ΠΠ±ΠΎΠ±ΡΠ΅Π½Π½ΡΠ΅ ΡΡΡΠ΄ΠΎΠ²ΡΠ΅ ΡΡΠ½ΠΊΡΠΈΠΈ | Π’ΡΡΠ΄ΠΎΠ²ΡΠ΅ ΡΡΠ½ΠΊΡΠΈΠΈ | ||||
ΠΊΠΎΠ΄ | Π½Π°ΠΈΠΌΠ΅Π½ΠΎΠ²Π°Π½ΠΈΠ΅ | ΡΡΠΎΠ²Π΅Π½Ρ ΠΊΠ²Π°Π»ΠΈΡΠΈΠΊΠ°ΡΠΈΠΈ | ΠΠ°ΠΈΠΌΠ΅Π½ΠΎΠ²Π°Π½ΠΈΠ΅ | ΠΊΠΎΠ΄ | ΡΡΠΎΠ²Π΅Π½Ρ (ΠΏΠΎΠ΄ΡΡΠΎΠ²Π΅Π½Ρ) ΠΊΠ²Π°Π»ΠΈΡΠΈΠΊΠ°ΡΠΈΠΈ |
A | ΠΡΠΎΠΈΠ·Π²ΠΎΠ΄ΡΡΠ²ΠΎ ΠΌΠ΅ΡΠ°Π»Π»ΠΎΠΏΡΠΎΠΊΠ°ΡΠ° ΠΈ ΡΡΡΠ± ΠΈΠ· ΡΠ΅ΡΠ½ΡΡ ΠΈ ΡΠ²Π΅ΡΠ½ΡΡ ΠΌΠ΅ΡΠ°Π»Π»ΠΎΠ² Π½Π° ΠΎΠ΄Π½ΠΎΠΊΡΠ°ΡΠ½ΡΡ Π²ΠΎΠ»ΠΎΡΠΈΠ»ΡΠ½ΡΡ ΡΡΠ°Π½Π°Ρ | 3 | ΠΡΠΏΠΎΠ»Π½Π΅Π½ΠΈΠ΅ ΠΏΠΎΠ΄Π³ΠΎΡΠΎΠ²ΠΈΡΠ΅Π»ΡΠ½ΡΡ ΠΎΠΏΠ΅ΡΠ°ΡΠΈΠΉ Π²ΠΎΠ»ΠΎΡΠ΅Π½ΠΈΡ ΠΌΠ΅ΡΠ°Π»Π»ΠΎΠΏΡΠΎΠΊΠ°ΡΠ° ΠΈ ΡΡΡΠ± ΠΈΠ· ΡΠ΅ΡΠ½ΡΡ ΠΈ ΡΠ²Π΅ΡΠ½ΡΡ ΠΌΠ΅ΡΠ°Π»Π»ΠΎΠ² Π½Π° ΠΎΠ΄Π½ΠΎΠΊΡΠ°ΡΠ½ΡΡ Π²ΠΎΠ»ΠΎΡΠΈΠ»ΡΠ½ΡΡ ΡΡΠ°Π½Π°Ρ | A/01.3 | 3 |
ΠΠ΅Π΄Π΅Π½ΠΈΠ΅ ΠΏΡΠΎΡΠ΅ΡΡΠ° Π²ΠΎΠ»ΠΎΡΠ΅Π½ΠΈΡ ΠΌΠ΅ΡΠ°Π»Π»ΠΎΠΏΡΠΎΠΊΠ°ΡΠ° ΠΈ ΡΡΡΠ± ΠΈΠ· ΡΠ΅ΡΠ½ΡΡ ΠΈ ΡΠ²Π΅ΡΠ½ΡΡ ΠΌΠ΅ΡΠ°Π»Π»ΠΎΠ² Π½Π° ΠΎΠ΄Π½ΠΎΠΊΡΠ°ΡΠ½ΡΡ Π²ΠΎΠ»ΠΎΡΠΈΠ»ΡΠ½ΡΡ ΡΡΠ°Π½Π°Ρ | A/02.3 | ||||
ΠΡΠΏΠΎΠ»Π½Π΅Π½ΠΈΠ΅ Π·Π°ΠΊΠ»ΡΡΠΈΡΠ΅Π»ΡΠ½ΡΡ ΠΎΠΏΠ΅ΡΠ°ΡΠΈΠΉ Π²ΠΎΠ»ΠΎΡΠ΅Π½ΠΈΡ ΠΌΠ΅ΡΠ°Π»Π»ΠΎΠΏΡΠΎΠΊΠ°ΡΠ° ΠΈ ΡΡΡΠ± ΠΈΠ· ΡΠ΅ΡΠ½ΡΡ ΠΈ ΡΠ²Π΅ΡΠ½ΡΡ ΠΌΠ΅ΡΠ°Π»Π»ΠΎΠ² Π½Π° ΠΎΠ΄Π½ΠΎΠΊΡΠ°ΡΠ½ΡΡ Π²ΠΎΠ»ΠΎΡΠΈΠ»ΡΠ½ΡΡ ΡΡΠ°Π½Π°Ρ | A/03.3 | ||||
B | ΠΡΠΎΠΈΠ·Π²ΠΎΠ΄ΡΡΠ²ΠΎ ΠΏΡΠΎΠ²ΠΎΠ»ΠΎΠΊΠΈ, ΡΠΏΠ΅ΡΠΈΠ°Π»ΡΠ½ΡΡ ΠΏΡΠΎΡΠΈΠ»Π΅ΠΉ ΠΈ ΡΡΡΠ± ΠΈΠ· ΡΠ΅ΡΠ½ΡΡ ΠΈ ΡΠ²Π΅ΡΠ½ΡΡ ΠΌΠ΅ΡΠ°Π»Π»ΠΎΠ² Π½Π° ΡΡΠ°Π½Π°Ρ Π±Π°ΡΠ°Π±Π°Π½Π½ΠΎΠ³ΠΎ ΡΠΈΠΏΠ° Ρ ΠΎΠ΄Π½ΠΎΠΊΡΠ°ΡΠ½ΡΠΌ ΠΈ ΠΌΠ½ΠΎΠ³ΠΎΠΊΡΠ°ΡΠ½ΡΠΌ Π²ΠΎΠ»ΠΎΡΠ΅Π½ΠΈΠ΅ΠΌ | 3 | ΠΡΠΏΠΎΠ»Π½Π΅Π½ΠΈΠ΅ ΠΏΠΎΠ΄Π³ΠΎΡΠΎΠ²ΠΈΡΠ΅Π»ΡΠ½ΡΡ ΠΎΠΏΠ΅ΡΠ°ΡΠΈΠΉ Π²ΠΎΠ»ΠΎΡΠ΅Π½ΠΈΡ ΠΏΡΠΎΠ²ΠΎΠ»ΠΎΠΊΠΈ, ΡΠΏΠ΅ΡΠΈΠ°Π»ΡΠ½ΡΡ ΠΏΡΠΎΡΠΈΠ»Π΅ΠΉ ΠΈ ΡΡΡΠ± ΠΈΠ· ΡΠ΅ΡΠ½ΡΡ ΠΈ ΡΠ²Π΅ΡΠ½ΡΡ ΠΌΠ΅ΡΠ°Π»Π»ΠΎΠ² Π½Π° ΡΡΠ°Π½Π°Ρ Π±Π°ΡΠ°Π±Π°Π½Π½ΠΎΠ³ΠΎ ΡΠΈΠΏΠ° Ρ ΠΎΠ΄Π½ΠΎΠΊΡΠ°ΡΠ½ΡΠΌ ΠΈ ΠΌΠ½ΠΎΠ³ΠΎΠΊΡΠ°ΡΠ½ΡΠΌ Π²ΠΎΠ»ΠΎΡΠ΅Π½ΠΈΠ΅ΠΌ | B/01.3 | 3 |
ΠΠ΅Π΄Π΅Π½ΠΈΠ΅ ΠΏΡΠΎΡΠ΅ΡΡΠ° Π²ΠΎΠ»ΠΎΡΠ΅Π½ΠΈΡ ΠΏΡΠΎΠ²ΠΎΠ»ΠΎΠΊΠΈ, ΡΠΏΠ΅ΡΠΈΠ°Π»ΡΠ½ΡΡ ΠΏΡΠΎΡΠΈΠ»Π΅ΠΉ ΠΈ ΡΡΡΠ± ΠΈΠ· ΡΠ΅ΡΠ½ΡΡ ΠΈ ΡΠ²Π΅ΡΠ½ΡΡ ΠΌΠ΅ΡΠ°Π»Π»ΠΎΠ² Π½Π° ΡΡΠ°Π½Π°Ρ Π±Π°ΡΠ°Π±Π°Π½Π½ΠΎΠ³ΠΎ ΡΠΈΠΏΠ° Ρ ΠΎΠ΄Π½ΠΎΠΊΡΠ°ΡΠ½ΡΠΌ ΠΈ ΠΌΠ½ΠΎΠ³ΠΎΠΊΡΠ°ΡΠ½ΡΠΌ Π²ΠΎΠ»ΠΎΡΠ΅Π½ΠΈΠ΅ΠΌ | B/02.3 | ||||
ΠΡΠΏΠΎΠ»Π½Π΅Π½ΠΈΠ΅ Π·Π°ΠΊΠ»ΡΡΠΈΡΠ΅Π»ΡΠ½ΡΡ ΠΎΠΏΠ΅ΡΠ°ΡΠΈΠΉ Π²ΠΎΠ»ΠΎΡΠ΅Π½ΠΈΡ ΠΏΡΠΎΠ²ΠΎΠ»ΠΎΠΊΠΈ, ΡΠΏΠ΅ΡΠΈΠ°Π»ΡΠ½ΡΡ ΠΏΡΠΎΡΠΈΠ»Π΅ΠΉ ΠΈ ΡΡΡΠ± ΠΈΠ· ΡΠ΅ΡΠ½ΡΡ ΠΈ ΡΠ²Π΅ΡΠ½ΡΡ ΠΌΠ΅ΡΠ°Π»Π»ΠΎΠ² Π½Π° ΡΡΠ°Π½Π°Ρ Π±Π°ΡΠ°Π±Π°Π½Π½ΠΎΠ³ΠΎ ΡΠΈΠΏΠ° Ρ ΠΎΠ΄Π½ΠΎΠΊΡΠ°ΡΠ½ΡΠΌ ΠΈ ΠΌΠ½ΠΎΠ³ΠΎΠΊΡΠ°ΡΠ½ΡΠΌ Π²ΠΎΠ»ΠΎΡΠ΅Π½ΠΈΠ΅ΠΌ | B/03.3 | ||||
C | ΠΡΠΎΠΈΠ·Π²ΠΎΠ΄ΡΡΠ²ΠΎ ΠΌΠΈΠΊΡΠΎΠΏΡΠΎΠ²ΠΎΠ»ΠΎΠΊΠΈ ΠΈΠ· ΡΠ΅ΡΠ½ΡΡ ΠΈ ΡΠ²Π΅ΡΠ½ΡΡ ΠΌΠ΅ΡΠ°Π»Π»ΠΎΠ² Π½Π° ΡΡΠ°Π½Π°Ρ ΠΌΠ½ΠΎΠ³ΠΎΠΊΡΠ°ΡΠ½ΠΎΠ³ΠΎ Π²ΠΎΠ»ΠΎΡΠ΅Π½ΠΈΡ | 3 | ΠΡΠΏΠΎΠ»Π½Π΅Π½ΠΈΠ΅ ΠΏΠΎΠ΄Π³ΠΎΡΠΎΠ²ΠΈΡΠ΅Π»ΡΠ½ΡΡ ΠΎΠΏΠ΅ΡΠ°ΡΠΈΠΉ Π²ΠΎΠ»ΠΎΡΠ΅Π½ΠΈΡ ΠΌΠΈΠΊΡΠΎΠΏΡΠΎΠ²ΠΎΠ»ΠΎΠΊΠΈ Π½Π° ΡΡΠ°Π½Π°Ρ ΠΌΠ½ΠΎΠ³ΠΎΠΊΡΠ°ΡΠ½ΠΎΠ³ΠΎ Π²ΠΎΠ»ΠΎΡΠ΅Π½ΠΈΡ | C/01.3 | 3 |
ΠΠ΅Π΄Π΅Π½ΠΈΠ΅ ΠΏΡΠΎΡΠ΅ΡΡΠ° Π²ΠΎΠ»ΠΎΡΠ΅Π½ΠΈΡ ΠΌΠΈΠΊΡΠΎΠΏΡΠΎΠ²ΠΎΠ»ΠΎΠΊΠΈ Π½Π° ΡΡΠ°Π½Π°Ρ ΠΌΠ½ΠΎΠ³ΠΎΠΊΡΠ°ΡΠ½ΠΎΠ³ΠΎ Π²ΠΎΠ»ΠΎΡΠ΅Π½ΠΈΡ | C/02.3 | ||||
ΠΡΠΏΠΎΠ»Π½Π΅Π½ΠΈΠ΅ Π·Π°ΠΊΠ»ΡΡΠΈΡΠ΅Π»ΡΠ½ΡΡ ΠΎΠΏΠ΅ΡΠ°ΡΠΈΠΉ Π²ΠΎΠ»ΠΎΡΠ΅Π½ΠΈΡ ΠΌΠΈΠΊΡΠΎΠΏΡΠΎΠ²ΠΎΠ»ΠΎΠΊΠΈ Π½Π° ΡΡΠ°Π½Π°Ρ ΠΌΠ½ΠΎΠ³ΠΎΠΊΡΠ°ΡΠ½ΠΎΠ³ΠΎ Π²ΠΎΠ»ΠΎΡΠ΅Π½ΠΈΡ | C/03.3 | ||||
Π’ΡΡΠ΄ΠΎΠ²ΡΠ΅ Π΄Π΅ΠΉΡΡΠ²ΠΈΡ | ΠΠΎΠ»ΡΡΠ΅Π½ΠΈΠ΅ (ΠΏΠ΅ΡΠ΅Π΄Π°ΡΠ°) ΠΈΠ½ΡΠΎΡΠΌΠ°ΡΠΈΠΈ ΠΏΡΠΈ ΠΏΡΠΈΠ΅ΠΌΠΊΠ΅-ΡΠ΄Π°ΡΠ΅ ΡΠΌΠ΅Π½Ρ ΠΎ ΡΠΌΠ΅Π½Π½ΠΎΠΌ ΠΏΡΠΎΠΈΠ·Π²ΠΎΠ΄ΡΡΠ²Π΅Π½Π½ΠΎΠΌ Π·Π°Π΄Π°Π½ΠΈΠΈ, ΠΎ ΡΠΎΡΡΠΎΡΠ½ΠΈΠΈ ΡΠ°Π±ΠΎΡΠ΅Π³ΠΎ ΠΌΠ΅ΡΡΠ° Π²ΠΎΠ»ΠΎΡΠΈΠ»ΡΡΠΈΠΊΠ°, Π½Π΅ΠΏΠΎΠ»Π°Π΄ΠΊΠ°Ρ Π² ΡΠ°Π±ΠΎΡΠ΅ ΠΎΠ±ΡΠ»ΡΠΆΠΈΠ²Π°Π΅ΠΌΠΎΠ³ΠΎ ΠΎΠ±ΠΎΡΡΠ΄ΠΎΠ²Π°Π½ΠΈΡ ΠΈ ΠΏΡΠΈΠ½ΡΡΡΡ ΠΌΠ΅ΡΠ°Ρ ΠΏΠΎ ΠΈΡ ΡΡΡΡΠ°Π½Π΅Π½ΠΈΡ | ||||
ΠΡΠΎΠ²Π΅ΡΠΊΠ° ΡΠΎΡΡΠΎΡΠ½ΠΈΡ ΠΎΠ³ΡΠ°ΠΆΠ΄Π΅Π½ΠΈΠΉ ΠΈ ΡΠ°Π±ΠΎΡΠΎΡΠΏΠΎΡΠΎΠ±Π½ΠΎΡΡΠΈ ΠΎΡΠ½ΠΎΠ²Π½ΠΎΠ³ΠΎ ΠΈ Π²ΡΠΏΠΎΠΌΠΎΠ³Π°ΡΠ΅Π»ΡΠ½ΠΎΠ³ΠΎ ΠΎΠ±ΡΠ»ΡΠΆΠΈΠ²Π°Π΅ΠΌΠΎΠ³ΠΎ ΠΎΠ±ΠΎΡΡΠ΄ΠΎΠ²Π°Π½ΠΈΡ, ΡΡΠ΅Π΄ΡΡΠ² ΠΈΠ½Π΄ΠΈΠ²ΠΈΠ΄ΡΠ°Π»ΡΠ½ΠΎΠΉ Π·Π°ΡΠΈΡΡ, ΡΠ²ΡΠ·ΠΈ, ΠΏΡΠΎΠΈΠ·Π²ΠΎΠ΄ΡΡΠ²Π΅Π½Π½ΠΎΠΉ ΡΠΈΠ³Π½Π°Π»ΠΈΠ·Π°ΡΠΈΠΈ, Π±Π»ΠΎΠΊΠΈΡΠΎΠ²ΠΎΠΊ, ΠΈΠ½ΡΡΡΡΠΌΠ΅Π½ΡΠ°, ΠΏΡΠΎΡΠΈΠ²ΠΎΠΏΠΎΠΆΠ°ΡΠ½ΠΎΠ³ΠΎ ΠΎΠ±ΠΎΡΡΠ΄ΠΎΠ²Π°Π½ΠΈΡ Π½Π° ΡΡΠ°ΡΡΠΊΠ΅ Π²ΠΎΠ»ΠΎΡΠ΅Π½ΠΈΡ | |||||
ΠΠΎΠ΄Π³ΠΎΡΠΎΠ²ΠΊΠ° ΠΊ ΡΠ°Π±ΠΎΡΠ΅ Π²ΠΎΠ»ΠΎΡΠΈΠ»ΡΠ½ΠΎΠ³ΠΎ ΠΎΠ±ΠΎΡΡΠ΄ΠΎΠ²Π°Π½ΠΈΡ, ΠΈΠ½ΡΡΡΡΠΌΠ΅Π½ΡΠ°, ΠΏΡΠΈΡΠΏΠΎΡΠΎΠ±Π»Π΅Π½ΠΈΠΉ ΠΈ ΡΠ΅Ρ Π½ΠΎΠ»ΠΎΠ³ΠΈΡΠ΅ΡΠΊΠΎΠΉ ΡΠΌΠ°Π·ΠΊΠΈ | |||||
Π£ΡΡΠ°Π½ΠΎΠ²ΠΊΠ° Π²ΠΎΠ»ΠΎΠΊ | |||||
ΠΡΠΎΠ²Π΅ΡΠΊΠ° ΠΏΠΎΡΡΡΠΏΠΈΠ²ΡΠ΅Π³ΠΎ ΠΌΠ΅ΡΠ°Π»Π»Π°, ΠΏΡΠ΅Π΄Π½Π°Π·Π½Π°ΡΠ΅Π½Π½ΠΎΠ³ΠΎ Π΄Π»Ρ Π²ΠΎΠ»ΠΎΡΠ΅Π½ΠΈΡ, Π½Π° ΡΠΎΠΎΡΠ²Π΅ΡΡΡΠ²ΠΈΠ΅ ΠΎΡΠ½ΠΎΠ²Π½ΡΠΌ ΡΡΠ΅Π±ΠΎΠ²Π°Π½ΠΈΡΠΌ ΡΡΠ°Π½Π΄Π°ΡΡΠΎΠ² ΠΈ ΡΠ΅Ρ Π½ΠΈΡΠ΅ΡΠΊΠΈΡ ΡΡΠ»ΠΎΠ²ΠΈΠΉ | |||||
ΠΠΎΠ΄Π³ΠΎΡΠΎΠ²ΠΊΠ° ΠΌΠ΅ΡΠ°Π»Π»Π° ΠΊ Π²ΠΎΠ»ΠΎΡΠ΅Π½ΠΈΡ | |||||
Π£ΡΡΠ°Π½ΠΎΠ²ΠΊΠ° Π±ΡΠ½ΡΠ°, ΠΊΠ°ΡΡΡΠΊΠΈ Π½Π° ΡΠ°Π·ΠΌΠΎΡΠΎΡΠ½ΠΎΠ΅ ΡΡΡΡΠΎΠΉΡΡΠ²ΠΎ Π²ΠΎΠ»ΠΎΡΠΈΠ»ΡΠ½ΠΎΠ³ΠΎ ΡΡΠ°Π½Π° | |||||
ΠΠ΅Π΄Π΅Π½ΠΈΠ΅ Π°Π³ΡΠ΅Π³Π°ΡΠ½ΠΎΠ³ΠΎ ΠΆΡΡΠ½Π°Π»Π° ΠΈ ΡΡΠ΅ΡΠ½ΠΎΠΉ Π΄ΠΎΠΊΡΠΌΠ΅Π½ΡΠ°ΡΠΈΠΈ Π²ΠΎΠ»ΠΎΡΠΈΠ»ΡΡΠΈΠΊΠ° | |||||
ΠΠ΅ΠΎΠ±Ρ ΠΎΠ΄ΠΈΠΌΡΠ΅ ΡΠΌΠ΅Π½ΠΈΡ | ΠΠΏΡΠ΅Π΄Π΅Π»ΡΡΡ Π²ΠΈΠ·ΡΠ°Π»ΡΠ½ΠΎ ΠΈΠ»ΠΈ Ρ ΠΈΡΠΏΠΎΠ»ΡΠ·ΠΎΠ²Π°Π½ΠΈΠ΅ΠΌ ΠΏΡΠΈΠ±ΠΎΡΠΎΠ² ΠΎΡΠΊΠ»ΠΎΠ½Π΅Π½ΠΈΡ ΠΏΠ°ΡΠ°ΠΌΠ΅ΡΡΠΎΠ² ΡΠ΅ΠΊΡΡΠ΅Π³ΠΎ ΡΠΎΡΡΠΎΡΠ½ΠΈΡ ΠΎΠ±ΡΠ»ΡΠΆΠΈΠ²Π°Π΅ΠΌΠΎΠ³ΠΎ ΠΎΡΠ½ΠΎΠ²Π½ΠΎΠ³ΠΎ ΠΈ Π²ΡΠΏΠΎΠΌΠΎΠ³Π°ΡΠ΅Π»ΡΠ½ΠΎΠ³ΠΎ ΠΎΠ±ΠΎΡΡΠ΄ΠΎΠ²Π°Π½ΠΈΡ ΠΎΠ΄Π½ΠΎΠΊΡΠ°ΡΠ½ΡΡ Π²ΠΎΠ»ΠΎΡΠΈΠ»ΡΠ½ΡΡ ΡΡΠ°Π½ΠΎΠ², ΡΡΠ΅Π΄ΡΡΠ² ΠΈΠ½Π΄ΠΈΠ²ΠΈΠ΄ΡΠ°Π»ΡΠ½ΠΎΠΉ Π·Π°ΡΠΈΡΡ, ΡΠ²ΡΠ·ΠΈ, ΠΏΡΠΎΠΈΠ·Π²ΠΎΠ΄ΡΡΠ²Π΅Π½Π½ΠΎΠΉ ΡΠΈΠ³Π½Π°Π»ΠΈΠ·Π°ΡΠΈΠΈ, Π±Π»ΠΎΠΊΠΈΡΠΎΠ²ΠΎΠΊ, Π°Π²Π°ΡΠΈΠΉΠ½ΠΎΠ³ΠΎ ΠΈΠ½ΡΡΡΡΠΌΠ΅Π½ΡΠ°, ΠΏΡΠΎΡΠΈΠ²ΠΎΠΏΠΎΠΆΠ°ΡΠ½ΠΎΠ³ΠΎ ΠΎΠ±ΠΎΡΡΠ΄ΠΎΠ²Π°Π½ΠΈΡ ΠΎΡ ΡΡΡΠ°Π½ΠΎΠ²Π»Π΅Π½Π½ΡΡ Π·Π½Π°ΡΠ΅Π½ΠΈΠΉ | ||||
ΠΠΏΡΠ΅Π΄Π΅Π»ΡΡΡ ΡΠΈΠΏ Π²ΠΎΠ»ΠΎΠΊΠΈ ΠΈ ΡΠ΅Ρ Π½ΠΎΠ»ΠΎΠ³ΠΈΡΠ΅ΡΠΊΡΡ ΡΠΌΠ°Π·ΠΊΡ Π² Π·Π°Π²ΠΈΡΠΈΠΌΠΎΡΡΠΈ ΠΎΡ Π²ΠΈΠ΄Π° ΠΏΡΠΎΠΈΠ·Π²ΠΎΠ΄ΠΈΠΌΠΎΠΉ ΠΏΡΠΎΠ΄ΡΠΊΡΠΈΠΈ | |||||
ΠΡΠ΅Π½ΠΈΠ²Π°ΡΡ ΠΊΠ°ΡΠ΅ΡΡΠ²ΠΎ ΠΈ Π½Π΅ΠΎΠ±Ρ ΠΎΠ΄ΠΈΠΌΠΎΠ΅ ΠΊΠΎΠ»ΠΈΡΠ΅ΡΡΠ²ΠΎ ΡΠ΅Ρ Π½ΠΎΠ»ΠΎΠ³ΠΈΡΠ΅ΡΠΊΠΎΠΉ ΡΠΌΠ°Π·ΠΊΠΈ Π² ΠΏΡΠΎΡΠ΅ΡΡΠ΅ Π²ΠΎΠ»ΠΎΡΠ΅Π½ΠΈΡ | |||||
Π£ΡΡΠ°Π½Π°Π²Π»ΠΈΠ²Π°ΡΡ ΡΠ΅Ρ Π½ΠΎΠ»ΠΎΠ³ΠΈΡΠ΅ΡΠΊΠΈΠΉ ΠΈΠ½ΡΡΡΡΠΌΠ΅Π½Ρ Π½Π° ΠΎΠ΄Π½ΠΎΠΊΡΠ°ΡΠ½ΡΡ Π²ΠΎΠ»ΠΎΡΠΈΠ»ΡΠ½ΡΡ ΡΡΠ°Π½Π°Ρ | |||||
ΠΠΈΠ·ΡΠ°Π»ΡΠ½ΠΎ ΠΎΠΏΡΠ΅Π΄Π΅Π»ΡΡΡ Π½Π°Π»ΠΈΡΠΈΠ΅ Π΄Π΅ΡΠ΅ΠΊΡΠΎΠ² Π½Π° ΠΏΠΎΠ²Π΅ΡΡ Π½ΠΎΡΡΠΈ ΠΌΠ΅ΡΠ°Π»Π»Π° ΠΏΠ΅ΡΠ΅Π΄ Π²ΠΎΠ»ΠΎΡΠ΅Π½ΠΈΠ΅ΠΌ | |||||
ΠΡΠΈΠΌΠ΅Π½ΡΡΡ ΠΊΠΎΠ½ΡΡΠΎΠ»ΡΠ½ΠΎ-ΠΈΠ·ΠΌΠ΅ΡΠΈΡΠ΅Π»ΡΠ½ΡΠΉ ΠΈΠ½ΡΡΡΡΠΌΠ΅Π½Ρ Π΄Π»Ρ ΠΈΠ·ΠΌΠ΅ΡΠ΅Π½ΠΈΡ Π³Π΅ΠΎΠΌΠ΅ΡΡΠΈΡΠ΅ΡΠΊΠΈΡ ΡΠ°Π·ΠΌΠ΅ΡΠΎΠ² ΠΏΠΎΡΡΡΠΏΠ°ΡΡΠ΅Π³ΠΎ ΠΌΠ΅ΡΠ°Π»Π»ΠΎΠΏΡΠΎΠΊΠ°ΡΠ° | |||||
ΠΠ±ΡΠ΅Π·Π°ΡΡ ΡΠΎΡΡΡ ΠΏΡΠΎΠ²ΠΎΠ»ΠΎΠΊΠΈ ΠΏΠ΅ΡΠΏΠ΅Π½Π΄ΠΈΠΊΡΠ»ΡΡΠ½ΠΎ ΠΊ Π΅Π΅ ΠΎΡΠΈ | |||||
ΠΠΎΠ΄Π°Π²Π°ΡΡ ΡΠΏΠ΅ΡΠΈΠ°Π»ΡΠ½ΡΠ΅ ΠΊΠΎΠΌΠ°Π½Π΄Ρ ΠΌΠ°ΡΠΈΠ½ΠΈΡΡΡ ΠΊΡΠ°Π½Π° Π² Ρ ΠΎΠ΄Π΅ ΡΠ΅Ρ Π½ΠΎΠ»ΠΎΠ³ΠΈΡΠ΅ΡΠΊΠΎΠ³ΠΎ ΠΏΡΠΎΡΠ΅ΡΡΠ° | |||||
ΠΡΠΎΠΈΠ·Π²ΠΎΠ΄ΠΈΡΡ Π½Π°Π»Π°Π΄ΠΊΡ ΡΠ΅Ρ Π½ΠΎΠ»ΠΎΠ³ΠΈΡΠ΅ΡΠΊΠΎΠ³ΠΎ ΠΎΠ±ΠΎΡΡΠ΄ΠΎΠ²Π°Π½ΠΈΡ ΠΎΠ΄Π½ΠΎΠΊΡΠ°ΡΠ½ΡΡ Π²ΠΎΠ»ΠΎΡΠΈΠ»ΡΠ½ΡΡ ΡΡΠ°Π½ΠΎΠ² | |||||
ΠΡΠΈΠΌΠ΅Π½ΡΡΡ ΡΡΠ΅Π΄ΡΡΠ²Π° ΠΈΠ½Π΄ΠΈΠ²ΠΈΠ΄ΡΠ°Π»ΡΠ½ΠΎΠΉ Π·Π°ΡΠΈΡΡ, ΠΏΠΎΠΆΠ°ΡΠΎΡΡΡΠ΅Π½ΠΈΡ ΠΈ ΠΏΠΎΠ»ΡΠ·ΠΎΠ²Π°ΡΡΡΡ Π°Π²Π°ΡΠΈΠΉΠ½ΡΠΌ ΠΈΠ½ΡΡΡΡΠΌΠ΅Π½ΡΠΎΠΌ Π½Π° ΡΡΠ°ΡΡΠΊΠ΅ Π²ΠΎΠ»ΠΎΡΠ΅Π½ΠΈΡ | |||||
ΠΡΠΈΠΌΠ΅Π½ΡΡΡ ΠΏΡΠΎΠ³ΡΠ°ΠΌΠΌΠ½ΠΎΠ΅ ΠΎΠ±Π΅ΡΠΏΠ΅ΡΠ΅Π½ΠΈΠ΅ ΡΠ°Π±ΠΎΡΠ΅Π³ΠΎ ΠΌΠ΅ΡΡΠ° Π²ΠΎΠ»ΠΎΡΠΈΠ»ΡΡΠΈΠΊΠ° | |||||
ΠΠ΅ΠΎΠ±Ρ ΠΎΠ΄ΠΈΠΌΡΠ΅ Π·Π½Π°Π½ΠΈΡ | Π£ΡΡΡΠΎΠΉΡΡΠ²ΠΎ, ΠΏΡΠΈΠ½ΡΠΈΠΏ ΡΠ°Π±ΠΎΡΡ ΠΈ ΠΏΡΠ°Π²ΠΈΠ»Π° ΡΠΊΡΠΏΠ»ΡΠ°ΡΠ°ΡΠΈΠΈ ΠΎΡΠ½ΠΎΠ²Π½ΠΎΠ³ΠΎ ΠΈ Π²ΡΠΏΠΎΠΌΠΎΠ³Π°ΡΠ΅Π»ΡΠ½ΠΎΠ³ΠΎ ΠΎΠ±ΠΎΡΡΠ΄ΠΎΠ²Π°Π½ΠΈΡ, Π²ΠΎΠ»ΠΎΡΠΈΠ»ΡΠ½ΠΎΠ³ΠΎ ΠΈΠ½ΡΡΡΡΠΌΠ΅Π½ΡΠ° ΡΡΠ°ΡΡΠΊΠ° Π²ΠΎΠ»ΠΎΡΠ΅Π½ΠΈΡ | ||||
Π£ΡΡΡΠΎΠΉΡΡΠ²ΠΎ, ΠΊΠΈΠ½Π΅ΠΌΠ°ΡΠΈΡΠ΅ΡΠΊΠΈΠ΅ ΡΡ Π΅ΠΌΡ ΠΈ ΠΏΡΠ°Π²ΠΈΠ»Π° Π½Π°Π»Π°Π΄ΠΊΠΈ ΠΎΠ΄Π½ΠΎΠΊΡΠ°ΡΠ½ΡΡ Π²ΠΎΠ»ΠΎΡΠΈΠ»ΡΠ½ΡΡ ΡΡΠ°Π½ΠΎΠ² | |||||
ΠΡΠΎΠΈΠ·Π²ΠΎΠ΄ΡΡΠ²Π΅Π½Π½ΠΎ-ΡΠ΅Ρ Π½ΠΈΡΠ΅ΡΠΊΠΈΠ΅ ΠΈΠ½ΡΡΡΡΠΊΡΠΈΠΈ ΠΏΠΎ Π²ΠΎΠ»ΠΎΡΠ΅Π½ΠΈΡ ΠΌΠ΅ΡΠ°Π»Π»ΠΎΠΏΡΠΎΠΊΠ°ΡΠ° ΠΈ ΡΡΡΠ± Π½Π° ΠΎΠ΄Π½ΠΎΠΊΡΠ°ΡΠ½ΡΡ Π²ΠΎΠ»ΠΎΡΠΈΠ»ΡΠ½ΡΡ ΡΡΠ°Π½Π°Ρ | |||||
ΠΡΠ°Π²ΠΈΠ»Π° ΠΏΡΠΈΠ΅ΠΌΠΊΠΈ ΠΌΠ΅ΡΠ°Π»Π»Π°, ΠΏΡΠ΅Π΄Π½Π°Π·Π½Π°ΡΠ΅Π½Π½ΠΎΠ³ΠΎ Π΄Π»Ρ Π²ΠΎΠ»ΠΎΡΠ΅Π½ΠΈΡ | |||||
ΠΠΈΠ΄Ρ Π΄Π΅ΡΠ΅ΠΊΡΠΎΠ² ΠΌΠ΅ΡΠ°Π»Π»Π°, Π½Π°ΠΏΡΠ°Π²Π»ΡΠ΅ΠΌΠΎΠ³ΠΎ Π½Π° Π²ΠΎΠ»ΠΎΡΠ΅Π½ΠΈΠ΅ | |||||
Π‘ΠΏΠΎΡΠΎΠ±Ρ ΠΏΠΎΠ΄Π³ΠΎΡΠΎΠ²ΠΊΠΈ ΠΌΠ΅ΡΠ°Π»Π»ΠΎΠΏΡΠΎΠΊΠ°ΡΠ° ΠΈ ΠΈΡ Π²Π»ΠΈΡΠ½ΠΈΠ΅ Π½Π° ΠΊΠ°ΡΠ΅ΡΡΠ²ΠΎ ΠΌΠ΅ΡΠ°Π»Π»Π° ΠΏΡΠΈ Π²ΠΎΠ»ΠΎΡΠ΅Π½ΠΈΠΈ | |||||
ΠΡΠ°Π²ΠΈΠ»Π° ΠΈ ΠΏΠΎΡΡΠ΄ΠΎΠΊ ΡΡΡΠ°Π½ΠΎΠ²ΠΊΠΈ (ΡΠΌΠ΅Π½Ρ) ΡΠ΅Ρ Π½ΠΎΠ»ΠΎΠ³ΠΈΡΠ΅ΡΠΊΠΎΠ³ΠΎ ΠΈΠ½ΡΡΡΡΠΌΠ΅Π½ΡΠ° Π½Π° ΡΡΠ°Π½Π°Ρ ΠΎΠ΄Π½ΠΎΠΊΡΠ°ΡΠ½ΠΎΠ³ΠΎ Π²ΠΎΠ»ΠΎΡΠ΅Π½ΠΈΡ | |||||
ΠΠΎΠ½ΡΡΡΡΠΊΡΠΈΡ ΠΈ ΠΏΠΎΡΡΠ΄ΠΎΠΊ ΡΠ±ΠΎΡΠΊΠΈ Π²ΠΎΠ»ΠΎΠΊΠΈ | |||||
Π’ΡΠ΅Π±ΠΎΠ²Π°Π½ΠΈΡ Π±ΠΈΡΠΎΡΠ½ΠΎΠΉ ΡΠΈΡΡΠ΅ΠΌΡ ΠΈ Π½Π°ΡΡΠ΄ΠΎΠ²-Π΄ΠΎΠΏΡΡΠΊΠΎΠ² Π½Π° ΡΡΠ°ΡΡΠΊΠ΅ Π²ΠΎΠ»ΠΎΡΠ΅Π½ΠΈΡ | |||||
ΠΠ°Π·Π½Π°ΡΠ΅Π½ΠΈΠ΅ ΠΈ ΠΏΡΠ°Π²ΠΈΠ»Π° ΠΏΡΠΈΠΌΠ΅Π½Π΅Π½ΠΈΡ ΠΊΠΎΠ½ΡΡΠΎΠ»ΡΠ½ΠΎ-ΠΈΠ·ΠΌΠ΅ΡΠΈΡΠ΅Π»ΡΠ½ΠΎΠ³ΠΎ ΠΈΠ½ΡΡΡΡΠΌΠ΅Π½ΡΠ° | |||||
Π’ΡΠ΅Π±ΠΎΠ²Π°Π½ΠΈΡ ΡΡ Π΅ΠΌ ΠΏΠ΅ΡΠ΅ΠΌΠ΅ΡΠ΅Π½ΠΈΡ ΠΈ ΡΠΊΠ»Π°Π΄ΠΈΡΠΎΠ²Π°Π½ΠΈΡ ΠΌΠ΅ΡΠ°Π»Π»Π° ΠΈ ΠΎΠ±ΠΎΡΡΠ΄ΠΎΠ²Π°Π½ΠΈΡ Π½Π° ΡΡΠ°ΡΡΠΊΠ΅ Π²ΠΎΠ»ΠΎΡΠ΅Π½ΠΈΡ | |||||
Π‘Π»Π΅ΡΠ°ΡΠ½ΠΎΠ΅ Π΄Π΅Π»ΠΎ ΠΏΡΠΈΠΌΠ΅Π½ΠΈΡΠ΅Π»ΡΠ½ΠΎ ΠΊ Π²ΡΠΏΠΎΠ»Π½ΡΠ΅ΠΌΡΠΌ ΡΠ°Π±ΠΎΡΠ°ΠΌ Π½Π° ΡΡΠ°ΡΡΠΊΠ΅ Π²ΠΎΠ»ΠΎΡΠ΅Π½ΠΈΡ | |||||
ΠΠ»Π°Π½ ΠΌΠ΅ΡΠΎΠΏΡΠΈΡΡΠΈΠΉ ΠΏΠΎ Π»ΠΎΠΊΠ°Π»ΠΈΠ·Π°ΡΠΈΠΈ ΠΈ Π»ΠΈΠΊΠ²ΠΈΠ΄Π°ΡΠΈΠΈ ΠΏΠΎΡΠ»Π΅Π΄ΡΡΠ²ΠΈΠΉ Π°Π²Π°ΡΠΈΠΉ Π½Π° ΡΡΠ°ΡΡΠΊΠ΅ Π²ΠΎΠ»ΠΎΡΠ΅Π½ΠΈΡ | |||||
Π’ΡΠ΅Π±ΠΎΠ²Π°Π½ΠΈΡ ΠΎΡ ΡΠ°Π½Ρ ΡΡΡΠ΄Π°, ΠΏΡΠΎΠΌΡΡΠ»Π΅Π½Π½ΠΎΠΉ, ΡΠΊΠΎΠ»ΠΎΠ³ΠΈΡΠ΅ΡΠΊΠΎΠΉ ΠΈ ΠΏΠΎΠΆΠ°ΡΠ½ΠΎΠΉ Π±Π΅Π·ΠΎΠΏΠ°ΡΠ½ΠΎΡΡΠΈ Π½Π° ΡΡΠ°ΡΡΠΊΠ΅ Π²ΠΎΠ»ΠΎΡΠ΅Π½ΠΈΡ | |||||
ΠΡΠΎΠ³ΡΠ°ΠΌΠΌΠ½ΠΎΠ΅ ΠΎΠ±Π΅ΡΠΏΠ΅ΡΠ΅Π½ΠΈΠ΅ ΡΠ°Π±ΠΎΡΠ΅Π³ΠΎ ΠΌΠ΅ΡΡΠ° Π²ΠΎΠ»ΠΎΡΠΈΠ»ΡΡΠΈΠΊΠ° | |||||
ΠΡΡΠ³ΠΈΠ΅ Ρ Π°ΡΠ°ΠΊΡΠ΅ΡΠΈΡΡΠΈΠΊΠΈ | — | ||||
Π’ΡΡΠ΄ΠΎΠ²ΡΠ΅ Π΄Π΅ΠΉΡΡΠ²ΠΈΡ | ΠΠΎΠ»ΡΡΠ΅Π½ΠΈΠ΅ (ΠΏΠ΅ΡΠ΅Π΄Π°ΡΠ°) ΠΈΠ½ΡΠΎΡΠΌΠ°ΡΠΈΠΈ ΠΏΡΠΈ ΠΏΡΠΈΠ΅ΠΌΠΊΠ΅-ΡΠ΄Π°ΡΠ΅ ΡΠΌΠ΅Π½Ρ ΠΎ Ρ Π°ΡΠ°ΠΊΡΠ΅ΡΠΈΡΡΠΈΠΊΠ°Ρ ΡΠ΅ΠΆΠΈΠΌΠ° Π²ΠΎΠ»ΠΎΡΠ΅Π½ΠΈΡ, ΠΏΡΠΈΡΠΈΠ½Π°Ρ ΠΏΠΎΠ»ΡΡΠ΅Π½ΠΈΡ Π½Π΅ΡΠΎΠΎΡΠ²Π΅ΡΡΡΠ²ΡΡΡΠ΅ΠΉ ΠΏΡΠΎΠ΄ΡΠΊΡΠΈΠΈ ΠΈ Π±ΡΠ°ΠΊΠ° ΠΈ ΠΏΡΠΈΠ½ΡΡΡΡ ΠΌΠ΅ΡΠ°Ρ ΠΏΠΎ ΠΈΡ ΡΡΡΡΠ°Π½Π΅Π½ΠΈΡ | ||||
ΠΡΠΎΠ²Π΅ΡΠΊΠ° ΡΠ°Π±ΠΎΡΠΎΡΠΏΠΎΡΠΎΠ±Π½ΠΎΡΡΠΈ ΠΎΠ±ΡΠ»ΡΠΆΠΈΠ²Π°Π΅ΠΌΠΎΠ³ΠΎ Π²ΠΎΠ»ΠΎΡΠΈΠ»ΡΠ½ΠΎΠ³ΠΎ ΠΎΠ±ΠΎΡΡΠ΄ΠΎΠ²Π°Π½ΠΈΡ ΠΈ ΠΌΠ΅Ρ Π°Π½ΠΈΠ·ΠΌΠΎΠ² | |||||
ΠΠ°ΡΡΡΠΎΠΉΠΊΠ° Π²ΠΎΠ»ΠΎΡΠΈΠ»ΡΠ½ΠΎΠ³ΠΎ ΡΡΠ°Π½Π° | |||||
ΠΡΠΎΠ±Π½ΠΎΠ΅ Π²ΠΎΠ»ΠΎΡΠ΅Π½ΠΈΠ΅ | |||||
ΠΠΎΠ½ΡΡΠΎΠ»Ρ ΠΏΠ°ΡΠ°ΠΌΠ΅ΡΡΠΎΠ² ΠΈΠ·Π΄Π΅Π»ΠΈΠΉ Π΄Π»Ρ Π΄Π°Π»ΡΠ½Π΅ΠΉΡΠ΅Π³ΠΎ Π·Π°ΠΏΡΡΠΊΠ° Π² ΠΏΡΠΎΠΈΠ·Π²ΠΎΠ΄ΡΡΠ²ΠΎ Π²ΡΠ΅ΠΉ ΠΏΠ°ΡΡΠΈΠΈ ΠΌΠ΅ΡΠ°Π»Π»Π° | |||||
ΠΠΎΠ½ΡΡΠΎΠ»Ρ ΠΊΠ°ΡΠ΅ΡΡΠ²Π° ΠΏΠΎΠ²Π΅ΡΡ Π½ΠΎΡΡΠΈ ΠΈ Π³Π΅ΠΎΠΌΠ΅ΡΡΠΈΡΠ΅ΡΠΊΠΈΡ ΡΠ°Π·ΠΌΠ΅ΡΠΎΠ² Ρ ΠΎΠ»ΠΎΠ΄Π½ΠΎΡΡΠ½ΡΡΠΎΠ³ΠΎ ΠΌΠ΅ΡΠ°Π»Π»Π° | |||||
Π Π΅Π³ΡΠ»ΠΈΡΠΎΠ²ΠΊΠ° ΠΏΠ°ΡΠ°ΠΌΠ΅ΡΡΠΎΠ² Π²ΠΎΠ»ΠΎΡΠ΅Π½ΠΈΡ | |||||
Π‘ΠΌΠ΅Π½Π° Π²ΠΎΠ»ΠΎΠΊ | |||||
ΠΠΎΠ½ΡΡΠΎΠ»Ρ ΠΊΠ°ΡΠ΅ΡΡΠ²Π° ΠΈ ΡΠ²ΠΎΠ΅Π²ΡΠ΅ΠΌΠ΅Π½Π½ΠΎΠΉ Π·Π°ΠΌΠ΅Π½Ρ ΡΠ΅Ρ Π½ΠΎΠ»ΠΎΠ³ΠΈΡΠ΅ΡΠΊΠΎΠ³ΠΎ ΠΈΠ½ΡΡΡΡΠΌΠ΅Π½ΡΠ° Π½Π° ΠΎΠ΄Π½ΠΎΠΊΡΠ°ΡΠ½ΡΡ Π²ΠΎΠ»ΠΎΡΠΈΠ»ΡΠ½ΡΡ ΡΡΠ°Π½Π°Ρ | |||||
ΠΠ±ΡΠ»ΡΠΆΠΈΠ²Π°Π½ΠΈΠ΅ ΡΠΌΠ°Π·ΠΎΡΠ½ΡΡ ΠΈ ΡΠΏΠ΅ΡΠΈΠ°Π»ΡΠ½ΡΡ Π½Π°ΠΌΠΎΡΠΎΡΠ½ΡΡ ΡΡΡΡΠΎΠΉΡΡΠ² ΠΈΠ»ΠΈ Π·Π°Π³ΡΡΠ·ΠΎΡΠ½ΡΡ ΠΊΠΎΠ½ΡΠΎΠ»Π΅ΠΉ ΠΈ Π½Π°ΠΊΠΎΠΏΠΈΡΠ΅Π»Π΅ΠΉ Π³ΠΎΡΠΎΠ²ΠΎΠΉ ΠΏΡΠΎΠ΄ΡΠΊΡΠΈΠΈ, ΡΡΠ΅ΠΌΠ½ΡΡ ΠΌΠ΅Ρ Π°Π½ΠΈΠ·ΠΌΠΎΠ² ΠΈ ΡΠΈΡΡΠ΅ΠΌ ΠΎΡ Π»Π°ΠΆΠ΄Π΅Π½ΠΈΡ ΠΏΡΠΈ Π²ΠΎΠ»ΠΎΡΠ΅Π½ΠΈΠΈ | |||||
ΠΠΎΠ½ΡΡΠΎΠ»Ρ Π½Π°ΠΌΠΎΡΠΊΠΈ ΠΌΠ΅ΡΠ°Π»Π»ΠΎΠΏΡΠΎΠΊΠ°ΡΠ° Π½Π° Π²ΠΎΠ»ΠΎΡΠΈΠ»ΡΠ½ΡΠ΅ Π±Π°ΡΠ°Π±Π°Π½Ρ, ΡΠΊΠ»Π°Π΄ΠΊΠΈ ΠΏΡΡΡΠΊΠΎΠ² Π½Π° ΠΏΡΠΈΠ΅ΠΌΠ½ΠΎΠ΅ ΠΏΡΠΈΡΠΏΠΎΡΠΎΠ±Π»Π΅Π½ΠΈΠ΅ | |||||
Π‘ΡΠ΅ΠΌ, ΡΠ²ΡΠ·ΠΊΠ° ΠΈ ΠΌΠ°ΡΠΊΠΈΡΠΎΠ²ΠΊΠ° ΠΌΠΎΡΠΊΠΎΠ², Π±ΡΠ½ΡΠΎΠ² ΠΈΠ»ΠΈ ΠΏΠ°ΡΠ΅ΠΊ ΠΏΡΠΎΠ΄ΡΠΊΡΠΈΠΈ | |||||
ΠΠ±ΡΠ΅Π·ΠΊΠ° Π·Π°ΠΏΡΠ°Π²ΠΎΡΠ½ΡΡ ΠΊΠΎΠ½ΡΠΎΠ² | |||||
Π‘Π±ΡΠΎΡ Π³ΠΎΡΠΎΠ²ΠΎΠΉ ΠΏΡΠΎΠ΄ΡΠΊΡΠΈΠΈ Π½Π° ΡΡΠ΅Π»Π»Π°ΠΆ ΠΈΠ»ΠΈ Π² Π½Π°ΠΊΠΎΠΏΠΈΡΠ΅Π»ΡΠ½ΡΠΉ ΠΊΠ°ΡΠΌΠ°Π½ | |||||
ΠΠ΅Π΄Π΅Π½ΠΈΠ΅ Π°Π³ΡΠ΅Π³Π°ΡΠ½ΠΎΠ³ΠΎ ΠΆΡΡΠ½Π°Π»Π° ΠΈ ΡΡΠ΅ΡΠ½ΠΎΠΉ Π΄ΠΎΠΊΡΠΌΠ΅Π½ΡΠ°ΡΠΈΠΈ Π²ΠΎΠ»ΠΎΡΠΈΠ»ΡΡΠΈΠΊΠ° | |||||
ΠΠ΅ΠΎΠ±Ρ ΠΎΠ΄ΠΈΠΌΡΠ΅ ΡΠΌΠ΅Π½ΠΈΡ | ΠΠΏΡΠ΅Π΄Π΅Π»ΡΡΡ Π²ΠΈΠ·ΡΠ°Π»ΡΠ½ΠΎ ΠΈΠ»ΠΈ Ρ ΠΈΡΠΏΠΎΠ»ΡΠ·ΠΎΠ²Π°Π½ΠΈΠ΅ΠΌ ΠΏΡΠΈΠ±ΠΎΡΠΎΠ² ΠΎΡΠΊΠ»ΠΎΠ½Π΅Π½ΠΈΡ ΠΏΠ°ΡΠ°ΠΌΠ΅ΡΡΠΎΠ² ΡΠ΅ΠΊΡΡΠ΅Π³ΠΎ ΡΠΎΡΡΠΎΡΠ½ΠΈΡ ΠΎΠ±ΡΠ»ΡΠΆΠΈΠ²Π°Π΅ΠΌΠΎΠ³ΠΎ ΠΎΡΠ½ΠΎΠ²Π½ΠΎΠ³ΠΎ ΠΈ Π²ΡΠΏΠΎΠΌΠΎΠ³Π°ΡΠ΅Π»ΡΠ½ΠΎΠ³ΠΎ ΠΎΠ±ΠΎΡΡΠ΄ΠΎΠ²Π°Π½ΠΈΡ ΠΎΠ΄Π½ΠΎΠΊΡΠ°ΡΠ½ΡΡ Π²ΠΎΠ»ΠΎΡΠΈΠ»ΡΠ½ΡΡ ΡΡΠ°Π½ΠΎΠ² ΠΈ ΡΡΡΡΠΎΠΉΡΡΠ² Π²ΠΎΠ»ΠΎΡΠ΅Π½ΠΈΡ ΠΎΡ ΡΡΡΠ°Π½ΠΎΠ²Π»Π΅Π½Π½ΡΡ Π·Π½Π°ΡΠ΅Π½ΠΈΠΉ | ||||
ΠΠΈΠ·ΡΠ°Π»ΡΠ½ΠΎ ΠΎΠΏΡΠ΅Π΄Π΅Π»ΡΡΡ Π½Π°Π»ΠΈΡΠΈΠ΅ Π΄Π΅ΡΠ΅ΠΊΡΠΎΠ² Π½Π° ΠΏΠΎΠ²Π΅ΡΡ Π½ΠΎΡΡΠΈ ΠΌΠ΅ΡΠ°Π»Π»Π° ΠΏΠ΅ΡΠ΅Π΄ Π²ΠΎΠ»ΠΎΡΠ΅Π½ΠΈΠ΅ΠΌ, Π² ΠΏΡΠΎΡΠ΅ΡΡΠ΅ ΠΈ ΠΏΠΎΡΠ»Π΅ Π²ΠΎΠ»ΠΎΡΠ΅Π½ΠΈΡ | |||||
ΠΡΡΡΠ΅ΡΡΠ²Π»ΡΡΡ ΠΏΡΠΎΠ²Π΅ΡΠΊΡ ΠΈΡΠΏΡΠ°Π²Π½ΠΎΡΡΠΈ ΡΠ΅Ρ Π½ΠΎΠ»ΠΎΠ³ΠΈΡΠ΅ΡΠΊΠΎΠ³ΠΎ ΠΈΠ½ΡΡΡΡΠΌΠ΅Π½ΡΠ° ΠΎΠ΄Π½ΠΎΠΊΡΠ°ΡΠ½ΡΡ Π²ΠΎΠ»ΠΎΡΠΈΠ»ΡΠ½ΡΡ ΡΡΠ°Π½ΠΎΠ² | |||||
ΠΠΎΠ΄Π±ΠΈΡΠ°ΡΡ ΡΠΈΠΏ Π²ΠΎΠ»ΠΎΠΊΠΈ ΠΈ ΡΠ΅Ρ Π½ΠΎΠ»ΠΎΠ³ΠΈΡΠ΅ΡΠΊΡΡ ΡΠΌΠ°Π·ΠΊΡ Π² Π·Π°Π²ΠΈΡΠΈΠΌΠΎΡΡΠΈ ΠΎΡ ΠΌΠ°ΡΠΊΠΈ ΠΈ Π²ΠΈΠ΄Π° ΠΊΠ°Π»ΠΈΠ±ΡΡΠ΅ΠΌΠΎΠ³ΠΎ ΠΌΠ΅ΡΠ°Π»Π»Π° | |||||
Π Π΅Π³ΡΠ»ΠΈΡΠΎΠ²Π°ΡΡ ΡΠΊΠΎΡΠΎΡΡΡ Π²ΠΎΠ»ΠΎΡΠ΅Π½ΠΈΡ Π½Π° ΠΎΠ΄Π½ΠΎΠΊΡΠ°ΡΠ½ΡΡ Π²ΠΎΠ»ΠΎΡΠΈΠ»ΡΠ½ΡΡ ΡΡΠ°Π½Π°Ρ | |||||
ΠΡΠΎΠ²Π΅ΡΡΡΡ Π²Π΅Π»ΠΈΡΠΈΠ½Ρ ΡΠ°ΠΊΡΠΈΡΠ΅ΡΠΊΠΎΠ³ΠΎ Π°Π±ΡΠΎΠ»ΡΡΠ½ΠΎΠ³ΠΎ ΠΎΠ±ΠΆΠ°ΡΠΈΡ | |||||
ΠΠΎΠ»ΡΠ·ΠΎΠ²Π°ΡΡΡΡ ΠΌΠ΅ΡΠΈΡΠ΅Π»ΡΠ½ΡΠΌ ΠΈΠ½ΡΡΡΡΠΌΠ΅Π½ΡΠΎΠΌ | |||||
ΠΡΠ΅Π½ΠΈΠ²Π°ΡΡ ΠΊΠ°ΡΠ΅ΡΡΠ²ΠΎ ΠΈ Π½Π΅ΠΎΠ±Ρ ΠΎΠ΄ΠΈΠΌΠΎΠ΅ ΠΊΠΎΠ»ΠΈΡΠ΅ΡΡΠ²ΠΎ ΡΠ΅Ρ Π½ΠΎΠ»ΠΎΠ³ΠΈΡΠ΅ΡΠΊΠΎΠΉ ΡΠΌΠ°Π·ΠΊΠΈ Π² ΠΏΡΠΎΡΠ΅ΡΡΠ΅ Π²ΠΎΠ»ΠΎΡΠ΅Π½ΠΈΡ | |||||
ΠΡΠΈΠΌΠ΅Π½ΡΡΡ ΠΊΠΎΠ½ΡΡΠΎΠ»ΡΠ½ΠΎ-ΠΈΠ·ΠΌΠ΅ΡΠΈΡΠ΅Π»ΡΠ½ΡΠΉ ΠΈΠ½ΡΡΡΡΠΌΠ΅Π½Ρ Π΄Π»Ρ ΠΎΠΏΡΠ΅Π΄Π΅Π»Π΅Π½ΠΈΡ Π³Π΅ΠΎΠΌΠ΅ΡΡΠΈΡΠ΅ΡΠΊΠΈΡ ΡΠ°Π·ΠΌΠ΅ΡΠΎΠ² ΠΏΠΎΡΡΡΠΏΠ°ΡΡΠ΅Π³ΠΎ ΠΌΠ΅ΡΠ°Π»Π»Π° | |||||
ΠΡΠΎΠΈΠ·Π²ΠΎΠ΄ΠΈΡΡ ΠΏΠΎΠ²Π΅ΡΠΊΡ ΠΌΠ΅ΡΠΈΡΠ΅Π»ΡΠ½ΠΎΠ³ΠΎ ΠΈΠ½ΡΡΡΡΠΌΠ΅Π½ΡΠ° | |||||
ΠΡΠΈΠΌΠ΅Π½ΡΡΡ ΡΡΠ΅Π΄ΡΡΠ²Π° ΠΈΠ½Π΄ΠΈΠ²ΠΈΠ΄ΡΠ°Π»ΡΠ½ΠΎΠΉ Π·Π°ΡΠΈΡΡ, ΠΏΠΎΠΆΠ°ΡΠΎΡΡΡΠ΅Π½ΠΈΡ ΠΈ ΠΏΠΎΠ»ΡΠ·ΠΎΠ²Π°ΡΡΡΡ Π°Π²Π°ΡΠΈΠΉΠ½ΡΠΌ ΠΈΠ½ΡΡΡΡΠΌΠ΅Π½ΡΠΎΠΌ Π½Π° ΡΡΠ°ΡΡΠΊΠ΅ Π²ΠΎΠ»ΠΎΡΠ΅Π½ΠΈΡ | |||||
ΠΡΠΈΠΌΠ΅Π½ΡΡΡ ΠΏΡΠΎΠ³ΡΠ°ΠΌΠΌΠ½ΠΎΠ΅ ΠΎΠ±Π΅ΡΠΏΠ΅ΡΠ΅Π½ΠΈΠ΅ ΡΠ°Π±ΠΎΡΠ΅Π³ΠΎ ΠΌΠ΅ΡΡΠ° Π²ΠΎΠ»ΠΎΡΠΈΠ»ΡΡΠΈΠΊΠ° | |||||
ΠΠ΅ΠΎΠ±Ρ ΠΎΠ΄ΠΈΠΌΡΠ΅ Π·Π½Π°Π½ΠΈΡ | Π£ΡΡΡΠΎΠΉΡΡΠ²ΠΎ, ΠΏΡΠΈΠ½ΡΠΈΠΏ ΡΠ°Π±ΠΎΡΡ ΠΈ ΠΏΡΠ°Π²ΠΈΠ»Π° ΡΠΊΡΠΏΠ»ΡΠ°ΡΠ°ΡΠΈΠΈ ΠΎΠ±ΡΠ»ΡΠΆΠΈΠ²Π°Π΅ΠΌΠΎΠ³ΠΎ ΠΎΡΠ½ΠΎΠ²Π½ΠΎΠ³ΠΎ ΠΈ Π²ΡΠΏΠΎΠΌΠΎΠ³Π°ΡΠ΅Π»ΡΠ½ΠΎΠ³ΠΎ ΠΎΠ±ΠΎΡΡΠ΄ΠΎΠ²Π°Π½ΠΈΡ ΡΡΠ°ΡΡΠΊΠ° Π²ΠΎΠ»ΠΎΡΠ΅Π½ΠΈΡ | ||||
Π£ΡΡΡΠΎΠΉΡΡΠ²ΠΎ, ΠΊΠΈΠ½Π΅ΠΌΠ°ΡΠΈΡΠ΅ΡΠΊΠΈΠ΅ ΡΡ Π΅ΠΌΡ ΠΈ ΠΏΡΠ°Π²ΠΈΠ»Π° Π½Π°Π»Π°Π΄ΠΊΠΈ ΠΎΠ΄Π½ΠΎΠΊΡΠ°ΡΠ½ΡΡ Π²ΠΎΠ»ΠΎΡΠΈΠ»ΡΠ½ΡΡ ΡΡΠ°Π½ΠΎΠ² | |||||
ΠΠ°Π·Π½Π°ΡΠ΅Π½ΠΈΠ΅ ΠΈ ΠΏΡΠ°Π²ΠΈΠ»Π° ΠΏΡΠΈΠΌΠ΅Π½Π΅Π½ΠΈΡ ΠΊΠΎΠ½ΡΡΠΎΠ»ΡΠ½ΠΎ-ΠΈΠ·ΠΌΠ΅ΡΠΈΡΠ΅Π»ΡΠ½ΡΡ ΠΏΡΠΈΠ±ΠΎΡΠΎΠ² ΠΈ ΠΌΠ΅ΡΠΈΡΠ΅Π»ΡΠ½ΠΎΠ³ΠΎ ΠΈΠ½ΡΡΡΡΠΌΠ΅Π½ΡΠ° | |||||
ΠΡΠΎΠΈΠ·Π²ΠΎΠ΄ΡΡΠ²Π΅Π½Π½ΠΎ-ΡΠ΅Ρ Π½ΠΈΡΠ΅ΡΠΊΠΈΠ΅ ΠΈΠ½ΡΡΡΡΠΊΡΠΈΠΈ ΠΏΠΎ Π²ΠΎΠ»ΠΎΡΠ΅Π½ΠΈΡ ΠΌΠ΅ΡΠ°Π»Π»ΠΎΠΏΡΠΎΠΊΠ°ΡΠ° ΠΈ ΡΡΡΠ± Π½Π° ΠΎΠ΄Π½ΠΎΠΊΡΠ°ΡΠ½ΡΡ Π²ΠΎΠ»ΠΎΡΠΈΠ»ΡΠ½ΡΡ ΡΡΠ°Π½Π°Ρ | |||||
ΠΡΠΎΠ±Π΅Π½Π½ΠΎΡΡΠΈ Π²ΠΎΠ»ΠΎΡΠ΅Π½ΠΈΡ ΠΌΠ΅ΡΠ°Π»Π»ΠΎΠΏΡΠΎΠΊΠ°ΡΠ° ΡΠ°Π·Π»ΠΈΡΠ½ΡΡ ΠΌΠ°ΡΠΎΠΊ | |||||
Π’ΠΈΠΏΡ Π²ΠΎΠ»ΠΎΠΊ (ΠΎΠ΄ΠΈΠ½Π°ΡΠ½Π°Ρ, ΡΠ±ΠΎΡΠ½Π°Ρ, ΡΠΎΠ»ΠΈΠΊΠΎΠ²Π°Ρ) | |||||
ΠΡΠ°Π²ΠΈΠ»Π° ΠΈ ΠΏΠΎΡΡΠ΄ΠΎΠΊ ΡΡΡΠ°Π½ΠΎΠ²ΠΊΠΈ (ΡΠΌΠ΅Π½Ρ) ΡΠ΅Ρ Π½ΠΎΠ»ΠΎΠ³ΠΈΡΠ΅ΡΠΊΠΎΠ³ΠΎ ΠΈΠ½ΡΡΡΡΠΌΠ΅Π½ΡΠ° Π½Π° ΡΡΠ°Π½Π°Ρ ΠΎΠ΄Π½ΠΎΠΊΡΠ°ΡΠ½ΠΎΠ³ΠΎ Π²ΠΎΠ»ΠΎΡΠ΅Π½ΠΈΡ | |||||
ΠΠ»ΠΈΡΠ½ΠΈΠ΅ ΡΠΊΠΎΡΠΎΡΡΠ½ΡΡ ΡΠ΅ΠΆΠΈΠΌΠΎΠ² Π½Π° ΠΏΡΠΎΡΠ΅ΡΡ Π²ΠΎΠ»ΠΎΡΠ΅Π½ΠΈΡ ΠΌΠ΅ΡΠ°Π»Π»Π° | |||||
ΠΠΎΡΠ»Π΅Π΄ΠΎΠ²Π°ΡΠ΅Π»ΡΠ½ΠΎΡΡΡ Π΄Π΅ΠΉΡΡΠ²ΠΈΠΉ ΠΏΡΠΈ Π·Π°ΠΏΡΡΠΊΠ΅ ΠΈΠ»ΠΈ ΠΎΡΠΊΠ»ΡΡΠ΅Π½ΠΈΠΈ, Π½Π°ΡΡΡΠΎΠΉΠΊΠ΅, ΠΊΠΎΠ½ΡΡΠΎΠ»Π΅ ΡΠ΅ΠΆΠΈΠΌΠ° ΡΠ°Π±ΠΎΡΡ ΠΎΠ±ΠΎΡΡΠ΄ΠΎΠ²Π°Π½ΠΈΡ | |||||
ΠΠ»ΠΈΡΠ½ΠΈΠ΅ ΡΠΏΠΎΡΠΎΠ±Π° ΠΏΠΎΠ΄Π³ΠΎΡΠΎΠ²ΠΊΠΈ ΠΌΠ΅ΡΠ°Π»Π»Π° Π½Π° ΠΊΠ°ΡΠ΅ΡΡΠ²ΠΎ ΠΏΡΠΎΠ΄ΡΠΊΡΠΈΠΈ ΠΏΡΠΈ Π²ΠΎΠ»ΠΎΡΠ΅Π½ΠΈΠΈ | |||||
Π‘ΠΈΡΡΠ΅ΠΌΠ° Π΄ΠΎΠΏΡΡΠΊΠΎΠ² ΠΈ ΠΏΠΎΡΠ°Π΄ΠΎΠΊ, ΠΊΠ²Π°Π»ΠΈΡΠ΅ΡΡ ΠΈ ΠΏΠ°ΡΠ°ΠΌΠ΅ΡΡΡ ΡΠ΅ΡΠΎΡ ΠΎΠ²Π°ΡΠΎΡΡΠΈ ΠΎΠ±ΡΠ°Π±Π°ΡΡΠ²Π°Π΅ΠΌΠΎΠ³ΠΎ ΠΌΠ΅ΡΠ°Π»Π»Π° | |||||
ΠΠ°Π²ΠΈΡΠΈΠΌΠΎΡΡΡ ΠΏΡΠΎΡΠ½ΠΎΡΡΠ½ΡΡ ΠΈ ΠΏΠ»Π°ΡΡΠΈΡΠ΅ΡΠΊΠΈΡ ΡΠ²ΠΎΠΉΡΡΠ² ΠΌΠ΅ΡΠ°Π»Π»Π° ΠΎΡ ΡΡΠ΅ΠΏΠ΅Π½ΠΈ Π΄Π΅ΡΠΎΡΠΌΠ°ΡΠΈΠΈ ΠΏΡΠΈ Π²ΠΎΠ»ΠΎΡΠ΅Π½ΠΈΠΈ ΠΌΠ΅ΡΠ°Π»Π»Π° | |||||
Π’ΡΠ΅Π±ΠΎΠ²Π°Π½ΠΈΡ Π»ΠΎΠΊΠ°Π»ΡΠ½ΠΎΠΉ Π½ΠΎΡΠΌΠ°ΡΠΈΠ²Π½ΠΎΠΉ Π΄ΠΎΠΊΡΠΌΠ΅Π½ΡΠ°ΡΠΈΠΈ, ΡΠ΅Π³Π»Π°ΠΌΠ΅Π½ΡΠΈΡΡΡΡΠ΅ΠΉ ΠΏΡΠΎΡΠ΅ΡΡΡ Π²ΠΎΠ»ΠΎΡΠ΅Π½ΠΈΡ | |||||
Π’ΡΠ΅Π±ΠΎΠ²Π°Π½ΠΈΡ ΡΡΠ°Π½Π΄Π°ΡΡΠΎΠ² ΠΈ ΡΠ΅Ρ Π½ΠΈΡΠ΅ΡΠΊΠΈΡ ΡΡΠ»ΠΎΠ²ΠΈΠΉ ΠΊ Π²ΡΠΏΡΡΠΊΠ°Π΅ΠΌΠΎΠΉ ΠΏΡΠΎΠ΄ΡΠΊΡΠΈΠΈ | |||||
ΠΠ΅Ρ Π°Π½ΠΈΡΠ΅ΡΠΊΠΈΠ΅ ΡΠ²ΠΎΠΉΡΡΠ²Π° ΠΎΠ±ΡΠ°Π±Π°ΡΡΠ²Π°Π΅ΠΌΠΎΠ³ΠΎ ΠΌΠ΅ΡΠ°Π»Π»Π° | |||||
ΠΠΈΠ΄Ρ Π±ΡΠ°ΠΊΠ° ΠΌΠ΅ΡΠ°Π»Π»ΠΎΠΏΡΠΎΠ΄ΡΠΊΡΠΈΠΈ, Π²ΡΡΠ²Π»ΡΠ΅ΠΌΡΠ΅ ΠΏΡΠΈ Π²ΠΎΠ»ΠΎΡΠ΅Π½ΠΈΠΈ ΠΌΠ΅ΡΠ°Π»Π»Π° | |||||
ΠΠΎΠΏΡΡΡΠΈΠΌΡΠ΅ Π²ΠΈΠ΄Ρ Π΄Π΅ΡΠ΅ΠΊΡΠΎΠ², ΠΎΠ±ΡΠ°Π·ΡΡΡΠΈΠ΅ΡΡ Π² ΠΏΡΠΎΡΠ΅ΡΡΠ΅ Π²ΠΎΠ»ΠΎΡΠ΅Π½ΠΈΡ | |||||
Π‘Π»Π΅ΡΠ°ΡΠ½ΠΎΠ΅ Π΄Π΅Π»ΠΎ ΠΏΡΠΈΠΌΠ΅Π½ΠΈΡΠ΅Π»ΡΠ½ΠΎ ΠΊ Π²ΡΠΏΠΎΠ»Π½ΡΠ΅ΠΌΡΠΌ ΡΠ°Π±ΠΎΡΠ°ΠΌ Π½Π° ΡΡΠ°ΡΡΠΊΠ΅ Π²ΠΎΠ»ΠΎΡΠ΅Π½ΠΈΡ | |||||
Π’ΡΠ΅Π±ΠΎΠ²Π°Π½ΠΈΡ Π±ΠΈΡΠΎΡΠ½ΠΎΠΉ ΡΠΈΡΡΠ΅ΠΌΡ ΠΈ Π½Π°ΡΡΠ΄ΠΎΠ²-Π΄ΠΎΠΏΡΡΠΊΠΎΠ² Π½Π° ΡΡΠ°ΡΡΠΊΠ΅ Π²ΠΎΠ»ΠΎΡΠ΅Π½ΠΈΡ | |||||
ΠΠ»Π°Π½ ΠΌΠ΅ΡΠΎΠΏΡΠΈΡΡΠΈΠΉ Π»ΠΎΠΊΠ°Π»ΠΈΠ·Π°ΡΠΈΠΈ ΠΈ Π»ΠΈΠΊΠ²ΠΈΠ΄Π°ΡΠΈΠΈ ΠΏΠΎΡΠ»Π΅Π΄ΡΡΠ²ΠΈΠΉ Π°Π²Π°ΡΠΈΠΉ Π½Π° ΡΡΠ°ΡΡΠΊΠ΅ Π²ΠΎΠ»ΠΎΡΠ΅Π½ΠΈΡ | |||||
Π’ΡΠ΅Π±ΠΎΠ²Π°Π½ΠΈΡ ΠΎΡ ΡΠ°Π½Ρ ΡΡΡΠ΄Π°, ΠΏΡΠΎΠΌΡΡΠ»Π΅Π½Π½ΠΎΠΉ, ΡΠΊΠΎΠ»ΠΎΠ³ΠΈΡΠ΅ΡΠΊΠΎΠΉ ΠΈ ΠΏΠΎΠΆΠ°ΡΠ½ΠΎΠΉ Π±Π΅Π·ΠΎΠΏΠ°ΡΠ½ΠΎΡΡΠΈ Π½Π° ΡΡΠ°ΡΡΠΊΠ΅ Π²ΠΎΠ»ΠΎΡΠ΅Π½ΠΈΡ | |||||
ΠΡΠΎΠ³ΡΠ°ΠΌΠΌΠ½ΠΎΠ΅ ΠΎΠ±Π΅ΡΠΏΠ΅ΡΠ΅Π½ΠΈΠ΅ ΡΠ°Π±ΠΎΡΠ΅Π³ΠΎ ΠΌΠ΅ΡΡΠ° Π²ΠΎΠ»ΠΎΡΠΈΠ»ΡΡΠΈΠΊΠ° | |||||
ΠΡΠΎΠ³ΡΠ°ΠΌΠΌΠ½ΠΎΠ΅ ΠΎΠ±Π΅ΡΠΏΠ΅ΡΠ΅Π½ΠΈΠ΅ ΡΠ°Π±ΠΎΡΠ΅Π³ΠΎ ΠΌΠ΅ΡΡΠ° Π²ΠΎΠ»ΠΎΡΠΈΠ»ΡΡΠΈΠΊΠ° | |||||
ΠΡΡΠ³ΠΈΠ΅ Ρ Π°ΡΠ°ΠΊΡΠ΅ΡΠΈΡΡΠΈΠΊΠΈ | — | ||||
Π’ΡΡΠ΄ΠΎΠ²ΡΠ΅ Π΄Π΅ΠΉΡΡΠ²ΠΈΡ | ΠΠ·Π²Π»Π΅ΡΠ΅Π½ΠΈΠ΅ Π²ΠΎΠ»ΠΎΠΊ ΠΈΠ· ΠΎΠΏΡΠ°Π², ΠΏΡΠΎΡΠΈΡΠΊΠ° Π²ΠΎΠ»ΠΎΠΊ | ||||
ΠΡΠ±ΠΎΡ ΠΎΠ±ΡΠ°Π·ΡΠΎΠ² ΠΏΡΠΎΠΈΠ·Π²Π΅Π΄Π΅Π½Π½ΠΎΠΉ ΠΏΡΠΎΠ΄ΡΠΊΡΠΈΠΈ Π½Π° ΡΠΈΠ·ΠΈΠΊΠΎ-ΠΌΠ΅ΡΠ°Π»Π»ΠΎΠ³ΡΠ°ΡΠΈΡΠ΅ΡΠΊΠΈΠ΅ ΠΈΡΠΏΡΡΠ°Π½ΠΈΡ | |||||
ΠΠΎΠ½ΡΡΠΎΠ»Ρ Π³Π΅ΠΎΠΌΠ΅ΡΡΠΈΡΠ΅ΡΠΊΠΈΡ ΠΏΠ°ΡΠ°ΠΌΠ΅ΡΡΠΎΠ² ΠΈ ΠΊΠ°ΡΠ΅ΡΡΠ²Π° ΠΏΠΎΠ²Π΅ΡΡ Π½ΠΎΡΡΠΈ Π³ΠΎΡΠΎΠ²ΠΎΠΉ ΠΏΡΠΎΠ΄ΡΠΊΡΠΈΠΈ | |||||
ΠΡΠΎΠ²Π΅Π΄Π΅Π½ΠΈΠ΅ Π°ΡΡΠ΅ΡΡΠ°ΡΠΈΠΈ ΠΏΡΠΎΠ΄ΡΠΊΡΠΈΠΈ ΠΏΠΎΡΠ»Π΅ Π²ΠΎΠ»ΠΎΡΠ΅Π½ΠΈΡ | |||||
ΠΡΠΎΡΠΌΠ»Π΅Π½ΠΈΠ΅ ΡΠΎΠΏΡΠΎΠ²ΠΎΠ΄ΠΈΡΠ΅Π»ΡΠ½ΠΎΠΉ Π΄ΠΎΠΊΡΠΌΠ΅Π½ΡΠ°ΡΠΈΠΈ Π½Π° ΠΏΡΠΎΠΈΠ·Π²Π΅Π΄Π΅Π½Π½ΡΡ ΠΏΡΠΎΠ΄ΡΠΊΡΠΈΡ | |||||
Π‘ΡΠ΅ΠΌ, ΡΠ²ΡΠ·ΠΊΠ°, ΠΌΠ°ΡΠΊΠΈΡΠΎΠ²ΠΊΠ°, ΡΠΏΠ°ΠΊΠΎΠ²ΠΊΠ° ΠΏΡΠΎΠ΄ΡΠΊΡΠΈΠΈ | |||||
ΠΠ·Π²Π΅ΡΠΈΠ²Π°Π½ΠΈΠ΅ ΠΏΡΠΎΠΈΠ·Π²Π΅Π΄Π΅Π½Π½ΠΎΠΉ ΠΏΡΠΎΠ΄ΡΠΊΡΠΈΠΈ | |||||
Π‘Π΄Π°ΡΠ° Π² ΡΠΈΠ»ΡΠ΅ΡΠ½ΡΡ ΠΌΠ°ΡΡΠ΅ΡΡΠΊΡΡ ΠΎΡΡΠ°Π±ΠΎΡΠ°Π½Π½ΡΡ Π²ΠΎΠ»ΠΎΠΊ | |||||
Π‘Π±ΠΎΡ, ΡΠΎΡΡΠΈΡΠΎΠ²ΠΊΠ° ΠΎΡΠ±ΡΠ°ΠΊΠΎΠ²Π°Π½Π½ΠΎΠ³ΠΎ ΠΌΠ΅ΡΠ°Π»Π»Π° ΠΈ ΠΎΡΡ ΠΎΠ΄ΠΎΠ² ΠΏΠΎ Π³ΡΡΠΏΠΏΠ°ΠΌ | |||||
Π§ΠΈΡΡΠΊΠ° ΠΎΠ±ΡΠ»ΡΠΆΠΈΠ²Π°Π΅ΠΌΠΎΠ³ΠΎ ΠΎΠ±ΠΎΡΡΠ΄ΠΎΠ²Π°Π½ΠΈΡ | |||||
Π‘Π±ΠΎΡ ΠΈΡΠΏΠΎΠ»ΡΠ·ΠΎΠ²Π°Π½Π½ΠΎΠΉ Π²Π΅ΡΠΎΡΠΈ Π² ΡΠΏΠ΅ΡΠΈΠ°Π»ΡΠ½ΡΠ΅ ΠΊΠΎΠ½ΡΠ΅ΠΉΠ½Π΅ΡΡ | |||||
Π£Π±ΠΎΡΠΊΠ° ΡΠ°Π±ΠΎΡΠ΅Π³ΠΎ ΠΌΠ΅ΡΡΠ° Π²ΠΎΠ»ΠΎΡΠΈΠ»ΡΡΠΈΠΊΠ° | |||||
ΠΠ΅Π΄Π΅Π½ΠΈΠ΅ Π°Π³ΡΠ΅Π³Π°ΡΠ½ΠΎΠ³ΠΎ ΠΆΡΡΠ½Π°Π»Π° ΠΈ ΡΡΠ΅ΡΠ½ΠΎΠΉ Π΄ΠΎΠΊΡΠΌΠ΅Π½ΡΠ°ΡΠΈΠΈ Π²ΠΎΠ»ΠΎΡΠΈΠ»ΡΡΠΈΠΊΠ° | |||||
ΠΠ΅ΠΎΠ±Ρ ΠΎΠ΄ΠΈΠΌΡΠ΅ ΡΠΌΠ΅Π½ΠΈΡ | ΠΡΠ±ΠΈΡΠ°ΡΡ ΠΏΡΠΎΠ±Ρ Π΄Π»Ρ ΠΎΠΏΡΠ΅Π΄Π΅Π»Π΅Π½ΠΈΡ ΡΠΈΠ·ΠΈΠΊΠΎ-ΠΌΠ΅ΡΠ°Π»Π»ΠΎΠ³ΡΠ°ΡΠΈΡΠ΅ΡΠΊΠΈΡ ΡΠ²ΠΎΠΉΡΡΠ² Π³ΠΎΡΠΎΠ²ΠΎΠ³ΠΎ ΠΌΠ΅ΡΠ°Π»Π»Π° | ||||
ΠΡΠΎΠ²Π΅ΡΡΡΡ ΠΈΡΠΏΡΠ°Π²Π½ΠΎΡΡΡ Π²Π΅ΡΠΎΠ² | |||||
ΠΠ·Π²Π»Π΅ΠΊΠ°ΡΡ ΠΎΡΡΠ°Π±ΠΎΡΠ°Π½Π½ΡΠ΅ Π²ΠΎΠ»ΠΎΠΊΠΈ ΠΈΠ· ΠΎΠΏΡΠ°Π² | |||||
ΠΡΠΈΠΌΠ΅Π½ΡΡΡ ΡΡΠ΅Π΄ΡΡΠ²Π° ΠΈΠ½Π΄ΠΈΠ²ΠΈΠ΄ΡΠ°Π»ΡΠ½ΠΎΠΉ Π·Π°ΡΠΈΡΡ, ΠΏΠΎΠΆΠ°ΡΠΎΡΡΡΠ΅Π½ΠΈΡ ΠΈ ΠΏΠΎΠ»ΡΠ·ΠΎΠ²Π°ΡΡΡΡ Π°Π²Π°ΡΠΈΠΉΠ½ΡΠΌ ΠΈΠ½ΡΡΡΡΠΌΠ΅Π½ΡΠΎΠΌ Π½Π° ΡΡΠ°ΡΡΠΊΠ΅ Π²ΠΎΠ»ΠΎΡΠ΅Π½ΠΈΡ | |||||
ΠΡΠΈΠΌΠ΅Π½ΡΡΡ ΠΏΡΠΎΠ³ΡΠ°ΠΌΠΌΠ½ΠΎΠ΅ ΠΎΠ±Π΅ΡΠΏΠ΅ΡΠ΅Π½ΠΈΠ΅ ΡΠ°Π±ΠΎΡΠ΅Π³ΠΎ ΠΌΠ΅ΡΡΠ° Π²ΠΎΠ»ΠΎΡΠΈΠ»ΡΡΠΈΠΊΠ° | |||||
ΠΠ΅ΠΎΠ±Ρ ΠΎΠ΄ΠΈΠΌΡΠ΅ Π·Π½Π°Π½ΠΈΡ | Π£ΡΡΡΠΎΠΉΡΡΠ²ΠΎ, ΠΏΡΠΈΠ½ΡΠΈΠΏ ΡΠ°Π±ΠΎΡΡ ΠΈ ΠΏΡΠ°Π²ΠΈΠ»Π° ΡΠΊΡΠΏΠ»ΡΠ°ΡΠ°ΡΠΈΠΈ ΠΎΠ±ΠΎΡΡΠ΄ΠΎΠ²Π°Π½ΠΈΡ Π΄Π»Ρ Π²Π·Π²Π΅ΡΠΈΠ²Π°Π½ΠΈΡ, ΠΌΠ°ΡΠΊΠΈΡΠΎΠ²ΠΊΠΈ ΠΈ ΡΠΏΠ°ΠΊΠΎΠ²ΠΊΠΈ ΠΌΠ΅ΡΠ°Π»Π»Π° | ||||
Π’ΡΠ΅Π±ΠΎΠ²Π°Π½ΠΈΡ Π½ΠΎΡΠΌΠ°ΡΠΈΠ²Π½ΠΎΠΉ Π΄ΠΎΠΊΡΠΌΠ΅Π½ΡΠ°ΡΠΈΠΈ ΠΊ ΠΏΠ°ΡΠ°ΠΌΠ΅ΡΡΠ°ΠΌ ΠΈ ΠΊΠ°ΡΠ΅ΡΡΠ²Ρ Π³ΠΎΡΠΎΠ²ΠΎΠΉ ΠΏΡΠΎΠ΄ΡΠΊΡΠΈΠΈ, ΠΊΡΠΈΡΠ΅ΡΠΈΠΈ ΠΎΡΠ΅Π½ΠΊΠΈ ΠΊΠ°ΡΠ΅ΡΡΠ²Π° Π³ΠΎΡΠΎΠ²ΠΎΠΉ ΠΏΡΠΎΠ΄ΡΠΊΡΠΈΠΈ, Π²ΠΈΠ΄Ρ Π±ΡΠ°ΠΊΠ° ΠΈ ΡΠΏΠΎΡΠΎΠ±Ρ Π΅Π³ΠΎ ΠΏΡΠ΅Π΄ΡΠΏΡΠ΅ΠΆΠ΄Π΅Π½ΠΈΡ, Π²ΡΡΠ²Π»Π΅Π½ΠΈΡ ΠΈ ΡΡΡΡΠ°Π½Π΅Π½ΠΈΡ | |||||
Π’ΡΠ΅Π±ΠΎΠ²Π°Π½ΠΈΡ ΠΊ ΠΏΡΠΎΠ²Π΅Π΄Π΅Π½ΠΈΡ ΠΎΡΠ±ΠΎΡΠ° ΠΏΡΠΎΠ± Π΄Π»Ρ ΠΈΡΠΏΡΡΠ°Π½ΠΈΠΉ ΠΌΠ΅ΡΠ°Π»Π»ΠΎΠΏΡΠΎΠ΄ΡΠΊΡΠΈΠΈ | |||||
ΠΠ΅ΡΠ΅ΡΠ΅Π½Ρ, ΠΏΠ΅ΡΠΈΠΎΠ΄ΠΈΡΠ½ΠΎΡΡΡ ΠΈ ΠΌΠ΅ΡΠΎΠ΄Ρ ΠΊΠΎΠ½ΡΡΠΎΠ»Ρ Ρ Π°ΡΠ°ΠΊΡΠ΅ΡΠΈΡΡΠΈΠΊ ΠΌΠ΅ΡΠ°Π»Π»ΠΎΠΏΡΠΎΠ΄ΡΠΊΡΠΈΠΈ | |||||
Π’ΡΠ΅Π±ΠΎΠ²Π°Π½ΠΈΡ ΠΊ ΠΊΠ°ΡΠ΅ΡΡΠ²Ρ Π³ΠΎΡΠΎΠ²ΠΎΠΉ ΠΌΠ΅ΡΠ°Π»Π»ΠΎΠΏΡΠΎΠ΄ΡΠΊΡΠΈΠΈ | |||||
ΠΡΠ°Π²ΠΈΠ»Π° ΡΠΊΠ»Π°Π΄ΠΊΠΈ, ΡΠ²ΡΠ·ΠΊΠΈ ΠΈ ΡΡΠ°Π½ΡΠΏΠΎΡΡΠΈΡΠΎΠ²ΠΊΠΈ Π³ΠΎΡΠΎΠ²ΠΎΠΉ ΠΏΡΠΎΠ΄ΡΠΊΡΠΈΠΈ | |||||
ΠΡΠ°Π²ΠΈΠ»Π° ΠΏΡΠΈΠ΅ΠΌΠΊΠΈ ΠΌΠ΅ΡΠ°Π»Π»Π° ΠΏΠΎΡΠ»Π΅ Π²ΠΎΠ»ΠΎΡΠ΅Π½ΠΈΡ | |||||
Π’ΡΠ΅Π±ΠΎΠ²Π°Π½ΠΈΡ Π±ΠΈΡΠΎΡΠ½ΠΎΠΉ ΡΠΈΡΡΠ΅ΠΌΡ ΠΈ Π½Π°ΡΡΠ΄ΠΎΠ²-Π΄ΠΎΠΏΡΡΠΊΠΎΠ² Π΄Π»Ρ ΡΠ°Π±ΠΎΡΠ΅Π³ΠΎ ΠΌΠ΅ΡΡΠ° Π²ΠΎΠ»ΠΎΡΠΈΠ»ΡΡΠΈΠΊΠ° | |||||
ΠΡΠ°Π²ΠΈΠ»Π° ΡΠΊΡΠΏΠ»ΡΠ°ΡΠ°ΡΠΈΠΈ ΠΏΠΎΠ΄ΡΠ΅ΠΌΠ½ΡΡ ΡΠΎΠΎΡΡΠΆΠ΅Π½ΠΈΠΉ | |||||
ΠΠ»Π°Π½ ΠΌΠ΅ΡΠΎΠΏΡΠΈΡΡΠΈΠΉ Π»ΠΎΠΊΠ°Π»ΠΈΠ·Π°ΡΠΈΠΈ ΠΈ Π»ΠΈΠΊΠ²ΠΈΠ΄Π°ΡΠΈΠΈ ΠΏΠΎΡΠ»Π΅Π΄ΡΡΠ²ΠΈΠΉ Π°Π²Π°ΡΠΈΠΉ | |||||
Π’ΡΠ΅Π±ΠΎΠ²Π°Π½ΠΈΡ ΠΎΡ ΡΠ°Π½Ρ ΡΡΡΠ΄Π°, ΠΏΡΠΎΠΌΡΡΠ»Π΅Π½Π½ΠΎΠΉ, ΡΠΊΠΎΠ»ΠΎΠ³ΠΈΡΠ΅ΡΠΊΠΎΠΉ ΠΈ ΠΏΠΎΠΆΠ°ΡΠ½ΠΎΠΉ Π±Π΅Π·ΠΎΠΏΠ°ΡΠ½ΠΎΡΡΠΈ Π½Π° ΡΡΠ°ΡΡΠΊΠ΅ Π²ΠΎΠ»ΠΎΡΠ΅Π½ΠΈΡ | |||||
ΠΡΠΎΠ³ΡΠ°ΠΌΠΌΠ½ΠΎΠ΅ ΠΎΠ±Π΅ΡΠΏΠ΅ΡΠ΅Π½ΠΈΠ΅ ΡΠ°Π±ΠΎΡΠ΅Π³ΠΎ ΠΌΠ΅ΡΡΠ° Π²ΠΎΠ»ΠΎΡΠΈΠ»ΡΡΠΈΠΊΠ° | |||||
ΠΡΡΠ³ΠΈΠ΅ Ρ Π°ΡΠ°ΠΊΡΠ΅ΡΠΈΡΡΠΈΠΊΠΈ | — | ||||
Π’ΡΡΠ΄ΠΎΠ²ΡΠ΅ Π΄Π΅ΠΉΡΡΠ²ΠΈΡ | ΠΠΎΠ»ΡΡΠ΅Π½ΠΈΠ΅ (ΠΏΠ΅ΡΠ΅Π΄Π°ΡΠ°) ΠΈΠ½ΡΠΎΡΠΌΠ°ΡΠΈΠΈ ΠΏΡΠΈ ΠΏΡΠΈΠ΅ΠΌΠΊΠ΅-ΡΠ΄Π°ΡΠ΅ ΡΠΌΠ΅Π½Ρ ΠΎ ΡΠΌΠ΅Π½Π½ΠΎΠΌ ΠΏΡΠΎΠΈΠ·Π²ΠΎΠ΄ΡΡΠ²Π΅Π½Π½ΠΎΠΌ Π·Π°Π΄Π°Π½ΠΈΠΈ, ΠΎ ΡΠΎΡΡΠΎΡΠ½ΠΈΠΈ ΡΠ°Π±ΠΎΡΠ΅Π³ΠΎ ΠΌΠ΅ΡΡΠ°, Π½Π΅ΠΏΠΎΠ»Π°Π΄ΠΊΠ°Ρ Π² ΡΠ°Π±ΠΎΡΠ΅ ΠΎΠ±ΡΠ»ΡΠΆΠΈΠ²Π°Π΅ΠΌΠΎΠ³ΠΎ ΠΎΠ±ΠΎΡΡΠ΄ΠΎΠ²Π°Π½ΠΈΡ ΠΈ ΠΏΡΠΈΠ½ΡΡΡΡ ΠΌΠ΅ΡΠ°Ρ ΠΏΠΎ ΠΈΡ ΡΡΡΡΠ°Π½Π΅Π½ΠΈΡ | ||||
ΠΡΠΎΠ²Π΅ΡΠΊΠ° ΡΠΎΡΡΠΎΡΠ½ΠΈΡ ΠΎΠ³ΡΠ°ΠΆΠ΄Π΅Π½ΠΈΠΉ ΠΈ ΠΈΡΠΏΡΠ°Π²Π½ΠΎΡΡΠΈ ΡΡΠ΅Π΄ΡΡΠ² ΠΈΠ½Π΄ΠΈΠ²ΠΈΠ΄ΡΠ°Π»ΡΠ½ΠΎΠΉ Π·Π°ΡΠΈΡΡ, ΡΡΠ΅Π΄ΡΡΠ² ΡΠ²ΡΠ·ΠΈ, ΠΏΡΠΎΠΈΠ·Π²ΠΎΠ΄ΡΡΠ²Π΅Π½Π½ΠΎΠΉ ΡΠΈΠ³Π½Π°Π»ΠΈΠ·Π°ΡΠΈΠΈ, Π±Π»ΠΎΠΊΠΈΡΠΎΠ²ΠΎΠΊ, Π°Π²Π°ΡΠΈΠΉΠ½ΠΎΠ³ΠΎ ΠΈΠ½ΡΡΡΡΠΌΠ΅Π½ΡΠ°, ΠΏΡΠΎΡΠΈΠ²ΠΎΠΏΠΎΠΆΠ°ΡΠ½ΠΎΠ³ΠΎ ΠΎΠ±ΠΎΡΡΠ΄ΠΎΠ²Π°Π½ΠΈΡ Π½Π° ΡΡΠ°ΡΡΠΊΠ΅ Π²ΠΎΠ»ΠΎΡΠ΅Π½ΠΈΡ | |||||
ΠΡΠΎΠ²Π΅ΡΠΊΠ° ΠΏΠΎΡΡΡΠΏΠΈΠ²ΡΠ΅Π³ΠΎ ΠΌΠ΅ΡΠ°Π»Π»Π° Π½Π° ΡΠΎΠΎΡΠ²Π΅ΡΡΡΠ²ΠΈΠ΅ ΠΎΡΠ½ΠΎΠ²Π½ΡΠΌ ΡΡΠ΅Π±ΠΎΠ²Π°Π½ΠΈΡΠΌ ΠΊ ΠΌΠ΅ΡΠ°Π»Π»Ρ, ΠΏΡΠ΅Π΄Π½Π°Π·Π½Π°ΡΠ΅Π½Π½ΠΎΠΌΡ Π΄Π»Ρ Π²ΠΎΠ»ΠΎΡΠ΅Π½ΠΈΡ | |||||
Π£ΡΡΠ°Π½ΠΎΠ²ΠΊΠ° Π²ΠΎΠ»ΠΎΠΊ | |||||
ΠΠΎΠ½ΡΡΠΎΠ»Ρ ΠΊΠ°ΡΠ΅ΡΡΠ²Π° ΠΏΠΎΠ΄ΡΠΌΠ°Π·ΠΎΡΠ½ΠΎΠ³ΠΎ ΡΠ»ΠΎΡ ΠΌΠ΅ΡΠ°Π»Π»ΠΎΠΏΡΠΎΠΊΠ°ΡΠ° ΠΏΠ΅ΡΠ΅Π΄ Π²ΠΎΠ»ΠΎΡΠ΅Π½ΠΈΠ΅ΠΌ | |||||
