Изготовление пуансонов — KUTR.RU
Изготовлением пуансонов занимается предприятие ООО Металлообработка. При необходимости нанесения на материал отпечатка сразу большого объема знаков, возможно заключение пуансона в обойму. В прессовальных, штамповочных и маркировочных работах одним из ключевых инструментов является пуансон. Его назначение – маркировка лицевой поверхности изделия под воздействием пресса. Суть его работы заключается в оказании давления на поверхность определенного материала.
Отправьте запрос на [email protected] или звоните 8 (3439) 389 801, 380 081.
ООО «Металлообработка» изготовит пуансоны по чертежам, на заказ из любого металла (9хс, 12хмф, У7, У8 и других марок) с закалкой.
Виды пуансонов.
В зависимости от выполняемых функций пуансоны бывают четырех видов: пробивные, вырубные, прошивные и просечные пуансоны. На данные детали могут оказываться тепловые либо силовые нагрузки. Исходя из сферы применения, для изготовления пуансонов используют износоустойчивые стали, обладающие высокой прочностью при воздействии высокими температурами либо повышенной прокаливаемостью.
При изготовлении пуансонов на ООО Металлообработка используют различные марки инструментальной углеродистой стали со степенью закалки в пределах 54-65 HRC. Легированная сталь не совсем подходит для таких целей, так как после воздействия высокой температуры она становится хрупкой.
Процесс производства пуансонов состоит из нескольких последовательных действий. Так, начинается действие с изготовления заготовки, которая поддается механической обработке. Далее проводится черновое и чистовое шлифование, закалка и заточка профиля.
Изготовить пуансоны цилиндрической формы предельно просто. Так, заготовка для таких изделий поддается металлообработке, полировке и шлифовке. Производство фасонных пуансонов гораздо сложнее. Изначально, при помощи металлорежущего оборудования, производится обработка контура пуансона, на основании которого делается оттиск. По готовому оттиску производится обработка пуансона, дальнейшая закалка и финальная обработка. В основном, закалка пуансонов производится при температуре около 780 градусов на протяжении восьми минут.
Изготовление пуансонов со сложным контуром возможно на нескольких видах оборудования. Так, пуансоны с фланцем и постоянным сечением желательно обрабатывать при помощи строгальных или фрезерных станков. Пуансоны с буртиками поддают обработке на фасонный-строгальных станках. Обработку производят, основываясь на оттиске либо по предварительно размеченному контуру.
При несоблюдении необходимых условий во время термообработки возможна деформация поверхности заготовки. Предприятие ООО Металлообработка занимается изготовлением пуансонов высокого качества, соблюдая все технологические требования во время производства. Изготовление пуансонов осуществляется с применением инновационных технологий профильной шлифовки, термообработки и маркировки. Благодаря хорошо налаженному производственному процессу существует возможность производства высококачественных пуансонов в сжатые сроки.
В зависимости от назначения, графическое изображение (цифры или буквы) может наноситься на пуансон как в прямом, так и в зеркальном отображении.
В большинстве случаев параллельно с пуансонами используют и матрицы. Изготовление штампов, матриц, пуансонов возможно с применением высокоточных станков, оснащенных программным управлением. Процесс производства этих деталей имеет много общего. Так, изначально заготовка матрицы либо пуансона поддается обработке на фрезерных станках вертикального типа. После этого поверхность заготовки подвергается шлифовке на специальном оборудовании. Далее происходит разметка рабочего контура с использованием слесарных и фрезерных станков, закалка в печи. Соответственно, изготовление пуансонов и матриц может производиться на одном и том же оборудовании, с разницей лишь в размерах деталей.
Изготовление пуансонов и матриц.
Пуансон должен быть несколько меньше, чем матрица. Если пуансон представляет собой более сложную конструкцию чем матрица, то в первую очередь следует производить пуансон, и на основании оттиска готового пуансона происходит изготовление матрицы. Очень важно при этом соблюдать необходимый зазор. Изготовление пуансонов и матриц в соответствии с зазором возможно путем независимой обработки или взаимной подгонки. Если предполагается производство большого количества одинаковых штампов, целесообразно применять метод независимой обработки.
В том случае, если контур пуансона представляет собой сложную фигуру, разметка отверстий в державке производится при помощи координатно-сверлильного станка. После закалки пуансон подвергается шлифовке. Закалка позволяет пуансону длительное время сохранять свою первоначальную форму во время воздействия силовых нагрузок.
В последнее время появилась возможность осуществлять изготовление матриц, пуансонов при помощи станков, укомплектованных системой фотоэлектрического копирования. Такое оборудование позволяет производить детали с высокой точностью обработки – ±0,025 мм.
В последнее время большое распространение получают прогрессивные технологии изготовления пуансонов. Например, на предприятии ООО Металлообработка широко применяется электроэрозионная технология производства, основанная на пропускании по заготовкам импульсного электрического тока. Не менее популярны и другие электрохимические технологии.
Матрица и пуансон на заказ
Матрица и пуансон на заказ
Металлические изделия – матрицы и пуансоны при производственных процессах металлообработки подвергаются механическим нагрузкам. Из-за чего относятся к категории изделий с высокой степенью износа. В результате воздействий практически все производственные фабрики, предприятия и компании сталкиваются с необходимостью поиска замены вышедших из строя элементов на новые.
Закажите матрицы и пуансоны на заказ, высылайте чертежи на [email protected] Цех +7 912 291 59 18. Высокое качество, выгодная цена!
- Мы изготовим на заказ по всей стране высококачественные пуансоны и матрицы. Наша продукция обладает высоким качеством и полностью отвечает всем указанным параметрам, ГОСТам и международным стандартам, пожеланиям клиентов.
Чем собой представляют матрицы и пуансоны?
Пуансон – это деталь из металла. Заготовка необходимой геометрической формы соответствующая основному профилю матрицы. Пуансон выполняет роль пресса и штампа. К тому же эта деталь может применяться в виде маркировщика. Пуансоны подразделяются на: вырубные типы, прошивочные, гибочные, пробивные, гибочные.
Матрица также является металлическим изделием и работает в паре с пуансоном. Стенки матрицы параллельны и без крышек. Изделия могут быть из разного материала, быть простыми, комбинированными и сложными. Первый вид матриц применяется при производстве определенного вида изделий, другие при изготовлении сразу нескольких видов изделий.
Пуансоны и матрицы для оборудования на заказ
Если у вас возникала необходимость заказать качественные виды деталей – матрицы и пуансоны обращайтесь к нам. Мы для изготовления особой точности деталей используем только современные станки с числовым программным управлением, а это говорит о высокой степени точности изделий при изготовлении и соблюдении всех требуемых размеров и других технических характеристик.
- Стоимость услуг и сроки поставки изделий из металла зависят в первую очередь от сложности элементов, поставки объема заказанной продукции и сложности.
- В общем, партнерские отношения с нашей компанией очень экономичны и взаимовыгодны, так как мы стараемся всегда клиента порадовать высоким качеством работ и своей лояльностью ценообразования.
- В итоге, сотрудничество с нашим металлообрабатывающим предприятием, клиент получает необходимые изделия высокой точности и особой прочности. Все детали подвергаются закалке, что не может не отражаться на длительности эксплуатационного срока.
Пуансоны и матрицы на заказ от производителя
- Промышленные ножи
- Пуансоны и матрицы
ООО Металлообрабатывающий завод «ЛИРА» предлагает изготовление матриц и пуансонов для любого вида пресс-ножниц (НГ5223, НГ5222, НВ5222,НВ5221, НВ 5224,Н513, НБ 633, С229А и т.д.).
Ввиду того, что в процессе работы пуансоны и матрицы подвергаются воздействию больших силовых и тепловых нагрузок, мы производим их из высокостойких сталей Х12МФ и 6ХВ2С.
Для рассмотрения возможности изготовления просим прислать чертежи или эскизы необходимых Вам матриц и пуансонов на электронную почту stnk@list. ru и [email protected] или сделать заказ через форму на сайте. Также можно проконсультироваться с нашими специалистами по телефонам 89036089030, 8(831)225-01-97, 228-70-10, 228-70-40, 218-06-94
Мы с удовольствием ответим на все интересующие Вас вопросы!
Обратите внимание ножи могут изготавливаться по любым размерам! — сделать заказМатрицы и пуансоны представляют собой качественные металлические изделия, используемые в металлообрабатывающей промышленности, на штамповочном и прессовом производстве.
Пуансон – важная деталь инструмента, необходимая для штамповки и прессования материалов. При прессовании пуансон давит на заготовку и выдавливает ее через матрицу, в результате чего получаются детали необходимой формы.
Изготовление пуансонов и матриц для нас очень ответственный и важный этап производства.
Вам требуется изготовление промышленных ножей различного назначения — Звоните!
8 (831) 225 01 97
8 (903) 608 90 30
На сайте нашей компании Вы можете найти большой выбор продукции для Вашего предприятия. Что такое пуансон и матрица? Поговорим об этом ниже. Ни один штамповочный и прессовый рабочий процесс не может обойтись без пуансона. Эта деталь используется при штамповке и обработке металла. Чтобы проштамповать готовые элементы на изделие производится непосредственное давление. Именно для производства такой тех. операции и предназначается пуансон. Конструкция детали бывает:
- Вырубной.
- Просечной.
- Прошивочный.
- Пробивной.
В момент прессования пуансон начинает давить на заготовку, которая выдавливается через матрицу. Так как деталь работает при больших нагрузках, ее делают из стали высокой прочности. Она устойчива к деформации под действием перепадов температур. Пуансоны и матрицы Вы можете заказать на нашем сайте. Также мы готовы выполнить изготовление на заказ по чертежам, эскизам и образцам клиента. Цена на производство рассчитывается в индивидуальном порядке.
Матрица принцип работы
Чтобы получить необходимую сложную форму изделия надо использовать матричную конструкцию, которая может быть сделана из различного материала: резина, полиуретан, сталь и т.
- Простая.
- Сложная.
- Комбинированная.
Особо сложные конструкции используются не часто, их делают по спецзаказу. Если Вам нужны высококачественные матрицы и пуансоны обращайтесь к менеджеру нашего металлообрабатывающего завода. Специалист оформит сделку. Проконсультироваться по возникшим вопросам можно по телефонному номеру 89036089030, 8(831)2250197, 2287010, 2287040, 2180694 или по электронной почте [email protected], [email protected] . Будем рады новому сотрудничеству!
Пуансон и штамп
На качестве поверхности среза сказывается притупление режущих кромок элементов, а также неточное распределение зазора по контуру. Если Вам нужна консультация профессионального мастера, который объяснит, как правильно установить зазор просто позвоните нам.
Звоните или оставляете заявку на сайте
Согласуем чертежи и стоимость изготовления
Изготавливаем и доставляем в оговоренные сроки
Изготовление в Казани пуансонов и матриц для пресса на заказ
Пуансоны и матрицы в процессе эксплуатации подвергаются постоянным нагрузкам, из-за чего относятся деталям, характеризующимся быстрым износом. В результате предприятия сталкиваются с необходимостью замены данных элементов. Компания «РосКомплект» заказать изготовление пуансонов и матриц в Казани на заказ. Изготавливаемая нами продукция обладает высоким качеством и полностью соответствует указанным заказчиком параметрам.
Что собой представляют пуансоны и матрицы?
Матрица — изделие из металла, имеющее параллельные стенки без крышки. Изделия могут быть простыми, сложными и комбинированными. Первые используются для изготовления одного вида деталей, последние — для производства нескольких различных изделий.
Пуансон представляет собой металлическую конструкцию, которая соответствует профилю матрицы. Элемент выполняет функции штампа или пресса. Также он может использоваться в качестве маркировщика.
Пуансоны делятся на несколько категорий и бывают:
- прошивочными;
- вырубными;
- пробивными;
- гибочными.
На практике их используются в паре с прессом, листогибом. Они используются для пробивки отверстий, сгибания металлических элементов для придания нужной формы.
Если возникла необходимость купить данные элементы в Казани, то следует обратиться в компания «РосКомплект». Для производства продукции использует современное оборудование с программным управлением, отличающееся высокой точностью. Цена и сроки изготовления зависят от объема работ и сложности элементов. В целом, сотрудничество с нами является экономически выгодным, так как мы стараемся придерживаться лояльной ценовой политики.
В результате сотрудничества заказчик получает изделия нужных габаритов, прошедшие процесс закаливание. Это обеспечивает их длительный срок службы
Что такое матрица и пуансон?
Особенности пуансонов и матриц
Оснастка промышленных станков отличается практичностью, многофункциональностью и простотой в обслуживании. Для нормальной работы станка требуется регулярная очистка поверхностей от остатков бетонной смеси и металла. Для этого применяют различные механические способы с использованием скребков, шпателей, щеток-сметок. Перед остановом вибропресса или станка его промывают под напором воды и просушивают.
Матрицы и пуансоны — это быстроизнашивающиеся детали, поэтому расходные части подлежат замене. В зависимости от сферы использования матрицы и пуансоны служат 4-6 лет. Составные части вибропрессов или штампов выпускают различных конфигураций и назначений. Это определяется формой, типом и размерами выпускаемых металлических деталей или бетонных изделий.
