Производство аммиака | ОАО «ГИАП»
Производство аммиака
За годы существования ГИАП на основе разработок его ученых и инженеров была создана крупнейшая в мире и передовая по уровню технических решений азотная промышленность. Было спроектировано и построено около 70 агрегатов аммиака мощностью от 55 до 450 тыс. тонн в год. Построен уникальный аммиакопровод Тольятти – Одесса, позволяющий экспортировать жидкий аммиак во многие регионы мира. В настоящее время в России и странах СНГ работает 22 агрегата аммиака мощностью 450000 тонн в год. По проектам института построены объекты азотной промышленности в Афганистане, Болгарии, Германии, Китае, Кубе, Румынии.
НОВЫЕ ТЕХНОЛОГИИ В ПРОИЗВОДСТВЕ АММИАКА
В рамках данного направления в настоящее время компанией осуществляется разработка и проектирование следующих технологий:
- Модернизация действующих производств аммиака
- Перевод избыточных производств аммиака на производство метанола
- Создание интегрированных производств аммиак-метанол, аммиак-водород и др.
- Разработка производства аммиака на базе новейших достижений технологии для замены действующих агрегатов
Для выполнения работ по перечисленным направлениям компания располагает знаниями и опытом практически по всем стадиям технологических линий производств аммиака, метанола, водорода и др. Сотрудники компании принимали участие в разработке технологии и аппаратуры для многих крупнотоннажных химических производств, а также в их пуске. В 1998 году при их участии было разработано и запущено производство аммиака в Китае с использованием наиболее современной энергосберегающей технологии, превосходящей мировой уровень. В настоящее время разработаны перспективные технологии производства аммиака с удельным энергопотреблением 6.64 Гкал на тонну NH3. Для модернизации производств разработаны технические решения по увеличению мощности крупных агрегатов аммиака до 1800 тонн в сутки, разработаны и осуществлены проекты реконструкции колонн синтеза аммиака и метанола, конверторов СО первой и второй ступени, смесителей для реакторов реформинга и др.
Технология ГИАП производства аммиака с низким потреблением энергии
При разработке концепции нового аммиачного агрегата мы принимали во внимание следующие аспекты проблемы:
Термодинамический аспект. Необходимо прежде всего снизить производство пара, ограничившись неизбежными технологическими нуждами, и производство механической энергии, используемой на компремирование технологических потоков и гидравлические потери. При этом неизбежную рекуперацию тепла следует проводить на наиболее высоком температурном уровне.
Экологический аспект. Можно полагать, что ограничения на используемое первичное топливо и производство пара скажется на количестве жидких и газовых выбросов в окружающую среду. Мы исходили из необходимости снизить вредные газовые выбросы в 3-4 раза и почти полностью исключить выбросы технологического конденсата.
Надежность и безопасность. Следует принять во внимание, что надежность и безопасность агрегата повышается, если удается уменьшить долю оборудования, работающего при наиболее высокой температуре и давлении, упростить компрессоры, исключить паропроводы высокого давления и турбины, использующие пар высокого давления. Система управления должна обеспечивать надежное функционирование всех установок агрегата, содержать подсистемы диагностирования состоянии оборудования, обрабатывать и выводить их информацию.
Технические решения. Термодинамические соображения, положенные в основу концепции энергосбережения могут быть реализованы путем использования новейших разработок ГИАП в области технологии, аппаратуры и катализаторов. В соответствии с этой концепцией аммиачного агрегата мы приняли следующие технические решения.
Базовые показатели потребления энергии аммиачных агрегатов по технологии ГИАП.
В приведенной ниже Таблице 1 приведены показатели по потреблению энергии на тонну аммиака. для агрегата с давлением синтеза 80 бар, в котором достигнуто наименьшее производство механической энергии – около 0,566 МВт на тонну аммиака.Таблица 1
БАЗОВЫЕ ПОКАЗАТЕЛИ РАСХОДА СЫРЬЯ, ЭНЕРГИИ И МАТЕРИАЛОВ ДЛЯ АММИАЧНЫХ АГРЕГАТОВ ПО ТЕХНОЛОГИИ ГИАП на 1 тонну NH3
Давление в цикле синтеза, бар | 80 |
Природный газ, м3 калорийность 8807 кал/м3 | 708,1 |
Кислород, м3 | 0 |
Электроэнергия, кВтч | 481,5 |
Питательная вода, м3 | 0,73 |
Охлаждающая вода, м3 | 80,6 |
Общее потребление энергии, ГДж | 28,01 |
Программное обеспечение инженерно-технологических решений.
При разработке современных технологий большее значение принимает программное обеспечение моделирования химико-технологических процессов. В нашем институте ведутся работы по созданию программных средств для расчёта процессов в каталитических реакторах, поскольку производство аммиака в значительной мере базируется на каталитических процессах, а его дальнейшее развитие связано с прогрессом в области исследований гетерогенного катализа. Любая разработка современной аммиачной технологии не может быть осуществлена без использования программ кинетических расчетов реакторов вторичного риформинга, конверсии СО, синтеза аммиака и др. Указанные программы созданы с учетом многолетних исследований ГИАП в области кинетики гетерогенного катализа и обобщают уникальный опыт внедрения разработок института в промышленности.
Сейчас мы перешли от одномерных моделей химико-технологических процессов с набором критериальных уравнений тепломассообмена к созданию программ более сложных двумерных моделей. Использование таких моделей уменьшает количество экспериментально определяемых параметров, которые на настоящий момент либо нельзя достаточно точно определить, либо они вообще не определяются существующими методами измерения. Кроме того, такие модели в несколько раз увеличивают объем получаемой полезной информации.
В частности разработана программа для расчета паровой конверсии природного газа по двухмерной модели катализаторного слоя, которая делает возможным:
- Предсказание получаемого состава газа на выходе из реактора с катализатором различных форм и размеров
- Определение производительности риформинга.
- Определение степени использования и ресурса дальнейшей работы катализатора.
- Расчет оптимального объема катализатора согласно требуемой производительности установки и с учетом возможного старения катализатора.
- Расчет радиального и аксиального распределения температур, концентраций, скоростей потоков и т. д.
Как и все программные разработки, сделанные в ГИАПе, она базируется на фундаментальных теоретических построениях и использовании значительного количества промышленных экспериментальных данных.
