Печи для производства угля — Корпорация «Лес Вологодчины»
Углевыжигательные печи Корпорация «Лес Вологодчины» производит с 2005 года. На данном этапе имеем огромный опыт успешной работы по выпуску и запуску углевыжигательных печей. Благодаря полученному опыту был разработан и протестирован широкий ассортимент печей с выходом качественного древесного угля категории (А). Все углевыжигательные печи изготавливаются с применением жаропрочной стали, что в разы увеличивает срок эксплуатации.
Печь для производства угля состоит из камеры со встроенным котлом и теплообменником, что позволяет экономить сырье, сократить время цикла. Не надо смотреть на технологии вчерашних дней и греть улицу внешним теплоносителем. За счет герметичности камеры и отсутствия контакта с дымовыми газами на выходе получается качественный древесный уголь с минимальным содержанием золы. Все печи укомплектованы системами дожига пиролизных газов, пароотведения, аварийной системой остывания, системой подачи воды.
Герметичная камера и дожиг пиролизных газов в топке делают производство древесного угля более экологически чистым. Эксплуатация углевыжигательной печи «Заря» проста и удобна, экономически выгодна, благодаря простой конструкции.
Печи для производства угля есть в наличии.
Более точная информация, цена, как заказать у менеджера по
т. +7921-232-71-15
Назад
Далее
Технические характеристики углевыжигательных печейМарка печи для угля | ПУ-1/1 | Малютка | Заря-14 | Заря-25 |
Полезный объём пиролизной камеры, м3 | 1 | 7 | 14 | 25 |
Загружаемый объём сырья (Р,0,4-0,6), м3 | 0,6 | 3 | 6-7 | 12-14 |
Выход угля, кг (за один цикл) | 90 | 450 | 900-1200 | 1800-2100 |
Количество циклов за месяц (в зависимости от влажности сырья) | 9-12 | 9-12 | 7-12 | 7-12 |
Теплоноситель | внутренний | внутренний | внутренний | внутренний |
Система дожига пиролизных газов | + | + | + | + |
Утеплитель базальтовый Вайред мат Rockwool 40 | + | + | + | + |
Размеры Д*Ш*В, мм | 1200*1200*1500 | 2700*2000*2200 | 4000*2000*2200 | 6400*2450*2600 |
Вес, кг | 600 | 1900 | 3000 | 5000 |
Территория для установки, мм | 4000*3000 | 6000*3000 | 8000*5000 | 12000*5000 |
Выслать коммерческое предложение с ценами
Видео обзор работы печей по запросу у менеджера
т.: +7921-232-71-15
Печь предназначена для переработки древесины в древесный уголь методом термического разложения без доступа кислорода. Данный метод обеспечивает максимальное качество получаемого продукта из любой породы дерева. Конструктивная особенность данной печи обеспечивает: экологическую чистоту процесса, большое загрузочные окно позволяет механизировать загрузочные работы, возможность поворота пиролизной камеры, сокращает время выгрузки и физические затраты. Время полного цикла, благодаря изменениям, значительно снижается.
Печь также можно использоваться для утилизации бытовых отходов, горючих отходов предприятий так как при сжигании все дымовые газы проходят через топку с температурой во время горения пиролизных газов 1100 Сº.
Печь состоит из пиролизной камеры, площадки крепления пиролизной камеры, подъемного устройства (лебёдки), конденсаторной емкости.
Полезный объём пиролизной камеры, м3 | 14 |
Загружаемый объём сырья (Р,0,4-0,6), м3 | 6-7 |
Выход угля, кг (за один цикл) | 900-1200 |
Количество циклов за месяц (в зависимости от влажности сырья) | 7-12 |
Теплоноситель | внутренний |
Система дожига пиролизных газов | + |
Утеплитель базальтовый Вайред мат Rockwool 40 | + |
Вес печи, кг | 4000 |
Внешние габариты Д*Ш*В, мм | 5000*2400*2400 |
Территория для установки, мм | 8000*6000 |
Выслать коммерческое предложение с ценами
Доставка, запуск оборудования для производства угля, обучение работников.
![]()
Внимание!
На некоторые печи действует
Скидка
Подробности у менеджера по т.: +7(8172)70-00-23
Или закажите обратный звонок, мы перезвоним Вам!
Технические характеристики шредера
Производительность, кг/час | до 300 |
Размер камеры измельчения Д/Ш, мм | 300/400 |
Количество валов | 2 |
Мощность основных двигателей, кВт | 0,55+0,55 |
Ширина ножа, мм | 12 |
Диаметр диска ножа, мм | 200 |
Количество режущих зубьев на ноже, шт. | 3 |
Размер получаемой фракции, мм | 50±30 |
Скорость вращения вала, об/мин | 40 |
Размеры Ш/Д/В | 1200/600/700 |
Вес, кг | 100 |
Выслать коммерческое предложение с ценами
Производство древесного угля «СВАРОЖИЧЪ» | Курский завод грануляторов
Описание
Производство древесного угля «Сварожичъ» — это комплекс состоящий из системы 4х автономных реторт.
