Опилкобетон, пропорции и изготовление | РЕМОНТ-УЗЕЛ
При подготовке к строительству какого-либо объекта встает вопрос, из каких материалов выкладывать стены. На сегодняшний день имеется много строительных материалов, но надо выбрать именно те, которые подходят к определенным требованиям застройщика: они должны быть экологичными, безопасными, огнестойкими, морозостойкими, паронепроницаемыми, влагостойкими и прочными.
Такими требованиями обладают опилкобетонные блоки. Они изготавливаются из натуральных материалов. Меняя наполнители и используя различные добавки, можно добиться нужных качественных характеристик и здорового микроклимата в жилых домах, построенных из опилкобетона.
Возможность придать этому материалу разные свойства позволяет сократить расходы на покупку строительных материалов.
Примером может служить одноэтажная постройка, где нет необходимости в использовании высокопрочных материалов, значит, можно уменьшить количество цемента — одного из самых дорогих компонентов в составе наполнителей.
Изготовление опилкобетона
Состав компонентов опилкобетона позволяет выполнить заготовку материалов за один день. В магазинах строительных материалов все есть. Процесс изготовления опилкобетона вручную очень трудоемкий, поэтому хорошо бы использовать растворомешалку (бетономешалку).
- Способ изготовления блоков заключается в следующем: высушенные опилки просеивают, затем добавляют песок, цемент и известь и перемешивают смесь до однородной массы. Продолжая перемешивать, добавляют нужное количество воды.
- Чтобы проверить, правильно ли приготовлена смесь, надо взять комок смеси и сжать ее в кулаке – она должна оставаться пластичной и сухой, без капелек воды.
- Затем нужно не откладывая переходить к изготовлению блоков. Смесь достаточно быстро твердеет. При укладке в форму смесь надо хорошо утрамбовать, чтобы не образовывались пузырьки. Для изготовления форм применяются деревянные ящики, покрытые внутри или пленкой, или чем-то другим, чтобы смесь не соприкасалась с доской, которая может поглощать влагу.
- Распалубку блоков следует проводить через несколько дней. Готовые блоки следует уложить под навес на просушку на 3 месяца. При укладке необходимо оставить зазор между блоками, чтобы просушка была равномерной.
Опилки надо обработать перед тем, как загрузить в смесь, особенно те, которые долго лежали, так как в них содержится влага. Обработка производится известковым молоком или раствором хлорида кальция (10%). Затем надо тщательно просушить. Опилкам из древесины хвойных пород дерева предварительная обработка не требуется.
Кстати, сегодня существует много видов бетон. По данной теме читайте: стеклофибробетон. А также пенобетон. А кого-то заинтересует декоративный бетон.
Свойства опилкобетона
Опилкобетон — хороший звукоизолирующий материал, способный обеспечить хороший микроклимат в доме. Очень важным показателем в строительстве является влажность материала. От состоянии влажности зависит не только комфортность проживания, но и морозоустойчивость.
Для снижения избыточной влаги применяются следующие способы: применение гидрофобизирующих добавок, обшивка пластиковыми панелями и многое другое. Следует обратить внимание, что облицовка стеновых блоков защитными облицовочными материалами проводится повсеместно.
Еще в советское время для производства санитарно-гигиенических кабин применялся гипс. После прокрашивания кабин гипс становился хорошим влагостойким материалом. Поэтому облицовка блоков из опилкобетонов защитно-декоративными материалами позволит снизить водопоглощение на 2-4 %.
пропорции изготовления опилкобетона
Опилкобетон относится к негорючим материалам, что позволяет широко применять его в строительстве. Например, его огнестойкость выше, чем у полистиролбетона. Это объясняется прежде всего тем, что древесные опилки, утрамбованные в цементно-песчаной смеси, практически не могут возгореться.
Опилкобетонные блоки обладают хорошими показателями на растяжение и изгиб, подтверждённые лабораторными испытаниями. Эти показатели обеспечивают наличие фибровидных частиц. По этим показателям опилкобетон намного опережает пенобетон, газобетон и другие строительные материалы.
Роль армированного материала в опилкобетонных блоках выполняют опилки и стружка. За счет этого появляется высокая прочность блоков. Расчеты при проектировании строительства показывают, что их можно использовать в многоэтажном строительстве.
Опилкобетон можно пилить, сверлить и забивать в него гвозди. Учитывая его низкую себестоимость, применение блоков в строительстве сократит расходы на строительство объектов. Опилкобетонные блоки являются хорошей основой для крепления защитно-декоративных покрытий, а применение клея дает очень прочное сцепление.
Меняя содержание наполнителя, а также состав вяжущей смеси, можно добиться различных свойств и характеристик опилкобетона. Это дает возможность широкого использования — начиная от возведения зданий разной этажности до строительства столбов и заборов, при этом сократив затраты на строительство.
А далее, как сделать бетон своими руками — читайте здесь.
Подписывайтесь на НАШ ТЕЛЕГРАММ КАНАЛ! Актуальные именно сегодня и полезные советы!
__________________________________________________________________________________
Получайте новые статьи с сайта на электронную почту
Опилкобетон: состав, пропорции, изготовление | Блоки
Разнообразие строительных материалов продиктовано поиском наиболее дешевых, простых в производстве и экологичных вариантов. Одной из интересных, но далеко не новых, технологий является производство опилкобетона. Он применяется в монолитном и блочном домостроении. Рассмотрим его основные характеристики и технологию изготовления.
Характеристика опилкобетона
В состав смеси входит вода, строительный песок, опилки и цемент; так же возможно применение дополнительных веществ. Благодаря натуральности компонентов материал получается экологически чистым. Процентное содержание опилок может достигать 70%. При этом материал не поддерживает горение, благодаря цементной оболочке. Сопротивление огню длится 3 часов при температуре 1200 °C.
Влагопоглощение материала составляет от 8 до 12%. Достигается показатель путем вымачивания опилок в жидком стекле. Низкая гигроскопичность увеличивает морозостойкость. При самых низких показателях влагопоглощения сопротивление минусовым температурам до 100 циклов.
Показатель теплопроводности экологичного бетона составляет 0,32 Вт/м°С. Для сравнения — 40 см стены из опилкобетона заменяют по 1 метр кирпичной кладки.
Конструкции, из рассматриваемого материала, имеют высокую сопротивляемость к механическим воздействиям. Опилки выступают, своего рода, арматурой, добавляя изделиям стойкость к растяжению.
Работать с опилкобетоном достаточно просто. Для обработки не нужны специальные приспособления. Материал можно, сверлить, забивать гвозди, резать фрезой или ножовкой. Опилкобетонные блоки применяются как для одноэтажного строительства, так и для домов до 4 этажей. В зависимости от конструктивных нагрузок используются различные маркировка, которая формируется исходя из соотношения компонентов
Таблица пропорций составляющих опилкобетона
Марка | Соотношение компонентов в указанном порядке (цемент, известь, песок, сухие опилки) |
5 | 1:1:0:2 |
10 | 1:2:8 |
15 | 1:1,2:5 |
25 | 1:1:1,2:4 |
При строительстве нужно помнить: чем меньше содержание опилок, тем прочнее изделие. При этом тепло- и шумоизоляционные свойства снижаются. Вес рассматриваемого бетона ниже многих строительных материалов, что позволяет уменьшить нагрузку на фундамент. Также отпадает необходимость в применении спецтехники.
