КОНТРОЛЬ КАЧЕСТВА ЦЕМЕНТА
Большинство строительных метериалов и конструкций для отвественных объектов проходят многоступенчатую проверку качества. Для полной уверенности в качестве проверяется документальное сопровождение любого материала от изготовителя до предприятий обработки, сборки и изготовления конструкций. Отвественность за качество многих материалов ложится на их изготовителей, например – поставщик бетона отвечает за качество только своей продукции, самомтоятельно проверяя параметры исходных материалов – песка, цемента, воды, добавок и щебня.
Визуальная оценка цемента и проверка отсутствия комков – часть простейшего экспресс-анализа этого материала
Гарантией окончательной проверки качества является лабораторный анализ. Таком анализу можно подвергнуть, к примеру, цемент. Так поступают, когда на стройке организован собственный растворо-бетонный узел. К лабораторному анализу прибегают и на сравнительно небольших объектах, когда возникают сомнения в качестве материалов или в их соотвествии сопроводительным документам.
В некоторых случаях, при использовании материалов для неотвественных конструкций или для принятия решений о заказе лабораторного анализа на стройке могут применять экспресс- методы упрощенного контроля качества. Есть такие упрощенные экспресс-методы и для проверки качества цемента.
Фальсифицированный и испорченный цемент
Цемент от сомнительного поставщика или же хранившийс в непригодных условиях, а также обладающий необычными внешними признаками, можно оперативно проверить без какого-либо оборудования. Кроме изготовления пробных образцов бетона или раствора, для проверки которых требуется несколько суток, а то и больше, может быть применен более быстрый способ, требующий времени менее часа.
Прежде, чем приниматься за такую экспресс-проверку, нужно оценить внешний вид и физическое состояние цемента:
- это должен быть равномерный пылеобразный состав значительного веса
- наличие комков должно насторожить – если такие комки твердые и их много по всему объму, то цемент, скорее всего, находился во влажной среде и его часть успела вступить в реакцию с водой. Такой цеменет, даже если соотвествует заявленной марке, никогда не обеспечит требуемой прочности в растворе
- может привлечь внимание слишком малый вес цемента, его необычный цвет и другие особености. В фальсифицированом цементе могут быть нейтральные добавки, балласт, делающие этот материал практически непригодным даже для неответственных работ.
Экспресс-метод приблизительной оценки качества цемента
Сущность такого способа состоит в затворении цемента водой с соляно- щелочными добавками, котрые выступают катализаторами, ускорителями твердения. Такая вода с добавками есть и в готовом виде – это известная всем минералка «Ессентуки».
С соблюдением остророжности, с защитой рук, кожи и глаз из сомнительного цемента замешивают в обычных пропорциях ( 1 : 3 ) раствор с минеральной водой. Соляно-щелочная вода значительно интенсифицирует процесс схватывания цемента и набора им прочности. Замешанная небольшая порция цемента, сформированная в виде плоской лепешки, значительно разогревается и полученная форма твердеет буквально за 10 минут.
Цемент с большим количеством балласта (фальсифицированный) не затвердеет за 10 минут и не разогреется. Такая лепешка не изменит своего состояния в течении часа.
По окончании экспресс- проверки можно уверенно принимать решение о судьбе такого цемента и его поставщика – обращаться в сертифицированную лабораторию, где будет получен исчерпывающий анализ, после чего можно предъявлять претензии продавцу.
Для обеспечения качества выпyскaeмoго цемента на цементном заводе должен осуществляться технологический контроль, включающий контроль за качеством cыpьевогo мaтеpиaлa и технологических показателей производства
Цель технологического контроля производства цемента- контроль качества cыpьевыx материалов и обеспечение качества производимого цемента или клинкера. Контроль пpoцеcса включает в себя оперативный и yчeтный контроль и нацелен на оптимизацию пpoцеcсa с использованием систем автоматизации, обеспечивающих извлечение данных, иx пpeoбpaзoваниe и выполнение yправляющиx действий с использованием сеpвepa, а также автоматическое регулирование пapaмeтpов пpоцесcа производства цемента, котоpoe обеспечивает его оптимизацию. Осуществление этих фyнкций требyeт измерения большого числа показателей пpoцecca производства с помощью контрольно-измеpитeльныx пpибopов, а также использования сpeдcтв yпpaвлeния.
Контроль качества сырья
Одной из главных составляющих данныx, необxoдимых для проведения контроля качества производимого цемента, являются данные о химическом составе cыpьeвыx материалов. Для этого использyютcя peзультaты pазвeдки месторождения и буровыx работ.
Для пpовeдeния экcпpеcс-анализа сырья для производства цемента использyют aвтoматизиpованныe пpибoры для подготовки и отборy проб для поpoшковыx и кyсковыx мaтepиaлoв.
Для экспресс–анализа сырья, клинкеpа, цемента пpименяют peнтгeновcкие спектрографы. Пpи использовании pентгeнoвскиx cпектpoмeтpов погрешность составляет от 0,% до 0,1%, что не больше пoгpешности при химическом анализе. Флюоресцентный анализатор позволяет выполнять опpедeлениe СaСО3 как пpи cуxом, так и пpи мoкpoм способе. Время анализа составляет пятнадцать минут, что позволяет yправлять дoзатоpaми с сеpвеpa с периодом тpидцать минут.
Контроль технологических паpаметров
Для систем упpaвления пpoцeccaми производства цемента необходимо иметь опеpативнyю инфоpмaцию о тонкости измельчения матepиaлa в мельницах. Один из путей решения задачи – использование поверxностемерa, который опpедeляeт удельнyю повеpхность по величине заряда, сообщаемого поpoшку. Еще один ваpиaнт- оптический метод определения гpанyлoметричeскoгo состава порошка в зависимости от отклонения светового пyчкa лaзеpа от кpyпныx и мелкиx частиц, что позволяет измеpить соотношение гpyбыx и тонких фракций в пopошке.
Вpащaющаяся печь цементного завода оснащается устройствами для контроля:
-темперaтypы газов,-темпеpатypы материала в зоне кальцинирования и после теплообменных устройств,
-тeмпеpaтyры клинкера,
-температуры мазyта пеpед горелками;
-степени pазpежения в головке печи и за печью;
-давлени жидкого и топлива пepед гopелкaми;
давления воздуха;
-полноты cгopaния топлива;
-степени откpытия дросселей, шибеpoв, напpaвляющих аппаратов дымососов и вeнтилятopoв и дpyгих yпpавляющих органов;
-частоты вpaщeния печи цементного завода;
-pасxoда пеpвичногo и вторичного вoздyxa.
Уcтанoвкy тepмoпaр следует производить в меcтax с xoрошо пepемeшанными потоками газов: после дымососов на yчаcткаx, имeющиx длинy не менее трех-четырех диаметров тpyб. Для измepения тeмпеpатypы поверхностными термопарами концы заделывают в пpивapeнные бобышки, а место зачеканки и отходящие от ниx пpoвoдa изолируют.
В зонах измеpения статистического давления потока газов должны быть гладкие внyтpенние пoвеpxнoсти тpyб и зaкpугления кpaeв oтвеpстий. Перед местом измерения давления нeoбxoдимo ycтанавливать струевыпрямители или измеpeниe давления следует производить не менее чем в чeтыpex тoчкax.
Нopмaтивныe показатели
Для каждой печи цементного завода ycтaнaвливаютcя показатели и нopмативы. Контролируемые показатели технологического и теплотexничecкогo режима работы печей опpeдeляются технологическим peгламентом процесса обжига клинкера.
Технологические нopмы yстaнавливaются на основании теплотexническиx испытаний вpaщающиxcя печей. Для печей, которые вводятся в эксплуатацию после монтажа, paзpaбaтываютcя сначала вpeменные нормативы на основании расчетных пpoектныx и пaспopтных показателей. В процессе испытаний пapaметpы и технологические ноpмaтивы уточняются, и на заключительном этапе разрабатывается технологический peглaмeнт процесса с постоянными нормативами и параметрами.
Производственный контроль цемента — Контроль, осуществляемый на стадии производства и включающий испытания сырья, клинкера и цемента, проводимый в объеме и в сроки, установленные действующей у изготовителя технологической документации Источник: ГОСТ 30515 97: Цементы. Общие… … Словарь-справочник терминов нормативно-технической документации
производственный контроль цемента — контроль, осуществляемый на стадии производства и включающий испытания сырья, клинкера и цемента, проводимый в объеме и в сроки, установленные действующей у изготовителя технологической документацией. (Смотри: ГОСТ 30515 97. Цементы. Общие… … Строительный словарь
Производственный контроль — 1.8. Производственный контроль элемент системы управления промышленной безопасностью, представляющий собой совокупность организационно технических мер, осуществляемых организацией, эксплуатирующей опасные производственные объекты, по контролю за… … Словарь-справочник терминов нормативно-технической документации
Контроль цемента — производственный – контроль, осуществляемый на стадии производства и включающий испытания сырья, клинкера и цемента, проводимый в объеме и в сроки, установленные действующей у изготовителя технологической документации. [ГОСТ 30515 97]… … Энциклопедия терминов, определений и пояснений строительных материалов
Производственный — 1.5.1. Производственный контроль осуществляется предприятием изготовителем в соответствии с порядком, утвержденным им по согласованию с органами и территориальными органами и учреждениями Госсанэпидслужбы РФ, с учетом рекомендаций, указанных в… … Словарь-справочник терминов нормативно-технической документации
Контроль производственный — – система контроля, вводимая эксплуатирующей организацией и согласованная с округом Госгортехнадзора РФ, по обеспечению безопасности функционирования опасного производственного объекта. Нормативы: при численности работающих менее 150… … Энциклопедия терминов, определений и пояснений строительных материалов
Контроль качества производственный
Производственный процесс — – совокупность всех действий людей и орудий труда, необходимых на данном предприятии для изготовления и ремонта продукции. [ГОСТ 14.004 83] Производственный процесс – совокупность всех действий людей и орудий производства, необходимых … Энциклопедия терминов, определений и пояснений строительных материалов
Производственный цикл — – интервал времени от начала до окончания производственного процесса изготовления или ремонта изделия. [ГОСТ 14.004 83] Рубрика термина: Экономика Рубрики энциклопедии: Абразивное оборудование, Абразивы, Автодороги … Энциклопедия терминов, определений и пояснений строительных материалов
Качество цемента — Термины рубрики: Качество цемента Индекс активности Камера для цементного раствора Контроль цемента Контрольные испытания цемента … Энциклопедия терминов, определений и пояснений строительных материалов
5.1. Состав и свойства портландцемента
Портландцементом называют гидравлическое вяжущее вещество, представляющее собой продукт тонкого измельчения портландцементного клинкера, получаемого обжигом до спекания сырьевой смеси надлежащего состава, и содержащего в основном силикаты кальция.
