Механическая обработка металла: виды и способы
Механическая обработка – это процесс, во время которого изменяются размеры и конфигурация заготовок и деталей. Если же говорить о металлических изделиях, то для их обработки используются специальные режущие инструменты, такие как резцы, протяжки, сверла, метчики, фрезы и т. д. Все операции выполняются на металлорежущих станках согласно технологической карте. В данной статье мы узнаем, какие бывают способы и виды механической обработки металлов.
Способы обработки
Механообработка подразделяется на две большие группы. В первую входят операции, которые происходят без снятия металла. К ним относят ковку, штамповку, прессование, прокат. Это так называемая механическая обработка с помощью давления или удара. Её применяют для того, чтобы придать необходимую форму заготовке. Для цветных металлов чаще всего используют ковку, а для черных – штамповку.
Вторая группа включает в себя операции, в ходе которых с заготовки снимается часть металла. Это необходимо для придания ей необходимых размеров. Такая механическая обработка металла называется резанием и выполняется при помощи металлорежущих станков. Наиболее распространенными способами обработки являются точение, сверление, зенкерование, шлифование, фрезерование, развертывание, долбление, строгание и протягивание.
От чего зависит вид обработки
Изготовление металлической детали из заготовки – трудоёмкий и достаточно сложный процесс. Он включает в себя множество различных операций. Одной из них является механическая обработка металла. Прежде чем к ней приступить, составляют технологическую карту и делают чертеж готовой детали с указанием всех необходимых размеров и классов точности. В некоторых случаях для промежуточных операций также подготавливают отдельный чертеж.
Кроме того, существует черновая, получистовая и чистовая механическая обработка металла. Для каждой из них выполняется расчет режимов резания и припусков. Вид обработки металла в целом зависит от обрабатываемой поверхности, класса точности, параметров шероховатости и размеров детали. Например, для получения отверстия по квалитету Н11 используют черновое сверление сверлом, а для получистого развертывания на 3 класс точности можно использовать развертку или же зенкер. Далее мы изучим способы механической обработки металлов более детально.
Точение и сверление
Точение выполняется на станках токарной группы при помощи резцов. Заготовка крепится в шпиндель, который вращается с заданной скоростью. А резец, закрепленный в суппорте, совершает продольно-поперечные движения. В новых ЧПУ-станках все данные параметры вводятся в компьютер, и устройство само выполняет необходимую операцию. В старых моделях, например, 16К20 продольно-поперечные движения выполняются вручную. На токарных станках возможно точение фасонных, конических и цилиндрических поверхностей.
Сверление – это операция, которую выполняют для получения отверстий. Главным рабочим инструментом является сверло. Как правило, сверление не обеспечивает высокий класс точности и является либо черновой, либо получистовой обработкой. Для получения отверстия с квалитетом ниже Н8 используют развертывание, рассверливание, растачивание и зенкерование. Кроме того, после сверления также могут выполнять нарезание внутренней резьбы. Такая механическая обработка металла выполняется при помощи метчиков и некоторых видов резцов.
Фрезерование и шлифование
Фрезерование – один из наиболее интересных способов обработки металлов. Данная операция выполняется при помощи самых разнообразных фрез на фрезерных станках. Различают концевую, фасонную, торцевую и периферийную обработку. Фрезерование может быть как черновым и получистовым, так и чистовым. Наименьший квалитет точности, получаемый при чистовой обработке,– 6. При помощи фрез вытачивают различные шпонки, канавки, колодцы, подсечки, фрезеруют профили.
Шлифование – механическая операция, используемая для повышения качества шероховатости, а также для снятия лишнего слоя металла вплоть до микрона. Как правило, данная обработка является завершающим этапом при изготовлении деталей, а значит, является чистовой. Для срезания используются абразивные круги, на поверхности которых расположено огромное количество зерен, имеющих разную форму режущей кромки. При такой обработке деталь очень сильно нагревается. Для того чтобы металл не деформировался и не надкололся, используют смазочно-охлаждающие жидкости (СОРЖ). Механическая обработка цветных металлов осуществляется при помощи алмазных инструментов. Это позволяет обеспечить наилучшее качество изготавливаемой детали.
fb.ru
Механическая обработка металлов: виды, способы
Механическая обработка металлов – необходимый процесс перед тем, как металлическую деталь можно будет использовать.
Работать с разными видами металлов можно разными способами – все они имеют свои плюсы и минусы и могут использовать в разных ситуациях в зависимости от ваших целей.
Из статьи вы узнаете, что такое механическая обработка металлов, и какие ее виды существуют, и сможете выбрать, какая процедура работы с металлом требуется именно вам.
Варианты обработки с давлением
Существуют всего две возможности финальной обработки металлических деталей: это может быть сделано с помощью давления или резания.
Чаще всего ее используют, когда нужно придать металлическому листу форму, либо в процессе создания деталей из сортового металлопроката.
Этот способ воздействия включает следующие виды работ: гибку, штамповку, высадку и пр. Ниже мы рассмотрим всевозможные способы воздействия на металл с помощью давления подробнее.
Для обработки цветных металлов часто используется ручная горячая кузнечная обработка.
Для ее осуществления, материал предварительно нагревается до температуры, превосходящую его рекристаллизацию, а затем ему придают нужную форму.
