Механические свойства и методы их определения
2 лекция
МАТЕРИАЛОВЕДЕНИЕ
Механические свойства и методы их определения
Механические свойства материалов определяют на специальных образцах.
Наиболее распространенными механическими характеристиками являются: твердость , пределы прочности и упругости , ударная вязкость
Испытания выполняются на разрывных машинах с использованием специальных образцов. Деформация может быть упругой или пластической . Упругая деформация полностью снимается (исчезает) после снятия
нагрузки. Пластическая деформация не исчезает после снятия нагрузки (согните алюминиевую проволоку, после того как нагрузка снята, проволока не разгибается — она пластически деформирована).
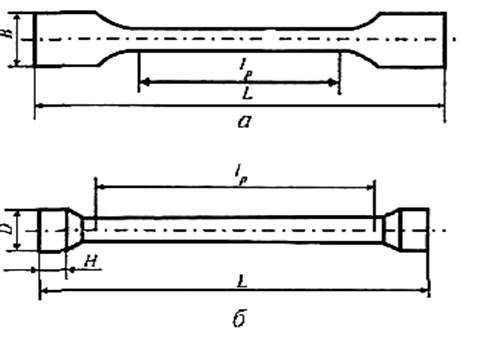
При этом определяются: предел прочности (sв) — напряжение, при котором происходит разрушение образца
Определение твердости
Твердость характеризует сопротивление материала большим пластическим деформациям.
Наиболее распространенные методы определения твердости связаны с внедрением специального тела, называемого индентором, в испытуемый материал с таким усилием, чтобы в материале остался отпечаток индентора.
Метод Бринелля (НВ )
Вдавливание шарика происходит при постоянной нагрузке, в результате на поверхности образца образуется отпечаток в виде сферической лунки.
Диаметр отпечатка измеряется в двух взаимно перпендикулярных направлениях с помощью микроскопа Бринелля — это лупа со шкалой.
Метод Роквелла
Принципиальное отличие этого метода от рассмотренного ранее заключается в том, что твердость определяется не площадью поверхности отпечатка индентора, а глубиной его проникновения в исследуемый образец.
В качестве индентора используют алмазный конус при испытаниях твердых материалов и стальной закаленный шарик при испытаниях мягких материалов. Значения твердости обозначаются:
HRC — алмазный конус, нагрузка 150 кгс; HRA — алмазный конус, нагрузка 60 кгс; HRB — шарик (например, 90 HRA). Шкала по измерению твердости HRC изменена в связи с изменением эталона, поэтому в измеряемые значения следует вносить поправку.Значения твердости в единицах HRC примерно в 10 раз меньше, чем в единицах НВ, т.е. твердость 30 HRC примерно соответствует 300НВ.
Метод Виккерса
Метод основан на вдавливании четырехгранной алмазной пирамидки с углом между противоположными гранями, равным 136°. Твердость (она обозначается HV ) определяется отношением нагрузки к площади поверхности отпечатка.
Значения твердости по Бринеллю и Виккерсу практически равны.
Метод Шора .
При измерении твердости по Шору груз вместе с укрепленным на нем индентором (обычно это стальной шарик) падает с высоты на образец перпендикулярно его поверхности. Твердость по Шору определяется по высоте отскока шарика(груз с индентором).
Определение ударной вязкости и вязкости разрушения
Для определения ударной вязкости используют образцы с надрезом, который служит концентратором напряжений. Образец устанавливают на маятниковом копре так, чтобы удар маятника происходил против надреза, раскрывая его. Маятник поднимают на высоту, при падении он разрушает образец, поднимаясь на высоту(так как часть запасенной при подъеме работы тратится на разрушение образца).
Ударная вязкость — это относительная работа разрушения, т.е. работа, отнесенная к площади образца до разрушения.
КЛАССОФИКАЦИЯ СТАЛЕЙ
Сплавы с содержанием углерода (С) до 2,14% называются сталями.
Стали классифицируются по химическому составу, способу производства, качеству, степени раскисления, назначению, структуре
По хим. Составу стали классифицируются на углеродистые и легированные.
Углеродистые делятся на: низкоуглеродистые – до 0,25% С,
среднеуглеродистые – 0,25-0,6% С,
высокоуглеродистые – более 0,6% С.
По содержанию легирующих элементов делятся:
низколегированные – до 2,5% лиг. эл.,
среднелегированные – 2,5-10% лиг. эл.,
высоколегированные – долее 10% л. э.
По способу производства различают:
конверторные,
мартеновские,
электростали,
стали особым методом выплавки.
По назначению стали классифицируются:
конструкционные,
строительные,
стали специального назначения с особыми свойствами.
По качеству различают:
обыкновенного качества,
качественные,
высококачественные,
особовысококачественные.
Качество стали зависит от вредных примесей, преимущественно от (серы, фосфора)
Качество углеродистых сталей отражается в маркировки.
Стали обыкновенного качества маркируют буквами Ст (Ст3).
В конце маркировки высококачественных сталей ставится буква А (У10А).
Все легированные стали производят как минимум качественными (10, 20, 45 — % С в 0,00).
Для производства особовысококачественных сталей применяют специальные виды улучшающие обработку, которые могут указываться в маркировках сталей.
ВИ (ВИТ) – переплавка в вакуумных индукционных печах,
ВД (ВДП) – переплавка в вакуумных дуговых печах,
Ш (ЭМП) – электрошлаковый переплав,
ШД – вакуумный дуговой переплав сталей после электрошлакового переплава,
ПДБ – плазменно-дуговая переплавка.
По степени раскисления различают:
спокойную (ст) которая раскислена марганцем. Кремнием и алюминием.
полуспокойную (пс) раскислена марганцем и алюминием.
кипящую (кп) раскисляется марганцем.
В ГОСТах маркировка сталей принято следующее комбинация, чисел и букв.
Первая цифра в маркировки указывает на содержание углерода в стали:
если цифра однозначная то в 0,0%,
если цифра двухзначная то в 0,00%,
если цифра не указана то ~ 1%.
ПРИМЕР 9ХС – 0,9% углерода
Для обозначение легирующих элементов входящих в состав стали каждому из них присвоена своя буква:
Н-никель, Д-медь, А-азот, Х-хром, Р-бор, П-фосфор, К-кобальт, Б-ниобий, М-малибден, Ц-цирконий, Т-титан, Г- марганец, С-кремний, Ф-ванадий, Ю-алюминий, В-вольфрам.
Цифры идущие после букв, указывают среднее содержание данного легирующего элемента в %. Если цифры нет то легирующего элемента ~ 1%.
Пример:
9ХС — 0,9% угл.,1% хрома,1% кремния.
Х12 – 1% угл., 12% хрома.
Степень раскисления сталей обозначается буквами в конце маркировки стали: СП — спокойная, ПС — полуспокойная, КП – кипящая.
Для некоторых сталей употребляется специальное условное обозначение:
Р – быстрорежущая сталь, цифра за которой указывается содержание вольфрама в % (Р18-быстрорежущая сталь с 18% вольфрама),
маркировка шарикоподшипниковых сталей начинается с буквы Ш и последующей цифры указывающей на содержание хрома в 0,0% (ШХ15 – шарикоподшипниковая сталь 1,5% хрома)
Углеродистые стали обыкновенного качества – Ст0, Ст1, Ст2, Ст3, СТ3Г, …- используется для металлоконструкций слабонагруженных.
Углеродистые конструкционные качественные стали – 08, 10, 15, 20, 25, 30, …85 – винты, гайки, болты.
Автоматные стали – А11,А20,А30,АС40 (С — свинец, Е — селен ) изделия не ответственные изготавливаются на автоматах.
Углеродистые инструментальные стали – У7, У8, У9, …У13.
Высококачественные – У7А, …У13А.
Легированные стали –
ст. средней прочности 15ХР,20ХМ и т.п.
ст. повышенной прочности – 12Х2Н3А, 18Х2НМА изготавливают поршневые кольца
Улучшаемые стали – 30Х,40Х, 50Х изготавливают коленчатые валы.
Хромокремнемарганцевые стали – 30ХГСА автомобильное производство.
Хромоникелевые стали – 40ХН шест-ни
Хромоникельмолибденовые стали – 40ХНМА, 38ХНЗМФА изготавливают сильно нагруженные детали.
Высокопрочные стали – 30ХГСНА, 30Х5МСФА.
Рессорно-пружинистые стали – 55С2, 60С2А, 70С3А изготавливают пружины вагонов, автомобильные рессоры.
Шарикоподшипниковые стали – ШХ15, ШХ15СГ изготавливают траки гусеничных танков, крестовины рельс.
Инструментальные стали – 9ХС, ХВГС, ХВ2, ХВ4 изготавливают плашки, протяжки.
Быстрорежущие стали – Р18, Р6М5, 10Р6М5 крупногабаритный инструмент работающий с знакопеременными нагрузками.
Жаростойкие стали – 15Х5, 12Х17, 15Х28, 25Х2М1 A используются в котлостроительстве.
Чугун — классификация и маркировка
В зависимости от степени графитизации, обусловливающей вид излома, — на серый, белый и половинчатый (или отбелённый).
В зависимости от формы включений графита — на чугун с пластинчатым, шаровидным (высокопрочный чугун), вермикулярным и хлопьевидным (ковкий чугун) графитом.
в зависимости от характера металлической основы — на перлитный, ферритный, перлитно-ферритный, аустенитный, бейнитный и мартенситный
В зависимости от назначения — на конструкционный и чугун со специальными свойствами; по химическому составу — на легированные и нелегированные.
Серый чугун — наиболее широко применяемый вид чугуна (машиностроение, сантехника, строительные конструкции) имеет высокий коэффициент поглощения колебаний при вибрациях деталей (в 2-4 раза выше, чем у стали).
Белый Чугун представляет собой сплав, в котором избыточный углерод, не находящийся в твёрдом растворе железа, присутствует в связанном состоянии в виде карбидов железа Fe3C (цементит)
Белый чугун вследствие низких механических свойств и хрупкости имеет ограниченное применение для деталей простой конфигурации, работающих в условиях повышенного абразивного износа
Половинчатый чугун содержит часть углерода в свободном состоянии в виде графита, а часть — в связанном в виде карбидовека. Применяется в качестве фрикционного материала, работающего в условиях сухого трения (тормозные колодки), а также для изготовления деталей повышенной износостойкости (прокатные, бумагоделательные, мукомольные валки).
mirznanii.com
Методы исследования механических свойств металлов
Строительные машины и оборудование, справочник
Категория:
Автомобильные эксплуатационные материалы
Методы исследования механических свойств металлов
Свойства металлов и сплавов определяются внутренним строением и природой атомов, из которых они состоят. Все свойства металлов разделяются на физические, химические, механические и технологические.
К физическим свойствам относятся: блеск, цвет, плотность, плавкость, тепловое расширение, тепло- и электропроводность, магнитность.
К химически м свойствам относится способность металлов вступать в химические реакции с другими элементами и сложными веществами, например с кислородом воздуха, углекислотой, водой и т. д. В результате могут происходить разрушения металлов и необратимые изменения их структуры и свойств.
Механические свойства металлов определяют способность сопротивляться прилагаемым усилиям. К таким свойствам относятся упругость, пластичность, прочность, твердость и т. д.
Технологические свойства характеризуют способность металлов поддаваться различным видам механической обработки: ковке, штамповке, прокатке, обработке режущим инструментом и т. д.
