Содержание статьи
- Описание термина – что такое легированная сталь
- Химический состав легированной стали
- Виды легированных сталей
- Что означают добавки легированной стали и их влияние на свойства
- Маркировка: какие марки стали называются легированными
- Применение легированной стали
- Сварка сплавов
В данной статье мы расскажем про один из наиболее распространенных методов, а также дадим ответ про легированную сталь – что это такое.
Любой металл, а также его сплав, имеет механические и химические характеристики. Такая наука, как материаловедение, вместе со всей металлургической промышленностью, занимаются изучением свойств материалов, а также находят способы для их улучшения.
В первую очередь отметим, что мы имеем дело не с отдельным веществом, а с составом, основные компоненты которого – железо (не менее 45%) и углерод. Но в отличие от классического в марки добавляют специализированные легирующие элементы. Их концентрация не очень большая, но даже эта небольшая доля (обычно от 1 до 3%) способствует значительному изменению в лучшую сторону характеристик материала.
Описание термина – что такое легированная сталь
Физические свойства, такие как прочность, пластичность, хрупкость, могут быть увеличены или уменьшены в несколько раз. Изменение кристаллической решетки материалов активно применяют в металлургии, а также при производстве многочисленных деталей и корпусов для автомобильного, машинного, станочного и прочего производства, а также для создания строительных конструкций и инструментов. Сфера применения настолько велика, что сплав начали изготавливать большими партиями, он постепенно вытесняет долю изготавливаемого железа и обычных стальных веществ.
Исходя из приведенной информации, легирование стали – это металлургический процесс выплавки, в ходе которого в состав добавляются материалы примесей. При этом есть два вида операции:
- Объемный – когда компоненты попадают в глубинную структуру. В расплав или шихту внедряются хром, никель и пр.
- Поверхностный – в ходе него происходит диффузионное или иное напыление, то есть покрывается только верхний слой.
Процесс начал использоваться относительно недавно. Впервые эксперименты начали проводить в 1882 году. И с первого же образца исследователи обнаружили, что вместе с улучшением физических свойств значительно снижается степень обрабатываемости. Простыми словами, с материалом просто стало сложно работать. Безусловно, к настоящему времени все дополнительные эффекты легирования изучены, поэтому составлены специальные ГОСТы для разных способов металлообработки.
Химический состав легированной стали
Есть постоянные компоненты – это те, которые есть в любом сплаве данной категории, есть также необязательные, легирующие ингредиенты. Сперва перечислим те, которые образуют классический материал:
- Железо. Это очень ковкий сам по себе металл, который добывается из руды. Особенность в том, что его довольно много находится в недрах земли, по добываемости он на втором месте после алюминия. Он хорошо вступает в реакции, именно по этой причине его можно сплавлять различными образами. В процентном соотношении его может быть от 45 до 97-99 процентов. Точное количество частей мы называть не будем, поскольку существует очень много марок сталей, состав которых разнится.
- Углерод. Это один из неотъемлемых компонентов. При совокупности данных веществ увеличиваются природные качества железа. В среднем его добавляют от 0,1% до 1,4% к общей массе. Чем больше его содержание, тем выше прочность. Все стальные изделия делят на углеродистые и низкоуглеродистые.
- Марганец. Интересный ингредиент, который также является легирующим. Хотя если его меньше, чем 1%, то особенных свойств он не придает. Сам по себе это очень красивый серебристый металл, именно от него слитки приобретают свой характерный перелив. Но основная заслуга марганца в том, что он является раскислителем, то есть способствует удалению из сплава кислорода, который, в свою очередь, негативно влияет на особенности. Есть интересные соединения (имени Гадфильда – создателя), которые содержат около 11 – 14 процентов. В таком случае сталь теряет свои магнитные качества, а также становится очень ударопрочной и износостойкой, поскольку при ударах упрочняется.
- Кремний – обязательный элемент, который при большом содержании (более 0,8%) имеет легирующие свойства. Он тоже является раскислителем, а также увеличивает стойкость, предел упругости, жаропрочность и некоторые другие особенности.
Кроме того, в составе обычно есть вредные и скрытые примеси. От них пытаются избавиться, но, к сожалению, полностью убрать не получается. Поэтому в крайне малых дозах в образцах есть:
- Сера, из-за которой увеличивается красноломкость – появляются трещины на разогретой заготовке.
- Фосфор, он приводит к увеличению хладноломкости, то есть хрупкости.
- Кислород, азот и водород – «разрыхляют» структуру.
- Окислы и нитриды – могут привести к надрывам.
Третья группа компонентов – это случайные. Они попадают в емкость вместе с шихтами, то есть со смесью исходных материалов, и не несут положительного влияния. Бывают безвредными или не очень полезными, но из-за малой доли содержания практически не важны. К ним относят:
- медь;
- цинк;
- свинец;
- хром;
- никель и пр.
И, наконец, четвертая группа – это специальные легирующие добавки. Эти элементы вводятся дополнительно для повышения определенных характеристик. Именно они делают из классического сплава упрочненный. Более подробно мы перечислим компоненты в соответствующем разделе статьи.
Виды легированных сталей
Основная классификация разделяет все марки на три подвида по количеству полезных примесей. Представим процентное соотношение в таблице:
Название | Процент добавок |
Низколегированная | Около 2,5%. Положительные качества прибавились, но при этом ковкость и прочие характеристики для металлообработки не сильно поменялись. |
Среднелегированная | От 2,5% до 10%. Используется такое соединение чаще всего. |
Высоколегированная | От 10% до 50%. Максимальная прочность и дороговизна – отличительные черты таких изделий. |
Помимо этого, все распространенные легированные стали различаются по маркам. Об этом более подробно расскажем в разделе про маркировку.
Классификация
Вне зависимости от того, какое процентное содержание легирующих веществ в сплаве, он также может быть разделен на три подвида:
- Конструкционный – применяется для изготовления разных деталей, механизмов и конструкций в машиностроении, станкостроении, прочих сферах промышленности и в строительстве. Это очень прочный материал, который может выдерживать большие статические и динамические нагрузки. Именно из таких марок изготавливаются двигатели и запчасти для автомобилей.
- Инструментальный – очень жаропрочный, который предназначен для создания инструментов – как ручных, так и станочных. Большинство фрез, резцов, сверл изготовлены именно из такой стали.
- С особыми свойствами. Если предыдущие два сорта скорее брали прочностью и надежностью, то данный подвид отличается химической или термической устойчивостью.
Последнюю категорию ряд исследователей даже классифицирует отдельно, утверждая, что ее можно поделить на:
- Жаропрочные – они выдерживают температуры вплоть до 1000 градусов.
- Устойчивые к коррозии металла, поэтому их можно применять в изделиях и конструкциях, которые предназначены для эксплуатации в условиях повышенной влажности.
- Жароустойчивые и окалиностойкие – характеристики отмечают их невосприимчивость к распаду.
Что означают добавки легированной стали и их влияние на свойства
Мы уже упоминали, что некоторые компоненты могут быть как обязательными, так и специальными примесями – в зависимости от их количества. Различные марки могут содержать:
Элемент | Влияние |
Хром | Значительно защищает от коррозии, способствует повышению твердости, а также ударопрочности. Показательно то, что много хрома добавляют в нержавейку. |
Никель | С добавлением данного вещества сплав становится более вязкий и пластичный, уменьшается его хрупкость, что очень важно, например, перед обработкой давлением – прессованием или штамповкой. |
Титан | Снижает зернистость, делает структуру более однородной, а значит, менее подверженной появлению трещин и расколов. Дополнительно улучшается восприимчивость к металлообработке и устойчивость к ржавлению. |
Ванадий | Как и после внедрения титана, можно заметить менее зернистую форму. Также характерно увеличение текучести и порога прочности на разрыв. |
Молибден | После него намного эффективнее процесс закалки, а также снижается хрупкость, появляется большая выносливость к ржавлению. |
Вольфрам | Кроме повышения твердости, он еще и помогает при термообработке – зернистость не увеличивается при нагреве, а при отпуске не сильно страдает ломкость. |
Кремний | Его задача – одновременное увеличение прочности и сохранение уровня вязкости. Но если его будет более 15%, то можно наблюдать за повышением магнитной проницаемости и сопротивляемости электричеству. однако нужно быть осторожным, поскольку сталь становится более хрупкой. |
Кобальт | Хорошо защищает от быстрого разрушения под воздействием высоких температур; делает выше ударопрочность |
Алюминий | Добавляет окалиностойкость, то есть при большом жаре не происходит быстрого окисления. |
Мы перечислили основные добавки, которые применяются при легировании. Также сделаем отдельную таблицу для примесей, которые невозможно полностью убрать из состава.
Элемент | Влияние |
Углерод | Очень сильно повышает прочность, твердость, ударостойкость, предел текучести. Но есть строгие ограничения по его добавлению. проще говоря, если его будет более 1,2 – 1,4 процента, то все перечисленные характеристики, напротив, пойдут на спад вместе с пластичностью. |
Марганец | Выше мы представили его значимость в качестве раскислителя. Но вещество защищает не только от кислорода, но и от серы, а зачем защищать, читаем ниже. |
Сера | Высоким называется уже ее содержание, превышающее 0,6%. Примесь в такой концентрации приводит к плохой свариваемости, сниженной прочности, пластичности и коррозионной устойчивости. в общем, этот ингредиент не приносит никакой пользы, только вред. |
Фосфор | Его наличие может привести к завышенному показателю хрупкости и текучести, а также к понижению вязкости и пластичности. |
Азот, водород и кислород | Газы способствуют разрыхлению структуры, из-за чего сплав становится хрупким, менее выносливым к нагрузкам и недостаточно вязким. |
Маркировка: какие марки стали называются легированными
Нормативный документ, который регламентирует название каждого нового подвида, – это ГОСТ 4543-71. Потребность в наличии такой систематизации возникла из-за огромного количества разновидностей, которые только увеличиваются с каждым годом, потому что открываются новые соединения и пропорции. Каждый вид предназначен для отдельной сферы деятельности и уникален по-своему. Чтобы их отличать, используют специальные нанесения. Вот как она выглядит:
Или так, на английском языке:
В первом случае букв указано не было, значит это просто классический сплав с добавками. Но во втором мы видим спереди «Х» – ее наличие говорит, что перед нами хромистая сталь. Если в начале стояли другие, они бы свидетельствовали о следующем:
- Ж – нержавеющая;
- Е – магнитная;
- Я – хромоникелевая нержавейка;
- Ш – шарикоподшипниковая;
- Р – быстрорежущая инструментальная.
Также аббревиатуры могут стоять справа. Например:
- А – высококачественная;
- Ш – особовысококачественная;
- Н – полученная способом нагартованного проката;
- ТО – использован термически обработанный прокат.
Теперь о цифрах и буквах внутри самой маркировки. Цифровое обозначение обычно показывает процентное соотношение вещества. Но так как нет возможности уточнять все до сотых частей, то принято округлять до целых. А если содержание не превышает 1%, то буквенный знак присутствует, а цифра не ставится. Сами элементы записываются либо по химическим формулам, либо по первым значениям. Посмотрим более полный перечень:
Если вы хотите исчерпывающие списки и перечни марок, следует заглянуть в вышеупомянутый ГОСТ.
Применение легированной стали
Сфер использования настолько много, что их сложно перечислить. Скажем только о некоторых производствах:
- Инструменты для медицины, в том числе острые режущие предметы.
- Лезвия.
- Подшипники и прочие детали с высокой радиальной и опорной нагрузкой.
- Резцы, фрезы, сверла и прочая оснастка для станков по металлообработке.
- Корпуса для техники и приборов.
- Нержавеющая посуда – ведра, тазы и пр.
- Делали для автомобилестроения.
Это и многое другое можно изготавливать из данного вещества. Любые задачи, которые требуют превосходных прочностных качеств, могут рассчитывать на легированную сталь.
Свойства
В зависимости от легирующих компонентов они могут быть различными, но в целом улучшаются следующие характеристики:
- Коррозийная устойчивость. Иногда достаточно только обработать верхний слой защитным составом, но как быть с деталями, которые постоянно соприкасаются с влагой и кислородом? Ответ простой – легировать.
- Прочность.
- Твердость.
- Отсутствие хрупкости.
- Стойкость к нагрузкам на растяжение и сжатие.
- Нужный уровень вязкости и предела текучести.
- Уменьшение намагниченности.
Производство
Основной способ – металлургический. В ходе него в расплавленный металл добавляют нужное количество примесей. Затем задаются дополнительные условия, в которых диффузия или иные реакции проходятся с более высокой скоростью.
Второй вариант легирования – нанесение поверхностного слоя таким образом, что вещества начинают взаимное проникновение друг в друга.
Сварка сплавов
Мы отмечали, что после добавления компонентов металлообработка, в том числе с помощью сварочного аппарата, затрудняется. Посмотрим, в чем особенности.
Низколегированных
Рекомендации:
- Нельзя допускать быстрого остывания шва – тогда могут появиться микротрещины.
- Аппарат должен быть с обратной полярностью и постоянным напряжением.
- Нужно использовать электроды с фтористо-кальциевым покрытием.
- Процесс – без перерыва, плавно со средней скоростью в 20 м/ч.
- Напряжение – 40 В и сила тока – 80 А.
Среднелегированных
Особенности:
- В электродах должно быть меньше легирующих веществ, чем в сплаве.
- Если лист шире, чем 5 мм, применяйте аргоновую сварку.
- При газовом аппарате используйте смесь из ацетилена и кислорода.
Высоколегированных
- Тепловой захват материала – минимальный.
- Электроды с фтористо-кальциевым покрытием.
- Не стоит применять газовую сварку.
В статье мы рассказали все про легированную сталь: что это значит, особенности получения, свойства и состав. Надеемся, что информация была для вас познавательной.
После того, как ознакомитесь со статьей, можете прочитать про наши товары. Компания «Рокта» уже 15 лет на российском рынке. За это время мы охватили практически все города страны.
Уже более 3 000 лет человечество обрабатывает железо изготавливая различные орудия, машины, домашнюю утварь. Несмотря на относительно высокие механические свойства этого металла его разрушение в результате коррозии не способствует долговременному использованию железных изделий на открытом воздухе.
Ещё одним существенным ограничением в использовании данного металла является его невысокие эстетические качества. Чтобы существенно улучшить данные свойства при производстве стали используются добавки придающие устойчивость к окислению, появлению на её поверхности блеска и существенному увеличению прочности металла.
