Что такое экструдер и экструзия, принципы работы
Экструзия исключает из производственного цикла трудоемкую механическую обработку. Это быстрый и недорогой способ получения пленок, труб, профиля и других изделий, выпускаемых погонажом из полимерного сырья. В статье расскажем, что такое экструдер, как происходит процесс экструзии полиэтилена, разберем тонкости экструзионной технологии.
Что такое экструзия полимеров?
Процесс экструзии происходит при нагреве полимеров максимум до 250 0С. Производство идет на скорости до 120 метров/минуту. Около 30 % всего объема полимеров перерабатывается по экструзионной технологии с помощью экструдеров. Попробуем разобраться в тонкостях этого процесса.
Экструзия полимеров — это технология получения формовочных изделий из термопластов и их композиций на шнековых прессах. Осуществляется путем продавливания (под давлением) однородного расплава через щель формовочной головки экструдера.
Щель имеет определенную форму, которая определяет геометрию изделия — сайдинг, пленка, оконный ПВХ профиль. В качестве сырья используются гранулы полиэтилена ПВД и ПНД, полипропилена, ПВХ, полистирола и других полимеров.
Экструзия включает в себя следующие этапы:
- получение однородного расплава в экструдере;
- формование;
- охлаждение продукции;
- натяжение и намотка (пленки), нарезка (профиль, труба).
Устройство и принцип работы экструдера, что это такое
Уже по тому, что слова «экструдер» и «экструзия» являются однокоренными, становится понятным, что экструдер — это основной рабочий орган экструзионной линии.
По длине экструдер для полимеров условно делится на три зоны: загрузки, сжатия расплава и дозирования.
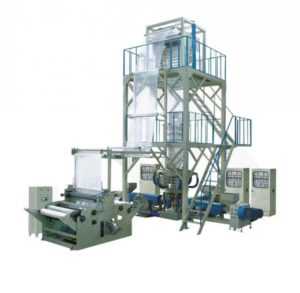
Экструдер для пленки
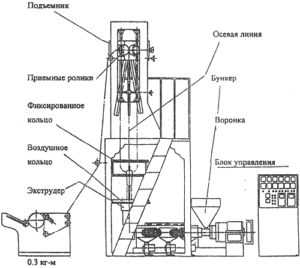
Схема экструдера для полиэтилена
- Зона загрузки. Гранулы (порошок, вторичное сырье) подаются в бункер самотеком или под напором сжатого компрессором воздуха. Шнек, который приводится в движение работой привода, вращается, и уплотняя полимер до состояния пробки, продвигает его к горячим секциям экструдера.
- Зона плавления. Здесь шаг между витками начинает уменьшаться. Как следствие один и тот же объем полимера пытается поместиться в уменьшившемся пространстве. Пробка прижимается к обогреваемым стенкам трубы экструдера, плавится, расплав перемешивается. Хотим уточнить, что плавление происходит, в основном, не за счет нагревателей (они лишь интенсифицируют процесс), а из-за огромных сдвиговых деформаций в уплотняющемся полимере.
- Зона дозирования. На выходе из экструдера полимер продавливается через систему фильтрующих сеток и проходит через формующее отверстие, профиль которого зависит от формы выпускаемой продукции.
Важно! Экструдер может различаться по типу и количеству шнеков. Выпускаются: одношнековые, двухшнековые и многошнековые, дисковые и многодисковые экструдеры.
О конструкции одношнекового экструдера.
Внутри толстостенного корпуса (трубы) вращается шнек — металлический стержень с винтовой навивкой. Шнек перемещает гранулы по направлению к экструзионной головке. Корпус опоясывают секции хомутовых нагревателей, которые греют металл и плавят полимер, прижимаемый винтом к внутренней поверхности трубы. «Горячую» часть оборудования помещают в водоохлаждаемый кожух, и сверху утепляют термочехлом.
Одношнековый экструдер, схема
Экструзия пленки
Наиболее популярными формовочными изделиями, которые получают с применением экструзии, являются пленки. Их изготавливают из полистирола, полипропилена, полиамида, лавсана, поликарбоната, ПВХ, но самыми востребованными из них являются, конечно же, пленки из экструдированного полиэтилена высокого и низкого давления. Именно на их примере мы рассмотрим, какие этапы этот материал проходит на выходе из экструдера.
Существует два метода экструдирования пленок:
- Метод раздува рукава.
- Метод плоскощелевой экструзии.
Читайте также какие дефекты могут возникнуть при экструзии пленки и как их устранить.
Метод раздува рукава.
Полимер выдувается из экструдера для пленки через кольцевую щель в формующей головке. Визуально это выглядит, как из фильеры поднимается сплошной пленочный цилиндр, раздуваемый изнутри воздухом. Воздух подается под давлением через дорн — отверстие в центре головки.
Охлаждение при экструзии полиэтилена, в зависимости от ориентации рукава, может производиться по двум схемам:
- Если рукав направлен вертикально вверх или горизонтально, то пленка обдувается воздухом, поступающим через охлаждающие кольца по периметру рукава;
Раздувной экструдер
- При отводе рукава вниз используется водяное охлаждение — такая схема сокращает время кристаллизации.
После остывания пленка складывается с помощью специальных «щек» в полотно и протягивается через отжимающие воздух валки. Готовый материал отправляется на намотку.
Чем быстрее охладить расплав полиэтилена на выходе из экструдера, тем выше будет прозрачность и блеск пленки. Почему так происходит? Дело в том, что при остывании в пленке образуется два вида молекулярных структур — кристаллическая и амфорная. Когда материал охлаждают медленно, то макромолекулы полимера успеют сформироваться в кристаллы, и экструдированная пленка будет мутной и неэластичной, но прочной. При быстром охлаждении кристаллы не успевают соединиться и пространство между ними заполняют амфорные связи, придающие пленке прозрачность, хорошую эластичность и гибкость.
Метод плоскощелевой экструзии.
Отверстие в фильере плоскощелевого экструдера протачивают в виде тончайшей щели. Пленка из формовочной головки выходит в виде непрерывного полотна определенной толщины и ширины.
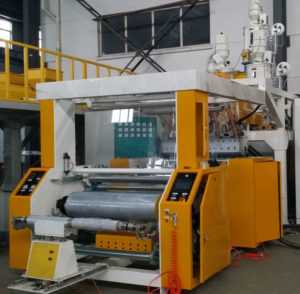
Плоскощелевой экструдер для производства стрейч-пленки
Существует два варианта охлаждения пленки полученной плоскощелевым методом:
- Первый, это когда экструзионный полиэтилен сразу же после формования подается на охлаждающий барабан, температура поверхности которого поддерживается на уровне 30…50 0С.
- Второй вариант — пленку пропускают через ванну с проточной водой. Такое шоковое охлаждение позволяет получать блестящий и прозрачный материал, но есть свои нюансы. Когда пленка заходит в воду, она вызывает рябь на ее поверхности, из-за которой на полиэтилене появляются пятна.
После охлаждения и сушки полиэтилен протягивается через натягивающие валы и идет на намотку.
Соэкструзия и коэкструзия.
Соэкструзия — это технология, использующаяся для получения многослойных пленок.
В качестве сырья может использоваться: полиэтилен низкой и высокой плотности, полипропилен, полиамидная пленка и др. полимеры. Гранулят этих пластических масс плавится в разных экструдерах, после чего соединяется и проходит через одну формовочную фильеру (головку). Для прочного склеивания нужно, чтобы молекулярная сетка полимеров была похожа по структуре. Но если нужно связать барьерный слой, например, EVOH и линейный полиэтилен, то потребуется специальные вяжущие сополимеры.
Соэкструзионные многослойные пленки используются для вакуумирования продуктов, как транспортная упаковка, с/х пленка (для мульчирования, пленка с эффектом антифог), упаковка фармацевтических препаратов.
По похожей технологии, которая получила название коэкструзия, изготавливают панели сайдинга и профиль ПВХ. Поливинилхлорид — основа профиля, занимает около 80% толщины панели, оставшиеся 20% — акрил. Как и в случае соэкструзии, используется работа двух коэкструдеров, где отдельно плавят ПВХ и акрил. Соединяются эти расплавы в щелевой филере, откуда выходят уже готовым спаянным изделием.