Π£ΡΡΠ°Π½ΠΎΠ²ΠΊΠ° Π±ΡΠ½ΡΠ°, ΠΊΠ°ΡΡΡΠΊΠΈ Π½Π° ΡΠ°Π·ΠΌΠΎΡΠΎΡΠ½ΠΎΠ΅ ΡΡΡΡΠΎΠΉΡΡΠ²ΠΎ | |||||
Π‘Π²Π°ΡΠΊΠ° ΠΊΠΎΠ½ΡΠΎΠ² ΠΏΡΠΎΠ²ΠΎΠ»ΠΎΠΊΠΈ Π² Π±ΡΠ½ΡΠ°Ρ ΠΈ ΠΏΡΠΎΠ²ΠΎΠ»ΠΎΠΊΠΈ Π½Π° ΠΊΠ°ΡΡΡΠΊΠ°Ρ | |||||
ΠΠ±ΡΠ»ΡΠΆΠΈΠ²Π°Π½ΠΈΠ΅ ΡΠΌΠ°Π·ΠΎΡΠ½ΡΡ ΠΈ ΡΠΏΠ΅ΡΠΈΠ°Π»ΡΠ½ΡΡ Π½Π°ΠΌΠΎΡΠΎΡΠ½ΡΡ ΡΡΡΡΠΎΠΉΡΡΠ², ΡΠ²Π°ΡΠΎΡΠ½ΡΡ Π°ΠΏΠΏΠ°ΡΠ°ΡΠΎΠ², ΡΡΠ΅ΠΌΠ½ΡΡ ΠΌΠ΅Ρ Π°Π½ΠΈΠ·ΠΌΠΎΠ² ΠΈ ΡΠΈΡΡΠ΅ΠΌΡ ΠΎΡ Π»Π°ΠΆΠ΄Π΅Π½ΠΈΡ ΠΏΡΠΈ Π²ΠΎΠ»ΠΎΡΠ΅Π½ΠΈΠΈ | |||||
ΠΡΠΎΠ²Π΅ΡΠΊΠ° ΠΈΡΠΏΡΠ°Π²Π½ΠΎΡΡΠΈ ΠΊΠΎΠ½ΡΡΠΎΠ»ΡΠ½ΠΎ-ΠΈΠ·ΠΌΠ΅ΡΠΈΡΠ΅Π»ΡΠ½ΡΡ ΠΈΠ½ΡΡΡΡΠΌΠ΅Π½ΡΠΎΠ² ΠΈ ΡΠΏΠ΅ΡΠΈΠ°Π»ΡΠ½ΡΡ ΠΏΡΠΈΡΠΏΠΎΡΠΎΠ±Π»Π΅Π½ΠΈΠΉ | |||||
ΠΠ΅Π΄Π΅Π½ΠΈΠ΅ Π°Π³ΡΠ΅Π³Π°ΡΠ½ΠΎΠ³ΠΎ ΠΆΡΡΠ½Π°Π»Π° ΠΈ ΡΡΠ΅ΡΠ½ΠΎΠΉ Π΄ΠΎΠΊΡΠΌΠ΅Π½ΡΠ°ΡΠΈΠΈ Π²ΠΎΠ»ΠΎΡΠΈΠ»ΡΡΠΈΠΊΠ° | |||||
ΠΠ΅ΠΎΠ±Ρ ΠΎΠ΄ΠΈΠΌΡΠ΅ ΡΠΌΠ΅Π½ΠΈΡ | ΠΠΏΡΠ΅Π΄Π΅Π»ΡΡΡ Π²ΠΈΠ·ΡΠ°Π»ΡΠ½ΠΎ ΡΠ°Π±ΠΎΡΠΎΡΠΏΠΎΡΠΎΠ±Π½ΠΎΡΡΡ Π²ΠΎΠ»ΠΎΡΠΈΠ»ΡΠ½ΠΎΠ³ΠΎ ΡΡΠ°Π½Π° ΠΈ ΡΡΡΡΠΎΠΉΡΡΠ² Π²ΠΎΠ»ΠΎΡΠ΅Π½ΠΈΡ | ||||
ΠΠ°ΡΡΡΠ°ΠΈΠ²Π°ΡΡ Π²ΠΎΠ»ΠΎΡΠΈΠ»ΡΠ½ΡΠΉ ΡΡΠ°Π½, ΡΡΡΡΠΎΠΉΡΡΠ²Π° Π²ΠΎΠ»ΠΎΡΠ΅Π½ΠΈΡ ΠΈ ΡΠ²Π°ΡΠΊΠΈ ΠΏΡΠΎΠ²ΠΎΠ»ΠΎΠΊΠΈ | |||||
ΠΡΠΎΠΈΠ·Π²ΠΎΠ΄ΠΈΡΡ ΡΠ΅Π³ΡΠ»ΠΈΡΠΎΠ²ΠΊΡ Π΄ΠΎΠΏΠΎΠ»Π½ΠΈΡΠ΅Π»ΡΠ½ΠΎΠ³ΠΎ ΠΎΠ±ΠΎΡΡΠ΄ΠΎΠ²Π°Π½ΠΈΡ | |||||
ΠΠΎΠ΄Π±ΠΈΡΠ°ΡΡ ΡΠΈΠΏ Π²ΠΎΠ»ΠΎΠΊΠΈ Π΄Π»Ρ Π²ΠΎΠ»ΠΎΡΠ΅Π½ΠΈΡ ΡΠ°Π·Π»ΠΈΡΠ½ΡΡ Π²ΠΈΠ΄ΠΎΠ² ΠΌΠ΅ΡΠ°Π»Π»ΠΎΠΏΡΠΎΠ΄ΡΠΊΡΠΈΠΈ | |||||
ΠΠΎΠ΄Π±ΠΈΡΠ°ΡΡ ΡΠ΅Ρ Π½ΠΎΠ»ΠΎΠ³ΠΈΡΠ΅ΡΠΊΡΡ ΡΠΌΠ°Π·ΠΊΡ Π² Π·Π°Π²ΠΈΡΠΈΠΌΠΎΡΡΠΈ ΠΎΡ Π²ΠΈΠ΄Π° ΠΏΡΠΎΠΈΠ·Π²ΠΎΠ΄ΠΈΠΌΠΎΠΉ ΠΏΡΠΎΠ΄ΡΠΊΡΠΈΠΈ | |||||
ΠΡΠ΅Π½ΠΈΠ²Π°ΡΡ ΠΊΠ°ΡΠ΅ΡΡΠ²ΠΎ ΠΈ Π½Π΅ΠΎΠ±Ρ ΠΎΠ΄ΠΈΠΌΠΎΠ΅ ΠΊΠΎΠ»ΠΈΡΠ΅ΡΡΠ²ΠΎ ΡΠ΅Ρ Π½ΠΎΠ»ΠΎΠ³ΠΈΡΠ΅ΡΠΊΠΎΠΉ ΡΠΌΠ°Π·ΠΊΠΈ Π² ΠΏΡΠΎΡΠ΅ΡΡΠ΅ Π²ΠΎΠ»ΠΎΡΠ΅Π½ΠΈΡ | |||||
ΠΠ±ΡΠ΅Π·Π°ΡΡ ΡΠΎΡΡΡ ΠΏΡΠΎΠ²ΠΎΠ»ΠΎΠΊΠΈ ΠΏΠ΅ΡΠΏΠ΅Π½Π΄ΠΈΠΊΡΠ»ΡΡΠ½ΠΎ ΠΊ Π΅Π΅ ΠΎΡΠΈ | |||||
ΠΠΎΠ΄Π°Π²Π°ΡΡ ΡΠΏΠ΅ΡΠΈΠ°Π»ΡΠ½ΡΠ΅ ΠΊΠΎΠΌΠ°Π½Π΄Ρ ΠΌΠ°ΡΠΈΠ½ΠΈΡΡΡ ΠΊΡΠ°Π½Π° Π² Ρ ΠΎΠ΄Π΅ ΡΠ΅Ρ Π½ΠΎΠ»ΠΎΠ³ΠΈΡΠ΅ΡΠΊΠΎΠ³ΠΎ ΠΏΡΠΎΡΠ΅ΡΡΠ° | |||||
ΠΡΠΎΠΈΠ·Π²ΠΎΠ΄ΠΈΡΡ ΠΏΠΎΠ²Π΅ΡΠΊΡ ΠΌΠ΅ΡΠΈΡΠ΅Π»ΡΠ½ΠΎΠ³ΠΎ ΠΈΠ½ΡΡΡΡΠΌΠ΅Π½ΡΠ° | |||||
ΠΡΠΈΠΌΠ΅Π½ΡΡΡ ΡΡΠ΅Π΄ΡΡΠ²Π° ΠΈΠ½Π΄ΠΈΠ²ΠΈΠ΄ΡΠ°Π»ΡΠ½ΠΎΠΉ Π·Π°ΡΠΈΡΡ, ΠΏΠΎΠΆΠ°ΡΠΎΡΡΡΠ΅Π½ΠΈΡ ΠΈ ΠΏΠΎΠ»ΡΠ·ΠΎΠ²Π°ΡΡΡΡ Π°Π²Π°ΡΠΈΠΉΠ½ΡΠΌ ΠΈΠ½ΡΡΡΡΠΌΠ΅Π½ΡΠΎΠΌ | |||||
ΠΡΠΈΠΌΠ΅Π½ΡΡΡ ΠΏΡΠΎΠ³ΡΠ°ΠΌΠΌΠ½ΠΎΠ΅ ΠΎΠ±Π΅ΡΠΏΠ΅ΡΠ΅Π½ΠΈΠ΅ ΡΠ°Π±ΠΎΡΠ΅Π³ΠΎ ΠΌΠ΅ΡΡΠ° Π²ΠΎΠ»ΠΎΡΠΈΠ»ΡΡΠΈΠΊΠ° | |||||
ΠΠ΅ΠΎΠ±Ρ ΠΎΠ΄ΠΈΠΌΡΠ΅ Π·Π½Π°Π½ΠΈΡ | Π£ΡΡΡΠΎΠΉΡΡΠ²ΠΎ, ΠΏΡΠΈΠ½ΡΠΈΠΏ ΡΠ°Π±ΠΎΡΡ, ΠΏΡΠ°Π²ΠΈΠ»Π° ΡΠ΅Ρ Π½ΠΈΡΠ΅ΡΠΊΠΎΠΉ ΡΠΊΡΠΏΠ»ΡΠ°ΡΠ°ΡΠΈΠΈ ΠΈ ΠΊΠΎΠ½ΡΡΡΡΠΊΡΠΈΠ²Π½ΡΠ΅ ΠΎΡΠΎΠ±Π΅Π½Π½ΠΎΡΡΠΈ Π²ΠΎΠ»ΠΎΡΠΈΠ»ΡΠ½ΠΎΠ³ΠΎ ΠΎΠ±ΠΎΡΡΠ΄ΠΎΠ²Π°Π½ΠΈΡ, ΡΠ°Π·ΠΌΠ°ΡΡΠ²Π°ΡΠ΅Π»Π΅ΠΉ, Π½Π°ΠΌΠ°ΡΡΠ²Π°ΡΠ΅Π»Π΅ΠΉ, ΠΏΡΠΈΡΠΏΠΎΡΠΎΠ±Π»Π΅Π½ΠΈΠΉ Π΄Π»Ρ ΠΎΡΡΡΠ΅Π½ΠΈΡ ΠΏΡΠΎΠ²ΠΎΠ»ΠΎΠΊΠΈ, ΡΠΌΠ°Π·ΠΎΡΠ½ΠΎΠ³ΠΎ ΠΎΠ±ΠΎΡΡΠ΄ΠΎΠ²Π°Π½ΠΈΡ, ΠΎΠ±ΠΎΡΡΠ΄ΠΎΠ²Π°Π½ΠΈΡ Π΄Π»Ρ ΠΎΠ±ΡΠ΅Π·ΠΊΠΈ Π±ΡΠ½ΡΠΎΠ², ΡΠ²Π°ΡΠΊΠΈ ΠΏΡΠΎΠ²ΠΎΠ»ΠΎΠΊΠΈ | ||||
Π£ΡΡΡΠΎΠΉΡΡΠ²ΠΎ ΠΏΡΠΈΠΌΠ΅Π½ΡΠ΅ΠΌΠΎΠ³ΠΎ ΠΊΠΎΠ½ΡΡΠΎΠ»ΡΠ½ΠΎ-ΠΈΠ·ΠΌΠ΅ΡΠΈΡΠ΅Π»ΡΠ½ΠΎΠ³ΠΎ ΠΈΠ½ΡΡΡΡΠΌΠ΅Π½ΡΠ° ΠΈ ΡΠΏΠ΅ΡΠΈΠ°Π»ΡΠ½ΡΡ ΠΏΡΠΈΡΠΏΠΎΡΠΎΠ±Π»Π΅Π½ΠΈΠΉ | |||||
Π£ΡΡΡΠΎΠΉΡΡΠ²ΠΎ, ΠΏΡΠΈΠ½ΡΠΈΠΏ ΡΠ°Π±ΠΎΡΡ ΠΈ ΠΏΡΠ°Π²ΠΈΠ»Π° ΡΠ΅Ρ Π½ΠΈΡΠ΅ΡΠΊΠΎΠΉ ΡΠΊΡΠΏΠ»ΡΠ°ΡΠ°ΡΠΈΠΈ ΡΠ²Π°ΡΠΎΡΠ½ΠΎΠ³ΠΎ Π°ΠΏΠΏΠ°ΡΠ°ΡΠ° | |||||
Π’ΡΠ΅Π±ΠΎΠ²Π°Π½ΠΈΡ Π½ΠΎΡΠΌΠ°ΡΠΈΠ²Π½ΠΎΠΉ Π΄ΠΎΠΊΡΠΌΠ΅Π½ΡΠ°ΡΠΈΠΈ, ΡΠ΅Π³Π»Π°ΠΌΠ΅Π½ΡΠΈΡΡΡΡΠ΅ΠΉ ΠΏΡΠΎΡΠ΅ΡΡΡ Π²ΠΎΠ»ΠΎΡΠ΅Π½ΠΈΡ (ΠΏΡΠΎΠΈΠ·Π²ΠΎΠ΄ΡΡΠ²Π΅Π½Π½ΠΎ-ΡΠ΅Ρ Π½ΠΎΠ»ΠΎΠ³ΠΈΡΠ΅ΡΠΊΠΈΡ ΠΈΠ½ΡΡΡΡΠΊΡΠΈΠΉ) | |||||
ΠΠΎΠ½ΡΡΡΡΠΊΡΠΈΠΈ ΠΈ ΠΏΠΎΡΡΠ΄ΠΎΠΊ ΡΠ±ΠΎΡΠΊΠΈ Π²ΠΎΠ»ΠΎΠΊ | |||||
Π‘ΠΏΠΎΡΠΎΠ±Ρ ΡΠ΅Π³ΡΠ»ΠΈΡΠΎΠ²Π°Π½ΠΈΡ Π΄ΠΎΠΏΠΎΠ»Π½ΠΈΡΠ΅Π»ΡΠ½ΠΎΠ³ΠΎ ΠΎΠ±ΠΎΡΡΠ΄ΠΎΠ²Π°Π½ΠΈΡ: ΡΠ°Π·ΠΌΠ°ΡΡΠ²Π°ΡΠ΅Π»Π΅ΠΉ, Π½Π°ΠΌΠ°ΡΡΠ²Π°ΡΠ΅Π»Π΅ΠΉ, ΠΏΡΠΈΡΠΏΠΎΡΠΎΠ±Π»Π΅Π½ΠΈΠΉ Π΄Π»Ρ ΠΎΡΡΡΠ΅Π½ΠΈΡ ΠΏΡΠΎΠ²ΠΎΠ»ΠΎΠΊΠΈ, ΡΠΌΠ°Π·ΠΎΡΠ½ΠΎΠ³ΠΎ ΠΎΠ±ΠΎΡΡΠ΄ΠΎΠ²Π°Π½ΠΈΡ, ΠΎΠ±ΠΎΡΡΠ΄ΠΎΠ²Π°Π½ΠΈΡ Π΄Π»Ρ ΠΎΠ±ΡΠ΅Π·ΠΊΠΈ Π±ΡΠ½ΡΠΎΠ², ΡΠ²Π°ΡΠΊΠΈ ΠΏΡΠΎΠ²ΠΎΠ»ΠΎΠΊΠΈ | |||||
ΠΡΠ°Π²ΠΈΠ»Π° ΠΏΡΠΈΠ΅ΠΌΠΊΠΈ ΠΌΠ΅ΡΠ°Π»Π»Π° Π΄Π»Ρ Π²ΠΎΠ»ΠΎΡΠ΅Π½ΠΈΡ | |||||
Π‘ΠΎΡΡΠ°ΠΌΠ΅Π½Ρ ΠΌΠ΅ΡΠ°Π»Π»Π°, ΠΎΡΠ½ΠΎΠ²Π½ΡΠ΅ ΡΠ²ΠΎΠΉΡΡΠ²Π° ΠΌΠ΅ΡΠ°Π»Π»Π° ΠΈ ΡΠΏΠ»Π°Π²ΠΎΠ², ΠΏΠΎΠ΄Π»Π΅ΠΆΠ°ΡΠΈΡ Π²ΠΎΠ»ΠΎΡΠ΅Π½ΠΈΡ | |||||
Π’ΡΠ΅Π±ΠΎΠ²Π°Π½ΠΈΡ Π½ΠΎΡΠΌΠ°ΡΠΈΠ²Π½ΠΎΠΉ Π΄ΠΎΠΊΡΠΌΠ΅Π½ΡΠ°ΡΠΈΠΈ ΠΊ ΠΌΠ΅ΡΠ°Π»Π»Ρ, Π½Π°ΠΏΡΠ°Π²Π»ΡΠ΅ΠΌΠΎΠΌΡ Π½Π° Π²ΠΎΠ»ΠΎΡΠ΅Π½ΠΈΠ΅ | |||||
ΠΡΠ°Π²ΠΈΠ»Π° Π½Π°Π½Π΅ΡΠ΅Π½ΠΈΡ ΠΏΡΠΎΠΌΠ΅ΠΆΡΡΠΎΡΠ½ΠΎΠΉ ΠΌΠ°ΡΠΊΠΈΡΠΎΠ²ΠΊΠΈ | |||||
Π’ΡΠ΅Π±ΠΎΠ²Π°Π½ΠΈΡ Π±ΠΈΡΠΎΡΠ½ΠΎΠΉ ΡΠΈΡΡΠ΅ΠΌΡ ΠΈ Π½Π°ΡΡΠ΄ΠΎΠ²-Π΄ΠΎΠΏΡΡΠΊΠΎΠ² Π΄Π»Ρ Π²ΠΎΠ»ΠΎΡΠΈΠ»ΡΡΠΈΠΊΠ° | |||||
ΠΠΎΡΡΠ΄ΠΎΠΊ ΠΈ ΠΏΡΠ°Π²ΠΈΠ»Π° ΠΏΡΠΎΠ²Π΅Π΄Π΅Π½ΠΈΡ ΡΡΡΠΎΠΏΠΎΠ²ΠΎΡΠ½ΡΡ ΡΠ°Π±ΠΎΡ | |||||
Π‘Π»Π΅ΡΠ°ΡΠ½ΠΎΠ΅ Π΄Π΅Π»ΠΎ ΠΏΡΠΈΠΌΠ΅Π½ΠΈΡΠ΅Π»ΡΠ½ΠΎ ΠΊ Π²ΡΠΏΠΎΠ»Π½Π΅Π½ΠΈΡ ΡΠ°Π±ΠΎΡ Π½Π° ΡΡΠ°ΡΡΠΊΠ΅ Π²ΠΎΠ»ΠΎΡΠ΅Π½ΠΈΡ | |||||
ΠΠ»Π°Π½ ΠΌΠ΅ΡΠΎΠΏΡΠΈΡΡΠΈΠΉ Π»ΠΎΠΊΠ°Π»ΠΈΠ·Π°ΡΠΈΠΈ ΠΈ Π»ΠΈΠΊΠ²ΠΈΠ΄Π°ΡΠΈΠΈ ΠΏΠΎΡΠ»Π΅Π΄ΡΡΠ²ΠΈΠΉ Π°Π²Π°ΡΠΈΠΉ Π½Π° ΡΡΠ°ΡΡΠΊΠ΅ Π²ΠΎΠ»ΠΎΡΠ΅Π½ΠΈΡ | |||||
Π’ΡΠ΅Π±ΠΎΠ²Π°Π½ΠΈΡ ΠΎΡ ΡΠ°Π½Ρ ΡΡΡΠ΄Π°, ΠΏΡΠΎΠΌΡΡΠ»Π΅Π½Π½ΠΎΠΉ, ΡΠΊΠΎΠ»ΠΎΠ³ΠΈΡΠ΅ΡΠΊΠΎΠΉ ΠΈ ΠΏΠΎΠΆΠ°ΡΠ½ΠΎΠΉ Π±Π΅Π·ΠΎΠΏΠ°ΡΠ½ΠΎΡΡΠΈ Π½Π° ΡΡΠ°ΡΡΠΊΠ΅ Π²ΠΎΠ»ΠΎΡΠ΅Π½ΠΈΡ | |||||
ΠΡΠΎΠ³ΡΠ°ΠΌΠΌΠ½ΠΎΠ΅ ΠΎΠ±Π΅ΡΠΏΠ΅ΡΠ΅Π½ΠΈΠ΅ ΡΠ°Π±ΠΎΡΠ΅Π³ΠΎ ΠΌΠ΅ΡΡΠ° Π²ΠΎΠ»ΠΎΡΠΈΠ»ΡΡΠΈΠΊΠ° | |||||
ΠΡΡΠ³ΠΈΠ΅ Ρ Π°ΡΠ°ΠΊΡΠ΅ΡΠΈΡΡΠΈΠΊΠΈ | — | ||||
Π’ΡΡΠ΄ΠΎΠ²ΡΠ΅ Π΄Π΅ΠΉΡΡΠ²ΠΈΡ | ΠΠΎΠ»ΡΡΠ΅Π½ΠΈΠ΅ (ΠΏΠ΅ΡΠ΅Π΄Π°ΡΠ°) ΠΈΠ½ΡΠΎΡΠΌΠ°ΡΠΈΠΈ ΠΏΡΠΈ ΠΏΡΠΈΠ΅ΠΌΠΊΠ΅-ΡΠ΄Π°ΡΠ΅ ΡΠΌΠ΅Π½Ρ ΠΎ Ρ Π°ΡΠ°ΠΊΡΠ΅ΡΠΈΡΡΠΈΠΊΠ°Ρ ΡΠ΅ΠΆΠΈΠΌΠ° Π²ΠΎΠ»ΠΎΡΠ΅Π½ΠΈΡ, ΠΏΡΠΈΡΠΈΠ½Π°Ρ ΠΏΠΎΠ»ΡΡΠ΅Π½ΠΈΡ Π½Π΅ΡΠΎΠΎΡΠ²Π΅ΡΡΡΠ²ΡΡΡΠ΅ΠΉ ΠΏΡΠΎΠ΄ΡΠΊΡΠΈΠΈ ΠΈ Π±ΡΠ°ΠΊΠ° ΠΈ ΠΏΡΠΈΠ½ΡΡΡΡ ΠΌΠ΅ΡΠ°Ρ ΠΏΠΎ ΠΈΡ ΡΡΡΡΠ°Π½Π΅Π½ΠΈΡ Π² ΡΠ΅ΡΠ΅Π½ΠΈΠ΅ ΡΠΌΠ΅Π½Ρ | ||||
ΠΡΠΎΠ²Π΅ΡΠΊΠ° ΠΊΠ°ΡΠ΅ΡΡΠ²Π° ΠΈ ΠΊΠΎΠ»ΠΈΡΠ΅ΡΡΠ²Π° ΡΠ΅Ρ Π½ΠΎΠ»ΠΎΠ³ΠΈΡΠ΅ΡΠΊΠΎΠΉ ΡΠΌΠ°Π·ΠΊΠΈ Π²ΠΎ Π²ΡΠ΅ΠΌΡ Π²ΠΎΠ»ΠΎΡΠ΅Π½ΠΈΡ | |||||
Π£ΠΏΡΠ°Π²Π»Π΅Π½ΠΈΠ΅ ΡΠ°Π±ΠΎΡΠΎΠΉ Π²ΠΎΠ»ΠΎΡΠΈΠ»ΡΠ½ΠΎΠ³ΠΎ ΡΡΠ°Π½Π° | |||||
Π£ΡΡΠ°Π½ΠΎΠ²ΠΊΠ° ΡΠΊΠΎΡΠΎΡΡΠΈ Π²ΠΎΠ»ΠΎΡΠ΅Π½ΠΈΡ ΠΏΠΎ Π·Π°Π΄Π°Π½Π½ΠΎΠΌΡ ΠΌΠ°ΡΡΡΡΡΡ ΠΈ ΡΠ΅ΠΆΠΈΠΌΡ Π²ΠΎΠ»ΠΎΡΠ΅Π½ΠΈΡ | |||||
ΠΠΎΠ½ΡΡΠΎΠ»Ρ Π΄ΠΈΠ°ΠΌΠ΅ΡΡΠ° ΠΈ ΠΏΡΠΎΡΠΈΠ»Ρ ΠΏΡΠΎΠ²ΠΎΠ»ΠΎΠΊΠΈ ΠΏΠΎ ΠΏΡΠΎΡΡΠΆΠΊΠ°ΠΌ ΠΈ ΠΊΠ°ΡΠ΅ΡΡΠ²Π° ΠΏΠΎΠ²Π΅ΡΡ Π½ΠΎΡΡΠΈ ΠΏΡΠΎΠ²ΠΎΠ»ΠΎΠΊΠΈ | |||||
ΠΠ°Π±Π»ΡΠ΄Π΅Π½ΠΈΠ΅ Π·Π° ΠΏΡΠΎΡΠ΅ΡΡΠΎΠΌ Π½Π°ΠΌΠΎΡΠΊΠΈ ΠΏΡΠΎΠ²ΠΎΠ»ΠΎΠΊΠΈ Π½Π° ΠΏΡΠΈΠ΅ΠΌΠ½ΠΎΠ΅ ΠΏΡΠΈΡΠΏΠΎΡΠΎΠ±Π»Π΅Π½ΠΈΠ΅ | |||||
Π‘Π±ΡΠΎΡ Π³ΠΎΡΠΎΠ²ΠΎΠ³ΠΎ ΠΌΠ΅ΡΠ°Π»Π»Π° Π½Π° ΡΡΠ΅Π»Π»Π°ΠΆ ΠΈΠ»ΠΈ Π² Π½Π°ΠΊΠΎΠΏΠΈΡΠ΅Π»ΡΠ½ΡΠΉ ΠΊΠ°ΡΠΌΠ°Π½ | |||||
ΠΠΎΠ΄Π½Π°Π»Π°Π΄ΠΊΠ° Π²ΠΎΠ»ΠΎΡΠΈΠ»ΡΠ½ΠΎΠ³ΠΎ ΠΎΠ±ΠΎΡΡΠ΄ΠΎΠ²Π°Π½ΠΈΡ | |||||
ΠΠ΅Π΄Π΅Π½ΠΈΠ΅ Π°Π³ΡΠ΅Π³Π°ΡΠ½ΠΎΠ³ΠΎ ΠΆΡΡΠ½Π°Π»Π° ΠΈ ΡΡΠ΅ΡΠ½ΠΎΠΉ Π΄ΠΎΠΊΡΠΌΠ΅Π½ΡΠ°ΡΠΈΠΈ Π²ΠΎΠ»ΠΎΡΠΈΠ»ΡΡΠΈΠΊΠ° | |||||
ΠΠ΅ΠΎΠ±Ρ ΠΎΠ΄ΠΈΠΌΡΠ΅ ΡΠΌΠ΅Π½ΠΈΡ | ΠΡΡΠ²Π»ΡΡΡ ΠΎΡΠΊΠ»ΠΎΠ½Π΅Π½ΠΈΡ ΡΠ΅ΠΊΡΡΠΈΡ ΠΏΠ°ΡΠ°ΠΌΠ΅ΡΡΠΎΠ² ΡΠ΅Ρ Π½ΠΎΠ»ΠΎΠ³ΠΈΡΠ΅ΡΠΊΠΎΠ³ΠΎ ΠΏΡΠΎΡΠ΅ΡΡΠ° ΠΈ ΡΠΎΡΡΠΎΡΠ½ΠΈΡ ΠΎΠ±ΠΎΡΡΠ΄ΠΎΠ²Π°Π½ΠΈΡ ΠΎΡ ΡΡΡΠ°Π½ΠΎΠ²Π»Π΅Π½Π½ΡΡ Π·Π½Π°ΡΠ΅Π½ΠΈΠΉ | ||||
ΠΡΡΠ²Π»ΡΡΡ ΠΎΡΠΊΠ»ΠΎΠ½Π΅Π½ΠΈΡ ΡΠ΅ΠΊΡΡΠΈΡ ΠΏΠ°ΡΠ°ΠΌΠ΅ΡΡΠΎΠ² ΡΠ΅Ρ Π½ΠΎΠ»ΠΎΠ³ΠΈΡΠ΅ΡΠΊΠΎΠ³ΠΎ ΠΏΡΠΎΡΠ΅ΡΡΠ° ΠΈ ΡΠΎΡΡΠΎΡΠ½ΠΈΡ ΠΎΠ±ΠΎΡΡΠ΄ΠΎΠ²Π°Π½ΠΈΡ ΠΎΡ ΡΡΡΠ°Π½ΠΎΠ²Π»Π΅Π½Π½ΡΡ Π·Π½Π°ΡΠ΅Π½ΠΈΠΉ | |||||
ΠΠΎΠ»ΡΠ·ΠΎΠ²Π°ΡΡΡΡ ΠΏΡΠΎΠ³ΡΠ°ΠΌΠΌΠ½ΡΠΌ ΠΎΠ±Π΅ΡΠΏΠ΅ΡΠ΅Π½ΠΈΠ΅ΠΌ Π΄Π»Ρ ΡΠΏΡΠ°Π²Π»Π΅Π½ΠΈΡ ΡΠ΅Ρ Π½ΠΎΠ»ΠΎΠ³ΠΈΡΠ΅ΡΠΊΠΈΠΌ ΠΏΡΠΎΡΠ΅ΡΡΠΎΠΌ Π²ΠΎΠ»ΠΎΡΠ΅Π½ΠΈΡ | |||||
ΠΠ°ΠΏΡΠ°Π²Π»ΡΡΡ ΠΏΡΠΎΠ²ΠΎΠ»ΠΎΠΊΡ Π² Π²ΠΎΠ»ΠΎΠΊΡ Π½Π° ΠΌΠΈΠ½ΠΈΠΌΠ°Π»ΡΠ½ΠΎΠΉ ΡΠΊΠΎΡΠΎΡΡΠΈ | |||||
ΠΡΠΎΠ²Π΅ΡΡΡΡ ΠΊΠ°ΡΠ΅ΡΡΠ²ΠΎ Π²ΠΎΠ»ΠΎΠΊΠΈ | |||||
Π Π΅Π³ΡΠ»ΠΈΡΠΎΠ²Π°ΡΡ ΡΠΊΠΎΡΠΎΡΡΡ Π²ΠΎΠ»ΠΎΡΠ΅Π½ΠΈΡ ΠΏΠΎ Π·Π°Π΄Π°Π½Π½ΠΎΠΌΡ ΠΌΠ°ΡΡΡΡΡΡ ΠΈ ΡΠ΅ΠΆΠΈΠΌΡ Π²ΠΎΠ»ΠΎΡΠ΅Π½ΠΈΡ | |||||
ΠΡΠΎΠΈΠ·Π²ΠΎΠ΄ΠΈΡΡ Π·Π°ΠΌΠ΅Π½Ρ Π²ΠΎΠ»ΠΎΠΊ | |||||
ΠΠΈΠ·ΡΠ°Π»ΡΠ½ΠΎ ΠΎΠΏΡΠ΅Π΄Π΅Π»ΡΡΡ ΠΊΠ°ΡΠ΅ΡΡΠ²ΠΎ ΠΏΠΎΠ²Π΅ΡΡ Π½ΠΎΡΡΠΈ ΠΌΠ΅ΡΠ°Π»Π»Π° | |||||
ΠΡΠΈΠΌΠ΅Π½ΡΡΡ ΠΊΠΎΠ½ΡΡΠΎΠ»ΡΠ½ΠΎ-ΠΈΠ·ΠΌΠ΅ΡΠΈΡΠ΅Π»ΡΠ½ΡΠΉ ΠΈΠ½ΡΡΡΡΠΌΠ΅Π½Ρ Π΄Π»Ρ ΠΎΠΏΡΠ΅Π΄Π΅Π»Π΅Π½ΠΈΡ Π³Π΅ΠΎΠΌΠ΅ΡΡΠΈΡΠ΅ΡΠΊΠΈΡ ΠΏΠ°ΡΠ°ΠΌΠ΅ΡΡΠΎΠ² ΠΌΠ΅ΡΠ°Π»Π»Π°, ΠΏΡΠΎΡΠ΅Π΄ΡΠ΅Π³ΠΎ Π²ΠΎΠ»ΠΎΡΠ΅Π½ΠΈΠ΅ | |||||
ΠΠΈΠ·ΡΠ°Π»ΡΠ½ΠΎ ΠΎΠΏΡΠ΅Π΄Π΅Π»ΡΡΡ ΡΠ°Π²Π½ΠΎΠΌΠ΅ΡΠ½ΠΎΡΡΡ ΡΠ»ΠΎΡ ΠΎΠΊΠΈΡΠ»ΠΎΠ², ΡΠ²Π΅Ρ ΠΏΠΎΠ±Π΅ΠΆΠ°Π»ΠΎΡΡΠΈ, Π²ΠΌΡΡΠΈΠ½Ρ ΠΈ ΠΏΠΎΡΠ΅ΡΡΠΎΡΡΠΈ ΠΎΡ ΡΠΎΠ»ΠΈΠΊΠΎΠ² | |||||
ΠΡΠΈΠΌΠ΅Π½ΡΡΡ ΡΡΠ΅Π΄ΡΡΠ²Π° ΠΈΠ½Π΄ΠΈΠ²ΠΈΠ΄ΡΠ°Π»ΡΠ½ΠΎΠΉ Π·Π°ΡΠΈΡΡ, ΠΏΠΎΠΆΠ°ΡΠΎΡΡΡΠ΅Π½ΠΈΡ ΠΈ ΠΏΠΎΠ»ΡΠ·ΠΎΠ²Π°ΡΡΡΡ Π°Π²Π°ΡΠΈΠΉΠ½ΡΠΌ ΠΈΠ½ΡΡΡΡΠΌΠ΅Π½ΡΠΎΠΌ Π½Π° ΡΡΠ°ΡΡΠΊΠ΅ Π²ΠΎΠ»ΠΎΡΠ΅Π½ΠΈΡ | |||||
ΠΡΠΈΠΌΠ΅Π½ΡΡΡ ΠΏΡΠΎΠ³ΡΠ°ΠΌΠΌΠ½ΠΎΠ΅ ΠΎΠ±Π΅ΡΠΏΠ΅ΡΠ΅Π½ΠΈΠ΅ ΡΠ°Π±ΠΎΡΠ΅Π³ΠΎ ΠΌΠ΅ΡΡΠ° Π²ΠΎΠ»ΠΎΡΠΈΠ»ΡΡΠΈΠΊΠ° | |||||
ΠΠ΅ΠΎΠ±Ρ ΠΎΠ΄ΠΈΠΌΡΠ΅ Π·Π½Π°Π½ΠΈΡ | Π£ΡΡΡΠΎΠΉΡΡΠ²ΠΎ, ΠΏΡΠΈΠ½ΡΠΈΠΏ ΡΠ°Π±ΠΎΡΡ, ΠΏΡΠ°Π²ΠΈΠ»Π° ΡΠ΅Ρ Π½ΠΈΡΠ΅ΡΠΊΠΎΠΉ ΡΠΊΡΠΏΠ»ΡΠ°ΡΠ°ΡΠΈΠΈ ΠΎΡΠ½ΠΎΠ²Π½ΠΎΠ³ΠΎ ΠΈ Π²ΡΠΏΠΎΠΌΠΎΠ³Π°ΡΠ΅Π»ΡΠ½ΠΎΠ³ΠΎ ΠΎΠ±ΠΎΡΡΠ΄ΠΎΠ²Π°Π½ΠΈΡ ΡΡΠ°ΡΡΠΊΠ° Π²ΠΎΠ»ΠΎΡΠ΅Π½ΠΈΡ | ||||
ΠΡΠΎΠΈΠ·Π²ΠΎΠ΄ΡΡΠ²Π΅Π½Π½ΠΎ-ΡΠ΅Ρ Π½ΠΈΡΠ΅ΡΠΊΠΈΠ΅ ΠΈΠ½ΡΡΡΡΠΊΡΠΈΠΈ ΠΏΠΎ Π²ΠΎΠ»ΠΎΡΠ΅Π½ΠΈΡ ΠΌΠ΅ΡΠ°Π»Π»ΠΎΠΏΡΠΎΠ΄ΡΠΊΡΠΈΠΈ Π½Π° ΡΡΠ°Π½Π°Ρ Π±Π°ΡΠ°Π±Π°Π½Π½ΠΎΠ³ΠΎ ΡΠΈΠΏΠ° Ρ ΠΎΠ΄Π½ΠΎΠΊΡΠ°ΡΠ½ΡΠΌ ΠΈ ΠΌΠ½ΠΎΠ³ΠΎΠΊΡΠ°ΡΠ½ΡΠΌ Π²ΠΎΠ»ΠΎΡΠ΅Π½ΠΈΠ΅ΠΌ | |||||
Π‘Ρ Π΅ΠΌΡ ΡΠ΅Ρ Π½ΠΎΠ»ΠΎΠ³ΠΈΡΠ΅ΡΠΊΠΎΠ³ΠΎ ΠΏΡΠΎΡΠ΅ΡΡΠ° Π²ΠΎΠ»ΠΎΡΠ΅Π½ΠΈΡ, Π²ΡΠΏΠΎΠ»Π½Π΅Π½ΠΈΡ ΠΏΡΠΎΠΌΠ΅ΠΆΡΡΠΎΡΠ½ΡΡ ΠΎΠΏΠ΅ΡΠ°ΡΠΈΠΉ | |||||
ΠΡΠΎΠ±Π΅Π½Π½ΠΎΡΡΠΈ Π²ΠΎΠ»ΠΎΡΠ΅Π½ΠΈΡ ΡΠ°Π·Π»ΠΈΡΠ½ΡΡ Π²ΠΈΠ΄ΠΎΠ² ΠΌΠ΅ΡΠ°Π»Π»ΠΎΠΏΡΠΎΠ΄ΡΠΊΡΠΈΠΈ | |||||
Π’ΠΈΠΏΡ Π²ΠΎΠ»ΠΎΠΊ (ΠΎΠ΄ΠΈΠ½Π°ΡΠ½Π°Ρ, ΡΠ±ΠΎΡΠ½Π°Ρ, ΡΠΎΠ»ΠΈΠΊΠΎΠ²Π°Ρ) | |||||
ΠΠ»ΠΈΡΠ½ΠΈΠ΅ ΡΠΏΠΎΡΠΎΠ±ΠΎΠ² ΠΏΠΎΠ΄Π³ΠΎΡΠΎΠ²ΠΊΠΈ ΠΌΠ΅ΡΠ°Π»Π»Π° Π½Π° ΠΊΠ°ΡΠ΅ΡΡΠ²ΠΎ Π³ΠΎΡΠΎΠ²ΠΎΠΉ ΠΏΡΠΎΠ΄ΡΠΊΡΠΈΠΈ | |||||
ΠΠ»ΠΈΡΠ½ΠΈΠ΅ ΡΠΊΠΎΡΠΎΡΡΠ½ΡΡ ΡΠ΅ΠΆΠΈΠΌΠΎΠ² Π½Π° ΠΏΡΠΎΡΠ΅ΡΡ Π²ΠΎΠ»ΠΎΡΠ΅Π½ΠΈΡ ΠΌΠ΅ΡΠ°Π»Π»Π° | |||||
ΠΠΎΡΠ»Π΅Π΄ΠΎΠ²Π°ΡΠ΅Π»ΡΠ½ΠΎΡΡΡ Π΄Π΅ΠΉΡΡΠ²ΠΈΠΉ ΠΏΡΠΈ Π·Π°ΠΏΡΡΠΊΠ΅ ΠΈΠ»ΠΈ ΠΎΡΠΊΠ»ΡΡΠ΅Π½ΠΈΠΈ, Π½Π°ΡΡΡΠΎΠΉΠΊΠ΅, ΠΊΠΎΠ½ΡΡΠΎΠ»Π΅ ΡΠ΅ΠΆΠΈΠΌΠ° ΡΠ°Π±ΠΎΡΡ ΠΎΠ±ΠΎΡΡΠ΄ΠΎΠ²Π°Π½ΠΈΡ | |||||
ΠΠ°Π²ΠΈΡΠΈΠΌΠΎΡΡΡ ΠΏΡΠΎΡΠ½ΠΎΡΡΠ½ΡΡ ΠΈ ΠΏΠ»Π°ΡΡΠΈΡΠ΅ΡΠΊΠΈΡ ΡΠ²ΠΎΠΉΡΡΠ² ΠΌΠ΅ΡΠ°Π»Π»Π° ΠΎΡ ΡΡΠ΅ΠΏΠ΅Π½ΠΈ Π΄Π΅ΡΠΎΡΠΌΠ°ΡΠΈΠΈ ΠΏΡΠΈ Π²ΠΎΠ»ΠΎΡΠ΅Π½ΠΈΠΈ ΠΌΠ΅ΡΠ°Π»Π»ΠΎΠΏΡΠΎΠ΄ΡΠΊΡΠΈΠΈ | |||||
Π’ΡΠ΅Π±ΠΎΠ²Π°Π½ΠΈΡ ΠΊ ΠΊΠ°ΡΠ΅ΡΡΠ²Ρ Π³ΠΎΡΠΎΠ²ΠΎΠΉ ΠΏΡΠΎΠ΄ΡΠΊΡΠΈΠΈ Π² ΡΠΎΠΎΡΠ²Π΅ΡΡΡΠ²ΠΈΠΈ Ρ Π·Π°ΠΊΠ°Π·ΠΎΠΌ | |||||
ΠΠΈΠ΄Ρ Π΄Π΅ΡΠ΅ΠΊΡΠΎΠ², ΠΎΠ±ΡΠ°Π·ΡΡΡΠΈΡ ΡΡ Π² ΠΏΡΠΎΡΠ΅ΡΡΠ΅ Π²ΠΎΠ»ΠΎΡΠ΅Π½ΠΈΡ | |||||
Π’ΡΠ΅Π±ΠΎΠ²Π°Π½ΠΈΡ ΡΡΠ°Π½Π΄Π°ΡΡΠΎΠ² ΠΊ Π³Π΅ΠΎΠΌΠ΅ΡΡΠΈΡΠ΅ΡΠΊΠΈΠΌ ΠΏΠ°ΡΠ°ΠΌΠ΅ΡΡΠ°ΠΌ, ΡΠ°Π²Π½ΠΎΠΌΠ΅ΡΠ½ΠΎΡΡΠΈ ΡΠ»ΠΎΡ ΠΎΠΊΠΈΡΠ»ΠΎΠ², ΡΠ²Π΅ΡΡ ΠΏΠΎΠ±Π΅ΠΆΠ°Π»ΠΎΡΡΠΈ, Π²ΠΌΡΡΠΈΠ½Π°ΠΌ ΠΈ ΠΏΠΎΡΠ΅ΡΡΠΎΡΡΡΠΌ ΠΎΡ ΡΠΎΠ»ΠΈΠΊΠΎΠ² | |||||
ΠΡΠ°Π²ΠΈΠ»Π° ΠΏΠΎΠ»ΡΠ·ΠΎΠ²Π°Π½ΠΈΡ ΠΊΠΎΠ½ΡΡΠΎΠ»ΡΠ½ΠΎ-ΠΈΠ·ΠΌΠ΅ΡΠΈΡΠ΅Π»ΡΠ½ΡΠΌΠΈ ΠΏΡΠΈΠ±ΠΎΡΠ°ΠΌΠΈ Π½Π° ΡΡΠ°ΡΡΠΊΠ΅ Π²ΠΎΠ»ΠΎΡΠ΅Π½ΠΈΡ | |||||
Π’ΡΠ΅Π±ΠΎΠ²Π°Π½ΠΈΡ Π±ΠΈΡΠΎΡΠ½ΠΎΠΉ ΡΠΈΡΡΠ΅ΠΌΡ ΠΈ Π½Π°ΡΡΠ΄ΠΎΠ²-Π΄ΠΎΠΏΡΡΠΊΠΎΠ² Π½Π° ΡΡΠ°ΡΡΠΊΠ΅ Π²ΠΎΠ»ΠΎΡΠ΅Π½ΠΈΡ | |||||
Π’ΡΡΠ΄ΠΎΠ²ΡΠ΅ Π΄Π΅ΠΉΡΡΠ²ΠΈΡ |
|
Π’ΡΠ΅Π±ΠΎΠ²Π°Π½ΠΈΡ ΠΊ ΠΎΠ±ΡΠ°Π·ΠΎΠ²Π°Π½ΠΈΡ ΠΈ ΠΎΠ±ΡΡΠ΅Π½ΠΈΡ |
|
Π’ΡΠ΅Π±ΠΎΠ²Π°Π½ΠΈΡ ΠΊ ΠΎΠΏΡΡΡ ΠΏΡΠ°ΠΊΡΠΈΡΠ΅ΡΠΊΠΎΠΉ ΡΠ°Π±ΠΎΡΡ |
|
ΠΠΎΠ»ΠΎΡΠΈΠ»ΡΠ½ΡΠΉ ΡΡΠ°Π½ — Ρ Π°ΡΠ°ΠΊΡΠ΅ΡΠΈΡΡΠΈΠΊΠΈ ΠΈ ΠΏΡΠΈΠΌΠ΅Π½Π΅Π½ΠΈΠ΅
Π‘Π΅Π³ΠΎΠ΄Π½Ρ ΠΏΡΠΎΠΈΠ·Π²ΠΎΠ΄ΡΡΠ²ΠΎ ΠΌΠ΅ΡΠ°Π»Π»ΠΈΡΠ΅ΡΠΊΠΈΡ ΠΈΠ·Π΄Π΅Π»ΠΈΠΉ ΡΠ²Π»ΡΠ΅ΡΡΡ Π½Π°ΠΈΠ±ΠΎΠ»Π΅Π΅ Π²ΠΎΡΡΡΠ΅Π±ΠΎΠ²Π°Π½Π½ΠΎΠΉ ΠΎΡΡΠ°ΡΠ»ΡΡ ΠΏΡΠΎΠΈΠ·Π²ΠΎΠ΄ΡΡΠ²Π°. Π ΡΡΠΈΠΌ ΡΠΈΠΏΠ°ΠΌ ΠΏΡΠΎΠΈΠ·Π²ΠΎΠ΄ΡΡΠ²Π° ΠΌΠΎΠΆΠ½ΠΎ ΠΎΡΠ½Π΅ΡΡΠΈ ΠΈ ΠΈΠ·Π³ΠΎΡΠΎΠ²Π»Π΅Π½ΠΈΠ΅ ΡΠ°ΠΊΠΈΡ ΠΈΠ·Π΄Π΅Π»ΠΈΠΉ ΠΈΠ· ΠΌΠ΅ΡΠ°Π»Π»Π°, ΠΊΠ°ΠΊ ΠΏΡΠΎΠ²ΠΎΠ»ΠΎΠΊΠ°, ΠΆΠ΅Π»Π΅Π·Π½ΡΠ΅ ΠΏΡΡΡΡ, ΠΏΡΠΎΡΠΈΠ»ΡΠ½ΠΎΠ³ΠΎ ΠΌΠ°ΡΠ΅ΡΠΈΠ°Π»Π° ΠΈ ΡΡΡΠ±Ρ Π½Π΅ ΡΠ»ΠΈΡΠΊΠΎΠΌ Π±ΠΎΠ»ΡΡΠΈΠ΅ ΠΏΠΎ Π΄ΠΈΠ°ΠΌΠ΅ΡΡΡ. Π‘ΡΠΎΠΈΡ ΠΎΡΠΌΠ΅ΡΠΈΡΡ, ΡΡΠΎ Π΄Π»Ρ ΠΈΠ·Π³ΠΎΡΠΎΠ²Π»Π΅Π½ΠΈΡ Π²ΡΠ΅Ρ ΡΡΠΈΡ ΠΌΠ΅ΡΠ°Π»Π»ΠΈΡΠ΅ΡΠΊΠΈΡ ΠΈΠ·Π΄Π΅Π»ΠΈΠΉ ΡΡΠ΅Π±ΡΠ΅ΡΡΡ Π½Π°Π»ΠΈΡΠΈΠ΅ ΡΠΏΠ΅ΡΠΈΠ°Π»ΡΠ½ΠΎΠ³ΠΎ ΠΎΠ±ΠΎΡΡΠ΄ΠΎΠ²Π°Π½ΠΈΡ, ΠΊ Π½Π΅ΠΌΡ Π½Π΅ΠΏΠΎΡΡΠ΅Π΄ΡΡΠ²Π΅Π½Π½ΠΎ ΠΎΡΠ½ΠΎΡΠΈΡΡΡ Π²ΠΎΠ»ΠΎΡΠΈΠ»ΡΠ½ΡΠΉ ΡΡΠ°Π½.
Π£ΡΡΡΠΎΠΉΡΡΠ²ΠΎ Π²ΠΎΠ»ΠΎΡΠΈΠ»ΡΠ½ΠΎΠ³ΠΎ ΡΡΠ°Π½Π°.
ΠΠ°Π½Π½ΠΎΠ΅ ΠΎΠ±ΠΎΡΡΠ΄ΠΎΠ²Π°Π½ΠΈΠ΅ ΠΏΡΠ΅Π΄Π½Π°Π·Π½Π°ΡΠ΅Π½ΠΎ Π΄Π»Ρ ΡΠΎΠ³ΠΎ, ΡΡΠΎΠ±Ρ ΠΏΡΠΎΡΡΠ³ΠΈΠ²Π°ΡΡ ΠΈΠ·Π΄Π΅Π»ΠΈΠ΅ ΡΠ΅ΡΠ΅Π· ΡΠ°ΠΊ Π½Π°Π·ΡΠ²Π°Π΅ΠΌΡΡ Π²ΠΎΠ»ΠΎΠΊΡ, ΠΈΠ½ΡΠΌΠΈ ΡΠ»ΠΎΠ²Π°ΠΌΠΈ ΡΠΏΠ΅ΡΠΈΠ°Π»ΡΠ½ΡΠΉ Π³Π»Π°Π·ΠΎΠΊ, Β ΠΏΡΠΈ ΡΡΠΎΠΌ ΡΠ°Π·ΠΌΠ΅Ρ Π΅Π³ΠΎ ΡΠ΅ΡΠ΅Π½ΠΈΡ ΡΠ²Π»ΡΠ΅ΡΡΡ ΠΌΠ΅Π½ΡΡΠΈΠΌ, Π½Π΅ΠΆΠ΅Π»ΠΈ ΡΠ°Π·ΠΌΠ΅Ρ ΡΠ΅ΡΠ΅Π½ΠΈΡ ΠΈΡΡ
ΠΎΠ΄Π½ΠΎΠ³ΠΎ ΠΌΠ°ΡΠ΅ΡΠΈΠ°Π»Π°. ΠΠΎΠ»ΠΎΡΠΈΠ»ΡΠ½ΡΠ΅ ΡΡΠ°Π½Ρ, Π² Π½Π΅ΠΏΠΎΡΡΠ΅Π΄ΡΡΠ²Π΅Π½Π½ΠΎΠΉ Π·Π°Π²ΠΈΡΠΈΠΌΠΎΡΡΠΈ ΠΎΡ ΠΈΡ
ΠΏΡΠΈΠ½ΡΠΈΠΏΠ° ΡΠ°Π±ΠΎΡΡ ΠΌΠΎΠ³ΡΡ ΠΏΠΎΠ΄ΡΠ°Π·Π΄Π΅Π»ΡΡΡΡΡ Π½Π° ΡΡΠ°Π½Ρ Π΄Π²ΠΈΠΆΠ΅Π½ΠΈΠ΅ ΠΌΠ΅ΡΠ°Π»Π»Π°, Π² ΠΊΠΎΡΠΎΡΡΡ
ΡΠ²Π»ΡΠ΅ΡΡΡ ΠΏΡΡΠΌΠΎΠ»ΠΈΠ½Π΅ΠΉΠ½ΡΠΌ. Π ΡΡΠ°Π½Ρ, Π² ΠΊΠΎΡΠΎΡΡΡ
ΠΎΠ±ΡΠ°Π±Π°ΡΡΠ²Π°Π΅ΠΌΡΠΉ ΠΌΠ΅ΡΠ°Π»Π» Π½Π°ΠΌΠ°ΡΡΠ²Π°Π΅ΡΡΡ Π½Π° Π±Π°ΡΠ°Π±Π°Π½Π½ΠΎΠ΅ ΡΡΡΡΠΎΠΉΡΡΠ²ΠΎ.
ΠΠΎΠ»ΠΎΡΠΈΠ»ΡΠ½ΡΠ΅ ΡΡΠ°Π½Ρ ΠΏΠ΅ΡΠ²ΠΎΠΉ ΠΊΠ°ΡΠ΅Π³ΠΎΡΠΈΠΈ ΠΌΠΎΠ³ΡΡ Π±ΡΡΡ ΡΠ΅Π΅ΡΠ½ΡΠΌΠΈ ΠΈ ΡΠ΅ΠΏΠ½ΡΠΌΠΈ. ΠΡ
ΠΈΡΠΏΠΎΠ»ΡΠ·ΡΡΡ Π΄Π»Ρ Π²ΠΎΠ»ΠΎΡΠ΅Π½ΠΈΡ ΠΈ ΠΊΠ°Π»ΠΈΠ±ΡΠΎΠ²ΠΊΠΈ ΡΠ°ΠΊΠΈΡ
ΠΈΠ·Π΄Π΅Π»ΠΈΠΉ, ΠΊΠ°ΠΊ ΠΏΡΡΡΠΊΠΈ, ΡΡΡΠ±Ρ Π½Π΅Π±ΠΎΠ»ΡΡΠΎΠ³ΠΎ Π΄ΠΈΠ°ΠΌΠ΅ΡΡΠ° ΠΈ Π΄ΡΡΠ³ΠΈΡ
ΠΏΠΎΠ΄ΠΎΠ±Π½ΡΡ
ΠΈΠ·Π΄Π΅Π»ΠΈΠΉ. Π’Π°ΠΊΠΎΠΉ ΠΌΠ°ΡΠ΅ΡΠΈΠ°Π» Π½Π΅ Π½ΡΠΆΠ½ΠΎ ΡΠΌΠ°ΡΡΠ²Π°ΡΡ Π² ΡΠΏΠ΅ΡΠΈΠ°Π»ΡΠ½ΡΠ΅ Π±ΡΡ
ΡΡ.
Β
Β
ΠΡΠΎΡΠΎΠΉ ΡΠΈΠΏ Π²ΠΎΠ»ΠΎΡΠΈΠ»ΡΠ½ΡΡ ΡΡΠ°Π½ΠΎΠ², ΠΌΠ΅ΡΠ°Π»Π» Π² ΠΊΠΎΡΠΎΡΡΡ Π½Π°ΠΌΠ°ΡΡΠ²Π°Π΅ΡΡΡ Π½Π° Π±Π°ΡΠ°Π±Π°Π½Π½ΠΎΠ΅ ΡΡΡΡΠΎΠΉΡΡΠ²ΠΎ, ΠΈΡΠΏΠΎΠ»ΡΠ·ΡΠ΅ΡΡΡ Π½Π°ΠΈΠ±ΠΎΠ»Π΅Π΅ ΡΠ°ΡΡΠΎ Π΄Π»Ρ ΠΈΠ·Π³ΠΎΡΠΎΠ²Π»Π΅Π½ΠΈΡ ΡΠ°ΠΊΠΈΡ ΠΌΠ°ΡΠ΅ΡΠΈΠ°Π»ΠΎΠ², ΠΊΠ°ΠΊ ΠΌΠ΅ΡΠ°Π»Π»ΠΈΡΠ΅ΡΠΊΠ°Ρ ΠΏΡΠΎΠ²ΠΎΠ»ΠΎΠΊΠ°, Π° ΡΠ°ΠΊ ΠΆΠ΅ ΡΠΏΠ΅ΡΠΈΠ°Π»ΡΠ½ΡΠΉ ΠΏΡΠΎΡΠΈΠ»ΡΠ½ΡΠΉ ΠΌΠ°ΡΠ΅ΡΠΈΠ°Π». Π‘ΡΠΎΠΈΡ ΠΎΡΠΌΠ΅ΡΠΈΡΡ, ΡΡΠΎ Π΄Π°Π½Π½ΡΠΉ ΡΠΈΠΏ ΡΡΠ°Π½Π° ΠΌΠΎΠΆΠ½ΠΎ, Π² ΡΠ²ΠΎΡ ΠΎΡΠ΅ΡΠ΅Π΄Ρ, ΠΏΠΎΠ΄ΡΠ°Π·Π΄Π΅Π»ΡΡΡ Π½Π° ΡΡΠ°Π½Ρ ΠΎΠ΄Π½ΠΎΠΊΡΠ°ΡΠ½ΠΎΠ³ΠΎ Π΄Π΅ΠΉΡΡΠ²ΠΈΡ. ΠΠ° ΠΌΠ½ΠΎΠ³ΠΎΠΊΡΠ°ΡΠ½ΡΠ΅ ΡΡΠ°Π½Ρ, ΠΊΠΎΡΠΎΡΡΠ΅ ΡΠ°Π±ΠΎΡΠ°ΡΡ ΡΠΎ ΡΠΊΠΎΠ»ΡΠΆΠ΅Π½ΠΈΠ΅ΠΌ. ΠΠ° ΡΡΠ°Π½Ρ ΠΌΠ½ΠΎΠ³ΠΎΠΊΡΠ°ΡΠ½ΡΠ΅, ΠΊΠΎΡΠΎΡΡΠ΅ ΡΠ°Π±ΠΎΡΠ°ΡΡ Π±Π΅Π· ΡΠΊΠΎΠ»ΡΠΆΠ΅Π½ΠΈΡ, ΠΈ Π½Π°ΠΊΠΎΠ½Π΅Ρ, Π½Π° ΡΡΠ°Π½Ρ ΠΌΠ½ΠΎΠ³ΠΎΠΊΡΠ°ΡΠ½ΠΎΠ³ΠΎ Π΄Π΅ΠΉΡΡΠ²ΠΈΡ, ΠΊΠΎΡΠΎΡΡΠ΅ ΡΠ°Π±ΠΎΡΠ°ΡΡ Ρ ΠΏΡΠΎΡΠΈΠ²ΠΎΠ½Π°ΡΡΠΆΠ΅Π½ΠΈΠ΅ΠΌ.
ΠΠ°Π½Π½ΠΎΠ΅ ΠΎΠ±ΠΎΡΡΠ΄ΠΎΠ²Π°Π½ΠΈΠ΅ Π²ΠΊΠ»ΡΡΠ°Π΅Ρ Π² ΡΠ΅Π±Ρ ΡΡΠΈ ΠΎΡΠ½ΠΎΠ²Π½ΡΡ
ΡΠ°Π±ΠΎΡΠΈΡ
ΡΠ»Π΅ΠΌΠ΅Π½ΡΠ°, ΡΡΠΈΠΌΠΈ ΡΠ°Π±ΠΎΡΠΈΠΌΠΈ ΡΠ°ΡΡΡΠΌΠΈ ΡΠ²Π»ΡΡΡΡΡ ΡΡΡΡΠΎΠΉΡΡΠ²ΠΎ Π΄Π»Ρ ΡΠ°Π·ΠΌΠΎΡΠΊΠΈ ΠΌΠ΅ΡΠ°Π»Π»ΠΈΡΠ΅ΡΠΊΠΎΠ³ΠΎ ΠΌΠ°ΡΠ΅ΡΠΈΠ°Π»Π°, ΡΠ°ΠΌΠ° ΡΠ°ΡΡΡ, ΠΊΠΎΡΠΎΡΠΎΠ΅ ΠΏΡΠΎΠΈΠ·Π²ΠΎΠ΄ΠΈΡ Π²ΠΎΠ»ΠΎΡΠ΅Π½ΠΈΠ΅, ΠΈ ΡΡΡΡΠΎΠΉΡΡΠ²ΠΎ Π΄Π»Ρ Π½Π°ΠΌΠΎΡΠΊΠΈ Π³ΠΎΡΠΎΠ²ΠΎΠ³ΠΎ ΠΈΠ·Π΄Π΅Π»ΠΈΡ.
ΠΡΠΈΠ½ΡΠΈΠΏ ΡΠ°Π±ΠΎΡΡ Π²ΠΎΠ»ΠΎΡΠΈΠ»ΡΠ½ΠΎΠ³ΠΎ ΡΡΠ°Π½Π°.
Β
Β
Β
ΠΡΠΈΠ½ΡΠΈΠΏ ΡΠ°Π±ΠΎΡΡ Π΄Π°Π½Π½ΠΎΠ³ΠΎ ΡΡΡΡΠΎΠΉΡΡΠ²Π° Π²ΡΠ³Π»ΡΠ΄ΠΈΡ ΡΠ»Π΅Π΄ΡΡΡΠΈΠΌ ΠΎΠ±ΡΠ°Π·ΠΎΠΌ. ΠΠ°ΡΠ΅ΡΠΈΠ°Π» ΠΏΠΎΠ΄Π»Π΅ΠΆΠ°ΡΠΈΠΉ Π²ΠΎΠ»ΠΎΡΠ΅Π½ΠΈΡ ΡΠ΅ΡΠ΅Π· ΠΊΠΎΡΠ·ΠΈΠ½Ρ ΠΏΡΠΈΠ΅ΠΌΠΎΡΠ½ΠΎΠ³ΠΎ ΠΎΡΠ΄Π΅Π»Π΅Π½ΠΈΡ Π° ΡΠ°ΠΊΠΆΠ΅ ΡΠ΅ΡΠ΅Π· ΡΠΏΠ΅ΡΠΈΠ°Π»ΡΠ½ΡΠ΅ ΡΠΎΠ»ΠΈΠΊΠΎΠ²ΡΠ΅ ΡΡΡΡΠΎΠΉΡΡΠ²Π°, Π½Π°ΠΏΡΠ°Π²Π»ΡΡΡΠ΅Π³ΠΎ Ρ Π°ΡΠ°ΠΊΡΠ΅ΡΠ° Π²ΡΠ΄Π°Π΅ΡΡΡ Π½Π° ΡΠΎΠ»ΠΈΠΊ, ΠΈ Π΄Π°Π»Π΅Π΅ Π½Π° ΡΠΎΠ»ΠΈΠΊ ΡΡΡΠ°Π½ΠΎΠ²Π»Π΅Π½Π½ΡΠΉ Π² ΠΊΠ°ΡΠ΅ΡΠΊΠ΅ ΠΊΠΎΠΌΠΏΠ΅Π½ΡΠΈΡΡΡΡΠ΅Π³ΠΎ ΡΠΈΠΏΠ°. Π£ΠΆΠ΅ Ρ ΡΡΠΎΠΉ ΠΊΠ°ΡΠ΅ΡΠΊΠΈ ΠΌΠ°ΡΠ΅ΡΠΈΠ°Π» Π²ΡΠ΄Π°Π΅ΡΡΡ ΠΏΡΡΠΌΠΎ Π½Π° ΡΠ°ΠΌΠΎ Π²ΠΎΠ»ΠΎΡΠΈΠ»ΡΠ½ΠΎΠ΅ ΡΡΡΡΠΎΠΉΡΡΠ²ΠΎ.
ΠΡΠΏΠΎΠ»ΡΠ·ΠΎΠ²Π°Π½ΠΈΠ΅ ΡΠ°ΠΊΠΎΠ³ΠΎ ΠΎΡΠ³Π°Π½Π°, ΠΊΠ°ΠΊ ΠΊΠΎΠΌΠΏΠ΅Π½ΡΠΈΡΡΡΡΠ°Ρ ΠΊΠ°ΡΠ΅ΡΠΊΠ° Π²Π°ΠΆΠ½ΠΎ Π΄Π»Ρ ΡΠΎΠ³ΠΎ, ΡΡΠΎΠ±Ρ ΠΏΡΠ΅Π΄ΠΎΡΠ²ΡΠ°ΡΠΈΡΡ ΠΎΠ±ΡΡΠ² ΠΏΡΠΎΠ²ΠΎΠ»ΠΎΠΊΠΈ, Π² ΡΠ»ΡΡΠ°Π΅ ΡΠ΅Π·ΠΊΠΎΠ³ΠΎ ΡΠΎΡΠΌΠΎΠΆΠ΅Π½ΠΈΡ Π²ΠΎΠ»ΠΎΠΊΠΈ ΠΈΠ»ΠΈ ΡΠ΅Π·ΠΊΠΎΠΉ ΠΎΡΡΠ°Π½ΠΎΠ²ΠΊΠΈ ΡΠ°Π±ΠΎΡΡ Π²ΡΠ΅Π³ΠΎ ΡΡΡΡΠΎΠΉΡΡΠ²Π°. Π‘ΡΡΡ ΡΡΠΎΠ³ΠΎ ΡΠ°Π±ΠΎΡΠ΅Π³ΠΎ ΠΌΠ΅Ρ
Π°Π½ΠΈΠ·ΠΌΠ° ΡΡΠ΅Π·Π²ΡΡΠ°ΠΉΠ½ΠΎ ΠΏΡΠΎΡΡΠ°: Π²ΠΎ Π²ΡΠ΅ΠΌΡ Π²Π½Π΅Π·Π°ΠΏΠ½ΠΎΠΉ ΠΎΡΡΠ°Π½ΠΎΠ²ΠΊΠΈ ΠΏΡΠΈ ΠΏΠΎΠ΄Π°ΡΠ΅ Π·Π°Π³ΠΎΡΠΎΠ²ΠΊΠΈ, Π±Π»ΠΎΠΊΠΈ ΠΎΠ±ΠΎΡΡΠ΄ΠΎΠ²Π°Π½ΠΈΡ Π΅ΡΠ΅ ΠΊΠ°ΠΊΠΎΠ΅-ΡΠΎ Π²ΡΠ΅ΠΌΡ ΠΏΡΠΎΠ΄ΠΎΠ»ΠΆΠ°ΡΡ Π²ΡΠ°ΡΠ΅Π½ΠΈΠ΅ ΠΈ ΡΠΎΠΎΡΠ²Π΅ΡΡΡΠ²Π΅Π½Π½ΠΎ ΡΡΠ΅Π±ΡΡΡ Π²ΡΠ΄Π°ΡΠΈ Π΅ΡΠ΅ ΠΊΠ°ΠΊΠΎΠ³ΠΎ-ΡΠΎ ΠΎΠΏΡΠ΅Π΄Π΅Π»Π΅Π½Π½ΠΎΠ³ΠΎ ΠΊΠΎΠ»ΠΈΡΠ΅ΡΡΠ²Π° Π·Π°Π³ΠΎΡΠΎΠ²ΠΎΡΠ½ΠΎΠ³ΠΎ ΠΌΠ°ΡΠ΅ΡΠΈΠ°Π»Π°. Π ΡΡΠΎ Π²ΡΠ΅ΠΌΡ ΠΊΠ°ΡΠ΅ΡΠΊΠ° ΠΊΠΎΠΌΠΏΠ΅Π½ΡΠΈΡΡΡΡΠ΅Π³ΠΎ ΡΠΈΠΏΠ° Π²ΠΎΠ»ΠΎΡΠΈΠ»ΡΠ½ΠΎΠ³ΠΎ ΡΡΠ°Π½Π° ΠΏΡΠΎΠΈΠ·Π²ΠΎΠ΄ΠΈΡ Π΄Π²ΠΈΠΆΠ΅Π½ΠΈΠ΅ ΠΏΠΎ Π½Π°ΠΏΡΠ°Π²Π»Π΅Π½ΠΈΡ Π²Π²Π΅ΡΡ
ΠΈ ΡΠ°ΠΊΠΈΠΌ ΠΎΠ±ΡΠ°Π·ΠΎΠΌ Β ΠΎΡΠ²ΠΎΠ±ΠΎΠΆΠ΄Π°Π΅Ρ Π½Π΅ΠΎΠ±Ρ
ΠΎΠ΄ΠΈΠΌΠΎΠ΅ ΠΊΠΎΠ»ΠΈΡΠ΅ΡΡΠ²ΠΎ ΠΌΠ°ΡΠ΅ΡΠΈΠ°Π»Π°, ΠΊΠΎΡΠΎΡΡΠΉ ΡΠΎΠ±ΡΡΠ²Π΅Π½Π½ΠΎ ΠΏΠΎΡΡΡΠΏΠ°Π΅Ρ Π½Π° Π²ΠΎΠ»ΠΎΡΠΈΠ»ΡΠ½ΠΎΠ΅ ΡΡΡΡΠΎΠΉΡΡΠ²ΠΎ ΠΈ ΡΠ°ΠΊΠΈΠΌ ΠΎΠ±ΡΠ°Π·ΠΎΠΌ ΠΎΠ±ΡΡΠ² Π½Π΅ ΠΈΠΌΠ΅Π΅Ρ ΠΌΠ΅ΡΡΠΎ.
ΠΠ° ΠΏΠΎΡΠ»Π΅Π΄Π½Π΅ΠΉ ΡΡΠ°Π΄ΠΈΠΈ Π²ΠΎΠ»ΠΎΡΠ΅Π½ΠΈΡ ΠΌΠ°ΡΠ΅ΡΠΈΠ°Π» ΠΏΡΠΎΡ
ΠΎΠ΄Ρ ΠΏΠΎΠ΄Π²Π΅ΡΠ³Π½ΡΡΡΠΉ Π²ΠΎΠ»ΠΎΡΠ΅Π½ΠΈΡ ΠΏΠΎΡΡΡΠΏΠ°Π΅Ρ Π½Π° Π½ΠΈΠΆΠ½ΠΈΠΉ Π²ΠΎΠ»ΠΎΡΠΈΠ»ΡΠ½ΡΠΉ Π±Π°ΡΠ°Π±Π°Π½ ΡΠ΄Π²ΠΎΠ΅Π½Π½ΠΎΠ³ΠΎ ΡΠΈΠΏΠ°, ΠΏΠΎΡΠ»Π΅ ΡΠ΅Π³ΠΎ ΠΏΠΎΡΡΠ΅Π΄ΡΡΠ²ΠΎΠΌ ΡΠΎΠ»ΠΈΠΊΠ° ΠΏΠ΅ΡΠ΅ΠΊΠΈΠ΄Π½ΠΎΠ³ΠΎ ΡΠΈΠΏΠ° ΠΎΠ½ Π²ΡΠ΄Π°Π΅ΡΡΡ Π½Π° Π±Π°ΡΠ°Π±Π°Π½ ΡΠ°ΡΠΏΠΎΠ»ΠΎΠΆΠ΅Π½Π½ΡΠΉ Π²Π²Π΅ΡΡ
Ρ, ΠΊΠΎΡΠΎΡΡΠΉ ΡΠ²Π»ΡΠ΅ΡΡΡ Π½Π°ΠΊΠΎΠΏΠΈΡΠ΅Π»ΡΠ½ΡΠΌ. ΠΠΌΠ΅Π½Π½ΠΎ ΠΏΠΎΡΡΠ΅Π΄ΡΡΠ²ΠΎΠΌ ΡΠΎΠ³ΠΎ, ΡΡΠΎ Π²Π΅ΡΡ
Π½ΠΈΠΉ Π±Π°ΡΠ°Π±Π°Π½ Π½Π°ΠΊΠ°ΠΏΠ»ΠΈΠ²Π°Π΅Ρ ΠΏΡΠΎΠ²ΠΎΠ»ΠΎΠΊΡ, Π΅Π΅ ΠΌΠΎΠΆΠ½ΠΎ Π±ΡΠ΄Π΅Ρ ΠΏΠΎΠ΄Π°ΡΡ Π² ΡΠ»ΡΡΠ°Π΅ ΡΠ΅Π·ΠΊΠΎΠ³ΠΎ ΡΠΎΡΠΌΠΎΠΆΠ΅Π½ΠΈΡ ΡΡΡΡΠΎΠΉΡΡΠ²Π°.
ΠΠΎΡΠ»Π΅ ΠΏΡΠΎΡΠ΅Π΄ΡΡΡ Π²ΠΎΠ»ΠΎΡΠ΅Π½ΠΈΡ, ΠΏΡΠΎΠ²ΠΎΠ»ΠΎΠΊΠ° Π²ΡΠ΄Π°Π΅ΡΡΡ Π½Π° ΡΠΏΠ΅ΡΠΈΠ°Π»ΡΠ½ΠΎΠ΅ ΡΠΈΡ
ΡΠΎΠ²Π°Π»ΡΠ½ΠΎΠ΅ ΡΡΡΡΠΎΠΉΡΡΠ²ΠΎ, ΠΊΠΎΡΠΎΡΠΎΠ΅ ΡΠ»ΡΠΆΠΈΡ Π΄Π»Ρ ΡΠΎΠ³ΠΎ, ΡΡΠΎΠ±Ρ ΠΏΡΠΈΠ΄Π°Π²Π°ΡΡ ΠΈΠ·Π΄Π΅Π»ΠΈΡ ΠΈΠ·Π³ΠΈΠ±Ρ ΠΈ Π·Π°Π΄Π°Π½Π½ΡΡ ΡΠΎΡΠΌΡ. Π Π°Π±ΠΎΡΠ° Π²ΠΎΠ»ΠΎΡΠΈΠ»ΡΠ½ΠΎΠ³ΠΎ ΡΡΠ°Π½Π° ΠΏΡΠΎΠΈΡΡ
ΠΎΠ΄ΠΈΡ Π½Π΅ΠΏΠΎΡΡΠ΅Π΄ΡΡΠ²Π΅Π½Π½ΠΎ ΠΎΡ ΡΠ»Π΅ΠΊΡΡΠΈΡΠ΅ΡΠΊΠΎΠ³ΠΎ Π΄Π²ΠΈΠ³Π°ΡΠ΅Π»Ρ.
ΠΠ-11-101-95
ΠΠ°ΡΠ° Π²Π²Π΅Π΄Π΅Π½ΠΈΡ 1996-07-01
Π Π°Π·ΡΠ°Π±ΠΎΡΠ°Π½Ρ ΠΈ Π²Π½Π΅ΡΠ΅Π½Ρ
Π£ΠΏΡΠ°Π²Π»Π΅Π½ΠΈΠ΅ΠΌ ΠΏΠΎ Π½Π°Π΄Π·ΠΎΡΡ Π² ΠΌΠ΅ΡΠ°Π»Π»ΡΡΠ³ΠΈΡΠ΅ΡΠΊΠΎΠΉ ΠΏΡΠΎΠΌΡΡΠ»Π΅Π½Π½ΠΎΡΡΠΈ
Π£ΡΠ²Π΅ΡΠΆΠ΄Π΅Π½Ρ
ΠΠΎΡΠ³ΠΎΡΡΠ΅Ρ
Π½Π°Π΄Π·ΠΎΡΠΎΠΌ Π ΠΎΡΡΠΈΠΈ ΠΠΎΡΡΠ°Π½ΠΎΠ²Π»Π΅Π½ΠΈΠ΅ N 45 ΠΎΡ 13.09.95 Π³.
Π Π΅Π΄Π°ΠΊΡΠΈΠΎΠ½Π½Π°Ρ
ΠΊΠΎΠ»Π»Π΅Π³ΠΈΡ:
Π.Π .ΠΠ΅ΡΠΊΠΎΠ²
(ΠΏΡΠ΅Π΄ΡΠ΅Π΄Π°ΡΠ΅Π»Ρ), Π.Π‘.ΠΠ°Π½ΠΈΠ½ (Π·Π°ΠΌΠ΅ΡΡΠΈΡΠ΅Π»Ρ ΠΏΡΠ΅Π΄ΡΠ΅Π΄Π°ΡΠ΅Π»Ρ), Π.Π€.ΠΠ°ΡΡΠΎΡ
ΠΈΠ½,
Π.Π.ΠΠ°ΡΡΠ»ΠΊΠΈΠ½Π°, Π.Π.ΠΠ»Π΅ΠΊΡΠ΅Π΅Π², Π.Π.ΠΠ·Π²ΠΎΠ·ΡΠΈΠΊΠΎΠ², Π.Π.ΠΠ»Π°ΡΡΠΈΠ½ΠΈΠ½,
Π.Π.Π¨Π°ΠΊΠΈΡΠ·ΡΠ½ΠΎΠ²Π°, Π.Π.Π¨ΠΈΠ³ΠΎΡΠΈΠ½, Π.Π€.Π’Π΅ΡΠ΅Π½ΡΡΠ΅Π²Π°
ΠΠ°ΡΡΠΎΡΡΠΈΠ΅ ΠΡΠ°Π²ΠΈΠ»Π°
ΡΠ°Π·ΡΠ°Π±ΠΎΡΠ°Π½Ρ ΠΠ°ΡΡΠ½ΠΎ-ΠΈΡΡΠ»Π΅Π΄ΠΎΠ²Π°ΡΠ΅Π»ΡΡΠΊΠΈΠΌ ΠΈΠ½ΡΡΠΈΡΡΡΠΎΠΌ ΠΎΡ
ΡΠ°Π½Ρ ΡΡΡΠ΄Π° ΠΈ
ΡΠ΅Ρ
Π½ΠΈΠΊΠΈ Π±Π΅Π·ΠΎΠΏΠ°ΡΠ½ΠΎΡΡΠΈ ΡΠ΅ΡΠ½ΠΎΠΉ ΠΌΠ΅ΡΠ°Π»Π»ΡΡΠ³ΠΈΠΈ (ΠΠΠΠ’ΠΡΠ΅ΡΠΌΠ΅Ρ) Π½Π° ΠΎΡΠ½ΠΎΠ²Π΅
ΡΡΠ²Π΅ΡΠΆΠ΄Π΅Π½Π½ΡΡ
ΠΠΈΠ½ΡΠ΅ΡΠΌΠ΅ΡΠΎΠΌ Π‘Π‘Π‘Π Π² 1987 Π³. ΠΡΠ°Π²ΠΈΠ» Π±Π΅Π·ΠΎΠΏΠ°ΡΠ½ΠΎΡΡΠΈ Π²
ΠΌΠ΅ΡΠΈΠ·Π½ΠΎΠΌ ΠΏΡΠΎΠΈΠ·Π²ΠΎΠ΄ΡΡΠ²Π΅, Ρ ΡΡΠ°ΡΡΠΈΠ΅ΠΌ ΠΠΎΡΠ³ΠΎΡΡΠ΅Ρ
Π½Π°Π΄Π·ΠΎΡΠ° Π ΠΎΡΡΠΈΠΈ, Π° ΡΠ°ΠΊΠΆΠ΅
Ρ ΡΡΠ΅ΡΠΎΠΌ Π·Π°ΠΌΠ΅ΡΠ°Π½ΠΈΠΉ ΠΈ ΠΏΡΠ΅Π΄Π»ΠΎΠΆΠ΅Π½ΠΈΠΉ ΠΏΡΠ΅Π΄ΠΏΡΠΈΡΡΠΈΠΉ,
Π½Π°ΡΡΠ½ΠΎ-ΠΈΡΡΠ»Π΅Π΄ΠΎΠ²Π°ΡΠ΅Π»ΡΡΠΊΠΈΡ
ΠΈ ΠΏΡΠΎΠ΅ΠΊΡΠ½ΡΡ
ΠΈΠ½ΡΡΠΈΡΡΡΠΎΠ², ΠΎΡΠ³Π°Π½ΠΎΠ²
ΠΠΎΡΠ³ΠΎΡΡΠ΅Ρ
Π½Π°Π΄Π·ΠΎΡΠ° ΠΈ Π¦Π΅Π½ΡΡΠ°Π»ΡΠ½ΠΎΠ³ΠΎ Π‘ΠΎΠ²Π΅ΡΠ° ΠΏΡΠΎΡΡΠΎΡΠ·Π°
Π³ΠΎΡΠ½ΠΎ-ΠΌΠ΅ΡΠ°Π»Π»ΡΡΠ³ΠΈΡΠ΅ΡΠΊΠΎΠΉ ΠΏΡΠΎΠΌΡΡΠ»Π΅Π½Π½ΠΎΡΡΠΈ Π ΠΎΡΡΠΈΠΈ.
Π
ΠΡΠ°Π²ΠΈΠ»Π°Ρ
ΠΈΠ·Π»ΠΎΠΆΠ΅Π½Ρ ΡΡΠ΅Π±ΠΎΠ²Π°Π½ΠΈΡ Π±Π΅Π·ΠΎΠΏΠ°ΡΠ½ΠΎΡΡΠΈ ΠΊ ΠΏΡΠΎΠΈΠ·Π²ΠΎΠ΄ΡΡΠ²Π΅Π½Π½ΡΠΌ
ΠΏΡΠΎΡΠ΅ΡΡΠ°ΠΌ ΠΈ ΠΎΡΠ³Π°Π½ΠΈΠ·Π°ΡΠΈΠΈ ΠΏΡΠΎΠΈΠ·Π²ΠΎΠ΄ΡΡΠ²Π° Π½Π° ΠΏΡΠ΅Π΄ΠΏΡΠΈΡΡΠΈΡΡ
ΠΏΠΎ
ΠΏΡΠΎΠΈΠ·Π²ΠΎΠ΄ΡΡΠ²Ρ ΠΌΠ΅ΡΠΈΠ·ΠΎΠ² (ΠΌΠ΅ΡΠΈΠ·Π½ΡΡ
ΠΈΠ·Π΄Π΅Π»ΠΈΠΉ) Π½Π΅Π·Π°Π²ΠΈΡΠΈΠΌΠΎ ΠΎΡ ΠΈΡ
ΠΏΡΠΈΠ½Π°Π΄Π»Π΅ΠΆΠ½ΠΎΡΡΠΈ, Π° ΡΠ°ΠΊΠΆΠ΅ ΠΏΠΎ ΡΡΡΡΠΎΠΉΡΡΠ²Ρ ΠΈ ΠΎΠ±Π΅ΡΠΏΠ΅ΡΠ΅Π½ΠΈΡ Π±Π΅Π·ΠΎΠΏΠ°ΡΠ½ΠΎΠΉ
ΡΠΊΡΠΏΠ»ΡΠ°ΡΠ°ΡΠΈΠΈ ΠΎΡΠ½ΠΎΠ²Π½ΠΎΠ³ΠΎ ΠΈ Π²ΡΠΏΠΎΠΌΠΎΠ³Π°ΡΠ΅Π»ΡΠ½ΠΎΠ³ΠΎ ΠΎΠ±ΠΎΡΡΠ΄ΠΎΠ²Π°Π½ΠΈΡ.
Π‘
Π²Π²Π΅Π΄Π΅Π½ΠΈΠ΅ΠΌ Π½Π°ΡΡΠΎΡΡΠΈΡ
ΠΡΠ°Π²ΠΈΠ» Π΄Π΅ΠΉΡΡΠ²ΠΈΠ΅ ΠΡΠ°Π²ΠΈΠ» Π±Π΅Π·ΠΎΠΏΠ°ΡΠ½ΠΎΡΡΠΈ Π² ΠΌΠ΅ΡΠΈΠ·Π½ΠΎΠΌ
ΠΏΡΠΎΠΈΠ·Π²ΠΎΠ΄ΡΡΠ²Π΅, ΡΡΠ²Π΅ΡΠΆΠ΄Π΅Π½Π½ΡΡ
Π² 1978 Π³., ΠΏΡΠ΅ΠΊΡΠ°ΡΠ°Π΅ΡΡΡ.
1. ΠΠΠ©ΠΠ ΠΠΠΠΠΠΠΠΠ―
ΠΠ°ΡΡΠΎΡΡΠΈΠ΅ ΠΡΠ°Π²ΠΈΠ»Π°
ΡΡΡΠ°Π½Π°Π²Π»ΠΈΠ²Π°ΡΡ ΡΡΠ΅Π±ΠΎΠ²Π°Π½ΠΈΡ ΠΊ ΠΏΡΠΎΠ΅ΠΊΡΠΈΡΡΠ΅ΠΌΡΠΌ, ΡΡΡΠΎΡΡΠΈΠΌΡΡ,
ΡΠ΅ΠΊΠΎΠ½ΡΡΡΡΠΈΡΡΠ΅ΠΌΡΠΌ ΠΈ Π΄Π΅ΠΉΡΡΠ²ΡΡΡΠΈΠΌ ΠΏΡΠ΅Π΄ΠΏΡΠΈΡΡΠΈΡΠΌ, ΡΠ΅Ρ
Π°ΠΌ,
ΠΎΠΏΡΡΠ½ΠΎ-ΠΏΡΠΎΠΌΡΡΠ»Π΅Π½Π½ΡΠΌ ΡΡΡΠ°Π½ΠΎΠ²ΠΊΠ°ΠΌ ΠΏΠΎ ΠΏΡΠΎΠΈΠ·Π²ΠΎΠ΄ΡΡΠ²Ρ ΠΌΠ΅ΡΠ°Π»Π»ΠΎΠΈΠ·Π΄Π΅Π»ΠΈΠΉ
(ΠΌΠ΅ΡΠΈΠ·ΠΎΠ²) Π² ΡΠ°ΡΡΠΈ ΠΎΠ±Π΅ΡΠΏΠ΅ΡΠ΅Π½ΠΈΡ Π±Π΅Π·ΠΎΠΏΠ°ΡΠ½ΠΎΡΡΠΈ ΡΡΡΠ΄Π° (ΡΠ°Π±ΠΎΡΠ°ΡΡΠΈΡ
) ΠΏΡΠΈ
Π²Π΅Π΄Π΅Π½ΠΈΠΈ ΡΠ΅Ρ
Π½ΠΎΠ»ΠΎΠ³ΠΈΡΠ΅ΡΠΊΠΈΡ
ΠΏΡΠΎΡΠ΅ΡΡΠΎΠ² ΠΈ ΡΠΊΡΠΏΠ»ΡΠ°ΡΠ°ΡΠΈΠΈ ΠΎΠ±ΠΎΡΡΠ΄ΠΎΠ²Π°Π½ΠΈΡ.
ΠΠ»Ρ ΡΠΊΠ°Π·Π°Π½Π½ΡΡ
ΠΏΡΠ΅Π΄ΠΏΡΠΈΡΡΠΈΠΉ
ΠΈ ΡΠ΅Ρ
ΠΎΠ² ΡΠ°ΠΊΠΆΠ΅ ΠΎΠ±ΡΠ·Π°ΡΠ΅Π»ΡΠ½Ρ ΠΠ±ΡΠΈΠ΅ ΠΏΡΠ°Π²ΠΈΠ»Π° Π±Π΅Π·ΠΎΠΏΠ°ΡΠ½ΠΎΡΡΠΈ Π΄Π»Ρ
ΠΏΡΠ΅Π΄ΠΏΡΠΈΡΡΠΈΠΉ ΠΈ ΠΎΡΠ³Π°Π½ΠΈΠ·Π°ΡΠΈΠΉ ΠΌΠ΅ΡΠ°Π»Π»ΡΡΠ³ΠΈΡΠ΅ΡΠΊΠΎΠΉ ΠΏΡΠΎΠΌΡΡΠ»Π΅Π½Π½ΠΎΡΡΠΈ (ΡΡΠ².
ΠΠΎΡΠ³ΠΎΡΡΠ΅Ρ
Π½Π°Π΄Π·ΠΎΡΠΎΠΌ Π‘Π‘Π‘Π 13.05.87 (Ρ ΠΈΠ·ΠΌΠ΅Π½Π΅Π½ΠΈΡΠΌΠΈ ΠΈ Π΄ΠΎΠΏΠΎΠ»Π½Π΅Π½ΠΈΡΠΌΠΈ
N 1 ΠΎΡ
25.09.95), Π° Π΄Π»Ρ ΡΠ΅Ρ
ΠΎΠ² Ρ
ΠΎΠ»ΠΎΠ΄Π½ΠΎΠΉ ΠΈ Π³ΠΎΡΡΡΠ΅ΠΉ ΠΏΡΠΎΠΊΠ°ΡΠΊΠΈ, ΠΊΡΠΎΠΌΠ΅ ΡΠΎΠ³ΠΎ,
ΠΡΠ°Π²ΠΈΠ»Π° Π±Π΅Π·ΠΎΠΏΠ°ΡΠ½ΠΎΡΡΠΈ Π² ΠΏΡΠΎΠΊΠ°ΡΠ½ΠΎΠΌ ΠΏΡΠΎΠΈΠ·Π²ΠΎΠ΄ΡΡΠ²Π΅* (ΡΡΠ².
ΠΠΎΡΠ³ΠΎΡΡΠ΅Ρ
Π½Π°Π΄Π·ΠΎΡΠΎΠΌ Π‘Π‘Π‘Π 26.07.77 ΠΈ ΠΠΈΠ½ΡΠ΅ΡΠΌΠ΅ΡΠΎΠΌ Π‘Π‘Π‘Π 25.05.77).
________________
*
ΠΠ° ΡΠ΅ΡΡΠΈΡΠΎΡΠΈΠΈ Π ΠΎΡΡΠΈΠΉΡΠΊΠΎΠΉ Π€Π΅Π΄Π΅ΡΠ°ΡΠΈΠΈ Π΄ΠΎΠΊΡΠΌΠ΅Π½Ρ Π½Π΅ Π΄Π΅ΠΉΡΡΠ²ΡΠ΅Ρ. ΠΠ΅ΠΉΡΡΠ²ΡΠ΅Ρ
ΠΠ
11-519-02. — ΠΡΠΈΠΌΠ΅ΡΠ°Π½ΠΈΠ΅ ΠΈΠ·Π³ΠΎΡΠΎΠ²ΠΈΡΠ΅Π»Ρ Π±Π°Π·Ρ Π΄Π°Π½Π½ΡΡ
.
ΠΠ°ΡΡΠΎΡΡΠΈΠ΅ ΠΡΠ°Π²ΠΈΠ»Π°
ΠΎΠ±ΡΠ·Π°ΡΠ΅Π»ΡΠ½Ρ Π΄Π»Ρ Π²ΡΠΏΠΎΠ»Π½Π΅Π½ΠΈΡ Π΄ΠΎΠ»ΠΆΠ½ΠΎΡΡΠ½ΡΠΌΠΈ Π»ΠΈΡΠ°ΠΌΠΈ ΠΈ ΠΈΡΠΏΠΎΠ»Π½ΠΈΡΠ΅Π»ΡΠΌΠΈ
ΡΠ°Π±ΠΎΡ ΠΏΡΠ΅Π΄ΠΏΡΠΈΡΡΠΈΠΉ, ΠΎΡΠ³Π°Π½ΠΈΠ·Π°ΡΠΈΠΉ ΠΈ ΡΡΡΠ΅ΠΆΠ΄Π΅Π½ΠΈΠΉ (Π½Π΅Π·Π°Π²ΠΈΡΠΈΠΌΠΎ ΠΎΡ ΡΠΎΡΠΌ
ΡΠΎΠ±ΡΡΠ²Π΅Π½Π½ΠΎΡΡΠΈ), ΡΠ²ΡΠ·Π°Π½Π½ΡΠΌΠΈ Ρ ΠΏΡΠΎΠ΅ΠΊΡΠΈΡΠΎΠ²Π°Π½ΠΈΠ΅ΠΌ, ΡΡΡΠΎΠΈΡΠ΅Π»ΡΡΡΠ²ΠΎΠΌ ΠΈ
ΡΠΊΡΠΏΠ»ΡΠ°ΡΠ°ΡΠΈΠ΅ΠΉ ΠΏΡΠ΅Π΄ΠΏΡΠΈΡΡΠΈΠΉ, ΡΠ΅Ρ
ΠΎΠ² ΠΈ ΡΡΡΠ°Π½ΠΎΠ²ΠΎΠΊ ΠΏΠΎ ΠΏΡΠΎΠΈΠ·Π²ΠΎΠ΄ΡΡΠ²Ρ
ΠΌΠ΅ΡΠΈΠ·ΠΎΠ². ΠΠ° ΠΎΡΠ½ΠΎΠ²Π°Π½ΠΈΠΈ ΡΡΠΈΡ
ΠΡΠ°Π²ΠΈΠ» Π΄Π»Ρ ΡΠ°Π±ΠΎΡΠΈΡ
Π΄ΠΎΠ»ΠΆΠ½Ρ Π±ΡΡΡ
ΡΠ°Π·ΡΠ°Π±ΠΎΡΠ°Π½Ρ ΡΠΎΠΎΡΠ²Π΅ΡΡΡΠ²ΡΡΡΠΈΠ΅ ΠΈΠ½ΡΡΡΡΠΊΡΠΈΠΈ.
1.1. ΠΠΏΠ°ΡΠ½ΡΠΉ ΠΈ Π²ΡΠ΅Π΄Π½ΡΠ΅ ΠΏΡΠΎΠΈΠ·Π²ΠΎΠ΄ΡΡΠ²Π΅Π½Π½ΡΠ΅ ΡΠ°ΠΊΡΠΎΡΡ
1.1.1. ΠΡΠΈ ΡΠ°Π·ΡΠ°Π±ΠΎΡΠΊΠ΅
ΠΏΡΠΎΠ΅ΠΊΡΠ½ΠΎΠΉ Π΄ΠΎΠΊΡΠΌΠ΅Π½ΡΠ°ΡΠΈΠΈ Π½Π° Π²Π½ΠΎΠ²Ρ ΡΡΡΠΎΡΡΠΈΠ΅ΡΡ ΠΈ ΡΠ΅ΠΊΠΎΠ½ΡΡΡΡΠΈΡΡΠ΅ΠΌΡΠ΅
ΠΌΠ΅ΡΠΈΠ·Π½ΡΠ΅ ΠΏΡΠΎΠΈΠ·Π²ΠΎΠ΄ΡΡΠ²Π° Π΄ΠΎΠ»ΠΆΠ½Ρ ΡΡΠΈΡΡΠ²Π°ΡΡΡΡ Π²ΠΎΠ·ΠΌΠΎΠΆΠ½ΡΠ΅ ΠΎΠΏΠ°ΡΠ½ΡΠ΅ ΠΈ
Π²ΡΠ΅Π΄Π½ΡΠ΅ ΠΏΡΠΎΠΈΠ·Π²ΠΎΠ΄ΡΡΠ²Π΅Π½Π½ΡΠ΅ ΡΠ°ΠΊΡΠΎΡΡ (ΠΏΠΎ ΠΊΠ»Π°ΡΡΠΈΡΠΈΠΊΠ°ΡΠΈΠΈ ΠΠΠ‘Π’
12.0.003) ΠΈ ΠΏΡΠ΅Π΄ΡΡΠΌΠ°ΡΡΠΈΠ²Π°ΡΡΡΡ ΠΌΠ΅ΡΡ, ΠΈΡΠΊΠ»ΡΡΠ°ΡΡΠΈΠ΅ ΠΈΡ
Π²ΠΎΠ·Π΄Π΅ΠΉΡΡΠ²ΠΈΠ΅
Π½Π° ΠΏΠ΅ΡΡΠΎΠ½Π°Π». ΠΠ° Π΄Π΅ΠΉΡΡΠ²ΡΡΡΠ΅ΠΌ ΠΏΡΠΎΠΈΠ·Π²ΠΎΠ΄ΡΡΠ²Π΅ ΠΏΠ΅ΡΠ΅ΡΠ΅Π½Ρ ΡΠ°ΠΊΡΠΎΡΠΎΠ² Π΄ΠΎΠ»ΠΆΠ΅Π½
Π±ΡΡΡ ΡΡΠ²Π΅ΡΠΆΠ΄Π΅Π½ Π³Π»Π°Π²Π½ΡΠΌ ΠΈΠ½ΠΆΠ΅Π½Π΅ΡΠΎΠΌ (ΡΠ΅Ρ
Π½ΠΈΡΠ΅ΡΠΊΠΈΠΌ Π΄ΠΈΡΠ΅ΠΊΡΠΎΡΠΎΠΌ).
