Исследование химического состава пироконденсата пиролизного производства
АННОТАЦИЯ
Приведены результаты исследования химического состава пироконденсата пиролизного производства – пиролизного дистиллята, тяжелой смолы пиролиза и тар-продукта на основе переработки природного газа Устюртского региона. Показано, что пиролизный дистиллят это легкая жидкость от желтого до светло-коречневого цвете с неприятным запахом.
Тяжелая смола пиролиза это маслянистая жидкость от темно-коричневого до темно-зеленого цвета с неприятным запахом. Тар-продукт вещество черного цвета, без запаха. Составы продуктов не стабильны и зависят от сырья пиролиза.
Пиролизный дистиллят содержит, в основном арены и олефины с числом углерода 6-12. Содержание олефинов составляет 23,7%, аренов 67,18%. Присутствуют также алканы, диены, циклоалканы.
Тяжелая смола пиролиза содержит в основном нафталин 41,51%, 2-метилнафталин 16,25%, а также инден – 9,33%, 1-метилнафталин и 1,6-диметилнафталин. Количественно-качественный анализ показал совпадение спектрограмм компонентов смолы с базой данных прибора «ИК-Фурье спектрометр Nicolet 6700 c микроскопом Continuum и Раман-модулем» на 90-97%.
ABSTRACT
Results of research of a chemical compound pyrocondensate pyrolystion manufactures –pyrolystion distillate, heavy pitch of pyrolysis and a tar-product on the basis of processing of natural gas of Ustjurt region are resulted. It is shown, that pyrolystion distillate is an easy liquid from yellow to light-brown colour with an unpleasant smell.
Heavy pitch of pyrolysis is an oily liquid from dark brown to dark green color with an unpleasant smell. The tar-product substance of black colour, without a smell. Structures of products are not stable and depend on pyrolysis raw materials.
Pyrolystion distillate contains, basically arenes and olephins with number of carbon 6-12. The maintenance olephins makes 23,7 %, arenes 67,18%. Are present also alkanes, diens, cycloalkanes.
Heavy pitch of pyrolysis contains basically naphthalene of 41,51%, 2-metil naphthalene 16,25%, and also indene — 9,33%, 1-methylnaphthalene and 1,6-dimethylnaphthalene. The quantitatively-qualitative analysis has shown coincidence of spectrograms of components of pitch to a device database «Infra red-Fourier spectrometer Nicolet 6700 with microscope Continuum and the Raman-module» on 90-97%.
Ключевые слова:пироконденсат, пиролизный дистиллят, тяжелая смола пиролиза, химический состав.
Keywords:pyrocondensate, pyrolystion distillate, heavy pitch of pyrolysis, chemical compound.
В последние годы химическая промышленность Узбекистана изменилась существенным образом — была проведена полномасштабная реформа, в которой во главу угла была поставлено производство продуктов с высоко добавленной стоимостью на основе глубокой переработки местных сырьевых ресурсов. В этом отношении особое значение приобретает освоение новых, импортозамещающей химической продукции на базе переработки имеющегося в Республике углеводородного сырья. Руководством страны уделяется большое внимание созданию новых высокотехнологичных химических промышленных объектов, таких как Шуртанский и Устюртский газохимические комплексы, позволившие Республике занять одно из лидирующих позиций по выпуску полимерной продукции в Центральной Азии.
Совместное предприятие ООО “Uz-Kor Gas Chemical”, является одним из крупнейших производителей полимерной продукции в Центральной Азии, на основе переработки природного газа Устюртского региона. Общая годовая производственная мощность комплекса составляет 387 тыс. тонн полиэтилена и 83 тыс. тонн полипропилена. При этом образуется более 102 тыс. тонн пиролизного дистиллята, 8 тыс. тонн пиролизного масла (ТСП — тяжелая смола пиролиза) и 10 тысяч тонн тар-продукта. Пиролизный дистиллят, пиролизное масло и тар-продукт не перерабатываются [5].
Пиролизный дистиллят и пиролизное масло являются вторичным сырьем для производства нафталина, ароматических углеводородов, индена, фталевого ангидрида и других ценных химических продуктов в которых нуждается промышленность. На СП ООО “Uz-Kor Gas Chemical” переработка этих фракций не предусмотрена проектом. Между тем тяжелые фракции жидких продуктов пиролиза являются сырьем, имеющим внушительный потенциал для дальнейшего применения, т.к. современные технологии позволяют производить ценные продукты гораздо более дорогие и более необходимые, чем топливо. Из-за отсутствия приемлемых технологий переработки пиролизных отходов с получением индена, нафталина и его гамологов в стране не производится фталевый ангидрид. Поэтому исследования направленные на разработку комплексной технологии переработки отходов газохимических комплексов является актуальной задачей и требует своего решения.
С целью использования жидких продуктов пиролиза в качестве вторичного сырья и разработки приемлемой для республики технологии их переработки проведены исследования химического состава пироконденсата пиролизного производства СП ООО “Uz-Kor Gas Chemical”.
Процесс термического пиролиза углеводородного сырья (нефти и её фракций) – основной способ получения низкомолекулярных ненасыщенных углеводородов – олефинов (алкенов) – этилена и пропилена. Наряду с производством этилена и пропилена, процесс пиролиза нефти — основной источник производства дивинила, выделяемого ректификацией из сопутствующей пиролизной С4 фракции и отгонов бензола, получаемого из жидких продуктов пиролиза. Около 80% мирового производства бутадиена и 39% производства бензола осуществляется пиролизом углеводородов [4].
Современная мировая структура сырья пиролиза выглядит следующим образом: этан 27,6% масс., сжиженные газы (пропан, бутан) 14,0% масс., прямогонный бензин (нафта) 53,1% масс., гидроочищенные керосино-газойлевые фракции 5,3% масс.
Использование этих видов сырья в отдельных странах различно. Так, в США и Канаде преобладающим сырьём является этан (49,1% масс. и 69,7% масс.), в Германии, Китае, Франции и Японии — нафта (57,4% масс., 73,3% масс., 60,0% масс.и 80,3% масс.). Кроме того, в Германии и Китае находят широкое применение гидроочищенные керосино-газойлевые фракции (32,0% масс. и 26,7% масс.) [2].
В Узбекистане преобладающим сырьём для термического пиролиза являются этан, пропан-бутановая фракция и газоконденсат.
Продукты пиролиза делятся на две группы: пирогаз и пироконденсат. Пирогаз – начиная с метана до пропилена, на выходе из пиролизной печи при охлаждении до комнатной температуры находится в газообразном состоянии и разделяется от пироконденсата – от дивинила до тяжелой смолы, который при комнатной температуре находится в жидко-твердом состоянии.
Пироконденсат в свою очередь разделяется на три группы веществ по температурам кипения – пиролизный дистиллят (начало температуры кипения 35oС, конец температуры кипения 180oС), тяжелая смола пиролиза (начало температуры кипения 170oС, конец температуры кипения 270oС), тар продукт (начало температура кипения 280oС). Количество образующегося пироконденсата составляет от 2% до 25% от общей массы продуктов пиролиза, в зависимо от сырья.
Пиролизный дистиллят – это легкая жидкость от желтого до светло коричневого цвета с неприятным запахом. Состав ее не стабилен и зависит от сырья пиролиза. Образцы пиролизного дистиллята СП ООО “Uz-Kor Gas Chemical”, для предварительного определения качественного и количественного состава, анализировали на газовом хроматографе с масс-селективным детектором Agilent 5977A [4]. Результаты анализов приведены на рисунке 1 и таблице 1.
Рисунок 1. Масс спектрограммы трех образцов (а, б и в) пиролизного дистиллята
Таблица 1.
Химический состав пиролизного дистиллята
Число углерода | Алканы | Диены | Олефины | Циклоалканы | Арены | Всего |
2 | 0 | 0 | 0 | 0 | 0 | 0 |
3 | 0 | 0 | 0 | 0 | 0 | 0 |
4 | 0 | 0 | 0 | 0 | 0 | 0 |
5 | 0,8 | 0,89 | 4,91 | 0,19 | 0 | 6,79 |
6 | 0,22 | 0,41 | 3,87 | 0,41 | 32,94 | 37,85 |
7 | 0,25 | 0,14 | 0,84 | 0,45 | 11,23 | 12,91 |
8 | 0,12 | 0,08 | 0,18 | 0,48 | 9,75 | 10,61 |
9 | 0,04 | 0,1 | 0,04 | 0,15 | 7,56 | 7,89 |
10 | 0,03 | 0,11 | 9,07 | 0,4 | 5,23 | 14,84 |
11 | 0,18 | 0,69 | 2,95 | 0 | 0,47 | 4,29 |
12 | 0 | 0,15 | 1,84 | 0 | 0 | 1,99 |
Всего | 1,64 | 2,57 | 23,7 | 2,08 | 67,18 | 97,17 |
Тяжелая смола пиролиза – это маслянистая жидкость от темно-коричневого до темно-зеленого цвета с неприятным запахом. Состав ее не стабилен и зависит от сырья пиролиза. Образцы тяжелой смолы пиролиза СП ООО «Uz-Kor Gas Chemical», для предварительного определения качественного и количественного состава анализировали на газовом хроматограф с масс-селективным детектором Agilent 5977A, Подготовленную пробу анализировали на хромато-масс-спектрометре «Agilent Technology» GС 6890 / МS 5973N с использованием капиллярной колонки размером 30м×0,25 мм с 5% фенилметилсилоксана в диметилсилоксане, газ носитель — водород, температура инжектора – 280оС, температура MS источника – 230оС, температура MS квадруполя – 180оС, при программировании температуры термостата колонок от 100 до 280оС, скорость подъема температуры 10оС мин, величина пробы 1 мкл., в режиме без деления потока. Результаты анализов приведены на рисунке 2. и таблице 2.