Технология изготовления опилкобетона
Кратко рассмотрим производство блоков из опилкобетона своими руками. Для начала работ из доски сбивается опалубка размером 390*190*190 мм. Чтобы блок лучше извлекался, на внутреннюю сторону короба набивают линолеум. Готовить сырье желательно при помощи бетономешалки. В таком случае блоки будут более однородными, что понизит водопоглащение. Вначале перемешиваются сухие компоненты, массовая доля которых зависит от необходимого объема готового продукта. В качестве наполнителя применяются опилки деревьев хвойных пород. Перед добавлением они вымачиваются в известковом растворе или жидком стекле.
Пропорции для раствора извести
- Опилки — 1 м3;
- Вода — 150-200 литров, в зависимости от влажности опилок;
- Известь — 2,5 кг.
Лучше применять цемент марки 400. Добавки должны составлять не более 3% от массы цемента.
В форме смесь уплотняется вибратором или вручную. Также для уплотнения массы применяются вибрационные столы. На вторые сутки блоки вынимаются из опалубки. Дальнейшая сушка происходит на улице в течение 10-14 дней при ясной погоде. Равномерность схватывания достигается периодическим смачиванием изделий.
Влияние пород древесины, обработки частицами и состава смеси
M. R. Garcez 1 , E. O. Garcez 2 , A. O. Machado 2 , D. A. Gatto 2
1 Interdiscipliarm, федеральный университет. Бразилия
2 Инженерный центр, Федеральный университет Пелотас (UFPel), Бразилия
Адрес для корреспонденции: М. Р. Гарсез, Междисциплинарный факультет, Федеральный университет Риу-Гранди-ду-Сул (UFRGS), Бразилия.
Электронная почта: |
Copyright © 2016 Научное и академическое издательство. Все права защищены.
Эта работа находится под лицензией Creative Commons Attribution International License (CC BY).
http://creativecommons.org/licenses/by/4.0/
Аннотация
Цель этого исследования заключалась в изучении влияния пород древесины, обработки частиц и пропорций смеси на физические (плотность) и механические (прочность на сжатие и динамический модуль упругости) свойства цементно-древесных композитов. Были исследованы различные пропорции смеси, основанные на соотношении цемент: древесина 0,3:0,7 по объему, с

Ключевые слова:
Pinus elliottii, E ucalyptus grandis, Известь, Цемент, Опилки, Отходы Ссылайтесь на эту статью: М. Р. Гарсез , Э. О. Гарсез , А. О. Мачадо , Д. А. Гатто , Цементно-древесные композиты: влияние пород древесины, обработки частиц и пропорций смеси, International Journal of Composite Materials , Vol. 6 № 1, 2016. С. 1-8. дои: 10.5923/j. cmaterials.20160601.01.
Описание статьи
- 1. Введение
- 2. Материалы и методы
- 2.1. Материалы
- 2.2. Пропорции смеси и производство
- 2.3. Физические и механические свойства
- 2.4. Статистический анализ
- 3. Результаты и обсуждение
- 3.1. Плотность
- 3.2. Прочность на сжатие
- 3.3. Динамический модуль упругости
- 4. Выводы
1. Введение
- Бразилия входит в пятерку крупнейших производителей делового круглого леса наряду с США, Канадой, Китаем, Российской Федерацией, Российской Федерацией, Российской Федерацией, Российской Федерацией, Китаем, Российской Федерацией, Канадой и Канадой. Эти страны произвели в 2013 г. 54% всего мирового производства [1]. Как следствие, лесопильные заводы ежегодно производят огромное количество древесных отходов, неправильная утилизация которых может нанести ущерб окружающей среде и вызвать экономические проблемы у лесопромышленных компаний.
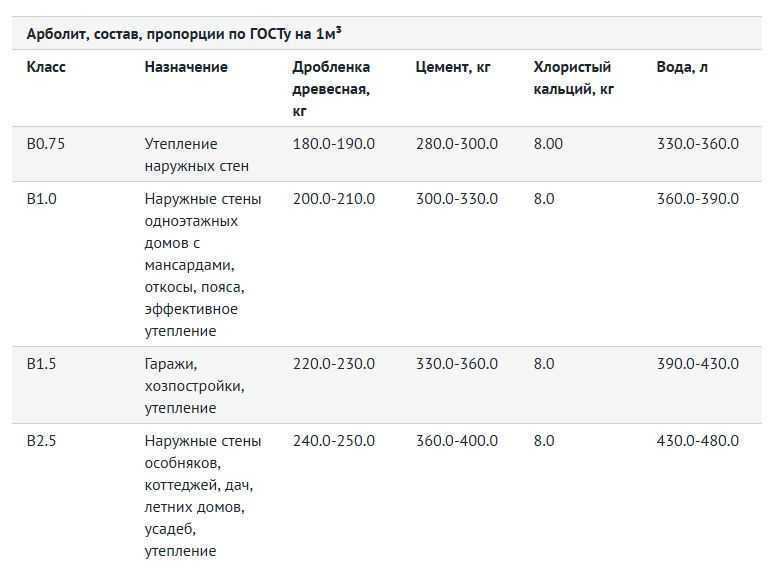
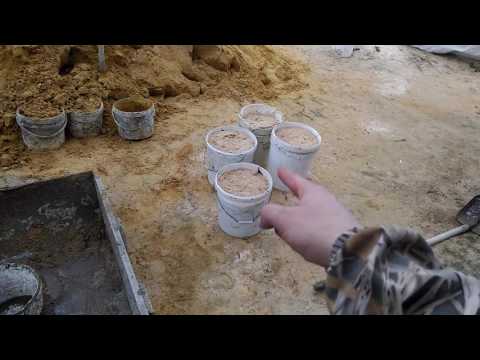

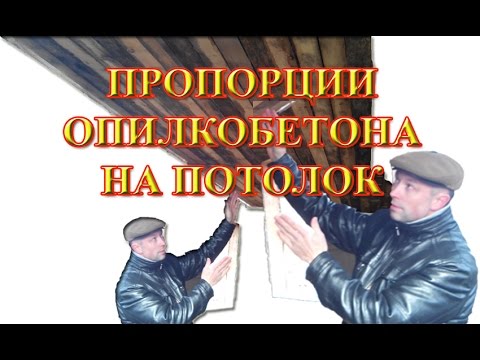
2. Материалы и методы
2.1. Материалы
- В качестве связующего использовался бразильский цемент CPV-ARI [12], аналогичный портландцементу типа III – HESC – высокопрочный цемент (ASTM C150-12). Pinus elliottii и Eucalyptus grandis отходы были получены от деревообрабатывающей промышленности, расположенной в Южной Бразилии. Были использованы две обработки частиц: Цементное покрытие [13], которое заключалось в смешивании влажных опилок и цемента с соотношением опилок:цемент 8:1 по объему; Погружение частиц опилок в насыщенный раствор извести [5], приготовленный с использованием гидроксида кальция типа CH II [14] с опилками: вода: Ca(OH) 2 в соотношении 1:1:0,05 по массе, в течение 24 часов с последующей кратковременной промывкой проточной водопроводной водой.