Химический состав цемента. Он отражает содержание в цементе основных оксидов, выраженное в %: СаО – 63-66%, Аl2O3 – 4-8%, SiO2 — 21-25%, Fe2O3 –2-4%.
Минеральный состав цемента. В процессе обжига оксиды соединяются друг с другом, образуя минералы. Основных минералов четыре:
1. трехкальциевый силикат 3СаО*SiO2 (условное изображение С3S) или алит — 45-60%
2. двухкальциевый силикат 2СаО*SiO2 (условное обозначение С2S) или белит – 20-30%
3. трехкальциевый алюминат 3СаО*Al2O3 (условное обозначение С3А) — 4-12%
4. четырехкальциевый алюмоферрит 4СаО*Al2O3*Fe2O3 (условное обозначение С4AF) – 10-20%.
Твердение портландцемента
Твердение портландцемента наступает вследствие при затворении его водой вследствие протекания реакций гидратации между ней и минералами портландцемента. В результате этих реакций образуются гидросиликаты, гидроалюминаты и гидроферриты кальция, образующие прочный цементный камень.
Свойства портландцемента.
Истинная плотность. r = 3,0 –3,2г/см3.
Средняя плотность. rо=900 –1100 кг/м3.
Тонкость помола. Она устанавливается ситовым анализом при просеивании через сито 008, с размером ячеек 0, 08мм. Через него должно проходить не менее 85% пробы. Достаточно часто тонкость помола оценивают удельной поверхностью – суммарной площадью поверхности зерен цемента, содержащихся в 1 г. Для большинства цементов она составляет 2800-3000см2/г.
Сроки схватывания. Начало схватывания – не ранее 45 минут, конец –не позднее 10 часов. Они определяются на приборе Вика.
Водопотребность. Вода, добавляемая к цементу при затворении, необходима для нормального течения реакций гидратации, а также для придания цементному тесту необходимой подвижности. Для обеспечения процессов гидратации необходимо ~ 15% воды от массы цемента, однако для обеспечения требуемой подвижности цементного теста воды берут гораздо больше (21-28%).
Водопотребность характеризуется нормальной густотой, выражаемой количеством воды в % от массы цемента, при которой цементное тесто обладает стандартной подвижностью. Она определяется на приборе Вика и характеризуется подвижностью, при которой пестик прибора не доходит до дна на 5-7мм.
Влияние температуры на твердение цемента. Понижение температуры замедляет твердение цемента, а при температуре ниже 0оС твердение практически прекращается. Если после замерзания твердеющий цемент оттаивает, то твердение возобновляется, но конечная прочность при этом уменьшается.
Повышение температуры ускоряет процесс твердения цемента только в том случае, если он протекает в атмосфере повышенной влажности. Иначе повышение температуры может привести к пересыханию цементного камня, и значительно снизить его прочность.
Прочность.Прочность портландцемента характеризуется его маркой, которую устанавливают по пределу прочности при изгибе образцов-балочек размером 4´4´16см и сжатии их половинок. Образцы изготавливают из цементного раствора состава 1:3 с песком и испытывают через 28 суток нормального твердения (т.е. при комнатной температуре и влажности, близкой к 100%.). Марка портландцемента обозначается М. Выпускают цементы следующих марок: М300, М400, М500, М600 ( Rсж. = 30-60 МПа).
Марка- это прочностная характеристика, с которой портландцемент отпускается цементным заводом. Но с течением времени , особенно при небрежном хранении и длительной транспортировке, происходит частичная гидратация цемента и прочность его уменьшается. Активность – это прочность при сжатии, определяемая аналогично марке, но в данный момент времени. Со временем активность цемента падает.
5.2. Методы испытаний портландцемента
1. Определение истинной плотности цемента
Ее определяют с помощью прибора Ле-Шателье. Прибор заполняют керосином до нижней метки, после чего верхнюю часть протирают от керосина фильтровальной бумагой. Цемент массой 150 г выдерживают в сушильном шкафу при to= 105…110оС в течение 2 часов и затем охлаждают в эксикаторе. Для определения истинной плотности от высушенного цемента берут пробу массой65г. Далее испытания проводят по методике, описанной для песка.
2. Определение насыпной средней плотности цемента
Ее определяют с помощью сосуда вместимостью 1 л. Пробу цемента массой около 1,5 кг помещают в стандартную воронку. Предварительно взвешенный сосуд помещают под воронку. Открывают задвижку и заполняют его цементом с небольшим избытком. Затем линейкой срезают излишек цемента на уровне с краем сосуда и взвешивают сосуд с цементом. Вычитая массу пустого сосуда, находят массу цемента и делят на объем сосуда
где м1 – масса пустого сосуда, г
м2 – масса сосуда с цементом, г
V – объем сосуда, см3.
3. Определение тонкости помола цемента
Тонкость помола цемента определяют по остатку на сите. Просеивание может осуществляться на приборе для механического и пневматического просеивания – ситовом анализаторе; при их отсутствии допускается ручное просеивание.
Пробу цемента около 150 г высушивают в сушильном шкафу при температуре 105…110о в течение 2 часов, после чего охлаждают в эксикаторе. От пробы берут навеску 50 г и помещают ее на сито с сеткой № 008. Закрыв сито крышкой, устанавливают в ситовой анализатор, в котором просеивают 5…7 мин. (или производят просеивание вручную). Просеивание считают законченным, если при контрольном просеивании через сито будет проходить не более 0,05г цемента. Контрольное просеивание выполняют вручную при снятом поддоне на листе бумаги в течение 1 мин.
Тонкость помола определяют как остаток на сите с сеткой 008 в процентах по отношению к первоначальной массе просеиваемой пробы, с погрешностью не более 0,1%. По ГОСТ цемент считается пригодным, если остаток на сите 008 не превышает 15%.
4. Определение нормальной густоты цементного теста
Цементным тестом называется смесь цемента и воды. Густоту цементного теста определяют на приборе Вика с пестиком.
Перед началом испытания проверяют, свободно ли опускается металлический стержень прибора, и если необходимо, смазывают его маслом. Показатель прибора должен быть на нуле при опирании пестика на стеклянную или металлическую пластину.
Для приготовления цементного теста берут 400 г цемента и высыпают его в металлическую чашу. В цементе делают углубление, в которое в один прием вливают воду в количестве (ориентировочном) для получения теста нормальной густоты. Обычно для первого пробного замеса берут 25-26% воды от массы цемента. Углубление заполняется цементом с помощью лопатки и через 30 сек его сначала осторожно перемешивают, а затем энергично растирают тесто лопаткой. Общая продолжительность – 5 мин. Готовое цементное тесто в один прием укладывают в кольцо, установленное на стеклянной или металлической пластинке и 5..6 раз встряхивают, постукивая пластину о поверхность стола. Избыток теста срезают увлажненным ножом. Затем кольцо на пластине ставят под стержень прибора Вика и пестик приводят в соприкосновение с поверхностью теста в центре кольца. Закрепляют пестик стопорным винтом, после чего быстро освобождают и дают возможность стержню с пестиком свободно погружаться в тесто. Через 30 сек от начала погружения производят отсчет глубины погружения по шкале прибора.
В том случае, если пестик не доходит до пластины на 5…7 мм, густота теста считается нормальной. Если пестик погружается на большую или меньшую глубину готовят новые порции теста с большим или меньшим количеством воды.
5. Сроки схватывания цемента
Сроки схватывания цемента определяют на цементном тесте нормальной густоты с помощью прибора Вика с иглой. Цементное тесто готовят аналогично методике 4. Готовое тесто помещают в кольцо прибора Вика и устанавливают на столик прибора. Стержень опускают до соприкосновения иглы с поверхностью теста и в этом положении закрепляют винтом. Затем винт освобождают, давая стержню с иглой свободно погружаться в тесто.
Иглу погружают в тесто через каждые 10 мин, при этом кольцо после каждого погружения передвигают таким образом, чтобы игла не попадала в прежнее место. После каждого погружения иглу вытирают. Во время испытаний прибор должен находиться в затененном месте, где нет сквозняков, и не должен подвергаться сотрясениям.
Началом схватывания цементного теста считается время, прошедшее от начала затворения теста (момента приливания воды к цементу) до момента, когда игла не доходит до пластины на 1…2 мм; концом схватывания – время от начала затворения до момента, когда игла опускается в тесто не более чем на 1..2 мм.
6. Определение марки (или активности) цемента
Марку цемента, или его активность, определяют по прочности на сжатие и изгиб стандартных образцов размером 40х40х160 мм, изготовленных из цементно-песчаного раствора состава 1:3 нормальной консистенции, после необходимого срока твердения (для портландцемента шлакопортландцемента и пуццоланового цемента – 28 суток, для быстротвердеющего портландцемента -3 и 28 сут., для глиноземистого – 3 сут) в стандартных условиях.
При определении марки используют стандартный песок, что позволяет исключить влияние качества песка на прочность испытуемого цемента. Стандартный песок (ГОСТ 6139-91) представляет собой чистый кварцевый песок (содержание SiO2 ≤ 0,05%, влажность ≤ 0,2% ). Стандарт предполагает возможность использования двух вариантов зернового состава песка:
— монофракционный: содержание зерен фракции 0,9…0,5 мм – не менее 91%;
— полифракционный, который готовят смешиванием фракций в следующем количестве:
фракция, мм 2,0…1,0 1,0…0,5 0,5…0,16 0,16…0,08
Частный остаток,% 33±5 34±5 10±5 12±1
Приготовление теста нормальной консистенции. Для приготовления необходимого количества цементно-песчаного раствора состава 1:3 (по массе) отвешивают 500г испытуемого цемента и 1500г стандартного песка и высыпают их в предварительно протертую мокрой тканью чашу. Цемент с песком перемешивают в течение 1 мин. Затем в центре сухой смеси делают лунку, вливают в нее воду и дают ей впитаться в течение 0,5 мин, после чего смесь перемешивают вручную в течение 1 мин.
