Коррозия трубопроводов — способы и методы их защиты
Коррозия трубопроводов представляет собой основную причину возникновения разгерметизации, в результате которой на поверхности трубы появляются трещины, разрывы и каверны. И поэтому, защита трубопроводов от коррозии является задачей не только строителей или изготовителей, но также специалистов создающих проекты и тех, кто будет ими пользоваться.
Причиной возникновения ржавчины и коррозии на стальных резервуарах может стать неподходящий состав протекающей по ним жидкости, неправильное сочетание различных металлов, а также недостаточная борьба с коррозией и плохо подобранные способы протекции. Опасность коррозии заключается в том, что она может стать причиной течи трубопроводов. Выполнить ремонт труб, после повреждения можно только используя сварку.
Причины возникновения
Коррозия стальных подземных труб представляет собой явление, основной причиной которого можно назвать реакции электрохимического окисления металлов от их постоянного взаимодействия с влагой. В результате таких реакций, состав металла меняется на ионном уровне, покрывается ржавчиной, распадается и просто пропадает с поверхности.
На процесс окисления может оказывать влияние характер жидкости, которая течет по подземному трубопроводу отопления или свойства среды, в которых он расположен. Именно по этой причине, выбирая подходящие средства для борьбы с ржавчиной необходимо учитывать все особенности, предшествовавшие ее возникновению. В противном случае, ремонт при помощи сварки неизбежен.
Виды защиты
На сегодняшний день существует несколько различных методов для обработки подземных труб отопления от ржавчины и коррозии. Все они основаны на принципе специальной обработки, в процессе которой металл, из которого сделаны резервуары, вступает в реакцию с вводимыми веществами и растворами. В результате таких действий образуется специальная пленка, которая и обеспечивает защиту.
Можно выделить несколько основных видов антикоррозийных способов защиты:
- обработка жидкости посредством реагентов химического характера;
- обработка стенок;
- блуждающий ток;
- катодная;
- анодная.
Обработка жидкости
Жидкость, которая протекает по трубопроводу, может иметь некоторые агрессивные качества. Агрессивный состав воды может стать следствием содержания в ней карбонатов, бикарбонатов или кислорода, которые становятся причиной того, что металл покрывается ржавчиной.
Выполнить качественную очистку стенок подземных труб или прочистить их полностью достаточно сложно технически. Основной задачей химической обработки воды является превращение ее состава из агрессивного в слабокальцирующий. Такая обработка подземных труб отопления от ржавчины зачастую сводиться к добавлению в воду соды, кальция или карбоната натрия.
На тех участках водопроводов, в которых вода может распределяться по отдельным точкам водозабора, ее дальнейшая обработка осуществляется при помощи добавления полифосфатов.
Антикоррозийная защита оцинкованных подземных резервуаров осуществляется при помощи добавления силикатов, фосфатов и поликарбонатов. Таким образом, на внутренней поверхности оцинкованных труб появляется специальная пленка, препятствующая возникновению коррозии.
Обработка стенок
Обработка стенок используется в качестве их защиты от коррозии уже много лет. Для выполнения такого комплекса мероприятий покрытие наносится на внешнюю или внутреннюю стенку подземной трубы.
Благодаря гальванике на поверхности формируется активная или пассивная пленка высокой прочности, которая не позволяет агрессивной среде проникнуть в глубокие слои металла. Эффект от таких действий может легко сохраняться на достаточно длительный период.
Как правило, на поверхность изделия наносится другой металл. Чаще всего для этого используется цинк, на который коррозия не воздействует. На поверхность металла может наноситься краска, лак или эмаль, которые также выступают в роли эффективной обработки газопроводов.
Для достижения максимального эффекта при борьбе с ржавчиной часто используются сплавы таких металлов как цинк или магний. Специалисты утверждают, что цинкование труб представляет собой самый популярный из всех существующих на сегодняшний день методов обработки.
Блуждающий ток
Блуждающий ток представляет собой ток, который образуется в грунтах при дисперсии электрифицированных путей. Энергия поступает к точке, являющейся катодом, и выходит в точке, которая является анодом.
В ходе процесса происходит электролиз, который может стать причиной появления ржавчины и повреждения резервуара. В этом случае, антикоррозийной изоляцией подземных трубопроводов является дренаж электрического характера.
Кабеля с низким сопротивлением подключаются к источнику тока в специально определенных местах.
Индуцированный ток
Катодная антикоррозийная протекция подземных резервуаров основана на использовании электрического тока, который подается в постоянном режиме и не дает пленке для защиты металла разрушаться.
Этот способ выполняется за счет использования кабеля с низким электросопротивлением, но при этом отличной изоляцией. Сам трубопровод в этом случае выполняет роль катода и таким образом защищается от возможных процессов коррозии.
Расходуемый анод
Еще одним довольно эффективным видом защиты от блуждающих токов является анодная химзащита. Заглубленный магниевый блок выполняет функции анода в коррозийной среде. Благодаря медленному разложению магния происходит изоляция магистральных стальных трубопроводов от подземных блуждающих токов. Такой вид защиты чаще всего используется для защиты изделий ограниченной длины или для резервуаров, которые выполнены из стали.
Как правило, анод помещается в мешок из хлопка или джута, который в свою очередь погружается в глинистую смесь. Основной задачей такой упаковки является обеспечение равномерности расхода анода, а также сохранения необходимого уровня влажности.
Такая система предотвратит появление пленки, которая может затруднить разложение анода.
