Механические свойства металлов | Металлы и сплавы
Основные механические свойства
К основным механическим свойствам относят прочность, пластичность, твердость, ударную вязкость и упругость. Большинство показателей механических свойств определяют экспериментально растяжением стандартных образцов на испытательных машинах.
Прочность — способность металла сопротивляться разрушению при действии на него внешних сил.
Пластичность — способность металла необратимо изменять свою форму и размеры под действием внешних и внутренних сил без разрушения.
Твердость — способность металла сопротивляться внедрению в него более твердого тела. Твердость определяют с помощью твердомеров внедрением стального закаленного шарика в металл (на приборе Бринелля) или внедрением алмазной пирамиды в хорошо подготовленную поверхность образца (на приборе Роквелла). Чем меньше размер отпечатка, тем больше твердость испытуемого металла. Например, углеродистая сталь до закалки имеет твердость 100 . . . 150 НВ (по Бринеллю) , а после закалки — 500 . . . 600 НВ.
Ударная вязкость — способность металла сопротивляться действию ударных нагрузок. Эта величина, обозначаемая КС (Дж/см2 или кгс • м/см ), определяется отношением механической работы А, затраченной на разрушение образца при ударном изгибе, к площади поперечного сечения образца.
Упругость — способность металла восстанавливать форму и объем после прекращения действий внешних сил. Эта величина характеризуется модулем упругости Е (МПа или кгс/мм2), который равен отношению напряжения а к вызванной им упругой деформации. Высокой упругостью должны обладать стали и сплавы для изготовления рессор и пружин.
Механические свойства металлов
Под механическими свойствами понимают характеристики, определяющие поведение металла (или другого материала) под действием приложенных внешних механических сил. К механическим свойствам обычно относят сопротивление металла (сплава) деформации (прочность) и сопротивление разрушению (пластичность, вязкость, а также способность металла не разрушаться при наличии трещин).
В результате механических испытаний получают числовые значения механических свойств, т. е. значения напряжений или деформаций, при которых происходят изменения физического и механического состояний материала.
Оценка свойств
При оценке механических свойств металлических материалов различают несколько групп их критериев.
- Критерии, определяемые независимо от конструктивных особенностей и характера службы изделий. Эти критерии находятся путем стандартных испытаний гладких образцов на растяжение, сжатие, изгиб, твердость (статические испытания) или на ударный изгиб образцов с надрезом (динамические испытания).
- Прочностные и пластические свойства, определяемые при статических испытаниях на гладких образцах хотя и имеют важное значение (они входят в расчетные формулы) во многих случаях не характеризуют прочность этих материалов в реальных условиях эксплуатации деталей машин и сооружений. Они могут быть использованы только для ограниченного числа простых по форме изделий, работающих в условиях статической нагрузки при температурах, близких к нормальной.
- Критерии оценки конструктивной прочности материала, которые находятся в наибольшей корреляции со служебными свойствами данного изделия и характеризуют работоспособность материала в условиях эксплуатации.
Конструкторская прочность металлов
Критерии конструктивной прочности металлических материалов можно разделить на две группы:
- критерии, определяющие надежность металлических материалов против внезапных разрушений (вязкость разрушения, работа, поглощаемая при распространении трещин, живучесть и др.). В основе этих методик, использующих основные положения механики разрушения, лежат статические или динамические испытания образцов с острыми трещинами, которые имеют место в реальных деталях машин и конструкциях в условиях эксплуатации (надрезы, сквозные отверстия, неметаллические включения, микропустоты и т. д.). Трещины и микронесплошности сильно меняют поведение металла под нагрузкой, так как являются концентраторами напряжений;
- критерии, которые определяют долговечность изделий (сопротивление усталости, износостойкость, сопротивление коррозии и т. д.).
Критерии оценки
Критерии оценки прочности конструкции в целом (конструкционной прочности), определяемые при стендовых, натурных и эксплуатационных испытаниях. При этих испытаниях выявляется влияние на прочность и долговечность конструкции таких факторов, как распределение и величина остаточных напряжений, дефектов технологии изготовления и конструирования металлоизделий и т. д.
Для решения практических задач металловедения необходимо определять как стандартные механические свойства, так и критерии конструктивной прочности.
Похожие материалы
МЕХАНИЧЕСКИЕ СВОЙСТВА МЕТАЛЛОВ
⇐ ПредыдущаяСтр 4 из 16Следующая ⇒И МЕТОДЫ ИХ ОПРЕДЕЛЕНИЯ
Цель работы: изучить способы определения основных механических свойств металлических материалов.
Теоретические сведения
Механические свойства определяют способность металлов сопротивляться воздействию внешних сил (нагрузок). Они зависят от химического состава металлов, их структуры, характера технологической обработки и других факторов. Зная механические свойства металлов, можно судить о поведении металла при обработке и в процессе работы машин и механизмов.
К основным механическим свойствам металлов относятся прочность, пластичность, твердость и ударная вязкость.
Прочность – способность металла не разрушаться под действием приложенных к нему внешних сил.
Пластичность – способность металла получать остаточное изменение формы и размеров без разрушения.
Твердость – способность металла сопротивляться вдавливанию в него другого, более твердого тела.
Ударная вязкость – степень сопротивления металла разрушению при ударной нагрузке.
Механические свойства определяют путем проведения механических испытаний.
Испытания на растяжение. Этими испытаниями определяют такие характеристики, как пределы пропорциональности, упругости, прочности и пластичность металлов. Для испытаний на растяжение применяют круглые и плоские образцы (рисунок 2.1, а, б), форма и размеры которых установлены стандартом. Цилиндрические образцы диаметром d0 = 10 мм, имеющие расчетную длину l0 = 10d0, называют нормальными, а образцы, у которых длина l0 = 5d0, – короткими. При испытании на растяжение образец растягивается под действием плавно возрастающей нагрузки и доводится до разрушения.
Разрывные машины снабжены специальным самопишущим прибором, который автоматически вычерчивает кривую деформации, называемую диаграммой растяжения. Диаграмма растяжения в координатах «нагрузка Р – удлинение ∆l» отражает характерные участки и точки, позволяющие определить ряд свойств металлов и сплавов (рисунок 2.1). На участке 0 — Рпц удлинение образца увеличивается прямо пропорционально возрастанию нагрузки. При повышении нагрузки свыше Рпц, на участке Рпц — Pупр прямая пропорциональность нарушается, но деформация остается упругой (обратимой). На участке выше точки Pvпр возникают заметные остаточные деформации, и кривая растяжения значительно отклоняется от прямой. При нагрузке
а, б – стандартные образцы для испытания на растяжение;
в – диаграмма растяжения образца из пластичного материала
Рисунок 2.1 – Испытание на растяжение
Усилия, соответствующие основным точкам диаграммы растяжения, дают возможность определить характеристики прочности, выраженные в мегапаскалях, МПа, по формуле
, (2.1)
где σi – напряжение, МПа;
Pi – соответствующая точка диаграммы растяжения, Н;
F0 – площадь поперечного сечения образца до испытания, мм2.
Предел пропорциональности σпц – это наибольшее напряжение, до которого сохраняется прямая пропорциональность между напряжением и деформацией:
, (2.2)
где Pпц – напряжение, соответствующее пределу пропорциональности, Н.
Предел упругости σупр
, (2.3)
где Pупр – напряжение, соответствующее пределу упругости, Н.
Предел текучести физический σт — напряжение, начиная с которого деформация образца происходит почти без дальнейшего увеличения нагрузки:
, (2.4)
где Pт – напряжение, соответствующее пределу текучести, Н.
Если площадка текучести на диаграмме растяжения данного материала отсутствует, то определяется условный предел текучести σ0,2 — напряжение, вызывающее пластическую деформацию, равную 0,2 %.
Предел прочности (временное сопротивление) σв — напряжение, равное отношению наибольшей нагрузки, предшествующей разрушению образца, к первоначальной площади его сечения:
, (2.5)
где Pв – напряжение, соответствующее пределу прочности, Н.
По результатам испытания на растяжение определяют характеристики пластичности металлов.
Показатели пластичности металлов — относительное удлинение и относительное сужение – рассчитывают по результатам замеров образца до и после испытания.
Относительное удлинение δ находится как отношение увеличения длины образца после разрыва к его первоначальной расчетной длине, выраженное в процентах:
где lk – длина образца после разрыва, мм;
l0 – расчетная (начальная) длина образца, мм.
Относительное сужение ψ определяется отношением уменьшения площади поперечного сечения образца после разрыва к первоначальной площади его поперечного сечения, выраженным в процентах:
, (2.7)
где F0 – начальная площадь поперечного сечения образца;
Fк – площадь поперечного сечения образца в месте разрушения.
Методы определения твердости.Наиболее распространенным методом определения твердости металлических материалов является метод вдавливания, при котором в испытуемую поверхность под действием постоянной статической нагрузки вдавливается другое, более твердое тело (наконечник). На поверхности материала остается отпечаток, по величине которого судят о твердости материала. Показатель твердости характеризует сопротивление материала пластической деформации, как правило, большой, при местном контактном приложении нагрузки.
Твердость определяют на специальных приборах – твердомерах, которые отличаются друг от друга формой, размером и материалом вдавливаемого наконечника, величиной приложенной нагрузки и способом определения числа твердости. Так как для измерения твердости испытывают поверхностные слои металла, то для получения правильного результата поверхность металла не должна иметь наружных дефектов (трещин, крупных царапин и т. д.).
Измерение твердости по Бринеллю. Сущность этого способа заключается в том, что в поверхность испытуемого металла вдавливается стальной закаленный шарик диаметром 10, 5 или 2,5 мм в зависимости от толщины образца под действием нагрузки, которая выбирается в зависимости от предполагаемой твердости испытуемого материала и диаметра наконечника по формулам:
Р = 2,5D2 (таблица 2.1).
Таблица 2.1 – Выбор диаметра шарика D и нагрузки Р
Материал образца | Твердость, кгс/мм2 | Толщина образца, мм | Диаметр шарика D, мм | P/D2, кгс/мм2 | Нагрузка Р, кгс | Выдержка под нагрузкой, с |
Черные металлы (сталь, чугун) | 450 — 140 | более 6 6 – 3 менее 3 | 2,5 | 187,5 | ||
Черные металлы | Менее 140 | более 6 6 – 3 менее 3 | 2,5 | 187,5 | ||
Твердые цветные металлы (латунь, бронза, медь) | 140 – 32 | более 6 6 – 3 менее 3 | 2,5 | 62,5 | ||
Мягкие цветные металлы (олово, алюминий и др.) | 35 — 8 | более 6 6 – 3 менее 3 | 2,5 | 2,5 | 62,5 15,6 |
На поверхности образца остается отпечаток (рисунок 2.2, а), по диаметру которого определяют твердость. Диаметр отпечатка измеряют специальной лупой с делениями.
Твердость рассчитывают по формуле
где НВ – твердость по Бринеллю, кгс/мм2;
Р – нагрузка при испытании, кгс или Н;
F – площадь полученного отпечатка, мм2;
D – диаметр наконечника, мм;
d – диаметр отпечатка, мм.
Рисунок 2.2 – Измерение твердости методами Бринелля (а),
Роквелла (б), Виккерса (в)
На практике пользуются специальными таблицами, которые дают перевод диаметра отпечатка в число твердости, обозначаемое НВ. Например: 120 НВ, 350 НВ и т.д. (Н – твердость, В – по Бринеллю, 120, 350 – число твердости в кгс/мм2, что соответствует 1200 и 3500 МПа).
Этот способ применяют, главным образом, для измерения твердости незакаленных металлов и сплавов: проката, поковок, отливок и др.
Твердомер Бринелля можно использовать в том случае, если твердость материала не превышает 450 кгс/мм2. В противном случае произойдет деформация шарика, что приведет к погрешностям в измерении. Кроме того, твердомер Бринелля не применяется для испытания тонких поверхностных слоев и образцов тонкого сечения.
Измерение твердости по Роквеллу. Измерение осуществляют путем вдавливания в испытуемый металл стального шарика диаметром 1,588 мм или алмазного конуса с углом при вершине 120° (см. рисунок 2.2, б).В отличие от метода Бринелля твердость по Роквеллу определяют не по диаметру отпечатка, а по глубине вдавливания наконечника.
Вдавливание производится под действием двух последовательно приложенных нагрузок — предварительной, равной ≈ 100 Н, и окончательной (общей) нагрузки, равной 1400, 500 и 900 Н. Твердость определяют по разности глубин вдавливания отпечатков. Для испытания твердых материалов (например, закаленной стали) необходима нагрузка 1500 Н, а вдавливание стальным шариком нагрузкой 1000 Н производят для определения твердости незакаленной стали, бронзы, латуни и других мягких материалов. Глубина вдавливания измеряется автоматически, а твердость после измерения отсчитывается по трем шкалам: А, В, С (таблица 2.2).
