Гранулятор своими руками | Изготовление пеллет своими руками
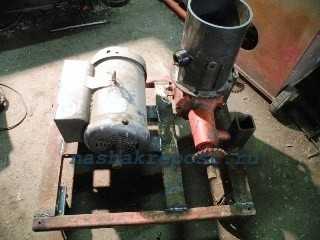
Большое количество различных механизмов, приобретение которых не целесообразно из-за очень высокой стоимости или не возможно из-за ограниченного предложения на рынке может быть изготовлено самостоятельно. Одним из таких механизмов является гранулятор – аппарат для изготовления кормовых или отопительных гранул (пеллет). Использование гранул позволяет значительно разнообразить рацион домашних животных, сохраняя питательные свойства различных видов растительного и животного корма. Применение топливных гранул уже нашло широкое применение в странах северной Европы как прекрасная альтернатива не только твердым (дрова, уголь), но и жидким (солярка, мазут) видам топлива. Для их изготовления используются такие виды отходов обработки древесины, как опилки и стружки. Иногда для получения сырья осуществляют измельчение макушек деревьев, остающихся при лесозаготовке, а так же сучьев и корней.
Предлагаемые к продаже заводские экземпляры имеют либо очень большую производительность, что не позволяет малым предприятиям осуществить их полную загрузку, либо очень высокую стоимость, что не дает возможности предпринимателям или частным подворьям быстро окупить свои данное оборудование. Предлагаем вниманию читателей описание технологии изготовления небольшого гранулятора своими руками для производства пеллет в домашних условиях, себестоимость которого значительно меньше многих промышленных аналогов.
Принцип работы гранулятора
По принципу работы все аппараты для производства гранул из отрубей или древесных пеллет делятся на две группы – с плоской или с кольцеобразной матрицей. Предлагаемый вниманию механизм относится к первой группе. Он состоит из сварной основы, на которую монтируется привод в виде электродвигателя требуемой мощности и редуктора с установленным на нем рабочим узлом. Процесс изготовления потребует выполнения сварочных работ, а так же использования некоторых готовых деталей, подбираемых в зависимости от размеров рабочего узла.
Изготовление основания для самодельного гранулятора
Изготовление агрегата начинаем с основания. Предварительно подготовьте достаточное количество стального проката в виде швеллера или прямоугольного профиля сечением 25×40 миллиметров. С помощью болгарки (угловой шлифовальной машинки) или слесарной ножовки осуществите раскрой материала на отдельные детали в соответствие с фото.
Используя сварочный аппарат или так же газовую сварку соедините детали основания гранулятора в рамную конструкцию с соответствующими площадками для крепления электродвигателя и рабочего узла. В случае изготовления не стационарного, а мобильного устройства установите по углам нижней рамы колеса на болтовом или сварочном соединении.
Рабочий механизм гранулятора для пеллет
Рабочий узел, соединяемый с электродвигателем посредством цепной передачи, состоит из редуктора и цилиндрической емкости, в которой устанавливается дискообразная матрица и пара установленных на валу специальных шестерен.
Матрица представляет собой металлический диск, имеющий толщину не менее восьми миллиметров с просверленными в нем отверстиями. Диаметр отверстий равен диаметру пеллет и составляет восемь – десять миллиметров. Форма отверстий выполнена в виде усеченного конуса, что обеспечивает постепенное обжимание гранулируемой смеси. Этот аспект значительно повышает плотность гранул, не зависимо от используемого сырья. В центре диск имеет отверстие с пазом для крепления на вращающемся выходном валу редуктора с помощью шпонки и крепящейся на болтах муфты.
Корпус рабочего узла состоит из двух полых цилиндров, имеющих прямоугольные прорези для установки пары червячных колёс, обеспечивающих при работе агрегата необходимое давление на гранулируемую массу.
В нижнем цилиндре корпуса имеется выходное отверстие для удаления готовых гранул (пеллет) в какую-либо приемную емкость. Принцип работы готового механизма основан на вращении диска-матрицы синхронно с установленными на валу шестернями. Вращение матрицы обеспечивается приводом редуктора от электродвигателя и жестким креплением рабочего диска. Попадающая через загрузочную верхнюю часть корпуса рабочего узла масса продавливается через отверстия, при этом сжимается и уплотняется, образуя достаточно твердые цилиндры небольшой длины. В зависимости от обрабатываемого сырья масса может дополнительно увлажняться в тех или иных пропорциях.
Описанный в данной статье гранулятор, сделанный своими руками, не требует больших расходов для изготовления и вполне может быть использован для работы небольшими деревообрабатывающими производствами, а так же животноводческими или зерновыми.
В данном видео продемонстрирована работа самодельного гранулятора:
Уважаемые читатели, комментируйте статью, задавайте вопросы, подписывайтесь на новые публикации — нам интересно ваше мнение 🙂
Статьи, которые Вам будут интересны:
nashakrepost.ru
технология производства топлива в домашних условиях, изготовление оборудования
Стоимость традиционных энергоносителей повышается, и все чаще владельцы частных домов решают использовать для отопления различные виды биомассы. Один из таких видов топлива — пеллетное. Оно представляет собой прессованные гранулы, а в качестве материалов можно использовать мелкие древесные опилки, торф, солому и т.д. Так как производство этого вида топлива в странах СНГ развито слабо, многие люди решают делать пеллеты своими руками.
Основные преимущества
Пеллеты представляют собой цилиндрические гранулы диаметром 4−10 мм и длиной 15−50 мм. В качестве сырья для их изготовления можно использовать различные природные материалы. Чаще всего пеллеты своими руками в домашних условиях делают из следующего сырья:
- Отходов деревообрабатывающих предприятий — наиболее качественными являются гранулы из опилок.
- Коры, веток, а также сухой хвои и листвы.
- Отходы агропромышленного комплекса.
- Торфа — использование этого вида топлива позволяет добиться максимальной теплоотдачи.
Качество гранул во многом зависит от используемого сырья. Лучше всего использовать топливо, изготовленное из древесных опилок. Так как древесные отходы в топливе премиум-класса имеют высокую степень очистки, то изготовить их самостоятельно довольно сложно.
Также промышленные сорта могут содержать и определенное количество примесей — кору, хвою, листья. Они обладают более высокой зольностью, но при этом показатель энергоемкость остается высоким. Для производства пеллет в домашних условиях чаще всего используют различные виды отходов деревообработки и сельхозпроизводства.
Среди основных преимуществ этого вида топлива можно отметить:
Содержание вредных веществ минимально, и при его сгорании в основном выделяется углекислый газ с водяным паром.
- Может использоваться в котлах длительного горения.
- Не требуется много места для хранения.
- Так как в процессе производства не нужно использовать химические ингредиенты, то риски развития аллергических реакций минимальны.
- Обладает высоким показателем теплоотдачи.
- Пеллетное топливо не подвержено процессам внутреннего гниения, что исключает самовозгорание.
Промышленная технология
Процесс производства пеллет можно разделить на несколько этапов. Сначала проводится подготовка и дробление сырья. В промышленных условиях материал также сортируется и после очистки от примесей поступает на линию предварительного дробления. После этого сырье в обязательном порядке сушится. Для этого применяются аэрационные или барабанные сушильные установки. Остаточная влажность древесных опилок должна быть ниже 14%.
Следующим этапом производства пеллетного топлива является тонкое дробление материала. Использование специального оборудования позволяет довести щепу до состояния муки. Максимальный размер фракции после этого процесса составляет 4 мм. Затем снова контролируется влажность материала, и при необходимости проводится вторичная сушка. В противном случае сырье не будет прессоваться.