Печь ретортного типа для выжигания угля — это металлическая ёмкость закрытого типа, в которой создаются условия для разложения древесины на углерод (угли) и газообразные летучие вещества.
Из газообразных веществ, в следствии определенных процессов производства древесного угля, выделяется пиролизный газ, который отапливает комплекс углевыжигательного завода.
Сырьё для производства древесного угля
Сырьё для производства древесного угля может быть самым разнообразным:
- Горбыль древесный, доска, рейка, брус, вагонка, лес
- Отходы древесной промышленности, щепа, ветки, древесный мусор, опилки, стружка, пиломатериалы
- Шишки, крупная твердая скорлупа орехов и т.д.
Как производили древесный уголь раньше?
Древесный уголь в России, начиная с ХVIII и до ХIХ века производили исключительно прибегая к ручному труду крестьян и заключенных, отбывавших наказание на каторгах. Во времена производства древесного угля появилась такая профессия как углежог. Высокоуглеродный уголь стал полуфабрикатом для металлургии, кузнечного дела, керамического производства и т.д. Бревна и лес, который работники заготавливали с апреля по сентябрь в глубоком овраге складывали особым способом — кучами, сверху покрывали дерном около 7 см, а затем толстым слоем земли. От едкого дыма, копоти и смрада, которые беспрерывно вздымались от тлеющих под дерном дров, у людей болели глаза, становилось тяжелым дыхание, у многих в груди появлялась боль, сильное сердцебиение.
Преимущества углевыжигательного комплекса «Сварожичъ»
Преимуществами оборудования для производства древесного угля является:
- Экологичность комплекса — дыма нет!!!
- Комплекс отапливает сам себя, после первого запуска печи
- Легкость в обслуживании и в эксплуатации
- Компактность размещения комплекса на территории
С чего начать производство древесного угля?
- Подобрать соответствующие производственные площади
- Проверить доступность исходного древесного сырья
- Подготовить древесное сырьё для переработки.
Подобрать фракцию
Как работает углевыжигательный комплекс «Сварожичъ»?
Производство древесного угля «Сварожичъ» рассчитано на беспрерывную — суточную работу 24/7.
Время от момента загрузки древесного сырья в ретортную печь до полной выгрузки готового продукта из неё называется Циклом.
Цикл работы одной ретортной печи — это время затраченное ретортой на процесс разложения исходной древесины на углерод и газообразные вещества путём нагревания без (или с ограничением) доступа воздуха, до момента окончания процесса термического пиролиза и полной выгрузки готового продукта (углей) в бак для охлаждения.
Цикл производства древесного угля «Сварожичъ» занимает в среднем от 10 — 14 часов.
Первый цикл системы «Сварожичъ» занимает больше всего времени, т.к. необходимо дополнительное время для разогрева системы и основного теплогенератора от 2 — 4 часов.
Принцип функционирования комплекса производства древесного угля «Сварожичъ».

Примерный алгоритм работы комплекса.
Алгоритм работы углевыжигательного комплекса представлен на примере выжигания сырья: горбыль сосновый, влажность 40 — 50%, фракция — бруски размером 5см*10см, заполнение реторт — 70% от общего объема.
Технологический процес производства древесного угля с помощью комплекса «Сварожичъ» включает в себя следующие этапы:
- Подготовка исходного древесного сырья
Измельчить излишне крупные куски древесины для дальнейшей подачи в бункер ленточного конвейерного транспортера.
- Загрузка исходного сырья в бункер питатель ленточного транспортера
- Подача древесины в Печь — реторту № 1 (заполняем реторту насыпью)
Печи — реторты № 2, № 3, № 4 на этом этапе НЕ загружаются!!!
- Подготовленными топочными дровами запускаем теплогенератор — основную печь, нагоняя температурный режим по первому основному датчику от 500 — до 800 °C
Температурный режим основного теплогенератора удерживаем до систематической подачи пиролизного газа в Печь — Реторту № 1.
При необходимости корректируем температурный режим первого датчика топочными дровами.
С момента запуска основной печи до начала пиролиза в реторте № 1 может пройти от 3 — до 4 часов работы печки.
- Через 4 часа работы основного теплогенератора, ленточным транспортером засыпаем Печь — реторту № 2
- Через 4 часа от момента запуска Реторты № 2, засыпаем Печь — реторту № 3
- Через 4 часа от момента запуска Реторты № 3, засыпаем Печь — реторту № 4
- Через 4 часа от момента запуска Реторты № 4, при условии окончания пиролиза в Реторте № 1, ее необходимо разгрузить.
