Переработка — железная руда — Большая Энциклопедия Нефти и Газа, статья, страница 1
Переработка — железная руда
Cтраница 1
Переработка железных руд осуществляется несколькими последовательными процессами: сначала из руды выплавляют чугун, затем его перерабатывают, получая сталь и ковкое железо. [1]
Переработка железной руды производится в специальных шахтных печах, называемых доменными, поэтому процесс получения чугуна из железных руд называется доменным процессом. Железная руда, кокс и флюс в требуемых количествах подаются в засыпное устройство в верхней части доменной печи. Снизу в домну поступает воздух, предварительно нагретый в воздухонагревателях. В результате сложного химического взаимодействия между рудой, флюсом, топливом и кислородом воздуха образуются чугун и шлак. Чугун стекает в нижнюю часть печи, откуда через летку выпускается в ковш. [2]
Переработка железных руд
При переработке железных руд получают чугун — сплав железа с углеродом ( 2 — 5 % углерода), твердую сталь — железоуглеродистый сплав ( 0 2 — 2 % углерода) и мягкую сталь ( железо), содержащую меньше 0 2 % углерода. [5]
При переработке железных руд получается чугун — сплав железа с углеродом, содержащий от 1 7 до 5 % углерода и примеси серы, кремния, фосфора, марганца и некоторых других элементов. Благодаря высокому содержанию углерода чугун не обладает ковкостью и тягучестью. [6]
При переработке цинксодержа-щих железных руд на ряде предприятий черной металлургии при очистке газов доменного и мартеновского производства образуются шла-мы, которые складируются на больших земельных площадях. Высокое содержание в них цинка и железа ( до 13 и 35 % соответственно) делает их ценным сырьем, использование которого в народном хозяйстве требует разработки экономически целесообразных схем комплексной переработки. [7]
Двухстадийный процесс переработки железной руды в сталь путем получения чугуна в домнах и выплавки из него стали в конвертерах, мартеновских и электросталеплавильных печах требует повышенных энергозатрат и экологически несовершенен, особенно стадия доменного производства чугуна. Поэтому шире начали использовать более экономичные процессы прямого восстановления железа из руд с последующей его плавкой в электропечах для получения стали. [9]
Технологический процесс переработки железной руды, угля, известняка и углеводородных топлив в конечный продукт может быть разбит на 3 — 4 основные стадии, которые осуществляются раздельно с получением определенного продукта, на следующей стадии перерабатываемого в продукт нового вида. Различные стадии процесса могут проходить в одной технологической установке. [10]
Доменные печи предназначены для переработки железной руды в чугун. В засыпное устройство, расположенное в верхней части печи, подают агломерат, кокс, флюсы при помощи специального подъемника, оборудованного скиповыми тележками, которые перемещаются по наклонному мосту. [11]
Во вращающихся печах возможна переработка различных железных руд, в том числе высококремнеземистых комплексных руд, пиритных огарков, колошниковой пыли, шлаков. В качестве восстановителей могут использоваться коксовая и угольная мелочь, буроугольный полукокс и другие виды низкосортного топлива. [12]
Металлургические фосфатные шлаки, образующиеся при переработке высокофосфористых железных руд, являются дополнительным источником фосфорных удобрений. В этом отношении они представляют интерес как щелочные удобрения, отличающиеся высокой агрохимической эффективностью на кислых дерново-подзолистых почвах. [13]
Намечается значительное увеличение их выпуска на базе переработки фосфористых железных руд Керченского, Кустанайского, Ангарского месторождений. Развивается также отечественное производство обесфторенных фосфатов. [14]
Новый этап в разведывании, добыче и переработке железных руд начался в 30 — х годах, когда голландский купец А. Д. Виниус, получив царскую жалованную грамоту на мельницы и всякое железное дело, приступил к строительству первых в стране вододействующих железоделательных заводов под Тулой, в 40 верстах от ранее разведанного Деди-ловского железорудного массива. [15]
Страницы: 1 2 3
www.ngpedia.ru
Параграф 7. Окускование
Представляет собой процесс превращения мелких частиц рудных концентратов и некоторых других материалов в более крупные куски (20 — 40 мм), удовлетворяющие требованиям доменной плавки. Для окускования применяются в основном два способа:
Известен и третий способ окускования – брикетирование. Однако, для руд металлургического производства брикетирование не нашло широкого применения ввиду сложности обработки брикетов для получения необходимой их прочности и низкой стойкостью инструмента.
Агломерация и получение окатышей относятся к термическим способам окускования, когда кусковой продукт получается в результате спекания и сплавления частиц шихты, нагретых до высоких температур (1300 — 1500 °С). Благодаря этому, кроме физического процесса спекания протекают и химико-минералогические превращения (разложение карбонатов, окисление серы, удаление гидратной влаги и др.), улучшающие качество агломерата и окатышей.
Параграф 8. Переработка железных руд
К черным металлам относятся железо и его сплавы, а также металлы, применяемые преимущественно в железных сплавах-марганец и хром. Поэтому к черной металлургии относятся производство и переработка железных сплавов, играющих исключительно важную роль во всех областях техники. Чистое железо получается электролитическим путем и имеет ограниченное применение. На практике применяются главным образом сплавы железа с различным металлами и другими веществами, из которых наибольшее значение имеет углерод. При переработке железных руд сначала получают чугун; затем чугун подвергают переделу в сталь. Лишь около 10 % всего количества выплавляемого чугуна используется непосредственно для производства чугунных отливок.
Переработка железной руды производится в специальных шахтных печах, называемых доменными, поэтому процесс получения чугуна из железных руд называется доменным процессом. Железная руда, кокс и флюс в требуемых количествах подаются в засыпное устройство в верхней части доменной печи. Снизу в домну поступает воздух, предварительно нагретый в воздухонагревателях. В результате сложного химического взаимодействия между рудой, флюсом, топливом и кислородом воздуха образуются чугун и шлак. Чугун стекает в нижнюю часть печи, откуда через летку выпускается в ковш. Производство чугуна – это первая стадия двухступенчатого процесса переработки железных руд в сталь, который в настоящее время преобладает.
