Шнековые мойки — Дробильное оборудование
Шнековые мойки используют для промывки песка и материала с кусками крупностью до 10 мм. Рабочий орган таких моек имеет вид сплошной спирали. Мойки бывают одно — и двухспиральными. Устанавливают их под углом 12…18°. Влажность выдаваемого материала 15…18%. Спирали армированы съемными износоустойчивыми пластинами.
Шнековая пескомойка-классификатор (рис. 34) представляет собой полуцилиндрическое корыто 1, внутри которого вращается спираль 2, приводимая в движение приводом 3 (электродвигатель, редуктор и пара зубчатых шестерен).
Рис. 34. Схема шнековой мойки: 1 — корыто, 2 — спираль, 3 — привод, 4 — механизм подъема спирали, 5 — загрузочная коробка, б — сливной желоб
При запуске мойки спираль 2 поднимают с помощью механизма 4, включают ее в работу и постепенно погружают в корыто. Материал с водой подается в мойку через загрузочную коробку 5 и спиралью транспортируется вверх к разгрузочному окну, расположенному в донной части корыта. Тонкие частицы материала переливаются с водой через сливной порог в желоб и удаляются по сливному патрубку.
Кроме отмыва глинистых и илистых частиц на шнековых пескомойках можно производить классификацию материалов по граничному зерну 0,15 мм.
Шнековые пескомойки для нерудных материалов выпускают двух марок: С-871 и С-872 производительностью соответственно 62…123 и 97…196 т/ч.
Основной недостаток машин с неподвижной ванной — ограниченная крупность питания. При увеличении крупности питания повышается вероятность заклинивания отдельных кусков между лопастями и стенками корыта, что приводит к деформации и поломке лопастей и валов.
Рис. 35. Схема работы промывочных барабанов: а — прямоточного, б — противоточного, в — противоточного с внутренней подпорной стенкой
arxipedia.ru
Шнековая мойка | Производителя | ETW International
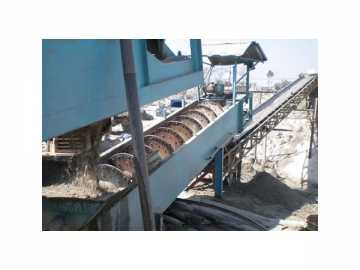
Известная своей способностью удалять глину и другие примеси с поверхности камня, шнековая мойка стала основным продуктом для обработки строительных материалов, дробления горных пород и обогащения руд. Модель шнековой мойки можно выбрать в зависимости от размера обрабатываемого камня, гравия или руды. По запросу мы можем спроектировать и произвести оборудование в соответствии с определенными требованиями заказчика.
Существуют и другие области применения данного оборудования, такие как строительство автомобильных дорог и водохранилищ, гидроэнергетика химическая и цементная промышленности.
Основные особенности
1. Шнековая мойка оснащена стандартными регулируемыми водосливами на переливном отверстии, которые позволяют менять уровень воды. Инновационная структура машины обеспечивает высокое качество получаемого продукта.
3. Моечное оборудование гарантирует смывание минимального количества песка, а также обеспечивает сортировку по размерам и модуль крупности готового продукта.
Принцип работы
Шнековая мойка серии XL устанавливается под наклоном. Вода подается из нижней части накопительного резервуара с загрузочной стороны. Мойка использует скребок шнека для осуществления процессов обезжиривания и очистки. Головка шнека погружена в накопительный бак. Шнек управляется двигателем через зубчатую передачу, он разделяет более легкие фракции от полезных материалов.