- Выгрузка готового продукта — древесного угля происходит в железный бак с крышкой, где готовый древесный уголь должен остывать в течение суток плотно закрытый крышкой, без доступа воздуха.
Цикл Реторты № 1 в этом случае составит 16 часов с момента запуска основного теплогенератора.
Внимание!!! Готовый продукт обязательно должен остывать в течение суток плотно закрытый крышкой, иначе может произойти самовозгорание древесного угля.
- После выгрузки Реторты № 1 ее необходимо сразу наполнить исходным сырьем.
- Выгрузка готового продукта из Реторты № 2 происходит через 4 часа с момента выгрузки Реторты № 1 и тут же происходит загрузка Реторты № 2
- Выгрузка готового продукта из Реторты № 3 происходит через 4 часа с момента выгрузки Реторты № 2 и тут же происходит загрузка Реторты № 3
- Выгрузка готового продукта из Реторты № 4 происходит через 4 часа с момента выгрузки Реторты № 3 и тут же происходит загрузка Реторты № 4
Циклы работы Реторт № 1,2,3,4 в этом случае составит уже 14 часов с момента загрузки исходного сырья.
Температурные режимы производства древесного угля
Комплекс производства древесного угля «Сварожичъ» включает в себя несколько температурных датчиков:
- Датчик контроля температуры с автоматической регулировкой сброса температуры и оповещением нехватки рабочей температуры расположен на основном теплогенераторе — печи.
- Дополнительные датчики расположены на каждой Реторте
Производительность комплекса «Сварожичъ»
Производительность комплекса «Сварожичъ» тестировалась на сырье: сосновая порода дерева из отходов древесной промышленности — древесном горбыле.
Исходная влажность древесины составляла от 40 % — 50 %. Размер фракции — бруски, куски после измельчения рубильной машиной размером 15см*10см*3см и более. При тестировании комплекса было установлено:
- В случае если исходная влажность сырья превышает показатель 50%, тогда время цикла увеличивается.
- В случае если фракция исходного сырья крупнее указанной, тогда реторта заполняется с большими воздушными пустотами (сотами), следовательно выход готового древесного угля незначительно уменьшается.
- В случае сели исходное сырьё мельче указанной фракции, реторта заполняется плотно, следовательно выход готового древесного угля увеличивается.
При производстве древесного угля из лиственных пород деревьев — производительность ориентированная на вес всегда будет больше, чем у хвойных пород деревьев.
На что необходимо обращать внимание при производстве древесного угля?
Какой процент содержания углерода в готовом древесном угле?
Угольная печь своими руками — Tim Tinker
Этот сайт содержит партнерские ссылки. Таким образом, я буду зарабатывать на соответствующих покупках без каких-либо дополнительных затрат для вас. Это помогает мне поддерживать этот веб-сайт, так что спасибо за вашу поддержку.
Самодельная угольная печь, которая может самостоятельно производить древесный уголь из древесных отходов, предварительно обжигая и полностью обжигая самодельную керамику.
Я не возражаю против небольшой двусмысленности в названии. Я могу быть краток и задать читателю вопрос: это устройство, которое производит древесный уголь или использует древесный уголь? В данном случае это и то, и другое, и оно может даже приготовить мне ужин или закоптить моих угрей!
Когда она в конце концов достигла точки плавления болотной обыкновенной студенческой глины, я решил назвать ее моей печью Навуходоносора, согласно библейскому рассказу, где Навуходоносор якобы сделал печь «……..в семь раз больше, чем обычно отапливать……». Не позволяйте фактам или физике мешать хорошей истории, но в моем случае печь выжила (и нуждалась в небольшом огнеупорном ремонте), и я достиг своей цели плавления белой глины!
Мотылинка Старшая
Знакомство с угольной печью своими руками
Этот пост находится в разработке.
Я играю с огнём и по возможности предпочитаю использовать отходы упавших деревьев для своей игры с огнем. Вероятно, я вырастил слишком много деревьев, и теперь у меня есть лишняя древесина, которая не нужна для обогрева моего дома, иначе она сгорела бы в загоне.
Древесный уголь из такой древесины при обдуве принудительным воздухом достигает самых высоких температур горения этого скромного топлива для обжига керамических изделий своими руками.
Я надеялся сделать печь, которую можно было бы использовать для получения древесного угля из древесных отходов. Это означало бы, что тепло от его пиролитического превращения в древесный уголь может производить умеренные температуры, которые можно использовать для других целей, таких как длительная и устойчивая подготовка керамики к их окончательному обжигу.
Полезными побочными продуктами могут быть другие процессы с использованием тепла, такие как плавление металлов, медленное приготовление пищи и даже копчение мяса. Дополнительный начальный бонус можно было бы получить, если сделать печь из огнеупорной смеси, которая по сути представляет собой почву. «Будет забавно посмотреть, сможет ли печь поджечь собственные стены, как в этом маленьком видео?»
