Горячая объемная штамповка и холодная штамповка деталей из листового металла
Горячая объемная штамповка представляет собой процесс намеренного деформирования нагретой заготовки из разного рода металла для изменения ее размеров и конфигурации.
Причем, геометрические характеристики изделия при этом меняются в нескольких измерениях, а не в одной плоскости. Технология нашла применение во многих отраслях промышленности и имеет весьма обширные перспективы для дальнейшего развития и совершенствования.
Содержание
- В каких областях промышленности технология нашла применение?
- Разновидности объемной штамповки
- Технологические схемы штамповки
- В закрытых штампах
- В открытых штампах, имеющих переменный зазор
- Инструменты и оборудование
- Подведем итог
В каких областях промышленности технология нашла применение?
Горячая объемная штамповка ‒ вид обработки металлозаготовок с помощью давления, который подразумевает использование специального инструмента, штампа, для формообразования поковки из разогретой заготовки.
Поверхности полостей и выступов отдельных частей штампа при этом ограничивают течение металла, поэтому в итоге операции происходит образование единственной замкнутой полости по конфигурации поковки. Такую полость называют ручьем.
Для данного вида обработки необходимы специальные штамповочные заготовки. Их изготавливают с применением проката профилей разных форм путем разрезания прутков на отдельные изделия кривошипными пресс-ножницами, механическими пилами, газовой резкой и т.п.
Горячая объемная штамповка.Достоинства такой технологии при сравнении заключается в следующем:
- высокие показатели производительности;
- более высокая точность изготовления деталей: допуски при штамповании поковок в 3 раза меньше, нежели при ковке.
Основными недостатками технологии являются дороговизна инструмента и его узкая направленность: конкретный штамповочный станок подходит для создания поковки одной формы и размера.
Помимо этого, для осуществления объемной горячей штамповки поковок потребуется в несколько раз больше усилий деформирования, нежели для ковки аналогичных поковок.
На заметку! Крупными называют поковки с массой в несколько сот килограммов, но они используются в редких случаях. Еще реже можно встретить изделия с массой 2-3 тонны. Наиболее распространенные формы имеют массу от 20 до 30 кг.
Технология активно применяется на производственных предприятиях металлообрабатывающей промышленности, которые имеют дело с алюминиевыми сплавами, латунью.
С помощью горячей штамповки прессом изготовляются заготовки для деталей легковых автомобилей, тракторов и других видов сельскохозяйственных машин, самолетов, железнодорожных вагонов, станков и т.п.
С учетом тенденции к росту серийности в машиностроении штамповка в будущем приобретет еще большую популярность и развитие.
https://youtu.be/0-1fp3iKrT4
Разновидности объемной штамповки
Существуют разные виды объемной штамповки: и горячая. Первая технология менее распространена, нежели горячая, так как для нее не требуется очень мощное оборудование.
Помимо этого, стоит отметить склонность большинства сталей и сплавов поддаваться обработке именно в горячем состоянии. Поэтому именно горячий вид штамповки и ковки предпочтителен для множества предприятий металлургической отрасли, которые предполагают изготовление изделий из листов металла.
Но и свои достоинства у холодной технологии создания поковок из металла присутствуют:
- в процессе работы не происходит нагревание металла;
- металлическая поверхность не окисляется при контакте с кислородом;
- можно изготовить изделия с более точными параметрами;
- низкие показатели шероховатости металлической поверхности;
- низкий расход металла;
- низкая трудоемкость производства изделий.
Отметим! При холодной объемной штамповке изделиям не нужна финишная обработка.
Горячий метод штамповки поковок отличается:
- высокими показателями производительности;
- отменной однородностью и прочностью готовых поковок;
- возможностью получения поковки сложной формы;
- высокой автоматизации рабочих процессов.
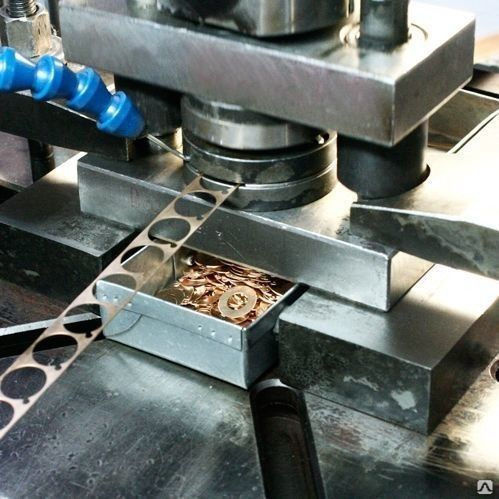
Различают разные способы горячей объемной штамповки, в зависимости от типа примененных штампов:
- открытая;
- закрытая;
- выдавливанием;
- прошивкой;
- в разъемных матрицах.
Именно такая классификация считается основной, потому что тип использованного в работе штампа является определяющим фактором для характера течения металла при формообразовании поковки.
Благодаря использованию технологии обработки металлов данным методом можно изготовить разнообразные по геометрическим параметрам поковки:
- Детали удлиненной формы: рычаги, шатуны. Для их производства потребуется штамповочный пресс.
Исходную заготовку поддают протягиванию и обрабатывают плашмя. В конце работы деталь фасонируют при помощи ковки. - Дисковые детали квадратной, круглой формы и небольшой длины: ступицы, шестеренки, фланцы, крышки.
Изготавливаются с помощью технологии осадки в торец заготовки. А их использование осуществляется с применением штамповочных переходов.
Путем штамповки крайне сложно изготовить абсолютно точные по размеру поковки, по этой причине существует такое понятие как допуски. Они учитывают недоштамповку изделия по высоте, износ ручья штампов, риск сдвига штампов в процессе использования и т.п.
Если допуски обуславливают чистоту поверхности и точность поковки, что удовлетворяет общим требованиям к конечным результатам работы, то в дальнейшем иных припусков не предполагают.
Если же предполагаемые заранее допуски или чистота поверхности металла на деле оказались неудовлетворительными, стоит рассмотреть возможность получения более точных параметров поковок путем калибровки, чеканки, улучшения качества самого процесса и нагрева.
Если же это решение не позволяет решить вопрос, то назначаются припуски для последующей обработке путем резки.
Технологические схемы штамповки
Станок горячей штамповки металла функционирует с применением специальных рабочих схем. С их помощью выполняется ковка и штамповка различных металлических изделий. Исходя из характеристик примененной рабочей схемы, можно определить будущие параметры готовой поковки.
Классифицировать такие схемы можно по типу задействованных в работе штампов:
В закрытых штампах
Штамповка заготовки.Полость штампа в процессе деформации закрыта, поэтому зазор между подвижной и неподвижной зонами минимален. Особенности устройства штампа закрытого типа определяет вид штамповочного станка.
В большинстве случаев верхняя часть штампа характеризуются выступом, а нижняя – представляет собой полость. Также можно встретить обратную ситуацию.
Применение подобных изделий на практике должно осуществляться с тщательной подготовкой и четким контролем над идентичностью объемов поковки и заготовки.
Несоблюдение данных требований может привести к частичному заполнению углов полости металлом, если его будет недостаточно.
Также проблемы могут возникнуть с высотой поковки при работе горячим методом: если металла будет чрезмерно много, высота поковки получится больше, чем запланировано. Чтобы штамповка проходила по оптимальной схеме, важно отрезать заготовки с максимальной точностью.
В открытых штампах, имеющих переменный зазор
В него вытекает определенный объем металла, что позволяет заполнить рабочую полость поковки в полной мере. Помимо этого, облой заполнится излишками металла на конечной стадии работы, что снизит запрос к точности заготовок по весу.
Холодная и горячая штамповка с применением таких изделий осуществляется в четыре стадии: осадка заготовки, совмещение стеночек изделия с заготовкой, вытекание лишнего металла в канавку при обжатии, удаление избыточного металла из полости.
Достоинством штампов для горячей штамповки является возможность произвести любой вид поковок.
Закрытые штампы также характеризуются определенными преимуществами:
- Более благоприятная структура поковок.
В данном случае не происходит перерезания волокон в облой в точке вытекания металла. Они обтекают поковочный контур, что позволяет достигнуть уникальной точности поверхности деталей без каких-либо видов шлифовки; - Отсутствие облоя при такой схеме.
Это позволяет значительным образом снизить расход металла. - Наличие возможности работать с малопластичными сплавами, характеризующимися высоким уровнем деформации под высоким напряжением неравномерного всестороннего сжатия.
Инструменты и оборудование
Штамповочное производство холодным и горячим методами требует наличия ряда инструментов и приспособлений. Применяемое для штамповки оборудование условно делится на основное и вспомогательное.
К первой группе инструментов причисляют штампы, разделяющиеся, в свою очередь, на ковочные для изготовления изделий и обрезные для ликвидации заусенцев после штамповки.
Все они предназначаются для создания исключительно заданной детали, но иногда можно встретить и варианты со съемными частями и блоками, которые позволяют выполнить переналадку.
Штамповочный инвентарь для горячей технологии производится из высококачественной легированной инструментальной стали, потому что на изделия в процессе эксплуатации оказывается высокое механическое давление и термическая нагрузка.
Но это довольно дорогой материал, поэтому для экономии денежных средств штампы производят со вставками из более дешевых металлов.
Холодная штамповка металла предполагает использование оборудования, работающего при высоких удельных нагрузках и обеспечивающего высокую точность форм и размеров изделий. Оно характеризуется высокой производительностью и увеличенным рабочим ходом, так как обладает высокой жесткостью конструкции.
Kо второй группе инструментов и приспособлений для осуществления штамповки относят:
- приспособления, позволяющие осуществить доставку и загрузку металла в печь, его подачу от печи к молоту и передачу заготовок от одного молота к последующему;
- инвентарь для подачи заготовок под штамповочный пресс с их последующим перекладыванием из одного ручья штампа в другой;
- инструменты для удаления поковки из штампов после изготовления;
- измерительные приборы и шаблоны для осуществления периодического контроля отштампованных поковок.
На заметку! В конструкции штампа необходимо иметь такие эксплуатационные параметры, чтобы она позволяла менять форму заготовки согласно конкретным требованиям, прочно фиксировалась на оборудовании, предоставляла возможность сохранить точность ее установки и комфортабельную транспортировку.
Для обработки деталей из металла методом горячей объемной штамповки потребуется следующее оборудование:
- молотовые штампы;
- горячештамповочные кривошипные прессы;
- горизонтально-ковочные агрегаты.
Самые распространенные варианты сегодня ‒ это паровоздушные молоты с двойным действием и простые приводные фрикционные молоты. Они работают за счет ударно-деформирующего воздействия на металлозаготовку.
Высококачественное перераспределение металла можно обеспечить при условии одновременного регулирования хода подвижных деталей и силы удара в сочетании с кантованием заготовки. Отметим, что молоты причисляются к категории довольно недорого штамповочного оборудования.
Также при горячем штамповании часто используются кривошипные прессы с жестким приводом, не позволяющим изменять направление ползуна.
Изготовленные с помощью прессов поковки отличаются большей точностью за счет жесткого хода. Это сводит к минимальной вероятности риск появления припусков на механическую обработку.
Недостаток такого оборудования заключается в необходимости проводить предварительную очистку заготовки от окалины, иначе она вжимается в тело поковки.
При соприкосновении разогретого металла со стеночками пресса происходит остывание заготовки из-за большого количества времени, потраченного на процесс деформации.
Подведем итог
Горячая и холодная штамповка – технологии, активно задействованные на предприятиях металлургической промышленности, в машино- и авиастроении и в иных производственных сферах при изготовлении разного типа деталей из стали и цветных металлов.
При этом горячая листовая штамповка встречается чаще, нежели холодная, так как позволяет работать практически со всеми металлами, и в том числе низкоплавкими.
Горячая объемная штамповка и сущность процесса
Метод горячей объемной штамповки использует одно из основных физических свойств металлов — пластичность. Это свойство металлического поликристалла изменять свои размеры при приложении к нему усилия.
Горячая объемная штамповка
Пластичность растет с повышением температуры, поэтому для изготовления сложных объемных деталей заготовки нагревают.
Таким способом изготавливают детали самой разнообразной формы — от деталей часов до колесных дисков автомобиля.
Содержание
Процесс горячей объемной штамповки
Метод заключается в том, что при приложении высокого давления металл горячей болванки подвергается серии последовательных деформаций, и, не нарушая своей целостности, затекает в свободное пространство специально подготовленных штампов, повторяя их пространственную форму и приходя к заданным размерам. Выступы и впадины в соответствующих локальных областях штампа ограничивают и направляют движение металла, приближая с каждым проходом конфигурацию и габариты болванки к параметрам конечного изделия. При последнем рабочем проходе они формируют замкнутый единый ручей (полость), совпадающий с конфигурацией готового изделия.
Технологический процесс горячей объемной штамповки
Термин горячая объемная штамповка металла указывает на то, что габариты и геометрия заготовки меняются не в одном, а в двух или трех измерениях.
Горячая штамповка в качестве болванок использует круглый или прямоугольный прокат, а также горячекатаный лист. Горячая объемная штамповка проводится и прямо из прутка, если конфигурация детали не очень сложная и достаточно одного-двух проходов. Впоследствии отдельные детали отрубают от прутка.
По своей форме конечные поковки подразделяют на два основных класса:
- Дисковые: фланцы, крышки, ступицы, прочие круглые (прямоугольные) поковки с длиной, малой относительно диаметра.
Здесь выбирают базовую технологическую схему осадки в торец исходной болванки.
- Удлиненные: рычаги, валы, шатуны и похожие на них по конфигурации детали. Болванка располагается на штампе плашмя, и в ходе нескольких черновых и штамповочных операций ей придают окончательную форму. До завершающего прохода исполняют формовку в ручьях и на вальцах.
По технологическим схемам активно применяются две наиболее употребительных:
- штамповка в закрытых штампах
- штамповка в открытых штампах
Горячая объемная штамповка в закрытых штампах осуществляется в штампе с небольшим зазором между его половинами. Подразумевается, что объемы заготовки и готового изделия совпадают. Эту оснастку снабжают двумя поверхностями разъединения, находящимися под некоторым углом. Схема используется в производстве сравнительно несложных по своей форме деталей и позволяет добиться наибольшей однородности внутреннего строения детали и меньшей шероховатости.
При применении схемы горячей объемной штамповки в открытых штампах нет точного соответствия объемов между заготовкой и конечным изделием, происходит активное перераспределение массы металла между частями поковки. Часть металла выдавливается за пределы штампа в специальную канавку и называется облоем. Схема позволяет штамповать детали практически любой конфигурации, поскольку позволяет проводить большое количество черновых и завершающих проходов с промежуточным кантованием болванки.
Преимущества и недостатки процесса
Горячая объемная штамповка обладает такими достоинствами, как:
- Изготовление поковок весьма сложной формы.
- Снижение потерь материалов.
- Снижение удельной трудоемкости.
- Нет необходимости в высокой квалификации штамповщика.
- Точность соблюдения габаритов и конфигурации.
К минусам метода горячей объемной штамповки относят
- Сложность операций
- Значительная энергоемкость
- Существенная стоимость и трудоемкость проектирования и изготовления оснастки. Штамп приходится делать из высококачественных материалов, и применим он только к данному изделию.
- Необходимость использовать большее усилие, чем при ковке
- Лимит веса готового изделия до 3-4 тонн.
Преимущества и недостатки
В целом горячую объемную штамповку имеет смысл применять при выпуске средних и больших серий, а также, если сложность формы и толщина детали не допускают применение обойтись холодной формовкой.
Технологический процесс горячей объемной штамповки охватывает множество подготовительных и рабочих операций, от поступления материала и до получения конечного изделия.
Схема горячей объемной штамповки
Проработка технологии включает такие этапы, как:
- Определяется схема горячей объемной штамповки — в открытых штампах или закрытая, выпускается конструкторская документация.
- Определяют переходы процесса, с учетом допусков выставляют размеры болванки.
- Исходя из потребного усилия горячей объемной штамповки выбирают оборудование (пресс, молот, и т. д.).
- Проектируются штампы.
- Задается метод нагревания и температурно-временной режим для каждой операции.
- Определяются отделочно-завершающие операции.
- Определяются технико-экономические характеристики проектируемого техпроцесса.
Горячая объемная штамповка требует от технологов, конструкторов и цехового персонала глубоких знаний по материаловедению и обширного практического опыта работы с данным процессом.
Сам процесс горячей объемной штамповки разделяется на следующие этапы:
- Нарезка проката на болванки,
- Доведение заготовок до рабочей температуры
- Штамповочные операции
- Удаление облоя
- Коррекция формы (при необходимости)
- Термообработка
- Удаление окалины
- Калибровка,
- Прием службой технического контроля.
Смазка для процесса горячей объемной штамповки
До подачи на штамп болванки требуется полностью и равномерно прогреть. На современных предприятиях этим процессом управляет автоматика, обеспечивая заданных график повышения температуры, равномерное прогревание всех заготовок по всему их объему и исключение образования оксидных пленок и зон пониженного содержания углерода. В качестве нагревателей применяют:
- электроконтактные установки. Нагрев осуществляется путем включения болванки в электрическую цепь и прохождению по ней сильного тока.
- индукционные системы. Нагрев производится вихревыми токами, возбуждаемыми в приповерхностном слое заготовки;
- газовые печи. Повышение температуры проходит в изолированной от атмосферы камере, заполненной инертным газом, исключающим образование окалины.
Удаление облоя и пробивка пленок применяется в случае открытой схемы горячей объемной штамповки. При этом используют специальные обрезные и пробивные штампы и кривошипные прессы.
