Прощай, мартен! Остановлена самая большая мартеновская печь в России | Экономика | Деньги
Все, что когда-то было экономически целесообразно, помогало выплавлять металл, необходимый для конских подков, паровозных колес и брони для танков, ушло в прошлое. Не поверите, но технология, которую придумал француз Пьер Мартен, работала 150 лет.
Что бы ни говорили об устаревшей технологии, тяжелом ручном труде, но сам процесс варки стали восхитительно красив. Сталевары словно танцуют у раскаленного зева печи. Мужчины идут по кругу, подхватывая по очереди на лопаты уголек, и точным броском отправляют его в бушующий огонь. Как хорошая хозяйка проверяет вкус супа в процессе готовки, так и здесь мастер берет пробу стали несколько раз. Черпак на длинной ручке опускается в котел, где металл семь часов кипит при температуре 1500 градусов. Веер искр, жар, гул.
Еще более романтичен разлив уже готовой стали по порционным ковшам, 250 тонн за раз. Кажется, что крошечные фигурки управляют извержением вулкана, ювелирно распределяя потоки раскаленной лавы туда, куда ей следует течь. Когда смотришь на слаженную работу гигантских механизмов и людей, словесный штамп «боги огня» совсем не кажется заезженным определением для такого труда.

Мартен на самом деле устарел давно. В Европе от этих печей отказались лет 60 назад. Современные электродуговые печи, которые пришли им на смену могут дать 24 плавки в сутки, а старичок мартен — максимум три. При этом выбрасывает в атмосферу много загрязняющих веществ, да и сталевар — профессия вредная для здоровья. Каждую смену обезвоживание организма работающего у печи человека доходит до критической отметки, страдают легкие, сердце.
На последней плавке в мартене присутствовала улыбчивая пожилая дама из Франции, мадам Катрин Калганофф, правнучка того самого Пьера Мартена.
— Я горжусь прадедом. Он герой, ведь своим изобретением он помог миру и России в том числе, — на грамотном русском языке произнесла мадам. На вопрос о том, как Мартены породнились с Россией, она отвечала охотно: «Мама влюбилась в русского эмигранта, дворянина Калганова. И потом родилась я».
На последней плавке, конечно, присутствовал весь коллектив сталеваров: триста человек. В последнюю очередь бросили в бурлящую печь цеховые часы, больше они здесь не понадобятся. Время мартена остановилось.
— Грустно, пришел сюда работать сразу после армии и другой работы не представляю, — вздыхает мастер цеха Алексей Каменсков. — На погасшую печь смотреть больно, но она еще два дня будет остывать даже на морозе. Пока жива наша старушка, 85 лет отработала!
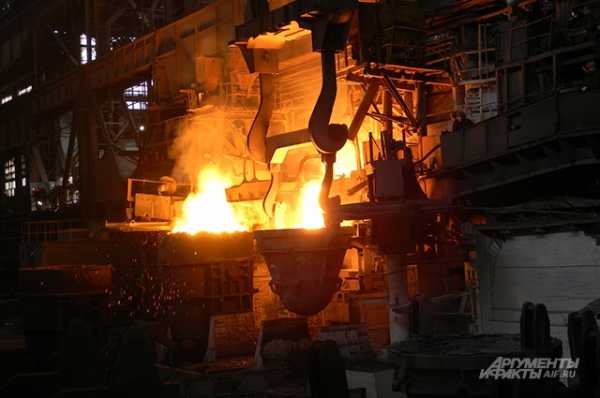
Один вопрос всех волнует: куда же пойдут работать люди, если цех закрыт навсегда? Председатель совета директоров Объединенной металлургической компании Анатолий Седых
www.aif.ru
Мартеновская печь — Большая советская энциклопедия
Марте́новская печь
(от имени П. Мартена)
пламенная регенеративная печь для переработки чугуна и стального лома в сталь заданного химического состава и качества.