Теоретическая база программы расчета конверсии природного газа в трубке с катализатором позволяет создавать аналогичные программы и для других процессов гетерогенного катализа, например, для моделирования процессов синтеза аммиака в радиально-противоточном реакторе.
www.giap-m.com
ИК ГЕОС посталяет установки по производству амиака
Аммиак относится к числу важнейших продуктов химической промышленности. Аммиак нашел широкое применение для производства азотных удобрений (нитрат и сульфат аммония, мочевина), взрывчатых веществ и полимеров, азотной кислоты, соды (по аммиачному методу) и других продуктов химической промышленности, также применяется в качестве хладагента. В 1955 г. во всем мире было произведено аммиака около 8 млн. т, в 1965г.— 20 млн. т, в 1970 г.— 66 млн. т, в 1980 г. — более 100 млн. т, а в 1985 г. более 120 млн. т. Сырьем к установкам по производству аммиака в основном служат природный газ (возможно применение сжиженного нефтяного газа, тяжелых углеводородов, нафты и даже угля) и азот.
Реакция получения аммиака основана на прямом взаимодействии водорода и азота:
Процесс получения:
Технологическая схема получения аммиака, прежде всего зависит от типа углеводородного сырья. Наиболее широкое использование получил природный газ, именно он является основой аммиачной промышленности. В основе процесса производства аммиака лежит паровой риформинг. Для этого исходный природный газ очищают от серы при помощи десульфатора. Далее очищенный природный газ смешивается с паром для процесса риформинга. В печи происходит сложная реакция с получением угарного газа, углекислого газа и водорода. Смесь этих газов и пара поступает в конвертер сдвига для получение дополнительного получения водорода. Далее возможны различные варианты технических решений. Первый — добавление в процесс технического воздуха (традиционный) или извлечение водорода методом КЦА с последующим смешением его с чистым азотом. Последний метод является наиболее энергоэффетивным. Синтез аммиака из газообразного водорода и азота является экзотермической реакцией. Ограничения термодинамического равновесия не позволяют получить полную конверсию водорода и азота в аммиак за один проход через реактор. Контур синтеза аммиака кроме реактора включает несколько теплообменников для предварительного нагрева и охлаждения, конденсации и отделения товарного аммиака. Непрореагировавший сингаз возвращается на компрессор рециркуляции для достижения полного синтеза.
Наиболее глобальным изменением подвергся блок синтеза аммиака. Главной чертой стало применение аксиально-радиального реактора с высокой степенью конверсии, что позволяет уменьшить количество циркуляционного газа, что также положительно отразилось на энергоэффективности из-за снижения потребляемой мощности компрессора, циркуляционного насоса и энергопотребления на охлаждение.
В таком аксиально-радиальном реакторе слой катализатора не имеет перекрытия сверху и некоторое количество газа поступает в осевом направлении. Количество газа, проходящего в осевом направлении, контролируется правильной схемой перфорированных отверстий и отчасти «изолированный» катализатор работает при условиях, аналогичных условиям катализатора в радиальной части слоя. Поэтому в данной конструкции достигается максимальная производительность объема загруженного катализатора. Технология постоянно совершенствуется и главным направлением мероприятий по ее улучшению является снижение энергоемкости самого процесса. Общее энергопотребление (расход сырья, топлива и электроэнергии) на тонну аммиака составляет от 6,6 до 7,1 Гкал в зависимости от местных условий и производительности установки. Для снижения энергопотребления мы проектируем установки с максимальной утилизацией тепла, современными более эффективными катализаторами, адсорбционное извлечение СО2, а также производство побочных продуктов для других химических производств.
Вместе с производством аммиака на установках можно побочно получать метанол, карбид, водород, кислород, аргон, монооксид углерода и диоксид углерода.
Современный завод по производству аммиака представляет из себя довольно сложный комплекс сооружений.
Наши специалисты помогут подобрать Вам оптимальную установку к требуемому технологическому процессу. Опыт наших специалистов позволяет реализовывать проект установки производства аммиака «под ключ» для нужд Заказчика.
geos-ltd.com
Оборудование + Технология изготовления 2019
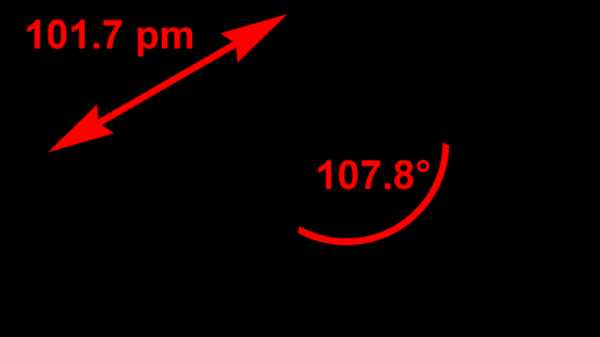
Аммиак (нитрид водорода, формула NH3) при нормальных условиях — это бесцветный газ с резким характерным запахом. Он относится к числу важнейших продуктов химической промышленности. Его ежегодное мировое производство достигает 150 млн. тонн. В основном он используется для изготовлении азотных удобрений (нитрат и сульфат аммония, мочевина), взрывчатых веществ и полимеров, азотной кислоты, соды (по аммиачному методу) и других продуктов химической промышленности. Жидкий аммиак используют в качестве растворителя.
В холодильной технике используется в качестве холодильного агента (R717).
В медицине 10% раствор аммиака, чаще называемый нашатырным спиртом, используется при обморочных состояниях (для возбуждения дыхания), для стимуляции рвоты, а также наружно — при невралгии, миозитах, укусах насекомых, для обработки рук хирурга. При неправильном использовании может вызвать ожоги пищевода и желудка (в случае приёма неразведённого раствора), рефлекторную остановку дыхания (при вдыхании в высокой концентрации).
Технология производства аммиака + видео как получают
В рамках этого направления сегодня многие компании стали заниматься разработкой и проектированием следующих технологий:
- Перевод избыточного количества аммиака на изготовление метанола.
- Разработка производства на основе современных технологий для подмены активных агрегатов.
- Создание интегрированного производства и модернизация.
На производство одной тонны аммиака в России расходуется в среднем 1200 нм³ природного газа, в Европе — 900 нм³. Белорусский «Гродно Азот» расходует 1200 нм³, после модернизации ожидается снижение расхода до 876 нм³. Украинские производители потребляют от 750 нм³ до 1170 нм³. По технологии UHDE заявляется потребление 6,7 — 7,4 Гкал энергоресурсов на тонну.
