Как получить сталь из чугуна в масштабах современного производства
Главная » Сталь
Автор perminoviv На чтение 4 мин Просмотров 386 Опубликовано
Сталь остается основным конструкционным материалом для строительной, машиностроительной и множества других отраслей промышленности. Разделение железоуглеродистых сплавов зависит от содержания углерода. Условно можно считать, что при содержании до 2% углерода это сталь, более 2% — чугун. В литературе в трудах великого материаловеда Гуляева уточняется, что граница раздела 2,14% справедливо только при ничтожно малом содержании любых других элементов, кроме железа и углерода. Не удивительно, что он используется при производстве на крупных комбинатах и небольших литейных цехах.
Использование высокоуглеродистых сплавов в сталеплавильном переделе может быть реализовано в холодном виде. Он имеет форму пирамидки, выплавленной предварительно на металлургических комбинатах из руды и флюсующих материалов и разлитых на специальных разливочных машинах. Преимуществом использования такого типа сырья является неограниченная логистика и гарантированный химический анализ такого материала. Это позволяет в сталеплавильных цехах произвести предварительные подготовительные работы по борьбе с серой, фосфором и другими элементами которые негативно влияют на физические свойства готовой продукции.
На крупных металлургических комбинатах с полным циклом для выплавки стали используют чугун в жидком виде. Перед тем как получит сталь из чугуна, его производят в доменном цехе. Во время выпуска из доменной печи, чугун сливается в ковши, защищенные футерованным слоем от высокой температуры. В этих ковшах его привозят в сталеплавильный цех, где его сливают в большую емкость, в которой смешивается до 1800 тонн чугуна из разных доменных печей. Эта емкость называется миксер. В ней происходит усреднение по химическому анализу и температурному показателю. На многих заводах применяют ковши – миксера. По команде сталевара печи, конвертера или начальника смены из миксера выдается взвешенная порция в ковшах на следующий передел.
К этому времени в сталеплавильном агрегате уже находится разогретый до определенной температуры стальной лом. Чугун заливается на этот лом. Дальше наводя и убирая шлак, меняя его основность и температуру, сталевар доводит расплав до необходимой температуры и химического состава. Такой процесс производства экономит большое количество энергоносителей и снижает себестоимость в производственных масштабах.
Основными агрегатами для использования чугуна при производстве стали являются конвертера, мартеновские, дуговые электрические, индукционные печи.
В мартеновских печах реализован процесс рекуперации тепла. Поток горячего воздуха, проходя над расплавленной ванной печи, нагревается и нагревает регенераторы. Через определенный промежуток времени меняется направление потока воздуха и он, соприкасаясь с регенераторами, нагревается. Более высокая температура воздуха повышает калорийность сжигания теплотворного газа. Изобретенная в 1864 году Пьером Мартеном этот агрегат сегодня считается перевернутой страницей в истории металлургии. Действующие мартены не в состоянии справиться с конкуренцией и требованиям, предъявляемых к выплавляемой стали.
Конвертер это агрегат, в котором скрап и передельный чугун в жидком виде продувается кислородом или воздухом. Окисление углерода происходит с дополнительным выделением тепла. Таким образом, решается одновременно две задачи – уменьшение углеродного эквивалента и достижение температурных показателей достаточных для борьбы с серой и рядом других элементов. Больше половины стали в мире производят в конвертерах.
Электродуговая печь является неотъемлемым элементом производства нержавеющих, легированных, специализированных сталей. Тепло в этой печи наводится электрической дугой, которая возникает между электродами и металлической ванной. Чугун ложится в завалку или заливается после предварительного нагрева металла. Дальше добавляются флюсующие материалы и вспениватели шлака. Это позволяет вывести серу и фосфор из металла.
В индукционной печи чугун преимущественно используется в виде холодного шихтовального материала при выплавке сталей. Невозможность влиять на содержание серы и фосфора при плавке в такой печи к чугуну предъявляют особо высокие требования по содержанию этих элементов.
Производство стали из чугуна оправданно в крупных масштабных производствах и небольших литейных цехах и участках.
