В составе фрикционной смеси тормозной колодки содержится в среднем от 20 до 30 различных составляющих, включая органические и неорганические волокна, абразивы, минеральные, синтетические и органические смазочные материалы, металлическую стружку и др. наполнители.
Сочетание этих компонентов в той или иной пропорции обеспечивает адресный подбор фрикционной смеси под тот или иной тип применения. К примеру, большее содержание абразивов увеличивает эффективность торможения, которая характеризуется безразмерной величиной, называемой коэффициентом трения. Чем выше коэффициент трения, тем меньше тормозной путь автомобиля.
Большое содержание абразивов в составе фрикционной смеси приводит к чрезмерному износу колодки, диска и повышенной шумности при торможении.
Однако слишком большое содержание абразивов в составе фрикционной смеси приводит к чрезмерному износу колодки, диска и повышенной шумности при торможении. Графит, сульфиды металлов в составе смеси выполняют роль смазки. Они снижают степень износа колодки и диска, уменьшают шум при торможении, но приводят к уменьшению коэффициента трения и повышению вибрации при торможении. Чрезмерное содержание стальной стружки и органических соединений в составе смеси увеличивает долю углеродистых отложений в продуктах износа колодки.
До середины 90-х годов XX века в составе фрикционных смесей активно использовался асбест, обеспечивающий высокий коэффициент трения и высокую температурную стабильность. Общее количество компонентов в составе фрикционной смеси асбестосодержащей колодки по сравнению с современной колодкой было значительно меньше (6–10 компонентов). Компания Ferodo первой на рынке еще за 16 лет до официального запрета асбеста наладила выпуск безасбестовых фрикционных смесей. Заменить асбест одним компонентом невозможно, поэтому общее количество составляющих в смеси увеличилось.
Медь до недавнего времени являлась одним из основных компонентов фрикционной смеси тормозной колодки с удельным весом до 20%. Медь выполняла следующие важные функции: обеспечение эффективности торможения, снижение шума при торможении, снижение пыльности при износе, обеспечение эффективного отвода тепла, обеспечение целостности и прочности фрикционной смеси. Однако медь – тяжелый металл, и в окружающей среде она окисляется, образуя вредные соединения. Мельчайшие частицы меди с продуктами износа фрикционного материала попадают на дорожное полотно и смываются дождями в водоемы, где медь оказывает негативное влияние на экосистему водной среды. Постепенное ограничение на использование меди во фрикционных смесях уже принято в ряде штатов США – к 2021 году ее содержание в тормозных колодках должно быть менее 5%, а к 2025 году – менее 0,5%, что принято считать нулевым содержанием. Похожие инициативы вводятся и в странах Европы. Предполагается, что к 2025 году содержание меди в составе фрикционной смеси тормозных колодок будет законодательно регламентировано или полностью запрещено во всем мире. И уже сегодня крупнейшие европейские автопроизводители требуют установки на свои автомобили тормозных механизмов с колодками с пониженным и нулевым содержанием меди.
Крупнейшие европейские автопроизводители требуют установки на свои автомобили тормозных механизмов с колодками с пониженным и нулевым содержанием меди.
При проектировании тормозной колодки должны учитываться основные тенденции в современном автомобилестроении. Увеличение доли автомобилей с электрическими и гибридными силовыми установками (требуются смеси с пониженной шумностью при торможении), использование электромеханического стояночного тормоза (требуются смеси с большим коэффициентом статического трения), применение производителями тормозных систем суппортов меньшего размера и веса для снижения неподрессоренных масс в подвеске автомобиля (уменьшение размера тормозной колодки – использование фрикционной смеси с обеспечением большей эффективности торможения), использование тормозных колодок с меньшим содержанием во фрикционной смеси стальной стружки и с меньшим или нулевым содержанием меди (существующие и грядущие законодательные ограничения) – все эти тенденции были учтены в недавно внедренной Federal-Mogul новой технологии тормозных колодок Ferodo Eco-Friction с низким или нулевым содержанием меди.
Основой для Ferodo Eco-Friction стала комбинация из 25 компонентов, в том числе сульфидов металлов, минералов, абразивов, волокон, керамических частиц и различных видов графита. Этот состав обеспечивает эффективность торможения, не уступающую медьсодержащим фрикционным материалам. Результаты независимого тестирования колодок по технологии Eco-Friction для популярных европейских автомобилей подтвердили их превосходство по эффективности торможения в сравнении со стандартными медьсодержащими колодками Ferodo Premier и с продукцией конкурентов (меньший тормозной путь и меньшая степень износа в паре трения колодка/диск). Благодаря успешным исследованиям Federal-Mogul стала мировым лидером в области создания фрикционных материалов с низким или нулевым содержанием меди.
Более 85% ассортимента колодок Ferodo для вторичного рынка выполнены по технологии Eco-Friction.
Серийный выпуск колодок Eco-Friction начался в 2014 году, когда компания Daimler выбрала продукцию Ferodo в качестве оригинальных комплектующих для нового Mercedes-Benz C-Class, а с сентября 2015 года колодки Eco-Friction устанавливаются и на Audi A4. Также эти колодки были рекомендованы для вторичного рынка автокомплектующих. Свыше 85% ассортимента колодок Ferodo для вторичного рынка выполнены по этой современной технологии.
До середины XX века фрикционная накладка дисковой тормозной колодки прикреплялась к несущей стальной пластине потайными заклепками во многих точках, но в середине XX века для соединения композитов с металлом были разработаны достаточно термостойкие и прочные клеи на основе термореактивных смол. В технологии производства дисковых тормозных колодок как для легковых, так и для грузовых автомобилей в настоящее время используется два основных способа формования фрикционного материала на стальной несущей пластине: прессование (только давление) и термопрессование (давление плюс нагрев). При производстве фрикционных накладок для грузовой техники используется метод термопрессования фрикционного материала. Для барабанных тормозов легковых и легких коммерческих автомобилей фрикционная накладка приклеивается к поверхности стального башмака. Фрикционные накладки барабанных тормозных механизмов для грузовых автомобилей закрепляются на тормозном башмаке с помощью заклепок. Это обуславливается большими габаритами тормозного механизма, более высокими нагрузками на фрикционную накладку при торможении, а также удобством и оптимизацией затрат при замене фрикционных накладок при регламентном обслуживании тормозной системы (без необходимости замены тормозных башмаков).
Фрикционные материалы: выбор, требования
Современное производственное оборудование обладает довольно сложной конструкцией. Фрикционные механизмы передают движение при помощи силы трения. Это могут быть муфты, зажимы, разжимы и тормоза.
Чтобы оборудование было долговечным, работало без простоев, к его материалам выдвигают особенные требования. Они постоянно растут. Ведь техника и оборудование постоянно совершенствуются. Увеличиваются их мощности, рабочие скорости, а также нагрузки. Поэтому в процессе их функционирования применяют различные фрикционные материалы. От их качества зависит надежность, долговечность оборудования. В некоторых случаях от этих элементов системы зависит безопасность и жизнь людей.
Общая характеристика
Фрикционные материалы – это неотъемлемые элементы узлов и механизмов, которые обладают возможностью поглощать механическую энергию и рассеивать ее в окружающую среду. При этом все элементы конструкции не должны быстро изнашиваться. Для этого представленные материалы обладают определенными свойствами.
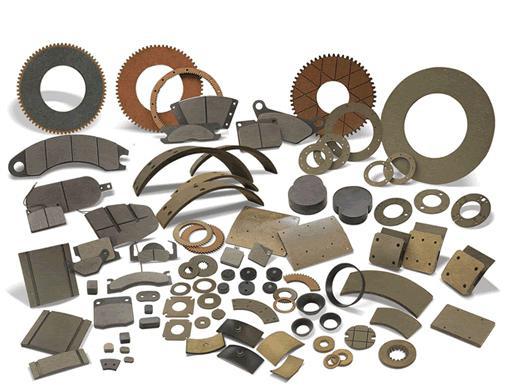
Коэффициент трения фрикционных материалов должен быть стабильным и высоким. Показатель износостойкости также обязан удовлетворять эксплуатационные требования. Такие материалы обладают хорошей термостойкостью и не подвержены механическим воздействиям.
Чтобы вещество, выполняющее фрикционные функции, не прихватывалось к рабочим поверхностям, оно наделяется достаточными адгезионными качествами. Совокупность таких свойств обеспечивает нормальную работу оборудования и систем.
Свойства материала
Фрикционные материалы обладают определенным набором свойств. Основные из них были перечислены выше. Это служебные качества. Именно они определяют эксплуатационные характеристики каждого вещества.
Но все служебные характеристики обуславливаются набором физико-механических и теплостатических показателей. Такие параметры меняются в процессе эксплуатации материала. Но их предельное значение учитывается в процессе выбора фрикционного вещества.
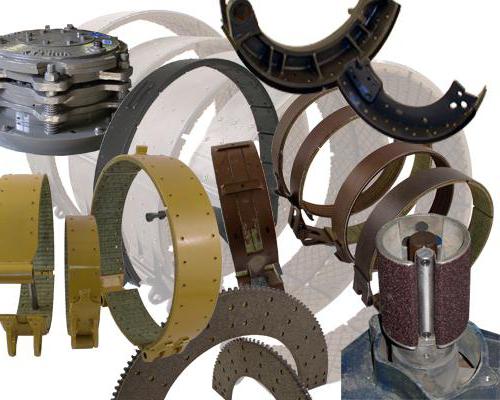
Существует разделение свойств на статические, динамические и опытные показатели. К первой группе параметров относят предел сжатия, прочности, изгиба и растяжения. Также сюда входят теплоемкость, теплопроводность и линейное расширение материала.
К показателям, определяемым в динамических условиях, причисляют термоустойчивость, теплостойкость. В опытной обстановке устанавливают коэффициент трения, износостойкость и стабильность.
Виды материалов
Фрикционные материалы системы тормозов и сцепления чаще всего изготавливают на медной или железной основе. Вторая группа веществ применяется в условиях повышенной нагрузки, особенно при сухом трении. Медные материалы используют для средних и легких нагрузок. Причем они подходят как для сухого трения, так и с применением смазочных жидкостей.
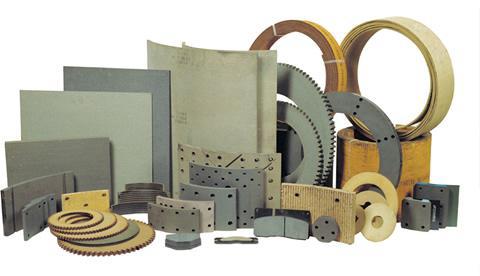
В современных условиях производства получили широкое применение материалы на каучуковой и смоляной основе. Также могут применяться различные наполнители из металлических и неметаллических компонентов.
Область применения
Существует классификация фрикционных материалов в зависимости от области их применения. В первую большую группу входят передаточные устройства. Это средние и слабонагруженные механизмы, которые работают без смазки.
Далее выделяются фрикционные материалы системы тормозов, предназначенные для средних и тяжелонагруженных механизмов. В этих узлах смазка не применяется.
К третьей группе относят вещества, применяемые в сцеплениях средних и тяжелонагруженных узлов. В них присутствует масло.
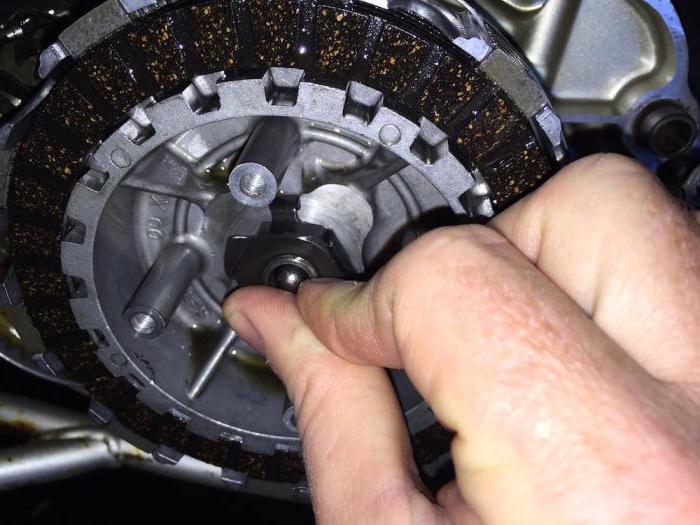
Также выделяют отдельной группой материалы тормозов, в которых присутствует жидкая смазка. Основные параметры механизмов определяют выбор фрикционных материалов.
В сцеплении нагрузка действует на элементы системы около 1 с, а в тормозе – до 30 с. Этот показатель определяет характеристики материалов узлов.
Металлические материалы
Как уже было сказано выше, основными металлическими фрикционными материалами системы сцепления, тормоза является железо и медь. Очень популярны сегодня сталь и чугун.
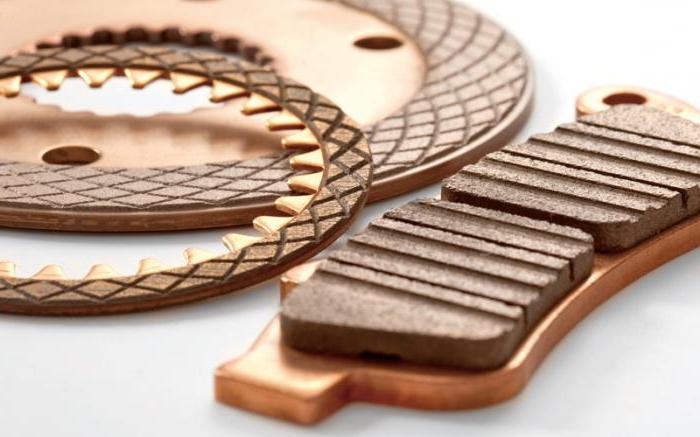
Они применимы в разных механизмах. Например, фрикционные материалы для тормозных колодок, состав которых содержит чугун, часто применяются в железнодорожных системах. Он не коробится, но резко теряет свои скользящие качества при температуре от 400 °С.
Неметаллические материалы
Фрикционные материалы сцепления или тормозов изготавливают также из неметаллических веществ. Их создают преимущественно на асбестовой основе (смола, каучук выступают связующими компонентами).
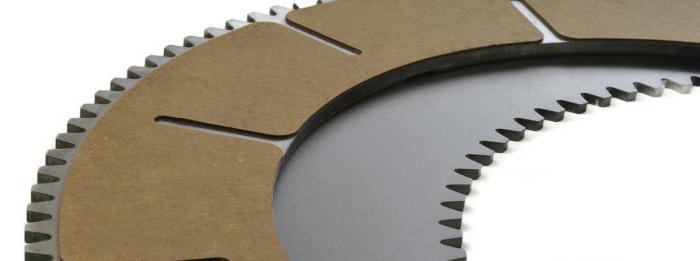
Коэффициент трения остается достаточно высоким до температуры 220 °С. Если связующим веществом является смола, материал характеризуется высокой износоустойчивостью. Но их коэффициент трения несколько ниже относительно других подобных материалов. Популярным материалом из пластмассы на такой основе выступает ретинакс. В его составе присутствует фенолформальдегидная смола, асбест, барит и прочие компоненты. Это вещество применимо для узлов и тормозных механизмов с тяжелыми эксплуатационными условиями. Оно сохраняет свои качества даже при нагреве до 1000 °С. Поэтому ретинакс применим даже в авиационных тормозных системах.
Асбестовые материалы изготавливают путем создания одноименной ткани. Ее пропитывают асфальтом, резиной или бакелитом и спрессовывают при высоких температурах. Короткие асбестовые волокна могут формировать также нетканые накладки. В них добавляется мелкая металлическая стружка. Иногда для усиления прочности в них вводится латунная проволока.
Спеченные материалы
Существует еще одна разновидность представленных компонентов систем. Это спеченные фрикционные материалы системы тормозов. Что это разновидность, станет понятнее из способа их изготовления. Их чаще всего изготавливают на стальной основе. В процессе сварки с ней спекаются другие, входящие в состав, компоненты. Предварительно спрессованные заготовки, состоящие из порошковых смесей, подвергают высокотемпературному нагреву.
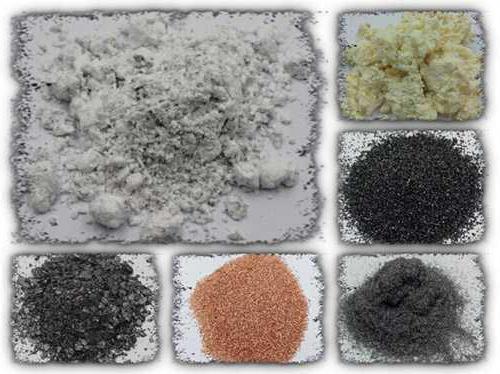
Такие материалы применяют чаще всего в тяжелонагруженных муфтах и тормозных системах. Их высокие показатели при эксплуатации определяются двумя группами компонентов, входящих в состав. Первые материалы обеспечивают хороший коэффициент трения и износоустойчивость, а вторые – стабильность и достаточный уровень адгезии.
Материалы на стальной основе для сухого трения
Выбор материала для различных систем осуществляется на основе экономической и технической целесообразности его изготовления и эксплуатации. Несколько десятилетий тому назад востребованными были такие материалы на железной основе, как ФМК-8, МКВ-50А, а также СМК. Фрикционные материалы для тормозных колодок, которые работали в тяжелонагруженных системах, позже стали изготавливать из ФМК-11.
МКВ-50А является более новой разработкой. Ее применяют при изготовлении накладок для дисковых тормозов. Он имеет преимущество перед группой ФМК по показателям стабильности, износостойкости.
В современном производстве большего распространения получили материалы типа СМК. В них повышено содержание марганца. Также в состав входят карбид и нитрид бора, дисульфид молибдена и карбид кремния.
Материалы на основе бронзы для сухого трения
В передаточных и тормозных системах различного назначения хорошо себя зарекомендовали материалы на основе оловянистой бронзы. Они гораздо меньше изнашивают сопряженные детали из чугуна или стали, чем фрикционные материалы на железной основе.
Представленную разновидность материалов применяют даже в авиационной промышленности. Для особых условий эксплуатации олово могут заменять такими веществами, как титан, кремний, ванадий, мышьяк. Это предотвращает образование межкристаллической коррозии.
Материалы на основе оловянистой бронзы широко применяют в автомобильной промышленности, а также при изготовлении сельскохозяйственной техники. Они выдерживают большие нагрузки. Входящие в состав сплава 5-10% олова обеспечивают повышенную прочность. Свинец и графит играют роль твердой смазки, а двуокись кремния или кремний повышают коэффициент трения.
Работа в условиях жидкой смазки
Материалы, применяемые в сухих системах, обладают существенным недостатком. Они подвержены быстрому износу. При попадании в них смазки из расположенных рядом узлов резко снижается их эффективность. Поэтому в последнее время все большего распространения получают материалы, предназначенные для работы в жидком масле.
Такое оборудование плавно включается, характеризуется высоким уровнем износоустойчивости. Оно легко охлаждается и просто герметизируется.
В зарубежной практике в последнее время растут объемы производства такого продукта, как фрикционный материал листовой для тормозов, муфт и прочих механизмов на основе асбеста. Его пропитывают смолой. В состав входят формованные элементы с высоким содержанием металлических наполнителей.
Чаще всего для смазочной среды применяют спеченные материалы, изготовленные на основе меди. Чтобы повысить фрикционные характеристики, в состав вводятся неметаллические твердые компоненты.
Улучшение свойств
В первую очередь улучшения требует износостойкость, которой обладают фрикционные материалы. От этого зависит экономическая и эксплуатационная целесообразность представленных компонентов. В этом случае технологи разрабатывают пути по устранению чрезмерного нагрева на трущихся поверхностях. Для этого совершенствуют свойства самого фрикционного материала, конструкцию устройства, а также регламентируют рабочие условия.
Если материалы применяются в условиях сухого трения, особое внимание уделяется их жаропрочности и устойчивости к окислению. Такие вещества менее подвержены износу абразивного типа. Но для систем со смазкой жаропрочность не имеет такого большого значения. Поэтому большее внимание уделяется их прочности.
Также технологи при повышении качества фрикционных материалов уделяют внимание их степени окисляемости. Чем она меньше, тем долговечнее компоненты механизмов. Еще одним направлением является уменьшение пористости материала.
Современное производство должно совершенствовать применяемые дополнительные материалы в процессе изготовления различных подвижных, передаточных устройств. Это позволит удовлетворить растущее потребительские и эксплуатационные требования, выдвигаемые к фрикционным материалам.
Фрикционные материалы — состав и классификация
Фрикционные материалы – это субстанции обеспечивающие функционирование деталей в условиях избыточного трения, создавая эффективное скольжение. Характеризуются субстанции повышенной фрикционной теплостойкостью, что выражается в сохранении износоустойчивости с коэффициента трения при различных температурах. Материалы имеют пониженную адгезию и сверхвысокую теплопроводность, прекрасно сочетающуюся с отличной теплоёмкостью и сопротивляемостью тепловым ударам, провоцируемым генерированием тепла в ходе трения.
Классификация фрикционных материалов
Фрикционные материалы бывают 3-х групп, принадлежность к которым определяет их физические и химические характеристики:
- металлические;
- неметаллические;
- спечённые.
Металлическими фрикционными материалами считаются стали и чугуны, последние традиционно используются для тормозных колодок, так как они не коробятся. Некоторые стали (65 Г, 45, 40) применяются при изготовлении фрикционных муфт, устанавливаемых на машины с гусеничным ходом.
Важно! Стали склонны к короблению, а в случае перегрева вполне может произойти схватывание.
Именно по этой причине металлические детали по мере возможности заменяются пластиковыми элементами.
Неметаллические материалы, преимущественно имеют асбестовую основу, однако здесь могут применять несколько типов связующих веществ:
- каучук;
- смола;
- канифоль.
Применяются разные наполнители: кремнезём; медь; латунь; сурик. Однако наилучшим материалом, относящимся к данной группе, является ретинакс, состоящий из фенолформальдегидной смолы. Дополнительно в составе присутствует асбест, также есть барит. Материал применяется при производстве тормозных узлов в авиационной промышленности.
Спечённые материалы имеют основу из стального или медного порошка, а наполнителем является металлический оксид и карбид. Благодаря внедрению в состав асбеста с графитом, удаётся избежать схватывания, а сопротивляемость скольжению создаётся посредством добавления муллита. Отменный тепловой режим формируется благодаря цветным металлам, например, алюминию и цинку. Сверхвысокая соединительная прочность формируется в ходе спекания, обеспечивающее надёжное соединение металлической основы и добавок с наполнителями.
Характеристики
Основной физической характеристикой материалов, является температурный режим, при котором они могут эксплуатироваться. Спечённые изделия, имеющие медную основу, обладают температурным пределом 300°C, а материалы из металлов, например, меди, никеля, хрома с добавлением асбеста и барита выдерживают 1200°C. Неметаллические изделия эксплуатируются при 1000°C, но это относится только к ретинаксу, а вот пластмассовые материалы способны выдержать трение, при котором температура достигает не более 250°C.
Область применения
Наиболее востребованными в народном хозяйстве и производственной сфере, являются спечённые материалы, обладающие прекрасными эксплуатационными характеристиками. Допускается их применение при создании фрикционных муфт, необходимых для комплектования тормозных устройств, работающих под высокой нагрузкой. Возможно их применение при изготовлении колодок, дисков и разных секторов.Изделия незаменимы в условиях, когда создаётся избыточное трение, что преимущественно происходит при торможении. Именно поэтому они незаменимы в транспортной промышленности, где активно используются для изготовления тормозных систем. Выбор материала зависит от температуры среды, нагнетаемой при эксплуатации.
Состав тормозных колодок: конструкция и нагрузки
Тормозные колодки – наиболее важный элемент тормозной системы. Именно от них зависит эффективность работы тормозов. Хорошие, правильные колодки будут не только долго и надежно выполнять свои функции, но и сохранят тормозной диск или барабан целым и невредимым долгие годы. Наоборот, плохие, некачественные колодки могут испортить тормозной диск, проделав в нем глубокие канавы, и т. д.