Иногда в ходе выемки изделий из штампа, обрубки облоя или термообработки происходит искривление осей изделия либо нарушение поперечных сечений. Тогда применяют операцию коррекции формы, или правку. Заготовки больших размеров либо изготовленные из высококачественных сталей подвергаются правке, будучи горячими. Операция проводится в чистовом ручье после удаления облоя. Иногда операцию правки совмещают с обрезкой. Изделия небольшого размера корректируют винтовыми прессами по окончании термообработки и остывания.
Термообработка в горячей объемной штамповке
Термообработку проводят с целью доведения физических свойств изделий до заданных параметров и для облегчения финальной обработки. Операция позволяет также снять остаточные напряжения, уменьшить зернистость, повысить вязкость и пластичность.
Объемная штамповка
Чтобы упростить операции контроля, обеспечить прецизионное позиционирование болванки и снизить износ инструмента на стадии механической обработки, проводят очистку изделий от окалины. Для этого применяются дробеструйные комплексы. В изолированной камере поковки воздухом под большим напором разгоняют стальную дробь и направляют ее на движущиеся, на транспортере изделия. Многочисленные соударения сбивают пленки и хлопья окислов в поверхности, придавая ей матовый внешний вид и одновременно уплотняя приповерхностный слой. Для мелких изделий применяют другую установку — галтовочный барабан. В нем большое количество деталей пересыпается вместе с добавляемыми к ним металлическими шариками или звездочками. Благодаря многочисленным соударениям деталей с них сбивается окалина.
Иногда в последовательность добавляют еще один переход — калибровку. Она проводится с целью избежать финишной обработки, оставляя только шлифовку. Посредством плоскостной калибровки достигают точности габаритов по вертикали. Объемная калибровка служит для доведения габаритов в нескольких направлениях, позволяя также и снизить шероховатость. Для калибровки используют специальные штампы с особо точными ручьями, повторяющими конфигурацию поковки.
Штамповочные ручьи и их виды
Для простых конфигураций изделий горячая объемная штамповка выполняется за один проход.
Штамповочные ручьи и их виды
Если же предстоит отштамповать замысловатое изделие с перепадами толщин и высот, выступы и изгибы — изготовление проводят за несколько проходов, в каждом из которых формовка делается отдельной впадиной на штампе — ручьем. Их подразделяются на два вида:
Заготовительные
Используются для фасонирования приведения материала болванки к пространственной конфигурации, позволяющей провести операции горячей объемной штамповки с минимальными потерями материала.
Заготовительные ручьи
Виды заготовительных ручьев:
- Протяжной — растягивает определенные части болванки, сужая их сечение. Применяется серия несильных ударов с переворотом болванки
- Податной — утолщает сечение болванки, «перегоняя» на это место материал с соседних участков. Применяется также серия несильных ударов с переворотом болванки
- Пережимной — плющит болванку в месте применения, вызывая увеличение местной ширины.
Используется 1-3 сильных удара,
- Гибочный – используется для деталей с выгнутой осью
- Осадочный — применяется для изделий, близких к круглой форме. Уменьшает высоту болванки, добиваясь нужной высоты и радиуса
Штамповочные
Используются в завершающей формовке, бывают черновыми и чистовыми.
Черновой используется для изделий сложной конфигурации и в целях снижения износа чистового. Предназначен для приближения габаритов и конфигурации болванки к окончательному изделию. Он глубже и уже, чем чистовой ручей, обладает большими радиусами и уклонами. Эти меры применяются для свободного размещения болванки в чистовом ручье.
Штамповочные ручьи
Чистовой ручей используется для формовки конечной продукции, изготавливается с припуском на усадку при охлаждении. Устанавливается в середине штампа, поскольку давление и возникающие напряжения при чистовой штамповке максимальны. Для отвода выдавливаемого металла вокруг ручья расположена облойная канавка.
Схемы штамповки
Конкретная конфигурация горячей объемной штамповки выбирается опытным технологом, принимающим во внимание следующие параметры:
- Размеры детали.
- Материал.
- Форма.
- Доступное оборудование.
- Лимиты трудоемкости и материальных затрат.
На текущий момент применяется две основные схемы горячей объемной штамповки:
- с открытым штампом;
- с закрытым штампом.
Штамповка в закрытом штампе проводится с небольшим зазором между его половинами. Подразумевается, что объемы болванки и конечной детали точно совпадают. Иногда делают две линии примыкания, находящиеся под углом друг к другу. Схема используется для формовки сравнительно несложных по конфигурации поковок и позволяет добиться наибольшей однородности внутреннего строения детали и меньшей шероховатости.
Схема штамповки в закрытых штампах
При применении схемы горячей объемной штамповки в открытых штампах нет соответствия объемов болванки и конечного изделия, происходит активное перераспределение массы металла между ее частями. Некоторая часть металла выдавливается за пределы штампа в приспособленную для этого канавку и называется облоем. Схема позволяет штамповать детали практически любой конфигурации, поскольку позволяет проводить большое количество черновых и завершающих проходов с промежуточными поворотами болванки.
Оборудование, используемое для горячей объемной штамповки
Оборудование для горячей объемной штамповки включает в себя:
- Молоты
- Кривошипные прессы
- Горизонтально-ковочные машины
Технология применения каждого класса установок связана с их конструкцией. Молоты допускают такие схемы, как открытая штамповка и штамповка в закрытых штампах
Горячая объемная штамповка на молотах
Технология использует явление преобразования кинетической энергии падающего массивного молота в энергию ударной деформации заготовки. Молоты поднимаются в исходное состояние сжатым воздухом или паром и имеют массу от 0.5 до 25 тонн.
Горячая объемная штамповка на молотах
Изменяя высоту подъема молота, можно регулировать силу удара. Ход молота также регулируется, это дает возможность для поворота заготовки во время очередного подъема молота и более точной штамповки. Доступны все подготовительные операции, включая протяжку и подкат.
Точность изготовления деталей на молотах оставляет желать лучшего, что объясняется неминуемым сдвигом частей штампа друг относительно друга в момент удара. Допуски при использовании молотов приходится давать большими, а для обеспечения возможности выемки изделий из пресса делаются большие штамповочные уклоны.
Горячая объемная штамповка на прессах
Горячая штамповка металла проводится и на кривошипных прессах. Главная характеристика оборудования — это развиваемое им усилие, варьирующееся от 6 до 110 МН.
Горячая объемная штамповка на прессах
Конструкция кривошипного горячештамповочного пресса имеет жесткий привод и не дает возможности регулировать ход пресса и его усилие. Эти факторы исключают из перечня допустимых операций протяжку и подкат, поскольку для них нужно постепенно увеличиваемое давление.
Отсутствие ударов, постоянный ход штампа и использование направляющих исключает сдвиг, что позволяет добиться точности обработки, принципиально недостижимой на молотах.
Соответственно допустимо задание существенно меньших допусков, штамповочных радиусов и уклонов, что снижает потери материалов и повышает производительность оборудования.
Кроме того, статическая деформация глубже проникает в болванку, чем динамическая, и это делает доступными для обработки материалы с низкой пластичностью.
Отрицательными особенностями кривошипных горячештамповочных прессов являются:
- окалина запрессовывается в поверхность, для борьбы с этим применяют нагрев в инертной атмосфере или глубокую зачистку болванки;
- ввиду продолжительного соприкосновения с пуансоном болванка остывает, снижается ее пластичность и заполняемость.
Штамповка на горизонтально-ковочных машинах
При горячей объемной штамповке этим методом, установка также приводится в действие кривошипным механизмом, главное деформирующее усилие прикладывается по горизонтали. В дополнение к этому применяется еще один ползун, размещенный под прямым углом. Матрица соответственно также составлена из двух частей, одна из которых является подвижной.
Штамповка на горизонтально-ковочных машинах
Доступны такие переходы, как высадка, прошивка и пробивка. Для штамповки стержней, колец, труб с утолщениями и отверстиями в качестве заготовок применяют круглый или квадратный пруток.
Эти специализированные устройства позволяют добиваться существенного повышения эффективности. В качестве минусов можно отметить узкую применимость и дороговизну.
Горячая штамповка металла и ее технология
Штамповка горячим способом металлической заготовки способствует ее деформации в нагретом состоянии, чтобы придать соответствующую форму изделию. Эти технологии применяются в тяжелом машиностроении, и они по-своему уникальны.
- Суть технологии
- Выбор технологии
- О схемах штампов
- Применяемое оборудование
- О работе механизмов
Суть технологии
Горячая штамповка металла заключается в нагревании изделия и давлением заданного штампа формируется деталь. При этом изменение температурного режима производится до состояния, который бы образовался при ковке.
Чтобы не было вытекания металла, в конструкции штампа предусматриваются специальные полости в виде выступов. Так формируется поверхность в виде ручья соответствующая замкнутому типу, а конфигурация выполненного изделия соответствует его форме.
Исполнение горячей штамповки производиться из разнопрофильных брусков сечения: прямоугольного, квадратного или круглого. В исключительных случаях технологический процесс штамповки изделий выполняется из прутка. Для начала производят поковку с заданными размерами, а после ее делят на части. Заготовки для штампов выполняют обычно из металлического прутка.
Эффективность технологического процесса заключается в том, что ее можно применять в производстве серийных заготовок.
При применении этой технологии предприятия имеют множество преимуществ:
- Снижается процент образования металлических отходов.
- Производительность труда растет.
- Возможность выполнения сложных конструктивных элементов.
- Обеспечение точности геометрических размеров.
- Заготовки отличаются высоким качеством поверхности.
Технология изготовления детали объемной штамповкой следующая:
- резка заготовки в размер;
- нагревание в печи;
- 1 переход;
- 2 переход;
- 3 переход;
- устранение облоя и обработка металла.
По технологии штамповки выполняется огромный перечень действий от загрузки болванки в обрабатываемую зону, завершая изыманием из печи. Алгоритм подразумевает выполнение работ:
- Штампы используются с закрытым или открытым ручьями.
- Выполнить конструкторскую документацию на разработку поковки.
- Продумать за какое количество переходов выполняется заготовка.
- Выбрать подходящее оборудование, продумать, какие использовать штампы.
- Произвести нагрев поковки, выбирая способ нагрева штампа и режимов работы оборудования.
- Исходя из требований качества обработки детали, произвести оценку, какие завершающие операции проводить.
- Подсчитать технико-экономические показатели заданного техпроцесса.
По отношению к ковке метод горячего штампования обладает своими достоинствами и недочетами:
№ п/п | Достоинства | Недостатки |
1. | Высокая производительность трудового процесса | Лимиты по массе получаемых деталей и заготовок, не более — 3,5 тонн |
2. | Качество обрабатываемой поверхности, допуском и припусков почти в 4 раза меньше; при выполнении калибровки получаемые допуски составляют 0,05 мм, поэтому мехобработке подвергаются лишь места сопряжений со смежными изделиями, а остальных поверхностей достаточная шероховатость и точность | Деформация выше, исходя из этого, используется мощное оборудование, это происходит, потому что деформации подвергается заготовка полностью, при этом течь металла подвергается сопротивлению, создаваемого стенками штампа |
3.![]() | Возможность получения конструктивных элементов сложной конфигурации | Достаточно высокая цена оборудования, так как оно сложное и выполняется из качественного материала, а применяется лишь для изготовления одного вида изделия |
4. | Простота выполняемых операций, для этого необязательно иметь большой стаж работы, программа обучения штамповщика несложная |
Для горячей штамповки металла применяется несколько известных технологий, зависимых от следующих параметров:
- выбора оборудования;
- геометрических размеров;
- материала заготовки.
Выбор технологии
По выбранной технологии можно производить несколько типов деталей:
► Удлиненные — к ним относятся рычаги, валы, воротки и иные. Обработка производится плашмя при использовании штамповочного пресса. Последним этапом этой работы является фасонирование, исполняемое в заготовительных вальцах для ковки.
► Дисковые – к ним относятся кольца, диски, шестерни, крышки и иные изделия. При выполнении данной операции используется метод осадки, производимый в торец заготовки. Для этого процесса применяются штамповочные переходы.
Таблица типовых изделий для разной формы поковок с подробным описанием:
№ п/п | Краткое описание характеристики | Типовые изделия |
Изделия удлиненной конфигурации | ||
1. | Прямая ось | Балки, валы, втулки, шатуны |
2. | Изогнутые по оси | Рычаги, предназначенные для рулевого управления |
Симметричные | ||
1. | Круглые изделия | Фланцы, шестеренки и ступицы |
2. | Квадратные и многоугольные | Гайки, фланцевые соединения и ступицы |
3. | Изделия, имеющие отростки | Типа вилки и крестовины |
Иные изделия | ||
1.![]() | Комбинированной формы | Коленвалы, поворотные кулачки |
2. | С количеством необрабатываемых поверхностей большего объема | Рычажные элементы для переключения передач, крюки для буксира и балки для параллельных осей |
3. | С внутренними отверстиями и заглублениями | Валы с полостями, шестеренчатые блоки и детали для фланцевых соединений |
► Штамповочные ручьи, которые в свою очередь подразделяются на:
- Протяжные (увеличивается длина отдельных элементов на обрабатываемой заготовки, именно по этой части производится нанесение ударов с кантованием детали).
- Заготовительные (выполнение фасонирования детали или равномерное перераспределение металлической массы с минимальными потерями).
- Пережимные (при этом одновременно уменьшается высота и увеличивается ширины обрабатываемой заготовки).
- Подкатные (диаметр отдельных участков увеличивается при распределении металла по оси заготовки).
- Гибочные (производится формирование поковки заготовки с изгибом по оси под 90 0).
► Разновидности штамповочных ручьев:
- Черновые – конфигурация обрабатываемого материала в большей степени приближена к форме поковки. К особенностям относятся увеличенная глубина, радиусы и уклоны по отношению к параметрам изделия, выполненного начисто.
- Чистовые – при приобретении требуемой формы увеличиваются размеры на ту величину, на которую увеличиваются усадки металлической заготовки. Металлопрокат располагают в центральной оси штампа, так как на его оказываются максимальные усилия.
О схемах штампов
► В производственном процессе применяются две схемы горячего штампования:
- Закрытого типа – по заданной технологии между частями штампа неподвижной и подвижной просвечиваются небольшие зазоры минимальны. Для исполнения изделий применяются прессы с выступом наверху рабочего инструмента, а внизу размещена полость. Или, напротив, на молотах при выступе снизу, в полости в верхней части используемого инструмента.
Этот способ применяется, когда объемы готового изделия и поковки соответствуют по параметрам. Штампы этой разновидности имеют одновременно две полости для разъема, расположенные под углом 900, относительно друг друга.
- Открытого типа – принцип их работы основан на том, что между неподвижной и подвижной частями обеспечивается зазор, в который выливается лишний металл. Их можно применять для поковок любого размера.
► Преимущества производства с использованием открытых типом штампов:
- Безупречное качество поверхности.
- Однородная структура материала.
- Экономия металла.
- Возможность применения материалов с невысокими показателями пластичности, так как воздействует высокое напряжение и обеспечивается неравномерность при сжатии.
Применяемое оборудование
Даже если обрабатываемый материал имеет мягкую структуру, использование оборудования для придания заданной формы обязательно. К этому оборудованию можно отнести:
- Гидравлические прессы.
- Гильотины.
- Кривошипно-шатунные механизмы.
Также нужно правильно выполнять расчеты по расходу материалов и выполнять чертежи, с учетом требований государственных стандартов.
Если рассматривать штамповочный станок, то в его состав входят следующие конструктивные элементы:
- исполнительный механизм, соответствующий типу станка;
- мотор для приведения оборудования в движение;
- передачи, обеспечивающей движение от одного механизма к другому.
Видео: горячая штамповка металла — автоматизированные линии.
О работе механизмов
► Кривошипно — шатунные прессы. Принцип действия его заключается во вращении привода, который, в свою очередь, преобразует движение в возвратно-поступательное на установленном ползуне. Детали технического устройства выполняются из стали прочной структуры с ребрами жесткости.
Движется ползун по заданному режиму, при этом на него воздействует усилие в 8000 т. Установки кривошипного типа, используемые на производствах, снижают себестоимость деталей, а также упрощают их изготовление. Экономия составляет около 30%. Станки подразделяются на: простые, с двойным действием или с тройным действием.
С помощью технического устройства можно выполнять следующие технологические решения:
- Производство штампованных деталей при открытых или закрытых матрицах.
- Исполнение заусенца.
- Выдавливание заготовок.
- Прошивку.
- Обработку одновременно несколькими способами.
Под воздействием одной ударной нагрузки механические прессы производят работу, но при ударе меньшей силой от гидравлического пресса получается лучшие эффект. В связи с этим гидравлику используют для крупногабаритных и толстостенных деталей.
► Гидравлические прессы. Завод — изготовитель выпускает оборудование для ковки, создания продавливающих усилий и проштамповывания поверхности. Переработка металлических отходов с их помощью тоже результативна. Принцип действия заключается в увеличении силы давления на изделие в несколько раз.
Выглядит пресс следующим образом: это два цилиндра, заполненные водой и между ними расположена труба. В каждом цилиндре находятся поршни, а основа принципа работы заложена на законе Паскаля.
► Радиально-ковочные механизмы. Заготовка располагается в модуле, в котором осуществляется нагрев по принципу индукции. После того как материал становиться мягким она подается на захват через конвейерный механизм непосредственно в зону обработки. В процессе приобретения нужной формы заготовка вращается, что обеспечивает ее равномерную обработку. Ковка детали осуществляется бойками.
Функционирование пресса производиться от мотора, присоединенного к клиноременным передачам. Их вертикальное размещение передает движение на боек и шатунный механизм. Для синхронности работы в устройстве расположены копирные барабаны. Червячные передачи приводят в работу держатель электромотором. Притормаживание движений осуществляется пружинной муфтой.