Оснастка вибропрессовальных и штамповочных станков должна иметь ровную поверхность без зазоров, заусениц, рванин и трещин. Цилиндрические пуансоны подвергают черновому и чистовому шлифованию, а также полировке и заточке. Фасонные пуансоны изготавливают оттиском, при этом деталь проходит закалку (процесс протекает при температуре 780 градусов в течение 8 минут) и финальную обработку. Оснастка со сложным контуром производится при помощи строгальных или фрезерных станков. На этом же оборудовании изготавливают матрицы, с учетом соответствующих размеров. Качественно изготовленные прессовальные формы обеспечивают чистую линию среза, с максимально точностью, при минимальном износе самого штампа.
Важную роль играет зазор между матрицей и пуансоном:
- При малом зазоре будет образовываться рванина и слоистость поверхности среза;
- При большом — происходит втягивание тонкого материала в станок с последующим разрывом. Изделие будет иметь заусенцы и затянутые края. Если материал имеет достаточную толщину, то готовая деталь будет иметь закругленные кромки;
- Допускается выпуск удовлетворительного качества деталей при острых режущих краях штампа и при зазоре до 30% от толщины.
Зазор зависит от рода и толщины материала (от 0,5 до 12 мм.) и колеблется в пределах 4-16% толщины исходника.
Только при грамотно настроенном зазоре между пуансоном и матрицей, а также остроты их кромок будет обеспечиваться качество выпускаемых деталей согласно заданным параметрам технического проекта.
Матрицы и пуансоны для штамповки маталла
Главная / Матрицы, пуансоны
Матрицы и пуансоны
Матрица и пуансон для печенья Почётный_гражданин_города_Вологды Матрицы на слайдер Матрицы и пуансоны Матрицы и пуансоны медалей и монет матрица и пуансон монеты
Для изготовления изделий методом штамповки или отливки, применяются матрица и пуансон. Это формообразующие части, между которыми заливается расплавленный материал, либо располагается заготовка для получения различных пресс-форм и металлоконструкций.
Матрица – это элемент, формообразующий будущее изделие. Стенки матрицы параллельны друг другу, с отсутствием крышки. Существуют простые, сложные и комбинированные виды матриц.
Пуансон – специальная конструкция, совпадающая с профилем матрицы. Является замыкающим элементом, с помощью которого изделие образуется сверху.
Виды пуансонов:
Классифицируется по способу воздействия на заготовку и типу конструкции:
1. Пробивные;
2. Прошивные;
3. Просечные;
4. Вырубные.
Выбор материалов для матриц и пуансонов.
Необходимо заострять внимание на материале, из которого будут производиться штампы и пуансоны. Чем хуже подобрана сталь, тем производительность оборудования будет ниже.
Объемные пуансоны, сложной формы, изготавливаются из высокохромистых и высокоуглеродистых сплавов стали.
Для изготовления штампов простых видов – используются углеродистые инструментальные стали У8А – У11А.
Для повышения износоустойчивости штампов, в наше производство введены материалы из твердых и быстрорежущих сплавов. Лучшие результаты в изготовлении прессовых деталей показали сплавы: сталинит и стеллит. Не нуждаясь в закаливании, они придают жесткость элементам.
Специалисты СТАНКОФИНЭКСПО грамотно подберут лучшие материалы для минимального износа, штампов и пуансонов.
Особенности производства матриц, пуансонов
Пуансоны и матрицы – это быстроизнашивающиеся детали, расходные части периодически подлежат замене. Матрицы и пуансоны в среднем эксплуатируются 4 – 6 лет, в зависимости от сферы использования. Составные части вибропресса или штампа выпускают различные конфигурации и назначения. Определяется это размерами, типом и формой производимых металлических деталей или бетонных изделий.
Оснастка наших вибропрессовальных и штамповочных станков имеет ровную поверхность без заусениц и зазоров, трещин и рванин.
Цилиндрические пуансоны проходят черновое и чистовое шлифование, заточку и полировку.
Изготовление фасонных пуансон производится оттиском, деталь же проходит закалку при температуре 780 градусов в течении 8мин.) и подвергается финишной обработке.
Для производства оснастки со сложным контуром используется фрезерные и строгальные станки, так же учитывается соответствующие размеры детали, на этом же оборудовании изготавливаются матрицы. Идеально чистую линию среза гарантирует высококачественно произведенные пресс-формы, при минимальном износе штампа с максимальной точностью.
Выбрав наше производство, вы получите высококачественно изготовленные пресс-формы, пуансоны с идеально точной линией среза. Срок эксплуатации и минимальный износ штампа, произведенного нашим оборудованием значительно превысит ваши ожидания.
Производство матрицы, пуансоны в России.
Производство матриц и пуансонов – это сложный, профессиональный процесс, требующий применения высокоточного оборудования. Инновационные разработки и достижения в металлообработке позволяют нам выполнять задачи, связанные с производством деталей на высочайшем уровне, соблюдая технические нормы и правила в соответствии с ГОСТ. Возможно производство матриц и пуансон в единичных количествах по индивидуальным чертежам, размерам заказчика.
Последние просмотренные страницы
Производство пуансонов и матриц
Формообразующая оснастка — это пуансоны и матрицы. Без этих приспособлений некоторые детали изготовить не представляется возможным. Для этой цели прессы, штампы и другое оборудование специально оснащается матрицами и пуансонами. Если они правильных геометрических размеров и с нормальным внешним видом, то и выпускаемые изделия будут качественнее.
Форму изделия образует, как правило, открытый короб — матрица. Они бывают двух типов: простые и комбинированные. Простые матрицы – применяются для изготовления, только одного вида изделий, комбинированные — для двух и более видов изделий. Наша компания выполняет заказы на изготовление матриц, применяемых в различных отраслях производства.
Комбинированные матрицы | Простые матрицы | Пуансоны |
Конструкция, совпадающая с матрицей – называется пуансон. Он также широко применяется в металлообработке, прессование металлов и при производстве строительных изделий. Пуансоны различаются по конструкции. Они бывают — пробивные, прошивные, просечные, вырубные. Пуансон часто используется как пресс, при помощи которого заготовку продавливают через матрицу. Пуансоны и матрицы быстро изнашиваются. Срок их использования варьируется в зависимости от сферы использования, и составляют от 4-х до шести лет. Конфигурация и назначение штампов и их составных частей очень разнообразны. Мы используем особые технологии для изготовления оснастки без дефектов: трещин, зазоров, заусениц. Пуансоны цилиндрической формы процесс шлифования проходят в два этапа, далее полировка и затачивание. Конечная обработка производится при помощи фрезерных и строгальных станков.
Фасонный пуансон изготавливается путем технологического оттиска. Потом при температуре 780 градусов по Цельсию деталь закаливают в термопечи около 8 минут, далее финишная обработка.
Оснастку более сложного контура изготавливают в основном при помощи фрезерного и строгального оборудования. Для изготовления матрицы такого же размера используется такое же оборудование. Чем качественнее изготовлены пресс-формы и точнее линия среза пуансона, штамп будет менее изнашиваться, и срок его использования будет больше.
Индивидуальный подход к каждому клиенту – это главный принцип работы специалистов нашей компании «Станметалломаркет». Все разработки будут выполнены с учетом пожеланий наших клиентов. Приобретение качественного оборудования поможет Вам в реализации планов и решении поставленных Вами задач.
Commercial Classics »Журнал» Природа шрифтов и шрифтов металла: краткое введение
Ящик пуансонов литейного производства Caslon. Это Трафальгарский № 1 Roman Open, вырезанный Кингом в 1830-х годах. Библиотека Святой Невесты.
1 из 3
Стальной пуансон, вырезанный Селкирком для Caslon, Son и Livermore до 1839 года. Two Line Great Primer Italian. Он имеет легкий блеск смазки, чтобы не ржаветь. Боковые стороны слегка скошены для облегчения работы с перфоратором. Библиотека Святой Невесты.2 из 3
Двухстрочный праймер Great Primer (около 36pt) с медной матрицей из литейного завода Фиггинса.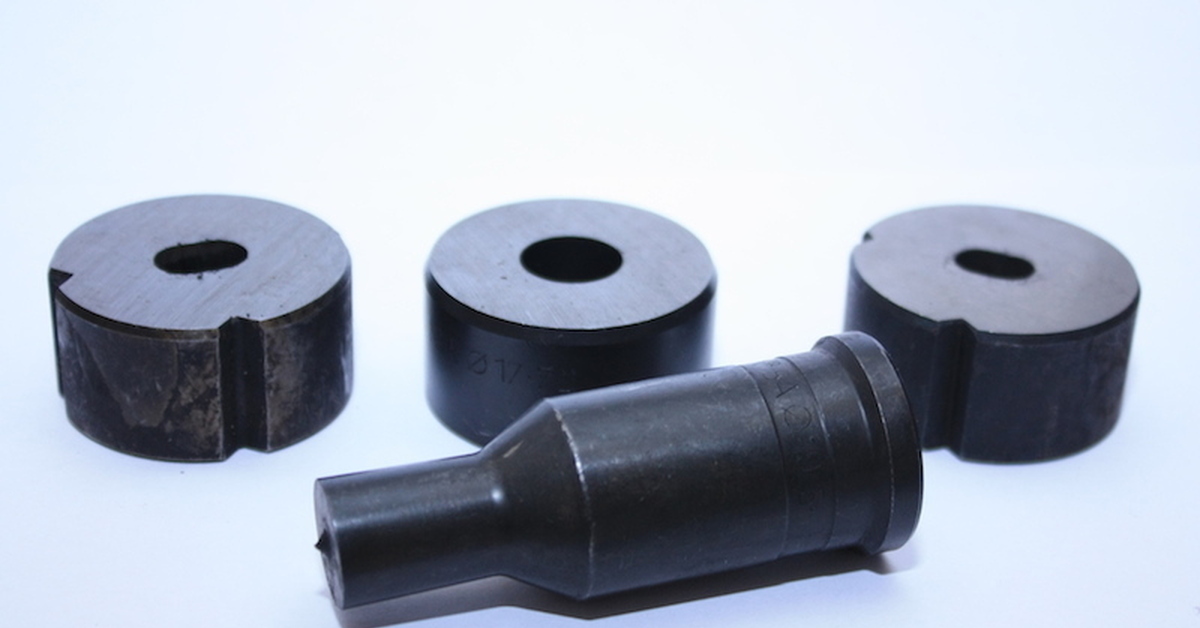
3 из 3
Сегодня методы создания, использования и просмотра шрифтов — это в основном цифровые процессы. Мы сделали все лица в библиотеке Commercial Classics в цифровом виде от начала до конца. Однако оригиналы, на которых они основывались, были изготовлены традиционным аналоговым методом, который использовался с пятнадцатого века, когда Гутенберг изобрел подвижный шрифт.Эти процессы производят физический продукт — как писал знаменитый типографский писатель Гарри Картер: «Типографский шрифт — это то, что вы можете взять и держать в руке».
Пьер-Симон Фурнье, Manuel typographique , 1764 и 1766 является одним из сделаны наиболее подробные отчеты о шрифтовом поиске. В 1930 году Гарри Картер, Фурнье сделал перевод текста « Manuel typographique ». Затем это было переиздано в 1973 году. В 1995 году было произведено факсимиле Manuel typographique с переводом Картера под редакцией Джеймса Мосли.
В последние годы голландский шрифтовой дизайнер Фред Смейерс написал и практиковал искусство вырезания пуансоном (но не литья шрифта), чтобы лучше понять это ремесло, особенно в шестнадцатом веке. Это подробно описано в его книге Counterpunch , Hyphen Press, London, 1996 и исправленном издании 2011 года.
Все вышеперечисленные издания предлагают библиографии, в которых перечислены другие ключевые работы. Сборник ссылок на шрифтовое дело и литературу по нему можно найти здесь: www.circuitousroot.com. — и эти процессы продолжались в промышленных масштабах до двадцатого века.
Пробойник за работой, используя ножницы и напильники для придания формы стальному пуансону. Используя окуляр, дырокол вырезает дырокол под размер текста. Иллюстрация Джо МакКендри.1 из 6
Пуансон после резки и закалки, стороны скошены для облегчения работы. Перфорация — это обратное изображение буквы, и это изображение будет на конце шрифта.Иллюстрация Джо МакКендри.2 из 6
Закаленный пуансон врезается в кусок меди под прямым углом. Это момент, когда удар может сломать потраченные впустую часы тяжелой работы. Иллюстрация Джо МакКендри.3 из 6
При первом ударе по матрице медь вытесняется.
4 из 6
Матрица теперь выровнена и для литья, благодаря чему изображение буквы может быть воспроизведено тысячи раз.Иллюстрация Джо МакКендри.5 из 6
Тип литой из металла (сплав свинца, олова и сурьмы). Ник в шрифте должен убедиться, что тип правильный. Иллюстрация Джо МакКендри.6 из 6
До наступления цифровой эры шрифт представлял собой кусок литого металла, где каждый отдельный символ представлял собой выпуклое перевернутое изображение буквы (или любого другого изображения). Когда шрифты были объединены вместе, они сделали составную форму, с которой можно было делать копии в процессе высокой печати.Сегодня шрифт — цифровой, и его можно масштабировать на компьютере без каких-либо усилий. Из одного дизайна можно создать множество размеров, от размеров настолько маленьких, что их едва можно увидеть, до самых больших рекламных щитов. С другой стороны, металлический тип как физический объект существовал только в том размере, в котором он был создан и отлит. Размер шрифта описывался не размером изображения буквы, а размером тела, на котором сидела буква. Даже когда тип больше не является физическим, он все еще описывается виртуальным телом. Это сделало процесс изготовления шрифта трудоемким, но также сделало форму и дизайн специфичными для его размера.
