Газодинамическое Напыление аппаратами ДИМЕТ — Технологии сварки
Газодинамическое Напыление аппаратами ДИМЕТ — Технологии сварки — Металлический форум Перейти к публикацииVexx 99
-
- Members
- 99
- 519 публикаций
- Город: Казахстан, Лисаковск
- Имя: Обросов Артём
Vexx 99
-
- Members
- 99
- 519 публикаций
- Город: Казахстан, Лисаковск
- Имя: Обросов Артём
Vexx 99
-
- Members
- 99
- 519 публикаций
- Город: Казахстан, Лисаковск
- Имя: Обросов Артём
Vexx 99
-
- Members
- 99
- 519 публикаций
- Город: Казахстан, Лисаковск
- Имя: Обросов Артём
Vexx 99
-
- Members
- 99
- 519 публикаций
- Город: Казахстан, Лисаковск
- Имя: Обросов Артём
andrey357 48
-
- Members
- 48
- 521 публикация
- Город: Подмосковные мы…
Vexx 99
-
- Members
- 99
- 519 публикаций
- Город: Казахстан, Лисаковск
- Имя: Обросов Артём
Vexx 99
-
- Members
- 99
- 519 публикаций
- Город: Казахстан, Лисаковск
- Имя: Обросов Артём
gve 465
-
- Members
- 465
- 2 275 публикаций
- Город: Новосибирск
- Имя: Григорий
Vexx 99
-
- Members
- 99
- 519 публикаций
- Город: Казахстан, Лисаковск
- Имя: Обросов Артём
ёжИК 29 18
-
- Members
- 18
- 152 публикации
- Город: Архангельск
- Имя: Александр
Vexx 99
-
- Members
- 99
- 519 публикаций
- Город: Казахстан, Лисаковск
- Имя: Обросов Артём
Vexx 99
-
- Members
- 99
- 519 публикаций
- Город: Казахстан, Лисаковск
- Имя: Обросов Артём
Dunhell 12
-
- Members
- 12
- 33 публикации
- Город: Алматы
www.chipmaker.ru
Мир современных материалов — Холодное газодинамическое напыление
Метод холодного газодинамического напыления металла (англ. – cold spray, cold gas dynamic spraying) состоит в том, что твердые частицы металла, температура которых значительно меньше их температуры плавления, разгоняются до сверхзвуковой скорости и закрепляются на поверхности при соударении с нею.
Сущность метода холодного газодинамического напыления металла включает в себя формирование в сопле сверхзвукового газового потока, подачу в этот поток порошкового материала с размерами частиц 0,01-50 мкм, его сверхзвуковое ускорение в сопле и направление частиц порошка на поверхность изделия. Ускорение частиц возможно в среде холодных или подогретых газов, таких как: воздух, гелий, азот. Значения температуры существенно ниже температуры плавления материала порошка (0,4-0,7Тпл). Технология холодного газодинамического напыления позволяет наносить металлические покрытия не только на металлы, но и на стекло, керамику, камень, бетон. Покрытия, нанесенные этим методом, механически прочны и имеют высокую адгезию к подложке.
Явление формирования покрытий методом холодного газодинамического напыления впервые было обнаружено в Институте теоретической и прикладной механики им. С.А. Христиановича Сибирского отделения Российской академии наук (ИТПМ СО РАН) в начале 80-х годов прошлого века. Они показали, что для формирования покрытия необязательно, чтобы частицы находились в расплавленном или предрасплавленном состоянии, а покрытия можно получать из частиц с температурой значительно ниже их температуры плавления, в отличие от традиционных методов напыления.
Рис. 1. Микрофотографии покрытий [1].
Основные экспериментальные факты:
1. Наиболее важным параметром при холодном напылении является скорость частиц, именно от ее величины зависят адгезия, пористость, микротвердость покрытий и др. Для всех частиц с диаметром d£50 мкм существует «пороговая» величина скорости взаимодействия их с подложкой (500-600 м/с). Если скорость ниже этого значения, то наблюдается процесс эрозии. При скорости выше «пороговой» процесс эрозии переходит в напыление.
2. Существует критическая величина расхода частиц, при котором напыление не происходит независимо от времени воздействия потока.
Рис. 2. Микрофотографии внешнего слоя (х150) и поперечного шлифа покрытия из частиц алюминия (электронный микроскоп, х300) [1].