На финальном этапе производства измельченный сухой материал поступает в специальные установки для прессования. Он продавливается через матрицу с конусообразными отверстиями определенных размеров. Благодаря особой форме каналов опилки уплотняются. Также под давлением увеличивается температура сырья и выделяется вещество лигнин. Оно содержится в составе любого вида древесины и способствует прочному склеиванию фракции. При выходе из прессовальной установки гранулы могут иметь температуру до +90°С, и их необходимо охладить.
Изготовление в домашних условиях
Технология производства пеллетного топлива кажется простой, но в домашних условиях его изготовление оказывается не всегда рентабельным и довольно трудным. Одной из главных проблем при создании производственной линии в частном хозяйстве является отсутствие специального оборудования — гранулятора. В продаже можно найти бытовые модели, но их стоимость довольно высока.
Безусловно, сделать пеллетайзер можно и самостоятельно, но это сложная задача. Недостаточно изготовить все необходимые для станка детали: во время сборки потребуется точная подгонка. Перед тем как начать делать пресс для пеллет своими руками, необходимо правильно оценить имеющиеся навыки.
Вторая проблема заключается в доступности материалов для изготовления пеллетного топлива. Думать о возможности производства гранул в домашних условиях стоит лишь в том случае, когда есть возможность регулярно получать сырье, причем оно должно быть бесплатным либо иметь минимальную стоимость. Только в такой ситуации появится возможность обеспечить себя качественным экологичным видом топлива.
Также следует сказать, что применение станков с плоскими матрицами позволяет избежать цикла вторичного дробления. В них установлены зубчатые ролики, благодаря которым щепа перетирается до требуемого состояния. Без сушки опилок обойтись не получится, и для решения поставленной задачи многие мастера собирают барабанные сушилки простой конструкции. Также следует помнить, что лучший материал для изготовления пеллетного топлива — хвойная древесина. Из тополя, липы или ивы сделать гранулы не получится.
Самодельный гранулятор
Чтобы сделать станок для производства пеллет своими руками, потребуется чертеж. Зачастую проблемы возникают уже на стадии его поиска, так как мастера редко делятся секретами своей работы. Некоторые из них предлагают приобрести у них готовый станок, но его стоимость будет высокой. Для создания самодельного гранулятора потребуется изготовить несколько основных узлов.
Одним из главных среди них является матрица. Следует предупредить, что самостоятельно сделать ее будет довольно сложно, так как потребуется профессиональное оборудование и хорошие навыки работы с ним. Похожая матрица используются для изготовления комбикорма, и стоит попробовать ее приобрести.
Если такой возможности нет, то из металла толщиной от 20 мм предстоит вырезать круглую заготовку. Затем на ней размечается и высверливается посадочное отверстие с пазом для фиксации на валу электродвигателя. Отверстия для прессовки должны иметь коническую форму. Без специальной фрезы их сделать невозможно. Также следует сказать, что наружный диаметр детали может быть любым, и чем он больше, тем выше окажется производительность оборудования.
Второй ответственный узел станка — мощные зубчатые катки. Они монтируются на вал с помощью подшипников качения. Кроме этого, на вале необходимо сделать осевое отверстие для крепления на вертикальном приводе. Сила прижима катков к матрице регулируется с помощью гайки.
Корпус можно изготовить из трубы либо сварить из листового металла. Его внутренний диаметр должен соответствовать размеру матрицы, обеспечивая ее вращение с минимальным зазором. Чтобы упростить обслуживание гранулятора, корпус стоит сделать разборным. Для изготовления пеллетного станка своими руками потребуется редуктор. Этот агрегат устанавливается в нижней части оборудования и предназначен для передачи вращения на рабочий вертикальный вал с частотой 70−100 об./мин.
Матрица и катки монтируются в верхней части гранулятора. Вся конструкция вместе с электромотором устанавливается на раму, выполненную из двутавра, швеллера либо уголка. Важно помнить, что нагрузки на станину будут высокими, и она должна их спокойно выдерживать.
Такая конструкция оборудования для изготовления топливных гранул — не единственно возможная. Обладая достаточными навыками и при доступе к профессиональному металлообрабатывающему оборудованию сделать самостоятельно гранулятор вполне реально. В такой ситуации главной проблемой станет поиск доступного и дешевого сырья.
kaminguru.com
Изготовление пеллет своими руками – советы эксперта – Свой дом мечты
Современные автономные котлы работают на пеллетах, которые представляют собой цилиндрические гранулы.
Для изготовления пеллет используются древесина, производственные отходы лесопильной промышленности, деревообрабатывающего и мебельного производства. Помимо этого освоено производство агропеллет, для получения которых в переработку идет солома, кукуруза, шелуха подсолнечника и иные подобные им материалы.
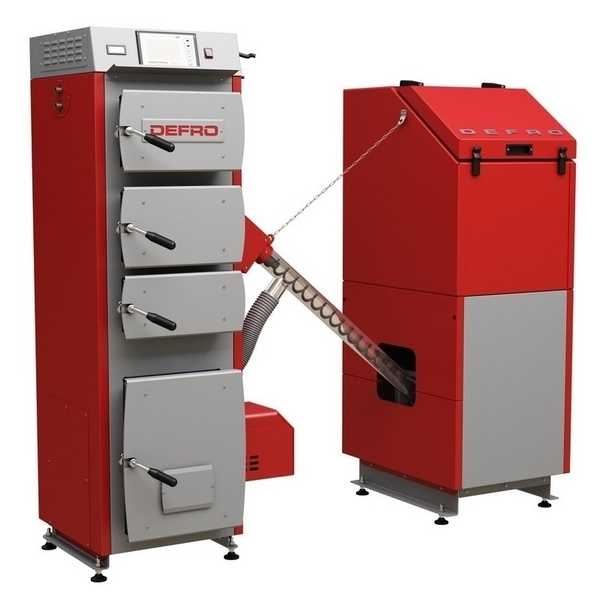
Требования к транспортировке и хранению такого топлива значительно ниже, по сравнению с жидким и газообразным. Это обстоятельство способствует росту популярности пеллет у хозяев частных домостроений.
ПеллетыДля формирования гранул необходимо давление в 300 атм., действующее в условиях повышенного температурного режима. В таких условиях из сырья выделяется лигнин, который соединяет между собой частицы в единую гранулу. Размеры пеллет находятся в пределах: по длине – 10-30 мм, по диаметру – 6-10 мм.
Вследствие того, что при производстве этого топлива применяются только натуральные материалы, то их экологичность вне всякого сомнения. При горении пеллет в котле образуется крайне незначительный объем углекислого газа, который можно сопоставить с процессами разложения древесины естественным образом.
Какие бывают сорта пеллет?
Пеллеты принято классифицировать на следующие виды.
Белые
Топливо этой группы принято относить к премиум-классу. Его, как правило, используют в современном высокотехнологичном котельном оборудовании. При сгорании образуется количество тепла, равное 17,2 Мдж/кг при зольности 0,5%.
Темные
Такие пеллеты называются индустриальными. В их производстве используется, помимо древесины, кора деревьев. Это топливо применяется в котлах, в которых удаление золы осуществляется чаще. Теплотворность его находится на уровне белых пеллет, а зольность несколько выше – 0,7%.
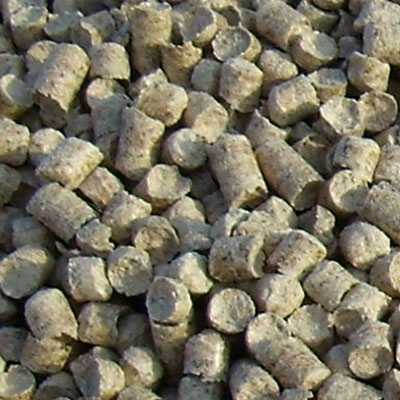
Агропеллеты
АгропеллетыИх относят к дешевому топливу, обладающему стандартным качеством. В качестве теплотехнического оборудования для сжигания агропеллет служат большие котлы, способные работать на таком топливе. В результате горения выделяемое количество энергии равно 15 МДж/кг, а зольность может быть более 3%.