Тар-продукт – это твердое вещество черного цвета без запаха. Состав не стабилен и зависит от сырья пиролиза. Образцы тар-продукта СП ООО «Uz-Kor Gas Chemical» для предварительного определения качественного состава анализировали на анализаторе ИК-Фурье спектрометр Nicolet 6700 c микроскопом Continuum и Раман-модулем. Результаты анализа приведены на рисунке 3.
Рисунок 2. Масс спектрограмма образца тяжелой смолы пиролиза производства
СП ООО Uz-Kor Gas Chemical”
Таблица 2.
Количественно – качественный состав тяжелой смолы пиролиза производства СП ООО «Uz-Kor Gas Chemical»
№ | Вещество | Количество, % | Совпадение с базой |
1. | Indene | 9.33 | 93 |
2. | 1-methylindene | 8.96 | 96 |
3. | Naphthalene | 41.51 | 90 |
4. | 1-мethylnaphthalene | 8.61 | 97 |
5. | 2-methyInaphthalene | 16.25 | 96 |
6. | 1-ethylnaphthalene | 1.77 | 90 |
7. | 1,6-Dimethylnaphthalene | 1.71 | 95 |
Рисунок 3. ИК-спектрограмма тар-продукта: 1 – тар-продукт, 2, 3 и 4 спектры базы прибора
Исследования химического состава пироконденсата пиролизного производства СП ООО «Uz-Kor Gas Chemical» были проведены для решения проблемы рационального использования тяжелых фракций жидких и твердых продуктов пиролиза. Результаты анализа пироконденсата пиролизного производства СП ООО «Uz-Kor Gas Chemical» для получения зависимости от фракционного состава исходного сырья и условий пиролиза показали, что в сравнении с литературными данными [6] в соответствии с данными таблицам 1 и 2 разница составляет от 3 до 10%, и т.о. пироконденсат может быть использован для дальнейшей переработки.
Основной проблемой эффективного использования ТСП является низкое качество, связанное с высоким содержанием асфальтенов и механических примесей. В связи с тенденцией утяжеления сырья пиролиза требуются дополнительные затраты на облагораживание смол. Вопрос подготовки сырья для производства углеводородных материалов становится ключевым при создания обоснованных композиционных рецептур с учетом данных экономического и экологического анализа. Например, композиции из ТСП и пека можно использовать в качестве «сухой анодной массы» металлургического производства [3].
Особенности химической природы пироконденсата пиролизного производства, большие масштабы производства, превращают пироконденсат из отходов в один из целевых продуктов при производстве различных типов материалов, что позволит повысить эффективность пиролизного производства СП ООО “Uz-Kor Gas Chemical”, благодаря получению новых видов химической продукции.
Список литературы:
1. Бёккер Ю. «Хроматография. Инструментальная аналитика: методы храмотографии и капиллярного элек-трофореза». Перевод с немецкого, Москва, Техносфера, 2009.
2. Бондалетов В.Г., Бондалетова Л.И., Нгуен Ван Тхань. «Использование жидких продуктов пиролиза угле-водородного сырья в синтезе нефтеполимерных смол» // Успехи современного естествознания. – 2015. –
№ 1-7. – С. 1130-1133.
3. Лебедева И.П., Дошлов О.И., Иванова К.К. «Утилизация смол пиролиза, образуемых в установке ЭП-300 ОАО «Ангарский завод полимеров»», Экологический вестник России. — 2010. — № 7. — С. 44-46.
4. Мухина Т.Н., Барабанов Н.Л., Бабаш С.Е. Пиролиз углеводородного сырья. — М.: Химия, 1987. — 240 с.
5. Официальный сайт СП ООО ”Uz-Kor Gas Chemical” http://www.uz-kor.com/index.php/ru/deyatelnost 2018 г.
6. Справочник нефтехимика. В двух томах. Т. 1. /Под ред С.К.Огородникова. Л.: Химия, 1978. – 496 с.
7universum.com
виды пиролиза, описание и оборудование для пиролиза
Процессы термического разложения органических и неорганических соединений называют пиролизом. Особенностью сжигания при этом методе считается ограничение доступа кислорода. Данный способ утилизации считается безотходным/малоотходным и позволяет создавать циклический механизм переработки не только ТБО, но также нефтепродуктов, загрязненной почвы, прочего.
На выходе такого деструктивного разрушения становятся продукты, характер и природа которых зависит от применяемого конкретно метода, а также состава вторичного сырья.
Выделяют два основных результирующих направления: обезвреживание отходов и сбор сырьевой базы. Последний вариант на сегодня наиболее актуальный. Прежде всего из-за возможности воссоздавать нефтехимические продукты, природный ресурс которых, как известно, невосполним.
Кроме того, в результате переработки органических отходов получают сразу два вида продуктов — кокс и жидкие компоненты: смолы, пиролизный газ. При осаждении или фильтрации последнего получают углеводороды. Дополнительно к этому вызывает интерес получение ароматических соединений.
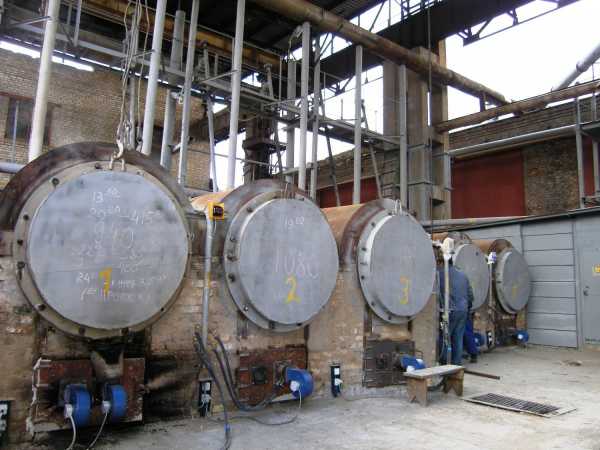
Оборудование для пиролиза резины
Виды пиролиза, причины их появления
Для реализации метода требуется дорогостоящее оборудование, необходима подготовка кадров. Несмотря на это заинтересованность в создании предприятий, занимающихся утилизацией ТБО по методу пиролиза есть.
- Во-первых, это эффективный метод использования вторичного сырья (фактически безотходный).
- Во-вторых, наблюдается заметный вклад в защиту экологической среды.
- В-третьих, не страдают жители территорий, прилегающих к заводам с таким методом переработки.
Появившись еще в 19 веке, пиролиз интенсивно развивался. Заинтересованные лица искали еще более приемлемые варианты для разложения отходов. Преследовались такие цели:
- сохранение безопасности для окружающей среды;
- сокращение расходов на переработку;
- создание условий для накопления результатов сжигания;
- получение экономической выгоды.
В итоге появились несколько видов метода, сосредоточимся на них. Формально их два: сухой и окислительный. Однако первый имеет собственные разновидности и характеристики.
Сухой пиролиз и его разновидности
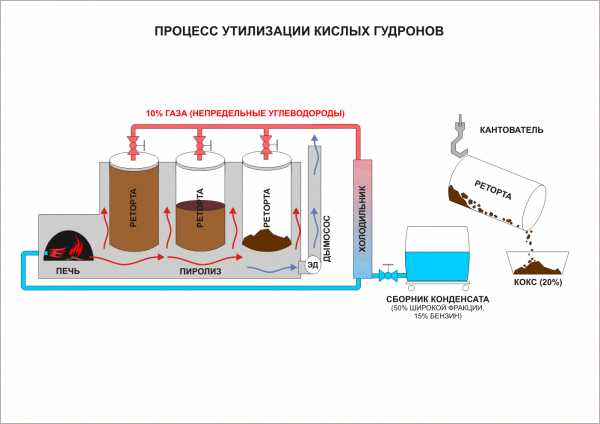
Утилизация кислых гудронов пиролизом
Метод преследует такие основные цели: обезвреживание вторичного сырья, получение топлива, различных химических соединений, используемых в промышленности. Главный сохраняемый принцип, которому следует сухой пиролиз, — рациональное использование невосполнимых природных ресурсов.
Способ позволяет получать пиролизный газ, жидкий продукт, твердые углеродистые компоненты. Сухой пиролиз может протекать при трех режимах температур:
- Низких.
- Средних.
- Высоких.
Пиролиз при Т 450-550 градусов по Цельсию относится к низкотемпературному. Методу характерно получение полукоксов в больших количествах, максимальная температура выхода пиролизного газа при образовании его в минимальных объемах. Также наблюдается получение смол, которые в дальнейшем используются для производства каучука. Образующиеся полукоксы применяют в качестве топлива для промышленных и бытовых нужд.
Среднетемпературный пиролиз происходит при 800 градусах по Цельсию. В ходе сжигания выделяется большое количество газа и гораздо меньше, жидких смол и непосредственно кокса, чем в предыдущем случае.
Высокотемпературный пиролиз протекает при Т выше 900 градусов по Цельсию. Этот метод дает минимальное количество твердых и жидких отходов. Образующиеся газы впоследствии используют, как топливо для транспортировки.
Окислительный пиролиз
Это процесс частичного или полного сжигания промышленного вторичного сырья при его контакте с продуктами сгорания топлива. Используется для обезвреживания жидких нефтесодержащих отходов, а также пластмасс, резины, прочего.
Этот метод используют для сжигания сырья, находящегося в пастообразном, жидком или даже газообразном состоянии. Под обработку окислительным способом подходят измельченный пластик, резина, а также промышленные стоки.