Коронарная обработка пленки после экструзии
Химическая инертность и малая поверхностная энергия пленки делают ее невосприимчивой к типографской или любой другой краске. Нанесение покрытия на поверхность полиэтилена станет возможным, если его поверхностная энергия будет хотя бы на 10 дин/см выше энергии наносимой краски. В ином случае краска будет просто собираться в капли. «Подзарядить» пленку можно коронированием. Каждая экструзивная линия оборудована активатором обработки коронным разрядом, который состоит из: генератора, трансформатора и электродов. При пропадании пленки в область электромагнитного поля растет ее поверхностная энергия и повреждается верхний слой макромолекул (микротравление).
Применение технологии экструзии
- Химическая промышленность. Почти все термопласты и их композиции могут перерабатываться экструзией в готовые изделия (пленки, трубы, оболочки изоляции, сайдинг, листы).
- Производство комбикорма. Измельченное сырье для производства комбикорма поступает в экструдер, где подвергается уплотнению, сжатию и температурной обработке при температуре до 200
0С. Этот способ переработки повышает питательность и усвояемость корма, сохраняет в нем витамины и препятствует размножению микроорганизмов. - Брикетирование твердого биотоплива. Переработка биомассы (торфа, угольной пыли, шелухи подсолнечника, отходов сахарного производства, соломы сои, щепы) и прессование ее в гранулы или брикеты производится на экструдерах;
- Пищевая промышленность. Макароны, кукурузные палочки и хлопья, жевательная резинка и чипсы, соевые продукты— все эти продукты изготавливают с помощью пищевой экструзии.
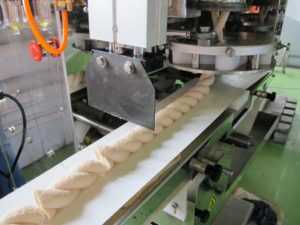
Экструзия теста, экструдер для теста
Развитие экструзионного производства сейчас идет сейчас по трем направлениям. Это: усовершенствование существующего оборудования, применение новых композиций полимеров, совершенствование автоматизированных систем управления. Последнее направление представляется наиболее актуальным — уже сейчас в России появились установки оборудованные АСУ на основе микропроцессора. Они позволяют автоматически контролировать не только работу экструдера, но и системы подготовки сырья, калибровки и обрезки готовых изделий.
oplenke.ru
Экструзия. Общее представление об экструзии
Рейтинг: 4.5/5 из 30Экструзия — метод формования в экструдере для пленки изделий или полуфабрикатов неограниченной длины продавливанием расплава полимера через формующую головку с каналами необходимого профиля.
Термопластичный полимер в процессе экструзии, не претерпевая химических превращений, последовательно переходит сначала из твердого состояния (в виде гранул или порошка) в расплав, а затем вновь в твердое состояние — после выхода из формующей оснастки.
При нагреве, с возрастанием температуры, увеличивается подвижность молекул, разрушаются кристаллические образования, молекулы принимают клубкообразную или спиральную форму и начинают смещаться относительно друг друга. Полимер из твердого состояния переходит в расплав. У полимеров кристаллической структуры этот переход отвечает узкому интервалу температур, а у аморфных — широкому. В интервале между температурами плавления и разложения полимер находится в вязкотекучем состоянии. Именно в состоянии расплава материал экструдируется. Реальный интервал температур переработки несколько уже, чем интервал между температурой плавления и разложения, так как, с одной стороны, необходимо иметь достаточно подвижный расплав, а с другой стороны, необходимо избежать разложения полимера при экструзии.
Переработка полимерного материала экструзией осуществляется на специальных машинах — экструдерах.
Схема агрегата для производства рукавной пленки представлена на рисунке ниже:
Основными элементами экструдера являются обогреваемый цилиндр, шнек (с охлаждением или без него), сетки, размещаемые на решетке, и формующая головка.
Технологический процесс экструзии складывается из последовательного перемещения материала вращающимся шнеком в его зонах: питания (I), пластикации (II), дозирования расплава (III), а затем продвижения расплава в каналах формующей головки.
Схема одношнекового экструдера
Основные типы шнеков
Деление шнека на зоны I-III осуществляется по технологическому признаку и указывает на то, какую операцию в основном выполняет данный участок шнека. Разделение шнека на зоны условно, поскольку в зависимости от природы перерабатываемого полимера, температурно-скоростного режима процесса и других факторов, начало и окончание определенных операций могут смещаться вдоль шнека, захватывая различные зоны или переходя из одного участка в другой.
Цилиндр также имеет определенные длины зон обогрева. Длина этих зон определяется расположением нагревателей на его поверхности и их температурой. Границы зон шнека I-III и зон обогрева цилиндра могут не совпадать. Для обеспечения успешного перемещения материала большое значение имеют условия продвижения твердого материала из загрузочного бункера и заполнение межвиткового пространства, находящегося под воронкой бункера.
Питание шнека зависит от формы частиц сырья и их плотности. Гранулы, полученные резкой заготовки на горячей решетке гранулятора, не имеют острых углов и ребер, что способствует их лучшей сыпучести. Гранулы, полученные холодной рубкой прутка-заготовки, имеют острые углы, плоское сечение среза, что способствует их сцеплению и, как следствие, худшей сыпучести. При длительной работе экструдера возможен перегрев цилиндра под воронкой бункера и самого бункера. В этом случае гранулы начнут слипаться и прекратится их подача на шнек. Для предотвращения перегрева этой части цилиндра в нем могут быть сделаны полости для циркуляции охлаждающей воды.
Зона питания I
Поступающие из бункера гранулы заполняют межвитковое пространство шнека зоны I и уплотняются. Продвижение гранул осуществляется вследствие разности значений силы трения полимера о внутреннюю поверхность корпуса цилиндра и о поверхность шнека. Поскольку поверхность контакта полимера с поверхностью шнека больше, чем с поверхностью цилиндра, необходимо уменьшить коэффициент трения полимера о шнек, так как в противном случае материал перестанет двигаться вдоль оси шнека, а начнет вращаться вместе с ним. В ряде случаев это достигается повышением температуры стенки цилиндра (нагревом) и понижением температуры шнека (охлаждением водой в зоне I).
В зоне I вследствие большого внешнего и внутреннего трения выделяется тепло, которое также расходуется на нагрев материала. В эту же зону подается тепло от нагревателей, расположенных по периметру цилиндра.
Если температура цилиндра такова, что начинается преждевременное плавление полимера у его стенки, то материал будет проскальзывать по этой поверхности, т.е. вращаться вместе со шнеком. Поступательное движение материала прекращается. При оптимальной температуре полимер спрессован, уплотнен и образует в межвитковом пространстве твердую пробку. Лучше всего, если такая скользящая пробка образуется и сохраняется на границе зон I и II. Свойства пробки во многом определяют производительность машины, стабильность транспортировки полимера, величину максимального давления и т.д.
Зона пластикации и плавления II
В начале зоны II происходит подплавление полимера, примыкающего к поверхности цилиндра. Расплав постепенно накапливается и воздействует на убывающую по ширине пробку. Поскольку глубина нарезки шнека уменьшается по мере продвижения материала от зоны I к зоне III, то возникающее давление заставляет пробку плотно прижиматься к горячей стенке цилиндра, где и происходит плавление полимера.
Схема плавления пробки материала в зоне II в межвитковом сечении шнека
Схема плавления пробки материала в зоне II в межвитковом сечении шнека
В зоне пластикации пробка плавится также и под действием тепла, выделяющегося вследствие внутреннего, вязкого трения в материале в тонком слое расплава, где происходят интенсивные сдвиговые деформации, — материал пластицируется, интенсивно гомогенизируется.
Конец зоны II характеризуется распадом пробки на отдельные фрагменты. Далее расплав полимера с остатками твердых частиц попадает в зону дозирования.
Зона дозирования III
Продвижение гетерогенного материала (расплав, частички твердого полимера) продолжает сопровождаться выделением внутреннего тепла, которое является результатом интенсивных сдвиговых деформаций в полимере. Расплавленная масса продолжает гомогенизироваться, что проявляется в окончательном плавлении остатков твердого полимера, усреднении вязкости и температуры расплавленной части. В межвитковом пространстве расплав имеет ряд потоков, основными из которых являются продольный и циркуляционный.
