Модернизация токарных станков по металлу и дереву
Человек постоянно пытается сделать труд более лёгким, а его результаты более точными и красивыми. Те или иные усовершенствования орудий труда касаются любых инструментов, а тем более станков, на которых производятся изделия для:
- промышленного оборудования;
- бытовой техники;
- сложные или тяжёлые детали, необходимые для отрасли пассажирских перевозок;
- деталей теплостанций для обеспечения городского населения теплом;
- и др.
Всё, что касается жизни и здоровья человека, должно быть выполнено с надлежащей точностью и аккуратностью. К сожалению, даже у самых высококлассных мастеров может дрогнуть рука, или произойти заминка в действиях на доли секунды, что может привести к браку. От этого никто не застрахован, кроме автомата, запрограммированного на точное выполнение операции.
В этой статье мы хотели бы рассказать об основных направлениях доработки и усовершенствования токарных станков по металлу и дереву.
Первое программирование станков, правда, ткацких, было произведено в самом начале VIX века. Для токарного оборудования подобная модернизация, оснащение ЧПУ – числовым программным управлением, коснулось в самом конце 2 Мировой войны. Это произошло в Америке. Использовались токарные станки с ЧПУ только для изготовления пропеллеров для вертолётов.
Далеко не просто происходило, да и сейчас происходит компьютеризация процесса. Только в 1954 году были поставлены на поток станки с числовым программным управлением. Сейчас всё больше, в цехах с массовым производством одинаковых изделий, можно встретить токарных станков с числовым программным управлением. Скорость производства деталей увеличилась на этих станках значительно, даже за счет того, что автомат на перекур не выходит в середине процесса. Брак фактически сведён к нулю, а изделия имеют практически идеальное качество. Многое зависит и от правильно составленной программы.
Не только новые станки управляются при помощи компьютерной программы, но и на старое оборудование можно установить ЧПУ. Цель та же – повысить конкурентоспособность изделий выпускаемых на старом оборудовании. Установленное ранее на станок автоматическое управление с годами устаревает, появляются новые разработки, да и износ узлов и частей на старых станках со временем даёт о себе знать.
При замене или установке на станке ЧПУ с ним вкупе меняется вся система КСУ – комплексная система управления:
- гидравлическая система;
- электродвигатель;
- шпиндельные узлы;
- автоматические системы станка;
- приводы.
Необходима установка автоматического управления с ЧПУ и для станков повышенной точности, как для производственных мощностей, так и для экспериментальных цехов при НИИ и других организаций, занимающихся разработками в области точной механики и сверх надёжной техники.
Как работает станок с ЧПУ
Не следует думать, что для работы на токарном станке с программным управлением нужно знать меньше, чем при работе на механическом или полуавтоматическом станке. Для работы на нём так же необходимо:
- уметь читать чертежи;
- знать, какая скорость подачи и скорость проведения определённой операции необходима;
- порядок обработки заготовок.
Выполняя длительное время одну и ту же операцию на станке, его нет необходимости перепрограммировать. Достаточно нажать кнопку пуск, после того как в кулачках была зажата заготовка, что осуществляется при помощи кнопок, находящихся снаружи закрываемого корпуса станка.
Для выполнения сложных деталей с различным внутренним диаметром отверстия и различной шириной внешнего диаметра детали, наиболее выгоден станок с револьверной головкой. Станок с ЧПУ не обязательно будет работать только в автоматическом режиме. Панель управления станком имеет кнопки для ручного управления, что даёт возможность, не меняя программы, по чертежу выполнить деталь другой формы, если после неё опять будут выполняться прежние.
Станки с ЧПУ имеют управляемую как в ручном, так и в автоматическом режиме, пиноль, удерживающую длинные заготовки.
В отличие от механических станков, компьютеризированный имеет транспортёрную ленту, вывозящую стружку за пределы станка. В нижнем резервуаре находится охлаждающая эмульсия. Её подача на заготовку программируется наравне со скоростью подачи резцов и скоростью вращения.
Физически работать на станке с ЧПУ легче, но прежде чем запустить станок в автоматическом режиме, необходимо представить в каком порядке были бы проведены операции в ручном режиме, и заложить все сведения при помощи кнопок на панели в программу станка. Теоретические знания и умение обращаться с электроникой – это второстепенно, главное заключается в опыте работы на станке без программного обеспечения. Ведь под панелью находится всё тот же токарный станок, с теми же системами и принципом работы, только усилий от токаря при закреплении заготовки в кулачках, настройке скоростей, фиксации задней бабки потребуется в разы меньше.
После пройденной всеми инструментами обработки, изделие отрезается резцом и падает в контейнер всё в том же автоматическом режиме. Чистота рабочего пространства оператора обеспечивается не только тем, что отходы по транспортёру вывозятся в специальный резервуар, но и тем, что весь процесс обработки происходит в закрытом режиме. При проведении обработки детали в ручном режиме, следить за ходом можно через большое смотровое оконце на крышке, которое даёт полный обзор обрабатываемой заготовки.
Есть у токарных станков с ЧПУ ещё одна интересная возможность – получение вида детали с компьютера по электронной почте или другими способами. Специальные программы способны поворачивать виртуальную деталь, считывая её параметры, что значительно упрощает перенос чертежа оператором с бумажного носителя в систему станка.
Сколько стоит модернизация
Существуют и станки, в работе которых постоянное перепрограммирование приведёт к снижению темпов производства. К таким видам токарных станков относятся те, что предназначаются для выполнения единичных изделий. Но и для этого ряда станков необходима модернизация, которая сделает работу на них более удобной и качественной.
Для токарных станков, используемых для изготовления штучных изделий, модернизация может заключаться:
- повышением точности, за счёт установки подшипников другого типа;
- облегчения самого станка ввиду ограничения в данном производстве диаметра и веса заготовки;
- изготовлением станины с выемкой, что вызвано удобством в обработке определённого вида заготовок.
Расходы на установку ЧПУ и всей сопутствующей модернизация станка могут составлять около половины суммы нового оборудования. Да и не каждый станок, отработавший немалый срок, сможет выдержать подобное усовершенствование. Для старого оборудования, безотказно работающего в своём формате, достаточно доработать или обновить некоторые узлы:
- повысить мощность, поставив электродвигатель нового поколения;
- увеличить число рабочих передач;
- повысить жёсткость;
- механизировать процесс закрепления и снятия заготовок.
Такие усовершенствования могут проходить по плану во время капитального ремонта станков, но если учесть их возраст и то, что запасные части для них уже не выпускаются, остаётся их дорабатывать методом подбора узлов, предназначенных для других моделей токарных станков или изготавливать самостоятельно.
Проводимая модернизация может способствовать выходу из строя других узлов. Например, при установке более мощного двигателя, могут не выдержать такой нагрузки:
- ременная передача;
- фрикционная муфта;
- зубчатое колесо и другие узлы и механизмы.
Устанавливая новые мощные узлы, необходимо заранее просчитать, не приведёт ли такая модернизация к выходу из строя других. Чтобы избежать случайностей, необходимо провести проверочный расчёт на прочность всего оборудования станка, и усилить более слабые его узлы. Только в этом случае усовершенствование будет целесообразным и принесёт доход, а не дополнительные траты на покупку и изготовление запчастей.
Модернизация очень старого станка может заключаться:
- в смене вида ременной передачи с плоской на клиновую;
- установке зубчатых колёс из более прочных сплавов и композитов;
- в повышении жёсткости путём установки станка на более широкие тумбы;
- в укреплении станины за счёт дополнительных рёбер жёсткости;
- в удлинении станины, если того требует производственный процесс;
- в оснащении револьверной головкой другого типа.
Любая модернизация производится для того, чтобы продлить срок службы станка и сделать его более современным и производительным.
Относительно приобретения нового, полная модернизация, с установкой автоматического узла управления на старый, обойдётся примерно в 2 раза дешевле.
Устройство токарного станка 16К20 — полезная информация Токарные станки по металлу
Сборочные единицы (узлы) и механизмы токарно-винторезного станка: 1 — передняя бабка, 2 — суппорт, 3 — задняя бабка, 4 — станина, 5 и 9 — тумбы, 6 — фартук, 7 — ходовой винт, 8 — ходовой валик, 10 — коробка подач, 11 — гитары сменных шестерен, 12 — электро -пусковая аппаратура, 13 — коробка скоростей, 14 — шпиндель.
Токарно-винторезные станки предназначены для обработки, включая нарезание резьбы, единичных деталей и малых групп деталей. Однако бывают станки без ходового винта. На таких станках можно выполнять все виды токарных работ, кроме нарезания резьбы резцом. Техническими параметрами, по которым классифицируют токарно-винторезные станки, являются наибольший диаметр D обрабатываемой заготовки (детали) или высота Центров над станиной (равная 0,5 D), наибольшая длина L обрабатываемой заготовки (детали) и масса станка. Ряд наибольших диаметров обработки для токарно-винторезных станков имеет вид: D = 100, 125, 160, 200, 250, 320, 400, 500, 630, 800, 1000, 1250, 1600, 2000 и далее до 4000 мм. Наибольшая длина L обрабатываемой детали определяется расстоянием между центрами станка. Выпускаемые станки при одном и том же значении D могут иметь различные значения L. По массе токарные станки делятся на легкие — до 500 кг (D = 100 — 200 мм), средние — до 4 т (D = 250 — 500 мм), крупные — до 15 т (D = 630 — 1250 мм) и тяжелые — до 400 т (D = 1600 — 4000 мм).
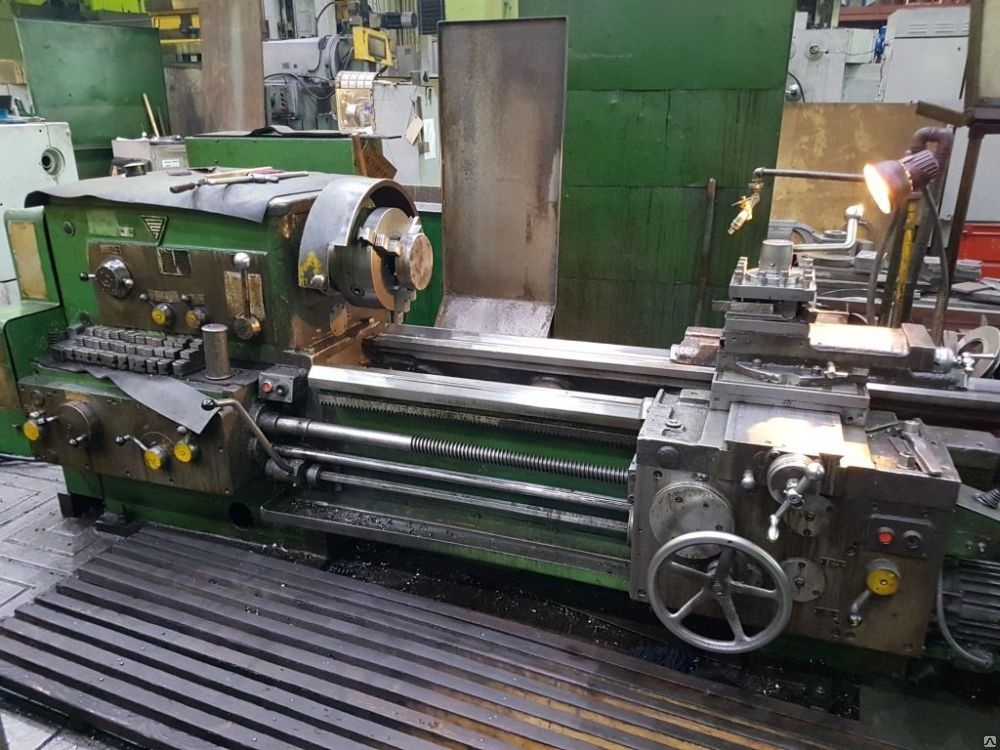
16К20 Характеристики станка 16К20 завода «Красный пролетарий»
.
Общий вид и размещение органов управления токарно-винторезного станка мод. 16К20:
Рукоятки управления: 2 — сблокированная управление, 3,5,6 — установки подачи или шага нарезаемой резьбы, 7, 12 — управления частотой вращения шпинделя, 10 — установки нормального и увеличенного шага резьбы и для нарезания многозаходных резьб, 11 — изменения направления нареза-ния резьбы (лево- или правозаходной), 17 — перемещения верхних салазок, 18 — фиксации пиноли, 20 — фиксации задней бабки, 21 — штурвал перемещения пиноли, 23 — включения ускоренных перемещений суппорта, 24 — включения и выключения гайки ходового винта, 25 — управления изменением направления вращения шпинделя и его остановкой, 26 — включения и выключения подачи, 28 — поперечного перемещения салазок, 29 — включения продольной автоматической подачи, 27 — кнопка включения и выключения главного электродвигателя, 31 — продольного перемещения салазок; Узлы станка: 1 — станина, 4 — коробка подач, 8 — кожух ременной передачи главного привода, 9 — передняя бабка с главным приводом, 13 — электрошкаф, 14 — экран, 15 — защитный щиток, 16 — верхние салазки, 19 — задняя бабка, 22 — суппорт продольного перемещения, 30 — фартук, 32 — ходовой винт, 33 — направляющие станины.
Механизм подач и коробка скоростей 16К20 токарного станка.
Главный привод станка. В передней бабке размещены коробка скоростей и шпиндель, которые приводят во вращение обрабатываемую деталь при выбранных глубине резания и подаче. На рисунке показано устройство коробки скоростей, которая работает следующим образом. Заготовка зажимается в кулачковом патроне, который крепится к фланцу шпинделя 13. Вращение от электродвигателя 1 через ременную передачу 2 и муфту включения 3 передается на вал 5.
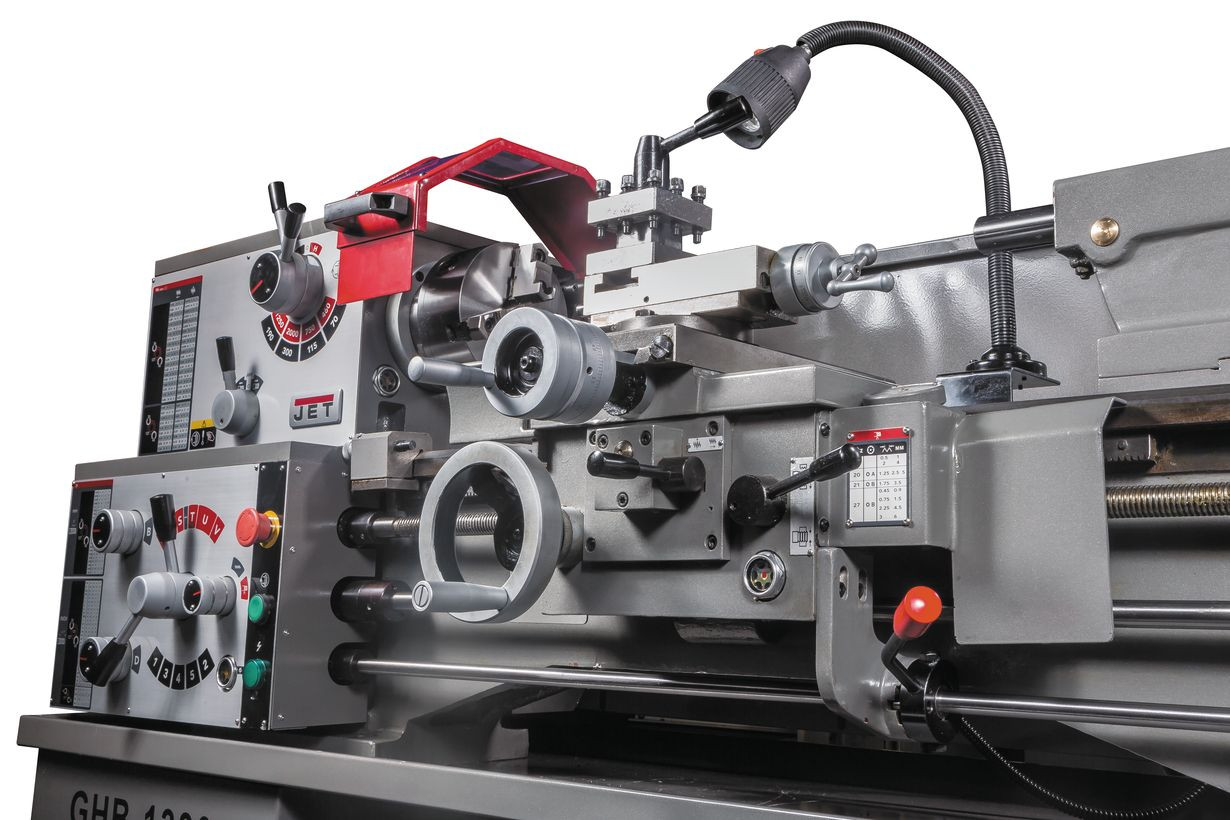
Привод этого механизма осуществляется от коробки скоростей через трензель (смотри рисунок справа), который состоит из четырех зубчатых колес а, б, в, г, связанных с рукояткой 19, переключением которой осуществляется реверс (т. е. изменение направления вращения) вала 20 (приводного вала суппорта). Позиции а, б, в, г, 19 и 20 (см. рисунки). При крайнем нижнем положении рукоятки 19 (положение А) зубчатые колеса а, б, в, г соединены последовательно и направление вращения вала 20 совпадает с направлением вращения шпинделя. При верхнем положении рукоятки 19 (положение В) соединены только зубчатые колеса а, в, г и направление вращения вала 20 изменяется на противоположное. В среднем положении рукоятки 19 (положение Б) зубчатые колеса б и в не соединяются с зубчатым колесом а и вал 20 не вращается.
