российские учёные создали самый огнеупорный материал в мире — РТ на русском
Материаловеды МИСиС создали керамический материал карбонитрид гафния, способный выдерживать рекордную температуру 4200 °C. Это подтверждают результаты компьютерного моделирования, предсказавшего огнеупорные свойства и высокую твёрдость такого материала. Ранее самым тугоплавким веществом с температурой плавления 3990 °C считался карбид тантала-гафния. После окончания пандемии коронавируса учёные планируют провести эксперимент, который определит температуру плавления нового материала.
Материаловеды Национального исследовательского технологического университета МИСиС создали самый огнеупорный в мире керамический материал карбонитрид гафния, способный выдержать температуру 4200 °C. Об этом сообщается в журнале Ceramics International.
До настоящего времени карбид тантала-гафния с температурой плавления 3990 °C считался самым огнеупорным соединением, созданным человеком. На идею создания более тугоплавкого вещества материаловедов МИСиС натолкнуло исследование американских коллег 2015 года, в котором с помощью компьютерного моделирования были предсказаны исключительные температурные свойства и высокая твёрдость композитного соединения гафния, углерода и азота.
«Для получения нового материала была использована тройная система гафний-углерод-азот. Методом самораспространяющегося высокотемпературного синтеза мы получили вещество карбонитрид гафния — насыщенный азотом карбид гафния», — сообщил в беседе с RT автор работы, директор научно-исследовательского центра конструкционных и керамических наноматериалов МИСиС Дмитрий Московских.
Также по теме
Менделеевские металлы: российские учёные открыли полупроводниковые соединения из рения, галлия и германияСотрудники химического факультета Московского государственного университета открыли новые интерметаллиды — соединения из рения, галлия…
Далее учёные сравнили плавкость двух материалов: исходного карбида гафния (плавится при 3990 °C) и полученного карбонитрида гафния. С помощью аккумулятора и молибденовых электродов они провели в глубоком вакууме одновременный нагрев двух материалов. В результате карбид оплавился, а карбонитрид остался в неизменном виде. Однако на данный момент, отмечают учёные, конкретную температуру плавления нового материала выше 4000 °С им определить не удалось.
Чтобы подтвердить все свойства нового материала, предсказанные компьютерным моделированием, учёным необходимо провести дополнительные эксперименты. Для этого, по словам Дмитрия Московских, было заключено соглашение с Объединённым институтом высоких температур РАН о проведении пирометрического анализа, который был отложен из-за пандемии COVID-19.
После снятия ограничений намечено проведение исследования, во время которого карбонитрид гафния будет расплавлен лазером с одновременным измерением теплофизических свойств, включая температуру плавления.
- Предварительные исследования показали, что карбонитрид гафния способен выдержать температуру 4200 °C
- © НИТУ МИСиС
По мнению учёных, разработка подобных высокотемпературных материалов будет востребована при создании авиационной, ракетно-космической и специальной военной техники. На гиперзвуковой скорости и при прохождении через атмосферу Земли двигатели, крылья и носовые обтекатели летательных аппаратов работают при температурах выше 2000 °С и должны быть защищены от воздействия внешней среды. В таких аппаратах применяется керамическая теплозащита с использованием наиболее прочных и тугоплавких композитных материалов.
В дальнейшем для проверки возможности применения карбонитрида гафния в аэрокосмической промышленности запланировано гиперзвуковое исследование для изучения абляции — испарения внешних слоёв материала.
Российские материаловеды разработали материал с рекордной температурой плавления
Материаловеды из НИТУ «МИСиС» синтезировали новый материал с ультравысокой температурой плавления — нестехиометрический карбонитрид гафния. Точно измерить его температуру плавления ученые пока не смогли, но она выше чем у карбида гафния, наиболее тугоплавкого из известных на сегодняшний день материалов. Результаты исследования опубликованы в журнале Ceramics International.
Соединения с ультравысокой — 2000 градусов Цельсия и выше — температурой плавления используются во многих областях современных технологий. Особенно востребованы такие материалы в аэрокосмической отрасли: например, из них изготавливают покрытия для носовых обтекателей и передних кромок крыльев многоразовых воздушно-космических самолетов — при выходе из атмосферы температура этих деталей может достигать 4000 градусов Цельсия. Чтобы найти материалы с высокой температурой плавления, а также подходящими механическими свойствами, материаловеды экспериментируют с различной керамикой: оксидами, нитридами, карбидам и боридами переходных металлов. В настоящее время самым тугоплавким материалом называют нестехиометрический карбид гафния HfC0.98 — для него была зафиксирована температура плавления 3927 градусов Цельсия.
Исследователи из Национального исследовательского технологического университета «МИСиС» под руководством Дмитрия Московских (Dmitry O. Moskovskikh) разработали новый материал с ультравысокой температурой плавления — нестехиометрический карбонитрид гафния.
Сотрудники «МИСиС» предложили для получения нестехиометрических карбонитридов гафния новый метод, который состоит из трех последовательных стадий. В начале порошок гафния смешивают с порошком угля в мольном соотношении 2:1 и перемалывают в высокоскоростной барабанно-шаровой мельнице в течение пяти минут. Помол проводится в инертной атмосфере — это нужно, чтобы избыток гафния не вступил в реакцию с кислородом. Активированный в шаровой мельнице композит Hf/C с размером частиц 20-100 микрон затем «сжигают» в азоте. Этот процесс называется самораспространяющийся высокотемпературный синтез, для него необходимо высокое давление азота — 8 атмосфер. На этой стадии азот внедряется в кристаллическую решетку композита, превращая его в нестехиометрический карбонитрид.
Измерить такие высокие значения температуры плавления в лабораторных условиях напрямую очень сложно. Поэтому авторы решили проверить температуру плавления нового материала косвенно — путем сравнения с действующим рекордсменом тугоплавкости, карбидом гафния HfC0.98. Для этого спрессованные образцы двух материалов разместили на графитовой пластине, имеющей форму гантели и сверху накрыли аналогичной пластиной, чтобы избежать тепловых потерь. Затем полученную конструкцию при помощи молибденовых электродов подключили к аккумулятору и пропустили через нее ток в 1200 Ампер. Под действием такого мощного электрического тока графит сильно разогревается, при этом самая высокая температура устанавливается в узкой части гантели — там где находятся образцы.
В дальнейшем авторы планируют уточнить температуру плавления методом высокотемпературной лазерной или электрической пирометрии, а также изучить стабильность нового материала в гиперзвуковых условиях, что будет актуальным для его дальнейшего применения в аэрокосмической промышленности.
В 2018 году материаловеды из «МИСиС» также предложили новый способ получения так называемых объемных MAX-фаз — слоистых смешанных карбидов, которые сочетают в себе свойства металлов и керамики. Для этого они использовали комбинацию методов самораспространяющегося высокотемпературного синтеза и сдвиговой деформации под давлением.
Свойства карбидов металлов (гафния, хрома, титана, вольфрама и др.)
Представлены сведения о химических и физических свойствах карбидов металлов: таких, как гафний, хром, титан, вольфрам и других. Физические свойства карбидов сведены в отдельные таблицы, в которых указана их плотность, твердость, температура плавления и кипения, а также электрические и тепловые свойства.
Карбид гафния GfC
В таблице приведены свойства карбида металла гафния. Карбид гафния представляет собой соединение серого цвета с температурой плавления 3890°С и высокой плотностью, которая при комнатной температуре составляет 12600 кг/м3. Энергия кристаллической решетки GfC равна 117,2·105 кДж/кмоль.
Карбид гафния полностью растворяется в ортофосфорной, азотной и серной кислотах. При температуре около 2000°С он начинает взаимодействовать с тугоплавкими металлами — такими, как молибден, вольфрам, тантал и ниобий.
Молекулярная масса | 190,5 |
Тип решетки | Кубическая |
Плотность, кг/м3 | 12600 |
Температура плавления, °С | 3890±150 |
Температура кипения, °С | 4160 |
Средний ТКЛР в интервале 20-1200°С, α·106, град-1 | 6,1 |
Молярная теплоемкость при 20°С, кДж/(кмоль·град) | 35,3 |
Теплопроводность карбида гафния с нулевой пористостью при температуре 300°С равна 9,2 Вт/(м·град). При нагревании коэффициент теплопроводности GfC увеличивается. Удельная теплоемкость карбида гафния относительно невысока и при росте температуры слабо увеличивается.
300 | 400 | 600 | 800 | 1000 | 1200 | |
---|---|---|---|---|---|---|
Удельная массовая теплоемкость, Дж/(кг·град) | 251 | 251 | 255 | 268 | 281 | 297 |
Коэффициент теплопроводности, Вт/(м·град) | 9,2 | 10 | 11,7 | 13,8 | 15,9 | 17,2 |
Карбиды хрома
Таблица содержит физические свойства карбидов хрома различного состава. Соединения с формулой Cr23C6 и Cr3C2 имеют серый цвет; Cr7C3 — серебристый.
Карбиды хрома Cr23C6 и Cr7C3 нерастворимы в царской водке. После длительного нагрева при 730…870°С карбид Cr7C3 превращается в Cr23C6. Карбид Cr3C2 нерастворим в воде. Изделия из него также практически нерастворимы в кислотах, их смесях и растворах щелочей. Однако, он может взаимодействовать с цинком при температуре 940°С. Температура начала окисления Cr3C2 составляет 900…1000°С.
Свойства/карбид | Cr4C | Cr23C6 | Cr7C3 | Cr3C2 |
---|---|---|---|---|
Молекулярная масса | 220 | 1265 | 400 | 180 |
Тип решетки | Кубическая | Кубическая | Гексагональная | Ромбическая |
Плотность, кг/м3 | — | 6970 | 6920 | 6680 |
Температура плавления, °С | 1520 | 1550 | 1700±50 | 1890 (разлаг.![]() |
Средний ТКЛР в интервале 20-800°С, α·106, град-1 | — | 10,1 | 10 | 10,3 |
Удельная массовая теплоемкость при 20°С, Дж/(кг·град) | — | 493 | 523 | 546 |
Молярная теплоемкость при 20°С, кДж/(кмоль·град) | — | 84 | 209 | 98 |
Коэффициент теплопроводности при 20°С, Вт/(м·град) | — | 18,7 | 16,6 | 16,2 |
Карбид титана TiC
Карбид титана TiC представляет собой соединение светло-серого цвета с металлическим блеском. Он химически инертен при комнатной температуре: плохо растворяется в кислотах, их смесях и некоторых щелочах в холодном и нагретом состояниях.
При высоких температурах (выше 2500°С) начинает реагировать с азотом. При взаимодействии с водородом обезуглероживается. Кроме того, окисляется углекислым газом при температурах выше 1200°С. Температура активного окисления карбида титана составляет 1100…1200°С.
Область температурной устойчивости TiC достигает 3140°С, он высокостоек в расплавленных легкоплавких металлах и металлах типа меди, алюминия, латунях, чугунах и сталях. Степень черноты карбида титана равна 0,9 (при длине волны 0,655 мкм).
Молекулярная масса | 59,9 |
Тип решетки | Кубическая |
Плотность, кг/м3 | 4930 |
Температура плавления, °С | 3147±50 |
Температура кипения, °С | 4305 |
Твердость по шкале Мооса | 8-9 |
Средний ТКЛР в интервале 20-2700°С, α·106, град-1 | 9,6 |
Молярная теплоемкость при 20°С, кДж/(кмоль·град) | 33,7 |
Удельная массовая теплоемкость при 25°С, Дж/(кг·град) | 842 |
Коэффициент теплопроводности при 20°С, Вт/(м·град) | 34…39 |
Удельное электрическое сопротивление при 20°С, ρ·108, Ом·м | 60 |
Карбиды вольфрама W
2C и WCКарбиды вольфрама W2C и WC представляют собой соединения серого цвета. Область температурной устойчивости для W2C составляет до 2750°С; для WC — до 2600°С. Тонкий порошок WC быстро окисляется на воздухе при 500…520°С. Температура начала окисления грубого порошка WC составляет 595°С. При 700°С изменение массы карбида вольфрама WC в результате часового окисления составляет 8,3 мг/(см2·ч).