4. Только малая доля частиц, разгоняемая сверхзвуковым потоком, в итоге напыляется на изделие, основная же доля отражается и уносится потоком газа. Масса напыленных частиц увеличивается с ростом расхода порошкового материала.
5. При формировании покрытия нагрев поверхности изделия незначителен. Разница температур для поверхности только обтекаемой потоком газа и при напылении покрытия составляет »45 градусов.
Существует 2 разновидности холодного газодинамического напыления: высокого и низкого давления. Сравнение типичных параметров оборудования для напыления по этим двум способам представлено в табл. 1. В общем, качество покрытий нанесенным методом высокого давления выше и требования к определенному размеру частиц порошка ниже. Главное достоинство метода низкого давления в более низкой стоимости оборудования и его меньших габаритах.
Таблица 1. Сравнение режимов холодного газодинамического напыления высокого (ХГНВД) и низкого давления (ХГННД).
Параметр |
ХГНВД |
ХГННД |
Газ |
Азот, гелий, смесь |
Сжатый воздух |
Давление, бар |
7-40 |
6-10 |
Температура нагрева, 0С |
20-550-800 |
20-650 |
Расход газа, м3/мин |
0,85-2,5 (азот), макс. 4,2 (гелий) |
0,3-0,4 |
Расход порошка, кг/ч |
4,5-13,5 |
0,3-3 |
Расстояние для напыления, мм |
10-50 |
5-15 |
Мощность, кВт |
17-47 |
3,3 |
Размер частиц, мкм |
5-50 |
5-30 |
На рис. 3 представлена принципиальная схема напыления покрытий холодным методом высокого давления. Газ под высоким давлением нагревается и смешивается с порошком, затем газопорошковая смесь поступает в сопло, где она ускоряется до сверхзвуковой скорости и направляется на подложку, формируя покрытие.
Рис. 3. Принципиальная схема холодного газодинамического напыления высокого давления.
Основное отличие сверхзвукового сопла для этих технологий заключается в том, что при напылении с низким давлением порошок поступает перпендикулярно газовому потоку прямо в сопле, а при технологии высокого давления в сопло поступает газопорошковая смесь (рис. 4, 5). Также отличием является то, что подогрев газа при высоком давлении осуществляется перед сверхзвуковым соплом, а при низком давлении непосредственно в нем.
Рис. 4. Конструкция сопла для холодного газодинамического напыления высокого давления [2].
Рис. 5. Конструкция сопла для холодного газодинамического напыления низкого давления.
При методе холодного напыления низкого давления обычно напыляют различные металлические порошки вместе с добавкой керамических частиц (Al2O3, SiC). Считается, что эти добавки активируют поверхность подложки, улучшая адгезию, и благодаря им прочищается сопло.
Холодный метод нанесения покрытий, в основном, применяют для восстановления различных металлических деталей в случае трещин, сколов, истирания. Также у них высокий потенциал в качестве антикоррозионных, теплопроводных покрытий. Предложено использовать такие покрытия в качестве защитных для контактных поверхностей кабельных наконечников [1]. В [3] приведены экспериментальные результаты испытаний разнообразных покрытий поверхностей сильноточных контактов, нанесенных холодным газодинамическим напылением низкого давления. Все варианты не прошли испытания, кроме специально разработанного композиционного покрытия (см. новость «Защитное композиционное покрытие для электрических контактов»
Source: http://worldofmaterials.ru/358-zashchitnoe-kompozitsionnoe-pokrytie-dlya-elektricheskikh-kontaktov»).
Литература:
1.Алхимов А.П., Клинков С.В., Косарев В.Ф., Фомин В.М. Холодное газодинамическое напыление. Теория и практика. – М.: Физматлит, 2010 — 536 с.
2. http://www.cmit.asiro.au/innovation/2003-08/cold_spray.cfm
3. Koktsinskaya E.M., Roshal A.G. et al. Aging Tests of the High Current Aluminum–Copper Contact Connections in the ITER DC Busbar System/ IEEE Transactions on Plasma Science. – 2014. -Volume:42 , Issue: 3, p. 443-448.