С помощью гитары устанавливают (настраивают) зубчатые колеса с определенным передаточным отношением, обеспечивающим необходимое перемещение суппорта на один оборот шпинделя. Расстояние L между валами 1 и 2 является постоянным. На валу 2 свободно установлен приклон 3 гитары, закрепленный болтом 4. Ось 5 промежуточных колес вис можно перемещать по радиальному пазу, тем самым изменяя расстояние А между центрами колес c и d. Дуговой паз приклона 3 позволяет регулировать размер В.
Коробка подач.
Назначение коробки подач — изменять скорости вращения ходового винта и ходового вала, чем достигается перемещение суппорта с выбранной скоростью в продольном и поперечном направлениях. Вал 14 в подшипниках 15 (сотри рисунок) коробки подач получает вращение от зубчатых колес гитары; вместе с ним вращается и имеет возможность перемещаться вдоль него зубчатое колесо П с рычагом 10.
Суппорт
Суппорт предназначен для перемещения во время обработки режущего инструмента, закрепленного в резцедержателе. Он состоит из нижних салазок (продольного суппорта) 1, которые перемещаются по направляющим станины с помощью рукоятки 15 и обеспечивают перемещение резца вдоль заготовки. На нижних салазках по направляющим 12 перемещаются поперечные салазки (поперечный суппорт) 3, которые обеспечивают перемещение резца перпендикулярно оси вращения заготовки (детали). На поперечных салазках 3 расположена поворотная плита 4, которая закрепляется гайкой 10. По направляющим 5 поворотной плиты 4 перемещаются (с помощью рукоятки 13) верхние салазки 11, которые вместе с плитой 4 могут поворачиваться в горизонтальной плоскости относительно поперечных салазок и обеспечивать перемещение резца под углом к оси вращения заготовки (детали). Резцедержатель (резцовая головка) 6 с болтами 8 крепится к верхним салазкам с помощью рукоятки 9, которая перемещается по винту 7. Привод перемещения суппорта производится от ходового винта 2, от ходового вала, расположенного под ходовым винтом, или вручную. Включение автоматических подач производится рукояткой 14.
Резцедержатель, фартук и разъемная гайка
Устройство резцедержателя показано на рисунке сверху. В центрирующей расточке верхних салазок 5 установлена коническая оправка 3 с резьбовым концом. На конусе оправки установлена четырехсторонняя резцовая головка 6. При вращении рукоятки 4 головка 2 перемещается вниз по резьбе конической оправки 3 и через шайбу 1 и упорный подшипник обеспечивает жесткую посадку резцовой головки 6 на конической поверхности оправки 3. От поворота при закреплении резцовая головка удерживается шариком, который заклинивается между поверхностями, образованными пазом на основании конической оправки 3 и отверстием в резцовой головке 6. При необходимости сменить позицию инструмента рукоятку 4 поворачивают против часовой стрелки. При этом головка 2 поворачивается и перемещается вверх по резьбе конической оправки 3, снимая усилие затяжки резцовой головки 6 на конусе конической оправки 3. Одновременно головка 2 поворачивает резцовую головку 6 посредством тормозных колодок, фрикционно связанных с поверхностью расточки головки 2 и соединенных с резцовой головкой 6 штифтами 7.
При этом шарик, расположенный у основания конической оправки 3, не препятствует повороту резцовой головки, так как он утапливается в отверстие, сжимая пружину. Если в процессе работы рукоятка 4 (в зажатом положении) стала останавливаться в неудобном положении, то, изменяя толщину шайбы 1, можно установить ее в удобное для рабочего положение. Продольное и поперечное перемещение салазок суппорта производится через фартук 2 (смотри рисунок справа), который крепится к нижней поверхности продольного суппорта 1. Ручная продольная подача производится маховиком, который через зубчатую передачу сообщает вращение зубчатому колесу 4, катящемуся по рейке 3, закрепленной на станине 5 станка, и перемещает продольный суппорт вместе с поперечным суппортом и фартуком 2. Продольная подача суппорта 1 от ходового винта 2 производится включением разъемной гайки рукояткой 14 (смотри рисунок слева). Разъемная гайка состоит из двух частей (1 и 2), которые перемещаются по направляющим А при повороте рукоятки 5.
При этом диск 4 посредством прорезей В, расположенных эксцентрично, перемещает пальцы 3, в результате чего обе части гайки сдвигаются или раздвигаются. Если обе части гайки охватывают ходовой винт, то производится продольная подача (перемещение) суппорта; если они раздвинуты, то подача отключается.
Задняя бабка 16К20
Устройство задней бабки показано на рисунке. В корпусе 1 (при вращении винта 5 маховиком 7) перемещается пиноль 4, закрепляемая рукояткой 3. В пиноли устанавливается центр 2 с коническим хвостовиком (или инструмент). Задняя бабка перемещается по направляющим станка вручную или с помощью продольного суппорта. В рабочем неподвижном положении задняя бабка фиксируется рукояткой 6, которая соединена с тягой 8 и рычагом 9. Сила прижима рычага 9 тягой 8 к станине регулируется гайкой 11 и винтом 12. Более жесткое крепление задней бабки производится с помощью гайки 13 и винта 14, который прижимает к станине рычаг 10.
История токарного станка — полезная информация Токарно-винторезные станки по металлу
История относит изобретение токарного станка к 650 гг. до н. э. Станок представлял собой два установленных центра, между которыми зажималась заготовка из дерева, кости или рога. Раб или подмастерье вращал заготовку (один или несколько оборотов в одну сторону, затем в другую). Мастер держал резец в руках и, прижимая его в нужном месте к заготовке, снимал стружку, придавая заготовке требуемую форму.
Позднее для приведения заготовки в движение применяли лук со слабо натянутой (провисающей) тетивой. Тетиву оборачивали вокруг цилиндрической части заготовки так, чтобы она образовала петлю вокруг заготовки. При движении лука то в одну, то в другую сторону, аналогично движению пилы при распиливании бревна, заготовка делала несколько оборотов вокруг своей оси сначала в одну, а затем в другую сторону.
В XIV — XV веках были распространены токарные станки с ножным приводом. Ножной привод состоял из очепа — упругой жерди, консольно закрепленной над станком. К концу жерди крепилась бечевка, которая была обернута на один оборот вокруг заготовки и нижним концом крепилась к педали. При нажатии на педаль бечевка натягивалась, заставляя заготовку сделать один — два оборота, а жердь — согнуться. При отпускании педали жердь выпрямлялась, тянула вверх бечевку, и заготовка делала те же обороты в другую сторону.
Примерно к 1430 г. вместо очепа стали применять механизм, включающий педаль, шатун и кривошип, получив, таким образом, привод, аналогичный распространенному в XX веке ножному приводу швейной машинки. С этого времени заготовка на токарном станке получила вместо колебательного движения вращение в одну сторону в течение всего процесса точения.
В 1500 г. токарный станок уже имел стальные центры и люнет, который мог быть укреплен в любом месте между центрами.
На таких станках обрабатывали довольно сложные детали, представляющие собой тела вращения, — вплоть до шара. Но привод существовавших тогда станков был слишком маломощным для обработки металла, а усилия руки, держащей резец, недостаточными, чтобы снимать большую стружку с заготовки. В результате обработка металла оказывалась малоэффективной. Необходимо было заменить руку рабочего специальным механизмом, а мускульную силу, приводящую станок в движение, более мощным двигателем.
Появление водяного колеса привело к повышению производительности труда, оказав при этом мощное революционизирующее действие на развитие техники. А с середины XIV в. водяные приводы стали распространяться в металлообработке.
В середине XVI Жак Бессон (умер в 1569 г.) — изобрел токарный станок для нарезки цилиндрических и конических винтов.
В начале XVIII века Андрей Константинович Нартов (1693-1756), механик Петра первого, изобретает оригинальный токарно-копировальный и винторезный станок с механизированным суппортом и набором сменных зубчатых колес. Чтобы по-настоящему понять мировое значение этих изобретений, вернемся к эволюции токарного станка.
В XVII в. появились токарные станки, в которых обрабатываемое изделие приводилось в движение уже не мускульной силой токаря, а с помощью водяного колеса, но резец, как и раньше, держал в руке токарь. В начале XVIII в. токарные станки все чаще использовали для резания металлов, а не дерева, и поэтому проблема жесткого крепления резца и перемещения его вдоль обрабатываемой поверхности стола весьма актуальной. И вот впервые проблема самоходного суппорта была успешно решена в копировальном станке А.К.Нартова в 1712 г.
К идее механизированного передвижения резца изобретатели шли долго. Впервые эта проблема особенно остро встала при решении таких технических задач, как нарезание резьбы, нанесение сложных узоров на предметы роскоши, изготовление зубчатых колес и т.д. Для получения резьбы на валу, например, сначала производили разметку, для чего на вал навивали бумажную ленту нужной ширины, по краям которой наносили контур будущей резьбы. После разметки резьбу опиливали напильником вручную. Не говоря уже о трудоемкости такого процесса, получить удовлетворительное качество резьбы таким способом весьма трудно.
А Нартов не только решил задачу механизации этой операции, но в 1718-1729 гг. сам усовершенствовал схему. Копировальный палец и суппорт приводились в движение одним ходовым винтом, но с разным шагом нарезки под резцом и под копиром. Таким образом, было обеспечено автоматическое перемещение суппорта вдоль оси обрабатываемой заготовки. Правда, поперечной подачи еще не было, вместо нее было введено качание системы «копир-заготовка». Поэтому работы над созданием суппорта продолжались. Свой суппорт создали, в частности, тульские механики Алексей Сурнин и Павел Захава. Более совершенную конструкцию суппорта, близкую к современной, создал английский станкостроитель Модсли, но А.К. Нартов остается первым, кто нашел путь к решению этой задачи.
Вторая половина XVIII в. в станкостроении ознаменовалась резким увеличением сферы применения металлорежущих станков и поисками удовлетворительной схемы универсального токарного станка, который мог бы использоваться в различных целях.
В 1751 г. Ж. Вокансон во Франции построил станок, который по своим техническим данным уже походил на универсальный. Он был выполнен из металла, имел мощную станину, два металлических центра, две направляющие V-образной формы, медный суппорт, обеспечивающий механизированное перемещение инструмента в продольном и поперечном направлениях. В то же время в этом станке отсутствовала система зажима заготовки в патроне, хотя это устройство существовало в других конструкциях станков. Здесь предусматривалось крепление заготовки только в центрах. Расстояние между центрами можно было менять в пределах 10 см. Поэтому обрабатывать на станке Вокансона можно было лишь детали примерно одинаковой длины.
В 1778 г. англичанин Д. Рамедон разработал два типа станков для нарезания резьб. В одном станке вдоль вращаемой заготовки по параллельным направляющим передвигался алмазный режущий инструмент, скорость перемещения которого задавалась вращением эталонного винта. Сменные шестерни позволяли получать резьбы с разным шагом. Второй станок давал возможность изготавливать резьбу с различным шагом на детали большей длины, чем длина эталона. Резец продвигался вдоль заготовки с помощью струны, накручивавшейся на центральную шпонку.
В 1795 г. французский механик Сено изготовил специализированный токарный станок для нарезки винтов. Конструктор предусмотрел сменные шестерни, большой ходовой винт, простой механизированный суппорт. Станок был лишен каких-либо украшений, которыми любили украшать свои изделия мастера прежде.
Накопленный опыт позволил к концу XVIII века создать универсальный токарный станок, ставший основой машиностроения. Его автором стал Генри Модсли. В 1794 г. он создал конструкцию суппорта, довольно несовершенную. В 1798 г., основав собственную мастерскую по производству станков, он значительно улучшил суппорт, что позволило создать вариант универсального токарного станка.
В 1800 г. Модсли усовершенствовал этот станок, а затем создал и третий вариант, содержавший все элементы, которые имеют токарно-винторезные станки сегодня. При этом существенно то, что Модсли понял необходимость унификации некоторых видов деталей и первым стал внедрять стандартизацию резьб на винтах и гайках. Он начал выпускать наборы метчиков и плашек для нарезки резьб.
Одним из учеников и продолжателей дела Модсли был Р. Робертс. Он улучшил токарный станок тем, что расположил ходовой винт перед станиной, добавил зубчатый перебор, ручки управления вынес на переднюю па нель станка, что сделало более удобным управление станком. Этот станок работал до 1909 г.
Другой бывший сотрудник Модсли — Д. Клемент создал лоботокарный станок для обработки деталей большого диаметра. Он учел, что при постоянной скорости вращения детали и постоянной скорости подачи по мере движения резца от периферии к центру скорость резания будет падать, и создал систему увеличения скорости.
В 1835 г. Д. Витворт изобрел автоматическую подачу в поперечном направлении, которая была связана с механизмом продольной подачи. Этим было завершено принципиальное совершенствование токарного оборудования.
Следующий этап — автоматизация токарных станков. Здесь пальма первенства принадлежала американцам. В США развитие техники обработки металлов началось позднее, чем в Европе. Американские станки первой половины XIХ в. значительно уступали станкам Модсли.
Во второй половине XIХ в. качество американских станков было уже достаточно высоким. Станки выпускались серийно, причем вводилась полная взаимозаменяемость деталей и блоков, выпускаемых одной фирмой. При поломке детали достаточно было выписать с завода аналогичную и заменить сломанную деталь на целую без всякой подгонки.
Во второй половине XIХ в. были введены элементы, обеспечивающие полную механизацию обработки — блок автоматической подачи по обеим координатам, совершенную систему крепления резца и детали. Режимы резания и подач изменялись быстро и без значительных усилий. В токарных станках имелись элементы автоматики — автоматический останов станка при достижении определенного размера, система автоматического регулирования скорости лобового точения и т.д.
Однако основным достижением американского станкостроения было не развитие традиционного токарного станка, а создание его модификации — револьверного станка. В связи с необходимостью изготовления нового стрелкового оружия (револьверов) С. Фитч в 1845 г. разработал и построил револьверный станок с восемью режущими инструментами в револьверной головке. Быстрота смены инструмента резко повысила производительность станка при изготовлении серийной продукции. Это был серьезный шаг к созданию станков-автоматов.
В деревообработке первые станки-автоматы уже появились: в 1842 г. такой автомат построил К. Випиль, а в 1846 г. Т. Слоан.
Первый универсальный токарный автомат изобрел в 1873г. Хр. Спенсер.
Суппорт токарного станка
Одним из важнейших достижений машиностроения в начале XIX века стало распространение металлорежущих станков с суппортами — механическими держателями для резца. Введение суппорта разом повлекло за собой усовершенствование и удешевление всех машин, дало толчок к новым усовершенствованиям и изобретениям.
Суппорт предназначен для перемещения во время обработки режущего инструмента, закрепленного в резцедержателе. Он состоит из нижних салазок (продольного суппорта) 1, которые перемещаются по направляющим станины с помощью рукоятки 15 и обеспечивают перемещение резца вдоль заготовки. На нижних салазках по направляющим 12 перемещаются поперечные салазки (поперечный суппорт) 3, которые обеспечивают перемещение резца перпендикулярно оси вращения заготовки (детали).