При комнатной температуре порошок карбида вольфрама практически не растворяется в сильных концентрированных кислотах. Однако он почти полностью растворим в кипящих H2SO4 и HNO3. При температуре 940°С WC слабо взаимодействует с расплавом цинка.
Свойства/карбид | W2C | WC |
---|---|---|
Молекулярная масса | 379,7 | 195,9 |
Тип решетки | Гексагональная | |
Плотность, кг/м3 | 1720 | 1560 |
Температура плавления, °С | 2730±15 | 2720 |
Температура кипения, °С | 6000 | |
Твердость по шкале Мооса | 9-10 | 9 |
Средний ТКЛР в интервале 20-2000°С, α·106, град-1 | 5,8 | |
Удельная массовая теплоемкость в интервале 0-100°С, Дж/(кг·град) | — | 184 |
Молярная теплоемкость при 25°С, кДж/(кмоль·град) | — | 36 |
Коэффициент теплопроводности при 20°С, Вт/(м·град) | 29,3 | 197 |
Карбид кальция CaC
2В таблице приведены физические свойства карбида кальция CaC2. По своим оптическим свойствам химически чистый карбид кальция — большие, почти бесцветные кристаллы с голубоватым оттенком. Технический CaC2 в зависимости от степени чистоты имеет серый, коричнево-желтый или черный цвет.
Предел температурной устойчивости для карбида кальция равен 2300°С. При температуре 20°С он полностью растворяется в воде (с выделением ацетилена) и концентрированной соляной кислоте.
Молекулярная масса | 64,1 |
Тип решетки | Тетрагональная, кубическая |
Плотность, кг/м3 | 2100 |
Температура плавления, °С | 2300 (разлаг.) |
Удельная массовая теплоемкость при 25°С, Дж/(кг·град) | 960 |
Молярная теплоемкость при 25°С, кДж/(кмоль·град) | 61,3 |
Карбид циркония ZrC
Карбид циркония представляет собой соединение серого цвета с металлическим блеском. Он химически инертен при комнатной температуре: плохо растворяется в концентрированных кислотах, их смесях и некоторых щелочах, как в холодном, так и нагретом состоянии. Карбид циркония нерастворим в воде, однако взаимодействует с азотом с образованием нитридов.
Температура активного окисления ZrC составляет 1100…1200°С, область температурной устойчивости — до 3530°С. Карбид циркония стоек в расплавах меди и медных сплавов, стали, чугуна и легкоплавких металлов.
Молекулярная масса | 103,2 |
Тип решетки | Кубическая |
Плотность, кг/м3 | 6730 |
Температура плавления, °С | 3530 |
Температура кипения, °С | 5100 |
Твердость по шкале Мооса | 8-9 |
Средний ТКЛР в интервале 20-1100°С, α·106, град-1 | 6,74 |
Молярная теплоемкость при 20°С, кДж/(кмоль·град) | 61,1 |
Удельная массовая теплоемкость при 25°С, Дж/(кг·град) | 456 |
Коэффициент теплопроводности при 0°С, Вт/(м·град) | 42 |
Удельное электрическое сопротивление при 20°С, ρ·108, Ом·м | 50 |
Карбиды ниобия Nb
2C и NbCВ таблице даны физические свойства карбидов ниобия Nb2C и NbC. Плотный карбид ниобия NbC имеет серовато-коричневый или бледно-лиловый металлический цвет. Порошок NbC имеет фиолетовый оттенок.
Карбиды ниобия при комнатной температуре химически инертны, обладают высокой химической стойкостью к действию кислот и их смесей даже в нагретом состоянии. Однако, они растворимы в смеси плавиковой и азотной кислоты.
При нагревании на воздухе NbC слегка обезуглероживается. До температуры 2500°С он устойчив в атмосфере азота. Температура активного окисления карбида ниобия составляет 900…1000°С. Область температурной устойчивости — до 3890°С. Он стоек в расплавах металлов (Cu, Al), имеет высокую твердость по шкале Мооса.
Свойства/карбид | Nb2C | NbC |
---|---|---|
Молекулярная масса | 197,8 | 105 |
Тип решетки | Гексагональная | Кубическая |
Плотность, кг/м3 | 7860 | 7560 |
Температура плавления, °С | 2927 | 3480 |
Температура кипения, °С | — | 4500 |
Твердость по шкале Мооса | — | 9-10 |
Средний ТКЛР в интервале 20-1100°С, α·106, град-1 | 6,5 | |
Удельная массовая теплоемкость при 20°С, Дж/(кг·град) | 315 | 355 |
Молярная теплоемкость при 25°С, кДж/(кмоль·град) | 30,36 | 37,35 |
Коэффициент теплопроводности при 20°С, Вт/(м·град) | — | 19 |
Удельное электрическое сопротивление при 20°С, ρ·108, Ом·м | 55 | 46 |
Источники:
- Чиркин В.
С. Теплофизические свойства материалов ядерной техники. М.: Атомиздат, 1967. — 474 с.
- Кржижановский Р. Е., Штерн З. Ю. Теплофизические свойства неметаллических материалов (карбиды). Справочник. Л.: Энергия, 1976. — 120 с.
Предсказан новый рекордсмен тугоплавкости
Фрагмент карты электронной плотности в структуре карбида гафния
Изображение: Qi-Jun Hong et al. / PRB, 2015
Химики из Университета Брауна (Провиденс) теоретически предсказали существование фазы смешанного карбида-нитрида гафния с рекордно высокой температурой плавления — свыше 4400 кельвинов. Об этом сообщает пресс-релиз университета, работа опубликована в журнале Physical Review B.
Для поиска соединения-рекордсмена авторы работы использовали методы компьютерного моделирования, позволяющие следить за динамикой атомов кристаллической решетки в процессе плавления. Программа моделировала фрагмент решетки соединения, содержащий около ста атомов. В качестве модельной рассматривалась система, содержащая карбиды и нитриды тантала и гафния.
Выбор данной системы авторы объясняют тремя основными факторами, влияющими на величину температуры плавления, выявленными в ходе исследования. Это, во-первых, наличие сильных ковалентных и ионных связей внутри соединения, во-вторых, наличие определенных дефектов в материале, которые могут существовать как в твердой, так и жидкой фазе — например, вакансии (отсутствие атомов) в решетке. За счет того, что такие системы еще в твердом виде менее упорядочены, их плавление дает меньший энтропийный выигрыш, что повышает температуру фазового перехода. Третьим фактором, влияющим на температуру плавления, является положение уровня Ферми в системе.
Трехмерная фазовая диаграмма в системе гафний-углерод-азот. Температура, предсказанная методами теории функционала плотности, отличается от экспериментальной примерно на пять процентов, поэтому теоретическая оценка Tплавления нового соединения — примерно 4400 кельвинов
Изображение: Qi-Jun Hong et al. / PRB, 2015
Оказалось, что добавление атомов азота в структуру исходных «рекордсменов» — карбидов тантала и гафния — способно увеличить энтропию твердого соединения и за счет этого получить выигрыш в температуре плавления. Обладателем максимальной температуры плавления, согласно моделированию, стала фаза HfN0.38C0. 51, плавящаяся при примерно 4400 кельвинах. Эта температура всего на полторы тысячи градусов меньше, чем температура поверхности Солнца.
На данный момент авторы обсуждают с материаловедами возможности синтеза и использования гипотетического вещества. Несмотря на высокую температуру плавления, для применения материала в различных сферах необходимо изучить также его стойкость к коррозии и многие другие особенности.
Температурой плавления выше четырех тысяч кельвинов обладают немногие соединения, из бинарных самыми характерными являются карбиды гафния(4160-4163 кельвина) и тантала (4153 кельвина). Современным рекордсменом температуры плавления является карбид тантала-гафния Ta4HfC5, плавящийся при 4215 кельвинах.
Физики определили самое тугоплавкое вещество
Дендритная структура, возникшая в месте плавления карбида тантала-гафния
Omar Cedillos-Barraza et al. / Scientific Reports, 2016
Физики из Имперского колледжа Лондона, Института трансурановых элементов (Карлсруэ) и Университета Лондона уточнили температуры плавления карбидов гафния и тантала. С помощью лазерных методов плавки ученые показали, что наибольшей температурой плавления обладает чистый карбид гафния — HfC0,98 — материал плавится при 3959 ±84 градусах Цельсия. Ранее считалось, что самым тугоплавким материалом из известных является смешанный карбид гафния-тантала, содержащий примерно 20 процентов гафния. Исследование опубликовано в журнале Scientific Reports, кратко о нем сообщает пресс-релиз колледжа.
Исследования температуры плавления карбидов гафния и тантала датируются еще первой половиной XX века. Для этого использовался метод Пирани-Алтертума: с помощью электрического тока нагревалась пластинка материала с отверстием в центре. За пластинкой следили с помощью пирометра. В момент плавления отверстие оказывалось заполнено материалом и изменяло свое свечение. Разброс температур плавления, определенных этим методом для карбида гафния составил почти двести градусов, и по результатам измерений трудно было однозначно определить, какой из карбидов гафния и тантала является самым тугоплавким.
Образцы карбидов после плавления лазером. Слева-направо: кабрид тантала, карбид тантала-гафния, карбид гафния
Omar Cedillos-Barraza et al. / Scientific Reports, 2016
Авторы новой работы, отметив несовершенство ранних пирометров и методик, предложили использовать новый подход для определения температуры плавления. В ней образец керамики плавился под действием мощного 4,5-киловаттного лазера, после чего исследователи следили за его свечением. Момент плавления определялся по изменению отражения от поверхности. После этого лазер отключался, а температура плавления определялась по плато на графике остывания образца: в момент затвердевания отводимая от образца теплота не меняет его температуры.
Слева: кривая температурной зависимости карбида гафния (черная) и производная сигнала отраженного света. Справа: температурные кривые для карбида тантала, гафния и тантала-гафния.
Omar Cedillos-Barraza et al. / Scientific Reports, 2016
В результате оказалось, что наименьшей температурой плавления обладает карбид тантала — она соответствует 3768 ± 77 градусам Цельсия. Интересно, что в некоторых ранних работах карбид тантала наоборот считался более тугоплавким, чем карбид гафния. Высокими температурами плавления обладал состав Ta0.8Hf0.2C, ранее считавшийся рекордсменом — порядка 3905 ± 82 градусов Цельсия. Остальные смешанные карбиды плавились при более низких температурах. Абсолютным рекордсменом, по данным новой работы, стал карбид гафния HfC0,98, материал плавится при 3959 ±84 градусах Цельсия. Для сравнения, самым тугоплавким металлом является вольфрам, плавящийся при 3422 градусах Цельсия.
Считается, что карбидные керамики могут найти применение при строительстве гиперзвуковых самолетов. При движении в атмосфере на скорости свыше пяти чисел Маха теплозащита должна выдерживать температуры в 2200 кельвин и выше.
Ранее химики из Университета Брауна (Провиденс) теоретически предсказали существование фазы смешанного карбида-нитрида гафния с рекордно высокой температурой плавления — свыше 4400 кельвин. Ее состав отвечает формуле HfN0. 38C0.51.
Владимир Королёв
В Новосибирске создали технологию быстрого получения самого тугоплавкого материала в мире — Сибирь
НОВОСИБИРСК, 5 июня. /ТАСС/. Ученые Сибирского отделения Российской академии наук (СО РАН) разработали технологию быстрого получения самого тугоплавкого из известных материалов — карбида гафния — и деталей из него за несколько минут, тогда как до сих пор для этого требовались часы. Как сообщила пресс-служба Института ядерной физики (ИЯФ) СО РАН, для получения материала, который плавится при температуре свыше 3900 градусов Цельсия и применяется в ядерной отрасли, использован метод электронно-лучевой сварки и послойное нанесение.
«Ученые ИЯФ и Института химии твердого тела и механохимии СО РАН получили карбид гафния с температурой плавления 3953 градуса Цельсия с помощью электронно-лучевой сварки. Технология заключается в измельчении гафния и углерода, формировании композита и нагревании направленным пучком электронов. Сырье добавляется послойно, как при печати на 3D-принтере. Новый метод позволяет получать готовые детали за несколько минут, тогда как при классическом способе уходит несколько часов», — говорится в сообщении.