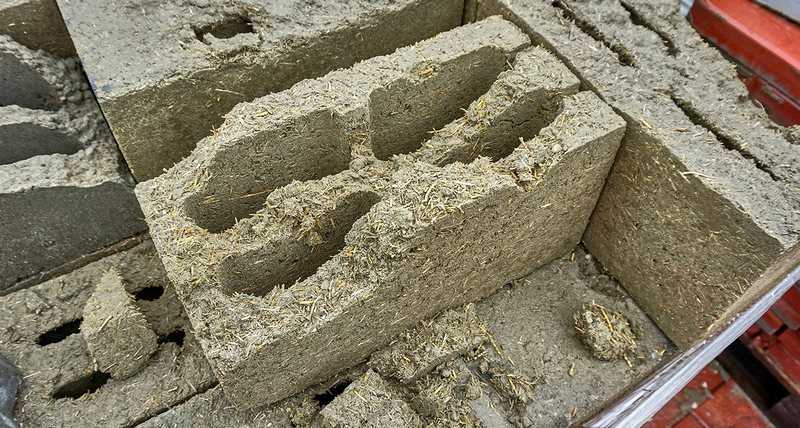
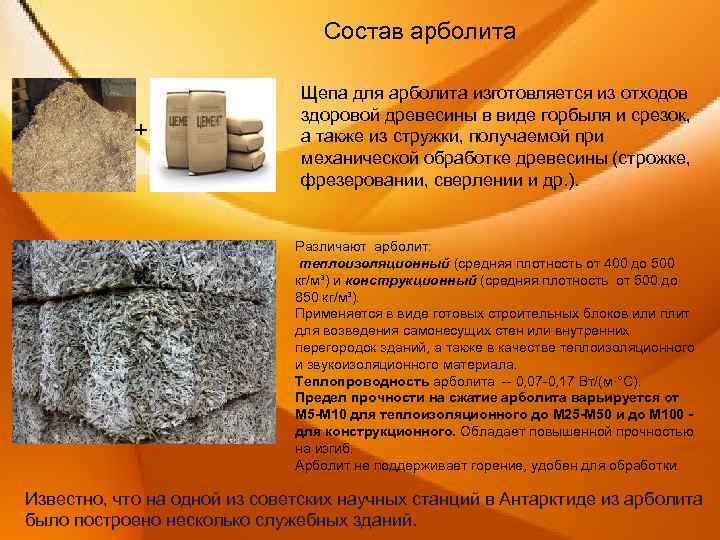
Рис 1 . В natura и предварительно обработанных опилках: (a) Pinus elliottii ; (b) Eucalyptus grandis |
|
F ig ure 2 . Гранулометрический состав: (a) Pinus elliottii ; (b) Eucalyptus grandis |
2.
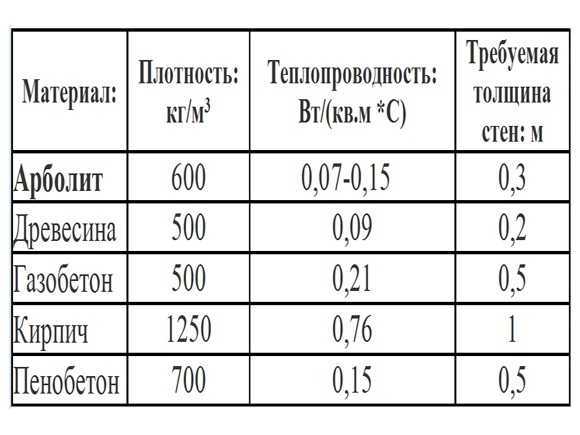
- Пропорции смеси были определены на основе соотношения цемент:древесина 0,3:0,7 по объему с Pinus elliottii и Eucalyptus grandis с процентным содержанием опилок 100-0, 75-25, 50. -50, 25-75 и 0-100, как показано в таблице 2.
|
|
2.
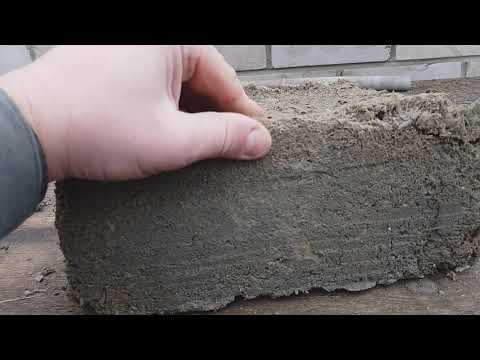
- Характеристики цементно-древесных композитов в отношении пород древесины, обработки частиц и пропорций смеси оценивались по физическим и механическим свойствам. Плотность Плотность определяли путем измерения массы и объема каждого образца в соответствии с уравнением 1, где M 0 — вес (г), V 0 — объем (см 3 ), а ρ — плотность (г/см 3 ). Результаты представляли как среднее значение пяти измерений.
(1) |

(2) |
2.4. Статистический анализ
- Дисперсионный анализ (ANOVA) выполняли с использованием коммерческого программного обеспечения Statgraphics. Критерий наименьшей значимой разницы Фишера (LSD) использовали для сравнения разницы между средними значениями свойств на уровне 0,05.
3. Результаты и обсуждение
- Тенденции в средних значениях свойств цементно-древесных композитов установить трудно, в основном потому, что древесные волокна являются биологическим материалом и имеют присущую изменчивость длины волокон и свойств [7]. Кроме того, обработка каждого древесного волокна может быть неравномерной по поверхности волокна. Тем не менее, образцы древесины, обработка и пропорции смеси, предложенные в этой экспериментальной программе, привели к набору данных, который позволил изучить явные тенденции в средних физических и механических свойствах цементно-древесных композитов, как обсуждается в этом разделе.
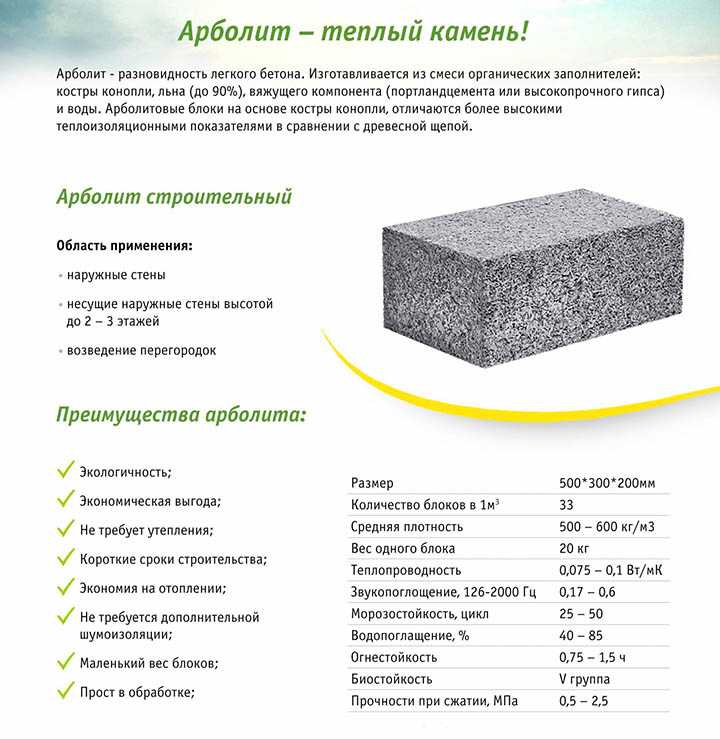
3.1. Плотность
- На рис. 3 представлены результаты определения плотности цементно-древесных композитов, значения которых представлены в табл. 3. Результаты согласуются с другими, опубликованными в литературе [3, 4, 8, 11, 19].