Таблица 2.2 – Наконечники и нагрузки для шкал А, В, С
Наконечник | Суммарная нагрузка Р, Н (кгс) | Отсчет по шкале | Обозначение твердости |
Стальной шарик | 1000 (100) | В (красная) | HRB |
Алмазный конус | 1500 (150) | С (черная) | HRC |
Алмазный конус | 600 (60) | А (черная) | HRA |
Твердость (число твердости) по Роквеллу обозначается следующим образом: 90 HRA, 80 HRB, 55 HRC (Н – твердость, Р – Роквелл, А, В, С – шкала твердости, 90, 80, 55 – число твердости в условных единицах).
Определение твердости по Роквеллу имеет широкое применение, так как дает возможность испытывать мягкие и твердые металлы без дополнительных измерений; размер отпечатков очень незначителен, поэтому можно испытывать готовые детали без их порчи.
Измерение твердости по Виккерсу. Данный метод позволяет измерять твердость как мягких, так и очень твердых металлов и сплавов. Он пригоден для определения твердости очень тонких поверхностных слоев (толщиной до 0,3мм). В этом случае в испытуемый образец вдавливается четырехгранная алмазная пирамида с углом при вершине 136о (см. рисунок 2.2, в). При таких испытаниях применяются нагрузки от 50 до 1200 Н. Измерение отпечатка производят по длине его диагонали, рассматривая отпечаток под микроскопом, входящим в твердомер. Число твердости по Виккерсу, обозначаемое НV, находят по формуле
, (2.9)
где Р – нагрузка, Н;
d – длина диагонали отпечатка, мм.
На практике число твердости НV находят по специальным таб-лицам.
Определение ударной вязкости производят на специальном маятниковом копре (рисунок 2.3). Для испытаний применяется стандартный надрезанный образец, который устанавливается на опорах копра. Маятник определенной массой поднимают на установленную высоту Н и закрепляют, а затем освобожденный от защелки маятник падает, разрушает образец и снова поднимается на некоторую вы-
соту h. Удар наносится по стороне образца, противоположной надрезу. Для испытаний используют призматические образцы с надрезами различных видов: U-образный, V-образный, T-образный (надрез с усталостной трещиной).
а – схема испытания; б – образцы для испытаний.
Рисунок 2.3 – Испытания на ударную вязкость
Ударная вязкость КС (Дж/см2) оценивается работой, затраченной маятником на разрушение стандартного надрезанного образца, отнесенной к сечению образца в месте надреза:
, (2.10)
где А – работа, затраченная на разрушение образца (определяется по разности энергий маятника до и после удара: А0 – А1), Дж;
F – площадь поперечного сечения образца в месте надреза, см2.
В зависимости от вида надреза в образце ударная вязкость обозначается KCU, KCV, KCТ (третья буква – вид надреза).
Материалы и принадлежности
· Образцы для испытания на растяжение, твердость и ударную вязкость.
· Разрывная испытательная машина.
· Твердомеры Бринелля, Роквелла, Виккерса.
· Маятниковый копер.
· Штангенциркуль.
Порядок выполнения работы
Испытания на растяжение
2.3.1.1 Измерить рабочую длину и диаметр образца перед испытанием, записать данные в протокол испытаний.
2.3.1.2 Подготовленный для испытания образец поместить в зажимы машины.
2.3.1.3 Включить электродвигатель.
2.3.1.4 Наблюдать за перемещением стрелки по шкале машины, зафиксировать нагрузку, соответствующую текучести образца, и наибольшую нагрузку, предшествующую разрушению образца, записать в соответствующие графы протокола испытаний.
2.3.1.5 После разрыва образца выключить электродвигатель, обе части образца вынуть из зажимов, снять с диаграммного аппарата часть бумажной ленты с записанной диаграммой.
2.3.1.6 Обе части образца плотно приложить одну к другой, измерить длину и диаметр образца в месте разрыва, записать данные в протокол испытаний.
2.3.1.7 Рассчитать характеристики прочности и пластичности материала, записать полученные данные.
Механические свойства металлов
Любое вещество, будь то газ, жидкость или твердое тело, обладает рядом специфических, только ему присущих свойств. Однако эти свойства позволяют не только индивидуализировать элементы, но и объединять их в группы по принципу схожести.
Посмотрите на металлы: с обывательской точки зрения это блестящие элементы, с высокой электро- и теплопроводностью, не восприимчивые к внешним физическим воздействиям, ковкие и легко свариваемые при высоких температурах. Достаточен ли этот перечень. чтобы объединить металлы в одну группу? Конечно же нет, металлы и их производные (сплавы) гораздо сложнее и обладают целым набором химических, физических, механических и технологических свойств. Сегодня мы поговорим лишь об одной группе: механических свойствах металлов.
Блок: 1/4 | Кол-во символов: 773
Источник: https://promplace.ru/vidy-metallov-i-klassifikaciya-staty/mehanicheskie-svoistva-metallov-1542.htm
Основные механические свойства
К основным механическим свойствам относят прочность, пластичность, твердость, ударную вязкость и упругость. Большинство показателей механических свойств определяют экспериментально растяжением стандартных образцов на испытательных машинах.
Прочность — способность металла сопротивляться разрушению при действии на него внешних сил.
Пластичность — способность металла необратимо изменять свою форму и размеры под действием внешних и внутренних сил без разрушения.
Твердость — способность металла сопротивляться внедрению в него более твердого тела. Твердость определяют с помощью твердомеров внедрением стального закаленного шарика в металл (на приборе Бринелля) или внедрением алмазной пирамиды в хорошо подготовленную поверхность образца (на приборе Роквелла). Чем меньше размер отпечатка, тем больше твердость испытуемого металла. Например, углеродистая сталь до закалки имеет твердость 100 . . . 150 НВ () , а после закалки — 500 . . . 600 НВ.
Ударная вязкость — способность металла сопротивляться действию ударных нагрузок. Эта величина, обозначаемая КС (Дж/см2 или кгс • м/см ), определяется отношением механической работы А, затраченной на разрушение образца при ударном изгибе, к площади поперечного сечения образца.
Упругость — способность металла восстанавливать форму и объем после прекращения действий внешних сил. Эта величина характеризуется модулем упругости Е (МПа или кгс/мм2), который равен отношению напряжения а к вызванной им . Высокой упругостью должны обладать стали и сплавы для изготовления рессор и пружин.
Блок: 2/4 | Кол-во символов: 1556
Источник: https://www.metalcutting.ru/content/mehanicheskie-svoystva-metallov
Таблица.1. Механические свойства основных промышленных сплавов
Техническое железо | Мембраны | |||
Чугун серый | 12—38 | до 0,25 | 143—220 | Отливки фасонные |
Чугун высокопрочный | 30—60 | 0,5—10 | 170—262 | Ответственные отливки |
Сталь малоуглеродистая (мягкая) | 32 — 70 | 11 — 28 | 100—130 | Котельное железо трубы, котлы |
Сталь среднеуглеродистая (средней твердости) | 50—70 | 12 — 16 | 170 — 200 | Оси, шатуны, валы, рельсы |
Сталь твердая после закалки и отпуска | 110—140 | до 9 | 400—600 | Инструмент ударный и режущий |
Бронза оловянистая | 15 — 25 | 3—10 | 70—80 | Детали, работающие на истирание и подверженные коррозии |
Бронза алюминиевая | 40—50 | 120 | То же | |
Латунь однофазная | 25 — 35 | 30-60 | 42—60 | Патронно-гильзовое производство |
Латунь двухфазная | 35—45 | 30—40 | _ | Детали, изготовленные горячей штамповкой |
Силумин | 21—23 | 1 — 3 | 65—100 | Детали в авиастроении и автостроении |
Сплавы магния | 24 — 32 | 10—16 | 60—70 | То же |
Блок: 2/2 | Кол-во символов: 1107
Источник: http://xn--80awbhbdcfeu.su/mehansv
Основные механические свойства металлов
Что это за свойства? Под механическими понимают такие свойства субстанции, которые отражают ее умение противостоять действиям извне. Известно девять основных механических свойств металлов:
— Прочность — означает, что приложение статической, динамической или знакопеременной нагрузки не приводит к нарушению внешней и внутренней целостности материала, изменению его строения, формы и размеров.
— Твердость (часто путают с прочностью) — характеризует возможность одного материала противостоять прониканию другого, более твердого предмета.
— Упругость — означает способность к деформированию без нарушения целостности под действием определенных сил и возвращению первоначальной формы после освобождения от нагрузки.
— Пластичность (часто путают с упругостью и наоборот) — также способность к деформации без нарушения целостности, однако в отличие от упругости, пластичность означает, что объект способен сохранить полученную форму.
— Стойкость к трещинам — под воздействием внешних сил (ударов, натяжений и пр.) материал не образует трещин и сохраняет наружную целостность.
— Вязкость или ударная вязкость — антоним ломкости, то есть возможность сохранять целостность материала при возрастающих физических воздействиях.
— Износостойкость — способность к сохранению внутренней и внешней целостности при длительном трении.
— Жаростойкость — длительная возможность противостоять изменению формы, размера и разрушению при воздействии больших температур.
— Усталость — время и количество циклических воздействий, которые материал может выдержать без нарушения целостности.
Часто, говоряо тех или иных свойствах, мы путаем их названия: технологические свойства относим к физическим, физические к механическим и наоборот. И это неудивительно, ведь несмотря на глубинные отличия, лежащие в основе той или иной группы свойств, механические свойства не только крайне тесно связаны с другими характеристиками металлов, но и напрямую зависят от них.
Блок: 2/4 | Кол-во символов: 2075
Источник: https://promplace.ru/vidy-metallov-i-klassifikaciya-staty/mehanicheskie-svoistva-metallov-1542.htm
Механические свойства металлов
Под механическими свойствами понимают характеристики, определяющие поведение металла (или другого материала) под действием приложенных внешних механических сил. К механическим свойствам обычно относят сопротивление металла (сплава) деформации (прочность) и сопротивление разрушению (пластичность, вязкость, а также способность металла не разрушаться при наличии трещин).
В результате механических испытаний получают числовые значения механических свойств, т. е. значения напряжений или деформаций, при которых происходят изменения физического и механического состояний материала.
Оценка свойств
При оценке механических свойств металлических материалов различают несколько групп их критериев.
- Критерии, определяемые независимо от конструктивных особенностей и характера службы изделий. Эти критерии находятся путем стандартных испытаний гладких образцов на растяжение, сжатие, изгиб, твердость (статические испытания) или на ударный изгиб образцов с надрезом (динамические испытания).
- Прочностные и пластические свойства, определяемые при статических испытаниях на гладких образцах хотя и имеют важное значение (они входят в расчетные формулы) во многих случаях не характеризуют прочность этих материалов в реальных условиях эксплуатации деталей машин и сооружений. Они могут быть использованы только для ограниченного числа простых по форме изделий, работающих в условиях статической нагрузки при температурах, близких к нормальной.
- Критерии оценки конструктивной прочности материала, которые находятся в наибольшей корреляции со служебными свойствами данного изделия и характеризуют работоспособность материала в условиях эксплуатации.
Блок: 3/4 | Кол-во символов: 1660
Источник: https://www.metalcutting.ru/content/mehanicheskie-svoystva-metallov
Физические свойства металлов
Наиболее взаимозависимы между собой механические и химические свойства металлов, ведь именно химический состав металла или сплава, его внутреннее строение (особенности кристаллической решетки) диктуют все остальные его параметры. Если говорить о механических и физических свойствах металлов, то их чаще других путают между собой, что обусловлено близостью данных определений.
Физические свойства часто неотделимы от механических. К примеру, тугоплавкие металлы еще и самые прочные. Главное же отличие лежит в природе свойств. Физические свойства — те что проявляется в покое, механические — только под воздействием извне. Не хуже других связаны механические и технологические свойства металлов. Например, механическое свойство металла «прочность» может быть результатом его грамотной технологической обработки (с этой целью нередко используют «закалку» и «старение»). Обратная взаимосвязь не менее важна, к примеру, ковкость проявление хорошей ударной вязкости.
Делая вывод, можно сказать, что зная некоторые химические, физические или технологические свойства можно предугадать, как будет вести себя металл под воздействием нагрузки (т.е. механически), и наоборот.
В чем отличия механических свойств металлов и сплавов?
Различаются ли механические свойства металлов и сплавов? Безусловно. Ведь любой металлический сплав изначально создается с целью получения каких-либо конкретных свойств. Некоторые сочетания легирующих элементов и основного металла в сплаве способны мгновенно преобразить легируемый элемент. Так алюминий ( не самый прочный и твердый металл в мире) в сочетании с цинком и магнием образует сплав по прочности сравнимый со сталью. Все это дает практически неограниченные возможности в получении веществ наиболее близких к требуемым.
Отдельное внимание следует уделить механическим свойствам наплавленных металлов. Наплавленным считается металл, с помощью которого производилась сварка двух или более частей какого-то металлического элемента или конструкции. Этот металл словно нитки соединяет разорванные части. От того, как будет вести себя «шов» под нагрузкой, будет зависеть безопасность и надежность всей конструкции. Исходя из этого, крайне важно, чтобы свойства наплавленного металла были не хуже, чем у главного металла.