Новая технология делает производство менее энергозатратным и повышает качество материала — при традиционном способе он получается пористым.
Сейчас карбид гафния применяется для изготовления оборудования ядерных реакторов.
«Материал с успехом может применяться в сфере ракетостроения, в качестве внешнего покрытия для теплозащитных оболочек возвращаемых космических аппаратов типа «Буран». При помощи послойного нанесения возможно создавать композиционные покрытия с градиентом теплопроводности: первый слой должен выдерживать высокие температуры, второй и последующие — плавно распределять тепло и изолировать от него внутреннею часть аппарата», — отмечается в сообщении.
Также разработчики считают, что технология позволит сделать более доступным производство соединений на основе других тугоплавких металлов — тантала, вольфрама, молибдена.
«Добрости» — совместная рубрика с «Жить», общероссийским социальным проектом, призванным поддержать людей, оказавшихся в сложной жизненной ситуации.
Ученые ИЯФ и ИХТТиМ СО РАН научились плавить карбид гафния
Публичный договор-оферта
на оказание платных услуг сайта navigato.ru1. Настоящий документ является Публичной офертой — официальным договором на оказание платных услуг сайта navigato.ru в дальнейшем — Исполнитель и содержит все условия предоставления услуг.
2. В соответствии с п.2 статьи 437 ГК РФ, в случае принятия изложенных ниже условий и расценок на размещение платных объявлений юридическое или физическое лицо, производящее акцепт настоящей оферты, именуется Заказчиком (п.3 статьи 437 ГК РФ — акцепт оферты равносилен заключению договора, на условиях, изложенных в оферте ).

3. Внимательно прочтите материалы договора публичной оферты, ознакомьтесь с правилами подачи объявления и платными услугами. В случае несогласия с условиями договора или одного из пунктов, Исполнитель предлагает Вам отказаться от использования платных услуг сайта navigato.ru.
4. Оферта — официальный публичный документ по оказанию платных услуг сайта navigato.ru , опубликованный по адресу http://navigato.ru/ (Юридическая информация).
5. Акцепт оферты — полное принятие Заказчиком условий настоящего договора путём оплаты услуг сайта navigato.ru , акцепт оферты создаёт договор оферты.
6. Заказчик — юридическое или физическое лицо, осуществившее акцепт оферты, и являющееся Заказчиком платных услуг Исполнителя по договору оферты.
7. Договор оферты — договор между Исполнителем и Заказчиком на оказание платных услуг, заключённый посредством акцепта оферты.
8. Оказание Заказчику платных услуг на условиях договора является предметом настоящей оферты.

9. Исполнитель имеет право в любой момент изменить условия настоящего договора и расценки на платные услуги без предварительного согласования с Заказчиком, обязуясь опубликовать изменения по адресу http://navigato.ru/ (Юридическая информация) не менее чем за один день до вступления изменений в силу.
10. Платные услуги доски объявлений предоставляются в полном объёме при условии 100% оплаты Заказчиком.
11. Ознакомившись с платными услугами и правилами подачи объявления создаёт объявление и оплачивает услугу через один из доступных на сайте платёжных сервисов.
12. После проведения Заказчиком оплаты выбранных услуг и перечисления денежных средств на счёт Исполнителя, договор оферты вступает в силу.
13. Исполнитель обеспечивает предоставление консультационных услуг Заказчику по выбранной им платной услуге.
14. Услуги считаются оказанными в полном объеме, если в течение 12 часов после оплаты услуги Заказчиком не выслан мотивированный отказ от услуги на e-mail Исполнителя.

15. По письменному требованию Заказчика Исполнитель может распечатать договор оферту с подписями Сторон, который будет представлять юридическую силу, равную юридической силе настоящего договора.
16. Исполнитель делает всё возможное для бесперебойного предоставления Заказчику оплаченных услуг в полном объеме.
17. Исполнитель не несёт ответственности за неисполнение оплаченных услуг, в случае если нарушение договора оферты вызвано не зависящими от него обстоятельствами непреодолимой силы — наводнением, землетрясением, действиями властей, отсутствием электроэнергии, сбоями в сети интернет, общественными беспорядками, другими стихийными бедствиями и прочими обстоятельствами, неподконтрольными Исполнителю, которые могут помешать исполнению условий настоящего договора оферты.
18. В случае невозможности исполнения условий договора оферты, Исполнитель обязуется произвести возврат денежных средств, оплаченных Заказчиком за выполнение услуги. В других случаях возврат денег не производится.
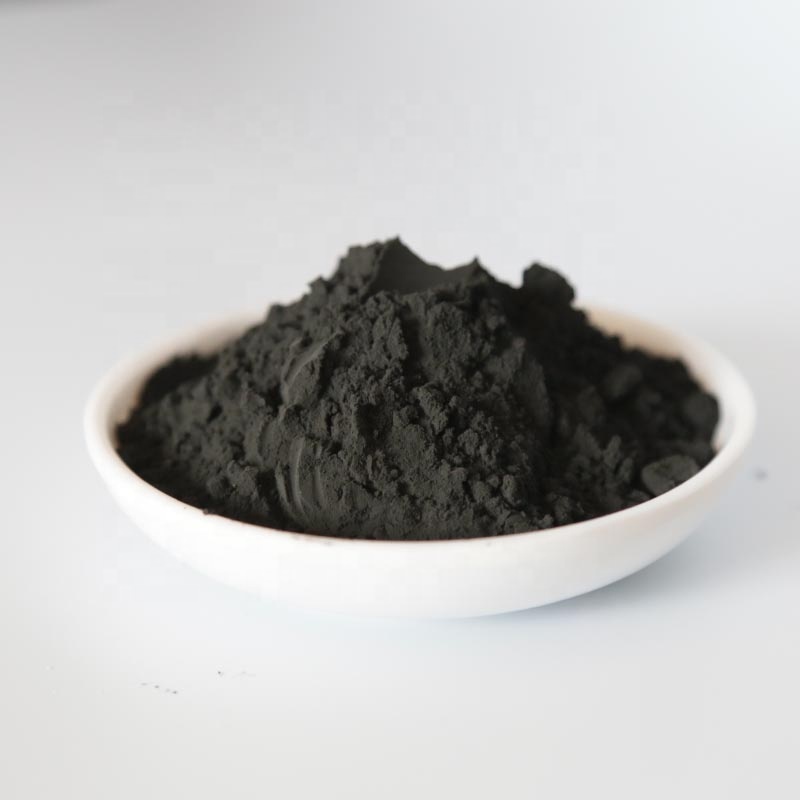
19. За невыполнение обязательств настоящего договора оферты Стороны несут ответственность в соответствии с законодательством Российской Федерации. Договор вступает в силу с момента акцепта оферты и действует до выполнения Сторонами своих обязательств. Спорные вопросы решаются путём переговоров Сторон.
Произошла ошибка при настройке пользовательского файла cookie
Этот сайт использует файлы cookie для повышения производительности. Если ваш браузер не принимает файлы cookie, вы не можете просматривать этот сайт.
Настройка вашего браузера для приема файлов cookie
Существует множество причин, по которым cookie не может быть установлен правильно. Ниже приведены наиболее частые причины:
- В вашем браузере отключены файлы cookie. Вам необходимо сбросить настройки вашего браузера, чтобы он принимал файлы cookie, или чтобы спросить вас, хотите ли вы принимать файлы cookie.
- Ваш браузер спрашивает вас, хотите ли вы принимать файлы cookie, и вы отказались.
Чтобы принять файлы cookie с этого сайта, нажмите кнопку «Назад» и примите файлы cookie.
- Ваш браузер не поддерживает файлы cookie. Если вы подозреваете это, попробуйте другой браузер.
- Дата на вашем компьютере в прошлом. Если часы вашего компьютера показывают дату до 1 января 1970 г., браузер автоматически забудет файл cookie. Чтобы исправить это, установите правильное время и дату на своем компьютере.
- Вы установили приложение, которое отслеживает или блокирует установку файлов cookie. Вы должны отключить приложение при входе в систему или проконсультироваться с системным администратором.
Почему этому сайту требуются файлы cookie?
Этот сайт использует файлы cookie для повышения производительности, запоминая, что вы вошли в систему, когда переходите со страницы на страницу. Чтобы предоставить доступ без файлов cookie
потребует, чтобы сайт создавал новый сеанс для каждой посещаемой страницы, что замедляет работу системы до неприемлемого уровня.
Что сохраняется в файле cookie?
Этот сайт не хранит ничего, кроме автоматически сгенерированного идентификатора сеанса в cookie; никакая другая информация не фиксируется.
Как правило, в файлах cookie может храниться только информация, которую вы предоставляете, или выбор, который вы делаете при посещении веб-сайта. Например, сайт не может определить ваше имя электронной почты, пока вы не введете его. Разрешение веб-сайту создавать файлы cookie не дает этому или любому другому сайту доступа к остальной части вашего компьютера, и только сайт, который создал файл cookie, может его прочитать.
Карбид гафния | AMERICAN ELEMENTS ®
РАЗДЕЛ 1. ИДЕНТИФИКАЦИЯ
Название продукта: Карбид гафния
Номер продукта: Все применимые коды продуктов American Elements, например HF-C-02 , HF-C-03 , HF-C-04 , HF-C-05
CAS #: 12069-85-1
Соответствующие установленные области применения вещества: Научные исследования и разработки
Информация о поставщике:
American Elements
10884 Weyburn Ave.
Лос-Анджелес, Калифорния
Тел .: +1 310-208-0551
Факс: +1 310-208-0351
Телефон экстренной связи:
Внутренний номер, Северная Америка: +1 800-424-9300
Международный: +1 703-527-3887
РАЗДЕЛ 2. ИДЕНТИФИКАЦИЯ ОПАСНОСТИ
Классификация вещества или смеси
Классификация в соответствии с Регламентом (ЕС) № 1272/2008
GHS02 Flame
Flam. Sol. 2 х328 Легковоспламеняющееся твердое вещество.
Классификация в соответствии с Директивой 67/548 / EEC или Директивой 1999/45 / EC
F; Легковоспламеняющийся
R11: Легковоспламеняющийся.
Информация, касающаяся особых опасностей для человека и окружающей среды:
Н / Д
Опасности, не классифицированные иным образом
Данные отсутствуют
Элементы маркировки
Маркировка в соответствии с Постановлением (ЕС) № 1272/2008
Вещество классифицируется и маркируется в соответствии с постановлением CLP .
Пиктограммы, обозначающие опасности
GHS02
Сигнальное слово: Осторожно
Краткая характеристика опасности
h328 Воспламеняющееся твердое вещество.
Меры предосторожности
P210 Беречь от тепла / искр / открытого огня / горячих поверхностей.Не курить.
P280 Пользоваться защитными перчатками / защитной одеждой / средствами защиты глаз / лица.
P240 Заземлить / связать контейнер и приемное оборудование.
P241 Использовать взрывозащищенное электрическое / вентиляционное / осветительное / оборудование.
P370 + P378 В случае пожара: Использовать для тушения: CO2, порошок или водяную струю.
Классификация WHMIS
B4 — Легковоспламеняющееся твердое вещество
Система классификации
Рейтинги HMIS (шкала 0-4)
(Система идентификации опасных материалов)
ЗДОРОВЬЕ
ПОЖАР
РЕАКТИВНОСТЬ
1
2
1
Здоровье (острые эффекты) = 1
Воспламеняемость = 2
Физическая опасность = 1
Другие опасности
Результаты оценки PBT и vPvB
PBT: нет данных
vPvB: нет данных
РАЗДЕЛ 3.СОСТАВ / ИНФОРМАЦИЯ ОБ ИНГРЕДИЕНТАХ
Вещества
Номер CAS / Название вещества:
12069-85-1 Карбид гафния
Идентификационный номер (а):
Номер ЕС: 235-114-1
Дополнительная информация:
Гафний обычно встречается с низкий уровень циркония, так как разделение двух элементов затруднено
РАЗДЕЛ 4.

