Легированные стали Статьи
Сталь, содержащая один или несколько легирующих элементов, вводимых для придания изделию определенных физико-механических свойств, называется легированной. Содержание некоторых элементов, когда они не являются легирующими, не должно превышать: кремния (Si) — 0,5%; марганца (Мп) — 0,8%; хрома (Сг) 0,3%; никеля (Ni) — 0,3%; меди (Си) -0,3% Легированные стали подразделяют на подклассы: низко— , средне— , и высоколегированные. Низколегированная сталь — это сталь, легированная одним элементом при содержании его не более 2% (по верхнему пределу) или несколькими элементами при суммарном их содержании 3,5% (по верхнему пределу). Среднелегированная сталь, легированная одним элементом, при содержании его не более 8% (по верхнему пределу) или несколькими элементами при суммарном их содержании, как правило, не более 12% (по верхнему пределу). Высоколегированная — это сталь с суммарным содержанием легирующих элементов не менее 10% (по верхнему пределу), при содержании одного из них не менее 8% (по нижнему пределу), при содержании железа более 45%. Маркировка всех легированных конструкционных сталей однотипная. Первые две цифры обозначают содержание углерода в сотых долях процента, буквы являются условным обозначением легирующих элементов, цифра после буквы обозначает содержание легирующего элемента в %, причем содержание, равное 1% и меньше, не ставится, буква «А» в конце марки показывает, что сталь высококачественная и имеет пониженное содержание серы и фосфора. Основными элементами, влияющими на свойства стали, являются углерод, марганец и кремний. Углерод при повышении его содержания в стали ведет к повышению прочности и твердости и уменьшению пластичности. Окисление углерода во время сварки вызывает появление большого количества газовых пор. Марганец повышает ударную вязкость и хладноломкость стали, являясь хорошим раскислителем, способствует уменьшению содержания кислорода в стали. При содержании марганца в стали более 1,5 % свариваемость ухудшается, так как увеличивается твердость стали, образуются закалочные структуры и могут появиться трещины.
Кремний вводится в сталь как раскислитель. При содержании кремния более 1 % свариваемость стали ухудшается, так как возникают тугоплавкие окислы, что ведет к появлению шлаковых включений. Сварной шов становится хрупким. Хром при значительном содержании в стали снижает ее свариваемость вследствие образования тугоплавких окислов и закалочных структур. Никель повышает прочность и пластичность шва и не ухудшает свариваемость. Алюминий — активный раскислитель стали, повышает окалиностой-кость. Вольфрам повышает прочность и твердость при повышенных температурах, ухудшает свариваемость, сильно окисляется. Ванадий затрудняет сварку, сильно окисляется, требует введения в зону плавления активных раскислителей. Медь улучшает свариваемость, повышая прочность, ударную вязкость и коррозионную стойкость сталей. Сера приводит к образованию горячих трещин. Фосфор вызывает при сварке появление холодных трещин. Как правило, повышение уровня легирования и прочности стали приводит к ухудшению ее свариваемости.
Первостепенная роль по влиянию на свойства сталей принадлежит углероду. Доля влияния каждого легирующего элемента может быть отнесена к доле влияния углерода. На этом основании о свариваемости легированных сталей можно судить по коэффициенту эквивалентности по углероду для различных элементов. При подсчете Сэ содержание химических элементов принимается в процентах. Если Сэ меньше 0,4% , то трещины в зоне термического влияния не возникают. При Сэ = (0,4 — 0,7%) — необходим предварительный подогрев. Если Сэ = (0,7 — 1,0%) — нужны предварительный и сопутствующий подогрев. При Сэ более 1,0% сталь не сваривается обычными (традиционными) методами сварки плавлением. Образование холодных трещин уменьшается путем выбора рационального способа и технологии сварки, предварительного подогрева, снижения содержания водорода в сварном соединении, применения отпуска после сварки. Элементами, обуславливающими возникновение горячих трещин, являются прежде всего сера, затем углерод, фосфор, кремний и др. Элементами, повышающими стойкость швов против трещин и нейтрализующими действие серы, являются: марганец, кислород, титан, хром, ванадий.
Предупреждение образования горячих трещин может быть достигнуто путем уменьшения количества и сосредоточения швов, выбора оптимальной формы разделки кромок, устранения излишней жесткости закреплений, предварительного подогрева, применения электродного металла с более низким содержанием углерода и кремния. Низколегированные стали хорошо свариваются всеми способами сварки плавлением. Получение при сварке равнопрочного сварного соединения, особенно термоупрочненных сталей, вызывает некоторые трудности и требует определенных технологических приемов. В зонах, удаленных от высокотемпературной области, возникает холодная пластическая деформация. При наложении последующих слоев эти зоны становятся участками деформационного старения, приводящего к снижению пластических и повышению прочностных свойств металла и соответственно к возможному появлению холодных трещин. В сталях, содержащих углерод по верхнему пределу и повышенное количество марганца и хрома, вероятность образования холодных трещин увеличивается (особенно с ростом скорости охлаждения).
Предварительный подогрев и последующая термо обработка позволяют снимать остаточные сварочные напряжения и получать необходимые механические свойства сварных соединений из низколегированных сталей. По разрезаемости легированные стали делятся на аналогичные четыре группы с соответствующим значением показателя эквивалента углерода.
Легированная сталь
Легированная сталь — это сталь, включающая в себя разные легирующие элементы, придающие стали нужные механические и физические свойства.
Также эти элементы значительно повышают стойкость к коррозии, стойкость к хрупкости и повышают прочность.
Элементы легированной стали можно вынести в такой список:
- азот;
- медь;
- никель;
- хром;
- ванадий.
Это классические добавки, которые максимально применяются в производстве. Легированная сталь разделяют на три основных класса:
- низколегированную;
- высоколегированную;
- среднелегированной.
Классификация легированных сталей производится из учета процентного содержания легируемых элементов. Каждый из этих типов стали получают металлургическим путем, однако в отдельных случаях может выполняться легирование только определенной поверхности, чтобы придать необходимые прочностные свойства изделиям и деталям. Легированная сталь приобретает свои свойства на различных этапах производства металла, по мере добавления легирующих элементов. Легированная сталь может включать в себя от одного до нескольких легируемых элементов, которые повышают конструкционную прочность сплава. Легированная сталь выпускают в нескольких основных типах:
- инструментальную;
- конструкционную;
- сталь, имеющая особые химические и физические свойства.
Маркировка легируемых сталей производится с помощью букв, которые показывают какой легирующий элемент содержится в сплаве, и цифрами, определяющими среднее содержание этого элемента в процентах. Цифры вначале названия марки указывают, сколько углерода содержит материал.
- Р — быстрорежущая;
- Ш – шарикоподшипниковая;
- А — автоматная;
- Л — полученная литьем;
- Э — электротехническая.
На содержание азота указывает буква А, находящаяся в середине марки. Две буквы А (АА), показывают состав особо чистой стали и эти буквы стоят в конце. Сталь особо высокого качества в конце марки имеет букву Ш. Примеры маркировки легированных сталей:
18ХГТ означает:
- 0,18% С;
- 1% Cr;
- 1% Mn;
- 0,1% Ti.
Сталь 30ХГСА содержит:
- 0,30% С;
- 0,8-1,1% Cr;
- 0,9-1,2% Mn;
- 0,8-1,25% Si.
Назначение легируемых сталей
Назначение легируемых сталей очень разнообразно, так как, имея в своем составе соответствующие легируемые добавки, такая сталь способна выдерживать разного рода нагрузки, в отличие от обычной. Большинство показателей можно регулировать с помощью добавления нужных легирующих элементов. Основное назначение легируемых сталей — изготовление хирургических инструментов, ювелирного оборудования, различных металлоконструкций, строительной арматуры, промышленных машин, механизмов, испытывающих большие нагрузки при работе. Марки инструментального назначения легируемых сталей используют для изготовления деталей, которые работают под высоким давлением, также их применяют при изготовлении эталонных шестерен, роликов сложной формы, секций кузнечных штампов и т.д.. Другие марки применяют для деталей с повышенной износостойкостью, хорошей прочностью на изгиб, контактной нагрузке, при необходимой замечательной упругости.
Виды легированной стали
Виды легированной стали различают соответственно процентному содержанию легирующих элементов в сплаве. Так классифицируются:
- низколегированные и содержат до 2,5% легирующих элементов;
- среднелегированные, имеющие от 2,5 до 10% легируемых элементов;
- высоколегированные имеют 10 — 50% таких элементов.
Виды легированной стали бывают разными. Классифицируются в зависимости от процентного соотношения высокоэффективных компонентов, допустим: циркония, ванадия, тантала, других химических элементов, например, углерода, а также структурной специфики:
- ледебуритные – наличие первичных карбидов;
- эвтектоидные – строение металла перлитное;
- заэвтектоидные – присутствие вторичных карбидов;
- доэвтектоидные – есть избыточный феррит.
По степени использования, назначения бывают стали: конструкционные, инструментальные, с особыми свойствами.
Виды легированной стали
включают в себя также нержавеющие, имеющие великолепные свойства стойкости к химической и электрохимической коррозии. Специальные жаростойкие, имеющие хорошую стойкость химическому разрушению в газовой среде при температуре выше 500 С, но при этом они работают в слабо нагруженном состоянии или не нагруженном. Жаропрочные стали, которые работают при больших нагрузках в течение достаточного времени и при этом сохраняющие достаточную жаростойкость.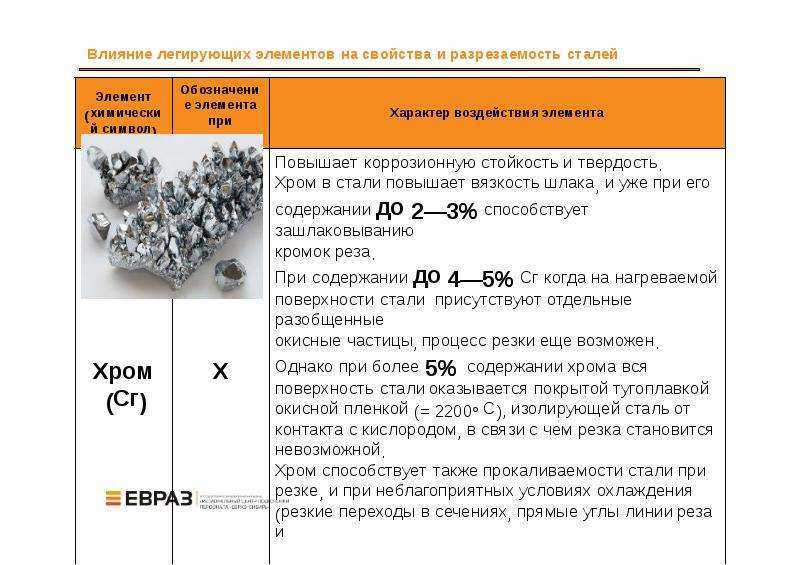
- качественной;
- высококачественной;
- очень высокого качества.