Что такое легированная сталь
Это углеродистая сталь для улучшения технологических свойств которой введены специальные легирующие элементы. Процент добавок в составе невелик, но даже при незначительной концентрации, физические свойства металла улучшаются в несколько раз.
В зависимости от вида используемых добавок при производстве стали металл приобретает следующие свойства:
- неподверженность коррозии;
- упругость;
- тугоплавкость;
- прочность.
Для придания перечисленных качеств в состав добавляют следующие металлы:
- хром;
- никель;
- молибден;
- вольфрам;
- медь.
Зачастую в углеродистую сталь достаточно добавить 1 — 3% легирующих элементов для придания ей необходимых свойств и качеств.
Видео:
Виды легированных сталей
От процентного содержания добавок стали разделяются на:
- Низколегированные — содержание добавок менее 2,5%
- Среднелегированные — 2,5 — 10%.
- Высоколегированные — более 10%.
Также легированные стали подразделяются на следующие виды:
- конструкционные;
- инструментальные;
- с особыми физическими свойствами.
Конструкционные и инструментальные изделия используются в тех областях применения металлов, где необходима повышенная прочность. Легированные стали с особыми физическими свойствами могут быть устойчивыми к коррозии, высокой температуре и к химически агрессивным средам.
Маркировка легированных сталей
Из-за большого разнообразия сплавов с улучшающими добавками появилась необходимость в их маркировке. Легированные стали классификация и маркировка которых будет приведена ниже очень легко идентифицировать по буквенному обозначению, а также по указанию процентного состава тех или иных веществ в металле.

Расшифровка
Маркировка включает в себя буквы, которые обозначают предназначение металла.
- Ж, Х, Е — обозначение нержавеющих, хромистых и магнитных сплавов.
- Я — хромоникелевая нержавеющая сталь.
- Ш — шарикоподшипниковая.
- Р — режущая.
- А, Ш — качественная и высококачественная легированная сталь.
Также в сплавах могут содержаться следующие элементы:
- Азот — А
- Алюминий — Ю
- Бериллий — М
- Бор — П
- Вольфрам — В
- Ванадий — Ф
- Кобальт — К
- Кремний — С
- Марганец — Г
- Медь — Д
- Молибден — М
- Магний — Ш
- Ниобий — Б
- Никель — Н
- Селен — Е
- Титан — Т
- Фосфор — П
- Хром — Х
- Цирконий — Ц
- Редкоземельные металлы — Ч
Если легированные стали маркировка которых после букв не имеет цифр не содержат ниобия, молибдена, ванадия, алюминия, азота, бора, титана, циркония и редкоземельных металлов, то это будет говорить о том, что в материале содержание легирующего элемента менее 1,5%. Для перечисленных выше металлов имеется исключение из данного правила, по причине влияния на механические свойства сплава даже десятых долей процента.
Если перед буквенным обозначением стоит цифра, то это показатель содержания кремния, а расположение цифр после буквы указывает процентное соотношение обозначенных химических элементов.
Видео:
Применение легированных сплавов
Благодаря высоким эксплуатационным характеристикам легированная сталь применение находит в машиностроении, изготовлении инструментов, труб и строительных материалов.
Детали машин обычно изготавливают из перлитных металлов. К этой категории материалов относятся низколегированные и среднелегированные стали, которые после отжига имеют структуру позволяющую легко обрабатывать металл с помощью режущего инструмента.
Низколегированные стали благодаря повышенным прочностным характеристикам позволяют существенно экономить денежные средства при строительстве крупногабаритных сооружений и машин. Например, в судостроительстве благодаря использованию материала удаётся уменьшить толщину применяемого металла.
Легированные стали с добавками хрома широко используются для производства изделий, которые устойчивы к воздействия молочной и уксусной кислоты, а также следующих деталей работающих под значительным давлением:
- Поршневые пальцы, карданные крестовины и другие изделия предназначенные для эксплуатации в условиях повышенного износа.
- Кулачковые муфты, плунжеры и шлицевые валики.
- Шестерни коробок передач и червячные валы, а также другие изделия для работы на малых и средних скоростях.
Высоколегированная сталь широко используется для производства деталей устойчивых к коррозионному разрушению. Такие изделия также устойчивы к высоким температурам и способны работать в условиях до +1100 градусов.
Некоторые виды сплавов благодаря особым тепловым качествам имеют специальное применение, например:
- ЭН42 — материал обладает коэффициентом расширения таким же как и у стекла, поэтому применяется в качестве электродов в лампах накаливания.
- Х8Н36 — обладает постоянной упругостью, которая не изменяется в температурных пределах от минус 50 до +100 градусов. Благодаря неизменяемой упругости такой материал широко используется для
- И36 — сплав обладает нулевым коэффициентом температурного расширения, поэтому идеально подходит для изготовления различных эталонов и калибровочных изделий.
Сварка легированных сталей: особенности
Легированные сплавы обладают хорошей пластичностью, поэтому из них можно изготовить сложные конструкции методом сварки. По причине различного содержания добавок каждый тип легированных изделий имеет свои особенности.
Сварка низколегированных сталей
Особенность сварных соединений низколегированных сталей заключается в высокой сопротивляемости холодным трещинам и хрупкому разрушению. Но, такие свойства соединительного шва можно достичь только при правильном сваривании.
Если процесс предварительного нагрева будет нарушен либо сварной шов подвергнется слишком быстрому остыванию металл может получить в местах соединения микроскопические повреждения, которые значительно уменьшат прочность всей конструкции.
Низколегированные стали марки 10Г2СД, а также 14ХГС и 15ХСНД свариваются с использованием аппарата постоянного тока с обратной полярностью. Электроды для сваривания должны иметь фтористо-кальциевое покрытие. Величина сварочного тока должна точно соответствовать типу электрода, толщине металла и типу сплава. Несоблюдение этого требования также отразится на качестве сварного шва и, как следствие, на прочности изготавливаемой конструкции.
Сварка низколегированной стали должна осуществляться без перерыва, чтобы весь шов был выполнен без при температуре металла не менее 200 градусов. Средняя скорость сварки составляет 20 м/ч, при напряжении 40 В и силе тока 80 А.
Видео:
Сварка среднелегированных сталей
При изготовлении конструкций из среднелегированных сталей необходимо использовать сварочные материалы, в которых содержание легирующих элементов должно быть меньше, чем в свариваемом материале.
Только при использовании таких материалов можно добиться получения шва с высокой устойчивостью к деформации. Если при изготовлении изделий из среднелегированных сталей толщина листа не превышает 5 мм, то высокого качества соединения можно достичь при использовании аргонодуговой сварки.
Если для соединения деталей используется газовая сварка, то в качестве источника горения следует применять ацетилен в смеси с кислородом.
Сварка высоколегированных сталей
Если для производства металлических деталей применяется высоколегированная сталь, то в этом случае следует применять сварочное оборудование с минимальным тепловым захватом материала. Это необходимо для снижения вероятности коробления металла во время сварки, по причине большого содержания в составе металла различных примесей.
Электрическая сварка высоколегированных сплавов осуществляется с использованием электродов с фтористокальциевым покрытием. В этом случае удаётся добиться высоких показателей механической и химической прочности сварного шва.
Применение газовой сварки при изготовлении конструкций из высоколегированных сталей нежелательно. В исключительных случаях возможно использование газовой сварки для соединения жаропрочного высоколегированного стального листа толщиной не более 2 мм.
Видео:
Заключение
Применение легированных сплавов при изготовлении металлических деталей и конструкций позволяет придать ним необходимые физические качества. При работе с такими металлами обозначение легирующих элементов в стали помогает подобрать заготовку с нужными параметрами, из которой затем будет изготовлена конструкция.
При использовании таких сплавов необходимо не только знать их состав, но и способы соединения при помощи сварки. Поэтому если следовать рекомендациям изложенным в данной статье, то можно получить высококачественное изделия с заданными параметрами.
Пожалуй, нет в мире такого человека, который бы не слышал про самый распространенный сплав железа на земле – сталь. Помимо того, что материал имеет немало разновидностей, он используется в производстве практически любых железных конструкций и предметов. Причем отдельного внимания заслуживает легированные сплавы, которые обладают особыми свойствами. В современной промышленности сложно найти какую-либо отрасль, где не используется легированная сталь. Что такое и чем данная разновидность отличается от всех остальных?
Что это за материал?
Обычная сталь – это соединение железа углерода и ряда примесей. Под определением «легированная сталь» (ЛС) подразумевается особый сплав, который получен путем внедрения некоторого количества химических элементов. Это делается с целью получения необходимых физических и химических свойств металла.
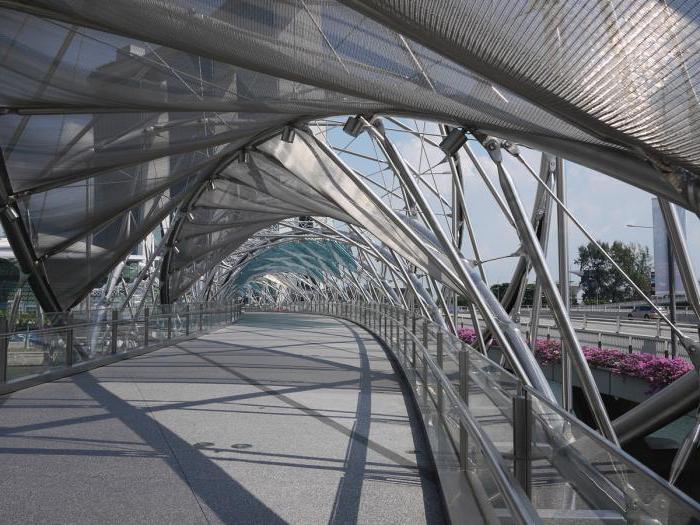
Как правило, добавляются такие элементы периодической таблицы Менделеева, без которых сложно обойтись в зависимости от конкретной ситуации:
- Никель – Н (Ni).
- Медь – М (Cu).
- Ниобий – Б (Nb).
- Хром – Х (Cr).
- Марганец – Г (Mn).
- Кремний – С (Si).
- Ванадий – Ф (V).
- Вольфрам – В (W).
- Молибден – М (Mo).
- Титан – Т (Ti).
- Алюминий – А (Al).
- Цирконий – Ц (Zr).
- Кобальт – К (Co).
Но помимо них находят применение молибден с алюминием. При этом каждый из этих элементов добавляется с определенной целью. И их количество напрямую влияет на получение необходимых качеств. Теперь уже становится немного понятно, что такое легированная сталь.
Добавки
Некоторые из них, повышая какие-то определенные свойства материала, занижают другие качества. К примеру, при помощи марганца можно существенно повысить прочность и твердость металла наряду с улучшением режущих качеств. В то же время это приводит к увеличению зерна, что снижает стойкость к ударным нагрузкам.
Добавление хрома, наоборот, может повысить эти качества и одновременно с этим увеличить жаропрочность. Благодаря никелю сплав становится более упругим, а если его количество преобладает, то металл приобретает высокие показатели коррозийной стойкости и жаропрочности. Нержавеющая сталь, о которой знает каждый, это как раз сплав из последних двух металлов либо материал с содержанием хрома 27 %.
Каждого, кто знает, что собой представляет легированная сталь, что такое легирование — понимает не до конца. Так вот, суть его как раз заключается в добавлении этих элементов. Но вернемся к нашим «примесям» – молибден с одной стороны повышает твердость, но с другой — приводит к уменьшению хрупкости. За счет вольфрама можно повысить не только твердость, но и прочность, а вместе с этим и режущие качества металла. К тому же при нагреве до высокой температуры (600-650 °С) эти свойства не теряются (красностойкость).
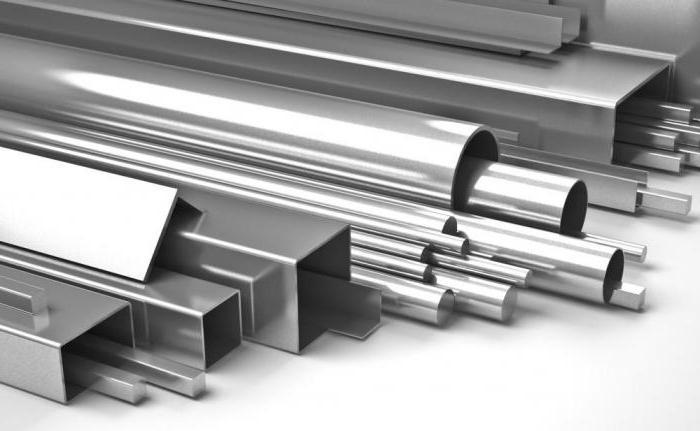
Кремний позволяет увеличить упругость материала, а также стойкость к воздействию кислот. Добавление ванадия способствует увеличению пластических свойств за счет уменьшения зерна. Титан позволяет получить более прочный материал.
Примеси
Теперь точно понятно, что такое легированная сталь. Но вместе с этим следует знать о наличии некоторых примесей, которые, вне зависимости от марки стали, в ней всегда присутствуют. В большинстве случаев это неметаллы:
- Углерод.
- Сера.
- Фосфор.
- Кислород и Азот.
- Водород.
Углерод больше всего оказывает влияние на свойства стали. Если его содержится не более 1,2 %, то материал отличается высокой твердостью и прочностью. Также увеличивается предел текучести. Превышение этой нормы приводит к снижению прочности и пластичности.
Большое содержание серы тоже не на пользу. Более 0,65 % – снижается ударная вязкость, коррозионная стойкость, пластичность. Но, помимо этого, существенно снижается свариваемость стали.
С фосфором надо быть предельно внимательным, поскольку его превышение, даже незначительно, отрицательно сказывается на металле. Снижается вязкость и пластичность, в то же время хрупкость и текучесть возрастают. Все это может отразиться на обработке легированных сталей.
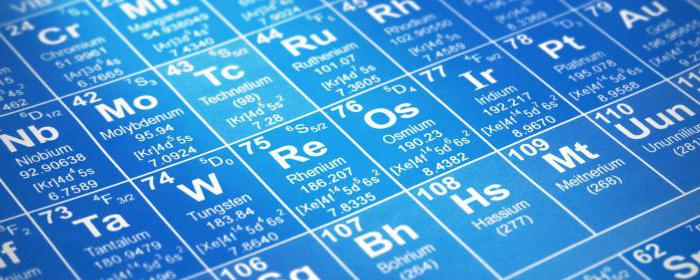
Превышение кислорода и азота приводит к излишней хрупкости материала, а также понижают его вязкость.
Высокое содержание водорода тоже наделяет металл хрупкостью, что нежелательно.