Металлы и сплавы используются в качестве основного конструкционного материала для деталей автомобилей, различных машин, механизмов и сооружений, работающих в условиях больших нагрузок. Поэтому для металлов важнейшими являются их механические свойства. Определение этих свойств производится при испытаниях, которые в зависимости от способа приложения усилия делятся на статические и динамические. При статических испытаниях нагрузка на образец металла возрастает медленно и плавно. При динамических испытаниях нагрузка увеличивается с большой скоростью или изменяется многократно по величине и направлению Вид испытаний определяется назначением и условиями применения деталей машин.
Наиболее распространенными испытаниями для исследования механических свойств металлов являются статические испытания на растяжение и твердость, а также динамические испытания на Удар и усталость.
Испытание на растяжение производится для образцов металлов на специальных разрывных машинах типа ИМ-12А, РМ-500 и др. При этом используются образцы определенной формы и размеров, изготовленные по стандарту. Образец закрепляют в захвате машины и подвергают нагрузке, увеличивая силу, растягивающую образец. По силоизмерительному прибору разрывной машины определяют величину растягивающей силы. Как только растягивающая сила превысит силу сопротивления металла, происходит разрыв образца. Напряжения, возникающие в металле при испытании, автоматически записываются на ленте самописца машины в виде диаграмм растяжения.
На диаграмме растяжения по оси ординат отложено растягивающее усилие Р (в кгс), а по оси абсцисс — деформация или абсолютное удлинение образца (в мм). Удлинение образца при возрастании нагрузки от точки О до точки А пропорционально этому возрастанию, а от точки А до точки Б пропорциональность нарушается. В интервале нагрузок Б — В металл начинает течь, т.е. происходит удлинение образца при постоянной силе Р. В точке Г диаграммы сила достигает максимального значения, на образце образуется шейка и в точке Д он разрывается.
Указанные характерные точки на диаграмме позволяют определить показатели механических свойств — величины напряжений или пределы пропорциональности, упругости, текучести, прочности, истинное сопротивление разрыву, относительное удлинение и относительное сужение.
Следует отметить, что текучесть металлов на участке Б — В характерна только для низкоуглеродистых сталей. Высокоуглеродистые стали не обладают текучестью и не имеют на диаграмме участка текучести. Поэтому для них находят условный предел текучести при остаточном удлинении, равном 0,2%.
Рис. 1. Диаграмма растяжения мягкой стали
Найденное значение твердости по шкалам В, С, А обозначают соответственно HRB, HRC, HRA.
Определение твердости по Роквеллу имеет широкое применение, так как позволяет испытывать твердые и мягкие металла прямо на готовых деталях.
Испытание на удар проводится с целью оценки сопротивляемости образца металла ударной нагрузке. Для этого используют специальную машину, называемую маятниковым копром (копры типа МК-15, PS 30 и др.). Испытуемый образец металла устанавливают на опоры копра и подвергают ударному воздействию массивным маятником, падающим с определенной высоты.
Работа Ау подсчитывается перемножением массы маятника на разность высот его подъема до удара и после удара.
Испытания на усталость позволяют выявить срок службы многих ответственных металлических деталей (шатуны, коленчатые валы двигателей, полуоси и др.), которые подвергаются в процессе работы действию повторных и знакопеременных нагрузок. Свойство металлов выдерживать большое число циклов переменных нагрузок называется выносливостью.
Единицей измерения при испытании на усталость является предел выносливости, т. е. величина допустимого напряжения, которое выдерживает металл без разрушения при заданном числе циклов нагрузки.
Испытания на усталость проводят в зависимости от назначения детали на различных машинах (типа МУИ-6000, ИВМ и др.). Наиболее распространены испытательные машины, нагрузка на которых прикладывается изгибом при вращении, растяжением-сжатием, кручением. Результатом испытания является кривая усталости,представляющая зависимость напряжения от числа циклов, причем минимальная величина напряжения, выдерживаемая металлом в конце испытания, и будет характеризовать предел выносливости.
Реклама:
Читать далее: Термическая обработка стали
Категория: — Автомобильные эксплуатационные материалы
Главная → Справочник → Статьи → Форум
stroy-technics.ru
Стандартные методы определения механических свойств. сварных и паяных соединений
Существует много стандартных методов определения механических свойств металлов. Это испытания на растяжение, испытания гладких образцов на статический изгиб и надрезанных образцов на ударный изгиб, определение твердости металла, испытание на длительную прочность и многие другие. Основное назначение этих испытаний состоит в получении количественных характеристик металла, необходимых для выполнения инженерных расчетов. Часть методов предназначена для получения характеристик металла, которые хотя и не участвуют как количественные в расчетах на прочность, но используются для качественной оценки работоспособности изготовляемых из него деталей или для установления соответствия металла техническим условиям на его поставку.
Большая часть этих методов испытаний может быть применена — также и для оценки механических свойств металла шва, около — шовных зон или даже сварных соединений. Тем не менее существует отдельный стандарт (ГОСТ 6996—66 «Сварные соединения. Методы определения механических свойств»), который специально регламентирует процедуру испытаний только сварных соединений.
Назначение этих методов испытаний состоит в определении механических свойств, которые используются для количественной и качественной оценки работоспособности сварных соединений и конструкций, а также для сравнения механических свойств основного металла и металла сварных соединений с целью оценки соответствия принятой технологии сварки тем требованиям, которые предъявлены к сварной конструкции. Рассмотрим основные требования к образцам и условиям проведения стандартных испытаний сварных соединений.
В испытаниях на статическое растяжение образцов (рис. 3.3) определяют условный или действительный предел текучести ат, временное сопротивление ав, относительное удлинение после разрыва б5 на образцах, рабочая длина /0 которых в пять раз больше диаметра d0, относительное сужение после разрыва ф. Образцы изготовляют из металла шва, участков околошовной зоны или
наплавленного металла. Отбор образцов ведут либо непосредственно из конструкции, либо из специально сваренных соединений. Такие образцы используются для испытаний при нормальной и пониженной температурах. Образцы с резьбой на концах используются при различных температурах, в том числе и при повышенных.
Для определения сопротивляемости металла разрушению при ударных нагрузках в присутствии концентратора испытания на ударный изгиб надрезанных образцов (рис. 3.4). Определяют так называемую ударную вязкость ан металла шва, околошовной зоны в различных участках и наплавленного металла. Надрез располагают в том месте, где необходимо определить свойства. Используют надрезы с различной остротой. Чем острее надрез, тем меньше работа, затрачиваемая на изгиб образца до появления трещины, и тем больше работа, идущая на распространение трещины по образцу аи = A IF, где А — работа, идущая на ударный излом образца; F— площадь поперечного сечения в зоне надреза. Величину аа в СИ выражают в Дж/м2 или (чаще) в кратных единицах — МДж/м2. Ранее применялась единица 1 кгс-м/см2 « «0,1 МДж/м2.
Измерение твердости металла позволяет косвенно судить о его механических свойствах и структурном состоянии, а также позволяет определить размеры закаленных и отпущенных зон, степень упрочнения и разупрочнения металла в сварном соединении. Измерение твердости основного металла, металла околошовной зоны и шва производят на приборах Виккерса, Роквелла и Бринелля
на макрошлифах поперечного сечения образцов. Твердость определяют вдавливанием в необходимые точки образца индентора — алмазной пирамиды (Виккерс), алмазного конуса (Роквелл) или стального шарика (Бринелль) — с последующим измерением размера отпечатка и пересчетом в соответствующие единицы твердости (HV, HRC, НВ).
Испытание сварного соединения на статическое растяжение предназначено для определения прочности сварного соединения. Для определения прочности стыковых соединений используют плоские образцы, представленные на рис. 3.5. Утолщение шва
снимают механическим путем. Разрушение происходит обычно по наименее прочному участку соединения. Уровень прочности, определяемый таким путем, характеризует прочность сварного соединения в целом, а не прочность отдельной слабой зоны (см. § 3).
Для определения прочности металла шва в образцах делают выкружку, ослабляющую среднюю часть образца (рис. 3.6). Определяют временное сопротивление по формуле
о’в = kP/F,
где k — поправочный коэффициент, для сталей k = 0,9; F — площадь наименьшего поперечного сечения до испытания.
Для определения пластичности металла стыковых сварных соединений проводят испытания образцов на статический изгиб. Образцы прямоугольной формы (рис. 3.7, а, б), вырезанные вдоль или поперек стыкового шва и механически обработанные со всех сторон, помещают на две опоры специального приспособления и производят изгиб образцов посередине пуансоном, имеющим радиус закругления, соответствующий конкретной толщине образца. Изгиб производят до появления трещины или надрывов длиной более 5 мм на растянутой стороне образца. Угол а (рис. 3.7, в) характеризует пластичность металла сварного соединения.
Свойства паяных соединений определяют при ударном и статическом нагружениях согласно ГОСТ 23046—78 и 23047—78. Стати-
а — шов расположен вдоль образца; б — шов расположен поперек образца; в — вид
образца после испытания
а)
а — на ударный изгиб; б — на ударный срез; в — на ударный изгиб для стыковых сое-
динений; г — на ударный изгиб для косых соединений
снимает наклеп, достигнутый при холодной прокатке металла. На рис. 3.11 показано распределение твердости в сварном соединении из сплава АМгб. Твердость шва и околошовной зоны близки к твердости отожженного металла. Предел прочности и пргдел текучести оказываются заметно
ниже, чем у основного ме — WK — Основной нагартобонный металл талла, а пластичность повы — 120 шается. Представление о размерах зоны и степени разупрочнения Дает также табл.3.1.
Зоны, где металл обладает пониженным пределом текучести по отношению к пределу текучести соседнего металла, называют мягкими прослойками.
Паяные стыковые соединения, припой в которых менее прочен, чем основной металл, также содержат мягкую прослойку. Прочность таких соединений зависит не только от прочности металла мягкой зоны, но и от ее относительного размера % = his, где h — ширина прослойки; s— толщина металла.
Таблица 3.1 Изменение свойств наклепанного металла в сварных стыковых соединениях
|
Другим типичным примером образования механической неоднородности и прослоек является сварка термически обработанных сталей. Будем для простоты рассматривать сварку без присадочного металла. Тогда шов и околошовная зона, нагретые до температуры выше ЛСз, в процессе охлаждения закаливаются и имеют более высокую твердость и прочность, чем основной металл.. Этот участок называют твердой прослойкой (рис. 3.12, а).
Рядом с ней по обе стороны находятся участки высокоотпущенного металла, который и по отношению к основному металлу, и по отношению к твердой прослойке имеет пониженный предел текучести. Эти зоны образуют две мягкие прослойки. В случае если термически обработанная сталь сваривается аустенитным швом (рис. 3.12, б), возникает еще более сложное сочетание мягкого аустенитного шва, двух твердых и двух мягких прослоек. Если отношение пределов текучести прослойки и соседнего участка больше единицы, то прослойка будет твердой; в обратном случае — мягкой.
Рис. 3.12. Твердые и мягкие прослойки в сварных соединениях
Необходимость изучения прослоек объясняется тем, что механические свойства сварных соединений, такие, как прочность, деформационная способность, энергоемкость при разрушении, а также
место и характер разрушения, зависят от степени и топографии механической неоднородности.
Механические свойства образца, вырезанного из мягкой прослойки и имеющего низкую прочность, еще не свидетельствуют о том, что сварное соединение в целом обладает такими же свойствами. Взаимодействие отдельных зон протекает сложным образом, и агрегатная прочность сварного соединения, как правило, не совпадает с прочностью какой-либо прослойки.