1.1.2. ΠΠΊΡΠΏΠ»ΡΠ°ΡΠ°ΡΠΈΠΎΠ½Π½ΡΠ΅
Π΄ΠΎΠΊΡΠΌΠ΅Π½ΡΡ Π² ΠΌΠ΅ΡΠΈΠ·Π½ΡΡ
ΠΏΡΠΎΠΈΠ·Π²ΠΎΠ΄ΡΡΠ²Π°Ρ
Π΄ΠΎΠ»ΠΆΠ½Ρ ΡΠΎΠ΄Π΅ΡΠΆΠ°ΡΡ ΡΡΡΠ°Π½ΠΎΠ²Π»Π΅Π½Π½ΡΠ΅
Π½ΠΎΡΠΌΠ°ΡΠΈΠ²Π°ΠΌΠΈ Π΄ΠΎΠΏΡΡΡΠΈΠΌΡΠ΅ ΠΏΠ°ΡΠ°ΠΌΠ΅ΡΡΡ (ΡΡΠΎΠ²Π½ΠΈ, ΠΏΠΎΠΊΠ°Π·Π°ΡΠ΅Π»ΠΈ) ΠΎΠΏΠ°ΡΠ½ΡΡ
ΠΈ
Π²ΡΠ΅Π΄Π½ΡΡ
ΡΠ°ΠΊΡΠΎΡΠΎΠ².
1.1.3. ΠΡΠΎΠΈΠ·Π²ΠΎΠ΄ΡΡΠ²Π΅Π½Π½ΡΠ΅
ΠΏΡΠΎΡΠ΅ΡΡΡ Π΄ΠΎΠ»ΠΆΠ½Ρ Π±ΡΡΡ ΠΎΡΠ³Π°Π½ΠΈΠ·ΠΎΠ²Π°Π½Ρ ΡΠ°ΠΊΠΈΠΌ ΠΎΠ±ΡΠ°Π·ΠΎΠΌ, ΡΡΠΎΠ±Ρ ΠΏΠ°ΡΠ°ΠΌΠ΅ΡΡΡ
ΠΎΠΏΠ°ΡΠ½ΡΡ
ΠΈ Π²ΡΠ΅Π΄Π½ΡΡ
ΠΏΡΠΎΠΈΠ·Π²ΠΎΠ΄ΡΡΠ²Π΅Π½Π½ΡΡ
ΡΠ°ΠΊΡΠΎΡΠΎΠ² Π½Π΅ ΠΏΡΠ΅Π²ΡΡΠ°Π»ΠΈ Π΄ΠΎΠΏΡΡΡΠΈΠΌΡΡ
ΠΏΡΠ΅Π΄Π΅Π»ΠΎΠ². Π ΡΠ»ΡΡΠ°Π΅ ΡΠ΅Ρ
Π½ΠΈΡΠ΅ΡΠΊΠΎΠΉ Π½Π΅Π²ΠΎΠ·ΠΌΠΎΠΆΠ½ΠΎΡΡΠΈ ΠΈΠ»ΠΈ Π½Π΅ΡΠ΅Π»Π΅ΡΠΎΠΎΠ±ΡΠ°Π·Π½ΠΎΡΡΠΈ
ΡΡΡΠ°Π½ΠΎΠ²Π»Π΅Π½ΠΈΡ ΠΈΠ»ΠΈ ΡΠΎΠ±Π»ΡΠ΄Π΅Π½ΠΈΡ Π΄ΠΎΠΏΡΡΡΠΈΠΌΡΡ
ΠΏΡΠ΅Π΄Π΅Π»ΠΎΠ² ΡΠ°ΠΊΠΈΡ
ΠΏΠ°ΡΠ°ΠΌΠ΅ΡΡΠΎΠ²
Π΄ΠΎΠ»ΠΆΠ½Ρ Π±ΡΡΡ ΡΠ°Π·ΡΠ°Π±ΠΎΡΠ°Π½Ρ ΠΌΠ΅ΡΡ ΠΏΠΎ ΠΈΡΠΊΠ»ΡΡΠ΅Π½ΠΈΡ Π½Π΅Π³Π°ΡΠΈΠ²Π½ΠΎΠ³ΠΎ Π²Π»ΠΈΡΠ½ΠΈΡ
ΠΎΠΏΠ°ΡΠ½ΡΡ
ΠΈ Π²ΡΠ΅Π΄Π½ΡΡ
ΡΠ°ΠΊΡΠΎΡΠΎΠ² Π½Π° ΡΠ΅Π»ΠΎΠ²Π΅ΠΊΠ°.
1.2. ΠΠΏΠ°ΡΠ½ΡΠ΅ Π²Π½Π΅ΡΠ½ΠΈΠ΅ Π²ΠΎΠ·Π΄Π΅ΠΉΡΡΠ²ΡΡΡΠΈΠ΅ ΡΠ°ΠΊΡΠΎΡΡ
1.2*. ΠΠ΄Π°Π½ΠΈΡ ΠΈ ΡΠΎΠΎΡΡΠΆΠ΅Π½ΠΈΡ
ΠΌΠ΅ΡΠΈΠ·Π½ΡΡ
ΠΏΡΠΎΠΈΠ·Π²ΠΎΠ΄ΡΡΠ² Π΄ΠΎΠ»ΠΆΠ½Ρ Π±ΡΡΡ ΠΎΠ±ΠΎΡΡΠ΄ΠΎΠ²Π°Π½Ρ ΠΌΠΎΠ»Π½ΠΈΠ΅Π·Π°ΡΠΈΡΠΎΠΉ ΠΈ
Π·Π°ΡΠΈΡΠΎΠΉ ΠΎΡ ΠΎΠΏΠ°ΡΠ½ΡΡ
ΡΠ°ΠΊΡΠΎΡΠΎΠ² Π΄ΡΡΠ³ΠΈΡ
ΠΏΡΠΈΡΠΎΠ΄Π½ΡΡ
ΡΠ²Π»Π΅Π½ΠΈΠΉ, ΡΡΡΠ°Π½ΠΎΠ²Π»Π΅Π½Π½ΡΡ
ΠΏΡΠΎΠ΅ΠΊΡΠ½ΠΎΠΉ Π΄ΠΎΠΊΡΠΌΠ΅Π½ΡΠ°ΡΠΈΠ΅ΠΉ, Π² ΡΠΎΠΎΡΠ²Π΅ΡΡΡΠ²ΠΈΠΈ Ρ ΡΡΠ΅Π±ΠΎΠ²Π°Π½ΠΈΡΠΌΠΈ ΡΡΡΠΎΠΈΡΠ΅Π»ΡΠ½ΡΡ
Π½ΠΎΡΠΌ ΠΈ ΠΏΡΠ°Π²ΠΈΠ».
__________________
* ΠΡΠΌΠ΅ΡΠ°ΡΠΈΡ ΡΠΎΠΎΡΠ²Π΅ΡΡΡΠ²ΡΠ΅Ρ ΠΎΡΠΈΠ³ΠΈΠ½Π°Π»Ρ. — ΠΡΠΈΠΌΠ΅ΡΠ°Π½ΠΈΠ΅ ΠΈΠ·Π³ΠΎΡΠΎΠ²ΠΈΡΠ΅Π»Ρ Π±Π°Π·Ρ Π΄Π°Π½Π½ΡΡ .
2. ΠΠΠ©ΠΠ Π’Π ΠΠΠΠΠΠΠΠ― ΠΠΠΠΠΠΠ‘ΠΠΠ‘Π’Π
ΠΠ° ΠΏΠΎΠ΄ΡΠ°Π·Π΄Π΅Π»Π΅Π½ΠΈΡ
ΠΏΡΠ΅Π΄ΠΏΡΠΈΡΡΠΈΠΉ ΠΌΠ΅ΡΠΈΠ·Π½ΡΡ
ΠΏΡΠΎΠΈΠ·Π²ΠΎΠ΄ΡΡΠ², ΠΈΡΠΏΠΎΠ»ΡΠ·ΡΡΡΠΈΡ
Π²Π·ΡΡΠ²ΠΎΠΎΠΏΠ°ΡΠ½ΡΠ΅ ΠΈ
Π²Π·ΡΡΠ²ΠΎΠΏΠΎΠΆΠ°ΡΠΎΠΎΠΏΠ°ΡΠ½ΡΠ΅ Ρ
ΠΈΠΌΠΈΡΠ΅ΡΠΊΠΈΠ΅ Π²Π΅ΡΠ΅ΡΡΠ²Π°, ΡΠ°ΡΠΏΡΠΎΡΡΡΠ°Π½ΡΡΡΡΡ
ΡΡΠ΅Π±ΠΎΠ²Π°Π½ΠΈΡ ΠΠ±ΡΠΈΡ
ΠΏΡΠ°Π²ΠΈΠ» Π²Π·ΡΡΠ²ΠΎΠ±Π΅Π·ΠΎΠΏΠ°ΡΠ½ΠΎΠΉ* Π΄Π»Ρ Π²Π·ΡΡΠ²ΠΎΠΏΠΎΠΆΠ°ΡΠΎΠΎΠΏΠ°ΡΠ½ΡΡ
Ρ
ΠΈΠΌΠΈΡΠ΅ΡΠΊΠΈΡ
, Π½Π΅ΡΡΠ΅Ρ
ΠΈΠΌΠΈΡΠ΅ΡΠΊΠΈΡ
ΠΈ Π½Π΅ΡΡΠ΅ΠΏΠ΅ΡΠ΅ΡΠ°Π±Π°ΡΡΠ²Π°ΡΡΠΈΡ
ΠΏΡΠΎΠΈΠ·Π²ΠΎΠ΄ΡΡΠ²**
(ΠΠΠΠ-88), ΡΡΠ²Π΅ΡΠΆΠ΄Π΅Π½Π½ΡΡ
ΠΠΎΡΠ³ΠΎΡΡΠ΅Ρ
Π½Π°Π΄Π·ΠΎΡΠΎΠΌ Π‘Π‘Π‘Π 06.09.88 Π³.
_________________
*
Π’Π΅ΠΊΡΡ Π΄ΠΎΠΊΡΠΌΠ΅Π½ΡΠ° ΡΠΎΠΎΡΠ²Π΅ΡΡΡΠ²ΡΠ΅Ρ ΠΎΡΠΈΠ³ΠΈΠ½Π°Π»Ρ;
** ΠΠ° ΡΠ΅ΡΡΠΈΡΠΎΡΠΈΠΈ
Π ΠΎΡΡΠΈΠΉΡΠΊΠΎΠΉ Π€Π΅Π΄Π΅ΡΠ°ΡΠΈΠΈ Π΄Π΅ΠΉΡΡΠ²ΡΡΡ Π€Π΅Π΄Π΅ΡΠ°Π»ΡΠ½ΡΠ΅
Π½ΠΎΡΠΌΡ ΠΈ ΠΏΡΠ°Π²ΠΈΠ»Π° Π² ΠΎΠ±Π»Π°ΡΡΠΈ ΠΏΡΠΎΠΌΡΡΠ»Π΅Π½Π½ΠΎΠΉ Π±Π΅Π·ΠΎΠΏΠ°ΡΠ½ΠΎΡΡΠΈ «ΠΠ±ΡΠΈΠ΅ ΠΏΡΠ°Π²ΠΈΠ»Π°
Π²Π·ΡΡΠ²ΠΎΠ±Π΅Π·ΠΎΠΏΠ°ΡΠ½ΠΎΡΡΠΈ Π΄Π»Ρ Π²Π·ΡΡΠ²ΠΎΠΏΠΎΠΆΠ°ΡΠΎΠΎΠΏΠ°ΡΠ½ΡΡ
Ρ
ΠΈΠΌΠΈΡΠ΅ΡΠΊΠΈΡ
,
Π½Π΅ΡΡΠ΅Ρ
ΠΈΠΌΠΈΡΠ΅ΡΠΊΠΈΡ
ΠΈ Π½Π΅ΡΡΠ΅ΠΏΠ΅ΡΠ΅ΡΠ°Π±Π°ΡΡΠ²Π°ΡΡΠΈΡ
ΠΏΡΠΎΠΈΠ·Π²ΠΎΠ΄ΡΡΠ²»,
ΡΡΠ²Π΅ΡΠΆΠ΄Π΅Π½Π½ΡΠ΅ ΠΡΠΈΠΊΠ°Π·ΠΎΠΌ
Π ΠΎΡΡΠ΅Ρ
Π½Π°Π΄Π·ΠΎΡΠ° ΠΎΡ 11.03.2013 N 96. — ΠΡΠΈΠΌΠ΅ΡΠ°Π½ΠΈΠ΅ ΠΈΠ·Π³ΠΎΡΠΎΠ²ΠΈΡΠ΅Π»Ρ
Π±Π°Π·Ρ Π΄Π°Π½Π½ΡΡ
.
ΠΡΠ΅Π΄Π΅Π»ΡΠ½ΠΎ Π΄ΠΎΠΏΡΡΡΠΈΠΌΡΠ΅
ΠΊΠΎΠ½ΡΠ΅Π½ΡΡΠ°ΡΠΈΠΈ Π²ΡΠ΅Π΄Π½ΡΡ
Π²Π΅ΡΠ΅ΡΡΠ² Π² Π²ΠΎΠ·Π΄ΡΡ
Π΅ ΡΠ°Π±ΠΎΡΠ΅ΠΉ Π·ΠΎΠ½Ρ ΠΈ ΠΎΠ±ΡΠΈΠ΅
ΡΡΠ΅Π±ΠΎΠ²Π°Π½ΠΈΡ Π±Π΅Π·ΠΎΠΏΠ°ΡΠ½ΠΎΡΡΠΈ ΠΎΠΏΡΠ΅Π΄Π΅Π»ΡΡΡΡΡ Π² ΡΠΎΠΎΡΠ²Π΅ΡΡΡΠ²ΠΈΠΈ Ρ ΠΠΠ‘Π’
12.1.005 ΠΈ ΠΠΠ‘Π’
12.1.007.
3. Π’Π ΠΠΠΠΠΠΠΠ― ΠΠ ΠΠΠΠΠΠΠ‘ΠΠΠ‘Π’Π ΠΠ ΠΠΠΠΠΠΠ‘Π’Π
3.1. ΠΡΠΎΠ²ΠΎΠ»ΠΎΠΊΠΈ ΠΈ ΠΊΠ°Π»ΠΈΠ±ΡΠΎΠ²Π°Π½Π½ΠΎΠ³ΠΎ ΠΌΠ΅ΡΠ°Π»Π»Π°
Π
ΠΎΠΏΠ°ΡΠ½ΡΠΌ ΠΈ Π²ΡΠ΅Π΄Π½ΡΠΌ ΠΏΡΠΎΠΈΠ·Π²ΠΎΠ΄ΡΡΠ²Π΅Π½Π½ΡΠΌ ΡΠ°ΠΊΡΠΎΡΠ°ΠΌ ΠΎΡΠ½ΠΎΡΡΡΡΡ:
ΠΏΠΎΠ²ΡΡΠ΅Π½Π½ΡΠ΅ ΡΠ΅ΠΌΠΏΠ΅ΡΠ°ΡΡΡΡ
ΠΏΠΎΠ²Π΅ΡΡ
Π½ΠΎΡΡΠ΅ΠΉ ΠΈ Π²ΠΎΠ·Π΄ΡΡ
Π° ΡΠ°Π±ΠΎΡΠ΅ΠΉ Π·ΠΎΠ½Ρ;
ΠΏΠΎΠ΄Π²ΠΈΠΆΠ½ΡΠ΅ ΡΠ°ΡΡΠΈ
ΠΏΡΠΎΠΈΠ·Π²ΠΎΠ΄ΡΡΠ²Π΅Π½Π½ΠΎΠ³ΠΎ ΠΎΠ±ΠΎΡΡΠ΄ΠΎΠ²Π°Π½ΠΈΡ;
ΠΏΠ΅ΡΠ΅Π΄Π²ΠΈΠ³Π°ΡΡΠΈΠ΅ΡΡ Π·Π°Π³ΠΎΡΠΎΠ²ΠΊΠΈ
ΠΈ ΠΈΠ·Π΄Π΅Π»ΠΈΡ;
Π΄Π²ΠΈΠΆΡΡΠΈΠ΅ΡΡ ΠΌΠ°ΡΠΈΠ½Ρ ΠΈ
ΠΌΠ΅Ρ
Π°Π½ΠΈΠ·ΠΌΡ;
ΠΏΠΎΠ²ΡΡΠ΅Π½Π½Π°Ρ Π·Π°ΠΏΡΠ»Π΅Π½Π½ΠΎΡΡΡ
Π²ΠΎΠ·Π΄ΡΡ
Π° ΡΠ°Π±ΠΎΡΠ΅ΠΉ Π·ΠΎΠ½Ρ;
ΠΏΠΎΠ²ΡΡΠ΅Π½Π½ΡΠΉ ΡΡΠΎΠ²Π΅Π½Ρ ΡΡΠΌΠ°
Π½Π° ΡΠ°Π±ΠΎΡΠ΅ΠΌ ΠΌΠ΅ΡΡΠ΅;
ΠΎΠΏΠ°ΡΠ½ΠΎΡΡΡ ΠΏΠΎΡΠ°ΠΆΠ΅Π½ΠΈΡ
ΡΠ»Π΅ΠΊΡΡΠΈΡΠ΅ΡΠΊΠΈΠΌ ΡΠΎΠΊΠΎΠΌ.
3.1.1. ΠΡΠΎΠΈΠ·Π²ΠΎΠ΄ΡΡΠ²ΠΎ ΠΏΡΠΎΠ²ΠΎΠ»ΠΎΠΊΠΈ ΠΌΠ΅ΡΠΎΠ΄ΠΎΠΌ Π²ΠΎΠ»ΠΎΡΠ΅Π½ΠΈΡ
3.1.1.1. ΠΠ»Ρ Π²ΠΎΠ»ΠΎΡΠΈΠ»ΡΠ½ΡΡ
ΡΡΠ°Π½ΠΎΠ² ΠΊΠ°ΠΆΠ΄ΡΠΉ Π±Π°ΡΠ°Π±Π°Π½ Ρ ΠΈΠ½Π΄ΠΈΠ²ΠΈΠ΄ΡΠ°Π»ΡΠ½ΡΠΌ ΠΏΡΠΈΠ²ΠΎΠ΄ΠΎΠΌ Π΄ΠΎΠ»ΠΆΠ΅Π½ ΠΈΠΌΠ΅ΡΡ
Π·Π°ΠΏΡΠ°Π²ΠΎΡΠ½ΡΡ ΡΠΊΠΎΡΠΎΡΡΡ Π½Π΅ Π±ΠΎΠ»Π΅Π΅ 30% ΠΌΠ°ΠΊΡΠΈΠΌΠ°Π»ΡΠ½ΠΎΠΉ ΡΠ°Π±ΠΎΡΠ΅ΠΉ ΡΠΊΠΎΡΠΎΡΡΠΈ Π΄Π»Ρ
Π΄Π°Π½Π½ΠΎΠ³ΠΎ ΡΠΈΠΏΠ° ΡΡΠ°Π½ΠΎΠ².
3.1.1.2. ΠΠΎΠ»ΠΎΡΠΈΠ»ΡΠ½ΡΠ΅
ΡΡΠ°Π½Ρ Π΄ΠΎΠ»ΠΆΠ½Ρ Π±ΡΡΡ ΠΎΠ±ΠΎΡΡΠ΄ΠΎΠ²Π°Π½Ρ ΠΏΡΠ»ΡΡΠ°ΠΌΠΈ ΡΠΏΡΠ°Π²Π»Π΅Π½ΠΈΡ.
ΠΠ»Ρ Π²ΠΎΠ»ΠΎΡΠ΅Π½ΠΈΡ ΡΠΎΠ½ΡΠ°ΠΉΡΠ΅ΠΉ ΠΈ
Π½Π°ΠΈΡΠΎΠ½ΡΠ°ΠΉΡΠ΅ΠΉ ΠΏΡΠΎΠ²ΠΎΠ»ΠΎΠΊΠΈ Π΄ΠΎΠΏΡΡΠΊΠ°Π΅ΡΡΡ ΡΠΊΡΠΏΠ»ΡΠ°ΡΠ°ΡΠΈΡ ΡΡΠ°Π½ΠΎΠ² Π±Π΅Π· ΠΏΡΠ»ΡΡΠΎΠ²
ΡΠΏΡΠ°Π²Π»Π΅Π½ΠΈΡ.
3.1.1.3. ΠΠ»Ρ Π°Π²Π°ΡΠΈΠΉΠ½ΠΎΠ³ΠΎ
Π²ΡΠΊΠ»ΡΡΠ΅Π½ΠΈΡ Π²ΠΎΠ»ΠΎΡΠΈΠ»ΡΠ½ΡΠ΅ ΡΡΠ°Π½Ρ Π΄ΠΎΠ»ΠΆΠ½Ρ ΠΎΠ±ΠΎΡΡΠ΄ΠΎΠ²Π°ΡΡΡΡ ΠΊΠ½ΠΎΠΏΠΊΠ°ΠΌΠΈ ΠΈΠ»ΠΈ
ΠΏΠ΅Π΄Π°Π»ΡΡ «ΠΠ»Π°Π²Π½ΡΠΉ ΡΡΠΎΠΏ». ΠΠ΄Π½Π° ΠΈΠ· ΠΊΠ½ΠΎΠΏΠΎΠΊ (ΠΏΠ΅Π΄Π°Π»Π΅ΠΉ) Π΄ΠΎΠ»ΠΆΠ½Π° Π½Π°Ρ
ΠΎΠ΄ΠΈΡΡΡΡ
Ρ ΡΠΈΡΡΠΎΠ³ΠΎ Π±Π°ΡΠ°Π±Π°Π½Π°, Π° Π΄ΡΡΠ³Π°Ρ — Ρ ΡΠ°Π·ΠΌΠΎΡΠΎΡΠ½ΠΎΠ³ΠΎ ΡΡΡΡΠΎΠΉΡΡΠ²Π°.
3.1.1.4. Π ΠΏΡΠΎΡΠ΅ΡΡΠ΅
Π²ΠΎΠ»ΠΎΡΠ΅Π½ΠΈΡ Π΄ΠΎΠ»ΠΆΠ½Π° ΠΏΡΠΈΠΌΠ΅Π½ΡΡΡΡΡ ΡΠΌΠ°Π·ΠΊΠ°, Π½Π΅ ΠΎΠΊΠ°Π·ΡΠ²Π°ΡΡΠ°Ρ Π²ΡΠ΅Π΄Π½ΠΎΠ³ΠΎ
Π²ΠΎΠ·Π΄Π΅ΠΉΡΡΠ²ΠΈΡ Π½Π° ΠΎΠ±ΡΠ»ΡΠΆΠΈΠ²Π°ΡΡΠΈΠΉ ΠΏΠ΅ΡΡΠΎΠ½Π°Π».
3.1.1.5. Π‘ΡΠ°Π½Ρ Π΄ΠΎΠ»ΠΆΠ½Ρ
ΠΈΠΌΠ΅ΡΡ Π²ΠΎΠ·Π΄ΡΡΠ½ΠΎΠ΅ ΠΈΠ»ΠΈ Π²ΠΎΠ΄ΡΠ½ΠΎΠ΅ ΠΎΡ
Π»Π°ΠΆΠ΄Π΅Π½ΠΈΠ΅ Π±Π°ΡΠ°Π±Π°Π½ΠΎΠ².
3.1.1.6. ΠΠ°ΡΠ°Π±Π°Π½Ρ
Π²ΠΎΠ»ΠΎΡΠΈΠ»ΡΠ½ΡΡ
ΡΡΠ°Π½ΠΎΠ² Π΄ΠΎΠ»ΠΆΠ½Ρ ΠΈΠΌΠ΅ΡΡ ΠΎΠ³ΡΠ°ΠΆΠ΄Π΅Π½ΠΈΠ΅, ΠΏΡΠ΅Π΄ΠΎΡΠ²ΡΠ°ΡΠ°ΡΡΠ΅Π΅ Π²ΡΠ±ΡΠΎΡ
ΠΏΡΠΎΠ²ΠΎΠ»ΠΎΠΊΠΈ ΠΏΡΠΈ ΠΎΠ±ΡΡΠ²Π΅ ΠΈΠ»ΠΈ ΠΏΡΠΈ ΠΏΠ΅ΡΠ΅ΠΏΠΎΠ»Π½Π΅Π½ΠΈΠΈ Π±Π°ΡΠ°Π±Π°Π½Π°, Π° ΡΠ°ΠΊΠΆΠ΅ Π²ΡΠ±ΡΠΎΡ
ΠΊΠ»Π΅ΡΠ΅ΠΉ ΠΏΡΠΈ ΠΎΠ±ΡΡΠ²Π΅ ΠΏΡΠΎΠ²ΠΎΠ»ΠΎΠΊΠΈ Π² ΠΌΠΎΠΌΠ΅Π½Ρ Π·Π°ΠΏΡΠ°Π²ΠΊΠΈ Π±Π°ΡΠ°Π±Π°Π½Π°. ΠΠ³ΡΠ°ΠΆΠ΄Π΅Π½ΠΈΠ΅
Π±Π°ΡΠ°Π±Π°Π½ΠΎΠ² Π΄ΠΎΠ»ΠΆΠ½ΠΎ Π±ΡΡΡ ΡΠ±Π»ΠΎΠΊΠΈΡΠΎΠ²Π°Π½ΠΎ Ρ ΠΏΡΡΠΊΠΎΠΌ ΡΡΠ°Π½Π° Π½Π° ΡΠ°Π±ΠΎΡΡΡ
ΡΠΊΠΎΡΠΎΡΡΡ ΠΈ ΠΎΠ±Π΅ΡΠΏΠ΅ΡΠΈΠ²Π°ΡΡ ΡΠ°Π±ΠΎΡΡ ΡΡΠ°Π½Π° Π½Π° ΡΠ°Π±ΠΎΡΠ΅ΠΉ ΡΠΊΠΎΡΠΎΡΡΠΈ ΡΠΎΠ»ΡΠΊΠΎ ΠΏΡΠΈ
Π·Π°ΠΊΡΡΡΠΎΠΌ ΠΎΠ³ΡΠ°ΠΆΠ΄Π΅Π½ΠΈΠΈ Π²ΡΠ΅Ρ
Π±Π°ΡΠ°Π±Π°Π½ΠΎΠ². ΠΠ΅ΡΠ²ΡΠΉ ΠΎΠ±ΠΆΠΈΠΌΠ½ΠΎΠΉ Π±Π°ΡΠ°Π±Π°Π½
Π²ΠΎΠ»ΠΎΡΠΈΠ»ΡΠ½ΡΡ
ΡΡΠ°Π½ΠΎΠ² Π΄ΠΎΠ»ΠΆΠ΅Π½ Π±ΡΡΡ ΠΎΠ±ΠΎΡΡΠ΄ΠΎΠ²Π°Π½ ΡΠ»Π΅ΠΊΡΡΠΎΡΠΎΡΠΌΠΎΠ·Π½ΡΠΌ
ΡΡΡΡΠΎΠΉΡΡΠ²ΠΎΠΌ, ΠΎΠ±Π΅ΡΠΏΠ΅ΡΠΈΠ²Π°ΡΡΠΈΠΌ Π°Π²Π°ΡΠΈΠΉΠ½ΡΡ ΠΎΡΡΠ°Π½ΠΎΠ²ΠΊΡ Π΅Π³ΠΎ Π½Π΅ Π±ΠΎΠ»Π΅Π΅ ΡΠ΅ΠΌ
ΡΠ΅ΡΠ΅Π· ΠΎΠ΄ΠΈΠ½ ΠΎΠ±ΠΎΡΠΎΡ ΠΏΠΎΡΠ»Π΅ Π²ΡΠΊΠ»ΡΡΠ΅Π½ΠΈΡ Π±Π°ΡΠ°Π±Π°Π½Π°. ΠΠ»Π΅ΠΊΡΡΠΎΡΠΎΡΠΌΠΎΠ·Π½ΡΠΌ
ΡΡΡΡΠΎΠΉΡΡΠ²ΠΎΠΌ Π² ΡΠ΅Π»ΡΡ
Π±ΡΡΡΡΠ΅ΠΉΡΠ΅ΠΉ ΠΎΡΡΠ°Π½ΠΎΠ²ΠΊΠΈ ΡΡΠ°Π½Π° Π² Π°Π²Π°ΡΠΈΠΉΠ½ΡΡ
ΡΠ»ΡΡΠ°ΡΡ
Π΄ΠΎΠ»ΠΆΠ½Ρ Π±ΡΡΡ ΠΎΠ±ΠΎΡΡΠ΄ΠΎΠ²Π°Π½Ρ Π²ΡΠ΅ Π±Π°ΡΠ°Π±Π°Π½Ρ Π²ΠΎΠ»ΠΎΡΠΈΠ»ΡΠ½ΡΡ
ΠΌΠ°ΡΠΈΠ½.
3.1.1.7 ΠΠ»Ρ Π°Π²Π°ΡΠΈΠΉΠ½ΠΎΠ³ΠΎ
Π²ΡΠΊΠ»ΡΡΠ΅Π½ΠΈΡ Π±Π°ΡΠ°Π±Π°Π½ΠΎΠ², Π½Π΅ ΠΎΠ±ΠΎΡΡΠ΄ΠΎΠ²Π°Π½Π½ΡΡ
Π·Π°ΡΠΈΡΠ½ΡΠΌΠΈ ΠΎΠ³ΡΠ°ΠΆΠ΄Π΅Π½ΠΈΡΠΌΠΈ,
Π΄ΠΎΠ»ΠΆΠ½Ρ Π±ΡΡΡ ΡΡΡΡΠΎΠ΅Π½Ρ Π±Π°ΡΡΠ΅ΡΠ½ΡΠ΅ Π²ΡΠΊΠ»ΡΡΠ°ΡΠ΅Π»ΠΈ, Π²ΡΠΏΠΎΠ»Π½Π΅Π½Π½ΡΠ΅ Π² Π²ΠΈΠ΄Π΅
ΡΡΠ°Π½Π³, ΡΠ°ΡΠΏΠΎΠ»ΠΎΠΆΠ΅Π½Π½ΡΡ
ΡΠΎ ΡΡΠΎΡΠΎΠ½Ρ ΡΠ°Π±ΠΎΡΠ΅Π³ΠΎ ΠΌΠ΅ΡΡΠ° Π²ΠΎΠ»ΠΎΡΠΈΠ»ΡΡΠΈΠΊΠ° Π½Π°
Π²ΡΡΠΎΡΠ΅ 0,7-0,8 ΠΌ.
ΠΠ°ΡΡΠ΅ΡΠ½ΡΠ΅ Π²ΡΠΊΠ»ΡΡΠ°ΡΠ΅Π»ΠΈ
Π΄ΠΎΠ»ΠΆΠ½Ρ Π±ΡΡΡ ΡΠ±Π»ΠΎΠΊΠΈΡΠΎΠ²Π°Π½Ρ Ρ ΡΠΎΡΠΌΠΎΠ·Π½ΡΠΌ ΡΡΡΡΠΎΠΉΡΡΠ²ΠΎΠΌ, ΠΎΠ±Π΅ΡΠΏΠ΅ΡΠΈΠ²Π°ΡΡΠΈΠΌ
Π²ΡΠΊΠ»ΡΡΠ΅Π½ΠΈΠ΅ Π±Π°ΡΠ°Π±Π°Π½ΠΎΠ² ΠΏΡΠΈ Π΄Π²ΠΈΠΆΠ΅Π½ΠΈΠΈ Π±Π°ΡΡΠ΅ΡΠ° Π² ΡΡΠΎΡΠΎΠ½Ρ ΡΡΠ°Π½Π°.
Π‘ΡΠ°Π½Ρ ΡΠΎΠ½ΡΠ°ΠΉΡΠ΅Π³ΠΎ ΠΈ
Π½Π°ΠΈΡΠΎΠ½ΡΠ°ΠΉΡΠ΅Π³ΠΎ Π²ΠΎΠ»ΠΎΡΠ΅Π½ΠΈΡ ΠΈ ΡΡΠ°Π½Ρ «ΠΡΡΠ½Π°» (ΠΊΡΠΎΠΌΠ΅ ΡΡΠ°Π½ΠΎΠ² ΠΌΠ°Π³Π°Π·ΠΈΠ½Π½ΠΎΠ³ΠΎ
ΡΠΈΠΏΠ°) Π±Π°ΡΡΠ΅ΡΠ½ΡΠΌΠΈ Π²ΡΠΊΠ»ΡΡΠ°ΡΠ΅Π»ΡΠΌΠΈ ΠΌΠΎΠ³ΡΡ Π½Π΅ ΠΎΠ±ΠΎΡΡΠ΄ΠΎΠ²Π°ΡΡΡΡ.
3.1.1.8. ΠΠ°ΡΠ°Π±Π°Π½Ρ
Π²ΠΎΠ»ΠΎΡΠΈΠ»ΡΠ½ΠΎΠ³ΠΎ ΡΡΠ°Π½Π° Π΄ΠΎΠ»ΠΆΠ½Ρ Π±ΡΡΡ ΠΎΠ±ΠΎΡΡΠ΄ΠΎΠ²Π°Π½Ρ Π°Π²ΡΠΎΠΌΠ°ΡΠΈΡΠ΅ΡΠΊΠΈΠΌ
ΡΡΡΡΠΎΠΉΡΡΠ²ΠΎΠΌ Π΄Π»Ρ ΠΎΡΡΠ°Π½ΠΎΠ²ΠΊΠΈ ΡΡΠ°Π½Π° ΠΏΡΠΈ ΠΎΠ±ΡΡΠ²Π΅ ΠΏΡΠΎΠ²ΠΎΠ»ΠΎΠΊΠΈ ΠΈΠ»ΠΈ Π²ΡΡ
ΠΎΠ΄Π΅ Π΅Π΅
ΠΊΠΎΠ½ΡΠ° ΠΈΠ· Π²ΠΎΠ»ΠΎΠΊΠΈ.
3.1.1.9. Π Π°Π±ΠΎΡΠ° Π½Π°
Π²ΠΎΠ»ΠΎΡΠΈΠ»ΡΠ½ΡΡ
Π±Π°ΡΠ°Π±Π°Π½Π°Ρ
Ρ Π½Π΅ΠΎΡΡΠ»ΠΈΡΠΎΠ²Π°Π½Π½ΠΎΠΉ ΠΈΠ»ΠΈ ΠΈΠ·Π½ΠΎΡΠ΅Π½Π½ΠΎΠΉ Π³Π°Π»ΡΠ΅Π»ΡΡ
Π·Π°ΠΏΡΠ΅ΡΠ°Π΅ΡΡΡ.
3.1.1.10. ΠΠ»Ρ ΡΠ²Π΅Π»ΠΈΡΠ΅Π½ΠΈΡ
Π΅ΠΌΠΊΠΎΡΡΠΈ Π±Π°ΡΠ°Π±Π°Π½ΠΎΠ² ΠΎΠ΄Π½ΠΎΠΊΡΠ°ΡΠ½ΡΡ
ΡΡΠ°Π½ΠΎΠ² ΠΈ ΡΠΈΡΡΠΎΠ³ΠΎ Π±Π°ΡΠ°Π±Π°Π½Π°
ΠΌΠ½ΠΎΠ³ΠΎΠΊΡΠ°ΡΠ½ΡΡ
ΡΡΠ°Π½ΠΎΠ², ΡΡΡΠ°Π½ΠΎΠ²Π»Π΅Π½Π½ΡΡ
Π΄ΠΎ Π²Π²Π΅Π΄Π΅Π½ΠΈΡ Π½Π°ΡΡΠΎΡΡΠΈΡ
ΠΡΠ°Π²ΠΈΠ»,
ΡΠ°Π·ΡΠ΅ΡΠ°Π΅ΡΡΡ Π½Π°ΡΠ°ΡΠΈΠ²Π°Π½ΠΈΠ΅ Π±Π°ΡΠ°Π±Π°Π½ΠΎΠ² Ρ ΠΎΠ³ΡΠ°Π½ΠΈΡΠΈΡΠ΅Π»ΡΠΌΠΈ ΠΏΡΠΎΡΠΈΠ² ΡΠ±ΡΠΎΡΠ°
Π²ΠΈΡΠΊΠΎΠ² ΠΏΡΠΎΠ²ΠΎΠ»ΠΎΠΊΠΈ. ΠΡΠ΅ΠΏΠ»Π΅Π½ΠΈΠ΅ ΡΠ΄Π»ΠΈΠ½ΠΈΡΠ΅Π»Π΅ΠΉ Π΄ΠΎΠ»ΠΆΠ½ΠΎ Π³Π°ΡΠ°Π½ΡΠΈΡΠΎΠ²Π°ΡΡ ΠΎΡ
Π²ΡΠ»Π΅ΡΠ° ΠΈΡ
Π²ΠΎ Π²ΡΠ΅ΠΌΡ Π²ΡΠ°ΡΠ΅Π½ΠΈΡ Π±Π°ΡΠ°Π±Π°Π½Π°. ΠΠΌΠΊΠΎΡΡΡ ΠΏΡΠΈΠ΅ΠΌΠ½ΠΎΠ³ΠΎ ΡΠΈΡΡΠΎΠ²ΠΎΠ³ΠΎ
Π±Π°ΡΠ°Π±Π°Π½Π° Π½Π΅ Π΄ΠΎΠ»ΠΆΠ½Π° ΠΏΡΠ΅Π²ΡΡΠ°ΡΡ Π²Π΅Π»ΠΈΡΠΈΠ½Ρ, ΡΡΡΠ°Π½ΠΎΠ²Π»Π΅Π½Π½ΠΎΠΉ Π·Π°Π²ΠΎΠ΄ΡΠΊΠΎΠΉ
Π΄ΠΎΠΊΡΠΌΠ΅Π½ΡΠ°ΡΠΈΠ΅ΠΉ.
3.1.1.11. ΠΡΠ»ΡΠ½ΠΈΡΡ Π΄ΠΎΠ»ΠΆΠ½Ρ
ΡΠ°ΡΠΏΠΎΠ»Π°Π³Π°ΡΡΡΡ Π½Π° ΡΠ°Π±ΠΎΡΠ΅ΠΌ ΡΡΠΎΠ»Π΅ Π½Π° ΡΠ°ΠΊΠΎΠΌ ΡΠ°ΡΡΡΠΎΡΠ½ΠΈΠΈ ΠΎΡ Π±Π°ΡΠ°Π±Π°Π½Π°,
ΡΡΠΎΠ±Ρ ΠΈΡΠΊΠ»ΡΡΠΈΡΡ Π²ΠΎΠ·ΠΌΠΎΠΆΠ½ΠΎΡΡΡ Π·Π°ΡΠ΅ΠΌΠ»Π΅Π½ΠΈΡ ΠΊΠ»Π΅ΡΠ΅ΠΉ ΠΌΠ΅ΠΆΠ΄Ρ Π±Π°ΡΠ°Π±Π°Π½ΠΎΠΌ ΠΈ
ΠΌΡΠ»ΡΠ½ΠΈΡΠ΅ΠΉ ΠΏΡΠΈ Π·Π°ΠΏΡΠ°Π²ΠΊΠ΅ ΠΏΡΠΎΠ²ΠΎΠ»ΠΎΠΊΠΈ Π½Π° Π±Π°ΡΠ°Π±Π°Π½.
ΠΡΠ΅ΠΏΠ»Π΅Π½ΠΈΠ΅ ΠΌΡΠ»ΡΠ½ΠΈΡ Π΄ΠΎΠ»ΠΆΠ½ΠΎ
Π±ΡΡΡ ΡΠ°ΡΡΡΠΈΡΠ°Π½ΠΎ Π½Π° ΡΠ΅ΡΡΡΠ΅Ρ
ΠΊΡΠ°ΡΠ½ΡΠΉ Π·Π°ΠΏΠ°Ρ ΠΏΡΠΎΡΠ½ΠΎΡΡΠΈ Ρ ΡΡΠ΅ΡΠΎΠΌ
ΠΌΠ°ΠΊΡΠΈΠΌΠ°Π»ΡΠ½ΠΎΠ³ΠΎ ΡΡΠΈΠ»ΠΈΡ Π΄Π»Ρ ΡΠ°Π·ΡΡΠ²Π° ΠΏΡΠΎΠ²ΠΎΠ»ΠΎΠΊΠΈ.
3.1.1.12. ΠΠΎΠ»ΠΎΠΆΠ΅Π½ΠΈΠ΅
Π½Π°ΠΏΡΠ°Π²Π»ΡΡΡΠΈΡ
ΡΠΎΠ»ΠΈΠΊΠΎΠ² ΠΌΡΠ»ΡΠ½ΠΈΡΡ Π΄ΠΎΠ»ΠΆΠ½ΠΎ ΠΎΠ±Π΅ΡΠΏΠ΅ΡΠΈΠ²Π°ΡΡ ΠΏΡΠ°Π²ΠΈΠ»ΡΠ½ΠΎΡΡΡ
Π½Π°Π±Π΅Π³Π°Π½ΠΈΡ ΠΏΡΠΎΠ²ΠΎΠ»ΠΎΠΊΠΈ Π½Π° Π±Π°ΡΠ°Π±Π°Π½.
3.1.1.13. ΠΠ° ΡΡΠ°Π½Π°Ρ
, Π½Π΅
ΠΎΠ±ΠΎΡΡΠ΄ΠΎΠ²Π°Π½Π½ΡΡ
Π·Π°ΡΠΈΡΠ½ΡΠΌΠΈ ΠΎΠ³ΡΠ°ΠΆΠ΄Π΅Π½ΠΈΡΠΌΠΈ Π±Π°ΡΠ°Π±Π°Π½ΠΎΠ², ΠΏΡΠΎΠ²ΠΎΠ»ΠΎΠΊΠ°,
ΠΏΠ΅ΡΠ΅Ρ
ΠΎΠ΄ΡΡΠ°Ρ Π² ΠΏΡΠΎΡΠ΅ΡΡΠ΅ Π²ΠΎΠ»ΠΎΡΠ΅Π½ΠΈΡ Ρ Π±Π°ΡΠ°Π±Π°Π½Π° Π½Π° Π±Π°ΡΠ°Π±Π°Π½, Π΄ΠΎΠ»ΠΆΠ½Π° Π±ΡΡΡ
Π·Π°ΠΊΠ»ΡΡΠ΅Π½Π° Π² ΡΠΏΠ΅ΡΠΈΠ°Π»ΡΠ½ΡΠ΅ Π·Π°ΡΠΈΡΠ½ΡΠ΅ ΡΡΡΠ±Ρ.
3.1.1.14. ΠΠ΅ΠΏΠΎΠ΄Π²ΠΈΠΆΠ½ΡΠ΅
ΡΠ°Π·ΠΌΠΎΡΠΎΡΠ½ΡΠ΅ ΡΡΡΡΠΎΠΉΡΡΠ²Π° Π΄ΠΎΠ»ΠΆΠ½Ρ Π±ΡΡΡ Π½Π°Π΄Π΅ΠΆΠ½ΠΎ Π·Π°ΠΊΡΠ΅ΠΏΠ»Π΅Π½Ρ ΠΈ ΡΠ½Π°Π±ΠΆΠ΅Π½Ρ
ΠΏΡΠΎΠ²ΠΎΠ΄ΠΊΠ°ΠΌΠΈ ΠΈΠ»ΠΈ Π½Π°ΠΏΡΠ°Π²Π»ΡΡΡΠΈΠΌΠΈ Π΄Π»Ρ ΠΏΡΠ°Π²ΠΈΠ»ΡΠ½ΠΎΠ³ΠΎ ΡΠ±Π΅Π³Π°Π½ΠΈΡ Π²ΠΈΡΠΊΠΎΠ²
ΠΏΡΠΎΠ²ΠΎΠ»ΠΎΠΊΠΈ.
3.1.1.15. ΠΡΠ°ΡΠ°ΡΡΠΈΠ΅ΡΡ
ΡΠΈΠ³ΡΡΠΊΠΈ, ΠΏΡΠΈΠΌΠ΅Π½ΡΠ΅ΠΌΡΠ΅ Π² ΠΊΠ°ΡΠ΅ΡΡΠ²Π΅ ΡΠ°Π·ΠΌΠΎΡΠΎΡΠ½ΠΎΠ³ΠΎ ΡΡΡΡΠΎΠΉΡΡΠ²Π°, ΠΌΠΎΠ³ΡΡ
ΠΈΡΠΏΠΎΠ»ΡΠ·ΠΎΠ²Π°ΡΡΡΡ ΡΠΎΠ»ΡΠΊΠΎ ΠΏΡΠΈ ΡΡΠ»ΠΎΠ²ΠΈΠΈ, Π΅ΡΠ»ΠΈ Π»ΠΈΠ½Π΅ΠΉΠ½Π°Ρ ΡΠΊΠΎΡΠΎΡΡΡ ΡΡ
ΠΎΠ΄Π°
Π²ΠΈΡΠΊΠΎΠ² Π½Π΅ ΠΏΡΠ΅Π²ΡΡΠ°Π΅Ρ 150 ΠΌ/ΠΌΠΈΠ½.
3.1.1.16. Π‘ΡΠ°Π½Ρ Ρ
Π²ΡΠ°ΡΠ°ΡΡΠΈΠΌΠΈΡΡ ΡΠΈΠ³ΡΡΠΊΠ°ΠΌΠΈ Π΄ΠΎΠ»ΠΆΠ½Ρ Π±ΡΡΡ ΡΠ½Π°Π±ΠΆΠ΅Π½Ρ ΡΠ»Π΅Π΄ΡΡΡΠΈΠΌΠΈ
ΡΡΡΡΠΎΠΉΡΡΠ²Π°ΠΌΠΈ:
ΠΏΡΠΈΡΠΏΠΎΡΠΎΠ±Π»Π΅Π½ΠΈΠ΅ΠΌ Π΄Π»Ρ
Π°Π²ΡΠΎΠΌΠ°ΡΠΈΡΠ΅ΡΠΊΠΎΠΉ ΠΎΡΡΠ°Π½ΠΎΠ²ΠΊΠΈ ΡΡΠ°Π½Π° Ρ ΡΠ΅Π»ΡΡ ΠΏΡΠ΅Π΄ΡΠΏΡΠ΅ΠΆΠ΄Π΅Π½ΠΈΡ ΠΎΠ±ΡΡΠ²Π°
ΠΏΡΠΎΠ²ΠΎΠ»ΠΎΠΊΠΈ ΠΏΡΠΈ Π΅Π΅ Π·Π°ΠΏΡΡΡΠ²Π°Π½ΠΈΠΈ Π½Π° ΡΠΈΠ³ΡΡΠΊΠ΅;
ΡΠΎΡΠΌΠΎΠ·Π½ΡΠΌ ΡΡΡΡΠΎΠΉΡΡΠ²ΠΎΠΌ Π΄Π»Ρ
ΠΏΡΠ΅Π΄ΠΎΡΠ²ΡΠ°ΡΠ΅Π½ΠΈΡ ΠΎΠ±ΡΠ°Π·ΠΎΠ²Π°Π½ΠΈΡ ΠΏΠ΅ΡΠ΅Π»Ρ ΠΏΡΠΈ Π²ΡΠ°ΡΠ΅Π½ΠΈΠΈ ΡΠΈΠ³ΡΡΠΊΠΈ; ΡΠΎΡΠΌΠΎΠ·Π½ΠΎΠ΅
ΡΡΡΡΠΎΠΉΡΡΠ²ΠΎ ΠΌΠΎΠΆΠ΅Ρ Π½Π΅ ΡΡΡΠ°Π½Π°Π²Π»ΠΈΠ²Π°ΡΡΡΡ Π½Π° ΡΠΈΠ³ΡΡΠΊΠ°Ρ
, ΠΏΡΠΈΠΌΠ΅Π½ΡΠ΅ΠΌΡΡ
Π΄Π»Ρ
Π²ΠΎΠ»ΠΎΡΠ΅Π½ΠΈΡ ΠΏΡΠΎΠ²ΠΎΠ»ΠΎΠΊΠΈ Π΄ΠΈΠ°ΠΌΠ΅ΡΡΠΎΠΌ Π±ΠΎΠ»Π΅Π΅ 6,0 ΠΌΠΌ;
ΠΏΡΠΈΡΠΏΠΎΡΠΎΠ±Π»Π΅Π½ΠΈΠ΅ΠΌ,
ΠΈΡΠΊΠ»ΡΡΠ°ΡΡΠΈΠΌ Π²ΠΎΠ·ΠΌΠΎΠΆΠ½ΠΎΡΡΡ ΡΠ±ΡΠ°ΡΡΠ²Π°Π½ΠΈΡ Π²ΠΈΡΠΊΠΎΠ² ΡΠ΅ΡΠ΅Π· Π²Π΅ΡΡ
ΡΠΈΠ³ΡΡΠΊΠΈ.
3.1.1.17. ΠΡΠΈ Π²ΠΎΠ»ΠΎΡΠ΅Π½ΠΈΠΈ
ΠΏΡΠΎΠ²ΠΎΠ»ΠΎΠΊΠΈ ΡΠΎ ΡΠΊΠΎΡΠΎΡΡΡΡ Π²ΡΠ°ΡΠ΅Π½ΠΈΡ ΡΠ°Π·ΠΌΠ°ΡΡΠ²Π°ΡΡΠ΅Π³ΠΎ ΡΡΡΡΠΎΠΉΡΡΠ²Π° Π±ΠΎΠ»Π΅Π΅ 80
ΠΌ/ΠΌΠΈΠ½, Π° ΡΠ°ΠΊΠΆΠ΅ ΠΏΡΠΈ ΡΠ°Π±ΠΎΡΠ΅ Ρ «ΡΡΠΆΠ΅Π»ΠΎΠ²Π΅ΡΠ½ΡΠΌΠΈ» ΠΌΠΎΡΠΊΠ°ΠΌΠΈ Π΄ΠΎΠ»ΠΆΠ½Ρ
ΠΏΡΠΈΠΌΠ΅Π½ΡΡΡΡΡ ΡΠ°Π·ΠΌΠΎΡΠΎΡΠ½ΡΠ΅ ΡΡΡΡΠΎΠΉΡΡΠ²Π° Π½Π΅ΠΏΠΎΠ΄Π²ΠΈΠΆΠ½ΠΎΠ³ΠΎ ΡΠΈΠΏΠ° ΠΈΠ»ΠΈ ΡΠ°Π·ΠΌΠΎΡΠΊΠ°
Π΄ΠΎΠ»ΠΆΠ½Π° ΠΏΡΠΎΠΈΠ·Π²ΠΎΠ΄ΠΈΡΡΡΡ Ρ ΠΊΠ°ΡΡΡΠ΅ΠΊ.
3.1.1.18. ΠΠ΅ΠΆΠ΄Ρ
ΡΠ°Π·ΠΌΠΎΡΠΎΡΠ½ΡΠΌ ΡΡΡΡΠΎΠΉΡΡΠ²ΠΎΠΌ Π½Π΅ΠΏΠΎΠ΄Π²ΠΈΠΆΠ½ΠΎΠ³ΠΎ ΡΠΈΠΏΠ° ΠΈ ΠΌΡΠ»ΡΠ½ΠΈΡΠ΅ΠΉ ΠΏΠ΅ΡΠ²ΠΎΠ³ΠΎ
Π±Π°ΡΠ°Π±Π°Π½Π° Π΄ΠΎΠ»ΠΆΠ½ΠΎ Π½Π°Ρ
ΠΎΠ΄ΠΈΡΡΡΡ Π½Π°ΠΏΠΎΠ»ΡΠ½ΠΎΠ΅ ΠΏΠ΅ΡΠ»Π΅ΡΠ»Π°Π²Π»ΠΈΠ²Π°ΡΡΠ΅Π΅ ΡΡΡΡΠΎΠΉΡΡΠ²ΠΎ,
ΠΏΡΠ΅Π΄Π½Π°Π·Π½Π°ΡΠ΅Π½Π½ΠΎΠ΅ Π΄Π»Ρ Π°Π²ΡΠΎΠΌΠ°ΡΠΈΡΠ΅ΡΠΊΠΎΠΉ ΠΎΡΡΠ°Π½ΠΎΠ²ΠΊΠΈ Π±Π°ΡΠ°Π±Π°Π½Π° ΠΈΠ»ΠΈ ΡΡΠ°Π½Π° Π²
ΡΠ»ΡΡΠ°Π΅ ΠΎΠ±ΡΠ°Π·ΠΎΠ²Π°Π½ΠΈΡ ΠΏΠ΅ΡΠ»ΠΈ ΠΈΠ»ΠΈ Π·Π°ΠΏΡΡΡΠ²Π°Π½ΠΈΡ Π²ΠΈΡΠΊΠΎΠ² ΠΏΡΠΎΠ²ΠΎΠ»ΠΎΠΊΠΈ. ΠΠ»Ρ
ΡΡΠ°Π½ΠΎΠ² Ρ Π΄ΠΈΠ°ΠΌΠ΅ΡΡΠΎΠΌ Π±Π°ΡΠ°Π±Π°Π½Π° 550 ΠΌΠΌ ΠΈ Π±ΠΎΠ»Π΅Π΅ Π΄ΠΎΠΏΡΡΠΊΠ°Π΅ΡΡΡ ΠΏΡΠΈΠΌΠ΅Π½Π΅Π½ΠΈΠ΅
ΠΏΡΠ΅Π΄ΠΎΡ
ΡΠ°Π½ΠΈΡΠ΅Π»ΡΠ½ΠΎΠ³ΠΎ ΠΊΠΎΠ»ΡΡΠ° Π±Π΅Π· Π±Π»ΠΎΠΊΠΈΡΠΎΠ²ΠΊΠΈ Π΄Π»Ρ Π·Π°ΡΠΈΡΡ ΡΠ°Π±ΠΎΡΠ΅Π³ΠΎ ΠΎΡ
ΡΠ΄Π°ΡΠΎΠ² ΠΊΠΎΠ½ΡΠΎΠΌ ΠΏΡΠΎΠ²ΠΎΠ»ΠΎΠΊΠΈ.
3.1.1.19. ΠΡΠΈ ΡΠ°Π·ΠΌΠΎΡΠΊΠ΅
ΠΏΡΠΎΠ²ΠΎΠ»ΠΎΠΊΠΈ Ρ ΠΊΠ°ΡΡΡΠ΅ΠΊ Π΄ΠΎΠ»ΠΆΠ½Ρ ΡΠΎΠ±Π»ΡΠ΄Π°ΡΡΡΡ ΡΠ»Π΅Π΄ΡΡΡΠΈΠ΅ ΡΡΠ΅Π±ΠΎΠ²Π°Π½ΠΈΡ:
ΠΊΠ°ΡΡΡΠΊΠΈ Π΄ΠΎΠ»ΠΆΠ½Ρ ΠΈΠΌΠ΅ΡΡ
Π½Π΅ΠΎΠ±Ρ
ΠΎΠ΄ΠΈΠΌΡΡ Π±Π°Π»Π°Π½ΡΠΈΡΠΎΠ²ΠΊΡ ΠΈ ΠΏΡΠΎΡΠ½ΠΎΡΡΡ, Π»Π΅Π³ΠΊΠΎ Π²ΡΠ°ΡΠ°ΡΡΡΡ Π½Π° ΠΎΡΠΈ ΠΈ
ΠΈΠΌΠ΅ΡΡ ΡΠΎΡΠΌΠΎΠ·Π½ΠΎΠ΅ ΡΡΡΡΠΎΠΉΡΡΠ²ΠΎ, ΠΏΡΠ΅Π΄ΠΎΡΠ²ΡΠ°ΡΠ°ΡΡΠ΅Π΅ ΠΎΠ±ΡΠ°Π·ΠΎΠ²Π°Π½ΠΈΠ΅ ΡΠ»Π°Π±ΠΈΠ½Ρ
ΠΏΡΠΎΠ²ΠΎΠ»ΠΎΠΊΠΈ ΠΏΡΠΈ ΠΈΠ½Π΅ΡΡΠΈΠΎΠ½Π½ΠΎΠΌ Π²ΡΠ°ΡΠ΅Π½ΠΈΠΈ;
Π΄Π»Ρ Π±ΡΡΡΡΠΎΠΉ ΠΎΡΡΠ°Π½ΠΎΠ²ΠΊΠΈ
ΠΊΠ°ΡΡΡΠΊΠΈ ΠΏΡΠΈ ΠΎΠ±ΡΡΠ²Π΅ ΠΏΡΠΎΠ²ΠΎΠ»ΠΎΠΊΠΈ ΠΈΠ»ΠΈ ΠΎΡΡΠ°Π½ΠΎΠ²ΠΊΠ΅ Π±Π°ΡΠ°Π±Π°Π½Π° Π΄ΠΎΠ»ΠΆΠ½ΠΎ Π±ΡΡΡ
ΠΏΡΠ΅Π΄ΡΡΠΌΠΎΡΡΠ΅Π½ΠΎ Π½Π΅Π·Π°Π²ΠΈΡΠΈΠΌΠΎΠ΅, Π°Π²ΡΠΎΠΌΠ°ΡΠΈΡΠ΅ΡΠΊΠΈ Π΄Π΅ΠΉΡΡΠ²ΡΡΡΠ΅Π΅ ΡΠΎΡΠΌΠΎΠ·Π½ΠΎΠ΅
ΡΡΡΡΠΎΠΉΡΡΠ²ΠΎ, ΡΠ±Π»ΠΎΠΊΠΈΡΠΎΠ²Π°Π½Π½ΠΎΠ΅ Ρ ΠΏΡΡΠΊΠΎΠΌ ΠΈ ΠΎΡΡΠ°Π½ΠΎΠ²ΠΊΠΎΠΉ Π±Π°ΡΠ°Π±Π°Π½Π°,
ΠΏΡΠ΅Π΄ΠΎΡΠ²ΡΠ°ΡΠ°ΡΡΠ΅Π΅ ΡΠΏΠ°Π΄Π°Π½ΠΈΠ΅ ΠΈ Π·Π°ΠΏΡΡΡΠ²Π°Π½ΠΈΠ΅ Π²ΠΈΡΠΊΠΎΠ² ΠΏΡΠΎΠ²ΠΎΠ»ΠΎΠΊΠΈ Π½Π°
ΠΊΠ°ΡΡΡΠΊΠ΅;
Π½Π΅ΠΏΠΎΠ΄Π²ΠΈΠΆΠ½ΡΠ΅ ΠΊΠ°ΡΡΡΠΊΠΈ
Π΄ΠΎΠ»ΠΆΠ½Ρ ΠΈΠΌΠ΅ΡΡ ΡΡΡΡΠΎΠΉΡΡΠ²ΠΎ Π΄Π»Ρ ΠΏΠ»Π°Π²Π½ΠΎΠ³ΠΎ ΡΡ
ΠΎΠ΄Π° ΠΏΡΠΎΠ²ΠΎΠ»ΠΎΠΊΠΈ.
3.1.1.20. ΠΠ°ΠΌΠΎΡΠΎΡΠ½ΡΠ΅
Π°ΠΏΠΏΠ°ΡΠ°ΡΡ Π²ΠΎΠ»ΠΎΡΠΈΠ»ΡΠ½ΡΡ
ΡΡΠ°Π½ΠΎΠ² Π΄ΠΎΠ»ΠΆΠ½Ρ Π±ΡΡΡ ΠΎΠ±ΠΎΡΡΠ΄ΠΎΠ²Π°Π½Ρ ΠΎΠ³ΡΠ°Π΄ΠΈΡΠ΅Π»ΡΠ½ΡΠΌΠΈ
ΡΡΠ΅Π΄ΡΡΠ²Π°ΠΌΠΈ ΠΏΡΠΎΡΠΈΠ² Π°Π²Π°ΡΠΈΠΉΠ½ΠΎΠ³ΠΎ Π²ΡΠ±ΡΠΎΡΠ° ΠΏΡΠΈΠ΅ΠΌΠ½ΠΎΠΉ ΠΊΠ°ΡΡΡΠΊΠΈ ΠΈΠ·
Π°ΠΏΠΏΠ°ΡΠ°ΡΠ°.
ΠΠ° Π²Π½ΠΎΠ²Ρ ΡΡΡΠ°Π½Π°Π²Π»ΠΈΠ²Π°Π΅ΠΌΡΡ
Π²ΠΎΠ»ΠΎΡΠΈΠ»ΡΠ½ΡΡ
ΡΡΠ°Π½Π°Ρ
Π½Π°ΠΌΠΎΡΠΎΡΠ½ΡΠΉ Π°ΠΏΠΏΠ°ΡΠ°Ρ Π΄ΠΎΠ»ΠΆΠ΅Π½ ΠΈΠΌΠ΅ΡΡ ΡΠΎΡΠΌΠΎΠ·Π½ΠΎΠ΅
ΡΡΡΡΠΎΠΉΡΡΠ²ΠΎ, ΡΠ±Π»ΠΎΠΊΠΈΡΠΎΠ²Π°Π½Π½ΠΎΠ΅ ΡΠΎ ΡΡΠ°Π½ΠΎΠΌ, ΠΈ ΠΎΠ³ΡΠ°ΠΆΠ΄Π΅Π½ΠΈΠ΅, ΠΈΡΠΊΠ»ΡΡΠ°ΡΡΠ΅Π΅
Π²ΠΎΠ·ΠΌΠΎΠΆΠ½ΠΎΡΡΡ ΡΠ°Π·Π»Π΅ΡΠ° ΠΊΠΎΠ½ΡΠΎΠ² ΠΏΡΠΎΠ²ΠΎΠ»ΠΎΠΊΠΈ ΠΏΡΠΈ Π΅Π΅ ΠΎΠ±ΡΡΠ²Π΅ ΠΈΠ»ΠΈ Π²ΡΡ
ΠΎΠ΄Π΅ Ρ
ΡΠΈΡΡΠΎΠ³ΠΎ Π±Π°ΡΠ°Π±Π°Π½Π°.
3.1.1.21. ΠΠΎΠ»ΠΎΡΠΈΠ»ΡΠ½ΡΠ΅
ΡΡΠ°Π½Ρ Ρ Π²Π΅ΡΡΠΈΠΊΠ°Π»ΡΠ½ΠΎΠΉ ΡΠ°Π·ΠΌΠΎΡΠΊΠΎΠΉ ΠΏΡΠΎΠ²ΠΎΠ»ΠΎΠΊΠΈ, ΡΠ°Π±ΠΎΡΠ°ΡΡΠΈΠ΅ Π½Π΅ Ρ
ΡΠ°Π·ΠΌΠ°ΡΡΠ²Π°ΡΡΠΈΡ
ΡΡΡΡΠΎΠΉΡΡΠ², Π° ΡΠΎ ΡΡΠ΅Π»Π»Π°ΠΆΠ΅ΠΉ, Π΄ΠΎΠ»ΠΆΠ½Ρ Π±ΡΡΡ ΠΎΠ±ΠΎΡΡΠ΄ΠΎΠ²Π°Π½Ρ
ΠΊΠΎΠ»ΠΎΠ½Π½Π°ΠΌΠΈ Π²ΡΡΠΎΡΠΎΠΉ 3,5-4,0 ΠΌ Ρ ΡΡΡΡΠΎΠΉΡΡΠ²ΠΎΠΌ Π½Π° Π½ΠΈΡ
ΠΏΠ΅ΡΠ»Π΅ΡΠ»Π°Π²Π»ΠΈΠ²Π°ΡΡΠ΅Π³ΠΎ
ΠΊΠΎΠ»ΡΡΠ°, Π°Π²ΡΠΎΠΌΠ°ΡΠΈΡΠ΅ΡΠΊΠΈ ΠΎΡΡΠ°Π½Π°Π²Π»ΠΈΠ²Π°ΡΡΠ΅Π³ΠΎ ΠΏΠ΅ΡΠ²ΡΠΉ Π±Π°ΡΠ°Π±Π°Π½ ΡΡΠ°Π½Π° Π²
ΡΠ»ΡΡΠ°Π΅ ΠΎΠ±ΡΠ°Π·ΠΎΠ²Π°Π½ΠΈΡ ΠΏΠ΅ΡΠ»ΠΈ.
ΠΠΎΠ»ΠΎΠ½Π½Ρ ΡΡΡΠ°Π½Π°Π²Π»ΠΈΠ²Π°ΡΡΡΡ
ΠΏΠ΅ΡΠ΅Π΄ ΠΏΠ΅ΡΠ²ΡΠΌ Π±Π°ΡΠ°Π±Π°Π½ΠΎΠΌ ΠΈ Π΄ΠΎΠ»ΠΆΠ½Ρ Π±ΡΡΡ ΠΎΠ±ΠΎΡΡΠ΄ΠΎΠ²Π°Π½Ρ Π»Π΅ΡΡΠ½ΠΈΡΠ°ΠΌΠΈ ΠΈ
ΠΏΠ»ΠΎΡΠ°Π΄ΠΊΠ°ΠΌΠΈ Π΄Π»Ρ ΡΡΡΡΠ°Π½Π΅Π½ΠΈΡ Π·Π°ΠΏΡΡΡΠ²Π°Π½ΠΈΡ ΠΏΡΠΎΠ²ΠΎΠ»ΠΎΠΊΠΈ Π² ΠΊΠΎΠ»ΡΡΠ΅.
Π‘ΡΠ΅Π»Π»Π°ΠΆ ΡΠΊΠ°Π·Π°Π½Π½ΡΡ
ΡΡΠ°Π½ΠΎΠ²
Π΄ΠΎΠ»ΠΆΠ΅Π½ Π±ΡΡΡ ΠΎΠ±ΠΎΡΡΠ΄ΠΎΠ²Π°Π½ ΡΠ»Π΅ΠΏΠΏΠ΅ΡΠ½ΡΠΌ ΠΌΠ΅Ρ
Π°Π½ΠΈΠ·ΠΌΠΎΠΌ, ΠΏΡΠ΅Π΄Π½Π°Π·Π½Π°ΡΠ΅Π½Π½ΡΠΌ Π΄Π»Ρ
ΠΏΠΎΠ΄ΡΡΠΆΠΊΠΈ Π±ΡΠ½ΡΠΎΠ² ΠΏΡΠΎΠ²ΠΎΠ»ΠΎΠΊΠΈ ΠΏΠΎΠ΄ ΠΊΠΎΠ»ΠΎΠ½Π½Ρ.
3.1.1.22. Π‘ΡΠ°Π½Ρ,
ΠΏΡΠ΅Π΄Π½Π°Π·Π½Π°ΡΠ΅Π½Π½ΡΠ΅ Π΄Π»Ρ Π³ΡΡΠ±ΠΎΠ³ΠΎ ΠΈ ΡΡΠ΅Π΄Π½Π΅Π³ΠΎ Π²ΠΎΠ»ΠΎΡΠ΅Π½ΠΈΡ ΠΏΡΠΎΠ²ΠΎΠ»ΠΎΠΊΠΈ, Π΄ΠΎΠ»ΠΆΠ½Ρ
Π±ΡΡΡ ΠΎΠ±ΠΎΡΡΠ΄ΠΎΠ²Π°Π½Ρ Π΄ΠΈΡΡΠ°Π½ΡΠΈΠΎΠ½Π½ΡΠΌΠΈ ΠΏΡΠ»ΡΡΠ°ΠΌΠΈ ΡΠΏΡΠ°Π²Π»Π΅Π½ΠΈΡ, Π½ΠΎΠΆΠ½ΠΈΡΠ°ΠΌΠΈ,
ΡΠ²Π°ΡΠΎΡΠ½ΡΠΌΠΈ Π°ΠΏΠΏΠ°ΡΠ°ΡΠ°ΠΌΠΈ Ρ ΡΠ°Π·ΠΌΠ°ΡΡΠ²Π°ΡΡΠΈΡ
ΠΈ ΡΠΌΠ°ΡΡΠ²Π°ΡΡΠΈΡ
ΡΡΡΡΠΎΠΉΡΡΠ².
3.1.1.23. Π‘ΡΠ°Π½Ρ ΠΏΠΎ
ΠΏΡΠΎΠΈΠ·Π²ΠΎΠ΄ΡΡΠ²Ρ ΠΏΡΠΎΠ²ΠΎΠ»ΠΎΠΊΠΈ Π² ΠΌΠΎΡΠΊΠΈ Π΄ΠΎΠ»ΠΆΠ½Ρ Π±ΡΡΡ ΠΎΠ±ΠΎΡΡΠ΄ΠΎΠ²Π°Π½Ρ ΠΌΠ΅Ρ
Π°Π½ΠΈΠ·ΠΌΠ°ΠΌΠΈ
Π΄Π»Ρ ΡΡΠ΅ΠΌΠ° ΠΌΠΎΡΠΊΠΎΠ² ΠΈ ΠΏΡΠΈΡΠΏΠΎΡΠΎΠ±Π»Π΅Π½ΠΈΡΠΌΠΈ Π΄Π»Ρ ΠΈΡ
ΡΠ²ΡΠ·ΠΊΠΈ.
3.1.1.24. ΠΠ»Ρ ΠΈΠ·ΠΌΠ΅Π½Π΅Π½ΠΈΡ
ΠΏΠΎΠ»ΠΎΠΆΠ΅Π½ΠΈΡ ΠΊΠ°ΡΡΡΠ΅ΠΊ ΠΌΠ°ΡΡΠΎΠΉ Π±ΠΎΠ»Π΅Π΅ 500 ΠΊΠ³ Π΄ΠΎΠ»ΠΆΠ½Ρ ΠΏΡΠΈΠΌΠ΅Π½ΡΡΡΡΡ
ΠΊΠ°Π½ΡΠΎΠ²Π°ΡΠ΅Π»ΠΈ.
3.1.1.25. Π‘ΡΠ°Π½ΠΊΠΈ Π΄Π»Ρ
ΠΎΡΡΡΠ΅Π½ΠΈΡ ΠΏΡΠΎΠ²ΠΎΠ»ΠΎΠΊΠΈ Π΄ΠΈΠ°ΠΌΠ΅ΡΡΠΎΠΌ Π±ΠΎΠ»Π΅Π΅ 1,0 ΠΌΠΌ Π΄ΠΎΠ»ΠΆΠ½Ρ ΠΎΠ±ΠΎΡΡΠ΄ΠΎΠ²Π°ΡΡΡΡ
ΠΈΠ½Π΄ΠΈΠ²ΠΈΠ΄ΡΠ°Π»ΡΠ½ΡΠΌΠΈ ΡΠ»Π΅ΠΊΡΡΠΎΠΏΡΠΈΠ²ΠΎΠ΄Π°ΠΌΠΈ. ΠΠ±ΡΠ΅Π·ΠΊΠ° ΠΏΡΠΎΠ²ΠΎΠ»ΠΎΠΊΠΈ Π΄ΠΎΠ»ΠΆΠ½Π°
ΠΏΡΠΎΠΈΠ·Π²ΠΎΠ΄ΠΈΡΡΡΡ ΠΌΠ΅Ρ
Π°Π½ΠΈΡΠ΅ΡΠΊΠΈΠΌΠΈ Π½ΠΎΠΆΠ½ΠΈΡΠ°ΠΌΠΈ.
3.1.1.26. ΠΠ»ΠΈΠ½Π° ΡΠ΅ΠΏΠΈ
Π·Π°ΡΡΠΆΠ½ΡΡ
ΠΊΠ»Π΅ΡΠ΅ΠΉ Π΄ΠΎΠ»ΠΆΠ½Π° Π±ΡΡΡ Π½Π΅ Π±ΠΎΠ»Π΅Π΅ 2-Ρ
Π΄ΠΈΠ°ΠΌΠ΅ΡΡΠΎΠ² Π±Π°ΡΠ°Π±Π°Π½Π°.
3.1.1.27. Π¦Π΅ΠΏΡ Ρ
ΡΠΊΡΠ΅ΠΏΠ»Π΅Π½Π½ΡΠΌ Π½Π° Π½Π΅ΠΉ ΠΊΡΡΡΠΊΠΎΠΌ ΠΈ ΠΊΠ»Π΅ΡΠ°ΠΌΠΈ Π΄ΠΎΠ»ΠΆΠ½Π° ΠΈΡΠΏΡΡΡΠ²Π°ΡΡΡΡ Π½Π°
ΡΠ΅ΡΡΠΈΠΊΡΠ°ΡΠ½ΡΠΉ Π·Π°ΠΏΠ°Ρ ΠΏΡΠΎΡΠ½ΠΎΡΡΠΈ ΠΎΡΠ½ΠΎΡΠΈΡΠ΅Π»ΡΠ½ΠΎΠ³ΠΎ* ΠΌΠ°ΠΊΡΠΈΠΌΠ°Π»ΡΠ½ΠΎΠ³ΠΎ ΡΡΠΈΠ»ΠΈΡ
Π²ΠΎΠ»ΠΎΡΠ΅Π½ΠΈΡ ΠΏΡΠΎΠ²ΠΎΠ»ΠΎΠΊΠΈ Π½Π° Π΄Π°Π½Π½ΠΎΠΌ ΡΡΠ°Π½Π΅.
_________________
*
Π’Π΅ΠΊΡΡ Π΄ΠΎΠΊΡΠΌΠ΅Π½ΡΠ° ΡΠΎΠΎΡΠ²Π΅ΡΡΡΠ²ΡΠ΅Ρ ΠΎΡΠΈΠ³ΠΈΠ½Π°Π»Ρ. — ΠΡΠΈΠΌΠ΅ΡΠ°Π½ΠΈΠ΅ ΠΈΠ·Π³ΠΎΡΠΎΠ²ΠΈΡΠ΅Π»Ρ
Π±Π°Π·Ρ Π΄Π°Π½Π½ΡΡ
.
3.1.1.28. ΠΠ»Ρ Π·Π°ΡΠΈΡΡΠΊΠΈ
ΡΠ²Π°ΡΠ½ΠΎΠ³ΠΎ ΡΠ²Π° ΠΏΡΠΎΠ²ΠΎΠ»ΠΎΠΊΠΈ Π½Π° ΡΡΠ°Π½Π°Ρ
ΡΠΎΠ½ΠΊΠΎΠ³ΠΎ ΠΈ ΡΠΎΠ½ΡΠ°ΠΉΡΠ΅Π³ΠΎ (ΠΌΠΎΠΊΡΠΎΠ³ΠΎ)
Π²ΠΎΠ»ΠΎΡΠ΅Π½ΠΈΡ Π½Π΅ΠΎΠ±Ρ
ΠΎΠ΄ΠΈΠΌΠΎ ΠΏΡΠΈΠΌΠ΅Π½ΡΡΡ Π°Π±ΡΠ°Π·ΠΈΠ²Π½ΡΠ΅ ΠΊΡΡΠ³ΠΈ Π΄ΠΈΠ°ΠΌΠ΅ΡΡΠΎΠΌ Π½Π΅ Π±ΠΎΠ»Π΅Π΅
150 ΠΌΠΌ, ΠΈ Π½Π° ΡΡΠ°Π½Π°Ρ
Π³ΡΡΠ±ΠΎ-ΡΡΠ΅Π΄Π½Π΅Π³ΠΎ Π²ΠΎΠ»ΠΎΡΠ΅Π½ΠΈΡ — Π½Π΅ Π±ΠΎΠ»Π΅Π΅ 200 ΠΌΠΌ.
Π§ΠΈΡΠ»ΠΎ ΠΎΠ±ΠΎΡΠΎΡΠΎΠ² Π²Π°Π»Π°
Π½Π°ΠΆΠ΄Π°ΡΠ½ΠΎΠ³ΠΎ ΡΡΠ°Π½ΠΊΠ°, Π½Π° ΠΊΠΎΡΠΎΡΠΎΠΌ ΡΡΡΠ°Π½ΠΎΠ²Π»Π΅Π½ ΠΊΡΡΠ³, Π΄ΠΎΠ»ΠΆΠ½ΠΎ Π±ΡΡΡ ΡΠ°ΠΊΠΈΠΌ,
ΡΡΠΎΠ±Ρ ΠΎΠΊΡΡΠΆΠ½Π°Ρ ΡΠΊΠΎΡΠΎΡΡΡ Π²ΡΠ°ΡΠ΅Π½ΠΈΡ ΠΊΡΡΠ³Π° Π½Π΅ ΠΏΡΠ΅Π²ΡΡΠ°Π»Π° 15 ΠΌ/ΡΠ΅ΠΊ.
3.1.1.29. ΠΠ»Ρ
ΠΎΠ±ΡΠ»ΡΠΆΠΈΠ²Π°Π½ΠΈΡ Π²ΠΎΠ»ΠΎΡΠΈΠ»ΡΠ½ΠΎΠ³ΠΎ ΡΡΠ°Π½Π° Π΄ΠΎΠ»ΠΆΠ½Ρ Π±ΡΡΡ ΠΏΡΠ΅Π΄ΡΡΠΌΠΎΡΡΠ΅Π½Ρ ΡΠ°Π±ΠΎΡΠ΅Π΅
ΠΌΠ΅ΡΡΠΎ ΠΈ ΠΏΡΠΎΡ
ΠΎΠ΄Ρ. Π Π°Π·ΠΌΠ΅ΡΡ ΡΠ°Π±ΠΎΡΠ΅Π³ΠΎ ΠΌΠ΅ΡΡΠ° Π΄ΠΎΠ»ΠΆΠ½Ρ Π±ΡΡΡ Π΄ΠΎΡΡΠ°ΡΠΎΡΠ½ΡΠΌΠΈ
Π΄Π»Ρ Π±Π΅Π·ΠΎΠΏΠ°ΡΠ½ΠΎΠ³ΠΎ ΠΈ ΡΠ΄ΠΎΠ±Π½ΠΎΠ³ΠΎ ΠΎΠ±ΡΠ»ΡΠΆΠΈΠ²Π°Π½ΠΈΡ ΠΎΡΠ½ΠΎΠ²Π½ΠΎΠ³ΠΎ ΠΈ
Π²ΡΠΏΠΎΠΌΠΎΠ³Π°ΡΠ΅Π»ΡΠ½ΠΎΠ³ΠΎ ΠΎΠ±ΠΎΡΡΠ΄ΠΎΠ²Π°Π½ΠΈΡ (Π½Π°ΠΆΠ΄Π°ΡΠ½ΠΎΠ³ΠΎ ΠΈ ΠΎΡΡΡΠΈΡΠ΅Π»ΡΠ½ΠΎΠ³ΠΎ ΡΡΠ°Π½ΠΊΠΎΠ² ΠΈ
ΡΠ²Π°ΡΠΎΡΠ½ΠΎΠ³ΠΎ Π°ΠΏΠΏΠ°ΡΠ°ΡΠ°) Ρ ΡΡΠ΅ΡΠΎΠΌ ΡΠ°Π·ΠΌΠ΅ΡΠ΅Π½ΠΈΡ ΡΡΠ΅Π»Π»Π°ΠΆΠ΅ΠΉ Π΄Π»Ρ ΠΌΠ΅ΡΠ°Π»Π»Π°,
ΠΏΡΠ»ΡΡΠΎΠ² ΡΠΏΡΠ°Π²Π»Π΅Π½ΠΈΡ, ΡΠ°Π·ΠΌΠΎΡΠΎΡΠ½ΡΡ
ΠΈ Π½Π°ΠΌΠΎΡΠΎΡΠ½ΡΡ
ΡΡΡΡΠΎΠΉΡΡΠ², ΡΠ²ΡΠ·ΠΎΡΠ½ΡΡ
ΡΡΠΎΠ»ΠΎΠ², ΠΊΠ°ΡΡΡΠ΅ΠΊ ΠΈ Ρ.Π΄.
3.1.1.30. ΠΠ»Ρ ΡΠ΅Π·ΠΊΠΈ
ΠΏΡΠΎΠ²ΠΎΠ»ΠΎΠΊΠΈ Π΄ΠΎΠ»ΠΆΠ½Ρ ΠΏΡΠΈΠΌΠ΅Π½ΡΡΡΡΡ Π½ΠΎΠΆΠ½ΠΈΡΡ ΠΈΠ»ΠΈ ΠΊΡΡΠ°ΡΠΊΠΈ. ΠΠΎΡΠ΅Π·ΠΊΠ°
Π²ΡΡΠΎΠΊΠΎΡΠ³Π»Π΅ΡΠΎΠ΄ΠΈΡΡΠΎΠΉ ΠΏΡΠΎΠ²ΠΎΠ»ΠΎΠΊΠΈ ΡΡΠ΅Π΄Π½Π΅ΠΉ ΠΈ Π±ΠΎΠ»ΡΡΠΎΠΉ ΡΠΎΠ»ΡΠΈΠ½Ρ Π΄ΠΎΠ»ΠΆΠ½Π° Π±ΡΡΡ
ΠΌΠ΅Ρ
Π°Π½ΠΈΠ·ΠΈΡΠΎΠ²Π°Π½Π°.
3.1.1.31. Π Π°Π±ΠΎΡΠΈΠ΅,
Π·Π°Π½ΡΡΡΠ΅ Π½Π° ΠΏΡΠΎΠΈΠ·Π²ΠΎΠ΄ΡΡΠ²Π΅ ΠΏΡΠΎΠ²ΠΎΠ»ΠΎΠΊΠΈ, Π΄ΠΎΠ»ΠΆΠ½Ρ ΡΠ°Π±ΠΎΡΠ°ΡΡ Π² Π·Π°ΡΠΈΡΠ½ΡΡ
ΠΎΡΠΊΠ°Ρ
ΠΈΠ»ΠΈ Π·Π°ΡΠΈΡΠ½ΡΡ
ΡΠΈΡΠΊΠ°Ρ
.
3.1.2. ΠΡΠΎΠΈΠ·Π²ΠΎΠ΄ΡΡΠ²ΠΎ ΠΊΠ°Π»ΠΈΠ±ΡΠΎΠ²Π°Π½Π½ΠΎΠ³ΠΎ ΠΌΠ΅ΡΠ°Π»Π»Π°
3.1.2.1. ΠΡΠΎΠΈΠ·Π²ΠΎΠ΄ΡΡΠ²ΠΎ
ΠΊΠ°Π»ΠΈΠ±ΡΠΎΠ²Π°Π½Π½ΠΎΠ³ΠΎ ΠΌΠ΅ΡΠ°Π»Π»Π° Π² ΠΌΠΎΡΠΊΠ°Ρ
Π΄ΠΎΠ»ΠΆΠ½ΠΎ ΠΎΡΠ²Π΅ΡΠ°ΡΡ ΡΡΠ΅Π±ΠΎΠ²Π°Π½ΠΈΡΠΌ
Π±Π΅Π·ΠΎΠΏΠ°ΡΠ½ΠΎΡΡΠΈ, ΠΈΠ·Π»ΠΎΠΆΠ΅Π½Π½ΡΠΌ Π² ΠΏΠΏ.3.1.1.1-3.1.1.31 Π½Π°ΡΡΠΎΡΡΠΈΡ
ΠΡΠ°Π²ΠΈΠ».
3.1.2.2. Π¦Π΅ΠΏΠ½ΡΠ΅
Π²ΠΎΠ»ΠΎΡΠΈΠ»ΡΠ½ΡΠ΅ ΡΡΠ°Π½Ρ Π΄ΠΎΠ»ΠΆΠ½Ρ Π±ΡΡΡ ΠΎΠ±ΠΎΡΡΠ΄ΠΎΠ²Π°Π½Ρ ΠΌΠ΅Ρ
Π°Π½ΠΈΠ·ΠΌΠ°ΠΌΠΈ Π΄Π»Ρ Π·Π°Π΄Π°ΡΠΈ
ΠΏΡΡΡΠΊΠΎΠ² Π² Π²ΠΎΠ»ΠΎΠΊΡ. ΠΠ° Π΄Π΅ΠΉΡΡΠ²ΡΡΡΠΈΡ
ΡΡΠ°Π½Π°Ρ
Π΄ΠΎΠΏΡΡΠΊΠ°Π΅ΡΡΡ ΠΏΡΠΈΠΌΠ΅Π½Π΅Π½ΠΈΠ΅
ΠΏΡΠΈΡΠΏΠΎΡΠΎΠ±Π»Π΅Π½ΠΈΠΉ Π΄Π»Ρ ΠΎΡΡΡΠ΅Π½ΠΈΡ ΡΡΠ°Π½Π³.
3.1.2.3. Π¦Π΅ΠΏΠ½ΡΠ΅
Π²ΠΎΠ»ΠΎΡΠΈΠ»ΡΠ½ΡΠ΅ ΡΡΠ°Π½Ρ Π΄ΠΎΠ»ΠΆΠ½Ρ Π±ΡΡΡ ΠΎΠ±ΠΎΡΡΠ΄ΠΎΠ²Π°Π½Ρ ΠΌΠ΅Ρ
Π°Π½ΠΈΠ·ΠΌΠ°ΠΌΠΈ ΡΠ±ΡΠ°ΡΡΠ²Π°Π½ΠΈΡ
ΠΌΠ΅ΡΠ°Π»Π»Π° Π² ΠΏΡΠΈΠ΅ΠΌΠ½ΡΠΉ ΠΊΠ°ΡΠΌΠ°Π½.
3.1.2.4. ΠΠΎΠ½ΡΡΡΡΠΊΡΠΈΡ
ΡΡΠ΅Π»Π»Π°ΠΆΠ° Π²ΠΎΠ»ΠΎΡΠΈΠ»ΡΠ½ΡΡ
ΡΠ΅ΠΏΠ½ΡΡ
ΡΡΠ°Π½ΠΎΠ² Π΄ΠΎΠ»ΠΆΠ½Π° ΠΈΡΠΊΠ»ΡΡΠ°ΡΡ Π²ΠΎΠ·ΠΌΠΎΠΆΠ½ΠΎΡΡΡ
ΠΏΠ°Π΄Π΅Π½ΠΈΡ Ρ Π½ΠΈΡ
ΠΏΡΡΡΠΊΠΎΠ². Π‘ΠΎ ΡΡΠΎΡΠΎΠ½Ρ ΡΠ°Π±ΠΎΡΠ΅Π³ΠΎ ΠΌΠ΅ΡΡΠ° ΡΡΠ΅Π»Π»Π°ΠΆΠΈ Π΄ΠΎΠ»ΠΆΠ½Ρ
Π±ΡΡΡ ΠΎΠ±ΠΎΡΡΠ΄ΠΎΠ²Π°Π½Ρ ΡΠΎΠ»ΠΈΠΊΠ°ΠΌΠΈ Π΄Π»Ρ ΠΎΠ±Π»Π΅Π³ΡΠ΅Π½ΠΈΡ ΠΏΠΎΠ΄Π°ΡΠΈ ΡΡΠ°Π½Π³ Π² Π²ΠΎΠ»ΠΎΠΊΡ.
3.1.2.5. ΠΠΎΠ΄Π°ΡΠ° ΡΠΌΠ°Π·ΠΊΠΈ Π½Π°
ΡΡΠ°Π½Π³Ρ Π΄ΠΎΠ»ΠΆΠ½Π° Π±ΡΡΡ ΠΌΠ΅Ρ
Π°Π½ΠΈΠ·ΠΈΡΠΎΠ²Π°Π½Π°.
3.1.2.6. ΠΡΠΈ
ΠΏΡΠΎΠ΅ΠΊΡΠΈΡΠΎΠ²Π°Π½ΠΈΠΈ Π½ΠΎΠ²ΡΡ
ΡΠ΅ΠΏΠ½ΡΡ
Π²ΠΎΠ»ΠΎΡΠΈΠ»ΡΠ½ΡΡ
ΡΡΠ°Π½ΠΎΠ² Π΄ΠΎΠ»ΠΆΠ½Ρ
ΠΏΡΠ΅Π΄ΡΡΠΌΠ°ΡΡΠΈΠ²Π°ΡΡΡΡ ΠΏΠ»Π°Π²Π½ΠΎΠ΅ ΠΏΠΎΠ²ΡΡΠ΅Π½ΠΈΠ΅ ΡΠΊΠΎΡΠΎΡΡΠΈ ΠΎΡ ΠΌΠΎΠΌΠ΅Π½ΡΠ° Π·Π°Ρ
Π²Π°ΡΠ°
ΠΏΡΡΡΠΊΠ° Π΄ΠΎ ΡΠ°Π±ΠΎΡΠ΅ΠΉ ΡΠΊΠΎΡΠΎΡΡΠΈ Π²ΠΎΠ»ΠΎΡΠ΅Π½ΠΈΡ ΠΈ ΠΏΠ»Π°Π²Π½ΡΠΉ Π²ΠΎΠ·Π²ΡΠ°Ρ ΡΠ΅Π»Π΅ΠΆΠΊΠΈ.
3.1.2.7. Π ΠΎΠ»ΠΈΠΊΠΎΠΏΡΠ°Π²ΠΈΠ»ΡΠ½ΡΠ΅
ΠΌΠ°ΡΠΈΠ½Ρ Π΄ΠΎΠ»ΠΆΠ½Ρ Π±ΡΡΡ ΠΎΠ±ΠΎΡΡΠ΄ΠΎΠ²Π°Π½Ρ ΡΠΎ ΡΡΠΎΡΠΎΠ½Ρ Π·Π°Π΄Π°ΡΠΈ ΠΌΠ΅ΡΠ°Π»Π»Π°
ΠΏΡΠΎΠ²ΠΎΠ΄ΠΊΠΎΠΉ.
3.1.2.8. ΠΠ΅ΠΆΠ΄Ρ ΠΏΡΠ°Π²ΠΈΠ»ΡΠ½ΠΎΠΉ
ΠΌΠ°ΡΠΈΠ½ΠΎΠΉ ΠΈ ΠΏΡΠΈΠ΅ΠΌΠ½ΡΠΌ ΡΡΠ΅Π»Π»Π°ΠΆΠΎΠΌ Π΄ΠΎΠ»ΠΆΠ½ΠΎ Π±ΡΡΡ ΡΡΡΠ°Π½ΠΎΠ²Π»Π΅Π½ΠΎ ΠΎΠ³ΡΠ°ΠΆΠ΄Π΅Π½ΠΈΠ΅.
Π ΠΎΠ»ΠΈΠΊΠΈ ΠΏΡΠ°Π²ΠΈΠ»ΡΠ½ΠΎΠΉ ΠΌΠ°ΡΠΈΠ½Ρ Π΄ΠΎΠ»ΠΆΠ½Ρ Π±ΡΡΡ ΠΎΠ³ΡΠ°ΠΆΠ΄Π΅Π½Ρ.
3.1.2.9. ΠΡΠ΅ΡΡ-Π½ΠΎΠΆΠ½ΠΈΡΡ
Π΄Π»Ρ ΠΎΠ±ΡΠ΅Π·ΠΊΠΈ ΠΊΠΎΠ½ΡΠΎΠ² Π΄ΠΎΠ»ΠΆΠ½Ρ ΠΈΠΌΠ΅ΡΡ ΠΏΡΠ΅Π΄ΠΎΡ
ΡΠ°Π½ΠΈΡΠ΅Π»ΡΠ½ΡΠ΅ ΡΠΈΡΡ,
ΠΏΡΠ΅Π΄ΠΎΡΠ²ΡΠ°ΡΠ°ΡΡΠΈΠ΅ Π²ΡΠ±ΡΠΎΡ (ΠΎΡΠ»Π΅ΡΠ°Π½ΠΈΠ΅) ΠΎΠ±ΡΠ΅Π·Π°Π΅ΠΌΡΡ
ΠΊΠΎΠ½ΡΠΎΠ² ΡΡΠ°Π½Π³.
3.1.2.10. Π‘ΡΠ΅Π»Π»Π°ΠΆΠΈ
ΠΏΡΠ°Π²ΠΈΠ»ΡΠ½ΡΡ
ΠΌΠ°ΡΠΈΠ½ ΠΈ Π½ΠΎΠΆΠ½ΠΈΡ Π΄ΠΎΠ»ΠΆΠ½Ρ Π±ΡΡΡ ΠΎΠ±ΠΎΡΡΠ΄ΠΎΠ²Π°Π½Ρ
ΠΏΡΠ΅Π΄ΠΎΡ
ΡΠ°Π½ΠΈΡΠ΅Π»ΡΠ½ΡΠΌΠΈ ΡΠΏΠΎΡΠ°ΠΌΠΈ, ΠΈΡΠΊΠ»ΡΡΠ°ΡΡΠΈΠΌΠΈ ΡΠΊΠ°ΡΡΠ²Π°Π½ΠΈΠ΅ Π½Π° ΠΏΠΎΠ», ΠΈ Π½Π΅
Π΄ΠΎΠΏΡΡΠΊΠ°ΡΡ ΠΏΠ°Π΄Π΅Π½ΠΈΡ ΠΊΠΎΡΠΎΡΠΊΠΈΡ
ΡΡΠ°Π½Π³.
3.1.2.11. ΠΡΠΈ
ΠΏΡΠΎΠ΅ΠΊΡΠΈΡΠΎΠ²Π°Π½ΠΈΠΈ Π½ΠΎΠ²ΡΡ
ΡΠ΅ΠΏΠ½ΡΡ
ΡΡΠ°Π½ΠΎΠ², ΠΎΡΡΡΠΈΠ»ΡΠ½ΡΡ
ΡΡΠ°Π½ΠΊΠΎΠ², ΠΏΡΠ°Π²ΠΈΠ»ΡΠ½ΡΡ
ΠΌΠ°ΡΠΈΠ½, ΠΏΡΠ΅ΡΡ-Π½ΠΎΠΆΠ½ΠΈΡ, ΡΠ»ΠΈΡΠΎΠ²Π°Π»ΡΠ½ΡΡ
ΠΈ ΠΏΠΎΠ»ΠΈΡΠΎΠ²Π°Π»ΡΠ½ΡΡ
ΡΡΠ°Π½ΠΊΠΎΠ² Π΄Π»Ρ
ΠΏΡΡΡΠΊΠΎΠ²ΠΎΠ³ΠΎ ΠΌΠ΅ΡΠ°Π»Π»Π°, Π° ΡΠ°ΠΊΠΆΠ΅ ΠΏΡΠΈ ΠΌΠΎΠ΄Π΅ΡΠ½ΠΈΠ·Π°ΡΠΈΠΈ Π΄Π΅ΠΉΡΡΠ²ΡΡΡΠ΅Π³ΠΎ
ΠΏΠ΅ΡΠ΅ΡΠΈΡΠ»Π΅Π½Π½ΠΎΠ³ΠΎ ΠΎΠ±ΠΎΡΡΠ΄ΠΎΠ²Π°Π½ΠΈΡ Π΄ΠΎΠ»ΠΆΠ½Π° Π±ΡΡΡ ΠΏΡΠ΅Π΄ΡΡΠΌΠΎΡΡΠ΅Π½Π° ΠΌΠ΅Ρ
Π°Π½ΠΈΡΠ΅ΡΠΊΠ°Ρ
Π·Π°Π΄Π°ΡΠ° ΠΏΡΡΡΠΊΠΎΠ².