М. п. состоит из следующих основных частей (рис.): рабочего пространства (под, передняя и задняя стенки, свод), где осуществляется плавка; головок (правой и левой), состоящих из собственно головок и вертикальных каналов для подачи топлива и воздуха в рабочее пространство и отвода из него продуктов сгорания; шлаковиков (воздушных и газовых) — для осаждения и накопления пыли и частиц шлака, выпадающих из проходящих через них продуктов сгорания; регенераторов (воздушных и газовых) — для подогрева поступающих в печь газа и воздуха теплом выходящих из рабочего пространства продуктов сгорания; боровов (каналов) для воздуха, газа и продуктов сгорания; системы перекидных клапанов, предназначенных для изменения направления подачи в печь топлива и воздуха и отвода из рабочего пространства продуктов сгорания; котла-утилизатора; дымовой трубы. Рабочее пространство и головки печи расположены выше рабочей площадки цеха и условно называются верхним строением печи. Остальные части находятся под рабочей площадкой и называются нижним строением. М. п. — агрегат симметричный: правая и левая её стороны относительно вертикальной оси одинаковы по устройству. Топливо и воздух для горения поступают в рабочее пространство поочерёдно то с правой, то с левой стороны; продукты сгорания отводятся из рабочего пространства соответственно с противоположной стороны. Изменение направления подачи топлива и воздуха, то есть изменение направления факела в рабочем пространстве, осуществляется системой клапанов и шиберов и называется «перекидкой» клапанов. Продукты сгорания поступают из шлаковика в регенератор сверху при температуре 1500— 1600 °C и, проходя по насадке (огнеупорная кладка регенераторов), передают ей значительную часть содержащегося в них тепла. При последующем прохождении через нагретую насадку холодного воздуха или газа они нагреваются до 1100— 1200 °С.
Все элементы М. п. выкладывают из огнеупорных материалов (см. Огнеупоры). В зависимости от характера огнеупорных материалов, из которых выложено рабочее пространство, М. п. делятся на основные и кислые. Для кладки основной М. п. применяют магнезитовый, магнезито-хромитовый, хромомагнезитовый кирпичи, магнезитовый порошок (для наварки пода), для кладки кислой М. п. — динасовый кирпич и кварцевый песок. В нижнем строении печи используются форстеритовый, высокоглинозёмистый, магнезитовый и шамотный кирпичи. Для придания строительной прочности всей конструкции печи кладка крепится металлической арматурой. Узлы и детали М. п., работающие в условиях высоких температур, постоянно охлаждаются.
М. п. бывают двух типов — стационарные и качающиеся. Большинство М. п. стационарные. Качающиеся М. п. обычно применяются для переработки фосфористых чугунов, так как при этом требуется несколько раз «скачивать» богатый фосфором шлак, что легче осуществлять на качающихся печах. М. п. могут отапливаться жидким (мазутом) или газообразным (природный, смешанный, генераторный газ) топливом. Смешанный газ (коксовый и доменный) и генераторный газ, обладающие недостаточной теплотой сгорания, перед поступлением в рабочее пространство подогреваются в регенераторах примерно до 1150 °С. Природный газ и мазут используются без подогрева. Кислород, служащий для интенсификации горения топлива, вводится через фурмы, помещенные в головках печи, а подаваемый для продувки ванны — через фурмы, опускаемые в отверстия в своде. Некоторое количество топлива может поступать вместе с кислородом в рабочее пространство печи с помощью топливо-кислородных горелок, также опускаемых через свод. Печи, отапливаемые низкокалорийными видами газообразного топлива, имеют две пары шлаковиков и две пары регенераторов (для подогрева газа и подогрева воздуха), располагаемых попарно соответственно под каждой головкой печи; отапливаемые мазутом или природным газом имеют под каждой головкой по одному шлаковику и одному регенератору — только для подогрева воздуха. Несмотря на наличие регенераторов, отходящие газы перед дымовой трубой имеют температуру 400—800 °С. Для утилизации этого тепла за М. п. устанавливают котлы-утилизаторы. Печи оборудованы контрольно-измерительной аппаратурой, позволяющей не только контролировать их работу, но и автоматически поддерживать заданный тепловой режим в различные периоды плавки.
Использование кислорода для интенсификации работы М. п. приводит к постепенному уменьшению роли регенераторов. В связи с этим в 60-х годах 20 века на ряде металлургических заводов были пущены в эксплуатацию так называемые двухванные печи (См. Двухванная печь), вообще не имеющие регенераторов.
Основные показатели, характеризующие работу М. п., — её производительность (годовая, часовая и съём стали с 1 м2 площади пода в сутки) и расход топлива. Годовая производительность наиболее полно характеризует работу печи, так как позволяет учесть все простои — горячие (без прекращения подачи топлива) и холодные (с отключением топлива) и объективно сравнивать работу однотипных печей. Производительность крупных М. п. превышает 0,5 млн. т стали в год. Съём стали с 1 м2 площади пода позволяет сравнивать работу печей разной ёмкости в различных условиях. Обычно съём стали составляет 12—13 т/м2. В СССР достигнуты наиболее высокие в мире технико-экономические показатели работы М. п.
Лит. см. при статье Мартеновское производство.
И. Б. Поляк.