Можно отметить, что лучшим способом защиты внутренней и внешней поверхности труб от возникновения коррозийных процессов будет использование материалов, которые менее всего им подвержены. И, тем не менее, даже на таких материалах в силу определенных причин могут возникать очаги коррозии и повреждения различного рода. И поэтому, лучше всего уже в процессе использования труб использования труб использоваться один из самых подходящих из используемых на сегодняшний день методов защиты.
kraska.guru
откуда берется ржавчина и как с ней бороться при помощи антикоррозионой защиты? + Видео
1 Причины возникновения и физика процесса
Коррозия трубопроводов начинается при возникновении электрохимической реакции окисления сплавов под воздействием влаги. Структура металла изменяется из-за влияния влаги и протекающих токов, в результате чего разрушается кристаллическая решетка и происходит «исчезание» металла с поверхности трубы. Причины появления коррозии трубопроводов заключаются в следующем:
- Сплавы с разным химическим составом обладают разными электрическими потенциалами, что вызывает протекание электрических токов по трубопроводу. Разные потенциалы могут быть обусловлены резким изменением грунта или окружающей среды.
- Влага, находящаяся в грунте.
- Химсостав и наличие кислот в грунте или окружающей среде.
- Состав транспортируемых веществ.
Существует несколько видов ржавления: поверхностная (по всей площади трубы), местная (участки поверхности) и щелевая. Коррозия на всей поверхности — крайне редкое явление. Самой опасной является местная коррозия, на которую приходится почти 90% всех повреждений. Щелевая тоже широко распространена, однако она редко приводит к серьезным повреждениям труб от коррозии.
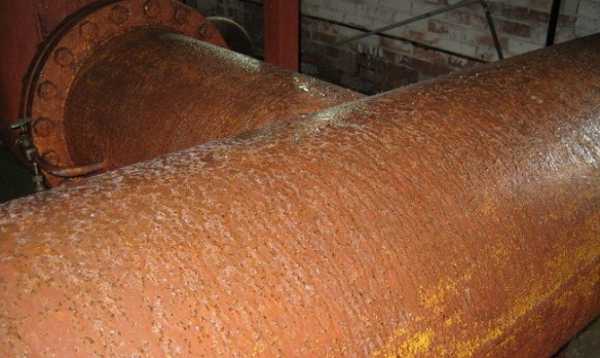
Поверхностное ржавление трубы
Рекомендуем ознакомиться
Наиболее часто коррозия развивается на участках, находящихся под железнодорожными или трамвайными путями, а также в случае нарушения СНИП и прокладкой труб под опорами электропередач. Скорость коррозии может колебаться в широких пределах от 3-4 мм до 20-30 мм год.
В зависимости от того, какие факторы вызывают появление ржавления, применяется различная антикоррозионная защита. О способах предотвращения ржавчины путепроводов рассказывается ниже.
2 Специальные защитные покрытия
Для предотвращения ржавчины абсолютно всех трубопроводов используется пассивная защита. Она заключается в создании изоляционного покрытия между металлом и окружающей средой. Для этого на трубу наносится вначале слой специальной антикоррозийной жидкости (грунтовки), затем объект либо красят либо наносят эпоксидную смолу.
Если накладывается слой эпоксидной смолы, возможно нанесение дополнительно битума, пеком (каменноугольным). Относительно новое средство защиты — полимерные ленты, однако они довольно дорогие.
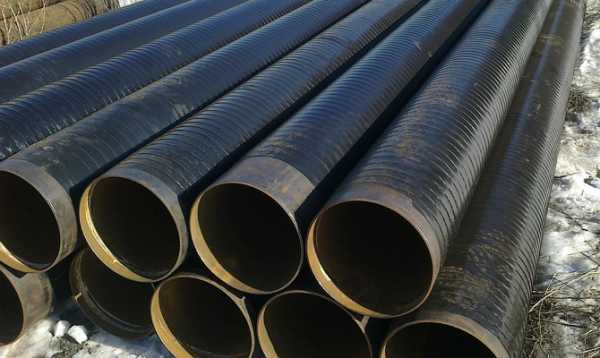
Защита от коррозии полимерными лентами
В идеальной системе нанесение защитных слоев позволяет полностью защитить объекты, однако в реальности это практически невыполнимо. Антикоррозийная защита не обеспечивает 100% защиты из-за деформаций или разрушений защитного слоя при транспортировке, укладке и монтаже. Даже визуально целое покрытие может иметь микротрещины или другие повреждения. Кроме того, защитные слои различных материалов имеют разные диффузионные и химические свойства. Защитное покрытие всегда подбирается под конкретный тип грунта (песок, супесок, суглинок и т. д.).
Таким образом, защитить объекты путем только нанесения покрытий нельзя. Состыкованные трубы с разными покрытиями может ускорить ржавление. Поэтому помимо покрытия поверхностей антикоррозийными материалами применяют и другие способы защиты.
3 Катодный способ
Защита трубопроводов от ржавления бывает и активной. Таковыми являются катодные и анодные защиты.
Активные способы основаны на понижении скорости реакции ржавления, с помощью смещения электрического потенциала до более низких значений (по сравнению с потенциалом окружающей среды). В начале 30-х годов прошлого века, ученым Робертом Куном было установлено, что смещение электрического потенциала на несколько десятых вольта позволяет замедлить скорость коррозийных реакций до 8-12 микрометров в год. Эта скорость развития ржавчины крайне мала и практически не существенна.