Рисунок 3. Плотность композитов цементной мыть0041 |
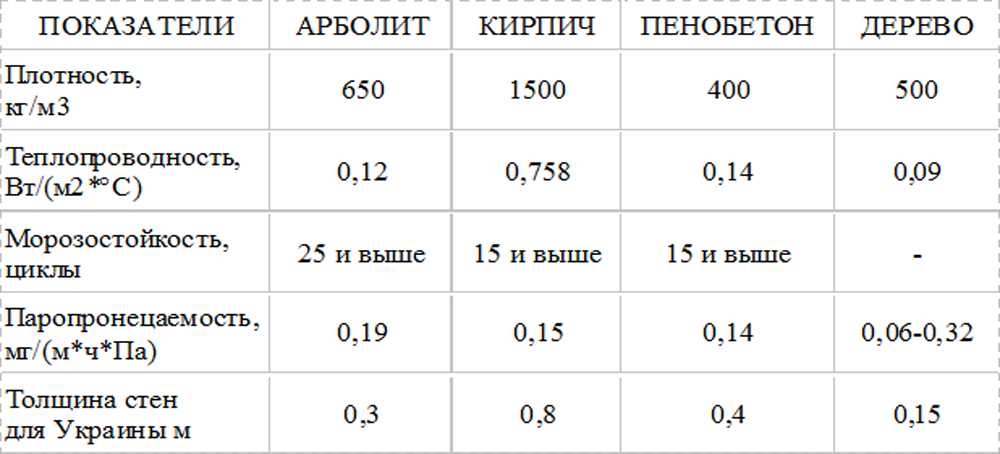
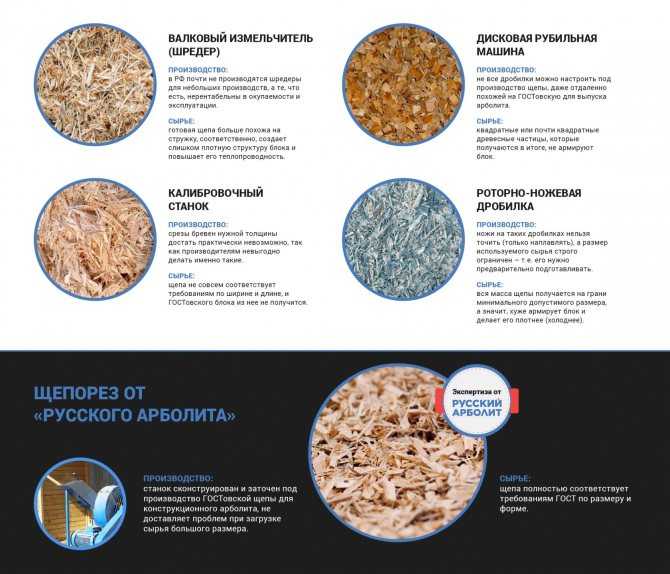
3.2. Прочность на сжатие
- На рис. 4 показаны результаты прочности на сжатие для цементно-древесных композитов, значения которых представлены в таблице 4. Результаты согласуются с другими данными, опубликованными в литературе [3, 4, 7, 8].
Рис 4 . Таблица 4.9 Таблица 4. Прочность на сжатие цементных композитов |
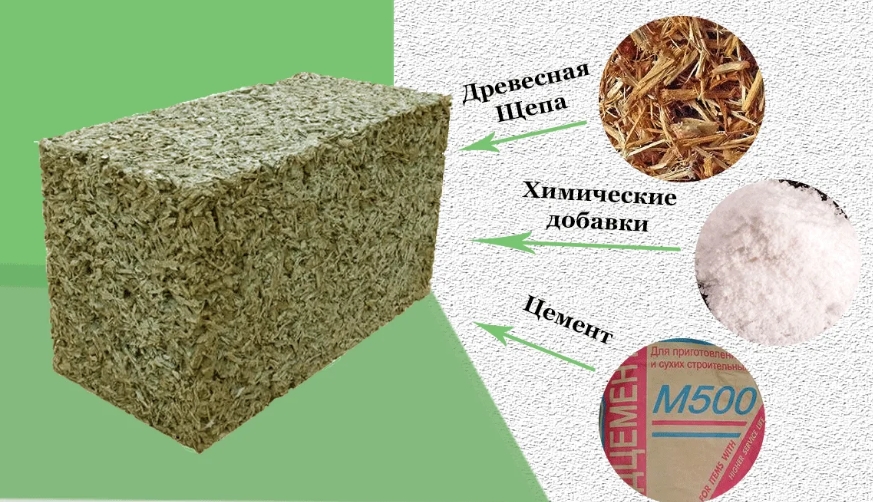
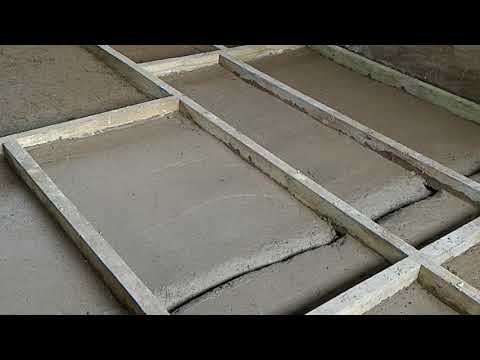
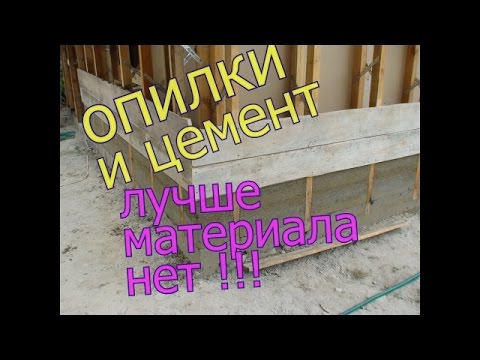
Рис. 5 . (a) Хрупкое поведение цементного теста; (b) Тяжелое поведение P100E0 CIM Композит цементного использования |
Рис. 6. Поведение цементно-древесных композитов с разным процентным содержанием в древесных опилках natura Eucaliptus grandis : (a) P75E25; (а) Р50Е50; (а) P25E75; (a) P0E100 |

3.3. Динамический модуль упругости
- Важность определения модуля упругости связана с тем фактом, что это механическое свойство напрямую связано с жесткостью, деформируемостью и контролем растрескивания цементно-древесных композитов [22]. Модуль упругости цементного теста зависит в основном от его пористости и соотношения вода:цемент. Однако в цементно-древесном композите соотношение между пастой и заполнителем, породой древесины и обработкой древесными частицами также может иметь значение. На рис. 7 представлены результаты определения динамического модуля упругости цементно-древесных композитов, значения которых представлены в табл. 5. Результаты согласуются с другими, опубликованными в литературе [3, 4, 8, 9].