Величина продольного (вдоль оси шнека) потока определяет производительность экструдера, а циркуляционного — качество гомогенности полимера или смешения компонентов. В свою очередь продольный поток складывается из трех потоков расплава: прямого, обратного (обусловлен наличием сеток, оснастки, трения о поверхность цилиндра и шнека) и потока утечек (часть материала перетекает в направлении противотока в зазор между гребнем шнека и поверхностью цилиндра).
Течение расплава через сетки и формующую оснастку
Расплав вращающимся шнеком продавливается через фильеру, к которой прижаты металлические сетки. Сетки фильтруют, гомогенизируют и создают сопротивление движению расплава, на них теряется часть давления. Проходя через систему фильтрующих сеток, порции полимерного расплава с большей вязкостью задерживаются на сетках. Этого времени должно хватить для того, чтобы порция расплава достигла нужной температуры. Сверхвысокомолекулярные фракции полимера и различные примеси задерживаются сетками и через некоторое время они вместе с сеткой удаляются из цилиндра экструдера. Перепад давления на фильтрующих сетках служит показателем засорения, т. е. увеличения сопротивления сеток, и, следовательно, служит сигналом к их замене.
После прохождения сеток гомогенизированный расплав под остаточным давлением (5,0/35 МПа) продавливается в формующую оснастку и, приобретая определенный профиль, выходит практически под очень небольшим избыточным давлением из кольцевого зазора головки. Сменный инструмент (формующая оснастка) устанавливается на выходе из отверстия цилиндра. Материал продавливается через каналы экструзионной головки под действием давления, развивающегося в пространстве винтового канала шнека.
Основные конструктивные элементы головок рассмотрим на примерах головок для производства рукавной пленки.
Любая головка имеет формующий канал, в данном примере кольцевой. Наружная поверхность рукава оформляется деталью, называемой мундштуком 3 (реже используют термины матрица, фильера). Внутренняя поверхность рукава оформляется дорном 1. Мундштук и дорн являются сменными инструментами головки.
Монтажная схема экструзионной головки
Экструзионная головка для экструзии ПЭНД
- дорн,
- рассекатель,
- мундштук,
- регулировочное кольцо,
- регулировочный болт.
Экструзионная головка для экструзии ПЭВД
- дорн,
- рассекатель,
- мундштук,
- регулировочное кольцо,
- регулировочный болт.
Расплав из экструдера через фильтр (набор сеток на фильере) подается в центральный канал головки 1, соединенный с несколькими расходящимися от него в радиальных направлениях цилиндрическими каналами 2. Из каждого радиального канала расплав попадает в кольцевую щель 4, по периметру которой распределяется коллекторным каналом 6, выполненным в теле дорна 3 по винтовой линии. Длина коллекторов такова, что распределенные по периметру щели осевые потоки от каждого из коллекторов взаимно перекрываются. Совмещаясь (суммируясь) на начальном участке щели 4а, в конце его (т. е. собственно в щели 4) они образуют единый монолитный кольцевой поток.
Как видно, поверхность стыка отдельных потоков ориентирована не радиально, а тангенциально, т.е. не пронизывает насквозь всю толщину стенки выходящего из головки рукава, что является важным преимуществом данной конструкции.
Схема головки с винтовыми коллекторами
Второе преимущество головки — развитая опора дорна 3 на корпусе 5 по большой поверхности с большим диаметром D. Это обеспечивает большую жесткость крепления дорна и, следовательно, соблюдение равенства высоты формующего канала по всему его периметру с большой точностью.
Наконец, третье преимущество — отсутствие развитого конического подводящего канала. Следовательно, в сотни раз меньше распределенное осевое усилие, действующее на дорн, и практически отсутствуют изгибающие моменты на нем из-за возможной неоднородности распределения этого усилия.
На рисунках представлены экструзионные головки, для производства пленок из ПЭНД и ПЭВД. Очевидно, что основное отличие этих конструкций заключается в том, что при экструзии ПЭНД дорн сужается в направлении выхода рукава из формующего канала, а в случае ПЭВД дорн, соответственно, расширяется.
Регулировка зазора формующего канала обеспечивается шестью и более в зависимости от диаметра головки болтами 5.
Источник: Линия по производству рукавной пленки: инструкция пользователя. Лебедев П.Г., Лебедева Т.М., Митина Л.Н.,
www.eximpack.com
устройство, принцип действия и разновидности
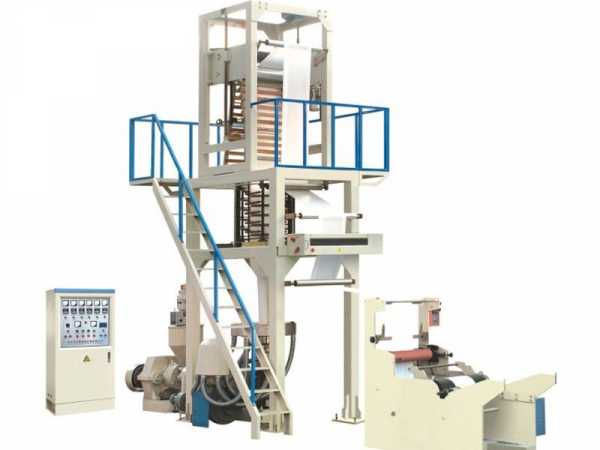
Одной из основных технологий переработки пластмасс и изготовления из них разнообразных деталей и профильной продукции является экструзия. Заключается она в приготовлении расплава полимеров с последующим продавливанием его через формующие сопла – специальные насадки, придающие материалу заданную форму. Главным элементом производственной линии, использующей подобную методику, является экструдер для пластика.
Принцип работы экструдера
Экструдер представляет собой электромеханическое устройство, непосредственное предназначенное для процесса формовки пластмассовых профильных деталей их полуфабрикатов. Общее устройство экструдера для пластика:
- Корпус с системой нагрева до необходимой температуры плавления полимеров. В качестве источника тепловой энергии могут использоваться привычные резистивные системы или индукционные, создающие высокие температуры за счет наведенных на их корпус высокочастотных индукционных токов Фуко.
- Узел загрузки, через который различными способами сырье поступает в полость корпуса.
- Рабочий орган, создающий необходимое давление для перемещения сырья от узла загрузки до формующих насадок. Используются различные физические принципы, так это механизм может быть поршневым, дисковым или шнековым. Наибольшее распространение получили именно шнековые экструдеры.
- Экструзионная головка (иначе – фильера), задающая форму получаемых изделий.
- Механический привод (двигатель и редукторная система), создающий и передающий на рабочий орган необходимое усилие.
- Системы контроля и управления, поддерживающие необходимый технологический режим.
Загруженное в виде гранул, порошка или лома сырье под действием рабочего органа перемещается в рабочую зону корпуса, где под действием давления, трения и подаваемой извне температуры нагревается и плавится до состояния, требуемого по условиям технологического процесса.
В ходе движения в полости корпуса сырье тщательно перемешивается до однородной гомогенизированной массы.
Под действием высокого давления расплав продавливается через сетчатые фильтры и формующие головки, где происходят его окончательная гомогенизация и придание заданного профиля.
Затем, охлаждаясь естественным или принудительным способом, он полимеризуются, и в итоге получаются изделия необходимой конфигурации с заданными физическими и механическими свойствами.
Видео: «Как работает экструдер?»
Виды экструдеров
Современные экструзионные установки различаются как по схеме рабочего органа, так и по своему целевому предназначению.
Экструдеры одношнековые и двухшнековые
Шнековые (червячные) экструдеры – наиболее распространенные, так как практически в полной мере отвечают всем требованиям технологического процесса. Рабочим органом выступает шнек экструдера (винт Архимеда, известный каждому хотя бы по домашним мясорубкам).
Лопасть шнека экструдера захватывает сырье в области загрузки и перемещает последовательно по всей длине цилиндра корпуса, через зону нагрева, гомогенизации и формовки. В зависимости от технологической карты и вида исходного материала шнеки могут быть нормальными или быстроходными, цилиндрической или конической формы, сужающиеся к выходу. Одним из главных параметров является соотношение рабочего диаметра шнека к его длине. Различаются также шнеки шагом витков и их глубиной.
