1.2. Классификация и маркировка чугунов.
В зависимости от состояния углерода в чугуне, различают: белые, серые, высокопрочные, ковкие чугуны и чугуны с вермикулярным графитом.
Белыми называют чугуны, в которых весь углерод находится в связанном состоянии в виде цементита (карбид железа).
В остальных видах чугунов (серые, высокопрочные, ковкие, с вермикулярным графитом) углерод в значительной степени или полностью находится в свободном состоянии в виде графита.
В серых чугунах – в пластинчатой или червеобразной форме; в высокопрочных – в шаровидной форме, в ковких – в хлопьевидной форме. Чугуны с вермикулярным графитом имеют две формы графита – шаровидную (до 40%) и вермикулярную (в виде мелких тонких прожилок).
Чугуны
маркируют двумя буквами, обозначающих
разновидность чугуна, и двумя цифрами,
соответствующими минимальному значению
временного сопротивления σ Серый чугун обозначают буквами «СЧ»
(ГОСТ 1412-85), высокопрочный — «ВЧ»
(ГОСТ 7293-85), ковкий — «КЧ» (ГОСТ
1215-85), чугун с вермикулярным графитом
– ЧВГ (ГОСТ 28384 -89):
СЧ 10 — серый чугун с пределом прочности при растяжении 100 МПа;
ВЧ 70 — высокопрочный чугун с пределом прочности при растяжении 700 МПа;
КЧ 35 — ковкий чугун с пределом прочности при растяжении 350 МПа;
ЧВГ 40 – чугун с вермикулярным графитом с пределом прочности при растяжении 400 МПа.
Различают еще чугуны с особыми свойствами:
антифрикционные чугуны (ГОСТ 1585-85) – обозначаются первыми буквами АЧ и порядковым номером, например,
АЧС-1 – антифрикционный серый чугун с порядковым номером марки 1;
АЧВ-2 – антифрикционный высокопрочный чугун с порядковым номером марки 2;
АЧК-2 – антифрикционный ковкий чугун с порядковым номером марки 2;
жаростойкие чугуны (ГОСТ 7769 – 82) – обозначаются буквами ЖЧ, после которых идет буквенное обозначение легирующих элементов (Н – никель, Д – медь и др.
, аналогично обозначению легирующих элементов в стали) и цифры, указывающие концентрацию элементов в %%; например,
ЖЧХ-2,5 – жаростойкий чугун хромистый с содержанием хрома 2,5%;
ЖЧС-5,5 – жаростойкий чугун, легированный кремнием с содержанием 5,5%;
2. Классификация и маркировка цветных металлов и сплавов.
2.1. Алюминий и алюминиевые сплавы.
Алюминий
– металл серебристо-белого цвета в
изломе, легкий (имеет малую плотность
2,7 г/см
В зависимости от степени чистоты алюминий согласно ГОСТ 11069-74 бывает особой (А999), высокой (А995, А95) и технической чистоты (А85, А7Е, АО и др.).
Алюминий
маркируют буквой «А» и цифрами,
обозначающими доли процента свыше
99,0% алюминия. Буква «Е» обозначает
повышенное содержание железа и пониженное
кремния.
Примеры:
А999 — алюминий особой чистоты, в котором содержится не менее 99,999% алюминия;
А5 — алюминий технической чистоты, в котором 99,5% алюминия. Алюминиевые сплавы разделяют на деформируемые и литейные. Те и другие могут быть не упрочняемые и упрочняемые термической обработкой.
Деформируемые алюминиевые сплавы хорошо обрабатываются прокаткой, ковкой, штамповкой. Их марки приведены в ГОСТ 4784-74. К деформируемым алюминиевым сплавам, не упрочняемым термообработкой, относятся сплавы системы алюминий-марганец (Al–Mn) и алюминий-магний (Al–Mg): AМц; АМг1; АМг4,5; АМг6. Аббревиатура включает в себя начальные буквы, входящих в состав сплава компонентов, и цифры, указывающие содержание легирующего элемента в процентах.
К
деформируемым алюминиевым сплавам,
упрочняемым термической обработкой,
относятся сплавы системы Al-Cu-Mg
с добавками некоторых элементов
(дуралюмины, ковочные сплавы), а также
высокопрочные и жаропрочные сплавы
сложного хим.
Чистый деформируемый алюминий обозначается буквами «АД» и условным обозначением степени его чистоты: АДОч (не менее 99,98% Al), АДООО (не менее 99,80% Аl), АДО (99,5% Аl), АД1 (99,30% Al), АД (не менее 98,80% Аl).
Литейные алюминиевые сплавы (ГОСТ 2685-75) обладают хорошей жидкотекучестью, имеет сравнительно не большую усадку и предназначены в основном для фасонного литья. Эти сплавы маркируются буквами «АЛ» с последующим порядковым номером: АЛ2, АЛ9, АЛ13, АЛ22, АЛЗО.
Иногда маркируют по составу: АК7М2; АК21М2,5Н2,5; АК4МЦ6. В этом случае «М» обозначает медь. «К» — кремний, «Ц» — цинк, «Н» — никель; цифра — среднее % содержание элемента.
Из
алюминиевых антифрикционных сплавов
(ГОСТ 14113-78) изготовляют подшипники и
вкладыши, как литьем, так и обработкой
давлением.