3.1.2.12. ΠΡΠΎΠ±Π΅ΠΌΠ΅ΡΠ½ΡΠ΅
ΡΡΡΠ°Π½ΠΎΠ²ΠΊΠΈ Π΄Π»Ρ ΠΎΡΠΈΡΡΠΊΠΈ ΡΡΠ°Π½Π³ ΠΎΡ ΠΎΠΊΠ°Π»ΠΈΠ½Ρ Π΄ΠΎΠ»ΠΆΠ½Ρ Π±ΡΡΡ ΠΎΠ±ΠΎΡΡΠ΄ΠΎΠ²Π°Π½Ρ:
ΡΠΈΡΡΠ΅ΠΌΠΎΠΉ Π²ΡΡΡΠΆΠ½ΠΎΠΉ
Π²Π΅Π½ΡΠΈΠ»ΡΡΠΈΠΈ ΠΈΠ· Π΄ΡΠΎΠ±Π΅ΠΌΠ΅ΡΠ½ΡΡ
ΠΊΠ°ΠΌΠ΅Ρ, ΡΠ±Π»ΠΎΠΊΠΈΡΠΎΠ²Π°Π½Π½ΠΎΠΉ Ρ ΠΏΡΡΠΊΠΎΠΌ
Π΄ΡΠΎΠ±Π΅ΠΌΠ΅ΡΠ½ΠΎΠΉ ΡΡΡΠ°Π½ΠΎΠ²ΠΊΠΈ;
Π²Ρ
ΠΎΠ΄Π½ΡΠΌΠΈ ΠΈ Π²ΡΡ
ΠΎΠ΄Π½ΡΠΌΠΈ
Π·Π°ΡΠ²ΠΎΡΠ°ΠΌΠΈ Π΄Π»Ρ ΠΏΠΎΠ΄Π°ΡΠΈ ΠΌΠ΅ΡΠ°Π»Π»Π°, ΠΈΡΠΊΠ»ΡΡΠ°ΡΡΠΈΠΌΠΈ Π²ΡΠ»Π΅Ρ Π΄ΡΠΎΠ±ΠΈ ΠΈΠ·
ΠΊΠ°ΠΌΠ΅Ρ;
Π±Π»ΠΎΠΊΠΈΡΠΎΠ²ΠΊΠΎΠΉ, ΠΈΡΠΊΠ»ΡΡΠ°ΡΡΠ΅ΠΉ
ΡΠ°Π±ΠΎΡΡ Π΄ΡΠΎΠ±Π΅ΠΌΠ΅ΡΠ½ΡΡ
ΠΊΠ°ΠΌΠ΅Ρ ΠΏΡΠΈ ΠΎΡΠΊΡΡΡΡΡ
Π΄Π²Π΅ΡΡΡ
ΠΈ Π»ΡΠΊΠ°Ρ
.
3.1.2.13. Π Π΅Π·ΡΠΎΠ²ΡΠ΅
Π³ΠΎΠ»ΠΎΠ²ΠΊΠΈ ΡΡΠ°Π½ΠΊΠΎΠ² Π΄Π»Ρ ΠΎΠ±ΡΠΎΡΠΊΠΈ (ΠΎΠ±Π΄ΠΈΡΠΊΠΈ) ΠΏΠΎΠ²Π΅ΡΡ
Π½ΠΎΡΡΠΈ ΠΌΠ΅ΡΠ°Π»Π»Π° Π΄ΠΎΠ»ΠΆΠ½Ρ
ΠΈΠΌΠ΅ΡΡ ΠΎΠ³ΡΠ°ΠΆΠ΄Π΅Π½ΠΈΠ΅, ΠΈΡΠΊΠ»ΡΡΠ°ΡΡΠ΅Π΅ Π²ΠΎΠ·ΠΌΠΎΠΆΠ½ΠΎΡΡΡ Π²ΡΠ»Π΅ΡΠ° ΡΡΡΡΠΆΠΊΠΈ. ΠΡΠΊΠΈ ΠΈ
ΠΎΠ³ΡΠ°ΠΆΠ΄Π΅Π½ΠΈΡ Π΄ΠΎΠ»ΠΆΠ½Ρ ΠΈΠΌΠ΅ΡΡ Π±Π»ΠΎΠΊΠΈΡΠΎΠ²ΠΊΡ, ΠΈΡΠΊΠ»ΡΡΠ°ΡΡΡΡ ΡΠ°Π±ΠΎΡΡ ΡΡΠ°Π½ΠΊΠ° ΠΏΡΠΈ
ΠΎΡΠΊΡΡΡΡΡ
ΠΎΠ³ΡΠ°ΠΆΠ΄Π΅Π½ΠΈΡΡ
ΠΈ Π»ΡΠΊΠ°Ρ
.
3.1.2.14. ΠΡΡΡΠΈΠ»ΡΠ½ΡΠ΅
ΡΡΠ°Π½ΠΊΠΈ Ρ ΡΠ΅Π·ΡΠΎΠ²ΠΎΠΉ Π³ΠΎΠ»ΠΎΠ²ΠΊΠΎΠΉ Π΄ΠΎΠ»ΠΆΠ½Ρ Π±ΡΡΡ ΠΎΠ±ΠΎΡΡΠ΄ΠΎΠ²Π°Π½Ρ:
ΠΌΠ΅Ρ
Π°Π½ΠΈΡΠ΅ΡΠΊΠΈΠΌΠΈ Π·Π°ΠΆΠΈΠΌΠ°ΠΌΠΈ
ΠΏΡΡΡΠΊΠΎΠ² ΠΏΠ΅ΡΠ΅Π΄ ΠΈΡ
ΠΏΠΎΠ΄Π°ΡΠ΅ΠΉ Π² Π·ΠΎΠ½Ρ ΡΠ΅Π·Π°Π½ΠΈΡ;
Π°Π²ΡΠΎΠΌΠ°ΡΠΈΡΠ΅ΡΠΊΠΈΠΌ
ΡΡΡΡΠΎΠΉΡΡΠ²ΠΎΠΌ Π·Π°ΠΊΡΡΠ²Π°Π½ΠΈΡ Π·ΠΎΠ½Ρ Π΄Π΅ΠΉΡΡΠ²ΠΈΡ ΡΠ΅Π·ΡΠΎΠ²;
ΠΌΠ΅Ρ
Π°Π½ΠΈΠ·ΠΌΠΎΠΌ ΠΏΠΎΠ΄Π°ΡΠΈ ΠΏΡΡΡΠΊΠΎΠ²
Π² Π·ΠΎΠ½Ρ Π΄Π΅ΠΉΡΡΠ²ΠΈΡ ΡΠ΅Π·ΡΠΎΠ².
3.1.2.15. Π¨Π»ΠΈΡΠΎΠ²Π°Π»ΡΠ½ΡΠ΅ ΠΈ
ΠΏΠΎΠ»ΠΈΡΠΎΠ²Π°Π»ΡΠ½ΡΠ΅ ΡΡΠ°Π½ΠΊΠΈ Π΄ΠΎΠ»ΠΆΠ½Ρ ΠΎΡΠ²Π΅ΡΠ°ΡΡ ΡΠ»Π΅Π΄ΡΡΡΠΈΠΌ ΡΡΠ΅Π±ΠΎΠ²Π°Π½ΠΈΡΠΌ:
ΡΠ»ΠΈΡΠΎΠ²Π°Π»ΡΠ½ΡΠ΅ ΠΈ
ΠΏΠΎΠ»ΠΈΡΠΎΠ²Π°Π»ΡΠ½ΡΠ΅ ΠΊΡΡΠ³ΠΈ Π΄ΠΎΠ»ΠΆΠ½Ρ Π±ΡΡΡ ΠΎΠ±ΠΎΡΡΠ΄ΠΎΠ²Π°Π½Ρ Π½Π°Π΄Π΅ΠΆΠ½ΡΠΌΠΈ Π·Π°ΡΠΈΡΠ½ΡΠΌΠΈ
ΠΎΠ³ΡΠ°ΠΆΠ΄Π΅Π½ΠΈΡΠΌΠΈ;
ΡΠ°Π·ΡΠ΅ΡΠ°Π΅ΡΡΡ ΠΏΡΠΈΠΌΠ΅Π½ΡΡΡ
ΡΠΎΠ»ΡΠΊΠΎ ΡΡΠ°Π½Π΄Π°ΡΡΠ½ΡΠ΅ ΠΊΡΡΠ³ΠΈ, ΠΏΡΠΎΡΠ΅Π΄ΡΠΈΠ΅ ΠΈΡΠΏΡΡΠ°Π½ΠΈΠ΅;
Π·ΠΎΠ½Π° Π²ΡΠ°ΡΠ΅Π½ΠΈΡ Π±ΡΠ½ΡΠ° Π½Π°
Π±ΡΠ½ΡΠΎΡΠ»ΠΈΡΠΎΠ²Π°Π»ΡΠ½ΡΡ
ΡΡΠ°Π½ΠΊΠ°Ρ
Π΄ΠΎΠ»ΠΆΠ½Π° ΠΈΠΌΠ΅ΡΡ ΠΎΠ³ΡΠ°ΠΆΠ΄Π΅Π½ΠΈΡ.
3.1.2.16. ΠΠΎΠΌΠ±ΠΈΠ½ΠΈΡΠΎΠ²Π°Π½Π½ΡΠ΅
Π»ΠΈΠ½ΠΈΠΈ Π΄Π»Ρ ΠΏΡΠΎΠΈΠ·Π²ΠΎΠ΄ΡΡΠ²Π° ΠΊΠ°Π»ΠΈΠ±ΡΠΎΠ²Π°Π½Π½ΠΎΠ³ΠΎ ΠΌΠ΅ΡΠ°Π»Π»Π° Π² ΠΏΡΡΡΠΊΠ°Ρ
Π΄ΠΎΠ»ΠΆΠ½Ρ Π±ΡΡΡ
ΠΎΠ±Π΅ΡΠΏΠ΅ΡΠ΅Π½Ρ ΠΏΠ΅ΡΠ΅Ρ
ΠΎΠ΄Π½ΡΠΌΠΈ ΠΌΠΎΡΡΠΈΠΊΠ°ΠΌΠΈ. ΠΡΠ΅ ΠΏΡΠΎΡ
ΠΎΠ΄Ρ Π½Π° ΡΡΠ°ΡΡΠΊΠ°Ρ
ΠΌΠ΅ΠΆΠ΄Ρ
ΠΎΠ±ΠΎΡΡΠ΄ΠΎΠ²Π°Π½ΠΈΠ΅ΠΌ Π΄ΠΎΠ»ΠΆΠ½Ρ ΠΈΠΌΠ΅ΡΡ ΠΎΠ³ΡΠ°ΠΆΠ΄Π΅Π½ΠΈΠ΅, ΡΠ±Π»ΠΎΠΊΠΈΡΠΎΠ²Π°Π½Π½ΠΎΠ΅ Ρ ΡΠ°Π±ΠΎΡΠΎΠΉ
Π»ΠΈΠ½ΠΈΠΈ, ΠΈΡΠΊΠ»ΡΡΠ°ΡΡΠ΅Π΅ Π΄ΠΎΡΡΡΠΏ ΠΊ ΠΎΠΏΠ°ΡΠ½ΠΎΠΉ Π·ΠΎΠ½Π΅.
3.2. ΠΡΠΎΠΈΠ·Π²ΠΎΠ΄ΡΡΠ²ΠΎ ΡΡΠ°Π»ΡΠ½ΡΡ ΠΊΠ°Π½Π°ΡΠΎΠ² ΠΈ ΠΌΠ΅ΡΠ°Π»Π»ΠΎΠΊΠΎΡΠ΄Π°
Π
ΠΎΠΏΠ°ΡΠ½ΡΠΌ ΠΈ Π²ΡΠ΅Π΄Π½ΡΠΌ ΠΏΡΠΎΠΈΠ·Π²ΠΎΠ΄ΡΡΠ²Π΅Π½Π½ΡΠΌ ΡΠ°ΠΊΡΠΎΡΠ°ΠΌ ΠΎΡΠ½ΠΎΡΡΡΡΡ:
ΠΏΠΎΠ΄Π²ΠΈΠΆΠ½ΡΠ΅ ΡΠ°ΡΡΠΈ
ΠΏΡΠΎΠΈΠ·Π²ΠΎΠ΄ΡΡΠ²Π΅Π½Π½ΠΎΠ³ΠΎ ΠΎΠ±ΠΎΡΡΠ΄ΠΎΠ²Π°Π½ΠΈΡ;
ΠΏΠ΅ΡΠ΅Π΄Π²ΠΈΠ³Π°ΡΡΠΈΠ΅ΡΡ
Π·Π°Π³ΠΎΡΠΎΠ²ΠΊΠΈ, ΠΈΠ·Π΄Π΅Π»ΠΈΡ;
ΠΏΠΎΠ²ΡΡΠ΅Π½Π½Π°Ρ Π·Π°ΠΏΡΠ»Π΅Π½Π½ΠΎΡΡΡ
Π²ΠΎΠ·Π΄ΡΡ
Π° ΡΠ°Π±ΠΎΡΠ΅ΠΉ Π·ΠΎΠ½Ρ;
ΠΏΠΎΠ²ΡΡΠ΅Π½Π½ΡΠΉ ΡΡΠΎΠ²Π΅Π½Ρ ΡΡΠΌΠ°
Π½Π° ΡΠ°Π±ΠΎΡΠ΅ΠΌ ΠΌΠ΅ΡΡΠ΅;
ΠΎΠΏΠ°ΡΠ½ΠΎΡΡΡ ΠΏΠΎΡΠ°ΠΆΠ΅Π½ΠΈΡ
ΡΠ»Π΅ΠΊΡΡΠΈΡΠ΅ΡΠΊΠΈΠΌ ΡΠΎΠΊΠΎΠΌ.
3.2.1. Π₯ΡΠ°Π½Π΅Π½ΠΈΠ΅ ΠΈ ΠΏΡΠΈΠ³ΠΎΡΠΎΠ²Π»Π΅Π½ΠΈΠ΅ ΡΠΌΠ°Π·ΠΊΠΈ
3.2.1.1. ΠΠ»Ρ Ρ
ΡΠ°Π½Π΅Π½ΠΈΡ ΠΈ
ΠΏΡΠΈΠ³ΠΎΡΠΎΠ²Π»Π΅Π½ΠΈΡ ΡΠΌΠ°Π·ΠΊΠΈ, ΠΏΡΠΈΠΌΠ΅Π½ΡΠ΅ΠΌΠΎΠΉ Π² ΠΊΠ°Π½Π°ΡΠ½ΠΎΠΌ ΠΏΡΠΎΠΈΠ·Π²ΠΎΠ΄ΡΡΠ²Π΅, Π΄ΠΎΠ»ΠΆΠ½Ρ
Π±ΡΡΡ ΡΠΏΠ΅ΡΠΈΠ°Π»ΡΠ½ΡΠ΅ ΠΏΠΎΠΌΠ΅ΡΠ΅Π½ΠΈΡ, ΠΎΠ±ΠΎΡΡΠ΄ΠΎΠ²Π°Π½Π½ΡΠ΅ Π΅ΠΌΠΊΠΎΡΡΡΠΌΠΈ Π΄Π»Ρ ΠΏΠΎΠ΄ΠΎΠ³ΡΠ΅Π²Π°
ΡΠΌΠ°Π·ΠΊΠΈ, ΠΊΠ°ΠΌΠ΅ΡΠΎΠΉ Π΄Π»Ρ ΡΠ°Π·ΠΎΠ³ΡΠ΅Π²Π° ΡΠΌΠ°Π·ΠΊΠΈ ΠΏΠ°ΡΠΎΠΌ ΠΈ ΡΠ»ΠΈΠ²Π° Π΅Π΅ Π²
Π΅ΠΌΠΊΠΎΡΡΠΈ.
3.2.1.2. ΠΠΎΠ΄Π°ΡΠ° Π±ΠΎΡΠ΅ΠΊ Ρ
ΠΊΠ°Π½Π°ΡΠ½ΠΎΠΉ ΡΠΌΠ°Π·ΠΊΠΎΠΉ Π² ΠΊΠ°ΠΌΠ΅ΡΡ ΡΠ°Π·ΠΎΠ³ΡΠ΅Π²Π° Π΄ΠΎΠ»ΠΆΠ½Π° Π±ΡΡΡ ΠΌΠ΅Ρ
Π°Π½ΠΈΠ·ΠΈΡΠΎΠ²Π°Π½Π°.
3.2.1.3. ΠΠΌΠΊΠΎΡΡΠΈ Π΄ΠΎΠ»ΠΆΠ½Ρ
Π±ΡΡΡ ΠΎΠ±ΠΎΡΡΠ΄ΠΎΠ²Π°Π½Ρ ΡΡΡΡΠΎΠΉΡΡΠ²ΠΎΠΌ, Π½Π΅ Π΄ΠΎΠΏΡΡΠΊΠ°ΡΡΠΈΠΌ ΠΎΠ±ΡΠ°Π·ΠΎΠ²Π°Π½ΠΈΡ Π² Π½ΠΈΡ
ΠΈΠ·Π±ΡΡΠΎΡΠ½ΠΎΠ³ΠΎ Π΄Π°Π²Π»Π΅Π½ΠΈΡ ΠΏΡΠΈ ΡΠ°Π·ΠΎΠ³ΡΠ΅Π²Π΅ ΡΠΌΠ°Π·ΠΊΠΈ.
3.2.2. ΠΠ°ΠΌΠΎΡΠΊΠ° ΠΏΡΠΎΠ²ΠΎΠ»ΠΎΠΊΠΈ ΠΈ ΠΏΡΡΠ΄Π΅ΠΉ Π½Π° ΠΊΠ°ΡΡΡΠΊΠΈ
3.2.2.1. ΠΠΎΠ½ΡΡΡΡΠΊΡΠΈΡ
Π½Π°ΠΌΠΎΡΠΎΡΠ½ΡΡ
ΡΡΠ°Π½ΠΊΠΎΠ² Π΄ΠΎΠ»ΠΆΠ½Π° ΠΎΠ±Π΅ΡΠΏΠ΅ΡΠΈΠ²Π°ΡΡ:
ΠΏΠ»ΠΎΡΠ½ΡΡ ΠΈ ΡΠ°Π²Π½ΠΎΠΌΠ΅ΡΠ½ΡΡ
Π½Π°ΠΌΠΎΡΠΊΡ ΠΏΠΎ ΡΠΈΡΠΈΠ½Π΅ ΠΈ ΠΏΠΎ Π²ΡΡΠΎΡΠ΅ ΠΊΠ°ΡΡΡΠΊΠΈ;
Π½Π°Π΄Π΅ΠΆΠ½ΡΡ Π½Π°ΡΡΡΠΎΠΉΠΊΡ
ΠΌΠ΅Ρ
Π°Π½ΠΈΠ·ΠΌΠ° ΡΠΊΠ»Π°Π΄ΠΊΠΈ Π² Π·Π°Π²ΠΈΡΠΈΠΌΠΎΡΡΠΈ ΠΎΡ Π΄ΠΈΠ°ΠΌΠ΅ΡΡΠ° ΠΏΡΠΎΠ²ΠΎΠ»ΠΎΠΊΠΈ ΠΈ ΡΠ°Π·ΠΌΠ΅ΡΠ°
ΠΊΠ°ΡΡΡΠΊΠΈ;
ΡΠ°Π²Π½ΠΎΠΌΠ΅ΡΠ½ΠΎΠ΅ Π½Π°ΡΡΠΆΠ΅Π½ΠΈΠ΅
ΠΏΡΠΎΠ²ΠΎΠ»ΠΎΠΊΠΈ ΠΏΡΠΈ ΡΠΌΠ°ΡΡΠ²Π°Π½ΠΈΠΈ Π΅Π΅ Ρ ΡΠΈΠ³ΡΡΠΊΠΈ ΠΈΠ»ΠΈ ΠΊΠ°ΡΡΡΠΊΠΈ;
Π°Π²ΡΠΎΠΌΠ°ΡΠΈΡΠ΅ΡΠΊΡΡ ΠΎΡΡΠ°Π½ΠΎΠ²ΠΊΡ
ΠΈ ΡΠΎΡΠΌΠΎΠΆΠ΅Π½ΠΈΠ΅ ΡΡΠ°Π½ΠΊΠ° ΠΏΠΎ ΠΎΠΊΠΎΠ½ΡΠ°Π½ΠΈΠΈ Π½Π°ΠΌΠΎΡΠΊΠΈ ΠΏΡΠΎΠ²ΠΎΠ»ΠΎΠΊΠΈ ΠΈΠ»ΠΈ Π² ΡΠ»ΡΡΠ°Π΅ Π΅Π΅
ΠΎΠ±ΡΡΠ²Π°;
Π±Π΅Π·ΠΎΠΏΠ°ΡΠ½ΡΡ ΡΡΡΠ°Π½ΠΎΠ²ΠΊΡ
ΠΌΠΎΡΠΊΠ° Π½Π° ΡΠΈΠ³ΡΡΠΊΡ, ΠΈΡΠΊΠ»ΡΡΠ°ΡΡΡΡ ΡΠΌΠ΅ΡΠ΅Π½ΠΈΠ΅ ΠΌΠΎΡΠΊΠ° ΠΏΠΎ ΠΎΡΠ½ΠΎΡΠ΅Π½ΠΈΡ ΠΊ ΠΎΡΠΈ
ΡΠΈΠ³ΡΡΠΊΠΈ, ΠΈ Π½Π°Π΄Π΅ΠΆΠ½ΠΎΠ΅ ΠΊΡΠ΅ΠΏΠ»Π΅Π½ΠΈΠ΅ ΠΊΠ°ΡΡΡΠΊΠΈ Π½Π° ΡΠΏΠΈΠ½Π΄Π΅Π»Π΅ Π³ΠΎΠ»ΠΎΠ²ΠΊΠΈ
ΡΡΠ°Π½ΠΊΠ°.
3.2.2.2. ΠΠ°ΠΌΠΎΡΠΎΡΠ½ΡΠ΅
ΡΡΠ°Π½ΠΊΠΈ Ρ Π΄ΠΈΠ°ΠΌΠ΅ΡΡΠΎΠΌ Π΄ΠΈΡΠΊΠ° ΠΊΠ°ΡΡΡΠΊΠΈ Π΄ΠΎ 150 ΠΌΠΌ Π΄Π»Ρ Π½Π°ΠΌΠΎΡΠΊΠΈ ΠΏΡΠΎΠ²ΠΎΠ»ΠΎΠΊΠΈ Ρ
ΠΌΠΎΡΠΊΠΎΠ² Π΄ΠΎΠ»ΠΆΠ½Ρ ΡΡΡΠ°Π½Π°Π²Π»ΠΈΠ²Π°ΡΡΡΡ ΡΠ°ΠΊΠΈΠΌ ΠΎΠ±ΡΠ°Π·ΠΎΠΌ, ΡΡΠΎΠ±Ρ ΠΎΡΡ ΠΊΠ°ΡΡΡΠΊΠΈ Π²
Π½Π°ΠΌΠΎΡΠΎΡΠ½ΠΎΠΌ ΡΡΠ°Π½ΠΊΠ΅ ΡΠ°ΡΠΏΠΎΠ»Π°Π³Π°Π»Π°ΡΡ Π½Π°Π΄ ΡΡΠΎΠ²Π½Π΅ΠΌ ΠΏΠΎΠ»Π° ΡΠ°Π±ΠΎΡΠ΅ΠΉ ΠΏΠ»ΠΎΡΠ°Π΄ΠΊΠΈ Π²
ΠΏΡΠ΅Π΄Π΅Π»Π°Ρ
0,8-1,0 ΠΌ.
3.2.2.3. ΠΠ½ΠΎΠ³ΠΎΠ³ΠΎΠ»ΠΎΠ²ΠΎΡΠ½ΡΠ΅
Π½Π°ΠΌΠΎΡΠΎΡΠ½ΡΠ΅ ΡΡΠ°Π½ΠΊΠΈ Π΄ΠΎΠ»ΠΆΠ½Ρ Π±ΡΡΡ ΠΎΡΠ½Π°ΡΠ΅Π½Ρ ΠΎΡΠ΄Π΅Π»ΡΠ½ΡΠΌΠΈ ΠΏΠ΅ΡΠ΅Π²ΠΎΠ΄Π½ΡΠΌΠΈ
ΠΌΠ΅Ρ
Π°Π½ΠΈΠ·ΠΌΠ°ΠΌΠΈ, ΠΈΡΠΊΠ»ΡΡΠ°ΡΡΠΈΠΌΠΈ ΡΠ°ΠΌΠΎΠΏΡΠΎΠΈΠ·Π²ΠΎΠ»ΡΠ½ΡΠΉ ΠΏΠ΅ΡΠ΅Ρ
ΠΎΠ΄ ΡΠ΅ΠΌΠ½Ρ Ρ
Ρ
ΠΎΠ»ΠΎΡΡΠΎΠ³ΠΎ Π½Π° ΡΠ°Π±ΠΎΡΠΈΠΉ ΡΠΊΠΈΠ². ΠΠ΅ΡΠ΅Π²ΠΎΠ΄Π½ΠΎΠΉ ΠΌΠ΅Ρ
Π°Π½ΠΈΠ·ΠΌ Π΄ΠΎΠ»ΠΆΠ΅Π½ ΠΎΠ±Π΅ΡΠΏΠ΅ΡΠΈΠ²Π°ΡΡ
ΠΎΡΡΠ°Π½ΠΎΠ²ΠΊΡ Π³ΠΎΠ»ΠΎΠ²ΠΊΠΈ ΠΊΠ°ΠΊ ΡΠΎ ΡΡΠΎΡΠΎΠ½Ρ ΠΊΠ°ΡΡΡΠΊΠΈ, ΡΠ°ΠΊ ΠΈ ΡΠΎ ΡΡΠΎΡΠΎΠ½Ρ
ΡΠΈΠ³ΡΡΠΊΠΈ.
3.2.2.4. Π€ΠΈΠ³ΡΡΠΊΠΈ Π΄Π»Ρ
ΡΠ°Π·ΠΌΠ΅ΡΠ΅Π½ΠΈΡ ΠΌΠΎΡΠΊΠΎΠ² ΠΏΠ΅ΡΠ΅ΠΌΠ°ΡΡΠ²Π°Π΅ΠΌΠΎΠΉ ΠΏΡΠΎΠ²ΠΎΠ»ΠΎΠΊΠΈ Π΄ΠΎΠ»ΠΆΠ½Ρ ΡΠΎΠΎΡΠ²Π΅ΡΡΡΠ²ΠΎΠ²Π°ΡΡ
ΡΠ°Π·ΠΌΠ΅ΡΠ°ΠΌ ΠΌΠΎΡΠΊΠΎΠ² ΠΈ ΠΎΠ±Π΅ΡΠΏΠ΅ΡΠΈΠ²Π°ΡΡ ΡΠ°Π·ΠΌΠ΅ΡΠ΅Π½ΠΈΠ΅ Π²ΡΠ΅Ρ
Π²ΠΈΡΠΊΠΎΠ² Π½Π° ΡΠΈΠ³ΡΡΠΊΠ΅,
Π±Π΅Π· ΠΎΡΠ΅Π΄Π°Π½ΠΈΡ ΠΈΡ
Π½Π° ΠΎΡΠ½ΠΎΠ²Π°Π½ΠΈΠΈ ΡΠΈΠ³ΡΡΠΊΠΈ.
3.2.2.5. Π Π°ΡΠΏΠΎΠ»ΠΎΠΆΠ΅Π½ΠΈΠ΅
ΡΠΈΠ³ΡΡΠΎΠΊ Π½Π° ΠΎΠ±ΡΠΈΡ
ΡΡΠ°Π½ΠΈΠ½Π°Ρ
Ρ Π½Π°ΠΌΠΎΡΠΎΡΠ½ΡΠΌΠΈ ΡΡΠ°Π½ΠΊΠ°ΠΌΠΈ Π΄ΠΎΠΏΡΡΠΊΠ°Π΅ΡΡΡ ΡΠΎΠ»ΡΠΊΠΎ
ΠΏΡΠΈ ΠΏΠ΅ΡΠ΅ΠΌΠΎΡΠΊΠ΅ ΠΌΠΎΡΠΊΠΎΠ² ΠΌΠ°Π»ΠΎΠ³ΠΎ ΡΠ°Π·ΠΌΠ΅ΡΠ° ΠΏΡΠΈ Π΄ΠΈΠ°ΠΌΠ΅ΡΡΠ°Ρ
ΠΏΡΠΎΠ²ΠΎΠ»ΠΎΠΊΠΈ Π΄ΠΎ 1
ΠΌΠΌ.
3.2.2.6. ΠΡΠΈ ΠΏΠ΅ΡΠ΅ΠΌΠΎΡΠΊΠ΅
ΠΌΠΎΡΠΊΠΎΠ² ΠΏΡΠΎΠ²ΠΎΠ»ΠΎΠΊΠΈ ΡΡΠ΅Π΄Π½Π΅Π³ΠΎ ΠΈ Π±ΠΎΠ»ΡΡΠΎΠ³ΠΎ ΡΠ°Π·ΠΌΠ΅ΡΠ° (Π΄ΠΈΠ°ΠΌΠ΅ΡΡΠΎΠΌ Π±ΠΎΠ»Π΅Π΅ 1 ΠΌΠΌ)
ΡΠΈΠ³ΡΡΠΊΠΈ Π΄ΠΎΠ»ΠΆΠ½Ρ ΡΠ°ΡΠΏΠΎΠ»Π°Π³Π°ΡΡΡΡ Π½Π° ΠΎΡΠ΄Π΅Π»ΡΠ½ΡΡ
ΡΡΡΠΎΠΉΡΠΈΠ²ΡΡ
ΠΎΡΠ½ΠΎΠ²Π°Π½ΠΈΡΡ
.
3.2.2.7. Π¨ΠΈΡΠΈΠ½Π° ΠΊΠ°ΡΡΡΠ΅ΠΊ
Π΄ΠΎΠ»ΠΆΠ½Π° ΡΠΎΠΎΡΠ²Π΅ΡΡΡΠ²ΠΎΠ²Π°ΡΡ ΡΠ°Π·ΠΌΠ΅ΡΡ ΠΊΠ°ΡΠ΅ΡΠΎΠΊ ΠΏΡΡΠ΄Π΅Π²ΡΡΡΠΈΡ
ΠΈ ΠΊΠ°Π½Π°ΡΠΎΠ²ΡΡΡΠΈΡ
ΠΌΠ°ΡΠΈΠ½.
3.2.2.8. ΠΡΠΈ ΠΎΡΠ²Π΅ΡΡΡΠΈΠΉ
ΠΊΠ°ΡΡΡΠ΅ΠΊ ΠΈ ΡΠΎΡΠΌΠΎΠ·Π½ΡΡ
ΡΠΊΠΈΠ²ΠΎΠ², Π·Π°ΠΊΡΠ΅ΠΏΠ»Π΅Π½Π½ΡΡ
Π½Π° Π΄ΠΈΡΠΊΠ°Ρ
ΠΊΠ°ΡΡΡΠ΅ΠΊ, Π΄ΠΎΠ»ΠΆΠ½Ρ
ΡΠΎΠ²ΠΏΠ°Π΄Π°ΡΡ Π΄Π»Ρ ΠΎΠ±Π΅ΡΠΏΠ΅ΡΠ΅Π½ΠΈΡ ΡΠ°Π²Π½ΠΎΠΌΠ΅ΡΠ½ΠΎΡΡΠΈ ΡΠΎΡΠΌΠΎΠΆΠ΅Π½ΠΈΡ ΠΊΠ°ΡΡΡΠ΅ΠΊ ΠΏΡΠΈ
ΡΠΌΠ°ΡΡΠ²Π°Π½ΠΈΠΈ Ρ Π½ΠΈΡ
ΠΏΡΠΎΠ²ΠΎΠ»ΠΎΠΊΠΈ Π² ΠΏΡΡΠ΄Π΅Π²ΡΡΡΠΈΡ
ΠΈ ΠΊΠ°Π½Π°ΡΠΎΠ²ΡΡΡΠΈΡ
ΠΌΠ°ΡΠΈΠ½Π°Ρ
.
3.2.2.9. ΠΠ»Ρ
ΡΡΠ°Π½ΡΠΏΠΎΡΡΠΈΡΠΎΠ²ΠΊΠΈ ΠΏΡΡΡΡΡ
ΠΊΠ°ΡΡΡΠ΅ΠΊ ΠΈ ΠΊΠ°ΡΡΡΠ΅ΠΊ Ρ ΠΏΡΠΎΠ²ΠΎΠ»ΠΎΠΊΠΎΠΉ Π΄ΠΎΠ»ΠΆΠ½Ρ
ΠΏΡΠΈΠΌΠ΅Π½ΡΡΡΡΡ ΠΏΠΎΠ΄ΡΠ΅ΠΌΠ½ΠΎ-ΡΡΠ°Π½ΡΠΏΠΎΡΡΠ½ΡΠ΅ ΠΌΠ΅Ρ
Π°Π½ΠΈΠ·ΠΌΡ.
3.2.2.10. Π‘ΠΎΠ΅Π΄ΠΈΠ½Π΅Π½ΠΈΠ΅
ΠΊΠΎΠ½ΡΠΎΠ² ΠΏΡΠΎΠ²ΠΎΠ»ΠΎΠΊΠΈ ΠΏΡΠΈ Π½Π°ΠΌΠΎΡΠΊΠ΅ Π½Π° ΠΊΠ°ΡΡΡΠΊΠΈ Π΄ΠΎΠ»ΠΆΠ½ΠΎ ΠΏΡΠΎΠΈΠ·Π²ΠΎΠ΄ΠΈΡΡΡΡ Π½Π°
ΡΠ»Π΅ΠΊΡΡΠΈΡΠ΅ΡΠΊΠΈΡ
Π°ΠΏΠΏΠ°ΡΠ°ΡΠ°Ρ
ΡΡΡΠΊΠΎΠ²ΠΎΠΉ ΡΠ²Π°ΡΠΊΠΈ, ΠΊΠΎΡΠΎΡΡΠ΅ Π΄ΠΎΠ»ΠΆΠ½Ρ Π±ΡΡΡ
Π·Π°Π·Π΅ΠΌΠ»Π΅Π½Ρ.
3.2.2.11. ΠΡΠ²ΠΎΠ±ΠΎΠΆΠ΄Π΅Π½ΠΈΠ΅
ΠΊΠ°ΡΡΡΠ΅ΠΊ ΠΎΡ ΠΎΡΡΠ°ΡΠΊΠ° ΠΏΡΠΎΠ²ΠΎΠ»ΠΎΠΊΠΈ Π΄ΠΎΠ»ΠΆΠ½ΠΎ ΠΏΡΠΎΠΈΠ·Π²ΠΎΠ΄ΠΈΡΡΡΡ Π½Π° ΡΡΠ°Π½ΠΊΠ°Ρ
,
ΠΎΡΠ½Π°ΡΠ΅Π½Π½ΡΡ
ΠΏΡΠΈΡΠΏΠΎΡΠΎΠ±Π»Π΅Π½ΠΈΠ΅ΠΌ Π΄Π»Ρ ΡΡΡΠ°Π½ΠΎΠ²ΠΊΠΈ ΠΊΠ°ΡΡΡΠ΅ΠΊ Ρ ΠΏΡΠΎΠ²ΠΎΠ»ΠΎΠΊΠΎΠΉ. ΠΠ»Ρ
ΠΏΠ΅ΡΠ΅ΠΌΠΎΡΠΊΠΈ ΠΏΡΠΎΠ²ΠΎΠ»ΠΎΠΊΠΈ Ρ ΠΊΠ°ΡΡΡΠ΅ΠΊ Π² ΠΌΠΎΡΠΊΠΈ ΠΏΠ΅ΡΠ΅ΠΌΠΎΡΠΎΡΠ½ΡΠΉ ΡΡΠ°Π½ΠΎΠΊ Π΄ΠΎΠ»ΠΆΠ΅Π½
Π±ΡΡΡ ΠΎΠ±ΠΎΡΡΠ΄ΠΎΠ²Π°Π½ Π±Π°ΡΠ°Π±Π°Π½ΠΎΠΌ, ΠΏΠ»ΠΎΡΠ½ΠΎΡΡΡ Π½Π°ΠΌΠΎΡΠΊΠΈ ΠΈ ΡΠΎΡΠΌΠΈΡΠΎΠ²Π°Π½ΠΈΠ΅ ΠΌΠΎΡΠΊΠ°
Π½Π° ΠΊΠΎΡΠΎΡΠΎΠΌ Π΄ΠΎΠ»ΠΆΠ½Ρ ΠΎΠ±Π΅ΡΠΏΠ΅ΡΠΈΠ²Π°ΡΡΡΡ Π½Π°ΡΡΠΆΠ΅Π½ΠΈΠ΅ΠΌ ΠΏΠ΅ΡΠ΅ΠΌΠ°ΡΡΠ²Π°Π΅ΠΌΠΎΠΉ
ΠΏΡΠΎΠ²ΠΎΠ»ΠΎΠΊΠΈ.
3.2.3. ΠΠ·Π³ΠΎΡΠΎΠ²Π»Π΅Π½ΠΈΠ΅ ΠΏΡΡΠ΄Π΅ΠΉ ΠΈ ΠΊΠ°Π½Π°ΡΠΎΠ²
3.2.3.1. ΠΡΡΠ΄Π΅Π²ΡΡΡΠΈΠ΅ ΠΈ
ΠΊΠ°Π½Π°ΡΠΎΠ²ΡΡΡΠΈΠ΅ ΠΌΠ°ΡΠΈΠ½Ρ Π΄ΠΎΠ»ΠΆΠ½Ρ Π±ΡΡΡ ΠΎΠ±ΠΎΡΡΠ΄ΠΎΠ²Π°Π½Ρ ΡΠ΅ΠΊΡΠΈΠΎΠ½Π½ΡΠΌΠΈ
ΠΎΠ³ΡΠ°ΠΆΠ΄Π΅Π½ΠΈΡΠΌΠΈ, ΡΠ΄ΠΎΠ±Π½ΡΠΌΠΈ Π΄Π»Ρ ΡΠΊΡΠΏΠ»ΡΠ°ΡΠ°ΡΠΈΠΈ ΠΊΠ°ΡΠ΅ΡΠΎΠΊ (ΡΠ°ΠΌ) ΠΌΠ°ΡΠΈΠ½.
ΠΡΠΊΡΡΠ²Π°ΡΡΠΈΠ΅ΡΡ ΠΈ ΡΠ°Π·Π΄Π²ΠΈΠΆΠ½ΡΠ΅ ΡΠ°ΡΡΠΈ ΠΎΠ³ΡΠ°ΠΆΠ΄Π΅Π½ΠΈΠΉ Π΄ΠΎΠ»ΠΆΠ½Ρ ΠΈΠΌΠ΅ΡΡ
Π±Π»ΠΎΠΊΠΈΡΠΎΠ²ΠΊΡ, ΠΈΡΠΊΠ»ΡΡΠ°ΡΡΡΡ ΠΏΡΡΠΊ ΠΈ ΡΠ°Π±ΠΎΡΡ ΠΌΠ°ΡΠΈΠ½Ρ ΠΏΡΠΈ ΠΎΡΠΊΡΡΡΡΡ
ΠΈΠ»ΠΈ
Π½Π΅ΠΏΠ»ΠΎΡΠ½ΠΎ Π·Π°ΠΊΡΡΡΡΡ
ΠΎΠ³ΡΠ°ΠΆΠ΄Π΅Π½ΠΈΡΡ
.
3.2.3.2. ΠΠ° ΡΠΈΠ³Π°ΡΠ½ΡΡ
ΠΌΠ°ΡΠΈΠ½Π°Ρ
Ρ ΠΊΠ°ΡΡΡΠΊΠ°ΠΌΠΈ Π΄ΠΈΠ°ΠΌΠ΅ΡΡΠΎΠΌ Π΄ΠΎ 315 ΠΌΠΌ Π΄ΠΎΠΏΡΡΠΊΠ°Π΅ΡΡΡ ΠΏΡΠΈΠΌΠ΅Π½ΡΡΡ
ΠΎΡΠΊΡΡΠ²Π°ΡΡΠΈΠ΅ΡΡ ΠΏΡΡΡΠΊΠΎΠ²ΡΠ΅, ΡΠ΅ΡΡΠ°ΡΡΠ΅ ΠΈΠ»ΠΈ ΠΏΠ΅ΡΡΠΎΡΠΈΡΠΎΠ²Π°Π½Π½ΡΠ΅ Π»ΠΈΡΡΠΎΠ²ΡΠ΅
ΠΎΠ³ΡΠ°ΠΆΠ΄Π΅Π½ΠΈΡ Π½Π° ΠΊΠ°ΠΆΠ΄ΠΎΠΉ ΡΠ΅ΠΊΡΠΈΠΈ. ΠΠ°ΡΠΈΠ½Ρ Ρ ΠΊΠ°ΡΡΡΠΊΠ°ΠΌΠΈ Π΄ΠΈΠ°ΠΌΠ΅ΡΡΠΎΠΌ Π±ΠΎΠ»Π΅Π΅ 315
ΠΌΠΌ Π½Π° ΠΊΠ°ΠΆΠ΄ΠΎΠΉ ΡΠ΅ΠΊΡΠΈΠΈ Π΄ΠΎΠ»ΠΆΠ½Ρ ΠΈΠΌΠ΅ΡΡ ΠΎΠ³ΡΠ°ΠΆΠ΄Π΅Π½ΠΈΡ ΠΈΠ· Π΄Π²ΡΡ
ΠΈΠ»ΠΈ Π½Π΅ΡΠΊΠΎΠ»ΡΠΊΠΈΡ
ΡΠ΄Π²ΠΈΠ³Π°ΡΡΠΈΡ
ΡΡ ΠΈΠ»ΠΈ ΠΎΡΠΊΡΡΠ²Π°ΡΡΠΈΡ
ΡΡ ΡΠ°ΡΡΠ΅ΠΉ.
3.2.3.3. ΠΠ³ΡΠ°ΠΆΠ΄Π΅Π½ΠΈΡ
ΠΊΠΎΡΠ·ΠΈΠ½ΠΎΡΠ½ΡΡ
ΠΌΠ°ΡΠΈΠ½ Π΄ΠΎΠ»ΠΆΠ½Ρ Π±ΡΡΡ ΡΡΡΠ°Π½ΠΎΠ²Π»Π΅Π½Ρ Π½Π° Π²ΡΡΠΎΡΡ Π½Π΅ ΠΌΠ΅Π½Π΅Π΅ Π²ΡΡΠΎΡΡ
ΡΠΎΡΠΎΡΠ° ΠΌΠ°ΡΠΈΠ½Ρ.
3.2.3.4. ΠΡΡΠ΄Π΅Π²ΡΡΡΠΈΠ΅ ΠΈ
ΠΊΠ°Π½Π°ΡΠΎΠ²ΡΡΡΠΈΠ΅ ΠΌΠ°ΡΠΈΠ½Ρ Π΄ΠΎΠ»ΠΆΠ½Ρ Π±ΡΡΡ ΠΎΠ±ΠΎΡΡΠ΄ΠΎΠ²Π°Π½Ρ ΡΡΡΡΠΎΠΉΡΡΠ²ΠΎΠΌ
Π°Π²ΡΠΎΠΌΠ°ΡΠΈΡΠ΅ΡΠΊΠΎΠΉ ΠΎΡΡΠ°Π½ΠΎΠ²ΠΊΠΈ ΠΏΡΠΈ ΠΎΠ±ΡΡΠ²Π΅ ΠΏΡΠΎΠ²ΠΎΠ»ΠΎΠΊΠΈ (ΠΏΡΡΠ΄ΠΈ) ΠΈΠ»ΠΈ ΠΏΡΠΈ
Π²ΡΡ
ΠΎΠ΄Π΅ ΠΈΡ
ΠΊΠΎΠ½ΡΠ°, Π° ΡΠ°ΠΊΠΆΠ΅ ΡΡΠ΅Π΄ΡΡΠ²Π°ΠΌΠΈ ΡΠΎΡΠΌΠΎΠΆΠ΅Π½ΠΈΡ ΠΌΠ°ΡΠΈΠ½Ρ.
3.2.3.5. Π¨Π΅ΡΡΠ΅ΡΠ½ΠΈ Π²
Π²Π΅ΡΡΠΈΠΊΠ°Π»ΡΠ½ΡΡ
ΠΊΠ°Π½Π°ΡΠΎΠ²ΡΡΡΠΈΡ
ΠΌΠ°ΡΠΈΠ½Π°Ρ
ΠΊΠΎΡΠ·ΠΈΠ½ΠΎΡΠ½ΠΎΠ³ΠΎ ΡΠΈΠΏΠ° Π΄ΠΎΠ»ΠΆΠ½Ρ Π±ΡΡΡ
Π½Π°Π΄Π΅ΠΆΠ½ΠΎ ΠΎΠ³ΡΠ°ΠΆΠ΄Π΅Π½Ρ ΠΎΡ Π²ΠΎΠ·ΠΌΠΎΠΆΠ½ΠΎΠ³ΠΎ ΠΏΠΎΠΏΠ°Π΄Π°Π½ΠΈΡ Π² Π½ΠΈΡ
ΠΊΠΎΠ½ΡΠΎΠ² ΠΏΡΡΠ΄Π΅ΠΉ.
3.2.3.6. ΠΠ°ΡΠ΅ΡΠΊΠΈ (ΡΠ°ΠΌΡ)
ΠΏΡΡΠ΄Π΅Π²ΡΡΡΠΈΡ
ΠΌΠ°ΡΠΈΠ½ Π΄ΠΎΠ»ΠΆΠ½Ρ Π±ΡΡΡ ΡΠΎΠ»ΡΠΊΠΎ ΡΡΠ°Π»ΡΠ½ΡΠΌΠΈ (Π»ΠΈΡΡΠΌΠΈ ΠΈΠ»ΠΈ
ΡΠ²Π°ΡΠ½ΡΠΌΠΈ).
3.2.3.7. ΠΠΎΠ½ΡΡΡΡΠΊΡΠΈΡ
ΠΊΠ°ΡΠ΅ΡΠΎΠΊ ΡΠΈΠ³Π°ΡΠ½ΡΡ
ΠΌΠ°ΡΠΈΠ½ Π΄ΠΎΠ»ΠΆΠ½Π° ΠΎΠ±Π΅ΡΠΏΠ΅ΡΠΈΠ²Π°ΡΡ ΠΈΡ
ΡΡΡΠΎΠΉΡΠΈΠ²ΠΎΡΡΡ Ρ
Π·Π°ΠΊΡΠ΅ΠΏΠ»Π΅Π½Π½ΡΠΌΠΈ Π² Π½ΠΈΡ
ΠΊΠ°ΡΡΡΠΊΠ°ΠΌΠΈ ΠΈ Π½Π΅ Π΄ΠΎΠΏΡΡΠΊΠ°ΡΡ Π²ΡΠ°ΡΠ΅Π½ΠΈΡ ΠΈΠ»ΠΈ ΠΊΠ°ΡΠ΅Π½ΠΈΡ
(Π±ΠΎΠ»Π΅Π΅ 30Β°) ΠΊΠ°ΡΠ΅ΡΠΎΠΊ ΠΏΡΠΈ Π²ΡΠ°ΡΠ΅Π½ΠΈΠΈ ΡΠΎΡΠΎΡΠ° ΠΌΠ°ΡΠΈΠ½Ρ.
3.2.3.8. ΠΠΎΠ½ΡΡΡΡΠΊΡΠΈΡ ΠΈ
ΠΏΡΠΎΡΠ½ΠΎΡΡΡ ΠΊΠ°ΡΠ΅ΡΠΎΠΊ, ΡΠΏΠΎΡΠΎΠ± ΠΊΡΠ΅ΠΏΠ»Π΅Π½ΠΈΡ ΠΈΡ
ΠΎΠΏΠΎΡΠ½ΡΡ
Ρ
Π²ΠΎΡΡΠΎΠ²ΡΡ
ΡΠ°ΡΡΠ΅ΠΉ,
ΡΠΏΠΎΡΠΎΠ± ΠΊΡΠ΅ΠΏΠ»Π΅Π½ΠΈΡ ΠΊΠ°ΡΡΡΠΊΠΈ ΠΊ ΠΊΠ°ΡΠ΅ΡΠΊΠ΅ Π΄ΠΎΠ»ΠΆΠ½Ρ ΠΈΡΠΊΠ»ΡΡΠ°ΡΡ Π²ΠΎΠ·ΠΌΠΎΠΆΠ½ΠΎΡΡΡ
Π²ΡΠ±ΡΠΎΡΠ° ΠΊΠ°ΡΡΡΠΊΠΈ ΠΈΠ· ΠΏΡΡΠ΄Π΅Π²ΡΡΡΠΈΡ
ΠΈ ΠΊΠ°Π½Π°ΡΠΎΠ²ΡΡΡΠΈΡ
ΠΌΠ°ΡΠΈΠ½.
3.2.3.9. ΠΠ°ΡΡΠ΄ΠΊΠ°
ΠΊΠ°Π½Π°ΡΠΎΠ²ΡΡΡΠΈΡ
ΠΈ ΠΏΡΡΠ΄Π΅Π²ΡΡΡΠΈΡ
ΠΌΠ°ΡΠΈΠ½ Π΄ΠΎΠ»ΠΆΠ½Π° ΠΏΡΠΎΠΈΠ·Π²ΠΎΠ΄ΠΈΡΡΡΡ ΡΠ΅ΠΏΠ½ΡΠΌΠΈ ΠΈΠ»ΠΈ
ΠΊΠ°Π½Π°ΡΠ½ΡΠΌΠΈ ΡΡΡΠΎΠΏΠ°ΠΌΠΈ.
3.2.3.10. ΠΠ»Ρ ΡΠΎΡΠΌΠΎΠΆΠ΅Π½ΠΈΡ
ΡΠΎΡΠΎΡΠ° ΠΊΠΎΡΠ·ΠΈΠ½ΠΎΡΠ½ΡΡ
ΠΌΠ°ΡΠΈΠ½ Π΄ΠΎΠ»ΠΆΠ½Ρ ΠΏΡΠΈΠΌΠ΅Π½ΡΡΡΡΡ Π±ΡΡΡΡΠΎΠ΄Π΅ΠΉΡΡΠ²ΡΡΡΠΈΠ΅
ΡΠΎΡΠΌΠΎΠ·Π° ΠΊΠΎΠ»ΠΎΠ΄ΠΎΡΠ½ΠΎΠ³ΠΎ ΡΠΈΠΏΠ°.
3.2.3.11. ΠΡΠΎΡΡΡΠ°Π½ΡΡΠ²ΠΎ
ΠΌΠ΅ΠΆΠ΄Ρ Π²ΡΡΡΠΆΠ½ΡΠΌ ΡΠΊΠΈΠ²ΠΎΠΌ ΠΈ Π½Π°ΡΡΠΈΠ»ΠΎΠΌ ΠΏΡΠΈΡΠΌΠΊΠ° Π²ΡΡΡΠΆΠ½ΠΎΠ³ΠΎ ΡΠΊΠΈΠ²Π° Π΄ΠΎΠ»ΠΆΠ½ΠΎ
Π±ΡΡΡ ΠΎΠ³ΡΠ°ΠΆΠ΄Π΅Π½ΠΎ Π±ΠΎΡΡΠΈΠΊΠΎΠΌ Π²ΡΡΠΎΡΠΎΠΉ Π½Π΅ ΠΌΠ΅Π½Π΅Π΅ 50 ΠΌΠΌ.
3.2.3.12. ΠΠΎΠ΄Π°ΡΠ° ΡΠΌΠ°Π·ΠΊΠΈ
Π΄ΠΎΠ»ΠΆΠ½Π° ΠΎΡΡΡΠ΅ΡΡΠ²Π»ΡΡΡΡΡ Π½Π°ΡΠΎΡΠΎΠΌ. ΠΠ°Π½Π½Ρ ΡΠΎ ΡΠΌΠ°Π·ΠΊΠΎΠΉ ΠΊΠ°Π½Π°ΡΠΎΠ²ΡΡΡΠΈΡ
ΠΈ
ΠΏΡΡΠ΄Π΅Π²ΡΡΡΠΈΡ
ΠΌΠ°ΡΠΈΠ½ Π΄ΠΎΠ»ΠΆΠ½Ρ Π±ΡΡΡ ΡΠ½Π°Π±ΠΆΠ΅Π½Ρ ΡΠ΅ΡΠΌΠΎΡΠ΅Π³ΡΠ»ΡΡΠΎΡΠΎΠΌ,
ΡΠ΅ΠΏΠ»ΠΎΠΎΠ±ΠΌΠ΅Π½Π½ΠΈΠΊΠΎΠΌ ΠΈ ΡΡΡΡΠΎΠΉΡΡΠ²ΠΎΠΌ, ΠΏΡΠ΅Π΄ΠΎΡΠ²ΡΠ°ΡΠ°ΡΡΠΈΠΌ ΡΠ°Π·Π±ΡΡΠ·Π³ΠΈΠ²Π°Π½ΠΈΠ΅
ΡΠΌΠ°Π·ΠΊΠΈ.
3.2.3.13. ΠΡΠΎΠ½ΡΡΠ΅ΠΉΠ½ ΠΈ
ΠΏΡΠΈΡΠΏΠΎΡΠΎΠ±Π»Π΅Π½ΠΈΡ Π΄Π»Ρ ΡΡΡΠ°Π½ΠΎΠ²ΠΊΠΈ ΠΊΠ°ΡΡΡΠ΅ΠΊ Ρ ΡΠ΅ΡΠ΄Π΅ΡΠ½ΠΈΠΊΠΎΠΌ ΠΈΠ»ΠΈ ΠΏΡΡΠ΄ΡΡ ΠΏΠ΅ΡΠ΅Π΄
ΠΏΡΡΠ΄Π΅Π²ΡΡΡΠΈΠΌΠΈ ΠΈ ΠΊΠ°Π½Π°ΡΠΎΠ²ΡΡΡΠΈΠΌΠΈ ΠΌΠ°ΡΠΈΠ½Π°ΠΌΠΈ Π΄ΠΎΠ»ΠΆΠ½Ρ Π±ΡΡΡ ΡΠ½Π°Π±ΠΆΠ΅Π½Ρ
ΡΠ΅Π³ΡΠ»ΠΈΡΡΠ΅ΠΌΡΠΌ ΡΠΎΡΠΌΠΎΠ·Π½ΡΠΌ ΡΡΡΡΠΎΠΉΡΡΠ²ΠΎΠΌ.
3.2.3.14. ΠΠΎΠ½ΡΠ°ΠΊΡΡ
ΡΠ»Π΅ΠΊΡΡΠΎΠ°ΠΏΠΏΠ°ΡΠ°ΡΠ° Π΄Π»Ρ ΡΠ΅Π·ΠΊΠΈ ΠΊΠ°Π½Π°ΡΠ° ΠΈΠ»ΠΈ ΠΏΡΡΠ΄ΠΈ Π΄ΠΎΠ»ΠΆΠ½Ρ Π±ΡΡΡ Π·Π°ΠΊΡΡΡΡ
ΡΠΈΡΠΊΠΎΠΌ ΠΎΡ Π²ΡΠ±ΡΠΎΡΠ° ΠΈΡΠΊΡ ΠΈΠ»ΠΈ ΠΎΠΏΠ»Π°Π²Π»Π΅Π½Π½ΡΡ
ΡΠ°ΡΡΠΈΡ ΠΈΠ· Π·ΠΎΠ½Ρ ΡΠ΅Π·Π°Π½ΠΈΡ.
3.2.3.15. ΠΠΈΡΠΊΠΈ
ΡΡΠΈΠΊΡΠΈΠΎΠ½Π½ΡΡ
ΠΏΠΈΠ» Π΄Π»Ρ ΡΠ΅Π·ΠΊΠΈ ΠΊΠ°Π½Π°ΡΠΎΠ² ΠΈ ΠΈΡ
ΠΏΡΠΈΠ²ΠΎΠ΄Ρ Π΄ΠΎΠ»ΠΆΠ½Ρ ΠΈΠΌΠ΅ΡΡ
ΠΎΠ³ΡΠ°ΠΆΠ΄Π΅Π½ΠΈΡ.
3.2.3.16. ΠΡΠΈ ΡΠ΅Π·ΠΊΠ΅
ΠΊΠ°Π½Π°ΡΠΎΠ² ΡΡΠΈΠΊΡΠΈΠΎΠ½Π½ΡΠΌΠΈ ΠΏΠΈΠ»Π°ΠΌΠΈ Π΄ΠΎΠ»ΠΆΠ½Ρ ΠΎΠ±Π΅ΡΠΏΠ΅ΡΠΈΠ²Π°ΡΡΡΡ ΠΏΡΠΎΡΠΈΠ²ΠΎΠΏΠΎΠΆΠ°ΡΠ½ΡΠ΅
ΠΌΠ΅ΡΡ.
3.2.3.17. ΠΠ»Ρ ΡΡΡΠ½ΠΎΠΉ
ΡΠ΅Π·ΠΊΠΈ ΠΊΠ°Π½Π°ΡΠΎΠ² Π΄ΠΎΠΏΡΡΠΊΠ°Π΅ΡΡΡ ΠΏΡΠΈΠΌΠ΅Π½ΡΡΡ Π½ΠΎΠΆΠ½ΠΈΡΡ ΡΡΡΠ°ΠΆΠ½ΠΎΠ³ΠΎ, Π²ΠΈΠ½ΡΠΎΠ²ΠΎΠ³ΠΎ
ΠΈΠ»ΠΈ Π³ΠΈΠ»ΡΠΎΡΠΈΠ½Π½ΠΎΠ³ΠΎ ΡΠΈΠΏΠ° Ρ ΡΡΡΠ½ΡΠΌ ΠΏΡΠΈΠ²ΠΎΠ΄ΠΎΠΌ. ΠΡΠΈΠΌΠ΅Π½ΡΡΡ Π΄Π»Ρ ΡΡΠΎΠΉ ΡΠ΅Π»ΠΈ
Π·ΡΠ±ΠΈΠ»ΠΎ Π·Π°ΠΏΡΠ΅ΡΠ°Π΅ΡΡΡ.
3.2.3.18. Π‘ΠΏΠ΅ΡΠΈΠ°Π»ΡΠ½ΡΠΉ Π½ΠΎΠΆ
Π΄Π»Ρ ΡΡΠ°ΡΠΈΠ²Π°Π½ΠΈΡ ΠΎΡΠ³Π°Π½ΠΈΡΠ΅ΡΠΊΠΈΡ
ΡΠ΅ΡΠ΄Π΅ΡΠ½ΠΈΠΊΠΎΠ² Π΄ΠΎΠ»ΠΆΠ΅Π½ ΠΈΠΌΠ΅ΡΡ
Π½Π΅ΠΌΠ΅ΡΠ°Π»Π»ΠΈΡΠ΅ΡΠΊΡΡ ΡΡΡΠΊΡ Π΄Π»ΠΈΠ½ΠΎΠΉ Π½Π΅ ΠΌΠ΅Π½Π΅Π΅ 120 ΠΌΠΌ. ΠΠ»Π°ΡΡΠΈΠ½Π° Π½ΠΎΠΆΠ° Π΄ΠΎΠ»ΠΆΠ½Π°
Π±ΡΡΡ ΠΈΠ·Π³ΠΎΡΠΎΠ²Π»Π΅Π½Π° ΠΈΠ· Π²ΡΠ·ΠΊΠΈΡ
ΡΡΠ°Π»Π΅ΠΉ ΡΠΎΠ»ΡΠΈΠ½ΠΎΠΉ 1,5-2,0 ΠΌΠΌ ΠΈ Π΄Π»ΠΈΠ½ΠΎΠΉ Π½Π΅
Π±ΠΎΠ»Π΅Π΅ 80 ΠΌΠΌ. ΠΠΎΠ½Π΅Ρ Π½ΠΎΠΆΠ° Π΄ΠΎΠ»ΠΆΠ΅Π½ Π±ΡΡΡ ΡΡΠΏΡΠΌ, ΠΎΠ²Π°Π»ΡΠ½ΠΎΠΉ ΠΈΠ»ΠΈ
ΠΏΡΡΠΌΠΎΡΠ³ΠΎΠ»ΡΠ½ΠΎΠΉ ΡΠΎΡΠΌΡ.
3.2.3.19. ΠΡΡΠ°ΡΠΊΠΈ Π΄ΠΎΠ»ΠΆΠ½Ρ
Π±ΡΡΡ Π·Π°ΡΠΎΡΠ΅Π½Ρ, Π½Π° ΡΠ΅ΠΆΡΡΠ΅ΠΉ ΡΠ°ΡΡΠΈ Π½Π΅ Π΄ΠΎΠ»ΠΆΠ½ΠΎ Π±ΡΡΡ Π²ΠΌΡΡΠΈΠ½ ΠΈ ΡΠΊΠΎΠ»ΠΎΠ².
3.2.3.20. ΠΡΠΈ
ΠΈΠ·Π³ΠΎΡΠΎΠ²Π»Π΅Π½ΠΈΠΈ ΠΏΠ»ΠΎΡΠΊΠΈΡ
ΠΊΠ°Π½Π°ΡΠΎΠ² Π΄ΠΎΠ»ΠΆΠ½Ρ ΠΏΡΠΈΠΌΠ΅Π½ΡΡΡΡΡ ΠΏΠΎΠ΄Π²ΠΈΠΆΠ½ΡΠ΅
ΠΏΠΎΠ²ΠΎΡΠΎΡΠ½ΡΠ΅ ΡΡΠΎΠ»Ρ-ΡΠ΅Π»Π΅ΠΆΠΊΠΈ.
3.2.3.21. Π‘Π½ΡΡΠΈΠ΅ ΠΎΡΡΠ°ΡΠΊΠΎΠ²
ΠΏΡΠΎΠ²ΠΎΠ»ΠΎΠΊΠΈ ΠΈ ΠΏΡΡΠ΄Π΅ΠΉ Ρ ΠΊΠ°ΡΡΡΠ΅ΠΊ Π΄ΠΎΠ»ΠΆΠ½ΠΎ Π²ΡΠΏΠΎΠ»Π½ΡΡΡΡΡ Π² ΡΠΏΠ΅ΡΠΈΠ°Π»ΡΠ½ΠΎ
ΠΎΡΠ²Π΅Π΄Π΅Π½Π½ΡΡ
ΠΌΠ΅ΡΡΠ°Ρ
, Π½ΠΎ Π½Π΅ Π² Π·ΠΎΠ½Π΅ ΡΠ°Π±ΠΎΡΡ ΠΌΠ°ΡΠΈΠ½Ρ.
3.2.3.22. ΠΠ° ΠΏΡΡΠ΄Π΅Π²ΡΡΡΠΈΡ
ΠΈ ΠΊΠ°Π½Π°ΡΠΎΠ²ΡΡΡΠΈΡ
ΠΌΠ°ΡΠΈΠ½Π°Ρ
ΠΈ Π½Π°ΠΌΠΎΡΠΎΡΠ½ΡΡ
ΡΡΠ°Π½ΠΊΠ°Ρ
, Π±ΠΎΠ»ΡΡΠΎΠΉ ΠΏΡΠΎΡΡΠΆΠ΅Π½Π½ΠΎΡΡΠΈ
ΠΏΠΎ ΡΡΠΎΠ½ΡΡ ΠΎΠ±ΡΠ»ΡΠΆΠΈΠ²Π°Π½ΠΈΡ ΠΌΠ°ΡΠΈΠ½Ρ (ΡΡΠ°Π½ΠΊΠ°), Π΄ΠΎΠ»ΠΆΠ½Ρ Π±ΡΡΡ ΡΡΡΠ°Π½ΠΎΠ²Π»Π΅Π½Ρ
Π΄ΡΠ±Π»ΠΈΡΡΡΡΠΈΠ΅ ΠΏΠΎΡΡΡ ΡΠΏΡΠ°Π²Π»Π΅Π½ΠΈΡ, ΡΠ΄Π°Π»Π΅Π½Π½ΡΠ΅ Π΄ΡΡΠ³ ΠΎΡ Π΄ΡΡΠ³Π° Π½Π΅ Π±ΠΎΠ»Π΅Π΅ ΡΠ΅ΠΌ
Π½Π° 6 ΠΌ. ΠΠ»Π΅ΠΊΡΡΠΎΡΡ
Π΅ΠΌΠ° ΡΠΏΡΠ°Π²Π»Π΅Π½ΠΈΡ Π΄ΠΎΠ»ΠΆΠ½Π° ΠΈΡΠΊΠ»ΡΡΠ°ΡΡ Π²ΠΎΠ·ΠΌΠΎΠΆΠ½ΠΎΡΡΡ
ΡΠΏΡΠ°Π²Π»Π΅Π½ΠΈΡ ΠΈΠΌΠΈ ΠΎΠ΄Π½ΠΎΠ²ΡΠ΅ΠΌΠ΅Π½Π½ΠΎ Ρ Π½Π΅ΡΠΊΠΎΠ»ΡΠΊΠΈΡ
ΠΏΠΎΡΡΠΎΠ².
3.2.3.23. ΠΠ³ΡΠ°ΠΆΠ΄Π΅Π½ΠΈΠ΅
ΠΊΠΎΠ½ΡΡΠ½ΠΎΠΉ ΡΠ°ΡΡΠΈ ΡΠ²ΠΈΠ²ΠΊΠΈ ΠΊΠ°Π½Π°ΡΠ° ΠΈΠ»ΠΈ ΠΏΡΡΠ΄ΠΈ Π΄ΠΎΠ»ΠΆΠ½ΠΎ ΠΈΠΌΠ΅ΡΡ Π±Π»ΠΎΠΊΠΈΡΠΎΠ²ΠΊΡ,
ΠΈΡΠΊΠ»ΡΡΠ°ΡΡΡΡ ΠΏΡΡΠΊ ΠΈ ΡΠ°Π±ΠΎΡΡ ΠΌΠ°ΡΠΈΠ½Ρ ΠΏΡΠΈ ΡΠ½ΡΡΠΎΠΌ ΠΎΠ³ΡΠ°ΠΆΠ΄Π΅Π½ΠΈΠΈ.
3.2.3.24. ΠΠ° ΡΡΠ°ΡΡΠΊΠ°Ρ
ΠΏΠ΅ΡΠ΅Ρ
ΠΎΠ΄Π° ΠΏΡΡΠ΄ΠΈ ΠΈΠ»ΠΈ ΠΊΠ°Π½Π°ΡΠ° Π½Π° Π²ΡΡΡΠΆΠ½ΠΎΠΉ ΡΠΊΠΈΠ² Π΄ΠΎΠ»ΠΆΠ½ΠΎ Π±ΡΡΡ
ΠΏΡΠ΅Π΄ΡΡΠΌΠΎΡΡΠ΅Π½ΠΎ Π·Π°ΡΠΈΡΠ½ΠΎΠ΅ ΠΏΡΠΈΡΠΏΠΎΡΠΎΠ±Π»Π΅Π½ΠΈΠ΅, ΠΏΡΠ΅Π΄ΠΎΡ
ΡΠ°Π½ΡΡΡΠ΅Π΅ ΠΏΠΎΠΏΠ°Π΄Π°Π½ΠΈΠ΅
ΠΏΠ°Π»ΡΡΠ΅Π² ΡΡΠΊ ΠΎΠ±ΡΠ»ΡΠΆΠΈΠ²Π°ΡΡΠ΅Π³ΠΎ ΠΏΠ΅ΡΡΠΎΠ½Π°Π»Π° ΠΏΠΎΠ΄ ΠΏΡΡΠ΄Ρ ΠΈΠ»ΠΈ ΠΊΠ°Π½Π°Ρ.
3.2.3.25. ΠΠ»Ρ ΡΠΊΠ»Π°Π΄ΠΊΠΈ
ΡΠΌΠ΅Π½Π½ΡΡ
Π΄Π΅ΡΠ°Π»Π΅ΠΉ, ΠΎΡΠ½Π°ΡΡΠΊΠΈ ΠΈ ΠΈΠ½ΡΡΡΡΠΌΠ΅Π½ΡΠ° Π΄ΠΎΠ»ΠΆΠ½Ρ ΠΏΡΠ΅Π΄ΡΡΠΌΠ°ΡΡΠΈΠ²Π°ΡΡΡΡ
ΡΠΏΠ΅ΡΠΈΠ°Π»ΡΠ½ΡΠ΅ ΡΡΠ΅Π»Π»Π°ΠΆΠΈ, ΡΡΠΈΠΊΠΈ ΠΈΠ»ΠΈ ΡΡΠΌΠ±ΠΎΡΠΊΠΈ.
3.2.3.26. ΠΠΎΠ½ΡΡΠΎΠ»ΡΠ½ΡΠ΅ ΠΈ
ΡΠΈΠ³Π½Π°Π»ΡΠ½ΡΠ΅ ΡΡΡΡΠΎΠΉΡΡΠ²Π°, ΠΏΡΠ΅Π΄ΡΠΏΡΠ΅Π΄ΠΈΡΠ΅Π»ΡΠ½ΡΠ΅ Π½Π°Π΄ΠΏΠΈΡΠΈ, ΡΠ°Π±Π»ΠΈΡΡ Π΄ΠΎΠ»ΠΆΠ½Ρ
Π±ΡΡΡ ΡΠ°ΡΠΏΠΎΠ»ΠΎΠΆΠ΅Π½Ρ Π² ΠΏΠΎΠ»Π΅ Π·ΡΠ΅Π½ΠΈΡ ΡΠ°Π±ΠΎΡΠ΅Π³ΠΎ.
3.2.3.27. ΠΠ΅ΠΆΠ΄Ρ ΠΏΡΠ»ΡΡΠΎΠΌ
ΡΠΏΡΠ°Π²Π»Π΅Π½ΠΈΡ ΠΈ ΡΡΠΎΠ½ΡΠΎΠΌ ΠΌΠ°ΡΠΈΠ½Ρ (ΡΡΠ°Π½ΠΊΠ°) Π΄ΠΎΠ»ΠΆΠ½ΠΎ Π±ΡΡΡ ΡΠ°ΡΡΡΠΎΡΠ½ΠΈΠ΅ Π½Π΅
ΠΌΠ΅Π½Π΅Π΅ 0,8 ΠΌ.
3.2.3.28. Π Π°ΡΡΡΠΎΡΠ½ΠΈΠ΅
ΠΌΠ΅ΠΆΠ΄Ρ Π½Π°ΠΌΠΎΡΠΎΡΠ½ΡΠΌΠΈ ΡΡΠ°Π½ΠΊΠ°ΠΌΠΈ ΠΏΠΎ ΡΡΠΎΠ½ΡΡ ΠΎΠ±ΡΠ»ΡΠΆΠΈΠ²Π°Π½ΠΈΡ Π² Π·Π°Π²ΠΈΡΠΈΠΌΠΎΡΡΠΈ ΠΎΡ
ΠΊΠΎΠ½ΡΡΡΡΠΊΡΠΈΠΈ ΡΡΠ°Π½ΠΊΠΎΠ² Π΄ΠΎΠ»ΠΆΠ½ΠΎ Π±ΡΡΡ Π½Π΅ ΠΌΠ΅Π½Π΅Π΅ 1,2 ΠΌ.
3.2.3.29. Π Π°ΡΡΡΠΎΡΠ½ΠΈΠ΅ ΠΎΡ
Π²ΡΡΡΡΠΏΠ°ΡΡΠΈΡ
ΠΊΠΎΠ½ΡΡΡΡΠΊΡΠΈΠΉ ΡΡΠ΅Π½ Π΄ΠΎ ΠΊΠ°ΡΡΡΠ΅ΠΊ ΠΈ ΡΠΈΠ³ΡΡΠΎΠΊ ΡΠΎ ΡΡΠΎΡΠΎΠ½Ρ
ΠΎΠ±ΡΠ»ΡΠΆΠΈΠ²Π°Π½ΠΈΡ Π΄ΠΎΠ»ΠΆΠ½ΠΎ Π±ΡΡΡ Π½Π΅ ΠΌΠ΅Π½Π΅Π΅ 1,5 ΠΌ.
Π Π°ΡΡΡΠΎΡΠ½ΠΈΡ ΠΎΡ ΠΊΠΎΠ»ΠΎΠ½Π½Ρ Π΄ΠΎ
Π±ΠΎΠΊΠΎΠ²ΡΡ
ΡΡΠΎΡΠΎΠ½ Π½Π°ΠΌΠΎΡΠΎΡΠ½ΡΡ
ΡΡΠ°Π½ΠΊΠΎΠ² Π΄ΠΎΠ»ΠΆΠ½Ρ Π±ΡΡΡ Π½Π΅ ΠΌΠ΅Π½Π΅Π΅ 0,8 ΠΌ, Π° ΡΠΎ
ΡΡΠΎΡΠΎΠ½Ρ ΡΠΈΠ³ΡΡΠΎΠΊ ΠΈ ΠΊΠ°ΡΡΡΠ΅ΠΊ — Π½Π΅ ΠΌΠ΅Π½Π΅Π΅ 1,2 ΠΌ.
3.2.3.30. Π Π°ΡΡΡΠΎΡΠ½ΠΈΠ΅
ΠΌΠ΅ΠΆΠ΄Ρ ΠΊΠ°Π½Π°ΡΠ½ΡΠΌΠΈ ΠΌΠ°ΡΠΈΠ½Π°ΠΌΠΈ ΡΠΎ ΡΡΠΎΡΠΎΠ½Ρ ΠΎΠ±ΡΠ»ΡΠΆΠΈΠ²Π°Π½ΠΈΡ ΠΊΠ°ΡΠ΅ΡΠΎΠΊ (ΡΠΈΡΠΈΠ½Π°
ΡΠ°Π±ΠΎΡΠ΅Π³ΠΎ ΠΌΠ΅ΡΡΠ°) Π΄ΠΎΠ»ΠΆΠ½ΠΎ Π±ΡΡΡ Π½Π΅ ΠΌΠ΅Π½Π΅Π΅ 1,2 ΠΌ. Π Π°ΡΡΡΠΎΡΠ½ΠΈΠ΅ ΠΌΠ΅ΠΆΠ΄Ρ
ΠΊΠΎΠ»ΠΎΠ½Π½Π°ΠΌΠΈ Π·Π΄Π°Π½ΠΈΡ ΠΈ ΠΌΠ°ΡΠΈΠ½Π°ΠΌΠΈ ΡΠΎ ΡΡΠΎΡΠΎΠ½Ρ, ΠΏΡΠΎΡΠΈΠ²ΠΎΠΏΠΎΠ»ΠΎΠΆΠ½ΠΎΠΉ ΡΠ°Π±ΠΎΡΠ΅ΠΌΡ
ΠΌΠ΅ΡΡΡ, Π΄ΠΎΠΏΡΡΠΊΠ°Π΅ΡΡΡ ΡΠΎΠΊΡΠ°ΡΠ°ΡΡ Π΄ΠΎ 1,0 ΠΌ.
3.2.3.31. ΠΡΠΈ
ΠΏΡΠΎΠ΅ΠΊΡΠΈΡΠΎΠ²Π°Π½ΠΈΠΈ ΠΈ ΡΠ΅ΠΊΠΎΠ½ΡΡΡΡΠΊΡΠΈΠΈ ΡΠ΅Ρ
ΠΎΠ² Ρ Π½Π°ΠΌΠΎΡΠΎΡΠ½ΡΡ
ΡΡΠ°Π½ΠΊΠΎΠ²,
ΠΏΡΡΠ΄Π΅Π²ΡΡΡΠΈΡ
ΠΈ ΠΊΠ°Π½Π°ΡΠΎΠ²ΡΡΡΠΈΡ
ΠΌΠ°ΡΠΈΠ½ Π΄ΠΎΠ»ΠΆΠ½Ρ Π±ΡΡΡ ΠΏΡΠ΅Π΄ΡΡΠΌΠΎΡΡΠ΅Π½Ρ
Π½Π΅ΠΎΠ±Ρ
ΠΎΠ΄ΠΈΠΌΡΠ΅ ΠΏΠ»ΠΎΡΠ°Π΄ΠΈ Π΄Π»Ρ ΡΠ΅ΠΌΠΎΠ½ΡΠ° ΠΈ Π΄Π΅ΠΌΠΎΠ½ΡΠ°ΠΆΠ° ΡΠ·Π»ΠΎΠ² ΠΎΠ±ΠΎΡΡΠ΄ΠΎΠ²Π°Π½ΠΈΡ.
3.2.3.32. ΠΠ°Π½Π°ΡΠΎΠ²ΡΡΡΠΈΠ΅ ΠΈ
ΠΏΡΡΠ΄Π΅Π²ΡΡΡΠΈΠ΅ ΠΌΠ°ΡΠΈΠ½Ρ Π΄ΠΎΠ»ΠΆΠ½Ρ Π±ΡΡΡ ΠΎΠ±ΠΎΡΡΠ΄ΠΎΠ²Π°Π½Ρ ΡΡΠ΅Π΄ΡΡΠ²Π°ΠΌΠΈ
ΡΡΠΌΠΎΠ³Π»ΡΡΠ΅Π½ΠΈΡ.
3.3. ΠΡΠΎΠΈΠ·Π²ΠΎΠ΄ΡΡΠ²ΠΎ ΠΊΡΠ΅ΠΏΠ΅ΠΆΠ½ΡΡ ΠΈΠ·Π΄Π΅Π»ΠΈΠΉ ΠΈ Π³Π²ΠΎΠ·Π΄Π΅ΠΉ
Π
ΠΎΠΏΠ°ΡΠ½ΡΠΌ ΠΈ Π²ΡΠ΅Π΄Π½ΡΠΌ ΠΏΡΠΎΠΈΠ·Π²ΠΎΠ΄ΡΡΠ²Π΅Π½Π½ΡΠΌ ΡΠ°ΠΊΡΠΎΡΠ°ΠΌ ΠΎΡΠ½ΠΎΡΡΡΡΡ:
ΠΏΠΎΠ΄Π²ΠΈΠΆΠ½ΡΠ΅ ΡΠ°ΡΡΠΈ
ΠΏΡΠΎΠΈΠ·Π²ΠΎΠ΄ΡΡΠ²Π΅Π½Π½ΠΎΠ³ΠΎ ΠΎΠ±ΠΎΡΡΠ΄ΠΎΠ²Π°Π½ΠΈΡ;
ΠΏΠ΅ΡΠ΅Π΄Π²ΠΈΠ³Π°ΡΡΠΈΠ΅ΡΡ ΠΈΠ·Π΄Π΅Π»ΠΈΡ,
Π·Π°Π³ΠΎΡΠΎΠ²ΠΊΠΈ;
ΠΏΠΎΠ²ΡΡΠ΅Π½Π½ΡΠΉ ΡΡΠΎΠ²Π΅Π½Ρ ΡΡΠΌΠ°
Π½Π° ΡΠ°Π±ΠΎΡΠ΅ΠΌ ΠΌΠ΅ΡΡΠ΅;
ΠΎΠΏΠ°ΡΠ½ΠΎΡΡΡ ΠΏΠΎΡΠ°ΠΆΠ΅Π½ΠΈΡ
ΡΠ»Π΅ΠΊΡΡΠΈΡΠ΅ΡΠΊΠΈΠΌ ΡΠΎΠΊΠΎΠΌ;
ΠΎΡΡΡΡΠ΅ ΠΊΡΠΎΠΌΠΊΠΈ, Π·Π°ΡΡΠ΅Π½ΡΡ
Π½Π° ΠΏΠΎΠ²Π΅ΡΡ
Π½ΠΎΡΡΠΈ Π·Π°Π³ΠΎΡΠΎΠ²ΠΎΠΊ, ΠΈΠ½ΡΡΡΡΠΌΠ΅Π½ΡΠΎΠ² ΠΈ ΠΎΠ±ΠΎΡΡΠ΄ΠΎΠ²Π°Π½ΠΈΡ.
3.3.1. ΠΠ±ΡΠΈΠ΅ ΡΡΠ΅Π±ΠΎΠ²Π°Π½ΠΈΡ ΠΊ ΡΡΠ°ΡΡΠΊΠ°ΠΌ ΠΈ ΠΎΠ±ΠΎΡΡΠ΄ΠΎΠ²Π°Π½ΠΈΡ
3.3.1.1. ΠΠ²ΡΠΎΠΌΠ°ΡΡ, Π²
ΡΠΈΡΡΠ΅ΠΌΠ°Ρ
ΡΠΏΡΠ°Π²Π»Π΅Π½ΠΈΡ ΠΊΠΎΡΠΎΡΡΡ
ΠΈΡΠΏΠΎΠ»ΡΠ·ΡΠ΅ΡΡΡ ΡΠΆΠ°ΡΡΠΉ Π²ΠΎΠ·Π΄ΡΡ
, Π΄ΠΎΠ»ΠΆΠ½Ρ
ΠΈΠΌΠ΅ΡΡ ΡΡΡΡΠΎΠΉΡΡΠ²ΠΎ, ΠΎΡΠΊΠ»ΡΡΠ°ΡΡΠ΅Π΅ ΠΏΡΠΈΠ²ΠΎΠ΄ ΠΏΡΠΈ ΠΏΠ°Π΄Π΅Π½ΠΈΠΈ Π΄Π°Π²Π»Π΅Π½ΠΈΡ Π½ΠΈΠΆΠ΅
ΡΡΡΠ°Π½ΠΎΠ²Π»Π΅Π½Π½ΠΎΠ³ΠΎ, ΠΈ ΡΠΎΠΎΡΠ²Π΅ΡΡΡΠ²ΡΡΡΠΈΠΉ ΡΠ²Π΅ΡΠΎΠ²ΠΎΠΉ ΡΠΈΠ³Π½Π°Π» Π½Π° ΠΏΡΠ»ΡΡΠ΅
ΡΠΏΡΠ°Π²Π»Π΅Π½ΠΈΡ: «ΠΠ΅Ρ Π΄Π°Π²Π»Π΅Π½ΠΈΡ Π²ΠΎΠ·Π΄ΡΡ
Π°».
3.3.1.2. ΠΠ°ΠΆΠ΄ΡΠΉ Π°Π²ΡΠΎΠΌΠ°Ρ
Π΄ΠΎΠ»ΠΆΠ΅Π½ ΠΎΠ±ΠΎΡΡΠ΄ΠΎΠ²Π°ΡΡΡΡ ΠΏΡΠ»ΡΡΠΎΠΌ ΡΠΏΡΠ°Π²Π»Π΅Π½ΠΈΡ, ΡΠ°ΡΠΏΠΎΠ»ΠΎΠΆΠ΅Π½Π½ΡΠΌ Π½Π° Π²ΡΡΠΎΡΠ΅
0,8-1,2 ΠΌ ΠΎΡ ΠΏΠΎΠ»Π° ΡΠ°Π±ΠΎΡΠ΅ΠΉ ΠΏΠ»ΠΎΡΠ°Π΄ΠΊΠΈ. ΠΠ°ΠΆΠ΄Π°Ρ ΠΊΠ½ΠΎΠΏΠΊΠ° ΠΏΡΠ»ΡΡΠ° ΡΠΏΡΠ°Π²Π»Π΅Π½ΠΈΡ
Π΄ΠΎΠ»ΠΆΠ½Π° ΠΈΠΌΠ΅ΡΡ Π½Π°Π΄ΠΏΠΈΡΡ Π½Π°Π·Π½Π°ΡΠ΅Π½ΠΈΡ.
3.3.1.3. ΠΡΠ΅ΡΡΡ
ΠΌΠ΅Ρ
Π°Π½ΠΈΡΠ΅ΡΠΊΠΈΠ΅ (ΠΊΡΠΈΠ²ΠΎΡΠΈΠΏΠ½ΡΠ΅, ΡΠ΅ΠΊΠ°Π½ΠΎΡΠ½ΡΠ΅, Π²ΠΈΠ½ΡΠΎΠ²ΡΠ΅, ΡΡΠΈΠΊΡΠΈΠΎΠ½Π½ΡΠ΅ ΠΈ Π΄Ρ.)
Π΄ΠΎΠ»ΠΆΠ½Ρ ΠΈΠΌΠ΅ΡΡ ΡΠΊΠ°Π·Π°ΡΠ΅Π»Ρ ΠΏΠΎΠ»ΠΎΠΆΠ΅Π½ΠΈΡ ΠΏΠΎΠ»Π·ΡΠ½Π°, Π³ΡΠ°ΡΠΈΠΊ ΡΡΠΈΠ»ΠΈΠΉ ΠΈΠ»ΠΈ ΡΠ½Π΅ΡΠ³ΠΈΠΈ
ΠΏΠΎ ΠΏΠΎΠ»Π·ΡΠ½Ρ ΠΈ ΠΊΠ°ΡΡΡ ΡΠΌΠ°Π·ΠΊΠΈ.
3.3.1.4. ΠΠ²ΡΠΎΠΌΠ°ΡΡ Π΄ΠΎΠ»ΠΆΠ½Ρ
Π±ΡΡΡ ΠΎΡΠ½Π°ΡΠ΅Π½Ρ ΠΌΠ΅ΡΡΠ½ΡΠΌ ΠΎΡΠ²Π΅ΡΠ΅Π½ΠΈΠ΅ΠΌ Π½Π°ΠΏΡΡΠΆΠ΅Π½ΠΈΠ΅ΠΌ Π½Π΅ Π²ΡΡΠ΅ 42 Π.
3.3.1.5. ΠΠ°ΡΡΡΠΎΠΉΠΊΠ°
Π°Π²ΡΠΎΠΌΠ°ΡΠΎΠ² ΠΈ ΠΏΡΠΎΠ±Π½Π°Ρ ΡΡΠ°ΠΌΠΏΠΎΠ²ΠΊΠ° Π·Π°Π³ΠΎΡΠΎΠ²ΠΎΠΊ Π΄ΠΎΠ»ΠΆΠ½Ρ ΠΏΡΠΎΠΈΠ·Π²ΠΎΠ΄ΠΈΡΡΡΡ Π½Π°
ΠΌΠΈΠ½ΠΈΠΌΠ°Π»ΡΠ½ΠΎΠΉ ΡΠΊΠΎΡΠΎΡΡΠΈ, Π½Π° ΠΎΠ΄ΠΈΠ½ΠΎΡΠ½ΡΡ
Ρ
ΠΎΠ΄Π°Ρ
.
ΠΠ±ΠΎΡΡΠ΄ΠΎΠ²Π°Π½ΠΈΠ΅ Π΄Π»Ρ Π²ΠΎΠ»ΠΎΡΠ΅Π½ΠΈΡ
Π‘ΠΎΠ΄Π΅ΡΠΆΠ°Π½ΠΈΠ΅ ΡΡΡΠ°Π½ΠΈΡΡ
Π§ΡΠΎ ΡΠ°ΠΊΠΎΠ΅ ΠΏΡΠΎΡΠ΅ΡΡ Π²ΠΎΠ»ΠΎΡΠ΅Π½ΠΈΡ
ΠΠΎΠ»ΠΎΡΠ΅Π½ΠΈΠ΅ β ΠΏΡΠΎΡΠ΅ΡΡ ΠΎΠ±ΡΠ°Π±ΠΎΡΠΊΠΈ Π΄Π°Π²Π»Π΅Π½ΠΈΠ΅ΠΌ, ΠΏΡΠΈ ΠΊΠΎΡΠΎΡΠΎΠΌ ΠΏΠ»Π°ΡΡΠΈΡΠ΅ΡΠΊΠ°Ρ Π΄Π΅ΡΠΎΡΠΌΠ°ΡΠΈΡ Π·Π°Π³ΠΎΡΠΎΠ²ΠΊΠΈ Π² Ρ ΠΎΠ»ΠΎΠ΄Π½ΠΎΠΌ ΡΠΎΡΡΠΎΡΠ½ΠΈΠΈ ΠΎΡΡΡΠ΅ΡΡΠ²Π»ΡΠ΅ΡΡΡ Π·Π° ΡΡΠ΅Ρ Π΅Π΅ ΠΏΡΠΎΡΡΠ³ΠΈΠ²Π°Π½ΠΈΡ Ρ ΡΡΠΈΠ»ΠΈΠ΅ΠΌ P ΡΠ΅ΡΠ΅Π· ΠΏΠΎΡΡΠ΅ΠΏΠ΅Π½Π½ΠΎ ΡΡΠΆΠ°ΡΡΠ΅Π΅ΡΡ ΠΎΡΠ²Π΅ΡΡΡΠΈΠ΅ Π² ΠΈΠ½ΡΡΡΡΠΌΠ΅Π½ΡΠ΅, Π½Π°Π·ΡΠ²Π°Π΅ΠΌΠΎΠΌ Π²ΠΎΠ»ΠΎΠΊΠΎΠΉ, ΠΈΠ»ΠΈ ΡΠΈΠ»ΡΠ΅ΡΠΎΠΉ (ΡΠΈΡ. 1).
Π ΠΈΡ. 1. Π‘Ρ Π΅ΠΌΡ Π²ΠΎΠ»ΠΎΡΠ΅Π½ΠΈΡ: Π° β ΠΏΡΡΡΠΎΠΊ; Π±, Π² β ΡΡΡΠ±Ρ; Π³ β ΠΏΡΠΈΠΌΠ΅ΡΡ ΠΏΠΎΠ»ΡΡΠ°Π΅ΠΌΡΡ ΠΏΡΠΎΡΠΈΠ»Π΅ΠΉ.
ΠΡΠΈ Π²ΠΎΠ»ΠΎΡΠ΅Π½ΠΈΠΈ Π·Π°Π³ΠΎΡΠΎΠ²ΠΊΠ° 1 ΠΏΡΠΎΡΠ°ΡΠΊΠΈΠ²Π°Π΅ΡΡΡ ΡΠ΅ΡΠ΅Π· ΡΠΈΠ»ΡΠ΅ΡΡ 2 Π² Ρ ΠΎΠ»ΠΎΠ΄Π½ΠΎΠΌ ΡΠΎΡΡΠΎΡΠ½ΠΈΠΈ, ΠΏΡΠΈΠΎΠ±ΡΠ΅ΡΠ°Ρ Π³Π»Π°Π΄ΠΊΡΡ ΠΏΠΎΠ²Π΅ΡΡ Π½ΠΎΡΡΡ (Ra = 1,6 ΠΌΠΊΠΌ) ΠΈ ΡΠΎΡΠ½ΠΎΡΡΡ ΠΏΠΎΠΏΠ΅ΡΠ΅ΡΠ½ΠΎΠ³ΠΎ ΡΠ°Π·ΠΌΠ΅ΡΠ° Π² ΠΏΡΠ΅Π΄Π΅Π»Π°Ρ 8-13-Π³ΠΎ ΠΊΠ²Π°Π»ΠΈΡΠ΅ΡΠΎΠ² (Π΄Π»Ρ ΠΊΡΡΠ³Π»ΠΎΠ³ΠΎ ΠΏΡΠΎΠΊΠ°ΡΠ°) ΠΡΠΈ Π²ΠΎΠ»ΠΎΡΠ΅Π½ΠΈΠΈ ΡΠ²Π΅ΡΠ΄ΠΎΡΡΡ ΠΈ ΠΏΡΠ΅Π΄Π΅Π» ΡΠ΅ΠΊΡΡΠ΅ΡΡΠΈ ΠΌΠ°ΡΠ΅ΡΠΈΠ°Π»Π° ΡΠ²Π΅Π»ΠΈΡΠΈΠ²Π°ΡΡΡΡ Π·Π° ΡΡΠ΅Ρ Π½Π°ΠΊΠ»Π΅ΠΏΠ° (ΡΠΏΡΠΎΡΠ½Π΅Π½ΠΈΡ) . ΠΠΎΠ»ΠΎΡΠ΅Π½ΠΈΠ΅ ΡΠ²Π»ΡΠ΅ΡΡΡ ΠΈΡΠΊΠ»ΡΡΠΈΡΠ΅Π»ΡΠ½ΡΠΌ ΠΌΠ΅ΡΠΎΠ΄ΠΎΠΌ Π΄Π»Ρ ΠΏΡΠΎΠΈΠ·Π²ΠΎΠ΄ΡΡΠ²Π° ΠΎΡΠ΅Π½Ρ ΡΠΎΠ½ΠΊΠΎΠΉ ΠΏΡΠΎΠ²ΠΎΠ»ΠΎΠΊΠΈ.
ΠΠ°ΡΠΈΠ½Ρ, ΠΎΠ±Π΅ΡΠΏΠ΅ΡΠΈΠ²Π°ΡΡΠΈΠ΅ Π²ΡΠΏΠΎΠ»Π½Π΅Π½ΠΈΠ΅ ΠΏΠ»Π°ΡΡΠΈΡΠ΅ΡΠΊΠΎΠΉ Π΄Π΅ΡΠΎΡΠΌΠ°ΡΠΈΠΈ ΠΌΠ΅ΡΠ°Π»Π»Π° Π²ΠΎΠ»ΠΎΡΠ΅Π½ΠΈΠ΅ΠΌ, Π½Π°Π·ΡΠ²Π°ΡΡ Π²ΠΎΠ»ΠΎΡΠΈΠ»ΡΠ½ΡΠΌΠΈ ΡΡΠ°Π½Π°ΠΌΠΈ. ΠΡΠ½ΠΎΠ²Π½ΡΠΌΠΈ ΠΈΡ ΡΠ»Π΅ΠΌΠ΅Π½ΡΠ°ΠΌΠΈ ΡΠ²Π»ΡΡΡΡΡ Π²ΠΎΠ»ΠΎΡΠΈΠ»ΡΠ½ΡΠΉ ΠΈΠ½ΡΡΡΡΠΌΠ΅Π½Ρ ΠΈ ΡΡΠ½ΡΡΠ΅Π΅ ΡΡΡΡΠΎΠΉΡΡΠ²ΠΎ ΠΡΠΈΠ½ΡΠΈΠΏ ΡΠ°Π±ΠΎΡΡ Π²ΠΎΠ»ΠΎΡΠΈΠ»ΡΠ½ΡΡ ΡΡΠ°Π½ΠΎΠ² ΠΌΠΎΠΆΠ΅Ρ Π±ΡΡΡ ΡΠ°Π·Π»ΠΈΡΠ½ΡΠΌ ΠΈ ΠΎΠΏΡΠ΅Π΄Π΅Π»ΡΠ΅ΡΡΡ Ρ Π°ΡΠ°ΠΊΡΠ΅ΡΠΎΠΌ ΡΠ°Π±ΠΎΡΡ ΡΡΠ½ΡΡΠ΅Π³ΠΎ ΡΡΡΡΠΎΠΉΡΡΠ²Π°.