Глава 6.4. Влияние легирующих элементов на структуру и свойства сталей — Купити в Харкові, Києві, Україні. Безкоштовне тестування
Легирующие элементы специально вводят в сталь с целью изменения ее структуры и свойств в отличие от примесей, попадающих в сталь при выплавке из руд, шихты. Стали, содержащие легирующие элементы, называются легированными.
В зависимости от содержания легирующих элементов (указанного в скобках) различают низколегированные (до 2…3 %), среднелегированные (3… 10%) и высоколегированные стали (более 10%).
Изменение структуры и свойств сталей возможно лишь в том случае, если элементы, вводимые в сталь, взаимодействуют с железом и (или) углеродом, тогда эти элементы и являются легирующими.
Основными легирующими элементами сталей являются металлы, которые с железом образуют твердые растворы замещения. Железо является полиморфным металлом и имеет две модификации: a-железо (ОЦК решетка) и γ-железо (ГЦК решетка). В a-железе хорошо растворяются элементы, имеющие ОЦК решетку. Соответственно в γ-железе — элементы с ГЦК решеткой.
К первой группе относятся хром, молибден, вольфрам, ванадий, титан и кремний. Сплавы железа с ними описываются диаграммой состояния с расширенной областью сплавов с ОЦК решеткой — a-твердых растворов. При этом область γ-твердых растворов резко уменьшается (рис. 6.1, а). Сплавы, не претерпевающие (α о γ)-превращения, т.е. лежащие правее точки а на оси концентраций, называются ферритными. Эти легирующие элементы повышают температуру А3 (точка G на диаграмме состояния системы Fe — Fe3C) и понижают А4 — температуру существования высокотемпературной модификации Feα (точка N в соответствии с диаграммой состояния системы Fe — Fc3C: см. подразд. 4.1).
Ко второй группе относятся марганец, никель и кобальт. Эти элементы образуют с железом сплавы, имеющие диаграмму состояния с расширенной областью сплавов с ГЦК решеткой — γ-твердых растворов — и уменьшенной областью существования a-твердых растворов (рис. 6.1, б). Сплавы, не претерпевающие (γ↔α) – превращения, т.е. лежащие правее точки α на оси концентраций, называются аустенитными. Эти легирующие элементы оказывают противоположное влияние на температуры А3 (понижают) и А4 (повышают).
По взаимодействию с углеродом легирующие элементы делятся на карбидообразующие элементы, которые образуют собственные карбиды; графитообразующие (графитизаторы) — способствующие распаду карбидов с выделением свободного углерода; нейтральные.
Карбидообразующими являются марганец, хром, молибден, вольфрам, ванадий и титан. В Периодической системе они располагаются слева от железа, и чем левее, тем больше (сильнее) выражена их карбидообразующая способность. Таким образом, самым сильным карбидообразующим является титан, а наиболее слабым (исключая железо) — марганец. Железо является еще более слабым карбидообразующим компонентом, чем марганец.
Рис. 6.1. Влияние легирующих элементов на вид диаграммы состояния сплава железо — легирующий элемент и температуру полиморфных превращений железа: а — легирующие элементы с ОЦК решеткой; б — легирующие элементы с ГЦК решеткой
При легировании сталей марганец (независимо от его количества), хром (до 2 %), а также вольфрам и молибден в малых количествах (десятые доли процента) растворяются в цементите, частично замещая атомы железа в его кристаллической решетке. Образуется легированный цементит, мало отличающийся по свойствам от обычного. Его формула в общем виде записывается как М3С, где М — атомы металлов. Таким образом, цементит может иметь состав (Fe, Сг)3С или (Fe, Мn)3С и т.д.
При повышенных концентрациях легирующие элементы в стали образуют собственные карбиды. Так, при содержании 2… 10% хрома в сталях образуется карбид Сг7С3, а при увеличении свыше 10 % — Сг23С6. Причем эти карбиды могут растворять в себе железо (значительное количество) и другие легирующие элементы. Тогда они обозначаются как М7С3 и М23С6. Вольфрам и молибден образуют сложные карбиды Fe3W3C и Fe3Mo3C (М6С). Все эти карбиды сравнительно легко растворяются в аустените при нагреве.
Сильные карбидообразующие элементы образуют карбиды типа МС (TiC, VC, WC, МоС). Вольфрам и молибден могут образовывать также карбиды типа М2С (W2C и Мо2С). Все эти карбиды практически не растворяются в аустените.
Энергия связи атомов углерода и сильных карбидообразующих элементов значительно выше, чем атомов углерода и железа. Это определяет большую твердость этих карбидов: твердость цементита — 800… 1000 HV, карбида титана (TiC) — 3200 HV. Кроме того, повышается устойчивость карбидов сильных карбидообразующих элементов при нагреве, они растворяются в аустените при более высоких температурах. Так, цементит начинает растворяться в аустените при 727 °С, карбиды хрома при 850… 900 °С, а карбиды ванадия (VC) и титана (TiC) практически не растворяются в аустените, так как температуры их растворения (около 1300 °С) выше температуры плавления сталей.
Графитизаторами являются никель и кремний. Так, кремний сильно ускоряет реакцию графитизации, т.е. происходит распад цементита с образованием свободного углерода. В качестве графитизатора его широко используют при выплавке чугунов (см. гл. 7).
К нейтральным элементам относится кобальт, который широко применяется в твердых сплавах в качестве металла-связки (см. подразд. 9.2.2).
В отожженном состоянии легированные стали имеют прочность и твердость большие, чем у углеродистых, но их ударная вязкость ниже (рис. 6.2). Это вызвано тем, что легирующие элементы, растворяясь в феррите, упрочняют его, особенно марганец и кремний.
Рис. 6.2. Влияние легирующих элементов на свойства феррита: а — изменение твердости; б — изменение ударной вязкости
Существенное влияние легирующие элементы оказывают на положение линий диаграммы состояния системы Fe — Fe3C. При нагреве они растворяются в аустените, искажают его кристаллическую решетку, уменьшая тем самым растворимость в нем углерода. В результате линия SE сдвигается влево, т.е. в сторону меньшего содержания углерода (рис. 6.3). Это приводит к тому, что структура перлита — эвтектоида и ледебурита — эвтектики у легированных сталей достигается при более низком содержании углерода, чем в углеродистых сталях. Так, сталь с 5 % хрома является заэвтектоидной при 0,6 % С, а при 1,5 % углерода уже содержит в структуре ледебурит, т. е. является чугуном, в то время как заэвтектоидные углеродистые стали содержат более 0,8 % углерода — точка S диаграммы состояния (см. рис. 4.2). В соответствии с диаграммой состояния системы Fe — Fe3C ледебурит появляется в структуре, если углерода более 2,14% — точка Е. Таким образом, наряду с делением на доэвтектоидные, эвтектоидные и заэвтектоидные, что характерно для углеродистых сталей (см. подразд. 4.2 и рис. 4.2), у легированных сталей появляется еще одна группа — ледебуритные стали со структурой, аналогичной доэвтектическим чугунам.
Рис. 6.3. Влияние легирующих элементов на положение точек S и Е диаграммы состояния системы Fe — Fe3C
Основные преимущества легированных сталей перед углеродистыми проявляются при термической обработке. Прежде всего это связано с изменением вида диаграммы изотермического превращения аустенита. Марганец и никель повышают устойчивость переохлажденного аустенита, при этом на С-образной диаграмме линия начала распада аустенита смещается вправо (рис. 6.4, а). Карбидообразующие элементы не только смещают эту линию вправо, но и меняют вид диаграммы принципиально: диаграмма раздваивается, на ней появляется два минимума устойчивости переохлажденного аустенита (рис. 6.4, б). При этом важен именно сдвиг во времени начала распада переохлажденного аустенита, который начинается позже и приводит к снижению критической скорости охлаждения, т.е. увеличению прокаливаемости.
Проиллюстрируем это с помощью рис. 6.5. Скорость охлаждения сердцевины детали из углеродистой стали меньше критической (vсер vкр) и структуру мартенсита по всему сечению (рис, 6.5, б). Твердость сталей 40 и 40Х в сечении 10 и 40 мм приведена на рис. 6.6.
Рис. 6.4. Диаграммы изотермического превращения аустенита в углеродистой стали и сталях, легированных Ni, Si, Мn (а) и сильными карбидообразующими элементами (б)
Рис. 6.5. Прокаливаемость углеродистой (а) и легированной (б) сталей: Ауст — устойчивый аустенит; Анеуст — неустойчивый (переохлажденный) аустенит; А — аустенит; М — мартенсит; П — перлит; С — сорбит; Т — троостит; vкр — критическая скорость охлаждения; — скорость охлаждения сердцевины детали; vсер — скорость охлаждения поверхности детали; Мн — температура начала мартенситного превращения; Мк — температура конца мартенситного превращения
Таким образом, из легированных сталей следует изготавливать детали большого сечения, которые необходимо упрочнять по всему сечению. Кроме того, важным преимуществом легированных сталей является возможность более медленного охлаждения при закалке (в масле или расплавленных солях, а не в воде, как детали из углеродистых сталей). Это уменьшает закалочные напряжения и, следовательно, деформацию деталей, предупреждает образование трещин. Поэтому детали сложной формы, склонные к деформациям при закалке, также следует изготавливать из легированных сталей.
Влияние легирующих элементов на вид С-образной диаграммы проявляется также в том, что большинство легирующих элементов снижает температуру мартенситных точек М и Мк (рис. 6.7, а). Это приводит к появлению в структуре закаленных сталей остаточного аустенита (рис. 6.7, б). Особенно сильно увеличивается его количество в высокоуглеродистых сталях. В этих случаях в технологии термической обработки деталей для устранения остаточного аустенита необходимо предусмотреть обработку холодом. Исключением являются алюминий и кобальт — они повышают температуры Мн и Мк, а также кремний, не оказывающий влияния на эти температуры.
Рис. 6.6. Твердость по сечению сталей 40 и 40Х
Легирующие элементы повышают устойчивость мартенсита при нагреве, т.е. задерживают выделение из него атомов углерода и уменьшают скорость коагуляции карбидов (рис. 6.8). Поэтому для получения одинаковой твердости и прочности детали из легированных сталей следует отпускать при более высокой температуре.
Рис. 6.7. Влияние легирующих элементов на температуру начала мартенситного превращения М„ (а) и количество остаточного аустенита (б) в стали с 1% С
Наряду с положительными свойствами легированные стали обладают рядом недостатков, которые практически не наблюдаются в углеродистых сталях.