Рассмотрим случай, когда растягивающая сила направлена вдоль шва и все прослойки испытывают одинаковые деформации. Деформационная способность соединения и, как показано ниже, его несущая способность ограничены пластичностью металла наименее пластичной прослойки. На рис. 3.13 показаны диаграммы зависимости напряжения от деформации в различных зонах сварного соединения. Точки Аъ А2 и А3 соответствуют разрушению образца. Разрушение наступит при е == ёа3; При этом напряжения од в основном металле, сг3 в шве и сг2 в твердой прослойке будут сильно различаться. Продольная растягивающая сила в основном воспринимается участком основного металла, так как его площадь
намного превосходит и площадь поперечного сечения шва, и площадь твердой прослойки. И хотя уровень напряжений сг2 в твердой прослойке будет велик, средние напряжения будут близки к аъ что существенно ниже разрушающих напряжений в точке Ах. Это означает, что прочность сварного соединения с твердой прослойкой, нагруженного вдоль шва, окажется ниже, чем прочность такого же элемента из основного металла, так как разрушение в последнем случае произойдет при напряжениях, близких к а1<о.4). Отрицательное влияние твердой прослойки сказывается сильнее, если по длине соединения встречаются резкие изменения сечения шва, вызывающие концентрацию напряжений, или еще хуже — поперечные трещины или другие дефекты в твердой прослойке.
При действии силы вдоль шва наличие малопрочных мягких прослоек практически не влияет на общую несущую способность нагруженного элемента, так как площадь прослоек обычно невелика.
Рассмотрим работу мягкой прослойки при растяжении стыкового соединения поперек шва (рис. 3.14) достаточно большой протяженности за плоскость чертежа. В упругой стадии нагружения мягкая прослойка и соседние участки деформируются однородно, и при достижении предела текучести материала мягкой прослойки сгТм в ней возникает пластическая деформация, в то время как соседние участки остаются в упругом состоянии. При дальнейшем повышении нагрузки и деформации коэффициент поперечной деформации р у прослойки будет выше, чем у соседнего металла. По мере развития пластической деформации в прослойке р 0,5, в то время как в упругих частях р — 0,3. Из-за неодинаковой поперечной деформации возникают касательные напряжения, максимальные на плоскостях. раздела. Они будут препятствовать поперечному сужению прослойки в направлении толщины листа. Чем уже прослойка, т. е. чем меньше х = his, тем меньшее поперечное сужение получает прослойка к моменту возникновения в ней истинных разрушающих напряжений сгр. Так как среднее истинное разрушающее напряжение Op меняется мало, то в более узких мягких прослойках площадь утоненного поперечного сечения прослойки Fy к моменту разрушения будет больше, а следовательно, будет больше и разрушающая сила Рр:
Рр—°Л* (злз)
В этом заключается причина повышения несущей способности (эффект контактного упрочнения). Повышение разрушающей силы
не может происходить беспредельно, так как соседние с мягкой прослойкой более прочные участки также при определенных уело — биях начнут пластически деформироваться. Чем более прочны соседние зоны, тем больше эффект контактного упрочнения. Твердые прослойки, находящиеся рядом с мягкими, усиливают этот эффект.
Можно рассматривать идеализированный случай работы мягкой прослойки, считая соседние с прослойкой участки металла абсолютно твердыми, недеформируемыми. Тогда будут выполняться условия плоской деформации, так как деформация в направлении за чертеж будет равна нулю (см. § 1). В этом случае временное сопротивление соединения с мягкой прослойкой ав можно определить по формуле
СГв = СГв/(х, (3.14)
м
где сгв/—временное сопротивление металла мягкой прослойки;
м
— коэффициент контактного упрочнения в случае плоской деформации:
Кх = (я + 1/*)/(2Уз)- (3.15)
Если прослойка не идеально прямоугольная, как это бывает в сварных соединениях, то х = F/s2,- где F—■ площадь поперечного сечения прослойки; s — толщина металла.
Прочность соединения достигнет прочности соседнего, более прочного металла, если временное сопротивление сгв в формуле (3.14) станет равным временному сопротивлению аВт более прочного металла. При этом Кхпрея = оВт/оВм. По формуле (3.15) определим предельную относительную толщину прослойки Хцред, при которой достигается равнопрочность соединения:
ипРсд= 1/(2У^З Лх|фе1 — я)* (3.16)
Например, если <тв /сгв = 1,2, то по формуле (3.16) получаем хнрел = 1. При Ку. > 1,2 относительная толщина мягкой прослойки «пред-Должна быть еще меньше. Следует, однако, иметь в виду, что повышение прочности соединения с мягкой прослойкой за счет уменьшения х ограничено уровнем истинного разрушающего напряжения металла мягкой прослойки.
Относительное поперечное сужение ф в мягкой прослойке и абсолютное удлинение образца А зависят от относительной толщины прослойки х и свойств металлов в соединении. На рис. 3.14 видно, что в широких прослойках, когда эффекта контактного упрочнения еще не наблюдается, ф остается постоянным при уменьшении х, а А постепенно падает по мере уменьшения доли длины участка мягкой прослойки в общей длине образца. В области контактного упрочнения ф резко падает, так как возрастают поперечные касательные напряжения, препятствующие сужению прослоек. Удлинение образца А при уменьшении х также сначала уменьшается, но затем, когда реализуется повышение прочности, А возрастает,
поскольку в пластическую деформацию в большей мере вовлекается основной металл.
При испытании соединений с мягкой прослойкой на изгиб до разрушения разрушающий момент Мр, при котором появляются трещины в прослойке, не зависит от относительной ширины прослойки к. Это можно объяснить тем, что разрушение при изгибе не связано с образованием шейки и изменением размеров поперечного сечения. Поэтому касательные напряжения, действующие вблизи границ мягкой прослойки, хотя и влияют на процесс пластической деформации во время нагружения, но не изменяют существенно толщины образца и его момента сопротивления. Разрушение наступает, когда максимальное напряжение в крайнем волокне достигает истинного разрушающего напряжения металла мягкой
прослойки (гр. Если принять, что зависимость напряжения сг от деформации е при а > сгг имеет линейный характер и к моменту разрушения эпюра напряжений в сечении выглядит, как показано на рис.[1] 3.15, то разрушающий момент равен
Mp—W (<гр + 0,5<гт), (3.17)
где W — момент сопротивления сечения; ат —> предел текучести металла мягкой прослойки.
При работе соединений с мягкой прослойкой в элементах конструкций влияние мягкой прослойки на прочность может несколько изменяться. В сосудах с внутренним давлением р, где сокр = 2оос, мягкая прослойка с малой к в кольцевом шве работает аналогично сварному соединению, которое растягивается вдоль прослойки. Пониженной прочности металла прослойки при этой схеме не обнаруживается, так как разрушение происходит вдоль сосуда. Если % велика, то мягкая прослойка удлиняется в окружном направлении сильнее, чем остальная часть сосуда, в результате чего искривляется прямолинейная образующая (рис. 3.16). Разрушение может наступить вдоль образующей сосуда в зоне прослойки вследствие Повышенной деформации в окружном направлении или даже по окружности из-за дополнительных деформаций изгиба и растяжения вдоль сосуда. Твердые прослойки в кольцевом сварном соединении разрушаются раньше, чем остальная часть сосуда достигает
предельной пластической деформации в окружном направлений. Этот случай аналогичен растяжению сварного соединения вдоль шва при наличии в нем твердой прослойки. Момент разрушения зависит от пластичности твердой прослойки.
Мягкая прослойка в продольном шве ведет себя примерно так же, как при испытании образцов на одноосное растяжение с поперечной мягкой прослойкой. Твердые прослойки в продольных швах сосуда, если они не попадают в зону концентрации напряжений, обычно не снижают прочности сосуда.
Выше были рассмотрены идеализированные случаи работы соединений с прямоугольной формой мягких прослоек. В сварных соединениях прослойки могут находиться под углом к направлению действия сил, иметь произвольную форму поперечного сечения
и иначе влиять на прочность. Однако общая тенденция их влияния оказывается такой же, как в случаях, рассмотренных в настоящем параграфе.
Одним из видов неоднородности механических свойств металла является анизотропия, она выражается в различии свойств металла при нагружении его в разных направлениях. Различными могут быть пластичность, прочность, ударная вязкость, коэффициент поперечной деформации, модуль упругости и другие свойства. Анизотропия металла возникает чаще всего во время прокатки. Прочность, пластичность, ударная вязкость, как правило, выше у образцов, вырезанных вдоль проката (рис. 3.17). Во время разрушения трещина, пересекая волокна, встречает большее сопротивление, чем двигаясь вдоль волокон. Особенно низкими бывают прочность и пластичность металла по толщине листа. При наличии расслоений в металле пластичность отдельных образцов в этом направлении близка к нулю. Во время термической резки или сварки, если усадка металла происходит в направлении толщины листа, в зоне расслоений появляются трещины. Передача растягивающих усилий в направлении толщины может предусматриваться при проектировании сварных конструкций лишь в тех случаях, когда есть полная уверенность, что используемый металл не склонен к образованию расслоений, а механические свойства в направлении толщины соответствуют уровню, предусмотренному техническими условиями.
Анизотропия может выражаться в различном сопротивлении металла пластической деформации, различном упрочнении и, как следствие, в различных коэффициентах поперечной деформации.
В этом случае анизотропию можно оценивать по отношению поперечных пластических деформаций Р = Є* /е^пл и R = £ffnJe’znjlt где є* и ej— поперечные пластические деформации соответственно в направлении длины и толщины проката при растяжении 0*|разца № 1; ъу и e’zпл — поперечные пластические деформации при растяжении образца № 2 (рис. 3.17).
Если материал изотропен во всех трех направлениях, то Р — = R = 1. Если материал изотропен в плоскости и анизотропен в направлении толщины, то Р — R ф 1. У некоторых видов тонколистового проката титановых сплавов анизотропия выражена сильно, сопротивление пластической деформации в направлении толщины значительно больше, чем в плоскости (Р = R = 4 — г- 7). При двухосном растяжении, например в сферическом или цилиндрическом сосуде давления, металл имеет возможность пластически деформироваться в плоскости листа только при утонении его по толщине. Ввиду большого сопротивления пластической деформации по толщине прочность при таких схемах нагружения заметно возрастает. Так, максимальное окружное условное напряжение в цилиндрическом тонкостенном сосуде давления из титанового сплава с содержанием 5 % А1 и 2,5 % Sn в 1,5 раза выше, чем максимальное условное напряжение при одноосном растяжении.
hssco.ru
Механические свойства металлов и методы их определения
МЕХАНИЧЕСКИЕ СВОЙСТВА МЕТАЛЛОВ И МЕТОДЫ ИХ ОПРЕДЕЛЕНИЯ
Введение
Механические свойства определяют способность металлов сопротивляться воздействию внешних сил (нагрузок). Они зависят от химического состава металлов, их структуры, характера технологической обработки и других факторов. Зная механические свойства металлов, можно судить о поведении металла при обработке и в процессе работы машин и механизмов.
К основным механическим свойствам металлов относятся прочность, пластичность, твердость и ударная вязкость.
Прочность — способность металла не разрушаться под действием приложенных к нему внешних сил.
Пластичность — способность металла получать остаточное изменение формы и размеров без разрушения.
Твердость — способность металла сопротивляться вдавливанию в него другого, более твердого тела.
