ΠΠ»ΡΠΌΠΈΠ½ΠΈΠΉ ΠΈ Π΅Π³ΠΎ ΡΠΏΠ»Π°Π²Ρ. ΠΡΠΎΠ±Π΅Π½Π½ΠΎΡΡΠΈ ΠΎΠ±ΡΠ°Π±ΠΎΡΠΊΠΈ
ΠΠ»ΡΠΌΠΈΠ½ΠΈΠΉ β ΠΌΡΠ³ΠΊΠΈΠΉ ΠΈ ΠΏΠ»Π°ΡΡΠΈΡΠ½ΡΠΉ ΠΌΠ΅ΡΠ°Π»Π», ΠΊΠΎΡΠΎΡΡΠΉ, Π² ΠΎΠ±ΡΠ΅ΠΌ ΡΠ»ΡΡΠ°Π΅, Ρ
ΠΎΡΠΎΡΠΎ ΠΏΠΎΠ΄Π΄Π°Π΅ΡΡΡ ΠΌΠ΅Ρ
Π°Π½ΠΈΡΠ΅ΡΠΊΠΎΠΉ ΠΎΠ±ΡΠ°Π±ΠΎΡΠΊΠ΅ (ΡΡΠ΅Π·Π΅ΡΠΎΠ²Π°Π½ΠΈΡ, ΡΠ²Π΅ΡΠ»Π΅Π½ΠΈΡ, Π³ΡΠ°Π²ΠΈΡΠΎΠ²Π°Π½ΠΈΡ). Π Π΅ΠΆΠΈΠΌΡ ΡΠ΅Π·Π°Π½ΠΈΡ ΠΏΡΠΈ ΡΡΠΎΠΌ ΠΌΠΎΠ³ΡΡ Π±ΡΡΡ Π½Π°ΠΌΠ½ΠΎΠ³ΠΎ Π²ΡΡΠ΅, ΡΠ΅ΠΌ ΠΏΡΠΈ ΠΎΠ±ΡΠ°Π±ΠΎΡΠΊΠ΅, Π½Π°ΠΏΡΠΈΠΌΠ΅Ρ, ΠΊΠΎΠ½ΡΡΡΡΠΊΡΠΈΠΎΠ½Π½ΡΡ
ΡΡΠ°Π»Π΅ΠΉ.
Π‘ ΠΎΠ΄Π½ΠΎΠΉ ΡΡΠΎΡΠΎΠ½Ρ, ΡΡΠΎ ΠΎΠ±ΡΡΠ»ΠΎΠ²Π»Π΅Π½ΠΎ ΠΌΠ΅Π½ΡΡΠΈΠΌΠΈ Π½Π°Π³ΡΡΠ·ΠΊΠ°ΠΌΠΈ ΠΏΡΠΈ ΡΠ½ΡΡΠΈΠΈ ΡΡΡΡΠΆΠΊΠΈ, Ρ Π΄ΡΡΠ³ΠΎΠΉ β Π²ΡΡΠΎΠΊΠΈΠΌ ΠΊΠΎΡΡΡΠΈΡΠΈΠ΅Π½ΡΠΎΠΌ ΡΠ΅ΠΏΠ»ΠΎΠΏΡΠΎΠ²ΠΎΠ΄Π½ΠΎΡΡΠΈ Π°Π»ΡΠΌΠΈΠ½ΠΈΡ, Π±Π»Π°Π³ΠΎΠ΄Π°ΡΡ ΠΊΠΎΡΠΎΡΠΎΠΌΡ ΡΠ΅ΠΏΠ»ΠΎ ΠΈΠ· Π·ΠΎΠ½Ρ ΡΠ΅Π·Π°Π½ΠΈΡ Ρ
ΠΎΡΠΎΡΠΎ ΠΎΡΠ²ΠΎΠ΄ΠΈΡΡΡ Π²ΠΌΠ΅ΡΡΠ΅ ΡΠΎ ΡΡΡΡΠΆΠΊΠΎΠΉ, Π½Π΅ Π²ΡΠ·ΡΠ²Π°Ρ ΠΏΠ΅ΡΠ΅Π³ΡΠ΅Π²Π° ΠΈΠ½ΡΡΡΡΠΌΠ΅Π½ΡΠ°.
ΠΠ½ΠΎΠ³Π΄Π° ΠΏΡΠΈ ΠΎΠ±ΡΠ°Π±ΠΎΡΠΊΠ΅ Π°Π»ΡΠΌΠΈΠ½ΠΈΡ ΠΌΠΎΠΆΠ½ΠΎ ΡΡΠΎΠ»ΠΊΠ½ΡΡΡΡΡ ΠΈ Ρ Π½Π΅Π³Π°ΡΠΈΠ²Π½ΡΠΌΠΈ ΡΡΡΠ΅ΠΊΡΠ°ΠΌΠΈ.
ΠΠ΅ΡΠ²ΡΠΉ β Π²ΡΡΠΎΠΊΠ°Ρ Π²ΡΠ·ΠΊΠΎΡΡΡ Π½Π΅ΠΊΠΎΡΠΎΡΡΡ
ΡΠΏΠ»Π°Π²ΠΎΠ². Π ΡΡΠΎΠΌ ΡΠ»ΡΡΠ°Π΅ ΡΡΡΠ΅ΡΡΠ²ΡΠ΅Ρ ΡΠ΅Π½Π΄Π΅Π½ΡΠΈΡ ΠΊ ΡΠΎΡΠΌΠΈΡΠΎΠ²Π°Π½ΠΈΡ Π΄Π»ΠΈΠ½Π½ΠΎΠΉ ΡΡΡΡΠΆΠΊΠΈ, ΠΊΠΎΡΠΎΡΠ°Ρ Π½Π°ΠΌΠ°ΡΡΠ²Π°Π΅ΡΡΡ Π½Π° ΠΈΠ½ΡΡΡΡΠΌΠ΅Π½Ρ ΠΈ Π·Π°Π±ΠΈΠ²Π°Π΅Ρ ΠΊΠ°Π½Π°Π²ΠΊΠΈ, ΡΡΠΎ ΠΏΡΠΈΠ²ΠΎΠ΄ΠΈΡ ΠΊ ΠΏΠΎΠ»ΠΎΠΌΠΊΠ΅ Π³ΡΠ°Π²ΠΈΡΠΎΠ²Π°Π»ΡΠ½ΠΎΠΉ ΡΡΠ΅Π·Ρ ΠΈΠ»ΠΈ ΡΠ²Π΅ΡΠ»Π°. ΠΠΎΡΡΠΎΠΌΡ, ΠΊΠ°ΠΊ ΠΏΡΠ°Π²ΠΈΠ»ΠΎ, Π½Π° ΠΈΠ½ΡΡΡΡΠΌΠ΅Π½ΡΠ΅ Π΄Π»Ρ ΠΎΠ±ΡΠ°Π±ΠΎΡΠΊΠΈ ΡΠΏΠ»Π°Π²ΠΎΠ² Π°Π»ΡΠΌΠΈΠ½ΠΈΡ Π΄Π΅Π»Π°ΡΡ Π±ΠΎΠ»ΡΡΠΈΠ΅ ΡΡΡΡΠΆΠ΅ΡΠ½ΡΠ΅ ΠΊΠ°Π½Π°Π²ΠΊΠΈ Π΄Π»Ρ ΠΎΠ±Π»Π΅Π³ΡΠ΅Π½Π½ΠΎΠ³ΠΎ ΡΡ
ΠΎΠ΄Π° ΡΡΡΡΠΆΠΊΠΈ, Ρ
ΠΎΡΡ ΡΡΠΎ ΠΈ ΠΎΠ³ΡΠ°Π½ΠΈΡΠΈΠ²Π°Π΅Ρ ΠΌΠ°ΠΊΡΠΈΠΌΠ°Π»ΡΠ½ΠΎΠ΅ ΠΊΠΎΠ»ΠΈΡΠ΅ΡΡΠ²ΠΎ Π·ΡΠ±ΡΠ΅Π² Π½Π° ΡΡΠ΅Π·Π΅ Π΄Π²ΡΠΌΡ Π»ΠΈΠ±ΠΎ ΡΡΠ΅ΠΌΡ.
ΠΡΠΎΡΠΎΠΉ Π½Π΅Π³Π°ΡΠΈΠ²Π½ΡΠΉ ΡΡΡΠ΅ΠΊΡ β Π½Π°ΡΠΎΡΡΠΎΠΎΠ±ΡΠ°Π·ΠΎΠ²Π°Π½ΠΈΠ΅. ΠΡΠΎ ΡΠ²Π»Π΅Π½ΠΈΠ΅, ΠΏΡΠΈ ΠΊΠΎΡΠΎΡΠΎΠΌ ΠΏΡΠΎΠΈΡΡ ΠΎΠ΄ΠΈΡ ΡΠΎΡΠ΅ΡΠ½Π°Ρ Π½Π°ΠΏΠ»Π°Π²ΠΊΠ° ΠΎΠ±ΡΠ°Π±Π°ΡΡΠ²Π°Π΅ΠΌΠΎΠ³ΠΎ ΠΌΠ°ΡΠ΅ΡΠΈΠ°Π»Π° Π½Π° ΡΠ΅ΠΆΡΡΡΡ ΠΊΡΠΎΠΌΠΊΡ ΠΈΠ½ΡΡΡΡΠΌΠ΅Π½ΡΠ° Π² Π·ΠΎΠ½Π΅ ΡΠ΅Π·Π°Π½ΠΈΡ. Π‘Π»Π΅Π΄ΡΡΠ²ΠΈΠ΅ΠΌ ΡΡΠΎΠ³ΠΎ ΡΠ²Π»ΡΠ΅ΡΡΡ ΠΏΡΠΈΡΡΠΏΠ»Π΅Π½ΠΈΠ΅ ΡΠ΅ΠΆΡΡΠ΅Π³ΠΎ ΠΊΠ»ΠΈΠ½Π° ΠΈ ΡΠ²Π΅Π»ΠΈΡΠ΅Π½ΠΈΠ΅ Π½Π°Π³ΡΡΠ·ΠΊΠΈ Π½Π° ΠΈΠ½ΡΡΡΡΠΌΠ΅Π½Ρ, Π° ΡΠ°ΠΊ ΠΆΠ΅ Π·Π°ΡΡΡΠ΄Π½Π΅Π½Π½ΡΠΉ ΡΡ ΠΎΠ΄ ΡΡΡΡΠΆΠΊΠΈ ΠΈΠ·-Π·Π° ΡΡ ΡΠ΄ΡΠ΅Π½ΠΈΡ ΡΠ΅ΡΠΎΡ ΠΎΠ²Π°ΡΠΎΡΡΠΈ ΠΏΠ΅ΡΠ΅Π΄Π½Π΅ΠΉ ΠΏΠΎΠ²Π΅ΡΡ Π½ΠΎΡΡΠΈ ΠΈΠ½ΡΡΡΡΠΌΠ΅Π½ΡΠ°. ΠΡΠΎΠΈΠ·Π²ΠΎΠ΄ΠΈΡΠ΅Π»ΠΈ ΠΈΠ½ΡΡΡΡΠΌΠ΅Π½ΡΠ° Π±ΠΎΡΡΡΡΡ Ρ ΡΡΠΈΠΌ ΡΠ²Π»Π΅Π½ΠΈΠ΅ΠΌ, ΠΏΠΎΠ²ΡΡΠ°Ρ Π³Π»Π°Π΄ΠΊΠΎΡΡΡ ΠΏΠ΅ΡΠ΅Π΄Π½Π΅ΠΉ ΠΏΠΎΠ²Π΅ΡΡ Π½ΠΎΡΡΠΈ (Π½Π°ΠΏΡΠΈΠΌΠ΅Ρ, Π·Π° ΡΡΠ΅Ρ Π΄ΠΎΠΏΠΎΠ»Π½ΠΈΡΠ΅Π»ΡΠ½ΠΎΠΉ ΠΏΠΎΠ»ΠΈΡΠΎΠ²ΠΊΠΈ ΠΈΠ»ΠΈ Π½Π°Π½Π΅ΡΠ΅Π½ΠΈΡ ΡΠ»ΡΡΡΠ°Π³Π»Π°Π΄ΠΊΠΎΠ³ΠΎ ΠΏΠΎΠΊΡΡΡΠΈΡ), Π° ΡΠ°ΠΊΠΆΠ΅ Π·Π°Π΄Π°Π²Π°Ρ ΠΎΠΏΡΠ΅Π΄Π΅Π»Π΅Π½Π½ΡΠ΅ Π·Π½Π°ΡΠ΅Π½ΠΈΡ ΠΏΠ΅ΡΠ΅Π΄Π½Π΅Π³ΠΎ ΠΈ Π·Π°Π΄Π½Π΅Π³ΠΎ ΡΠ³Π»ΠΎΠ² ΡΠ΅ΠΆΡΡΠ΅Π³ΠΎ ΠΊΠ»ΠΈΠ½Π°.
ΠΡΠΈ Π½Π°ΠΏΠ»Π°Π²ΠΊΠ΅ ΠΌΠ°ΡΠ΅ΡΠΈΠ°Π»Π°, ΠΏΡΠΎΠΈΡΡ
ΠΎΠ΄ΠΈΡ Π·Π°Π±ΠΈΠ²Π°Π½ΠΈΠ΅ ΠΊΠ°Π½Π°Π²ΠΊΠΈ, ΡΡΠΎ Π²Π΅Π΄Π΅Ρ ΠΊ Π΄ΠΈΡΠ±Π°Π»Π°Π½ΡΡ ΠΈΠ½ΡΡΡΡΠΌΠ΅Π½ΡΠ°. ΠΡΠΈ Π·Π°ΡΡΠΏΠ»Π΅Π½ΠΈΠΈ ΡΠ΅ΠΆΡΡΠ΅ΠΉ ΠΊΡΠΎΠΌΠΊΠΈ, ΠΏΡΠΎΠΈΡΡ
ΠΎΠ΄ΠΈΡ ΠΏΠ΅ΡΠ΅Π³ΡΠ΅Π² ΠΈΠ½ΡΡΡΡΠΌΠ΅Π½ΡΠ°, ΡΡΠΎ ΠΌΠΎΠΆΠ΅Ρ ΠΏΡΠΈΠ²Π΅Π·ΡΠΈ ΠΊ Π·Π°ΠΊΠ»ΠΈΠ½ΠΈΠ²Π°Π½ΠΈΡ ΠΈ ΠΊΠ°ΠΊ ΡΠ»Π΅Π΄ΡΡΠ²ΠΈΠ΅, ΠΊ ΠΏΠΎΠ»ΠΎΠΌΠΊΠ΅ Π΄ΠΎΡΠΎΠ³ΠΎΡΡΠΎΡΡΠ΅Π³ΠΎ ΠΈΠ½ΡΡΡΡΠΌΠ΅Π½ΡΠ°.
ΠΠ° ΡΡΠ΅ΠΏΠ΅Π½Ρ ΠΈ Π³Π»ΡΠ±ΠΈΠ½Ρ Π½Π°ΠΏΠ»Π°Π²ΠΊΠΈ ΠΌΠ°ΡΠ΅ΡΠΈΠ°Π»Π°, Π²Π»ΠΈΡΡΡ ΡΠ΅ΠΆΠΈΠΌΡ ΡΠ΅Π·Π°Π½ΠΈΡ, Π³Π΅ΠΎΠΌΠ΅ΡΡΠΈΡ ΡΠ΅ΠΆΡΡΠ΅Π³ΠΎ ΠΈΠ½ΡΡΡΡΠΌΠ΅Π½ΡΠ°, ΡΡΠ΅ΠΏΠ΅Π½Ρ Π΅Π³ΠΎ Π·Π°ΡΡΠΏΠ»Π΅Π½ΠΈΡ, Ρ.Π΅. Π²ΡΠ΅ ΡΠ°ΠΊΡΠΎΡΡ, ΠΎΠΏΡΠ΅Π΄Π΅Π»ΡΡΡΠΈΠ΅ ΠΏΡΠΎΡΠ΅ΠΊΠ°Π½ΠΈΠ΅ ΠΏΠ»Π°ΡΡΠΈΡΠ΅ΡΠΊΠΎΠΉ Π΄Π΅ΡΠΎΡΠΌΠ°ΡΠΈΠΈ Π² Π·ΠΎΠ½Π΅ ΡΠ΅Π·Π°Π½ΠΈΡ.
Π£Π²Π΅Π»ΠΈΡΠ΅Π½ΠΈΠ΅ ΡΠΊΠΎΡΠΎΡΡΠΈ ΡΠ΅Π·Π°Π½ΠΈΡ ΡΠΏΠΎΡΠΎΠ±ΡΡΠ²ΡΠ΅Ρ ΡΠΌΠ΅Π½ΡΡΠ΅Π½ΠΈΡ Π³Π»ΡΠ±ΠΈΠ½Ρ ΠΈ ΡΡΠ΅ΠΏΠ΅Π½ΠΈ Π½Π°ΠΏΠ»Π°Π²ΠΊΠΈ, Π° ΠΏΠΎΠ΄Π°ΡΠΈ ΠΈ Π³Π»ΡΠ±ΠΈΠ½Ρ ΡΠ΅Π·Π°Π½ΠΈΡ β ΠΊ ΠΈΡ ΡΠ²Π΅Π»ΠΈΡΠ΅Π½ΠΈΡ!
ΠΠ»Ρ ΡΡΡΡΠ°Π½Π΅Π½ΠΈΡ Π½Π΅Π³Π°ΡΠΈΠ²Π½ΡΡ ΡΡΡΠ΅ΠΊΡΠΎΠ² ΠΏΡΠΈ ΠΎΠ±ΡΠ°Π±ΠΎΡΠΊΠ΅ Π°Π»ΡΠΌΠΈΠ½ΠΈΠ΅Π²ΡΡ ΡΠΏΠ»Π°Π²ΠΎΠ² ΡΠ΅ΠΊΠΎΠΌΠ΅Π½Π΄ΡΠ΅ΡΡΡ ΠΈΡΠΏΠΎΠ»ΡΠ·ΠΎΠ²Π°ΡΡ ΡΠΏΠ΅ΡΠΈΠ°Π»ΡΠ½ΡΠ΅ ΡΠ΅ΡΠΈΠΈ ΡΠ²Π΅ΡΠ΄ΠΎΡΠΏΠ»Π°Π²Π½ΠΎΠ³ΠΎ ΠΈΠ½ΡΡΡΡΠΌΠ΅Π½ΡΠ°.
ΠΠ»Ρ ΠΌΠ΅Ρ Π°Π½ΠΈΡΠ΅ΡΠΊΠΎΠΉ ΠΎΠ±ΡΠ°Π±ΠΎΡΠΊΠΈ Π½Π° ΡΡΠ΅Π·Π΅ΡΠ½ΡΡ ΠΈ ΡΠΎΠΊΠ°ΡΠ½ΡΡ ΡΡΠ°Π½ΠΊΠ°Ρ , ΡΠ°ΡΠ΅ Π²ΡΠ΅Π³ΠΎ ΠΈΡΠΏΠΎΠ»ΡΠ·ΡΡΡ ΠΌΠ°ΡΠΊΠΈ Π΄ΡΡΠ°Π»ΠΈ Π16 Π»ΠΈΠ±ΠΎ Π16Π’ (Π16Π’Π).
Π16Π’ Π»ΡΡΡΠ΅ Π²ΡΠ΅Π³ΠΎ ΠΏΠΎΠ΄Ρ ΠΎΠ΄ΠΈΡ Π΄Π»Ρ ΠΌΠ΅Ρ Π°Π½ΠΈΡΠ΅ΡΠΊΠΎΠΉ ΠΎΠ±ΡΠ°Π±ΠΎΡΠΊΠΈ Π½Π° ΡΡΠ΅Π·Π΅ΡΠ½ΡΡ ΠΈ ΡΠΎΠΊΠ°ΡΠ½ΡΡ ΡΡΠ°Π½ΠΊΠ°Ρ . ΠΠ»Π°Π³ΠΎΠ΄Π°ΡΡ ΡΠ΅ΡΠΌΠΎΠΎΠ±ΡΠ°Π±ΠΎΡΠΊΠ΅, Π΄Π°Π½Π½ΡΠΉ ΠΌΠ°ΡΠ΅ΡΠΈΠ°Π» ΠΈΠΌΠ΅Π΅Ρ Π±ΠΎΠ»Π΅Π΅ Ρ ΡΡΠΏΠΊΡΡ ΡΡΡΡΠΊΡΡΡΡ, ΡΡΠΎ ΠΏΠΎΠ»ΠΎΠΆΠΈΡΠ΅Π»ΡΠ½ΠΎ Π²Π»ΠΈΡΠ΅Ρ Π½Π° ΡΠ΅ΠΆΠΈΠΌΡ Π΅Π³ΠΎ ΡΠ΅Π·Π°Π½ΠΈΡ.
ΠΡΠΈ ΡΡΠ΅Π·Π΅ΡΠΎΠ²Π°Π½ΠΈΠΈ Π16Π’, Π»ΡΡΡΠ΅ Π²ΡΠ΅Π³ΠΎ ΠΈΡΠΏΠΎΠ»ΡΠ·ΠΎΠ²Π°ΡΡ Π½Π΅ΠΏΡΠ΅ΡΡΠ²Π½ΡΡ ΠΏΠΎΠ΄Π°ΡΡ Π‘ΠΠ Π»ΠΈΠ±ΠΎ ΡΠΈΡΡΠ΅ΠΌΡ ΠΎΡ
Π»Π°ΠΆΠ΄Π΅Π½ΠΈΠ΅ ΠΈΠ½ΡΡΡΡΠΌΠ΅Π½ΡΠ° ΠΌΠ°ΡΠ»ΡΠ½ΡΠΌ ΡΡΠΌΠ°Π½ΠΎΠΌ.
ΠΡΠΈ ΠΎΠΏΠ΅ΡΠ°ΡΠΈΡΡ
Ρ Π½Π΅Π±ΠΎΠ»ΡΡΠΈΠΌΠΈ ΡΡΠ΅ΠΌΠ°ΠΌΠΈ Π·Π° ΠΏΡΠΎΡ
ΠΎΠ΄, Π16Π’ ΠΌΠΎΠΆΠ½ΠΎ ΠΎΠ±ΡΠ°Π±Π°ΡΡΠ²Π°ΡΡ βΠ½Π° ΡΡΡ
ΡΡβ, Π»ΠΈΠ±ΠΎ ΠΏΠ΅ΡΠΈΠΎΠ΄ΠΈΡΠ΅ΡΠΊΠΈ ΠΎΠΏΡΡΡΠΊΠΈΠ²Π°Ρ Π²ΡΡΡΠ½ΡΡ Π·ΠΎΠ½Ρ ΡΠ΅Π·Π°Π½ΠΈΡ.
Π‘ΠΏΠ»Π°Π² Π16, ΡΠ°ΠΊ ΠΆΠ΅ ΡΠ΄ΠΎΠ±Π΅Π½ Π΄Π»Ρ ΠΌΠ΅Ρ Π°Π½ΠΈΡΠ΅ΡΠΊΠΎΠΉ ΠΎΠ±ΡΠ°Π±ΠΎΡΠΊΠΈ. ΠΠ³ΠΎ ΡΠΎΠΏΡΠΎΡΠΈΠ²Π»Π΅Π½ΠΈΠ΅ ΡΡΠ΅Π·Π° Π½Π΅ ΠΏΡΠ΅Π²ΡΡΠ°Π΅Ρ 15 ΠΊΠ³/ΠΌΠΌ2. ΠΡΠ½ΠΎΠ²Π½ΡΠΌ ΠΎΡΠ»ΠΈΡΠΈΠ΅ΠΌ Π΄Π°Π½Π½ΠΎΠ³ΠΎ ΡΠΏΠ»Π°Π²Π°, ΠΎΡΠ½ΠΎΡΠΈΡΠ΅Π»ΡΠ½ΠΎ ΡΠ΅ΡΠΌΠΎΠΎΠ±ΡΠ°Π±ΠΎΡΠ°Π½Π½ΠΎΠ³ΠΎ Π16Π’, ΡΠ²Π»ΡΠ΅ΡΡΡ ΡΡΡΡ Π±ΠΎΠ»Π΅Π΅ Π²ΡΡΠΎΠΊΠΈΠΉ ΠΏΠ°ΡΠ°ΠΌΠ΅ΡΡ Π²ΡΠ·ΠΊΠΎΡΡΠΈ.
ΠΡΠΈ Π½Π΅ ΠΊΠΎΡΡΠ΅ΠΊΡΠ½ΡΡ ΡΠ΅ΠΆΠΈΠΌΠ°Ρ ΡΠ΅Π·Π°Π½ΠΈΡ, Π»ΠΈΠ±ΠΎ ΠΏΡΠΈ Π½Π΅ ΠΏΡΠ°Π²ΠΈΠ»ΡΠ½ΠΎ ΠΏΠΎΠ΄ΠΎΠ±ΡΠ°Π½Π½ΠΎΠΌ ΠΈΠ½ΡΡΡΡΠΌΠ΅Π½ΡΠ΅, ΠΌΠΎΠΆΠ΅Ρ ΠΏΡΠΎΠΈΡΡ ΠΎΠ΄ΠΈΡΡ Π½Π°ΠΌΠ°ΡΡΠ²Π°Π½ΠΈΠ΅ ΡΡΡΡΠΆΠΊΠΈ Π½Π° ΠΈΠ½ΡΡΡΡΠΌΠ΅Π½Ρ.
ΠΡΠΈ ΠΎΠ±ΡΠ°Π±ΠΎΡΠΊΠ΅ Π16, ΠΈΡΠΏΠΎΠ»ΡΠ·ΡΡΡ Π½Π΅ΠΏΡΠ΅ΡΡΠ²Π½ΡΡ ΠΏΠΎΠ΄Π°ΡΡ Π‘ΠΠ Π² Π·ΠΎΠ½Ρ ΡΠ΅Π·Π°Π½ΠΈΡ.
ΠΠ½ΡΡΡΡΠΌΠ΅Π½Ρ β ΠΌΠ°ΠΊΡΠΈΠΌΠ°Π»ΡΠ½ΠΎ ΠΎΡΡΡΠΎ Π·Π°ΡΠΎΡΠ΅Π½Π½ΡΠΉ.
Π‘Π°ΠΌΡΠΌ ΡΠ»ΠΎΠΆΠ½ΡΠΌ Π΄Π»Ρ ΡΡΠ΅Π·Π΅ΡΠ½ΠΎΠΉ ΠΈ ΡΠΎΠΊΠ°ΡΠ½ΠΎΠΉ ΠΎΠ±ΡΠ°Π±ΠΎΡΠΊΠΈ ΡΠ²Π»ΡΠ΅ΡΡΡ ΡΠΈΡΡΡΠΉ Π°Π»ΡΠΌΠΈΠ½ΠΈΠΉ ΠΈ Π΅Π³ΠΎ ΡΠΏΠ»Π°Π² Ρ ΠΌΠ°Π³Π½ΠΈΠ΅ΠΌ (ΠΠΠ).
ΠΠ°Π½Π½ΡΠ΅ ΡΠΏΠ»Π°Π²Ρ ΠΈΠΌΠ΅ΡΡ ΡΠ΄ΠΎΠ²Π»Π΅ΡΠ²ΠΎΡΠΈΡΠ΅Π»ΡΠ½ΡΡ ΠΏΡΠΎΡΠ½ΠΎΡΡΡ, Ρ
ΠΎΡΠΎΡΡΡ ΠΏΠ»Π°ΡΡΠΈΡΠ½ΠΎΡΡΡ ΠΈ Π²ΡΡΠΎΠΊΡΡ ΠΊΠΎΡΡΠΎΠ·ΠΈΠΉΠ½ΡΡ ΡΡΠΎΠΉΠΊΠΎΡΡΡ. Π‘ ΡΠΎΡΡΠΎΠΌ ΡΠΎΠ΄Π΅ΡΠΆΠ°Π½ΠΈΡ ΠΌΠ°Π³Π½ΠΈΡ, ΡΡΡΠ΅ΡΡΠ²Π΅Π½Π½ΠΎ ΡΠ²Π΅Π»ΠΈΡΠΈΠ²Π°Π΅ΡΡΡ ΠΏΡΠΎΡΠ½ΠΎΡΡΡ ΠΠΠ.
ΠΠ· Π²ΡΠ΅Ρ
ΡΠΏΠ»Π°Π²ΠΎΠ² Π°Π»ΡΠΌΠΈΠ½ΠΈΡ, Π΄Π°Π½Π½ΡΠΉ ΡΠΏΠ»Π°Π² ΡΠ²Π»ΡΠ΅ΡΡΡ ΡΠ°ΠΌΡΠΌ Π²ΡΠ·ΠΊΠΈΠΌ.
ΠΡΠΈ ΠΎΠ±ΡΠ°Π±ΠΎΡΠΊΠ΅ ΠΠΠ Π½Π° ΡΡΠ΅Π·Π΅ΡΠ½ΡΡ
ΡΡΠ°Π½ΠΊΠ°Ρ
Ρ Π§ΠΠ£ Π»ΠΈΠ±ΠΎ Π½Π° ΡΠΎΠΊΠ°ΡΠ½ΡΡ
ΡΡΠ°Π½ΠΊΠ°Ρ
Ρ Π§ΠΠ£, ΠΎΠΏΠ΅ΡΠ°ΡΠΎΡ ΠΌΠΎΠΆΠ΅Ρ ΡΡΠ°Π»ΠΊΠΈΠ²Π°ΡΡΡΡ Ρ ΠΏΡΠΎΠ±Π»Π΅ΠΌΠΎΠΉ Π·Π°Π±ΠΈΠ²Π°Π½ΠΈΡ ΠΊΠ°Π½Π°Π²ΠΎΠΊ ΠΈΠ½ΡΡΡΡΠΌΠ΅Π½ΡΠ° ΡΡΡΡΠΆΠΊΠΎΠΉ.
Π‘ΠΎΠ±Π»ΡΠ΄Π°Ρ ΡΡΠΈ ΠΏΡΠ°Π²ΠΈΠ»Π°, ΠΌΠΎΠΆΠ½ΠΎ ΠΎΠ±ΡΠ°Π±Π°ΡΡΠ²Π°ΡΡ ΠΠΠ Π±Π΅Π· ΠΎΠΏΠ°ΡΠ½ΠΎΡΡΠΈ Π΄Π»Ρ ΠΈΠ½ΡΡΡΡΠΌΠ΅Π½ΡΠ° ΠΈ ΠΏΠΎΠ»ΡΡΠ°ΡΡ Π½Π΅ΠΎΠ±Ρ ΠΎΠ΄ΠΈΠΌΡΡ ΡΠ΅ΡΠΎΡ ΠΎΠ²Π°ΡΠΎΡΡΡ.
ΠΡΡΠ°Π»ΡΠ½ΡΠ΅ ΡΠΏΠ»Π°Π²Ρ Π°Π»ΡΠΌΠΈΠ½ΠΈΡ, Π½Π΅ ΡΠ°ΠΊ ΡΠ°ΡΠΏΡΠΎΡΡΡΠ°Π½Π΅Π½Ρ ΠΏΡΠΈ ΠΌΠ΅Ρ Π°Π½ΠΈΡΠ΅ΡΠΊΠΎΠΉ ΠΎΠ±ΡΠ°Π±ΠΎΡΠΊΠ΅ Π½Π° Π’ΠΎΠΊΠ°ΡΠ½ΡΡ ΠΈ ΡΡΠ΅Π·Π΅ΡΠ½ΡΡ ΡΡΠ°Π½ΠΊΠ°Ρ Ρ Π§ΠΠ£.
technograv.ru
Π₯ΠΈΠΌΠΈΡΠ΅ΡΠΊΠ°Ρ ΠΎΠ±ΡΠ°Π±ΠΎΡΠΊΠ° Π°Π»ΡΠΌΠΈΠ½ΠΈΡ | ΠΡΡ ΠΎ ΠΊΡΠ°ΡΠΊΠ°Ρ
Π₯ΠΈΠΌΠΈΡΠ΅ΡΠΊΠ°Ρ ΠΎΠ±ΡΠ°Π±ΠΎΡΠΊΠ° ΠΏΠΎΡΠ²ΠΈΠ»Π°ΡΡ ΠΏΠΎΠ·ΠΆΠ΅, ΡΠ΅ΠΌ ΡΠ»Π΅ΠΊΡΡΠΈΡΠ΅ΡΠΊΠ°Ρ ΠΈ Π² Π½Π°ΡΡΠΎΡΡΠ΅Π΅ Π²ΡΠ΅ΠΌΡ ΡΠΈΡΠΎΠΊΠΎ Π΅Π΅ Π·Π°ΠΌΠ΅Π½ΡΠ΅Ρ. ΠΠ»Π°Π²Π½ΡΠΌ ΠΏΡΠ΅ΠΈΠΌΡΡΠ΅ΡΡΠ²ΠΎΠΌ ΡΡΠΈΡ ΠΏΡΠΎΡΠ΅ΡΡΠΎΠ² ΡΠ²Π»ΡΡΡΡΡ Π³ΠΎΡΠ°Π·Π΄ΠΎ Π±ΠΎΠ»Π΅Π΅ Π½ΠΈΠ·ΠΊΠ°Ρ ΡΡΠΎΠΈΠΌΠΎΡΡΡ, ΠΏΡΠΈΡΠ΅ΠΌ Π½Π΅ ΡΠΎΠ»ΡΠΊΠΎ Π½Π° ΡΠ»Π΅ΠΊΡΡΠΎΡΠ½Π΅ΡΠ³ΠΈΠΈ, Π½ΠΎ ΠΈ ΡΠ΅Π·Π΅ΡΠ²ΡΠ°ΡΠΎΠ² ΠΈ ΠΊΡΠ΅ΠΏΠ»Π΅Π½ΠΈΠΉ. ΠΡΠ»Π΅Π΄ΡΡΠ²ΠΈΠ΅ ΡΠΎΠ³ΠΎ, ΡΡΠΎ Π² Π΄Π°Π½Π½ΠΎΠΌ ΡΠ»ΡΡΠ°Π΅ Π½Π΅ ΡΡΠ΅Π±ΡΠ΅ΡΡΡ ΡΠ»Π΅ΠΊΡΡΠΈΡΠ΅ΡΠΊΠΈΠΉ ΡΠΎΠΊ ΠΈ ΠΏΠΎΠ΄Π²ΠΈΠΆΠ½ΡΠΉ Π°Π½ΠΎΠ΄Π½ΠΎΠ³ΠΎ ΡΡΠ΅ΡΠΆΠ½Ρ, ΡΠ°Π±ΠΎΡΡ ΠΌΠΎΠΆΠ½ΠΎ ΠΏΡΠΎΠ²ΠΎΠ΄ΠΈΡΡ Π² ΠΊΠΎΡΠ·ΠΈΠ½Π°Ρ ΠΈ Ρ ΠΏΡΠΎΡΡΡΠΌΠΈ Π·Π°ΠΆΠΈΠΌΠ°ΠΌΠΈ.Π ΠΎΡΠ½ΠΎΠ²Π½ΠΎΠΌ, ΠΏΡΠΈΠ½ΡΠΈΠΏ Ρ ΠΈΠΌΠΈΡΠ΅ΡΠΊΠΎΠΉ ΠΎΠ±ΡΠ°Π±ΠΎΡΠΊΠΈ ΠΏΠΎΡ ΠΎΠΆ Π½Π° ΠΏΡΠΈΠ½ΡΠΈΠΏ Π³Π°Π»ΡΠ²Π°Π½ΠΈΡΠ΅ΡΠΊΠΎΠΉ ΠΎΠ±ΡΠ°Π±ΠΎΡΠΊΠΈ, ΠΎΠ΄Π½Π°ΠΊΠΎ Π²ΠΌΠ΅ΡΡΠΎ ΡΠ»Π΅ΠΊΡΡΠΈΡΠ΅ΡΠΊΠΎΠ³ΠΎ ΡΠΎΠΊΠ° Π·Π΄Π΅ΡΡ ΠΈΡΠΏΠΎΠ»ΡΠ·ΡΡΡΡΡ Ρ ΠΈΠΌΠΈΡΠ΅ΡΠΊΠΈΠ΅ ΠΎΠΊΠΈΡΠ»ΠΈΡΠ΅Π»ΠΈ. ΠΠ²ΠΈΠΆΡΡΠ΅ΠΉ ΡΠΈΠ»ΠΎΠΉ Ρ ΠΈΠΌΠΈΡΠ΅ΡΠΊΠΎΠΉ ΠΎΠ±ΡΠ°Π±ΠΎΡΠΊΠΈ ΡΠ²Π»ΡΠ΅ΡΡΡ ΡΠ°Π·Π½ΠΎΡΡΡ ΡΠ»Π΅ΠΊΡΡΠΎΡ ΠΈΠΌΠΈΡΠ΅ΡΠΊΠΈΡ ΠΏΠΎΡΠ΅Π½ΡΠΈΠ°Π»ΠΎΠ² ΠΌΠ΅ΠΆΠ΄Ρ Π°Π½ΠΎΠ΄Π½ΡΠΌΠΈ ΠΈ ΠΊΠ°ΡΠΎΠ΄Π½ΡΠΌΠΈ ΡΡΠ°ΡΡΠΊΠ°ΠΌΠΈ ΠΏΠΎΠ²Π΅ΡΡ Π½ΠΎΡΡΠΈ.
ΠΠΎΡΡΡΠΈΡΠΈΠ΅Π½Ρ Π·Π΅ΡΠΊΠ°Π»ΡΠ½ΠΎΠ³ΠΎ ΠΎΡΡΠ°ΠΆΠ΅Π½ΠΈΡ Π³Π»Π°Π΄ΠΊΠΎΠ³ΠΎ ΠΏΡΠΎΠΊΠ°ΡΠ°Π½Π½ΠΎΠ³ΠΎ Π°Π»ΡΠΌΠΈΠ½ΠΈΡ ΠΏΡΠΈ Π°Π½ΠΎΠ΄ΠΈΡΠΎΠ²Π°Π½ΠΈΠΈ Π·Π°ΠΌΠ΅ΡΠ½ΠΎ ΠΏΠ°Π΄Π°Π΅Ρ, Π΅ΡΠ»ΠΈ ΠΏΠ΅ΡΠ΅Π΄ ΡΡΠΈΠΌ ΠΎΠ½ Π½Π΅ ΠΏΠΎΠ΄Π²Π΅ΡΠ³Π°Π΅ΡΡΡ ΠΎΠ±ΡΠ°Π±ΠΎΡΠΊΠ΅ Ρ ΠΈΠΌΠΈΡΠ΅ΡΠΊΠΈΠΌ ΠΈΠ»ΠΈ ΡΠ»Π΅ΠΊΡΡΠΈΡΠ΅ΡΠΊΠΈΠΌ ΡΠΏΠΎΡΠΎΠ±ΠΎΠΌ Π² ΡΠ΅ΡΠ΅Π½ΠΈΠ΅ ΠΊΠΎΡΠΎΡΠΊΠΎΠ³ΠΎ ΠΏΡΠΎΠΌΠ΅ΠΆΡΡΠΊΠ° Π²ΡΠ΅ΠΌΠ΅Π½ΠΈ. ΠΠΎΠ΄ΠΎΠ±Π½ΠΎΠ΅ ΡΠΌΠ΅Π½ΡΡΠ΅Π½ΠΈΠ΅ ΠΊΠΎΡΡΡΠΈΡΠΈΠ΅Π½ΡΠ° Π·Π΅ΡΠΊΠ°Π»ΡΠ½ΠΎΠ³ΠΎ ΠΎΡΡΠ°ΠΆΠ΅Π½ΠΈΡ Π½Π°Π±Π»ΡΠ΄Π°Π΅ΡΡΡ ΠΈ Π½Π° Π½Π°ΡΠ°Π»ΡΠ½ΡΡ ΡΡΠ°Π΄ΠΈΡΡ Ρ ΠΈΠΌΠΈΡΠ΅ΡΠΊΠΎΠΉ ΠΎΠ±ΡΠ°Π±ΠΎΡΠΊΠΈ, ΠΎΠ΄Π½Π°ΠΊΠΎ Π·Π°ΡΠ΅ΠΌ ΡΠ»Π΅Π΄ΡΠ΅Ρ ΠΏΠΎΠ²ΡΡΠ΅Π½ΠΈΠ΅ ΠΊΠΎΡΡΡΠΈΡΠΈΠ΅Π½ΡΠ° Π·Π΅ΡΠΊΠ°Π»ΡΠ½ΠΎΠ³ΠΎ ΠΎΡΡΠ°ΠΆΠ΅Π½ΠΈΡ, ΠΊΠΎΡΠΎΡΡΠΉ ΠΌΠΎΠΆΠ΅Ρ Π΄ΠΎΡΡΠΈΠ³Π°ΡΡ 90% (ΠΌΠ°ΠΊΡΠΈΠΌΠ°Π»ΡΠ½ΠΎ Π²ΠΎΠ·ΠΌΠΎΠΆΠ½ΡΠΉ ΠΊΠΎΡΡΡΠΈΡΠΈΠ΅Π½Ρ Π΄Π»Ρ Π°Π»ΡΠΌΠΈΠ½ΠΈΡ), ΠΏΡΠΈ ΡΠΎΠ±Π»ΡΠ΄Π΅Π½ΠΈΠΈ Π²ΡΠ΅Ρ ΡΡΠ»ΠΎΠ²ΠΈΠΉ Ρ ΠΈΠΌΠΈΡΠ΅ΡΠΊΠΎΠΉ ΠΎΠ±ΡΠ°Π±ΠΎΡΠΊΠΈ. Π’ΠΎΡ ΠΆΠ΅ ΠΏΡΠΎΡΠ΅ΡΡ Π½Π°Π±Π»ΡΠ΄Π°Π΅ΡΡΡ ΠΈ ΠΏΡΠΈ Π³Π°Π»ΡΠ²Π°Π½ΠΈΡΠ΅ΡΠΊΠΎΠΉ ΠΎΠ±ΡΠ°Π±ΠΎΡΠΊΠ΅. ΠΡΠΈ Π°Π½ΠΎΠ΄ΠΈΡΠΎΠ²Π°Π½ΠΈΠΈ ΠΊΠΎΡΡΡΠΈΡΠΈΠ΅Π½Ρ Π·Π΅ΡΠΊΠ°Π»ΡΠ½ΠΎΠ³ΠΎ ΠΎΡΡΠ°ΠΆΠ΅Π½ΠΈΡ Π°Π»ΡΠΌΠΈΠ½ΠΈΡ, ΠΏΠΎΠ²Π΅ΡΠ³Π½ΡΡΠΎΠ³ΠΎ ΡΠ»Π΅ΠΊΡΡΠΈΡΠ΅ΡΠΊΠΎΠΉ ΠΈΠ»ΠΈ Ρ ΠΈΠΌΠΈΡΠ΅ΡΠΊΠΎΠΉ ΠΎΠ±ΡΠ°Π±ΠΎΡΠΊΠ΅ ΠΎΡΡΠ°ΡΡΡΡ Π²ΡΡΠΎΠΊΠΈΠΌ (Ρ ΠΎΡΡ ΠΈ Π½Π°Π±Π»ΡΠ΄Π°Π΅ΡΡΡ Π½Π΅Π±ΠΎΠ»ΡΡΠΎΠ΅ Π΅Π³ΠΎ ΡΠΌΠ΅Π½ΡΡΠ΅Π½ΠΈΠ΅ Ρ ΡΠ²Π΅Π»ΠΈΡΠ΅Π½ΠΈΠ΅ΠΌ Π²ΡΠ΅ΠΌΠ΅Π½ΠΈ Π½Π°Ρ ΠΎΠΆΠ΄Π΅Π½ΠΈΡ Π² Π²Π°Π½Π½Π΅ Π΄Π»Ρ Π°Π½ΠΎΠ΄ΠΈΡΠΎΠ²Π°Π½ΠΈΡ, Π²ΡΠ·Π²Π°Π½Π½ΠΎΠ΅ ΠΌΠ΅Π΄Π»Π΅Π½Π½ΡΠΌ ΡΠ°ΡΡΠ²ΠΎΡΠ΅Π½ΠΈΠ΅ΠΌ ΠΈ Π»ΡΠ³ΠΊΠΎΠΉ ΡΠ΅ΡΠΎΡ ΠΎΠ²Π°ΡΠΎΡΡΡΡ Π²Π½Π΅ΡΠ½Π΅ΠΉ ΠΏΠΎΠ²Π΅ΡΡ Π½ΠΎΡΡΠΈ Π°Π½ΠΎΠ΄Π½ΠΎΠΉ ΠΏΠ»ΡΠ½ΠΊΠΈ). ΠΠΎΡΡΠΎΠΌΡ ΠΏΡΠΎΠΌΡΡΠ»Π΅Π½Π½ΡΠΉ ΠΏΡΠΎΡΠ΅ΡΡ Π³Π»ΡΠ½ΡΠ΅Π²Π°Π½ΠΈΡ ΠΌΠ΅ΡΠΎΠ΄ΠΎΠΌ Π°Π½ΠΎΠ΄ΠΈΡΠΎΠ²Π°Π½ΠΈΡ ΠΎΠ±ΡΡΠ½ΠΎ Π²ΠΊΠ»ΡΡΠ°Π΅Ρ Π² ΡΠ΅Π±Ρ Ρ ΠΈΠΌΠΈΡΠ΅ΡΠΊΡΡ ΠΎΠ±ΡΠ°Π±ΠΎΡΠΊΡ Π½Π΅ΠΏΠΎΡΡΠ΅Π΄ΡΡΠ²Π΅Π½Π½ΠΎ ΠΏΠ΅ΡΠ΅Π΄ Π°Π½ΠΎΠ΄ΠΈΡΠΎΠ²Π°Π½ΠΈΠ΅ΠΌ.