Тормозные колодки бывают разными. Причем речь идет не о конструкции и дизайне, а в первую очередь о материале фрикционных накладок, которые собственно и осуществляют торможение. Фрикционных смесей на сегодня существует превеликое множество. У каждой фирмы своя рецептура и свои ингредиенты. В состав смеси могут входить 15 и более различных компонентов. Их пропорции четко выдержаны. Любое изменение доли того или иного компонента может существенно изменить свойства будущих тормозных накладок, вплоть до их полной неработоспособности.
Основа фрикционной смеси – армирующий компонент. Именно от него зависит прочность, термостойкость и стабильность тормозных свойств изделия. В последние годы сложились устойчивые виды фрикционных изделий, получивших свое название, именно основываясь на их армирующем компоненте. Выделяются асбестовые, безасбестовые и органические (на основе органических волокон) компоненты.
Первые, как видно из названия, в качестве армирующего элемента используют асбест. Вредность этого материала для человека уже стала притчей во языцех. Во многих руководствах по ремонту и обслуживанию автомобилей говорится, что менять асбестосодержащие тормозные колодки и даже снимать колеса (если у вас такие тормоза) необходимо предельно осторожно, заблаговременно позаботившись о защите органов дыхания и зрения.
Безасбестовые представляют собой фрикционный материал, в котором роль армирующего компонента выполняют иные составляющие. Это может быть стальная вата, медная, латунная стружка, различные полимерные композиции и т. д. В бюджетных колодках производители используют смесь органических и неорганических волокон, балансируя между коэффициентом трения, изностойкостью и конечной ценой колодки. Если речь идет о дорогих колодках, хотя и предназначенных для дорожных автомобилей, то производители могут включать гранулы мягких металлов и искусственного графита, кевларовых и карбоновых волокон, таким образом увеличивая термостабильность фрикционного материала.
Самые современные на данный момент фрикционные материалы выполняют на основе органических волокон. У таких колодок наилучшие тормозные свойства. Недаром именно они устанавливаются на современные болиды Формула-1, где нагрузки на тормоза (по меркам городских автомобилей) просто запредельные. Ведь им приходится за считанные секунды или даже доли секунды снижать скорость машины с 300 до 60 км/ч. К сожалению, как и любых высокотехнологичных и наукоемких изделий, стоимость таких колодок доступна лишь таким «денежным» видам автоспорта.
И еще раз вспомним о тепле. Колодки также должны охлаждаться, но, в отличие от дисков, они как раз должны не пропускать тепло через себя. Нагреваясь, сами, они обязательно начнут греть рабочие тормозные цилиндры, а они, в свою очередь, тормозную жидкость, и если она закипит, тормоза перестанут работать, со всеми вытекающими последствиями. Вот почему столь важно обеспечить тепловой барьер между фрикционными накладками и металлической основой тормозной колодки.
Содержание статьи
Нагрузки на передние и задние тормозные колодки
При торможении передние тормозные колодки испытывают основную нагрузку, поэтому они изнашиваются быстрее задних тормозных колодок. Часто приходится слышать, что пока поменяешь задние тормозные колодки, износишь три раза передние тормозные колодки. В принципе, соотношение 1:3 верное.
Многие производители ставят на передние и задние тормозные колодки специальные устройства, предупреждающие об износе этого компонента. Они бывают механические и электронные. В первом случае изношенная задняя или передняя тормозная колодка начинает неприятно скрипеть. Во втором – в случае износа передней или задней тормозной колодки на панели приборов зажигается специальный индикатор.
При замене тормозных колодок лучше поменять все колодки. Например, если вы меняете задние тормозные колодки, то поменяйте колодки сразу на обоих задних колесах. В случае передних тормозных колодок поступайте аналогично. Это позволит избежать ситуации, когда новые и уже износившиеся колодки будут по-разному тормозить колеса, отчего автомобиль будет терять в управляемости.
Фрагменты статьи Ю.Буцкого и В.Карпицкого “О тормозных колодках потребителю – только факты”
Физика безопасности

