Классификация сварки плавлением | Рудетранс
Все существующие способы сварки можно разделить на две основные группы: сварку давлением (контактная, газопрессовая, трением, холодная, ультразвуком) и сварку плавлением (газовая, термитная, электродуговая, электрошлаковая, электронно-лучевая, лазерная).
Простейшие виды сварки плавлением известны с глубокой древности, например литейная сварка. Современная схема сварки плавлением показана на рисунке.
К соединяемым деталям в месте сварки подводят сварочное пламя; производят местное расплавление деталей до образования общей сварочной ванны жидкого металла. После удаления сварочного пламени металл ванны быстро охлаждается и затвердевает, в результате детали оказываются соединёнными в одно целое. Перемещая пламя по линии сварки, можно получить сварной шов любой длины. Сварочное пламя должно иметь достаточную тепловую мощность и температуру; сварочную ванну нужно образовывать на сравнительно холодном металле: теплопроводность металлов высока и быстро образовать ванну может только очень горячее пламя.
Сварочное пламя расплавляет как металл, так и загрязнения на его поверхности, образующиеся шлаки всплывают на поверхность ванны. Горячее пламя сильно нагревает металл на поверхности, значительно выше точки плавления; в результате меняется химический состав металла и его структура после затвердевания; изменяются и механические свойства. Затвердевший металл ванны, так называемый металл сварного шва обычно по своим свойствам отличается от основного металла, незатронутого сваркой. Сварка плавлением отличается значительной универсальностью; современными сварочными источниками легко могут быть расплавлены почти все металлы, возможно соединение разнородных металлов.
Характерный признак сварки плавлением; выполнение её за один этап-нагрев сварочным пламенем, в отличие от сварки давлением.
Самое широкое распространение получили различные способы электрической сварки плавлением, а ведущее место занимает дуговая сварка, при которой источником теплоты служит электрическая дуга.
Электрическую сварку плавлением в зависимости от характера источников нагрева и расплавления свариваемых кромок можно разделить на следующие основные виды сварки:
- электрическая дуговая, где источником тепла является электрическая дуга;
- электрошлаковая
- электронно-лучевая , при которой нагрев и расплавление кромок соединяемых деталей производят направленным потоком электронов, излучаемых раскалённым катодом;
- лазерная , при которой нагрев и расплавление кромок соединяемых деталей производят направленным сфокусированным мощным световым лучом микрочастиц-фотонов.
При электрической дуговой сварке основная часть теплоты, необходимая для нагрева и плавления металла, получается за счет дугового разряда, возникающего между свариваемым металлом и электродом. Под действием теплоты дуги кромки свариваемых деталей и торец плавящегося электрода расплавляются, образуя сварочную ванну, которая некоторое время находится в расплавленном состоянии. При затвердевании металла образуется сварное соединение. Энергия, необходимая для образования и поддержания дугового разряда, получается от источников питания дуги постоянного или переменного тока. Классификация дуговой сварки производится в зависимости от степени механизации процесса сварки, рода тока и полярности, типа дуги, свойств электрода, вида защиты зоны сварки от атмосферного воздуха и др.
По степени механизации различают сварку вручную, полуавтоматическую и автоматическую сварку. Отнесение процессов к тому или иному способу зависит от того, как выполняются зажигание и поддержание определенной длины дуги, манипуляция электродом для придания шву нужной формы, перемещение электрода по линии наложения шва и прекращения процесса сварки.
При ручной сварке указанные операции, необходимые для образования шва, выполняются рабочим-сварщиком вручную без применения механизмов.
При полуавтоматической сварке плавящимся электродом механизируются операции по подаче электродной проволоки в сварочную зону, а остальные операции процесса сварки осуществляются вручную.
При автоматической сварке под флюсом механизируются операции по возбуждению дуги, поддержанию определённой длины дуги, перемещению дуги по линии наложения шва. Автоматическая сварка плавящимся электродом ведётся сварочной проволокой диаметром 1-6 мм; при этом режим сварки (ток, напряжение, скорость перемещения дуги и др.) более стабилен, что обеспечивает однородность качества шва по его длине, в то же время требуется большая точность в подготовке и сборке деталей под сварку.
По роду тока различают дуги, питаемые постоянным током прямой (минус на электроде) или обратной (плюс на электроде) полярности или переменным током.
По типу дуги различают дугу прямого действия (зависимую дугу) и дугу косвенного действия (независимую дугу). В первом случае дуга горит между электродом и основным металлом, который также является частью сварочной цепи, и для сварки используется теплота, выделяемая в столбе дуги и на электродах; во втором — дуга горит между двумя электродами. Основной металл не является частью сварочной цепи и расплавляется преимущественно за счёт теплоотдачи от газов столба дуги. В этом случае питание дуги осуществляется обычно переменным током, но она имеет незначительное применение из-за малого коэффициента полезного действия дуги (отношение полезно используемой тепловой мощности дуги к полной тепловой мощности).
По свойствам электрода различают способы сварки плавящимся электродом и неплавящимся (угольным, графитовым и вольфрамовым). Сварка плавящимся электродом является самым распространённым способом сварки; при этом дуга горит между основным металлом и металлическим стержнем, подаваемым в зону сварки по мере плавления. Этот вид сварки можно производить одним или несколькими электродами. Если два электрода подсоединены к одному полюсу источника питания дуги, то такой метод называют двухэлектродной сваркой, а если больше — многоэлектродной сваркой пучком электродов. Если каждый из электродов получает независимое питание — сварку называют двухдуговой (многодуговой) сваркой. При дуговой сварке плавлением КПД дуги достигает 0,7-0,9.
По условиям наблюдения за процессом горения дуги различают открытую, закрытую и полуоткрытую дугу. При открытой дуге визуальное наблюдение за процессом горения дуги производится через специальные защитные стёкла — светофильтры. Открытая дуга применяется при многих способах сварки: при ручной сварке металлическим и угольным электродом и сварке в защитных газах.
По роду защиты зоны сварки от окружающего воздуха различают следующие способы сварки: без защиты (голым электродом, электродом со стабилизирующим покрытием), со шлаковой защитой (толстопокрытыми электродами, под флюсом), шлакогазовой (толстопокрытыми электродами), газовой защитой (в среде газов) с комбинированной защитой (газовая среда и покрытие или флюс). Стабилизирующие покрытия представляют собой материалы, содержащие элементы, легко ионизирующие сварочную дугу. Наносятся тонким слоем на стержни электродов (тонкопокрытые электроды), предназначенных для ручной дуговой сварки.
Наибольшее применение имеют средне — и толстопокрытые электроды, предназначенные для ручной дуговой сварки и наплавки, изготовляемые в специальных цехах или на заводах.
Применяются также магнитные покрытия, которые наносятся на проволоку в процессе сварки за счёт электромагнитных сил, возникающих между находящейся под током электродной проволокой и ферромагнитным порошком, находящемся в бункере, через который проходит электродная проволока при полуавтоматической или автоматической сварке. Иногда это ещё сопровождается дополнительной подачей защитного газа.
классификация и характеристика способов сварки
Сварочное соединение считается одним из самых прочных, поэтому используется в строительстве, изготовлении техники и других областях.Но видов сварки существует несколько. Принцип действия везде один — разогрев двух сторон металла до перемешивания состава, чтобы получилась общая молекулярная решетка. Достигается это разными методами. Рассмотрим, какие бывают виды сварки металлов, чтобы лучше ориентироваться при выборе сварочного оборудования.
В этой статье:
- Термитная сварка
- Электродуговая контактная сварка
- Газопламенная сварка
- Электрошлаковая сварка
- Плазменная сварка
- Термомеханический класс сварки
Термитная сварка
Соединение металлов осуществляется путем разогрева кромок при помощи термита. Это специальный порошок, состоящий из мелкой фракции алюминия и железной окалины. Вместо алюминия допустимо применение в составе магния.
Суть термитной сварки состоит в сведении двух сторон изделия, между которыми предусматривается зазор. Концы помещаются в огнеупорную форму, изолирующую металл от внешней среды и задающую ширину и высоту сварочного соединения. К форме подведен бункер (тигль) с термитным порошком.
Стороны изделия предварительно разогревают. Обычно используют пропано-кислородное или керосино-кислородное пламя. После этого термит поджигают в бункере пламенем или запалом и накрывают крышкой. Одновременно открывают подачу из бункера снизу в зону стыковки.
Жидкий металл заливает форму и расплавляет собой окончательно кромки. Происходит сваривание сторон. Затем выжидают, пока изделие не остынет, и убирают форму. На поверхности возможны неровности, наплывы, поэтому может потребоваться механическая обработка.
Термическая сварка применяется для соединения:
Подходит для сварки углеродистых сталей и чугуна толщиной 10-15 см. В миниатюрном варианте таким методом сплавляют кабеля и провода. Технология позволяет соединять металлы большого сечения в труднодоступных местах, экономит время. Но швы получаются очень грубыми и нуждаются в шлифовке, поэтому для фасадной части изделий не подходят.
Чаще всего при помощи термитной сварки ремонтируют железнодорожные пути. Соединения выполняют по ГОСТ Р 57179-2016, а стыки обозначаются аббревиатурой «ССР» — «стыковое соединение рельсов».
Электродуговая контактная сварка
Сварка электрической дугой является одной из самых распространенных, поскольку подходит для соединения большинства типов металлов и проста в реализации. Все подвиды электродуговой сварки имеют общий принцип — задействуется ток с пониженным напряжением (для безопасности сварщика) и повышенной силой (для расплавления металла).
Между положительным и отрицательным концами, подключенными к источнику тока, при касании, возбуждается электрическая дуга. Если удерживать зазор между полюсами в 3-5 мм, дуга горит стабильно и выделяет температуру до 5000º С. Этого достаточно, чтобы плавить кромки основного металла. Способ защиты сварочной ванны и заполнение стыка осуществляются по-разному, от чего электродуговая контактная сварка делится на несколько разновидностей.
Ручная дуговая сварка (ММА, РДС)
После остывания соединения на поверхности образуется шлаковая корка. Она удаляется шлакоотделителем и шов осматривается на предмет дефектов. Выполняется ММА сварка на переменном или постоянном токе, для чего задействуются трансформаторы или инверторы, выпрямители.
При помощи ручной дуговой сварки (РДС) можно соединять:
Для создания однородного шва используются электроды с аналогичным составом стержня. Сварка возможна во всех пространственных положениях, но отличается низкой производительностью. Возможно сваривание сторон толщиной до 30 мм с глубокой разделкой кромок.
Аргоновая сварка (TIG)
Аргоновой сваркой соединяют:
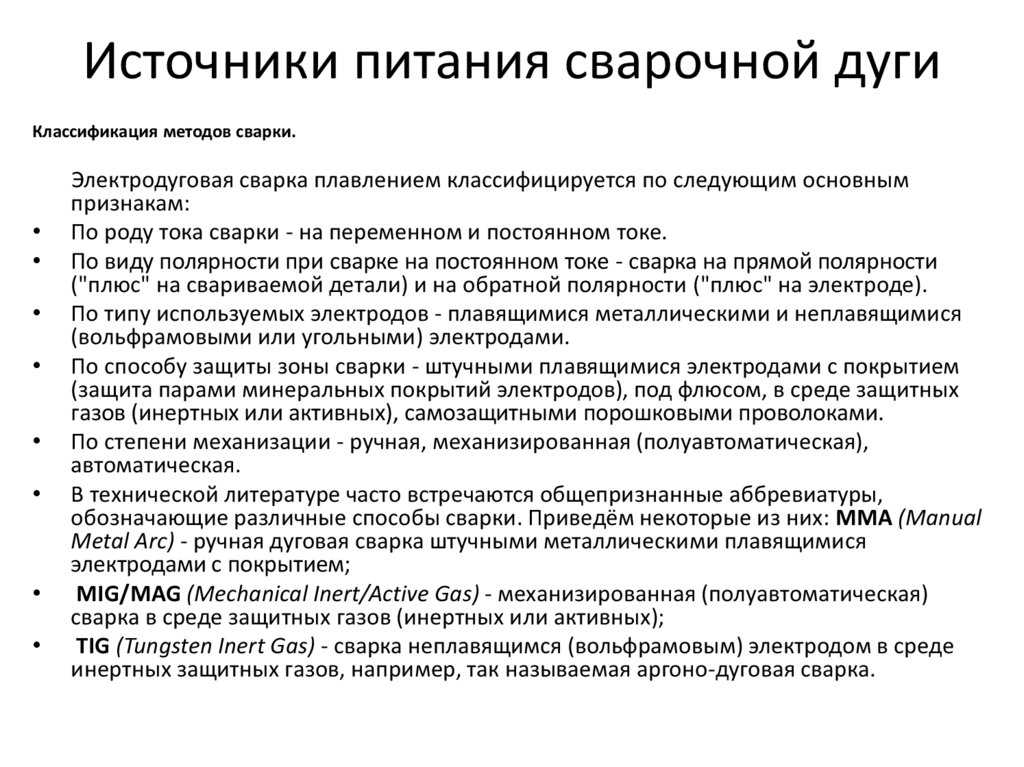
Аргоно-дуговая сварка обеспечивает высокое качество проплавления и универсальна по свариваемым материалам. Возможна на переменном или постоянном токе, швы не нуждаются в зачистке, но стоят аппараты для TIG сварки дороже, чем для ММА.
Сварка полуавтоматом (MIG/MAG)
Полуавтоматы бывают моноблочными и с раздельным исполнением источника тока и подающего механизма. Есть оборудование с жидкостным и водяным охлаждением. Максимальная сила тока возможна до 500 А. Благодаря полуавтоматической сварке швы качественные, аккуратные, не нуждаются в зачистке, а скорость выполнения высокая. При установке соответствующей проволоки, MIG сваркой соединяют:
Существует разновидность полуавтоматической сварки без газа. Тогда сварочная ванна защищается газом от порошка, расположенного в полой части проволоки. Порошковая проволока позволяет выполнять соединение металлов, не используя громоздкий баллон, что упрощает транспортировку. Но качество швов порошковой проволокой значительно проигрывает сварке в газовой среде, поэтому подходит только для неответственных изделий или применения в полевых условиях, труднодоступных местах.
Сварка под флюсом
Газопламенная сварка
Ведется при помощи пламени от горелки. Для создания пламени используется ацетилен или пропан (в качестве горючего газа) и кислород (для увеличения мощности пламени). Температура факела достигает 2800-3100º С, что позволяет плавить кромки металла. Для заполнения сварочной ванны используется присадочная проволока, подающаяся свободной рукой сварщика.
Газовой сваркой чаще всего соединяют черные металлы, трубы, латают емкости. Энергонезависимость разрешает применять сварку в полевых условиях, на крышах, в тоннелях, подвалах. Подключение к баллонам выполняется через редукторы с манометрами. У кислородного редуктора манометров два — высокого и низкого давления. Потребуются дополнительные комплектующие (шланги, мундштуки, ниппели), чтобы все соединить в одну систему.
Горелки рабочей части и диаметру сопла:
Электрошлаковая сварка
Суть электрошлаковой сварки заключается в соединении двух сторон металла за счет тепла, выделяемого шлаковой ванной. Для этого зону стыковки заполняют токопроводящим флюсом. К нему подводится сварочный электрод (проволока), который разогревает флюс, образуя жидкий шлак. Электрод продолжает проводить ток, будучи погруженным в сварочную шлаковую ванну. Метод бездуговой. Температура повышается и кромки металла сплавляются между собой.
Диапазон толщины свариваемых металлов таким методом составляет 20-3000 мм. Шлаковой сваркой можно соединять:

Задействуется технология в химической промышленности, машиностроении, кораблестроении, авиационной промышленности.
Плазменная сварка
Для расплавления кромок и присадочного металла используется плазма. Оборудование состоит из источника постоянного тока, газового аргонового баллона, плазмотрона. Для отвода лишнего тепла от сопла плазмотрона (горелки), нередко предусматривается водяное охлаждение.
Газ подается в плазмотрон и нагревается электрической дугой. Благодаря этому он увеличивается в объеме до 100 раз. За счет теплового расширения он начинает истекать из сопла на высокой скорости. Это и есть плазма. Ее температура составляет 30 000º С, что превосходит характеристики других методов сварки.
По реализации технологии возможно два варианта:

При помощи плазменной сварки соединяют металлы толщиной до 9 мм во всех пространственных положениях. Метод подходит для сваривания:
Термомеханический класс сварки
Все перечисленные выше виды сварки относятся к термическому классу. В них соединение сторон осуществляется за счет высокой температуры, вырабатываемой дугой, пламенем или прохождением тока.