Промышленный способ получения аммиака основан на прямом взаимодействии водорода и азота:
N2 + 3H2 ⇄ 2NH3+ + 91,84 кДж
Это так называемый процесс Габера (немецкий физик, разработал физико-химические основы метода). Реакция происходит с выделением тепла и понижением объёма. Следовательно, исходя из принципа Ле-Шателье, реакцию следует проводить при возможно низких температурах и при высоких давлениях — тогда равновесие будет смещено вправо. Однако скорость реакции при низких температурах ничтожно мала, а при высоких увеличивается скорость обратной реакции. Проведение реакции при очень высоких давлениях требует создания специального, выдерживающего высокое давление оборудования, а значит, и больших капиталовложений. Кроме того, равновесие реакции даже при 700°C устанавливается слишком медленно для практического её использования. Выход аммиака (в объёмных процентах) в процессе Габера при различных температурах и давлении имеет следующие значения:
100 ат | 300 ат | 1000 ат | 1500 ат | 2000 ат | 3500 ат | |
---|---|---|---|---|---|---|
400 °C | 25,12 | 47,00 | 79,82 | 88,54 | 93,07 | 97,73 |
450 °C | 16,43 | 35,82 | 69,69 | 84,07 | 89,83 | 97,18 |
500 °C | 10,61 | 26,44 | 57,47 | Нет данных | ||
550 °C | 6,82 | 19,13 | 41,16 |
Применение катализатора (пористое железо с примесями Al2O3 и K2O) позволило ускорить достижение равновесного состояния. Интересно, что при поиске катализатора на эту роль пробовали более 20 тысяч различных веществ.
Учитывая все вышеприведённые факторы, процесс получения проводят при следующих условиях:
- температура 500 °C;
- давление 350 атмосфер;
- катализатор.
Выход аммиака при таких условиях составляет около 30%. В промышленных условиях использован принцип циркуляции — аммиак удаляют охлаждением, а непрореагировавшие азот и водород возвращают в колонну синтеза. Это оказывается более экономичным, чем достижение более высокого выхода реакции за счёт повышения давления. Для его получения в лаборатории используют действие сильных щелочей на соли аммония:
NH4Cl + NaOH → NH3↑ + NaCl + H2O
Обычно лабораторным способом аммиак получают слабым нагреванием смеси хлорида аммония с гашеной известью.
2NH4Cl + Ca(OH)2 → CaCl2 + 2NH3↑ + 2H2O
Для осушения аммиака его пропускают через смесь извести с едким натром. Очень сухой можно получить, растворяя в нём металлический натрий и впоследствии перегоняя. Это лучше делать в системе, изготовленной из металла под вакуумом. Система должна выдерживать высокое давление (при комнатной температуре давление насыщенных паров около 10 атмосфер). На промышленном производстве обычно для сушки используют абсорбционные колонны.
Видео как делают:
Производство аммиака не должно обходить стороной технический прогресс. В основном это касается энергосбережения. В ходе разработки современных технологий большое значение отводится программному обеспечению, необходимому для моделирования химических и технологических процессов.
Загрузка…moybiznes.org
Мини производство удобрений — Оборудование мини производства
Когда беседа поднимается о комбинатах, в основном думают, что это: парк техники, множество рабочих, большое количество разного технологического оборудования, территория с внушительными длинными терминалами. Большинство отечественных фабрик таким образом организованы, однако они являются не оптимизированными. Рентабельность хорошего комбината обусловлена не мощностью, а покупкой оптимального производственного оборудования. Мини заводы приходят вместо заводов старого типа.
Мини производство удобрений
Предлагаем Вам комплект оборудования для производства удобрений и биогаза, который снизит Ваши затраты на утилизацию органических отходов (коровий, птичий, свиной и др. навоз) и дополнительно позволит выпускать высокоэффективное экологически чистое жидкое органическое удобрение «КОУД». Установив оборудование, вы сможете забыть о покупке дорогостоящих минеральных удобрений и полностью обеспечить потребности своего хозяйства в подкормке сельхохозяйственных культур.
Кроме этого, оборудование вырабатывает источник энергии – биогаз, который можно использовать для получения электроэнергии, для нагрева воды в технологических целях и т.д.
Установка предназначена для безотходной, экологически чистой переработки органических отходов сельскохозяйственного производства (навоза, помета, фекалий, твердых бытовых отходов, пищевых отходов, растительных остатков), имеющего КРС или других домашних животных (свиньи, овцы, козы, лошади, пушные звери и т.д.) и птицу (куры, гуси, утки, индюшки и т.д.) в газообразное топливо – биогаз, конвертируемый далее в электрическую и тепловую энергию, экологически чистые жидкие или твердые органические удобрения, лишенные нитратов и нитритов, семян сорняков, патогенной микрофлоры, яиц гельминтов, специфических запахов.
Она осуществляет биотехнологическую переработку всех видов органических отходов (навоза, помета) фермы крупного рогатого скота (КРС) на 15-20 голов, или свинофермы на 150-180 голов, или птицефермы на 1500-1800 голов и позволяет наладить непрерывное производство удобрений.
Производительность:
— количество перерабатываемых отходов при влажности 85% т/сутки – до 0,6
— выход по биогазу с общей теплотворной способностью 480 тыс. кДж/сутки (эквивалент 17 кг топочного мазута) до 24 куб. м. в сутки
— общее количество вырабатываемой тепловой энергии, 432 тыс. кДж в сутки
— эквивалент по электроэнергии 48 кВт*ч в сутки
— количество вырабатываемых органических удобрений до 0,6 тонн в сутки
— расход тепла на собственные нужды не более 30% от вырабатываемого
Продукты:
— биогаз, содержит 60% метана, 40% углекислого газа, не содержит сероводорода, теплотворная способность 20-22 тыс. кДж/куб.м. используется в любых бытовых газовых приборах
— тепловая энергия – горячая вода (70-90 гр.С) для отопления бытовых и производственных помещений площадью 75-90 кв.м.
— электрическая энергия – переменный ток 220-380 В, 50 Гц
— жидкие удобрения
Срок эксплуатации 10 лет. Процесс непрерывный.
Установка может собираться в батареи из 2-х и более блок-модулей и обрабатывать, соответственно, отходы от 30-40 и более голов КРС или другой живности.
В базовую комплектацию входят биореактор и газгольдер.
При Вашем желании изготовим и установим любое дополнительно оборудование для полной автоматизации работы биореактора и использования его продуктов.
Мини-комплектация системы.
Предназначена для использования частными лицами, имеющими небольшое количество КРС, свиней, птиц.
Стандартная комплектация имеет объем биореактора 1 куб.м. и позволяет перерабатывать отходы от 2 до 4 коров, от 25 до 30 свиней, от 250 до 300 птиц. Комплектация может быть изменена.
Использование этой системы позволит получать ежедневно 100 кг высококачественного удобрения «КОУД». При комплектации газгольдером возможно получение биогаза для использования в бытовых целях.