Металлургические фосфатные шлаки, образующиеся при переработке высокофосфористых железных руд, являются дополнительным источником фосфорных удобрений. В этом отношении они представляют интерес как щелочные удобрения, отличающиеся высокой агрохимической эффективностью на кислых дерново-подзолистых почвах.
Завод черной металлургии с полным технологическим циклом осуществляет переработку железной руды последовательно в чугун, сталь и прокат. В силу технологической специализации общий производственный комплекс (предприятие) естественно разделен на ряд отдельных участков производства. Это разделение прежде всего происходит по основным фазам производственного процесса, так называемым переделам (коксохимическому, аглодоменному, сталеплавильному, прокатному), и далее на цехи и участки.
Таблица 1.1 – Рейтинг стран по добычи железной руды
Место | Страна | Объем производства железной руды, млн. тонн |
1 | Китай | 900 |
2 | Австралия | 420 |
3 | Бразилия | 370 |
4 | Индия | 260 |
5 | Россия | 100 |
6 | Украина | 72 |
7 | ЮАР | 55 |
8 | США | 49 |
9 | Канада | 35 |
10 | Иран | 33 |
Таблица 1.2 – Рейтинг компаний по добычи железной руды
Компания | Страновая принадлежность | На территории каких стран добывают руду | Объем производства железной руды, млн. тонн |
Vale | Бразилия | Бразилия | 255 |
BHP Billiton | Австралия | Австралия, Бразилия | 160 |
Rio Tinto | Великобритания | Австралия, Индия, Канада, Гвинея | 153 |
ArcelorMittal | Великобритания | Канада, США, Мексика, Бразилия, Украина, Казахстан, Алжир, Либерия | 79 |
Fortescue Metals | Австралия | Австралия | 55 |
Евразхолдинг | Россия, Великобритания, Люксембург | Россия, Украина | 50 |
Металлоинвест | Россия | Россия | 44 |
AnBen | Китай | Китай | 44 |
Метинвест Холдинг | Украина | Украина | 43 |
Anglo American | ЮАР | ЮАР | 41 |
studfiles.net
Польза железной руды — MicroArticles
Считается, что человек познакомился с железом метеоритного происхождения раньше, чем с другими металлами. В древности и в средние века семь известных тогда металлов сопоставляли с семью планетами, что символизировало связь между металлами и небесными телами и небесное происхождение металлов. Затем железо сопоставлялось с Меркурием и называлось меркурием, но позднее его стали сопоставлять с Марсом и называть марс, что, в частности подчеркивало внешнее сходство красноватой окраски Марса с красными железными рудами.
Вначале люди узнали метеоритное железо. В переводе со многих языков древнего мира оно означало «небесный металл». Метеоритное железо всегда самородное. Оно сверх чистое, его можно ковать холодным. Чистое железо не ржавеет, примером этого служит колонна в Индии, которая стоит уже много столетий несмотря на влажный и жаркий климат. Самым крупным железным метеоритом является метеорит, найденный в 1920 году на юго-западе Африки весом 60т. Самородное железо обнаружено на Марсе и на Луне.
Впрочем, некоторые народы не связывали название железа с небесным происхождением металла. Так, у славянских народов название «железо» прямо указывает на функцию предметов, изготовлявшихся из железа, режущих инструментов и оружия.
Позднее изобрели способ получения железа непосредственно из руды в специальных печах (доменные печи). Способ этот назывался «сыродутным», так как «сырую» болотную или луговую руду закладывали в обмазанную глиной яму вместе с древесным углем, а затем через отверстие в нижней части ямы дули ручными, а позднее механическими мехами. В результате этого, окись железа превращалась в металл, а пустая порода стекала вниз.
Таким образом, анализ происхождения слова «железо» в различных языках подтверждает тот факт, что впервые на Земле было обнаружено метеоритное железо, попавшее к нам из космоса, а в дальнейшем люди научились получать его из руды.
Ученые открыли важную роль железа в жизни растений, животных и человека. Железо обусловливает красную окраску гемоглобина, от которого зависит цвет крови человека и животных. В организме взрослого человека содержится 3 г чистого железа, входящего в состав гемоглобина. Основная роль гемоглобина — перенос кислорода из легких к тканям, а в обратном направлении – углекислого газа. В организм железо поступает вместе с пищей. Если человек плохо пережевывает пищу, железо не усваивается организмом.
Железо необходимо и растениям. Растения, выращенные без железа, имеют белые листья. Маленькая добавка железа и они приобретают зеленый цвет. Если белый лист смазать раствором соли, содержащей железо, то вскоре смазанное место зеленеет.
Так от одной и той же причины – наличия железа в соках и тканях — весело зеленеют листья растений и ярко румянятся щеки человека.
Почти все используемые человечеством металлы – это сплавы на основе железа. Железа выплавляется в мире очень много, гораздо больше, чем других металлов. Сплавы на основе железа универсальны, технологичны, доступны, дешевы. Железу еще долго быть фундаментом цивилизации.
Более того, в последнее время некоторые ученые полагают, что в ядре Земли находится расплавленное железо, которое способствует поддержанию магнитного поля планеты.
Известный микробиолог Майкл Дентон в своей книге “Предназначение природы” приводит такой комментарий:
“Среди всех металлов железо является самым жизненно необходимым и важным для человека. Накопление железа в ядре звезды провоцирует её взрыв и, таким образом, дает возможность распространяться по всей Вселенной атомам железа, необходимым для жизни. Температура, которую формировали атомы железа, и сила гравитации внутри ядра на первоначальной стадии формирования Земли стали причиной химических изменений нашей планеты и в результате обеспечили предпосылки для развития атмосферы и гидросферы. Расплавленное железо, находящееся внутри ядра Земли, исполняет функцию мощнейшего магнита и формирует магнитный пояс Земли. Благодаря этому поясу Земля защищена от воздействия испепеляющей космической радиации и от разрушения озонового слоя Земли под воздействием космических лучей…»
Если бы не существовало атомов железа, то невозможно было бы само возникновение жизни, не было бы сверхновых звезд, Земля не достигла бы той температуры, что существовала на первоначальном этапе ее формирования, не было бы атмосферы и гидросферы, не было бы защитного магнитного пояса, не существовало бы озонового слоя, не было бы никаких металлов.