Фрикционная накладка- важнейшая деталь тормозной колодки. Основные ее задачи- получение необходимых сил трения в процессе торможения и обеспечение стабильности коэффициента трения при изменении скорости вращения тормозного диска и давления в системе. Естественное желание изготовителей автомобилей (как, впрочем, и разработчиков и производителей тормозных накладок)- получение коэффициента трения, близкого к константе при любых условиях эксплуатации. Выполнить это требование нелегко, о чем свидетельствует весь мировой опыт. Можно говорить лишь о поиске оптимального сочетания свойств накладки.
Большинство современных тормозных накладок имеет коэффициент трения 0,35-0,45. Почему так? Чем плохи значения 0,28 или, положим, 0,55? С первой цифрой все понятно: заниженные фрикционные свойства приводят к увеличению времени торможения и тормозного пути, что отрицательно сказывается на безопасности. А хороши ли высокие фрикционные свойства? На первый взгляд — да. Но только на первый. На деле же увеличение коэффициента трения сужает диапазон воздействий на педаль от начала торможения до блокировки колес. И начинаются неприятности.
Судите сами: блокировка приводит к скольжению или юзу. Это недопустимо, как минимум, по двум причинам. Во-первых, ухудшаются устойчивость и управляемость автомобиля. Ведь сцепление колес с дорогой становится одинаковым во всех направлениях — что в курсовом, что в боковом. Во-вторых, увеличивается тормозной путь, поскольку сцепление с дорогой при скольжении колес значительно меньше, чем при качении.
Поэтому при высоком коэффициенте трения накладок требуется осторожность в «топтании педали», определенные навыки вождения и быстрая реакция. Особо опасны дороги, где чередуются участки с хорошим и плохим сцеплением колеса. Например, асфальт, гололед, асфальт, снег, снова гололед и это тянется на много километров. Или так: слева асфальт, а справа, ближе к обочине, жидкая грязь. В подобных ситуациях на машинах без ABS торможение может привести к потере управляемости и непредсказуемым последствиям. Такие случаи особенно опасны в условиях интенсивного движения с высокой скоростью.
О конструкции: взаимодействие осей
В подавляющем большинстве случаев на передней и задней осях автомобиля устанавливаются разные тормозные механизмы. Секрет прост: осям требуется неодинаковая эффективность торможения. Сегодня на многих легковых автомобилях и легких грузовиках наиболее распространена система Д-Б — то есть с дисковыми механизмами на передней оси и барабанными — на задней. Тормозные накладки в этих схемах различны — и по технологии изготовления и по набору компонентов фрикционной композиции. Однако они должны правильно взаимодействовать, то есть иметь согласованные фрикционные характеристики.
Напомним, что опережающая блокировка колес передней оси нарушает управляемость автомобиля, а опережающая блокировка колес задней оси приводит к потере устойчивости, провоцируя занос и опрокидывание. Поэтому эффективность торможения каждой из осей должна находиться строго в своих рамках — это и есть основа безопасности. Коэффициент трения зависит от давления между накладкой и контртелом (диском или барабаном), от скорости и, конечно, от температуры.
Более стабильными являются дисковые тормозные механизмы. Они в меньшей степени теряют эффективность с ростом указанных факторов. Кроме того, им не так страшно попадание воды, масла и грязи на поверхности трения. А вот накладки барабанных тормозов более капризны. Многие знакомы с ситуацией, когда после форсирования большой лужи барабанные тормозные механизмы просто-напросто перестают работать. При интенсивном пользовании тормозами эффективность торможения каждой из осей автомобиля изменяется — причем (внимание!) не пропорционально друг другу. Отсюда видно, сколь легко может быть нарушено правильное взаимодействие передних и задних механизмов в процессе торможения.
Накладка фрикционная тормозная – это часть тормозной колодки автомобиля, благодаря которой создается тормозной момент. В основе работы устройства – сила трения. В момент торможения изделие взаимодействует с металлическим барабаном, поглощая кинетическую энергию автомобиля.
Снижение скорости и остановка транспорта происходит благодаря силе трения. Плотно прикрепленная к металлической части тормозной колодки накладка способствует торможению. Кинетическая энергия движения транспортного средства преобразуется в тепловую, которую колодка и тормозной диск рассеивают в окружающей среде.
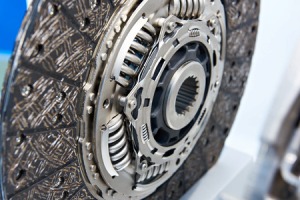
легковых машин;
грузовиков;
сельскохозяйственной и промышленной техники.
ОАО «Тамбов АТИ» специализируется на производстве накладок тормозных для грузовых автомобилей отечественного и иностранного производства, а также для высоконагруженных транспортных средств (ракетовозов, автомобильных кранов и т.п.)
Качественные накладки на тормозные колодки обеспечивают эффективное торможение даже при высокой частоте и сложных условиях.
Разновидности тормозных накладок
По назначению накладки бывают для тормозных механизмов:барабанных;
дисковых.
Накладки для барабанных тормозных механизмов выполнены в виде дугообразной пластины, наружный радиус которой равен внутреннему радиусу барабана. Устанавливаются в каждом колесном тормозном механизме по две штуки.
Накладки в виде плоских серпообразных пластины используют для дисковых тормозов.
По месту монтажа:
установка в колесных тормозных механизмах;
установка в механизме стояночного тормоза.
Материалы изготовления накладок
Изготавливают накладки тормозных колодок из смеси полимеров, асбестов и других веществ. Раствор включает в себя множества различных компонентов. В качестве основы выступает либо асбест, либо полимер.Поэтому все эти накладки делятся на две большие категории: асбестовые и безасбестовые.
Асбестовые
В основе изделия – асбестовые волокна, в частности хризотил-асбест. Он используется в качестве каркаса, скрепляя и удерживая остальные составляющие. Изделия получаются мягкими, но отличаются высоким коэффициентом трения. Значительно снижают износ тормозного механизма.
Безасбестовые
В качестве основного компонента используются полимеры или минеральные волокна. Более жесткие и шумные, по сравнению с асбестовыми. Но являются менее вредными для окружающей среды.
В качестве дополнительных компонентов каждый производитель использует разные материалы: металлическую стружку, каучук, керамику, медь, полимеры.
Состав смеси постоянно дорабатывается, меняется процентное соотношение компонентов. Производители держат в секреты собственные рецепты и разработки.
Наше предприятие производит фрикционные накладки тормозных колодок как из асбестовых, так и безасбестовых материалов.
Способы производства тормозных накладок
Для производства тормозных фрикционных накладок готовят смесь из основного компонента и дополнительных веществ. Затем помешают в форму и под пресс либо при стандартных температурах, либо при высоких.При стандартных температурах
Смешанные компоненты укладывается в подготовленные формы, попадают по пресс без какого-либо воздействия температур. Некоторые компании подвергают накладки воздействию высоких температур уже после формовки. Такие изделия стоят дешевле, но не отличаются долговечностью.
При высоких температурах
Раствор укладывают в форму и прессуют под воздействием высокой температуры. Изготовленные таким способом фрикционные тормозные накладки отличаются долгим сроком службы. Независимо от типа прессования, конечный этап изготовления – шлифование.
Производители фрикционных накладок учитывают конструктивные и технические особенности транспортных средств, поэтому для каждого автомобиля создаются отдельные модели накладок.
Для определения степени износа тормозных накладок и необходимости их замены используют один из трех индикаторов: специальную метку, углубление или ступеньку. Некоторые производители рекомендуют менять накладки каждые 15 000 км пробега.
Ассортимент фрикционных накладок тормозных колодок производства ОАО «Тамбов АТИ» можно посмотреть в Каталоге.
Также у нас вы можете заказать изготовление тормозных накладок по чертежу.
Выбирая подходящие тормозные колодки для автомобиля, мы решаем более приземленную задачу, чем разработка системы мгновенной остановки поездов. Однако и с колодками все не так просто. С чего начать поиски нужных колодок, куда смотреть, чему верить? Попробуем разобраться.
Какие имена на «тормозном рынке» России можно считать самыми надежными?
Поскольку высшая честь для производителя — поставлять комплектацию на конвейеры автозаводов, то можно назвать три имени: Federal-Mogul, TMD Friction и Galfer. Эти компании лидируют в первичной поставке тормозных колодок для европейского рынка по легковой тематике. Крупнейший поставщик — Federal-Mogul.
Это еще не все. Автозаводу отдельно взятые колодки не нужны: его интересуют тормозные системы «под ключ». В частности, колодки должны быть совместимы различными электронными устройствами тормозной системы (ABS, EBD, EDS, ASR и т.п). Вот почему на конвейер колодки поставляются через производителей тормозных систем, крупнейшими из которых для европейских автопроизводителей легковых автомобилей являются TRW, Brembo, Continental (ATE), Akebono, CBI.
На оригинальной колодке крупно нанесен логотип автопроизводителя и логотип производителя тормозной системы. Поэтому конечные потребители иногда ошибочно полагают, что бренд, относящийся к логотипу производителя тормозной системы, и есть бренд реального производителя тормозной колодки.
А на какие бренды в первую очередь смотреть в магазине?
Например, вот на эти: Ferodo,Wagner, Textar, Mintex, Pagid, Galfer, Brembo, ATE, TRW, Bosch, Icer, Remsa, LPR и др.
С чего начать выбор нужной мне колодки?
С номера оригинальной детали. Его найти несложно — в дилерском центре всегда подскажут. Деталь с таким номером могут производить несколько фирм. Но следует помнить, что оригинальная колодка будет по определению и самой дорогой. Если вопрос об экономии не стоит, то это — лучший выбор. Продукция, идущая на конвейер, распространяется в основном через авторизованные дилерские центры, но иногда поступает и в обычные автоцентры. Но уж если решили не экономить, то лучше платить у официалов. Это будет стопроцентное попадание «в оригинал».
А если хочется сэкономить? Тогда нас ждет продукция для вторичного рынка.
Чем вторичный рынок хуже первичного?
Ничем! Так обычно говорят производители. Мол, тот же конвейер, та же технология. Но не всегда это именно так. К примеру, если конвейерная колодка испытывается по десятку с лишним параметров, то ее вторичная подруга — преимущественно по трем. Это плотность крепления материала к несущей пластине, тест на сжимаемость фрикционного материала и динамометрические испытания по замеру трения. Это обязательные тесты для вторичного рынка Европы. На такую продукцию ставят клеймо R90 на соответствие одноименным правилам. Без этого клейма колодка не может быть продана на вторичном рынке в странах Евросоюза.
Так чем же хуже вторичные колодки?
У них может быть несколько иной состав фрикционной смеси. Они могут чуть хуже тормозить, иметь меньший ресурс. Однако разница с оригиналом исчисляется несколькими процентами — не более.
Проблема совсем в другом. Соответствие правилам R90 не обсуждается — наличие клейма обязательно. Но номер такой колодки будет отличаться от оригинального, а потому для покупателя возможны приключения.
Какие — понятно, в общем-то… Предстоит обнаружить кросс-ссылку, которая выведет вас с номера оригинальной колодки на неоригинальную. Тут может помочь продавец — в профильных торговых точках всегда есть база данных: например, база TecDoc. В нее загружают информацию большинство серьезных поставщиков, в том числе и упомянутые выше.
Перед покупкой желательно сопоставить свою старую колодку с новой: компьютеры тоже умеют подвирать. Но и тут возможны «приключения»: следует помнить, что различия по внешнему виду вполне допустимы! Колодки могут отличаться, допустим, покрытием, которое снижает вибрации и шум. Колодка премиум-класса имеет, как правило, металлическую антишумовую пластину. А вот колодки эконом-класса и среднего сегмента — резиновое, типа мастики, как правило, с неровной поверхностью. По своим характеристикам эти типы покрытий могут быть идентичными, но металлическая антишумовая пластина выглядит намного эстетичнее и меньше подвержена повреждениям в сравнении с покрытием типа мастики.
Можно ли ставить такие колодки на дорогую машину? Тут опять некоторое лукавство — многое зависит от владельца. Один даже «старушку» будет гонять к официалам, другой сразу же после окончания гарантии уйдет «налево». И в этом случае он будет искать только бюджетный вариант.
Где купить вторичную колодку?
Лучше всего — у тех же официалов: они, как правило, предлагают как оригинальные запчасти, так и более доступные по цене — для послегарантийных машин. Опять-таки, речь идет о надежности продавца.
Понятно, что к автодилерам поедут далеко не все, потому что изначальная цель поиска вторичных колодок была простая: сэкономить. Есть и более дешевые места — сетевые розничные магазины вроде «Авто-49», и интернет-магазины типа Exist. Но с этого момента опять начинается лотерея, потому что, не будучи специалистом, отличить колодки премиум-качества от собратьев более низкого ранга уже почти невозможно. Некоторые производители, например, Federal-Mogul (колодки Ferodo Premier) или Continental (колодки ATE), используют систему PrioSpot для защиты своей продукции от подделок. Однако простому смертному разобраться в этом очень тяжело.
Часто предлагают экзотику: скажем, полностью керамические колодки. Что это за изделия?
Чаще всего это маркетинговый ход производителей. Практически любые колодки содержат керамику в том или ином процентном соотношении. В тех колодках, которые называют керамическими, как правило, процент содержания этих керамических частиц выше, чем в остальных.
Асбест — это плохо или нет?
Это идеальный материал для тормозных колодок. Он обладает высоким коэффициентом трения и стабильностью при высоких температурах. Почему его запретили — вопрос дискуссионный, но это уже давно свершившийся факт. Евросоюз отказался от него в середине 90-х. Взамен пошли органические соединения, сульфиды металлов, синтетические смазочные вещества и др. Раньше в асбестосодержащих колодках было около десятка компонентов, сейчас их 25.
А чем провинилась медь?
Ее тоже объявили вредной. И теперь автопроизводители требуют от поставщиков, чтобы они поставляли на конвейер колодки с нулевым или низким содержанием меди в составе фрикционной смеси. Первым автомобилем в Европе, который стал оснащаться немедесодержащими колодками, стало новое поколение Mercedes-Benz S-класса, анонсированного в 2014 году. А с сентября 2015 года список пополнил Audi A4 — на конвейер по его производству идут колодки с нулевым содержанием меди от Federal-Mogul по технологии Ferodo Eco-Friction. Такие колодки при той же себестоимости лучше тормозят. И у них меньшая степень износа. Немедесодержащая колодка щадящим образом относится к тормозному диску и обеспечивает износ в паре колодка/диск до 60% ниже, чем при использовании медьсодержащей колодки. Сейчас все идет к тому, что вскоре одна замена колодки будет приходиться на одну замену диска, поскольку срок службы тормозной колодки увеличивается.
Кто служит дольше? Колодки или диск?
Сегодня — диск, конечно же. Как правило, 2–3 замены колодки — одна замена диска. Но диск не вечен, у него обычно есть маркировка по минимально допустимой толщине. Допустим она составляет 9 мм, однако человек упрямо может ездить до момента, пока диск не износится, скажем, до 4 мм. В этом случае выделяемое тепло уже не будет эффективно отводиться. Масса диска становится меньше, от перегрева он начинает деформироваться, его может «повести», а в худшем случае рабочая часть может отсоединиться от ступичной. Это — реальность.
Когда надо заменять колодки?
На большинстве современных автомобилей колодки оснащены датчиками износа. Принцип работы простой — электрический контакт интегрируется в структуру фрикционного материала тормозной колодки. Считается, что колодка подлежит замене, когда остаточная толщина фрикционного материала на несущей пластине достигает значения 3 мм. Если он меньше 3 мм, то колодку надо менять, даже если нет датчика износа. При производстве любой тормозной колодки на стальную несущую пластину наносят термоизоляционный слой толщиной 2–3 мм. Когда колодка изнашивается, вы уже тормозите не фрикционным материалом, а именно этим составом. А при полном износе со стальным диском контактирует уже стальная несущая пластина колодки — здесь уже начинается активный износ диска.
Нужно ли притирать новые колодки?
Да, это очень желательно. Общее пожелание понятно: в начальный период хорошо бы не ездить излишне активно, а также не перегружать машину. А рекомендуемый алгоритм притирки такой: торможение со скорости 80 км/ч до 30 км/ч — и так 20 раз с перерывом примерно 30 секунд. Это позволяет сгладить вершины микронеровностей пары колодка/диск.
Часто на форумах советуют применять колодки от другого автомобиля, отпилив от них лишнее «по месту»…
Вообще-то, ни один профессионал такого издевательства не посоветует, поскольку колодка — это критически важный элемент безопасности автомобиля. Но, если исходная колодка взята для премиум-автомобиля похожего класса, и фрикционная смесь обеспечивает требуемую эффективность торможения, скажем, тормозные диски одного размер
что нужно знать о тормозных колодках
Автовладельцы нередко оперируют понятиями «жесткие» и «мягкие» в отношении тормозных колодок, а продавцы автозапчастей уверенно оценивают ассортимент того или иного производителя по этому параметру. В реальности — характеристики торможения зависят совсем от других параметров, а производители тормозных колодок отказываются понимать такую «градацию».
Разработчики тормозных колодок понимают «жесткость» в буквальном смысле — как способность фрикционного материала сжиматься под нагрузкой. Этот параметр регулируется и согласно Европейскому стандарту испытаний тормозных колодок автомобилей ECE-R90 не должен превышать 2% при температуре окружающей среды и 5% при нагреве до 400 °С. Прежде всего, этот параметр нормируется для того, чтобы тормозные колодки обеспечивали адекватное «чувство педали тормоза». Дело в том, что «мягкие» колодки с хорошим коэффициентом трения и параметрами комфорта сделать проще, но тогда может пострадать безопасность.