Источник: http://bmpa.narod.ru/page7.html
Мини производство удобрений
Аммиак / Вода аммиачная / Диамонийфосфат / Запчасти к арматуре промышленной / Запчасти к компрессорам / Запчасти к насосам / Изделия из пластмасс / Карбамид / Пленки полимерные полиолефиновые / Селитра аммиачная / Удобрения / Смолы
Продукция: Зерновые / Подсолнечник / Мясо птицы / Яйца птицы / Паштеты из мяса птицы / Сухой куриный помет
Источник: http://www.poshuk.com/kved/Ind.24.15.0
Мини производство удобрений
Самое главное в бизнесе по производству удобрений – это постоянное внедрение инноваций. Зачастую бывает мало просто освоить их производство, нужно постоянно разрабатывать новые возможности упрощения технологического процесса, разрабатывать проектно-конструкторскую документацию, осваивать новые виды продукции, быть в курсе новостей в данной области и так далее. Это – достаточно динамичная отрасль. Разработка новых схем получения неорганических удобрений – также может стать одним из направлений деятельности.
Основной потребитель минеральных удобрений – это представители сельскохозяйственной отрасли. Ее сейчас невозможно представить без применения минеральных удобрений в том или ином количестве, таким образом, отрасль их производства всегда будет востребована. Однако, несмотря на это, на рынке уже имеется большое количество их производителей, поэтому конкуренцию могут выдержать лишь те, кто основывает и внедряет инновации.
Оборудование для производства удобрений
Завод по производству удобрений должен иметь необходимое оборудование для совершения своей деятельности. Получение разрешений в данной сфере деятельности обязательно. Также важно соблюдать е только нормы пожаробезопасности или производства химической продукции, но также и экологические. Очень важно заранее выбрать поставщиков качественного оборудования для производства минеральных удобрений. Здесь можно выбрать как российские машиностроительные заводы, так и зарубежные. Зачастую в поставке европейского оборудования нет особой необходимости, поскольку отечественные производители также предлагают достаточно неплохие по качеству конструкции, которые порой даже бывают более адаптированы к местному производству.
Производство удобрений — документы и разрешения
Источник: http://promplace.ru/article_single.php?arc=98
Мини производство удобрений
Юрий Слащинин:
Предлагаются вам не чертежи, а метод и технология.
Я не знаю ваших условий и возможностей. А вы, зная их, можете легко приспособить к ним предлагаемую технологию. Она общедоступна, проста, а значит, истинна. Истинна, потому что исходит из главного секрета урожайности: чем больше в почве бактерий, тем выше урожай.
Исходя из этого закона, не трудно сделать вывод, что для получения высоких урожаев требуется ускоренное размножение в почве бактерий и прочего «живого вещества». Именно этому земледелец должен научиться в наших новых условиях. Научиться делать это «размножение» с виртуозной легкостью во всех возможных вариантах, используя имеющуюся органику, оборудование и даже окружающую среду.
Говорю это к тому, что совсем не обязательно вывозить на поля тысячи тонн органики. Надо там же и оставлять ее, как делали первые земледельцы Земли, следуя законам природы. Они уносили с поля колосья, плоды, овощи. А все оставшееся тут же запахивали в землю. У нас же предписано: солому — в скирды, стерню — сжечь, ботву — на межу, листья — на свалку и т.д. И все под благовидными предлогами борьбы с сорняками и вредителями, а по сути — с единственной целью увести подальше от возможности получить повышенный урожай.
И для производства органических удобрений вовсе не требуется 2-3 лет. Факт деления бактерий в среднем за 20 минут известен давно. Надо пользоваться этим и делать все возможное для размножения бактерий, а не губить их химией и глубокой пахотой, как предписывается ныне действующей агротехникой.
Предлагаемая технология производства органических удобрений направлена на создание всего возможного для размножения полезных бактерий почвы в максимальном объеме при минимально коротких сроках.
В зависимости от оснащенности мини-завода этот срок будет колебаться от 2-х недель до 1 суток.
А это, как понимаете, уже поточное производство продукции, эквивалентной зерну, овощам и фруктам, в которые превратятся отходы нашей жизнедеятельности.
И последняя оговорка для уточнения. У некоторых читателей наших изданий может сложиться мнение, что мы полностью отвергаем минеральные удобрения. Это не так. Мы — сторонники органического земледелия — всегда знали, что минералы и микроэлементы растениям нужны.
Так же, как и человеку.
Но ведь вы, садясь обедать, не подаете в тарелках вместо супа растворы железного купороса с кусочками калия, блестками серы и зеленью ядовитого хрома, медного купороса. Почему же растениям сгружается все это под благовидным предлогом «накормить» и повысить урожай?
Минералы и микроэлементы растениями нужны. Но, во-первых, многие из них растения получают из почвы, воздуха и воды. Во–вторых, самый главный их поставщик в сбалансированном виде (как уже говорилось) — это отжившие бактерии, их переГНОЙ. А в случае, когда первое и второе не в состоянии обеспечить растения всем необходимым для полноценного развития, то минералы и микроэлементы просто необходимо внести в почву.
Мы же будем это делать не только напрямую, но и окольно. То есть использовать бактерии. Пусть возьмут в себя, сколько в состоянии вобрать, а после своей короткой жизни передадут все растениям в усвояемом виде. Вот тогда и не будут накапливаться в зерне, овощах и фруктах нитраты и прочая химическая гадость.
Схема мини-завода
Перед вами схема основного модуля мини-завода. Назовем ее так:
Установка
для превращения органических отходов
в чернозем повышенного плодородия
Компоненты органических составляющих поступают на приемную площадку. При необходимости измельчаются измельчителем (1) и подаются в бункер-накопитель (2), откуда поступают на ленту транспортера (4) в заданных задвижками (3) количествах. Транспортер сбрасывает компоненты в вильчатый смеситель-разрыхлитель (5), где они перемешиваются, рыхлятся и транспортером (6) подаются в биореактор (7).
Биореактор представляет собой кирпичный туннель с брезентовым, легко съемным покрытием (8). На полу уложены перфорированные трубы (9), в которые подается пар из парогенератора (10). Загруженная в биореактор масса быстро увлажняется и нагревается паром до температуры 60-70 0 С, при которой гарантированно погибают гельменты и патогенная микрофлора, и процесс компостирования органических компонентов термофильной биофлорой идет в оптимальном, ускоренном режиме. Установленные внутри биореактора датчики автоматически поддерживают температуру и влажность через блок управления.
Процесс переработки органики в питательную массу для «живого вещества» или животных (в случае производства кормов) ускоряется в сотни раз и длится 1-3 суток.