Описание мер первой помощи
При вдыхании:
Обеспечить пациента свежим воздухом. Если не дышит, сделайте искусственное дыхание.Держите пациента в тепле.
Немедленно обратитесь за медицинской помощью.
При попадании на кожу:
Немедленно промыть водой с мылом; тщательно промыть.
Немедленно обратитесь за медицинской помощью.
При попадании в глаза:
Промыть открытый глаз под проточной водой в течение нескольких минут. Проконсультируйтесь с врачом.
При проглатывании:
Обратитесь за медицинской помощью.
Информация для врача
Наиболее важные симптомы и воздействия, как острые, так и замедленные
Данные отсутствуют
Указание на необходимость немедленной медицинской помощи и специального лечения
Нет данных
РАЗДЕЛ 5.МЕРЫ ПОЖАРОТУШЕНИЯ
Средства пожаротушения
Надлежащие средства тушения
Специальный порошок для металлических пожаров. Не используйте воду.
Средства пожаротушения непригодны из соображений безопасности
Вода
Особые опасности, исходящие от вещества или смеси
При пожаре могут образоваться следующие вещества:
Окись углерода и углекислый газ
Дым оксида металла
Рекомендации для пожарных
Защитный оборудование:
Надеть автономный респиратор.
Надеть полностью защитный непромокаемый костюм.
РАЗДЕЛ 6. МЕРЫ ПРИ СЛУЧАЙНОМ ВЫБРОСЕ
Меры личной безопасности, защитное снаряжение и порядок действий в чрезвычайной ситуации
Используйте средства индивидуальной защиты. Не подпускайте незащищенных людей.
Обеспечьте соответствующую вентиляцию.
Не приближайтесь к источникам возгорания.
Меры по защите окружающей среды:
Не допускайте попадания материала в окружающую среду без официального разрешения.
Не допускать попадания продукта в канализацию, канализацию или другие водоемы.
Не допускайте попадания материала в землю или почву.
Методы и материалы для локализации и очистки:
Хранить вдали от источников возгорания.
Обеспечьте соответствующую вентиляцию.
Предотвращение вторичных опасностей:
Хранить вдали от источников возгорания.
Ссылка на другие разделы.
См. Раздел 7 для получения информации о безопасном обращении.
См. Раздел 8 для получения информации о средствах индивидуальной защиты.
Информацию об утилизации см. В Разделе 13
РАЗДЕЛ 7.ОБРАЩЕНИЕ И ХРАНЕНИЕ
Обращение
Меры предосторожности при обращении
Хранить контейнер плотно закрытым.
Хранить в сухом прохладном месте в плотно закрытой таре.
Обеспечьте хорошую вентиляцию на рабочем месте.
Информация о защите от взрывов и пожаров:
Защищать от электростатических зарядов.
Условия безопасного хранения с учетом несовместимости
Требования, предъявляемые к складским помещениям и таре:
Хранить в прохладном месте.
Информация о хранении в одном общем хранилище:
Хранить вдали от окислителей.
Дополнительная информация об условиях хранения:
Держать емкость плотно закрытой.
Хранить в прохладном, сухом месте в хорошо закрытых емкостях.
Специфическое конечное использование
Данные отсутствуют
РАЗДЕЛ 8. КОНТРОЛЬ ВОЗДЕЙСТВИЯ / ЛИЧНАЯ ЗАЩИТА
Дополнительная информация о конструкции технических систем:
Правильно работающий вытяжной шкаф для химических веществ, предназначенный для опасных химикатов и имеющий среднюю скорость потока воздуха не менее 100 футов в минуту.
Контрольные параметры
Компоненты с предельными значениями, требующие контроля на рабочем месте:
Гафний, металл и соединения в виде Hf
мг / м3
ACGIH TLV 0.5
Австрия MAK 0,5
Бельгия TWA 0,5
Дания TWA 0,5
Финляндия TWA 0,5
Франция VME 0,5
Германия MAK 0,5
Корея TLV 0,5
Нидерланды MAC-TGG 0,5
Норвегия TWA 0,5
Польша TWA 0,5
Швейцария MAK-W 0,5
TWA Соединенного Королевства 0,5; 1.5-STEL
USA PEL 0.5
Дополнительная информация: Нет данных
Контроль воздействия
Средства индивидуальной защиты
Соблюдайте типичные защитные и гигиенические методы обращения с химическими веществами.
Хранить вдали от продуктов питания, напитков и кормов.
Немедленно снимите всю грязную и загрязненную одежду.
Мыть руки перед перерывами и по окончании работы.
Поддерживайте эргономичную рабочую среду.
Дыхательное оборудование:
При высоких концентрациях использовать подходящий респиратор.
Защита рук:
Непроницаемые перчатки
Осмотрите перчатки перед использованием.
Пригодность перчаток должна определяться как материалом, так и качеством, последнее из которых может варьироваться в зависимости от производителя.
Время проницаемости материала перчаток (в минутах)
Нет данных
Защита глаз: Защитные очки
Защита тела: Защитная рабочая одежда.
РАЗДЕЛ 9. ФИЗИЧЕСКИЕ И ХИМИЧЕСКИЕ СВОЙСТВА
Информация об основных физических и химических свойствах
Внешний вид:
Форма: Твердое вещество в различных формах
Цвет: Серый
Запах: Без запаха
Порог запаха: Нет данных.
pH: нет данных
Точка плавления / интервал плавления: 3890 ° C (7034 ° F)
Точка кипения / интервал кипения: данные отсутствуют
Температура сублимации / начало: данные отсутствуют
Температура вспышки: нет
воспламеняемость ( твердое, газовое): Легковоспламеняющийся.
Температура возгорания: Данные отсутствуют.
Температура разложения: Данные отсутствуют.
Самовоспламенение: Данные отсутствуют.
Взрывоопасность: данные отсутствуют.
Пределы взрываемости:
Нижняя: данные отсутствуют
Верхние: данные отсутствуют
Давление пара: нет данных
Плотность при 20 ° C (68 ° F): 12,2 г / см 3 (101,809 фунта / галлон)
относительная плотность: Нет данных.
Плотность пара: Нет данных
Скорость испарения: Нет данных
Растворимость в воде (H 2 O): Нерастворимый
Коэффициент распределения (н-октанол / вода): данные отсутствуют.
Вязкость:
Динамическая: нет данных
Кинематическая: нет
Другая информация
Данные отсутствуют
РАЗДЕЛ 10. СТАБИЛЬНОСТЬ И РЕАКЦИОННАЯ СПОСОБНОСТЬ
Реакционная способность
Данные отсутствуют
Химическая стабильность
Стабилен при рекомендуемых условиях хранения.
Термическое разложение / условия, которых следует избегать:
Разложение не произойдет при использовании и хранении в соответствии со спецификациями.
Возможность опасных реакций
Опасные реакции неизвестны
Условия, которых следует избегать
Данные отсутствуют
Несовместимые материалы:
Данные отсутствуют
Опасные продукты разложения:
Окись углерода и двуокись углерода
Дым оксидов металлов
РАЗДЕЛ 11.ТОКСИКОЛОГИЧЕСКАЯ ИНФОРМАЦИЯ
Информация о токсикологическом воздействии
Острая токсичность: Эффекты неизвестны.
Значения LD / LC50, которые имеют отношение к классификации: Нет данных
Раздражение или разъедание кожи: Может вызывать раздражение
Раздражение или разъедание глаз: Может вызывать раздражение
Сенсибилизация: Сенсибилизирующие эффекты неизвестны.
Мутагенность зародышевых клеток: Эффекты неизвестны.
Канцерогенность:
Нет данных о классификации канцерогенных свойств этого материала от EPA, IARC, NTP, OSHA или ACGIH.
Репродуктивная токсичность: Эффекты неизвестны.
Специфическая системная токсичность, поражающая отдельные органы-мишени — многократное воздействие: Эффекты неизвестны.
Специфическая системная токсичность, поражающая отдельные органы-мишени — однократное воздействие: Эффекты неизвестны.
Опасность при вдыхании: Эффекты неизвестны.
От подострой до хронической токсичности:
Гафний и соединения гафния могут вызывать раздражение кожи и глаз. Имеются сообщения о повреждении печени от воздействия гафния.
От подострой до хронической токсичности: Эффекты неизвестны.
Дополнительная токсикологическая информация:
Насколько нам известно, острая и хроническая токсичность этого вещества полностью не изучена.
РАЗДЕЛ 12. ЭКОЛОГИЧЕСКАЯ ИНФОРМАЦИЯ
Токсичность
Водная токсичность:
Нет данных
Стойкость и разлагаемость
Нет данных
Биоаккумуляционный потенциал
Нет данных
Мобильность в почве
Нет данных
Дополнительная экологическая информация:
Не допускать попадание материала в окружающую среду без официальных разрешений.
Избегать попадания в окружающую среду.
Результаты оценки PBT и vPvB
PBT: N / A
vPvB: N / A
Другие побочные эффекты
Нет данных
РАЗДЕЛ 13.СООБРАЖЕНИЯ ПО УТИЛИЗАЦИИ
Методы обработки отходов
Рекомендация
Обратитесь к официальным инструкциям, чтобы обеспечить надлежащую утилизацию.
Неочищенная тара:
Рекомендация:
Утилизация должна производиться в соответствии с официальными предписаниями.
РАЗДЕЛ 14. ТРАНСПОРТНАЯ ИНФОРМАЦИЯ
Номер ООН
DOT, IMDG, IATA
UN3178
Собственное транспортное наименование ООН
DOT
Легковоспламеняющееся твердое неорганическое вещество, н.у.к. (Карбид гафния)
IMDG, IATA
Легковоспламеняющееся твердое вещество, НЕОРГАНИЧЕСКОЕ, N.ОПЕРАЦИОННЫЕ СИСТЕМЫ. (Карбид гафния)
Класс (ы) опасности при транспортировке
DOT
Класс
4.1 Легковоспламеняющиеся твердые вещества, самореактивные вещества и твердые десенсибилизированные взрывчатые вещества.
Этикетка
4. 1
Класс
4.1 (F3) Легковоспламеняющиеся твердые вещества, самореактивные вещества и твердые десенсибилизированные взрывчатые вещества
Этикетка
4.1
IMDG, IATA
Класс
4.1 Воспламеняющиеся твердые вещества, самореактивные вещества и твердые десенсибилизированные взрывчатые вещества.
Этикетка
4,1
Группа упаковки
DOT, IMDG, IATA
III
Опасности для окружающей среды: N / A
Особые меры предосторожности для пользователя
Предупреждение: легковоспламеняющиеся твердые вещества, самореактивные вещества и твердые десенсибилизированные взрывчатые вещества
Транспортировка навалом в соответствии с Приложением II к MARPOL73 / 78 и код IBC
N / A
Транспортировка / Дополнительная информация:
DOT
Морской загрязнитель (DOT):
№
Типовой регламент ООН:
UN3178, Легковоспламеняющееся твердое вещество, неорганическое, n.Операционные системы. (Карбид гафния), 4.1, III
РАЗДЕЛ 15.

Нормативы / законы по безопасности, охране здоровья и окружающей среды, относящиеся к веществу или смеси
Национальные правила
Все компоненты этого продукта перечислены в списке токсичных веществ Агентства по охране окружающей среды США. Закон о контроле за веществами Реестр химических веществ.
Все компоненты этого продукта внесены в Канадский список веществ, не предназначенных для домашнего использования (NDSL).
SARA Раздел 313 (списки конкретных токсичных химических веществ)
Вещество не указано.
Предложение штата Калифорния 65
Предложение 65 — Химические вещества, вызывающие рак
Вещество не указано в списке.
Prop 65 — Токсичность для развития
Вещество не указано.
Правило 65 — Токсичность для развития, женщины.
Вещество не перечислено.
Правило 65 — Токсичность для развития, мужчины.
Вещество не указано.
Информация об ограничении использования:
Для использования только технически квалифицированными специалистами.
Другие постановления, ограничения и запретительные постановления
Вещество, вызывающее очень серьезную озабоченность (SVHC) в соответствии с Регламентом REACH (EC) No.1907/2006.
Вещества нет в списке.