Основы получения чугуна и стали
СТРОИТЕЛЬНЫЕ МАТЕРИАЛЫ
Чугун получают в ходе доменного процесса, основанного на восстановлении железа из его природных оксидов, содержащихся в железных рудах, коксом при высокой температуре. Кокс, сгорая, образует углекислый газ. При прохождении через раскаленный кокс он превращается в оксид углерода, который и восстанавливает железо в верхней части печи по обобщенной схеме: Fe203—*Fe304—►FeO—»Fe. Опускаясь в нижнюю горячую часть печи, железо плавится в соприкосновении с коксом и, частично растворяя его, превращается в чугун. В готовом чугуне содержится около 93% железа, до 5% углерода и небольшое количество примесей кремния, марганца, фосфора, серы и некоторых других элементов, перешедших в чугун из пустой породы. В зависимости от количества и формы связи углерода и примесей с железом, чугуны имеют разные свойства, в том числе цвет, подразделяясь по этому признаку на белые и серые.
Сталь получают из чугуна путем удаления из него части углерода и примесей. Существуют три основных способа производства стали: конвертерный, мартеновский и электроплавильный.
Конвертерный основан на продувке расплавленного чугуна в больших грушевидных сосудах-конвертерах сжатым воздухом. Кислород воздуха окисляет примеси, переводя их в шлак; углерод выгорает. При малом содержании в чугуне фосфора конвертеры футеруют кислыми огнеупорами, например динасом, при повышенном — основными, периклазовыми. Соответственно выплавляемую в них сталь по традиции называют бессемеровской и томасовской. Конвертерный способ отличается высокой производительностью, обусловившей его широкое распространение. К недостаткам его относятся повышенный угар металла, загрязнение шлаком и наличие пузырьков воздуха, ухудшающих качество стали. Применение вместо воздуха кислородного дутья в сочетании с углекислым газом и водяным паром значительно улучшает качество конвертерной стали.
Мартеновский способ осуществляется в специальных печах, в которых чугун сплавляется вместе с железной рудой и металлоломом (скрапом). Выгорание примесей происходит за счет кислорода воздуха, поступающего в печь вместе с горючими газами и железной рудой в составе оксидов. Состав стали хорошо поддается регулированию, что позволяет получать в мартеновских печах высококачественные стали для ответственных конструкций.
Электроплавление является наиболее совершенным способом получения высококачественных сталей с заданными свойствами, но требует повышенного расхода электроэнергии. По способу ее подведения электропечи подразделяются на дуговые и индукционные. Наибольшее применение в металлургии имеют дуговые печи. В электропечах выплавляют специальные виды сталей — средне — и высоколегированные, инструментальные, жаропрочные, магнитные и другие.
Экологически чистые строительные материалы
В связи с развитием промышленности состояние окружающей среды каждый год ухудшается. Главный вопрос, который стоит перед человечеством: как уберечь природу от пагубного воздействия человека? Эта проблема касается всех сфер человеческой …
Асфальтовые бетоны и растворы
Для приготовления асфальтовых растворов и бетонов применяют асфальтовое вяжущее, представляющее смесь нефтяного битума с тонкомолотыми минеральными порошками (известняка, доломита, мела, асбеста, шлака). Минеральный наполнитель не только уменьшает расход битума, но …
Дегтевые вяжущие вещества
Деготь представляет собой густую вязкую массу чернокоричневого цвета, образующуюся при нагревании без доступа воздуха твердых видов топлива (каменного и бурого углей, горючего сланца, торфа, древесины). В строительстве применяют главным образом …
Преобразование чугуна в кованое железо — The Teamon Process
Share на Facebook
Share в Twitter
Share на Reddit
Share на Linkedin
Акции по электронной почте
Печать
Открытие дешевого и простого способа освобождения чугуна от углерода уже давно является предметом серьезного исследования ученых и практиков. Способ производства кованого железа и стали, предложенный мистером Джоном Хитоном, кажется, по общему признанию, является наиболее быстрым и тщательным методом, но для многих все еще остается открытым вопрос, достаточно ли он экономичен.
Наши читатели уже знают, что в основе метода лежит превращение углерода с помощью нитратов соды или калия.