Модель | Спираль | Накопительный бак | Размер получаемого продукта | Пропускная способность | Скорость шнека | Расход воды | Мощность двигателя | Вес | Габариты |
Диаметр | Длина | ||||||||
мм | мм | мм | т/ч | об/мин | т/ч | кВт | т | мм | |
LSX915 | 915 | 7585 | ≤ 10 | 100 | 21 | 11 | 10-80 | 6.5 | 8500 × 2950 × 1930 |
2LSX915 | 915 | 7585 | ≤ 10 | 200 | 21 | 2 × 11 | 20-160 | 11.8 | 8420 × 3765 × 2030 |
LSX1115 | 1115 | 9782 | ≤ 10 | 175 | 17 | 15 | 20-150 | 10.18 | 10970 × 3945 × 4720 |
2LSX1115 | 1115 | 9782 | ≤ 10 | 350 | 17 | 2 × 15 | 40-300 | 17.94 | 10970 × 5250 × 4720 |
XSD2610 | 2600 | 3220 | ≤ 10 | 50 | 0.8 | 5.5 | 4-4.5 | 2.7 | 3220 × 2125 × 2670 |
XSD3016 | 3000 | 3810 | ≤ 10 | 80 | 0.8 | 7.5 | 16.3 | 3.2 | 3400 × 2615 × 2800 |
Схожие названия
Спиральная мойка камня | Оборудование для очистки камня | Гравиемойка
www.etwinternational.ru
Мойка для полимеров — первый этап переработки вторичного пластика
Октябрь 19, 2016, Energylogia Автор Energylogia , Категория Пластик, Просмотров: 10 723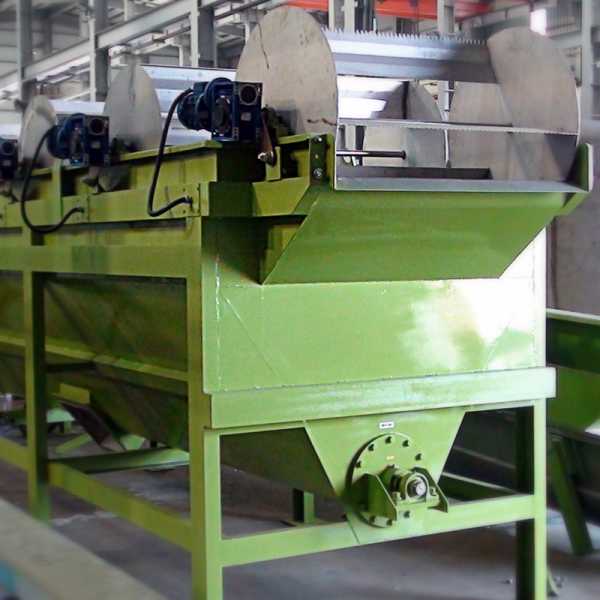
Из грязной пластмассы невозможно сделать качественный агломерат или гранулят для повторной отливки в пресс-формах. Поэтому для отмывки полигонных отходов перед дальнейшей переработкой применяется специальное оборудование — мойки для полимеров.
Технология мойки загрязненных пластмасс
Моющее оборудование не может функционировать само по себе. Оно действует в составе производственной линии, чья задача – комплексно подготовить грязный пластик к следующим операциям – агломерации либо грануляции.
Линия мойки занимает первое место в технологической цепочке переработки полимеров, привезенных с полигонов бытовых отходов или других мест, где они успели загрязниться.
При очистке пластмассы делятся на 2 группы:
- полиэтилентерефталат (ПЭТ) и полиэтиленгликольтерефталат (ПЭТФ), из которых изготавливают пищевую пластмассовую тару;
- прочие виды пластика — ППР, ПВД, ПА, ПНД и так далее.
Такое разделение требуется из-за разной плотности материалов. ПЭТ и ПЭТФ тяжелее воды и тонут в ней, в то время как остальные пластмассы всплывают. Поэтому технология их мойки тоже отличается, а линии, предназначенные для очистки пленок ПВД, не дадут требуемого результата при подготовке отходов ПЭТ.
Процесс отмывки ПЭТ-бутылок
Технологический процесс отмывания использованных ПЭТ-бутылок более сложный, нежели обработка различных пленок. Он состоит из таких операций:
- Сортировка. Здесь вручную происходит разделение отходов на разные группы и отбор инородного мусора. Отходы медленно перемещаются сортировочным транспортером, автоматически удаляющим металлические включения с помощью встроенных электромагнитов (магнитный сепаратор).
- Измельчение (дробление), совмещенное с первичной мойкой.
- Сушка на центрифуге с предварительным удалением легких фракций — остатков этикеток и прочих инородных частиц.
- Флотация в специальной ванной. Цель операции – отделить тяжелый ПЭТ, оседающий на дно ванны, от крышек и колец для бутылок, сделанных из других видов пластмасс. Вместе с дроблеными пробками на поверхность всплывают остатки этикеток и прочего мусора.