Тестирование прототипа. Я сделал небольшой прототип печи из четырех кирпичей, земли и листа металла, и во время фазы устойчивого горения древесного угля температура печи достигла 1250°C. У него было много утечек, плохая изоляция, обеспечиваемая верхней крышкой из листового металла, и ограниченный приток воздуха, подаваемый небольшим вентилятором USB. Я предположил, что смогу достичь гораздо более высоких температур с помощью хорошо спроектированной печи с минимальными утечками, хорошей изоляцией и нагнетанием воздуха мощного пылесоса. Вот небольшое видео прототипа в действии.
Миниатюрный прототип печи из кирпича и огнемета USB. Он очень примитивен, но может нагреваться до 1250°C, когда он закрыт крышкой из листового металла.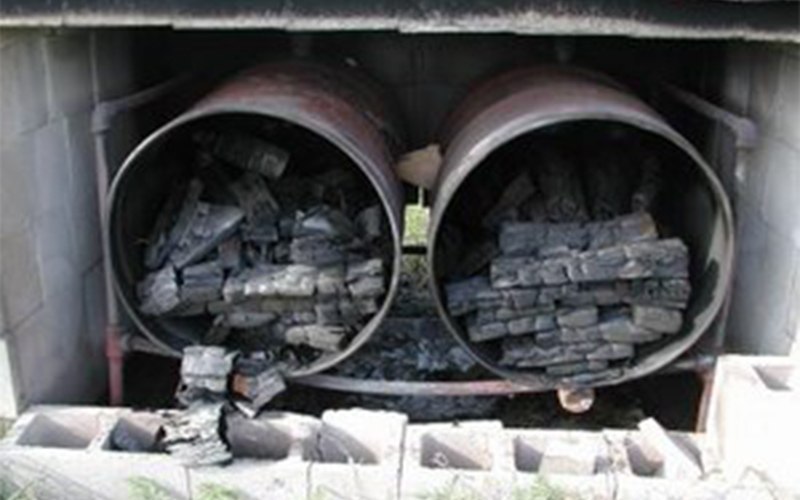
Испытание футеровки печи. Во время испытаний прототипа печи я также поместил образец предложенной мной самодельной теплоизоляционной футеровки печи, чтобы посмотреть, как она справляется с суровыми условиями этой адской дыры. Это была смесь перлита, мелкоизмельченного суглинка (без глины) и силиката натрия. Подробнее читайте в моем посте о огнеупорах из силиката натрия своими руками.
Он уцелел, немного треснул, но в него впилась сетка из птичьей проволоки. Он стал очень легким и приобрел стеклянную текстуру. Может потребоваться еще одно окончательное покрытие, чтобы уменьшить остекление, если печь достигает значительно более высоких температур. Я нанес тальк на каждую сторону тестового образца. Похоже, это предотвратило чрезмерное застекление, которое я наблюдал в предыдущих тестах. Это достигается за счет повышения температуры плавления поверхности.
Экспериментальная керамическая футеровка печи после сушки на воздухе и затем в печи до 220°С. Он состоит из перлита, тонкоизмельченного суглинка (без глины, я называю его постямным грунтом) и силиката натрия.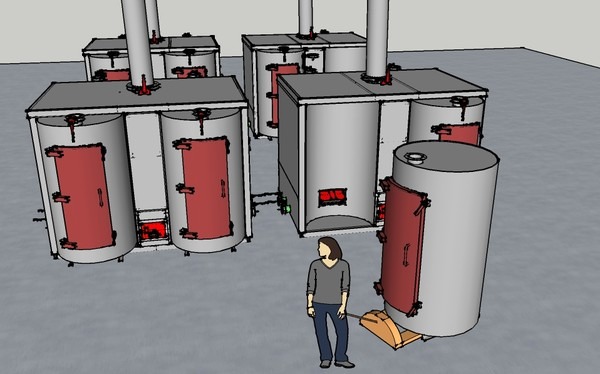
Отверждение углекислым газом. Я часто использую силикат натрия для изготовления огнеупоров, а отверждение изделий перед полным обжигом требует умеренных температур в диапазоне ~200-300°C для удаления химически связанной воды.
Также высокая концентрация двуокиси углерода в воздухе ускоряет превращение силиката обратно в двуокись кремния (при подготовке к превращению в стеклокерамику при высоких температурах). Такое тепло и богатые пары углекислого газа образуются при пиролизе древесины в древесный уголь.
Впоследствии я обнаружил, что температура в печи может легко достигать 200-300°С в верхней части топочной камеры во время сжигания древесины с естественной тягой для производства древесного угля. Это должно обеспечить устойчивые условия сушки/отверждения перед высокотемпературным обжигом древесного угля.