Существует еще термомеханический класс, где воздействие теплом комбинируется с давлением или прижатием. К таким видам сварки относятся: контактная стыковая, газопрессовая, диффузионная. Кромки металла разогреваются прохождением тока, за счет возросшего сопротивления в зоне контакта двух сторон, а затем дополнительно сдавливаются для лучшего соединения. Это образует сплошной, прочный шов. Нагрев может быть местным или общим. Метод применяется при выпуске металлопроката, кузнечной продукции, сборки конструкций.
Источник видео: FUBAG
Ответы на вопросы: какие виды сварки бывают: способы и классификации
Какой вид сварки легче всего освоить?
СкрытьПодробнее
Легче всего научиться варить полуавтоматом. Проволока подается автоматически, вылет электрода постоянный, хорошо видно сварочную ванну (нет шлака).
Какой аппарат купить для гаража, дачи?
СкрытьПодробнее
Зависит от будущих решаемых задач. Для сварки мангала, калитки — хватит простого ММА инвертора. Чтобы варить двери, ворота, теплицы — купите полуавтомат MIG. Если предстоит работать с нержавейкой или алюминием, используйте инвертор TIG AC/DC.
Существуют ли универсальные аппараты?
СкрытьПодробнее
Да, есть сварочное оборудование 2 в 1 или 3 в 1. В них сочетается ММА с MIG или TIG, или все три режима сразу. Купив такой аппарат, можно легко переключаться с одной задачи по сварке на другую.
Чем газовая сварка пропаном отличается от сварки ацетиленом?
СкрытьПодробнее
По принципу выполнения — ничем. По характеристикам — у ацетилена температура факела достигает 3100 градусов, а у пропана — 2800º С. Если предстоит варить толстые металлы 4-5 мм — используйте ацетилен. Для сварки тонких трубок больше подойдет пропан
Взаимозаменяемы ли пропановая и ацетиленовые горелки?
СкрытьПодробнее
Нет! У них разная форма мундштуков.
Остались вопросы
Оставьте Ваши контактные данные и мы свяжемся с Вами в ближайшее время
Обратная связь
Вернуться к списку
1.2 Классификация видов сварки.
По используемой энергии виды сварки можно разделить на следующие группы: механическая, химическая, электрическая, электромеханическая, химико-механическая.
Примерами применения механической энергии для сварки являются холодная сварка, сварка взрывом сварка трением.
Виды сварки, использующие химическую энергию, характеризуются нагревом металла посредством превращения химической энергии в тепловую. Примером такого использования химической энергии является газовая сварка плавлением.
Электрические
виды сварки основаны на превращении электрической
энергии в тепловую. Это превращение
осуществляется при использовании дуги,
выделении тепла при протекании тока
через шлаки, посредством превращения
в тепло кинетической энергии пучка
электронов, индуктированием тока
различных частот.
Электромеханические виды сварки основаны на нагреве металла путем превращения электрической энергии в тепловую с последующим пластическим деформированием нагретого металла путем сдавливания.
Химико-механические виды сварки известны давно. Путем превращения химической энергии в тепловую металл нагревается до пластического состояния и далее подвергается пластическому деформированию. Примером может служить кузнечная, газопрессовая сварка и др.
По состоянию в сварочной зоне в момент сварки все ее виды разделяются на сварку давлением и сварку плавлением.
Сварка давлением обычно осуществляется при температурах ниже Тпл свариваемых металлов, и их сваривание происходит в твердом состоянии посредством приложения давления, достаточного для создания необходимой пластической деформации.
Сварка
давлением имеет определенные преимущества
перед сваркой плавлением: ниже температура
нагрева, т. е. металл подвергается меньшему
тепловому воздействию, которое может
быть вредным для его свойств; более
низкий нагрев позволяет затрачивать
меньше энергии на сварочную операцию.
Однако некоторые факторы ограничивают широкое применение сварки давлением. К ним относятся необходимость применения больших сдавливающих сил и соответственно довольно сложных приспособлений для зажатия и сдавливания свариваемых деталей, а также необходимость обеспечения чистоты поверхностей в момент их сваривания.
Сварка плавлением осуществляется с местным расплавлением свариваемых частей. В сравнении со сваркой давлением она обладает рядом преимуществ, из которых основным является большая универсальность.
Для
ее выполнения требуется только достаточно
мощный источник тепла, обеспечивающий
локальное (местное) расплавление; в
случае подвижного источника тепла
расплавление происходит от участка к
участку. Таким образом, общее увеличение
сечения свариваемых элементов не влечет
за собой необходимости создания
громоздких сварочных машин.
Если при сварке давлением в большинстве случаев для выполнения сварочных операций изделие должно подаваться к машине, то при сварке плавлением обычно источник тепла подается к изделию, что позволяет изготавливать весьма крупногабаритные сварные конструкции.
Однако расплавление металла при сварке плавлением неизбежно сопровождается усилением взаимодействия жидкого металла с окружающей средой, приводя к ряду реакций, характерных для металлургических процессов при производстве металлов. В ряде случаев эти реакции могут значительно ухудшить свойства закристаллизовавшегося при сварке металла. В целях регулирования металлургических процессов при сварке в желаемом направлении применяют флюсы, газовую защиту места сварки.
Основные виды сварки металлов при их классификации по технологическому признаку приведены в табл. 1.
Сварка металлов | |
Сварка плавлением | Сварка давлением |
Термитная сварка | Холодная сварка |
Газовая сварка | Ультразвуковая сварка |
Электрошлаковая сварка | Газопрессовая сварка |
Электроннолучевая сварка | Индукционная сварка Диффузионная |
Сварка взрывом | |
Электродуговая сварка
| Контактная сварка
|
принципы классификации.

1 / 1
Мосты, корабли, самолёты – всё, чем так гордится человечество, первоначально строилось при помощи ковки либо клёпки. В конце 19-го века были проделаны первые опыты по свариванию металлов. Уже в начале 20-го века появились значительные успехи сварки в области создания ответственных конструкций.
Первый мост, созданный методом сваривания, был сделан в СССР в городе Киеве. Он соединил левый и правый берега Днепра. Мощный толчок развитию сварочных технологий, как ни странно, принесла беда. В годы Великой Отечественной Войны на заводах, эвакуированных за Урал, танки стали собирать сваркой. Время потребовало технологию быстрой и качественной сборки, и она была создана в кратчайшие сроки.
После окончания войны, необходимость быстрого восстановления страны подтолкнула внедрение сварочных технологий в различные отрасли народного хозяйства. Не осталась в стороне от этой прогрессивной технологии и космонавтика. Поскольку Советский Союз был пионером в освоении космоса, то сварка на орбите впервые в мире была произведена на советском космическом корабле «Союз-6» в 1969 году.
Именно в это время сваривание металлов прочно вошло во все отрасли народного хозяйства. Клёпка и ковка остались разве что в арсенале мастеров художественных изделий.
Дальнейшее развитие сварочных технологий в современном мире пошло в сторону улучшения самого процесса, наращивания возможностей сварочных аппаратов и расширения областей применения этой прогрессивной техники.
Принципы классификации сварки
Количество способов и видов сваривания различных материалов уверенно перевалило за полторы сотни. Для того, чтобы качественно сварить металлы, необходимо правильно выбрать метод сваривания. В этом поможет классификация видов сварки. Существует множество «самодельных» классификаций, которые создают хаос в данном вопросе и способствуют закупке оборудования, несоответствующего поставленным задачам. Единственно правильным подходом следует считать практику классифицирования по принципу осуществления физического воздействия, степени технического обеспечения и применению различных технологий.
Признаки физического воздействия
Для определения класса сварки необходимо рассмотреть форму приложенной энергии.
Различают три класса сварки:
-
термический;
-
термомеханический;
-
механический.
Термический класс объединяет в себе процессы, происходящие за счёт использования различных видов тепловой энергии. Наибольший объём работ в этом классе выполняется дуговой и газовой сваркой. Эти два вида обязательны в любых производствах, связанных с созданием металлических конструкций или их ремонтом.
Термомеханический класс предполагает два вида воздействия: нагрев и давление. Ярким примером служит контактная сварка, когда электроды одновременно разогревают и сжимают детали. Гораздо реже встречаются другие представители этого класса: дугопрессовая, диффузионная и кузнечная.
Состав механического класса не велик, но достаточно интересен. С одной стороны это экономически выгодные виды сварки, а с другой стороны, они требуют столь специфических условий, что имеют очень малую область применения. Экономическая выгода обусловлена отсутствием нагрева. К этому классу относят холодную сварку давлением (гипербарическая), сварку трением, ультразвуковую сварку и сварку взрывом.
Технические признаки
Для этой классификации задействованы такие принципы:
-
принцип защиты от окисления;
-
непрерывность процесса;
-
уровень механизации.
Качество шва зависит от степени защиты от окисления. Наиболее распространёнными считаются технологии сваривания в среде защитных газов. Часто встречается защита флюсом, пеной и различными комбинированными способами.
Классификация видов сварки по непрерывности процесса не требует особых разъяснений и имеет всего два вида: непрерывные процессы или прерывистые. По степени механизации тоже сильно не мудрили и остановились на следующем варианте классификации:
-
ручные;
-
механизированные;
-
автоматизированные;
-
автоматические.
Классификация по технологическим принципам
По технологическим принципам виды сварки классифицируются в зависимости от того, какие технологии лежат в основе процесса сваривания. Это очень разветвлённая и не лишённая противоречий классификация, которая постоянно уточняется и обновляется. Например, в отдельный вид выделена технология дуговой сварки, здесь же она разделяется на mig/mag, mma, tig, которые, в свою очередь, разделяются по виду сварочного тока, диаметру и виду электрода и многим другим признакам.
Виды сварки
Ручная дуговая сварка (MMA)
Это основа всех основ. Именно с этого вида сваривания начинался победный марш сварочных технологий по различным отраслям производства. В те времена достаточно было иметь сварочный трансформатор и пачку электродов, чтобы варить везде: от судостроения, трубопроводов, до ворот на даче. В наше время источники сварочного тока стали на порядок легче, намного экономичнее и мощнее. Разработано множество технологий сваривания в зависимости от пространственного положения шва, химического состава и толщины металла.
Основное преимущество данного вида сварки – простота и доступность оборудования, возможность выдвинуться в любую точку на местности (при наличии электросети или мобильного генератора). Из недостатков можно отметить небольшой перечень свариваемых материалов. В основном, это чёрные металлы. Как любой вид ручной работы, требует значительной квалификации сварщика. Особенно это касается сваривания потолочных и вертикальных швов, сваривания толстых листов металла.
Аргонодуговая сварка неплавящимся электродом (TIG)
Этим видом сваривания охвачено не более 1% от всей массы сварочных работ. Но обойтись без него невозможно, если речь идет о цветных металлах. Этот способ позволяет варить практически всё. Причем шов получается высочайшего качества, даже при сваривании тонких листов металла. Отсюда и область применения этого метода распространяется на судостроение, авиастроение, создание космических аппаратов. Самое массовое применение этого вида сваривания можно наблюдать в автомобилестроении и кузовном ремонте.
Сварка осуществляется вольфрамовым или графитовым электродом в среде, которая создаётся подачей защитного газа в район сварочной ванны. Применяются смеси из активных и инертных газов, в зависимости от материала свариваемых деталей. Основными недостатками этого метода принято считать значительную стоимость работ, которая складывается из дорогого оборудования, расхода газов и использования сварщиков высокой квалификации.
Полуавтоматическая сварка (MIG/MAG)
Этот вид соединения деталей очень похож на предыдущий, но в качестве электрода здесь используется специальная проволока, которая подаётся в зону сваривания автоматически. Для этого в аппаратах MIG/MAG предусмотрен подающий механизм. Защита сварочной ванны от воздействия кислорода воздуха может производиться либо подачей защитного газа, либо применением порошковой проволоки, либо флюсом. Основная область применения полуавтоматов – сваривание цветных металлов и легированных сталей.
Чаще всего в качестве защитного газа используется углекислый газ. Работа на полуавтомате не требует высокой квалификации у сварщика. Ещё один плюс этого вида – его высокая производительность. Поэтому повсеместно распространено использование этого способа на массовых производствах, где имеет место сваривание длинных швов на листовых металлах.
Газовая сварка
Этот вид сваривания имеет больше недостатков, чем преимуществ, но остаётся актуальным более 100 лет. Сразу хочется отметить те преимущества, которые позволяют ему оставаться на плаву:
-
простота оборудования;
-
высокая мобильность;
-
широчайший перечень свариваемых материалов;
-
сварка и резка «в одном флаконе».
Недостатки, которые сдерживают её применение на производстве, в основном, определяются неизбежно широкой зоной нагрева. Из-за этого процессы происходят медленно с большим расходом газа, что сказывается на себестоимости работ. Ещё один минус – это невозможность автоматизации таких процессов и как следствие — необходимость высокой квалификации сварщика.
Точечная (контактная) сварка
В более широком понимании эта сварка называется контактной, но большее распространение получила одна из её разновидностей – точечная сварка, поэтому в обиходе этот вид соединения деталей называют точечной сваркой. Чаще всего, таким образом сваривают листовую сталь. Листы укладывают внахлёст, сильно сдавливают электродами, по которым пропускается электрический ток в тысячи ампер.
Этот вид не требует особой рабочей квалификации, но невозможен без дорогого оборудования и ограничен в толщине и форме соединяемых деталей. Зато точечная сварка хорошо автоматизируется и имеет высокую производительность. Наибольшее распространение она получила на массовых производствах, конвейерных линиях. Самый яркий и весомый пример – сварочные роботы в автомобильной промышленности.
Механическая сварка
Чаще её называют сваркой взрывом. С её помощью покрывают одни металлы другими. Выполняется за счёт нагрева, который образуется при трении одного металла о другой.
Электрошлаковая сварка
Очень редкий вид, применяется для получения ковано-сварных изделий. Сварочный ток пропускают через шлак, используя в качестве электродов проволоку, стержни и т.п. Результатом прохождения тока получается плавление кромок и присадочных материалов, которые при остывании образуют шов.
Плазменная сварка
Один из тепловых видов сваривания и резки металлов. Очень производительный вид, поддающийся полной автоматизации. Характеристика плазмотрона позволяет создать мощный концентрированный поток плазмы, которым и производится сваривание (чаще резка) металла.
Электронно-лучевая сварка
В этом виде сваривания тепло создаётся электронным лучом. Понятно, что работы должны проводиться в вакуумной камере или на выходе из неё. Вид очень редкий, требует специального дорогого оборудования и применяется в редких случаях.
Лазерная сварка
В отличие от предыдущего вида, лазерная сварка нашла широкое применение в различных отраслях промышленности. Созданы разные типы лазеров (твердотельные, газовые, жидкостные, полупроводниковые), доступные широким слоям населения. Кроме промышленных установок, имеется большое количество самодельных станков с ЧПУ, созданных на основе лазера и микроконтроллерного управления.
Диффузионная сварка
Одна из разновидностей тепломеханической сварки. Детали разогревают и сдавливают одновременно. Для качественного прохождения процессов необходим вакуум. Как следствие, возникает необходимость создания дорогих установок, поэтому применяется только в очень ответственных узлах космической, авиационной и электронной промышленности.
Сварка высокочастотными токами
Специфический вид создания неразъёмных соединений, который традиционно закрепился на автоматизированных линиях по изготовлению трубопроводов. Очень высокопроизводительный и максимально автоматизированный метод. К месту сваривания труб подводится специальный высокочастотный индуктор и через несколько секунд разогретые токами высокой частоты трубы соединены. Ни огня, ни копоти.