Вас также может заинтересовать:
worldofmaterials.ru
Газодинамическая технология холодного напыления (ХГН) от компании ДИМЕТ
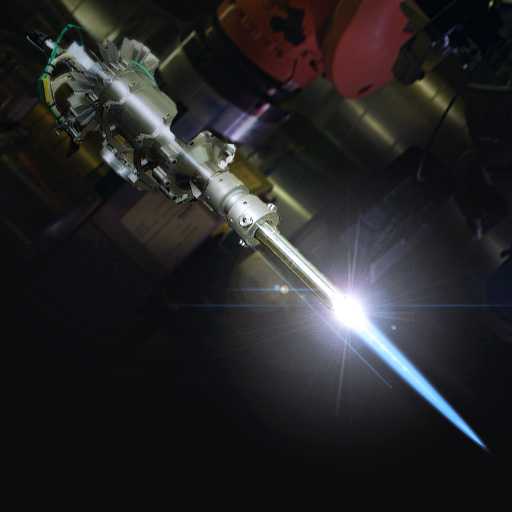
По сути, газодинамическая технология холодного напыления – более продвинутый вариант давно уже зарекомендовавшего себя газотермического способа восстановления различных металлических деталей и поверхностей. Cold Spray или просто ХГН значительно расширяет возможности «горячего» метода обработки изделий.
В настоящее время, бесспорно, это самая передовая технология восстановления и защиты материалов, получившая широкое распространение как в промышленном секторе, так и гражданской сфере.
Принцип действия, плюсы и минусы ХГН
ХГН имеет два основных отличия от газотермического метода реставрации. Во-первых, напыление защитного или восстановительного покрытия происходит при пониженной температуре, не превышающей 150 °С, что в свою очередь не вызывает напряжения в обрабатываемых деталях и их деформации. Во-вторых, «холодная» технология позволяет создавать слой регулируемой толщины и в точно заданных границах. О других плюсах и минусах расскажем чуть позже, а пока об авторах метода и о том, как он работает.
Его разработчиком является «Обнинский центр порошкового напыления» (Россия). Производимое ими оборудование получило название ДИМЕТ®. Оно сертифицировано по системе ГОСТ Р и защищено патентами России, США, Канады и других стран. В основу технологии заложен принцип сверхзвукового воздействия мельчайшими частицами легкоплавких и других материалов на обрабатываемую поверхность. В основном это полимеры или сплавы карбидов с металлами с размером частиц 0,01-0,5 мкм. Смешиваясь с газом они подаются на изделие со скоростью 500-1000 м/с.
В зависимости от состава расходного материала (порошка) и изменения режимов его нанесения можно получить однородное или композиционное покрытие с твердой или пористой структурой и своей функциональной задачей. Это может быть: восстановление геометрии изделия, упрочнение и защита металла от коррозии, повышение тепло- и электропроводности материала, а также образование износостойкого покрытия, выдерживающего воздействие химически активных сред, высоких тепловых нагрузок и т. д.
Кстати, обнинские инженеры разработали уже несколько модификаций установок ДИМЕТ®. Учитывая широкую востребованность данного оборудования, сейчас серийно выпускаются как ручные, так и автоматизированные аппараты холодного газодинамического напыления, что позволяет использовать их в промышленности, нефтегазовой отрасли, а также в малом бизнесе для обработки небольших деталей. Тем более, что ничего особо сложного в самой технологии нет. Для работы комплекса (помимо материала для напыления) необходим только сжатый воздух (подается под давлением 0,6-1,0 МПа и расходом 0,3-0,4 м3/мин.) и электросеть напряжением 220 В.
Теперь ещё о преимуществах и недостатках метода. Во-первых, в отличие от газотермического способа ХГН может эффективно применяться при обычном давлении, в любом температурном диапазоне и уровне влажности. В-вторых, он экологически абсолютно безопасен. В-третьих, благодаря большой скорости, может применяться и для абразивной чистки поверхности. Ну, а единственным недостатком технологии является возможность нанесения покрытий только из относительно пластичных металлов, таких как медь, алюминий, цинк, никель и др.
Область применения ХГН
Более подробно хотелось бы остановиться на сферах использования технологии холодного газодинамического напыления порошковыми материалами, чтобы наглядно показать насколько она сегодня востребована.
Устранение дефектов, восстановление поверхностей и герметизация
Всё это – работа, которой могут заниматься даже малые предприятия. К примеру, в небольших мастерских можно ремонтировать детали из легких сплавов (части автомобильной конструкции, допустим), прежде всего, алюминиевых и алюминиевомагниевых. Причем, легко устраняются дефекты, возникшие как в процессе производства, так и в процессе эксплуатации. А отсутствие сильного нагрева и низкая энергетика метода позволяют чинить даже тонкостенные изделия.