Таинственная и теснейшая связь между существованием жизни, красным цветом крови и железом, находящемся в ядре Земли, показывает степень важности данного металла для жизни.
До 20-го века люди не располагали информацией о том, что железо присутствует и в ядре земли, и в крови человека, не знали и о роли железа в поддержании жизни. Однако, в наше время медики открыли еще одно удивительное свойство железа – способность излечивать некоторые тяжелые заболевания у людей..
Таким образом, железо играет значительную роль в нашей жизни, поскольку при недостаточном содержании данного химического элемента в крови, человек может заболеть; растения теряют свою окраску и гибнут; при отсутствии его в ядре Земли пропадет магнитный пояс нашей планеты, что приведет к исчезновению защиты от воздействия космической радиации и от разрушения озонового слоя Земли.
www.microarticles.ru
Переработка и обогащение железных руд
Министерство образования и науки РФ
Федеральное государственное бюджетное образовательное учреждение высшего образования
«Уральский Государственный Горный Университет»
Кафедра обогащения полезных ископаемых
Курсовая работа
Группа ОПИ — 13
Студент Кожевников А.О.
Преподаватель Овчинникова Т.Ю.
Екатеринбург
2016
Содержание
Глава 1. Переработка и обогащение железных руд 3
Параграф 1. Обогащение железных руд 3
Параграф 2. Промывка 4
Параграф 3. Гравитационный способ 5
Параграф 4. Электромагнитный способ 7
Параграф 5. Флотация 8
Параграф 6. Усреднение руд 9
Параграф 7. Окускование 11
Параграф 8. Переработка железных руд 12
Глава 2. Практика 15
Параграф 9. Технологический баланс продуктов обогащения 15
Параграф 10. Раскрытие минералов 21
Параграф 11. Построение кривых обогатимости и контрастности 35
Параграф 12. Роза ветров города Качканар 36
Для заметок 41
Список литературы 42
Глава 1. Переработка и обогащение железных руд
Параграф 1. Обогащение железных руд
Обогащение руд представляет собой процесс обработки полезных ископаемых, целью которого является повышение содержания полезного компонента и снижения содержания вредных примесей путем отделения рудного минерала от пустой породы. В результате обогащения получают концентрат, более богатый по содержанию определенного металла, чем исходная руда, и остаточный продукт – хвосты, более бедный, чем исходная руда.
В настоящее время более 90 процентов железных руд подвергаются обогащению. Применяемые на практике разнообразные способы обогащения основаны на общем принципе разделения зерен полезного минерала и пустой породы. Наиболее распространенными способами обогащения железных руд являются:
Параграф 2. Промывка
Используется для обогащения руд с глинистой и песчаной пустой породой. Обычно для этой цели используют вращающиеся барабаны, так называемые бутары, имеющие решетчатый конусный корпус. Руда внутри барабана продвигается вперед, скользя и перекатываясь по его стенкам. Под действием ударов кусков друг о друга пустая порода разрушается и смывается струями воды, подаваемой в барабан. Растворенная часть пустой породы вместе с водой проходит через отверстия барабана, образуя отходы (хвосты), а отмытый материал (концентрат) удаляется через разгрузочное устройство.
Рисунок 1.1 – Схема конической бутары
Параграф 3. Гравитационный способ
Используется в случае, когда имеется существенное различие плотностей полезного минерала и пустой породы. Различают динамическое гравитационное обогащение и статическое (в тяжелых суспензиях).
Динамическое гравитационное обогащение основано на различии скоростей падения частиц различной массы в жидкости. При этом используют аппараты, называемые отсадочными машинами, а способ обогащения – отсадкой. Дробленую руду загружают на решетку, закрепленную в верхней части камеры, заполненной водой. Кривошипно-шатунный механизм сообщает диафрагме колебательные движения, благодаря чему периодически изменяется уровень воды. Когда диафрагма входит внутрь камеры, поток воды движется вверх через слой руды на решетке, взвешивая частички руды. При этом скорость перемещения более легких (пустая порода) больше, чем более тяжелых зерен (полезный минерал). При движении потока вниз быстрее опускаются тяжелые зерна. В результате такого попеременного движения потока воды через слой руды происходит расслаивание его. В нижней части, ближе к решетке скапливаются тяжелые зерна концентрата, а в поверхностном слое – зерна пустой породы, которые смываются с решетки поверхностным слоем воды.
Рисунок 1.2 – Схема отсадочной машины
1 – решетка; 2 – привод диафрагмы; 3 – диафрагма.