ΠΡΠ»ΠΏΠ°Π½ ΠΈ ΠΡΡΠΎΡΡΠΌΠΈΡΠΏΡΠΎΠΈΠ·Π²Π΅Π»ΠΈ ΠΈΠ·ΠΌΠ΅ΡΠ΅Π½ΠΈΡ ΠΈΠ·ΠΌΠ΅Π½Π΅Π½ΠΈΡ ΠΊΠΎΡΡΡΠΈΡΠΈΠ΅Π½ΡΠ° Π·Π΅ΡΠΊΠ°Π»ΡΠ½ΠΎΠ³ΠΎ ΠΎΡΡΠ°ΠΆΠ΅Π½ΠΈΡ Π²ΠΎ Π²ΡΠ΅ΠΌΡ Ρ ΠΈΠΌΠΈΡΠ΅ΡΠΊΠΎΠΉ ΠΎΠ±ΡΠ°Π±ΠΎΡΠΊΠΈ Π°Π»ΡΠΌΠΈΠ½ΠΈΡ, Π° Π·Π°ΡΠ΅ΠΌ Ρ ΠΏΠΎΠΌΠΎΡΡΡ ΡΠ»Π΅ΠΊΡΡΠΎΠ½Π½ΠΎΠ³ΠΎ ΠΌΠΈΠΊΡΠΎΡΠΊΠΎΠΏΠ° Π½Π°Π±Π»ΡΠ΄Π°Π»ΠΈ Π·Π° ΡΠΎΠΎΡΠ²Π΅ΡΡΡΠ²ΡΡΡΠΈΠΌΠΈ ΠΈΠ·ΠΌΠ΅Π½Π΅Π½ΠΈΡΠΌΠΈ ΡΡΡΡΠΊΡΡΡΡ ΠΏΠΎΠ²Π΅ΡΡ Π½ΠΎΡΡΠΈ. ΠΡΠΎΡΠ΅ΡΡ Ρ ΠΈΠΌΠΈΡΠ΅ΡΠΊΠΎΠΉ ΠΎΠ±ΡΠ°Π±ΠΎΡΠΊΠΈ Π½Π°ΡΠ°Π»ΡΡ Ρ ΡΠ΅Π·ΠΊΠΎΠ³ΠΎ ΡΠΌΠ΅Π½ΡΡΠ΅Π½ΠΈΡ ΠΊΠΎΡΡΡΠΈΡΠΈΠ΅Π½ΡΠ° Π·Π΅ΡΠΊΠ°Π»ΡΠ½ΠΎΠ³ΠΎ ΠΎΡΡΠ°ΠΆΠ΅Π½ΠΈΡ, Π²ΡΠ·Π²Π°Π½Π½ΠΎΠ³ΠΎ ΡΡΠ°Π²Π»Π΅Π½ΠΈΠ΅ΠΌ, Π·Π°ΡΠ΅ΠΌ ΠΏΠΎΡΠ»Π΅Π΄ΠΎΠ²Π°Π»ΠΎ Π΅Π³ΠΎ ΠΏΠΎΠ²ΡΡΠ΅Π½ΠΈΠ΅, Π° ΠΏΠΎ Π΄ΠΎΡΡΠΈΠΆΠ΅Π½ΠΈΠΈ ΠΌΠ°ΠΊΡΠΈΠΌΠ°Π»ΡΠ½ΠΎΠ³ΠΎ Π·Π½Π°ΡΠ΅Π½ΠΈΡ ΠΎΠ½ ΡΡΠ°Π» ΡΠΌΠ΅Π½ΡΡΠ°ΡΡΡΡ. ΠΠ° ΠΏΠ΅ΡΠ²ΠΎΠΌ ΡΡΠ°ΠΏΠ΅ Π½Π°Π±Π»ΡΠ΄Π°Π»ΡΡ ΡΠΎΡΡ ΠΈ ΡΠ»ΠΈΠ²Π°Π½ΠΈΠ΅ ΡΠ»ΡΡΠ°ΠΉΠ½ΠΎ ΡΠ°ΡΠΏΠΎΠ»ΠΎΠΆΠ΅Π½Π½ΡΡ ΡΠΌΠΎΠΊ ΡΡΠ°Π²Π»Π΅Π½ΠΈΡ, ΡΡΠΎ ΠΏΡΠΎΠΈΡΡ ΠΎΠ΄ΠΈΠ»ΠΎ Π΄ΠΎ ΡΠ΅Ρ ΠΏΠΎΡ, ΠΏΠΎΠΊΠ° ΠΏΠ΅ΡΠ²ΠΎΠ½Π°ΡΠ°Π»ΡΠ½Π°Ρ ΠΏΠΎΠ²Π΅ΡΡ Π½ΠΎΡΡΡ Π½Π΅ Π±ΡΠ»Π° ΠΏΠΎΠ»Π½ΠΎΡΡΡΡ ΡΠ΄Π°Π»Π΅Π½Π°. ΠΡΡΠ΅ΡΡΠ²Π΅Π½Π½ΡΠΉ ΠΎΠΊΠΈΡΠ΅Π» Π±ΡΠ» Π·Π°ΠΌΠ΅Π½ΡΠ½ ΡΠΏΠ»ΠΎΡΠ½ΠΎΠΉ ΠΏΡΠΎΡΠ½ΠΎΠΉ ΠΏΠ»ΡΠ½ΠΊΠΎΠΉ, ΠΏΠΎ ΠΊΠΎΡΠΎΡΠΎΠΉ ΠΏΡΠΎΠ΄ΠΎΠ»ΠΆΠ°Π»Π°ΡΡ Ρ ΠΈΠΌΠΈΡΠ΅ΡΠΊΠ°Ρ ΠΎΠ±ΡΠ°Π±ΠΎΡΠΊΠ°. Π₯ΠΎΠ°Ρ ΠΏΡΠ΅Π΄ΠΏΠΎΠ»ΠΎΠΆΠΈΠ», ΡΡΠΎ ΡΡΠ° ΠΏΠ»ΡΠ½ΠΊΠ° ΡΠ²Π»ΡΠ»Π°ΡΡ ΠΎΠΊΠΈΡΠ»ΠΎΠΌ, ΡΠΎΠ΄Π΅ΡΠΆΠ°ΡΠΈΠΌ Π·Π½Π°ΡΠΈΡΠ΅Π»ΡΠ½ΠΎΠ΅ ΠΊΠΎΠ»ΠΈΡΠ΅ΡΡΠ²ΠΎ Π°Π½ΠΈΠΎΠ½ΠΎΠ² ΠΈΠ· ΡΠ°ΡΡΠ²ΠΎΡΠ°. ΠΡΠ°ΠΏ ΡΡΠ°Π²Π»Π΅Π½ΠΈΡ Π½Π΅ΠΎΠ±Ρ ΠΎΠ΄ΠΈΠΌ Π΄Π»Ρ Π·Π°ΠΌΠ΅Π½Ρ Π΅ΡΡΠ΅ΡΡΠ²Π΅Π½Π½ΠΎΠ³ΠΎ ΠΎΠΊΠΈΡΠ»Π° Π½Π° ΡΠΎΠ½ΠΊΡΡ ΠΏΡΠΎΡΠ½ΡΡ ΠΏΠ»ΡΠ½ΠΊΡ, ΠΎΠ±Π»Π°Π΄Π°ΡΡΡΡ Ρ Π°ΡΠ°ΠΊΡΠ΅ΡΠΈΡΡΠΈΠΊΠ°ΠΌΠΈ, Π½Π΅ΠΎΠ±Ρ ΠΎΠ΄ΠΈΠΌΡΠΌΠΈ Π΄Π»Ρ ΠΎΡΡΡΠ΅ΡΡΠ²Π»Π΅Π½ΠΈΡ ΠΎΠ±ΡΠ°Π±ΠΎΡΠΊΠΈ. Π ΡΡΡΠ΅ΡΡΠ²ΠΎΠ²Π°Π½ΠΈΠΈ ΡΡΠ°Π΄ΠΈΠΈ ΡΡΠ°Π²Π»Π΅Π½ΠΈΡ Π΄Π°Π²Π½ΠΎ ΡΠΆΠ΅ Π±ΡΠ»ΠΎ ΠΈΠ·Π²Π΅ΡΡΠ½ΠΎ ΠΏΡΠΎΠΌΡΡΠ»Π΅Π½Π½ΠΈΠΊΠ°ΠΌ, ΠΊΠΎΡΠΎΡΡΠ΅ Π½Π°Π±Π»ΡΠ΄Π°Π»ΠΈ Π΅Ρ Π² ΡΠ΅ΡΠ΅Π½ΠΈΠ΅ ΠΏΠ΅ΡΠ²ΡΡ 30 ΡΠ΅ΠΊΡΠ½Π΄ ΠΏΡΠΎΡΠ΅ΡΡΠ° Ρ ΠΈΠΌΠΈΡΠ΅ΡΠΊΠΎΠΉ ΠΎΠ±ΡΠ°Π±ΠΎΡΠΊΠΈ ΠΈ ΠΏΡΠΈΠΏΠΈΡΡΠ²Π°Π»ΠΈ ΡΡΠΎ Π°ΠΊΡΠΈΠ²Π½ΠΎΡΡΠΈ ΠΏΡΠΎΠΊΠ°ΡΠ°Π½Π½ΠΎΠΉ ΠΈΠ»ΠΈ ΠΏΠΎΠ»ΠΈΡΠΎΠ²Π°Π»ΡΠ½ΠΎΠΉ ΠΏΠΎΠ²Π΅ΡΡ Π½ΠΎΡΡΠΈ. ΠΠΊΠΈΡΠ΅Π», ΡΠΌΠ°Π·ΠΎΡΠ½ΠΎ-ΠΎΡ Π»Π°ΠΆΠ΄Π°ΡΡΠ°Ρ ΠΆΠΈΠ΄ΠΊΠΎΡΡΡ Π΄Π»Ρ ΠΏΡΠΎΠΊΠ°ΡΠΊΠΈ ΠΈ Π΄Π΅ΡΡΠΈΡ, Π½Π°Π½ΠΎΡΠΈΠΌΡΠ΅ Π½Π° ΠΏΠΎΠ²Π΅ΡΡ Π½ΠΎΡΡΡ, ΡΡΠΈΡΠ°Π»ΠΈΡΡ ΠΏΡΠΈΡΠΈΠ½ΠΎΠΉ Π½Π°Π»ΠΈΡΠΈΡ ΡΡΠΎΠΉ Π½Π°ΡΠ°Π»ΡΠ½ΠΎΠΉ ΡΡΠ°Π΄ΠΈΠΈ ΡΡΠ°Π²Π»Π΅Π½ΠΈΡ, Π·Π° ΠΊΠΎΡΠΎΡΠΎΠΉ, ΠΏΠΎΡΠ»Π΅ ΡΠ΄Π°Π»Π΅Π½ΠΈΡ ΡΠ»ΠΎΡ ΠΠ΅ΠΉΠ»Π±ΠΈ, ΡΠ»Π΅Π΄ΠΎΠ²Π°Π»Π° ΠΎΠ±ΡΠ°Π±ΠΎΡΠΊΠ°. ΠΡΠΎ ΡΠ°ΠΊ ΠΆΠ΅ ΠΏΠΎΠ΄ΡΠ²Π΅ΡΠ΄ΠΈΠ»ΠΈ ΠΡΡΠΎΡΡΠΌΠΈΡ ΠΈ Π‘Π²ΠΈΠ»ΠΈΠ½ΡΠΊΠΈ, ΠΎΠ±Π½Π°ΡΡΠΆΠΈΠ²ΡΠΈΠ΅, ΡΡΠΎ Π²ΡΠ΅ΠΌΡ ΡΠ΄Π°Π»Π΅Π½ΠΈΡ ΡΠ»ΠΎΡ Π΅ΡΡΠ΅ΡΡΠ²Π΅Π½Π½ΠΎΠ³ΠΎ ΠΎΠΊΠΈΡΠ»Π° Π·Π°Π²ΠΈΡΠ΅Π»ΠΎ ΠΎΡ Π΅Π³ΠΎ ΡΠΎΠ»ΡΠΈΠ½Ρ. ΠΡΠ»ΠΏΠ°Π½ ΠΈ ΠΡΡΠΎΡΡΠΌΠΈΡ ΠΈΠ·ΡΡΠ°Π»ΠΈ ΡΠΎΠ»Ρ ΠΌΠ΅Π΄ΠΈ Π² ΡΠ°ΡΡΠ²ΠΎΡΠ°Ρ ΡΠΎΡΡΠΎΡΠ½ΠΎΠΉ/ΡΠ΅ΡΠ½ΠΎΠΉ/Π°Π·ΠΎΡΠ½ΠΎΠΉ ΠΊΠΈΡΠ»ΠΎΡ, ΠΈ ΠΏΡΠΈΡΠ»ΠΈ ΠΊ Π²ΡΠ²ΠΎΠ΄Ρ, ΡΡΠΎ ΠΌΠ΅Π΄Ρ Π½Π΅ΠΎΠ±Ρ ΠΎΠ΄ΠΈΠΌΠ° Π΄Π»Ρ ΠΏΡΠΈΠ΄Π°Π½ΠΈΡ ΠΏΠΎΠ²Π΅ΡΡ Π½ΠΎΡΡΠΈ ΠΌΠ°ΠΊΡΠΈΠΌΠ°Π»ΡΠ½ΠΎΠ³ΠΎ Π±Π»Π΅ΡΠΊΠ°. ΠΠ½ΠΈ ΡΡΠΈΡΠ°Π»ΠΈ, ΡΡΠΎ ΠΏΡΠΎΡΠ΅ΡΡ Ρ ΠΈΠΌΠΈΡΠ΅ΡΠΊΠΎΠΉ ΠΎΠ±ΡΠ°Π±ΠΎΡΠΊΠΈ Π²ΠΊΠ»ΡΡΠ°Π΅Ρ Π² ΡΠ΅Π±Ρ ΡΡΠΈ ΡΡΠ°ΠΏΠ°: ΡΡΠ°Π²Π»Π΅Π½ΠΈΠ΅, ΠΎΠ±ΡΠ°Π±ΠΎΡΠΊΠ° ΠΈ ΠΎΠ³ΡΡΠ±Π»Π΅Π½ΠΈΠ΅. ΠΠ°ΠΊΡΠΈΠΌΠ°Π»ΡΠ½ΡΠΉ ΡΡΠΎΠ²Π΅Π½Ρ Π±Π»Π΅ΡΠΊΠ° Π΄ΠΎΡΡΠΈΠ³Π°Π΅ΡΡΡ ΠΏΠΎΡΠ»Π΅ ΠΏΡΠΎΠ²Π΅Π΄Π΅Π½ΠΈΡ ΠΎΠ±ΡΠ°Π±ΠΎΡΠΊΠΈ ΠΈ ΠΏΠ΅ΡΠ΅Π΄ ΠΎΠ³ΡΡΠ±Π»Π΅Π½ΠΈΠ΅ΠΌ. ΠΡΠ»ΠΈ Π½Π° ΠΏΠΎΠ²Π΅ΡΡ Π½ΠΎΡΡΡ Π½Π°Π½Π΅ΡΡΠΈ Π½Π΅Π΄ΠΎΡΡΠ°ΡΠΎΡΠ½ΠΎΠ΅ ΠΊΠΎΠ»ΠΈΡΠ΅ΡΡΠ²ΠΎ ΠΌΠ΅Π΄ΠΈ, ΡΡΠ°Π΄ΠΈΡ ΡΡΠ°Π²Π»Π΅Π½ΠΈΡ Π±ΡΠ΄Π΅Ρ Π½Π΅ ΠΏΠΎΠ»Π½ΠΎΡΡΡΡ Π·Π°ΠΌΠ΅Π½Π΅Π½Π° ΠΏΠΎΠ»ΠΈΡΠΎΠ²ΠΎΡΠ½ΠΎΠΉ ΡΡΡΡΠΊΡΡΡΠΎΠΉ Π΄ΠΎ Π½Π°ΡΠ°Π»Π° ΠΎΠ³ΡΡΠ±Π»Π΅Π½ΠΈΡ. ΠΡΠΈ ΠΏΡΠ΅Π²ΡΡΠ΅Π½ΠΈΠΈ ΠΎΠΏΡΠΈΠΌΠ°Π»ΡΠ½ΠΎΠ³ΠΎ ΠΊΠΎΠ»ΠΈΡΠ΅ΡΡΠ²Π° ΠΌΠ΅Π΄ΠΈ, Π½Π° ΠΏΠΎΠ²Π΅ΡΡ Π½ΠΎΡΡΠΈ ΠΎΠ±ΡΠ°Π·ΡΡΡΡΡ Π±ΠΎΠ»ΡΡΠΈΠ΅ ΡΠΊΠΎΠΏΠ»Π΅Π½ΠΈΡ ΡΠ°ΡΡΠΈΡ ΠΌΠ΅Π΄ΠΈ, ΡΠΎΠ·Π΄Π°ΡΡΠΈΠ΅ Π½Π° Π½Π΅ΠΊΠΎΡΠΎΡΡΡ ΡΡΠ°ΡΡΠΊΠ°Ρ ΡΠΎΠΊ Π±ΠΎΠ»ΡΡΠΎΠΉ ΠΏΠ»ΠΎΡΠ½ΠΎΡΡΠΈ, Π²ΡΠ»Π΅Π΄ΡΡΠ²ΠΈΠ΅ ΡΠ΅Π³ΠΎ ΡΡΠ°Π΄ΠΈΡ ΠΎΠ³ΡΡΠ±Π»Π΅Π½ΠΈΡ Π½Π°ΡΡΡΠΏΠ°Π΅Ρ ΠΎΡΠ΅Π½Ρ Π±ΡΡΡΡΠΎ. ΠΠΎΡΡΠΎΠΌΡ ΡΡΠΈΡΠ°Π΅ΡΡΡ, ΡΡΠΎ ΡΠΎΠ»Ρ ΠΌΠ΅Π΄ΠΈ Π² Π΄Π°Π½Π½ΠΎΠΌ ΡΠ»ΡΡΠ°Π΅ β ΡΡΠΎ ΡΡΠΈΠΌΡΠ»ΡΡΠΈΡ ΠΎΠ±ΡΠ°Π·ΠΎΠ²Π°Π½ΠΈΡ ΠΏΡΠΎΡΠ½ΠΎΠΉ ΠΏΠ»ΡΠ½ΠΊΠΈ Π½Π° ΠΏΠΎΠ²Π΅ΡΡ Π½ΠΎΡΡΠΈ ΠΌΠ΅ΡΠ°Π»Π»Π°. ΠΠ° ΡΡΠΎ ΡΠ°ΠΊΠΆΠ΅ ΡΠΊΠ°Π·ΡΠ²Π°Π΅Ρ ΡΠΎΡ ΡΠ°ΠΊΡ, ΡΡΠΎ ΡΠΎΠ΄Π΅ΡΠΆΠ°ΡΠΈΠ΅ ΠΌΠ΅Π΄Ρ ΡΠ°ΡΡΠ²ΠΎΡΡ ΠΈΠΌΠ΅ΡΡ ΠΌΠ΅Π½ΡΡΡΡ ΡΠΊΠΎΡΠΎΡΡΡ ΡΠ½ΡΡΠΈΡ ΠΌΠ΅ΡΠ°Π»Π»Π°, Π½Π΅ΠΆΠ΅Π»ΠΈ ΡΠ°ΡΡΠ²ΠΎΡΡ, Π½Π΅ ΡΠΎΠ΄Π΅ΡΠΆΠ°ΡΠΈΠ΅ ΠΌΠ΅Π΄ΠΈ. ΠΡΠ΅ ΡΡΠΈ ΡΠ΅ΠΎΡΠΈΠΈ ΠΏΡΠ΅Π΄ΠΏΠΎΠ»Π°Π³Π°ΡΡ Π½Π°Π»ΠΈΡΠΈΠ΅ ΡΡΠΆΡΠ»ΡΡ ΠΌΠ΅ΡΠ°Π»Π»ΠΎΠ² Π² ΡΠ°ΡΡΠ²ΠΎΡΠ°Ρ Π΄Π»Ρ Ρ ΠΈΠΌΠΈΡΠ΅ΡΠΊΠΎΠΉ ΠΎΠ±ΡΠ°Π±ΠΎΡΠΊΠΈ, ΠΎΠ΄Π½Π°ΠΊΠΎ, Π½Π΅ ΠΈΡΠΊΠ»ΡΡΠ΅Π½ΠΎ, ΡΡΠΎ ΡΠ°ΠΊΠΎΠ²ΡΡ ΠΌΠΎΠΆΠ΅Ρ ΠΈ Π½Π΅ Π±ΡΡΡ Π² ΡΠΎΡΡΠ°Π²Π΅ ΡΠ°ΡΡΠ²ΠΎΡΠΎΠ². ΠΡΠΈ ΠΎΡΡΡΡΡΡΠ²ΠΈΠ΅ ΠΊΠ°ΡΠΎΠ΄Π½ΠΎΠ³ΠΎ ΠΌΠ΅ΡΠ°Π»Π»Π° ΡΠΎΠ»Ρ ΠΊΠ°ΡΠΎΠ΄Π° ΠΌΠΎΠΆΠ΅Ρ Π²ΡΠΏΠΎΠ»Π½ΡΡΡ Π·Π΅ΡΠ½ΠΎ, ΠΎΡΠ»ΠΈΡΠ½ΠΎΠ΅ ΠΎΡ ΠΌΠ΅ΠΆΠ·ΡΡΠ΅Π½Π½ΠΎΠΉ Π³ΡΠ°Π½ΠΈΡΡ Π² Π½Π°ΡΠ°Π»Π΅ ΡΠ΅Π°ΠΊΡΠΈΠΈ, ΠΎΠ΄Π½Π°ΠΊΠΎ ΠΏΠΎ Ρ ΠΎΠ΄Ρ ΡΠ΅Π°ΠΊΡΠΈΠΈ ΠΏΠ»ΡΠ½ΠΊΠ° ΠΎΠΊΠΈΡΠ»Π° ΡΠ°ΠΌΠ° ΠΌΠΎΠΆΠ΅Ρ ΡΡΠ°ΡΡ ΠΊΠ°ΡΠΎΠ΄Π½ΠΎΠΉ ΠΎΠ±Π»Π°ΡΡΡΡ. ΠΠ΅ΠΉΠ΅Ρ ΠΈ ΠΡΠ°ΡΠ½ ΠΎΠ±Π½Π°ΡΡΠΆΠΈΠ»ΠΈ, ΡΡΠΎ Π΄ΠΎΠ±Π°Π²Π»Π΅Π½ΠΈΠ΅ ΠΎΠΊΠΈΡΠ»ΠΈΡΠ΅Π»Ρ, Π° ΠΈΠΌΠ΅Π½Π½ΠΎ Π°Π·ΠΎΡΠ½ΠΎΠΉ ΠΊΠΈΡΠ»ΠΎΡΡ, ΠΏΠΎΠΌΠΎΠ³Π°Π΅Ρ ΡΠ½ΠΈΠ·ΠΈΡΡ ΡΡΠΎΠ²Π΅Π½Ρ ΡΠ°ΡΡΠ²ΠΎΡΠΈΠΌΠΎΡΡΠΈ Π°Π»ΡΠΌΠΈΠ½ΠΈΡ Π² ΡΠΎΡΡΠΎΡΠ½ΠΎΠΉ ΠΊΠΈΡΠ»ΠΎΡΠ΅, Π° Π² ΡΠ°ΡΡΠ²ΠΎΡΠ°Ρ Π½Π° Π±Π°Π·Π΅ ΡΠΎΡΡΠΎΡΠ½ΠΎΠΉ ΠΊΠΈΡΠ»ΠΎΡΡ ΡΡΠΎ ΠΌΠΎΠΆΠ΅Ρ ΡΠΏΠΎΡΠΎΠ±ΡΡΠ²ΠΎΠ²Π°ΡΡ ΠΎΠ±ΡΠ°Π·ΠΎΠ²Π°Π½ΠΈΡ ΠΏΡΠΎΡΠ½ΠΎΠΉ ΠΏΠ»ΡΠ½ΠΊΠΈ.
ΠΠ»ΠΈΡΡΠΎΡΠ΄ ΠΈ ΠΡΡΠΎΡΡΠΌΠΈΡ ΠΏΡΠ΅Π΄ΠΏΠΎΠ»ΠΎΠΆΠΈΠ»ΠΈ, ΡΡΠΎ Π°Π·ΠΎΡΠ½Π°Ρ ΠΊΠΈΡΠ»ΠΎΡΠ° Π²ΡΠΏΠΎΠ»Π½ΡΠ΅Ρ Π΅ΡΡ ΠΎΠ΄Π½Ρ ΡΡΠ½ΠΊΡΠΈΡ, ΡΠ²ΡΠ·Π°Π½Π½ΡΡ Ρ ΠΎΡΠ°ΠΆΠ΄Π΅Π½ΠΈΠ΅ΠΌ ΠΌΠ΅Π΄ΠΈ, ΠΈ ΡΡΠΎ ΠΏΡΠΈ Π΅Ρ ΠΎΠΏΡΠΈΠΌΠ°Π»ΡΠ½ΠΎΠΉ ΠΊΠΎΠ½ΡΠ΅Π½ΡΡΠ°ΡΠΈΠΈ ΡΠ°ΡΡΠΈΡΡ ΠΌΠ΅Π΄ΠΈ, ΠΎΡΠ°ΠΆΠ΄Π°Π΅ΠΌΡΠ΅ Π½Π° ΠΏΠΎΠ²Π΅ΡΡ Π½ΠΎΡΡΠΈ, Π΄ΠΎΠ»ΠΆΠ½Ρ ΠΈΠΌΠ΅ΡΡ ΠΌΠ°Π»ΡΠΉ ΡΠ°Π·ΠΌΠ΅Ρ ΠΈ Π±ΡΠ΄ΡΡ ΡΠ°ΡΠΏΡΠ΅Π΄Π΅Π»Π΅Π½Ρ Π΄ΠΎΡΡΠ°ΡΠΎΡΠ½ΠΎ ΡΠ°Π²Π½ΠΎΠΌΠ΅ΡΠ½ΠΎ. ΠΡΠΈ Π½ΠΈΠ·ΠΊΠΎΠΌ ΡΡΠΎΠ²Π½Π΅ ΠΊΠΎΠ½ΡΠ΅Π½ΡΡΠ°ΡΠΈΠΈ Π°Π·ΠΎΡΠ½ΠΎΠΉ ΠΊΠΈΡΠ»ΠΎΡΡ ΡΠ°ΡΠΏΡΠ΅Π΄Π΅Π»Π΅Π½ΠΈΠ΅ ΡΠ°ΡΡΠΈΡ ΠΌΠ΅Π΄ΠΈ ΠΏΠ΅ΡΠ΅ΡΡΠ°ΡΡ Π±ΡΡΡ ΡΠ°Π²Π½ΠΎΠΌΠ΅ΡΠ½ΡΠΌ, Π° ΡΠΌΠΊΠΈ ΠΎΠ³ΡΡΠ±Π»Π΅Π½ΠΈΡ ΠΎΠΊΠ°Π·ΡΠ²Π°ΡΡΡΡ ΡΠ²ΡΠ·Π°Π½Π½ΡΠΌΠΈ Ρ ΠΊΡΡΠΏΠ½ΡΠΌΠΈ ΡΠ°ΡΡΠΈΡΠ°ΠΌΠΈ. ΠΡΠ»ΠΈ ΠΊΠΎΠ½ΡΠ΅Π½ΡΡΠ°ΡΠΈΡ Π°Π·ΠΎΡΠ½ΠΎΠΉ ΠΊΠΈΡΠ»ΠΎΡΡ ΡΠ»ΠΈΡΠΊΠΎΠΌ Π²ΡΡΠΎΠΊΠ°, ΡΠΎ Π² ΡΠ΅Π·ΡΠ»ΡΡΠ°ΡΠ΅ Π½Π°ΡΠ°Π»ΡΠ½ΠΎΠ³ΠΎ ΡΡΠ°ΠΏΠ° ΡΡΠ°Π²Π»Π΅Π½ΠΈΡ ΠΏΡΠΎΡΠ΅ΡΡΠ° ΠΎΠ±ΡΠ°Π±ΠΎΡΠΊΠΈ ΠΏΠΎΠ»ΡΡΠ°Π΅ΡΡΡ Π·Π΅ΡΠ½ΠΈΡΡΠ°Ρ ΠΏΠΎΠ²Π΅ΡΡ Π½ΠΎΡΡΡ ΡΠ²Π΅ΡΠ° ΠΎΡΠΈΡΠ΅Π½Π½ΠΎΠ³ΠΎ Π°ΠΏΠ΅Π»ΡΡΠΈΠ½Π°, ΠΈ ΡΡΠΎ Π½Π΅ ΠΏΠΎΠ΄Π΄Π°ΡΡΡΡ ΠΈΠ·ΠΌΠ΅Π½Π΅Π½ΠΈΡ ΠΏΡΡΡΠΌ ΠΎΠ±ΡΡΠ½ΠΎΠΉ ΠΎΠ±ΡΠ°Π±ΠΎΡΠΊΠΈ.
ΠΠΎ Π€ΠΈΡΠ΅ΡΡ ΠΈ ΠΠΎΡ Ρ ΠΌΠ΅Ρ Π°Π½ΠΈΠ·ΠΌ ΡΠ΅Π°ΠΊΡΠΈΠΈ Ρ ΠΈΠΌΠΈΡΠ΅ΡΠΊΠΎΠΉ ΠΎΠ±ΡΠ°Π±ΠΎΡΠΊΠΈ Π·Π°Π²ΠΈΡΠΈΡ ΠΎΡ Π΄Π²ΡΡ ΠΏΡΠΎΡΠ΅ΡΡΠΎΠ²:
1.ΠΠ½ΠΎΠ΄ΠΈΡΠΎΠ²Π°Π½ΠΈΠ΅: ΡΠ°ΡΡΠ²ΠΎΡΠ΅Π½ΠΈΠ΅ Π°Π»ΡΠΌΠΈΠ½ΠΈΡ Π»ΠΎΠΊΠ°Π»ΡΠ½ΠΎΠ³ΠΎ Π³Π°Π»ΡΠ²Π°Π½ΠΈΡΠ΅ΡΠΊΠΎΠ³ΠΎ ΡΠ»Π΅ΠΌΠ΅Π½ΡΠ° ΠΏΡΠΈ ΡΠΎΠΊΠ΅ Π΄ΠΎΡΡΠ°ΡΠΎΡΠ½ΠΎΠΉ ΠΏΠ»ΠΎΡΠ½ΠΎΡΡΠΈ Π΄Π»Ρ ΠΎΠ±ΡΠ°Π·ΠΎΠ²Π°Π½ΠΈΡ Π½Π΅ΠΎΠ±Ρ ΠΎΠ΄ΠΈΠΌΠΎΠΉ ΠΏΠΎΡΠΈΡΡΠΎΠΉ ΠΏΡΠΎΡΠ½ΠΎΠΉ ΠΏΠ»ΡΠ½ΠΊΠΈ, ΠΈ
2.ΠΠ°ΡΠΎΠ΄Π½Π°Ρ ΡΠ΅Π°ΠΊΡΠΈΡ: Π²ΠΎΡΡΡΠ°Π½ΠΎΠ²Π»Π΅Π½ΠΈΠ΅ Π΄Π΅ΠΏΠΎΠ»ΡΡΠΈΠ·ΡΡΡΠΈΡ ΠΎΠΊΠΈΡΠ»ΠΈΡΠ΅Π»Π΅ΠΉ Π½Π° ΠΊΠ°ΡΠΎΠ΄Π½ΡΡ ΡΡΠ°ΡΡΠΊΠ°Ρ , Π½Π°ΠΏΡΠΈΠΌΠ΅Ρ, ΠΏΡΠΈ ΠΎΡΠ°ΠΆΠ΄Π΅Π½ΠΈΠΈ ΠΌΠ΅Π΄ΠΈ.
ΠΡΠΎΠΌΠ΅ ΡΠΎΠ³ΠΎ, Π½Π° Π°Π½ΠΎΠ΄Π½ΡΡ ΡΡΠ°ΡΡΠΊΠ°Ρ ΠΌΠΎΠΆΠ΅Ρ ΠΈΠΌΠ΅ΡΡ ΠΌΠ΅ΡΡΠΎ Π²ΡΠ΄Π΅Π»Π΅Π½ΠΈΠ΅ ΠΊΠΈΡΠ»ΠΎΡΠΎΠ΄Π°, ΡΠΎΠ³Π΄Π° ΠΊΠ°ΠΊ Π½Π° ΠΊΠ°ΡΠΎΠ΄Π½ΡΡ ΡΡΠ°ΡΡΠΊΠ°Ρ ΠΌΠΎΠΆΠ΅Ρ ΠΏΡΠΎΠΈΡΡ ΠΎΠ΄ΠΈΡΡ ΠΎΡΠ°ΠΆΠ΄Π΅Π½ΠΈΠ΅ ΠΌΠ΅Π΄ΠΈ ΠΈ Π²ΠΎΠ΄ΠΎΡΠΎΠ΄Π°, ΠΏΡΠΈΡΠ΅ΠΌ ΡΡΠΈ Π΄Π²Π° ΠΏΡΠΎΡΠ΅ΡΡΠ° ΠΏΡΠΎΡ ΠΎΠ΄ΡΡ Π»ΠΈΠ±ΠΎ ΠΎΠ΄Π½ΠΎΠ²ΡΠ΅ΠΌΠ΅Π½Π½ΠΎ, Π»ΠΈΠ±ΠΎ ΠΏΠΎΠΎΡΠ΅ΡΡΠ΄Π½ΠΎ.
ΠΠ½ΠΎΠ΄Π½ΡΡ ΡΠ΅Π°ΠΊΡΠΈΡ ΠΌΠΎΠΆΠ½ΠΎ Π·Π°ΠΏΠΈΡΠ°ΡΡ ΡΠ»Π΅Π΄ΡΡΡΠΈΠΌ ΠΎΠ±ΡΠ°Π·ΠΎΠΌ: Al β Al
Π ΡΠ΅Ρ ΡΠ»ΡΡΠ°ΡΡ , ΠΊΠΎΠ³Π΄Π° Π°Π·ΠΎΡΠ½Π°Ρ ΠΊΠΈΡΠ»ΠΎΡΠ° Π²Ρ ΠΎΠ΄ΠΈΡ Π² ΡΠΎΡΡΠ°Π² ΡΠ°ΡΡΠ²ΠΎΡΠ° Π΄Π»Ρ Ρ ΠΈΠΌΠΈΡΠ΅ΡΠΊΠΎΠΉ ΠΎΠ±ΡΠ°Π±ΠΎΡΠΊΠΈ, ΠΌΠΎΠΆΠ΅Ρ Π½Π°Π±Π»ΡΠ΄Π°ΡΡΡΡ ΡΠ»Π΅Π΄ΡΡΡΠ°Ρ ΡΠΈΡΡΠ°ΡΠΈΡ:
a)ΠΠ·ΠΎΡΠ½Π°Ρ ΠΊΠΈΡΠ»ΠΎΡΠ° ΠΌΠΎΠΆΠ΅Ρ Π²ΡΡΡΠΏΠΈΡΡ Π² ΡΠ΅Π°ΠΊΡΠΈΡ Ρ ΠΌΠ΅ΡΠ°Π»Π»ΠΎΠΌ Π² Π½Π΅Π΄ΠΈΡΡΠΎΡΠΈΠΈΡΠΎΠ²Π°Π½Π½ΠΎΠΌ ΡΠΎΡΡΠΎΡΠ½ΠΈΠΈ OH.NO2. ΠΡΠ° ΡΠ΅Π°ΠΊΡΠΈΡ ΠΏΡΠΎΠΈΡΡ ΠΎΠ΄ΠΈΡ Ρ Π±Π»Π°Π³ΠΎΡΠΎΠ΄Π½ΡΠΌΠΈ ΠΌΠ΅ΡΠ°Π»Π»Π°ΠΌΠΈ, Π½Π°ΠΏΡΠΈΠΌΠ΅Ρ, ΠΌΠ΅Π΄Ρ, ΠΈ Π² Π΅Ρ ΡΠ΅Π·ΡΠ»ΡΡΠ°ΡΠ΅ ΠΎΠ±ΡΠ°Π·ΡΠ΅ΡΡΡ ΠΎΠΊΡΠΈΠ΄ ΠΌΠ΅ΡΠ°Π»Π»Π° ΠΈ ΠΎΠΊΡΠΈΠ΄Ρ Π°Π·ΠΎΡΠ°. ΠΠ°ΡΠΎΠ΄Π½Π°Ρ ΡΠ΅Π°ΠΊΡΠΈΡ ΠΌΠΎΠΆΠ΅Ρ ΡΠ²Π»ΡΡΡΡΡ Π²ΠΎΡΡΡΠ°Π½ΠΎΠ²Π»Π΅Π½ΠΈΠ΅ΠΌ OH.NO2 Π΄ΠΎ Π³ΠΈΠ΄ΡΠΎΠΊΡΠΈΠ»ΡΠ½ΠΎΠ³ΠΎ ΠΈΠΎΠ½Π° ΠΏΠ»ΡΡ Π°Π·ΠΎΡΠΈΡΡΠ°Ρ ΠΊΠΈΡΠ»ΠΎΡΠ° ΠΈ, Π²ΠΏΠΎΡΠ»Π΅Π΄ΡΡΠ²ΠΈΠΈ, ΠΎΠΊΡΠΈΠ΄ΠΎΠ² Π°Π·ΠΎΡΠ°. ΠΠΎΠ½Π΅ΡΠ½ΡΠΉ ΡΠ΅Π·ΡΠ»ΡΡΠ°Ρ ΡΠ΅Π°ΠΊΡΠΈΠΈ ΠΌΠΎΠΆΠ½ΠΎ Π·Π°ΠΏΠΈΡΠ°ΡΡ ΠΊΠ°ΠΊ:
2 Al + 3OH.NO2 β A12O3 + 3HNO2
Π±) ΠΠ·ΠΎΡΠ½Π°Ρ ΠΊΠΈΡΠ»ΠΎΡΠ° ΠΌΠΎΠΆΠ΅Ρ Π²ΡΡΡΠΏΠΈΡΡ Π² ΡΠ΅Π°ΠΊΡΠΈΡ Ρ ΠΌΠ΅ΡΠ°Π»Π»ΠΎΠΌ Π² Π΄ΠΈΡΡΠΎΡΠΈΠΈΡΠΎΠ²Π°Π½Π½ΠΎΠΉ ΡΠΎΡΠΌΠ΅ H+ + NO3β.
Π§Π°ΡΠ΅ Π²ΡΠ΅Π³ΠΎ ΡΡΠ° ΡΠ΅Π°ΠΊΡΠΈΡ Π½Π°Π±Π»ΡΠ΄Π°Π΅ΡΡΡ Π² ΡΠ΅Ρ ΡΠ»ΡΡΠ°ΡΡ , ΠΊΠΎΠ³Π΄Π° Π°Π·ΠΎΡΠ½Π°Ρ ΠΊΠΈΡΠ»ΠΎΡΠ° Π½Π°Ρ ΠΎΠ΄ΠΈΡΡΡ Π² ΠΊΠΎΠ½ΡΠ°ΠΊΡΠ΅ Ρ ΠΌΠ΅Π½Π΅Π΅ Π±Π»Π°Π³ΠΎΡΠΎΠ΄Π½ΡΠΌΠΈ ΠΌΠ΅ΡΠ°Π»Π»Π°ΠΌΠΈ ΡΠΈΠΏΠ° Π°Π»ΡΠΌΠΈΠ½ΠΈΡ, Π³Π΄Π΅ ΡΠ°Π·ΡΡΡΠ΅Π½ΠΈΠ΅ ΠΈΠΎΠ½ΠΎΠ² Π²ΠΎΠ΄ΠΎΡΠΎΠ΄Π° ΡΠ°ΡΠ΅ ΠΏΡΠΎΠΈΡΡ ΠΎΠ΄ΠΈΡ Π² ΠΊΠ°ΡΠ΅ΡΡΠ²Π΅ ΠΊΠ°ΡΠΎΠ΄Π½ΠΎΠΉ ΡΠ΅Π°ΠΊΡΠΈΠΈ.