Стерилизованная масса из биореактора выгребается шнековым погрузчиком (11) в смеситель (12), куда одновременно подаются для смешивания почвенные аэробные бактерии из питателя (13) и микроэлементы из питателя (14). И готовая продукция отгружается на поля.
При этом не потребуется заниматься лишней работой. Например, возить с полей солому или ботву на мини-завод, а ЗАТЕМ ВНОВЬ транспортировать на поля. Тратя при этом силы, рабочее время, горючее и т.д. Проще максимум органики сразу оставлять на полях, при уборке, а к ней добавлять бактериальную «закваску», приготовленную на нашем мини-заводе. И не просто закваску, но еще и запас минеральных веществ, микроэлементов, всевозможных стимуляторов для увеличивающихся масс бактерий, которые разовьются на органике полей. Этот запас именуется «затравкой». Затравка совместно с «закваской» оздоровят почву. В итоге — меньше затрат и больше пользы.
Мини-завод введет вас в кругооборот высоких урожаев. Раньше эту образующую круговорот функцию выполняла корова и вообще скот, навоз от которого поступал на поля, удобрял, увеличивая урожай, и часть урожая вновь возвращалась скоту… и так продолжалось до бесконечности… А теперь все это обеспечит мини-завод. Причем обеспечит на новой качественной основе, гарантирующей повышенный урожай в земледелии и повышенную продуктивность в животноводстве.
Если убедил скептиков, вернемся к мини-заводу.
Что. Зачем. Почему.
Осознанно и умышленно вам предлагается схема, а не проектный чертеж мини-завода. Почему?
А потому что чертеж — это предписание: делай так, а не иначе. По умолчанию здесь предполагается условие: если не сделаешь по-нашему — мы не отвечаем за последствия. В чем-то такой подход правильный. А в чем-то и уловка, насилие.
Например, почему я должен делать «так и не иначе», если придумал «лучше и эффективнее»? Вот ради такого раскрепощения вашей творческой мысли, ради расширения простора по использованию ваших ресурсов, имеющегося оборудования, которое можно приспособить, вам предлагается именно схема мини-завода.
Итак, общая для всех идея — построить мини-завод по производству Закваски и Затравки для бактерий почвы.
Для завода, даже малого, потребуется территория, стены… И каждый сейчас их представляет по-разному, исходя из того, что имеет или может иметь.
А можно обойтись и без стен с крышей. В конце главы изложен общедоступный дешевый вариант производства методом буртового компостирования на открытых площадках.
Правда, процесс производства будет, естественно, растянут по срокам за счет холодных периодов. Но летом все получится как надо. Вот вам уже и вариант на случай крайней нужды.
Поставите над буртом крышу — возможности расширятся. Разместите бурты в каком-либо приспособленном помещении — еще лучше. А если помещение отапливается, имеет электричество и воду, тогда — совсем прекрасно.
Юрий Слащинин Разумное земледелие
продолжение следует.
odtdocs.ru/biolog/608
Источник: http://ogorodnikam.temaretik.com/393834072286432148/mini-zavod-po-proizvodstvu-organicheskih-udobrenij—yuriya-slaschinina-chast-1/
02 августа 2019 годаЧасто читают…
- Мини завод по производству цемента производство цена
Если речь поднимается о комбинатах, в основном представляют: множество трудящихся, огромное количество машин, множество станков, территория с большими терминалами. Множество предприятий РФ таким образом устроены, но…
- Оборудование для производства силикатного кирпича Продажа оборудования цена
Во время того, как поднимается беседа о комбинатах, в основном воображают: тысячи трудящихся, множество техники, площади с огромными помещениями, парк транспорта….
- История производства кирпича
Когда поднимается разговор о комбинатах, в основном воображают: множество трудящихся, множество разной техники, сотни единиц техники, площади…
mini-proizvodstvo.ru
Наименование объекта
| Наименование услуги
| Заказчик
| Страна
| Год
|
Производство аммиака на промышленной площадке АО «Минудобрения», г. Россошь | Разработка различных вариантов концепции развития производства аммиака | АО «Минудобрения», г. Россошь | Россия | в работе |
Изотермические резервуары жидкого аммиака завода азотных удобрений | Освидетельствование резервуаров | Quimimpex | Куба | в работе |
Техническое перевооружение агрегата аммиака с увеличением мощности до 2100 т/сутки | Разработка проектной документации, рабочей документации, конструкторской документации | ПАО “Дорогобуж” | Россия | в работе |
Реконструкция агрегата АМ-76 для достижения суточной производительности 1750 т/сутки | Разработка исходных данных для проектирования | ООО “Газпром нефтехим Салават” | Россия | 2019 |
Техническое перевооружение отделения жидкого аммиака для выполнения опрессовки ж/д цистерн с установкой сигнализаторов сдвига железнодорожных вагонов-цистерн | Разработка основных технических решений и проектной документации | АО “Апатит”, Балаковский филиал | Россия | 2018 |
Отвод от действующего аммиакопровода Тольятти – Одесса до склада жидкого аммиака | Согласование постоянного технологического регламента | АО “Апатит”, Балаковский филиал | Россия | 2018 |
Отвод от действующего аммиакопровода Тольятти – Одесса до склада жидкого аммиака | Согласование постоянного технологического регламента | АО “Апатит”, Балаковский филиал | Россия | 2018 |
Установка водяных завес для подавления распространения облака газообразного аммиака при аварийных проливах на складах жидкого аммиака | Разработка Рабочей документации | АО “Минудобрения” г. Россошь | Россия | 2018 |
Повышение надежности узла регулирования уровня в паросборнике 109 в цехе АМ-2 | Разработка Рабочей документации | АО “Минудобрения” г. Россошь | Россия | 2018 |
Приведение технологических схем цеха Аммиак-2 к нормам ГОСТ | Оказание технических услуг | АО “НАК “Азот”, г. Новомосковск | Россия | 2018 |
Замена межступенчатых холодильников компрессора синтез-газа поз. 401: АВО поз. 429-1,3,4 ступени | Техническое сопровождение строительства | АО “Апатит”, Череповецкий комплекс | Россия | 2018 |
Склад жидкого аммиака (СЖА) вместимостью 490 тонн | Разработка основных технических решений | АО “НИУИФ”, г. Волхов | Россия | 2018 |
Постоянный технологический регламент отделения жидкого аммиака | Согласование постоянного технологического регламента | АО “Апатит”, Балаковский филиал | Россия | 2017 |