Сущность статического гравитационного обогащения (в тяжелых суспензиях) способа заключается в том, что измельченную руду загружают в резервуар с жидкостью (суспензией), имеющей плотность больше плотности пустой породы, но ниже плотности рудного минерала. В этом случае пустая порода всплывает на поверхность жидкости, а зерна полезного минерала опускаются на дно резервуара. В качестве тяжелой жидкости обычно используют смесь воды с тонкоизмельченным ферросилицием.
studfiles.net
Способ переработки железных руд
Изобретение относится к подготовке железосодержащего сырья к металлургической переработке. Руду рассеивают на крупный, средний и мелкий классы крупности. Руду крупного класса подвергают сенсорной сепарации с выделением чернового концентрата и отвальных хвостов, черновой концентрат додрабливают до крупности среднего класса и подвергают магнитной сепарации с получением отвальных хвостов и концентрата. Руду среднего класса подвергают сенсорной сепарации с получением отвальных хвостов и чернового концентрата, черновой концентрат подвергают магнитной сепарации с получением отвальных хвостов и концентрата. Концентраты, полученные из руды крупного и среднего классов, подвергают грохочению с получением подрешетного продукта с крупностью, равной крупности мелкого класса и надрешетного продукта, используемого как металлургическое сырье. При этом руду мелкого класса подвергают магнитной сепарации с выделением отвальных хвостов и концентрата, концентрат объединяют с подрешетными продуктами, полученными из крупного и среднего классов, и брикетируют. Изобретение позволяет получить окускованный материал с высоким содержанием железа, являющийся высококачественным сырьем для металлургической промышленности, при одновременном упрощении процесса. 1 з.п. ф-лы, 3 ил., 2 пр.
Изобретение относится к области переработки железосодержащего сырья, конкретно методом окускования, и служит для подготовки железосодержащего сырья к металлургической переработке.
Известен способ подготовки шихтового материала в виде брикетов к плавке (патент RU №2154680, опубл. 05.03.1999 г.), в котором производят смешивание предварительно подготовленных железосодержащих отходов металлургического производства с тонко измельченным углеродосодержащим материалом в количестве 15-60% по углероду от массы отходов и связующим, обработку полученной смеси водным раствором жидкого стекла, прессование и последующую сушку. В качестве связующего используют механическую смесь суглинка, глины или полевого шпата и карбоната натрия. Причем смесь подвергают совместному размолу до фракции 0,85 мм и менее.
Основные недостатки способа заключаются в том, что брикеты при хранении теряют прочность, при нагреве в печи полностью разрушаются, также в готовых брикетах снижается содержание железа, производство брикетов весьма трудоемко из-за необходимости размола до 0,85 мм и сложного состава связующего.
Известен способ получения брикетов из мелкодисперсных оксидов металлов (патент RU №198940, опубл. 20.02.2003 г.), в котором для получения брикетов, предназначенных для восстановления тепловой обработкой в газовой атмосфере, производят смешение оксидов металлов с водным раствором жидкого стекла и гидрофобными жидкими углеводородами с температурой кипения выше 300°C и последующее прессование.
Основными недостатками способа являются сложность его осуществления, разубоживание брикетов по содержанию полезных компонентов.
Известен способ окускования мелкодисперсных железосодержащих материалов для металлургического передела с использованием органического связующего (патент RU №2272848, опубл. 27.03.2006 г.), в котором окусковывают измельченные железосодержащие материалы. В качестве железосодержащего материала используют железорудный концентрат, железную руду, шламы металлургического производства, измельченную окалину и другие мелкодисперсные железосодержащие материалы. По крайней мере, один железосодержащий материал и связующее смешивают, осуществляют агрегирование смеси и упрочнение полученных агрегатов. В качестве связующего материала используют синтетический сополимер акриламида и акрилата натрия, в котором мольная доля акрилата натрия может составлять от 0,5 до 99,5%, молекулярная масса в диапазоне от 1·104 до 2·107. Дозировка синтетического сополимера акриламида и акрилата натрия составляет от 0,02 до 0,10 кг на тонну железосодержащего материала. Сополимер акриламида и акрилата натрия может быть использован в виде сухого порошка, раствора, эмульсии, суспензии или аэрозоля, в чистом виде или в смеси с дополнительным материалом.
Основным недостатком способа является высокая трудоемкость производства.
Известен способ безобжиговой переработки мелкозернистых железосодержащих отходов металлургического производства, содержащих замасленную окалину (патент RU №2292405, опубл. 27.01.2007 г.), в котором производится измельчение исходных компонентов, дозирование, смешивание исходных материалов со связующим с последующим добавлением воды, окусковывание смеси и упрочнение окускованного материала, отличающийся тем, что в исходную смесь добавляют углеродсодержащий материал, а в качестве связующего используют известь, или портландцемент, или портландцементный клинкер при следующем соотношении компонентов, мас. %: железосодержащие отходы — 35-83, связующее — 10-50, углеродсодержащий материал — 7-25, при этом содержание замасленной окалины в железосодержащих отходах составляет 36,4 или 40, или 50, или 100%.
Недостатки способа заключаются в том, что в брикетах снижается содержание железа, и способ весьма трудоемок из-за сложного состава связующего и необходимости измельчения исходных компонентов.
Известен способ подготовки железной руды к металлургической переработке (патент РФ №2463362, опубл. 10.10.2012 г.), принятый за прототип, в котором железную руду дозируют, смешивают со связующим, брикетируют методом прессования и сушат. При этом исходную железную руду рассеивают на классы крупности и для брикетирования используют класс мельче 5 мм, в качестве связующего используют серную кислоту в количестве 0,5-5 мас. % и дорзин в количестве 5-20 мл/т шихты. Перед рассевом железная руда может быть раздроблена до крупности 20 мм.
Недостатки способа в сравнительно высокой трудоемкости процесса, невозможности использовать железную руду при пониженном содержании железа в ней.
Техническим результатом является упрощение процесса, при одновременном получении окускованного материала с высоким содержанием полезного компонента.
Технический результат достигается тем, что в способе переработки железных руд руду рассеивают на классы крупности, дробят, смешивают со связующим, брикетируют, сушат брикеты, при этом руду разделяют на крупный, средний и мелкий классы крупности, крупный класс подвергают сенсорной сепарации с выделением чернового концентрата и отвальных хвостов, черновой концентрат додрабливают до крупности среднего класса и подвергают магнитной сепарации с получением отвальных хвостов и концентрата; средний класс подвергают сенсорной сепарации с получением отвальных хвостов и чернового концентрата, черновой концентрат подвергают магнитной сепарации с получением отвальных хвостов и концентрата; концентраты, полученные из крупного и среднего классов, подвергают грохочению с получением подрешетного продукта с крупностью, равной крупности мелкого класса и надрешетного продукта, используемого как металлургическое сырье; мелкий класс подвергают магнитной сепарации с выделением отвальных хвостов и концентрата, концентрат объединяют с подрешетными продуктами, полученными из крупного и среднего классов и брикетируют. Концентрат магнитной сепарации мелкого класса, объединенный с подрешетными продуктами, полученными из крупного и среднего классов, может брикетироваться методом экструзии.