- . В результате механические свойства цементно-древесных композитов, особенно в отношении жесткости и деформируемости, могут значительно различаться при использовании смесей древесных пород.
Экспериментальные результаты (Таблица 5) показали влияние породы древесины на модуль упругости. Хотя композиты с высоким содержанием 9Опилки 0049 Eucaliptus grandis (P25E75 и P0E100) показали самые высокие значения прочности на сжатие (рис. 4), такие композиты не показали такого же поведения в отношении модуля упругости. Высокий коэффициент вариации (Таблица 5) может быть результатом неоднородности образцов цементно-древесного материала, но также может возникать из-за того, что на ультразвуковые измерения могут влиять несколько факторов, таких как длина оптического пути, содержание влаги, температура, форма и размер образца. Влияние заполнителя на модуль упругости иногда может иметь большее значение, чем прочность или возраст. Для композитов с разным типом заполнителя это влияние может быть еще более сложным [23]. В этом исследовании было обнаружено, что разные композиты с одинаковым диапазоном прочности могут иметь очень разные модули упругости, и предполагается, что эти результаты получены из-за совокупного влияния.
На рис. 8 показан динамический модуль упругости цементно-древесных композитов со статистическими данными сравнения средних значений, где одинаковые буквы означают обработку эквивалентными средними значениями. Композит П75Э25 с частицами, предварительно обработанными цементным покрытием, показал самое высокое значение модуля упругости.
Цементно-древесные композиты со 100%, 75% и 50% опилок Pinus elliottii и частиц, предварительно обработанных цементным покрытием, показали лучшие характеристики в отношении модуля упругости. Композиты P100E0 и P50E50 не показали статистической разницы между средними значениями для частиц, предварительно обработанных погружением в щелочной раствор. Композиты со 100% содержанием опилок Eucaliptus grandis показали наилучшие результаты в отношении модуля упругости для в natura опилок с последующим покрытием цементом и погружением в обработку щелочным раствором.Рис. 8 Динамический модуль упругости цементно-древесных композитов со статистическими данными сравнения средних значений Прочность межфазной связи между волокном и цементной матрицей зависит от содержания влаги из-за пониженной прочности на изгиб влажного волокна, что делает его более гибким и с меньшей вероятностью препятствует растрескиванию цементной матрицы [3]. Таким образом, учитывая гигроскопическое поведение древесины, модуль упругости цементно-древесного композита ниже, чем модуль упругости самого цементного теста, и имеет тенденцию к снижению по мере увеличения процентного содержания древесины.
Рис 7 . Таблица 50041 |
4. Выводы
- Результаты показали, что порода древесины, обработка частиц и пропорции смеси могут влиять на физические и механические свойства цементно-древесных композитов. Смеси Eucalyptus grandis и опилок Pinus ellioti давали промежуточные значения плотности, от промежуточных до более низких значений прочности на сжатие и от промежуточных до более высоких значений динамического модуля упругости. Композиты со 100% содержанием
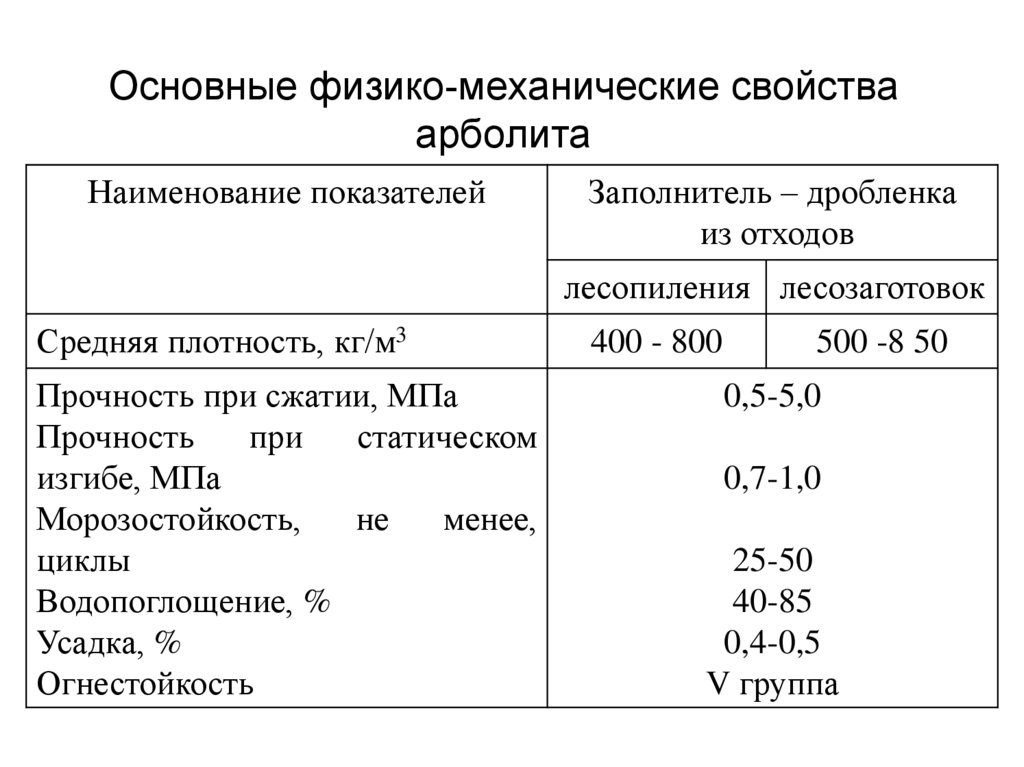
Каталожные номера
[1] | К. Юргенсен, В. Коллерт, А. Лебедис, 2014 г., Оценка производства делового круглого леса из лесонасаждений, Серия рабочих документов по лесонасаждениям и деревьям, ФАО FP/48/E. |
[2] | Н. Солтани, А. Бахрами, М.И. Печ-Канул, Л.А. Гонсалес, 2015 г., Обзор физико-химической обработки рисовой шелухи для производства современных материалов, Журнал химической инженерии, 264, 899-935. |
[3] | С. Фрайборт, Р. Мауриц, А. Тайшингер, У. Мюллер, 2008 г.![]() |
[4] | Р. М. Ронким, Ф. С. Ферро, Ф. Х. Ичимото, К. И. Кампос, М. с. Бертолини, А. Л. Христофоро, Ф. А. Р. Лар, 2014, Физические и механические свойства древесно-цементного композита с лигноцеллюлозными отходами, Международный журнал композитных материалов, 4 (2), 69-72. |
[5] | М. Фан, М.К. Ндиконтар, С. Чжоу, Дж. Х. Нгамвенг, 2012, Цементные композиты из тропических пород древесины: совместимость древесины и цемента, Строительство и строительные материалы, (36), 135 –140. |
[6] | X. Лин, М. Р. Силсби, Д. М. Рой, Р. Кесслер, П. Р. Бланкенхорн, 1994, Подходы к улучшению свойств цементных композитов, армированных древесным волокном, Исследование цемента и бетона, 24 (8), 1558-1566 гг. |
[7] | J. L. Pehanicha, P.R. Blankenhorna, M.R.![]() |
[8] | Бертолини М.С., Кампос К.И., Соуза А.М., Панзера Т.Х., Христофоро А.Л., Лар Ф.А.Р., 2014, Древесно-цементные композиты из отходов Pinus sp. дерево: Эффект обработки частиц. International, Journal of Composite Materials, 4(2), 146-149. |
[9] | А. Ашори, Т. Табарса, Ф. Амоси, 2012, Оценка использования железнодорожных шпал из отходов древесины в древесно-цементных композитных материалах, Строительство и строительные материалы, 27, 126–129. |
[10] | А. Бахрами, Н. Солтани, М.И. Печ-Канул, К.А. Гутьеррес, 2016, Разработка композитов с металлической матрицей из промышленных/сельскохозяйственных отходов и их производных, Критические обзоры в области науки и техники об окружающей среде, 46, 143-208.![]() |
[11] | F C. Jorge, C. Pereira, JMF Ferreira, 2004, Древесно-цементные композиты: обзор, Holz Roh Werkst, 62, 370–377. |
[12] | АБНТ. Бразильская ассоциация технических стандартов. NBR 5733: Портландцемент с высокой начальной прочностью. Рио-де-Жанейро, 19 лет91. |
[13] | S. A. Costa, «Incorporação de serrim em argamassas cimentícias», M. Eng. Диссертация, Universidade do Minho, Гимарайнш, Португалия, 2012 г. |
[14] | ABNT. Бразильская ассоциация технических стандартов. NBR 7115: Гидроксид кальция для строительных растворов. Требования. Рио-де-Жанейро, 2003 г. |