Ударная вязкость — степень сопротивления металла разрушению при ударной нагрузке.
Механические свойства определяют путем проведения механических испытаний.
1. Испытания на растяжение
Этими испытаниями определяют такие характеристики, как пределы пропорциональности, упругости, прочности и пластичность металлов. Для испытаний на растяжение применяют круглые и плоские образцы (рисунок 2.1, а, б), форма и размеры которых установлены стандартом. Цилиндрические образцы диаметром d0 = 10 мм, имеющие расчетную длину l0 = 10d0, называют нормальными, а образцы, у которых длина l0 = 5d0, — короткими. При испытании на растяжение образец растягивается под действием плавно возрастающей нагрузки и доводится до разрушения.
Разрывные машины снабжены специальным самопишущим прибором, который автоматически вычерчивает кривую деформации, называемую диаграммой растяжения. Диаграмма растяжения в координатах «нагрузка Р — удлинение ∆l» отражает характерные участки и точки, позволяющие определить ряд свойств металлов и сплавов (рисунок 2.1). На участке 0 — Рпц удлинение образца увеличивается прямо пропорционально возрастанию нагрузки. При повышении нагрузки свыше Рпц, на участке Рпц — Pупр прямая пропорциональность нарушается, но деформация остается упругой (обратимой). На участке выше точки Pvпр возникают заметные остаточные деформации, и кривая растяжения значительно отклоняется от прямой. При нагрузке Рт появляется горизонтальный участок диаграммы — площадка текучести Т-Т1, которая наблюдается, главным образом, у деталей из низкоуглеродистой стали. На кривых растяжения хрупких металлов площадка текучести отсутствует. Выше точки Рт нагрузка возрастает до точки А, соответствующей максимальной нагрузке Рв, после которой начинается ее падение, связанное с образованием местного утонения образца (шейки). Затем нагрузка падает до точки В, где и происходит разрушение образца. С образованием шейки разрушаются только пластичные металлы.
а, б — стандартные образцы для испытания на растяжение;
в — диаграмма растяжения образца из пластичного материала
Рисунок 2.1 — Испытание на растяжение
Усилия, соответствующие основным точкам диаграммы растяжения, дают возможность определить характеристики прочности, выраженные в мегапаскалях, МПа, по формуле
, 2.1)
где σi — напряжение, МПа;i — соответствующая точка диаграммы растяжения, Н;0 — площадь поперечного сечения образца до испытания, мм2.
Предел пропорциональности σпц — это наибольшее напряжение, до которого сохраняется прямая пропорциональность между напряжением и деформацией:
, .2)
где Pпц — напряжение, соответствующее пределу пропорциональности, Н.
Предел упругости σупр — напряжение, при котором пластические деформации впервые достигают некоторой малой величины, характеризуемой определенным допуском (обычно 0,05 %):
, .3)
где Pупр — напряжение, соответствующее пределу упругости, Н.
Предел текучести физический σт — напряжение, начиная с которого деформация образца происходит почти без дальнейшего увеличения нагрузки:
, .4)
где Pт — напряжение, соответствующее пределу текучести, Н.
Если площадка текучести на диаграмме растяжения данного материала отсутствует, то определяется условный предел текучести σ0,2 — напряжение, вызывающее пластическую деформацию, равную 0,2 %.
Предел прочности (временное сопротивление) σв — напряжение, равное отношению наибольшей нагрузки, предшествующей разрушению образца, к первоначальной площади его сечения:
, .5)
где Pв — напряжение, соответствующее пределу прочности, Н.
По результатам испытания на растяжение определяют характеристики пластичности металлов.
Показатели пластичности металлов — относительное удлинение и относительное сужение — рассчитывают по результатам замеров образца до и после испытания.
Относительное удлинение δ находится как отношение увеличения длины образца после разрыва к его первоначальной расчетной длине, выраженное в процентах:
, .6)
где lk — длина образца после разрыва, мм;
l0 — расчетная (начальная) длина образца, мм.
Относительное сужение ψ определяется отношением уменьшения площади поперечного сечения образца после разрыва к первоначальной площади его поперечного сечения, выраженным в процентах:
, 7)
где F0 — начальная площадь поперечного сечения образца;к — площадь поперечного сечения образца в месте разрушения.
. Методы определения твердости
Наиболее распространенным методом определения твердости металлических материалов является метод вдавливания, при котором в испытуемую поверхность под действием постоянной статической нагрузки вдавливается другое, более твердое тело (наконечник). На поверхности материала остается отпечаток, по величине которого судят о твердости материала. Показатель твердости характеризует сопротивление материала пластической деформации, как правило, большой, при местном контактном приложении нагрузки.
Твердость определяют на специальных приборах — твердомерах, которые отличаются друг от друга формой, размером и материалом вдавливаемого наконечника, величиной приложенной нагрузки и способом определения числа твердости. Так как для измерения твердости испытывают поверхностные слои металла, то для получения правильного результата поверхность металла не должна иметь наружных дефектов (трещин, крупных царапин и т. д.).
Измерение твердости по Бринеллю. Сущность этого способа заключается в том, что в поверхность испытуемого металла вдавливается стальной закаленный шарик диаметром 10, 5 или 2,5 мм в зависимости от толщины образца под действием нагрузки, которая выбирается в зависимости от предполагаемой твердости испытуемого материала и диаметра наконечника по формулам: Р = 30D2; Р = 10D2; Р = 2,5D2 (таблица 2.1).
Таблица 2.1 — Выбор диаметра шарика D и нагрузки Р
Материал образца | Твердость, кгс/мм2 | Толщина образца, мм | Диаметр шарика D, мм | P/D2, кгс/мм2 | Нагрузка Р, кгс | Выдержка под нагрузкой, с |
Черные металлы (сталь, чугун) | 450 — 140 | более 6 6 — 3 менее 3 | 10 5 2,5 | 30 | 3000 750 187,5 | 10 |
Черные металлы | Менее 140 | более 6 6 — 3 менее 3 | 10 5 2,5 | 30 | 3000 750 187,5 | 30 |
Твердые цветные металлы (латунь, бронза, медь) | 140 — 32 | более 6 6 — 3 менее 3 | 10 5 2,5 | 10 | 1000 250 62,5 | 30 |
Мягкие цветные металлы (олово, алюминий и др.) | 35 — 8 | более 6 6 — 3 менее 3 | 10 5 2,5 | 2,5 | 250 62,5 15,6 | 60 |
На поверхности образца остается отпечаток (рисунок 2.2, а), по диаметру которого определяют твердость. Диаметр отпечатка измеряют специальной лупой с делениями.
Твердость рассчитывают по формуле
, (2.8)
где НВ — твердость по Бринеллю, кгс/мм2;
Р — нагрузка при испытании, кгс или Н;- площадь полученного отпечатка, мм2;- диаметр наконечника, мм;- диаметр отпечатка, мм.
Рисунок 2.2 — Измерение твердости методами Бринелля (а), Роквелла (б), Виккерса (в)
На практике пользуются специальными таблицами, которые дают перевод диаметра отпечатка в число твердости, обозначаемое НВ. Например: 120 НВ, 350 НВ и т.д. (Н — твердость, В — по Бринеллю, 120, 350 — число твердости в кгс/мм2, что соответствует 1200 и 3500 МПа).
Этот способ применяют, главным образом, для измерения твердости незакаленных металлов и сплавов: проката, поковок, отливок и др.
Твердомер Бринелля можно использовать в том случае, если твердость материала не превышает 450 кгс/мм2. В противном случае произойдет деформация шарика, что приведет к погрешностям в измерении. Кроме того, твердомер Бринелля не применяется для испытания тонких поверхностных слоев и образцов тонкого сечения.
Измерение твердости по Роквеллу. Измерение осуществляют путем вдавливания в испытуемый металл стального шарика диаметром 1,588 мм или алмазного конуса с углом при вершине 120° (см. рисунок 2.2, б). В отличие от метода Бринелля твердость по Роквеллу определяют не по диаметру отпечатка, а по глубине вдавливания наконечника.
Вдавливание производится под действием двух последовательно приложенных нагрузок — предварительной, равной ≈ 100 Н, и окончательной (общей) нагрузки, равной 1400, 500 и 900 Н. Твердость определяют по разности глубин вдавливания отпечатков. Для испытания твердых материалов (например, закаленной стали) необходима нагрузка 1500 Н, а вдавливание стальным шариком нагрузкой 1000 Н производят для определения твердости незакаленной стали, бронзы, латуни и других мягких материалов. Глубина вдавливания измеряется автоматически, а твердость после измерения отсчитывается по трем шкалам: А, В, С (таблица 2.2).
Таблица 2.2 — Наконечники и нагрузки для шкал А, В, С
Наконечник | Суммарная нагрузка Р, Н (кгс) | Отсчет по шкале | Обозначение твердости |
Стальной шарик | 1000 (100) | В (красная) | HRB |
Алмазный конус | 1500 (150) | С (черная) | HRC |
Алмазный конус | 600 (60) | А (черная) | HRA |
Твердость (число твердости) по Роквеллу обозначается следующим образом: 90 HRA, 80 HRB, 55 HRC (Н — твердость, Р — Роквелл, А, В, С — шкала твердости, 90, 80, 55 — число твердости в условных единицах).
Определение твердости по Роквеллу имеет широкое применение, так как дает возможность испытывать мягкие и твердые металлы без дополнительных измерений; размер отпечатков очень незначителен, поэтому можно испытывать готовые детали без их порчи.
Измерение твердости по Виккерсу. Данный метод позволяет измерять твердость как мягких, так и очень твердых металлов и сплавов. Он пригоден для определения твердости очень тонких поверхностных слоев (толщиной до 0,3 мм). В этом случае в испытуемый образец вдавливается четырехгранная алмазная пирамида с углом при вершине 136о (см. рисунок 2.2, в). При таких испытаниях применяются нагрузки от 50 до 1200 Н. Измерение отпечатка производят по длине его диагонали, рассматривая отпечаток под микроскопом, входящим в твердомер. Число твердости по Виккерсу, обозначаемое НV, находят по формуле
, (2.9)
где Р — нагрузка, Н;- длина диагонали отпечатка, мм.
На практике число твердости НV находят по специальным таблицам.
. Определение ударной вязкости
Определение ударной вязкости производят на специальном маятниковом копре (рисунок 2.3). Для испытаний применяется стандартный надрезанный образец, который устанавливается на опорах копра. Маятник определенной массой поднимают на установленную высоту Н и закрепляют, а затем освобожденный от защелки маятник падает, разрушает образец и снова поднимается на некоторую высоту h. Удар наносится по стороне образца, противоположной надрезу. Для испытаний используют призматические образцы с надрезами различных видов: U-образный, V-образный, T-образный (надрез с усталостной трещиной).
а — схема испытания; б — образцы для испытаний.
Рисунок 2.3 — Испытания на ударную вязкость
Ударная вязкость КС (Дж/см2) оценивается работой, затраченной маятником на разрушение стандартного надрезанного образца, отнесенной к сечению образца в месте надреза:
, (2.10)
где А — работа, затраченная на разрушение образца (определяется по разности энергий маятника до и после удара: А0 — А1), Дж;- площадь поперечного сечения образца в месте надреза, см2.
stud24.ru
II. Определение механических свойств металлов
Основными механическими свойствами металлов являются прочность, упругость, пластичность, твердость и вязкость. Механические свойства металлов определяют испытанием специальных образцов на соответствующих испытательных машинах.