Катодный способ может быть осуществлен электрически и гальванически.
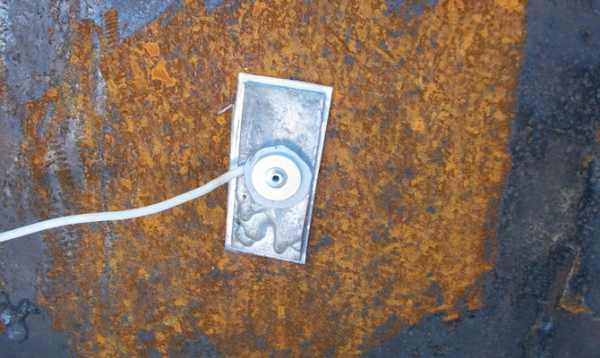
Катодный способ защиты труб от ржавчины
Гальванический метод (использование анодов из специальных сплавов) основан на следующем явлении: все металлы в одном и том же электролите обладают разными потенциалами. Поэтому при помещении металла, имеющего меньший потенциал в грунт, он будет являться анодом и разрушаться первым, защищая таким образом объект. В зависимости от типа грунта и сплава, из которого изготовлен трубопровод, подбирается материал для «жертвенного анода». Обычно используют магниевые, цинковые и алюминиевые сплавы.
Применение такой защиты возможно только в средах, имеющих низкое сопротивление (менее 40-50 Ом*м). Для сред с более высоким сопротивлением такая защита от коррозии бессмысленна.
Несмотря на большой выбор защитных средств, ржавлению ежегодно подвержены сотни километров трубопроводов. Именно на ржавчину приходится до 60% всех повреждений. В основном, это происходит из-за не соблюдений правил по уходу за путепроводами, поэтому своевременная проверка и уход крайне обязательны.
tutmet.ru
2. Причины и механизм коррозии трубопроводов
Основной причиной коррозии металла трубопроводов и резервуаров является термодинамическая неустойчивость металлов. Именно поэтому подавляющее большинство металлов в земной коре находится в связанном состоянии в виде окислов, солей и других соединений. Согласно второму закону термодинамики, любая система стремится перейти из состояния с большей энергией в состояние с меньшей энергией.
Энергия, которой обладают вещества, называется химической энергией.
Она создается движением электронов на электронных орбитах атомов и молекул. При определенных условиях химическая энергия может превращаться в другие виды энергии, совершать работу (например, работу образования химических соединений).
Применительно к веществам 2-й закон термодинамики звучит так: самопроизвольно совершаются только такие химические превращения, в результате которых образуются вещества с меньшей химической энергией. Практически для всех металлов (кроме золота) при образовании окислов, солей и т. д. это правило выполняется. Поэтому окисление металлов, т. е. их коррозия, в естественных условиях процесс неизбежный.
Практически круговорот металла в природе выглядит так. Металлургическая промышленность, затрачивая большое количество энергии, осуществляет восстановление металлов из руд в свободное состояние, то есть переводит их на более высокий энергетический уровень. Однако, когда этот металл уже в виде какой-то конструкции подвергается действию окислителей (кислорода), он самопроизвольно переходит в более стабильное окисленное состояние.
Влияние неоднородности состава металла
Для строительства трубопроводов применяют малоуглеродистые и низколегированные стали. Кроме железа они содержат углерод (до 2 %), легирующие примеси (хром, никель, марганец, медь) и примеси, которые невозможно полностью удалить в металлургическом процессе (сера, фосфор, кислород, азот, водород). Неоднородный состав сталей благоприятствует возникновению коррозионных пар в соответствующей среде.
Влияние неоднородности условий на поверхности металла
Для возникновения тока при электрохимической коррозии металла необходимо наличие катодной и анодной зон. В анодной зоне протекает реакция окисления, заключающаяся в потере металлом своих электронов и образовании ион-атомов
Me →Ме n+ + n ∙ẽ.
Переходя в раствор электролита, ион-атомы металла вызывают его постепенное разрушение — коррозию.
О2 + 4Н+ + 4 ẽ → 2Н2О — в кислой среде,
О2 + 2Н2О + 4 ẽ → 4(ОН) — в щелочной среде,
то такая реакция называется реакцией кислородной деполяризации.
Из рассмотрения механизма электрохимической коррозии следует, что интенсивность процесса зависит от скорости образования ион-атомов металла (и свободных электронов), а также наличия кислорода и воды. Учитывая, что на скорость образования ион-атомов влияет температура, концентрация раствора электролита и другие внешние условия, можно сделать заключение, что если на поверхности одного и того же металла создать различные условия, то одна часть его поверхности станет анодом по отношению к другой.
Примеры образования гальванических элементов из одного металла приведены на рис. 2.
Рисунок 2 — Примеры образования гальванических элементов
В первом случае анодом является электрод, помещенный в подогретый электролит. Это связано с тем, что в подогретом электролите растворение металла происходит более интенсивно. Аналогичная картина наблюдается и в слабоконцентрированном растворе собственной соли по сравнению с концентрированным раствором этой соли. Наконец, при подаче к одному из электродов воздуха на нем облегчается протекание реакции кислородной деполяризации, характерной для катода.
Рисунок 4 — Примеры возникновения коррозионных элементов на трубопроводе в результате различия условий на поверхности металла: А — анодная зона; К — катодная зона (стрелки указывают направление движения ион-атомов метала
К образованию коррозионных элементов на поверхности трубопроводов приводит различный доступ кислорода к разным участкам его поверхности, разная влажность грунта, неоднородность микроструктуры металла. Примеры возникновения коррозионных элементов приведены на рисунке 4.