Однако одношнековые экструдеры не всегда применимы. Например, если в качестве сырья используется порошковый полуфабрикат, один винт не справится с тщательным его перемешиванием в ходе расплавления и гомогенизации.
В подобных случаях применяют двухшнековые экструдеры, винты которых могут находиться во взаимном зацеплении, совершать параллельное или встречное вращательное движение, иметь прямую или коническую форму.
В результате процессы разогрева, смешения и гомогенизации проводятся более тщательно, и на головку поступает полностью однородная и дегазированная масса.
Нельзя не отметить, что в некоторых технологических процессах применяются экструдеры и с большим количеством шнеков – до четырех, а кроме того, существуют и планетарные автоматы, когда вокруг центрального винта вращается до 12 сателлитных.
Это бывает необходимым при работе с некоторыми видами пластиков, которые под действием высоких температур имеют свойство к деструкции – потере физических качеств. Таким образом, их нагрев в подобных экструдерах осуществляется за счет силы трения и создаваемого высокого давления.
Экструдер для ПВХ профиля
Производство пластиковых или композитных профилей в большинстве случаев производится именно методом экструзии. Для этого, в зависимости от материала и сложности формы изделия, используют одно- или двухшнековые аппараты с соответствующими формующими головками.
Ассортимент весьма обширен – от тонких нитей или полос до листов, крупных панелей и сложных по геометрии профилей. Ставшие всем привычные пластиковые оконные и дверные системы собираются из ПВХ-профилей, изготовленных именно таким способом.
Добавка в полимер специальных компонентов позволяет выпускать сложные композиты, например, дерево-пластиковые конструкции, которые также часто применяются при изготовлении различных строительных конструкций.
Экструдер для производства труб
При производстве трубной продукции очень важным условием является отсутствие в гомогенизированной смеси пузырьков газа, поэтому экструдеры для труб в обязательном порядке оснащаются системой дегазации. Обычно это – двухшнековые установки, в которых, помимо прочего, применяются так называемые барьерные шнеки, надежно разделяющие еще твердый полуфабрикат от полностью расплавленного. Это обеспечивает полную однородность состава, что очень важно для эксплуатационных качеств выпускаемой трубы.
Экструдеры для полиэтилена
Все полимерные пленки изготавливаются исключительно способом экструзии. Для производства плёнок используется выдувной экструдер. Формующий узел экструдера для стрейч пленки может быть выполнен в виде узкой щели –на выходе получается однослойная пленка необходимой толщины и ширины.
В некоторых моделях используются круглые щелевые фильеры большого диаметра – пленка получается в виде рукава.
Мини экструдеры для пленки производят полиэтилен шириной рукава до 300мм и толщиной до 600 мкм. Небольшой размер устройства позволяет установить его даже в обычном помещении.
Экструзионные линии
В промышленных условиях экструдер – это один из главных компонентов целой экструзионной линии, которая включает, помимо него, ряд других установок и механизмов:
- Система подготовки и загрузки сырья – иногда полуфабрикат нуждается в предварительной просушке и калибровании перед подачей в загрузочный бункер.
- Система охлаждения – устанавливается на выходе экструдера для ускорения процесса полимеризации изделий. Могут быть различного типа – воздушные или в виде охлаждающих ванн.
- Механизмы протяжки готовых профилей.
- Маркирующие и ламинирующие системы различного принципа действия.
- Намоточные и отрезные механизмы для приведения изделий в требуемый для складского хранения и транспортировки вид.
Могут использоваться и другие механизмы и технологические устройства для автоматизации непрерывного процесса производства.
Производители экструзионных линий
Экструзионные линии пользуются огромным спросом, и их производство налажено во многих странах Европы и Азии. Традиционными лидерами в производстве подобного оборудования считаются австрийские производители, практикующие выпуск подобных линий еще с середины прошлого столетия. Европейские системы всегда отличали высочайшее качество, использование самых современных инновационных разработок в области технологии обработки пластмасс.
В последнее время на рынок экструзионных линий активно поставляется продукция китайских производителей. Вопреки расхожему мнению, это вовсе не говорит о ее низком качестве – и надёжность, и характеристики выпускаемого оборудования в целом отвечают современным требованиям. Кроме того, цены на экструдеры из Китая могут быть значительно ниже европейских.
Стараются не отстать от жизни и отечественные промышленники. Так, пользуются спросом экструзионные линии «Полипром Кузнецк», выпускаемые в Пензенской области, или «Группы компаний СТР» из подмосковных Подольска и Воскресенска.
Цена на экструдеры для пластика варьируются от страны-производителя и индивидуальных характеристик устройства.
promresursy.com
что это такое? Описание экструдера. Как изготовить своими руками?
Экструзия представляет собой способ получения полуфабрикатов или изделий из полимерных материалов неограниченной длины. Применяется этот процесс также в пищевой и комбикормовой промышленности. Головкой экструдера расплав полимера выдавливается в формующую головку с нужным профилем. Этот способ изготовления, наряду с литьем пластмасс под давлением, на данный момент один из самых популярных. Экструзии подвержены почти все основные типы полимерных материалов: эластомеры, термопласты, реактопласты и прочие. Итак, сам процесс понятен, поэтому стоит рассмотреть экструдер: что это такое, как он работает, а также другие моменты, связанные с ним.
Принцип действия и конструкция
Экструзионная технология существует уже более шестидесяти лет, и за это время появилось много конструкций машин, предназначенных для ее реализации. Принцип действия прибора определяется сутью самого технологического процесса. Итак, если рассматривать экструдер, что это такое, становится понятно после определения того, что данный сложный физико-химический процесс протекает под влиянием механических усилий при условии высокотемпературного воздействия и присутствия влаги. Продукт при переработке нагревается за счет того, что механическая энергия превращается в тепло, выделяемое в процессе борьбы с внутренним трением, а также пластической деформации продукта либо благодаря внешнему нагреву.
В процессе экструзионной обработки имеется несколько сменных параметров, а именно: состав сырья, его влажность и природа. Во время производства может изменяться температура, давление, а также интенсивность и продолжительность воздействия на сырье.
Методы работы
Рассматривая экструдер, что это такое, будем разбираться по порядку. Существует три основных метода работы: холодная формовка, горячая экструзия и теплая обработка. Наиболее распространен в последнее время метод горячей формовки, осуществляемый при высоком давлении и скорости, когда имеется значительный переход механической энергии в тепловую. Чтобы реализовать процесс, можно использовать шнековый экструдер, у которого основным рабочим органом служит шнек специальной конструкции, осуществляющий вращение в цилиндрическом корпусе. Формообразующая матрица находится на выходе.
Схема экструдера предполагает, что в конструкции его рабочей части шнеки и камеры смонтированы для точного выполнения поставленных задач. Имеется загрузочная камера, куда осуществляется ввод сырья и разнородных добавок, закрытые камеры, в которых есть отверстия для измерения давления и температуры, а также добавление жидких веществ и отбор проб. Шнеки можно оснастить дополнительными элементами, благодаря чему перемещение продукта будет осуществляться под дополнительным сопротивлением, а также все будет перемешиваться в процессе.
Экструдер: что это такое и как он устроен?
Рабочую часть механизма с учетом стадий процесса обработки можно разделить условно на три зоны: первая, отвечающая за прием сырья; вторая, отвечающая за пластификацию и сжатие; третья — зона выпрессовывания продукта. Рабочая часть шнековых экструдеров может иметь одну из нескольких разных конструкций:
— одинарные шнеки: цилиндрические с постоянным или переменным шагом, конический, винтовой, конический с шагом, уменьшающимся к выходу;
— сдвоенные шнеки: вращающиеся в одном или разных направлениях;
— сдвоенные шнеки, входящие в зацепление: вращающиеся в одном направлении и самоочищающиеся, вращающиеся в разных направлениях и частично очищающиеся.
Использование
Экструдер зерновых работает за счет того, что в частицах зерна, находящихся в камере закрытого типа, при нагревании происходит нарастание внутреннего давления за счет испарений влаги. Из-за мгновенной разгерметизации камеры происходит расширение паровоздушной смеси, что приводит к увеличению объема зерновых частиц.