Комплект тормозных колодок Textar, выполненных по стандарту ECE R90.
Если говорить о свойствах, которые действительно должны интересовать покупателя, то характеристики колодки напрямую зависят от рецептуры фрикционного материала, которая сегодня представляет собой сложное сочетание многих ингредиентов, количество которых может насчитывать несколько десятков, ведь колодка должна отвечать многим, порой противоречащим друг другу требованиям. Так, колодка должна обеспечивать эффективное торможение в широком диапазоне температур окружающей среды и оставаться стабильной при нагреве без таких сопутствующих явлений, как перегрев, дымление, кипение, прихватывание к тормозному диску, замыливание при длительном торможении. В разумных пределах должно быть пылеобразование, чтобы пыль не забивала подвижные элементы тормозных механизмов и отверстия вентилируемых тормозных дисков, сама пыль не была бы вредной для людей и окружающей среды, а колодки изнашивались бы равномерно с тормозными дисками.
Все материалы фрикционных накладок тормозных колодок можно разделить на 2 большие группы. «Европейские» — материалы группы «low steel» (с низким содержанием стали) и «азиатские» — группы NAO (безасбестовая органика). Есть еще третья группа — фрикционные смеси под общим названием Semi Metallic, которые содержат от 40 до 65% стальных волокон. «Наполовину стальные» колодки отличает эффективное торможение, высокая, даже избыточная теплопроводность, шумность, высокое пылеобразование и не бережное отношение к тормозному диску, поэтому в настоящее время применяются они чаще для легкого коммерческого транспорта.

