нанесение аппликаторов) механизированным способом в трассовых условиях трудновыполнима.
Техническая задача, решаемая предлагаемым изобретением, заключается в формировании монолитного беспористого покрытия с повышенными температурами эксплуатации (до 100°С) в трассовых условиях, непосредственно на трубопроводе, при использовании термоусаживающихся лент с клеевым слоем, с обеспечением высокой стойкости покрытия к сдвиговым нагрузкам по всей поверхности трубопровода, включая зоны продольных и поперечных швов, и влагостойкости.
Поставленная задача решается за счет того, что в способе нанесения полимерного защитного покрытия на изолируемые поверхности стальных трубопроводов, преимущественно в трассовых условиях, включающем предварительную очистку и нагрев изолируемой поверхности, нанесение на нее спиральной намоткой с одновременной прикаткой роликом ленты термоусаживающегося полимерного материала покрытия с термопластичным слоем из адгезионной композиции, согласно изобретению, нагрев поверхности производят до температуры плавления адгезионной композиции слоя, и на изолируемую поверхность дополнительно наносят намоткой ленту адгезионного термопластичного материала, армированного сеткой, а для защитного покрытия используют двухслойную термоусаживающуюся ленту и наносят ее с натяжением перед прикатывающим роликом, причем после нанесения поверхность двухслойной термоусаживающейся ленты дополнительно нагревают до температуры усадки с помощью источника лучистого нагрева.
При изоляции трубопроводов необходимо надежно защитить изоляционным материалом поверхность трубопровода и области сварных соединений. Качество изоляционного покрытия, полученного при нанесении на подогретую трубу с использованием соответствующих материалов, выше, чем при нанесении покрытия на основе материалов холодного нанесения.
На предварительно очищенную и нагретую поверхность трубопровода последовательно, слой на слой наносят адгезионный термопластичный слой в виде армированной сеткой ленты и слой полимерного защитного покрытия в виде ленты с адгезионным термопластичным слоем. Армирование адгезионного слоя сеткой необходимо для придания ленте равнопрочности по длине и ширине и возможности ее минимального натяжения при нанесении для исключения провисания.
Оба слоя наносят последовательно с использованием двух рулонов материалов, расположенных диаметрально относительно оси трубы, спиральной намоткой лент по длине трубопровода, обеспечивая натяжение полимерного защитного покрытия перед упругим прикатывающим роликом. Первый слой (адгезионный) при контакте с нагретой трубой переходит в термопластичное состояние и под усилием прикатывающего ролика, воздействующего через защитный полимерный слой покрытия, заполняет каверны и другие неровности на поверхности трубопровода, исключая образование пустот в зоне перехода от усиления сварного шва к поверхности трубы. Кроме того, при прикатке обеспечивается исключение воздушных пузырей между слоями покрытия и склеивание нахлестов полимерной защитной ленты. После прикатки осуществляют нагрев термоусаживающегося полимерного защитного покрытия с наружной стороны, что обеспечивает его усадку и, как следствие, нормативную адгезию покрытия к металлу трубы и между его слоями. Таким образом, обеспечивается полная изоляция наружной поверхности трубопровода от вредного воздействия внешней среды, в том числе, гарантированная защита сварных соединений.
Способ осуществляют следующим образом. На трубопроводе с подготовленной поверхностью (после пескоструйной обработки) устанавливают кольцевую разъемную камеру нагрева, приводом которой служит устройство, обеспечивающее равномерность передвижения камеры. После камеры нагрева, по ходу движения изолировочного комплекса на трубопроводе размещают изолировочную машину, оснащенную двумя шпулями и двумя дополнительными прикаточными устройствами. На шпулях установлены рулон ленты с адгезионным термопластичным армированным сеткой слоем и второй рулон двухслойной термоусаживающейся ленты для нанесения полимерного защитного покрытия. Шпули и прикаточное устройство расположены с одной стороны машины. Их взаимное осевое расположение таково, что сначала наносят адгезионный термопластичный армированный слой с нахлестом не менее 10 мм, через 90° по окружности на него наносят полимерный защитный слой с нахлестом не менее 30 мм и с прикаткой упругим роликом в момент наложения термоусаживающейся ленты на трубу. А затем еще одним прикаточным роликом через 90° осуществляют дополнительную прикатку покрытия с уже размягченным адгезионным слоем. При этом после изолировочной машины на трубопроводе размещают усадочную кольцевую нагревательную камеру. При движении этого комплекса оборудования вдоль трубопровода происходит непрерывный процесс нагрева трубопровода, нанесения и термоусадки покрытия, обеспечивающие надежную защиту поверхности трубопровода и зон сварных соединений. Остановка процесса предусмотрена для смены рулонов изоляционных материалов.