Металлический шрифт был создан в процессе подбора шрифтов. Более конкретно, определение типа описывает конец операции, когда расплавленный металл использовался для отливки физического объекта (типа). Первоначальная форма шрифта была вырезана как пуансон, который затем использовался для формирования матрицы. В матрицу была встроена буква пуансона, которая затем использовалась для отливки металлического шрифта, копии исходного пуансона с буквой на концах.
К восемнадцатому и девятнадцатому векам процесс набора текста был в основном отделен от деятельности печатника. Литейные предприятия, такие как Caslon, продавали бы свои литые печатные машины на коммерческой основе любому типографу, который хотел бы их купить. Эти литейные заводы либо нанимали, либо нанимали квалифицированных мастеров для создания штампов. Некоторые специализировались на вырубных штампах, другие были просто опытными граверами-фрилансерами, которые могли выгравировать любую букву или изображение на предметах. Начиная со стального стержня со сплющенным концом, они использовали различные инструменты (граверы и пилки) для создания выпуклого и плоского обратного изображения буквы размером с последний кусок шрифта.Как вы понимаете, в то время как шрифт большого размера был бы виден невооруженным глазом, для меньшего и меньшего размера требовалось использование инструментов увеличения и яркого света.
Поскольку сталь трудно резать, вы можете себе представить, что это был медленный и трудоемкий процесс. Электротипирование, изобретенное в конце 1830-х годов, позволяло вырезать штампы из металла, который был намного мягче и легче формовать, поэтому один или два штампа обычно можно было сделать за день. (В последние годы Фред Смейерс на основании личного опыта предположил, что это число выше.По мере того, как дыроколы довольствовались буквой, они создавали дымовую пробу изображения, беря масляную свечу, которая переносила сажу на конец дырокола. Затем это было вдавлено в бумагу и получилось хрупкое изображение письма. По мере того, как создавалось все больше и больше персонажей, их можно было сравнивать друг с другом.
Количество штампов, которые они наносили для гарнитуры, зависело от того, была ли форма для текста или для отображения. Если бы это было для демонстрации, количество ударов было минимальным: иногда просто A – Z с основной пунктуацией, иногда с цифрами и валютой (в Британии девятнадцатого века фунт стерлингов был необходим для лотерей и аукционов в афишах).В размерах текста набор символов обычно был больше за счет добавления звездочки, кинжалов, знаков раздела, прописных букв и лигатур. Возможно, акценты были добавлены, но по сравнению даже с самыми скромными современными шрифтами, это были небольшие наборы символов.
Хотя технический процесс изготовления штампов ведется, мы не знаем, как была выбрана форма письма.У нас есть записи XVI века о Плантене, знаменитом печатнике Антверпена, заказывающем штампы в Гранжоне; но хотя спецификация касается размера и функции необходимой буквы, в ней не указывается, как она должна выглядеть. Как только формы букв были хорошо установлены, можно представить, что новые штампы были вырезаны, чтобы заменить старые штампы, которые изнашивались, или чтобы заполнить потребность в шрифте определенного размера, и что форма соответствовала современным стилям. Каждый размер будет отличаться, так как они сделаны вручную, но стилистически они все равно будут подходить друг к другу.Только когда стили менялись, форма обсуждалась, будь то копирование стиля другого литейного производства или форма современной надписи. Например, как был определен внешний вид Джона Баскервилля? Поставлял ли Баскервиль своему перфоратору Джону Хэнди подробные инструкции или визуальные заметки? С рисунками букв? Или это был более простой процесс? Можно представить, что основатели часто давали указания перфораторам: «Нам нужно новое лицо в закрашенном египетском стиле для двойной пики». Закройщик понимает эти термины и создает что-то стилистически соответствующее этому, но в деталях просто делает то, что считает лучшим. Из доказательств от литейного завода Caslon видно, что по доказательствам были сделаны комментарии, но они не являются исчерпывающими. Было ли это потому, что к этому моменту лицо уже было обсуждено и прокомментировано (они часто являются частью серии стилей или размеров), или потому, что они просто не сделали так много комментариев по доказательствам? Сравните количество комментариев к доказательству с теми, которые мы видим у современных дизайнеров; комментарий, который вы найдете сегодня к доказательству, кажется гораздо более предписывающим и подробным.
Когда работа с перфоратором была завершена, пуансон закаливали, нагревая его и затем погружая в холодную воду. Затем стальные штампы использовались для создания отпечатка на поверхности куска меди. Это впечатление было зеркальным отражением удара. Нанести удар кулаком по меди было умелой работой; пуансон должен был ударить его прямо и чисто, чтобы произвести безупречное впечатление. Каждый удар пуансона также был чреват опасностью — пуансон, хотя и был сделан из закаленной стали и вдавливался в более мягкий металл — медь, все же мог быть поврежден, часто без возможности восстановления.Половина или день рабочего времени могли быть потеряны. Хотя удар может образовывать несколько матриц, количество ударов каждой буквы часто бывает единичным.
Медная матрица будет искажена впечатлением от пуансона, расширяясь и теряя свои плоские стороны. Затем эти выпуклости были удалены, чтобы получить обоснованную и правдивую матрицу. Затем его вставляли в ручную форму (или, позже, в литейную машину), и из нее производили отливку. Пробойник, создавший форму буквы, не отвечал за то, как буква будет отлита на ее теле, сколько места будет слева или справа от буквы, или сколько места сверху и снизу.Пробойник будет знать, насколько большим будет размер шрифта, и вносит коррективы; он решал, насколько велики отношения между высотой прописной буквы и нижним регистром (если он сокращал один), насколько велики были восходящие и нисходящие элементы, но его окончательное размещение на теле шрифта происходило позже, когда матрица была сделал. Качество шрифта — это не просто сама буква, а то, как эти буквы сочетаются друг с другом. Сегодня шрифтовый дизайн — это единый вид деятельности; рисование букв и расстановка между ними происходит одновременно.
К концу девятнадцатого века был изобретен новый метод нанесения ударов. Пантографический гравировальный станок резал сталь. По чертежам большого размера можно было изготовить штампы разных размеров и в большом количестве, что в значительной степени сделало перфоратор устаревшим. С появлением новых технологий литейных машин Monotype и Linotype старые литейные предприятия потеряли большую часть своей торговли.В Великобритании это привело к исчезновению Кэслона в 30-х годах, Миллера и Ричарда в 50-х и Стивенса Шэнкса к 70-м годам. Материал набора имел ограниченные значения: цена стального лома для пуансонов и более низкая стоимость меди матриц. Изготовленные вручную матрицы можно было перепроектировать, чтобы они подходили к машинам Monotype, но в основном они были списаны. Однако многое уцелело в Британии: Стивенсон Блейк, который был последним литейным заводом в Британии, продал свой печатный материал в то, что сейчас является Типовым архивом в Стоквелле, Лондон.Некоторые матрицы и удары Стивенса Шэнкса, преемника Фиггинса, были спасены усилиями Джеймса Мосли и находятся в библиотеке Сент-Брайд. Литейный завод Caslon был продан на аукционе; Стивенсон Блейк купил то, что было годным к употреблению (например, Caslon Old Face), а остальное было продано на металлолом. Основная часть пуансонов (более тысячи коробок, относящихся к истокам литейного производства в восемнадцатом веке) была куплена Monotype в качестве источника потенциальных дизайнов. Они были подарены издательству Oxford University Press и в конечном итоге попали в Сент-Брайд.
Ассоциация европейских музеев печати ~ Монотипная штамповка
Ричард Арда, The Type Archive, Лондон (Великобритания)
Выступление Ричарда Ардага , The Type Archive, Лондон, Соединенное Королевство, на конференции Ассоциации европейских музеев печати, Защита нематериального наследия: передача технологий печати будущим поколениям , проходившей в Национальном музее van de Speelkaart, Турнхаут, Бельгия, 23-26 мая 2019 г.
Я хотел бы тепло поблагодарить AEPM за предоставленную мне возможность выступить и начать с извинений: я не академик, поэтому мой сегодняшний доклад будет сделан через призму моего собственного опыта, а не основан на научных исследованиях.
В рамках этой конференции я удачно получил нематериальное наследие печати, которое вы хотите сохранить, и очень благодарен за это. Я определенно тот, кто лучше всего учится на практике, и я наслаждался возможностью поучаствовать в моем ученичестве в Type Archive, которому удалось сохранить навыки, о которых я собираюсь рассказать, и сохранить им жизнь. через практику вот уже четверть века.
Итак, чтобы представиться: я графический дизайнер со своей собственной практикой, в основном занимаюсь дизайном книг.Мой интерес к типографике и печати привел меня к высокой печати, и, почувствовав вкус к ней, я с тех пор все больше и больше проваливался в кроличью нору. Я также являюсь партнером New North Press, студии высокой печати в Лондоне, и именно от имени New North Press в 2014 году я заказал прототип шрифта высокой печати, напечатанного на 3D-принтере, под названием A23D. Этот проект был очень интересным упражнением — с тонкостями, в которые я не буду сейчас вдаваться, — но, несмотря на то, что в то время я неплохо разбирался в высокой печати, он действительно заставил меня осознать, насколько ограниченным было мое понимание традиционных методов создания шрифтов.Я видел, как работают литейщики Monotype и Linotype, но путь преобразования формы буквы из нарисованного эскиза в физическую часть шрифта был чем-то вроде загадки или, по крайней мере, тем, что я мог описать, только цитируя то, что я читал в книгах. Поэтому, когда появилась возможность наблюдать, а позже и практиковать этапы штамповки и изготовления матриц, я сразу ухватился за нее.
Архив типов занимается инженерией слова и хранит типографские артефакты, датируемые многими веками, но одной из первоначальных причин его существования было сохранение системы монотипирования типов горячего металла.Эта система привела к механизации как производства шрифта, так и его настройки, и Monotype Corporation предоставила всему миру оборудование, которое сделало это возможным: клавиатуры, композиционные и суперкастеры, матрицы и штампы; все это она производила и распространяла.
После распада компании в 1996 году 900 тонн машин и оборудования были перевезены с базы Monotype в Солфордс, графство Суррей, в бывшую ветеринарную больницу в Стоквелле, Южный Лондон, которая впоследствии стала Типовым архивом.(Для доставки 23 000 ящиков пуансонов и матриц потребовалось два десятитонных грузовика с ежедневными посещениями в течение семи недель. А на установку и оборудование ушла еще неделя с двумя шестнадцатитонными грузовиками. Этот шаг получил название «Операция Ганнибал».)
Корпорация «Монотипия» была огромной операцией. Фактически, оборудования, которое поступило в Стоквелл, было достаточно для завода, чтобы поддерживать производство. Это означало, по большей части, по одному на каждую машину, плюс архив штампов, матриц, диаграмм и записей.
Оглядываясь назад, я могу сказать, что первое впечатление от посещения архива было трепетным, как по поводу степени детализации различных процессов, так и по поводу масштаба, в котором когда-то все происходило. Также произошла ментальная адаптация, которая пришла постепенно, когда я понял, что, хотя я подходил с точки зрения дизайна, на самом деле я столкнулся с точной инженерией. Там, где я видел Баскервиля, другие сотрудники видели число: 169 (серийный номер «Монотипия»).
На этом слайде показана диаграмма для 252 (или Кентавра для вас и меня).Он показывает размеры шкалы и размещения каждого символа в шрифте в единицах десятитысячных дюйма. Это 14pt, для каждого размера шрифта есть отдельные таблицы. И все они написаны от руки.
В цехе штамповки на Monotype ежедневно работали 10 станков, и это был всего лишь один отдел на огромной производственной линии, на которой работали тысячи человек. На заводе, как правило, каждая задача была разделена: если вы просверлили конические отверстия, вы не использовали бы боковой фрезерный станок.Так что мне очень повезло, что мой наставник, Кумар, был достаточно дружелюбен со своим мастером, чтобы пойти против этого соглашения, и сумел научиться использовать все машины, участвующие в производстве матриц.
Парминдер Кумар Раджпут — это тот, у кого я учился, и тот факт, что я могу стоять здесь и говорить сегодня, действительно является данью его терпению и поддержке. Обладая почти 60-летним опытом, он, безусловно, мастер, а я — новичок. В Monotype период обучения навыкам штамповки составлял от 3 до 5 месяцев, полный рабочий день: пять дней в неделю.Мой ученик был один день в неделю в течение полутора лет, пока занимался другими проектами, так что мне еще предстоит пройти немалый путь, прежде чем я смогу уверенно называть себя профессионалом.