Форма гранул пеллет и физико-геометрические характеристики обуславливают хорошую сыпучесть топлива. Таким образом, появляется возможность автоматизации подачи его в котел, что в свою очередь позволяет работать длительное время автономно без участия людей.
Основные достоинства
Высокая экологичность топлива является главным достоинством пеллет. Процесс их сжигания сопровождается образованием углекислого газа и паров воды. Объем газа находится на таком уровне, что усвоение его растениями не оставляет никакого следа в атмосфере.
При сжигании пеллет возможно осуществить процесс пиролиза, который применяется в котлах, имеющих длительный период горения.
Возможность автоматизации процесса загрузки топлива практически исключает необходимость в участии человека в работе оборудования.
Компактность гранул существенно снижает потребности в складских площадях и упрощает их транспортировку.
Технология производства пеллет исключает необходимость введения в состав сырья различных добавок, что не способствует выделению неприятных запахов при горении.
В случае применения топлива высокого качества, показатель теплоотдачи существенно превышает аналогичный показатель у традиционного твердого топлива.
Высокая пожаробезопасность пеллет обуславливается отсутствием процессов гниения или прения. Применение качественного гранулированного топлива и высокотехнологичных котлов сокращают расходы на отопление.
Также имеется возможность освоить изготовление пеллет своими руками, что приведет к снижению затрат.
Следует понимать, что при всех несомненных положительных качествах этого топлива, стоимость его значительна.
Технологический процесс
Условно процесс получения пеллет можно разделить на следующие стадии.
Измельчение сырья
Для получения требуемых для производства размеров материала применяются дробилки, или их еще называют рубительные машины. Необходимая ширина сырья составляет 25 мм при толщине 2 мм.
После этого требуется произвести сушку полученного материала. С уменьшением его размера затраты энергии возрастают.
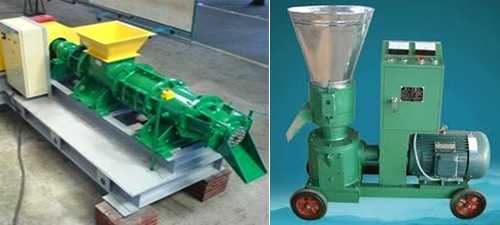
Сушка и дополнительное измельчение
Влажность при осуществлении технологического процесса играет важную роль, она должна быть 10+/- 2 %. При ее повышении требуется проведение дополнительной сушки. В случае чрезмерно сухого сырья его придется увлажнять до требуемой величины.
Для сушки используется оборудование, которое по своим конструктивным особенностям может быть барабанным или ленточным. Использование ленточной сушилки более предпочтительно в плане безопасности эксплуатации, несмотря на то, что дороже.
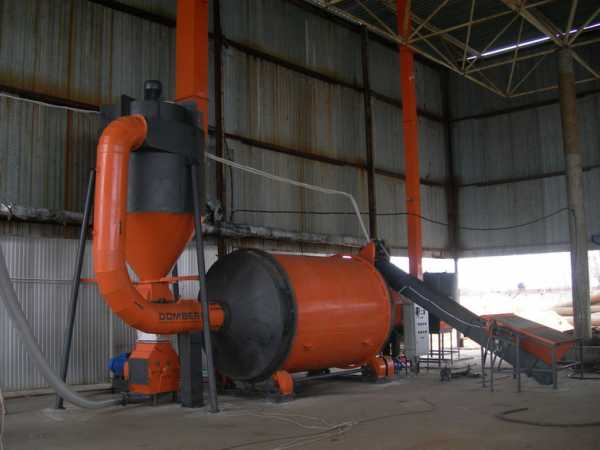
Нормальный технологический процесс прессования может быть осуществлен при условии, что величина частиц сырья составляет не более 4 мм. После подсушивания сырье поступает на дополнительное измельчение на дезинтеграторе.
Водоподготовка
При снижении показателя влажности до 8% и менее крайне затрудняется прессование древесины. С целью достижения требуемого уровня этого показателя материал загружается для увлажнения в специальные агрегаты. Для этой цели хорошо подходят смесители шнекового типа, в которых используются пар или вода.
Если сырье для производства пеллет получено из древесины твердых пород, то применение пара позволит уменьшить прочностные характеристики и повысить пластичность. Конструкция некоторых прессов такова, что отпадает необходимость в использовании пара.
Прессование
Этот процесс производится на прессах различной конструкции, которые отличаются формой матрицы. Они могут быть оборудованы матрицей:
- круглой. Такие прессы изначально применялись в пищевой и химической промышленностях, а также для производства комбикормов;
- плоской. Они проектировались для переработки ТБО.
При наличии конструктивных различий, принцип их действия одинаков. Под воздействием усилия происходит смятие материала на матрице. В ходе этого процесса происходит продавливание сырья через ее отверстия, а получающиеся гранулы срезаются при помощи специальных ножей. В ходе такой обработки происходит троекратное уплотнение материала.
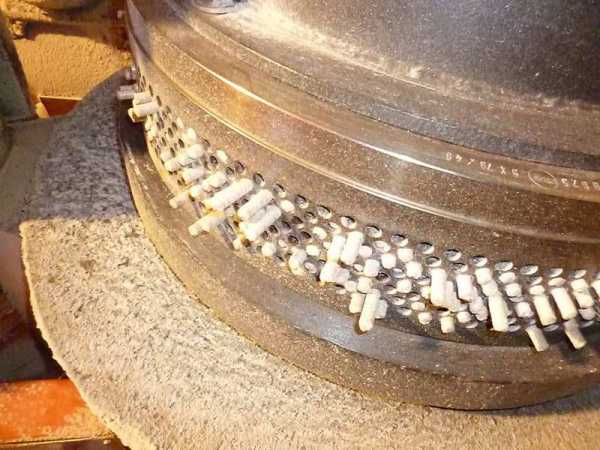
Процесс, происходящий в рабочей зоне пресса, является адиабатическим. Сжатие в этом случае сопровождается ростом температуры до 100 градусов Цельсия. Значительные нагрузки, воздействующие на оборудование, требуют использования материалов с высокой прочностью.
Охлаждение и очистка
Формирование и качество гранул зависят от приложенного усилия и температуры, образующейся в ходе процесса. При этом максимально допустимой температурой является значение в 120 градусов Цельсия. Превышение его отрицательно отражается на качестве изделия.
Полученные пеллеты должны быть охлаждены. В результате чего происходит их сушка и упрочнение. Затем следует процедура очистки готовой продукции для придания ей товарного вида.
Завершающим этапом производственного процесса получения пеллет является фасовка и упаковка в тару, объем которой соответствует потребностям заказчика.
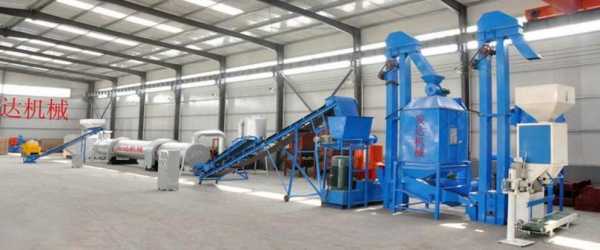
Производство пеллет в личном хозяйстве
При наличии сырьевой базы организация производства пеллет в домашних условиях будет хорошим подспорьем в хозяйстве. Организация технологического цикла получения гранулированного топлива требует такого оборудования, как:
- устройство для дробления;
- приспособление для сушки;
- сито;
- гранулятор.