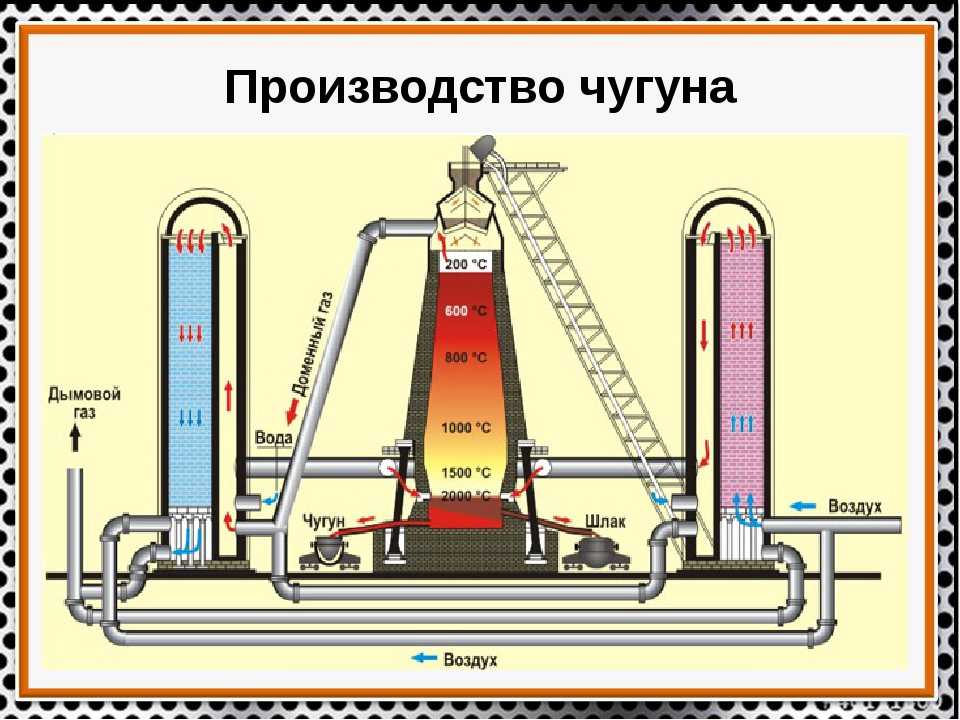



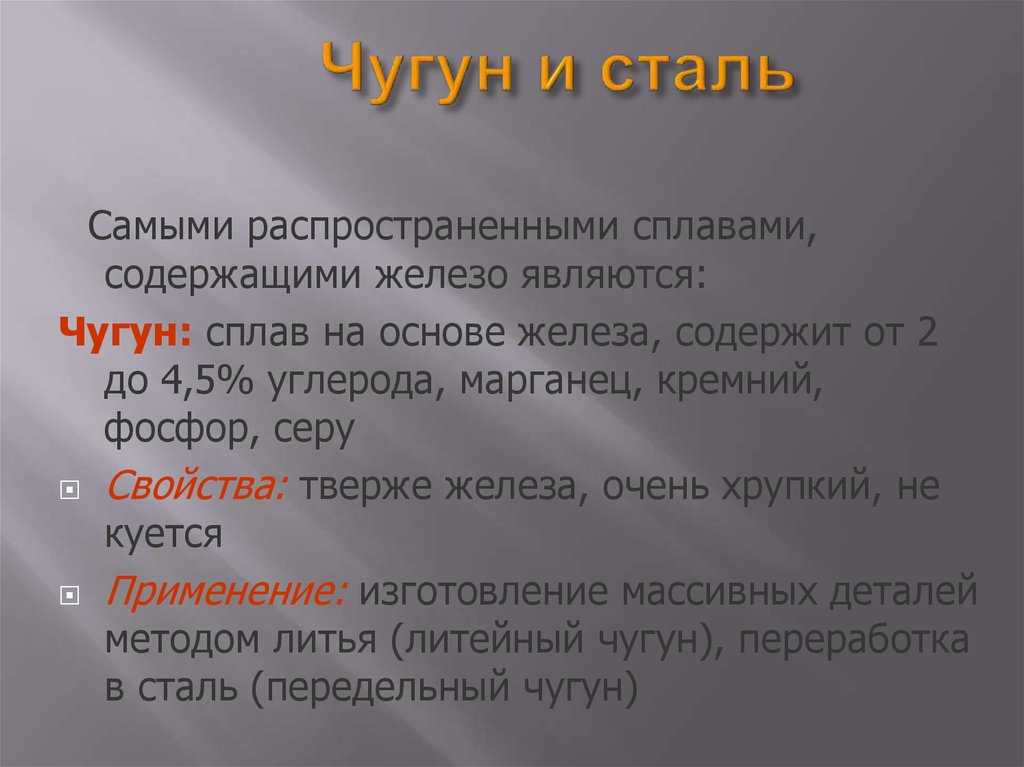
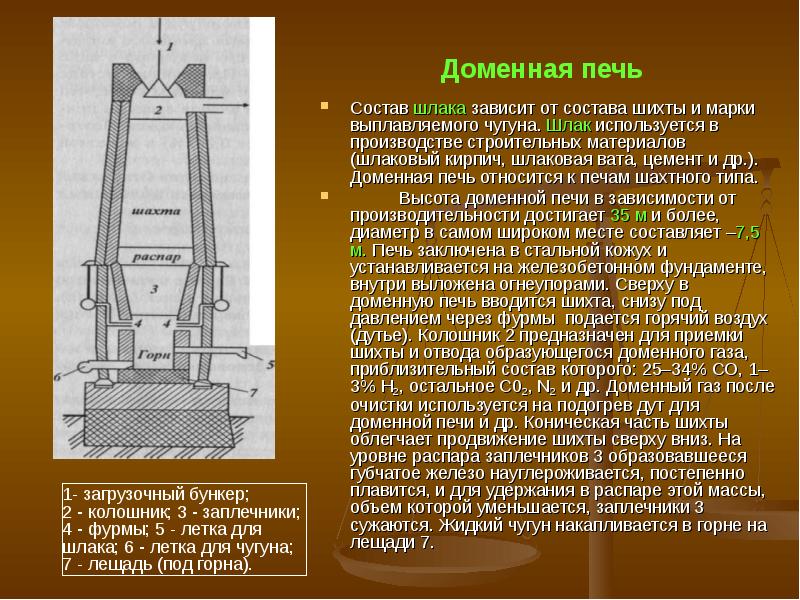
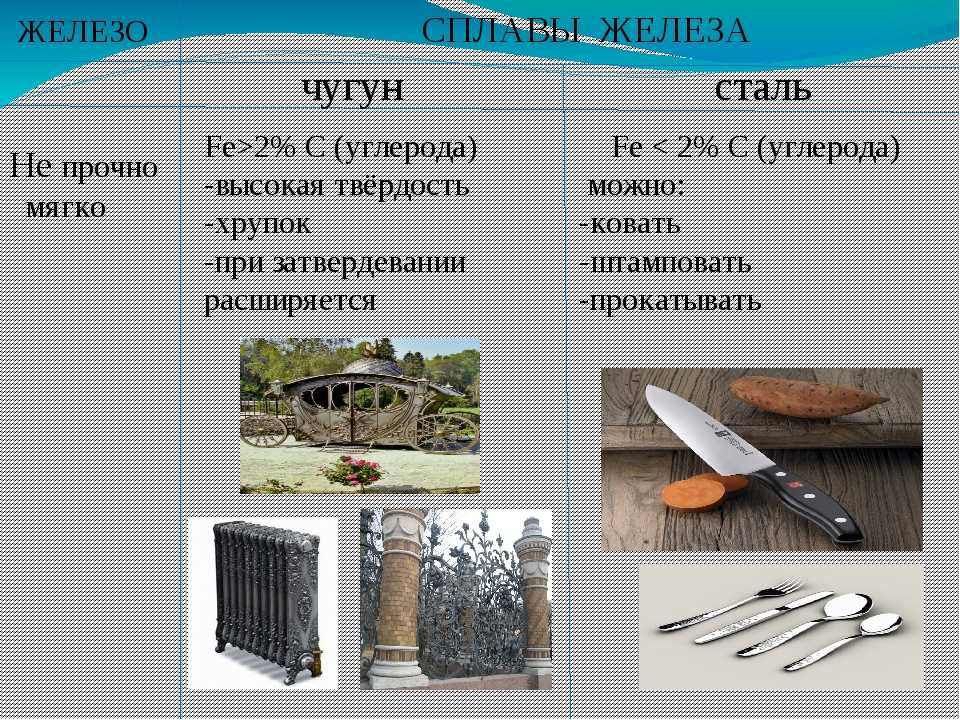
Эта статья была первоначально опубликована под названием «Преобразование чугуна в кованое железо — процесс Хитона» в журнале Scientific American 20, 14, 218 (апрель 1869 г.)
doi:10.1038/scientificamerican04031869-218a
В чем разница между Литое и кованое железо?