Republished by Blog Post Promoter
Виды штамповки металла
Штамповка металла — процесс контролируемой деформации, при котором тело меняет свою форму под воздействием избыточного давления. Благодаря такой обработке металлическим изделиям придают самые разнообразные формы, которые необходимы им для выполнения своих функциональных обязанностей. Штамповке поддаются детали небольшой толщины, так как сгибать толстую продукцию весьма проблематично.
Холодная штамповка металла
Существует два вида штамповки металлов: холодная и горячая. Первый вариант подразумевает обработку заготовки без ее предварительного нагревания. Этот метод дешевле с точки зрения промышленного производства, так как не требует затрат энергии на доведение металла до определенной температуры. Таким способом обрабатывают в основном тонкие листы, которые и без нагревания хорошо поддаются воздействию.
Процесс холодной штамповки листового металла разбит на несколько этапов, каждый из которых играет важную роль для получения конечного результата. На начальном этапе выполняется процесс уплотнения, который снижает пластичность металла, чтобы изделие лучше держало полученную в результате штамповки форму. Технологически процесс представляет собой прессование металлической заготовки под большим давлением.
На втором этапе производится отжиг изделий при температурах 550-620 градусов по Цельсию в специальных печах. Это позволяет провести процедуру рекристаллизации металлической решетки и внедрению в нее атомов углерода на молекулярном уровне, что позволяет значительно повысить прочность металла. Время отжига зависит от состава сплава и размеров обрабатываемых деталей. Когда подготовка окончена, изделие отправляется на пресс для холодной штамповки металла, который придаст ему нужную форму.
По времени процедура занимает считанные секунды и не требует вмешательство человека. На прессах используются специальные матрицы, изготовленные из твердых сортов стали, реже из других сплавов. Они предназначены для длительной эксплуатации, в процессе которой сохраняют свою первоначальную форму с точностью до миллиметра. Это очень важно, так как холодная штамповка металла производится под конкретные нужды, и отклонения по форме готовой продукции недопустимы, так как это может привести к не состыковкам с другими деталями. Данный способ безвреден для рабочего персонала, так как им не приходится находиться в зоне с высокими температурами. Кроме того отсутствие необходимости предварительного нагрева позволяет довольно просто провести автоматизацию рабочего процесса.
Горячая штамповка металла
Горячая штамповка металла позволяет обрабатывать более толстые заготовки, так как в раскаленном сплаве гораздо слабее межмолекулярные связи, и он лучше поддается сгибанию. Металлические изделия перед началом процедуры проходят те же самые подготовительные этапы, как и в случае с холодной штамповкой. Но оборудование для штамповки металла уже существенно отличается. Оно состоит из двух основных частей: печи и пресса. Печь используется для предварительного нагрева заготовки до температуры красного каления. В таком виде сплав хорошо поддается физическому воздействию и при этом полностью отсутствует риск его пережога.
Для создания оптимальных условий внутри печи современные станки оборудуются высокоточной автоматизированной системой управления. Она требует лишь выставления начальных параметров, которые зависят от типа обрабатываемой детали. Обо всем остальном позаботится компьютер. Прессы для штамповки металла горячим способом изготавливают из твердых, высоколегированных марок стали, которые проходят дополнительную обработку для повышения стойкости к термическим нагрузкам. Они должны выдержать определенное количество технологических операций без потери своих первоначальных характеристик, поэтому очень важно использовать наиболее качественный материал для их производства.
Горячая штамповка требует непосредственного участия человека в производственном процессе. Заготовка быстро остывает в нормальных условиях, так что ее необходимо оперативно доставлять от печи к станку для штамповки металла. Этим занимается рабочий, который при помощи кузнечных клещей переносит изделие на нужное место. Работа в среде с постоянно высоким температурным режимом негативно отражается на организме, поэтому необходимо правильно рассчитывать продолжительность смен, чтобы минимизировать вредное влияние условий на работников. Автоматизация процесса также сталкивается с большими трудностями и требует высоких затрат, поэтому практически нигде не используется.
Для охлаждения деталей не применяют дополнительного оборудования, они остывают естественным путем. В большинстве случаев после штамповки не требуется дополнительной обработки деталей. Исключение составляют изделия для автомобильной промышленности, которые подвергаются процедуре оцинковке. Иногда при штамповке листового металла возникает необходимость обрезать лишние элементы. Для этого используется специальный станок с высокоточным резаком.
Жидкая штамповка металла
Кроме двух перечисленных способов существует еще один, который применяется значительно реже. Он подразумевает жидкую штамповку металла или так называемое литье под давлением, когда сплав заливается в закрытый штамп в жидком состоянии, а окончательное формирование изделия происходит уже в твердом виде. Это позволяет получать детали идеальной формы с улучшенными механическими свойствами. Широкому распространению метода на данном этапе мешает дороговизна и сложность технологического процесса.
Технология штамповки металлов используется для производства большого ассортимента продукции для различных отраслей. Таким способом получают детали автомобильного кузова, разнообразные панели и отделочные материалы, корпуса для бытовой техники. Штамповка является одним из древнейших методов обработки металлов, который дошел до наших дней. Изменилась технология, но принцип остался тот же самый, что и много лет назад.
При помощи объемной штамповки металла получают изделия самой разнообразной формы. Это и специальные уголки, которые используются в анкерных крепях, и разнообразные элементы для оборудования, и детали, используемые в производстве приборов, узлов и агрегатов для всех отраслей промышленности.
Штамповка изделий из металла позволяет получить деталь практически любой формы, чего нельзя добиться при других видах обработки. Это с успехом используется на металлургических заводах, которые могут быстро подстраиваться к новым потребностям рынка. Нужно всего лишь изготовить штамп необходимой формы и можно приступать к выпуску новой продукции.
Объемная штамповка металла
Главная » Разное » Объемная штамповка металла
Объёмная штамповка изделий из металла
В технике под объемной штамповкой подразумевается такой технологический процесс, в результате которого происходит пространственное изменение различных объемных заготовок, имеющих простейшую геометрическую конфигурацию (цилиндрическую, призматическую и т.п.), для того, чтобы изготовить из них детали гораздо более сложной формы. По окончании штамповки изделие соответствует той форме, что имеет полость штампов – основных рабочих инструментов. С точки зрения физики штамповка металла представляет собой ни что иное, как происходящий в результате пластической деформации процесс перераспределения материала, из которого изготовлена исходная заготовка. Специалисты подразделяют объемную
штамповку на горячую и холодную.
Холодная объемная штамповка
Главной отличительной характеристикой холодной объемной штамповки является то, что она производится без нагревания заготовки. В качестве исходного материала для нее используются штучные (мерные) заготовки, которые нарезаются из калиброванных прутков, или же отрезки проволоки, поставляемые на производства в бухтах (бунтах).
Холодная объемная штамповка используется в тех случаях, когда необходимо выпустить детали, имеющие стабильные и высокие механические характеристики, используемые в ответственных узлах и механизмах. В ходе этого технологического процесса в заготовках не происходит рекристаллизация металла, к тому же он существенно упрочняется. В отдельных случаях поковки, которые получаются в результате штампования, представляют собой готовые детали и не требуют последующей обработки.
Одним из существенных недостатков холодной объемной штамповки является то, что при осуществлении этого технологического процесса штампы быстро изнашиваются, поскольку они испытывают на себе значительные механические нагрузки.
Горячая объемная штамповка
При осуществлении горячей объемной штамповки заготовки разогреваются до температуры от +200 °С до +1300 °С (конкретная величина этого показателя зависит от условий обработки и состава сплава). Исходным материалом для горячей штамповки являются заготовки разрезанные на отдельные отрезки, которые по своему объему равны будущим готовым изделиям. По своей физической сущности процесс горячей объемной штамповки практически идентичен свободной ковке, однако наиболее существенное его отличие состоит в том, что производится он с использованием специальных, предварительно изготовленных штампов.
С использованием технологического процесса горячей объемной штамповки изготавливают такие поковки, которые имеют сравнительно высокую точность, структурную однородность, а также достаточно сложную конфигурацию, которая недостижима при использовании технологии свободной ковки.
Основным рабочим органом, используемым при горячей объемной штамповке, являются штампы, которые состоят из двух частей: матриц и пуансонов. При установке в специальных вертикальных прессах и молотах матрицы являются неподвижными, а пуансоны – подвижными. Для осуществления процедуры объемной штамповки используются так называемые открытые штампы, в которых плоскость разъема их составных частей расположена перпендикулярно направлению штамповки. Еще одним технологическим способом осуществления этого процесса является использование закрытых штампов. Они характеризуются тем, что в них плоскость разъема располагается непосредственно по периметру поковки.
Открытые штампы универсальны в применении и просты по своему устройству, однако их использование ведет к образованию заусенца (он располагается в специальной канавке и затем обрезается на отрезном станке). В закрытых штампах заусенцев или нет вообще, или они совсем невелики, однако эти рабочие органы не отличаются универсальностью применения.
Для получения методом штамповки деталей высокой точности по своим объемным характеристикам применяются закрытые штампы, снабженные компенсаторами. Они представляют собой дополнительные полости, предназначенные для удаления избыточного металла заготовки, и находятся в тех местах, куда металл проникает в последнюю очередь. Этот материал неизбежно идет в отход, и поэтому использование компенсаторов является неэкономичным.
Еще одним широко используемым при горячей штамповке методом является применение штамповочных уклонов. Они проделываются в полостях штампов для того, чтобы облегчить извлечение из них готовых деталей. При этом, однако, форма готовой поковки оказывается несколько искаженной.
Для достижения достаточно высокой точности готовых деталей способом горячей объемной штамповки их нередко выпускают в так называемых разъемных матрицах. Они представляют собой специальные
штампы, имеющие две и более плоскости разъема. Такие матрицы хорошо подходят для штамповки в кривошипных и гидровинтовых прессах, а одной из их отличительных особенностей является отсутствие уклонов.
Штамповка металла (горячая, холодная) — технология, плюсы и минусы
Штамповка металла — процесс изменения формы и размеров металлических заготовок под действием давления. Подробное знакомство с технологией проведения работ поможет понять секреты популярности данного способа обработки металлопроката.
Горячая объемная штамповка металла
Особенностью метода заключается в деформации заготовки после нагревания ее до определенной температуры. Формообразование происходит в результате принудительного перераспределения разогретого металла по выемкам внутренней поверхности штампа.
Особенности горячего штампования
Процесс основан на использовании пластичности металла, которая увеличивается при нагревании. Перед началом формовки болванки равномерно прогреваются на специальных установках с автоматическим управлением. Они обеспечивают поддержание необходимой температуры по всему объему заготовок и исключают образование оксидных пленок.
Оборудование, применяемое для термообработки:
- Электроконтактные установки. Нагрев осуществляется электрическим током, проходящим по заготовке.
- Индукционные системы. Прогревание болванки происходит за счет вихревых токов, возникающих в поверхностном слое болванки.
- Газовые печи. Температура заготовок повышается в изолированной камере, наполненной инертным газом.
Горячая объемная штамповка металла проводится обученным персоналом, обладающим практическими навыками и опытом работы на данном виде производства.
Данным способом производят два вида деталей:
- Удлиненные. Это могут быть: рычаги, валы, воротки и другие. Работа проводится плашмя и завершается фасонированием в заготовительных вальцах ковки.
- Дисковые. В их число входят: кольца, диски, шестерни, крышки. В данном случае применяется метод осадки в торец заготовки с применением штамповочных переходов.
Закрытый способ
Для получения изделий необходимой формы используются прессы с выступом наверху и пустотами внизу. Между неподвижной и подвижной частями имеется минимальный зазор. Полости для разъема располагаются по отношению друг к другу под углом 90°. Метод используется, в тех случаях, когда размеры готового изделия и поковки совпадают по параметрам.
Открытый способ
В данном случае между рабочими деталями имеется больший зазор для стекания лишнего металла. Для удаления облоя используются обрезные и пробивные штампы и кривошипные прессы. Технология может применяться для штамповки изделий любого размера. Безупречная поверхность, однородная структура и экономия металла – преимущества открытого способа.
Штамповочные ручьи
Создание сложных форм с перепадами толщин и высот, выступами и изгибами осуществляется благодаря поверхностям, имеющим специальные впадины, заготовительные и штамповочные ручьи.
Они бывают нескольких видов:
- Протяжные.
Применяются для увеличения длины отдельных участков путем нанесения частых ударов с одновременным кантованием детали.
- Заготовительные. Необходимы для фасонирования заготовки и придания готовому изделию формы с минимальным отходом металла.
- Пережимные. Используются для уменьшения высоты с одновременным увеличением ширины отдельного участка заготовки.
- Подкатные. Обеспечивают равномерное распределение металла по оси заготовки с увеличением диаметра отдельных частей.
- Гибочные. Применяются для формирования поковки, угол изгиба которой составляет 90°.
Окончательное необходимое формоизменение детали происходит в штамповочных ручьях. Они бывают:
- Черновые. Для приближения размеров заготовки к требуемым габаритам детали и снижения износа чистового ручья.
- Чистовые. Они устанавливаются в середине штампа, и используется окончательной формовки изделий. При его изготовлении учитываются припуски на усадку. Выдавливаемый металл оттекает через облойную канавку.
Дополнительные операции
На заключительном этапе после удаления лишнего материала в чистовом ручье проводится коррекция формы детали. Это требуется для правки ее искривленных осей. Изделия из легированных сталей и больших размеров обрабатываются в горячем состоянии. Продукция мелкого калибра корректируется после термообработки и остывания.
Доведение физических свойств до необходимых значений происходит во время заключительного нагревания. Термообработка снимает остаточное напряжение, уменьшает зернистость и повышает пластичность.
Очистка от окалины проводится механической обработкой. Процедура для крупных изделий проходит в дробеструйных комплексах. Мелкие детали очищаются в галтовочных барабанах.
Для снижения шероховатости и получения точных размеров применяется калибровка продукции. После нее не требуется проводить финишную обработку, достаточно отшлифовать полученные детали. Для работы применяются специальные штампы с особо точными ручьями, повторяющими конфигурацию поковки.
Преимущества и недостатки горячей штамповки
Достоинства:
- Экономия металла за счет снижения потерь.
- Возможность изготовления деталей сложных форм.
- Снижение трудоемкости.
- Получение изделий точной формы и конфигурации.
- Высокий уровень производительности.
К минусам метода относятся:
- Высокая стоимость проектирования и изготовления оснастки.
- Сложность и энергоемкость процесса.
- Максимальный вес не превышает 4 тонны.
Горячий метод используется для выпуска больших серий и в случаях, когда сложность форм и толщина изделий не позволяет провести штампование холодным способом.
Холодная штамповка металла
Холодный способ представляет собой технологическую операцию, при которой металлическая заготовка без предварительного нагрева подвергается деформации.
Листовое штампование
Детали данным методом изготовляют прессованием металлических листов, полос или рулонов. Толщина получаемой продукции не превышает 10 мм. Листовая штамповка металла востребована при массовом производстве изделий, абсолютно идентичных по форме и размерам.
Для проведения работ используется два вида прессов:
- Универсальные. Они предназначены для вырубки, сгибания и вытяжки.
- Специальные. С их помощью осуществляется глубокая вытяжка и специфическое выгибание деталей.
Листовая штамповка металла может проводиться на механизированном оборудовании или на пресс-автоматах.
Заготовки для работ при необходимости нарезаются с помощью механических или гидравлических ножниц. Широкие листы режутся на дисковых инструментах с цилиндрическими ножками. Криволинейный контур выполняется дисковыми или коническими ножницами.
Виды операций, проводимые во время листовой штамповки
Детали изготавливают двумя способами:
- Формоизменяющий. К нему относятся: скручивание, прогибание, навивание, обжим, формование, вытягивание, отбортовка.
За время прохождения операции материал заготовки не разрушается, меняется только форма и размер.
- Разделяющий. В него входят: нарезка, прокалывание, обрезка, пробивка и зачистка. Заготовки в данном случае разделяются во время сдвига по заданному контуру.
Плюсы и минусы метода
К недостаткам холодного листового штампования металла относится высокая стоимость оборудования. Окупаемость процесса происходит быстро только в серийном производстве.
Преимуществами данного метода являются:
- Возможность выполнять параллельно несколько операций.
- Получение взаимозаменяемых деталей.
- Рост производительности и эффективности.
- Экономичность массового и серийного производства.
- Получение прочных деталей с сохранением их минимальной массы.
- Точность размеров и высокое качество поверхности.
Холодное штампование рассчитано на производство изделий массой, не превышающей 1 тонну. Производство изделий большего веса не рекомендуется.
Объемная холодная штамповка
Этот универсальный метод востребован в производстве разнообразных изделий из металла. Существует несколько видов объемного штампования.
Холодное выдавливание
Заготовка помещается в полость, из которой металл выдавливается в отверстия, расположенные в рабочем механизме. Проводится на кривошипных или гидравлических прессах. Различают четыре варианта выдавливания:
- прямое;
- обратное;
- боковое;
- комбинированное.
Возможность получения изделий без разрушения и деформации заготовок – плюсы выдавливания.
Высадка
Процесс осуществляется на специальных автоматах. Штамповке подвергается прут или проволока. Они размещаются в рабочую зону и разрезаются на заготовки установленных размеров. Отрезанные части переносятся в штамповочный механизм.
Холодная объемная штамповка металла в открытых штампах
Способ основан на формовании деталей путем заполнения металлом полости штампа. Чтобы облегчить процесс и ослабить сопротивление металлической основы, детали расчленяют на переходы, между которыми они подвергаются отжигу. Благодаря этому повышается пластичность металла, сокращается риск разрушения деталей и увеличивается допустимая степень формоизменения.