Устройство мартеновской печи: 1 — рабочее пространство; 2 — свод; 3 — подина; 4 — сталевыпускное отверстие; 5 — отверстие для спуска шлака; 6 — завалочные окна; 7 — передняя стенка; 8 — задняя стенка; 9 — головки; 10 — вертикальные каналы; 11 — шлаковик; 12 — регенераторы: 13 — насадка регенераторов; 14 — борова; 15 — рабочая площадка.
Источник: Большая советская энциклопедия на Gufo.megufo.me
Мартеновская печь Википедия
Пьер Мартен предложил новый способ получения литой стали в регенеративных пламенных печах. Использовав разработанный в 1856 году немецким инженером К. В. Сименсом принцип регенерации тепла продуктов горения, Мартен применил его для подогрева не только воздуха, но и газа. Благодаря этому удалось получить температуру, достаточную для выплавки стали. Первая плавка была осуществлена Мартеном на одном из французских заводов 8 апреля 1864 года. Мартеновский способ стал широко применяться в металлургии в последней четверти XIX века, а в начале XX века в мартеновских печах выплавляли половину общего мирового производства стали [1].
Распространению мартеновского способа выплавки стали в Европе способствовал высокий спрос на рельсы и возможность добавления в шихту мартеновских печей до 30 % стального и железного лома (в том числе изношенных рельсов). Проблема повышенного содержания фосфора в европейских рельсах первоначальной укладки решалась добавлением в печь ферромарганца. Таким образом, мартеновская и бессемеровская сталь в 1860-х годах практически заменили тигельную в производстве колёсных бандажей, рессор, осей и рельсов
В России первая мартеновская печь была построена С. И. Мальцевым в 1866—1867 годах на Ивано-Сергиевском железоделательном заводе Мальцевского фабрично-заводского округа. 16 марта 1870 года были осуществлены первые плавки 2,5-тонной печи на Сормовском заводе[3]. Основатель завода — греческий купец, принявший российское подданство, Дмитрий Егорович Бенардаки привёз в 1870 году молодого инженера Александра Износкова, который построил печь. В 1998 году мартеновские печи на Сормовском заводе перестали действовать. В июне 2005 года было заключено охранное обязательство на здание цеха, где была установлена первая российская мартеновская печь, между заводом и министерством культуры Нижегородской области. В мае 2012 года был произведён демонтаж здания прокатного цеха в нарушение требований федерального закона «Об объектах культурного наследия (памятниках истории и культуры) народов РФ»[4][5].
В 1879 году Джон Юз запустил первую мартеновскую печь на Юзовском заводе[6].
Начиная со второй половины XX века доля мартеновской стали в общем объёме производства снижается во всех основных странах-производителях. При этом происходит замещение сталью, выплавляемой в кислородных конвертерах и электропечах. Так, например, в период с 1960 по 2005 годы в СССР (России) доля мартеновской стали в общем объёме производства снизилась с 85 до 25 %; в США — с 87 до нуля %; на Украине — с 53 до 45 %; в Китае — с 25 до нуля %; в Германии — с 47 до нуля %; в Японии — с 68 до нуля %[7]. Начиная с 1970-х годов новые мартеновские печи в мире более не строятся[8]. Мартеновский процесс практически вытеснен гораздо более эффективным кислородно-конвертерным способом (около 63 % мирового производства), а также электроплавкой (более 30 %). По результатам 2008 года на мартеновский способ производства приходится не более 2,2 % мировой выплавки стали[8]. Наибольший удельный вес выплавки стали мартеновским спо
ruwikiorg.ru
Мартеновская печь — Machinepedia
Марте́новская печь (марте́н) — плавильная печь для переработки передельного чугуна и лома в сталь нужного химического состава и качества. Название произошло от фамилии французского инженера и металлурга Пьера Мартена, создавшего первую печь такого образца в 1864 году.
Описание
В зависимости от состава огнеупорных материалов подины печи мартеновский способ выплавки стали может быть основным (в составе огнеупора преобладают СаО и MgO) и кислым (подина состоит из SiO2). Выбор футеровки зависит от предполагаемого состава шлака в процессе плавки.
Основной принцип действия — вдувание раскаленной смеси горючего газа и воздуха в печь с низким сводчатым потолком, отражающим жар вниз, на расплав. Нагревание воздуха происходит посредством продувания его через предварительно нагретый регенератор (специальная камера, в которой выложены каналы огнеупорным кирпичом). Нагрев регенератора до нужной температуры осуществляется очищенными горячими печными газами. Происходит попеременный процесс: сначала нагрев регенератора продувкой печных газов, затем продувка холодного воздуха.