На поперечных салазках 3 расположена поворотная плита 4, которая закрепляется гайкой 10. По направляющим 5 поворотной плиты 4 перемещаются (с помощью рукоятки 13) верхние салазки 11, которые вместе с плитой 4 могут поворачиваться в горизонтальной плоскости относительно поперечных салазок и обеспечивать перемещение резца под углом к оси вращения заготовки (детали).
Резцедержатель (резцовая головка) 6 с болтами 8 крепится к верхним салазкам с помощью рукоятки 9, которая перемещается по винту 7. Привод перемещения суппорта производится от ходового винта 2, от ходового вала, расположенного под ходовым винтом, или вручную. Включение автоматических подач производится рукояткой 14.
Устройство поперечного суппорта показано на рисунке ниже. По направляющим продольного суппорта 1 ходовым винтом 12, оснащенным рукояткой 10, перемещаются салазки поперечного суппорта. Ходовой винт 12 закреплен одним концом в продольном суппорте 1, а другим — связан с гайкой (состоящей из двух частей 15 и 13 и клина 14), которая крепится к поперечным салазкам 9. Затягивая винт 16, раздвигают (клином 14) гайки 15 и 13, благодаря чему выбирается зазор между ходовым винтом 12 и гайкой 15.
Величину перемещения поперечного суппорта определяют по лимбу 11. К поперечному суппорту крепится (гайками 7) поворотная плита 8, вместе с которой поворачиваются верхние салазки 6 и резцедержатель 5. На некоторых станках на поперечных салазках 9 устанавливается задний резцедержатель 2 для проточки канавок, отрезки и других работ, которые могут быть выполнены перемещением поперечного суппорта, а также кронштейн 3 с щитком 4, защищающим рабочего от попадания стружки и смазочно-охлаждающей жидкости.
Токарный станок имеет весьма древнюю историю, причем с годами его конструкция менялась очень незначительно. Приводя во вращение кусок дерева, мастер с помощью долота мог придать ему самую причудливую цилиндрическую форму. Для этого он прижимал долото к быстро вращающемуся куску дерева, отделял от него круговую стружку и постепенно давал заготовке нужные очертания. В деталях своего устройства станки могли довольно значительно отличаться друг от друга, но вплоть до конца XVIII века все они имели одну принципиальную особенность: при обработке заготовка вращалась, а резец находился в руках мастера.
Исключения из этого правила были очень редкими, и их ни в коем случае нельзя считать типичными для этой эпохи. Например, держатели для резца получили распространение в копировальных станках. С помощью таких станков работник, не обладавший особыми навыками, мог изготовлять затейливые изделия очень сложной формы. Для этого пользовались бронзовой моделью, имевшей вид изделия, но большего размера (обычно 2:1). Нужное изображение получали на заготовке следующим образом.
Станок оборудовался двумя суппортами, позволявшими вытачивать изделия без участия руки работника: в одном был закреплен копировальный палец, в другом — резец. Неподвижный копировальный палец имел вид стержня, на заостренном конце которого помешался маленький ролик. К ролику копировального пальца специальной пружиной постоянно прижималась модель. Во время работы станка она начинала вращаться и в соответствии с выступами и впадинами на своей поверхности совершала колебательные движения.
Эти движения модели через систему зубчатых колес передавались вращающейся заготовке, которая повторяла их. Заготовка находилась в контакте с резцом, подобно тому, как модель находилась в контакте с копировальным пальцем. В зависимости от рельефа модели заготовка то приближалась к резцу, то удалялась от него. При этом менялась и толщина стружки. После многих проходов резца по поверхности заготовки возникал рельеф, аналогичный имевшемуся на модели, но в меньшем масштабе.
Копировальный станок был очень сложным и дорогим инструментом. Приобрести его могли лишь весьма состоятельные люди. В первой половине XVIII века, когда возникла мода на точеные изделия из дерева и кости, токарными работами занимались многие европейские монархи и титулованная знать. Для них большей частью и предназначались копировальные станки.
Но широкого распространения в токарном деле эти приспособления не получили. Простой токарный станок вполне удовлетворял всем потребностям человека вплоть до второй половины XVIII века. Однако с середины столетия все чаще стала возникать необходимость обрабатывать с большой точностью массивные железные детали. Валы, винты различной величины, зубчатые колеса были первыми деталями машин, о механическом изготовлении которых встал вопрос тотчас же после их появления, так как они требовались в огромном количестве.
Особенно остро нужда в высокоточной обработке металлических заготовок стала ощущаться после внедрения в жизнь великого изобретения Уатта. Изготовление деталей для паровых машин оказалось очень сложной технической задачей для того уровня, которого достигло машиностроение XVIII века.
Обычно резец укреплялся на длинной крючкообразной палке. Рабочий держал его в руках, опираясь как на рычаг на специальную подставку. Этот труд требовал больших профессиональных навыков и большой физической силы. Любая ошибка приводила к порче всей заготовки или к слишком большой погрешности обработки.
В 1765 году из-за невозможности рассверлить с достаточной точностью цилиндр длиной в два фута и диаметром в шесть дюймов Уатт вынужден был прибегнуть к ковкому цилиндру. Расточка цилиндра длиною в девять футов и диаметром в 28 дюймов допускала точность до «толщины маленького пальца».
С начала XIX века начался постепенный переворот в машиностроении. На место старому токарному станку один за другим приходят новые высокоточные автоматические станки, оснащенные суппортами. Начало этой революции положил токарный винторезный станок английского механика Генри Модсли, позволявший автоматически вытачивать винты и болты с любой нарезкой.
Нарезка винтов долго оставалась сложной технической задачей, поскольку требовала высокой точности и мастерства. Механики давно задумывались над тем, как упростить эту операцию. Еще в 1701 году в труде Ш. Плюме описывался способ нарезки винтов с помощью примитивного суппорта.
Для этого к заготовке припаивали отрезок винта в качестве хвостовика. Шаг напаиваемого винта должен был быть равен шагу того винта, который нужно было нарезать на заготовке. Затем заготовку устанавливали в простейших разъемных деревянных бабках; передняя бабка поддерживала тело заготовки, а в заднюю вставлялся припаянный винт. При вращении винта деревянное гнездо задней бабки сминалось по форме винта и служило гайкой, вследствие чего вся заготовка перемещалась в сторону передней бабки. Подача на оборот была такова, что позволяла неподвижному резцу резать винт с требуемым шагом.
Подобного же рода приспособление было на токарно-винторезном станке 1785 года, который был непосредственным предшественником станка Модсли. Здесь нарезка резьбы, служившая образцом для изготавливаемого винта, наносилась непосредственно на шпиндель, удерживавший заготовку и приводивший ее во вращение. (Шпинделем называют вращающийся вал токарного станка с устройством для зажима обрабатываемой детали.) Это давало возможность делать нарезку на винтах машинным способом: рабочий приводил во вращение заготовку, которая за счет резьбы шпинделя, точно так же как и в приспособлении Плюме, начинала поступательно перемещаться относительно неподвижного резца, который рабочий держал на палке.
Таким образом, на изделии получалась резьба, точно соответствующая резьбе шпинделя. Впрочем, точность и прямолинейность обработки зависели здесь исключительно от силы и твердости руки рабочего, направлявшего инструмент. В этом заключалось большое неудобство. Кроме того, резьба на шпинделе была всего 8-10 мм, что позволяло нарезать только очень короткие винты.
Винторезный станок, сконструированный Модсли, представлял собой значительный шаг вперед. История его изобретения так описывается современниками. В 1794-1795 годах Модсли, еще молодой, но уже весьма опытный механик, работал в мастерской известного изобретателя Брамы.
Перед Брамой и Модсли стояла задача увеличить число деталей, изготавливаемых на станках. Однако старый токарный станок был для этого неудобен. Начав работу по его усовершенствованию, Модсли в 1794 году снабдил его крестовым суппортом.
Нижняя часть суппорта (салазки) устанавливались на одной раме с задней бабкой станка и могла скользить вдоль ее направляющей. В любом ее месте суппорт мог быть прочно закреплен при помощи винта. На нижних салазках находились верхние, устроенные подобным же образом. С помощью них резец, закрепленный винтом в прорези на конце стального бруска, мог перемещаться в поперечном направлении.
Движение суппорта в продольном и поперечном направлениях происходило с помощью двух ходовых винтов. Подвинув резец с помощью суппорта вплотную к заготовке, жестко установив его на поперечных салазках, а затем перемещая вдоль обрабатываемой поверхности, можно было с большой точностью срезать лишний металл. При этом суппорт выполнял функцию руки рабочего, удерживающего резец. В описываемой конструкции, собственно, не было еще ничего нового, но она была необходимым шагом к дальнейшим усовершенствованиям.
Уйдя вскоре после своего изобретения от Брамы, Модсли основал собственную мастерскую и в 1798 году создал более совершенный токарный станок. Этот станок стал важной вехой в развитии станкостроения, так как он впервые позволил автоматически производить нарезку винтов любой длины и любого шага.
Слабым местом прежнего токарного станка было то, что на нем можно было нарезать только короткие винты. Иначе и быть не могло ведь там не было суппорта, рука рабочего должна была оставаться неподвижной, а двигалась сама заготовка вместе с шпинделем. В станке Модсли заготовка оставалась неподвижной, а двигался суппорт с закрепленным в нем резцом.
Для того чтобы заставить суппорт перемещаться на нижних салазках вдоль станка, Модсли соединил с помощью двух зубчатых колес шпиндель передней бабки с ходовым винтом суппорта. Вращающийся винт вкручивался в гайку, которая тянула за собой салазки суппорта и заставляла их скользить вдоль станины. Поскольку ходовой винт вращался с той же скоростью, что и шпиндель, то на заготовке нарезалась резьба с тем же шагом, что была на этом винте. Для нарезки винтов с различным шагом при станке имелся запас ходовых винтов.
Автоматическое нарезание винта на станке происходило следующим образом. Заготовку зажимали и обтачивали до нужных размеров, не включая механической подачи суппорта. После этого соединяли ходовой винт со шпинделем, и винтовая нарезка осуществлялась за несколько проходов резца. Обратный отход суппорта каждый делался вручную после отключения самоходной подачи. Таким образом, ходовой винт и суппорт полностью заменяли руку рабочего. Мало того, они позволяли нарезать резьбу гораздо точнее и быстрее, чем на прежних станках.
В 1800 году Модсли внес замечательное усовершенствование в свой станок – взамен набора сменных ходовых винтов он применил набор сменных зубчатых колес, которые соединяли шпиндель и ходовой винт (их было 28 с числом зубьев от 15 до 50).
На своем станке Модсли выполнял нарезку резьб с такой изумительной точностью и аккуратностью, что это казалось современникам почти чудом. Он, в частности, нарезал регулировочные винт и гайку для астрономического прибора, который в течение долгого времени считался непревзойденным шедевром точности. Винт имел пять футов длины и два дюйма в диаметре с 50-ю витками на каждый дюйм. Резьба была такой мелкой, что ее невозможно было рассмотреть невооруженным глазом. В скором времени усовершенствованный Модсли станок получил повсеместное распространение и послужил образцом для многих других металлорежущих станков. В 1817 году был создан строгальный станок с суппортом, позволивший быстро обрабатывать плоские поверхности. В 1818 году Уитни придумал фрезерный станок. В 1839 году появился карусельный станок и т.д.
Нартов Андрей Константинович (1683 — 1756)
Деятель времени Петра Великого. Русский механик и изобретатель. Учился в Школе математических и навигацких наук в Москве. Около 1718 года был послан царем за границу для усовершенствования в токарном искусстве и «приобретения знаний в механике и математике». По указанию Петра I, Нартов вскоре был переведен в Петербург и назначен личным токарем царя в дворцовой токарной мастерской.
Работая здесь в 1712-1725, Нартов изобрел и построил ряд совершенных и оригинальных по кинематической схеме токарных станков (в том числе копировальных), часть которых была снабжена механическими суппортами. С появлением суппорта решалась задача изготовления частей машин строго определенной геометрической формы, задача производства машин машинами.
В 1726-1727 и в 1733 Нартов работал при Московском монетном дворе, где создал оригинальные монетные станки. В том же 1733 году Нартов создал механизм для подъема «Царь колокола». После смерти Петра, Нартову было поручено сделать «триумфальный столп» в честь императора, с изображением всех его «баталий».
Когда в Академию Наук были сданы все токарные принадлежности и предметы Петра, а также и «триумфальный столп», то, по настоянию начальника академии, барона Корфа, считавшего Нартова единственным человеком, способным окончить «столп», он был переведен в академию «к токарным станкам», для заведывания учениками токарного и механического дела и слесарями. Петровская токарня, превращенная Нартовым в академические мастерские, послужила базой для последующих работ М. В. Ломоносова, а затем И. П. Кулибина (особенно в области приборостроения).
В 1742 году Нартов принес Сенату жалобу на советника академии Шумахера, с которым у него происходили пререкания по денежному вопросу, а затем добился назначения следствия над Шумахером, на место которого был определен сам Нартов. В этой должности он пробыл только 1,5 года, потому что оказался «ничего кроме токарного художества незнающим и самовластным»; он велел запечатать архив академической канцелярии, грубо обращался с академиками, и наконец, довел дело до того, что Ломоносов и другие члены стали просить возвращения Шумахера, который вновь вступил в управление академией в 1744 году, а Нартов сосредоточил свою деятельность «на пушечно-артиллерийском деле».
1738-1756, работая в Артиллерийском ведомстве, Нартов создал станки для сверления канала и обточки цапф пушек, оригинальные запалы, оптический прицел; предложил новые способы отливки пушек и заделки раковин в канале орудия. В 1741 Нартов изобрел скорострельную батарею из 44 трехфунтовых мортирок. В этой батарее впервые в истории артиллерии был применен винтовой подъемный механизм, который позволял придавать мортиркам желаемый угол возвышения.
В обнаруженной рукописи Нартова «Ясное зрелище махин» описывается более 20 токарных, токарно-копировальных, токарно-винторезных станков различных конструкций. Выполненные Нартовым чертежи и технические описания свидетельствуют о его больших инженерных познаниях. Он издал также: «Достопамятные повествования и речи Петра Великого» и «Театрум махинарум».
Генри Модсли (Maudslay Henry 1771-1831)
Английский механик и промышленник. Создал токарно-винторезный станок с механизированным суппортом (1797), механизировал производство винтов, гаек и др. Ранние годы провел в Вулвиче под Лондоном.
В 12 лет стал работать набивальщиком патронов в Вулвичском арсенале, а в 18 лет он лучший кузнец арсенала и слесарь-механик, в мастерской Дж. Брама — лучшей мастерской Лондона. Позже открыл собственную мастерскую, потом завод в Ламбете.
Создал «Лабораторию Модсли». Дизайнер. Машиностроитель. Создал механизированный суппорт токарного станка, собственной конструкции. Придумал оригинальный набор сменных зубчатых колес. Изобрел поперечно-строгальный станок с кривошипно-шатунным механизмом. Создал или усовершенствовал большое количество различных металлорежущих станков. Строил для России паровые корабельный машины.
Фрезерный столик своими руками к мини токарному станку
(Из книги Е. Васильева «Маленькие станки»)
Это столик
Для расширения возможностей станочка (токарного — прим.) заказал на заводе две дополнительных детали. Первая — это столик. Столик имеет 30 отверстий с резьбой М5, закален и отшлифован.
Угольник
Вторая дополнительная деталь — угольник вот такой хитрой формы. Сталь 45, закалён и отшлифован.
На станке сделал кое-какие мелкие переделки: перенёс гайку ходового винта продольной подачи с правой стороны суппорта на левую. Результат такой модернизации: если снять заднюю бабку, суппорт можно отводить вправо до самого конца станины, на место задней бабки. Снял верхние салазки и на их место прикрутил угольник. Верхние салазки поставил вертикально и прикрутил к угольнику за шпильку резцедержки.
К основанию верхних салазок прикрутил столик. Получилось приспособление для горизонтального фрезерования. (Правильнее сказать: «для вертикального фрезерования», так как инструмент расположен вертикально к столу, как на вертикально-фрезерном станке, и работа подразумевается преимущественно концевыми фрезами).
Один из крепёжных болтиков угольника проходит через полукруглую прорезь, позволяя в некоторых пределах поворачивать угольник в горизонтальной плоскости.