Чугуны, классификация чугунов, свойства
Чугун – сплав железа с углеродом, в котором углерода больше 2.14%.
Рис. 11. Классификация чугунов
Белый и серый чугун. Серый и белый чугуны резко различаются по свойствам. Белые чугуны очень твердые и хрупкие, плохо обрабатываются режущим инструментом, идут на переплавку в сталь и называются передельными чугунами. Часть белого чугуна идет на получение ковкого чугуна.

Серый
чугун получают при добавлении в
расплавленный металл веществ,
способствующих распаду цементита и
выделению углерода в виде графита. Для
серого чугуна графитизатором является
кремний. При введении в сплав кремния
около 5% цементит серого чугуна практически
полностью распадается и образуется
структура из пластичной ферритной
основы и включений графита. С уменьшением
содержания кремния цементит, входящий
в состав перлита, частично распадается
и образуется ферритно-перлитная
структура с включениями графита. При
дальнейшем уменьшении содержания
кремния формируется структура серого
чугуна на перлитной основе с включениями
графита.
Механические свойства серых чугунов зависят от металлической основы, а также формы и размеров включений графита. Наиболее прочными являются серые чугуны на перлитной основе, а наиболее пластичными —серые чугуны на ферритной основе. Поскольку графит имеет очень малую прочность и не имеет связи с металлической основой чугуна, полости, занятые графитом, можно рассматривать как пустоты, надрезы или трещины в металлической основе чугуна, которые значительно снижают его прочность и пластичность. Наибольшее снижение прочностных свойств вызывают включения графита
По
физико-механическим характеристикам
серые чугуны условно можно разделить
на четыре группы: малой прочности,
повышенной прочности, высокой
прочности и со специальными свойствами.
Легированный серый чугун имеет мелкозернистую структуру и лучшее строение графита за счет присадки небольших количеств никеля и хрома, молибдена и иногда титана или меди.
Модифицированный
серый чугун имеет однородное строение
по сечению отливки и более мелкую
завихренную форму графита. Химический
состав шихты для изготовления
модифицированного чугуна подбирают
таким, чтобы обычный модифицированный
чугун затвердевал бы в отливке с отбелом
(т.е. белым или половинчатым). Модификаторы
— ферросилиций, силикоалюминий,
силикокальций и др. — добавляют в
количестве 0,1 —0,3% от массы чугуна
непосредственно в ковш во время его
заполнения. В структуре отливок из
модифицированного серого чугуна не
содержится ледебуритного цементита.
Вследствие малого количества вводимого
в чугун модификатора его химический
состав практически остается неизменным.
Жидкий модифицированный чугун необходимо
немедленно разливать в литейные
формы, так как эффект модифицирования
исчезает через 10—15 мин.
Высокопрочный чугун. Механические свойства высокопрочного чугуна позволяют применять его для изготовления деталей машин, работающих в тяжелых условиях, вместо поковок или отливок из стали. Из высокопрочного чугуна изготовляют детали прокатных станов, кузнеч но-прессового оборудования, паровых турбин (лопатки направляющего аппарата), тракторов, автомобилей (коленчатые валы, поршни) и др. Так, например, коленчатый вал легковой автомашины «Волга» изготовляют из высокопрочного чугуна следующего состава: 3,4-3,6% С; 1,8-2,2% Si; 0,96-1,2% Mn; 0,16-0,30% Cr; <0,01 % S; <0,06% P и 0,01-0,03% Mg. Низкое содержание серы и фосфора и небольшие пределы содержания других химических элементов обеспечиваются тем, что такой чугун выплавляют не в вагранке, а в электрической печи. После термической обработки механические свойства чугуна получаются весьма высокими: Ов= 620-650 МПа; §= 8-12 % и твердость НВ = 192-240.
Ковкий
чугун. Ковкий чугун — условное название более
пластичного чугуна по сравнению с серым. Ковкий чугун никогда не куют. Отливки
из ковкого чугуна получают длительным
отжигом отливок из белого чугуна с
перлитнс-цементитной структурой. Толщина
стенок отливки не должна превышать
40—50 мм. При отжиге цементит белого
чугуна распадается с образованием
графита хлопьевидной формы. У отливокс
толщиной стенокболее 50 мм при отжиге
будет образовываться нежелательный
пластинчатый графит.
Ковкий
чугун широко применяют в автомобильном,
сельскохозяйственном и текстильном
машиностроении. Из него изготовляют
детали высокой прочности, способные
воспринимать повторно-переменные и
ударные нагрузки и работающие в
условиях повышенного износа, такие как
картер заднего моста, тормозные колодки,
ступицы, пальцы режущих аппаратов
сельскохозяйственных машин, шестерни,
крючковые цепи и др. Широкое распространение
ковкого чугуна, занимающего по
механическим свойствам промежуточное
положение между серым чугуном и сталью,
обусловлено лучшими по сравнению со
сталью литейными свойствами белого
чугуна, что позволяет получать отливки
сложной формы. Ковкий чугун характеризуется
достаточно высокими антикоррозионными
свойствами и хорошо работает в среде
влажного воздуха, топочных газов и воды.
Чугуны со специальными свойствами. Такие чугуны используют в различных отраслях машиностроения тогда, когда отливка, кроме прочности, должна обладать теми или иными специфическими свойствами (износостойкостью, химической стойкостью, жаростойкостью и т. п.). Из большого количества чугунов со специальными свойствами приведем в качестве примеров следующие.