Виды пиролиза по типу сжигаемого материала
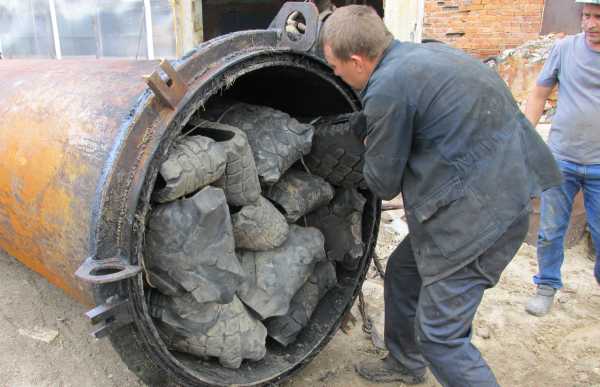
Самодельная установка для пиролиза старых покрышек
Россия страна богатая древесиной. В ней сложилась одна из наиболее фундаментальных школ пиролиза этого вида сырья. Происходит процесс при низкотемпературном режиме. На выходе получают такие вещества: жидкие — метиловый спирт, уксусная кислота, ацетон, смола и др, твердые – древесный уголь.
Пиролиз метана производится при высоких температурах и получаемый в результате ацетилен, тут же отправляют на производство искусственного каучука. Такие сложности связаны с тем, что переработка метана для добычи конечного продукта ацетилена экономически невыгодна.
Между тем пиролиз метана имеет ряд уравнений для решения проблемы утилизации этого продукта. Для протекания реакций, кроме специфической температуры периодически требуются дополнительные вещества.
Например, тримеризация ацетилена протекает в низкотемпературном режиме, но обязательно с присутствием активированного угля. Более того, специфика данного процесса в его скорости: данный вид пиролиза относится к низкоскоростному, что подразумевает медленную подачу источника возгорания.
Предварительный этап получения ацетилена протекает наоборот при высоких температурах и в скоростном режиме. Формула реакции такова: 2СН4 = С2Н2 + 3Н2. Однако попутно протекает еще целый ряд побочных реакций.
Пиролиз и крекинг предельных углеводородов – это среднетемпературный процесс, в результате него получают: этилен, пропилен, бензол и ряд подобных продуктов. Нефтегазовое сырье перерабатывают по методу крекинга еще с 1877 года, автор идеи также россиянин, химик Александр Александрович Летним.
Пиролиз мусора и ТБО подразумевает в том числе переработку шин, пластмасс, прочего, о чем речь уже шла ранее. Поэтому стоит выделить лишь основные моменты или трудности, с которыми сталкиваются в ходе осуществления данного процесса.
Видео — Пиролиз или нефтехимия в деталях:
Необходимость в пиролизных установках
Главная проблема утилизации мусора и других отходов ТБО обсуждаемым методом, это найти эффективный и недорогостоящий способ для улавливания испарений, возникающих во время сжигания. При горении выделяются хлор, фосфор, сера. Более того, некоторые отдельно взятые случаи сжигания отличаются присутствием реакции взаимодействия хлора с другими продуктами сжигания, в результате чего могут образовываться просто ядовитые соединения.
Современные установки решают ряд описанных трудностей. Например, ограниченность доступа кислорода сокращает вероятность образования токсинов: фуран, бензапирен, прочих.
Возможность создания циклических комплексов переработки отходов ведет к почти безотходному производству. Достигается максимальная экономия энергетических ресурсов. Кроме того, образующийся в результате шлак идет на ремонт дорог, что дополнительно повышает экономическую значимость переработки.
Расширяется круг вероятных мест размещения заводов (даже на территории городов). Поскольку в идеале не должно быть выбросов в окружающую среду: отсутствие газообразных ядовитых испарений, исключение образования производственных стоков (все собирается и циклически перерабатывается).
Последнее преимущество, все перечисленные возможности выполняются на довольно компактном оборудовании, без огромных труб, высоких устрашающих зданий. Организовать производство вторичных отходов вполне реально в небольшом ангаре.
Видео — пиролизные установки для утилизации отходов:
Внедрение метода на бытовом уровне
Жить в пригороде становится все более популярно. Однако далеко не все горожане готовы к заготовке дров, а газификация поселков и дачных участков решается довольно туго.
Альтернативой традиционным способам утепления жилых помещений выступают бытовые пиролизные котлы. Сегодня они не просто становятся источником энергии практически из мусора, но оснащены современной электроникой и принудительной вентиляцией. Бытовые котлы «Пиролиз 43» — одна из популярных моделей, представленная рынке подобных товаров. Оборудование имеет два котла сжигания, что гарантирует дожег образующих паров, газов, прочего. Это делает их использование преимущественным во всех отношениях: экономично, безопасно, эффективно.
Причем для использования данной модели котла также подходят дрова, но специалисты подчеркивают: топливо в котлах скорее тлеет, чем горит, плюс дополнительный дожег, — обеспечивают существенную экономию ресурсов.
Зола почти не образуется, а значит владельцам не придется долго думать над очисткой оборудования в процессе эксплуатации. Последнее, что важно для бытовых пользователей – это возможность выбирать котел подходящего дизайна (в том числе и его цвет).
Духовой шкаф с пиролитической очисткой
Подобные возможности современного бытового оборудования лишний раз заставляют задуматься о целесообразности приобретения газовой или электрической плиты.
Реализация пиролитической очистки возможна только для последнего варианта. Эта технология значительно эффективней, чем гидролиз или электролиз, также находящие место для бытового применения.
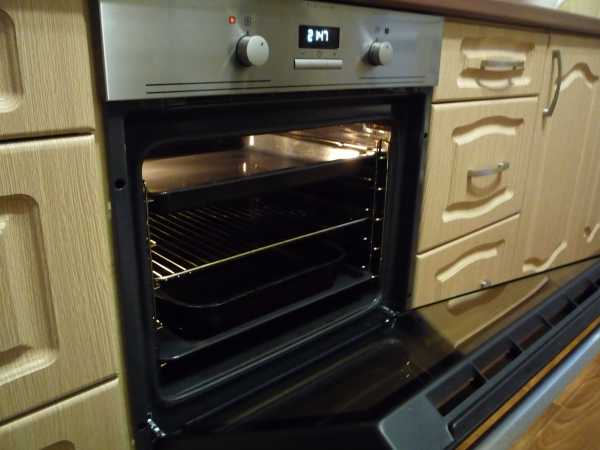
Духовой шкаф с пиролитической очисткой
Система с пиролитической очисткой не требует смены никаких фильтров и сохраняет работоспособность на весь гарантийный срок духового шкафа. Если предельно просто описать процессы, происходящие при подобной очистке, все выглядит примерно так:
- загрязненный духовой шкаф разогревается до максимально возможных температур;
- далее происходит сжигание жиров, накипи, прочих наслоений на стенках оборудования;
- газ уходит по каналам вентилирования;
- на дне поддона образуется зола, которую можно просто выбросить.
Сегодня достаточно много форумов собирает аудиторию, заинтересованную данным вопросом. Поскольку такие блюда, как курочка-гриль или шашлычок в духовке, не приготовишь в кулинарном рукаве. С другой стороны, выпечка после такого использования печки получается просто ужасная. Вот и выходит, что многим действительно необходимы действенные, одновременно экономичные методы очистки, каковым и является пиролиз.
xlom.ru
Пиролизная переработка | Бизнес Промышленность
В нынешнее время чтобы термическим путём переработать углеродсодержащие отходы применяют две технологии: термическую газификацию и пиролизную переработку.
Считается, что вторая технология более эффективная и предпочтительная для переработки отходов кокса, угля, пластика, торфа, деревообработки, резинотехнических изделий и т.д.
Технология пиролизной переработки
Пиролизная переработка – это процесс термической дисперсии органических соединений при отсутствии воздуха. Этот процесс абсолютно исключает выделение различных загрязняющих и канцерогенных веществ, которые образуются в процессе окисления.
Пиролиз углеродсодержащего сырья способствует образованию двух продуктов:
- неочищенного конденсируемого пиролизного газа;
- полукоксового порошка.
После охлаждения и очистки полученного газа образуется пиролизный дистиллят. Количество полукоксового порошка составляет около 30% от общей массы исходного сырья.
Кроме вышеперечисленных продуктов, при пиролизе получается и тепловая энергия, проходя внутренние экзотермические реакции в реакторах установок для пиролиза.
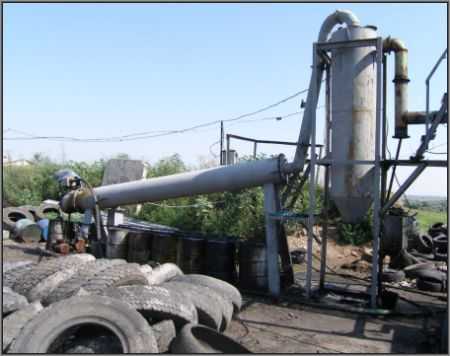
Температура реакций
Пиролизная переработка происходит при температуре от 350 до 850°. От температуры зависит соотношение количества продуктов пиролиза на выходе, поскольку при увеличении температуры одновременно увеличивается выход газового компонента.
Соответственно, более низкая температура способствует увеличению выхода полукокса и жидкой фракции. Оптимальной считается температура пиролиза в 500° для основных видов применяемого в процессе углеродсодержащего сырья, а также 550-800° – для горючего сланца или измельченного угля.
Факторы эффективности пиролизной переработки
Одним из факторов, влияющих на КПД пиролизной переработки, является влажность сырья. Этот показатель должен лежать в диапазоне 18-19%. Также частицы сырья обязаны иметь достаточно мелкие размеры, дабы обеспечить быстрый и глубокий нагрев для того, чтобы обеспечить высокую производительности и эффективность технологического процесса.
