производство фланцев, завод по производству фланцев
Фланцы, несмотря на кажущуюся простоту, распространенный элемент в строительстве коммуникаций и на производствах, поскольку практически любой трубопровод связан с фланцевыми креплениями. Исходя из возлагаемых на этот элемент задач, производство фланцев всегда связано с жестким контролем качества и современным оборудованием, поскольку нарушения в технологии могут повлечь за собой выходы из строя целых трубопроводов, что приносит огромные убытки.
Фланцы могут производиться различными методами, среди которых ковка, штамповка, литейный способ, а также нарезка из проката. Все они имеют собственные плюсы и минусы, поэтому уместно будет рассмотреть основные из них.
Способы производства фланцев
Один из самых технологичных способов производства фланцев – ковка. К несомненным плюсам метода, безусловно, относится его простота и надежность, а также низкая себестоимость подготовки процесса (изготовление матрицы). Однако сортовой прокат, из которого производятся кованые фланцы, постоянно колеблется по стоимости (при этом низких цен на него не бывает), а каждый типоразмер фланца нуждается в собственной ковочной форме, что существенно сказывается на цене, особенно в условиях заказа маленьких партий изделий. Отражается на цене и необходимость дальнейшей механической обработки изделий.
Другой популярный способ, посредством которого происходит производство фланцев – это штамповка. Больше всего данный метод подходит для крупных партий изделий и отличается высокой степенью надежности. Однако под каждый размер фланца необходимо подбирать собственный штамп, а еще сама продукция производится только из высококачественной стали, что влечет удорожание готового изделия.
Другой технологичный способ – нарезка из листового проката и гибка. Это метод с низкими затратами, но очень эффективный. Он в своих стандартах допускает (по ГОСТ) даже сварку двух сегментов. Минус метода – размер фланцев напрямую зависит от диапазона работы гибочного станка. Технологически подходит только для плоских приварных фланцев, и сам метод не очень производителен.
Что касается литейного способа, то он также распространен. При таком методе возможно производить фланцы любого размера с учетом всех необходимых параметров под различные цели и задачи. Среди литейных методов можно выделить литье в кокиль, литье под давлением и особенно центробежное электрошлаковое литье. Этот метод в качестве сырья использует металлолом, что значительно уменьшает экономические затраты на металл, однако высока стоимость литейных форм.
Выбор метода производства фланцев необходимо совершать, прежде всего, по степени экономической целесообразности. Поэтому всегда стоит проконсультироваться со специалистами, прежде чем заказывать партию изделий.
что это? Изготовление, устройство, виды фланцев
Фланец — это метизная деталь. Его предназначение — соединять трубы, сальники или подобные пустотелые металлические конструкции цилиндрической формы. Чтобы прочно и надежно соединить два предмета, нужно дополнительно использовать мягкие прокладки. Для их изготовления используют мягкие материалы. И на вопрос: «Фланец — что это за деталь?» — можно ответить, что это метиз (сокращение от «металлическое изделие»), который создает хорошую герметизацию в местах соединений цилиндрических элементов.
Устройство
Стандартные фланцы по внешнему виду напоминают металлическое кольцо, на котором расположены специальные отверстия для шпилек либо болтов. На некоторых видах этих элементов могут быть выступы, впадины, шипы, пазы.
Изготовление фланцев
Для изготовления применяются различные марки стали: 13ХФА, 20/09Г2С, 12Х18Н10Т, 15Х5 М и другие. Кроме того, они могут быть стальными и нержавеющими. Технология используется различная. Производители используют ковку, штамповку, литье. Для каждого способа применяется специальное оборудование, формы. Выпуская свою продукцию, производители тщательно проверяют ее на качество. Применяя в своей работе специальные тесты, сотрудники ОТК проверяют их на прочность, надежность. Также проверяются на влагоустойчивость фланцы. Что это такое? Так как они относятся к крепежным элементам и участвуют в соединении металлических деталей, которые могут контактировать с водой, важно, чтобы они не были подвержены коррозии. Именно поэтому используются водоустойчивые металлические сплавы. Часто производители покрывают поверхность фланцев дополнительным защитным слоем.
Виды фланцев
Итак, фланец — что это? Это, прежде всего, метиз. В зависимости от применения данные детали могут быть плоскими, воротниковыми, свободными. Конструктивное исполнение не сильно отличается. На воротниковых фланцах имеется небольшой выступ, напоминающий конус. Часто его и называют воротником. Такой тип фланцев применяют тогда, когда нужно приварить детали встык. Этот выступ помогает плотно соединить между собой соединительные части у трубопроводов. Также они необходимы тогда, когда трубопроводы подводятся к емкостям или другому техническому оборудованию. Главным достоинством таких фланцев является то, что их можно использовать несколько раз. Изготовлены данные метизы из прочных материалов, и это позволяет их применять в работе, где температура колеблется от –253 и до +600 градусов по Цельсию.
Плоский фланец — что это? Это метиз, который напоминает плоский диск с отверстиями. Его используют, когда нужно соединить части арматуры, валы, сосуды, трубопроводы, приборы и тому подобное. При помощи этого элемента можно плотно закрепить части трубопроводов.
Свободный фланец — что это? Этот вид не сильно отличается от вышеперечисленных. Он состоит из двух частей: из обычного фланца и кольца. Важно, чтобы они были сделаны из одного материала и имели одинаковый диаметр и давление. Их применяют там, где работы наиболее трудны, где сложно выполнить монтаж. За счет двух частей соединение будет плотным и прочным. Сначала подсоединяется обычный фланец (он приваривается), а другое кольцо затем во время работы можно спокойно поворачивать.
Другая классификация
Для некоторых видов работ сделаны особенные виды элементов. Специальный фланец — что это? Это те же метизы, но для того чтобы сделать некоторые работы удобными, конструкция их немного видоизменена. Они также могут быть приварными, свободными, литыми, резьбовыми. Только на них вырезаны пазы или приварены выступы. Для их изготовления сначала разрабатываются специальные чертежи и отливаются формы. Такие метизы делают по заказу предприятий.
fb.ru
Технология изготовления фланцев
СОДЕРЖАНИЕ
Введение.
1. Анализ служебного назначения детали.
2. Анализ технологичности конструкции детали.
3. Определение типа производства.
4. Выбор заготовки и его экономическое обоснование.
5. Анализ существующего технологического процесса.
6. Выбор варианта технологического маршрута и его экономическое обоснование.