Разновидности ЛС
В зависимости от количества легирующих добавок сталь может разделяться на три вида:
- Низколегированная сталь – содержит не более 2,5 % добавок.
- Среднелегированная сталь – количество легирующих элементов варьируется от 2,5 до 10 %.
- Высоколегированная сталь – здесь речь идет о большем содержании 10 % и выше.
При этом учитывается именно суммарное количество легирующих добавок.
Чтобы получить определенные качества, легированные стали проходят процесс нормализации. Это когда материал нагревается до температуры 900 °C, а после этого он охлаждается на воздухе.
Исходя из этого, «маркировка» легированных сталей может выглядеть так:
- Перлитная – содержание легирующих добавок у таких сталей колеблется от 5 % до 7 %. Получаются следующие структуры: перлит, сорбит, тростит.
- Мартенситная – здесь легирующих элементов больше 7-15 %, углерода при этом не более 0,55 %.
- Аустенитная – помимо содержания легирующих элементов (более 15 %), здесь присутствует никель (8 %) и марганец (13 %). Содержание же углерода здесь не более 0,2 %.
- Ферритная – у такой структуры углерода также содержится не больше 0,2 %. В то время как хрома здесь 17-30 %, кремния 2,5 % (не менее). Такие стали можно отнести к малоуглеродистым.
- Карбидная (ледебуритная) – это уже высокоуглеродистые марки (0,7 % С). В основном содержат вольфрам, ванадий, молибден и хром.
Получение разной марки легированной стали, точнее ее структуры, зависит не только от скорости охлаждения металла на воздухе, но и от количества легирующих добавок и углерода.
Особенности маркировки ЛС
В начале статьи в списке легирующих элементов возле каждого из них стоят буквы, что не случайно. Именно ими производится маркировка подобных металлов, но помимо них присутствуют еще цифры. Пример приведен ниже.
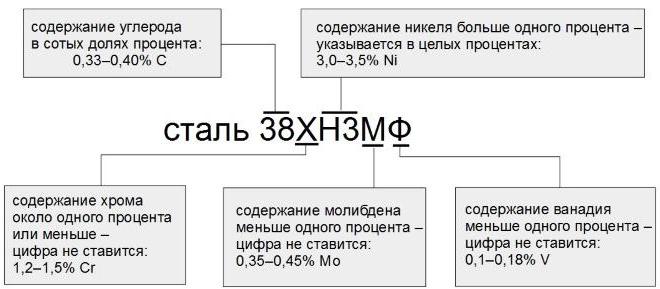
Все это делается согласно ГОСТу 4543-71. Буквенно-цифровое обозначение принято неслучайно, ведь все легированные стали имеют широкий ассортимент. А в таком многообразии несложно запутаться, и поэтому возникла необходимость в систематизации.
При этом каждая буква кириллицы (идет первой) в обозначении указывает на присутствие того или иного элемента, а цифра (как правило, после буквы) — содержание в процентах. При этом, если речь идет о количестве менее 0,99 %, то число обычно не ставится.
Иногда в сплав могут быть добавлены и редкоземельные металлы, такие как иттрий, лантан и ряд прочих. В этом случае в обозначении стали легированной по ГОСТу указывается лишь одна буква – Ч. В маркировке стали есть и другие особенности:
- Первые две цифры всегда указывают на процентное содержание углерода, который буквенно никогда не обозначается.
- Если это быстрорежущая сталь, то содержание вольфрама указывается в целых долях процента. Хрома в таких сплавах обычно 4 %.
- Для шарикоподшипниковой стали после букв ШХ следует обозначение содержание хрома в десятых долях процента.
- Присутствие двух литер «А» указывает на особо чистую легированную сталь.
Возьмем для примера две маркировки:
- 03Х13АГ19 – ЛС содержит 0,03 % углерода, 13 % хрома, 1 % азота и 19 % марганца.
- 18ХГТ – у этой стали углерода 0,18 %, а хрома, титана и марганца по 1 %.
Помимо этого, в самом начале какой-либо маркировки легированных сталей может стоять буква, которая указывает на материал специального назначения:
- Электротехническая – Э.
- Быстрорежущая – Р.
- Шарикоподшипниковая – Ш.
- Автоматная – А.
Легированные стали еще могут принадлежать категории высококачественных или особенно высококачественных металлов.
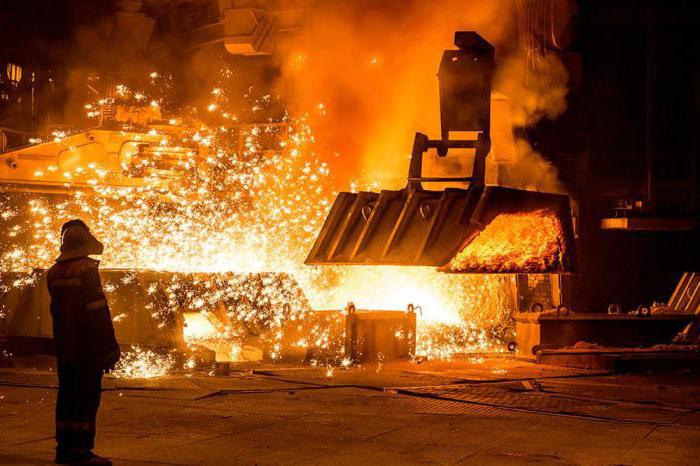
В этом случае в конце маркировки будет стоять литера «А» либо «Ш» соответственно.
Преимущества
Все легированные стали обладают рядом ценных преимуществ, среди которых стоит выделить:
- повышенную стойкость к деформациям пластинчатого характера;
- высокую твердость;
- стойкость к хладоломкости и вязкости;
- технологические качества на высоком уровне.
Помимо этого, такая сталь не склона к короблению или появлению прочих дефектов в ходе процесса закалки.
Недостатки
При всех очевидных достоинствах, которыми обладают легированные инструментальные стали либо прочие, недостатки тоже присутствуют:
- Для них характерна дендритная ликвация, но, к счастью, этого можно избежать проведением диффузионного отжига.
- Высоколегированные марки могут содержать остаточный аустенит, из-за чего снижается сопротивляемость к усталости и твердости материала.
- Не исключается появление флокенов – так называемых трещин в структуре стали. Данного дефекта можно избежать путем замедления охлаждения металла, а также снижения содержания водорода в ходе выплавки.
В зависимости от разновидности термической обработки позволяют избежать появления большинства дефектов. В результате чего сталь приобретает необходимые, порой уникальные качества.
Производство ЛС
Процесс производства легированных инструментальных сталей или иных проходит в несколько этапов с использованием электродуговых печей:
- Железная руда очищается.
- Плавление металла.
- Добавление легирующих элементов.
В процессе очистки железная руда избавляется от нежелательных примесей, таких как сера и фосфор. Все это происходит в плавильной печи открытого типа. Также используется технология внепечной обработки стали. Другой технологический необходимый процесс – это вакуумная плавка, в результате которого удаляется мышьяк и ряд примесей цветных металлов.
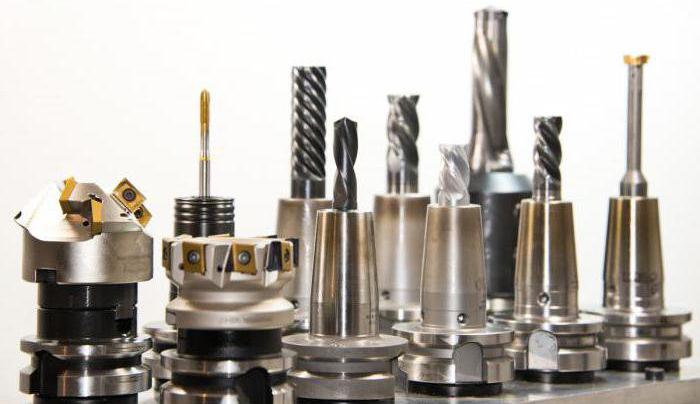
Для плавки металла уже используется электродуговая печь, для чего в ней сырье разогревается до высокой температуры 400-600 °C. Здесь железо начинает превращаться в чугун, для которого характерна неустойчивая кристаллическая решетка. Но посредством стабилизации из него получается какая-нибудь марка легированной стали.
Делается это следующим образом. В рабочую камеру поступает кислород, при сгорании которого атмосфера камеры снабжается углеродом. Он начинает смешиваться с железом, что и ведет к образованию стали.
Потом уже в сырье начинают добавлять различные добавки в зависимости от необходимых свойств металла. Кристаллическая решетка становится более плотной, и в результате получается легированная продукция.
Термообработка ЛС
На выплавке производство ЛС не заканчивается. После этого необходимо ее закалить. Выплавленные образцы проходят процедуру закаливания при температуре 1100 °C. После нее нужен отпуск углеродистых и легированных сталей, причем делается он постепенно, во избежание появления трещин.
Этот процесс необходим для всех закаленных деталей. Его главная задача заключается в снятии внутренних напряжений. При этом снижается твердость, а пластичность увеличивается. Для отпуска могут использоваться разные средства:
- Ванны:
- масляные;
- селитровые;
- с расплавленной щелочью.
- Печь с принудительной воздушной циркуляцией.
Что касается температуры отпуска, то она зависит от марки ЛС и необходимой твердости материала. К примеру, для HRC 59-60 это 150-200 °C. Для быстрорежущих ЛС нужен температурный режим чуть больше – 540-580 °C. Это еще называется как вторичное отвердение, поскольку твердость детали возрастает.
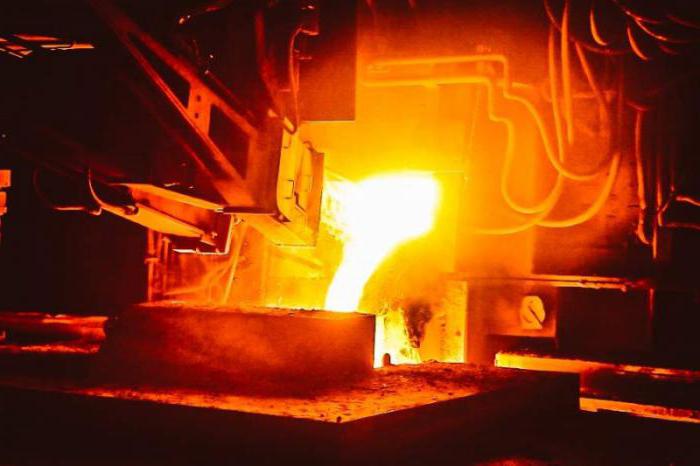
Как правило, после процесса отпуска сталь охлаждается на открытом воздухе. Но хромоникелевые изделия исключение – для них нужна ванна с водой или маслом. Если охлаждение затянется, это приведет к излишней хрупкости металла.
Область применения
Что касается назначения легированных сталей, то это практически любая сфера человеческой жизнедеятельности. Инструментальный металл идет на производство резцов, фрез, штампов, измерительных устройств, шестерен, пружин, подвесок, растяжек и многого другого. Нержавеющая ЛС идеальна для изготовления посуды, корпусов бытовой техники.
Сварка ЛС
Процесс сварки ЛС в полной мере зависит от химического состава металла. Причем в отличие от легирующих элементов больше всего оказывает влияние углерод. В то же время сами добавки по-разному воздействуют на сварку. К примеру, наличие хрома и марганца в большей степени приводит к образованию трещин, нежели никель. А вот титан на этот процесс действует вполне благоприятным образом.
Из-за большого количества серы, фосфора и растворенных газов свариваемость стали в разы ухудшается. Поэтому их содержание не должно быть более 0,020-0,055 %, что никоим образом не отразится на сварке легированных сталей.
Легированная сталь
пер.Каштановый 8/14 51100 пгт.Магдалиновка

Nikolaenko Dmitrij
Легированная сталь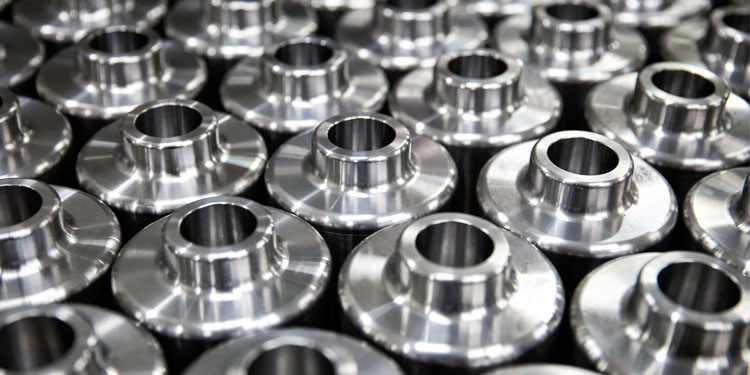
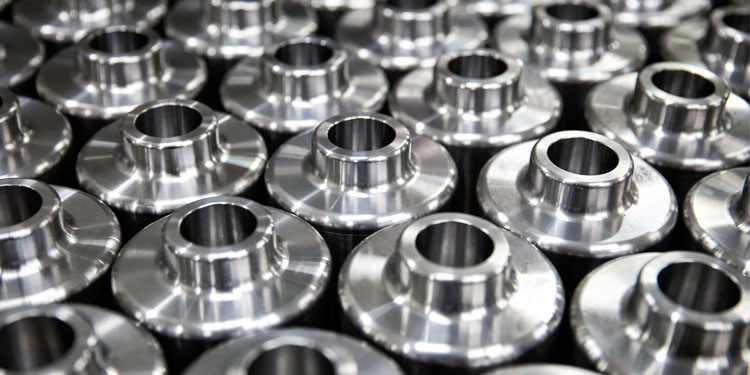
- 5
- 4
- 3
- 2
- 1
Легированная сталь — это сталь, включающая в себя разные легирующие элементы, придающие стали нужные механические и физические свойства.
Также эти элементы значительно повышают стойкость к коррозии, стойкость к хрупкости и повышают прочность.
Элементы легированной стали можно вынести в такой список:
- азот;
- медь;
- никель;
- хром;
- ванадий.
Это классические добавки, которые максимально применяются в производстве. Легированная сталь разделяют на три основных класса:
- низколегированную;
- высоколегированную;
- среднелегированной.
Классификация легированных сталей производится из учета процентного содержания легируемых элементов. Каждый из этих типов стали получают металлургическим путем, однако в отдельных случаях может выполняться легирование только определенной поверхности, чтобы придать необходимые прочностные свойства изделиям и деталям. Легированная сталь приобретает свои свойства на различных этапах производства металла, по мере добавления легирующих элементов. Легированная сталь может включать в себя от одного до нескольких легируемых элементов, которые повышают конструкционную прочность сплава. Легированная сталь выпускают в нескольких основных типах:
- инструментальную;
- конструкционную;
- сталь, имеющая особые химические и физические свойства.