Рис. 6.8. Влияние температуры отпуска на твердость стали: 1 — углеродистой; 2 — легированной
Отпускная хрупкость — резкое снижение ударной вязкости после отпуска. Различают два вида отпускной хрупкости (рис. 6.9). Необратимая отпускная хрупкость (I рода) проявляется у всех сталей при отпуске в интервале температур 250…350 °С. Она не зависит от скорости охлаждения при отпуске и присуща и углеродистым, и легированным сталям. Обратимая отпускная хрупкость (II рода) наблюдается только у легированных (чаще всего хромистых) сталей при высоком отпуске, но лишь в том случае, когда охлаждение после отпуска медленное — на воздухе. Подавить отпускную хрупкость II рода можно быстрым охлаждением (например, не на воздухе, а в масле). Однако при этом возникает опасность коробления, тем более что отпуск легированных сталей выполняется при более высоких температурах, чем углеродистых. Кроме того, быстрое охлаждение невозможно для крупногабаритных деталей. Для предупреждения отпускной хрупкости II рода эффективно легирование молибденом и вольфрамом в небольших количествах (0,5 %). Стали, легированные таким образом (например, 40ХНМА), не склонны к отпускной хрупкости.
Рис. 6.9. Влияние температуры отпуска на ударную вязкость легированной стали: I — зона необратимой отпускной хрупкости; II — зона обратимой отпускной хрупкости
Флокенами называются мелкие внутренние трещины, появляющиеся в кованых или катаных сталях. Они наиболее часто встречаются в сталях, содержащих хром (хромистых, хромоникелевых, хромомарганцовистых и т. д.). Как всякие трещины, флокены сильно понижают механические свойства стали. Флокены тем более опасны, чем большую прочность должна иметь сталь (при отсутствии дефектов), так как из таких сталей изготавливают наиболее нагруженные детали.
Причиной образования флокенов является присутствие в стали повышенного количества водорода (выше 0,0008%). Флокены появляются при быстром охлаждении стали в интервале 250…20 °С после окончания пластической деформации. В этом случае водород создает большие давления, которые и приводят к образованию трещин. Если сталь в указанном температурном интервале охлаждать медленно, то водород успевает выделиться из стали и флокены не возникают. Флокены редко образуются в литой стали, так как пористость, характерная для литой структуры, облегчает удаление водорода из стали.
Флокены устраняются ковкой или прокаткой на меньший размер. При этом происходит залечивание, «заварка» трещин. Флокены практически не встречаются в сечениях с толщиной (диаметром) меньше 25 мм.
Шиферный (слоистый) излом наблюдается после горячей деформации. При прокате усадочные раковины и пузыри вытягиваются в виде слоев загрязненного металла. При разрушении излом получается слоистым, с острыми зазубринами и выступами. Термической обработкой шиферный излом не исправляется. Исправить структуру можно только перековкой стали.
Карбидная ликвация (неоднородность) наблюдается в средне- и высокоуглеродистых легированных сталях в виде строчек и местных скоплений карбидов. Этот порок очень опасен, особенно в инструментальной стали, так как скопления карбидов вызывают понижение стойкости инструмента вследствие резкого изменения механических свойств по сечению. Чем больше карбидная неоднородность, тем ниже эксплуатационные свойства стали.
Устранить карбидную ликвацию термической обработкой невозможно. Карбидная неоднородность тем меньше, чем больше степень пластической деформации при обработке (ковке, прокате) стали.
Нарушения режимов термической обработки легированных сталей вызывают дефекты, рассмотренные ранее, которые характерны и для углеродистых сталей (обезуглероживание, перегрев, пережог, закалочные трещины и т.д.).
- Попередня
- Наступна
Высоколегированная сталь
Высоколегированные стали – это железоуглеродистые сплавы с содержанием легирующих добавок более 10% и до 50%, а железа – свыше 45%.
Легирующие элементы образуют с железом химические связи, что существенно влияет на свойства материала и улучшает его качество. Химические добавки вводятся в сплав с учетом его назначения и необходимых характеристик, например:
- жаростойкость увеличивают Al, Si, Co;
- красностойкость – Mo;
- плотность – Ti, V;
- кислотоупорность – Si;
- прочность, износостойкость – Cr, V, Ti, Ni, Mn;
- твердость – Cr, V;
- упругость – Cr;
- стойкость к температурным расширениям – W;
- антикоррозионные качества – Ni, Mo, Ti, Cr;
- устойчивость перед ударными нагрузками – Mn, Co;
- прочность молекулярной решетки – W.
Сферы применения
Сложно переоценить, что значит высоколегированная сталь для нефтяной и химической промышленности, энергетики, машино- и авиастроения. Из таких сплавов производятся конструкции, используемые в агрессивных средах и при температурных перепадах. В газовой промышленности применяются коррозиестойкие легированные стали с содержанием углерода, уменьшенным до 0,12%. Элементы из окалиностойких сплавов используются в печах и в роли нагревательных элементов.
Классификация
Такие сплавы классифицируются:
- По структуре – бывают аустенитные, аустенитно-ферритные и ферритные, аустенитно-мартенситные и мартенситные. Наиболее популярные аустенитные составы. Содержание легирующих веществ у них достигает 55%. В качестве основных компонентов используются хром (18%) и никель (до 8%). Остальные примеси вводятся в зависимости от необходимых свойств материала.
- По преобладающей составляющей – сплавы на никелевой основе (50% Ni или более) и на железоникелевой (свыше 65% Fe и Ni в соотношении 1,5:1).
- По свойствам – коррозиестойкие, жаростойкие, жаропрочные.
- По доминирующему компоненту, которым легировали сплав, – хромистые, хромомарганцевые, хромоникелевые.
- По тепловым характеристикам:
- элинвар (Х8Н36) – имеет стабильный модуль упругости и рабочий температурный диапазон от -50 до +100 °С, используется для изготовления часовых пружин и деталей измерительных приборов;
- инвар (И36) – не склонен к температурным расширениям, применяется для изготовления эталонных деталей и калибровочных элементов;
- платинит (ЭН42) – по тепловому расширению идентичен стеклу, используется для производства электродов ламп накаливания.
- По магнитным свойствам – магнитные (магнитомягкие и магнитотвердые) и немагнитные.
Марки высоколегированных сталей
Марка | Содержание химических компонентов, % | ||||||
---|---|---|---|---|---|---|---|
C | Mn | Si | S | P | B | Al | |
СН1А | |||||||
1006АК | 0,25–0,4 | ˃0,02 | |||||
1008АК | 0,3–0,5 | ˃0,02 | |||||
1010АК | 0,08–0,13 | 0,3–0,6 | ˃0,02 | ||||
1012АК | 0,1–0,15 | 0,3–0,6 | ˃0,02 | ||||
1015АК | 0,13–0,18 | 0,3–0,6 | ˃0,02 | ||||
1018АК | 0,15–0,2 | 0,7–0,9 | ˃0,02 | ||||
1018SK | 0,15–0,2 | 0,7–0,9 | 0,1–0,35 | ||||
1022AK | 0,18–0,23 | 0,7–1 | ˃0,02 | ||||
1022SK | 0,18–0,23 | 0,7–1 | 0,1–0,35 | ||||
S25C | 0,22–0,28 | 0,22–0,28 | 0,15–0,35 | ||||
10B21 | 0,18–0,23 | 0,7–1 | ˃0,0005 | ||||
10B33 | 0,32–0,36 | 0,7–1 | 0,15–0,35 | ˃0,0005 | |||
1541 | 0,36–0,44 | 1,35–1,65 |
Характеристики
Свойства высоколегированных сталей зависят от марки, формулы сплава, легирующих веществ и их процентного содержания. При помощи термообработки и легирования определенными компонентами материалам придаются необходимые характеристики:
- прочность;
- твердость;
- сопротивление ползучести при нагреве;
- упругость;
- пластичность;
- устойчивость к деформации, истиранию, коррозии, износу;
- жаростойкость;
- жаропрочность;
- другие требуемые качества.
Например, по технологии штампосварки из таких сплавов производят изделия, выдерживающие сверхнизкие температуры до -253 °С. При обработке кремнием получают ферросилиды, устойчивые к кислотным средам.
Все легированные сплавы пригодны к сварке и другим видам обработки. Главное – учитывать состав стали и ее свойства, использовать подходящий режим нагрева и четко соблюдать технологию. Чтобы получить надежное соединение, следует учитывать малую теплопроводность высоколегированных сплавов, их значительное электрическое сопротивление и склонность к линейному расширению.
Компания «Металлист» выполняет комплекс услуг по обработке высоколегированной стали:
- лазерная резка металла;
- плазменная резка металла;
- гибка металла;
- слесарные работы по металлу;
- порошковая покраска изделий из металла.
Легирующие элементы и примеси в сталях
1. ЛЕГИРОВАНИЕ СТАЛЕЙ
1.1. Легирующие элементы и примеси в сталях
1.1.1. Основные понятия и определения
Углеродистые стали часто не удовлетворяют повышенным требованиям, которые предъявляются развивающимися отраслями промышленности к материалам. Они имеют недостаточную прочность, вязкость, сопротивление хрупкому разрушению, низкую теплостойкость, прокаливаемость, коррозионную стойкость. Кроме того, углеродистые стали не обладают рядом физико-химических свойств: немагнитностью, жаростойкостью, особыми магнитными, электрическими и тепловыми свойствами и т.д.
Эти недостатки углеродистых сталей можно исправить легированием – введением в сталь легирующих элементов.
Легирующими элементами называют химические элементы, специально введенные в сталь для получения требуемых строения, структуры, физико-химических и механических свойств.
Основными легирующими элементами в сталях являются Мn, Si, Сг, Ni, Мо W, Со, Сu, Тi, V, Zr, Nb, Аl, В. В некоторых сталях легирующими элементами могут быть также Р, S, N, Se, Те, Рb, Се, Lа и др.
Легированные стали — это сплавы на основе железа, в химический состав которых специально введены легирующие элементы, обеспечивающие при определенных способах производства и обработки требуемую структуру и свойства.
Некоторые легирующие элементы (V, Nb, Тi, Zr, В) могут оказывать существенное влияние на структуру и свойства стали при содержании их в сотых долях процента (В — в тысячных долях процента). Такие стали иногда называют микролегированными.
1.1.2. Классификация легирующих элементов
Согласно общепринятой классификации железо и сплавы на его основе относятся к черным металлам, а все остальные металлы и сплавы на их основе — к цветным. Легирующие элементы – металлы можно условно разделить на следующие группы:
металлы железной группы — к ним относятся металлы кобальт, никель, а также близкий к ним по свойствам марганец;
тугоплавкие металлы — к ним относятся металлы, имеющие температуру плавления выше, чем у железа, т.е. выше 1539°С. Из тугоплавких металлов, наиболее часто используемых в качестве легирующих элементов в стали, можно отметить вольфрам, молибден, ниобий, а также ванадий и хром;
легкие металлы — из этой группы легирующих элементов наиболее часто применяют титан и алюминий;
редкоземельные металлы (РЗМ) — к этой группе относятся лантан, церий, неодим, а также близкие к ним по свойствам иттрий и скандий. Редкоземельные металлы часто используют в виде так называемого мишметалла, содержащего 40-45% церия и 45-50% всех других редкоземельных металлов.