Способ переработчики железных руд поясняется следующими фигурами:
фиг. 1 — схема переработки железных руд;
фиг. 2 — таблица результаты переработки рядовой железной руды;
фиг. 3 — таблица результаты переработки богатой железной руды.
Способ осуществляется следующим образом. Исходная руда поступает на предварительное грохочение I фиг. 1, где ее разделяют на три класса крупности. Затем крупный класс подвергают сенсорной сепарации с выделением отвальных хвостов I и чернового концентрата I, который дробят и направляют на магнитную сепарацию II. В ходе магнитной сепарации выделяют отвальные хвосты IV и концентрат IV, который подвергают грохочению II. Надрешетный I продукт грохочения отправляют на непосредственную металлургическую переработку, а порешетный I продукт на брикетирование.
Средний класс крупности подвергают сенсорной сепарации II, в ходе которой выделяют отвальные хвосты II и черновой концентрат II. Черновой концентрат II подвергают магнитной сепарации, в ходе которой выделяют отвальные хвосты V и концентрат V. Концентрат V в ходе грохочения III разделяют на надрешетный II продукт, который транспортируют на металлургическую переработку. Подрешетный II продукт грохочения отправляют на брикетирование. Мелкий класс подвергают магнитной сепарации с выделением отвальных хвостов III и концентрата III, который поступает на брикетирование.
Брикеты используются как компонент шихты для производства чугуна и стали.
Конкретная крупность грохочения может свободно меняться в достаточно широких пределах и зависит от свойств руды и требований потребителя.
Пример 1. Исходная окисленная железная руда КМА с максимальной крупностью куска около 250 мм, содержащая около 45% железа, разделялась в ходе грохочения I на классы + 100 мм, — 100+10 мм и — 10 мм. Далее переработка производилась по схеме, приведенной на фиг. 1. Результаты разделения представлены на фиг. 2.
Пример 2. Исходная окисленная железная руда КМА с максимальной крупностью куска около 230 мм, содержащая около 56% железа, разделялась в ходе грохочения I на классы + 100 мм, — 100+10 мм и — 10 мм. Далее переработка производилась по схеме, приведенной на фиг. 1. Результаты разделения представлены на фиг. 3.
Таким образом, заявляемый способ позволяет получить окускованный материал с высоким содержанием железа, являющийся высококачественным сырьем для металлургической промышленности. Одновременно происходит упрощение процесса производства.
1. Способ переработки железных руд, включающий рассев руды на крупный, средний и мелкий классы крупности, дробление, смешивание со связующим, брикетирование и сушку брикетов, отличающийся тем, что руду крупного класса подвергают сенсорной сепарации с выделением чернового концентрата и отвальных хвостов, черновой концентрат додрабливают до крупности среднего класса и подвергают магнитной сепарации с получением отвальных хвостов и концентрата, руду среднего класса подвергают сенсорной сепарации с получением отвальных хвостов и чернового концентрата, черновой концентрат подвергают магнитной сепарации с получением отвальных хвостов и концентрата, и концентраты, полученные из руды крупного и среднего классов, подвергают грохочению с получением подрешетного продукта с крупностью, равной крупности мелкого класса и надрешетного продукта, используемого как металлургическое сырье, при этом руду мелкого класса подвергают магнитной сепарации с выделением отвальных хвостов и концентрата, концентрат объединяют с подрешетными продуктами, полученными из крупного и среднего классов, и брикетируют.
2. Способ по п.1, отличающийся тем, что концентрат магнитной сепарации мелкого класса, объединенный с подрешетными продуктами, полученными из руды крупного и среднего классов, брикетируют методом экструзии.
findpatent.ru
Проблемы недостатка полезной руды
21 декабря 2011
Для решения сырьевой проблемы существует вторичная переработка. Это касается и металлургической сферы. Путем переработки металлолома решаются экономические и экологические проблемы, что в последнее время является актуальным. Не смотря на то, что объемы металла, его запасы в недрах Земли колоссальны, объем поступающего металла в утиль так же велик. Это всегда востребованная отрасль промышленности, а потому спрос на услуги переработки металла остается стабильно высоким.
Существуют специальные предприятия по переработке отходов металла, множество фирм. Какие же плюсы есть в переработке металла? Вот самые главные из них:
- сокращается нагрузка в местах месторождений металлов;
- улучшается экологическая обстановка;
- сокращаются объемы топлива, идущие на получение металлов;
- меньше рассеиваются и распыляются металлы в глобальных масштабах.
Решаются все эти проблемы путем сложного технологического процесса с изменением форм и размеров вторсырья, придавая новые желаемые формы путем различных методов.
Использование сырья комплексно позволяет рационально извлекать основные и сопутствующие элементы, утилизировать отходы добычи, обогащений руды с избеганием нанесения урона окружающей среде. Металлургия – земле- и водоемкая отрасль. Ценные попутные компоненты из железной руды извлекаются при помощи имеющихся технологий, но на многих комплексных месторождениях полезный материал сбрасывается в отвалы. Стоит заметить, что в некоторых черных металлах встречаются и редкие металлы и их компоненты – вольфрам, никель, кобальт, титан, медь, цинк. При условии правильной обработке, обогащение и обработка руд позволит сделать из отходов товарный продукт. Так же в извлеченной породе можно встретить и нерудные полезные ископаемые – мел, сланец, глина и суглинка, кварцевый песок, мергель, гранит и гнейс. Все эти материалы широко используются в различных отраслях промышленности и являются популярным сырьем.