В комбикормовой промышленности чаще всего используются одношнековые механизмы с постоянным шагом и цилиндрической формой шнека. Производство экструдеров такой конструкции использует набор шнеков, а между ними в четко определенной последовательности находится несколько подпорных шайб, а шнеки и шайбы на шпильке закрепляются при помощи болта с конусной головкой. Кожух рабочей части изнутри оснащается несколькими продольными каналами, которые гарантируют, что продукт не будет перекручиваться во время перемещения. На выходе кожуха имеется обычная конусная гайка, снабженная отверстием. Регулирование зазора между конусами болта крепления шнеков с выходной гайкой позволяет регулировать температуру продукта. Так устроен экструдер. Что это такое, вам уже понятно, теперь осталось разобраться с иными моментами.
Производство механизмов
Разные модели экструдеров характеризуются различным конструктивным исполнением элементов, включенных в рабочую часть, числом рабочих камер, присутствием дополнительных систем, с помощью которых расширяются технологические возможности приборов, особенностью приводов, питателей и прочих частей. Форма цилиндра признана самой технологичной в плане изготовления, что делает ее себестоимость самой низкой.
Технология сегодня
Итак, можно рассмотреть, как работает экструдер. Что это такое, было описано ранее, а теперь стоит определиться с некоторыми важными моментами. Современные конструкции механизмов реализуют технологию сухой экструзии. Она так названа из-за того, что весь процесс осуществляется при помощи тепла, выделяемого в процессе прохождения продукта сквозь рабочую часть механизма. Имеется возможность использования пара при экструдировании. Для этого у прибора имеется камера предварительной паровой обработки сырья. Использование пара позволяет увеличить производительность и уменьшить износ основных частей и узлов механизма.
Сухая экструзия
Весь процесс занимает не более 30 секунд. Этого времени хватает для измельчения, тепловой обработки, обезвоживания, смешивания, обеззараживания, стабилизации и увеличения объема. Можно сделать экструдер своими руками, работающий по данной технологии. Для этого потребуется приобрести все элементы для будущего механизма, которые в дальнейшем будут соединены в соответствии со схемой прибора. Вам понадобится шнек подходящей конфигурации, электродвигатель, который станет основой механизма, корпус будущего прибора, подающая емкость и емкость на выходе, камера, в которой будет создаваться вакуум.
Альтернативные примеры
Процесс экструзии может использоваться не только при производстве. Существует такой прибор, как ручной сварочный экструдер, который предназначен для соединения полимерных материалов, а именно пленок, между собой посредством нагрева их краев с одновременной стыковкой. Чаще всего такой прибор используется для соединения элементов из термопластов. Эти вещества встречаются сейчас повсеместно. Это тазики, шланги, ведра, бочки, люки, емкости, канализационные решетки, элементы наружной и внутренней отделки помещений. Перечень можно составить достаточно длинный. Такое обилие термопластов привело к тому, что промышленные производители разработали весьма компактные приборы, которые предназначены для работы с этими материалами на местах их использования. Именно для этого был разработан сварочный экструдер. Его использование заметно упростило работы по сварке изделий из синтетических термопластов: поливинилхлорида, полиэтилена и полипропилена.
fb.ru
Оборудование-ЭКСТРУДЕР|ЭКСТРУЗИОННАЯ ЛИНИЯ ДЛЯ ПОЛИМЕРНЫХ ЛИСТОВ|QINGDAO LEADER MACHINERY CO., LTD.
Одношнековые экструдеры серии LSJ производства компании Qingdao Leader Machinery Co.,Ltd. (Циндао ООО Лидер Экструзионное Оборудование) является головным устройством в линиях, оснащенными соответствующими головками и дополнительным оборудованием, для переработки различных полимерных материалов ПНД, ПП, АБС, ПВХ, ПЭТ, ПК, ПС в трубы, профили, листы, гранулы и т.п. 1.Основн… Далее>>
Двухшнековые конические экструдеры серии LSZ характеризуется равномерным плавлением материала без его разложения, что гарантирует высокое качество продукции и высокую скорость экструзии изделий из ПВХ. Является головным устройством в линиях, оснащенными соответствующими головками (фильерами) и дополнительным оборудованием, для производства труб, лист… Далее>>
По составу оборудования линии для производства геомембран не отличаются от обычных линий для производства листовых материалов. Основные технические параметры: 1. Ширина листов: 1000 — 8000мм 2. Толщина листов: 0,5 — 3мм Геомембраны применяются в качестве гидроизоляционного материала: 1.в строительстве для гидроизоляции крыш и фундаментов; 2.при создании ис… Далее>>
Экструзионная линия предназначена для производства кровельного гофрированного листа ПВХ в виде шифера (черепицы). ПВХ шифер — материал с высокими эксплуатационными свойствами, является отличной альтернативой традиционной керамической черепице, шиферу и другим кровельным материалам. Внешний слой изготавливается из ПВХ с добавкой ультрафиолетов… Далее>>
Преимущества: Экструзионная линия предназначена для производства листов сотового поликарбоната, от одного до четырех слоев, в зависимости от требований покупателя Использование: реклама и дизайн; строительство, где сотовый поликарбонат используется для наружного и внутреннего остекления как легкий прочный конструкционный материал в строительс… Далее>>
Экструзионная линия предназначена для производства вспененных жестких ПВХ листов по технологии CELUKA. Технология заключается в том, что после выхода из экструдера газонасыщенная масса ПВХ поступает в калибратор, где происходит выделение газа из верхнего и нижнего слоев непосредственно соприкасающихся с металлическими пластинами. В этих местах проис… Далее>>
Данная производственная линия использует двухшнековый экструдер, плоскощелевую головку, трехваковский каландр и другие вспомогательные оборудования. Наша компания Данная производственная линия использует двухшнековый экструдер, плоскощелевую головку, трехвалковый каландр и другое вспомогательное оборудование. К комплектному производственному… Далее>>
Основные технические параметры: Ширина листа: 600-1800мм Толщина листа: 0.2-2мм Применения: Выпускаемые листы прочные, имеют высокую термостойкость, коррозионную стойкость. На поверхности можно сделать тиснение. Как полуфабрикаты можно использовать для изготовления подарочных пакетов, рекламы, папок, абажуров, ковриков для мыши, для пищевой упа… Далее>>
Экструзионная каландровая линия предназначена для производства однослойных или многослойных ПЭТ листов. Линия позволяет выпускать пленку и- или листы с различными свойствами: прозрачные, светорассеивающие, бесцветные, цветные, УФ – защитой. Использование: защитное остекление, санитарно-техническое использование, реклама и строительство, тара и упа… Далее>>
Основные технические параметры: Толщина листа: 0,2-2мм Ширина листа: 500-1500мм Характеристика экструзионной линии: 1. Экструдер / зкструдеры двухшнековый 2. Устройство замены сетки фильтра 3. Насос расплава (по требованию заказчика) 4. Плоскощелевая Т-образная головка 5. Трехвалковый каландр наклонный / вертикальный 6. Конвейе… Далее>>
Экструзионная каландровая линия предназначена для производства однослойных или многослойных ПЭ, ПП, ПС, АБС, ПВХ листов. Использование: тара и упаковка, санитарно-техническое использование, реклама и строительство и т.д. Основные технические параметры: 1. Ширина листов: 700мм/900мм/1020мм/1200мм/1300мм/1400мм/1500мм/1700мм/1800мм/2100мм/2200мм 2. Толщина листов: … Далее>>
Состав комплектной линии: Ленточный конвейер→Дробилка с водой→Одношнековый загрузчик сырья→Одношнековый высокоскоростной фрикционный промыватель→Шнековый конвейер №1→Ванна промывания→Шнековый конвейер №2→Горизонтальная машина обезвоживания→Циклон Характеристики: 1. Дробилка с 4 комплектами фиксированных ножей обеспечивает высокую… Далее>>