Правильный выбор – основа успеха
Классификация способов сварки Категория: Сварка металлов Классификация способов сварки Способы сварки можно классифицировать, например, по виду энергии, используемой при сварке, степени механизации процесса сварки, виду свариваемого металла и т. п. Вполне совершенной системы классификации, охватывающей все способы сварки, не существует. Достаточно совершенную систему классификации можно создать, взяв за основу давление, производящее так называемую осадку при сварке. По этому признаку все существующие способы сварки можно разделить на две большие группы: 1) сварка давлением; 2) сварка без давления или сварка плавлением. Рис. 1. Классификация способов сварки Первая группа характеризуется применением давления для осадки металла, остальные признаки, в том числе состояние металла не принимаются во внимание. Во второй группе самопроизвольное (спонтанное) объединение металла соединяемых частей в монолитное целое без приложения давления возможно лишь при жидком состоянии металла, т. е. металл в зоне сварки должен быть обязательно расплавлен. Приложение давления хотя бы и при наличии расплавления в зоне сварки заставляет отнести способ к группе сварки давлением, как например, при электрической контактной сварке. К сварке плавлением примыкает пайка, отличающаяся тем, что расплавляется лишь присадочный металл (припой), а основной свариваемый металл остается нерасплавленным, в то время как при сварке частично расплавляется и основной металл. В предлагаемой классификации, показанной на рис. 1, каждый из методов сварки разделен на несколько способов. Простейшие виды сварки плавлением известны с глубокой древности, например литейная сварка. Современная схема сварки плавлением показана на рис. 2. К соединяемым деталям в месте сварки подводят сварочное пламя; производят местное расплавление деталей до образования общей сварочной ванны жидкого металла. Сварочное пламя расплавляет как металл, так и загрязнения на его поверхности, образующиеся шлаки всплывают на поверхность ванны. Горячее пламя сильно нагревает металл на поверхности значительно выше точки плавления; в результате меняется химический состав металла и его структура после затвердевания; изменяются и механические свойства. Характерный признак сварки плавлением; выполнение ее за один этап — нагрев сварочным пламенем, в отличие от сварки давлением, где необходимы нагрев и давление. Автогенная сварка примерно эквивалентна понятию «газовая» или «газоплавильная сварка», отсюда постепенно развился своеобразный технический жаргон с безграмотными выражениями вроде «он варит автогеном», «автогенная резка», и т, п., засоряющими язык. Термин «автогенная сварка» не рекомендуется употреблять в технической литературе. Рис. 2. Схема сварки плавлением В процессе сварки давлением собранные детали сдавливают усилием Р (рис. 4). Операция сдавливания называется осадкой, а прилагаемое давление — осадочным давлением. При осадке выдавливаемый металл образует утолщение у сварного стыка, в которое уходит металл с поверхностей сварки со всеми загрязнениями, адсорбированными газами, на поверхность выходят свежие, так называемые ювенильные слои металла, которые участвуют в образовании сварного соединения. Сравнительно невысокий нагрев металла и затрудненный доступ воздуха в зону сварки позволяют сохранить почти неизменными химический состав и структуру, а следовательно, и механические свойства металла в сварном соединении. При сварке давлением иногда возможно получить тождественность и металлографическую неотличимость зоны сварки с остальным металлом. Способы сварки давлением также достаточно универсальны, охватывают большинство технически важных металлов, возможно соединение разнородных металлов. Рис. 3. Схема сварки давлением Достаточно интересна и в некоторых случаях удобна система классификации, основанная на виде энергии, преимущественно используемой при сварке. По этому признаку все способы сварки можно разделить на четыре большие группы по преобладающему виду энергии: По объему применений и промышленному значению первое место занимает электросварка, использующая электрическую энергию для нагрева металла. В химических способах для нагрева металла используется энергия экзотермических химических реакций, из них наибольшее значение имеют газовая сварка и термитная сварка. В механических способах преобладающее значение имеет механическая энергия; сюда относятся, например, такие способы сварки, как прессовая, кузнечная (горновая), холодная, сварка трением. Сварка лучевая или радиационная обеспечивает высокую чистоту и стерильность процесса, источник энергии может быть расположен весьма далеко от объекта сварки. Рис. 4. Энергетическая классификация способов сварки Для способов, в которых существенное значение имеют два вида энергии, можно образовать промежуточные группы, например электромеханическую для контактной сварки, электрохимическую для дуговой сварки в активном защитном газе, химико-механическую для газопрессовой сварки и т. д. Особого распространения подобная классификация не получила. Реклама:Читать далее:Виды дуговой сварки
Статьи по теме:
Главная → Справочник → Статьи → Блог → Форум |

1
Первый слайд презентации: Классификация видов сварки: термический класс, механический класс, термомеханический класс
Изображение слайда
2
Слайд 2
ГОСТ 19521-74 – Сварка металлов. Классификация Основные признаки и ступени классификации
Изображение слайда
3
Слайд 3: Классификация сварки металлов по физическим признакам
К термическому классу относятся такие виды сварки, которые осуществляются плавлением с использованием тепловой энергии, а именно: дуговая, электрошлаковая, электронно-лучевая, плазменная, ионно-лучевая, тлеющим разрядом, световая, индукционная, газовая, термитная и литейная.
Изображение слайда
4
Слайд 4
К механическому классу сварки относятся такие виды сварки, которые осуществляются с использованием механической энергии и давления, а именно: холодная, взрывом, ультразвуковая, трением и магнитно-импульсная.
Изображение слайда
5
Слайд 5
К термомеханическому классу сварки относятся такие виды сварки, которые осуществляются с использованием тепловой энергии и давления, а именно: контактная, диффузионная, индукционно-прессовая, газопрессовая, термокомпрессионная, дугопрессовая, шлакопрессовая, термитно-прессовая и печная
Изображение слайда
6
Слайд 6: Классификация сварки металлов по техническим признакам
К техническим признакам относятся: способ защиты металла в зоне сварки, непрерывность процесса и степень механизации сварки
По способу защиты металла различают сварку в воздухе, вакууме, защитных газах, под флюсом, по флюсу, в пене и с комбинированной защитой;
По непрерывности процесса различают непрерывные и прерывистые виды сварки;
По степени механизации — ручные, механизированные, автоматизированные и автоматические.
Изображение слайда
7
Слайд 7: Дуговая сварка
Дуговая сварка – это процесс сваривания, при котором воздействие тепловой энергии оплавляет соединяемые детали
Изображение слайда
8
Слайд 8
Схема классификации дуговой сварки
Изображение слайда
9
Слайд 9: Электрошлаковая сварка
Плавление свариваемого и присадочного металлов осуществляется теплом, выделяющимся при прохождении электрического тока через расплавленный шлак в период установившегося процесса сварки.
Изображение слайда
10
Слайд 10: Электронно-лучевая сварка
Электронно-лучевая сварка. Этот вид сварки выполняется в камерах с разрежением. Тепло образуется за счет бомбардировки поверхности металла электронами, имеющими большие скорости, анодом является свариваемая деталь, а катодом — вольфрамовая спираль.
Изображение слайда
11
Слайд 11: Плазменная сварка
Этот вид сварки основан на пропускании электрического тока большой плотности через газовую среду, находящуюся под некоторым давлением, в результате чего газ получает ионизированное состояние, называемое плазмой.
Изображение слайда
12
Слайд 12: Газовая сварка
Газовая сварка основана на плавлении свариваемого и присадочного металлов высокотемпературным газокислородным пламенем.
Изображение слайда
13
Слайд 13: Световая сварка
Этот вид сварки основан на применении специального светового луча, который плавит металл. Для получения сильного светового луча используют особые установки, называемые лазерами.
Изображение слайда
14
Слайд 14: Термитная сварка
свариваемые детали помещают в огнеупорную форму, а в установленный сверху тигель засыпают термит — порошкообразную смесь алюминия с железной окалиной. При горении термита развивается высокая температура (более 2000°С), образуется жидкий металл, который при заполнении формы оплавляет кромки свариваемых изделий, заполняет зазор, образуя сварной шов.
Изображение слайда
15
Слайд 15: Контактная сварка
При контактной сварке место соединения разогревается и расплавляется теплом, выделяемым при прохождении электрического тока через контактируемые места свариваемых деталей; при приложении в этом месте сжимающего усилия образуется сварное соединение
Изображение слайда
16
Слайд 16: Диффузионная сварка
Осуществляется за счет взаимной диффузии атомов контактирующих частей при относительно длительном воздействии повышенной температуры и при незначительной пластической деформации.
Изображение слайда
17
Слайд 17: Газопрессовая сварка
Газопрессовая сварка основана на нагревании концов стержней или труб по всей длине окружности многопламенными горелками до пластического состояния или плавления и последующего сдавливания стержней внешним усилием.
Изображение слайда
18
Слайд 18: Ультразвуковая сварка
Ультразвуковая сварка основана на совместном воздействии на свариваемые детали механических колебаний ультразвуковой частоты и небольших сжимающих усилий.
Изображение слайда
19
Слайд 19: Сварка трением
Сварка трением. При вращении одного из стержней и соприкосновении его торца с торцом закрепленного стержня концы стержней разогреваются и с приложением осевого усилия свариваются.
Изображение слайда
20
Слайд 20: Холодная сварка
Холодная сварка основана на способности срастания кристаллов металла при значительном давлении.
Изображение слайда
21
Последний слайд презентации: Классификация видов сварки: термический класс, механический класс,: Индукционно-прессовая сварка
Индукционно-прессовая сварка. Этот вид сварки основан на разогреве токами высокой частоты концов стыкуемых стержней или труб до пластического состояния с последующим приложением осевых усилий для получения неразъемного соединения.
Изображение слайда
4 различных типа сварочных процессов 2022
Если вы думаете о карьере сварщика, важно определить область, в которой вы хотели бы специализироваться. Существует более 30 различных типов сварочных процессов, от газокислородной к более сложным практикам лазерного луча. Тем не менее, эти разновидности обычно делятся на четыре основных типа.
4 основных типа сварочных процессов
- Подайте заявку на получение степени сварщика в NEIT!
Загрузка…
Существует четыре основных типа сварки: дуговая сварка металлическим электродом в среде защитного газа (GMAW/MIG), дуговая сварка вольфрамовым электродом в среде защитного газа (GTAW/TIG), дуговая сварка металлическим электродом в среде защитного газа (SMAW) и дуговая сварка порошковой проволокой (FCAW).
В этом посте мы подробно расскажем об особенностях, назначенных каждому процессу, и выделим различия между ними. Продолжайте читать, чтобы узнать все, что вам нужно знать о четырех основных типах сварки и о том, для чего они используются.
Дуговая сварка металлическим газом (GMAW/MIG)
Этот процесс, также известный как сварка в среде инертного газа или MIG, использует тонкую проволоку в качестве электрода. Проволока нагревается по мере прохождения через сварочный аппарат к месту сварки. Защитный газ должен использоваться для защиты сварного шва от загрязняющих веществ в воздухе.
Обычно это двуокись углерода, кислород, аргон или гелий. Этот метод часто используется для обработки таких металлов, как нержавеющая сталь, медь, никель, углеродистая сталь, алюминий и т. д. Из всех сварочных процессов этот наиболее популярен в строительной и автомобильной промышленности.
Дуговая сварка металлическим электродом в среде защитного газа считается одной из самых простых в освоении технологий сварки, что делает ее особенно интересной для начинающих сварщиков. Он также требует минимальной очистки, обеспечивает высокую скорость сварки и лучший контроль над более тонкими материалами.
Некоторые недостатки, связанные с этим типом процесса сварки, связаны с затратами на получение защитного газа, а также с невозможностью сваривать более толстые металлы или выполнять вертикальную или потолочную сварку.
Дуговая сварка вольфрамовым электродом в среде защитного газа (GTAW/TIG)
Этот тип сварки, также известный как сварка вольфрамовым электродом в среде инертного газа или сварка TIG, обычно используется для сварки тонких и цветных материалов, таких как алюминий, медь, свинец или никель. Это обычно применяется к производству велосипедов или самолетов.
В отличие от других типов сварки, при сварке TIG для получения сварного шва используется неплавящийся вольфрамовый электрод. Вам по-прежнему потребуется внешний источник газа, обычно это аргон или смесь аргона и гелия.
Этот метод сварки считается одним из самых сложных для освоения, и он обеспечивает самое высокое качество сварных швов.
Поскольку между дугой и областью сварки находится лишь крошечная область, для выполнения требуется огромная точность и мастерство. Сварные швы, полученные этим методом, известны своей чрезвычайной прочностью.
Дуговая сварка в защитном металле (SMAW)
Этот тип сварки основан на ручной технике с использованием плавящегося электрода, покрытого флюсом. Этот метод, как правило, наиболее популярен среди сварщиков на дому. Этот процесс также более неофициально известен как сварка стержнем.
Прозвище относится к электроду, используемому для сварки металла, который имеет форму «палки». Поскольку дуговая сварка защитным металлом требует минимального оборудования, это один из самых недорогих процессов.
Этот вид сварки не требует защитного газа и может выполняться на открытом воздухе при ветре или дожде. Он также хорошо работает с грязью и ржавыми материалами. Тем не менее, недостатки действительно существуют.
Сварка электродом обычно не позволяет производить продукцию самого высокого качества. Они склонны к пористости, трещинам и неглубокому проникновению. В целом, сварные швы менее долговечны, чем другие виды сварки.
Дуговая сварка порошковой проволокой (FCAW)
Подобно сварке MIG, дуговая сварка с флюсовой проволокой вращается вокруг процесса непрерывной подачи проволоки. Существует два отдельных процесса, связанных с дуговой сваркой с флюсовой проволокой.
В одном из них используется защитный газ, а в другом используются самозащитные вещества, образующиеся при разложении флюса внутри проволоки.
Этот вид сварки известен тем, что он недорогой и простой в освоении. Подобно процессу сварки MIG, это отличный способ для начинающих сварщиков начать свою карьеру в этой области.
Также позволяет сварщикам выполнять работу на открытом воздухе (ветер не повлияет на сварку). Полуавтоматическая дуга обеспечивает высокую скорость сварки и портативность, что делает ее популярным процессом для строительных проектов.
Начните свою карьеру сварщика в Технологическом институте Новой Англии
Степень младшего специалиста в области технологии сварки в NEIT, одной из лучших школ сварки в стране, дает интенсивный практический опыт, необходимый для начала карьеры в области сварки.
Программа предназначена для того, чтобы помочь учащимся овладеть навыками сварки и монтажа трубопроводов, познакомить их с САПР, проектированием зданий и научить читать чертежи. Дополнительная теория и практика также включены в учебную программу.
Выпускникибудут подготовлены к ряду различных отраслевых должностей, включая инженера по сварке, сварщика на производстве, техника по промышленному проектированию, инженера по контролю качества, дизайнера CADD, техника CADD, продавца сварочной промышленности и техника по испытанию материалов.
Учащиеся также будут подготовлены к будущим сертификационным экзаменам посредством имитационного квалификационного теста сварщика.
Классификация сварочных процессов (с таблицей) | Соединение металлов
РЕКЛАМА:
Сварка в целом подразделяется на два типа:
I. Сварка пластмасс :
В этом случае два соединяемых куска металла нагревают до пластического состояния и завершают сварку их форсированием. В этом случае наполнитель не добавляется.
РЕКЛАМА:
II. Сварка плавлением:
В этом случае два куска металла нагревают и доводят до расплавленного состояния, добавляют наполнитель и дают ему затвердеть.
Процессы сварки пластмасс и плавлением далее классифицируются следующим образом:
I. Сварка пластика:(а) Кузнечная сварка:
РЕКЛАМА:
Это старейший метод соединения двух металлических частей. В этом случае тепло создается кузнечным огнем, и два соединяемых куска металла нагреваются и доводятся до пластического состояния. Затем они накладываются друг на друга и сбиваются, образуя соединение.
(b) Сварка сопротивлением:
В этом случае через соединяемые куски металла пропускают сильный электрический ток. Затем из-за электрического сопротивления металлы нагреваются до пластического состояния и, приложив усилие, можно завершить сварку.
В этом случае дополнительный присадочный материал не требуется, а металлические детали запрессовываются в два медных электрода.
РЕКЛАМА:
(i) Точечная сварка:
Используется для сварки черных и цветных металлов толщиной до 8 мм. Свариваемые листы удерживаются между неподвижным и подвижным электродами, как показано на рисунке. Затем электроды прижимаются нажатием ножного рычага. При прижатии электродов протекает ток, и две детали в точках прижатия доводятся до пластического состояния. Затем этот пластичный металл смешивается, затвердевает, образуя соединение.
(ii) Выступающая сварка:
Это слегка модифицированная форма процесса точечной сварки. В этом случае ток и давление локализуют в точках сварки, делая выступы для верхнего листа металла, как показано на рис. 40.9.. Два металлических листа удерживаются на месте между неподвижным рычагом и верхним подвижным рычагом. Затем пропускают ток и получают сварные швы во всех точках выступов за счет сплющивания выступов.
Эта шовная сварка используется для получения непрерывных швов между двумя перекрывающимися листами. В этом случае два листа, подлежащие шовной сварке, удерживаются, как показано, между электродами. Когда электродные колеса вращаются, будет производиться непрерывный шов.
(iii) Шовная сварка:
(II) Сварка плавлением:
(а) Газовая сварка:
РЕКЛАМА:
При газовой сварке тепловая энергия, необходимая для нагрева поверхностей, получается путем сжигания смеси двух газов. Обычно кислород и ацетилен используются для газовой сварки. Эти газы смешиваются в соответствующих пропорциях в сварочной горелке. Эта сварочная горелка снабжена двумя регуляторами для регулирования газов.
Пламя, возникающее в результате горения, используется для нагрева металлических поверхностей до пластического состояния, и сварка завершается добавлением присадочного материала, как показано на рисунке.