ΠΠ° ΡΠ°ΠΌΠΎΠΌ Π΄Π΅Π»Π΅ ΠΈΡΠΏΠΎΠ»ΡΠ·ΠΎΠ²Π°Π½ΠΈΠ΅ ΠΊΠΎΠ½ΡΠ΅Π½ΡΡΠΈΡΠΎΠ²Π°Π½Π½ΠΎΠΉ Π°Π·ΠΎΡΠ½ΠΎΠΉ ΠΊΠΈΡΠ»ΠΎΡΡ ΠΏΠΎΠ·Π²ΠΎΠ»ΡΠ΅Ρ ΡΠΎΠ·Π΄Π°ΡΡ Π½Π° Π°Π»ΡΠΌΠΈΠ½ΠΈΠΈ ΠΎΡΠ΅Π½Ρ ΡΠΎΠ½ΠΊΡΡ ΡΡΡΠΎΠΉΡΠΈΠ²ΡΡ ΠΏΠ°ΡΡΠΈΠ²ΠΈΡΡΡΡΡΡ ΠΏΠ»ΡΠ½ΠΊΡ, ΡΠΎΠ»ΡΠΈΠ½Π° ΠΊΠΎΡΠΎΡΠΎΠΉ Π΄ΠΎΡΡΠΈΠ³Π°Π΅Ρ ΠΌΠ°ΠΊΡΠΈΠΌΡΠΌΠ°. ΠΠ½Π°ΡΠ΅Π½ΠΈΠ΅ ΠΌΠ°ΠΊΡΠΈΠΌΡΠΌΠ° Π·Π°Π²ΠΈΡΠΈΡ ΠΎΡ ΡΠΏΠΎΡΠΎΠ±Π° ΠΏΠΎΠ΄Π³ΠΎΡΠΎΠ²ΠΊΠΈ ΠΏΠΎΠ²Π΅ΡΡ Π½ΠΎΡΡΠΈ , ΠΏΠΎΡΠ»Π΅ ΠΊΠΎΡΠΎΡΠΎΠ³ΠΎ ΠΎΠ½Π° ΠΏΡΠΈΠΎΠ±ΡΠ΅ΡΠ°Π΅Ρ ΠΏΠΎΡΡΠΎΡΠ½Π½ΠΎΠ΅ Π·Π½Π°ΡΠ΅Π½ΠΈΠ΅. ΠΠ°ΠΌΠ»ΠΈΠ½ ΡΡΠΈΡΠ°Π», ΡΡΠΎ Ρ ΠΈΠΌΠΈΡΠ΅ΡΠΊΡΡ ΡΠ΅Π°ΠΊΡΠΈΡ ΠΎΠ±ΡΠ°Π·ΠΎΠ²Π°Π½ΠΈΡ ΠΎΠΊΠΈΡΠ»Π° ΠΏΡΠΎΡΡΠ°Π²ΠΊΠΈ Π½Π° Π°Π»ΡΠΌΠΈΠ½ΠΈΠ΅Π²ΠΎΠΉ ΠΏΠΎΠ²Π΅ΡΡ Π½ΠΎΡΡΠΈ ΠΌΠΎΠΆΠ½ΠΎ Π·Π°ΠΏΠΈΡΠ°ΡΡ ΡΠ»Π΅Π΄ΡΡΡΠΈΠΌ ΠΎΠ±ΡΠ°Π·ΠΎΠΌ:
14Al + 10 HNO3 β7 Al2O3 + 4N2 +2NO2 + 5H2O
Π’Π°ΠΊ ΠΊΠ°ΠΊ ΠΎΠΊΠΈΡΠ΅Π» ΠΎΠ±ΡΠ°Π·ΡΠ΅ΡΡΡ Π½Π° ΠΏΠΎΠ²Π΅ΡΡ Π½ΠΎΡΡΠΈ ΠΌΠ΅ΡΠ°Π»Π»Π°, ΡΠΎ ΡΠΎΡΡΠΎΡΠ½Π°Ρ ΠΊΠΈΡΠ»ΠΎΡΠ° ΠΎΠ΄Π½ΠΎΠ²ΡΠ΅ΠΌΠ΅Π½Π½ΠΎ ΡΠ°ΡΡΠ²ΠΎΡΡΠ΅Ρ Π΅Π³ΠΎ Π² ΠΎΠ±Π»Π°ΡΡΠΈ ΠΊΠΎΠ½ΡΠ°ΠΊΡΠ° ΡΠ°ΡΡΠ²ΠΎΡΠ° ΠΈ ΠΎΠΊΡΠΈΠ΄Π°:
Al2O3 + 6 H3PO4 β2Al(H2PO4)3 + 3 H2O
Π§Π°ΡΡΠ΅ΡΠ΄ΠΆΠΈΠΏΡΠΎΠ²Π΅Π» ΠΈΡΡΠ»Π΅Π΄ΠΎΠ²Π°Π½ΠΈΠ΅ ΡΠ°ΡΡΠ²ΠΎΡΠΎΠ² ΡΠΎΡΡΠΎΡΠ½ΠΎΠΉ, ΡΠ΅ΡΠ½ΠΎΠΉ ΠΈ Π°Π·ΠΎΡΠ½ΠΎΠΉ ΠΊΠΈΡΠ»ΠΎΡ ΠΈ ΠΎΠ±Π½Π°ΡΡΠΆΠΈΠ», ΡΡΠΎ ΡΠ°ΡΡΠ²ΠΎΡΡ, ΠΏΡΠΈΠ΄Π°ΡΡΠΈΠ΅ ΠΌΠ°ΠΊΡΠΈΠΌΠ°Π»ΡΠ½ΡΠΉ Π±Π»Π΅ΡΠΊ ΠΏΠΎΠ²Π΅ΡΡ Π½ΠΎΡΡΠΈ Π²ΠΎ Π²ΡΠ΅ΠΌΡ Ρ ΠΈΠΌΠΈΡΠ΅ΡΠΊΠΎΠΉ ΠΎΠ±ΡΠ°Π±ΠΎΡΠΊΠΈ, Ρ Π°ΡΠ°ΠΊΡΠ΅ΡΠΈΠ·ΠΎΠ²Π°Π»ΠΈΡΡ ΠΌΠ΅Π½ΡΡΠΈΠΌΠΈ ΠΈΠ·ΠΌΠ΅Π½Π΅Π½ΠΈΡΠΌΠΈ ΠΏΠ»ΠΎΡΠ½ΠΎΡΡΠΈ ΡΠΎΠΊΠ° Π²ΠΎ Π²ΡΠ΅ΠΌΡ ΡΠ΅Π°ΠΊΡΠΈΠΈ Ρ Π²ΡΠ΄Π΅Π»Π΅Π½ΠΈΠ΅ΠΌ Π²ΠΎΠ΄ΠΎΡΠΎΠ΄Π°, ΠΌΠ΅Π½ΡΡΠ΅ΠΉ ΠΊΠΎΡΡΠΎΠ·ΠΈΠΉΠ½ΡΠΌ ΡΠΎΠΊΠΎΠΌ, Π±ΠΎΠ»ΡΡΠΈΠΌ Π²ΠΎΠ΄ΠΎΡΠΎΠ΄Π½ΡΠΌ ΠΏΠ΅ΡΠ΅Π½Π°ΠΏΡΡΠΆΠ΅Π½ΠΈΠ΅ΠΌ ΠΈ Π±ΠΎΠ»Π΅Π΅ Π±Π»Π°Π³ΠΎΡΠΎΠ΄Π½ΡΠΌ ΠΊΠΎΡΡΠΎΠ·ΠΈΠΉΠ½ΡΠΌ ΠΏΠΎΡΠ΅Π½ΡΠΈΠ°Π»ΠΎΠΌ, ΡΠ΅ΠΌ ΠΌΠΎΠΆΠ½ΠΎ ΠΏΠΎΠ»ΡΡΠΈΡΡ ΠΏΡΠΈ ΠΏΠΎΠΌΠΎΡΠΈ Π΄ΡΡΠ³ΠΈΡ ΡΠΎΡΡΠ°Π²Π½ΡΡ ΠΊΠΈΡΠ»ΠΎΡ ΠΈΠ»ΠΈ ΠΈΡ ΡΠΌΠ΅ΡΠ΅ΠΉ.
Π£ΡΠΈΡΡΠ²Π°Ρ ΡΠ°ΡΡΠ²ΠΎΡΡΡΡΡΡ ΡΠΈΠ»Ρ, Ρ ΠΈΠΌΠΈΡΠ΅ΡΠΊΠΎΠ΅ Π΄Π΅ΠΉΡΡΠ²ΠΈΠ΅ ΠΈ ΡΠ»Π΅ΠΊΡΡΠΎΡ ΠΈΠΌΠΈΡΠ΅ΡΠΊΠΈΠ΅ ΡΠ²ΠΎΠΉΡΡΠ²Π° ΡΡΠΈΡ ΡΠ°ΡΡΠ²ΠΎΡΠΎΠ² Π§Π°ΡΡΠ΅ΡΠ΄ΠΆΠΈ ΡΠΎΠ·Π΄Π°Π» ΡΠ°ΡΡΠ²ΠΎΡ Π±Π΅Π· ΡΠΎΡΡΠΎΡΠ½ΠΎΠΉ ΠΊΠΈΡΠ»ΠΎΡΡ, ΡΠΎΠ΄Π΅ΡΠΆΠ°ΡΠΈΠΉ Π²Π°Π½Π°Π΄ΠΈΠ΅Π²ΠΎ-ΠΊΠΈΡΠ»ΡΠΉ Π°ΠΌΠΌΠΎΠ½ΠΈΠΉ Π΄Π»Ρ Π±ΠΎΠ»ΡΡΠΎΠΉ Π²ΡΠ·ΠΊΠΎΡΡΠΈ, ΠΊΠ°ΠΊ Ρ ΡΠ°ΡΡΠ²ΠΎΡΠΎΠ² Π½Π° ΠΎΡΠ½ΠΎΠ²Π΅ ΡΠΎΡΡΠΎΡΠ½ΠΎΠΉ ΠΊΠΈΡΠ»ΠΎΡΡ.
ΠΡΡΡΡΡΡΠ²ΠΈΠ΅ Π² ΠΏΡΠΎΠ΄ΡΠΊΡΠΎΠ² Π²ΠΎΡΡΡΠ°Π½ΠΎΠ²Π»Π΅Π½ΠΈΡ Π°Π·ΠΎΡΠ½ΠΎΠΉ ΠΊΠΈΡΠ»ΠΎΡΡ ΡΠ°ΡΡΠ²ΠΎΡΠ΅ E.W. ΠΏΡΠ΅Π΄ΠΏΠΎΠ»Π°Π³Π°Π΅Ρ Π²ΠΎΠ·ΠΌΠΎΠΆΠ½ΠΎΡΡΡ ΡΠ°Π·Π»ΠΈΡΠ½ΠΎΠΉ ΡΠ΅Π°ΠΊΡΠΈΠΈ Π² Π΄Π°Π½Π½ΠΎΠΌ ΡΠ°ΡΡΠ²ΠΎΡΠ΅. ΠΠ°Π΄ΠΎ Π·Π°ΠΌΠ΅ΡΠΈΡΡ, ΡΡΠΎ ΠΡΠΎΡΡΠΌΠΈΡ ΠΈ ΠΡΠ½Π½ΠΈΠ½Π³Π°ΠΌ Π² ΠΏΡΠΎΡΠ΅ΡΡΠ΅ ΠΈΠ·ΡΡΠ΅Π½ΠΈΡ ΡΠ°ΡΡΠ²ΠΎΡΠΎΠ² ΡΠΈΠΏΠ° ΠΡΡΡΠ²Π΅ΡΠΊ (E.W.) ΠΏΠΎΠΊΠ°Π·Π°Π»ΠΈ, ΡΡΠΎ Π² Π΄Π°Π½Π½ΠΎΠΌ ΡΠ»ΡΡΠ°Π΅ ΠΌΠ΅Ρ Π°Π½ΠΈΠ·ΠΌ ΠΎΠ±ΡΠ°Π±ΠΎΡΠΊΠΈ Π±ΡΠ΄Π΅Ρ ΡΠ°ΠΊΠΈΠΌ ΠΆΠ΅, ΠΊΠ°ΠΊ ΠΈ ΠΏΡΠΈ ΠΈΡΠΏΠΎΠ»ΡΠ·ΠΎΠ²Π°Π½ΠΈΠΈ ΡΠ°ΡΡΠ²ΠΎΡΠΎΠ² Ρ ΡΠΎΡΡΠΎΡΠ½ΠΎΠΉ, ΡΠ΅ΡΠ½ΠΎΠΉ ΠΈ Π°Π·ΠΎΡΠ½ΠΎΠΉ ΠΊΠΈΡΠ»ΠΎΡΠΎΠΉ, ΠΎΠ΄Π½Π°ΠΊΠΎ ΠΏΡΠΈ ΡΡΠΎΠΌ ΠΎΠ½ΠΈ ΠΎΡΠΌΠ΅ΡΠ°ΡΡ, ΡΡΠΎ ΠΊΠΎΠ½ΡΡΠΎΠ»Ρ Π²ΡΠ΅ ΠΆΠ΅ ΠΈΠ³ΡΠ°Π΅Ρ Π΄ΠΎΡΡΠ°ΡΠΎΡΠ½ΠΎ Π±ΠΎΠ»ΡΡΡΡ ΡΠΎΠ»Ρ. Π ΡΠ΅Π·ΡΠ»ΡΡΠ°ΡΠ΅ ΠΏΡΠΎΠ²Π΅Π΄Π΅Π½Π½ΡΡ ΠΈΠΌΠΈ ΠΈΠ·ΠΌΠ΅ΡΠ΅Π½ΠΈΠΉ ΠΏΠΎΡΠ΅Π½ΡΠΈΠ°Π»Π° Π² ΠΏΡΠΎΡΠ΅ΡΡΠ΅ Ρ ΠΈΠΌΠΈΡΠ΅ΡΠΊΠΎΠΉ ΠΎΠ±ΡΠ°Π±ΠΎΡΠΊΠΈ Π±ΡΠ»Π° ΠΏΡΠΎΠ΄Π΅ΠΌΠΎΠ½ΡΡΡΠΈΡΠΎΠ²Π°Π½Π° Π²Π°ΠΆΠ½ΠΎΡΡΡ Π°Π·ΠΎΡΠ½ΠΎΠΉ ΠΊΠΈΡΠ»ΠΎΡΡ Π΄Π»Ρ ΠΏΡΠΎΠΈΠ·Π²ΠΎΠ΄ΡΡΠ²Π° ΠΎΠΊΡΠΈΠ΄Π½ΠΎΠΉ ΠΏΠ»Π΅Π½ΠΊΠΈ Π½Π° ΠΏΠΎΠ²Π΅ΡΡ Π½ΠΎΡΡΠΈ ΡΠ°ΠΊΠΈΠΌ ΠΎΠ±ΡΠ°Π·ΠΎΠΌ, ΡΡΠΎΠ±Ρ ΠΎΠ±Π΅ΡΠΏΠ΅ΡΠΈΡΡ Π²ΠΎΠ·ΠΌΠΎΠΆΠ½ΠΎΡΡΡ ΠΏΡΠΎΠΈΠ·Π²Π΅Π΄Π΅Π½ΠΈΡ ΠΎΠ±ΡΠ°Π±ΠΎΡΠΊΠΈ. ΠΡΠΈ ΡΠ»ΠΈΡΠΊΠΎΠΌ ΠΌΠ°Π»ΠΎΠΌ ΠΊΠΎΠ»ΠΈΡΠ΅ΡΡΠ²Π΅ Π°Π·ΠΎΡΠ½ΠΎΠΉ ΠΊΠΈΡΠ»ΠΎΡΡ Π½Π°Π±Π»ΡΠ΄Π°Π΅ΡΡΡ ΠΎΠ±ΡΠ΅Π΅ ΡΡΠ°Π²Π»Π΅Π½ΠΈΠ΅ ΠΏΠΎΠ²Π΅ΡΡ Π½ΠΎΡΡΠΈ, Π° ΠΏΡΠΈ ΡΠ»ΠΈΡΠΊΠΎΠΌ Π±ΠΎΠ»ΡΡΠΎΠΌ β ΡΠΎΡΠ΅ΡΠ½Π°Ρ ΠΊΠΎΡΡΠΎΠ·ΠΈΡ. ΠΡΠΈ ΡΠ²Π΅Π»ΠΈΡΠ΅Π½ΠΈΠΈ ΡΠΎΠ΄Π΅ΡΠΆΠ°Π½ΠΈΡ Π°Π»ΡΠΌΠΈΠ½ΠΈΡ Π² Π²Π°Π½Π½Π΅ ΠΏΡΠΎΠΈΡΡ ΠΎΠ΄ΠΈΡ ΠΎΡΠ°ΠΆΠ΄Π΅Π½ΠΈΠ΅ (Al(Nh5 F2)3 , ΠΏΠΎΡΡΠΎΠΌΡ Π΄Π»Ρ ΠΏΠΎΠ΄Π΄Π΅ΡΠΆΠ°Π½ΠΈΡ ΡΠΎΠΎΡΠ²Π΅ΡΡΡΠ²ΡΡΡΠ΅Π³ΠΎ ΡΠΎΠΎΡΠ½ΠΎΡΠ΅Π½ΠΈΡ HNO3 :Nh5 HF2 Π½Π΅ΠΎΠ±Ρ ΠΎΠ΄ΠΈΠΌΠΎ ΠΏΡΠΎΠΈΠ·Π²ΠΎΠ΄ΠΈΡΡ Π΄ΠΎΠ±Π°Π²Π»Π΅Π½ΠΈΠ΅ Π±ΠΈΡΡΠΎΡΠΈΠ΄Π° Π°ΠΌΠΌΠΎΠ½ΠΈΡ. Π ΠΎΠ»Ρ ΡΠ²ΠΈΠ½ΡΠ° Π² Π΄Π°Π½Π½ΠΎΠΌ ΡΠ°ΡΡΠ²ΠΎΡΠ΅, ΠΏΡΠΈΡΡΡΡΡΠ²ΡΡΡΠ΅Π³ΠΎ Π² ΠΊΠ°ΡΠ΅ΡΡΠ²Π΅ ΠΏΡΠΈΠΌΠ΅ΡΠΈ ΠΈΠ»ΠΈ Π΄ΠΎΠ±Π°Π²Π»Π΅Π½Π½ΠΎΠ³ΠΎ Π½ΠΈΡΡΠ°ΡΠ° ΡΠ²ΠΈΠ½ΡΠ°, ΡΡ ΠΎΠ΄Π½Π° Ρ ΡΠΎΠ»ΡΡ, ΠΊΠΎΡΠΎΡΡΡ Π²ΡΠΏΠΎΠ»Π½ΡΠ΅Ρ ΠΌΠ΅Π΄Ρ Π² ΡΠ°ΡΡΠ²ΠΎΡΠ°Ρ Π΄Π»Ρ Π³Π»ΡΠ½ΡΠ΅Π²Π°Π½ΠΈΡ. ΠΠ½ ΠΎΡΠ°ΠΆΠ΄Π°Π΅ΡΡΡ Π½Π° ΠΈΠ½Π΅ΡΡΠΌΠ΅ΡΠ°Π»Π»ΠΈΠ΄ ΠΏΠΎΠ²Π΅ΡΡ Π½ΠΎΡΡΠΈ ΠΈ Π²Π»ΠΈΡΠ΅Ρ Π½Π° ΠΊΠ°ΡΠΎΠ΄Π½ΠΎΠ΅ Π²ΡΠ΄Π΅Π»Π΅Π½ΠΈΠ΅ Π²ΠΎΠ΄ΠΎΡΠΎΠ΄Π°.
ΠΡΠΎΡΠΎΠΉ ΡΠΈΠΏ Ρ ΠΈΠΌΠΈΡΠ΅ΡΠΊΠΎΠΉ ΠΎΠ±ΡΠ°Π±ΠΎΡΠΊΠΈ Ρ Π°ΡΠ°ΠΊΡΠ΅ΡΠΈΠ·ΡΠ΅ΡΡΡ Π½ΠΈΠ·ΠΊΠΈΠΌ ΠΊΠΎΡΡΡΠΈΡΠΈΠ΅Π½ΡΠΎΠΌ ΡΠ°ΡΡΠ²ΠΎΡΠ΅Π½ΠΈΡ Π² ΠΌΠ΅Π½Π΅Π΅ ΠΊΠΎΠ½ΡΠ΅Π½ΡΡΠΈΡΠΎΠ²Π°Π½Π½ΡΡ ΡΠ°ΡΡΠ²ΠΎΡΠΎΠ². ΠΠ»Ρ Π°Π»ΡΠΌΠΈΠ½ΠΈΡ ΠΏΡΠΈΠΌΠ΅ΡΠΎΠΌ ΠΌΠΎΠ³ΡΡ ΠΏΠΎΡΠ»ΡΠΆΠΈΡΡ ΡΠ°ΡΡΠ²ΠΎΡΡ Π½Π° ΠΎΡΠ½ΠΎΠ²Π΅ ΠΏΠ΅ΡΠ΅ΠΊΠΈΡΠΈ Π²ΠΎΠ΄ΠΎΡΠΎΠ΄Π°, ΠΎΠΏΠΈΡΠ°Π½Π½ΡΠ΅ Π½ΠΈΠΆΠ΅, Π° ΡΠ°ΠΊΠΆΠ΅ Π½Π΅ΠΊΠΎΠ½ΡΠ΅Π½ΡΡΠΈΡΠΎΠ²Π°Π½Π½ΡΠ΅ ΡΠ°ΡΡΠ²ΠΎΡΡ ΠΠ°ΠΉΠ·Π΅ΡΠ° ΠΈ ΠΠΆΠ΅Π½Π΅ΡΠ°Π» ΠΠΎΡΠΎΡΠ·, ΡΠΎΠ΄Π΅ΡΠΆΠ°ΡΠΈΠ΅ Π² ΠΊΠ°ΡΠ΅ΡΡΠ²Π΅ ΠΎΠΊΠΈΡΠ»ΠΈΡΠ΅Π»Ρ Π°Π·ΠΎΡΠ½ΡΡ ΠΈ Ρ ΡΠΎΠΌΠΎΠ²ΡΡ ΠΊΠΈΡΠ»ΠΎΡΡ. Π ΡΡΠΎΠΌ ΡΠ»ΡΡΠ°Π΅ ΡΠ΅ΡΡ ΠΈΠ΄ΡΡ Π½Π΅ ΠΎ ΡΠ³Π»Π°ΠΆΠΈΠ²Π°Π½ΠΈΠΈ, ΠΊΠΎΡΠΎΡΠΎΠ΅ ΠΈΠΌΠ΅Π΅Ρ ΠΌΠ΅ΡΡΠΎ ΠΏΡΠΈ ΠΏΡΠΈΠΌΠ΅Π½Π΅Π½ΠΈΠΈ ΡΠ°ΡΡΠ²ΠΎΡΠΎΠ² Π½Π° ΠΎΡΠ½ΠΎΠ²Π΅ ΡΠΎΡΡΠΎΡΠ½ΠΎΠΉ ΠΊΠΈΡΠ»ΠΎΡ. Π Π΄Π°Π½Π½ΠΎΠΌ ΡΠ»ΡΡΠ°Π΅ Π±Π»Π΅ΡΠΊ Π²ΡΠ·Π²Π°Π½ ΡΠ°ΠΌΠΈΠΌ ΠΎΠ±ΡΠ°Π·ΠΎΠ²Π°Π½ΠΈΠ΅ΠΌ ΠΏΡΠΎΡΠ½ΠΎΠΉ ΠΏΠ»ΡΠ½ΠΊΠΈ.Π‘ΡΠΈΡΠ°Π΅ΡΡΡ, ΡΡΠΎ ΡΡΠΎ Π²ΡΠ·Π²Π°Π½ΠΎ ΡΠ΅ΠΌ, ΡΡΠΎ ΡΡΠ»ΠΎΠ²ΠΈΡ Π΄Π»Ρ ΠΎΠ±ΡΠ°Π·ΠΎΠ²Π°Π½ΠΈΡ ΠΎΠΊΠΈΡΠ»Π° Π²ΠΎ Π²ΠΏΠ°Π΄ΠΈΠ½Π°Ρ Π΄ΠΎΡΡΠΈΠ³Π°ΡΡΡΡ Π½Π΅ΡΠΊΠΎΠ»ΡΠΊΠΎ Π±ΡΡΡΡΠ΅Π΅, ΡΠ΅ΠΌ Π½Π° Π²ΡΡΡΡΠΏΠ°Ρ . Π’Π°ΠΊΠΈΠΌ ΠΎΠ±ΡΠ°Π·ΠΎΠΌ ΡΡΠ°Π½ΠΎΠ²ΠΈΡΡΡ Π²ΠΎΠ·ΠΌΠΎΠΆΠ½ΡΠΌ ΡΠ°ΡΡΠ²ΠΎΡΠ΅Π½ΠΈΠ΅ Π±ΠΎΠ»ΡΡΠ΅Π³ΠΎ ΠΊΠΎΠ»ΠΈΡΠ΅ΡΡΠ²Π° ΠΌΠ΅ΡΠ°Π»Π»Π° Π½Π° Π²ΡΡΡΡΠΏΠ°Ρ ΠΏΠ΅ΡΠ΅Π΄ ΠΎΠ±ΡΠ°Π·ΠΎΠ²Π°Π½ΠΈΠ΅ΠΌ ΠΏΠ»ΡΠ½ΠΊΠΈ, Π² ΡΠΎ ΠΆΠ΅ Π²ΡΠ΅ΠΌΡ Π±ΠΎΠ»Π΅Π΅ Π±ΡΡΡΡΠΎΠ΅ Π½Π°ΡΠ°ΡΡΠ°Π½ΠΈΠ΅ ΠΎΠΊΠΈΡΠ»Π° Π½Π° Π±ΠΎΠ»Π΅Π΅ Π²ΡΡΠΎΠΊΠΈΡ ΡΡΠ°ΡΡΠΊΠ°Ρ ΠΏΠΎΠ²Π΅ΡΡ Π½ΠΎΡΡΠΈ ΠΌΠΎΠΆΠ΅Ρ ΡΠ°ΠΌΠΎ ΠΏΡΠΈΠ²Π΅ΡΡΠΈ ΠΊ ΡΠ³Π»Π°ΠΆΠΈΠ²Π°Π½ΠΈΡ ΡΠ΅ΡΠΎΡ ΠΎΠ²Π°ΡΠΎΡΡΠ΅ΠΉ. Π’Π°ΠΊΠΈΠΌ ΠΎΠ±ΡΠ°Π·ΠΎΠΌ ΠΎΠ±ΡΠ°Π±ΠΎΡΠΊΠ° Π°Π»ΡΠΌΠΈΠ½ΠΈΡ ΡΡΠ°Π»Π° Π²ΠΎΠ·ΠΌΠΎΠΆΠ½ΠΎΠΉ ΠΏΡΡΡΠΌ ΠΏΠΎΠΏΠ΅ΡΠ΅ΠΌΠ΅Π½Π½ΠΎΠ³ΠΎ Π°Π½ΠΎΠ΄ΠΈΡΠΎΠ²Π°Π½ΠΈΡ ΠΈ ΡΠ°ΡΡΠ²ΠΎΡΠ΅Π½ΠΈΡ ΠΏΠΎΠΊΡΡΡΠΈΡ. ΠΡΠΎΡΠ΅ΡΡ Π³Π°Π»ΡΠ²Π°Π½ΠΈΡΠ΅ΡΠΊΠΎΠΉ ΠΎΠ±ΡΠ°Π±ΠΎΡΠΊΠΈ, ΠΎΠΏΠΈΡΠ°Π½Π½ΡΠΉ ΠΠ²Π°Π½ΡΠΎΠΌ ΠΈ Π£ΠΈΡΡΠΎΠΌΠΎΠΌ, ΠΎΡΠ½ΠΎΠ²ΡΠ²Π°Π΅ΡΡΡ Π½Π° ΡΠ΅Ρ ΠΆΠ΅ ΠΏΡΠΈΠ½ΡΠΈΠΏΠ°Ρ .
Π ΡΠ»ΡΡΠ°Π΅ ΠΏΡΠΈΠΌΠ΅Π½Π΅Π½ΠΈΡ Π΄Π°Π½Π½ΡΡ ΡΠΏΠΎΡΠΎΠ±ΠΎΠ² Ρ ΠΈΠΌΠΈΡΠ΅ΡΠΊΠΎΠΉ ΠΎΠ±ΡΠ°Π±ΠΎΡΠΊΠΈ ΠΏΠΎΠΎΡΠ΅ΡΡΠ΄Π½ΠΎΠ΅ Π½Π°ΡΠ°ΡΡΠ°Π½ΠΈΠ΅ ΠΈ ΡΠ°ΡΡΠ²ΠΎΡΠ΅Π½ΠΈΠ΅ ΠΏΡΠΎΡΠ½ΠΎΠΉ ΠΏΠ»ΡΠ½ΠΊΠΈ ΠΏΡΠΎΠΈΡΡ ΠΎΠ΄ΠΈΡ Π²ΡΠ·Π²Π°Π½Π½ΠΎΠ΅ ΠΏΠ΅ΡΠΈΠΎΠ΄ΠΈΡΠ΅ΡΠΊΠΎΠΉ ΠΏΠ°ΡΡΠΈΠ²Π½ΠΎΡΡΡΡ, ΠΊΠΎΡΠΎΡΠ°Ρ, Π²ΠΎΠ·ΠΌΠΎΠΆΠ½ΠΎ, Π²ΠΎΠ·Π½ΠΈΠΊΠ°Π΅Ρ ΠΈΠ·-Π·Π° ΠΈΠ·ΠΌΠ΅Π½Π΅Π½ΠΈΠΉ ΡΡΠΎΠ²Π½Ρ ΡΠ ΡΠ°ΡΡΠ²ΠΎΡΠ° Π² Π½Π΅ΠΏΠΎΡΡΠ΅Π΄ΡΡΠ²Π΅Π½Π½ΠΎΠΉ Π±Π»ΠΈΠ·ΠΎΡΡΠΈ ΠΎΡ ΠΏΠΎΠ²Π΅ΡΡ Π½ΠΎΡΡΠΈ. Π ΠΏΠΎΠ΄ΠΎΠ±Π½ΡΡ ΡΠ»ΡΡΠ°ΡΡ ΠΏΡΠΎΡΠ½Π°Ρ ΠΏΠ»ΡΠ½ΠΊΠ° Π½Π°ΡΠ°ΡΡΠ°Π΅Ρ Π±Π»Π°Π³ΠΎΠ΄Π°ΡΡ ΠΏΠΎΠ²ΡΡΠ΅Π½ΠΈΡ ΡΡΠΎΠ²Π½Ρ ΡΠ, Π²ΡΠ·Π²Π°Π½Π½ΠΎΠΌΡ ΠΊΠ°ΡΠΎΠ΄Π½ΡΠΌΠΈ ΡΠ΅Π°ΠΊΡΠΈΡΠΌΠΈ, ΡΠ½ΠΈΡΡΠΎΠΆΠ΅Π½ΠΈΠ΅ΠΌ ΠΈΠΎΠ½ΠΎΠ² Π²ΠΎΠ΄ΠΎΡΠΎΠ΄Π° ΠΈΠ»ΠΈ ΠΎΠ±ΡΠ°Π·ΠΎΠ²Π°Π½ΠΈΡ Π³ΠΈΠ΄ΡΠΎΠΊΡΠΈΠ»ΡΠ½ΡΡ ΠΈΠΎΠ½ΠΎΠ². Π ΡΠΎ ΠΆΠ΅ Π²ΡΠ΅ΠΌΡ Π½Π°Π±Π»ΡΠ΄Π°Π΅ΡΡΡ ΠΊΠΎΠ½ΡΠ΅Π½ΡΡΠ°ΡΠΈΡ ΠΈΠΎΠ½ΠΎΠ² ΡΡΠΆΡΠ»ΡΡ ΠΌΠ΅ΡΠ°Π»Π»ΠΎΠ² Π½Π° ΠΏΠΎΠ²Π΅ΡΡ Π½ΠΎΡΡΠΈ. ΠΠ°ΡΠ΅ΠΌ, ΠΊΠΎΠ½ΡΠ΅Π½ΡΡΠ°ΡΠΈΡ Π³ΠΈΠ΄ΡΠΎΠΊΡΠΈΠ»ΡΠ½ΡΡ ΠΈΠΎΠ½ΠΎΠ² ΡΠΌΠ΅Π½ΡΡΠ°Π΅ΡΡΡ Π² ΡΠ΅Π·ΡΠ»ΡΡΠ°ΡΠ΅ ΠΎΠ±ΡΠ°Π·ΠΎΠ²Π°Π½ΠΈΡ ΠΏΠ°ΡΡΠΈΠ²ΠΈΡΡΡΡΠ΅ΠΉ ΠΏΠ»ΡΠ½ΠΊΠΈ, Π² ΡΠΎ Π²ΡΠ΅ΠΌΡ ΠΊΠ°ΠΊ Π² ΠΏΠ°ΡΡΠΈΠ²Π½ΡΠΉ ΠΏΠ΅ΡΠΈΠΎΠ΄ Π΄ΠΈΡΡΡΠ·ΠΈΡ ΡΠ°ΠΊΠΆΠ΅ ΠΏΠΎΠΌΠΎΠ³Π°Π΅Ρ Π²ΠΎΡΡΡΠ°Π½ΠΎΠ²Π»Π΅Π½ΠΈΡ ΡΡΠΎΠ²Π½Ρ ΡΠ, ΠΏΡΠΈ ΠΊΠΎΡΠΎΡΠΎΠΌ ΠΎΠΊΠΈΡΠ΅Π» ΡΠ°ΡΡΠ²ΠΎΡΡΠ΅ΡΡΡ, ΠΈ ΡΠΈΠΊΠ» ΠΏΠΎΠ²ΡΠΎΡΡΠ΅ΡΡΡ. Π ΡΡΠ°Π²Π½ΠΈΡΠ΅Π»ΡΠ½ΠΎ ΠΌΠ°Π»ΠΎ ΠΊΠΎΠ½ΡΠ΅Π½ΡΡΠΈΡΠΎΠ²Π°Π½Π½ΡΡ ΡΠ°ΡΡΠ²ΠΎΡΠ°Ρ ΠΏΠ΅ΡΠ΅ΠΊΠΈΡΠΈ Π²ΠΎΠ΄ΠΎΡΠΎΠ΄Π° Π±Π»Π°Π³ΠΎΠ΄Π°ΡΡ ΠΎΠ±ΡΠ°Π·ΠΎΠ²Π°Π½ΠΈΡ Π·Π°ΡΠΈΡΠ½ΠΎΠΉ ΠΏΠ»ΡΠ½ΠΊΠΈ ΠΏΠΎΡΠ΅Π½ΡΠΈΠ°Π» Π°Π»ΡΠΌΠΈΠ½ΠΈΡ ΠΏΠΎΠ΄Π½ΠΈΠΌΠ°Π΅ΡΡΡ Π΄ΠΎ ΡΠ»Π΅ΠΊΡΡΠΎΠΏΠΎΠ»ΠΎΠΆΠΈΡΠ΅Π»ΡΠ½ΡΡ Π·Π½Π°ΡΠ΅Π½ΠΈΠΉ. ΠΠ΄Π½Π°ΠΊΠΎ, Π΅ΡΠ»ΠΈ ΡΡΠΎΠ²Π΅Π½Ρ ΡΠ ΠΏΠΎΠ΄Π½ΠΈΠΌΠ°Π΅ΡΡΡ Π²ΡΡΠ΅ Π·Π½Π°ΡΠ΅Π½ΠΈΡ 5, ΡΡΠΎ ΠΏΡΠΈΠ²ΠΎΠ΄ΠΈΡ ΠΊ ΡΠ°Π·ΡΡΠ²Ρ ΠΏΠ»Π΅Π½ΠΊΠΈ, ΡΠ°ΠΊ ΠΊΠ°ΠΊ ΠΌΠ΅Π½ΡΠ΅ΡΡΡ ΡΠ΅Π°ΠΊΡΠΈΡ ΠΏΠ΅ΡΠ΅ΠΊΠΈΡΠΈ Π²ΠΎΠ΄ΠΎΡΠΎΠ΄Π° ΠΈ ΠΌΠ΅ΡΠ°Π»Π»Π°.Π§ΡΠΎ ΠΊΠ°ΡΠ°Π΅ΡΡΡ ΡΠ°ΡΡΠ²ΠΎΡΠΎΠ² ΠΏΠ΅ΡΠ΅ΠΊΠΈΡΠΈ Π²ΠΎΠ΄ΠΎΡΠΎΠ΄Π°, ΡΠΎΠ΄Π΅ΡΠΆΠ°ΡΠΈΡ ΠΊΠΈΡΠ»ΠΎΡΡ, ΡΡΠΎΠΌΡ ΠΌΠ΅Ρ Π°Π½ΠΈΠ·ΠΌΡ ΡΠΏΠΎΡΠΎΠ±ΡΡΠ²ΡΠ΅Ρ ΡΠΎΡ ΡΠ°ΠΊΡ, ΡΡΠΎ ΠΏΠ΅ΡΠ΅ΠΊΠΈΡΡ Π²ΠΎΠ΄ΠΎΡΠΎΠ΄Π° ΡΠ²Π»ΡΠ΅ΡΡΡ ΠΎΠΊΠΈΡΠ»ΠΈΡΠ΅Π»Π΅ΠΌ ΡΠΎΠ»ΡΠΊΠΎ ΠΏΡΠΈ Π½ΠΈΠ·ΠΊΠΎΠΌ ΡΡΠΎΠ²Π½Π΅ ΡΠ, ΡΠΎΠ³Π΄Π° ΠΊΠ°ΠΊ Π² Π±ΠΎΠ»Π΅Π΅ ΡΠ΅Π»ΠΎΡΠ½ΡΡ ΡΠ°ΡΡΠ²ΠΎΡΠ°Ρ ΠΎΠ½Π° ΠΊΠ°ΡΠ°Π»ΠΈΡΠΈΡΠ΅ΡΠΊΠΈ ΡΠ°ΡΠΏΠ°Π΄Π°Π΅ΡΡΡ Ρ ΠΎΠ±ΡΠ°Π·ΠΎΠ²Π°Π½ΠΈΠ΅ΠΌ ΠΊΠΈΡΠ»ΠΎΡΠΎΠ΄Π°. ΠΠ΅ΡΠΈΠΎΠ΄ΠΈΡΠ΅ΡΠΊΠΈΠ΅ Π²ΡΠ΄Π΅Π»Π΅Π½ΠΈΡ ΠΊΠΈΡΠ»ΠΎΡΠΎΠ΄Π° Π² ΡΠ°ΠΊΠΈΡ ΡΠ°ΡΡΠ²ΠΎΡΠ°Ρ Π±ΡΠ»ΠΈ Π·Π°ΠΌΠ΅ΡΠ΅Π½Ρ ΠΠ°ΡΡΠ°Π»Π»ΠΎΠΌ Π½Π° ΠΆΠ΅Π»Π΅Π·Π΅, ΠΈ ΡΡΠΈ Π²ΡΠ΄Π΅Π»Π΅Π½ΠΈΡ Π³Π°Π·Π° Π²ΠΎΠ·ΠΌΠΎΠΆΠ½ΠΎ ΠΎΠ±ΠΎΠ·Π½Π°ΡΠ°ΡΡ ΠΏΠ΅ΡΠΈΠΎΠ΄ ΡΠΎΡΠΌΠΈΡΠΎΠ²Π°Π½ΠΈΡ ΠΏΠ»ΡΠ½ΠΊΠΈ Π΄ΠΎ ΡΠΎΠ³ΠΎ ΠΌΠΎΠΌΠ΅Π½ΡΠ°, ΠΊΠΎΠ³Π΄Π° ΠΏΠΎΠ½ΠΈΠΆΠ΅Π½ΠΈΠ΅ ΡΡΠΎΠ²Π½Ρ ΡΠ Π½Π΅ Π²ΡΠ·ΡΠ²Π°Π΅Ρ ΡΠ΅Π³Π΅Π½Π΅ΡΠ°ΡΠΈΠΈ ΠΌΠ΅ΡΠ°Π»Π»Π° ΠΈ ΠΏΠΎΠ²ΡΠΎΡΠ½ΠΎΠ΅ ΠΏΡΠ΅ΠΎΠ±ΡΠ°Π·ΠΎΠ²Π°Π½ΠΈΠ΅ ΠΏΠ΅ΡΠ΅ΠΊΠΈΡΠΈ Π²ΠΎΠ΄ΠΎΡΠΎΠ΄Π° Π² ΠΎΠΊΠΈΡΠ»ΠΈΡΠ΅Π»Ρ.
vseokraskah.net
Π’Π΅ΡΠΌΠΎΠΎΠ±ΡΠ°Π±ΠΎΡΠΊΠ° Π°Π»ΡΠΌΠΈΠ½ΠΈΠ΅Π²ΡΡ ΡΠΏΠ»Π°Π²ΠΎΠ²: Π²ΠΈΠ΄Ρ ΠΈ ΡΠ΅ΠΆΠΈΠΌΡ
Π’Π΅ΡΠΌΠΈΡΠ΅ΡΠΊΠ°Ρ ΠΎΠ±ΡΠ°Π±ΠΎΡΠΊΠ° Π°Π»ΡΠΌΠΈΠ½ΠΈΠ΅Π²ΡΡ ΡΠΏΠ»Π°Π²ΠΎΠ² ΠΏΡΠ΅Π΄Π½Π°Π·Π½Π°ΡΠ΅Π½Π° Π΄Π»Ρ ΠΊΠΎΡΡΠ΅ΠΊΡΠΈΡΠΎΠ²ΠΊΠΈ Ρ Π°ΡΠ°ΠΊΡΠ΅ΡΠΈΡΡΠΈΠΊ ΠΌΠ°ΡΠ΅ΡΠΈΠ°Π»Π° Ρ ΠΏΠΎΠΌΠΎΡΡΡ Π²ΠΎΠ·Π΄Π΅ΠΉΡΡΠ²ΠΈΡ Π²ΡΡΠΎΠΊΠΈΡ ΡΠ΅ΠΌΠΏΠ΅ΡΠ°ΡΡΡ. Π Π°Π·Π»ΠΈΡΠ½ΡΠΌΠΈ ΡΠΏΠΎΡΠΎΠ±Π°ΠΌΠΈ ΠΎΠ±ΡΠ°Π±ΠΎΡΠΊΠΈ ΠΌΠΎΠΆΠ½ΠΎ Π΄ΠΎΠ±ΠΈΡΡΡΡ ΡΠΈΡΠΎΠΊΠΎΠ³ΠΎ ΡΠ°Π·Π½ΠΎΠΎΠ±ΡΠ°Π·ΠΈΡ ΡΡΡΡΠΊΡΡΡΡ ΠΈ ΡΠ²ΠΎΠΉΡΡΠ².