Тормозные колодки Nisshinbo.

Тормозная колодка Nisshinbo, «выпеченная» из смеси NAO.
Современные рецептуры Low Steel, содержащие от 20 до 30% стальных волокон, распространены на европейском рынке. За счет замещения стали другими ингредиентами, которые производители обычно содержат в секрете, удалось добиться коэффициента трения в диапазоне 0,38–0,5, высокой температурной и скоростной стабильности, информативности педали тормоза, большей прочности и отличного очищения ржавчины с тормозных дисков. Это материалы с высокими характеристиками торможения, отлично подходящие для скоростного движения, которое компенсирует еще достаточно высокое пылеобразование, давая возможность пыли выветриться из тормозных механизмов.

Сравнительные характеристики фрикционных материалов (чем дальше от центра, тем лучше).
Минимальное же пылеобразование достигнуто рецептурами, которые вообще не содержат стали. Гамма рецептур, в которых сталь замещена альтернативными волокнами и керамикой, известных под названием NAO (Non-Asbestos Organic — безасбестовая органика), была разработана в Японии как для внутреннего потребления, так и для рынка США, на котором начали жестко регулировать содержание металлов в тормозных колодках. Рецептуры NAO практически не пылят, не шумят, то есть они обеспечивают комфортное вождение, но имеют меньший коэффициент трения и температурную стабильность и в целом уступают по эффективности торможения рецептурам Low Steel. Поэтому одна и та же модель японского автомобиля на американский рынок поставляется с колодками NAO, а на более требовательный к эффективности тормозов европейский рынок — с колодками Low Steel. Среди производителей тормозных колодок, имеющих статус поставщика на конвейер, можно выделить немецкий бренд Textar — как поставщика колодок группы Low Steel и японский Nisshinbo — как приверженца группы NAO. Как правило, колодки NAO дороже Low Steel. Однако в ассортименте Textar компании TMD Friction есть колодки серии epad, которые не только обладают всеми преимуществами материалов NAO, но и имеют необычайно высокий для этой группы коэффициент трения и температурную стабильность, то есть вписываются в рамки 0,35–0,45 в температурном диапазоне от 100 до 320 °С при пониженном пыле-образовании. Такие свойства обеспечивает уникальная рецептура фрикционной смеси, в которую входят 25 ингредиентов — ноу-хау компании TMD Friction.
Компания проводит интенсивные стендовые испытания и ходовые испытания на собственных треках, на которых в том числе имитируются горные и гоночные условия. На одну колодку приходится до 1000 стендовых часов и до 300 000 километров на треке. В итоге тормозные колодки Textar превосходят требования стандарта ECE R90. Все изделия Textar соответствуют требованиям ведущих европейских автопроизводителей — Audi, BMW, Mercedes-Benz, MINI, Seat, Skoda, Volvo, Volkswagen и других — и уровню качества ОЕМ.
Хочу получать самые интересные статьи
Производители фрикционных материалов | Поставщики фрикционных материалов
Список производителей фрикционных материалов
Применения
Применения включают в себя системы сцепления и тормоза, операционные системы, автомобильное оборудование, системы зубьев зубчатых колес и промышленное оборудование, которые все должны быть в состоянии остановить или замедлить свои процессы. Компоненты, такие как фрикционные колодки и накладки и колодки дискового тормоза, изготовлены из фрикционных материалов.
Отрасли, которые часто используют эти продукты, включают строительство, автомобилестроение, лесное хозяйство, нефтегазовую отрасль и добычу полезных ископаемых.
Тормозные системы
Фрикционные материалы используются в тормозных системах для замедления колес или их остановки, а также для полного предотвращения движения других компонентов. Нажатие на тормоз активирует систему, где фрикционный материал помещается на движущийся диск, тем самым замедляя соединительные колеса.
История фрикционных материалов
Трение — это закон природы, и с незапамятных времен люди пытались им манипулировать.Например, одним из первых способов, которым люди научились разжигать огонь, было создание трения между горючими материалами, такими как дерево.
Некоторые из самых ранних научных заметок, которые мы связали с целью смягчения трения, включают в себя те, которые были написаны древнегреческими и римскими мыслителями. Примеры этих людей включают Плиния Старшего, Аристотеля и Витрувия.
В 1493 году в посмертно опубликованных тетрадях Леонардо да Винчи писал о своем открытии классических законов трения скольжения.Гийом Амонтон заново открыл эти же законы в 1699 году. Он опубликовал свое открытие, и эти законы были названы тремя законами сухого трения Амонтона. После этого другие ученые быстро обнаружили другие вещи о трении, которые были равны классической эмпирической модели трения. Эта модель состоит из статического, кинетического и трения качения. Сначала ученые обнаружили разницу между статическим трением и кинетическим трением. Затем, в 1734 году, Джон Феофил Дезагюльер обнаружил, что трение является достаточно мощной силой, чтобы разрывать прилипшие поверхности.В 1833 году Артур Жюль Мартин опубликовал различие между трением скольжения и трением качения. Законы трения, которые они обнаружили, все еще используются сегодня.
Фрикционные материалы — ProTec Friction Group В 1888 году женщина по имени Берта Бенц изобрела тормозные колодки после того, как она подумала о них, взяв один из первых в мире приводов на дальние расстояния. (Она поехала через Германию.) Ее тормозные колодки и другие ранние тормозные колодки были сделаны с использованием асбестовых фрикционных материалов. Хотя асбест был невероятно эффективным, примерно через 100 лет ученые объявили, что асбест может вызывать рак и заболевания легких.(Национальный институт здравоохранения выпустил официальное объявление в 1989 году.) С тех пор фрикционные материалы из асбеста были отправлены на пыльную книжную полку истории. Его заменили в основном синтетическими арамидными волокнами. Керамика также стала популярным фрикционным материалом благодаря своим термостойким свойствам.
Постоянное развитие отрасли и ее приложений побудило производителей фрикционных материалов и тормозов сохранить свои составы и достижения в секрете.Они делают это, чтобы отличить себя от конкурентов. Например, внедрение керамики в промышленность открыло многочисленные двери для повышения эффективности и долговечности изделий из фрикционных материалов. Снижение шума и более быстрая остановка стали обычными требованиями для тормозов и сцепления. Технологические разработки являются постоянными в этой отрасли, и, таким образом, качество фрикционно-стойких материалов прошло долгий путь и будет продолжать расти.
Design
Материалы
Поскольку тепловая энергия является побочным продуктом процесса создания трения, производители обычно используют материалы, устойчивые к нагреву, для изготовления фрикционных материалов.Самым популярным выбором для фрикционных материалов были волокна из асбеста. Однако из-за растущих проблем со здоровьем, связанных с воздействием асбеста, керамика стала популярным материалом для использования в качестве альтернативы.
Керамика обладает высокой износостойкостью и устойчивостью к нагреванию и поэтому используется в средах с высоким коэффициентом трения. Фрикционные материалы должны выдерживать большие физические нагрузки, поскольку износ материала неизбежно приводит к трению.
Кроме того, производители производили такие изделия, как полуметаллические тормозные материалы, используя латунь, медь и стальную вату, склеенные смолой.Эти элементы похожи на керамику с точки зрения долговечности.
Особенности и настройка
Тип используемого материала в значительной степени зависит от необходимого типа трения. Типы трения включают статическое, кинетическое и трения качения.
Статическое трение , возникает, когда два твердых объекта не движутся относительно друг друга, и движение вообще предотвращается. Важной вещью, которую следует учитывать при реализации этого типа трения, является уклон поверхности.
Кинетическое трение , или динамическое трение, происходит, когда два объекта движутся относительно друг друга. Одна поверхность может двигаться вдоль неподвижного объекта, или обе поверхности могут двигаться.
Трение качения предполагает использование колес или шариков. Во время трения качения грубый материал ловит колесо или шар, предотвращая его скольжение или скольжение. Например, когда автомобильная шина вращается на льду или снегу, трение препятствует ее захвату на земле и позволяет ей продолжать вращаться.
Чтобы определить лучшие фрикционные материалы для работы, производители также думают о том, как быстро трение должно остановить объект или систему (чем выше трение, тем быстрее объект может быть остановлен), как часто будет использоваться фрикционный материал , бюджет, требуемая химическая стойкость, требуемая износостойкость, допустимое выделение тепла, необходимое поглощение энергии и коэффициент трения.
Для обеспечения дополнительного трения и, следовательно, повышения их эффективности фрикционные материалы текстурированы или имеют шероховатую поверхность.Производители используют более гладкие поверхности для более эффективной транспортировки материалов. Кроме того, производители могут добавить резину, чтобы повысить способность тормозной системы производить поверхностное трение. Однако чем больше текстуры добавлено к поверхности, тем больше энергии требуется для ее перемещения. Чтобы обсудить ваши возможности дизайна фрикционных материалов, поговорите с поставщиком сегодня.
Особенности
Вы можете использовать фрикционные материалы несколькими различными способами. В основном они работают как тормоза на автомобилях и других моторизованных транспортных средствах.Чтобы замедлить или остановить обычный автомобиль, фрикционные материалы преобразуют кинетическую энергию в тепло. Однако, чтобы замедлить гибридные и электрические транспортные средства, фрикционные материалы используют регенеративное торможение, процесс, во время которого трение преобразует кинетическую энергию в электрическую энергию.
Типы
Продукция, изготовленная из фрикционных материалов, включает в себя: тормозные колодки, тормозные колодки, фрикционные диски, диски сцепления (дисковые муфты), накладки сцепления, тормозные накладки, комплекты сцепления и тормозные колодки (тормозные ленты).
Тормозные колодки — это блоки из твердого фрикционного материала. Они замедляют колеса при нажатии на обод этих колес, где они обеспечивают трение, необходимое для замедления системы. Они довольно распространены на велосипедах.
Тормозные колодки , также известные как фрикционные колодки, представляют собой металлические пластины, используемые в качестве металлической половины фрикционных тормозных систем.
Фрикционные диски , также известные как фрикционные диски или фрикционные диски, используются в автомобильных тормозных системах.Они состоят из металлической пластины, скрепленной фрикционным материалом. Фрикционные диски обычно изготавливаются из металла. Однако использование металла имеет недостаток, который представляет собой шум шлифования, создаваемый при приложении трения. Поэтому зачастую производители покрывают металлические компоненты торможения другими материалами с высоким коэффициентом трения, такими как резина, чтобы они не были такими громкими.
Диски сцепления , или диски фрикционной муфты, являются подтипом фрикционного диска. Они связывают двигатель автомобиля с входным валом коробки передач, где они облегчают временное разъединение, которое происходит, когда водитель переключает передачи.
Облицовка сцепления — это фрикционный материал, используемый с дисками сцепления. Они помогают сцеплению запускать и останавливать поток энергии между ведомым валом и ведущим валом. Они делают это благодаря низкому коэффициенту трения. Поскольку они работают с более низким коэффициентом трения, чем аналогичные фрикционные материалы, они создают исключительно тихие, стабильные и гладкие системы.
Тормозные накладки представляют собой слои фрикционного материала, связанные с тормозными колодками и накладки на них. Тормозные накладки являются термостойкими, что предотвращает возникновение трения от искр или пожара.
Тормозные колодки , также известные как тормозные ленты, состоят из металлической пластины, прикрепленной к поверхности трения, такой как тормозная накладка. Тормозные колодки доступны в широком диапазоне конфигураций, таких как колодки барабанного тормоза и колодки дискового тормоза.
Правильный уход за фрикционными материалами
Фрикционные материалы используются постоянно, настолько, что они изнашиваются довольно быстро. К сожалению, вы мало что можете сделать, чтобы продлить срок их службы лифта. Вместо этого вам нужно знать, когда их заменить, чтобы не повредить автомобиль или машину.
В тормозной системе характерным признаком износа тормоза является визг. Когда ваш тормоз начинает визжать, проверьте их и посмотрите, нужно ли их заменить. Хотя вам не нужно удалять их при первых признаках износа, вы не хотите ждать, пока они не будут полностью уничтожены. Эксплуатация оборудования без достаточного набивки и трения может привести к повреждению или даже несчастному случаю. Лучше быть в безопасности, чем потом сожалеть. Если вы слышите или чувствуете скрипучий звук при нажатии на тормоза, вы слишком долго ждали, и ваша тормозная система, вероятно, была повреждена.
Еще одна вещь, которую вы должны остерегаться — это повреждение в результате попадания масла или утечки тормозной жидкости. Одним из наиболее распространенных признаков загрязнения тормозов является «тормозная стук» или вибрационный шум, исходящий от тормозов. Если вы слышите или видите стук в тормозе, вам необходимо найти и устранить утечку, а затем заменить тормозные колодки. Вы должны заменить не один, а оба из них. При одновременной замене тормозных колодок убедитесь, что тормозные фрикционные материалы имеют одинаковую толщину. Неровные фрикционные материалы вызывают неравномерное торможение.
Стандарты
Некоторые стандарты, которым должны соответствовать ваши фрикционные материалы, зависят от вашего местоположения. Например, в Соединенных Штатах ваши фрикционные материалы должны соответствовать правилам безопасности, опубликованным EPA (Агентство по защите окружающей среды). Если вы планируете отправлять продукцию за пределы Соединенных Штатов, мы рекомендуем, чтобы ваши фрикционные материалы соответствовали директиве ЕС RoHS (Ограничение использования опасных веществ). Другие стандарты, достойные вашего времени, включают стандарты, разработанные FMSI (Институт стандартов на фрикционные материалы) и SAE International.
Что нужно учитывать
Когда вы рассматриваете фрикционные материалы или изделия из фрикционных материалов, вам необходимо работать с подходящим поставщиком из отрасли. Это ключ к вашему успеху. Чтобы помочь вам на вашем пути, мы составили полный список поставщиков фрикционных материалов высшего качества. Вы найдете их профили по всей этой странице. Прежде чем просматривать их, если вы еще этого не сделали, запишите список своих спецификаций. Не забудьте указать свой бюджет, график, требования к доставке и стандартные требования.Как только вы подготовили свой список, вы можете просмотреть производителей, которые мы перечислили. Часто смотрите свой список, как вы это делаете. Выберите трех или четырех поставщиков, с которыми вы хотели бы поговорить напрямую, а затем обратитесь к своим спецификациям. Не бойтесь задавать вопросы представителям службы поддержки, поэтому они здесь! После того, как вы закончите свои разговоры, сравните и сопоставьте свои заметки и выберите производителя, который, по вашему мнению, лучше всего вам подойдет. Удачи!
Фрикционные материалы Информационное видео
. фрикционные материалы | Тормоза для автомобилей | Продукция | Продукты и технологии
Дисковые и барабанные тормоза оснащены фрикционным материалом, который называется тормозными колодками и тормозными накладками соответственно.