7. Расчёт общих и межоперационных припусков.
8. Расчёт режимов резания.
9. Нормирование технологического процесса.
10. Расчёт и проектирование приспособления.
11. Механизация и автоматизация процесса изготовления детали.
12.Охрана труда.
Заключение.
Список используемых источников литературы.
Приложение.
В ВЕДЕНИЕ
Технология машиностроения – это наука об изготовлении машин требуемого качества в установленном производственной программой количестве и в заданные сроки при наименьших затратах живого и овеществленного труда, т.е. при наименьшей себестоимости.
Производственный процесс представляет собой совокупность всех действий людей и орудий производства, необходимых на данном предприятии для изготовления или ремонта выпускаемых изделий.
В соответствии с ГОСТ 3.1109 – 82 технологический процесс – это часть производственного процесса, содержащая целенаправленные действия по изменению и (или) определению состояния предмета труда.
Технологическая операция – это законченная часть технологического процесса, выполняемая на одном рабочем месте. Применительно к условиям механосборочного производства стандартизированное определение операции можно представить в следующем виде: технологическая операция – это часть технологического процесса, выполняемого непрерывно на одном рабочем месте, над одним или несколькими одновременно обрабатываемыми или собираемыми изделиями, одним или несколькими рабочими.
Целью данного проекта является модернизация базового среднесерийного технологического процесса для снижения материалоемкости, повышения производительности и уменьшения себестоимости.
Курсовой проект представляет собой разработку технологического процесса механической обработки детали «Фланец».
1. АНАЛИЗ СЛУЖЕБНОГО НАЗНАЧЕНИЯ ДЕТАЛИ
В курсовом проекте рассмотрена деталь «Фланец» рис.1
Фланец – неотъемлемая часть трубопроводной арматуры. Область применения фланцев чрезвычайно широка, фланцы применяются как соединительный компонент труб, так же фланец может служить соединением вращающихся деталей. По внешнему виду фланец представляет парную конструкцию плоского сечения кольцевой или дисковой формы. Крепление фланцев осуществляется через диаметрально расположенные отверстия одного и другого фланца путем резьбового соединения. Это болты или шпильки, стягивающие два фланца. Различаются фланцы по размерам, по вариантам соединения фланцев между собой, по лицевой форме и так же по вариантам уплотнителей между двумя стыкующимися поверхностями фланца. Надежность фланца в соединениях трубопроводов от вакуума в 10-13 мбар до вариантов, когда фланцы соединяют трубопроводы с давлением в 200 бар, делает фланцы востребованным элементом соединительных конструкций. В соответствии с ГОСТом фланцы выпускаются трех видов: фланцы стальные плоские, воротниковые и фланцы свободные на кольце, закрепленном методом сварки. Фланцы первого вида служат как соединительный элемент трубопровода между собой и с аналогичным фланцем другого элемента системы. Крепятся фланцы к трубе либо на резьбовом соединении, либо на сварном. Такие фланцы способны выдерживать температурные режимы от -75 до 450 градусов, но следует учитывать что фланцы в зависимости от величины диаметра самой трубы и предполагаемых величин давления и региональных условий эксплуатации имеют до десяти подвидов прокладочных соединений. Плоские фланцы способны выдерживать еще больший диапазон температур, поэтому соединяют такие фланцы сваркой, не используя для прокладок между плоскими фланцами дополнительных материалов. Воротниковые фланцы крепятся встык, фланцы такого типа распространены для крепления различных приборов, посредством соединения с фланцами различной арматуры и патрубков дополнительного оборудования. Фланцы каждого типа и вида снабжены отдельными таблицами характеристик.
Фланцы являются соединительной частью труб, валов, резервуаров. Они представляют собой плоские стальные диски или кольца с отверстиями для шпилек или болтов. Применяются фланцы при соединении различных изделий арматуры с основными трубопроводами. Кроме этого, их используют для скрепления между собой отдельных участков трубопровода или присоединения к оборудованию. Соединение с помощью фланца способно обеспечить прочность, герметичность конструкции, а также упрощает процесс сборки и разборки. По белорусским стандартам фланцы выпускают стальные резьбовые, устьевые, а также для аппаратов и сосудов под прокладку.
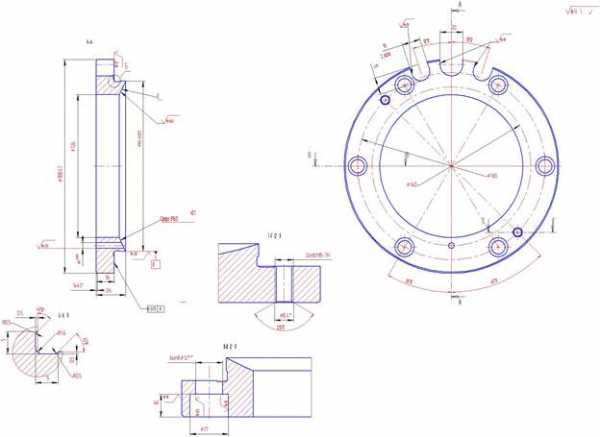
Фланец- рисунок 1 изготавливается из Стали 45 ГОСТ 1050-74, который состоит из 6отв. Ø17 служащие для крепежа фланца, 2-х резьбовых отверстий предназначенных для вытягивания фланца из узла и одного отверстия под штифт Ø
, так же по посадке выполнена шейка Ø и имеется сфера R.Для проектирования используют справочные материалы: рекомендации по улучшению технологичности конструкции изделия, каталоги сборочного и подъемно-транспортного оборудования, альбомы сборочной технологической оснастки, нормативы по нормированию сборочных работ, примеры сборки аналогичных изделий.
Цель технологических разработок – дать подробное описание процессов сборки изделия, выявить необходимые средства производства, площади, рабочую силу, трудоемкость и себестоимость сборки изделия.
Применение приспособлений позволяет: устранить разметку заготовок перед обработкой, повысить ее точность, увеличить производительность труда на операции, снизить себестоимость продукции, облегчить условия работы и обеспечить ее безопасность, расширить технологические
возможности оборудования, организовать многостаночное обслуживание, применить технически обоснованные нормы времени, сократить число рабочих, необходимых для выпуска продукции.
Таким образом, я установил что деталь полностью соответствует своему назначению.
2.АНАЛИЗ ТЕХНОЛОГИЧНОСТИ КОНСТРУКЦИИ ДЕТАЛИ
Качественный анализ детали на технологичность.