Если древесное сырье представляет собой опилки, то необходимость в использовании дробилки отпадает. Размер опилок приемлем для запуска их в работу. В качестве камеры для сушки можно использовать металлическую бочку. Просеивание исходного материала при помощи сита дает возможность удалить крупную фракцию и неделовые примеси, негативно влияющие на качество продукции. Основным агрегатом данного производства является гранулятор.
Процесс изготовления гранулятора
Перед изготовлением гранулятора важно определиться, какого типа он будет. Конструкция гранулятора с плоской матрицей более доступна для исполнения в кустарных условиях, чем изготовление шнекового с цилиндрической матрицей.
Устройство малогабаритного гранулятора
Процесс изготовления гранулятора заключается в операциях по сборке отдельных узлов, которые можно приобрести в готовом виде. К ним относятся такие модули:
- электрический двигатель;
- редуктор;
- рабочий узел;
- трансмиссия.
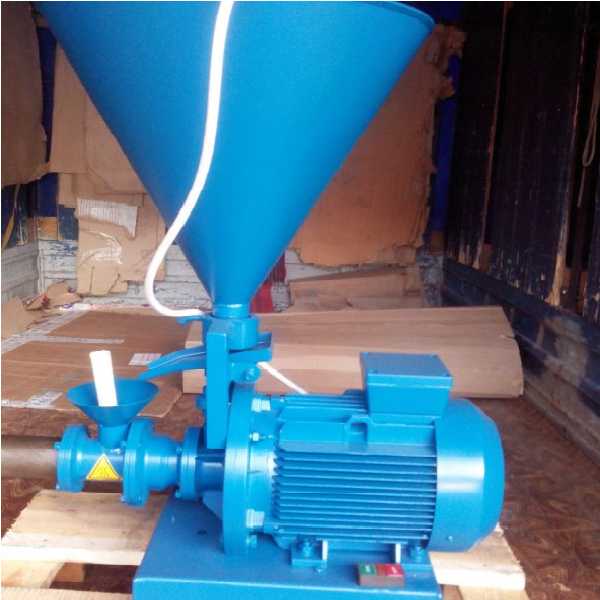
Некоторые детали под силу изготовить самостоятельно.
Изготовление матрицы
Для ее изготовления необходима толстолистовая сталь, толщина которой должна быть 8-20 мм. Из нее вырезают круг с необходимым диаметром. В центре круглой заготовки выполняется отверстие с диаметром, соответствующим валу электродвигателя. На поверхности диска производится перфорация, которая имеет форму усеченного конуса, меньшее основание которого равняется диаметру готовой продукции.
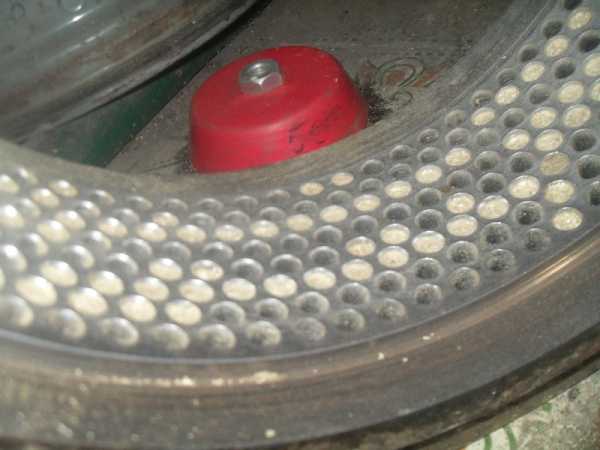
Сборка устройства
Два катка червячного типа монтируются на валу, который устанавливается на матрице в перпендикулярном направлении к ее плоскости. Эти шестерни производят измельчение и прессование материала. При этом происходит выдавливание сырья через отверстия в матрице.
Установка рабочего узла осуществляется в корпусе, который представляет собой вертикальный цилиндр. Монтаж должен быть выполнен так, чтобы вращению механизма ничего не мешало, но зазор при этом был минимальным.
В конструкции предусматриваются отверстия: вверху – для подачи сырья, снизу – для поступления гранул. Нижняя часть оснащается емкостью для их приема.
Приводом агрегата является электрический двигатель, вал которого соединен с рабочим узлом. Вся конструкция жестко крепится к раме.
Работа малогабаритной установки
Работа малогабаритной установкиПроизводство пеллет своими руками не представляет сложности при использовании самодельного гранулятора. Для этого производится загрузка в приемник, расположенный в верхней части устройства, подготовленной массы опилок. При попадании в рабочую зону происходит продавливание ее в отверстие матрицы. Проходя через нее, сырье приобретает форму и размер, соответствующий этим отверстиям. При этом гранулы получают требуемую плотность. На следующем этапе производства осуществляется извлечение цилиндров из емкости накопителя и производится их сушка.
Самодельная установка шнекового типа
Гранулятор с одним шнеком можно сделать самостоятельно. Его конструкция состоит из:
- корпуса, который представляет собой стальную трубу;
- шнека, который можно позаимствовать из оборудования, пришедшего в негодность;
- загрузочного узла;
- привода, в качестве которого используется электродвигатель;
- редуктора;
- подшипника упорного типа;
- головки для профилирования.

Смотрите также
small-house.ru
Пеллеты своими руками. Производство пеллет своими руками :: SYL.ru
В последнее время владельцы частных домов, в которых нет центрального отопления, изготавливают пеллеты своими руками. Это связано с тем, что стоимость топлива постоянно растет. Пеллеты представляют собой экологически чистое топливо, которое можно самостоятельно изготовить, используя отходы древесного производства, а также сельского хозяйства.
Разновидности пеллет
При производстве пеллет используют биомассу, которая имеет высокую энергетическую ценность. В качестве особенности сырья должна выступать способность к прессованию. Самым распространенным при изготовлении пеллет сырьем выступает кора, щепа, опилки и иные отходы лесозаготовки, а также деревообработки. Топливо можно получить и из растительных отходов, в роли которых может выступить шелуха, солома, подсолнечная лузга и другие культуры. Менее распространены торфяные пеллеты или те, что выполнены из куриного помета.
Преимущества пеллет
Производство пеллет своими руками позволяет получить такое топливо, которое дает такую теплоотдачу, которую невозможно сравнить с той, что получается из досок, щепы или традиционной коры. Хранить такое прессованное топливо тоже гораздо удобнее, так как оно занимает гораздо меньше места по сравнению с досками или щепой. Это обусловлено тем, что помещение может иметь гораздо меньшую площадь. Помимо этого, пеллеты можно располагать в непосредственной близости с жилыми постройками, так как подобное топливо не представляет опасности для здоровья.
Рекомендации по использованию пеллет
После того как пеллеты своими руками будут изготовлены, использовать их рекомендуется в специальных котлах. Особенность их работы заключается в постоянной подаче кислорода в процессе горения. Более того, современные котлы автоматического действия требуют не столь частой загрузки пеллет.
Технология производства пеллет
Изготовление описываемого топлива происходит в несколько этапов, первый из которых предусматривает первоначальное дробление древесины, после чего получаются достаточно крупные частицы. Затем сырье проходит процесс сушки и претерпевает мелкое дробление. Основа должна быть насыщена паром, который иногда заменяют на воду, что позволяет подготовить материал. В таком состоянии он легче поддается прессованию, а затем полученные гранулы охлаждаются.