Дисковые и барабанные тормоза оснащены фрикционным материалом, который называется тормозными колодками и тормозными накладками соответственно.
Фрикционные материалы играют важную роль в тормозной системе, поскольку в тормозах используется трение для торможения (замедления и остановки).
Тормозные колодки и тормозные накладки изготавливаются из смеси не менее 10-20 видов сырья. Смешивание подходящих материалов для требуемого состояния и производительности — очень сложная задача, требующая специализированных ноу-хау, которые включают передовой опыт Akebono.
Качество фрикционных материалов также меняется в зависимости от производственного процесса. Благодаря технологиям разработки и производства, усовершенствованным на протяжении многих лет, Akebono предлагает высокопроизводительные и высококачественные фрикционные материалы, которые отвечают потребностям наших клиентов.

Смесь сырья для наших фрикционных материалов (тормозные колодки, тормозные накладки)
колодки дискового тормоза и накладки барабанного тормоза изготовлены из смеси от 10 до 20 видов сырья. В зависимости от их конкретной роли сырье делится на три категории; «связующий материал», «элемент жесткости» и «материал для регулирования трения».
Связующий материал отверждает сырье и придает материалу его интенсивность.В основном используется фенольная смола.
Элемент жесткости придает фрикционным материалам дополнительную интенсивность. Используются различные виды органических и неорганических волокон, такие как арамидные и металлические волокна.
Материал для регулировки трения в основном регулирует эффективность фрикционных материалов. Он используется для усиления эффективности или стабилизации характеристик фрикционных материалов. При необходимости смешивают различные виды сырья, такие как смазочные материалы, органические наполнители, неорганические наполнители, абразивные материалы и металлический порошок.
Фрикционное сырье
Типы фрикционных материалов

- * 1 Спеченный сплав. Явления, при которых частицы порошкового материала объединяются и превращаются в твердое вещество, создавая давление и создавая порошковый материал и нагревая его при температуре ниже температуры плавления. Материал, который производится не плавлением металла, а спеканием металлических порошков, называется спеченным сплавом.
Композит- * 2 C / C: Углеродный армированный углеродный композит. Углеродный композитный материал был усилен углеродным волокном. Это чрезвычайно термостойкий и легкий. Этот материал часто используется для тормозных роторов и тормозных колодок для самолетов и гоночных автомобилей.
Требования к рабочим характеристикам фрикционных материалов (тормозные колодки, тормозные накладки)
Кроме того, фрикционные материалы необходимы для обеспечения стабильной эффективности (минимальное колебание эффективности) при различных условиях, таких как скорость транспортного средства, масса в груженом состоянии или изменение температуры в результате использования тормоза, а также при различных воздействиях окружающей среды, включая влажность, воду и грязь. ,Прочность, чтобы противостоять тепловым помехам, и механическая прочность также являются важными критериями проектирования.
Долговечность является еще одним важным свойством фрикционных материалов, поскольку они изнашиваются по мере использования. Кроме того, когда применяются тормоза, визг, шум и вибрации должны быть сведены к минимуму. Кроме того, фрикционные материалы не должны вызывать повреждения материала, с которым они контактируют, например, дисковые роторы. Фрикционные материалы также должны иметь низкую теплопроводность для предотвращения повышения температуры самих тормозов или тормозного масла.
Основные эксплуатационные требования к фрикционным материалам:
- — Оптимальная эффективность, то есть соответствующий коэффициент трения (μ)
- — Стабильная эффективность при различных условиях использования и / или условиях окружающей среды
- — прочность против тепловых помех и механическая прочность
- — Высокий уровень прочности
- — Минимизированный визг тормоза, шум и вибрации
- — Низкое повреждение материала контакта, такого как дисковый ротор
- — низкая теплопроводность
Фрикционные материалы Akebono (тормозные колодки, тормозные накладки)
Akebono разрабатывает и производит широкий ассортимент тормозных колодок и тормозных накладок, в том числе для автомобилей, сверхскоростных пассажирских экспрессов и высокопроизводительных автомобилей для автоспорта.Различные типы материалов используются в зависимости от того, где используются тормоза. Когда для торможения требуется высокая интенсивность при высокой температуре и условиях высокой нагрузки, таких как скоростные поезда Shinkansen, движущиеся со скоростью, используются металлические фрикционные материалы. Для автомобилей, используемых в Европе, где торможение на высоких скоростях относительно распространено, используются фрикционные материалы с низким содержанием стали.
Для легковых автомобилей, как правило, используются «не стальные» тормозные колодки из-за их сбалансированных характеристик эффективности, интенсивности и сопротивления визгу тормозов.«Не стальные» тормозные колодки являются основными продуктами Akebono.
Akebono продолжает разрабатывать высокопроизводительные тормоза с целью усовершенствования новейших тормозных технологий. Высокопроизводительные тормоза Akebono поставляются различным командам автоспорта. Опыт, приобретенный в автоспорте, который использует тормоза до предела, применяется для разработки тормозных колодок и тормозных накладок для легковых автомобилей.
-

Тормозные колодки для 24-часовой гонки на выносливость на Нюрбургринге
-

10-цилиндровые тормозные колодки для высокопроизводительных легковых автомобилей
-

6-горшковые тормозные колодки для высокопроизводительных автомобилей
Разработка фрикционных материалов (тормозные колодки, тормозные накладки)
Для разработки фрикционных материалов необходимо учитывать как производительность, так и качество, обеспечивающее длительный срок службы.Это достигается путем нахождения правильной комбинации сырья, а также путем оптимизации условий производства. Есть много шагов, которые необходимо предпринять, прежде чем продукт будет доставлен нашим клиентам. Это может занять несколько месяцев или даже несколько лет. Оценены физико-химические свойства фрикционных материалов. Испытательный инструмент, называемый динамометром, на котором можно установить реальный тормоз, используется для оценки свойств трения. Фактические автомобили используются для оценки совместимости автомобиля и тормоза.Мы также разрабатываем сырье, которое минимизирует воздействие на окружающую среду.
В Akebono мы постоянно стремимся стать экспертами в области фрикционных материалов. У нас есть собственные средства тестирования, с помощью которых мы можем оценить основные свойства от ранних стадий разработки до конечной стадии оценки с использованием реального транспортного средства.
Процесс изготовления фрикционных материалов (тормозные колодки, тормозные накладки)
Фрикционные материалы производятся в процессе производства, контроля и испытаний перед их изготовлением.