Должны соблюдаться условия ограничений согласно Статье 67 и Приложению XVII Регламента (ЕС) № 1907/2006 (REACH) для производства, размещения на рынке и использования.
Вещества нет в списке.
Приложение XIV Правил REACH (требуется разрешение на использование)
Вещество не указано.
REACH — Предварительно зарегистрированные вещества
Вещество внесено в список.
Оценка химической безопасности:
Оценка химической безопасности не проводилась.
РАЗДЕЛ 16. ПРОЧАЯ ИНФОРМАЦИЯ
Паспорт безопасности в соответствии с Регламентом (ЕС) № 1907/2006 (REACH). Вышеупомянутая информация считается правильной, но не претендует на исчерпывающий характер и должна использоваться только в качестве руководства. Информация в этом документе основана на текущем уровне наших знаний и применима к продукту с учетом соответствующих мер безопасности. Это не является гарантией свойств продукта. American Elements не несет ответственности за любой ущерб, возникший в результате обращения или контакта с вышеуказанным продуктом.Дополнительные условия продажи см. На обратной стороне счета-фактуры или упаковочного листа. АВТОРСКИЕ ПРАВА 1997-2021 AMERICAN ELEMENTS. ЛИЦЕНЗИОННЫМ ДАННЫМ РАЗРЕШЕНО ИЗГОТОВЛЕНИЕ НЕОГРАНИЧЕННЫХ КОПИЙ БУМАГИ ТОЛЬКО ДЛЯ ВНУТРЕННЕГО ИСПОЛЬЗОВАНИЯ.
Сферические вмятины на углеродно-углеродных композитах с покрытием из карбида гафния и карбида кремния после испытания на термоудар на воздухе
Реферат
В данном исследовании высокотемпературное окисление и вмятины на карбиде кремния (SiC) и карбиде гафния ( Композиты углерод-углерод (C / C) с покрытием HfC были исследованы для предотвращения окисления композитов C / C на воздухе.Слои SiC и HfC были покрыты для защиты композита от окисления на воздухе при высокой температуре. Испытания на высокотемпературное окисление проводились при 500 ° C, 1000 ° C, 1350 ° C и 1500 ° C в течение 1 часа на воздухе с последующим охлаждением до комнатной температуры путем теплового удара. Этот цикл повторяли до тех пор, пока слой покрытия не был поврежден. В результате измерения изменения веса в соответствии с тепловым циклом и наблюдения за повреждением волокна в композитах C / C было установлено, что сопротивление окислению HfC превосходит сопротивление SiC.Изменение механических свойств было исследовано с помощью испытания на вдавливание шариком из карбида вольфрама с радиусом 3,18 или 7,93 мм до и после испытания на высокотемпературное окисление при тепловом ударе. Относительный модуль упругости был спрогнозирован на основе наклона кривой нагрузка-смещение при вдавливании во время нагружения или наклона кривой во время разгрузки. Относительная твердость также анализировалась на основе остаточного смещения после вдавливания. Твердость и модуль упругости покрытия HfC и SiC были выше, чем у композитов C / C, а механические свойства C / C-композита с покрытием HfC были относительно хорошими по сравнению с таковыми у композитов с покрытием SiC до теплового удара. контрольная работа.
В частности, в этом исследовании было обнаружено, что механические свойства C / C-композитов с покрытием HfC, подвергнутых воздействию температур> 1000 ° C на воздухе, были перенесены с эластичных на квазипластические. Квазипластичность слоя покрытия HfC была оценена как превосходная с точки зрения его устойчивости к механическим повреждениям, поскольку слой покрытия нелегко отслаивать или повредить даже при окислении.
Ключевые слова
Углерод-углеродные композиты
Покрытие
Карбид гафния
Вмятины
Механические свойства
Рекомендуемые статьи Цитирующие статьи (0)
© 2020 Elsevier Ltd и Techna Group S.r.l. Все права защищены.
Рекомендуемые статьи
Цитирующие статьи
Производство волокон из карбида тантала и гафния с помощью ForcespinningTM для сверхвысокотемпературных применений
В этой работе предлагается новый метод производства ультратонких волокон из карбида тантала и гафния с использованием технологии Forcespinning4 TM исследован золь-гель процесс на основе негалогенидов. Оптимальный диапазон вязкости раствора систематически определялся с помощью реологических исследований чистого ПАН / ДМФ в зависимости от образования волокон.Впоследствии параметры Forcespinning TM также были систематически изучены для определения оптимальной скорости вращения и расстояния от фильеры до собирающего стержня, необходимых для идеального формирования волокна. Волокна TaC и HfC были синтезированы методом Forcespinning TM с использованием смеси ПАН и тугоплавких алкоксидов переходных металлов (т.е. этоксида тантала (V) и трет-бутоксида гафния (IV)) в растворе ДМФ на основе оптимальных условий, определенных из чистого ПАН. / ДМФ. Во всех случаях после прокаливания порошковая дифракция рентгеновских лучей (PXRD) и энергодисперсионная спектроскопия (EDS) показали, что были получены волокна TaC и HfC.ТГА / ДСК подтвердили химическую стабильность полученных волокон.
1. Введение
Хотя тугоплавкие карбиды переходных металлов (RTM-C) изучались еще в 1800-х годах, интерес к этим материалам возрос в конце 1950-х, когда космическая гонка усилилась [1]. Исследования RTM-C привлекли еще больший интерес в конце 1980-х годов для аэрокосмических приложений [1]. Поскольку гиперзвуковые технологии развивают скорость выше 5 Маха, температура поверхности может достигать 2000 ° C в присутствии высокореактивных газов [1].Следовательно, материалы, которые могут выжить / смягчить эти экстремальные условия, имеют решающее значение для будущего применения гиперзвуковых технологий. В настоящее время композиты углерод / углерод (C / C) являются предпочтительным материалом из-за их механических, термических и ударных свойств. К сожалению, углерод подвержен окислению при высокой температуре в различных средах и имеет низкую стабильность в условиях сильной эрозии [2]. Волокна из карбида кремния (SiC) также исследовались в качестве замены углеродных волокон.Однако волокна SiC могут сохранять свои механические свойства только до 1900 ° C. SiC генерирует газообразные продукты реакции в результате естественного окисления в сочетании с температурой> 1100 ° C, высоким давлением и внешним потоком газа [3].
Из-за теплового ограничения углеродных и карбидокремниевых волокон, затрудняющих работу при сверхвысоких температурах, материалы RTM-C для использования в высокотемпературных средах были определены как жизнеспособные заменители [4]. Материалы RTM-C обладают прочной ковалентной связью и степенью металлической связи, что приводит к высоким температурам плавления (> 3700 ° C (4000 K)), высокой твердости, хорошей жаропрочности, высокой стойкости к окислению, отличной электропроводности и исключительной устойчивость к агрессивным химическим и термическим средам [2, 5–7].Эта комбинация свойств позволяет RTM-C выжить в более экстремальных условиях, чем существующие конструкционные материалы. Следовательно, использование этих материалов в качестве армирующих волокон в композитах значительно повысит термическое сопротивление, а также устойчивость к повреждениям в сверхвысокотемпературных композитах [2–7].
Для использования этих материалов RTM-C в качестве армирующих волокон в композитах критически важен легко масштабируемый способ производства высококачественных материалов в форме волокна. Способы производства материалов из гафния и карбида тантала (HfC и TaC) из литературы описывают несколько путей, которые привели к успешному производству этих материалов в виде волокна и порошка [8].Однако в большинстве этих методов используются агрессивные реагенты и галогенидные предшественники тугоплавкого переходного металла, которые, как известно, приводят к образованию примесей при разложении (т.е. загрязнении Cl). Золь-гель процесс продемонстрировал возможность использования алкоголятов металлов (группы IV, V и VI) для синтеза частиц и волокон практически без примесей [9–12].
Кроме того, не все эти методы позволяют производить качественные волокна традиционными методами. В настоящее время наиболее распространенными способами изготовления волокон являются методы формования из расплава, самосборки, разделения фаз и электроспиннинга [13].Благодаря простоте и дешевизне электропрядения, это наиболее часто используемый метод изготовления нановолокон. К сожалению, этот метод имеет ограничения по материалу / растворителю из-за электростатических полей и по своей сути низкой производительности при традиционном производстве методом электроспиннинга в лабораторных масштабах, которое, как было показано, позволяет производить только около 0,1 г / ч волокон [14, 15]. С другой стороны, Oregon et al. произвел волокна поликапролактона (PCL) с расходом 0,32 г за две минуты (с увеличением до 9,6 г / ч) с помощью технологии Forcespinning TM , что соответствует увеличению выхода на 3000% [14].Силовое вращение TM — это процесс, разработанный Sarker et al. что похоже на электроспиннинг. Однако он использует центробежные силы вместо электростатических сил для создания волокон из раствора, выбрасываемого из вращающейся металлической головки [15]. Это приводит к быстрому производству волокнистых материалов от нанометров до микронных [16]. Благодаря использованию центробежных сил, возможные варианты материалов для Forcespinning TM не ограничиваются их диэлектрическими свойствами, что позволяет использовать широкий спектр комбинаций материалов [17–20].Благодаря сочетанию Forcespinning TM с золь-гель процессом ранее были успешно синтезированы сверхвысокотемпературные керамические волокна, такие как карбид кремния (SiC), и волокна RTM-C, такие как карбид титана (TiC) и карбид циркония (ZrC).
Хотя Firbas et al. были первыми, кто производил волокна из TiC и ZrC методом Forcespinning TM , TaC и HfC с более высокой температурой плавления еще не были синтезированы этим методом [17].
В данной работе представлен способ получения стабильных волокон TaC и HfC с использованием техники Forcespinning TM и золь-гелевых металлических прекурсоров на основе негалогенидов.Во-первых, идеальная вязкость раствора систематически определялась с помощью реологических исследований чистого ПАН / ДМФ. Затем параметры Forcespinning TM были систематически изучены для определения оптимальной угловой скорости и расстояния от фильеры до собирающего стержня, необходимых для идеального формирования волокна. Наконец, для волокон TaC и HfC были представлены приготовление золь-гель, параметры обработки волокна и характеристики. Насколько нам известно, это первый раз, когда волокна TaC и HfC были синтезированы с помощью метода Forcespinning TM .Благодаря этим результатам, высокопроизводительное производство волокон RTM-C для армирования композитов стало возможным благодаря технологии Forcespinning TM .
2. Материалы и методы
2.1. Материалы
Все синтезы проводили в перчаточном боксе, заполненном аргоном, и все химические вещества использовали в том виде, в котором они были получены, если не указано иное. Безводный диметилформамид (DMF), безводная уксусная кислота, полиакрилонитрил (PAN, молекулярная масса 150 000) и этоксид тантала (V) были приобретены у Sigma Aldrich.Трет-бутоксид гафния (IV) был приобретен у Alfa Aesar.
2.2. Приготовление раствора PAN
Растворы PAN были приготовлены с различными массовыми процентами от 10 до 20% мас. / Мас. Для приготовления растворов желаемые количества ПАН и ДМФ добавляли в химический сосуд с магнитной мешалкой. Затем раствор герметично закрывали и оставляли перемешиваться до полного растворения PAN. Аликвоту раствора PAN объемом 3 мл отбирали для процесса прядения, а аликвоту объемом 1 мл отбирали для реологических исследований, чтобы сравнить различные процентные содержания раствора PAN по массе.
2.