Мартеновский способ также зависит от состава шихты, используемой при плавке. Различают такие разновидности мартеновского способа выплавки стали: скрап-процесс, при котором шихта состоит из стального лома (скрапа) и 25—45 % чушкового передельного чугуна; процесс применяют на заводах, где нет доменных печей, но расположенных в промышленных центрах, где много металлолома скрап-рудный процесс, при котором шихта состоит из жидкого чугуна (55—75 %), скрапа и железной руды; процесс применяют на металлургических заводах, имеющих доменные печи.
Технологии
C 1999 года, в мартеновском производстве началась новая эра — эра интенсификации процесса за счет использования бескислородного дутья малой интенсивности. Предложенная технология «скрытой» донной продувки основывалась на подаче нейтрального газа через дутьевые элементы, установленные в кладке подины, и применении для ее набивки специальных огнеупорных порошков. За 6 лет на эту технологию были переведены 32 мартеновские печи различной емкости — от 110 до 400 т, их них 26 — работающих скрап-процессом. В зависимости от емкости печи в подине устанавливались 3 — 5 дутьевых элемента с расходом 30 — 100 л/мин. на элемент. Эта технология кардинальным образом обеспечила повышение эффективности и конкурентоспособности мартеновского процесса, продлив жизнь этому способу производства стали. Так, практически на всех заводах за время использования донной продувки улучшились показатели работы не только отдельных печей, но и всего цеха.
- существенно снизились горячие и холодные простои, в том числе на ремонт пода;
- на 10 — 20 % сократилась длительность плавки;
- на 12 — 18 % увеличилась производительность печей в фактический час и производство стали в цехе;
- снизились расходы условного топлива, заправочных материалов и печных огнеупоров;
- в 1,3 — 2 раза увеличилась стойкость свода и длительность кампании в межремонтный период.
В настоящее время мартеновский способ производства стали практически вытеснен гораздо более эффективным кислородно-конвертерным способом (около 63 % мирового производства), а также электроплавкой (более 30 %). Начиная с 1970-х годов новые мартеновские печи в мире более не строятся. По результатам 2008 года на мартеновский способ производства приходится 2,2 % мировой выплавки стали. Так, объем выпуска мартеновской стали в СССР/России упал с 52 % в 1990 до 22 % в 2003 году и 16,5 % в 2008 году. Наибольший удельный вес выплавки стали мартеновским способом в мире по результатам 2008 года наблюдался на Украине (свыше 40 %).
machinepedia.org
Мартеновская печь — Справочник химика 21
Х-38. Поточная диаграмма теплового баланса мартеновской печи. [c.387]Температура предварительного подогрева котельных топлив лимитируется их температурой вспышки. Она должна быть не ниже 90 — 140° С при определении в открытом тигле для топочных и не ниже 80—90 С при определении в закрытом тигле для флотских мазутов. Содержание воды в котельных топливах не должно превышать 1—2 вес. %, а серы во флотских мазутах должно быть не более 0,80—2,0 вес. %, в топочных мазутах марок 40, 100 и 200 — не более 0,5 пес. % при малосернистом сырье, 2,0 вес. % при сернистом сырье и 3,5 вес. % при высокосернистом. В топливе МП для мартеновских печей содержание серы ограничивают величиной О,.5 вес. %. [c.135]
Взаимодействие огнеупорной футеровки с плавильной пылью. Под сводом электроплавильных и мартеновских печей во все периоды плавки находится плавильная пыль, которая взаимодействует со сводовыми огнеупорами, полностью впитываясь в них или оставляя на поверхности расплывчатые пятна, а также тонкозернистые бугорки металла. [c.99]
Топливо нефтяное — мазут (ГОСТ 10585—03) выпускается шести марок мазут флотский Ф5 и Ф12, мазут топочный 40 100 200 и топливо МП для мартеновских печей. Марки мазутов определяются максимально допустимой вязкостью прп 50° С в °ВУ (До 1965 г. мазут флотский выпускался по ГОСТ 1626—57 трех марок ФС5, Ф12 и Ф20, а топочный — по ГОСТ 1501—57 шести марок 20, 40, 60, 80, 100 и 200.) [c.212]
Кроме котельного топлива указанных марок вырабатывают топливо для мартеновских печей, норма и качество которого регулируются ГОСТ 14298—69 [c.11]
Рис, 1Х-37. Схема мартеновской печи. [c.386]
Коксовым газом называется газ, получаемый нагреванием каменного угля до 900—1100°С без доступа воздуха. Этот газ в чистом виде или в смеси с природным газом используется в качестве топлива для нагревания мартеновских печей, печей стекольной и керамической промышленности, а также в коммунальном хозяйстве. Кроме того, коксовый газ служит сырьем три синтезе химических продуктов. [c.449]