Процесс производства: Ленточный конвейер→Барабаное отделение→Стол для ручной сортировки→Металлоискатель→Ленточный конвейер→Дробилка→Устройство для снятия этикеток→Паровой горячий промыватель № 1 →Фрикционный промыватель→Паровой горячий промыватель № 2→Высокоскоростный фрикционный промыватель→Ванна промывания →Промывание оросител… Далее>>
Состав комплектной линии: Двухстадийный смеситель, двухшнековый конический экструдер, головка, гранулятор, двухшаговый воздушный транспортер и циклон для выпускаемых гранул. Данная линия производит гранулы методом горячей отрезки для переработки ПВХ. Особенность линии: передовая технология, универсальность, высокая производительность. Основ… Далее>>
Состав данной линии: Одношнековый экструдер, гидравлическое устройство для смены фильтров, гранулятор, центробежное обезвоживающее устройство, воздушный транспортёр и циклон для выпускаемых гранул. Специальная головка с водяным затвором пригодна для разного сырья: ПП, ПЭ и т.д. Линии отличаются высокой эффективностью, малой удельной энергоемкост… Далее>>
Каскадная грануляционная линия состоит из экструдера с устройством принудтельной подачи сырья, второго одношнекового экструдера, вакуумного устройства дегазации, устройства для быстрой замены фильтров, отрезного устройства для гранул и т д. Увеличен диаметр секции подачи сырья у шнека. Компрессор с большим объемом коэффициента сжатия. Устройство вакуу… Далее>>
Данная линия используется для грануляции полимерных материалов с высоким индексом вязкости, например, ПП, ПС, АБС, ПК. Шнек спроектирован для гранулирования различных материалов. Роторный гранулятор обладает стабильной работой; обеспечивая энергосбережение, безопасность в эксплуатации и т. д. Пресс-форма специально спроектирована для выпуска высококаче… Далее>>
Применения: Данная линия использует в качестве сырья ПВД. Применяя полимеры разных характеристик экструдируются односторонние или двухсторонние самоклеящиеся стрейч-пленки, которые имеют высокую прочности на растяжение, сопротивление на прокола и ударопрочность. Стрейч-пленки имеют хорошую прозрачность и расширение, широко используются для упако… Далее>>
Особенности: 1. Головка, дорны имеют спиральную конструкцию. Головка с непрерывным вращением 360 градусов. 2. Устройство для быстрой замены фильтров с легкой сменой сетки. 3. К линии установляются рад комплектных элементов: устройство расчета длины, продольное отрезное устройство, форсунки для воды охлаждения, циклон дл… Далее>>
Применения: Данная линия для производства термоусадочной пленки из ПЭ ПНД, выпускаемая пленка широко используется как упаковочная пленка, сельскохозяйственная укрывающая пленка и т.п. Основные технические параметры: Модель YD-C50 YD-C55 YD-C65 YD-C65-1 Диаметр шнека, мм 50 … Далее>>
www.extruder-cn.com
Описание экструзионной линии на примере линии EXT 2200/120/320| VFMSPB.RU
Назначение экструзионной линии
Экструзионная линия EXT 2200/120/320 предназначена для изготовления листов из ПНД, ПВД, АБС, ПС, ПП, ПЭТ и других термопластичных полимеров методом экструзии (выдавливания) расплавленной пластмассы через формующий инструмент, каландрования (точной калибровки по толщине, придания заданных прочностных свойств и необходимой чистоты поверхности), непрерывной обрезки краев в процессе движения материала (с целью получения листа заданной ширины), и периодической отрезки листов заданной длины.
Состав линии
В состав линии EXT 2200/120/320, (см. Рис.1) входят: шнековый (винтовой) экструдер (1), загрузочный бункер (2), фильтр очистки массы (3),
формующий инструмент — щелевая головка (4), калибровочное устройство-каландр (5), роликовый транспортер-рольганг (6), вытяжное устройство (7),
устройство отрезки листа (9) и централизованный пульт управления (ЦПУ) (8).
Исходный материал представляет собой дозированную смесь гранул сырья и суперконцентрата красителя или дробленых отходов предыдущего производства.
Материал засыпается в загрузочный бункер, откуда поступает в экструдер (рис. 2).
Подробное описание технологии экструзии(Рис. 2 и Рис. 1)
Экструдер
ЭКСТРУДЕР предназначен для размягчения (пластификации) исходного материала.
Принцип устройства экструдера(Рис. 2)
Рабочим органом экструдера является вращающийся винт-шнек(1), диаметром 120мм., установленный в отверстие гильзы(2). Вращение шнека с заданной скоростью обеспечивается управляемым приводом. Привод вращения шнека экструдера образован управляемым электродвигателем(3) и редуктором(4).
Вал электродвигателя и входной вал редуктора, а также выходной вал редуктора и хвостовик шнека, соединены между собой муфтами(5), имеющими упругий элемент для сглаживания колебаний нагрузки на привод, возникающей вследствие разницы давления материала по длине шнека.
Задание скорости вращения шнека производится с пульта управления привода(9).
Питание экструдера
Питание экструдера осуществляется блоком питания(7), на верхней панели кожуха которого установлена кнопка экстренного выключения питания в случае возникновения аварийной ситуации.
Установка экструдера(крепление)
Все рабочие органы экструдера размещены на станине(15). При этом, гильза(2) неподвижно закреплена на опорах станины, электродвигатель(3) и редуктор(4) зафиксированы болтами. Хвостовик шнека(1) установлен в подшипниковую опору(6):, фланец корпуса которой жестко соединен винтами с концевым фланцем гильзы(2).
Подача материала
Вращаясь, шнек(1) захватывает материал из загрузочного бункера(Рис.1 (2)) и подает через гильзу(2) и фильтр(Рис.1 (3)) в щелевую головку(Рис.1 (4)). В процессе подачи в гильзе(2) производится постепенный нагрев материала до требуемой температуры.
Устройство нагрева
Устройство нагрева исходного материала(13) представляет собой набор нагревательных элементов — спиралей, облегающих наружную
поверхность гильзы(2) по всей ее длине, соединенных параллельно, и образующими 6 зон регулируемого нагрева.
Зоны с 1-ой по 6-ую расположены в направлении от загрузочного бункера(Рис.1 (2)) к щелевой головке(Рис.1 (4)).
Общее количество элементов — 19.
Температура нагрева в каждой зоне задается собственным регулятором-измерителем(10) и фиксируется собственным датчиком (термопарой).
Система задания температурного режима экструдера включает в себя 6 регуляторов — измерителей ТРМ1, которые расположены на станине(15).
На ЦПУ имеется индикаторная панель, содержащая пояснительную схему компоновки системы нагрева и выдающую всю необходимую для оценки состояния
процесса информацию.
Каждая зона нагрева защищена кожухом(14).
Кроме того, в качестве дополнительного устройства стабилизации температуры, каждая зона оснащена вентилятором. Включение вентиляторов
производится при необходимости.
Последовательность повышения температуры нагрева от зоны 1 к зоне 6 обеспечивает необходимую для формования пластификацию материала.
При подаче, материал оказывает сопротивление движению, в результате чего в гильзе создается значительное давление на стенки и шнек.
Следствием этого является то, что шнек в процессе работы испытывает большие осевые нагрузки. Для восприятия этих нагрузок в опоре шнека
установлен упорный подшипник(6). Подшипниковая опора(6) образована радиальным подшипником, осуществляющим центровку
шнека и воспринимающим радиальную нагрузку, и упорным подшипником, воспринимающим осевую нагрузку.
Подшипники установлены и закреплены в собственном корпусе.
Для устранения опасности заклинивания шнека в случае попадания инородных (непластмассовых) предметов внутрь шнековой машины, конструкция шнека
EXT 2200/120/320 предусматривает постоянную глубину витка. Создание давления в зоне сжатия обеспечивается уменьшением шага винта.
ФИЛЬТР
ФИЛЬТР предназначен для воспрепятствования попадания в щелевую головку инородных тел и, в процессе работы, подлежит периодической очистке. Фильтр расположен между экструдером и щелевой головкой (см. Рис.1) и установлен в корпусе, образованном двумя фланцами, один из которых присоединен к гильзе, а другой к щелевой головке. На фильтр прикрепляется сетка.
ЩЕЛЕВАЯ ГОЛОВКА
ЩЕЛЕВАЯ ГОЛОВКА установлена на выходе экструдера и состоит из верхней и нижней части, которые неподвижно соединены между собой болтами и, в сборе, закреплены на станине.