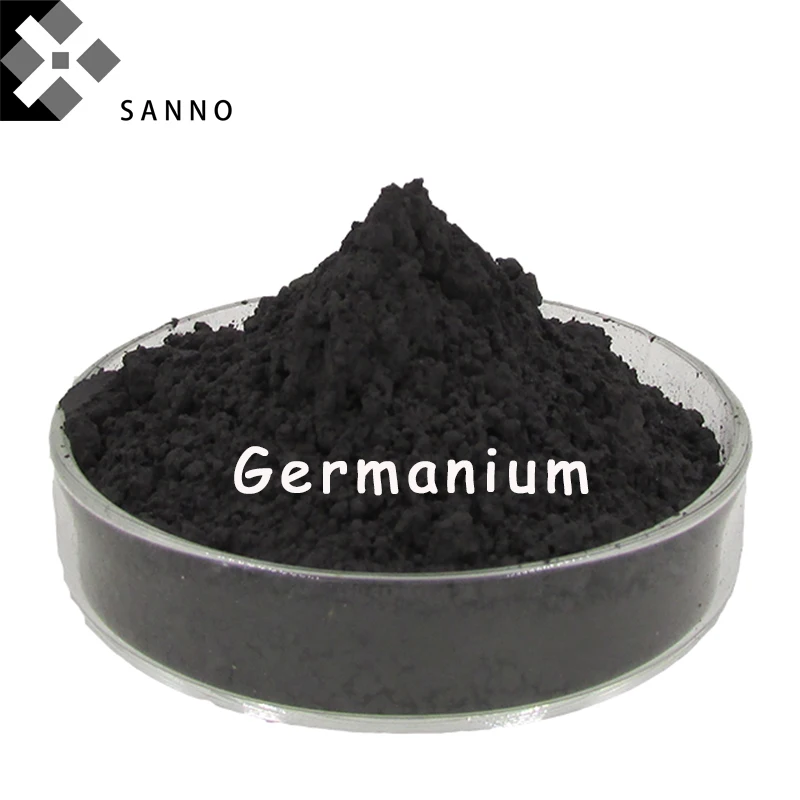
Раствор предшественника волокна состоял из объединенного раствора PAN и раствора этоксида тантала (V). Рецепт раствора PAN (13% масс.) Состоял из 3,897 г PAN и 30,00 г DMF. Реагенты добавляли в химический сосуд с магнитной мешалкой; раствор герметично закрывали и оставляли перемешиваться до полного растворения ПАН. Для раствора этоксида тантала (V) 4,500 г этоксида тантала (V) и 9,000 г уксусной кислоты добавляли в химический сосуд с магнитной мешалкой; раствор герметично закрывали и оставляли перемешиваться до растворения.«Раствор волокон» представлял собой раствор этоксида тантала (V) / уксусная кислота, смешанный с раствором PAN / DMF, который перемешивали в течение ночи. Наконец, была отобрана аликвота раствора волокна объемом 3 мл для процесса прядения, а аликвота объемом 1 мл была взята для реологических исследований для сравнения с оптимальным чистым раствором PAN. Тот же процесс был использован с трет-бутоксидом гафния (IV) вместо этоксида тантала (V) для получения HfC-волокон.
2.4. RTM-C Fiber Preparation
Волокна были получены с использованием системы циклона FibeRio L-1000 M Cyclone Forcespinning TM .Технология Forcespinning TM использует центробежную силу для выдавливания раствора из металлических головок на вертикальные металлические стержни на выбранных расстояниях радиального разделения. Систематически изучались скорость вращения и расстояние собирающей удочки, результаты представлены в рукописи и вспомогательной информации. Систематические исследования привели к идеальной программе, представляющей собой многоступенчатую программу, состоящую из отжима при 1000 об / мин в течение пяти секунд и последующего увеличения до 3500 об / мин в течение 1200 секунд. Металлических стержней было размещено 17.78 см от фильеры. Затем полученные волокна собирали и помещали в коробчатую печь при 220 ° C со скоростью линейного изменения 5 ° C в минуту, а затем выдерживали при 220 ° C в течение двух часов. После охлаждения до комнатной температуры волокна затем помещали в трубчатую печь при 1600 ° C со скоростью линейного изменения 5 ° C в минуту в потоке аргона и выдерживали в течение двух часов. Полученные волокна были охарактеризованы с помощью PXRD, SEM / EDS и TGA.
2,5. Определение характеристик волокна
Порошковые дифракционные рентгенограммы (PXRD) были получены на дифрактометре PANalytical X’Pert Pro (5–70 ° два тета) с использованием излучения CuK α (1.5406 Å) и детектор RTMS X’Celerator со скоростью сканирования 0,02 ° / сек с использованием держателя с нулевым фоном. Картины PXRD анализировали с использованием программного обеспечения JADE 9.6.0 (Materials Data Inc., Ливермор, Калифорния) и индексировали с помощью файла порошковой дифракции PDF-4 +. Термогравиметрические анализы (ТГА) / дифференциальная сканирующая калориметрия (ДСК) проводили в атмосфере проточного воздуха и азота от комнатной температуры до 1000 ° С со скоростью 10 ° С / мин с использованием системы Mettler Toledo STARe. Сканирующую электронную микроскопию проводили с использованием Hitachi S-5200 FE-SEM с приставкой Oxford Instruments X-MAX EDAX, работающей с ускоряющим напряжением 20 кВ.
3. Результаты и обсуждение
3.1. Реологические испытания
Производство волокнистых материалов нетривиально и зависит от множества синтетических и инструментальных переменных. Из многих параметров вязкость золь-геля наиболее легко адаптируется для производства волокнистых материалов в любом приборе. Поэтому были проведены реологические исследования растворов PAN / DMF для определения оптимальной вязкости раствора, необходимой для производства волокон посредством Forcespinning TM с использованием нашего оборудования.
Реологические испытания чистых растворов ПАН / ДМФ с различным массовым процентом от 10 до 20 мас.% Были измерены как функция скорости сдвига. Растворы полимера Forcespinning TM обычно имеют более высокое содержание полимера, чем растворы для электропрядения, из-за различий в генерировании струи и расширении обоих методов. Чистый раствор служил суррогатом для определения оптимальных условий для растворов RTM-C, и их результаты профиля вязкости показаны на рисунке 1 (а). При 10 мас.% (Минимальная нагрузка) раствор ПАН / ДМФ демонстрирует почти ньютоновское поведение, вплоть до скорости сдвига ~ 200 л / с, с вязкостью 570 мПа с.
По мере увеличения содержания ПАН растворы полимеров демонстрируют возрастающие уровни вязкости, и переход к разжижению при сдвиге происходит при прогрессивно более низких скоростях сдвига, поскольку система показывает дальнейшее перепутывание цепей. Ожидается, что все эти растворы будут иметь характер запутывания цепей, исходя из предшествующей литературы о растворах PAN / DMF [20].Стабильное формирование волокна требует концентрации полимера, достаточной для получения перепутывания цепей. Wang et al. представили реологические характеристики растворов ПАН / ДМФА, которые определили минимальную концентрацию ( ° C мин ) для входа в режим перепутывания цепей при приблизительно 5 мас.%. Для растворов полимеров выше ° C мин , Wang et al. обнаружили, что удельная вязкость подчиняется степенному закону η sp ∼ 4. 78 [21].На рисунке 1 (b) представлены графики зависимости удельной вязкости от объемного% PAN для оценки степенного закона, характерного для этих растворов. Приготовленные здесь растворы с более высокой концентрацией различаются по молекулярной массе и имеют показатель степени, равный 6,25, что указывает на быстрое развитие эластичности при сушке.
Производство волокон включает в себя поверхностное натяжение и вязкость раствора полимера, перепутывание цепей и динамику релаксации раствора полимера, скорость испарения растворителя и силы растяжения на волокне при переходе от наконечника отверстия к системе коллектора [ 22].Производство волокна компанией Forcespinning TM впервые было протестировано на чистых растворах ПАН / ДМФ, чтобы связать вязкость раствора с образованием волокна, поскольку вязкоупругая нестабильность может привести к образованию шариков при низкой вязкости. Как можно видеть на Фигуре 2, средняя вязкость, полученная при скорости сдвига в диапазоне от 0 до 1000 л / с для различных растворов, увеличивалась по мере увеличения мас. % ПАН. Раствор 10–13 мас.% Дает плохую морфологию нановолокон с каплями и шариками из-за низкой вязкости, как показано на Рисунке S2.При содержании 17–20 мас.% Образуются короткие нановолокна с низким выходом, что указывает на то, что вязкость раствора слишком высока для данной центробежной силы, как показано на Рисунке S2. Однако 15 мас.% Давали однородные волокна без капель. Измеренная вязкость на рисунке 1 (а) представляет собой разжижение при сдвиге, и поэтому для характеристики производства подходящего волокна были выбраны значения при максимальной скорости сдвига 1000 л / с. Это дает 2,80 Па · с в качестве целевой вязкости для раствора предшественника RTM-C.
Контроль свойств волокна, включая диаметр, регулярность и форму, требует настройки параметров обработки для процесса Forcespinning TM .На практике есть три параметра прибора, которые можно изменять для управления формированием волокна: угловая скорость, Ω, расстояние до коллектора и концентрация полимера. Forcespinning TM имеет пятиступенчатый процесс формирования волокна. Этапы включают (1) выход струи, (2) орбитальную траекторию, (3) аэродинамическую вибрацию волокна, (4) орбитальное расширение и (5) сбор волокна. Существует критическая угловая скорость для создания струи, но есть вторая критическая угловая скорость, при которой диаметр струи уменьшается значительно ниже диаметра отверстия наконечника [8].Таким образом, размер волокна относительно нечувствителен к диаметру отверстия, что важно для капиллярного противодавления, необходимого для индуцирования потока к наконечнику. Существует минимальная скорость вращения, связанная с фазой вытягивания волокна, а также предотвращающая вытягивание волокон обратно к валу фильеры, и максимальная скорость, связанная с разрывом струи раствора полимера. Таким образом, раствор 15 мас.% ПАН был исследован при различных скоростях и расстояниях коллектора для определения оптимальных условий.Как видно на Рисунке S3, на формирование волокна сильно влияют различные скорости вращения и расстояния сбора.
Низкие обороты (≤2000 об / мин) приводят к образованию капель из-за того, что не превышает вторую критическую угловую скорость, необходимую для уменьшения диаметра волокна ниже диаметра отверстия. Слишком высокая (≥5000 об / мин) скорость вращения приводит к очень мелким волокнам, которым не хватает прочности для образования непрерывных волокон. Расстояние сбора также необходимо оптимизировать, чтобы определить, на каком расстоянии от фильеры волокна полностью сформированы.Поэтому мы исследовали расстояния для коллектора в диапазоне от 15 до 18 см. Систематическое исследование этих переменных, основанное на формировании волокна и выходе, привело к скорости 3500 об / мин и расстоянию сбора 17,78 см, что является оптимальной скоростью и расстоянием, необходимым для наилучшего формирования волокна.
Ожидалось, что добавление раствора этоксида тантала (V) / уксусной кислоты к 15% -ному раствору ПАН / ДМФ повысит вязкость, что в конечном итоге приведет к изменению характеристик раствора при ранее определенных условиях. Согласно предыдущим исследованиям с чистым раствором ПАН / ДМФ, оптимальная вязкость раствора, необходимая для наших приборов, составляла 2,80 Па · с. Чтобы учесть дополнительное притяжение между этоксидом Та и ПАН, мы снизили концентрацию ПАН / ДМФ до 13 мас.%, Что привело к получению в общей сложности 33 мас.% Раствора этоксида тантала (V) / уксусной кислоты для получения «раствора волокна». Реология раствора волокон была исследована по сравнению с чистым 15% -ным раствором ПАН / ДМФ, и их поведение было сопоставимо, как показано на рисунке 1 (c).При низкой скорости сдвига вязкость раствора волокна-предшественника TaC выше, чем у 15% раствора PAN / DMF, что указывает на то, что этоксид Ta создает дополнительное взаимодействие между цепями PAN. Вязкость предшественника TaC при скорости сдвига 1000 1 / с составляла 3,07 Па с, что сравнимо с 15% -ным раствором PAN / DMF, который был определен как оптимальный. Эту процедуру повторили для раствора трет-бутоксида Hf / уксусная кислота. Таким образом, эти решения использовались на протяжении всей остальной работы. После приготовления раствора RTM-C волокнистые материалы генерировались со скоростью 3500 об / мин с собирающими стержнями на 17.78 см от фильеры.