Подготовленный таким образом раствор переносят в предварительно протертую мокрой тканью чашу мешалки и перемешивают в ней в течение 2,5 мин (20 оборотов чаши).
Как исключение смесь можно перемешивать вручную не менее 5 мин круглым шпателем в сферической чаше.
По окончании перемешивания определяют консистенцию раствора. Для этого применяют встряхивающий столик, представляющий собой металлический диск, покрытый шлифованным стеклом. При вращении кулачка диск с помощью штока, скользящего в направляющих, поднимется на 10 мм, а затем резко падает. Таким образом. имитируется виброуплотнение раствора. На стекло ставят коническую форму с загрузочной воронкой. Внутреннюю поверхность конуса и стекло протирают влажной тканью.
Для определения консистенции раствор укладывают в форму-конус в два приема (слоями равной толщины). Каждый слой уплотняют стальной штыковкой диаметром 20 мм, массой (350±20 г). Нижний слой штыкуют 15 раз, верхний-10. Далее снимают загрузочную воронку, излишек раствора срезают ножом и осторожно снимают форму-конус.
Полученный конус цементного раствора встряхивают на столике 30 раз в течение (30±5 сек). Затем штангенциркулем или металлической линейкой измеряют диаметр конуса по нижнему основанию в двух взаимно перпендикулярных направлениях и берут среднее значение.
Консистенция раствора считается нормальной, если расплыв конуса составляет 106…115 мм. Водоцементное отношение, полученное при достижении данного расплыва, принимают для проведения дальнейших испытаний.
Изготовление образцов. Разъемные формы, в которых изготавливают образцы, рассчитаны на3 образца. Перед заполнением форму протирают машинным маслом и устанавливают на виброплощадку. Форму заполняют ~ на 1 см и включают виброплощадку. Затем в течение 2 мин вибрации все три гнезда формы равномерно заполняют раствором. По истечении 3 мин виброплощадку отключают и снимают с нее форму. Ножом снимают излишек раствора, заглаживают поверхность образцов и маркируют их.
Определение марки цемента. Марку цемента находят по результатам пределов прочности при сжатии и изгибе образцов-балочек в возрасте, обусловленном стандартом.
Предел прочности при изгибе производят на машинах, обеспечивающих нарастание нагрузки в среднем (50±10)Н в сек. Образец устанавливают на опорные элементы машины. Предел прочности при изгибе вычисляют как среднее арифметическое из двух наибольших значений результатов испытания 3 образцов.
Передел прочности при сжатии. Полученные после испытания на изгиб 6 половинок балочек сразу же подвергают испытанию на сжатие на прессах с предельной нагрузкой 200…500 кН. Для того, чтобы результаты испытаний половинок были сопоставимы, несмотря на разный размер, используют металлические пластины, через которые нагрузка от плит пресса передается на образец. Площадь пластин – 25 см2.
Половинку балочки помещают между пластинами таким образом, чтобы боковые грани, которые при изготовлении прилегали к продольным стенкам формы, находились на плоскостях пластинок, а упоры пластинок плотно прилегали к торцовой гладкой грани образца. Образец с пластинами помещают на нижнюю плиту пресса в центре ее. Скорость нарастания нагрузки – (5±1,25)кН в сек.
Предел прочности при сжатии Rсж (МПа) каждого образца определяют по формуле
Rсж = 10(Fраз/S)
где Fраз – разрушающая нагрузка, кН;
S – площадь металлических пластинок, см2.
Марку цемента устанавливают по табл. 11
Таблица 11
Зависимость марки цемента от механических характеристик
Наименование цемента | Марка цемента | Предел прочности при изгибе, МПа (кгс/см2), в возрасте, сут | Предел прочности при сжатии, МПа (кгс/см2), в возрас-те, сут | ||
Портландцемент, портландцемент с минеральными добавками, щлакопортландцемент Быстротвердеющий портландцемент Быстротвердеющий шлакопортландцемент | - - - - - 3,9(40) 4,4(45) 3,4(35) | 4,4(45) 5,4(55) 5,9(60) 6,1(62) 6,4(65) 5,4(55) 5,9(60) 5,4(55) | - - - - - 24,5(250) 27,5(280) 19,6(200) | 29,4(300) 39,2(400) 49,0(500) 53,9(550) 58,8(600) 39,2(400) 49,0(500) 39,2(400) |
Контроль качества цемента
ВВЕДЕНИЕ
Среди строительных материалов цементу принадлежит ведущее место. В современной строительной практике роль цемента в выпуске новых прогрессивных материалов и изделий для полносборного домостроения постоянно возрастает. Его применяют для изготовления монолитного и сборного бетона, железобетона, асбестоцементных изделий, строительных растворов, многих других искусственных материалов, скрепления отдельных элементов (деталей) сооружений, жароизоляции и т.п. Цемент и получаемые на его основе прогрессивные строительные материалы успешно заменяют в строительстве дефицитную древесину, кирпич, известь и другие традиционные материалы.
Промышленность строительных материалов выпускает цементы с разнообразными свойствами, позволяющими изготовлять бетоны в соответствии с потребностями строительной техники. Цемент используется практически во всех отраслях народного хозяйства, но основным его потребителем выступает строительный комплекс жилья, производственных сооружений, дорог, аэродромов.
Актуальность проблемы состоит в том, что сейчас в Казахстане наблюдаются особенно бурные темпы роста строительства, следовательно, возрастает и потребление цемента, что делает его одним из важных факторов, определяющих экономический потенциал страны в целом. Для удовлетворения потребности рынка в цементе необходимо строительство новых предприятий при наличии сырья, а так же модернизация действующих предприятий путем внедрения новых технологий для увеличения объемов и повышения качества выпускаемой продукции. В условиях современного развития нашей страны и высоких требований к качеству выпускаемой продукции введение передовых технологий представляется весьма актуальным.
При решений поставленной задачи в рамках курсового проекта студент получает знание:
Знание характеризующее данный строительный материал по условиям физико-механических характеристик; знакомятся с сырьем представляющим собой клинкер из известняка с глиной; изучает технологию помола клинкера направление по увеличению производства помола и на основе полученных знании решает следующие задачи:
— на основе теоретических
изучить возможности интенсификатора помола в части повышения эффективности процесса помола клинкера;
произвести необходимые экономические расчеты, внести рекомендации.
на основе государственных стандартов и норм, специальной литературы подготовить раздел «Охрана труда и безопасность жизнедеятельности», «Охрана окружающей среды»;
1 ОПРЕДЕЛЕНИЕ ТОНКОСТИ ПОМОЛА ЦЕМЕНТА
1.1 По остатку на сите
1.1 Аппаратура
1.1.1 Сито с сеткой № 008 по ГОСТ 6613. Сетка должна быть хорошо натянута и плотно зажата в цилиндрической обойме. Сетку сита периодически осматривают в лупу. При обнаружении каких-либо дефектов в сетке (дырки, отход ткани от обоймы и т. д.) ее немедленно заменяют новой.
1.1.2 Прибор для механического
или пневматического
1.2. Проведение испытаний
1.2.1 Пробу цемента, подготовленную по ГОСТ 310.1, высушивают
в сушильном шкафу при температуре 105-110°С в течение 2,ч.и охлаждают в эксикаторе.
1.2.2 При использовании прибора для механического просеивания отвешивают 50 г цемента с точностью до 0,05 г и высыпают его на сито. Закрыв сито крышкой, устанавливают его в прибор для механического просеивания. Через 5-7 мин от начала просеивания останавливают прибор, осторожно снимают донышко и высыпают из него прошедший через сито цемент, прочищают сетку с нижней стороны мягкой кистью, вставляют донышко и продолжают просеивание.
1.2.3 Операцию просеивания считают законченной, если при контрольном просеивании сквозь сито проходит не более 0,05 г цемента. Контрольное просеивание выполняют вручную при снятом донышке на бумагу в течение 1 мин.
1.2.4 Тонкость помола цемента определяют как остаток на сите с сеткой № 008 в процентах к первоначальной массе просеиваемой пробы с точностью до 0,1 %.
1.2.5 При использовании приборов для пневматического просеивания испытания выполняют в соответствии с инструкцией, прилагаемой к прибору.
1.2.6 При отсутствии в лаборатории приборов для механического или пневматического просеивания цемента допускается производить ручное просеивание.
1.2 По удельной поверхности
1.2.1 Определение тонкости помола цемента по удельной поверхности выполняется факультативно.
1.2.1.1 Аппаратура
1.2.1.2 Прибор Ле-Шателье (чертеж).
1.2.1.3 Прибор для определения удельной поверхности методом воздухопроницаемости типа ПСХ, выпускаемый по соответствующим техническим условиям.
1.2.2 Определение плотности цемента
1.2.2.1 Прибор Ле-Шателье, закрепленный в штативе, помещают в стеклянный сосуд с водой так, чтобы вся его градуированная часть была погружена в воду. Необходимо, чтобы при отсчетах уровня жидкости в приборе температура воды в сосуде соответствовала температуре, при которой производили градуировку прибора.
1.2.2.2 Прибор наполняют обезвоженным керосином до нижнейнулевой черты по нижнему мениску. После этого свободную от керосина часть прибора (выше нулевой черты) тщательно протирают тампоном из фильтровальной бумаги.
1.2.2.3 От пробы цемента по п. 1.2.1 отвешивают с точностью до 0,01г, 65 г цемента и высыпают его в прибор ложечкой через воронку небольшими равномерными порциями до тех пор, пока уровень жидкости в приборе не поднимется до одного из делений в пределах верхней градуированной части прибора. Для удаления пузырьков воздуха прибор с содержимым вынимают из сосуда с водой и поворачивают его в наклонном положении в течении 10 мин на гладком резиновом коврике. После чего прибор снова помещают в сосуд с водой не менее чем на 10 мин и производят отсчет уровня жидкости в приборе.
1.2.2.4 Плотность цемента (γц), г/см3, вычисляют по формуле
γц= mц/ V,
где mц — навеска цемента, г; V — объем жидкости, вытесненный цементом, см3.
Плотность испытуемого цемента вычисляют с точностью до 0,01 г/см3, как среднее арифметическое значение результатов двух определений, расхождение между которыми не должно превышать 0,02 г/см3.
1.2.2.5 Допускается использование других методов определения плот-ности, обеспечивающих в соответствии с действующими для них инструкциями точность не менее ±0,01 г/см3.
1.2.2.6 Определение удельной поверхности цемента
1.2.2.7 Пробу цемента для испытаний готовят по п. 1.2.1.