В вертикальной плоскости столик также может быть немного повёрнут в ту или другую сторону. Закрепив деталь на столике, а фрезу в патроне, можно выполнить нехитрые фрезерные работы.
Изготовил прижимы, с помощью которых при фрезерной работе на столике можно закрепить или деталь, или тиски, как показано на фото. Прижимы крепятся к столику винтами М5. Сами лапки сделал из старого лобзика (и слегка закалил), а винты специально купил в магазине крепежа, по несколько штук каждой длины.
Возникла необходимость изготовить деталь из дюрали. Заготовка — пруток Д16Т диаметром 50 мм.
Отпилил необходимый кусочек ножовкой, отторцевал на токарном станочке, предварительно снял лишнее снова ножовкой, так как во фрезерном приспособлении пока ещё не всё работает как надо, и снимать много металла получается долго.
Потихоньку фрезерую, одновременно подбирая оснастку, инструмент, и приспосабливаясь к норову станка при такой работе.
Фрезу закрепляю в сверлильном патроне, в котором нарезал резьбу, как на шпинделе: М12х1. Биение фрезы в патроне чуть меньше 0,05 мм. Меньше сделать не получилось, так как биение меняется примерно на пару соток при отвинчивании-навинчивании патрона, и ещё на пару соток — при перезажиме инструмента. Оставил пока, как есть — эти пять соток не мешают, да и патрон этот не того качества, чтобы с ним хотелось возиться.
Любопытно, что в отличие от токарной обработки, при фрезеровании управление педалью оказалось абсолютно неудобным.
Первая проба фрезерного приспособления.
Источник: Е. Васильев «Маленькие станки»
Наибольший диаметр устанавливаемой заготовки, мм | |
— над станиной, — над суппортом, — над выемкой в станине |
1000 650 1400* |
Наибольший диаметр обрабатываемой заготовки, мм: | |
— над станиной, — над суппортом |
1000 650 |
Наибольшая длина обрабатываемой заготовки, мм | 1000; 3000; 5000; 6000; 8000; 10000; 12000 |
Длина выемки в станине от зеркала патрона, мм | 390* |
Наибольший вес устанавливаемой заготовки, кг | 8000**; 10000 |
Высота резца, устанавливаемого в резцедержателе, мм | 50 |
Размер конца шпинделя передней бабки по DIN | 2-15М |
Внутренний конус в шпинделе бабки шпиндельной (метрический) | 140 |
Количество ступеней частот вращения шпинделя | 24 |
Диаметр цилиндрического отверстия в шпинделе, мм | 128 |
Пределы частот вращения шпинделя, об./мин. | 5-500 |
. | |
Пределы рабочих подач, мм/об. | |
— продольных, — поперечных, — резцовых салазок |
0,06-2,42 (0,06-19,36***) 0,022-0,88 (0,022-7,04***) 0,022-0,88 (0,022-7,04***) |
Пределы шагов нарезаемых резьб | |
— метрических, мм — дюймовых, ниток на дюйм — модульных, модуль — питчевых, питч |
1-96 24-0,25 0,5-24 96-1 |
Ускоренное перемещение суппорта, мм/мин. | |
— продольное, — поперечное и резцовых салазок |
3000 1000 |
Наибольшее усилие резания, кН | 41 |
Наибольший крутящий момент на шпинделе, кНм | 9,5 |
Мощность главного привода, кВт | 22 |
. | |
Габаритные размеры, мм | |
— длина — ширина — высота |
4100; 6140; 8180; 9190; 11380; 13210; 15210 2200 1770**; 1880 |
Масса, кг | 9850; 12800; 15750; 16140; 17730; 20300; 23500 |
Настольный токарный станок RED S712
Когда для габаритного оборудования просто нет места, но токарную обработку изделий выполнять всё же необходимо, то оптимальным решением будет купить настольный универсальный токарно-винторезный станок RED S712 по низкой цене. Данный станок является отличным вариантом для домашней мастерской, автосервиса, а также школьных мастерских. Этот небольшой, но в тоже время функциональный помощник способен превосходно справиться с выполнением таких операций как: нарезка резьбы, зенкерование, сверление, обточка поверхностей.
Настольный токарный станок RED S712 обладает рядом преимуществ:
- Удобное управление. Даже токарь имеющий скромный опыт работы может с лёгкостью выполнять необходимые операции на этом оборудовании;
- Эргономичная защита трёхкулачкового патрона диаметром 100 мм;
- Рукоятки оснащены удобными лимбами;
- Надёжная защита ходового винта. Исключено попадание металлической стружки, а это значит, что данный элемент станка прослужит гораздо дольше;
- Стальной механизм гитары зубчатых колёс. Специальная система смазки;
- Индукционно закалённые направляющие станины. Гарантия длительного срока службы;
- Таблица с указанием выбора режимов резания размещённая на торце крышки шпиндельной бабки;
- Высокая жесткость при скромных габаритных размерах.
Компактные размеры станка позволяют реализовать свои конструкторские задумки. Оборудование потребляет минимум электрической энергии, обладает очень незначительной шумностью и длительным сроком службы. Качество станка подтверждено соответствующими сертификатами.
Модель обладает удобным стандартным набором управления, понятным любому токарю без переучивания.
Модель оснащена трехкулачковым патроном диаметром 100 мм, и эргономичной защитой патрона.
Все рукоятки оснащены четкими и удобными лимбами.
Вылет пиноли задней бабки составляет – 50 мм.
Все рукоятки станка обладают высокой эргономичностью, что позволяет полностью сосредоточиться на обработке заготовки.
12-позиционный резьбоуказатель позволяет быстро и удобно нарезать нужную резьбу.
Станок оснащен защитой ходового винта, предотвращающей попадание стружки и дальнейший износ.
Механизм гитары зубчатых колес оснащен металлическими шестернями, обладающими большим ресурсом и повышенной износостойкостью
Направляющие станины прошли закалку токами высокой частоты (ТВЧ)
На торце крышки шпиндельной бабки расположена таблица выбора режимов резания
Станок обладает компактными размерами
Стандартная комплектация:
- Трехкулачковый патрон Ø 100 мм;
- Набор сменных шестерён для нарезания резьбы;
- 4-х позиционный резцедержатель;
- 12-ти позиционный резьбоуказатель;
- Обратные кулачки;
- Упорный центр MK-2;
- Защитный экран патрона;
- Защитная задняя стенка;
- Поддон для сбора стружки.
Техническая характеристика Токарного винторезного станка CDS6250B/1000 | ||
Электропитание | ||
Мощность двигателя шпинделя | 7,5 кВт (опция: 11 кВт) | |
Станочные данные | ||
Диаметр обработки над станиной | 500 мм | |
Диаметр обработки над суппортом | 290 мм | |
Диаметр обработки в выемке станины | 760 мм | |
Длина выемки станины | 280 мм | |
Межцентровое расстояние | 1000 мм | |
Ширина станины | 394 мм | |
Максимальный вес обрабатываемой заготовки | 300 кг | |
Шпиндель | ||
Число оборотов шпинделя | 26 — 2000 об/мин | |
Количество скоростей шпинделя | 16 | |
Проходное отверстие шпинделя | 82 мм (опция: 105 мм) | |
Фланец шпинделя | Camlock D8 (DIN 55029, ISO 702/II) | |
Внутренний конус шпинделя | метрический 90 мм (1:20) | |
Крутящий момент шпинделя | 2370 Нм | |
Подачи и резьбы | ||
Продольная подача (45 подач) | 0,044 — 1,48 мм/об | |
Поперечная подача (45 подач) | 0,022 — 0,74 мм/об | |
Быстрый ход в продольном направлении | 4200 мм/мин | |
Быстрый ход в поперечном направлении | 2100 мм/мин | |
Пределы шага нарезаемых метрических резьб (73 шага) | 0,35 — 80 мм | |
Пределы шага нарезаемых дюймовых резьб (47 шагов) | 80 — 7/16 ниток/дюйм | |
Пределы шага нарезаемых модульных резьб (45 шагов) | модуль 0,2 — 40 | |
Пределы шага нарезаемых питчевых резьб (47 шагов) | 160 — 7/8 DP | |
Диаметр / шаг продольного ходового винта | 40 / 12 мм | |
Резцедержатель | ||
Размер державки резца | 25 х 25 мм | |
Угол поворота верхней каретки суппорта | ± 45° | |
Ход верхней каретки суппорта | 130 мм | |
Ход поперечной каретки суппорта | 348 мм | |
Задняя бабка | ||
Конус пиноли задней бабки | МК5 | |
Диаметр пиноли задней бабки | 75 мм | |
Ход пиноли задней бабки | 150 мм | |
Поперечное перемещение задней бабки | ± 15 мм | |
Габаритные размеры | ||
Длина | 2600 мм | |
Ширина х Высота | 1230 х 1440 мм | |
Масса станка | 2170 кг |
| Марка:
В нашем домашнем магазине есть токарный станок по металлу Jet GBH-1340A с цифровым считывающим устройством (DRO), и мы обсуждали возможность добавления ЧПУ, потому что некоторые типы деталей чрезвычайно сложно изготавливать с высокой точностью без компьютера в драйвере. сиденье.
Этот проект со страниц Make: Magazine. Подпишитесь сегодня!Но мы подошли к проекту с некоторым откладыванием.Изначально мы выбрали контроллер частотно-регулируемого привода (VFD) для шпинделя, шаговых двигателей NEMA 34 и приводов для осей токарного станка на основе того, что мы нашли внутри нашего фрезерного станка Tormach 770. Мы также нашли в Интернете плату управления параллельным ЧПУ. Одним из наших основных соображений в отношении выбранных нами деталей было «дешево», хотя в конечном итоге это будет стоить нам.
Прибыли детали, и мы отложили их примерно на год, в то время как другие проекты имели приоритет, лишь изредка пересматривая этот проект, чтобы провести измерения или подумать, как именно установить степперы.Это был внезапный отказ двигателя шпинделя Jet, который снова привлек внимание к этому проекту. Мы вытащили детали и всерьез приступили к конверсии.
НЕОБХОДИМОЕ ВРЕМЯ:
Много выходных
ТРУДНОСТЬ:
Продвинутый
СТОИМОСТЬ:
2500–2 800 долл. США
МАТЕРИАЛЫ
- Станок струйный металлообрабатывающий с цифровым считыванием (УЦИ)
- 3-х фазный мотор Marathon # 145THFR5329, 500 $, для замены сгоревшего шпиндельного мотора
- Контроллер двигателя с частотно-регулируемым приводом (VFD) Emerson Commander SK, 450 долл. США
- Плата управления ЧПУ, параллельный порт, например, многофункциональная плата ЧПУ C11G, 68 долларов США, CNC4PC.com
- Шаговые двигатели, NEMA 34 (2) для осей X и Z, модель 34HS38-3008S, 110 долларов США за штуку
- Платы цифрового шагового драйвера (2) GeckoDrive G213V, 150 долларов США за штуку Компьютер
- , работающий под управлением Linux, программное обеспечение ЧПУ, которое можно бесплатно загрузить с linuxcnc.org. Мы использовали древнюю машину Pentium 4.
- Roxburgh EMC фильтр для шумоподавления
- Шарико-винтовая передача, 40 ″, с шариковой гайкой $ 225
- Подшипники упорные (4)
- Пользовательские крепления двигателя (2) из нержавеющей стали и алюминия на нашем стане с ЧПУ Tormach 770
- Балочные муфты (2), также известные как муфты гибких валов, от 5 до 50 долларов на Amazon в зависимости от размера
- Блок управления, сталь, 24 ″ × 16 ″ × 10 ″
- Выключатели питания, защитного отключения и т. Д.
- Провод: 12ga, 14ga и 22ga
- Реле, переключатели и т. Д., Бывшие в употреблении от неиспользуемых частей токарного станка
ИНСТРУМЕНТЫ
- Фрезы с ЧПУ, концевые фрезы, расточные оправки, токарные инструменты для обработки опор двигателя
- Сверло, отвертки, гаечные ключи, устройства для зачистки проводов, щипцы для обжима и т. Д.
- Паяльник и припой
Преобразование ЧПУ состоит из трех основных частей. Это: (1) модификация самой машины, (2) конструкция блока управления и (3) установка и настройка управляющего ПК.
Плата параллельного управления / интерфейсная карта.МОДИФИКАЦИЯ СТАНКА, ЧАСТЬ ПЕРВАЯ
Наш токарный станок по металлу 40 дюймов, предварительная переоборудование.Наш токарный станок имеет поворотный механизм 13 дюймов и длинную ось 40 дюймов. Скорость вращения шпинделя обычно регулируется через редуктор за шпинделем, приводимый в действие однофазным двигателем 230 В. Никаких изменений в передаче не потребовалось; мы просто выбрали оптимальную настройку передачи, и под ЧПУ скорость будет контролироваться контроллером VFD. Неисправность оригинального однофазного двигателя была на самом деле удачей, потому что замена его трехфазным двигателем обеспечила больший контроль и позволила достичь максимальной скорости почти вдвое большей, чем 1750 об / мин, которые мог выдержать оригинальный двигатель.Лучше всего то, что частотно-регулируемый привод смог преобразовать 220 В из однофазного в трехфазное. Оригинальный электрический блок управления был удален с задней части токарного станка, а некоторые управляющие реле и другие части были разобраны для использования в новом блоке управления.
Фрезеруется первая опора двигателя оси Z.Каретка, в которой удерживаются режущие инструменты, имела два варианта управления движением по оси Z. (На токарном станке ось Z направлена влево-вправо, а ось X управляет диаметром.) Есть основной ходовой винт для резания общего назначения и второй ходовой винт, который вращается синхронно со шпинделем для нарезания резьбы.Оба они приводятся в действие одной и той же коробкой передач и используются для перемещения каретки с помощью рычагов управления на самой каретке. Мы решили удалить ходовой винт нарезания резьбы и стержень, который управлял первичным ходовым винтом. Это позволило бы нам приводить в движение первичный ходовой винт через шаговый двигатель, установленный на противоположном конце и прикрепленный ремнем и шкивами. Первичный ходовой винт совершил чуть более 50 оборотов, чтобы переместить каретку на 1 дюйм, и мы надеялись, что это обеспечит некоторую степень точности управления.
Первая попытка привода двигателя по оси Z.Используя фрезерный станок с ЧПУ, мы изготовили опору двигателя, которая крепится болтами к токарному станку на вертлюге, почти так же, как генератор в автомобиле устанавливается для натяжения ремня.
Замена поперечных суппортов: Оригинальная рукоятка оси X.Для оси X, также известной как поперечный суппорт, очевидным выбором был прямой привод от шагового двигателя. Мы сняли рукоятки со станка и фрезеровали еще одно алюминиевое крепление. Ходовой винт был прикреплен к шаговому двигателю с помощью балочной муфты для снятия напряжения.
Мотор с поперечным суппортом в сборе: новый шаговый двигатель по оси X.В заднюю бабку токарного станка доработок не производилось. Это будет оставаться под ручным управлением, пока компьютер выполняет тяжелую работу по осям X и Z.
КОНСТРУКЦИЯ БЛОКА УПРАВЛЕНИЯ
Первоначальный блок управления Jet был слишком мал, чтобы вместить все компоненты, необходимые для управления токарным станком, поэтому мы нашли в сети коробку 24 ″ × 16 ″ × 10 ″, которая подошла бы ко всему. Возможно, глубина в 10 дюймов была излишней, но на боковой стороне корпуса оставалось достаточно места для установки охлаждающих вентиляторов и переключателей.И он был достаточно прочным, чтобы при установке на токарном станке мог поддерживать монитор и стоять.
Выкладка контрольных частей.Мы установили компоненты на алюминиевый лист толщиной 1/8 дюйма, который можно было вынуть из коробки для облегчения доступа и который также мог бы служить радиатором. В алюминии и задней части коробки были вырезаны отверстия для набора ручных органов управления шпинделем.
Проводка в процессе.Были добавлены кабельные каналы с открытыми пазами, чтобы провода не спутывались.
Тщательно промаркированный переход.На протяжении всего процесса в Visio поддерживалась схема, в которой все соединения были тщательно пронумерованы, а провода были помечены на обоих концах, чтобы они соответствовали друг другу.
Блок управления в сборе (с головой Стэна внутри)
Блок управления в сборе, первое тестирование.
Всего на сборку блока управления ушло около 60 часов.