3.2. PXRD
После отверждения сырого тела при 220 ° C и карбонизации реагентов при 1600 ° C для изолированных продуктов были собраны данные PXRD. Как видно на Рисунке 3 (а), продукт из Та «волокнистого раствора» давал дифракционные пики при 35,5 ° (111), 40,7 ° (200), 58,9 ° (220) и 70,0 ° (311), которые были проиндексированы как TaC (PDF № 00-035-0801) [6, 21–26]. Было некоторое присутствие оксида тантала (Ta 2 O 5 , PDF № 00-025-0922), поскольку это типично при использовании алкоксидов металлов в качестве предшественника металла [11].Используя полуколичественный (SQ) фазовый анализ в программном обеспечении Bruker Diffrac Eva V5.2, было установлено, что Ta-волокна содержат 91,8% TaC (00-035-0801) и 8,2% Ta 2 O 5 (00-025- 0922).
На рис. 3 (б) представлены спектры PXRD продукта, полученного из раствора Hf. В спектрах наблюдались дифракционные пики при 33,4 ° (111), 38,8 ° (200) и 56,1 ° (220), которые были проиндексированы как HfC (PDF № 00-039-1491). Как видно из спектров, присутствуют остатки оксида гафния (HfO 2 , PDF № 00-053-0560), поскольку это типично при использовании алкоксидов металлов в качестве предшественника металла, но основным продуктом является HfC [11].Используя полуколичественный (S-Q) фазовый анализ в Bruker Diffrac Eva V5.2, было установлено, что Hf-волокна содержат 96,8% HfC (00-039-1491) и 3,2% HfO 2 (00-053-0560).
3.3. SEM / EDS
На рис. 4 показаны СЭМ-изображения синтезированных волокон TaC. Волокна TaC имели средний диаметр 475 нм. На рис. 5 представлено СЭМ-изображение вместе с ЭДС-изображениями тантала и углерода, собранными на волокнах TaC. Анализ EDS подтверждает присутствие тантала и углерода в выбранной области, как показано на нижнем изображении.На рис. 6 показаны СЭМ-изображения синтезированных волокон HfC. Волокна HfC имели диаметр со средним размером 340 нм. На рисунке 7 представлено изображение SEM вместе с изображениями EDS гафния и углерода, собранными на волокнах HfC. Анализ EDS подтверждает присутствие гафния и углерода в выбранной области, как показано на нижнем изображении.
3.4. Температурное поведение волокон RTM-C
Кривая ТГА на рисунке 8 (а) показывает, что волокна TaC были термически стабильны при температуре ниже 450 ° C на воздухе.После 450 ° C наблюдалось увеличение веса, которое объясняется окислением TaC до Ta 2 O 5 , что дополнительно подтверждается PXRD, как показано в S4 [6, 22]. Следует отметить, что величина этого увеличения веса указывает на то, что окисление может ограничиваться поверхностью TaC за счет образования формируемого пассивирующего слоя Ta 2 O 5 . Механизм окисления TaC следующий [27] [29]:
Примерно после 560 ° C потеря веса была вызвана окислением любого присутствующего свободного углерода и потерей CO 2 из системы [20].Кроме того, как видно на Фигуре 8 (b), волокна не показали изменения массы (разложения) согласно N 2 . Кривая ТГА на Рисунке 8 показывает, что синтезированные волокна HfC демонстрируют термическую стабильность ниже примерно 500 ° C на воздухе.
После 500 ° C наблюдалось увеличение массы из-за окисления HfC до HfO 2 и подтверждено с помощью PXRD (S4). Окисление HfC происходит следующим образом [21, 22]:
Примерно после 650 ° C потеря веса была вызвана окислением любого присутствующего свободного углерода и потерей CO 2 из системы [20].Кроме того, как видно на Фигуре 8 (b), волокна не показали изменения массы (разложения) согласно N 2 . Обратите внимание, что вес увеличивается примерно при 500 ° C, а вес уменьшается примерно при 650 ° C, что меньше, чем у волокон TaC. Это может быть связано с возможностью того, что волокна TaC имели больше захваченного свободного углерода, чем волокна HfC. Рамановские спектры представлены на рисунке S4.
4. Выводы
Волокна TaC и HfC были успешно синтезированы методом Forcespinning TM .Реология различных мас.% ПАН и ДМФ была определена, чтобы понять перепутывание и оптимизировать раствор предшественника для формирования волокна. Этот суррогатный образец раствора привел к оптимальным параметрам раствора для производства волокон RTM-C. Волокна RTM-C были охарактеризованы, чтобы подтвердить их образование, кристаллическую структуру и стабильность. После успешной термообработки волокна PXRD подтвердил образование кристаллических волокон TaC и HfC. Анализ ТГА показал, что волокна RTM-C сохраняют стойкость к окислению и термическую стабильность на воздухе до 450 ° C.Микроскопический анализ показал, что средний диаметр волокон составлял 475 нм и 340 нм для волокон TaC и HfC соответственно. Также микроскопия показала, что Hf и Ta были равномерно распределены по волокну. Этот метод позволяет простой и быстрый синтез этих волокон с возможностью быстрого получения граммов волокон. Текущие исследования будут изучать механическое поведение, уменьшение содержания оксидов и включение волокна в композит.
Доступность данных
В статью включены данные реологического анализа, порошковой дифракции рентгеновских лучей, сканирующей электронной микроскопии / энергодисперсионной спектроскопии и термогравиметрического анализа.
Конфликт интересов
Авторы заявляют об отсутствии конфликта интересов.
Выражение признательности
Эта работа была поддержана программой исследований и разработок под руководством лаборатории Sandia National Laboratories, многопрофильной лаборатории, управляемой и управляемой National Technology and Engineering Solutions of Sandia LLC, дочерней компанией Honeywell International Inc., находящейся в полной собственности компании Honeywell International Inc. Национальное управление ядерной безопасности Министерства энергетики США по контракту DE-NA0003525.
Дополнительные материалы
Дополнительная информация включает в себя подробные изображения формирования волокна PAN при различных скоростях и расстояниях собирающих стержней, PXRD-спектры волокон после термогравиметрического анализа на воздухе и спектры комбинационного рассеяния волокон в исходном состоянии. (Дополнительные материалы)
Порошок карбида гафния высокой чистоты по меньшей цене Быстрая доставка
По вопросам, связанным с покупкой, напишите нам по адресу [email protected], sales5 @ nanoshel.com, [email protected]
На главную »Порошок карбида гафния (HfC, чистота: 99,9%, 400-500 нм)
инвентарный № | CAS | Паспорт безопасности материалов | Спецификация | COA | Каталог |
---|---|---|---|---|---|
NS6130-02-297 | 12069-85-1 |
(HfC, чистота: 99.9%, APS: 400-500 нм)
Доступный размер упаковки: 10Gms, 25Gms, 50Gms, 100Gms, 250Gms, 500Gms, 1Kg и оптовые заказы
SEM — наночастицы HfC
Анализ размера частиц
Порошок карбида гафния
Продукт | Порошок карбида гафния / нанопорошок | |
Арт. | NS6130-02-297 | |
CAS | 12069-85-1 | Подтвердить |
APS | 400-500 нм | Подтвердить |
Чистота | 99,9% | Подтвердить |
Молекулярная формула | HfC | Подтвердить |
Молекулярный вес | 190.50 г / моль | Подтвердить |
Плотность | 12,2 г / см³ | Подтвердить |
Точка плавления | 3890 ° С | Подтвердить |
Растворимость | Не растворим в воде | |
Контроль качества | Каждая партия порошка карбида гафния / нанопорошка была успешно протестирована. | |
Main Inspect Verifier | Менеджер КК |
Типичный химический анализ
Анализ | 99,9% |
Другой металл | 850 частей на миллион |
Порошок карбида гафния
Свяжитесь с нами:
У нас вы можете легко приобрести порошок карбида гафния по отличным ценам.Разместите онлайн-заказ, и мы отправим его через DHL, FedEx, UPS. Вы также можете запросить коммерческое предложение, отправив нам письмо по адресу [email protected]. Мы приглашаем вас связаться с нами для получения дополнительной информации о нашей компании и наших возможностях. В Nanoshel мы будем рады быть вам полезными. Мы с нетерпением ждем ваших предложений и отзывов.
sales5 @ nanoshel.com
Подписывайтесь на нас:Примечание * Обмен материалов / продуктов не разрешен. Nanoshel не предлагает возврат средств. * Чеки в долларах США не принимаются, принимаются только банковские TT / кредитные карты
фактов о гафнии | Живая наука
Гафний — блестящий серебристо-серый переходный металл. Обнаруженный в 1923 году, это был предпоследний элемент со стабильными ядрами, который был добавлен в таблицу Менделеева (последним был рений в 1925 году).Гафний назван в честь латинского слова Копенгаген: Hafnia . Этот элемент имеет несколько очень важных коммерческих применений, в том числе его использование в атомной энергетике, электронном оборудовании, керамике, электрических лампочках и в производстве суперсплавов.
Гафний редко встречается в природе в свободном виде, вместо этого он присутствует в большинстве минералов циркония в концентрации до 5 процентов. Фактически, гафний настолько химически похож на цирконий, что разделить два элемента чрезвычайно сложно.Большая часть товарного гафния производится как побочный продукт при рафинировании циркония.
Гафний — 45-й по численности элемент на Земле, составляющий около 3,3 частей на миллион (ppm) земной коры по весу, согласно Chemicool. Гафний довольно устойчив к коррозии из-за образования оксидной пленки на открытых поверхностях. Фактически, он не подвержен действию воды, воздуха и всех щелочей и кислот, кроме фтороводорода.
Карбид гафния (HfC) имеет самую высокую температуру плавления из всех известных двухэлементных соединений, составляющую около 7 034 градуса по Фаренгейту (3890 градусов по Цельсию), по данным лаборатории Джефферсона.Составной нитрид гафния (HfN) также имеет высокую температуру плавления, около 5 981 градус по Фаренгейту (3305 градусов Цельсия). Согласно Chemistry World, среди соединений трех элементов смешанный карбид вольфрама и гафния имеет самую высокую температуру плавления среди всех известных соединений, составляющую 7 457 градусов по Фаренгейту (4 125 градусов по Цельсию). Некоторые другие соединения гафния включают фторид гафния (HfF 4 ), хлорид гафния (HfCl 4 ) и оксид гафния (HfO 2 ).
Просто факты
- Атомный номер (количество протонов в ядре): 72
- Атомный символ (в периодической таблице элементов): Hf
- Атомный вес (средняя масса атома): 178.49
- Плотность: 13,3 грамма на кубический сантиметр
- Фаза при комнатной температуре: твердое вещество
- Точка плавления: 4 051 градус Фаренгейта (2233 градуса Цельсия)
- Точка кипения: 8 317 градусов F (4 603 градуса C)
- Количество изотопов ( атомов одного и того же элемента с другим числом нейтронов): 32, период полураспада которых известен с массовыми числами от 154 до 185
- Наиболее распространенные изотопы: Hf-174, Hf-176, Hf-177, Hf-178, Hf- 179 и Hf-180.
Discovery
По данным Chemistry World, присутствие гафния было предсказано за десятилетия до его открытия.Этот элемент оказался довольно неуловимым, так как было практически невозможно отличить его химически от гораздо более распространенного циркония.
Гафний был еще неизвестен, когда русский химик и изобретатель Димитрий Менделеев разработал Периодический закон — предсовременную версию периодической таблицы элементов — в 1869 году. Однако в своей работе Менделеев правильно предсказал, что будет элемент, свойства которого были похожи на цирконий и титан, но тяжелее их.
В 1911 году французский химик Жорж Урбен, который уже открыл редкоземельный элемент лютеций, считал, что наконец обнаружил недостающий элемент 72, который, согласно Chemicool, он назвал целцием.Однако несколько лет спустя было показано, что его открытие представляет собой комбинацию уже открытых лантаноидов (15 металлических элементов с атомными номерами от 57 до 71 в периодической таблице).
По-прежнему было неясно, будет ли отсутствующий элемент 72 переходным или редкоземельным металлом, поскольку он попал на границу между этими двумя типами элементов в таблице. По данным Chemistry World, химики, которые считали, что это редкоземельный элемент, провели много бесплодных поисков среди минералов, содержащих редкоземельные элементы.