Анализ технологичности конструкции детали состоит из технологического контроля чертежей и технологического анализа конструкции.
Рабочий чертеж обрабатываемой детали содержит все необходимые сведения, дающие представление о детали, т.е. все проекции, виды, разрезы и сечения. На чертеже указаны все размеры с необходимыми допусками, шероховатость обрабатываемых поверхностей, допускаемые отклонения от правильных геометрических форм, а также взаимного положения поверхностей. Чертеж содержит все необходимые сведения о свойствах материала детали.
Основное значение при обработке детали имеют технологические базовые поверхности детали. В качестве базовых поверхностей при обработке детали
Проанализировав конструктивные элементы детали. Мы установили что деталь практически по всем показателям является технологичной. Так как для её изготовления не требуется специальный инструмент. Поверхности детали не содержат сложной геометрии, что тоже упрощает её изготовления. Заготовка из трубного проката будет максимально приближена по конструкции к форме детали. При данной заготовки себестоимость детали и отход материала будет минимальным. Что уменьшит затраты на материал.
Таблица 1
Химический состав стали 45, %(ГОСТ 1050-88)
Таблица 2
Физико-механические свойства стали 45 ( ГОСТ 1050-88),
В качестве материала заменителя можно применить схожую сталь Ст40.
Количественный анализ детали на технологичность не ведем, так как из чертежа видно, что все поверхности детали унифицированы, спец. инструмент не используется. Трудоемких операций — таких как долбление, строгание нет — деталь технологична.
3.ОПРЕДЕЛЕНИЕ ТИПА ПРОИЗВОДСТВА
Исходные данные:
Годовая программа изделий N1 =5000 шт.;
Количество деталей на изделие m=1 шт.;
Запасные части β=2%;
Режим работы предприятия – 2 смены в сутки;
mirznanii.com
ПРОИЗВОДСТВО ФЛАНЦЕВ ОМСК. Производители, поставка фланцев. Детали трубопроводов компания «Метизно-фланцевый завод»
Производим детали трубопроводов, специализируемся на производстве фланцев больших диаметров, нестандартных фланцев. Производим фланцы по чертежам.
Наше предприятие является производителем фланцев больших диаметров (до 3000 мм, массой до 3000 кг).
Завод специализируется на производстве: деталей трубопроводов высокого давления, деталей вращения больших диаметров.
Производство — фланцы стандартные, фланцы специальные, в том числе: фланцы переходные, фланцы по чертежу (согласовывается чертеж).
Производство нержавеющих фланцев (фланцы 08Х18Н10Т, фланцы 8Х18Н10Т, фланцы 12Х18Н10Т, фланцы 06ХН28МДТ, фланцы 6ХН28МДТ, фланцы 10Х17Н13М2Т) ГОСТ, DIN, ANSI, ASME.
Серийное и мелкосерийное производство фланцев.
Технологические возможности нашего предприятия позволяют изготавливать фланцы, детали вращения диаметром до 3000 мм и массой до 3000 кг: заготовки фланцев, фланцы, заглушки, переходы, прокладки, обечайки, втулки, шестерни, звездочки, зубчатые венцы — а также толстостенные тройники; проводятся испытания механических свойств изделий и другие исследования.
Наш метод производства основан на применении электрошлаковых технологий, разработанных в Институте Электросварки им. Е.О.Патона. Омские инженеры дополнили и модернизировали эти производственные установки разработок 70х годов. В результате мы получили современную, высокопроизводительную установку с электронной системой управления.
Установка центробежного электрошлакового литья (ЦЭШЛ) обеспечивает высокое качество литого металла за счет его рафинирования в процессе электрошлаковой плавки.
Механические свойства заготовки, при этом, не уступают кованной, но превосходят их по показателям пластичности, ударной вязкости при одинаковой прочности.
Электрошлаковое литье фланцев и других деталей трубопроводов имеет ряд преимуществ перед другими аналогичными технологиями. Получаемый металл после переплава имеет более высокие характеристики, при этом данная технология обеспечивает возможность активного воздействия на расплав металла: легирование, модификация металла в тигле, а также гарантируется стабильность химического состава металла в процессе плавки, даже при наличии в нем легкоокисляющихся элементов. Электрошлаковые тигельные печи значительно превосходят открытые сталеплавильные печи по степени рафинирования и стабильности химического состава сплава. Содержание серы при электрошлаковой плавке снижается в среднем в 1,5 – 2 раза при неизменном содержании основных легирующих элементов. При электрошлаковом литье тигельные печи значительно дешевле и проще в эксплуатации, чем современные индукционные печи. В отличие от индукционных печей, в ЭШЛ печах с керамическим тиглем, применяется не специальные источники питания повышенной частоты, а стандартные сварочные трансформаторы.
В процессе ЭШЛ тигельной плавки плавление металла происходит в результате выделения теплоты в жидком электропроводном шлаке при прохождении через него электрического тока. В качестве исходного сырья используют расходуемые электроды цельные или собранные из фрагментов. Электроды могут состоять из проката или металлического лома. Расплавленный металл, проходя через слой жидкого шлака, температура которого обычно на 150 – 200 С выше температуры плавления металла, интенсивно рафинируется от вредных примесей и неметаллических включений.
Получаемый таким образом металл является заготовкой для получения деталей для следующих отраслей: нефтегазовой промышленности, энергетики, горнодобывающей промышленности и других отраслей промышленности.
Себестоимость получаемых деталей, при их высоком качестве, значительно ниже, чем аналогичные соединительные детали трубопроводов, полученные по другой технологии. Так как в ЭШЛ используется лом, то для получения новой заготовки можно использовать старую, тем самым значительно уменьшается стоимость заготовки. Электроустановки ЭШЛ просты и занимают малую площадь, при этом получаемый металл имеет отличные механические свойства и другие характеристики, а сырьем является металлолом.
Металлургические плавильные установки компании «Метизно-фланцевый завод» позволяют изготавливать детали вращения: фланцы стальные, фланцы нержавеющие, заглушки, переходы, обечайки стальные, кольцевые заготовки весом от 20 до 3000 кг с условным проходом от 200 мм (внутренний диаметр) и более. Изготавливаем толстостенные литые тройники. Заготовка для воротниковых фланцев может изготавливаться на кузнечном оборудовании (смотреть на видео).