Предлагаемый способ был опробован при нанесении защитного изоляционного покрытия на участке магистрального газопровода «Бухара-Урал» диаметром 1020 мм.
На участке трубопровода после его очистки смонтировали кольцевую разъемную передвижную нагревательную камеру. После камеры нагрева по ходу движения изолировочного комплекса установили изолировочную машину ИММ-1020, оснащенную двумя рулонами лент и двумя прикаточными устройствами. В качестве адгезионного термопластичного слоя использовали армированную ленту-заполнитель, выполненную из сополимера полиэтилена, шириной 430 мм с армирующей сеткой из стекловолокна, пропитанного органическим составом, обеспечивающим влагонепроницаемость стекловолокнистой сетки, а в качестве защитного полимерного покрытия использовали двухслойную термоусаживающуюся ленту «ТЕРМА-СТМП» шириной 450 мм. Материалы наносили последовательно слой на слой спиральной намоткой лент с нахлестом в наружном слое не менее 30 мм при натяжении термоусаживающейся ленты перед упругим прикатывающим роликом с усилием не менее 15 н/см, при этом прикатку проводили эластичным резиновым роликом при наложении защитного покрытия на трубу с усилием не менее 30 н/см. После прикатки защитное покрытие нагревали в камере с инфракрасным излучением для его усадки и надежной защиты трубопровода.
Производительность изоляционных работ составила 30 м/час. Испытания полученного покрытия показали, что адгезия к металлу трубы составляет 100-130 н/см. Отслаивание покрытия по всей поверхности трубы происходило по когезионному типу. Все остальные испытания покрытия были проведены в соответствии с ГОСТ Р51164-98, получены нормативные значения покрытия.
Использование предлагаемого способа позволит гарантированно защитить поверхность трубопроводов и зон сварных соединений в условиях капитального ремонта протяженных участков магистральных трубопроводов при нанесении защитного покрытия с использованием механизированного трассового оборудования.
Способ нанесения полимерного защитного покрытия на изолируемые поверхности стальных трубопроводов, преимущественно в трассовых условиях, включающий предварительную очистку и нагрев изолируемой поверхности, нанесение на нее спиральной намоткой с одновременной прикаткой роликом ленты термоусаживающегося полимерного материала защитного покрытия с адгезионным термопластичным слоем из адгезионной композиции, отличающийся тем, что нагрев поверхности производят до температуры плавления адгезионной композиции и на изолируемую поверхность дополнительно наносят намоткой ленту адгезионного термопластичного материала, армированного сеткой, а для защитного покрытия используют двухслойную термоусаживающуюся ленту и наносят ее с натяжением перед прикатывающим роликом, причем после нанесения поверхность двухслойной термоусаживающейся ленты дополнительно нагревают до температуры усадки с помощью источника лучистого нагрева.
findpatent.ru
Полиэтиленовое покрытие труб наружное — фото и видео
Ржавление (коррозия) элементов трубопровода – явление, происходящее при химической реакции окисления металлоповерхности от активного взаимодействия с влагой. Влага проникает в структуру материала и вызывает в ней изменения на ионном уровне, из-за которых структура металла постепенно разрушается.
Темпы коррозионного процесса зависят от того, с каким видом влаги контактирует металл, от условий внешней среды, в которых расположена система. Своевременная противокоррозионная обработка трубных изделий позволит избежать негативных последствий и продлить сроки эксплуатации системы в целом. Какие виды наружных покрытий труб существуют в современной промышленности – расскажем подробно в следующих разделах статьи.
Покрытие битумно-мастичного типа
До середины века 20-го для противокоррозионной наружной обработки труб на предприятиях применяли два вида изоляционного покрытия – битумную мастику и специальные липкие ленты на полимерной основе (фото). Изоляция проводилась прямо на месте прокладки трубопровода, покрытия не имели достаточной устойчивости к механическому воздействию и потому могли предохранить поверхность изделий от коррозионных процессов на срок в десять- двенадцать лет и не более. Рассмотрим свойства каждого вида покрытия обстоятельно.