Особенности первоначального дробления
Для того чтобы изготовить пеллеты своими руками, необходимо, как было сказано, подвергнуть древесину дроблению. В процессе этого необходимо использовать специальную дробилку, после выхода из которой получатся элементы с размерами в пределах 25х25х2 мм. Подобные габариты позволяют качественно просушить материал, в ходе чего следует применять сушильные аппараты. Только после этого элементы могут быть еще раз измельчены.
Если сырье окажется не в достаточной степени просушено, то его будет очень сложно спрессовать, да и использовать для печи или котла такие пеллеты не представится возможным. Это указывает на то, что этап сушки никак нельзя миновать. После этого влага покидает сырье в объеме 8-12 %. Правила производства регламентируют нормальную влажность материала в пределах 10 %. Использовать при изготовлении топлива можно аппарат для сушки ленточного или барабанного типа.
Правила сушки и мелкого дробления
Для того чтобы изготовить пеллеты своими руками, необходимо использовать энергию, получаемую от 1 м3 древесины, что верно для одной тонны сырья. Но стоит учесть, что в процессе сушки в качестве топлива предпочтительнее использовать кору или опилки, тогда изготовление обойдется дешевле.
Недопустимо запускать на этапе прессования сырье, размер одного элемента которого превышает 4 мм. Такого результата можно добиться только при использовании специальной дробилки. Масса качественного продукта после прохождения этапа дробления составляет примерно 150 кг на 1 м3. Специалисты рекомендуют применять молотковые мельницы, так как они позволяют добиться желаемого результата.
Этап насыщения влагой
Изготовление пеллет своими руками должно сопровождаться поступлением сырья на этап прессования с нормальной влажностью. Иногда процесс сушки лишает нормальной влажности материал. Для того чтобы она достигла 10 %, необходимо погрузить материал в емкость, где он будет претерпевать воздействие пара. При влажности в 8 % сырье не станет склеиваться, получить пеллеты не удастся. Если в работе предполагается использовать мягкую породу, то не потребуется применять особо сложное оборудование.
Технология прессования и охлаждения
Чтобы изготовить пеллеты своими руками, чертежи оборудования вам не понадобятся, за исключением того случая, если установку вы планируете сделать самостоятельно. Ее схематичный рисунок можно увидеть в статье. После завершения прессования удастся получить цилиндры, диаметр которых может быть разным и, как правило, варьируется в пределах 6-25 мм. Прессование происходит при повышенной температуре, это сопровождается выделением вещества, которое называется лигнином.
Ввиду того что температура гранул достигает 90 0С, они требуют охлаждения и сушки. По окончании данного этапа топливо можно упаковывать. Если вы изготавливали самостоятельно пеллеты, оборудование своими руками тоже можно изготовить, но не стоит оставлять материал после завершения процесса производства в бункере, так как это может снизить его качество. Необходимо делать топливо в небольших количествах, которое будет возможно использовать за короткое время или упаковать в полиэтиленовые пакеты.
Если вы решили заняться производством пеллет в домашних условиях, на территории собственного участка, то можно облегчить работу и приобрести мобильный гранулятор, который представлен прессом. Еще одним вариантом облегчения процесса послужит приобретение, а не самостоятельная подготовка сырья.
Станок и гранулятор своими руками
Если вас интересует самостоятельное производство пеллет, оборудование своими руками можно изготовить. Например, дробилка может быть сделана из сит, которые имеют заданные габариты ячеек. Их рекомендуется изготовить из мелкой стальной сетки, которая фиксируется на деревянном каркасе. Сушилка может иметь барабанный тип. Ее допустимо изготовить из стальных бочек, которые предварительно следует лишить дна. После чего бочки свариваются между собой. Полученную трубу следует зафиксировать на станину, обеспечив перемешивание посредством шкива от электродвигателя. А вот сушка будет осуществляться методом подачи воздуха.
Гранулятор для пеллет своими руками можно изготовить из электродвигателя и редуктора. Основание будет состоять из металлопроката, выполненного в виде швеллера, в качестве альтернативного решения можно использовать прямоугольный профиль 40х25 мм. Разрезать стальные элементы можно УШМ, а вот сопряжение следует производить с помощью сварочного аппарата. Если к конструкции прикрепить колеса, то установка обретет мобильность, ее с легкостью можно будет перевозить по помещению.
Основной рабочий узел описываемой установки должен быть сопряжен с электрическим мотором с помощью цепной передачи. Цилиндрическая емкость и редуктор лягут в основу узла. В емкости должна быть расположена матрица, которая имеет вид диска и обладает отверстиями. Не следует забывать о наличии шестерен, их необходимо установить на валу в количестве двух штук.
Матрицей выступит стальной диск, максимальная толщина которого равна 12 мм, предварительно в этом элементе необходимо проделать нужное число отверстий. В зависимости от того, какие в итоге должны быть получены гранулы, необходимо проделать соответствующие отверстия, они могут иметь диаметр 8-10 мм. А вот их форма обязательно должна получиться конусной, чтобы гранулы прессовались.
Корпус имеет вид пары полых цилиндров с прямоугольными отверстиями, предназначенными для червячных колес, именно они станут гарантировать необходимое давление на материал в ходе проведения работы. Для того чтобы гранулы имели возможность покидать установку, для них следует сделать отверстие, расположенное в нижней части. Принцип функционирования установки заключается в одновременном вращении шестерен и матрицы, что делает возможным продавливание материала сквозь отверстия.
Если вы постоянно нуждаетесь в топливе, то самостоятельное изготовление пеллет окажется намного выгоднее по сравнению с их приобретением.
www.syl.ru
Устройство гранулятора пеллет: от матриц до роликов
Здравствуйте уважаемые читатели и подписчики блога, на связи с вами Андрей Ноак! Сегодня я расскажу вам про устройство гранулятора пеллет.
Введение
С гранулятором я познакомился в далеком 2010 году, когда на нашем огромном производстве запускали новый цех по производству пеллет. В то время я работал технологом на этом участке и мне приходилось достаточно много времени проводить в цеху пока отлаживалась технология изготовления пеллет.
Настройка пресса занимала первое в отлаживании технологии. Первое время практически каждую неделю у нас не шел пеллет и цех простаивал по три – четыре дня пока мы настроим гранулятор. Так как мы запускали уже не первый цех по деревообработке, то понимали – это нормально когда пуско наладка оборудования проходит именно в таком режиме.
За время настроек пресса мы его изучили от и до, кроме этого пришлось даже его несколько раз полностью разбирать. А пресс у нас был от фирмы “Amandus Kahl” с плоской матрицей. Как я уже говорил такие пресса с плоскими матрицами используются для жестких материалов, а это более твердые породы древесины, резиновые покрышки и многое другое. Но кроме этого их преимущество состоит и в том, что на них можно перерабатывать и мягкое сырье, к примеру различные корма, солому и многое другое.
Информация данная в данной статье взята с моей новой книги – «ТИПИЧНЫЕ ОШИБКИ ПРОИЗВОДИТЕЛЕЙ ОБОРУДОВАНИЯ ДЛЯ ПРОИЗВОДСТВА ПЕЛЛЕТ», нет не думайте что я там «засаживаю» производителей, я там даю ценнейшую информацию как подбирать оборудование и разговаривать с производителем линий для того чтобы потом избежать типичных ошибок. Более подробно в разделе «МОИ КНИГИ».
Кроме этой информации я также могу предоставить помощь при выборе оборудования, проектировании предприятия, помочь с поиском линии, оказать информационные услуги по модернизации производства. Более подробно в разделе «УСЛУГИ»
Устройство гранулятора с плоской матрицей
Итак гранулятор с плоской матрицей состоит из:
- Пуансона;
- Роликов;
- Матрицы;
- Разравнивающих лопаток;
- Регулирующего, подъем пуансона с роликами, устройства;
- Червяка;
- Системы шкивов передающих крутящий момент от двигателя к червяку;
- Двигатель, у нас на прессе с производительностью 1,5 – 2 тонны в час, мощность была 250 кВт.