Отвод от действующего аммиакопровода Тольятти – Одесса до склада жидкого аммиака | Авторский надзор за строительством | АО “Апатит”, Балаковский филиал | Россия | 2017 |
Установка водяных завес для подавления распространения облака газообразного аммиака при аварийных проливах на складах жидкого аммиака | Разработка основных технических решений | АО “Минудобрения” г. Россошь | Россия | 2017 |
Дополнительные системы защиты котла поз. 101-BU агрегата №2 и №3 производства аммиака ПАО “Акрон” | Разработка основных технических решений | ООО “Новгородский ГИАП”, г. Великий Новгород | Россия | 2017 |
Производство аммиака | Капитальный ремонт цеха АММИАК-4, в т.ч. вакуумирование катализатора синтеза аммиака в среде азота, загрузка и восстановление катализатора; вывод агрегата на рабочий режим | ООО НАК “Азот” | Россия | 2017 |
Комплекс по производству Аммиака – Карбамида – Меламина на основе продувочного газа производства метанола на ПАО «Метафракс», г. Губаха | Технический аудит ПД результатов ИИ по объекту | ПАО “Метафракс” | Россия | 2017 |
Техническое обследование для технического переоснащения агрегата аммиака мощностью до 2100 т/сутки | Приёмка и адаптация базового проекта иностранного лицензиара, во всех частях и по техническим нормам и правилам проектирования РФ. Разработка Проектной документации для прохождения экспертизы промбезопасности, Разработка рабочей документации | ПАО “Дорогобуж” | Россия | 2017 |
Отделение очистки газа от CO2 в цехе “Аммиак № 1” | Разработка технического проекта, анализ и разработка основных технических решений (реконструкция) | AB ACHEMA | Литва | 2016 |
Установка осушки свежего синтез-газа для агрегата аммиака-2 | Разработка проектной документации и рабочего проекта. Разработка и поставка комплектного оборудования. Шеф-надзор за монтажом установки и проведением пуско-наладочных работ | AB ACHEMA | Литва | 2016 |
Агрегат производства аммиака АМ-70 Агрегат производства аммиака АМ-76 | Технологический аудит. Обследование и выявление узких мест в производстве (реконструкция, увеличение мощностей) | КАО “Азот” | Россия | 2016 |
Строительство установки утилизации аммиака из танковых и продувочных газов производства аммиака с получением раствора аммиачной селитры | Разработка проектной документации, рабочей документации. Поставка оборудования | ТОО “КазАзот” | Казахстан | 2016 |
Строительство агрегата аммиака мощностью 2060 т/сутки | Приемка базового проекта иностранного лицензиара. Разработка проектной и рабочей документации. Получение положительного заключения Госэкспертизы. Инженерное сопровождение поставок оборудования. Авторский надзор документации. Получение разрешения на применение | ОАО “Акрон” | Россия | 2016 |
Агрегаты производства аммиака АМ-70, АМ-76 | Разработка перечня параметров ПАЗ | ОАО “ЗМУ КЧХК” | Россия | 2015 |
Склад жидкого аммиака | Разработка рабочей документации (реконструкция заводского склада со строительством дополнительного изотермического хранилища вместимостью 10000т. Ресивер воздуха КИП) | ОАО “КуйбышевАзот” | Россия | 2015 |
Санитарная колонна утилизации потоков газообразного аммиака | Разработка рабочей и проектной документации (узлы приема аммиачной воды от производства аммиака “ЛиндеАзотТольятти” и склада изотермического хранения жидкого аммиака в резервуары корп. 460) | ОАО “КуйбышевАзот” | Россия | 2015 |
Производство аммиака | Разработка рабочей документации с целью технического перевооружения АХУ с установкой дополнительных конденсаторов испарительного типа в цехе №2. | ОАО “Минудобрения” | Россия | 2015 |
Оборудование аппаратного отделения АХУ № 1 компрессорного цеха | Разработка рабочей и проектной документации. Сопровождение прохождения экспертизы промышленной безопасности | ОАО “Московский хладокомбинат №14 | Россия | 2015 |
Агрегаты производства аммиака АМ-76 | Разработка и согласование ОТР, Разработка МТБ, Разработка проектной документации. Экспертиза промышленной безопасности | ОАО “ТольяттиАзот” | Россия | 2015 |
Изотермический резервуар | Сопровождение прохождения экспертизы промышленной безопасности | ОАО “ТольяттиАзот” | Россия | 2015 |
Техническое перевооружение агрегата №6 аммиака №6 (АМ-76) с увеличением производительности до 1750 т/сутки аммиака | Разработка проектной документации | ОАО “ТольяттиАзот” | Россия | 2015 |
Производство аммиака | Разработка и поставка оборудования для системы утилизации тепла печи первичного риформинга | ОАО НАК “Азот” | Россия | 2015 |
Выделение водорода из продувочных газов синтеза в производстве аммиака | Разработка и согласование ОТР, Технико-экономическое обоснование | ОАО НАК “Азот” | Россия | 2015 |
Производство аммиака (цех Аммиак-3) | Разработка эксплуатационной документации (технологических регламентов инструкций и т.д.) | ОАО НАК “Азот” | Россия | 2015 |
Производство аммиака | Разработка проектной и рабочей документации системы утилизации тепла печи первичного риформинга в агрегате аммиака | ОАО НАК “Азот” | Россия | 2015 |
Система утилизации тепла печи первичного риформингав цехе Аммиак-3 | Разработка проектной документации с целью технического перевооружения. Сопровождение прохождения экспертизы промышленной безопасности | ОАО НАК “Азот” | Россия | 2015 |
Склад жидкого аммиака | Технология складирования жидкого аммиака. Схема приема, хранения, отпуска потребителю, наполнение баллонов. Разработка схемы приема, хранения, отпуска потребителю, наполнение баллонов (Техническое перевооружение) | ООО “Менделеевсказот” | Россия | 2015 |
Реакционные трубы, стояки, нижних коллекторов радиантной части печи первичного риформинга агрегата производства аммиака | Сопровождение прохождения экспертизы промышленной безопасности | ПАО “Дорогобуж” | Россия | 2015 |
Технические устройства агрегата аммиака | Сопровождение прохождения экспертизы промышленной безопасности | ПАО “Дорогобуж” | Россия | 2015 |
Установка утилизации аммиака из танковых и продувочных газов производства аммиака | Разработка рабочей документации | ТОО “КазАзот” | Казахстан | 2015 |
Агрегат аммиака № 2 (АМ-80) | Разработка базового проекта (исходных данных), рабочего проекта и комплектная поставка лицензионного оборудования | AB ACHEMA | Литва | 2015 |
Аммиакопровод “Тольятти-Одесса” – БФ АО “Апатит” | Разработка рабочей документации (отвод от действующего магистрального аммиакопровода “Тольятти-Одесса” до БФ АО “Апатит”) | АО “Апатит”, Балаковский филиал | Россия | 2015 |