Π‘ΡΠ°Π½Ρ ΠΌΠΎΠ³ΡΡ Π±ΡΡΡ Ρ ΠΏΡΡΠΌΠΎΠ»ΠΈΠ½Π΅ΠΉΠ½ΡΠΌ Π΄Π²ΠΈΠΆΠ΅Π½ΠΈΠ΅ΠΌ ΠΏΡΠΎΡΡΠ³ΠΈΠ²Π°Π΅ΠΌΠΎΠ³ΠΎ ΠΌΠ΅ΡΠ°Π»Π»Π° (ΡΠ΅ΠΏΠ½ΡΠ΅, ΡΠ΅Π΅ΡΠ½ΡΠ΅, Π³ΠΈΠ΄ΡΠ°Π²Π»ΠΈΡΠ΅ΡΠΊΠΈΠ΅ ΠΈ Π΄Ρ. ) ΠΈ Ρ Π½Π°ΠΌΠ°ΡΡΠ²Π°Π½ΠΈΠ΅ΠΌ Π½Π° Π±Π°ΡΠ°Π±Π°Π½ (Π±Π°ΡΠ°Π±Π°Π½Π½ΡΠ΅) ΠΠ΅ΡΠ²ΡΠΉ ΡΠΈΠΏ ΠΌΠ°ΡΠΈΠ½ ΠΏΡΠΈΠΌΠ΅Π½ΡΠ΅ΡΡΡ Π΄Π»Ρ Π²ΠΎΠ»ΠΎΡΠ΅Π½ΠΈΡ ΠΏΡΠΎΡΠΈΠ»Π΅ΠΉ, ΡΠΌΠ°ΡΡΠ²Π°Π½ΠΈΠ΅ Π² Π±ΡΠ½ΡΡ ΠΊΠΎΡΠΎΡΡΡ Π²ΡΠ·ΡΠ²Π°Π΅Ρ ΠΎΠΏΡΠ΅Π΄Π΅Π»Π΅Π½Π½ΡΠ΅ ΡΡΡΠ΄Π½ΠΎΡΡΠΈ. ΠΠ°ΡΠ°Π±Π°Π½Π½ΡΠ΅ Π²ΠΎΠ»ΠΎΡΠΈΠ»ΡΠ½ΡΠ΅ ΡΡΠ°Π½Ρ ΠΈΡΠΏΠΎΠ»ΡΠ·ΡΡΡ Π΄Π»Ρ Π²ΠΎΠ»ΠΎΡΠ΅Π½ΠΈΡ ΠΏΡΠΎΠ²ΠΎΠ»ΠΎΠΊΠΈ, Π° ΡΠ°ΠΊΠΆΠ΅ ΡΠΏΠ»ΠΎΡΠ½ΡΡ ΠΈ ΠΏΠΎΠ»ΡΡ ΠΏΡΠΎΡΠΈΠ»Π΅ΠΉ Π½Π΅Π±ΠΎΠ»ΡΡΠΈΡ ΡΠ΅ΡΠ΅Π½ΠΈΠΉ ΠΈΠ· ΡΠ΅ΡΠ½ΡΡ ΠΈ ΡΠ²Π΅ΡΠ½ΡΡ ΠΌΠ΅ΡΠ°Π»Π»ΠΎΠ², ΠΊΠΎΡΠΎΡΡΠ΅ Π½Π΅ ΠΏΠΎΠ²ΡΠ΅ΠΆΠ΄Π°ΡΡΡΡ ΠΏΡΠΈ ΡΠΌΠ°ΡΡΠ²Π°Π½ΠΈΠΈ Π² Π±ΡΡ ΡΡ
1. Π‘ΡΠ°Π½Ρ Ρ ΠΏΡΡΠΌΠΎΠ»ΠΈΠ½Π΅ΠΉΠ½ΡΠΌ Π΄Π²ΠΈΠΆΠ΅Π½ΠΈΠ΅ΠΌ ΠΏΡΡΡΠΊΠ°
Π‘ΡΠ°Π½Ρ Ρ ΠΏΡΡΠΌΠΎΠ»ΠΈΠ½Π΅ΠΉΠ½ΡΠΌ Π΄Π²ΠΈΠΆΠ΅Π½ΠΈΠ΅ΠΌ ΠΏΡΡΡΠΊΠ° ΠΏΡΠΈ Π²ΠΎΠ»ΠΎΡΠ΅Π½ΠΈΠΈ ΡΡΡΠΎΡΡ ΡΠ°ΡΠ΅ Π²ΡΠ΅Π³ΠΎ ΡΠ΅ΠΏΠ½ΡΠΌΠΈ. ΠΡΠ½ΠΎΠ²Π½ΡΠΌΠΈ ΡΠ»Π΅ΠΌΠ΅Π½ΡΠ°ΠΌΠΈ ΡΠ°ΠΊΠΎΠ³ΠΎ ΡΡΠ°Π½Π° (ΡΠΈΡ. 2) ΡΠ²Π»ΡΡΡΡΡ ΡΡΠ°Π½ΠΈΠ½Π° 3, Π±Π΅ΡΠΊΠΎΠ½Π΅ΡΠ½Π°Ρ ΡΠ΅ΠΏΡ 2, ΡΠ΅Π»Π΅ΠΆΠΊΠ° Ρ Π·Π°Ρ Π²Π°ΡΠΎΠΌ 4, ΡΡΠΎΠΉΠΊΠ° Π΄Π»Ρ ΠΊΡΠ΅ΠΏΠ»Π΅Π½ΠΈΡ Π²ΠΎΠ»ΠΎΠΊΠΈ 5, Π΄Π²ΠΈΠ³Π°ΡΠ΅Π»Ρ ΠΈ ΠΏΠ΅ΡΠ΅Π΄Π°ΡΡΠΈΠ΅ Π΄Π²ΠΈΠΆΠ΅Π½ΠΈΠ΅ ΠΌΠ΅Ρ Π°Π½ΠΈΠ·ΠΌΡ 1. Π ΡΠ΅ΠΏΠ½ΡΡ ΡΡΠ°Π½Π°Ρ ΡΠΎΠ²ΡΠ΅ΠΌΠ΅Π½Π½ΠΎΠΉ ΠΊΠΎΠ½ΡΡΡΡΠΊΡΠΈΠΈ ΠΈΠΌΠ΅ΡΡΡΡ ΡΡΡΡΠΎΠΉΡΡΠ²Π° Π΄Π»Ρ Π°Π²ΡΠΎΠΌΠ°ΡΠΈΡΠ΅ΡΠΊΠΎΠ³ΠΎ Π²ΠΎΠ·Π²ΡΠ°ΡΠ΅Π½ΠΈΡ ΡΠ΅Π»Π΅ΠΆΠΊΠΈ Ρ Π·Π°Ρ Π²Π°ΡΠΎΠΌ, ΠΏΡΠΈΡΠΏΠΎΡΠΎΠ±Π»Π΅Π½ΠΈΡ Π΄Π»Ρ Π½Π°Π΄Π΅Π²Π°Π½ΠΈΡ ΡΡΡΠ± ΠΈ ΡΠ±ΡΠ°ΡΡΠ²Π°Π½ΠΈΡ ΠΈΡ ΠΏΠΎΡΠ»Π΅ Π²ΠΎΠ»ΠΎΡΠ΅Π½ΠΈΡ Ρ ΠΎΠΏΡΠ°Π²ΠΊΠΈ, Π°Π²ΡΠΎΠΌΠ°ΡΠΈΡΠ΅ΡΠΊΠΎΠ³ΠΎ Π·Π°Ρ Π²Π°ΡΠ° ΠΏΡΡΡΠΊΠΎΠ² ΠΈ ΠΏΡ ΠΠ½ΠΎΠ³ΠΎΠ½ΠΈΡΠΎΡΠ½ΡΠ΅ Π²ΠΎΠ»ΠΎΡΠΈΠ»ΡΠ½ΡΠ΅ ΡΡΠ°Π½Ρ ΡΡΠ½ΡΡ ΠΎΠ΄Π½ΠΎΠ²ΡΠ΅ΠΌΠ΅Π½Π½ΠΎ Π΄ΠΎ 10 Π·Π°Π³ΠΎΡΠΎΠ²ΠΎΠΊ.
ΠΠ»ΠΈΠ½Π° ΠΏΡΠΎΡΡΠ³ΠΈΠ²Π°Π΅ΠΌΠΎΠ³ΠΎ Π½Π° ΡΠ΅ΠΏΠ½ΡΡ ΡΡΠ°Π½Π°Ρ ΠΈΠ·Π΄Π΅Π»ΠΈΡ ΠΎΠ³ΡΠ°Π½ΠΈΡΠΈΠ²Π°Π΅ΡΡΡ ΡΠ°Π·ΠΌΠ΅ΡΠ°ΠΌΠΈ ΡΡΠ°Π½ΠΈΠ½Ρ ΠΈ ΡΠ°ΡΠ΅ Π²ΡΠ΅Π³ΠΎ Π½Π΅ ΠΏΡΠ΅Π²ΡΡΠ°Π΅Ρ 15 ΠΌ. ΠΠ΄Π½Π°ΠΊΠΎ ΠΈΠΌΠ΅ΡΡΡΡ ΡΡΠ°Π½Ρ, Π½Π° ΠΊΠΎΡΠΎΡΡΡ ΠΏΡΠΎΡΡΠ³ΠΈΠ²Π°ΡΡ ΠΏΡΡΡΠΊΠΈ ΠΈ ΡΡΡΠ±Ρ Π΄Π»ΠΈΠ½ΠΎΠΉ Π΄ΠΎ 50 ΠΌ.
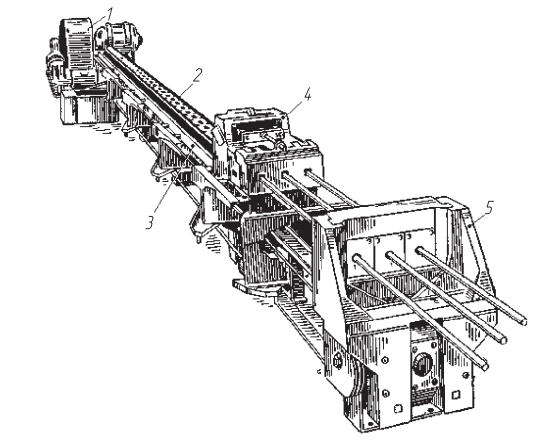
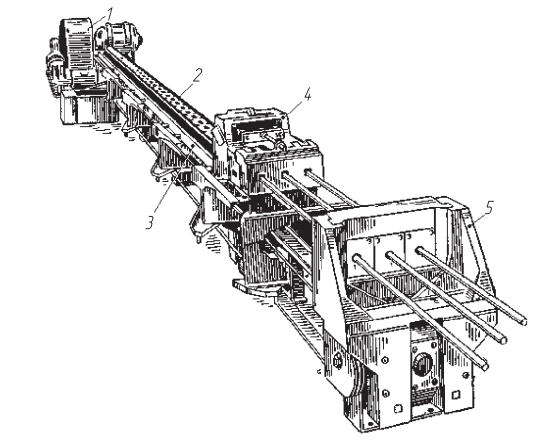
Π ΠΈΡ. 2. ΠΠ±ΡΠΈΠΉ Π²ΠΈΠ΄ ΡΠ΅ΠΏΠ½ΠΎΠ³ΠΎ ΠΌΠ½ΠΎΠ³ΠΎΠΏΡΡΡΠΊΠΎΠ²ΠΎΠ³ΠΎ Π²ΠΎΠ»ΠΎΡΠΈΠ»ΡΠ½ΠΎΠ³ΠΎ ΡΡΠ°Π½Π°
Π¦Π΅ΠΏΠ½ΡΠ΅ ΡΡΠ°Π½Ρ ΡΡΡΠΎΡΡ Ρ ΡΡΠΈΠ»ΠΈΠ΅ΠΌ Π²ΠΎΠ»ΠΎΡΠ΅Π½ΠΈΡ ΠΎΡ 5 Π΄ΠΎ 1500 ΠΊΠ. Π‘ΠΊΠΎΡΠΎΡΡΡ Π²ΠΎΠ»ΠΎΡΠ΅Π½ΠΈΡ Π½Π° Π½ΠΈΡ ΠΏΡΠΈ ΠΎΠ±ΡΠ°Π±ΠΎΡΠΊΠ΅ ΠΎΡΠ½ΠΎΡΠΈΡΠ΅Π»ΡΠ½ΠΎ ΠΊΠΎΡΠΎΡΠΊΠΈΡ ΠΏΡΡΡΠΊΠΎΠ² (ΠΏΠΎΡΡΠ΄ΠΊΠ° 5. . . 8 ΠΌ) ΡΠΎΡΡΠ°Π²Π»ΡΠ΅Ρ 0,03. . . 0,5 ΠΌ/Ρ. ΠΡΠΈ Π²ΠΎΠ»ΠΎΡΠ΅Π½ΠΈΠΈ Π΄Π»ΠΈΠ½Π½ΡΡ ΠΏΡΡΡΠΊΠΎΠ² ΡΠΊΠΎΡΠΎΡΡΡ Π²ΠΎΠ»ΠΎΡΠ΅Π½ΠΈΡ Π΄ΠΎΡΡΠΈΠ³Π°Π΅Ρ 1,5. . . 3,3 ΠΌ/Ρ. Π ΠΏΠΎΡΠ»Π΅Π΄Π½Π΅ΠΌ.ΡΠ»ΡΡΠ°Π΅.ΠΏΡΠ΅Π΄ΡΡΠΌΠ°ΡΡΠΈΠ²Π°Π΅ΡΡΡ.Π°Π²ΡΠΎΠΌΠ°ΡΠΈΡΠ΅ΡΠΊΠ°Ρ.ΡΠ΅Π³ΡΠ»ΠΈΡΠΎΠ²ΠΊΠ°. ΡΠΊΠΎΡΠΎΡΡΠΈ, ΡΠ°ΠΊ ΠΊΠ°ΠΊ Π²ΠΊΠ»ΡΡΠ΅Π½ΠΈΠ΅ ΡΡΠ½ΡΡΠ΅ΠΉ ΡΠ΅Π»Π΅ΠΆΠΊΠΈ Π½Π° Π±ΠΎΠ»ΡΡΠΈΡ ΡΠΊΠΎΡΠΎΡΡΡΡ ΡΠ²Π΅Π»ΠΈΡΠΈΠ²Π°Π΅Ρ Π²Π΅ΡΠΎΡΡΠ½ΠΎΡΡΡ ΠΎΠ±ΡΡΠ²Π° ΠΏΠ΅ΡΠ΅Π΄Π½Π΅Π³ΠΎ Π·Π°ΠΎΡΡΡΠ΅Π½Π½ΠΎΠ³ΠΎ ΠΊΠΎΠ½ΡΠ° Π·Π°Π³ΠΎΡΠΎΠ²ΠΊΠΈ Π² Π½Π°ΡΠ°Π»ΡΠ½ΡΠΉ ΠΌΠΎΠΌΠ΅Π½Ρ Π²ΠΎΠ»ΠΎΡΠ΅Π½ΠΈΡ.
Π‘ΠΈΡΡΠ΅ΠΌΡ ΡΠΏΡΠ°Π²Π»Π΅Π½ΠΈΡ ΡΠΎΠ²ΡΠ΅ΠΌΠ΅Π½Π½ΡΡ Π²ΠΎΠ»ΠΎΡΠΈΠ»ΡΠ½ΡΡ ΡΡΠ°Π½ΠΎΠ² ΠΏΠΎΡΡΡΠΎΠ΅Π½Ρ Π½Π° ΠΈΡΠΏΠΎΠ»ΡΠ·ΠΎΠ²Π°Π½ΠΈΠΈ ΠΏΡΠΎΠ³ΡΠ°ΠΌΠΌΠΈΡΡΠ΅ΠΌΡΡ ΠΊΠΎΠ½ΡΡΠΎΠ»Π»Π΅ΡΠΎΠ² Ρ Π°Π²ΡΠΎΠΌΠ°ΡΠΈΡΠ΅ΡΠΊΠΎΠΉ ΡΠΈΡΡΠ΅ΠΌΠΎΠΉ Π΄ΠΈΠ°Π³Π½ΠΎΡΡΠΈΠΊΠΈ.
2. ΠΠ°ΡΠ°Π±Π°Π½Π½ΡΠ΅ ΡΡΠ°Π½Ρ
Π Π·Π°Π²ΠΈΡΠΈΠΌΠΎΡΡΠΈ ΠΎΡ Ρ Π°ΡΠ°ΠΊΡΠ΅ΡΠ° ΡΠ°Π±ΠΎΡΡ ΠΈ ΠΊΠΎΠ»ΠΈΡΠ΅ΡΡΠ²Π° Π±Π°ΡΠ°Π±Π°Π½ΠΎΠ² ΡΡΠ°Π½Ρ Π΄Π΅Π»ΡΡ Π½Π° ΠΎΠ΄Π½ΠΎΠΊΡΠ°ΡΠ½ΡΠ΅, ΠΈΠ»ΠΈ ΠΎΠ΄Π½ΠΎΠ±Π°ΡΠ°Π±Π°Π½Π½ΡΠ΅, ΠΈ ΠΌΠ½ΠΎΠ³ΠΎΠΊΡΠ°ΡΠ½ΡΠ΅, ΠΈΠ»ΠΈ ΠΌΠ½ΠΎΠ³ΠΎΠ±Π°ΡΠ°Π±Π°Π½Π½ΡΠ΅, ΠΊΠΎΡΠΎΡΡΠ΅ ΠΌΠΎΠ³ΡΡ ΠΏΠΎΠ΄ΡΠ°Π·Π΄Π΅Π»ΡΡΡΡΡ ΠΏΠΎ ΡΠΏΠΎΡΠΎΠ±Ρ Π²ΡΠΏΠΎΠ»Π½Π΅Π½ΠΈΡ Π½Π° Π½ΠΈΡ Π²ΠΎΠ»ΠΎΡΠ΅Π½ΠΈΡ Π½Π° ΡΠ»Π΅Π΄ΡΡΡΠΈΠ΅ Π²ΠΈΠ΄Ρ: ΠΌΠ½ΠΎΠ³ΠΎΠΊΡΠ°ΡΠ½ΡΠ΅, ΡΠ°Π±ΠΎΡΠ°ΡΡΠΈΠ΅ Π±Π΅Π· ΡΠΊΠΎΠ»ΡΠΆΠ΅Π½ΠΈΡ, ΠΌΠ½ΠΎΠ³ΠΎΠΊΡΠ°ΡΠ½ΡΠ΅, ΡΠ°Π±ΠΎΡΠ°ΡΡΠΈΠ΅ ΡΠΎ ΡΠΊΠΎΠ»ΡΠΆΠ΅Π½ΠΈΠ΅ΠΌ, ΠΈ ΠΌΠ½ΠΎΠ³ΠΎΠΊΡΠ°ΡΠ½ΡΠ΅, ΡΠ°Π±ΠΎΡΠ°ΡΡΠΈΠ΅ Ρ ΠΏΡΠΎΡΠΈ- Π²ΠΎΠ½Π°ΡΡΠΆΠ΅Π½ΠΈΠ΅ΠΌ. ΠΠ½ΠΎΠ³ΠΎΠ±Π°ΡΠ°Π±Π°Π½Π½ΡΠ΅ ΡΡΠ°Π½Ρ ΠΌΠΎΠ³ΡΡ ΠΈΠΌΠ΅ΡΡ Π΄ΠΎ 30 Π²ΠΎΠ»ΠΎΠΊ.
ΠΠ΄Π½ΠΎΠΊΡΠ°ΡΠ½ΡΠ΅ ΡΡΠ°Π½Ρ ΠΈΡΠΏΠΎΠ»ΡΠ·ΡΡΡ ΠΏΡΠΈ Π²ΠΎΠ»ΠΎΡΠ΅Π½ΠΈΠΈ ΡΠΎΠ»ΡΡΠΎΠΉ ΠΏΡΠΎΠ²ΠΎΠ»ΠΎΠΊΠΈ ΠΈ ΠΏΡΡΡΠΊΠΎΠ² ΡΠ°ΡΠ΅ Π²ΡΠ΅Π³ΠΎ Π΄ΠΈΠ°ΠΌΠ΅ΡΡΠΎΠΌ ΠΎΡ 4 Π΄ΠΎ 25 ΠΌΠΌ. ΠΠΎ ΡΠΏΠΎΡΠΎΠ±Ρ ΡΠΊΠ»Π°Π΄ΠΊΠΈ ΠΌΠ΅ΡΠ°Π»Π»Π° Π½Π° Π±Π°ΡΠ°Π±Π°Π½Π΅ ΠΈΡ ΠΈΠ·Π³ΠΎΡΠΎΠ²Π»ΡΡΡ Ρ Π²Π΅ΡΡΠΈΠΊΠ°Π»ΡΠ½ΡΠΌ ΠΈ Π³ΠΎΡΠΈΠ·ΠΎΠ½ΡΠ°Π»ΡΠ½ΡΠΌ ΡΠ°ΡΠΏΠΎΠ»ΠΎΠΆΠ΅Π½ΠΈΠ΅ΠΌ ΠΎΡΠΈ Π±Π°ΡΠ°Π±Π°Π½Π° Π ΠΏΠΎΡΠ»Π΅Π΄Π½Π΅ΠΌ ΡΠ»ΡΡΠ°Π΅ ΡΠΏΡΠΎΡΠ°ΡΡΡΡ Π·Π°ΠΏΡΠ°Π²ΠΊΠ° ΠΏΡΠΎΠ²ΠΎΠ»ΠΎΠΊΠΈ ΠΈ ΡΠ½ΡΡΠΈΠ΅ Π±ΡΠ½ΡΠ° Ρ Π±Π°ΡΠ°Π±Π°Π½Π°. ΠΠΈΠ°ΠΌΠ΅ΡΡ Π±Π°ΡΠ°Π±Π°Π½Π° ΠΎΠΏΡΠ΅Π΄Π΅Π»ΡΠ΅ΡΡΡ ΡΠ΅ΡΠ΅Π½ΠΈΠ΅ΠΌ ΠΏΡΠΎΡΡΠ³ΠΈΠ²Π°Π΅ΠΌΠΎΠ³ΠΎ ΠΈΠ·Π΄Π΅Π»ΠΈΡ. Π’Π°ΠΊ, ΠΏΡΠΈ Π΄ΠΈΠ°ΠΌΠ΅ΡΡΠ΅ ΠΏΡΠΎΠ²ΠΎΠ»ΠΎΠΊΠΈ 4 ΠΌΠΌ Π΄ΠΈΠ°ΠΌΠ΅ΡΡ Π±Π°ΡΠ°Π±Π°Π½Π° ΡΠ°Π²Π΅Π½ 450 ΠΌΠΌ, ΠΏΡΠΈ Π΄ΠΈΠ°ΠΌΠ΅ΡΡΠ΅ ΠΏΡΡΡΠΊΠ° 25 ΠΌΠΌ β 1000 ΠΌΠΌ.
ΠΠ»Ρ ΡΠΎΠ³ΠΎ ΡΡΠΎΠ±Ρ Π²ΠΈΡΠΊΠΈ ΠΏΡΠΎΠ²ΠΎΠ»ΠΎΠΊΠΈ ΠΏΠΎ ΠΌΠ΅ΡΠ΅ Π½Π°ΠΌΠ°ΡΡΠ²Π°Π½ΠΈΡ ΠΌΠΎΠ³Π»ΠΈ ΡΠ²ΠΎΠ±ΠΎΠ΄Π½ΠΎ ΡΠ΄Π²ΠΈΠ³Π°ΡΡΡΡ ΠΏΠΎ Π±Π°ΡΠ°Π±Π°Π½Ρ, ΠΏΠΎΡΠ»Π΅Π΄Π½ΠΈΠΉ Π΄Π΅Π»Π°ΡΡ Π² Π²ΠΈΠ΄Π΅ ΡΡΠ΅ΡΠ΅Π½Π½ΠΎΠ³ΠΎ ΠΊΠΎΠ½ΡΡΠ° ΠΈΠ»ΠΈ ΡΠΎΡΡΠΎΡΡΠΈΠΌ ΠΈΠ· ΡΡΠ΅ΡΠ΅Π½Π½ΠΎΠ³ΠΎ ΠΊΠΎΠ½ΡΡΠ° ΠΈ ΡΠΈΠ»ΠΈΠ½Π΄ΡΠ° ΠΠ°ΡΠ°Π±Π°Π½ ΠΏΠ΅ΡΠ΅Π΄Π°Π΅Ρ ΡΡΠΈΠ»ΠΈΠ΅ Π²ΠΎΠ»ΠΎΡΠ΅Π½ΠΈΡ ΠΏΡΠΎΠ²ΠΎΠ»ΠΎΠΊΠ΅. Π Π°Π±ΠΎΡΠΈΠΉ ΡΡΠ°ΡΡΠΎΠΊ Π±Π°ΡΠ°Π±Π°Π½Π° ΠΈΡΠΏΡΡΡΠ²Π°Π΅Ρ Π·Π½Π°ΡΠΈΡΠ΅Π»ΡΠ½ΡΠ΅ Π½Π°Π³ΡΡΠ·ΠΊΠΈ ΠΎΡ Π΄Π°Π²Π»Π΅Π½ΠΈΡ Π½Π°ΠΌΠ°ΡΡΠ²Π°Π΅ΠΌΠΎΠΉ ΠΏΡΠΎΠ²ΠΎΠ»ΠΎΠΊΠΈ, ΠΏΠΎΡΡΠΎΠΌΡ Π΅Π³ΠΎ ΡΠ°Π±ΠΎΡΠ°Ρ ΠΏΠΎΠ²Π΅ΡΡ Π½ΠΎΡΡΡ Π΄ΠΎΠ»ΠΆΠ½Π° ΠΈΠΌΠ΅ΡΡ Π²ΡΡΠΎΠΊΡΡ ΡΠ²Π΅ΡΠ΄ΠΎΡΡΡ ΠΠ½Π° Π²ΡΠΏΠΎΠ»Π½ΡΠ΅ΡΡΡ ΠΈΠ· ΠΊΠΎΠ²Π°Π½ΠΎΠΉ ΡΡΠ°Π»ΠΈ Ρ ΡΠ²Π΅ΡΠ΄ΠΎΡΡΡΡ ΠΏΠΎΠ²Π΅ΡΡ Π½ΠΎΡΡΠΈ ΠΎΠΊΠΎΠ»ΠΎ 62 HRC. ΠΠΎΠ»ΠΎΡΠΈΠ»ΡΠ½ΡΠ΅ Π±Π°ΡΠ°Π±Π°Π½Ρ ΠΈΠΌΠ΅ΡΡ Π²Π½ΡΡΡΠ΅Π½Π½ΡΡ ΡΠΈΡΡΠ΅ΠΌΡ ΠΎΡ Π»Π°ΠΆΠ΄Π΅Π½ΠΈΡ.
Π‘ΠΊΠΎΡΠΎΡΡΡ Π²ΠΎΠ»ΠΎΡΠ΅Π½ΠΈΡ Π½Π° ΠΎΠ΄Π½ΠΎΠΊΡΠ°ΡΠ½ΡΡ ΡΡΠ°Π½Π°Ρ ΡΠ°ΡΠ΅ Π²ΡΠ΅Π³ΠΎ ΡΠΎΡΡΠ°Π²Π»ΡΠ΅Ρ 1. . . 2 ΠΌ/Ρ ΠΈ ΠΎΠ±ΡΡΠ½ΠΎ Π½Π΅ ΠΏΡΠ΅Π²ΡΡΠ°Π΅Ρ 5 ΠΌ/Ρ. Π Π·Π°Π²ΠΈΡΠΈΠΌΠΎΡΡΠΈ ΠΎΡ ΡΠ΅ΡΠ΅Π½ΠΈΡ ΠΈ Π²ΠΈΠ΄Π° ΠΏΡΠΎΡΡΠ³ΠΈΠ²Π°Π΅ΠΌΠΎΠ³ΠΎ ΠΌΠ΅ΡΠ°Π»Π»Π° ΡΡΠ°Π½Ρ ΠΎΠ΄Π½ΠΎΠΊΡΠ°ΡΠ½ΠΎΠ³ΠΎ Π²ΠΎΠ»ΠΎΡΠ΅Π½ΠΈΡ ΡΡΡΠΎΡΡ Π² ΡΠ°ΡΡΠ΅ΡΠ΅ Π½Π° ΡΡΠΈΠ»ΠΈΠ΅ Π²ΠΎΠ»ΠΎΡΠ΅Π½ΠΈΡ ΠΎΡ 0,05 Π΄ΠΎ 100 kH.
ΠΡΠΈΠ²ΠΎΠ΄ Π²ΠΎΠ»ΠΎΡΠΈΠ»ΡΠ½ΡΡ Π±Π°ΡΠ°Π±Π°Π½ΠΎΠ² ΠΎΡΡΡΠ΅ΡΡΠ²Π»ΡΠ΅ΡΡΡ Ρ ΠΏΠΎΠΌΠΎΡΡΡ Π΄Π²ΠΈΠ³Π°ΡΠ΅Π»Π΅ΠΉ ΠΏΠ΅ΡΠ΅ΠΌΠ΅Π½Π½ΠΎΠ³ΠΎ ΡΠΎΠΊΠ° Ρ ΡΠ°ΡΡΠΎΡΠ½ΡΠΌ ΡΠ΅Π³ΡΠ»ΠΈΡΠΎΠ²Π°Π½ΠΈΠ΅ΠΌ. ΠΠ»Π΅ΠΊΡΡΠΎΠ΄Π²ΠΈΠ³Π°ΡΠ΅Π»ΠΈ Π΄Π»Ρ ΠΎΠ±Π»Π΅Π³ΡΠ΅Π½ΠΈΡ ΡΠ΅Π³ΡΠ»ΠΈΡΠΎΠ²ΠΊΠΈ ΡΠ΅ΠΌΠ΅Π½Π½ΠΎΠΉ ΠΏΠ΅ΡΠ΅Π΄Π°ΡΠΈ ΠΌΠΎΠ½ΡΠΈΡΡΡΡ Π½Π° Π½Π°ΠΊΠ»ΠΎΠ½Π½ΡΡ Π½Π°ΠΏΡΠ°Π²Π»ΡΡΡΠΈΡ . ΠΠ½ΠΎΠ³ΠΎΠΊΡΠ°ΡΠ½ΠΎΠ΅ Π²ΠΎΠ»ΠΎΡΠ΅Π½ΠΈΠ΅ Π±Π΅Π· ΡΠΊΠΎΠ»ΡΠΆΠ΅Π½ΠΈΡ Π²ΡΠΏΠΎΠ»Π½ΡΠ΅ΡΡΡ ΡΠ°ΠΊ, ΡΡΠΎ ΠΏΡΠΎΡΡΠ³ΠΈΠ²Π°Π΅ΠΌΠ°Ρ ΠΏΡΠΎΠ²ΠΎΠ»ΠΎΠΊΠ° Π½Π°ΠΌΠ°ΡΡΠ²Π°Π΅ΡΡΡ Π½Π° ΡΡΠ½ΡΡΠΈΠΉ Π΅Π΅ Π±Π°ΡΠ°Π±Π°Π½ 2, 4, 5, ΠΊΠ°ΠΊ ΠΏΡΠΈ ΠΎΠ΄Π½ΠΎΠΊΡΠ°ΡΠ½ΠΎΠΌ Π²ΠΎΠ»ΠΎΡΠ΅Π½ΠΈΠΈ. Π‘ΡΠ°Π½ (ΡΠΈΡ. 3) ΡΠΎΡΡΠΎΠΈΡ ΠΈΠ· Π½Π΅ΡΠΊΠΎΠ»ΡΠΊΠΈΡ ΠΏΠΎΡΠ»Π΅Π΄ΠΎΠ²Π°ΡΠ΅Π»ΡΠ½ΠΎ ΡΠ°ΡΠΏΠΎΠ»ΠΎΠΆΠ΅Π½Π½ΡΡ Π²ΠΎΠ»ΠΎΠΊ 1 ΠΈ ΡΡΠ½ΡΡΠΈΡ Π±Π°ΡΠ°Π±Π°Π½ΠΎΠ², ΠΊΠΎΡΠΎΡΡΠ΅, Ρ ΠΎΡΡ ΠΈ ΡΠ²ΡΠ·Π°Π½Ρ Π½Π΅ΠΏΡΠ΅ΡΡΠ²Π½ΠΎΡΡΡΡ ΠΏΡΠΎΡΠ΅ΡΡΠ°, ΠΌΠΎΠ³ΡΡ ΡΠ°Π±ΠΎΡΠ°ΡΡ Π½Π΅Π·Π°Π²ΠΈΡΠΈΠΌΠΎ Π΄ΡΡΠ³ ΠΎΡ Π΄ΡΡΠ³Π°.
Π‘ΠΌΠ°ΡΡΠ²Π°Π½ΠΈΠ΅ ΠΏΡΠΎΠ²ΠΎΠ»ΠΎΠΊΠΈ Ρ Π±Π°ΡΠ°Π±Π°Π½Π° 2 ΠΈ 4 Π²ΠΎ Π²ΡΠ΅ΠΌΡ Π²ΠΎΠ»ΠΎΡΠ΅Π½ΠΈΡ ΠΈΠ»ΠΈ ΠΏΡΠΈ Π΅Π³ΠΎ ΠΎΡΡΠ°Π½ΠΎΠ²ΠΊΠ΅, ΡΡΠΎΠ±Ρ ΠΈΠ·Π±Π΅ΠΆΠ°ΡΡ Π΅Π΅ ΡΠΊΡΡΡΠΈΠ²Π°Π½ΠΈΡ, ΠΏΡΠΎΠΈΠ·Π²ΠΎΠ΄ΠΈΡΡΡ ΡΠ΅ΡΠ΅Π· ΡΠΈΡΡΠ΅ΠΌΡ ΡΠΎΠ»ΠΈΠΊΠΎΠ² 3, ΠΎΠ΄ΠΈΠ½ ΠΈΠ· ΠΊΠΎΡΠΎΡΡΡ , ΡΠ°ΡΠΏΠΎΠ»ΠΎΠΆΠ΅Π½Π½ΡΠΉ Π½Π°Π΄ Π±Π°ΡΠ°Π±Π°Π½ΠΎΠΌ, ΠΈΠΌΠ΅Π΅Ρ Π²ΠΎΠ·ΠΌΠΎΠΆΠ½ΠΎΡΡΡ ΡΠ²ΠΎΠ±ΠΎΠ΄Π½ΠΎ Π²ΡΠ°ΡΠ°ΡΡΡΡ Π²ΠΎΠΊΡΡΠ³ ΠΎΡΠΈ Π±Π°ΡΠ°Π±Π°Π½Π° Π‘ΠΊΠΎΡΠΎΡΡΡ Π²ΡΠ°ΡΠ΅Π½ΠΈΡ Π±Π°ΡΠ°Π±Π°Π½Π° ΡΠΈΠ½Ρ ΡΠΎΠ½ΠΈΠ·ΠΈΡΡΠ΅ΡΡΡ ΡΠ΅Π½ΡΠΎΡΠ½ΡΠΌ ΡΠΎΠ»ΠΈΠΊΠΎΠΌ, ΠΊΠΎΡΠΎΡΡΠΉ Π°Π²ΡΠΎΠΌΠ°ΡΠΈΡΠ΅ΡΠΊΠΈ ΡΠ΅Π³ΡΠ»ΠΈΡΡΠ΅Ρ Π΅Π΅ Π² ΡΠΎΠΎΡΠ²Π΅ΡΡΡΠ²ΠΈΠΈ Ρ ΠΎΠ±ΠΆΠ°ΡΠΈΠ΅ΠΌ ΠΏΡΠΎΠ²ΠΎΠ»ΠΎΠΊΠΈ.
Π ΠΈΡ. 3. ΠΠ½ΠΎΠ³ΠΎΠ±Π°ΡΠ°Π±Π°Π½Π½ΡΠΉ Π²ΠΎΠ»ΠΎΡΠΈΠ»ΡΠ½ΡΠΉ ΡΡΠ°Π½, ΡΠ°Π±ΠΎΡΠ°ΡΡΠΈΠΉ Π±Π΅Π· ΡΠΊΠΎΠ»ΡΠΆΠ΅Π½ΠΈΡ: Π° β ΡΡ Π΅ΠΌΠ°; Π± β ΠΎΠ±ΡΠΈΠΉ Π²ΠΈΠ΄ ΡΡΠ°Π½Π° SCWD-600
Π‘ΠΊΠΎΡΠΎΡΡΡ Π²ΠΎΠ»ΠΎΡΠ΅Π½ΠΈΡ Π½Π° ΡΡΠ°Π½Π°Ρ Π±Π΅Π· ΡΠΊΠΎΠ»ΡΠΆΠ΅Π½ΠΈΡ ΠΌΠΎΠΆΠ΅Ρ Π΄ΠΎΡΡΠΈΠ³Π°ΡΡ 20 ΠΌ/Ρ. ΠΠΎΠ΄ΠΎΠ±Π½ΡΠ΅ ΡΡΠ°Π½Ρ ΠΈΠ·Π³ΠΎΡΠΎΠ²Π»ΡΡΡ ΠΊΠ°ΠΊ Ρ Π³ΡΡΠΏΠΏΠΎΠ²ΡΠΌ, ΡΠ°ΠΊ ΠΈ Ρ ΠΈΠ½Π΄ΠΈΠ²ΠΈΠ΄ΡΠ°Π»ΡΠ½ΡΠΌ ΠΏΡΠΈΠ²ΠΎΠ΄ΠΎΠΌ Π΄Π»Ρ ΠΊΠ°ΠΆΠ΄ΠΎΠ³ΠΎ Π±Π°ΡΠ°Π±Π°Π½Π°. ΠΠ° ΠΊΠ°ΡΡΡΠΊΠΈ ΠΌΠΎΠΆΠ΅Ρ Π½Π°ΠΌΠ°ΡΡΠ²Π°ΡΡΡΡ Π΄ΠΎ 4000 ΠΊΠ³ ΠΏΡΠΎΠ²ΠΎΠ»ΠΎΠΊΠΈ.
Π‘ΡΠ°Π½Ρ ΠΌΠ½ΠΎΠ³ΠΎΠ±Π°ΡΠ°Π±Π°Π½Π½ΠΎΠ³ΠΎ Π²ΠΎΠ»ΠΎΡΠ΅Π½ΠΈΡ, ΡΠ°Π±ΠΎΡΠ°ΡΡΠΈΠ΅ ΡΠΎ ΡΠΊΠΎΠ»ΡΠΆΠ΅Π½ΠΈΠ΅ΠΌ (ΡΠΈΡ. 4), ΠΈΠΌΠ΅ΡΡ ΡΡΡΠ΅ΡΡΠ²Π΅Π½Π½ΠΎΠ΅ ΠΎΡΠ»ΠΈΡΠΈΠ΅ ΠΎΡ ΡΡΠ°Π½ΠΎΠ², ΡΠ°Π±ΠΎΡΠ°ΡΡΠΈΡ Π±Π΅Π· ΡΠΊΠΎΠ»ΡΠΆΠ΅Π½ΠΈΡ ΠΡΠΈ Π²ΠΎΠ»ΠΎΡΠ΅Π½ΠΈΠΈ ΡΠΎ ΡΠΊΠΎΠ»ΡΠΆΠ΅Π½ΠΈΠ΅ΠΌ ΠΏΡΠΎΡΡΠ³ΠΈΠ²Π°Π΅ΠΌΡΡ ΠΏΡΠΎΠ²ΠΎΠ»ΠΎΠΊΡ ΠΎΠ±ΠΎΡΠ°ΡΠΈΠ²Π°ΡΡ Π²ΠΎΠΊΡΡΠ³ ΡΠ°Π±ΠΎΡΠΈΡ ΡΠΊΠΈΠ²ΠΎΠ² 3 (Π±Π°ΡΠ°Π±Π°Π½ΠΎΠ²) ΠΎΠ΄ΠΈΠ½ ΠΈΠ»ΠΈ Π½Π΅ΡΠΊΠΎΠ»ΡΠΊΠΎ ΡΠ°Π· ΡΠ°ΠΊ, ΡΡΠΎΠ±Ρ ΡΡΠ³ΠΎΠ²ΠΎΠ΅ ΡΡΠΈΠ»ΠΈΠ΅ Π½Π° ΠΊΠ°ΠΆΠ΄ΠΎΠΌ ΡΠΊΠΈΠ²Π΅ ΠΏΡΠ΅ΠΎΠ΄ΠΎΠ»Π΅Π²Π°Π»ΠΎΡΡ Π΄Π΅ΠΉΡΡΠ²ΠΈΠ΅ΠΌ ΡΠΈΠ» ΡΡΠ΅Π½ΠΈΡ ΠΌΠ΅ΠΆΠ΄Ρ ΠΏΠΎΠ²Π΅ΡΡ Π½ΠΎΡΡΡΡ ΡΠΊΠΈΠ²Π° ΠΈ ΠΎΠ±Ρ Π²Π°ΡΡΠ²Π°ΡΡΠ΅ΠΉ Π΅Π³ΠΎ Π² ΠΏΡΠΎΡΠ΅ΡΡΠ΅ Π²ΠΎΠ»ΠΎΡΠ΅Π½ΠΈΡ ΠΏΡΠΎΠ²ΠΎΠ»ΠΎΠΊΠΎΠΉ. ΠΠΎ Π²ΡΠ΅ΠΌΡ ΡΠ°Π±ΠΎΡΡ Π·Π° ΠΊΠ°ΠΆΠ΄ΡΠΉ ΠΎΠ±ΠΎΡΠΎΡ Π±Π°ΡΠ°Π±Π°Π½Π° (ΡΠΊΠΈΠ²Π°) Π½Π° Π½Π΅Π³ΠΎ Π½Π°ΠΌΠ°ΡΡΠ²Π°Π΅ΡΡΡ ΠΎΠ΄ΠΈΠ½ Π²ΠΈΡΠΎΠΊ ΠΏΡΠΎΠ²ΠΎΠ»ΠΎΠΊΠΈ ΠΈ Π²ΠΌΠ΅ΡΡΠ΅ Ρ ΡΡΠΈΠΌ ΠΎΠ΄ΠΈΠ½ Π²ΠΈΡΠΎΠΊ ΡΠΌΠ°ΡΡΠ²Π°Π΅ΡΡΡ.
Π ΠΈΡ. 4. Π‘Ρ Π΅ΠΌΠ° ΡΡΠ°Π½Π° ΠΌΠ½ΠΎΠ³ΠΎΠ±Π°ΡΠ°Π±Π°Π½Π½ΠΎΠ³ΠΎ Π²ΠΎΠ»ΠΎΡΠ΅Π½ΠΈΡ, ΡΠ°Π±ΠΎΡΠ°ΡΡΠ΅Π³ΠΎ ΡΠΎ ΡΠΊΠΎΠ»ΡΠΆΠ΅Π½ΠΈΠ΅ΠΌ: 1 β ΠΏΠΎΠ΄Π°ΡΡΠΈΠΉ Π±Π°ΡΠ°Π±Π°Π½; 2 β Π²ΠΎΠ»ΠΎΠΊΠ°; 3 β ΡΠ°Π±ΠΎΡΠΈΠΉ ΡΠΊΠΈΠ²; 4 β ΠΏΡΠΈΠ΅ΠΌΠ½ΡΠΉ Π±Π°ΡΠ°Π±Π°Π½.
Π‘ΠΊΠΎΡΠΎΡΡΡ Π²ΡΡ ΠΎΠ΄Π° ΠΌΠ΅ΡΠ°Π»Π»Π° ΠΈΠ· Π²ΠΎΠ»ΠΎΠΊΠΈ Π½Π΅ ΠΌΠΎΠΆΠ΅Ρ ΠΎΠΊΠ°Π·Π°ΡΡΡΡ Π±ΠΎΠ»ΡΡΠ΅ ΠΎΠΊΡΡΠΆΠ½ΠΎΠΉ ΡΠΊΠΎΡΠΎΡΡΠΈ ΠΏΠΎΡΠ»Π΅Π΄ΡΡΡΠ΅Π³ΠΎ Π·Π° Π½Π΅ΠΉ Π±Π°ΡΠ°Π±Π°Π½Π°, ΠΈΠ±ΠΎ Π²ΠΎΠ»ΠΎΡΠ΅Π½ΠΈΠ΅ Π²ΡΠΏΠΎΠ»Π½ΡΠ΅ΡΡΡ ΡΡΠ½ΡΡΠΈΠΌ ΡΡΠΈΠ»ΠΈΠ΅ΠΌ ΡΡΠΎΠ³ΠΎ Π±Π°ΡΠ°Π±Π°Π½Π°. ΠΠ°Π½Π½ΠΎΠ΅ ΠΎΠ±ΡΡΠΎΡΡΠ΅Π»ΡΡΡΠ²ΠΎ ΡΡΠ΅Π±ΡΠ΅Ρ ΠΏΡΠΈ ΡΠ°Π±ΠΎΡΠ΅ Π½Π° ΡΡΠ°Π½Π°Ρ ΡΠΎ ΡΠΊΠΎΠ»ΡΠΆΠ΅Π½ΠΈΠ΅ΠΌ Π²ΡΠ±ΠΈΡΠ°ΡΡ ΠΎΠΊΡΡΠΆΠ½ΡΡ ΡΠΊΠΎΡΠΎΡΡΡ ΡΠ°Π±ΠΎΡΠΈΡ ΡΠΊΠΈΠ²ΠΎΠ² ΡΠ°ΠΊΠΎΠΉ, ΡΡΠΎΠ±Ρ ΠΎΠ½Π° Π±ΡΠ»Π° Π½Π° 2. . . 4 % Π±ΠΎΠ»ΡΡΠ΅ ΡΠΊΠΎΡΠΎΡΡΠΈ Π²ΠΎΠ»ΠΎΡΠ΅Π½ΠΈΡ. ΠΡΠ° ΡΠ°Π·Π½ΠΈΡΠ° (Π·Π° ΠΈΡΠΊΠ»ΡΡΠ΅Π½ΠΈΠ΅ΠΌ ΠΏΠΎΡΠ»Π΅Π΄Π½Π΅Π³ΠΎ Π±Π°ΡΠ°Π±Π°Π½Π°) Π²ΡΠ·ΡΠ²Π°Π΅Ρ ΠΏΡΠΎΡΠΊΠ°Π»ΡΠ·ΡΠ²Π°Π½ΠΈΠ΅ ΠΌΠ΅ΡΠ°Π»Π»Π° ΠΏΠΎ ΡΠ°Π±ΠΎΡΠΈΠΌ ΡΠΊΠΈΠ²Π°ΠΌ, ΠΈ ΡΠ°ΠΊΠΎΠ΅ Π²ΠΎΠ»ΠΎΡΠ΅Π½ΠΈΠ΅ Π½Π°Π·ΡΠ²Π°Π΅ΡΡΡ Π²ΠΎΠ»ΠΎΡΠ΅Π½ΠΈΠ΅ΠΌ ΡΠΎ ΡΠΊΠΎΠ»ΡΠΆΠ΅Π½ΠΈΠ΅ΠΌ Π‘ΡΠ°Π½Ρ ΡΠΎ ΡΠΊΠΎΠ»ΡΠΆΠ΅Π½ΠΈΠ΅ΠΌ ΠΈΡΠΏΠΎΠ»ΡΠ·ΡΡΡ Π³Π»Π°Π²Π½ΡΠΌ ΠΎΠ±ΡΠ°Π·ΠΎΠΌ Π΄Π»Ρ Π²ΠΎΠ»ΠΎΡΠ΅Π½ΠΈΡ ΠΌΠ΅Π΄Π½ΠΎΠΉ, Π°Π»ΡΠΌΠΈΠ½ΠΈΠ΅Π²ΠΎΠΉ ΠΈ ΡΡΠ°Π²Π½ΠΈΡΠ΅Π»ΡΠ½ΠΎ ΠΌΡΠ³ΠΊΠΎΠΉ ΡΡΠ°Π»ΡΠ½ΠΎΠΉ ΠΏΡΠΎΠ²ΠΎΠ»ΠΎΠΊΠΈ. ΠΡ ΠΈΠ·Π³ΠΎΡΠΎΠ²Π»ΡΡΡ Ρ Π³ΠΎΡΠΈΠ·ΠΎΠ½ΡΠ°Π»ΡΠ½ΡΠΌ ΠΈ Π²Π΅ΡΡΠΈΠΊΠ°Π»ΡΠ½ΡΠΌ ΡΠ°ΡΠΏΠΎΠ»ΠΎΠΆΠ΅Π½ΠΈΠ΅ΠΌ ΡΠ°Π±ΠΎΡΠΈΡ ΡΠΊΠΈΠ²ΠΎΠ² ΠΠ° Π½ΠΈΡ Π²ΡΠΏΠΎΠ»Π½ΡΠ΅ΡΡΡ Π²ΠΎΠ»ΠΎΡΠ΅Π½ΠΈΠ΅ Π² ΠΆΠΈΠ΄ΠΊΠΎΠΉ ΡΠΌΠ°Π·ΠΊΠ΅, ΡΡΠΎ ΠΎΠ±Π΅ΡΠΏΠ΅ΡΠΈΠ²Π°Π΅Ρ Π²ΠΎΠ·ΠΌΠΎΠΆΠ½ΠΎΡΡΡ ΠΏΡΠΈΠΌΠ΅Π½Π΅Π½ΠΈΡ Π²ΡΡΠΎΠΊΠΎΡΠΊΠΎΡΠΎΡΡΠ½ΠΎΠ³ΠΎ Π²ΠΎΠ»ΠΎΡΠ΅Π½ΠΈΡ (Π΄ΠΎ 40 ΠΌ/Ρ) Π ΠΊΠ°ΡΠ΅ΡΡΠ²Π΅ ΡΠΌΠ°Π·ΠΊΠΈ ΠΏΡΠΈ Π²ΠΎΠ»ΠΎΡΠ΅Π½ΠΈΠΈ ΠΏΡΠΈΠΌΠ΅Π½ΡΡΡ ΠΌΠΈΠ½Π΅ΡΠ°Π»ΡΠ½ΠΎΠ΅ ΠΌΠ°ΡΠ»ΠΎ, Π³ΡΠ°ΡΠΈΡ, ΠΌΡΠ»ΠΎ ΠΈΠ»ΠΈ ΡΠΌΡΠ»ΡΡΠΈΠΈ. ΠΠ°ΠΊ Π΄Π»Ρ ΡΠΌΠ°Π·ΠΊΠΈ ΠΎΠ±ΠΎΡΡΠ΄ΡΡΡ ΠΎΡ Π»Π°ΠΆΠ΄Π΅Π½ΠΈΠ΅ΠΌ.
ΠΡΠΎΡΠΈΠ²ΠΎΠ½Π°ΡΡΠΆΠ΅Π½ΠΈΠ΅ ΠΏΡΠΈ Π²ΠΎΠ»ΠΎΡΠ΅Π½ΠΈΠΈ ΠΏΠΎΠ»ΠΎΠΆΠΈΡΠ΅Π»ΡΠ½ΠΎ ΡΠΊΠ°Π·ΡΠ²Π°Π΅ΡΡΡ Π½Π° ΡΠΈΠ»ΠΎΠ²ΡΡ ΡΡΠ»ΠΎΠ²ΠΈΡΡ ΠΏΡΠΎΡΠ΅ΡΡΠ°, ΡΡΠΎ Π²Π»Π΅ΡΠ΅Ρ Π·Π° ΡΠΎΠ±ΠΎΠΉ ΡΠΌΠ΅Π½ΡΡΠ΅Π½ΠΈΠ΅ ΠΈΠ·Π½ΠΎΡΠ° Π²ΠΎΠ»ΠΎΠΊ, ΡΠ»Π΅Π΄ΠΎΠ²Π°ΡΠ΅Π»ΡΠ½ΠΎ, ΠΏΠΎΠ²ΡΡΠ°Π΅ΡΡΡ ΡΠΎΡΠ½ΠΎΡΡΡ ΡΠ°Π·ΠΌΠ΅ΡΠΎΠ² ΠΏΡΠΎΠ²ΠΎΠ»ΠΎΠΊΠΈ. ΠΠ΅Π»ΠΈΡΠΈΠ½Ρ ΠΏΡΠΎΡΠΈΠ²ΠΎΠ½Π°ΡΡΠΆΠ΅Π½ΠΈΡ ΡΡΡΠ°Π½Π°Π²Π»ΠΈΠ²Π°ΡΡ Π² ΠΏΡΠ΅Π΄Π΅Π»Π°Ρ ΠΎΡ 10 Π΄ΠΎ 30 % ΠΎΡ ΡΡΠΈΠ»ΠΈΡ Π²ΠΎΠ»ΠΎΡΠ΅Π½ΠΈΡ.
ΠΠ»Ρ ΡΠΎΡΠ½ΠΎΠ³ΠΎ ΡΠ΅Π³ΡΠ»ΠΈΡΠΎΠ²Π°Π½ΠΈΡ ΠΏΡΠΎΡΠΈΠ²ΠΎΠ½Π°ΡΡΠΆΠ΅Π½ΠΈΡ ΡΡΠ°Π½Ρ ΠΎΠ±ΠΎΡΡΠ΄ΠΎΠ²Π°Π½Ρ Π°Π²ΡΠΎΠΌΠ°ΡΠΈΡΠ΅ΡΠΊΠΎΠΉ ΡΡΡΠ°Π½ΠΎΠ²ΠΊΠΎΠΉ ΡΠΊΠΎΡΠΎΡΡΠΈ ΡΠ°Π±ΠΎΡΠΈΡ Π±Π°ΡΠ°Π±Π°Π½ΠΎΠ² ΠΠ°ΠΆΠ΄ΡΠΉ Π±Π°ΡΠ°Π±Π°Π½ ΠΏΡΠΈΠ²ΠΎΠ΄ΠΈΡΡΡ ΠΈΠ½Π΄ΠΈΠ²ΠΈΠ΄ΡΠ°Π»ΡΠ½ΡΠΌ ΠΏΡΠΈΠ²ΠΎΠ΄ΠΎΠΌ Ρ ΡΠ΅Π³ΡΠ»ΠΈΡΡΠ΅ΠΌΠΎΠΉ ΡΠΊΠΎΡΠΎΡΡΡΡ. Π‘ΡΠ°Π½Ρ ΠΎΡΠ½Π°ΡΠ°ΡΡ ΡΡΡΡΠΎΠΉΡΡΠ²ΠΎΠΌ Ρ Π³ΠΈΠ΄ΡΠ°Π²Π»ΠΈΡΠ΅ΡΠΊΠΈΠΌ ΠΏΡΠΈΠ²ΠΎΠ΄ΠΎΠΌ Π΄Π»Ρ ΡΠ½ΡΡΠΈΡ Π½Π°ΠΏΡΡΠΆΠ΅Π½ΠΈΠΉ Ρ ΠΏΡΠΎΠ²ΠΎΠ»ΠΎΠΊΠΈ.
3. ΠΠΎΠ»ΠΎΡΠΈΠ»ΡΠ½ΡΠΉ ΡΡΠ°Π½ Π΄Π»Ρ ΡΡΡΠ±
ΠΠΎΠ»ΠΎΡΠ΅Π½ΠΈΠ΅ ΡΡΡΠ± ΠΌΠΎΠΆΠ½ΠΎ ΠΏΡΠΎΠΈΠ·Π²ΠΎΠ΄ΠΈΡΡ Π½Π° ΠΎΠΏΡΠ°Π²ΠΊΠ΅ (ΡΠΌ. ΡΠΈΡ. 1, Π±) ΠΈ Π±Π΅Π· ΠΎΠΏΡΠ°Π²ΠΊΠΈ (ΡΠΌ. ΡΠΈΡ. 1, Π²), Π΅ΡΠ»ΠΈ ΡΡΠ΅Π±ΡΠ΅ΡΡΡ ΡΠΌΠ΅Π½ΡΡΠΈΡΡ Π½Π°ΡΡΠΆΠ½ΡΠΉ Π΄ΠΈΠ°ΠΌΠ΅ΡΡ ΠΈ ΡΠΎΠ»ΡΠΈΠ½Ρ ΡΡΠ΅Π½ΠΊΠΈ ΠΡΠΈ ΡΡΠΎΠΌ ΠΌΠΎΠ³ΡΡ ΠΏΡΠΈΠΌΠ΅Π½ΡΡΡΡΡ ΠΎΠΏΡΠ°Π²ΠΊΠΈ, Π΄Π²ΠΈΠΆΡΡΠΈΠ΅ΡΡ Π²ΠΌΠ΅ΡΡΠ΅ Ρ ΡΡΡΠ±ΠΎΠΉ, ΠΆΠ΅ΡΡΠΊΠΎ Π·Π°ΠΊΡΠ΅ΠΏΠ»Π΅Π½Π½ΡΠ΅ ΠΈ ΡΠ°ΠΌΠΎΡΡΡΠ°Π½Π°Π²Π»ΠΈΠ²Π°ΡΡΠΈΠ΅ΡΡ ΠΎΠΏΡΠ°Π²ΠΊΠΈ ΠΠΎΠ»ΠΎΡΠ΅Π½ΠΈΠ΅ Π½Π° ΠΎΠΏΡΠ°Π²ΠΊΠ°Ρ ΠΏΠΎΠ·Π²ΠΎΠ»ΡΠ΅Ρ ΠΏΠΎΠ»ΡΡΠΈΡΡ ΡΡΡΠ±Ρ Ρ Π²ΡΡΠΎΠΊΠΈΠΌΠΈ ΡΠΎΡΠ½ΠΎΡΡΡΡ ΡΠ°Π·ΠΌΠ΅ΡΠΎΠ² ΠΈ ΠΊΠ°ΡΠ΅ΡΡΠ²ΠΎΠΌ Π²Π½ΡΡΡΠ΅Π½Π½Π΅ΠΉ ΠΏΠΎΠ²Π΅ΡΡ Π½ΠΎΡΡΠΈ.
Π ΠΈΡ. 5. ΠΠΎΠ»ΠΎΡΠΈΠ»ΡΠ½ΡΠΉ ΡΡΠ°Π½ Π΄Π»Ρ ΡΡΡΠ±
ΠΠΎΠ»ΠΎΡΠΈΠ»ΡΠ½ΡΠΉ ΡΡΠ°Π½ Π΄Π»Ρ ΡΡΡΠ± (ΡΠΈΡ. 5) ΠΈΠΌΠ΅Π΅Ρ Π΄Π²Π΅ Π±Π΅ΡΠΊΠΎΠ½Π΅ΡΠ½ΡΠ΅ ΡΠ΅ΠΏΠΈ ΠΠ°Π»Ρ 3, ΡΠΌΠΎΠ½ΡΠΈΡΠΎΠ²Π°Π½Π½ΡΠ΅ Π½Π° ΡΡΠ°Π»ΡΠ½ΠΎΠΉ ΡΠ°ΠΌΠ΅-ΡΡΠ°Π½ΠΈΠ½Π΅ ΠΈ ΠΏΡΠΈΠ²ΠΎΠ΄ΠΈΠΌΡΠ΅ Π² Π΄Π²ΠΈΠΆΠ΅Π½ΠΈΠ΅ ΠΎΡ Π²Π΅Π΄ΡΡΠΈΡ Π·Π²Π΅Π·Π΄ΠΎΡΠ΅ΠΊ, ΠΊΠΎΡΠΎΡΡΠΌ ΠΏΠΎΡΡΠ΅Π΄ΡΡΠ²ΠΎΠΌ Π·ΡΠ±ΡΠ°ΡΠΎΠΉ ΠΏΠ΅ΡΠ΅Π΄Π°ΡΠΈ 4 ΡΠΎΠΎΠ±ΡΠ°Π΅ΡΡΡ Π²ΡΠ°ΡΠ΅Π½ΠΈΠ΅ ΠΎΡ ΠΌΠΎΡΠΎΡΠ°. ΠΠ° ΠΊΠΎΠ½ΡΠ΅ ΡΠ°ΠΌΡ ΡΠΊΡΠ΅ΠΏΠ»Π΅Π½Ρ Π³ΠΎΠ»ΠΎΠ²ΠΊΠΈ 1 Ρ ΡΠΈΠ»ΡΠ΅ΡΠ°ΠΌΠΈ, ΠΈΠ·Π³ΠΎΡΠΎΠ²Π»Π΅Π½Π½ΡΠΌΠΈ ΠΈΠ· ΡΠ²Π΅ΡΠ΄ΠΎΠ³ΠΎ ΡΠΏΠ»Π°Π²Π°. ΠΠ° ΡΡΠ°Π½ΠΈΠ½Π΅ ΠΊΠ°ΡΡΡΡΡ Π΄Π²Π΅ ΡΠ΅Π»Π΅ΠΆΠΊΠΈ 2 Ρ ΠΊΠ»Π΅ΡΠ°ΠΌΠΈ Π΄Π»Ρ Π·Π°Ρ Π²Π°ΡΠ° ΠΏΡΠΎΡΡΠ³ΠΈΠ²Π°Π΅ΠΌΠΎΠΉ ΡΡΡΠ±Ρ, ΠΊΠΎΡΠΎΡΡΠ΅ ΡΠ²ΠΎΠΈΠΌΠΈ ΠΊΡΡΡΠΊΠ°ΠΌΠΈ ΠΌΠΎΠ³ΡΡ Π±ΡΡΡ Π·Π°Ρ Π²Π°ΡΠ΅Π½Ρ Π·Π° Π»ΡΠ±ΠΎΠ΅ Π·Π²Π΅Π½ΠΎ ΡΠ΅ΠΏΠΈ. ΠΡΠΎΡΡΠΆΠΊΠ° ΡΡΡΠ±Ρ Π²Π΅Π΄Π΅ΡΡΡ Π½Π° ΠΊΠΎΡΠΎΡΠΊΠΎΠΉ ΠΈΠ»ΠΈ Π΄Π»ΠΈΠ½Π½ΠΎΠΉ ΠΎΠΏΡΠ°Π²ΠΊΠ΅.
Π§ΠΈΡΠ»ΠΎ ΠΏΡΠΎΡΡΠΆΠ΅ΠΊ ΡΡΡΠ± Π·Π°Π²ΠΈΡΠΈΡ ΠΎΡ ΠΈΡΡ ΠΎΠ΄Π½ΡΡ ΠΈ Π·Π°Π΄Π°Π½Π½ΡΡ ΡΠ°Π·ΠΌΠ΅ΡΠΎΠ². ΠΠ»Ρ ΡΠΎΠ½ΠΊΠΎΡΡΠ΅Π½Π½ΡΡ ΡΡΡΠ± ΠΌΠ°Π»ΠΎΠ³ΠΎ Π΄ΠΈΠ°ΠΌΠ΅ΡΡΠ° ΠΌΠΎΠΆΠ΅Ρ Π²ΡΠΏΠΎΠ»Π½ΡΡΡΡΡ ΡΠ²ΡΡΠ΅ 13 ΠΏΡΠΎΡΡΠΆΠ΅ΠΊ. ΠΠΎ ΠΌΠ΅ΡΠ΅ ΡΠ΄Π»ΠΈΠ½Π΅Π½ΠΈΡ ΡΡΡΠ±Ρ ΡΠ°Π·ΡΠ΅Π·Π°ΡΡΡΡ Π΄ΠΈΡΠΊΠΎΠ²ΠΎΠΉ ΠΏΠΈΠ»ΠΎΠΉ
ΠΡΠΎΡΠΌΠΎΡΡΠΎΠ²: 867
ΠΠΎΠ»ΠΎΡΠΈΠ»ΡΠ½ΡΠ΅ ΡΡΠ°Π½Ρ
ΠΠΎΠ»ΠΎΡΠΈΠ»ΡΠ½ΡΠ΅ ΡΡΠ°Π½Ρ, ΠΏΡΠ΅Π΄Π½Π°Π·Π½Π°ΡΠ΅Π½Ρ Π΄Π»Ρ ΠΏΡΠΎΠΈΠ·Π²ΠΎΠ΄ΡΡΠ²Π° ΠΏΡΠΎΠ²ΠΎΠ»ΠΎΠΊΠΈ ΠΌΠ΅Π½ΡΡΠ΅Π³ΠΎ Π΄ΠΈΠ°ΠΌΠ΅ΡΡΠ° ΠΈΠ· ΠΊΠ°ΡΠ°Π½ΠΊΠΈ (Π³ΡΡΠ±ΠΎΠ΅ Π²ΠΎΠ»ΠΎΡΠ΅Π½ΠΈΠ΅) ΠΈΠ»ΠΈ ΠΈΠ· ΠΏΡΠΎΠ²ΠΎΠ»ΠΎΠΊΠΈ Π±ΠΎΠ»ΡΡΠ΅Π³ΠΎ Π΄ΠΈΠ°ΠΌΠ΅ΡΡΠ°.ΠΡΠΈΠΌΠ΅ΡΠ½ΡΠ΅ Π΄ΠΈΠ°ΠΏΠ°Π·ΠΎΠ½Ρ Π²ΠΎΠ»ΠΎΡΠ΅Π½ΠΈΡ:
- ΠΡΡΠ±ΠΎΠ΅ Π²ΠΎΠ»ΠΎΡΠ΅Π½ΠΈΠ΅: Π²Ρ ΠΎΠ΄Π½ΠΎΠΉ Π΄ΠΈΠ°ΠΌΠ΅ΡΡ Π² ΡΠ°ΠΊΠΈΡ ΠΌΠ°ΡΠΈΠ½Π°Ρ 8ΠΌΠΌ Π΄Π»Ρ ΠΌΠ΅Π΄ΠΈ ΠΈ 12-9.5 Π΄Π»Ρ Π°Π»ΡΠΌΠΈΠ½ΠΈΡ, Π²ΡΡ ΠΎΠ΄Π½ΠΎΠΉ ΠΎΡ 4ΠΌΠΌ Π΄ΠΎ 1.2ΠΌΠΌ.
- Π‘ΡΠ΅Π΄Π½Π΅Π΅ Π²ΠΎΠ»ΠΎΡΠ΅Π½ΠΈΠ΅: Π²Ρ ΠΎΠ΄Π½ΠΎΠΉ Π΄ΠΈΠ°ΠΌΠ΅ΡΡ 1.8ΠΌΠΌ — 3.5ΠΌΠΌ, Π²ΡΡ ΠΎΠ΄Π½ΠΎΠΉ ΠΎΡ 1.5ΠΌΠΌ — 0.2ΠΌΠΌ.
- Π’ΠΎΠ½ΠΊΠΎΠ΅ Π²ΠΎΠ»ΠΎΡΠ΅Π½ΠΈΠ΅: Π²Ρ ΠΎΠ΄Π½ΠΎΠΉ Π΄ΠΈΠ°ΠΌΠ΅ΡΡ, 1.0ΠΌΠΌ — 1.8ΠΌΠΌ, Π²ΡΡ ΠΎΠ΄Π½ΠΎΠΉ 0.5ΠΌΠΌ β 0.05ΠΌΠΌ.
Π ΠΎΡΠ»ΠΈΡΠΈΠΈ ΠΎΡ Π°Π»ΡΠΌΠΈΠ½ΠΈΡ, ΠΏΡΠΈ Π²ΠΎΠ»ΠΎΡΠ΅Π½ΠΈΠΈ ΠΌΠ΅Π΄ΠΈ ΡΠ°ΡΡΠΎ ΠΈΡΠΏΠΎΠ»ΡΠ·ΡΠ΅ΡΡΡ ΠΎΡΠΆΠΈΠ³ ΠΏΡΠΎΠ²ΠΎΠ»ΠΎΠΊΠΈ Π΄Π»Ρ ΠΏΠΎΠ»ΡΡΠ΅Π½ΠΈΡ ΠΏΡΠΎΠ²ΠΎΠ»ΠΎΠΊΠΈ ΠΌΠ°ΡΠΊΠΈ ΠΠ (ΠΌΠ΅Π΄Ρ ΠΌΡΠ³ΠΊΠ°Ρ), Π±Π΅Π· ΠΎΡΠΆΠΈΠ³Π° ΡΠΎΠΎΡΠ²Π΅ΡΡΡΠ²Π΅Π½Π½ΠΎ ΠΠ’ (ΠΌΠ΅Π΄Ρ ΡΠ²Π΅ΡΠ΄Π°Ρ). ΠΡΠΆΠΈΠ³ ΠΏΡΠΎΠΈΡΡ ΠΎΠ΄ΠΈΡ Π·Π° ΡΡΠ΅Ρ ΠΏΡΠΎΠΏΡΡΠΊΠ°Π½ΠΈΡ ΡΠ»Π΅ΠΊΡΡΠΈΡΠ΅ΡΠΊΠΎΠ³ΠΎ ΡΠΎΠΊΠ° Π±ΠΎΠ»ΡΡΠΎΠ³ΠΎ Π½Π°ΠΏΡΡΠΆΠ΅Π½ΠΈΡ, ΡΠ΅ΡΠ΅Π· ΡΡΠ°ΡΡΠΎΠΊ ΠΏΡΠΎΠ²ΠΎΠ»ΠΎΠΊΠΈ Π½Π°Ρ ΠΎΠ΄ΡΡΠΈΠΉΡΡ ΠΌΠ΅ΠΆΠ΄Ρ Π΄Π²ΡΡ ΡΠΎΠ»ΠΈΠΊΠΎΠ²-ΠΊΠΎΠ½ΡΠ°ΠΊΡΠΎΠ².
ΠΠΏΡΠ΅Π΄Π΅Π»ΠΈΡΠ΅ΡΡ Ρ ΠΏΡΠΈΠ΅ΠΌΠ½ΡΠΌ ΡΡΡΡΠΎΠΉΡΡΠ²ΠΎΠΌ. ΠΡΠΎΠ²ΠΎΠ»ΠΎΠΊΠ° ΠΌΠΎΠΆΠ΅Ρ ΡΠΊΠ»Π°Π΄ΡΠ²Π°ΡΡΡΡ Π² ΠΊΠΎΡΠ·ΠΈΠ½Ρ ΠΈΠ»ΠΈ Π½Π°ΠΌΠ°ΡΡΠ²Π°ΡΡΡΡ Π½Π° Π±ΠΎΠ±ΠΈΠ½Ρ. ΠΠ° Π±ΠΎΠ±ΠΈΠ½Ρ Π½Π°ΠΌΠ°ΡΡΠ²Π°ΡΡΡΡ ΠΎΠ½Π° ΠΌΠΎΠΆΠ΅Ρ ΠΊΠ°ΠΊ Ρ ΠΏΠΎΠΌΠΎΡΡΡ ΠΏΡΠΎΡΡΠΎΠ³ΠΎ ΠΎΠ΄ΠΈΠ½Π°ΡΠ½ΠΎΠ³ΠΎ ΠΏΡΠΈΠ΅ΠΌΠ½ΠΈΠΊΠ°, ΡΠ°ΠΊ ΠΈ Ρ ΠΏΠΎΠΌΠΎΡΡΡ Π΄Π²ΠΎΠΉΠ½ΠΎΠ³ΠΎ Π°Π²ΡΠΎΠΌΠ°ΡΠΈΡΠ΅ΡΠΊΠΎΠ³ΠΎ (Π΄Π»Ρ ΡΠΊΠΎΡΠΎΡΡΠ½ΡΡ ), ΠΊΠΎΡΠΎΡΡΠΉ ΠΏΠΎΠ·Π²ΠΎΠ»ΡΠ΅Ρ Π½Π΅ ΠΎΡΡΠ°Π½Π°Π²Π»ΠΈΠ²Π°Ρ ΡΡΠ°Π½, ΠΌΠ΅Π½ΡΡΡ Π±ΠΎΠ±ΠΈΠ½Ρ.
Π‘Π»Π΅Π΄ΡΠ΅Ρ ΠΏΠΎΠΌΠ½ΠΈΡΡ, ΡΡΠΎ ΠΏΡΠΎΡΠ΅ΡΡ Π²ΠΎΠ»ΠΎΡΠ΅Π½ΠΈΡ ΡΡΠ΅Π±ΡΠ΅Ρ Π½Π΅ΠΏΡΠ΅ΡΡΠ²Π½ΠΎΠΉ ΡΠΌΠ°Π·ΠΊΠΈ Ρ ΠΈΡΠΏΠΎΠ»ΡΠ·ΠΎΠ²Π°Π½ΠΈΠ΅ΠΌ ΡΠΌΡΠ»ΡΡΠΈΠΈ. ΠΠ»Ρ ΡΡΠΎΠ³ΠΎ Π½Π΅ΠΎΠ±Ρ ΠΎΠ΄ΠΈΠΌΠΎ ΡΠΎΠΎΡΡΠ΄ΠΈΡΡ ΠΌΠ°ΡΠ»ΠΎΡΡΠ°Π½ΡΠΈΡ, Π²ΠΊΠ»ΡΡΠ°ΡΡΡΡ Π² ΡΠ΅Π±Ρ Π½Π°ΡΠΎΡΡ, ΡΠ΅Π·Π΅ΡΠ²ΡΠ°Ρ Π΄Π»Ρ ΡΠΌΡΠ»ΡΡΠΈΠΈ ΠΈ Π² Π·Π°Π²ΠΈΡΠΈΠΌΠΎΡΡΠΈ ΠΎΡ ΡΠ΅Π³ΠΈΠΎΠ½Π° Π΄ΠΎΠΏΠΎΠ»Π½ΠΈΡΠ΅Π»ΡΠ½ΡΠ΅ ΡΡΡΡΠΎΠΉΡΡΠ²Π° ΠΎΡ Π»Π°ΠΆΠ΄Π΅Π½ΠΈΡ, ΠΊΠ°ΠΊ Π½Π°ΠΏΡΠΈΠΌΠ΅Ρ ΡΠ°Π΄ΠΈΠ°ΡΠΎΡΡ ΠΈΠ»ΠΈ Π³ΡΠ°Π΄ΠΈΡΠ½ΠΈ.
ΠΠ΅ ΡΠ»Π΅Π΄ΡΠ΅Ρ ΠΏΡΠ΅Π½Π΅Π±ΡΠ΅Π³Π°ΡΡ ΡΠΈΡΡΠ΅ΠΌΠΎΠΉ ΡΠΈΠ»ΡΡΡΠ°ΡΠΈΠΈ ΡΠΌΡΠ»ΡΡΠΈΠΈ. ΠΡΠΎΠ±Π΅Π½Π½ΠΎ ΡΠ°ΠΊΠ°Ρ ΡΠΈΡΡΠ΅ΠΌΠ° Π²Π°ΠΆΠ½Π° Π² ΡΠ»ΡΡΠ°Π΅ Π΄Π°Π»ΡΠ½Π΅ΠΉΡΠ΅Π³ΠΎ Π²ΠΎΠ»ΠΎΡΠ΅Π½ΠΈΡ ΠΏΡΠΎΠ²ΠΎΠ»ΠΎΠΊΠΈ, ΡΠ°ΠΊ ΠΊΠ°ΠΊ ΠΌΠΈΠΊΡΠΎΡΠ°ΡΡΠΈΡΡ ΠΌΠ΅Π΄ΠΈ, ΠΏΠΎΠΏΠ°Π΄Π°ΡΡΠΈΠ΅ Π²ΠΌΠ΅ΡΡΠ΅ Ρ ΡΠΌΡΠ»ΡΡΠΈΠ΅ΠΉ Π² ΡΠΈΠ»ΡΠ΅ΡΡ Π² ΠΌΠΎΠΌΠ΅Π½Ρ ΠΏΡΠΎΡΡΠΆΠΊΠΈ, Π²ΠΏΡΠ΅ΡΡΠΎΠ²ΡΠ²Π°ΡΡΡΡ Π² ΠΏΡΠΎΠ²ΠΎΠ»ΠΎΠΊΡ ΠΈ ΡΠ²Π»ΡΡΡΡΡ ΠΌΠ΅ΡΡΠΎΠΌ ΡΠ°Π·ΡΡΠ²Π° ΠΏΡΠΈ ΡΠ»Π΅Π΄ΡΡΡΠ΅ΠΌ ΡΡΠ°ΠΏΠ΅ Π²ΠΎΠ»ΠΎΡΠ΅Π½ΠΈΡ.
ΠΡΠΎΠΌΠ΅ ΡΠΎΠ³ΠΎ, Π»ΠΈΠ½ΠΈΡ Π²ΠΎΠ»ΠΎΡΠ΅Π½ΠΈΡ Π΄ΠΎΠ»ΠΆΠ½Π° Π±ΡΡΡ ΡΠΊΠΎΠΌΠΏΠ»Π΅ΠΊΡΠΎΠ²Π°Π½Π° Π΄ΠΎΠΏΠΎΠ»Π½ΠΈΡΠ΅Π»ΡΠ½ΡΠΌΠΈ ΡΡΠ°Π½ΠΊΠ°ΠΌΠΈ ΠΈ ΠΎΠ±ΠΎΡΡΠ΄ΠΎΠ²Π°Π½ΠΈΠ΅ΠΌ, ΡΠ°ΠΊΠΈΠΌΠΈ ΠΊΠ°ΠΊ ΠΎΡΡΡΠΈΠ»ΡΠ½ΠΎ- Π·Π°ΡΡΠΆΠ½ΠΎΠΉ ΡΡΠ°Π½ΠΎΠΊ, Π°ΠΏΠΏΠ°ΡΠ°Ρ Ρ ΠΎΠ»ΠΎΠ΄Π½ΠΎΠΉ ΠΈ/ΠΈΠ»ΠΈ Π³ΠΎΡΡΡΠ΅ΠΉ ΡΠ²Π°ΡΠΊΠΈ. Π’Π°ΠΊ ΠΆΠ΅ ΡΡΠ΄Π° ΠΌΠΎΠΆΠ½ΠΎ ΠΎΡΠ½Π΅ΡΡΠΈ ΠΈ ΡΠΈΠ»ΡΠ΅ΡΡ (Π²ΠΎΠ»ΠΎΠΊΠΈ), ΠΊΠΎΠΌΠΏΠ»Π΅ΠΊΡ Π·Π°Π²ΠΈΡΠΈΡ ΠΎΡ ΡΠΎΠ³ΠΎ, ΠΊΠ°ΠΊΠΎΠΉ Π½ΡΠΆΠ΅Π½ Π΄ΠΈΠ°ΠΌΠ΅ΡΡ Π½Π° Π²ΡΡ ΠΎΠ΄Π΅. ΠΡΠ½ΠΎΠ²Π½ΡΠΌΠΈ ΠΏΠΎΠΊΠ°Π·Π°ΡΠ΅Π»ΡΠΌΠΈ ΠΊΠ°ΡΠ΅ΡΡΠ²Π° ΠΏΡΠΎΠ΄ΡΠΊΡΠΈΠΈ (ΠΏΡΠΎΠ²ΠΎΠ»ΠΎΠΊΠΈ/ΠΆΠΈΠ»Ρ) ΡΠ²Π»ΡΡΡΡΡ ΡΠΎΠΏΡΠΎΡΠΈΠ²Π»Π΅Π½ΠΈΠ΅ ΠΈ ΠΊΠΎΡΡΡΠΈΡΠΈΠ΅Π½Ρ ΡΠ΄Π»ΠΈΠ½Π΅Π½ΠΈΡ.
ΠΡΠ»ΠΈ ΠΡ ΠΏΠ»Π°Π½ΠΈΡΡΠ΅ΡΠ΅ ΠΏΡΠΎΠ΄Π°Π²Π°ΡΡ ΠΏΡΠΎΠ΄ΡΠΊΡΠΈΡ ΠΏΠΎΡΠ»Π΅ Π²ΠΎΠ»ΠΎΡΠ΅Π½ΠΈΡ, ΡΠΎ Π²ΠΎΠ·ΠΌΠΎΠΆΠ½ΠΎ ΠΏΠΎΠ½Π°Π΄ΠΎΠ±ΠΈΡΡΡΡ Π»Π°Π±ΠΎΡΠ°ΡΠΎΡΠ½ΠΎΠ΅ ΠΎΠ±ΠΎΡΡΠ΄ΠΎΠ²Π°Π½ΠΈΠ΅ Π΄Π»Ρ ΠΈΠ·ΠΌΠ΅ΡΠ΅Π½ΠΈΡ ΡΡΠΈΡ ΠΏΠΎΠΊΠ°Π·Π°ΡΠ΅Π»Π΅ΠΉ ΠΈ Π΅ΡΠ»ΠΈ Π΄Π»Ρ ΠΈΠ·ΠΌΠ΅ΡΠ΅Π½ΠΈΡ ΡΠΎΠΏΡΠΎΡΠΈΠ²Π»Π΅Π½ΠΈΡ ΠΊΠΎΠΌΠΏΠ»Π΅ΠΊΡ ΡΡΠΎΠΈΡ Π½Π΅ Π΄ΠΎΡΠΎΠ³ΠΎ, ΡΠΎ Π΄Π»Ρ ΠΈΠ·ΠΌΠ΅ΡΠ΅Π½ΠΈΡ ΡΠ΄Π»ΠΈΠ½Π΅Π½ΠΈΡ ΡΡΠΎ Π΄ΠΎΡΠΎΠ³ΠΎΠ΅ ΠΎΠ±ΠΎΡΡΠ΄ΠΎΠ²Π°Π½ΠΈΠ΅, ΠΎΡΠΎΠ±Π΅Π½Π½ΠΎ Π΄Π»Ρ Π±ΠΎΠ»ΡΡΠΈΡ Π΄ΠΈΠ°ΠΌΠ΅ΡΡΠΎΠ².
ΠΡΠ»ΠΈ ΠΡ ΠΏΠ»Π°Π½ΠΈΡΡΠ΅ΡΠ΅ ΠΈΡΠΏΠΎΠ»ΡΠ·ΠΎΠ²Π°ΡΡ ΠΏΠΎΠ»ΡΡΠ΅Π½Π½ΡΡ ΠΏΡΠΎΠ΄ΡΠΊΡΠΈΡ ΡΠ°ΠΌΠΎΡΡΠΎΡΡΠ΅Π»ΡΠ½ΠΎ, ΡΠΎ Π²ΠΏΠΎΠ»Π½Π΅ ΠΌΠΎΠΆΠ½ΠΎ ΠΎΠ±ΠΎΠΉΡΠΈΡΡ ΠΏΡΠΎΡΡΡΠΌ ΡΠ΅ΡΡΠ΅ΡΠΎΠΌ Π΄Π»Ρ ΠΈΠ·ΠΌΠ΅ΡΠ΅Π½ΠΈΡ ΡΠΎΠΏΡΠΎΡΠΈΠ²Π»Π΅Π½ΠΈΡ, Π° ΡΠ΄Π»ΠΈΠ½Π΅Π½ΠΈΠ΅ ΠΌΠΎΠΆΠ½ΠΎ ΠΈΠ·ΠΌΠ΅ΡΠΈΡΡ, ΡΠΎΠΎΡΡΠ΄ΠΈΠ² Π½Π΅ Ρ ΠΈΡΡΠΎΠ΅ ΠΏΡΠΈΡΠΏΠΎΡΠΎΠ±Π»Π΅Π½ΠΈΠ΅ Π΄Π»Ρ ΡΠ°ΡΡΡΠ³ΠΈΠ²Π°Π½ΠΈΡ ΠΏΡΠΎΠ²ΠΎΠ»ΠΎΠΊΠΈ.
ΠΡΡΠ±ΠΎΠ΅ Π²ΠΎΠ»ΠΎΡΠ΅Π½ΠΈΠ΅ ΡΠ½Π΅ΡΠ³ΠΎΠ΅ΠΌΠΊΠΈΠΉ ΠΏΡΠΎΡΠ΅ΡΡ, Π² ΠΊΡΠΏΠ΅ Ρ ΠΎΡΠΆΠΈΠ³ΠΎΠΌ, ΡΠΊΠΎΡΠΎΡΡΠ½ΡΠ΅ Π»ΠΈΠ½ΠΈΠΈ ΠΏΠΎΡΡΠ΅Π±Π»ΡΡΡ ΠΎΠΊΠΎΠ»ΠΎ 300 ΠΊΠΡ/Ρ. Π Π°Π±ΠΎΡΠ°ΡΡ Π½Π° ΡΠ°ΠΊΠΈΡ
Π»ΠΈΠ½ΠΈΡΡ
, ΠΊΠ°ΠΊ ΠΏΡΠ°Π²ΠΈΠ»ΠΎ, ΠΏΠΎ 2 ΠΎΠΏΠ΅ΡΠ°ΡΠΎΡΠ°. ΠΠ°ΡΡΠ°ΡΡ ΡΠ»Π΅ΠΊΡΡΠΎΡΠ½Π΅ΡΠ³ΠΈΠΈ ΠΏΡΠΈ ΡΡΠ΅Π΄Π½Π΅ΠΌ Π²ΠΎΠ»ΠΎΡΠ΅Π½ΠΈΠΈ ΠΎΠΊΠΎΠ»ΠΎ 100 ΠΊΠΡ, ΠΏΡΠΈ ΡΠΎΠ½ΠΊΠΎΠΌ ΠΎΠΊΠΎΠ»ΠΎ 50ΠΊΠΡ.
1.4 ΠΡΠΎΠ΄ΡΠΊΡΠΈΡ, ΠΏΠΎΠ»ΡΡΠ°Π΅ΠΌΠ°Ρ Π²ΠΎΠ»ΠΎΡΠ΅Π½ΠΈΠ΅ΠΌ
ΠΠ²Π΅Π΄Π΅Π½ΠΈΠ΅
ΠΡΠΎΠΈΠ·Π²ΠΎΠ΄ΡΡΠ²ΠΎ ΠΌΠ΅ΡΠΈΠ·ΠΎΠ² ΡΠ²Π»ΡΠ΅ΡΡΡ ΡΠ°ΠΌΠΎΡΡΠΎΡΡΠ΅Π»ΡΠ½ΠΎΠΉ ΠΎΠ±Π»Π°ΡΡΡΡ ΠΌΠ΅ΡΠ°Π»Π»ΠΎΠΎΠ±ΡΠ°Π±ΠΎΡΠΊΠΈ. ΠΠ΅ΡΠΈΠ·Π°ΠΌΠΈ ΡΡΠ»ΠΎΠ²Π½ΠΎ ΠΏΡΠΈΠ½ΡΡΠΎ Π½Π°Π·ΡΠ²Π°ΡΡ Π³ΡΡΠΏΠΏΡ ΡΠΈΡΠΎΠΊΠΎ ΠΏΡΠΈΠΌΠ΅Π½ΡΠ΅ΠΌΡΡ Π² Π½Π°ΡΠΎΠ΄Π½ΠΎΠΌ Ρ ΠΎΠ·ΡΠΉΡΡΠ²Π΅ ΠΌΠ΅ΡΠ°Π»Π»ΠΈΡΠ΅ΡΠΊΠΈΡ ΠΈΠ·Π΄Π΅Π»ΠΈΠΉ ΠΏΡΠΎΠΌΡΡΠ»Π΅Π½Π½ΠΎΠ³ΠΎ Π½Π°Π·Π½Π°ΡΠ΅Π½ΠΈΡ, Π΄Π»Ρ ΠΈΠ·Π³ΠΎΡΠΎΠ²Π»Π΅Π½ΠΈΡ ΠΊΠΎΡΠΎΡΡΡ ΠΈΡΠΏΠΎΠ»ΡΠ·ΡΡΡ ΠΊΠ°ΡΠ°Π½ΠΊΡ, ΠΌΠ΅Π»ΠΊΠΎΡΠΎΡΡΠ½ΡΠΉ ΠΏΡΠΎΠΊΠ°Ρ, ΠΊΠ°Π»ΠΈΠ±ΡΠΎΠ²Π°Π½Π½ΡΠΉ ΠΌΠ΅ΡΠ°Π»Π», ΠΏΡΠΎΠ²ΠΎΠ»ΠΎΠΊΡ ΠΈ ΠΊΠ°ΡΠ°Π½ΡΠ΅ ΠΏΠΎΠ»ΠΎΡΡ. Π ΡΡΠΎΠΉ Π³ΡΡΠΏΠΏΠ΅ ΠΈΠ·Π΄Π΅Π»ΠΈΠΉ, ΠΎΡΠ½ΠΎΡΡΡΠ΅ΠΉΡΡ ΠΊ ΠΏΡΠΎΠ΄ΡΠΊΡΠΈΠΈ ΡΠ΅ΡΠ²Π΅ΡΡΠΎΠ³ΠΎ ΠΏΠ΅ΡΠ΅Π΄Π΅Π»Π° ΡΠ΅ΡΠ½ΠΎΠΉ ΠΌΠ΅ΡΠ°Π»Π»ΡΡΠ³ΠΈΠΈ (ΡΡΠΈΡΠ°Ρ ΠΏΠ΅ΡΠ²ΡΠΌ — ΠΏΡΠΎΠΈΠ·Π²ΠΎΠ΄ΡΡΠ²ΠΎ ΡΡΠ³ΡΠ½Π°, Π²ΡΠΎΡΡΠΌ β ΡΡΠ°Π»ΠΈ, ΡΡΠ΅ΡΡΠΈΠΌ β ΠΏΡΠΎΠΊΠ°ΡΠ°), ΠΎΡΠ½ΠΎΡΡΡΡΡ: ΠΏΡΠΎΠ²ΠΎΠ»ΠΎΠΊΠ°, ΠΊΠ°Π½Π°ΡΠ½ΡΠ΅ ΠΈΠ·Π΄Π΅Π»ΠΈΡ, ΠΌΠ΅ΡΠ°Π»Π»ΠΎΠΊΠΎΡΠ΄, Π²ΠΈΡΠ°Ρ Π°ΡΠΌΠ°ΡΡΡΠ°, ΠΌΠ΅ΡΠ°Π»Π»ΠΈΡΠ΅ΡΠΊΠΈΠ΅ ΡΠ΅ΡΠΊΠΈ, ΠΊΡΠ΅ΠΏΠ΅ΠΆΠ½ΡΠ΅ ΠΈΠ·Π΄Π΅Π»ΠΈΡ ΠΈ Π΄Ρ.
ΠΠ±ΡΠ°Π±ΠΎΡΠΊΠ° ΠΌΠ΅ΡΠ°Π»Π»Π° Π²ΠΎΠ»ΠΎΡΠ΅Π½ΠΈΠ΅ΠΌ, Ρ.Π΅. ΠΏΡΠΎΡΡΠ³ΠΈΠ²Π°Π½ΠΈΠ΅ Π·Π°Π³ΠΎΡΠΎΠ²ΠΊΠΈ ΡΠ΅ΡΠ΅Π· ΠΎΡΠ²Π΅ΡΡΡΠΈΠ΅, Π²ΡΡ ΠΎΠ΄Π½ΡΠ΅ ΡΠ°Π·ΠΌΠ΅ΡΡ ΠΊΠΎΡΠΎΡΠΎΠ³ΠΎ ΠΌΠ΅Π½ΡΡΠ΅, ΡΠ΅ΠΌ ΠΈΡΡ ΠΎΠ΄Π½ΠΎΠ΅ ΡΠ΅ΡΠ΅Π½ΠΈΠ΅ Π·Π°Π³ΠΎΡΠΎΠ²ΠΊΠΈ, Π½Π°Ρ ΠΎΠ΄ΠΈΡ ΡΠ°ΠΌΠΎΠ΅ ΡΠΈΡΠΎΠΊΠΎΠ΅ ΠΏΡΠΈΠΌΠ΅Π½Π΅Π½ΠΈΠ΅ Π² ΡΠ°Π·Π»ΠΈΡΠ½ΡΡ ΠΎΡΡΠ°ΡΠ»ΡΡ ΠΏΡΠΎΠΌΡΡΠ»Π΅Π½Π½ΠΎΡΡΠΈ. ΠΠ·Π΄Π΅Π»ΠΈΡ, ΠΏΠΎΠ»ΡΡΠ°Π΅ΠΌΡΠ΅ Π²ΠΎΠ»ΠΎΡΠ΅Π½ΠΈΠ΅ΠΌ, ΠΎΠ±Π»Π°Π΄Π°ΡΡ Π²ΡΡΠΎΠΊΠΈΠΌ ΠΊΠ°ΡΠ΅ΡΡΠ²ΠΎΠΌ ΠΏΠΎΠ²Π΅ΡΡ Π½ΠΎΡΡΠΈ ΠΈ Π²ΡΡΠΎΠΊΠΎΠΉ ΡΠΎΡΠ½ΠΎΡΡΡΡ ΡΠ°Π·ΠΌΠ΅ΡΠΎΠ² ΠΏΠΎΠΏΠ΅ΡΠ΅ΡΠ½ΠΎΠ³ΠΎ ΡΠ΅ΡΠ΅Π½ΠΈΡ.
ΠΠΎΠ»ΠΎΡΠ΅Π½ΠΈΠ΅ Π²ΡΠ³ΠΎΠ΄Π½ΠΎ ΠΎΡΠ»ΠΈΡΠ°Π΅ΡΡΡ ΠΎΡ ΠΌΠ΅Ρ Π°Π½ΠΈΡΠ΅ΡΠΊΠΎΠΉ ΠΎΠ±ΡΠ°Π±ΠΎΡΠΊΠΈ ΠΌΠ΅ΡΠ°Π»Π»Π° ΡΠ΅Π·Π°Π½ΠΈΠ΅ΠΌ (ΡΡΡΠΎΠ³Π°Π½ΠΈΠ΅ΠΌ), ΡΡΠ΅Π·Π΅ΡΠΎΠ²Π°Π½ΠΈΠ΅ΠΌ, ΠΎΠ±ΡΠΎΡΠΊΠΎΠΉ ΠΈ ΠΏΡ., ΡΠ°ΠΊ ΠΊΠ°ΠΊ ΠΏΡΠΈ ΡΡΠΎΠΌ ΠΎΡΡΡΡΡΡΠ²ΡΡΡ ΠΎΡΡ ΠΎΠ΄Ρ ΠΌΠ΅ΡΠ°Π»Π»Π° Π² Π²ΠΈΠ΄Π΅ ΡΡΡΡΠΆΠΊΠΈ, Π° ΡΠ°ΠΌ ΠΏΡΠΎΡΠ΅ΡΡ Π·Π°ΠΌΠ΅ΡΠ½ΠΎ ΠΏΡΠΎΠΈΠ·Π²ΠΎΠ΄ΠΈΡΠ΅Π»ΡΠ½Π΅Π΅ ΠΈ ΠΌΠ΅Π½Π΅Π΅ ΡΡΡΠ΄ΠΎΠ΅ΠΌΠΎΠΊ.