При разработке фрикционных материалов, где должны соблюдаться различные требования к рабочим характеристикам, эффективное смешивание различных видов сырья является одним из наиболее важных технологических знаний. То, как производятся материалы, также влияет на качество, поэтому важна и технология производства. Akebono способен обеспечить стабильные рабочие характеристики и качество благодаря своим дисковым тормозным колодкам благодаря своим разработкам и технологиям производства, усовершенствованным за эти годы.
Процессы контроля и испытаний фрикционных материалов (тормозные колодки, тормозные накладки)
Для контроля и испытаний фрикционных материалов используются различные методы для проверки их качества. Процессы включают оценку физических свойств, таких как твердость и интенсивность фрикционных материалов, а также химический анализ органических материалов. Для проверки эффективности, износа и визга тормоза используется динамометр, на котором можно установить и проверить настоящий тормоз.
Для тестирования наших фрикционных материалов с точки зрения клиента мы используем «Ай-Ринг», который является крупнейшим испытательным полигоном в своем роде среди производителей автомобильных запчастей.
На полигоне «Ай-Ринг» могут проводиться различные испытания тормозов, от оценок на испытательном стенде до оценок на реальном автомобиле.
Решение вопросов, связанных с ингредиентами наших фрикционных материалов 

На протяжении долгой истории разработки и производства фрикционных материалов Akebono последовательно преследовал тему «безопасность и спокойствие».»
Примерно до 2000 года асбест широко использовался в качестве сырья для фрикционных материалов благодаря его благоприятным свойствам для тормозов, таким как превосходная термическая стабильность. В 1970-х годах из-за границы поступали сообщения об опасностях для здоровья асбеста. Сразу после этого Akebono стала одной из первых компаний в Японии, которая приступила к разработке неасбестовой продукции. Мы лидировали в отрасли по выпуску неасбестовой продукции, и в 1992 году вся продукция OEM (для автомобильных заводов) для легковых автомобилей была переведена на неасбестовую.За этим последовал полный переход на не асбестовые OEM-продукты для коммерческих транспортных средств в 1994 году. Начиная с 2000 года, производство асбестовых изделий, включая запасные части, было прекращено.
Принимая во внимание экологические нормы в отношении меди, которая используется для фрикционных материалов из-за ее термической стабильности, мы приступили к разработке и производству фрикционных материалов, не содержащих медь * . С 2007 года мы поставляем запасные части без содержания меди, а с 2014 года — оригинальные фрикционные материалы.Технологии следующего поколения также находятся в стадии разработки. Akebono разрабатывает тормозные колодки, сделанные из растительных ресурсов (биомассы), а также тормозные колодки, которые не генерируют тормозную пыль.
- * Не содержащий меди фрикционный материал: материалы с содержанием меди ниже указанного значения.
, Анализ влияния структуры задней накладки тормозной колодки и материала накладки на трение на шум дискового тормоза
В данном исследовании предлагается трехслойная конструкция тормозной колодки, на которой создана динамическая модель тормозной накладки тормозного диска с шестью степенями свободы, и факторы влияющие на нестабильность системы анализируются. Анализ показывает, что изменение массы и жесткости тормозной колодки будет влиять на устойчивость системы. Из анализа линейных комплексных собственных значений прогнозируются нестабильные режимы вибрации тормозной системы, а эффективность модели анализа комплексного режима подтверждается стендовыми испытаниями тормозной системы.Разработаны тормозные колодки различной конструктивной формы и проанализировано их влияние на устойчивость тормозной системы. Результаты показывают, что конструкция трехслойной структуры и конструкция прорезей тормозной колодки могут эффективно уменьшить возникновение визга тормоза, особенно шума высокочастотного визга.
1. Введение.За последние три десятилетия доля дискового тормоза, используемого в седане, росла год от года. Можно предположить, что дисковые тормоза будут постепенно заменять барабанные тормоза в седане. Однако проблема тормозного шума дисковых тормозов все еще существует, и многие явления тормозного шума до сих пор не были объяснены рационально [1–3]. Процесс автомобильного торможения вызывает вибрацию, а нестабильная вибрация не только приводит к шуму, который одновременно влияет на комфорт вождения и вызывает акустическое загрязнение окружающей среды, но также вызывает усталостный износ автомобильной тормозной системы [4]. Ларс прорезали и обнажили поверхность тормозного диска и экспериментально доказали, что улучшенный тормозной диск может уменьшить появление визга тормоза [5]. Оберст и Лай использовали теорию хаоса для изучения механизма тормозного шума, который имеет большое руководящее значение [6]. Кунг и соавт. вычислил свободный модальный компонент в тормозе и получил компоненты и связанные модальные условия с наибольшей скоростью вклада неустойчивой моды с помощью комплексного анализа собственных значений [7].В дополнение к использованию сложного анализа собственных значений для изучения тормозного шума, динамический анализ переходных процессов впервые используется Nagy et al. Частоты четырех мод, полученные из результатов динамического анализа переходных процессов, совпадают с экспериментальным шумом [8]. Недостатки переходной динамики состоят в том, что она занимает слишком много времени на вычисления и занимает много места на диске, а также затрудняет непосредственное использование данных для внесения изменений в проект. Кроме того, из-за высокой частоты визга тормоза явный шаг интегрального времени очень мал, тогда как неявный интеграл может иметь большой шаг времени, но он ослабит высокочастотный режим.Комплексный анализ собственных значений и переходный динамический анализ используются AbuBakar и Ouyang [9] для изучения визга тормоза при той же модели и граничных условиях. Результаты вышеупомянутых двух анализов идентичны с различным механизмом контакта и интегральным методом. При анализе шума тормозной системы использование комплексного анализа собственных значений в сочетании с разумной комбинацией переходного динамического анализа может быть способом анализа механизма генерации шума.
В эксперименте по скольжению с трением на плоской пластине Чен [3] обнаружил, что мгновенный визг не может быть вызван модальной связью, а переходное возбуждение между диском и блоком может быть ключевым механизмом визга.Тем не менее, этот тип возбуждения с переменной нагрузкой является переходным процессом, который трудно уловить в экспериментах. Динамический анализ переходных процессов может более четко показать процесс и выявить причины этого явления. Для динамической модели тормозного диска и тормозной колодки Zhang et al. Предложили модель фрикционного генератора с четырьмя степенями свободы. [10], чтобы исследовать разницу между линейным анализом и нелинейным анализом шума тормозной системы, и приведены соответствующие меры по улучшению.
В этом контексте на основе теории модального сцепления устанавливается модель движения с шестью степенями свободы тормозного диска и тормозной колодки. В сочетании с конечно-элементным комплексным модальным анализом и стендовыми испытаниями он имеет большое значение для улучшения характеристик NVH за счет улучшения свойств материала тормозной колодки и оптимизации структуры задней панели тормозной колодки, чтобы подавить шум визга тормоза и исследовать шум. Механизм торможения шума, который обеспечивает теоретическую основу для снижения шума визга тормоза.
2. Кинематическая модель Six-DOF тормозной дисковой тормозной колодки
Модель тормозной муфты, созданная Festjens et al. [11] показывает, что структура и демпфирование задней пластины тормозной колодки оказывают важное влияние на тормозной шум. Аналогичным образом, величина демпфирования материала фрикционной накладки также будет оказывать значительное влияние на шум при торможении. Благодаря исследованию, проведенному Ruhai et al. [12], известно, что добавление определенной части вязкоупругого материала к фрикционной накладке может уменьшить резонансную тенденцию между тормозной колодкой и тормозным диском, тем самым, в некоторой степени подавляя визг тормоза.Исходя из важного влияния фрикционной накладки, она разделена на две части, а именно: подложка футеровки и смесь фрикционной накладки. Поскольку состав материала подложки футеровки обладает более сильными демпфирующими характеристиками, чем смесь фрикционной футеровки, он должен рассматриваться по-разному в процессе моделирования и симуляции.
Кинематическая модель с шестью степенями свободы для тормозной дисковой тормозной колодки изображена на рисунке 1. Из-за небольшого демпфирования системы эффект демпфирования игнорируется при анализе кинематики.Тормозная колодка состоит из задней пластины тормозной колодки, подложки накладки и фрикционной накладки. имеет степень свободы z z 1 ; имеет z — степень свободы направления z 2 ; и имеет степень свободы направления z z 3 и степень свободы направления x x 3 ; Тормозной диск имеет две степени свободы, соответственно, x — направление x , d и z — направление z , d ., и — коэффициент трения, сила поршня, действующая на тормозную колодку, и положительная сила, действующая на тормоз
. сверлильных и щелевых дисковых тормозных роторов
Без сомнения, тормоза — самая мощная система в вашем автомобиле. Неважно, сколько у вас лошадиных сил, это бесполезно, если вы не можете сбросить достаточную скорость, чтобы не дать заднему концу машину перед вами. Ваши заводские тормоза обеспечивают достаточную тормозную мощность для случайных поездок на работу или случайного непредвиденного прекращения паники, но для энтузиастов с высокими эксплуатационными характеристиками лучше выбрать модернизированный набор роторов с отверстиями или пазами.Так в чем же разница между сверлильными и щелевыми тормозными роторами? Здесь мы обсудим преимущества и недостатки каждого из них, чтобы вы могли принять собственное обоснованное решение.

Smooth Rotors
Гладкие тормозные роторы
Комплект гладких роторов премиум-класса обеспечивает более чем достаточную тормозную мощность при нормальных условиях вождения. Вот почему 99,9% новых автомобилей все еще идут с ними с завода.Они обеспечивают большую площадь поверхности по сравнению с просверленными или прорезанными роторами и, следовательно, очень эффективны в качестве теплоотвода, а именно для этого предназначен тормозной ротор. Они также не так подвержены растрескиванию при экстремальном использовании, как просверленные роторы. Отсутствие пазов или отверстий позволяет гладким роторам сохранять максимальную структурную целостность, что делает их пригодными для умеренного использования гусениц в сочетании с тормозными колодками с высокими эксплуатационными характеристиками и тормозной жидкостью с высокой температурой кипения. Существует несколько разновидностей, от прямой замены до высококачественных оцинкованных роторов, для борьбы с поверхностной ржавчиной и сохранения их нового облика на многие мили.

Щелевые Роторы
щелевых тормозных роторов
У щелевых роторов, как следует из названия, есть канавки, вырезанные вдоль поверхности ротора, где контактная площадка контактирует. Это связано с тем, что при многократном резком торможении, когда температура вашей тормозной системы увеличивается, между колодкой и ротором образуется слой газа и пыли в результате переноса материала, вызванного трением. Прорези в роторе обеспечивают путь для выхода скопившихся газов. Это позволяет большей площади поверхности тормозной колодки контактировать с ротором, что приводит к лучшему прикусу колодки и более последовательным упорам.Кроме того, этот увеличенный контакт с поверхностью приводит к более высокому коэффициенту трения, поэтому вы фактически используете меньше энергии, чтобы замедлить автомобиль на ту же величину. Вентиляция, обеспечиваемая роторами с прорезями, является одним из основных способов борьбы с затуханием тормозов и поддержания постоянной тормозной способности, круг за кругом. Имейте в виду, однако, что некоторые выделенные «гоночные» роторы с прорезями на самом деле используют острый край на прорезях, чтобы врезать в тормозную колодку небольшое количество для лучшего прикуса, но это может значительно ускорить износ тормоза.