Холодное объемное штампование осуществляется в открытых штампах. В условиях холодной деформации закрытая штамповка используются для получения изделий из цветных металлов.
Достоинства и недостатки объемной штамповки
Основным минусом данного метода является быстрое изнашивание штампов. Причиной тому служат значительные механические нагрузки, которые испытывает на себе применяемое оборудование.
Преимущества объемной штамповки:
- Получение высококачественных изделий без окалины.
- Прочность произведенных деталей и точность размеров за счет отсутствия окисления.
- Высокая производительность.
- Минимальная шероховатость поверхности изделий.
- Возможность полной или частичной автоматизации.
- Не нужно нагревать материал.
- Эффективность использования металла.
Качество изготовления продукции зависит от правильной сборки и работы штампа.
Заключение
Штамповка металла – востребованный способ для выпуска продукции. Секрет популярности данного способа обработки деталей состоит в высокой скорости производства изделий любых размеров и форм.
Используемая литература и источники:
- Холодная объемная штамповка. Справочник под редакцией Навроцкого Г. А., Машиностроение, 1973.
- Основы технологии автоматизированного холодновысадочного производства Амиров М. Г., Лавриненко Ю. А. Уфа.: 1992
- Пластичность, её прогнозирование и использование при обработке металлов давлением Дзугутов М. Я., Металлургия, 1984.
- Статья на Википедии про штамповку
Холодная штамповка из металла на заказ
Завод Металл СЗПК оперативно выполнит заказ на холодную листовую и объемную штамповку деталей из металла.
- Прогрессивная штамповка на прессах с усилием 25-160 тн
- Проектирование и изготовление штамповой оснастки
- Изготовление деталей на оснастке Заказчика
- Толщина металла до 8 мм
Изготовление изделий и деталей на пресс автомате из листов, полос, лент, кругов, профильного проката. Холодная листовая штамповка — цена от 50 копеек за удар пресса
- Расчет стоимости — 1 день
При изготовление продукции по чертежам Заказчика на нашей оснастке — мы за свой счет проектируем и изготавливаем штамп, Вы платите только за изделие!
Примеры работ. Мы выполняем заказы любой сложности:
Холодная штамповка — короткий видеоролик с производства
- Листовая холодная штамповка
- Объемная холодная штамповка
- Штамповая оснастка
- Дополнительная обработка изделий
Технологии и методы холодной штамповки деталей из металла
Холодная штамповка из металла производится с помощью кривошипных и пневматических прессов различного усиления, непосредственно на которые устанавливаются штампы. Такой способ штампования позволяет получить готовые детали, не требующие доработки и с минимальным образованием отходов.
Прогрессивная листовая штамповка деталей
Холодная листовая металлоштамповка является наиболее прогрессивным методом, результатом которого являются изделия, не требующие дальнейшей обработки. Листовая металлоштамповка выполняется без нагрева холодным способом, обработка давлением, в результате чего на поверхности металла не возникает окалин. Посредством листовой холодной металлобработки можно получить детали точных размерностей любых нужных форм, с гладкой поверхностью и повышенными износостойкими качествами. Широкая линейка прессов с усилием от 25 до 160т позволяет проводить прогрессивную листовую штамповку металла для любых целей.
К преимуществам прогрессивной холодной обработки из листового металла относится:
- Простота процессов штамповки;
- Высокая производительность;
- Минимальное количество отходов;
- Штамповка листового металла может быть целесообразна как при массовом использовании, так и при изготовлении одной детали;
- Отсутствие температурного воздействия;
Листовая металлоштамповка дает возможность производить детали из металла на заказ любой точности и сложности, толщиной металла от 0,7 до 8мм.
![]()
Объемная холодная штамповка
Холодная объемная штамповка, производительный метод изготовления детали из стали и цветных металлов сложных форм и малых размеров. Отсутствие нагрева при деформации изделий позволяет получить более точные размеры с боле чистой поверхностью. Метод включает операции: осадка, формовка, выдавливание, высадка, чеканка, клеймение.
Объемная металлоштамповка чаще применяется при изготовлении таких деталей как болты, гайки, подшипники, цилиндрические и конические формы.
Штамповая оснастка
Штамповая оснастка состоит из матрицы и пуансона, которые изготавливаются из износостойкого и твердого материала. С помощью пресса заготовка деформируется по форме матрицы. Оснастка включает в себя специальные прессы и молоты, которые и приводят в действие весь механизм.
Подробнее, штамповая оснастка
Изготовление оснастки возможно при предоставлении чертежа или образца изделия. Стоимость штампа может быть включена в стоимость детали.
Обращаем внимание, что при массовом изготовлении больших партий, рекомендуется иметь от двух комплектов штамповой оснастки во избежание простоев в случае поломки или износа. Ресурс штампа рассчитывается исходя из количества выпущенных изделий.
Дополнительная обработка изделий
Последующая обработка деталей может включать механическую обработку и нанесение защитного порошкового покрытия или гальваническое цинкование.
Прогрессивная металлоштамповка
ЗАКАЗАТЬ
Мы работаем с понедельника по пятницу с 10 утра до 18 вечера и готовы обсудить с Вами интересующие Вас вопросы в это время.
Приложить файл Вам перезвонить?
Горячая объемная штамповка. Технология горячей объемной штамповки. Схемы штамповки. Штамповка в открытых и закрытых штампах.
Горячая объемная штамповка
Основная операция горячей объемной штамповки (ГОШ) может быть выполнена за один или несколько переходов. При каждом переходе формообразование осуществляется специальной рабочей полостью штампа – ручьем (гравюрой). Переходы и ручьи делятся на две группы: заготовительные и штамповочные. Схема технологического процесса получения сложной заготовки в нескольких ручьях представлена на рисунке 1.
Стадии получения сложной поковки в нескольких ручьях
Рис. 1: 1 – черновой ручей; 2 – подкатной ручей; 3 – протяжной ручей; 4 – чистовой ручей; 5 – гибочный ручей
Виды штамповочных ручьев
Заготовительные ручьи предназначены для фасонирования в штампах. Фасонирование – перераспределение металла заготовки с целью придания ей формы, обеспечивающей последующую штамповку с малым отходом металла. К заготовительным ручьям относятся протяжной, подкатной, гибочный и пережимной, а также площадка для осадки.
Протяжной ручей предназначен для увеличения длины отдельных участков заготовки за счет уменьшения площади их поперечного сечения, выполняемого воздействием частых слабых ударов с кантованием заготовки.
Подкатной ручей служит для местного увеличения сечения заготовки (набора металла) за счет уменьшения сечения рядом лежащих участков, то есть для распределения объема металла вдоль оси заготовки в соответствии с распределением его в поковке. Переход осуществляется за несколько ударов с кантованием.
Пережимной ручей предназначен для уменьшения вертикального размера заготовки в местах, требующих уширения. Выполняется за 1…3 удара.
Гибочный ручей применяют только при штамповке поковок, имеющих изогнутую ось. Служит для придания заготовке формы поковки в плоскости разъема. Из гибочного ручья в следующий заготовку передают с поворотом на 90 0.
При штамповке поковок, имеющих в плане форму окружности или близкую к ней, часто применяют осадку исходной заготовки до требуемых размеров по высоте и диаметру. Для этого на плоскости штампа предусматривают площадку для осадки.
Штамповочные ручьи предназначены для получения готовой поковки. К штамповочным ручьям относятся черновой (предварительный) и чистовой (окончательный).
Черновой ручей предназначен для максимального приближения формы заготовки к форме поковки сложной конфигурации. Глубина ручья несколько больше, а поперечные размеры меньше, чем у чистового ручья (чтобы заготовка свободно укладывалась в чистовой ручей). Радиусы скругления и уклоны увеличиваются. В открытых штампах черновой ручей не имеет облойной канавки. Применяется для снижения износа чистового ручья, но может отсутствовать.
Чистовой ручей служит для получения готовой поковки, имеет размеры «горячей поковки», то есть больше, чем у холодной поковки, на величину усадки. В открытых штампах по периметру ручья предусмотрена облойная канавка, для приема избыточного металла. Чистовой ручей расположен в центре штампа, так как в нем возникают наибольшие усилия при штамповке.
Технология горячей объемной штамповки
Технологический процесс ГОШ отличается значительным разнообразием и определяется выбором самого изделия и применяемым оборудованием. Технологический процесс зависит от формы поковки. По форме в плане поковки делятся на две группы: диски и поковки удлиненной формы.
К первой группе относятся круглые или квадратные поковки, имеющие сравнительно небольшую длину: шестерни, диски, фланцы, ступицы, крышки и др. Штамповка таких поковок производится осадкой в торец исходной заготовки с применением только штамповочных переходов.
Ко второй группе относятся поковки удлиненной формы: валы, рычаги, шатуны и др. Штамповка таких поковок производится протяжкой исходной заготовки (плашмя). Перед окончательной штамповкой таких поковок в штамповочных ручьях требуется фасонирование исходной заготовки в заготовительных ручьях штампа, свободной ковкой или на ковочных вальцах.
Схемы штамповки
Так как характер течения металла в процессе штамповки определяется типом штампа, то этот признак можно считать основным для классификации способов штамповки. В зависимости от типа штампа выделяют штамповку в открытых и закрытых штампах (рисунок 2).
Схемы штамповки
Рис. 2
Штамповка в открытых штампах (рисунок 2, позиция а) характеризуется переменным зазором между подвижной и неподвижной частями штампа. В этот зазор вытекает часть металла – облой, который закрывает выход из полости штампа и заставляет остальной металл заполнить всю полость. В конечный момент деформирования в облой выжимаются излишки металла, находящиеся в полости, что позволяет не предъявлять высокие требования к точности заготовок по массе. Штамповкой в открытых штампах можно получить поковки всех типов.
Штамповка в закрытых штампах (рисунок 2, позиция б) характеризуется тем, что полость штампа в процесс деформирования остается закрытой. Зазор между подвижной и неподвижной частями штампа постоянный и небольшой, образование в нем облоя не предусмотрено. Устройство таких штампов зависит от типа машины, на которой штампуют. Например, нижняя половина штампа может иметь полость, а верхняя – выступ (на прессах), или верхняя – полость, а нижняя – выступ (на молотах). Закрытый штамп может иметь две взаимно перпендикулярные плоскости разъема (рисунок 2, позиция в).
При штамповке в закрытых штампах необходимо строго соблюдать равенство объемов заготовки и поковки, иначе при недостатке металла не заполняются углы полости штампа, а при избытке размер поковки по высоте будет больше требуемого. Отрезка заготовок должна обеспечивать высокую точность.
Существенное преимущество штамповки в закрытых штампах – уменьшение расхода металла из-за отсутствия облоя. Поковки имеют более благоприятную структуру, так как волокна обтекают контур поковки, а не перерезаются в месте выхода металла в облой. Металл деформируется в условиях всестороннего неравномерного сжатия при больших сжимающих напряжениях, это позволяет получать большие степени деформации и штамповать малопластичные сплавы.
Штамповка металла – услуги штамповки деталей из листового металла в Москве| Новомосковский завод
Комплексную обработку любых металлов и сплавов предлагает Новомосковский завод металлоконструкций. Одним из направлений нашей деятельности является предоставление услуги штамповки металла на заказ.
Штамповка деталей из листового металла. Что мы можем
Техническая оснащённость предприятия и его специализация позволяют нам выполнять штамповку любых видов. Заказчикам доступна:
- Объёмная штамповка:
- o Холодная. Предусматривает, что предварительного нагрева обрабатываемой заготовки не требуется;
- o Горячая. Деталь обрабатывается после предварительного прогрева;
- o Жидкая. (Иное наименование – литьё под давлением). Даёт идеальный результат, но очень дорогой метод.
- Листовая штамповка.
Эти процессы включают:
- Гибку металла;
- Его вытяжку;
- Выполнение отбортовки;
- Обжим заготовки;
- Её формовку.
Горячая объёмная штамповка металла многократно превосходит ковку по производительности и качеству готовых деталей. В ГК «НЗМК» эта технология применяется при выполнении заказа на изготовление элементов со сложной формой, масса которых не превышает 300 кг, при их серийном заказе.
Работы выполняются в следующей последовательности:
- Разделка материала на заготовки;
- Их нагревание;
- Собственно штамповка;
- Выполнение термической обработки полученных поковок;
- Обрубка детали;
- Отделка.
Объёмная штамповка деталей выполняется на Новомосковском заводе металлоконструкций двумя способами: в открытых и закрытых штампах.
Первый вариант изначально допускает определённый процент отходов металла, поступающего в облой (до 20% общей массы заготовки). Он менее экономичен, с данной точки зрения. Но процесс штамповки проще. Мы используем его при изготовлении коленвалов, шестерён, рычагов, шатунов и т.п.
Закрытый штамп позволяет работать без отходов. Штамповка изделий из металла, с его использованием, позволяет получать детали, которым не требуется последующая доводка.
Услуги штамповки металла на заказ. Разновидности выполнения работ
Заказчик может рассчитывать, что горячая штамповка металла, при выполнении его заказа, будет выполнена на одноручьевых штампах (если они имеют простую форму), либо на многополостных штампах, в которых выполняется поэтапное приближение формы заготовки к виду требуемой поковки. При этом заготовка перемещается из одного ручья, в другой в заданной последовательности.
При выполнении заказов на изготовление крепежа применяется способ, так называемой, холодной высадки. При этом трудоёмкость данной операции ≥ 200 раз превосходит изготовление аналогичных деталей на станках.
Если клиенту необходима штамповка деталей из листового металла, НЗМК готов предложить:
- Разделительную обработку:
- o Обрезка;
- o Пробивка;
- o Вырубка;
- o Отрезание;
- формообразующую обработку.
Если заказчику требуется изготовить из стальных тонких листов профили гнутые различного вида и формы, мы готовы выполнить данный заказ на специальных прессах, предназначенных для гибки листа.
123456 (Объемная штамповка и обработка металлов резанием) — документ
Содержание
1. Объёмная штамповка
Введение
Объемная штамповка
Штампы
Технологический процесс изготовления
Нагрев металлов перед обработкой давлением
Нагревательное устройство
Оборудование для горячей объемной штамповки
Отделочные операции
1. 8.1 Обрезка заусенца и пробивка пленок
1.8.2 Правка штамповочных поковок
1.8.3 Очистка поковок от окалины
1.8.4 Калибровка поковок
1.8.5 Контроль качества
1.9 Расчетная часть
2. Обработка металлов резанием
Введение
Основные типы токарных станков
Классификация токарно-винторезных станков
Элементы резцов
2.5.1 Основные положения
2.5.2 Геометрические параметры режущей части резцов
2.5.3 Типы токарных резцов
2.6 Приспособления
Назначение приспособлений
Основные конструктивные элементы приспособлений
Кулачковые патроны
Центры
Хомутики
Цанговые патроны
Способы закрепления заготовок на станке
Вспомогательный инструмент
2.7 Обработка заготовок на токарно-винторезных станках
Список использованной литературы
1. Объёмная штамповка
1.1 Введение
Штамповка — способ обработки металлов давлением, при котором течение металла ограничено поверхностями полостей и выступов штампа. Верхняя и нижняя части штампа образуют замкнутую полость по форме изготовляемой детали – штамповки. В зависимости от формы заготовки (лист, прокат и т. д.), оборудования и технологических приемов различают объемную штамповку и листовую штамповку. Кроме того, штамповку можно осуществлять с нагревом и без нагрева. Прообразом штамповки можно считать чеканку монет. Широкое применение процесса штамповки началось в конце XVIII – начале XIX вв. в связи с переходом на промышленный выпуск изделий, в частности первый патент на изготовление штампованием латунных гильз был выдан в 1796 (Германия). С появлением паровых машин на штамповочных прессах стали осуществлять различные пробивные и вырубные операции, например пробивку отверстий под заклепки. Наибольшее развитие штамповка получила в середине ХХ в. с ростом серийного и массового производства в приборо- и машиностроении, радиоэлектронной промышленности и других отраслях, так как является в десятки раз производительнее ковки. Штампованные детали имеют в 2-3 раза меньшие припуски на обработку, чем кованные, то есть выше процент использования металла. Штамповку осуществляют на молотах с массой падающих частей 0,5-30 т, кривошипных горячештамповочных прессах с усилием от 6 до 100 Мн (600-10 000 тс), гидравлических прессах с усилием до 750 Мн (75 000 тс), горизонтально-ковочных машинах, кузнечно-штамповочных автоматах, гидровинтовых пресс-молотах. Чтобы сократить отход металла, уменьшить последующую обработку применяют безоблойное штампование. При горячей штамповке на молотах окалина удаляется в промежутках между первыми ударами. На прессах штамповку выполняют за один ход. В связи с этим применяют так называемую безокислительный нагрев заготовок (обычно прокат), например в индукционных печах. Это обеспечивает получение изделий почти без окалины. Труднодеформируемые материалы штампуют, как правило, на гидравлических прессах в штампах, нагретых до температуры обрабатываемого материала (например, для титановых сплавов до 800 С), — так называемая изотермическая штамповка.
Для обеспечения более высокой чистоты поверхности, большей точности размеров изделия применяют холодную штамповку, процесс которой аналогичен горячей штамповке, но исключает нагрев.