Всепогодный и мобильный. Было бы лучше, если бы печь была защищена от непогоды, чтобы ее можно было безопасно хранить снаружи, возможно, в шапке от дождя. Мобильность означает, что его можно перемещать, если он мешает, или его можно переместить в место, наиболее подходящее для его потенциального использования (например, угольщик для копчения или тихий курильщик угря). Следовательно, прочное круглое бетонное основание казалось хорошей отправной точкой для формирования бочкообразной огнеупорной стены печи.
Основание угольной печи
Основание из портландцемента. Я изготовил цилиндрический профиль из листового металла (нижний и без верха), чтобы отлить в него основание печи. Я приварил колено для подачи воздуха диаметром ~40 мм, которое отлил в середину основания. Внутренний выход трубы был направлен вверх к зазору с небольшим сменным фитингом для решетки, который предотвратил бы падение больших кусков угля в трубу.
Планировалось использовать этот воздухозаборник в качестве устройства с ограниченным доступом воздуха для производства древесного угля и отверждения углекислым газом с использованием естественной тяги печной трубы. В качестве альтернативы, его можно использовать для небольшой принудительной подачи воздуха из небольшого пожарного вентилятора USB (как показано на некоторых фотографиях ниже, где огнеупорная штукатурка была отверждена пламенем и углекислым газом). Наконец, для окончательного высокотемпературного сплавления керамики он мог бы нагнетать воздух из пылесоса, работающего от сети. «Пылесосы, которые выбрасывают повсюду, потому что они стали излишними благодаря революции стиля Дайсона».
Основание печи выполнено из простого песка и портландцементной смеси.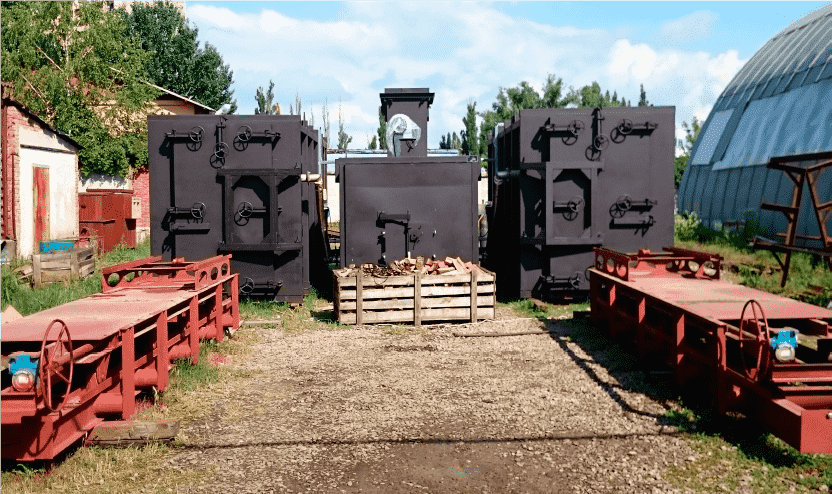
Нижняя часть отливки была выполнена из смеси портландцемента и песка с добавлением армирующей проволоки и легкой сетки для защиты от катаклизмического растрескивания основания. Я не ожидаю, что он станет настолько горячим, что портландцемент разрушится.
Высокотемпературный изоляционный цемент. Затем я добавил щедрый слой перлита, смешанного с высокотемпературным цементом и водой. «Высокая доля перлита в цементе делает смесь странной, поскольку перлит просто плавает в цементном порошке, как рисовые пузыри и сахар, пока не будет добавлено небольшое количество воды». Он хорошо наливался и утрамбовывался, и его можно было обрабатывать, как обычный цемент, с щедрой трамбовкой. Гранулы перлита ведут себя как мелкие агрегаты. Я также оставил возможность добавить дополнительный горячий рендер лица, если это когда-нибудь понадобится. Тем не менее, мой опыт работы с очень горячими воздухонагревателями показывает, что тепло не уходит вниз через вездесущий слой золы. Время покажет.
Стенка печи. Не знаю, как назвать, но стена сойдет. Это будет изолированный корпус, куда будет поступать древесное топливо, формироваться древесный уголь, а керамические творения будут купаться в пламени древесного газа, а затем излучаться интенсивным теплом от сжигания древесного угля с принудительной подачей воздуха.
Боковой порт для печной трубы. Я надеюсь сделать отверстие для дымохода, чтобы его можно было использовать для создания естественной тяги для медленного горения, когда не требуются самые высокие температуры. Это означало бы, что купол можно закрыть простой круглой огнеупорной крышкой. В качестве альтернативы можно нагреть сверху кастрюлю для медленного приготовления или коптильню.