(i) Ацетиленовая сварка :
Как следует из названия, в данном случае используются два газа: кислород и ацетилен. Следует отметить, что кислород и ацетилен коммерчески доступны в баллонах. При необходимости ацетилен может быть получен путем химической реакции между карбидом кальция и водой, как показано ниже.0003
И химическая реакция горения ацетилена,
Когда происходит горение, мы получаем пламя на кончике факела, как показано на рисунке.
В основном существует 3 типа пламени:
(i) Нейтральное пламя:
Получается путем смешивания равных количеств ацетилена и кислорода. Он используется для сварки всех металлов, таких как черные металлы, медь и алюминиевые сплавы.
Когда мы изменим пропорции Кислорода и ацетилена. Можно получить науглероживающее и окислительное пламя.
(ii) Пламя науглероживания:
Получается большим количеством ацетилена. Он очень подходит для сварки стали, так как скорость сварки этим пламенем выше.
(iii) Окислительное пламя:
Может быть получено большим количеством кислорода. В основном используется для сварки латуни. Он также очень подходит для операций резки.
Преимущества:
(1) Газовая сварка больше подходит для тонких листов.
(2) Оборудование портативное, поэтому подходит для наружных ремонтных работ.
(3) Заменив сопло в горелке, горелку можно использовать для газовой резки.
Ограничения:
(1) Это медленный процесс по сравнению с дуговой сваркой.
(2) Газы, используемые при газовой сварке, более дорогие.
Обратите внимание, что мы будем изучать сварочную горелку и другое сварочное оборудование во время изучения газовой резки.
Воздушно-ацетиленовая сварка. Как следует из названия, в этом случае в качестве газов для образования пламени используются воздух и ацетилен. В этом случае получаемые температуры ниже, чем при других процессах газовой сварки. Этот метод обычно используется для сварки свинца.
(б) Дуговая сварка:
(i) Дуговая сварка металлическим электродом:
На рис. 40.8 показана схема дуговой сварки. Он в основном состоит из сварочного выпрямителя, держателя электрода (или сварочного стержня), сварочного стержня и заготовки.
Когда сварочный стержень касается заготовки, возникает дуга и выделяется огромное количество тепла. Температура дуги составляет около 3600°C. Эта тепловая энергия используется для плавления заготовки и сварочного прутка. Так образуется небольшая лужа расплавленного металла. Этот расплавленный металл перемешивается под действием дуги, металл идеально перемешивается и после охлаждения дает прочное соединение.
Примечание:
(i) Напряжение зажигания дуги составляет 60-100 В.
(ii) Напряжение поддержания дуги составляет 25–45 В.
(iii) Источником питания может быть переменный ток. или постоянный ток
(iv) Зазор между сварочным стержнем и заготовкой должен составлять 3 мм.
(v) Расплавленный металл в ванне при контакте с воздухом образует в стали оксиды и нитриды при взаимодействии с кислородом и азотом воздуха. Это ослабляет сварное соединение и снижает коррозионную стойкость. Поэтому, чтобы избежать этого, сварочные стержни снабжены флюсовым покрытием. Этот флюс после сварки образует шлаковую корку на сварном соединении и препятствует окислению. Затем этот шлак необходимо отщепить.
Применение:
Эта дуговая сварка чаще всего используется при изготовлении резервуаров, сосудов, ферм, рам, котлов, автомобильных шасси и корпусов и т. д.
(ii) Дуговая сварка под флюсом (SAW):
Это усовершенствованный процесс дуговой сварки, который используется для производства стыковых швов толстых стальных листов.
В этом случае образующаяся дуга погружается (покрывается) в флюс, отсюда и название дуговой сварки под флюсом. Через бункер для флюса подается флюс, а механизм подачи проволоки непрерывно подает оголенную проволоку.
В этом случае образующаяся дуга погружена в флюс. Из-за тепла дуги проволока и основной металл плавятся и образуют ванну расплавленного металла. Таким образом, расплавленная ванна после охлаждения образует сварное соединение.
(iii) Дуговая сварка вольфрамовым электродом в среде защитного газа (GTAW):
Он также известен как сварка вольфрамовым электродом в среде инертного газа (TIG).
Это быстрый процесс, обеспечивающий чистые сварные швы и способный сваривать металлы, сварка которых считается невозможной. TIG-сварка использует неплавящийся электрод в специальном держателе, отдельный присадочный материал и инертный газ, т.е. баллон с аргоном, источник питания.
Когда вольфрамовый электрод ударяет по заготовке, возникает дуга. Вокруг дуги образуется защитный слой из инертного газа, когда газ выходит из горелки. Из-за тепла дуги заготовка и присадочный материал расплавляются и образуют расплавленную ванну. Эта расплавленная ванна после охлаждения образует прочный сварной шов в среде инертного газа.
Преимущества сварки TIG:
1. Сварные соединения прочнее, пластичнее и устойчивее к коррозии, чем другие швы, выполненные другими способами.
2. Сварка цветных металлов упрощается, так как не требуется лен.
3. Разнородные металлы также легко свариваются.
4. За счет наличия инертного газа меньше дыма.
5. Дуга прозрачна благодаря защитному инертному газу, поэтому сварочный газ может четко наблюдать за сваркой во время ее выполнения.
Ограничения сварки TIG :
1. Процесс работает относительно медленно.
2. Обратная сторона сварного шва должна быть защищена от атмосферы.
3. Стоимость инертного газа достаточно высока.
4. Соединения A1 требуют надлежащей очистки перед сваркой, поскольку инертный газ не оказывает никакого очищающего или флюсующего действия.
(iv) Дуговая сварка металлическим газом (GMAW):
Он также известен как сварка в среде инертного газа (MIG). При сварке MIG мы получаем чистые и качественные сварные швы, а также высокую скорость наплавки присадочного металла. Он использует высокий сварочный ток, который используется для разрушения шариков расплавленного металла на мелкие брызги.
На рис. 40.11 показана принципиальная схема сварки МИГ. MIG использует расходуемый электрод. Он подается через электрододержатель в дугу. Затем с той же скоростью электрод плавится и наплавляется в сварной шов. Небольшой двигатель с регулируемой скоростью будет использоваться для снятия проволоки с катушки и подачи ее в дугу.
Обычно CO 2 или аргон используются в качестве защитных газов. В основном процесс был разработан для сварки алюминия и титана. Но в настоящее время он имеет широкое применение, так как его можно использовать для сварки во всех положениях; и для работы с этой установкой требуются менее квалифицированные операторы.
(c) Термитная сварка:
Этот процесс сварки используется при ремонте тяжелых деталей, таких как спицы ведущих колес, сломанные шатуны, другие детали двигателя и т. д.
Так, кислород из оксида железа соединяется с алюминием и образует оксид алюминия или шлак и будет образовываться перегретая термитная сталь. Температура термита будет около 2700°C, что почти вдвое больше по сравнению с температурой плавления стали.
В процессе термитной сварки свариваемые детали помещаются в форму, как показано на рисунке. Затем перегретая термитная сталь выливается из тигля с огнеупорной футеровкой, как показано на рисунке. За счет тепла термитной стали поверхности свариваемых металлов доводятся до пластического состояния и при необходимости для завершения сварки прикладывается некоторое механическое давление.
Главная ›› Машиностроение ›› Соединение металлов ›› Процессы ›› Сварка ›› Классификация сварки
Что такое сварка и ее виды – Полное объяснение
Это процесс соединения металлов и термопластов с помощью высокой температуры, которая расплавляет металлы и сплавляет их вместе, образуя при охлаждении прочный сварной шов. В некоторых случаях также применяется давление, чтобы металлы сплавились вместе во время охлаждения сварного шва. В некоторых случаях присадочный металл используется для соединения металлических частей вместе. В отличие от пайки твердым припоем и пайки, при которых основной металл не плавится, в процессе сварки основной металл плавится.
Для выполнения процесса сварки у нас есть несколько сварочных аппаратов, которые помогают в процессе соединения.
Различное сварочное оборудование —
- Сварная машина
- Сварные электроды
- Металлы наполнителя
- Держатель электродов
Оборудование для обеспечения безопасности, которое очень необходимо для безопасного рабочего
- 29002 Healling Helping Helping Оборудование, которое очень необходимо для безопасного рабочего
- . Held Held Held Held Held Helding Held Supending, который очень необходим для безопасного рабочего
- 9.meld Held Held Held Helding Helding Helding Helding Helding Held. Перчатки
- Защитные очки
- Маска или респиратор
- Ушил
- Обувь
СОДЕРЖАНИЕ
Классификация сваркиСварка может быть классифицирована в основном в 5 типов, а это: 9003
.
Дуговая сваркаСварка
3. Сварка сопротивлением
4. Сварка энергетическим лучом
5. Сварка твердого телаПроцесс соединения двух или более металлических деталей вместе с помощью электрической дуги называется дуговой сваркой. Дуга создается источником электропитания. Для создания дуги в дуговой сварке можно использовать постоянный ток (DC) или переменный ток (AC). Электрод, используемый в этом типе сварки, может быть плавящимся или неплавящимся. Защитный газ используется для защиты зоны сварки от загрязнения из атмосферы. Тип используемого защитного газа может быть инертным или полуинертным. Присадочный материал также иногда используется для сварки двух деталей вместе.
Различные типы дуговой сварки:
1. Дуговая сварка в среде защитного газа (SMAW)
Газовая сварка
2. Дуговая сварка металлическим электродом в среде защитного газа (GMAW), сварка в среде инертного газа или сварка MIG
3.Дуговая сварка с флюсовой проволокой (FCAW)
4. Дуговая сварка вольфрамовым электродом (GTAW): сварка вольфрамовым электродом в среде инертного газа (TIG)
5. Дуговая сварка под флюсом (SAW)
6. Сварка атомным водородом
7. Электрошлаковая сварка (ESW)
8. Электрогазовая сварка
9. Дуговая сварка сварка
10. Плазменно-дуговая сварка (PAW)
11. Углеродная дуговая сварка (CAW)Это старейший процесс сварки, при котором ацетиленовый газ сжигается в присутствии кислорода, образуя пламя, которое может обеспечить температуру сварки около 3100 градусов Цельсия.
- Его также называют кислородно-кислородной сваркой или кислородно-ацетиленовой сваркой .
- Оборудование простое и недорогое. Дуга, образующаяся при такой сварке, менее концентрированная по сравнению с дуговой сваркой, что может привести к более медленному охлаждению сварного шва, что приводит к большим остаточным напряжениям и деформации.
- Менее популярный процесс в промышленных работах и широко используется при сварке труб, труб и в ремонтных работах.
Читайте также:
- Что такое плазменно-дуговая обработка (ПАМ) и как она работает?
- Ультразвуковая обработка (USM) – основные части, принцип работы, преимущества и недостатки применения
- Что такое процесс электроэрозионной обработки (EDM) и как он работает?
Это метод сварки, при котором электрический ток используется для соединения двух металлических деталей. Сопротивление материала используется для выработки тепла в свариваемых соединениях. Через металлы пропускают ток силой от 100 до 100 000 А которые должны быть соединены. В этом случае сжатие также используется для соединения деталей в процессе сварки.
- Эта сварка широко используется при производстве стальных труб и при сборке автомобилей.
- A В процессе образуется очень мало загрязнений, и это эффективный процесс.
- Единственным ограничением контактной сварки является то, что ее можно использовать для сварки только тонких металлических деталей.
Наиболее часто используемые типы контактной сварки:
1. Точечная сварка
0 Energy Beam Сварка
2. Шовная сварка
3. Стыковая сварка
4. Сварка оплавлением
5. Выступающая сварка
6. Сварка с осадкойВ этом методе сварки используется луч высокой энергии, который воздействует на зону сварки. Эти методы сварки включают сварку лазерным лучом и сварку электронным лучом.
Обе сварки почти одинаковы, но если внимательно приглядеться, они отличаются источником энергии. При лазерной сварке используется очень сильно сфокусированный луч лазера для выработки тепла для создания соединения, а при электронно-лучевой сварке используется электронный луч очень высокой плотности.
EBW делается в вакууме. Они используются в приложениях с высокой производительностью.
Преимущества
- Плотность энергии этих методов сварки очень высока.
- Обеспечивает очень глубокое проплавление и уменьшает площадь сварного шва.
- их можно легко автоматизировать для крупного производства.
Недостатки
- Высокая стоимость оборудования.
Типы этих методов сварки:
1. Лазерная сварка
Сварка в твердом состоянии
2. Электронно-лучевая сваркавместе без плавления, т. е. соединения образуются в твердом состоянии. например, ультразвуковая сварка, при которой две металлические детали свариваются вместе с использованием очень высокочастотной вибрации под высоким давлением.
Типы сварки в твердом состоянии:
1.
Ультразвуковая сварка
2. Сварка взрывом
3. Сварка трением
4. Сварка трением с перемешиванием
5. Магнитно-импульсная сварка
6. Холодная сварка
7. Диффузионная сварка
8. Экзотермическая сварка/ Термитная сварка
9. Высокочастотная сварка
10. Сварка горячим давлением
11. Индукционная сварка
12. Склеивание валкамиВ этой статье мы вкратце узнали о том, что такое сварка, ее основные виды. Если вы нашли эту информацию ценной и полезной, не забудьте поставить лайк и поделиться ею.
Ссылки:
- https://en.wikipedia.org/wiki/Welding
Классификация сварочных процессов — ExtruDesign
Сварное соединение представляет собой неразъемное соединение. Это сварное соединение может быть выполнено сплавлением кромок двух соединяемых частей вместе с приложением давления и присадочным материалом или без него. На основании этого процесс сварки классифицируется. В этой статье мы собираемся обсудить классификацию сварочных процессов.
Процесс сварки широко используется в производстве в качестве альтернативного метода литья или ковки, а также в качестве замены болтовых и заклепочных соединений.
В большинстве случаев процесс сварки также используется в качестве средства ремонта. Это означает воссоединение металла в месте трещины, наращивание отколовшейся небольшой детали, например, зуба шестерни, или восстановление изношенной поверхности, например поверхности подшипника.
Классификация процессов сварки
Процессы сварки можно разделить на две основные группы. это
- Сварка плавлением : При сварке плавлением требуется только тепло.
- Кузнечная сварка : При кузнечной сварке мы используем как тепло, так и давление.
Давайте обсудим это подробно.
Сварка плавлением
В случае сварки плавлением соединяемые детали удерживаются на месте, в то время как расплавленный металл подается к месту сварки.
Рис.Пример сварки плавлением ( Источник: Workshopinsider.com )
Расплавленный металл может исходить из поставляемого присадочного металла или расплавленного металла из них самих (основной металл). Сами детали или присадочный металл обычно имеют состав основного металла. Под действием тепла расплавленного присадочного металла или другого источника тепла поверхность стыка становится пластичной или даже расплавленной. Таким образом, когда расплавленный металл затвердевает или плавится, образуется сварное соединение.
Что такое производственный процесс…
Пожалуйста, включите JavaScript
Сварка плавлением в зависимости от способа выделения тепла может быть классифицирована как
- Термитная сварка
- Газовая сварка
- Электродуговая сварка
1. Термитная сварка
При термитной сварке смесь оксида железа и алюминий, называемый термитом, воспламеняется, а оксид железа превращается в расплавленное железо. Расплавленный чугун заливается в форму, сделанную вокруг стыка, и сплавляется со свариваемыми деталями.
Это показано на приведенном ниже примере изображения этого процесса сварки. Рис. Пример процесса термитной сварки (Источник: Викимедиа)
Основным преимуществом термитной сварки является то, что все части сварного шва расплавляются одновременно, а сварной шов остывает почти равномерно. Это приводит к минимальной проблеме с остаточными напряжениями. По сути, это процесс плавления и литья.
Как мы видели на примере, эта термитная сварка часто используется для соединения железных и стальных деталей, которые слишком велики для изготовления одной детали, таких как рельсы, рамы грузовиков, рамы локомотивов, другие большие профили, используемые на паровых и железных дорогах. , для кормовых шпангоутов, шпангоутов и т.п.
На сталелитейных заводах термитная электросварка применяется для замены сломанных зубьев шестерен, приварки новых шеек валков и шестерен, ремонта сломанных ножниц.
2. Газовая сварка
Газовая сварка производится путем воздействия пламени кислородно-ацетиленового или водородного газа сварочной горелки на поверхности подготовленного соединения.
Рис. Образец процесса газовой сваркиНа следующем изображении показано, как это делается.