Однако новые данные, полученные как из области химии, так и из физики, подтвердили идею о том, что элемент 72 будет переходным элементом. Например, ученые знали, что элемент 72 находится ниже титана и циркония в периодической таблице, и оба они были известными переходными элементами. Кроме того, датский физик Нильс Бор, один из основателей квантовой теории, предсказал, что элемент 72 будет переходным металлом на основе его электронной конфигурации элемента, согласно Chemistry World.
В 1921 году Бор призвал венгерского химика Георга фон Хевеши и голландского физика Дирка Костерто — двух молодых исследователей в его институте в то время — искать элемент 72 в циркониевой руде. Основываясь на своей квантовой теории атомной структуры, Бор знал, что новый металл будет иметь химическую структуру, аналогичную цирконию, поэтому, согласно Chemicool, была большая вероятность того, что эти два элемента будут найдены в одних и тех же рудах.
Фон Хевеши и Костер последовали совету Бора и приступили к изучению циркониевой руды с помощью рентгеновской спектроскопии.По данным Chemical and Engineering News, они использовали теорию Бора о том, как электроны заполняют оболочки и подоболочки внутри атомов, чтобы предсказать различия между рентгеновскими спектрами двух элементов. Этот метод в конечном итоге привел к открытию гафния в 1923 году. Это открытие было одним из шести оставшихся пробелов в периодической таблице Менделеева. Они назвали новый элемент в честь родного города Бора Копенгагена ( Hafnia на латыни).
Использует
Гафний чрезвычайно устойчив к коррозии и является отличным поглотителем нейтронов, что позволяет использовать его в атомных подводных лодках и стержнях управления ядерными реакторами — важной технологии, используемой для поддержания реакций деления.Управляющие стержни поддерживают активную цепную реакцию деления, но также предотвращают ее неконтролируемое ускорение.
Гафний используется в электронном оборудовании, таком как катоды и конденсаторы, а также в керамике, фотовспышках и нити накаливания ламп. По данным лаборатории Джефферсона, он используется в вакуумных трубках в качестве газопоглотителя — вещества, которое соединяется с газами и удаляет из них следовые газы. Гафний обычно сплавлен с другими металлами, такими как титан, железо, ниобий и тантал. Например, жаропрочные гафний-нобиевые сплавы используются в аэрокосмической отрасли, например, в космических ракетных двигателях.
Соединение карбида гафния имеет самую высокую температуру плавления среди всех соединений, состоящих всего из двух элементов, что позволяет использовать его для облицовки высокотемпературных печей и обжиговых печей, согласно Chemicool.
Кто знал?
- Гафний пирофорен (самовоспламеняется) в виде порошка.
- Английский химик Генри Мозли был ученым, который понял, что элемент Жоржа Урбена «кельций» не является истинным элементом, находящимся под цирконием. К сожалению, Первая мировая война прервала важные исследования этого молодого ученого.Мозли послушно поступил на службу в Королевские инженеры британской армии и был убит снайпером в 1915 году. Его смерть заставила Англию установить новую политику, запрещающую выдающимся ученым участвовать в боях.
- В 1925 году голландские химики Антон Эдуард ван Аркель и Ян Хендрик де Бур разработали метод получения гафния высокой чистоты. Для этого ученые разложили тетраиодид гафния на горячей вольфрамовой проволоке, в результате чего получился кристаллический стержень из чистого гафния, согласно Chemicool.Этот метод называется процессом кристаллического бруска.
- Ядерный изомер гафния долгое время обсуждался как потенциальное оружие. В «Споре о гафнии» ученые обсуждают, способен ли этот элемент вызывать быстрое высвобождение энергии.
- Хотя цирконий химически очень похож на гафний, он отличается от гафния тем, что очень плохо поглощает нейтроны. Поэтому цирконий используется во внешнем слое топливных стержней, где важно, чтобы нейтроны могли легко перемещаться.
Датирование слоев Земли гафнием
В недавнем исследовании международная группа исследователей смогла подтвердить, что первая кора Земли сформировалась около 4,5 миллиардов лет назад, благодаря химическому анализу гафния в редком метеорите. Исследователи полагают, что метеорит произошел от астероида Веста после сильного удара, в результате которого на Землю были отправлены фрагменты горной породы, говорится в пресс-релизе исследования, опубликованном в Science Daily. По мнению исследователей, метеориты — это части первоначального материала, из которого сформированы все планеты.Для исследования они измерили соотношение изотопов гафния-176 и гафния-177 в метеорите. Это дало им отправную точку для построения Земли. Они сравнили результаты с самыми старыми породами на Земле, по сути подтвердив, что кора уже сформировалась на поверхности Земли около 4,5 миллиардов лет назад. Их результаты опубликованы в Proceedings of the National Academy of Sciences (PNAS).
Цена на карбид гафния— ALB Materials Inc
Тантал 09.07.2020
карбид гафния цена
КАРБИД ГАФНИЯ цена, купить КАРБИД ГАФНИЯ
Продукт назван карбид гафния, 99.5
% (металлы без Zr), Zr <1%; Чистота: Упаковка: 100 г, 500 г, 1 кг; Цена: 330 ~ 3300 долларов США
Карбид гафния (HfC) представляет собой химическое соединение гафния и углерода, которое является одним из самых тугоплавких бинарных соединений, известных человеку, с температурой плавления приблизительно 3900 ℃.
Порошок карбида гафния получают восстановлением оксида гафния углеродом при температуре от 1800 до 2000 ℃, при которой требуется длительное время обработки для удаления всего кислорода.
Он обладает наивысшей температурой плавления среди всех известных бинарных сплавов, из-за чего имеет множество высокотемпературных применений.
Он считается кандидатом для применения в условиях экстремально высоких температур, таких как сопла ракет и компоненты ГПВРД.
Карбид гафния также может использоваться в твердых покрытиях, которые часто наносятся с помощью таких процессов, как плазменное напыление.
Кроме того, из конструкционных пен HfC можно производить высокотемпературные компоненты или использовать их в качестве теплоизоляционного материала.
Он также используется в керамической промышленности.
Больше цен на сопутствующие товары
Порошок карбида гафния особой чистоты за меньшую цену Быстрая доставка
Порошок карбида гафния (HfC)
Точка плавления: 3890 ° C
Молекулярная формула: HfC
Молекулярный вес: 190,50 г / моль
Плотность: 12,2 г / см³
Порошок карбида гафния — очень твердый материал.
Используется в твердых покрытиях.
Он также используется в качестве материала горловины сопла ракеты и в металлокерамических материалах.
Он имеет низкую стойкость к окислению, окисление начинается при температуре до 430 ° C.
Порошок карбида гафния пластичен и имеет блестящий серебряный блеск.
Металл имеет плотноупакованную гексагональную кристаллическую структуру.
Он демонстрирует отличные механические свойства и очень хорошую коррозионную стойкость.
В электронной промышленности используется соединение на основе гафния, которое можно использовать в изоляторах затвора в интегральных схемах поколения 45 нм.
Соединения на основе карбида гафния представляют собой практически высокие диэлектрики, позволяющие снизить ток утечки затвора, что улучшает характеристики в таких масштабах.
Кроме того, благодаря своей термостойкости и близости к кислороду и азоту гафний является хорошим поглотителем кислорода и азота в газонаполненных лампах и лампах накаливания.
Гафний также используется в качестве электрода при плазменной резке из-за его способности сбрасывать электроны в воздух.
Это соединение с самой высокой известной температурой плавления: 3890 ° C.
Теоретически деталь, изготовленная из композитного волокна и матрицы из карбида гафния, выдержит температуры, которые могут привести к размягчению или плавлению даже тугоплавких сплавов металл-металл, таких как смеси рений-вольфрам.
HfC имеет примерно 60 процентов плотности металлических сплавов, поэтому критически важные компоненты ракет, ракет и аэрокосмической отрасли, изготовленные из композитов HfC, будут соответственно легче.
Порошок карбида гафния
У нас вы можете легко приобрести порошок карбида гафния по отличным ценам.
Порошок карбида гафния
В последнее десятилетие улучшения в нанотехнологиях были вызваны заметными достижениями в синтезе наноматериалов и, кроме того, многообещающей информацией о приложениях в биомедицине, электронике и энергетике.
Инновации в области наноматериалов могут решить ряд крупнейших научных проблем современности, начиная от потребности в более эффективных альтернативных энергетических технологиях, более быстрой и гибкой электронике и заканчивая улучшенной диагностикой и лечением заболеваний.
Отличительные свойства наноматериалов включают большое отношение поверхности к объему, благоприятную проводимость, уникальные оптические эффекты и эффекты ограничения, а также многие другие.
Сегодня трудно представить себе существование без нанотехнологий.
Нанотехнологии, а точнее наноматериалы, уже используются во многих продуктах и в промышленных приложениях.
Наша база данных продуктов и приложений для нанотехнологий на данный момент дает общее представление о том, как наноматериалы и приложения наноструктур используются сегодня в промышленных и коммерческих приложениях в различных отраслях промышленности.
ALB предлагает огромную коллекцию наноматериалов, которые перемещаются по Периодической таблице, включая золото, серебро, оксид железа, металл и металлические композиты, оксиды, нитриды и керамику.
Мы также предлагаем широкий выбор нанопроволок, нанопорошков и дисперсий наночастиц, магнитных нанопорошков, наночастиц и квантовых пятен.
Органические наноматериалы, например углеродные нанотрубки, графен и оксид графена, а также фуллерены, доступны с различными степенями чистоты и модификациями поверхности.
Мы также предлагаем дендримеры, которые представляют собой органические наноматериалы с четко определенными химическими группами поверхности и размерами, подходящими для исследований и разработок в области доставки лекарств.
Мы верим, что нанотехнологии будут стимулировать реальные будущие обновления производственных технологий в химии, биотехнологии, электронике, медицине, материаловедении, альтернативной энергии, смазочных материалах и сельском хозяйстве.
Карбид гафния (HfC) порошок
ALB предлагает высококачественный порошок карбида гафния (HfC) по конкурентоспособным ценам.
Это сырье для мишеней для распыления солнечной энергии на топливных элементах CVD.
Применение HFC
карбид тантала гафния
Карбид нано-гафния производится в области высоких технологий и новых технологий, а также из высокопроизводительных твердых сплавов, аэрокосмической отрасли, атомной энергетики, электроники, покрытий, кремневых тонких пленок и ключевых материалов для автоматизации металлургии. Очень подходит для ракетного сопла, может вернуть в атмосферу части носового конуса космической ракеты.Используется в керамической промышленности и т. Д. Серый металлический порошок — это один из новых материалов, который производится с помощью нового ремесла. Высокая чистота, равномерное распределение зерен, высокая поверхностная активность, термостабильность, стойкость к окислению, высокая интенсивность, степень твердости. высокая, теплопроводность хорошая, ударная вязкость хорошая, является одним из видов важных высокопрочных, высокопрочных и антикоррозионных высокотемпературных конструкционных материалов.
Порошок карбида тантала (TaC), 99,7%, наши клиенты получают порошок карбида тантала высочайшего качества и чистоты по конкурентоспособной цене.
ALB Materials специализируется на производстве, поставках и распространении порошка карбида тантала по всему миру.
Наш опыт в области наноматериалов, современной керамики, редкоземельных химикатов, порошков для термического напыления, материалов твердооксидных топливных элементов (ТОТЭ), катализаторов, наномагнетиков, гальваники и биотехнологий позволяет нам поставлять нашим клиентам порошок карбида тантала высочайшее качество и чистота по конкурентоспособной цене.
Наш порошок карбида тантала доступен в широком диапазоне количеств и спецификаций, чтобы удовлетворить ваши конкретные промышленные или научные применения.
Часть содержания этой статьи воспроизводится с других носителей с целью передачи дополнительной информации и не означает, что этот веб-сайт согласен с его взглядами или подтверждает подлинность своего содержания. Он не несет прямой и солидарной ответственности за нарушение таких работ. p>
Если в содержании этой страницы есть какие-либо нарушения, неверная информация, исправление ошибок и другие проблемы, свяжитесь с нами по адресу info @ albmaterials.com p>
Ссылка на эту статью: https://www.albmaterials.com/knowledge/blog/hafnium-carbide-price.html
.