Для этого используют самые простые инструменты: ручной молот или молоток. Степень нагревания материала зависит от его свойств: насколько в нем много углерода.
Видео:
Чем меньше это значение, тем выше должна быть рабочая температура.
Подобная механическая отделка разных типов металлов считается достаточно эффективной, поскольку дает возможность создавать сплошные детали высокой прочности, не теряя при этом природных свойств материала.
Существует и более совершенный – механический способ горячей обработки.
В этом случае материал также разогревается до нужной температуры, но воздействие проводится с помощью специального устройства.
Механическая ковка может быть свободной, либо производиться с помощью кузнечного штампа.
В первом случае воздействие на металлическое покрытие происходит с помощью наковальни и молотка, которым воздействуют на металл.
Другой вариант – когда на металл оказывается воздействие специальным прессом, который придает ему нужную форму.
И молот, и пресс – механические устройства, но первое придает заготовкам нужную форму ударами, а второе – с помощью давления.
Устройство-молот может быть паровым, паровоздушным, падающим с фрикционным диском или пружинным.
Пресс может быть гидравлическим, парогидравлическим, винтовым, фрикционным, эксцентриковым, кривошипным или пружинным.
Механическая обработка молотом используется реже, поскольку она очень шумная и менее эффективная и используется только на крупных производствах.
Помимо горячего воздействия, бывает также холодное — оно применяется чаще, поскольку способно придать заготовкам из цветных и черных металлов нужную форму, при это не влияя на ее физические характеристики.
В отличие от горячего воздействия, при холодном способе нагревать поверхность не нужно – вся работа производится при комнатной температуре.
Холодный способ воздействия называют штамповкой, она делится на разные виды. Штамповка может быть одно или многооперационной в зависимости от функций конкретного устройства.
Видео:
Работа с материалом может проводиться как с сохранением сплошного покрытия, так и с его разделением – это тоже зависит от типа устройства, с помощью которого заготовке придается нужная форма.
Наиболее популярные виды холодного воздействия прессом следующие: воздействие с помощью гибки, вытягивания, обжатия, формования, выпучивания или разбортовывания.
Гибка позволяет изменить осевую форму детали, ее делают с помощью специальных тисков, которые устанавливают на гибочные штампы и прессы.
С помощью вытягивания можно сделать детали сложных форм. Для этого вида работ необходим давильный станок.
С помощью обжатия поперечное сечение полой детали уменьшается, а формование позволяет превратить заготовку в деталь, имеющую пространственную форму.
Для этого вида обработки требуются вытяжные или специальные формовочные штампы.
При выпучивании заготовка так же приобретает вид пространственной формы, а при разбортовывании на детали создаются бортики и прочие дополненные элементы.
Обработка с помощью резки
Механическая обработка разных типов металлов путем резки также требует специального оборудования. Это более сложный процесс, поэтому и виды станков здесь используются более сложные.
Для цветных металлов, устойчивых к внешнему воздействию и сложно поддающихся деформации, чаще всего для обработки используют специальный лазер, либо метод плазменный обработки, который после появления лазера стал менее актуален.
Видео:
Сегодня механическая обработка металла на станках и линиях производится с помощью волоконного лазера, который состоит из резонатора, световода и специального накачивающего модуля.
Лазерный луч при этом способе воздействия попадает на поверхность металла через специальный световод, сохраняющий энергию луча, за счет чего мощность устройства оказывается достаточной для качественной резки цветных металлов.
С волоконным лазером довольно просто работать – он автоматизирован и отличается высокими качественными характеристиками: помимо резки, обеспечивает охлаждение изделия, а также способен выдерживать высокие мощности и температуры.
Этот инструмент имеет функции не только резки, но и другие виды обработки: гравировки и сварки.
Существуют следующие виды обработки металла путем резки: обточка, сверление, фрезерование, строгание и шлифование.
При обточке материала его изменения минимальны, поскольку эта процедура производится в тех случаях, когда размер заготовки практически соответствует конечному размеру детали.
Сделать обточку можно на оборудовании разного типа: для этого может подойти токарный, сверлильный, шлифовальный и другие виды станков.
Обточку детали чаще всего делают на токарном станке с помощью специального резца, который эффективно снимает лишний слой металла и приводит заготовку к нужному размеру.
С помощью сверления можно сделать в заготовках нужные отверстия, тем самым изменив их форму.
Видео:
Для этого типа обработки подойдет любое оборудование, имеющее сверло и тиски: между ними нужно установить заготовку, сверло будет находить на нее поступательно, и в результате мы получим отверстие нужного нам размера и формы.
С помощью фрезерования форма детали также изменяется. Это довольно сложный вид обработки, требующий наличия специального оборудования — горизонтально-фрезерного станка.
Обработка заготовки выполняется с помощью фрезы, которая есть на этом устройстве.
Фреза воздействует на заготовку под углом, при этом сама деталь не двигается – до начала работы ее нужно четко зафиксировать на поверхности оборудования.
Строгальный метод работы заключается в воздействии на заготовку резца. Для этого процесса требуется специальный строгальный станок, т.к. только он оснащен нужным инструментом.
Во время работы резец постепенно входит в металл, а затем выходит обратно, выполняя прерывистые движения.
Это сложный способ обработки цветных металлов, т.к. он требует расчетов холостых и рабочих ходов для правильного выполнения работы.