Интенсивное тепло белого конуса пламени нагревает локальные поверхности до точки плавления, в то время как оператор манипулирует сварочным стержнем, чтобы подавать металл для сварки. Таким образом, расплавленный металл сварочного стержня и оплавленные поверхности образуют соединение. Для удаления шлака используется флюс. Поскольку скорость нагрева при газовой сварке низкая, этот метод сварки используется, когда необходимо сваривать более тонкие материалы.
3. Электродуговая сварка
При электродуговой сварке работа готовится так же, как и при газовой сварке. В этой электродуговой сварке присадочный металл подается металлическим сварочным электродом. Оператор с защищенными глазами и лицом зажигает дугу, касаясь электродом основного металла. Основной металл на пути потока дуги плавится, образуя ванну расплавленного металла, которая, кажется, вытесняется из ванны взрывом дуги, как показано на следующем рисунке электродуговой сварки.
Дуговая сварка ( Источник: Workshopinsider.com )
В основном металле образуется небольшое углубление, и расплавленный металл осаждается по краю этого углубления, которое называется дуговым кратером. Шлак счищается после остывания шва.
Дуговая сварка не требует предварительного нагрева металла, а так как температура дуги достаточно высока, то расплавление металла происходит практически мгновенно. Существует два вида дуговой сварки в зависимости от типа электрода.
а) Дуговая сварка без защиты
б) Дуговая сварка под защитойа) Дуговая сварка без защиты
Когда для сварки используется большой электрод или присадочный стержень, это называется дуговой сваркой без защиты. В этом случае наплавленный металл шва, пока он горячий, будет поглощать кислород и азот из атмосферы. Это снижает прочность металла шва, снижает его пластичность и коррозионную стойкость.
b) Дуговая сварка в среде защитного газа
Рис. Принципиальная схема дуговой сварки в среде защитного газаПри дуговой сварке в защитных газах используются сварочные стержни, покрытые твердым материалом, как показано на приведенной выше принципиальной схеме.
Образовавшийся выступ покрытия фокусируется на концентрированном потоке дуги, который защищает глобулы металла от воздуха и предотвращает поглощение большого количества вредного кислорода и азота.
Кузнечная сварка
При кузнечной сварке соединяемые детали сначала нагревают до необходимой температуры в печи или кузнице, а затем куют. В настоящее время этот метод сварки используется редко. Электросварка сопротивлением является примером кузнечной сварки. Рис. Пример кузнечной сварки ( Источник: Марк Аспери )
В этом случае соединяемые детали прижимаются друг к другу и от одной части к другой пропускают электрический ток до тех пор, пока металл не нагреется до температуры плавления соединения. Принцип приложения тепла и давления, последовательного или одновременного, широко используется в процессах, известных как точечная, шовная, выступающая, осадочная и оплавлением.
Заключение
Это основная классификация различных сварочных процессов.
Кроме того, существует множество сварочных процессов, классифицируемых как дуговая сварка, газовая сварка. О них мы говорили в отдельных статьях. Дайте нам знать, что вы думаете об этом в разделе комментариев ниже.
ИСО — 25.160.10 — Сварочные процессы
ISO 857-1:1998
Сварка и родственные процессы. Словарь. Часть 1. Процессы сварки металлов
95,99 ИСО/ТК 44/ПК 7 ISO 857:1979
Определения сварочных процессов
95,99 ИСО/ТК 44 ISO 857:1990
Процессы сварки и пайки.
Словарь
95,99 ИСО/ТК 44/ПК 7 ISO 3834:1978
Сварка. Факторы, которые следует учитывать при оценке фирм, использующих сварку в качестве основного средства производства
95,99 ИСО/ТК 44 ISO 4063:1990
Сварка, пайка и пайка металлов. Номенклатура процессов и ссылочные номера для условного обозначения на чертежах
95,99 ИСО/ТК 44/ПК 7 ISO 6213:1983
Сварка.
Вопросы, которые необходимо учитывать для обеспечения качества сварных конструкций
95,99 ИСО/ТК 44/ПК 10 ISO 6213:1989
Сварка. Факторы, которые необходимо учитывать для обеспечения качества сварных конструкций
95,99 ИСО/ТК 44/ПК 10 ISO 9013:1992
Сварка и родственные процессы. Классификация качества и допуски на размеры термически обработанных (кислород/пламя горючего газа) поверхностей
95,99 ИСО/ТК 44/ПК 8 ISO 9013:2002
Термическая резка.
Классификация термической резки. Геометрические характеристики изделия и допуски по качеству
95,99 ИСО/ТК 44/ПК 8 ISO 9013:2017
Термическая резка. Классификация термической резки. Геометрические характеристики изделия и допуски по качеству
90,93 ИСО/ТК 44/ПК 8 ISO 9692-2:1998
Сварка и родственные процессы. Подготовка соединения.
Часть 2. Дуговая сварка сталей под флюсом
90,93 ИСО/ТК 44/ПК 7 ISO 9692-3:2000
Сварка и родственные процессы. Рекомендации по подготовке соединений. Часть 3. Сварка металла в среде инертного газа и сварка вольфрамом в среде инертного газа алюминия и его сплавов
95,99 ИСО/ТК 44/ПК 7 ISO 9692-3:2016
Сварка и родственные процессы.
Типы подготовки швов. Часть 3. Сварка металла в среде инертного газа и сварка вольфрамом в среде инертного газа алюминия и его сплавов
90,93 ИСО/ТК 44/ПК 7 ISO 9956-1:1995
Спецификация и утверждение процедур сварки металлических материалов. Часть 1. Общие правила сварки плавлением
95,99 ИСО/ТК 44/ПК 10 ISO 9956-1:1995/Изм. 1:1998
Спецификация и утверждение процедур сварки металлических материалов.
Часть 1. Общие правила сварки плавлением. Поправка 1
95,99 ИСО/ТК 44/ПК 10 ИСО 9956-2:1995
Спецификация и утверждение процедур сварки металлических материалов. Часть 2. Спецификация процедур дуговой сварки
95,99 ИСО/ТК 44/ПК 10 ISO 9956-2:1995/Amd 1:1998
Спецификация и утверждение процедур сварки металлических материалов. Часть 2. Спецификация процедур дуговой сварки.
Поправка 1
95,99 ИСО/ТК 44/ПК 10 ISO 9956-3:1995
Спецификация и утверждение процедур сварки металлических материалов. Часть 3. Испытания процедур дуговой сварки сталей
95,99 ИСО/ТК 44/ПК 10 ISO 9956-3:1995/Amd 1:1998
Спецификация и утверждение процедур сварки металлических материалов. Часть 3. Испытания процедур дуговой сварки сталей. Поправка 1
95,99 ИСО/ТК 44/ПК 10 ISO 9956-4:1995
Спецификация и утверждение процедур сварки металлических материалов.
Часть 4. Испытания процедур дуговой сварки алюминия и его сплавов
95,99 ИСО/ТК 44/ПК 10 ISO 9956-4:1995/Amd 1:1998
Спецификация и утверждение процедур сварки металлических материалов. Часть 4. Испытания процедур дуговой сварки алюминия и его сплавов. Поправка 1
95,99 ИСО/ТК 44/ПК 10 ИСО 9956-5:1995
Спецификация и одобрение процедур сварки металлических материалов.
Часть 5. Утверждение с использованием утвержденных сварочных материалов для дуговой сварки
95,99 ИСО/ТК 44/ПК 10 ISO 9956-6:1995
Спецификация и одобрение процедур сварки металлических материалов. Часть 6: Утверждение, связанное с предыдущим опытом
95,99 ИСО/ТК 44/ПК 10 ISO 9956-7:1995
Спецификация и утверждение процедур сварки металлических материалов.
Часть 7. Утверждение стандартной процедуры дуговой сварки
95,99 ИСО/ТК 44/ПК 10 ISO 9956-8:1995
Спецификация и одобрение процедур сварки металлических материалов. Часть 8. Утверждение путем предпроизводственных сварочных испытаний
95,99 ИСО/ТК 44/ПК 10 ISO 9956-10:1996
Спецификация и утверждение процедур сварки металлических материалов. Часть 10.
Спецификация процедуры сварки для электронно-лучевой сварки
95,99 ИСО/ТК 44/ПК 10 ИСО 9956-11:1996
Спецификация и утверждение процедур сварки металлических материалов. Часть 11. Спецификация процедур сварки для лазерной сварки
95,99 ИСО/ТК 44/ПК 10 ISO 11970:2001
Спецификация и утверждение процедур сварки для производственной сварки стальных отливок
95,99 ИСО/ТК 17/ПК 11 ISO 11970:2016
Спецификация и квалификация сварочных процедур для производственной сварки стальных отливок
90,92 ИСО/ТК 17/ПК 11 ISO 12996:2013
Механическое соединение.
Разрушающие испытания соединений. Размеры образцов и методика испытания на растяжение и сдвиг отдельных соединений
90,93 ИСО/ТК 44/ПК 6 ИСО 13469:2014
Механическое соединение. Заклепки с геометрическим замыканием и (замковые) болтовые соединения. Спецификации и квалификация процедур испытаний
90,93 ИСО/ТК 44/ПК 6 ISO 13916:1996
Сварка.
Руководство по измерению температуры предварительного нагрева, межпроходной температуры и температуры поддержания предварительного подогрева
95,99 ИСО/ТК 44/ПК 10 ISO 13916:2017
Сварка. Измерение температуры предварительного нагрева, межпроходной температуры и температуры поддержания предварительного подогрева
60,60 ИСО/ТК 44/ПК 10 ISO 13918:2008
Сварка.
Шпильки и керамические втулки для дуговой приварки шпилек
95,99 ИСО/ТК 44/ПК 10 ИСО 13918:2017
Сварка. Шпильки и керамические втулки для дуговой приварки шпилек
60,60 ИСО/ТК 44/ПК 10 ISO 13918:2017/Amd 1:2021
Сварка. Шпильки и керамические втулки для дуговой приварки шпилек. Поправка 1
60,60 ИСО/ТК 44/ПК 10 ISO 13920:1996
Сварка.
Общие допуски для сварных конструкций. Размеры длин и углов. Форма и положение
90,60 ИСО/ТК 44/ПК 10 ISO 14327:2004
Сварка сопротивлением. Методы определения зоны свариваемости контактной точечной, выступающей и шовной сваркой
95,99 ИСО/ТК 44/ПК 6 ISO 14344:2010
Сварочные материалы. Закупка присадочных материалов и флюсов
90,93 ИСО/ТК 44/ПК 3 ISO 14373:2006
Сварка сопротивлением.
Процедура точечной сварки низкоуглеродистых сталей без покрытия и с покрытием
95,99 МИС ISO 14373:2015
Сварка сопротивлением. Процедура точечной сварки низкоуглеродистых сталей без покрытия и с покрытием
90,92 ИСО/ТК 44/ПК 6 ISO/CD 14373
Сварка сопротивлением. Процедура точечной сварки низкоуглеродистых сталей без покрытия и с покрытием
30,99 ИСО/ТК 44/ПК 6 ISO 14555:1998
Сварка.
Дуговая сварка металлических материалов шпильками
95,99 ИСО/ТК 44/ПК 10 ISO 14555:2006
Сварка. Дуговая сварка металлических материалов
95,99 ИСО/ТК 44/ПК 10 ISO 14555:2014
Сварка. Дуговая сварка металлических материалов
95,99 ИСО/ТК 44/ПК 10 ISO 14555:2017
Сварка.
Дуговая сварка металлических материалов
90,60 ИСО/ТК 44/ПК 10 ISO 15011-1:2002
Здоровье и безопасность при сварке и родственных процессах. Лабораторный метод отбора проб дыма и газов, образующихся при дуговой сварке. Часть 1. Определение интенсивности выбросов и отбор проб для анализа дыма в виде твердых частиц
95,99 ИСО/ТК 44/ПК 9 ISO 15011-1:2009
Здоровье и безопасность при сварке и родственных процессах.
Лабораторный метод отбора проб дыма и газов. Часть 1. Определение скорости выделения дыма при дуговой сварке и сбор дыма для анализа
90,93 ИСО/ТК 44/ПК 9 ISO 15011-2:2003
Охрана здоровья и безопасность при сварке и родственных процессах. Лабораторный метод отбора проб дыма и газов, образующихся при дуговой сварке. Часть 2. Определение интенсивности выбросов газов, кроме озона
95,99 ИСО/ТК 44/ПК 9 ИСО 15011-2:2009
Здоровье и безопасность при сварке и родственных процессах.
Лабораторный метод отбора проб дыма и газов. Часть 2. Определение интенсивности выбросов моноксида углерода (CO), диоксида углерода (CO2), моноксида азота (NO) и диоксида азота (NO2) ) при дуговой сварке, резке и строжке
90,93 ИСО/ТК 44/ПК 9 ISO 15011-3:2002
Здоровье и безопасность при сварке и родственных процессах. Лабораторный метод отбора проб дыма и газов, образующихся при дуговой сварке. Часть 3. Определение концентрации озона с помощью измерений в фиксированной точке
95,99 ИСО/ТК 44/ПК 9 ISO 15011-3:2009
Здоровье и безопасность при сварке и родственных процессах.
Лабораторный метод отбора проб дыма и газов. Часть 3. Определение скорости выделения озона при дуговой сварке
90,93 ИСО/ТК 44/ПК 9 ISO 15011-4:2006
Здоровье и безопасность при сварке и родственных процессах. Лабораторный метод отбора проб дыма и газов. Часть 4. Паспорта дыма
95,99 ИСО/ТК 44/ПК 9 ISO 15011-4:2006/Amd 1:2008
Здоровье и безопасность при сварке и родственных процессах.
Лабораторный метод отбора проб дыма и газов. Часть 4. Паспорта дымовых газов. Поправка 1
95,99 ИСО/ТК 44/ПК 9 ISO 15011-4:2017
Здоровье и безопасность при сварке и родственных процессах. Лабораторный метод отбора проб дыма и газов. Часть 4. Паспорта дыма
90,93 ИСО/ТК 44/ПК 9 ISO 15011-5:2011
Здоровье и безопасность при сварке и родственных процессах.
Лабораторный метод отбора проб дыма и газов. Часть 5. Идентификация продуктов термического разложения, образующихся при сварке или резке изделий, полностью или частично состоящих из органических материалов методом пиролиз-газовой хроматографии-масс-спектрометрии
90,93 ИСО/ТК 44/ПК 9 ISO/TS 15011-5:2006
Здоровье и безопасность при сварке и родственных процессах. Лабораторный метод отбора проб дыма и газов. Часть 5. Идентификация продуктов термического разложения, образующихся при сварке или резке изделий, полностью или частично состоящих из органические материалы
95,99 ИСО/ТК 44/ПК 9 ISO/TS 15011-6:2012
Здоровье и безопасность при сварке и родственных процессах.
Лабораторный метод отбора проб дыма и газов. Часть 6. Процедура количественного определения дыма и газов при контактной точечной сварке
90,93 ИСО/ТК 44/ПК 9 ISO/TS 15011-6:2012/Cor 1:2012
Здоровье и безопасность при сварке и родственных процессах. Лабораторный метод отбора проб дыма и газов. Часть 6. Процедура количественного определения дыма и газов при контактной точечной сварке. Техническое исправление 1
60,60 ИСО/ТК 44/ПК 9 ISO 15607:2003
Спецификация и квалификация процедур сварки металлических материалов.
Общие правила
95,99 ИСО/ТК 44/ПК 10 ISO 15607:2003/Cor 1:2005
Спецификация и квалификация процедур сварки металлических материалов. Общие правила. Техническое исправление 1
95,99 ИСО/ТК 44/ПК 10 ISO 15607:2019
Спецификация и аттестация процедур сварки металлических материалов. Общие правила
60,60 ИСО/ТК 44/ПК 10 ISO 15609-1:2004
Спецификация и квалификация процедур сварки металлических материалов.
Спецификация процедуры сварки. Часть 1: Дуговая сварка
95,99 ИСО/ТК 44/ПК 10 ISO 15609-1:2004/Cor 1:2005
Спецификация и квалификация процедур сварки металлических материалов. Спецификация процедуры сварки. Часть 1: Дуговая сварка. Техническое исправление 1
95,99 ИСО/ТК 44/ПК 10 ISO 15609-1:2019
Спецификация и квалификация процедур сварки металлических материалов.
Спецификация процедуры сварки. Часть 1: Дуговая сварка
60,60 ИСО/ТК 44/ПК 10 ИСО 15609-2:2001
Спецификация и квалификация процедур сварки металлических материалов. Спецификация процедур сварки. Часть 2: Газовая сварка
95,99 ИСО/ТК 44/ПК 10 ISO 15609-2:2019
Спецификация и аттестация процедур сварки металлических материалов. Спецификация процедуры сварки.