Итак, теперь, когда я дал вам контекст, я перейду к специфике процесса штамповки. Я попытался обобщить то, что научился описывать вам сегодня, но стоит отметить, что в действительности изготовление штампов и матриц не так просто, как следующие инструкции. Понимание цели каждого процесса, а также того, как управлять машинами, которые могут быть темпераментными, является необходимым ингредиентом.Иметь такого человека, как Кумар, чтобы направлять меня, напоминать мне и снова напоминать мне, пока техники и причины не встанут на свои места, было решающим.
Что такое вырубка дыроколом? Пуансоны — это мастер-буквы и первый значительный этап перевода рисунка в металлический шрифт. Обычно они вырезаются из стали и забиваются в матрицу или матрицу, из которой можно легко отливать кратные детали. На протяжении веков штамповка выполнялась вручную резцом; метод изготовления, зависящий от высококвалифицированных мастеров.Но, перефразируя литературу по Monotype, когда удар сломался во время удара по матрице, никакие человеческие навыки не могли гарантировать, что любой второй удар может быть нанесен настолько точно, чтобы он был микроскопически неотличим от первого: такой подвиг возможен только машина.
Вертикальный пантограф в Типовом архиве был разработан Фрэнком Хинманом Пирпонтом и производился Monotype Lanston Corporation с 1907 года. В принципе, он очень похож на конструкции Линн Бойда Бентона 1880-х годов.Оператор использует перо на нижнем конце, чтобы проследить контур увеличенного рисунка символа. На верхнем конце находится стальной пуансон, который вращается вокруг режущего инструмента, вращающегося с очень высокой скоростью (10 000 оборотов в минуту).
Однако перед тем, как приступить к нарезке пуансона, необходимо пройти несколько этапов. Каждый символ дизайна шрифта отображается как контурный рисунок размером 10 x 10 дюймов, на основе которого можно установить пропорции и границы в 18-элементной системе Monotype.Это уменьшено до образца четверти размера, на котором персонаж приподнят с поверхности. Традиционно для этого использовали воск и формировали медную пластину. К сожалению, средства для использования этой техники не сохранились, но мы смогли изготовить эквивалентные шаблоны с помощью фрезерования с ЧПУ.
При таком большом существующем архиве штампов и матриц в Type Archive потребность в нарезании новых штампов не велика. Однако мне повезло, что мое ученичество совпало с выдающимся заказом: созданием Hungry Dutch, шрифта, разработанного Расселом Маретом, и первой новой серией Monotype для составления композиций за более чем 40 лет.Эта комиссия предоставила практическую причину для понимания, практики и документирования процесса вырезания пуансоном и представляет собой очень полезный пример. На этой неделе мы только что получили образцы для последних 10 глифов, поэтому мы можем вырезать удары, которые завершат набор римских символов.
Вот пустой стальной пуансон толщиной 0,2 дюйма (примерно 5 мм). При резке металл относительно мягкий, затвердевание наступает позже. Поверхности пуансона, особенно лицевая часть, перед резкой гладко натираются о различные сорта индийского камня, чтобы обеспечить абсолютно ровную и безупречную поверхность.Смазка также наносится повторно на протяжении всего процесса резки.
Вставив пуансон в верхнюю часть машины и закрепив рисунок внизу, можно начать резку с обводки персонажа стилусом и серией следящих элементов, которые размещены в картридже выше для облегчения доступа.
Последователи представляют собой диски различного размера, прикрепленные к концу иглы в порядке уменьшения диаметра, при этом глубина фрезы также регулируется для работы до забоя.Резак режет все мельче по мере приближения к лицевой стороне буквы с каждым контуром. Существует целый кабинет последователей, выбор которого зависит от масштаба требуемого готового типа.
Здесь мы видим фрезы и справа увеличенные модели, используемые для обучения. Первый — это фрезерный инструмент, используемый для удаления больших нежелательных участков вокруг персонажа; второй — долоторез, который начинает определять контур; и, наконец, окончательные разрезы выполняются точечным инструментом.Процесс постепенный, обычно с использованием 2 долотных фрез перед окончательной обработкой. В некоторых окончательных разрезах удаляется только 0,00004 ″ (0,001 мм) металла.
Стоит отметить, что эти фрезы должны быть тщательно заточены в несколько этапов. Фрезы проверяются на станке, называемом Shadowgraph, который увеличивает инструмент в 200 раз, чтобы обеспечить точность до 10 000 долей дюйма перед резкой.
Это анимация, в которой примерно 30 этапов выполняются последовательно.
Стороны пуансона должны быть скошены, чтобы его можно было удалить без повреждений при ударе по матрице. Для силы фишки персонажа приподняты, а «спасательные» клинья защищают тонкие стены снаружи.
После того, как все измерения будут сверены с таблицей и все заусенцы будут удалены, пуансон можно закалить для подготовки к нанесению ударов. Пуансоны помещают попарно в печь на 6 минут при температуре 850 градусов, затем опускают в ведро с маслом.Затем штампы проверяются на прочность с помощью промышленного манометра. Измерения снова проверяются, и штампы «оправдываются».
Тогда матрица может быть поражена. Штамповочная машина оказывает давление 20 тонн. Если при нанесении удара имело место какое-либо искажение, лепет измельчается для компенсации, чтобы положение на матрице было точным. (Если лепет слишком велик с одной стороны, тиснение может отодвинуть положение символа от цели.) Искажение внешних размеров матрицы будет исправлено позже.
Я был очень горд видеть законченный шрифт, уходящий от литейщика композиции. Но, согласно литературе Monotype, окончательное удовлетворение еще предстоит реализовать: «Пробойник только при печати готового шрифта, когда чернильные оттиски персонажей появляются на бумаге и образуют узнаваемые формы слов под взглядом читателя. видит конечный продукт своего мастерства ».
Я должен прояснить, что проект Hungry Dutch — это не только результат моего труда.Мне нужно отметить Ника Гилла, чтобы он вдохнул в него первоначальную жизнь; Грэм Шеппард, создавший рисунки; Кумару за то, что он применил свои знания и умения и поделился ими со мной; Дункану Эйвери за управление проектом; и, конечно же, Расселу Марету за его дизайн и терпение. Также Сью Шоу за ее постоянную преданность Типовому архиву.
Type Archive — это поистине уникальное место, где собраны не только выдающиеся коллекции по истории типографского производства, но и продвигается их сложное понимание и практические навыки благодаря своему преданному своему делу персоналу.Теперь он готов предложить фантастические возможности тем, кто хочет углубить свои знания в области типографской инженерии, и приглашает всех желающих заявить о себе. Как признают все присутствующие в этом зале, существует постоянная необходимость сохранять эти навыки и передавать бесценные знания, которые мы помогли сохранить.
Я хотел бы закончить этой мыслью: сохранение традиционных навыков посредством практики важно, но, возможно, не менее важно придумывать новые способы их использования.
Диаметр пуансона — обзор
Испытание в форме шляпы
Методика образца в форме шляпы часто используется в компрессионном стержне Хопкинсона (рис. 2.8), который был изобретен в 1977 году Мейером и Хартманном в Институте Фраунгофера (IFAM, Бремен). , Германия) и использовался Hartmann et al. [26] и цитируется Meyer et al. [27]. Образец сдвига (в форме шляпы) расположен между входным и выходным стержнем. Они исследовали различные стали на предмет механических свойств и образования полос сдвига.Образец шляпы часто используют Мейерс [28–31] и Битти и др. [32] (рисунок 2.9).
Рисунок 2.8. Инструментальный аппарат Гопкинсона для получения белых полос в лаборатории, согласно Hartmann et al. [26].
Рисунок 2.9. Геометрия образца в форме шляпы, согласно Beatty et al. [32].
Преимущество теста в форме шляпы заключается в том, что его можно использовать для получения полос сдвига даже в очень пластичных материалах в компрессионной установке Хопкинсона, а также в том, что можно проводить сравнение между малыми и большими деформациями разрушения [33].Благодаря геометрии можно достичь очень высоких деформаций при высоких скоростях деформации, но на измерение напряжения сдвига влияют краевые эффекты. Деформируемость при сдвиге можно измерить и оценить. Чтобы исследовать микроструктуру образования полос сдвига, смещение образца шляпы можно легко ограничить в осевом направлении с помощью стопорных колец.
Битти и др. [32] провели эксперименты со сталью AISI 4340, используя образец шляпы, чтобы изучить образование полос сдвига высокопрочных сталей при высоких скоростях нагружения.Они исследовали влияние температуры аустенизации на потребление энергии при сдвиговом нагружении.
Не обращая внимания на шляпообразную геометрию [32], где диаметр пуансона и отверстия одинакового размера, в литературе существует несколько исследований, в которых диаметр пуансона меньше диаметра отверстия; большинство исследований проводится на образцах, у которых диаметр пуансона больше диаметра отверстия. Эта конфигурация приводит к дополнительной сжимающей нагрузке, такой как гидростатическое давление.
Образец, у которого диаметр пуансона меньше диаметра отверстия, использовали Миннаар и Чжоу [34] (рис. 2.10). Образцы были загружены в сжатый стержень Гопкинсона и по-разному остановлены, чтобы исследовать эволюцию сдвига. Исследуемые материалы: HY-80, HY-100, HSLA-80, 4340 VAR и Ti – 6Al – 4V. Титан в этом исследовании является самым твердым материалом и показывает ранний выход из строя в отличие от мягких сталей. С подобной геометрией образца, как показано на рис. 2.10, Chung et al.[35] провели динамические испытания в стержне Гопкинсона для стали AISI 4340. Ширина сдвига почти такая же, но общий диаметр больше.
Рисунок 2.10. Образец в форме шляпы, по мнению Миннаара и Чжоу [34].
Пурше [36] и Пурше и Мейер [37] исследовали поведение разрушения при сдвиге различных закаленных и отпущенных сталей с образцом в форме шляпы, у которого диаметр пуансона также меньше диаметра отверстия (рис. 2.11A). Этот образец аналогичен образцу Мейера и Крюгера [33] (рис. 2.11Б). Пурше обнаружил линейную корреляцию между разрушением при сдвиге для шляпообразного образца и деформациями разрушения, обнаруженными в условиях двухосного сдвига при сжатии (рис. 2.94).
Рисунок 2.11. Образец в форме шляпы, согласно Пурше [36] (A) и Мейеру и Крюгеру [33] (B).
Изменяя диаметры, если диаметр пуансона больше диаметра отверстия, создаются различные состояния напряжения сдвига при сжатии (гидростатическое давление). Это напряженное состояние препятствовало разрушению, и хрупкий материал может быть проанализирован на предмет предрасположенности к адиабатическому сдвигу.Сюэ [38] использовал такой образец шляпы (рис. 2.12) для исследования статического и динамического поведения нержавеющей стали 304, титана и Ti – 6Al – 4V. Для стали 304 было проанализировано влияние размера зерна.
Рисунок 2.12. Образец в форме шляпы со степенью сжатия по Сюэ [38].
Meyers et al. [28] исследовали микроструктуру материалов, подвергнутых сдвигу, таких как медь, титан и тантал. Методами испытаний были образцы в форме шляпы, загруженные в стержень Гопкинсона, и испытание на толстостенный цилиндр (TWC), которое будет объяснено позже.
Крюгер [39] и Мейер и др. [40] обнаружили, что дополнительное радиальное сжимающее напряжение в зоне сдвига шляпообразного образца уменьшало деформацию разрушения титанового сплава (рисунок 2.13A) и увеличивало деформацию разрушения тяжелого сплава вольфрама (рисунок 2.13B). Компонент радиального сжатия был вызван не самой геометрией образца, а внешним цилиндром для создания радиального давления в зоне сдвига образца.
Рисунок 2.13. Согласно Крюгеру [39] и Мейеру и др., Влияние дополнительного радиального сжимающего напряжения на поведение при разрушении шляпообразных образцов при комнатной температуре.[40].
Couque [41] использовал прямой стержень Гопкинсона (рис. 2.14) для исследования разрушения при сдвиге тяжелого сплава вольфрама и стали при различных боковых давлениях на образце шляпки (рис. 2.15). Кук обнаружил, что длина полосы адиабатического сдвига в калибровочной секции сильно зависит от скорости нагружения. При более высоком боковом давлении деформация разрушения при сдвиге для вольфрамового сплава увеличивается, аналогично результатам Крюгера [39]. Кук объяснил это поведение уменьшающейся частью пластической работы, преобразующейся в тепло при увеличении давления.
Рисунок 2.14. Прямая сборка Хопкинсона, согласно Couque [41] и Teng et al. [42].
Рисунок 2.15. Образец в форме шляпы с дополнительным напряжением сжатия, согласно Couque [41] и Teng et al. [42].
Teng et al. [42] провели численное исследование на образце в форме шляпы с геометрически индуцированными напряжениями взаимного сжатия, как показано на рис. 2.15 [41]. Использованы материальные данные экспериментальных исследований Couque. Тэн смоделировал формирование и распространение полос адиабатического сдвига и последующее распространение трещин.Тэн сравнил смоделированные длины полос сдвига с экспериментальными данными. Он предположил, что горячие точки в полосе сдвига являются местами зарождения трещин. Таким образом, образование трещины в полосе сдвига напоминает соединение небольших трещин.