В щелевой головке происходит формование пластичного материала в непрерывную ленту. Необходимым условием качественного и безотказного формования является температурный режим. Щелевая головка имеет собственную систему задания и контроля температурного режима, которая включает в себя совокупность нагревательных элементов, регуляторов-измерителей
и датчиков температуры. В качестве нагревательных элементов используются трубчатые электронагреватели (ТЭНы). Производится независимый нагрев верхней и нижней частей щелевой
головки, верхней и нижней кромок на выходе формуемого материала (губок).
Количество нагревательных элементов верхней части — 22, нижней части — 14.
Количество зон управляемого нагрева в верхней части — 10, в нижней части -6.
Подогрев губок производится отдельными ТЭНами (температура не задается, но регулируется). Задание температуры нагрева производится для каждой зоны.
В качестве устройств задания используются 10 регуляторов-измерителей ТРМ1 (на Рис. 2 устройство 10) и 1 восьмиканальный регулятор-изменритель
ТРМ-138 (на Рис. 2 устройство 11). В каждой зоне нагрева установлен собственный датчик температуры (термопара).
Температурный режим работы экструдера и щелевой головки является основным параметром технологии, устанавливается в результате тщательной отработки для каждого вида изделий,
и требует постоянного и внимательного наблюдения. Наблюдение за работой системы проводится по показаниям на индикаторной панели, которая расположена на ЦПУ(8).
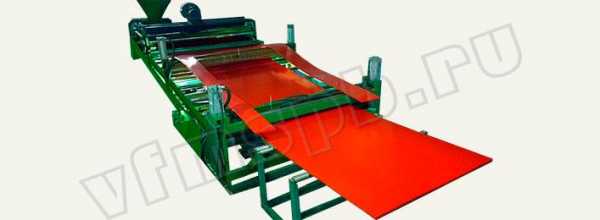
КАЛАНДР
КАЛАНДР расположен последовательно после щелевой головки и представляет собой механическую систему из трех валов (1-3), последовательно расположенных в вертикальной плоскости. При этом валы образуют две пары (верхний — средний и средний — нижний), в которых каждый из валов вращается в противоположном направлении.
Все исполнительные устройства и механизмы каландра размещены на станине, имеющей возможность перемещения относительно экструдера и фиксации на определенном расстоянии от
щелевой головки. Расстояние между щелевой головкой и каландром определяется в процессе отработки технологии данной продукции и фиксируется установочными винтами.
Каландр образован Валами, диаметром 320 мм. каждый, установленных в подшипниковых опорах, связанных со станиной. При этом опоры вала неподвижны,
а опоры валов имеют возможность перемещения по направляющим станины и фиксации, с помощью винтов, относительно вала на определенном расстоянии.
Скорость вращения валов каландра задается управляющим устройством-инвертором с Пульта.
Каландр имеет собственную систему стабилизации температурного режима. Теплоносителем является специальная жидкость (эмульсия),которая непрерывно циркулирует внутри
валов. Эмульсия заливается в расширительный бак до необходимого уровня. В баке эмульсия разогревается. Нагревательные элементы закреплены в крышке бака,
там же установлен датчик температуры. Средством подачи жидкости в систему является центробежный насос. Кроме того, в системе имеется радиатор, необходимый для охлаждения жидкости. Управление температурой осуществляется терморегулятором, который расположен на станине экструдера.
На выходе каландра, на станине, закреплено устройство продольной обрезки краев материала. На штанге, симметрично, с двух сторон установлены обрезные ножи и прижимы.
В работе ножи должны быть надежно зафиксированы на штанге (гайками, с двух сторон). Материал протягивается между верхним и средним, затем между средним и нижним валами с заданной скоростью, в результате чего приобретает требуемую прочность,
гладкость и равнотолщинность, необходимую толщину и ширину ленты.
РОЛЬГАНГ
РОЛЬГАНГ (роликовый транспортер) размещен на станине и представляет собой комплект роликов, закрепленных с возможностью их свободного вращения. Продукция в виде непрерывной ленты заданной толщины и ширины перемещается по транспортеру под воздействием вытяжного устройства и продолжает охлаждаться.
Вытяжное устройство образовано парой обрезиненных валов, которые синхронно вращаются в противоположном направлении, обеспечивая подачу
полимерной ленты к устройству обрезки. Скорость валов регулируется иныерторным регулятором частоты.
Устройство резки производит отрезку готовых листов от экструдируемого полотна.
vfmspb.ru
Экструзионная линия — Справочник химика 21
В области переработки пластмасс экструзией наметилась общая тенденция увеличения производительности экструзионных линий и установок на 35-40% по сравнению с существующими. Модернизация экструзионного оборудования создает возможности для такого увеличения, а также способствует повышению качества выпускаемой продукции. Важное значение в модернизации узлов экструзионных линий имеет совершенствование основного агрегата — экструдера. [c.236]
Экструзионные линии для производства профилей и труб [c.202]
Для нанесения покрытий из термопластичных полимерных материалов на электрические провода, кабели, стальные трубы, на деревянные планки и другие полуфабрикаты применяются экструзионные линии на базе одночервячных пластицирующих экструдеров, причем широкое использование получили экструзионные агрегаты в кабельной промышленности. Например, для [c.208]
Роботизация технологических процессов делает актуальной проблему получения реологических характеристик на встраиваемых в перерабатывающее оборудование вискозиметрах. В частности, описа на [32] конструкция нового промышленного реометра капиллярного типа, встроенного непосредственно в экструзионную линию двухшнекового экструдера. В работе [33] проведена сопоставительная оценка реологических характеристик термопластов, полученных на встраиваемом вискозиметре постоянного расхода и на капиллярном вискозиметре постоянного давления. В диапазоне скоростей сдвига, характерном для процессов переработки, обнаружены отклонения в 3-5%, а для полиэтилена — 10-14 % однако эту систематическую разницу можно учитывать с помощью коэффициентов корреляции. [c.452]
Пленка формуется посредством экструзии из расплава. Экструзионный процесс включает в себя серию операций, каждая из которых влияет на стабильность и устойчивость экструдата, а следовательно, и пленки. Процессы, происходящие в экструдере, — это загрузка, плавление, смешение, измерение и фильтрация. Кольцевая экструзионная головка формует полимерный рукав, который раздувается воздухом, поступающим в головку. Раздув рукава увеличивает размер пленки и ориентирует полимерный материал. Рукав проходит через зоны холодного воздуха, который отверждает полимер и управляет кристаллизацией [10]. На рис. 1.4 приведена схема экструзионной линии. [c.23]
В производственных условиях при переработке пластмасс возникновение и накопление зарядов статического электричества может происходить при засыпке полимерного материала в бункер литьевой машины при централизованной подаче сырья к литьевой машине пневмотранспортом в экструзионных линиях и агрегатах при пересыпании гранул, движении пленки или листов при таблетировании во время загрузки материала в бункер и перемещении таблеток по отводящему лотку при вальцевании и каландровании при производстве пленок и листов из термопластиков в производстве стеклопластиков и при получении изделий из газонаполненных пластмасс и т. п. [c.97]
Экструзионные линии для производства листов и плоских пленок [c.205]
Экструзионные линии для нанесения полимерных покрытий [c.208]
Экструзионная линия должна быть способна перерабатывать широкий спектр полиэтиленов с различными молекулярной массой, молекулярно-мас-совым распределением, содержанием и распределением сомономера. Менее мощные экструзионные линии используются только для переработки ПЭНП, поскольку их свойство снижения вязкости с увеличением скорости сдвига способствует переработке большого количества сырья при пониженной мощности. В процессе экструзии может потребоваться введение таких добавок, как антиоксиданты, ультрафиолетовые стабилизаторы, лубриканты (смазочная добавка), веществ, снижающих трение и повышающих клейкость поэтому может оказаться необходимым устройство для их раздельного впуска или сухого смешения. Экструзионная установка должна иметь устройство для плавления (пластикации) и перемещения расплавленного полимера через головку. Как правило, для этого используется одношнековый экструдер он наиболее подходит для распределительного смешения. Распределительное смешение используется для гомогенизации расплава, когда достаточно лишь хорошо перемешать компоненты. Двухшнековые экструдеры обеспечивают более интенсивное смешение и по- [c.24]
Особенности комплектующих устройств экструзионных линий описаны ниже. [c.207]