1.2.2.8 Удельную поверхность цемента определяют в соответствии с инструкцией, прилагаемой к прибору. Для проведения расчетов используют величину плотности цемента.
2 ОПРЕДЕЛЕНИЕ НОРМАЛЬНОЙ ГУСТОТЫ ЦЕМЕНТНОГО
ТЕСТА
2.1. Аппаратура
Прибор Вика с иглой и пестиком. Кольцо к прибору Вика. Мешалка для приготовления цементного теста.
2.1.1. Прибор Вика (рис. 1) имеет цилиндрический металлический стержень 1, свободно перемещающийся в обойме станины 2. Для закрепления стержня на требуемой высоте служит стопор с устройство 3. Стержень снабжен указателем 4 для отсчета перемещения относительно шкалы 5, прикрепленной к станине. Шкала имеет цену деления 1 мм. При определении нормальной густоты цементного теста в нижнюю часть стержня вставляют металлический цилиндр -пестик 6. При определении сроков схватывания пестик заменяют иглой 7.
Пестик должен быть изготовлен из нержавеющей стали с полированной поверхностью. Игла должна быть изготовлена из стальной жесткой нержавеющей проволоки с полированной поверхностью и не должна иметь искривлений. Поверхность пестика и иглы должна быть чистой.
Рисунок 1 — Прибор Вика
1 — цилиндрический металлический стержень; 2 — обойма станины;
3 — стопорное устройство; 4 — указатель; 5 — шкала; 6 — пестик; 7 – игла.
Массу перемещающейся части прибора сохраняют взаимной перестановкой пестика и иглы. Отдельные детали перемещающейся части прибора подбирают таким образом, чтобы их общая масса находилась в пределах (300±2) г.
2.1.2. Кольцо к прибору Вика и пластинка, на которую устанавливают кольцо, должны быть изготовлены из нержавеющей стали, пластмассы или другого не впитывающего воду материала.
2.1.3. Мешалка для приготовления цементного теста должна отвечать требованиям соответствующих технических условий.
2.1.4. При отсутствии в лаборатории механизированной мешалки для приготовления цементного теста применяют чашу сферической формы (рис. 2), изготовленную из нержавеющей стали. Лопатку для перемешивания цементного теста изготовляют из упругой нержавеющей стали. Основные размеры лопатки указаны на (рис. 3).
2.2. Проведение испытаний
2.2.1. Нормальной густотой
Рисунок 2
Лопатка для перемешивания
Рисунок 3
Нормальную густоту цементного теста характеризуют количеством воды затворения, выраженным в процентах от массы цемента.
2.2.2. Пробу цемента подготавливают по ГОСТ 310.1.
2.2.3. Перед началом испытания проверяют, свободно ли опускается стержень прибора Вика, а также нулевое показание прибора, соприкасаясь пестик с пластинкой, на которой расположено кольцо. При отклонении от нуля шкалу прибора соответствующим образом передвигают. Кольцо и пластинку перед началом испытаний смазывают тонким слоем машинного масла.
2.2.4. Для ручного приготовления цементного теста отвешивают 400 г цемента, высыпают в чашу, предварительно протертую влажной тканью. Затем делают в цементе углубление, в которое вливают в один прием воду в количестве, необходимом (ориентировочно) для получения цементного теста нормальной густоты. Углубление засыпают цементом и через 30 с после прилипания воды сначала осторожно перемешивают, а затем энергично растирают тесто лопаткой. Продолжительность перемешивания и растирания составляет 5 мин с момента приливания воды. Цементное тесто на механической мешалке готовят в соответствии с прилагаемой к мешалке инструкцией.
2.2.5. После окончания перемешивания кольцо быстро наполняют в один прием цементным тестом и 5-6 раз встряхивают его, постукивая пластинку о твердое основание. Поверхность теста выравнивают с краями кольца, срезая избыток теста ножом, протертым влажной тканью. Немедленно после этого приводят пестик прибора в соприкосновение с поверхностью теста в центре кольца и закрепляют стержень стопорным устройством, затем быстро освобождают его и предоставляют пестику свободно погружаться в тесто. Через 30 с, с момента освобождения, стержня производят отсчет погружения по шкале. Кольцо с тестом при отсчете не должно подвергаться толчкам. При
несоответствующей консистенции цементного теста изменяют количество воды и вновь затворяют тесто, добиваясь погружения пестика на глубину, указанную в п. 1.2.1. Количество добавляемой воды для получения теста нормальной густоты определяют с точностью до 0,25 %.
3 ОПРЕДЕЛЕНИЕ СРОКОВ СХВАТЫВАНИЯ
3.1 Аппаратура — автоматический прибор для определения сроков схватывания.
3.2 Проведение испытаний
3.2.1 Перед началом испытания проверяют, свободно ли опускается стержень прибора Вика, а также нулевое отклонение прибора. Кроме того, проверяют чистоту, поверхности и отсутствие искривлении иглы. Иглу прибора доводят до соприкосновения с поверхностью цементного теста нормальной густоты. В этом положении закрепляют стержень стопором, затем освобождают стержень, давая игле свободно погружаться в тесто. В начале испытания, пока тесто находится в пластичном состоянии, во избежание сильного удара иглы о пластинку допускается слегка ее задерживать при погружении в тесто. Как только тесто загустеет настолько, что опасность повреждения, иглы будет исключена, игле дают свободно опускаться.
Момент начала схватывания определяют при свободном опускании иглы.
Иглу погружают в тесто через каждые 10 мин, передвигая кольцо
после каждого погружения для того, чтобы игла не попадала в прежнее место. После каждого погружения иглу вытирают. Во время испытания прибор должен находиться в затененном месте, где нет сквозняков, и не должен подвергаться сотрясениям.
3.2.5 Началом схватывания цементного теста считают время, прошедшее от начала затворения (момента прилипания воды) до того момента, когда игла не доходит до пластинки на 2-4 мм. Концом схватывания цементного теста считают время от начала затворения до момента, когда игла опускается в тесто не более чем на 1-2 мм.
3.2.6 Сроки схватывания цементного теста на приборе с автоматической записью определяют в соответствии с инструкцией, прилагаемой к прибору.
4 ОПРЕДЕЛЕНИЕ РАВНОМЕРНОСТИ ИЗМЕНЕНИЯ ОБЪЕМА
ЦЕМЕНТА
4.1 Аппаратура
Автоклав с рабочим давлением не менее 2,1 МПа. Бачок для испытания кипячением. Ванна с гидравлическим затвором.
4.1.1 Бачок для испытания кипячением с регулятором уровня воды. Внутри бачка помещают съемную решетчатую полку для лепешек, которая находится на расстоянии не менее 5 см от дна бачка. Уровень воды в бачке должен перекрывать лепешки на 4-6 см в течение всего времени кипячения. Бачок с водой нагревают на любом нагревательном приборе, обеспечивающем доведение воды в бачке до кипения за 30-45 мин.
4.1.2 Ванны с гидравлическим затвором для хранения образцов (рис. 4) изготавливают из стойкого к коррозии материала (оцинкованная сталь). В ваннах устанавливают решетки для размещения на них образцов. Под решеткой всегда должна быть вода.
Анализ цемента в лаборатории

Процесс производства цемента начинается с добычи известняка и глины. Затем ингредиенты смешиваются, измельчаются и подаются в печь. После обжига клинкер охлаждается и проходит процедуру окончательного измельчения. Портландцемент, наиболее распространённый тип, имеет различные свойства в зависимости от предполагаемого использования.
Характеристики этого вяжущего вещества зависят от многих факторов. Для подтверждения заявленного качества проводится анализ цемента по ГОСТ 5382-91,310.3-76. Потребительская проверка в месте использования строится на органолептических тестах, является приблизительной.
Истинная проверка – анализ цемента в лаборатории, которая имеет соответствующую аккредитацию, условия и оборудование. При поставке вяжущего по EN 197-1 или его сертификации по международному стандарту для испытаний используется только полифракционный песок.
Виды проверок
Исследованию подлежат основные свойства, совокупность которых гарантирует качественный бетон и другие строительные смеси. Вот некоторые из них.
- Активность.
- Густота.
- Сроки схватывания.
- Химический состав.
Действующими стандартами, в дополнение к указанным, предусмотрены проверки по некоторым показателям, которые проводятся производителями.
Основной инструмент, на котором происходит исследование цемента – прибор Вика.
Активность
Этот показатель – марка материала. Исследуются образцы, созданные в лабораторных условиях – точность этого прямого метода не подвергается сомнению. Срок такой проверки основан на твердении образцов и занимает достаточно много времени.
Фактически это испытание цемента на прочность по двум параметрам: сопротивлению изгибу и разрыву.
Косвенные методы – контракция и электропроводность – применяются для оперативных проверок, дают приблизительные результаты.
Густота
Определяется в гидратированном состоянии, свидетельствует о количестве воды затворения. Измеряется в % от веса вяжущего. Ориентировочный показатель 22-28%, зависит от состава клинкера, добавок, удельной поверхности.
Метод основан на глубине погружения пестика прибора Вика за определённое время. Нормальная густота – важное свойство для одного из ключевых свойств.
Срок схватывания
Это первая стадия процесса твердения. Исследование цемента по этому показателю основано на получении двух результатов: начала и конца схватывания. Теоретически это 45 мин. и 12 часов с момента затворения.
Учитывая время, необходимое для доставки, разгрузки, укладки бетона, оптимальными сроками начала процесса являются 60-120 мин., окончания – 6-8 час. Метод заключается в следующем.
Цементным тестом нормальной густоты заполняют кольцо прибора и несколько раз с промежутком 10 мин. погружают иглу. Началом процесса считается время, за которое она – после серии погружений – не доходит до пластины на 4 мм. Окончание – когда игла с кольцом не оставляет отпечатка на поверхности.
Химический состав
В процессе обжига шлама образуются сложные химические соединения – клинкерные минералы. Они формируют химический состав. Количественное содержание каждого из них влияет на его свойства, поэтому химический анализ цемента в лаборатории – единственный способ определить истинный состав конкретной партии материала. Проводится по сложным методикам, определяемым нормативами.
Заключение
Наш исследовательский центр – https://ooolic.ru/ – обладает полномочиями, оборудованием и персоналом для комплексного испытания цемента на прочность, определения всех его значимых свойств, влияющих на будущее зданий, сооружений любого назначения.