Блок: 3/4 | Кол-во символов: 2340
Источник: https://promplace.ru/vidy-metallov-i-klassifikaciya-staty/mehanicheskie-svoistva-metallov-1542.htm
Конструкторская прочность металлов
Критерии конструктивной прочности металлических материалов можно разделить на две группы:
- критерии, определяющие надежность металлических материалов против внезапных разрушений (вязкость разрушения, работа, поглощаемая при распространении трещин, живучесть и др.). В основе этих методик, использующих основные положения механики разрушения, лежат статические или динамические испытания образцов с острыми трещинами, которые имеют место в реальных деталях машин и конструкциях в условиях эксплуатации (надрезы, сквозные отверстия, неметаллические включения, микропустоты и т. д.). Трещины и микронесплошности сильно меняют поведение металла под нагрузкой, так как являются концентраторами напряжений;
- критерии, которые определяют долговечность изделий (сопротивление усталости, износостойкость, сопротивление коррозии и т. д.).
Критерии оценки
Критерии оценки прочности конструкции в целом (конструкционной прочности), определяемые при стендовых, натурных и эксплуатационных испытаниях. При этих испытаниях выявляется влияние на прочность и долговечность конструкции таких факторов, как распределение и величина , дефектов технологии изготовления и конструирования металлоизделий и т. д.
Для решения практических задач металловедения необходимо определять как стандартные механические свойства, так и критерии конструктивной прочности.
Блок: 4/4 | Кол-во символов: 1456
Источник: https://www.metalcutting.ru/content/mehanicheskie-svoystva-metallov
Как определить механические свойства?
Экспериментальным путем. Среди основных методов определения механических свойств металлов можно выделить:
— испытания на растяжение;
— метод вдавливания по Бринеллю;
— определение твердости металла по Роквеллу;
— оценка твердости по Виккерсу;
— определение вязкости с помощью маятникового копра;
Механические свойства имеют весьма серьезное значение. Их знание позволяет использовать металлы и их сплавы с наибольшей эффективностью и отдачей.
Блок: 4/4 | Кол-во символов: 545
Источник: https://promplace.ru/vidy-metallov-i-klassifikaciya-staty/mehanicheskie-svoistva-metallov-1542.htm
Количество использованных доноров: 3
Информация по каждому донору:
- https://www.metalcutting.ru/content/mehanicheskie-svoystva-metallov: использовано 3 блоков из 4, кол-во символов 4672 (41%)
- https://promplace.ru/vidy-metallov-i-klassifikaciya-staty/mehanicheskie-svoistva-metallov-1542.htm: использовано 4 блоков из 4, кол-во символов 5733 (50%)
- http://xn--80awbhbdcfeu.su/mehansv: использовано 1 блоков из 2, кол-во символов 1107 (10%)
Любое вещество, будь то газ, жидкость или твердое тело, обладает рядом специфических, только ему присущих свойств. Однако эти свойства позволяют не только индивидуализировать элементы, но и объединять их в группы по принципу схожести.
Посмотрите на металлы: с обывательской точки зрения это блестящие элементы, с высокой электро- и теплопроводностью, не восприимчивые к внешним физическим воздействиям, ковкие и легко свариваемые при высоких температурах. Достаточен ли этот перечень. чтобы объединить металлы в одну группу? Конечно же нет, металлы и их производные (сплавы) гораздо сложнее и обладают целым набором химических, физических, механических и технологических свойств. Сегодня мы поговорим лишь об одной группе: механических свойствах металлов.
Основные механические свойства металлов
Что это за свойства? Под механическими понимают такие свойства субстанции, которые отражают ее умение противостоять действиям извне. Известно девять основных механических свойств металлов:
— Прочность — означает, что приложение статической, динамической или знакопеременной нагрузки не приводит к нарушению внешней и внутренней целостности материала, изменению его строения, формы и размеров.
— Твердость (часто путают с прочностью) — характеризует возможность одного материала противостоять прониканию другого, более твердого предмета.
— Упругость — означает способность к деформированию без нарушения целостности под действием определенных сил и возвращению первоначальной формы после освобождения от нагрузки.
— Пластичность (часто путают с упругостью и наоборот) — также способность к деформации без нарушения целостности, однако в отличие от упругости, пластичность означает, что объект способен сохранить полученную форму.
— Стойкость к трещинам — под воздействием внешних сил (ударов, натяжений и пр.) материал не образует трещин и сохраняет наружную целостность.
— Вязкость или ударная вязкость — антоним ломкости, то есть возможность сохранять целостность материала при возрастающих физических воздействиях.
— Износостойкость — способность к сохранению внутренней и внешней целостности при длительном трении.
— Жаростойкость — длительная возможность противостоять изменению формы, размера и разрушению при воздействии больших температур.
— Усталость — время и количество циклических воздействий, которые материал может выдержать без нарушения целостности.
Часто, говоряо тех или иных свойствах, мы путаем их названия: технологические свойства относим к физическим, физические к механическим и наоборот. И это неудивительно, ведь несмотря на глубинные отличия, лежащие в основе той или иной группы свойств, механические свойства не только крайне тесно связаны с другими характеристиками металлов, но и напрямую зависят от них.
Физические свойства металлов
Наиболее взаимозависимы между собой механические и химические свойства металлов, ведь именно химический состав металла или сплава, его внутреннее строение (особенности кристаллической решетки) диктуют все остальные его параметры. Если говорить о механических и физических свойствах металлов, то их чаще других путают между собой, что обусловлено близостью данных определений.
Физические свойства часто неотделимы от механических. К примеру, тугоплавкие металлы еще и самые прочные. Главное же отличие лежит в природе свойств. Физические свойства — те что проявляется в покое, механические — только под воздействием извне. Не хуже других связаны механические и технологические свойства металлов. Например, механическое свойство металла «прочность» может быть результатом его грамотной технологической обработки (с этой целью нередко используют «закалку» и «старение»). Обратная взаимосвязь не менее важна, к примеру, ковкость проявление хорошей ударной вязкости.
Делая вывод, можно сказать, что зная некоторые химические, физические или технологические свойства можно предугадать, как будет вести себя металл под воздействием нагрузки (т.е. механически), и наоборот.
В чем отличия механических свойств металлов и сплавов?
Различаются ли механические свойства металлов и сплавов? Безусловно. Ведь любой металлический сплав изначально создается с целью получения каких-либо конкретных свойств. Некоторые сочетания легирующих элементов и основного металла в сплаве способны мгновенно преобразить легируемый элемент. Так алюминий ( не самый прочный и твердый металл в мире) в сочетании с цинком и магнием образует сплав по прочности сравнимый со сталью. Все это дает практически неограниченные возможности в получении веществ наиболее близких к требуемым.
Отдельное внимание следует уделить механическим свойствам наплавленных металлов. Наплавленным считается металл, с помощью которого производилась сварка двух или более частей какого-то металлического элемента или конструкции. Этот металл словно нитки соединяет разорванные части. От того, как будет вести себя «шов» под нагрузкой, будет зависеть безопасность и надежность всей конструкции. Исходя из этого, крайне важно, чтобы свойства наплавленного металла были не хуже, чем у главного металла.
Как определить механические свойства?
Экспериментальным путем. Среди основных методов определения механических свойств металлов можно выделить:
— испытания на растяжение;
— метод вдавливания по Бринеллю;
— определение твердости металла по Роквеллу;
— оценка твердости по Виккерсу;
— определение вязкости с помощью маятникового копра;
Механические свойства имеют весьма серьезное значение. Их знание позволяет использовать металлы и их сплавы с наибольшей эффективностью и отдачей.
Механические свойства металлов — Студопедия
Отклонение частоты
f = f – fноом [ Гц ]
f = ± 0,1 Гц – допускаемое значение
f = ± 0,2 Гц – предельно допускаемое значение
f = ± 0,4 Гц – аварийно допускаемое значение
Изменение нагрузки потребителей в сети может быть различным . При малом изменении нагрузки требуется небольшой резерв мощности. В этих случаях автоматическое регулирование частоты одной так называемой частотно-регулируемой станцией.
При больших изменениях нагрузки, автоматическое регулирование частоты должно быть предусмотрено на значительном числе станций. Для этого составляются графики изменения нагрузок электростанций.
При отключении мощных линий электропередач в послеаварийных режимах, система может оказаться разделенной на отдельно не синхронно работающие части.
На электростанциях, на которых мощности может оказаться не достаточно, произойдет снижение производительности оборудования собственных нужд (питательных и циркуляционных насосов), следовательно вызовет значительное снижение мощности станции , вплоть до выхода ее из строя.
В подобных случаях для предотвращения аварий предусматриваются устройства АЧР, отключающие в таких случаях часть менее ответственных потребителей, а после включения резервных источников питания, устройства ЧАПВ включают отключенных потребителей.
Механические свойства характеризуют способность материала сопротивляться деформации (упругой и пластической) и разрушению. Для металлов и сплавов, работающих как конструкционные материалы, эти свойства являются определяющими. Выявляют их испытаниями при воздействии внешних нагрузок.
Количественные характеристики механических свойств: упругость, пластичность, прочность, твердость, вязкость, усталость, трещиностойкость, хладостойкость, жаропрочность. Эти характеристики необходимы для выбора материалов и режимов их технологической обработки, расчетов на прочность деталей и конструкций, контроля и диагностики их прочностного состояния в процессе эксплуатации.
Под действием внешней нагрузки в твердом теле возникают напряжение и деформация.
Напряжение — это нагрузка (сила) P, отнесенная к первоначальной площади поперечного сечения F0 образца:
Деформация — это изменение формы и размеров твердого тела под действием внешних сил или в результате физических процессов, возникающих в теле при фазовых превращениях, усадке и т.п. Деформация может быть упругая (исходные размеры образца восстанавливаются после снятия нагрузки) и пластическая (сохраняется после снятия нагрузки).
Напряжение s измеряют в паскалях (Па), деформацию e — в процентах (%) относительного удлинения (Dl/l)×100 или сужения площади сечения (DS/S)×100.
При все возрастающей нагрузке упругая деформация, как правило, переходит в пластическую, и далее образец разрушается (рис.1). В зависимости от способа приложения нагрузки методы испытания механических свойств металлов, сплавов и других материалов делятся на статические, динамические и знакопеременные.
Прочность — способность металлов оказывать сопротивление деформации или разрушению статическим, динамическим или знакопеременным нагрузкам. Прочность металлов при статических нагрузках испытывают на растяжение, сжатие, изгиб и кручение. Испытание на разрыв является обязательным. Прочность при динамических нагрузках оценивают удельной ударной вязкостью, а при знакопеременных нагрузках — усталостной прочностью.
Прочность при испытании на растяжение оценивают следующими характеристиками (рис.1).
Предел прочности на разрыв (предел прочности или временное сопротивление разрыву) sв — это напряжение, отвечающее наибольшей нагрузке Рmax, предшествующей разрушению образца:
.
Эта характеристика является обязательной для металлов.
Предел пропорциональности sпц — это условное напряжение Рпц, при котором начинается отклонение от пропорциональной зависимости между деформацией и нагрузкой:
.
Предел текучести sт — это наименьшее напряжение Рт, при котором образец деформируется (течет) без заметного увеличения нагрузки:
.
Условный предел текучести s0,2 — напряжение, после снятия которого остаточная деформация достигает величины 0,2 %.
Если же на кривой напряжение — деформация за пределом упругости образуется площадка текучести (рис.1), то за предел текучести sт принимают напряжение, отвечающее площадке текучести.
Если после того, как напряжение превысило sт, его снять, то деформация уменьшится по пунктирной линии. Отрезок ОО¢ показывает остаточную пластическую деформацию.
Величина sт чрезвычайно чувствительна к скорости деформации (продолжительности действия нагрузки) и к температуре. Если прикладывать к материалу напряжение меньше sт в течение длительного времени, то оно может вызвать пластическую (остаточную) деформацию. Это медленное и непрерывное пластическое деформирование воздействием постоянной нагрузки называют ползучестью (криппом).
Пластичность — свойство металлов деформироваться без разрушения под действием внешних сил и сохранять измененную форму после снятия этих сил. Пластичность — одно из важных механических свойств металла, которое в сочетании с высокой прочностью делает его основным конструкционным материалом. Ее характеристиками являются относительное удлинение перед разрывом d и относительное сужение перед разрывом y. Эти характеристики определяют при испытании металлов на растяжение, а их численные значения вычисляют по формулам (в процентах):
,
,
где l0 и lр — длина образца до и после разрушения соответственно;
F0и Fр — площадь поперечного сечения образца до и после разрушения.
Упругость — свойство металлов восстанавливать свою прежнюю форму после снятия внешних сил, вызывающих деформацию. Упругость — свойство, обратное пластичности.
Твердость — способность металлов оказывать сопротивление проникновению в них более твердого тела. Испытания на твердость — самый доступный и распространенный вид механических испытаний. Наибольшее применение в технике получили статические методы испытания на твердость при вдавливании индентора: метод Бринелля, метод Виккерса и метод Роквелла. Твердость, согласно этим методам, определяют следующим образом.