[15] | ABNT. Бразильская ассоциация технических стандартов. NM 248: Распределение частиц по размерам. Рио-де-Жанейро, 2003 г. |
[16] | АБНТ. Бразильская ассоциация технических стандартов.![]() |
[17] | ABNT. Бразильская ассоциация технических стандартов. NBR 15630: Строительные растворы. Определение динамического модуля упругости при распространении ультразвуковой волны. Rio de Janeiro, 2008. |
[18] | M. R Garcez, T. Santos, D. A. Gatto, 2013, Avaliação das propriedades físicas e mecânicas de concretos pré-moldados com adição de serragem em substituição ao agregado miúdo, Ciência & Engenharia, 22, 95-104. |
. -493. | |
[20] | В. Кастро, Р. Д. Араужо, К. Пархен, С. Ивакири, 2014, Avaliação dos efeitos de pré-tratamentos da madeira de Eucalyptus benthamii de Camatibilid de Camatibilio & compbage de Maidenau , Арворе, 38(5), 935-942. |
[21] | А. Л. Беральдо, Дж. В. Карвалью, 2004, Compósito de Eucalyptus Grandis – cimento Portland, Scientia Forestalis, 65, 150-161.![]() |
. , 610-615. | |
[23] | А. Л. Гутьеррес, М. Ф. Кановаз, Модуль упругости высокопрочного бетона, 1995, Материалы и конструкции, 28, 559-568. |
Патент США на строительный материал и способ изготовления того же патента (Патент № 4,402,751, выдан 6 сентября 1983 г.)
ПРЕДПОСЫЛКИ ИЗОБРЕТЕНИЯ
строительные материалы и, более конкретно, но не ограничиваясь этим, к строительному материалу и способу его изготовления из обычно отходов.
2. Описание предшествующего уровня техники
Производство строительных материалов, таких как бетон и т.п., из смеси компонентов, включающих древесные волокна, изучалось в течение многих лет. На самом деле, использование соломы для изготовления кирпичей практиковалось еще древними египтянами, а попытки использовать опилки и тому подобное исследовались и экспериментировались в течение многих лет. Уолтер Р. Фриберг провел обширное исследование использования опилок в производстве бетона и является автором публикации Университета Айдахо от 19 октября.53, касающийся его деятельности в этой области. Использование древесных волокон, таких как опилки, в производстве бетона приводит к получению легкого и теплоизоляционного продукта, что очень желательно, но предшествующие эксперименты по использованию опилок в сочетании с цементом для производства бетона были в значительной степени неэффективными, поскольку они требовали больших количеств цемент в пропорции к опилкам для достижения необходимой прочности конечного продукта. В результате получился строительный материал, который был и дорогим, и тяжелым. В методе Фриберге было обнаружено, что добавление диатомитового материала к опилкам, как правило, устраняет некоторые из предыдущих недостатков. Диатомит обычно добывают открытым способом, и предложение явно намного превышает спрос, но добыча продукта является очевидным экологическим недостатком.
Кроме того, г-н Фриберге признает, что диатомитовый раствор является волокнистым и затрудняет ручное смешивание. Были предприняты другие эксперименты с использованием волокнистых материалов в сочетании с цементом для производства строительного материала, такие как те, которые показаны в Erricks U.S. Re. № 24003, патент США Weiss. № 1631171, Бриджфорд, патент США. № 3533725, Marra, патент США. № 3671377, Breslauer, патент США. № 3705837 и патент США Tjannberg. № 4 228 202. Ссылка Breslauer относится к древесным стружкам, покрытым портландцементом; Weiss относится к изготовлению стеновых досок из древесной пасты; Erricks показывает стабилизатор для целлюлозных материалов; Bridgeford использует древесные волокна, смешанные с полимером; Марра показывает древесную массу, смешанную со связующим; и Tjannberg раскрывает способ придания огнестойкости целлюлозному материалу. Ни один из предшествующих источников и экспериментов, по-видимому, не позволил успешно решить проблему строительных материалов на волокнистой основе.
СУЩНОСТЬ ИЗОБРЕТЕНИЯ
Настоящее изобретение относится к строительному материалу, в котором волокна или другие отходы используются в качестве компонента строительного материала, и к способу изготовления строительного материала, который был специально разработан для преодоления вышеизложенного. недостатки. В новом методе используются органические отходы, которые обычно считаются экономическими потерями и многие из которых представляют собой загрязняющие вещества или вредны для окружающей среды. В широком смысле новый процесс включает добавление извести, которая может представлять собой печную пыль (распространенный отход) или тому подобное, в предварительно выбранных или заранее определенных количествах или соотношениях по объему к органическим отходам. Примерами отходов являются опилки, хлопковая шелуха, скорлупа орехов, кукурузная шелуха или другие растительные волокна. Известковая смесь затем выдерживается и отверждается в течение заданного периода времени в соответствии с химическими характеристиками используемых отходов. Материал на этом этапе может быть «удержан» для использования на месте, например, для заливки стен и т.п., или может быть доставлен на производственный завод для формования или формирования кирпичей, листов, блоков или панелей для обеспечения низкой стоимости. , легкие, в значительной степени огнестойкие, легко обрабатываемые строительные материалы для строительных блоков, изоляции и т.п. Заполнитель, полученный данным способом, может быть смешан с цементом, смесью цемента и золы-уноса или быстротвердеющим гипсовым цементом с высокими испытаниями для получения конечного продукта. Другими словами, шлам можно использовать в любой хорошо известной рецептуре для производства бетонного материала. Когда растительное волокно представляет собой опилки, или измельченную шелуху, или измельченные заусенцы, необходимое дополнительное количество воды сначала смешивают с цементом, а заполнитель или опилки добавляют в увлажненный цемент в заранее отмеренных количествах.