При обработке руда в доменных печах образуются шлаки основные, нейтральные и кислые. Различаются они входящими в них компонентами, их соотношением. Если использовать мартеновский способ для выплавки металла, удаляются примеси серы и фосфора благодаря основным шлакам. Сам по себе шлак является ценным сырьем и применяется в строительных и дорожно-строительных отраслях. Так щебень и пемза имеют свою себестоимость в несколько раз меньше из-за подобного способа добычи, а их удельные затраты сводятся к минимуму. При раскислении стали на вторичной переработке металла с применением шлаков сокращаются расходы ферросилиция, который на сегодня дефицит. Шлаками очищают днища судов, применяют при гидротехническом строительстве.
Богатые месторождения хрома истощаются, нужно постоянно наращивать мощность добычи, обогащать бедную руду. Благодаря специально разработанному процессу с прокалкой на воздухе дробленых руд, измельчению пека, приготовлению водной суспензии, карбонатизации, появилась возможность получения углеродистого феррохрома.
Пыль, появляющаяся при металлургическом процессе в значительном количестве, должна улавливаться и утилизироваться с последующим извлечением из нее металлов и, конечно, для охраны окружающей среды. Есть сухое и мокрое пылеулавливание, которое осложняется содержанием в пыли цинка и свинца.
Благодаря различным методам утилизации и переработке отходов металлов, решаются проблемы недостатка полезной руды в автодорожной отрасли, железнодорожной, сельской, строительной и других отраслях.
Читайте также:metalurg.su
Способ переработки железной руды с получением пигмента и брикетов
Изобретение относится к способу получения природных (несинтетических) железоокисных пигментов, которые могут использоваться в специальных антикоррозионных грунтовках, применяемых в том числе и для нужд кораблестроения с одновременным получением сырья для металлургической промышленности в виде брикетов. Также способ может быть использован для производства редких и особо дорогих марок пигментов, включая и транспарентные, для нужд фармацевтической, косметической и пищевой промышленности.
Известен «Способ получения красного железоокисного пигмента» (патент RU №2303046, опубл. 20.07.2007). Способ получения красного железоокисного пигмента включает окисление водных растворов сульфата или суспензий гидроксида железа (II) кислородом воздуха при квазистационарных значениях температуры и рН реакционной среды, гидротермальную термообработку суспензии из оксигидроксидов железа (III) в периодическом или непрерывном режиме в автоклавах, отмывку пигмента от водорастворимых солей, сушку и размол пигмента. В процессе гидротермальной термообработки на суспензию FeOOH воздействуют наносекундными электромагнитными импульсами со следующими характеристиками: длительность импульса 0,5-5 нс, амплитуда импульсов 4-10 кВ, частота повторения импульсов 200-1000 Гц, процесс проводят при температуре 130-200°С.
Основные недостатки способа в сложности получения пигмента, экологической вредности процесса.
Известен способ «Получение железной слюдки микронного класса крупности» (патент RU №2354672, опубл. 10.05.2009). Изобретение относится к оксиду железа (III) пластинчатой структуры, который может быть использован в качестве пигмента. Природный механически измельченный оксид железа (III), пластинчатая структура которого составляет по меньшей мере 50 вес.%, предпочтительно 75 вес.%, содержит частицы размером менее 10 мкм в количестве, по меньшей мере, 50 вес.%, предпочтительно 70 вес.%, особо предпочтительно 90 вес.%. Соотношение толщины к максимальному диаметру пластин оксида железа (III) составляет 1:5, предпочтительно, 1:10. Для получения такого оксида железа (III) его механически измельчают в ударно-отражательной мельнице или в струйной мельнице. Полученный в результате механического измельчения оксид железа (III) разделяют по крупности частиц, например, посредством воздушного сепаратора.
Основные недостатки способа в сложности получения высококачественного пигмента по предлагаемой «сухой» технологии, низком выходе готового пигмента.
Известен «Способ получения железоокисного пигмента из спекулярита» (патент RU №2366674, опубл. 10.09.2009). Для получения железоокисного пигмента из спекулярита сначала ведут измельчение спекулярита до размера частиц более 1 мм — 5 мм, затем проводят обогащение методом магнитной сепарации до содержания Fe2O3 более 60,0 мас.%, после чего обогащенный спекулярит снова измельчают. Из обогащенного спекулярита может быть получен пигмент с матовым блеском, состоящий из железной слюдки с содержанием Fe2O3 более 85 мас.%, которая включает тонкие чешуйчатые пластинки в количестве более 50 мас.%, и характеризующийся остатком после мокрого просеивания на сите с размером отверстий 63 мкм не более 35 мас.%.
Основными недостатками способа являются низкий выход кондиционного пигмента из исходного сырья, трудность получения высококачественного пигмента.
Известен способ получения природного красного железоокисного пигмента из руды (Кусков В.Б., Кускова Я.В. «Разработка технологии получения железооксидных пигментов». Металлург. №3, 2010, стр.70-72), принятый за прототип. Дробленую железную руду подвергают магнитной сепарации с разделением на магнитную и немагнитную фракции, немагнитную фракцию измельчают и классифицируют в 4 стадии, включающих основную классификацию, первое перечистное, первое контрольное и второе контрольное гидроциклирование с отделением песков основной классификации. Затем слив подвергают окислительной деструкции, сгущают и сушат с одновременной дезинтеграцией и воздушной классификацией пигмента.
Основным недостатком способа является невозможность получения нескольких сортов, в частности высококачественных, пигмента и сравнительно невысокий выход готового пигмента.
Техническим результатом изобретения является повышение качества готового пигмента, расширение возможностей способа и повышение комплексности использования железной руды.