В сплавах железо — углерод классификацию легирующих элементов можно проводить по степени сродства легирующих элементов к углероду по сравнению со сродством к нему железа. По этому признаку различают карбидообразующие и некарбидообразующие легирующие элементы. Карбидообразующие легирующие элементы (Тi, Zr, V, Nb, Та, Сr, Мо, W, Мn), а также железо могут образовывать в стали карбиды. Некарбидообразующие элементы (Сu, Ni, Со, Si, Аl) карбидов в стали не образуют. Склонность к карбидообразованию у легирующих элементов тем сильнее, чем менее достроена d-оболочка у металлического атома.
Ранее была принята буквенно-цифровая система обозначения марок сталей и сплавов.
Углеродистые конструкционные качественные стали обозначают двухзначным числом, указывающим среднее содержание углерода в сотых долях процента (например, 05; 08; 10; 15; 20; 25…80; 85).
Для сталей, полностью не раскисленных (при С<0,20 %), в обозначение добавляются индексы: кп — кипящая сталь (£0,07% Si) – 15кп, пс — полуспокойная сталь, например, 20пс (0,05- 0,17% Si). Для спокойных сталей индекс не указывается (0,12-0,30% Si). Углеродистые инструментальные стали обозначают буквой «У » и следующей за ней цифрой, указывающей среднее содержание углерода и десятых долях процента (например, У7; У8; У9; У10; У11; У12; У13).
В легированных сталях основные легирующие элементы обозначаются буквами: А (в середине марки) — N, К — Co, Т — Ti, Б — Nb, В — W, Г — Mn, Д — Cu, Е — Se, М — Mo, Н — Ni, П — P, Р — B, С — Si, Ф — V, Х — Cr, Ц — Zr, Ю — Al, Ч- РЗМ (La, Pr, Ce и др.).
Цифры после буквы в обозначении марки стали показывают примерное количество того или иного элемента, округленное до целого числа. При среднем содержании легирующего элемента до 1,5 % цифру за буквенным индексом не приводят. Содержание углерода указывается в начале марки в сотых (конструкционные стали) или десятых (инструментальные стали) долях процента.
Так, конструкционная сталь, содержащая 0,42- 0,50% С; 0,5-0,8% Мn; 0,8-1,0% Сr; 1,3-1,8,% Ni; 0,2-0,3%Мо и 0,10-0,18%V, обозначается маркой 45ХН2МФ. Инструментальная сталь (штамповая) состава: 0,32-0,40% С; 0,80-1,20 % Si; 0,15-0,40 % Мn; 4,5- 5,5 % Сr; 1,20-1,50 % Мо и 0,3-0,5 % V обозначается 4Х5МФС.
Если содержание углерода в инструментальных легированных сталях 1 % и более, то цифру в начале марки иногда вообще не ставят (например, X, ХВГ).
Буква «А » в конце марки указывает, что сталь относится к категории высококачественной (ЗОХГСА), если та же буква в середине марки — то сталь легирована азотом (16Г2АФ), а в начале марки буква «А » указывает на то, что сталь автоматная повышенной обрабатываемости (А35Г2). Индекс «АС » в начале марки указывает, что сталь автоматная со свинцом (АС35Г2).
Особовысококачественная сталь обозначается добавлением через дефис в конце марки буквы «Ш » (ЗОХГС-Ш или ЗОХГСА-Ш).
Сталь, не содержащая в конце марки букв «А » или «Ш » , относится к категории качественных (ЗОХГС).
В марках быстрорежущих сталей вначале приводят букву «Р » , за ней следует цифра, указывающая содержание вольфрама. Во всех быстрорежущих сталях содержится около 4% Сг, поэтому в обозначении марки буквы «X » нет. Ванадий, содержание которого в различных марках колеблется в пределах от 1 до 5 %, указывается в марке, если его среднее содержание 2,0 % и более. Так как содержание углерода в быстрорежущих сталях пропорционально количеству ванадия, то содержание углерода в маркировке стали не указывается. Если в быстрорежущих сталях содержится молибден или кобальт, количество указывается в марке. Например, сталь состава: 0,7-0,8 % С; 3,8-4,4 % Сr; 17,0-18,5 % W; 1,0-1,4 % V обозначается маркой Р18, а сталь: 0,95-1,05% С; 3,8-4,4% Сr; 5,5-6% W; 4,6- 5,2 % Мо; 1,8-2,4 % V и 7,5-8,5 % Со обозначается Р6М5Ф2К8.
Высоколегированные стали сложного состава иногда обозначают упрощенно по порядковому номеру разработки и освоения стали на металлургическом заводе. Перед номером стали ставят индексы «ЭИ » (исследовательская), «ЭП » (пробная) — завод «Электросталь » .
Например, упомянутая быстрорежущая сталь Р6М5Ф2К8 упрощенно обозначается ЭП658, а жаропрочная 37Х12Н8Г8МФБ — ЭИ481.
Маркировка марок жаропрочных и жаростойких сплавов на железоникелевой и никелевой основах состоит только из буквенных обозначений элементов, за исключением никеля, после которого указывается цифра, обозначающая его среднее содержание в процентах (ХН77ТЮР, ХН62ВМКЮ и др.).
Примесями называют химические элементы, перешедшие в состав стали в процеесе ее производства как технологические добавки или как составляющие шихтовых материалов.
Примеси в стали по классификации Н.Т. Гудцова подразделяют на постоянные (обыкновенные), случайные и скрытые (вредные).
Постоянными примесями являются элементы, которые вводятся в сталь по технологическим соображениям (технологические добавки).
Постоянными примесями в стали являются марганец и кремний, которые как примеси имеются практически во всех промышленных сталях. Содержание марганца в конструкционных сталях обычно находится в пределах 0,3-0,8 % (если марганец не является легирующим элементом), в инструментальных сталях его содержание несколько меньше (0,15-0,40 %). Введение марганца как технологической добавки в таких количествах необходимо для перевода серы из сульфида железа в сульфид марганца. Кремний в хорошо раскисленных (спокойных) сталях обычно содержится в пределах 0,17-0,37 %. В неполной мере раскисленных низкоуглеродистых (£0,2% С) сталях его содержится меньше: в полуспокойных 0,05-0,017 %, в кипящих <0,07 %. В нержавеющих и жаропрочных, нелегированных кремнием сталях его может содержаться до 0,8 %.
Случайными примесями в стали могут быть практически любые элементы, случайно попавшие в сталь из скрапа, природно-легированной руды или раскислителей. Чаще всего это Сr, Ni, Сu, Мо, W, А1, Т1 и др. в количествах, ограниченных для примесей.
Скрытыми примесями в стали являются сера, фосфор, мышьяк и газы: водород, азот и кислород. Однако в последнее время азот, серу, фосфор иногда используют в качестве легирующих добавок для обеспечения ряда особых свойств сталей.
По марочному химическому составу стали можно определить, какие элементы являются легирующими добавками, а какие — примесями. Если в марочном химическом составе стали устанавливают нижний (не менее) и верхний (не более) пределы содержания в стали данного элемента, то он будет легирующим. Как правило, для примесей устанавливается только верхний предел содержания. Исключение составляют лишь марганец и кремний, количество которых регламентируется нижним и верхним пределом, как для примесей, так и для легирующих добавок.
Содержание примесей в стали обычно ограничивается следующими пределами:
Mn £ 0,8%, Si £ 0,4%, Сr £ 0,3%, Ni £ 0,3%, Сu £ 0,3%, Мо £ 0,1%, W £ 0,2%, P £ 0,025%,
S £ 0,015-0,05%.
Вредные примеси сера, фосфор и газы присутствуют практически во всех сталях и в зависимости от типа стали они могут оказывать на свойства различное влияние.
В настоящее время в металлургии широко используют различные технологические процессы и способы производства стали, в результате которых достигается существенное уменьшение загрязненности металла неметаллическими включениями, и становится возможным регулирование их состава, размера и характера распределения. К таким процессам и способам относятся: рафинирующие переплавы (электрошлаковый, вакуумно-дуговой), вакуумная индукционная плавка, внепечная обработка стали синтетическими шлаками, вакуумирование в ковше и др.
Сера
При комнатной температуре растворимость серы в α-железе практически отсутствует. Поэтому вся сера в стали связана в сульфиды железа и марганца и частично в сульфиды легирующих элементов. С повышением температуры сера растворяется в α- и γ-железе, хотя и незначительно, но до вполне определенных концентраций (0,02 % в α-железе при 913 °С и 0,05 % S в γ-железе при 1365 °С). Поэтому сернистые включения могут видоизменяться при термической обработке стали.
Если сера связана в сульфид железа FeS, то при относительно низких температурах горячей деформации стали вследствие расплавления эвтектики сульфида железа (896 °С), с температурой плавления 988 °С, наблюдается красноломкость стали. При более высоких температурах горячей пластической деформации возможна горячеломкость стали, обусловленная расплавлением находящегося по границам первичных зерен аустенита, собственно сульфида железа (1188°С). Введение в сталь марганца в отношении Mn: S>8-10 приводит практически к полному связыванию серы в тугоплавкий сульфид марганца MnS (Тпл=1620 °С) и исключает образование легкоплавкой сульфидной эвтектики. Это позволяет избежать красноломкости и горячеломкости сталей при их горячей обработке давлением.
Увеличение содержания серы в стали мало влияет на прочностные свойства, но существенно изменяет вязкость стали и ее анизотропию в направлениях поперек и вдоль прокатки. Особенно сильно анизотропия выражена при высоких содержаниях серы.
В жаропрочных аустенитных сталях повышение содержания серы заметно уменьшает пределы ползучести и длительной прочности, т.е. сера снижает жаропрочные свойства.
Фосфор
Растворимость фосфора в α- и γ-железе значительно выше, чем содержание фосфора в стали как примеси. Поэтому фосфор в стали целиком находится в твердом растворе, и его влияние на свойства сказывается через изменения свойств феррита и аустенита. Вредное действие фосфора на свойства может усугубляться из-за сильной склонности его к ликвации (степень ликвации достигает 2-3).
Действие фосфора на свойства феррита проявляется в его упрочняющем влиянии и особенно в усилении хладноломкости стали, т.е. повышении температуры перехода из вязкого в хрупкое состояние.
Фосфор относится к сильным упрочнителям. Несмотря на то, что содержание его в стали обычно не превышает 0,030-0,040 %, он увеличивает предел текучести феррита на 20…30 МПа. В то же время увеличение содержания фосфора в пределах сотых долей процента может вызывать повышение порога хладноломкости на несколько десятков градусов (~20-25°С на 0,01 % Р) благодаря сильному уменьшению работы распространения трещины (рис.1).
Рекомендуем посмотреть лекцию «Психопрофилактика».
Рисунок 1 – Влияние фосфора на σв и σт и ударную вязкость KCU низкоуглеродистой феррито-перлитной стали (0,2 % С, 1 % Мn).
В конструкционных улучшаемых сталях содержание фосфора оказывает основное влияние на явление обратимой отпускной хрупкости. В этом случае влияние его на порог хладноломкости особенно сильно (0,010 % Р повышает температуру перехода на ~ 40 °С).
В сталях, выплавленных на базе керченских руд, содержится мышьяк. Его влияние на свойства стали аналогично фосфору, но вредное действие мышьяка значительно слабее, чем фосфора. Поэтому в качественной стали такого производства допускается до 0,08 % As.