НАСТРОЙКА УПРАВЛЯЮЩЕГО ПК
Хотя многие проекты с ЧПУ используют параллельный порт для управления станком, они часто не используют новейшее и лучшее аппаратное обеспечение ПК.Во-первых, многие современные ПК не имеют параллельных портов, но также многие современные процессоры имеют оптимизацию, которая делает их очень хорошими при работе с программным обеспечением, но очень плохими при прямом изменении битов портов ввода-вывода для чувствительного ко времени управления оборудованием. Это не проблема для ПК, управляющего принтером, потому что USB избавил от тяжелой работы, но, по нашему опыту работы с фрезерным станком с ЧПУ, неправильная конфигурация оборудования / программного обеспечения может привести к сокращению на десятки тысячных долей от того, что G-код попросил о.
К счастью, в основных вариантах программного обеспечения ЧПУ есть списки компьютеров, которые были протестированы, поэтому требуется меньше догадок.Мы выбрали старый Dell Optiplex с процессором Pentium 4 под управлением LinuxCNC. Мы смогли купить два из них (так что у нас был запасной) по 30 долларов за штуку в местном магазине переработанных компьютеров.
LinuxCNC предлагает очень эффективный набор опций управления и хорошо поддерживается сообществом преданных компьютерных фанатов. Следуя инструкциям с веб-сайта, установка LinuxCNC была простой и хорошо работала на нашем древнем ПК. Используя их программу StepConf, мы смогли настроить отдельные выводы параллельного порта так, как нам хотелось.Мы обнаружили, что было бы целесообразно установить LinuxCNC до того, как мы купим какое-либо из наших управляющих устройств. У них были конфигурации по умолчанию для нескольких различных типов оборудования, о некоторых из которых мы не знали, когда делали наши первоначальные покупки.
Это не заняло много времени, и наша параллельная панель управления загоралась, как рождественская елка, когда мы нажимали кнопки. Волшебный дым не выходил. Мы должны были быть золотыми. Вместо этого ничего не работало.
ДЕШЕВЫЕ ЗАПЧАСТИ ВЕРНУТЬСЯ НА УКЛЮЧЕНИЕ
Возможно, будет несправедливо сказать, что ничего не работало.Были намеки на то, что кое-что было почти правильным. Один из шаговых двигателей издавал один звук, когда мы приказывали ему повернуться. Светодиод на одном из драйверов шагового двигателя будет оставаться зеленым до этого момента, а затем станет красным. Другой шаговый водитель демонстративно покраснел, как только было подано питание, и сидел, глядя на нас, как
глаз Саурона.
Мы проверили всю проводку. Мы сравнили нашу установку с тем, как был подключен Тормах; нет проблем. Когда мы позаимствовали осциллограф, чтобы проверить выход нашей платы управления ЧПУ, мы обнаружили первую проблему: напряжение выходного сигнала поднималось только до половины уровня, требуемого для шаговых драйверов.Наша плата управления за 20 долларов была мусором. Мы решили немного ослабить кошелек и нашли доску за 99 долларов на другом сайте. Когда он прибыл, он имел другой веб-сайт: CNC4PC.com. Кроме того, это было шесть аппаратных ревизий, устаревших по сравнению с их новейшим предложением. Он действительно обеспечивал нужные уровни напряжения, поэтому мы назвали это «извлеченным уроком» и надеялись, что степперы могут работать лучше. Они не.
Ранее я упоминал, что многое из того, что мы помещаем в наш собственный блок управления, основано на том, что мы нашли на нашем заводе.Эти шаговые приводы были той же модели MA860H, что и мельница, поэтому с видением счетов за ремонт мельницы в наших головах мы начали заменять подозрительные детали на мельницу. Шаговые двигатели были первыми, и, к нашему большому облегчению, оба работали отлично. Следующими пошли драйверы шагового двигателя, и ни один из них не работал. Глаз Саурона продолжал насмехаться над нами. Подозревая, что это могла быть наша вина, мы заказали новую пару такой же модели. Оба они тоже были мертвы по прибытии. Один вообще не работал бы на мельнице, а другой вращался бы, но только в одном направлении.Ясно, что эти драйверы не были надежным решением.
Водитель Франкенштейна: новые приводы GeckoDrives, установленные в туше неисправного водителя.Дополнительные онлайн-исследования наконец-то привели нас к GeckoDrive, и мы очень счастливы. Эти платы работали хорошо, когда мы их подключили в первый раз, и оба модуля Gecko вместе уместились в том же пространстве, что и один из более ранних, более дешевых драйверов. При требуемом напряжении GeckoDrives потребуется радиатор (не входит в комплект). Более дешевые драйверы включали в себя большой радиатор и вентилятор, и поскольку вентилятор был той частью этого драйвера, которая работала надежно, мы нашли большое удовлетворение, установив GeckoDrives в выдолбленный каркас мертвого драйвера.Это решило сразу две проблемы.
Детали управления собраны, пока не в корпусе.Новая плата параллельного управления была намного больше оригинальной, и теперь мы могли установить ее в пространстве, оставленном одним из оригинальных шаговых драйверов.
Одно замечание о шаговых драйверах: они бывают аналоговыми и цифровыми. На YouTube вы найдете видео, в которых сравнивается их поведение. Это показывает, и мы согласны с тем, что цифровые драйверы обеспечивают более плавную и тихую работу шагового двигателя. Они кажутся стоящими добавленной цены.
СОСТАВЛЯЕМ ВСЕ ВМЕСТЕ
Все детали были на своих местах. Мы могли управлять шаговыми двигателями с помощью кнопок пользовательского интерфейса или инструкций G-кода, а с помощью элементарного присоединения двигателей к ходовым винтам мы могли перемещать каретку по обеим осям.
Мы не знали точного отношения вращения ходового винта к поперечному перемещению, поэтому потребовалось немного проб и ошибок, чтобы найти правильные настройки в программе LinuxCNC StepConf. StepConf запрашивает несколько значений: количество шагов двигателя на оборот, микрошаг привода, соотношение зубьев шкива и шаг ходового винта.Если вы не уверены в этих значениях, обратите внимание, что они просто умножаются на одно значение, которое означает «шаги на дюйм». Если вы установите для всех этих значений, кроме одного, значение 1 (не имеет значения, какое именно), вы получите оставшееся значение, которое будет большим числом, которое можно настроить с большой точностью. Процесс, которому мы следовали:
- Переместите каретку примерно в известное положение, двигаясь слева направо. В пользовательском интерфейсе ЧПУ сбросьте смещения, чтобы положение было 0 .
- Измерьте положение каретки.
- Используя G-код, переместите каретку на 1 дюйм вправо, т.е. Z1 .
- Измерьте новое положение каретки и вычислите разницу в дюймах.
- Разделите ваше значение «шагов на дюйм» на пройденное расстояние, чтобы получить новое значение шагов на дюйм. Например, если ваши шаги на дюйм равны 20000 , а вы перемещаетесь на 1,015 ″, ваши новые шаги на дюйм будут равны 20 000 / 1,015 или 19704 .
- Повторяйте до тех пор, пока выдача команды на перемещение на 1 дюйм не приведет к уверенному перемещению на 1 дюйм.
Очень важно, чтобы измерения всегда производились после перемещения каретки в одном и том же направлении, поскольку ходовой винт почти наверняка будет иметь люфт. Если вы измеряете после движения в противоположных направлениях, ваши измерения будут отклоняться до величины люфта.
УЦИ все еще было прикреплено к токарному станку, и это значительно упростило процесс сравнения инструкций на ПК с реальным движением каретки. Следуя нашему процессу, мы должны были прийти к значению шагов на дюйм, которое дало бы стабильные результаты независимо от того, где на оси мы измеряли.Он работал по оси X, но по оси Z измерения менялись на целых 0,012 дюйма в зависимости от того, где они были сняты. Что-то было ужасно неправильно.
МОДИФИКАЦИЯ ТОКАРНОГО СТАНКА,
ЧАСТЬ ВТОРАЯ
Ходовые винты могут быть неточными, но винт должен быть очень плохим, чтобы погрешность увеличивалась и уменьшалась снова и снова более чем на 40 дюймов. Проблема заключалась в том, что помимо головного винта в движении по оси Z участвовали другие шестерни и червячные передачи. Нам нужно было учесть неточности по всему поезду.Люфт оси Z был таким же ужасным. В LinuxCNC есть способы компенсировать это, но для этого потребовалось бы найти ошибку в каждой точке на оси 40 дюймов. Было бы почти невозможно достичь желаемой точности. Зубчатая передача должна уйти.
Измерение места для крепления крепления двигателя оси Z.Прецизионная шарико-винтовая пара может практически устранить люфт за свою цену. Одна компания предложила 3500 долларов за шарико-винт диаметром 40 дюймов. В конце концов, мы купили шарико-винт и гайку за 225 долларов в компании Roton Products в штате Миссури.Потребовалась модификация, чтобы соответствовать подшипникам, которые мы приобрели за 336 долларов в местной шлифовальной мастерской. Шарико-винтовая передача Roton имела люфт в 0,007 дюйма, но, по крайней мере, он был стабильным и легко компенсировался в LinuxCNC.
Наше второе крепление для двигателя оси Z: на полпути через фрезерование, завершено и установлено с помощью шарико-винтовой передачиМы также решили отказаться от ремня и шкивов и создать новое крепление для шарико-винтовой передачи, чтобы мы могли осуществлять прямой привод от шагового двигателя.
Крепление шпиндельной бабки по оси Z.Каждый конец вала удерживается парой упорных подшипников, установленных спина к спине, чтобы исключить движение, но при этом допускать вращение, а сам вал устанавливается с небольшим натяжением между двумя опорами подшипников
Модифицированный токарный станок с новыми моторами, готовыми для шаговых двигателей..
Любому ЧПУ нужны концевые выключатели, чтобы станок мог найти исходное положение для каждой оси.
Монтаж концевого выключателя.К счастью, когда мы разобрали блок ручного управления, мы обнаружили два переключателя мгновенного действия, идеально подходящие для этой цели, поэтому мы установили их в удобном положении для каждого приводного винта.
Для прокладки кабелей обычно используются кабельные трассы, но мы избежали этого для оси X, просто позволив проводам, идущим от блока управления сзади к оси X, приводимой спереди, свободно свисать под машиной.
ОТДЕЛКИ
Токарный станок с ЧПУ работает во время первого пробного запуска.У нас появился действующий токарный станок с ЧПУ. LinuxCNC работал хорошо, хотя пользовательский интерфейс выглядел как старое приложение для Windows 98.
Снимок экрана LinuxCNC (программа не загружена, пока я не выясню, как заставить ее игнорировать тот факт, что она не подключена).К счастью, после изучения их пользовательских форумов мы обнаружили два альтернативных пользовательских интерфейса, оба из которых выглядели и работали намного лучше.
Как это обычно бывает с Linux, будьте готовы прочитать множество форумов и документации и редактировать текстовые файлы, чтобы получить нужную конфигурацию.
Приспособление для заточки лезвий ножей. Ручки изготовлены на токарном станке с ЧПУ! Шаблон для окончательной заточкиМы также планируем следующие усовершенствования в будущем:
- Мы потеряли возможность нарезать резьбу в этом проекте. Однако LinuxCNC поддерживает это, если вы можете предоставить обратную связь от оптического датчика скорости шпинделя.
- Жидкая охлаждающая жидкость может быть очень полезной даже на токарном станке без крышки при низких оборотах.
- Мы можем ограничить люфт, заказав новые шариковые гайки, у которых каждый четвертый или пятый шарик имеет другой размер, чтобы уменьшить допуск между шарико-винтовой парой и гайкой.
- Шарико-винтовые пары необходимо защитить. Нам нужно сделать несколько покрытий или кистей, чтобы они оставались чистыми.
Taig Micro с ЧПУ
Преобразование токарного станка Taig Micro 2-осевой токарный станок Taig Micro с числовым программным управлением (ЧПУ) Преобразование
Последнее обновление Вторник, 11 мая 2021 г., 06:46:31
гора Часовой пояс США
ДОМ
Микротокарный станок с ЧПУ, Ходовой винт оси X, Ходовой винт оси Z,
Шаговые двигатели, Шкивы двигателя шпинделя, Тахометр,
Индекс шпинделя, Концевые выключатели, E-stop,
QCTP,
Фильм о резьбонарезании с ЧПУ,
Машинный рабочий свет
CNC Mill
Схема системы
CNCzone
Форум поддержки Mach
Конфигурация Mach4
Калькулятор машиниста
Mach4Turn Руководство
Руководство по настройке нарезания резьбы Mach4
График на поверхности футов в минуту (SFM) 1
SFM 2
SFM 3
Микротокарный станок с ЧПУ
Тайг Микротокарный станок преобразован в ЧПУ.
На фото показана резка в первую очередь
конус без компаунда.
Поскольку Фрезерные станки с ЧПУ компьютер коммутационная плата,
контроллер шагового двигателя и
MPG уже были
на месте,
было очень рентабельно преобразовать Taig Micro
Токарный станок с ЧПУ от
установка другого провода
винты,
кронштейны для шаговых двигателей и
добавочные концевые выключатели. Шаговый двигатель
Панель управления
была легко перепроектирован и переделан
для обеспечения переключаемых выходов осей X и Z.
Возврат к базовой конфигурации токарного станка.
Устанавливается на 1/8 »
алюминиевая пластина.
Более книги по механообработке
Нажмите на связанные эскизы #ad
Ходовой винт оси X
Три винта 6-32 удерживают монтажную пластину двигателя.
Шаговый
крепится четырьмя болтами 10-32 с цилиндрической головкой.
Двигатель имеет кромку диаметром 1,5 дюйма, которая входит в & центрирует
на NEMA 23
размер отверстия для кронштейна двигателя.
Первоначальная конструкция кронштейна с использованием 1/4 »
алюминиевая пластина.
Перфоратор для выравнивания.
Покомпонентное изображение
беззазорная муфта шлицевого вала
с изготовленным
Адаптер ходового винта 1 / 4-20, левый.
Муфта вала без люфта в сборе.
Секунда, попроще
переходник тоже был сделан.
Основной кронштейн удерживается под кареткой с помощью
OEM
болты, направляющие латунную планку.
Исходные резьбы 4-40
были увеличены до 8-32 для повышения прочности.
Не перетягивайте эти болты, так как это повредит упор.
Заменил муфту на использование простого адаптера размера вала.
(цилиндр) с отверстием
чтобы установочный винт прошел насквозь.
Обратите внимание на плоские поверхности ходового винта, так что 3/16 дюйма с открытым концом.
гаечный ключ
можно использовать, чтобы удерживать его от поворота
когда
затягивает / откручивает стопорную гайку на другом конце, где
бронза
расположены радиальные / упорные подшипники.
Поскольку шаговые двигатели не имеют упорных подшипников,
лучше всего их изолировать
от этих сил.
Вдоль оси ходового винта пластиковая муфта имеет
малый зазор 1 мм так что невозможно передать
тяга
сил правда это маловероятно т.к. передняя тяга
Подшипник
имеет
почти исключено любое движение.
Такие же меры предосторожности приняты и для муфты ходового винта оси Z
.
Радиальные и упорные подшипники изготовлены из пропитанной маслом
спеченная бронза (OISB).Он проникает в исходное место.
Ходовой винт изготовлен из Стержень с резьбой 1 / 4-20 SS LH.
Геометрия
OEM была воспроизведена
но с более жесткими допусками.
Обратите внимание, пропитанная маслом бронза мягкая и может раздавиться / деформироваться.
Узел упорного подшипника в разобранном виде.
Левая и правая
торцы корпуса действуют как опорные поверхности.
Корпус (0,711 дюйма OAL) имеет резьбу 5 / 16-24 NF и
0,462 дюйма длины, которые такие же
как часть OEM.
Обработка и резка 6-32 дюйма длиной 0,42 дюйма
резьба на ходовом винте
конец.
Вал без резьбы имеет длину 0,82 дюйма.
Вал имеет диаметр OAL 1,24 дюйма x 0,14125 дюйма.
Ходовой винт обработанный квадратный / плоский с подшипниками
прямо напротив (правой) стороны
упорного подшипника.
Стальной хомут
черного цвета является сохраненной деталью OEM.
Тяга OISB диаметром 0,32 дюйма и толщиной 0,128 дюйма
Шайба
находится на (левой) стороне подшипника.
Контргайка регулируется до отсутствия люфта или заедания.
Нейлоновая гайка из желудя фиксирует первую гайку
и закрывает острый
потоки.