Последний способ работ с металлом – шлифовальный. Это довольно простой метод, который часто можно выполнить своими руками, если шлифовальный круг есть в наличии.
Для профессиональной же обработки используются специальные шлифовальные станки.
Работа с заготовками из цветных металлов происходит за счет вращательных движений с прямолинейной и круговой подачей.
Видео:
Этот способ воздействия используется для получения деталей, имеющих цилиндрическую форму.
Если же обработке подвергается плоская заготовка, то направление подачи может быть только прямым.
rezhemmetall.ru
Механическая обработка металлов
Во многих областях промышленности не обойтись без такого процесса, как механическая обработка металлов. Машины, станки и инструменты постоянно совершенствуются, из года в год операции осуществляются все быстрее. На производственных предприятиях работают станки специализированного и общего назначения. С помощью таких станков легко раскроить заготовки листового, профильного или другого типа. Широко применяются также методы разделения материала: резка ножовочным полотном, фрезой, ленточной пилой и прочие.
Технологические процессы механической обработки металлов
Механическая обработка металлов — достаточно сложный процесс, в результате которого получаются детали определенных размеров и заданных форм. Существует два способа механического воздействия на материал. Первый способ выражается в снятии верхнего слоя с рабочей поверхности. При этом глубина может быть разной зависимо от требований, предъявляемых к размерам детали. Во втором способе материал никак не повреждается при первичном воздействии, он может лишь прессоваться, штамповаться, коваться, прокатываться. Как правило, за таким способом воздействия следует этап дальнейшей работы над деталью.
Комплекс технологических операций по приданию определенного размера и формы деталям предусматривает различные виды механической обработки металлов. Основные из них – это работы по точению, фрезерованию, строганию, шлифованию и сверлению. Сейчас все операции проводятся на современных многофункциональных станках. Так, одна и та же машина может выполнять последовательно разные функции. Для этого просто необходимо правильно установить программы и вовремя применять нужные инструменты. Многие названия инструментов говорят об их предназначении: сверло — для сверления, фреза – для фрезерования и так далее.
Все виды механической обработки металлов разнообразны, им свойственные собственные отличия и нюансы. Самым современным способом, отвечающим высокотехнологичным требованиям, является обработка на токарном станке. Они бывают автоматическими, полуавтоматическими и с ЧПУ. Как правило, для обработки фасонных или плоских поверхностей используется фрезерование разных видов: торцевое, концевое или фасонное.
Сейчас множество современных производств предлагают услуги по механической обработке металла. Станков для проведения этих работ существует также немало, но время диктует свои условия, поэтому машины постоянно совершенствуются. Так, примитивные станки уже почти везде заменены на автоматические линии. Динамично развивающиеся предприятия стараются как можно больше расширить производство с помощью высокотехнологического оборудования. Таким образом, с большой долей вероятности можно гарантировать высокое качество выпускаемой продукции и минимальные сроки обработки заказов. Любое производство выигрывает, если принимает за приоритетное направление хорошую выработку качественных изделий, независимо от объема заказа и его сложности.
Оборудование для механической обработки металлов
Как правило, услуги по механической обработке металла выполняются быстро и в полном соответствии со всеми стандартами, когда за работу берется квалифицированный персонал. Кроме этого, каждое перспективное предприятие обеспечивает для работы оптимальные условия: достаточное наличие производственных площадей, необходимое оборудование. Стоит отметить, что для успешного и быстрого выполнения заказа персоналу нужно предоставить станки, сварочное и технологическое оборудование.
Итак, для выполнения работ следует правильно выбрать оборудование механической обработки металлов. Конечно, за основную работу – снятие стружки, отвечает токарное и фрезерное направление. Самое распространенное оборудование в данной сфере – токарные центры с ЧПУ и центры вертикально-фрезерные. Современные модели позволяют изготовлять детали, соответствующие самым высоким требованиям относительно геометрических параметров изделия и шероховатости его поверхности. Преимуществами новых моделей станков являются: точность, скорость, улучшенные параметры рабочих зон.
Оборудование механической обработки металлов на настоящий момент представлено в широком ассортименте. Среди многообразия моделей имеются как самые популярные, так и достаточно редкие (относительно часты применения). К примеру, карусельный станок, который способен обработать деталь, имеющую диаметр до девяти метров. Такой станок применяется не часто и не везде. Достаточно востребованы координатно-расточные станки, обеспечивающие качественную расточку под любым углом и станки расточные с поворотными столами. Каждое предприятие, сфера деятельности которого – механическая обработка металла, старается иметь в наличии фрезерные, зубофрезерные, радиально-, горизонтально- и вертикально-сверлильные станки.
promplace.ru
Виды механической обработки металлов: точение, фрезерование, сверление, строгание, долбление, шлифование
Большинство деталей машин изготовляется путем обработки резанием. Заготовками таких деталей служат прокат, отливки, поковки, штамповки и др.
Процесс обработки деталей резанием основан на образовании новых поверхностей путем деформирования и последующего отделения поверхностных слоев материала с образованием стружки. Та часть металла, которая снимается при обработке, называется припуском. Или, говоря иначе, припуск — это избыточный (сверх чертежного размера) слой заготовки, оставляемый для снятия режущим инструментом при операциях обработки резанием.