ΠΠΎΠ»ΠΎΡΠ΅Π½ΠΈΠ΅ ΠΏΡΠ΅Π΄ΡΡΠ°Π²Π»ΡΠ΅Ρ ΡΠΎΠ±ΠΎΠΉ ΠΎΠ΄ΠΈΠ½ ΠΈΠ· Π΄ΡΠ΅Π²Π½Π΅ΠΉΡΠΈΡ ΡΠΏΠΎΡΠΎΠ±ΠΎΠ² ΠΎΠ±ΡΠ°Π±ΠΎΡΠΊΠΈ ΠΌΠ΅ΡΠ°Π»Π»Π° Π΄Π°Π²Π»Π΅Π½ΠΈΠ΅ΠΌ. ΠΠΏΠ΅ΡΠ²ΡΠ΅ Π²ΠΎΠ»ΠΎΡΠ΅Π½ΠΈΠ΅ Π½Π°ΡΠ°Π»ΠΈ ΠΏΡΠΈΠΌΠ΅Π½ΡΡΡ 3-3,5 ΡΡΡ. Π»Π΅Ρ Π΄ΠΎ Π½Π°ΡΠ΅ΠΉ ΡΡΡ. Π Π½Π°ΡΠ°Π»Π΅ XYIII Π²Π΅ΠΊΠ° Π½Π° Π·Π°Π²ΠΎΠ΄Π°Ρ Π£ΡΠ°Π»Π° ΡΠ°Π±ΠΎΡΠ°Π»ΠΎ 16 Π²ΠΎΠ»ΠΎΡΠΈΠ»ΡΠ½ΡΡ ΡΡΠ°Π½ΠΎΠ² ΠΎΡ Π²ΠΎΠ΄ΡΠ½ΠΎΠ³ΠΎ ΠΏΡΠΈΠ²ΠΎΠ΄Π°, Π²ΡΠΏΡΡΠΊΠ°Π²ΡΠΈΡ ΠΎΠΊΠΎΠ»ΠΎ 45 ΡΠΎΠ½Π½ ΠΆΠ΅Π»Π΅Π·Π½ΠΎΠΉ ΠΏΡΠΎΠ²ΠΎΠ»ΠΎΠΊΠΈ Π² Π³ΠΎΠ΄. Π 1838 Π³ΠΎΠ΄Ρ Π²ΠΏΠ΅ΡΠ²ΡΠ΅ Π±ΡΠ»ΠΎ ΠΏΡΠΈΠΌΠ΅Π½Π΅Π½ΠΎ ΠΌΠ½ΠΎΠ³ΠΎΠΊΡΠ°ΡΠ½ΠΎΠ΅ Π²ΠΎΠ»ΠΎΡΠ΅Π½ΠΈΠ΅ Π½Π° Π±ΠΎΠ»ΡΡΠΈΡ ΡΠΊΠΎΡΠΎΡΡΡΡ 30-60 ΠΌ/ΠΌΠΈΠ½. Π 1922 Π³ΠΎΠ΄Ρ Π½Π° ΠΠ΅Π»ΠΎΡΠ΅ΡΠΊΠΎΠΌ ΡΡΠ°Π»Π΅ΠΏΡΠΎΠ²ΠΎΠ»ΠΎΡΠ½ΠΎ-ΠΊΠ°Π½Π°ΡΠ½ΠΎΠΌ Π·Π°Π²ΠΎΠ΄Π΅ Π±ΡΠ» Π²Π½Π΅Π΄ΡΠ΅Π½ ΡΠΏΠ΅ΡΠΈΠ°Π»ΡΠ½ΡΠΉ Π²ΠΈΠ΄ ΡΠ΅ΡΠΌΠΈΡΠ΅ΡΠΊΠΎΠΉ ΠΎΠ±ΡΠ°Π±ΠΎΡΠΊΠΈ ΠΊΠ°ΡΠ°Π½ΠΊΠΈ — ΠΏΠ°ΡΠ΅Π½ΡΠΈΡΠΎΠ²Π°Π½ΠΈΠ΅, Ρ ΠΏΠΎΠΌΠΎΡΡΡ ΠΊΠΎΡΠΎΡΠΎΠ³ΠΎ Π±ΡΠ»Π° ΠΏΠΎΠ»ΡΡΠ΅Π½Π° ΠΏΡΠΎΡΠ½Π°Ρ ΡΡΠ°Π»ΡΠ½Π°Ρ ΠΏΡΠΎΠ²ΠΎΠ»ΠΎΠΊΠ°. ΠΠ΅ΡΠ΅Ρ ΠΎΠ΄ ΠΎΡ Π²ΠΎΠ»ΠΎΡΠ΅Π½ΠΈΡ Π½Π° ΠΎΠ΄Π½ΠΎΠΊΡΠ°ΡΠ½ΡΡ ΠΌΠ°ΡΠΈΠ½Π°Ρ ΠΊ Π²ΠΎΠ»ΠΎΡΠ΅Π½ΠΈΡ Π½Π° ΠΌΠ½ΠΎΠ³ΠΎΠΊΡΠ°ΡΠ½ΡΡ ΡΡΠ°Π½Π°Ρ ΠΏΠΎΠ·Π²ΠΎΠ»ΠΈΠ» Π·Π½Π°ΡΠΈΡΠ΅Π»ΡΠ½ΠΎ ΠΏΠΎΠ΄Π½ΡΡΡ ΠΏΡΠΎΠΈΠ·Π²ΠΎΠ΄ΠΈΡΠ΅Π»ΡΠ½ΠΎΡΡΡ. Π‘ΠΊΠΎΡΠΎΡΡΡ Π²ΠΎΠ»ΠΎΡΠ΅Π½ΠΈΡ Π²ΠΎΠ·ΡΠΎΡΠ»Π° Π±ΠΎΠ»Π΅Π΅ ΡΠ΅ΠΌ Π² 15 ΡΠ°Π·.
Π‘ΡΠ°Π»Π΅ΠΏΡΠΎΠ²ΠΎΠ»ΠΎΡΠ½ΠΎΠ΅ ΠΏΡΠΎΠΈΠ·Π²ΠΎΠ΄ΡΡΠ²ΠΎ ΡΠ΅Ρ Π½ΠΈΡΠ΅ΡΠΊΠΈ ΠΏΠΎΡΡΠΎΡΠ½Π½ΠΎ ΡΠΎΠ²Π΅ΡΡΠ΅Π½ΡΡΠ²ΡΠ΅ΡΡΡ. ΠΠ·ΠΌΠ΅Π½Π΅Π½Π° ΡΡΡΡΠΊΡΡΡΠ° ΠΏΡΠΎΠΈΠ·Π²ΠΎΠ΄ΡΡΠ²Π°: ΡΠ²Π΅Π»ΠΈΡΠ΅Π½Π° Π΄ΠΎΠ»Ρ Π²ΡΠΏΡΡΠΊΠ° ΠΏΡΠΎΠ²ΠΎΠ»ΠΎΠΊΠΈ ΠΎΡΠ²Π΅ΡΡΡΠ²Π΅Π½Π½ΠΎΠ³ΠΎ Π½Π°Π·Π½Π°ΡΠ΅Π½ΠΈΡ, Π±ΠΎΠ»Π΅Π΅ ΡΠΎΠ½ΠΊΠΎΠΉ ΠΈ ΠΏΡΠΎΡΠ½ΠΎΠΉ. ΠΡΠ²ΠΎΠ΅Π½Ρ Π²ΡΡΠΎΠΊΠΈΠ΅ ΡΠΊΠΎΡΠΎΡΡΠΈ Π²ΠΎΠ»ΠΎΡΠ΅Π½ΠΈΡ.
ΠΡΠΎΠ²ΠΎΠ»ΠΎΠΊΡ ΠΎΡΠ½ΠΎΠ²Π½ΠΎΠ³ΠΎ ΡΠΎΡΡΠ°ΠΌΠ΅Π½ΡΠ° ΠΏΡΠΎΠΈΠ·Π²ΠΎΠ΄ΡΡ ΠΏΠΎ ΡΠΎΠ²ΡΠ΅ΠΌΠ΅Π½Π½ΡΠΌ, Π΄ΠΎΡΡΠ°ΡΠΎΡΠ½ΠΎ ΡΡΡΠ΅ΠΊΡΠΈΠ²Π½ΡΠΌ ΡΠ΅Ρ Π½ΠΎΠ»ΠΎΠ³ΠΈΡΠ΅ΡΠΊΠΈΠΌ ΡΡ Π΅ΠΌΠ°ΠΌ Π½Π° Π²ΡΡΠΎΠΊΠΎΠΏΡΠΎΠΈΠ·Π²ΠΎΠ΄ΠΈΡΠ΅Π»ΡΠ½ΠΎΠΌ ΠΎΠ±ΠΎΡΡΠ΄ΠΎΠ²Π°Π½ΠΈΠΈ. Π‘ΡΠ°Π»Π΅ΠΏΡΠΎΠ²ΠΎΠ»ΠΎΡΠ½ΠΎΠ΅ ΠΏΡΠΎΠΈΠ·Π²ΠΎΠ΄ΡΡΠ²ΠΎ ΠΎΡΠ½Π°ΡΠ΅Π½ΠΎ ΠΏΠΎΡΠΎΡΠ½ΡΠΌΠΈ Π°Π³ΡΠ΅Π³Π°ΡΠ°ΠΌΠΈ, Π½Π° ΠΊΠΎΡΠΎΡΡΡ ΡΠΎΠ²ΠΌΠ΅ΡΠ΅Π½Ρ ΠΎΠΏΠ΅ΡΠ°ΡΠΈΠΈ ΡΠ΅ΡΠΌΠΈΡΠ΅ΡΠΊΠΎΠΉ ΠΎΠ±ΡΠ°Π±ΠΎΡΠΊΠΈ ΠΈ ΠΏΠΎΠ΄Π³ΠΎΡΠΎΠ²ΠΊΠΈ ΠΏΠΎΠ²Π΅ΡΡ Π½ΠΎΡΡΠΈ, Π²ΠΊΠ»ΡΡΠ°Ρ Π½Π°Π½Π΅ΡΠ΅Π½ΠΈΠ΅ ΠΌΠ΅ΡΠ°Π»Π»ΠΈΡΠ΅ΡΠΊΠΈΡ ΠΏΠΎΠΊΡΡΡΠΈΠΉ.
ΠΠ΅ΡΠΈΠ·Π½Π°Ρ ΠΏΡΠΎΠΌΡΡΠ»Π΅Π½Π½ΠΎΡΡΡ ΠΎΠ±Π΅ΡΠΏΠ΅ΡΠΈΠ²Π°Π΅Ρ ΠΏΠ΅ΡΠ΅ΡΠ°Π±ΠΎΡΠΊΡ 90-95% ΠΏΡΠΎΠΈΠ·Π²ΠΎΠ΄ΠΈΠΌΠΎΠΉ ΠΊΠ°ΡΠ°Π½ΠΊΠΈ Π² ΠΏΡΠΎΠ²ΠΎΠ»ΠΎΠΊΡ. ΠΠ°ΡΡΠ΄Ρ Ρ ΠΏΠΎΠ²ΡΡΠ΅Π½ΠΈΠ΅ΠΌ ΠΏΡΠΎΡΠ½ΠΎΡΡΠΈ ΠΏΡΠΎΠ²ΠΎΠ»ΠΎΠΊΠΈ ΠΈ ΡΠ½ΠΈΠΆΠ΅Π½ΠΈΠ΅ΠΌ Π²Π΅Π»ΠΈΡΠΈΠ½Ρ Π΅Π΅ ΠΏΠ»ΡΡΠΎΠ²ΡΡ Π΄ΠΎΠΏΡΡΠΊΠΎΠ² Π½Π° Π΄ΠΈΠ°ΠΌΠ΅ΡΡ Π·Π½Π°ΡΠΈΡΠ΅Π»ΡΠ½ΠΎ ΡΠΊΠΎΠ½ΠΎΠΌΠΈΡΡΡ ΠΌΠ΅ΡΠ°Π»Π». ΠΡΠΎΠΌΡ ΠΆΠ΅ ΡΠΏΠΎΡΠΎΠ±ΡΡΠ²ΡΠ΅Ρ ΡΠ²Π΅Π»ΠΈΡΠ΅Π½ΠΈΠ΅ Π΄ΠΎΠ»ΠΈ Π²ΡΠΏΡΡΠΊΠ° ΠΏΡΠΎΠ²ΠΎΠ»ΠΎΠΊΠΈ Ρ Π·Π°ΡΠΈΡΠ½ΡΠΌΠΈ ΠΏΠΎΠΊΡΡΡΠΈΡΠΌΠΈ ΠΈ Ρ ΡΠ°ΡΠΎΠ½Π½ΡΠΌ ΠΏΠΎΠΏΠ΅ΡΠ΅ΡΠ½ΡΠΌ ΡΠ΅ΡΠ΅Π½ΠΈΠ΅ΠΌ Π²ΠΌΠ΅ΡΡΠΎ ΠΊΡΡΠ³Π»ΠΎΠΉ, ΡΡΠΎ ΠΏΠΎΠ·Π²ΠΎΠ»ΡΠ΅Ρ ΡΠ½ΠΈΠ·ΠΈΡΡ ΠΌΠ°ΡΡΡ ΡΠ°ΠΌΠΎΠ³ΠΎ ΠΈΠ·Π΄Π΅Π»ΠΈΡ ΠΈ Π²ΡΠ΅ΠΉ ΠΏΠΎΡΡΠ΅Π±Π»ΡΠ΅ΠΌΠΎΠΉ ΠΏΡΠΎΠ²ΠΎΠ»ΠΎΠΊΠΈ.
ΠΠΠ Β«Π§Π‘ΠΠΒ» ΡΠ²Π»ΡΠ΅ΡΡΡ ΠΊΡΡΠΏΠ½ΡΠΌ ΠΏΡΠ΅Π΄ΠΏΡΠΈΡΡΠΈΠ΅ΠΌ ΠΌΠ΅ΡΠΈΠ·Π½ΠΎΠΉ ΠΏΡΠΎΠΌΡΡΠ»Π΅Π½Π½ΠΎΡΡΠΈ, Π² Π½ΠΎΠΌΠ΅Π½ΠΊΠ»Π°ΡΡΡΠ΅ ΠΈΠ·Π΄Π΅Π»ΠΈΠΉ ΠΊΠΎΡΠΎΡΠΎΠ³ΠΎ ΠΏΡΠ΅Π΄ΡΡΠ°Π²Π»Π΅Π½Π° ΡΠΈΡΠΎΠΊΠ°Ρ Π³Π°ΠΌΠΌΠ° ΠΌΠ΅ΡΠΈΠ·ΠΎΠ². Π Π½Π°ΡΡΠΎΡΡΠ΅Π΅ Π²ΡΠ΅ΠΌΡ Π΄ΠΎΠ»Ρ Β«Π§Π‘ΠΠΒ» Π² ΠΎΡΠ³ΡΡΠ·ΠΊΠ΅ ΡΠΎΠ²Π°ΡΠ½ΠΎΠΉ ΠΏΡΠΎΠ΄ΡΠΊΡΠΈΠΈ ΡΡΠ΅Π΄ΠΈ ΠΏΡΠ΅Π΄ΠΏΡΠΈΡΡΠΈΠΉ Π°ΡΡΠΎΡΠΈΠ°ΡΠΈΠΈ Β«ΠΡΠΎΠΌΠΌΠ΅ΡΠΈΠ·Β» ΡΠΎΡΡΠ°Π²Π»ΡΠ΅Ρ 38%.
30 Π΄Π΅ΠΊΠ°Π±ΡΡ 1967 Π³ΠΎΠ΄Π° Π±ΡΠ» ΠΈΠ·Π΄Π°Π½ ΠΏΡΠΈΠΊΠ°Π· ΠΠΈΠ½ΠΈΡΡΠ΅ΡΡΡΠ²Π° ΡΠ΅ΡΠ½ΠΎΠΉ ΠΌΠ΅ΡΠ°Π»Π»ΡΡΠ³ΠΈΠΈ Π‘Π‘Π‘Π ΠΎ ΡΠΎΠ·Π΄Π°Π½ΠΈΠΈ Π§Π΅ΡΠ΅ΠΏΠΎΠ²Π΅ΡΠΊΠΎΠ³ΠΎ ΡΡΠ°Π»Π΅ΠΏΡΠΎΠΊΠ°ΡΠ½ΠΎΠ³ΠΎ Π·Π°Π²ΠΎΠ΄Π° Π½Π° Π±Π°Π·Π΅ Π²ΡΠ²Π΅Π΄Π΅Π½Π½ΠΎΠ³ΠΎ ΠΈΠ· ΡΠΎΡΡΠ°Π²Π° ΠΌΠ΅ΡΠ°Π»Π»ΡΡΠ³ΠΈΡΠ΅ΡΠΊΠΎΠ³ΠΎ Π·Π°Π²ΠΎΠ΄Π° ΠΌΠ΅ΡΠΈΠ·Π½ΠΎΠ³ΠΎ ΠΏΡΠΎΠΈΠ·Π²ΠΎΠ΄ΡΡΠ²Π°.
Π Π½Π°ΡΡΠΎΡΡΠ΅Π΅ Π²ΡΠ΅ΠΌΡ ΠΠΠ Β«Π§Π‘ΠΠΒ» ΡΠ°Π·Π΄Π΅Π»Π΅Π½ΠΎ Π½Π° ΡΡΠΈ Π±ΠΎΠ»ΡΡΠΈΡ ΠΏΡΠΎΠΈΠ·Π²ΠΎΠ΄ΡΡΠ²Π°:
ΠΌΠ΅ΡΠΈΠ·Π½ΠΎΠ΅ ΠΏΡΠΎΠΈΠ·Π²ΠΎΠ΄ΡΡΠ²ΠΎ Π² ΡΠΎΡΡΠ°Π²Π΅ ΡΡΠ°Π»Π΅ΠΏΡΠΎΠ²ΠΎΠ»ΠΎΡΠ½ΠΎΠ³ΠΎ ΡΠ΅Ρ Π° β 1 ΠΌΠΎΡΠ½ΠΎΡΡΡΡ 450 ΡΡΡ. ΡΠΎΠ½Π½ ΠΏΡΠΎΠ²ΠΎΠ»ΠΎΠΊΠΈ Π² Π³ΠΎΠ΄; Π³Π²ΠΎΠ·Π΄ΠΈΠ»ΡΠ½ΠΎΠ³ΠΎ ΡΠ΅Ρ Π° ΠΌΠΎΡΠ½ΠΎΡΡΡΡ 70 ΡΡΡ. ΡΠΎΠ½Π½ Π³Π²ΠΎΠ·Π΄Π΅ΠΉ Π² Π³ΠΎΠ΄; ΡΠ΅Ρ Π° ΠΌΠ΅ΡΠ°Π»Π»ΠΈΡΠ΅ΡΠΊΠΈΡ ΡΠ΅ΡΠΎΠΊ ΠΌΠΎΡΠ½ΠΎΡΡΡΡ 30 ΡΡΡ. ΡΠΎΠ½Π½ ΡΠ΅ΡΠΊΠΈ ΠΈ ΡΠ΅ΡΡΠ°ΡΡΡ ΠΊΠΎΠ½ΡΡΡΡΠΊΡΠΈΠΉ Π² Π³ΠΎΠ΄; ΡΠ»Π΅ΠΊΡΡΠΎΠ΄Π½ΠΎΠ³ΠΎ ΡΠ΅Ρ Π° ΠΌΠΎΡΠ½ΠΎΡΡΡΡ 66 ΡΡΡ. ΡΠΎΠ½Π½ ΡΠ»Π΅ΠΊΡΡΠΎΠ΄ΠΎΠ² ΠΈ ΠΏΠΎΡΠΎΡΠΊΠΎΠ²ΠΎΠΉ ΠΏΡΠΎΠ²ΠΎΠ»ΠΎΠΊΠΈ Π² Π³ΠΎΠ΄;
ΠΊΠ°Π»ΠΈΠ±ΡΠΎΠ²ΠΎΡΠ½ΠΎΠ΅ ΠΏΡΠΎΠΈΠ·Π²ΠΎΠ΄ΡΡΠ²ΠΎ Π² ΡΠΎΡΡΠ°Π²Π΅ ΠΊΠ°Π»ΠΈΠ±ΡΠΎΠ²ΠΎΡΠ½ΠΎΠ³ΠΎ ΡΠ΅Ρ Π° ΠΌΠΎΡΠ½ΠΎΡΡΡΡ 500 ΡΡΡ. ΡΠΎΠ½Π½ ΠΊΠ°Π»ΠΈΠ±ΡΠΎΠ²Π°Π½Π½ΠΎΠ³ΠΎ ΠΌΠ΅ΡΠ°Π»Π»Π° Π² Π³ΠΎΠ΄; ΠΊΡΠ΅ΠΏΠ΅ΠΆΠ½ΠΎΠ³ΠΎ ΡΠ΅Ρ Π° ΠΌΠΎΡΠ½ΠΎΡΡΡΡ 15 ΡΡΡ. ΡΠΎΠ½Π½ ΠΊΡΠ΅ΠΏΠ΅ΠΆΠ° Π² Π³ΠΎΠ΄; ΡΠ΅Ρ Π° ΡΡΠ°Π»ΡΠ½ΡΡ ΡΠ°ΡΠΎΠ½Π½ΡΡ ΠΏΡΠΎΡΠΈΠ»Π΅ΠΉ ΠΌΠΎΡΠ½ΠΎΡΡΡΡ 20 ΡΡΡ. ΡΠΎΠ½Π½ ΡΠ°ΡΠΎΠ½Π½ΡΡ ΠΏΡΠΎΡΠΈΠ»Π΅ΠΉ Π² Π³ΠΎΠ΄;
ΡΡΠ°Π»Π΅ΠΏΡΠΎΠ²ΠΎΠ»ΠΎΡΠ½ΠΎ-ΠΊΠ°Π½Π°ΡΠ½ΠΎΠ΅ ΠΏΡΠΎΠΈΠ·Π²ΠΎΠ΄ΡΡΠ²ΠΎ Π² ΡΠΎΡΡΠ°Π²Π΅ ΡΡΠ°Π»Π΅ΠΏΡΠΎΠ²ΠΎΠ»ΠΎΡΠ½ΠΎΠ³ΠΎ ΡΠ΅Ρ Π° β 2 ΠΌΠΎΡΠ½ΠΎΡΡΡΡ 120 ΡΡΡ. ΡΠΎΠ½Π½ ΠΏΡΠΎΠ²ΠΎΠ»ΠΎΠΊΠΈ Π² Π³ΠΎΠ΄ ΠΈ ΠΊΠ°Π½Π°ΡΠ½ΠΎΠ³ΠΎ ΡΠ΅Ρ Π° ΠΌΠΎΡΠ½ΠΎΡΡΡΡ 75 ΡΡΡ. ΡΠΎΠ½Π½ ΡΡΠ°Π»ΡΠ½ΡΡ ΠΈ Π°ΡΠΌΠ°ΡΡΡΠ½ΡΡ ΠΊΠ°Π½Π°ΡΠΎΠ² Π² Π³ΠΎΠ΄.
Π ΡΡΡΡΠΊΡΡΡΡ Π·Π°Π²ΠΎΠ΄Π° Π²ΠΊΠ»ΡΡΠ΅Π½ ΡΡΠ΄ ΡΠ»ΡΠΆΠ± ΠΈ Π²ΡΠΏΠΎΠΌΠΎΠ³Π°ΡΠ΅Π»ΡΠ½ΡΡ ΡΠ΅Ρ ΠΎΠ²: ΡΠ½Π΅ΡΠ³ΠΎΡΠ΅Ρ , ΠΈΠ½ΡΡΡΡΠΌΠ΅Π½ΡΠ°Π»ΡΠ½ΡΠΉ, ΡΠ΅ΠΌΠΎΠ½ΡΠ½ΠΎ-ΠΌΠ΅Ρ Π°Π½ΠΈΡΠ΅ΡΠΊΠΈΠΉ, ΡΠ°ΡΠ½ΡΠΉ, ΡΡΡΠΎΠΈΡΠ΅Π»ΡΠ½ΡΠΉ, ΡΡΠ°Π½ΡΠΏΠΎΡΡΠ½ΠΎ-Π³ΡΡΠ·ΠΎΠ²ΠΎΠΉ, ΠΈ Π΄Ρ. ΠΠ±Π΅ΡΠΏΠ΅ΡΠ΅Π½ΠΈΠ΅ ΠΏΡΠΎΠΈΠ·Π²ΠΎΠ΄ΡΡΠ²Π° ΡΡΡΡΠ΅ΠΌ ΠΈ ΠΌΠ°ΡΠ΅ΡΠΈΠ°Π»Π°ΠΌΠΈ ΠΎΡΡΡΠ΅ΡΡΠ²Π»ΡΠ΅Ρ Π΄ΠΈΡΠ΅ΠΊΡΠΈΡ ΠΏΠΎ ΠΎΠ±Π΅ΡΠΏΠ΅ΡΠ΅Π½ΠΈΡ ΠΌΠ°ΡΠ΅ΡΠΈΠ°Π»ΡΠ½ΠΎ-ΡΠ΅Ρ Π½ΠΈΡΠ΅ΡΠΊΠΈΠΌΠΈ ΡΠ΅ΡΡΡΡΠ°ΠΌΠΈ, Π΄ΠΈΡΠ΅ΠΊΡΠΈΡ ΠΏΠΎ ΠΌΠ°ΡΠΊΠ΅ΡΠΈΠ½Π³Ρ ΠΈ ΡΠ±ΡΡΡ ΠΎΡΡΡΠ΅ΡΡΠ²Π»ΡΠ΅Ρ ΡΠ°Π±ΠΎΡΡ Ρ ΠΊΠ»ΠΈΠ΅Π½ΡΠ°ΠΌΠΈ, ΠΏΠ»Π°Π½ΠΈΡΠΎΠ²Π°Π½ΠΈΠ΅ ΠΏΡΠΎΠ΄Π°ΠΆ ΠΈ ΠΈΠ·ΡΡΠ΅Π½ΠΈΠ΅ ΡΡΠ½ΠΊΠ° ΡΠ±ΡΡΠ°.
ΠΡΠΏΠΎΠ»ΡΠ·ΠΎΠ²Π°Π½Π° ΠΈΠ½ΡΠΎΡΠΌΠ°ΡΠΈΡ ΠΈΠ· βΠΠΎΡΠΎΠ±ΠΈΡ Π²ΠΎΠ»ΠΎΡΠΈΠ»ΡΡΠΈΠΊΠ°β.
1. ΠΠ»Π°ΡΡΠΈΡΠΈΠΊΠ°ΡΠΈΡ Π²ΠΎΠ»ΠΎΡΠΈΠ»ΡΠ½ΡΡ ΡΡΠ°Π½ΠΎΠ²
ΠΠΎΠ»ΠΎΡΠΈΠ»ΡΠ½ΡΠΉ ΡΡΠ°Π½ — ΡΡΠΎ ΠΌΠ°ΡΠΈΠ½Π°, ΡΠ»ΡΠΆΠ°ΡΠ°Ρ Π΄Π»Ρ ΠΎΠ±ΡΠ°Π±ΠΎΡΠΊΠΈ ΠΌΠ΅ΡΠ°Π»ΒΠ»Π° Π²ΠΎΠ»ΠΎΡΠ΅Π½ΠΈΠ΅ΠΌ, .Ρ.Π΅.ΠΏΡΠΎΡΡΠ³ΠΈΠ²Π°Π½ΠΈΠ΅ΠΌ ΠΌΠ΅ΡΠ°Π»Π»ΠΈΡΠ΅ΡΠΊΠΈΡ Π·Π°Π³ΠΎΡΠΎΠ²ΠΎΠΊ Π² Ρ ΠΎΠ»ΠΎΠ΄ΒΠ½ΠΎΠΌ ΡΠΎΡΡΠΎΡΠ½ΠΈΠΈ ΡΠ΅ΡΠ΅Π· Π²ΠΎΠ»ΠΎΡΠΈΠ»ΡΠ½ΡΠΉ ΠΈΠ½ΡΡΡΡΠΌΠ΅Π½Ρ Π΄Π»Ρ ΠΏΠΎΠ»ΡΡΠ΅Π½ΠΈΡ ΠΌΠ΅Π½ΡΡΠΈΡ ΡΠ°Π·ΠΌΠ΅ΡΠΎΠ² ΠΏΠΎΠΏΠ΅ΡΠ΅ΡΠ½ΠΎΠ³ΠΎ ΡΠ΅ΡΠ΅Π½ΠΈΡ Π³ΠΎΡΠΎΠ²ΠΎΠ³ΠΎ ΠΈΠ·Π΄Π΅Π»ΠΈΡ — ΠΏΡΠΎΠ²ΠΎΠ»ΠΎΠΊΠΈ. ΠΠΎΠ»ΠΎΒΡΠ΅Π½ΠΈΠ΅ΠΌ ΠΎΠ±ΡΠ°Π±Π°ΡΡΠ²Π°Π΅ΡΡΡ ΠΏΡΠΎΠ²ΠΎΠ»ΠΎΠΊΠ° ΠΊΡΡΠ³Π»ΡΡ ΠΈ ΡΠ°ΡΠΎΠ½Π½ΡΡ ΡΠ΅ΡΠ΅Π½ΠΈΠΉ ΠΈ ΠΎΠ±Π΅ΡΒΠΏΠ΅ΡΠΈΠ²Π°Π΅ΡΡΡ Π²ΡΡΠΎΠΊΠ°Ρ ΡΠΎΡΠ½ΠΎΡΡΡ ΠΏΡΠΎΡΠΈΠ»Ρ ΠΈ ΡΠΈΡΡΠ°Ρ Π³Π»Π°Π΄ΠΊΠ°Ρ ΠΏΠΎΠ²Π΅ΡΡ Π½ΠΎΡΡΡ. ΠΡΠΈ Ρ ΠΎΠ»ΠΎΠ΄Π½ΠΎΠΌ Π²ΠΎΠ»ΠΎΡΠ΅Π½ΠΈΠΈ Π·Π½Π°ΡΠΈΡΠ΅Π»ΡΠ½ΠΎ ΠΏΠΎΠ²ΡΡΠ°Π΅ΡΡΡ ΠΏΡΠ΅Π΄Π΅Π» ΡΠ΅ΠΊΡΡΠ΅ΡΡΠΈ ΠΈ ΠΏΡΠΎΡΠ½ΠΎΡΡΠΈ, Π° ΡΠ°ΠΊΠΆΠ΅ ΡΠ²Π΅ΡΠ΄ΠΎΡΡΡ ΠΏΡΠΎΡΡΠ³ΠΈΠ²Π°Π΅ΠΌΠΎΠ³ΠΎ ΠΌΠ΅ΡΠ°Π»Π»Π°.
Π Π·Π°Π²ΠΈΡΠΈΠΌΠΎΡΡΠΈ ΠΎΡ ΠΊΠΎΠ½ΡΡΡΡΠΊΡΠΈΠ²Π½ΡΡ ΠΎΡΠΎΠ±Π΅Π½Π½ΠΎΡΡΠ΅ΠΉ ΠΈ Π½Π°Π·Π½Π°ΡΠ΅Π½ΠΈΡ Π²ΠΎΠ»ΠΎΡΠΈΠ»ΡΠ½ΡΠ΅ ΡΡΠ°Π½Ρ Π΄Π΅Π»ΡΡΡΡ Π½Π° Π΄Π²Π΅ Π³ΡΡΠΏΠΏΡ: ΡΡΠ°Π½Ρ Ρ ΠΊΡΡΠ³ΠΎΠ²ΡΠΌ Π΄Π²ΠΈΠΆΠ΅ΒΠ½ΠΈΠ΅ΠΌ ΠΏΡΠΎΠ²ΠΎΠ»ΠΎΠΊΠΈ ΠΏΡΠΈ Π½Π°ΠΌΠΎΡΠΊΠ΅ Π½Π° Π±Π°ΡΠ°Π±Π°Π½ ΠΈ Ρ ΠΏΡΡΠΌΠΎΠ»ΠΈΠ½Π΅ΠΉΠ½ΡΠΌ Π΄Π²ΠΈΠΆΠ΅Π½ΠΈΠ΅ΠΌ Π³ΠΎΡΠΎΠ²ΠΎΠ³ΠΎ ΠΈΠ·Π΄Π΅Π»ΠΈΡ ΠΏΡΠΈ ΠΏΠΎΠΌΠΎΡΠΈ ΡΡΠ½ΡΡΠΈΡ ΡΠ΅Π»Π΅ΠΆΠ΅ΠΊ. ΠΠΎ ΠΏΡΠΈΠ½ΡΠΈΠΏΡ ΡΠ°Π±ΠΎΡΡ Π²ΠΎΠ»ΠΎΡΠΈΠ»ΡΠ½ΡΠ΅ ΡΡΠ°Π½Ρ ΠΊΠ»Π°ΡΡΠΈΡΠΈΡΠΈΡΡΡΡΡΡ Π½Π° Π²ΠΎΠ»ΠΎΡΠΈΠ»ΡΠ½ΡΠ΅ ΡΡΠ°Π½Ρ Π±Π΅Π· ΡΠΊΠΎΠ»ΡΠΆΠ΅Π½ΠΈΡ ΠΏΡΠΎΠ²ΠΎΠ»ΠΎΠΊΠΈ Π½Π° ΡΡΠ³ΠΎΠ²ΡΡ Π±Π°ΡΠ°Π±Π°Π½Π°Ρ ΠΈ ΡΡΠ°Π½Ρ ΡΠΎ ΡΠΊΠΎΠ»ΡΠΆΠ΅Π½ΠΈΠ΅ΠΌ ΠΏΡΠΎΠ²ΠΎΠ»ΠΎΠΊΠΈ Π½Π° Π±Π°ΡΠ°Π±Π°Π½Π°Ρ , ΠΊΡΠΎΠΌΠ΅ ΠΏΠΎΡΠ»Π΅Π΄Π½Π΅Π³ΠΎ, ΡΠΈΡΡΠΎΠ²ΠΎΠ³ΠΎ.
ΠΠ΅ΡΠ²ΡΠ΅, Π² ΡΠ²ΠΎΡ ΠΎΡΠ΅ΡΠ΅Π΄Ρ, ΠΏΠΎΠ΄ΡΠ°Π·Π΄Π΅Π»ΡΡΡΡΡ Π½Π° ΡΡΠ°Π½Ρ Ρ Π½Π°ΠΊΠΎΠΏΠ»Π΅ΒΠ½ΠΈΠ΅ΠΌ ΠΏΡΠΎΠ²ΠΎΠ»ΠΎΠΊΠΈ Π½Π° ΠΏΡΠΎΠΌΠ΅ΠΆΡΡΠΎΡΠ½ΡΡ Π±Π°ΡΠ°Π±Π°Π½Π°Ρ ΠΈ Π½Π° ΡΡΠ°Π½Ρ Ρ Π°Π²ΡΠΎΠΌΠ°ΡΠΈΒΡΠ΅ΡΠΊΠΈΠΌ ΡΠ΅Π³ΡΠ»ΠΈΡΠΎΠ²Π°Π½ΠΈΠ΅ΠΌ ΡΠ°ΡΡΠΎΡΡ Π²ΡΠ°ΡΠ΅Π½ΠΈΡ ΠΏΡΠΎΠΌΠ΅ΠΆΡΡΠΎΡΠ½ΡΡ Π±Π°ΡΠ°Π±Π°Π½ΠΎΠ² Π½Π° ΠΏΡΡΠΌΠΎΡΠΎΡΠ½ΡΡ ΡΡΠ°Π½Π°Ρ .
ΠΠΎ ΠΊΡΠ°ΡΠ½ΠΎΡΡΠΈ Π²ΠΎΠ»ΠΎΡΠ΅Π½ΠΈΡ Π²ΠΎΠ»ΠΎΡΠΈΠ»ΡΠ½ΡΠ΅ ΡΡΠ°Π½Ρ ΠΏΠΎΠ΄ΡΠ°Π·Π΄Π΅Π»ΡΡΡΡΡ Π½Π°
ΠΎΠ΄Π½ΠΎΠΊΡΠ°ΡΠ½ΡΠ΅ ΠΈ ΠΌΠ½ΠΎΠ³ΠΎΠΊΡΠ°ΡΠ½ΡΠ΅. ΠΠΎ ΠΊΠΈΠ½Π΅ΠΌΠ°ΡΠΈΡΠ΅ΡΠΊΠΎΠΌΡ ΠΏΡΠΈΠ½ΡΠΈΠΏΡ — ΡΡΠ°Π½Ρ Ρ ΠΈΠ½Π΄ΠΈΠ²ΠΈΠ΄ΡΠ°Π»ΡΠ½ΡΠΌ ΠΏΡΠΈΠ²ΠΎΠ΄ΠΎΠΌ ΠΊΠ°ΠΆΠ΄ΠΎΠ³ΠΎ Π±Π°ΡΠ°Π±Π°Π½Π° ΠΈ ΡΡΠ°Π½Ρ Ρ Π³ΡΡΠΏΠΏΠΎΠ²ΡΠΌ ΠΏΡΠΈΒΠ²ΠΎΠ΄ΠΎΠΌ Π²ΡΠ΅Ρ Π±Π°ΡΠ°Π±Π°Π½ΠΎΠ². Π Π·Π°Π²ΠΈΡΠΈΠΌΠΎΡΡΠΈ ΠΎΡ Π΄ΠΈΠ°ΠΌΠ΅ΡΡΠ° ΠΏΡΠΎΡΡΠ³ΠΈΠ²Π°Π΅ΠΌΠΎΠΉ ΠΏΡΠΎΠ²ΠΎΠ»ΠΎΠΊΠΈ ΡΡΠ°Π½Ρ ΠΏΠΎΠ΄ΡΠ°Π·Π΄Π΅Π»ΡΡΡΡΡ: Π΄Π»Ρ ΠΎΡΠΎΠ±ΠΎ ΡΠΎΠ»ΡΡΠΎΠ³ΠΎ Π²ΠΎΠ»ΠΎΡΠ΅Π½ΠΈΡ (ΠΏΡΠΈ Π΄ΠΈΠ°ΠΌΠ΅ΡΡΠ΅ ΠΏΡΠΎΠ²ΠΎΠ»ΠΎΠΊΠΈ Π±ΠΎΠ»Π΅Π΅ 6.0 ΠΌΠΌ), Π³ΡΡΠ±ΠΎΠ³ΠΎ Π²ΠΎΠ»ΠΎΡΠ΅Π½ΠΈΡ (3.0-6.0 ΠΌΠΌ), ΡΡΠ΅Π΄Π½Π΅Π³ΠΎ Π²ΠΎΠ»ΠΎΡΠ΅Π½ΠΈΡ (1.8-3.0 ΠΌΠΌ), ΡΠΎΠ½ΠΊΠΎΠ³ΠΎ Π²ΠΎΠ»ΠΎΡΠ΅Π½ΠΈΡ (0.8-1.8 ΠΌΠΌ), ΡΠΎΠ½ΡΠ°ΠΉΡΠ΅Π³ΠΎ Π²ΠΎΠ»ΠΎΡΠ΅Π½ΠΈΡ (0.5-0.8 ΠΌΠΌ), Π½Π°ΠΈΡΠΎΠ½ΡΠ°ΠΉΡΠ΅Π³ΠΎ Π²ΠΎΠ»ΠΎΡΠ΅Π½ΠΈΡ (0.1-0.5 ΠΌΠΌ) ΠΈ Π²ΠΎΠ»ΠΎΡΠ΅Π½ΠΈΡ ΠΏΡΠΎΠ²ΠΎΠ»ΠΎΠΊΠΈ Π΄ΠΈΠ°ΠΌΠ΅ΡΡΠΎΠΌ ΠΌΠ΅Π½Π΅Π΅ 0.1 ΠΌΠΌ.
ΠΠΎ ΡΠ΅ΡΠΌΠΈΡΠ΅ΡΠΊΠΈΠΌ ΡΡΠ»ΠΎΠ²ΠΈΡΠΌ Π΄Π΅ΡΠΎΡΠΌΠ°ΡΠΈΠΈ Π²ΠΎΠ»ΠΎΡΠ΅Π½ΠΈΠ΅ ΠΏΡΠΎΠ²ΠΎΠ»ΠΎΠΊΠΈ ΠΏΠΎΠ΄ΒΡΠ°Π·Π΄Π΅Π»ΡΠ΅ΡΡΡ Π½Π°:
Π³ΠΎΡΡΡΠ΅Π΅ Π²ΠΎΠ»ΠΎΡΠ΅Π½ΠΈΠ΅ — Π²ΠΎΠ»ΠΎΡΠ΅Π½ΠΈΠ΅ Π² ΡΡΠ»ΠΎΠ²ΠΈΡΡ Π·Π°ΡΠ΅ΠΊΡΠΈΡΡΠ°Π»Π»ΠΈΠ·Π°ΡΠΈΠΎΠ½Π½ΡΡ ΡΠ΅ΠΌΠΏΠ΅ΡΠ°ΡΡΡ (Π΄ΠΎ 900Β°Π‘), ΠΏΡΠΈΠΌΠ΅Π½ΡΠ΅ΠΌΠΎΠ΅ Π΄Π»Ρ ΡΠ°ΠΊΠΈΡ ΠΌΠ΅ΡΠ°Π»Π»ΠΎΠ², ΠΊΠ°ΠΊ Π²ΠΎΠ»ΡΡΡΠ°ΠΌ, ΠΌΠΎΠ»ΠΈΠ±Π΄Π΅Π½, ΡΠΏΠ»Π°Π²Ρ ΡΠΈΡΠ°Π½Π° ΠΈ Π°Π»ΡΠΌΠΈΠ½ΠΈΡ, ΡΠ°ΠΊ ΠΊΠ°ΠΊ ΠΎΠ½ΠΈ ΠΎΠ±Π»Π°Π΄Π°ΡΡ ΠΏΡΠΈ ΠΎΠ±ΡΡΠ½ΡΡ ΡΠ΅ΠΌΠΏΠ΅ΡΠ°ΡΡΡΠ°Ρ Π½Π΅Π΄ΠΎΡΡΠ°ΡΠΎΡΠ½ΠΎΠΉ ΠΏΠ»Π°ΡΡΠΈΡΠ½ΠΎΡΡΡΡ ΠΈ ΠΏΡΠΎΡΠ²Π»ΡΡΡ Ρ ΡΡΠΏΠΊΠΎΡΡΡ; ΡΠ΅ΠΏΠ»ΠΎΠ΅ Π²ΠΎΠ»ΠΎΡΠ΅Π½ΠΈΠ΅ — Π²ΠΎΠ»ΠΎΡΠ΅Π½ΠΈΠ΅ Π² ΡΡΠ»ΠΎΠ²ΠΈΡΡ Π΄ΠΎ ΠΈΠ»ΠΈ ΠΎΠΊΠΎΠ»ΠΎ ΡΠ΅ΠΊΡΠΈΡΡΠ°Π»Π»ΠΈΠ·Π°ΡΠΈΠΎΠ½Π½ΠΎΠ³ΠΎ ΠΏΠΎΡΡΠ΄ΠΊΠ° (Π΄ΠΎ 500Β°Π‘,) ΠΈΡΠΏΠΎΠ»ΡΠ·ΡΠ΅ΡΠ΅Π΅ΡΡ Π΄Π»Ρ Π²ΠΎΒΠ»ΠΎΡΠ΅Π½ΠΈΡ ΠΏΡΠΎΠ²ΠΎΠ»ΠΎΠΊΠΈ ΠΈΠ· Π±ΡΡΡΡΠΎΡΠ΅ΠΆΡΡΠΈΡ ΠΌΠ°ΡΠΎΠΊ ΡΡΠ°Π»Π΅ΠΉ ΡΠΈΠΏΠ° Π -9, Π -18; Π½ΠΈΠ·ΠΊΠΎΡΠ΅ΠΌΠΏΠ΅ΡΠ°ΡΡΡΠ½ΠΎΠ΅ Π²ΠΎΠ»ΠΎΡΠ΅Π½ΠΈΠ΅ — Π²ΠΎΠ»ΠΎΡΠ΅Π½ΠΈΠ΅ Π² ΠΈΠ½ΡΠ΅ΡΠ²Π°Π»Π΅ ΡΠ΅ΠΌΒΠΏΠ΅ΡΠ°ΡΡΡ ΠΎΡ 60Β°Π‘ Π΄ΠΎ 180Β°Π‘, ΠΏΡΠΈΠΌΠ΅Π½ΡΡΡΠ΅Π΅ΡΡ ΠΏΡΠΈ ΠΏΡΠΎΠΈΠ·Π²ΠΎΠ΄ΡΡΠ²Π΅ ΠΏΡΠΎΠ²ΠΎΠ»ΠΎΠΊΠΈ ΠΈΠ· Π²ΡΡΠΎΠΊΠΎΠ»Π΅Π³ΠΈΡΠΎΠ²Π°Π½Π½ΡΡ ΡΡΠ°Π»Π΅ΠΉ Ρ Π°ΡΡΡΠ΅Π½ΠΈΡΠ½ΠΎΠΉ ΠΈ Π°ΡΡΡΠ΅Π½ΠΈΡΠ½ΠΎ-ΡΠ΅ΡΡΠΈΡΠ½ΠΎΠΉ ΡΡΡΡΠΊΡΡΡΠΎΠΉ.
ΠΡΠΎΠΌΠ΅ ΡΡΠΎΠ³ΠΎ, ΠΏΡΠΎΡΠ΅ΡΡ Π²ΠΎΠ»ΠΎΡΠ΅Π½ΠΈΡ ΠΌΠΎΠΆΠ΅Ρ ΠΏΡΠΎΠ²ΠΎΠ΄ΠΈΡΡΡΡ Ρ ΠΏΡΠΎΡΠΈΠ²ΠΎΠ½Π°-ΡΡΠΆΠ΅Π½ΠΈΠ΅ΠΌ, ΠΊΠ°ΠΊ ΡΡΠΎ ΠΏΡΠΎΠΈΡΡ ΠΎΠ΄ΠΈΡ Π½Π° ΠΏΡΡΠΌΠΎΡΠΎΡΠ½ΡΡ Π²ΠΎΠ»ΠΎΡΠΈΠ»ΡΠ½ΡΡ ΡΡΠ°Π½Π°Ρ -ΠΏΠ΅ΡΠ΅Π΄ ΡΠΎΠΎΡΠ²Π΅ΡΡΡΠ²ΡΡΡΠ΅ΠΉ Π²ΠΎΠ»ΠΎΠΊΠΎΠ½ ΠΏΡΠΎΡΡΠ³ΠΈΠ²Π°Π΅ΠΌΠΎΠΉ ΠΏΡΠΎΠ²ΠΎΠ»ΠΎΠΊΠ΅ ΡΠΎΠ·Π΄Π°Π΅ΡΡΡ ΠΏΡΠ΅Π΄Π²Π°ΡΠΈΡΠ΅Π»ΡΠ½ΠΎΠ΅ Π½Π°ΡΡΠΆΠ΅Π½ΠΈΠ΅ ΠΎΡ ΠΏΡΠ΅Π΄ΡΠ΄ΡΡΠ΅Π³ΠΎ Π±Π°ΡΠ°Π±Π°Π½Π°.
ΠΠΈΠ±ΡΠ°ΡΠΈΠΎΠ½Π½ΠΎΠ΅ Π²ΠΎΠ»ΠΎΡΠ΅Π½ΠΈΠ΅ — Π²ΠΎΠ»ΠΎΡΠ΅Π½ΠΈΠ΅ Ρ Π½Π°Π»ΠΎΠΆΠ΅Π½ΠΈΠ΅ΠΌ Π²ΠΈΠ±ΡΠ°ΡΠΈΠΉ Π½Π° ΠΏΡΠΎΠ²ΠΎΠ»ΠΎΠΊΡ ΠΈΠ»ΠΈ Π²ΠΎΠ»ΠΎΠΊΡ Ρ ΡΠ°ΡΡΠΎΡΠΎΠΉ ΠΎΡ 200 Π΄ΠΎ 1000 ΠΡ, ΡΡΠΎ ΠΏΡΠΈΠ²ΠΎΒΠ΄ΠΈΡ ΠΊ ΡΠΌΠ΅Π½ΡΡΠ΅Π½ΠΈΡ ΡΠΈΠ»Ρ Π²ΠΎΠ»ΠΎΡΠ΅Π½ΠΈΡ Π½Π° 35-45%.
ΠΠΎΠ»ΠΎΡΠ΅Π½ΠΈΠ΅ ΡΠ΅ΡΠ΅Π² Π²ΡΠ°ΡΠ°ΡΡΡΡΡΡ Π²ΠΎΠ»ΠΎΠΊΡ ΡΠ°ΠΊΠΆΠ΅ ΡΠΌΠ΅Π½ΡΡΠ°Π΅Ρ ΡΠΈΠ»Ρ Π²ΠΎΠ»ΠΎΡΠ΅Π½ΠΈΡ, Π½ΠΎ Π΄Π»Ρ Π²ΡΠ°ΡΠ΅Π½ΠΈΡ Π²ΠΎΠ»ΠΎΠΊΠΈ Π½Π΅ΠΎΠ±Ρ ΠΎΠ΄ΠΈΠΌ ΡΠΏΠ΅ΡΠΈΠ°Π»ΡΠ½ΡΠΉ ΠΏΡΠΈΠ²ΠΎΠ΄.
ΠΠΎΠ»ΠΎΡΠ΅Π½ΠΈΠ΅ ΠΏΡΠΎΠ²ΠΎΠ»ΠΎΠΊΠΈ ΡΠ΅ΡΠ΅Π· Π½Π΅ΠΏΡΠΈΠ²ΠΎΠ΄Π½ΡΠ΅ ΡΠΎΠ»ΠΈΠΊΠΎΠ²ΡΠ΅ Π²ΠΎΠ»ΠΎΠΊΠΈ, ΠΏΡΠΈΒΠΌΠ΅Π½ΡΡΡΠΈΠ΅ΡΡ Π΄Π»Ρ Π²ΡΡΠΎΠΊΠΎΠΏΡΠΎΡΠ½ΡΡ ΡΡΠ°Π»Π΅ΠΉ, Π°Π½Π°Π»ΠΎΠ³ΠΈΡΠ½ΠΎ ΠΎΠ±ΡΠ°Π±ΠΎΡΠΊΠ΅ Π΄Π°Π²Π»Π΅ΒΠ½ΠΈΠ΅ΠΌ ΠΌΠ΅ΡΠΎΠ΄ΠΎΠΌ ΠΏΡΠΎΠΊΠ°ΡΠΊΠΈ Ρ Π½Π΅ΠΏΡΠΈΠ²ΠΎΠ΄Π½ΡΠΌΠΈ Π²Π°Π»ΠΊΠ°ΠΌΠΈ.
ΠΠΎΡΠ²Π»Π΅Π½ΠΈΠ΅ Π² 1927-28 Π³Π³. ΡΠ²Π΅ΡΠ΄ΠΎΡΠΏΠ»Π°Π²Π½ΠΎΠ³ΠΎ Π²ΠΎΠ»ΠΎΡΠΈΠ»ΡΠ½ΠΎΠ³ΠΎ ΠΈΠ½ΡΡΡΡΒΠΌΠ΅Π½ΡΠ° ΠΏΡΠΎΠΈΠ·Π²Π΅Π»ΠΎ ΡΠ²ΠΎΠ΅Π³ΠΎ ΡΠΎΠ΄Π° ΡΠ΅Π²ΠΎΠ»ΡΡΠΈΡ Π² Π²ΠΎΠ»ΠΎΡΠΈΠ»ΡΠ½ΠΎΠΌ ΠΏΡΠΎΠΈΠ·Π²ΠΎΠ΄ΡΡΠ²Π΅.
1.1 ΠΠΎΠ»ΠΎΡΠΈΠ»ΡΠ½ΡΠ΅ ΡΡΠ°Π½Ρ Π΄Π»Ρ ΠΎΠ΄Π½ΠΎΠΊΡΠ°ΡΠ½ΠΎΠ³ΠΎ Π²ΠΎΠ»ΠΎΡΠ΅Π½ΠΈΡ ΠΏΡΠΎΠ²ΠΎΠ»ΠΎΠΊΠΈ
ΠΠ΄Π½ΠΎΠΊΡΠ°ΡΠ½ΡΠ΅ Π²ΠΎΠ»ΠΎΡΠΈΠ»ΡΠ½ΡΠ΅ ΡΡΠ°Π½Ρ ΠΏΡΠ΅Π΄Π½Π°Π·Π½Π°ΡΠ΅Π½Ρ Π΄Π»Ρ Π²ΠΎΠ»ΠΎΡΠ΅Π½ΠΈΡ ΠΏΡΠΎΠ²ΠΎΠ»ΠΎΠΊΠΈ ΠΈΠ· Π·Π°Π³ΠΎΡΠΎΠ²ΠΎΠΊ ΡΠΎΠ»ΡΡΡΡ ΡΠ°Π·ΠΌΠ΅ΡΠΎΠ² — ΠΎΡ 8.0 Π΄ΠΎ 20.0 ΠΌΠΌ. ΠΠΈΠ°ΠΌΠ΅ΡΡ ΡΡΠ½ΡΡΠΈΡ Π±Π°ΡΠ°Π±Π°Π½ΠΎΠ² ΡΠΎΡΡΠ°Π²Π»ΡΠ΅Ρ 550-750 ΠΌΠΌ.
Π‘Ρ Π΅ΠΌΠ° ΡΠ°Π±ΠΎΡΡ ΠΎΠ΄Π½ΠΎΠΊΡΠ°ΡΠ½ΠΎΠ³ΠΎ Π²ΠΎΠ»ΠΎΡΠΈΠ»ΡΠ½ΠΎΠ³ΠΎ ΡΡΠ°Π½Π° ΠΏΠΎΠΊΠ°Π·Π°Π½Π° Π½Π° ΡΠΈΡ.1.1. ΠΡΠΎΡΡΠ³ΠΈΠ²Π°Π΅ΠΌΠ°Ρ Π·Π°Π³ΠΎΡΠΎΠ²ΠΊΠ° 2 ΡΠΌΠ°ΡΡΠ²Π°Π΅ΡΡΡ Ρ ΡΠ°Π·ΠΌΠΎΡΠΎΡΠ½ΠΎΠ³ΠΎ ΡΡΡΡΠΎΠΉΡΡΠ²Π° 1. ΠΠΎΡΠ»Π΅ ΠΏΡΠΎΡ ΠΎΠΆΠ΄Π΅Π½ΠΈΡ ΡΠ΅ΡΠ΅Π· Π²ΠΎΠ»ΠΎΡΠΈΠ»ΡΠ½ΡΠΉ ΠΈΠ½ΡΡΡΡΠΌΠ΅Π½Ρ (Π²ΠΎΒΠ»ΠΎΠΊΡ) 3, ΠΏΡΠΎΡΡΠ½ΡΡΠ°Ρ Π½Π° Π½Π΅ΠΎΠ±Ρ ΠΎΠ΄ΠΈΠΌΡΠΉ ΡΠ°Π·ΠΌΠ΅Ρ (Π΄ΠΈΠ°ΠΌΠ΅ΡΡ) ΠΏΡΠΎΠ²ΠΎΠ»ΠΎΠΊΠ° 4 Π½Π°ΠΌΠ°ΡΡΠ²Π°Π΅ΡΡΡ Π½Π° ΡΡΠ½ΡΡΠΈΠΉ Π±Π°ΡΠ°Π±Π°Π½ Π±, ΠΊΠΎΡΠΎΡΡΠΉ ΠΏΡΠΈΠ²ΠΎΠ΄ΠΈΡΡΡ Π²ΠΎ Π²ΡΠ°ΡΠ΅Π½ΠΈΠ΅ ΠΎΡ ΡΠ»Π΅ΠΊΡΡΠΎΠ΄Π²ΠΈΠ³Π°ΡΠ΅Π»Ρ 7 ΡΠ΅ΡΠ΅Π· ΡΠ΅Π΄ΡΠΊΡΠΎΡ ΠΈΠ»ΠΈ ΠΊΠΎΡΠΎΠ±ΠΊΡ ΡΠΊΠΎΡΠΎΡΡΠ΅ΠΉ 6.
ΠΠΎΠ»ΠΎΡΠΈΠ»ΡΠ½ΡΠΉ ΡΡΠ°Π½ (ΡΠΈΡ.1.2) ΠΏΡΠ΅Π΄ΡΡΠ°Π²Π»ΡΠ΅Ρ ΡΠΎΠ±ΠΎΠΉ ΡΠ°ΠΌΠΎΡΡΠΎΡΡΠ΅Π»ΡΒΠ½ΡΠΉ Π±Π»ΠΎΠΊ, ΡΠΎΡΡΠΎΡΡΠΈΠΉ ΠΈΠ· Π»ΠΈΡΠΎΠ³ΠΎ ΠΊΠΎΡΠΏΡΡΠ° 11, Π½Π° ΠΊΠΎΡΠΎΡΠΎΠΌ ΡΠΌΠΎΠ½ΡΠΈΡΠΎΠ²Π°Π½ ΡΡΠ³ΠΎΠ²ΡΠΉ Π²ΠΎΠ»ΠΎΡΠΈΠ»ΡΠ½ΡΠΉ Π±Π°ΡΠ°Π±Π°Π½ 5.ΠΠ°ΡΠ°Π±Π°Π½ ΠΏΠΎΠ»ΡΡΠ°Π΅Ρ Π²ΡΠ°ΡΠ΅Π½ΠΈΠ΅ ΠΎΡ ΡΠ»Π΅ΠΊΡΒΡΠΎΠΏΡΠΈΠ²ΠΎΠ΄Π°, ΡΠΎΡΡΠΎΡΡΠ΅Π³ΠΎ ΠΈΠ· ΡΠ»Π΅ΠΊΡΡΠΎΠ΄Π²ΠΈΠ³Π°ΡΠ΅Π»Ρ 3, ΠΊΠ»ΠΈΠ½ΠΎΡΠ΅ΠΌΠ΅Π½Π½ΠΎΠΉ ΠΏΠ΅ΡΠ΅Π΄Π°ΒΡΠΈ, ΡΠ΅ΡΡΡΠ΅Ρ ΡΠΊΠΎΡΠΎΡΡΠ½ΠΎΠΉ ΠΊΠΎΡΠΎΠ±ΠΊΠΈ ΠΏΠ΅ΡΠ΅Π΄Π°Ρ 4, ΠΊΠΎΠ½ΠΈΡΠ΅ΡΠΊΠΎΠΉ ΠΈ ΡΠΈΠ»ΠΈΠ½Π΄ΡΠΈΡΠ΅ΡΒΠΊΠΎΠΉ ΠΏΠ°Ρ Π·ΡΠ±ΡΠ°ΡΡΡ ΠΊΠΎΠ»Π΅Ρ.
ΠΡΠ½Ρ Π·Π°Π³ΠΎΡΠΎΠ²ΠΊΠΈ, ΠΏΠΎΠ΄Π»Π΅ΠΆΠ°ΡΠ΅ΠΉ Π²ΠΎΠ»ΠΎΡΠ΅Π½ΠΈΡ, Π½Π°Π΄Π΅Π²Π°Π΅ΡΡΡ Π½Π° ΠΊΠΎΠ½ΡΠΎΠ»Ρ 1 ΠΈΠ»ΠΈ ΡΠΈΠ³ΡΡΠΊΡ 2. ΠΠΎΠ½Π΅Ρ ΠΏΡΠΎΠ²ΠΎΠ»ΠΎΠΊΠΈ ΠΏΠΎΡΠ»Π΅ Π·Π°ΠΎΡΡΡΠ΅Π½ΠΈΡ Π½Π° ΠΎΡΡΡΠΈΠ»ΡΠ½ΠΎΠΌ ΡΡΠ°Π½ΠΊΠ΅ ΠΏΡΠΎΠΏΡΡΠΊΠ°ΡΡ ΡΠ΅ΡΠ΅Π· ΠΎΡΠ²Π΅ΡΡΡΠΈΠ΅ Π²ΠΎΠ»ΠΎΠΊΠΈ 9, ΠΏΠΎΡΠ»Π΅ ΡΠ΅Π³ΠΎ Π·Π°Ρ Π²Π°ΡΡΠ²Π°ΒΡΡ Π²ΡΡΡΠΆΠ½ΡΠΌΠΈ ΠΊΠ»Π΅ΡΠ°ΠΌΠΈ. ΠΠ»Π΅ΡΠΈ ΠΏΡΠΈ ΠΏΠΎΠΌΠΎΡΠΈ ΠΏΠ»Π°ΡΡΠΈΠ½ΡΠ°ΡΠΎΠΉ ΡΠ΅ΠΏΠΈ Ρ ΠΊΡΡΠΊΠΎΠΌ Π½Π° Π΄ΡΡΠ³ΠΎΠΌ ΠΊΠΎΠ½ΡΠ΅ ΡΠΎΠ΅Π΄ΠΈΠ½ΡΡΡΡΡ Ρ Π±Π°ΡΠ°Π±Π°Π½ΠΎΠΌ 5.ΠΠ° Π·Π°ΠΏΡΠ°Π²ΠΎΡΠ½ΠΎΠΉ (ΠΌΠ΅Π΄Π»Π΅Π½ΒΠ½ΠΎΠΉ) ΡΠΊΠΎΡΠΎΡΡΠΈ Π½Π° Π±Π°ΡΠ°Π±Π°Π½ Π½Π°ΠΌΠ°ΡΡΠ²Π°Π΅ΡΡΡ Π½Π΅ΡΠΊΠΎΠ»ΡΠΊΠΎ Π²ΠΈΡΠΊΠΎΠ² ΠΏΡΠΎΠ²ΠΎΠ»ΠΎΒΠΊΠΈ, ΠΏΠΎΡΠ»Π΅ ΡΠ΅Π³ΠΎ ΠΊΠ»Π΅ΡΠΈ ΡΠ½ΠΈΠΌΠ°ΡΡΡΡ, Π° ΡΠ²ΠΎΠ±ΠΎΠ΄Π½ΡΠΉ ΠΊΠΎΠ½Π΅Ρ ΠΏΡΠΎΠ²ΠΎΠ»ΠΎΠΊΠΈ Π·Π°ΠΊΒΡΠ΅ΠΏΠ»ΡΠ΅ΡΡΡ Π·Π° ΡΠΏΠΈΡΡ 6 Π±Π°ΡΠ°Π±Π°Π½Π°. ΠΠΎΡΠ»Π΅ ΡΡΠΎΠ³ΠΎ ΡΡΠ°Π½ Π²ΠΊΠ»ΡΡΠ°Π΅ΡΡΡ Π½Π° ΡΠ°ΒΠ±ΠΎΡΡΡ ΡΠΊΠΎΡΠΎΡΡΡ.
ΠΠΎΡΠ»Π΅ Π½Π°ΠΊΠΎΠΏΠ»Π΅Π½ΠΈΡ Π½Π° Π±Π°ΡΠ°Π±Π°Π½Π΅ ΠΎΠΏΡΠ΅Π΄Π΅Π»Π΅Π½Π½ΠΎΠ³ΠΎ ΠΊΠΎΠ»ΠΈΡΠ΅ΡΡΠ²Π° Π²ΠΈΡΠΊΠΎΠ² ΠΏΡΠΎΠ²ΠΎΠ»ΠΎΠΊΠΈ, ΡΡΠ°Π½ ΠΎΡΡΠ°Π½Π°Π²Π»ΠΈΠ²Π°Π΅ΡΡΡ, ΠΏΠΎΠ»ΡΡΠ΅Π½Π½ΡΠΉ ΠΌΠΎΡΠΎΠΊ ΠΏΡΠΎΠ²ΠΎΠ»ΠΎΠΊΠΈ (ΠΈΠ»ΠΈ ΠΏΠ΅ΡΠ΅Π΄Π΅Π»ΡΠ½ΠΎΠΉ Π·Π°Π³ΠΎΡΠΎΠ²ΠΊΠΈ) ΡΠ½ΠΈΠΌΠ°Π΅ΡΡΡ ΠΈ ΡΠΊΠ»Π°Π΄ΡΠ²Π°Π΅ΡΡΡ Π½Π° ΡΠ²ΡΠ·ΠΎΡΠ½ΡΡ ΡΠΈΒΠ³ΡΡΠΊΡ 8.
ΠΡΠ΅ ΠΎΠΏΠ΅ΡΠ°ΡΠΈΠΈ ΠΏΠΎ ΡΠΊΠ»Π°Π΄ΠΊΠ΅ Π±ΡΠ½ΡΠ° Π·Π°Π³ΠΎΡΠΎΠ²ΠΊΠΈ Π½Π° ΡΠ°Π·ΠΌΠΎΡΠΎΡΠ½ΠΎΠ΅ ΡΡΡΒΡΠΎΠΉΡΡΠ²ΠΎ ΠΈ ΡΡΠ΅ΠΌ ΠΌΠΎΡΠΊΠ° ΠΏΡΠΎΠ²ΠΎΠ»ΠΎΠΊΠΈ ΠΌΠ΅Ρ Π°Π½ΠΈΠ·ΠΈΡΠΎΠ²Π°Π½Ρ.
ΠΠΎΠ»ΠΎΡΠΈΠ»ΡΠ½ΡΠΉ Π±Π°ΡΠ°Π±Π°Π½ ΠΎΠ±ΡΠ»ΡΠΆΠΈΠ²Π°Π΅ΡΡΡ ΠΏΠΎΠ΄ΡΠ΅ΠΌΠ½ΠΈΠΊΠ°ΠΌΠΈ, Π° ΡΠΊΠ»Π°Π΄ΠΊΠ° Π±ΡΠ½ΡΠ° ΠΎΡΡΡΠ΅ΡΡΠ²Π»ΡΠ΅ΡΡΡ ΡΠ΅Π»ΡΡΠ΅ΡΠΎΠΌ 7. ΠΠ°ΡΡΠ° Π±ΡΠ½ΡΠΎΠ² Ρ ΠΏΡΠΎΠ²ΠΎΠ»ΠΎΡΠ½ΡΡ ΠΏΡΠΎ ΠΊΠ°ΡΠ½ΡΡ ΡΡΠ°Π½ΠΎΠ² ΡΠΎΡΡΠ°Π²Π»ΡΠ΅Ρ 1.0-1.5 Ρ, Π΄Π»Ρ ΠΈΡ ΡΠΊΡΡΠΏΠ½Π΅Π½ΠΈΡ ΠΏΡΠΈΠΌΠ΅Π½ΡΠ΅ΡΡΡ ΡΡΡΠΊΠΎΠ²Π°Ρ ΡΠ²Π°ΡΠΊΠ° Ρ ΠΏΠΎΠΌΠΎΡΡΡ ΡΠΏΠ΅ΡΠΈΠ°Π»ΡΠ½ΡΡ ΡΠ²Π°ΡΠΎΡΠ½ΡΡ Π°ΠΏΠΏΠ°ΡΠ°ΡΠΎΠ² 10, ΠΊΠΎΒΡΠΎΡΡΠΌΠΈ ΠΎΠ±ΠΎΡΡΠ΄ΠΎΠ²Π°Π½ ΠΊΠ°ΠΆΠ΄ΡΠΉ ΡΡΠ°Π½.
ΠΠ°ΠΌΠΎΡΠΊΠ° ΠΏΡΠΎΠ²ΠΎΠ»ΠΎΠΊΠΈ ΠΌΠΎΠΆΠ΅Ρ ΠΏΡΠΎΠΈΠ·Π²ΠΎΠ΄ΠΈΡΡΡΡ Π½Π΅ ΡΠΎΠ»ΡΠΊΠΎ Π² Π±ΡΠ½ΡΡ, Π½ΠΎ ΠΈ Π½Π° ΠΊΠ°ΡΡΡΠΊΠΈ Π²ΠΌΠ΅ΡΡΠΈΠΌΠΎΡΡΡΡ Π΄ΠΎ 2.0 Ρ ΠΏΡΠΈ ΠΏΠΎΠΌΠΎΡΠΈ ΡΠΏΠ΅ΡΠΈΠ°Π»ΡΠ½ΡΡ Π½Π°ΠΌΠΎΒΡΠΎΡΠ½ΡΡ ΡΡΡΡΠΎΠΉΡΡΠ², ΠΊΠΎΡΠΎΡΡΠ΅ ΠΌΠΎΠ³ΡΡ Π±ΡΡΡ ΡΡΡΠ°Π½ΠΎΠ²Π»Π΅Π½Ρ Π² ΠΎΠ΄Π½ΠΎΠΉ Π»ΠΈΠ½ΠΈΠΈ Ρ Π²ΠΎΠ»ΠΎΡΠΈΠ»ΡΠ½ΡΠΌΠΈ ΡΡΠ°Π½Π°ΠΌΠΈ. ΠΡΠΎ ΠΏΠΎΠ·Π²ΠΎΠ»ΡΠ΅Ρ ΠΏΠΎΠ²ΡΡΠΈΡΡ ΠΏΡΠΎΠΈΠ·Π²ΠΎΠ΄ΠΈΡΠ΅Π»ΡΠ½ΠΎΡΡΡ Π²ΠΎΠ»ΠΎΡΠΈΠ»ΡΠ½ΠΎΠ³ΠΎ ΡΡΠ°Π½Π° Π·Π° ΡΡΠ΅Ρ ΡΠ½ΠΈΠΆΠ΅Π½ΠΈΡ Π²ΡΠ΅ΠΌΠ΅Π½ΠΈ Π½Π° ΡΡΡΠ½ΡΠ΅ ΠΎΠΏΠ΅ΡΠ°ΡΠΈΠΈ (ΡΡΠ΅ΠΌ ΠΌΠΎΡΠΊΠ° ΠΏΡΠΎΠ²ΠΎΠ»ΠΎΠΊΠΈ Ρ Π±Π°ΡΠ°Π±Π°Π½Π° ΠΈ Π΄Ρ.) ΠΈ ΡΠ²Π΅Π»ΠΈΡΠ΅Π½ΠΈΡ ΠΌΠ°ΡΠΈΠ½Π½ΠΎΠ³ΠΎ Π²ΡΠ΅ΠΌΠ΅Π½ΠΈ. ΠΡΠΈ ΡΡΠΎΠΌ ΡΠ»ΡΡΡΠ°Π΅ΡΡΡ ΠΊΠ°ΡΠ΅ΡΡΠ²ΠΎ Π³ΠΎΡΠΎΠ²ΠΎΠΉ ΠΏΡΠΎΠ΄ΡΠΊΡΠΈΠΈ, ΡΠΌΠ΅Π½ΡΡΠ°ΒΡΡΡΡ ΠΎΡΡ ΠΎΠ΄Ρ, ΠΈΡΠΊΠ»ΡΡΠ°Π΅ΡΡΡ ΠΏΠ΅ΡΠ΅ΠΏΡΡΡΠ²Π°Π½ΠΈΠ΅ ΠΏΡΠΎΠ²ΠΎΠ»ΠΎΠΊΠΈ ΠΈ Ρ.Π΄.
ΠΡΠΈΠ²ΠΎΠ΄ Π² ΡΡΠ°Π½Π°Ρ ΠΎΠ΄Π½ΠΎΠΊΡΠ°ΡΠ½ΠΎΠ³ΠΎ Π²ΠΎΠ»ΠΎΡΠ΅Π½ΠΈΡ ΠΌΠΎΠΆΠ΅Ρ ΠΎΡΡΡΠ΅ΡΡΠ²Π»ΡΡΡΡΡ ΠΎΡ ΡΠ»Π΅ΠΊΡΡΠΎΠ΄Π²ΠΈΠ³Π°ΡΠ΅Π»Π΅ΠΉ ΠΊΠ°ΠΊ ΠΏΠ΅ΡΠ΅ΠΌΠ΅Π½Π½ΠΎΠ³ΠΎ, ΡΠ°ΠΊ ΠΈ ΠΏΠΎΡΡΠΎΡΠ½Π½ΠΎΠ³ΠΎ ΡΠΎΠΊΠ°.
ΠΡΠΈΠ²ΠΎΠ΄ Π΄ΠΎΠ»ΠΆΠ΅Π½ ΠΎΠ±Π΅ΡΠΏΠ΅ΡΠΈΠ²Π°ΡΡ:
Π·Π°ΠΏΡΡΠΊ ΡΡΠ°Π½Π° ΠΏΡΠΈ Π·Π°ΠΏΡΠ°Π²ΠΊΠ΅ Π½Π° ΠΌΠ΅Π΄Π»Π΅Π½Π½ΠΎΠΉ, ΠΏΠΎΠ»Π·ΡΡΠ΅ΠΉ ΡΠΊΠΎΡΠΎΡΡΠΈ ΠΈ ΠΏΠ»Π°Π²Π½ΡΠΉ ΡΠ°Π·Π³ΠΎΠ½, ΠΈΡΠΊΠ»ΡΡΠ°ΡΡΠΈΠΉ ΠΎΠ±ΡΡΠ² ΠΏΡΠΎΠ²ΠΎΠ»ΠΎΠΊΠΈ;
Π±ΡΡΡΡΡΠΉ ΡΠ°Π·Π³ΠΎΠ½ Π΄Π»Ρ ΠΎΠ±Π΅ΡΠΏΠ΅ΡΠ΅Π½ΠΈΡ ΠΌΠ°ΠΊΡΠΈΠΌΠ°Π»ΡΠ½ΠΎΠΉ ΠΏΡΠΎΠΈΠ·Π²ΠΎΠ΄ΠΈΡΠ΅Π»ΡΒ Π½ΠΎΡΡΠΈ;
ΡΠΈΡΠΎΠΊΠΈΠΉ Π΄ΠΈΠ°ΠΏΠ°Π·ΠΎΠ½ ΡΠ΅Π³ΡΠ»ΠΈΡΠΎΠ²Π°Π½ΠΈΡ ΡΠΊΠΎΡΠΎΡΡΠΈ Π²ΠΎΠ»ΠΎΡΠ΅Π½ΠΈΡ Π² Π·Π°Π²ΠΈΒ ΡΠΈΠΌΠΎΡΡΠΈ ΠΎΡ Π²Π΅Π»ΠΈΡΠΈΠ½Ρ ΠΏΠΎΠΏΠ΅ΡΠ΅ΡΠ½ΠΎΠ³ΠΎ ΡΠ΅ΡΠ΅Π½ΠΈΡ ΠΈ ΠΌΠ°ΡΠΊΠΈ ΠΏΡΠΎΡΡΒ Π³ΠΈΠ²Π°Π΅ΠΌΠΎΠ³ΠΎ ΠΌΠ°ΡΠ΅ΡΠΈΠ°Π»Π°;
Π±ΡΡΡΡΡΡ ΠΎΡΡΠ°Π½ΠΎΠ²ΠΊΡ ΡΡΠ°Π½Π° Π² Π°Π²Π°ΡΠΈΠΉΠ½ΡΡ ΡΠ»ΡΡΠ°ΡΡ .
ΠΠ΅ΡΠΌΠΎΡΡΡ Π½Π° ΡΠΎ, ΡΡΠΎ ΡΠΎΠ²ΡΠ΅ΠΌΠ΅Π½Π½ΡΠ΅ ΠΎΠ΄Π½ΠΎΠΊΡΠ°ΡΠ½ΡΠ΅ ΡΡΠ°Π½Ρ ΠΏΡΠΎΠ΅ΠΊΡΠΈΡΡΒΡΡ Π΄Π»Ρ ΡΠ°Π±ΠΎΡΡ Ρ ΠΏΠΎΠ²ΡΡΠ΅Π½Π½ΡΠΌΠΈ ΡΠΊΠΎΡΠΎΡΡΡΠΌΠΈ Π²ΠΎΠ»ΠΎΡΠ΅Π½ΠΈΡ, ΠΎΠ½ΠΈ ΠΈΠΌΠ΅ΡΡ ΡΠ»Π΅ΒΠ΄ΡΡΡΠΈΠ΅ Π½Π΅Π΄ΠΎΡΡΠ°ΡΠΊΠΈ:
Π·Π° ΠΎΠ΄Π½Ρ, Π° ΠΈΠ½ΠΎΠ³Π΄Π° Π·Π° Π΄Π²Π΅ ΠΏΡΠΎΡΡΠΆΠΊΠΈ (ΠΏΡΠΈ ΡΡΡΠΏΠ΅Π½ΡΠ°ΡΠΎΠΌ, ΡΠ΄Π²ΠΎΠ΅Π½Β Π½ΠΎΠΌ Π±Π°ΡΠ°Π±Π°Π½Π΅) Π½Π΅Π»ΡΠ·Ρ ΠΏΠΎΠ»ΡΡΠ°ΡΡ Π²ΡΡΠΎΠΊΠΈΠ΅ ΠΎΠ±ΠΆΠ°ΡΠΈΡ;
ΠΎΠ³ΡΠ°Π½ΠΈΡΠ΅Π½Π½Π°Ρ ΡΠΊΠΎΡΠΎΡΡΡ Π²ΠΎΠ»ΠΎΡΠ΅Π½ΠΈΡ Π²ΡΠ΅ΡΠ΅Π»ΠΎ ΠΎΠΏΡΠ΅Π΄Π΅Π»ΡΠ΅ΡΡΡ Π΄ΠΎΠΏΡΡΡΠΈΠΌΠΎΠΉ ΡΠΊΠΎΡΠΎΡΡΡΡ ΡΡ ΠΎΠ΄Π° Π·Π°Π³ΠΎΡΠΎΠ²ΠΊΠΈ Ρ ΡΠΈΠ³ΡΡΠΊΠΈ;
— Π²Π²ΠΈΠ΄Ρ ΡΠΎΠ³ΠΎ, ΡΡΠΎ Π΄ΠΈΠ°ΠΌΠ΅ΡΡ Π·Π°Π³ΠΎΡΠΎΠ²ΠΊΠΈ Π΄ΠΎΠ²ΠΎΠ»ΡΠ½ΠΎ Π²Π΅Π»ΠΈΠΊ, Π° ΠΌΠ°ΡΠΈΠ½Β Π½ΠΎΠ΅ Π²ΡΠ΅ΠΌΡ Π½Π° ΠΎΠ΄ΠΈΠ½ Π±ΡΠ½Ρ Π·Π°Π³ΠΎΡΠΎΠ²ΠΊΠΈ ΠΌΠ°Π»ΠΎ, ΡΡΠ°Π½ ΡΠ°ΡΡΠΎ ΠΏΡΠΈΡ ΠΎΠ΄ΠΈΡΡΡ ΠΎΡΒ ΡΠ°Π½Π°Π²Π»ΠΈΠ²Π°ΡΡ Π΄Π»Ρ Π·Π°ΠΌΠ΅Π½Ρ Π±ΡΠ½ΡΠ°, Π° ΡΠ°ΠΊΠΆΠ΅ ΡΡΠ΅ΠΌΠ° ΠΌΠΎΡΠΊΠ° ΠΏΡΠΎΠ²ΠΎΠ»ΠΎΠΊΠΈ, Π΅ΡΠ»ΠΈ ΠΏΠΎΡΠ»Π΅Π΄Π½ΡΡ Π½Π°ΠΊΠ°ΠΏΠ»ΠΈΠ²Π°Π΅ΡΡΡ Π½Π° Π±Π°ΡΠ°Π±Π°Π½Π΅.
ΠΠ΄Π½ΠΎΠΊΡΠ°ΡΠ½ΡΠ΅ Π²ΠΎΠ»ΠΎΡΠΈΠ»ΡΠ½ΡΠ΅ ΡΡΠ°Π½Ρ Π½Π°Ρ ΠΎΠ΄ΡΡ ΡΠΈΡΠΎΠΊΠΎΠ΅ ΠΏΡΠΈΠΌΠ΅Π½Π΅Π½ΠΈΠ΅ Π΄Π»Ρ ΠΏΡΠΎΠΈΠ·Π²ΠΎΠ΄ΡΡΠ²Π° ΠΏΡΠΎΠ²ΠΎΠ»ΠΎΠΊΠΈ ΡΠ°ΡΠΎΠ½Π½ΡΡ ΠΏΡΠΎΡΠΈΠ»Π΅ΠΉ (ΡΠ΅ΡΠ΅Π½ΠΈΠΉ), ΠΏΡΠΈ Π²ΠΎΠ»ΠΎΡΠ΅Π½ΠΈΠΈ ΡΡΡΠ΄Π½ΠΎΠ΄Π΅ΡΠΎΡΠΌΠΈΡΡΠ΅ΠΌΡΡ ΠΌΠ°ΡΠΎΠΊ ΡΡΠ°Π»Π΅ΠΉ, ΠΏΡΠΈ ΠΊΠ°Π»ΠΈΠ±ΡΠΎΠ²ΠΊΠ΅ ΡΠΎΠ»ΡΡΠΎΠΉ ΠΏΡΠΎΠ²ΠΎΠ»ΠΎΒΠΊΠΈ, Π° ΡΠ°ΠΊΠΆΠ΅ ΠΏΡΠΈ ΡΠ΅ΠΏΠ»ΠΎΠΌ Π²ΠΎΠ»ΠΎΡΠ΅Π½ΠΈΠΈ Ρ ΠΏΡΠ΅Π΄Π²Π°ΡΠΈΡΠ΅Π»ΡΠ½ΡΠΌ ΠΏΠΎΠ΄ΠΎΠ³ΡΠ΅Π²ΠΎΠΌ ΠΌΠ΅ΒΡΠ°Π»Π»Π° (Π·Π°Π³ΠΎΡΠΎΠ²ΠΊΠΈ).
Π ΡΠ°Π±Π».2.1 ΠΏΡΠΈΠ²Π΅Π΄Π΅Π½Π° ΡΠ΅Ρ Π½ΠΈΡΠ΅ΡΠΊΠ°Ρ Ρ Π°ΡΠ°ΠΊΡΠ΅ΡΠΈΡΡΠΈΠΊΠ° Π½Π°ΠΈΠ±ΠΎΠ»Π΅Π΅ ΡΠ°ΡΠΏΡΠΎΡΡΡΠ°Π½Π΅Π½Π½ΡΡ ΡΠΈΠΏΠΎΠ² Π²ΠΎΠ»ΠΎΡΠΈΠ»ΡΠ½ΡΡ ΡΡΠ°Π½ΠΎΠ² ΠΊΠ°ΠΊ Π΄Π»Ρ ΠΎΠ΄Π½ΠΎΠΊΡΠ°ΡΠ½ΠΎΠ³ΠΎ, ΡΠ°ΠΊ ΠΈ Π΄Π»Ρ ΠΌΠ½ΠΎΠ³ΠΎΠΊΡΠ°ΡΠ½ΠΎΠ³ΠΎ Π²ΠΎΠ»ΠΎΡΠ΅Π½ΠΈΡ ΠΊΠΎΠ½ΡΡΡΡΠΊΡΠΈΠΈ ΠΠΠΠΠΠΠ’ΠΠΠ¨Π°.
ΠΠΈΠ½Π΅ΠΌΠ°ΡΠΈΡΠ΅ΡΠΊΠΈΠ΅ ΡΡ Π΅ΠΌΡ ΠΏΡΠΈΠ²ΠΎΠ΄ΠΎΠ² ΡΡΠ°Π½ΠΎΠ² ΠΠ‘Π 1/650, ΠΠ‘Π 1/550 ΠΈ ΠΠ‘Π 1/750 ΠΏΡΠΈΠ²Π΅Π΄Π΅Π½Ρ Π½Π° ΡΠΈΡ. 1.3-1.5.
Π ΠΈΡ.1.1. Π‘Ρ Π΅ΠΌΠ° ΡΠ°Π±ΠΎΡΡ ΠΎΠ΄Π½ΠΎΠΊΡΠ°ΡΠ½ΠΎΠ³ΠΎ Π²ΠΎΠ»ΠΎΡΠΈΠ»ΡΠ½ΠΎΠ³ΠΎ ΡΡΠ°Π½Π°:
1 — ΡΠ°Π·ΠΌΠΎΡΠΎΡΠ½ΠΎΠ΅ ΡΡΡΡΠΎΠΉΡΡΠ²ΠΎ; 2 — ΠΏΡΠΎΠ²ΠΎΠ»ΠΎΠΊΠ° — Π·Π°Π³ΠΎΡΠΎΠ²ΠΊΠ°; 3 — Π²ΠΎΠ»ΠΎΡΠΈΠ»ΡΠ½ΡΠΉ ΠΈΠ½ΡΡΡΡΠΌΠ΅Π½Ρ; 4 — ΠΏΡΠΎΡΡΠ½ΡΡΠ°Ρ ΠΏΡΠΎΠ²ΠΎΠ»ΠΎΠΊΠ°; 5 — ΡΡΠ½ΡΡΠΈΠΉ Π±Π°ΡΠ°Π±Π°Π½; 6 — ΡΠ΅Π΄ΡΠΊΡΠΎΡ; 7 — ΡΠ»Π΅ΠΊΡΡΠΎΠ΄Π²ΠΈΠ³Π°ΡΠ΅Π»Ρ
Π ΠΈΡ.1.2. ΠΠ±ΡΠΈΠΉ Π²ΠΈΠ΄ Π²ΠΎΠ»ΠΎΡΠΈΠ»ΡΠ½ΠΎΠ³ΠΎ ΡΡΠ°Π½Π° ΠΠ‘Π 1/650:
1-ΠΊΠΎΠ½ΡΠΎΠ»Ρ Π΄Π»Ρ Π·Π°Π³ΠΎΡΠΎΠ²ΠΊΠΈ Π² ΠΌΠΎΡΠΊΠ°Ρ ; 2-Π²ΡΠ°ΡΠ°ΡΡΠΈΠ΅ΡΡ ΡΠΈΠ³ΡΡΠΊΠΈ Π΄Π»Ρ ΠΌΠΎΡΠΊΠΎΠ²;3-ΡΠ»Π΅ΠΊΡΡΠΎΠ΄Π²ΠΈΠ³Π°ΡΠ΅Π»Ρ ΠΏΡΠΈΠ²ΠΎΠ΄Π°; 4-ΠΊΠΎΡΠΎΠ±ΠΊΠ° ΠΏΠ΅ΡΠ΅Π΄Π°Ρ; 5-Π²ΠΎΠ»ΠΎΡΠΈΠ»ΡΠ½ΡΠΉ,ΡΡΠ½ΡΡΠΈΠΉ Π±Π°ΡΠ°Π±Π°Π½;6-ΡΠΏΠΈΡΡ Π΄Π»Ρ Π½Π°ΠΊΠΎΠΏΠ»Π΅Π½ΠΈΡ ΠΏΡΠΎΠ²ΠΎΠ»ΠΎΠΊΠΈ; 7-ΠΊΠΎΠ»ΠΎΠ½Π½Π° ΡΡΠ΅ΠΌΠ½ΠΈΠΊΠ°: 8-ΡΠΈΠ³ΡΡΠΊΠ° Π΄Π»Ρ ΡΠ²ΡΠ·ΠΊΠΈ ΠΌΠΎΡΠΊΠ°; 9-ΡΠΈΠ»ΡΠ΅ΡΠΎΠ΄Π΅ΡΠΆΠ°ΡΠ΅Π»Ρ; 10-ΡΠ²Π°ΡΠΎΡΠ½ΡΠΉ Π°ΠΏΠΏΠ°ΡΠ°Ρ; 11-ΠΊΠΎΡΠΏΡΡ Π±Π»ΠΎΠΊΠ° ΡΡΠ°Π½Π°; 12-ΡΠ»Π΅ΠΊΡΡΠΎΡΠΊΠ°Ρ; 13-Π½Π°ΠΆΠ΄Π°ΠΊ
. 1.2 ΠΠΎΠ»ΠΎΡΠΈΠ»ΡΠ½ΡΠ΅ ΡΡΠ°Π½Ρ Π΄Π»Ρ ΠΌΠ½ΠΎΠ³ΠΎΠΊΡΠ°ΡΠ½ΠΎΠ³ΠΎ Π²ΠΎΠ»ΠΎΡΠ΅Π½ΠΈΡ
ΠΏΡΠΎΠ²ΠΎΠ»ΠΎΠΊΠΈ
ΠΠ° ΠΌΠ½ΠΎΠ³ΠΎΠΊΡΠ°ΡΠ½ΡΡ Π²ΠΎΠ»ΠΎΡΠΈΠ»ΡΠ½ΡΡ ΡΡΠ°Π½Π°Ρ ΠΏΡΠΎΠ²ΠΎΠ»ΠΎΠΊΠ° — Π·Π°Π³ΠΎΡΠΎΠ²ΠΊΠ° ΠΏΡΠΎΒΡ ΠΎΠ΄ΠΈΡ ΠΏΠΎΡΠ»Π΅Π΄ΠΎΠ²Π°ΡΠ΅Π»ΡΠ½ΠΎ ΡΠ΅ΡΠ΅Π· Π½Π΅ΡΠΊΠΎΠ»ΡΠΊΠΎ Π²ΠΎΠ»ΠΎΠΊ, ΠΈΠ·ΠΌΠ΅Π½ΡΡ ΠΏΠΎΡΠ»Π΅ ΠΊΠ°ΠΆΠ΄ΠΎΠΉ
ΠΠΎΠ»ΠΎΡΠΈΠ»ΡΠ½ΡΠΉ ΡΡΠ°Π½ ΡΠΈΠΏΠ° UDZSA 5000/6
Π¨Π΅ΡΡΠΈΠΊΡΠ°ΡΠ½ΡΠΉ Π²ΠΎΠ»ΠΎΡΠΈΠ»ΡΠ½ΡΠΉ ΡΡΠ°Π½ Π±Π»ΠΎΡΠ½ΠΎΠ³ΠΎ ΡΠΈΠΏΠ° ΠΌΠΎΠ΄Π΅Π»ΠΈ UDZSA 5000/6 Ρ ΠΌΠ°ΠΊΡΠΈΠΌΠ°Π»ΡΠ½ΡΠΌ ΡΡΠΈΠ»ΠΈΠ΅ΠΌ Π²ΠΎΠ»ΠΎΡΠ΅Π½ΠΈΡ Π½Π° ΠΏΠ΅ΡΠ²ΠΎΠΌ ΡΠ΅ΡΠ½ΠΎΠ²ΠΎΠΌ Π±Π»ΠΎΠΊΠ΅ ΡΠ°Π²Π½ΡΠΌ 50 ΠΊΠ (5000 ΠΊΠ³), ΠΏΡΠ΅Π΄Π½Π°Π·Π½Π°ΡΠ΅Π½ Π΄Π»Ρ Π²ΠΎΠ»ΠΎΡΠ΅Π½ΠΈΡ ΡΡΠ°Π»ΡΠ½ΠΎΠΉ ΡΠ³Π»Π΅ΒΡΠΎΠ΄ΠΈΡΡΠΎΠΉ ΠΏΡΠΎΠ²ΠΎΠ»ΠΎΠΊΠΈ ΠΏΡΠΈ Π΄ΠΈΠ°ΠΌΠ΅ΡΡΠ΅ Π·Π°Π³ΠΎΡΠΎΠ²ΠΊΠΈ Π΄ΠΎ 12 ΠΌΠΌ. ΠΡΠΈ Π²ΠΎΠ»ΠΎΡΠ΅Π½ΠΈΠΈ ΠΌΠ΅Π΄Π½ΠΎΠΉ ΠΈΠ»ΠΈ Π°Π»ΡΠΌΠΈΠ½ΠΈΠ΅Π²ΠΎΠΉ ΠΏΡΠΎΠ²ΠΎΠ»ΠΎΠΊΠΈ Π΄ΠΈΠ°ΠΌΠ΅ΡΡ Π·Π°Π³ΠΎΡΠΎΠ²ΠΊΠΈ ΠΌΠΎΠΆΠ΅Ρ Π±ΡΡΡ Π±ΠΎΠ»ΡΡΠ΅. ΠΠ±ΡΠΈΠΉ Π²ΠΈΠ΄ Π²ΠΎΠ»ΠΎΡΠΈΠ»ΡΠ½ΠΎΠ³ΠΎ ΡΡΠ°Π½Π° UDZSA 5000/6 ΠΏΡΠΈΠ²Π΅Π΄Π΅Π½ Π½Π° ΡΠΈΡ.3.1.
ΠΡΠ΅ Π±Π»ΠΎΠΊΠΈ Π΄Π°Π½Π½ΠΎΠ³ΠΎ ΡΡΠ°Π½Π° ΠΈΠΌΠ΅ΡΡ ΠΎΠ΄ΠΈΠ½Π°ΠΊΠΎΠ²ΡΡ ΠΊΠΎΠ½ΡΡΡΡΠΊΡΠΈΡ. ΠΡΠ»ΠΈΒΡΠΈΡΠ΅Π»ΡΠ½ΡΡ ΠΎΡΠΎΠ±Π΅Π½Π½ΠΎΡΡΡ ΠΈΠΌΠ΅Π΅Ρ ΡΠΈΡΡΠΎΠ²ΠΎΠΉ Π±Π°ΡΠ°Π±Π°Π½, ΡΠ½Π°Π±ΠΆΠ΅Π½Π½ΡΠΉ ΡΠΏΠ΅ΡΠΈΒΠ°Π»ΡΠ½ΡΠΌΠΈ ΡΠΏΠΈΡΠ°ΠΌΠΈ Π΄Π»Ρ ΡΠ±ΠΎΡΠ° Π²ΠΈΡΠΊΠΎΠ² Π³ΠΎΡΠΎΠ²ΠΎΠΉ ΠΏΡΠΎΠ²ΠΎΠ»ΠΎΠΊΠΈ Π² ΠΌΠΎΡΠΎΠΊ. ΠΡΠ»ΠΈ Π²ΠΎΠ»ΠΎΡΠΈΠ»ΡΠ½ΡΠΉ ΡΡΠ°Π½ ΡΠ½Π°Π±ΠΆΠ΅Π½ Π½Π°ΠΌΠΎΡΠΎΡΠ½ΡΠΌ Π°ΠΏΠΏΠ°ΡΠ°ΡΠΎΠΌ, ΡΠΎ Π³ΠΎΡΠΎΠ²Π°Ρ ΠΏΡΠΎΠ²ΠΎΒΠ»ΠΎΠΊΠ° Π½Π°ΠΌΠ°ΡΡΠ²Π°Π΅ΡΡΡ Π½Π° ΠΊΠ°ΡΡΡΠΊΠΈ Π²ΠΌΠ΅ΡΡΠΈΠΌΠΎΡΡΡΡ Π΄ΠΎ 1000 ΠΊΠ³.
ΠΠ°ΠΆΠ΄ΡΠΉ Π±Π»ΠΎΠΊ ΡΡΡΠ°Π½Π°Π²Π»ΠΈΠ²Π°Π΅ΡΡΡ Π½Π° ΡΠΎΠ±ΡΡΠ²Π΅Π½Π½ΠΎΠΌ ΠΆΠ΅Π»Π΅Π·ΠΎΠ±Π΅ΡΠΎΠ½Π½ΠΎΠΌ ΡΡΠ½Π΄Π°ΠΌΠ΅Π½ΡΠ΅, ΠΏΡΠΎΡΠ½ΠΎ ΠΏΡΠΈΠΊΡΠ΅ΠΏΠ»ΡΠ΅ΡΡΡ ΠΊ Π½Π΅ΠΌΡ Π°Π½ΠΊΠ΅ΡΠ½ΡΠΌΠΈ Π±ΠΎΠ»ΡΠ°ΠΌΠΈ. Π Π±Π»ΠΎΒΠΊΠ°ΠΌ ΠΏΠΎΠ΄Π²ΠΎΠ΄ΡΡΡΡ Π½Π΅ΠΎΠ±Ρ ΠΎΠ΄ΠΈΠΌΡΠ΅ ΠΊΠΎΠΌΠΌΡΠ½ΠΈΠΊΠ°ΡΠΈΠΈ: ΡΡΡΠ±ΠΎΠΏΡΠΎΠ²ΠΎΠ΄Ρ Π΄Π»Ρ Π²ΠΎΠ΄ΡΠ½ΠΎΒΠ³ΠΎ ΠΎΡ Π»Π°ΠΆΠ΄Π΅Π½ΠΈΡ Π±Π°ΡΠ°Π±Π°Π½ΠΎΠ² ΠΈ Π²ΠΎΠ»ΠΎΠΊΠΎΠ΄Π΅ΡΠΆΠ°ΡΠ΅Π»Π΅ΠΉ, ΡΠ»Π΅ΠΊΡΡΠΎΠΏΠΈΡΠ°Π½ΠΈΠ΅ , ΡΠΈΡΒΡΠ΅ΠΌΡ ΡΠΏΡΠ°Π²Π»Π΅Π½ΠΈΡ ΠΈ Ρ.Π΄.
Π Π·Π°Π²ΠΈΡΠΈΠΌΠΎΡΡΠΈ ΠΎΡ ΡΠ΅Ρ Π½ΠΎΠ»ΠΎΠ³ΠΈΡΠ΅ΡΠΊΠΈΡ ΠΎΡΠΎΠ±Π΅Π½Π½ΠΎΡΡΠ΅ΠΉ ΠΈΠ·Π³ΠΎΡΠΎΠ²Π»Π΅Π½ΠΈΡ ΠΏΡΠΎΠ²ΠΎΠ»ΠΎΠΊΠΈ ΠΈ ΠΏΠΎΠ»ΡΡΠ΅Π½ΠΈΡ Π½Π΅ΠΎΠ±Ρ ΠΎΠ΄ΠΈΠΌΡΡ ΠΌΠ΅Ρ Π°Π½ΠΈΡΠ΅ΡΠΊΠΈΡ ΡΠ²ΠΎΠΉΡΡΠ² Π½Π° Π³ΠΎΡΠΎΠ²ΠΎΠΌ ΡΠ°Π·ΠΌΠ΅ΡΠ΅ Π²ΠΎΠ»ΠΎΡΠΈΠ»ΡΠ½ΡΠ΅ ΡΡΠ°Π½Ρ ΠΌΠΎΠ³ΡΡ ΠΊΠΎΠΌΠΏΠ»Π΅ΠΊΡΠΎΠ²Π°ΡΡΡΡ Π² ΠΎΠ΄Π½ΠΎΠΉ Π»ΠΈΠ½ΠΈΠΈ Ρ ΡΠ°Π·Π»ΠΈΡΠ½ΡΠΌ ΡΠΈΡΠ»ΠΎΠΌ Π±Π»ΠΎΠΊΠΎΠ² (ΠΎΡ ΠΎΠ΄Π½ΠΎΠ³ΠΎ Π΄ΠΎ ΡΠ΅ΡΡΠΈ).ΠΡΠ½ΠΎΠ²Π½ΡΠ΅ ΡΠ΅Ρ Π½ΠΈΡΠ΅ΡΠΊΠΈΠ΅ Ρ Π°ΡΠ°ΠΊΡΠ΅ΡΠΈΡΡΠΈΠΊΠΈ Π²ΠΎΠ»ΠΎΡΠΈΠ»ΡΠ½ΡΡ ΡΡΠ°Π½ΠΎΠ² UDZSA 5000/1-6, 2500/1-6, 1250/1-10 ΠΈ 630/1-10 ΠΏΡΠΈΠ²Π΅Π΄Π΅Π½Ρ Π² ΡΠ°Π±Π».3.2.