Листовая штамповка – способ получения тонкостенных изделий плоской или пространственной формы. Тонколистовой материал (до 4 мм) штампуют без нагрева, толстолистовой (свыше 4 мм) – с нагревом. Получаемые этим способом детали имеют точные размеры и обычно не нуждаются в дальнейшей обработке резанием. В мелкосерийном и серийном производствах применяют универсальные машины и оснастку; в крупносерийном и массовом производствах используют многооперационные штампы. Штамповку выполняют на кривошипных прессах с усилием 63-50 000 кн (6,3-5000 тс), с числом ходов от 5 до 15 в мин, на листоштамповочных автоматах с усилием 50-40 000 кн (5-4000 тс), с числом ходов до 120 в мин, на гидравлических вытяжных прессах с усилием от 8 до 200 Мн (800 – 20 000 тс). В массовом производстве особое значение при листовой штамповке приобретают использование комбинированных штампов, механизация и автоматизация целых участков, автоматические линии.
При производстве однотипных деталей из листа (толщина алюминиевого листа 1,5-2 мм, стального – 0,5-0,6 мм), в частности в авиационной промышленности, большое распространение получила так называемая штамповка резиной, позволяющая удешевить инструмент, упростить конструкцию пресса. На гидравлическом прессе простого действия укрепляется подушка из резины или другого упругого материала в металлическом коробе, установленном на подвижных частях пресса. Нижний боек штампа имеет форму штампуемой детали. Пока штампуются одни детали, подготавливают новые заготовки.
При гидравлической вытяжке, являющейся также разновидностью листовой штамповки, деформирование заготовки осуществляется непосредственно жидкостью.
В 50-х годах ХХ века разработаны и начали успешно внедряться принципиально новые технологические процессы, позволяющие обрабатывать труднодеформируемые материалы (жаропрочные стали, титановые, молибденовые, вольфрамовые и другие сплавы).
При взрывном штамповании ударная волна, возникающая при сгорании заряда взрывчатого вещества, деформирует заготовку, придавая ей нужную форму. Вследствие кратковременности процесса (мсек – мксек) штампы можно изготовлять не только из дешевых малоуглеродистых сталей, но и из таких материалов, как бетон, дерево, пластмасса и так далее.
Высокоскоростная штамповка – способ обработки труднодеформируемых материалов с высокой точностью на молотах, скорость падающей части (бабы) которых при ударе достигает 40-60 м/сек. У обычных молотов не выше 8 м/сек. Масса соударяющихся частей у высокоскоростных молотов при одинаковой энергии удара во много раз меньше, чем у обычных молотов.
1.2 Объемная штамповка
Объемная штамповка, технологический процесс, заключающийся в изменении простейших объемных заготовок (цилиндрической, призматической и другой формы) в более сложные изделия, форма которых соответствует полости специализированных инструментов – штампов. Объемная штамповка как процесс перераспределения металла заготовки происходит в результате пластической деформации.
Основные операции объемной штамповки – осадка, высадка, протяжка, выдавливание, гибка, плющение, калибровка, образование выступов, утолщений, углублений, осуществляемые на кузнечно-прессовых машинах – молотах, прессах и машинах специального назначения. Из штампованных поковок после обработки резанием и термической обработки получают различные детали: шатуны, коленчатые валы, рычаги, зубчатые колеса, лопатки турбин, крепежные детали, шары, ролики и кольца подшипников и др.
Различают холодную и горячую объемные штамповки.
Холодная штамповка осуществляется без нагрева. Исходный материал – калиброванные прутки, нарезаемые на мерные (штучные) заготовки, или проволока в бунтах. Масса получаемых изделий от нескольких г до нескольких кг; точность по 3-2-му классам; шероховатость поверхности соответствует 7-10-му классам чистоты. Холодной объемной штамповкой получают ответственные детали с высокими и стабильными механическими свойствами, что объясняется отсутствием рекристаллизации в металле и упрочнением. Так как заготовки не нагреваются, на поверхности поковок не происходит образование окалины, обезуглероживания, обесцинкования и тому подобного, что улучшает качество поковок в целом и сохраняет припуски на дальнейшую обработку. В ряде случаев поковки не требуют дополнительной обработки, являясь готовыми деталями (коэффициент использования металла составляет 1). Однако для осуществления холодной объемной штамповки требуются значительные усилия – до 2500 Мн/м2 (1 Мн=100 тс) и более, что отрицательно влияет на стойкость штампов. Существенно снизить усилия (в 10-15 раз) позволяет нагрев заготовок, то есть горячая объемная штамповка.
Горячая объемная штамповка осуществляется с нагревом до температуры 200-1300 С в зависимости от состава сплава и условий обработки. Исходный материал – прокатные прутки, разделенные на мерные заготовки, равные по объему будущей поковке (с учетом неизбежных отходов). Масса получаемых изделий от нескольких г до 6-8 т; точность размеров поковок зависит от их массы и конфигурации и может быть повышена последующей холодной калибровкой; шероховатость поверхности соответствует 3-7-му классам чистоты. Процесс горячей объемной штамповки аналогичен по физической сущности свободной ковке, но осуществляется в штампах. Горячей объемной штамповкой получают поковки, однородные по структуре, сравнительно высокой точности, сложной конфигурации, которой невозможно добиться при свободной ковке. Однако средний коэффициент использования металла при горячей объемной штамповке 0,5-0,6 (то есть до 50-40 % металла идет в отход), при холодной штамповке этот коэффициент значительно выше.
Штампы для объемной штамповки чаще всего состоят из 2 половин – верхней и нижней или из пуансона и матрицы. Обычно при штамповке на молотах и вертикальных прессах нижняя часть штампа неподвижна, а верхняя подвижна. Объемную штамповку выполняют в открытых штампах – с плоскостью разъема, перпендикулярной направлению штамповки, или в закрытых штампах- с плоскостью разъема по периметру поковки. Открытый штамп отличается простотой устройства и универсальностью применения, но горячая штамповка в нем связана с образованием заусенца, который обеспечивает заполнение сложного рельефа полости штампа. Для размещения заусенца в штампе предусматривается специальная канавка. После штамповки заусенец обрезают в штампе на обрезном прессе. Отход металла при этом составляет 5-20%, иногда достигает 50-80%. В закрытых штампах, применяемых при горячей и холодной объемных штамповках, заусенец либо весьма невелик (не более 1%), либо совсем отсутствует, так как поковка формируется из всего объема металла. Однако эти штампы менее универсальны, например в них нельзя получать поковки в форме шара. В тех случаях, когда нужно получить исходные заготовки достаточно высокой точности по объему, применяют закрытые штампы с компенсаторами – дополнительными полостями, в которые вытекает избыточный металл заготовки. Компенсаторы располагаются в таком месте штампа, в которое металл поступает в последнюю очередь, чтобы предотвратить преждевременное и чрезмерное попадание металла в компенсатор. Однако этот способ неэкономичен, так как металл, поступающий в компенсатор, идет в отход. Другим технологическим приемом при горячей объемной штамповке является применение штамповочных уклонов, которые делают в полости штампов с целью облегчения выталкивания готовых изделий.
Поковка получается искаженной формы, например вместо цилиндра – усеченный конус. Обычно в молотовых штампах уклоны 5-7 . Излишек металла на поковке (напуск) также является отходом. Для осуществления объемной штамповки с меньшим уклоном (1-2 ) в штампах применяют выталкиватели: при штамповке на молотах – только нижние, на прессах – верхние и нижние.
Одним из рациональных решений является горячая объемная штамповка в разъемных матрицах, то есть в штампах с 2 или несколькими плоскостями разъема, чаще всего на горизонтально-ковочных машинах. Матрицы этих штампов не имеют уклонов, в них можно штамповать даже поковки, расширяющиеся ко дну матрицы. В разъемных матрицах можно также вести штамповку на гидровинтовых и кривошипных прессах. Поковки для одной и той же детали можно получить методами горячей объемной штамповки как на молоте, так и на прессе. В этих двух случаях заготовки будут внешне отличаться, иметь разные припуски.
Объемная штамповка применяется как однопереходный процесс для получения простейших поковок и многопереходный – для деталей сложных форм. При многопереходной объемной штамповке производят подготовительные операции (так называемое фасонирование заготовок), а затем осуществляют окончательную штамповку. Многопереходную объемную штамповку производят с использованием средств механизации или на автоматах, на гидравлических прессах с усилием 750 Мн, молотах с массой падающих частей до 20-25 тс, кривошипных горячештамповочных прессах с усилием до 80 Мн, на автоматах для одно- и многопозиционной штамповки, на прессах холодного выдавливания, машинах для раскатки, ковочных вальцах и другом специализированном оборудовании. При штамповке на гидровинтовых прессах и высокоскоростных молотах можно получать поковки с тонкими сечениями. На многопозиционных холодно- и горячештамповочных автоматах осуществляется объемная штамповка изделий с наибольшими диаметрами: при холодной штамповке до 50 мм с производительностью до 500 шт/мин, при горячей – до 120 мм с производительностью до 70 шт/мин.
Штампы – точный, сложный и дорогой инструмент, поэтому применение объемной штамповки целесообразно главным образом в крупносерийном и массовом производствах.
Перспективы дальнейшего развития объемной штамповки определяются расширением применения штампов для горячей малоотходной штамповки и конструированием мощного оборудования для холодной штамповки, а также внедрением новых процессов деформации металлов с использованием явлений сверхпластичности, применением гидростатических методов и др.
Штамповка металла по доступной цене – Завод ОПС
Заказать штамповку металла
Штамповка представляет собой один из способов обработки металлов давлением, который заключается в пластической деформации заготовки в результате силового воздействия. Это воздействие оказывается инструментом, специально изготавливаемым с учетом необходимой геометрии и размеров готового изделия — штампом, состоящим из матрицы и пуансона. Штамповка металла выполняется с помощью пресса, который посредством ползуна передает усилие пуансону и далее на заготовку, заставляя ее принять форму жестко закрепленной матрицы.
Виды штамповки
Операции штамповки делятся на разделительные и формоизменяющие. Первый вид предполагает отделение части заготовки по замкнутому контуру или по прямой линии. Это отрезка, обрезка, пробивка и вырубка. Второй вид обработки используется для изготовления из заготовки детали с измененными размерами и параметрами без механического разрушения. К формоизменяющим операциям относят отбортовку, обжим, вытяжку, формовку, гибку и пуклёвку.
Листовая и объемная штамповка
По характеру обрабатываемых заготовок различают листовую и объемную штамповку. Первый вариант широко применяется при изготовлении деталей машин и механизмов, металлической посуды, корпусов различных устройств и элементов декора. Полученные методом листовой штамповки детали, как правило, не нуждаются в доводке. Что касается объемной штамповки, то результатом этой операции, заключающейся в продавливании в формах холодного или раскаленного металла, чаще бывает заготовка, требующая дальнейшей обработки.
Холодная и горячая штамповка
Штамповка может быть холодной или горячей. Оба вида требуют предварительного расчета, проектирования и изготовления специально оснастки — штампа с нужными параметрами. При этом учитывается масса будущего изделия и характеристики металла, который будет подвергнут штамповке — его твердость, электропроводность, теплопроводность, вязкость и устойчивость к коррозии.
Холодная штамповка применяется для изготовления деталей из низкоуглеродистых сталей (Ст35, Ст25), меди, алюминия. Она обеспечивает большую точность размеров и улучшенное качество поверхности (до 8-го квалитета). Это простой, экономичный и высокопроизводительный способ металлообработки, который широко применяется на производстве. Недостатком является снижение пластичности материала в результате обработки, хрупкость получаемого изделия.
При обработке методом горячей штамповки перед механическим воздействием на металл его нагревают (степень нагрева зависит от температуры пластической деформации конкретного вида материала), используя для этого газовую, электрическую или индукционную печь. После этого заготовку подвергают деформации в разных плоскостях, изменяя ее сечение и конфигурацию. Обработка методом горячей штамповки позволяет минимизировать количество отходов, сделать структуру материала однороднее и плотнее, но есть и побочный эффект — окалина, которую потом приходится удалять. Горячую штамповку применяют для обработки легированной и углеродистой стали (чем выше содержание легирующих элементов и углерода, тем выше необходимая температура нагрева заготовки). Так, к примеру, сталь Ст 90ХФ подвергают штамповке, нагревая до температуры 1050 — 1100⁰С, а для марки Ст45 достаточно 830 — 850⁰С.
Оборудование для штамповки металла
Станки для штамповки металла — это прессы с различными типами привода, характеристиками, дополнительным оборудованием, количеством выполняемых операций, производительностью. Конкретный тип и модели станков для промышленных предприятий подбираются исходя из специфики выпускаемых изделий и масштабов производства. При изготовлении каждого типа оборудования, предназначенного для штамповки металла, руководствуются действующими ГОСТами и межгосударственными стандартами, которые регламентируют его рабочие параметры, размеры и нормы точности.
Для штамповки металла используются:
- кривошипно-шатунные прессы;
- гидравлические прессы;
- электромагнитные прессы.
Гидравлические прессы
Гидравлические прессы по мощности значительно превосходят кривошипные и электромагнитные. Сложная система гидравлики позволяет поршню, перемещающемуся под давлением масла, передавать ползуну серьезное усилие, которое тот, в свою очередь, направляет на обрабатываемую поверхность посредством пуансона. Пуансон по всей длине рабочего хода давит равномерно, но его движение очень медленное, поэтому производительность гидравлических прессов невысока.
Электромагнитные прессы
Что касается электромагнитных прессов, то здесь давление создается сердечником, выталкиваемым из катушки под воздействием силового электрического поля. Из-за низкой мощности и эффективности, а также неравномерности усилия в разных точках рабочего хода такое оборудование на крупных металлообрабатывающих предприятиях практически не используется.
Кривошипно-шатунные прессы
Кривошипно-шатунные прессы вращательное движение привода преобразуют в возвратно-поступательное движение ползуна с закрепленным на нем пуансоном. Пресс может иметь до 4-х ползунов, приводимых в движение одним или двумя кривошипами. На промышленном оборудовании с четырьмя ползунами, работающими от одного привода, изготавливают габаритные изделия из листового металла, подвергая его серьезной деформации. Пример таких изделий — кузовные детали автомобилей.
На московском заводе ОПС установлены многопозиционные листоштамповочные автоматы для последовательной многооперационной листовой штамповки из металлической рулонной ленты с автоматическим переносом штампуемой детали с позиции на позицию. Это точное высокопроизводительное оборудование, соответствующее ГОСТ 8260-88. Предприятие принимает заказы на изготовление продукции методом холодной и горячей штамповки.
Открытая штамповка и штамповка
Металлические изделия в зависимости от назначения, массы, размеров могут быть изготовлены различными методами: литьем, механической обработкой или ковкой. Открытая штамповка и штамповка имеют то преимущество, что полученный элемент отличается высоким прочностным свойством и не имеет недостатков.
Основными материалами для поковок марок и являются конструкционные углеродистые и легированные стали, а также цветные металлы и их сплавы.
Открытая поковка
Заключается в деформации металла в любом направлении с применением наковален специальной формы и различных видов инструментов и приспособлений, придающих форму фрагментам поковки. Применяемые операции над элементом: удлинение, сплющивание, осадка, штамповка, резка, гибка, скручивание и сварка. Кузнечно-штамповочное производство применяют обычно для небольших серий, когда производство штампов невыгодно, или для производства поковок большой массы и размера.При регенерации и ремонте инструментов и оборудования мастерских, а также при производстве запасных частей и в целях капитального ремонта. Максимальный вес сырья, т.е. слитков для поковок, составляет 500 тонн. Мелкие поковки изготавливают из предварительно прокатанной шихты, а крупные из слитков.
Для свободной ковки применяют молоты и гидравлические прессы, обжимные и электрообжимные машины, наковальни, клещи, зубила.
Поковки в открытых штампах включают:
- кованые кольца и втулки
- плоские и квадратные круглые прутки
- квадратные и прямоугольные блоки
- многоступенчатые валы
- полные диски и с отверстиями
- контакты штифты
- , головки
Входящие материалы:
- слитки — поковки больших размеров и массы обычно выковываются непосредственно из слитков соответствующих размеров, отлитых в форме усеченной пирамиды с шести-, восьми- или двенадцатигранным поперечным сечением.
- Плиты кованые или катаные — с квадратным сечением, вогнутыми сторонами и закругленными кромками. Катаные заготовки или прутки обычно используются для более легких поковок. Заготовки имеют поперечное сечение, очень близкое к квадратному, а сортовой прокат может иметь квадратное, прямоугольное или круглое сечение.
Получателями свободной поковки обычно являются предприятия машиностроительной, оборонной, энергетической, судостроительной, горнодобывающей, буровой и автотранспортной отраслей.Они имеют множество применений в качестве компонентов и узлов в различных отраслях промышленности:
- для рессор для автомобилей
- для нагруженных шестерен, шестерен, поршневых пальцев
- для фитингов
- для лопаток турбин, валов турбин
- для болтов и деталей котлов
- для частей судовых рулей
- для болтов сцепления, осей локомотивов, осей вагонов
- для тяжелонагруженных деталей машин и двигателей в автомобильной и аэрокосмической промышленности.
- для оправок, для деталей самолетов
- на детали и комплектующие для космической техники
- для специальных сверл и опорных роликов
Поковка
Штамповка, как следует из названия, заключается в формировании объекта в штампе.Качество кованых изделий выше по сравнению с аналогичными изделиями, изготовленными другим способом обработки стали. Кованый, а затем термообработанный металл обладает лучшими механическими свойствами и прочностью, поэтому наиболее нагруженные детали машин изготавливаются из поковок. Широкое использование штамповок обусловлено многими преимуществами процессов штамповки. Высокое качество поковок, эффективность оборудования и широкая степень использования.