Маркировка легируемых сталей
Маркировка легируемых сталей производится с помощью букв, которые показывают какой легирующий элемент содержится в сплаве, и цифрами, определяющими среднее содержание этого элемента в процентах. Цифры вначале названия марки указывают, сколько углерода содержит материал. Если указано две цифры — содержаться сотые доли процента, если одна — десятые. Маркировка легируемых сталей может иметь дополнительные обозначения. Например, присутствуют распространенные обозначения:
- Р — быстрорежущая;
- Ш – шарикоподшипниковая;
- А — автоматная;
- Л — полученная литьем;
- Э — электротехническая.
На содержание азота указывает буква А, находящаяся в середине марки. Две буквы А (АА), показывают состав особо чистой стали и эти буквы стоят в конце. Сталь особо высокого качества в конце марки имеет букву Ш. Примеры маркировки легированных сталей:
18ХГТ означает:
- 0,18% С;
- 1% Cr;
- 1% Mn;
- 0,1% Ti.
Сталь 30ХГСА содержит:
- 0,30% С;
- 0,8-1,1% Cr;
- 0,9-1,2% Mn;
- 0,8-1,25% Si.
Назначение легируемых сталей
Назначение легируемых сталей очень разнообразно, так как, имея в своем составе соответствующие легируемые добавки, такая сталь способна выдерживать разного рода нагрузки, в отличие от обычной. Большинство показателей можно регулировать с помощью добавления нужных легирующих элементов. Основное назначение легируемых сталей — изготовление хирургических инструментов, ювелирного оборудования, различных металлоконструкций, строительной арматуры, промышленных машин, механизмов, испытывающих большие нагрузки при работе. Марки инструментального назначения легируемых сталей используют для изготовления деталей, которые работают под высоким давлением, также их применяют при изготовлении эталонных шестерен, роликов сложной формы, секций кузнечных штампов и т.д.. Другие марки применяют для деталей с повышенной износостойкостью, хорошей прочностью на изгиб, контактной нагрузке, при необходимой замечательной упругости.
Виды легированной стали
Виды легированной стали различают соответственно процентному содержанию легирующих элементов в сплаве. Так классифицируются:
- низколегированные и содержат до 2,5% легирующих элементов;
- среднелегированные, имеющие от 2,5 до 10% легируемых элементов;
- высоколегированные имеют 10 — 50% таких элементов.
Виды легированной стали бывают разными. Классифицируются в зависимости от процентного соотношения высокоэффективных компонентов, допустим: циркония, ванадия, тантала, других химических элементов, например, углерода, а также структурной специфики:
- ледебуритные – наличие первичных карбидов;
- эвтектоидные – строение металла перлитное;
- заэвтектоидные – присутствие вторичных карбидов;
- доэвтектоидные – есть избыточный феррит.
По степени использования, назначения бывают стали: конструкционные, инструментальные, с особыми свойствами.
Виды легированной стали включают в себя также нержавеющие, имеющие великолепные свойства стойкости к химической и электрохимической коррозии. Специальные жаростойкие, имеющие хорошую стойкость химическому разрушению в газовой среде при температуре выше 500 С, но при этом они работают в слабо нагруженном состоянии или не нагруженном. Жаропрочные стали, которые работают при больших нагрузках в течение достаточного времени и при этом сохраняющие достаточную жаростойкость. Виды легированной стали конструкционной бывают:
- качественной;
- высококачественной;
- очень высокого качества.
В век перепроизводства разве что младенец не знает, что существует легированная сталь. Но часто происходит подмена понятий и многие обыватели считают, что единственным достоинством такого материала является его высокая антикоррозионная стойкость. На самом деле, кроме нержавейки, существует колоссальное количество стальных сплавов, содержащих легирующие добавки и имеющие различные механические и эксплуатационные характеристики. Ну а теперь все по порядку.
Легированные стали: определение и классификация
Легированные сплавы имеют сложный состав на основе железа и углерода, содержащие различные химические элементы, которые влияют на структурные преобразования металлов на молекулярном уровне. Процентное содержание таких добавок и организация процесса раскисления, легирования и дегазации сталей определяют их физико-химические свойства.
Интересный факт. Началом массового производства немагнитных сплавов считается выплавка стали англичанином Робертом Гадфильдом в конце XIX века. Конечно, человечество и раньше знало, что такое легированная сталь, но организовать потоковое производство и оценить все преимущества ее применения люди смогли только в эпоху глобальной индустриализации и, к сожаленью, с появлением новых военных технологий. Благодаря высокому сопротивлению износу и ударным нагрузкам сталь Гадфильда вплоть до середины XX века становится наиболее используемым сплавом для производства железнодорожных крестовин, танковых траков, пехотных шлемов и даже тюремных решеток.
Отличия от углеродистых сталей
Любой стальной сплав содержит железо и углерод. Причем содержание последнего может составлять 0,02 – 0,15% и напрямую определяет его свойства и марку. Он повышает твердость и прочность, но при увеличении концентрации снижает пластичность. Увеличивает режущую способность, электрическое сопротивление и коэрцитивную силу. Снижает температуру плавления и плотность.
Обыкновенные углеродистые стали, также как легированные, могут содержать кремний, марганец, медь, серу, хром, фосфор, водород, азот и алюминий, только их количество значительно ниже, а используются они в основном для раскисления сплава. При этом Si и Mn вводятся для улучшения прочностных показателей и физико-химических свойств. Другие вещества попадают в расплавленную сталь из шихты или печных газов и соответственно считаются вредными примесями. При плавке легированных сталей их свойства моделируются за счет целенаправленного введения оптимизирующих веществ.
Легирующие добавки
Наиболее распространенными элементами, использующимися для улучшения физических и химических свойств стальных сплавов являются: хром, марганец, никель, кремний, вольфрам, молибден, ванадий, титан, медь, кобальт, алюминий, бор, ниобий, цирконий, азот, мышьяк, сера и фосфор. Но, несмотря на такой обширный список, все же наиболее используемыми являются лишь несколько из вышеперечисленных элементов.
Таблица 1
Элемент |
Химическое обозначение |
Обозначение в маркировке |
Содержание, % |
Особенности применения |
Марганец |
Mn |
Г |
1,25 – 13 |
Аустенитобразующее вещество, улучшает прокаливаемость и увеличивает порог жидкотекучести металла. Повышает сопротивление истиранию и ударным нагрузкам. |
Кремний |
Si |
С |
0,8 – 14,0 |
Ферритообразующий компонент. Не влияет на вязкостные свойства, при этом повышает предел прочности и текучести, магнитную проницаемость и электропроводимость. Улучшает пластичность, кислотостойкость и прочностные показатели. |
Алюминий |
Al |
Ю |
0,7 – 1,2 |
Минимизирует процессы старения. Повышает пластичность. |
Фосфор |
P |
П |
0,05 – 0,35 |
Улучшает антикоррозионные свойства и обрабатываемость. В количестве менее 0,03% провоцирует хладоломкость. |
Хром |
Cr |
Х |
0,5 – 30 |
Ферритообразующий компонент. Широко используется как самостоятельный легирующий агент, так и в комплексе с другими веществами. Его введение способствует расширению температурного интервала затвердевания, увеличивает прочность и твердость без изменения показателей пластичности. Содержание 1% улучшает механические свойства. С повышением концентрации хрома до 5% увеличивается теплостойкость, а кислотостойкие и жаропрочные сплавы уже содержат более высокий процент хрома, который может достигать до 28%. |
Никель |
Ni |
Н |
1,0 – 25 |
Аустенитообразующий компонент. Улучшает ударную вязкость и термоокислительную стабильность. Повышает прокаливаемость и окалиностойкость. |
Молибден |
Mo |
М |
0,2 – 5,0/6,5 |
Значительно повышает показатели твердости, прочности и пластичности. В наибольшей концентрации содержится в жаропрочных сталях, а в конструкционных марках его количество обычно не превышает 0,4%. |
Вольфрам |
W |
В |
1,0 – 18,0 |
Карбидообразующая присадка, повышающая пределы прочности и твердости. Вводится в быстрорежущие инструментальные сплавы до 18% и оптимизирует термопрочность и сопротивление ударным нагрузкам. |
Ванадий |
V |
Ф |
0,15 – 2,0 |
Карбидообразующий агент, который увеличивает прочность и повышает вязкость. Ванадийсодержащие сплавы демонстрируют прецизионную ударную стойкость и инертность к напряжениям, но очень дорого стоят. |
Титан |
Ti |
Т |
0,4 – 0,15 |
Связывая углерод в прочные карбиды, измельчает зерна аустенита и снижает склонность к межкристаллической коррозии. Повышает кислотоупорность и минимизирует самозакаливаемость металлов. |
Ниобий |
Ni |
Б |
0,1 – 0,25 |
Сильно карбидообразующий элемент. В нержавеющие сплавы вводится для минимизации межкристаллической коррозии, в марганцовистую – для снижения отпускной хрупкости. |
Медь |
Cu |
Д |
0,5 – 4,0 |
Ее присаживание увеличивает предел текучести, пластичность, сопротивляемость коррозионным процессам. В судостроении позволяет эффективно решить проблему обрастания подводной части корпуса водорослями и ракушками. |
Бор |
B |
Р |
0,002 – 0,004 |
Увеличивает прокаливаемость. Является лучшей альтернативой для замены дорогостоящего молибдена и никеля. |
Кобальт |
Co |
К |
12,0 – 50,0 |
Используется для жаростойких и быстрорежущих марок. Его присадка позволяет режущей плоскости сохранять свои свойства даже при температурах красного каления и защищает конструктивные части теплогенерирующих элементов от окисления при воздействии агрессивных сред и критических температур. |
Редко-земельные металлы |
Ce, La |
Ч |
0,05 – 0,3 |
Одновременно выступают дегазаторами и десульфураторами. В значительной мере оптимизирующее влияют на обрабатываемость и физико-химические свойства. Улучшают жидкотекучесть, свариваемость и ковкость. |
Сера |
S |
— |
0,1 – 0,3 |
Несмотря на то, что наличие серы активизирует процессы ржавления, она используется в автоматных марках для облегчения станочной обработки. |
На заметку. Даже в составе технически чистого железа обязательно присутствуют около 20 химических примесей. Но их суммарное количество не превышает 0,25 процента.
Общая классификация легированных сталей
Она основывается на том, в каком количестве добавка введена в состав сплава, и определяет основные группы, исходя из химической структуры, целевого назначения и уникальных свойств. Таким образом, различают следующие категории.
Классификация стальных сплавов по процентному содержанию всех легирующих компонентов:
- не более 2,5 % — низколегированные;
- в интервале от 2,5 до 10,0% – среднелегированные;
- более 10% — высоколегированные.
Классификация легированных сталей по назначению:
- конструкционные. Используются для изготовления металлоконструкций, деталей машин, агрегатов и механизмов;
- инструментальные. Применяются при изготовлении высококачественного мерительного и режущего инструмента и ударо-штамповочного оснастки;
- с особыми свойствами (жаростойкие, нержавеющие и прочие).
В своей профессиональной деятельности металлурги и инженеры часто прибегают к более широкой номенклатуре. Например, профессионалами используется классификация таких сплавов по их микроструктуре в нормализованном состоянии (перлитные, аустенитные, карбидные и мартенситные) или в равновесном состоянии (доэвтектоидные, эвтектоидные, заэвтектоидные).
Характеристика легированных сталей
Фазовые превращения в твердых растворах железа определяются общими законами взаимной растворимости и межатомных взаимодействий всех элементов, включая углерод и легирующие добавки. Поэтому легированная сталь имеет одновременно схожие и уникальные характеристики:
- химические: жаростойкость, кислотостойкость, нержавление;
- физические: тепловые, магнитные, электрические;
- специальные: износостойкость, сопротивляемость ползучести.
Среди преимуществ и достоинств, которыми обладает данный металлопрокат, следует выделить повышенное сопротивление хладостойкости, ударным и пластичным деформациям, улучшенная прокаливаемость, повышенная вязкость. При этом для большинства сплавов, содержащих разное количество легирующих присадок, характерно:
- наличие остаточного аустенита после термозакалки;
- склонность к образованию флокенов;
- механическая прочность;
- тугоплавкость.
На заметку. В зависимости от химической природы вводимых элементов легированная сталь изменяет свойства жидкотекучести и поверхностного натяжения. А также снижает температуру плавления следующим образом:
Элемент |
Снижение T для 1% элемента в жидком р/р, ˚С |
Элемент |
Снижение T для 1% элемента в жидком р/р, ˚С |
Элемент |
Снижение T для 1% элемента в жидком р/р, ˚С |
Углерод |
90 |
Кремний |
6 |
Никель |
2,9 |
Сера |
40 |
Фосфор |
28 |
Титан |
17 |
Марганец |
1,7 |
Медь |
2,6 |
Бор |
100 |
Хром |
1,8 |
Молибден |
1,5 |
Вольфрам |
1 |
Алюминий |
5 |
Ванадий |
1,3 |
Кобальт |
1,5 |
Данные таблицы показывают, что по сравнению с малоуглеродистым обычным стальным сплавом у высоколегированной марки, содержащей около 50% присадок, температура ликвидуса ниже почти на 100˚С.
Маркировка легированных сплавов и основные марки
В мировой практике используется несколько документов, регламентирующих маркировку легированных сталей. Но в любом случае они все предполагают использование буквенно-цифровых обозначений.
Стандарты стран СНГ
Процентная величина массовой доли углерода маркируется первыми двумя цифрами без использования буквенного обозначения. Далее в порядке уменьшения указываются легирующие компоненты и их доля в сплаве в среднем эквиваленте. Буквенные обозначения химических элементов указаны в таблице 1. Легирующие присадки, количество которых менее 1,0% указываются только в расшифрованной номенклатуре, так как обозначение тогда бы приняло очень громоздкий вид.
Учитывая обширный сортамент, также марка стальных сплавов может включать дополнительные символы, более расширенно описывающие свойства или особенности: А – автоматные, Е – магнитные, Ж – нержавеющие, Р – режущие, Х – хромистые, Ш – шарикоподшипниковые, Э — электротехнические, Я – хромоникелевые. Также маркировка может предполагать исключения от общих правил обозначения. Так в зависимости химического состава конструкционные сплавы разделяют на качественные и высококачественные. Например, в конце маркировки буква «А» указывает, что структура сплава особо чистая по отношению к содержанию фосфора и серы, а буква «Ш» относит их к высококачественным.