Влияние состава среды
Нефти представляют собой смесь различных углеводородов с неуглеводородными компонентами (спирты, фенолы, соединения серы, кислорода и др.). Если предельные и непредельные углеводороды совершенно инертны к металлам, то неуглеводородные компоненты вступают с ними в химическую реакцию. Особенно опасны сернистые соединения (элементарная сера, сероводород, меркаптаны), которые являются причиной от 3 до 20 % случаев коррозионного повреждения внутренней поверхности трубопроводов. Сернистые соединения нефти попадают при ее переработке и в нефтепродукты.
Большую опасность в коррозионном отношении представляют также органические кислоты, образующиеся в результате окисления углеводородной и неуглеводородной составляющих товарных топлив при их хранении и применении.
Таким образом, нефтепродукты в той или иной мере являются коррозионно-активными.
Механизм наведения блуждающих токов на подземные металлические сооружения и их разрушения
Появление блуждающих токов в подземных металлических сооружениях связано с работой электрифицированного транспорта и электрических устройств, использующих землю в качестве токопровода. Источниками блуждающих токов являются линии электрифицированных железных дорог, трамваев, линии электропередачи, установки катодной защиты и др.
При работе электрифицированного транспорта ток совершает движение от положительной шины тяговой подстанции по контактному проводу к двигателю транспортного средства, а затем через колеса попадает на рельсы, по которым возвращается к отрицательной шине тяговой подстанции. Однако из-за нарушения перемычек между рельсами (увеличение сопротивления цепи), а также низкого переходного сопротивления «рельсы — грунт» часть тока стекает в землю. Здесь она натекает на подземные металлические сооружения, имеющие низкое продольное сопротивление, и распространяется до места с нарушенной изоляцией, расположенного недалеко от сооружения с еще меньшим продольным сопротивлением. В месте стекания блуждающих токов металл сооружения теряет свои ион-атомы, т. е. разрушается.
Блуждающие токи опасны тем, что они стекают, как правило, с небольшой площади поверхности, что приводит к образованию глубоких язв в металле в течение короткого времени.
Закономерности коррозионного растрескивания под напряжением (КРН)
Коррозионное растрескивание под напряжением (стресс-коррозия, карбонатное растрескивание) — это разрушение металла вследствие возникновения и развития трещин при одновременном воздействии растягивающих напряжений и коррозионной среды.
Впервые упоминания о КРН появились в начале 60-х годов XX века после того, как данное явление было зафиксировано на газопроводах высокого давления в Австралии, Канаде и США. В начале 80-х годов оно было идентифицировано на газопроводах, проложенных в пустынных и полупустынных районах Средней Азии и Казахстана. В настоящее время, по данным Ростех-надзора, КРН является главной причиной разрушения линейной части магистральных газопроводов.
Внешне КРН выглядит как группы трещин, ориентированных преимущественно вдоль оси трубы. Трещины могут проникать в тело трубы на различную глубину. Нарушение целостности газопровода происходит в результате протяженного разрушения, когда трещины или группы трещин достигают критического размера и происходит быстрый, так называемый «долом».
Трещины зарождаются на внешней поверхности трубопровода в нижней части трубы в районе 5.. .7 часов условного циферблата. Коррозионному растрескиванию подвергаются как основной металл труб, так и сварные соединения. Наиболее часто КРН развивается в 20-километровой зоне после компрессорной станции, а также при наличии водных потоков, которые направлены вдоль трубопроводов или пересекают их.
Зонами риска с точки зрения КРН являются участки с пересеченной местностью, где трубопровод не прилегает ко дну траншеи, поэтому между ними существует воздушный зазор. 40 % всех аварий по причине КРН связано с нарушением целостности изоляционного покрытия.
Все стресс-коррозионные разрушения последних лет происходят в нейтральных и слабокислых грунтах (рН=4,5…7). Многочисленные наблюдения аварийных разрушений за рубежом свидетельствуют, что КРН во многих случаях провоцируется локальной коррозией, и поэтому развитие КРН напрямую связано с коррозионной активностью грунтов.
Единого мнения о механизме КРН пока нет. Один из возможных «сценариев» ее развития выглядит следующим образом:
1) под некачественно нанесенное или поврежденное изоляционное покрытие трубопровода попадает грунтовая вода;
2) в результате действия катодной защиты, обеспечивающей наложение отрицательного потенциала на трубопровод, большая часть катионов водорода, содержащихся в грунтовой воде, превращается в атомы и молекулы водорода на поверхности металла 2Н+ +ẽ →Н2), что приводит к дополнительному отслоению изоляционного покрытия;
3) часть атомов или катионов водорода проникает в металл, нарушая его структуру и приводя к его охрупчиванию;
4) от действия переменной нагрузки на поверхности металла образуются трещины, в которые проникает почвенный электролит, и описанный выше процесс повторяется;
5) при достижении одной из трещин критических размеров наступает «внезапное» разрушение трубопровода.
Подводя итоги вышесказанному, можно сделать неутешительный вывод, что коррозия трубопроводов — процесс неизбежный. Однако человек, вооруженный знанием механизма коррозии, может затормозить его таким образом, чтобы обеспечить сохранение работоспособности трубопроводов в течение достаточно длительного времени.
studfiles.net
17. Внутренняя коррозия трубопроводов. Причины, методы борьбы.