Магнитный чугун используют для изготовления корпусов электрических машин, рам, щитов и др. Для этой цели наилучшим является ферритный чугун с шаровидным графитом.
Немагнитный
чугун используют для изготовления
кожухов и бандажей различных электрических
машин. Для этого применяют
никеле-марган-цовистый чугун, содержащий
7-10% Мп и 7-9%
Ni,
а также марганцево-меднистый чугун, в
котором содержится 9,8% Мn
и 1,2-2,0% Си.
Жаростойкий чугун — чугаль содержит 20-25% А1.
К чугунам со специальными свойствами относят также упомянутые ранее ферросплавы — ферромарганец, ферросилиций и т.д., предназначенные для раскисления и легирования стали при ее выплавке.
Классификация легированных чугунов
ГЛАВНАЯ > Блог
Чугун с общим сплавом можно разделить на три категории: износостойкий чугун, жаропрочный чугун и коррозионностойкий чугун.
Износостойкий чугун можно условно разделить на две категории в зависимости от условий его работы: одна представляет собой антифрикционный чугун, который работает в условиях смазки, например направляющие станков, гильзы цилиндров, кольца и подшипники; другой — из несмазанных абразивных материалов. Износостойкие чугуны, которые работают в условиях износа, например, плуги, валки и детали шаровых мельниц. Антифрикционный чугун работает в условиях смазанного и адгезионного износа, например, рельсы станков, гильзы цилиндров двигателей, поршневые кольца, подшипники и т. Д. Структура антифрикционного чугуна обычно прочно заделана твердой упрочняющей фазой на мягкую матрицу. На основе обычного серого чугуна содержание фосфора увеличивают до 0,4-0,6% с образованием чугуна с высоким содержанием фосфора. Фосфор добавляли путем добавления феррофосфора, и он может образовывать фосфорную эвтектику (F+Fe3P, P+Fe3P или F+P+Fe3P) с ферритом или перлитом, которая распределяется на подложке прерывистой сеткой, образуя твердую фазу на мягкая подложка, что значительно повышает износостойкость чугуна. Износостойкий чугун работает в условиях сухого трения и абразивного изнашивания. Таких как валки, лемеха, мелющие шары и т.д. Этот вид чугуна не только сильно изнашивается, но и подвергается большим нагрузкам, и должен иметь высокую и равномерную твердость.
Белый чугун относится к этому типу чугуна. Однако он хрупок и не выдерживает ударных нагрузок. Его можно использовать только для изготовления лемехов, корпусов насосов, вкладышей для шлифовальных машин и мелющих шаров.
Жаропрочный чугун относится к чугуну с хорошей стойкостью к окислению и росту при высоких температурах. Изготовление деталей из высокотемпературного чугуна, таких как подовая плита печи, теплообменник, тигель, выпускная труба и форма для литья под давлением, должны быть изготовлены из жаропрочного чугуна. Обычно кремний, алюминий, хром и другие легирующие элементы добавляются в виде кремнеуглеродного сплава, слитка алюминия или феррохрома в чугун для повышения критической температуры чугуна для получения однофазной ферритовой матрицы для устранения явления роста, вызванного разложением цементита; обычно он также может образовывать плотную и устойчивую оксидную пленку, обладающую хорошим защитным эффектом, предотвращающим непрерывное окисление и рост чугуна. При добавлении сфероидизирующего агента и легирующих элементов, таких как хром и никель, графит способствует рафинированию и сфероидизации. Отключение шаровидного графита может предотвратить или уменьшить проникновение окисляющего газа в чугун.
В нефтехимической, судостроительной и других отраслях промышленности различные детали из чугуна, такие как арматура, трубы, корпуса насосов, емкости и т.п., часто работают в атмосфере, морской воде, кислоте, щелочи, соли и других средах, требующих высокой коррозионной стойкости. Стойкий к коррозии чугун может предотвратить или замедлить коррозию агрессивных сред. Коррозионностойкий чугун можно разделить на легированный чугун с высоким содержанием кремния, никелевый аустенитный чугун, чугун с высоким содержанием хрома, алюминиевый чугун, низколегированный чугун и т. д.
Типы чугуна (стр. 1), серый и ковкий чугун
Марки чугуна
Для большинства современных автомобильных и потребительских применений чугун делится на 4 отдельные категории:
- Серый чугун (эта страница)
- Высокопрочный чугун ( эта страница)
- Ковкий чугун с аустенитным отпуском (страница 2)
- Чугун с уплотненным графитом Страница 2)
В Северной Америке есть 2 промышленных общества, которые берут на себя ответственность за организацию и управление программами по регулированию и совершенствованию технологических процессов:
- Американское общество литейщиков (AFS)
- Общество ковкого чугуна (DIS)
Сравнение графита — микрофотографические исследования
Серый чугун — Пример микрофотографии Ковкий чугун — Пример микрофотографии Высокопрочный чугун с аустенитным отпуском – микрофотографияЧугун с уплотненным графитом – микрофотография Чугун представляет собой сплав железо-углерод-кремний, содержащий более 2% углерода, который заливают в форму, содержащую негатив желаемой окончательной формы. Механические свойства и поведение материала зависят от морфологии графита, который образуется в железной матрице в результате терморегулирования процесса и добавления элементов для получения желаемой формы графита. Все чугуны затвердевают в результате сложной эвтектической реакции, в которой участвуют Fe, C и Si. Есть также влияние Cu, Mn, S и P.