Маркировка легированных сталей для речного и морского судостроения часто осуществляется в соответствии с ГОСТ 5521-86 и требованиями Международной ассоциации классификационных обществ. Это означает, что такие сплавы классифицируют на категории A, B, D и Е с учетом предела текучести, показателям прочности, хрупкости и сопротивлению ударным нагрузкам.
Европейские стандарты
EN 10027 определяет порядок обозначения всех сталей. Легированные сплавы имеют маркировку 1.20ХХ – 1.89ХХ, где первая цифра определяет, что данный материал относится к сталям, вторая и третья цифра определяют номер группы сталей и две последние — порядковый номер сплава в этой группе. Например, категория инструментальных сталей идентифицируется как 1.20ХХ – 1.28ХХ, а нержавеющих как 1.40ХХ – 1.45ХХ.
Североамериканские стандарты ASTM/ASME и AISI
В США действует наиболее обширная система маркировки стальных сплавов. Например, маркировка ASTM предполагает обозначение основных химических элементов, предел прочности и форму проката. В системе AISI используют 4 цифры, где первые две указывают номер группы, две последующие – процентное количество углерода. Буквенные символы демонстрируют наличие соответствующих присадок.
Марки, наиболее востребованные в инжиниринге
- 09Г2С – низколегированная сталь, сочетающая механическую прочность, хорошую обрабатываемость и доступную стоимость;
- S355AR – конструкционная марка, широко используемая в машиностроении и строительстве;
- 40Х и ее аналог AISI 5135 – основной конструкционный материал для изготовления деталей и оборудования промышленного сектора и трубопроводной арматуры;
- 10Г2С1 – кремнемарганцевая марка, демонстрирующая хладостойкость, неплохую свариваемость и повышенную коррозионную стойкость, благодаря чему востребована при сооружении мостов, газопроводов и объектов повышенной надежности;
- 10Х11Н23Т3МР – жаропрочный сплав из аустенитного класса, использующийся для производства пружин, деталей крепежа и сварочных электродов.
Использование легированных сталей
Сегодня практически невозможно перечислить все сферы, где применяется легированная сталь. Это тракторостроение и машиностроение, химико-технологический и промышленно-производственный комплекс, нефтегазодобывающая отрасль и сельское хозяйство. Например:
- из хромосодержащих сплавов изготавливают детали для оборудования, эксплуатируемого в условия прямого или вероятного контакта с агрессивными средами: плунжера и шлицы, валы и зубчатые колеса, поршневые пальцы и карданные крестовины;
- низколегированные конструкционные сплавы чаще всего востребованы в строительстве, массово используется при сооружении каркасных металлоконструкций и для изготовления труб, сортового и фасонного металлопроката. Несмотря на обширный сортамент, легированная сталь марки 09Г2С и S355AR является наиболее использованной в этой сфере;
- инструментальный сплав – универсальный материал для клейм, пресс-форм, эталонных калибров и штампов. А из ледебуритных марок изготавливаются быстрорежущего инструмента и шарошечных долот.
Также не стоит забывать, что физические особенности легированных сплавов проявляются в термообработанном состоянии. Именно поэтому их широко используют для термонапрягаемых деталей, высокоскоростных и тяжелонагруженных пар трения.
В связи с интенсивным развитием современных технических отраслей, легированная сталь находит применение в гражданской и военной авиации, в турбостроении и в альтернативной электроэнергетике. Так же можно купить металл в Украине, а именно легированную сталь для изготовления мультикоптеров и беспилотников, ядерных реакторов, ракетно-космических систем. В то же время стремительное расширение сферы применения легированных сталей обуславливает ужесточение требований к их качеству и мотивирует к разработке новых сплавов.
Легированная сталь — сталь, которая кроме обычных примесей содержит элементы, специально вводимые в определённых количествах для обеспечения требуемых физических или механических свойств. Эти элементы называются легирующими.
Легирующие добавки повышают прочность, коррозийную стойкость стали, снижают опасность хрупкого разрушения. В качестве легирующих добавок применяют хром, никель, медь, азот (в химически связанном состоянии), ванадий и др.
Легированную сталь по степени легирования разделяют на: низколегированную (легирующих элементов до 2,5 %), среднелегированную (от 2,5 до 10 %), высоколегированную (от 10 до 50 %).
Маркировка
Легированные стали маркируются цифрами и буквами, указывающими примерный состав стали. Буква показывает, какой легирующий элемент входит в состав стали.
Стоящая за буквой цифра обозначает среднее содержание элемента в процентах. Если элемента содержится менее 1 %, то цифры за буквой не ставятся. Первые две цифры указывают среднее содержание углерода в сотых долях процента, если цифра одна, то содержание углерода в десятых долях процента.
Дополнительные обозначения в начале марки:
- Р — быстрорежущая;
- Ш — шарикоподшипниковая;
- А — автоматная;
- Э — электротехническая;
и др.
Исключения:
- содержание в шарикоподшипниковых сталях хрома в десятых долях процента(например ШХ4 — Cr 0,4 %)
- в марке быстрорежущей стали, цифра после «Р» — содержание вольфрама в %, и во всех быстрорежущих сталях содержание хрома 4 %.
Буква А в середине марки стали показывает содержание азота, а в конце — сталь высококачественная.
Пример:
- сталь 18ХГТ — 0,18 %, 1 Сr, 1 Мn, около 0,1 Тi;
- сталь 38ХНЗМФА — 0,38 %, 1,2—1,5 Сr; 3 Ni, 0,3—0,4 Мо, 0,1—0,2 V;
- сталь 30ХГСА — 0,30 %, 0,8—1,1 Сr, 0,9—1,2 Мn, 0,8—1,251 Si;
- сталь 03Х13АГ19 — 0,03 %, 13 Сr, 0,2—0,3 N, 19 Мn.
См. также
Ссылки
марки, состав, свойства, область применения
Чтобы улучшить технические характеристики металлов, сплавов, проводится технологический процесс, называемый легированием. Он подразумевает под собой введение в состав соединения материалов дополнительных добавок, которые изменяют его свойства. Зависимо от того, сколько процентов дополнительных компонентов добавляется, выделяется три группы получаемых материалов. Любой мастер металлообработки должен знать низколегированные стали, их марки.


Состав
Прежде чем начинать разбираться со свойствами, необходимо узнать состав низколегированных сталей. Количество легирующих добавок не должно превышать 5% (некоторые источники указывают максимальное количество дополнительных компонентов — до 2.5%). Углерод не считается легирующим компонентом.
К наиболее популярным, недорогим дополнительным добавкам относятся:
- Ванадий — отвечает за равномерную структуру.
- Молибден — увеличивает устойчивость соединения к высоким температурам.
- Ниобий — повышает показатель прочности.
- Вольфрам — увеличивает теплостойкость.
- Титан — повышает показатель износоустойчивости.
- Никель, кремний — повышают удароустойчивость, сопротивляемость току.
Свойства низколегированных сталей
Чтобы понимать возможности, сферы применения низколегированных материалов, требуется разобраться с их физическими, химическими свойствами:
- Высокая износостойкость.
- Высокая коррозийная стойкость.
- Повышенные механические свойства.
- Высокая поверхностная твердость.
Классификация легированных сталей
С развитием новых технологий, появлением разных легированных сталей, их нужно было классифицировать.
Разделение по количеству углерода, содержащегося в сплаве:
- Высокоуглеродистые — более 0.65%.
- Среднеуглеродистые — от 0.25% до 0.65%.
- Низкоуглеродистые — менее 0.25%.
Разделение по процентному содержанию легирующих добавок:
- Низколегированные — до 5% (по некоторым источникам до 2.5%).
- Среднелегированные — до 10%.
- Высоколегированные — 10–50%.
По внутренней структуре легированные стали бывают:
- Эвтектоидные — перлитная структура.
- Ледебуритные — наличие первичных карбидов в структуре.
- Доэвтектоидные — присутствие избыточных ферритов, насыщающих состав.
- Заэвтектоидные — наличие вторичных карбидов в сплаве.
По назначения эти материалы можно разделить на две больших группы:
- Строительные — для изготовления металлоконструкций, которые во время последующей эксплуатации не будут подвергаться критическим температурам.
- Машиностроительные — используются при изготовлении деталей для разных механизмов, корпусов.
Машиностроительные стали бывают:
- Цементуемые — при изготовлении проходят процесс цементации, а затем закалки.
- Жаропрочные — среднеуглеродистые стали. Применяются при изготовлении изделий, использующихся в сфере энергетики.
- Улучшаемые — материалы, проходящие дополнительную закалку. Из них изготавливаются детали, подвергающиеся большим нагрузкам.


Легирующие элементы и их влияние на свойства сталей
Выше описывалось несколько легирующих добавок, которые добавляются в состав соединений наиболее часто. Чтобы понимать, как воздействуют все дополнительные компоненты на технические характеристики сплава, требуется разобраться с ними по отдельности более подробно:
- Титан — зернистость структуры уменьшается, повышаются показатели плотности, прочности.
- Сера — этого компонента не должно быть более 0.65% в составе. В противном случае снизится устойчивость к коррозии, пластичность, ударная вязкость.
- Углерод — содержание не более 1.2% повышает показатели прочности, твердости. Если количество будет увеличено, технические параметры снизятся.
- Фосфор — не подходит в качестве легирующей добавки. Увеличение его количества в составе приводит к резкому снижению технических параметров.
- Алюминий — чтобы повысить окалиностойкость, добавляется этот компонент.
- Никель — способствует повышению коррозийной стойкости, вязкости, пластичности.
- Хром — увеличивает твердость, прочность, коррозийную стойкость.
- Кремний — содержание этого компонента не должно превышать 15%. Увеличивает электросопротивление, магнитопроницаемость.
- Марганец — содержание до 0.8% причисляется к одной из технологических примесей. Снижает негативное воздействие серы на сплав.
- Кислород, азот — большое количество пузырьков газов в составе делает металл более хрупким.
- Водород — металлурги стараются снизить количество этого компонента в составе, чтобы сделать материал более прочным.
Маркировка
Маркировка металла несет в себе множество информации для покупателей, людей, работающих с продукцией. Марки низколегированной стали указываются по ГОСТу 4543-71. Маркировка представляет собой набор букв, цифр, каждая из которых имеет определенное значение. Стандартная расшифровка:
- На первом месте идет буква. Она определяет свойства металла, относит его к определенный подгруппе. Например, буква «Ж» указывает на основу из нержавейки.
- Цифра, идущая после первой буквы, обозначает процентное содержание углерода в составе. Например, 5 — 0.05%.
- Далее обозначаются легирующие добавки по периодической таблице.
- После обозначений дополнительных компонентов, указываются цифры, говорящие об их процентном содержании в соединении.
Применяются низколегированные стали в разных направлениях промышленности. Область применения:
- Изготовление облегченных конструкций из металла.
- Корпуса для бытовой техники.
- Детали для промышленного оборудования.
- Режущие инструменты.
Из-за высокой цены на подобные материалы, их используются в тех случаях, когда аналоги не могут справиться с поставленными задачами.


Сварка
Чтобы соединить детали из низколегированной стали с помощью сварки, нужно учитывать несколько нюансов:
- Изготавливать вертикальные, потолочные швы.
- Сварочный стержень должен быть не менее 4 мм по сечению.
- Чтобы снизить скорость охлаждение металла, требуется выполнять стыковые или бортовые швы.
- Сваривая заготовки толщиной, не превышающей 6 мм, требуется выполнять только один проход.
- Чтобы придать соединению высокую пластичность, нужно использовать электроды Э42А.
- Если металл содержит малое количество углерода, требуется применять электроды с покрытием из фтора, кальция.
Для проведения сварочных работ, требуется использовать специальную присадку Св-10Г2.
Низколегированные стали имеют повышенные технические параметры, благодаря добавлению дополнительных компонентов в состав. Их используют в тех направлениях промышленности, где нужно применять детали, металлоконструкции высокой прочности, износоустойчивости. Для соединения отдельных деталей, нужно учитывать ряд нюансов использования сварочного оборудования.
Сталь является одним из самых популярных материалов, используемых в строительной отрасли. По данным Всемирной ассоциации производителей стали, в 2018 году во всем мире было произведено около 1808 миллионов тонн сырой стали, и около 50% этой продукции было использовано строительной промышленностью. Кроме того, они также заявляют, что существует 3500 различных марок стали, и каждая марка обладает экологическими, химическими и физическими свойствами, уникальными для этой марки стали.Сталь претерпела значительные изменения во времени, и за последние 20 лет было разработано около 75% всех типов современной стали. Интересно отметить, что если бы Эйфелева башня (построенная в 1887 году) была построена в наши дни, для нее потребовалась бы только треть используемой в то время стали.
Типы стали
По сути, сталь — это сплав железа с низким содержанием углерода. Существуют тысячи различных типов сталей, которые созданы для различных применений.Они широко делятся на 4 типа — углеродистая сталь, инструментальная сталь, нержавеющая сталь и легированная сталь. Углеродистые стали составляют большинство сталей, производимых сегодня в мире. Инструментальные стали используются для изготовления деталей машин, штампов и инструментов. Нержавеющая сталь используется для изготовления обычных предметов домашнего обихода. Легированные стали изготавливаются из железа, углерода и других элементов, таких как ванадий, кремний, никель, марганец, медь и хром.
Легированная сталь
Когда в углеродистую сталь добавляются другие элементы, содержащие металлы и неметаллы, образуется легированная сталь.Эти легированные стали демонстрируют различные экологические, химические и физические свойства, которые могут варьироваться в зависимости от элементов, используемых для легирования. Здесь пропорция легирующих элементов может обеспечивать различные механические свойства.
Эффекты легирования
Виды легированной стали
Существует два вида легированной стали — низколегированная и высоколегированная.Как упоминалось ранее, состав и пропорция легирующих элементов определяют различные свойства легированной стали. Низколегированные стали содержат до 8% легирующих элементов, тогда как высоколегированные стали содержат более 8% легирующих элементов.