Часть 2: Газовая сварка
60,60 ИСО/ТК 44/ПК 10 ISO 15609-3:2004
Спецификация и аттестация процедур сварки металлических материалов. Спецификация процедуры сварки. Часть 3. Электронно-лучевая сварка
90,93 ИСО/ТК 44/ПК 10 ISO 15609-4:2004
Спецификация и аттестация процедур сварки металлических материалов. Спецификация процедуры сварки.
Часть 4. Лазерная сварка
95,99 ИСО/ТК 44/ПК 10 ISO 15609-4:2009
Спецификация и квалификация процедур сварки металлических материалов. Спецификация процедуры сварки. Часть 4. Лазерная сварка
90,93 ИСО/ТК 44/ПК 10 ISO 15609-5:2004
Спецификация и аттестация процедур сварки металлических материалов. Спецификация процедуры сварки. Часть 5: Сварка сопротивлением
95,99 ИСО/ТК 44/ПК 6 ISO 15609-5:2011
Спецификация и квалификация процедур сварки металлических материалов.
Спецификация процедуры сварки. Часть 5. Сварка сопротивлением
90,93 ИСО/ТК 44/ПК 6 ISO 15609-6:2013
Спецификация и аттестация процедур сварки металлических материалов. Спецификация процедуры сварки. Часть 6. Лазерно-дуговая гибридная сварка
90,93 ИСО/ТК 44/ПК 10 ISO 15610:2003
Спецификация и аттестация процедур сварки металлических материалов.
Аттестация на основе испытанных сварочных материалов
90,92 ИСО/ТК 44/ПК 10 ISO/FDIS 15610
Спецификация и аттестация процедур сварки металлических материалов. Аттестация на основе испытанных сварочных материалов
50.00 ИСО/ТК 44/ПК 10 ИСО 15612:2004
Спецификация и аттестация процедур сварки металлических материалов. Аттестация путем принятия стандартной процедуры сварки
95,99 ИСО/ТК 44/ПК 10 ISO 15612:2018
Спецификация и аттестация процедур сварки металлических материалов.
Аттестация путем принятия стандартной спецификации процедуры сварки
60,60 ИСО/ТК 44/ПК 10 ISO 15613:2004
Спецификация и аттестация процедур сварки металлических материалов. Квалификация на основе предпроизводственных сварочных испытаний
90,92 ИСО/ТК 44/ПК 10 ISO/DIS 15613
Спецификация и аттестация процедур сварки металлических материалов.
Аттестация на основе предпроизводственных сварочных испытаний
40.20 ИСО/ТК 44/ПК 10 ISO 15614-1:2004
Спецификация и аттестация процедур сварки металлических материалов. Проверка процедуры сварки. Часть 1: Дуговая и газовая сварка сталей и дуговая сварка никеля и никелевых сплавов
95,99 ИСО/ТК 44/ПК 10 ISO 15614-1:2004/Изм. 1:2008
Спецификация и аттестация процедур сварки металлических материалов.
Проверка процедуры сварки. Часть 1. Дуговая и газовая сварка сталей и дуговая сварка никеля и никелевых сплавов. Поправка 1
95,99 ИСО/ТК 44/ПК 10 ISO 15614-1:2004/Cor 1:2005
Спецификация и квалификация процедур сварки металлических материалов. Проверка процедуры сварки. Часть 1. Дуговая и газовая сварка сталей и дуговая сварка никеля и никелевых сплавов. Техническое исправление 1
95,99 ИСО/ТК 44/ПК 10 ISO 15614-1:2004/Изм.
2:2012
Спецификация и аттестация процедур сварки металлических материалов. Проверка процедуры сварки. Часть 1. Дуговая и газовая сварка сталей и дуговая сварка никеля и никелевых сплавов. Поправка 2
95,99 ИСО/ТК 44/ПК 10 ISO 15614-1:2017
Спецификация и аттестация процедур сварки металлических материалов. Проверка процедуры сварки. Часть 1. Дуговая и газовая сварка сталей и дуговая сварка никеля и никелевых сплавов
90,60 ИСО/ТК 44/ПК 10 ИСО 15614-1:2017/Изм.
1:2019
Спецификация и аттестация процедур сварки металлических материалов. Проверка процедуры сварки. Часть 1. Дуговая и газовая сварка сталей и дуговая сварка никеля и никелевых сплавов. Поправка 1
60,60 ИСО/ТК 44/ПК 10 ISO 15614-2:2005
Спецификация и аттестация процедур сварки металлических материалов. Проверка процедуры сварки. Часть 2. Дуговая сварка алюминия и его сплавов
90,92 ИСО/ТК 44/ПК 10 ISO 15614-2:2005/Cor 1:2005
Спецификация и квалификация процедур сварки металлических материалов.
Проверка процедуры сварки. Часть 2. Дуговая сварка алюминия и его сплавов. Техническое исправление 1
60,60 ИСО/ТК 44/ПК 10 ISO 15614-2:2005/Cor 2:2009
Спецификация и квалификация процедур сварки металлических материалов. Проверка процедуры сварки. Часть 2. Дуговая сварка алюминия и его сплавов. Техническое исправление 2
60,60 ИСО/ТК 44/ПК 10 ISO/DIS 15614-2
Спецификация и аттестация процедур сварки металлических материалов.
Проверка процедуры сварки. Часть 2. Дуговая сварка алюминия и его сплавов
40,99 ИСО/ТК 44/ПК 10 ISO 15614-3:2008
Спецификация и аттестация процедур сварки металлических материалов. Проверка процедуры сварки. Часть 3. Сварка плавлением нелегированных и низколегированных чугунов
90,93 ИСО/ТК 44/ПК 10 ISO 15614-4:2005
Спецификация и аттестация процедур сварки металлических материалов.
Испытание процедуры сварки. Часть 4. Чистовая сварка алюминиевых отливок
90,92 ИСО/ТК 44/ПК 10 ISO 15614-4:2005/Cor 1:2007
Спецификация и аттестация процедур сварки металлических материалов. Проверка процедуры сварки. Часть 4. Чистовая сварка алюминиевых отливок. Техническое исправление 1
60,60 ИСО/ТК 44/ПК 10 ISO/DIS 15614-4
Спецификация и аттестация процедур сварки металлических материалов.
Испытание процедуры сварки. Часть 4. Чистовая сварка алюминиевых отливок
40,60 ИСО/ТК 44/ПК 10 ISO 15614-5:2004
Спецификация и аттестация процедур сварки металлических материалов. Проверка процедуры сварки. Часть 5. Дуговая сварка титана, циркония и их сплавов
90,92 ИСО/ТК 44/ПК 10 ISO/DIS 15614-5
Спецификация и аттестация процедур сварки металлических материалов.
Проверка процедуры сварки. Часть 5. Дуговая сварка титана, циркония и их сплавов
40,99 ИСО/ТК 44/ПК 10 ISO 15614-6:2006
Спецификация и аттестация процедур сварки металлических материалов. Проверка процедуры сварки. Часть 6. Дуговая и газовая сварка меди и ее сплавов
90,92 ИСО/ТК 44/ПК 10 ISO/DIS 15614-6
Спецификация и аттестация процедур сварки металлических материалов.
Проверка процедуры сварки. Часть 6. Дуговая и газовая сварка меди и ее сплавов
40,60 ИСО/ТК 44/ПК 10 ISO 15614-7:2007
Спецификация и аттестация процедур сварки металлических материалов. Проверка процедуры сварки. Часть 7. Наплавка
95,99 ИСО/ТК 44/ПК 10 ISO 15614-7:2016
Спецификация и аттестация процедур сварки металлических материалов.
Проверка процедуры сварки. Часть 7. Наплавка
90,93 ИСО/ТК 44/ПК 10 ISO 15614-8:2002
Спецификация и аттестация процедур сварки металлических материалов. Проверка процедуры сварки. Часть 8. Приварка труб к соединениям трубной доски
95,99 ИСО/ТК 44/ПК 10 ИСО 15614-8:2016
Спецификация и аттестация процедур сварки металлических материалов.
Проверка процедуры сварки. Часть 8. Приварка труб к соединениям трубной доски
90,92 ИСО/ТК 44/ПК 10 ISO 15614-10:2005
Спецификация и аттестация процедур сварки металлических материалов. Испытания процедуры сварки. Часть 10. Гипербарическая сухая сварка
90,93 ИСО/ТК 44/ПК 15 ISO 15614-11:2002
Спецификация и аттестация процедур сварки металлических материалов.
Проверка процедуры сварки. Часть 11. Электронно- и лазерно-лучевая сварка
90,92 ИСО/ТК 44/ПК 10 ISO/DIS 15614-11
Спецификация и аттестация процедур сварки металлических материалов. Проверка процедуры сварки. Часть 11. Электронно- и лазерно-лучевая сварка
40.20 ИСО/ТК 44/ПК 10 ISO 15614-12:2004
Спецификация и аттестация процедур сварки металлических материалов.
Проверка процедуры сварки. Часть 12. Точечная, шовная и выступающая сварка
95,99 ИСО/ТК 44/ПК 6 ISO 15614-12:2014
Спецификация и аттестация процедур сварки металлических материалов. Проверка процедуры сварки. Часть 12. Точечная, шовная и выступающая сварка
95,99 ИСО/ТК 44/ПК 6 ISO 15614-12:2021
Спецификация и аттестация процедур сварки металлических материалов.
Проверка процедуры сварки. Часть 12. Точечная, шовная и рельефная сварка
60,60 ИСО/ТК 44/ПК 6 ISO 15614-13:2005
Спецификация и аттестация процедур сварки металлических материалов. Проверка процедуры сварки. Часть 13. Стыковая сварка сопротивлением и сварка оплавлением
95,99 ИСО/ТК 44/ПК 6 ISO 15614-13:2012
Спецификация и аттестация процедур сварки металлических материалов.
Проверка процедуры сварки. Часть 13. Сварка с осадкой (сопротивление встык) и сварка оплавлением
95,99 ИСО/ТК 44/ПК 6 ISO 15614-13:2021
Спецификация и аттестация процедур сварки металлических материалов. Проверка процедуры сварки. Часть 13. Сварка с осадкой (сопротивление встык) и сварка оплавлением
90,92 ИСО/ТК 44/ПК 6 ISO/CD 15614-13
Спецификация и аттестация процедур сварки металлических материалов.
Проверка процедуры сварки. Часть 13. Сварка с осадкой (сопротивление встык) и сварка оплавлением
30,99 ИСО/ТК 44/ПК 6 ISO 15614-14:2013
Спецификация и аттестация процедур сварки металлических материалов. Проверка процедуры сварки. Часть 14. Лазерно-дуговая гибридная сварка сталей, никеля и никелевых сплавов
90,93 ИСО/ТК 44/ПК 10 ISO 15620:2000
Сварка.
Сварка трением металлических материалов
95,99 ИСО/ТК 44/ПК 10 ISO 15620:2019
Сварка. Сварка трением металлических материалов
60,60 ИСО/ТК 44/ПК 10 ISO 16432:2006
Сварка сопротивлением. Процедура рельефной сварки низкоуглеродистых сталей без покрытия и с покрытием с использованием рельефных выступов
90,93 ИСО/ТК 44/ПК 6 ISO 16433:2006
Сварка сопротивлением.
Процедура шовной сварки низкоуглеродистых сталей без покрытия и с покрытием
90,93 ИСО/ТК 44/ПК 6 ISO 17652-1:2003
Сварка. Испытания заводских грунтовок в отношении сварки и родственных процессов. Часть 1. Общие требования
90,93 ИСО/ТК 44/ПК 10 ISO 17652-2:2003
Сварка. Испытание межоперационных грунтовок в отношении сварки и родственных процессов.
Часть 2. Сварочные свойства межоперационных грунтовок
90,93 ИСО/ТК 44/ПК 10 ISO 17652-3:2003
Сварка. Испытание заводских грунтовок в отношении сварки и родственных процессов. Часть 3. Термическая резка
90,93 ИСО/ТК 44/ПК 10 ISO 17652-4:2003
Сварка. Испытание заводских грунтовок в отношении сварки и родственных процессов.
Часть 4. Выброс дыма и газов
90,93 ИСО/ТК 44/ПК 10 ИСО 17657-1:2005
Сварка сопротивлением. Измерение сварочного тока при контактной сварке. Часть 1. Руководство по измерению
90,93 ИСО/ТК 44/ПК 6 ISO 17657-2:2005
Сварка сопротивлением. Измерение сварочного тока для контактной сварки. Часть 2. Измеритель сварочного тока с токоизмерительной катушкой
90,93 ИСО/ТК 44/ПК 6 ISO 17657-3:2005
Сварка сопротивлением.
Измерение сварочного тока для контактной сварки. Часть 3. Катушка измерения тока
90,93 ИСО/ТК 44/ПК 6 ISO 17657-4:2005
Сварка сопротивлением. Измерение сварочного тока для контактной сварки. Часть 4. Система калибровки
90,93 ИСО/ТК 44/ПК 6 ISO 17657-5:2005
Сварка сопротивлением. Измерение сварочного тока для контактной сварки.
Часть 5. Проверка системы измерения сварочного тока
90,93 ИСО/ТК 44/ПК 6 ISO 17658:2002
Сварка. Дефекты при кислородной, лазерной и плазменной резке. Терминология
90,93 ИСО/ТК 44/ПК 7 ISO 17660-1:2006
Сварка. Сварка арматурной стали. Часть 1. Несущие сварные соединения
90,92 ИСО/ТК 44/ПК 10 ISO 17660-2:2006
Сварка.
Сварка арматурной стали. Часть 2. Ненесущие сварные соединения
90,92 ИСО/ТК 44/ПК 10 ISO/TR 17671-1:2002
Сварка. Рекомендации по сварке металлических материалов. Часть 1. Общее руководство по дуговой сварке
90,93 ИСО/ТК 44/ПК 10 ISO/TR 17671-2:2002
Сварка. Рекомендации по сварке металлических материалов. Часть 2.
Дуговая сварка ферритных сталей
90,93 ИСО/ТК 44/ПК 10 ISO/TR 17671-3:2002
Сварка. Рекомендации по сварке металлических материалов. Часть 3. Дуговая сварка нержавеющих сталей
90,93 ИСО/ТК 44/ПК 10 ISO/TR 17671-4:2002
Сварка. Рекомендации по сварке металлических материалов. Часть 4. Дуговая сварка алюминия и алюминиевых сплавов
90,93 ИСО/ТК 44/ПК 10 ISO/TR 17671-5:2004
Сварка.
Рекомендации по сварке металлических материалов. Часть 5. Сварка плакированных сталей
90,93 ИСО/ТК 44/ПК 10 ISO/TR 17671-6:2005
Сварка. Рекомендации по сварке металлических материалов. Часть 6. Лазерная сварка
90,93 ИСО/ТК 44/ПК 10 ISO/TR 17671-7:2004
Сварка. Рекомендации по сварке металлических материалов.
Часть 7. Электронно-лучевая сварка
90,93 ИСО/ТК 44/ПК 10 ISO 17677-1:2009
Сварка сопротивлением. Словарь. Часть 1. Точечная, выступающая и шовная сварка
95,99 ИСО/ТК 44/ПК 6 ISO 17677-1:2019
Сварка сопротивлением. Словарь. Часть 1. Точечная, выступающая и шовная сварка
95,99 ИСО/ТК 44/ПК 6 ISO 17677-1:2021
Сварка сопротивлением.
Словарь. Часть 1. Точечная, выступающая и шовная сварка
60,60 ИСО/ТК 44/ПК 6 ISO/TR 17844:2004
Сварка. Сравнение стандартных методов предотвращения холодных трещин
90,93 ИСО/ТК 44/ПК 10 ISO 17916:2016
Безопасность машин для термической резки
90,93 ИСО/ТК 44/ПК 9 ISO 18594:2007
Точечная, рельефная и шовная сварка сопротивлением.
Метод определения переходного сопротивления на алюминиевых и стальных материалах
90,93 ИСО/ТК 44/ПК 6 ISO 18595:2007
Сварка сопротивлением. Точечная сварка алюминия и алюминиевых сплавов. Свариваемость, сварка и испытания
95,99 ИСО/ТК 44/ПК 6 ISO 18595:2021
Сварка сопротивлением. Точечная сварка алюминия и алюминиевых сплавов.
Свариваемость, сварка и испытания
60,60 ИСО/ТК 44/ПК 6 ISO/DIS 18595
Сварка сопротивлением. Точечная сварка алюминия и алюминиевых сплавов. Свариваемость, сварка и испытания
40,98 ИСО/ТК 44/ПК 6 ISO 18785-4:2018
Точечная сварка трением с перемешиванием. Алюминий. Часть 4. Спецификация и квалификация процедур сварки
60,60 МИС ISO 18785-5:2018
Точечная сварка трением с перемешиванием.