Агрегат аммиака № 3 | Разработка рабочей документации (привязка водяного холодильника поз.1118-с агрегата №2 для охлаждения азотоводородной смеси) | ОАО “Акрон” | Россия | 2015 |
Агрегат аммиака № 2 (АМ-80) | Разработка базового проекта и проектной документации на модернизацию агрегата аммиака с целью снижения удельного энергопотребления не менее чем на 0,5 Гкал/тонну аммиака | AB ACHEMA | Литва | 2014 |
Агрегат производства аммиака “Аммиак 4” мощностью 2060 т/сутки | Разработка технических проектов нестандартизированного оборудования (технический проект абсорбера СО2 поз.С303В) | ОАО “Акрон” | Россия | 2014 |
Склад жидкого аммиака | Разработка проектной документации с целью размещения нового склада жидкого аммиака с изотермическим резервуаром | ОАО “Акрон” | Россия | 2014 |
Технические устройства производства аммиака “Аммиак 4” мощностью 2060 т/сутки | Сопровождение прохождения экспертизы промышленной безопасности | ОАО “Акрон” | Россия | 2014 |
Производство аммиака | Разработка ОТР | ОАО “ЗМУ КЧХК” | Россия | 2014 |
Производство аммиака | Разработка рабочей документации (Отделение очистки конвертированного газа от диоксида углерода в цехе №1) | ОАО “КуйбышевАзот” | Россия | 2014 |
Отделение очистки конвертированного газа от диоксида углерода в цехе №1 производства аммиака | Сопровождение прохождения экспертизы промышленной безопасности | ОАО “КуйбышевАзот” | Россия | 2014 |
Отделение очистки конвертированного газа от диоксида углерода в цехе №1 производства аммиака | Сопровождение прохождения экспертизы промышленной безопасности | ОАО “КуйбышевАзот” | Россия | 2014 |
Аммиакопровод Тольятти – Одесса | Разработка экспертного заключения | ОАО “Минудобрения” | Россия | 2014 |
Производство аммиака | Разработка рабочей документации (дооборудование узла хранения серной кислоты и едкого натра отделения деминерализации воды цеха №1) | ОАО “Минудобрения” | Россия | 2014 |
Производство аммиака | Разработка технических решений | ОАО “Московский хладокомбинат №14 | Россия | 2014 |
Змеевики парогазовой и паровоздушной смеси, расположенные в зоне БТА агрегата аммиака АМ-76 №6 | Разработка проектной и рабочей документации. Сопровождение прохождения экспертизы промышленной безопасности | ОАО “ТольяттиАзот” | Россия | 2014 |
Печь первичного риформинга цеха аммиака | Разработка эксплуатационной документации (технологических регламентов инструкций и т.д.) | ПАО “Дорогобуж” | Россия | 2014 |
Технические устройства производства аммиака | Сопровождение прохождения экспертизы промышленной безопасности | ПАО “Дорогобуж” | Россия | 2014 |
Факельная установка цеха производства аммиака 1Б | Разработка экспертного заключения | Филиал “Азот” АО “ОХК “УРАЛХИМ” | Россия | 2014 |
Агрегат аммиака №2 с увеличением производительности до 1750 т/сутки | Разработка проектной документации | ОАО “Акрон” | Россия | 2014 |
www.alvigo-group.com
Аммиак — Находкинский завод минеральных удобрений
Что такое аммиак
Аммиак, или нитрид водорода — одно из соединений азота. Это бесцветный газ с резким характерным запахом, обладающий химической формулой Nh4. При замораживании или под давлением аммиак переходит в жидкую форму.
Аммиак широко применяется в промышленности, а также является ключевым компонентом в производстве азотных удобрений. Азот необходим растениям для правильного развития и роста. Использование удобрений повышает содержание азота в почве, увеличивая урожайность.
Использование аммиака в сельском хозяйстве
Аммиак в основном используется для производства множества видов азотных удобрений, таких как карбамид и нитрат (аммиачная селитра) и сульфат аммония. Большая часть производимого в мире аммиака продается сельскохозяйственным или промышленным потребителям.
Широкое использование в промышленности
Аммиак – одно из важнейших веществ для химической промышленности. Его используют для получения полимеров, текстиля, взрывчатки, этанола. Применяется аммиак и в качестве растворителя и охлаждающего вещества. Аммиак используется при производстве лекарств и косметики.
Производство аммиака
Аммиак производится путем соединения азота и водорода при температурах 380 — 500 градусов по Цельсию и давлении 250 атм в присутствии катализатора.
В качестве сырья для производства аммиака может быть использован уголь, кокс и коксовый газ, но в основном аммиак производят из природного газа. Производство аммиака отличается высокой энергоемкостью, показатель потребления природного газа – один из важнейших факторов, определяющих рентабельность.
Использование аммиака
В качестве удобрения
Самостоятельно в качестве удобрения применяется безводный аммиак, который получают путем сжижения газообразного аммиака под высоким давлением . Он представляет собой жидкость с содержанием азота 82,3%, что делает его наиболее концентрированным и экономически эффективным азотным удобрением.
Из аммиака производят много видов азотных удобрений. Наиболее важные из них карбамид, аммиачная селитра и сульфат аммония.
Карбамид (мочевина) изготавливается из аммиака и диоксида углерода. Он поставляется в виде гранул и микро гранул и содержит 46% азота, что делает его самым концентрированных азотным удобрением.
Аммиачная селитра (NH4NO3) – наиболее распространенное универсальное азотное удобрение, содержащее 35% азота, применяется в качестве основного удобрения и для подкормки.
Сульфат аммония содержит 21% азота и до 24% серы, поэтому является также источником серного питания. Хорошо впитывается, не вымывается из почвы, используется под все сельскохозяйственные культуры.
Промышленное использование
Аммиак относится к числу важнейших продуктов химической промышленности. Вещества, производимые из аммиака, служат основой для производства пропилена, текстильных волокон, проводов, труб, тары, шин, деталей автомобилей и телефонов. Из аммиака производят также взрывчатые вещества.
Жидкий аммиак используют в качестве растворителя и хладагента. Аммиак применяют и как противоморозную добавку к сухим строительным растворам.
Производные аммиака амины используются в области медицины. Это нашатырный спирт, компоненты косметики и лекарственных средств.
Водный раствор аммиака используется в качестве источника азота в процессе производства дрожжей. В мире растет спрос на этанол, а дрожжи — единственный вид микроорганизмов, используемый для превращения сахара в этанол.