Штамповка позволяет сэкономить много материала и, следовательно, является экономичным методом обработки.Согласно статистическим данным, замена механической обработки штамповкой позволяет на каждый миллион тонн партии экономить 25 000 тонн металла. По сравнению с свободной ковкой штамповка имеет большие преимущества. Он обеспечивает большую точность изготовления поковок, дает возможность формообразования поковок, чего нельзя получить свободной ковкой. Предметы сложной формы можно выковать быстро и легко. Высокая эффективность и простота позволяют снизить затраты. Экономьте время и труд.Однако необходимо закупать часто дорогостоящие приспособления и штампы, которые рентабельны только при больших сериях.
Кузнечная штамповка отличается от свободной ковки тем, что имеет четкую разделительную линию, а характерным признаком является заусенец, если это открытая штамповка. Ковка в закрытых штампах происходит без образования грата. Его роль выполняет компенсатор, размещенный в районе болванки, впоследствии залитой металлом.
Поковки включают:
- шестерни
- коленчатые валы
- опорные катки
Штамповка имеет ряд преимуществ, в первую очередь возможность производить большое количество деталей за короткое время.
.
Что такое ковка?
Ковка методом штамповки — это процесс металлообработки, при котором из нагретого куска металла постепенно формируется слиток. Он включает в себя формирование слитка с повторяющимися ударами молотка или штампа, которые поднимаются, а затем падают на деталь, сплющиваются или вдавливаются в форму. В зависимости от сложности конструкции детали процесс иногда требует использования нескольких штампов. Процесс ковки обычно приближается к готовой детали, но обычно требуется дополнительная обработка для достижения допуска.Штамповка широко используется в автомобильной промышленности для изготовления различных деталей двигателей, коробок передач и мостов.
Штампы, используемые в штамповке, обычно изготавливаются из высоколегированной стали, называемой инструментальной сталью. Кузнечные штампы спроектированы так, чтобы противостоять ударам и истиранию, и, как правило, могут выдерживать тысячи быстрых циклов нагрева и охлаждения. Штампы для ковки обычно изготавливаются из двух половин. Верхняя половина, называемая молотком, прикреплена к блоку, который поднимают и опускают на слиток.Нижняя половина, известная как наковальня, обычно является стационарной матрицей, на которой куется стержень.
Ковка в штампах выполняется штампами, которые не полностью окружают заготовку. Матрицы обычно плоские, хотя также могут использоваться контурные или режущие штампы. Открытая структура позволяет стержню расширяться при забивании до нужной толщины.
Методы, обычно связанные с ковкой в открытых штампах, включают насечку и окантовку.Зубчатая обработка — это процесс постепенного сплющивания прутка или слитка по длине. Этот процесс используется для достижения желаемой толщины, после чего его можно обрезать. Кромки обычно изготавливаются вогнутой матрицей. Этот метод концентрирует и формирует материал по сторонам и концам кованой детали для получения однородных краев и правильной ширины.
Пресс-формы используются для штамповки, иногда называемой штамповкой. Когда молоток падает на заготовку, горячий металл вдавливается в полости штампа, придавая окончательную форму детали.По мере того как металл приспосабливается к матрице, лишний материал, известный как заусенец, выдавливается. Заусенец должен быть удален после завершения ковки.
Другим распространенным типом штамповки является химическая штамповка. Этот процесс также называют настоящей штамповкой, так как заготовка полностью закрыта штампом, что предотвращает образование заусенцев. Многие производители предпочитают ковку, а не ковку, поскольку заусенец, полученный при штамповке, может составлять почти половину исходного слитка.
ДРУГИЕ ЯЗЫКИ
.
Ковка | Нержавеющая сталь: база знаний Нержавеющая сталь: база знаний
По сравнению с свободной ковкой штамповка дает большие преимущества — при сопоставимой серии и размерах получаемых поковок.
Принимая во внимание вышеизложенные предположения, штамповка методом штамповки имеет следующие преимущества по сравнению с ковкой в свободном штампе:
- возможность использования меньших технологических припусков,
- повышенная точность поковок,
- возможность формообразования поковок, которое не может быть дано открытой штамповкой,
- возможность легкой и быстрой ковки изделий сложной формы,
- низкая трудоемкость и высокая производительность,
- значительная экономия трудозатрат,
- легко определить время ковки, что позволяет точно рассчитать стоимость.
Недостатки штамповки следующие:
- необходимость применения ковочных машин с повышенной точностью направления штампа,
- дополнительные расходы, связанные с прессами для обрезки заусенцев,
- большая стоимость оснастки,
- рентабельность для больших серий поковок,
- малые размеры изготавливаемых поковок.
Штампованные поковки обычно изготавливают из шихты, предварительно прокатанной и разрезанной на секции, соответствующие массе одной поковки или нескольких поковок в зависимости от требований разработанного технологического процесса.
Штамповка , как и открытая поковка, характеризуется трехосным напряженным состоянием, где все основные напряжения сжимающие.
При штамповке в закрытых штампах расширение материала ограничивается стенкой инструмента.
Следовательно, существует состояние трехосного сжатия во всем объеме материала. При ковке в закрытых штампах единичное давление в 2 раза выше, чем при ковке в открытых штампах, и в 3–6 раз, чем при свободной ковке. Удельное давление, вызывающее пластическую деформацию, примерно в 15 раз больше, чем давление, используемое при свободной штамповке. Экструдированный материал обладает очень высокой пластичностью.
Классификация заготовок для штамповки:
Группа I. Применяется к поковкам переменного сечения
Группа II. Применяются для поковок, требующих изгиба и асимметричного перемещения металла
Группа III. Используется для поковок, требующих высадки
Группа IV. Используется для поковок сложной поперечной формы
При ковке на прессах применяют только те операции, которые можно выполнить одним ходом ползуна пресса, например предварительная штамповка и чистовая обработка, осадка, сужение, гибка и формовка (формовка). Вышеуказанные операции выполняются так же, как и с молотками.
Правильная отработка технологического процесса штамповки зависит также от правильной конструкции поковки, в том числе радиуса закруглений и технологических припусков, в том числе конструкции днища. Радиусы скругления в поковках бывают трех видов: наружные, внутренние и в местах изменения поперечного сечения поковок.
Радиусы кривых имеют большое влияние на процесс ковки и срок службы инструмента.
Расчет объема партии. Идеальная поковка — это поковка, представляющая собой вращающееся твердое тело, поперечное сечение которого равно сумме соответствующих сечений поковки и облоя.
.
Кузнечное дело | Флудра
Кузнечное дело включает процессы ковки, используемые для изготовления изделий из стали, а также цветных металлов и их сплавов. К таким процессам относятся:
- подготовка материала для ковки, т.е. резка, очистка, предварительный нагрев,
- поковка,
- чистовая обработка поковок, т.е. полировка, рихтовка, штамповка, обрезка.
Различают ручную и механическую (машинную) ковку. В ручных операциях ковки используются наковальня и различные инструменты, в то время как механическая ковка осуществляется с помощью кузнечных машин.
Различают следующие способы ковки: кузнечная, обжимная и кузнечная.
Ручная ковка обычно представляет собой горячий процесс, проводимый после нагревания материала до оптимальной температуры в горне. Примеры ручных инструментов показаны на рис.7-1.
К основным кузнечным операциям относятся: резка, прошивка, волочение, осадка, гибка, смещение и сварка.
Резка ведется на наковальне наборами и долотами.
Пробивка может выполняться на наковальне или обжимном блоке.
Волочение материала выполняется молотком или долом на наковальне (рис. 7-2). Волнистую поверхность заготовки, образовавшуюся в результате более полного использования, сглаживают наборным молотком.
Осадка заключается в забивании заготовкой, помещенной на наковальню в вертикальное положение (рис.7-3а, б), чтобы сделать его короче в одном измерении и толще в другом. Для того чтобы осадить определенный участок заготовки (например, его середину или конец), его следует подвергнуть точечному нагреву.
Операция гибки показана на рис.7-3в,г
Смещение относится к операции по уменьшению толщины заготовки на ее конце путем удлинения смещенного участка путем кузнечной ковки на наковальне с использованием дола.
Сварка заключается в соединении элементов из низкоуглеродистой стали путем их нагрева до высокой температуры (ок.1200 °С) и сбивания их между собой (рис. 7-3д, е, ж). Концы свариваемых заготовок обрезают под углом, тщательно зачищают от окалины и соединяют под достаточным давлением.
Обжатие включает использование различных обжимных блоков, верхних обжимных элементов, штампов и подходящих обжимных элементов.
.
404 — страница не найдена
Ошибка 404 — страница не найдена
Ваш город Красноярск?
При выборе изменится адрес и контакты представительства в вашем городе, а также актуальный ассортимент товаров.
- Россия
- Казахстан
- Белоруссия
- Кыргызстан
- Узбекистан
- Таджикистан
Выберите ваш город
Россия
Россия Казахстан Белоруссия Кыргызстан Узбекистан Таджикистан
А
АнгарскАрхангельскАстрахань
Б
БалаковоБарнаулБелгородБийскБлаговещенскБратскБрянск
В
Великий НовгородВладивостокВладикавказВладимирВолгоградВолжскийВологдаВоронеж
Г
Грозный
Д
Дзержинск
Е
Екатеринбург
И
ИвановоИжевскИркутск
Й
Йошкар-Ола
К
КазаньКалининградКалугаКемеровоКировКостромаКраснодарКрасноярскКурганКурск
Л
Липецк
М
МагнитогорскМахачкалаМоскваМурманск
Н
Набережные ЧелныНижневартовскНижнекамскНижний НовгородНижний ТагилНовокузнецкНовороссийскНовосибирскНоябрьск
О
ОмскОрёлОренбургОрск
П
ПензаПермьПетрозаводскПсков
Р
Ростов-на-ДонуРыбинскРязань
С
СалехардСамараСанкт-ПетербургСаранскСаратовСевастопольСеверодвинскСимферопольСмоленскСочиСтавропольСтарый ОсколСтерлитамакСургутСыктывкар
Т
ТаганрогТамбовТверьТольяттиТомскТулаТюмень
У
Улан-УдэУльяновскУфа
Х
ХабаровскХанты-Мансийск
Ч
ЧебоксарыЧелябинскЧереповецЧита
Ш
Шахты
Э
Энгельс
Я
ЯкутскЯрославль
А
АктауАктобеАлматыАтырауАшхабад
Д
Душанбе
Ж
Жезказган
К
КарагандаКокшетауКостанайКызылорда
Н
Нур-Султан (Астана)
П
ПавлодарПетропавловск
С
Семей
Т
ТалдыкорганТаразТуркестан
У
УральскУсть-Каменогорск
Ш
Шымкент
Б
Брест
В
Витебск
Г
ГомельГродно
М
МинскМогилёв
Б
БаткенБишкек
Д
Джалал-Абад
К
Каракол
Н
Нарын
О
Ош
Т
Талас
А
Андижан
Б
Бухара
Н
Нукус
С
Самарканд
Т
Ташкент
Ф
Фергана
Б
БохтарБустон
В
Вахдат
Г
ГиссарГулистон
Д
Душанбе
И
ИстаравшанИстиклолИсфара
К
КанибадамКулябКурган-Тюбе
Л
Левакант
Н
Нурек
П
Пенджикент
Р
Рогун
Т
Турсунзаде
Х
ХорогХуджанд
Обратный звонок
Введите имя Введите номер телефонаНажимая на кнопку, вы соглашаетесь на обработку персональных данных
Оформление заказа
Введите имя Введите номер телефонаНажимая на кнопку, вы соглашаетесь на обработку персональных данных
Запрос цены
Введите имя Введите номер телефонаНажимая на кнопку, вы соглашаетесь на обработку персональных данных
Товар добавлен!
Горячее тиснение 101 | Macrodyne
Что такое горячее тиснение?
Горячая штамповка, известная как закалка под прессом в Европе и горячая штамповка в Азии, представляет собой процесс термической формовки листового металла, при котором формование и металлургическая термообработка происходят во время процесса штамповки. Закалка под прессом была первоначально разработана в 1970-х годах для производства сельскохозяйственных инструментов из закаленной стали, но с тех пор она оказала большое коммерческое влияние на производство легких и высокопрочных белых кузовов в автомобильной промышленности. Снижение расхода топлива и безопасность транспортных средств привели к повсеместному использованию компонентов из сверхвысокопрочной стали, что стало возможным благодаря появлению процесса горячей штамповки.
Раннее развитие и продвижение горячей штамповки было сосредоточено на низкоуглеродистой стали 22MnB5, легированной марганцем и бором, из-за традиционного использования и доступности в секторе белого тела. При нагреве листа 22MnB5 выше 900 °C микроструктура металла преобразуется из ферритной стали в аустенитную, затем при быстром охлаждении в штампе стальная фаза превращается в мартенситную с пределом прочности до 1500 МПа [220 KSI ]. С тех пор были разработаны более высокоуглеродистые марки стали со специальными покрытиями и усовершенствованными химическими составами с пределом прочности до 2000 МПа [29]. 0 KSI] и множество существенных преимуществ процесса и свойств материала.
Для горячей штамповки требуется программируемый сервогидравлический пресс с высокими скоростями подачи и возможностью выдержки для многократного контроля веса в процессах горячей штамповки и охлаждения. Вспомогательное оборудование обычно включает в себя печь с роликовым подом или штабелированную печь для нагрева листового металла, робототехнику или устройства подачи материала, систему охлаждения матрицы и операции обрезки деталей. Тип рамы пресса, системы направляющих, скорость, грузоподъемность, направление подачи материала, быстрая смена штампа и возможность загрузки вне центра должны быть тщательно оценены, чтобы убедиться, что пресс оптимизирован для конкретных операций горячего тиснения.
Соображения по материалам
Любой металл, поддающийся термообработке или трудно поддающийся формованию, может выиграть от горячей штамповки, когда производство сложных высокопрочных деталей является преимуществом. Некоторые примеры материалов представлены в таблице 1 ниже.
Material | Grade | Strength | ||||||||||||||||||||||||||||||||||||||||||||||||||||||||||||||||||||||||||||
Boron Alloy Steel, 0.22% C | 22MnB5 | 1500 MPa | ||||||||||||||||||||||||||||||||||||||||||||||||||||||||||||||||||||||||||||
Boron Alloy Steel, 0.30% C | 30MnB5 | 1800 MPa | ||||||||||||||||||||||||||||||||||||||||||||||||||||||||||||||||||||||||||||
Boron Alloy Steel, 0.37% C | 37MnB5 | 2000 MPa | ||||||||||||||||||||||||||||||||||||||||||||||||||||||||||||||||||||||||||||
Aluminum Alloy, 6000 series | 6061-T6 | 300 MPa | ||||||||||||||||||||||||||||||||||||||||||||||||||||||||||||||||||||||||||||
Aluminum Alloy, 7000 series | 7075-T76 | 500 MPa | ||||||||||||||||||||||||||||||||||||||||||||||||||||||||||||||||||||||||||||
Magnesium Alloy | AZ31B-H | 300 MPa | ||||||||||||||||||||||||||||||||||||||||||||||||||||||||||||||||||||||||||||
Titanium Alloy 9Таблица 1
Не все металлы будут демонстрировать высокую прочность, характерную для борсодержащих сталей, при горячей штамповке. Добавление бора в углеродистые стали способствует фазовому превращению в мартенсит при быстром охлаждении.
Коррозия, обезуглероживание и образование накипи на листовых материалах при высоких температурах в печи являются проблемой для горячей штамповки. Для стали без покрытия требуется атмосфера инертного газа, чтобы свести к минимуму образование накипи. Коррозионно-стойкие покрытия, такие как алюминий-кремний, часто наносят на листовую сталь, чтобы исключить необходимость удаления окалины. Добавление определенных легирующих элементов также может уменьшить коррозию и в некоторых случаях снизить потребность в охлаждении, необходимом для поддержания твердости, и сделать возможным многоэтапное формование.
Металлурги и производители стали приложили значительные усилия для улучшения материалов, используемых для горячей штамповки. На рисунке 1 ниже показано соотношение между удлинением и пределом прочности на разрыв для борсодержащей стали 22MnB5 в отожженном и горячештампованном состояниях по сравнению с другими составами стали, такими как мягкая сталь и обычные высокопрочные стали. Наложенная справа фазовая диаграмма температура-время иллюстрирует условия, необходимые для производства мартенситной стали, а также временные и температурные зоны, в которых в 22MnB5 могут возникать другие фазы. Рис. 1: Свойства материала и циклы охлаждения для 22MnB5.Преимущества горячей штамповки Преимуществами конструкционных компонентов горячей штамповки являются исключительный предел прочности при растяжении в состоянии после формования и сложные геометрические формы, которые могут быть сформированы. Повышенная прочность горячештампованных деталей позволяет снизить вес компонентов за счет использования более тонкого листового металла, сохраняя при этом как структурную целостность, так и ударопрочность.
Когда использовать горячую штамповку Горячую штамповку лучше всего использовать, когда требуются сверхвысокопрочные сплавы с высокой прокаливаемостью, которые очень трудно формовать при комнатной температуре, для удовлетворения строгих требований к продукции. В качестве распространенного примера низкоуглеродистые стали, легированные бором, и другие стальные сплавы с улучшенными составами используются для изготовления белых деталей кузова легковых автомобилей, таких как стойки, бамперы, дверные балки и рейлинги на крыше. На этом высококонкурентном и строго регулируемом рынке количество деталей кузова, формируемых горячим способом, и степень снижения веса продолжают расти.