Добавлена пружина для дальнейшего уменьшения люфта на гайке ходового винта.
Регулируемый левый кронштейн использует Т-образную гайку,
шайба, гайка и болт 10-32.
Пружина не влияет на геометрию кронштейна.
Добавлена вторая внутренняя пружина.
Добавлен верхний
Кронштейн жесткости для шагового двигателя оси X.
Левая кромка скошена до
очистить кулачок.
Деталь болтами к каретке и корпусу концевого выключателя.
Имеет две выемки
которые входят в зацепление с кромками сопрягаемых деталей.
Два правых болта должны были освободить
канал кулачка, расположенный только
выше.
Вкручиваются в глухие резьбовые отверстия.
Другой вид выемки в фиксируемом кронштейне.
Ходовой винт оси Z
Прецизионное развертывание a
Отверстие 1/4 дюйма
в блок для установки
двух пропитанных маслом бронзовых гаек ходового винта.
Бронза с масляной пропиткой
материал подшипника
с резьбой для прецизионного ходового винта 1 / 4-20 RH.
Наружный диаметр ходового винта
гаек, обработанных до 0,750 дюйма и
разрезать.
Остался дополнительный материал для изготовления шестигранной гайки
для регулировки гаечного ключа.
Покомпонентное изображение корпуса гайки ходового винта
, а также
нижнюю часть винтов кронштейна двигателя.
Обратите внимание на квадратную канавку в гайках ходового винта и
точка полусобака
установочные винты
которые их привлекают.
Опорный блок ходового винта удерживается снизу
г.
кронштейн двигателя с помощью четырех болтов 10-32 с головкой под ключ.
Люфт снимается регулировкой одной гайки
против
Другой. Шестигранная гайка имеет размер 11/16 «.
Небольшое отверстие между двумя правыми болтами,
обеспечивает доступ к 6-32
болт кронштейна с колпачковой головкой.
Еще два аналогичных установочных винта были добавлены в верхнюю часть
, чтобы добавить прочности и удерживать настройки,
лучше.
Корпус гайки ходового винта оси Z
приподнят как можно ближе к токарному станку.
кровать, по возможности.
Прокладка выровняла оси ходового винта и двигателя.
Не самая сильная установка, так что
кронштейн жесткости
был добавлен для значительного увеличения прочности.
Шаговые двигатели
Шаговый двигатель большего размера предназначен для
каретка и двигатель среднего размера
для поперечного суппорта; оба — 3А.
Восемь выводов двигателя подключены к шестиконтактному разъему
Molex. Кабели длиной 7 футов
использовать 18
калибр проволоки.
Кронштейны с ходовыми винтами
5/8 »
Наружный диаметр, внутренний диаметр 1/2 дюйма
радиальные упорные шариковые и бронзовые подшипники с пропиткой маслом
.
Радиальные подшипники удерживаются зеленой проникающей
Loctite. Эта модель
подшипник (глубокая канавка)
предназначен для восприятия как радиальных, так и осевых сил, но он
не казался крепким
достаточно для применения,
, поэтому в конструкцию были добавлены бронзовые упорные шайбы.
Деталь кронштейна ходового винта. Бронзовые шайбы
имеют неглубокую,
Зенковка
с внешним диаметром 0,38 дюйма для ступицы радиального подшипника
зазор при вращении.
Отверстие 1/2 дюйма в скамейке
Верхняя часть позволяет полностью спрятать разъем и кабель двигателя
снизу.
Конец шлицевой муфты ходового винта
со снятой одной стороной.
Бронзовая шайба (скрытая) действует как левая
тяга (лафет
движется вправо) несущую поверхность.
Двигатель ходового винта оси Z соответствует жесткому допуску,
1,5 »
Зенковка для крепления NEMA 23.
Шкивы двигателя шпинделя
Кронштейн двигателя распространяется на оба
левый и правый к
удерживают добавление система с тремя шкивами для более медленных
скоростей и
шпиндельный тахометр, датчик
под шкив шпинделя соответственно.
Промежуточный вал или промежуточный вал
Компактный промежуточный вал (или промежуточный вал)
3-й
шкивная система на 178 об / мин; удобно для
Нарезание резьбы с ЧПУ.
Повернул ходовой винт
Кронштейн 180 градусов для лучшего доступа
к стопорным болтам с шестигранной головкой
гаечный ключ.
Для под головки винтов сделана распорная планка стальная;
намного лучше, чем
шайбы перекосились над прорезью.
Шаговый двигатель полностью контактирует с металлом.
верхняя пластина
обеспечивая дополнительный эффективный отвод тепла.
Когда мотор шпинделя наклонен вперед,
сейчас отдыхает
против резинового бампера.
Все детали удаляются друг от друга, когда мотор шпинделя
наклонен
жду поменять ремень на шкивах.
Нажмите на связанные ссылки
#ad
Радиальный / упорный подшипник и кронштейн
на другом конце
ходового винта.
Точность Ходовой винт 1 / 2-20
это запчасть
, оставшаяся от
Тайг
Проект преобразования ЧПУ Micro Mill.
Бронзовая пропитанная маслом шайба действует как правая
тяга
(каретка перемещается влево) опорная поверхность.
Заменена дополнительная плита на
1/8 »
сталь
, чтобы резьба была прочнее.
Его крепежные болты проходят через
скамейка.
Для под головки винтов сделана распорная планка стальная;
намного лучше, чем
шайбы перекосились над прорезью.
Добавлена еще одна масляная бронзовая упорная шайба
со стопорным кольцом для
дополнительная сила.
Изогнуты углы кронштейна.
Тахометр
QRB1114 Датчик тахометра NIR EO
схема.
Поскольку изначально он был разработан для ShumaTech
ДРО-350, требовалось
тахометр / буфер
схема
буферная схема для достижения
надежные показания Mach4.
Эта схема была заменена на
NTE 3100
фотонно-связанный модуль прерывателя датчик
для шпинделя токарного станка с ЧПУ
но все еще используется
для тахометра фрезерного шпинделя с ЧПУ
схема.
QRB1114 фиксируется коническим штифтом, который
в
мелкий канал нарезан концевой фрезой со сферической головкой 1/8 дюйма.
Сделал прорезь сзади, чтобы можно было подбирать
для вставки и
для простоты установки.
Датчик тахометра определяет темноту
винт проходит мимо.
В
установочный винт был покрашен в черный цвет.
Двухжильный провод с тефлоновым покрытием проложен под
скамейка вместе с
кабели шагового и концевого выключателя.
Входы тахометров для фрезерных и токарных станков
на Mach4 переключаются
аналогично Схема переключения выхода шагового двигателя.
Направление микровыключателя уровня указывает на которое
мини-стерео входное гнездо
связан с
разразиться
доска.
Переключаются только сигнал тахометра (белый) и 5 В постоянного тока (красный).
Две площадки
связаны вместе у доски.
Нажмите на связанные эскизы #ad
Этот подход с переключением датчика был изменен на
разместить
указатель дискового типа с прорезями для токарного станка.
Переключатель больше не нужен, как фрезерный станок и токарный станок.
тахометры сейчас используют
отдельные входные каналы.
Шпиндель
Индекс
Светоотражающий тахометр
достаточно для индикации числа оборотов
, но мне нужно было больше точности для Нарезание резьбы с ЧПУ.
Установлены 4-кулачковый патрон и поворотный стол с ЧПУ.
на станину мельницы Тайг для
ручное управление через Mach4.
Чтобы изготовить и смонтировать диск с прорезью, сначала
1/2 «-3/8»
ступенчатая беседка сделана для
удерживайте шкив Taig в 4-х кулачках.
Съемный,
5/8 «сталь
колышек показан в
место.
Показанный шкив утрамбован
в 4-кулачковом патроне.
Штифт 5/8 «центрирует 0,0625»
толстая алюминиевая пластина глубиной 1/2 дюйма, отверстия
# 43 просверливаются через каждые 90 градусов. Нарезание резьбы и установка 4-40
Винт
после каждого отверстия помог сделать настройку
становится все более жестким.
В
5/8 «центральный штифт удален.
между каждыми 4-40 нажатиями.
С центральным штифтом и 4 винтами, 3,5 дюйма
Диск диаметром
фрезерован с использованием
серия более глубоких разрезов.
Индексирующая выемка фрезерована до расчетного размера.
с использованием
эти формулы из документации Mach4.
Этот паз с квадратными краями, глубиной 0,25 дюйма и шириной 0,32 дюйма является
немного завышен для
максимальная скорость 8200 об / мин.
Mach4 больше не поддерживает многослотовую синхронизацию.
альфа
(угол паза) = 0.0012 x N (максимальная частота вращения шпинделя)
W (ширина паза) = 0,0088 x альфа x D (диаметр диска)
Примечание: если D в дюймах (или мм), тогда W в дюймах (или мм).
Центр имеет зенковку для
очистки ступицы шпинделя
правильно.
Диск с прорезями, полностью установленный на шкив.
Шпиндель.
Нанесен алюминиевый противозадирный состав.
перед установкой
терморасширенный шкив.
Для одного слота установите
параметры индексации LPT1 и пин входа #.
Эта установка с ЧПУ использует LPT1 контакт 15 для токарного станка и LPT1.
контакт 11 вход для
мельница. Увидеть
система
схематический.
После этого шкив был отцентрирован в
4-кулачковый патрон на
Токарный станок 9×20 и небольшие вариации
в передней / задней / краевых поверхностях диска были удалены.
Дисковое биение теперь
сведены к минимуму. Все края были тщательно зачищены от заусенцев
, чтобы уменьшить вероятность
режет при вращении с высокой скоростью.
Большое отверстие в монтажной пластине позволяет
Мини-стереоразъем
и провод для пропуска через стол.
Кронштейн шагового двигателя оси Z должен был иметь несколько
площадей
открыт для провода от тахометра.
г. NTE 3100
Кронштейн модуля фотонного прерывателя
обеспечивает доступ для проскальзывания провода
на место.
Обратите внимание на возможность вертикальной регулировки, обеспечиваемую
прорезной кронштейн с двумя
4-40 саморезов с шайбами из нержавеющей стали.
В верхней части фрезеровано неглубокое углубление, чтобы
Модуль
от поворота после
продлить воздействие вибрации.
Резьбовое отверстие позволяет вкручивать винт 4-40 с
Шайба из нержавеющей стали для удержания модуля на месте.
Кронштейны установлены. Верхние отверстия L-образных кронштейнов
прорезь
чтобы обеспечить окончательное осевое выравнивание двигателя и ходового винта.
Для окончательной центровки ходового винта поперечный суппорт
полностью опустился на
правый кронштейн подшипника
, который затем затягивается. Затем поперечный суппорт перемещается в
крайний левый
перед окончательной затяжкой кронштейна
самостоятельно выровняйте детали.Этот метод также используется для выравнивания всех
осей фрезерно-токарных
Весы / кронштейны УЦИ.
Шаговый двигатель переустановлен.
Кронштейн модуля был перемещен в положение, позволяющее
г.
диск, который нужно вставить на место через большую выемку.
Для центрирования диска в пазу шпиндель
был отрегулирован вдоль станины типа «ласточкин хвост».
Кронштейн модуля был тогда
установлен в правильное положение.
Отверстия под болты кронштейна (посередине) позволили окончательно
совмещение вала шагового двигателя с ходовым винтом.
Модуль датчика E-O подключен к
показатель
Импульсная плата и
соединены с коммутационной платой системы.
Концевые выключатели
Концевой выключатель оси X
механизм. Латунный стержень 1/4 дюйма образует кулачок
против микровыключателя, удерживаемого внутри
скобка.
Стержень скользит в отверстии с прецизионным рассверливанием; очень плотно прилегает.
Привод с круглым кулачком сделать проще, так как
не имеет точной ориентации с
уважение к переключателю.
Корпус концевого выключателя также действует
как массивное усиление
скобка.
Деталь кулачка латунной тяги.
Обратите внимание, что два кулачка находятся на
спереди и сзади.
Кулачок вставляется в Т-образный паз с правой стороны поперечного суппорта
.
Штифт удерживает шток на поперечном суппорте.
Есть немного
играть, чтобы предотвратить связывание.
Практически никакая стружка не может попасть в механизм переключателя
при нормальной работе, так как стержень удерживает
отверстие заблокировано
, если кулачок полностью не погружен под
, только самое большое внутрь (-X)
экскурсия в вагоне
, которая может произойти в особых условиях эксплуатации
, например, при использовании заднего
отрезной резцедержатель.
В нижней части кронштейна фрезерован карман.
г.
Микровыключатель удерживается на дополнительной плите. Два пластиковых монтажных отверстия переключателя
были нарезаны на 3-48, как и пластина.
Верхняя часть переключателя крепится к нижней части фрезерованного кармана.
Только выступ на рычаге переключателя выступает через
удлиненный,
Отверстие 1/4 дюйма
перпендикулярно направляющей кулачка.
Для размыкания нормально замкнутого переключателя необходим ход 0,050 дюйма.
с тефлоновым покрытием
провод используется для соединений.
Сторона кармана была освобождена, чтобы освободить
места для переключателя толщиной 0,0625 дюйма
тарелка.
Концевые выключатели оси Z устанавливаются снизу.
мотор
кронштейн для защиты от стружки.
Край двухпроводной розетки Molex сидит
в маленьком кармане и есть
захватывается зажимом.
Этот разъем позволяет использовать шаговый двигатель и ограничить
цепей, которые необходимо отделить от
скобка.
Гнездо Molex зафиксировано зажимом.
Три NC-переключателя последовательно подключены к
розетка Molex с использованием провода с тефлоновой изоляцией.
Уменьшил зажим розетки и сдвинул предел
переключатели
далее под кронштейном для большей защиты.
Регулируемые латунные упоры концевых выключателей оси Z.
Латунные упоры зажимаются на L-образном кронштейне.
Винт с накатанной головкой 6-32 фиксирует упор в любой точке
рельса. Слот — это
плотно прилегает к рейке.
Все кромки ограничителей имеют закругленные углы.
Прецизионные стальные весы были
крепится тонким двусторонним скотчем
. Сначала обезжирить все контактные поверхности
изопропиловым спиртом (C 3 H 8 O).
Кабель концевого выключателя подключен к схема коммутационной платы.
Концевые выключатели и кабели шагового двигателя
в оболочке и затем фрезерованный под скамейкой.
E-stop
Выключатель аварийного останова токарного станка подключается последовательно с
два
выключатели аварийной остановки мельницы.
Три
концевые выключатели токарного станка
соединены последовательно с
предел в пять мельниц
переключатели.
Все 12 переключателей
для токарных и фрезерных станков (включая
кулон) должен
быть
NC для работы любого станка.Длина скамьи
теперь составляет 5 упоров.
(включая клавиатуру ESC).
Нажмите на
связанные эскизы #ad
Нажмите на связанные эскизы #ad
QCTP
Размещение стойки инструмента быстрой смены (QCTP) на
Крестовая горка Taig
должен быть повторяемым, таким образом, находя
Установлено
дюбелей для выравнивания основания.Показано, что пилотное отверстие
пробурено на 7/64 дюйма перед расширением на 1/8 дюйма.
Перед сверлением Т-образная гайка и основание QCTP были выровнены с помощью
размещение на Поверхностная пластина и использование
поверхностный датчик.
Дюбели 1/8 дюйма выравнивают основание QCTP и сталь.
Гайка с Т-образным пазом в глухие отверстия в
поперечный слайд.
Обратите внимание на установочные отверстия в основании QCTP.
Их можно легко
удаляется, если необходимо повернуть QCTP.
Все детали собраны и зафиксированы на поперечных суппортах.
Токарный станок с ЧПУ Taig выполняет пробный чистовой пропил.
Mach4 Mill также содержит Mach4 Turn для управления вашим ЧПУ токарный ход.
График 1 на поверхности футов в минуту (SFM) SFM 2 SFM 3 Калькулятор машиниста
Токарный станок с полусферической резкой с внешним диаметром 0,3 дюйма.
Штанга удерживается с помощью
Цанговый адаптер Taig ER-16.
ЧПУ
Резьба фильм
Два фильма, показывающие ЧПУ Taig
на токарном станке
нарезание алюминиевого болта 3 / 8-16.
В Mach4 шпиндель должен быть включен
(желтый
светодиод
горит)
чтобы программа считывала поворот шпинделя на
оборотов. Также рекомендуется усреднение скорости шпинделя.