Meyers et al. [43] исследовали полосы сдвига из нержавеющей стали AISI 304L, которые были получены с образцом в форме шляпы в стержне Кольского и с испытаниями TWC. Полосы сдвига исследуются с помощью методов дифракции обратного рассеяния электронов (EBSD) и просвечивающего электронного микроскопа (ТЕМ).
Clos et al. [44] провели испытания образцов в форме шляпы с двумя различными геометрическими формами: классический цилиндрический образец и образец в форме плоской шляпы с нагрузкой в стержне Гопкинсона (рис. 2.16). Образец в форме плоской шляпы был разработан для уменьшения краевых эффектов. Кроме того, плоский образец позволяет измерять повышение температуры во время деформации с помощью инфракрасного датчика. Clos et al. варьировали состояние напряжения сжатия / сдвига и использовали различные пределы деформации для изучения развития процесса сдвига.Clos использовала стали с содержанием углерода 0,15% и 0,45% и сплав Inconel 718. В стали с содержанием углерода 0,45% и инконелем 718 он обнаружил белые полосы травления (шириной до 20 мкм), а в стали с содержанием углерода 0,15% он обнаружил только темные полосы травления (около 200 мкм). Clos разделил поведение нагрузки-смещения на три этапа. Стадия I — это фаза до локализации, стадия II — это фаза локализации, а стадия III — это фаза после локализации. Локализация создавалась не только нестабильностью равномерно напряженной зоны, но и краевыми эффектами.Разрушение не происходит одновременно по всей зоне сдвига. Полосы сдвига образовывались на этапе постлокализации в результате трения. Измеренные температуры 0,45% углеродистой стали в начале локализации составляют около 200–250 ° C, 500 ° C в начале фазы после локализации и 850 ° C в конце фазы после локализации.
Рисунок 2.16. Образец шляпы как цилиндрической, так и плоской формы, согласно Clos et al. [44].
Сюэ и Грей [45] исследовали отожженную нержавеющую сталь AISI 316L в сборке стержня Гопкинсона с использованием шляпообразных образцов с определенным сжимающим напряжением.Они охарактеризовали формирование полосы сдвига посредством этапов деформации с различным временем нагружения. Комплексные исследования микроструктуры, включая наблюдения с помощью ПЭМ, этой стали были выполнены Xue et al. [46]. Xue et al. [47] провели геометрические эксперименты с материалами, подвергнутыми предварительному удару (304 и 316L), с тем же образцом в форме шляпы. Состояние материала, подвергшегося предварительному удару, показывает более высокий предел текучести и более короткую стадию деформационного упрочнения, чем материал без ударов. Деформация разрушения также ниже по сравнению с состоянием без сотрясения.
Lins et al. [48] также использовали шляпообразный образец с дополнительным напряжением сжатия для исследования горячекатаной стали без зазоров в узле Гопкинсона с различными пределами деформации для исследования микроструктурного внешнего вида полос сдвига.
Ли и др. [49] использовали образец в форме шляпы с немного большим диаметром пуансона в качестве отверстия. Исследуемые материалы представляли собой углеродистые стали с содержанием углерода 0,15%, 0,45% и 1,16%. Испытания проводятся с использованием стержня Хопкинсона.Ли исследовал образование полос адиабатического сдвига. Деформированная полоса для 0,15% -ной стали и преобразованные полосы, для которых наблюдается среднее и высокое содержание углерода. Ли также исследовал влияние скорости нагружения на формирование полосы сдвига.
Xu et al. [29] исследовали микроструктурные аспекты локализации адиабатического сдвига на различных материалах, таких как низкоуглеродистая сталь, нержавеющая сталь, титан и его сплавы, алюминиевый сплав и другие. Материалы были испытаны среди других методов с образцами в форме шляпы в сборке стержня Гопкинсона.
Peirs et al. [50] провели динамические испытания шляпообразных образцов Ti – 6Al – 4V с стержнем Гопкинсона. Он исследовал влияние радиуса кромки образца и ширины сдвига на формирование полос сдвига. Ширина обеспечивает однородность распределения напряжения и деформации, а также гидростатического давления. Конфигурация радиуса определяет возникновение полос адиабатического сдвига. Были проведены дополнительные исследования относительно эволюции полос сдвига и расчетов методом конечных элементов (КЭ).
Образец в форме шляпы использовался для титана Ti – 6Al – 4V [30], титанового сплава Ti – 6Al – 4V [51], алюминиевого сплава [38,52], тантала [31,53], циркония [54]. ] и медь [55].
Пробивные прессы — обзор
11.4.3 Производственный процесс
Изготовление деталей кожуха из оцинкованного листового металла и конструкционной стали. В качестве сырья для большинства кондиционеров используются стальные конструкции и листовая сталь. По мере того, как листовой металл перерабатывается в производственные ячейки или рабочие ячейки, его разрезают, формуют, штампуют, просверливают, разрезают и / или сгибают до нужной формы или формы.Кожухи или обертки — металл, которым окружают наружные блоки, — изготовлены из оцинкованного листового металла для защиты от коррозии. Оцинкованный листовой металл также используется для изготовления нижней панели, лицевых панелей и различных опорных кронштейнов кондиционера. Этот листовой металл разрезается на срезном прессе в производственной ячейке вскоре после доставки со склада или складских запасов. Профили из конструкционной стали вырезаются и скошиваются на ленточной пиле, чтобы сформировать полезные кронштейны и опоры.
Пробивной пресс для форм из листового металла. Из пресса-ножницы листовой металл загружается на пробивной пресс с ЧПУ (ЧПУ). Пробивной пресс имеет возможность получать свою компьютерную программу из программы CAD / CAM (автоматизированное черчение / производство с помощью компьютера) или из независимо написанной программы ЧПУ. Программа CAD / CAM преобразует чертеж или модель детали на компьютере в файл, который может быть прочитан пробивным прессом, сообщая ему, где пробивать отверстия в листовом металле. Плашки и другие штамповочные инструменты хранятся в машине и механически подаются к штамповочному рычагу, где их можно использовать для прохождения сквозь лист.Листогибочные прессы с числовым программным управлением (NC) сгибают лист в его окончательную форму, используя компьютерный файл для программирования. Различные гибочные матрицы используются для разных форм и конфигураций и могут быть изменены для каждого компонента.
Некоторые кронштейны, ребра и листовые компоненты передаются на аутсорсинг другим предприятиям или компаниям для производства в больших количествах. На сборочный завод их привозят только тогда, когда они нужны для сборки. Многие кронштейны производятся на гидравлическом или механическом прессе, где кронштейны различной формы и конфигурации могут быть изготовлены из свернутого в рулон листа и непрерывно разматываться в машину.Могут изготавливаться большие объемы деталей, потому что пресс часто может производить детали сложной формы одним ударом.
Очистка деталей. Перед нанесением порошкового покрытия все детали должны быть чистыми и свободными от грязи, масла, жира и смазочных материалов. Для выполнения этой необходимой задачи используются различные методы очистки. Большие емкости для раствора, заполненные чистящим растворителем, взбалтывают и сбивают масло, когда детали погружаются в воду. В системах распылительной мойки используются чистящие растворы под давлением для удаления грязи и жира.Обезжиривание паром, подвешивание деталей над резким чистящим паром, использует кислотный раствор и оставляет детали свободными от нефтепродуктов. Для дополнительной защиты от коррозии многие детали будут загрунтованы в ванне с фосфатной грунтовкой перед тем, как попасть в сушильный шкаф, чтобы подготовить их к нанесению порошкового покрытия.
Порошковая покраска. Перед тем, как скобы, сковороды и обертки будут собраны вместе, они подвергаются процессу порошкового покрытия. Система порошкового покрытия распыляет похожий на краску сухой порошок на детали, когда они подаются через кабину на подвесной конвейер.Это можно сделать с помощью роботизированных опрыскивателей, которые запрограммированы, где распылять, когда каждая деталь проходит через кабину на конвейере. Детали статически заряжены, чтобы порошок прилипал к глубоким щелям и изгибам внутри каждой детали. Детали с порошковым покрытием затем подают через печь, обычно с той же конвейерной системой, где порошок постоянно спекается на металле. Процесс занимает менее 10 мин.
Изгиб трубок конденсатора и испарителя. Конденсатор и испаритель действуют как теплообменник в системах кондиционирования воздуха и изготовлены из медных или алюминиевых трубок, изогнутых в форме змеевика, чтобы максимально увеличить расстояние, через которое проходит рабочая жидкость.Противоположная жидкость, или охлаждающая жидкость, проходит по трубкам, когда рабочая жидкость отводит свое тепло в испарителе. Для этого нужно взять множество медных трубок малого диаметра, изогнутых одинаковой формы, и закрепить их с помощью направляющих стержней и алюминиевых пластин. Рабочая жидкость или хладагент протекает через медные трубки, а противоположная жидкость течет вокруг них между алюминиевыми пластинами. Трубы часто заканчиваются изгибом шпильки, выполняемым гибочными станками с ЧПУ по тому же принципу, что и листогибочным прессом с ЧПУ.Каждый изгиб идентичен следующему. В гибочных станках используются предварительно выпрямленные трубы для сгибания неподвижной матрицы с оправкой, проходящей через внутренний диаметр, чтобы предотвратить ее сжатие во время гибки. По окончании изгиба оправка загибается назад через внутреннюю часть трубы.
НКТ, поставляемые производителю в виде бухты, проходят через разматыватель и выпрямитель перед подачей через гибочный станок. Часть трубок будет разрезана на нужную длину абразивной пилой, которая разрежет несколько маленьких трубок за один ход.Алюминиевые пластины вырубают на штамповочном прессе и формуют на механическом прессе для создания углублений или волн на пластине. Эти волны максимизируют термодинамическую теплопередачу между рабочей жидкостью и противоположной средой. Когда медные трубы закончены в ячейке гибки, они транспортируются с помощью автоматически управляемого транспортного средства (AGV) в сборочную ячейку, где они укладываются на направляющие стержни и проходят через пластины или ребра.
Соединение медных трубок с алюминиевыми пластинами .Основная часть сборки — соединение медных трубок с алюминиевыми пластинами. Эта сборка становится испарителем и достигается за счет того, что уложенные друг на друга медные трубки в их конфигурации шпильки и механически сплавлены с алюминиевыми пластинами. Сплав происходит, когда пуля или оправка пропускаются через медную трубку, чтобы расширить ее и прижать к внутренней части отверстия в пластине. Это обеспечивает бережное, но полезное соединение между трубкой и пластиной, обеспечивая теплопередачу.
Конденсатор изготавливается аналогичным образом, за исключением того, что противодействующей средой обычно является воздух, который охлаждает медные или алюминиевые змеевики конденсатора без пластин. Они удерживаются скобами, поддерживающими гибкую трубу, и соединяются с испарителем с помощью фитингов или муфт. Конденсатор обычно представляет собой одну трубку, которую можно согнуть в нескольких изгибах шпильки. Расширительный клапан, который обычно передается на аутсорсинг, устанавливается в трубопроводе после конденсатора.Это позволяет давлению рабочей жидкости снижаться и повторно поступать в насос.
Установка помпы. Насос обычно покупается. Предназначенный для повышения давления в системе и циркуляции рабочей жидкости, насос соединяется с системой с помощью фитингов и фиксируется на месте с помощью опорных кронштейнов и основания. Он скреплен болтами с другими конструктивными элементами кондиционера и покрыт кожухом из листового металла. Кожух скрепляется заклепками или болтами для обеспечения надлежащей защиты внутренних компонентов.
ВИДЫ ПУАНСОНОВ: КОНСТРУКЦИЯ И ОБСЛУЖИВАНИЕ
Виды штампов, применяемых при изготовлении штампов в металлургической промышленности, их конструирование и ремонт.
Во всех штампах или матрицах, используемых в металлургической промышленности, между их компонентами есть пробойник. Внутри матрицы пуансон удерживается в пластине держателя пуансона, и его функция заключается в объединении с лезвием — или резаком — и формировании покрытий — или другого элемента — из полосы олова, которая подается поперек прессу, на котором он находится. установлен.
Типы пуансонов — одна из важнейших частей штампа , так как именно эта деталь выполняет наиболее значительную работу. Пуансон выполняет различные задачи . Основные из них сделаны вашей губой — см. Рисунок №1 — а это:
— Сделайте разрез материала путем удара его «режущей кромки» о край лезвия.
— Плотно прижмите обрезанный материал к верхней поверхности прижимного кольца, пока деталь формируется.Это делается основанием его «нижней губы».
Anuncios
— Посредством «радиуса выступа» облегчить поток внешней части материала внутрь для формирования соответствующего профиля крышки или инкрустированного контейнера.
— Определите внешний диаметр крышки или контейнера, который определяется диаметром «внутренней части выступа» пуансона.
— Практически все элементы, составляющие верхнюю часть матрицы, устанавливаются внутри пуансона или вокруг него.
Рисунок № 1: Разрез типовой формы пуансона и обозначение частей его выступа
Рисунок №1 воспроизводит классический силуэт дырокола для крышек / низов. Его основная часть — это нижняя область или выступ, и на нем появляются критические точки, контакт между ним и оловом или материалом, используемым для производства продукта, который должен быть получен.
На протяжении этой работы мы подробно обсудим важность их, их конструкцию и обслуживание.Фактически, его характеристики варьируются в зависимости от того, для чего предназначен кристалл.