- Плавающая масса направляется барабанами в отдельную емкость.
- Измельченный ПЭТ-пластик доставляется вместе с водой в установку интенсивной мойки, выполняемой за счет трения, подогрева и применения химических средств. Задача – начисто отмыть сырье от грязи и клея, используемого для этикеток.
- Окончательная сушка во второй центрифуге и накопление в бункере, предназначенном для наполнения сырьем биг-бегов.
Для перемещения сырья между установками используются шнековые и ленточные транспортеры. Также в линиях от различных производителей может применяться пневмотранспорт и перекачивание отходов вместе с водой насосами.
Очистка тонкостенных полимеров
Эта категория отходов включает в себя разнообразные полиэтиленовые пакеты, упаковки и тару, коими полны полигоны всех городов. Отмывать их от грязи проще, чем ПЭТ-бутылки, поскольку отходы содержат очень мало клея и имеют более мягкую структуру.
Соответственно, в технологию мойки входит меньше операций:
- сортировка;
- дробление с предварительной отмывкой;
- мойка во флотационной ванне;
- сушка в центрифуге;
- сбор в бункер – накопитель и наполнение биг-бегов.
Чтобы организовать законченный цикл переработки, в конце моющей линии зачастую устанавливают агломератор, получая готовое сырье для грануляции и отливки изделий в термопласт-автоматах.
Дополнительные технологические операции
В зависимости от степени загрязнения полимерных отходов и финансовых возможностей предприятия – переработчика технология мойки полимеров может дополняться различными операциями. Цель — увеличить производительность и повысить качество сырья на выходе, дабы расширить сферу применения вторичного пластика.
Пример.
Нередко производители различных напитков, работающие на территории постсоветского пространства, используют для этикеток дешевый резиновый клей, который тяжело удаляется. Из-за этого технологический процесс необходимо расширить, добавив операции удаления этикеток и мойку с подогревом.
При необходимости этап сортировки может быть усовершенствован за счет следующих мероприятий:
- Для ПЭТ-бутылок, собранных в тюки, вместо сортировочного конвейера поставить стол для ручной разделки.
- Ускорить и автоматизировать процесс разделки тюков поможет установка специального аппарата — кипоразбивателя.
- Вместо ручного отбора мусора от пластика применить автоматический просеиватель или грохот.
С помощью отделителя этикеток не только повышается качество работы всей линии, но и уменьшается количество отходов бумаги в ванне.
Чтобы отделить мелкие частицы мусора и различных пластмасс после дробления, в технологический процесс добавляется операция воздушной сортировки. Под напором воздуха в установке значительная часть легких фракций отделяется, а во флотационную ванну попадает больше однородного ПЭТ-сырья.
Для лучшей очистки полимеров мойка делится на 2 этапа:
- промывка с применением химикатов в воде, нагретой до 85—90 °С;
- фрикционная мойка с трением и полосканием для удаления химии.
Технологическая вода, применяемая на всех этапах, должна циркулировать в замкнутом цикле. Поэтому для ее очистки устанавливается отдельная ванна, разделенная на несколько отсеков. В одном с помощью вибросита отделяются нерастворимые частицы величиной до 33 мкм, в остальных вода проходит фильтрацию и химическую очистку.
На последнем этапе переработки вторичного сырья может применяться циклон – накопитель, объединяющий в себе 2 функции: дополнительную сушку и дозирование готовой массы в биг-беги.
Оборудование моечной линии
Состав производственной линии лучше всего рассматривать на примере отмывки ПЭТ-бутылок, поскольку данная технология – самая сложная.
Итак, базовый вариант линии мойки включает в себя следующие машины и установки (в порядке очередности):
- ленточный конвейер для ручной сортировки либо разделочный стол;
- наклонный конвейер, загружающий отходы в бункер дробилки;
- моющая дробильная установка;
- центрифуга №1;
- флотационная ванна с дополнительной емкостью для накопления остатков этикеток и пробок;
- фрикционная мойка;
- центрифуга №2;
- накопительный бункер.
Для начальной загрузки отходов и дальнейшей их передачи от одной установки к другой применяются ленточные и шнековые конвейеры.