По Бринеллю — в испытуемый образец с определенной силой вдавливается закаленный стальной шарик диаметром D под действием нагрузки P, и после снятия нагрузки измеряется диаметр отпечатка d (рис.2,а). Число твердости по Бринеллю — НВ, характеризуется отношением нагрузки P, действующей на шарик, к площади поверхности сферического отпечатка M:
.
Чем меньше диаметр отпечатка d, тем больше твердость образца. Диаметр шарика D и нагрузку P выбирают в зависимости от материала и толщины образца. Метод Бринелля не рекомендуется применять для материалов с твердостью более 450 HB, так как стальной шарик может заметно деформироваться, что внесет погрешность в результаты испытаний.
При испытании на твердость по методу Виккерса в поверхность материала вдавливается алмазная четырехгранная пирамида с углом при вершине a = 136° (рис.2,б). После снятия нагрузки вдавливания измеряется диагональ отпечатка d1. Число твердости по Виккерсу HV подсчитывается как отношение нагрузки Р к площади поверхности пирамидального отпечатка М:
.
Число твердости по Виккерсу обозначается символом HV с указанием нагрузки Р и времени выдержки под нагрузкой, причем размерность числа твердости (кгс/мм2) не ставится. Продолжительность выдержки индентора под нагрузкой принимают для сталей 10-15 с, а для цветных металлов — 30 с. Например, 450 HV10/15 означает, что число твердости по Виккерсу 450 получено при Р = 10 кгс (98,1 Н), приложенной к алмазной пирамиде в течение 15 с.
Преимущество метода Виккерса по сравнению с методом Бринелля заключается в том, что методом Виккерса можно испытывать материалы более высокой твердости из-за применения алмазной пирамиды.
При испытании на твердость по методу Роквелла в поверхность материала вдавливается алмазный конус с углом при вершине 120° или стальной шарик диаметром 1,588 мм. Однако, согласно этому методу, за условную меру твердости принимается глубина отпечатка. Схема испытания по методу Роквелла показана на рис.2,в. Вначале прикладывается предварительная нагрузка Р0,под действием которой индентор вдавливается на глубину h0. Затем прикладывается основная нагрузка Р1, под действием которой индентор вдавливается на глубину h1. После этого снимают нагрузку Р1,но оставляют предварительную нагрузку Р0.
При этом под действием упругой деформации индентор поднимается вверх, но не достигает уровня h0. Разность (h – h0) зависит от твердости материала; чем тверже материал, тем меньше эта разность. Глубина отпечатка измеряется индикатором часового типа с ценой деления 0,002 мм. При испытании мягких металлов методом Роквелла в качестве индентора применяется стальной шарик. Последовательность операций такая же, как и при испытании алмазным конусом. Число твердости, определенное методом Роквелла, обозначается символом HR. Однако в зависимости от формы индентора и значений нагрузок вдавливания к этому символу добавляется буква А, С, или В, обозначающая соответствующую шкалу измерений.
Числа твердости по Роквеллу определяют в условных единицах по формулам:
;
,
где 100 и 130 — предельно заданное число делений индикатора часового типа с ценой деления 0,002 мм.
Трещиностойкость — свойство материалов сопротивляться развитию трещин при механических и других воздействиях.
Трещины в материалах могут быть металлургического и технологического происхождения, а также возникать и развиваться в процессе эксплуатации. В случае возможности хрупкого разрушения для безопасной работы элементов конструкций необходимо количественно оценивать размеры допустимых трещиноподобных дефектов.
Количественной характеристикой трещиностойкости материала является критический коэффициент интенсивности напряжений в условиях плоской деформации в вершине трещины KIс.
Многие конструкции при эксплуатации испытывают ударные нагрузки. Для решения вопроса об их долговечности и надежности в этих условиях очень важными являются результаты динамических испытаний (нагрузка прилагается ударом с большой силой).
Переход от статических нагружений к динамическим вызывает изменение всех свойств металлов и сплавов, связанных с пластической деформацией.
Для оценки склонности материала к хрупкому разрушению применяют испытания на ударный изгиб образцов с надрезом, в результате которых определяют ударную вязкость.
Ударная вязкость — работа, затраченная при динамическом разрушении надрезанного образца, отнесенная к площади поперечного сечения в месте надреза.
Вязкость — свойство, обратное хрупкости. Ударная вязкость ответственных деталей должна быть высокой.
Кроме числовых значений, получаемых при испытании на удар, важным критерием является характер излома. Волокнистый матовый излом без характерного металлического блеска свидетельствует о вязком разрушении. Хрупкое разрушение дает кристаллический блестящий излом.
Ударная вязкость зависит от многих факторов. Наличие в изделиях резких переходов в сечении, надрезов, вырезов и т. п. вызывает неравномерное распределение напряжений по сечению и их концентрацию. Ударная вязкость зависит также и от состояния поверхности образца. Риски, царапины, следы механической обработки и другие дефекты снижают ударную вязкость.
Динамическое нагружение вызывает повышение предела упругости и предела текучести, не переводя материал в хрупкое состояние. Но при понижении температуры, сопротивление удару резко уменьшается. Это явление называется хладоломкостью.
К хладоломким металлам относятся металлы с объемноцентрированной кубической решеткой (например, a-Fe, Mo, Cr). Для этой группы металлов при определенной минусовой температуре наблюдается резкое снижение ударной вязкости. К нехладоломким металлам можно отнести металлы с гранецентрированной кубической решеткой (g-Fe, Al, Ni и др.). Хладоломкость у крупнозернистого материала наступает при более высокой температуре, чем у мелкозернистого.
Характер падения ударной вязкости напоминает порог, что привело к выражению «порог хладоломкости».
Температура, при которой происходит определенное падение ударной вязкости, называется критической температурой хрупкости Tкр.
Большинство разрушений деталей и конструкций при эксплуатации происходит в результате циклического нагружения. Причем в ряде случаев разрушение происходит при напряжениях, лежащих ниже предела упругости.
Усталость — процесс постепенного накопления повреждений в материале при действии циклических нагрузок, приводящий к образованию трещин и разрушению.
Термин «усталость» часто заменяют термином «выносливость», который показывает сколько перемен нагрузок может выдержать металл или сплав без разрушения. Сопротивление усталости характеризуется пределом выносливости s-1. Число циклов условно принято для сталей равным 107, для цветных металлов — 10-8.
Явление усталости наблюдается при изгибе, кручении, растяжении-сжатии и при других способах нагружения.
Большое влияние на выносливость оказывают микроскопическая неоднородность, неметаллические включения, газовые пузыри, химические соединения, а также надрезы, риски, царапины, наличие обезуглероженного слоя и следов коррозии на поверхности изделий, которые приводят к неравномерному распределению напряжений и снижают сопротивление материала повторно-переменным нагрузкам.
Износостойкость — сопротивление металлов изнашиванию вследствие процессов трения. Износ заключается в отрыве с трущейся поверхности отдельных ее частиц и определяется по изменению геометрических размеров или массы детали.
Усталостная прочность и износостойкость дают наиболее полное представление о долговечности деталей в конструкциях, а ударная вязкость и трещиностойкость характеризует надежность этих деталей.
Жаропрочность — способность металлов и сплавов длительно сопротивляться началу и развитию пластической деформации и разрушению под действием постоянных нагрузок при высоких температурах. Предел кратковременной прочности, предел ползучести и предел длительной прочности — численные характеристики жаропрочности.
2. Механические свойства металлов
Механические свойства металлов определяются следующими характеристиками: предел упругости ?Т, предел текучести ?Е, предел прочности относительное удлинение ?, относительное сужение ? и модуль упругости Е, ударная вязкость, предел выносливости, износостойкость.
Твердость, определяемая простейшими неразрушающими методами, зависит в основном от содержания углерода и условий термической обработки стали. Для грубой оценки прочности можно пользоваться следующим соотношением: ?В = НВ/3.
Все металлические детали машин в процессе эксплуатации подвергаются воздействию различных внешних нагрузок, которые могут производиться плавно, постепенно (статически) или мгновенно (динамически). Воздействуя на детали, внешние нагрузки изменяют их форму, т. е. деформируют Свойство материалов из металла и сплавов принимать первоначальную форму после прекращения действия внешних сил называется упругостью, а деформация, исчезающая после снятия нагрузки, получила название упругой. Если к металлической детали приложить большие усилия и после прекращения их действия она не примет своей первоначальной формы, а останется деформированной, то такая деформация называется пластической. Способность металлических материалов и деталей деформироваться под воздействием внешних нагрузок, не разрушаясь, и сохранять измененную форму после прекращения действия усилий называется пластичностью. Материалы из металлов, не способные к пластическим деформациям, называются хрупкими.
Важным свойством материалов и деталей из металлов наряду с упругостью и пластичностью является прочность. Металлические детали или инструмент в зависимости от условий работы должны обладать определенными механическими свойствами – прочностью, упругостью, пластичностью.
При длительной эксплуатации металлические детали машин подвергаются повторно—переменным нагрузкам (растяжение – сжатие). При напряжениях, меньших предела текучести или предела упругости, они могут внезапно разрушиться. Это явление называется усталостью металлов. Пределом выносливости (усталости) называют максимальное напряжение, которое выдерживают материалы и детали из металлов, не разрушаясь, при достаточно большом числе повторно—переменных нагружений (циклов).
Для стальных образцов эту характеристику устанавливают при 10 млн циклов, для цветных металлов – при 100 млн циклов. Предел выносливости обозначают греческой буквой? –1 и измеряют в Па.
В процессе работы многие детали машин нагреваются до высоких температур, достигающих 1000 °C и более. Для таких деталей важной характеристикой является жаропрочность – способность материалов из металлов и сплавов сохранять необходимую прочность при высоких температурах. У металлов и сплавов, работающих длительное время под нагрузкой при высоких температурах, наблюдается явление ползучести, т. е. непрерывная пластическая деформация под действием постоянной нагрузки (металл «ползет»).
Данный текст является ознакомительным фрагментом.Читать книгу целиком
Поделитесь на страничке«Какие бывают свойства металлов?» – Яндекс.Кью
Материалы, используемые в машиностроении В машиностроении любое изделие, оборудование, деталь из которых они состоят, изготавливают из материалов, которые удовлетворяют техническим, экологическим, экономическим, эксплуатационным и другим требованиям, обеспечивая при этом выполнение их назначения. Такие материалы называются конструкционными. Такие детали несомненно должны выдерживать как внешнее, так и внутреннее физическое воздействие (шумоизоляция, теплоизоляция, герметизация и т.п.). Данные способности материалов проверяются при анализе их свойств. Существует довольно широкий спектр конструкционных материалов, выбором наиболее подходящего для того или иного изделия материала, удовлетворяющего все требования и себестоимость, занимаются конструкторы. Металлы и сплавы В машиностроении под металлами может пониматься как химический элемент, так и его примеси, или сплавы, которые различаются рядом свойств: Металлический блеск Высокая тепло- и электропроводность Непрозрачность Способность подвергаться обработке в холодном и горячем состоянии Металлы хорошо образуют химические соединения с неметаллами (оксиды, нитриды, бориды и т.п.), а также с другими металлами (интерметаллиды). Машиностроительные предприятия активно используют более 60 видов металлов, на их основе более 5000 сплавов. Сплав – это твердый материал, образованный путем смешивание двух и более компонентов Сплавы могут создаваться как при чистом физическом процессе (плавка, растворение, перемешивание), так и химическими воздействиями между элементами. Сплавы на основе металлов называются черными, на основе других элементов – цветными. Легкие цветные металлы сделаны на основе алюминия, магния, титана и имеют малую плотность, тяжелые же, с высокой плотностью изготовлены на основе олова, свинца, меди. Чугун Один из наиболее распространенных металлов в машиностроении. Чугун подразделяется на белый, серый, ковкий, высокопрочный. Белый чугун используется в основном для переделки в сталь, он получается при быстром охлаждении при заливки металла в форму. Имеет уменьшенное количество кремния или повышенное содержание магния. При долгом отжиге белого чугуна получают ковкий чугун, он довольно хрупкий и применяется при производстве зубчатых колес, звеньев цепей, хомуты, муфты и т.п., так как не предусматривает механического воздействия. Серый чугун имеет повышенное содержание кремния, и является основным материалом для изготовления отливок. Со временем путем воздействия на графит в момент нахождения в жидком состоянии, удалось вывести модифицированный чугун, который имеет повышенную прочность. Сталь Сталь наиболее распространенный материал в машиностроении. Он обладает ковкостью, высокой прочностью, вязкостью, хорошо обрабатывается. Стали разделяются на углеродистые и легированные. Из стали изготавливаются такие изделия как: прокат, штамповые болты, штыри, свариваемые детали, сверла, зубила, валу, зубчатые колеса и т.п. Твердые сплавы Свое место твердые сплавы нашли в горнодобывающей, металлообрабатывающей и других отраслях промышленности. Режущие инструменты, изготовленные из твердых сплавов могут работать в несколько раз более производительнее, чем простые режущие сплавы. Одним из самых прочных, но довольно молодых сплавов считается титан. К тому же такие сплавы вдвое легче. Такие сплавы применяются в изготовлении сверхзвуковых самолетов, так как титан способен выдерживать температуры превышающие 500 градусов. К тому же титан обладает коррозийной стойкостью, не окисляясь в агрессивной среде. Алюминий и алюминиевые сплавы Алюминиевые сплавы широко применяются при производстве автомобилей, самолетов, приборостроении, тракторной промышленности, многие отрасли промышленности используют алюминий на производстве. Алюминий наиболее распространенный химический элемент после кислорода. Отлично поддается штамповки, ковке, и отливу. К тому же он гораздо легче чугуна и стали. Обладает хорошей электропроводностью. Другие металлы Медь широко применяется в производстве токопроводящих деталей. Медь тяжелее стали и чугуна. Обладает хорошей пластичностью. Свинец плохой проводник тепла и тока. В промышленности применяется при производстве аккумуляторов, кабеля и т.п. Он очень мягкий и пластичный. Часто используется в соединении с другими металлами. Цинк, своего рода тяжелый металл с сильным металлическим блеском. Большое количество цинка используется для шинкования деталей. В основном цинк применяется в сплавах. Так же цинк применяют при производстве белил. Олово, довольно мягкий металл, широко применяемы в быту и промышленности, за счет устойчивости к воздуху, воды, слабым кислотам. Так же олово входит в состав припоев, антифрикционных сплавов и бронз. Баббиты – это сплав на основе меди, цинка и олова, алюминия. В основном применяются для заливки подшипников в двигателях, турбин, насосов и т.п. Бронза, разделяется на оловянную бронзу и без оловянную. Оловянные бронзы обладают высокой антикоррозийностью, а также высокими литейными свойствами. Но широкого применения они не нашли, так как олово достаточно дорогой и дефицитный металл. Зато без оловянные бронзы нашли широкое применение в промышленности. Неметаллические материалы, используемые в машиностроении Основой машиностроения служат металлы, но также свое применение находят и ряд неметаллических материалов. Практически все они плохо передают тепло, прочные, легкие, а также на порядок дешевле металлов. Примеры неметаллических материалов: Стекло органическое Пресс-материал, используется для изготовления различных деталей путем прессования. Текстолит конструкционный Гетинакс, применяется для изготовления подшипников, маховиков и тп. Паронит, служит для выпуска прокладок между неподвижными металлическими деталями Пластины резиновые и резинотканевые Войлок технический Водостойкий, обивочный картон Ткань асбестовая
Механические свойства металлов
Механические свойства металлов определяют диапазон полезности металла и определяют ожидаемое обслуживание. Механические свойства также используются, чтобы помочь определить и идентифицировать металлы. Наиболее распространенными из рассматриваемых свойств являются прочность, твердость, пластичность и ударопрочность.