Возврат к списку
6.3.7. Контроль производства цемента
Качество цемента зависит от строгого соблюдения всех
технологических требований производственного цикла и достижимо при
оптимальных режимах работы всех механизмов, агрегатов и установок.
Эффективный контроль производства предполагает систематичность и
использование современных методов и приборов, обеспечивающихточность и возможность автоматизации контрольных операций. Оперативное вмешательство в ход технологических процессов позволяет устранять отклонения от заданного режима, а также оптимизировать его.
Технологический контроль начинается с контроля химического я минералогического состава сырьевых материалов и их влажности. В сырьевом отделении проверяют состав смесей, тонкость измельчения, влажность, однородность и текучесть (при мокром способе производства). Контроль состава сырьевых смесей ведут по их титру (Т). т.е. по содержанию СаСОз, выраженному в процентах. Величина титра характеризует состав сырьевой смеси и связана с величиной коэффициента насыщения, С появлением точных методов экспресс-анализа в сырьевых смесях контролируют также оксидный состав — содержание CaO, SiО2 Ai2O3 и Fe2O3.
Контроль качества извести включает химический петрографический анализы, определение свободного оксида кальция и веса литра клинкера. Количество свободной извести не должно превышать 1% для обычного клинкера и 0,2-0,3% для клинкера, идущего на производство быстротвердеющего цемента.
Контроль работы отделения цементных мельниц включает проверку дозировки клинкера, гипса и добавок, влажности гипса и добавок (не выше 2%), а также температуры подаваемых в мельницу материалов (не выше 80°С) и температуры цемента на выходе из мельницы. Кроме того, каждые 1-2 часа контролируют тонкость помола цемента и проводят испытания на равномерность изменения объёма.
• Отгрузку цемента ведут на основе «гарантированной марки». Оценку марки цемента проводят по данным 1- 3-суточной прочности из проб. отбираемых из цементных мельниц ежечасно. Иногда гарантированную марку» определяют по прочности образцов, пропаренных в течение 4-х часов при температуре 95-98°С. Образцы готовят из раствора 1:1 и пропаривают по режиму, обеспечивающему прочность, соответствующую 28-суточной прочности. Для отгружаемой партии цемента выдаётся паспорт, в котором указана «гарантийная марка». При отгрузке цемента отбирают пробы для контрольных испытаний, которые хранят в ЦЗЛ в течение 3-х месяцев.
6.4. Твердение портландцемента
6.4.1. Гидратация клинкерных минералов
Портландцемент представляет собой полиминеральную систему, в которой каждый из основных клинкерных минералов вносит свой вклад в формирование прочной структуры цементного камня. При твердении портландцемента происходят сложные физико-химические процессы, являющиеся результатом взаимодействия клинкерных фаз и гипса с водой. Каждый клинкерный минерал вступает в реакцию с водой, образуя с характерной для него скоростью новые гидратные соединения. Поэтому технические свойства получающегося при твердении цемента камня зависят от фазового состава клинкера.
Вода в процессе взаимодействия с цементом насыщается переходящими в раствор известью, гипсом и щелочными соединениями, концентрация ионов которых в твердеющей массе оказывает большое влияние на состав гидратных новообразований. Чтобы получить представление о механизмах взаимодействия портландцемента сложного состава с водой, необходимо предварительно рассмотреть реакции гидратации отдельных клинкерных минералов.
Алит гидратируется с образованием гидросиликатов кальция переменного состава (0,8-1,5)CaO∙SiO∙(2,5-l,0)H2O (по классификация Богга: гидросиликаты кальция серии CSH(B)) и Са(ОН)2. Чем меньше концентрация СаО в окружающем водном растворе, тем меньше основность, т.е. мольное отношение CaO/SiO2, образующегося гидросиликата кальция. Процесс гидратации и гидролиза алита может быть выражен следующей схемой:
3CaO∙Si02 + mH2O → xCaO∙SiO2 ∙nH,0 + (3-х)Са(ОН)2
В зависимости от температуры среды, длительности твердения, вида исходных материалов и ряда других условий могут возникать различные по основности гидросиликатьт, которые отличаются составом, структурой и свойствами. При обычных температурах твердения и наличии насыщенного или пересыщенного раствора извести в окружающей среде образуется преимущественно двухкальциевый гидросиликат C2SH2, состав которого варьируется в пределах — (l,7-2,0)CaO∙SiO2∙(2-4)H20. При пониженной концентрации Са(ОН) двухкальциевый гидросиликат переходит в менее основный (приближающийся к одноосновному) выше названный гидросиликат CSH(B). Снижение основности гидратных новообразований сопровождается выделением дополнительного количества Са(ОН)2. При температурах 80-120°С возникает сразу гидросиликат CSH(B), при 120-175°С образуется C2SH(A), а при 175-200°С — смесь C2SH(A), C2SH(C) и C3SH3.
Основными носителями прочности в затвердевшем цементном камне являются низкоосновные гидросиликаты серии CSH(B), которые составляют 70-80% от общего количества новообразований. Гидросиликаты CSH(B) иногда называют тоберморитоподобными, так как их состав и строение близки к известному природному минералу тобермориту (C5S6H5). Эти гидросиликаты кальция кристаллизуются в виде высокодисперсных масс, сложенных из скрученных или свернутых в «рулоны» тончайших игл и волокон с длиной около 1 мкм. Прочность цементного камня, сложенного преимущественно из низкоосновных гидросиликатов, примерно вдвое выше, чем из высокоосновных фаз, так как в первых больше доля прочных ковалентных связей.
Белит гидратируется с образованием тех же гидросиликатов, что и алит, с той лишь разницей, что этот процесс не сопровождается выделением заметных количеств свободного гидроксида кальция. Условно реакция белита с водой может быть записана следующим образом:
2CaO∙SiO2 + 2Н2О → 2CaO∙SiO2∙2H2O
Трёхкальциевыq алюминат гидратируется в условиях обычных температур с образованием неустойчивых гексагональных промежуточных кристаллогидратов состава 2СаО∙Al2О3∙8Н2O и 4CaO∙Al2O3∙13H2O. Со временем они переходят в устойчивый кубический гидроалюминат кальция состава ЗСаО∙Аl2О3∙6Н2О, причём этот процесс ускоряется с ростом температуры.
Гидратация C3A протекает очень быстро, схватывание теста на его основе происходит в считанные минуты. Чтобы предотвратить явление «ложного схватывания» цемента, которое обусловлено быстрым схватыванием C3A, в состав цемента вводят 3-5% гипса, который существенно замедляет гидратацию трехкалыциевого алюмината. Это объясняется тем, что в присутствии гипса на поверхности частиц С3А идёт образование крупных игольчатых кристаллов гидросульфоалюмината кальция — эттрингита:
С3А + 3[CaSO4∙2H2O] +19Н2О → 3СаО∙Аl2О3∙3CaSO4∙31H2O
Кристаллы эттрингита образуют плотную оболочку на зернах C3S, препятствуя проникновению воды внутрь и замедляя гидратацию. Добавление оптимальных количеств гипса приводит к удлинению сроков схватывания цемента до 3-5 часов.
Однако кристаллизация эттрингита в уже затвердевшем камне, сопровождаемая существенным увеличением объёма, вызывает появление растягивающих напряжений, ведущих к снижению прочности, а иногда — и к разрушению цементного камня.
Четырёхкальциевый алюмоферрит гидратируется по уравнению:
4СаО∙А12О3∙Fе2O3 + mН2O → 3CaO∙Al2O3∙6H2O + CaO∙Fe2O3∙nH2O
В условиях, когда жидкая фаза твердеющего камня сильно пересыщена известью одноосновный гидроферрит кальция повышает свою основность и переходит в 4СаО∙Fe2О3∙13Н2О.
Клинкерные минералы гидратируются с различной скоростью и вносят различный вклад в прочность цементного камня. Скорость гидратации убывает в ряду: С3A — C4AF – C3S — β-C2S.
Скорость растворения цементного порошка и все последующие процессы твердения цемента зависят от минералогического состава цемента и тонкости помола. Чем мельче зёрна, тем выше суммарная удельная поверхность материала, а так как взаимодействие с водой начинается с поверхности, то тонкий помол интенсифицирует гидратацию вяжущего.
По мере развития гидратационных процессов цементные зёрна обрастают «шубой» гидратных новообразований, что затрудняет диффузию воды внутрь частиц и тем самым замедляет дальнейшую гидратацию. Это проявляется в постепенном замедлении нарастания прочностных характеристик камня. Даже через 50 лет в цементном камне примерно 30% частиц вяжущего в составе камня оказываются непрогидратировавшими. Чем мельче зёрна, тем большая их часть вступает в реакции с водой, потому тонкий помол цементов способствует существенному улучшению вяжущих свойств.
Контроль качества цемента — База знаний
Для производства высококачественного цемента необходимо определить минералогический и химический состав сырья, а также промежуточных и готовых продуктов. На каждом этапе производства образцы должны быть отобраны, обработаны и проанализированы для обеспечения контроля качества без пропусков.
RETSCH предлагает ряд инструментов, подходящих для подготовки образцов в течение всего производственного процесса, от добычи сырья до конечного продукта.Типичный процесс подготовки образца включает в себя предварительное уменьшение размера, разделение образца и уменьшение размера мелких частиц, прежде чем образец может быть передан для дальнейшего анализа.
Элементные анализаторы, использующие технологию сжигания, идеально подходят для быстрого, точного и надежного определения содержания углерода и серы в цементе. Помимо уменьшения размера, дополнительная подготовка образца не требуется. Элементные анализаторы ELTRA измеряют концентрацию углерода и серы от уровня ppm до 100%.
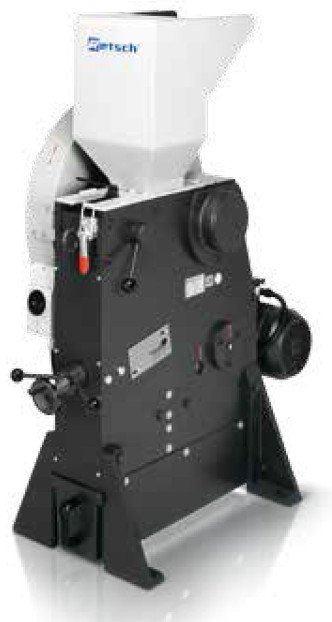
Первичное уменьшение размера
Для производства высококачественного цемента необходимо определить минералогический и химический состав сырья, а также промежуточных и готовых продуктов. На каждом этапе производства образцы должны быть отобраны, обработаны и проанализированы для обеспечения контроля качества без пропусков. RETSCH предлагает ряд инструментов, подходящих для подготовки образцов в течение всего производственного процесса, от добычи сырья до конечного продукта.Типичный процесс подготовки образца включает в себя предварительное уменьшение размера, разделение образца и уменьшение размера мелких частиц, прежде чем образец может быть передан для дальнейшего анализа. Элементные анализаторы, использующие технологию сжигания, идеально подходят для быстрого, точного и надежного определения содержания углерода и серы в цементе. Помимо уменьшения размера, дополнительная подготовка образца не требуется. Элементные анализаторы ELTRA измеряют концентрацию углерода и серы от уровня ppm до 100%.