Алюминий. Часть 5. Требования к качеству и контролю
60,60 МИС ISO/TR 22824:2003
Сварочные материалы. Расчетное и измеренное значение FN в спецификациях. Заявление экспертов Комиссии IIW IX
90,92 МИС ISO/DTR 22824
Сварочные материалы. Расчетное и измеренное значение FN в спецификациях. Заявление экспертов Комиссии IIW IX
30,99 МИС ISO 25239-1:2011
Сварка трением с перемешиванием.
Алюминий. Часть 1. Словарь
95,99 МИС ISO 25239-1:2020
Сварка трением с перемешиванием. Алюминий. Часть 1. Словарь
60,60 МИС ISO 25239-2:2011
Сварка трением с перемешиванием. Алюминий. Часть 2. Расчет сварных соединений
95,99 МИС ISO 25239-2:2020
Сварка трением с перемешиванием.
Алюминий. Часть 2. Расчет сварных соединений
60,60 МИС ISO 25239-3:2011
Сварка трением с перемешиванием. Алюминий. Часть 3. Квалификация сварщиков
95,99 МИС ISO 25239-3:2020
Сварка трением с перемешиванием. Алюминий. Часть 3. Квалификация сварщиков
60,60 МИС ISO 25239-4:2011
Сварка трением с перемешиванием.
Алюминий. Часть 4. Спецификация и квалификация процедур сварки
95,99 МИС ISO 25239-4:2020
Сварка трением с перемешиванием. Алюминий. Часть 4. Спецификация и аттестация процедур сварки
60,60 МИС ISO 25239-5:2011
Сварка трением с перемешиванием. Алюминий. Часть 5. Требования к качеству и контролю
95,99 МИС ISO 25239-5:2020
Сварка трением с перемешиванием.
Алюминий. Часть 5. Требования к качеству и контролю
60,60 МИС ISO/TR 25901-1:2016
Сварка и родственные процессы. Словарь. Часть 1. Общие термины
90,60 ИСО/ТК 44/ПК 7 ISO/FDIS 25901-2
Сварка и родственные процессы. Словарь. Часть 2. Здоровье и безопасность
50. 20
ИСО/ТК 44/ПК 7 ISO/TR 25901-3:2016
Сварка и родственные процессы. Словарь. Часть 3. Сварочные процессы
90,60 ИСО/ТК 44/ПК 7 ISO/TR 25901-4:2016
Сварка и родственные процессы. Словарь. Часть 4. Дуговая сварка
90,60 ИСО/ТК 44/ПК 7 ISO/TR 25901:2007
Сварка и родственные процессы.
Словарь
95,99 ИСО/ТК 44/ПК 7 ISO 25980:2014
Здоровье и безопасность при сварке и родственных процессах. Прозрачные сварочные шторы, полосы и экраны для процессов дуговой сварки
90,92 ИСО/ТК 44/ПК 9 ИСО/ДИС 25980
Охрана здоровья и безопасность при сварке и родственных процессах. Прозрачные сварочные шторы, полосы и экраны для процессов дуговой сварки
40. 20
ИСО/ТК 44/ПК 9 Сварочные процессы – IspatGuru
Сварочные процессы
- satyendra
- 10 апреля 2014 г.
- 1 Комментарий
- электроды, MIG, MMA, SMAW, TIG, сварка,
Сварочные процессы
Сварка – это производственный процесс, при котором материалы соединяются путем коалесценции. Сварка обычно осуществляется путем расплавления заготовок и добавления присадочного материала для образования ванны расплавленного материала, который охлаждается, образуя прочное соединение, либо под давлением, иногда используемым в сочетании с теплом, либо сам по себе для получения сварного шва. Это отличается от пайки и пайки, которые включают плавление материала с более низкой температурой плавления между заготовками для образования связи между ними без плавления заготовок. Для сварки обычно требуется источник тепла для создания высокотемпературной зоны для плавления материала, хотя можно сварить две металлические детали без значительного повышения температуры.
Существуют методы с твердофазным соединением. В этих методах не происходит плавления электродов, хотя в процессе выделяется тепло. Кроме того, поскольку детали плотно прижаты друг к другу, в процессе соединения исключается попадание воздуха. При обычной сварке расплавленный и затвердевший материал обычно слабее деформируемого материала того же состава. При соединении в твердой фазе такого плавления не происходит, поэтому данный метод позволяет получать соединения высокого качества. Этими методами можно также легко сваривать разнородные по природе металлы. В обычном процессе сварки соединение разнородных металлов представляет проблемы, так как при плавлении образуются хрупкие интерметаллические соединения.
Современная технология сварки зародилась незадолго до конца 19 века, когда были разработаны методы создания высокой температуры в локализованных зонах. Существуют различные принятые методы и стандарты, и все еще ведется непрерывный поиск новых и улучшенных методов сварки.
Хотя различные сварочные процессы имеют свои преимущества и ограничения и требуются для особых и специфических применений, ручная дуговая сварка металлическим электродом (ММА) по-прежнему занимает доминирующее положение с точки зрения общего наплавленного металла. Сварочные процессы можно классифицировать на основе следующих критериев.
- Сварка с присадочным материалом или без него – Сварка может выполняться с применением присадочного материала или без него. Когда сварка выполняется без присадочного материала, она называется автогенной сваркой. Раньше только газовая сварка представляла собой процесс плавления, при котором соединение могло быть достигнуто с присадочным материалом или без него. Однако с развитием многих других сварочных процессов (например, TIG, электронная и т. д.) такая классификация создала путаницу, поскольку эти процессы подпадают под обе категории.
- Источник энергии сварки. Используется ряд источников энергии, таких как химическая, электрическая, световая, звуковая, механическая энергия и т.
д. Однако, кроме химической энергии, все другие формы энергии генерируются из электрической энергии. Таким образом, этот критерий не является хорошим критерием для правильной классификации.
- Дуговая и бездуговая сварка. В этой классификации все процессы дуговой сварки относятся к одному классу, а все остальные процессы относятся к классу недуговой сварки. Однако трудно отнести какой-либо класс к таким процессам, как электрошлаковая сварка (ЭШС), стыковая сварка оплавлением и т. д. в соответствии с этой классификацией, и, следовательно, такая классификация также не является идеальной.
- Сварка плавлением и давлением. Эта классификация является наиболее широко используемой классификацией, поскольку она охватывает все процессы в обеих категориях, независимо от источника тепла и сварки с присадочным материалом или без него. Сварка плавлением включает в себя все те процессы, при которых расплавленный металл свободно затвердевает при сварке давлением: расплавленный металл, если он задерживается в замкнутом пространстве (например, контактная точечная сварка или дуговая сварка шпилек), затвердевает под давлением или полутвердый металл охлаждается под давлением.
Процессы сварки плавлением и сваркой давлением показаны на рис. 1 и рис. 2 соответственно.
Рис. 1. Процессы сварки плавлением
Рис. 2. Процессы сварки давлением
Основные процессы сварки кратко описаны ниже.
Газовая сварка – Кислородно-ацетиленовая газовая сварка является наиболее важным процессом, используемым для соединения различных металлов. Другие горючие газы, такие как сжиженный нефтяной газ, метан, водород и т. д., также могут использоваться вместо ацетилена при газовой сварке. В зависимости от соотношения кислорода в газе можно получить три типа пламени, а именно (i) восстановительное пламя, (ii) нейтральное пламя и (iii) окислительное пламя. Восстановительное пламя (также называемое науглероживающим пламенем) содержит несгоревший углерод, который может добавляться к сварному шву во время сварки. Науглероживающее пламя может подходить для сварки высокоуглеродистых сталей или для науглероживания поверхности низкоуглеродистых или мягких сталей.
Нейтральное пламя неизменно используется для сварки сталей и других металлов. В окислительном пламени внутренняя зона становится очень маленькой, и возникает громкий шум. Окислительное пламя дает максимально возможную температуру. Максимальная температура кислородно-ацетиленового пламени составляет около 3200 градусов по Цельсию, а центр этой концентрации тепла находится сразу за крайней вершиной белого конуса. Окислительное пламя обычно вводит кислород в металл сварного шва и не является предпочтительным для сварки сталей.
Сварочная горелка имеет камеру смешения, в которой смешиваются кислород и ацетилен, и эта смесь воспламеняется на конце горелки. Сварка может осуществляться двумя способами. В переднем методе горелка движется в направлении сварки с наклоном горелки под углом 65 градусов к наплавленному металлу. В технике обратной руки горелка наклонена под углом 45 градусов к несвариваемому участку. Газовая сварка больше подходит для тонких пластин и листов, так как ее пламя не такое пронзительное, как при дуговой сварке.
Время сварки сравнительно больше, а зона термического влияния (ЗТВ) и деформация больше, чем при дуговой сварке
Сварка ММА или дуговая сварка в среде защитного газа (SMAW) – Также известна как сварка электродом или дуговая сварка в среде защитного флюса (FSAW). Это очень гибкий и широко используемый процесс дуговой сварки. Он включает в себя зажигание дуги между покрытым металлическим электродом и заготовкой. Тепло дуги расплавляет основной металл и электрод, которые смешиваются вместе, образуя при охлаждении сплошную твердую массу. Электрический ток в виде переменного или постоянного тока от сварочного источника питания используется для образования электрической дуги между электродом и соединяемыми металлами. По мере наложения шва флюсовое покрытие электрода распадается, выделяя пары, служащие защитным газом, и образуя слой шлака. Оба они защищают зону сварки от атмосферного загрязнения. Сварку ММА можно использовать для соединения стали, нержавеющей стали, чугуна и многих цветных металлов.
Для многих мягких и высокопрочных углеродистых сталей этот метод соединения является предпочтительным.
Дуговая сварка под флюсом (SAW) – процесс сварки назван так потому, что зона сварки и дуги погружаются под слой флюса. SAW нагревает металлы с помощью электрической дуги между оголенным электродом и основным материалом под слоем флюсового материала. Флюс становится проводящим, когда он расплавлен, создавая путь для прохождения тока между электродом и заготовкой. В этом процессе используется сплошной сплошной проволочный электрод, экранированный флюсом. Флюс стабилизирует дугу во время сварки, защищая сварочную ванну от атмосферы. Покрытие из флюса предотвращает брызги и искры, а также защищает от ультрафиолетового излучения и паров, которые обычно являются частью SMAW. Он также покрывает и защищает сварной шов во время охлаждения и может влиять на состав сварного шва и его свойства. SAW обычно автоматизирован, но также доступны полуавтоматические системы. Ток может быть как переменным, так и постоянным, а для автоматизированных систем электроды могут представлять собой один провод или несколько сплошных или трубчатых проводов или полос.
Сварку можно выполнять только в горизонтальном или горизонтальном положении из-за использования гранулированного флюса и текучести расплавленной сварочной ванны. С помощью этого процесса можно достичь высокой скорости наплавки и сваривать очень толстые и тонкие материалы.
Дуговая сварка с флюсовой проволокой (FCAW) – FCAW была разработана в начале 1950-х годов как альтернатива SMAW. Преимущество FCAW перед SMAW заключается в том, что он исключает использование стержневых электродов. Это помогло FCAW преодолеть многие ограничения, связанные с SMAW. Этот процесс широко используется из-за его высокой скорости сварки и портативности. Это полуавтоматический или автоматический процесс сварки, предназначенный для углеродистой, нержавеющей и низколегированной стали. В нем используется электрическая дуга для создания коалесценции между сплошным трубчатым электродом из присадочного металла и основными материалами, и его можно выполнять с защитным газом или без него. Для FCAW требуется расходуемый трубчатый электрод с непрерывной подачей, содержащий флюс и постоянное напряжение, или, реже, источник сварочного тока постоянного тока.
Иногда используется защитный газ извне, но часто сам флюс обеспечивает необходимую защиту от атмосферы, создавая как газообразную защиту, так и жидкий шлак, защищающий сварной шов. При использовании порошковой проволоки в среде защитного газа защитные агенты обеспечиваются флюсом, содержащимся внутри трубчатого электрода. Подаваемый извне газ расширяет основные элементы электрода, чтобы предотвратить атмосферное загрязнение расплавленного металла. При использовании защитного газа технологическое оборудование практически такое же, как при дуговой сварке в среде защитного газа. С помощью специальных фидеров, чувствительных к напряжению, можно выполнять высококачественную сварку порошковой проволокой с источником сварочного тока постоянного тока. Этот процесс подходит для сварки во всех положениях с правильным выбором присадочного металла и параметров.
Дуговая сварка металлическим электродом в среде защитного газа (GMAW) – также называется сваркой в среде инертного газа (MIG).
GMAW — это процесс дуговой сварки, который включает в себя автоматическую подачу непрерывного сплошного плавящегося электрода, обычно защищенного подачей газа извне. Этот процесс используется для сварки металлов, таких как сталь, алюминий, нержавеющая сталь и медь, и может использоваться для сварки в любом положении при выборе соответствующих параметров сварки и оборудования. GMAW использует положительную полярность электрода постоянного тока (DCEP), а оборудование обеспечивает автоматическое управление дугой. Сварщик должен выполнять только ручное управление позиционированием горелки, направлением и скоростью перемещения. В этом процессе присадочный металл хранится на катушке и перемещается роликами (ток подается в проволоку) через трубу в «факел». Большое количество присадочной проволоки на катушке означает, что процесс можно считать непрерывным, и можно легко выполнять длинные непрерывные сварные швы. Инертный газ также подается по трубе в горелку и существует вокруг проволоки. Между проволокой и заготовкой зажигается дуга, и из-за высокой температуры дуги почти мгновенно образуется сварочная ванна.
При этом ключевыми вопросами являются выбор правильной газовой смеси, ее расхода, скорости сварочной проволоки и силы тока. После того, как они будут установлены, требуемый уровень квалификации будет ниже, чем при использовании кислородно-ацетиленового процесса. Процесс можно легко автоматизировать. Сварка GMAW в настоящее время обычно выполняется роботами. Процесс сварки GMAW широко используется для стали и алюминия. Хотя защитный слой из инертного газа поддерживает чистоту сварного шва, в зависимости от настроек процесса могут быть брызги металлических шариков рядом со сварным швом, которые ухудшают его внешний вид, если их не удалить.
Тандемная сварка — по сравнению с обычной системой GMAW, тандемная сварка использует две проволоки, расположенные одна за другой. Сварочная проволока подается одновременно и плавится с помощью независимых контактных наконечников, установленных в одной горелке. Результатом является превосходное качество сварки с небольшим разбрызгиванием и до трех раз большей скоростью наплавки и скоростью перемещения по сравнению с обычными системами.
Процесс имеет идеальные характеристики для автоматизированных приложений.
Вольфрамовая сварка в среде инертного газа (TIG) или дуговая сварка вольфрамовым электродом (GTAW ) — это процесс ручной сварки, в котором используется неплавящийся вольфрамовый электрод, смесь инертных или полуинертных газов и отдельный присадочный материал. Особенно полезный для сварки тонких материалов, этот метод характеризуется стабильной дугой и высоким качеством сварных швов, но требует значительных навыков оператора и может выполняться только на относительно низких скоростях. В этом процессе используется неплавящийся вольфрамовый электрод, и между ним и поверхностью заготовки зажигается дуга. GTAW можно использовать практически для всех свариваемых металлов, хотя чаще всего он применяется для нержавеющей стали и легких металлов. Он часто используется, когда качество сварных швов чрезвычайно важно.
Плазменно-дуговая сварка (PAW) – PAW является разновидностью GTAW. В процессе используется вольфрамовый электрод, но для создания дуги используется плазменный газ.
Дуга более концентрированная, чем дуга GTAW, что делает поперечный контроль более важным и, таким образом, в целом ограничивает технику механизированным процессом. Процесс сужения значительно увеличивает напряжение дуги и степень ионизации. Помимо повышения температуры дуги, самая горячая область плазмы выходит за пределы сопла вниз к рабочей поверхности. Общий результат — более концентрированный источник тепла при более высокой температуре, что значительно повышает эффективность теплопередачи, позволяя увеличить скорость движения. При ручном использовании требуется высокий уровень квалификации оператора. Из-за стабильного тока этот метод можно использовать для материалов с более широким диапазоном толщин, чем метод GTAW. Это намного быстрее и может быть применено ко всем материалам, как в GTAW, кроме магния. Одним из важных применений процесса является автоматизированная сварка нержавеющей стали.
Лазерная сварка (LBW) – LBW представляет собой автоматизированный процесс, использующий тепло от концентрированного луча когерентного света для соединения двух материалов.