Механические свойства металлов определяют диапазон полезности металла и установить сервис, который можно ожидать.механический свойства также используются, чтобы помочь определить и идентифицировать металлы. Большинство Рассматриваются такие общие свойства, как прочность, твердость, пластичность и удар. сопротивление.Сила
Сила металла заключается в его способности противостоять действию внешних силы не ломаясь. Прочность на растяжение, также называемая пределом прочности, максимальная прочность, развиваемая в металле при испытании на растяжение. испытание на растяжение представляет собой метод определения поведения металла под фактическая нагрузка на растяжение.Этот тест обеспечивает предел упругости, удлинение, предел текучести, предел текучести, предел прочности и сокращение площади. Испытания на растяжение обычно проводятся по стандартизированным комнатные температуры, но также могут быть сделаны при повышенных температурах.
Многие машины для испытания на растяжение оборудованы для построения кривой, которая показывает нагрузка или напряжение и деформация или движение, возникающие во время испытания операция. В процессе тестирования нагрузка увеличивается постепенно и образец будет растягиваться или удлиняться пропорционально растягивающей нагрузке.
Образец будет удлиняться прямо пропорционально нагрузке во время упругая часть кривой до точки А. В этот момент образец будет продолжать удлиняться, но без увеличения нагрузки. Это известный как предел текучести стали и является концом упругой часть. В любой точке до точки А, если нагрузка устранена, образец вернется к своему первоначальному размеру.
Уступка происходит из точки А в точку Б, и это площадь пластическая деформация.Если нагрузка была устранена в точке B, образец не вернется к своему первоначальному размеру, но вместо этого взять постоянный набор. После точки B нагрузка должна быть увеличена до дальше растянуть образец.
Нагрузка увеличится до точки C, которая является пределом прочности материал. В точке C образец сломается и нагрузка больше не будет несется. Предел прочности материала при растяжении достигается путем деление предельной нагрузки на площадь поперечного сечения оригинала образец.Это обеспечивает предел прочности при растяжении в ньютонах на квадратный миллиметр (мегапаскаль, МПа) или фунты на квадратный дюйм.
Предел текучести или предел текучести получается путем деления нагрузки на урожайность. или в точке А исходной областью. Это обеспечивает показатель в фунтах на квадратный дюйм или МПа. Чрезвычайно пластичные металлы не имеют предела текучести. Они растягиваются или дают при низких нагрузках. Для этих металлов предел текучести определяется изменением удлинения.Две десятых одного процента удлинение произвольно устанавливается в качестве предела текучести. Предел текучести это предел, на который рассчитываются конструкции.
Пластичность
Пластичность металла — это свойство, которое позволяет ему растягиваться или иным образом изменил форму, не нарушая и сохранить измененный форма после того, как нагрузка была снята.Пластичность металла может быть определена из испытания на растяжение. Это сделано путем определения процента удлинения.Калибровочные метки сделаны двумя дюймов друг от друга через точку, где произойдет перелом. Увеличение калибровочная длина, относящаяся к исходной длине, умноженной на 100 удлинения Это сделано, делая метки центрального удара на расстоянии в два дюйма в уменьшенном разделе тестового купона, тестируя купон, плотно удерживая две части вместе и повторно измеряя расстояние между отметки центрального удара. Исходные два дюйма вычитаются из измеренная длина и разница делится на два и умножается на 100, чтобы получить процент удлинения.
Сокращение площади
Уменьшение площади является еще одной мерой пластичности и получается из испытание на растяжение путем измерения исходной площади поперечного сечения образец и связь его с площадью поперечного сечения после отказа.Для круглого образца измеряется диаметр и поперечное сечение Площадь рассчитывается. После того, как испытательный стержень сломан, измеряется диаметр в самой маленькой точке. Площадь поперечного сечения снова рассчитывается. Разница в области делится на исходную площадь и умножается на 100, чтобы дать процентное уменьшение площади.Эта цифра меньшее значение, чем удлинение, но обычно сообщается, когда даны механические свойства металла.
Образец для испытания на растяжение также обеспечивает другое свойство металла известный как его модуль упругости, также называемый модулем Юнга. это отношение напряжения к упругой деформации. Это относится к наклон кривой до предела текучести. Модуль упругости важно для дизайнеров и заложено во многих формулах дизайна.
Твердость
Твердость металла определяется как устойчивость металла к местное проникновение более тяжелого вещества. Твердость металлов измеряется выталкивая закаленный стальной шар или алмаз в поверхность образец под определенным весом в машине для испытания на твердость.Brinell является одним из наиболее популярных типов машин для измерения твердость. Он обеспечивает твердость по Бринеллю (BHN), которая находится в килограмм на квадратный миллиметр в зависимости от нагрузки, приложенной к закаленной мяч в килограммах и делится на площадь отпечатка, оставленного мяч в квадратных миллиметрах.
Существует несколько других систем измерения твердости. Популярная машина твердомер Роквелла, который использует алмаз, который принудительно в поверхность образца. Различные нагрузки используются для обеспечения разный масштаб. Меньшие нагрузки используются для более мягких материалов. Другой Метод с помощью твердомера Виккерса, который читает прямо, как алмаз вдавливается в поверхность металла. Другим способом является Береговый склероскоп, который использует небольшой вес, который будет подпрыгивать от поверхности металла, обеспечивающей измерение твердости.
Ударопрочность
Стойкость металла к ударам оценивается с точки зрения ударной вязкости. Металл может обладать удовлетворительной пластичностью при статических нагрузках, но может выходить из строя при динамических нагрузках или ударах.Ударная вязкость чаще всего определяется с помощью теста Шарпи. Иногда измеряется тестом Изоде. Оба типа тестов используют один и тот же тип маятниковая испытательная машина. Испытательный образец Шарпи — это балка на опоре на обоих концах и содержит выемку в центре.Образец помещен на опорах и ударил маятником на стороне, противоположной выемке. Точность и расположение выемки имеет огромное значение. Там несколько типов образцов Шарпи; тип V-образного надреза является наиболее популярный.
Ударная вязкость металла определяется путем измерения энергии впитывается в перелом. Это равно весу маятника умножить высоту, на которой высвобождается маятник, и высоту который маятник качается после того, как он ударил образец.В стандарте Метрическая практика, ударопрочность измеряется двумя способами. Один в джоулях основанный на поглощенной энергии и, два, в джоулях на квадратный сантиметр площадь разрушенной поверхности или площадь поперечного сечения под метка В англосаксонских терминах ударная вязкость — это фунт-фут. поглощенной энергии.
Твердость: Твердость — это свойство металлов, которое позволяет им противостоять вдавливанию или надрезу. Менее закаленный металл может быть легко обработан. Напротив, когда твердость металла увеличивается, обрабатываемость металла уменьшается. Когда металл слишком сильно упрочняется, он делает металл ломким, что, в свою очередь, может сделать металл неуправляемым. Увеличение содержания углерода в стали может привести к увеличению ее твердости и, следовательно, сделать ее хрупкой и менее обрабатываемой.Характер термической обработки металлов после литья с помощью процесса литья в песчаную форму, литья по выплавляемым моделям или других процессов определяет твердость металлов.
В керамике хрупкость является еще одним важным свойством. Некоторые керамики являются хрупкими, и это делает их неубиваемыми. Небольшие вмятины на этих материалах могут привести к образованию трещин, что приводит к поломке.
Размер и форма металла: Это еще один жизненно важный фактор, который определяет, насколько легко или сложно металлы могут быть обработаны.Между металлами толщиной от 50 до 400 мм, которые, по вашему мнению, легко могут быть станком? То, что размером 50 мм, может быть легко обработано, чем другое, потому что его толщина меньше, чем у другого.
Металлические формы, с другой стороны, влияют на их легкость или сложность резки на станке. Металл, который имеет полую форму, может быть легко обработан, чем квадратный толстый металлический блок.
Тип используемого станка: Обрабатываемость зависит от типа станка, используемого в процессе резки.Время, необходимое для резки металла, который работает со скоростью 20 об / сек, не может быть одинаковым, когда тот же металл режется на машине, которая имеет скорость 50 об / сек. Это с 50 об / сек будет иметь более высокую обрабатываемость, чем с оборотом 20 в секунду. Причина в том, что режущий диск первого охватывает большее расстояние в металле, чем последний.
Кроме того, твердость станка также определяет, насколько обрабатываемым может быть материал. Хорошо известно, что обработка на станках, изготовленных из алмаза, не может быть одинаковой, если один и тот же материал обрабатывается станками с низкой прочностью.Алмаз, являющийся самым твердым из известных материалов, может легко обрабатывать многие материалы благодаря своей прочности.
Охлаждающие жидкости / смазочные материалы: Охлаждающие жидкости и смазочные материалы играют важную роль при обработке материала. Поскольку смазочные материалы применяются в процессе механической обработки, обрабатываемость металлов повышается. Это связано с тем, что смазочные материалы снижают силы трения, действующие между машиной и материалом, являющимся машиной.
Кроме того, охлаждающие жидкости играют свою роль в снижении температуры обрабатывающего инструмента и обрабатываемого материала.Это уменьшает разрывную операцию, которая может возникнуть из-за чрезмерного выделения тепла. Примерами охлаждающих жидкостей, которые можно использовать при обработке, являются жидкий водород, жидкий азот и жидкий гелий.
Коэффициент трения: С идеей физики отмечено, что коэффициент трения µ прямо пропорционален силе трения F по формуле µ = F / R . В формуле R — нормальная реакция между поверхностью обрабатываемой детали и поверхностью режущего инструмента.
Согласно формуле, когда коэффициент статического трения увеличивается, сила трения между двумя поверхностями в контакте также увеличивается. Таким образом, более высокий коэффициент трения, обусловленный высокой силой трения, повышает обрабатываемость металлов. В этом контексте сила трения — это сила, необходимая для преодоления трения между двумя поверхностями, соприкасающимися в процессе обработки. Обратите внимание, что µ не может быть единица, т. Е. 100 процентов.
Свариваемость
Это свойство металла, которое указывает на легкость, с которой два одинаковых или разнородных металла соединяются плавлением (с применением давления или без него) и с использованием или без использования присадочных металлов.Капиллярное действие должно происходить между металлами, которые должны быть сварены вместе.
Перед сваркой свариваемые части очищаются от загрязнений. Примеси могут быть в форме жира, масла или даже оксидов. Смазка на свариваемом участке может быть удалена с помощью обезжиривающих средств. Примеси оксидов могут быть удалены путем флюсования. Если примеси не будут удалены, свариваемость металла будет зависеть до и после сварки.