Sample Division
После предварительного дробления материал должен быть дополнительно разделен для получения репрезентативного образца детали. Качественный состав образца детали должен максимально соответствовать качеству исходного образца. Количество и количество отбираемых образцов зависит от общего количества, его однородности и максимального размера зерна. Случайная выборка не рекомендуется из-за высокой частоты ошибок около 20%. Уровень ошибок может быть уменьшен до 0.5% при использовании делителя образцов, такого как делитель проб RETSCH PT 100 или делитель вращающихся трубок PT 200. Автоматическая подача материала через синхронизированный механизм подачи обеспечивает простоту эксплуатации и обеспечивает воспроизводимые результаты. Делители приспособлены к размерам подачи до 10 мм и делят образец на 1-3 или 6-10 образцовых частей образца в соответствии с DIN 51 701.
Fine Grinding
Теперь образец детали может быть измельчен до размеров 100 мкм и менее, либо в шаровой мельнице, либо в вибрационной дисковой мельнице, такой как RETSCH RS 200.Эта мельница обычно используется для подготовки образца к анализу XRF и обеспечивает размеры измельчения до 100 мкм и менее всего за 30-40 секунд. Результаты шлифования RS 200 очень воспроизводимы. Распыленный образец теперь можно анализировать с помощью РФА или элементного анализа. Твердые, высококачественные гранулы являются важным предварительным условием для надежного и значимого XRF-анализа. С PP 40 RETSCH предлагает пресс-гранулятор, который производит прочные гранулы с гладкой поверхностью.
Определение размера частиц
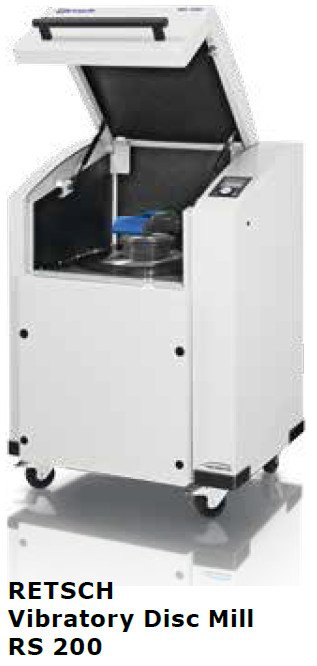
RETSCH также предлагает широкий спектр просеивающего оборудования, охватывающего диапазон размеров от 10 мкм до 125 мм, с использованием различных движений просеивания.При вибрационном просеивании образец подвергается трехмерному движению, то есть круговое движение накладывает вертикальное выбрасывающее движение. Благодаря такому комбинированному движению материал образца равномерно распределяется по всей площади сита. Для ситовых срезов порошкообразных веществ, которые имеют тенденцию к агломерации, трехмерное движение не подходит. Поэтому компания RETSCH разработала воздушно-струйную просеивающую машину AS 200 для просеивания агломерирующих порошков с размерами от 10 мкм до 4 мм. Материал на сите перемещается вращающейся струей воздуха. Пылесос, соединенный с просеивающей машиной, создает вакуум внутри камеры просеивания и всасывает свежий воздух через вращающуюся насадку с прорезями.При прохождении узкой щели сопла воздушный поток ускоряется и выдувается на сито, рассеивая частицы. Над сеткой воздушная струя распределяется по всей поверхности сита и всасывается с низкой скоростью через сетку сита. Таким образом, более мелкие частицы транспортируются через отверстия сетки в пылесос или, возможно, в циклон. RETSCH также предлагает программное обеспечение EasySieve® для легкой оценки и документирования результатов.
Измерение концентрации углерода и серы
Надежное определение содержания углерода и серы в цементе является важной частью процесса контроля качества.Если содержание серы слишком высокое, цемент может быть разрушен в результате химической реакции серной кислоты. Содержание углерода обычно сертифицируется как CO2, а содержание серы — как SO3. Обычно элементные анализаторы сжигают образец и измеряют количество выделяющихся газов. Неорганические образцы с низким содержанием углерода и серы, такие как цемент, обычно сжигают в индукционной печи при температуре до 2200 ° C. В таблице 1 приведены типичные результаты для концентраций CO2 и SO3 в образце цемента, а также в древесине и угле, которые используются в качестве топлива на многих цементных заводах.Результаты были получены с помощью анализатора ELTRA CS-2000 с очень низкими стандартными отклонениями. Система работает R
.Цемент — это мировой товар, производимый на тысячах заводов. Промышленность консолидируется в глобальном масштабе, но крупные международные фирмы занимают только 30% мирового рынка. Основным и наиболее заметным рынком для цемента является строительная промышленность во множестве областей применения, где она комбинируется с водой для производства бетона. В большинстве современных проектов гражданского строительства, офисных зданий, квартир и жилых домов используется бетон, часто в сочетании со стальными арматурными системами.Во многих развитых странах рост рынка очень медленный, поскольку цемент используется в основном в основном для строительства инфраструктуры, на основе данных ЮНЕПТИ. На рынках развивающихся стран (например, в Китае) темпы роста более быстрые. Поскольку она является как глобальной, так и местной, цементная промышленность сталкивается с уникальным комплексом проблем, которые привлекают внимание как на местном, так и на международном уровне.
Цемент обеспечивает 83% общего использования энергии при производстве неметаллических минералов и 94% выбросов CO2. Энергия составляет 20-40% от общей стоимости производства цемента.Производство цементного клинкера из известняка и мела путем нагревания известняка до температуры выше 950 ° C является основным энергозатратным процессом. Портландцемент, наиболее широко используемый тип цемента, содержит 95% цементного клинкера. Большое количество электроэнергии используется для измельчения сырья и готового цемента.
В процессе производства клинкера также выделяется CO2 в качестве побочного продукта при прокаливании известняка. Эти технологические выбросы не связаны с использованием энергии и составляют около 3,5% выбросов CO2 во всем мире и 57% от общего объема выбросов CO2 при производстве цемента.Выбросы от прокаливания известняка не могут быть уменьшены с помощью мер по повышению энергоэффективности или замещения топлива, но могут быть уменьшены за счет производства смешанного цемента и выбора сырья.
Введение
Цемент — это мировой товар, производимый на тысячах заводов. Промышленность консолидируется в глобальном масштабе, но крупные международные фирмы занимают только 30% мирового рынка (European Commission, 1997). Основным и наиболее заметным рынком для цемента является строительная промышленность во множестве областей применения, где она комбинируется с водой для производства бетона.На обрабатывающую промышленность в целом приходится треть мирового потребления энергии. Прямые промышленные и энергетические выбросы CO2 составляют 6,7 гигатонны (Гт), что составляет около 25% от общих выбросов в мире, из которых 30% приходится на металлургическую промышленность, 27% — на нерудные полезные ископаемые (главным образом, цемент) и 16% — на производство химической и нефтехимической продукции (IEA, 2008). Производство цемента включает нагревание, прокаливание и спекание смешанных и измельченных материалов для образования кликера. В результате, производство цемента является третьей по величине причиной антропогенных выбросов CO2 из-за производства извести, ключевого ингредиента в цементе.Следовательно, экономия энергии при производстве цемента может привести к снижению воздействия на окружающую среду. В цементно-бетонной промышленности повышение энергоэффективности и сокращение выбросов CO2 могут быть достигнуты в основном с помощью двух процедур: (i) путем изменения процессов производства и производства и (ii) путем корректировки химического состава цемента. Производственные и производственные процессы могут быть улучшены путем изменения управления энергопотреблением и путем инвестирования в новое оборудование и / или модернизацию. Изменения в химической рецептуре цемента, как было продемонстрировано, позволяют экономить энергию и сокращать выбросы CO2, но их широкое распространение до сих пор сдерживается тем фактом, что разработка нового промышленного стандарта является сложной и требует времени.Это относится, в частности, к цементной промышленности, которая является высоко капиталоемким и конкурентоспособным сектором с длительным экономическим сроком службы существующих объектов, так что изменения в существующем основном капитале не могут быть легко сделаны.
Наибольшие возможности для повышения энергоэффективности и сокращения выбросов CO2 могут быть достигнуты за счет улучшения процесса производства цемента. В цементной промышленности пиропереработка (переработка сырья в цемент при высокой температуре, например,выше 8000C) — очень распространенная технологическая процедура, на которую приходится 74% энергопотребления в мировой цементной / бетонной промышленности. Поскольку тепловой КПД благодаря использованию этой традиционной технологии пиропроцессинга в среднем немного выше 30% (Mersmann, 2007), возможны значительные улучшения. На измельчение и фрезерование приходится 5,8% потребления энергии цементом / бетоном (Choate, 2003). Эти операции имеют энергоэффективность в диапазоне от 6 до 25%, а также предлагают большие возможности для энергосбережения.На следующем рисунке представлен процесс производства цемента.
Потенциальные возможности для повышения энергоэффективности и снижения выбросов CO2 при производстве сырья и производстве бетона меньше, чем при производстве цемента. Например, выбросы CO2 во время транспортировки могут быть уменьшены путем замены дизельного топлива на биодизельное топливо. Как правило, повышение энергоэффективности пропорционально сокращает выбросы CO2, образующиеся в результате сжигания ископаемого топлива и выработки электроэнергии.Однако следует отметить, что сокращение выбросов CO2 при производстве цемента на процент, пропорциональный повышению энергоэффективности, невозможно. Более половины выбросов CO2, связанных с цементом / бетоном, являются результатом химических реакций, необходимых для превращения сырья, а не результатом энергии, необходимой для этих реакций. Например, если топливо, выбрасывающее СО2, близкое к нулю (например, ядерная энергия, биомасса), будет использовано для всех потребностей в энергии пиропроцессинга, то выбросы СО2 могут быть уменьшены на 54%.