К этому всему зольность сырья должна быть максимум 50%. Зола, которая находится в составе сырья, не поддаётся переработке, она увеличивает энергозатраты и уменьшает полезный выход продуктов распада. Поэтому пиролизная переработка сырья, у которого зольность более 50%, будет практически нерентабельна.
Применение продуктов пиролиза
При дальнейшей глубокой переработке продуктов пиролиза возможно получение множества высоколиквидных энергетических продуктов, таких как:
- заменитель природного газа,
- печное топливо,
- полукокс с очень развитой микропорной поверхностью,
- электрическая энергия,
- тепловая энергия, а также разнообразные топливные жидкие продукты.
Социальные закладки
www.business-equipment.ru
Деятельность
Награды проекта
- 2012 год — Признан лучшим проектно-финансовым соглашением в нефтехимическом и газохимическом секторах международным изданием «Project Finance International».
- 2012 год — Удостоен международных премий «Лучшая сделка 2012 года» изданиями Trade Finance Magazine и Global Trade Review.
- 2014 год — Присуждена премия «Глобальная сделка 2014 года в нефтегазовой сфере» международным изданием Infrastucture Journal
Производственные мощности
- Ежегодная добыча и транспортировка более 3,0 млрд. кубических метров природного газа с месторождения «Сургиль»;
- Ежегодная добыча, предварительная подготовка и транспортировка более 115 тысяч тонн газового конденсата с месторождения «Сургиль»;
- Глубокая многоступенчатая переработка природного газа с извлечением ценных компонентов на Устюртском газохимическом комплексе.
Общая годовая производственная мощность комплекса составляет:
387 тыс. тонн полиэтилена;
83 тыс. тонн полипропилена;
102 тыс. тонн пиролизного дистиллята;
8 тыс. тонн пиролизного масла.
Завод разделения газа.
Завод разделения газа, был построен команией «Samsung Engineering Co. Ltd.» за 36 месяцев. С августа 2015 года на заводе разделения газа, начат прием природного газа с месторождений Сургиль, Западный и Восточный Бердах. На сегодняшний день завод осуществляет разделение поступающего природного газа на такие фракции как метан (товарный газ), этан, сжиженный углеводородный газ и газоконденсат.
Завод по производству этилена.
Строительство завода по производству этилена, осуществлялось компанией «GS Engineering & Construction Corp.», в течении 40 месяцев, базируясь на основании технологии производства этилена и пропилена, компании KBR, по лицензии которой работают более 100 заводов более чем в 27 странах
Заводы по производству полиэтилена и полипропилена.
Первый полиэтилен высокой плотности, производства Устюртского ГХК был получен 25 октября 2015 года, и с 5 ноября 2015 года начато производство полипропилена с разновидностью марок. Заводы были спроектированы и построены компанией «Samsung Engineering Co. Ltd.», в течении 38 месяцев, лицензиаром технологии является всемирно известная компания «Lotte Chemical», по лицензии которой работают крупные производства в 18 странах мира.
На заводе полимеров, осуществляются реакции полимеризации, сепарация, осушка и грануляция полиэтилена и полипропилена.
Завод обеспечения энергоресурсами.
Был спроектирован и построен компанией «Hynudai Engineering» в течении 36 месяцев. Завод обеспечивет производственные нужды всего комплекса электроэнергией, газовым азотом, техническим воздухом, паром высокого давления, технической и повторно очищенной водой. Также в рамках проекта Устюртского ГХК в эксплуатации находятся газотурбинныее генераторы компании «Siemens», которые обеспечивают максимальную энергоэффективность всего комплекса в целом, одновременно осуществляя поставку электроэнергию во внешнюю энергосеть.
На сегодняшний день производимая полимерная продукция, реализуется на экспорт, в страны Центральной и Восточной Азии, СНГ и Европы, а так же на внутренний рынок через торговую площадку УзРТСБ.
Пиролизный дистиллят и пиролизное масло, направляется в Бухарский нефтеперерабатывающий завод, для дальнейшей переработки и получения топлива.
www.uz-kor.com
Пиролизное сырье — Справочник химика 21
Тяжелый газойль гидрокрекинга рассматривается как хорошее пиролизное сырье для получения этилена, а фракции С5—85°С и 85—193 °С, богатые нафтеновыми углеводородами, — как превосходное сырье для каталитического риформинга, направленного на производство ароматических углеводородов. Легкий газойль обычно используется как компонент дизельного топлива. [c.49]Вследствие этого значительная часть потребности установок пиролиза в сырье будет обеспечиваться жидкими углеводородными продуктами. К таковым относятся газовый бензин, рафинаты каталитического риформинга, а также при необходимости низкооктановый прямогонный бензин. В некоторых случаях в качестве пиролизного сырья могут быть использованы и более высококипя-щие фракции нефтепереработки. [c.36]
Основные способы производства бутадиена одно- и двухстадийное дегидрирование бутана, дегидрирование бутиленов. выделение из пиролизной фракции С4 и метод Лебедева (на основе этилового спирта). Последний метод устарел, и объем производства по нему сокращается. Наиболее экономичным, по-видимому, является процесс получения бутадиена из пиролизного сырья. Себестоимость бутадиена, выделенного из газов пиролиза, примерно на 40% ниже себестоимости бутадиена, получаемого двухстадийным каталитическим дегидрированием бутана. Но пиролизный метод пока не получил широкого распространения, так как основное сырье для пиролиза в СССР составляют легкие углеводороды, и количество бутадиена, извлекаемого из продуктов пиролиза, незначительно. С увеличением доли более тяжелых фракций в балансе сырья пиролиза выход бутадиена (в %) возрастает [c.184]
Получаемый на стадии дистилляции пропан можно использовать для бытового газоснабжения или в качестве пиролизного сырья. [c.70]
Некоторое количество керосино-газойлевых фракций, составляющих 6—7 % на перерабатываемую нефть (в годовом разрезе), расходуется в качестве сырья на установках каталитического крекинга в Баку, а также на Гурьевском нефтеперерабатывающем заводе, что, естественно, снижает выход товарной продукции. Дистилляты пиролизного сырья и керо-сино-газойлевой фракции для каталитического крекинга не подвергаются выщелачиванию и направляются на указанные установки в сыром виде, что приводит и к потере некоторых ресурсов нафтеновых кислот. [c.120]
Таким образом, все дистилляты, получаемые с установок первичной перегонки нефти, за исключением керосино-газойлевых фракций и пиролизного сырья, являются товарной продукцией и направляются на нужды народного хозяйства. [c.120]
Таким образом, перевод пирогенных установок на режим пиролиза бензиновых фракций при условии выработки тех же количеств газа позволит сэкономить жидкое пиролизное сырье примерно в 2 раза. [c.370]
ТЕХНОЛОГИЯ ПРОИЗВОДСТВА НЕФТЯНОГО ПЕКА ИЗ ПИРОЛИЗНОГО СЫРЬЯ [c.86]
В странах Западной Европы выход бензина из нефти за последние годы снизился с 22 до 15,5% и все же 8—10% вырабатываемого бензина остается в избытке. Поэтому здесь большая часть бензина используется в качестве пиролизного сырья для производства этилена, пропилена, ароматических углеводородов. Для обеспечения тепловых электростанций применяется мазут, выходы которого составляют 33—35% на перерабатываемую нефть [14]. [c.14]
В США природный газ в больших размерах Используется в качестве пиролизного сырья в производстве -этилена и пропилена, а также топлива на тепловых электростанциях. Основным же направлением использования нефти является производство моторных топлив, главным образом автомобильного бензина. [c.14]
Это положение можно наглядно показать на примере производства этилена, одного из наиболее многотоннажных нефтехимических продуктов, продукция которого непрерывно и быстро возрастает. До начала 70-х годов основным пиролизным сырьем для производства этилена в США служили этан и пропан, выделяемые из природного газа. В случае пиролиза этана получались самые высокие выходы этилена с минимальными выходами сухого газа и пиролизной смолы (ароматических углеводородов). В странах Западной Европы основным пиролизным сырьем служила бензиновая фракция, производство которой на нефтеперерабатывающих заводах значительно превышало потребность в автомобильном бензине. Резкое повышение цен на этан, пропан и нефть в начале 70-х годов сделало экономически нерентабельными эти виды сырья в пиролизных процессах производства этилена [11, 12]. В качестве сырья в процессах пиролиза начали применять более тяжелые виды нефтяных продуктов [13] и даже сырую нефть. Выходы этилена и пропилена из этого сырья, конечно, значительно ниже, чем при пиролизе этана, пропана и бензина, а выходы жидких продуктов пиролиза, в том числе бензола и его гомологов, выше. Это значит, что удельный вес пиролизного бензола и его [c.250]
В капиталистических странах з связи с энергетическим кризисом сложилась обстановка перспективного дефицита традиционных видов исходного сырья для процессов пиролиза, таких, как этан, пропан, бутан и их смеси, а также низкокипящие бензиновые и бензино-лигроиновые фракции. Это вызвало новую волну обширных исследовательских, проектно-конструкторских и других работ по применению в качестве пиролизного сырья более тяжелых нефтепродуктов — легких и тяжелых газойлей, вакуумных отгонов и других, а также сырых нефтей. [c.4]