Битумно-мастичное покрытие состояло из следующих слоев:
- В первую очередь поверхность трубы плотно покрывалась грунтовкой битумной или битумно-полимерной;
- Далее наносилась собственно сама мастика. Мастичных слоев нужно было положить несколько (два или три), а между ними обязательно проложить армирующий слой из стеклосетки или стеклохолста;
- На последнем этапе работ труба закрывалась оберточным материалом (крафт-бумагой, бризолом, гидроизолом).
От указанного метода противокоррозионной обработки труб не отказались и в современной промышленности, однако у него есть множество недостатков. Применение битумной изоляции может проводиться в ограниченном температурном диапазоне. При слишком низких температурах битумный слой делается хрупким, легко разрушается при незначительных механических воздействиях на него. При высоких температурах – мастика буквально «плывет», делается мягкой и само покрытие легко продавливается под весом грунта. Еще один минус данного наружного покрытия для труб – высокая способность к поглощению влаги.
Изоляция изделий полимерной лентой
Полимерная лента показала себя как материал более технологичный, кроме того такое покрытие было более устойчиво к применению в условиях перепада температур. Лента выдерживала диапазон от минус двадцати градусов Цельсия до плюс сорока! Материал отличался также низким влагопоглощением, отличной водонепроницаемостью. Но, однако, при всех достоинствах у полимерных лент нашелся существенный минус – они плохо прилегали к стальной поверхности, и потому постепенно покрытие начинало сдвигаться с поверхности изделия, что под воздействием некоторых внешних факторов приводило к быстрому ржавлению трубы и ее механическому разрушению.
Указанные материалы в наши дни применяются редко, ведь им на смену пришли другие, более инновационные типы покрытий.
Ленточно-полиэтиленовая изоляция
Ленточно-полиэтиленовая изоляция появилась в ходе попыток изобрести тонкое полиэтиленовое покрытие. Трубы с наружным полиэтиленовым покрытием данного типа не пользовались спросом у потребителя, так как напыленный слой полимерных веществ не обладал нужной степенью водостойкости и был чувствителен к температурным перепадам.
Чуть позднее в промышленности появились полиэтиленово-мастичные покрытия. Изолирующий слой такого покрытия состоял из полиэтилена экструдированного типа, который наносился на мастику.
Но все указанные способы наружной изоляции стальных труб оставались либо достаточно дорогими, либо технологически неприменимыми в определенных условиях. А потому было разработано покрытие комбинированного типа – ленточно-полиэтиленовая изоляция. Этим изолятором покрывались трубные изделия по 530 диаметр включительно и главным отличием данного изолятора от прочих аналогов, являлось то, что в нем появился особенный слой – ударопрочный.
Полиэтиленовое наружное покрытие труб
Стальные трубы с полиэтиленовым покрытием (фото) впервые стали выпускаться в конце 60-х годов прошлого века: после изобретения немецкими промышленниками особого сополимера, которым и стали обрабатывать трубные изделия для получения прочной двухслойной изоляции. Позднее появились и другие сополимеры, и клеевые композиции, которые позволяли обеспечить высокую адгезию изолятора с металлической поверхностью. Двухслойная полиэтиленовая изоляция стала основным способом наружной противокоррозионной обработки труб на долгие годы. Она стала чрезвычайно востребована в нефтепромышленности, благодаря своим технологическим характеристикам.
Трехслойное полиэтиленовое покрытие труб можно смело назвать инновацией, потому что появилось оно в начале 80-х годов 20-го века. В изоляторе данного типа появился еще один слой, слой эпоксидного праймера. Как создается трехслойная изоляция — можно детально изучить на видео-инструкции к статье.
Защитное покрытие из разнообразных сополимеров наносится не только на трубы из стали. Труба полиэтиленовая с защитным покрытием применяется в строительстве современных систем водоснабжения, отопления, газоснабжения. Изолятор прекрасно выдерживает механические воздействия, не пропускает влагу, но при необходимости (монтажных работах) его легко удалить с поверхности изделия в местах установки соединений или спайки. Ценятся такие изделия и за безопасность и экологичность в эксплуатации.