Производство и поставка фланцев в регионы России
Производство и поставка деталей трубопроводов (фланцы) осуществляется во все города России:
- Центральный федеральный округ
- Северо-Западный федеральный округ
- Приволжский федеральный округ
- Южный федеральный округ
- Уральский федеральный округ
- Сибирский федеральный округ
- Дальневосточный федеральный округ
Сроки изготовления и комплектации в зависимости от сложности заказа — от 3 до 30 дней. Выполняем срочные заказы по просьбе клиента. По вашему запросу быстро производим расчет сроков изготовления и стоимости деталей. Высылаем прайс лист по факсу или email.
www.12821-80.ru
ИЗГОТОВЛЕНИЕ ФЛАНЦЕВ
Количество просмотров публикации ИЗГОТОВЛЕНИЕ ФЛАНЦЕВ — 1025
Технические условия на изготовление колпачков
Изготовление колпачков тарелок колонных аппаратов
В колонных аппаратах применяют тарелки колпачковые, которые комплектуются колпачками стальными, медными, чугунными, керамическими.
Стальные колпачки (Рис. 26.7.) изготавливают с наружным диаметром 60, 80, 100 и 150 мм с открытыми и закрытыми прорезями.
Рисунок 26.7 – Колпачки капсульные с прорезями:
а – открытыми; б – закрытыми.
Колпачки следует изготавливать из листового проката. Наибольшее отклонение наружного диаметра колпачка по нижней кромке зубьев для колпачков: D = 80 + 3 мм; D = 100 +4 мм; D = 15 + 6 мм.
Предельное отклонение угла прорези колпачка + 10. Смещение оси отверстия под болт относительно оси колпачка – не более 1,5 мм. Глубина рисок на наружной поверхности колпачка должна быть не более 0,2 мм.
Технология изготовления стального колпачка следующая.
1. Расконсервация.
2. Правка на листоправильной машине.
3. Резка листа на полосы на гильотинных ножницах с плоскими ножами.
4. Вырубка заготовки (диска) на прессе.
5. Вытяжка первая в штампе на прессе.
6. Термическая операция: нагреть токами высокой частоты (установка ТВЧ) колпачок из стали МСт 3 кп до температуры 600–650 °С и охладить на воздухе; колпачок из стали 08Х18Н10Т – до 1050–1100 °С, охладить в воде.
7. Вытяжка вторая – в штампе на прессе.
8. Контрольная операция. Проверить размеры колпачка, перекос вытяжки, отсутствие трещин.
9. Подрезка торца на токарно-винторезном станке.
10. Прессовая. Вырубка центрального отверстия.
11. Слесарная. Снять заусенцы после пробивки центрального отверстия.
12. Прессовая. Вырубка боковых отверстий.
13. Слесарная. Снять заусенцы после вырубки пазов.
14. Контрольная.
15. Моечная. Промыть колпачки растворителем. Просушить.
Параметры и размеры. Фланцы (рис. 27.1) трубопроводов и соединительных частей, а также входные и выходные фланцы арматуры машин, приборов, аппаратов и резервуаров, применяемых в химической, нефтеперерабатывающей и нефтехимической отраслях промышленности, изготавливают в соответствии с ОСТ 26-830—73, ОСТ 26-842—73, ГОСТ 28759.1-90-28759.8-90. В табл. 27.1 приведены области применения различных типов фланцев.
Рисунок 27.1 – Типы стальных фланцев: а — плоский приварной;
б— свободный на приваренном кольце; в— литой; г — приварной встык
При изготовлении теплообменных аппаратов фланцы корпусов распределительных камер и крышек для аппаратов диаметром 400 мм и выше, рассчитанных на условное давление 15,7 МПа, должны соответствовать действующим отраслевым стандартам, а для аппаратов с рабочей температурой одной или обеих сред 300 °С и более фланцы выполняют приварными встык с уплотнительной поверхностью выступ-впадина, для Ру–6,4 МПа – с уплотнительной поверхностью под металлическую прокладку восьмигранного сечения. Уплотнительную поверхность шип–паз можно применять только с прокладками, которые крайне важно помещать в замкнутый объём, к примеру, с прокладками из фторопласта. У теплообменных аппаратов, работающих под вакуумом, на корпуса, распределительные камеры и крышки устанавливают корпусные фланцы не менее чем РУ=1 МПа.
Таблица 27.1 – Области применения различных типов фланцев
Тип фланцев (стальных) | Условный диаметр, ДУ, мм | Условное давление Р , МПа | ОСТ |
Плоские приварные | 10–1600 ‘ | 0,1–2,45 | 26-830–73 26-831–73 26-832–73 |
Свободные на приварном кольце | 100–500 | 0,1–2,45 | 26-833–73 26-834–73 26-835–73 |
Литые | 15–600 | 1,57–15,7 | 26-836–73 26-837–73 26-838–73 |
Приварные встык | 10–800 | 0,59–15,7 | 26-839–73 26-840–73 26-841–73 26-842–73 |
Технические требования на изготовление фланцев должны соответствовать ОСТ 26-843–73 и ОСТ 26-291–94. Материал для изготовления фланцев выбирают исходя из температуры и среды, в которой они должны работать. Это в основном стали ВСт3сп3, 20К, 16ГС, 12Х18Н10Т, 10Х17Н13М2Т.
Предельные отклонения размеров фланцев следующие.
Смещение осей отверстий d от номинального расположения должно быть не более: 1 мм – для отверстий d = 12–18 мм; 1,6 мм– для отверстий d = 23–33-мм; 2 мм – для отверстий d = 40–52 мм.
Торцевое биение поверхности Б – по ХІІ степени точности ГОСТ 10356. Непараллельность поверхностей А и Б – 0,1 мм в пределах наружного диаметра гайки.
Допускается изготовление фланцев сварными из нескольких частей полосового проката с последующей сваркой мест стыка при условии выполнения швов с полным проваром по всему сечению фланца и 100 %-ного контроля качества швов. В этом случае допускается располагать отверстия на сварных швах.
Важно заметить, что для сосудов и аппаратов из двухслойной стали фланцы изготавливают из стали основного слоя двухслойной стали (или из стали этого же класса) с защитой уплотнительной и внутренней поверхностей фланца от коррозии наплавкой. Толщина наплавленного слоя после механической обработки должна быть не менее 4+2-1 мм, а при наличии требований по межкристаллитной коррозии — не менее 6+2-1 мм. Допускается защита уплотнительной и внутренней поверхностей фланцев облицовкой из хромоникелевой аустенитной стали. Толщина облицовки должна быть не менее 3 мм.