По данным экономистов, долевое участие этана, пропана и нефтезаводских газов в производстве этилена и других олефинов в США к 1980 г. будет уменьшаться за счет вовлечения значительных объемов прямогонных бензинов и других жидких нефтепродуктов в качестве пиролизною сырья [80 81 120]. Ожидается [1071, что в 1983 г. 50—55% этилена будет производиться из этана, пропана и бутана (в 1973 г.— 67%), 5—10% — из нефтезаводских газов, а остальные 35—45% — пиролизом бензиновых фракций и газойлей (в 1973 г.— 20 %). [c.11]
Стремление к максимальному и пользованию в качестве пиролизного сырья газов и бензиновых фракций для производства низших олефинов как за рубежом, так и в СССР до последних лет обусловливается двумя основными причинами. Во-первых, они являются наиболее благоприятными для получения олефинов, так как по сравнению с другими более тяжелыми фракциями обеспечивают наивысший выход этилена, а в случае необходимости — и пропилена. Во-вторых, современные трубчатые печи, составляющие основную техническую базу процесса пиролиза, не в состоянии эффективно перерабатывать в низшие олефины более тяже- [c.14]
Эффективным источником пиролизного сырья могут быть нефтезаводские газы при получении их в достаточно больших количествах. [c.15]
В качестве пиролизного сырья как в Советском Союзе, так и в зарубежных странах (особенно в странах Западной Европы и Японии) наиболее широкое распространение получили прямогонные легкие бензины и бензино-лигроиновые фракции с концом кипения до 200° С, а в последнее время также рафинаты платформинга. [c.17]
В последние годы как в Советском Союзе, так и во многих странах Западной Европы, а также Японии и США большое внимание уделяется использованию в качестве пиролизного сырья легких и тяжелых прямогонных газойлевых фракций, выкипающих соответственно в пределах 200—380 и 250—540 С [69 88 П2 120]. [c.17]
Проблема широкого применения газойлей в качестве пиролизного сырья для США, Японии и стран Западной Европы связана с их ценой. Технико-экономические расчеты показывают [58 69 1201, что использование газойлей на установках пиролиза целесообразно при условии, если стоимость последних будет на 20—30% ниже стоимости бензиновых фракций. В случае стоимости газойлей на 30% ниже стоимости бензиновых фракций многочисленные пиролизные установки будут проектироваться для работы на атмосферном газойле с пределами кипения 230—330° С. [c.18]
При переработке нефтяных газов особенно большое значение приобрело производства этилена и пропилена для прогрессивных видов пластических масс (полиэтилена, полипропилена), бутадиена и изопрена -для синтеза высококачественных каучуков (полибутадиена и полиизопрена), заменяющих натуральные. В настоящее время сжиженные газы, получаемые на ГПЗ, занимают большой удельный вес в структуре сырья для производства этилена. Являясь относительно эффективным пиролизным сырьем (главным образом пропан), ресурсы сжиженных газов не смогут полностью обеспечить весь объем производства этилена в стране. Пропан и бутаны одновременно необходимы для нужд в качестве бытового топлива в сельской местности. Бутаны дополнительно в большом количестве требуются в качестве сырья для синтеза бутадиена. [c.48]
Таким образом, изменяя режимы пиролиза и рециркулируя образующиеся газообразные углеводороды, можно в широких пределах изменять выходы и соотношения как этилена, так и побочных продуктов реакции. Выбор того или иного режима диктуется обычно спросом на отдельные продукты и экономической эффективностью их реализации, а также структурой цен на сырье и получаемые продукты. Изменение режимов пиролиза дает аналогичные возможности широкого варьирования выходами продуктов также при использовании газойлей в качестве пиролизного сырья. [c.23]
На ГПЗ из нефтяных и природных газов получают большое количество пропана — в США около 65% пропана вырабатывают на газоперерабатывающих заводах [8]. В чистом виде или в смеси с бутаном пропан используют в качестве нефтехимического (пиролизного) сырья, коммунально-бытового и моторного топлива, для огневой культивации почвы, сушки сельскохозяйственной продукции и других целей. Кроме этана и пропана, из нефтяных и природных газов извлекают н-бутан, изобутан, н-пентан и изопентан, которые используют для производства синтетического каучука, коммунально-бытового и моторного топлива. [c.10]
В Советском Союзе часть ресурсов прямогонных бензиновых фракций перерабатывается по прямому назначению в процессах каталитического реформинга. В дальнейшем расход бензиновых фракций с целью производства бензола, толуола и ксилолов возрастет, следовательно, резко сократятся их ресурсы для пиролиза. Кроме того, развитие нефтехимической промышленности экономически целесообразно базировать на преимущественном использовании бензиновых фракций (в качестве пиролизного сырья) только в тех случаях, когда осуществляется комбинирование производств с нефтеперерабатывающей (по топливно-масляной схеме) и нефтехимической ветвями в составе крупных комбинатов. [c.23]
Применение сырых нефтей в качестве пиролизного сырья целесообразно, так как они доступны, дешевы, не требуют специальной предварительной подготовки и транспортабельны на любые экономически оправданные расстояния. Кроме того, использование сырых нефтей для пиролиза не связано с конкретными схемами нефтеперерабатывающих заводов, от ритмичной работы и возможностей которых во многом зависит своевременное и полное обеспечение сырьем нефтехимических производств. Решение проблемы использования сырых нефтей и тяжелых нефтепродуктов для пиролиза до последних лет встречает трудности из-за отсутствия [c.23]
Природные газы содержат 93—98% метана, до 2% этана и до 1% пропана. Поскольку для пиролиза пригодны только этан и пропан, природные газы считаются малоценным сырьем пиролиза. Попутный газ и продукты стабилизации нефти содержат 60—70% этана, пропана и более высококипящих парафиновых углеводородов и поэтому представляют собой ценное пиролизное сырье. Иногда пиролизу подвергают не весь попутный газ, а только выделенные из него этан, пропан и бутан. [c.204]
Интеграл кинетической функции жесткости по длине реакционного змеевика определяет степень разложения сырья на выходе из последнего. Константа скорости реакции является характеристикой пиролизного сырья. [c.33]
Ресурсы пиролизного сырья в нашей стране и почти во всех странах в основном складываются из сжиженных газов и низкокачественных прямогонных бензиновых фракций (депентанизированный газовый бензин, конденсаты газоконденсатных месторождений, низкооктановые бензиновые фракции и др.). Тем не менее ресурсы прямогонных бензиновых фракций недостаточны для перспективного развития производства низших непредельных углеводородов Сз—С4. Поэтому во все возрастающих количествах в процессах пиролиза применяется тяжелое сырье. [c.159]
Однако учитывая большое значение проблемы вовлечения сырых нефтей и тяжелых нефтепродуктов в сферу производства олефинов в процессах пиролиза, важно экономическое обоснование этой целесообразности. Целесообразность и эффективность применения сырых нефтей в качестве пиролизного сырья прежде всего обосновывается их доступностью и сравнительной дешевизной, а также тем, что они не требуют предварительной подготовки и транспортабельны на любые экономически оправдываемые расстояния. Кроме того, использование сырых нефтей для пиролиза не связывается с какими-либо конкретными схемами нефтеперерабатывающих (на топлива и масла) заводов, от ритмичной работы которых во многом зависит устой- [c.162]
А вот с метаном на пиролизном производстве сделать пока ничего не могут. Это безвозвратная потеря, когда относительно дорогое пиролизное сырье обращается в топливный газ. Хуже всего, что выход метана трудно уменьшить, так как он возрастает с повышением жесткости пиролиза. [c.108]
В последние годы в структуре пиролизного сырья начала увеличиваться доля жидкого нефтяного сырья — низкооктанового бензина и рафинатов. [c.54]
Отстоявшееся пиролизное сырье было перекачано по следующему участку нефтепровода от промежуточной станции до конечного пункта без изменения режима перекачки. [c.156]
Модель оптимального баланса пиролизного сырья. [c.156]
Первым шагом к использованию химических веществ в трубопроводах стало применение продуктов нефтепереработки керосиновых и бензиновых дистиллятов для отмывки трубопроводов с одновременным пропуском большого количества скребков. Таким способом еще в 1927 г. был удален весь рыхлый слой церезина со стенок трубопровода Грозный-Махачкала, построенного в 1913 г. и транспортирующего парафинистую нефть и мазут. Летом 1932 г. для выяснения возможности перевода нефтепровода с перекачки нефти на перекачку светлых продуктов была успешно осуществлена промывка керосиновыми и бензиновыми дистиллятами перегона Грозный-Калаус. В 1956 г. путем промывки пиролизным сырьем была решена проблема с отложениями парафина на стенках нефтепровода Туймазы-Омск. [c.43]
Тогда решили промыть трубопровод пиролизным сырьем. Прокачку подогретой нефти и пиролизного сырья производили при обычном режиме работы нефтепровода — со скоростью 1-1,2 м/с. Пиролизное сырье продвигалось по нефтепроводу пробкой длиной 36 км при общей длине обрабатываемого участка 165 км. Так сырье перекачивали до промежуточной перекачивающей станции, расположенной примерно на середине трассы нефтепровода, где оно было принято в один из резервуаров этой станции. [c.156]