Пуансон и ролики
Про пуансон можно сказать только то, что количество катков на нем может колебаться от двух до пяти. На каждый материал ставятся свои ролики и их число. К примеру у нас на прессе стояло пять роликов, когда приехал немец, то сказал что пять роликов это для гранулирования травы, а для древесины нужно ставить четыре ролика, но они должны быть больше в диаметре.
Дело в том что когда становится больше диаметр ролика, то плавнее происходит вдавливание материала в матрицу, таким образом не разрушается будущий пеллет и образуется меньше отсева. Когда же увеличивается количество роликов, увеличивается производительность пресса.
Думаю все понятно, чем больше диаметр ролика – тем лучше качество прессуемого материала, чем больше количество роликов – тем больше производительность пресса.
Катки бывают двух видов для травы и для дерева, покупая б/у оборудование часто можно встретить такие ситуации когда вместо роликов и пуансона по дереву, продается оборудование для гранулирования травы.
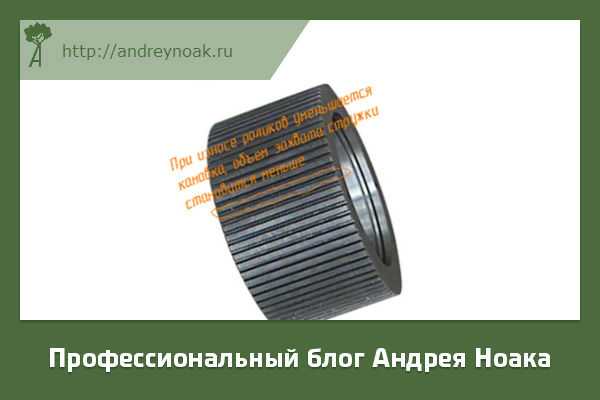
При износе катков гранулятора, каемки становятся меньше и захват сырья на матрицу становится меньше. На фото ролики для травы…
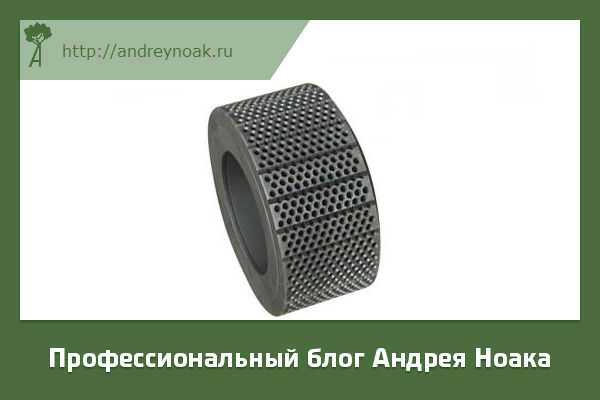
Каток по дереву. Древесина набивается в отверстия и потом не дает ему сильно давить на матрицу, при уменьшении контакта между ними, увеличивается ресурс обоих…
При работе пуансон и ролики выходят из строя, на пуансоне это износ, изгибы валов для посадки катков. Ролики же изнашиваются в местах соприкосновения с матрицей, на них появляется выработка, могут подгарать и подклинивать. Еще одним слабым местом являются подшипники роликов, они клинят или подгорают.
За нормой расхода матрицы, катков и подшипников нужно следить, как, я рассказал в вышеупомянутой книге. Кроме этого дал практические рекомендации для увеличения ресурса работы всего инструмента.
Матрица
Не только от пуансона и катков зависит производительность оборудования, огромное влияние на качество гранул и скорость прессования оказывает и матрица. И первый ее параметр это толщина.
На самом деле по логике вещей толщина должна зависеть от перерабатываемого материала. Если матрица слишком толстая, то производительность оборудования будет снижена, а затраты энергии на производство одной тонны гранул будут возрастать, так как готовые пеллет нужно будет проталкивать через отверстие.
Кроме этого слишком большая толщина будет поджигать пеллет, делая его темнее и менее конкурентоспособным. А еще на толстой матрице чаще забиваются отверстия.
На слишком тонком инструменте вы не получите качественных гранул, так как она не пропресуется до нужной плотности и прочности.
Вообще задача производителя вам рекомендовать какие то толщины для определенного материала, а задача деревообработчика это протестировать под себя, сделать все замеры и подобрать себе оптимальные варианты, как это сделать я написал в своей книге «Типичные ошибки производителей оборудования при производстве пеллет».
При работе этот инструмент также периодически выходит из строя. Признаками износа служат получаемые гранулы завышенного диаметра, к примеру гранулируете на матрице 8 мм, а получаете окатыши диаметром 9,5 – 10мм. Еще признаками считают тонкие стенки между ячейками, откалывание стенок, механические повреждения, неравномерное продавливание гранул, это когда заглядываете при гранулировании на матрицу, а там в одном месте идет выходят гранулы, а в другом просто идет отсев, конечно это еще может быть и неправильная настройка.
Что касается последнего пункта про неравномерный выход гранул, то одной из причин может быть неправильная выставка матрицы или ее болтание на корпусе. В таких случаях будет повышенное количество отсева, а пеллет не будет иметь достаточной прочности. Мы к примеру на производстве периодически протачивали посадочное отверстие под матрицу, как это сделать, я также рассказал в своей книге.
Для того чтобы увеличить ресурс работы матрицы, увеличить производительность, уменьшить количество отсева, необходимо периодически проводить обслуживание и зенковку. Зенкование матрицы производится примерно каждые 200 тонн пеллет.
Разравнивающие лопатки
Про них я упоминал в статье про пресс гранулятор, но сегодня также расскажу. Основной функцией как вы уже догадались по названию является разравнивание перед роликом древесной массы, чтобы масса была равномерно распределена по ширине ролика нагрузка на ролик была минимальна. За состоянием лопаток нужно периодически следить. Я знаю предприятия где лопаток вообще не стоит на грануляторе и они работают. На вопрос почему они так делают, они отвечают что все и так работает. Работать то работает, но вот износ происходит не равномерный, нагрузки неравномерные и соответственно ресурс работы оборудования снижается.
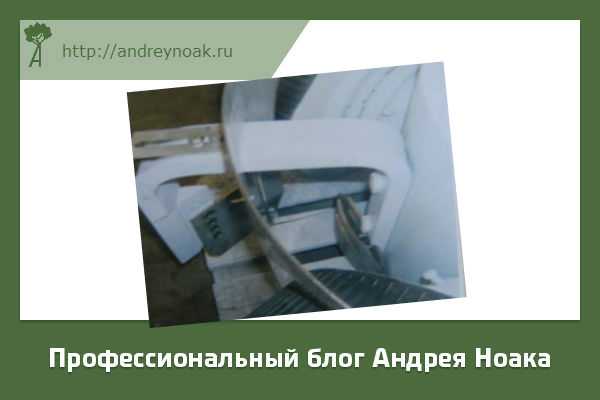
Направляющие щитки отвечающие за равномерное распределение прессуемого материала по поверхности матрицы должны выставляться согласно инструкциям… Тогда сырье распределяется равномерно по площади матрицы гранулятора…
Червячный механизм
Это сердце гранулятора, без которого ничего бы не прессовалось, он в процессе обслуживания никак не вскрывается. Необходимо чтобы в нем всегда имелось масло по нужному уровню. Сама марка масла заливается строго по регламенту от предприятия производителя.