Первые оснащаются электродвигателями небольшой мощности (от 1,5 кВт) с ременной либо редукторной передачей, приводящей в движение основной вал и транспортерную ленту. Есть возможность регулировать угол подачи сырья.
Шнековые транспортеры, перемещающие измельченную ПЭТ-флексу вперемешку с остатками пробок, оборудованы более мощным двигателем (от 4 кВт) и приводом от редуктора. В них также реализована возможность регулировки угла подачи дробленого пластика к следующей машине.
Остальное оборудование имеет более сложную конструкцию и заслуживает того, чтобы его рассмотреть по отдельности.
Моющая дробилка
Машины, предназначенные для измельчения полимеров, относятся к роторному типу дробилок. От их производительности зависит мощность всей линии мойки.
Существует 3 разновидности измельчителей:
- одновальные, где дробление пластика происходит между роторными и стационарными ножами;
- двухвальные, в них отходы дробятся между двумя группами роторных и стационарных ножей;
- четырехвальные.
Принцип действия установки следующий:
- Отходы подаются конвейером в бункер, откуда они падают в роторный механизм дробилки. Он представляет собой один или несколько валов (роторов) с закрепленными ножами (от 4 до 16 шт.). Есть и стационарные ножи, установленные внутри стального корпуса аппарата, их количество бывает разным.
- Бутылки, проходя сквозь этот механизм, превращаются в мелкую фракцию (ПЭТ-флексу), падающую на сетку с ячейками определенного размера (выбирается по желанию заказчика).
- Проваливаясь сквозь решетку, мелкий пластик смывается водой в сторону шнековой выгрузки.
- В процессе первичной отмывки удаляется грязь и отделяется часть бумажных и полимерных этикеток. Вся масса увлекается шнеком к следующей операции — центрифугированию.
- Скорость вращения роторов в установках от разных производителей колеблется в диапазоне 500—1000 об/мин, а мощность электродвигателя зависит от перерабатываемого материала и расчетной производительности машины.
Пример.
Дробилка производительностью до 200 кг/ч, предназначенная для измельчения ПЭТ, оснащена двигателем мощностью 11 кВт с ременным приводом. На установке для дробления пленки и старых биг-бегов применен электродвигатель 30 кВт, обеспечивающий производительность до 300 кг/ч.
Дробильная машина, действующая в составе автоматизированной производственной линии, управляется с общего пульта, хотя может комплектоваться собственным шкафом. Здесь важно синхронизировать работу подающего конвейера со скоростью измельчения установки, дабы добиться максимального эффекта, но не перегружать бункер.
Сушильная центрифуга
Основой этой машины является перфорированный барабан из нержавеющей стали толщиной от 3 мм.
Для обработки ПЭТ-флексы используется вертикальная модель центрифуги с неподвижным барабаном, внутри которого размещен ротор сложной конфигурации, напоминающей шнек. Сверху агрегата находится загрузочный бункер, внизу – шнековая выгрузка.
Алгоритм работы сушилки:
- Хлопья ПЭТ вместе с водой подаются от дробилки в загрузочный бункер центрифуги посредством конвейера.
- Вращаясь с большой скоростью, ротор прогоняет дробленый пластик мимо отверстий в барабане, отжимая из него воду.
- Одновременно происходит механическое отделение различных инородных примесей.
- Отжатую массу шнековая выгрузка перемещает на операцию флотации.
Центрифуги, рассчитанные на отжим отходов ПВД, ПНД, ПВХ и других видов полимеров, работают несколько по-другому.
В них вращается сам перфорированный барабан, а внутренний ротор отсутствует. В установках предусматривается периодическая очистка барабана потоком воды.
Справка.
Для повышения производительности и уменьшения влажности сырья практикуется использование шнековых отжимных прессов, действующих по принципу соковыжималки и предназначенных для сушки тонкостенных полимеров.
Частота вращения ротора (в других моделях — барабана) и мощность привода зависит от назначения машины и ее производительности.