Коррозия – это разрушение металлов в результате химического или электрохимического воздействия окружающей среды, это окислительно-восстановительный гетерогенный процесс, происходящий на поверхности раздела фаз.
Хотя механизм коррозии в разных условиях различен, по виду разрушения поверхности металла различают:
Равномерную или общую коррозию, т.е. равномерно распределенную по поверхности металла.
Местную или локальную коррозию, т.е. сосредоточенную на отдельных участках поверхности.
Межкристаллитную коррозию – характеризующуюся разрушением металла по границам кристаллитов (зерен металла).
Избирательную коррозию – избирательно растворяется один или несколько компонентов сплава, после чего остается пористый остаток, который сохраняет первоначальную форму и кажется неповрежденным.
Коррозионное растрескивание происходит, если металл подвергается постоянному растягивающему напряжению в коррозионной среде. КР может быть вызвано абсорбцией водорода, образовавшегося в процессе коррозии.
По механизму протекания различают химическую и электрохимическую коррозию.
Химическая коррозия характерна для сред не проводящих электрический ток.
Коррозия стали в водной среде происходит вследствие протекания электрохимических реакций, т.е. реакций сопровождающихся протеканием электрического тока. Скорость коррозии при этом возрастает.
Электрохимическая коррозия возникает в результате работы множества макро- или микрогальванопар в металле, соприкасающемся с электролитом.
Причины коррозии:
1. Температура и рН воды
Можно выделить 3 зоны:
1) рН < 4,3 . Скорость коррозии чрезвычайно быстро возрастает с понижением рН.
2) 4,3 < рН < 9-10. Скорость коррозии мало зависит от рН.
3) 9-10 < рН < 13. Скорость коррозии убывает с ростом рН и коррозия практически прекращается при рН = 13. (Сильнощелочная среда).
Повышение температуры ускоряет анодные и катодные процессы, так как увеличивает скорость движения ионов, а, следовательно, и скорость коррозии.
2. Содержание кислорода в воде
Как было отмечено выше, железо труб подвергается интенсивной коррозии в кислой среде при рН < 4,3 и практически не корродирует при рН > 4,3, если в воде отсутствует растворенный кислород. Если в воде есть растворенный кислород, то коррозия железа будет идти и в кислой, и в щелочной среде.
3. Парциальное давления СО2
Огромное влияние на разрушение металла труб коррозией оказывает свободная углекислота (СО2), содержащаяся в пластовых водах. Известно, что при одинаковом рН коррозия в углекислотной среде протекает более интенсивно, чем в растворах сильных кислот .
Минерализация воды
Растворенные в воде соли являются электролитами, поэтому увеличение их концентрации до определенного предела повысит электропроводность среды и, следовательно, ускорит процесс коррозии.
Уменьшение скорости коррозии связано с тем, что:
1) уменьшается растворимость газов, СО2 и О2, в воде;
2) возрастает вязкость воды, а, следовательно, затрудняется диффузия, подвод кислорода к поверхности трубы.
6. Давление
Повышение давления увеличивает процесс гидролиза солей и увеличивает растворимость СО2.
7. Структурная форма потока
Относительные скорости течения фаз (газа и жидкости) в газожидкостных смесях (ГЖС) в сочетании с их физическими свойствами (плотностью, вязкостью, поверхностным натяжением и т.д.) и размерами и положением в пространстве трубопровода определяют формирующиеся в них структуры двухфазных (многофазных) потоков. Можно выделить семь основных структур: пузырьковая, пробковая, расслоенная, волновая, снарядная, кольцевая и дисперсная.
Каждая структура ГЖС влияет на характер коррозионного процесса.
8. Биокоррозия, коррозия под действием микроорганизмов.
Итак, коррозионную агрессивность воды характеризуют природа и количество растворенных солей, рН, жесткость воды, содержание кислых газов.
Степень влияния этих факторов зависит от температуры, давления, структуры потока и количественного соотношения воды и углеводородов в системе.
Способы предупреждения внутренней коррозии трубопроводов подразделяются на технические (механические), химические и технологические.
Кардинальным средством борьбы с коррозионным повреждением стальных труб является замена их на пластмассовые.
Для предотвращения внутренней коррозии нефтесборных трубопроводов в ОАО «Татнефть», например, выбраны следующие направления:
— для перекачки беспарафинистых серосодержащих нефтей используются металло-пластмассовые трубы, коррозионно-стойкие гибкие трубы производства КВАРТ;
— для парафинистых нефтей применяются трубы со специальным защитным покрытием, выдерживающем температуру эксплуатации до 150 оС.
С 1988г. стеклопластиковые трубы безотказно работают в качестве НКТ, диаметр 89 мм. В основе последней разработки компании Ameron (Нидерланды), специализирующейся на выпуске стеклопластиковых труб для нефтяной промышленности — технология стальной полосы, применяемая компанией British Aerospace для изготовления высокопрочных оболочек двигателей космических ракет. Новый материал SSL — это ламинированный композитный материал, который сочетает преимущества высокопрочной стали с коррозионной стойкостью стекловолокна.
Задача надежности защиты от внутренней коррозии решается с помощью технологии футерования трубных плетей полиэтиленом и специальной конструкцией стыка. Однако, единой методики выбора типа покрытия в зависимости от свойств транспортируемой среды и условий эксплуатации трубопровода не выработано.