Изоляция труб полиэтиленом широко востребована не только в сферах промышленных и связанных с добычей природных ресурсов, в домашних коммуникациях также часто применяют гофрированную нержавейку марки 25а, защищенную слоем полиэтилена. Полиэтиленовая изоляция помогает предохранить металлическую поверхность от запотевания и последующих коррозионных процессов.
trubygid.ru
способ нанесения полимерного защитного покрытия на внутреннюю поверхность трубопровода — патент РФ 2028210
Использование: футерование внутренней поверхности металлических труб полимерными термопластичными трубами. Сущность изобретения: используют рукав из полиэтилена или композиций на его основе, предварительно подвергнутый радиационной обработке с последующим продольным растяжением , а нагревание рукава в трубопроводе производят до температуры от 200 до 400°С и скорости перемещения зоны нагрева от 0,3 до 1,0 м/мин. 1 табл. Изобретение относится к нанесению защитных покрытий на внутреннюю поверхность труб и трубопроводов различного назначения при их изготовлении, монтаже или ремонте. Известен способ футерования внутренней поверхности металлической трубы пластмассовой термопластичной трубой (оболочкой), наружный диаметр которой несколько больше внутреннего диаметра. Пластмассовую трубу облучают излучением, затем ее нагревают до 140оС и растягивают, подвешивая груз, до удлинения на 25%, после чего производят медленное охлаждение. Затем пластмассовую трубу вводят в металлическую и пакет нагревают до температуры 140оС, выдерживают в течение 100 мин и медленно охлаждают. При этом происходит восстановление исходного диаметра пластмассовой трубы — расширение за счет сокращения длины, т.е. происходит собственно футерование внутренней поверхности металлической трубы [1]. Данный способ требует использования громоздкого и энергоемкого оборудования для нагрева футеруемых труб до 140-150оС и поэтому пригоден только для футерования труб в заводских условиях. Известен являющийся наиболее близким к изобретению способ нанесения полимерного защитного покрытия, на внутреннюю поверхность трубопровода, включающий введение в полость трубопровода рукава из полимерного термопластичного материала, закрепление одного из концов рукава на конце трубопровода, последовательные нагрев и прижатие рукава к стенке трубы с перемещением зоны нагрева перед зоной прижатия [2]. В данном способе нагрев производят до оплавления поверхности рукава, соприкасающейся со стенкой трубы, при этом нагрев производят кольцевой индукционной печью изнутри рукава, а прижатие рукава к внутренней поверхности трубопровода производят сжатым воздухом, подаваемым внутрь рукава. Данный способ также требует использования громоздкого оборудования для нагрева футеруемых труб до 140-150оС. Кроме того, требуется система для прижатия рукава сжатым воздухом, необходима герметизация рукава. Способ пригоден для получения футеровки из полимеров с температурой 150оС полиэтилена, поливинилхлорида и других, имеющих температуру эксплуатации не выше 100оС, требуется предварительная подготовка внутренней поверхности трубопровода-очистка и т.п. Способ непригоден для ремонта дефектных участков со сквозными повреждениями труб, не пригоден он также в принципе для футеровки подземных, подводных и т.п. трубопроводов. Целью изобретения является упрощение технологии нанесения полимерного защитного покрытия на внутреннюю поверхность трубопровода, снижение энергоемкости и повышение скорости процесса, расширение области применения полимерных покрытий из термопластов в трубопроводах с температурой транспортируемой среды до 150оС, высокоагрессивных сред, для футеровки подземных участков трубопроводов без вскрытия грунта, подводных — без извлечения их на поверхность, установленных на различных сооружениях и оборудовании без демонтажа последних. Достигается поставленная техническая задача тем, что используют рукав из полиэтилена или композиций на его основе, предварительно подвергнутый радиационной обработке с последующим продольным растяжением, а нагревание рукава в трубопроводе производят до температуры 200-400оС и скорости перемещения зоны нагрева от 0,3 до 1 м/мин. Способ нанесения полимерного защитного покрытия на внутреннюю поверхность трубопровода осуществляется