Стенка печи. Я сделал стену достаточно высокой, в виде плавно сужающейся конической формы с большим отверстием наверху. Емкость намного больше, чем все, что я могу выстрелить. Тем не менее, я надеялся, что его можно будет загрузить большим количеством необработанной древесины, которая может пиролизоваться в древесный уголь и со временем падать вниз, чтобы пополнить древесный уголь, который будет ближе всего к соплу воздушной струи.
Внутренняя форма купола была изготовлена из 22-литровой бочки из-под растительного масла, которую я разрезал в четырех местах. Я снова собрал барабан, чтобы он был конусообразным и его можно было легко извлечь после того, как купол был оштукатурен изолирующим огнеупором. Пластиковый лист был обернут вокруг конуса, чтобы при необходимости он мог легко отделяться от рендера.
Фундамент угольной печи с формообразующим конусом для стены купола устанавливается на место с укладкой вокруг него слоя армирующей сетки. Стена купола угольной печи. Самый внутренний слой купола представляет собой самодельный огнеупор, сделанный из суглинка (в основном не содержащего глины), силиката натрия и перлита, чтобы сделать его изолирующим и довольно легким (как описано выше). Слой легкой оцинкованной проволоки, мы надеемся, защитит от катастрофического обрушения.
«Как только я закончил смешивать первую партию огнеупорной штукатурки, как всегда пошел дождь. Поэтому я быстро опробовал портативность угольной печи, поставив ее на тележку для мешков, и ее было восхитительно легко перемещать под навесом. .»
Основание угольной печи с первым огнеупорным и изоляционным слоем, нанесенным на каркас временной стены купола. Штукатурка наносится очень легко, но начинает оседать при толщине более 15-20 мм. Я решил, что для хорошей изоляции потребуется второй слой той же огнеупорной смеси. Это также даст удобную возможность добавить второй слой армирующей сетки в виде спирали из птичьей проволоки. В любом случае потребуется значительное количество времени на сушку/отверждение для набора прочности перед следующей обработкой. Или будет?
Когда снимать куполообразную форму?
Я могу снять формовочную форму после высыхания штукатурки, но тогда она может дать усадку и сильно треснуть или застрять в форме. С другой стороны, если бы я удалил форму, пока рендер был «зеленым», я бы избежал усадки и застрял на сценариях. Раннее удаление плесени значительно увеличит скорость высыхания, а силикатная штукатурка способна заживать, пока она зеленая. Я взял плоскодонку и удалил форму, пока рендер был в этом деликатно твердом зеленом состоянии. «Похоже, эта авантюра окупилась»
Тонкая стена купола печи ненадежно держится вместе с высокотемпературной штукатуркой с высоким содержанием силиката почвы в ее зеленом состоянии после удаления внутренней формы. У меня возникло искушение попытаться заполнить небольшие пустоты, оставленные в рендере выпуклостями в пластиковой пленке. Однако при этом я ткнул пальцем в стену и на данном этапе отказался от этой идеи как от плохой.
Немедленно стрелять, чтобы ускорить лечение или нет? Отказавшись от косметического ремонта, я почувствовал, что удача еще со мной. Я решил ускорить отверждение зеленого рендера, зажег внутри него небольшой огонь. «В конце концов, это то, для чего это нужно!» Такой нагрев огнем ускоряет отверждение за счет его высыхания и значительного увеличения концентрации двуокиси углерода, которая участвует в превращении силиката в форму двуокиси кремния при подготовке к высокотемпературному превращению в стекловидный кремнезем.
Поджигание огнеупорной штукатурки стены противопожарного купола для ускорения высыхания/отверждения огнеупорного материала из силиката натрия. Это быстро сделает его намного прочнее, если вы нанесете дополнительные слои стены купола. Установите еще больший огонь, чтобы быстро вылечить рендер огненного купола. Обжиг рендера достиг 550°C (максимальная температура по термометру) в верхней части купола, а в нижней зоне температура превышала 550°C. Эта температура в сочетании с высоким содержанием углекислого газа делала внутреннюю часть печи твердой и твердой. Вот небольшое видео обстрела.
Эти температуры означают, что это хорошее предварительное отверждение, которое делает штукатурку готовой к полному обжигу керамики. «Это небольшое видео показывает обжиг рендера и его трансформацию в хард-финиш. Это всего лишь концепция керамики, ее настоящее рождение происходит при гораздо более высокой температуре, когда она становится стекловидной субстанцией. Это произойдет, пока печь будет введена в эксплуатацию.
Следующий внешний слой должен был состоять из смеси портландцемента и песка с перлитом. Однако я подумал, что для большей глубины изоляции необходим дополнительный слой силикатного перлита почвы. «В любом случае, это чертовски дешево!» Окончательные внешние слои портландцемента придадут дополнительную прочность и стойкость к истиранию, а внутренние слои будут хорошо защищены от нагревания.