Например, агрегат, способный высушить и очистить до 300 кг флексы за 1 ч, оснащен мотором на 5,5 кВт, а диаметр ротора составляет 38 см. Производительность 600 кг/ч обеспечит ротор Ø500 мм и двигатель на 15 кВт. Такая же центрифуга устанавливается в конце технологического цикла и сушит окончательно вымытое сырье.
Ванна флотации
Конструкция этих установок отличается в зависимости от перерабатываемого вида пластмассы.
Существуют такие разновидности ванн:
- наклонная мойка для ПЭТ-флексы малой производительности;
- горизонтальная высокопроизводительная ванна для отмывания флексы;
- мойка с барабанами для других видов пластика.
Особенность данного оборудования заключается в том, что ванну для очистки хлопьев ПЭТ нельзя применять с целью отмывания других полимеров.
Сырье из пластиковых бутылок обладает плотностью выше единицы и тонет в воде, в отличие от прочих пластмасс.
Поэтому конструкция флотационных установок состоит из таких элементов:
- ванна, имеющая наклонное дно, либо в сечении повторяет форму перевернутой пирамиды;
- по дну ванны проходит шнек, приводимый в действие двигателем с редуктором;
- шнековый конвейер, выгружающий измельченный ПЭТ под водой;
- система пополнения воды, сливаемой вместе с отходами в отдельную емкость.
Когда конвейер распыляет под водой измельченную массу, то тяжелый ПЭТ опускается на дно, а остальные полимеры, из которых сделаны пробки, кольца и этикетки; всплывают на поверхность. Оттуда они сливаются вместе с водой, после чего проходят через малый пресс для отжима.
ПЭТ-флекса увлекается шнеком, расположенным на дне, и выходит с другой стороны для прохождения процедуры мойки. То есть, флотационная ванна в линии переработки бутылок служит только для разделения пластмасс.
Хлопья других видов пластика отмываются во флотационной мойке с подогревом, оснащенной 4 барабанами с лопастями различной конфигурации для захвата лоскутов разных размеров.
Отличия от ванн для ПЭТ следующие:
- Сама емкость — двухстенная прямоугольного сечения. Между стенками заложен утеплитель и встроены электронагреватели.
- Над дном установлена сетка, отделяющая крупные частицы.
- Над поверхностью расположены барабаны (от 4 шт.), вращаемые двумя электродвигателями посредством редукторов. Лопасти барабанов сделаны различной ширины и повернуты под разными углами.
- Для очистки воды задействована система рециркуляции.
- Отходы пленок моются во флотационной ванне с применением химических реагентов и подогрева воды до температуры 85—90 °С. После они направляются на полоскание и сушку.
Если необходимо осуществить горячую химическую мойку ПЭТ-полимеров, то после ванны флотации дополнительно ставится специальная машина цилиндрической формы с утепленными стенками и встроенными ТЭНами. Внутри емкости сделаны лопасти – ворошители, перемешивающие отмываемую массу дробленной флексы.
Фрикционная мойка
Как легко понять по названию, очистка пластмасс в этой установке производится за счет трения хлопьев друг о друга, о сетку и детали шнека. За счет этого отмывается 95% всех загрязнений, что вполне приемлемо для получения вторичного сырья.
Агрегат состоит из таких элементов:
- наклонный корпус в виде узкого желоба, закрытого со всех сторон;
- шнек с редукторным приводом от электродвигателя, проходящий по всей длине корпуса;
сетка, окружающая шнек внутри желоба; - загрузочный проем в нижней части;
- проем для выгрузки в верхней части.
Для доступа к внутренней полости желоб оборудован откидными крышками. Некоторые модели, предназначенные для химической мойки с подогревом, имеют утепленный корпус и электронагреватели.
Принцип действия машины прост: хлопья или лоскуты полимеров загружаются внутрь желоба, где за счет вращения шнека трутся между собой. По пути вверх грязь удаляется вместе с водой через сетку, а сверху выходит чистое сырье, направляемое для сушки в центрифугу №2.
Фрикционные мойки весьма производительны и функционируют непрерывно. Например, агрегат с мощностью привода 11 кВт способен промыть 2 тыс. кг ПЭТ-флексы за 1 час. При этом технологическая вода циркулирует по кругу, проходя очистку в отдельной ванне.