В зависимости от характера действия нагрузки испытания могут быть статическими, динамическими, циклическими. При статических испытаниях нагружение проводится плавно, в отличие от резкого нагружения при динамических испытаниях. При циклических испытаниях изменяются направления действия нагрузки или ее величина, или оба фактора вместе.
К статическим испытаниям обычно относятся испытания на растяжение и сжатие, проводимые на разрывных машинах, и испытания твердости, проводимые на приборах Бринелля, Роквелла, Виккерса.
К динамическим испытаниям относятся испытания на ударный изгиб, которые проводятся на маятниковых копрах.
Циклические испытания проводятся на машинах с циклически изменяемой нагрузкой для определения сопротивляемости металлов усталостному разрушению.
III. Физические методы исследования
Для изучения структуры металлов и сплавов используются различные физические методы, позволяющие на основании регистрации известных физических величин анализировать структуру и состояние вещества, а также выявлять характер превращений, протекающих в твердом теле под воздействием внешних причин (нагрев, охлаждение, деформация и др.).
К этим методам относятся электронная микроскопия, рентгеноструктурный анализ, резистометрический, дилатометрический, магнитный и другие методы.
В данной работе необходимо познакомиться с установками и их работой для проведения электронно-микроскопического и рентгеноструктурного анализов.
Электронно-микроскопический анализ относится к прямому методу наблюдения и изучения структуры вещества. Анализ проводится на просвечивающих и растровых электронных микроскопах. По темпам развития и количеству моделей РЭМ опережает просвечивающие электронные микроскопы, хотя последние разработаны и используются значительно раньше РЭМ.
В лабораторной работе необходимо ознакомиться с прибором РЭМ-200 и его работой.
В растровых электронных микроскопах поверхность исследуемого образца облучается стабильным во времени тонко сфокусированным (диаметр до 5–10 нм) электронным зондом, совершающим возвратно-поступательное движение по линии или развертывающимся в растр. Растром называется совокупность близко расположенных параллельных линий движения зонда, по которым зонд сканирует (обегает) выбранный участок на поверхности образца. При взаимодействии зонда с веществом образца в каждой точке поверхности происходит ряд эффектов, которые регистрируются датчиками. Эти эффекты служат основой для получения информации о строении исследуемых объектов. Изображение объекта формируется на экране электронно-лучевой трубки, с которого фиксируется на фотографическую пленку.
Рентгеноструктурный анализ основан на явлении интерференции рентгеновских лучей, отраженных от атомных плоскостей кристалла. Этот метод позволяет изучить фазовый состав сплава, определить степень совершенства кристаллов, их ориентировку, определить оптимальные режимы технологии изготовления и обработки разнообразных кристаллических материалов. В настоящее время наибольшее распространение в качестве рентгеновских аппаратов получили дифрактометры, которые позволяют регистрировать интенсивность отраженного рентгеновского излучения на диаграммную ленту самописца. ДРОН-2,0, ДРОН-3,0 ДРОН-3М – дифрактометры рентгеновские общего назначения, выпускаемые в нашей стране, широко используется в научных и заводских лабораториях.
studfiles.net
Способ определения механических свойств металлов
Изобретение относится к области определения прочностных свойств металлов и их сплавов путем приложения растягивающих нагрузок к стандартным плоским или круглым образцам исследуемых металлов, геометрические размеры которых регламентируются ГОСТ 10006-80. Сущность: осуществляют осевое растяжение плоских и круглых образцов с фиксированной скоростью деформации, и определение температуры испытания. Коэффициент динамической вязкости металлов и эффективную энергию разрушения определяют по формулам: для плоского и круглого образца, используя значения предела прочности, предела текучести, относительного удлинения металлов при растяжении стандартных образцов, скорости деформации, при которой растягивается образец, модуля Юнга и скорости звука продольных волн в металле. Технический результат: возможность при исследовании конструкций из металла под действием реальных нагрузок и скоростей деформаций вплоть до разрушения основывать прогноз по эксплуатационной надежности выбранного материала на основании количественных оценок параметров (σb, σ02, δ5, έ, µ, А*). 3 табл.
Изобретение относится к области определения прочностных свойств металлов и их сплавов путем приложения растягивающих нагрузок к стандартным плоским или круглым образцам исследуемых металлов. Ресурсосберегающая стратегия по разработке новых материалов для различных отраслей промышленности, а также изготовление из них конструкций является важнейшим направлением в механике разрушения. Необходимо сегодня констатировать, что в мировой практике обоснование прочности и эксплуатационной надежности металлов при различных нагрузках основываются на использовании линейной, упругой механики разрушения.
Известно [1-2], что для металлов наиболее близка, с точки зрения физики твердого тела, модель вязкопластической среды, где свойства материала-металла характеризуются следующими параметрами (σ02, δ5, µ, έ), где µ — коэффициент динамической вязкости материала. Эта величина отражает количественную характеристику внутреннего трения материала при заданной скорости деформации έ и температуре испытаний. Соответственно σ02, δ5 — предел текучести и относительное удлинение при растяжении плоского или круглого стандартного образца до разрушения, согласно ГОСТ 10006-80.
Добавляя к рассматриваемой модели вязкопластической среды энергетический критерий разрушения [3], получим замкнутую систему уравнений [4], которая позволяет описать динамику деформирования плоского или круглого металлического образца при растяжении вплоть до разрушения. Здесь появляется еще один параметр характеристики материала А* — эффективная энергия динамического разрушения, размерность которого совпадает с размерностью параметра ударной вязкости Ак (ГОСТ 9454-78), но имеет принципиально другой физический смысл и не связан, например, с конфигурацией «надреза» в образце Шарпи или Менаже ([5], с. 165-166).
Известный способ определения ударной вязкости металлов (ГОСТ 9454-78) основан на фундаменте упругой механики твердого тела, где относительное удлинение δ5≤1%, что для пластичных металлов не приемлемо. Во-вторых, параметр Ак выражает скорее методологическую характеристику системы «образец-надрез-копер», чем характеристику материала. Это подтверждается, в частности, большим разбросом экспериментальных данных.
Наиболее близким по технической сущности к изобретению является способ определения механических свойств материала при растяжении плоских или круглых образцов при фиксированной скорости деформации и температуры испытаний (ГОСТ 10006-80, ГОСТ 1497-77).
Недостатком данного способа является малая информативность по эксплуатационной надежности металлов и прогнозированию сопротивления их к разрушению.
Целью изобретения является прогнозирование эксплуатационной надежности металлов и сопротивления их к разрушению за счет определения в схеме вязкопластической среды математических зависимостей [6-7]: коэффициента динамической вязкости материала µ и энергии разрушения А* от основных параметров σ02, δ5, µ, έ, полученных при испытаниях на растяжение плоских и круглых стандартных образцов согласно ГОСТ 10006-80, ГОСТ 1497-77.
Поставленная цель достигается тем, что коэффициент динамической вязкости металлов µ и эффективную энергию разрушения А* определяют по формулам: для плоского образца µ=(σb-σ02)/2έ, A*=3cµδ5σ02/4Е и для круглого образца µ=(σb-σ02)3έ, А*=3сµδ5σ02/Е.
Здесь σb, σ02, δ5 — соответственно предел прочности, предел текучести и относительное удлинение металлов при растяжении стандартных образцов. А также έ — скорость деформации, при которой растягивается образец, Е — модуль Юнга, с — скорость звука продольных волн в металле.
Таким образом, в дальнейшем предлагается при исследовании конструкций из металла под действием реальных нагрузок и скоростей деформаций вплоть до разрушения основывать прогноз по эксплуатационной надежности выбранного материала на основании количественных оценок параметров (σb, σ02, δ5, έ, µ, А*).
Принимая во внимание уже полученные решения математических моделей в схеме вязкопластической среды для основных конструктивных элементов: для плоского образца [6], круглого [7], цилиндра [8], шара [9], можно перейти к конкретным практическим расчетам для прогнозирования, например, оптимального материала для конкретной конструкции или изделия.
Первый пример. Рассмотрим данные ГОСТ 21945-76, где регламентируются механические свойства (σb, σ02, δ5, Ак) бесшовных горячекатанных труб из сплавов на основе титана при температуре +20°C плоских образцов (ГОСТ 10006-80), при скорости деформаций έ=0,25·10-2 1/с. Усредняя данные мехсвойств (табл. 3, ГОСТ 21945-76), в табл.1 представлены механические свойства основных титановых сплавов ПТ1М, ПТ7М, ПТ3В, ОТ4, 14, которые имеют широкое применение в судостроении и авиации. В табл. 1, на основании формул (1), представлены расчетные значения µ, А* для рассматриваемых титановых сплавов. В расчетах приняты следующие значения постоянных: модуль нормальной упругости Е-103 ГПа, скорость звука в титане с=3260 м/с, скорость деформации έ=0,25·10-2 1/с. Принимая во внимание, что коэффициент динамической вязкости µ является характеристикой внутреннего трения материала, а А* — есть работа, затрачиваемая при разрыве единицы сечения материала, который находится под нагрузкой вплоть до разрушения, отсюда следует, что при максимальных значениях µ, А*, рассматриваемые титановые сплавы имеют максимальное сопротивление к разрушению Как следует из данных табл. 1, из названных сплавов ПТ1М, ПТ7М, ПТ3В, ОТ4, 14 наибольшим сопротивлением к разрушению будет обладать конструкция, изготовленная из сплава ПТ7М. Из анализа данных табл. 1 относительно ударной вязкости Ак (образец Менаже) самая высокая величина Ак=0,88 МДж/м2 для сплава ПТ1М. На практике наиболее ответственные детали конструкции не из сплава ПТ1М (корпус подлодки из сплава ПТ3В, трубы для теплообменников, работающие на морских турбинах из сплавов ПТ7М и т.д.).
Второй пример. В качестве примера оценки броневой надежности конкретных сталей в табл. 2 представлены механические свойства отечественной броневой стали 30Х2Н2М1Ф-Ш при различных режимах отжига ([10], с. 252). Здесь указаны значения ударной вязкости Aк (KCU) при температуре испытаний +20°C и -40°C (ГОСТ9454-78), а механические свойства указаны при растяжении плоских образцов при έ=0,25·10-2 1/с, согласно ГОСТ 1497-77. Расчеты значений µ, А* по формуле (1) определяются для сталей: модуль Юнга Е=200 ГПа, скорость звука с=5050 м/с. Из данных табл. 2 следует перспективность броневой стали 30Х2Н2М1Ф-Ш при режиме отжига п.3, табл. 2.
Третий пример. Рассмотрим экспериментальные данные для броневых плит фирмы CLJ (Франция). В табл. 3 представлены основные марки и механические свойства ([10], с. 289), включая значения ударной вязкости Ак (KCV) при температуре испытания -40°C плоских образцов. Значения µ, А* в табл. 3 рассчитаны по формуле (1) при έ=0,25·10-2 1/с, Е=200 ГПа, с=5050 м/с. Из данных табл. 3 относительно µ, А* следует, что броневая сталь MAPS240 наиболее надежная к динамическим нагрузкам по сравнению с другими представленными сталями. Наиболее «проблемная» — MAPS300, у которой прочность при этом наиболее высокая. По одному значению Ак (KCV, KCU) невозможно спрогнозировать перспективность рассматриваемых материалов (см. табл. 1, 2, 3).