Система шкивов и двигатель
Тут особо сказать нечего, нужно следить чтобы ремни были натянуты, шкивы хорошо закреплены и обязательно присутствовала защита на ременной передаче.
Что касаемо двигателя, то он должен быть настроен под максимальную нагрузку, дабы не сгореть. При забивании пресса и достижении максимальной нагрузки двигатель останавливается. Кроме этого на двигатель должна быть обязательно поставлена защита в виде автомата и теплового реле. Все это делается чтобы предупредить выход из строя, так как большие электродвигатели стоят много денег.
Видео устройства
Удачи и до новых встреч, с вами был Андрей Ноак!
andreynoak.ru
как сделать своими руками, схема сборки гранулятора, изготовления топлива и его хранение
Уголь или дрова — топливо недешёвое, в качестве альтернативы им можно использовать более доступные отходы сельского хозяйства и деревоперерабатывающей промышленности. Однако засыпать листья, солому или опилки в топливное отверстие неудобно. Поэтому их спрессовывают в специальные гранулы (пеллеты). Обычно такое топливо производят в промышленных условиях, но можно сделать пеллеты своими руками и дома.
Плюсы и минусы пеллет
В современном мире под пеллетами подразумевают не только продукцию из древесных стружек или ненужной бумаги, но и любые отходы сельского хозяйства и столярной промышленности, спрессованные в гранулы.
Для их производства подходит всё, что может гореть, но ранее неэффективно утилизировалось. Дополнительные преимущества пеллет:
- Нет необходимости покупать готовые гранулы, домашний мастер может освоить технологию их изготовления даже без специальных навыков. Кроме того, производство пеллет своими руками в домашних условиях может стать неплохим бизнесом.
- Обогревать помещения пеллетами дешевле, чем другими видами топлива.
- Экологическая чистота сырья.
- Пониженное количество выделяемых продуктов горения.
К минусам можно отнести лишь особые условия хранения — помещение должно быть сухим и хорошо защищённым от случайных возгораний. Очевидно, что плюсов у брикетов гораздо больше.
Пеллеты своими руками.
Категории гранул
Сырьё для производства гранулированного топлива может быть разным, поэтому и характеристики его различаются.
Пеллеты делят на несколько категорий:
- Премиум (белый). Это топливо высшего качества, получаемое из мелких опилок и отходов мягких древесных пород, очищенных от примесей. Главная характеристика белых пеллет — низкая зольность (около 0,5 процента от общего объёма гранул).
- Индустриальный (серый). Изготавливается из древесных опилок. Может содержать часть хвои, коры и прочих примесей. Зольность составляет около 1,5 процента.
- Промышленный (тёмный). На изготовление идёт солома, жмых, сухие листья, различные древесные отходы и даже птичий помёт. Зольность такого топлива намного выше — примерно 5 процентов от общего объёма.
Первые две категории обычно используются для индивидуального отопления. Промышленная группа отлично подходит для топки котельных. Небольшая стоимость и высокая теплоотдача делают этот вид весьма выгодным.
Что такое пеллеты? www.teplomet.ru
Перечень оборудования
Чтобы сделать пеллеты в домашних условиях, можно использовать отходы столярного производства, прошлогодние листья, мелкий хворост, солому и т. п. Обязательный комплекс механизмов для производства состоит из дробилки и гранулятора (пресса). В некоторых случаях может понадобиться сушилка и дополнительный измельчитель.
Основной элемент производства — гранулятор (пеллетайзер). Мастеру необходимо принять решение, покупать готовое оборудование или сделать его самому. Промышленные аппараты просты в управлении, обладают высокой производительностью, позволяют получать материал отличного качества. Однако стоит промышленный гранулятор довольно дорого, и срок его окупаемости составит несколько лет. Поэтому тем, кто хочет сэкономить на оборудовании, стоит попробовать собрать пеллетайзер самостоятельно.
Сделать чертёж гранулятора для опилок своими руками довольно просто. Аппарат состоит из матрицы, редуктора, барабана, электрического двигателя и катков. Все необходимые компоненты, кроме двигателя, можно приобрести в магазине или сделать самостоятельно.
Чаще всего используют два вида матриц. Одна производит цилиндрические, другая — плоские пеллеты. Пеллетайзер первого типа актуален для крупных производств. Второй тип больше подходит для личных хозяйств. В такой аппарат сырьё засыпается сверху, а катки, прокатываясь по нему, выдавливают массу.
Матрицу можно присоединить и к прессу ручного типа. Следует учитывать, что в таких аппаратах изготавливают пеллеты только из мягких материалов — лузги, жмыха, листвы и т. п. Производительность ручного гранулятора довольно низкая, а сила сжатия — небольшая. Поэтому для заготовки топлива понадобится немало сил и времени.
Самостоятельная сборка гранулятора
Основу для гранулятора следует варить из железного листа или отрезка трубы. Каркас прибора состоит из двух частей: в одной гранулы формируются, в другой обрезаются.
Форма устанавливается к первой части таким образом, чтобы между стенками корпуса и формой остался небольшой зазор. В нижней части корпуса с помощью подшипников и муфты крепится редукторный вал.
Чтобы упростить процесс очистки, основу корпуса лучше сделать разъёмной, скрепив место соединения болтами. Сам аппарат прочно прикрепляют к раме из металлических уголков. Рядом с корпусом устанавливается двигатель, к которому нужно подключить вал.
Бесплатное отопление. Гранулятор. Изготовление комбикорма и пеллет.
Процесс изготовления альтернативного топлива
Когда станок для производства пеллет готов, можно приступать к работе.
Схема изготовления прессованного топлива такова:
- Подготовить сырьё. Для этого измельчить ветки, кору и прочие крупные фрагменты. Оптимальный вариант — использование дробилки. Этого этапа можно избежать, если удалось приобрести качественные мелкие опилки столярного производства, лузгу или жмых. Солома также не нуждается в дробилке, её режут специальными ножницами.
- Подсушить полученный материал. Его влажность не должна быть выше 9−15% от общей массы сырья.
- Смесь необходимо снова увлажнить. Если влажность материала будет ниже 8%, готовые пеллеты будут просто рассыпаться сразу после выхода из гранулятора.
- Засыпать массу в форму, включить двигатель, запустить пресс. При давлении смесь сцепляется, благодаря выделяющемуся из дерева лигнина (вещество содержится в растительных клетках и играет роль клея).
- Просушить готовые изделия.
Стоит иметь в виду, что на выходе пеллеты нагреты до 90 градусов и довольно хрупкие. Поэтому обращаться с ними нужно осторожно. Для просушки изделия раскладывают в проветриваемом помещении или на улице, прикрыв от прямого солнечного света. Следует беречь продукцию от дождя и снега.
Правила хранения пеллет
Хранить прессованное топливо рекомендуется в сухих сараях и подвалах, защищённых от случайного огня. Хотя сами пеллеты довольно инертны и к легковоспламеняющимся веществам не относятся, внезапно загоревшееся топливо погасить будет сложно. Общая температура помещения значения не имеет.
Если пеллетное топливо хранится на улице, обязательно нужно прикрыть его листами шифера, тепличной плёнкой, рубероидом или другим влагонепроницаемым материалом. Необходимо следить, чтобы гранулы не соприкасались с землёй.
Очень удобно сложить пеллеты в мешки весом 20 или 10 кг каждый и убрать в подходящее место. Так топливо займёт совсем немного места, а если было изготовлено для продажи, его будет удобно отпускать покупателям.
Если сделать станок для производства пеллет своими руками, можно наладить изготовление альтернативного топлива на дому. Такое производство довольно трудоёмкое, но экономически выгодное.