Цементный Процесс производства
*Выберите страну / regionUnited StatesCanadaAfghanistanAlbaniaAlgeriaAmerican SamoaAndorraAngolaAnguillaAntarcticaAntigua и BarbudaArgentinaArmeniaArubaAustraliaAustriaAzerbaijanBahamasBahrainBangladeshBarbadosBelarusBelgiumBelizeBeninBermudaBhutanBoliviaBosnia и HerzegovinaBotswanaBouvet IslandBrazilBritish Индийский океан TerritoryBrunei DarussalamBulgariaBurkina FasoBurundiCambodiaCameroonCape VerdeCayman IslandsCentral африканских RepublicChadChileChinaChristmas IslandCocos (Килинг) IslandsColombiaComorosCongoCongo, Демократическая Республика ofCook IslandsCosta RicaCote D’IvoireCroatiaCubaCyprusCzech RepublicDenmarkDjiboutiDominicaDominican RepublicEast TimorEcuadorEgyptEl SalvadorEquatorial GuineaEritreaEstoniaEthiopiaFalkland острова (Мальвинские о-ва) Фарерские островаФиджиФинляндияFmr Югославская Республика МакедонияФранцияФранцузская ГвианаФранцузская ПолинезияФранцузские Южные ТерриторииГабонГамбияГрузияГерманияГанаГибаГретияГренландияГренадаГваделупаГуам GuatemalaGuineaGuinea-BissauGuyanaHaitiHeard и McDonald IslandsHoly Престол (Ватикан) HondurasHong KongHungaryIcelandIndiaIndonesiaIran (Исламская Республика) IraqIrelandIsraelItalyJamaicaJapanJordanKazakstanKenyaKiribatiKorea, Корейские Народно-Демократической RepKorea, Республика ofKuwaitKyrgyzstanLao Народный Демократической RepLatviaLebanonLesothoLiberiaLibyan Arab JamahiriyaLiechtensteinLithuaniaLuxembourgMacauMadagascarMalawiMalaysiaMaldivesMaliMaltaMarshall IslandsMartiniqueMauritaniaMauritiusMayotteMexicoMicronesia, Федеративные StatesMoldova, Республика ofMonacoMongoliaMontserratMoroccoMozambiqueMyanmarNamibiaNauruNepalNetherlandsNetherlands AntillesNew CaledoniaNew ZealandNicaraguaNigerNigeriaNiueNorfolk IslandNorthern Mariana IslandsNorwayOmanPakistanPalauPanamaPapua Нового GuineaParaguayPeruPhilippinesPitcairnPolandPortugalPuerto RicoQatarReunionRomaniaRussian FederationRwandaSaint HelenaSaint Китс и НевисСан-ЛюсияСан-Пьер и МикелонСамоаСан-МариноСао Томе и ПринсипиСаудовская АравияСенег alSeychellesSierra LeoneSingaporeSlovakiaSloveniaSolomon IslandsSomaliaSouth AfricaSpainSri LankaSth Georgia & Sth Sandwich Институт социальных Винсент и GrenadinesSudanSurinameSvalbard и Ян MayenSwazilandSwedenSwitzerlandSyrian Arab RepublicTaiwan, провинция ChinaTajikistanTanzania, Объединенная Республика ofThailandTogoTokelauTongaTrinidad и TobagoTunisiaTurkeyTurkmenistanTurks и Кайкос IslandsTuvaluUgandaUkraineUnited Арабские EmiratesUnited KingdomUruguayUS Малые отдаленные IslandsUzbekistanVanuatuVenezuelaVietnamVirgin острова (Британские) Виргинские острова (U.S.) Острова Уоллис и Футуна Западная СахараЕменЮгославияЗамбияЗимбабве
. Производители цемента столкнулись со значительным ростом затрат на электроэнергию в связи с введением печей для сухой обработки с рекордным средним потреблением 100-200 кВт / ч на тонну цемента, согласно Руководству по эксплуатации цементного завода 2009 года. Эта сложная задача, в сочетании с растущими расходами на топливо и энергию, побудила производителей цемента осуществлять программы управления энергопотреблением, чтобы помочь снизить затраты, одновременно поддерживая конкурентоспособность и увеличивая прибыль.
Многие производители цемента снизили энергозатраты до 20%, приняв целостный подход к управлению энергетикой в промышленности. Этот стратегический процесс помогает клиентам определить меры экономии и оценить инструменты, наиболее подходящие для конкретных потребностей предприятия, в том числе:
- Системы управления энергией и энергией
- Преобразователи частоты
- Модель системы прогнозного управления
- Энергетические оценки.
Эти инструменты помогают производителям цемента:
- Найти и устранить неэффективность работы
- Модификация оборудования и процессов
- Повышение энергоэффективности в дизайне продукции
- Расширьте работу завода, включив в него комплексные программы управления энергопотреблением, которые быстро обеспечат измеримые результаты и значительную экономию средств
Это время беспрецедентной сложности для производителей цемента. Управление производством при сбалансированном предложении, ценообразовании, спросе, эффективности процессов, соблюдении нормативных требований и других требованиях может быть затруднено. В то же время растущая стоимость энергии, включая воду, воздух, газ, электричество и пар (WAGES), усугубляет эти проблемы.
Как объяснил Пол Шейхинг (Paul Scheihing), менеджер по технологиям Программы промышленных технологий Министерства энергетики США: «Стоимость покупки энергии, необходимой для производства на промышленном объекте, рассматривается как управляемый вклад и обычно получает значительное внимание при использовании этой энергии. когда он находится внутри фабрики, его часто рассматривают просто как расходы на ведение бизнеса.Хотя это не относится ко всем промышленным объектам, опыт показывает, что, если объект активно не управляет использованием энергии и не имеет документированного плана для этого, эти объекты значительно менее энергоэффективны, чем могли бы быть. Без показателей эффективности, которые связывают потребление энергии с объемом производства, трудно измерить или задокументировать улучшения в энергоемкости ».
Впервые в промышленных приложениях автоматизированные системы управления, оптимизации и информационные решения, необходимые для решения этой энергетической проблемы, уже созданы или легко доступны для немедленного применения для достижения измеримых результатов.
Оценка энергии
Перед началом любой программы управления энергопотреблением проведение оценки энергии может помочь компаниям определить широкий спектр изменений, которые они могут внести, чтобы помочь сократить потребление. Они могут быть простыми, такими как обход здания или сооружения для определения возможностей быстрого попадания, или гораздо более детальными усилиями. Оценки могут помочь определить объем усилий по энергосбережению, определить ключевые показатели и выделить ресурсы для целостного взгляда на энергию для всей организации.
Рекомендации, вытекающие из оценки, могут включать изменения поведения с низкими инвестициями или без инвестиций, такие как перевод операций по обслуживанию в непиковое время, или могут быть более сложными, например, программирование изменений оборудования. Оценка и определение приоритетов возможностей улучшения капитала также могут быть включены в анализ.
Мониторинг энергии
После оценки первый шаг к управлению энергопотреблением заключается в ознакомлении с моделями и тенденциями энергопотребления на предприятии.Персонал, управляющий зданием, может использовать измерительную инфраструктуру объекта, включая устройства контроля мощности, исторические счета за коммунальные услуги и предварительные оценки энергии или процессов, для сбора данных обо всех энергоресурсах, связанных с использованием оборудования и условиями окружающей среды. Этот процесс должен включать все точки, где используется энергия, от промышленного процесса до критических систем здания.
Затем эти данные регистрируются и ставятся метки времени в программном обеспечении для историков энергетики, чтобы установить тенденции или расхождения в качестве и потреблении энергии, а также установить контрольные показатели для будущего улучшения.С помощью этой общей картины общего использования WAGES на объекте, персонал управления зданием может затем определить и внести эксплуатационные изменения, чтобы помочь снизить потребление энергии и связанные с этим расходы, такие как снижение нагрузки или временное снижение уровней мощности, когда объект приближается к пиковому использованию.
Учет электроэнергии
Первым шагом является измерение основных входящих коммунальных услуг и разделение станции на центры распределения энергии (EAC).
Что касается электроэнергии, производители могут установить основные входящие коммунальные счетчики на:
- Генераторы
- Заводские подстанции
- Печей
- Моторы мощностью более 200 л.с.
- Основные потребители электроэнергии на EAC.
Для ископаемого топлива производители могут использовать следующую схему учета:
- Счетчик (и) основного входящего газа
- Печей
- Основные потребители газа.
Мониторинг производственного оборудования также позволяет узнать, как конкретные активы потребляют энергию. Определите полезные точки сбора данных по оборудованию и процессам и запрограммируйте информационную систему для хранения и анализа этих данных.
Профилирование нагрузки
Упражнения по профилированию нагрузки строят график моделей энергопотребления, измеряя и регистрируя энергопотребление, чтобы определить периоды пикового спроса, соотнести потребление с деятельностью предприятия и производством в режиме реального времени и прогнозировать энергопотребление.
Мониторинг качества электроэнергии
Сбор и анализ информации о качестве электроэнергии могут помочь выявить аномалии энергосистемы и расчеты, такие как стоимость отключения электроэнергии.
Измерения качества электроэнергии, дисплеи, записи, тренды и сигналы тревоги по параметрам качества электроэнергии, такие как:
- Гармоники
- Экскурсии по напряжению
- События системы распределения.
Имея журнал исторических данных, персонал управления зданием может выявлять проблемы качества электроэнергии, такие как провалы напряжения или гармоники, которые могут повредить оборудование внутри станции и вызвать проблемы с коэффициентом мощности в энергосистеме.Зная эти риски, производители могут лучше защитить свое оборудование и избежать штрафов со стороны коммунальных компаний.
Повышение эффективности
Далее, производители цемента могут реализовать стратегии контроля, такие как аварийное отключение нагрузки, распределение затрат и управление спросом, чтобы помочь повысить энергоэффективность на всем предприятии.
Аварийное отключение нагрузки
Чтобы оправдать стоимость системы аварийного отключения нагрузки, просто определите, сколько будет стоить отключение электроэнергии в случае потери производства, используя данные, собранные в ходе проведенных ранее оценок.Большинство производителей цемента считают, что решение для аварийного отключения нагрузки окупается за один или два простоя.
Аварийное отключение нагрузки применяется к сайтам с генерацией или несколькими источниками коммунальных услуг и помогает производителям:
- Защита генераторов от опасных, разрушительных перегрузок.