ΠΠ»ΠΎΠΊΠΈ Π²ΠΎΠ»ΠΎΡΠΈΠ»ΡΠ½ΠΎΠ³ΠΎ ΡΡΠ°Π½Π° UDZSA 5000/6 ΠΈΠΌΠ΅ΡΡ Π² ΡΠ²ΠΎΠ΅ΠΌ ΡΠΎΡΡΠ°Π²Π΅ ΠΏΡΠΈΠ²ΠΎΠ΄ ΠΎΡ ΡΠ»Π΅ΠΊΡΡΠΎΠ΄Π²ΠΈΠ³Π°ΡΠ΅Π»Ρ ΠΏΠ΅ΡΠ΅ΠΌΠ΅Π½Π½ΠΎΠ³ΠΎ ΡΠΎΠΊΠ°, ΠΊΠ»ΠΈΠ½ΠΎΡΠ΅ΠΌΠ΅Π½Π½ΡΡ ΠΏΠ΅ΡΠ΅ΒΠ΄Π°ΡΡ, ΡΠ΅ΡΡΡΠ΅Ρ ΡΡΡΠΏΠ΅Π½ΡΠ°ΡΡΡ ΠΊΠΎΡΠΎΠ±ΠΊΡ ΠΏΠ΅ΡΠ΅Π΄Π°Ρ, Π΄Π²Π΅ ΡΠΈΠ»ΠΈΠ½Π΄ΡΠΈΡΠ΅ΡΠΊΠΈΠ΅ ΠΈ ΠΎΠ΄Π½Ρ ΠΊΠΎΠ½ΠΈΡΠ΅ΡΠΊΡΡ Π·ΡΠ±ΡΠ°ΡΡΡ ΠΏΠ΅ΡΠ΅Π΄Π°ΡΡ, ΠΏΡΠΈΠ²Π΅Π΄Π΅Π½Π½ΡΠ΅ Π½Π° ΡΠΈΡ.3.2. ΠΡΠ΅ ΠΌΠ΅Ρ Π°Π½ΠΈΠ·ΠΌΡ ΡΡΡΠ°Π½ΠΎΠ²Π»Π΅Π½Ρ Π² Π»ΠΈΡΠΎΠΌ ΡΡΠ°Π»ΡΠ½ΠΎΠΌ ΠΊΠΎΡΠΏΡΡΠ΅, ΠΎΠ±Π΅ΡΠΏΠ΅ΡΠΈΒΠ²Π°ΡΡΠ΅ΠΌ Π΄ΠΎΡΡΠ°ΡΠΎΡΠ½ΡΡ ΠΏΡΠΎΡΠ½ΠΎΡΡΡ ΠΈ ΠΆΠ΅ΡΡΠΊΠΎΡΡΡ. ΠΠ°Π»Ρ Π·ΡΠ±ΡΠ°ΡΡΡ ΠΊΠΎΠ»Π΅Ρ ΠΈΠΌΠ΅ΡΡ ΠΎΠΏΠΎΡΡ Π½Π° ΠΏΠΎΠ΄ΡΠΈΠΏΠ½ΠΈΠΊΠ°Ρ ΠΊΠ°ΡΠ΅Π½ΠΈΡ. Π‘ΠΌΠ°Π·ΠΊΠ° Π·ΡΠ±ΡΠ°ΡΡΡ ΠΊΠΎΠ»Π΅Ρ ΠΈ ΠΏΠΎΠ΄ΡΠΈΠΏΠ½ΠΈΠΊΠΎΠ²ΡΡ ΡΠ·Π»ΠΎΠ² — ΠΊΠ°ΡΡΠ΅ΡΠ½Π°Ρ, ΠΎΠΊΡΠ½Π°Π½ΠΈΠ΅ΠΌ ΠΈ ΡΠ°Π·Π±ΡΡΠ·Π³ΠΈΠ²Π°Π½ΠΈΠ΅ΠΌ. ΠΡΠ±ΡΡ ΠΊΠΎΠ»Π΅Ρ Π΄Π»Ρ ΡΠ²Π΅Π»ΠΈΡΠ΅Π½ΠΈΡ ΡΡΠΎΠΉΠΊΠΎΡΡΠΈ ΠΏΠΎΠ΄Π²Π΅ΡΠ³Π°ΡΡΡΡ Π·Π°ΠΊΠ°Π»ΠΊΠ΅ ΠΈ ΡΠ»ΠΈΒΡΠΎΠ²Π°Π½ΠΈΡ Π»ΠΈΠ±ΠΎ ΠΏΡΠΈΡΠΈΡΠΊΠ΅. Π£ΠΏΡΠΎΡΠ½Π΅Π½ΠΈΡ Π·Π°ΠΊΠ°Π»ΠΊΠΎΠΉ ΠΏΠΎΠ΄Π²Π΅ΡΠ³Π°ΡΡΡΡ ΠΈ ΡΠΎΠ»ΠΈΒΠΊΠΈ Π΄ΠΈΡΡΠ΅ΡΠ΅Π½ΡΠΈΠ°Π»Π°, ΡΠ°Π±ΠΎΡΠ°ΡΡΠΈΠ΅ Π² ΡΡΠ»ΠΎΠ²ΠΈΡΡ ΡΡΠΆΠ΅Π»ΠΎΠ³ΠΎ Π½Π°Π³ΡΡΠΆΠ΅Π½ΠΈΡ.
ΠΠ°ΠΆΠ΄ΡΠΉ Π²ΠΎΠ»ΠΎΡΠΈΠ»ΡΠ½ΡΠΉ ΡΡΠ°Π½ ΠΎΡΠ½Π°ΡΠ°Π΅ΡΡΡ Π·Π°ΠΏΡΠ°Π²ΠΎΡΠ½ΠΎΠΉ ΡΠ°Π½Π³ΠΎΠΉ Π΄Π»Ρ ΠΏΡΠΎΡΡΠ³ΠΈΠ²Π°Π½ΠΈΡ ΠΊΠΎΠ½ΡΠ° ΠΏΡΠΎΠ²ΠΎΠ»ΠΎΠΊΠΈ ΡΠ΅ΡΠ΅Π· Π²ΠΎΠ»ΠΎΡΠΈΠ»ΡΠ½ΡΠΉ ΠΈΠ½ΡΡΡΡΠΌΠ΅Π½Ρ ΠΈ Π½Π°ΠΌΠ°ΒΡΡΠ²Π°Π½ΠΈΡ Π½Π° Π±Π°ΡΠ°Π±Π°Π½ Π½Π΅ΡΠΊΠΎΠ»ΡΠΊΠΈΡ Π²ΠΈΡΠΊΠΎΠ² ΠΏΡΠΎΠ²ΠΎΠ»ΠΎΠΊΠΈ Π΄Π»Ρ Π΄Π°Π»ΡΠ½Π΅ΠΉΡΠ΅Π³ΠΎ Π²ΠΎΠ»ΠΎΡΠ΅Π½ΠΈΡ. ΠΡΡΠ³ΠΎΠΉ ΠΊΠΎΠ½Π΅Ρ ΡΠ°Π½Π³ΠΈ ΠΈΠΌΠ΅Π΅Ρ ΠΊΡΡΡΠΎΠΊ, ΠΊΠΎΡΠΎΡΡΠΉ Π·Π°ΡΠ΅ΠΏΠ»ΡΠ΅ΡΡΡ Π·Π° ΡΠΏΠ΅ΡΠΈΠ°Π»ΡΠ½ΡΠ΅ ΠΎΡΠ²Π΅ΡΡΡΠΈΡ Π² Π±Π°ΡΠ°Π±Π°Π½Π΅. ΠΠΎΡΠ»Π΅ Π½Π°ΠΌΠ°ΡΡΠ²Π°Π½ΠΈΡ Π½Π΅ΡΠΊΠΎΠ»ΡΠΊΠΈΡ Π²ΠΈΡΠΊΠΎΠ² ΠΏΡΠΎΠ²ΠΎΠ»ΠΎΠΊΠΈ (ΠΎΠΊΠΎΠ»ΠΎ 10) ΡΠ°Π½Π³Π° ΡΠ½ΠΈΠΌΠ°Π΅ΡΡΡ ΠΈ ΡΡΠ°Π½ Π²ΠΊΠ»ΡΡΠ°Π΅ΡΡΡ Ρ Π·Π°ΠΏΡΠ°Π²ΠΎΡΠ½ΠΎΠΉ ΡΠΊΠΎΡΠΎΡΡΠΈ Π½Π° Π½ΠΎΡΠΌΠ°Π»ΡΠ½ΡΡ ΡΠ°Π±ΠΎΡΡΡ. ΠΠΎ Π²ΡΠ΅ΠΌΡ Π·Π°ΠΏΡΠ°Π²ΠΊΠΈ Π½ΡΠΆΠ½ΠΎ Π±ΡΡΡ ΠΎΡΠ΅Π½Ρ Π²Π½ΠΈΠΌΠ°ΡΠ΅Π»ΡΠ½ΡΠΌ ΠΈ ΠΏΡΠ΅Π΄ΠΎΡ ΡΠ°Π½ΡΡΡ ΡΡΠΊΠΈ ΠΎΡ Π²ΠΎΠ·ΠΌΠΎΠΆΠ½ΠΎΠ³ΠΎ Π·Π°ΡΡΠ³ΠΈΠ²Π°Π½ΠΈΡ ΠΈΡ Π²ΠΈΡΠΊΠ°ΠΌΠΈ Π½Π°ΠΌΠ°ΡΡΠ²Π°Π΅ΠΌΠΎΠΉ ΠΏΡΠΎΠ²ΠΎΠ»ΠΎΠΊΠΈ.
ΠΠ±ΡΠΈΠΉ Π²ΠΈΠ΄ ΠΏΡΠΎΠΌΠ΅ΠΆΡΡΠΎΡΠ½ΠΎΠ³ΠΎ Π±Π°ΡΠ°Π±Π°Π½Π° Π²ΠΎΠ»ΠΎΡΠΈΠ»ΡΠ½ΠΎΠ³ΠΎ ΡΡΠ°Π½Π° UDZSA 5000/ΠΏ ΠΏΠΎΠΊΠ°Π·Π°Π½ Π½Π° ΡΠΈΡ.3.2.
ΠΠ°Π³ΠΎΡΠΎΠ²ΠΊΠ° ΠΈΠ»ΠΈ ΠΏΡΠΎΠ²ΠΎΠ»ΠΎΠΊΠ° ΠΏΡΠΎΠΌΠ΅ΠΆΡΡΠΎΡΠ½ΠΎΠ³ΠΎ ΡΠ°Π·ΠΌΠ΅ΡΠ°, ΠΏΡΠΎΡ ΠΎΠ΄Ρ ΡΠ΅ΡΠ΅Π· Π²ΠΎΠ»ΠΎΡΠΈΠ»ΡΠ½ΡΠΉ ΠΈΠ½ΡΡΡΡΠΌΠ΅Π½Ρ, ΡΡΡΠ°Π½ΠΎΠ²Π»Π΅Π½Π½ΡΠΉ Π² Π²ΠΎΠ»ΠΎΠΊΠΎΠ΄Π΅ΡΠΆΠ°ΡΠ΅Π»Π΅ 10, Π½Π°ΠΌΠ°ΒΡΡΠ²Π°Π΅ΡΡΡ Π½Π° ΡΡΠ³ΠΎΠ²ΡΠΉ Π±Π°ΡΠ°Π±Π°Π½ ΠΈ ΠΏΠΎΡΠ»Π΅ Π½Π°ΠΊΠΎΠΏΠ»Π΅Π½ΠΈΡ Π½Π΅ΠΊΠΎΡΠΎΡΠΎΠ³ΠΎ ΠΎΠ±ΡΠ΅ΠΌΠ° ΠΏΡΠΎΠΏΡΡΠΊΠ°Π΅ΡΡΡ ΡΠ΅ΡΠ΅Π· ΡΠΎΠ»ΠΈΠΊ 13 ΡΠΎΡΠΌΠΎΠ·Π½ΠΎΠ³ΠΎ Π΄ΠΈΡΡΠ΅ΡΠ΅Π½ΡΠΈΠ°Π»Π° ΠΈ Π΄Π°Π»Π΅Π΅ ΡΠ΅ΒΡΠ΅Π· Π½Π°ΠΏΡΠ°Π²Π»ΡΡΡΠΈΠΉ Π±Π»ΠΎΠΊ 14, ΡΡΡΠ°Π½ΠΎΠ²Π»Π΅Π½Π½ΡΠΉ Π½Π° Π²Π΅ΡΡΠΈΠΊΠ°Π»ΡΠ½ΠΎΠΉ ΡΡΠΎΠΉΠΊΠ΅, ΠΊ Π²ΠΎΠ»ΠΎΠΊΠΎΠ΄Π΅ΡΠΆΠ°ΡΠ΅Π»Ρ ΡΠ»Π΅Π΄ΡΡΡΠ΅Π³ΠΎ Π±Π»ΠΎΠΊΠ° Π²ΠΎΠ»ΠΎΡΠΈΠ»ΡΠ½ΠΎΠ³ΠΎ ΡΡΠ°Π½Π°.
ΠΠΊΠ»ΡΡΠ΅Π½ΠΈΠ΅ Π±Π»ΠΎΠΊΠ° Π²ΠΎΠ»ΠΎΡΠΈΠ»ΡΠ½ΠΎΠ³ΠΎ ΡΡΠ°Π½Π° ΠΏΡΠΎΠΈΠ·Π²ΠΎΠ΄ΠΈΡΡΡ ΠΊΠ½ΠΎΠΏΠΊΠΎΠΉ 9.. «ΠΡΡΠΊ», Π° ΠΎΡΡΠ°Π½ΠΎΠ²ΠΊΠ° ΠΊΠ½ΠΎΠΏΠΊΠΎΠΉ 8 «Π‘ΡΠΎΠΏ». Π£ΠΏΡΠ°Π²Π»Π΅Π½ΠΈΠ΅ ΡΠΈΡΡΠ΅ΠΌΠΎΠΉ ΠΎΡ Π»Π°ΠΆΒΠ΄Π΅Π½ΠΈΡ Π²ΠΎΠ»ΠΎΡΠΈΠ»ΡΠ½ΠΎΠ³ΠΎ ΠΈΠ½ΡΡΡΡΠΌΠ΅Π½ΡΠ° ΠΎΡΡΡΠ΅ΡΡΠ²Π»ΡΠ΅ΡΡΡ ΠΏΠ΅ΡΠ΅ΠΏΡΡΠΊΠ½ΡΠΌ ΠΊΠ»Π°ΠΏΠ°ΒΠ½ΠΎΠΌ 7, Π° ΠΎΡ Π»Π°ΠΆΠ΄Π΅Π½ΠΈΠ΅ Π±Π°ΡΠ°Π±Π°Π½Π° — ΠΊΠ»Π°ΠΏΠ°Π½ΠΎΠΌ 6.
ΠΠΎ Π²ΡΠ΅ΠΌΡ Π·Π°ΠΏΡΠ°Π²ΠΊΠΈ ΠΏΡΠΎΠ²ΠΎΠ»ΠΎΠΊΠΈ Π½Π° Π±Π°ΡΠ°Π±Π°Π½Π΅ ΠΈ Π½Π°ΡΡΠΎΠΉΠΊΠ΅ ΡΡΠ°Π½Π° Π½ΠΎΠΆΠ½ΠΎΠΉ Π²ΡΠΊΠ»ΡΡΠ°ΡΠ΅Π»Ρ «ΠΏΠΎΠ»Π·ΡΡΠ΅ΠΉ» ΠΌΠ΅Π΄Π»Π΅Π½Π½ΠΎΠΉ ΡΠΊΠΎΡΠΎΡΡΠΈ ΠΏΡΠΈΠ²ΠΎΠ΄Π° Π±Π»ΠΎΠΊΠ° -ΠΊΠΎΠ½Π΅ΡΠ½ΡΠΉ Π²ΡΠΊΠ»ΡΡΠ°ΡΠ΅Π»Ρ 1. Π§Π°ΡΡΠΎΡΠ° Π²ΡΠ°ΡΠ΅Π½ΠΈΡ Π±Π°ΡΠ°Π±Π°Π½Π° ΠΊΠΎΠ½ΡΡΠΎΠ»ΠΈΡΡΠ΅ΡΡΡ ΡΠ°Ρ ΠΎΠ³Π΅Π½Π΅ΡΠ°ΡΠΎΡΠΎΠΌ 2.
ΠΠ΅ΡΠ΅ΠΊΠ»ΡΡΠ΅Π½ΠΈΠ΅ ΡΡΡΠΏΠ΅Π½Π΅ΠΉ Π·ΡΠ±ΡΠ°ΡΡΡ ΠΏΠ΅ΡΠ΅Π΄Π°Ρ ΠΊΠΎΡΠΎΠ±ΠΊΠΈ ΡΠΊΠΎΡΠΎΡΡΠ΅ΠΉ Π½Π° Π±Π»ΠΎΠΊΠ΅ ΠΎΡΡΡΠ΅ΡΡΠ²Π»ΡΠ΅ΡΡΡ ΡΡΡΠ°Π³Π°ΠΌΠΈ 16 ΠΈ 17, ΠΏΡΠΈΡΠ΅ΠΌ ΠΎΠ΄Π½ΠΎΠ²ΡΠ΅ΠΌΠ΅Π½Π½ΠΎ ΠΎΠ΄Π½Π° ΠΈ ΡΠ°ΠΆΠ΅ ΡΠΊΠΎΡΠΎΡΡΡ (ΠΏΠ΅ΡΠ΅Π΄Π°ΡΠ°) ΡΡΡΠ°Π½Π°Π²Π»ΠΈΠ²Π°Π΅ΡΡΡ Π½Π° Π²ΡΠ΅Ρ Π±Π»ΠΎΠΊΠ°Ρ . Π£Π²Π΅Π»ΠΈΒΡΠ΅Π½ΠΈΠ΅ Π»ΠΈΠ½Π΅ΠΉΠ½ΠΎΠΉ ΡΠΊΠΎΡΠΎΡΡΠΈ Π²ΠΎΠ»ΠΎΡΠ΅Π½ΠΈΡ ΠΈΠ»ΠΈ ΠΎΠΊΡΡΠΆΠ½ΠΎΠΉ ΡΠΊΠΎΡΠΎΡΡΠΈ Π±Π°ΡΠ°Π±Π°Π½ΠΎΠ² ΠΎΡ ΠΏΠ΅ΡΠ²ΠΎΠ³ΠΎ Π΄ΠΎ ΠΏΠΎΡΠ»Π΅Π΄Π½Π΅Π³ΠΎ ΡΠΈΡΡΠΎΠ²ΠΎΠ³ΠΎ ΠΎΡΡΡΠ΅ΡΡΠ²Π»ΡΠ΅ΡΡΡ Π·Π° ΡΡΠ΅Ρ ΡΠ°Π·Π»ΠΈΡΒΠ½ΠΎΠ³ΠΎ ΡΠΈΡΠ»Π° Π·ΡΠ±ΡΠ΅Π² Za ΠΈ Zb Π² ΠΊΠΈΠ½Π΅ΠΌΠ°ΡΠΈΡΠ΅ΡΠΊΠΎΠΉ ΡΡ Π΅ΠΌΠ΅ Π² ΠΊΠ°ΠΆΠ΄ΠΎΠΌ Π±Π»ΠΎΠΊΠ΅.
ΠΠ»ΠΎΠΊΠΈΡΡΡΡΠΈΠΉ ΠΊΠΎΠ½ΡΠ°ΠΊΡ 15 ΠΎΡΠΊΠ»ΡΡΠ°Π΅Ρ Π³Π»Π°Π²Π½ΡΠΉ ΠΏΡΠΈΠ²ΠΎΠ΄Π½ΠΎΠΉ ΡΠ»Π΅ΠΊΡΡΠΎΠ΄ΒΠ²ΠΈΠ³Π°ΡΠ΅Π»Ρ ΠΏΡΠΈ ΠΎΡΠΊΡΡΡΠΎΠΉ Π΄Π²Π΅ΡΡΠ΅ Π·Π°ΡΠΈΡΡ. ΠΡΠ΅ ΠΌΠ΅Ρ Π°Π½ΠΈΠ·ΠΌΡ ΡΠΌΠΎΠ½ΡΠΈΡΠΎΠ²Π°Π½Ρ Π½Π° Π»ΠΈΡΠΎΠΌ ΠΊΠΎΡΠΏΡΡΠ΅ 18.
ΠΠ° ΡΠΈΡ. 3.3 ΠΏΡΠ΅Π΄ΡΡΠ°Π²Π»Π΅Π½Π° ΠΊΠΈΠ½Π΅ΠΌΠ°ΡΠΈΡΠ΅ΡΠΊΠ°Ρ ΡΡ Π΅ΠΌΠ° ΠΎΠ΄Π½ΠΎΠ³ΠΎ Π±Π»ΠΎΠΊΠ° Π²ΠΎΠ»ΠΎΡΠΈΠ»ΡΠ½ΠΎΠ³ΠΎ ΡΡΠ°Π½Π° UDZSA 5000/6, Π° Π² ΡΠ°Π±Π». 3.3 — Π΄Π°Π½Π½ΡΠ΅ ΡΠΈΡΠ΅Π»
Π ΠΈΡ. 3.2. ΠΠ±ΡΠΈΠΉ Π²ΠΈΠ΄ Π±Π»ΠΎΠΊΠ° Π²ΠΎΠ»ΠΎΡΠΈΠ»ΡΠ½ΠΎΠ³ΠΎ ΡΡΠ°Π½Π° UDZSA 5000/ΠΏ: 1 — Π½ΠΎΠΆΠ½Π°Ρ ΠΊΠ½ΠΎΠΏΠΊΠ°»Π‘ΡΠΎΠΏ»; 2 — ΡΠ°Ρ ΠΎΠ³Π΅Π½Π΅ΡΠ°ΡΠΎΡ; 3 — ΡΠ»Π΅ΠΊΡΡΠΎΠ΄Π²ΠΈΠ³Π°ΡΠ΅Π»Ρ; 4 — Π³Π»Π°Π²Π½ΡΠΉ ΠΏΡΠΈΠ²ΠΎΠ΄Π½ΠΎΠΉ ΡΠ»Π΅ΠΊΡΡΠΎΠ΄Π²ΠΈΠ³Π°ΡΠ΅Π»Ρ; 5 — ΠΊΠΎΡΠΎΠ±ΠΊΠ° ΡΠ»Π΅ΠΊΡΡΠΎΠΊΠ»Π΅ΠΌΠΌ; 6 — ΠΏΠ΅ΡΠ΅ΠΏΡΡΠΊΠ½ΠΎΠΉ ΠΊΠ»Π°ΠΏΠ°Π½ Π΄Π»Ρ ΠΎΡ Π»Π°ΠΆΠ΄Π΅Π½ΠΈΡ Π±Π°ΡΠ°Π±Π°Π½Π°; 7 — ΠΏΠ΅ΡΠ΅ΠΏΡΡΠΊΠ½ΠΎΠΉ ΠΊΠ»Π°ΠΏΠ°Π½ Π΄Π»Ρ ΠΎΡ Π»Π°ΠΆΠ΄Π΅Π½ΠΈΡ ΠΈΠ½ΡΡΡΡΠΌΠ΅Π½ΡΠ°; 8 — ΠΊΠ½ΠΎΠΏΠΊΠ° «Π‘ΡΠΎΠΏ»; 9 — ΠΊΠ½ΠΎΠΏΠΊΠ° «ΠΡΡΠΊ»; 10 — Π½Π°ΠΏΡΠ°Π²Π»ΡΡΡΠΈΠΉ ΡΠΎΠ»ΠΈΠΊ ΠΏΠ΅ΡΠ΅Π΄ ΡΠΈΠ»ΡΠ΅ΡΠΎΠ΄Π΅ΡΠΆΠ°ΡΠ΅Π»Π΅ΠΌ; 11 -ΠΊΡΡΡΠΊΠ° Π±Π°ΠΊΠ° Ρ ΠΎΡ Π»Π°ΠΆΠ΄Π°ΡΡΠ΅ΠΉ ΠΆΠΈΠ΄ΠΊΠΎΡΡΡΡ; 12 — ΡΡΠ½ΡΡΠΈΠΉ Π±Π°ΡΠ°Π±Π°Π½; 13 -ΡΠΎΡΠΌΠΎΠ· Π΄ΠΈΡΡΠ΅ΡΠ΅Π½ΡΠΈΠ°Π»Π°; 14 — Π²Π΅ΡΡ Π½ΠΈΠΉ Π½Π°ΠΏΡΠ°Π²Π»ΡΡΡΠΈΠΉ ΡΠΎΠ»ΠΈΠΊ; 15 — Π±Π»ΠΎΒΠΊΠΈΡΡΡΡΠΈΠΉ ΠΊΠΎΠ½ΡΠ°ΠΊΡ ΠΏΡΠΈ ΠΎΡΠΊΡΡΠ²Π°Π½ΠΈΠΈ Π·Π°ΡΠΈΡΠ½ΠΎΠ³ΠΎ ΠΎΠ³ΡΠ°ΠΆΠ΄Π΅Π½ΠΈΡ; 16 — ΡΡΡΠ°Π³ Π΄Π»Ρ Π²ΠΊΠ»ΡΡΠ΅Π½ΠΈΡ 2-ΠΉ ΠΈ 4-ΠΉ ΠΏΠ΅ΡΠ΅Π΄Π°ΡΠΈ; 17 — ΡΡΡΠ°Π³ Π΄Π»Ρ Π²ΠΊΠ»ΡΡΠ΅Π½ΠΈΡ 1-ΠΉ ΠΈ 3-ΠΉ ΠΏΠ΅ΡΠ΅Π΄Π°Ρ; 18 — ΠΊΠΎΡΠΏΡΡ Π±Π»ΠΎΠΊΠ°
1.3 ΠΠΎΠ»ΠΎΡΠΈΠ»ΡΠ½ΡΠ΅ ΡΡΠ°Π½ΡΒ ΡΠ°Π·Π΄Π΅Π»ΡΡΡ Π½Π° Π΄Π²Π° ΡΠΈΠΏΠ°: Π±Π°ΡΠ°Π±Π°Π½Π½ΡΠ΅ ΠΈ ΡΠ΅ΠΏΠ½ΡΠ΅.
Β
Π ΠΈΡ.
1.3.1. ΠΡΠΎΠ΄ΠΎΠ»ΡΠ½ΡΠΉ ΡΠ°Π·ΡΠ΅Π· Π²ΠΎΠ»ΠΎΠΊΠΈ (Π°) ΠΈ ΡΡ
Π΅ΠΌΡ
Π±Π°ΡΠ°Π±Π°Π½Π½ΠΎΠ³ΠΎ (Π±) ΠΈ ΡΠ΅ΠΏΠ½ΠΎΠ³ΠΎ (Π²) Π²ΠΎΠ»ΠΎΡΠΈΠ»ΡΠ½ΡΡ
ΡΡΠ°Π½ΠΎΠ²
ΠΠ°ΡΠ°Π±Π°Π½Π½ΡΠ΅ ΡΡΠ°Π½ΡΒ (ΡΠΈΡ. 1.3.1, Π±) ΡΠ»ΡΠΆΠ°Ρ Π΄Π»Ρ Π²ΠΎΠ»ΠΎΡΠ΅Π½ΠΈΡ ΠΏΡΠΎΠ²ΠΎΠ»ΠΎΠΊΠΈ ΠΈ ΡΡΡΠ± Π½Π΅Π±ΠΎΠ»ΡΡΠΎΠ³ΠΎ Π΄ΠΈΠ°ΠΌΠ΅ΡΡΠ°, Π½Π°ΠΌΠ°ΡΡΠ²Π°Π΅ΠΌΡΡ Π½Π° Π²Π΅ΡΡΡΡΠΊΡ 1. ΠΡΠ΅Π΄Π²Π°ΡΠΈΡΠ΅Π»ΡΠ½ΠΎ Π·Π°ΠΎΡΡΡΠ΅Π½Π½ΡΠΉ ΠΊΠΎΠ½Π΅Ρ ΠΏΡΠΎΠ²ΠΎΠ»ΠΎΠΊΠΈ ΠΏΡΠΎΠΏΡΡΠΊΠ°Π΅ΡΡΡ ΡΠ΅ΡΠ΅Π· ΠΎΡΠ²Π΅ΡΡΡΠΈΠ΅ Π²ΠΎΠ»ΠΎΠΊΠΈ 2 ΠΈ Π·Π°ΠΊΡΠ΅ΠΏΠ»ΡΠ΅ΡΡΡ Π½Π° Π±Π°ΡΠ°Π±Π°Π½Π΅ 3, ΠΊΠΎΡΠΎΡΡΠΉ ΠΏΡΠΈΠ²ΠΎΠ΄ΠΈΡΡΡ Π²ΠΎ Π²ΡΠ°ΡΠ΅Π½ΠΈΠ΅ ΠΎΡ ΡΠ»Π΅ΠΊΡΡΠΎΠ΄Π²ΠΈΠ³Π°ΡΠ΅Π»Ρ ΡΠ΅ΡΠ΅Π· ΡΠ΅Π΄ΡΠΊΡΠΎΡ ΠΈ Π·ΡΠ±ΡΠ°ΡΡΡ ΠΏΠ΅ΡΠ΅Π΄Π°ΡΡ 4. Π‘ΡΡΠ΅ΡΡΠ²ΡΡΡ ΡΠ°ΠΊΠΆΠ΅ ΡΡΠ°Π½Ρ ΠΌΠ½ΠΎΠ³ΠΎΠΊΡΠ°ΡΠ½ΠΎΠ³ΠΎ Π²ΠΎΠ»ΠΎΡΠ΅Π½ΠΈΡ, ΠΈΠΌΠ΅ΡΡΠΈΠ΅ Π΄ΠΎ 20 Π±Π°ΡΠ°Π±Π°Π½ΠΎΠ² Ρ ΡΡΡΠ°Π½ΠΎΠ²Π»Π΅Π½Π½ΡΠΌΠΈ ΠΏΠ΅ΡΠ΅Π΄ ΠΊΠ°ΠΆΠ΄ΡΠΌ ΠΈΠ· Π½ΠΈΡ Π²ΠΎΠ»ΠΎΠΊΠ°ΠΌΠΈ.
Π¦Π΅ΠΏΠ½ΡΠ΅ ΡΡΠ°Π½ΡΒ Ρ ΠΏΡΡΠΌΠΎΠ»ΠΈΠ½Π΅ΠΉΠ½ΡΠΌ Π΄Π²ΠΈΠΆΠ΅Π½ΠΈΠ΅ΠΌ ΡΡΠ½ΡΡΠ΅Π³ΠΎ ΡΡΡΡΠΎΠΉΡΡΠ²Π° (ΡΠΈΡ. 1.3.1, Π²) ΠΏΡΠΈΠΌΠ΅Π½ΡΡΡ Π΄Π»Ρ Π²ΠΎΠ»ΠΎΡΠ΅Π½ΠΈΡ ΠΏΡΡΡΠΊΠΎΠ² ΠΈ ΡΡΡΠ±, ΠΊΠΎΡΠΎΡΡΠ΅ Π½Π΅ ΠΌΠΎΠ³ΡΡ Π½Π°ΠΌΠ°ΡΡΠ²Π°ΡΡΡΡ Π² Π±ΡΠ½ΡΡ. ΠΠ° ΡΡΠΎΠΌ ΡΡΠ°Π½Π΅ ΠΊΠΎΠ½Π΅Ρ ΠΏΡΡΡΠΊΠ° ΠΏΡΠΎΠΏΡΡΠΊΠ°ΡΡ ΡΠ΅ΡΠ΅Π· ΠΎΡΠ²Π΅ΡΡΡΠΈΠ΅ Π²ΠΎΠ»ΠΎΠΊΠΈ 2 ΠΈ Π·Π°Ρ Π²Π°ΡΡΠ²Π°ΡΡ ΠΊΠ»Π΅ΡΠ°ΠΌΠΈ 5, ΠΊΠΎΡΠΎΡΡΠ΅ Π·Π°ΠΊΡΠ΅ΠΏΠ»Π΅Π½Ρ Π½Π° ΠΊΠ°ΡΠ΅ΡΠΊΠ΅ 6. ΠΠ°ΡΠ΅ΡΠΊΠ° ΡΠ΅ΡΠ΅Π· ΡΡΠ³ΠΎΠ²ΡΠΉ ΠΊΡΡΠΊ 7 ΠΏΠ΅ΡΠ΅ΠΌΠ΅ΡΠ°Π΅ΡΡΡ ΠΏΠ»Π°ΡΡΠΈΠ½ΡΠ°ΡΠΎΠΉ ΡΠ΅ΠΏΡΡ 8, ΠΏΡΠΈΠ²ΠΎΠ΄ΠΈΠΌΠΎΠΉ Π² Π΄Π²ΠΈΠΆΠ΅Π½ΠΈΠ΅ ΠΎΡ Π·Π²Π΅Π·Π΄ΠΎΡΠΊΠΈ 9, ΠΊΠΎΡΠΎΡΠ°Ρ Π²ΡΠ°ΡΠ°Π΅ΡΡΡ ΠΎΡ ΡΠ»Π΅ΠΊΡΡΠΎΠ΄Π²ΠΈΠ³Π°ΡΠ΅Π»Ρ 11 ΡΠ΅ΡΠ΅Π· ΡΠ΅Π΄ΡΠΊΡΠΎΡ 10.
ΠΠΎΠ»ΠΎΡΠ΅Π½ΠΈΠ΅,
ΠΊΠ°ΠΊ ΠΏΡΠ°Π²ΠΈΠ»ΠΎ, ΠΎΡΡΡΠ΅ΡΡΠ²Π»ΡΡΡ Π² Ρ
ΠΎΠ»ΠΎΠ΄Π½ΠΎΠΌ
ΡΠΎΡΡΠΎΡΠ½ΠΈΠΈ, Π° ΠΏΠΎΡΠΎΠΌΡ ΠΎΠ½ΠΎ ΡΠΎΠΏΡΠΎΠ²ΠΎΠΆΠ΄Π°Π΅ΡΡΡ
ΡΠΏΡΠΎΡΠ½Π΅Π½ΠΈΠ΅ΠΌ (Π½Π°ΠΊΠ»Π΅ΠΏΠΎΠΌ) ΠΌΠ΅ΡΠ°Π»Π»Π°. ΠΡΡ
ΠΎΠ΄Π½ΡΠΌΠΈ
Π·Π°Π³ΠΎΡΠΎΠ²ΠΊΠ°ΠΌΠΈ ΡΠ»ΡΠΆΠ°Ρ ΠΏΡΠΎΠΊΠ°ΡΠ°Π½Π½ΡΠ΅ ΠΈΠ»ΠΈ
ΠΏΡΠ΅ΡΡΠΎΠ²Π°Π½Π½ΡΠ΅ ΠΏΡΡΡΠΊΠΈ ΠΈ ΡΡΡΠ±Ρ ΠΈΠ· ΡΡΠ°Π»ΠΈ,
ΡΠ²Π΅ΡΠ½ΡΡ
ΠΌΠ΅ΡΠ°Π»Π»ΠΎΠ² ΠΈ ΠΈΡ
ΡΠΏΠ»Π°Π²ΠΎΠ². ΠΠ΅Π»ΠΈΡΠΈΠ½Π°
Π΄Π΅ΡΠΎΡΠΌΠ°ΡΠΈΠΈ Π·Π° ΠΎΠ΄ΠΈΠ½ ΠΏΡΠΎΡ
ΠΎΠ΄ ΠΎΠ³ΡΠ°Π½ΠΈΡΠ΅Π½Π°:Β =
1,25-1,45. ΠΡΠ»ΠΈ Π΄Π»Ρ ΠΏΠΎΠ»ΡΡΠ΅Π½ΠΈΡ Π½Π΅ΠΎΠ±Ρ
ΠΎΠ΄ΠΈΠΌΡΡ
ΠΏΡΠΎΡΠΈΠ»Π΅ΠΉ ΡΡΠ΅Π±ΡΠ΅ΡΡΡ Π±ΠΎΠ»ΡΡΠ°Ρ Π΄Π΅ΡΠΎΡΠΌΠ°ΡΠΈΡ,
ΡΠΎ ΠΏΡΠΈΠΌΠ΅Π½ΡΡΡ Π²ΠΎΠ»ΠΎΡΠ΅Π½ΠΈΠ΅ Π·Π° Π½Π΅ΡΠΊΠΎΠ»ΡΠΊΠΎ
ΠΏΠ΅ΡΠ΅Ρ
ΠΎΠ΄ΠΎΠ² ΠΏΡΠΎΡΡΠ³ΠΈΠ²Π°Π½ΠΈΠ΅ΠΌ ΡΠ΅ΡΠ΅Π· ΡΡΠ΄
ΠΏΠΎΡΡΠ΅ΠΏΠ΅Π½Π½ΠΎ ΡΠΌΠ΅Π½ΡΡΠ°ΡΡΠΈΡ
ΡΡ ΠΏΠΎ Π²Π΅Π»ΠΈΡΠΈΠ½Π΅
ΠΎΡΠ²Π΅ΡΡΡΠΈΠΉ. ΠΠ»Ρ ΡΠ½ΡΡΠΈΡ Π½Π°ΠΊΠ»Π΅ΠΏΠ° ΠΏΠΎΡΠ»Π΅
ΠΊΠ°ΠΆΠ΄ΠΎΠ³ΠΎ ΠΏΠ΅ΡΠ΅Ρ
ΠΎΠ΄Π° ΠΌΠ΅ΡΠ°Π»Π» ΠΏΠΎΠ΄Π²Π΅ΡΠ³Π°ΡΡ
ΠΏΡΠΎΠΌΠ΅ΠΆΡΡΠΎΡΠ½ΠΎΠΌΡ ΠΎΡΠΆΠΈΠ³Ρ. ΠΠ»Ρ ΡΠΌΠ΅Π½ΡΡΠ΅Π½ΠΈΡ
ΡΠΈΠ»Ρ ΡΡΠ΅Π½ΠΈΡ ΠΌΠ΅ΡΠ°Π»Π»Π° ΠΎΠ± ΠΈΠ½ΡΡΡΡΠΌΠ΅Π½Ρ
ΠΏΠΎΠ»ΠΈΡΡΡΡ ΠΎΡΠ²Π΅ΡΡΡΠΈΠ΅ Π² Π²ΠΎΠ»ΠΎΠΊΠ΅ ΠΈ ΠΏΡΠΈΠΌΠ΅Π½ΡΡΡ
ΡΠ°Π·Π»ΠΈΡΠ½ΡΠ΅ ΡΠΌΠ°Π·ΠΊΠΈ — ΠΌΠΈΠ½Π΅ΡΠ°Π»ΡΠ½ΡΠ΅ ΠΌΠ°ΡΠ»Π°,
ΠΎΠ»ΠΈΡΡ, Π³ΡΠ°ΡΠΈΡ, ΡΠ°Π»ΡΠΊ, ΠΌΡΠ»Π°, ΡΠΎΡΡΠ°ΡΠ½ΡΠ΅ ΠΈ
ΠΌΠ΅ΡΠ°Π»Π»ΠΈΡΠ΅ΡΠΊΠΈΠ΅ ΠΏΠΎΠΊΡΡΡΠΈΡ ΠΈ Π΄Ρ.
Π‘ΠΎΡΡΠ°ΠΌΠ΅Π½Ρ ΠΈΠ·Π΄Π΅Π»ΠΈΠΉ, ΠΈΠ·Π³ΠΎΡΠΎΠ²Π»Π΅Π½Π½ΡΡ Π²ΠΎΠ»ΠΎΡΠ΅Π½ΠΈΠ΅ΠΌ, ΠΎΡΠ΅Π½Ρ ΡΠ°Π·Π½ΠΎΠΎΠ±ΡΠ°Π·Π΅Π½: ΠΏΡΠΎΠ²ΠΎΠ»ΠΎΠΊΠ° 0,002-10 ΠΌΠΌ ΠΈ ΡΠ°ΡΠΎΠ½Π½ΡΠ΅ ΠΏΡΠΎΡΠΈΠ»ΠΈ (ΡΠΈΡ. 1.3.1, Π±), ΡΡΡΠ±Ρ Π΄ΠΈΠ°ΠΌΠ΅ΡΡΠΎΠΌ ΠΎΡ 0,3 Π΄ΠΎ 500 ΠΌΠΌ Ρ ΡΠΎΠ»ΡΠΈΠ½ΠΎΠΉ ΡΡΠ΅Π½ΠΊΠΈ ΠΎΡ 0,05 Π΄ΠΎ 5-6 ΠΌΠΌ.
Β
Π ΠΈΡ.
3.47. Π‘Ρ
Π΅ΠΌΠ° Π²ΠΎΠ»ΠΎΡΠ΅Π½ΠΈΡ ΡΡΡΠ±Ρ (Π°) ΠΈ ΠΏΡΠΈΠΌΠ΅ΡΡ
ΠΏΡΠΎΡΠΈΠ»Π΅ΠΉ, ΠΏΠΎΠ»ΡΡΠ°Π΅ΠΌΡΡ
Π²ΠΎΠ»ΠΎΡΠ΅Π½ΠΈΠ΅ΠΌ (Π±)
ΠΠΎΠ»ΠΎΡΠ΅Π½ΠΈΠ΅ ΡΡΡΠ± ΠΌΠΎΠΆΠ½ΠΎ Π²ΡΠΏΠΎΠ»Π½ΡΡΡ Π±Π΅Π· ΠΎΠΏΡΠ°Π²ΠΊΠΈ, Π΄Π»Ρ ΡΠΌΠ΅Π½ΡΡΠ΅Π½ΠΈΡ ΡΠΎΠ»ΡΠΊΠΎ Π²Π½Π΅ΡΠ½Π΅Π³ΠΎ Π΄ΠΈΠ°ΠΌΠ΅ΡΡΠ°Β (ΡΠ΅Π΄ΡΡΠΈΡΠΎΠ²Π°Π½ΠΈΠ΅), ΠΈ Ρ ΠΎΠΏΡΠ°Π²ΠΊΠΎΠΉ (Π΄Π»Ρ ΡΠΌΠ΅Π½ΡΡΠ΅Π½ΠΈΡ Π²Π½Π΅ΡΠ½Π΅Π³ΠΎ Π΄ΠΈΠ°ΠΌΠ΅ΡΡΠ° ΠΈ ΡΠΎΠ»ΡΠΈΠ½Ρ ΡΡΠ΅Π½ΠΊΠΈ). ΠΠ° ΡΠΈΡ. 3.47, Π°, ΠΏΠΎΠΊΠ°Π·Π°Π½Π° ΡΡ Π΅ΠΌΠ° Π²ΠΎΠ»ΠΎΡΠ΅Π½ΠΈΡ ΡΡΡΠ±Ρ 1 Π½Π° Π΄Π»ΠΈΠ½Π½ΠΎΠΉ Π·Π°ΠΊΡΠ΅ΠΏΠ»Π΅Π½Π½ΠΎΠΉ ΠΎΠΏΡΠ°Π²ΠΊΠ΅ 3. Π ΡΡΠΎΠΌ ΡΠ»ΡΡΠ°Π΅ ΠΏΡΠΎΡΠΈΠ»Ρ ΠΏΠΎΠ»ΡΡΠ΅Π½Π½ΠΎΠΉ ΡΡΡΠ±Ρ ΠΎΠΏΡΠ΅Π΄Π΅Π»ΡΠ΅ΡΡΡ Π·Π°Π·ΠΎΡΠΎΠΌ ΠΌΠ΅ΠΆΠ΄Ρ Π²ΠΎΠ»ΠΎΠΊΠΎΠΉ 2 ΠΈ ΠΎΠΏΡΠ°Π²ΠΊΠΎΠΉ 3. ΠΠΎΠ»ΠΎΡΠ΅Π½ΠΈΠ΅ ΠΎΠ±Π΅ΡΠΏΠ΅ΡΠΈΠ²Π°Π΅Ρ Π²ΡΡΠΎΠΊΡΡ ΡΠΎΡΠ½ΠΎΡΡΡ ΡΠ°Π·ΠΌΠ΅ΡΠΎΠ² (ΡΡΠ°Π»ΡΠ½Π°Ρ ΠΏΡΠΎΠ²ΠΎΠ»ΠΎΠΊΠ° Π΄ΠΈΠ°ΠΌΠ΅ΡΡΠΎΠΌ 1,0-1,6 ΠΌΠΌ ΠΈΠΌΠ΅Π΅Ρ Π΄ΠΎΠΏΡΡΠΊ 0,02 ΠΌΠΌ), Π²ΡΡΠΎΠΊΠΎΠ΅ ΠΊΠ°ΡΠ΅ΡΡΠ²ΠΎ ΠΏΠΎΠ²Π΅ΡΡ Π½ΠΎΡΡΠΈ, ΠΏΠΎΠ»ΡΡΠ΅Π½ΠΈΠ΅ ΠΎΡΠ΅Π½Ρ ΡΠΎΠ½ΠΊΠΈΡ ΠΏΡΠΎΡΠΈΠ»Π΅ΠΉ. ΠΠ΅ΡΠΎΠ΄ Π΄Π°Π΅Ρ Π²ΠΎΠ·ΠΌΠΎΠΆΠ½ΠΎΡΡΡ ΡΠΈΡΠΎΠΊΠΎ Π²Π°ΡΡΠΈΡΠΎΠ²Π°ΡΡ (Π·Π° ΡΡΠ΅Ρ Π½Π°ΠΊΠ»Π΅ΠΏΠ°, Π° ΡΠ°ΠΊΠΆΠ΅ ΡΠ΅ΡΠΌΠΈΡΠ΅ΡΠΊΠΎΠΉ ΠΎΠ±ΡΠ°Π±ΠΎΡΠΊΠΈ) Π΄ΠΈΠ°ΠΏΠ°Π·ΠΎΠ½ ΠΏΡΠΎΡΠ½ΠΎΡΡΠ½ΡΡ ΠΈ ΠΏΠ»Π°ΡΡΠΈΡΠ΅ΡΠΊΠΈΡ ΡΠ²ΠΎΠΉΡΡΠ² ΠΌΠ΅ΡΠ°Π»Π»Π° Π³ΠΎΡΠΎΠ²ΠΎΠ³ΠΎ ΠΈΠ·Π΄Π΅Π»ΠΈΡ, ΡΠ΅Π·ΠΊΠΎ ΡΠΎΠΊΡΠ°ΡΠ°Π΅Ρ ΠΎΡΡ ΠΎΠ΄Ρ ΠΈ ΡΠ²Π΅Π»ΠΈΡΠΈΠ²Π°Π΅Ρ ΠΏΡΠΎΠΈΠ·Π²ΠΎΠ΄ΠΈΡΠ΅Π»ΡΠ½ΠΎΡΡΡ. ΠΡΠ»ΠΈΡΠΈΡΠ΅Π»ΡΠ½ΠΎΠΉ ΡΠ΅ΡΡΠΎΠΉ ΠΏΡΠΎΡΠ΅ΡΡΠ° Π²ΠΎΠ»ΠΎΡΠ΅Π½ΠΈΡ ΡΠ²Π»ΡΠ΅ΡΡΡ Π΅Π³ΠΎ ΡΠ½ΠΈΠ²Π΅ΡΡΠ°Π»ΡΠ½ΠΎΡΡΡ (ΠΏΡΠΎΡΡΠΎΡΠ° ΠΈ Π±ΡΡΡΡΠΎΡΠ° Π·Π°ΠΌΠ΅Π½Ρ ΠΈΠ½ΡΡΡΡΠΌΠ΅Π½ΡΠ°), ΡΡΠΎ Π΄Π΅Π»Π°Π΅Ρ Π΅Π³ΠΎ ΠΎΡΠ΅Π½Ρ ΡΠ°ΡΠΏΡΠΎΡΡΡΠ°Π½Π΅Π½Π½ΡΠΌ.
2. Π₯Π°ΡΠ°ΠΊΡΠ΅ΡΠΈΡΡΠΈΠΊΠ° Π²ΡΠΏΠΎΠΌΠΎΠ³Π°ΡΠ΅Π»ΡΠ½ΠΎΠ³ΠΎ ΠΎΠ±ΠΎΡΡΠ΄ΠΎΠ²Π°Π½ΠΈΡ Π²ΠΎΠ»ΠΎΡΠΈΠ»ΡΠ½ΡΡ ΡΡΠ°Π½ΠΎΠ².
2.1 Π Π°Π·ΠΌΠΎΡΠΎΡΠ½ΡΠ΅ ΡΡΡΡΠΎΠΉΡΡΠ²Π°
Π Π°Π·ΠΌΠΎΡΠΎΡΠ½ΡΠ΅ ΡΡΡΡΠΎΠΉΡΡΠ²Π° ΠΏΡΠ΅Π΄Π½Π°Π·Π½Π°ΡΠ΅Π½Ρ Π΄Π»Ρ ΡΠ°Π·ΠΌΠ°ΡΡΠ²Π°Π½ΠΈΡ ΠΏΡΠΎΒΠ²ΠΎΠ»ΠΎΠΊΠΈ-Π·Π°Π³ΠΎΡΠΎΠ²ΠΊΠΈ ΠΏΠ΅ΡΠ΅Π΄ Π²ΠΎΠ»ΠΎΡΠΈΠ»ΡΠ½ΡΠΌ ΡΡΠ°Π½ΠΎΠΌ Ρ ΡΠ΅Π»ΡΡ Π΅Π΅ ΠΏΠΎΡΠ»Π΅Π΄ΡΡΒΡΠ΅Π³ΠΎ Π²ΠΎΠ»ΠΎΡΠ΅Π½ΠΈΡ. Π Π·Π°Π²ΠΈΡΠΈΠΌΠΎΡΡΠΈ ΠΎΡ ΡΠΎΠ³ΠΎ, Π² ΠΊΠ°ΠΊΠΎΠΌ Π²ΠΈΠ΄Π΅ ΠΏΠΎΡΡΡΠΏΠ°Π΅Ρ ΠΏΡΠΎΠ²ΠΎΠ»ΠΎΠΊΠ° Π΄Π»Ρ Π΄Π°Π»ΡΠ½Π΅ΠΉΡΠ΅ΠΉ ΠΏΠ΅ΡΠ΅ΡΠ°Π±ΠΎΡΠΊΠΈ: Π² ΠΌΠΎΡΠΊΠ°Ρ (Π±ΡΠ½ΡΠ°Ρ ) ΠΈΠ»ΠΈ Π½Π° ΠΊΠ°ΒΡΡΡΠΊΠ°Ρ Π±ΠΎΠ»ΡΡΠΎΠΉ Π²ΠΌΠ΅ΡΡΠΈΠΌΠΎΡΡΠΈ (Π΄ΠΎ 1000 ΠΊΠ³ ΠΈ Π±ΠΎΠ»Π΅Π΅), ΠΊΠΎΠ½ΡΡΡΡΠΊΡΠΈΠ²Π½ΠΎ ΡΠ°Π·ΠΌΠ°ΡΡΠ²Π°ΡΡΠΈΠ΅ ΡΡΡΡΠΎΠΉΡΡΠ²Π° ΡΠ°Π·Π΄Π΅Π»ΡΡΡΡΡ Π½Π° ΡΡΠΈ ΡΠΈΠΏΠ°:
ΡΠ°Π·ΠΌΠΎΡΠΊΠ° Ρ Π²ΡΠ°ΡΠ°ΡΡΠΈΡ ΡΡ ΡΠΈΠ³ΡΡΠΎΠΊ;
ΡΠ°Π·ΠΌΠΎΡΠΊΠ° ΡΠΎ ΡΡΠ°ΡΠΈΠΎΠ½Π°ΡΠ½ΠΎ ΡΡΡΠ°Π½ΠΎΠ²Π»Π΅Π½Π½ΡΡ ΠΊΡΠΎΠ½ΡΡΠ΅ΠΉΠ½ΠΎΠ², ΠΊΠΎΠ½ΡΠΎΒ Π»Π΅ΠΉ;
ΡΠ°Π·ΠΌΠΎΡΠΊΠ° Ρ ΡΡΡΡΠΎΠΉΡΡΠ²Π° ΠΏΠΈΠ½ΠΎΠ»ΡΠ½ΠΎΠ³ΠΎ ΡΠΈΠΏΠ° Π΄Π»Ρ ΡΡΡΠ°Π½ΠΎΠ²ΠΊΠΈ ΠΊΠ°ΡΡΒ ΡΠ΅ΠΊ.
Π ΡΠ°Π·ΠΌΠΎΡΠΎΡΠ½ΡΠΌ ΡΡΡΡΠΎΠΉΡΡΠ²Π°ΠΌ ΠΏΡΠ΅Π΄ΡΡΠ²Π»ΡΡΡΡΡ ΡΡΠ΅Π±ΠΎΠ²Π°Π½ΠΈΡ:
ΠΎΠ±Π΅ΡΠΏΠ΅ΡΠ΅Π½ΠΈΠ΅ ΡΠ°Π²Π½ΠΎΠΌΠ΅ΡΠ½ΠΎΠ³ΠΎ ΡΡ ΠΎΠ΄Π° ΠΏΡΠΎΠ²ΠΎΠ»ΠΎΠΊΠΈ-Π·Π°Π³ΠΎΡΠΎΠ²ΠΊΠΈ Π±Π΅Π· Π·Π°Β ΠΏΡΡΡΠ²Π°Π½ΠΈΡ ΠΈ ΠΏΠΎΠ΄ ΠΎΠΏΡΠ΅Π΄Π΅Π»Π΅Π½Π½ΡΠΌ ΡΠ³Π»ΠΎΠΌ;
Π²ΠΎΠ·ΠΌΠΎΠΆΠ½ΠΎΡΡΡ ΡΠ΅Π³ΡΠ»ΠΈΡΠΎΠ²Π°Π½ΠΈΡ ΡΠΈΠ»Ρ Π½Π°ΡΡΠΆΠ΅Π½ΠΈΡ Π² Π·Π°Π²ΠΈΡΠΈΠΌΠΎΡΡΠΈ ΠΎΡ Π΄ΠΈΠ°ΠΌΠ΅ΡΡΠ° ΠΏΡΠΎΠ²ΠΎΠ»ΠΎΠΊΠΈ;
Π²ΠΎΠ·ΠΌΠΎΠΆΠ½ΠΎΡΡΡ ΡΠ²Π°ΡΠΈΠ²Π°Π½ΠΈΡ ΠΊΠΎΠ½ΡΠΎΠ² ΠΏΡΠΎΠ²ΠΎΠ»ΠΎΠΊΠΈ Π±Π΅Π· ΠΎΡΡΠ°Π½ΠΎΠ²ΠΊΠΈ Π²ΠΎΒ Π»ΠΎΡΠΈΠ»ΡΠ½ΠΎΠ³ΠΎ ΡΡΠ°Π½Π°;
ΠΎΠ±Π΅ΡΠΏΠ΅ΡΠ΅Π½ΠΈΠ΅ Π±Π΅Π·ΠΎΠΏΠ°ΡΠ½ΠΎΠΉ ΡΠ°Π±ΠΎΡΡ ΠΎΠ±ΡΠ»ΡΠΆΠΈΠ²Π°ΡΡΠ΅Π³ΠΎ ΠΏΠ΅ΡΡΠΎΠ½Π°Π»Π°;
ΠΌΠ΅Ρ Π°Π½ΠΈΠ·Π°ΡΠΈΡ Π·Π°Π³ΡΡΠ·ΠΊΠΈ ΡΠ°Π·ΠΌΠ°ΡΡΠ²Π°ΡΡΠΈΡ ΡΡΡΡΠΎΠΉΡΡΠ²;
Π²ΠΎΠ·ΠΌΠΎΠΆΠ½ΠΎΡΡΡ ΠΈΡΠΏΠΎΠ»ΡΠ·ΠΎΠ²Π°Π½ΠΈΡ Π±ΠΎΠ»ΡΡΠΈΡ ΡΠΊΠΎΡΠΎΡΡΠ΅ΠΉ ΡΡ ΠΎΠ΄Π° ΠΏΡΠΎΠ²ΠΎΠ»ΠΎΒ ΠΊΠΈ Ρ ΡΠ°Π·ΠΌΠ°ΡΡΠ²Π°ΡΡΠΈΡ ΡΡΡΡΠΎΠΉΡΡΠ² Π΄Π»Ρ ΠΎΠ±Π΅ΡΠΏΠ΅ΡΠ΅Π½ΠΈΡ ΡΠΊΠΎΡΠΎΡΡΠ½ΠΎΠ³ΠΎ ΠΈ Π²ΡΡΠΎΠΊΠΎΡΠΊΠΎΡΠΎΡΡΠ½ΠΎΠ³ΠΎ Π²ΠΎΠ»ΠΎΡΠ΅Π½ΠΈΡ ΠΏΡΠΎΠ²ΠΎΠ»ΠΎΠΊΠΈ.
ΠΡΠΈ ΡΠ°Π·ΠΌΠΎΡΠΊΠ΅ ΠΏΡΠΎΠ²ΠΎΠ»ΠΎΠΊΠΈ ΠΈΠ· ΠΌΠΎΡΠΊΠΎΠ², ΡΠ»ΠΎΠΆΠ΅Π½Π½ΡΡ Π½Π° Π²ΡΠ°ΡΠ°ΡΡΡΡΡΡ ΡΠΈΠ³ΡΡΠΊΡ, ΠΏΠΎΠ»ΠΎΠΆΠΈΡΠ΅Π»ΡΠ½ΡΠΌ ΠΏΡΠ΅ΠΈΠΌΡΡΠ΅ΡΡΠ²ΠΎΠΌ ΡΠ²Π»ΡΠ΅ΡΡΡ ΡΠΎ, ΡΡΠΎ ΠΏΡΠΎΠ²ΠΎΠ»ΠΎΠΊΠ°., ΡΠΌΠ°ΡΡΠ²Π°ΡΡΡ Ρ ΡΠΈΠ³ΡΡΠΊΠΈ, Π½Π΅ Π·Π°ΠΊΡΡΡΠΈΠ²Π°Π΅ΡΡΡ Π²ΠΎΠΊΡΡΠ³ ΡΠ²ΠΎΠ΅ΠΉ ΠΎΡΠΈ, ΡΡΠΎ Π²Π°ΠΆΒΠ½ΠΎ ΠΏΡΠΈ Π²ΠΎΠ»ΠΎΡΠ΅Π½ΠΈΠΈ ΠΏΡΠΎΠ²ΠΎΠ»ΠΎΠΊΠΈ ΡΠ°ΡΠΎΠ½Π½ΠΎΠ³ΠΎ ΠΏΡΠΎΡΠΈΠ»Ρ ΠΏΠΎ ΡΠ΅ΡΠ΅Π½ΠΈΡ. ΠΠΎ ΠΏΡΠΈ Π±ΠΎΠ»ΡΡΠΈΡ ΠΌΠ°ΡΡΠ°Ρ ΠΌΠΎΡΠΊΠ° ΠΈ Π±ΠΎΠ»ΡΡΠΎΠΉ ΡΠ°ΡΡΠΎΡΠ΅ Π²ΡΠ°ΡΠ΅Π½ΠΈΡ ΡΠΈΠ³ΡΡΠΊΠΈ ΠΈΠ·-Π·Π° Π½Π΅ΒΡΠΎΡΠ½ΠΎΠΉ Π±Π°Π»Π°Π½ΡΠΈΡΠΎΠ²ΠΊΠΈ ΠΌΠΎΡΠΊΠ° ΠΎΡΠ½ΠΎΡΠΈΡΠ΅Π»ΡΠ½ΠΎ ΠΎΡΠΈ Π²ΡΠ°ΡΠ΅Π½ΠΈΡ Π²ΠΎΠ·Π½ΠΈΠΊΠ°ΡΡ Π±ΠΎΠ»ΡΡΠΈΠ΅ ΡΠ΅Π½ΡΡΠΎΠ±Π΅ΠΆΠ½ΡΠ΅ ΡΠΈΠ»Ρ ΠΈΠ½Π΅ΡΡΠΈΠΈ, ΠΊΠΎΡΠΎΡΡΠ΅ Π²ΡΠ·ΡΠ²Π°ΡΡ Π±ΡΡΡΡΡΠΉ ΠΈΠ·Π½ΠΎΡ ΠΏΠΎΠ΄ΡΠΈΠΏΠ½ΠΈΠΊΠΎΠ²ΡΡ ΠΎΠΏΠΎΡ, Π° ΡΠ»Π΅Π΄ΠΎΠ²Π°ΡΠ΅Π»ΡΠ½ΠΎ, ΠΈ ΡΠ°ΡΡΡΠΉ ΠΈΡ ΡΠ΅ΠΌΠΎΠ½Ρ. ΠΠ° Π²ΡΠ°ΒΡΠ°ΡΡΠΈΡ ΡΡ ΡΡΡΡΠΎΠΉΡΡΠ²Π°Ρ ΠΌΠΎΠΆΠ½ΠΎ ΡΠ°Π·ΠΌΠ°ΡΡΠ²Π°ΡΡ ΠΏΡΠΎΠ²ΠΎΠ»ΠΎΠΊΡ ΡΠΎΠ»ΡΡΡΡ ΠΈ ΡΡΠ΅Π΄ Π½ΠΈΡ ΡΠ°Π·ΠΌΠ΅ΡΠΎΠ². Π‘Π²Π°ΡΠΊΠ° ΠΆΠ΅ ΠΊΠΎΠ½ΡΠΎΠ² ΠΏΡΠΎΠ²ΠΎΠ»ΠΎΠΊΠΈ Π±Π΅Π· ΠΎΡΡΠ°Π½ΠΎΠ²ΠΊΠΈ ΡΠΈΠ³ΡΡΠΊΠΈ, Π° ΡΠ»Π΅Π΄ΠΎΠ²Π°ΡΠ΅Π»ΡΠ½ΠΎ, ΠΈ Π²ΠΎΠ»ΠΎΡΠΈΠ»ΡΠ½ΠΎΠ³ΠΎ ΡΡΠ°Π½Π° Π½Π΅Π²ΠΎΠ·ΠΌΠΎΠΆΠ½Π°, ΠΏΠΎΡΡΠΎΠΌΡ ΡΠ²Π΅Π»ΠΈΒΡΠΈΠ²Π°Π΅ΡΡΡ Π²ΡΠ΅ΠΌΡ, Π·Π°ΡΡΠ°ΡΠΈΠ²Π°Π΅ΠΌΠΎΠ΅ Π½Π° ΡΡΡΠ½ΡΠ΅ ΠΎΠΏΠ΅ΡΠ°ΡΠΈΠΈ.
ΠΡΠΈ ΡΡΡΠ°Π½ΠΎΠ²ΠΊΠ΅ ΠΌΠΎΡΠΊΠΎΠ² ΠΏΡΠΎΠ²ΠΎΠ»ΠΎΠΊΠΈ Π½Π° ΠΊΡΠΎΠ½ΡΡΠ΅ΠΉΠ½Π°Ρ ΠΈΠΌΠ΅Π΅ΡΡΡ Π²ΠΎΠ·ΠΌΠΎΠΆΒΠ½ΠΎΡΡΡ ΡΠ²Π°ΡΠΈΠ²Π°Π½ΠΈΡ ΠΊΠΎΠ½ΡΠΎΠ² ΠΏΡΠΎΠ²ΠΎΠ»ΠΎΠΊΠΈ ΠΏΡΠΈ ΡΠ°Π±ΠΎΡΠ°ΡΡΠ΅ΠΌ ΡΡΠ°Π½Π΅. ΠΠΎ ΠΏΡΠΈ ΡΡΠΎΠΌ ΡΠΏΠΎΡΠΎΠ±Π΅ ΡΠ°Π·ΠΌΠ°ΡΡΠ²Π°Π½ΠΈΡ ΠΏΡΠΎΠ²ΠΎΠ»ΠΎΠΊΠ°, ΡΡ ΠΎΠ΄Ρ Ρ ΠΊΡΠΎΠ½ΡΡΠ΅ΠΉΠ½Π°, ΠΏΠΎΠ»ΡΡΠ°Π΅Ρ ΠΎΡΠ΅Π²ΠΎΠ΅ Π·Π°ΠΊΡΡΡΠΈΠ²Π°Π½ΠΈΠ΅ Π·Π° ΠΊΠ°ΠΆΠ΄ΡΠΉ Π²ΠΈΡΠΎΠΊ Π½Π° ΠΎΠ΄ΠΈΠ½ ΠΏΠΎΠ»Π½ΡΠΉ ΠΎΠ±ΠΎΡΠΎΡ, Ρ.Π΅. Π½Π° 360Β°. ΠΡΠΎΠ²ΠΎΠ»ΠΎΠΊΠ° ΠΏΠΎΠ΄Ρ ΠΎΠ΄ΠΈΡ ΠΊ ΠΏΠ΅ΡΠ²ΠΎΠΌΡ Π²ΠΎΠ»ΠΎΠΊΠΎΠ΄Π΅ΡΠΆΠ°ΡΠ΅Π»Ρ ΡΡΠ°Π½Π° Π²ΠΎΠ»ΒΠ½ΠΈΡΡΠΎΠΉ. Π§ΡΠΎΠ±Ρ ΡΠΌΠ΅Π½ΡΡΠΈΡΡ ΡΡΠ΅ΠΏΠ΅Π½Ρ Π²ΠΎΠ»Π½ΠΈΡΡΠΎΡΡΠΈ, ΠΊΡΠΎΠ½ΡΡΠ΅ΠΉΠ½Ρ ΡΡΡΠ°Π½Π°Π²ΒΠ»ΠΈΠ²Π°ΡΡΡΡ Π½Π° Π·Π½Π°ΡΠΈΡΠ΅Π»ΡΠ½ΠΎ Π±ΠΎΠ»ΡΡΠ΅ΠΌ ΡΠ°ΡΡΡΠΎΡΠ½ΠΈΠΈ, ΡΠ΅ΠΌ Π²ΡΠ°ΡΠ°ΡΡΠΈΠ΅ΡΡ ΡΠΈΒΠ³ΡΡΠΊΠΈ, ΠΎΡ Π²ΠΎΠ»ΠΎΡΠΈΠ»ΡΠ½ΠΎΠ³ΠΎ ΡΡΠ°Π½Π°, ΡΡΠΎ ΡΠ²Π΅Π»ΠΈΡΠΈΠ²Π°Π΅Ρ ΠΏΡΠΎΠΈΠ·Π²ΠΎΠ΄ΡΡΠ²Π΅Π½Π½ΡΠ΅ ΠΏΠ»ΠΎΡΠ°Π΄ΠΈ.
ΠΠ»Ρ ΠΏΡΠ΅Π΄ΠΎΡ ΡΠ°Π½Π΅Π½ΠΈΡ ΡΠ°ΠΌΠΎΠΏΡΠΎΠΈΠ·Π²ΠΎΠ»ΡΠ½ΠΎΠ³ΠΎ ΡΡ ΠΎΠ΄Π° Π²ΠΈΡΠΊΠΎΠ² ΠΈ ΠΈΡ Π·Π°ΠΏΡΒΡΡΠ²Π°Π½ΠΈΡ Π½Π° ΠΊΡΠΎΠ½ΡΡΠ΅ΠΉΠ½Π΅ ΡΡΡΠ°Π½Π°Π²Π»ΠΈΠ²Π°Π΅ΡΡΡ ΡΠΏΠ΅ΡΠΈΠ°Π»ΡΠ½ΡΠΉ ΡΡΡΠ°Π³, Π·Π°Π΄Π΅ΡΒΠΆΠΈΠ²Π°ΡΡΠΈΠΉ Π²ΠΈΡΠΊΠΈ ΡΠΈΠ»ΠΎΠΉ ΡΠΎΠ±ΡΡΠ²Π΅Π½Π½ΠΎΠΉ ΠΌΠ°ΡΡΡ. ΠΠΈΠΆΠ½ΠΈΠΉ ΡΡΡΠ°Π³ ΡΠ°ΠΊΠΆΠ΅ ΠΏΡΠ΅ΒΠΏΡΡΡΡΠ²ΡΠ΅Ρ Π²ΠΈΡΠΊΠ°ΠΌ ΠΏΡΠΎΠΈΠ·Π²ΠΎΠ»ΡΠ½ΠΎΠ³ΠΎ ΡΡ ΠΎΠ΄Π°. ΠΠ°ΠΆΠ΄ΡΠΉ ΡΠ½ΠΈΠΌΠ°Π΅ΠΌΡΠΉ Π²ΠΈΡΠΎΠΊ ΠΏΡΠΈΒΠΏΠΎΠ΄Π½ΠΈΠΌΠ°Π΅Ρ ΡΡΡΠ°Π³ΠΈ ΠΈ ΠΎΠ½ΠΈ, ΡΠ΄Π°ΡΡΡΡΡ ΠΎ ΡΠ²ΠΎΠΈ ΠΎΠΏΠΎΡΡ, ΠΈΠ·Π΄Π°ΡΡ ΡΡΡΠΊ-Ρ Π»ΠΎ ΠΏΠΎΠΊ. ΠΠ΅ΡΠΊΠΎΠ»ΡΠΊΠΎ ΡΠ°ΠΊΠΈΡ ΡΠ°Π±ΠΎΡΠ°ΡΡΠΈΡ ΡΠ°Π·ΠΌΠ°ΡΡΠ²Π°ΡΠ΅Π»Π΅ΠΉ ΡΠΎΠ·Π΄Π°ΡΡ Π² ΡΠ΅Ρ Π΅ Π΄ΠΎΒΠΏΠΎΠ»Π½ΠΈΡΠ΅Π»ΡΠ½ΡΠΉ ΡΡΠΌ Π² Π²ΠΈΠ΄Π΅ ΠΏΠ΅ΡΠΈΠΎΠ΄ΠΈΡΠ΅ΡΠΊΠΈΡ ΡΠ΄Π°ΡΠΎΠ².
Π Π°Π·ΠΌΠ°ΡΡΠ²Π°ΡΠ΅Π»Ρ Π² Π²ΠΈΠ΄Π΅ ΠΏΠΎΠ΄Π²Π΅ΡΠΊΠΈ Π΄Π»Ρ Π΄Π²ΡΡ Π±ΡΠ½ΡΠΎΠ² ΠΎΠ΄Π½ΠΎΠ²ΡΠ΅ΠΌΠ΅Π½Π½ΠΎ ΡΡΠ°Π½ΡΠΏΠΎΡΡΠΈΡΡΠ΅ΡΡΡ ΠΊΡΠ°Π½ΠΎΠΌ ΠΈΠ»ΠΈ ΠΊΡΠ°Π½-Π±Π°Π»ΠΊΠΎΠΉ ΠΈΠ· ΠΎΡΠ΄Π΅Π»Π΅Π½ΠΈΡ Π΄Π»Ρ ΠΏΠΎΠ΄Π³ΠΎΒΡΠΎΠ²ΠΊΠΈ ΠΏΠΎΠ²Π΅ΡΡ Π½ΠΎΡΡΠΈ ΠΏΡΠΎΠ²ΠΎΠ»ΠΎΠΊΠΈ ΠΊ Π²ΠΎΠ»ΠΎΡΠ΅Π½ΠΈΡ Π² Π²ΠΎΠ»ΠΎΡΠΈΠ»ΡΠ½ΠΎΠ΅ ΠΎΡΠ΄Π΅Π»Π΅Π½ΠΈΠ΅. ΠΠ±ΡΠ°Ρ Π³ΡΡΠ·ΠΎΠΏΠΎΠ΄ΡΠ΅ΠΌΠ½ΠΎΡΡΡ ΠΏΠΎΠ΄Π²Π΅ΡΠΊΠΈ Π΄ΠΎ 1.5 Ρ. ΠΠΎΠΊΠ° Ρ ΠΎΠ΄Π½ΠΎΠΉ ΠΏΠΎΠ΄Π²Π΅ΡΠΊΠΈ ΠΈΠ΄Π΅Ρ ΡΠ°Π·ΠΌΠ°ΡΡΠ²Π°Π½ΠΈΠ΅, Π½Π° Π²ΡΠΎΡΠΎΠΉ ΠΏΠΎΠ΄Π³ΠΎΡΠ°Π²Π»ΠΈΠ²Π°Π΅ΡΡΡ ΠΊΠΎΠ½Π΅Ρ Π±ΡΠ½ΡΠ° Π΄Π»Ρ ΡΠ²Π°ΡΠΊΠΈ Ρ Π·Π°Π΄Π½ΠΈΠΌ ΠΊΠΎΠ½ΡΠΎΠΌ ΠΏΠ΅ΡΠ²ΠΎΠ³ΠΎ Π±ΡΠ½ΡΠ°.
Π Π°Π·ΠΌΠΎΡΠΊΠ° ΠΏΡΠΎΠ²ΠΎΠ»ΠΎΠΊΠΈ Ρ ΠΊΠ°ΡΡΡΠΊΠΈ Π² Π½Π°ΡΡΠΎΡΡΠ΅Π΅ Π²ΡΠ΅ΠΌΡ ΠΈΠΌΠ΅Π΅Ρ ΡΠ°ΠΌΠΎΠ΅ Π±ΠΎΠ»ΡΡΠΎΠ΅ ΡΠ°ΡΠΏΡΠΎΡΡΡΠ°Π½Π΅Π½ΠΈΠ΅ ΠΈ, Π³Π΄Π΅ ΡΡΠΎ Π²ΠΎΠ·ΠΌΠΎΠΆΠ½ΠΎ, Π·Π°ΠΌΠ΅Π½ΡΠ΅Ρ ΡΠ°Π·ΠΌΠΎΡΠΊΡ ΠΈΠ· Π±ΡΠ½ΡΠΎΠ². Π’Π°ΠΊ ΠΊΠ°ΠΊ ΠΌΠ°ΡΡΠ° ΠΏΡΠΎΠ²ΠΎΠ»ΠΎΠΊΠΈ Π½Π° ΠΊΠ°ΡΡΡΠΊΠ°Ρ Π±ΠΎΠ»ΡΡΠΎΠΉ Π²ΠΌΠ΅ΡΡΠΈΠΌΠΎΡΡΠΈ Π² Π½Π΅ΡΠΊΠΎΠ»ΡΠΊΠΎ ΡΠ°Π· Π±ΠΎΠ»ΡΡΠ΅ ΠΌΠ°ΡΡΡ ΠΌΠΎΡΠΊΠ°, Π·Π½Π°ΡΠΈΡΠ΅Π»ΡΠ½ΠΎ ΡΠΎΠΊΡΠ°ΡΠ°Π΅ΡΡΡ ΡΡΡΠ½ΠΎΠ΅ Π²ΡΠ΅ΠΌΡ Π½Π° Π·Π°ΠΌΠ΅Π½Ρ Π·Π°Π³ΠΎΡΠΎΠ²ΠΊΠΈ. Π£Π»ΡΡΡΠ°ΡΡΡΡ ΡΡΠ»ΠΎΠ²ΠΈΡ ΡΡΠ°Π½ΡΠΏΠΎΡΡΠΈΡΠΎΠ²ΠΊΠΈ ΠΈ Ρ ΡΠ°Π½Π΅Π½ΠΈΡ ΠΏΡΠΎΠ²ΠΎΠ»ΠΎΠΊΠΈ, ΡΠΌΠ΅Π½ΡΡΠ°Π΅ΡΡΡ Π²ΠΎΠ·ΠΌΠΎΠΆΠ½ΠΎΡΡΡ Π·Π°ΠΏΡΡΡΠ²Π°Π½ΠΈΡ Π²ΠΈΡΠΊΠΎΠ², Π° ΡΠ»Π΅Π΄ΠΎΠ²Π°ΡΠ΅Π»ΡΠ½ΠΎ, ΡΠ½ΠΈΠΆΠ°ΡΡΡΡ ΠΎΡΡ ΠΎΠ΄Ρ ΠΌΠ΅ΡΠ°Π»Π»Π°. ΠΡΠ°ΠΊΡΠΈΡΠ΅ΡΠΊΠΈ Π²ΠΎΠ·ΠΌΠΎΠΆΠ½Π° Π»ΡΠ±Π°Ρ ΡΠΊΠΎΡΠΎΡΡΡ ΡΠΌΠ°ΡΡΠ²Π°Π½ΠΈΡ, Π½Π΅ΠΎΠ±Ρ ΠΎΠ΄ΠΈΠΌΠ°Ρ ΠΏΡΠΈ Π²ΠΎΠ»ΠΎΡΠ΅Π½ΠΈΠΈ, ΡΠ°Π±ΠΎΡΠ° ΡΠ°Π·ΒΠΌΠΎΡΠΎΡΠ½ΠΎΠ³ΠΎ ΡΡΡΡΠΎΠΉΡΡΠ²Π° Π±Π΅ΡΡΡΠΌΠ½Π°Ρ.
Π Π°Π·ΠΌΠΎΡΠΎΡΠ½ΠΎΠ΅ ΡΡΡΡΠΎΠΉΡΡΠ²ΠΎ ΠΈΠΌΠ΅Π΅Ρ Π΄Π²Π΅ ΡΠ°ΠΌΠΎΡΡΠΎΡΡΠ΅Π»ΡΠ½ΡΠ΅ ΡΡΠΎΠΉΠΊΠΈ Ρ Π²ΡΠ°ΡΠ°ΡΡΠΈΠΌΠΈΡΡ ΠΏΠΈΠ½ΠΎΠ»ΡΠΌΠΈ. ΠΠ΄Π½Π° ΠΈΠ· ΠΏΠΈΠ½ΠΎΠ»Π΅ΠΉ Π΄ΠΎΠ»ΠΆΠ½Π° ΠΈΠΌΠ΅ΡΡ ΠΏΠ΅ΡΠ΅ΠΌΠ΅ΡΠ΅Π½ΠΈΠ΅
Π²Π΄ΠΎΠ»Ρ ΡΠ²ΠΎΠ΅ΠΉ ΠΎΡΠΈ Π΄Π»Ρ ΠΎΠ±Π΅ΡΠΏΠ΅ΡΠ΅Π½ΠΈΡ ΡΡΡΠ°Π½ΠΎΠ²ΠΊΠΈ ΠΊΠ°ΡΡΡΠ΅ΠΊ ΡΠ°Π·Π»ΠΈΡΠ½ΡΡ ΠΏΠΎ ΡΠ²ΠΎΠ΅ΠΉ ΡΠΈΡΠΈΠ½Π΅. Π’Π°ΠΊ, Π½Π°ΠΏΡΠΈΠΌΠ΅Ρ, Π½Π° ΠΎΠ΄Π½ΠΎΠΌ ΡΠ°Π·ΠΌΠ°ΡΡΠ²Π°ΡΡΠ΅ΠΌ ΡΡΡΡΠΎΠΉΡΡΠ²Π΅ ΠΌΠΎΠ³ΡΡ ΠΏΡΠΈΠΌΠ΅Π½ΡΡΡΡΡ ΠΊΠ°ΡΡΡΠΊΠΈ ΡΠ°Π·ΠΌΠ΅ΡΠΎΠΌ 630, 800 ΠΈ 1000 ΠΌΠΌ ΠΏΠΎ Π΄ΠΈΠ°ΠΌΠ΅ΡΡΡ Π΄ΠΈΡΠΊΠ°. ΠΠ»Ρ Π±ΠΎΠ»ΡΡΠ΅Π³ΡΡΠ·Π½ΡΡ ΠΊΠ°ΡΡΡΠ΅ΠΊ ΠΏΡΠ΅Π΄ΡΡΠΌΠ°ΡΡΠΈΠ²Π°ΡΡΡΡ Π³ΡΡΠ·ΠΎΠΏΠΎΠ΄ΡΠ΅ΠΌΠ½ΡΠ΅ ΡΡΡΡΠΎΠΉΡΡΠ²Π°, ΠΎΠ±ΡΡΠ½ΠΎ Π³ΠΈΠ΄ΡΠ°Π²Π»ΠΈΡΠ΅ΡΠΊΠΎΠ³ΠΎ ΡΠΈΠΏΠ°. ΠΠ»Ρ ΠΎΠ±Π΅ΡΠΏΠ΅ΡΠ΅Π½ΠΈΡ ΡΠΎΡΠΌΠΎΠΆΠ΅ΒΠ½ΠΈΡ ΠΊΠ°ΡΡΡΠ΅ΠΊ, Π΄Π»Ρ ΡΠΎΠ·Π΄Π°Π½ΠΈΡ Π½Π°ΡΡΠΆΠ΅Π½ΠΈΡ ΡΡ ΠΎΠ΄ΡΡΠ΅ΠΉ ΠΏΡΠΎΠ²ΠΎΠ»ΠΎΠΊΠΈ ΠΈΠΌΠ΅Π΅ΡΡΡ ΡΠΎΡΠΌΠΎΠ·Π½ΠΎΠ΅ ΡΡΡΡΠΎΠΉΡΡΠ²ΠΎ ΠΊΠΎΠ»ΠΎΠ΄ΠΎΡΠ½ΠΎΠ³ΠΎ ΠΈΠ»ΠΈ Π»Π΅Π½ΡΠΎΡΠ½ΠΎΠ³ΠΎ ΡΠΈΠΏΠ°, ΠΏΠΎΠ·Π²ΠΎΠ»ΡΡΡΠ΅Π΅ ΡΠ΅Π³ΡΠ»ΠΈΡΠΎΠ²Π°ΡΡ ΡΠΈΠ»Ρ Π½Π°ΡΡΠΆΠ΅Π½ΠΈΡ ΠΏΡΠΎΠ²ΠΎΠ»ΠΎΠΊΠΈ Π² Π·Π°Π²ΠΈΡΠΈΠΌΠΎΡΡΠΈ ΠΎΡ Π΅Π΅ Π΄ΠΈΠ°ΠΌΠ΅ΡΒΡΠ°.
Π Π½Π΅ΠΊΠΎΡΠΎΡΡΡ ΡΠ»ΡΡΠ°ΡΡ ΡΡΠΈΠΊΡΠΈΠΎΠ½Π½ΡΠ΅ ΡΠΎΡΠΌΠΎΠ·Π½ΡΠ΅ ΡΠΈΡΡΠ΅ΠΌΡ ΡΠ°Π±ΠΎΡΠ°ΡΡ Π½Π΅Π΄ΠΎΡΡΠ°ΡΠΎΡΠ½ΠΎ ΠΏΠ»Π°Π²Π½ΠΎ ΠΈ ΡΡΡΠΎΠΉΡΠΈΠ²ΠΎ. ΠΠΎΡΡΠΎΠΌΡ Π² ΡΡΠΈΡ ΡΠ»ΡΡΠ°ΡΡ Π² ΠΊΠ°ΡΠ΅ΡΡΒΠ²Π΅ ΡΠΎΡΠΌΠΎΠ·Π° ΡΡΡΠ°Π½Π°Π²Π»ΠΈΠ²Π°ΡΡ ΡΠ»Π΅ΠΊΡΡΠΎΠ΄Π²ΠΈΠ³Π°ΡΠ΅Π»Ρ, ΡΠ°Π±ΠΎΡΠ°ΡΡΠΈΠΉ Π² Π³Π΅Π½Π΅ΡΠ°ΒΡΠΎΡΠ½ΠΎΠΌ ΡΠ΅ΠΆΠΈΠΌΠ΅ ΠΈ ΡΠΎΠ·Π΄Π°ΡΡΠΈΠΉ ΠΏΠ»Π°Π²Π½ΠΎΠ΅ ΡΠΎΡΠΌΠΎΠΆΠ΅Π½ΠΈΠ΅. ΠΠ΅Π»ΠΈΡΠΈΠ½ΠΎΠΉ Π½Π°Π³ΡΡΠ·ΠΊΠΈ Π½Π° ΡΠ»Π΅ΠΊΡΡΠΎΠ΄Π²ΠΈΠ³Π°ΡΠ΅Π»Ρ-Π³Π΅Π½Π΅ΡΠ°ΡΠΎΡ ΠΌΠΎΠΆΠ½ΠΎ Π² ΡΠΈΡΠΎΠΊΠΈΡ ΠΏΡΠ΅Π΄Π΅Π»Π°Ρ ΡΠ΅Π³ΡΠ»ΠΈΡΠΎΒΠ²Π°ΡΡ ΡΠΈΠ»Ρ Π½Π°ΡΡΠΆΠ΅Π½ΠΈΡ ΠΏΡΠΎΠ²ΠΎΠ»ΠΎΠΊΠΈ, ΡΠΌΠ°ΡΡΠ²Π°ΡΡΠ΅ΠΉΡΡ Ρ ΠΊΠ°ΡΡΡΠΊΠΈ.
ΠΠ°ΠΆΠ½ΡΠΌ ΡΠ»Π΅ΠΌΠ΅Π½ΡΠΎΠΌ ΡΠ°Π·ΠΌΠ°ΡΡΠ²Π°ΡΡΠΈΡ ΡΡΡΡΠΎΠΉΡΡΠ², ΠΎΡΠΎΠ±Π΅Π½Π½ΠΎ Ρ ΠΌΠΎΡΠΊΠΎΠ², ΡΠ²Π»ΡΠ΅ΡΡΡ Π½Π°Π»ΠΈΡΠΈΠ΅ ΠΊΠΎΠ½Π΅ΡΠ½ΡΡ Π²ΡΠΊΠ»ΡΡΠ°ΡΠ΅Π»Π΅ΠΉ, ΠΏΡΠ΅Π΄Π½Π°Π·Π½Π°ΡΠ΅Π½Π½ΡΡ Π΄Π»Ρ ΠΎΡΠΊΒΠ»ΡΡΠ΅Π½ΠΈΡ Π²ΠΎΠ»ΠΎΡΠΈΠ»ΡΠ½ΠΎΠ³ΠΎ ΡΡΠ°Π½Π° Π² ΡΠ»ΡΡΠ°Π΅ Π·Π°ΠΏΡΡΡΠ²Π°Π½ΠΈΡ Π²ΠΈΡΠΊΠΎΠ² ΠΏΡΠΎΠ²ΠΎΠ»ΠΎΠΊΠΈ ΠΈ Π΅Π΅ Π·Π°ΡΡΠΆΠΊΠΈ, Π° ΡΠ°ΠΊΠΆΠ΅ ΠΏΡΠΈ ΠΎΠΊΠΎΠ½ΡΠ°Π½ΠΈΠΈ ΠΌΠΎΡΠΊΠ° ΠΏΡΠΎΠ²ΠΎΠ»ΠΎΠΊΠΈ. ΠΠ½ΠΈ ΡΡΡΠ°Π½Π°Π²ΒΠ»ΠΈΠ²Π°ΡΡΡΡ ΠΌΠ΅ΠΆΠ΄Ρ ΡΠ°Π·ΠΌΠΎΡΠΎΡΠ½ΡΠΌ ΡΡΡΡΠΎΠΉΡΡΠ²ΠΎΠΌ ΠΈ Π²ΠΎΠ»ΠΎΡΠΈΠ»ΡΠ½ΡΠΌ ΡΡΠ°Π½ΠΎΠΌ.
Π£ΠΏΡΠ°Π²Π»Π΅Π½ΠΈΠ΅ ΠΊΠΎΠ½Π΅ΡΠ½ΡΠΌ Π²ΡΠΊΠ»ΡΡΠ°ΡΠ΅Π»Π΅ΠΌ ΠΎΡΡΡΠ΅ΡΡΠ²Π»ΡΠ΅ΡΡΡ ΠΏΠΎΠ²ΠΎΡΠΎΡΠ½ΡΠΌ ΡΡΡΠ°Π³ΠΎΠΌ-ΡΠΊΠΎΠ±ΠΎΠΉ, ΡΠ΅ΡΠ΅Π· ΠΊΠΎΡΠΎΡΡΡ ΠΏΡΠΎΠΏΡΡΠΊΠ°Π΅ΡΡΡ ΠΏΡΠΎΠ²ΠΎΠ»ΠΎΠΊΠ°. ΠΠ° Π½Π΅ΠΊΠΎΡΠΎΒΡΡΡ Π²ΠΎΠ»ΠΎΡΠΈΠ»ΡΠ½ΡΡ ΡΡΠ°Π½Π°Ρ ΡΡΡΠ°Π½Π°Π²Π»ΠΈΠ²Π°ΡΡΡΡ ΠΏΠ΅ΡΠ»Π΅Π²ΡΠ΅ ΠΊΠΎΠΌΠΏΠ΅Π½ΡΠ°ΡΠΎΡΡ, ΠΊΠΎΒΡΠΎΡΡΠ΅ Π·Π° ΡΡΠ΅Ρ ΡΠ΄Π»ΠΈΠ½Π΅Π½ΠΈΡ ΠΈΠ»ΠΈ ΡΠΊΠΎΡΠΎΡΠ΅Π½ΠΈΡ ΠΏΠ΅ΡΠ»ΠΈ ΠΏΡΠΎΠ²ΠΎΠ»ΠΎΠΊΠΈ ΡΠΎΠ³Π»Π°ΡΡΡΡ ΡΠ°Π±ΠΎΡΡ ΡΠ°Π·ΠΌΠΎΡΠΎΡΠ½ΠΎΠ³ΠΎ ΡΡΡΡΠΎΠΉΡΡΠ²Π° Ρ Π²ΠΎΠ»ΠΎΡΠΈΠ»ΡΠ½ΡΠΌ ΡΡΠ°Π½ΠΎΠΌ, ΡΠ°ΠΊΠΆΠ΅ ΠΏΡΠ΅ΒΠ΄ΠΎΡ ΡΠ°Π½ΡΡ ΠΎΠ±ΡΡΠ²Π½ΠΎΡΡΡ ΠΏΡΠΎΠ²ΠΎΠ»ΠΎΠΊΠΈ.
ΠΠ° ΡΠ°Π±ΠΎΡΠ΅ΠΉ ΠΏΠ»ΠΎΡΠ°Π΄ΠΊΠ΅ ΡΠ°Π·ΠΌΠΎΡΠΎΡΠ½ΡΡ ΡΡΡΡΠΎΠΉΡΡΠ² ΡΡΡΠ°Π½Π°Π²Π»ΠΈΠ²Π°ΡΡΡΡ Π½ΠΎΠΆΠ½ΠΈΡΡ Π΄Π»Ρ ΠΎΠ±ΡΠ΅Π·ΠΊΠΈ ΠΊΠΎΠ½ΡΠΎΠ² ΠΏΠ΅ΡΠ΅Π΄ ΡΠ²Π°ΡΠΊΠΎΠΉ. ΠΡΠΎΠ²ΠΎΠ»ΠΎΠΊΠ° ΡΠΎΠ½ΠΊΠΈΡ ΠΈ ΡΡΠ΅Π΄Π½ΠΈΡ Π΄ΠΈΠ°ΠΌΠ΅ΡΡΠΎΠ² ΠΌΠΎΠΆΠ΅Ρ Π±ΡΡΡ ΠΎΠ±ΡΠ΅Π·Π°Π½Π° ΠΌΠ΅Ρ Π°Π½ΠΈΡΠ΅ΡΠΊΠΈΠΌΠΈ Π½ΠΎΠΆΠ½ΠΈΡΠ°ΠΌΠΈ, ΡΡΡΠ°Π½Π°Π²Π»ΠΈΠ²Π°Π΅ΠΌΡΠΌΠΈ Π½Π° ΠΎΡΡΡΠΈΠ»ΡΠ½ΡΡ Π°ΠΏΠΏΠ°ΡΠ°ΡΠ°Ρ . ΠΠ»Ρ Π±ΠΎΠ»Π΅Π΅ ΡΠΎΠ»ΡΡΠΎΠ³ΠΎ Π΄ΠΈΠ°ΒΠΌΠ΅ΡΡΠ° ΠΎΡ 0.8 ΠΌΠΌ ΠΈ Π±ΠΎΠ»Π΅Π΅ ΡΠΈΡΠΎΠΊΠΎ Π·Π°ΡΠ΅ΠΊΠΎΠΌΠ΅Π½Π΄ΠΎΠ²Π°Π»ΠΈ ΡΠ΅Π±Ρ Π² ΡΠ°Π±ΠΎΡΠ΅ Π½ΠΎΠΆΒΠ½ΠΈΡΡ Ρ Π³ΠΈΠ΄ΡΠΎΠΏΡΠΈΠ²ΠΎΠ΄ΠΎΠΌ Ρ ΡΠΈΠ»ΠΎΠΉ ΡΠ΅Π·Π°Π½ΠΈΡ Π΄ΠΎ 150 ΠΊΠ (15 ΡΡ), ΠΈΠΌΠ΅ΡΡΠΈΠ΅ Π°Π²ΡΠΎΠ½ΠΎΠΌΠ½ΡΡ ΡΡΠ°Π½ΡΠΈΡ ΡΠΎ Π²ΡΠ΅ΠΌ Π½Π΅ΠΎΠ±Ρ ΠΎΠ΄ΠΈΠΌΡΠΌ ΠΎΠ±ΠΎΡΡΠ΄ΠΎΠ²Π°Π½ΠΈΠ΅ΠΌ. Π Π°Π±ΠΎΡΠ΅Π΅ Π΄Π°Π²ΒΠ»Π΅Π½ΠΈΠ΅ Π² Π³ΠΈΠ΄ΡΠΎΡΠΈΡΡΠ΅ΠΌΠ΅ Π΄ΠΎΡΡΠΈΠ³Π°Π΅Ρ 16 ΠΠΠ° (160 ΠΊΠ³Ρ/ΡΠΌ2).
Π Π°Π·ΠΌΠΎΡΠΎΡΠ½ΡΠ΅ ΡΡΡΡΠΎΠΉΡΡΠ²Π° Ρ ΠΊΠ°ΡΡΡΠ΅ΠΊ AVS 630T ΠΈ AVS 800T
Π Π°Π·ΠΌΠΎΡΠΎΡΠ½ΡΠ΅ ΡΡΡΡΠΎΠΉΡΡΠ²Π° ΡΠΊΠ°Π·Π°Π½Π½ΡΡ ΡΠΈΠΏΠΎΠ² ΠΏΡΠ΅Π΄Π½Π°Π·Π½Π°ΡΠ΅Π½Ρ Π΄Π»Ρ ΡΠ°Π·ΠΌΠ°ΡΡΠ²Π°Π½ΠΈΡ ΠΏΡΠΎΠ²ΠΎΠ»ΠΎΠΊΠΈ-Π·Π°Π³ΠΎΡΠΎΠ²ΠΊΠΈ ΠΏΠ΅ΡΠ΅Π΄ Π²ΠΎΠ»ΠΎΡΠΈΠ»ΡΠ½ΡΠΌ ΡΡΠ°Π½ΠΎΠΌ Ρ ΠΊΠ°ΡΡΒΡΠ΅ΠΊ Π΄ΠΈΠ°ΠΌΠ΅ΡΡΠΎΠΌ 315-630 ΠΌΠΌ Π½Π° AVS 630T ΠΈ Π΄ΠΈΠ°ΠΌΠ΅ΡΡΠΎΠΌ 500-800 ΠΌΠΌ Π΄Π»Ρ AVS 800T. ΠΠ°ΠΊΡΠΈΠΌΠ°Π»ΡΠ½ΠΎ Π΄ΠΎΠΏΡΡΡΠΈΠΌΠ°Ρ ΠΌΠ°ΡΡΠ° ΠΏΡΠΎΠ²ΠΎΠ»ΠΎΠΊΠΈ Π΄Π»Ρ ΠΏΠ΅ΡΠ²ΠΎΠ³ΠΎ ΡΡΡΒΡΠΎΠΉΡΡΠ²Π° Π΄ΠΎ 700 ΠΊΠ³, Π° Π΄Π»Ρ Π²ΡΠΎΡΠΎΠ³ΠΎ — Π΄ΠΎ 1200 ΠΊΠ³.