Волокна растительного происхождения, которые могут быть получены в результате лущения, прессования, распиловки и формовки и т. п., подлежащие обработке, сначала высушиваются и помещаются в раствор, который, как правило, представляет собой одну часть извести на восемь объемных частей воды. Сухой материал переходит в побелочную смесь (известковую воду) и, видимо, пытается впитать влагу. Кроме того, оказывается, что известь прикрепляется к клеточной стенке растительных волокон и внедряется в нее, и когда продукт высыхает, сухой продукт сохраняет свой расширенный объем. Известь может образовывать кладочный цемент (химическая связь), поскольку известь и портландцемент, например, становятся кладочным цементом.
Для ускорения процесса может быть желательно использовать воду, содержащуюся в любом отработанном шламе, используемом для смешивания извести или летучей золы. Требуется время отверждения, в течение которого известь проходит через массу, чтобы остановить все химические реакции (например, устранить запахи), и может быть необходимо периодически перемешивать смесь через определенные промежутки времени во время операции отверждения. Известь, используемая в процессе, часто сама по себе является отходом и обычно доступна в огромных количествах, например летучая зола, являющаяся отходом от сжигания угля, хвостов и т.п. Известь регулирует фактор PH волокнистых компонентов, запечатывает сахара и останавливает другие химические реакции. Затем известкованные материалы можно использовать в качестве заполнителя, по существу, в любой хорошо известной операции смешивания бетона. Новый способ не только позволяет получить легкий, по существу, огнеупорный изоляционный строительный материал, но также решает многие экологические проблемы, связанные с тем, что в качестве основного ингредиента в процессе можно использовать отходы, которые в противном случае трудно утилизировать. Способ по изобретению принимает органические волокнистые материалы либо в сухой форме, такой как опилки, шелуха, заусенцы, стебли и т.п., либо как часть шлама, выводимого из древесной массы, бумажных фабрик, заводов по переработке, тряпичной или льняной бумаги.
мельницы и другие подобные установки, сбрасывающие шламы, содержащие значительный объем воды или жидкостей и волокон. После того, как шлам был обработан этим способом, шлам сохнет очень медленно, и когда он становится полностью сухим, он, по-видимому, не будет «снова намокать». Как следствие, предпочтительно выполнить некоторую сушку, но не полную сушку до завершения всего процесса. Затем обработанный шлам может храниться для будущего использования по мере необходимости. Новый строительный материал экономичен и долговечен в использовании, прост и эффективен в производстве.
ПОДРОБНОЕ ОПИСАНИЕ ПРЕДПОЧТИТЕЛЬНОГО ВАРИАНТА ВОПЛОЩЕНИЯ
Многие промышленные процессы производят большое количество продуктов шлама отходов, содержащих волокнистые компоненты. По существу любой из этих отработанных шламовых материалов может быть использован или обработан настоящим способом для получения заполнителя для использования при создании прочного легкого эффективного строительного материала. Кроме того, в процессе могут использоваться сухие волокнистые материалы, такие как опилки, шелуха, заусенцы, стебли и другие растительные волокна. Новый процесс действует для регулирования фактора PH шлама или сухих волокнистых материалов, чтобы противодействовать кислотным условиям, обычно присутствующим в них. Процесс останавливает биологические и бактериологические процессы и уплотнения и содержит сахара, смолы и химические группы, выделяемые из волокон, и после соответствующего времени отверждения процесс производит заполнитель, который может использоваться в качестве ингредиента в гипсе, известковом растворе, наполнителе или в предпочтительный продукт соответствует конкретному строительному материалу.
В целях пояснения новый процесс можно рассматривать в двух формах, первая форма представляет собой процесс, применяемый к «сухим» органическим волокнистым материалам, а вторая представляет собой процесс, применяемый к «влажным» массам волокнистого материала, который часто называют как «шлак». Для дальнейшего уточнения процесса следующие определения применяются к продуктам, на которые ссылаются в процессе:
Известь, используемая в этом процессе, была получена из отходов «хвостов» завода по гидратации извести, из опасных для окружающей среды промышленных отходов извести и из стандартные каменщики известковые строительные.
Побелка представляет собой раствор извести в воде. Диапазон отношения извести к воде варьируется в зависимости от химического состава обрабатываемого органического волокнистого материала.
Добавки для побелки: При наличии отходов, отличных от органических волокнистых материалов, таких как сточные воды, содержащие фекальные колиформные бактерии, или когда условия позволяют установить ферментацию до начала процесса очистки, летучая зола (отходы угольных электростанций ) можно добавлять в небольших количествах. В шламы, которые имеют тенденцию образовывать «комки» и сопротивляются равномерной обработке, сухие или влажные силикаты, такие как силикат натрия или кальция, могут быть введены в побелку сразу после стадии побелки для облегчения равномерного отверждения.
Сухие органические волокнистые материалы: Термин «сухой» используется для обозначения класса материалов, которые представляют собой по существу сухие частицы, не входящие в состав какой-либо массы непрерывного формуемого материала. Эти сухие органические волокнистые отходы имеют диапазон содержания влаги от «мягко-сухого» до довольно влажного.
Цементная смесь: органический волокнистый материал, обработанный способом по изобретению, становится заполнителем для легкого бетоноподобного материала, который можно назвать «фибробетон».
Цемент, который становится вяжущим или цементным раствором, может представлять собой портландцемент, кладочный цемент, гипсовый цемент или подобные широко используемые продукты, или может представлять собой комбинацию, например, цемента (портландского типа) и летучей золы с подходящими характеристиками. Соотношение цемента и золы-уноса в диапазоне от небольшого количества золы-уноса до 30% по массе цемента и до 70% золы-уноса использовалось с хорошими результатами.
Что касается, в частности, «сухого» способа для нового процесса, то можно использовать органические волокнистые материалы, такие как древесные отходы, включая опилки, стружку, осколки, скорлупу орехов пекан, миндаля, грецких орехов и других орехов, которые были расколоты и удаленное мясо, скорлупа или кожура масличных орехов, арахис, соевые бобы и аналогичные материалы, хлопковая шелуха и другие отходы переработки растительных продуктов. Частицы этих сухих органических волокнистых материалов могут быть обработаны в довольно широком диапазоне размеров. Однако на конечный продукт сильно влияет размер частиц в заполнителе. Для более прочных «фибробетонов» предпочтительно не должно быть больших комков или «комков» волокон без цементного раствора. По этим причинам некоторые материалы, такие как ватные жернова, могут потребовать измельчения в любой подходящей простой операции, прежде чем приступить к новому процессу.