Π‘ΠΏΠ»Π°Π²Ρ, ΠΊΠΎΡΠΎΡΡΠ΅ ΡΠΎΠ΄Π΅ΡΠΆΠ°Ρ ΠΏΡΠΈΠΌΠ΅ΡΠΈ Π² ΡΠ°Π·ΠΌΠ΅ΡΠ΅ 15-18%, ΠΈΠΌΠ΅ΡΡ Π²ΠΈΠ΄ ΡΠ²Π΅ΡΠ΄ΠΎΠ³ΠΎ ΡΠ°ΡΡΠ²ΠΎΡΠ°. Π ΠΊΠ°ΡΠ΅ΡΡΠ²Π΅ Π΄ΠΎΠΏΠΎΠ»Π½ΠΈΡΠ΅Π»ΡΠ½ΡΡ ΠΊΠΎΠΌΠΏΠΎΠ½Π΅Π½ΡΠΎΠ² ΠΏΡΠΈΠΌΠ΅Π½ΡΡΡΡΡ ΠΌΠ΅Π΄Ρ, ΠΌΠ°Π³Π½ΠΈΠΉ, ΡΠΈΠ½ΠΊ, ΠΊΡΠ΅ΠΌΠ½ΠΈΠΉ ΠΈ Π΄ΡΡΠ³ΠΈΠ΅ Π²Π΅ΡΠ΅ΡΡΠ²Π°, ΡΠ°Π·Π»ΠΈΡΠ½ΠΎΠ΅ ΡΠΎΡΠ΅ΡΠ°Π½ΠΈΠ΅ ΠΊΠΎΡΠΎΡΡΡ ΠΈ ΠΈΡ ΠΏΡΠΎΡΠ΅Π½ΡΠ½ΠΎΠ΅ ΡΠΎΠΎΡΠ½ΠΎΡΠ΅Π½ΠΈΠ΅ ΠΏΡΡΠΌΠΎ ΠΏΡΠΎΠΏΠΎΡΡΠΈΠΎΠ½Π°Π»ΡΠ½ΠΎ Π²Π»ΠΈΡΡΡ Π½Π° ΡΠ²ΠΎΠΉΡΡΠ²Π° ΠΌΠ°ΡΠ΅ΡΠΈΠ°Π»Π°.
Π ΠΎΠ±ΡΡΠ½ΠΎΠΌ ΡΠΎΡΡΠΎΡΠ½ΠΈΠΈ Π°Π»ΡΠΌΠΈΠ½ΠΈΠ΅Π²ΡΠ΅ ΡΠΏΠ»Π°Π²Ρ Π½Π΅ ΠΎΡΠ»ΠΈΡΠ°ΡΡΡΡ Π²ΡΡΠΎΠΊΠΎΠΉ ΠΏΡΠΎΡΠ½ΠΎΡΡΡΡ, ΠΏΡΠΈ ΡΡΠΎΠΌ Π΄ΠΎΠ²ΠΎΠ»ΡΠ½ΠΎ ΠΏΠ»Π°ΡΡΠΈΡΠ½Ρ. ΠΠ°ΠΈΠ±ΠΎΠ»Π΅Π΅ Π½Π΅ΡΡΡΠΎΠΉΡΠΈΠ²ΡΠ΅ ΡΠΏΠ»Π°Π²Ρ Π²ΠΊΠ»ΡΡΠ°ΡΡ Π² ΡΠΎΡΡΠ°Π² Π±ΠΎΠ»ΡΡΠΎΠ΅ ΠΊΠΎΠ»ΠΈΡΠ΅ΡΡΠ²ΠΎ Π»Π΅Π³ΠΈΡΡΡΡΠΈΡ ΠΊΠΎΠΌΠΏΠΎΠ½Π΅Π½ΡΠΎΠ², ΠΊΠΎΡΠΎΡΡΠ΅ Π²Π»ΠΈΡΡΡ Π½Π° ΡΠ°Π²Π½ΠΎΠ²Π΅ΡΠ½ΡΡ ΡΡΡΡΠΊΡΡΡΡ.
ΠΠ»Ρ ΡΠΏΡΠΎΡΠ½Π΅Π½ΠΈΡ Π°Π»ΡΠΌΠΈΠ½ΠΈΠ΅Π²ΡΡ ΡΠΏΠ»Π°Π²ΠΎΠ² ΠΏΡΠΈΠΌΠ΅Π½ΡΠ΅ΡΡΡ ΠΌΠ΅ΡΠΎΠ΄Ρ ΡΠ΅ΡΠΌΠΎΠΎΠ±ΡΠ°Π±ΠΎΡΠΊΠΈ. ΠΡΡΠ΅ΠΌ ΡΠ°Π²Π½ΠΎΠΌΠ΅ΡΠ½ΠΎΠ³ΠΎ Π½Π°Π³ΡΠ΅Π²Π°, ΠΊΠΎΡΠΎΡΡΠΉ ΡΠ΅Π³Π»Π°ΠΌΠ΅Π½ΡΠΈΡΡΠ΅ΡΡΡ ΡΠ΅Ρ Π½ΠΈΡΠ΅ΡΠΊΠΈΠΌΠΈ ΡΡΠ»ΠΎΠ²ΠΈΡΠΌΠΈ, ΠΏΠΎΠ»ΡΡΠ°ΡΡ ΡΠΎΠΎΡΠ²Π΅ΡΡΡΠ²ΡΡΡΡΡ ΡΡΡΡΠΊΡΡΡΡ, Π½Π΅ΠΎΠ±Ρ ΠΎΠ΄ΠΈΠΌΡΡ Π΄Π»Ρ Π½Π°ΡΠ°Π»ΡΠ½ΠΎΠΉ ΡΡΠ°Π΄ΠΈΠΈ ΡΠ°ΡΠΏΠ°Π΄Π° ΡΠ²Π΅ΡΠ΄ΠΎΠ³ΠΎ ΡΠ°ΡΡΠ²ΠΎΡΠ°.
Π‘ ΠΏΠΎΠΌΠΎΡΡΡ ΡΠ΅ΡΠΌΠΎΠΎΠ±ΡΠ°Π±ΠΎΡΠΊΠΈ ΠΌΠΎΠΆΠ½ΠΎ ΠΏΠΎΠ»ΡΡΠΈΡΡ ΠΌΠ½ΠΎΠΆΠ΅ΡΡΠ²ΠΎ ΡΠΈΠΏΠΎΠ² ΡΡΡΡΠΊΡΡΡΡ ΠΌΠ°ΡΠ΅ΡΠΈΠ°Π»Π°, ΠΊΠΎΡΠΎΡΡΠ΅ ΡΠΎΠΎΡΠ²Π΅ΡΡΡΠ²ΡΡΡ ΡΡΠ΅Π±ΠΎΠ²Π°Π½ΠΈΡΠΌ ΠΏΡΠΎΠΈΠ·Π²ΠΎΠ΄ΡΡΠ²Π°. Π’Π΅ΡΠΌΠΈΡΠ΅ΡΠΊΠ°Ρ ΠΎΠ±ΡΠ°Π±ΠΎΡΠΊΠ° ΠΏΠΎΠ·Π²ΠΎΠ»ΡΠ΅Ρ ΡΠΎΠ·Π΄Π°ΡΡ ΡΡΡΡΠΊΡΡΡΡ, Π½Π΅ ΠΈΠΌΠ΅ΡΡΡΡ Π°Π½Π°Π»ΠΎΠ³ΠΎΠ².
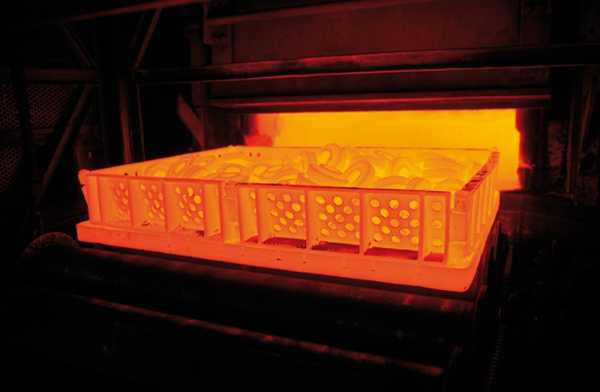
ΠΠ° ΡΠ΅Π³ΠΎΠ΄Π½ΡΡΠ½ΠΈΠΉ Π΄Π΅Π½Ρ ΡΠ°Π·ΡΠ°Π±ΠΎΡΠ°Π½ΠΎ ΠΌΠ½ΠΎΠΆΠ΅ΡΡΠ²ΠΎ ΠΌΠ΅ΡΠΎΠ΄ΠΎΠ² ΡΠ΅ΡΠΌΠΎΠΎΠ±ΡΠ°Π±ΠΎΡΠΊΠΈ Π°Π»ΡΠΌΠΈΠ½ΠΈΠ΅Π²ΡΡ ΠΈΠ·Π΄Π΅Π»ΠΈΠΉ, ΡΡΠ΅Π΄ΠΈ ΠΊΠΎΡΠΎΡΡΡ Π½Π°ΠΈΠ±ΠΎΠ»ΡΡΡΡ ΠΏΠΎΠΏΡΠ»ΡΡΠ½ΠΎΡΡΡ ΠΎΠ±ΡΠ΅Π»ΠΈ ΡΡΠΈ: ΠΎΡΠΆΠΈΠ³, Π·Π°ΠΊΠ°Π»ΠΊΠ°, ΡΡΠ°ΡΠ΅Π½ΠΈΠ΅.
ΠΡΠΎΠ±Π΅Π½Π½ΠΎΡΡΠΈ ΡΠ΅ΡΠΌΠΎΠΎΠ±ΡΠ°Π±ΠΎΡΠΊΠΈ Π°Π»ΡΠΌΠΈΠ½ΠΈΠ΅Π²ΡΡ ΡΠΏΠ»Π°Π²ΠΎΠ²
ΠΠ»ΡΠΌΠΈΠ½ΠΈΠΉ ΠΈ Π΅Π³ΠΎ ΡΠΏΠ»Π°Π²Ρ ΡΡΠ΅Π±ΡΡΡ ΠΎΡΠΎΠ±ΠΎΠ³ΠΎ ΠΏΠΎΠ΄Ρ ΠΎΠ΄Π° ΠΊ ΡΠ΅ΡΠΌΠΎΠΎΠ±ΡΠ°Π±ΠΎΡΠΊΠ΅ Π΄Π»Ρ Π΄ΠΎΡΡΠΈΠΆΠ΅Π½ΠΈΡ ΠΎΠΏΡΠ΅Π΄Π΅Π»Π΅Π½Π½ΠΎΠΉ ΠΏΡΠΎΡΠ½ΠΎΡΡΠΈ ΠΈ ΡΡΡΡΠΊΡΡΡΡ ΠΌΠ°ΡΠ΅ΡΠΈΠ°Π»Π°. ΠΡΠ΅Π½Ρ ΡΠ°ΡΡΠΎ ΠΏΡΠΈΠΌΠ΅Π½ΡΡΡ Π½Π΅ΡΠΊΠΎΠ»ΡΠΊΠΎ ΠΌΠ΅ΡΠΎΠ΄ΠΎΠ² ΡΠ΅ΡΠΌΠΎΠΎΠ±ΡΠ°Π±ΠΎΡΠΊΠΈ. ΠΠ±ΡΡΠ½ΠΎ, ΠΏΠΎΡΠ»Π΅ Π·Π°ΠΊΠ°Π»ΠΊΠΈ ΡΠ»Π΅Π΄ΡΠ΅Ρ ΡΡΠ°ΡΠ΅Π½ΠΈΠ΅. ΠΠΎ Π½Π΅ΠΊΠΎΡΠΎΡΡΠ΅ ΡΠΈΠΏΡ ΠΌΠ°ΡΠ΅ΡΠΈΠ°Π»ΠΎΠ² ΠΌΠΎΠ³ΡΡ ΠΏΠΎΠ΄Π²Π΅ΡΠ³Π°ΡΡΡΡ ΡΡΠ°ΡΠ΅Π½ΠΈΡ Π±Π΅Π· Π·Π°ΠΊΠ°Π»ΠΊΠΈ.
Π’Π°ΠΊΠ°Ρ Π²ΠΎΠ·ΠΌΠΎΠΆΠ½ΠΎΡΡΡ ΠΏΠΎΡΠ²Π»ΡΠ΅ΡΡΡ ΠΏΠΎΡΠ»Π΅ ΠΎΡΠ»ΠΈΠ²ΠΊΠΈ, ΠΊΠΎΠ³Π΄Π° ΠΊΠΎΠΌΠΏΠΎΠ½Π΅Π½ΡΡ, ΠΏΡΠΈ ΠΏΠΎΠ²ΡΡΠ΅Π½Π½ΠΎΠΉ ΡΠΊΠΎΡΠΎΡΡΠΈ ΠΎΡ Π»Π°ΠΆΠ΄Π΅Π½ΠΈΡ, ΠΌΠΎΠ³ΡΡ ΠΏΡΠΈΠ΄Π°ΡΡ ΠΌΠ΅ΡΠ°Π»Π»Ρ Π½Π΅ΠΎΠ±Ρ ΠΎΠ΄ΠΈΠΌΡΡ ΡΡΡΡΠΊΡΡΡΡ ΠΈ ΠΏΡΠΎΡΠ½ΠΎΡΡΡ. ΠΡΠΎ ΠΏΡΠΎΠΈΡΡ ΠΎΠ΄ΠΈΡ Π²ΠΎ Π²ΡΠ΅ΠΌΡ Π»ΠΈΡΡΡ ΠΏΡΠΈ ΡΠ΅ΠΌΠΏΠ΅ΡΠ°ΡΡΡΠ΅ ΠΎΠΊΠΎΠ»ΠΎ 180 Π³ΡΠ°Π΄ΡΡΠΎΠ². ΠΡΠΈ ΡΠ°ΠΊΠΎΠΉ ΡΠ΅ΠΌΠΏΠ΅ΡΠ°ΡΡΡΠ΅ ΠΏΠΎΠ²ΡΡΠ°Π΅ΡΡΡ ΡΡΠΎΠ²Π΅Π½Ρ ΠΏΡΠΎΡΠ½ΠΎΡΡΠΈ ΠΈ ΡΠ²Π΅ΡΠ΄ΠΎΡΡΠΈ, Π° ΡΠ°ΠΊΠΆΠ΅ ΡΠ½ΠΈΠΆΠ°Π΅ΡΡΡ ΡΡΠ΅ΠΏΠ΅Π½Ρ ΡΡΠ³ΡΡΠ΅ΡΡΠΈ.
ΠΠ°ΠΆΠ΄ΡΠΉ ΠΈΠ· ΠΌΠ΅ΡΠΎΠ΄ΠΎΠ² ΡΠ΅ΡΠΌΠΎΠΎΠ±ΡΠ°Π±ΠΎΡΠΊΠΈ ΠΈΠΌΠ΅Π΅Ρ Π½Π΅ΠΊΠΎΡΠΎΡΡΠ΅ ΠΎΡΠΎΠ±Π΅Π½Π½ΠΎΡΡΠΈ, ΠΊΠΎΡΠΎΡΡΠ΅ ΡΡΠΎΠΈΡ ΡΡΠΈΡΡΠ²Π°ΡΡ ΠΏΡΠΈ ΠΎΠ±ΡΠ°Π±ΠΎΡΠΊΠ΅ Π°Π»ΡΠΌΠΈΠ½ΠΈΠ΅Π²ΡΡ ΠΈΠ·Π΄Π΅Π»ΠΈΠΉ.
ΠΡΠΆΠΈΠ³ Π½Π΅ΠΎΠ±Ρ ΠΎΠ΄ΠΈΠΌ Π΄Π»Ρ ΠΏΡΠΈΠ΄Π°Π½ΠΈΡ ΠΎΠ΄Π½ΠΎΡΠΎΠ΄Π½ΠΎΠΉ ΡΡΡΡΠΊΡΡΡΡ Π°Π»ΡΠΌΠΈΠ½ΠΈΠ΅Π²ΠΎΠΌΡ ΡΠΏΠ»Π°Π²Ρ. Π‘ ΠΏΠΎΠΌΠΎΡΡΡ ΡΡΠΎΠ³ΠΎ ΠΌΠ΅ΡΠΎΠ΄Π° ΡΠΎΡΡΠ°Π² ΡΡΠ°Π½ΠΎΠ²ΠΈΡΡΡΡ Π±ΠΎΠ»Π΅Π΅ ΠΎΠ΄Π½ΠΎΡΠΎΠ΄Π½ΡΠΌ, Π°ΠΊΡΠΈΠ²ΠΈΠ·ΠΈΡΡΠ΅ΡΡΡ ΠΏΡΠΎΡΠ΅ΡΡ Π΄ΠΈΡΡΡΠ·ΠΈΠΈ ΠΈ Π²ΡΡΠ°Π²Π½ΠΈΠ²Π°Π΅ΡΡΡ ΡΠ°Π·ΠΌΠ΅Ρ Π±Π°Π·ΠΎΠ²ΡΡ ΡΠ°ΡΡΠΈΡ. Π’Π°ΠΊΠΆΠ΅ ΠΌΠΎΠΆΠ½ΠΎ Π΄ΠΎΠ±ΠΈΡΡΡΡ ΡΠ½ΠΈΠΆΠ΅Π½ΠΈΡ Π½Π°ΠΏΡΡΠΆΠ΅Π½ΠΈΡ ΠΊΡΠΈΡΡΠ°Π»Π»ΠΈΡΠ΅ΡΠΊΠΎΠΉ ΡΠ΅ΡΠ΅ΡΠΊΠΈ. Π’Π΅ΠΌΠΏΠ΅ΡΠ°ΡΡΡΠ° ΠΎΠ±ΡΠ°Π±ΠΎΡΠΊΠΈ ΠΏΠΎΠ΄Π±ΠΈΡΠ°Π΅ΡΡΡ ΠΈΠ½Π΄ΠΈΠ²ΠΈΠ΄ΡΠ°Π»ΡΠ½ΠΎ, ΠΈΡΡ ΠΎΠ΄Ρ ΠΈΠ· ΠΎΡΠΎΠ±Π΅Π½Π½ΠΎΡΡΠ΅ΠΉ ΡΠΏΠ»Π°Π²Π°, Π½Π΅ΠΎΠ±Ρ ΠΎΠ΄ΠΈΠΌΡΡ ΠΊΠΎΠ½Π΅ΡΠ½ΡΡ Ρ Π°ΡΠ°ΠΊΡΠ΅ΡΠΈΡΡΠΈΠΊ ΠΈ ΡΡΡΡΠΊΡΡΡΡ ΠΌΠ°ΡΠ΅ΡΠΈΠ°Π»Π°.
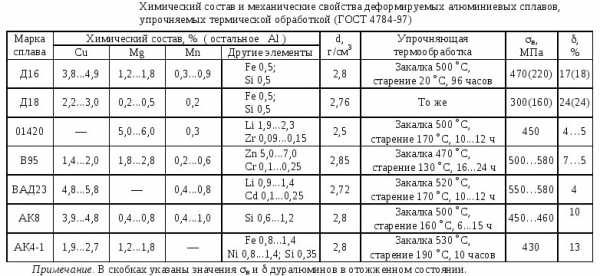
Π‘ΠΎΡΡΠ°Π² ΠΈ ΡΠ²ΠΎΠΉΡΡΠ²Π° Π°Π»ΡΠΌΠΈΠ½ΠΈΠ΅Π²ΡΡ ΡΠΏΠ»Π°Π²ΠΎΠ², ΡΠΏΡΠΎΡΠ½ΡΠ΅ΠΌΡΡ ΡΠ΅ΡΠΌΠΈΡΠ΅ΡΠΊΠΎΠΉ ΠΎΠ±ΡΠ°Π±ΠΎΡΠΊΠΎΠΉ
ΠΠ°ΠΆΠ½ΡΠΌ ΡΡΠ°ΠΏΠΎΠΌ ΠΎΡΠΆΠΈΠ³Π° ΡΠ²Π»ΡΠ΅ΡΡΡ ΠΎΡ Π»Π°ΠΆΠ΄Π΅Π½ΠΈΠ΅, ΠΊΠΎΡΠΎΡΡΠ΅ ΠΌΠΎΠΆΠ½ΠΎ ΠΏΡΠΎΠ²ΠΎΠ΄ΠΈΡΡ Π½Π΅ΡΠΊΠΎΠ»ΡΠΊΠΈΠΌΠΈ ΡΠΏΠΎΡΠΎΠ±Π°ΠΌΠΈ. ΠΠ±ΡΡΠ½ΠΎ ΠΏΡΠΎΠ²ΠΎΠ΄ΡΡ ΠΎΡ Π»Π°ΠΆΠ΄Π΅Π½ΠΈΡ Π² ΠΏΠ΅ΡΠΈ ΠΈΠ»ΠΈ Π½Π° ΠΎΡΠΊΡΡΡΠΎΠΌ Π²ΠΎΠ·Π΄ΡΡ Π΅. Π’Π°ΠΊΠΆΠ΅ ΠΏΡΠΈΠΌΠ΅Π½ΡΠ΅ΡΡΡ ΠΏΠΎΡΡΠ°ΠΏΠ½ΠΎΠ΅ ΠΊΠΎΠΌΠ±ΠΈΠ½ΠΈΡΠΎΠ²Π°Π½Π½ΠΎΠ΅ ΠΎΡ Π»Π°ΠΆΠ΄Π΅Π½ΠΈΠ΅, ΡΠ½Π°ΡΠ°Π»Π° Π² ΠΏΠ΅ΡΠΈ, Π° ΠΏΠΎΡΠΎΠΌ Π½Π° Π²ΠΎΠ·Π΄ΡΡ Π΅.
ΠΡ ΡΠΊΠΎΡΠΎΡΡΠΈ ΡΠ½ΠΈΠΆΠ΅Π½ΠΈΡ ΡΠ΅ΠΌΠΏΠ΅ΡΠ°ΡΡΡΡ Π½Π°ΠΏΡΡΠΌΡΡ Π·Π°Π²ΠΈΡΡΡ Ρ Π°ΡΠ°ΠΊΡΠ΅ΡΠΈΡΡΠΈΠΊΠΈ Π³ΠΎΡΠΎΠ²ΠΎΠ³ΠΎ ΠΌΠ°ΡΠ΅ΡΠΈΠ°Π»Π°. ΠΡΡΡΡΠΎΠ΅ ΠΎΡ Π»Π°ΠΆΠ΄Π΅Π½ΠΈΠ΅ ΡΠΏΠΎΡΠΎΠ±ΡΡΠ²ΡΠ΅Ρ ΠΎΠ±ΡΠ°Π·ΠΎΠ²Π°Π½ΠΈΡ ΠΏΠ΅ΡΠ΅Π½Π°ΡΡΡΠ΅Π½Π½ΠΎΡΡΠΈ ΡΠ²Π΅ΡΠ΄ΠΎΠ³ΠΎ ΡΠ°ΡΡΠ²ΠΎΡΠ°, Π° ΠΌΠ΅Π΄Π»Π΅Π½Π½ΠΎΠ΅ β Π·Π½Π°ΡΠΈΡΠ΅Π»ΡΠ½ΠΎΠ³ΠΎ ΡΡΠΎΠ²Π½Ρ ΡΠ°ΡΠΏΠ°Π΄Π° ΡΠ²Π΅ΡΠ΄ΠΎΠ³ΠΎ ΡΠ°ΡΡΠ²ΠΎΡΠ°.
ΠΠ°ΠΊΠ°Π»ΠΊΠ° ΡΡΠ΅Π±ΡΠ΅ΡΡΡ Π΄Π»Ρ ΡΠΏΡΠΎΡΠ½Π΅Π½ΠΈΡ ΠΌΠ°ΡΠ΅ΡΠΈΠ°Π»Π° ΠΏΡΡΠ΅ΠΌ ΠΏΠ΅ΡΠ΅Π½Π°ΡΡΡΠ΅Π½ΠΈΡ ΡΠ²Π΅ΡΠ΄ΠΎΠ³ΠΎ ΡΠ°ΡΡΠ²ΠΎΡΠ°. ΠΡΠΎΡ ΠΌΠ΅ΡΠΎΠ΄ ΠΎΡΠ½ΠΎΠ²Π°Π½ Π½Π° Π½Π°Π³ΡΠ΅Π²Π΅ ΠΈΠ·Π΄Π΅Π»ΠΈΠΉ ΡΠ΅ΠΌΠΏΠ΅ΡΠ°ΡΡΡΠ°ΠΌ ΠΈ Π±ΡΡΡΡΠΎΠΌ ΠΎΡ Π»Π°ΠΆΠ΄Π΅Π½ΠΈΠΈ. ΠΡΠΎ ΡΠΏΠΎΡΠΎΠ±ΡΡΠ²ΡΠ΅Ρ ΠΏΠΎΠ»Π½ΠΎΡΠ΅Π½Π½ΠΎΠΌΡ ΡΠ°ΡΡΠ²ΠΎΡΠ΅Π½ΠΈΡ ΡΠΎΡΡΠ°Π²Π½ΡΡ ΡΠ»Π΅ΠΌΠ΅Π½ΡΠΎΠ² Π² Π°Π»ΡΠΌΠΈΠ½ΠΈΠΈ. ΠΡΠΏΠΎΠ»ΡΠ·ΡΠ΅ΡΡΡ Π΄Π»Ρ ΠΎΠ±ΡΠ°Π±ΠΎΡΠΊΠΈ Π΄Π΅ΡΠΎΡΠΌΠΈΡΡΠ΅ΠΌΡΡ Π°Π»ΡΠΌΠΈΠ½ΠΈΠ΅Π²ΡΡ ΡΠΏΠ»Π°Π²ΠΎΠ².
ΠΠ»Ρ ΠΈΡΠΏΠΎΠ»ΡΠ·ΠΎΠ²Π°Π½ΠΈΡ ΡΡΠΎΠ³ΠΎ ΡΠΏΠΎΡΠΎΠ±Π° Π½ΡΠΆΠ½ΠΎ ΠΏΡΠ°Π²ΠΈΠ»ΡΠ½ΠΎ ΡΠ°ΡΡΡΠΈΡΠ°ΡΡ ΡΠ΅ΠΌΠΏΠ΅ΡΠ°ΡΡΡΡ ΠΎΠ±ΡΠ°Π±ΠΎΡΠΊΠΈ. Π§Π΅ΠΌ Π²ΡΡΠ΅ ΡΡΠ΅ΠΏΠ΅Π½Ρ, ΡΠ΅ΠΌ ΠΌΠ΅Π½ΡΡΠ΅ Π²ΡΠ΅ΠΌΠ΅Π½ΠΈ ΡΡΠ΅Π±ΡΠ΅ΡΡΡ Π½Π° Π·Π°ΠΊΠ°Π»ΠΊΡ. ΠΡΠΈ ΡΡΠΎΠΌ ΡΡΠΎΠΈΡ ΠΏΠΎΠ΄ΠΎΠ±ΡΠ°ΡΡ ΡΠ΅ΠΌΠΏΠ΅ΡΠ°ΡΡΡΡ ΡΠ°ΠΊ, ΡΡΠΎΠ±Ρ ΠΎΠ½Π° ΠΏΡΠ΅Π²ΡΡΠ°Π»Π° Π·Π½Π°ΡΠ΅Π½ΠΈΠ΅, Π½Π΅ΠΎΠ±Ρ ΠΎΠ΄ΠΈΠΌΠΎΠ΅ Π΄Π»Ρ ΡΠ°ΡΡΠ²ΠΎΡΠΈΠΌΠΎΡΡΠΈ ΠΊΠΎΠΌΠΏΠΎΠ½Π΅Π½ΡΠΎΠ², Π½ΠΎ Π±ΡΠ»Π° ΠΌΠ΅Π½ΡΡΠ΅ Π³ΡΠ°Π½ΠΈΡΡ ΡΠ°ΡΠΏΠ»Π°Π²Π° ΠΌΠ΅ΡΠ°Π»Π»Π°.
ΠΠ΅ΡΠΎΠ΄ΠΎΠΌ ΡΡΠ°ΡΠ΅Π½ΠΈΡ Π΄ΠΎΡΡΠΈΠ³Π°Π΅ΡΡΡ ΡΠ²Π΅Π»ΠΈΡΠ΅Π½ΠΈΠ΅ ΠΏΡΠΎΡΠ½ΠΎΡΡΠΈ Π°Π»ΡΠΌΠΈΠ½ΠΈΠ΅Π²ΠΎΠ³ΠΎ ΡΠΏΠ»Π°Π²Π°. ΠΡΠΈΡΠ΅ΠΌ Π½Π΅ΠΎΠ±ΡΠ·Π°ΡΠ΅Π»ΡΠ½ΠΎ ΠΏΠΎΠ΄Π²Π΅ΡΠ³Π°ΡΡ ΠΈΠ·Π΄Π΅Π»ΠΈΡ ΠΈΡΠΊΡΡΡΡΠ²Π΅Π½Π½ΠΎΠΌΡ ΡΡΠ°ΡΠ΅Π½ΠΈΡ, ΡΠ°ΠΊ ΠΊΠ°ΠΊ Π²ΠΎΠ·ΠΌΠΎΠΆΠ΅Π½ ΠΏΡΠΎΡΠ΅ΡΡ Π΅ΡΡΠ΅ΡΡΠ²Π΅Π½Π½ΠΎΠ³ΠΎ ΡΡΠ°ΡΠ΅Π½ΠΈΡ.
Π Π·Π°Π²ΠΈΡΠΈΠΌΠΎΡΡΠΈ ΠΎΡ ΡΠΈΠΏΠ° ΡΡΠ°ΡΠ΅Π½ΠΈΡ ΠΈΠ·ΠΌΠ΅Π½ΡΠ΅ΡΡΡ ΡΠΊΠΎΡΠΎΡΡΡ ΡΡΡΡΠΊΡΡΡΠ½ΡΡ ΠΈΠ·ΠΌΠ΅Π½Π΅Π½ΠΈΠΉ. ΠΠΎΡΡΠΎΠΌΡ ΠΈΡΠΊΡΡΡΡΠ²Π΅Π½Π½ΠΎΠ΅ ΡΡΠ°ΡΠ΅Π½ΠΈΠ΅ Π±ΠΎΠ»Π΅Π΅ ΠΏΡΠ΅Π΄ΠΏΠΎΡΡΠΈΡΠ΅Π»ΡΠ½ΠΎ, ΡΠ°ΠΊ ΠΊΠ°ΠΊ ΠΎΠ½ΠΎ ΠΏΠΎΠ·Π²ΠΎΠ»ΡΠ΅Ρ ΠΏΠΎΠ²ΡΡΠΈΡΡ ΠΏΡΠΎΠΈΠ·Π²ΠΎΠ΄ΠΈΡΠ΅Π»ΡΠ½ΠΎΡΡΡ ΡΠ°Π±ΠΎΡ. ΠΠΎΠ΄Π±ΠΎΡ ΡΠ΅ΠΌΠΏΠ΅ΡΠ°ΡΡΡΡ ΠΈ Π²ΡΠ΅ΠΌΠ΅Π½ΠΈ ΠΎΠ±ΡΠ°Π±ΠΎΡΠΊΠΈ Π·Π°Π²ΠΈΡΠΈΡ ΠΎΡ ΡΠ²ΠΎΠΉΡΡΠ² ΠΌΠ°ΡΠ΅ΡΠΈΠ°Π»Π° ΠΈ Ρ Π°ΡΠ°ΠΊΡΠ΅ΡΠΈΡΡΠΈΠΊ Π»Π΅Π³ΠΈΡΡΡΡΠΈΡ ΠΊΠΎΠΌΠΏΠΎΠ½Π΅Π½ΡΠΎΠ².
ΠΡΠ°Π²ΠΈΠ»ΡΠ½ΠΎΠ΅ ΡΠΎΡΠ΅ΡΠ°Π½ΠΈΠ΅ ΡΡΠΎΠ²Π½Ρ Π½Π°Π³ΡΠ΅Π²Π° ΠΈ Π²ΡΠ΅ΠΌΠ΅Π½ΠΈ Π²ΡΠ΄Π΅ΡΠΆΠΊΠΈ ΠΏΠΎΠ·Π²ΠΎΠ»ΡΠ΅Ρ ΠΏΠΎΠ²ΡΡΠΈΡΡ ΠΏΡΠΎΡΠ½ΠΎΡΡΡ ΠΈ ΠΏΠ»Π°ΡΡΠΈΡΠ½ΠΎΡΡΡ. Π’Π°ΠΊΠΎΠΉ ΠΏΡΠΎΡΠ΅ΡΡ Π½Π°Π·ΡΠ²Π°Π΅ΡΡΡ ΡΡΠ°Π±ΠΈΠ»ΠΈΠ·Π°ΡΠΈΠ΅ΠΉ.
ΠΠ΅ΡΠΎΠ΄Ρ ΠΎΡΠΆΠΈΠ³Π° Π°Π»ΡΠΌΠΈΠ½ΠΈΠ΅Π²ΡΡ Π»ΠΈΡΡΠΎΠ²
ΠΡΠΆΠΈΠ³ Π°Π»ΡΠΌΠΈΠ½ΠΈΠ΅Π²ΡΡ ΡΠΏΠ»Π°Π²ΠΎΠ² Π½Π΅ ΡΠ²Π»ΡΠ΅ΡΡΡ ΠΎΠ±ΡΠ·Π°ΡΠ΅Π»ΡΠ½ΡΠΌ ΠΊ ΠΏΡΠΈΠΌΠ΅Π½Π΅Π½ΠΈΡ. ΠΠΎ Π² Π½Π΅ΠΊΠΎΡΠΎΡΡΡ ΡΠ»ΡΡΠ°ΡΡ Π±Π΅Π· ΡΡΠΎΠ³ΠΎ ΡΠΏΠΎΡΠΎΠ±Π° ΡΠ΅ΡΠΌΠΎΠΎΠ±ΡΠ°Π±ΠΎΡΠΊΠΈ Π½Π΅Π²ΠΎΠ·ΠΌΠΎΠΆΠ½ΠΎ Π΄ΠΎΡΡΠΈΡΡ ΠΆΠ΅Π»Π°Π΅ΠΌΡΡ Ρ Π°ΡΠ°ΠΊΡΠ΅ΡΠΈΡΡΠΈΠΊ ΠΌΠ°ΡΠ΅ΡΠΈΠ°Π»Π°.
ΠΡΠΈΡΠΈΠ½ΠΎΠΉ ΠΏΡΠΈΠΌΠ΅Π½Π΅Π½ΠΈΡ ΠΎΡΠΆΠΈΠ³Π° ΠΌΠΎΠΆΠ΅Ρ ΡΡΠ°ΡΡ ΠΎΡΠΎΠ±ΠΎΠ΅ ΡΠΎΡΡΠΎΡΠ½ΠΈΠ΅ ΡΠΏΠ»Π°Π²Π°, ΠΊΠΎΡΠΎΡΠΎΠ΅ ΠΌΠΎΠΆΠ΅Ρ Π²ΡΡΠ°ΠΆΠ°ΡΡΡΡ Π² ΠΏΠΎΠ½ΠΈΠΆΠ΅Π½ΠΈΠΈ ΠΏΠ»Π°ΡΡΠΈΡΠ½ΠΎΡΡΠΈ ΠΌΠ°ΡΠ΅ΡΠΈΠ°Π»Π°.
ΠΡΠΈΠΌΠ΅Π½Π΅Π½ΠΈΠ΅ ΠΎΡΠΆΠΈΠ³Π° ΡΠ΅ΠΊΠΎΠΌΠ΅Π½Π΄ΡΠ΅ΡΡΡ ΠΏΡΠΈ Π½Π°Π±Π»ΡΠ΄Π΅Π½ΠΈΠΈ ΡΡΠ΅Ρ ΡΠΈΠΏΠΎΠ² ΡΠΎΡΡΠΎΡΠ½ΠΈΠΉ:
- Π‘Π²ΠΎΠΉΡΡΠ²Π΅Π½Π½ΠΎΠ΅ Π»ΠΈΡΡΠΌ ΠΈΠ·Π΄Π΅Π»ΠΈΡΠΌ Π½Π΅ΡΠ°Π²Π½ΠΎΠ²Π΅ΡΠ½ΠΎΠ΅ ΡΠΎΡΡΠΎΡΠ½ΠΈΠ΅ ΡΠ²ΡΠ·Π°Π½ΠΎ Ρ ΡΠ°Π·Π½ΠΈΡΠ΅ΠΉ ΡΠ΅ΠΌΠΏΠ΅ΡΠ°ΡΡΡΠ½ΡΡ ΡΠ΅ΠΆΠΈΠΌΠΎΠ². Π‘ΠΊΠΎΡΠΎΡΡΡ ΠΎΡ Π»Π°ΠΆΠ΄Π΅Π½ΠΈΡ Π»ΠΈΡΡΡ ΠΈΠ·Π΄Π΅Π»ΠΈΠΉ Π·Π½Π°ΡΠΈΡΠ΅Π»ΡΠ½ΠΎ ΠΏΡΠ΅Π²ΡΡΠ°Π΅Ρ ΡΠ΅ΠΊΠΎΠΌΠ΅Π½Π΄ΡΠ΅ΠΌΡΡ, ΠΏΡΠΈ ΠΊΠΎΡΠΎΡΠΎΠΉ Π΄ΠΎΡΡΠΈΠ³Π°Π΅ΡΡΡ ΡΡΡΠ΅ΠΊΡ ΡΠ°Π²Π½ΠΎΠ²Π΅ΡΠ½ΠΎΠΉ ΠΊΡΠΈΡΡΠ°Π»Π»ΠΈΠ·Π°ΡΠΈΠΈ.
- ΠΠ»Π°ΡΡΠΈΡΠ΅ΡΠΊΠ°Ρ Π΄Π΅ΡΠΎΡΠΌΠ°ΡΠΈΡ. Π’Π°ΠΊΠΎΠ΅ ΡΠΎΡΡΠΎΡΠ½ΠΈΠ΅ ΠΌΠΎΠΆΠ΅Ρ Π±ΡΡΡ Π²ΡΠ·Π²Π°Π½ΠΎ ΡΠ΅Ρ Π½ΠΎΠ»ΠΎΠ³ΠΈΡΠ΅ΡΠΊΠΈΠΌΠΈ ΡΡΠ΅Π±ΠΎΠ²Π°Π½ΠΈΡΠΌΠΈ ΠΊ Ρ Π°ΡΠ°ΠΊΡΠ΅ΡΠΈΡΡΠΈΠΊΠ°ΠΌ ΠΈ ΡΠΎΡΠΌΠ΅ Π³ΠΎΡΠΎΠ²ΠΎΠ³ΠΎ ΠΈΠ·Π΄Π΅Π»ΠΈΡ.
- ΠΠ΅ΠΎΠ΄Π½ΠΎΡΠΎΠ΄Π½Π°Ρ ΡΡΡΡΠΊΡΡΡΠ° ΠΌΠ°ΡΠ΅ΡΠΈΠ°Π»Π°, Π²ΡΠ·Π²Π°Π½Π½Π°Ρ ΠΈΠ½ΡΠΌΠΈ ΠΌΠ΅ΡΠΎΠ΄Π°ΠΌΠΈ ΡΠ΅ΡΠΌΠΎΠΎΠ±ΡΠ°Π±ΠΎΡΠΊΠΈ, Π² ΡΠΎΠΌ ΡΠΈΡΠ»Π΅ Π·Π°ΠΊΠ°Π»ΠΊΠΎΠΉ ΠΈ ΡΡΠ°ΡΠ΅Π½ΠΈΠ΅ΠΌ. Π ΡΠ°ΠΊΠΎΠΌ ΡΠ»ΡΡΠ°Π΅ ΠΏΡΠΎΠΈΡΡ ΠΎΠ΄ΠΈΡ Π²ΡΠ΄Π΅Π»Π΅Π½ΠΈΠ΅ ΠΎΠ΄Π½ΠΎΠ³ΠΎ ΠΈΠ· Π»Π΅Π³ΠΈΡΡΡΡΠΈΡ ΠΊΠΎΠΌΠΏΠΎΠ½Π΅Π½ΡΠΎΠ² Π² ΠΈΠ½ΡΠ΅ΡΠΌΠ΅ΡΠ°Π»Π»ΠΈΠ΄Π½ΡΡ ΡΠ°Π·Ρ, ΡΠΎΠΏΡΠΎΠ²ΠΎΠΆΠ΄Π°ΡΡΡΡΡΡ ΠΏΠ΅ΡΠ΅Π½Π°ΡΡΡΠ΅Π½ΠΈΠ΅ΠΌ ΠΊΠΎΠΌΠΏΠΎΠ½Π΅Π½ΡΠΎΠ².
ΠΡΡΠ΅ΡΠΊΠ°Π·Π°Π½Π½ΡΠ΅ ΠΏΡΠΎΠ±Π»Π΅ΠΌΡ ΠΌΠΎΠ³ΡΡ ΡΡΡΡΠ°Π½ΡΡΡΡ ΠΌΠ΅ΡΠΎΠ΄ΠΎΠΌ ΠΎΡΠΆΠΈΠ³Π°. ΠΠΎΡΠΌΠ°Π»ΠΈΠ·Π°ΡΠΈΡ ΡΡΡΡΠΊΡΡΡΡ ΠΈ ΡΠΎΡΡΠΎΡΠ½ΠΈΡ Π°Π»ΡΠΌΠΈΠ½ΠΈΠ΅Π²ΠΎΠ³ΠΎ ΡΠΏΠ»Π°Π²Π° ΡΠΎΠΏΡΠΎΠ²ΠΎΠΆΠ΄Π°Π΅ΡΡΡ ΠΏΠΎΠ²ΡΡΠ΅Π½ΠΈΠ΅ΠΌ ΠΏΠ»Π°ΡΡΠΈΡΠ½ΠΎΡΡΠΈ. Π Π·Π°Π²ΠΈΡΠΈΠΌΠΎΡΡΠΈ ΠΎΡ ΡΠΈΠΏΠ° Π½Π΅ΡΠ°Π²Π½ΠΎΠ²Π΅ΡΠ½ΠΎΠ³ΠΎ ΡΠΎΡΡΠΎΡΠ½ΠΈΡ ΠΏΠΎΠ΄Π±ΠΈΡΠ°ΡΡΡΡ ΡΠ°Π·Π»ΠΈΡΠ½ΡΠ΅ ΠΌΠ΅ΡΠΎΠ΄Ρ ΠΎΡΠΆΠΈΠ³Π°.