Таким образом, формулы позволяют оценить эксплуатационную надежность металлов при их испытании на растяжение стандартных образцов без надреза, что позволяет отказаться от испытаний образцов Шарпи, Менаже на ударную вязкость с помощью маятниковых копров. Принимая во внимание достаточную точность и трудоемкость при изготовлении образца 10×10×55 мм с (U, V)-образным надрезом глубиной 2 мм и радиусом надреза 1 мм с жесткими геометрическими допусками (см. ГОСТ 9454-78), цена при их изготовлении колеблется от 250 руб/шт. до 1300 руб/шт. в зависимости от материала образца (низкоуглеродистая сталь или высоколегированная сталь, сплав титана). На каждую плавку, чаще всего и на партию готовой продукции, регламентируются испытания на ударную вязкость. При этом отбираются по два-три образца, а для труб — с обеих сторон (см. ГОСТ 21945-76). Например, на одном только Челябинском трубопрокатном заводе (ОАО «ЧТПЗ») в испытательном центре и цеховых лабораториях изготавливают более 50000 образцов в год для определения ударной вязкости и примерно 85000 в год для определения механических свойств. В итоге тратится ~38,75 млн руб только на изготовление образцов с надрезом, а еще затраты на содержание оборудования и сами испытания, обработка результатов. И это только для одного предприятия, изготавливающего трубы и отводы для нефтегазовой промышленности и ВПК.
Таблица 1 | |||||||
Механические характеристики титановых сплавов (усредненные, согласно ГОСТ 21945-76 при +20°C) и расчетные данные коэффициента динамической вязкости µ и эффективной энергии динамического разрушения A* | |||||||
№ | Сплав титана | σв (МПа) | σ02(МПа) | δ5(%) | Ударная вязкость Aк (МДж/м2) | µ ГПа·с | A* ГДж/м2 |
1 | ПТ1М | 441 | 245 | 24 | 0,88 | 39,2 | 108 |
2 | ПТ7М | 578 | 372 | 18 | 0,78 | 41,2 | 129,7 |
3 | ПТЗВ | 710 | 519 | 10 | 0,64 | 38,3 | 114,7 |
4 | ОТ4 | 784 | 637 | 10 | 0,34 | 29,4 | 88,0 |
5 | 14 | 980 | 784 | 8 | 0,40 | 39,0 | 115,0 |
Таблица 2 | ||||||||||
Механические свойства броневых сталей при различных режимах отжига | ||||||||||
№ | Сталь | Режим отжига | σв (МПа) | σ02 (МПа) | δ5 (%) | A (KCU) при +20°C (МДж/м2) | A (KCU) при -40°C (МДж/м2) | µ (ГПа·с) | А* (ГДж/м2) | |
аустенизация | Изотермическая выдержка | |||||||||
1 | 3ОХ2Н2М1Ф-Ш | 900°C, 3 ч | 630°C, 100 ч | 1380 | 1270 | 15,3 | 1,18 | 0,94 | 22 | 81,3 |
2 | 3ОХ2Н2М1Ф-Ш | 900°C, 3 ч | 650°C, 48 ч | 1400 | 1300 | 13,8 | 1,03 | 0,95 | 20 | 68,2 |
3 | 3ОХ2Н2М1Ф-Ш | 900°C, 3 ч | 630°C, 100 ч | 1300 | 1180 | 15,5 | 1,56 | 1,36 | 24 | 83,4 |
4 | 3ОХ2Н2М1Ф-Ш | 850°C, 3 ч | 650°C, 48 ч | 1343 | 1227 | 15,3 | 1,36 | 1,14 | 23 | 82,0 |
Таблица 3 | |||||||
Основные марки и механические свойства броневых сталей фирмы GLJ (Франция) | |||||||
№ | Сталь | σв (МПа) | σ02 (МПа) | δ5 (%) | A (KCV) при -40°C(МДж/м2) | µ (ГПа·с) | A* (ГДж/м2) |
1 | MARS 190 | 1250 | 1150 | 14,0 | 0,60 | 20 | 61,2 |
2 | MARS 240 | 1750 | 1350 | 13,0 | 0,40 | 80 | 267 |
3 | MARS 270 | 1900 | 1500 | 10,5 | 0,30 | 80 | 228 |
4 | MARS 300 | 2250 | 1700 | 7,0 | 0,15 | 11 | 24,9 |
СПИСОК ЛИТЕРАТУРЫ
1. Ильюшин А.А. Деформация вязкопластического тела. — Учен. зап. МГУ. Механика, Москва, 1940, вып.39, с.1-81.
2. Ишлинский А. Ю. Прикладные задачи механики. Кн.1. Механика вязкопластических и не вполне упругих тел. Москва, «Наука», 1986, 405 с.
3. Иванов А.Г. О природе катастрофических разрушений трубопроводов. — Докл. АН СССР, Москва, 1985, т.285, №2, с.257-259.
4. Сериков С. В. Исследование деформации и разрушения титановых сплавов методом моделирования. — Журнал Титан, Москва, 2006, №1, с.53-59.
5. Фридман Я.Б. Механические свойства металлов. Изд. 3-е перераб. В двух частях. Часть вторая. Механические испытания. Москва, «Машиностроение», 1974, 308 с.
6. Сериков С.В. Двуосная неустановившаяся деформация прямолинейной полосы в схеме сжимаемой вязкопластической среды. — Журнал прикладной механики и технической физики. — Новосибирск, 1982, №6, с.123-133.
7. Сериков С.В. Неустановившаяся деформация круглого прутка в схеме сжимаемой вязкопластической среды. — Динамика сплошной среды, Новосибирск, Ин-т гидродинамики СО АН СССР, 1982, вып.55, с.79-89.
8. Сериков С.В. Оценка предельной деформации при разрушении металлических труб под действием интенсивных нагрузок. — Журнал прикладной механики и технической физики. — Новосибирск, 1987, №1, с.155-161.
9. Сериков С.В. Оценка осколкообразования при разрушении шаровой оболочки. — Журнал прикладной механики и технической физики. — Новосибирск, 1987, №3, с.125-132.
10. Гладышев С.А., Григорян В.А. Броневые стали. — Москва, Интермет Инжиниринг, 2010, 336 с.
11. ГОСТ 1497-77, ГОСТ 9454-78, ГОСТ 10006-80, ГОСТ 21945-76, Москва, Издательство стандартов.
Способ определения механических свойств металлов, включающий осевое растяжение плоских и круглых образцов с фиксированной скоростью деформации, и температуры испытания, отличающийся тем, что, коэффициент динамической вязкости металлов µ и эффективную энергию разрушения А* определяют по формулам: для плоского образца µ=(σb-σ02)/2έ, А*=3сµδ5σ02/4E и для круглого образца µ=(σb-σ02)/3έ, А*=3µδ5σ02/E,
здесь σb, σ02, δ5 — соответственно предел прочности, предел текучести и относительное удлинение металлов при растяжении стандартных образцов, а также έ — скорость деформации, при которой растягивается образец, Е — модуль Юнга, с — скорость звука продольных волн в металле.
www.findpatent.ru
Механические свойства металлов и методы их определения
Механические свойства металлов и методы их определения [c.287]МЕХАНИЧЕСКИЕ СВОЙСТВА МЕТАЛЛОВ И МЕТОДЫ ИХ ОПРЕДЕЛЕНИЯ [c.73]
Механические и другие свойства металлов и методы их определения. Используемые для изготовления различных изделий материалы прежде всего должны иметь определенный запас механических свойств, обеспечивающих неразрушение изделий эксплуатационными нагрузками. [c.14]
Механические и технологические свойства металлов и методы их определения [c.46]
Механические характеристики металла элементов конструкций и методы их определения описаны в большом объеме научно-технической литературы и нормативных документов. Однако конструктивные элементы аппаратов имеют некоторые особенности, которые вытекают из условий эксплуатаций и которые накладывают специальные требования к методам определения механических свойств. [c.277]
В ней рассмотрены структура, физические, химические, механические и технологические свойства металлов и изложены методы их определения описаны неметаллические материалы (пластмассы, абразивные материалы) приведены сведения о металлургии черных и цветных металлов, литейном производстве, обработке металлов давлением, о сварке металлов, резании, термической обработке. [c.2]
Стандарт устанавливает методы определения механических свойств металла шва и сварного соединения, свариваемых всеми видами сварки, из всех свариваемых металлов и их сплавов и распространяется на испытания, проводимые при определении качества продукции, присадочных материалов и при установлении квалификации сварщиков [c.537]
Свойства металлов И сплавов зависят от состава и структуры. Их определяют различными методами, которые нужно разделить на механические, физические, технологические, химические и специальные (определение жаропрочности, коррозионной стойкости и т. д.). [c.81]
Работоспособность конструктивных элементов оборудования представляет собой очень широкое и комплексное понятие, охватывающее возможность выполнять свои рабочие функции без разрушений и аварий в течение длительного, но определенного и ограниченного времени. При этом должна быть обеспечена безопасность и надежность эксплуатации, соответствующая объектам такого ответственного назначения, как сосуды и аппараты, работающие под внутренним давлением. При оценке работоспособности конструктивных элементов аппаратов необходимо опираться на данные о реальной их дефектности и данные о реальных механических характеристиках металла с учетом эффектов старения. Диагностическое оборудование должно давать возможность производить измерения всех основных параметров повреждаемости, определяющих работоспособность элементов. Необходимо иметь методы, позволяющие оценивать работоспособность по данным о дефектах, свойствах металла в процессе эксплуатации, параметрах нагруженности с учетом перепадов давления, состояния коррозионной защиты и др. [c.277]
Для определения твердости покрытия можно пользоваться лишь методом царапания с применением склерометра типа Мартенса или методом затухающих колебаний на маятниковом приборе Кузнецова. Все другие известные методы испытания твердости (методы вдавливания и методы упругого отскакивания бойка) не пригодны для испытания твердости покрытий, так как при их применении на получающиеся результаты оказывают влияние механические свойства основного металла. Объясняется это незначительностью толщины слоя покрытий, наносимых на детали. Исключить влияние основного металла можно, лишь увеличивая толщину слоя покрытая на испытываемых образцах. [c.546]
Легирование является наиболее распространенным методом повышения механических свойств металлических материалов. Увеличение прочностных характеристик материалов происходит благодаря влиянию легируюш,их элементов на исходное состояние сплава и на его изменение в процессе пластической деформации и проявляется в повышении предела текучести и возникновении более интенсивного деформационного упрочнения. Известно, что при деформировании в металлах и сплавах происходит образование дислокаций и формирование определенной для каждого материала и условий дислокационной структуры. В связи с этим становится ясным, что в основе повышения прочности металлов и сплавов лежит взаимодействие дислокаций с барьерами, которыми могут быть различные дефекты, границы, растворимые атомы, включения или дисперсные частицы. [c.76]
В технике используются механические колебания в очень широком интервале частот — от нескольких герц до 200 МГц, или от инфразвука до ультразвука. Широкий интервал применяемых частот обусловлен тем, что характер их распространения и поглощения зависит от частоты. Ею определяются контролируемая зона, минимальная измеряемая толщина, степень поглощения и характер возбужденных волн. В ультразвуковой дефектоскопии используется целая гамма различных видов волн, которые отличаются друг от друга как направлениями распространения колебаний, так и характером колебаний. Механические колебания используются для выявления нарушения сплошности и измерения толщины. Свойство их поглощения при прохождении через контролируемую среду используется для нахождения мелких рассеянных инородных включений и пустот, оценки неоднородности зерна, структуры, определения плотности массы, внутренних напряжений, коэффициента вязкости, межкристаллитной коррозии, зоны поверхностного распространения. Большим достоинством методов и средств неразрушающего ультразвукового контроля является их универсальность — возможность применения как для металлов и сплавов, так и для керамики, полупроводников, пластических масс, бетона, фарфора, стекла, ферритов, твердых сплавов, т. е. таких синтетических материалов, которые находят все большее применение в технике. [c.548]
Сварные соединения. Методы определения механических свойств. Стандарт содержит виды испытаний и область применения, отбор образцов, условия проведения испытаний и оценки их результатов, испытание металла различных участков сварного соединения и наплавленного металла на статическое (кратковременное) растяжение, на ударный изгиб (на надрезанных образцах), на стойкость против механического старения, измерение твердости различных участков металла сварного соединения, испытание сварного соединения на статическое растяжение, на статический изгиб, на ударный разрыв. [c.501]
К специальным методам контроля относятся также определение механических свойств сварного соединения, металлографические исследования структуры сварного соединения, анализ химического состава металла шва или наплавленного металла, определение коррозионной стойкости сварного соединения в определенной среде. Необходимость их применения устанавливается ТУ на изготовление и приемку конструкций. [c.131]