В начале 80-х годов в связи с ростом коррозионной активности добываемых жидкостей и увеличением протяженности трубопроводов стали применяться гибкие трубы. В первую очередь гибкие трубы начали применяться в системе ППД на месторождениях с особо агрессивными средами
В зависимости от коррозионных свойств скв продукции, условий экспл и коррозионной стойкости материалов рекомендуется предусматривать специальные способы защиты оборудования и трубопроводов от коррозии:
Термобработка аппаратов, труб и сварных швов;
Применение коррозионно-стойких материалов;
Химическая нейтрализация агрессивной среды;
Защита оборудования антикоррозионным покрытием;
Применение ингибиторов коррозии
studfiles.net
Классификация процессов внутренней и наружной коррозии на магистральных и промысловых трубопроводах — электронный каталог продукции,разработка мобильных приложений,АОС,автоматизированные обучающие системы,семинары по нефтегазовой тематике,разработка СТУ,СТУ
Коррозией (от лат. «corrosio» — «разъедание») металлов называется разрушение их поверхности в результате окисляющего воздействия окружающей среды. В процессе эксплуатации металлических магистральных и промысловых трубопроводов всегда происходит коррозия с образованием и развитием дефектов под воздействием внешних и внутренних факторов (воздействие коррозионной среды, статических и динамических напряжений, температуры и т.д.) и, как следствие, их разрушение. Коррозионное состояние трубопроводов определяется степенью коррозионного влияния на них окружающей среды и уровнем защиты от этого влияния.
Степень коррозионного влияния наиболее объективно определяется свободной скоростью роста коррозионных повреждений (Vкорр), измеряемой в мм/год. Многообразие природно-климатических условий РФ создает широкий диапазон скоростей почвенной наружной коррозии: от 0,25 — 0,3 мм/год в районах Сибири и Приполярья до 0,8-1,2 мм/год в южных регионах РФ и на Кавказе. Факторами дополнительной опасности являются значительные блуждающие токи (скорость роста дефектов: 0,1….10 мм/год) и индукционная коррозия (скорость роста дефектов: 0,05….3 мм/год) в промышленных районах центральной России. Скорость роста коррозионных дефектов в результате микробиологической наружной коррозии составляет 0,1…1,5 мм/год. В целом, наружную коррозионную опасность для объектов нефтегазового комплекса РФ можно характеризовать средней скоростью разрушения трубопроводов в 0,4….0,7 мм/год. Скорость роста внутренних коррозионных дефектов существенно превышает вышеуказанные цифры и может составлять до 10 мм/год. Существенной особенностью трубопроводов является то, что для них опасно появление даже самого мелкого сквозного проржавления, нарушающего их герметичность. У трубопроводов при этом возникают большие утечки транспортируемых продуктов, вызывающие опасность для окружающей среды, а иногда и опасность серьезных аварий вплоть до взрывов.
Указанные скорости роста обусловлены протеканием нескольких видов коррозионных процессов, различающихся между собой по механизму протекания: химическая коррозия, электрохимическая коррозия и коррозионное растрескивание под напряжением.
Химическая коррозия металлов — это гетерогенное взаимодействие металла с коррозионной средой, при котором окисление металла и восстановление окислителя происходит одновременно. Движущей силой процесса химической коррозии является уменьшение общей свободной энергии системы окислитель-восстановитель вследствие протекания химической реакции. Наиболее распространенным видом химической коррозии является коррозия металлов в газах, особенно при повышенных температурах.
На объектах нефтегазового комплекса наиболее часто встречается электрохимическая коррозия. Причиной протекания данного процесса является возникновение на поверхности металла, соприкасающегося с электролитом, большого количества коррозионных гальванических элементов. Возникновение таких коррозионных элементов вызвано различными величинами собственных потенциалов отдельных участков поверхности металла.
Это различие потенциалов на поверхности металла обусловливается как внутренними, так и внешними факторами. К числу внутренних факторов относятся: природа металла, его кристаллическое строение, наличие внутренних напряжений, температура, различный характер обработки поверхности металла, наличие загрязнений в металле (сегрегации, шлак и т. д.). К числу внешних факторов, влияющих на возникновение различных потенциалов на поверхности металла, относятся: природа и концентрация электролита, его температура, скорость движения, доступ окислителей к поверхности металла. В результате наличия разных потенциалов на поверхности металла образуется коррозионный гальванический элемент, в цепи которого возникает электрический ток.
Важной особенностью коррозионного процесса является то, что разрушения при электрохимической коррозии происходят только на анодах, в то время как на катодах происходит процесс деполяризации и разрушение металла не имеет места.
Коррозионное растрескивание под напряжением (КРН) труб в подземных трубопроводах является одной из форм инициируемых внешней средой разрушений. Его определяют как макрохрупкое разрушение, развивающееся в результате одновременного воздействия на металл коррозионной среды и растягивающих напряжений. В отличие от воздействия общей и локальной коррозии КРН приводит к снижению несущей способности, как правило, без существенного изменения толщины стенок.
В то же время, для объектов нефтегазового комплекса наиболее естественно классифицировать процессы коррозионного разрушения на протекающие на наружной и внутренней поверхности металлического объекта. В зависимости от условий протекания различают несколько видов наружной или внутренней коррозии стальных сооружений добычи, транспортировки и хранения нефти и газа.