Серый чугун
Серый чугун — это самая простая, самая распространенная и самая дешевая форма чугуна в мире. Микроструктура железа характеризуется качествами «чешуйчатого графита» в виде: а) типа, б) размера и в) матрицы.
Серый чугун обладает превосходными свойствами литья и механической обработки, что делает его очень ценным для деталей, которые могут быть тяжелыми. Кроме того, серый чугун обладает превосходными демпфирующими и тепловыми свойствами, что делает его идеальным для автомобильных тормозных систем. Хотя он прочный, он также хрупкий.
Типы чешуйчатого графита
Серый чугун на сегодняшний день является наиболее распространенным из чугунов. Наряду со сталью это наиболее широко используемый инженерный сплав. В 1 веке автомобильной промышленности это был предпочтительный материал для блоков цилиндров, головок и многих других компонентов трансмиссии. Название происходит от внешнего вида поверхности излома, которая имеет серый цвет. В сером чугуне графит затвердевает в виде взаимосвязанных чешуек, как показано выше в 3D-микроскопии с помощью сканирующего электронного микроскопа. Сгруппированные формы графита сравнивают с картофельными чипсами, склеенными вместе в центральном месте. Центральная точка — исходное графитовое ядро. Каждый кластер чешуек определяет эвтектическую ячейку в сером чугуне. Эвтектические ячейки несколько аналогичны зернам в других металлах. Прочность железа повышается за счет более мелких размеров ячеек.
Форма графита в сером чугуне является важным фактором, определяющим свойства сплава. Форма и размер графита могут заметно различаться в зависимости от скорости охлаждения и содержания сплава. Наиболее распространенная форма, как описано в предыдущем абзаце, называется Type A . Пять типов графита в сером чугуне классифицируются как b ASTM.
Тип A Чешуйчатая структура
Графит типа A имеет равномерное распределение и случайную ориентацию. Как правило, он обеспечивает наилучшие свойства и обычно используется для компонентов трансмиссии.
Серый чугун — Тип АСтруктура чешуек типа B
Графит типа B выглядит как розетки со случайной ориентацией. Это чаще всего происходит в почти эвтектических сплавах, которые неправильно модифицированы и содержат очень мало зародышей графита. Графит типа B часто встречается на поверхности отливки, где в остальном он относится к типу A.
Серый чугун — тип BСтруктура чешуек типа C
Графит типа C встречается в заэвтектических чугунах (CE больше 4,3), в которых графит образуется в качестве первичной фазы. Этот первичный графит называется графитом Киша. Его присутствие снижает свойства при растяжении, что может быть желательным для некоторых специальных применений.
Серый чугун — Тип CСтруктура чешуек типа D
Графит типа D возникает в результате междендритной сегрегации в быстро охлажденных чугунах. Он состоит из мелких беспорядочно ориентированных чешуек между аустенитными дендритами. Тип D может привести к более высоким свойствам при растяжении, но может быть трудным для термической обработки из-за сегрегации.
Структура чешуек типа E
Графит типа E похож на тип D, но с ориентированными чешуйками между ветвями аустенитных дендритов. Чаще всего это происходит в чугунах с очень низким углеродным эквивалентом.
Серый чугун — Тип EРазмер чешуйчатого графита
В дополнение к типу графита ASTM установила спецификации для размера графита. Это определяется путем сравнения количества хлопьев на микрофотографии со 100-кратным увеличением со стандартной диаграммой.
Механические свойства серого чугуна Как правило, серый чугун имеет низкую прочность и очень низкую пластичность. Чешуйки графита действуют как крошечные внутренние трещины, которые создают усиление напряжения. Это позволяет трещинам очень легко распространяться по материалу, что снижает прочность, пластичность и ударную вязкость (вязкость разрушения). Серый чугун определяется номером класса, который соответствует номинальной прочности сплава на растяжение. Например, серый чугун класса 30, который был типичным для блока цилиндров, имеет номинальную прочность на растяжение 30 000 фунтов на квадратный дюйм (207 МПа). Поскольку серый чугун имеет очень низкую пластичность, предел текучести и процентное удлинение, эти свойства редко измеряются или указываются. Поскольку YTS и UTS настолько близки (удлинение менее 1%), серый чугун классифицируется как «хрупкий материал». Другой способ определения серого чугуна — по твердости материала. Общество инженеров-автомобилестроителей (SAE) опубликовало стандарт материала для чугуна SAE J431, учитывающий как свойства прочности на растяжение, так и свойства твердости. Кроме того, каждый автомобильный OEM-производитель имеет собственный набор стандартов, регулирующих свойства серого чугуна, и специальные методы испытаний, необходимые для измерения качества материала.
Прочность и твердость
Прочность и твердость серого чугуна зависит как минимум от четырех основных факторов:
- Углеродный эквивалент
- Содержание сплава
- Модификация
- Скорость затвердевания
- Скорость затвердевания 900 Углеродный эквивалент.