Контроль качества сварного соединения с помощью образцов-свидетелей. Для контроля качества сварных соединений применяют периодические испытания контрольных технологических образцов-свидетелей. Эти образцы удобны для проведения испытаний и измерений, и их легко изготовить. При обеспечении одинаковых условий сварки образцов и сварных изделий (однородность материала, подготовка свариваемых поверхностей, режим сварки и др.) можно по измеренным характеристикам сварного соединения образцов судить о качестве сварного соединения готовых изделий. Качество сварки на контрольных образцах оценивают по результатам испытаний и измерений, проводимых соответственно требованиям, предъявляемым к сварным соединениям. Кроме механической прочности, нередко предъявляются требования особых свойств. Например, сохранение электрических свойств одного из металлов без изменения их в зоне сварного соединения или сохранение оптических свойств в сварной зоне и геометрических размеров изделий, получаемых способом ДС кварцевых элементов, и т. д. В ряде случаев к сварным соединениям не предъявляются повышенные требования по прочности. Например, для элементов электродов электролизеров, изготовленных способом ДС из пористых и сетчатых материалов, основной является электрохимическая характеристика, полученная при различных плотностях тока. Имея указанные выше данные, необходимо провести статистическую обработку результатов испытаний и измерений, используя математические методы. Основной задачей такой обработки является оценка среднего значения характеристики того или иного свойства и ошибки в определении этого среднего, а также выбор минимально необходимого количества образцов (или замеров) для оценки среднего с требуемой точностью. Эта задача является стандартной для любых измерений и подробно рассматривается во многих руководствах [8]. Следует иметь в виду, что, несмотря на одинаковые условия сварки образцов и изделий, качество соединения может быть различным по следующим причинам. При сварке деталей, имеющих значительно большие размеры по сравнению с контрольными образцами, возможны неравномерность нагрева вдоль поверхности соединения, а также неравномерность передачи давления. Образцы и изделия вообще имеют различную кривизну свариваемых поверхностей, что не обеспечивает идентичности условий формирования соединения. В ряде случаев, особенно для соединений ответственного назначения, перед разрушающими испытаниями образцов и изделий целесообразно, если это возможно, проводить неразрушающий контроль качества сварного соединения, а также другие возможные исследования для установления корреляции между различными измеряемыми характеристиками. Основные методы определения механических свойств сварного соединения и его отдельных зон устанавливает ГОСТ 6996—66. Имеются стандарты для испытаний на растяжение, ударную вязкость, коррозионную стойкость и т. д. [18]. В этих ГОСТах даны определения характеристик, оцениваемых в результате испытания, типовые формы и размеры образцов, основные требования к испытательному оборудованию, методика проведения испытания и подсчета результатов. [c.249]
Следовало бы различать понятия прочности сцепления, как результата физико-химического взаимодействия защитного покрытия с металлом, выражающей действительную связь между ними, и прочности покрытия к различным видам механического воздействия, нарушающим эту связь. Однако отсутствие доступных методов определения действительных сил связи, равно как силы, необходимой для их преодоления, приводит к необходимости пользоваться относительными способами определения столь важной характеристики, как прочность сцепления защитного покрытия с металлом, пренебрегая отличием свойств самого покрытия на испытуемых образцах и относя полученные результаты измерений всецело к рассматриваемой характеристике. [c.42]
Авторы предлагаемой книги предприняли попытку систематизировать и обобщить основные методы и методики научно-технического прогнозирования, применяемые в отечественной и зарубежной практике. Оценка приведенных методов дается с позиции возможности их использования при прогнозировании развития конструкционных материалов для машиностроения. Приводится целый ряд конкретных примеров, сформулированы основные принципы построения автоматизированной системы прогнозирования материалов. Известное ленинское выражение металл — это хлеб промышленности ярко характеризует тот факт, что технический прогресс любой отрасли народного хозяйства связан с производством материалов, обладающих определенным комплексом физических, механических, специальных свойств. [c.3]
Несмотря на прогрессивные методы получения изделий из этих материалов, такие, как намотка, прессование, определенный (порой весьма существенный) объем механической обработки остается. Механическая обработка необходима для получения высокой точности и требуемой, иногда весьма сложной, формы изделий. В то же время из-за специфических свойств этих материалов их механическая обработка отличается от существующих способов обработки металлов. [c.3]
Прибор автоматически молсет регистрировать диаграмму вдавливания в координатах Р, h, а также в координатах Pjh, h. При подсчете Н по методу Бриыелля через глубину невосстановленного отпечатка, т. е. Н = Р1(кОк), отношение P/h связано с Н постоянным для данного шара коэффициентом 1/(я 1), что позволяет просто оценить значение Н в любой точке диаграммы. Совершенствование приборов для автоматической записи диаграммы вдавливания, детальное исследование диаграмм и их связи с диаграммами растяисения представляют основную задачу при дальнейшей разработке безобразцовых методов определения механических свойств металлов по характеристикам твердости. [c.348]
Отсутствие совершенных средств контроля зарождения и развития повреждений металла, общепринятых принципов назначения новых сроков службы оборудования и трубопроводов с учетом их фактического состояния и условий работы не позволяют осуществлять высокоточное прогнозирование момента отказа конструкции. Оценку показателей надежности и определение остаточного ресурса оборудования и трубопроводов по зафиксированным параметрам их технического состояния проводят согласно научно-технической документации [57, 62-65] и методикам [30, 64, 66-81, 89 91]. Оценку фактической нагруженности оборудования и трубопроводов выполняют расчетными методами с учетом фактической геометрии и размеров конструкций, вида и величины выявленных дефектов и вызываемой ими концентрации напряжений, а также результатов экспериментальных исследований напряженно-деформированного состояния металла и изменения его физико-механических свойств. За исключением трещин механического или коррозионного происхождения развитие остальных повреждений трубопроводов прогнозируют по результатам внутритруб-ной или наружной дефектоскопии и контроля коррозии. [c.139]
Общую и локальную виды коррозии контролируют не реже 2 раз в месяц по зондам электросопротивления или аналогичным, но другого типа по всей технологической линии в жидких фазах, газовой фазе и по возможности на границах раздела, а также не менее 1 раза в год по образцам-свидетелям и замерам толщины стенок ультразвуковым или другим дефектоскопом. За сероводородным растрескиванием ведется наблюдение косвенным методом по степени водородпроницаемости водородных зондов на первой стадии (в течение года) не реже 1 раза в неделю и на последующей—1 раза в квартал по напряженным образцам и образцам для гиба-перегиба — не реже 1 раза в год. По мере проведения ремонтных работ необходимы вырезка образцов металла и полный анализ их состояния определение механических свойств, содержания водорода, стойкости к сероводородному растрескиванию, а также металлографические исследования. Кроме того, периодически проводится визуальный осмотр внешнего состояния и не реже 1 раза в год — внутренний осмотр сосудов с проведением соответствующих замеров и техническим освидетельствованием их. [c.176]
Можно сформулировать несколько требований к методам интенсивной пластической деформации, которые следует учитывать при их развитии для получения наноструктур в объемных образцах и заготовках. Это, во-первых, важность получения ультра-мелкозернистых структур, имеющих преимущественно большеугловые границы зерен, поскольку именно в этом случае происходит качественное изменение свойств материалов (гл. 4,5). Во-вторых, формирование наноструктур, однородных по всему объему образца, что необходимо для обеспечения стабильности свойств полученных материалов. В-третьих, образцы не должны иметь механических повреждений или разрущений несмотря на их интенсивное деформирование. Эти требования не могут быть реализованы путем использования обычных методов обработки металлов давлением, таких как прокатка, вытяжка или экструзия. Для формирования наноструктур в объемных образцах необходимым является использование специальных механических схем деформирования, позволяющих достичь больших деформаций материалов при относительно низких температурах, а также определение оптимальных режимов обработки материалов. К настоящему времени большинство результатов получено с использованием двух методов ИПД — кручения под высоким давлением и РКУ-прессования. Имеются также работы по получению нано- и субмикрокристаллических структур в ряде металлов и сплавов путем использования всесторонней ковки [16, 17 и др.], РКУ-вытяжки [18], метода песочных часов [19]. [c.9]
Безобразцовый метод основан на инденторшлх испытаниях материалов, в результате которых определяют специальные характеристики твердости и пересчитывают их на показатели других механических свойств. Главное его достоинство заключается в возможности ускоренной оценки механических характеристик металла готовых изделий, не выводя их из строя и не вырезая из них образцов. Поэтому этот метод получил название безобразцового метода определения механических свойств. [c.49]
Применение двух- и многослойных сталей и сплавов, обладающих взаимодополняющими физико-механическими свойствами, позволяет значительно снизить металлоемкость элементов конструкций. Проблема проектирования, создания и эксплуатации биметаллических конструкций повышенного ресурса, в частности высоконагру-женного оборудования АЭС, делает весьма актуальными экспериментальные исследования, направленные на разработку методов оценки несущей способности таких конструкций не только по интегральным характеристикам прочности, но и с учетом наличия трещиноподобных дефектов на стадиях инициации разрущения, а также распространения и остановки трещин. Развитие методов определения критериев сопротивления разрушению и их анализ необходимы для оптимизации свойств биметалла путем правильного выбора сочетания разнородных составляющих соединения, назначения технологического способа его изготовления и определения рационального соотношения толщин основного металла и плакирующего слоя. Кроме того, это необходимо при проведении расчетов на прочность и оценке ресурса биметаллических элементов конструкций, определении допускаемых размеров дефектов, выборе методов и средств дефектоскопии. [c.107]
Предлагаемый читателю первый том справочника Металловедение и термическая обработка стали посвящен изложению методик изучения тонкого строения и структуры сталей и определению их разнообразных свойств (механических, физических, эксплуатационных). Такое построение многотомного справочника представляется правильным, если иметь в виду преимущественно экспериментальный характер науки о металлах. В этом томе, наряду с традиционными методами изучения структуры и свойств (макро- и микроанализ, рентгеновская дифракто-метрия, электронная микроскопия, определение механических свойств при растяжении, ударе, циклическом нагружении и т.п.), рассмотрены развитые в последние годы тонкие методы структурых исследований (спектроскопические, резонансные, микроспектральные и др.) и методы определения сопротивления разрушению в различных условиях нагружения (параметры вязкости разрушения, кавитационное разрушение, износостойкость, сопротивление газовой коррозии) в сочетании с подробным изложением методик фрактографического анализа. Все эти новые разделы отличают настоящее издание от предыдущих. [c.8]