Легирующие элементы
Существует около 20 легирующих элементов, которые можно добавлять в углеродистую сталь для производства различных марок легированной стали. Они предоставляют различные типы свойств. Некоторые из используемых элементов и их эффекты включают в себя:
- Алюминий — может избавить сталь от фосфора, серы и кислорода
- Хром — может повысить прочность, твердость и износостойкость
- Медь — может повысить коррозионную стойкость и использовать жгут
- Марганец — может повысить жаропрочность, износостойкость, пластичность и прокаливаемость
- Никель — может повысить коррозионную стойкость, стойкость к окислению и прочность
- Silicon — может увеличить магнетизм и прочность
- Вольфрам — может увеличить прочность и твердость
- Ванадий — может повысить коррозионную стойкость, ударопрочность, прочность и ударную вязкость
Другие легирующие элементы, которые обеспечивают различные свойства, включают висмут, кобальт, молибден, титан, селен, теллур, свинец, бор, серу, азот, цирконий и ниобий.Эти легирующие элементы могут использоваться по отдельности или в различных комбинациях в зависимости от желаемых свойств.
Обратитесь к ближайшим дилерам Top Steel и получите бесплатные котировки
Изделия из легированной стали и их применение
Существуют сотни изделий, которые могут быть изготовлены из легированных сталей различного состава. К ним относятся трубы и трубки из легированной стали, пластины из легированной стали, листы и рулоны, прутки из легированной стали, стержни и провода, кованые фитинги из легированной стали, стыковые фитинги из легированной стали, фланцы из легированной стали, крепежные элементы и многое другое.Легированные стали имеют множество применений в различных отраслях промышленности, таких как автомобили, горнодобывающая промышленность, машины и оборудование, железные дороги, дорожное строительство, здания, бытовая техника и оффшорные применения.
Применение в строительстве больших конструкций
В строительстве и строительстве легированные стали используются для очень больших современных конструкций, таких как аэропорты, мосты, небоскребы и стадионы в виде стального каркаса. Легированные стали обеспечивают необходимую высокую прочность для поддержки таких больших конструкций.Даже бетонные конструкции используют легированные стали в качестве усиления, чтобы увеличить прочность и уменьшить общий вес конструкций. Меньшие предметы, такие как винты, гвозди и болты из легированной стали, используются в строительстве.
Применение в строительстве мостов
Мосты используют специальные легированные стали, известные как стали выветривания. Они обеспечивают улучшенную защиту от коррозии благодаря присутствию никеля, меди и хрома в качестве легирующих элементов. Атмосферные стали также находят применение в зданиях в качестве облицовочного материала для улучшения эстетики.Атмосферная сталь предлагает несколько преимуществ, которые включают в себя высокую безопасность, легкость и быстроту конструкции, эстетичный внешний вид, малую глубину конструкции, низкие эксплуатационные расходы и подвержены изменениям в будущем. Из-за его естественного выветривания отделка не требует покраски, что позволяет избежать экологических проблем, вызванных красками. Выветривающиеся стали чрезвычайно рентабельны в долгосрочной перспективе.
Прокат из легированной стали
Легированные стали используются для изготовления плоских изделий — листов и полос.Пластины доступны в широком ассортименте сортов и размеров. Они используются в строительстве при сварке плит в изготовленные секции.
Ленты и катушки из легированной стали Полосы
доступны в виде горячекатаных и холоднокатаных полос и оцинкованных в горячем состоянии рулонов. Оцинкованные в горячем состоянии катушки используются для изготовления строительных изделий, которые включают в себя облицовку стен и крыш, боковые ограждения, балки крыши, легкие стальные рамы и перемычки.
Легированная сталь, длинные изделия
Легированные стали используются для производства длинномерных изделий, используемых в строительной промышленности, таких как балки, конструкционные профили, стержни, рельсы, стержни и проволоки.
Фланцы из легированной стали
Еще одним важным продуктом из легированных сталей являются фланцы. Они используются в трубопроводах из нержавеющей стали. Эти фланцы могут быть выполнены для различных применений. Некоторые из них включают в себя фланцы с приваренной горловиной, которые имеют ту же толщину и наклон, что и трубы, и могут хорошо работать в жестких условиях высокого давления, высокой температуры или отрицательных температур. Фланцы внахлестки — это вставные фланцы, подходящие для трубопроводов из легированной стали, которые требуют регулярного технического обслуживания и осмотра.
Труба из легированной стали Трубы из легированной стали
являются важными материалами для строительства и строительства благодаря своим эксплуатационным характеристикам, таким как пластичность, простота монтажа без термической обработки и высокая долговечность. Это сплав нержавеющей стали, хрома и никеля. Некоторые специальные типы труб из легированной стали включают сварные трубы большого диаметра, электросварные сварные трубы, сварные трубы и бесшовные трубы. Они чрезвычайно полезны для высокотемпературных или коррозионных применений помимо сред высокого давления.
Цена из легированной стали
Поскольку легированные стали обладают специфическими свойствами, необходимыми для конкретных применений, цены значительно варьируются в зависимости от марок, включающих состав легирующих элементов, процесс изготовления и размер. Цены на легированные стали, имеющиеся в Индии, обычно варьируются в диапазоне от 90 580 рупий (1294 долл. США) за тонну до 4 088 730 рупий (5839 долл. США) за тонну.
Как видно из вышеизложенного, легированные стали играют важную роль в строительстве, а также в других отраслях.Легированные стали отличаются экономичностью, высокой эффективностью, коррозионной стойкостью, долговечностью, высокой прочностью, высоким соотношением прочности и веса, высокими эксплуатационными характеристиками в суровых условиях и широким ассортиментом продуктов, подходящих для большинства применений.
Обратитесь к ближайшим дилерам Top Steel и получите бесплатные котировки
Понимание низколегированной стали
Знание типа низколегированной стали и соответствие его правильному присадочному металлу имеет решающее значение для достижения целостности сварного шва.
Благодаря добавлению определенных сплавов низколегированные стали обладают точным химическим составом и обеспечивают лучшие механические свойства, чем многие обычные мягкие или углеродистые стали. Эти сплавы обычно составляют от 1 до 5 процентов содержания стали и добавляются на основе их способности обеспечивать очень специфический атрибут.Например, добавление молибдена улучшает прочность материала; никель добавляет прочность; а хром увеличивает температурную прочность, твердость и коррозионную стойкость. Марганец и кремний, другие распространенные легирующие элементы, обеспечивают отличные раскисляющие свойства.
К счастью, несмотря на добавление этих элементов, низколегированные стали не обязательно трудно сваривать. Тем не менее, точное знание того, какой тип низколегированной стали у вас есть, имеет решающее значение для достижения хорошей целостности сварного шва, как и правильный выбор присадочного металла.
Распространенное использование низколегированной стали
Первым шагом в понимании низколегированной стали является знание ее общего использования — все это сильно различается во многих отраслях промышленности. Область применения низколегированных сталей варьируется от военных транспортных средств, землеройных и строительных машин и кораблей до магистральных трубопроводов, сосудов под давлением и трубопроводов, нефтяных буровых платформ и конструкционных сталей.
Несколько общих групп низколегированных сталей, начиная со сталей HY 80, HY 90 и HY 100, используются для строительства корпусов судов, подводных лодок, мостов и внедорожных транспортных средств.Эти низколегированные стали содержат никель, молибден и хром, которые повышают свариваемость материала, ударную вязкость и предел текучести. При сварке этих низколегированных сталей предварительный нагрев и последующий нагрев обычно не требуются. Всегда обращайтесь к процедуре сварки, чтобы определить требования.
Другой тип низколегированной стали — высокопрочный низколегированный (HSLA) — отличается от других низколегированных марок тем, что каждый тип был создан для удовлетворения определенных механических требований, а не заданного химического состава.Применения HSLA включают военные корабли, конструкционную сталь и другие, известные своей прочностью.
Предназначенные для прочности, ударной вязкости при низких температурах и пластичности, стали ASTM A514, A517 и T1 подвергаются закалке и отпуску и используются в таких областях, как производство тяжелого оборудования, а также изготовление котлов и сосудов под давлением.
Стали для атмосферных воздействий, такие как ASTM A242, A588 и A709, класс 50W, полагаются на некоторые сплавы для создания защитного коррозионно-стойкого слоя. Этот слой также дает выветренный вид готовой стали и был впервые представлен как COR-TEN®.Закаленные стали популярны в художественных работах, мостах и в качестве облицовочного материала на зданиях для достижения особой эстетики.
Поиск совпадения присадочного металла
Наплавленные металлы, используемые для сварки низколегированных сталей (независимо от конкретного типа), обычно соответствуют химическому и механическому составу основного металла. Хотя присадочный металл может быть указан в технических заданиях, все же важно знать, как различные провода взаимодействуют с различными низколегированными базовыми материалами.Затем вы можете выбрать правильный низколегированный присадочный металл, сравнив имеющуюся информацию о базовом металле со спецификациями AWS для каждой проволоки.
Как правило, низколегированные присадочные металлы классифицируются по пределу прочности при растяжении в фунтах на квадратный дюйм — 80 KSI или выше — и они содержат легирующие элементы, такие как хром, никель или молибден. Эти присадочные металлы предназначены для соответствия конкретным низколегированным основным материалам, их химическому составу, прочности металла сварного шва и требованиям применения.
Для обеспечения успеха сварки, присадочные металлы для низколегированных сталей должны соответствовать или превышать предел прочности и предел текучести основного металла, а также его свойства удлинения и вязкости (с V-образным надрезом по Шарпи). Однако идеальное совпадение не всегда возможно, поэтому необходимо найти наиболее близкое из возможных — за некоторыми исключениями, конечно.
Например, при сварке разнородных низколегированных сталей обычно рекомендуется подбирать присадочные металлы с базовым материалом с более низкой прочностью.И наоборот, для получения меньшего сварного шва в поперечном сечении вы можете превзойти прочность основного материала. Превышение происходит, когда используемый присадочный металл имеет более высокую прочность, чем основной материал. Эта практика сложна, так как может привести к растрескиванию (особенно, если прочность металла сварного шва намного превышает прочность основного металла), например, когда используется низколегированный присадочный металл с более высоким содержанием хром-молибдена, чем основной металл. Вы должны выходить за рамки только тогда, когда конкретный дизайн соединения указывает, что это лучшая процедура.
Другим фактором, который необходимо учитывать при подборе низколегированных присадочных металлов, является толщина низколегированной стали, которую вы планируете сваривать. Например, закаленные и отпущенные стали, такие как A514, имеют специфические характеристики растяжения, текучести и относительного удлинения, если их толщина остается меньше 21/2 дюйма. Его механические свойства изменяются, если материал толще этого. За это изменение отвечает процесс закалки и отпуска, так как более толстый материал закаливается медленнее и приводит к снижению минимального предела текучести и прочности на растяжение.Поэтому для более толстого материала могут потребоваться присадки с более низкой прочностью.
Само приложение также определит ваш низколегированный присадочный металл. Например, соединение, которое требует термообработки после сварки (PWHT), использует присадочный металл, легированный молибденом, чтобы гарантировать, что материал сохраняет свою прочность. Такие применения включают PWHT сосудов под давлением, что помогает улучшить ударные или ударные свойства и уменьшить любые остаточные напряжения в сварном шве, которые могут привести к преждевременному выходу его из строя.
Другим примером является применение с высокой усталостью, такое как землеройное оборудование, для которого требуется присадочный металл с более высокой ударной вязкостью. Присадочный металл, легированный никелем, обеспечивает большую устойчивость к циклическим нагрузкам и усталости в такой ситуации, а также предлагает более высокую прочность и лучшую ударную вязкость, чем мягкая сталь при низких температурах.
Классификации присадочного металла
Как и другие присадочные металлы, низколегированные присадочные металлы классифицируются AWS.
На рисунке 1 показаны классификации AWS, в частности, для низколегированных проводов с металлическим сердечником, экранированных газом, в то время как на рисунке 2 показаны классификации для низколегированных проводов с сердечником из флюса.
В обоих случаях первое место в классификации просто указывает «электрод». Следующие два пробела относятся к пределу прочности на разрыв (x 10 KSI) и возможностям сварочного положения, за которыми следует, является ли это сплошной (S) или композитной (C) проволокой. Окончательный химический состав металла шва (также известный как класс продукта) является последним пробелом. В каждой из этих классификаций химический состав, соответствующий прочности на разрыв, направляет вас к подходящему присадочному металлу.
Буква в области химического состава указывает класс продукта присадочного металла.Каждый класс продукции, в свою очередь, отвечает специфическим химическим и механическим требованиям в зависимости от сплава, содержащегося в присадочном металле. Эти сплавы затем определяют общую свариваемость и удобство использования присадочного металла, характеристики окончательного сварного шва и область применения, для которой он предназначен.
Например, в низколегированных присадочных металлах класса продукта B (B2, B3, B6 и B8 / 9) добавляются различные количества хрома и молибдена для повышения их коррозионной стойкости.Эти присадочные металлы обычно предназначены для высокотемпературных применений. Аналогично, низколегированные присадочные металлы в классе продуктов K (K2, K3 и K4) имеют различное количество смеси марганец-никель-молибден для повышения прочности, что делает их идеальными для сварки сталей HSLA.
На рисунке 3 приведены подробные сведения о других классах изделий из низколегированных присадочных металлов и их включенных сплавах, характеристиках и рекомендуемых применениях. Эта информация должна помочь вам выбрать подходящий низколегированный присадочный металл для вашей низколегированной стали.
Как и в любом сварочном процессе, образование является ключом к пониманию низколегированных сталей и присадочных металлов, используемых для их сварки. Фактически, вооружение этими знаниями может означать разницу между существенными механическими неисправностями и продолжающимся успехом сварки. Кроме того, всегда тщательно консультируйтесь со сварочными процедурами для вашего конкретного применения. Наконец, помните, что обращение к надежному сварочному дистрибьютору или производителю присадочного металла часто может решить любые дополнительные вопросы, которые могут у вас возникнуть.N
,Инструктор: | Анастасия Михайловская |
---|
Краткое содержание курса
Целью курса является изучение различных металлов и металлических сплавов, их структуры, свойств и областей применения. Анализ влияния состава и структуры на свойства сплавов; выбор режимов термообработки; выбор сплавов для различных применений.
Формат курса
Часы лекции | Часы практики | Часы в лаборатории | Часы самостоятельной работы | Общее количество часов |
---|---|---|---|---|
12 | 24 | 10 | 144 | 180 |
Содержание курса
- Введение: основные предметы и задачи курса
- Микроструктуры, свойства и применение сталей и чугунов
- Влияние легирующих элементов на микроструктуру и свойства сталей
- Основные методы термообработки материалов на основе Fe
- Основные методы термообработки цветных сплавов
- Микроструктуры, свойства и применение сплавов на основе алюминия
- Микроструктуры, свойства и применение сплавов на основе магния
- Микроструктуры, свойства и применение сплавов на основе титана
- Микроструктуры, свойства и применение сплавов на основе меди
- Фазовый анализ и особенности микроструктуры в промышленных сплавах: лабораторные занятия
Рединг
Основной учебник:
- Дэвид Э.Лафлин, Хоно Казухиро, физическая металлургия, Elsevier, 2014
Дополнительные учебники:
- ASM РУКОВОДСТВО. Свойства и выбор: железо, сталь и высокопрочные сплавы. Т.1. Информационная компания материалов, 2010.