ΠΠ° ΡΠ΅Π³ΠΎΠ΄Π½ΡΡΠ½ΠΈΠΉ Π΄Π΅Π½Ρ Π²ΡΠ΄Π΅Π»ΡΡΡ ΡΡΠΈ ΡΠ΅ΠΆΠΈΠΌΠ° ΠΎΡΠΆΠΈΠ³Π°:
- ΠΠΎΠΌΠΎΠ³Π΅Π½ΠΈΠ·Π°ΡΠΈΡ. ΠΡΠ΅Π΄Π½Π°Π·Π½Π°ΡΠ΅Π½ Π΄Π»Ρ ΠΎΠ±ΡΠ°Π±ΠΎΡΠΊΠΈ Π»ΠΈΡΡΡ ΡΠ»ΠΈΡΠΊΠΎΠ². Π ΠΏΡΠΎΡΠ΅ΡΡΠ΅ ΡΠ΅ΡΠΌΠΈΡΠ΅ΡΠΊΠΎΠΉ ΠΎΠ±ΡΠ°Π±ΠΎΡΠΊΠΈ ΡΠ»ΠΈΡΠΊΠΎΠ² ΠΏΡΠΈ Π²ΡΡΠΎΠΊΠΈΡ ΡΠ΅ΠΌΠΏΠ΅ΡΠ°ΡΡΡΠ°Ρ Π΄ΠΎΡΡΠΈΠ³Π°Π΅ΡΡΡ ΡΠ°Π²Π½ΠΎΠΌΠ΅ΡΠ½Π°Ρ ΡΡΡΡΠΊΡΡΡΠ°. ΠΡΠΎ ΠΏΠΎΠ·Π²ΠΎΠ»ΡΠ΅Ρ ΡΠΏΡΠΎΡΡΠΈΡΡ ΠΏΡΠΎΡΠ΅ΡΡ ΠΏΡΠΎΠΊΠ°ΡΠ° Ρ ΡΠΌΠ΅Π½ΡΡΠ΅Π½ΠΈΠ΅ΠΌ ΠΊΠΎΠ»ΠΈΡΠ΅ΡΡΠ²Π° ΠΏΡΠΎΠΈΠ·Π²ΠΎΠ΄ΡΡΠ²Π΅Π½Π½ΡΡ ΡΠ°ΡΡ ΠΎΠ΄ΠΎΠ². Π Π½Π΅ΠΊΠΎΡΠΎΡΡΡ ΡΠ»ΡΡΠ°ΡΡ ΠΌΠΎΠΆΠ΅Ρ ΠΏΡΠΈΠΌΠ΅Π½ΡΡΡΡΡ Π΄Π»Ρ ΠΏΠΎΠ²ΡΡΠ΅Π½ΠΈΡ ΠΊΠ°ΡΠ΅ΡΡΠ²Π° Π΄Π΅ΡΠΎΡΠΌΠΈΡΠΎΠ²Π°Π½Π½ΡΡ ΠΈΠ·Π΄Π΅Π»ΠΈΠΉ. Π’Π΅ΠΌΠΏΠ΅ΡΠ°ΡΡΡΠ° ΠΎΡΠΆΠΈΠ³Π° ΡΠΎΠ±Π»ΡΠ΄Π°Π΅ΡΡΡ Π² ΠΏΡΠ΅Π΄Π΅Π»Π°Ρ 500 Π³ΡΠ°Π΄ΡΡΠΎΠ² Ρ ΠΏΠΎΡΠ»Π΅Π΄ΡΡΡΠ΅ΠΉ Π²ΡΠ΄Π΅ΡΠΆΠΊΠΎΠΉ. ΠΡ Π»Π°ΠΆΠ΄Π΅Π½ΠΈΠ΅ ΠΌΠΎΠΆΠ½ΠΎ ΠΏΡΠΎΠ²ΠΎΠ΄ΠΈΡΡ Π½Π΅ΡΠΊΠΎΠ»ΡΠΊΠΈΠΌΠΈ ΡΠΏΠΎΡΠΎΠ±Π°ΠΌΠΈ.
- Π Π΅ΠΊΡΠΈΡΡΠ°Π»Π»ΠΈΠ·Π°ΡΠΈΡ. ΠΡΠΈΠΌΠ΅Π½ΡΠ΅ΡΡΡ Π΄Π»Ρ Π²ΠΎΡΡΡΠ°Π½ΠΎΠ²Π»Π΅Π½ΠΈΡ Π΄Π΅ΡΠΎΡΠΌΠΈΡΠΎΠ²Π°Π½Π½ΡΡ Π΄Π΅ΡΠ°Π»Π΅ΠΉ. ΠΡΠΈ ΡΡΠΎΠΌ ΡΡΠ΅Π±ΡΠ΅ΡΡΡ ΠΏΡΠ΅Π΄Π²Π°ΡΠΈΡΠ΅Π»ΡΠ½Π°Ρ ΠΎΠ±ΡΠ°Π±ΠΎΡΠΊΠ° ΠΏΡΠ΅ΡΡΠΎΠΌ. Π’Π΅ΠΌΠΏΠ΅ΡΠ°ΡΡΡΠ° ΠΎΡΠΆΠΈΠ³Π° Π²Π°ΡΡΠΈΡΡΠ΅ΡΡΡ Π² Π΄ΠΈΠ°ΠΏΠ°Π·ΠΎΠ½Π΅ ΠΎΡ 350 Π΄ΠΎ 500 Π³ΡΠ°Π΄ΡΡΠΎΠ². ΠΡΠ΅ΠΌΡ Π²ΡΠ΄Π΅ΡΠΆΠΊΠΈ Π½Π΅ ΠΏΡΠ΅Π²ΡΡΠ°Π΅Ρ 2-Ρ ΡΠ°ΡΠΎΠ². Π‘ΠΊΠΎΡΠΎΡΡΡ ΠΈ ΡΠΏΠΎΡΠΎΠ± ΠΎΡ Π»Π°ΠΆΠ΄Π΅Π½ΠΈΡ Π½Π΅ ΠΈΠΌΠ΅Π΅Ρ ΠΎΡΠΎΠ±ΡΡ ΡΠ°ΠΌΠΎΠΊ.
- ΠΠ΅ΡΠ΅ΡΠΎΠ³Π΅Π½ΠΈΠ·Π°ΡΠΈΡ. ΠΠΎΠΏΠΎΠ»Π½ΠΈΡΠ΅Π»ΡΠ½Π°Ρ ΠΎΡΠΆΠΈΠ³ ΠΏΠΎΡΠ»Π΅ Π΄ΡΡΠ³ΠΈΡ ΠΌΠ΅ΡΠΎΠ΄ΠΎΠ² ΡΠ΅ΡΠΌΠΎΠΎΠ±ΡΠ°Π±ΠΎΡΠΊΠΈ. ΠΡΠΎΡ ΠΌΠ΅ΡΠΎΠ΄ Π½Π΅ΠΎΠ±Ρ ΠΎΠ΄ΠΈΠΌ Π΄Π»Ρ ΡΠ°Π·ΡΠΏΡΠΎΡΠ½Π΅Π½ΠΈΡ Π°Π»ΡΠΌΠΈΠ½ΠΈΠ΅Π²ΡΡ ΡΠΏΠ»Π°Π²ΠΎΠ². ΠΠ°Π½Π½ΡΠΉ ΠΌΠ΅ΡΠΎΠ΄ ΠΎΠ±ΡΠ°Π±ΠΎΡΠΊΠΈ ΠΏΠΎΠ·Π²ΠΎΠ»ΡΠ΅Ρ ΠΏΠΎΠ½ΠΈΠ·ΠΈΡΡ ΡΡΠ΅ΠΏΠ΅Π½Ρ ΠΏΡΠΎΡΠ½ΠΎΡΡΡ Ρ ΠΎΠ΄Π½ΠΎΠ²ΡΠ΅ΠΌΠ΅Π½Π½ΡΠΌ ΠΏΠΎΠ²ΡΡΠ΅Π½ΠΈΠ΅ΠΌ ΡΡΠΎΠ²Π½Ρ ΠΏΠ»Π°ΡΡΠΈΡΠ½ΠΎΡΡΠΈ. ΠΡΠΆΠΈΠ³ ΠΏΡΠΎΠΈΠ·Π²ΠΎΠ΄ΠΈΡΡΡ ΠΏΡΠΈΠΌΠ΅ΡΠ½ΠΎ ΠΏΡΠΈ 400 Π³ΡΠ°Π΄ΡΡΠ°Ρ Π¦Π΅Π»ΡΡΠΈΡ. ΠΡΠ΄Π΅ΡΠΆΠΊΠ° ΠΎΠ±ΡΡΠ½ΠΎ ΡΠΎΡΡΠ°Π²Π»ΡΠ΅Ρ 1-2 ΡΠ°ΡΠ°. ΠΡΠΎΡ ΡΠΈΠΏ ΠΎΡΠΆΠΈΠ³Π° Π·Π½Π°ΡΠΈΡΠ΅Π»ΡΠ½ΠΎ ΡΠ»ΡΡΡΠ°Π΅Ρ ΡΠΊΡΠΏΠ»ΡΠ°ΡΠ°ΡΠΈΠΎΠ½Π½ΡΠ΅ Ρ Π°ΡΠ°ΠΊΡΠ΅ΡΠΈΡΡΠΈΠΊΠΈ ΠΌΠ΅ΡΠ°Π»Π»Π° ΠΈ ΠΏΠΎΠ²ΡΡΠ°ΡΡ ΡΡΠ΅ΠΏΠ΅Π½Ρ ΡΠΎΠΏΡΠΎΡΠΈΠ²Π»Π΅Π½ΠΈΡ ΠΊΠΎΡΡΠΎΠ·ΠΈΠΈ.
ΠΠ°ΠΊΠ°Π»ΠΊΠ° Π°Π»ΡΠΌΠΈΠ½ΠΈΠ΅Π²ΡΡ ΠΎΡΠ»ΠΈΠ²ΠΎΠ²
ΠΠ°ΠΊΠ°Π»ΠΊΠ° ΠΏΠΎΠ΄Ρ ΠΎΠ΄ΠΈΡ Π½Π΅ Π΄Π»Ρ Π²ΡΠ΅Ρ ΡΠΈΠΏΠΎΠ² Π°Π»ΡΠΌΠΈΠ½ΠΈΠ΅Π²ΡΡ ΡΠΏΠ»Π°Π²ΠΎΠ². ΠΠ»Ρ ΡΡΠΏΠ΅ΡΠ½ΠΎΠ³ΠΎ ΡΡΡΡΠΊΡΡΡΠ½ΠΎΠ³ΠΎ ΠΈΠ·ΠΌΠ΅Π½Π΅Π½ΠΈΡ, ΡΠΏΠ»Π°Π² Π΄ΠΎΠ»ΠΆΠ΅Π½ ΡΠΎΠ΄Π΅ΡΠΆΠ°ΡΡ ΡΠ°ΠΊΠΈΠ΅ ΠΊΠΎΠΌΠΏΠΎΠ½Π΅Π½ΡΡ ΠΊΠ°ΠΊ ΠΌΠ΅Π΄Ρ, ΠΌΠ°Π³Π½ΠΈΠΉ, ΡΠΈΠ½ΠΊ, ΠΊΡΠ΅ΠΌΠ½ΠΈΠΉ ΠΈΠ»ΠΈ Π»ΠΈΡΠΈΠΉ. ΠΠΌΠ΅Π½Π½ΠΎ ΡΡΠΈ Π²Π΅ΡΠ΅ΡΡΠ²Π° ΡΠΏΠΎΡΠΎΠ±Π½Ρ ΠΏΠΎΠ»Π½ΠΎΡΠ΅Π½Π½ΠΎ ΡΠ°ΡΡΠ²ΠΎΡΠΈΡΡΡ Π² ΡΠΎΡΡΠ°Π²Π΅ Π°Π»ΡΠΌΠΈΠ½ΠΈΡ, ΡΠΎΠ·Π΄Π°Π² ΡΡΡΡΠΊΡΡΡΡ, ΠΈΠΌΠ΅ΡΡΡΡ ΠΎΡΠ»ΠΈΡΠ½ΡΠ΅ ΠΎΡ Π°Π»ΡΠΌΠΈΠ½ΠΈΡ ΡΠ²ΠΎΠΉΡΡΠ²Π°.
ΠΠ°Π½Π½ΡΠΉ ΡΠΈΠΏ ΡΠ΅ΡΠΌΠΎΠΎΠ±ΡΠ°Π±ΠΎΡΠΊΠΈ ΠΏΡΠΎΠ²ΠΎΠ΄ΠΈΡΡΡΡ ΠΏΡΠΈ ΠΈΠ½ΡΠ΅Π½ΡΠΈΠ²Π½ΠΎΠΌ Π½Π°Π³ΡΠ΅Π²Π΅, ΠΏΠΎΠ·Π²ΠΎΠ»ΡΡΡΠ΅ΠΌ ΡΠΎΡΡΠ°Π²Π½ΡΠΌ ΡΠ»Π΅ΠΌΠ΅Π½ΡΠ°ΠΌ ΡΠ°ΡΡΠ²ΠΎΡΠΈΡΡΡΡ Π² ΡΠΏΠ»Π°Π²Π΅, Ρ Π΄Π°Π»ΡΠ½Π΅ΠΉΡΠΈΠΌ ΠΈΠ½ΡΠ΅Π½ΡΠΈΠ²Π½ΡΠΌ ΠΎΡ Π»Π°ΠΆΠ΄Π΅Π½ΠΈΠ΅ΠΌ Π΄ΠΎ ΠΎΠ±ΡΡΠ½ΠΎΠ³ΠΎ ΡΠΎΡΡΠΎΡΠ½ΠΈΡ.
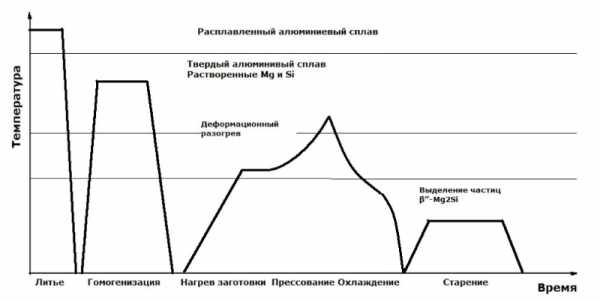
Π’Π΅ΡΠΌΠΈΡΠ΅ΡΠΊΠΈΠ΅ ΠΏΡΠ΅Π²ΡΠ°ΡΠ΅Π½ΠΈΡ Π² ΡΠΏΠ»Π°Π²Π°Ρ 6060, 6063, ΠΠ31
ΠΡΠΈ Π²ΡΠ±ΠΎΡΠ΅ ΡΠ΅ΠΌΠΏΠ΅ΡΠ°ΡΡΡΠ½ΠΎΠ³ΠΎ ΡΠ΅ΠΆΠΈΠΌΠ° ΡΠ»Π΅Π΄ΡΠ΅Ρ ΠΎΡΠΈΠ΅Π½ΡΠΈΡΠΎΠ²Π°ΡΡΡΡ Π½Π° ΠΊΠΎΠ»ΠΈΡΠ΅ΡΡΠ²ΠΎ ΠΌΠ΅Π΄ΠΈ. Π’Π°ΠΊΠΆΠ΅, Π½ΡΠΆΠ½ΠΎ ΡΡΠΈΡΡΠ²Π°ΡΡ ΡΠ²ΠΎΠΉΡΡΠ²Π° Π»ΠΈΡΡΡ ΠΈΠ·Π΄Π΅Π»ΠΈΠΉ.
Π ΠΏΡΠΎΠΌΡΡΠ»Π΅Π½Π½ΡΡ ΡΡΠ»ΠΎΠ²ΠΈΡΡ ΡΠ΅ΠΌΠΏΠ΅ΡΠ°ΡΡΡΠ° Π½Π°Π³ΡΠ΅Π²Π° ΠΏΠΎΠ΄ Π·Π°ΠΊΠ°Π»ΠΊΡ ΠΊΠΎΠ»Π΅Π±Π»Π΅ΡΡΡ Π² Π΄ΠΈΠ°ΠΏΠ°Π·ΠΎΠ½Π΅ ΠΎΡ 450 Π΄ΠΎ 560 Π³ΡΠ°Π΄ΡΡΠΎΠ². ΠΡΠ΄Π΅ΡΠΆΠΊΠ° ΠΈΠ·Π΄Π΅Π»ΠΈΠΉ ΠΏΡΠΈ ΡΠ°ΠΊΠΎΠΉ ΡΠ΅ΠΌΠΏΠ΅ΡΠ°ΡΡΡΠ΅ ΠΎΠ±Π΅ΡΠΏΠ΅ΡΠΈΠ²Π°Π΅Ρ ΡΠ°ΡΠΏΠ»Π°Π²Π»Π΅Π½ΠΈΠ΅ ΠΊΠΎΠΌΠΏΠΎΠ½Π΅Π½ΡΠΎΠ² Π² ΡΠΎΡΡΠ°Π²Π΅. ΠΡΠ΅ΠΌΡ Π²ΡΠ΄Π΅ΡΠΆΠΈ Π·Π°Π²ΠΈΡΠΈΡ ΠΎΡ ΡΠΈΠΏΠ° ΠΈΠ·Π΄Π΅Π»ΠΈΡ, Π΄Π»Ρ Π΄Π΅ΡΠΎΡΠΌΠΈΡΠΎΠ²Π°Π½Π½ΡΡ ΠΎΠ±ΡΡΠ½ΠΎ Π½Π΅ ΠΏΡΠ΅Π²ΡΡΠ°Π΅Ρ Π±ΠΎΠ»Π΅Π΅ ΡΠ°ΡΠ°, Π° Π΄Π»Ρ Π»ΠΈΡΡΡ β ΠΎΡ Π½Π΅ΡΠΊΠΎΠ»ΡΠΊΠΈΡ ΡΠ°ΡΠΎΠ² Π΄ΠΎ Π΄Π²ΡΡ ΡΡΡΠΎΠΊ.
Π‘ΠΊΠΎΡΠΎΡΡΡ ΠΎΡ Π»Π°ΠΆΠ΄Π΅Π½ΠΈΡ ΠΏΡΠΈ Π·Π°ΠΊΠ°Π»ΠΊΠ΅ Π½Π΅ΠΎΠ±Ρ ΠΎΠ΄ΠΈΠΌΠΎ ΠΏΠΎΠ΄Π±ΠΈΡΠ°ΡΡ ΡΠ°ΠΊ, ΡΡΠΎΠ±Ρ ΡΠΎΡΡΠ°Π² Π°Π»ΡΠΌΠΈΠ½ΠΈΠ΅Π²ΠΎΠ³ΠΎ ΡΠΏΠ»Π°Π²Π° Π½Π΅ ΠΏΠΎΠ΄Π²Π΅ΡΠ³Π°Π»ΡΡ ΡΠ°ΡΠΏΠ°Π΄Ρ. ΠΠ° ΠΏΡΠΎΠΌΡΡΠ»Π΅Π½Π½ΠΎΠΌ ΠΏΡΠΎΠΈΠ·Π²ΠΎΠ΄ΡΡΠ²Π΅ ΠΎΡ Π»Π°ΠΆΠ΄Π΅Π½ΠΈΠ΅ ΠΏΡΠΎΠ²ΠΎΠ΄ΡΡ Ρ ΠΏΠΎΠΌΠΎΡΡΡ Π²ΠΎΠ΄Ρ. ΠΠ΄Π½Π°ΠΊΠΎ ΡΠ°ΠΊΠΎΠΉ ΡΠΏΠΎΡΠΎΠ± Π½Π΅ Π²ΡΠ΅Π³Π΄Π° ΠΎΠΏΡΠΈΠΌΠ°Π»ΡΠ½ΠΎ ΠΏΠΎΠ΄Ρ ΠΎΠ΄ΠΈΡ, ΡΠ°ΠΊ ΠΊΠ°ΠΊ ΠΏΡΠΈ ΠΎΡ Π»Π°ΠΆΠ΄Π΅Π½ΠΈΠΈ ΡΠΎΠ»ΡΡΡΡ ΠΈΠ·Π΄Π΅Π»ΠΈΠΉ ΠΏΡΠΎΠΈΡΡ ΠΎΠ΄ΠΈΡ Π½Π΅ΡΠ°Π²Π½ΠΎΠΌΠ΅ΡΠ½ΠΎΠ΅ ΡΠ½ΠΈΠΆΠ΅Π½ΠΈΠ΅ ΡΠ΅ΠΌΠΏΠ΅ΡΠ°ΡΡΡΡ Π² ΡΠ΅Π½ΡΡΠ΅ ΠΈ ΠΏΠΎ ΠΊΡΠ°ΡΠΌ ΠΈΠ·Π΄Π΅Π»ΠΈΡ. ΠΠΎΡΡΠΎΠΌΡ Π΄Π»Ρ ΠΊΡΡΠΏΠ½ΠΎΠ³Π°Π±Π°ΡΠΈΡΠ½ΡΡ ΠΈ ΡΠ»ΠΎΠΆΠ½ΡΡ ΠΈΠ·Π΄Π΅Π»ΠΈΠΉ ΠΏΡΠΈΠΌΠ΅Π½ΡΡΡΡΡ Π΄ΡΡΠ³ΠΈΠ΅ ΠΌΠ΅ΡΠΎΠ΄Ρ ΠΎΡ Π»Π°ΠΆΠ΄Π΅Π½ΠΈΡ, ΠΊΠΎΡΠΎΡΡΠ΅ ΠΏΠΎΠ΄Π±ΠΈΡΠ°ΡΡΡΡ ΠΈΠ½Π΄ΠΈΠ²ΠΈΠ΄ΡΠ°Π»ΡΠ½ΠΎ.
Π‘ΡΠ°ΡΠ΅Π½ΠΈΠ΅ Π°Π»ΡΠΌΠΈΠ½ΠΈΠ΅Π²ΡΡ ΡΠΏΠ»Π°Π²ΠΎΠ²
Π‘ΡΠ°ΡΠ΅Π½ΠΈΠ΅ ΠΏΡΠΎΠ²ΠΎΠ΄ΠΈΡΡΡ Π΄Π»Ρ ΡΠ»ΡΡΡΠ΅Π½ΠΈΡ ΠΏΡΠΎΡΠ½ΠΎΡΡΠ½ΡΡ Ρ Π°ΡΠ°ΠΊΡΠ΅ΡΠΈΡΡΠΈΠΊ ΠΈΠ·Π΄Π΅Π»ΠΈΡ. ΠΡΠΎΡ Π²ΠΈΠ΄ ΡΠ΅ΡΠΌΠΈΡΠ΅ΡΠΊΠΎΠΉ ΠΎΠ±ΡΠ°Π±ΠΎΡΠΊΠΈ Π·Π°ΠΊΠ»ΡΡΠ°Π΅ΡΡΡ Π² Π²ΡΠ΄Π΅ΡΠΆΠΊΠ΅ Π² ΡΡΠ»ΠΎΠ²ΠΈΡΡ ΠΎΠ±ΡΡΠ½ΠΎΠ³ΠΎ ΡΠ΅ΠΌΠΏΠ΅ΡΠ°ΡΡΡΠ½ΠΎΠ³ΠΎ ΡΠ΅ΠΆΠΈΠΌΠ°.
ΠΠΎΠ²ΡΡΠ΅Π½ΠΈΠ΅ ΠΏΡΠΎΡΠ½ΠΎΡΡΠΈ Π΄ΠΎΡΡΠΈΠ³Π°Π΅ΡΡΡ ΠΏΡΡΠ΅ΠΌ ΡΠ°ΡΠΏΠ°Π΄Π° ΡΠ²Π΅ΡΠ΄ΠΎΠ³ΠΎ ΡΠ°ΡΡΠ²ΠΎΡΠ°, ΡΡΠΎ Π½Π΅ΠΎΠ±Ρ ΠΎΠ΄ΠΈΠΌΠΎ ΠΏΠΎΡΠ»Π΅ Π·Π°ΠΊΠ°Π»ΠΊΠΈ, ΡΠ°ΠΊ ΠΊΠ°ΠΊ Π·Π°ΠΊΠ°Π»ΠΊΠ° ΠΏΡΠΈΠ²ΠΎΠ΄ΠΈΡ ΠΊ ΠΏΡΠ΅ΡΡΡΠ΅Π½Π½ΠΎΡΡΠΈ ΠΌΠ΅ΡΠ°Π»Π»Π°.
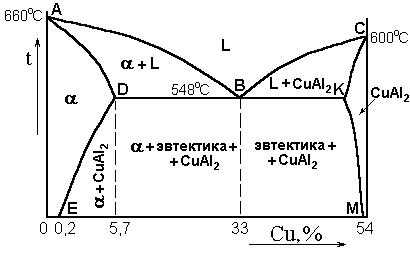
Π’Π΅ΡΠΌΠΎΠΎΠ±ΡΠ°Π±ΠΎΡΠΊΠ° Π΄ΡΡΠ°Π»ΡΠΌΠΈΠ½ΠΈΡ
Π‘ΡΡΠ΅ΡΡΠ²ΡΠ΅Ρ Π΄Π²Π° ΡΠΏΠΎΡΠΎΠ±Π° ΡΡΠ°ΡΠ΅Π½ΠΈΡ Π°Π»ΡΠΌΠΈΠ½ΠΈΠ΅Π²ΡΡ ΡΠΏΠ»Π°Π²ΠΎΠ²: Π΅ΡΡΠ΅ΡΡΠ²Π΅Π½Π½ΠΎΠ΅ ΠΈ ΠΈΡΠΊΡΡΡΡΠ²Π΅Π½Π½ΠΎΠ΅.
ΠΡΡΠ΅ΡΡΠ²Π΅Π½Π½ΠΎΠ΅ ΡΡΠ°ΡΠ΅Π½ΠΈΠ΅ ΠΏΡΠΎΠΈΡΡ ΠΎΠ΄ΠΈΡ Π±Π΅Π· ΠΏΡΠ΅Π΄Π²Π°ΡΠΈΡΠ΅Π»ΡΠ½ΠΎΠ³ΠΎ Π½Π°Π³ΡΠ΅Π²Π° ΠΏΡΠΈ ΠΎΠ±ΡΡΠ½ΡΡ ΡΠ΅ΠΌΠΏΠ΅ΡΠ°ΡΡΡΠ°Ρ . ΠΡΠΎ ΠΌΠΎΠΆΠ΅Ρ ΠΏΡΠΎΠΈΡΡ ΠΎΠ΄ΠΈΡΡ Π² ΡΡΠ»ΠΎΠ²ΠΈΡΡ ΠΎΠ±ΡΡΠ½ΠΎΠ³ΠΎ ΡΠΊΠ»Π°Π΄Π° ΠΈΠ»ΠΈ ΠΏΡΠΎΠΌΡΡΠ»Π΅Π½Π½ΠΎΠ³ΠΎ ΠΏΠΎΠΌΠ΅ΡΠ΅Π½ΠΈΡ, Π³Π΄Π΅ ΡΠ΅ΠΌΠΏΠ΅ΡΠ°ΡΡΡΠ° Π²ΠΎΠ·Π΄ΡΡ Π° Π½Π΅ ΠΏΡΠ΅Π²ΡΡΠ°Π΅Ρ 30 Π³ΡΠ°Π΄ΡΡΠΎΠ².
ΠΡΡΠ΅ΡΡΠ²Π΅Π½Π½ΠΎΠ΅ ΡΡΠ°ΡΠ΅Π½ΠΈΠ΅ Π²ΠΎΠ·ΠΌΠΎΠΆΠ½ΠΎ ΠΈΠ·-Π·Π° ΠΎΡΠΎΠ±ΠΎΠ³ΠΎ ΡΠ²ΠΎΠΉΡΡΠ²Π° Π°Π»ΡΠΌΠΈΠ½ΠΈΡ, ΠΊΠΎΡΠΎΡΠΎΠ΅ Π½Π°Π·ΡΠ²Π°Π΅ΡΡΡ Β«ΡΠ²Π΅ΠΆΠ΅Π·Π°ΠΊΠ°Π»Π΅Π½Π½ΠΎΠ΅ ΡΠΎΡΡΠΎΡΠ½ΠΈΠ΅Β». Π‘Π²ΠΎΠΉΡΡΠ²Π° ΠΈΠ·Π΄Π΅Π»ΠΈΠΉ Π·Π½Π°ΡΠΈΡΠ΅Π»ΡΠ½ΠΎ ΠΎΡΠ»ΠΈΡΠ°ΡΡΡΡ ΡΡΠ°Π·Ρ ΠΏΠΎΡΠ»Π΅ Π·Π°ΠΊΠ°Π»ΠΊΠΈ ΠΈ ΠΏΠΎΡΠ»Π΅ Π½Π΅ΠΊΠΎΡΠΎΡΠΎΠ³ΠΎ Π²ΡΠ΅ΠΌΠ΅Π½ΠΈ ΠΏΡΠ΅Π±ΡΠ²Π°Π½ΠΈΡ Π½Π° ΡΠΊΠ»Π°Π΄Π΅.
ΠΡΠΊΡΡΡΡΠ²Π΅Π½Π½ΠΎΠ΅ ΡΡΠ°ΡΠ΅Π½ΠΈΠ΅ ΠΏΡΠΎΠ²ΠΎΠ΄ΠΈΡΡΡ ΠΏΡΡΠ΅ΠΌ Π½Π°Π³ΡΠ΅Π²Π° ΠΈΠ·Π΄Π΅Π»ΠΈΠΉ Π΄ΠΎ ΡΠ΅ΠΌΠΏΠ΅ΡΠ°ΡΡΡΡ 200 Π³ΡΠ°Π΄ΡΡΠΎΠ². ΠΡΠΎ Π°ΠΊΡΠΈΠ²ΠΈΡΡΠ΅Ρ ΠΏΡΠΎΡΠ΅ΡΡ Π΄ΠΈΡΡΡΠ·ΠΈΠΈ, ΡΡΠΎ ΡΠΏΠΎΡΠΎΠ±ΡΡΠ²ΡΠ΅Ρ ΡΠ»ΡΡΡΠ΅Π½Π½ΠΎΠΌΡ ΡΠ°ΡΡΠ²ΠΎΡΠ΅Π½ΠΈΡ ΡΠΎΡΡΠ°Π²Π½ΡΡ ΡΠ»Π΅ΠΌΠ΅Π½ΡΠΎΠ². ΠΡΠ΄Π΅ΡΠΆΠΊΠ° ΡΠΎΡΡΠ°Π²Π»ΡΠ΅Ρ ΠΎΡ Π½Π΅ΡΠΊΠΎΠ»ΡΠΊΠΈΡ ΡΠ°ΡΠΎΠ² Π΄ΠΎ Π½Π΅ΡΠΊΠΎΠ»ΡΠΊΠΈΡ ΡΡΡΠΎΠΊ.
Π‘Π»Π΅Π΄ΡΠ΅Ρ ΠΎΡΠΌΠ΅ΡΠΈΡΡ, ΡΡΠΎ ΠΈΡΠΊΡΡΡΡΠ²Π΅Π½Π½ΠΎ ΡΠΎΡΡΠ°ΡΠ΅Π½Π½ΡΠ΅ ΡΠΏΠ»Π°Π²Ρ ΠΌΠΎΠΆΠ½ΠΎ Π²Π΅ΡΠ½ΡΡΡ ΠΊ ΠΈΠ·Π½Π°ΡΠ°Π»ΡΠ½ΠΎΠΌΡ ΡΠΎΡΡΠΎΡΠ½ΠΈΡ. ΠΠ»Ρ ΡΡΠΎΠ³ΠΎ Π½ΡΠΆΠ½ΠΎ Π½Π°Π³ΡΠ΅ΡΡ ΠΈΠ·Π΄Π΅Π»ΠΈΠ΅ Π΄ΠΎ 250 Π³ΡΠ°Π΄ΡΡΠΎΠ² Ρ Π²ΡΠ΄Π΅ΡΠΆΠΊΠΎΠΉ Π΄ΠΎ ΠΎΠ΄Π½ΠΎΠΉ ΠΌΠΈΠ½ΡΡΡ. ΠΡΠ΄Π΅ΡΠΆΠΊΠ° Π΄ΠΎΠ»ΠΆΠ½Π° ΠΏΡΠΎΠ²ΠΎΠ΄ΠΈΡΡΡ Π² ΡΠ΅Π»ΠΈΡΡΡΠ½ΠΎΠΉ Π²Π°Π½Π½Π΅ Π² ΡΡΡΠΎΠ³ΠΎ ΠΎΠΏΡΠ΅Π΄Π΅Π»Π΅Π½Π½ΠΎΠ΅ Π²ΡΠ΅ΠΌΡ, Ρ ΡΠΎΡΠ½ΠΎΡΡΡΡ Π΄ΠΎ Π½Π΅ΡΠΊΠΎΠ»ΡΠΊΠΈΡ ΡΠ΅ΠΊΡΠ½Π΄.
ΠΡΠΈΡΠ΅ΠΌ ΠΏΠΎΠ΄ΠΎΠ±Π½ΡΠΉ Π²ΠΎΠ·Π²ΡΠ°Ρ ΠΌΠΎΠΆΠ½ΠΎ Π²ΡΠΏΠΎΠ»Π½ΡΡΡ Π½Π΅ΡΠΊΠΎΠ»ΡΠΊΠΎ ΡΠ°Π·, Π±Π΅Π· ΠΏΠΎΡΠ΅ΡΠΈ ΠΏΡΠΎΡΠ½ΠΎΡΡΠΈ ΠΌΠ°ΡΠ΅ΡΠΈΠ°Π»Π°, Π½ΠΎ Ρ Π½Π΅Π±ΠΎΠ»ΡΡΠΈΠΌ ΠΈΠ·ΠΌΠ΅Π½Π΅Π½ΠΈΠ΅ΠΌ ΡΠ²ΠΎΠΉΡΡΠ². ΠΠΎΠ·Π²ΡΠ°Ρ ΡΠΎΡΡΠ°ΡΠ΅Π½Π½ΠΎΠ³ΠΎ ΠΌΠ΅ΡΠ°Π»Π»Π° ΠΎΠ±ΡΡΠ½ΠΎ ΠΏΡΠΎΠ²ΠΎΠ΄ΡΡ Ρ ΡΠ΅Π»ΡΡ Π²ΠΎΡΡΡΠ°Π½ΠΎΠ²Π»Π΅Π½ΠΈΡ ΠΏΠ»Π°ΡΡΠΈΡΠ½ΠΎΡΡΠΈ, Π½Π΅ΠΎΠ±Ρ ΠΎΠ΄ΠΈΠΌΠΎΠΉ Π΄Π»Ρ ΠΈΠ·ΠΌΠ΅Π½Π΅Π½ΠΈΡ ΡΠΎΡΠΌΡ ΠΈΠ·Π΄Π΅Π»ΠΈΡ.
ΠΡΠ±ΠΎΠΉ ΠΈΠ· ΡΠΈΠΏΠΎΠ² ΡΠ΅ΡΠΌΠΎΠΎΠ±ΡΠ°Π±ΠΎΡΠΊΠΈ ΡΠΈΡΠΎΠΊΠΎ ΠΈΡΠΏΠΎΠ»ΡΠ·ΡΠ΅ΡΡΡ Π² ΠΏΡΠΎΠΌΡΡΠ»Π΅Π½Π½ΠΎΡΡΠΈ. ΠΠ»Π°Π³ΠΎΠ΄Π°ΡΡ ΡΠ΅ΠΌΡ Ρ ΠΏΡΠΎΠΈΠ·Π²ΠΎΠ΄ΠΈΡΠ΅Π»Π΅ΠΉ Π΅ΡΡΡ Π²ΠΎΠ·ΠΌΠΎΠΆΠ½ΠΎΡΡΡ ΠΏΠΎΠ»ΡΡΠ΅Π½ΠΈΡ ΠΌΠ°ΡΠ΅ΡΠΈΠ°Π»ΠΎΠ², ΠΏΠΎΠ»Π½ΠΎΡΡΡΡ ΡΠΎΠΎΡΠ²Π΅ΡΡΡΠ²ΡΡΡΠΈΡ ΡΡΠ΅Π±ΠΎΠ²Π°Π½ΠΈΡΠΌ ΠΏΡΠΎΠΈΠ·Π²ΠΎΠ΄ΡΡΠ²Π°. ΠΡΠΈΡΠ΅ΠΌ ΡΠ°ΠΊΠ°Ρ ΠΎΠ±ΡΠ°Π±ΠΎΡΠΊΠ° ΡΠΏΠ»Π°Π²ΠΎΠ² ΠΏΠΎΠ·Π²ΠΎΠ»ΡΠ΅Ρ Π·Π½Π°ΡΠΈΡΠ΅Π»ΡΠ½ΠΎ ΡΠ»ΡΡΡΠΈΡΡ ΡΠ²ΠΎΠΉΡΡΠ²Π° Π°Π»ΡΠΌΠΈΠ½ΠΈΡ ΠΈ ΠΏΠΎΠ»ΡΡΠΈΡΡ ΠΌΠ°ΡΠ΅ΡΠΈΠ°Π», Π½Π΅ ΠΈΠΌΠ΅ΡΡΠΈΠΉ Π°Π½Π°Π»ΠΎΠ³ΠΎΠ².
ΠΠ»Π°Π²Π½ΠΎΠ΅ ΡΡΠ»ΠΎΠ²ΠΈΠ΅ ΠΏΡΠΈ ΡΠ΅ΡΠΌΠΎΠΎΠ±ΡΠ°Π±ΠΎΡΠΊΠ΅ β ΡΠΎΠ±Π»ΡΠ΄Π΅Π½ΠΈΠ΅ ΡΡΠ΅Π±ΠΎΠ²Π°Π½ΠΈΠΉ ΠΈ ΡΠ΅ΠΊΠΎΠΌΠ΅Π½Π΄Π°ΡΠΈΠΉ ΠΊ ΡΠ΅ΠΌΠΏΠ΅ΡΠ°ΡΡΡΠ½ΠΎΠΌΡ ΡΠ΅ΠΆΠΈΠΌΡ ΠΎΠ±ΡΠ°Π±ΠΎΡΠΊΠΈ ΠΈ Π²ΡΠ΅ΠΌΠ΅Π½ΠΈ Π²ΡΠ΄Π΅ΡΠΆΠΊΠΈ. ΠΠ°Π»Π΅ΠΉΡΠΈΠ΅ ΠΎΡΠΊΠ»ΠΎΠ½Π΅Π½ΠΈΡ ΠΌΠΎΠ³ΡΡ ΠΏΡΠΈΠ²Π΅ΡΡΠΈ ΠΊ Π½Π΅ΠΎΠ±ΡΠ°ΡΠΈΠΌΡΠΌ ΠΈΠ·ΠΌΠ΅Π½Π΅Π½ΠΈΡΠΌ ΡΠ²ΠΎΠΉΡΡΠ² ΠΌΠ°ΡΠ΅ΡΠΈΠ°Π»Π°.
ΠΡΠ»ΠΈ Π²Ρ Π½Π°ΡΠ»ΠΈ ΠΎΡΠΈΠ±ΠΊΡ, ΠΏΠΎΠΆΠ°Π»ΡΠΉΡΡΠ°, Π²ΡΠ΄Π΅Π»ΠΈΡΠ΅ ΡΡΠ°Π³ΠΌΠ΅Π½Ρ ΡΠ΅ΠΊΡΡΠ° ΠΈ Π½Π°ΠΆΠΌΠΈΡΠ΅ Ctrl+Enter.
stankiexpert.ru
ΠΠ±ΡΠ°Π±ΠΎΡΠΊΠ° Π°Π»ΡΠΌΠΈΠ½ΠΈΡ β studvesna73.ru
Π₯ΠΈΠΌΠΈΡΠ΅ΡΠΊΠ°Ρ ΠΎΠ±ΡΠ°Π±ΠΎΡΠΊΠ° ΠΏΠΎΡΠ²ΠΈΠ»Π°ΡΡ ΠΏΠΎΠ·ΠΆΠ΅, ΡΠ΅ΠΌ ΡΠ»Π΅ΠΊΡΡΠΈΡΠ΅ΡΠΊΠ°Ρ ΠΈ Π² Π½Π°ΡΡΠΎΡΡΠ΅Π΅ Π²ΡΠ΅ΠΌΡ ΡΠΈΡΠΎΠΊΠΎ Π΅Π΅ Π·Π°ΠΌΠ΅Π½ΡΠ΅Ρ. ΠΠ»Π°Π²Π½ΡΠΌ ΠΏΡΠ΅ΠΈΠΌΡΡΠ΅ΡΡΠ²ΠΎΠΌ ΡΡΠΈΡ ΠΏΡΠΎΡΠ΅ΡΡΠΎΠ² ΡΠ²Π»ΡΡΡΡΡ Π³ΠΎΡΠ°Π·Π΄ΠΎ Π±ΠΎΠ»Π΅Π΅ Π½ΠΈΠ·ΠΊΠ°Ρ ΡΡΠΎΠΈΠΌΠΎΡΡΡ, ΠΏΡΠΈΡΠ΅ΠΌ Π½Π΅ ΡΠΎΠ»ΡΠΊΠΎ Π½Π° ΡΠ»Π΅ΠΊΡΡΠΎΡΠ½Π΅ΡΠ³ΠΈΠΈ, Π½ΠΎ ΠΈ ΡΠ΅Π·Π΅ΡΠ²ΡΠ°ΡΠΎΠ² ΠΈ ΠΊΡΠ΅ΠΏΠ»Π΅Π½ΠΈΠΉ. ΠΡΠ»Π΅Π΄ΡΡΠ²ΠΈΠ΅ ΡΠΎΠ³ΠΎ, ΡΡΠΎ Π² Π΄Π°Π½Π½ΠΎΠΌ ΡΠ»ΡΡΠ°Π΅ Π½Π΅ ΡΡΠ΅Π±ΡΠ΅ΡΡΡ ΡΠ»Π΅ΠΊΡΡΠΈΡΠ΅ΡΠΊΠΈΠΉ ΡΠΎΠΊ ΠΈ ΠΏΠΎΠ΄Π²ΠΈΠΆΠ½ΡΠΉ Π°Π½ΠΎΠ΄Π½ΠΎΠ³ΠΎ ΡΡΠ΅ΡΠΆΠ½Ρ, ΡΠ°Π±ΠΎΡΡ ΠΌΠΎΠΆΠ½ΠΎ ΠΏΡΠΎΠ²ΠΎΠ΄ΠΈΡΡ Π² ΠΊΠΎΡΠ·ΠΈΠ½Π°Ρ ΠΈ Ρ ΠΏΡΠΎΡΡΡΠΌΠΈ Π·Π°ΠΆΠΈΠΌΠ°ΠΌΠΈ.Π ΠΎΡΠ½ΠΎΠ²Π½ΠΎΠΌ, ΠΏΡΠΈΠ½ΡΠΈΠΏ Ρ ΠΈΠΌΠΈΡΠ΅ΡΠΊΠΎΠΉ ΠΎΠ±ΡΠ°Π±ΠΎΡΠΊΠΈ ΠΏΠΎΡ ΠΎΠΆ Π½Π° ΠΏΡΠΈΠ½ΡΠΈΠΏ Π³Π°Π»ΡΠ²Π°Π½ΠΈΡΠ΅ΡΠΊΠΎΠΉ ΠΎΠ±ΡΠ°Π±ΠΎΡΠΊΠΈ, ΠΎΠ΄Π½Π°ΠΊΠΎ Π²ΠΌΠ΅ΡΡΠΎ ΡΠ»Π΅ΠΊΡΡΠΈΡΠ΅ΡΠΊΠΎΠ³ΠΎ ΡΠΎΠΊΠ° Π·Π΄Π΅ΡΡ ΠΈΡΠΏΠΎΠ»ΡΠ·ΡΡΡΡΡ Ρ ΠΈΠΌΠΈΡΠ΅ΡΠΊΠΈΠ΅ ΠΎΠΊΠΈΡΠ»ΠΈΡΠ΅Π»ΠΈ. ΠΠ²ΠΈΠΆΡΡΠ΅ΠΉ ΡΠΈΠ»ΠΎΠΉ Ρ ΠΈΠΌΠΈΡΠ΅ΡΠΊΠΎΠΉ ΠΎΠ±ΡΠ°Π±ΠΎΡΠΊΠΈ ΡΠ²Π»ΡΠ΅ΡΡΡ ΡΠ°Π·Π½ΠΎΡΡΡ ΡΠ»Π΅ΠΊΡΡΠΎΡ ΠΈΠΌΠΈΡΠ΅ΡΠΊΠΈΡ ΠΏΠΎΡΠ΅Π½ΡΠΈΠ°Π»ΠΎΠ² ΠΌΠ΅ΠΆΠ΄Ρ Π°Π½ΠΎΠ΄Π½ΡΠΌΠΈ ΠΈ ΠΊΠ°ΡΠΎΠ΄Π½ΡΠΌΠΈ ΡΡΠ°ΡΡΠΊΠ°ΠΌΠΈ ΠΏΠΎΠ²Π΅ΡΡ Π½ΠΎΡΡΠΈ.