Особенности технологии изготовления. В качестве заготовок для изготовления фланцев используют поковки, штамповки, профильный прокат, бандажные и сварные заготовки. При выборе способа получения заготовки для фланца крайне важно учитывать материал и габаритные размеры фланца, размеры сечения обода, коэффициент использования металла, трудоемкость изготовления и другие факторы. В табл. 27.2 приведены рекомендации по областям применения каждого из указанных способов.
О целесообразности применения заготовок каждого из указанных видов решают исходя из конкретных условий производства.
При штамповке фланцев на молотах обеспечиваются: высокая производительность, точность размеров заготовок, благодаря чему значительно уменьшается отход металла в стружку и снижается трудоемкость обработки. Штамповка на кривошипных горячештамповочных прессах имеет ряд преимуществ перед штамповкой на молотах: повышается производительность труда и точность исполнения размеров поковки, увеличивается коэффициент использования металла в результате уменьшения штамповочных уклонов, уменьшается расход электроэнергии и улучшаются условия труда. Гибку с последующей сваркой выгодно применять в том случае, когда сечение обода фланца относительно небольшое и когда материал фланца обладает хорошей свариваемостью. В табл. 27.3 приведены сравнительные технико-экономические показатели изготовления заготовок фланцев ковкой в подкладном кольце и гибкой из профильного проката с последующей сваркой встык.
Таблица 27.2 – Области применения различных способов получения заготовок для фланцев
Наименование способа | Условный диаметр Ду, мм | Характер производства |
Штамповка намолотах свободной ковкой | 10–250 | Серийный |
Штамповка на кривошипных горячештамповочных прессах | 10–150 | Серийный, массовый |
Гибка профильного проката | >250 | Серийный |
Из бандажных заготовок | 400–2400 | Массовый |
Из сваренных секторов | >400 | Индивидуальный |
Таблица 27.3 – Сравнительные технико-экономические показатели изготовления заготовок фланцев ковкой и гибкой из профильного проката
Показатели | Способ изготовления фланца | |
Гибка профиля с последующей сваркой | Ковка в подкладочном кольце | |
Масса, кг: | ||
заготовки | 18,8 | 69,0 |
поковки | — | 41,0 |
фланца | 13,5 | 15,4 |
Коэффициент использования металла | 0,8 | 0,2–0,25 |
трудозатраты, чел.-ч: | ||
на поковку | 0,2 | 1,2 |
на токарную обработку | 0,25 | 3,25 |
Выпуск фланцев на единицу производственного оборудования за одну смену, шт. |
Получение заготовок ковкой с последующей прокаткой на кольцепрокатном стане. Степень проработки материала фланца во всех направлениях, отсутствие сварного шва, сравнительно высокий коэффициент использования металла позволяют рекомендовать данный способ при серийном изготовлении крупногабаритных фланцев. Получение заготовок, сваренных из отдельных секторов, применяют, как правило, для фланцев больших размеров, изготавливаемых из проката большой толщины (более 40 мм) или из марок сталей, на которые отсутствует стандартный профильный прокат.
Штамповкана молотах. Типовой технологический процесс изготовления заготовок приваренных встык фланцев (DY == 150 — 250 мм) приведен в технологических документах ЕСКД.
Операция штамповочная. Фланцы чаще всего штампуют в открытых штампах, на зеркале которых размещают площадку для осадки заготовок площадью более 30 % всей площади зеркала штампа.
Заготовки крупных фланцев (до 200—250 мм) осаживают на ковочном молоте, а остальные операции выполняют на штамповочном молоте. Выбирая размеры формы штампа, крайне важно учитывать усадку при остывании (15 %). Для предотвращения застревания фланца в штампе боковые стенки ручьев изготавливают с уклоном 3—10°.
Рисунок 27.2 – Комбинированный штамп для прошивки отверстия и обрезки заусенцев (I – начальное положение штампа; II – положение штампа после обрезки и прошивки): 1 – обрезной пуансон; 2 – поковка; 3 – обрезная матрица; 4 – выдра; 5 – прошивной пуансон; 6 – заусенец | Рисунок 27.3 – Штамп для безоблойный штамповки фланцев: 1 — верхняя часть; 2 — нижняя часть |
За один ход пресса прошивают отверстия и обрезают заусеницы на кривошипных прессах в комбинированных штампах (рис. 27.2). Во время прошивки отверстия и обрезки заусенцев во фланцах (DY = 100 мм) одновременно правят их по плоскости. Фланцы большего диаметра правят на молоте в чистовом ручье штампа.
По причине того, что стойкость штампов, имеющих сравнительно малые размеры выступов, низкая, воротниковые фланцы (DY = 30 мм) штампуют без прошивки отверстия. В некоторых случаях для увеличения срока службы штампов выступы выполняют сменными, по мере износа их заменяют.
Конструкция штампов для безоблойной штамповки предусматривает возможность заполнения формы штампа металлом, прежде чем он достигнет выхода в облойную канавку. Большое влияние на заполнение формы’ штампа в процессе безоблойной штамповки оказывает форма исходной заготовки, которая должна приближаться к окончательной форме поковки. Указанное достигается предварительной штамповкой в черновых ручьях. Штампы для безоблойной штамповки фланцев схематически изображены на рис. 27.3 Объем исходной заготовки должен соответствовать объёму ручья.
Vзаг= Vпок+ Vугар
где Vпок – объём поковки, определяемый по чертежу; Vугар – объём потери металла на угар (1,5–2,0 % объёма заготовки).
Припуски, допуски и штамповочные уклоны для поковок, изготавливаемых безоблойным методом, назначаются по ГОСТ 7505-74.
Для лучшего извлечения поковок из ручьев штампа, уменьшения усилия, крайне важно го для штамповки на молотах, а также для повышения стойкости штампов в качестве смазок применяют графитовые суспензии, коллоидный графит на водной или масляной основе.
Штамповка на кривошипных горячештамповочных прессах. Наиболее производительным оборудованием для резки заготовок являются сортовые ножницы. При этом резка заготовок из легированных сталей на ножницах вызывает образование торцевых трещин. Для предотвращения этого явления сортовой прокат перед резкой нагревают в специальных печах до температуры 450—650 °С. Расчетный диаметр исходной заготовки для штамповки фланцев на кривошипных горячештамповочных прессах, мм:
где — объём заготовки, мм3; m – отношение высоты заготовки к ее диаметру, ĸᴏᴛᴏᴩᴏᴇ рекомендуется брать в пределах от 1,6 до 2,2.