Люди могут подумать, что термин «чугун» относится ко всем ранним изделиям из железа, или что ранние изделия из железа всегда были «коваными», или что и то, и другое может быть правдой. Они были бы неправы. На самом деле, основное различие между ними простое:
Чугун — это расплавленное железо, залитое в форму и остывшее.
Кованое железо — это железо, которое было нагрето, а затем обработано инструментами. На самом деле термин «обрабатывал» происходит от причастия прошедшего времени слова «работал».
Но давайте углубимся в детали.
Чугун
«Чугун» — это общий термин, который относится к ряду сплавов железа, но обычно ассоциируется с наиболее распространенным серым чугуном. Хотя чугун может звучать как литая форма чистого железа, на самом деле это сплав, содержащий от 2 до 4% углерода, а также небольшое количество кремния и марганца. Другие примеси, такие как сера и фосфор, также распространены.
Чугун образуется путем плавки железной руды или переплавки чугуна (продукт добычи железной руды) и смешивания с металлическим ломом и другими сплавами. Жидкую смесь разливают по формам и дают остыть и затвердеть. Из-за более высокого содержания углерода чугун затвердевает как гетерогенный сплав, поэтому в его микроструктуре содержится несколько материалов в разных фазах, что влияет на его физические свойства.
Например, в микроструктуре чугуна есть частицы углерода, которые при охлаждении металла образуют удлиненные графитовые чешуйки. Графит имеет низкую плотность и твердость, но обладает высокой смазывающей способностью. Таким образом, он предлагает мало структурных преимуществ, но он ставит под угрозу окружающую железную матрицу, создавая внутренние точки напряжения, которые могут привести к трещинам.
По сравнению с кованым железом или сталью чугун является хрупким, твердым и не податливым. Его нельзя согнуть, растянуть или придать форму. Его слабая прочность на растяжение означает, что он сломается до того, как согнется или деформируется. Однако он обладает хорошей прочностью на сжатие и широко использовался в строительстве зданий до появления сталелитейной промышленности в начале 20 века.
По сравнению со сталью чугун имеет более низкую температуру плавления, более текучий и менее вступающий в реакцию с материалами формы, что делает его подходящим для литья. Это значительно менее трудоемкий процесс, чем изготовление изделий из кованого железа, поэтому он был важной формой производства на протяжении 18 и 19 веков.й века. Чугун в значительной степени был заменен сталью в строительной отрасли, но он по-прежнему используется во многих промышленных целях.
Кованое железо
Кованое железо состоит в основном из железа с добавлением от 1 до 2% шлака, побочного продукта плавки железной руды, обычно смеси оксидов кремния, серы, фосфора и алюминия. Во время производства железо снимается с огня и обрабатывается молотком, пока оно еще горячее, чтобы придать ему намеченную окончательную форму.
Кованое железо часто имеет волокнистый внешний вид, но оно также мягче и пластичнее чугуна. Кованое железо очень пластично, а это означает, что его можно нагревать и повторно нагревать, а также придавать ему различные формы. На самом деле, он становится сильнее, чем больше он работает.
Кованое железо имеет гораздо более высокую прочность на растяжение, чем чугун, что делает его более подходящим для изготовления горизонтальных балок в строительстве. В общем, сильно сопротивляется усталости. Он безотказно деформируется, если только не перегружен сверх своих возможностей или не деформируется от воздействия сильного тепла (например, от огня).
Он широко использовался в строительстве зданий в 19 веке, но в 20 веке его заменила сталь. Сегодня кованое железо используется в основном для декоративных целей.
Коррозия
Литое и кованое железо подвержены коррозии, когда открытые поверхности подвергаются воздействию кислорода в присутствии влаги. В отличие от других металлов, образующих защитное окислительное покрытие, железо со временем полностью ржавеет и отслаивается. Это может быть сложной задачей для наружной среды, где воздействие осадков и влажности может быть постоянным.
Чтобы предотвратить ржавчину, изделия из железа должны быть покрыты для предотвращения воздействия.