ΠΠΎΡΡΡΠΈΡΠΈΠ΅Π½Ρ Π·Π΅ΡΠΊΠ°Π»ΡΠ½ΠΎΠ³ΠΎ ΠΎΡΡΠ°ΠΆΠ΅Π½ΠΈΡ Π³Π»Π°Π΄ΠΊΠΎΠ³ΠΎ ΠΏΡΠΎΠΊΠ°ΡΠ°Π½Π½ΠΎΠ³ΠΎ Π°Π»ΡΠΌΠΈΠ½ΠΈΡ ΠΏΡΠΈ Π°Π½ΠΎΠ΄ΠΈΡΠΎΠ²Π°Π½ΠΈΠΈ Π·Π°ΠΌΠ΅ΡΠ½ΠΎ ΠΏΠ°Π΄Π°Π΅Ρ, Π΅ΡΠ»ΠΈ ΠΏΠ΅ΡΠ΅Π΄ ΡΡΠΈΠΌ ΠΎΠ½ Π½Π΅ ΠΏΠΎΠ΄Π²Π΅ΡΠ³Π°Π΅ΡΡΡ ΠΎΠ±ΡΠ°Π±ΠΎΡΠΊΠ΅ Ρ ΠΈΠΌΠΈΡΠ΅ΡΠΊΠΈΠΌ ΠΈΠ»ΠΈ ΡΠ»Π΅ΠΊΡΡΠΈΡΠ΅ΡΠΊΠΈΠΌ ΡΠΏΠΎΡΠΎΠ±ΠΎΠΌ Π² ΡΠ΅ΡΠ΅Π½ΠΈΠ΅ ΠΊΠΎΡΠΎΡΠΊΠΎΠ³ΠΎ ΠΏΡΠΎΠΌΠ΅ΠΆΡΡΠΊΠ° Π²ΡΠ΅ΠΌΠ΅Π½ΠΈ. ΠΠΎΠ΄ΠΎΠ±Π½ΠΎΠ΅ ΡΠΌΠ΅Π½ΡΡΠ΅Π½ΠΈΠ΅ ΠΊΠΎΡΡΡΠΈΡΠΈΠ΅Π½ΡΠ° Π·Π΅ΡΠΊΠ°Π»ΡΠ½ΠΎΠ³ΠΎ ΠΎΡΡΠ°ΠΆΠ΅Π½ΠΈΡ Π½Π°Π±Π»ΡΠ΄Π°Π΅ΡΡΡ ΠΈ Π½Π° Π½Π°ΡΠ°Π»ΡΠ½ΡΡ ΡΡΠ°Π΄ΠΈΡΡ Ρ ΠΈΠΌΠΈΡΠ΅ΡΠΊΠΎΠΉ ΠΎΠ±ΡΠ°Π±ΠΎΡΠΊΠΈ, ΠΎΠ΄Π½Π°ΠΊΠΎ Π·Π°ΡΠ΅ΠΌ ΡΠ»Π΅Π΄ΡΠ΅Ρ ΠΏΠΎΠ²ΡΡΠ΅Π½ΠΈΠ΅ ΠΊΠΎΡΡΡΠΈΡΠΈΠ΅Π½ΡΠ° Π·Π΅ΡΠΊΠ°Π»ΡΠ½ΠΎΠ³ΠΎ ΠΎΡΡΠ°ΠΆΠ΅Π½ΠΈΡ, ΠΊΠΎΡΠΎΡΡΠΉ ΠΌΠΎΠΆΠ΅Ρ Π΄ΠΎΡΡΠΈΠ³Π°ΡΡ 90% (ΠΌΠ°ΠΊΡΠΈΠΌΠ°Π»ΡΠ½ΠΎ Π²ΠΎΠ·ΠΌΠΎΠΆΠ½ΡΠΉ ΠΊΠΎΡΡΡΠΈΡΠΈΠ΅Π½Ρ Π΄Π»Ρ Π°Π»ΡΠΌΠΈΠ½ΠΈΡ), ΠΏΡΠΈ ΡΠΎΠ±Π»ΡΠ΄Π΅Π½ΠΈΠΈ Π²ΡΠ΅Ρ ΡΡΠ»ΠΎΠ²ΠΈΠΉ Ρ ΠΈΠΌΠΈΡΠ΅ΡΠΊΠΎΠΉ ΠΎΠ±ΡΠ°Π±ΠΎΡΠΊΠΈ. Π’ΠΎΡ ΠΆΠ΅ ΠΏΡΠΎΡΠ΅ΡΡ Π½Π°Π±Π»ΡΠ΄Π°Π΅ΡΡΡ ΠΈ ΠΏΡΠΈ Π³Π°Π»ΡΠ²Π°Π½ΠΈΡΠ΅ΡΠΊΠΎΠΉ ΠΎΠ±ΡΠ°Π±ΠΎΡΠΊΠ΅. ΠΡΠΈ Π°Π½ΠΎΠ΄ΠΈΡΠΎΠ²Π°Π½ΠΈΠΈ ΠΊΠΎΡΡΡΠΈΡΠΈΠ΅Π½Ρ Π·Π΅ΡΠΊΠ°Π»ΡΠ½ΠΎΠ³ΠΎ ΠΎΡΡΠ°ΠΆΠ΅Π½ΠΈΡ Π°Π»ΡΠΌΠΈΠ½ΠΈΡ, ΠΏΠΎΠ²Π΅ΡΠ³Π½ΡΡΠΎΠ³ΠΎ ΡΠ»Π΅ΠΊΡΡΠΈΡΠ΅ΡΠΊΠΎΠΉ ΠΈΠ»ΠΈ Ρ ΠΈΠΌΠΈΡΠ΅ΡΠΊΠΎΠΉ ΠΎΠ±ΡΠ°Π±ΠΎΡΠΊΠ΅ ΠΎΡΡΠ°ΡΡΡΡ Π²ΡΡΠΎΠΊΠΈΠΌ (Ρ ΠΎΡΡ ΠΈ Π½Π°Π±Π»ΡΠ΄Π°Π΅ΡΡΡ Π½Π΅Π±ΠΎΠ»ΡΡΠΎΠ΅ Π΅Π³ΠΎ ΡΠΌΠ΅Π½ΡΡΠ΅Π½ΠΈΠ΅ Ρ ΡΠ²Π΅Π»ΠΈΡΠ΅Π½ΠΈΠ΅ΠΌ Π²ΡΠ΅ΠΌΠ΅Π½ΠΈ Π½Π°Ρ ΠΎΠΆΠ΄Π΅Π½ΠΈΡ Π² Π²Π°Π½Π½Π΅ Π΄Π»Ρ Π°Π½ΠΎΠ΄ΠΈΡΠΎΠ²Π°Π½ΠΈΡ, Π²ΡΠ·Π²Π°Π½Π½ΠΎΠ΅ ΠΌΠ΅Π΄Π»Π΅Π½Π½ΡΠΌ ΡΠ°ΡΡΠ²ΠΎΡΠ΅Π½ΠΈΠ΅ΠΌ ΠΈ Π»ΡΠ³ΠΊΠΎΠΉ ΡΠ΅ΡΠΎΡ ΠΎΠ²Π°ΡΠΎΡΡΡΡ Π²Π½Π΅ΡΠ½Π΅ΠΉ ΠΏΠΎΠ²Π΅ΡΡ Π½ΠΎΡΡΠΈ Π°Π½ΠΎΠ΄Π½ΠΎΠΉ ΠΏΠ»ΡΠ½ΠΊΠΈ). ΠΠΎΡΡΠΎΠΌΡ ΠΏΡΠΎΠΌΡΡΠ»Π΅Π½Π½ΡΠΉ ΠΏΡΠΎΡΠ΅ΡΡ Π³Π»ΡΠ½ΡΠ΅Π²Π°Π½ΠΈΡ ΠΌΠ΅ΡΠΎΠ΄ΠΎΠΌ Π°Π½ΠΎΠ΄ΠΈΡΠΎΠ²Π°Π½ΠΈΡ ΠΎΠ±ΡΡΠ½ΠΎ Π²ΠΊΠ»ΡΡΠ°Π΅Ρ Π² ΡΠ΅Π±Ρ Ρ ΠΈΠΌΠΈΡΠ΅ΡΠΊΡΡ ΠΎΠ±ΡΠ°Π±ΠΎΡΠΊΡ Π½Π΅ΠΏΠΎΡΡΠ΅Π΄ΡΡΠ²Π΅Π½Π½ΠΎ ΠΏΠ΅ΡΠ΅Π΄ Π°Π½ΠΎΠ΄ΠΈΡΠΎΠ²Π°Π½ΠΈΠ΅ΠΌ.
ΠΡΠ»ΠΏΠ°Π½ ΠΈ ΠΡΡΠΎΡΡΠΌΠΈΡ ΠΏΡΠΎΠΈΠ·Π²Π΅Π»ΠΈ ΠΈΠ·ΠΌΠ΅ΡΠ΅Π½ΠΈΡ ΠΈΠ·ΠΌΠ΅Π½Π΅Π½ΠΈΡ ΠΊΠΎΡΡΡΠΈΡΠΈΠ΅Π½ΡΠ° Π·Π΅ΡΠΊΠ°Π»ΡΠ½ΠΎΠ³ΠΎ ΠΎΡΡΠ°ΠΆΠ΅Π½ΠΈΡ Π²ΠΎ Π²ΡΠ΅ΠΌΡ Ρ ΠΈΠΌΠΈΡΠ΅ΡΠΊΠΎΠΉ ΠΎΠ±ΡΠ°Π±ΠΎΡΠΊΠΈ Π°Π»ΡΠΌΠΈΠ½ΠΈΡ, Π° Π·Π°ΡΠ΅ΠΌ Ρ ΠΏΠΎΠΌΠΎΡΡΡ ΡΠ»Π΅ΠΊΡΡΠΎΠ½Π½ΠΎΠ³ΠΎ ΠΌΠΈΠΊΡΠΎΡΠΊΠΎΠΏΠ° Π½Π°Π±Π»ΡΠ΄Π°Π»ΠΈ Π·Π° ΡΠΎΠΎΡΠ²Π΅ΡΡΡΠ²ΡΡΡΠΈΠΌΠΈ ΠΈΠ·ΠΌΠ΅Π½Π΅Π½ΠΈΡΠΌΠΈ ΡΡΡΡΠΊΡΡΡΡ ΠΏΠΎΠ²Π΅ΡΡ Π½ΠΎΡΡΠΈ. ΠΡΠΎΡΠ΅ΡΡ Ρ ΠΈΠΌΠΈΡΠ΅ΡΠΊΠΎΠΉ ΠΎΠ±ΡΠ°Π±ΠΎΡΠΊΠΈ Π½Π°ΡΠ°Π»ΡΡ Ρ ΡΠ΅Π·ΠΊΠΎΠ³ΠΎ ΡΠΌΠ΅Π½ΡΡΠ΅Π½ΠΈΡ ΠΊΠΎΡΡΡΠΈΡΠΈΠ΅Π½ΡΠ° Π·Π΅ΡΠΊΠ°Π»ΡΠ½ΠΎΠ³ΠΎ ΠΎΡΡΠ°ΠΆΠ΅Π½ΠΈΡ, Π²ΡΠ·Π²Π°Π½Π½ΠΎΠ³ΠΎ ΡΡΠ°Π²Π»Π΅Π½ΠΈΠ΅ΠΌ, Π·Π°ΡΠ΅ΠΌ ΠΏΠΎΡΠ»Π΅Π΄ΠΎΠ²Π°Π»ΠΎ Π΅Π³ΠΎ ΠΏΠΎΠ²ΡΡΠ΅Π½ΠΈΠ΅, Π° ΠΏΠΎ Π΄ΠΎΡΡΠΈΠΆΠ΅Π½ΠΈΠΈ ΠΌΠ°ΠΊΡΠΈΠΌΠ°Π»ΡΠ½ΠΎΠ³ΠΎ Π·Π½Π°ΡΠ΅Π½ΠΈΡ ΠΎΠ½ ΡΡΠ°Π» ΡΠΌΠ΅Π½ΡΡΠ°ΡΡΡΡ. ΠΠ° ΠΏΠ΅ΡΠ²ΠΎΠΌ ΡΡΠ°ΠΏΠ΅ Π½Π°Π±Π»ΡΠ΄Π°Π»ΡΡ ΡΠΎΡΡ ΠΈ ΡΠ»ΠΈΠ²Π°Π½ΠΈΠ΅ ΡΠ»ΡΡΠ°ΠΉΠ½ΠΎ ΡΠ°ΡΠΏΠΎΠ»ΠΎΠΆΠ΅Π½Π½ΡΡ ΡΠΌΠΎΠΊ ΡΡΠ°Π²Π»Π΅Π½ΠΈΡ, ΡΡΠΎ ΠΏΡΠΎΠΈΡΡ ΠΎΠ΄ΠΈΠ»ΠΎ Π΄ΠΎ ΡΠ΅Ρ ΠΏΠΎΡ, ΠΏΠΎΠΊΠ° ΠΏΠ΅ΡΠ²ΠΎΠ½Π°ΡΠ°Π»ΡΠ½Π°Ρ ΠΏΠΎΠ²Π΅ΡΡ Π½ΠΎΡΡΡ Π½Π΅ Π±ΡΠ»Π° ΠΏΠΎΠ»Π½ΠΎΡΡΡΡ ΡΠ΄Π°Π»Π΅Π½Π°. ΠΡΡΠ΅ΡΡΠ²Π΅Π½Π½ΡΠΉ ΠΎΠΊΠΈΡΠ΅Π» Π±ΡΠ» Π·Π°ΠΌΠ΅Π½ΡΠ½ ΡΠΏΠ»ΠΎΡΠ½ΠΎΠΉ ΠΏΡΠΎΡΠ½ΠΎΠΉ ΠΏΠ»ΡΠ½ΠΊΠΎΠΉ, ΠΏΠΎ ΠΊΠΎΡΠΎΡΠΎΠΉ ΠΏΡΠΎΠ΄ΠΎΠ»ΠΆΠ°Π»Π°ΡΡ Ρ ΠΈΠΌΠΈΡΠ΅ΡΠΊΠ°Ρ ΠΎΠ±ΡΠ°Π±ΠΎΡΠΊΠ°. Π₯ΠΎΠ°Ρ ΠΏΡΠ΅Π΄ΠΏΠΎΠ»ΠΎΠΆΠΈΠ», ΡΡΠΎ ΡΡΠ° ΠΏΠ»ΡΠ½ΠΊΠ° ΡΠ²Π»ΡΠ»Π°ΡΡ ΠΎΠΊΠΈΡΠ»ΠΎΠΌ, ΡΠΎΠ΄Π΅ΡΠΆΠ°ΡΠΈΠΌ Π·Π½Π°ΡΠΈΡΠ΅Π»ΡΠ½ΠΎΠ΅ ΠΊΠΎΠ»ΠΈΡΠ΅ΡΡΠ²ΠΎ Π°Π½ΠΈΠΎΠ½ΠΎΠ² ΠΈΠ· ΡΠ°ΡΡΠ²ΠΎΡΠ°. ΠΡΠ°ΠΏ ΡΡΠ°Π²Π»Π΅Π½ΠΈΡ Π½Π΅ΠΎΠ±Ρ ΠΎΠ΄ΠΈΠΌ Π΄Π»Ρ Π·Π°ΠΌΠ΅Π½Ρ Π΅ΡΡΠ΅ΡΡΠ²Π΅Π½Π½ΠΎΠ³ΠΎ ΠΎΠΊΠΈΡΠ»Π° Π½Π° ΡΠΎΠ½ΠΊΡΡ ΠΏΡΠΎΡΠ½ΡΡ ΠΏΠ»ΡΠ½ΠΊΡ, ΠΎΠ±Π»Π°Π΄Π°ΡΡΡΡ Ρ Π°ΡΠ°ΠΊΡΠ΅ΡΠΈΡΡΠΈΠΊΠ°ΠΌΠΈ, Π½Π΅ΠΎΠ±Ρ ΠΎΠ΄ΠΈΠΌΡ
studvesna73.ru
Π Π΅ΠΆΡΡΠΈΠΉ ΠΈΠ½ΡΡΡΡΠΌΠ΅Π½Ρ Π΄Π»Ρ ΠΎΠ±ΡΠ°Π±ΠΎΡΠΊΠΈ Π°Π»ΡΠΌΠΈΠ½ΠΈΡ
Π‘ΠΌ. ΡΠ°ΠΊΠΆΠ΅ ΠΠ΅Ρ Π°Π½ΠΈΡΠ΅ΡΠΊΠ°Ρ ΠΎΠ±ΡΠ°Π±ΠΎΡΠΊΠ° Π°Π»ΡΠΌΠΈΠ½ΠΈΡ
ΠΠΎΠ½ΡΡΡΡΠΊΡΠΈΡ ΡΠ΅ΠΆΡΡΠ΅Π³ΠΎ ΠΈΠ½ΡΡΡΡΠΌΠ΅Π½ΡΠ°
ΠΠ»ΠΈΡΠ½ΠΈΠ΅ ΠΊΠΎΠ½ΡΡΡΡΠΊΡΠΈΠΈ ΡΠ΅ΠΆΡΡΠ΅Π³ΠΎ ΠΈΠ½ΡΡΡΡΠΌΠ΅Π½ΡΠ° Π½Π° ΠΊΠ°ΡΠ΅ΡΡΠ²ΠΎ ΠΏΠΎΠ²Π΅ΡΡ Π½ΠΎΡΡΠΈ Π·Π°ΠΊΠ»ΡΡΠ°Π΅ΡΡΡ Π² Π΅Π³ΠΎ ΡΠΏΠΎΡΠΎΠ±Π½ΠΎΡΡΠΈ ΠΎΠ±ΡΠ°Π·ΠΎΠ²ΡΠ²Π°ΡΡ Β«ΠΏΡΠ°Π²ΠΈΠ»ΡΠ½ΡΡΒ» ΡΡΡΡΠΆΠΊΡ. ΠΠ°ΠΆΠ½ΠΎ, ΡΡΠΎΠ±Ρ ΡΡΡΡΠΆΠΊΠ° ΠΌΠΎΠ³Π»Π° Π³Π»Π°Π΄ΠΊΠΎ ΠΏΡΠΎΡ ΠΎΠ΄ΠΈΡΡ ΡΠ΅ΠΆΡΡΡΡ ΠΏΠΎΠ²Π΅ΡΡ Π½ΠΎΡΡΡ ΠΈΠ½ΡΡΡΡΠΌΠ΅Π½ΡΠ°. ΠΡΠΎ Π·Π½Π°ΡΠΈΡ, ΡΡΠΎ ΠΏΠ΅ΡΠ΅Π΄Π½ΠΈΠΉ ΡΠ³ΠΎΠ» Π·ΡΠ±Π° Π΄ΠΎΠ»ΠΆΠ΅Π½ Π±ΡΡΡ Π΄ΠΎΡΡΠ°ΡΠΎΡΠ½ΠΎ Π±ΠΎΠ»ΡΡΠΎΠΉ, ΡΠΌΠ°Π·ΠΊΠ° Π΄ΠΎΠ»ΠΆΠ½Π° Π±ΡΡΡ Π΄ΠΎΡΡΠ°ΡΠΎΡΠ½ΠΎΠΉ, Π° ΠΏΠΎΠ²Π΅ΡΡ Π½ΠΎΡΡΡ ΡΠ΅ΠΆΡΡΠ΅Π³ΠΎ ΠΈΠ½ΡΡΡΡΠΌΠ΅Π½ΡΠ° Π΄ΠΎΡΡΠ°ΡΠΎΡΠ½ΠΎ Π³Π»Π°Π΄ΠΊΠΎΠΉ. Π₯ΠΎΡΠΎΡΡΡ Π³Π»Π°Π΄ΠΊΡΡ ΠΏΠΎΠ²Π΅ΡΡ Π½ΠΎΡΡΡ Π½Π΅Π»ΡΠ·Ρ ΠΏΠΎΠ»ΡΡΠΈΡΡ ΠΏΡΠΈ ΡΠ°Π±ΠΎΡΠ΅ Ρ ΠΈΠ·Π½ΠΎΡΠ΅Π½Π½ΡΠΌ ΡΠ΅ΠΆΡΡΠΈΠΌ ΠΈΠ½ΡΡΡΡΠΌΠ΅Π½ΡΠΎΠΌ.
ΠΡΠ½ΠΎΠ²Π½ΡΠ΅ ΡΠ°ΠΊΡΠΎΡΡ, ΠΊΠΎΡΠΎΡΡΠ΅ Π²Π»ΠΈΡΡΡ Π½Π° ΠΊΠ°ΡΠ΅ΡΡΠ²ΠΎ ΠΏΠΎΠ²Π΅ΡΡ Π½ΠΎΡΡΠΈ ΠΏΡΠΈ ΠΌΠ΅Ρ Π°Π½ΠΈΡΠ΅ΡΠΊΠΎΠΉ ΠΎΠ±ΡΠ°Π±ΠΎΡΠΊΠ΅ Π°Π»ΡΠΌΠΈΠ½ΠΈΡ, Π·Π°Π΄Π°ΡΡ ΡΠ΅ΡΡΡΠ΅ ΠΎΡΠ΄Π΅Π»ΡΠ½ΡΡ ΠΎΠ±Π»Π°ΡΡΠΈ ΠΊΠ°ΡΠ΅ΡΡΠ²Π° ΠΌΠ΅Ρ Π°Π½ΠΈΡΠ΅ΡΠΊΠΎΠΉ ΠΎΠ±ΡΠ°Π±ΠΎΡΠΊΠΈ (ΡΠΈΡΡΠ½ΠΎΠΊ 1):
Π ΠΈΡΡΠ½ΠΎΠΊ 1 β ΠΠ°Π²ΠΈΡΠΈΠΌΠΎΡΡΡ ΠΊΠ°ΡΠ΅ΡΡΠ²Π° ΠΏΠΎΠ²Π΅ΡΡ
Π½ΠΎΡΡΠΈ ΠΈ
ΡΠΊΠΎΡΠΎΡΡΡ ΡΠ΅Π·Π°Π½ΠΈΡ ΠΏΡΠΈ ΠΌΠ΅Ρ
Π°Π½ΠΈΡΠ΅ΡΠΊΠΎΠΉ ΠΎΠ±ΡΠ°Π±ΠΎΡΠΊΠ΅ Π°Π»ΡΠΌΠΈΠ½ΠΈΡ
- ΠΠ±Π»Π°ΡΡΡ I: ΠΠ·-Π·Π° Π½Π°Π»ΠΈΠΏΠ°Π½ΠΈΡ Π½Π° ΡΠ΅ΠΆΡΡΡΡ ΠΊΡΠΎΠΌΠΊΡ ΠΊΠ°ΡΠ΅ΡΡΠ²ΠΎ ΠΏΠΎΠ²Π΅ΡΡ Π½ΠΎΡΡΠΈ ΡΠ²Π»ΡΠ΅ΡΡΡ Π½Π΅ΡΠ΄ΠΎΠ²Π»Π΅ΡΠ²ΠΎΡΠΈΡΠ΅Π»ΡΠ½ΡΠΌ; Π²ΠΌΠ΅ΡΡΠΎ ΡΠ΅Π·Π°Π½ΠΈΡ ΠΌΠ°ΡΠ΅ΡΠΈΠ°Π» ΠΏΠΎΠ΄Π²Π΅ΡΠ³Π°Π΅ΡΡΡ ΡΠ°Π·ΡΡΠ²Π°ΠΌ. ΠΡΠΎΠΉ ΠΎΠ±Π»Π°ΡΡΠΈ ΠΏΠ°ΡΠ°ΠΌΠ΅ΡΡΠΎΠ² Π½ΡΠΆΠ½ΠΎ ΠΈΠ·Π±Π΅Π³Π°ΡΡ.
- ΠΠ±Π»Π°ΡΡΡ II: Π‘Π½ΠΈΠΆΠ΅Π½ΠΈΠ΅ ΡΠ΅ΡΠΎΡ ΠΎΠ²Π°ΡΠΎΡΡΠΈ Ρ ΡΠ²Π΅Π»ΠΈΡΠ΅Π½ΠΈΠ΅ΠΌ ΡΠΊΠΎΡΠΎΡΡΠΈ ΡΠ΅Π·Π°Π½ΠΈΡ.
- ΠΠ±Π»Π°ΡΡΡ III: Π£Π²Π΅Π»ΠΈΡΠ΅Π½ΠΈΠ΅ Π²Π»ΠΈΡΠ½ΠΈΡ ΠΈΠ½ΡΡΡΡΠΌΠ΅Π½ΡΠ° ΠΈ ΠΎΠ±ΠΎΡΡΠ΄ΠΎΠ²Π°Π½ΠΈΡ, Π½Π°ΠΏΡΠΈΠΌΠ΅Ρ, Π²ΠΈΠ±ΡΠ°ΡΠΈΠΈ ΡΠ΅Π·ΡΠ° ΠΈΠ»ΠΈ ΠΏΠΈΠ»Ρ, Π² ΡΠΎΠΉ ΠΎΠ±Π»Π°ΡΡΠΈ, ΠΊΠΎΡΠΎΡΠ°Ρ, Π² ΠΏΡΠΈΠ½ΡΠΈΠΏΠ΅, Π±Π»Π°Π³ΠΎΠΏΡΠΈΡΡΠ½Π° Π΄Π»Ρ ΠΌΠ΅Ρ Π°Π½ΠΈΡΠ΅ΡΠΊΠΎΠΉ ΠΎΠ±ΡΠ°Π±ΠΎΡΠΊΠΈ Π°Π»ΡΠΌΠΈΠ½ΠΈΡ. ΠΠΎΡΡΠΎΠΌΡ, ΡΡΠΎΠ±Ρ Π΄ΠΎΠ±ΠΈΡΡΡΡ Π»ΡΡΡΠΈΡ ΡΠ΅Π·ΡΠ»ΡΡΠ°ΡΠΎΠ² ΠΏΡΠΈ ΡΡΠΎΠΉ ΡΠΊΠΎΡΠΎΡΡΠΈ ΡΠ΅Π·Π°Π½ΠΈΡ Π½Π΅ΠΎΠ±Ρ ΠΎΠ΄ΠΈΠΌΠΎ ΠΏΡΠΈΠΌΠ΅Π½ΡΡΡ ΠΎΠ±ΠΎΡΡΠ΄ΠΎΠ²Π°Π½ΠΈΠ΅, ΠΊΠΎΡΠΎΡΠΎΠ΅ ΡΠ°Π·ΡΠ°Π±ΠΎΡΠ°Π½ΠΎ ΡΠΏΠ΅ΡΠΈΠ°Π»ΡΠ½ΠΎ Π΄Π»Ρ Π°Π»ΡΠΌΠΈΠ½ΠΈΡ.
- ΠΠ±Π»Π°ΡΡΡ IV: ΠΠ»ΠΎΡ ΠΎΠ΅ ΠΊΠ°ΡΠ΅ΡΡΠ²ΠΎ ΠΏΠΎΠ²Π΅ΡΡ Π½ΠΎΡΡΠΈ. Π‘ΡΡΡΠΆΠΊΠ° ΡΠΎΠ±ΠΈΡΠ°Π΅ΡΡΡ Π½Π° ΠΎΠ±ΡΠ°Π±Π°ΡΡΠ²Π°Π΅ΠΌΠΎΠΌ ΠΌΠ°ΡΠ΅ΡΠΈΠ°Π»Π΅ ΠΈ Π½Π°Π»ΠΈΠΏΠ°Π΅Ρ (ΠΏΡΠΈΠ²Π°ΡΠΈΠ²Π°Π΅ΡΡΡ) ΠΊ ΡΠ΅ΠΆΡΡΠ΅ΠΌΡ ΠΈΠ½ΡΡΡΡΠΌΠ΅Π½ΡΡ, ΡΡΠΎ ΠΏΡΠΈΠ²ΠΎΠ΄ΠΈΡ ΠΊ ΠΏΠΎΠ²ΡΠ΅ΠΆΠ΄Π΅Π½ΠΈΡ ΠΎΠ±ΡΠ°Π±Π°ΡΡΠ²Π°Π΅ΠΌΠΎΠΉ ΠΏΠΎΠ²Π΅ΡΡ Π½ΠΎΡΡΠΈ. Π’Π°ΠΊΠΎΠ΅, Π½Π°ΠΏΡΠΈΠΌΠ΅Ρ, ΠΏΡΠΎΠΈΡΡ ΠΎΠ΄ΠΈΡ ΠΏΡΠΈ ΠΌΠ΅Ρ Π°Π½ΠΈΡΠ΅ΡΠΊΠΎΠΉ ΠΎΠ±ΡΠ°Π±ΠΎΡΠΊΠ΅ Π»ΠΈΡΠ΅ΠΉΠ½ΡΡ ΡΠΏΠ»Π°Π²ΠΎΠ² ΠΏΡΠΈ ΠΏΡΠΈΠΌΠ΅Π½Π΅Π½ΠΈΠΈ ΠΈΠ·Π½ΠΎΡΠ΅Π½Π½ΠΎΠ³ΠΎ ΡΠ΅ΠΆΡΡΠ΅Π³ΠΎ ΠΈΠ½ΡΡΡΡΠΌΠ΅Π½ΡΠ° ΠΈ Π²ΡΡΠΎΠΊΠΈΡ ΡΠΊΠΎΡΠΎΡΡΠ΅ΠΉ ΡΠ΅Π·Π°Π½ΠΈΡ.
ΠΠ·Π½ΠΎΡ ΡΠ΅ΠΆΡΡΠ΅Π³ΠΎ ΠΈΠ½ΡΡΡΡΠΌΠ΅Π½ΡΠ°
ΠΠ·Π½ΠΎΡΠ° ΡΠ΅ΠΆΡΡΠ΅Π³ΠΎ ΠΈΠ½ΡΡΡΡΠΌΠ΅Π½ΡΠ° Ρ ΠΎΠ±ΡΠ°Π·ΠΎΠ²Π°Π½ΠΈΠ΅ΠΌ ΡΠ°ΡΠ°ΠΏΠΈΠ½, ΠΊΠ°ΠΊ ΡΡΠΎ Ρ Π°ΡΠ°ΠΊΡΠ΅ΡΠ½ΠΎ ΠΏΡΠΈ ΠΌΠ΅Ρ Π°Π½ΠΈΡΠ΅ΡΠΊΠΎΠΉ ΠΎΠ±ΡΠ°Π±ΠΎΡΠΊΠ΅ ΡΡΠ°Π»ΠΈ, Π½Π΅ Π½Π°Π±Π»ΡΠ΄Π°Π΅ΡΡΡ ΠΏΡΠΈ ΠΌΠ΅Ρ Π°Π½ΠΈΡΠ΅ΡΠΊΠΎΠΉ ΠΎΠ±ΡΠ°Π±ΠΎΡΠΊΠ΅ Π°Π»ΡΠΌΠΈΠ½ΠΈΡ ΠΈ Π°Π»ΡΠΌΠΈΠ½ΠΈΠ΅Π²ΡΡ ΡΠΏΠ»Π°Π²ΠΎΠ². ΠΠ·Π½ΠΎΡ ΠΈΠ½ΡΡΡΡΠΌΠ΅Π½ΡΠ° ΠΏΡΠΈ ΠΌΠ΅Ρ Π°Π½ΠΈΡΠ΅ΡΠΊΠΎΠΉ ΠΎΠ±ΡΠ°Π±ΠΎΡΠΊΠ΅ Π°Π»ΡΠΌΠΈΠ½ΠΈΡ ΠΏΡΠΎΠΈΡΡ ΠΎΠ΄ΠΈΡ Π·Π° ΡΡΠ΅Ρ ΠΈΡΡΠΈΡΠ°Π½ΠΈΡ ΡΠ΅ΠΆΡΡΠ΅ΠΉ ΠΏΠΎΠ²Π΅ΡΡ Π½ΠΎΡΡΠΈ. ΠΠΎΡΡΠΎΠΌΡ ΡΠ΅ΡΠ°ΡΡΠΈΠΌ ΠΊΡΠΈΡΠ΅ΡΠΈΠ΅ΠΌ Π΄Π»Ρ ΠΎΡΠ΅Π½ΠΊΠΈ ΡΡΠΎΠΊΠ° ΡΠ»ΡΠΆΠ±Ρ ΡΠ΅ΠΆΡΡΠ΅Π³ΠΎ ΠΈΠ½ΡΡΡΡΠΌΠ΅Π½ΡΠ° ΠΎΠ±ΡΠ΅ΠΊΡΠΈΠ²Π½ΠΎ ΡΠ²Π»ΡΠ΅ΡΡΡ ΡΠΈΡΠΈΠ½Π° ΠΈΠ·Π½ΠΎΡΠ° VB, ΠΏΠΎΠΊΠ°Π·Π°Π½Π½Π°Ρ Π½Π° ΡΠΈΡΡΠ½ΠΊΠ΅ 2. ΠΠ·Π½ΠΎΡ ΡΠ΅ΠΆΡΡΠ΅ΠΉ ΠΏΠΎΠ²Π΅ΡΡ Π½ΠΎΡΡΠΈ Π·Π°Π²ΠΈΡΠΈΡ ΠΎΡ ΡΠ΅ΠΌΠΏΠ΅ΡΠ°ΡΡΡΡ ΠΈ ΠΏΡΠΎΠΈΡΡ ΠΎΠ΄ΠΈΡ Π² ΠΎΡΠ½ΠΎΠ²Π½ΠΎΠΌ ΠΏΡΡΠ΅ΠΌ ΠΈΡΡΠΈΡΠ°Π½ΠΈΡ. ΠΡΠΈ ΠΈΡΠΏΠΎΠ»ΡΠ·ΠΎΠ²Π°Π½ΠΈΠΈ ΠΈΠ½ΡΡΡΡΠΌΠ΅Π½ΡΠ° Ρ ΠΊΠ°ΡΠ±ΠΈΠ΄Π½ΡΠΌΠΈ Π½Π°ΡΠ°Π΄ΠΊΠ°ΠΌΠΈ ΠΌΠ°ΠΊΡΠΈΠΌΠ°Π»ΡΠ½Π°Ρ Π²Π΅Π»ΠΈΡΠΈΠ½Π° 0,3-0,5 ΠΌΠΌ Π΄Π»Ρ Π²Π΅Π»ΠΈΡΠΈΠ½Ρ ΠΈΠ·Π½ΠΎΡΠ° VB ΡΡΠΈΡΠ°Π΅ΡΡΡ Π½ΠΎΡΠΌΠ°Π»ΡΠ½ΠΎΠΉ.
Π ΠΈΡΡΠ½ΠΎΠΊ 2 β ΠΠ·Π½ΠΎΡ ΡΠ΅ΠΆΡΡΠ΅ΠΉ ΠΊΡΠΎΠΌΠΊΠΈ
ΠΠ° ΠΈΠ·Π½ΠΎΡ ΡΠ΅ΠΆΡΡΠ΅Π³ΠΎ ΠΈΠ½ΡΡΡΡΠΌΠ΅Π½ΡΠ° ΠΎΠΊΠ°Π·ΡΠ²Π°ΡΡ Π²Π»ΠΈΡΠ½ΠΈΠ΅ ΠΊΠ°ΠΊ ΠΌΠ°ΡΠ΅ΡΠΈΠ°Π» ΠΎΠ±ΡΠ°Π±Π°ΡΡΠ²Π°Π΅ΠΌΠΎΠΉ Π΄Π΅ΡΠ°Π»ΠΈ, ΡΠ°ΠΊ ΠΏΠ°ΡΠ°ΠΌΠ΅ΡΡΡ ΡΠ΅Π·Π°Π½ΠΈΡ.
ΠΠ°ΡΠ΅ΡΠΈΠ°Π» Π΄Π΅ΡΠ°Π»ΠΈ ΠΈΠΌΠ΅Π΅Ρ ΠΎΡΠΎΠ±Π΅Π½Π½ΠΎ Π±ΠΎΠ»ΡΡΠΎΠ΅ Π²Π»ΠΈΡΠ½ΠΈΠ΅ Π½Π° ΠΈΠ·Π½ΠΎΡ ΡΠ΅ΠΆΡΡΠ΅Π³ΠΎ ΠΈΠ½ΡΡΡΡΠΌΠ΅Π½ΡΠ°:
- ΠΠ·Π½ΠΎΡ ΡΠ²Π΅Π»ΠΈΡΠΈΠ²Π°Π΅ΡΡΡ Ρ ΡΠ²Π΅Π»ΠΈΡΠ΅Π½ΠΈΠ΅ΠΌ ΠΊΠΎΠ»ΠΈΡΠ΅ΡΡΠ²Π° ΠΊΡΡΠΏΠ½ΡΡ ΡΠ²Π΅ΡΠ΄ΡΡ ΡΠ°ΡΡΠΈΡ, ΠΊΠΎΡΠΎΡΡΠ΅ Π²Π½Π΅Π΄ΡΠ΅Π½Ρ Π² Π°Π»ΡΠΌΠΈΠ½ΠΈΠ΅Π²ΡΡ ΠΌΠ°ΡΡΠΈΡΡ. Π’Π°ΠΊΠΈΠΌΠΈ ΡΠ°ΡΡΠΈΡΠ°ΠΌΠΈ ΡΠ²Π»ΡΡΡΡΡ, Π½Π°ΠΏΡΠΈΠΌΠ΅Ρ, ΠΏΠ΅ΡΠ²ΠΈΡΠ½ΡΠ΅ Π²ΡΠ΄Π΅Π»Π΅Π½ΠΈΡ ΡΠ°ΡΡΠΈΡ ΠΊΡΠ΅ΠΌΠ½ΠΈΡ Π² Π·Π°ΡΠ²ΡΠ΅ΠΊΡΠΈΡΠ΅ΡΠΊΠΎΠΌ Π°Π»ΡΠΌΠΈΠ½ΠΈΠ΅Π²ΠΎΠΌ ΡΠΏΠ»Π°Π²Π΅. ΠΠΎ ΡΡΠΎΠΉ ΠΏΡΠΈΡΠΈΠ½Π΅ Π°Π»ΡΠΌΠΈΠ½ΠΈΠ΅Π²ΡΠ΅ ΠΎΡΠ»ΠΈΠ²ΠΊΠΈ Π²ΡΠ·ΡΠ²Π°ΡΡ ΡΠΈΠ»ΡΠ½ΡΠΉ ΠΈΠ·Π½ΠΎΡ ΡΠ΅ΠΆΡΡΠ΅Π³ΠΎ ΠΈΠ½ΡΡΡΡΠΌΠ΅Π½ΡΠ°. ΠΡΠΎΡ ΠΈΠ·Π½ΠΎΡ ΠΎΡΠΎΠ±Π΅Π½Π½ΠΎ Π²ΡΡΠΎΠΊΠΈΠΉ Π² ΡΠ»ΡΡΠ°Π΅ Π»ΠΈΡΠ΅ΠΉΠ½ΡΡ Π·Π°ΡΠ²ΡΠ΅ΠΊΡΠΈΡΠ΅ΡΠΊΠΈΡ ΠΏΠΎΡΡΠ½Π΅Π²ΡΡ Π°Π»ΡΠΌΠΈΠ½ΠΈΠ΅Π²ΡΡ ΡΠΏΠ»Π°Π²ΠΎΠ². Π‘ Π΄ΡΡΠ³ΠΎΠΉ ΡΡΠΎΡΠΎΠ½Ρ, Π΄Π΅ΡΠΎΡΠΌΠΈΡΡΠ΅ΠΌΡΠ΅ ΡΠΏΠ»Π°Π²Ρ Ρ Π½ΠΈΠ·ΠΊΠΈΠΌ ΡΠΎΠ΄Π΅ΡΠΆΠ°Π½ΠΈΠ΅ΠΌ ΠΊΡΠ΅ΠΌΠ½ΠΈΡ Π²ΡΠ·ΡΠ²Π°ΡΡ ΠΌΠΈΠ½ΠΈΠΌΠ°Π»ΡΠ½ΡΠΉ ΠΈΠ·Π½ΠΎΡ.