Наружная коррозия может быть подразделена на:
- почвенную коррозию, происходящую в условиях заложения металла в почву;
- атмосферную коррозию, происходящую в условиях влажного воздуха;
- микробиологическую коррозию, вызываемую или усиливаемую микроорганизмами, содержащимися в грунте;
- коррозионное растрескивание под напряжением (КРН), вызываемое следующими последовательными процессами: наводораживание, коррозионное и механическое разрушение объекта;
- электрокоррозию, вызываемую почвенными постоянными или переменными блуждающими токами от внешнего источника;
- индукционную коррозию, возникающую в результате индукционного влияния линий электроснабжения на участках их параллельного следования и пересечения.
Внутренняя коррозия сооружений нефтегазового комплекса обычно подразделяется на следующие классы:
На практике часто приходится сталкиваться с одновременным совместным протеканием нескольких коррозионных процессов.
Хотите узнать больше о коррозии металлических конструкций и методах противокоррозионной защиты?
Скачайте наше специализированное учебно-справочное приложение «Защита от коррозии»
transenergostroy.ru
Наружная коррозия | Коррозия подземных трубопроводов
Здравствуйте! Наружная коррозия трубопроводов, проложенных под землей, является одной из главных причин аварий и внештатных ситуаций в тепловых сетях.
Наружная коррозия бывает двух видов: сплошной равномерной и язвенной очаговой. Более опасной считается (и так оно и есть на самом деле) язвенная очаговая коррозия. Денный вид коррозии приводит к сквозным повреждениям, по другому свищам. Скорость распространения в трубопроводах теплоснабжения язвенной очаговой коррозии достигает 1,4 – 1,8 мм/год. В сравнении с этим сплошная равномерная коррозия менее опасна, скорость ее распространения – 0,1 – 0,2 мм/год.
Наружная коррозия надземных трубопроводов подразделяется по видам: химическая, электрохимическая, электрическая (от блуждающих токов).
Химическая коррозия – это коррозия, которая возникает в результате воздействия на металл труб различных веществ (газов, жидкостей). Эти вещества попадают на поверхность трубопроводов через изоляцию. Химическая коррозия – это сплошная коррозия, процесс ее распространения происходит равномерно. При этом труба «съедается» коррозией постепенно, без резких скачков.
Электрохимическая коррозия – эта коррозия возникает в результате того, что металл (электрод) вступает в реакцию с химически агрессивным грунтом (растворами электролита). Коррозия здесь происходит в анодной зоне, в которой осуществляется выход ионов металла в грунт. При электрохимической коррозии на трубах теплоснабжения появляются местные язвы, пробоины довольно большой глубины, которые затем могут развиться в сквозные отверстия в стенке трубопровода.
Электрическая коррозия, как правило, появляется в результате воздействия на трубу тока, «блуждающего» в грунте. В грунт ток зачастую попадает в результате его утечки из рельсов электротранспорта. Что же здесь происходит? Такой блуждающий ток попадает на трубу, затем движется по ней, а вблизи тяговой подстанции выходит в грунт. На трубе же, в месте выхода блуждающего тока, образуется очаг электрокоррозии.
На интенсивность и быстроту протекания коррозии оказывают влияние следующие факторы: 1) температурный режим трубопроводов теплоснабжения; 2) наличие влаги, кислорода; 3) химически активные и агрессивные соли и кислоты грунта, грунтовых вод.
Температура поверхности трубопроводов оказывает большое влияние на интенсивность поступления к трубе кислорода, углекислого газа и других агрессивных газов. Когда температура повышается, то увеличивается скорость выхода кислорода из воды. Это с одной стороны, а с другой уменьшается растворимость кислорода в воде, из-за того, что снижается коэффициент абсорбции и парционального давления кислорода. В результате всех этих процессов происходит подсушивание теплоизоляции перемещение влаги к периферии.
Важно знать, что скорость наружной коррозии сначала растет, достигает максимума при 65 – 75 °С, а затем начинает снижаться. А при температуре 100 С и выше коррозия практически отсутствует. Это можно наблюдать на примере паропроводов, где температура теплоносителя как раз выше 100 °С.
При снижении температуры происходит процесс притока влаги из грунта, в которой содержится кислород и другие агрессивные газы. Процесс этот происходит через изоляцию трубопроводов, то есть получается, что переменная температура теплоносителя увеличивает наружную коррозию. Также при влажном грунте и теплоизоляции возрастает электропроводимость, что приводит к увеличению опасности электрической и электрохимической коррозии.
teplosniks.ru
Коррозия трубопроводов и способы её предупреждения (2 часа).
Коррозия — это процесс разрушения металла в результате электрохимического или химического воздействия окружающей среды. Для промысловых трубопроводов различают наружную и внутреннюю коррозию.
Химическая коррозия внутренней поверхности труб происходит при добыче сернистых нефтей, которые разрушают металл. Химическая коррозия характеризуется равномерным разрушением металла по всей поверхности. Она обычно менее интенсивная, чем электрохимическая.
Природа электрохимической коррозии состоит в том, что металл трубы не химически чистый элемент, а технический сплав,- в котором содержатся вкрапления элементов, отличающихся по своей активности. Когда поверхность металла смочена полярной (электропроводной) жидкостью — водой, то между вкраплениями, отличающимися по активности, возникает электрический ток. При соприкосновении с полярной водой атомы металла, расположенные на поверхности, подвергаются воздействию силового поля молекул воды. Это взаимодействие может быть настолько сильным, что происходит ослабление связи атома металла со своими внешними электронами и ион металла (Fe2+) с более активного вкрапления, несущий положительный заряд, покидает узел кристаллической решетки и переходит в волу. При этом на поверхности более активного вкрапления металла (анодного участка) остаются освобождающиеся электроны 2е, перемещающиеся по металлу к менее активным вкраплениям (катодный участок). На катодных участках эти электроны взаимодействуют с кислородом и в результате его ионизации, происходит образование гидроксильной группы ОН, несущей отрицательный заряд.