Посмотреть
Руководство по настройке нарезания резьбы Mach4.
Нажмите на связанные эскизы #ad
3 / 8-16 ниток в нейлоне.
Машинный рабочий свет
Модернизированный рабочий фонарь для рабочего / машинного оборудования (США)
для ЧПУ
установка микротокарного станка.
Используется галогенная лампа
или лампа накаливания мощностью до 100 Вт (максимум). Магнитная база.
Плафон двустенный с
Радиатор из ребристого алюминия
сохраняет тепло на ощупь и продлевает срок службы переключателя.
Лампа
прочный, отличный
голова может быть направлена
более эффективно
чем предыдущий свет.
Заменил магнитный
база с 1 / 4-20
с резьбой,
1/4 »
толстая алюминиевая опорная плита для высокой жесткости.
Нажмите на связанные эскизы #ad
Микротокарный станок с ЧПУ, Ходовой винт оси X, Ходовой винт оси Z,
Шаговые двигатели,
Шкивы двигателя шпинделя, Тахометр,
Индекс шпинделя, Концевые выключатели, E-stop,
QCTP,
Фильм о резьбонарезании с ЧПУ,
Машинный рабочий свет
ДОМ
Хотя длинный стержень с резьбой вдоль станины первоначально назывался ведущим винтом , ведущим винтом или , в настоящее время его обычно называют ходовым винтом .Любой ходовой винт должен изготавливаться очень точно (они часто производятся специализированными производителями, а не самими производителями станков) с прямой, квадратной или другой формой резьбы, оптимизированной для этой задачи, но никогда не со стандартной формой Витворта или метрической формы, как К сожалению, встречается на многих более дешевых станках с Дальнего Востока. Ходовой винт будет воспроизводить свой точный шаг (отсюда и необходимость в точности) на материале, на который будет нарезана резьба — при условии, что он может каким-либо образом приводиться в движение непосредственно от шпинделя передней бабки — обычно с помощью обычных прямозубых шестерен, но иногда с помощью конических шестерен, планетарных передач. или даже, в некоторых случаях, с использованием зубчатых ремней.Конечно, с появлением компьютерного управления относительными движениями шпинделя и каретки легко управлять с помощью электроники — следовательно, теперь можно создавать резьбу без необходимости какого-либо механического соединения между шпинделем и кареткой). Формовка резьбы вручную : |
токарно-винторезный станок — Перевод на французский — примеры английский
Эти примеры могут содержать грубые слова, основанные на вашем поиске.
Эти примеры могут содержать разговорные слова, основанные на вашем поиске.
Продажа б / у, Берлин Германия, Стол / полка для кухонного оборудования, Бак, Нарезной станок / резьбонарезной станок / Токарно-винторезный станок , Общее оборудование
Vente Occasion, Berlin Allemagne, Стол / одежда для кухни, Стол; Plan de Travail, Гастрономия и Agroalimentaires
Produktionsmaterial 10 машин для литья под давлением от 60 до 80 тонн, 4 станка для лазерной резки и гравировки (CO2 и Yag), токарно-винторезный станок , 10 станков для токарной обработки пуговиц (все материалы), с филиалом в Тунисе (токарные станки и лазер)
Изготовление материалов 10 прессов для инъекций от 60 до 80 тонн, 4 машины для декомпрессии и гравирования лазера (CO2 и Yag), тур по декольте , 10 туров в бутон (toutes matières), avec filiale tunisienne (туры и лазер)Предложите пример
Другие результаты
Оригинальный токарно-винторезный станок Модслея находится в Музее науки в Лондоне.
Le prototype du tour à usiner de Maudslay est aujourd’hui Exposé au Science Museum de Londres.Бетононасосные станции Стационарные, Станок токарно-винторезный , Ленточнопильный стан.
В 2004 году два оператора токарно-винторезных станков в Верхней Савойе, Франция, Фредерик АНТУАН и Паскаль ЖАККАРД решили открыть производство в Румынии, чтобы дать им возможность проводить свою политику снижения цен.
В 2004 году, два декольте франсэ де Верхняя Савойя: Фредерик АНТУАН и Паскаль ЖАККАР приняли участие в производстве в Румынии для того, чтобы ответить на политическую позицию базового уровня.Затем он переехал в Лондон, где нашел работу на Генри Модсли, изобретателя токарно-винторезного станка , вместе с такими людьми, как Джеймс Нэсмит (изобретатель парового молота) и Ричард Робертс.
Puis il partit pour londres, et travailla aussi bien for Henry Maudslay, l’inventeur du tour à tarauder , que pour James Nasmyth (l’inventeur du marteau-pilon) и Ричард Робертс.Прецизионные токарно-винторезные и прутковые токарные . Отточенная техника, полная комплектация …
Примером стандартизации был шаг резьбы в 1841 году, названный в честь изобретателя винторезного станка и токарного станка с подающим валом , сэра Джозефа Уитворта (1803 — 1887).
Единственным примером стандартизации является исключение файлов, датированных 1841 годом, и портом, именуемым конструктором туров , колесницей и файловой службой сэра Джозефа Витворта (1803–1887).ТОКАРНО-ВИНТОВО-РЕЗАЛЬНЫЙ СТАНОК С ПОДАЧЕЙ ПРУТКА
2 Станки токарные и резьбонарезные
Это полезно для нарезания винтов .
СПОСОБ И УСТРОЙСТВО ДЛЯ ПОДАЧИ БРУСОВ НА РЕЖУЩИЙ СТАНОК
Зеркала (54, 56, 60, 62) имеют единые отражающие и поддерживающие структуры, образованные либо алмазным токарным станком , либо прецизионным формованием пластмассы.
Les miroirs (54, 56, 60, 62) представляют собой единый объект отражения и структуры, формирующие форму в доме , на улице , в купе по адресу , в том, что касается деталей из пластика.Описание: Токарные станки с ЧПУ для резки металла , высокоточные и производительные, инструменты, используемые в станке токарный станок
Описание: CNC Metal Cutting Tills , Haute précision et productif, Outils utilisés dans la machine de tourОсновные виды деятельности Восстановление и шлифование конусов шпинделя.Реконструкция станков и резьбонарезных станков токарно-фрезерных .
Принципиальные действия по пересмотру и исправлению де cône de broche. Реконструкция МО и туры с декольте .Инструмент для отрезания стружки для нарезания резьбы и внутренней винтовой нарезки методом
Международная Саморезно-винторезная Станкостроительная выставка каждые 2 года 08.03 — 11.03 2016
Международный салон машины декольте ts les deux ans 08.03 — 11.032016Основные виды деятельности Industriel , нарезание винтов из металлических материалов.
Принципы деятельности Декольте Industriel de matériaux métallique.Основные виды деятельности Нарезание винтов на большие партии деталей, отвечающих требованиям безопасности или нормативным требованиям.
Принципы деятельности Декольте de pièces de grandes séries ayant des exigences sécurité ou réglementaires.У нас также есть цех вторичной обработки, который комплектует винторезный .
Nous Disposons également d’un atelier de reprise, qui vient Compléter l ‘ usinage .Адаптация подающих винтов к токарному станку по дереву — Дискуссионные форумы
Обратите внимание, что это заархивированная тема , поэтому она заблокирована, и на нее невозможно ответить. Однако вы можете начать новую тему и обратиться к ней со ссылкой: http://www.banjohangout.org/archive/189050
Quickstep192 — Добавлено — 15.10.2010: 07:39:24
Кто-нибудь когда-нибудь приспосабливал / изобретал поперечные суппорты с подающими винтами к токарному станку по дереву, чтобы имитировать присущую им возможность управления подачей фрезы токарный станок по металлу?
У меня хороший токарный станок по дереву, и 90% того, что я делаю, — это точение дерева, но я хотел бы иметь возможность время от времени поворачивать металлическую деталь или просто лучше контролировать подачу при токарной обработке дерева.Здесь довольно изобретательная группа, поэтому я подумал, что проверю.
dickinnorwich — Опубликовано — 15.10.2010: 07:48:03
Хороший вопрос.
Я экспериментировал с той же идеей, используя тиски для дрели двойного действия, прикрепленные к станине. Но правда в том, что до тех пор, пока моя зрительно-моторная координация остается в порядке, есть что-то действительно приятное в том, чтобы делать это вручную. Я не хочу терять процесс, который мне чертовски нравится.
mhickler — Добавлено — 15.10.2010: 14:11:44
Quickstep, на моем сайте шесть примеров этой идеи: hicklerbanjo.ru / lathe_diy.html. Подходы включают преобразование Shop Smith, преобразование стандартного токарного станка по дереву и создание токарного станка с нуля. Мне также удалось сделать версию с ЧПУ.
mike gregory — Опубликовано — 15.10.2010: 20:35:30
цитата:id = «quote»>
Первоначально опубликовано mhicklerQuickstep, на моем сайте есть шесть примеров этой идеи: hicklerbanjo.com/lathe_diy .html. Подходы включают преобразование Shop Smith, преобразование стандартного токарного станка по дереву и создание токарного станка с нуля.Мне также удалось сделать версию с ЧПУ.
Боже, когда я увидел «Shopsmith», я щелкнул ссылку и получил
404 — Файл или каталог не найдены.
Ресурс, который вы ищете, возможно, был удален, изменилось его имя или временно недоступен.
Will1717 — Опубликовано — 15.10.2010: 21:47:06
Quickstep192:
Обязательно загляните на сайт Марка Хиклерса. Он тот парень, который испробовал почти все комбинации того, что вы хотите делать.Я уверен, что Марк согласится с одной вещью, что для устойчивости вам понадобится достаточно хорошее поперечное скольжение. То, что вы хотите сделать, вполне выполнимо + отличный способ.
Билл Рикард
5strings3picks1banjo — Опубликовано — 15.10.2010: 21:56:42
В итоге я купил старый токарный станок по металлу. Для меня много преимуществ. Я могу повернуть почти на 16 дюймов после того, как вырезал кровать под патроном.
Я заплатил 1200 долларов. У меня есть автоподача и нарезка нити, вперед и назад.Я люблю это.
Я согласен с Уиллом, Марк Хиклер знает свое дело, и, если бы я был в Штатах, думаю, я бы скопировал его идеи.
Свяжитесь с ним, и я уверен, что он поведет вас в правильном направлении.
Майк Грегори — Опубликовано — 16.10.2010: 04:00:15
Цитата:id = «quote»>
Первоначально отправлено 5strings3picks1banjoПривет Марк, ваша ссылка не работает.
Это та ссылка, которую вы хотели? Hicklerbanjo.com/lathe_diy.htmlВот идея, которая у меня возникла давным-давно.Я не знаю, какой у вас токарный станок, но чтобы адаптировать его к моей модели, требуется приварить станину к боковой стороне оригинальной станины для установки этого типа устройства.
wttool.com/product-exec/produc…Vises_WT_
ЭТА ссылка работает.
Если Джефф Крамер — это тот же Джефф Крамер, которого я встречал, то он не так уж далеко, прямо здесь, в Висконсине.
mhickler — Добавлено — 16.10.2010: 05:54:53
Есть. Это случилось снова. Я предполагаю, что форум сбрасывает www .Просто добавьте www . себя, и вы доберетесь туда.
Frisco Fred — Опубликовано — 16.10.2010: 07:21:38
цитата:id = «quote»>
Первоначально отправлено 5strings3picks1banjoПривет, Отметьте, что ваша ссылка не работает.
Это та ссылка, которую вы хотели? Hicklerbanjo.com/lathe_diy.htmlВот идея, которая у меня возникла давным-давно. Я не знаю, какой у вас токарный станок, но чтобы адаптировать его к моей модели, требуется приварить станину к боковой стороне оригинальной станины для установки этого типа устройства.
wttool.com/product-exec/produc…Vises_WT_
Чтобы не лопнуть чей-то пузырь … но эти дешевые двухосные штучки — ВЕДРО. Упоры, винты Acme и все остальное сделано из грязного грубого железа. Что делает инструмент точным, так это закаленные, отшлифованные движущиеся части с малым допуском … Простой и понятный
Найдите хороший бывший в употреблении американский, европейский или японский и прикрепите его жесткий и надежно к станине токарного станка. Может быть, соединение от демонтированного старого токарного станка по металлу.
Dogfeathers — Опубликовано — 16.10.2010: 08:09:16
Quickstep сказал:
«У меня хороший токарный станок по дереву, и 90% того, что я делаю, это токарная обработка дерева, но я бы хотел иметь возможность чтобы иногда _поворачивать металлическую деталь_ или просто лучше контролировать подачу при токарной обработке дерева ».
**********************
Ненавижу дождь на этом красивом параде, но я хочу предостеречь Quickstep (и других) от попыток превратить токарный станок по дереву в токарный станок по металлу. Опасность для вашего черепа, головы, рук, пальцев, глаз и окружающих.Есть много причин, по которым токарный станок по дереву, который может повернуть обод диаметром 12 дюймов, весит несколько сотен фунтов, а токарный станок по металлу, который может повернуть 12 дюймов, весит несколько тонн. Жесткость — это главный фактор, который позволит безопасно отделить куски металла от заготовки без изгиба всей рамы, захвата инструмента / заготовки и размахивания ею по комнате с огромной силой … достаточно легко, чтобы убить вас или вас. Меньше всего сломай себе беспокойную и ковыряющую руку. Отслаивание красивой волокнистой древесины — это одно дело, использование той же машины для обработки металла — это совершенно другой мир, и я предлагаю не рисковать своей шеей, пытаясь сэкономить несколько долларов.Если вы действительно хотите заниматься этим видом работы, потратите деньги и найдите старый токарный станок по металлу и не бездельничайте. Экономия в баке, бывшая в употреблении техника сейчас дешевая, (хотя их перемещение по-прежнему затруднительно). Я проработал в сфере металлообработки около 35 лет и был инспектором по технике безопасности в моей последней компании, и обычно я был вторым человеком. на месте оказания первой помощи до приезда скорой помощи.
Мораль истории …… сэкономленный пенни … потерянный палец! … и это наверняка ограничит ваш стиль выбора.
Собачьи перья … тревожный старик … у которого все еще остались пальцы.
SF Bay Area
Отредактировал — Dogfeathers 17.10.2010 07:31:12
mhickler — Добавлено — 16.10.2010: 11:09:28
Первоначально предлагалось не превратить токарный станок по дереву в токарный станок по металлу, а иметь средство, с помощью которого можно было бы механически перемещать фрезу. поперечного слайда. Даже с моими крестовыми суппортами Enco Asian (правда, отсутствующими) я могу рассчитывать на точность плюс-минус 5 тысячных дюйма.Здесь я говорю о диаметре, что означает, что я могу точно переместить мои фрезы на половину этого диаметра. Если бы я мог позволить себе более качественные поперечные слайды, я бы купил их в первую очередь.
У меня нет проблем с установкой тонера или фланца настолько туго или свободно, как того требует заказчик.
Плюс-минус 5 тысячных — это смешно в мире металлообработки, но мы говорим здесь о банджо, а не о реактивных двигателях.
Более того, Дэн Пеннингтон, Дэйв Хольцер и Джефф Крамер успешно использовали одни и те же поперечные слайды.В дополнение к этим производителям есть еще двое, которым я продал свои прототипы токарных станков один и два.
Quickstep192 — Опубликовано — 16.10.2010: 15:31:29
Mark,
Где вы взяли эти симпатичные крестообразные слайды с «ласточкиными хвостами»?
mhickler — Добавлено — 16.10.2010: 18:20:37
Приобрел их от Enco (use-enco.com). Enco — отличный источник всех видов приспособлений для металлообработки. Это ссылка на кросс-слайд Фазы II.use-enco.com/CGI/INSRIT?PMAKA=201-2826 . Текущая «веб-цена» составляет около 90 долларов. Стандартная цена смехотворна, и они все время рассылают листовки с более низкой ценой. На своем первом токарном станке я использовал один из них: use-enco.com/CGI/INSRIT?PMAKA=201-2536 . Во всех смыслах лучше, но дороже.
Как обычно, форум удаляет все префиксы «www», поэтому эти ссылки не будут работать, пока вы их не введете.
ronwalker49 — Опубликовано — 16.10.2010: 18:42:06
Я занимаюсь этим сейчас и опубликую несколько фотографий, когда закончу….
banjeaux bob — Опубликовано — 16.10.2010: 22:16:31
Помимо экономии, я считаю, что Оливер сделал токарный станок с такими встроенными функциями. цветные металлы без проблем с безопасностью.