Газы в стали
В сталях в определенных количествах обычно присутствуют водород, кислород, азот. Содержание их в сталях зависит прежде всего от способа выплавки. Водород может входить в состав твердого раствора стали и выделяться в газообразном состоянии, скапливаясь в порах металла, при этом в стали образуются флокены. Кислород обычно связан в неметаллические включения. Азот отрицательно влияет на свойства стали, если он находится в твердом растворе или образует нитриды железа, вызывая старение стали. Положительное влияние азота на свойства стали проявляется при связывании его в прочные нитриды A1N, VN, NbN или карбонириды V(C, N), Nb(C, N) и др., что используется в сталях с карбонитридным упрочнением. Кроме того, азот широко применяется в качестве аустенитообразующего элемента в коррозионностойких и жаропрочных сталях.
В заключение необходимо отметить, что борьбу с вредными примесями в стали в основном проводят при выплавке стали. Уменьшение содержания вредных примесей в стали требует немалых затрат для осуществления определенных технологических приемов и применения специальных методов выплавки.
Легирование стали
Сталь экологически безвредный материал. Он может быть на 100 % использован повторно путем переплава (стопроцентная утилизация). Желательные свойства стали достигаются путем введения в железо в период выплавки других элементов. Эта операция получила название легирования (от немецкого слова legieren сплавлять металлы), а вводимые элементы называются легирующими элементами (ЛЭ).
Под легирующими понимают элементы, вводимые в сталь для целенаправленного изменения ее свойств, то есть ЛЭ:
Изменяют температуру фазовых превращений железа. По этому признаку ЛЭ делятся:
элементы,
расширяющие температурную область -Fe(Ni,Co,Mn,
C, N2). Ni, Co, Mnне ограничено растворяются в-Fe;
C, N2образуют
область ограниченной растворимости;
элементы, расширяющие температурную область -Fe (Si,Al,P,Cr,V,Mo,W).Siвводится в сталь для получения однородных ферритных структур. Действие хрома отличается от этой картины. При хроме менее 13% он действует как аустенитообразующий элемент. При хроме более 13%выступает как типичный ферритообразующий элемент (Х18Н9).
Влияние на процессы дисперсионного твердения может протекать по двум направлениям:
за счет образования карбидов или нитридов, то есть за счет образования неметаллических включений. К карбидо- и нитридообразующим элементам относятся Cr,V,Nb,W,Ti,Zr. Их введение преследует цель образования карбидов или нитридов, которые в дисперсном состоянии упрочняют металл;
за
счет образования интерметаллидных фаз
с железом. Склонность к образованию
интерметаллидных фаз в безуглеродистой
стали проявляют W,Mo,Ti.
Легирующими могут быть как элементы, не встречающиеся в обычной стали, так и элементы, которые в каких-то количествах содержатся во всякой стали (С, Mn,Si,S,P).
По степени растворения в железе ЛЭ делятся на группы:
Металлы полностью растворимые в железе (Al, Ce, Mn, Cr, Ni, V, Cu, Si, Ti, Be).
Металлы частично растворимые в железе (W, Mo, Zr).
Металлы, растворимость которых при температуре сталеварения точно не установлена, т.к. они при высоких температурах испаряются (Ca,Cd,Li,Mg,Na).
Металлы, практически не растворимые в железе (Pb, Ag, Bi).
Неметаллы, частично растворимые в железе (С, S, P, N, As).
Ряд
легирующих элементов образует в железе
растворы близкие к идеальным (Mn,Co,Ni,Cr,Mo,Al), из
которых только Со иMnдействительно образуют практически
идеальные растворы; при образовании
остальных приходится учитывать теплоту
смешения.
Легирующие добавки вводятся в металл в небольших количествах, и они образуют с железом растворы, которые можно считать «бесконечно разбавленными».
На практике сталь часто легируется не одним элементом, а несколькими. При определении технологии легирования принимается во внимание степень сродства ЛЭ к кислороду. Такие элементы как Мо, Сu, Со,Niимеют сродство к кислороду меньше, чем железо, во время плавки они не окисляются и поэтому вводятся в металл вместе с шихтовыми материалами или по ходу плавки без опасения получить значительный их угар.
Другая
группа элементов (Ti,V,Cr,Si,Mn,Al) имеет сродство к
кислороду более высокое, чем железо.
Эти элементы под воздействием кислорода
газовой фазы, окислов железа шлака и
кислорода, растворенного в металле,
окисляются. Поэтому их вводят в металл
в конце плавки или часто в ковш с
предварительно раскисленным металлом.
Кроме того, принимаются специальные
меры по предотвращению окисления металла
при разливке (закрытые струи, защита
струи подачей инертного газа и др. ).
ЛЭ вводят в металл в виде чистых материалов (бруски никеля, алюминия, куски серы, графитовый порошок и т.д.) или в виде сплавов с железом (ферромарганец, ферросилиций, феррованадий и т.п.). Усвоение элемента, вводимого в виде сплава с железом, несколько выше. Однако приходится учитывать, что при этом увеличивается масса холодных материалов вводимых в металл. Металл, в который вводится большая масса легирующих добавок, приходится перегревать, а это не всегда желательно (повышается содержание газов в металле, снижается стойкость футеровки, повышается расход электроэнергии, топлива).
Кроме указанных выше способов, легированные добавки вводят в виде соединений (оксидов, карбидов, нитридов). Так, например, при производстве стали, содержащей ванадий, для легирования используют шлак, содержащий оксиды ванадия и т.д.
ЛЭ
− дорогие примеси, следовательно, их
нужно экономить. Однако производство
легированной стали экономически
оправдано получением особых ее свойств
и соответственно, уменьшением массы
металлических конструкций, повышением
их долговечности и надежности. Учитывая
высокую стоимость легированной стали,
все мероприятия, связанные со снижением
расхода легирующих добавок дают
значительный экономический эффект. К
таким мероприятиям относятся: использование
отходы легированных сталей и
совершенствование методов их ввода в
жидкую сталь.
32
сталь| Состав, свойства, типы, сорта и факты
производство
Посмотреть все СМИ
- Ключевые люди:
- Эндрю Карнеги Генри Бессемер Сэр Уильям Сименс Джон Огастес Роблинг Чарльз М. Шваб
- Похожие темы:
- Дамасская сталь углеродистая сталь перлит литая сталь мартенситная сталь
Просмотреть весь соответствующий контент →
Резюме
Прочтите краткий обзор этой темы
сталь , сплав железа и углерода, в котором содержание углерода колеблется до 2 процентов (при более высоком содержании углерода материал определяется как чугун). На сегодняшний день это наиболее широко используемый материал для строительства инфраструктуры и промышленности в мире, он используется для изготовления всего, от швейных иголок до нефтяных танкеров. Кроме того, инструменты, необходимые для изготовления таких изделий, также изготавливаются из стали. Как показатель относительной важности этого материала, в 2013 году мировое производство необработанной стали составило около 1,6 миллиарда тонн, а производство следующего по важности технического металла, алюминия, составило около 47 миллионов тонн. (Для списка производства стали по странам, см. ниже Мировое производство стали.) Основными причинами популярности стали являются относительно низкие затраты на ее производство, формовку и обработку, обилие двух сырьевых материалов (железной руды и металлолома) и беспрецедентный ассортимент механические свойства.
Свойства стали
Основной металл: железо
Изучение производства и структурных форм железа от феррита и аустенита до легированной стали
Посмотреть все видео к этой статье Основным компонентом стали является железо, металл, который в его чистое состояние ненамного тверже меди. За исключением самых крайних случаев, железо в твердом состоянии, как и все другие металлы, поликристаллично, т. е. состоит из многих кристаллов, смыкающихся друг с другом на своих границах. Кристалл — это хорошо упорядоченное расположение атомов, которые лучше всего можно представить в виде сфер, соприкасающихся друг с другом. Они упорядочены в плоскостях, называемых решетками, которые особым образом проникают друг в друга. Для железа расположение решетки лучше всего представить единичным кубом с восемью атомами железа в углах. Важным для уникальности стали является аллотропность железа, то есть его существование в двух кристаллических формах. В объемно-центрированной кубической (ОЦК) конфигурации в центре каждого куба находится дополнительный атом железа. В гранецентрированной кубической (ГЦК) конфигурации в центре каждой из шести граней единичного куба находится один дополнительный атом железа. Существенно, что стороны гранецентрированного куба или расстояния между соседними решетками в ГЦК конфигурации примерно на 25 процентов больше, чем в ОЦК компоновке; это означает, что в ГЦК-структуре больше места, чем в ОЦК-структуре, для удержания инородных ( , т.
е. сплавов) атомов в твердом растворе.
Железо имеет аллотропию ОЦК ниже 912°C (1674°F) и от 1394°C (2541°F) до температуры плавления 1538°C (2800°F). Называемое ферритом, железо в его ОЦК-образовании также называется альфа-железом в диапазоне более низких температур и дельта-железом в зоне более высоких температур. Между 912° и 1394°С железо находится в ГЦК-порядке, который называется аустенитным или гамма-железом. Аллотропное поведение железа сохраняется, за немногими исключениями, в стали, даже когда сплав содержит значительное количество других элементов.
Существует также термин бета-железо, который относится не к механическим свойствам, а скорее к сильным магнитным характеристикам железа. Ниже 770 ° C (1420 ° F) железо является ферромагнитным; температуру, выше которой он теряет это свойство, часто называют точкой Кюри.
Викторина «Британника»
Строительные блоки предметов повседневного обихода
Из чего сделаны сигары? К какому материалу относится стекло? Посмотрите, на что вы действительно способны, ответив на вопросы этого теста.
В чистом виде железо мягкое и обычно непригодно для использования в качестве конструкционного материала; основной метод его упрочнения и превращения в сталь — добавление небольшого количества углерода. В твердой стали углерод обычно встречается в двух формах. Либо он находится в твердом растворе в аустените и феррите, либо находится в виде карбида. Форма карбида может быть карбидом железа (Fe 3 C, известным как цементит) или карбидом легирующего элемента, такого как титан. (С другой стороны, в сером чугуне углерод проявляется в виде чешуек или скоплений графита из-за присутствия кремния, подавляющего образование карбидов.)