- Избегайте образования карбидов (цементит)
- Поощрение формирования графита
- Уменьшите сегрегацию
- Уменьшение ухудшения
- Улучшение Маханируемости
- . однородная структура
- Увеличение пластичности
- Извлечение Mg при конверсии = 20-25%
- Десульфурация основного сплава перед конверсией важна
- Реакция бурная и не рекомендуется для обеспечения безопасности
- Извлечение магния при конверсии = 40-45%
- Десульфуризация основного сплава перед конверсией важна
- Реакция бурная, но снижается, поскольку ковш глубже и имеет карман для обработки
- Все еще дымится во время конверсии и нуждается в вентиляционном колпаке
Конверсия промежуточного ковша
- Извлечение магния при конверсии = 60-65%
- Десульфурация основного сплава менее критична 90% от конверсии в открытом ковше
Конвертерный метод Джорджа Фишера
- Извлечение магния = 70% (используется магниевая стружка)
- Десульфурация основного сплава обычно не требуется
- Закрытый конверсионный сосуд содержит реакционную смесь
- Безопасен для больших объемов ковша
Конверсия в литейной форме
- Извлечение магния при конверсии = 70% (используется магниевая стружка)
- Десульфурация основного сплава менее критична реакция
- Обычно в сочетании с автоматическим разливочным ковшом для регулирования потока
Конверсия магния
Конверсия в разливочном ковше является наиболее распространенным методом конверсии и считается безопасным:
Извлечение Mg на 60-65%, низкое содержание дыма, снижение потерь углерода.Существуют и другие методы конверсии с различной степенью безопасности и эффективности извлечения магния: конверсия в открытом ковше (извлечение 20–25% Mg), конверсия в сэндвич-ковше (извлечение 40–45 Mg), конвертер Джорджа Фишера (извлечение 70% Mg), Конверсия в форме (извлечение 75% Mg)
Разливочный ковш — поперечное сечениеВыцветание магния
Еще одна проблема, связанная с образованием комков, заключается в выцветании Mg с течением времени, то есть в тенденции Mg постепенно испаряться (или окисляться) из раствора, когда поверхность ковша находится в контакте с воздухом. Когда Mg исчезает из состава сплава, уменьшается шаровидность, и механические свойства неожиданно меняются. Для предотвращения выгорания в открытом ковше сплав необходимо разливать в течение фиксированного промежутка времени (как правило, 10-12 минут). Однако при использовании закрытой автоматической разливочной станции этот срок может быть увеличен до часа, если используется инертный защитный газ для предотвращения контакта расплава с воздухом, тем самым предотвращая окисление магния.
Модификация
Последним этапом перед заливкой является модификация, которая также выполняется теми же методами, что и серый чугун. Как описано в разделе, посвященном серому чугуну, сплавы ферросилиция обычно добавляют в расплав непосредственно перед заливкой, чтобы обеспечить места для зародышеобразования графита. Более совершенные и более поздние методы инокуляции обеспечат более мелкое распределение конкреций и высокую плотность конкреций (количество конкреций на мм²). Количество узелков 200 и более часто указывается для более тонких срезов, но такого более высокого количества трудно достичь в толстых или тяжелых срезах.
Сравнительная таблица плотности конкреций из ковкого чугуна (100x)Ферритовые и перлитно-графитовые конструкции
Из-за высокой степени удлинения, достижимой для литого ферритного сорта ковкого чугуна, автомобильные конструкторы, ответственные за критически важные для безопасности конструкции шасси, предпочитают использовать ковкий чугун.
Для дизайнеров автомобилей ковкий чугун считается ценным материалом, потому что он дешевле, чем альтернативы, такие как кованая сталь, кованый алюминий или даже алюминиевые отливки, обработанные раствором. Благодаря высоким свойствам относительного удлинения и ударной вязкости, присущим литым конструкционным деталям из ковкого чугуна, конструкторы автомобильных шасси имеют низкозатратный производственный процесс, который позволяет их конструкциям пройти строгие требования к краш-тестам. Однако, когда эти же конструкторы рассматривают возможность снижения общего веса автомобиля, они начинают указывать более прочные марки ковкого чугуна. Однако в то же время конструкторы также требуют высокой пластичности, измеряемой % удлинения при обычных производственных испытаниях на растяжение. Таким образом, теперь у нас есть марки железа, которые зависят от некоторого количества перлита в морфологии железа для увеличения YTS, но при этом сохраняют удлинение > 8%. Поэтому тщательный анализ морфологии железа должен сочетаться с проверкой механических свойств, чтобы можно было строго контролировать химический состав сплава, чтобы получить ожидаемые результаты после извлечения образцов из литых деталей.
Металлографический анализ
Возможность оценки микроструктуры ковкого чугуна в литейном производстве особенно важна при использовании составов сплавов, в которые в сплав добавляют олово (Sn) или медь (Cu) с целью поднятия перлитных образований вокруг графитовых конкреций. Интерпретация этих типов микрофотографий и их корреляция с механическими свойствами очень важны для установления значимых пределов химического состава сплава, когда железо плавится и заливается на производственную линию.