BanjeauX Bob
uncle.fogey — Добавлено — 17.10.2010: 14:14:55
Если бы мне действительно нужна была поперечная подача, я бы просто купил большой токарный станок и покончил с этим. Если бы я точил металлические детали, я бы ОБЯЗАТЕЛЬНО купил токарный станок.
В течение многих лет я использовал большой токарный станок по дереву Powermatic с дублирующим устройством, которое состояло из стержня, на котором можно зажимать шаблон, и фрезы, установленной на каретке, которая двигалась вдоль шаблона. Вы могли использовать его для параллельных резов — для деревянных ободов банджо этого было более чем достаточно. Теперь у меня есть большой токарный станок по дереву на 800 фунтов, и я делаю каждый обод банджо с лицевой панелью.
Я бы сказал, просто используйте лицевые панели и делайте приспособления — это работает для меня — каковы ваши требования к допуску или ожидания от дерева?
Лучшим станком для токарного станка с банджо для работы с кондуктором может стать токарный станок с планшайбами со станиной 14 дюймов, длиной 3 дюйма и поперечной подачей.
Quickstep192 — Добавлено — 20.10.2010: 04:55:36
Я имею в виду две вещи.
Я хочу убрать немного со своего прядильного кольца. Хотя я понимаю, что лучше всего это сделать на токарном станке по металлу, мне сложно сделать такие инвестиции для разовой сделки.
Еще я хотел бы уметь точно поворачивать диски; точнее, выступы. Я не собираюсь обращаться с допусками, которые можно было бы ожидать от металла; Я просто хотел бы иметь возможность «подкрасться» к разрезу лучше, чем я могу сделать это вручную.
Преобразование ручного токарного станка в токарный станок с ЧПУ
При рассмотрении вопроса о преобразовании ручного токарного станка в токарный станок с ЧПУ вам необходимо принять во внимание типичное использование токарного станка и определить, улучшит ли переход на токарный станок с ЧПУ ваш процесс. Преобразование токарных станков с ЧПУ (с числовым программным управлением) выгодно при переходе на какой-либо тип производства и если вы действительно знаете, что делаете. Однако, если вы просто мастерите или занимаетесь своим хобби, преобразование может оказаться невыгодным.Токарные станки с ЧПУ хорошо справляются с обработкой дерева и металла, но могут также сверлить отверстия, нарезать резьбу, выполнять сложные и точные пропилы и выполнять множество других различных работ.
Перед преобразованием
Компьютеры управляют токарными станками с ЧПУ, и их популярность растет из-за простоты настройки проектов и упрощенного управления ими. Оператору ЧПУ необходимо точно знать, что он делает, и обладать высокой квалификацией в токарном процессе. Большинство преобразований токарного станка допускают как ручное управление, так и функции ЧПУ на токарном станке, поэтому пользователь может выбрать, какой атрибут использовать в любой момент времени.В результате большинства преобразований будет получен мини- или небольшой токарный станок с ЧПУ, который можно использовать дома или в мастерской, но при этом он будет производить более высокую производительность, чем ручные токарные станки.
Преобразование токарного станка
Большинство преобразований выиграют от перехода на ШВП, но это остается на ваше усмотрение в зависимости от того, сколько времени и денег вы готовы потратить. Вам также понадобится двигатель для автоматического привода машины. При преобразовании в ЧПУ есть 2 основных типа двигателей на выбор; Сервоприводы и степперы.Сервомоторы позволяют создавать проекты с высоким ускорением и регулируемой скоростью и являются предпочтительным вариантом. Однако для новичков рекомендуется использовать шаговый двигатель, потому что степперы могут подключать двигатель к токарному станку с помощью алюминиевой муфты. На противоположных концах муфты имеются отверстия, обрезанные по размеру вала, которые удерживаются вместе с помощью установочных винтов. Степперы намного дешевле и не требуют особых знаний.
Компьютерный аспект
Следующие несколько шагов больше связаны с компьютером, и именно здесь необходимость компьютерных знаний вступит в игру в проекте.Теперь вам нужно получить драйверы и блок питания для драйверов. После подключения блока питания вам необходимо подключить драйверы с питанием к параллельному порту вашего компьютера. Когда ваш компьютер будет готов к обмену данными с токарным станком, вам потребуется установить интерпретатор G-кода.
На этом этапе вы готовы к работе. Однако по мере того, как вы станете более продвинутыми, рекомендуется приобрести программное обеспечение CAD / CAM. Это программное обеспечение позволит вам получить более динамичный доступ к проектам.
Прочтите онлайн-версию «Зубчатые передачи токарных станков для нарезания шурупов», Брайан Вуд
Указатель
ВведениеЭта книга не является руководством по изготовлению вещей и не является руководством по тому, «как делать», например, сама операция нарезания шурупов; по этим темам уже есть много информации. Это в основном справочная информация, предназначенная специально для инженеров для использования в их мастерских. Он призван избавить их от хлопот и времени, затрачиваемых на разработку промежуточных передаточных чисел, необходимых для нарезания резьбы винта — передаточных чисел, которые не соответствуют языку резьбонарезания, для которого была построена их машина, или которые становятся необходимыми из-за необычного шага .
Включение редуктора для нарезания резьбы на токарном станке дает удобный и компактный способ быстрого выбора из ряда различных вариантов зубчатой передачи в коробке передач для получения альтернативных шагов винта без необходимости вносить какие-либо изменения в сменные колеса вне коробки передач. . В токарных станках, оборудованных отдельным подающим валом для наплавки и поперечной резки, изменения в редукторе также влияют на них, поскольку они обычно связаны между собой зубчатой передачей. Однако эта книга ориентирована исключительно на шаг резьбы винта, поскольку другие подачи обычно определяются на самом станке с помощью некоторого простого фиксированного отношения к шагу резьбы винта.
Любой шаг, который выходит за пределы выбора, доступного для самого редуктора, требует изменения внешнего зубчатого колеса вниз от шпинделя токарного станка, как это было бы в случае на токарном станке без редуктора. Производители обычно прикрепляют пластины к крышке сменного колеса для английских или метрических преобразований (в зависимости от машины), хотя другие преобразования, например, для шагов BA, могут быть указаны только в справочнике.
В этой книге показаны подробные таблицы наладки зубчатых зацеплений для токарных станков, которые чаще всего используются в модельных мастерских и других мастерских легкой техники, за одним заметным исключением.Охватывается широкий диапазон шагов, и впервые многие из них представлены путем включения шагов вне более обычных преобразований, таких как метрическая система из британской. Некоторые малоизвестные темы включены для тех, кто занимается реставрационными проектами.
В случае токарного станка Myford, оснащенного редуктором компании, описан радикально другой подход к преобразованию зубчатой передачи, который сохраняет очень ценную настройку точной подачи для всех шагов. Когда преобразование выполняется в соответствии с опубликованными изготовителями способами, настройка точной подачи больше недоступна, что является неудобным последствием преобразования токарного станка для резки с шагом не в британской системе.Чтобы исправить это, необходимо внести некоторые незначительные и незаметные изменения в оборудование токарных станков Myford. Они просты и полностью описаны с необходимыми рисунками; все они доступны любому инженеру-практику. Я не извиняюсь за то, что проявляю предвзятое отношение к токарным станкам Myford, являющимся владельцем более пятидесяти лет, но справедливое отношение к другим, часто лучше построенным и более мощным станкам представлено таким же несложным образом.
Вся цель этой книги состояла в том, чтобы как можно больше избежать математики и мистики вычисления передаточных чисел — что для некоторых может быть ужасной задачей — чтобы сделать работу с токарным станком более приятной. насколько возможно.
Одно из наиболее универсальных применений токарного станка в качестве станка — нарезание резьбы винта с широким изменением шага, не ограниченного диаметром обрабатываемой детали. Эта свобода просто невозможна с резьбонарезными штампами фиксированного размера, а поскольку сам токарный станок обычно используется для определения размеров заготовки в первую очередь, любая такая нарезка резьбы в качестве дальнейшей операции также будет гарантированно коаксиальной с заготовкой.
Зубчатые колеса (более правильные в данном контексте называемые сменными колесами, как теперь они будут называться) могут быть расположены по желанию для изменения передаточного числа между шпинделем токарного станка и, в конечном итоге, ходовым винтом каретки, чтобы изменять шаг полученная винтовая резьба, которую можно производить.
Рис. 0.1 Типичный токарный станок со станиной с зазором, показывающий соответствующие детали (рисунок Гэри Вудинга).
Рис. 0.1 представляет собой упрощенный чертеж типичного токарно-винторезного станка, на котором обозначены эти основные особенности. Поскольку задняя бабка не участвует в расчетах нарезания резьбы, чертеж не включает заднюю бабку. Показано положение винторезного редуктора; это последний элемент в цепи зубчатой передачи между шпинделем в передней бабке и ходовым винтом, который перемещает каретку инструмента, по той очень веской причине, что оператор токарного станка легко может использовать его по мере необходимости.
РАЗРАБОТКА ВИНТОВОРЕЗНЫХ СТАНКОВСо страниц Википедии мы узнаем, что Леонардо да Винчи рисовал эскизы токарно-винторезных станков; один из них был оснащен двумя ходовыми винтами и сменными колесами для изменения шага.
В конце восемнадцатого века Джесси Рамсден построил первый узнаваемый современный токарно-винторезный станок; он был оборудован ходовым винтом, суппортом для инструментов и механизмом смены колеса. Генри Модслей приписывают эту успешную конструкцию в мире в 1800 году в качестве станка, который можно было надежно и механически направлять для резки металлических винтов с шагом винта.С тех пор стало возможным крупномасштабное промышленное производство резьбовых деталей.
В 1841 году именно Джозеф Уитворт принес очень необходимый заказ, а также систему для классификации и консолидации множества резьбовых соединений, которые к тому времени производились несколькими компаниями. До Уитворта не было надежды сходить в строительный магазин за винтом или гайкой на замену; у всех этих компаний были свои неизменные стандарты. В этой книге вы найдете таблицы питча для потоков, происхождение которых восходит к тем ранним временам.Некоторые из них использовались на фабрике стрелкового оружия в Энфилде, Англия, а другие с конца восемнадцатого века лондонскими мастерами Holtzapffell при производстве токарных станков для декоративных работ.
Промышленные требованияМетоды сменных колес позволяют получить очень широкий диапазон шагов при поставке сменных колес. Однако использование методов сменного колеса для изменения шага токарно-нарезных винтов не очень хорошо подходит для требований промышленного производства, поскольку работает слишком медленно.
Первоначально, конечно, не было альтернативы изменению колесных формул вручную, после чего необходимо было произвести правильное зацепление выбранных колес. Чтобы справиться с медленными темпами производства, вызванными этими ограничениями, вполне вероятно, что разные токарные станки были настроены для выполнения разных задач нарезания резьбы вместе с оператором на каждом станке, чтобы получить некоторую скорость производства. Промышленное давление в то время постоянно росло, чтобы ускорить весь процесс, и в конечном итоге родился редуктор для селективного нарезания винтов.
Сегодня такая операция будет выполняться автоматом с кулачковым приводом, выпускающим десятки тысяч отдельных шурупов за раз. Даже подача прутка из бункера для хранения в машину автоматическая, поэтому она будет работать днем и ночью.
Исторические патентыВ ходе исследования разработки, приведшей к созданию успешного винторезного редуктора, я обратил внимание на небольшую книгу Оскара Э. Перриго, которая была опубликована в Нью-Йорке в 1903 году. ¹ В своей книге Перриго обратил внимание инженера на список патентов, относящихся к редуктору для нарезания резьбы; в то время в патентном ведомстве США находилось 164 штуки, которые были выпущены за период чуть менее полувека с 1854 по 1903 год. работать над списком из двадцати девяти патентов. Он считал, что они содержат зародыш идей и изобретательности, многие из которых были приняты другими, и поэтому они оказали наибольшее влияние на результат.Делая свой выбор, он отказался от «также-ран» с точки зрения практичности или долговечности. Он считал, что многие из них, должно быть, облагали патентное ведомство налогом при установлении достоинств новой заявки на патент по сравнению с чем-то очень похожим. Здесь мы должны помнить, что прочитать и понять патентную заявку непросто, а начинать с новой темы становится вдвойне сложно.
Чтобы подытожить его работу как можно более кратко, концепция конуса шестерен, из которого можно выбирать людей для зацепления ходового винта, возникла у Джона Хамфриса из Чикопи, штат Массачусетс, когда она появилась в патенте 83,774, выданном 3 ноября 1868 года.
Затем последовало множество вариаций на эту тему с некоторыми чрезвычайно опасными изобретениями, все с открытыми механизмами и множеством различных форм. Сам по себе беспорядок из-за того, что масло стекает с этих устройств, и шум, производимый ими в процессе использования, сделали бы их машинами крайне неприятными в использовании. Некоторые из них также были чрезвычайно сложными с множеством конусов зубчатых колес, которые необходимо было правильно соединить — задача, безусловно, выше обычного токаря, который, как ожидалось, осознал всю сложность и использовал ее для получения результатов.
Первый редуктор: NortonИз всего этого появилось первое устройство, содержащее весь необходимый механизм, надлежащим образом уплотненный, чтобы поместиться в отдельную коробку, которая может быть установлена в приводе на ходовой винт токарного станка. Он содержал двенадцатиступенчатый конус шестерен, напрямую соединенных с ходовым винтом, и простые надежные средства доступа к отдельным шестерням в конусе.
Рис. 0.2 Выписка из патента, выданного Вендаллу П. Нортону (с любезного разрешения Управления по патентам и товарным знакам США).
Этот дизайн стал явным лидером, и патент США 470 591 был выдан 8 марта 1892 года Вендаллу П. Нортону, затем из Маунт-Вернон, Нью-Йорк, а затем в Торрингтоне, Коннектикут, когда он добавил реверсивный уточнение в следующем патенте. Его имя теперь прочно ассоциируется во всем мире с резьбонарезными редукторами. Рис. 0.2 — это копия чертежа из этого патента, представленная оператору токарного станка. Передняя бабка токарного станка находится вверху рисунка.
Дизайн Norton с тех пор полностью взял на себя в этом отношении, и промышленные токарные станки оснащались редукторами, которые в целом соответствовали ему уже более века. Нортону явно повезло: он нашел покровителя в компании Hendey Company в Торрингтоне, штат Коннектикут, в самый подходящий момент для промышленного применения своего дизайна.
Хенди установил коробку передач своей конструкции на свой токарный станок в том же году, когда был выдан патент. Эта комбинация продвинула Norton на передний план, и другие компании, производящие станки, серьезно обратили на это внимание.Одна только развивающаяся автомобильная промышленность США имела огромный аппетит на станки всех видов, и Hendey была лишь одной из многих компаний, которые поставляли эту продукцию. Менее чем за тридцать лет компания Hendey выпускала токарные станки, оборудованные редуктором для нарезания резьбы Norton, на полномасштабной производственной линии.
Итак, по крайней мере, с коммерческой точки зрения, приз достается Венделлу П. Нортону за производство коробки передач компактной формы, основанной на первоначальной идее Джона Хамфри о конусе шестерен, общая конструкция которой используется до сих пор.
На некоторых современных токарных станках для инструментальных цехов эти редукторы могут стать довольно сложными с выбором рычага или, самое большее, одной легко реверсивной кластерной шестерни для обеспечения доступа к другим шагам. После этого через коробку передач может быть обеспечен быстрый выбор из другого диапазона других шагов.
Рис. 0.3 Изображение современного винторезного редуктора, установленного на немецком станке для инструментального цеха (с любезного разрешения www.lathes.co.uk).
Пример от немецкого производителя показан на Рис.0.3, что свидетельствует об уровне сложности, который может быть встроен в сложную коробку передач для нарезания резьбы. Основной зубчатый конус хорошо виден в правой половине, в данном случае это двенадцатиступенчатая версия. Однако способ смешивания передаточных чисел в левой части корпуса коробки передач был бы откровенно сбит с толку без соответствующих указаний в виде таблицы, в которой перечислены все возможные варианты. Вполне вероятно, что в нем есть передача для других языков, к которой можно просто получить доступ по положению рычага.
Для того, что можно было бы назвать любительским рынком в Великобритании, стоимость и размер даже простых редукторов не позволяли включать их в токарные станки меньшего размера, производимые для этого рынка.