Воздействие углерода лучше всего иллюстрируется диаграммой равновесия железа и углерода. Линия A-B-C представляет точки ликвидуса (, т. е. температуры, при которых расплавленное железо начинает затвердевать), а линия H-J-E-C представляет точки солидуса (при которых затвердевание завершается). Линия A-B-C показывает, что температура затвердевания снижается по мере увеличения содержания углерода в расплаве железа. (Это объясняет, почему серый чугун, содержащий более 2 процентов углерода, обрабатывается при гораздо более низких температурах, чем сталь.) Расплавленная сталь, содержащая, например, 0,77 процента углерода (показана вертикальной пунктирной линией на рисунке), начинает затвердевает при температуре около 1475 ° C (2660 ° F) и полностью затвердевает при температуре около 1400 ° C (2550 ° F). С этой точки и ниже все кристаллы железа находятся в аустенитной — , т. е. ГЦК — компоновка и содержат весь углерод в твердом растворе. При дальнейшем охлаждении резкое изменение происходит примерно при 727 ° C (1341 ° F), когда кристаллы аустенита превращаются в тонкую пластинчатую структуру, состоящую из чередующихся пластинок феррита и карбида железа. Эта микроструктура называется перлитом, а изменение называется эвтектоидным превращением. Перлит имеет твердость алмазной пирамиды (DPH) примерно 200 кгс на квадратный миллиметр (285 000 фунтов на квадратный дюйм), по сравнению с DPH 70 кгс на квадратный миллиметр для чистого железа.
Охлаждающая сталь с более низким содержанием углерода ( , например, 0,25 процента) приводит к микроструктуре, содержащей около 50 процентов перлита и 50 процентов феррита; это мягче, чем перлит, с DPH около 130. Сталь с содержанием углерода более 0,77%, например, 1,05%, содержит в своей микроструктуре перлит и цементит; он тверже перлита и может иметь DPH 250.
Получите подписку Britannica Premium и получите доступ к эксклюзивному контенту. Подпишитесь сейчас
Нержавеющая сталь — общая информация
Легирующие элементы в нержавеющей стали
Нержавеющие стали содержат ряд легирующих элементов в соответствии с определенной маркой и составом. Ниже перечислены легирующие добавки с указанием причины их присутствия, а в приложении представлена сводная таблица.
Углерод (C): Железо сплавляется с углеродом для изготовления стали и увеличивает твердость и прочность железа. Чистое железо не может быть закалено или упрочнено термической обработкой, но добавление углерода обеспечивает широкий диапазон твердости и прочности. В аустенитных и ферритных нержавеющих сталях нежелательно высокое содержание углерода, особенно при сварке, из-за угрозы выделения карбидов.
Марганец (Mn): Марганец добавляется в сталь для улучшения свойств горячей обработки и повышения прочности, ударной вязкости и прокаливаемости. Марганец, как и никель, является элементом, образующим аустенит, и использовался в качестве заменителя никеля в аустенитных нержавеющих сталях серии AISI200, например AISI 202 вместо AISI 304.
Хром (Cr): Хром добавляют в сталь для повышения стойкости к окислению. Это сопротивление увеличивается по мере добавления хрома. «Нержавеющие стали содержат минимум 10,5% хрома (традиционно 11 или 12%). Это дает очень заметную степень общей коррозионной стойкости по сравнению со сталями с более низким процентным содержанием хрома. Коррозионная стойкость обусловлена образованием самовосстанавливающегося пассивного слоя оксида хрома на поверхности нержавеющей стали.
Никель (Ni): никель добавляют в больших количествах, более примерно 8%, в нержавеющие стали с высоким содержанием хрома для образования наиболее важного класса коррозионностойких и жаропрочных сталей. Это аустенитные нержавеющие стали, типичным примером которых является 18-8 (304/1.4301), в которых склонность никеля к образованию аустенита отвечает за большую ударную вязкость (ударную вязкость) и высокую прочность как при высоких, так и при низких температурах. Никель также значительно повышает устойчивость к окислению и коррозии.
Молибден (Mo): молибден при добавлении в хромоникелевые аустенитные стали повышает устойчивость к точечной и щелевой коррозии, особенно в средах, содержащих хлориды и серу.
Азот (N): Азот увеличивает стабильность аустенита в нержавеющих сталях и, как и в случае никеля, является элементом, образующим аустенит. Предел текучести значительно повышается при добавлении азота в нержавеющие стали, как и устойчивость к точечной коррозии.
Медь (Cu): Медь обычно присутствует в нержавеющей стали в качестве остаточного элемента. Однако его добавляют в некоторые сплавы для придания им свойств дисперсионного твердения или для повышения коррозионной стойкости, особенно в среде морской воды и серной кислоты.
Титан (Ti): Титан добавляется для стабилизации карбида, особенно при сварке материала. Он соединяется с углеродом с образованием карбидов титана, которые достаточно стабильны и плохо растворяются в стали, что сводит к минимуму возникновение межкристаллитной коррозии. Добавление примерно 0,25/0,60% титана вызывает соединение углерода с титаном, а не с хромом, предотвращая связывание устойчивого к коррозии хрома в виде межкристаллитных карбидов и сопутствующую потерю коррозионной стойкости на границах зерен. Однако в последние годы использование титана постепенно сокращается из-за способности производителей стали поставлять нержавеющие стали с очень низким содержанием углерода, которые легко свариваются без стабилизации.
Фосфор (P): Фосфор обычно добавляют с серой для улучшения обрабатываемости. Фосфор, присутствующий в аустенитных нержавеющих сталях, увеличивает прочность. Однако он пагубно влияет на коррозионную стойкость и повышает склонность материала к растрескиванию при сварке.
Сера (S): При добавлении в небольших количествах сера улучшает обрабатываемость. Однако, как и фосфор, он отрицательно влияет на коррозионную стойкость и свариваемость.
Селен (Se): Селен ранее использовался в качестве добавки для улучшения обрабатываемости.
Ниобий/коломбий (Nb): ниобий добавляется в сталь для стабилизации углерода, и поэтому действует так же, как описано для титана. Ниобий также обладает эффектом упрочнения сталей и сплавов для работы при высоких температурах.
SiIicon (Si): Кремний используется в качестве раскислителя (раскислителя) при плавке стали, поэтому большинство сталей содержат небольшой процент кремния.
Кобальт (Co): Кобальт становится высокорадиоактивным при воздействии интенсивного излучения ядерных реакторов, и в результате любая нержавеющая сталь, используемая в ядерной сфере, будет иметь ограничение содержания кобальта, обычно не более 0,2%. Эта проблема особенно актуальна, поскольку в никеле, используемом при производстве аустенитных нержавеющих сталей, обычно присутствует остаточное содержание кобальта.
Кальций (Ca): Небольшие добавки используются для улучшения обрабатываемости без вредного воздействия серы, фосфора и селена на другие свойства.
Как различные сплавы изменяют свойства стали
Архитекторы и производители используют сталь на протяжении сотен лет из-за ее прочности и долговечности. И до недавнего времени для нужд этих творцов подходила любая сталь. Их стали не нужно было выдерживать высокие температуры и давления, которые сталь выдерживает сегодня. Эти современные требования делают стальные сплавы необходимыми практически во всех отраслях и областях применения.
Сплавы стали обладают другими свойствами, чем сама сталь. Они по-прежнему обладают прочностью и долговечностью стали, но в одних случаях умножают ее, а в других — вообще добавляют новые свойства. Ниже вы можете найти более подробное описание свойств различных сплавов.
1. Сплавы стали и алюминия
Алюминий раскисляет и дегазирует сталь, что контролирует размер зерна стали и делает ее более тонкой. При использовании в сочетании с азотом алюминий может превратить сталь в однородно твердый корпус. Алюминий помогает стали формироваться медленнее, а это значит, что из алюминиево-стальных сплавов можно делать более сложные детали. Это также делает сталь легче.
2. Сплавы стали и углерода
Углерод повышает прочность стали на растяжение, делая ее более твердой, менее пластичной, более жесткой и более устойчивой к износу. В зависимости от того, сколько углерода добавляет производитель, сталь может иметь разную степень прочности и твердости.
3. Сплавы стали и хрома
Хром, также называемый хромом, представляет собой второй основной компонент нержавеющей стали. Когда вы добавляете хром в сталь, это повышает ее характеристики несколькими способами. С одной стороны, это усложняет и усложняет жизнь. Это также делает зерно стали более мелким и делает ее устойчивой к царапинам, пятнам, ржавчине и вмятинам. Он также сохраняет форму стали при более высоких температурах и придает ей характерный серебристый блеск.
4. Сплавы стали и кобальта
Вы, наверное, знаете, что металл имеет тенденцию становиться более ковким при более высоких температурах. Это может оказаться катастрофическим или даже опасным в определенных обстоятельствах, таких как производство. К счастью, производители могут обратиться к сплавам стали и кобальта в качестве безопасного решения. Кобальт повышает прочность стали и сохраняет эту прочность при высоких температурах. Это делает его идеальным для использования в режущих инструментах.
В сочетании с никелем и алюминием сплавы стали и кобальта также создают мощные магниты альнико.
5. Сплавы стали и меди
Обычно стальные сплавы не содержат преднамеренно добавленную медь, но когда производители добавляют ее, она создает свойства дисперсионного твердения.
6. Сплавы стали со свинцом
Свинец улучшает характеристики обработки стали. Это снижает трение в местах контакта рабочих кромок друг с другом и улучшает образование стружки.
7. Сплавы стали и марганца
Если вам нужна особо прочная сталь, выбирайте сплавы стали и марганца. Сам по себе марганец обладает хрупкими, но чрезвычайно прочными свойствами. Он медленно остывает, и после остывания его довольно трудно разрезать.
Износ также делает поверхность еще более твердой. Так что если вам нужно отлить дробилки руды или железнодорожные переезды, выбирайте марганцовистую сталь.
8. Сплавы стали и молибдена
Молибден, как и марганец, кобальт и хром, также повышает прочность стали. Он добавляет твердости и позволяет стали выдерживать более высокие температуры и более сильные удары. Это также дает стали дополнительное преимущество сопротивления ползучести. Вы часто найдете этот сплав в автомобильных деталях и высококачественном оборудовании.
При использовании в сочетании с другими сплавами усиливает их действие.
9. Сплавы стали и никеля
В сплаве со сталью никель действует подобно марганцу. Это увеличивает прочность и твердость материала, но не делает его менее пластичным. Никель помогает стали противостоять ржавчине и придает ей большую эластичность. Это означает, что когда на него воздействуют силы, он может вернуться в свою первоначальную форму. При использовании с хромом он позволяет нержавеющей стали противостоять коррозии при высоких температурах.
10. Сплавы стали и азота
Азот повышает стабильность стали и предел текучести. Это делает сплав менее хрупким в целом.
11. Сплавы стали и фосфора
Сам по себе фосфор просто повышает прочность стали и устойчивость к коррозии. Однако он также может сделать сталь более восприимчивой к растрескиванию, поэтому производители обычно используют его в сочетании с марганцем и серой. Сильные стороны серы подробнее ниже.
12. Сплавы стали и кремния
Как и алюминий, кремний раскисляет сталь, что делает ее в целом прочнее. Это также увеличивает магнитную проницаемость стали.
13. Сплавы стали и серы
При соединении стали и серы полученный материал имеет низкую свариваемость и пластичность. Он также имеет меньшую ударную вязкость, поэтому расколется при достаточной силе. Однако он обладает улучшенной обрабатываемостью, и при использовании его с марганцем он теряет все свои недостатки.
14. Сплавы стали и титана
Титан сам по себе имеет репутацию прочного металла. Когда вы сочетаете его со сталью, другим прочным металлом, вы создаете нечто еще более прочное. Производители обычно вводят углерод в реакцию при создании титановой стали, и полученный металл обладает невероятной прочностью и коррозионной стойкостью.