При работе со сваркой, включающей использование присадочных металлов, для достижения оптимальной свариваемости используемый присадочный металл должен соответствовать основным металлам, которые должны быть сварены вместе.Существуют подходящие присадочные металлы для соединения некоторых основных металлов. Например, медь может использоваться в качестве присадочного металла при изготовлении стальных соединений.
Фактор, влияющий на свариваемость
Существуют уникальные факторы, которые влияют на свариваемость соединений. Эти факторы включают в себя:
- Состав металла;
- Тепловые свойства;
- Сварка техническая;
- Флюс; и
- Правильная обработка до и после сварки
Состав металла: Элементы, состоящие из металла, влияют на его свариваемость.Материалы с более высоким содержанием серы и фосфора имеют более низкую свариваемость. Если взять, например, серое железо, его свариваемость низкая из-за высокого содержания в нем серы и фосфора. Опять же, когда интерес представляет чугун с шаровидным графитом, его свариваемость больше, чем у серого чугуна, потому что он содержит меньшее количество серы и фосфора.
Тепловые свойства: Слово тепловое может использоваться вместо тепловой энергии. Скорость, с которой любой металл проводит тепло, влияет на свариваемость этого металла.Любой металл, который имеет хорошую теплопроводность, также имеет хорошую свариваемость.
Техника сварки: Специальные знания о сварке также определяют свариваемость любого соединения. Между сваркой, выполненной сварщиком, который много лет имел хороший опыт в сварке, и «молодым мальчиком», который только учится сварке, есть четкие различия. Когда эксперт сваривает соединение, его свариваемость выглядит лучше и сильнее, чем когда его проводит простой ученик. Таким образом, свариваемость любого соединения зависит от применяемого навыка сварки, а также от технологии, используемой в процессе сварки.
Флюсование и присадочный металл: Флюсование выполняется на металлах во время сварки для удаления примесей; особенно оксидные примеси. Материал для флюса определяет вид флюса, который будет использоваться на нем. Когда флюс делается на деталях, чтобы соединиться вместе, капиллярное воздействие на металл может легко иметь место.
Правильная обработка до и после сварки: Это важный фактор, который определяет свариваемость любого металла. Обработка поверхностей перед сваркой может определить, насколько сварным может быть соединение.Частями обработки могут быть правильная сборка двух металлов, подлежащих сварке, а также сглаживание двух точек для обеспечения хорошего соединения между ними. Опять же, определенные обработки на сваренной части могут продлить срок службы части.
Castable
Что такое литейность? Литейность — это свойство металла, которое указывает на легкость изготовления отливок с меньшими затратами, меньшими дефектами и с меньшими затратами времени. При изготовлении отливки должна быть тенденция к отливке без каких-либо дефектов.Это одна из причин, по которой отливки подвергаются проверке после их изготовления. Отливка без дефектов не может легко выйти из строя в результате коррозии или напряжения.
- Пластичность: Это способность металла вытягиваться в тонкий лист или в проволоку. Это может быть достигнуто путем установки давления на металл и последующего вытягивания под действием большой силы или приложения силы путем операции вытягивания. Литые или изготовленные металлы обычно демонстрируют направленные свойства, особенно в отношении пластичности, и обычно литой металл является менее пластичным, чем металл в кованом или отожженном состоянии («Механические свойства металлов» Дональда Маклина).
МЕХАНИЧЕСКИЕ СВОЙСТВА МЕТАЛЛОВ И СПЛАВОВ
Механические свойства имеют первостепенное значение в более крупных промышленных применениях металлов, поэтому они требуют большого внимания при их исследовании.
Сила. — Прочность материала является свойством сопротивления внешним нагрузкам или нагрузкам без повреждения конструкции. Термин предел прочности относится к удельному напряжению (фунт на квадратный дюйм), создаваемому в материале максимальной медленно прикладываемой нагрузкой, которой материал может противостоять без разрыва при испытании на растяжение.Испытание на растяжение чаще всего применяется к металлам, поскольку оно говорит об их свойствах намного больше, чем любое другое испытание. В металлургии разрушение часто называют разрушением, разрывом или разрушением; разрушение металла — это название поверхности, на которой произошел разрыв.
Прочность металлов и сплавов зависит от двух факторов: прочности кристаллов, из которых построены металлы, и прочности сцепления между этими кристаллами.Самым сильным из известных веществ является вольфрамовая проволока электрических ламп накаливания. Чистое железо слабое, но при сплавлении с углеродом для производства стали сталь может быть прочнее любого из чистых металлов, кроме вольфрама.
Стресс и напряжение. — Напряжение — это сила внутри тела, которая сопротивляется деформации из-за внешней нагрузки. Если эта нагрузка действует на поверхность единичной площади, она называется единичной силой, а напряжение, противостоящее ей, составляет единичных напряжений. Таким образом, в количественном отношении напряжение представляет собой силу на единицу площади; на европейском континенте это выражается в килограммах на квадратный миллиметр, в Соединенных Штатах — фунтов на квадратный дюйм, в то время как в Англии обычно используются длинные тонны на квадратный дюйм.
Когда внешняя сила действует на упругий материал, материал деформируется, и деформация пропорциональна нагрузке. Это искажение или деформация — это деформация , деформация измеряется в Соединенных Штатах и в Англии в дюймах на дюйм, а в Европе — в сантиметрах на сантиметр. Единица деформации, то есть отношение расстояний или длин.
Эластичность. — Любой материал, подверженный внешней нагрузке, искажается или деформируется.Упругие напряженные материалы возвращаются к своим первоначальным размерам, когда нагрузка освобождается, если нагрузка не слишком велика. Такое искажение или деформация пропорциональны величине нагрузки до определенной точки, но когда нагрузка слишком велика, материал постоянно деформируется, а когда нагрузка увеличивается до определенной точки, материал разрушается. Свойство восстановления первоначальных размеров после снятия внешней нагрузки известно как упругость .
Модуль упругости. — В пределах предела упругости отношение напряжения к деформации известно как модуль упругости (т.е. мера упругости).
Модуль упругости выражает жесткость материала. Для стали и большинства металлов это постоянное свойство, на которое очень мало влияют термическая обработка, горячая или холодная обработка или фактическая предел прочности металла. Их модули упругости показывают, что когда одинаковые по размеру стержни из стали и алюминия подвергаются одинаковой нагрузке, результирующая упругая деформация в алюминии будет почти в три раза выше, чем в стальном стержне.
Пропорциональный предел упругости. — Металлы обычно не эластичны во всем диапазоне нагрузок. Предел пропорциональности напряжения к деформации известен как пропорциональный предел . Предел упругости — это наибольшее удельное напряжение, которое выдержит испытываемый образец и все еще вернется к своим первоначальным размерам при снятии нагрузки. Предел пропорциональности и предел упругости в металлах очень близки друг к другу, настолько, что их часто путают, и в настоящее время принято объединять их в единый термин пропорциональный предел упругости. Это важное свойство, напряжение, которое не должно превышаться при проектировании.
Природа упругости. — Эластичность металлического вещества является функцией сопротивления его атомов разделению, сжатию или вращению друг относительно друга и, таким образом, является фундаментальным свойством материала. Таким образом, упругость демонстрируется как функция атомных сил. Это объясняет, почему модуль упругости прочной и хрупкой термически обработанной легированной стали точно такой же, как и у сравнительно слабой и пластичной отожженной стали.
Доходность. — Это точка на кривой напряжение-деформация, при которой напряжение снижается или фактически уменьшается, пока деформация продолжается. Этот термин строго применим только к мягким сталям, поскольку определяющая его характеристика не встречается ни в других металлах, ни в легированных сталях, ни даже в холоднокатаных или нормализованных низкоуглеродистых сталях.
Максимальная сила. — Наибольшая нагрузка, которую выдержал образец, деленная на первоначальную площадь поперечного сечения, называется пределом прочности на растяжение или пределом прочности детали.
Пластичность. — Пластичность — это способность металла постоянно деформироваться при растяжении без разрушения. В частности, термин обозначает способность вытягиваться от большего к меньшему диаметру проволоки. Такая операция, очевидно, включает в себя как удлинение, так и уменьшение площади, и значения этих двух характеристик металла, определенные в испытании на растяжение, обычно берут за меру пластичности металла.
Стойкость. — Прочность была определена как свойство поглощения значительной энергии до разрушения. Это мера общей энергопоглощающей способности материала, включая энергию как упругой, так и пластической деформации при постепенно прикладываемой нагрузке. Одним из наиболее распространенных испытаний на ударную вязкость является «испытание на удар, при котором измеряется энергия, поглощенная при разрушении образца внезапным ударом.
Природа выносливости. — Прочность металла определяется величиной скольжения, которое может произойти внутри кристаллов, не приводя к разрыву металла.Возможно, это результат попеременных проскальзываний и заклиниваний, которые каждая клиновидная кристаллографическая плоскость удерживает до тех пор, пока не будет приложено большее напряжение. Хрупкий металл или сплав либо не прекратит скольжение после достижения упругой деформации, либо остановится только на короткий период перед разрушением. Очевидно, что последовательная остановка и скольжение вызовут деформацию; следовательно, жесткие металлы и сплавы часто являются наиболее пластичными и пластичными.
Иногда кристаллы металла могут быть жесткими, но границы кристаллов могут содержать примеси, так что наименьшая деформация кристаллической массы может привести к растрескиванию хрупкого материала с границами зерен.Это относится к стали, содержащей значительное количество фосфора, и меди, содержащей висмут.
Гибкость. — Растяжимость — это свойство металла, которое допускает постоянную деформацию при сжатии без разрыва. В частности, это означает, что можно свернуть или забить тонкие листы. Свойство пластичности аналогично пластичности, но не одинаково, и разные металлы не обладают двумя свойствами в одинаковой степени: хотя свинец и олово относительно высоки в отношении пластичности, им не хватает необходимой прочности на растяжение быть втянутым в тонкую проволоку.Большинство металлов имеют повышенную пластичность и пластичность при более высоких температурах. Например, железо и никель очень податливы при ярко-красной жаре (1000 ° С).
Хрупкость. — Хрупкость подразумевает внезапную неудачу. Это свойство разрушения без предупреждения, то есть без видимой постоянной деформации. Это противоположность прочности в том смысле, что хрупкое тело имеет небольшое сопротивление разрыву после того, как оно достигает своего предела упругости. Хрупкость является противоположностью пластичности в том смысле, что она предполагает разрыв без значительной деформации.Часто твердые металлы являются хрупкими, но их не следует путать или использовать как синонимы.
Усталостный сбой. — Если металл подвергается частым повторениям напряжения, он в конечном итоге разорвется и разрушится.
Чередование стресса будет вызывать сбой быстрее, чем повторение стресса. Под «чередованием напряжений» подразумевается чередование растяжения и сжатия в любом волокне. Разрушение металлов и сплавов при повторяющихся или переменных напряжениях, слишком маленькое, чтобы вызывать постоянную деформацию при статическом применении, называется усталостным разрушением .
Коррозия Усталость. — Если элемент подвергается воздействию также агрессивных веществ, таких как влажная атмосфера или масло, не освобожденное от кислоты, напряжение, необходимое для разрушения, значительно ниже. Сильнейшие стали будут разрушаться при усталости и коррозии с напряжением на единицу волокна не более 24000 фунтов на квадратный дюйм, даже когда их предел прочности может указывать на то, что они могут выдержать гораздо более высокое напряжение. Интересно отметить, что удельное напряжение чрезвычайно прочной термически обработанной легированной стали, подверженной коррозионной усталости, будет не больше, чем у относительно слабой конструкционной стали.Важность защиты поверхностей усталостных элементов от коррозии путем цинкования, металлизации и т. Д., Если и когда это возможно, очевидна.
Твердость. — Качество твердости является сложным, и детальное исследование показало, что оно представляет собой сочетание ряда физико-механических свойств. Он чаще определяется в терминах метода, используемого для его измерений, и обычно означает устойчивость вещества к вдавливанию. Твердость также может быть определена с точки зрения устойчивости к царапанию и, таким образом, связана с износостойкостью.Термин твердость иногда используется для обозначения жесткости или характера деформируемых изделий, поскольку твердость металла при вдавливании тесно связана с его прочностью на растяжение.
В инженерной практике стойкость металла к проникновению твердым режущим инструментом обычно принимается как определяющая твердость. Был разработан ряд стандартизированных испытательных машин и пенетраторов, наиболее распространенными из которых являются машины Бринелля, Роквелла и Виккерса.
В тесте Бринелля шарик из закаленной стали диаметром 10 мм вдавливается в поверхность испытуемого материала под нагрузкой 500 или 3000 кг и измеряется площадь вдавливания.Затем твердость по Бринеллю выражается как отношение приложенной нагрузки к площади отпечатка.
В тестах Rockwell используется ряд различных шкал тестирования с использованием различных пенетраторов и нагрузок. Наиболее часто используемые весы — это шкала «C», в которой используется алмазный пенетратор с большой нагрузкой 150 кг, и шкала «B», в которой используется шарик из закаленной стали диаметром 1/16 дюйма при большой нагрузке 100 кг. В этом испытании в качестве меры твердости принимается разница глубины проникновения между той, которая создается небольшой нагрузкой в 10 кг, и наложенной большой нагрузкой.