согласно изобретению следующим образом. Для футеровки предлагается использовать гибкий тонкостенный рукав из радиационно-модифицированного (сшитого) полиэтилена или композиций на его основе, изготовленный по известной технологии [3]. Изделия из сшитого полиэтилена имеют повышенную формоустойчивость при температурах эксплуатации до 150оС, а также повышенную коррозионную стойкость. В предлагаемом способе рукав-заготовку после облучения ориентируют по длине — растягивают при нагревании до размягчения, уменьшая соответственно ее диаметр до технологически необходимого. Операция может производиться как на заводе, так и непосредственно на участке футеровки, в том числе на участке ремонта или санации трубопровода. Для растяжения (ориентации) рукава может использоваться традиционное оборудование и оснастка для ремонтных работ трубопроводов, для нагрева рукава — газовые горелки, паяльные лампы, а для растяжения по длине — барабаны, лебедки для перемотки тросов и т.п. В результате ориентации по длине рукаву придается «память формы», он становится «терморасширяющимся» по диаметру. Собственно процесс футерования внутренней поверхности с использованием предварительно подвергнутого радиационной обработке с последующим продольным растяжением рукава производится следующим образом. Рукав с заранее введенным в него тяговым тросом протаскивают в трубу. Конец рукава нагревают и, пластически деформируя, отбортовывают — закрепляют на конце трубы. К тяговому тросу присоединяют прижимное устройство, с помощью которого при протягивании его внутри рукава, находящегося в трубе, производят нагрев рукава, что приводит к его терморасширению, в результате чего происходит прижатие и напряженная в процессе охлаждения термофиксация рукава на стенке трубы. Прижимное устройство может представлять собой любой подходящий нагреватель — ТЭН или блок ТЭНов по ГОСТ 13236-83, выполненных в форме усеченного конуса с диаметром, близким к диаметру футеруемой трубы, или в случае футерования трубы некруглого сечения иметь форму проходного сечения футеруемой трубы — т.е. типа дорна. Нагреватель должен иметь температуру поверхности от 200 до 400оС и может быть инфракрасным излучателем, или газовым нагревательным устройством (для труб диаметром (d) 350 мм и более). Термофиксация покрытия на стенке трубы при охлаждении рукава (в основном за счет теплообмена со стенкой) может производиться эластичным гибким элементом с низким коэффициентом трения по поверхности рукава, который может быть отрезком гофрированного фторопластового шланга, отрезком фторопластового рукава, заполненного жидкостью; пружинным элементом с антифрикционным покрытием и т.п. Для определенных условий, например для труб с d 350 мм, могут применяться прикатывающие или пневматические конструкции. Скорость перемещения устройства подбирается опытным путем на отрезке трубы, но она должна быть не менее 0,3 м/мин и не более 1,0 м/мин. Скорость охлаждения тонкостенного рукава при прижатии его к стенке трубы высокая и значительно превышает скорость нагрева рукава нагревателем с температурой поверхности 200-400оС, вследствие большой теплоемкости трубы и возникающего большого температурного градиента, особенно при ремонте или санации трубопровода, находящегося в грунте или воде. Скорость перемещения прижимного устройства зависит практически только от его удельной мощности и температуры его поверхности. Толщина покрытия и, соответственно, толщина рукава определяется назначением покрытия, его функцией. Для футеровки трубопроводов, не имеющих сквозных повреждений — новых или безнапорных, достаточно, как показывает практика, покрытие толщиной 1 мм. Такой слой обеспечивает надежную защиту от коррозии в течение всего проектного срока эксплуатации трубопровода. Для труб со сквозными повреждениями особенно при ремонте или санации напорных трубопроводов, расчет толщины покрытия проводится по обычным методикам расчета прочности, так как в этом случае футеровка должна выполнять кроме защитной еще и силовую функцию. При расчете следует учитывать, что основную нагрузку при механических воздействиях несут сами ремонтируемые или санируемые трубы, а не рукав. Силы при терморасширении и остаточное напряжение в гибком тонкостенном (1-3 