2е + 1/2О2 + Н2О = 2ОН ионы Fe2+ взаимодействуют в растворе с образованием закиси железа Fe2+ + 2OH = Fe(OH)2; при наличии в воде свободного кислорода закись железа окисляется до окиси железа, которая выпадает в осадок:
Интенсивность протекания электрохимической реакции в основном зависит от водородного показателя рН среды. Если рН < 7 — среда кислая, если рН > 7 — щелочная, а при рН =7 — нейтральная. Среда считается сильно коррозионно-агрессивной, если рН < 4. Наличие в пластовой воде сероводорода H2S и углекислого газа СО2 сильно повышает кислотность среды, поэтому эти вещества считаются коррозионно-агрессивными.
Электрохимическая коррозия существенно увеличивается при наличии блуждающих электрических токов.
Способы защиты трубопроводов от наружной коррозии подразделяются на пассивные и активные. Пассивные способы защиты предусматривают изоляцию наружной поверхности трубы от контакта с грунтовыми водами и от блуждающих электрических токов, которая осуществляется с помощью противокоррозионных диэлектрических покрытий, обладающих водонепроницаемостью, прочным сцеплением с металлом, механической прочностью.
Для изоляции промысловых трубопроводов применяют покрытия на битумной основе и на основе полимеров. Для повышения прочности и долговечности битумных покрытий используют бризол и стекловолокнистые материалы.
Активные способы защиты трубопроводов от наружной коррозии предусматривают создание такого электрического тока, в котором весь металл трубопровода становится катодом, а анодом является дополнительно размещенный в грунте металл. Существуют два вида активной способы защиты трубопроводов от наружной коррозии — катодная и протекторная. Дополнительно размещаемый в грунте металл как в катодной, так и в протекторной защите, подвергается разрушению, а наружная коррозия трубопроводов не происходит.
Способы предупреждения внутренней коррозии трубопровода подразделяют на механические, химические и технологические.
К механическим способам относятся покрытия внутренней поверхности трубопровода различными лаками, эпоксидными смолами, цинко-силикатными покрытиями.
Химический способ – применение — ингибиторов коррозии. Наиболее эффективные ингибиторы коррозии И-1-А и ИКСГ-1. Эффективность их защитного действия составляет 95-98 %.
Таблица 5.1 — Расход ингибитора коррозии зависит от скорости коррозии
Скорость коррозии, мм/ год | до 0, 55 | 0,55-1,1 | 1,1 |
Расход ингибитора, г/м3 | 50-70 | 80-100 | 120 — 150 |
Блочные автоматизированные установки для приготовления и дозировки деэмульгаторов и ингибиторов коррозии типа БР-2,5, БР — 10Г БР-23 могут быть использованы в любой-точке трубопровода промысловой системы сбора и подготовки нефти на участке от скважин до установки комплексной подготовки нефти.
Установки типа БР-2,5, БР-Ш смонтированы на раме-санях в теплоизоляционной будке, которая герметично разделена на два отсека: технологический и отсек системы контроля и управления. Отсеки обогреваются взрыво-защищенными электронагревателями. В технологическом отсеке смонтирована технологическая ёмкость с вмонтированным трубчатым электронагревателем, шестеренный и дозировочные насосы, запорно-регулирующая арматура и датчики системы контроля и управления. Технологическая ёмкость предназначена для хранения и подогрева реагента. С помощью насоса заполняют ёмкость, проводят периодическую циркуляцию реагента по линии ёмкость-насос-емкость для поддержания постоянной его концентрации в ёмкости и предотвращения загустевания ингибитора коррозии. Насос включается и выключается автоматически по заданной программе.
Таблица 5.2 — Техническая характеристика блочных автоматизированных установок
Параметры | Тип установки | ||
БР-2,5 | БР-10 | БР-25 | |
Размер дозы, г/т | 10-50 | 10-50 | 10-50 |
Пропускная способность | 500-1000 | 1000-5000 | 5000-10000 |
сырьевого трубопровода, т/сут. | |||
Наибольшая подача насоса, л/ч | 2,5 | ||
Наибольшее давление нагнетания, МПа: | |||
при дозировке концентриро- | |||
ванных реагентов; | |||
При дозировке водных растворов реагентов. | - | ||
Кинематическая вязкость реагентов, м2/с не более | |||
Температура дозируемого реагента, °С - | 20 — 60 | 20 — 60 | 2 0 — 60 |
Температура окружающей среды, °С | |||
Масса, кг |
Дозировочным насосом непрерывно подают реагент в трубопровод. Размер дозы регулируют вручную поворотом лимба регулировочного механизма. Установка типа БР-25 состоит из двух автономных блоков — технологического блока и ёмкости, каждый блок смонтирован на раме-санях. В технологическом отсеке смонтированы дополнительно резервный насос-дозатор, насос для воды и смеситель. Подавая в смеситель в определенных соотношениях воду и концентрированный реагент, в установке можно приготовить и дозировать водный раствор реагентов заданной концентрации.
Похожие статьи:
poznayka.org