15. Сплавы стали и вольфрама
Подобно хрому и кобальту, вольфрам сохраняет прочность стали при высоких температурах. Это также повышает прочность материала в целом. Материал не только остается твердым, но и не ломким. Его прочность не позволяет ему сломаться после воздействия мощных сил.
16. Сплавы стали и ванадия
Ванадий сам по себе обладает хрупкими свойствами, но в сочетании со сталью полученный материал не имеет этой слабости. В итоге вы получаете мелкозернистую сталь, способную противостоять сильным ударам, поэтому вы часто найдете ее в автомобильных пружинах, шестернях и других деталях, которые постоянно вибрируют.
Теперь, когда вы знаете немного больше о стальных сплавах, вы знаете, какие легированные элементы искать в следующий раз, когда вам понадобится сталь в приложении. Позвоните своему местному производителю, чтобы получить стальной сплав, необходимый для вашего следующего проекта.
Полное руководство по углеродистой стали и стальным сплавам
Сталь является наиболее часто используемым металлом в мире, который находит применение в компонентах, продуктах и конструкциях в самых разных отраслях промышленности. Эта популярность во многом связана с присущей материалу прочностью, твердостью и долговечностью. Однако при рассмотрении стали в качестве материала для производственного проекта важно отметить, что сталь — это не отдельный металл, а скорее общий термин для группы металлов, состоящей в основном из железа и углерода, а также часто в различных количествах других элементов. Он доступен в многочисленных вариациях, каждая из которых имеет несколько иной состав и несколько отличающийся набор характеристик, что делает его пригодным для различных применений.
По некоторым данным, доступно более 3500 видов стали. Этот широкий выбор позволяет профессионалам отрасли найти сталь, которая точно соответствует их потребностям, но также усложняет выбор правильной стали. В следующем руководстве мы представляем обзор всего, что вам нужно знать об углеродистой стали и стальных сплавах. В нем обсуждается, что такое сталь, доступные типы и типичные области применения материала, чтобы помочь читателям лучше понять сталь и определить, какая из них подходит для проекта.
Что такое сталь?
Сталь представляет собой сплав железа и углерода. Его первичный компонент — железо — в чистом виде очень слаб и мягок. Добавление углерода к элементу значительно увеличивает его прочность на растяжение, твердость и сопротивление износу и истиранию, но снижает его пластичность, обрабатываемость и ударную вязкость. Однако общее добавленное количество должно быть менее 2%, чтобы полученный металл можно было классифицировать как сталь. Металл с содержанием углерода более 2% классифицируется как чугун.
В дополнение к углероду в процессе производства стали могут быть введены другие элементы для дальнейшего улучшения характеристик стали. Если сталь содержит по весу один или несколько легирующих элементов в стандартном процентном соотношении, она классифицируется как легированная сталь. Точные свойства, проявляемые конкретной легированной сталью, зависят от включенных элементов и их пропорций. В целом легированные стали демонстрируют огромную прочность, твердость и универсальность. Кроме того, они легко перерабатываются, что позволяет профессионалам отрасли повторно использовать и перепрофилировать их снова и снова без потери прочности или качества материала.
Углеродистая сталь состоит в основном из железа и углерода и основана на углероде в качестве основного упрочняющего элемента. Обычно их делят на три подкатегории: низкоуглеродистая сталь (от 0,03% до 0,15% углерода), среднеуглеродистая сталь (от 0,25% до 0,50% углерода) и высокоуглеродистая сталь (от 0,55% до 1,10% углерода). Чем выше содержание углерода, тем тверже получаемый материал и, следовательно, труднее с ним работать. По этой причине в производственных операциях чаще используются низкоуглеродистые стали, чем высокоуглеродистые.
Сплавы стали Сплавы стали сочетают углеродистую сталь с другими легирующими элементами для добавления или улучшения конкретных характеристик материала, таких как прочность, твердость или коррозионная стойкость. Их можно сгруппировать по сплаву или проценту сплава. Высоколегированные стали содержат более высокий процент легирующих элементов (более 8%, но обычно не менее 10%), в то время как низколегированные стали содержат низкий процент легирующих элементов (обычно от 1% до 5%, но могут иметь до 8%). Свойства стального сплава сильно зависят от добавленных легирующих элементов. Некоторые распространенные легирующие элементы перечислены ниже.
- Хром
- Кобальт
- Медь
- Марганец
- Молибден
- Никель
- Кремний
- Вольфрам
Помимо состава, существует множество других факторов, влияющих на характеристики стального сплава. Различные организации по стандартизации разработали системы классификации, чтобы обеспечить методы классификации углеродистых сталей и стальных сплавов по всем этим факторам. В Соединенных Штатах обычно используются AISI (Американский институт чугуна и стали), SAE (Общество автомобильных инженеров) и ASTM (Американское общество испытаний и материалов).
- В системах классификации AISI/SAE используется унифицированная система нумерации (UNS).
Каждому металлу присваивается четырехзначный номер, где первые две цифры указывают на тип стали и концентрацию легирующих элементов, а последние две цифры указывают на концентрацию углерода.
- Система классификации ASTM также использует классификацию UNS для металлов. Каждому металлу присваивается буква, обозначающая его общую категорию (А используется для железных и стальных материалов), и число, соответствующее его конкретным свойствам.
Стальные сплавы обладают превосходной прочностью, долговечностью и, в зависимости от того, из чего и как они сделаны, множеством других преимущественных характеристик. Эти качества делают их идеальным материалом для многих производственных и строительных проектов. Типичные области применения стальных сплавов включают:
- Строительные материалы (например, стержни, балки, рулоны, плиты, стержни, листы, проволоку, крепеж и т.
д.)
- Автомобильное и тяжелое оборудование (например, шестерни, шлицы, шкивы, валы, роторы и т. д.)
- Нефть и газ (например, трубы, трубы, фитинги, резервуары и т. д.)
- Горнодобывающая промышленность (например, машины, буры, инструменты и т. д.)
- Производство/станки (например, штампы, пресс-формы, конвейеры и т. д.)
- Ручные инструменты (например, гаечные ключи, отвертки, головки и т. д.)
Углеродистая сталь и стальные сплавы используются для изготовления широкого спектра деталей и изделий. Специалисты Grob Inc. используют его для производства различных холоднокатаных изделий, в том числе шлицевых валов, цилиндрических зубчатых колес, шкивов зубчатых ремней и многого другого. Чтобы узнать больше о возможностях холодной прокатки в Grob, посетите страницу холоднокатаной продукции. Свяжитесь с нами сегодня, чтобы обсудить ваши потребности в холодной прокатке с одним из наших экспертов.
Легирующие элементы|Нержавеющая сталь Outokumpu | Оутокумпу
Различные легирующие элементы оказывают особое влияние на свойства нержавеющей стали. Именно совокупное воздействие всех легирующих элементов, термической обработки и, в некоторой степени, примесей определяет профиль свойств конкретной марки стали. Следует отметить, что влияние легирующих элементов в некоторой степени различается между различными типами нержавеющей стали.
Алюминий (Al)
При добавлении в значительных количествах алюминий улучшает стойкость к окислению и используется для этой цели в некоторых жаростойких марках. В дисперсионно-твердеющих сталях алюминий используется для образования интерметаллических соединений, повышающих прочность в состаренном состоянии.
Углерод (C)
Углерод является мощным аустенитообразователем, который также значительно увеличивает механическую прочность. В ферритных марках углерод значительно снижает ударную вязкость и коррозионную стойкость. В мартенситных сортах углерод увеличивает твердость и прочность, но снижает ударную вязкость.
Церий (Ce)
Церий является одним из редкоземельных металлов (РЗМ) и добавляется в небольших количествах к некоторым термостойким сортам для повышения устойчивости к окислению при высоких температурах.
Хром (Cr)
Хром является наиболее важным легирующим элементом, так как он придает нержавеющей стали ее общую коррозионную стойкость. Все нержавеющие стали имеют содержание Cr не менее 10,5%. Кроме того, коррозионная стойкость увеличивается при более высоком содержании хрома. Хром также повышает устойчивость к окислению при высоких температурах и способствует формированию ферритной микроструктуры.
Кобальт (Co)
Кобальт используется в мартенситных сталях, где он повышает твердость и сопротивление отпуску, особенно при более высоких температурах.
Медь (Cu)
Медь улучшает коррозионную стойкость к некоторым кислотам и поддерживает аустенитную микроструктуру. Его также можно добавлять для уменьшения наклепа в сплавы, предназначенные для улучшения обрабатываемости. Кроме того, его также можно добавить для улучшения формуемости.
Молибден (Mo)
олибден значительно повышает стойкость как к равномерной, так и к локальной коррозии. Он немного повышает механическую прочность и сильно способствует формированию ферритной микроструктуры. Однако молибден также увеличивает риск образования вторичных фаз в ферритных, дуплексных и аустенитных сталях. В мартенситных сталях молибден повышает твердость при более высоких температурах отпуска из-за его влияния на выделение карбидов.
Марганец (Mn)
Марганец обычно используется для улучшения пластичности в горячем состоянии. Его влияние на баланс феррит/аустенит меняется в зависимости от температуры: при низких температурах марганец является стабилизатором аустенита, но при высоких температурах он стабилизирует феррит. Марганец увеличивает растворимость азота и используется для получения высокого содержания азота в дуплексных и аустенитных нержавеющих сталях. Марганец, как аустенитообразователь, также может частично заменить никель в нержавеющей стали.
Никель (Ni)
Никель обычно повышает пластичность и ударную вязкость. Основной причиной добавления никеля является создание аустенитной микроструктуры. Он также снижает скорость коррозии в активном состоянии и поэтому предпочтителен в кислых средах. В дисперсионно-твердеющих сталях никель также используется для образования интерметаллических соединений, используемых для повышения прочности. Добавление никеля в мартенситные марки в сочетании со снижением содержания углерода улучшает свариваемость.
Ниобий (Nb)
Ниобий является сильным феррито- и карбидообразователем и, как и титан, способствует образованию ферритной структуры. В аустенитные стали добавляют ниобий для повышения стойкости к межкристаллитной коррозии (стабилизированные марки). Кроме того, он улучшает механические свойства при высоких температурах. В ферритные марки иногда добавляют ниобий и/или титан для повышения ударной вязкости и минимизации риска межкристаллитной коррозии. В мартенситных сталях ниобий снижает твердость и повышает стойкость к отпуску. В США ниобий обозначается как Колумбий (Cb).
Азот (N)
Азот является очень мощным аустенитообразователем, который также значительно повышает механическую прочность. Он также повышает устойчивость к локальной коррозии, особенно в сочетании с молибденом. В ферритной нержавеющей стали азот сильно снижает ударную вязкость и коррозионную стойкость. В мартенситных сплавах азот увеличивает как твердость, так и прочность, но снижает ударную вязкость.