Использование в авиации, аэрокосмической промышленности, обороне и на других развивающихся рынках начинает ощущать преимущества более высокой прочности и меньшего веса, которые стали возможными благодаря горячей штамповке труднодеформируемых усовершенствованных сплавов. Вопросы процесса Принятие решения о том, является ли горячая штамповка предпочтительным процессом изготовления деталей, является сложной задачей. Необходимо учитывать объемы производства, производительность, стоимость детали, функцию детали и производственные допуски. Особое внимание необходимо уделить выбору подходящего сорта материала, который может извлечь выгоду из процесса термообработки для получения наилучшей возможной детали. Альтернативные процессы Процессы, позволяющие достичь аналогичных результатов, включают;
Штамповка металла [Холодный]: если формуемый материал достаточно пластичен при комнатной температуре, то аналогичные высокопрочные детали можно изготавливать без необходимости нагревания и отжига листового металла. Для производства точных деталей обычно требуются более традиционные методы проектирования деталей и штампов для управления возвратом пружины.
Горячая штамповка: Обычно используется для сплавов цветных металлов, которые трудно деформировать при комнатной температуре. После формовки часто требуется контролируемый процесс охлаждения и старения для восстановления микроструктур, затвердевших на твердый раствор, которые присутствовали до отжига листа путем нагревания.
Гидроформинг: Усовершенствованный процесс формования листов и труб, в котором используется гидравлическое давление вместо фиксированного пуансона для получения геометрических форм, не подходящих для штамповки, включая формы с подрезами или выпуклости.
Изготовление: Для прототипирования или мелкосерийного производства детали могут быть изготовлены из нескольких листов с помощью сварки или других способов соединения. В большинстве случаев изготовление подходит только тогда, когда объем производства недостаточно высок, чтобы оправдать стоимость специального инструмента. Процесс горячей штамповки Обзор Горячая штамповка включает быструю закалку сверхвысокопрочных сталей, которые были нагреты и отформованы. Процесс начинается с раскладки заготовки, которую загружают в печь или топку для нагрева. Нагретая заготовка с помощью системы подачи пресса передается в гидравлический пресс для горячей штамповки, который очень быстро закрывается для создания тоннажа, а затем удерживает деталь, пока она не остынет. Рис. 3: Элементы процесса прямого и непрямого горячего тиснения Прямое горячее тиснение более распространено в промышленности. Непрямая горячая штамповка добавляет стадию холодной штамповки перед нагревом. Факторы успехаПрямое горячее тиснение более распространено в промышленности. Непрямая горячая штамповка добавляет стадию холодной штамповки перед нагревом. Всестороннее изучение всех параметров, влияющих на горячее тиснение, выходит за рамки данной статьи. Вместо этого мы рассмотрим несколько ключевых факторов, влияющих на приемлемую экономику процесса: свойства материалов, закалочные инструменты, производительность и снижение дефектов.
Свойства материала: Высокая прокаливаемость материала обеспечивает более высокую прочность, что напрямую снижает вес детали.
Инструменты для формовки и закалки: Хорошо спроектированный инструмент для формовки и закалки имеет решающее значение для успешного производства детали. Зоны высокой прочности должны быть быстро закалены, чтобы получить желаемые свойства материала. Изолированные зоны компонентов, требующие большей пластичности, охлаждаются медленнее, а в некоторых случаях инструмент нагревается для достижения надлежащей микроструктуры. Специализированные стали для инструментов для горячей обработки, которые могут выдерживать суровые условия многократного термоциклирования, необходимы для минимизации износа матрицы и уменьшения выхода инструмента из строя.
Производительность: Закалка под прессом — это значительно более медленный процесс, чем традиционная штамповка, главным образом из-за времени, необходимого для закалки детали. Типичная скорость цикла прессования составляет от 10 до 30 секунд, при этом более толстые материалы занимают больше времени из-за дополнительного времени, необходимого для закалки. Дополнительная задержка также может быть связана с необходимостью лазерной обрезки, когда закаленная деталь слишком тверда для постобработки прессом и штамповки. Одним из методов, который использовался для сокращения времени цикла, является добавление кремния в состав сплава, что позволяет обеспечить более высокую температуру закалки для облегчения более быстрого многоэтапного формования с штамповкой горячим прессованием и обрезкой.
Уменьшение дефектов: Горячая штамповка приводит к тому, что в результате процесса отжига становится возможным формование глубоких и сложных форм, но высокие температуры делают сталь липкой. Высокая температура также означает, что на лист нельзя наносить смазку, и трение представляет собой серьезную проблему. Кроме того, покрытия материалов, используемые для предотвращения обезуглероживания и образования накипи во время нагрева заготовки, могут быть очень абразивными по отношению к поверхностям инструмента. В результате управление трением имеет решающее значение, чтобы избежать чрезмерного утончения, расщепления и растрескивания детали, а также чрезмерного износа штампа в результате истирания. Конструкция деталей и инструментов для предотвращения дефектов Конструкция деталей и пресс-инструментов для уменьшения и предотвращения дефектов в процессе горячей штамповки в первую очередь сосредоточена на поддержании температуры формования и управлении потоком материала.
Сведение к минимуму отрицательного воздействия трения и поддержание текучести материала является серьезной проблемой для горячей штамповки. Повышенные температуры не позволяют использовать какие-либо формовочные смазки, а в горячем состоянии металл становится очень мягким и липким. Насколько это возможно, конструкция должна минимизировать контакт поверхности между геометрией детали и заготовкой из листового металла. Минимизация контакта позволит обеспечить более свободный поток материала, однако поток также необходимо контролировать во время цикла, чтобы предотвратить образование складок на фланце и смещение деталей.
Поддержание температуры листового металла, достаточной для предотвращения затвердевания и растрескивания в процессе формовки, является еще одной серьезной проблемой. Некоторые общие методы для продвижения успешной детали и дизайна инструментов перечислены ниже в таблице 2.
Таблица 2: Стратегии проектирования деталей и инструментов. Обновлено в сентябре 2021 г. Конфигурация пресса Основные параметрыНастройка пресса для производства горячештампованных деталей начинается с требований к процессу изготовления детали. Для конфигурации требуется информация о типе материала, спецификациях деталей, объеме производства, скорости производства и целевых ценах. Затем эти факторы оказывают непосредственное влияние на требования к обработке, формованию и закалке, которые, в свою очередь, влияют на характеристики установки и оснастки. На приведенной ниже диаграмме зависимости температуры от времени процесса показаны этапы процесса, которые будут определять требования к процессу и достижимую производительность. Рис. 4: Температура в зависимости от времени процесса горячего штамповкиПри покупке пресса для горячего тиснения или полностью автоматизированной линии для горячего тиснения следует учитывать несколько ключевых переменных.
Размер станины Станина пресса должна вмещать в себя самый большой предполагаемый набор инструментов. Тоннаж и скорость Система управления гидравлическим прессом для горячей штамповки должна обеспечивать полностью программируемое и воспроизводимое управление тоннажем для оптимизации процесса и снижения энергопотребления. Пресс должен быть в состоянии произвести достаточное усилие, чтобы сформировать деталь и удерживать/затвердеть, но следует избегать чрезмерного усилия. Тоннаж, который применяется сверх необходимого, может привести к избыточному потреблению энергии и износу инструмента. Типичный диапазон тоннажа для горячей штамповки составляет от 500 до 1500 тонн.
Нагретая заготовка начинает быстро остывать сразу после извлечения из печи, поэтому очень важно, чтобы пресс закрывался и создавал массу для очень быстрого формования детали. Ход и дневной свет Между полностью втянутым пуансоном и поверхностью штампа должно быть достаточно дневного света, чтобы можно было снять готовую деталь с пресса. На практике это соответствует дневному свету, который примерно в три раза превышает ход пресса. Если пресс будет использоваться для производства более чем одной детали, ход и дневной свет должны соответствовать ожидаемому размеру инструмента. Дополнительные зазоры могут потребоваться для обеспечения охлаждения штампа, нагрева штампа, доступа к роботу или подающему устройству, а также быстросменного инструмента. Расширенные возможности Некоторые расширенные возможности горячей штамповки включают:
Ссылки на изображения
Посетите нашу страницу «Прессы горячего тиснения», чтобы узнать больше о специальных прессах горячего тиснения. Свяжитесь с нами, чтобы узнать о ваших потребностях в гидравлическом прессе. 10 Часто задаваемые вопросы по быстрорежущей стали горячего тиснения1. Что такое горячая штамповка В самом простом определении горячая штамповка, также называемая горячей штамповкой или закалкой под давлением, представляет собой процесс формовки металла в очень горячем состоянии (свыше 900°C) с последующей его закалкой (охлаждение это быстро) в штампе. 2. Как работает процесс?Материал, упрочняемый прессованием — борсодержащая сталь или алюминизированная сталь — нагревается более чем на 900 градусов до температуры аустенита в печи на первой ступени линии прессования. Материал быстро переносится на пресс, и деталь формируется, пока материал очень горячий. Затем деталь закаливают, удерживая ее в полости матрицы с водяным охлаждением в течение нескольких секунд в нижней части хода, когда зернистая структура материала преобразуется из аустенитного состояния в мартенситное. 3. Почему горячая печать? «На первый взгляд, процесс горячей штамповки кажется довольно простым — нагрейте стальную заготовку, пока она не раскалится докрасна, вдавите ее в полость штампа и держите там несколько секунд, пока она не остынет. Весь процесс представляет собой колдовство. У меня возникло видение кузнеца, работающего с раскаленной заготовкой над наковальней с кувалдой и закалочным ведром рядом с ним», — сказал Рич Марандо, президент Graebener Group Technologies, Наполеон, штат Огайо. Высокая прочность на растяжение. «В случае современной горячей штамповки относительно сложные детали могут быть сформированы в одностадийной штампе», — продолжил Марандо. «В результате получается сложная деталь почти чистой формы с пределом текучести во много раз выше, чем у детали из мягкой стали». Борсодержащая сталь в исходном состоянии имеет предел прочности при растяжении около 50 тысяч фунтов на квадратный дюйм, но после горячего формования она составляет около 200 тысяч фунтов на квадратный дюйм. Сложные компоненты. Поскольку горячая штамповка позволяет формовать сложные детали за один проход, многокомпонентные сборки могут быть переработаны и сформированы как один компонент, исключая некоторые последующие процессы соединения, такие как сварка. Без пружинного возврата. Возможно, самым значительным преимуществом горячей штамповки, помимо ее упрочняющей способности, является ее способность снимать напряжения, которая решает проблемы с пружинением и деформацией, распространенной проблемой при формовании высокопрочной стали (HSS) и усовершенствованной высокопрочной стали (AHSS). Cosma International Inc., Трой, штат Мичиган, подразделение Magna International, проектирует, разрабатывает и производит автомобильные системы, узлы, модули и компоненты. Поставщик уровня 1 поделился своим опытом горячей штамповки в статье «Горячее формование: прочность в сочетании со светом; между NHTSA и CAFE», опубликованной в выпуске The FABRICATOR® за май 2006 года. Одна из проблем, присущих штамповке из AHSS, заключается в том, что детали из AHSS, штампованные методом холодной штамповки, имеют тенденцию пружинить. «Это мешает подгонке и вызывает трудности при сварке и сборке», — сказал Свами Котагири, директор отдела исследований и разработок. Холодная штамповка сложных, угловатых деталей или деталей с трехмерным изгибом становится очень сложной, когда они изготовлены из очень высокопрочных материалов — от 150 до 200 KSI. 4. Какие компоненты подвергаются горячей штамповке? Проще говоря, горячая штамповка лучше всего подходит для изготовления деталей, которые должны быть одновременно легкими и очень прочными. Горячее тиснение чаще всего применяется для структурных автомобильных компонентов, таких как стойки кузова, коромысла, рейлинги на крыше, бамперы и дверные балки. Компания Cosma искала пути выполнения конструктивных требований Национальной администрации безопасности дорожного движения (NHTSA) по повышению безопасности транспортных средств. Требование уменьшить проникновение крыши в пространство салона при опрокидывании стало еще более жестким. «Стандарты разрушения крыши основаны на полной массе транспортного средства [GVW]», — сказал Котагири. «По сути, стандарт гласит, что если полная масса транспортного средства составляет 4000 фунтов, оно должно выдерживать силу, в 1,5 раза превышающую 4000 фунтов, или 6000 фунтов, при испытании на разрушение крыши, предназначенном для имитации опрокидывания. Чтобы соответствовать этим требованиям, материал компонентов должен быть прочнее — обычно это достигается за счет увеличения толщины и веса. Очевидное противоречие заключается в том, что компоненты также должны быть максимально легкими, чтобы соответствовать все более строгим корпоративным стандартам средней экономии топлива (CAFE) по снижению выбросов, сказал он. «Поэтому цель состоит в том, чтобы получить требуемые структурные характеристики, но при этом добавить как можно меньше веса», — сказал Котагири. 5. Каковы уникальные требования к прессу и оснастке?Система отопления. Печь или система индукционного нагрева должны быть установлены перед станцией формования на линии пресса для нагрева заготовки примерно до 960 градусов C. Система охлаждения. Пресс также должен быть оборудован системой охлаждения с большим количеством охлаждающих контуров с переменным управлением. Автоматизированная обработка . Поскольку нагретая деталь очень горячая на ощупь, в систему необходимо интегрировать автоматизированную систему обработки деталей, такую как шаттл или роботизированная система перемещения. Возможность задержки. Гидравлический пресс или пресс с сервоприводом с возможностью выдержки необходим для поддержания тоннажа в нижней части хода во время закалки детали. Безопасность. Пресс-система должна соответствовать всем требованиям безопасности для работы в горячем состоянии. Инструменты. Штамп для горячего тиснения представляет собой одноступенчатый штамп с внутренними каналами охлаждения и должен быть изготовлен из инструментальных материалов, устойчивых к тепловому удару. 6. Как это влияет на последующие процессы? Поскольку глубокую формовку можно выполнить одним ударом, составные сборки можно формировать как единый сложный компонент. «В прошлом, чтобы повысить безопасность боковых ударных балок, решение заключалось в добавлении деталей — добавлении большего количества металла в боковины кузова. Во многих случаях с помощью горячей штамповки мы можем устранить нужны дополнительные детали», — сказал Котагири в статье. «Допустим, у вас есть внутренняя часть центральной стойки со стороны кузова, усиление центральной стойки и наружная часть средней стойки. Если я использую в этой сборке компоненты, изготовленные горячим формованием, теперь я могу исключить усиление. В примерах разрушения крыши там, где обычные штамповки и усиления были заменены горячештампованными компонентами, масса снижается примерно на 30–40 процентов», — сказал он. Шкала. После формовки деталь может нуждаться в специальной обработке для удаления окалины и повышения коррозионной стойкости. Для борсодержащей стали без покрытия требуется богатая азотом (или другим инертным газом) атмосфера в печи; в противном случае, когда он подвергается воздействию атмосферы, на нем образуется окалина, которую необходимо удалить дробеструйной или пескоструйной обработкой. 7. Каковы другие аспекты возможностей?Меньший тоннаж Требование . Котагири сказал, что потребность в тоннаже для горячей формовки высокопрочной стальной детали значительно ниже, чем для холодной формовки. По его словам, для горячей формовки вытяжной части центральной стойки требуется всего от 30 до 40 процентов тоннажа, необходимого для ее холодной штамповки с использованием материала аналогичной прочности. Таким образом, деталь, для холодной штамповки которой требуется 1000 тонн, требует только 300-400 тонн для горячей штамповки, сказал он. Элементы сложной детали. Горячее формование позволяет получить очень сложную геометрию с высокой прочностью, которую нельзя формировать в холодном виде. «Честно говоря, сегодня нет ни одного другого процесса, при котором можно было бы сформировать деталь, подобную А-образной опоре, с такой же прочностью из-за упругости и из-за требований к тоннажу и прочности», — сказал Котагири. 8. Каковы ограничения горячего тиснения?Лазерная накладка. Окончательная обрезка должна выполняться с помощью лазера, поскольку после закалки детали ее становится слишком сложно обрезать с помощью традиционных стальных штампов для обрезки. Стоимость материалов. Бористая сталь стоит дороже, чем низкоуглеродистые материалы. Нельзя переформировать. Горячее тиснение — это одноэтапный процесс, фактически невозможно выполнить несколько процессов, таких как дополнительная вытяжка или отбортовка, поскольку материал затвердевает. Медленное формирование. Процесс горячей штамповки медленнее, чем холодная штамповка. От удара до удара проходит примерно 15-20 секунд. Ограниченные материалы. Этот процесс горячей штамповки нельзя применять к оцинкованной или предварительно окрашенной стали; только материалы из бора могут подвергаться горячей штамповке. 9. Как сравнить затраты?Расчет разницы в весе и стоимости может быть сложной задачей, поскольку прямое сравнение детали, изготовленной методом холодной штамповки, с деталью, изготовленной методом горячей штамповки, будет неточным, сказал Котагири. «Например, вы не можете взять центральную стойку холодной штамповки и сравнить ее с горячештампованной центральной стойкой и спросить: «Какова разница в стоимости?» потому что вы получаете больше от своей части в процессе горячей штамповки», — сказал Котагири. «Вопрос в следующем: «Нам нужна эта производительность; теперь дайте нам свой дизайн с горячим тиснением и расскажите, сколько вы сэкономили в массе». 10. Каково будущее горячего тиснения? Котагири из Cosma ожидает, что растущие требования к высокому соотношению прочности к весу повысят спрос на компоненты горячей штамповки. В настоящее время проводятся исследования и разработки, направленные на сокращение продолжительности цикла закалки и улучшение проверки целостности деталей, а также методов смазки и обрезки. Также проводятся исследования по улучшению контроля над концентрацией теплового напряжения, чтобы можно было варьировать прочность и напряжение по всему компоненту. Котагири сказал, что одним из наиболее важных аспектов успешного применения технологии горячей штамповки является возможность понять, как влияет на материал процесс нагрева в печи, а также понять технологию закалки в штампе. «‘Как я могу последовательно изготавливать детали в течение определенного периода времени и точно знать, как быстро они остыли, насколько они остыли, и контролировать температуру детали?» Мы нашли применение и способы массового производства компонентов с использованием этого процесса. Горячая штамповка и штамповка прототиповПерейти к содержимомуШтамповка металла обеспечивает повторяемость, не всегда достижимую при использовании других технологий изготовления, а также возможность создавать сложные детали с жесткими допусками, которые превышают производственные спецификации.Преимущества и области примененияМы понимаем, что нет одинаковых штамповочных штампов, поэтому крайне важно, чтобы у нас был запас прессов для удовлетворения потребностей наших клиентов. Опираясь на прочный фундамент возможностей штамповки листового металла, мы вложили средства в уникальные методы штамповки, такие как горячая штамповка. Горячее тиснение позволяет прессовать сложные детали с высокой прочностью на растяжение, создавая форму в едином легком изделии, что является растущим требованием в автомобильной и аэрокосмической промышленности. Другим дорогостоящим методом штамповки является штамповка с глубокой вытяжкой, основная компетенция нашей компании Duggan’s. В дополнение к нашим возможностям с точки зрения штамповки, мы не только разрабатываем и производим инструменты собственными силами, но и располагаем ведущей в отрасли металлургической лабораторией, позволяющей нам проверять и контролировать качество на протяжении всей операции штамповки, что позволяет поставлять детали более экономично и быстро. точность выше производственных допусков. ПроизводительностьОт прототипирования и мелкосерийного производства до мелкосерийного производства — у нас есть возможности и мощности на нашем предприятии площадью 105 000 кв. футов для удовлетворения потребностей наших клиентов в штамповке. Duggan может закрыть пробелы, с которыми сталкиваются наши клиенты, когда им нужны детали для производства. Наш обширный парк из более чем 60 прессов позволяет Duggan предоставлять услуги как по запросу, экстренная штамповка, мелкосерийное производство, так и крупносерийное производство деталей. ВОЗМОЖНОСТИ ШТАМПОВКИ ЛИСТОВОГО МЕТАЛЛА