Заготовки перед штамповкой нагревают в пламенных печах или в индукционных нагревателях. Существенным недостатком нагрева в пламенных печах является обезуглероживание заготовок и образование окалины, что ухудшает качество поверхности поковки и снижает стойкость штампа.
Эти недостатки устраняют применением защитной атмосферы или заменой пламенного нагрева электрическим.
Наиболее рационален нагрев заготовок в индукционных нагревателях, при этом слой окалины уменьшается в 4–5 раз, а обезуглераживание практически не происходит. На кривошипных горячештамповочных прессах фланцы штампуют за три перехода: осадка заготовки, штамповка, обрезка заусенцев и прошивка отверстия. Осадка исходной заготовки, выполняемая на осадочной площадке штампа, позволяет очистить поверхность заготовки от окалины, способствует лучшему заполнению металлом формовочного ручья штампа.
В чистовом формовочном ручье штампа поковка формуется за один ход пресса. В отличие от штамповки на молотах заполнение полости ручья верхней и нижней частей штампа в данном случае происходит с одинаковой скоростью. Минимальный уклон при штамповке на кривошипных прессах должна быть доведен до 1,5 –2°, а в отдельных случаях до 30°.
В ряде случаев при изготовлении фланцев на кривошипных горячештамповочных прессах применяют совмещенную штамповку двух фланцев различных размеров, что позволяет сократить расход металла и увеличить выпуск готовой продукции с единицы кузнечного оборудования.
При штамповке фланцев на кривошипных прессах особо важное значение имеет правильный выбор пресса по номинальному усилию. В случае если усилие пресса недостаточно, то возникает опасность его заклинивания или поломки. Расчетное усилие пресса, крайне важно е для штамповки фланцев, можно определить по формуле, МН;
где – максимальный диаметр поковки в плане, м; – площадь проекции поковки (без заусенцев) на плоскость разъема штампа, м2; – предел прочности при сжатии штампуемого металла при температуре окончания штамповки, МН/м2.
Рисунок 27.4 – Совмещенная штамповка фланцев: 1 – заусенец; 2 – основная поковка; 3 – дополнительная поковка | Рисунок 27.5 – Штамп для вырубки фланцев: 1, 7 – выталкиватели; 2 – верхняя плита; 3 –гайка; 4 – прижимная скоба; 5 – нижняя плита; 6 – кольцо; 9 – заготовка фланца; 9 – отход |
Обрезают заусенцы и прошивают отверстия на обрезных прессах в простых, последовательных или комбинированных штампах. В простых штампах используют два пресса (на одном обрезают заусенцы, на другом прошивают отверстие). В случае если размеры стола пресса достаточны для установки последовательного штампа, то обрезают заусенцы и прошивают отверстие на одном прессе в двух ручьях – обрезном и прошивном. Чаще всего эти две операции выполняют в комбинированном штампе, позволяющем за один ход пресса обрезать заусенцы и прошить отверстие.
На рис. 27.5 показан штамп для вырубки заготовок фланцев на кривошипном прессе. Обычно заготовки рассчитаны на три–четыре фланца, которые можно вырубить после одного нагрева. Заготовки нагревают в газовой печи до температуры штамповки. Отходы с пуансона снимаются выталкивающим устройством пресса и системой выталкивателей штампа, а заготовки фланца – верхним выталкивателем. После вырубки по наружному контуру заготовку фланца нагревают вторично и пробивают внутреннее отверстие.
Гибка заготовок из проката. Технологический процесс изготовления заготовок по этому методу состоит в разрезке полосы или профиля на мерные заготовки, гибке в кольцо и стыковой сварке.
На рис. 27.6 показана фланцегибочная машина, предназначенная для гибки в горячем состоянии колец и полуколец для фланцев больших диаметров и толщин.
Техническая характеристика фланцегибочной машины
Диаметр изгибаемой полосы, мм 600–1600
Частота вращения стола, об/мин 2
Усилие прижатия ролика при рабочем давлении
в гидроцилиндре машины 10 МН/м2, МН 0,2
Наибольшее поперечное сечение заготовки из
стали ВСтЗсп при 850 °С, мм 120х70
Мощность электродвигателя, кВт 28
Размеры, мм 4750х2400х1170
Конец полосы 3 заводят между эксцентриком 15 и шаблоном 17. При вращении стола по часовой стрелке происходит самозатягивание эксцентрика и изгибание полосы по шаблону. Для получения полного кольца крайне важно эксцентрик отвести от изогнутой полосы, что становится возможным при вращении стола против часовой стрелки. Отжимают эксцентрик упором 2. При гибке полосы ручка эксцентрика доходит до упора, а эксцентрик поворачивается, полоса освобождается от зажима. Стол 18 поворачивается и эксцентрик зажимают полосу в положении, показанном на рисунке штриховой линией. Зажав полосу эксцентриком, ее окончательно обкатывают гибочным роликом и снимают заготовку.
Рисунок 27.6 – Фланцегибочная машина:
1 – электромеханический привод; 2 – выдвижной упор: 3 – полоса; 4 – валик; 5 – штанга;
6 – гидропривод; 7 – гидроцилиндр; 8 – рама; 9 – консоль; 10 – пульт управления;
11 – шестерня; 12 – рукоятка; 13 – гибочный ролик; 14 – винт; 15 – зажимной эксцентрик; 16 – зубчатое колесо; 17 – сменный шаблон; 18 – поворотный стол; 19 – станина; 20 – ось;
21 – вал; 22 – коническая передача; 23 – редуктор; 24 – электродвигатель
Рисунок 27.7 – Схемы гибки полос на профилегибочном станке:
а – круглого фланца; б — фланца в форме эллипса
Рисунок 27.8 – Ролики с направляющими пазами: 1 — полоса; 2 — ролики
Эллипсные фланцы можно изготавливать также гибкой полосы на профилегибочном станке, к примеру, модели ПГ-5А. Полосу заготовки, соответствующую длине развертки эллипса вставляют в направляющие пазы гибочных роликов станка (рис.27.7) и изгибают в кольцо, после чего сваривают стык электросваркой. Установкой соответствующего расстояния между роликами из кольцевой заготовки симметричной раскаткой противоположных сторон получают эллипс необходимых размеров. Оснастка станка представляет собой универсальные съемные ролики с направляющими пазаи (рис.27.8). Высоту и ширину паза регулируют исходя из толщины и высоты полос.