При отстое пиролизного сырья из него на днище резервуара выпало кусками и виде жижи около 1000 тонн парафиновых отложений. [c.156]
Сжиженные газы — сырье для химических и нефтехимических производств. С высокими экономическими показателями сжиженные газы используют в качестве пиролизного сырья для получения олефиновых углеводородов, включая этилен, пропилен и бути-лены. Из отдельных фракций углеводородов получают газовую сажу, синтетические спирты и каучуки, различные пластические массы и много других продуктов, находящих все более широкое применение в народном хозяйстве и в быту. [c.25]
Весьма ценным пиролизным сырьем являются сжиженные попутные газы нефтедобычи (пропан и бутан). Важнейшими направлениями использования этих газов в СССР явятся бытовое газоснабжение и приготовление автотоплив, в особенности для городского автотранспорта. Большие количества н-бутана будут направляться на заводы синтетического каучука для дегидрирования в дивинил. Подсчитано, что после обеспечения сырьем указанных выше потребителей, оставшихся ресурсов сжиженных газов будет недостаточно для производства необходимых количеств этилена. [c.36]
Бутан применяется в качестве пиролизного сырья сравнительно редко. Обычно пиролиз бутана ведут при высокой конверсии, достигающей 95—96%, с целью максимального использования его за один проход, исключения рециркуляции, а также значительного облегчения выделения бутиленов и бутадиена из фракции С,. За один проход при 90%-ной конверсии бутана образуется 29% по массе чтилена и 23% пропилена. При этом змеевики печи коксуются в незначительной степени [120]. [c.16]
В настоящее время введено в промышленную эксплуатацию значительное количество газоконденсатных месторождений, газоконденсат которых может быть с успехом использован как пиролизное сырье в производстве этилена. В связи с этим выполнен ряд работ по пиролизу сырых и деарома-тизированных газоконденсатных остатков в лабораторных условиях в трубчатом реакторе и рекомендованы для них режимы ведения процесса. [c.178]
Общей чертой всех процессов термоконтактнЬго пиролиза является наличие теплоносителя, который нагревается в специальном аппарате. Затем нагретый теплоноситель транспортируется в реактор, где вступает в контакт с пиролизным сырьем. К теплоносителю предъявляются требования высокой теплоемкости, механической и термической прочности, низкой абразивной способности. В качестве теплоносителя применяются шамот, кокс, кварцевый песок и др. [c.213]
Второй вариант раздельной переработки малосернистого и сернистого сырья (или на двухпоточной установке одновременная переработка двух видов сырья) может быть реализовав на заводах, имеющих крупные установки пиролиза ЭП-300. В этом случае есть хорощая возможность дая выработки малосернистого кокса за счет вовлечения большой массы пиролизного сырья. Для этого только потребуется замена прямогонного бензина на керосино-газойлевую фракцию на установке пиролиза ЭП-300. Это мероприятие позволит вырабатывать до 250-260 тыс. т тяжелой смолы пиролиза с содержанием серы 0,2%. Коксование смеси тяжелой смолы пиролиза и дистиллятного крекинг-остатка в соотношениях 50 50 и 30 70 позволяет получить коксы со следующими характеристиками [c.78]
В Западной Европе после открытия крупных месторождений природного газа повысился интерес к легкому пиролизному сырью, поскольку из этана можно вырабатывать до 25% этилена. Повышенный интерес к этому сырью объясняется тем, что использование этана в химической и нефтехимической промышленности позволяет улучшить структуру пиролизного сырья и обеспечить высокую сбалансированность производства и потребления этилена с одной стороны, бутадиена и других побочных продуктов пиролиза бензина, с другой стороцьь [c.8]
Пропан используют в чистом виде илн в смеси с бутаном в кач-ве пиролизного сырья, топлива для дизельных двигателей и коммунальио-бытового топлива, при получении уксусной к-ты, ацетона и др. Бутан, изобутан, пентан и изопентан применяют в произ-ве СК, а также топлив для автомобильного транспорта и коммунально-бытового обслуживания. Стабильный газовый бензин служит компонентом автомобильных бензинов, а также р-рителем. При содержании не менее 3-5% H S и 0,05% Не целесообразно использовать Г. н. п. для получения соотв. дешевой товарной серы и гелия. [c.477]
chem21.info
Способ переработки жидких продуктов пиролиза углеводородного сырья
СОЮЗ СОВЕТСНИХ
СОЦИАЛИСТИЧЕСНИХ
РЕСПУБЛИК
Д,511 4 С 10 G 7/00
ГОСУДАРСТВЕННЫЙ НОМИТЕТ СССР
ПО ДЕЛА14 ИЗОБРЕТЕНИЙ И ОТКРЫТИЙ с.„. 11
ОПИСАНИЕ ИЗОБРЕТЕНИЯ /
К А BTOPCHOMY СВИДЕТЕЛЬСТВУ (21) 3821961/23-04 (22) 11.12.84 (46) 30.05.86. Бюл. № 20 (71) Уральский ордена Трудового Красного Знамени политехнический институт им. С.М. Кирова (72) Г.Б. Лехова, Н.А. Кудряшова, Г.Д. Харлампович, Т.М. Велик, А.Д. Беренц, Т.H. Мухина и Л.Д. Гуловская (53) 66.048(088.8) (56) Патент ЧССР № 144683, кл. С 10 G 7/00, опублик. 1972.
Патент ЧССР ¹ 149220, кл. С 10 С 7/00, опублик. 1973.
„„SU„„1234418 A 1 (54) (57) 1. СПОСОБ ПЕРЕРАБОТКИ ЖИДКИХ
ПРОДУКТОВ ПИРОЛИЗА УГЛЕВОДОРОДНОГО о
СЫРЬЯ, выкипающих выше 200 С, путем подачи сырья в змеевик печи однократного испарения с получением дистиллята и пека и ректификации дистиллята с выделением целевых фракции, отличающийся тем, что, с целью расширения ассортимента целевых фракций и упрощения технологии, сырье подают в змеевик печи с линейной скоростью 0,04-0,06 м/с, однократное испарение проводят при давлении 25-101,3 кПа при поддержании массового соотношения дистиллят.— пек 0,7-0,75:0,25-0,3 и ректификацию ведут при атмосферном давлении.
1лл4418
2. Способ по п.1, о т л и ч а ю — линовую, 245-250 — алкилнафталиношийся тем, что при ректификации вую, 275-280 — аценафтеновую, 290дистиллята отбирают фракции в диапа- 295 — флуореновую и 335-340 — антрао зоне температур, С: 280-225 — нафта ценфенантреновую.
Изобретение относится к получению иэ жидких продуктов пиролиза углеводородного сырья, выкипающих выше
200 С, фракций, в которых сосредоточены ресурсы индивидуальных ароматических полициклических.соединений — аценафтена, флуорена, фенантрена, антрацена, с одновременным получением нефтяного пиролизного пека и фракций, содержащих нафталин, монометилнафталины и диметилнафталины, и может найти применение в нефтехимической, сланцеперерабатывающей и коксохимической отраслях промышленности, Целью изобретения является расширение ассортимента продуктов и упрощение технологии процесса.
На фиг. 1 приведена принципиальная технологическая схема разделения жидких продуктов пиролиза на пиролизный пек и шесть целевых фракций.
Исходное сырье — тяжелую смолу пиролиэа бензинов (ТСП) — подают по линии 1 в печь 2 однократного испарения, откуда по линии 3 нагретое сырье попадает в испаритель 4.
Полученный в процессе однократного испарения иэ испарителя 4 дистиллят ТСП по линии 5 направляется в ректификационную колонну 6, в которой происходит разделение на фракции с пределами температур кипения 200270 С (дистиллят) и 270-380 С (кубовый продукт). Соотношение дистиллята и кубового продукта в колонне 6 составляет 0,66:0,34 °
Полученный пиролизный пек отводят по линии 7. Дистиллят колонны 6, в состав которого входят легкая, нафталиновая и алкилнафталиновая фракции, подается в качестве питания по линии 8 в колонну 9.
В колонне 9 в виде головного продукта отделяется легкая фракция (190-210″ С) по линии 10. Соотношение дистиллята и кубового продукта в этой колонне 0,2:0,8.
Кубовый продукт (210-270 С) колонны 9 подается в виде питания по линии 11 в колонну 12, где происходит его разделение на нафталиновую и алкилнафталиновую фракции, отводимые по линиям 13 и 14, соотношение фракций 0,52:0,48.
1О Кубовый продукт колонны 6 направляется по линии 15 на переработку в колонну 16. Конечными продуктами разделения этой колонны являются аценафтенфлуореновая фракция, отделяемая
t5 в качестве дистиллята по линии 17, финантренантраценовая фракция, отбираемая с одной иэ нижних ступеней колонны по линии 18, и кубовая фракция, представляющая продукты полиме20 риэации компонентов дистиллята ТСП.
Этот продукт может быть направлен в пекоприемник по линии 19 и использован в качестве добавки к высокоплавкому пеку, полученному в процессе однократного испарения. Соотношение потоков в колонне 16 — дистиллят:
:фракция:куб 0,43:0,23:0,34.
Аценафтенфлуореновая фракция подается в виде питания по линии 17 в
30 колонну 20.
В колонне 20 по линии 21 в дистиллят отбирается узкая фракция, в состав которой входят гомологи нафталина и аценафтен.
Кубовый продукт содержит смолистые высококипящие неидентифицированные компоненты с примесью антрацена и фенантрена. Аценафтеновая фракция (275-285 С) отбирается на уровне 35-й
4О теоретической ступени, считая снизу колонны по линии 22 а флуореновая
У на уровне 10-й теоретической ступени по линии 23. Соотношение конечных продуктов колонны 20, считая сверху
4 колонны, дистиллят:фракция:фракция: .:кубовый продукт 0,1:0,3:0,3:0,3.
i,0681
225
Плотность, г/см
ММ
Иодное число, r I /100r
Вязкость кинема57
15 тическая, м /cx10 при
Т, С
10,8
20
5,4
100
2,6
140
Отгон, мас.Е, до Т, С
200
40
250
380
Температура вспышки, С 104 подвергаются однократному испарению (ОИ) на установке непрерывного действия при давлении 101 3 кПа, 365-370 С скорости движения смолы в змеевике
0,04 м/с. Отделенный в испарителе 4 в количестве 25 мас.7 пек представляет собой темную массу со следующими параметрами.