Микроструктура пластин толщиной 2,5 мм: нелегированная – слева, легированная 0,5 % меди – справа. Нитал травленый.Изображение предоставлено для приведенных выше изображений микроструктуры:
Стефанеску, Дору М. и др., «Металлургия и механические свойства при растяжении тонкостенных чугунов с сфероидальным графитом», Международный журнал исследований литых металлов, 2003 г., том. 16 № 1-3.
https://www.researchgate.net/publication/260037434_The_Metallurgy_and_Tensile_Mechanical_Properties_of_Thin_Wall_Spheroidal_Graphite_IronsПерлитный ковкий чугун
Когда свойства удлинения не так важны, как YTS и UTS, обычно используются контролируемые добавки Cu и Sn для стимулирования образования перлита вокруг графитовых конкреций. Было обнаружено, что количество образовавшегося перлита пропорционально улучшенной прочности на растяжение с экспоненциальным уменьшением % удлинения.
Изображение предоставлено:
DIS Рисунок 3.16 Свойства при растяжении в зависимости от добавок Cu и Sn
Общество ковкого чугуна рис. 3.16
https://www.ductile.org/didata/Section3/Figures/pfig3_16.htmОтраслевые спецификации
На приведенной ниже диаграмме Общество автомобильных инженеров (SAE) публикует красивую диаграмму, в которой добавки к сплаву используются для изменения структуры от 100% феррита до повышения уровня перлита в морфологии железа.
SAE классифицирует материалы по UTS (минимальное ожидание) и ожидаемому % удлинения. Как показано на рисунке 3.16 DIS, % удлинения уменьшается экспоненциально, в то время как механические свойства увеличиваются логарифмически.
Изображение предоставлено для диаграммы выше:
Общество ковкого чугуна – РАЗДЕЛ XII. СПЕЦИФИКАЦИИ
https://www.ductile.org/didata/Section12/12intro.htmИспытания свойств на растяжение
Литейный цех по производству ковкого чугуна должен иметь возможность проводить более тщательные испытания образцов на растяжение, чем литейный цех по производству серого чугуна. Оценка ковкого чугуна в соответствии с любой основной технической спецификацией потребует измерения YTS, UTS, % удлинения, образцов для удара по Шарпи и твердости по Бринеллю. Таким образом, в дополнение к проведению спектрографического и металлографического анализа литейный цех должен иметь точный прибор для испытаний на растяжение.
Определение YTS (предела текучести при растяжении)
В связи с требованием высокой прочности при растяжении и минимальной потери пластичности, измеряемой в % относительного удлинения, особое внимание следует уделить испытаниям на растяжение как части производственного процесса.
Теперь у нас есть марки железа, которые зависят от некоторого количества перлита в морфологии железа для увеличения YTS, но при этом сохраняют удлинение > 8%. Поэтому тщательный анализ морфологии железа должен сочетаться с проверкой механических свойств, чтобы можно было строго контролировать химический состав сплава, чтобы получить ожидаемые результаты после извлечения образцов из литых деталей. Имея это в виду, определение YTS на основе метода смещения 0,2% должно основываться на использовании принятой интерпретации на основе программного обеспечения. Кроме того, все испытательные лаборатории, связанные с измерением свойств при растяжении для данной категории продуктов, должны сравнивать результаты с «циклическими» формами испытаний. Все задействованные лаборатории должны демонстрировать разумную взаимосвязь между объектами и операторами.
Дополнительная информация:
Таблица 1.
0 Структурные эффекты элементных добавок к чугуну
Элемент
ТипЭффект при затвердевании
Эффект во время
ЭвтектоидАлюминий
.
Сурьма
.
.
Висмут
.
.
Бор ≤ 0,15%
.
Бор > 0,15%
.
Хром
.
.
.
Медь
.
Марганец
.
Молибден
.
Никель
.
Кремний
.
Теллериум
.
.
.
Олово
.
.
Титан < 0,25%
.
ВанадийСильный графитизатор
.
Маленький эффект в использованном количестве
.
Карбидный промотор, но не карбидный формирователь
.
Сильный графитизатор
.
Твердосплавный стабилизатор
.
Сильный карбидный формирователь. Образует сложные карбиды, которые очень стабильны
.
Мягкий графитизатор
.
Мягкий твердосплавный формирователь
.
Мягкий твердосплавный формирователь
.
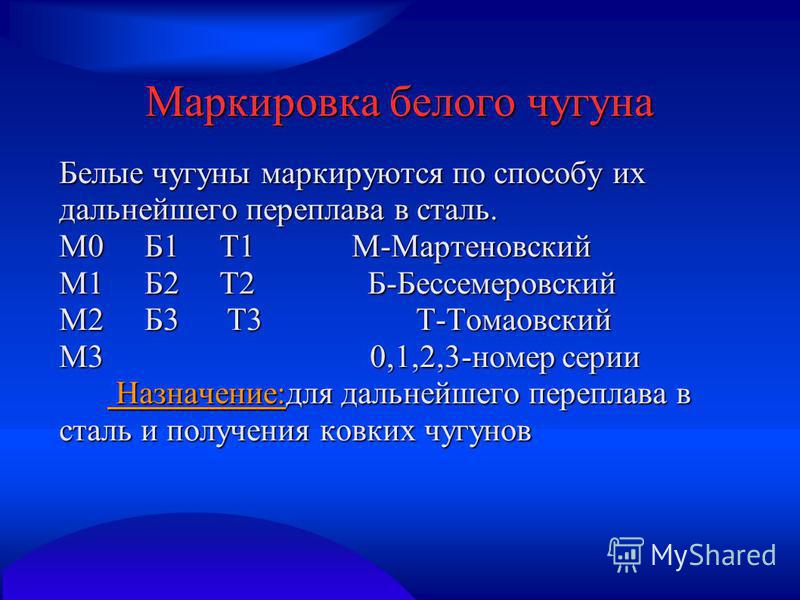
Углеродный эквивалент (CE)
Для чугуна формула углеродного эквивалента (CE) используется для понимания того, как легирующие элементы будут влиять на характеристики отливки. Он используется в качестве предиктора прочности чугуна, поскольку дает приблизительный баланс аустенита и графита в конечной структуре.