После снятия припуска на металлорежущих станках обрабатываемая деталь приобретает форму и размеры, соответствующие рабочему чертежу детали. Для уменьшения трудоемкости и себестоимости изготовления детали, а также ради экономии металла, размер припуска должен быть минимальным, но в то же время достаточным для получения хорошего качества детали и с необходимой шероховатостью поверхности.
В современном машиностроении имеется тенденция снижать объем обработки металлов резанием за счет повышения точности исходных заготовок.
Основные методы обработки металлов резанием. В зависимости от характера выполняемых работ и вида режущего инструмента различают следующие методы обработки металлов резанием: точение, фрезерование, сверление, зенкерование, долбление, протягивание, развертывание и др. (рис. 12).
Точение — операция обработки тел вращения, винтовых и спиральных поверхностей резанием при помощи резцов на станках токарной группы. При точении (рис. 12.1) заготовке сообщается вращательное движение (главное движение), а режущему инструменту (резцу) — медленное поступательное перемещение в продольном или поперечном направлении (движение подачи).
Фрезерование — высокопроизводительный и распространенный процесс обработки материалов резанием, выполняемое на фрезерных станках. Главное (вращательное) движение получает фреза, а движение подачи в продольном направлении — заготовка (рис. 12.2).
Сверление — операция обработки материала резанием для получения отверстия. Режущим инструментом служит сверло, совершающее вращательное движение (главное движение) резания и осевое перемещение подачи. Сверление производится на сверлильных станках (рис. 12.3).
Строгание — способ обработки резанием плоскостей или линейчатых поверхностей. Главное движение (прямолинейное возвратно-поступательное) совершает изогнутый строгальный резец, а движение подачи (прямолинейное, перпендикулярное главному движению, прерывистое) — заготовка. Строгание производится на строгательных станках (рис. 12.4).
Долбление — способ обработки резцом плоскостей или фасонных поверхностей. Главное движение (прямолинейное возвратно-поступательное) совершает резец, а движение подачи (прямолинейное, перпендикулярное главному движению, прерывистое) — заготовка. Долбление производят на долбежных станках (рис. 12.5).
Шлифование — процесс чистовой и отделочной обработки деталей машин и инструментов посредством снятия с их поверхности тонкого слоя металла шлифовальными кругами, на поверхности которого расположены абразивные зерна.
Рис. 12
Главное движение вращательное, которое осуществляется шлифовальным кругом. При круглом шлифовании (рис. 12.6) вращается одновременно и заготовка. При плоском шлифовании продольная подача осуществляется обычно заготовкой, а поперечная подача — шлифовальным кругом или заготовкой (рис. 12.7).
Протягивание — процесс, производительность при котором в несколько раз больше, чем при строгании и даже фрезеровании. Главное движение прямолинейное и реже вращательное (рис. 12.8).
cherch.ru
Механическая обработка металлов: технология, виды услуг
Механическая обработка металлов предполагает воздействие на заготовку контролируемым давлением, которое транслирует матрица (плита) пресса (молота) или режущая кромка обрабатывающего инструмента.
В данной статье мы рассмотрим современные технологии механической обработки, а равно и результаты их применения. Руководствуясь этими сведениями, вы сможете заказать интересующие вас услуги по механической обработке металла у «правильных» исполнителей, обладающих соответствующим станочным парком.
Методы механической обработки металлов
Механическая обработка предполагает всего две методики воздействия на заготовку, а именно:
- Контролируемое давление на плоскость. На этой методике базируются такие операции, как гибка, штамповка, высадка и так далее. Обрабатывающее усилие, в данном случае, генерирует верхняя плита пресса или гильотины.
- Резание (отделение «лишнего» объема специальным инструментом) вращающейся или неподвижной заготовки. Эта методика легла в основу таких операций, как токарная и фрезерная обработка, строгание, сверление и так далее. Обрабатывающее усилие, в данном случае, генерирует режущий инструмент, вдавливаемый в тело заготовки.
Причем первая методика – обработка давлением – используется в процессах формообразования полуфабрикатов или в производстве заготовок из сортового металлопроката.
Вторя методика – обработка резанием – позволяет получить из заготовки или полуфабриката готовую продукцию, обработанную в соответствии с определенными квалитетами качества (с контролируемыми величинами допусков, напусков и припусков).
Виды механической обработки металлов давлением
С помощью контролируемого давления можно реализовать следующие технологические операции:
- Изменение формы листовой или балочной заготовки, вплоть до формирования нового рельефа или нового поперечного сечения.
- Отделение от сортового металлопроката, в процессе которого из листовой или балочной заготовки будет «вырезан» полуфабрикат с нужными габаритами.
Технологические операции первого типа реализуются на прессах, механизированных кузнечных молотах, гибочных станках, прокатных станах (ротационных прессах). С помощью этих агрегатов можно согнуть, разогнуть, вытянуть или уплотнить любую металлическую деталь. При этом качество обработанной поверхности оставляет желать лучшего, а в поверхностных слоях металла накапливаются усталостные напряжения.
Технологические операции второго типа практикуют в процессе формирования полуфабрикатов самой разной формы, которые получают методом штамповки, резки на гильотинах, вырубки. Все вышеупомянутые операции можно проделать на типовых или специализированных прессах.