Отлично подходит ХГН и для восстановления изношенных поверхностей. Например, такой трудоемкий процесс, как «наращивание» металла в посадочных местах подшипников, теперь могут осуществлять даже малые предприятия, не говоря уже о восстановлении герметизации (когда применение жидких герметиков невозможно) в трубопроводах, теплообменниках или сосудах для рабочих газов, жидкостей.
Высокоточное восстановление деталей различных механизмов, токопроведение
ХГН очень эффективен в ремонте сложных изделий, где требуется точное восстановление геометрических параметров, устранение скрытых дефектов, но при этом с сохранением всех эксплуатационных характеристик, а также товарного вида. Именно поэтому данный метод активно используется в оборонно-промышленном комплексе, железнодорожной и авиационной промышленности, сельском хозяйстве, газоперекачке и пр.
Не обойтись без этой технологии и в создании контактных площадок. Благодаря возможности легкого нанесения покрытий на любые металлические, керамические и стеклянные поверхности ХГН применяется и в производстве электротехнических изделий. Например, в процессах меднения, создании силовых токонесущих сетей, нанесении токовводов, изготовлении подслоев под пайку и т. д.
Антикоррозийная обработка и устранение глубоких дефектов
Напыление так называемого антифрикционного покрытия – высокоэффективный способ избавления от локальных повреждений (глубоких сколов, задиров, царапин). Это позволяет избежать процедуры полной перезаливки или даже замены изделия, что, естественно, экономически не выгодно.
А в антикорроизонной обработке и защите от высокотемпературной коррозии различных коммуникаций данному методу вообще нет равных. К слову, различные модификации оборудования ДИМЕТ® обеспечивают качественную обработку внутренней поверхности труб диаметром от 100 мм и длиной до 12 м.
Владислав Пермин, специально для Equipnet.ru
www.equipnet.ru
Газодинамическое напыление по технологии ДИМЕТ при помощи роботов Kawasaki
Роботы Kawasaki применяют в комплексах напыления по технологии ДИМЕТ. Эта технология позволяет наносить металлический слой на различные поверхности: металл, стекло, керамика, камень. Особенностью технологии является возможность нанесения металлического порошка на несовместимые для сварки и пайки металлы. Например, удается эффективно наносить медь на алюминий, что представляет большую ценность для электротехнического производства.
О технолигии
Технология газодинамического напыления порошкового металла и преобразования его в монолитное покрытие реализуется на оборудовании ДИМЕТ выпускаемом Обнинским Центром Порошкового Напыления. Покрытия формируются на любой твердой поверхности, такой, как металл, стекло, керамика, камень. Материал покрытия выбирается при решении конкретной производственной или творческой задачи, поскольку решение может быть получено с помощью разного типа порошковых материалов.
Сжатый воздух (5-8 атм) нагревается (300-600°C) и подается в сопло, где формируется сверхзвуковой поток:
- в этот поток вводятся порошки, содержащие металлические и керамические частицы
- частицы ускоряются газовым потоком до скорости несколько сот метров в секунду и в нерасплавленном состоянии направляются на подложку
- при ударе о подложку кинетическая энергия частиц преобразуется в тепло, а затем в энергию связи частиц с подложкой
- в результате таких высокоскоростных ударов частицы закрепляются на подложке и формируют плотное покрытие.
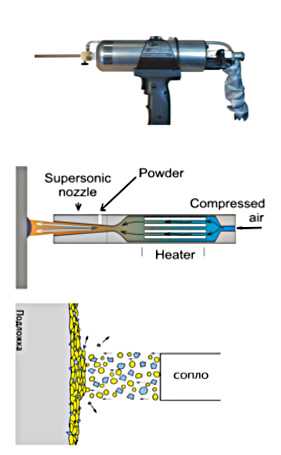
Основные процессы, определяющие сцепление частиц с подложкой и друг с другом:
- Тесное соприкосновение кристаллических решеток частиц и подложки (или разных частиц) до образования металлических связей, по крайней мере, на отдельных участках пятна контакта. При этом нигде не происходит плавления частицы или подложки. Этот механизм сцепления аналогичен механизму сцепления при сварке взрывом.
- На отдельных выступах и неровностях падающих частиц может происходить их плавление и осуществляться точечная микросварка.