CE = %C + 0,33 (%Si) + 0,33 (%P) – 0,027 (%Mn) + 0,4 (%S)
CE < 4,3%, доэвтектическое поведение при затвердевании
CE = 4,3, эвтектическое поведение при затвердевании
CE > 4,3%, заэвтектическое поведение во время затвердевания
Содержание сплава
Наиболее эффективными элементами для серого чугуна являются углерод и кремний. Когда цель состоит в том, чтобы разлить чугун по эвтектике, чтобы предотвратить образование карбидов железа, можно использовать ковшовые добавки кремния для модификации расплавленного сплава, чтобы всегда достигался эвтектический эквивалент. Используя расчет CE и подтверждая соответствующее количество добавок ферросиликата, клиновидный блок используется для подтверждения того, что серый чугун находится на желаемом уровне CE.
Углерод и кремний
По сравнению с обычными марками стали содержание углерода в сером чугуне примерно в десять раз выше. Поскольку стальной лом составляет большую часть шихты расплава для чугунолитейного производства, углерод обычно приходится добавлять в какой-то момент процесса либо в основную шихту, либо после того, как железо находится в расплавленном состоянии. Поскольку в стальном шихтовом ломе очень мало углерода, металлургу необходимо учитывать все металлические шихтовые материалы (сталь, железный лом, чугун) в основной печи. Добавки, повышающие содержание углерода, в значительной степени зависят от метода плавки (плавка в вагранке с коксом приводит к повышению уровня углерода), количества используемого кремния и наличия дешевого графита. Однако по мере перехода чугунолитейной промышленности от вагранки к индукционной плавке с аналогичными высокими добавками стального лома в шихту требуются альтернативные добавки в ковше, в потоке или в литейной форме для получения чешуек типа А в сером чугуне.
Методы модифицирования
С переходом на индукционную плавку литейные заводы тщательно загружают в свои индукционные ковши тщательно взвешенные количества стального лома, лома железа и более дорогого чугуна. Сегодня большее количество низкоуглеродистой стали может быть получено за счет добавления модификаторов ферросилиция (FeSi). Процесс модифицирования включает добавление от 0,05 до 1% специального сплава FeSi, содержащего контролируемые количества одного или нескольких тщательно отобранных элементов для дальнейшего улучшения морфологии графита. Объяснение того, как эти тщательно отобранные элементарные добавки, включая Al, Ca, Ba, Sr, Ce, La, Mn, Bi, S, O и Zr, можно найти в Таблице 1.0 Структурные эффекты элементарных добавок к чугуну, показанной ниже. . В дополнение к повышению уровня кремния модификатор создает центры зародышеобразования, которые способствуют осаждению и росту графита, а также затвердеванию железа на основе стабильной системы Fe-C.
Когда необходимо приобрести углерод для добавления, дополнительный материал обычно имеет форму графита. Добавки графита часто поступают из угольных электродов, ранее использовавшихся в сталеплавильных печах.
Цель модифицирования
Целью модифицирования является стимулирование гетерогенного зародышеобразования графита путем введения элементов, образующих подходящие субстраты, которые будут действовать как зародыши и инициировать желаемое образование графита. Способствуя стабильному затвердеванию эвтектики, модифицирование позволяет C выходить из раствора в подходящей форме графита, а не в виде карбида железа.
с осторожным контролем, использование инокулятного добавления поможет:
Эффект модифицирования представлен на рисунке ниже (Эффект модифицирования), где кривые охлаждения для немодифицированного железа обозначены черной пунктирной линией, а для модифицированного железа указаны в виде синей сплошной линии.
Модифицирование может происходить при выпуске, в ковше, в потоке во время литья или даже внутри формы. Модифицирующие сплавы доступны в гранулированной форме, упакованы в проволоку или отлиты/прессованы в различные формы. Размер регулируется в зависимости от точки добавления, времени и температуры, доступных для растворения в расплавленном железе. Как правило, количество добавок может быть уменьшено, если модифицирование происходит как можно ближе к заливке чугуна в форму, поэтому модифицирование «в потоке» гранулами FeSi является наиболее распространенным методом добавления.
Эффект модифицирования
На кривых охлаждения для железа без модифицирования (черная пунктирная линия) и модифицированного железа (синяя сплошная линия) влияние проявляется как снижение степени переохлаждения до образования графита (красная стрелка). ). Модификация также продлевает образование и рост графита, тем самым увеличивая время затвердевания (зеленая стрелка).
Влияние прививки на кривую охлаждения Формы испытания на охлаждение — результаты показывают стабильность состава железа и обработки для предотвращения образования карбидов.