Управление линией и работа персонала
Управление всеми машинами осуществляется с единого пульта, находящегося в удобном месте, откуда есть хороший обзор. Поскольку оборудование поставляется одним производителем, общий пульт совместим со всеми установками моющей линии. В самом бюджетном исполнении общий пульт может отсутствовать, а машины запускаться с помощью собственных шкафов управления. Также от стоимости оборудования и завода — изготовителя зависит набор функций, выполняемых с пульта.
Большинство производителей моечных комплексов утверждают, что работу всех агрегатов может обслуживать 1 человек. Это соответствует действительности, когда линия полностью автоматизирована и на нее подаются отсортированные отходы одного вида.
В противном случае для сортировки придется привлечь 2—4 человека как минимум.
Но даже при высокой степени автоматизации расклад по обслуживающему персоналу выглядит так:
- Специально обученный рабочий обслуживает линию;
- Для подвоза отходов и замены полных биг-бегов нужно использовать вилочный погрузчик либо тельфер, значит, необходим водитель или стропальщик.
- На предприятии должен постоянно находиться дежурный электрик для ремонта электросетей и наладчик, способный устранить неполадки в любой из машин во время работы.
- Еще один работник — ответственное лицо за функционирование участка.
Задача персонала – обеспечить безостановочную и безаварийную работу моющего комплекса.
Практика показывает, что проблемы могут возникать по таким причинам:
- При переработке ПЭТ-тары в отходы попадают бутылки из ПВХ, что недопустимо и в отдельных случаях может привести к остановке оборудования.
- Смешивание полимеров по видам и цветам дает некачественное сырье на выходе.
Несвоевременная очистка емкостей от грязи, собирающейся при мойке пластика. Проблема возникает при переходе на более загрязненные отходы. - Попадание мелких частиц металлов, разрушающих ножи дробилок, шнеки и другие рабочие детали машин.
Отдельная история – проблема с отмыванием различных клеящих составов для этикеток.
Если не удалить клей подчистую, то при агломерации либо грануляции он может придать желтоватый оттенок цвету полимера. Поэтому для очистки от нерастворимых в воде составов необходимо применять соответствующие химические компоненты, за что несет ответственность технолог предприятия.
Контроль качества очистки полимерных хлопьев состоит из трех операций:
- визуальный осмотр на предмет разноцветных включений;
- измерение влажности, которая не должна превышать определенных значений;
- проверка на наличие остатков клея, выполняемая термическим способом в лабораторном шкафу.
Недостаточно просушенное сырье, как и частицы клеящих составов, ухудшает качество этого полимера при грануляции. Из разноцветных хлопьев выйдет агломерат неопределенного оттенка, и его сфера применения будет ограничена, а цена существенно снизится. Отсюда и жесткие требования к соблюдению технологии и ответственности обслуживающего персонала.
energylogia.com
Шнековая и шнеко-барабанная моечные машины для крупы
Для мойки круп чаще всего используют шнеко-барабанные моечные машины (рис. 4). Работа на шнеко-барабанной моечной машине осуществляется следующим образом. Крупу из зернового сепаратора или промежуточной емкости направляют в шнек машины 1, в который непрерывно поступает вода. По мере продвижения крупы по шнеку легкие примеси всплывают и удаляются с избытком воды через переливную воронку. Продвигаясь вдоль шнека, крупа в связи с трением отдельных крупинок друг о друга, а также о винт и корпус шнека освобождается от прилипшей грязи и в конце шнека сбрасывается в передаточную коробку 2, откуда лопастями передается в ополаскивающий барабан 3. При продвижении крупы вдоль барабана она промывается струями воды, что способствует лучшему отделению минеральной примеси.
Рис. 4. Шнеко-барабанная моечная машина для крупы.
Для мойки круп и зернобобовых используют также шнековую моечную машину.
Шнековая моечная машина (рис. 5) состоит из приемного устройства 1 и корыта, в котором проходит шнек 2, передаточного патрубка 3 и вибрационного сита 4. Работа машины заключается в следующем. Продукт подается в приемное устройство, которое заполнено водой до верхнего сливного отверстия 5. По мере поступления крупа оседает в корыто шнека и шнеком транспортируется к передаточному патрубку. Легкие примеси (лузга, мучель и т. п.) всплывают на поверхность воды и удаляются через сливное отверстие. Камни оседают в камнеотборнике (на схеме не показан).