ВИДЫ ПУАНСОНОВA Первая классификация типов пуансонов , используемых в этой отрасли, может быть сделана в зависимости от их использования. Итак, вы можете поговорить о:
— A: Пробойники для крышек / днищ. № Используемые при изготовлении этих элементов, они отличаются тонкой кромкой из-за небольшой разницы между диаметром резания и внешней стороной крышки.Обычно они изготавливаются цельными.
— B: Пуансоны для упаковки капсул и колбас. То есть сотрудники для крышек для стеклянных банок, небольших контейнеров для сосисок или первой операции с контейнерами типа DRD или DWI. Высота юбки полученной детали позволяет выступу пуансона иметь толстую стенку. Обычно они состоят из нескольких частей, установленных концентрически друг в друге.
Их также можно классифицировать по типу инструмента, на котором они установлены, например:
— A: Пуансоны для штампов с направляющими колоннами .Они устанавливаются на пластине с пуансонами и имеют форму, показанную на рисунке 5.
— B: Пуансоны для штампов без колонн или сборки в воздухе. У них обычно есть ручка или пуансон, позволяющий прикрепить его к прессу. Его конфигурация показана на рисунке 2
.Другая классификация связана с присвоенной степенью твердости. Так их может быть:
— A: Мягкая штамповка . Они подвергаются термообработке, поэтому их твердость составляет 40-42 HRc.Они используются в паре со стальными лезвиями твердостью 60 — 62 HRc, просты в обслуживании и используются в основном для некруглых производств и небольших производств. Мы вернемся к этому позже.
— B: Жесткие удары . Они изготовлены из недеформируемой стали для инструментов и имеют твердость около 60 HRc. Они используются со стальными лезвиями или лучше со вставкой из карбида вольфрама. Его использование широко распространено на крупных производствах.
Anuncios
В этой работе мы начнем с классификации, основанной на ее использовании.
ВИДЫ ПУАНСОНОВ МАШИНМы уже говорили, что у них тонкая губа. Ваша критическая область, требующая пристального внимания, — это губа. Чтобы изучить их более подробно, сделаем это по окончательной твердости.
1º.- МЯГКИЕ ИЛИ ПОЛУЗАКРЕПЛЕННЫЕ ПУАНСОНЫ
Это те, чья работа восходит к истокам этой отрасли. Они изготовлены из хромоникелевой стали, которая может поставляться предварительно обработанной до конечной твердости 40 — 42 HRc, что позволяет полностью механизировать с использованием соответствующих инструментов, облегчая, таким образом, окончательную отделку, так как не требуется подвергать деталь после обработки.термический.
Они образуют рабочую пару со стальными лезвиями, более твердыми, чем пуансоны — от 60 до 62 HRc — из недеформируемой стали для инструментов. Время работы между ремонтами у этих пуансонов меньше, чем у их лезвий.
Его применение очень полезно для прямоугольных, овальных или некруглых штампов . Большим преимуществом является то, что он облегчает обработку профиля режущей кромки, которая обычно является сложной, основанной на составном радиусе и прямых кривых, поскольку ее твердость позволяет механическому регулировщику подкрашивать вручную в банке, делая использование приспособлений для регулировки.Также можно использовать этот тип пробойников для малопригодных инструментов из-за его экономии.
Его конструкция соответствует типу, показанному на рисунке 2. Он имеет рабочую кромку с углом 12º для штампов прямоугольной формы и более 15º или 16º для круглых и радиусом примерно 1 мм. Если хотите сэкономить сталь, можно разместить ручку или перфоратор из углеродистой стали.
Рисунок № 2: Мягкая матрица для прямоугольных крышек 1/4 булавы
Основным недостатком этого типа пуансонов является сокращенный срок службы их режущей кромки, так как они легко изнашиваются.Каждый раз, когда это происходит, мы должны переделывать его, что влечет за собой уменьшение его высоты. Уменьшая этот размер, также необходимо отрегулировать высоту деталей, находящихся внутри него. Для этого внутри пуансона и ниже его центра помещается прокладка, высота которой уменьшается каждый раз, когда вам нужно восстановить конец выступа. Другой вариант для круглых пуансонов — сначала оставить толстую стенку в ее основании, которая служит опорой для ее центральной части, чтобы ее можно было утопить при необходимости.
Из-за вышеперечисленных характеристик использование этих пуансонов следует ограничивать при работе с материалами — белой жестью или TFS — с низкой температурой, так как таким образом время использования без необходимости обслуживания будет больше.
Ремонт полутвердых пуансонов (40-43 Rockwell C)
Если требуется ремонт этих пуансонов, действуйте следующим образом:
- A) Обработайте отверстие пуансона под углом 30 ° и получите плоскую поверхность 1.5 мм с таким наклоном. прежде чем подчеркивать.
- B) Усильте в достаточной мере мундштук пуансона, чтобы внешняя часть пуансона могла быть исправлена до нужного размера на высоте не менее 2,5 мм., И чтобы внутренний диаметр пуансона мог быть исправлен до соответствующего размер, если необходимо. Целью этой осадки является увеличение диаметра резания, чтобы впоследствии должным образом приспособиться к диаметру матрицы. Исходя из того, что это напряжение прикладывается к холодному оружию, при надлежащей осторожности на кромке пуансона могут быть трещины.Предпочтительнее выполнять высадку двумя или тремя сериями небольших движений, чем выполнять заключительную серию движений большей интенсивности. Важно медленно поворачивать пуансон при ударе, чтобы удары молотка не оставляли следов в одном и том же месте, поэтому мы получим новую кромку пуансона за два оборота или прохода.
В случае небольших трещин в выступе пуансона при выполнении этой задачи необходимо обработать эту область до исчезновения трещины , а затем снова приступить к повторной высадке.Очень важно, чтобы ударная поверхность молотка была как можно более гладкой. Используемый молоток должен быть от 0,5 до 1 кг.
Anuncios
- C) Убедитесь, что поверхность гнезда пуансона плоская и без заусенцев, и при необходимости исправьте дефектные условия. Предлагаемый метод шлифования задней поверхности пуансона состоит в том, чтобы после операции осадки сначала поместить пуансон с этой задней поверхностью на плоский шлифовальный станок для шлифования напряженной поверхности, а затем перевернуть пуансон и отшлифовать поверхность позже.При установке пуансона для этих операций шлифования необходимо следить за тем, чтобы цилиндрическая поверхность монтажной или посадочной площадки оставалась перпендикулярной задней поверхности пуансона.
- D) Установите пуансон на круглошлифовальный станок, центрируя его от центрального гнезда пуансона, и проверьте, являются ли внешний и внутренний диаметры концентричными, и проверьте их размер, при необходимости исправив их до указанных средств.
- E) Необходимо отрегулировать высоту, либо опуская внутреннюю прокладку там, где находится центр пуансона, либо, если это не такая конструкция, углубить центральное седло непосредственно на пуансоне.Еще раз проверьте сборку пуансона с индикатором, чтобы убедиться, что он не сдвинулся, и закончите шлифовку седла. Углубление гнезда прокладки или центра пуансона может потребоваться для исправления дефекта на поверхности или для восстановления высоты между этим гнездом и лицевой стороной пуансона. В связи с этим следует проверить длину всех крепежных винтов, чтобы они не оставались в своих резьбовых отверстиях.
- F) В случае штампов для двойных штампов важно, чтобы посадочные места центров пуансона или регулировочных шайб находились на одном уровне высоты при установке указанных пуансонов, чтобы получить правильные средства в обеих матрицах.Следовательно, высота от задней поверхности пуансонов до посадочных мест центров должна находиться в пределах указанных допусков. Указание метода проверки можно увидеть на рисунке 3
Рисунок № 3: Проверка высоты пуансона
На этом чертеже представлен пуансон без ручки.
G) После зоны регулировки 2,5 мм между пуансоном и лезвием диаметр пуансона должен быть уменьшен на 0,15 мм примерно на 15 мм от передней поверхности пуансона.Это сделано для ограничения трения режущей кромки лезвия и ступеней о стенки пуансона. Что касается последнего, тот же эффект достигается за счет внутреннего опускания кромки протектора и заполнения ее латунным сварным швом, который является мягким материалом. В случае штампов для некруглых крышек это последнее решение легче осуществить.
H) Когда угол устья пуансона исправлен, рекомендуется оставить небольшую плоскую и горизонтальную область в несколько десятых миллиметра на краю режущей кромки, чтобы усилить ее и не порезать.Как мы уже указывали, для прямоугольных пуансонов этот угол составляет около 12 °, а для круглых — еще немного. В любом случае, оно должно быть точно таким же для прижимного кольца, чтобы обеспечить адекватное разглаживание материала во время операции перфорации.
Anuncios
Мы должны проявлять особую осторожность при переделке градусов прямоугольного пуансона в области четырех углов, потому что, если мы не примем меры предосторожности, мы можем удалить слишком много материала в этой области, и когда будет сформировано крыло крышки он не покинет его с правильным наклоном, так как будет выглядеть приподнятым краем.
Последним важным этапом настройки пуансона должно быть формирование радиуса. Его можно сделать вручную, используя специальные камни в зерне и должным образом смазанные. Радиус должен быть идеально отполирован и должен находиться в пределах от 0,75 мм до 1,25 мм.
I) После завершения исправления или ремонта необходимо проверить концентричность диаметров пуансона перед его снятием со станка. См. Рисунок № 4
.Рисунок № 4: Проверка соосности диаметра на пуансоне
Значительная часть приведенных здесь указаний действительна также, когда штампы предназначены для капсул или контейнеров для сосисок.Мы вернемся к этому.
2º.- ЖЕСТКИЙ ПУАНСОН
Это тип штампов более общего назначения. Его использование удобно при условии, что это формат больших производственных крышек. Они изготовлены из недеформируемой стали для инструментов и имеют твердость порядка 60 HRc. Лезвия, используемые с ними, могут быть стальными с немного более высокой твердостью — 62 HRc — или лучше того типа, который имеет твердосплавную пластину в зоне резания.
Его конструкция соответствует типу, показанному на рисунке No.5. Приведенные на нем размеры выражены в дюймах. Принципиальные отличия мягкого пуансона, помимо твердости:
— Наклон режущей кромки, увеличивающийся примерно до 30 °
— Радиус этого выступа, который обычно делают несколько больше, порядка 1,25 мм
— При сплющивании режущей кромки, которая уменьшена примерно до 0,25 мм
Рисунок № 5: Типичный жесткий удар для денежных средств
Обычно другие варианты:
— Снятие ручки или держателя пуансона.
— Быть деталью без дна, чтобы облегчить его исправление и сборку.
Эти последние отличия обусловлены конструкцией матрицы в целом, поскольку на инструментах с направляющими колоннами всегда используются жесткие пуансоны, а также, по крайней мере, двойные пуансоны.
Ремонт закаленных пуансонов (61 — 62 Rockwell C)
При использовании жестких пуансонов процедура регулировки менее сложна, чем для полутвердых пуансонов. Необходимо предпринять следующие шаги:
Измерьте износ внутреннего диаметра пуансона.Если будет обнаружено, что он изношен на 0,04 мм сверх максимального предела изготовления, то есть если внутренняя поверхность выступа «штампа» — та, которая образует изгиб крыла крышки — представляет собой износ — увеличение диаметра — более 0,04 мм, кромка должна быть восстановлена - да, позволяет — или деталь забракована. Вы также должны проверить режущую кромку, если она сохраняет свою остроту или требует шлифовки.
Anuncios
Исправление отверстия пуансона для формирования новой режущей кромки будет выполняться на круглошлифовальном станке, при этом необходимо удалить необходимый материал для получения новой чистой и острой кромки.Пуансоны двойных матриц должны быть исправлены до одинаковой длины. Чтобы восстановить исходную высоту их граней после их посадки на пластине держателя пуансона, рекомендуется использовать вставки с минимальной толщиной 0,40 мм. Будут предприняты усилия, чтобы количество добавок было минимум
.Перед снятием пуансона со шлифовального станка необходимо исправить радиус кромки, доведя его до правильной спецификации, — хорошее значение может составлять 1,25 мм — соедините его с прилегающими поверхностями и тщательно отполируйте.Не рекомендуется ремонтировать радиоприемник вручную, потому что этот метод приведет к получению неправильного и эксцентричного радиоприемника, что может создать проблемы при производстве. Твердые пуансоны для днищ имеют тенденцию к износу своего диаметра после производства примерно 10 миллионов единиц на пуансон.
Хотя это не очень часто, край рта сильного удара может быть поврежден или заклепан. С помощью этого метода добавляется достаточно материала для увеличения внешнего диаметра пуансона, что позволяет исправить его до исходного диаметра.На чертеже № 6 подробно описан этот способ, который отличается от метода, используемого для штампов с полувыдерживаемой закалкой, описанного выше.