Причем такие технологии практикуют лишь при массовом производстве, когда из листового и балочного проката формируют огромное количество однотипных заготовок.
Механическая обработка резанием
Обработка металла резанием дает возможность реализовать следующие технологические операции:
Токарную обработку, предполагающую изменение формы и размеров заготовок, образованных телами вращения (цилиндрами, конусами, сферами). Этот тип обработки реализуется на особых токарных и токарно-винторезных станках (последние используются для образования резьбовых поверхностей), в шпинделе которых закрепляют заготовку. Обрабатывающие инструменты – резцы – крепят в суппорте. Причем шпиндель совершает вращательное движение (вместе с заготовкой) а суппорт – возвратно-поступательное перемещение (вместе с режущим инструментом).
Сверление, предполагающее формирование глухих или сквозных отверстий с помощью вращающегося пруткового инструмента – сверла. Заготовка крепится к столу и остается неподвижной. Шпиндель режущего инструмента не только вращает сверло, но и перемещает его вниз и вверх.
Фрезерование – обработка фасонных или плоских поверхностей, формирование пазов, канавок. Фрезерный станок укомплектован инструментальным шпинделем и подвижным столом, к которому крепят заготовку. Шпиндель вращает фрезу (режущий инструмент), а стол обеспечивает продольную и поперечную подачу заготовки. В итоге, на таких агрегатах обрабатываются детали любой формы, а не только тела вращения.
Абразивная обработка, предполагающая использование особого режущего инструмента – абразивного круга, с помощью которого можно реализовать и шлифование поверхности, и глубокое резание, и доводку до нужного класса точности. Схема станка для абразивной обработки похожа на конструкцию агрегата для фрезерования. То есть, инструментальный шпиндель обеспечивает вращение абразивного круга, а за подачу отвечает привод рабочего стола, на котором крепят деталь.
Необходимо заметить, что любая металлообработка механическим способом предполагает генерацию обрабатывающего усилия в точке соприкосновения инструмента и заготовки, за счет перехода крутящего момента в силу резания. Причем крутящий момент может генерировать и инструмент (сверло, фреза) и заготовка (в токарном станке).
В итоге, качество обработки зависит от синхронизации крутящего момента инструмента или заготовки с поступательными перемещениями суппорта или рабочего стола.
Механическая обработка на станках с ЧПУ
Уровень качества, который обеспечивает любая технология механической обработки металлов, в первую очередь зависит от мастерства оператора того или иного станка или агрегата.
Поэтому, в целях повышения качества обработанной поверхности и точности габаритов получаемых деталей, обработку металлов резанием или давлением стараются проводить без участия человека (оператора), делегируя исполнение и контроль качества особому прибору – блоку числового программного управления.
Такие станки стоят недешево. К тому же, каждый обрабатывающий процесс начинается с создания «программы», управляющей работой привода и суппорта. Но впоследствии эту программу можно «запускать» уже в автоматическом режиме, получая гарантировано качественный результат (при условии стабильности габаритов режущих кромок у обрабатывающих инструментов).
Поэтому станки с ЧПУ имеет смысл использовать лишь в массовом производстве или для изготовления особо точных деталей.
steelguide.ru
Механическая обработка деталей из металла
Изготовление детали – трудоёмкий процесс, включающий в себя огромное количество различных видов обработки. Как правило, он начинается с составления маршрутной технологии и выполнения чертежа. В данной документации и содержатся все необходимые данные для изготовления детали. Механическая обработка – достаточно важный этап, включающий в себя огромное количество различных операций. Рассмотрим их детальнее.
Материал
В зависимости от требуемой детали выбирают и металлический материал. При последующей его обработке получают готовое изделие. Иными словами, металлический материал – это заготовка. Она бывает нескольких видов: штамповка, ковка, прокат, металлокерамика. Каждый вид заготовки отличается способом изготовления. Если, например, для ковки, в мелкосерийном производстве используют ковочные молоты, то для получения металлокерамического материала — прессовку металлических порошков в пресс-формах под давлением 100-600 Мпа.
Обработка плоских и цилиндрических поверхностей
Плоские поверхности обрабатывают при помощи фрезерования, строгания, протягивания. Как правило, к таким заготовкам относится листовой прокат и металлокерамика.
Строгание осуществляют на поперечно- и продольно-строгальных станках. При обработке на первом главное движение осуществляет резец, а движение подачи – стол станка. На продольно-строгальном – все наоборот. Кроме того, такая механическая обработка считается малопродуктивной, поскольку она имеет слишком маленькую скорость резания. Рабочий инструмент теряет много времени на обратный холостой ход. Преимуществами такой обработки является обеспечение прямолинейности и прямопропорциональности.
Фрезерование
Одним из наиболее высокопродуктивных методов обработки как плоских, так и цилиндрических поверхностей считается именно фрезерование. Это объясняется тем, что его осуществляют одновременно несколькими зубьями фрезы. Механическая обработка может проводиться последовательным, параллельным, последовательно-параллельным и непрерывным способом. Фрезерованием можно обработать поверхности с шероховатостью Rz=0,8 — 0,63 мкм и такая обработка будет называться тонкой.