- ASM HANDBOOK Свойства и выбор: Цветные сплавы и материалы специального назначения V.2. Информационная компания материалов, 2010.
- ASM РУКОВОДСТВО. Металлография и микроструктуры V.9. Информационная Компания Материалов, 2010.
- Деформация и обработка конструкционных материалов. Под редакцией З. Х. Го, Woodhead Publishing Limited, 2005.
- Обозначения и пределы химического состава алюминиевых сплавов в виде отливок и слитков, Алюминиевые ассоциации, 2008
- Обозначения и пределы химического состава для алюминиевых сплавов, Алюминиевые ассоциации, 2008
- Титан и титановые сплавы. Основы и приложения. Под редакцией Кристофа Лейенса, Манфреда Питерса.Copyright © 2003 WILEY-VCH Verlag GmbH & Co. KGaA, Weinheim
Оценка
Класс участия и домашние задания | 20% |
Промежуточные испытания и лабораторные работы | 30% |
Итоговый экзамен | 50% |
На самом деле, различные типы материалов для режущего инструмента использовались в промышленности, учитывая их особые свойства для конкретного применения, где требуется сбалансированное смешение необходимых характеристик. Существуют важные различия между режущими инструментами, и только хорошее знание их свойств может помочь разработчику / производителю выбрать подходящий для конкретного применения и для резки различных материалов.
Как правило, резание должно выполняться с использованием материала, который является более твердым, чем материал, который должен быть разрезан, и в то же время он должен иметь определенную геометрию, причем зазоры должны быть сконструированы таким образом, чтобы режущая кромка могла соответствующим образом взаимодействуйте с обрабатываемым куском, не перетаскивая остальную часть инструмента на поверхности куска. Эффективный режущий инструмент должен обладать (i) хорошей износостойкостью, чтобы быть способным сохранять его целостность против эрозии во время эксплуатации, (ii) достаточной ударной вязкостью, чтобы быть способным поглощать энергию, создаваемую различными нагрузками / вибрациями нагрузки / разгрузки, и (iii) соответствующая твердость, чтобы быть способной выдерживать постоянные изменения формы и геометрии во время резки.Однако экстремальная твердость, безусловно, не является предпочтительным свойством, поскольку она напрямую связана с хрупкостью инструмента и его хрупкостью. Твердость становится более значительной, когда обработка выполняется в экстремальных условиях, и инструмент должен сохранять свою целостность при высоких температурах.
1.1. Обзор различных типов материалов для режущих инструментов
В течение этого времени использовались различные материалы для режущих инструментов, и их разработка все еще находится в постоянном развитии. Резка и формование материалов на разные части для особых целей важны, особенно когда речь идет о высокой скорости резания и высоких температурах.По этим причинам материал инструмента должен проявлять такие свойства, чтобы предотвратить слишком сильный износ и разрушение при разрушении во время эксплуатации. Чтобы противостоять этим вредным условиям, режущий инструмент должен демонстрировать достаточную (i) твердость и прочность и поддерживать их при высокой температуре, (ii) ударную вязкость для поглощения энергии без разрушения, (iii) износостойкость, (iv) химическую инертность, и (v) теплопроводность. Как правило, режущие инструменты должны быть изготовлены с использованием механически более твердого материала по сравнению с материалом, который должен быть разрезан.Кроме того, использование режущего инструмента с определенной геометрией является предпочтительным, когда угол его зазора спроектирован таким образом, чтобы обеспечить идеальное взаимодействие между режущей кромкой и обрабатываемым куском, без замедления остальной части инструмента. другие поверхности близки к интересующей. Знание различий между характеристиками режущих материалов имеет важное значение [1–5] для их правильного выбора для резки обрабатываемых материалов.
Самыми старыми инструментальными материалами являются углеродистые стали (CS), но их реальное использование ограничено.Они редко используются для резки металла и сплавов, так как они быстро перегреваются при умеренно низкой температуре резки. Эти типы сталей содержат около 0,6–1,5% С и небольшие количества Si, Cr, Mn и V. В 1868 году Роберт Форестер Муше обнаружил, что твердость стали может быть повышена путем добавления W [6], и это отправная точка для обнаружения быстрорежущих сталей (HSSs) [7] незаменима в случае высоких скоростей резания (именно поэтому они называются быстрорежущими сталями) и повышенной температуры.Добавление легирующих элементов для упрочнения и укрепления основного материала и получения более стойкого в экстремальных условиях делает разницу между CS и HSS [8]. HSS может быть закален до различной глубины с помощью подходящей термообработки. Как правило, Mn, Cr, W, V, Мо, Со и Nb используются в качестве легирующих элементов в составе HSS. Co является ключевым элементом для обеспечения более высокой твердости (называемой холодной твердости ) HSS при высокой температуре, чем у CS. Они используются в качестве материалов для режущего инструмента, когда геометрия устройства и механика формирования стружки сложны или когда хрупкие инструменты не подходят ниже ударной нагрузки.HSS подходят для непрерывной резки и используются для разработки инструментов сложной формы, таких как сверла или зуборезы. Типичные скорости резания находятся в диапазоне 10–60 м / мин. Обычно используемые HSS подразделяются на типы M (инструментальные стали с Mo) и T (инструментальные стали с W), и они имеют различные классы: каждый работает для определенной цели, давая важные преимущества при точном использовании.
За это время эффективность УСЗ была повышена за счет изменения их свойств и условий поверхности с помощью различных методов: (i) уточнение их микроструктуры, (ii) производство с высоким уровнем содержания Co и V для усиления их горячей твердости и износостойкость тоже, (iii) использование порошковой металлургии для их производства, (iv) нанесение путем термического и химического осаждения паров (CVD) или физического осаждения из паров (PVD) (особенно TiC и TiN).С помощью этих процедур удалось повысить скорость их резания и, следовательно, весь срок службы инструмента примерно в три раза [9].
В начале 1920-х годов был введен немагнитный, износостойкий и коррозионно-стойкий сплав Co-Cr, известный как Stellite [10], который можно использовать на несколько более высоких скоростях, чем HSS. Из-за его низкой способности к шлифованию и для разработки цементированных / спеченных карбидов, использование Stellite очень скоро устарело. В настоящее время одним из важнейших инструментальных материалов, представленных в 1930-х годах, является цементированный карбид.По той причине, что они имеют высокую твердость в широком диапазоне температур, высокую теплопроводность и высокий модуль упругости, можно использовать во многих применениях. По сравнению с HSS они могут достигать скорости резания в 3–5 раз выше. Карбид вольфрама (WC), карбид титана (TiC), карбид тантала (TaC x ) и карбид ниобия (NbC / Nb 2 C) являются наиболее знакомыми твердыми карбидами, которые встроены в матрицу Co через процедуру спекания.На производительность твердосплавных инструментов существенно влияют тип карбида и содержание Co, и в зависимости от их состава они могут использоваться в различных областях применения. Более высокая твердость может быть достигнута с 3–6% Co, в то время как более высокий уровень Co (до 15%) обеспечивает превосходную ударную вязкость, но снижает твердость, износостойкость и прочность. При увеличении уровня W износостойкость увеличивается, однако это отрицательно влияет на прочность инструмента. TiC придает инструменту относительно более высокую износостойкость и меньшую ударную вязкость, чем WC [11–13].
Непрерывная индустриальная эволюция и потребность в более совершенных рабочих характеристиках для инструментальных материалов приводят к разработке инструментов с покрытием, увеличению срока службы инструмента и созданию более высоких скоростей резания. Как правило, слой / слои покрытия были реализованы методами PVD или CVD с использованием порошков TiN, TiC, TiCN и Al 2 O 3 , и обычно реализуется диапазон толщины 2-10 мкм. Для многофазных и керамических покрытий на твердосплавных инструментах предпочтительнее использовать технологию CVD, в то время как слой TiN, напыленный PVD, имеет некоторые положительные характеристики, такие как более высокая прочность режущей кромки, незначительное трение, более низкое сродство при создании наростной кромки и более гладкие и более постоянные по толщине (обычно в диапазоне 2–4 мкм).На самом деле, в основном для многофазного покрытия можно применять среднетемпературное химическое осаждение из паровой фазы (MTCVD), что приводит к более высокой устойчивости к распространению трещин, чем для режущих инструментов с CVD-покрытием. В середине двадцатого века были представлены спеченные режущие инструменты, изготовленные из керамики, содержащие Al 2 O 3 (белая или холодная штамповка керамики), Si 3 N 4 (черная или из прессованной керамики), SiAlON частицы [14–18].
В 1960-х годах были разработаны керметы [11–13], содержащие обычно 70% Al 2 O 3 и 30% TiC, с некоторыми небольшими количествами MoC, NbC, TaC, что дает некоторые преимущества.Добавление TiC и ZrO 2 к этим соединениям изменяет некоторые характеристики керамических инструментов: ZrO 2 улучшает вязкость разрушения, но в то же время снижает твердость и теплопроводность. По сравнению с HSS и карбидами керметы демонстрируют более высокую стойкость к истиранию, горячую твердость и химическую стабильность, но они имеют меньшую склонность к образованию заусенцев, имеют низкую прочность и низкую прочность на растяжение. Особые меры необходимы при работе с керамическими инструментами, чтобы избежать раннего выхода из строя инструмента.Эти инструменты подходят для непрерывной работы на очень высокой скорости. В любом случае, хрупкость и высокая стоимость керметов были проблематичными, и их характеристики расположены между характеристиками карбидов и керамики. Наиболее важной причиной разработки оксидно-металлических композиционных материалов было использование некоторых преимуществ хорошо известных характеристик или реализация различных свойств путем объединения различных элементов. Возможность снижения высокой хрупкости чистой оксидной керамики и повышение сопротивления при высокой температуре являются наиболее важными особенностями, которые показывают путь для разработки более сложного материала, такого как керметы.
С течением времени развитие режущих инструментов постоянно увеличивается. Начинается внедрение новых материалов, таких как кубический нитрид бора (cBN), поликристаллический cBN и поликристаллический алмазный инструмент. Они обеспечивают очень высокую износостойкость и прочность режущей кромки. При высокой температуре cBN химически инертен к Fe и Ni, и по этим причинам они обычно подходят для резки закаленных черных и жаропрочных сплавов. В то же время особое внимание должно быть уделено уравновешиванию его хрупкости во время службы.Самым твердым материалом является алмаз, и поскольку режущий инструмент демонстрирует высокую износостойкость, он сохраняет острую режущую кромку и часто используется, когда требуется хорошая чистота поверхности и точность размеров, особенно когда обрабатываются мягкие цветные сплавы и абразивные неметаллические материалы. Из-за его высокого химического сродства к Fe алмаз не подходит для резки стальных материалов [19–24].
Дальнейшее улучшение было достигнуто с разработкой армированных вискерами нанокристаллических инструментальных материалов с улучшенными свойствами, состоящих в использовании усов в качестве армирующих волокон в композитных инструментальных материалах.Это решение иногда расширяется добавлением ZrO 2 , который обеспечивает высокую вязкость разрушения, отличную жаропрочность, отличную стойкость к тепловому удару и прочность режущей кромки. Эволюция наноматериалов открывает отличные возможности для разработки новых усовершенствованных инструментальных материалов [25–28].
Идеальный инструмент не самый дорогой, но он тщательно отобран для профессионального, быстрого и экономичного выполнения запланированной операции резки.Обычно, когда прочность режущего инструмента увеличивается, его твердость при высокой температуре уменьшается. На рис. 1 показано, что для сравнения не существует идеального материала для режущего инструмента (без информации о материалах, армированных усиками, алмазом и усами). Каждый тип режущих материалов обладает своими типичными свойствами, которые необходимо понимать, чтобы эффективно использовать их в качестве режущего материала.
Рисунок 1.
Качественный показатель эволюции износостойкости и вязкости для различных инструментальных материалов.
1.1.1. Твердые металлы: обзор и некоторые свойства
Твердые металлы относятся к семейству композитных материалов, изготовленных из твердых материалов (металлические или неметаллические), которые соединены металлическими элементами. Обычно спекание или горячее прессование используется для изготовления компонентов, содержащих металлические твердые металлы, и некоторые из них могут использоваться без фаз связующего вследствие их собственной хрупкости.
Обычно гексагональный WC считается наиболее распространенным карбидом, а Co из-за его более высоких смачивающих свойств по сравнению с другими материалами в основном используется в качестве связующего материала [29–31].Когда при высокой температуре требуются определенные свойства, используют кубический TaC, TiC и NbC с добавлением небольшого количества V и Cr. Обычно используемые карбиды получают с помощью порошковой металлургии (PM), а затем компоненты смешивают и измельчают вместе, используя связующий материал (обычно органического типа), сушат распылением в агломератах и затем прессуют для получения зеленых форм, которые спекают для удаления их пористость и в то же время повысить их механическую прочность. В случае материалов, которые образуют короткие стружечные заготовки, такие как серый чугун, основными важными типами твердых металлов являются WC-Co, в то время как используются в случае материалов, которые обеспечивают длинную стружку, таких как стали, WC-TiC-Co / WC-TiC-TaC-Co [32-40].
Стандартизация материалов режущего инструмента очень трудна из-за различных видов производственных маршрутов, которые обычно используют порошковую металлургию (PM) различными альтернативными способами, чтобы лучше удовлетворить требования. Стандарт ISO 513: 2012 предусматривает классификацию по шести группам на основе обрабатываемых материалов: (1) все виды стали и литой стали и , кроме нержавеющей стали с аустенитной структурой, (2) нержавеющая сталь и аустенитная / ферритная сталь и литейная сталь , (3) чугун , чугун со сфероидальным графитом , чугун литейный , (4) цветные металлы (алюминий и другие металлы и неметаллические материалы), ( 5) жаропрочных сплавов и Ti (жаропрочные специальные сплавы на основе Fe, Ni и Co, Ti и его сплавов) и (6) твердые материалы (закаленная сталь, закаленные чугунные материалы, охлажденное литье) железо) [41].