При промышленном производстве чугуна модифицируют как серый, так и ковкий чугун, но серый чугун обычно требует меньших модифицирующих добавок, в зависимости от состава железного сплава, метода плавки и состава шихты. Внесение ферросилиция преобразует структуру из переохлажденного графита (графит типа E в сером чугуне) в полностью чешуйчатый или сфероидальный графит, как показано ниже.
Влияние модифицирования на структуру графита в сером и ковком чугунеДругие элементы
Поскольку прочность чугуна зависит от содержания феррита по отношению к содержанию перлита, для повышения прочности добавляются легирующие элементы, подавляющие образование феррита и увеличивающие количество перлита. Для изучения аффектов был изучен ряд элементов и даны общие описания. Для этой цели используются легирующие элементы, такие как хром (Cr), молибден (Mo) и вольфрам (W). Эти элементы способствуют образованию карбидов и повышают твердость железа. Дополнительную информацию см. в Таблице 1.0 Структурные эффекты добавок элементов к чугуну, приведенной ниже.
Ковкий чугун
Ковкий чугун (также называемый графитом с шаровидным графитом и шаровидным графитом) прочнее серого чугуна, более прочен и намного дешевле для литья сложных деталей, чем формование стали. Микроструктура железа характеризуется качеством «Узловатость» (округлость), размером узелков и плотностью узлов (узелков на мм²).
Ковкий чугун считается прочным материалом для деталей шасси (например, сталь), если его морфология является ферритной. В то время как прочность может быть увеличена путем использования добавок к сплаву для продвижения перлита вокруг конкреций, результирующий % удлинения снижается.
Резюме
Ковкий чугун прочнее и пластичнее (жестче), чем серый чугун. Он образуется путем обработки железа с относительно высоким углеродным эквивалентом узелковым агентом, таким как магний (наиболее распространенный) или церий, для образования графитовых сфер, которые растут во время затвердевания. Наиболее распространены автомобильные детали, требующие высокой прочности и ударной вязкости при воздействии нагрузок, связанных с термоциклированием или ударами. Типы деталей включают: коленчатые валы, распределительные валы, выпускные коллекторы, поворотные кулаки, рычаги подвески, держатели дифференциала, пружинные хомуты и тому подобное. В сантехнике и трубопроводной промышленности использование ковкого чугуна стало большим достижением в производстве труб, соединений и клапанов, которые были менее дорогими, чем альтернатива из ковкого чугуна. При всех этих применениях ковкий чугун получает все большее применение, часто вытесняя конструкции из серого чугуна, так что можно добиться снижения веса за счет улучшенных механических свойств.
На ежегодной конференции AFS 1948 г. участникам конференции была представлена новая морфология железа: ковкий чугун. Создателем этого нового материала обычно считается Кит Миллс, однако в первоначальном патенте 1949 года, переданном Международной никелевой компании (INCO), указаны три человека: Кит Дуайт Миллис, Альберт Пол Ганнебин и Норман Боден Пиллинг. В своем патенте (US 2485760A) изобретателям приписывают изобретение «литого ферросплава для производства ковкого чугуна путем обработки магнием».
Являясь патентообладателем ковкого чугуна с обработкой магнием, INCO продвигала преимущества свойств материала и представляла ковкий чугун дизайнерам и инженерам, распространяя техническую литературу и проводя семинары. По мере распространения знаний о свойствах и экономичности ковкого чугуна его использование резко возросло в пятидесятых и начале шестидесятых годов. После прекращения продвижения INCO ковкого чугуна в 1966 году рост рынка ковкого чугуна продолжал опережать рост рынка литья других черных металлов, но по мере того, как инженеры и дизайнеры, которые извлекли выгоду из первых усилий INCO по продвижению, ушли на пенсию, их заменило новое поколение, которое не было ознакомились с технологией процесса из своей академической подготовки. По этой причине было создано Общество ковкого чугуна (DIS) для обучения и ликвидации разрыва в знаниях с новыми поколениями металлургов, инженеров-конструкторов и инженеров-технологов.
Десульфурация
Обработка ковкого чугуна имеет чрезвычайно важное значение для определения его свойств. Начальным этапом производства ковкого чугуна является удаление избыточной серы из расплавленного чугуна. В серый чугун иногда добавляют серу, поскольку она способствует образованию графитовых чешуек. По этой причине он должен быть практически исключен из расплавов ковкого чугуна. Есть некоторые литейные заводы, которые перерабатывают как серый, так и ковкий чугун из одного и того же шихтового материала, поэтому любой лом серого чугуна, перерабатываемый внутри компании, будет содержать серу, которую необходимо удалить. Удаление серы включает добавление CaO или какого-либо другого агента. Следует отметить, что литейные заводы, которые специализируются только на обработке ковкого чугуна, могут иметь возможность избежать обширных процедур десульфурации, но они всегда должны следить за этим при измерении химического состава.
Нодуляризация с использованием конверсии магния
Уникальной стадией обработки ковкого чугуна является шаровидная обработка графита. На этом этапе к расплавленному сплаву добавляют магний для создания остаточного уровня Mg примерно 0,03-0,06%, что является количеством, необходимым для образования сфероидов из графита. К сожалению, Mg испаряется при температуре значительно ниже температуры плавления чугуна с шаровидным графитом, поэтому для достижения такой конверсии были разработаны инновационные методы конверсии:
Конверсия в открытом ковше