Технический результат достигается тем, что в способе переработки железной руды с получением пигмента и брикетов, включающем дробление железной руды, магнитную сепарацию, измельчение немагнитной фракции, ее гидравлическую классификацию, включающую основную и одну перечистную классификацию, ультразвуковую окислительную деструкцию, сгущение и сушку, железную руду сначала дробят и измельчают, а затем подвергают мокрой магнитной сепарации, немагнитную фракцию подвергают сначала ультразвуковой окислительной деструкции, а затем стадиальной гидравлической классификации, включающей основную классификацию и не менее двух перечистных классификаций для получения готового пигмента, при этом магнитную фракцию и пески основной классификации брикетируют с использованием в качестве связующего вещества мелассы в количестве 1-5 мас.% при влажности брикетируемой шихты 8-12%.
Магнитная сепарация и стадиальная гидравлическая классификация может быть осуществлена в гравитационно-центробежно-магнитном сепараторе.
Дробление и измельчение железной руды позволяет в достаточной степени раскрыть сростки минералов для их дальнейшего разделения.
Мокрая магнитная сепарация позволяет выделить в магнитную фракцию большую часть «непигментных» минералов, которые обладают большей удельной магнитной восприимчивостью, чем «пигментные» минералы.
Осуществление ультразвуковой окислительной деструкции для немагнитной фракции перед стадиальной гидравлической классификацией позволяет удалить сульфидные минералы из немагнитной фракции и повысить качество пигмента.
Стадиальная гидравлическая классификация, включающая основную гидравлическую классификацию и не менее двух перечистных гидравлических классификаций, позволяет получить сразу несколько сортов пигмента, отличающихся крупностью и укрывистостью.
Брикетирование магнитной фракции и песков основной классификации позволяет расширить возможности способа, а именно получить полностью готовый к металлургической переработке и легко транспортируемый брикет.
Использование в качестве связующего мелассы позволяет получить прочные брикеты, а сама меласса положительно влияет на металлургический процесс. Количество мелассы меньше 1 мас.% не позволяет получить достаточно прочный брикет, количество больше 5 мас.% не повышает прочность брикета.
Влажность брикетируемой шихты 8-12% обеспечивает равномерное перемешивание всех компонентов, формирование структурных связей и лучшее формование брикетов, что увеличивает их прочность. Влажность менее 8% затрудняет перемешивание компонентов брикетируемой шихты, влажность более 12% избыточна, снижает формуемость смеси, понижает прочность полученных брикетов.
Использование гравитационно-центробежно-магнитного сепаратора позволяет осуществить операции магнитной сепарации и классификации в одном аппарате, что снижает затраты, и позволяет получить пигменты нескольких сортов и исходный материал для получения брикетов.
Способ осуществляют следующим образом. Схема способа представлена на фиг.1. Железную руду сначала дробят в дробилках, мелкодробленую руду 1 измельчают в мельницах 2, а затем подвергают мокрой магнитной сепарации в мокром магнитном сепараторе 3. Магнитную фракцию 4 накапливают и используют для брикетирования. Немагнитную фракцию 5 подвергают сначала ультразвуковой окислительной деструкции 6, а затем стадиальной гидравлической классификации, включающей основную классификацию 7, и, например, первую 9, вторую 16 и третью 21 перечистные классификации. Слив основной гидравлической классификации 8 подают на первую перечистную гидравлическую классификацию в гидроциклон 9. Пески первой перечистной гидравлической классификации 10 возвращают на основную гидравлическую классификацию. Слив первой перечистной гидравлической классификации делят на два потока. Один из потоков 11 направляют на сгущение 12 и сушку 13 с получением готового пигмента третьего сорта 14. Другой поток 15 подают на вторую перечистную гидравлическую классификацию в гидроциклон 16 (меньшего объема). Пески второй перечистной гидравлической классификации 17 направляют в питание первой перечистной классификации. Слив второй перечистной гидравлической классификации также делят на два потока. Один из потоков 18 направляют на сгущение 12 и сушку 13 с получением готового пигмента второго сорта 19. Другой поток 20 подают на третью перечистную гидравлическую классификацию в гидроциклон 21 (еще меньшего объема). Пески третьей перечистной гидравлической классификации 22 направляют в питание второй перечистной классификации, а слив 23 на сгущение 12 и сушку 13, при этом получается готовый пигмент первого сорта 24.
Магнитную фракцию 4 и пески основной классификации 25 брикетируют 26 со связующим. Связующее приготавливают из мелассы 27 путем растворения ее в воде 28 из расчета по влажности брикетируемой шихты 8-12%. Раствор мелассы 29 смешивают 30 с магнитной фракцией 4 и песками основной классификации 25 и брикетируют 29. Мелассу используют в количестве 1-5 мас.% при влажности брикетируемой шихты 8-12%. Готовые брикеты 31 используют для металлургических целей, например, в доменном процессе.
В качестве сырья можно использовать богатые гематитовые, мартитовые, гидрогематитовые руды и т.п. железные руды.
Пример. Используют мартитовую и мартит-гидрогематитовую железную руду Яковлевского месторождения. Получена опытная партия пигмента и брикетов из железной руды. Исходную железную руду, крупностью 350-0 мм, дробят в две стадии на молотковых дробилках до размера крупности 10 мм, затем измельчают в шаровой мельнице мокрым способом до 75% класса мельче 40 мкм и подвергают мокрой магнитной сепарации на барабанном сепараторе. После окислительной деструкции в ультразвуковом реакторе немагнитную фракцию (выход 87% от операции магнитной сепарации) подвергают стадиальной гидравлической классифицикации в 4 стадии. Основную классификацию проводят в спиральном классификаторе. Первое перечистное гидроциклирование проводят в гидроциклоне диаметром 250 мм, второе перечистное гидроциклирование, в гидроциклоне диаметром 160 мм, и третье перечистное гидроциклирование — 100 мм. Часть слива первого перечистного гидроциклирования выводилась как готовый продукт и после сгущения в пастовом сгустителе, сушки, пылеулавливания отгружалась как готовый пигмент третьего сорта. Часть слива второго перечистного гидроциклонирования выводилась как готовый продукт и после сгущения в пастовом сгустителе, сушки, пылеулавливания отгружалась как готовый пигмент второго сорта. Слив третьего перечистного гидроциклонирования после сгущения в пастовом сгустителе, сушки, пылеулавливания отгружалась как готовый пигмент первого сорта. Выход, крупность и укрывистость полученного пигмента приведены на фиг.2 и составляли:
Третий сорт — выход 19-23%, крупность 32-38 мкм, укрывистость 16-20 г/м2;
Второй сорт — выход 14-18%, крупность 18-26 мкм, укрывистость 10-12 г/м2;
Первый — выход 10-17%, крупность 8-12 мкм, укрывистость 7-9 г/м2.