- При тесном соприкосновении ювенильных поверхностей разнородных материалов может проявляться межмолекулярное взаимодействие этих материалов. Типичным примером такого механизма является напыление зеркального алюминиевого покрытия на стекло.
- Определенную роль может играть механическое сцепление при условии глубокого проникновения частиц в подложку. Конкретное соотношение относительной роли различных механизмов сцепления в различных случаях может существенно отличаться друг от друга и является предметом отдельного исследования.
Области применения
Отрасль | Применение | Покрытия |
---|---|---|
Литейное производство |
Ремонт дефектов литьевых деталей -под давлением -в кокиль -по выплавляемым моделям |
Покрытия для восстановления формы и размеров деталей. Герметизирующие покрытия (низкая газопроницаемость) |
Металлургическое производство |
Снижение электросопротивления контактов электролизёров Защита от высокотемпературной коррозии |
Электропроводящие покрытия Жаростойкие покрытия |
Автомобилестроение |
Ремонт литых деталей |
-Покрытия для восстановления формы и размеров деталей. -Герметизирующие покрытия -Антикоррозионные покрытия |
Авторемонт |
-Покрытия при ремонте механических повреждений ГБЦ, БЦ, агрегатов -Герметизация трещин ГБЦ, БЦ, радиаторов, трубопроводов, кондиционеров -Защита от коррозии локальных очагов -Восстановление формы кузовных деталей из алюминия без шпатлевки |
-Покрытия для восстановления формы и размеров деталей. -Герметизирующие покрытия -Антикоррозионные покрытия |
Авиастроение, авиаремонт |
Ремонт литьевых и производственных дефектов алюминиевых деталей |
-Покрытия для восстановления формы и размеров деталей. -Герметизирующие покрытия
|
Ракетная и космическая техника |
Специальное |
-Покрытия для герметизации изделий из термоупрочненного алюминия -Теплоизлучающие покрытия |
Судостроение, судоремонт |
Протекторная защита сварных швов -Предотвращение от схватывания высоконагруженных резьбовых соединений -Восстановление подшипников скольжения -Восстановление посадочных мест подшипников |
-Покрытия для восстановления формы и размеров деталей -Антикоррозионные покрытия -Герметизирующие покрытия
|
Нефтегазовая промышленность |
-Восстановление геометрии деталей газоперекачивающих агрегатов -Предотвращение от схватывания высоконагруженных резьбовых соединений -Восстановление подшипников скольжения |
-Покрытия для восстановления формы и размеров деталей -Антисхватывающие покрытия -Антифрикционные |
Электротехническое производство |
-Металлизация электроконтактных площадок -Нанесение электропроводных гальванически совместимых покрытий -Металлизация для теплопередачи -Подслои по алюминию и стекло под пайку |
Электропроводящие покрытия |
Инструментальное производство |
Восстановление форм для пластиковой и стеклянной упаковки Восстановление форм для прессования резиновых изделий Восстановление оснастки для прессовки деталей из прессматериалов (АГ4, ДСВ, карболит) Изготовление искрозащищенного инструмента |
-Покрытия для восстановления формы и размеров деталей -Искробезопасные покрытия |
Реставрация памятников и скульптур |
Восстановление утраченных элементов памятников. Защита от коррозии |
-Покрытия для восстановления формы и размеров деталей -Антикоррозионные покрытия |
Реализованный проект
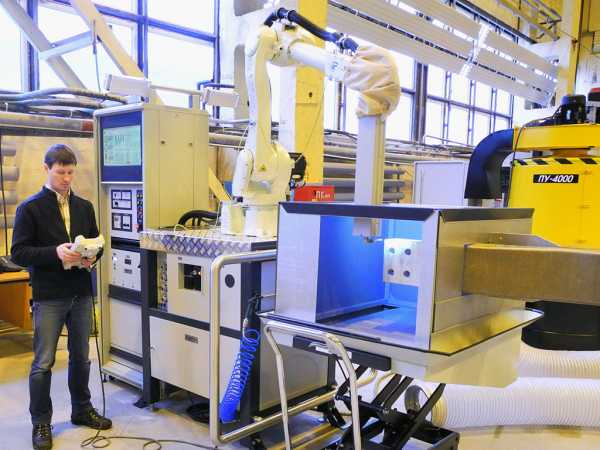
Схема комплекса:
Решенная задача:
Напыление двухслойного медного покрытия на плоские электроконтактные поверхности алюминиевых токопроводящих шин. Площадка напыления — до 0,5м2, сами шины достигают длины 12 метров и массы 4 тонны.