Тянущее, отрезное и приемное устройства в зависимости от типоразмера экструзионной линии должны иметь автономные или раздельные приводы, но с обязательным автоматическим согласованием скоростей перемещения заготовки через устройства комплектующего оборудования. [c.211]
Наложение изоляции на провода и кабель явилось одной из первых областей применения экструзии. Схема экструзионной линии для изолирования провода представлена на рис. 1.1. Полимер наносится на токопроводящую жилу, образуя первичный изолирующий слой. Металлический провод подается к фильере с отдающего устройства, проходя по пути в угловую головку через правильник и подогреватель (рис. 1.2). Изолированный провод выходит из фильеры и попадает в водяную охлаждающую ванну. Затем он проходит через электрический контроллер, где проверяется целостность изоляции, и поступает на тянущий кабестан, оттуда направляется к приемному устройству (намотка на бобину). [c.16]
При подготовке оборудования к пуску проверяют наличие воды, конденсата, сжатого воздуха и электроэнергии производят внешний осмотр экструзионной линии, чтобы убедиться в отсутствии посторонних включений в загрузочной воронке, посторонних предметов в зоне обслуживания, в исправности систем блокировки, контрольно-измерительных приборов, ограждения движущихся частей. [c.216]
Работу оборудования экструзионной линии проверяют на холостом ходу. Нельзя включать червячный пресс, в цилиндре которого материал находится в холодном состоянии, т. е. с температурой ниже температуры плавления (стеклования). [c.216]
В процессе пуска экструзионной линии в работу после включения червячного пресса не разрешается проталкивать материал к червяку механическими предметами в случае необходимости принудительной подачи материала и при отсутствии специального питающего устройства используют для этой цели предметы из цветного металла или дерева. [c.222]
В качестве примера на рис. 7.8 приведены варианты расположения экструзионных линий по производству листов для разных групп [c.223]
Экструзионная линия для производства пленки с раздуванием рукава вверх приведена на рис. 10-У. Выдав- [c.140]
Особенности обслуживания и ремонта экструзионных линий [c.158]
Выбор материалов для изготовления основных деталей экструзионных линий, а также методов механической и термохимической обработки определяется свойствами перерабатываемых пластмасс, требованиями к прочности и долговечности деталей. Обычно основные детали экструзионных линий должны отличаться высокой коррозионной стойкостью, твердостью, прочностью и степенью шероховатости. Поэтому при их изготовлении применяют высоколегированные стали, подвергнутые специальным видам термохимической обработки — азотированию, хромированию, наплавке или напылению твердых сплавов, алмазной или обычной шлифовке (табл. 14-У). [c.158]
Материалы и виды термохимической обработки деталей экструзионных линий [c.159]
При эксплуатации экструзионных линий следует соблюдать необходимую чистоту рабочего помещения, исключающую загрязнение перерабатываемого материала и особенно попадание в него металлических включений производить чистку оборудования сразу же после окончания работы, пока оно не охладилось более чем на 5—10° С ниже температуры плавления термопласта применять для чистки деталей головок, насадок от перерабатываемой пластмассы только деревянный, медный нли латунный инструмент смазывать детали байонетных затворов, винтовых соединений, которые работают при высоких температурах и находятся под давлением, суспензией графита в воде обеспечивать плотное прилегание нагревательных элементов к нагреваемой поверхности во избежание быстрого выхода элементов из строя. [c.159]
Эта машина устанавливается в экструзионной линии, непосредственно после автоматической пилы и соединяется со столом, с которого нарезанные трубы подаются на сварку, а фитинги под действием силы тяжести подастся в бункеры. [c.77]
Во время первых попыток экструзии каучука с рецептурой А (табл. 3.3) с определенными реологическими и другими физическими свойствами (табл. 3.4) было установлено, что когда материал достигает туннеля с горячим воздухом, пористая труба начинает разрушаться. Схема процесса в экструзионной линии приведена на рис. 3.3. [c.46]
Наложение ПЗО и ТЗО на ОВ проводят с помощью экструзионных линий с, диаметром шнека 25—32 мм (рис. 8.1). В некоторых случаях вместо ПЗО из экструдируемых материалов используют специальные УФ-отверждаемые акрилатные полимеры, наносимые протягиванием ОВ через фильеру. Технические данные применяемого материала приведены в табл. 3.3. [c.163]
Различные схемы экструзионных линий с охлаждаю-. щими валками показаны на рис. 102, а, б и в. Вадки охлаждаются водой и спроектированы так, чтобы обеспечить максимальную теплопередачу равномерно по всей длине. На рис. 102 показаны два охлаждающих валка, хотя при высоких скоростях работы применяются и три аналогичных валка. [c.212]
Рассмотрим экструзионную линию для производства голубых пакетов из рулона пленки, полученной методом раздува. Можно изготовить пакеты из такого рулона и оценить однородность их окраски. Если все пакеты на вид одинаково окрашены, а количественная оценка показывает, что они содержат фактически одно и то же количество голубого пигмента, значит пленка совершенно макрооднородна. И напротив, если анализ показывает, что общая концентрация пигмента практически одинакова во всех пакетах, но внешний вид отдельных пакетов неодинаков, и они имеют пятна, полосы, прослойки и т. д., то это означает наличие определенной текстуры. Следовательно, такой анализ позволяет обнаружить как различия в содержании пигмента в отдельных пакетах, так и различия в текстуре. Если смесь, поступающая в экструдер, неоднородна по составу, то с большой вероятностью можно обнаружить на рулоне пленки участки, окрашенные в голубой цвет и совсем не окрашенные, или участки с широкой гаммой оттенков голубого цвета. [c.186]
Экструзионная линия для покрытия провода резиной, которую требуется подвергнуть термической вулканизации, описана Родесом и Влеком . Кабель проходит вертикально вниз через экструзионную головку и вулканизационный туннель. Затем он охлаждается. При-че 1 вначале кабель проходит под водяным дущем, а затем пропускается через охлаждающую ванну. Далее провод поступает на тянущее устройство и приемное оборудование обычной конструкции. [c.208]
Моноволо кна изготавливаются из полиэтилена, полистирола, найлона, сарана, поливинилхлорида и полипропилена диаметром от 0,09 до 1,5 мм и обычно имеют круглое поперечное Сечение, о могут иметь и другие профили. -Схемы экструзионных линий для производства хмоноволокон из различных материалов приведены на рис. 124. [c.242]Упаковочные средства зачастую предназначены лншь для разового использования, поэтому они должны быть как можно более дешевыми. Выполнение этого требования обеспечивается применением ваккум-формования листовых (или пленочных) материалов в многогнездных формах. Агрегаты для упаковки в настоящее время специализированы на изготовлении определенных изделий. Они представляют собой комбинацию различных устройств, в число которых входит и узел вакуумного формования. Такого рода агрегаты могут состоять из экструзионной линии, машины для формования заготовки, хтройства для [c.416]
Наладчик экструзионных линий обязан проверить, кроме того, исправносгь используемых грузоподъемных приспособлений и крепежного инструмента. [c.224]
В США известно повторное применение упаковок из ударопрочного полистирола. Упаковку измельчают на ножевых дробилках. Однотипность перерабатывающего материала обеспечивает применение метода всплытия — осаждения . Размолотый материал промывают, просушивают и на экструзионной линии переплавляют в регранулят [96]. Подобный процесс переработки известен и для упаковки из полипропилена. [c.87]
Наложение изоляции производится на экструзионной линии для обычных ТФП. Дополнительным требованием к головке экструдера является необходимость обеспечения строгой симметричности потока расплава в головке, поэтому головки с рассекателем являются более предпочтительными. Применяют инструмент с обжатием, угол матрицы около 30°, а длина формующей части около 1—1,5 М М, угол дорна 15—20°, дорн имеет направляющую трубку длиной около 25 мм, которая утоплена в матрицу на 1—1,5 мм. Инструмент рассчитывают следующим образом. Внутренний диаметр направляющей трубки Dbh выбирают на 0,15—0,20 мм больще диаметра жилы D. Толщина стенки направляющей трубки А около 0,25 мм. Диаметр матрицы Dm зависит KaiK от типа 1и количества материала, используемого в качестве центров активации порообразования, так и от количества газа и окончательно устанавливается экспериментально. Ориентировочно >м может быть рассчитан по формуле [c.121]
chem21.info