В тесте Виккерса используется индентор с алмазной пирамидой на квадратной основе, который может быть загружен от 1 до 120 кг. Как и в тесте Бринелля, твердость выражается в единицах приложенной нагрузки, деленной на площадь поверхности пирамидального оттиска.
Тест Бринелля обычно используется только для довольно толстых сечений, таких как прутки и поковки, в то время как тест Роквелла обычно используется как для толстых, так и для тонких сечений, таких как полоса и трубы. Поверхностный камень Роквелла можно использовать на кусках толщиной до 0.010 дюйма. Тестер Vickers чаще всего используется в качестве лабораторного инструмента для очень точных измерений твердости, а не в качестве инструмента контроля производства.
Тест склероскопа по Шору измеряет устойчивость, а не твердость, хотя эти две взаимосвязи. Склероскоп измеряет отскок падающего молотка от испытательной поверхности, и число твердости выражается как высота отскока в терминах максимального отскока от полностью закаленной высокоуглеродистой стали.
Природа твердости и мягкости. — Сопротивление металла проникновению другого тела, очевидно, частично зависит от сопротивления его межатомных связей. На это указывает почти точная параллель порядка твердости металлов и их модулей упругости. Единственным известным исключением является соотношение магния и алюминия. Магний будет царапать алюминий, хотя его модуль упругости и его средняя прочность межатомных связей меньше.
Дата: 2015-12-24; просмотр: 1083
.
Механические свойства материалов | MechaniCalc
ПРИМЕЧАНИЕ. Эта страница использует JavaScript для форматирования уравнений для правильного отображения. Пожалуйста, включите JavaScript.
Механические свойства материала влияют на его поведение при загрузке. Модуль упругости материала влияет на то, насколько он отклоняется под нагрузкой, а прочность материала определяет напряжения, которые он может выдержать до того, как он выйдет из строя. Пластичность материала также играет важную роль в определении момента разрушения материала при его загрузке за пределы его предела упругости.Поскольку каждая механическая система подвергается нагрузкам во время работы, важно понимать, как ведут себя материалы, из которых состоят эти механические системы.
На этой странице описаны механические свойства материалов, которые имеют отношение к проектированию и анализу механических систем.
Содержание
стресс и напряжение
Соотношение между напряжением и деформацией в материале определяют, подвергая образец материала испытанию на растяжение или сжатие.В этом испытании к испытательному образцу прикладывается неуклонно увеличивающаяся осевая сила, а прогиб измеряется при увеличении нагрузки. Эти значения могут быть нанесены в виде кривой отклонения нагрузки. Прогиб образца для испытаний зависит как от модуля упругости материала, так и от геометрии образца (площадь и длина). Поскольку нас интересует поведение материала вне зависимости от геометрии, полезно обобщить данные, чтобы устранить влияние геометрии. Это делается путем преобразования значений нагрузки в значения напряжения и преобразования значений прогиба в значения деформации:
В уравнении для напряжения P — это нагрузка, а A 0 — исходная площадь поперечного сечения образца для испытаний.В уравнении для деформации L — текущая длина образца, а L 0 — исходная длина.
Кривая напряжения-деформации
Значения напряжения и деформации, определенные по испытанию на растяжение, можно построить в виде кривой напряжения-деформации , как показано ниже:
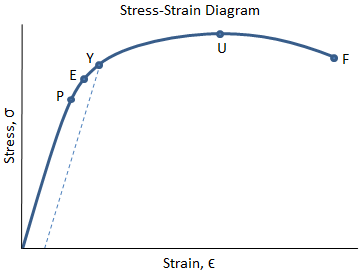
На диаграмме выше есть несколько интересных мест:
- P: Это предел пропорциональности , который представляет максимальное значение напряжения, при котором кривая напряжения-деформации является линейной.
- E: Это предел упругости , который представляет собой максимальное значение напряжения, при котором нет постоянного набора. Даже если кривая не является линейной между пределом пропорциональности и пределом упругости, материал все еще остается упругим в этой области, и если нагрузка будет снята в этой точке или ниже, образец вернется к своей первоначальной длине.
- Y: Это предел текучести , который представляет значение напряжения, выше которого напряжение начнет быстро расти.Напряжение в точке текучести называется пределом текучести , S или . Для материалов без четко определенного предела текучести он обычно определяется с использованием метода смещения 0,2% , в котором рисуется линия, параллельная линейной части кривой, которая пересекает ось х при значении деформации 0,002. Точка, в которой линия пересекает кривую напряжение-деформация, обозначается как предел текучести.
- U: Эта точка соответствует пределу прочности , S или , который является максимальным значением напряжения на диаграмме напряжения-деформации.Предел прочности также упоминается как прочность на растяжение . После достижения предельного напряжения образцы пластичных материалов будут иметь шейку , в которой площадь поперечного сечения в локализованной области образца значительно уменьшается.
- F: Это точка разрушения или точка разрушения , которая является точкой, в которой материал разрушается и разделяется на две части.
Кривые напряжения-деформации обычно необходимы при анализе сконструированного компонента.Однако данные о напряжении не всегда могут быть легко доступны. В этом случае довольно просто аппроксимировать кривую напряжения-деформации материала, используя уравнение Рамберга-Осгуда.
Истинный стресс и напряжение
Инженеры обычно работают с инженерным напряжением , которое представляет собой силу, деленную на исходную площадь образца перед нагрузкой: σ = P / A 0 . Однако при загрузке материала площадь уменьшается. истинное напряжение , является величиной напряжения в материале с учетом фактической площади образца.Поскольку площадь уменьшается при загрузке материала, истинное напряжение выше, чем инженерное напряжение.
На рисунке ниже показана техническая кривая напряжения-деформации по сравнению с истинной кривой деформации-напряжения. Поскольку инженерное напряжение рассчитывается как сила, деленная на исходную площадь (которая является постоянной величиной), кривая инженерного напряжения-деформации имеет ту же форму, что и кривая нагрузки-прогиба. Кривая инженерного напряжения-деформации падает после достижения предельной прочности, потому что сила, которая может поддерживаться материалом, падает, когда он начинает сужаться.Однако значение напряжения в истинной кривой напряжение-деформация всегда увеличивается при увеличении деформации. Это потому, что мгновенное значение площади используется при расчете истинного напряжения. Даже когда сила, поддерживаемая материалом, падает, уменьшение площади образца перевешивает уменьшение силы, и напряжение продолжает увеличиваться.
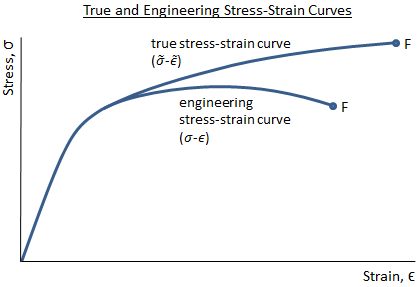
Следует отметить, что инженерное напряжение и истинное напряжение по существу одинаковы в линейно-упругой области кривой напряжение-деформация.Поскольку инженеры, как правило, работают в этой линейно-упругой области (проектирование конструкции, которая предназначена для работы за пределами предела упругости, нечасто), допустимо работать с инженерным напряжением, а не с настоящим напряжением.
Техническая деформация — это изменение длины, деленное на исходную длину: ε = ΔL / L 0 . Вместо того, чтобы просто рассчитывать одно значение ΔL, учтите, что изменение длины делится на множество небольших приращений ΔL j .Деформация также рассчитывается с небольшими приращениями: ε j = ΔL j / L j , где ΔL j — изменение длины приращения, а L j — длина в начале приращение. Когда эти приращения становятся бесконечно малыми, суммация деформаций приближается к истинной деформации:
Если предполагается, что объем постоянен на всем протяжении отклонения, то истинное напряжение и деформация могут быть рассчитаны как:
True Stress: | |
Истинный штамм: |
где и — истинные напряжения и деформации, а σ и ε — инженерные напряжения и деформации.
закон Гука
Ниже предела пропорциональности кривой напряжение-деформация зависимость между напряжением и деформацией является линейной. Наклон этой линейной части кривой напряжения-деформации представляет собой модуль упругости , E, также называемый модулем Юнга и модулем упругости . Закон Гука выражает взаимосвязь между модулем упругости, напряжением и деформацией в материале в линейной области:
σ = E ε
, где σ — значение напряжения, а ε — значение напряжения.
закон Гука в сдвиге
Закон Гука также имеет форму, касающуюся касательных напряжений и деформаций:
τ = G γ
где τ — значение напряжения сдвига, γ — значение напряжения сдвига, а G — модуль упругости сдвига. Модуль упругости и модуль сдвига связаны:
где ν — коэффициент Пуассона.
Более подробную информацию о законе Гука можно найти здесь.
коэффициент Пуассона
При приложении нагрузки к материалу материал удлиняется, а площадь поперечного сечения уменьшается.Это уменьшение площади поперечного сечения называется боковой деформации , и оно связано с осевой деформацией по коэффициенту Пуассона , ν. Для круглого образца это уменьшение площади реализуется как уменьшение диаметра, а коэффициент Пуассона рассчитывается как:
Коэффициент Пуассона применяется только в пределах области упругости кривой напряжение-деформация, и обычно он составляет около 0,3 для большинства металлов. Теоретический максимальный предел коэффициента Пуассона составляет 0,5.
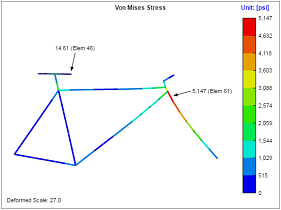
Упрочнение деформации
После того, как материал уступает, он начинает испытывать высокую скорость пластической деформации.Как только материал уступает, он начинает деформироваться, что увеличивает прочность материала. На приведенных ниже кривых напряжение-деформация видно, что прочность материала увеличивается между пределом текучести Y и пределом прочности в точке U. Это увеличение прочности является результатом деформационного упрочнения.
Пластичный материал на рисунке ниже способен выдерживать нагрузку даже после достижения предела прочности. Однако после достижения предельной прочности в точке U увеличение прочности из-за деформационного упрочнения опережает снижение несущей способности из-за уменьшения площади поперечного сечения.Между пределом прочности в точке U и точкой F разрушения инженерная прочность материала уменьшается и происходит образование шей.
На приведенной ниже кривой напряженно-деформированного состояния для хрупкого материала показана очень небольшая область деформационного упрочнения между пределом текучести Y и пределом прочности U. Обратите внимание, однако, что хрупкий материал может фактически не проявлять какого-либо деформирующего поведения или деформационного упрочнения вообще — в этом случае материал потерпит неудачу на линейной части кривой.Это чаще встречается в таких материалах, как керамика или бетон.
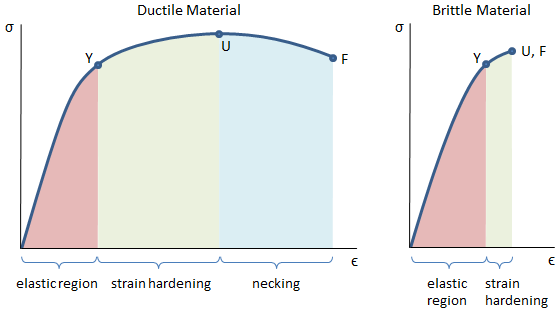
Поскольку область деформационного упрочнения находится между пределом текучести и пределом текучести, отношение предельной прочности к пределу текучести иногда используется в качестве меры степени деформационного упрочнения в материале. Это соотношение : коэффициент деформационного упрочнения :
коэффициент деформационного упрочнения = S tu / S ty
Согласно Доулингу, типичные значения коэффициента деформационного упрочнения в металлах колеблются примерно от 1.От 2 до 1,4.
Если материал нагружен сверх предела упругости, он подвергнется постоянной деформации. После выгрузки материала упругая деформация будет восстановлена (возврат к нулю), но пластическая деформация сохранится.
На рисунке ниже показана кривая напряжения-деформации материала, который был загружен за пределы предела текучести Y. При первой загрузке материала напряжение и деформация соответствовали кривой OY-Y ‘, а затем нагрузка была удалена после того, как стресс достиг точки Y ‘.Поскольку материал был загружен за пределы предела упругости, восстанавливается только упругая часть деформации — в материале теперь имеется некоторая постоянная деформация. Если материал должен был быть загружен снова, он следовал бы за линией O’-Y’-F, где O’-Y ‘- предыдущая линия разгрузки. Точка Y ‘является новой точкой доходности. Обратите внимание, что линия O’-Y ‘является линейной с наклоном, равным модулю упругости, и точка Y’ имеет более высокое значение напряжения, чем точка Y. Следовательно, материал теперь имеет более высокий предел текучести, чем был ранее, что является результатом деформационного упрочнения, которое произошло при нагружении материала сверх предела упругости.