Π ΡΠ²Π°ΡΠ½ΠΎΠΌ ΠΊΠΎΡΠΏΡΡΠ΅1 (ΡΠΈΡ.2.1) ΡΠ°ΡΠΏΠΎΠ»ΠΎΠΆΠ΅Π½Ρ Π΄Π²Π΅ ΡΡΡΠ°ΠΆΠ½ΡΠ΅ ΠΎΠΏΠΎΡΡ 5 ΠΈ 7. ΠΠΏΠΎΡΡ ΠΏΠ΅ΡΠ΅ΠΌΠ΅ΡΠ°ΡΡΡΡ ΠΏΠΎΡΡΡΠΏΠ°ΡΠ΅Π»ΡΠ½ΠΎ ΠΏΠΎ ΠΎΡΠΈ 4 ΠΏΡΠΈ ΠΏΠΎΠΌΠΎΡΠΈ Ρ ΠΎΠ΄ΠΎΠ²ΠΎΠ³ΠΎ Π²ΠΈΠ½ΡΠ° 6 Ρ Π»Π΅Π²ΠΎΠΉ ΠΈ ΠΏΡΠ°Π²ΠΎΠΉ ΡΠ΅Π·ΡΠ±ΠΎΠΉ, Π²ΡΠ°ΡΠ°ΡΡΠ΅Π³ΠΎΡΡ Π²ΡΡΡΠ½ΡΡ ΠΎΡ ΡΡΡΡΠ²Π°Π»Π° 3. ΠΠ°ΠΆΠΈΠΌΠ½ΡΠ΅ ΠΊΠΎΠ½ΡΡΡ 9 ΠΈΠΌΠ΅ΡΡ ΡΠΏΠ΅ΡΠΈΠ°Π»ΡΠ½ΡΡ ΡΠΎΡΠΌΡ, ΡΡΠΈΡΡΠ²Π°ΡΡΡΡ ΡΠ°Π·ΠΌΠ΅ΡΡ ΠΎΡΠ²Π΅ΡΡΡΠΈΠΉ ΠΊΠ°ΡΡΡΠ΅ΠΊ ΡΠ°Π·Π»ΠΈΡΠ½ΡΡ Π΄ΠΈΠ°ΠΌΠ΅ΡΡΠΎΠ². ΠΠ»Ρ ΠΏΠΎΠ΄ΡΠ΅ΠΌΠ° ΠΊΠ°ΡΡΡΠ΅ΠΊ ΡΠΎ ΡΡΠ°Π½ΠΈΠ½Ρ, ΠΏΠΎΡΠ»Π΅ Π·Π°ΠΆΠ°ΡΠΈΡ ΠΈΡ ΠΊΠΎΠ½ΡΡΠ°ΠΌΠΈ, ΡΠ»ΡΠΆΠΈΡ ΡΠΊΡΡΠ΅Π½ΡΡΠΈΠΊΠΎΠ²ΡΠΉ ΠΌΠ΅Ρ Π°Π½ΠΈΠ·ΠΌ 2 Ρ ΠΏΡΠΈΠ²ΠΎΠ΄ΠΎΠΌ ΠΎΡ ΡΡΠΊΠΎΡΡΠΊΠΈ-ΡΡΡΠ°Π³Π° 8. ΠΠΏΡΡΠΊΠ°Ρ ΡΡΡΠ°Π³ Π΄ΠΎ Π³ΠΎΡΠΈΠ·ΠΎΠ½ΡΠ°Π»ΡΠ½ΠΎΠ³ΠΎ ΠΏΠΎΠ»ΠΎΠΆΠ΅Π½ΠΈΡ, ΠΊΠ°ΡΡΡΠΊΠ° ΡΡΡΠ°Π½Π°Π²Π»ΠΈΠ²Π°Π΅ΡΡΡ Π² ΡΠ°Π±ΠΎΡΠ΅Π΅ ΠΏΠΎΠ»ΠΎΠΆΠ΅Π½ΠΈΠ΅. ΠΠ° ΠΎΠ΄Π½ΠΎΠΌ ΠΈΠ· ΠΊΠΎΠ½ΡΡΠΎΠ² ΡΡΡΠ°Π½ΠΎΠ²Π»Π΅Π½ ΡΠΎΡΠΌΠΎΠ·Π½ΠΎΠΉ ΡΠΊΠΈΠ² 10, ΡΠ°Π±ΠΎΡΠ°ΡΡΠΈΠΉ ΠΏΠΎ ΠΏΡΠΈΠ½ΡΠΈΠΏΡ Π»Π΅Π½ΡΠΎΡΠ½ΠΎΠ³ΠΎ ΡΠΎΡΠΌΠΎΠ·Π°, ΠΈ ΡΠ΅Π³ΡΠ»ΠΈΡΠΎΠ²Π°Π½ΠΈΠ΅ Π½Π°ΡΡΠΆΠ΅Π½ΠΈΡ ΡΡ ΠΎΠ΄ΡΡΠ΅ΠΉ Π·Π°Π³ΠΎΡΠΎΠ²ΠΊΠΈ ΠΏΡΠΎΠΈΠ·Π²ΠΎΠ΄ΠΈΡΡΡ Π²ΠΈΠ½ΡΠΎΠΌ Π’-ΠΎΠ±ΡΠ°Π·Π½ΠΎΠΉ ΡΠΎΡΠΌΡ.
Π ΠΈΡ.2.1. Π Π°Π·ΠΌΠΎΡΠΎΡΠ½ΠΎΠ΅ ΡΡΡΡΠΎΠΉΡΡΠ²ΠΎ AVS 630T ΠΈ AVS 800T
ΠΠ°ΠΌΠΎΡΠΎΡΠ½ΡΠ΅ Π°ΠΏΠΏΠ°ΡΠ°ΡΡ Π΄Π»Ρ Π²ΠΎΠ»ΠΎΡΠΈΠ»ΡΠ½ΡΡ ΡΡΠ°Π½ΠΎΠ²
ΠΠ°ΠΌΠΎΡΠΎΡΠ½ΡΠ΅ Π°ΠΏΠΏΠ°ΡΠ°ΡΡ, ΡΡΡΠ°Π½Π°Π²Π»ΠΈΠ²Π°Π΅ΠΌΡΠ΅ Π² ΠΎΠ΄Π½ΠΎΠΉ Π»ΠΈΠ½ΠΈΠΈ Ρ Π²ΠΎΠ»ΠΎΡΠΈΠ»ΡΠ½ΡΠΌΠΈ ΡΡΠ°Π½Π°ΠΌΠΈ, ΠΏΡΠ΅Π΄Π½Π°Π·Π½Π°ΡΠ΅Π½Ρ Π΄Π»Ρ Π½Π°ΠΌΠ°ΡΡΠ²Π°Π½ΠΈΡ ΠΏΡΠΎΠ²ΠΎΠ»ΠΎΠΊΠΈ Π³ΠΎΡΠΎΠ²ΠΎΠ³ΠΎ ΡΠ°Π·ΠΌΠ΅ΡΠ° Π½Π° ΠΊΠ°ΡΡΡΠΊΠΈ Π±ΠΎΠ»ΡΡΠΎΠΉ Π²ΠΌΠ΅ΡΡΠΈΠΌΠΎΡΡΠΈ: 250, 500 ΠΈ 1000 ΠΊΠ³, Π° ΠΈΠ½ΠΎΠ³Π΄Π° ΠΈ Π±ΠΎΠ»Π΅Π΅. ΠΠ»Π°Π³ΠΎΠ΄Π°ΡΡ Π±ΠΎΠ»ΡΡΠΎΠΉ Π²ΠΌΠ΅ΡΡΠΈΠΌΠΎΡΡΠΈ ΠΊΠ°ΡΡΡΠΊΠΈ ΠΏΠΎ ΡΡΠ°Π²Π½Π΅Π½ΠΈΡ Ρ ΠΌΠ°ΡΡΠΎΠΉ ΠΌΠΎΡΠΊΠ° Π½Π° ΡΠΈΡΡΠΎΠ²ΠΎΠΌ Π±Π°ΡΠ°Π±Π°Π½Π΅ Π²ΠΎΠ»ΠΎΡΠΈΠ»ΡΠ½ΠΎΠ³ΠΎ ΡΡΠ°Π½Π°, ΠΎΠ±ΡΡΠ½ΠΎ Π½Π΅ ΠΏΡΠ΅Π²ΡΡΠ°ΡΡΠ΅ΠΉ 70-80 ΠΊΠ³, ΡΠ²Π΅Π»ΠΈΡΠΈΠ²Π°Π΅ΡΡΡ ΠΏΡΠΎΠΈΠ·Π²ΠΎΠ΄ΠΈΡΠ΅Π»ΡΠ½ΠΎΡΡΡ ΡΡΠ°Π½Π° Π·Π° ΡΡΠ΅Ρ ΡΠΎΠΊΡΠ°ΡΠ΅Π½ΠΈΡ ΡΠΈΡΠ»Π° Π΅Π³ΠΎ ΠΎΡΡΠ°Π½ΠΎΠ²ΠΎΠΊ Π΄Π»Ρ ΡΡΠ΅ΠΌΠ° Π³ΠΎΡΠΎΠ²ΠΎΠΉ ΠΏΡΠΎΠ²ΠΎΠ»ΠΎΠΊΠΈ, Ρ.Π΅. ΡΠ²Π΅Π»ΠΈΡΠΈΠ²Π°Π΅ΡΡΡ Π΄ΠΎΠ»Ρ ΠΌΠ°ΡΠΈΠ½Π½ΠΎΠ³ΠΎ Π²ΡΠ΅ΠΌΠ΅Π½ΠΈ ΠΈ ΡΠΎΠΊΡΠ°ΡΠ°Π΅ΡΡΡ Π²ΡΠ΅ΠΌΡ Π½Π° ΡΡΡΠ½ΡΠ΅ ΠΎΠΏΠ΅ΡΠ°ΡΠΈΠΈ.
ΠΠ°ΠΌΠΎΡΠ°Π½Π½Π°Ρ ΠΏΡΠΎΠ²ΠΎΠ»ΠΎΠΊΠ° Π½Π° ΠΊΠ°ΡΡΡΠΊΠ°Ρ Π»Π΅Π³ΠΊΠΎ ΡΠ°Π·ΠΌΠ°ΡΡΠ²Π°Π΅ΡΡΡ Π±Π΅Π· Π·Π°ΠΏΡΡΡΠ²Π°Π½ΠΈΡ ΠΏΡΠΈ ΠΏΠΎΡΠ»Π΅Π΄ΡΡΡΠΈΡ ΡΠ΅Ρ Π½ΠΎΠ»ΠΎΠ³ΠΈΡΠ΅ΡΠΊΠΈΡ ΠΏΡΠΎΡΠ΅ΡΡΠ°Ρ , Π½Π°ΠΏΡΠΈΠΌΠ΅Ρ, ΠΏΡΠΈ ΠΏΠ΅ΡΠ΅ΠΌΠΎΡΠΊΠ΅ ΠΏΡΠΎΠ²ΠΎΠ»ΠΎΠΊΠΈ Π½Π° Π·Π°ΡΡΠ΄Π½ΡΠ΅ ΠΊΠ°ΡΡΡΠΊΠΈ Π² ΠΊΠ°Π½Π°ΡΠ½ΡΡ ΡΠ΅Ρ Π°Ρ . Π ΡΠ΅Π·ΡΠ»ΡΡΠ°ΡΠ΅ ΡΠΌΠ΅Π½ΡΡΠ°Π΅ΡΡΡ ΠΊΠΎΠ»ΠΈΡΠ΅ΡΡΠ²ΠΎ ΠΎΡΡ ΠΎΠ΄ΠΎΠ² ΠΏΡΠΈ ΠΏΠ΅ΡΠ΅ΠΌΠΎΡΠΊΠ΅.
ΠΠ° ΡΡΠ°Π½Π°Ρ Π±Π»ΠΎΡΠ½ΠΎΠ³ΠΎ ΡΠΈΠΏΠ° Π½Π°ΠΌΠΎΡΠΎΡΠ½ΡΠ΅ Π°ΠΏΠΏΠ°ΡΠ°ΡΡ ΡΠ²Π»ΡΡΡΡΡ ΡΠ°ΠΌΠΎΡΡΠΎΡΡΠ΅Π»ΡΠ½ΡΠΌΠΈ Π°Π³ΡΠ΅Π³Π°ΡΠ°ΠΌΠΈ, ΡΠ°Π±ΠΎΡΠ° ΠΊΠΎΡΠΎΡΡΡ Π΄ΠΎΠ»ΠΆΠ½Π° Π±ΡΡΡ ΡΡΡΠΎΠ³ΠΎ ΡΠΎΠ³Π»Π°ΡΠΎΠ²Π°Π½Π½ΠΎΠΉ Ρ ΡΠ°Π±ΠΎΡΠΎΠΉ Π²ΠΎΠ»ΠΎΡΠΈΠ»ΡΠ½ΠΎΠ³ΠΎ ΡΡΠ°Π½Π°, ΡΠΎΡΠ½Π΅Π΅ ΡΠΊΠΎΡΠΎΡΡΡ Π½Π°ΠΌΠΎΡΠΊΠΈ ΠΏΡΠΎΠ²ΠΎΠ»ΠΎΠΊΠΈ Π½Π° ΠΊΠ°ΡΡΡΠΊΡ Π΄ΠΎΠ»ΠΆΠ½Π° Π±ΡΡΡ ΡΠΈΠ½Ρ ΡΠΎΠ½ΠΈΠ·ΠΈΡΠΎΠ²Π°Π½Π° ΡΠΎ ΡΠΊΠΎΡΠΎΡΡΡΡ Π΅Π΅ Π΄Π²ΠΈΠΆΠ΅Π½ΠΈΡ Ρ ΡΠΈΡΡΠΎΠ²ΠΎΠ³ΠΎ Π±Π°ΡΠ°Π±Π°Π½Π°.
ΠΠ°ΠΌΠΎΡΠΎΡΠ½ΡΠ΅ Π°ΠΏΠΏΠ°ΡΠ°ΡΡ, ΠΊΠ°ΠΊ ΡΠ°ΠΌΠΎΡΡΠΎΡΡΠ΅Π»ΡΠ½ΡΠ΅ Π°Π³ΡΠ΅Π³Π°ΡΡ, ΠΈΠΌΠ΅ΡΡ ΠΈΠ½Π΄ΠΈΠ²ΠΈΠ΄ΡΠ°Π»ΡΠ½ΡΠ΅ ΠΏΡΠΈΠ²ΠΎΠ΄Ρ, ΠΊΠΎΡΠΎΡΡΠ΅ Π΄ΠΎΠ»ΠΆΠ½Ρ ΠΎΠ±Π΅ΡΠΏΠ΅ΡΠΈΠ²Π°ΡΡ ΡΠΈΡΠΎΠΊΠΈΠΉ Π΄ΠΈΠ°ΠΏΠ°Π·ΠΎΠ½ ΡΠΊΠΎΡΠΎΡΡΠ΅ΠΉ Π½Π°ΠΌΠΎΡΠΊΠΈ Π² ΡΠΎΠΎΡΠ²Π΅ΡΡΡΠ²ΠΈΠΈ ΡΠΎ ΡΠΊΠΎΡΠΎΡΡΡΠΌΠΈ Π²ΠΎΠ»ΠΎΡΠ΅Π½ΠΈΡ ΠΏΡΠΎΠ²ΠΎΠ»ΠΎΠΊΠΈ Π½Π° Π²ΠΎΠ»ΠΎΡΠΈΠ»ΡΠ½ΠΎΠΌ ΡΡΠ°Π½Π΅. ΠΡΠΈΠ²ΠΎΠ΄ Π½Π°ΠΌΠΎΡΠΎΡΠ½ΠΎΠ³ΠΎ Π°ΠΏΠΏΠ°ΡΠ°ΡΠ° Π΄ΠΎΠ»ΠΆΠ΅Π½ ΠΎΠ±Π΅ΡΠΏΠ΅ΡΠΈΠ²Π°ΡΡ ΠΏΠΎΡΡΠΎΡΠ½Π½ΠΎΠ΅ ΠΈ ΡΠ°Π²Π½ΠΎΠΌΠ΅ΡΠ½ΠΎΠ΅ Π½Π°ΡΡΠΆΠ΅Π½ΠΈΠ΅ ΠΏΡΠΎΠ²ΠΎΠ»ΠΎΠΊΠΈ ΠΏΡΠΈ Π΅Π΅ Π½Π°ΠΌΠΎΡΠΊΠ΅ Π½Π° ΠΊΠ°ΡΡΡΠΊΡ ΠΈ ΠΏΠΎ ΠΌΠ΅ΡΠ΅ ΡΠ²Π΅Π»ΠΈΡΠ΅Π½ΠΈΡ Π΄ΠΈΠ°ΠΌΠ΅ΡΡΠ° Π½Π°ΠΌΠΎΡΠΊΠΈ. ΠΠΎ Π²ΡΠ΅ΠΌΡ ΠΏΡΡΠΊΠ° Π²ΠΎΠ»ΠΎΡΠΈΠ»ΡΠ½ΠΎΠ³ΠΎ ΡΡΠ°Π½Π° Π½Π΅ Π΄ΠΎΠ»ΠΆΠ½ΠΎ Π±ΡΡΡ ΡΠ»Π°Π±ΠΈΠ½Ρ ΠΏΡΠΎΠ²ΠΎΠ»ΠΎΠΊΠΈ, ΠΈΠ½Π°ΡΠ΅ ΠΏΡΠΎΠΈΠ·ΠΎΠΉΠ΄Π΅Ρ ΠΏΡΠΎΡΠΊΠ°Π»ΡΠ·ΡΠ²Π°Π½ΠΈΠ΅ Π²ΠΈΡΠΊΠΎΠ² ΠΏΡΠΎΠ²ΠΎΠ»ΠΎΠΊΠΈ Π½Π° ΡΠΈΡΡΠΎΠ²ΠΎΠΌ Π±Π°ΡΠ°Π±Π°Π½Π΅ Π²ΠΎΠ»ΠΎΡΠΈΠ»ΡΠ½ΠΎΠ³ΠΎ ΡΡΠ°Π½Π° ΠΈ, ΠΊΠ°ΠΊ ΡΠ»Π΅Π΄ΡΡΠ²ΠΈΠ΅, ΠΎΠ±ΡΡΠ² ΠΏΡΠΎΠ²ΠΎΠ»ΠΎΠΊΠΈ. ΠΠ½Π°Π»ΠΎΠ³ΠΈΡΠ½ΠΎ, ΠΏΡΠΈ ΠΎΡΡΠ°Π½ΠΎΠ²Π΅ ΡΡΠ°Π½Π°, ΡΠΎΡΠΌΠΎΠΆΠ΅Π½ΠΈΠΈ Π½Π΅ Π΄ΠΎΠ»ΠΆΠ½ΠΎ Π±ΡΡΡ ΡΡΠ΅Π·ΠΌΠ΅ΡΠ½ΠΎΠ³ΠΎ Π½Π°ΡΡΠΆΠ΅Π½ΠΈΡ ΠΏΡΠΎΠ²ΠΎΠ»ΠΎΠΊΠΈ ΠΌΠ΅ΠΆΠ΄Ρ ΠΊΠ°ΡΡΡΠΊΠΎΠΉ ΠΈ ΡΠΈΡΡΠΎΠ²ΡΠΌ Π±Π°ΡΠ°Π±Π°Π½ΠΎΠΌ.
Π€ΡΠ΅Π·Π΅ΡΠΎΠ²Π°Π½ΠΈΠ΅
ΠΠΏΡΠ΅Π΄Π΅Π»Π΅Π½ΠΈΡ ΡΡΠ΅Π·Π΅ΡΠ½ΠΎΠΉ ΠΏΠ»Π°ΡΡΠΈΠ½Ρ
ΠΡΡΠ°Π²ΡΡΠ΅ Π³Π΅ΠΎΠΌΠ΅ΡΡΠΈΡ
ΠΠΎΠ»Π΅Π΅ Π΄Π΅ΡΠ°Π»ΡΠ½ΠΎΠ΅ ΠΈΠ·ΡΡΠ΅Π½ΠΈΠ΅ Π³Π΅ΠΎΠΌΠ΅ΡΡΠΈΠΈ ΡΠ΅ΠΆΡΡΠ΅ΠΉ ΠΊΡΠΎΠΌΠΊΠΈ ΠΏΠΎΠΊΠ°Π·ΡΠ²Π°Π΅Ρ Π΄Π²Π° Π²Π°ΠΆΠ½ΡΡ ΡΠ³Π»Π° Π½Π° ΠΏΠ»Π°ΡΡΠΈΠ½Π΅:
ΠΏΠ΅ΡΠ΅Π΄Π½ΠΈΠΉ ΡΠ³ΠΎΠ» (Ξ³)
ΡΠ³ΠΎΠ» ΡΠ΅ΠΆΡΡΠ΅ΠΉ ΠΊΡΠΎΠΌΠΊΠΈ (Ξ²)
ΠΠ°ΠΊΡΠΎ Π³Π΅ΠΎΠΌΠ΅ΡΡΠΈΡ ΡΠ°Π·ΡΠ°Π±ΠΎΡΠ°Π½Π° Π΄Π»Ρ ΡΠ°Π±ΠΎΡΡ Π² Π»Π΅Π³ΠΊΠΈΡ , ΡΡΠ΅Π΄Π½ΠΈΡ ΠΈΠ»ΠΈ ΡΡΠΆΠ΅Π»ΡΡ ΡΡΠ»ΠΎΠ²ΠΈΡΡ .
L (ΠΠ΅Π³ΠΊΠ°Ρ) Π³Π΅ΠΎΠΌΠ΅ΡΡΠΈΡ ΠΈΠΌΠ΅Π΅Ρ Π±ΠΎΠ»Π΅Π΅ ΠΏΠΎΠ»ΠΎΠΆΠΈΡΠ΅Π»ΡΠ½ΡΠΉ, Π½ΠΎ Π±ΠΎΠ»Π΅Π΅ ΡΠ»Π°Π±ΡΠΉ ΠΊΡΠ°ΠΉ (Π±ΠΎΠ»ΡΡΠΎΠΉ Ξ³, ΠΌΠ°Π»Π΅Π½ΡΠΊΠΈΠΉ Ξ²)
H (ΡΡΠΆΠ΅Π»Π°Ρ) Π³Π΅ΠΎΠΌΠ΅ΡΡΠΈΡ ΠΈΠΌΠ΅Π΅Ρ Π±ΠΎΠ»Π΅Π΅ ΡΠΈΠ»ΡΠ½ΡΠΉ, Π½ΠΎ ΠΌΠ΅Π½Π΅Π΅ ΠΏΠΎΠ»ΠΎΠΆΠΈΡΠ΅Π»ΡΠ½ΡΠΉ ΠΊΡΠ°ΠΉ (ΠΌΠ°Π»Π΅Π½ΡΠΊΠΈΠΉ Ξ³, Π±ΠΎΠ»ΡΡΠΎΠΉ Ξ²)
ΠΠ°ΠΊΡΠΎ Π³Π΅ΠΎΠΌΠ΅ΡΡΠΈΡ Π²Π»ΠΈΡΠ΅Ρ Π½Π° ΠΌΠ½ΠΎΠ³ΠΈΠ΅ ΠΏΠ°ΡΠ°ΠΌΠ΅ΡΡΡ Π² ΠΏΡΠΎΡΠ΅ΡΡΠ΅ ΡΠ΅Π·ΠΊΠΈ.ΠΡΡΠ°Π²ΠΊΠ° Ρ ΠΏΡΠΎΡΠ½ΠΎΠΉ ΡΠ΅ΠΆΡΡΠ΅ΠΉ ΠΊΡΠΎΠΌΠΊΠΎΠΉ ΠΌΠΎΠΆΠ΅Ρ ΡΠ°Π±ΠΎΡΠ°ΡΡ ΠΏΡΠΈ Π±ΠΎΠ»Π΅Π΅ Π²ΡΡΠΎΠΊΠΈΡ Π½Π°Π³ΡΡΠ·ΠΊΠ°Ρ , Π½ΠΎ ΡΠ°ΠΊΠΆΠ΅ Π³Π΅Π½Π΅ΡΠΈΡΡΠ΅Ρ Π±ΠΎΠ»Π΅Π΅ Π²ΡΡΠΎΠΊΠΈΠ΅ ΡΠΈΠ»Ρ ΡΠ΅Π·Π°Π½ΠΈΡ, ΠΏΠΎΡΡΠ΅Π±Π»ΡΠ΅Ρ Π±ΠΎΠ»ΡΡΠ΅ ΡΠ½Π΅ΡΠ³ΠΈΠΈ ΠΈ Π²ΡΠ΄Π΅Π»ΡΠ΅Ρ Π±ΠΎΠ»ΡΡΠ΅ ΡΠ΅ΠΏΠ»Π°. ΠΠΏΡΠΈΠΌΠΈΠ·ΠΈΡΠΎΠ²Π°Π½Π½ΡΠ΅ Π³Π΅ΠΎΠΌΠ΅ΡΡΠΈΠΈ ΠΌΠ°ΡΠ΅ΡΠΈΠ°Π»Π° ΠΎΠ±ΠΎΠ·Π½Π°ΡΠ΅Π½Ρ Π±ΡΠΊΠ²ΠΎΠΉ ΠΊΠ»Π°ΡΡΠΈΡΠΈΠΊΠ°ΡΠΈΠΈ ISO. ΠΠ°ΠΏΡΠΈΠΌΠ΅Ρ, Π³Π΅ΠΎΠΌΠ΅ΡΡΠΈΡ Π΄Π»Ρ ΡΡΠ³ΡΠ½Π°: -KL, -KM ΠΈ -KH.

ΠΡΡΠ°Π²ΠΈΡΡ ΡΠ³Π»ΠΎΠ²ΠΎΠΉ Π΄ΠΈΠ·Π°ΠΉΠ½
ΠΠ°ΠΈΠ±ΠΎΠ»Π΅Π΅ Π²Π°ΠΆΠ½ΠΎΠΉ ΡΠ°ΡΡΡΡ ΡΠ΅ΠΆΡΡΠ΅ΠΉ ΠΊΡΠΎΠΌΠΊΠΈ Π΄Π»Ρ ΠΈΠ·Π³ΠΎΡΠΎΠ²Π»Π΅Π½ΠΈΡ ΠΏΠΎΠ²Π΅ΡΡ Π½ΠΎΡΡΠΈ ΡΠ²Π»ΡΠ΅ΡΡΡ ΠΏΠ°ΡΠ°Π»Π»Π΅Π»ΡΠ½ΡΠΉ ΡΡΠ°ΡΡΠΎΠΊ b Ρ 1 ΠΈΠ»ΠΈ, Π΅ΡΠ»ΠΈ ΠΏΡΠΈΠΌΠ΅Π½ΠΈΠΌΠΎ, Π²ΡΠΏΡΠΊΠ»ΡΠΉ ΡΡΠ°ΡΡΠΎΠΊ ΡΡΠ΅ΠΊΠ»ΠΎΠΎΡΠΈΡΡΠΈΡΠ΅Π»Ρ b Ρ 2 ΠΈΠ»ΠΈ ΡΠ°Π΄ΠΈΡΡ ΡΠ³Π»Π°, r Ξ΅ ,

Π£Π³Π»ΠΎΠ²ΠΎΠΉ ΡΠ°Π΄ΠΈΡΡ, r ΠΠ°ΡΠ°Π»Π»Π΅Π»ΡΠ½ΡΠΉ ΡΡΠ°ΡΡΠΎΠΊ ( b Ρ 1) Π£ΡΠ°ΡΡΠΎΠΊ ΡΡΠ΅ΠΊΠ»ΠΎΠΎΡΠΈΡΡΠΈΡΠ΅Π»Ρ ( b Ρ 2)
ΠΠΏΡΠ΅Π΄Π΅Π»Π΅Π½ΠΈΡ ΡΡΠ΅Π·
Π£Π³ΠΎΠ» Π²Ρ ΠΎΠ΄Π°, ( k r ) (Π³ΡΠ°Π΄ΡΡΡ)
ΠΡΠ½ΠΎΠ²Π½ΠΎΠΉ ΡΠ³ΠΎΠ» ΡΠ΅ΠΆΡΡΠ΅ΠΉ ΠΊΡΠΎΠΌΠΊΠΈ ( k, , r, ) ΡΡΠ΅Π·Ρ ΡΠ²Π»ΡΠ΅ΡΡΡ Π΄ΠΎΠΌΠΈΠ½ΠΈΡΡΡΡΠΈΠΌ ΡΠ°ΠΊΡΠΎΡΠΎΠΌ, ΡΠ°ΠΊ ΠΊΠ°ΠΊ ΠΎΠ½ Π²Π»ΠΈΡΠ΅Ρ Π½Π° Π½Π°ΠΏΡΠ°Π²Π»Π΅Π½ΠΈΠ΅ ΡΠΈΠ»Ρ ΡΠ΅Π·Π°Π½ΠΈΡ ΠΈ ΡΠΎΠ»ΡΠΈΠ½Ρ ΡΡΡΡΠΆΠΊΠΈ.
ΠΠΈΠ°ΠΌΠ΅ΡΡ ΡΡΠ΅Π·Ρ, D c (ΠΌΠΌ)
ΠΠΈΠ°ΠΌΠ΅ΡΡ ΡΡΠ΅Π·Ρ ( D c ) ΠΈΠ·ΠΌΠ΅ΡΡΠ΅ΡΡΡ ΠΏΠΎ ΡΠΎΡΠΊΠ΅ (PK), Π³Π΄Π΅ ΠΎΡΠ½ΠΎΠ²Π½Π°Ρ ΡΠ΅ΠΆΡΡΠ°Ρ ΠΊΡΠΎΠΌΠΊΠ° Π²ΡΡΡΠ΅ΡΠ°Π΅ΡΡΡ Ρ ΠΏΠ°ΡΠ°Π»Π»Π΅Π»ΡΠ½ΠΎΠΉ ΠΏΠΎΠ²Π΅ΡΡ Π½ΠΎΡΡΡΡ.
ΠΠ°ΠΈΠ±ΠΎΠ»Π΅Π΅ Π²Π°ΠΆΠ½ΡΠΌ ΠΈΠ· ΡΠ°ΡΡΠΌΠ°ΡΡΠΈΠ²Π°Π΅ΠΌΡΡ Π΄ΠΈΠ°ΠΌΠ΅ΡΡΠΎΠ² ΡΠ²Π»ΡΠ΅ΡΡΡ ( D ΠΊΠΎΠ»ΠΏΠ°ΡΠΎΠΊ ) — ΡΡΡΠ΅ΠΊΡΠΈΠ²Π½ΡΠΉ Π΄ΠΈΠ°ΠΌΠ΅ΡΡ ΡΠ΅Π·Π°Π½ΠΈΡ Π½Π° ΡΠ°ΠΊΡΠΈΡΠ΅ΡΠΊΠΎΠΉ Π³Π»ΡΠ±ΠΈΠ½Π΅ ΡΠ΅Π·Π°Π½ΠΈΡ ( a p ) — ΠΈΡΠΏΠΎΠ»ΡΠ·ΡΠ΅ΠΌΡΠΉ Π΄Π»Ρ ΡΠ°ΡΡΠ΅ΡΠ° ΠΈΡΡΠΈΠ½Π½ΠΎΠΉ ΡΠΊΠΎΡΠΎΡΡΠΈ ΡΠ΅Π·Π°Π½ΠΈΡ. D 3 — ΡΠ°ΠΌΡΠΉ Π±ΠΎΠ»ΡΡΠΎΠΉ Π΄ΠΈΠ°ΠΌΠ΅ΡΡ ΠΏΠ»Π°ΡΡΠΈΠ½Ρ, Π΄Π»Ρ Π½Π΅ΠΊΠΎΡΠΎΡΡΡ ΡΠ΅Π·ΡΠΎΠ² ΠΎΠ½ ΡΠ°Π²Π΅Π½ D c .
ΠΠ»ΡΠ±ΠΈΠ½Π° ΡΠ΅Π·Π°Π½ΠΈΡ, a p (ΠΌΠΌ)
ΠΠ»ΡΠ±ΠΈΠ½Π° ΡΠ΅Π·Π°Π½ΠΈΡ ( a p ) — ΡΡΠΎ ΡΠ°Π·Π½ΠΈΡΠ° ΠΌΠ΅ΠΆΠ΄Ρ Π½Π΅ΠΎΠ±ΡΠ΅Π·Π°Π½Π½ΠΎΠΉ ΠΈ ΡΠ΅ΠΆΡΡΠ΅ΠΉ ΠΏΠΎΠ²Π΅ΡΡ Π½ΠΎΡΡΡΡ Π² ΠΎΡΠ΅Π²ΠΎΠΌ Π½Π°ΠΏΡΠ°Π²Π»Π΅Π½ΠΈΠΈ.ΠΠ°ΠΊΡΠΈΠΌΡΠΌ Π° Ρ Π² ΠΎΡΠ½ΠΎΠ²Π½ΠΎΠΌ ΠΎΠ³ΡΠ°Π½ΠΈΡΠ΅Π½ ΡΠ°Π·ΠΌΠ΅ΡΠΎΠΌ Π²ΡΡΠ°Π²ΠΊΠΈ ΠΈ ΠΌΠΎΡΠ½ΠΎΡΡΡΡ ΠΌΠ°ΡΠΈΠ½Ρ.
ΠΡΠ΅ ΠΎΠ΄Π½ΠΈΠΌ ΠΊΡΠΈΡΠΈΡΠ΅ΡΠΊΠΈΠΌ ΡΠ°ΠΊΡΠΎΡΠΎΠΌ ΠΏΡΠΈ ΡΠ΅ΡΠ½ΠΎΠ²ΠΎΠΉ ΠΎΠ±ΡΠ°Π±ΠΎΡΠΊΠ΅ ΡΠ²Π»ΡΠ΅ΡΡΡ ΠΊΡΡΡΡΡΠΈΠΉ ΠΌΠΎΠΌΠ΅Π½Ρ, Π° ΠΏΡΠΈ ΡΠΈΡΡΠΎΠ²ΠΎΠΉ ΠΎΠ±ΡΠ°Π±ΠΎΡΠΊΠ΅ — Π²ΠΈΠ±ΡΠ°ΡΠΈΡ.
Π¨ΠΈΡΠΈΠ½Π° ΡΠ΅Π·Π°, a e (ΠΌΠΌ)
Π Π°Π΄ΠΈΠ°Π»ΡΠ½Π°Ρ ΡΠΈΡΠΈΠ½Π° ΡΠ΅Π·Π°ΠΊΠ° (, , ΠΈ ), Π·Π°Π½ΡΡΠΎΠ³ΠΎ ΡΠ΅Π·Π°Π½ΠΈΠ΅ΠΌ. ΠΡΠΎΠ±Π΅Π½Π½ΠΎ Π²Π°ΠΆΠ½ΠΎ ΠΏΡΠΈ Π²ΡΠ΅Π·Π°Π½ΠΈΠΈ Π½Π° ΡΠ°Π³ ΠΈ ΠΏΡΠΈ Π²ΠΈΠ±ΡΠ°ΡΠΈΠΈ ΠΏΡΠΈ ΡΡΠ΅Π·Π΅ΡΠΎΠ²Π°Π½ΠΈΠΈ ΡΠ³Π»ΠΎΠ², Π³Π΄Π΅ ΠΌΠ°ΠΊΡΠΈΠΌΡΠΌ ΠΈ e ΠΎΡΠΎΠ±Π΅Π½Π½ΠΎ Π²Π°ΠΆΠ½Ρ.
Π Π°Π΄ΠΈΠ°Π»ΡΠ½ΠΎΠ΅ ΠΏΠΎΠ³ΡΡΠΆΠ΅Π½ΠΈΠ΅, a e / D c
Π Π°Π΄ΠΈΠ°Π»ΡΠ½ΠΎΠ΅ ΠΏΠΎΠ³ΡΡΠΆΠ΅Π½ΠΈΠ΅ ( a e / D c ) — ΡΠΈΡΠΈΠ½Π° ΡΠ΅Π·Π° ΠΏΠΎ ΠΎΡΠ½ΠΎΡΠ΅Π½ΠΈΡ ΠΊ Π΄ΠΈΠ°ΠΌΠ΅ΡΡΡ ΡΡΠ΅Π·Ρ.
ΠΠΎΠ»ΠΈΡΠ΅ΡΡΠ²ΠΎ ΡΡΡΠ΅ΠΊΡΠΈΠ²Π½ΡΡ ΡΠ΅ΠΆΡΡΠΈΡ ΠΊΡΠΎΠΌΠΎΠΊ Π½Π° ΠΈΠ½ΡΡΡΡΠΌΠ΅Π½ΡΠ΅, z c
ΠΠ»Ρ ΠΎΠΏΡΠ΅Π΄Π΅Π»Π΅Π½ΠΈΡ ΠΏΠΎΠ΄Π°ΡΠΈ ΡΡΠΎΠ»Π° ( v f ) ΠΈ ΠΏΡΠΎΠΈΠ·Π²ΠΎΠ΄ΠΈΡΠ΅Π»ΡΠ½ΠΎΡΡΠΈ. ΠΡΠΎ ΡΠ°ΡΡΠΎ ΠΎΠΊΠ°Π·ΡΠ²Π°Π΅Ρ ΠΊΡΠΈΡΠΈΡΠ΅ΡΠΊΠΎΠ΅ Π²Π»ΠΈΡΠ½ΠΈΠ΅ Π½Π° ΡΠ΄Π°Π»Π΅Π½ΠΈΠ΅ ΡΡΡΡΠΆΠΊΠΈ ΠΈ ΡΡΠ°Π±ΠΈΠ»ΡΠ½ΠΎΡΡΡ ΡΠ°Π±ΠΎΡΡ.
ΠΠ±ΡΠ΅Π΅ ΠΊΠΎΠ»ΠΈΡΠ΅ΡΡΠ²ΠΎ ΡΠ΅ΠΆΡΡΠΈΡ ΠΊΡΠΎΠΌΠΎΠΊ Π½Π° ΠΈΠ½ΡΡΡΡΠΌΠ΅Π½ΡΠ΅, z n
Π Π°ΡΡΡΠΎΡΠ½ΠΈΠ΅ ΠΌΠ΅ΠΆΠ΄Ρ ΡΡΡΠ΅ΠΊΡΠΈΠ²Π½ΡΠΌΠΈ ΡΠ΅ΠΆΡΡΠΈΠΌΠΈ ΠΊΡΠΎΠΌΠΊΠ°ΠΌΠΈ, u
ΠΠ»Ρ ΠΎΠΏΡΠ΅Π΄Π΅Π»Π΅Π½Π½ΠΎΠ³ΠΎ Π΄ΠΈΠ°ΠΌΠ΅ΡΡΠ° ΡΡΠ΅Π·Ρ Π²Ρ ΠΌΠΎΠΆΠ΅ΡΠ΅ Π²ΡΠ±ΠΈΡΠ°ΡΡ ΠΌΠ΅ΠΆΠ΄Ρ ΡΠ°Π·Π»ΠΈΡΠ½ΡΠΌΠΈ ΡΠ°Π³Π°ΠΌΠΈ: Π³ΡΡΠ±ΡΠΉ (-L), Π±Π»ΠΈΠ·ΠΊΠΈΠΉ (-M), ΡΠ²Π΅ΡΡ Π±Π»ΠΎΡΠ½ΡΠΉ (-H). X, Π΄ΠΎΠ±Π°Π²Π»Π΅Π½Π½ΡΠΉ ΠΊ ΠΊΠΎΠ΄Ρ, ΠΎΠ±ΠΎΠ·Π½Π°ΡΠ°Π΅Ρ Π²Π΅ΡΡΠΈΡ ΡΠ΅Π·Π°ΠΊΠ°, ΡΠ°Π³ ΠΊΠΎΡΠΎΡΠΎΠ³ΠΎ Π½Π΅ΠΌΠ½ΠΎΠ³ΠΎ Π±Π»ΠΈΠΆΠ΅, ΡΠ΅ΠΌ Π΅Π³ΠΎ ΠΎΡΠ½ΠΎΠ²Π½ΠΎΠΉ Π΄ΠΈΠ·Π°ΠΉΠ½.
ΠΠΈΡΡΠ΅ΡΠ΅Π½ΡΠΈΠ°Π»ΡΠ½ΡΠΉ ΡΠ°Π³
Π£ΠΊΠ°Π·ΡΠ²Π°Π΅Ρ Π½Π° Π½Π΅ΡΠ°Π²Π½ΠΎΠ΅ ΡΠ°ΡΡΡΠΎΡΠ½ΠΈΠ΅ ΠΌΠ΅ΠΆΠ΄Ρ Π·ΡΠ±ΡΡΠΌΠΈ ΡΡΠ΅Π·Ρ.ΠΡΠΎ ΠΎΡΠ΅Π½Ρ ΡΡΡΠ΅ΠΊΡΠΈΠ²Π½ΡΠΉ ΡΠΏΠΎΡΠΎΠ± ΠΌΠΈΠ½ΠΈΠΌΠΈΠ·ΠΈΡΠΎΠ²Π°ΡΡ Π²ΠΈΠ±ΡΠ°ΡΠΈΠΎΠ½Π½ΡΠ΅ ΡΠ΅Π½Π΄Π΅Π½ΡΠΈΠΈ. ,
ΠΡ Π½Π°ΡΠ»ΠΈ Π½Π°Ρ ΠΏΡΠΎΡΡΠΎΠΉ Π±Π΅ΡΠΏΠ»Π°ΡΠ½ΡΠΉ ΠΎΠ½Π»Π°ΠΉΠ½-ΠΊΠ°Π»ΡΠΊΡΠ»ΡΡΠΎΡ ΠΏΠΎΠ΄Π°ΡΠΈ ΠΈ ΡΠΊΠΎΡΠΎΡΡΠΈ, ΠΊΠΎΡΠΎΡΡΠΉ ΠΈΡΠΏΠΎΠ»ΡΠ·ΡΠ΅Ρ ΠΊΠ»Π°ΡΡΠΈΡΠ΅ΡΠΊΠΈΠ΅ ΡΠΎΡΠΌΡΠ»Ρ, ΠΊΠΎΡΠΎΡΡΠ΅ ΠΏΡΠ΅ΠΏΠΎΠ΄Π°ΡΡΡΡ Π½Π° ΡΡΠΎΠΊΠ°Ρ Π² ΠΌΠ°Π³Π°Π·ΠΈΠ½Π΅. Π‘ ΠΊΠ°Π»ΡΠΊΡΠ»ΡΡΠΎΡΠΎΠΌ Π²Π°ΠΌ Π½Π΅ Π½ΡΠΆΠ½ΠΎ Π±Π΅ΡΠΏΠΎΠΊΠΎΠΈΡΡΡΡ ΠΎ ΡΠΎΠΌ, ΠΊΠ°ΠΊ ΡΠ°ΡΡΡΠΈΡΠ°ΡΡ ΡΠΊΠΎΡΠΎΡΡΡ ΠΏΠΎΠ΄Π°ΡΠΈ Π΄Π»Ρ ΡΡΠ΅Π·Π΅ΡΠΎΠ²Π°Π½ΠΈΡ ΠΈΠ»ΠΈ ΡΠΊΠΎΡΠΎΡΡΡ (ΠΎΠ± / ΠΌΠΈΠ½). ΠΡΠΎΡΡΠΎ Π²Π²Π΅Π΄ΠΈΡΠ΅ ΠΏΠ°ΡΠ°ΠΌΠ΅ΡΡΡ, ΠΈ Π½Π°Ρ ΠΊΠ°Π»ΡΠΊΡΠ»ΡΡΠΎΡ Π½Π°ΠΉΠ΄Π΅Ρ Π΄Π»Ρ Π²Π°Ρ ΠΎΡΠ²Π΅Ρ.
ΠΡ ΠΏΡΠ΅Π΄Π»Π°Π³Π°Π΅ΠΌ ΠΊΠ°ΠΊ Π±Π΅ΡΠΏΠ»Π°ΡΠ½ΡΠΉ ΠΎΠ½Π»Π°ΠΉΠ½-ΠΊΠ°Π»ΡΠΊΡΠ»ΡΡΠΎΡ ΡΠΈΠ΄ΠΎΠ² ΠΈ ΡΠΊΠΎΡΠΎΡΡΠ΅ΠΉ Ρ ΠΈΡΠΏΠΎΠ»ΡΠ·ΠΎΠ²Π°Π½ΠΈΠ΅ΠΌ ΠΏΡΠΎΡΡΡΡ ΡΠΎΡΠΌΡΠ» ΠΌΠ°Π³Π°Π·ΠΈΠ½Π°, ΡΠ°ΠΊ ΠΈ Π±Π΅ΡΠΏΠ»Π°ΡΠ½ΡΠΉ (Π½Π° ΠΎΠ³ΡΠ°Π½ΠΈΡΠ΅Π½Π½ΠΎΠ΅ Π²ΡΠ΅ΠΌΡ) ΠΏΠΎΠ»Π½ΠΎΡΡΠ½ΠΊΡΠΈΠΎΠ½Π°Π»ΡΠ½ΡΠΉ ΠΊΠ°Π»ΡΠΊΡΠ»ΡΡΠΎΡ, ΠΊΠΎΡΠΎΡΡΠΉ ΡΠ²Π»ΡΠ΅ΡΡΡ Π²Π΅Π΄ΡΡΠΈΠΌ Π² ΠΎΡΡΠ°ΡΠ»ΠΈ ΠΊΠ°Π»ΡΠΊΡΠ»ΡΡΠΎΡΠΎΠΌ ΡΠΊΠΎΡΠΎΡΡΠ΅ΠΉ ΠΈ ΡΠΈΠ΄ΠΎΠ².ΠΠΆΠ΅Π΄Π½Π΅Π²Π½ΠΎ Π΅Π³ΠΎ ΠΈΡΠΏΠΎΠ»ΡΠ·ΡΡΡ ΡΡΡΡΡΠΈ Π»ΡΡΡΠΈΡ ΠΌΠΈΡΠΎΠ²ΡΡ ΠΏΡΠΎΠΈΠ·Π²ΠΎΠ΄ΠΈΡΠ΅Π»Π΅ΠΉ.
ΠΠ½ΠΈ Π·Π½Π°ΡΡ, ΡΡΠΎ Π΄Π΅Π»Π°ΡΡ, ΠΈ Π½Π΅ Π±ΡΠ΄ΡΡ ΡΡΠ°ΡΠΈΡΡ Π²ΡΠ΅ΠΌΡ ΠΈ Π΄Π΅Π½ΡΠ³ΠΈ, Π΅ΡΠ»ΠΈ ΠΏΡΠΎΠ³ΡΠ°ΠΌΠΌΠ½ΠΎΠ΅ ΠΎΠ±Π΅ΡΠΏΠ΅ΡΠ΅Π½ΠΈΠ΅ Π½Π΅ ΡΠ°Π±ΠΎΡΠ°Π΅Ρ.
ΠΠ΅Π»ΠΎ Π² ΡΠΎΠΌ, Π·Π°ΡΠ΅ΠΌ ΠΈΡΠΏΠΎΠ»ΡΠ·ΠΎΠ²Π°ΡΡ ΡΡΠΎΡ ΠΏΡΠΎΡΡΠΎΠΉ Π±Π΅ΡΠΏΠ»Π°ΡΠ½ΡΠΉ ΠΊΠ°Π»ΡΠΊΡΠ»ΡΡΠΎΡ, Π΅ΡΠ»ΠΈ Π²Ρ ΠΌΠΎΠΆΠ΅ΡΠ΅ ΠΏΠΎΠ»ΡΡΠΈΡΡ Π½Π°Ρ ΠΏΠΎΠ»Π½ΠΎΡΡΠ½ΠΊΡΠΈΠΎΠ½Π°Π»ΡΠ½ΡΠΉ ΠΊΠ°Π»ΡΠΊΡΠ»ΡΡΠΎΡ G-Wizard ΠΈ ΠΊΠ°Π»ΡΠΊΡΠ»ΡΡΠΎΡ ΡΠΊΠΎΡΠΎΡΡΠ΅ΠΉ ΡΠΎΠ²Π΅ΡΡΠ΅Π½Π½ΠΎ Π±Π΅ΡΠΏΠ»Π°ΡΠ½ΠΎ Π² ΡΠ΅ΡΠ΅Π½ΠΈΠ΅ 30 Π΄Π½Π΅ΠΉ?
ΠΠ°ΠΊ Π²Ρ ΠΏΡΠΎΠΈΠ³ΡΡΠ²Π°Π΅ΡΠ΅ Ρ ΡΡΠΎΠΉ ΡΠ΄Π΅Π»ΠΊΠΎΠΉ?
ΠΠ»Ρ Π·Π°Π³ΡΡΠ·ΠΊΠΈ ΠΈ Π½Π°ΡΠ°Π»Π° ΠΈΡΠΏΠΎΠ»ΡΠ·ΠΎΠ²Π°Π½ΠΈΡ G-Wizard ΡΡΠ΅Π±ΡΠ΅ΡΡΡ Π²ΡΠ΅Π³ΠΎ 37 ΡΠ΅ΠΊΡΠ½Π΄.ΠΡΠΎ Π½ΠΈΡΠ΅Π³ΠΎ Π½Π΅ ΡΡΠΎΠΈΡ, ΠΈ Π²Ρ ΠΌΠΎΠΆΠ΅ΡΠ΅ ΠΏΠΎΠ»ΡΡΠΈΡΡ ΠΎΡΠ»ΠΈΡΠ½ΡΡ ΡΠΊΠΎΡΠΎΡΡΡ ΠΈ ΡΠΊΠΎΡΠΎΡΡΡ Π² ΡΠ΅ΡΠ΅Π½ΠΈΠ΅ ΡΠ»Π΅Π΄ΡΡΡΠΈΡ 30 Π΄Π½Π΅ΠΉ. ΠΡΠ»ΠΈ ΠΏΠΎΡΠ»Π΅ ΡΡΠΎΠ³ΠΎ Π²Ρ Π·Π°Ρ ΠΎΡΠΈΡΠ΅ Π²Π΅ΡΠ½ΡΡΡΡΡ ΠΊ Π½Π°ΡΠ΅ΠΌΡ Π±Π΅ΡΠΏΠ»Π°ΡΠ½ΠΎΠΌΡ ΠΎΠ½Π»Π°ΠΉΠ½-ΠΊΠ°Π»ΡΠΊΡΠ»ΡΡΠΎΡΡ, Π½Π΅ Π±Π΅ΡΠΏΠΎΠΊΠΎΠΉΡΠ΅ΡΡ.
ΠΠΎ Π²Ρ ΡΠ°ΠΊΠΆΠ΅ ΠΌΠΎΠΆΠ΅ΡΠ΅ ΡΠΏΡΠ°Π²Π»ΡΡΡ Π²ΡΡΠΎΠΊΠΎΠΏΡΠΎΠΈΠ·Π²ΠΎΠ΄ΠΈΡΠ΅Π»ΡΠ½ΠΎΠΉ ΠΌΠΎΠ΄Π΅Π»ΡΡ, Π΅ΡΠ»ΠΈ ΠΎΠ½Π° Π±Π΅ΡΠΏΠ»Π°ΡΠ½Π°, Π²Π΅ΡΠ½ΠΎ?
G-Wizard ΠΈΠΌΠ΅Π΅Ρ ΡΡΠ½ΠΊΡΠΈΠΈ Π΄Π»Ρ ΠΊΠ°ΠΆΠ΄ΠΎΠ³ΠΎ ΡΠΈΠΏΠ° ΠΌΠ°ΡΠΈΠ½Ρ
ΠΡΠ΅ Π΅ΡΠ΅ Π½Π΅ ΡΠ²Π΅ΡΠ΅Π½Ρ? Π£ΡΡΠΈΡΠ΅, ΡΡΠΎ G-Wizard ΠΈΠΌΠ΅Π΅Ρ ΡΠΏΠ΅ΡΠΈΡΠΈΡΠ΅ΡΠΊΠΈΠ΅ ΡΡΠ½ΠΊΡΠΈΠΈ Π΄Π»Ρ ΠΊΠ°ΠΆΠ΄ΠΎΠ³ΠΎ ΡΠΈΠΏΠ° ΠΌΠ°ΡΠΈΠ½Ρ. ΠΠΎ ΡΡΡΠΈ, Π²Ρ ΠΏΠΎΠ»ΡΡΠ°Π΅ΡΠ΅ 3 ΠΊΠ°Π»ΡΠΊΡΠ»ΡΡΠΎΡΠ° Π² ΠΎΠ΄Π½ΠΎΠΌ:
Π©Π΅Π»ΠΊΠ½ΠΈΡΠ΅ ΠΏΠΎ ΠΊΠ°ΠΆΠ΄ΠΎΠΌΡ ΠΈΠ· Π½ΠΈΡ , ΡΡΠΎΠ±Ρ ΡΠ²ΠΈΠ΄Π΅ΡΡ ΡΡΠ½ΠΊΡΠΈΠΈ, Π°Π΄Π°ΠΏΡΠΈΡΠΎΠ²Π°Π½Π½ΡΠ΅ ΠΊ ΡΠΈΠΏΡ ΠΌΠ°ΡΠΈΠ½Ρ.
ΠΠ»ΠΈ ΠΏΡΠΎΡΡΠΎ Π²ΠΎΡΠΏΠΎΠ»ΡΠ·ΡΠΉΡΠ΅ΡΡ Π½Π°ΡΠΈΠΌ ΠΏΡΠΎΡΡΡΠΌ ΠΎΠ½Π»Π°ΠΉΠ½-ΠΊΠ°Π»ΡΠΊΡΠ»ΡΡΠΎΡΠΎΠΌ ΡΠΊΠΎΡΠΎΡΡΠΈ ΡΠ΅Π·Π°Π½ΠΈΡ ΠΈ ΠΏΠΎΠ΄Π°ΡΠΈ:
ΠΠ΄Π΅ΡΡ Π²Ρ ΠΌΠΎΠΆΠ΅ΡΠ΅ ΡΠΎΠ·Π΄Π°ΡΡ ΠΊΠΎΠ½ΡΠ΅Π½Ρ, ΠΊΠΎΡΠΎΡΡΠΉ Π±ΡΠ΄Π΅Ρ ΠΈΡΠΏΠΎΠ»ΡΠ·ΠΎΠ²Π°ΡΡΡΡ Π² ΠΌΠΎΠ΄ΡΠ»Π΅.
,- Π‘ΡΠ°Π½ΠΊΠΈ ΠΏΠΎΡΡΡΠΎΠ΅Π½Ρ ΠΏΠΎ ΠΌΠΎΠ΄ΡΠ»ΡΠ½ΠΎΠΉ ΠΊΠΎΠ½ΡΡΡΡΠΊΡΠΈΠΈ Π² ΠΊΠΎΠΌΠ±ΠΈΠ½Π°ΡΠΈΠΈ Π±Π»ΠΎΠΊΠΎΠ² ΠΈ Π½Π΅ ΡΡΠ΅Π±ΡΡΡ ΡΠΏΠ΅ΡΠΈΠ°Π»ΡΠ½ΠΎΠ³ΠΎ ΡΡΠ½Π΄Π°ΠΌΠ΅Π½ΡΠ°.
- ΠΠΎΠ²ΡΡΠ΅Π½ΠΈΠ΅ ΠΏΡΠΎΠΈΠ·Π²ΠΎΠ΄ΠΈΡΠ΅Π»ΡΠ½ΠΎΡΡΠΈ Π±Π»Π°Π³ΠΎΠ΄Π°ΡΡ Π±ΠΎΠ»Π΅Π΅ Π²ΡΡΠΎΠΊΠΎΠΉ ΡΠΊΠΎΡΠΎΡΡΠΈ Π²ΠΎΠ»ΠΎΡΠ΅Π½ΠΈΡ Π±Π»Π°Π³ΠΎΠ΄Π°ΡΡ ΡΠ°Π±ΠΎΡΠ΅ Π±Π΅Π· ΠΏΠ΅ΡΠ΅ΠΊΡΡΡΠΈΠ²Π°Π½ΠΈΡ.
- ΠΡΠΎΡΡΠΎΡΠ° Π² ΡΠΊΡΠΏΠ»ΡΠ°ΡΠ°ΡΠΈΠΈ ΠΈ Π±ΡΡΡΡΠ°Ρ Π·Π°ΠΏΡΠ°Π²ΠΊΠ°.
- ΠΡΡΠΎΠΊΠΎΠ΅ Π΄Π°Π²Π»Π΅Π½ΠΈΠ΅ Π£Π·ΠΊΠΈΠΉ Π·Π°Π·ΠΎΡ, Π²Π½ΡΡΡΠ΅Π½Π½Π΅Π΅ Π²ΠΎΠ΄ΡΠ½ΠΎΠ΅ ΠΎΡ Π»Π°ΠΆΠ΄Π΅Π½ΠΈΠ΅ Π΄Π»Ρ Π²ΡΡΠΎΠΊΠΎΡΡΡΠ΅ΠΊΡΠΈΠ²Π½ΠΎΠ³ΠΎ ΠΎΡ Π»Π°ΠΆΠ΄Π΅Π½ΠΈΡ ΠΏΡΠΎΠ²ΠΎΠ»ΠΎΠΊΠΈ.
- ΠΡΡΠΎΠΊΠ°Ρ ΡΡΠ΅ΠΏΠ΅Π½Ρ Π½Π°Π΄Π΅ΠΆΠ½ΠΎΡΡΠΈ — ΠΌΠ°Π»ΠΎΠ΅ Π²ΡΠ΅ΠΌΡ ΠΏΡΠΎΡΡΠΎΡ Π±Π»Π°Π³ΠΎΠ΄Π°ΡΡ ΠΌΠ΅Π½ΡΡΠ΅ΠΌΡ ΠΈΠ·Π½ΠΎΡΡ Π΄Π΅ΡΠ°Π»Π΅ΠΉ.
- ΠΠΎΡΠ°Π·Π΄ΠΎ Π»ΡΡΡΠ΅Π΅ ΠΊΠ°ΡΠ΅ΡΡΠ²ΠΎ ΠΎΡΠ΄Π΅Π»ΠΊΠΈ ΠΏΡΠΎΠ²ΠΎΠ»ΠΎΠΊΠΈ Π±Π»Π°Π³ΠΎΠ΄Π°ΡΡ Π±ΠΎΠ»Π΅Π΅ ΠΌΡΠ³ΠΊΠΎΠΌΡ ΠΎΠ±ΡΠ°ΡΠ΅Π½ΠΈΡ Ρ ΠΏΡΠΎΠ²ΠΎΠ»ΠΎΠΊΠΎΠΉ Π²ΠΎ Π²ΡΠ΅ΠΌΡ ΠΏΡΠΎΡΠ΅ΡΡΠ° Π²ΠΎΠ»ΠΎΡΠ΅Π½ΠΈΡ (ΠΌΠ΅Π½ΡΡΠ΅Π΅ ΠΎΡΠΊΠ»ΠΎΠ½Π΅Π½ΠΈΠ΅ ΠΏΡΠΎΠ²ΠΎΠ»ΠΎΠΊΠΈ, Π½ΠΈΠ·ΠΊΠΎΠ΅ ΡΠΊΡΡΡΠΈΠ²Π°Π½ΠΈΠ΅ ΠΈ Ρ. Π.), Π ΡΠ°ΠΊΠΆΠ΅ ΠΎΠΏΡΠΈΠΌΠΈΠ·ΠΈΡΠΎΠ²Π°Π½Π½ΠΎΠ΅ ΠΎΡ Π»Π°ΠΆΠ΄Π΅Π½ΠΈΠ΅ ΠΏΡΠΎΠ²ΠΎΠ»ΠΎΠΊΠΈ.
Π²ΠΎΠ»ΠΎΡΠ΅Π½ΠΈΡ ΠΏΡΠΎΠ²ΠΎΠ»ΠΎΠΊΠΈ ΠΌΠ΅Π»ΡΠ½ΠΈΡΠ°
ΡΠΎΠ²Π°ΡΡ | Unit | Tops-10/560 |
Π΄ΠΈΠ°ΠΌΠ΅ΡΡ ΠΡΠΏΡΡΠ°Π½ | ΠΌΠΌ | 560 (600) |
Π§Π΅ΡΡΠ΅ΠΆΠ½ΡΠΉ ΡΡΠ°ΠΌΠΏ | Π²ΡΠ΅ΠΌΡ | 10 |
ΠΠ°ΠΊΡ. ΠΠΈΠ°ΠΌΠ΅ΡΡ Π½Π° Π²Ρ ΠΎΠ΄Π΅ | ΠΌΠΌ | Ο6.5-5,5 |
ΠΠΈΠ½. ΠΠΈΠ°ΠΌΠ΅ΡΡ Π½Π° Π²ΡΡ ΠΎΠ΄Π΅ | ΠΌΠΌ | Ο2-2.7 |
Π‘ΠΊΠΎΡΠΎΡΡΡ Π²ΠΎΠ»ΠΎΡΠ΅Π½ΠΈΡ | ΠΌ / ΠΌΠΈΠ½ | 460 | 9002
ΠΠΠ° (ΠΌΠ°ΠΊΡ.) | 1300 | |
ΠΠ±ΡΠ°Ρ ΡΡΠ΅ΠΏΠ΅Π½Ρ ΡΠΆΠ°ΡΠΈΡ | % | 90,53-89.29 |
ΠΠΎΡΠ½ΠΎΡΡΡ Π΄Π²ΠΈΠ³Π°ΡΠ΅Π»Ρ | ΠΊΠΡ | 30-22 |
000000
Custom Cnc Π€ΡΠ΅Π·Π΅ΡΠ½ΡΠΉ ΠΠΎΠ²ΠΎΡΠΎΡΠ½ΡΠΉ Π§Π΅ΡΡΠ΅ΠΆ
Π’ΠΎΠΊΠ°ΡΠ½ΠΎ-ΡΡΠ΅Π·Π΅ΡΠ½ΡΠ΅ Π΄Π΅ΡΠ°Π»ΠΈ Ρ Π§ΠΠ£
ΠΠΏΠΈΡΠ°Π½ΠΈΠ΅ ΠΏΡΠΎΠ΄ΡΠΊΡΠ°
Π’ΠΈΠΏ ΠΏΡΠΎΠ΄ΡΠΊΡΠ° | ΠΠ΅ΡΠ°Π»ΠΈ ΠΌΠ°ΡΠΈΠ½ | |
Π Π°Π·ΠΌΠ΅Ρ | 00ΠΠ°ΠΊΠ°Π·Π½ΠΎΠΉ ΠΠ°ΡΠ΅ΡΠΈΠ°Π»: | Π£Π³Π»Π΅ΡΠΎΠ΄ΠΈΡΡΠ°Ρ ΡΡΠ°Π»Ρ, Π»Π°ΡΡΠ½Ρ, Π°Π»ΡΠΌΠΈΠ½ΠΈΠΉ, Π½Π΅ΡΠΆΠ°Π²Π΅ΡΡΠ°Ρ ΡΡΠ°Π»Ρ, ΠΏΠ»Π°ΡΡΠΈΠΊ, POM, Delrin ΠΈ Ρ. Π. |
ΠΠ΅ΡΠΎΠ΄ ΠΎΠ±ΡΠ°Π±ΠΎΡΠΊΠΈ | ΠΠ±ΡΠ°Π±ΠΎΡΠΊΠ° Ρ Π§ΠΠ£, ΡΠΎΠΊΠ°ΡΠ½Π°Ρ ΠΎΠ±ΡΠ°Π±ΠΎΡΠΊΠ°, ΡΡΠ΅Π·Π΅ΡΠΎΠ²Π°Π½ΠΈΠ΅, ΡΠ²Π΅ΡΠ»Π΅Π½ΠΈΠ΅, ΡΠ»ΠΈΡΠΎΠ²Π°Π½ΠΈΠ΅, ΠΏΡΠΎΠ²ΠΎΠ»ΠΎΠΊΠ° EDM ΠΈ Ρ. Π. | |
ΠΡΠ½ΠΎΠ²Π½ΠΎΠ΅ ΠΎΠ±ΠΎΡΡΠ΄ΠΎΠ²Π°Π½ΠΈΠ΅ | 1.CNC Π²Π΅ΡΡΠΈΠΊΠ°Π»ΡΠ½ΡΠΉ ΠΎΠ±ΡΠ°Π±Π°ΡΡΠ²Π°ΡΡΠΈΠΉ ΡΠ΅Π½ΡΡ, 2. ΠΠΎΡΠΈΠ·ΠΎΠ½ΡΠ°Π»ΡΠ½ΠΎ-ΡΠ°ΡΡΠΎΡΠ½ΠΎΠΉ ΡΡΠ°Π½ΠΎΠΊ Ρ Π§ΠΠ£. 3. ΠΡΡΠΎΠΊΠΎΡΠΊΠΎΡΠΎΡΡΠ½ΡΠ΅ ΡΠΎΠΊΠ°ΡΠ½ΡΠ΅ ΡΡΠ°Π½ΠΊΠΈ Ρ Π§ΠΠ£ 4. Π€ΡΠ΅Π·Π΅ΡΠ½ΡΠΉ ΡΡΠ°Π½ΠΎΠΊ Ρ Π§ΠΠ£. 5. ΠΠ±ΡΠΈΠ΅ ΡΡΠ΅Π·Π΅ΡΠ½ΡΠ΅ ΡΡΠ°Π½ΠΊΠΈ. 6. ΠΠ±ΡΠΈΠ΅ ΡΡΡΠ½ΡΠ΅ ΡΠΎΠΊΠ°ΡΠ½ΡΠ΅ ΡΡΠ°Π½ΠΊΠΈ, 7.Flarness Gridning machines, 8. Π ΡΡΠ½ΠΎΠΉ ΡΠ²Π΅ΡΠ»ΠΈΠ»ΡΠ½ΡΠΉ ΡΡΠ°Π½ΠΎΠΊ, 9. ΠΠ»Π΅ΠΊΡΡΠΎΡΡΠΎΠ·ΠΈΠΎΠ½Π½ΡΠΉ ΠΎΡΡΠ΅Π·Π½ΠΎΠΉ ΡΡΠ°Π½ΠΎΠΊ 9.Wire | |
ΠΠ±ΡΠ°Π±ΠΎΡΠΊΠ° ΠΏΠΎΠ²Π΅ΡΡ Π½ΠΎΡΡΠΈ | Π₯ΡΠΎΠΌΠΈΡΠΎΠ²Π°Π½ΠΈΠ΅ ΠΠ½ΠΎΠ΄ΠΈΡΠΎΠ²Π°Π½ΠΈΠ΅ ΠΠΎΡΠΎΡΠΊΠΎΠ²ΠΎΠ΅ ΠΏΠΎΠΊΡΡΡΠΈΠ΅ Π§Π΅ΡΠ½ΠΎΠ΅ ΠΎΠΊΠΈΡΠ»Π΅Π½ΠΈΠ΅ Π§Π΅ΡΠ½ΠΎΠ΅ ΠΎΠΊΠΈΡΠ»Π΅Π½ΠΈΠ΅ Π²Π·ΡΡΠ²Π½ΡΠ΅ ΡΠ°Π±ΠΎΡΡΠ§ΠΈΡΡΠΊΠ° ΠΈ Π²ΡΠΏΠ»Π΅ΡΠΊΠΈΠ²Π°Π½ΠΈΠ΅ ΠΠ»Π΅ΠΊΡΡΠΎΡΠΎΡΠ΅Π· | |
ΠΠΎΠΏΡΡΠΊ | +/- 0.01mm | |
ΠΠ±ΡΠ»ΡΠΆΠΈΠ²Π°Π½ΠΈΠ΅ OEM / ODM | ΠΠΎΡΡΡΠΏΠ½ΠΎ | |
ΠΠΎΡΡΠ°Π²ΠΊΠ° ΠΎΠ±ΡΠ°Π·ΡΠΎΠ² | 5-7Π΄Π½Π΅ΠΉ | |
ΠΡΠΎΠ³ΡΠ°ΠΌΠΌΠ½ΠΎΠ΅ ΠΎΠ±Π΅ΡΠΏΠ΅ΡΠ΅Π½ΠΈΠ΅ Π΄Π»Ρ ΠΏΡΠΎΠ΅ΠΊΡΠΈΡΠΎΠ²Π°Π½ΠΈΡ | ||
Π£ΡΠ»ΠΎΠ²ΠΈΡ ΡΠΎΡΠ³ΠΎΠ²Π»ΠΈ | FOB, CIF, EXW | |
Π£ΡΠ»ΠΎΠ²ΠΈΡ ΠΎΠΏΠ»Π°ΡΡ | T / T, L / C, Western Union | |
Π‘ΠΈΡΡΠ΅ΠΌΠ° ΠΊΠΎΠ½ΡΡΠΎΠ»Ρ ΠΊΠ°ΡΠ΅ΡΡΠ²Π° | ΠΡΠ΅Π΄ΠΎΡΡΠ°Π²ΠΈΡΡ ΠΎΡΡΠ΅Ρ ΠΎ ΠΏΡΠΎΠ²Π΅ΡΠΊΠ΅ | |
Π£ΠΏΠ°ΠΊΠΎΠ²ΠΊΠ° | ΠΠ°ΡΡΠΎΠ½, ΡΡΠ°Π½Π΄Π°ΡΡΠ½ΡΠ΅ ΡΠ°Π½Π΅ΡΠ½ΡΠ΅ ΡΡΠΈΠΊΠΈ | |
ΠΠΎΡΡΠ°Π²ΠΊΠ° 35 ΡΠ°Π±ΠΎΡΠΈΡ
Π΄Π½Π΅ΠΉ ΠΏΠΎΡΠ»Π΅ ΠΏΠΎΠ΄ΡΠ²Π΅ΡΠΆΠ΄Π΅Π½ΠΈΡ Π·Π°ΠΊΠ°Π·Π° | ||
Π£ΡΠ»ΠΎΠ²ΠΈΡ ΠΎΡΠ³ΡΡΠ·ΠΊΠΈ | 1) 0-100 ΠΊΠ³: (DHL / TNT / UPS / FEDEX) / ΠΠ²ΠΈΠ°ΠΏΠ΅ΡΠ΅Π²ΠΎΠ·ΠΊΠΈ | |
2)> 100 ΠΊΠ³: ΠΌΠΎΡΡΠΊΠΈΠ΅ ΠΏΠ΅ΡΠ΅Π²ΠΎΠ·ΠΊΠΈ ΠΈΠ»ΠΈ Π² ΡΠΎΠΎΡΠ²Π΅ΡΡΡΠ²ΠΈΠΈ Ρ ΡΡΠ΅Π±ΠΎΠ²Π°Π½ΠΈΡΠΌΠΈ Π·Π°ΠΊΠ°Π·ΡΠΈΠΊΠ° | ||
ΠΠ±Π»Π°ΡΡΡ ΠΏΡΠΈΠΌΠ΅Π½Π΅Π½ΠΈΡ | ΠΠ²ΡΠΎΠ·Π°ΠΏΡΠ°ΡΡΠΈ, ΠΊΠΎΠΌΠΏΠ»Π΅ΠΊΡΡΡΡΠΈΠ΅ Π΄Π»Ρ Hareware, Π³ΠΈΠ΄ΡΠ°Π²Π»ΠΈΠΊΠ°, ΠΊΠΎΠΌΠΏΡΠ΅ΡΡΠΎΡΡ, Π‘ΡΡΠΎΠΈΡΠ΅Π»ΡΠ½Π°Ρ ΡΠ΅Ρ Π½ΠΈΠΊΠ°, ΠΠ½ΠΆΠ΅Π½Π΅Ρ-ΠΌΠ΅Ρ Π°Π½ΠΈΠΊ, ΠΡΠΎΠΌΡΡΠ»Π΅Π½Π½ΠΎΠ΅ ΠΎΠ±ΠΎΡΡΠ΄ΠΎΠ²Π°Π½ΠΈΠ΅, Π΄Π΅ΡΠ°Π»ΠΈ ΡΡΠ°Π½ΡΠΌΠΈΡΡΠΈΠΈ ΠΈ Ρ. Π. |
ΠΡΠΎΠΈΠ·Π²ΠΎΠ΄ΡΡΠ²Π΅Π½Π½ΡΠΉ ΠΏΡΠΎΡΠ΅ΡΡ
Π£ΠΏΠ°ΠΊΠΎΠ²ΠΊΠ° ΠΈ ΠΎΡΠ³ΡΡΠ·ΠΊΠ°
ΠΡΠ·ΡΠ²Ρ ΠΏΠΎΠΊΡΠΏΠ°ΡΠ΅Π»Π΅ΠΉ
Π§Π°ΡΡΠΎ Π·Π°Π΄Π°Π²Π°Π΅ΠΌΡΠ΅ Π²ΠΎΠΏΡΠΎΡΡ
2
A 1) ΠΡΠΎΡΠ΅ΡΡΠΈΠΎΠ½Π°Π»ΡΠ½ΡΠΉ ΡΡΠ°Π½ΠΎΠΊ Ρ Π§ΠΠ£ Π΄Π»Ρ Π²ΡΠ΅Ρ
Π²Π°ΡΠΈΡ
ΠΈΠ½Π΄ΠΈΠ²ΠΈΠ΄ΡΠ°Π»ΡΠ½ΡΡ
ΠΏΠΎΡΡΠ΅Π±Π½ΠΎΡΡΠ΅ΠΉ.
2) Π£Π½ΠΈΠ²Π΅ΡΡΠ°Π»ΡΠ½ΡΠΉ ΡΠ΅Ρ
ΠΎΡΠ²Π΅ΡΠ°Π΅Ρ Π²Π°ΡΠΈΠΌ ΡΡΠ΅Π±ΠΎΠ²Π°Π½ΠΈΡΠΌ ΠΎΠ±ΡΠ°Π±ΠΎΡΠΊΠΈ Π½Π° ΡΡΠ°Π½ΠΊΠ°Ρ
Ρ Π§ΠΠ£, ΡΡΠ΅Π·Π΅ΡΠΎΠ²Π°Π½ΠΈΡ, ΡΠΎΠΊΠ°ΡΠ½ΠΎΠΉ ΠΎΠ±ΡΠ°Π±ΠΎΡΠΊΠΈ, ΡΠ²Π΅ΡΠ»Π΅Π½ΠΈΡ, ΡΠ°ΡΡΠ°ΡΠΈΠ²Π°Π½ΠΈΡ, ΠΎΠ±ΡΠ°Π±ΠΎΡΠΊΠΈ ΡΠ΅ΡΠΊΠΈ, ΡΠ²Π°ΡΠΊΠΈ ΠΈ ΠΈΠ·Π³ΠΎΡΠΎΠ²Π»Π΅Π½ΠΈΡ.
3) ΠΠ°ΡΠ΅ΡΡΠ²Π΅Π½Π½ΡΠ΅ Π΄Π΅ΡΠ°Π»ΠΈ Π±ΡΠ»ΠΈ ΡΠΊΡΠΏΠΎΡΡΠΈΡΠΎΠ²Π°Π½Ρ Π² Π‘Π¨Π, ΠΠ΅Π»ΠΈΠΊΠΎΠ±ΡΠΈΡΠ°Π½ΠΈΡ, FR ΠΈ RU.
4). ΠΡ ΡΡΠ°Π·Ρ ΡΠ°Π±ΡΠΈΠΊΠ° ΡΠΎΡΡΠ΅Π΄ΠΎΡΠΎΡΠΈΡΡΡΡ Π½Π° ΠΏΡΠ΅Π΄ΠΎΡΡΠ°Π²Π»Π΅Π½ΠΈΠ΅ ΡΡΠ»ΡΠ³ Π½Π° Π·Π°ΠΊΠ°Π· ΠΎΠ±ΡΠ°Π±ΠΎΡΠΊΠΈ.
5). ΠΠ±ΡΠ°Π±ΠΎΡΠΊΠ° ΠΊΠΎΠΌΠΏΠΎΠ½Π΅Π½ΡΠΎΠ² Ρ ΠΎΡΠ΅Π½Ρ ΠΆΠ΅ΡΡΠΊΠΈΠΌ Π΄ΠΎΠΏΡΡΠΊΠΎΠΌ ΠΈ ΠΎΡΠ΅Π½Ρ ΡΠ»ΠΎΠΆΠ½ΠΎΠΉ Π³Π΅ΠΎΠΌΠ΅ΡΡΠΈΠ΅ΠΉ
6). MOQ ΠΌΠ°Π»ΠΎ Π΄Π°ΠΆΠ΅ ΠΏΡΠΈΠ΅ΠΌΠ»Π΅ΠΌΠΎ Π² Π½Π΅ΠΊΠΎΡΠΎΡΡΡ
ΠΎΡΠΎΠ±ΡΡ
ΡΡΠ»ΠΎΠ²ΠΈΡΡ
.
7).Π³Π°ΡΠ°Π½ΡΠΈΡΠΎΠ²Π°Π½ΠΎ ΠΊΠ²Π°Π»ΠΈΡΠΈΡΠΈΡΠΎΠ²Π°Π½Π½ΡΡ
ΠΈ ΠΎΠΏΡΡΠ½ΡΡ
ΡΠ°Π±ΠΎΡΠ½ΠΈΠΊΠΎΠ², ΡΠΏΡΠ°Π²Π»ΡΡΡΠ΅ΠΉ ΡΠΈΡΡΠ΅ΠΌΡ ΠΈ ΡΠΎΡΡΠΎΡΠ½ΠΈΠ΅ ΠΎΠ±ΠΎΡΡΠ΄ΠΎΠ²Π°Π½ΠΈΡ Π²ΡΡΡΠ΅Π³ΠΎ ΠΊΠ°ΡΠ΅ΡΡΠ²Π°.
8). Π ΡΠ΄ΠΎΠΌ Ρ ΠΏΠΎΡΡΠΎΠΌ Π¨Π°Π½Ρ
Π°ΠΉ ΠΈ ΠΏΠΎΡΡΠΎΠΌ ΠΠΈΠ½Π±ΠΎ, ΡΠ΄ΠΎΠ±Π½Π°Ρ ΡΡΠ°Π½ΡΠΏΠΎΡΡΠ½Π°Ρ ΡΠ°Π·Π²ΡΠ·ΠΊΠ°
Q 2. ΠΠ°ΠΊ Π³Π°ΡΠ°Π½ΡΠΈΡΠΎΠ²Π°ΡΡ ΠΊΠ°ΡΠ΅ΡΡΠ²ΠΎ?
A 1) ΠΡ ΠΏΡΠΎΠΈΠ·Π²ΠΎΠ΄ΠΈΠΌ ΠΎΠ±ΡΠ°Π·ΡΡ Π΄Π»Ρ ΠΏΡΠΎΠ²Π΅ΡΠΊΠΈ ΠΊΠ°ΡΠ΅ΡΡΠ²Π° ΠΏΠ΅ΡΠ΅Π΄ ΡΠ΅ΡΠΈΠΉΠ½ΡΠΌ ΠΏΡΠΎΠΈΠ·Π²ΠΎΠ΄ΡΡΠ²ΠΎΠΌ.
2) ΠΠ΅ΡΡΠΎΠ½Π°Π» ΠΠ ΠΏΡΠΎΠ²Π΅ΡΠΈΡ Π΄Π΅ΡΠ°Π»ΠΈ ΠΏΠ΅ΡΠ΅Π΄ ΠΎΡΠΏΡΠ°Π²ΠΊΠΎΠΉ.
3) ΠΡ Π½Π΅ΡΠ΅ΠΌ ΠΎΡΠ²Π΅ΡΡΡΠ²Π΅Π½Π½ΠΎΡΡΡ Π·Π° ΠΊΠ°ΡΠ΅ΡΡΠ²ΠΎ Π½Π°ΡΠ΅ΠΉ ΠΏΡΠΎΠ΄ΡΠΊΡΠΈΠΈ.
Q 3. Π‘Π΅ΡΠ²ΠΈΡ ODM
A ΠΠ°ΠΉΡΠ΅ Π½Π°ΠΌ Π·Π½Π°ΡΡ Π²Π°ΡΡ ΠΈΠ΄Π΅Ρ ΠΈ ΡΠΎ, ΡΡΠΎ Π²Ρ Ρ
ΠΎΡΠΈΡΠ΅. ΠΠ°ΡΠ΅ ΠΌΠ°ΡΠΈΠ½ΠΎΡΡΡΠΎΠ΅Π½ΠΈΠ΅ ΠΌΠΎΠΆΠ΅Ρ ΡΠΏΡΠΎΠ΅ΠΊΡΠΈΡΠΎΠ²Π°ΡΡ ΠΏΠ΅ΡΠ°ΡΡ.
Solidworks, autoCAD, UG Π΄ΠΎΡΡΡΠΏΠ½Ρ Π΄Π»Ρ Π²ΡΠ΅Ρ
Π²ΠΈΠ΄ΠΎΠ² ΠΏΠΎΡΡΠ΅Π±Π½ΠΎΡΡΠ΅ΠΉ.
Q 4.ΠΠ±ΡΠ»ΡΠΆΠΈΠ²Π°Π½ΠΈΠ΅ OEM
A ΠΠ°ΡΠ° ΠΏΡΠΎΡΠ΅ΡΡΠΈΠΎΠ½Π°Π»ΡΠ½Π°Ρ ΠΌΠ΅Ρ
Π°Π½ΠΈΡΠ΅ΡΠΊΠ°Ρ ΠΌΠ°ΡΡΠ΅ΡΡΠΊΠ°Ρ Ρ Π§ΠΠ£ ΠΏΡΠ΅Π΄ΠΎΡΡΠ°Π²Π»ΡΠ΅Ρ ΡΡΠ»ΡΠ³ΠΈ ΠΎΠ±ΡΠ°Π±ΠΎΡΠΊΠΈ, ΡΠΎΡΠ΅Π½ΠΈΡ, ΡΡΠ΅Π·Π΅ΡΠΎΠ²Π°Π½ΠΈΡ, ΡΠ²Π΅ΡΠ»Π΅Π½ΠΈΡ, ΡΠ»ΠΈΡΠΎΠ²Π°Π½ΠΈΡ, ΡΠ°ΡΡΠ°ΡΠΈΠ²Π°Π½ΠΈΡ, ΡΠ²Π°ΡΠΊΠΈ, ΡΠ²Π°ΡΠΊΠΈ
Ρ Π§ΠΠ£ ΠΈ ΠΈΠ·Π³ΠΎΡΠΎΠ²Π»Π΅Π½ΠΈΡ. ΠΡ ΠΌΠΎΠΆΠ΅ΠΌ ΡΠ΄ΠΎΠ²Π»Π΅ΡΠ²ΠΎΡΠΈΡΡ Π²Π°ΡΠΈ ΡΡΠ΅Π±ΠΎΠ²Π°Π½ΠΈΡ.
Q 5. ΠΠ°ΠΊ Ρ Π½Π°ΠΌΠΈ ΡΠ²ΡΠ·Π°ΡΡΡΡ?
A 1) ΠΡ ΠΌΠΎΠΆΠ΅ΡΠ΅ ΠΎΡΡΠ°Π²ΠΈΡΡ Π½Π°ΠΌ ΡΠΎΠΎΠ±ΡΠ΅Π½ΠΈΠ΅ Π½Π° alibaba.
2) ΠΏΠΎΡΠ΅ΡΠΈΡΠ΅ Π½Π°ΡΡ Π²Π΅Π±-ΡΡΡΠ°Π½ΠΈΡΡ, ΡΡΠΎΠ±Ρ ΠΏΠΎΠ»ΡΡΠΈΡΡ ΠΊΠΎΠ½ΡΠ°ΠΊΡΠ½ΡΡ ΠΈΠ½ΡΠΎΡΠΌΠ°ΡΠΈΡ
,
1) ΠΡΠΎΡΠ΅ΡΡΠΈΠΎΠ½Π°Π»ΡΠ½ΡΠΉ ΡΡΠ°Π½ΠΎΠΊ Ρ Π§ΠΠ£ Π΄Π»Ρ Π²ΡΠ΅Ρ Π²Π°ΡΠΈΡ ΠΈΠ½Π΄ΠΈΠ²ΠΈΠ΄ΡΠ°Π»ΡΠ½ΡΡ ΠΏΠΎΡΡΠ΅Π±Π½ΠΎΡΡΠ΅ΠΉ.
2) Π£Π½ΠΈΠ²Π΅ΡΡΠ°Π»ΡΠ½ΡΠΉ ΡΠ΅Ρ ΠΎΡΠ²Π΅ΡΠ°Π΅Ρ Π²Π°ΡΠΈΠΌ ΡΡΠ΅Π±ΠΎΠ²Π°Π½ΠΈΡΠΌ ΠΎΠ±ΡΠ°Π±ΠΎΡΠΊΠΈ Π½Π° ΡΡΠ°Π½ΠΊΠ°Ρ Ρ Π§ΠΠ£, ΡΡΠ΅Π·Π΅ΡΠΎΠ²Π°Π½ΠΈΡ, ΡΠΎΠΊΠ°ΡΠ½ΠΎΠΉ ΠΎΠ±ΡΠ°Π±ΠΎΡΠΊΠΈ, ΡΠ²Π΅ΡΠ»Π΅Π½ΠΈΡ, ΡΠ°ΡΡΠ°ΡΠΈΠ²Π°Π½ΠΈΡ, ΠΎΠ±ΡΠ°Π±ΠΎΡΠΊΠΈ ΡΠ΅ΡΠΊΠΈ, ΡΠ²Π°ΡΠΊΠΈ ΠΈ ΠΈΠ·Π³ΠΎΡΠΎΠ²Π»Π΅Π½ΠΈΡ.
3) ΠΠ°ΡΠ΅ΡΡΠ²Π΅Π½Π½ΡΠ΅ Π΄Π΅ΡΠ°Π»ΠΈ Π±ΡΠ»ΠΈ ΡΠΊΡΠΏΠΎΡΡΠΈΡΠΎΠ²Π°Π½Ρ Π² Π‘Π¨Π, ΠΠ΅Π»ΠΈΠΊΠΎΠ±ΡΠΈΡΠ°Π½ΠΈΡ, FR ΠΈ RU.
4). ΠΡ ΡΡΠ°Π·Ρ ΡΠ°Π±ΡΠΈΠΊΠ° ΡΠΎΡΡΠ΅Π΄ΠΎΡΠΎΡΠΈΡΡΡΡ Π½Π° ΠΏΡΠ΅Π΄ΠΎΡΡΠ°Π²Π»Π΅Π½ΠΈΠ΅ ΡΡΠ»ΡΠ³ Π½Π° Π·Π°ΠΊΠ°Π· ΠΎΠ±ΡΠ°Π±ΠΎΡΠΊΠΈ.
5). ΠΠ±ΡΠ°Π±ΠΎΡΠΊΠ° ΠΊΠΎΠΌΠΏΠΎΠ½Π΅Π½ΡΠΎΠ² Ρ ΠΎΡΠ΅Π½Ρ ΠΆΠ΅ΡΡΠΊΠΈΠΌ Π΄ΠΎΠΏΡΡΠΊΠΎΠΌ ΠΈ ΠΎΡΠ΅Π½Ρ ΡΠ»ΠΎΠΆΠ½ΠΎΠΉ Π³Π΅ΠΎΠΌΠ΅ΡΡΠΈΠ΅ΠΉ
6). MOQ ΠΌΠ°Π»ΠΎ Π΄Π°ΠΆΠ΅ ΠΏΡΠΈΠ΅ΠΌΠ»Π΅ΠΌΠΎ Π² Π½Π΅ΠΊΠΎΡΠΎΡΡΡ ΠΎΡΠΎΠ±ΡΡ ΡΡΠ»ΠΎΠ²ΠΈΡΡ .
7).Π³Π°ΡΠ°Π½ΡΠΈΡΠΎΠ²Π°Π½ΠΎ ΠΊΠ²Π°Π»ΠΈΡΠΈΡΠΈΡΠΎΠ²Π°Π½Π½ΡΡ ΠΈ ΠΎΠΏΡΡΠ½ΡΡ ΡΠ°Π±ΠΎΡΠ½ΠΈΠΊΠΎΠ², ΡΠΏΡΠ°Π²Π»ΡΡΡΠ΅ΠΉ ΡΠΈΡΡΠ΅ΠΌΡ ΠΈ ΡΠΎΡΡΠΎΡΠ½ΠΈΠ΅ ΠΎΠ±ΠΎΡΡΠ΄ΠΎΠ²Π°Π½ΠΈΡ Π²ΡΡΡΠ΅Π³ΠΎ ΠΊΠ°ΡΠ΅ΡΡΠ²Π°.
8). Π ΡΠ΄ΠΎΠΌ Ρ ΠΏΠΎΡΡΠΎΠΌ Π¨Π°Π½Ρ Π°ΠΉ ΠΈ ΠΏΠΎΡΡΠΎΠΌ ΠΠΈΠ½Π±ΠΎ, ΡΠ΄ΠΎΠ±Π½Π°Ρ ΡΡΠ°Π½ΡΠΏΠΎΡΡΠ½Π°Ρ ΡΠ°Π·Π²ΡΠ·ΠΊΠ°
2. ΠΠ°ΠΊ Π³Π°ΡΠ°Π½ΡΠΈΡΠΎΠ²Π°ΡΡ ΠΊΠ°ΡΠ΅ΡΡΠ²ΠΎ?
1) ΠΡ ΠΏΡΠΎΠΈΠ·Π²ΠΎΠ΄ΠΈΠΌ ΠΎΠ±ΡΠ°Π·ΡΡ Π΄Π»Ρ ΠΏΡΠΎΠ²Π΅ΡΠΊΠΈ ΠΊΠ°ΡΠ΅ΡΡΠ²Π° ΠΏΠ΅ΡΠ΅Π΄ ΡΠ΅ΡΠΈΠΉΠ½ΡΠΌ ΠΏΡΠΎΠΈΠ·Π²ΠΎΠ΄ΡΡΠ²ΠΎΠΌ.
2) ΠΠ΅ΡΡΠΎΠ½Π°Π» ΠΠ ΠΏΡΠΎΠ²Π΅ΡΠΈΡ Π΄Π΅ΡΠ°Π»ΠΈ ΠΏΠ΅ΡΠ΅Π΄ ΠΎΡΠΏΡΠ°Π²ΠΊΠΎΠΉ.
3) ΠΡ Π½Π΅ΡΠ΅ΠΌ ΠΎΡΠ²Π΅ΡΡΡΠ²Π΅Π½Π½ΠΎΡΡΡ Π·Π° ΠΊΠ°ΡΠ΅ΡΡΠ²ΠΎ Π½Π°ΡΠ΅ΠΉ ΠΏΡΠΎΠ΄ΡΠΊΡΠΈΠΈ.
3. Π‘Π΅ΡΠ²ΠΈΡ ODM
ΠΠ°ΠΉΡΠ΅ Π½Π°ΠΌ Π·Π½Π°ΡΡ Π²Π°ΡΡ ΠΈΠ΄Π΅Ρ ΠΈ ΡΠΎ, ΡΡΠΎ Π²Ρ Ρ ΠΎΡΠΈΡΠ΅. ΠΠ°ΡΠ΅ ΠΌΠ°ΡΠΈΠ½ΠΎΡΡΡΠΎΠ΅Π½ΠΈΠ΅ ΠΌΠΎΠΆΠ΅Ρ ΡΠΏΡΠΎΠ΅ΠΊΡΠΈΡΠΎΠ²Π°ΡΡ ΠΏΠ΅ΡΠ°ΡΡ.
Solidworks, autoCAD, UG Π΄ΠΎΡΡΡΠΏΠ½Ρ Π΄Π»Ρ Π²ΡΠ΅Ρ Π²ΠΈΠ΄ΠΎΠ² ΠΏΠΎΡΡΠ΅Π±Π½ΠΎΡΡΠ΅ΠΉ.
4.ΠΠ±ΡΠ»ΡΠΆΠΈΠ²Π°Π½ΠΈΠ΅ OEM
ΠΠ°ΡΠ° ΠΏΡΠΎΡΠ΅ΡΡΠΈΠΎΠ½Π°Π»ΡΠ½Π°Ρ ΠΌΠ΅Ρ Π°Π½ΠΈΡΠ΅ΡΠΊΠ°Ρ ΠΌΠ°ΡΡΠ΅ΡΡΠΊΠ°Ρ Ρ Π§ΠΠ£ ΠΏΡΠ΅Π΄ΠΎΡΡΠ°Π²Π»ΡΠ΅Ρ ΡΡΠ»ΡΠ³ΠΈ ΠΎΠ±ΡΠ°Π±ΠΎΡΠΊΠΈ, ΡΠΎΡΠ΅Π½ΠΈΡ, ΡΡΠ΅Π·Π΅ΡΠΎΠ²Π°Π½ΠΈΡ, ΡΠ²Π΅ΡΠ»Π΅Π½ΠΈΡ, ΡΠ»ΠΈΡΠΎΠ²Π°Π½ΠΈΡ, ΡΠ°ΡΡΠ°ΡΠΈΠ²Π°Π½ΠΈΡ, ΡΠ²Π°ΡΠΊΠΈ, ΡΠ²Π°ΡΠΊΠΈ
Ρ Π§ΠΠ£ ΠΈ ΠΈΠ·Π³ΠΎΡΠΎΠ²Π»Π΅Π½ΠΈΡ. ΠΡ ΠΌΠΎΠΆΠ΅ΠΌ ΡΠ΄ΠΎΠ²Π»Π΅ΡΠ²ΠΎΡΠΈΡΡ Π²Π°ΡΠΈ ΡΡΠ΅Π±ΠΎΠ²Π°Π½ΠΈΡ.
5. ΠΠ°ΠΊ Ρ Π½Π°ΠΌΠΈ ΡΠ²ΡΠ·Π°ΡΡΡΡ?
1) ΠΡ ΠΌΠΎΠΆΠ΅ΡΠ΅ ΠΎΡΡΠ°Π²ΠΈΡΡ Π½Π°ΠΌ ΡΠΎΠΎΠ±ΡΠ΅Π½ΠΈΠ΅ Π½Π° alibaba.
2) ΠΏΠΎΡΠ΅ΡΠΈΡΠ΅ Π½Π°ΡΡ Π²Π΅Π±-ΡΡΡΠ°Π½ΠΈΡΡ, ΡΡΠΎΠ±Ρ ΠΏΠΎΠ»ΡΡΠΈΡΡ ΠΊΠΎΠ½ΡΠ°ΠΊΡΠ½ΡΡ ΠΈΠ½ΡΠΎΡΠΌΠ°ΡΠΈΡ