В качестве гравитационно-центробежно-магнитного сепаратора использовали круглый вращающийся концентрационный стол, снабженный электромагнитным индуктором бегущего поля. При этом также были получены три сорта пигмента:
Третий сорт — выход 18,8% — крупность 33 мкм, укрывистость 18 г/м2;
Второй сорт — выход 18,7%, крупность 22 мкм, укрывистость 11 г/м2;
Первый сорт — выход 19%, крупность 9 мкм, укрывистость 7 г/м2.
Свойства полученных брикетов приведены на фиг.3. Брикеты, полученные с количеством мелассы 0,8 мас.%, имели среднюю прочность на одноосное сжатие 4,13 МПа; 1 мас.% — 7,5 МПа; 2 мас.% — 8,5 МПа; 3 мас.% — 10,9 МПа; 4 мас.% — 15,3 МПа; 5 мас.% — 15,3 МПа.
Брикеты изготавливались размером 22×20×18 мм, средняя масса брикета около 30 г. Влажность шихты менялась в пределах 8-12%.
Таким образом, способ расширяет свои возможности и позволяет повысить качество готового пигмента и обеспечивает комплексность использования железной руды.
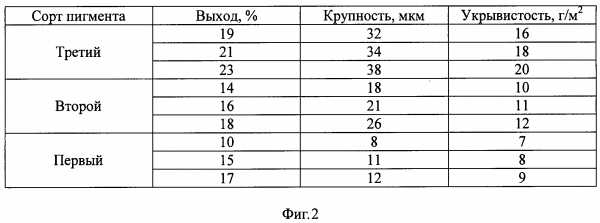
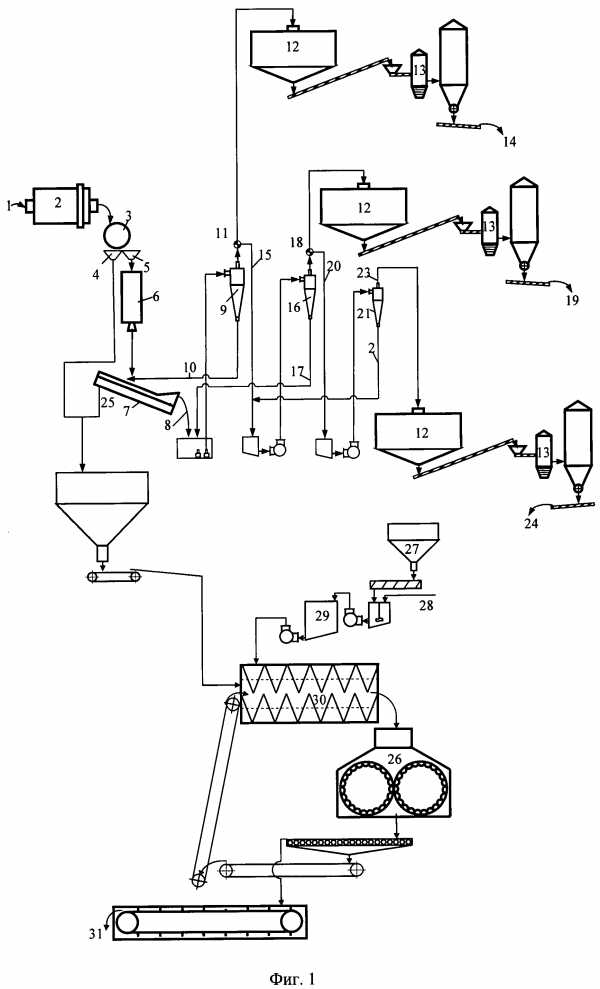
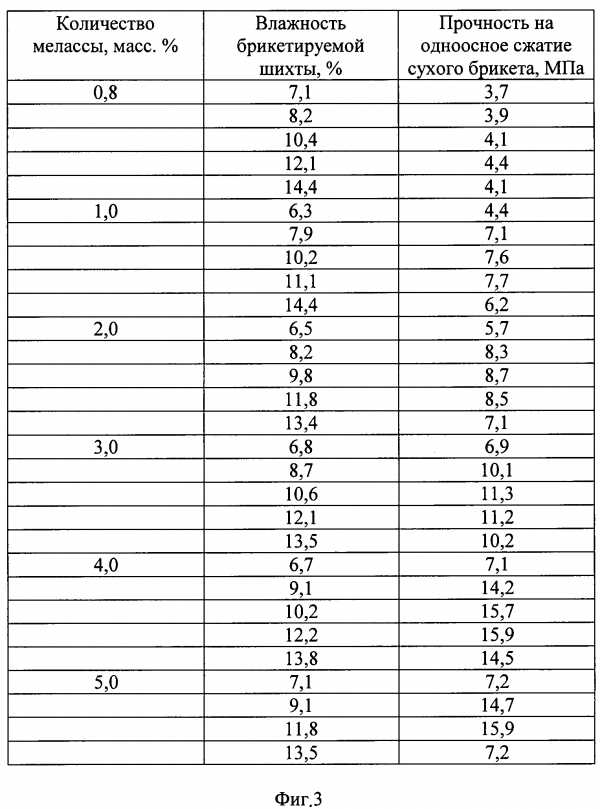
edrid.ru