Производство твердых металлов происходит в несколько этапов, которые могут быть дополнительно разделены на два основных семейства: первое предназначено для получения уплотненных порошков, а второе — для обжига, называемого спеканием, для склеивания отдельные частицы вместе обеспечивают превосходную прочность полученного материала. Первый этап является очень сложным, начиная с производства порошков, их точного смешивания с использованием прессующего агента / связующего материала, дробления и заканчивая процедурой прессования.В связи с этим спекание начинается с устранения отжимающего агента (депарафинизация) в контролируемых условиях (в присутствии H 2 или вакуума) при температуре около 600 ° C с последующей реальной обработкой спеканием в диапазоне температур 1350–1500 °. С в зависимости от состава твердого металла, который должен быть получен, обычно в вакууме или в восстановительной атмосфере. Когда порошки не могут быть спрессованы в их окончательной форме, обычно используется непрямое формование. Эта процедура начинается с прессованной заготовки и после удаления прессующего агента (при температуре около 600 ° C) или после предварительного спекания (до 1000 ° C) заготовка должна приобрести достаточную прочность, чтобы принять ее окончательную форму, полученную путем поворота, дробления и бурение.Обычно, когда необходимо получить большие пресс-формы, применяется процесс под давлением, и в зависимости от природы и состава пресс-форм это может быть холодное изостатическое или горячее изостатическое прессование.
Микроструктура, как и ожидалось, контролирует наиболее важные свойства и, в частности, на механические свойства в основном влияют два аспекта: средний размер карбидных зерен и их распределение в металлической матрице.
Используемое сырье и содержание уровня связующего, приложенное давление, время спекания и температура определяют рост зерен в структуре.Во время спекания увеличение размера зерна происходит в результате укрупнения. В то же время некоторые зерна имеют тенденцию увеличиваться по-разному и приобретать необычайно большие размеры, которых следует избегать, поскольку они действуют как места инициирования растрескивания, следовательно, снижая механические свойства материала. Для контроля размера зерна во время спекания можно использовать ингибиторы, чтобы сдерживать рост зерна и получать мелкозернистые карбиды [42].
Связь между прочностью, составом и размером гранул твердых металлов широко исследована в литературе [43–45].Высокотемпературные механические свойства твердого металла WC-Co, как предпочтительного материала для режущих инструментов, исследованы, например, в [46]. В этой главе рассматривается влияние размера зерен WC с содержанием Co на механические характеристики твердого металла с точки зрения модуля Юнга, коэффициента Пуассона, предела текучести, усталостной прочности и вязкости разрушения. Согласно этому исследованию, с ростом температуры и содержания Co модуль Юнга уменьшается. В [47] более выраженная потеря была подтверждена при температуре выше 800 ° C и независимости от размера зерна WC при комнатной температуре.Температура, содержание Co и размер зерна WC не влияют на коэффициент Пуассона. Чем выше температура и содержание Co, тем ниже предел текучести, в то время как до 700 ° C уровень Co и размеры гранулята WC не оказывают существенного влияния на вязкость разрушения твердых металлов WC-Co в соответствии с другими исследованиями [48–50]. При температуре выше 800 ° C более 8% Co значительно возрастает, эти свойства находятся в хорошем согласии с предыдущими исследованиями [48, 51], поскольку при этой температуре пластическая зона выше по сравнению с ситуацией при комнатной температуре, и это меняет распространение траектория перелома.Предлагаются различные теории пластической деформации твердых металлов WC-Co: в соответствии с [52–54] деформация материала происходит внутри фазы связующего, в то время как в [43, 44] наличие постоянной системы WC Предполагается, что карбидная сеть деформируется одновременно со связующим Co.
Как упомянуто в ссылках. [6, 55, 56], твердые металлы WC-Co, полученные из ультратонких или нанозернистых частиц, демонстрируют превосходную твердость по сравнению с их более крупнозернистыми, в то время как Lankford [57] указывает, что прочность на сжатие этих твердых металлов увеличивается, когда содержание связующего уменьшается.Влияние скорости нагружения на прочность при сжатии твердого металла WC-Co проиллюстрировано в [52] как функция содержания Co, и авторы обнаружили, что фрагменты становятся более мелкими после сжимающей нагрузки с увеличением скорости деформации и содержания Co. уменьшается, прочность на сжатие увеличивается из-за возрастающего уровня разрушения, которое характеризуется возникновением трещин, характерных для хрупкого материала. Распространение трещин вызывает локальное снятие напряжения. Этот аспект хорошо согласуется с тонкостью фрагментов, описанных в [53–64].
Из-за высокого промышленного запроса на режущие инструменты на основе карбонитрида титана (Ti (C, N)) с высокими и стабильными механическими свойствами, научное сообщество уделяло большое внимание этой проблеме [65]. Чтобы повысить твердость и механические свойства при высокой температуре таких режущих инструментов, добавление Mo, Ni-Co, WC, TaC, HfC было предложено в [66], и их влияние было оценено с помощью микроструктурных характеристик, которые напрямую связаны с механическим поведением системы.По мере увеличения содержания Ni-Co микроструктура материала становится более тонкой; более 4% добавления Мо отрицательно влияет на механические свойства. По мнению авторов [67, 68] предполагается, что для твердого металла, полученного с небольшим количеством Ni-Co и 4–8% (мас.) Мо, наилучшие механические свойства могут быть достигнуты. Добавление TaC увеличивает прочность на изгиб, а HfC увеличивает твердость твердого металла Ti (C, N). Кроме того, в некоторых исследованиях [65, 69, 70] сообщалось о положительном влиянии WC на смачиваемость между заинтересованными фазами, что дает более тонкую микроструктуру и более высокие механические свойства, но в то же время из-за низкой температуры окисления WC это оказывает негативное влияние. на его производительность резки, особенно в высокоскоростной обработке.В таких случаях целесообразно частично или полностью заменить частицы WC TaC [71], как указано также в [69, 70–72]. Нанокристаллические цементированные карбиды, полученные методом импульсного плазменного спекания, по сравнению со стандартным методом, полученным методом горячего изостатического прессования, демонстрируют более высокую твердость и более высокую относительную плотность, как показано в [73].
Исследование возможности использования нанотехнологий для повышения качества и эффективности обработки ограничено. В последнее время использование наночастиц, в том числе углеродных нанотрубок (УНТ), в инструментах для дробления и полировки, а также в качестве материалов для покрытий, стало очень привлекательным [74–79], и опубликованные данные [74] показывают, что добавление УНТ имеет тенденцию к снижению размер зерна структурной составляющей связующего, определяющий более высокую прочность и характеристики металлического связующего.
Процессы химического осаждения из паровой фазы и физического осаждения из паровой фазы использовались с 1970 года для осаждения различных твердых тонких слоев на цементированные карбиды [80–83] для увеличения срока их службы, в частности на активных частях инструментов. Матей и соавт. [84] сообщили о благоприятном влиянии некоторых слоев покрытия (TiN, TiC, TiAlN) на рабочие характеристики модифицированных инструментов WC-Co в чистой атмосфере с учетом их коррозионной стойкости по сравнению с инструментами без покрытия. Авторы обнаружили, что среди материалов, используемых для нанесения покрытия, слой TiN является наиболее перспективным для более эффективной защиты подложки.
1.2. Производство материалов для режущих инструментов
Растущее использование материалов для инструментов требует высокой целостности и улучшенных характеристик, которые представляют собой надежную поддержку для увеличения срока службы технических компонентов и их надежности без ущерба для безопасности. Экономическое влияние и сложность этих режущих материалов могут оправдать огромные усилия, которые они предпринимают в течение времени, для их разработки и обработки для различных применений. Получение изотропной микроструктуры, которая характеризуется однородным распределением элементов без сегрегации, имеет первостепенное значение при использовании материалов для резки.
Использование маршрута PM позволяет получать передовые инструментальные материалы, которые способны достичь очень высокой производительности и выдерживать суровые условия эксплуатации без преждевременного выхода из строя. Метод PM позволяет комбинировать порошки различной природы и характеристик, которые трудно спрессовать в противном случае, получая плотный конечный материал с гибридными или новыми свойствами. Способность PM выполнять все фазы обработки в твердом состоянии и превращать порошки непосредственно в конечную или полуфинальную форму можно рассматривать как основное преимущество такой технологии.Кроме того, с помощью этой технологии могут быть получены порошки со значительно различными температурами плавления с очень разными плотностями. Возможность использования различных компонентов, которые имеют ограниченные взаимную растворимость в жидком состоянии или, когда жидкий металл имеет высокое сродство к огнеупорной или другому субъекту ПМ является весьма перспективной технологией.
Процесс PM очень полезен в случае композитных материалов, содержащих алмаз и нитрид бора, а также твердых металлов.После Второй мировой войны (Второй мировой войны) эта технология стала важной для производства керметов первого поколения и с течением времени становится особенно важной для керметов второго поколения (содержащих карбиды, бориды, нитриды, силициды и т. Д.) И совершенствования в то же время их сопротивление при высокой температуре и их износостойкость по сравнению с первыми разработанными керметами.
В случае стальных материалов, в частности, свинец ПМ приобретает исключительные или улучшенные свойства, которые не могут быть реализованы традиционными производственными процедурами.В частности, в инструментальных сталях, получаемых традиционным способом, жидкий металл заливают в форму, затем слиток сковывают и раскатывают, после чего проводят стадию отжига. Из-за условий на стадии отверждения в обычных способах изготовления на слиток влияют явления макросегрегации, особенно в виде карбидов. Напротив, во время процесса PM жидкий металл транспортируется через небольшое сопло, и благодаря наличию высокого давления поток жидкости превращается в сферическую каплю с однородным составом; они могут быть собраны после их быстрого затвердевания без какой-либо возможности сегрегации.Быстрое охлаждение определяет выделение мелких карбидов, которые сохраняют свои свойства во время HIP и фрезерования. Технология PM производит изотропный материал с однородной микроструктурой, где действительно точное распределение карбидов способствует повышению их износостойкости и пластичности. В стандартно изготовленных HSS высокая пластичность может быть достигнута за счет потери износостойкости. Кроме того, PM HSS имеет тенденцию быстро реагировать на термообработку с более высокой предсказуемостью, чем обычно производимые HSS.
Как правило, разница между традиционно полученными материалами и материалами, полученными с помощью PM, связана не только с производственным маршрутом, но и с различными преимуществами, особенно в случае компонентов сложной формы и с высокой степенью точности.
Помимо преимуществ, существуют также некоторые недостатки, связанные с маршрутом РМ, в основном связанные с относительно высокой стоимостью металлических порошков и инструментов и материалов, используемых для уплотнения порошков, производительности пресса и т. Д.Тем не менее, многие из этих трудностей могут быть уменьшены в ходе эволюции с помощью правильного производственного плана на начальном этапе, который будет сопровождаться устоявшимся и важным массовым производством.
Обычно PM включает в себя различные технологии для изготовления конечных компонентов, а именно:
Традиционный процесс PM, состоящий из различных этапов, состоит из смешивания порошков элемент / сплав, прессования смеси в форме, а затем спекания происходит в контролируемая среда для металлургического связывания частиц.
Литье под давлением металлов (MIM) касается производства сложных форм в больших количествах с использованием тонкодисперсных металлических порошков (обычно <20 мкм), которые изготовлены по индивидуальному заказу со связующим (различные термопласты, воски и другие материалы) в сырье, которое подается в полость традиционного литьевого устройства. Связующее извлекают термической обработкой или обработкой растворителем, а зеленый спекают. Процесс MIM очень похож на литье под высоким давлением, но он ограничен относительно небольшими и очень сложными деталями.Самая важная особенность этой процедуры связана с ее способностью производить компоненты с механическими свойствами, сопоставимыми с деформируемыми материалами.
Изостатическое прессование — это процесс формования ТЧ, который применяется к порошку для уплотнения одинакового давления во всех направлениях, создавая однородную микроструктуру, и по сравнению с одноосным прессованием геометрические ограничения отсутствуют. Изостатическое прессование может быть реализовано: (i) холодным, когда он используется для уплотнения зеленого при комнатной температуре, и (ii) горячим (HIP), когда используется для полного объединения деталей при высоких температурах посредством твердотельной диффузии.HIP также может быть использован для устранения остаточной пористости из спеченной части PM. HIP является дорогостоящим методом, и на самом деле предпочтение отдается альтернативной более дешевой процедуре без использования давления при высокой температуре, а также с положительным результатом для окружающей среды.
Горячее прессование объединяет этапы уплотнения и обжига для получения умеренно простых симметричных фигур, которые создаются, исходя из сырья, введенного в высокотемпературную форму, в то время как оно все еще поддерживается под нагрузкой.Что касается горячего изостатического прессования (HIP), это процесс спекания порошков при постоянном давлении в простые или более сложные формы. Разница между HIP и изостатическим прессованием связана с тем, как во время спекания применяется давление, и в первом случае оно является равномерным.
На самом деле, производство металлических добавок (AM) стало очень популярным. Тем не менее, он используется для производства некоторых нишевых изделий из-за необходимости иметь больше знаний, прежде чем стать точной технологией для массового производства.
Цементированные карбиды, как правило, спекаются методом жидкофазного спекания в диапазоне температур 1350–1650 ° C с получением более или менее беспористого материала. Во время спекания Co становится жидким и легко растворяет W и C, поступающие из WC, и в то же время понижает температуру плавления. Кроме того, уровень C имеет первостепенное значение, поскольку он приводит к получению нежелательного соединения [42] в спеченном материале.
Влияние жидкой фазы на спекание важно, поскольку оно влияет на время спекания: полное уплотнение конечного продукта возможно в течение 1 часа.Идеальный уровень жидкости в сочетании с высокой растворимостью твердого вещества в жидкой фазе, а также полным смачиванием твердых и жидких частиц являются наиболее важными параметрами, влияющими на процесс спекания. Основными фазами спекания, графически проиллюстрированными на рисунке 2, являются:
Перегруппировка: образование жидкости и смачивание твердых элементов, участвующих в процессе, с последующим перераспределением в более компактную форму;
Перераспределение раствора: медленно происходит реорганизация структуры и происходит укрупнение частиц;
Твердотельное спекание: «уплотненная сборка» «обжигается» в конечный продукт [42].
Рисунок 2.
Схема наиболее важных этапов жидкофазного спекания [42].
Реактивное спекание, как одна из инновационных процедур спекания, является признаком постоянного улучшения различных производственных маршрутов с целью получения улучшенных свойств экономически удобным способом. В любом случае, из-за некоторых проблем, связанных с контролем процедуры, широкое промышленное использование таких методов все еще ограничено. Тепло, необходимое для спекания, обеспечивается экзотермической реакцией между основными порошками, и в результате этого получается достаточно для превращения уплотненных порошков в твердый материал [42].