Кремний (Si)
Кремний повышает устойчивость к окислению как при высоких температурах, так и в сильно окисляющих растворах при более низких температурах. Это способствует ферритной микроструктуре и увеличивает прочность.
Сера (S)
Сера добавляется в некоторые нержавеющие стали для улучшения их обрабатываемости. На уровнях, присутствующих в этих сортах, сера немного снижает коррозионную стойкость, пластичность, свариваемость и формуемость. На Outokumpu торговая марка PRODEC (PRODuction EConomy) используется для некоторых марок со сбалансированным содержанием серы для улучшения обрабатываемости. Можно добавить меньшее количество серы, чтобы уменьшить деформационное упрочнение и улучшить формуемость. Несколько повышенное содержание серы также улучшает свариваемость стали.
Титан (Ti)
Титан является сильным феррито- и карбидообразователем, который снижает эффективное содержание углерода и способствует формированию ферритной структуры двумя способами. За счет добавления титана в аустенитных сталях повышается стойкость к межкристаллитной коррозии (стабилизированные марки), а также улучшаются содержание углерода и механические свойства при высоких температурах. В ферритные марки добавляется титан для улучшения ударной вязкости, формуемости и коррозионной стойкости. В мартенситных сталях титан в сочетании с углеродом снижает твердость мартенсита и повышает стойкость к отпуску. В дисперсионно-твердеющих сталях титан используется для образования интерметаллических соединений, которые используются для повышения прочности.
Вольфрам (W)
Вольфрам присутствует в качестве примеси в большинстве нержавеющих сталей, хотя его добавляют в некоторые специальные марки, например, в супердуплексную сталь марки 4501, для повышения стойкости к точечной коррозии.
Ванадий (V)
Ванадий образует карбиды и нитриды при более низких температурах, продвигает феррит в микроструктуре и повышает ударную вязкость. Это увеличивает твердость мартенситных сталей из-за его влияния на тип присутствующего карбида. Это также повышает устойчивость к отпуску. Он используется только в нержавеющих сталях, которые могут быть закалены.
Глоссарий
Прочность
Способность поглощать энергию в пластическом диапазоне.
Активный
(1) Состояние металла, которое подвергается коррозии без значительного влияния продукта реакции.
(2) Более низкий или более низкий потенциал отрицательного электрода.
Повышение прочности стальных сплавов
Содержание
- Легирование азотом
- Применение сверхвысокого давления
- Преимущества легирования азотом
- Применение сталей, легированных азотом
- Дополнительные преимущества сталей, легированных азотом
- Статус патента
Улучшение прочности и других свойств стальных сплавов.
Подход
Исследования Горнорудного управления США показывают, что стали, расплавленные и затвердевшие под высоким давлением азота, приобретают предел текучести и прочность на растяжение, которые в четыре раза превышают прочность сопоставимых сплавов нержавеющей стали без азота. Усталостная прочность, сопротивление ползучести и другие механические свойства также улучшаются. Упрочнение происходит по двум механизмам: (1) увеличение растворенного азота в решетке и (2) образование дисперсных фаз нитрида металла.
Легирование стали азотом обычно осуществляется путем введения нитридов металлов во время плавки стали. Концентрация азота ограничивается его равновесной растворимостью при 1 атмосфере. Для гранецентрированного кубического (платного) железа эта растворимость составляет приблизительно 0,4 весовых процента (мас.%). Для объемно-центрированного кубического (ОЦК) железа растворимость составляет 0,05% масс. Это ограничение растворимости можно преодолеть, расплавив металл в сосуде под давлением.
Европейские производители стали в настоящее время имеют системы обработки металлов, которые могут плавить и разливать тонны стали под давлением азота, превышающим 4 мегапаскаля (МПа) (40 атмосфер). Они достигли концентрации азота в этих (нержавеющих) сталях до 1,0 мас.%. Прочность на растяжение примерно в два раза выше, чем у аналогичных сталей без азота.
Исследователи Бюро недавно плавили стали в горячей печи изостатического давления с азотом при давлении от 0,1 до 200 МПа. При более высоких давлениях исследователи Бюро наблюдали те же тенденции, отмеченные европейскими производителями стали: более высокие концентрации азота и более высокие значения прочности на растяжение как для ГЦК-, так и для ОЦК-железных сплавов. При 200 МПа концентрации азота превышали 4 мас.% в сплавах шихтового железа и 1,0 мас.% в ОЦК-сплавах железа.
Растворимость азота в сплавах железа зависит как от кристаллической структуры, так и от состава сплава. Растворимость азота в стали увеличивается с концентрацией хрома или марганца и уменьшается с концентрацией никеля. Например, в некоторых сталях, где марганец заменяет никель в качестве основного компонента аустенитизирующего сплава, растворимость азота увеличивается в 2 раза. В аустенитных нержавеющих сталях концентрация азота в твердом растворе увеличивается линейно с давлением до тех пор, пока она не станет достаточной, чтобы вызвать фазовый переход или вызвать образование второй фазы.
Применение сверхвысокого давления Для сплавов ОЦК железа увеличение избыточного давления азота с 0,1 до 100 МПа, а затем до 200 МПа увеличило концентрацию азота в стали с 0,03 до 0,3 % масс. , а затем до 1,2 % масс. . Для сплавов исходного железа тот же режим давления увеличил концентрацию с 0,03 до 0,3 мас.%, а затем до более чем 4,0 мас.%.
Металлические заряды нагревали до 1650°С и выдерживали под давлением в течение часа. Затем заряды охлаждались (под давлением) до затвердевания металла. Таким образом, железо и железные сплавы подвергались термообработке и обработке давлением:
- Чистое железо плавили под давлением азота 50 МПа. Образовались нитриды железа второй фазы Fe4N и Fe2N. Сплавы железо-хром
- выплавлялись под давлением азота 100 МПа. Образовался нитрид хрома (CrN).
- Три серии сплавов — железо-никель (Fe-Ni), железо-хром (Fe-Cr) и железо-хром-никель (Fe-Cr-Ni) — были выплавлены при различных давлениях азота и в течение разного времени при температуре . Размер и морфология выделений нитридов зависели от состава сплава и давления азота; возможно, они также зависели от времени при температуре. В сплавах Fe-Cr-Ni наблюдались концентрации CrN до 25%, что приводило к композитной микроструктуре нитрида металла.
- Коммерческие аустенитные нержавеющие стали (Fe-18Cr-8Ni), которые были выплавлены под давлением азота 200 МПа, также образовывали CrN. Образование большого количества CrN приводило к уменьшению содержания хрома в матрице до менее 10 мас.%, но аустенитная микроструктура сохранялась.
Обрабатываемость сплавов Fe-Cr-Ni с высоким содержанием азота была сравнима с обрабатываемостью тех же сплавов без азота. Сплавы легко обрабатывались при обычных температурах горячей обработки от 800 до 1050°С. Хотя дендритные микроструктуры CrN разрушались во время горячей обработки, растворения или разложения не наблюдалось. Предполагается, что из-за стабильной высокой концентрации азота в матрице фаза CrN остается в термодинамическом равновесии.
Литые сплавы Fe-Cr-Ni с высоким содержанием азота обладают высокой прочностью на растяжение, но являются хрупкими. Горячедеформированные сплавы продемонстрировали не только более высокую прочность на растяжение, чем их литые аналоги, но и удлинение при растяжении более чем на 25%. Предел текучести горячедеформированных сплавов Fe-18Cr-8Ni с высоким содержанием азота по сравнению с их исходными сплавами, техническими низкоуглеродистыми аналогами, повышен примерно со 170 МПа до более чем 700 МПа. После горячей обработки сплавы также подвергались холодной обработке для дальнейшего повышения прочности на растяжение.
Азот входит в сталь в виде атомов внедрения и образует твердый раствор. Концентрацию азота в сталях можно контролировать, регулируя как состав сплава, так и избыточное давление азота. Термодинамические расчеты можно использовать для оценки взаимодействий между азотом и элементами сплава по мере увеличения концентрации азота, то есть, какой тип нитридов будет образовываться и при каких условиях.
Азот и углерод конкурируют за междоузлия в металлической решетке. Из-за этой конкуренции присутствие углерода снижает растворимость азота.
Однако, поскольку азот более растворим в железе, чем углерод, до образования соответствующих осадков хрома, в ГЦК-железе предпочтительнее легирование азотом.
Добавление больших количеств азота к металлам, особенно к сплавам железа, является новым. Возникающий в результате рост нитридных сеток в расплавленном металле повышает возможность производства новых композиционных материалов на основе нитрида металла. В сплавах железо-азот различные легирующие элементы могут быть объединены с образованием только избранных нитридов. Проводимые в настоящее время исследования показывают, что при добавлении алюминия или кремния в нержавеющие стали преимущественно осаждается нитрид алюминия или кремния, AlN или Si3N4, а количество образующегося CrN уменьшается.
Применимость сталей, легированных азотом Лабораторные плавки сталей, легированных азотом, имеют значительно более высокое содержание азота, чем полученное ранее. Условия, в которых были приготовлены эти стали, легированные азотом, находятся в пределах допустимых температуры и давления многих коммерческих горячих печей изостатического давления, предназначенных для спекания керамических материалов. Следовательно, существуют предприятия, которые могли бы производить коммерческие количества этих сплавов с высоким содержанием азота.
Сегодня для многих применений передовых материалов требуется высокая прочность на растяжение, высокая износостойкость и превосходная стойкость к коррозии и окислению. Сплавы с высоким содержанием азота и композиты из осажденного нитрида металлов обещают удовлетворить некоторые из этих требований с материалами на основе железа.
Кроме того, плавка металлов под высоким давлением газа является новой технологией, которая может быть применима к другим системам газовых сплавов.
Дополнительные преимущества сталей, легированных азотом Добавление азота в аустенитные нержавеющие стали (содержащие около 19% хрома по весу и 9% по весу никеля) увеличивает усталостную долговечность и снижает скорость ползучести при постоянном уровне приложенного напряжения. Таким образом, срок службы для многих высокотемпературных применений, таких как паровые и атомные электростанции, может быть увеличен за счет использования легирования азотом.
Добавление азота повышает стабильность аустенитной структуры. Следовательно, сплавы с высоким содержанием азота, как правило, содержат меньше феррита или мартенсита и больше аустенита. Ферритная и мартенситная структуры имеют меньшую ударную вязкость и более высокие скорости роста усталостных трещин, особенно при низких температурах. Следовательно, легирование азотом повышает сопротивление как разрушению, так и росту усталостной трещины в метастабильных аустенитных сплавах.
Присутствие азота приводит к образованию пассивных оксидных пленок, которые лучше защищают аустенитные сплавы от коррозии. Снижается питтинговая коррозия и повышается коррозионная стойкость к кислотам. Однако все виды коррозионной стойкости по-прежнему зависят от наличия достаточного количества хрома в пассивных пленках.
Ожидается, что повышенная устойчивость к усталости, ползучести и коррозии приведет к использованию сталей, легированных азотом, в энергетике, судостроении, химических и криогенных процессах и сосудах под давлением.