Состав комплекса:
- ПЛК Овен;
- Робот Kawasaki RS006L;
- Камера напыления;
- Контроллер E01;
- …
Реализованный комплекс дает возможность выполнения следующих задач:
- исполнение технологического процесса с функцией программного контроля и управления параметрами;
- движение напылителя по заданной траектории, синхронизирующееся с работой технологического оборудования, посредством передачи информационных сообщений;
- визуализация параметров технологического процесса на сенсорном экране оператора, а также средства изменения режимов работы, организованные на базе элементов диалоговых окон.
Если у вас есть потребность в подобном решении — оставьте свои контактные данные в форме заявки. Наши специалисты проконсультируют вас и оговорят детали сотрудничества.
Галерея проекта
Схема сотрудничества
www.robowizard.ru
Газодинамическое напыление металла -Услуги
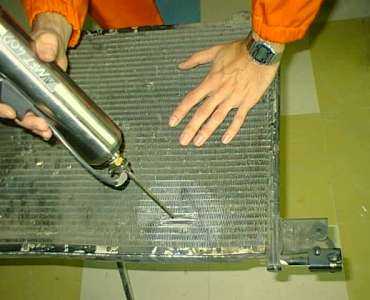
Работа оборудования ДИМЕТ®, разработанного и серийно выпускаемого «Обнинским центром порошкового напыления» (ООО «ОЦПН»), основана на эффекте закрепления частиц металла, если они движутся со сверхзвуковой скоростью, на поверхности при соударении с ней, газодинамическое напыление металлов ДИМЕТ®. Технология позволяет наносить металлические покрытия не только на металлы, но и на стекло, керамику, камень, бетон. К настоящему времени технология ДИМЕТ® позволяет наносить покрытия из алюминия, цинка, меди, олова, свинца, баббитов, никеля и наносить их не только на металлы, но и на стекло, керамику, камень, бетон.
Важно, что температуры при нанесении покрытий ДИМЕТ® не превышают 150 градусов, т.е. температуры работающего двигателя, что позволяет широко применять ДИМЕТ® в авторемонтных работах, а именно:
- —Ремонт головки блока цилиндров двигателя;
- —Герметизация топливных баков;
- —Ремонт радиаторов;
- —Ремонт и восстановление кондиционеров автомобиля;
- —Ремонт посадочных мест коленвалов и постелей распредвалов;
- —Ремонт обогревателей заднего стекла;
- —Цинкование, антикоррозийная обработка и многое другое.
Основные элементы технологии холодного газодинамического напыления
Технология газодинамического напыления металлов ДИМЕТ® включает в себя нагрев сжатого газа (воздуха), дальнейшее поступление его в сверхзвуковое сопло с формированием в сопле воздушного потока сверхзвуковой скорости. Далее питатель подает в сверхзвуковой поток металлический порошок (особым образом подготовленный), частицы металла разгоняются и направляются на поверхность детали.
Ремонт ГБЦ, отремонтированный блок цилиндров
В качестве порошковых материалов используются порошки металлов, сплавов или\и их смеси с керамическими порошками. Все составы порошков разработаны специально «Обнинским центром порошкового напыления» именно для оборудования ДИМЕТ®. Изменяя режимы работы оборудования можно либо проводить эрозионную (струйно-абразивную) обработку поверхности изделия, либо наносить металлические покрытия требуемых составов.
Преимущества метода газодинамического напыления в следующем:
- —Нанесение покрытий при любых значениях температуры и влажности окружающей среды, в обычных условиях мастерской;
- —Покрытие не нагреваентся свыше 100-150 градусов, следовательно нет внутренних напряжений деталий, деформаций и окисления материалов покрытия и детали;
- —Безопасность — отсутствуют высокие температуры, опасные газы и излучения, нет химически агрессивных отходов, требующих специальной нейтрализации;
- —ДИМЕТ® компактный, мобильный (вес от 11 до 20 кг в зависимости от модели), работа оборудованием интуитивно удобно, специальных навыков не требуется;
- —Оборудование используем не только в стационарных условиях но и в полевых;
altushka.com
Установка газодинамического напыления Димет | Яхта Стальная Крыса
В продолжении темы об оборудовании для нанесения цинкового покрытия на стальной корпус яхты, я побывал в Обнинском Центре Порошкового напыления и собственноручно затестировал установку газодинамического напыления Димет-405. Установка впечатляет. Под катом много много фоток напыленных поверхностей, над которыми мы немного поизголялись.