Хранение и перевозка
При замораживании или под давлением аммиак переходит в жидкую форму и требует специального оборудования и техники для транспортировки и хранения.
Жидкий аммиак хранится в соединенных между собой резервуарах, оснащенных предохранительными клапанами. Для повышения безопасности резервуары окапывают, устанавливают дополнительные поддоны и стенки.
При хранении больших объемов углеводородных газов наиболее эффективны подземные газохранилища. Широкое распространение получило хранение аммиака в изотермических газгольдерах.
Транспортировка аммиака проводится в специальных транспортных емкостях железнодорожным, водным и автотранспортом или по магистральным трубопроводам.
Основные потребители
Основной спрос на продукт предъявляет Китай, предприятия которого потребляют около 30% производимого в мире аммиака. Еще несколько стран и регионов демонстрируют примерно одинаковый уровень потребления аммиака: это США (10%), страны СНГ и Западной Европы (по 8-9%), Индия (8%).
Спрос на аммиак
Согласно прогнозам экспертов, в 2020 году производство аммиака составит около 190 млн тонн в год. Около трех четвертей производимого в мире аммиака используется для производства удобрений, около 50% идет на производство только карбамида.
В настоящее время на мировом рынке растет спрос на карбамид, поэтому прогнозируется, что спрос на аммиак, из которого он производится, в период до 2020 года будет расти с темпами не менее 2% в год.
Прогнозируемое повышение спроса на продукт создает возможности для вновь строящихся предприятий по производству карбамида.
nzmu.ru
Производство аммиака 💲
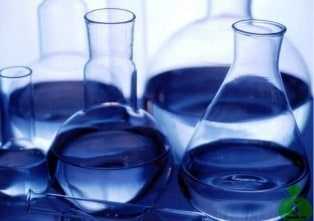
Аммиак относится к числу важнейших продуктов химической промышленности. Его ежегодное мировое производство достигает 150 млн. тонн. В основном он используется для изготовлении азотных удобрений (нитрат и сульфат аммония, мочевина), взрывчатых веществ и полимеров, азотной кислоты, соды (по аммиачному методу) и других продуктов химической промышленности. Жидкий аммиак используют в качестве растворителя.
В холодильной технике используется в качестве холодильного агента (R717).
В медицине 10% раствор аммиака, чаще называемый нашатырным спиртом, используется при обморочных состояниях (для возбуждения дыхания), для стимуляции рвоты, а также наружно — при невралгии, миозитах, укусах насекомых, для обработки рук хирурга. При неправильном использовании может вызвать ожоги пищевода и желудка (в случае приёма неразведённого раствора), рефлекторную остановку дыхания (при вдыхании в высокой концентрации).
Технология производства аммиака + видео
В рамках этого направления сегодня многие компании стали заниматься разработкой и проектированием следующих технологий:
- Перевод избыточного количества аммиака на изготовление метанола.
- Разработка производства на основе современных технологий для подмены активных агрегатов.
- Создание интегрированного производства и модернизация.
На производство одной тонны аммиака в России расходуется в среднем 1200 нм? природного газа, в Европе — 900 нм?. Белорусский «Гродно Азот» расходует 1200 нм?, после модернизации ожидается снижение расхода до 876 нм?. Украинские производители потребляют от 750 нм? до 1170 нм?. По технологии UHDE заявляется потребление 6,7 — 7,4 Гкал энергоресурсов на тонну аммиака.
Промышленный способ получения аммиака основан на прямом взаимодействии водорода и азота:
N2 + 3H2 ? 2NH3+ + 91,84 кДж
Это так называемый процесс Габера (немецкий физик, разработал физико-химические основы метода). Реакция происходит с выделением тепла и понижением объёма. Следовательно, исходя из принципа Ле-Шателье, реакцию следует проводить при возможно низких температурах и при высоких давлениях — тогда равновесие будет смещено вправо. Однако скорость реакции при низких температурах ничтожно мала, а при высоких увеличивается скорость обратной реакции. Проведение реакции при очень высоких давлениях требует создания специального, выдерживающего высокое давление оборудования, а значит, и больших капиталовложений. Кроме того, равновесие реакции даже при 700°C устанавливается слишком медленно для практического её использования. Выход аммиака (в объёмных процентах) в процессе Габера при различных температурах и давлении имеет следующие значения:
100 ат | 300 ат | 1000 ат | 1500 ат | 2000 ат | 3500 ат | |
---|---|---|---|---|---|---|
400 °C | 25,12 | 47,00 | 79,82 | 88,54 | 93,07 | 97,73 |
450 °C | 16,43 | 35,82 | 69,69 | 84,07 | 89,83 | 97,18 |
500 °C | 10,61 | 26,44 | 57,47 | Нет данных | ||
550 °C | 6,82 | 19,13 | 41,16 |
Применение катализатора (пористое железо с примесями Al2O3 и K2O) позволило ускорить достижение равновесного состояния. Интересно, что при поиске катализатора на эту роль пробовали более 20 тысяч различных веществ.
Читают сейчас:
Учитывая все вышеприведённые факторы, процесс получения проводят при следующих условиях:
- температура 500 °C;
- давление 350 атмосфер;
- катализатор.
Выход аммиака при таких условиях составляет около 30%. В промышленных условиях использован принцип циркуляции — аммиак удаляют охлаждением, а непрореагировавшие азот и водород возвращают в колонну синтеза. Это оказывается более экономичным, чем достижение более высокого выхода реакции за счёт повышения давления. Для получения аммиака в лаборатории используют действие сильных щелочей на соли аммония:
NH4Cl + NaOH ? NH3? + NaCl + H2O
Обычно лабораторным способом аммиак получают слабым нагреванием смеси хлорида аммония с гашеной известью.
2NH4Cl + Ca(OH)2 ? CaCl2 + 2NH3? + 2H2O
Для осушения аммиака его пропускают через смесь извести с едким натром. Очень сухой аммиак можно получить, растворяя в нём металлический натрий и впоследствии перегоняя. Это лучше делать в системе, изготовленной из металла под вакуумом. Система должна выдерживать высокое давление (при комнатной температуре давление насыщенных паров около 10 атмосфер). На промышленном производстве обычно для сушки используют абсорбционные колонны.
Видео как делают:
Производство аммиака не должно обходить стороной технический прогресс. В основном это касается энергосбережения. В ходе разработки современных технологий большое значение отводится программному обеспечению, необходимому для моделирования химических и технологических процессов.
Мало информации по теме? Поиск подскажет:
Автор статьи: Максим Миллер — о авторе. Бизнесмен, инвестор, финансовый консультант Facebook |
inask.ru