мм) радиационно-модифицированном рукаве составляют 10-30 кгс/см2 и могут достигать 1/3 прочности исходного полимерного материала. Поэтому при футеровке по предлагаемому способу практически отпадает необходимость в расплавлении полимерного рукава, как в известном способе (2) и нагреве трубы для обеспечения его адгезии к стенке. При использовании тонкостенного терморасширяющегося рукава практически не требуется подготовки внутренней поверхности трубопровода, достаточно проверки и обеспечения минимально необходимого сечения на всей длине трубы для беспрепятственного протаскивания рукава и протяжного устройства. С помощью гибкого рукава можно футеровать изогнутые до 90о переменного по форме и величине сечения трубы (цилиндры) — прямоугольные, овальные и другие. Упругость тонкостенного рукава при футеровке металлических труб облегчает проблему компенсации большого различия в линейном расширении металлов и пластмасс, по крайней мере в диапазоне температур (-60)-(+150)оС. Примеры осуществления способа. В примерах футерованию подвергается внутренняя поверхность стальной неоцинкованной (черной) сварной трубы, применяемой для водо- и газопроводов, систем отопления, изготовленной по ГОСТ 3262-75, с условным проходом 50 мм, внутренним диаметром 54 мм, толщиной стенки 3 мм. Длина трубы — 12 м. Труба предназначена для монтажа трубопровода распределительной тепловой сети категории 4 («Правила устройства и безопасной эксплуатации трубопроводов пара и горячей воды Госгортехнадзора СССР»). Транспортируемая среда — перегретый и насыщенный пар, горячая вода с температурой до 105оС. П р и м е р 1. Футеровку стальной трубы производят радиационнообработанным рукавом из полиэтилена. На заводе-изготовителе рукава из полиэтилена высокого давления марки 15303-003 ГОСТ 16336-77 на экструдере изготавливают рукав (трубу) с наружным диаметром 54-56 мм, толщиной стенки 1,5 мм; на ускорителе электронов ИЛУ-6 рукав облучают до поглощенной дозы 0,1-0,2 МГр. На участке футеровки отрезок рукава длиной 12,1 м последовательно нагревают до температуры 250оС (размягчения) и растягивают в длине до 13,3 м, при которой наружный диаметр рукава становится равным 50 мм (периметр — 157 мм). Этот диаметр на 10% меньше внутреннего диаметра футеруемой трубы и позволяет без затруднений ввести рукав в трубу, т.е. обеспечивает технологичность установки его в трубе. Внутри рукава пропускают тросик, конец рукава вместе с тросиком прикрепляют к концу другого тросика, заранее введенного в трубу, и с его помощью вводят рукав в трубу. Затем второй тросик отсоединяют, а к концу первого тросика присоединяют любым подходящим способом прижимное устройство для нагрева и прижатия рукава к стенке (термофиксации). Со стороны ввода прижимного устройства конец рукава длиной 0,7 м выводят за пределы трубы, нагревают теплоэлектровентилятором или газовой горелкой и вручную или с помощью подходящих приспособлений развальцовывают (отбортовывают) на наружной поверхности трубы. Затем прижимное устройство с помощью введенного внутрь рукава тросика протягивают внутри рукава со скоростью 0,3 м/мин, осуществляя нагрев рукава до 300оС, терморасширение и прижатие его на внутренней поверхности трубы (термофиксацию). В таблице приведены примеры 2 и 3 реализации способа. Полученная таким способом футеровка обеспечивает защиту трубы от воздействия транспортируемых пара или горячей воды с температурой до 135оС в течение не менее 30 лет. При коррозии трубы снаружи до сквозных повреждений размером до 10 мм футерованная труба сохраняет работоспособность при давлении среды до 6 ати.ФОРМУЛА ИЗОБРЕТЕНИЯ
СПОСОБ НАНЕСЕНИЯ ПОЛИМЕРНОГО ЗАЩИТНОГО ПОКРЫТИЯ НА ВНУТРЕННЮЮ ПОВЕРХНОСТЬ ТРУБОПРОВОДА, включающий введение в полость трубопровода рукава из полимерного термопластичного материала, закрепление одного из концов рукава на конце трубопровода, последовательные нагрев и прижатие рукава к стенке трубы с перемещением зоны нагрева перед зоной прижатия, отличающийся тем, что используют рукав из полиэтилена или композиций на его основе, предварительно подвергнутый радиационной обработке с последующим продольным растяжением, а нагревание рукава в трубопроводе производят до 200 — 400oС и скорости перемещения зоны нагрева 0,3 — 1,0 м/мин.www.freepatent.ru