Огнеупорная штукатурка, покрывающая горячую поверхность печи
Думаю, я немного поторопился с обжигом первого огнеупорного слоя, пока он был «сырым» или не отвержденным всухую. «Конечно, у него не было такой жесткой текстуры безе, как на тестовом образце, показанном выше». Он был немного рыхлым и недостаточно прочным для загрузки грубых дров. Поэтому я сделал мягкую мелкую штукатурку из талька (детская присыпка) и силиката натрия (40 г силиката: 40 г талька: 80 г воды). Она была преднамеренно насыщена силикатом и довольно «жидкая», и я очень аккуратно нанес штукатурку кистью на потрескавшуюся и рассыпчатую поверхность. Влага и растворенный силикат быстро впитывались в первоначальную поверхность, и тальк начал заполнять трещины и отверстия. Поверхность, обработанная таким образом, быстро становилась очень стабильной, а штукатурка быстро затвердевала.
Я сделал больше штукатурки и сразу же смог нанести второй слой, в результате чего получилась гладкая, прочная и плотная поверхность. «На этот раз я бы не стал спешить с обжигом керамического покрытия».
Печь на древесном угле, на довольно тонкую и рассыпчатую изолирующую огнеупорную стенку была нанесена тонкая горячая штукатурка из порошка талька/силиката натрия.
Еще одно огнеупорное покрытие горячей поверхности печи
Принимая во внимание улучшение поверхности талько-силикатной штукатурки, я подумал, что было бы неплохо нанести дополнительное более толстое покрытие горячей поверхности. У меня заканчивалась детская присыпка, поэтому я использовал немного гранатового порошка (отходы из поддона станка для гидроабразивной резки). «Из опыта я знал, что он может сделать огнеупор твердым, как камень для заточки ножей». Итак, огнеупорная смесь была такой (40 г силиката: 40 г талька: 400 г порошка граната: 100 г воды).
Это была очень густая смесь, которую я обильно нанесла кистью, чтобы полностью покрыть белый цвет тальковой штукатурки. Эта смесь застряла в щетине кисти, так как жидкая фаза втягивалась в поверхность во время чистки. Поэтому я использовал две заливки ~100 г воды во второй кастрюле, чтобы смягчить и удалить рендер с кисти. Постепенно эти дополнительные горшки с водой стали похожи на рендер, и я использовал их, чтобы смочить или загрунтовать поверхность, прежде чем быстро нанести окончательный рендер. Таким образом, ни один компонент рендера не был потрачен впустую, все ушло на горячую поверхность или на нее.
Внешняя поверхность угольной печи
Чтобы сделать печь снаружи прочной, я нанес толстый слой штукатурки из песка и портландцемента. Этот рендер был нанесен через слой тонкой оцинкованной проволоки для птиц. Последней штукатуркой будет белый цемент с добавлением гидроизоляции «влажного слоя». «Этот последний рендер был использован только ради красоты и тщеславия, а также потому, что у меня остались остатки в мастерской, и он заставляет уродливый цемент выглядеть великолепно, как дома на греческих островах».
Угольная печь покрыта двумя слоями портландцементной штукатурки снаружи после добавления цилиндра сетки из птичьей проволоки.
Кто забыл встроить порты для датчика термопары печи?
Рендеринг прошел так быстро, что я забыл добавить порты для термопар. Я сделал три маленькие трубки из нержавеющей стали, которые собирался вставить в стену печи, чтобы можно было вставить дешевый термопарный зонд для контроля температуры. Один наверху, где я мог бы готовить и курить, один посередине в зоне пиролиза и один в зоне высокотемпературного сжигания древесного угля. Неважно, этот рефрактор можно очень легко просверлить после затвердевания, поэтому я все еще могу добавить порты и продолжить визуализацию вокруг них.
Вот фотография модернизированных портов для термопар. Просверлив отверстия с помощью сверла по каменной кладке, я вставил в стену портовые трубки из нержавеющей стали для термопары с помощью моей чудодейственной алюминиевой фольги и расширяющегося огнеупора из силиката натрия. «Это волшебная штука, поскольку она пузырится, пенится и расширяется сама по себе, когда ее помещают в маленькое место, и становится огнеупорным огнеупором, который просто смеется над огнем».
Функциональные температуры для изготовления огнеупоров
В конце концов я остановился только на двух портах контроля температуры. Я обнаружил, что температура в печи достигала 200-300°С в верхней части с естественной тягой, где новые огнеупоры можно было аккуратно высушить и затвердеть, одновременно готовя древесный уголь для окончательного обжига. Зона в месте расположения среднего порта (показана на фото выше) достигла температуры около 1050С, что согласно вышеприведенному посту Апровечо должно обеспечить адекватный обжиг печных огнеупоров. Я отказался от идеи порта внизу в слое древесного угля, так как ожидал, что температура выйдет далеко за пределы 1300C для моей термопары K-типа.