Температура размягчения, С 195-200
Коксовый остаток, мас.Е 50-55
Плотность, г/см 1,22- 1,23
Содержание серы, мас.Х О, 1-0,2
Дистиллят ТСП подвергается ректификации с выделением целевых фракций.
В табл. 1 приведена характеристика дистиллята ТСП, в табл. 2 — характеристика целевых фракций.
Технологические параметры работы ректификационных колонн приведены в табл. 3.
Пример 2. Состав сырья, давление и температура соответствуют данным, приведенным в примере 1 Скорость движения смолы в змеевике
0,06 м/с. Соотношение дистиллята
35
45
3 12344
Дистиллят и кубовый продукт колонны 20, содержащие ценные компоненты, возвращаются в цикл: дистиллят пода ется на питание колонны 6, а кубовый продукт вместе с питанием по линии 24 — на колонну 16.
П р и и е р 1. Исходное сырье (ТСП бензинов) со следующими физико-химическими характеристиками:
18 4 и пека, качество пека, состав дистиллята и фракций, выделяемых ректификацией, соответствуют данным примера 1.
45-50
Пример 5. Состав сырья, давление и скорость движения смолы соответствуют приведенным в примере 4. о
Температура ОИ 315-320 С. Массовое соотношение дистиллята и пека
0,7:0,3.
Пример 3. Состав сырья, давление и скорость движения смолы соответствуют данным примера 1.
Температура ОИ 350-355 С, массовое соотношение дистиллята и пека 0,7:0,3.
Качество пека, получаемого при этих параметрах:
Температура размягчения, С 180-185
Коксовый остаток, мас.Ж 45-.47
Плотность, г/см i 21-1,22
Содержание серы, мас.7 0,2-0,1
Составы дистиллята и фракций, вьщеляемых ректификацией, идентичны (в пределах погрешности хроматографического анализа 5-10 отн.7) приведенным в примере 1 (см. табл. 1).
Пример 4. Состав основные физико-химические характеристики исходного сырья аналогичны, приведенным в примере 1. Давление ОИ 40 кПа, температура процесса 335-340 С, скорость движения смолы 0,04 м/с, массовое соотношение дистиллята и пека
0,75:0,25.
Полученный пек обладает следующими свойствами:
Температура размягчения, С 180-185
Коксовый остаток, мас.7
Плотность, г/смз 1,19-1 20
Содержание серы, мас.7. 0,1
Состав дистиллята, получаемого при данных условиях ОИ, приведен в табл.
Как видно из этих данных, качество дистиллята принципиально не отличается от приведенного в табл. 1 (в пределах ошибки анализа). Состав узких фракций, выделяемых в процессе переработки на колоннах, также идентичен приведенным в табл. 1.
1234418
35-40
1, 19-1, 20
35-40
1,19 — 1,2
30-35
1, 18-1, 19
Пек имеет следующие свойства:
Температура размягчения, С 165-170
Коксовый остаток, мас.7
Плотность, г/см
Содержание серы, мас.Ж 0,1 0,2
Состав дистиллята и узких фракций идентичен приведенному в примере 4.
Пример 6. Давление ОИ
25 кПа, температура процесса 320325 С, скорость движения смолы
0,04 м/с, массовое соотношение дистиллят:пек 0,75:0,25.
Полученный пек имеет следующие свойства:
Температура размягчения, ОС 160-165 2б
Коксовый остаток, мас.Ж
Плотность, г/см
Содержание серы, мас.X 0,1-0,2 25
Состав дистиллята приведен в табл. 4
Параметры работы колонн по разделению дистиллята на целевые фракции принципиально не отличаются от изложенных в примерах 1-5.
Пример 7. Давление ОИ и скорость движения сырья соответствуют приведенным в примере 6. Температура
295-300 С. Массовое соотношение дис0 тиллят: пек О, 7-:0,3 ..
Качество пека:
Температура размягчения, С 150-155
Коксовый остаток, мас.%
4О
Плотность, г/cM
Содержание серы, мас. 7. 0,1 — 0,2
При давлениях ниже 25 кПа (200 мм рт.ст.) резко возрастают затраты на осуществление процесса однократного испарения за счет роста потребляемой в этих условиях энергии.
Изменение температуры однократного испарения в выбранном диапазоне давлений происходит достаточно плавно (фиг. 2), поэтому незначительные колебания давлений (температуры) не влияют на качество получаемых дистиллятов (см. пример 1 и 4).
Явления, связанные с изменением физико-химических характеристик сырья при пониженных давлениях (сближение температур кипения и кристаллизации, увеличение вязкости, усиление сублимации таких компонентов, как нафталин, антрацен и др.), — забивка коммуникаций, увеличение сопротивления аппаратов и связанное с ними увеличение мощности насосов и приводов — отсутствуют.
При выбранном диапазоне скоростей подачи сырья в печь однократного испарения успевают пройти как процессы полимеризации, так и процессы деполимеризации, и конечные продукты процесса стабилизируются. При этих условиях в качестве жидкой фазы в испарителе отделяется пиролизный пек, содержащий пониженное количество полимеров.
На фиг. 3 приведены данные по выходу основных компонентов тяжелой смолы пиролиза в дистиллятную часть в зависимости от соотношения дистиллята и пека при осуществлении процесса однократного испарения.
Предлагаемый способ, сущность которого состоит в применении процессов однократного испарения и ректификации, позволяет получить шесть целевых фракций, из которых при дальнейшей переработке могут быть выделены аценафтен, флуорен, антрацен, фенантрен, с одновременным получением нафталина, моно- и диметиланафталинов с высоким выходом от потенциала в ис— ходном сырье (аценафтена 83, флуорена 77,, антрацена 85 и фенантрена 85X) и содержанием основного вещества 9698 мас.Е. Получаемый в процессе однократного испарения остаточный пек с пределами температур размягчения 150-2О0 С обеспечивает возможность его специфического применения (не приемлемого для полимерного связующего) в производстве некоторых видов углеграфитовых материалов, технология которых предусматривает использование высокоплавкого связующего, например высокотемпературных электрощеток сажевых марок на основе совместного вибропомола и вибросмешения компонентов °
12344 18
Т ° банда 1
Хомо хна пт фр
8,5 12,Ь
42,7
2,0
1,3 ментов
Нетмлмндеиы!
2,0 .13.7
38,7
6,7 10,2
1,6
18,5 29,,0 45 ° 1
19,9 28,6
10,3
Дмиетнлнндены
14 ° 2 17,9
8,8
7,5 11,0
2-Нетмлиафталии
15,7
12,6 13,3
8,0 11,0
I-Нетилнафталмн
16,4
13,4 12,2
8,7
4,3
2,3 3,5
Этилнафталииы
9 ° 6
4,8
Ь,9
6,8
6,2 5,5
Аде аафтеа 2, С
6 ° 8
3,3
9,7 флуорен
5,3
1,9
6,9
19,9
36 5
15,0
27 ° 1 94, 7
3,6
9,7
0,4 40 ° 3
1,3
8,2
19,0
0,7 38,5 29,5
2,7
14,7
22,8
6,1
70,5
Стюен не гаолян ллммх ноилоДииетилнафталииы
Иетил° це наф тею, трние тяп нафталины
Нетнлфпуорем, не тмп адемафте мы
Антрацаа, фенантрем
7,2 10 ° 7
2,1 3,2
Состав немодного сха>ьа и продуктов ректнфима!аню aoaoaa. при 101,3 аПа, иас.I
14,2 15,5 — — 92,0 2! ° 0
14,5 1,8 — 4,9 45 ° 2 1 ° 3
21 I 2 2 — 3 1 32 Ь. 36 ° 3
t1,3 2,2 — — .! 0 35,,3 1,3
1234418
Таблица 2
Фракции, получаемые при разделении фракции 206-380 С
ТСП бензинов
Показатели аценафте- флуореновая 22 новая 23 легкая нафтали10 новая 13
5,9
3,3
3,3
Выход от ТСП, мас.X 10
Пределы температур, ОС н ° к. — 210 210-230 230-270 275-285 285-305 310-370 кипения отбора фракций
195-200 220-225 245-250 275-280 290-295 335-340
125 135
0,935 1,005
165 195
1,020 1,104
t40
155
Молекулярная масса р г/см3 1o l,006 1,010
25 20-25 20-25 35
Таблица 3
Колонны
1 1
Параметры
6 9 12 16 20
Число теоретических ступеней
30
20
6-8
4-6
4-6
Флегмовое число
Место подачи исходного сырья, т.ст. (считая снизу колонны) 22
15
Доля отбора дистиллята (от исходного сырья на колонну) 0,66 0,2
0,52 0,43 0,1 о
Температура, С конденсации дисти.пля та
225 295 270
200
230 кипения кубового продукта
250 390 320
240 320 285
230
320
220
260 питания*
* Исходное сырье и колонны подается в виде кипящей жидкости
Иодное число, г I2/100 г алкилнафталино» вая 14 антраценфенантреновая 18
12344 18
Таблица 4
Состав.неводного саа7ле и продуктов ректафниац1вк conosa
Юи 101,3 кПа ° мас.Z
42,0 2,5 1,0
Нетнлныдезн4 14,0
10,1 1,5
39,2
7,0
Нафталин 29,1
18,8 29,1
46,0 10,9
Лвметнлнкдеем 11,2
17,7 8,6
14,1
2-Нетнлвафталнл 10, 5
I3,О i5,г
11,9
12,2 16,0
13,7
10,2
8,5
4,5
3,0
3,3
4,2
9 ° 5
5,5
6,5
7,3
14 ° 5 16,1
14,7
7,0
2,2
1 ° 5
21,4 2,4 — 4,3 33,5 35,1
11,0 2,0 — — 1,0 36,1 1,5
9,S
5,6
Фпуорел
36 ° 2 IS! — — » 273 950
19,7
1,0
19,0
0,2 36,3 32,0
2,5
22,6
5 ° 7
68,0
Сумма лег« кокнплцвх комналеатоэ 13,2
Нетнлаце вафтеme, трнметил вафт аллам
Иетнл- флуорею4 ° ме тю ацеыафтевм
Автрацев, фенактрав
НетвлфеаTPC Shl ° метвлавтр аде
ЮВ
10,1 0,4 42,0
90,0 20,5
5,7 45,0
12344 iI 8 тао
Н7ф7/71 ОРФФ
gg 70 80
Ц цццц фц дрцддЯщ(7 ТСПi и С %1
Фиг.Я
Составитель Е. Горлов
Техред Л. Олейник
Редактор Л. Веселовская
Корректор M.Ñàìáîðñêàÿ
Закал ?95?/30 Тираж 482 Подписное
ВНИИПИ Государственного комитета СССР по делам изобретений и открытий
113035, Москва, Ж-35, Раушская наб., д. 4/5
1рои олственно-полиграфическое предприятие, г. Ужгород, ул. Проектная, 4 с
4 »
3 f0 ф И ь, с о 0
ШО О0 N0 КО 500 00 700 800
0с паптчное Во5пение, мирт. ст.