Установка малогабаритная, в зависимости от модификации весит 10-19 кг, потребляет 0.3-0.4 куба воздуха и порядка 3 КВт электричества. Напыляет как распространенные металлы и смеси (цинк, алюминий), так и специфические (никель, баббит). Принцип действия- т.н. газодинамическое напыление- воздух от компрессора дополнительно нагревается и ускоряется в сопле до сверхзвуковых скоростей (типа 700 м/c), в него подается мелкодисперсный порошок (частица 50 мкм) металла или керамики, частицы которого разгоняются и впечатываются в деталь. Единственный минус установки для меня — низкая производительность. Цинковать корпус придется долго. Ну и ценник конечно тоже впечатляет.
Теперь про покрытие. Обещают прилипание к отпескоструенной поверхности порядка 50 МПа. Для сравнения- лучшие клеи дают в районе 20. Тоесть вроде как держаться должно прочнее краски)) Покрытие получается шероховатое- как раз то что нужно для последующего грунтования. Правда есть некоторые вопросы по слабоприлипшим частицам- нужно ли их пытаться удалять и если да то как?
2. Сам процесс прост до безобразия — стараемся обеспечить нормальное направление факела к обрабатываемой поверхности и выдерживаем дистанцию от сопла до детали порядка 10-15мм:
3. Стандартный образец, выдающийся клиентам. Взял два- один погрызли, другой замочили в солевом растворе)) Треугольные наплывы на образце- это массив напыленного металла на плоской стальной подложке:
4. Слева — медь. Справа- алюминий.
5.
6.
7. Сточенный надфилем участок напыленного алюминиевого образца. Весь этот массив был напылен:
8.
9. шлиф медного напыленного участка
10. шлиф алюминиевого напыленного участка
11.
12. А это одни из моих образцов, которые я привез с собой:
13. На эти образцы напылялся цинк без предварительной пескоструйки:
14. Оцинкованная поверхность крупным планом:
15. Крупный план напыленного цинкового покрытия (здесь и далее- если картинка двойная- сверху оригинал без обработки, снизу- задранная контрастность):
16.
17. Фаска напыляется хуже за счет изменения угла напыления. Идеально напылять перпендикулярно поверхности. 45 — предельный угол. Лучше не пылить под углом более 30 градусов:
18.
19. А это стандартный тест на прочность покрытия- я нацарапал сеточку с шагом 1-2мм острием чертилки:
20. При царапании давил изо всех сил- ни один кусочек покрытия из сеточки не вывалился и неоткрошился:
21.
22.
23. Граница напыления. Видна зона неполного напыления:
24.
25. Видны непропыленные участки:
26.
27. Испытание трением. Если потереть образцы друг о друга напыленными местами- цинк начинает полироваться:
28.
29.
30. Стоимость оборудования Димет. Стоимость высокая, чего тут говорить. Самая младшая модель — 220 тыщ, нормальная — 300:
Порошки алюминия, цинка, меди стоят сравнительно недорого- 600-800 руб за кг. Никель- 2500. Также можно пылить свинцом, оловом, баббитом.
———————
Хороший аппарат. Сильно хочется оцинковать корпус перед покраской.
www.steelratboat.ru
Оборудование для холодного газодинамического напыления металлов ДИМЕТ
ПРОФЕССИОНАЛЬНОЕ ПОРТАТИВНОЕ ОБОРУДОВАНИЕ ДИМЕТ® для «холодного газодинамического напыления»
Приглашаем Вас посмотреть короткометражный фильм о технологии ДИМЕТ® на портале «Российские технологии и научные разработки».
Смотреть видеоролик «Применение аппарата ДИМЕТ® в авторемонте».
Наше участие в выставках и демонстрация оборудования в работе.