Рисунок № 6: Загрунтованный штампом из закаленного металла
Это увеличение материала во время клепки не влияет на внутренний диаметр пуансона. По окончании шлифования следует проверить концентричность пуансона перед его снятием со станка, как описано ранее на рис. 4
.Независимо от того, нагружен он или нет, всегда должно выполняться то, что в пуансоне задние поверхности пуансона и его режущая кромка должны быть идеально плоскими и параллельными друг другу.Предел допускаемой погрешности 0,05 мм. Кромка пуансона обычно имеет наклон 30 ° и должна точно совпадать с кромкой гладильного кольца. Для этого их необходимо исправить вместе, используя ту же регулировку шлифовального станка. Режущая кромка должна иметь небольшую плоскую и горизонтальную поверхность 0,25 мм. примерно по ширине. Величину диаметра резания необходимо выдерживать минимум на участке 2,5 мм, затем его обычно понижают, чтобы уменьшить контакт с кромкой лезвия. (См. Рисунок № 7)
Рисунок № 7: Детали режущей кромки жесткого пуансона и ее перекрытие с лезвием
ПУАНСЫ ДЛЯ КОЛБАСНЫХ ПАКЕТОВ И КАПСУЛКак мы уже указывали, для них характерна толстая губная стенка.Это возможно, потому что важна разница между диаметром режущей кромки и стороной формируемой детали, тем более что высота этой стороны. Поэтому они очень прочные и обычно состоят из нескольких частей. Как и в случае с пуансонами для тапаса, изучим их по твердости
Anuncios
1º.- МЯГКИЕ ИЛИ ПОЛУЗАКРЕПЛЕННЫЕ ПУАНСОНЫ
Можно повторить почти те же соображения, которые были сделаны выше для пуансонов, предназначенных для колпачков, это действительно то, что уже было сказано о стали, которая будет использоваться, ее твердости, конструкции, характеристиках используемых лезвий и т. Д.
Если учесть, что эти пуансоны обычно делаются двумя штуками. Наружная часть, где находится режущая кромка, отвечающая свойствам твердости и т. Д., И другая внутренняя часть в виде внутренней рубашки. Эта вторая деталь, предназначенная для утюжения и придания формы стенке капсулы или контейнера. напротив центра матрицы, изготовлен из недеформируемой стали для инструментов, обработанной с твердостью, превышающей твердость внешнего корпуса — порядка 55 HRc -. Тот же самый, идеально отполированный по всей площади контакта с белой жестью, имеет более длительный срок службы, так как он меньше изнашивается и не должен подвергать его столько раз, сколько внешний ремонт его внутреннего диаметра. , хотя из его высоты и радио.На рисунке № 8 представлен пуансон для капсул этого типа.
Ремонт полутвердых пуансонов для капсул или колбасной упаковки:
Что касается пуансонов для этого использования, действуйте следующим образом:
Прежде всего, сделайте высадку, как указано выше, то есть с той же процедурой, что и для перфорации покрытия / фонда. См. Рисунок № 8
Рисунок № 8: Пробойник для капсул с грунтовкой
После выполнения осадки вторым этапом является шлифовка кромки пуансона с соответствующими степенями и подгонка ее внешнего диаметра к режущей матрице.Подходящий угол кромки пуансона составляет 10 °
, чтобы соответствовать внешнему диаметру мишени по матрице. Un ángulo adecuado del labio del punzón es de 10 º
В качестве критерия регулировки необходимо небольшое давление на матрицу, чтобы она поместилась внутри пуансона. Совершенная полировка шлифованной поверхности абсолютно необходима.
Третий этап — формирование рабочего радиуса аппарели. Обычно радиус делается вручную с использованием ручного камня с соответствующей зернистостью и должным образом смазанного.Радиоприемники от 0,75 до 1,25 мм дают хорошие результаты. Изменение значения этого радиуса иногда можно использовать для увеличения или уменьшения высоты стенки капсулы или контейнера.
Обычно радиоприемник проверяет образец корпуса, который был возвращен производственным отделом рядом с кристаллом, когда он был выведен из эксплуатации. Если длина юбки капсулы (высота капсулы) в этом образце удовлетворительна, такой же радиус будет сохраняться в отремонтированных пуансонах.В случае их изготовления реализация малых радиусов должна выполняться очень осторожно, потому что слишком малый радиус может привести к частичным трещинам в олове или также вызвать чрезмерную «выгибку» (orejeado) на краю юбки.
Anuncios
Очень важно обработать спицы надлежащим образом и с очень тонкой полировкой специальной наждачной бумагой, если возможно, уже использованной и смазанной, и, прежде всего, с использованием системы, которая не вызывает износа внутри пуансона.
2º.- ПУАНСЫ ЖЕСТКИЕ
Они также являются наиболее часто используемыми штампами для упаковки колбасных изделий. Как и крышки, они изготовлены из недеформируемой стали для инструментов и имеют твердость порядка 60 HRc
.Его конструкция может быть как цельной, так и тройной. Последний вариант является наиболее целесообразным. На рисунке 9 представлена часть этого варианта. В данном случае он состоит из:
— A: Основной корпус пуансона с режущей кромкой
— B: Формовочная добавка или внутренняя вставка, которая утюжит материал и определяет внешний диаметр контейнера.В этом изделии очень важен радиус вашей губы, по которому скользит материал.
— C: Прокладка, которая позволяет идеально промыть грани двух предыдущих деталей, составляющих нижнюю часть пуансона.
Рисунок № 9: Твердый пуансон, состоящий из трех частей
Детали A и B обработаны жестко, а обувь — нет. После регулировки они соединяются винтами.
Ремонт закаленных пуансонов (61 — 62 Rockwell C)
Когда режущая кромка изнашивается, действовать можно следующим образом:
— A: Снимите пуансон и открутите его детали.
— B: Исправить режущую поверхность его основного тела, переделав край массы.
— C: Если тренировочный комплект сохраняет свой радиус и внутреннюю поверхность в пределах спецификаций, не выполняйте с ним никаких действий.
— D: Уменьшите высоту регулировочной шайбы на то же значение, которое было устранено при шлифовании пуансона.
— E: Если необходимо изменить радиус формующей детали, необходимо принять во внимание ее окончательную высоту, чтобы определить высоту регулировочной шайбы.
— F: После того, как три части снова собраны, необходимо проверить их идеальное совмещение, чтобы режущая поверхность была точно разрушена. Если это не так, потребуется один последний финальный проход.
Мы не будем вдаваться в подробности того, как выполнять эти операции в ремонтной мастерской, поскольку они аналогичны указанным выше.
ПРИЛОЖЕННЫЕ ТИПЫ ПУАНСОНОВRECALCADO SOBRE PRENSA
Полуобработанные пуансоны, как для крышек / дна, так и для заделанных капсул / контейнеров, можно прижимать или приклепывать непосредственно к прессу.Эта процедура более неточна, чем процедура, выполняемая в мастерской по техническому обслуживанию и уже описанная выше, но она действительна для небольшого ремонта, и, таким образом, можно избежать частой разборки матрицы и ее отправки в мастерскую. Поэтому его можно использовать несколько раз, прежде чем прибегать к его разборке.
Этот метод высадки различается на каждом предприятии и в некоторой степени зависит от опыта механиков производства. Некоторые используют то, что обычно называют «чечевицей» — своего рода плоский молоток, который облегчает его введение между пуансоном и матрицей — другие используют стальной стержень, молоток или специальное устройство, которое вставляется в лезвие.
Anuncios
Цель состоит в том, чтобы немного увеличить внешний диаметр режущей кромки пуансона с помощью любого из этих методов. Но нужно следить за тем, чтобы не давить слишком сильно, потому что это сократит срок службы штампа.
Затем, когда пуансон впервые проникает в лезвие, он удаляет небольшое количество лишнего металла с края пуансона и, таким образом, изготавливается заново. Пуансон должен быть нагружен достаточно точно, чтобы получилась утопленная поверхность, когда пуансон входит в режущее лезвие, поскольку чрезмерный заусенец имеет тенденцию повреждать режущую кромку лезвия и сокращать срок службы пуансона.
Пуансоны следует заклепать ровно настолько, чтобы они вернулись к диаметру резания без потери материала. Это можно сделать, расположив шаблон — например, бумагу — между каждым этапом в шахматном порядке, чтобы определить, требуется ли дополнительная корректировка для получения идеального шаблона.
Если следовать этой практике, затраты на ремонт штампов будут значительно сокращены.
ОснованиеType — Типографская печать Commons
С момента изобретения Гутенбергом «подвижного типа» в 1400-х годах до середины 1800-х годов литье по существу оставалось неизменным — металл заливался вручную в форму, закрытую матрицей.С промышленной революцией и ростом грамотности и сопутствующим ростом спроса на печатные материалы изобретатели обратили внимание на механизацию литейного оборудования. Первые успешные машины были разработаны для компаний, занимающихся продажей шрифтов для принтеров. Хотя эти машины улучшили скорость производства и качество литейного типа, они ничего не изменили на полу компоновочного цеха — процесс установки и распределения шрифта оставался таким же трудоемким, как и в 1400-х годах.Неудивительно, что первая коммерчески успешная печатная машина Linotype была продана не за качество своего типа, а за экономию рабочей силы. Для дальнейшего обсуждения линотипа и других машин, которые последовали за ним, необходимы некоторые основные термины и концепции, лежащие в основе типов.
Основные детали
Практически все оборудование для литья, используемое в настоящее время, состоит из одних и тех же основных частей: нагретый горшок , наполненный расплавленным металлом, который содержит насос , который при срабатывании отпускает плунжер , который затем сжимает жидкий металл через сопло или мундштук , ускоряющий типовой металл в форму , которая образует корпус типа или заготовки, которая покрыта матрицей , которая образует печатную поверхность типа или слизняк.Хотя эти детали являются общими для всех машин, существует огромная разница в точной геометрии и конструкции от машины к машине.
Горшки — можно отапливать газом или электричеством. Многие из них (Linotype, Intertype, Ludlow и Thompson) имеют встроенный корпус насоса, называемый скважиной .
Насос— одна группа машин, разработанных и построенных корпорацией Monotype, использовала свободно плавающий насос в баке, который, будучи более сложным, обеспечивал большую гибкость производительности.
Плунжер — размер соответствует насосу или скважине, его ход определяет объем металла, проталкиваемого через сопло или мундштук. Обычно с пружинным приводом.
Сопло или мундштук — служит для ускорения струи определенного металла и фокусировки ее места для правильного входа в форму. Неправильно отрегулированные или смещенные от центра сопла делают текст пористым или с плохой печатной поверхностью.
Mold — создает тело типа или пули. Большинство из них легко заменяются для соответствия разным кеглям.В случае Ludlow тип обычно приводится к телу с фиксированной точкой. Linotypes и Intertypes использовали систему вкладышей, соответствующих типу и размеру пресс-формы. На машинах, которые отливают индивидуальный тип, форму изменяют или модифицируют, чтобы отливать другие размеры.
Матрица — создает лицевую сторону шрифта. «Глубина забивки» или глубина выемки должна соответствовать используемой пресс-форме, чтобы создать правильный тип высокого размера. Глубина прохождения зависит от стиля матрицы и от страны к стране.
Jeff Shay
Матрицы Ладлоу
Jeff Shay
Матрицы линотипов
Изготовление матриц
Есть три способа создать матрицу. Первоначально матрицы изготавливались с использованием ручных стальных пуансонов для создания выемки, в которую вставляется металл. Следующим нововведением стало использование гальванопластики для создания матрицы. Для этого необходимо скопировать «тип шаблона». Этот тип шаблона может быть либо существующим типом, либо новым дизайном, вырезанным из металла.Многие матрицы XIX века изготавливались таким способом путем ручной резки и гальванопластики. Разработка достаточно точных пантографов в 1880-х годах позволила механизировать вырубку штампов и шаблонов, а также позволила прямую фрезеровку матриц. Первые матрицы с прямой разводкой в Америке были вырезаны в 1882 году на заводе Central Type Foundry в Сент-Луисе. В 1880-х и 1890-х годах появилось несколько независимых фирм по матричной резке. Также в 1880-х годах Линн Бойд Бентон разработал необычайно сложный пантограф для гравировки типов рисунков и пуансонов, который был сдан в аренду нескольким компаниям по производству матриц и литейных машин, включая Linotype и Lanston Monotype.В 1899 году он модернизировал эту машину для прямой гравировки матриц, хотя для матриц с большим объемом производства, таких как линотип, штамповка по-прежнему была предпочтительным методом производства.
Jeff Shay
Матричные штампы линотипа
Тип Металл
Хотя его часто называют «свинцовым», на самом деле это сплав с переменным содержанием свинца, состоящий из 54–86% свинца, 11–28% сурьмы и 3–18% олова. Сурьма укрепляет металл. Олово укрепляет металл, уменьшая хрупкость сурьмы, а также увеличивая текучесть расплавленного металла.Точный выбор сплава зависит от типа машины, в которой он будет использоваться. По мере увеличения содержания сурьмы и олова в типе металла, твердость и долговечность этого типа также возрастают. Обратной стороной этого является то, что температуры литья также должны повышаться, чтобы легирующие элементы оставались в растворе. Сплавы с самым низким процентным содержанием сурьмы и олова используются в литейных установках без водяного охлаждения, которые работают при самых низких температурах электролизера. Сплавы с наивысшим содержанием легирующих элементов используются в традиционных литейных цехах, разливаются с помощью литейных машин высокой температуры и давления, таких как Barth Typecaster.Даже самые высокие температуры отливки значительно ниже точки «кипения» свинца, поэтому расплавленный металл не выделяет пары свинца — деталь, которую часто неправильно понимают.