На приведенных ниже фотографиях показаны керамические пробные шайбы, обожженные в печи. Шайбы практически не видны при самой высокой температуре на первом фото, сразу после поднятия крышки топки. Когда печь немного остынет, шайбы станут видны.
Вот небольшое видео показаний термопары при работающей печи и еще одно в ночное время.
Посмотрев на эту печную адскую дыру, я думаю, пора подумать о наших храбрых братьях и сестрах Украины:
Удивительно, до злости и досады, Когда вы обманываете свою молодость, чтобы вторгнуться в другую нацию, Армия Голиафов погублена собственной воинственностью, Против стойкой защиты Родины Давида, Кроме того, помните, во что обойдется вашей стране возмещение ущерба за войну!
Кто забыл отверстие для удаления золы?
Для человека, который так много играет с огнем, я не должен был бы удивиться, обнаружив, что удалить пепел из такой печи довольно сложно. Возможно, со временем я вырежу зольник и сделаю для него керамическую заглушку.
Раньше накопление золы происходило, когда я использовал печь с естественной тягой или с крошечным USB-огнедувкой. К счастью, когда я разжег печь с помощью бластера с принудительной подачей воздуха, сделанного из старого «двойного» пылесоса Electrolux. «Попробуй сделать это со своим Дайсоном!» Взрыв был настолько сильным, что не нужно было удалять значительного количества пепла, поскольку он просто оставил небольшой вулканический конус пепла вокруг входного отверстия для воздуха. «Хорошее изоляционное покрытие для следующего использования». Вот небольшое видео работы доменной печи на полной мощности.
Заключение
Этот самодельный огнеупорный проект показал, что печь на древесном угле можно сделать из почвы и силиката натрия. При наличии терпения его можно использовать для самовоспламенения, чтобы он стал изолирующим и жаростойким огнеупором. Затем он сможет удобно вулканизировать и обжигать другие огнеупорные изделия при высоких температурах, используя древесные отходы от упавших веток.
Тим
Приложение
После небольшого количества проб и ошибок мне удалось нагреть печь до устойчивой температуры, при которой можно обжечь «белую студенческую глину», чтобы она плавилась должным образом и даже начала плавиться и немного оседать. .
Предметы из бумажной глины, которые были обожжены в моей самой горячей печи Навуходоносора с полной загрузкой качественных дров.
Высокоэффективная печь для карбонизации для производства древесного угля
Перейти к содержимому Печь карбонизации- Посмотреть увеличенное изображение
Представление печи для карбонизации
Печь для карбонизации является идеальным оборудованием для производства брикетов из древесного угля. Это ключевое оборудование для всего процесса производства древесного угля. Печь для карбонизации использует новейшие технологии и разумную конструкцию, которая увеличивает коэффициент карбонизации и сокращает время карбонизации.
Применение печи для карбонизации
Печи для карбонизации широко используются для переработки древесного угля с брикетами биомассы, древесиной и лесохозяйственными отходами. Брикеты из биомассы изготавливаются из опилок и других сельскохозяйственных отходов, таких как солома, рисовая шелуха, бамбуковая стружка, травы, с использованием машины для брикетирования древесного угля А древесина и отходы лесного хозяйства, такие как сосновая древесина, ивовая древесина, бамбук, также могут использоваться в качестве сырья для печей карбонизации, которые непосредственно поступают в печь карбонизации и превращаются в древесный уголь без дробления и процесса брикетирования. Брикеты из древесного угля, изготовленные в печах для карбонизации, отличаются высокой плотностью, малым объемом, легко сгорают и подходят для семейного и промышленного использования.
Печь для карбонизации Классификация
Печь для карбонизации включает три различных типа, а именно: печь для карбонизации с воздушным потоком , печь для карбонизации с самовоспламенением , печь для карбонизации с подъемным механизмом . Самовоспламенение имеет уникальную подвижную конструкцию из стальных пластин, а выхлопные трубы соединены с сепаратором смолы и вытяжным вентилятором. Печь для карбонизации воздушным потоком изготовлена из огнеупорного материала и использует передовую технологию карбонизации горячим воздухом. В то время как энергосберегающая печь для карбонизации подъемного типа является типом печи для карбонизации, подходящей для семейной карбонизации древесно-угольных брикетов. Внутренний горшок можно повесить снаружи, что сэкономит много времени на охлаждение, поэтому производительность значительно возрастет.
Отличительные особенности печи для карбонизации
2. Простота в эксплуатации и экономия труда. Одновременно человек может обслуживать 3-5 печей карбонизации.
3. Принять уникальное оборудование для обеззараживания дыма, чтобы печь была экологически чистой.
4. Высокая скорость карбонизации и высокая эффективность. Степень карбонизации составляет около 40-60%, а скорость готовой продукции выше 9.5%.
5. Прочный. Печи изготовлены из специальных материалов и могут использоваться в течение 4 или 5 лет.