Фиг. Г
www.findpatent.ru
описание процесса, сырье, состав газа
Содержание: [скрыть]
- Суть процесса
- Заготовка сырья
- Оборудование
- Процесс перегонки
- Продукты пиролиза
- Перегонка древесины в домашних условиях
Большую часть древесины составляют органические соединения. Под воздействием высоких температур в условиях вакуума или минимального притока воздуха они распадаются на твердые, полужидкие и газообразные составляющие. Этот процесс называют сухой перегонкой, смолокурением, пиролизом. Он отличается от горения большей сохранностью разлагаемых компонентов. Химические реакции проходят очень быстро и без образования пламени и дыма.
Технология перегонки появилась в XII веке. Тогда в качестве сырья использовались сосновые и другие хвойные породы. Из них добывали смолу для пропитки деревянных частей судов и канатов, древесный уголь. В XIX веке с помощью деструкции углеродсодержащей массы стали получать уксусную кислоту.
Суть процесса
Обычное горение древесины с участием кислорода приводит к воспламенению и испарению выделяющихся газов, полному разрушению твердых составляющих, превращению их в дым, копоть, золу и пепел. Температура пламени при этом достигает 1000°С. Пиролиз — тоже термодеструкция. Результат этого процесса — образование продуктов распада лигнина, целлюлозы и гемицеллюлозы. Сухая перегонка осуществляется в замкнутом пространстве при постоянной температуре в 250–450°С, образующиеся газы и жидкие выделяемые компоненты сразу отводятся и охлаждаются. Процесс сопровождается большой отдачей тепла, но дым и копоть не образуются. Полученные остатки затем можно использовать в промышленных целях или домашнем хозяйстве.
Заготовка сырья
В качестве исходного материала применяют малопригодную для других нужд древесину, отходы производства, в том числе опилки. Принято выделять несколько групп сырья:
- твердолиственные: бук, береза, ильм, дуб, граб, клен, ясень;
- мягколиственные: липа, ольха, осина, тополь;
- хвойные: лиственница, сосна, кедр, пихта, ель.
Существует строгий производственный регламент, согласно которому все поступающие на перерабатывающие заводы лесоматериалы распиливаются, нарезаются и собираются в кучи определенной ширины и высоты на специальных складах. Их размещают на ровных участках, обеспечивают доступ воздуха и освещения.
Подготовка к пиролизу предполагает предварительное высушивание. Этот процесс может быть затруднен, особенно в случае работы с массивом осины или тополя, которые при повышенной сырости склонны к поражению грибком и развитию гниения.
Сушка производится на проветриваемой территории складов естественным образом. Для ускорения процесса материал раскалывают на мелкие отрезки. Подходящей для дальнейшей обработки считается древесина воздушно-сухого состояния: около 12–15%.
Иногда применяют быструю сушку: массив измельчают, помещают в печи или обдают сухим горячим воздухом.
Оборудование
Разложение древесины осуществляется в ретортных печах. Корпуса — цилиндрические емкости, сваренные из металла. Толщина их стенок — около 15 мм. Наверху находится загрузочное отверстие, внутри — решетки для размещения сырья, система подачи теплоносителей, отведения и охлаждения выделяемых жидких продуктов, газов и древесного угля, внизу — порт выгрузки получаемых компонентов.
Промышленное оборудование имеет различные размеры. Чаще используют большие печи, камеры сгорания которых около 2–2,5 м в диаметре. Применяют следующие системы разогрева:
- наружная: металлические стенки реторты раскаляются, запуская процесс разложения древесины;
- внутренняя подача тепла: температура поддерживается смесью выделяемых газов, их КПД обычно в несколько раз ниже, чем у нагреваемых извне.
Оборудование бывает непрерывного, полунепрерывного и периодического действия. В первом случае все этапы цикла происходят одновременно. Когда очередная партия древесины поступает внутрь, из выходного отверстия выгружают готовый уголь. У полунепрерывных устройств процесс упорядочен. Сначала полную обработку проходит первая партия сырья, после выгрузки поступает следующая. Вид оборудования влияет на скорость, с которой происходит разложение древесины.
Существуют котлы, сходные с промышленными, но более компактные. Они предназначены для пиролиза в небольших масштабах.
На результат перегонки влияют условия, в которых происходит процесс, и состояние поступающего материала.
Процесс перегонки
Если загружаемая партия древесины недостаточно сухая, после измельчения ее сушат в закрытой камере при температуре 130°С. Этот этап самый энергоемкий, т. к. требует обязательного внешнего источника тепла. Испарение влаги сопровождается первичным распадом некоторых компонентов древесины.
Дальнейшее нагревание до 155–200°С приводит к началу выделения и испарения газообразных веществ.
Непосредственное разложение всей массы материала происходит при последующем нагреве до 280–420°С. При этом выделяются и отводятся смолы, уксусная кислота, карбонильные соединения. В это же время образуется древесный уголь.
Финальный этап — прокаливание. Температура внутри реторты поднимается до 500°С и выше. Из древесного остатка удаляются тяжелые смолы, углеродистые соединения. Затем продукты охлаждают и выгружают из камеры.
Количество получаемого материала, скорость процесса и затраты энергии зависят от вида и размера кусков древесины, систем оборудования. Быстрый пиролиз с использованием внешних источников тепла приводит к получению большего количества угля и высокой его чистоте при относительно небольших затратах энергии.
Продукты пиролиза
Главные составляющие, ради которых осуществляют перегонку древесины, — уголь и уксусная кислота.
Уголь
Количество получаемого твердого остатка зависит от породы дерева. У твердолиственных бука и березы выход составляет около 25% от первичного материала. У хвойных пород он несколько выше. Меньше всего угля дают мягколиственные растения. Пиролиз опилок позволяет получать угольную муку. При этом выше выход жидкого остатка.
Качественный уголь не имеет трещин, бурого или белесого налета, горит без дыма. Бракованный продукт получается при нарушении технологии пиролиза: недостаточная температура, проникновение воздуха в печи.
Древесный уголь — экологичный и доступный вид топлива, который используется для промышленных и бытовых печей, домашних каминов. Он выделяет большое количество тепла, при сгорании практически не образует побочных продуктов и запаха, имеет низкую себестоимость. Уголь применяют в металлургической отрасли, сельском хозяйстве, для производства фильтров, пластмассы, красителей, стекла, медицинских препаратов.
Конденсат
Жидкие продукты пиролиза, или конденсат, содержат смолистые соединения, называемые жижкой. Количество ее достигает 50% от всего остатка и зависит от породы и влажности древесины, вида пиролиза. В состав жижки входят кетоны, смолы, альдегиды, спирты, сложные эфиры, вода. В результате многоэтапных реакций из нее образуется уксусная кислота — соединение, используемое в химической, текстильной, фармацевтической, косметологической, пищевой отраслях.
Из жижки получают муравьиную и масляную кислоты, ацетон, метиловый и изопропиловый спирты, формальдегид, смолы.
Газы
Газообразные соединения, выделяющиеся в результате перегонки, образуются в количестве 20–25%. В состав пиролизных газов входят:
- CO: 40–50%;
- CO2: 28–38%;
- CH4: 8–20%;
- H2: 1–2%;
- углеродные примеси: около 1%.
В среднем во время сухой перегонки 1м³ древесины выделяется около 70–80 м³ газообразных соединений.
Перегонка древесины в домашних условиях
Выполнить пиролиз древесины или ее отходов можно и в домашних условиях. При этом удастся получить только уголь.
В качестве реторты используют металлические бочки большого объема. Нельзя брать емкости из-под химикатов. Необходим чистый контейнер с несколькими маленькими отверстиями для выведения газов.
Вначале готовят платформу:
- На землю кладут большой лист железа.
- Устанавливают на ребро несколько огнеупорных кирпичей, между которыми раскладывают дрова.
- Разводят костер.
Бочку наполняют высушенной нарубленной древесиной, герметично закрывают. После этого ее устанавливают на платформу с костром. Когда емкость раскалится и начнется окисление, из отверстий пойдет газ. Процесс может занять несколько часов.
Когда выход газа прекратится, бочку в течение 30 минут оставляют на костре. После остывания снимают крышку и достают готовый древесный уголь. Его можно использовать для растопки бань, домашних печек, каминов. После перегонки опилок полученную муку добавляют в садовый грунт, используют для обработки срезов растений.
derevo-s.ru