Джефф Шэй, Редактор секции Дэвид Макмиллан, Рэймонд НельсонEngineering and Technology History Wiki
Массовое воспроизведение: в Библии Гутенберга использовалось четыре миллиона букв. Даже с учетом повторного использования требовались мелкие детали в больших масштабах. Никаких современных записей о печатных инструментах Гутенберга не существует; Возможно, он использовал такие формы, как эти французские образцы 17-го века.Эта статья изначально была написана Робертом Вудсом, научным сотрудником ASME. Эта статья содержит материалы, опубликованные в журнале «Машиностроение» за октябрь 2005 г. Авторское право 2005 г. Американское общество инженеров-механиков,
Мы привыкли считать изделия машинного производства практически идентичными. Например, никого не волнует, что новые лезвия бритвы не подходят к самой бритве.
Такая взаимозаменяемость — отличительная черта массового производства. Эли Уитни приписывают введение концепции взаимозаменяемых частей, когда он начал использовать приспособления и приспособления для производства функционально идентичных компонентов для мушкетов.Генри Форд довел массовое производство до его нынешнего состояния, когда представил сборочную линию, которая была не чем иным, как средством упрощения сборки номинально идентичных деталей.
Обычно мы рассматриваем массовое производство как достижение 20-го века, уходящее корнями в 19-е. Фактически, это убеждение не соответствует истине почти на пять веков. Доказательство очевидно, как и украденное письмо По: мы постоянно смотрим на доказательства и не видим их.
Любая современная книга о массовом производстве будет начинаться на странице, состоящей примерно из тысячи номинально идентичных.письма. Это настоящее массовое производство, и мы знаем, что оно датируется временами Гутенберга. Он начал все это в 1454 году.
Хотя Гутенберг обычно славится изобретением подвижного шрифта, акцент на самом шрифте игнорирует реальное новшество, которым был метод получения неограниченного количества каждой буквы. Первобытный подвижный тип, обычно в виде деревянных блоков, существовал до Гутенберга. Он перенес шрифт на следующий шаг.
Уитни производила мушкеты в ничтожных количествах, порядка нескольких тысяч.Первое издание Библии Гутенберга включало около четырех миллионов отдельных букв. Даже с учетом того, что он запустил три нажатия одновременно и, вероятно, набрал страницы, а затем повторно использовал шрифт, для этого потребовалось огромное количество отдельных битов.
Есть некоторый вопрос относительно средств, которыми был произведен первый образец Гутенберга. Было высказано предположение, что он, возможно, начал с чего-то столь же примитивного, как литье в песчаные формы.
У нас нет хорошей ранней документации, потому что, к сожалению для нас, слава Гутенберга развивалась так медленно, что никто не потрудился делать наброски его оборудования почти через сто лет после его банкротства в 1467 или 1968 году (никто точно не знает, когда) .Поэтому нам неясно, как именно были произведены все эти знаменитые подвижные элементы.
Как бы он ни начинал, он продолжал создавать технологию производства шрифтов, которая использовалась без принципиальных изменений в течение пяти столетий.
Его достижением было создание приспособлений, форм, которые позволяли отливать неограниченное количество копий каждой буквы. Для этого он с помощью ручных инструментов изготовил оборудование, которое даже современному машинисту было бы сложно.
Письменные записи о машинописи начинаются спустя много времени после смерти Гутенберга.Считается, что более поздние создатели шрифтов использовали методы, во многом похожие на методы Гутенберга. Они не могли бы поступить иначе.
Процесс изготовления шрифта начался с ручной вырезания зеркального изображения каждой буквы на конце пуансона из мягкой стали, который позже был закален. Пуансон наносился на более мягкую металлическую матрицу, обычно из меди. Затем матрица использовалась в качестве основы для формы, которая формировала отдельную деталь типа. Тип был отлит из свинцово-оловянного сплава смеси Гутенберга (теперь называемого типовым металлом), который из-за примеси сурьмы имел свойство слегка расширяться при затвердевании.Таким образом, он точно воспроизводит форму буквы, нанесенной в матрицу. Знания Гутенберга об этом сплаве, вероятно, выросли из его более раннего опыта в производстве ювелирных изделий, в котором для изготовления украшений использовалась аналогичная техника литья. Работа с ювелирными изделиями, несомненно, требовала от него развития ловкости рук, необходимой для нанесения ударов.
Форма, которая удерживала матрицу, была настоящим ключом к массовому производству, и она была намного сложнее, чем известная форма для сферической пули.Он должен был удовлетворить ряд требований. По сути, одна форма должна быть регулируемой, чтобы приспособиться к вариациям ширины разных букв. Например, для буквы «I» требуется более узкая форма, чем для буквы «W», хотя обе должны быть одинаковой высоты. Каждая форма должна была иметь строго прямоугольное поперечное сечение и сохранять вертикальное положение и угол (совмещение) каждой буквы. Форма должна была быстро открываться, чтобы удалить тип после затвердевания, и должна была учитывать тот факт, что внешние размеры матриц были произвольными.Это потребовало точного зажима плоских пластин разных размеров. Тонкая настройка сборки, чтобы каждая буква оставалась правильно ориентированной и разнесенной относительно соседних букв, требовала большого мастерства. Целый класс мастеров специализировался только на том, чтобы делать эти корректировки.
После того, как форма была правильно выровнена, она была готова к массовому производству. Это была работа шрифтовика, который на самом деле заливал расплавленный металл. Типовой металл выливался из нагретого котла с помощью ковша размером чуть больше наперстка.Постукивание по форме после заливки для обеспечения полного заполнения полости было само по себе искусством. Опытный шрифтовик мог бросать фишку каждые 10 или 12 секунд.
Металл заливался в форму через клиновидный литник, или выступ, который позже был сломан. Даже сегодня изготовителю инструмента и штампа было бы сложно изготовить такую сборку.
Развитию полиграфического искусства способствовали современные технологические инновации. Увеличительная линза прибыла в Северную Европу как раз вовремя, чтобы пригодиться.
Жизненно важным фактором, без которого были бы невозможны массовые публикации, было искусство изготовления бумаги, которое только-только достигло зрелости в Европе, хотя давно уже было известно на Востоке. Публикация ушла из стадии соскабливания пергамента или плетения папируса.
Первые формы букв, шрифты, дублировали готический шрифт, созданный вручную писцами. Это должно было сделать раннюю штамповочную резку относительно простой, потому что печатные буквы использовались для подделки рукописных документов.Следовательно, они имели размер и форму, удобные для ручного изготовления.
Примерно в 1500 году набор шрифтов стал более требовательным, когда появились более сложные формы букв, копирующие надписи на римских памятниках. Образцы этих шрифтов сохранились до наших дней; Фактически, многие современные шрифты имеют генеалогию, которая восходит к 15 и 16 векам.
Вырезание дыроколом считалось частной собственностью, и техника держалась в секрете. Это искусство было исследовано в книге «Counter Punch» 1996 года Фреда Смейерса под редакцией Робина Кинросса (Hyphen Press).Это может звучать как трактат по боксу, но название относится к инструменту, который используется для тиснения планки, которая в конечном итоге станет ударом. В нем задокументировано то, что Смейерс узнал, скопировав оригинальные методы для изучения процесса.
В его книге также обсуждается эстетика формирования букв. Прорисовка букв — это настоящее искусство. Доработки включают, например, небольшую корректировку формы идентичных букв, чтобы сохранить их характер при изменении размера.
Ручное искусство, связанное с высечкой пуансона, по-прежнему остается поистине выдающимся. До появления оптических или механических средств формирования букв, чего не было до прошлого века, каждый удар был делом рук одного художника. Шрифтам даже давали имена собственные. Никаких вспомогательных средств в виде механизмов не было, пока не прибыли высокоскоростные вращающиеся механизмы. Заманчиво представить себе, что использовался какой-то редуцирующий пантограф, но такое оборудование было невозможно до промышленной революции, поскольку это было связано с высокоскоростными вращающимися фрезами.
Самая известная новаторская попытка применить современные методы для набора текста была предпринята Линном Бойдом Бентоном, ныне очень уважаемым именем в области набора текста. В 1906 году он описал «машину для рисования», которая использовала пантограф, который рисовал большой рисунок шрифта и производил стальной штамп в значительно уменьшенном масштабе. Это был очень впечатляющий пример конструкции точных механизмов. В качестве демонстрации Бентон смог вырезать шрифт, в котором строчные буквы были высотой 0,0044 дюйма. Резка производилась вращающимся инструментом 0.0005 дюймов в диаметре. Он использовал это как рекламный трюк наравне со знакомой «Отче наш» на булавочной головке.
Буквы высотой до 0,055 дюйма (4-точечный шрифт) производятся регулярно. Иногда делаются даже более мелкие шрифты. Создавать их ручными напильниками и скребками — виртуозное исполнение.
Создание узнаваемой буквы — это только начало. Каждой букве должен быть придан отличительный характер путем изменения толщины и формы, которые требуют корректировки порядка 0.0001-дюйм.
Ранние штамповщики стали обычным делом объединяться в дома, чьим продуктом были тисненые матрицы. Они были проданы создателям шрифтов, которые отлили шрифт и продали его типографам.
Johannes Gensfleisch zur Laden zum Gutenberg родился в Майнце, Германия, вероятно, в 1398 году в семье, которая переехала в Гутенберг и приняла это имя. О его молодости мало что известно. Он, по-видимому, научился гравировать, что привело к его изобретению книгопечатания, когда он работал с ювелиром.Хотя его имя сейчас широко известно, Гутенберг не добился финансового успеха. Его первым предприятием в полиграфическом бизнесе было массовое производство индульгенций, крупный бизнес, в котором большое внимание уделялось массовому производству. Известно, что было напечатано около 150 000 экземпляров одного, и было много других. Продажа этих печатных карточек была одним из основных факторов, обеспокоивших Лютера и приведших к протестантской Реформации 50 лет спустя.
Введение Гутенберга в печать через религию, вероятно, привело к его решению продолжить выпуск Библии.Хотя это решение было важной вехой в истории человечества, лично ему оно не принесло пользы. Доходы от знаменитого библейского прайминга, проведенного в 1456 году, пошли только его сотрудникам после того, как он был вынужден уступить им свой бизнес. Он проиграл несколько судебных процессов, связанных с невыполнением обязательств по кредитам. После Библии у него была умеренно успешная попытка издать молитвенник в 1460 году. Он умер, живя на пенсию архиепископа Майнца.
Слава Гутенберга, которая является полностью посмертной, зафиксирована в Майнце статуями и музеем Гутенберга.Примечательно, что скульптору его статуи пришлось работать с воображением. Слава Гутенберга при его жизни была настолько скудной, что не существует ни его портретов, ни изображений его литейной мастерской.
Через три столетия после Гутенберга Бенджамин Франклин отдал своего внука, Бенджамина Франклина Баша, в известную французскую типографию Франсуа Дидо.
Внук изучал это искусство и даже научился, если не особо выдающийся, вырезать дыроколом. После того, как он привез в Штаты целую литейную фабрику, он и его знаменитый дед основали мастерскую, но внуку это не понравилось.Он действительно предпочитал публикации. Среди его предприятий был радикальный журнал под названием «Аврора», который, среди других примеров сомнительного политического суждения, резко критиковал Джорджа Вашингтона. Предприятие не имело большого успеха и окончательно потерпело крах в 1806 году. Однако некоторые из его технических новшеств, такие как введение пики, которая является эталоном типовой меры, сохранились и по сей день.
Сегодня идея вдавить крашеный металл в бумагу довольно необычна. Шрифты сделаны из электрических импульсов.Но наследие принтеров эпохи Возрождения осталось с нами.
Этот текст в том виде, в каком он был изначально напечатан, был набран шрифтом под названием Bembo, современной интерпретацией лица, созданного легендарным перфоратором Франческо Гриффо, который также изобрел идею курсива. Он вырезал ее в Венеции в 1495 году для своего начальника, издателя Альдуса Манутиус, который использовал ее для печати работы кардинала по имени Пьетро Бембо.
Книга была об одной из самых известных природных достопримечательностей Европы, горе Этна. Как и все вулканы, Этна может менять форму почвы, на которой она стоит.Однако гарнитуры вроде Bembo изменили весь мир.
Дополнительная литература
Существует значительный интерес к сохранению истории печати и набора текста. В Голландии. В музее Плантена-Моретуса представлены артефакты. датируется 1499 годом. относится к одному из первых издательств, которые нажились на изобретении Гутенберга.
Существует ряд современных публикаций, описывающих ранний типографский поиск. Среди них «Краткая история печатного слова» Уоррена Чаппелла.первоначально опубликовано в 1970 году в The New York Times и переиздано Hartley & Marks в 1999 году с дополнениями Роберта Брингхерста. История графического дизайна Филиппа Б. Меггса. последний раз был опубликован John Wiley & Sons в 1998 году. Книга Гарри Картера «Взгляд на раннюю типографику» (Hyphen Press. 2002) подробно исследует эту тему.
Библия шрифтовой индустрии. через 300 лет. это все еще «Механические упражнения по всему искусству печати» Джозефа Моксона.
.