Раскатка на кольцепрокатных станах. В качестве исходного материала при изготовлении цельнокатаных фланцев могут служить слитки или кованые цилиндрические заготовки, которые разрезают чаще всего на мощных многорезцовых станках, оставляя по осиразрезаемых заготовок шейку диаметром 50–60 мм. Надрезанные таким образом слитки поступают на специальный пресс (слитколоматель), на котором мерные заготовки отделяются друг от друга. При производстве фланцев из высоколегированных сталей экономически выгоден анодноискровой способ разрезки кованых заготовок.
Наиболее ответственными технологическими операциями при производстве цельнокатаных фланцев являются осадка, прошивка, раскатка на оправке и прокатка на стане. При этом на поверхности заготовок, в особенности из малопластичных высоколегированных сталей, часто появляются дефекты в виде разрывов и трещин, которые при последующей обработке давлением приводят к неисправимому браку фланцев. Промежуточные заготовки с подобными дефектами перед их дальнейшей обработкой передают на зачистку или обдирку. Раскатку на оправке (рис. 27.9 а, б) применяют для увеличения внутреннего и наружного диаметров прошитой заготовки в результате уменьшения начальной толщины кольца. При раскатке на роговой оправке можно получать профиль поперечного сечения обода кольцевой заготовки, приближенный к конечному профилю фланца. Внутренний диаметр кольцевой заготовки после раскатки должен быть наименьшим, но достаточным для надевания ее на нажимной валок кольцепрокатного стана.
Рисунок 27.9 – Схема раскатки кольцевой заготовки на скобе с двумя опорными плечами (а) и на роговой оправке (б): 1 – верхний боек; 2 — заготовка; 3 — рог; 4 — нижний боек
Заготовки диаметрами 120–420 мм раскатывают на специализированных машинах типа РМ300 и РМ500.
Усилие пресса, крайне важно е для раскатки гладких кольцевых заготовок на оправке, можно определить по формуле, Н:
,
где – среднее нормальное давление на контактной поверхности Н/м2;
– горизонтальная проекция контактной площади, м2,
В0 – ширина раскатываемого кольца, м; – средняя длина горизонтальной проекции очага деформации, м.
Величина при раскатке кольцевых заготовок на оправке зависит от геометрических размеров раскатываемого кольца, формы и размеров рабочей поверхности бойка, диаметра оправки и степени обжатия. При раскатке кольцевых заготовок на оправке плоским бойком, м:
где и – внутренний и наружный радиусы кольцевой заготовки, м; – величина абсолютного обжатия; К. – коэффициент, зависящий от отношения ;- радиус оправки, м.
Прокатку фланцев осуществляют также на специальном кольцепрокатном стане (рис. 27.11). Кольцепрокатный стан имеет два консольных валка 1, 2 и два упорных ролика 5. Валок 1 внешнего касания (нажимной) является приводным и передает усилие от гидравлического плунжера на прокатываемую кольцевую заготовку. Валок 2 внутреннего касания (ведомый) получает вращение от гидропривода 4. Под действием усилия валка 1 заготовка 3 входит в профильный калибр ведущего валка и за счёт сил трения начинает вращаться вместе с нажимным валком. Фланец на стане прокатывают до окончательных размеров за несколько оборотов кольцевой заготовки. С каждым оборотом кольца диаметр фланца увеличивается, в связи с этим число оборотов ограничивается заданным конечным диаметром фланца.
Рисунок 27.10 – Заготовка фланца, полученная на бандажепрокатном стане | Рисунок 27 11 – Схема прокатки фланца на кольцепрокатном стане |
referatwork.ru
Изготовления фланцев штучное и серийное производство в Санкт-Петербурге
Фланцы используют для соединения деталей. Их изготавливают разными методами, среди которых выделяют следующие способы: литье, ковка, нарезка и штамповка. В зависимости от варианта производства, каждый метод связан с определенными нюансами и имеет как преимущества, так и недостатки. Планируя заказать изготовление фланцев, выбирайте наиболее подходящий вариант.
Уважаемые клиенты! Сделать заказ и задать интересующие вас вопросы вы можете:
По телефонам: +7 (812) 400-5-800, +7 (812) 903-23-81;
По email [email protected] или через форму «Отправить заявку».
Кованые фланцы
Метод изменения форм заготовки посредством воздействия ударного инструмента. Может производиться как вручную, так и при помощи специального оборудования. Первый вариант слишком трудоемок. Второй способ более целесообразен.
Достоинства:
- подготовительные мероприятия не требуют больших вложений;
- довольно простой метод изготовления фланцев;
- хорошая производительность процесса.
Недостатки:
- на цену деталей влияет стоимость сортового проката, которая может колебаться;
- требуется индивидуальное изготовление форм, используемых в процессе ковки деталей различных размеров;
- небольшой коэффициент использования материала;
- дороговизна оборудования, применяемого при производстве деталей;
- при заказе небольших партий деталей, их производство является экономически невыгодным.
Штампованные фланцы
Целесообразно использование данной методики, если планируется заказ больших партий деталей. Увеличение производительности достигается путем автоматизации процесса.
Достоинства:
- простота изготовления;
- высокопроизводительный процесс;
- высокая точность получаемых фланцев;
- надежность и качество получаемой продукции.
Недостатки:
- так как в изготовлении деталей применяют сортовой металл, цена на который сравнительно высока, то и стоимость исходного сырья не маленькая;
- высокая себестоимость производимых деталей;
- небольшой коэффициент использования материала;
- требуется индивидуальное производство штампа для деталей разного размера.
Изготовление фланцев нарезкой
В качестве сырья для данного процесса используют гибку или же листовой прокат. Методом нарезки производят изготовление фланцев плоских форм.
Достоинства:
- относительно низкие затраты;
- простота технологического процесса;
- высокая эффективность методики;
- большой коэффициент использования металла;
- допускается сваривание сегментов фланца;
Недостатки:
- из-за узкого диапазона станка присутствует ограниченность типоразмера деталей;
- в качестве сырья для производства деталей применяется листовой прокат;
- низкая производительность процесса;
- ограниченность технологического производства, так как годится лишь для изготовления плоских приварных деталей.