Начальная стадия сухого процесса включает смешивание извести с водой в базовом соотношении один объем извести к восьми объемам воды в любом подходящем смесительном баке. Затем к смеси для побелки в чане добавляют сухие опилки или другие сухие материалы. Предпочтительно должен быть избыток жидкости для побелки, чтобы обеспечить тщательное перемешивание, перемешивание и пропитку добавленного к ней сухого волокнистого материала. Основное время перемешивания и замачивания смеси составляет примерно двадцать пять минут. Затем волокнистый материал может быть просеян на подходящем дренажном устройстве, а любые излишки побелки могут стекать обратно в ванну для обработки для повторного использования.
Было обнаружено, что несколько видов изделий из древесины и некоторые раковины реагируют характерным образом с образованием остатков, слизи или пленок. Когда это происходит, может быть желательным удалить такие выбросы и продолжить процесс замачивания с одним или несколькими вариантами, такими как увеличение количества извести в смеси для побелки, удлинение операции замачивания-смешивания до тридцати или тридцати пяти минут и / или введение добавки, такой как небольшое количество летучей золы, для разработки стандартной процедуры для этого конкретного сорта древесины или ракушек.
Некоторые общие рекомендации и контрольные точки для получения наилучших результатов при использовании сухих волокон можно резюмировать следующим образом:
1. Чем суше состояние используемого органического волокна, тем быстрее и полнее будет поглощение известкового раствора и наилучшие результаты контроля всех факторов, влияющих на конечный продукт.
2. Должно быть достаточное количество извести, абсорбированной и прилипшей к отдельным частицам и/или покрывающей их, чтобы они были видны и чтобы остановить дальнейшее брожение или разложение волокнистого продукта.
3. Соотношение извести и воды может быть отрегулировано как для экономии, так и для эффективности практически с любым органическим волокном, а смесь извести и воды или побелки будет герметизировать или противодействовать кислотности, сахару, маслу, смолам, скипидару и другим соединениям или компонентам. обычно считается вредным при использовании цемента для производства бетона. Например, для получения оптимального конечного результата для одного сорта орехового дерева предпочтительно требуется одна часть извести на шесть частей воды.
4. Многие из «сухих» органических волокон желательны для заполнителя, когда для строительных материалов требуется более высокая прочность на сжатие. Для этого заполнитель должен быть сухим для достижения наилучших прочностных характеристик и удерживаться в смесителе до тех пор, пока цемент и вода не будут тщательно перемешаны или перемешаны, после чего заполнитель можно добавлять в цементно-водную смесь.
5. Появление значительного количества слизи или пены на поверхности чана для обработки свидетельствует о возможности добавления извести после удаления реакционного материала, накопившегося в ванне.
6. Внешний вид и запах в целом являются удовлетворительными показателями хороших результатов лечения. После обработки волокнистый заполнитель можно складировать и хранить в течение длительного времени перед использованием в производстве строительного материала.
Как указано выше, процесс или способ изобретения могут быть эффективно применены к промышленным отходам, содержащим органические волокнистые материалы, выбрасываемые в виде шлама, и которые могут включать минералы, земли и другие материалы в воде. Кроме того, эти шламы часто содержат опасные для окружающей среды количества химических веществ и тяжелых металлов, а хранение и утилизация шламов представляет собой большую проблему. Предпочтительный метод обработки этих шламов заключается в первоначальном отсеивании волокнистых материалов в самой ранней точке сброса, например, в месте сброса с промышленного предприятия, удалении твердых частиц, которые легче воды, с помощью простых систем или других подобных устройств и пропускании твердых частиц. тяжелее воды для осаждения на дно резервуара для шлама перед сбором в отстойниках, после чего они могут быть перенесены в технологическую систему изобретения. Как более тяжелые, так и более легкие твердые частицы, собранные в отстойнике и полученные в процессе просеивания, поступают в чан и сразу же смешиваются с известью в базовом соотношении один объем извести на восемь объемов шлама. Эта базовая смесь затем может быть адаптирована для обработки шламов в особых условиях, а добавка летучей золы или силиката может улучшить действие в определенных шламах.
Затем обработанный известью шлам можно медленно взбалтывать в среде, которая позволяет воде высвобождаться из массы. В некоторые шламы или «влажные» волокна в массу могут быть введены добавки летучей золы или силиката. Благодаря эффекту вспенивания обработанный шлам может доставляться на подходящую дренажную станцию, которая может быть специально спроектирована для обеспечения выхода воды из массы. Если устройство для сбивания представляет собой передвижной смеситель или подобное устройство, подача шлама в зону слива относительно проста. Конечно, если операция сбивания выполняется в других емкостях, взбитый шлам может быть доставлен в зону слива любым подходящим способом.
Обработанный органический волокнистый материал предпочтительно «отвержден» во влажном состоянии. Для некоторых материалов желательно отверждать массу примерно в течение двадцати четырех часов для эффективного управления биологическими, бактериологическими и химическими процессами. Время отверждения следует контролировать и корректировать по мере необходимости, чтобы свести к минимуму «время трубопровода» или «время процесса» при эффективном сдерживании и контроле нежелательного материала или активности массы. Как и в случае «сухих» волокнистых материалов, обработанные шламовые материалы могут складироваться, транспортироваться или храниться для использования по мере необходимости.
После того, как шлам или сухие волокнистые материалы были обработаны новым способом, и после того, как остаток или материал-заполнитель полностью высохли, он, очевидно, не будет снова «увлажняться», как указано выше. Во многих случаях время высыхания может быть ускорено применением тепла. Заполнитель можно использовать обычным образом практически в любой рецептуре для создания цементоподобного строительного продукта. После обработки волокнистых изделий либо на сухой стадии, либо на мокрой стадии процесс создания строительного материала в основном такой же, как широко используемый сегодня.
Строительные изделия, изготовленные с использованием волокнистого заполнителя, полученного способом по изобретению, обладают отличными изоляционными свойствами, они легкие, прочные и могут использоваться обычным образом для гипсокартона, бетона и т. п. Строительные блоки и т.п., изготовленные из заполнителя, принимают гвозди и другие строительные инструменты обычным образом, как и в современном строительстве.
Из вышеизложенного будет очевидно, что настоящее изобретение обеспечивает новый способ создания строительного материала превосходного качества из волокнистого материала, который обычно считается отходами и неблагоприятным для окружающей среды. Сухие продукты и/или влажные продукты могут использоваться с одинаковой эффективностью в процессе, таким образом, не только производя эффективные строительные материалы, но и решая широко распространенную сегодня экологическую проблему и проблему загрязнения.
Хотя изобретение было описано с определенной степенью конкретности, очевидно, что многие изменения могут быть сделаны в деталях конструкции и расположении компонентов без отклонения от сущности и объема настоящего раскрытия. Понятно, что изобретение не ограничено вариантами осуществления, изложенными здесь в целях иллюстрации, а должно быть ограничено только объемом прилагаемой формулы или формулы изобретения, включая полный диапазон эквивалентности, на который распространяется каждый его элемент.