Четвертая группа-горючее для котельных установок и промышленных печей. Это топлива для стационарных котельных, электростанций и для транспортных котельных установок (силовые установки кораблей). Сюда же относят топлива для промышленных печей, например топливо для мартеновских печей. [c.9]
В качестве пылегазового потока использовались отходящие дымовые газы мартеновских печей, содержащие плавильную пыль концентрацией в среднем около 0,4 г-м размер частиц пыли до 2 мкм. При прохождении пылегазового потока через фильтровальную перегородку, толщина которой составляла несколько сантиметров, по истечении 30—40 с от начала фильтрования на глубине 5—6 мм от поверхности перегородки возникала узкая горизонтальная полоска, которая была окрашена в характерный для плавильной пыли буро-коричневый цвет. Эта полоска с течением времени расширялась в направлении к поверхности фильтровальной перегородки до тех пор, пока не заполняла весь ее лобовой слой. При этом окрашенный слой почти не распространялся в более глубокие зоны перегородки. На основании полученных сведений высказана гипотеза, объ- [c.110]
В 1962 г. амортизационный лом, включающий и вышедшие из строя вследствие коррозии металлические конструкции, составил, в нашей стране 16,3 млн. т , или примерно 1/5 годового производства стали. Значительная часть амортизационного лома используется путем переплавки в мартеновских печах. Однако стоимость изготовления конструкций, которая в большинстве случаев значительно превосходит стоимость израсходованного на их изготовление металла, при этом полностью теряется. [c.9]
Формула получена для струйных форсунок высокого давления на основе практики работы мартеновских печей. Для большинства других форсунок она требует экспериментальной проверки. [c.154]
Определить объем заполнения сталью 350-тонно-г(. кислородного конвертера, у которого форма бл зкa к нгаровидной, а внутренний диаметр 8 м. Рассчтать высоту слоя стали в 600-тонной мартеновской печи, если плавильное пространство ее имеет длину 17 м и ширину 7 м. Плотность жидкой стали 7200 кг/м . [c.223]
В рабочем пространстве мартеновской печи печная газовая среда окислительная. [c.40]
Современный промышленный опыт получения многих видов продуктов в печах определил для каждого из них режимы, необходимую печную среду, один или несколько конструктивных типов, источники и место теплогенерации. Например, варка стекла осуществляется в газопламенных ванных печах, стали — в электрических дуговых ванных печах и газопламенных мартеновских печах, обжиг кускового материала — в газопламенных шахтных или вращательных печах и т. д. [c.60]
Топливо для мартеновских печей — продукт нефтяного происхождения. [c.211]
Особо важные преимущества природного газа проявляются при интенсификации тепловых процессов. Так, в черной металлургии при использовании природного газа повышается производительность доменных печей на 4—5% (в отдельных случаях до 10%), сокращается расход кокса на 10—20% и снижается себестоимость чугуна на 2—12%, производительность мартеновских печей повышается на 5—10%, сокращается расход топлива (до 10%) и продолжительность плавки стали. При использовании природного газа в нагревательных печах, помимо интенсификации процесса, сокращается в два раза и более угар металла, который при обычном нагреве (мазутные печи) составляет от 1,5 до 3,0%. [c.90]
В мартеновском процессе чугун (200—500 т) плавят в широкой печи (мартеновская печь), в которой высокую темпе )атуру создает [c.555]
Выплавка стали в мартеновских печах [c.92]
Топливо нефтяное для мартеновских печей [c.585]
Действующие современные мартеновские печи — это крупные сталеплавильные агрегаты сложной конструкции с большим количеством различных дополнительных устройств. Строительство их связано с крупными капитальными затратами. Поэтому одновременный отказ от мартеновского способа производства стали и переход к кислородно-конвертерному и электросталеплавильному способам экономически нецелесообразен. Этим объясняется высокая доля мартеновской стали, выплавляемой до настоящего времени в нашей стране. [c.92]
При выплавке стали в мартеновских печах протекают процессы окисления углерода и примесей в шихте и образования шлаков аналогичные тем, которые идут в кислородном конвертере. Однако мартеновский процесс имеет ряд существенных особенностей. К ним относятся [c.92]
Опыт работы газоочистных установок на Макеевском металлургическом заводе им. С. М. Кирова показал, что внедрение магнитной обработки промывной воды перед подачей к оросителям труб Вентури способствует стабилизации давления в рабочем пространстве мартеновской печи, улучшению условий труда, экономии реагентов на очистку
www.chem21.info