Пеллеты из опилок и соломы как бизнес идея
oventilyacii.ru
Пеллеты своими руками — Делаем гранулятор для производства пеллет!
Делаем пеллеты своими руками: Инструкция по изготовлению пеллет
Для топки дровяных печей и каминов, а также твердотопливных котлов в последние годы используют не только дрова, но и прессованные гранулы или брикеты из отходов деревообработки – пеллеты. В отличие от сжигания дров, наносящего вред экологии, использование пеллет решает проблему утилизации опила, щепы, коры древесины, и позволяет получить высокоэффективное и экологически чистое топливо.
Пеллеты своими руками
Брикеты промышленного производства имеют низкую остаточную влажность, хорошо разгораются, длительно поддерживают горение и не вызывают появления копоти, нагара и сажи, что особенно удобно при топке камина. Однако, цена их сопоставима со стоимостью сухих березовых дров. Поэтому при наличии больших объемов древесных отходов целесообразно сделать установку для изготовления пеллет своими руками.
Оборудование для производства пеллет
Пеллеты делают из опила, щепы, коры деревьев, а также из отходов сельскохозяйственной деятельности – жмыха, лузги, соломы. Сырье предварительно измельчают до размера частиц 3-5 см, просушивают в сушилках до влажности 15%, после чего помещают в дробилку мелкого дробления. Полученную массу с величиной фракции не более 2 мм загружают в пресс, где сырье прессуется. На выходе из пресса получаются гранулы с влажностью не более 12%, размер гранул зависит от конструкции оборудования. Гранулы собирают в мешки, укупоривают и используют для розжига и топки печей и котлов.
Таким образом, для самостоятельного изготовления пеллет понадобится такое оборудование:
- Дробилка или измельчитель древесины. Если в качестве сырья вы планируете использовать опилки или лузгу, этот этап производства можно пропустить. Для использования обрезков пиломатериалов, веток, коры, некондиционной доски дробление является обязательным этапом.
- Сушилка для сырья барабанного или аэродинамического типа. Сушилку можно изготовить своими руками из металлической бочки.
- Дробилка мелкого дробления, в которой происходит измельчение крупного сырья до состояния опилок.
- Пресс для пеллет или гранулятор с плоской или цилиндрической матрицей. Применение гранулятора исключает необходимость мелкого дробления сырья, так как в нем происходит одновременное перемалывание и прессование гранул.
Наиболее рациональным выходом для домашнего производства пеллет можно считать использование гранулятора с матрицей плоского типа – этот вид оборудования можно сделать своими руками, не прибегая к покупке дорогостоящих комплектующих. Измельчитель и дробилка в этом случае вам не понадобятся, а необходимость в сушильной камере зависит от влажности сырья.
Требования к сырью
Как уже говорилось, основным параметром, от которого зависит качество получаемыхпеллет – это влажность исходного сырья. Для изготовления гранул, хорошо удерживающих форму и горение, нужна измельченная древесина с влажностью 12-15%. Достичь такой влажности можно двумя путями: использовать опилки и щепу от высушенной древесины или досушивать сырье в сушильном барабане.
Из древесных отходов наиболее популярны опилки хвойных пород – благодаря высокому содержанию смолы и лигнина, гранулирование происходит быстрее, а готовые пеллеты лучше держат форму. В сырье не должно содержаться крупных включений, посторонних предметов, металлических деталей. Для этого его необходимо не только просушить, но и просеять.
Конструкция гранулятора для пеллет
Гранулятор – это емкость с установленной внутри плоской или цилиндрической матрицей. Цилиндрическая матрица – это перфорированный барабан, внутри которого вращаются катки. Уплотненная масса с помощью катков вдавливается в прессовальные каналы – отверстия в барабане, и после прессования гранул и выхода их с внешней стороны срезается ножами.
Схема гранулятора для пеллет
Гранулятор с плоской матрицей работает по тому же принципу, но матрица в нем представляет собой перфорированный диск, жестко закрепленный на валу. При вращении матрицы катки аналогичным образом спрессовывают сырье и вдавливают его в отверстия в диске. Прессовальные каналы имеют форму сужающийся к выходу конус, что позволяет максимально уплотнять гранулы. Диаметр отверстий обычно не превышает 8-10 мм.
Для установки по прессованию пеллет можно взять готовую матрицу и катки – их продают в качестве запчастей производители грануляторов для комбикорма, а можно изготовить самостоятельно из листового металла толщиной не менее 20 мм и подходящих шестерен, закрепленных на валу.
Приводом для гранулятора обычно служит электродвигатель мощностью не менее 15 кВт, и редуктор. Частота вращения матрицы должна находиться в пределах 60-100 оборотов в минуту. Вал, на котором закреплена плоская матрица, может быть ориентирован как вертикально, так и горизонтально, при этом необходимо предусмотреть емкость для загрузки сырья и выгрузки готовых гранул.
Технология изготовления гранулятора
- Изготовление матрицы. Если вы решили изготовить матрицу самостоятельно, вам понадобится заготовка в виде диска толщиной не менее 20 мм. При меньшей толщине матрица быстро деформируется. Диаметр матрицы может быть любым, от него зависит производительность. Так, при диаметре 50 мм и двигателе 25-30 кВт вполне можно получать 300-350 кг пеллет в час. Для меньших объемов достаточно матрицы 25-30 см в диаметре. В центре диска сверлят отверстие по диаметру вала редуктора и выполняют паз для жесткой посадки. Отверстия для прессования и выхода гранул выполняют в виде конуса.
Матрица для гранулятора
- Шестерни или ролики для катков подбирают так, чтобы их ширина соответствовала рабочей зоне матрицы. Шестерни надевают на вал, который впоследствии будет закреплен перпендикулярно оси выходного вала редуктора с помощью муфты.
Шестерни для катков
- По размерам матрицы сваривают цилиндрический корпус гранулятора из трубы или листового металла. Корпус состоит из двух частей: в верхнюю загружают сырье, и после прохождения через систему роликов и матрицы готовые гранулы попадают в нижнюю часть корпуса, откуда по лотку высыпаются в подготовленную емкость.Матрица должна свободно вращаться внутри верхней части корпуса, при этом зазор должен быть минимальным.В нижней части корпуса делают отверстие для выхода готовыхпеллет, к нему приваривают лоток из трубы или листового металла.
Корпус для гранулятора
- Выходной вал редуктора закрепляют в нижней части корпуса гранулятора с помощью муфты и подшипников.
Выходной вал редуктора
- Для удобства чистки и обслуживания верхнюю и нижнюю часть корпуса выполняют разъемными с соединением на болты через приваренные ушки. Устанавливают матрицу и ролики в корпус.
Крепим верхнюю и нижнюю часть гранулятора для пеллет болтами
- Гранулятор устанавливают на раму, сваренную из уголка или швеллера, жестко закрепляя на ней. Крепят электродвигатель и подсоединяют его выходной вал к редуктору.
Устанавливаем гранулятор на раму сваренную из швеллера
- Раму и все детали гранулятора с внешней стороны окрашивают краской по металлу. Подключают двигатель в электросети и выполняют пробный запуск.
Процесс изготовления пеллет с помощью гранулятора
Гранулятор с матрицей плоского типа для изготовления пеллет, сделанный своими руками, способен решить проблему отопления дома площадью до 150 квадратных метров. Полученные гранулы можно использовать как для сжигания в печи или камине, так и для твердотопливных котлов. При этом вам не придется задумываться об утилизации отходов переработки древесины и сельскохозяйственного сырья.
Возможно вас заинтересует: Для того чтобы ремонт пищевого оборудования вам обошелся не дорого, обращайтесь к нам.
www.a-t.com.ua