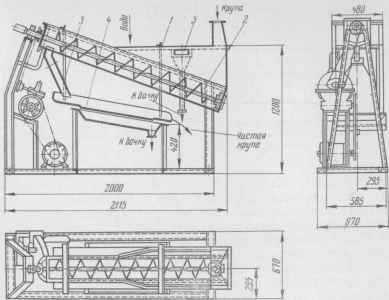
Рис. 5. Шнековая моечная машина для крупы.
Крупа, поднявшись до передаточного патрубка, сбрасывается через него на вибрационное сито.
Последние лопасти шнека имеют мелкие отверстия, через которые вода стекает вниз. На вибрационном сите крупа окончательно освобождается от воды.
Производительность шнековой моечной машины 1-1,5 т крупы в час, потребная мощность 1,7 кВт, число оборотов вала шнека в минуту 930. Габаритные размеры: длина 2115 мм, ширина 670 мм, высота 1420 мм. Масса машины 308 кг.
При мойке круп и зернобобовых применяют обычную водопроводную воду температурой 10-12° С и только пшено моют при температуре 45-47° С.
Расход воды на описанных моечных машинах составляет 2-2,5 л на 1 кг крупы.
Технологический эффект работы этих моечных машин достаточно высок. Зерно полностью освобождается от минерального загрязнения, доброкачественность его повышается. Так, доброкачественность гороха после мытья с 97,20% повысилась до 98,20%, овсяной крупы — с 98,20 до 98,80%. Значительно снижается содержание необрушенных зерен, сорной примеси, мучели и т. п.
При мойке овсяной крупы, например, отходы (исключая неучтенные — мучель и грязь) составляют примерно 0,43% к массе мытой крупы. Эти отходы состоят из семян дикорастущих растений, органического сора и т. п.
Показатели работы шнеко-барабанной моечной машины представлены в табл. 11.
Таблицa 11.
Продукты | Производительность машины кг/ч | Расход воды, л/кг | Потери сухих веществ, % | Влажность после мойки, % |
Горох лущеный | 1500 | 2,5 | 2,40 | 25-27 |
Рис | 1300 | 2,0 | 3,60 | 25-27 |
Овсяная крупа | 1700 | 2,1 | 1,10 | 25-27 |
Пшено | 1700 | 2,5 | 1,50 | 28-30 |
www.comodity.ru
Моечная машина шнековая ММШ | ЭлеМаш
Информация Технические характеристики Видео
Машина моечная шнековая ММШ применяется для мойки сыпучих продуктов (семечек, зерна, зелени, семян тыквы, круп и т. п.), имеющих небольшие загрязнения.
Продукт поступает из бункера, оснащенного заслонкой для регулировки потока. Мойка происходит в ёмкости, оборудованной шнековым питателем, который перемешивает продукт и одновременно подаёт его в зону выгрузки, где удаляется лишняя влага и продукт удаляется из машины.
Мойка осуществляется проточной водой, которая после мойки фильтруется от мусора и, по желанию заказчика, может сливаться в канализацию или пускаться по замкнутому циклу. Оператор может регулировать производительность моечной машины, расход воды, длительность мойки. Моечная машина используется на производствах зерновых хлебов, линиях жарки семечек, переработки пластмасс.
Технические характеристики являются справочными. Точную информацию уточняйте у наших менеджеров. Технические характеристики
Параметры Модель | ММШ-350 | ММШ-600 |
Производительность по зерну | 100-450 кг/час | 200-900 кг/час |
Длительность мойки | 15-100 сек | 15-100 сек |
Расход воды | 2-8 литров/мин | 3-15 литров/мин |
Мощность привода | 0,37 кВт | 0,55 кВт |
Напряжение питания | 1 фаза, 220 В, 50 Гц | |
Габариты (ДхШхВ) | 2100х480х1580 мм. | 2100х550х1600 мм. |
Масса | 180 кг. | 230 кг. |
Технические характеристики являются справочными. Точную информацию уточняйте у наших менеджеров. Видео по данному оборудованию не найдено!
Информация Технические характеристики Видео
elemash-m.ru