Этот процесс используется для сварки всех металлов, включая сталь, нержавеющую сталь, алюминий, титан, никель и медь, и обеспечивает высокие механические свойства и скорость перемещения, малую деформацию, отсутствие шлака или брызг. Сварные швы могут выполняться с присадочным металлом или без него, и во многих случаях для защиты расплавленной ванны используется защитный газ. Используемое оборудование требует значительных капиталовложений и высокого уровня квалификации оператора из-за очень высоких скоростей сварки и малой площади воздействия лазерного луча,
Электросварка сопротивлением – это процесс сварки не плавлением. Тепло выделяется, когда сильный электрический ток проходит через небольшую площадь двух контактирующих металлических поверхностей. Выделяемое тепло H определяется выражением H = I² × R × t, где I — ток, R — сопротивление поверхности раздела, а t — время приложения тока. Когда повышение температуры является достаточным, на нагретую поверхность прикладывается большое давление для образования сварного соединения.
Переменными процесса являются ток, время приложения тока, давление, продолжительность приложения давления, свариваемые материалы и их толщина. Существует пять основных видов контактной сварки. Это (i) точечная сварка, (ii) шовная сварка, (iii) рельефная сварка, (iv) стыковая сварка с осадкой и (v) стыковая сварка оплавлением.
- Точечная сварка. При точечной сварке свариваемые пластины располагаются одна над другой после очистки двух соприкасающихся поверхностей. По обеим сторонам пластины располагаются два штыревых электрода. К электродам прикладывается давление, которое поддерживается в течение определенного интервала времени, известного как время сжатия, перед началом дальнейшей работы. Затем ток пропускают через электроды. Время приложения тока, известное как время сварки, измеряется количеством циклов. Давление сохраняется и в это время. После отключения тока давление поддерживается в течение короткого времени, известного как время выдержки, так что нагретый металл затвердевает и образует сварной шов.
По истечении времени выдержки давление будет сброшено, и перед началом следующей операции точечной сварки будет дано время отключения. Слишком большой ток вызывает отрыв сварного шва, кавитацию и растрескивание сварного шва, снижение механических свойств и застревание электрода в поверхности. С другой стороны, меньший ток приводит к неплавлению поверхности и плохому сварному шву. Высокое давление увеличивает контакт и уменьшает контактное сопротивление, поэтому выделяется меньше тепла. Это может привести к деформации и сокращению срока службы электрода. Большее время подачи тока может привести к вскипанию, пористости, росту самородков до поверхности электрода. Проводимость материалов играет важную роль в определении толщины пластин, которые можно легко сваривать точечной сваркой. Точечная сварка высокоуглеродистых сталей требует термической обработки после сварки (PWHT). Преимуществами точечной сварки являются ее приспособленность к массовому производству, высокая скорость работы, чистота, отсутствие сварочных стержней и меньшая эксплуатационная квалификация.
Материалы, обладающие высокой тепло- и электропроводностью, плохо поддаются сварке точечной сваркой и требуют специальной технологии.
- Шовная сварка – При шовной сварке используются электроды роликового типа. Ролики вращаются по ходу сварки. Контролируя подачу питания, можно добиться хорошего контроля нагрева. Шов охлаждается под давлением через определенные промежутки времени. Сварной шов имеет меньше поверхностных нарушений. По мере сварки подаваемый ток пытается пройти через уже сваренный участок, тем самым уменьшая нагрев свариваемого участка. Одним из способов преодоления этой трудности является увеличение силы тока по ходу сварки. Иногда используется внешний нагрев, такой как высокочастотный нагрев, чтобы компенсировать эффект пониженного тока из-за шунтирования. Во время сварки выделяется большое количество тепла, поэтому ролики необходимо охлаждать с помощью устройств водяного охлаждения, чтобы избежать деформации роликов. Прерывание тока также может быть использовано таким образом, что ток течет в течение определенного времени для подачи необходимого тепла к сварному шву, а затем прекращается на другой заданный период времени до начала следующей точечной сварки.
Таким образом также контролируется нагрев роликов. Шовную сварку можно проводить на сталях, алюминиевых, магниевых и никелевых сплавах и не рекомендуется для меди и ее сплавов. Высокочастотная шовная сварка подходит для оребренных труб и других труб.
- Выступающая сварка – аналогична точечной сварке, за исключением того, что сварка выполняется в тех местах материала, где для этой цели сделаны выступы. Проекции создаются нажатием на выбранные места листа. Сопротивление нагреву, заключенному в свариваемых выступах между деталями, обеспечивается приложением соответствующего давления в соответствующее время в этих точках контакта. Выступающая сварка особенно применима в массовом производстве и вполне подходит там, где требуется много точечных сварных швов в ограниченном пространстве. Этот метод сварки используется при сварке кронштейнов, тяжелых стальных штамповок, при герметизации тиристоров и т. д.
- Стыковой шов с осадкой. Стыковой шов с осадкой получается путем соединения двух металлических частей вплотную друг к другу под давлением с последующим пропусканием тока от одной части к другой.
Контактные поверхности должны быть максимально гладкими. При сварке с осадкой (а также при стыковой сварке оплавлением) получается кузнечная структура в отличие от литой структуры, получаемой при точечной и рельефной сварке. Приварка инструментов к хвостовику осуществляется сваркой осадкой. Для соединения труб используется контактная стыковая сварка
- Стыковая сварка оплавлением. В этом методе сварки две свариваемые детали прижимаются друг к другу с применением давления, так что контакт происходит в точках из-за шероховатости поверхности. Пропускается большой сварочный ток. Поверхности нагреваются до расплавленного состояния, и по мере того, как одна деталь медленно приближается к другой, расплавленный металл испаряется. После того, как грани достигают стадии пластичности, применяется осадочное давление, приводящее к склеиванию двух граней. Стыковая сварка оплавлением отличается от контактной сварки давлением в том смысле, что в этом сварном шве контакты между двумя поверхностями осуществляются в какой-то момент только из-за шероховатости поверхности.
При стыковой сварке сопротивлением предпочтительна гладкая поверхность полного контакта.
В этом методе сварки поверхностные загрязнения удаляются брызгами во время оплавления, а расплавленный металл выбрасывается на заключительном этапе операции ковки. На сварном шве образуется небольшой ребр, состоящий из оставшегося расплавленного металла и оксидов. Этот плавник можно обрезать шлифовкой. Преимущество этого процесса заключается в том, что расплавленный металл и дуга обеспечивают эффективную защиту пластичного металла, который в конечном итоге образует сварной шов, так что можно избежать опасности окисления.
Прикладываемое давление в холодном (без предварительного нагрева) состоянии зависит от типа материала. При предварительном нагреве прикладываемое давление может быть снижено примерно до половины нормального значения. Стыковая сварка оплавлением легко применяется к высоколегированным сталям, которые не могут быть удовлетворительно сварены другими способами.
Электрошлаковая сварка (ЭШС) – ЭШС обеспечивает хорошую производительность и качество при изготовлении тяжелых конструкций и сосудов высокого давления.
Металл шва в процессе ЭШС получают сплавлением электродной проволоки под слоем флюса. Теплота для плавления получается как теплота сопротивления при прохождении тока через шлаковую ванну, покрывающую всю поверхность металла шва. Между кромками свариваемых деталей и подвижными формовочными башмаками образуется лужа расплавленного шлака. Металлический электрод погружают в расплавленный шлак. Ток, проходящий через электрод и расплавленный шлак, нагревает ванну шлака. Температура плавления шлака выше, чем у проволоки и основного металла. Следовательно, электродная проволока плавится, а расплавленный металл оседает на дно шлаковой ванны и затвердевает, образуя металл сварного шва. Для стабильной сварки необходимо, чтобы шлаковая ванна сохраняла свою температуру.
При ЭШС шлаковая ванна имеет глубину 40-50 мм и обеспечивает токопроводящий путь между электродом и основным металлом. Таким образом, ток сохраняется после гашения дуги. Напротив, в случае SAW, который похож на ESW, дуга остается стабильной под расплавленным шлаком, так как напряжение дуги составляет около 25-30 В, а слой шлака довольно неглубокий.
В ESW используются как нерасходуемые, так и расходуемые направляющие. В методе нерасходуемой направляющей используется контактная трубка, которая направляет проволочный электрод в шлаковую ванну. Сварочная головка плавно движется вверх вместе с башмаками по мере наплавки. В расходуемой направляющей используется расходуемая трубка. Сварочная головка остается неподвижной в верхней части соединения. Ось шва вертикальна. Сварочный аппарат перемещается вверх в соответствии со скоростью наплавки. Количество шлака остается постоянным. В шлак необходимо добавить небольшое количество флюса. Когда сварка завершена, сварочный аппарат можно убрать. Выбранная сварочная проволока должна соответствовать основному материалу.
Процесс ЭШО полностью непрерывен, поэтому производительность выше. Подготовка кромок соединяемых деталей не требуется. Будет экономия на количестве присадочного металла и флюса. После процесса сварки свариваемые детали нуждаются в термообработке. Процесс должен быть непрерывным и не должен прерываться.
В случае прерывания расплавленный металл будет сжиматься, образуя полость в центре. Обычные дефекты сварки, такие как шлаковые включения, пористость, подрезы, надрезы и т. д., в процессе ЭШС не встречаются.
Индукционная сварка давлением – Это сварка в твердой фазе, полученная с использованием высокочастотного индукционного нагрева и одновременного приложения давления. Окисления можно избежать путем продувки газообразным водородом. Соединяемые поверхности нагреваются индукционным током, создаваемым катушкой индуктивности, соединенной последовательно с двумя конденсаторами, питаемой от трансформатора с двумя высокочастотными генераторами переменного тока. Индуцированный ток течет по продольной петле вдоль свариваемых кромок, нагревая их равномерно по толщине на определенной длине. Ковочные валки, затем сваривают оплавленные кромки, оставляя небольшой внешний заусенец, который затем удаляют. Нормальная скорость сварки зависит от подаваемой мощности. Индукционная сварка давлением широко используется для соединения труб из котельной хромомолибденовой стали.
Электронно-лучевая сварка (ЭЛС) – Электронно-лучевая сварка – это процесс, в котором тепло, необходимое для плавления, получается в результате воздействия высокоскоростного потока электронов высокой плотности на заготовку. При ударе кинетическая энергия электронов преобразуется в тепловую энергию, вызывая как испарение, так и плавление. Испарение материала под балкой позволяет лучу проникать в свариваемый материал, при этом луч и пар образуют отверстие. При движении луча вдоль стыка расплавленный металл обтекает отверстие, выходя из сварного шва вслед за лучом. EBW имеет отношение глубины к ширине более 10:1 из-за чрезвычайно высокой концентрации тепла. Луч очень узкий, а скорость сварки высокая. Полезная тепловая нагрузка очень низкая.
Эмиттер электронов представляет собой катодно-анодную систему в камере с очень высоким вакуумом. Катод делается из тантала или вольфрама и нагревается примерно до 2560°С. Таким образом, вблизи его поверхности создается электронное облако.
Рядом с катодом закреплен металлический экран, который делает электрическое поле более резким и регулирует поток электронов. Электрическое поле между катодом и анодом ускоряет электроны и освобождает их со значительной энергией. Таким образом создается электронный луч, который падает на свариваемые детали. Магнитные линзы используются для фокусировки луча на заготовке. Магнитные катушки также используются для отклонения луча и управления пятном луча на заготовке.
Скорость сварки, которая зависит от ширины и глубины шва, должна контролироваться надлежащим образом. В противном случае это приводит либо к неполному провару, либо к перегреву. Поскольку зона сплавления в сварном соединении очень узкая, в основном материале возникают очень небольшие нарушения. Необходимый расчетный допуск на усадку невелик по сравнению с другими методами дуговой сварки, и остаточные напряжения, возникающие в компоненте, также малы. Поскольку фокусное расстояние системы EB довольно велико, EB-пистолет может быть размещен на расстоянии до одного метра от обрабатываемых деталей, в отличие от электродуговой или плазменно-струйной сварки.
Таким образом, с помощью ЭЛС возможна сварка узких и ограниченных участков. Сварку можно выполнять в широком диапазоне толщин (от 0,1 мм до 100 мм), а разнородные металлы можно легко сваривать благодаря точному контролю температуры. Скорость сварки ЭП значительно выше электродуговых методов, что позволяет сократить время сварки. Также повторяемость сварных швов EB высока по сравнению с другими процессами.
Сварка взрывом (EW) – EW представляет собой процесс, основанный на контролируемом применении огромной мощности, генерируемой детонирующими взрывчатыми веществами. Поверхности соединяемых деталей должны быть чистыми, без загрязнения окислами и т. д. Эти чистые поверхности прессуются под давлением порядка миллиона кг/кв. см, создаваемым взрывчатым веществом. Комбинация разнородных металлов — алюминия со сталью или титана со сталью — может быть легко получена с помощью этого процесса. Металлы, которые слишком хрупкие, чтобы выдержать воздействие взрыва, не могут быть сварены этим процессом.
EW – это хорошо подходящий процесс для нанесения плакирования. Верхнего предела толщины подложки нет.
Сварка трением (FW) – Трение между двумя поверхностями сварки используется для создания тепла до такой степени, что материал на двух поверхностях становится пластичным. Сварка осуществляется приложением осевого усилия. Процесс сварки трением делится на два различных режима, а именно (i) сварку трением с обычным приводом и (ii) сварку инерцией.
При обычной приводной сварке трением детали выравниваются по оси. Один компонент вращается с постоянной скоростью с помощью прямого привода, в то время как другой приводится в контакт с каркасом под действием осевого давления. Для выработки тепла дается достаточно времени, чтобы температура поверхности раздела сделала материал пластичным и позволила ковать компоненты вместе. На этом этапе вращение быстро останавливают, в то время как давление все еще сохраняется для консолидации сустава.
Хотя основной принцип тот же, при инерционной сварке кинетическая энергия вращающейся системы маховиков используется для нагрева поверхностей свариваемых компонентов.
Один компонент прикреплен к маховику, вращающемуся с высокой скоростью. Другой компонент помещается лицом к первому, так что трение между ними генерирует тепло. Энергия маховика используется для получения хорошей связи между компонентами.
Основными переменными в этом процессе являются относительная скорость, давление нагрева и ковки и продолжительность нагрева. Второстепенными факторами являются повышение давления при нагреве и ковке, замедление при торможении и свойства свариваемого материала. Периферийные скорости в диапазоне от 75 до 105 метров в минуту дают удовлетворительные сварные швы. Слишком высокая скорость может привести к расширению ЗТВ. Более низкие скорости не смогут генерировать достаточное количество тепла и поднять температуру до необходимого уровня. Давление ковки зависит от горячей прочности свариваемого сплава. Выбранное давление должно быть достаточным для сварки поверхностей. Продолжительность времени нагрева зависит от скорости вращения, трения и давления.
Время нагрева определяет тепловложение. Стали всех сортов, нержавеющие стали, медь и ее сплавы легко свариваются методом сварки трением.
Диффузионное соединение (DB) – DB представляет собой процесс соединения, который требует высокой температуры для улучшения диффузии, но включает очень небольшую макроскопическую деформацию. Соединение формируется без присадочного металла, а микроструктура и состав на границе раздела такие же, как у основных металлов. Прикладывается давление, вызывающее локальную пластическую деформацию и деформацию ползучести при температуре эксплуатации. Склеивание происходит за счет диффузии и зависит от температуры, времени и приложенного давления. Для улучшения характеристик склеивания можно использовать межслойную фольгу или покрытие. Рекристаллизация и миграция границ зерен на границе раздела происходят на заключительных стадиях склеивания, и эти процессы необходимы для получения высокопрочных соединений и устранения плоской границы раздела.
Давление можно прикладывать к соединяемым поверхностям через плиту. Для достижения того же можно использовать давление газа. Для сохранения чистоты поверхности склеивание можно проводить в вакууме. Если для приложения нагрузки используется давление газа, то можно использовать газовую камеру с аргоном. Важными переменными, влияющими на качество соединения, являются (i) шероховатость поверхности и (ii) поверхностные оксидные пленки. Ниже приведены основные преимущества БД.
- Прочность соединения может приближаться к прочности основного металла.
- Спеченные изделия, разнородные материалы, включая металл и керамику, могут быть соединены этим процессом.
- Склеивание предполагает минимальную деформацию и деформацию, поэтому возможен тщательный контроль размеров.
- В соединениях металлокерамики остаточные напряжения могут быть снижены за счет нескольких прокладок.
- Тонкие листы мелкозернистых сверхпластичных материалов можно легко соединить и придать им любую желаемую форму и контур путем диффузионной сварки.
- . Held Held Held Held Held Helding Held Supending, который очень необходим для безопасного рабочего