- ΠΠ·Π½ΠΎΡ Π²ΠΎΠ·ΡΠ°ΡΡΠ°Π΅Ρ Ρ ΡΠ²Π΅Π»ΠΈΡΠ΅Π½ΠΈΠ΅ΠΌ ΠΏΡΠΎΡΠ½ΠΎΡΡΠΈ Π°Π»ΡΠΌΠΈΠ½ΠΈΠ΅Π²ΡΡ ΡΠΏΠ»Π°Π²ΠΎΠ². Π’Π²Π΅ΡΠ΄ΡΠ΅ ΡΠ°ΡΡΠΈΡΡ, ΠΊΠΎΡΠΎΡΡΠ΅ Π½Π°Ρ ΠΎΠ΄ΡΡΡΡ Π² ΠΌΡΠ³ΠΊΠΎΠΉ Π°Π»ΡΠΌΠΈΠ½ΠΈΠ΅Π²ΠΎΠΉ ΠΌΠ°ΡΡΠΈΡΠ΅, Π΄ΠΎΠ²ΠΎΠ»ΡΠ½ΠΎ Π»Π΅Π³ΠΊΠΎ ΠΈΠ· Π½Π΅Π΅ Π²ΡΡΡΠ²Π°ΡΡΡΡ, Π½Π΅ Π½Π°Π½ΠΎΡΡ Π±ΠΎΠ»ΡΡΠΎΠ³ΠΎ Π²ΡΠ΅Π΄Π° ΠΈΠ½ΡΡΡΡΠΌΠ΅Π½ΡΡ. ΠΠ΄Π½Π°ΠΊΠΎ, Π΅ΡΠ»ΠΈ Π°Π»ΡΠΌΠΈΠ½ΠΈΠ΅Π²Π°Ρ ΠΌΠ°ΡΡΠΈΡΠ° ΠΈΠΌΠ΅Π΅Ρ ΠΏΠΎΠ²ΡΡΠ΅Π½Π½ΡΡ ΡΠ²Π΅ΡΠ΄ΠΎΡΡΡ, ΡΠΎ Π²ΠΊΠ»ΡΡΠ΅Π½ΠΈΡ Π²ΡΡΡΠ²Π°ΡΡΡΡ ΡΠΆΠ΅ ΡΡΡΠ΄Π½Π΅Π΅ ΠΈ ΠΏΠΎΡΡΠΎΠΌΡ ΠΏΡΠΈΡΠΈΠ½ΡΡΡ ΠΈΠ½ΡΡΡΡΠΌΠ΅Π½ΡΡ Π±ΠΎΠ»ΡΡΠΈΠΉ ΠΈΠ·Π½ΠΎΡ.
- ΠΠ°ΠΊΠΎΠ½Π΅Ρ, ΠΈΠ·Π½ΠΎΡ ΠΈΠ½ΡΡΡΡΠΌΠ΅Π½ΡΠ° Π·Π°Π²ΠΈΡΠΈΡ ΠΎΡ ΡΠΎΠΏΡΠΎΡΠΈΠ²Π»Π΅Π½ΠΈΡ ΠΈΠ·Π½ΠΎΡΡ ΡΠ°ΠΌΠΎΠ³ΠΎ ΠΈΠ½ΡΡΡΡΠΌΠ΅Π½ΡΠ°.
ΠΠ»ΠΈΡΠ½ΠΈΠ΅ ΡΠΊΠΎΡΠΎΡΡΠΈ ΡΠ΅Π·Π°Π½ΠΈΡ Π½Π° ΠΈΠ·Π½ΠΎΡ ΠΈΠ½ΡΡΡΡΠΌΠ΅Π½ΡΠ°
Π§ΡΠΎ ΠΊΠ°ΡΠ°Π΅ΡΡΡ ΡΡΠ»ΠΎΠ²ΠΈΠΉ ΡΠ΅Π·Π°Π½ΠΈΡ, ΡΠΎ ΡΠΊΠΎΡΠΎΡΡΡ ΡΠ΅Π·Π°Π½ΠΈΡ ΠΈΠΌΠ΅Π΅Ρ ΡΠ°ΠΌΠΎΠ΅ Π±ΠΎΠ»ΡΡΠΎΠ΅ Π²Π»ΠΈΡΠ½ΠΈΠ΅ Π½Π° ΡΡΠΎΠΊ ΡΠ»ΡΠΆΠ±Ρ ΡΠ΅ΠΆΡΡΠ΅Π³ΠΎ ΠΈΠ½ΡΡΡΡΠΌΠ΅Π½ΡΠ°. ΠΠ° ΡΠΈΡΡΠ½ΠΊΠ΅ 5 ΠΏΡΠ΅Π΄ΡΡΠ°Π²Π»Π΅Π½ ΠΏΡΠΈΠΌΠ΅Ρ Π·Π°Π²ΠΈΡΠΈΠΌΠΎΡΡΠΈ ΡΡΠΎΠΊΠ° ΡΠ»ΡΠΆΠ±Ρ ΡΠ΅ΠΆΡΡΠ΅Π³ΠΎ ΠΈΠ½ΡΡΡΡΠΌΠ΅Π½ΡΠ° ΠΏΡΠΈ ΠΌΠ΅Ρ Π°Π½ΠΈΡΠ΅ΡΠΊΠΎΠΉ ΠΎΠ±ΡΠ°Π±ΠΎΡΠΊΠ΅ Π°Π»ΡΠΌΠΈΠ½ΠΈΠ΅Π²ΡΡ ΡΠΏΠ»Π°Π²ΠΎΠ² Π΄Π»Ρ Π»ΠΈΡΡΡ Π² ΠΊΠΎΠΊΠΈΠ»Ρ. Π ΡΠ»ΡΡΠ°Π΅ Π΄Π΅ΡΠΎΡΠΌΠΈΡΡΠ΅ΠΌΡΡ Π°Π»ΡΠΌΠΈΠ½ΠΈΠ΅Π²ΡΡ ΡΠΏΠ»Π°Π²ΠΎΠ² ΡΡΠΎΠΊ ΡΠ»ΡΠΆΠ±Ρ ΡΠ΅ΠΆΡΡΠ΅Π³ΠΎ ΠΈΠ½ΡΡΡΡΠΌΠ΅Π½ΡΠ° ΠΈΠ·ΠΌΠ΅ΡΡΠ΅ΡΡΡ ΡΠΊΠΎΡΠ΅Π΅ Π² ΡΠΌΠ΅Π½Π°Ρ ΠΈΠ»ΠΈ Π΄Π½ΡΡ , ΡΠ΅ΠΌ Π² ΠΌΠΈΠ½ΡΡΠ°Ρ , ΠΊΠ°ΠΊ Π΄Π»Ρ Π»ΠΈΡΠ΅ΠΉΠ½ΡΡ ΡΠΏΠ»Π°Π²Π°Ρ Ρ Π²ΡΡΠΎΠΊΠΈΠΌ ΡΠΎΠ΄Π΅ΡΠΆΠ°Π½ΠΈΠ΅ΠΌ ΠΊΡΠ΅ΠΌΠ½ΠΈΡ.
ΠΠΎΡΠΊΠΎΠ»ΡΠΊΡ ΠΈΠ·Π½ΠΎΡ ΡΠ΅ΠΆΡΡΠ΅Π³ΠΎ ΠΈΠ½ΡΡΡΡΠΌΠ΅Π½ΡΠ° Π·Π°Π²ΠΈΡΠΈΡ ΡΠ°ΠΊΠΆΠ΅ ΠΎΡ Π΄ΡΡΠ³ΠΈΡ ΠΏΠ°ΡΠ°ΠΌΠ΅ΡΡΠΎΠ² ΠΌΠ΅Ρ Π°Π½ΠΈΡΠ΅ΡΠΊΠΎΠΉ ΠΎΠ±ΡΠ°Π±ΠΎΡΠΊΠΈ, ΡΠΎ ΡΡΠΎΠΊ ΡΠ»ΡΠΆΠ±Ρ ΠΌΠΎΠΆΠ½ΠΎ ΠΎΡΠ΅Π½ΠΈΠ²Π°ΡΡ ΡΠΎΠ»ΡΠΊΠΎ Π΄Π»Ρ ΠΎΠΏΡΠ΅Π΄Π΅Π»Π΅Π½Π½ΠΎΠ³ΠΎ Π½Π°Π±ΠΎΡΠ° ΠΏΠ°ΡΠ°ΠΌΠ΅ΡΡΠΎΠ². ΠΡΡΠ³ΠΈΠΌ ΠΏΠ°ΡΠ°ΠΌΠ΅ΡΡΠ°ΠΌΠΈ, ΠΊΠΎΡΠΎΡΡΠ΅ Π²Π»ΠΈΡΡΡ Π½Π° ΠΈΠ·Π½ΠΎΡ ΡΠ΅ΠΆΡΡΠ΅Π³ΠΎ ΠΈΠ½ΡΡΡΡΠΌΠ΅Π½ΡΠ° ΡΠ²Π»ΡΡΡΡΡ:
- Π‘ΠΌΠ°Π·ΠΎΡΠ½ΠΎ-ΠΎΡ Π»Π°ΠΆΠ΄Π°ΡΡΠΈΠ΅ ΡΠΌΡΠ»ΡΡΠΈΠΈ β ΡΡΡΠ΅ΠΊΡΠΈΠ²Π½ΠΎΠ΅ ΠΎΡ Π»Π°ΠΆΠ΄Π΅Π½ΠΈΠ΅ ΡΠ½ΠΈΠΆΠ°Π΅Ρ ΠΈΠ·Π½ΠΎΡ ΠΈΠ½ΡΡΡΡΠΌΠ΅Π½ΡΠ°.
- ΠΡΠ΅ΡΡΠ²ΠΈΡΡΠΎΡΡΡ ΡΠ΅Π·Π°Π½ΠΈΡ, Π½Π°ΠΏΡΠΈΠΌΠ΅Ρ, ΠΏΡΠΈ Π½Π°Π»ΠΈΡΠΈΠΈ Π² ΠΌΠ°ΡΠ΅ΡΠΈΠ°Π»Π΅ ΠΏΠΎΡ, ΠΏΠΎΠ²ΡΡΠ°Π΅Ρ ΠΈΠ·Π½ΠΎΡ ΠΈΠ½ΡΡΡΡΠΌΠ΅Π½ΡΠ°.
- Π‘ΠΊΠΎΡΠΎΡΡΡ ΠΏΠΎΠ΄Π°ΡΠΈ ΠΈ Π³Π»ΡΠ±ΠΈΠ½Π° ΡΠ΅Π·Π°Π½ΠΈΡ. ΠΠ·Π½ΠΎΡ ΠΈΠ½ΡΡΡΡΠΌΠ΅Π½ΡΠ° ΡΠ²Π΅Π»ΠΈΡΠΈΠ²Π°Π΅ΡΡΡ Ρ ΡΠ²Π΅Π»ΠΈΡΠ΅Π½ΠΈΠ΅ΠΌ ΡΠΎΠ»ΡΠΈΠ½Ρ ΠΏΠΎΠΏΠ΅ΡΠ΅ΡΠ½ΠΎΠ³ΠΎ ΡΠ΅ΡΠ΅Π½ΠΈΡ ΡΡΡΡΠΆΠΊΠΈ.
Π£ΡΠΈΠ»ΠΈΠ΅ ΡΠ΅Π·Π°Π½ΠΈΡ ΠΏΡΠΈ ΠΌΠ΅Ρ Π°Π½ΠΈΡΠ΅ΡΠΊΠΎΠΉ ΠΎΠ±ΡΠ°Π±ΠΎΡΠΊΠ΅ Π°Π»ΡΠΌΠΈΠ½ΠΈΡ
ΠΠ»Ρ ΠΎΡΠ΅Π½ΠΊΠΈ Π²Π»ΠΈΡΠ½ΠΈΡ ΠΌΠ°ΡΠ΅ΡΠΈΠ°Π»Π° Π½Π° ΡΡΠ»ΠΎΠ²ΠΈΡ ΡΠ΅Π·Π°Π½ΠΈΡ ΠΏΡΠΈΠΌΠ΅Π½ΡΡΡ ΡΠ°ΠΊ Π½Π°Π·ΡΠ²Π°Π΅ΠΌΠΎΠ΅ ΡΠ΄Π΅Π»ΡΠ½ΠΎΠ΅ ΡΡΠΈΠ»ΠΈΠ΅ ΡΠ΅Π·Π°Π½ΠΈΡ. ΠΡΠΎ ΡΠ΄Π΅Π»ΡΠ½ΠΎΠ΅ ΡΡΠΈΠ»ΠΈΠ΅ ΡΠ΅Π·Π°Π½ΠΈΡ ΠΈΠΌΠ΅Π΅Ρ ΠΊΠΎΡΡΠ΅Π»ΡΡΠΈΡ Ρ ΡΠ΅ΠΆΡΡΠΈΠΌ ΡΡΠΈΠ»ΠΈΠ΅ΠΌ, ΠΌΠ°ΡΠ΅ΡΠΈΠ°Π»ΠΎΠΌ ΠΈ ΡΠ°Π·ΠΌΠ΅ΡΠ°ΠΌΠΈ ΡΡΡΡΠΆΠΊΠΈ. Π ΠΎΠ±ΡΠ΅ΠΌ ΡΠ»ΡΡΠ°Π΅ ΠΏΡΠΈΠΌΠ΅Π½ΡΡΡΡΡ ΡΠ»Π΅Π΄ΡΡΡΠΈΠ΅ ΠΏΠΎΠ»ΠΎΠΆΠ΅Π½ΠΈΡ:
- Π Π°Π·Π»ΠΈΡΠ½ΡΠ΅ Π°Π»ΡΠΌΠΈΠ½ΠΈΠ΅Π²ΡΠ΅ ΡΠΏΠ»Π°Π²Ρ ΠΈΠΌΠ΅ΡΡ ΡΠ°Π·Π»ΠΈΡΠΈΡ Π² ΡΠ΄Π΅Π»ΡΠ½ΡΡ ΡΠ΅ΠΆΡΡΠΈΡ ΡΡΠΈΠ»ΠΈΡΡ , Π½ΠΎ ΠΎΡΠ½ΠΎΡΠΈΡΠ΅Π»ΡΠ½ΠΎ Π½Π΅Π±ΠΎΠ»ΡΡΠΎΠ΅.
- ΠΠ±ΡΡΠ½ΠΎ ΠΏΡΠΈΠ½ΠΈΠΌΠ°ΡΡ, ΡΡΠΎ ΡΠ΄Π΅Π»ΡΠ½ΠΎΠ΅ ΡΠ΅ΠΆΡΡΠ΅Π΅ ΡΡΠΈΠ»ΠΈΠ΅ Π΄Π»Ρ Π°Π»ΡΠΌΠΈΠ½ΠΈΡ ΠΈ Π°Π»ΡΠΌΠΈΠ½ΠΈΠ΅Π²ΡΡ ΡΠΏΠ»Π°Π²ΠΎΠ² ΡΠΎΡΡΠ°Π²Π»ΡΠ΅Ρ 30 % ΠΎΡ ΡΠ°ΠΊΠΎΠ³ΠΎ ΡΡΠΈΠ»ΠΈΡ Π΄Π»Ρ ΡΡΠ°Π»ΠΈ.
- ΠΠ΅Π»ΠΈΡΠΈΠ½Ρ ΡΠ΄Π΅Π»ΡΠ½ΠΎΠ³ΠΎ ΡΠ΅ΠΆΡΡΠ΅Π³ΠΎ ΡΡΠΈΠ»ΠΈΡ Π°Π»ΡΠΌΠΈΠ½ΠΈΠ΅Π²ΠΎΠ³ΠΎ ΡΠΏΠ»Π°Π²Π° Π½Π΅Π»ΡΠ·Ρ Π²ΡΠ²Π΅ΡΡΠΈ ΠΈΠ· Π΅Π³ΠΎ Ρ ΠΈΠΌΠΈΡΠ΅ΡΠΊΠΎΠ³ΠΎ ΡΠΎΡΡΠ°Π²Π° ΠΈΠ»ΠΈ ΡΠΈΠ·ΠΈΡΠ΅ΡΠΊΠΈΡ ΡΠ²ΠΎΠΉΡΡΠ².
- Π£Π΄Π΅Π»ΡΠ½ΠΎΠ΅ ΡΠ΅ΠΆΡΡΠ΅Π΅ ΡΡΠΈΠ»ΠΈΠ΅ Π½ΡΠΆΠ½ΠΎ ΠΎΠΏΡΠ΅Π΄Π΅Π»ΡΡΡ ΡΠΊΡΠΏΠ΅ΡΠΈΠΌΠ΅Π½ΡΠ°Π»ΡΠ½ΠΎ Π΄Π»Ρ ΠΊΠ°ΠΆΠ΄ΠΎΠ³ΠΎ ΠΎΡΠ΄Π΅Π»ΡΠ½ΠΎΠ³ΠΎ ΡΠ»ΡΡΠ°Ρ.
ΠΠ΅ΠΎΠ±Ρ ΠΎΠ΄ΠΈΠΌΠΎΠ΅ ΡΠ΅ΠΆΡΡΠ΅Π΅ ΡΡΠΈΠ»ΠΈΠ΅ Π·Π°Π²ΠΈΡΠΈΡ Π½Π΅ ΡΠΎΠ»ΡΠΊΠΎ ΠΎΡ ΡΠ°Π·ΠΌΠ΅ΡΠΎΠ² ΡΡΡΡΠΆΠΊΠΈ, Π½ΠΎ ΡΠ°ΠΊΠΆΠ΅ ΠΎΡ ΡΠΌΠ°Π·ΠΎΡΠ½ΠΎ-ΠΎΡ Π»Π°ΠΆΠ΄Π°ΡΡΠ΅ΠΉ ΡΠΌΡΠ»ΡΡΠΈΠΈ ΠΈ ΠΊΠΎΠ½ΡΡΡΡΠΊΡΠΈΠΈ ΡΠ΅ΠΆΡΡΠ΅Π³ΠΎ ΠΈΠ½ΡΡΡΡΠΌΠ΅Π½ΡΠ°:
- Π‘ΠΌΠ°Π·ΠΎΡΠ½ΠΎ-ΠΎΡ Π»Π°ΠΆΠ΄Π°ΡΡΠ°Ρ ΡΠΌΡΠ»ΡΡΠΈΡ ΠΎΠΊΠ°Π·ΡΠ²Π°Π΅Ρ Π΄Π²Π° ΠΏΡΠΎΡΠΈΠ²ΠΎΠΏΠΎΠ»ΠΎΠΆΠ½ΡΡ Π΄Π΅ΠΉΡΡΠ²ΠΈΡ. Π‘ ΠΎΠ΄Π½ΠΎΠΉ ΡΡΠΎΡΠΎΠ½Ρ, ΠΎΡ Π»Π°ΠΆΠ΄Π΅Π½ΠΈΠ΅ ΡΠ½ΠΈΠΆΠ°Π΅Ρ ΡΠ΅ΠΌΠΏΠ΅ΡΠ°ΡΡΡΡ Π² Π·ΠΎΠ½Π΅ ΡΠ΅Π·Π° ΠΈ ΡΠ΅ΠΌ ΡΠ°ΠΌΡΠΌ ΠΏΠΎΠ²ΡΡΠ°Π΅Ρ Π²Π΅Π»ΠΈΡΠΈΠ½Ρ ΡΡΠ΅Π±ΡΠ΅ΠΌΠΎΠ³ΠΎ ΡΠ΅ΠΆΡΡΠ΅Π³ΠΎ ΡΡΠΈΠ»ΠΈΡ. Π‘ Π΄ΡΡΠ³ΠΎΠΉ ΡΡΠΎΡΠΎΠ½Ρ, ΡΠΌΠ°Π·ΠΊΠ° ΠΎΠ±Π»Π΅Π³ΡΠ°Π΅Ρ Π΄Π²ΠΈΠΆΠ΅Π½ΠΈΠ΅ ΡΡΡΡΠΆΠΊΠΈ ΠΈ ΡΠ½ΠΈΠΆΠ°Π΅Ρ Π²Π΅Π»ΠΈΡΠΈΠ½Ρ ΡΡΠ΅Π±ΡΠ΅ΠΌΠΎΠ³ΠΎ ΡΡΠΈΠ»ΠΈΡ ΡΠ΅Π·Π°Π½ΠΈΡ.
- ΠΠ΅ΠΎΠΌΠ΅ΡΡΠΈΡ ΡΠ΅ΠΆΡΡΠ΅Π³ΠΎ ΠΈΠ½ΡΡΡΡΠΌΠ΅Π½ΡΠ° Π²Π»ΠΈΡΠ΅Ρ Π½Π° ΡΡΠΈΠ»ΠΈΠ΅ ΡΠ΅Π·Π°Π½ΠΈΡ ΡΠ΅ΡΠ΅Π· ΠΏΠ΅ΡΠ΅Π΄Π½ΠΈΠΉ ΡΠ³ΠΎΠ» Π·ΡΠ±Π° Ξ³. Π§Π΅ΠΌ Π±ΠΎΠ»ΡΡΠ΅ ΡΡΠΎΡ ΡΠ³ΠΎΠ», ΡΠ΅ΠΌ ΠΌΠ΅Π½ΡΡΠ΅ ΡΠΆΠ°ΡΠΈΠ΅ ΡΡΡΡΠΆΠΊΠΈ ΠΈ Π½ΠΈΠΆΠ΅ ΡΡΠΈΠ»ΠΈΠ΅ ΡΠ΅Π·Π°Π½ΠΈΡ (ΡΠΈΡΡΠ½ΠΎΠΊ 3).
- Π‘ΡΠ΅ΠΏΠ΅Π½Ρ ΠΈΠ·Π½ΠΎΡΠ° ΡΠ΅ΠΆΡΡΠ΅ΠΉ ΠΊΡΠΎΠΌΠΊΠΈ ΠΈΠΌΠ΅Π΅Ρ ΠΎΡΠ½ΠΎΡΠΈΡΠ΅Π»ΡΠ½ΠΎ Π±ΠΎΠ»ΡΡΠΎΠ΅ Π²Π»ΠΈΡΠ½ΠΈΠ΅. ΠΠΎΡΡΠΎΠΌΡ Π² Ρ ΠΎΠ΄Π΅ Π΄Π»ΠΈΡΠ΅Π»ΡΠ½ΠΎΠΉ ΠΌΠ΅Ρ Π°Π½ΠΈΡΠ΅ΡΠΊΠΎΠΉ ΠΎΠ±ΡΠ°Π±ΠΎΡΠΊΠΈ Π²Π΅Π»ΠΈΡΠΈΠ½Π° ΡΠ΅ΠΆΡΡΠ΅Π³ΠΎ ΡΡΠΈΠ»ΠΈΡ Π²ΠΎΠ·ΡΠ°ΡΡΠ°Π΅Ρ.
Π ΠΈΡΡΠ½ΠΎΠΊ 3 β ΠΠ°Π²ΠΈΡΠΈΠΌΠΎΡΡΡ ΡΡΠΈΠ»ΠΈΡ ΡΠ΅Π·Π°Π½ΠΈΡ ΠΏΡΠΈ ΠΌΠ΅Ρ
Π°Π½ΠΈΡΠ΅ΡΠΊΠΎΠΉ ΠΎΠ±ΡΠ°Π±ΠΎΡΠΊΠ΅ Π°Π»ΡΠΌΠΈΠ½ΠΈΡ Π² Π·Π°Π²ΠΈΡΠΈΠΌΠΎΡΡΠΈ ΠΎΡ ΠΏΠ΅ΡΠ΅Π΄Π½Π΅Π³ΠΎ ΡΠ³Π»Π° Π·ΡΠ±Π° ΠΈ ΡΠΊΠΎΡΠΎΡΡΠΈ ΡΠ΅Π·Π°Π½ΠΈΡ
ΠΡΡΠΎΡΠ½ΠΈΠΊ: TALAT 3100
aluminium-guide.ru
Π’ΠΎΠΊΠ°ΡΠ½Π°Ρ ΠΎΠ±ΡΠ°Π±ΠΎΡΠΊΠ° Π°Π»ΡΠΌΠΈΠ½ΠΈΡ | Π‘ΡΠ°Π½ΠΊΠΎΠ½
Π’ΠΎΠΊΠ°ΡΠ½Π°Ρ ΠΎΠ±ΡΠ°Π±ΠΎΡΠΊΠ° Π°Π»ΡΠΌΠΈΠ½ΠΈΡ Π² ΡΠΈΡΡΠΎΠΌ Π²ΠΈΠ΄Π΅ β ΡΠ»ΠΎΠΆΠ½ΡΠΉ ΠΏΡΠΎΡΠ΅ΡΡ, ΡΡΠ΅Π±ΡΡΡΠΈΠΉ Π·Π½Π°ΡΠΈΡΠ΅Π»ΡΠ½ΡΡ Π·Π°ΡΡΠ°Ρ ΡΠ°Π±ΠΎΡΠ΅Π³ΠΎ Π²ΡΠ΅ΠΌΠ΅Π½ΠΈ. ΠΠ»Ρ ΠΏΡΠΎΠΈΠ·Π²ΠΎΠ΄ΡΡΠ²Π° Π΄Π΅ΡΠ°Π»Π΅ΠΉ ΡΠ°ΡΡΠΎ ΠΈΡΠΏΠΎΠ»ΡΠ·ΡΠ΅ΡΡΡ ΡΠΎΠΊΠ°ΡΠ½Π°Ρ ΠΎΠ±ΡΠ°Π±ΠΎΡΠΊΠ° Π°Π»ΡΠΌΠΈΠ½ΠΈΠ΅Π²ΡΡ ΡΠΏΠ»Π°Π²ΠΎΠ², ΠΊΠΎΡΠΎΡΡΠ΅ Ρ ΠΎΡΠΎΡΠΎ ΠΏΠΎΠ΄Π΄Π°ΡΡΡΡ ΡΠ΅Π·Π°Π½ΠΈΡ ΠΈ Π΄ΡΡΠ³ΠΈΠΌ Π²ΠΈΠ΄Π°ΠΌ ΠΌΠ΅Ρ Π°Π½ΠΈΡΠ΅ΡΠΊΠΎΠΉ ΠΌΠ΅ΡΠ°Π»Π»ΠΎΠΎΠ±ΡΠ°Π±ΠΎΡΠΊΠΈ.
Π‘ΠΏΠ»Π°Π²Ρ ΠΈΠ· Π°Π»ΡΠΌΠΈΠ½ΠΈΡ ΠΈΠΌΠ΅ΡΡ ΡΠ²ΠΎΠΉΡΡΠ²ΠΎ Π΄Π΅Π»ΠΈΡΡΡΡ Π½Π° ΡΠ²ΠΎΡ ΠΊΠ²Π°Π»ΠΈΡΠΈΠΊΠ°ΡΠΈΡ. ΠΠ½ΠΈ ΠΌΠΎΠ³ΡΡ Π±ΡΡΡ Π»ΠΈΡΠ΅ΠΉΠ½ΡΠ΅ ΠΈ Π΄Π΅ΡΠΎΡΠΌΠΈΡΡΠ΅ΠΌΡΠ΅. Π‘Π΅Π³ΠΎΠ΄Π½Ρ Π°ΠΊΡΠΈΠ²Π½ΠΎΠ΅ ΠΌΠ΅ΡΡΠΎ Π½Π° ΡΡΠ½ΠΊΠ΅ Π·Π°Π½ΠΈΠΌΠ°ΡΡ ΠΈΠΌΠ΅Π½Π½ΠΎ Π΄Π΅ΡΠΎΡΠΌΠΈΡΡΠ΅ΠΌΡΠ΅ ΡΠΏΠ»Π°Π²Ρ, ΠΎ Π½ΠΈΡ ΠΌΡ ΠΈ Π±ΡΠ΄Π΅ΠΌ Π³ΠΎΠ²ΠΎΡΠΈΡΡ.
Π‘ΠΏΠ»Π°Π²Ρ Π΄Π΅ΡΠΎΡΠΌΠΈΡΡΠ΅ΠΌΠΎΠ³ΠΎ Ρ Π°ΡΠ°ΠΊΡΠ΅ΡΠ° ΠΌΠΎΠ³ΡΡ ΡΠ°Π·Π΄Π΅Π»ΡΡΡΡΡ ΠΏΠΎ ΡΠ²ΠΎΠ΅ΠΉ ΠΊΠ²Π°Π»ΠΈΡΠΈΠΊΠ°ΡΠΈΠΈ, ΠΊ ΠΊΠΎΡΠΎΡΠΎΠΉ ΠΎΡΠ½ΠΎΡΠΈΡΡΡ ΡΠΏΠΎΡΠΎΠ± ΡΠΏΡΠΎΡΠ½Π΅Π½ΠΈΡ. Π’ΠΎΠΊΠ°ΡΠ½ΡΠ΅ ΡΠ°Π±ΠΎΡΡ Ρ ΡΠ°ΠΊΠΈΠΌΠΈ ΡΠΏΠ»Π°Π²Π°ΠΌΠΈ ΠΌΠΎΠ³ΡΡ ΠΏΡΠΎΠ²ΠΎΠ΄ΠΈΡΡΡΡ Π½Π° Π»ΡΠ±ΡΡ ΡΡΡΡΠΎΠΉΡΡΠ²Π°Ρ ΠΎΠ±ΡΠ°Π±ΠΎΡΠΊΠΈ. ΠΠ΄Π½Π°ΠΊΠΎ ΡΠ»Π΅Π΄ΡΠ΅Ρ ΠΏΠΎΠΌΠ½ΠΈΡΡ, ΡΡΠΎ ΡΠΏΠΎΡΠΎΠ± ΡΠΏΡΠΎΡΠ½Π΅Π½ΠΈΡ ΠΏΠΎΠ΄ΡΠ°Π·ΡΠΌΠ΅Π²Π°Π΅Ρ ΠΏΠΎΠ΄ ΡΠΎΠ±ΠΎΠΉ ΡΠΏΡΠ°Π²Π»Π΅Π½ΠΈΠ΅ Π°Π»ΡΠΌΠΈΠ½ΠΈΠ΅Π²ΡΠΌΠΈ ΡΠΏΠ»Π°Π²Π°ΠΌΠΈ ΠΏΡΠΈ ΠΏΠΎΠΌΠΎΡΠΈ ΡΠ΅ΠΌΠΏΠ΅ΡΠ°ΡΡΡΡ ΠΈ Π΄Π°Π²Π»Π΅Π½ΠΈΡ. ΠΠΎ Π²ΡΠ΅ΠΌΡ ΡΠΎΠΊΠ°ΡΠ½ΠΎΠΉ ΠΎΠ±ΡΠ°Π±ΠΎΡΠΊΠΈ ΠΌΠ°ΡΠ΅ΡΠΈΠ°Π»Ρ ΠΏΠΎΠ΄Π΄Π°ΡΡΡΡ ΡΠΏΠ΅ΡΠΈΠ°Π»ΡΠ½ΠΎΠΌΡ Π²ΠΎΠ·Π΄Π΅ΠΉΡΡΠ²ΠΈΡ. ΠΡΠΈ ΠΎΠ±ΡΠ°Π±ΠΎΡΠΊΠ΅ ΡΠΎΠΊΠ°ΡΠ½ΡΡ ΡΠ»Π΅ΠΌΠ΅Π½ΡΠΎΠ² ΡΠ»Π΅Π΄ΡΠ΅Ρ ΠΎΠ±ΡΠ°ΡΠ°ΡΡ Π²Π½ΠΈΠΌΠ°Π½ΠΈΠ΅ Π½Π° Π²ΡΠ΅ Π΄Π΅ΡΠ°Π»ΠΈ.
ΠΡΠΎΠΌΠ΅ ΡΡΠΎΠ³ΠΎ ΡΠ»Π΅Π΄ΡΠ΅Ρ ΠΎΠ±ΡΠ°ΡΠΈΡΡ Π²Π½ΠΈΠΌΠ°Π½ΠΈΠ΅ Π½Π° ΡΠ²ΠΎΠΉΡΡΠ²Π° Π°Π»ΡΠΌΠΈΠ½ΠΈΠ΅Π²ΡΡ Π²Π΅ΡΠ΅ΡΡΠ². Π‘ΠΏΠ»Π°Π²Ρ ΡΠ°ΠΊΠΎΠ³ΠΎ Ρ Π°ΡΠ°ΠΊΡΠ΅ΡΠ° ΠΌΠΎΠ³ΡΡ Π΄Π΅Π»ΠΈΡΡΡΡ ΠΏΠΎ ΡΠ²ΠΎΠ΅ΠΉ ΠΏΡΠΎΡΠ½ΠΎΡΡΠΈ Π½Π° ΠΏΡΠΎΡΠ½ΠΎΡΡΡ Π½ΠΈΠ·ΠΊΠΎΠ³ΠΎ ΡΡΠΎΠ²Π½Ρ, ΡΡΠ΅Π΄Π½Π΅Π³ΠΎ ΠΈ Π²ΡΡΠΎΠΊΠΎΠ³ΠΎ. Π’ΠΎΡΠ΅Π½ΠΈΠ΅ Π»ΡΡΡΠ΅ Π²ΡΠ΅Π³ΠΎ ΠΏΡΠΎΠΈΡΡ ΠΎΠ΄ΠΈΡ Π½Π° ΡΡΠ΅Π΄Π½Π΅ΠΌ ΡΡΠΎΠ²Π½Π΅. ΠΠ° ΡΡΠ΅Π΄Π½Π΅ΠΌ ΡΡΠΎΠ²Π½Π΅ ΠΏΠ»ΠΎΡΠ½ΠΎΡΡΡ ΡΠ»Π΅ΠΌΠ΅Π½ΡΠΎΠ² ΠΎΡΠ΅Π½Ρ Π²ΡΡΠΎΠΊΠ°, ΡΡΠΎ ΠΏΠΎΠ·Π²ΠΎΠ»ΡΠ΅Ρ Π²ΠΎ Π²ΡΠ΅ΠΌΡ ΠΎΠ±ΡΠ°Π±ΠΎΡΠΊΠΈ ΡΠΎΠΊΠ°ΡΠ½ΡΡ ΠΈΠ·Π΄Π΅Π»ΠΈΠΉ Π²ΡΠΏΠΎΠ»Π½ΡΡΡ Π²ΡΠ΅ ΠΏΠ°ΡΠ°ΠΌΠ΅ΡΡΡ ΠΊΠ°ΡΠ΅ΡΡΠ²Π°.
ΠΠ΅ΡΠ΅ΡΡΠ²Π° ΠΈΠ· ΠΌΡΠ³ΠΊΠΎΠ³ΠΎ ΠΌΠ΅ΡΠ°Π»Π»Π°, ΠΊΠΎΡΠΎΡΡΠ΅ ΡΠ°Π·ΡΠ°Π±Π°ΡΡΠ²Π°ΡΡΡΡ ΠΏΠΎΠ΄ Π΄Π°Π²Π»Π΅Π½ΠΈΠ΅ΠΌ ΠΈΠΌΠ΅ΡΡ ΡΠ²ΠΎΠΉΡΡΠ²ΠΎ ΡΠΏΡΠΎΡΠ½ΡΡΡΡΡ ΡΠΎΠ»ΡΠΊΠΎ Ρ ΠΎΠ»ΠΎΠ΄Π½ΠΎΠΉ ΠΏΡΠΎΠΊΠ°ΡΠΊΠΎΠΉ. ΠΠ΅ΡΠΎΡΠΌΠΈΡΠΎΠ²Π°Π½ΠΈΠ΅ ΡΠ°ΠΊΠΎΠ³ΠΎ ΠΎΠ±ΡΠ°Π·ΡΠ° ΠΏΡΠΈΠ²ΠΎΠ΄ΠΈΡ ΠΊ ΡΠΎΠΌΡ, ΡΡΠΎ ΡΠΏΠ»Π°Π²Ρ Π°Π»ΡΠΌΠΈΠ½ΠΈΠ΅Π²ΠΎΠ³ΠΎ Ρ Π°ΡΠ°ΠΊΡΠ΅ΡΠ° ΡΡΠ°Π½ΠΎΠ²ΡΡΡΡ ΠΏΡΠΎΡΠ½ΡΠΌΠΈ ΠΈ ΡΠ²Π΅ΡΠ΄ΡΠΌΠΈ. ΠΠ· ΠΌΠΈΠ½ΡΡΠΎΠ² ΠΌΠΎΠΆΠ½ΠΎ ΠΎΡΠΌΠ΅ΡΠΈΡΡ ΡΠΎΡ ΡΠ°ΠΊΡ, ΡΡΠΎ ΡΠΌΠ΅Π½ΡΡΠ°Π΅ΡΡΡ ΠΏΠ»Π°ΡΡΠΈΡΠ½ΠΎΡΡΡ. ΠΠ΄Π½Π°ΠΊΠΎ ΡΡΠΎ Π½Π΅ ΡΠΈΠ»ΡΠ½ΠΎ ΠΎΡΡΠ°ΠΆΠ°Π΅ΡΡΡ, ΠΏΠΎ ΠΏΡΠΈΡΠΈΠ½Π΅ ΡΠΎΠ³ΠΎ, ΡΡΠΎ ΠΏΠ»Π°ΡΡΠΈΡΠ½ΠΎΡΡΡ ΠΌΠΎΠΆΠ½ΠΎ Π²ΠΎΡΡΡΠ°Π½ΠΎΠ²ΠΈΡΡ ΡΠ΅ΠΊΡΠΈΡΡΠ°Π»Π»ΠΈΠ·Π°ΡΠΈΠΎΠ½Π½ΡΠΌ ΠΌΠ΅ΡΠΎΠ΄ΠΎΠΌ.
Π‘ΡΡΠ΅ΡΡΠ²ΡΠ΅Ρ ΡΡΠ΄ Π²Π°ΡΠΈΠ°Π½ΡΠΎΠ² ΠΏΠΎΠ΄Π»Π΅ΠΆΠ°ΡΠΈΡ ΡΠ΅ΡΠΌΠ°Π»ΡΠ½ΠΎΠΉ ΠΎΠ±ΡΠ°Π±ΠΎΡΠΊΠ΅. Π ΠΏΡΠΈΠ½ΡΠΈΠΏΠ΅ Π°Π»ΡΠΌΠΈΠ½ΠΈΠΉ Ρ ΠΎΡΠΎΡΠΎ ΠΏΠΎΠ΄Π΄Π°ΡΡΡΡ ΡΡΠΎΠΌΡ ΠΏΡΠΎΡΠ΅ΡΡΡ. Π’Π΅ΠΌ Π±ΠΎΠ»Π΅Π΅ ΠΊΠ°ΠΊ ΡΠ°ΠΊΠΎΠ²ΠΎΠΉ ΡΠΏΠ»Π°Π², β ΠΎΠ½ ΠΎΡΠ΅Π½Ρ ΡΠ΅Π½ΠΈΡΡΡ. Π‘Π°ΠΌΡΠΌΠΈ ΡΠ°ΡΠΏΡΠΎΡΡΡΠ°Π½Π΅Π½Π½ΡΠΌΠΈ ΡΠ²Π»ΡΡΡΡΡ ΡΠ»Π΅Π΄ΡΡΡΠ΅ ΡΠΏΠ»Π°Π²Ρ ΠΈΠ· Π°Π»ΡΠΌΠΈΠ½ΠΈΡ, ΠΊΠΎΡΠΎΡΡΠ΅ ΠΎΡΡΠ°ΠΆΠ°ΡΡ ΠΌΠ°ΡΠΊΠΈΡΠΎΠ²ΠΊΡ ΠΏΡΠΎΠΊΠ°ΡΠ°:
- Π±Π΅Π· ΠΎΠ±ΠΎΠ·Π½Π°ΡΠ΅Π½ΠΈΡ;
- ΠΎΡΠΎΠΆΠΆΠ΅Π½Π½ΡΠ΅;
- ΠΏΡΠΎΡΠ½ΠΎΠ΅ ΡΡΠ΅Π΄Π½Π΅Π³ΠΎ ΠΊΠ»Π°ΡΡΠ°;
- ΠΏΡΠΎΡΠ½ΠΎΠ΅ Π²ΡΡΠΎΠΊΠΎΠ³ΠΎ ΠΊΠ»Π°ΡΡΠ°;
ΠΠ΅ΠΊΠΎΡΠΎΡΡΠ΅ ΡΠΎΠ΅Π΄ΠΈΠ½Π΅Π½ΠΈΡ Π΄ΠΎΠ»ΠΆΠ½Ρ ΠΏΡΠΎΡ ΠΎΠ΄ΠΈΡΡ ΡΠ΅ΡΠΌΠΎΠΌΠ΅Ρ Π°Π½ΠΈΡΠ΅ΡΠΊΡΡ ΠΎΠ±ΡΠ°Π±ΠΎΡΠΊΡ. Π ΠΎΡΠ½ΠΎΠ²Π½ΠΎΠΌ ΡΡΠΎ ΠΏΡΠΎΠΈΠ·Π²ΠΎΠ΄ΠΈΡΡΡ Ρ ΠΏΠΎΠΌΠΎΡΡΡ ΡΠΏΡΠΎΡΠ½Π΅Π½ΠΈΡ ΠΌΠ°ΡΠ΅ΡΠΈΠ°Π»ΠΎΠ² Π½Π° Π²ΡΡΠΎΠΊΠΎΠΉ ΡΠ΅ΠΌΠΏΠ΅ΡΠ°ΡΡΡΠ΅. Π ΡΡΠΎΠΌ ΡΠ»ΡΡΠ°Π΅ Π½Π°Π³Π°ΡΡΠΎΠ²ΠΊΠ° Π²ΡΠΏΠΎΠ»Π½ΡΠ΅ΡΡΡ ΠΏΠΎΡΠ»Π΅ ΠΏΡΠΎΡΠ΅ΡΡΠ° Π·Π°ΠΊΠ°Π»ΠΊΠΈ. ΠΠΎΠ³Π΄Π° Π²ΡΠΏΠΎΠ»Π½ΡΠ΅ΡΡΡ ΡΡΠΎΡ ΠΏΡΠΎΡΠ΅ΡΡ, ΠΌΠ°ΡΠΊΠΈΡΠΎΠ²ΠΎΡΠ½ΡΠ΅ ΡΠ»Π΅ΠΌΠ΅Π½ΡΡ ΠΎΠ±ΠΎΠ·Π½Π°ΡΠ°ΡΡΡΡ ΠΊΠ°ΠΊ: Π’Π ΠΈΠ»ΠΈ Π’1Π. ΠΡΡΡ ΡΡΠ΄ ΠΈ Π΄ΡΡΠ³ΠΈΡ ΡΠ΅ΠΆΠΈΠΌΠΎΠΌ, ΠΊ ΠΊΠΎΡΠΎΡΡΠΌ ΠΎΡΠ½ΠΎΡΠΈΡΡΡ Π’2, Π’5. ΠΠ΄Π½Π°ΠΊΠΎ ΠΈΡ ΡΠ΅ΠΆΠ΅ ΠΈΡΠΏΠΎΠ»ΡΠ·ΡΡΡ, ΡΠ°ΠΊ ΠΊΠ°ΠΊ ΠΏΡΠΎΡΠ½ΠΎΡΡΡ ΠΈΡ Π½Π° ΡΡΠ΄ ΠΌΠ΅Π½ΡΡΠ΅, Π° ΡΡΠΎ ΡΠΏΠΎΡΠΎΠ±ΡΡΠ²ΡΠ΅Ρ ΠΏΠΎΡΠ²Π»Π΅Π½ΠΈΡ ΠΊΠΎΡΡΠΎΠ·ΠΈΠΉ ΠΈ Π² ΠΏΠΎΡΠ»Π΅Π΄ΡΡΠ²ΠΈΠΈ ΡΠ°Π·ΡΡΡΠ΅Π½ΠΈΠΈ Π°Π»ΡΠΌΠΈΠ½ΠΈΡ.