Литые фланцы
Этот метод изготовления деталей довольно распространен. Процесс литья в свою очередь подразделяется на несколько вариантов. У каждого из них есть плюсы и минусы. Все они выполняют определенные задачи. При соблюдении технологии производства получаются надежные, качественные детали. На данный момент наиболее высокотехнологичным из существующих методик литья считается центробежное электрошлаковое.
Преимущества:
- в качестве сырья для производства деталей используют недорогой металлолом;
- высокое качество готовых деталей, не уступающих фланцам производимых посредством штамповки или ковки;
- высокая ударная вязкость получаемых изделий, превосходящая фланцы, полученные другими методами;
- высокая, в сравнении с другими методиками производства, пластичность;
- примечательная однородность металла, отмеченная при помощи ультразвукового анализа;
- большой коэффициент использования металла;
- высокая производительность;
- низкая себестоимость.
Недостатки:
- достаточно высокий расход электроэнергии;
- изготовление форм для электрошлакового литья, которые включают четыре элемента, обходится недешево.
Помимо промежуточного контроля качества изготавливаемых фланцев, осуществляется окончательная проверка их соответствия нормам. При этом обращают внимание на геометрические размеры деталей, механические свойства, отсутствие дефектов.
Экономическая целесообразность – вот основной критерий выбора методики изготовления фланцев.
В каждом случае подбор производится индивидуально, исходя из требуемого результата. Каждый заказчик самостоятельно определяется с выбором технологии производства, опираясь на экономическую составляющую.
www.dsnspb.ru
Изготовление фланцев
В качестве заготовок для изготовления фланцев служат штамповка, литье, профильный прокат.
Штамповка производится горячей вырубкой из «карточек», нарезанных из листа.
Линия укомплектована четырьмя токарными станками, вертикально-сверлильными и тремя специальными, из которых два станка для многошпиндельного сверления и один станок для клеймения. Кроме того, на линии установлена ванна для консервации. Универсальные токарные станки модернизированы и оснащены пневматическими патронами, пневмоцилиндрами для перемещения задней бабки, автоматическими остановами и быстродействующими резцовыми головками. Токарная обработка ведется резцами со специальной заточкой для стружколомания. На линии применяется быстропереналаживаемая оснастка.
Принципиальная схема работы полуавтомата для клеймения фланцев заключается в следующем:
По лотку, имеющему наклон 40°, фланцы стальные поступают вниз до упора в отсекатель каретки. Каретка имеет возвратно-поступательное движение, которое осуществляется гидравлическим цилиндром по направлению, перпендикулярному наклонному потоку.
В момент переключения обратного хода каретки на рабочий ход два имеющихся на каретке ролика захватывают очередной плоский фланец и при рабочем ходе перекатывают его по клейму, установленному на специальном суппорте, который поджимается к фланцу гидроцилиндром.
После нанесения клейма каретка возвращается в исходное положение, а при обратном движении захватывает очередную деталь. Питание гидроцилиндров для движения каретки и поджима клейма осуществляется от установки гидронасоса с электромотором.
Заготовки на поточную линию подаются партиями в специальной таре на автокарах непосредственно к первым трем токарным станкам. Каждый из этих станков обрабатывает отдельный типоразмер ответных фланцев.
Обработанные фланцы по специальному желобообразному скату направляются на следующие операции. После нее по таким же скатам детали передаются на станок для клеймения и далее — в ванну для консервации. Наряду со скатами у рабочих мест имеются рольганги, где устанавливаются ящики-накопители для деталей, поступающих с предыдущей операции.
Корпусные фланцы изготовляются из бандажных колец либо из профильного металла гибкой на специальных профилегибочных станках.
Кольца изготовляются из стали марки 20-25 по ГОСТ 1050—60 в термически обработанном состоянии. По техническим условиям на поставку кривизна и эллипсность, а также поверхностные дефекты допускаются в пределах, обеспечивающих получение чистовых размеров после механической обработки. Для окончательного получения фланцев для труб заготовки подвергают чистовой механической обработке и сверлят отверстия.
Из полосового проката фланцы изготовляются по ГОСТ 103—57. При этом полоса режется на сортовых ножницах H-137. Полосы из нержавеющей стали разрезаются на дисковой пиле.
Партия нарезанных заготовок подается на приемный стол газовой печи с шагающим подом. Перемещаясь к выходному отверстию, заготовки нагреваются до необходимой температуры и поступают на рольганг, а затем — на стол гибочного станка.
Гибка заготовок на специальной машине осуществляется вращением поворотного стола машины с установленным на нем гибочным шаблоном. При вращении стола заготовка, предварительно закрепленная на нем передним концом, упирается в неподвижно стоящий гибочный ролик и вследствие этого огибается вокруг гибочного шаблона При гибке в холодном состоянии конструкция машины предусматривает гибку по спирали.
Сварка стыков производится на стыкосварочной машине типа МСТР-500-4 завода «Электрик» либо на установке для сварки в среде углекислого газа.
При сварке в среде углекислого газа источником тока являются сварочные генераторы ПС-500 или ПСАА-300. Автоматом для сварки служит переоборудованный трактор ТС-17М.
Перед сваркой поверхности изделий очищают от окалины, грязи и масла проволочной щеткой. В качестве флюса применяют стандартный флюс АН-348. В данном случае флюс выполняет следующие функции;
а) обеспечивает равное формирование обратной стороны шва;
б) создает дополнительную защиту в виде тонкой пленки на поверхности расплавленной ванны;
в) предохраняет выгорание легирующих элементов проволоки при сварке корня шва;
г) при сварке плоских фланцев толщиной более 35 мм с поворотом благодаря флюсовой подушке уменьшается сухой вылет электродной проволоки, тем самым уменьшаются выгорание легирующих элементов проволоки и образование пор.
Основная защита сварочной ванны осуществляется углекислым газом. Сварка производится по слою флюса в изложнице, боковые стенки которой изготовлены из меди и охлаждаются водой, а снизу шов формируется на охлаждаемой медной подкладке.
После зачистки грата производится контроль сварного шва гамма-лучами. Просвечивание производится по ГОСТ 7512—55 радиоактивным цезим—137.
После контроля фланцы 12820 из нержавеющих сталей проходят термообработку и травление.
Правка фланцев производится на правильном прессе типа ПБ-192. После травки фланцы плоские приварные поступают на механическую обработку. Между рабочими местами фланцы транспортируются рольгангами, кран-укосинами, монорельсами.
skyprom.ru