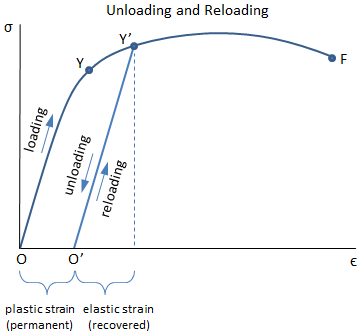
Благодаря деформационному упрочнению материал теперь имеет большую упругую область и более высокий предел текучести, но его пластичность уменьшена (деформация между точками Y’-F меньше, чем деформация между точками Y-F).
Упругий и пластиковый штамм
До предела упругости деформация материала также является упругой и будет восстановлена после снятия нагрузки, чтобы материал вернулся к своей первоначальной длине.Однако, если материал нагружен за предел упругости, в материале будет происходить постоянная деформация, которая также называется пластической деформацией.
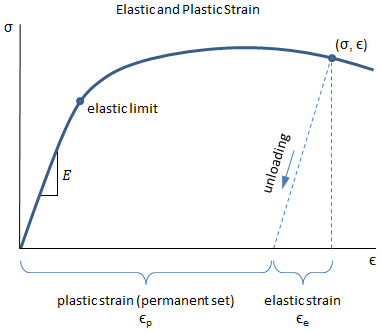
На рисунке выше в материале существуют как упругие, так и пластические деформации. Если нагрузка снимается в указанной точке (σ, ε), напряжение и деформация в материале будут следовать линии разгрузки, как показано. Упругая деформация и пластическая деформация указаны на рисунке и рассчитываются как:
Упругий штамм: | ε e = σ / E |
Пластиковый штамм: | ε p = ε — ε e |
где σ — напряжение в указанной точке, ε — деформация в указанной точке, а E — модуль упругости.
Пластичность
Пластичность является показателем того, сколько пластической деформации материал может выдержать, прежде чем он сломается. Пластичный материал может выдерживать большие нагрузки даже после того, как он начал давать. Общие показатели пластичности включают % удлинения и сокращения в области , как обсуждалось в этом разделе.
После разрушения образца во время испытания на растяжение измеряется окончательная длина образца и рассчитывается пластическая деформация при разрушении, также известная как деформация при разрыве :
где L f — конечная длина образца после разрыва, а L o — начальная длина образца.Важно отметить, что после разрушения образца упругая деформация, существовавшая в то время, когда образец находился под нагрузкой, восстанавливается, поэтому измеренная разница между конечной и начальной длинами дает пластическую деформацию при разрушении. Это показано на рисунке ниже:
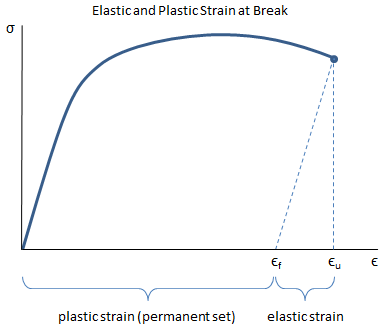
На чертеже видно, что пластическая деформация при разрушении, ε f , представляет собой деформацию, остающуюся в материале после восстановления упругой деформации.Предельная деформация, ε u , представляет собой общую деформацию при разрушении (пластическая деформация плюс упругая деформация).
Удлинение % рассчитывается по пластической деформации при разрушении следующим образом:
Процентное удлинение является обычно предоставляемым свойством материала, поэтому пластическая деформация при разрушении обычно рассчитывается из процентного удлинения:
ε f = EL / 100%
Предельная деформация учитывает как пластическую, так и упругую деформацию при разрушении:
ε u = ε f & plus; S tu / E
Другим важным свойством материала, которое можно измерить во время испытания на растяжение, является уменьшение в области , которое рассчитывается по формуле:
Помните, что на процент удлинения и уменьшения площади приходится пластмассовых компонентов, — осевое и боковое деформации соответственно.
ковкие и хрупкие материалы
Пластичный материал может противостоять большим деформациям даже после того, как он начал давать, тогда как хрупкий материал может противостоять небольшому или никакому пластическому напряжению. На рисунке ниже показаны типичные кривые напряжения-деформации для пластичного материала и хрупкого материала.
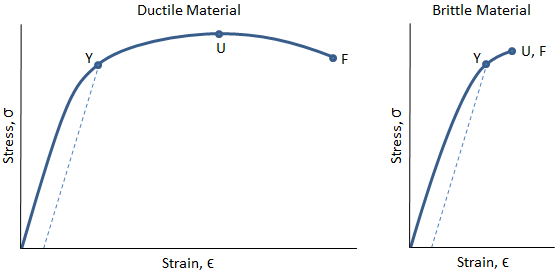
На рисунке выше видно, что пластичный материал значительно деформируется до точки разрушения F.Существует длинная область между пределом текучести в точке Y и пределом прочности в точке U, где материал подвергается деформационному упрочнению. Существует также длинная область между пределом прочности в точке U и точкой F разрушения, в которой площадь поперечного сечения материала быстро уменьшается и происходит сужение.
Видно, что хрупкий материал на рисунке выше разрушается вскоре после предела текучести. Кроме того, предел прочности совпадает с точкой разрушения.В этом случае шеек не происходит.
Поскольку площадь под кривой напряжения-деформации для пластичного материала выше, чем площадь под кривой напряжения-деформации для хрупкого материала, пластичный материал имеет более высокий модуль ударной вязкости — он может поглощать гораздо больше энергии деформации, прежде чем он брейки. Кроме того, поскольку пластичный материал сильно деформируется перед разрушением, его прогибы до разрушения будут очень высокими. Таким образом, будет визуально очевидно, что отказ неизбежен, и могут быть предприняты действия для разрешения ситуации до того, как произойдет катастрофа.
Типичная кривая напряжения-деформации для хрупкого материала показана ниже. Эта кривая показывает напряжение и деформацию для растягивающей и сжимающей нагрузки. Обратите внимание, что материал гораздо более устойчив к сжатию, чем к растяжению, как с точки зрения напряжения, которое он может выдержать, так и с точки зрения деформации до разрушения. Это типично для хрупкого материала.
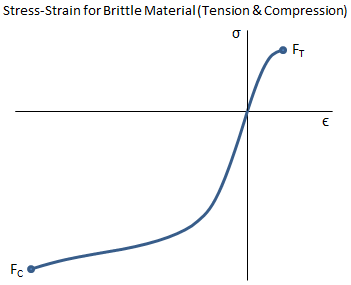
Энергия деформации
Когда сила прикладывается к материалу, материал деформируется и накапливает потенциальную энергию, как пружина.Энергия деформации (то есть количество потенциальной энергии, накопленной вследствие деформации) равна работе, затраченной на деформацию материала. Общая энергия деформации соответствует площади под кривой отклонения нагрузки и имеет единицы измерения in-lbf в стандартных единицах США и N-m в единицах СИ. Энергия упругой деформации может быть восстановлена, поэтому, если деформация остается в пределах предела упругости, тогда вся энергия деформации может быть восстановлена.
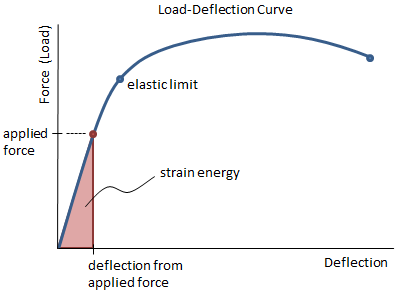
Энергия деформации рассчитывается как:
Общая форма: | U = работа = ∫ F dL | (область под кривой отклонения нагрузки) |
В пределах упругого предела: | (область под кривой отклонения нагрузки) | |
(потенциальная энергия пружины) |
Обратите внимание, что есть два уравнения для энергии деформации в пределах предела упругости.Первое уравнение основано на площади под кривой отклонения нагрузки. Второе уравнение основано на уравнении для потенциальной энергии, запасенной в пружине. Оба уравнения дают одинаковый результат, они просто выводятся несколько по-разному.
Плотность энергии деформации
Иногда более удобно работать с плотностью энергии деформации , которая является энергией деформации на единицу объема. Это равно площади под диаграммой напряжения-деформации:
где пределы в интеграле, приведенном выше, составляют от деформации от 0 до ε около , которая представляет собой деформацию, существующую в загруженном материале.
Обратите внимание, что единицы плотности энергии деформации — это фунты на кв. Дюйм в обычных единицах США и Па в единицах СИ.
Модуль упругости
Модуль упругости представляет собой количество энергии деформации на единицу объема (то есть плотность энергии деформации), которое материал может поглотить без возникновения постоянной деформации. Модуль упругости рассчитывается как площадь под кривой напряжение-деформация до предела упругости. Однако, поскольку предел упругости и предел текучести, как правило, очень близки, упругость может быть аппроксимирована как площадь под кривой напряжения-деформации до предела текучести.Поскольку кривая напряжения-деформации очень близка к пределу упругости, эта область является треугольной.
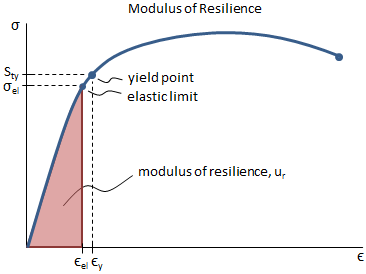
Модуль упругости рассчитывается как:
общая форма | |
треугольной формы |
где эл и эл — это напряжение и деформация на пределе упругости, S ty — предел текучести при растяжении, а Е — модуль упругости.
Обратите внимание, что единицы модуля упругости такие же, как единицы плотности энергии деформации, которые в фунтах на квадратный дюйм в обычных единицах США и Па в единицах СИ.
Модуль Прочности
Модуль ударной вязкости представляет собой количество энергии деформации на единицу объема (то есть плотность энергии деформации), которое материал может поглотить непосредственно перед тем, как разрушится. Модуль ударной вязкости рассчитывается как площадь под кривой напряжения-деформации до точки разрушения.
Точный расчет общей площади под кривой напряжение-деформация для определения модуля ударной вязкости несколько сложен. Тем не менее, грубое приближение может быть сделано путем деления кривой напряжения-деформации на треугольное сечение и прямоугольное сечение, как показано на рисунке ниже. Высота секций равна среднему пределу текучести и пределу прочности.
Модуль ударной вязкости может быть аппроксимирован как:
где S ty — предел текучести при растяжении, S tu — предел прочности при растяжении, ε y — деформация при растяжении, ε u — предел прочности при растяжении (общая деформация при разрушении), а E — это предел текучести. модуль упругости.
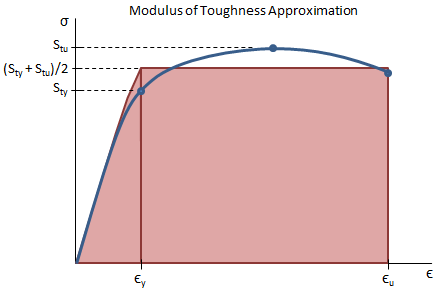
Лучшее вычисление модуля ударной вязкости можно сделать, используя уравнение Рамберга-Осгуда для аппроксимации кривой напряжение-деформация, а затем интегрируя площадь под кривой.
Следует отметить, насколько сильно площадь под пластической областью кривой напряжения-деформации (то есть прямоугольной части) влияет на ударную вязкость материала. Поскольку пластичный материал может выдерживать намного большую пластическую деформацию, чем хрупкий материал, пластичный материал, следовательно, будет иметь более высокий модуль ударной вязкости, чем хрупкий материал с таким же пределом текучести.Несмотря на то, что конструкции обычно предназначены для удержания напряжений в упругой области, пластичный материал с более высоким модулем ударной вязкости лучше подходит для применений, в которых может произойти случайная перегрузка.
Обратите внимание, что единицы измерения модуля ударной вязкости совпадают с единицами плотности энергии деформации, которые в фунтах на квадратный дюйм в обычных единицах США и Па в единицах СИ.
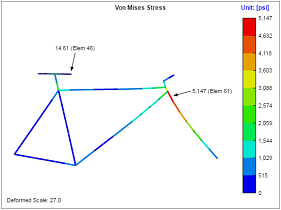
Приближение деформации от напряжения
Кривые напряжения-деформации для материалов обычно необходимы; однако без репрезентативных данных испытаний необходимо составить аппроксимацию кривой.Уравнение Рамберга-Осгуда может быть использовано для аппроксимации кривой напряжения-деформации для материала, знающего только предел текучести, предел прочности, модуль упругости и относительное удлинение материала в процентах (все из которых являются общими и легко доступными свойствами).
Уравнение Рамберга-Осгуда для полной деформации (упругой и пластической) как функции напряжения:
где σ — значение напряжения, E — модуль упругости материала, S ty — предел текучести материала при растяжении, а n — показатель деформационного упрочнения материала, который можно рассчитать по известным свойствам материала как показано позже в этом разделе. (Примечание 1)
Объяснение вывода уравнения Рамберга-Осгуда приводится в следующих разделах.
Уравнение Рамберга-Осгуда
Рамберг и Осгуд предложили взаимосвязь, которая часто используется для аппроксимации кривой напряжения-деформации для материала. Это соотношение является экспоненциальным и используется для описания пластической деформации в материале. Кривая напряжение-деформация в пластической области может быть аппроксимирована:
,