Протягивание
Этим способом обрабатывают детали в массовом и крупносерийном производстве. В некоторых случаях протягивание возможно заменить шлифованием и долблением. Такая механическая обработка имеет очень высокую точность. Протягивание может выполняться как в вертикальном направлении, так и в горизонтальном. Такая обработка применяется для операций, связанных с повышенной точностью, а режущий инструмент работает в условиях огромных нагрузок, таких как сжатие, изгиб, растяжение.
Например, протягивание используют при обработке отверстий в огнестрельном оружии, для нарезания шпоночных канавок и шлицев. В качестве режущего инструмента используют протяжки, как цельные, так и сборные. Их изготавливают из быстрорежущих и среднелегированных инструментальных сталей.
Обработка отверстий и резьбы
Механическая обработка деталей не обходится без таких важных инструментов, как сверла, зенкеры, метчики, развертки. Для того чтобы просверлить отверстие необходимого диаметра, обязательно выполняют расчет режима резания для данного процесса. Как правило, отверстие сверлят на необходимый диаметр с учетом припуска на последующую обработку. Для того чтобы обеспечить наилучшую точность, используют развертку, а для получистовой обработки возможно применение зенкера.
Механическая обработка деталей также может выполняться при помощи метчика. Данный инструмент предназначен для нарезания резьбы в уже существующих отверстиях. Различают метчики для глухих и сквозных отверстий. Для нарезания наружной резьбы используют резцы и плашки. Перед их использованием необходимо немного проточить заготовку. Для того чтобы создать качественный и эффективный заход режущего инструмента, перед началом операции снимают фаску на торце изделия. Она должна иметь такую же высоту, как и профиль резьбы.
Механическая обработка деталей из металла и обработка резьбы в редких случаях производится при помощи винторезных головок. Они крепятся в пиноли хвостовиком. В ней могут быть призматические, радиальные или же круглые гребенки. Они не контактируют с нарезанной резьбой при обратном ходе, поскольку по окончании процесса в автоматическом режиме расходятся.
Механическая обработка металла на станках и линиях изучается во многих колледжах и университетах. Специальность имеет код 36-01-54 и подразделяется на такие направления: фрезеровщик, токарь, шлифовальщик, контролер слесарных и станочных работ, оператор автоматических (АЛ) и полуавтоматических линий. Поскольку современные технологии не стоят на месте, очень актуально изучать механическую обработку металлов на станках с ЧПУ и на АЛ.
Такое оборудование значительно облегчает работу операторов. Их главной задачей является контроль, наладка и загрузка-разгрузка деталей и заготовок. Все операции автоматические линии выполняют при помощи специальных компьютерных программ и практически не требуют вмешательства операторов. Применение АЛ позволяет значительно снизить себестоимость обработки и время изготовления деталей.
fb.ru
Обработка металлов резанием: механическая
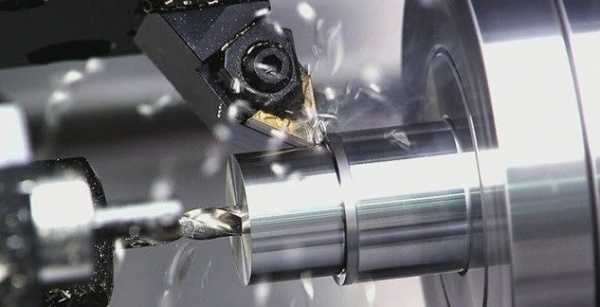
В машиностроительной, металлообрабатывающей отраслях, в строительстве используют различные способы обработки металла, резание – один из их разновидностей.
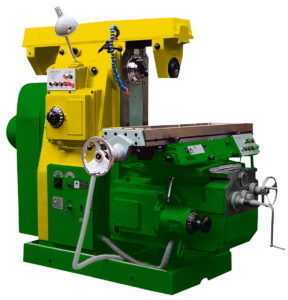
Поскольку металлических деталей существует огромное множество, они различаются по форме, размеру, весу, составу сплава, поэтому и обработка металлов резанием также осуществляется несколькими способами. Можно выделить основные:
- точение;
- сверление;
- фрезерование;
- строгание;
- шлифование.
Каждый вид предполагает использование специализированного оборудования – часто это стационарные станки.
Точение металлических деталей
Этот способ применяется, когда исходную заготовку необходимо в незначительной мере доводить до нужных размеров и конфигурации. Для этого специалисты используют токарный станок, комплект сверл или резцов. Деталь, которую нужно обработать, помещают в специальное вращательное устройство, вокруг которого движется режущий механизм.
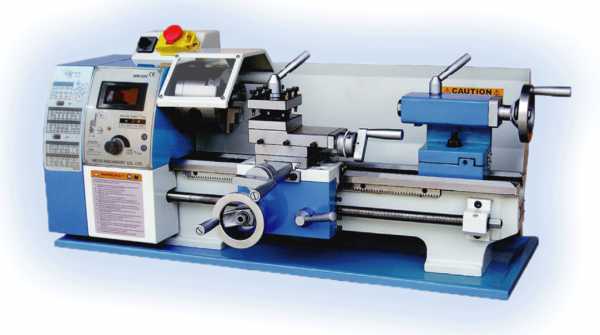
Благодаря оказываемому усилию кромка острия сверла врезается в деталь и удаляет лишний слой, который превращается в разного рода стружку. В зависимости от того какого вида выполняется резка стружка может быть:
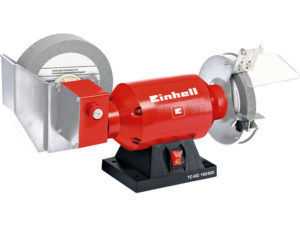
- элементная – получается при обработке сверхтвердого металла, такого как титан, процессы выполняются на низких скоростях;
- слитая – образовывается при высокоскоростной токарной обработке деталей из нетвердой стали, меди, олова, пластмассы;
- надлом – возникает в результате резки металлопластичных деталей;
- ступенчатая стружка получается, в результате обработки металлов средней твердости.