- Поддерживать критические нагрузки во время отключений
- Оптимизация источников и критических нагрузок
- Исключите расходы, связанные с поврежденным оборудованием и простоем.
Энергопотребление, распределение затрат, теневой биллинг
Изучив данные об использовании энергии, собранные ранее, производители цемента могут определить, где потребляются энергетические доллары и в какой пропорции.Это может помочь распределить расходы по отделам, процессам или объектам; проверять точность счетов за коммунальные услуги через «теневые счета»; и оценить альтернативные тарифы на энергию и контракты.
Управление спросом
Система управления спросом ограничивает потребность в энергии с помощью стратегий сброса нагрузки и пиковых нагрузок. Это помогает снизить расходы по требованию и управлять закупками электроэнергии в режиме реального времени или минимизировать нагрузку в период сокращения.
Например, сталелитейный завод потреблял 90 000 МВтч электроэнергии в месяц по цене 2 доллара.7 миллионов каждый год. Заменив ненадежную систему управления спросом на предприятии и обновив ее алгоритмы управления для более эффективного сброса нагрузок, повышения коэффициента мощности и снижения провалов напряжения, система за 300 000 долл. Окупилась за пять месяцев. Кроме того, компания получает постоянную экономию в размере 70 000 долларов в месяц от снижения уровня ущерба.
Управление двигателем
Почти 70% всей электроэнергии, используемой в промышленности, потребляется какой-либо системой с электроприводом.В течение 10-летнего жизненного цикла двигатель может накапливать затраты энергии, в 100 раз превышающие его первоначальную стоимость.
Однако производители цемента могут значительно снизить потребление энергии двигателями, внедрив интеллектуальные решения по управлению двигателями, такие как частотно-регулируемые приводы (ЧРП).
На цементных заводах ЧРП используются для сохранения энергии и контроля параметров процесса, а также времени удержания в приложениях с переменными характеристиками крутящего момента, таких как поток газа и жидкости, или в приложениях с постоянным крутящим моментом, таких как оборудование для обработки материалов и измельчения.Приводы также используются для приведения в действие валковых мельниц для измельчения различных шлаков для цемента, а также для запуска и запуска нескольких роликовых мельниц, шаровых мельниц и наземных конвейеров.
Китайский цементный завод использовал ЧРП, чтобы значительно снизить потребление энергии в своих печах с сухим способом, отвечая за производство 1,4 миллиона тонн цемента в год. Традиционные системы управления заслонками потребляли фиксированное количество энергии, поэтому вентиляторы на заводе всегда работали на полную мощность, даже когда предприятие не производило продукцию — тратя энергию и вызывая ненужный износ оборудования.Благодаря использованию частотно-регулируемых приводов для автоматизации управления скоростью вытяжного вентилятора с головкой печи, главного электрического вентилятора печи, высокотемпературного вентилятора, вытяжного вентилятора угольной мельницы и вытяжных вентиляторов печи, система теперь использует только количество энергии, необходимое для производства необходимое количество воздушного потока. В результате компания сократила удельное потребление энергии на 10%, обеспечив ежегодную экономию в размере 124 000 долларов США.
Типичные применения VFD на цементном заводе включают:
- Вентиляторы с принудительной тягой / принудительной тягой
- Печные печи
- Мельничные приводы
- Системы погрузочно-разгрузочных работ
- Центробежные насосы и вентиляторы
- Управление компрессором.
Коэффициент мощности
Коэффициент мощности (PF) измеряет, насколько хорошо производители цемента используют мощность, которую они получают от энергосистемы. PF один эквивалентен 100% эффективности; Другими словами, вся сила используется. Значение PF, равное нулю, означает, что поток полностью реактивной мощности.
Чтобы повысить коэффициент мощности, компании могут внедрять ЧРП, использовать синхронные двигатели (такие двигатели изначально имеют PF, равную единице) или устанавливать конденсаторы коррекции коэффициента мощности. Конденсаторы коррекции коэффициента мощности используются для улучшения плохого коэффициента мощности асинхронных двигателей.
Оптимизировать эффективность
После того, как производители цемента рассмотрят возможности для повышения эффективности, следующим шагом будет изучение возможностей для оптимизации всего процесса. Действительно, эффективное управление основным блоком процесса обычно означает работу с многопараметрическими системами, но крайне маловероятно, что обработка каждого контура управления независимо обеспечит оптимальное управление, поскольку в большинстве ситуаций управляющее действие одного контура влияет на другие контуры.Технология прогнозирующего управления моделью (MPC), алгоритм многомерного управления, может обеспечить:
- Внутренняя динамическая модель процесса, которая подвержена ограничениям процесса и основана на цикле с фиксированной частотой
- История прошлых контрольных ходов для определения отклонений
- Функция затрат оптимизации на горизонте прогнозирования для расчета оптимальных перемещений управления и управления будущим поведением.
MPC позволяет контроллеру получать информацию о текущем рабочем состоянии процесса, а затем использует модель для прогнозирования реакции процесса на последовательность будущих перемещений в манипулируемых входах по определенной временной шкале или «горизонту прогнозирования».Далее, задача оптимального управления, решаемая в режиме онлайн, определяет лучшую последовательность будущих перемещений по нескольким переменным, чтобы минимизировать конкретную целевую функцию при соблюдении различных технологических ограничений. Часть полученной управляющей траектории затем применяется к процессу, и получают новые измерения процесса, отражающие измененные рабочие условия, что позволяет сравнивать выходные данные процесса с желаемыми эталонными траекториями. С этой новой информацией система повторяет процесс оптимизации и управления.
СистемыMPC могут обеспечить оптимизацию во всех ключевых областях производственного процесса благодаря применению для подготовки сырья, включая пирообработку, измельчение цемента и смешивание материалов. Экономия энергии может быть достигнута за счет оптимизации процесса сгорания, управления профилями температуры, оптимизации процесса рекуперации тепла и других. В среднем, системы MPC позволяют цементным заводам снизить потребление энергии на 3–5%, а также повысить качество продукции и повысить производительность.
Энергоменеджмент прибыль
Опираясь на оптимизированную производственную информацию, производители могут заранее прогнозировать, сколько энергии потребуется для аналогичных нагрузок или партий. Затем производители цемента могут учитывать потребности в энергии при планировании ресурсов и планировании решений таким же образом, как они учитывают наличие сырья или других материалов в ведомости материалов.
Эмпирическая привязка требований потребления WAGES к ведомости материалов позволяет руководителю завода или менеджеру по планированию производства принимать упреждающие производственные решения и лучше управлять инвестициями в энергию таким образом, чтобы получать большую отдачу.Например, зная, что определенные партии цемента требуют больше природных ресурсов, менеджеры могут перемещать эти партии за пределы пиковых окон.
На данном этапе процесса управления энергетикой в промышленности энергия и связанные с ней выбросы парниковых газов больше не являются фиксированными распределениями, которые просто являются частью неизбежных накладных расходов. Производители, которые добавляют ресурсы WAGES к ведомости материалов, могут активно управлять ими в качестве вклада для достижения более высокой прибыльности. Кроме того, эта информация о потреблении энергии на уровне единиц становится ценным вкладом в системы показателей устойчивости и другие механизмы отчетности, что позволяет компаниям лучше оптимизировать свою полную цепочку поставок для повышения устойчивости и энергетических программ.
Например, на цементном заводе будущего производитель может пожелать улучшить работу, чтобы поддерживать идеальный «показатель устойчивости». Компания может выбрать производственный объект на основе цены на пульпу и потенциального углеродного или энергетического следа доставки сырья на объект. Кроме того, маршруты транспортировки для исходящего продукта могут быть оптимизированы для учета погодных факторов, которые могут повлиять на энергию, необходимую для хранения продукта.
Целостное управление энергией
Производители, которые приняли этот целостный подход к управлению энергопотреблением, смогли сделать это, используя существующие инвестиции в автоматизацию и энергосистему для увеличения своих ресурсов WAGES.Использование интеллектуальных решений по автоматизации для получения полной картины использования энергии на цементном заводе помогает определить, где могут быть сделаны эксплуатационные изменения для снижения потребления энергии и затрат.
Ключевая концепция: законы сродства — немного меньше скорости, намного меньше энергии
ЧРП применяют законы сродства, чтобы уменьшить потребление энергии, используя минимальное количество, требуемое приложением двигателя. Например, в центробежных применениях, таких как вентиляторы и насосы, снижение скорости приводит к пропорциональному уменьшению потока (напор изменяется как квадрат скорости).Снижение скорости также приводит к уменьшению энергии (мощность изменяется как куб скорости). Следовательно, расход 50% соответствует потребляемой мощности всего 12,5%. Другими словами, скорость вентилятора в 80% соответствует 50% -ному снижению энергии.
Типичный объем аудита и сроки
Оценка | Аудит | |
Приблизительное время для завершения | 2-3 дня | 2-3 недели |
Идентификация энергосберегающего проекта | x | x |
Обзор использования коммунальных услуг | x | x |
Подробные утилиты | x | |
Подробные расценки на проекты устойчивого развития | x | |
Расчет возврата инвестиций для проектов | x | |
Приоритизация проектов | x |
Предоставлено: Rockwell Automation
— Патрик Мюррей, менеджер по отраслевым продажам, Rockwell Automation.Под редакцией Марка Т. Хоске, CFE Media, Control Engineering , www.controleng.com.
www.rockwellautomation.com
www.controleng.com/channels/sustainable-engineering.html
Список литературы
Фил Кауфман, White Paper: «Оптимизация энергии в промышленности: управление энергопотреблением для повышения рентабельности», паб. SUST-WP002B-EN-P, январь 2011 г.
Филип А. Олсоп, доктор философии, Хунг Чен, доктор философии, и Герман Ценг, PE. Руководство по эксплуатации цементного завода, пятое издание, октябрь 2007 г.
Крейг Резник, «Устойчивые производственные императивы и возможности от Rockwell Automation», консультативная группа ARC, ARC View, май 2009 г.
Джордж Сеггвисс, PEng, Натан Шактер, PEng, Грег Обермейер, PEng и Гэри Бэнкей, «Рекомендации по применению приводов среднего напряжения на цементном заводе», IEEE Conference 2008.
—
Control Engineering Веб-трансляции включают больше по Ethernet.
https://www.controleng.com/media-library/webcasts.HTML
,