На многих машиностроительных предприятиях, потребителях металлопродукции, испытания механических свойств не проводят, вопрос о выборе наиболее эффективного направления использования поступающего металла решают по результатам входного контроля химического состава. При отсутствии надежных методов испытаний некоторых свойств на металлургических предприятиях определение этих свойств также заменяется установлением содержания влияющих на качество металла элементов и т.д. Таким образом, в общем комплексе взаимосвязанных проблем повышения технико-экономической эффективности выплавки черных металлов и их качественных показателей важная роль принадлежит мероприятиям, гарантирующим получение надежной измерительной информации о химическом составе шихтовых материалов, полуфабрикатов и готовой продукции. Не меньшее значение имеет основанная на измерениях химического состава информация о стабильности технологических процессов, обеспечивающая возможность их регулирования. Отмеченными причинами объясняется повышенное внимание, которое уделнется в промышленно раз- [c.12]
Надежность работы в значительной мере зависит от соответствия примененных материалов и их качества требованиям нормативнотехнологической документации. Действующие нормы и правила предусматривают механические испытания и металлографический анализ основного металла и сварных соединений котлов, трубопроводов пара и горячей воды и сосудов, работающих под давлением. Объемы и методы механических испытаний и металлографических исследований строго регламентированы [23, 24, 25]. Механические испытания ставят своей задачей определение механических свойств при комнатной и рабочей температуре, без знания которых нельзя правильно выбрать материал для изготовления детали и оценить состояние металла в процессе эксплуатации. Основными видами механических испытаний являются испытания на растяжение, твердость и на ударный изгиб (динамические испытания). Технологические испытания на загиб, раздачу и свариваемость служат для оценки возможности проведения технологических операций, необходимых для изготовления и монтажа оборудования (сварки, гибки, вальцовки и т. п.). Такие важнейшие для котельных материалов испытания, как испытания на ползучесть, длительную прочность, сопротивление усталости, релаксацию напряжений, не предусматриваются действующими правилами котлонадзора в качестве контрольных и служат в основном для выбора допускаемых напряжений и установления ресурса работы элементов, изготовленных из различных сталей. [c.8]
При участии автора книги в СССР были разработаны РД 50.344— 82 «Методические указания. Расчеты и испытания на прочность в машиностроении. Методы механических испытаний металлов. Определение характеристик вязкости разрушения (трещиностойкости) при циклическом нагружении», являющиеся первым межотраслевым нормативно-методическим документом по испытаниям металлов на трещиностойкость. Определяемые в соответствии с этими методическими указаниями характе 1стики могут быть использованы (наряду с другими характеристиками механических свойств) для суждения о сопротивлении материала развитию трещины и определения влияния на него различных металлургических, технологических и эксплуатационных факторов сопоставления материалов при обосновании их выбора для машин и конструкций контроля качества материалов оценки долговечности элементов конструкций на основании данных об их дефектности и напряженном состоянии установления Критерия неразрушающего контроля и анализа причин разрушения конструкций. [c.49]
Современные методы расчёта (см. гл. П — X зтого тома) отражают влияние динамичности нагрузок, формы и жёсткости деталей, типа напряжённого состояния, пластичности, усталости, ползучести и ряда других факторов на несущую способность, поддающихся расчётному или экспериментальпо.му определению. Ряд факторов не поддаётся таким определениям, и их влияние должпо быть отражено в запасе прочности на основании наблюдений за работой деталей и узлов, статистического анализа данных эксплоатации и испытания машин. И. С. Стрелецким [47] и А. Р. Ржаницыным [21] на основании статистических кривых распределения возникающих усилий и отклонений механических свойств, а также анализа основных факторов отклонения между действительными и расчётными усилиями, обоснована каноническая структура запаса прочности п в виде произведения минимального числа сомножителей п = 1- г,2- Щ, каждый из которых отражает важнейшие факторы отклонения между рассчитываемой и фактической несущей способностью детали или конструкции [31]. К одной группе факторов относятся а) разница в величине нагрузок, вводимых Б расчёт, и нагрузок действительных (определение последних в ряде случаев затруднительно, например, нагрузки, развиваемые при горячей и холодной обработке металлов, нагрузки на ходовую часть автомобилей, динамические усилия на лопатки турбин и т. д.) б) разница в величине уси- [c.383]
В отличие от предложенных ранее безобразцовых способов данный метод базируется на определении твердости (ГОСТ 18661-73) и учитывает индивидуальные особенности материала. Разработанный метод определения механических свойств позволяет осуществлять контроль качества металла 100% изделий без нарушения их целостности. Время на проведение испытаний сокращается более чем в 10 раз. Экономия металла за счет отказа от вырезки образцов составляет около 4 кг на каждую трубу паропровода диаметром 273X20 мм. [c.284]
При дуговой сварке никеля и его сплавов пет необходимости всегда стремиться к получению металла пша, обладаюгцего таким же химическим составом и структурой, как свариваемый материал. Например, технически чистый никель не удается сварить без пор, трещип, с достаточно высокими показателями механических и коррозионных свойств шва, если его химический состав и структура будут индептичными основному металлу. Для получения сварных швов, удовлетворяющих разнообразным требованиям, часто приходится прибегать к комплексному легированию их элементами, не содержащимися в основном металле, и одновременно препятствовать обогащению шва вредными примесями. В зависимости от метода сварки никеля могут быть применены различные способы легирования металла шва. Наиболее надежно легирование электродной проволокой определенного состава в сочегашш с пассивным нелегирующим электродным покрытием, флюсом плп защитой инертным газом. При этом должны быть обеспечены условия, обеспечивающие полное усвоение сварочной ванной легирующих элементов, содержащихся в основном и присадочном металлах. Во время ручной сварки легирование шва может осуществляться через электродное покрытие, в состав которого вводятся соответствующие порошки металлов пли ферросплавов. При сварке под обычными плавлеными флюсами легирование металла шва является следствием физико-химических процессов между окислами флюса и никелем. [c.181]
Часто различные образцы металлов и сплавов испытывают на сжатие, кручение, срез, изгиб, удар и т. д. Испытания образцов материала на растяжение, кручение и т. д. и построение при этом диаграмм деформация— напряжение обязательно связано с разрушением образцов. Очень часто образцы нельзя разрушать испытанием, так как нужно определить механические свойства заготовок или готовых изделий. В этом случае и, кроме того, для ускорения прочностных испытаний можно получить представление о механических свойствах материалов путем определения их сопротивляемости местной деформации, которые принято называть твердостью материалов. Такая деформация создается вдавливанием в испытуемый образец практически недефор-мируемого тела определенной формы, обычно шарика или алмазной пирамиды под определенной нагрузкой. Испытания на твердость проводятся быстро и не требуют изготовления сложных образцов. Наиболее распространенный метод измерения твердости — способ ее определения по площади отпечатка, который остается после вдавливания в испытуемый материал закаленного стального шарика диаметром от 2,5 до 10 мм при определенной нагрузке (от 62,5 кг до 3000 кг). Этот метод определения твердости называется методом Бринеля. [c.138]
ХРУПКОСТЬ МЕТАЛЛОВ, свойство металла при статической нагрузке рваться, ломаться или разрушаться без заметной остаточной деформации. Если металл перед разрывом обнару- кивает пластич. деформации (см. Деформация пластическая), а остаточных деформаций не получается только при ударной нагрузке, то это свойство называется ударной хрупкостью. X. м. при низких и обыкновенных иногда называется холодноломко-с т ь ю, а X. м. в раскаленном состоянии—к р а с-н о л о м к о с т ь ю. Хрупкость зависит от целого ряда факторов от структуры металла, ориентации кристаллитов, от примесей, от самого метода испытания и т. д. Один и тот же слиток металла в одном направлении м. б. хрупким, а в другом пластичным. Начиная приблизительно с 1920 года, металловедение сделало большие успехи благодаря тому, что был открыт ряд способов получения металлич. монокристаллов, т. е. одиночных кристаллов, в виде стержней. Детальные исследования механических свойств этих монокристаллов, произведенные нем. физиками (Полани, Э. Шмид, Закс и их сотрудники) и англ. металловедами (Тейлор, Карпентер, мисс Элам и др.), дали весьма ценные ре-. ультаты для понимания механизма хрупкости и пластичности (см.). Эти исследования показали, что в металлич. монокристаллах существуют вполне определенные кристаллографич. плоскости—плоскости с наиболее плотной упаковкой атомов, по к-рым начинается трансляция, или скольжение, одних слоев относительно других. Это явление начинается тогда, когда с двигающее, или скалывающее, напряжение в данной плоскости и по вполне определенному направлению достигает некоторого критич. значения 5. Кристаллографич. направление в плоскости скольжения, по которому атомы расположены наиболее близко друг к другу, является направлением скольжения. [c.319]
Вторая особенность определения хладостойкости сварных соединений состоит в оптимизации условий сварки. Ориентируясь на наименее хладостойкую зону, варьируют режимы сварки, чаще всего погонную энергию, добиваясь наилучших показателей по ударной вязкости. Существуют методы испытаний, использующие образцы, по форме и размерам близкие к натуральным сварным соединениям или даже узлам. Они позволяют оценить агрегатную сопротивляемость соединения или сварного узла. При испытании таких образцов определяют вторую критическую температуру Гкр , при которой Оср.р = ао,2- Следует заметить, что в лабораторных условиях сварные узлы обычно дают более низкие критические температуры из-за малого числа испытываемых образцов. Рассеяние свойств металлов, режимов сварки, форм концентраторов, а главное, их радиусов приводит на практике к тому, что отдельные экземпляры изделий имеют более высокую критическую температуру хрупкости. Чтобы выявить свойства сварных узлов при температуре выше Ткрг, определяют пластичность как при низких, так и при более высоких температурах. Значения температуры, при которых регистрируются стабильные высокие результаты по пластичности, обеспечивают максимально возможные механические свойства. При наличии отдельных выпадов низкой пластичности данная температура не может рассматриваться как исключающая хрупкие разрушения. [c.172]
В 50—70-х годах XIX в. в самостоятельную дисциплину, тесно связанную с инструментоведением, оформляется теория оптических инструментов, с помощью которой на основе достижений в расчетах оптических систем, разработке теории аберраций и технологии оптического стекла стали успешно решать задачу установления оптимальных условий для получения правильного изображения наблюдаемого объекта, подобного ему по геометрическому виду и по распределению яркости. Именно в этот период немецкий ученый К. Ф. Гаусс, отказавшись от понятия идеальной оптической системы, разработал методику расчета оптических систем с учетом толщины оптических деталей, положенную в основу современных оптических расчетов. Именно в этот период были разработаны и внедрены в производство прогрессивные методы варки оптического стекла с заданными свойствами. В значительной степени быстрому развитию точного приборостроения способствовало создание ряда оптических инструментов, предназначенных для сборки, юстировки и контроля точных приборов в процессе их изготовления и эксплуатации. Новая отрасль — металлография позволила применять при изготовлении приборов металлы, удовлетворяющие определенным механическим (повышенная твердость, незначительный износ), физическим (малый коэффициент расширения, иногда отсут- [c.360]
mash-xxl.info