Как мы делаем это лучше За годы штамповки и изготовления деталей мы многому научились, и мы знаем, что может пойти не так, и как организовать эффективный процесс при производстве высококачественных деталей. Этот опыт облегчает Даггану стандартизацию и внедрение подхода, имитирующего процессы массового производства. Механизмы Poka-yoke, вспомогательные средства проверки, сериализация и датчики ключевых функций — вот лишь несколько примеров таких процессов. Во многих случаях это делает объемы производства металлических штамповок наших клиентов идеальными для производства Duggan. Инструменты, которые мы используем, во многих случаях выдерживают не менее 100 000 деталей, и мы можем применять извлеченные уроки, чтобы наше ноу-хау стало конкурентным преимуществом для наших клиентов. ШТАМПОВКА ГЛУБОКОЙ ВЫТЯЖКОЙ
Штамповка глубокой вытяжкой Инструментальная стратегия, которую использует Duggan, в сочетании с нашими инвестициями в оборудование и опытом в этой категории деталей, делает это основной компетенцией. В настоящее время у нас есть более 15 амортизирующих прессов, что является передовым подходом к изготовлению штамповок из металла глубокой вытяжки. Дополнительная оснастка разработана как более сложный инструмент из трех частей, который способствует текучести металла. Мы также используем программное обеспечение для моделирования, чтобы убедиться, что наш подход не пропускает ни одной слепой зоны. ГОРЯЧАЯ ШТАМПОВКА
Горячая штамповка Горячая штамповка Сложные детали можно легко формовать на гидравлическом прессе с одноступенчатой матрицей. Эта способность создавать легкие детали делает горячую штамповку отличной для производства любого типа транспортных средств. Процесс горячей штамповки звучит просто: нагрейте заготовку из борсодержащей стали, титана или алюминия до красна (более 900 градусов), вдавите его в полость штампа с водяным охлаждением и держите там несколько секунд, пока он не остынет. К сожалению, вам нужно нечто большее. У нас есть не только многолетний опыт горячей штамповки деталей, но и металлургическая лаборатория для проверки прочности на растяжение и предел текучести в штамповках, опыт проектирования инструментов, который способствует охлаждению деталей, и такие процессы, как лазерная и электроэрозионная резка проволоки, которые могут быстро резать «собачку». срезы костей», которые можно быстро протестировать. ГИБОЧНЫЙ ТОРМОЗ
Листогибочный пресс Если это небольшой кронштейн, большие рельсы или что-то промежуточное, мы справимся. Наши листогибочные прессы имеют грузоподъемность до 350 тонн для гибки толстых или тонких деталей. Наш обширный ассортимент инструментов включает пуансон и матрицу практически для каждой формы канала. Все наши инструменты изготовлены из термообработанной инструментальной стали и отшлифованы для обеспечения точности. Мы предлагаем радиусные пуансоны всех размеров, от ножевого пуансона до радиуса 1 ». Для гнутых деталей с нечетным радиусом или очень большим радиусом мы можем использовать ступенчатую гибку. Ступенчатая гибка — это когда листогибочный пресс с ЧПУ запрограммирован на выполнение последовательности до 100 небольших ударов, которые при последовательном выполнении создают один большой радиус. Мы инвестировали в широкий спектр инструментов и создали большое разнообразие пуансонов и штампов. Это преимущество по двум причинам. Во-первых, работа может быть обработана сразу же после получения заказа без задержек, связанных с ожиданием поставки инструментов. Материалы, с которыми мы работаем
Сертификаты
Перейти к началу Все о горячей штамповке в производствеЧто такое горячее тиснение? Горячее тиснение — это процесс литографической печати, в котором используются нагретые формы для изображений или штампы для тиснения для переноса металлической фольги или предварительно высушенных красок на поверхность. Обычно процесс работает следующим образом: машина для горячего тиснения нагревает форму или штамп с гравировкой, которые затем прижимают маркировочную фольгу к поверхности. Фольга наносится только там, где горячий штамп соприкасается с материалом изделия, что позволяет инженерам создавать элегантные тисненые рисунки на деталях и узлах на этапе постпроизводства. Фольга для горячего тиснения имеет три слоя: цветной слой (который может быть пигментным или металлическим), адгезионная основа и разделительный слой. Инновации в цифровой печати позволяют даже горячее тиснение трехмерных изображений голографической фольгой. Горячее тиснение — это универсальный, точный и эффективный метод печати на поверхностях, который часто используется для персонализации или украшения продуктов. Вот краткое изложение некоторых ключевых преимуществ процесса горячего тиснения, а также основных соображений, о которых следует помнить. Четыре ключевых преимущества горячего тиснения Одним из наиболее значительных преимуществ горячего тиснения является то, что его можно использовать для обработки широкого спектра обычных материалов, включая пластмассы, резину и металлы, в дополнение к более специализированным материалам, таким как дерево, кожа и стекло. Пособие №1Горячее тиснение также является чистым и невероятно эффективным процессом. Поскольку машины для горячего тиснения фольгой работают с рулонами металлической фольги или с предварительно высушенными красками, инженеры могут избежать смешивания жидких красок и очистки грязных пятен. Пособие №2Горячее тиснениетакже неизменно дает высококачественные результаты — независимо от пигмента или металлической окраски фольги, адгезивные основы созданы для надежного сцепления с поверхностью продукта. Тем не менее, некоторые материалы, такие как кожа, требуют специальной фольги для правильного приклеивания, что важно помнить менеджерам по продукции. Пособие №3 Хотя фольга для маркировки рассчитана на долговечность, условия окружающей среды могут привести к ее выцветанию со временем. Пособие №4Несмотря на то, что метод горячего тиснения в основном используется для отделки, он также имеет и другие применения. Например, в автомобилестроении можно использовать горячую штамповку, чтобы максимизировать ковкость стали. Процесс похож на теплую формовку; однако штампы холодные при вдавливании в нагретую сталь, что создает мартенситные микроструктуры в стали, которые придают детали исключительную прочность. Это делает горячую штамповку полезной при производстве прочных кабин транспортных средств и каркасов безопасности, а также других деталей. Ограничения и соображения по горячему тиснению Единственным существенным ограничением процесса изготовления фольги для горячего тиснения является то, что он не позволяет печатать очень маленькие буквы без потери четкости. Еще одним ключевым моментом является выбор материала матрицы, прижимающей фольгу для тиснения. Обычно используются такие металлы, как латунь, медь, магний и сталь. Магниевые штампы проще и дешевле всего изготовить, но они менее долговечны. Медь и латунь обладают большей долговечностью и требуют больших затрат на производство, в то время как штампы из закаленной стали практически не поддаются разрушению и обеспечивают наилучший перенос фольги. Стальные штампы дороги в производстве, но благодаря своей долговечности становятся невероятно рентабельными при использовании в крупносерийном производстве. Изделия для горячего тиснения со сложными формами или не идеально плоскими поверхностями представляют собой сложную задачу. Комплексное и непревзойденное производственное обслуживание по запросу с помощью Fast RadiusВ конечном счете, горячее тиснение является эффективным средством индивидуальной настройки или украшения деталей или повышения пластичности таких материалов, как сталь. В любом случае процесс универсален и относительно прост. Производственные группы, надеющиеся использовать горячую штамповку в своем следующем проекте, не должны смотреть дальше. Fast Radius работает над расширением границ возможностей современного производства. Наша команда инженеров и дизайнеров тесно сотрудничает с каждым клиентом на каждом этапе жизненного цикла продукции — от проектирования до постпроизводственной отделки. Мы создаем больше, чем просто детали — мы строим доверительные партнерские отношения, ориентированные на своевременное производство высококачественных компонентов и узлов. Посетите ресурсный центр Fast Radius, чтобы узнать о нашем обширном списке предложений по производственным процессам, включая Digital Light Synthesis™ от Carbon, а также о разнообразии материалов, с которыми мы работаем. Готовы создавать свои детали с помощью Fast Radius?Начните предложение Ножи для горячего тиснения и холодного тиснения | Плюсы и минусыhttps://i0.wp.com/buckeyeengraving.com/wp-content/uploads/2021/07/knife-banner.jpg?fit=1024%2C678&ssl=1 1024 678 Бакай Гравюра Бакай Гравюра https://i0.wp.com/buckeyeengraving.com/wp-content/uploads/2021/07/knife-banner.jpg?fit=1024%2C678&ssl=1 Вопросы о горячем тиснении и холодном тиснении в основном возникают в наших беседах с производителями ножей, которые ищут нестандартный ножевой штамп или штамп. Наш ответ всегда начинается с вопроса: «Как вы делаете свой нож?» Когда производители ножей хотят поставить клеймо своего производителя, их процесс изготовления во многом определяет то, как они будут штамповать свои шедевры. Хотя мы отказываемся вступать в дискуссию о ковке ножа и обрезании ножа (мы любим и то, и другое!), мы действительно хотим помочь всем производителям ножей добиться красивого штриха на их конечном продукте. Ниже специалисты Buckeye Engraving делятся с производителями ножей (а также с кузнецами, кузнецами и другими мастерами по металлу) некоторыми знаниями о горячем тиснении и холодном тиснении, чтобы они могли с уверенностью выбрать процесс касания в соответствии со своими потребностями и получить желаемые результаты впечатления. Горячая штамповка для ковки ножа Ковка ножа включает создание формы, размера и толщины лезвия путем придания формы нагретому металлу с помощью молотка и наковальни. ГОРЯЧАЯ ШТАМПОВКА METAL PROSГорячая штамповка вашего ножа или других кованых изделий имеет много преимуществ. Поскольку металл более податлив во время процесса горячего тиснения 1. Вы можете нанести клеймо производителя или логотип большего размера, чем при холодном тиснении. 2. Даже жирные рисунки могут быть крупнее, чем при холодном тиснении. 3. Ручное тиснение и тиснение прессом позволяют получать четкие и чистые метки. По сути, горячая штамповка, как и сам процесс ковки, основана на перемещении металла для его формирования и придания формы. Этот момент важно отметить, так как количество силы будет играть роль в конечном результате штампованного изображения: чем больше дизайн сенсорной метки, тем больше силы вам потребуется, чтобы сместить больше металла при создании оттиска. ГОРЯЧАЯ ШТАМПОВКА МЕТАЛЛА МИНУСЫКак и все хорошие вещи, горячая штамповка имеет некоторые недостатки. В частности, горячая штамповка требует, чтобы металл был горячим! В результате во время штамповки необходимо использовать перчатки и другое защитное снаряжение, а некоторые металлурги считают, что громоздкие перчатки, фартуки и щипцы мешают им манипулировать штампом так осторожно, как им хотелось бы. Конечно, при достаточной практике мейкеры легко преодолевают эту неловкость. Чтобы устранить эти недостатки горячего тиснения, Buckeye Engraving предлагает несколько решений.
Стоит повторить, что горячее тиснение в значительной степени ограничивается производителями, занимающимися ковкой металла, поскольку оно зависит от температуры металла при штамповке. Так что, если вы ковите свой нож или другое металлическое изделие , а не , вы, вероятно, хотите узнать больше о холодной штамповке перед термообработкой ниже. Холодная штамповка для изготовления съемных ножей Изготовление ножей для снятия припуска включает в себя формирование лезвия путем снятия стального материала со стальной детали с помощью абразивов, пил и ленточных шлифовальных станков. ХОЛОДНАЯ ШТАМПОВКА METAL PROSВарианты холодной штамповки универсальны, так как холодную штамповку можно выполнять с помощью молотка или пресса, как и в случае с горячей штамповкой. Однако холодная штамповка имеет три важных преимущества, которые следует учитывать: 1. Холодная штамповка обеспечивает большую точность. Отсутствие беспокойства о горячем металле облегчает приближение, выравнивание и обращение с штампом или прессом во время холодной штамповки. Для многих этот уровень точности является всем. 2. Окончательный оттиск может быть более темным и глубоким благодаря процессам, происходящим после штамповки. Поскольку металл подвергается термообработке после процесса штамповки (помните, никогда нельзя штамповать холодный закаленный или термообработанный металл!), штампованный оттиск приобретает дополнительную темноту и глубину в результате этого процесса. 3. Холодная штамповка для самых разных процессов изготовления. В отличие от горячей штамповки, которая ограничивается процессом ковки, холодная штамповка подходит для производителей, которые работают с цветными металлами, отожженной сталью перед термообработкой и незакаленными металлами, которые не будут подвергаться термообработке.
COLD STAMPING METAL CONSПовышенная точность, безусловно, является большим плюсом для холодной штамповки, но опять же, у холодной штамповки есть ограничения.
Мы предлагаем быстрые и бесплатные оценки для вашего индивидуального штампа или штампа. Заполните нашу простую онлайн-форму бесплатного предложения сегодня, чтобы начать. Преимущества штамповки холоднокатаного металла по сравнению с горячекатаной штамповкой металлаАвтор: American Industrial, В зависимости от вашего применения, вы можете задаться вопросом, является ли горячекатаная или холоднокатаная штамповка металла лучшим выбором. Каждый из них обеспечивает преимущества для различных приложений. Однако химический состав марки материала может различаться в зависимости от производственного процесса. В этом блоге будут рассмотрены различия между горячекатаной и холоднокатаной сталью и способы выбора наилучшего процесса формовки для вашего применения. Что такое холоднокатаная штамповка металла по сравнению с горячекатаной штамповкой?Штамповка холоднокатаного металла Холоднокатаный металл формуется путем проталкивания через ряд роликов при комнатной температуре. Идеально подходят толстые куски металла, которые формуются под высоким давлением, что позволяет прокатывать материал до точных размеров и обеспечивает гладкую поверхность. Поскольку нагрев не требуется, штамповка холоднокатаного металла создает более прочный продукт без дополнительных ресурсов для его нагрева и охлаждения. Штамповка горячекатаного металлаКогда металл нагревается выше температуры рекристаллизации, он становится ковким. Затем его можно раскатать и придать желаемую форму. Однако высокие температуры, необходимые для нагревания, означают, что продукт также необходимо охлаждать при комнатной температуре, чтобы предотвратить разрушение под напряжением, что приводит к усадке и сухому чешуйчатому покрытию. К сожалению, невозможно точно предсказать различия в форме, размере и отделке горячекатаного металла.Каковы преимущества и области применения штамповки холоднокатаного металла?Штамповка холоднокатаного металлаобеспечивает повышенную эффективность, быструю обработку, точность штамповки и жесткие допуски. Штамповка горячекатаного металла может выполняться только для ограниченного числа типов, таких как борсодержащая сталь, в то время как холодная штамповка подходит для широкого круга металлов. Холоднокатаные металлы имеют более четкие и точные очертания, повышенную прочность и твердость, а также более высокую техническую и косметическую точность, чем горячекатаные, что делает их предпочтительными для многих применений, в том числе:
Почему вы должны выбрать штамповку металла с американским промышленным American Industrial является лидером в сфере услуг по штамповке металлов. Наши возможности обслуживают автомобильную, строительную, светотехническую и горнодобывающую отрасли, среди многих других. Мы работаем с нашими клиентами на каждом этапе производства, от проектирования до прототипа и готового продукта. Наше сертифицированное по ISO 9001:2015 предприятие с лучшими штамповочными машинами, машинами для контроля качества и ремесленниками производит продукцию, отвечающую самым строгим спецификациям и требовательным срокам. Наша команда также может обеспечить изготовление на заказ с возможностью штамповки металла, например:
Нужен ли вам очень сложный заказ компонентов, изготовленных в несколько этапов, или одноразовый прототип, наша команда всегда готова вам помочь. Последние сообщения
Архивы: |