ΠΠ° ΡΡΠΎ ΡΠ»Π΅Π΄ΡΠ΅Ρ ΠΎΠ±ΡΠ°ΡΠΈΡΡ Π²Π½ΠΈΠΌΠ°Π½ΠΈΠ΅?
ΠΠΎΠ½ΡΠ΅Π½ΡΡΠ°ΡΠΈΡ ΠΌΠ°ΡΠ΅ΡΠΈΠ°Π»ΠΎΠ² ΠΈΠ· Π°Π»ΡΠΌΠΈΠ½ΠΈΡ Π΄ΠΎΠ»ΠΆΠ½Π° Π±ΡΡΡ Π² ΡΠ°ΠΉΠΎΠ½Π΅ 2,7 Π³/ΡΠΌ. ΠΠ½Π° ΠΈΠ·ΠΌΠ΅ΡΡΠ΅ΡΡΡ Π²ΠΎ Π²ΡΠ΅ΠΌΡ Π²ΡΡΠΎΠΊΠΎΠΊΠ²Π°Π»ΠΈΡΠΈΡΠΈΡΠΎΠ²Π°Π½Π½ΡΡ ΡΠ°Π±ΠΎΡ ΠΎΡ 2,65 Π³/ΡΠΌ Π΄ΠΎ 2,85 Π³/ΡΠΌ, Π² ΠΎΡΠ½ΠΎΠ²Π½ΠΎΠΌ ΠΈΡΠΏΠΎΠ»ΡΠ·ΡΠ΅ΡΡΡ Π΄Π»Ρ B95.
ΠΠ·-Π·Π° ΠΌΠ°Π»ΠΎΠΉ ΠΏΠ»ΠΎΡΠ½ΠΎΡΡΠΈ ΡΠΏΠ»Π°Π²Π° ΠΎΠΏΡΠ΅Π΄Π΅Π»ΡΠ½Π½ΡΠ΅ Π·Π½Π°ΡΠ΅Π½ΠΈΡ ΠΏΡΠΎΡΠ½ΠΎΡΡΠΈ, ΡΠΏΡΡΠ³ΠΎΠ³ΠΎ ΠΌΠΎΠ΄ΡΠ»Ρ Π΄Π»Ρ ΠΊΠ°ΡΠ΅ΡΡΠ²Π΅Π½Π½ΡΡ ΠΌΠ°ΡΠ΅ΡΠΈΠ°Π»ΠΎΠ² ΠΈΠ· Π°Π»ΡΠΌΠΈΠ½ΠΈΡ ΡΠΎΠΏΠΎΡΡΠ°Π²ΠΈΠΌΡ Ρ ΡΠ΄Π΅Π»ΡΠ½ΡΠΌΠΈ Π²Π΅Π»ΠΈΡΠΈΠ½Π°ΠΌΠΈ Π²Π΅ΡΠ΅ΡΡΠ² ΠΈΠ· ΡΠΈΡΠ°Π½Π° ΠΈΠ»ΠΈ ΡΡΠ°Π»ΠΈ. ΠΡΠΎ ΡΠ²Π»ΡΠ΅ΡΡΡ Π²Π΅ΡΠΎΠΌΡΠΌ Π°ΡΠ³ΡΠΌΠ΅Π½ΡΠΎΠΌ. ΠΠΌΠ΅Π½Π½ΠΎ ΠΏΠΎ ΡΡΠΎΠΉ ΠΏΡΠΈΡΠΈΠ½Π΅ Ρ Π°Π»ΡΠΌΠΈΠ½ΠΈΡ Π΅ΡΡΡ Π²ΠΎΠ·ΠΌΠΎΠΆΠ½ΠΎΡΡΡ ΠΊΠΎΠ½ΠΊΡΡΠΈΡΠΎΠ²Π°ΡΡ Ρ ΡΠΈΡΠ°Π½ΠΎΠΌ ΠΈΠ»ΠΈ ΡΡΠ°Π»ΡΡ, ΠΎΠ΄Π½Π°ΠΊΠΎ ΡΡΠΎ Π²ΠΎΠ·ΠΌΠΎΠΆΠ½ΠΎ Π΄ΠΎ ΠΎΠΏΡΠ΅Π΄Π΅Π»ΡΠ½Π½ΡΡ ΡΠ΅ΠΌΠΏΠ΅ΡΠ°ΡΡΡΠ½ΡΡ ΡΡΠ»ΠΎΠ²ΠΈΠΉ, ΠΊΠΎΡΠΎΡΡΠ΅ Π½Π΅ ΠΏΡΠ΅Π²ΡΡΠ°ΡΡ 200 Π³ΡΠ°Π΄ΡΡΠΎΠ².
ΠΠ΅ΠΊΠΎΡΠΎΡΡΠ΅ ΡΠΎΠ΅Π΄ΠΈΠ½Π΅Π½ΠΈΡ ΠΈΠΌΠ΅ΡΡ Π½Π΅Π²ΡΡΠΎΠΊΠΎΠ΅ ΠΊΠ°ΡΠ΅ΡΡΠ²ΠΎ ΡΠ»Π΅ΠΊΡΡΠΎΠΏΡΠΎΠ²ΠΎΠ΄Π½ΠΎΡΡΠΈ ΠΈ ΡΠ΅ΠΏΠ»ΠΎΠΏΡΠΎΠ²ΠΎΠ΄Π½ΠΎΡΡΠΈ, ΡΡΠΎ Π²ΡΠ·ΡΠ²Π°Π΅Ρ ΠΊΠΎΡΡΠΎΠ·ΠΈΡ Π² ΡΠ΅ΡΠ΅Π½ΠΈΠ΅ Π½Π΅ΡΠΊΠΎΠ»ΡΠΊΠΎ Π»Π΅Ρ.
ΠΠ°Π²Π°ΠΉΡΠ΅ ΠΏΠ΅ΡΠ΅ΠΉΠ΄ΡΠΌ ΠΊ ΡΠ²ΠΎΠΉΡΡΠ²Ρ ΠΊΠΎΡΡΠΎΠ·ΠΈΠΈ, ΡΡΠΎ Π½Π΅ΠΎΠ±Ρ ΠΎΠ΄ΠΈΠΌΠΎ Π·Π½Π°ΡΡ ΠΎ Π½Π΅ΠΉ?
ΠΠΎ ΡΡΠ°ΡΠΈΡΡΠΈΠΊΠ΅ ΠΈΠ·Π²Π΅ΡΡΠ½ΠΎ, ΡΡΠΎ ΡΠΏΠ»Π°Π²Ρ, Π² ΠΊΠΎΡΠΎΡΡΠ΅ Π²Ρ ΠΎΠ΄ΡΡ ΠΠΡ ΠΈ ΠΠΠ³ ΠΈΠΌΠ΅ΡΡ Π»ΡΡΡΠΈΠ΅ ΠΊΠΎΡΡΠΎΠ·ΠΈΠΎΠ½Π½ΡΠ΅ ΡΠ²ΠΎΠΉΡΡΠ²Π°. ΠΠ΄Π½Π°ΠΊΠΎ Ρ ΡΠ΄ΡΠΈΠΌΠΈ Π±ΡΠ»ΠΈ Π·Π°ΠΌΠ΅ΡΠ΅Π½Ρ ΠΌΠ°ΡΠ΅ΡΠΈΠ°Π»Ρ Π16, B95 (ΠΎ ΠΊΠΎΡΠΎΡΠΎΠΌ ΡΠΆΠ΅ Π±ΡΠ»Π° ΠΈΠ½ΡΠΎΡΠΌΠ°ΡΠΈΡ Π² Π½Π°ΡΠ΅ΠΉ ΡΡΠ°ΡΡΠ΅ ΠΈ ΠΠ). ΠΡΠΎΠΌΠ΅ ΡΡΠΎΠΉ ΠΈΠ½ΡΠΎΡΠΌΠ°ΡΠΈΠΈ ΡΠ»Π΅Π΄ΡΠ΅Ρ ΡΡΠΈΡΡΠ²Π°ΡΡ, ΡΡΠΎ ΡΠ²ΠΎΠΉΡΡΠ²Π° Π²Π΅ΡΠ΅ΡΡΠ² ΡΠ°ΠΊΠΆΠ΅ ΡΠΈΠ»ΡΠ½ΠΎ Π·Π°Π²ΠΈΡΡΡ ΠΎΡ ΡΠ΅ΠΆΠΈΠΌΠ° Π·Π°ΠΊΠ°Π»ΠΊΠΈ ΠΈ Π²ΠΎΠ·ΡΠ°ΡΡΠ°. ΠΡΠΌΠ΅ΡΠΈΠΌ, ΡΡΠΎ Π½Π΅ΠΎΠ±Ρ ΠΎΠ΄ΠΈΠΌΠΎ ΡΠ°ΠΊΠΆΠ΅ ΠΎΠ±ΡΠ°ΡΠ°ΡΡ Π²Π½ΠΈΠΌΠ°Π½ΠΈΠ΅ Π½Π° ΡΠΎ, Π³Π΄Π΅ ΠΈΡΠΏΠΎΠ»ΡΠ·ΡΡΡΡΡ Π²Π΅ΡΠ΅ΡΡΠ²Π° ΠΈΠ»ΠΈ Π΄Π»Ρ ΡΠ΅Π³ΠΎ ΠΎΠ½ΠΈ ΠΏΡΠ΅Π΄Π½Π°Π·Π½Π°ΡΠ°ΡΡΡΡ. Π ΠΏΡΠΈΠΌΠ΅ΡΡ, ΡΠΏΠ»Π°Π² D16 ΠΏΡΠΈΠΌΠ΅Π½ΡΠ΅ΡΡΡ ΠΈΡΠΊΠ»ΡΡΠΈΡΠ΅Π»ΡΠ½ΠΎ Π² ΡΠΎΡΡΠΎΡΠ½ΠΈΠΈ, ΠΏΡΠΈΠ±Π»ΠΈΠΆΠ΅Π½Π½ΠΎΠΌ ΠΊ ΡΠΎΡΡΠ°ΡΠ΅Π½Π½ΠΎΠΌΡ. Π’Π΅ΠΌ Π½Π΅ ΠΌΠ΅Π½Π΅Π΅ ΠΏΠΎΡΠ»Π΅ 80 Π³ΡΠ°Π΄ΡΡΠΎΠ² ΠΏΠΎ Π¦Π΅Π»ΡΡΠΈΡ Π΅Π³ΠΎ ΠΊΠ°ΡΠ΅ΡΡΠ²Π° Π½Π°ΠΌΠ½ΠΎΠ³ΠΎ ΡΠΈΠ»ΡΠ½Π΅Π΅ ΡΡ ΡΠ΄ΡΠ°ΡΡΡΡ, ΡΡΠΎ Π²Π»Π΅ΡΡΡ Π·Π° ΡΠΎΠ±ΠΎΠΉ Π½Π΅Π³Π°ΡΠΈΠ²Π½ΡΠ΅ ΡΠ΅Π·ΡΠ»ΡΡΠ°ΡΡ. ΠΠΎ Π²ΡΠ΅ΠΌΡ ΡΠ°Π±ΠΎΡΡ Π½Π° ΡΠΎΠΊΠ°ΡΠ½ΠΎΠΌ ΡΡΠ°Π½ΠΊΠ΅ ΡΠ°ΡΡΠΎ ΠΌΠΎΠΆΠ½ΠΎ ΡΡΠ»ΡΡΠ°ΡΡ ΡΠ°Π·Π³ΠΎΠ²ΠΎΡΡ ΠΎ ΠΊΠΎΡΡΠΎΠ·ΠΈΠΈ, ΠΎΠ΄Π½Π°ΠΊΠΎ Π±ΠΎΠ»ΡΡΠΈΠ½ΡΡΠ²ΠΎ Π²Π΅ΡΠ΅ΡΡΠ² ΠΏΠΎΠ΄Π²Π΅ΡΠ³Π°ΡΡΡΡ ΠΊΠΎΡΡΠΎΠ·ΠΈΠΈ ΠΏΠΎΠ΄ ΡΠΈΠ»ΡΠ½ΡΠΌ Π½Π°ΠΏΡΡΠΆΠ΅Π½ΠΈΠ΅ΠΌ.
ΠΠΎ Π²ΡΠ΅ΠΌΡ ΠΎΠ±ΡΠ°Π±ΠΎΡΠΊΠΈ ΡΠ°ΠΊΠΆΠ΅ ΡΠ°ΡΡΠΎ ΡΠ΄Π΅Π»ΡΡΡ Π²Π½ΠΈΠΌΠ°Π½ΠΈΠ΅ ΠΈ ΡΠ²Π°ΡΠΈΠ²Π°Π΅ΠΌΠΎΡΡΠΈ Π²Π΅ΡΠ΅ΡΡΠ². ΠΠ΅Π΄Ρ Π²ΡΠ΅ΠΌ Ρ ΠΎΡΠΎΡΠΎ ΠΈΠ·Π²Π΅ΡΡΠ½ΠΎ Π² ΠΌΠ΅ΡΠ°Π»Π»ΠΎΠΎΠ±ΡΠ°Π±ΠΎΡΠΊΠ΅, ΡΡΠΎ ΡΠ²Π°ΡΠΈΠ²Π°Π΅ΠΌΠΎΡΡΡ ΠΏΡΠΎΡ ΠΎΠ΄ΠΈΡ Ρ ΠΏΠΎΠΌΠΎΡΡΡ Π²ΡΠ΅Ρ Π²ΠΈΠ΄ΠΎΠ² ΡΠ²Π°ΡΠΊΠΈ, ΡΠ°ΠΊΠΈΡ ΠΊΠ°ΠΊ ΠΠΡ ΠΈ ΠΠΠ³. ΠΠΎ Π²ΡΠ΅ΠΌΡ ΡΠ²Π°ΡΠΊΠΈ Π½Π΅Π³Π°ΡΡΠΎΠ²Π°Π½Π½ΠΎΠ³ΠΎ ΠΏΡΠΎΠΊΠ°ΡΠ°, ΡΠ°ΠΌ, Π³Π΄Π΅ Π½Π°Ρ ΠΎΠ΄ΠΈΡΡΡ ΡΠΎΠ² ΠΏΡΠΎΠ²ΠΎΠ΄ΡΡ ΠΎΡΠΆΠΈΠ³, ΠΏΠΎ ΡΡΠΎΠΉ ΠΏΡΠΈΡΠΈΠ½Π΅ ΡΠΎΠ² ΡΠΎΠΎΡΠ²Π΅ΡΡΡΠ²ΡΠ΅Ρ Π²ΡΠ΅ΠΌ ΠΏΠ°ΡΠ°ΠΌΠ΅ΡΡΠ°ΠΌ ΠΊΠ°ΡΠ΅ΡΡΠ²Π°, Π° ΡΠΎΡΡΠΎΡΠ½ΠΈΠ΅ ΡΠΎΠΎΡΠ²Π΅ΡΡΡΠ²ΡΠ΅Ρ ΡΠΎΡΡΠΎΡΠ½ΠΈΡ ΠΊΠ°ΡΠ΅ΡΡΠ²Π΅Π½Π½ΠΎΠΉ ΡΠ°Π±ΠΎΡΡ.
ΠΠ°ΡΠ΅ΡΠΈΠ°Π»Ρ ΡΠ΅ΡΠΌΠΎΡΠΏΡΠΎΡΠ½ΡΠ΅ΠΌΠΎΠ³ΠΎ ΡΠΎΡΠΌΠ°ΡΠ° ΠΌΠΎΠ³ΡΡ Π±ΡΡΡ Π±ΠΎΠ»Π΅Π΅ ΡΠΏΡΠΎΡΠ½Π΅Π½Π½ΡΠΌΠΈ ΠΏΠΎΡΠ»Π΅ ΡΠΎΠ³ΠΎ, ΠΊΠ°ΠΊ ΠΏΡΠΎΡ ΠΎΠ΄ΡΡ Π²ΡΠ΅ ΡΠ°Π±ΠΎΡΡ. ΠΠ΄Π½Π°ΠΊΠΎ ΡΠ»Π΅Π΄ΡΠ΅Ρ ΠΎΡΠΌΠ΅ΡΠΈΡΡ, ΡΡΠΎ ΠΈΡΡ ΠΎΠ΄Π½ΡΠ΅ ΠΏΠΎΠ»ΡΡΠ°Π±ΡΠΈΠΊΠ°ΡΡ Π½Π΅ Π΄ΠΎΠ»ΠΆΠ½Ρ ΠΏΠΎΠ΄Π²Π΅ΡΠ³Π°ΡΡΡΡ ΡΠ΅ΡΠΌΠΈΡΠ΅ΡΠΊΠΎΠΉ ΠΎΠ±ΡΠ°Π±ΠΎΡΠΊΠ΅, ΠΈΠ½Π°ΡΠ΅ ΡΠ²ΠΎΠΉΡΡΠ²ΠΎ Π°Π»ΡΠΌΠΈΠ½ΠΈΡ Π±ΡΠ΄Π΅Ρ ΠΎΡΠ΅Π½Ρ Π½ΠΈΠ·ΠΊΠΈΠΌ.
ΠΡΠΌΠ΅ΡΠΈΠΌ, ΡΡΠΎ ΡΠ΅Π³ΠΎΠ΄Π½Ρ ΠΈΠ·Π³ΠΎΡΠ°Π²Π»ΠΈΠ²Π°Π΅ΡΡΡ ΠΌΠ½ΠΎΠ³ΠΎ ΠΌΠ°ΡΠ΅ΡΠΈΠ°Π»ΠΎΠ², Π³Π΄Π΅ ΠΎΡΠ½ΠΎΠ²Π½ΠΎΠΉ ΡΠΎΡΡΠ°Π²Π»ΡΡΡΠ΅ΠΉ ΡΠ²Π»ΡΠ΅ΡΡΡ Π°Π»ΡΠΌΠΈΠ½ΠΈΠΉ: Π°Π»ΡΠΌΠΈΠ½ΠΈΠ΅Π²ΡΠ΅ ΠΏΡΠΎΡΠΈΠ»ΠΈ Π΄Π»Ρ ΠΏΠ°Π½Π΅Π»Π΅ΠΉ, Π°Π»ΡΠΌΠΈΠ½ΠΈΠ΅Π²ΡΠ΅ Π²ΡΡΠ»ΠΊΠΈ ΠΈ ΠΌΠ½ΠΎΠ³ΠΎ Π΄ΡΡΠ³ΠΈΡ . ΠΡΠΎΠ±ΠΎ ΡΠ΅Π½ΡΡΡΡ ΠΏΠΎΡΠ»Π΅ ΠΎΠ±ΡΠ°Π±ΠΎΡΠΊΠΈ Π»ΠΈΡΡΡ, Π³Π΄Π΅ ΡΠΎΡΡΠ°Π²Π»ΡΡΡΠ΅ΠΉ ΡΠ²Π»ΡΠ΅ΡΡΡ Π°Π»ΡΠΌΠΈΠ½ΠΈΠΉ.
Π Π·Π°Π²Π΅ΡΡΠ΅Π½ΠΈΠΈ ΡΠ»Π΅Π΄ΡΠ΅Ρ ΡΠΊΠ°Π·Π°ΡΡ, ΡΡΠΎ ΡΠΏΠ»Π°Π²Ρ, ΠΊΠΎΡΠΎΡΡΠ΅ Ρ ΠΎΡΠΎΡΠΎ ΠΏΠΎΠ΄Π»Π΅ΠΆΠ°Ρ ΠΏΡΠΎΡΠ΅ΡΡΡ ΡΠ²Π°ΡΠΊΠΈ ΠΈ ΠΈΠΌΠ΅ΡΡ Π²ΡΡΠΎΠΊΠΈΠΉ ΠΏΠΎΠΊΠ°Π·Π°ΡΠ΅Π»Ρ ΠΊΠΎΡΡΠΎΠ·ΠΈΠΎΠ½Π½ΠΎΠΉ ΡΡΠΎΠΉΠΊΠΎΡΡΠΈ, ΡΡΠΎ: ΠΠ, ΠΠ31, ΠΠ35, ΠΠ33.
ΠΠ° Π²ΡΠ΅ΠΌΡ Π½Π°ΡΠ΅ΠΉ ΠΏΡΠ°ΠΊΡΠΈΠΊΠΈ ΠΌΡ ΡΡΠ°Π»ΠΊΠΈΠ²Π°Π»ΠΈΡΡ Ρ ΡΠ°Π·Π½ΡΠΌΠΈ ΠΏΡΠΎΡΠ΅ΡΡΠ°ΠΌΠΈ ΡΠΎΠΊΠ°ΡΠ½ΠΎΠΉ Π΄Π΅ΡΡΠ΅Π»ΡΠ½ΠΎΡΡΠΈ, ΠΎΠ΄Π½Π°ΠΊΠΎ Π»ΡΡΡΠΈΠΉ ΠΏΠΎΠΊΠ°Π·Π°ΡΠ΅Π»Ρ ΡΡΠΎΠΉΠΊΠΎΡΡΠΈ Ρ Π½Π°ΡΠ΅ΠΉ ΡΠΎΡΠΊΠΈ Π·ΡΠ΅Π½ΠΈΡ β ΡΡΠΎ ΠΠ-33.
Π’ΠΎΡΠ΅Π½ΠΈΠ΅ ΠΌΠ΅ΡΠ°Π»Π»Π° Π·Π°Π²ΠΈΡΠΈΡ ΠΎΡ ΡΠ°Π·Π½ΡΡ ΠΏΡΠΎΡΠ΅ΡΡΠΎΠ², ΡΠ°ΠΊΠΈΡ ΠΊΠ°ΠΊ ΠΊΠΎΠ²ΠΊΠ°, Π»ΠΈΡΡΠ΅ ΠΈ Π΄ΡΡΠ³ΠΈΠ΅. Π’Π°ΠΊΠΆΠ΅ ΠΏΠΎΠΌΠ½ΠΈΡΠ΅, ΡΡΠΎ Π²ΠΎ Π²ΡΠ΅ΠΌΡ ΡΠ΅ΠΆΡΡΠ΅Π³ΠΎ ΠΏΡΠΎΡΠ΅ΡΡΠ° ΡΠ³Π»Ρ ΠΎΡΠ΅Π½Ρ ΠΎΡΡΡΡΠ΅, Π½Π΅ΠΎΠ±Ρ ΠΎΠ΄ΠΈΠΌΠΎ Π±ΡΡΡ ΠΎΡΡΠΎΡΠΎΠΆΠ½ΡΠΌ. ΠΠ»Π°ΡΡΠΈΡΠΈΡΠΈΡΡΡ ΠΏΠ°ΡΠ°ΠΌΠ΅ΡΡΡ, Π½Π΅ΠΎΠ±Ρ ΠΎΠ΄ΠΈΠΌΠΎ ΠΎΠ±ΡΠ°ΡΠΈΡΡ Π²Π½ΠΈΠΌΠ°Π½ΠΈΠ΅ Π½Π° ΠΈΠ·Π½ΠΎΡΠΎΡΡΠΎΠΉΠΊΠΎΡΡΡ, ΠΏΠΎΠΊΡΡΡΠΈΠ΅, ΡΠ²ΠΎΠΉΡΡΠ²Π° ΠΎΠ±ΡΠ°Π±ΠΎΡΠΊΠΈ. ΠΠ»Ρ ΠΎΠ±ΡΠ°Π±ΠΎΡΠΊΠΈ Π²Π΅ΡΠ΅ΡΡΠ² Π΄Π°Π½Π½ΠΎΠ³ΠΎ ΡΠΎΡΠΌΠ°ΡΠ° Ρ ΠΏΡΠΎΡΠ΅Π½ΡΠΎΠΌ ΠΊΡΠ΅ΠΌΠ½ΠΈΡ 13% Π½Π΅ΠΎΠ±Ρ ΠΎΠ΄ΠΈΠΌΠΎ ΠΈΡΠΏΠΎΠ»ΡΠ·ΠΎΠ²Π°ΡΡ CD05. ΠΠ±ΡΠ°ΡΠΈΡΠ΅ Π²Π½ΠΈΠΌΠ°Π½ΠΈΠ΅, ΡΡΠΎ Π΄Π»Ρ ΠΎΠ±ΡΠ°Π±ΠΎΡΠΊΠΈ ΠΏΡΠΈ Π²ΡΡΠΎΠΊΠΎΠΌ ΠΊΠ°ΡΠ΅ΡΡΠ²Π΅ Π»ΡΡΡΠ΅ ΡΠ°ΡΡΠΌΠ°ΡΡΠΈΠ²Π°ΡΡ CD15. Π’Π°ΠΊΠΆΠ΅ Π΄Π»Ρ ΠΎΠ±ΡΠ°Π±ΠΎΡΠΊΠΈ ΡΠΏΠ»Π°Π²ΠΎΠ² ΠΈΡΠΏΠΎΠ»ΡΠ·ΡΠ΅ΡΡΡ ΠΎΡ Π»Π°ΠΆΠ΄Π°ΡΡΠ°Ρ ΠΆΠΈΠ΄ΠΊΠΎΡΡΡ, ΠΊΠΎΡΠΎΡΠ°Ρ ΡΠΏΠΎΡΠΎΠ±ΡΡΠ²ΡΠ΅Ρ ΡΡΡΡΠ°Π½Π΅Π½ΠΈΡ ΡΡΡΡΠΆΠΊΠΈ.
Π’ΠΎΠΊΠ°ΡΠ½Π°Ρ ΠΎΠ±ΡΠ°Π±ΠΎΡΠΊΠ° Π°Π»ΡΠΌΠΈΠ½ΠΈΠ΅Π²ΡΡ ΡΠΏΠ»Π°Π²ΠΎΠ² Π½Π° ΡΡΠ°Π½ΠΊΠ°Ρ Ρ Π§ΠΠ£ β ΠΎΠ΄ΠΈΠ½ ΠΈΠ· Π²ΠΈΠ΄ΠΎΠ² ΡΡΠ»ΡΠ³, ΠΏΡΠ΅Π΄ΠΎΡΡΠ°Π²Π»ΡΠ΅ΠΌΡΡ ΠΊΠΎΠΌΠΏΠ°Π½ΠΈΠ΅ΠΉ Β«Π‘ΡΠ°Π½ΠΊΠΎΠ½Β».
ΠΠ±ΡΠ°ΡΠ½Π°Ρ ΡΠ²ΡΠ·Ρ
stankon.ru
ΠΠ±ΡΠ°Π±ΠΎΡΠΊΠ° Π°Π»ΡΠΌΠΈΠ½ΠΈΡ | Π£Π½ΠΈΠ²Π΅ΡΡΠ°Π»46
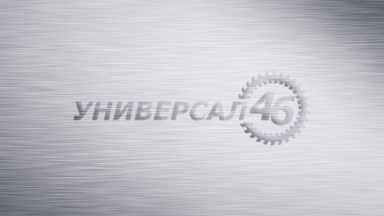
ΠΠ»ΡΠΌΠΈΠ½ΠΈΠΉ, ΠΎΠ±Π»Π°Π΄Π°Ρ ΡΠ°ΠΊΠΈΠΌΠΈ ΡΠ²ΠΎΠΉΡΡΠ²Π°ΠΌΠΈ, ΠΊΠ°ΠΊ ΠΌΠ°Π»Π°Ρ ΠΏΠ»ΠΎΡΠ½ΠΎΡΡΡ, Π²ΡΡΠΎΠΊΠ°Ρ ΡΠ΅ΠΏΠ»ΠΎΠΏΡΠΎΠ²ΠΎΠ΄Π½ΠΎΡΡΡ ΠΈ Π½ΠΈΠ·ΠΊΠΎΠ΅ ΡΠ»Π΅ΠΊΡΡΠΈΡΠ΅ΡΠΊΠΎΠ΅ ΡΠΎΠΏΡΠΎΡΠΈΠ²Π»Π΅Π½ΠΈΠ΅, Π²ΡΡΠΎΠΊΠ°Ρ ΠΏΠ»Π°ΡΡΠΈΡΠ½ΠΎΡΡΡ ΠΈ ΠΊΠΎΡΡΠΎΠ·ΠΈΠΎΠ½Π½Π°Ρ ΡΡΠΎΠΉΠΊΠΎΡΡΡ, Π΄ΠΎΡΡΠ°ΡΠΎΡΠ½ΠΎ Π²ΡΡΠΎΠΊΠ°Ρ ΠΏΡΠΎΡΠ½ΠΎΡΡΡ, ΠΏΠΎΠ»ΡΡΠΈΠ» ΡΠΈΡΠΎΠΊΠΎΠ΅ ΡΠ°ΡΠΏΡΠΎΡΡΡΠ°Π½Π΅Π½ΠΈΠ΅ Π² ΡΠ°Π·Π»ΠΈΡΠ½ΡΡ ΠΎΠ±Π»Π°ΡΡΡΡ ΡΠΎΠ²ΡΠ΅ΠΌΠ΅Π½Π½ΠΎΠΉ ΡΠ΅Ρ Π½ΠΈΠΊΠΈ. Π’Π°ΠΊΠΆΠ΅, ΡΠΈΡΠΎΠΊΠΎΠ΅ ΠΏΡΠΈΠΌΠ΅Π½Π΅Π½ΠΈΠ΅ Π°Π»ΡΠΌΠΈΠ½ΠΈΡ ΠΎΠ±ΡΡΠ»ΠΎΠ²Π»Π΅Π½ΠΎ Π΅Π³ΠΎ Π½ΠΈΠ·ΠΊΠΎΠΉ ΡΡΠΎΠΈΠΌΠΎΡΡΡΡ ΠΎΡΠ½ΠΎΡΠΈΡΠ΅Π»ΡΠ½ΠΎ Π΄ΡΡΠ³ΠΈΡ ΡΠ²Π΅ΡΠ½ΡΡ ΠΌΠ΅ΡΠ°Π»Π»ΠΎΠ².
ΠΠ»ΡΠΌΠΈΠ½ΠΈΠΉ ΠΎΡΠ½ΠΎΡΠΈΡΡΡ ΠΊ ΠΊΠ°ΡΠ΅Π³ΠΎΡΠΈΠΈ Π»Π΅Π³ΠΊΠΈΡ ΠΌΠ΅ΡΠ°Π»Π»ΠΎΠ². ΠΠ°ΠΈΠ±ΠΎΠ»Π΅Π΅ Ρ Π°ΡΠ°ΠΊΡΠ΅ΡΠ½ΡΠ΅ ΡΠ²ΠΎΠΉΡΡΠ²Π° ΡΠΈΡΡΠΎΠ³ΠΎ Π°Π»ΡΠΌΠΈΠ½ΠΈΡ β ΠΌΠ°Π»Π°Ρ ΠΏΠ»ΠΎΡΠ½ΠΎΡΡΡ (2,7 Π³/ΡΠΌ3), ΠΈ Π½ΠΈΠ·ΠΊΠ°Ρ ΡΠ΅ΠΌΠΏΠ΅ΡΠ°ΡΡΡΠ° ΠΏΠ»Π°Π²Π»Π΅Π½ΠΈΡ (660β°Π‘). ΠΠΎ ΡΡΠ°Π²Π½Π΅Π½ΠΈΡ Ρ ΠΆΠ΅Π»Π΅Π·ΠΎΠΌ, Ρ ΠΊΠΎΡΠΎΡΠΎΠ³ΠΎ ΠΏΠ»ΠΎΡΠ½ΠΎΡΡΡ ΡΠΎΡΡΠ°Π²Π»ΡΠ΅Ρ 7,8 Π³/ΡΠΌ3, Π° ΡΠ΅ΠΌΠΏΠ΅ΡΠ°ΡΡΡΠ° ΠΏΠ»Π°Π²Π»Π΅Π½ΠΈΡ β 1535β°Π‘, Π°Π»ΡΠΌΠΈΠ½ΠΈΠΉ ΠΈΠΌΠ΅Π΅Ρ ΠΏΠΎΡΡΠΈ Π² ΡΡΠΈ ΡΠ°Π·Π° Π±ΠΎΠ»Π΅Π΅ Π½ΠΈΠ·ΠΊΡΡ ΠΏΠ»ΠΎΡΠ½ΠΎΡΡΡ, Π² ΡΠ»Π΅Π΄ΡΡΠ²ΠΈΠ΅ ΡΠ΅Π³ΠΎ Π°Π»ΡΠΌΠΈΠ½ΠΈΠΉ ΠΈ Π΅Π³ΠΎ ΡΠΏΠ»Π°Π²Ρ ΡΠΈΡΠΎΠΊΠΎ ΠΏΡΠΈΠΌΠ΅Π½ΡΡΡ ΡΠ°ΠΌ, Π³Π΄Π΅ ΠΌΠ°Π»Π°Ρ ΠΏΠ»ΠΎΡΠ½ΠΎΡΡΡ ΠΈ Π±ΠΎΠ»ΡΡΠ°Ρ ΡΠ΄Π΅Π»ΡΠ½Π°Ρ ΠΏΡΠΎΡΠ½ΠΎΡΡΡ ΠΈΠΌΠ΅ΡΡ Π²Π°ΠΆΠ½ΠΎΠ΅ Π·Π½Π°ΡΠ΅Π½ΠΈΠ΅.
ΠΠ»ΡΠΌΠΈΠ½ΠΈΠ΅Π²ΡΠ΅ ΡΠΏΠ»Π°Π²Ρ ΠΌΠΎΠΆΠ½ΠΎ ΡΠ°Π·Π΄Π΅Π»ΠΈΡΡ Π½Π° Π΄Π²Π΅ Π±ΠΎΠ»ΡΡΠΈΠ΅ Π³ΡΡΠΏΠΏΡ β Π»ΠΈΡΠ΅ΠΉΠ½ΡΠ΅ ΠΈ Π΄Π΅ΡΠΎΡΠΌΠΈΡΡΠ΅ΠΌΡΠ΅ (ΠΊΠΎΠ½ΡΡΡΡΠΊΡΠΈΠΎΠ½Π½ΡΠ΅). ΠΠ΅ΡΠΎΡΠΌΠΈΡΡΠ΅ΠΌΡΠ΅ ΡΠΏΠ»Π°Π²Ρ Π² ΡΠ²ΠΎΡ ΠΎΡΠ΅ΡΠ΅Π΄Ρ Π΄Π΅Π»ΡΡΡΡ Π½Π° ΡΠ΅ΡΠΌΠΈΡΠ΅ΡΠΊΠΈ ΠΎΠ±ΡΠ°Π±ΠΎΡΠ°Π½Π½ΡΠ΅ ΠΈ ΡΠ΅ΡΠΌΠΈΡΠ΅ΡΠΊΠΈ Π½Π΅ΠΎΠ±ΡΠ°Π±ΠΎΡΠ°Π½Π½ΡΠ΅ ΡΠΏΠ»Π°Π²Ρ.
Π ΡΠ΅ΡΠΌΠΈΡΠ΅ΡΠΊΠΈ Π½Π΅ΠΎΠ±ΡΠ°Π±ΠΎΡΠ°Π½Π½ΡΠΌ ΡΠΏΠ»Π°Π²Π°ΠΌ ΠΎΡΠ½ΠΎΡΡΡΡΡ ΠΠΡ ΠΈ ΠΠΠ³. ΠΠ°ΡΠ³Π°Π½Π΅Ρ ΡΠ»ΡΡΡΠ°Π΅Ρ ΠΊΠΎΡΡΠΎΠ·ΠΈΠΎΠ½Π½ΡΡ ΡΡΠΎΠΉΠΊΠΎΡΡΡ ΡΠΏΠ»Π°Π²Π°. ΠΠ°Π³Π½ΠΈΠΉ ΡΠ²Π»ΡΠ΅ΡΡΡ ΠΏΠΎΠ»Π΅Π·Π½ΡΠΌ Π»Π΅Π³ΠΈΡΡΡΡΠΈΠΌ ΡΠ»Π΅ΠΌΠ΅Π½ΡΠΎΠΌ, Ρ.ΠΊ. ΠΏΠΎΠ²ΡΡΠ°Π΅Ρ ΠΊΠΎΡΡΠΎΠ·ΠΈΠΎΠ½Π½ΠΎΠ΅ ΡΠΎΠΏΡΠΎΡΠΈΠ²Π»Π΅Π½ΠΈΠ΅, ΡΠΌΠ΅Π½ΡΡΠ°Π΅Ρ ΠΏΠ»ΠΎΡΠ½ΠΎΡΡΡ Π°Π»ΡΠΌΠΈΠ½ΠΈΠ΅Π²ΠΎΠ³ΠΎ ΡΠΏΠ»Π°Π²Π° (Ρ.ΠΊ. ΠΎΠ½ Π»Π΅Π³ΡΠ΅ Π°Π»ΡΠΌΠΈΠ½ΠΈΡ), ΠΏΠΎΠ²ΡΡΠ°Π΅Ρ ΠΏΡΠΎΡΠ½ΠΎΡΡΡ, Π½Π΅ ΡΠ½ΠΈΠΆΠ°Ρ Π΅Π³ΠΎ ΠΏΠ»Π°ΡΡΠΈΡΠ½ΠΎΡΡΡ. ΠΠ΅ΡΠΎΡΠΌΠΈΡΡΠ΅ΠΌΡΠ΅ Π°Π»ΡΠΌΠΈΠ½ΠΈΠ΅Π²ΡΠ΅ ΡΠΏΠ»Π°Π²Ρ ΡΠ²Π»ΡΡΡΡΡ ΠΎΡΠ½ΠΎΠ²Π½ΡΠΌΠΈ ΠΊΠΎΠ½ΡΡΡΡΠΊΡΠΈΠΎΠ½Π½ΡΠΌΠΈ ΠΌΠ°ΡΠ΅ΡΠΈΠ°Π»Π°ΠΌΠΈ, ΡΠΈΡΠΎΠΊΠΎ ΠΏΡΠΈΠΌΠ΅Π½ΡΡΡΠΈΠΌΠΈΡΡ Π² Π°Π²ΠΈΠ°- ΠΈ Π°Π²ΡΠΎΡΡΡΠΎΠ΅Π½ΠΈΠΈ ΠΈ Π² Π΄ΡΡΠ³ΠΈΡ ΠΎΠ±Π»Π°ΡΡΡΡ ΠΌΠ°ΡΠΈΠ½ΠΎΡΡΡΠΎΠ΅Π½ΠΈΡ.
ΠΠ°ΠΏΡΠΈΠΌΠ΅Ρ, ΡΠΏΠ»Π°Π² Π°Π»ΡΠΌΠΈΠ½ΠΈΡ ΠΌΠ°ΡΠΊΠΈ ΠΠΠ³2 Π²ΡΠ΄Π΅Π»ΡΠ΅ΡΡΡ ΡΡΠ΅Π΄ΠΈ Π΄ΡΡΠ³ΠΈΡ ΠΊΠΎΡΡΠΎΠ·ΠΈΠΎΠ½Π½ΠΎΠΉ ΡΡΠΎΠΉΠΊΠΎΡΡΡΡ, ΠΏΠ»Π°ΡΡΠΈΡΠ½ΠΎΡΡΡΡ, Π° ΡΠ°ΠΊΠΆΠ΅ ΡΠ΅ΠΌ, ΡΡΠΎ Ρ ΠΎΡΠΎΡΠΎ ΡΠ²Π°ΡΠΈΠ²Π°Π΅ΡΡΡ. ΠΠ½ ΠΏΡΠ΅Π²ΠΎΡΡ ΠΎΠ΄ΠΈΡ ΠΏΠΎ ΠΏΡΠΎΡΠ½ΠΎΡΡΠΈ ΠΠΡ, Π² ΡΠΎ ΠΆΠ΅ Π²ΡΠ΅ΠΌΡ ΡΠ΅ΠΏΠ»ΠΎΠΏΡΠΎΠ²ΠΎΠ΄Π½ΠΎΡΡΡ ΠΈ ΡΠ»Π΅ΠΊΡΡΠΎΠΏΡΠΎΠ²ΠΎΠ΄Π½ΠΎΡΡΡ Ρ Π½Π΅Π³ΠΎ Π½ΠΈΠΆΠ΅, ΡΠ΅ΠΌ Ρ Π°Π»ΡΠΌΠΈΠ½ΠΈΠΉ-ΠΌΠ°ΡΠ³Π°Π½ΡΠ΅Π²ΠΎΠ³ΠΎ ΡΠΏΠ»Π°Π²Π°. Π₯ΠΈΠΌΠΈΡΠ΅ΡΠΊΠΈΠΉ ΡΠΎΡΡΠ°Π² ΠΠΠ³2 ΠΌΠΎΠΆΠ½ΠΎ Π½Π°Π·Π²Π°ΡΡ ΡΠ±Π°Π»Π°Π½ΡΠΈΡΠΎΠ²Π°Π½Π½ΡΠΌ. Π‘ΠΎΠ΄Π΅ΡΠΆΠ°Π½ΠΈΠ΅ ΠΌΠ°Π³Π½ΠΈΡ Π² Π½ΡΠΌ Π½Π΅ ΠΏΡΠ΅Π²ΡΡΠ°Π΅Ρ 4 %, ΡΡΠΎ ΠΏΠΎΠ»ΠΎΠΆΠΈΡΠ΅Π»ΡΠ½ΡΠΌ ΠΎΠ±ΡΠ°Π·ΠΎΠΌ ΡΠΊΠ°Π·ΡΠ²Π°Π΅ΡΡΡ Π½Π° ΠΏΠ»Π°ΡΡΠΈΡΠ½ΠΎΡΡΠΈ, ΠΊΠΎΡΡΠΎΠ·ΠΈΠΎΠ½Π½ΠΎΠΉ ΡΡΠΎΠΉΠΊΠΎΡΡΠΈ ΠΈ ΡΠ²Π°ΡΠΈΠ²Π°Π΅ΠΌΠΎΡΡΠΈ Π΄Π°Π½Π½ΠΎΠ³ΠΎ ΠΌΠ°ΡΠ΅ΡΠΈΠ°Π»Π°. Π ΡΠΎ ΠΆΠ΅ Π²ΡΠ΅ΠΌΡ ΡΠΎΠ΄Π΅ΡΠΆΠ°Π½ΠΈΠ΅ Mg ΠΏΡΠ΅Π²ΡΡΠ°Π΅Ρ 2 %, ΡΡΠΎ ΠΏΠΎΠ»ΠΎΠΆΠΈΡΠ΅Π»ΡΠ½ΡΠΌ ΠΎΠ±ΡΠ°Π·ΠΎΠΌ ΡΠΊΠ°Π·ΡΠ²Π°Π΅ΡΡΡ Π½Π° ΠΏΡΠΎΡΠ½ΠΎΡΡΠΈ ΡΠΏΠ»Π°Π²Π°.
ΠΡ ΠΏΡΠ΅Π΄Π»Π°Π³Π°Π΅ΠΌ Π»Π°Π·Π΅ΡΠ½ΡΡ ΡΠ΅Π·ΠΊΡ ΠΈ Π³ΠΈΠ±ΠΊΡ Π°Π»ΡΠΌΠΈΠ½ΠΈΡ ΡΠΎΠ»ΡΠΈΠ½ΠΎΠΉ Π΄ΠΎ 4,0 ΠΌΠΌ
universal46.ru