Для разных видов металла подбирается подходящая скорость, так тугоплавкие и сверхтвердые металлы нужно точить на минимальной скорости. Ее рассчитывают перед началом работ и задают в параметры точильного станка, далее скорость поддерживается автоматически.
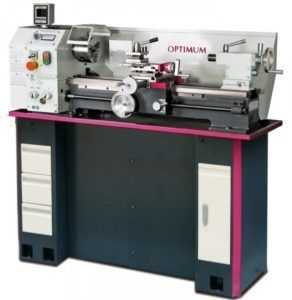
Необходимо понимать, что более точные и чистые работы обеспечиваются на меньшей скорости, а черновые можно осуществлять на максимально допустимой.
Важным моментом являются сплавы металлов, из которых изготовлены резцы. Точило должно быть выполнено из более прочного сплава, чем деталь, которую планируется резать. Наиболее часто для резцов используют титан, вольфрам, тантал.
В зависимости от того какого рода необходима обточка, резцы имеют различные формы и размеры, разнообразие режущих элементов позволит выполнить работы с высокой точностью и меньшим количеством стружки, то есть без значительных отходов.
Резец можно классифицировать по основным видам обработки:
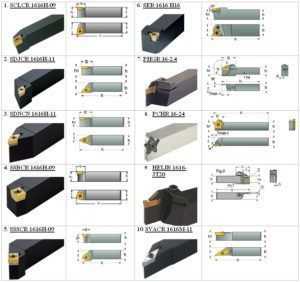
- расточный;
- резьбовый;
- канавочный;
- проходной;
- отрезной;
- подрезной;
- фасонный.
Сам токарный станок может быть механический и автоматизированный с программным пультом управления. Последний дает наибольшую точность и скорость работы, этот вид станков пришел на смену механическим и постепенно вытесняет их с производства.
Все расчеты – скорость, необходимые углы, направления резьбы рассчитываются в программном комплексе, это открывает широкие возможности для производства нестандартных деталей. Если бы для них использовался механический, потребовалось бы значительное время на настройку и не исключен большой процент брака при этом.
Сверление металлических заготовок
Еще одним видом резания металлических деталей является сверление, оно выполняется на соответствующем оборудовании, а сам резак называется сверлом. Суть способа сводится к тому, что сверло или зенкер приводятся в действие механическим способом и вращается вокруг своей оси.
Сверлильный станок. Настройка и другие хитрости
За счёт таких движений инструмент врезается в металлическую деталь, делая отверстие в ней. Сверло приводится в действие ручным приспособлением, механическими и автоматизированными станками. С помощью сверла можно получить отверстия в металлической заготовке разного вида, размера и глубины:
- перовое;
- спиральное;
- центровочное.
Чаще всего встречается спиральный вид сверла, оно состоит из трех частей: рабочей части, шейки и хвостовика. Режущий отрезок имеет две кромки, расположенные под определенным углом по отношению друг к другу, например, для резки чугунной детали необходим угол 118о.
Сверлильный станок из рулевой рейки
Хвостовик нужен чтобы закрепить сверло в патрон станка или дрель. Он может иметь две формы: цилиндрическую или коническую. На конце хвостовика установлена лапка, которая нужна для выталкивания сверла после использования из гнезда.
Шейка сверла – переходное звено, которое необходимо для обеспечения выхода в процессе шлифования абразивного круга. На шейке ставится маркировка сверла.
Перед началом сверления нужно разметить деталь, центр лучше сделать углубленным с помощью кернера, чтобы в начале работы сверло не слетело с намеченного пункта.
Для сверления металлических деталей могут применяться различные инструменты:
- трещотка – ручной механизм, приводится в действие с помощью поворота рукоятки, она дает вращательное движение собачке, в нее вставлен паз храповика со шпинделем, в который установлено сверло. Таким способом, выполняется сверление. Использовать трещотку более эффективно, когда нужно получить отверстие большого диаметра; Дрель пневматическая WESTER BM-10
- ручная дрель – приводится в действие с помощью вращения рукояти одной рукой, и давления, оказываемого на нагрудник. Коническая шестерня сообщает поступательное вращение сверлу. Этот способ позволяет делать отверстия диаметром до 8 мм;
- пневматическая дрель будет более эффективна для обработки деталей с отверстием, которое должно иметь диаметр до 75 мм. Приводится в действие от давления, которое оказывает сжатый воздух, аппарат имеет небольшую массу и габаритные размеры;
- электрическая дрель работает от мотора, который приводит в действие сверло. Модель позволяет не только делать отверстие, но и производить завинчивание гаек и винтов, развертывание, а также шлифование;
- сверлильный станок предназначен для промышленного производства, или в случаях, когда предполагаются большие объемы работы. Станки характеризуются высокой скоростью и имеют максимальную точность резки металла, а также они легки в управлении.