Портативные установки газодинамического напыления ДИМЕТ® обеспечивают нанесение высококачественных металлических покрытий из порошковых материалов (алюминиевые, медные, цинковые, никелевые, оловянные, свинцовые, баббитовые). Технология напыления «Димет» основывается на процессе газодинамического напылении металлов — «холодное газодинамическое напыление», и позволяет проводить широкий спектр авторемонтных, восстановительных работ, при которых ремонтируемая деталь нагревается не больше температуры работающего двигателя, локально и точно! Чрезвычайно важна малая температура нагрева напыляемого металла при ремонте радиаторов, трубок кондиционеров, нанесении и восстановлении электропроводящих покрытий. Из-за сравнительно низких температур напыления металлов, технологию ДИМЕТ® часто называют «холодной сваркой», что все же не совсем правильно. Оборудование предназначено для нанесения металлов в производстве изделий и при выполнении широкого спектра авторемонтных и восстановительных работ. Вес аппаратов от 10,3 кг до 19,3 кг, поэтому аппараты ДИМЕТ® широко используются в автосервисах и авторемонтных мастерских.
Оборудование ДИМЕТ® прекрасно себя зарекомендовало при применении в следующих областях (примеры с фотографиями в колонке справа):
• При повышении мощности и КПД газотурбинных установок магистральных газопроводов.
• Авторемонт (здесь ДИМЕТ получил широкое распространение — для устранения повреждений двигателя, ремонта автокондиционеров, агрегатов и кузова автомобиля).
• Восстановление посадочных мест подшипников.
• Защита сварных швов (например — глушителя автомобиля).
• Герметизация течей жидкостей и газов (ремонт автокондиционеров и радиаторов охлаждения автомобилей).
• Восстановление утраченных объемов металла (ремонт ГБЦ, коленвалов, узлов и деталей автомобиля, дефектов литья, механических дефектов деталей).
• Нанесение электропроводящих покрытий (обогрев заднего стекла автомобиля).
• Нанесение жаростойких покрытий.
• Антикоррозионная защита кузова автомобиля.
• Нанесение подслоев для пайки.
• Различные спецприменения (реставрация скульптур, декоративные работы и т.д.).
Малый вес и компактные габариты позволяют использовать оборудование ДИМЕТ® не только в стационарных условиях автомастерской, но и полевых условиях (выезд к клиенту для авторемонта, устранение дефектов габаритных узлов и агрегатов).
Мы всегда рекомендуем пройти бесплатное обучение работе с оборудованием ДИМЕТ® в специализированной лаборатории, наши специалисты поделятся с Вами наработками и навыками. На оборудование предоставляется гарантия производителя, осуществляется постгарантийное обслуживание. Обеспечивается поставка всех расходных материалов — порошков, сменных элементов.
Телефон и факс: +7(48439)2-17-80, +7(495)785-61-49, 8-916-918-97-54
E-mail: [email protected] [email protected]
Технология напыления металлов. ДИМЕТ
Технология нанесения металлов на поверхность деталей и изделий, реализуемая оборудованием ДИМЕТ® производимого «Обнинским центром порошкового напыления», использует газодинамический метод нанесения покрытий. Процесс является относительно новым, а основанная на нем технология динамической металлизации ДИМЕТ («DYMET» — «dynamic metallization») пока не изложена в учебниках. Однако уже накоплен опыт применения технологии ДИМЕТ® как на многих крупных предприятиях так и на предприятиях малого бизнеса.
На основе алюминия, меди, цинка, никеля, олова, свинца в настоящее время разработано более десятка видов порошковых материалов для нанесения покрытий. Все эти порошки могут быть нанесены в разных режимах с помощью оборудования ДИМЕТ®.
Газодинамическим методом наносятся жаростойкие покрытия, которые обеспечивают защиту вплоть до 1000-1100 градусов Цельсия. Электропроводность в среднем составляет 80-90 % электропроводности объемного материала. Коррозионная стойкость зависит от характеристик агрессивной среды.
Метод разработан на основе открытого в 80-х годах прошлого столетия эффекта закрепления твердых частиц, движущихся со сверхзвуковой скоростью, на поверхности при соударении с ней. Технология напыления реализованная в установках ДИМЕТ® хорошо известна на предприятиях металлургического, нефтегазового и энергетического комплекса России, и получила заслуженное признание.
Оборудование ДИМЕТ® сертифицировано по системе ГОСТ Р. Сертификат соответствия N РОСС RU.ТН02.Н00580.
_______________________________________________________________________
Разработчик и производитель ДИМЕТ®: Обнинский центр порошкового напыления (ООО»ОЦПН»)
Россия, 249040,
Калужская область,
г.Обнинск, пос. Кабицино, дом №1,
Телефон и факс: +7(48439)2-17-80, +7(495)785-61-49, 8-916-918-97-54
E-mail: [email protected] [email protected]
www.dymet-rus.ru