Фрезерование металлических деталей
Обработка металлов резанием с помощью фрезы – это один из самых распространенных способов. Главным режущим элементом в конструкции станка является фреза – круглое колесо, имеющее зубчатые края. Электрический мотор приводит в действие режущий механизм, на большой скорости фреза врезается в металлическую заготовку и снимает слои в нужных местах.
Токарно-фрезерный станок DMG CTX gamma 2000
В итоге получается срез в детали и стружка отработанного материала. Ранее фрезерные станки управлялись только специалистом, из-за больших скоростей и диаметра колеса, получалось много отходов и бракованных деталей. Современные станки управляются программным обеспечением, благодаря чему достигнут высокий уровень точности резки.
Фрезерный станок по металлу корвет 416 Энкор
Фрезы могут быть разных размеров и форм и применяются в зависимости от необходимой величины разреза, вида обрабатываемого металла.
Станки последнего поколения оснащены лазером, который позволяет не только достичь максимальной точности, но и выполнять работы по сложной фигурной резке. Тепловой лазер выжигает кромку в нужных местах, а шлифовальный лазер проходит по нескольку раз по кромке, разрезая металл, такой подход обеспечивает снятие минимального слоя материала заготовки. На выходе получается чистый разрез, без заусениц и сколов, такая деталь не потребует дальнейшей зачистки.
Строгальная резка металла
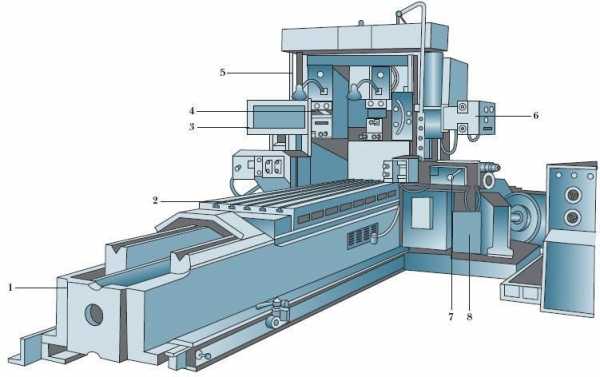
Обработка металла резанием строгальным способом предусматривает снятие верхних слоев поверхности детали, которая обрабатывается. Этот вид обработки предполагает использование специализированных станков:
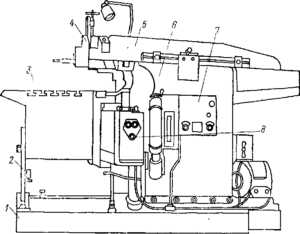
- строгально-долбежных;
- поперечного и продольного сечения;
- кромкострогальных.
Отличаются станки способом движения режущего механизма, производительностью, качеством обработки металла.
Особенностью строгальных установок является использование только прямых строгальных резцов, они устанавливаются на малых вылетах, поскольку не отличаются виброустойчивостью, но достаточно просты в управлении.
Недостаток таких резцов – невозможность получения максимально точных результатов резки. Для устранения этого недостатка некоторые станки имеют возможность для монтажа нескольких резцов.
В работе со строгальными станками важно учитывать, что режущие части достаточно мощные и способны с первого нажатия погрузиться в металл на большую глубину, что может испортить изделие.
Шлифование как способ резки металла
Шлифовальный метод для резки металлических деталей предусматривает использование различных абразивных кругов. Они состоят из мелких зерен, минерального происхождения, которые соединены друг с другом связкой.
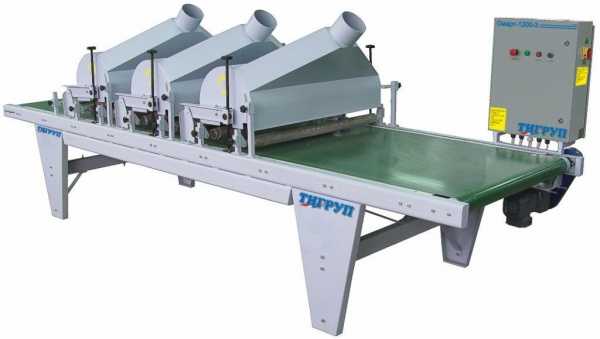
Техника резания сводится к следующему процессу: при движении абразивных насадок, острые грани срезают верхние слои металла и оставляют за собой гладкую выемку. Все движения осуществляются на очень большой скорости, иногда она достигает 3000 метров в одну минуту, для сравнения, при токарной обработке максимальная скорость составляет 30 метров.
Из-за высокой скорости и хаотичного расположения зерен получается очень мелкая стружка, которая разлетается во все стороны и на несколько метров. Эту особенность следует учитывать при организации безопасных условий работника.
Шлифовка позволяет добиться точных результатов резки, однако, при этом станок потребляет очень много электроэнергии, в 10 раз больше, чем, например, токарная установка. Еще одной особенностью шлифовки является высокая степень нагрева самой металлической детали, в некоторых случаях до 1000о. Это необходимо учитывать при обработке мягких металлов, таких как медь, олово, чугун и прочих, от действия шлифовального круга они могут попросту расплавиться.
Реклама партнеров
Видео: Удивительные возможности станков с ЧПУ
Похожие статьи
promtu.ru