Ротор с перекрестным бурением
Тормозные роторы с перекрестным бурением
перфорированных тормозные диски выглядят неоспоримо охладиться выглянуть из-за множеством кричащих колес, и они держат свои тормоза точно так же — круто. В первые дни гонок просверленные роторы были эффективным способом вентиляции слоя газа и пыли, который неизбежно накапливался между асбестовыми тормозными колодками и ротором при многократном резком торможении. Однако по мере развития технологий и материалов тормозных колодок выделение газа становится все менее серьезной проблемой.В наши дни, несмотря на то, что они по-прежнему выглядят великолепно и хорошо работают, отверстия для сверления больше по эстетическим соображениям, чем что-либо еще. Для эффективной работы роторы с прорезями стали предпочтительным выбором, поскольку роторы с поперечным бурением более подвержены растрескиванию под напряжением при экстремальном использовании. Достаточно взглянуть на спицы на колесе любого современного гоночного автомобиля — в поле зрения не будет просверленного ротора. На улице, однако, температура, с которой сталкиваются ваши тормоза, никогда не приближается к уровням, которые они испытывают на трассе.Таким образом, вентиляционные свойства просверленных роторов обеспечивают дополнительные преимущества, заключающиеся в поддержании температуры при нормальном движении для продления срока службы колодок, а также улучшенные характеристики в сырую погоду, позволяя воде выходить из поверхности ротора, увеличивая первоначальный прикус колодки.

Ротор с отверстиями и прорезями
Сверлильные и прорезные тормозные роторы
Роторы с отверстиями и пазами обеспечивают внешний вид и функциональность как роторов с поперечным бурением, так и роторов с пазами.Хотя они по-прежнему не идеальны для злоупотреблений, они будут страдать на ипподроме (то есть, в отверстиях, подверженных растрескиванию под напряжением), одно из мест, где просверлены и прорезаны роторы, находится на тяжелых транспортных средствах, буксирующих тяжелые грузы. Чем тяжелее транспортное средство, тем больше энергии требуется, чтобы замедлить его до безопасной и надежной остановки. Тормоза преобразуют кинетическую энергию (движение) в тепловую энергию, а более тяжелые транспортные средства неизменно выделяют больше тепла в своих тормозных системах. Таким образом, ротор, который работает более прохладно (с поперечным бурением) в сочетании с ротором, который поддерживает чистую поверхность контакта между собой и тормозной колодкой (с прорезями), когда он не выдвинут за пределы своего теплового порога, может обеспечить дополнительный уровень безопасности и долговечности.Помните, что название игры поддерживает постоянную силу остановки каждый раз, когда вы нажимаете на тормоза. Если вы когда-нибудь буксировали полностью загруженный трейлер по горному перевалу, вы знаете, какое ужасное ощущение затухания тормозов. Набор роторов с поперечными отверстиями и пазами может дать вам дополнительное спокойствие, поддерживая температуру и поверхность ротора в чистоте. Не забывайте сочетать роторы с отверстиями и пазами с высококачественным набором тормозных колодок, разработанных для вашего автомобиля, а также свежей тормозной жидкостью DOT-3 или DOT-4 для достижения наилучших результатов.
Выбор правильного тормозного ротора
Есть несколько вещей, которые следует иметь в виду при выборе тормозных роторов с поперечным бурением или пазами. Что касается уличных транспортных средств, то они одинаково хорошо работают и не испытывают никаких вредных побочных эффектов. Это просто сводится к личным предпочтениям того стиля, который вы предпочитаете. Однако роторы с прорезями или крестовинами не уменьшат исходный тормозной путь вашего автомобиля. Их цель — рассеивать тепло и газы для борьбы с затуханием тормозов и обеспечивать постоянные остановки после продолжительного злоупотребленияДля того, чтобы вытащить значительный кусок из вашего тормозного пути, рекомендуется набор липких шин и специальные тормозные колодки с высокими эксплуатационными характеристиками. Для движения по гусеницам роторы с прорезями являются предпочтительным выбором из-за их способности выпускать газы, не ослабляя их структуру. Для привлекательных, высококлассных стилей, просверленные или просверленные и прорезанные роторы обязательно поворачивают головы. Для ежедневного вождения любое из вышеперечисленного обеспечивает более чем достаточную тормозную способность.
Метки: роторы
,
Так чем же хуже вторичные колодки?
У них может быть несколько иной состав фрикционной смеси. Они могут чуть хуже тормозить, иметь меньший ресурс. Однако разница с оригиналом исчисляется несколькими процентами — не более.
Проблема совсем в другом. Соответствие правилам R90 не обсуждается — наличие клейма обязательно. Но номер такой колодки будет отличаться от оригинального, а потому для покупателя возможны приключения.
Какие — понятно, в общем-то… Предстоит обнаружить кросс-ссылку, которая выведет вас с номера оригинальной колодки на неоригинальную. Тут может помочь продавец — в профильных торговых точках всегда есть база данных: например, база TecDoc. В нее загружают информацию большинство серьезных поставщиков, в том числе и упомянутые выше.
Перед покупкой желательно сопоставить свою старую колодку с новой: компьютеры тоже умеют подвирать. Но и тут возможны «приключения»: следует помнить, что различия по внешнему виду вполне допустимы! Колодки могут отличаться, допустим, покрытием, которое снижает вибрации и шум. Колодка премиум-класса имеет, как правило, металлическую антишумовую пластину. А вот колодки эконом-класса и среднего сегмента — резиновое, типа мастики, как правило, с неровной поверхностью. По своим характеристикам эти типы покрытий могут быть идентичными, но металлическая антишумовая пластина выглядит намного эстетичнее и меньше подвержена повреждениям в сравнении с покрытием типа мастики.
Можно ли ставить такие колодки на дорогую машину? Тут опять некоторое лукавство — многое зависит от владельца. Один даже «старушку» будет гонять к официалам, другой сразу же после окончания гарантии уйдет «налево». И в этом случае он будет искать только бюджетный вариант.
Где купить вторичную колодку?
Лучше всего — у тех же официалов: они, как правило, предлагают как оригинальные запчасти, так и более доступные по цене — для послегарантийных машин. Опять-таки, речь идет о надежности продавца.
Понятно, что к автодилерам поедут далеко не все, потому что изначальная цель поиска вторичных колодок была простая: сэкономить. Есть и более дешевые места — сетевые розничные магазины вроде «Авто-49», и интернет-магазины типа Exist. Но с этого момента опять начинается лотерея, потому что, не будучи специалистом, отличить колодки премиум-качества от собратьев более низкого ранга уже почти невозможно. Некоторые производители, например, Federal-Mogul (колодки Ferodo Premier) или Continental (колодки ATE), используют систему PrioSpot для защиты своей продукции от подделок. Однако простому смертному разобраться в этом очень тяжело.
Часто предлагают экзотику: скажем, полностью керамические колодки. Что это за изделия?
Чаще всего это маркетинговый ход производителей. Практически любые колодки содержат керамику в том или ином процентном соотношении. В тех колодках, которые называют керамическими, как правило, процент содержания этих керамических частиц выше, чем в остальных.
Асбест — это плохо или нет?
Это идеальный материал для тормозных колодок. Он обладает высоким коэффициентом трения и стабильностью при высоких температурах. Почему его запретили — вопрос дискуссионный, но это уже давно свершившийся факт. Евросоюз отказался от него в середине 90-х. Взамен пошли органические соединения, сульфиды металлов, синтетические смазочные вещества и др. Раньше в асбестосодержащих колодках было около десятка компонентов, сейчас их 25.
А чем провинилась медь?
Ее тоже объявили вредной. И теперь автопроизводители требуют от поставщиков, чтобы они поставляли на конвейер колодки с нулевым или низким содержанием меди в составе фрикционной смеси. Первым автомобилем в Европе, который стал оснащаться немедесодержащими колодками, стало новое поколение Mercedes-Benz S-класса, анонсированного в 2014 году. А с сентября 2015 года список пополнил Audi A4 — на конвейер по его производству идут колодки с нулевым содержанием меди от Federal-Mogul по технологии Ferodo Eco-Friction. Такие колодки при той же себестоимости лучше тормозят. И у них меньшая степень износа. Немедесодержащая колодка щадящим образом относится к тормозному диску и обеспечивает износ в паре колодка/диск до 60% ниже, чем при использовании медьсодержащей колодки. Сейчас все идет к тому, что вскоре одна замена колодки будет приходиться на одну замену диска, поскольку срок службы тормозной колодки увеличивается.
Кто служит дольше? Колодки или диск?
Сегодня — диск, конечно же. Как правило, 2–3 замены колодки — одна замена диска. Но диск не вечен, у него обычно есть маркировка по минимально допустимой толщине. Допустим она составляет 9 мм, однако человек упрямо может ездить до момента, пока диск не износится, скажем, до 4 мм. В этом случае выделяемое тепло уже не будет эффективно отводиться. Масса диска становится меньше, от перегрева он начинает деформироваться, его может «повести», а в худшем случае рабочая часть может отсоединиться от ступичной. Это — реальность.
Когда надо заменять колодки?
На большинстве современных автомобилей колодки оснащены датчиками износа. Принцип работы простой — электрический контакт интегрируется в структуру фрикционного материала тормозной колодки. Считается, что колодка подлежит замене, когда остаточная толщина фрикционного материала на несущей пластине достигает значения 3 мм. Если он меньше 3 мм, то колодку надо менять, даже если нет датчика износа. При производстве любой тормозной колодки на стальную несущую пластину наносят термоизоляционный слой толщиной 2–3 мм. Когда колодка изнашивается, вы уже тормозите не фрикционным материалом, а именно этим составом. А при полном износе со стальным диском контактирует уже стальная несущая пластина колодки — здесь уже начинается активный износ диска.
Нужно ли притирать новые колодки?
Да, это очень желательно. Общее пожелание понятно: в начальный период хорошо бы не ездить излишне активно, а также не перегружать машину. А рекомендуемый алгоритм притирки такой: торможение со скорости 80 км/ч до 30 км/ч — и так 20 раз с перерывом примерно 30 секунд. Это позволяет сгладить вершины микронеровностей пары колодка/диск.
Часто на форумах советуют применять колодки от другого автомобиля, отпилив от них лишнее «по месту»…
Вообще-то, ни один профессионал такого издевательства не посоветует, поскольку колодка — это критически важный элемент безопасности автомобиля. Но, если исходная колодка взята для премиум-автомобиля похожего класса, и фрикционная смесь обеспечивает требуемую эффективность торможения, скажем, тормозные диски одного размер
что нужно знать о тормозных колодках
Автовладельцы нередко оперируют понятиями «жесткие» и «мягкие» в отношении тормозных колодок, а продавцы автозапчастей уверенно оценивают ассортимент того или иного производителя по этому параметру. В реальности — характеристики торможения зависят совсем от других параметров, а производители тормозных колодок отказываются понимать такую «градацию».
Разработчики тормозных колодок понимают «жесткость» в буквальном смысле — как способность фрикционного материала сжиматься под нагрузкой. Этот параметр регулируется и согласно Европейскому стандарту испытаний тормозных колодок автомобилей ECE-R90 не должен превышать 2% при температуре окружающей среды и 5% при нагреве до 400 °С. Прежде всего, этот параметр нормируется для того, чтобы тормозные колодки обеспечивали адекватное «чувство педали тормоза». Дело в том, что «мягкие» колодки с хорошим коэффициентом трения и параметрами комфорта сделать проще, но тогда может пострадать безопасность.

Комплект тормозных колодок Textar, выполненных по стандарту ECE R90.
Если говорить о свойствах, которые действительно должны интересовать покупателя, то характеристики колодки напрямую зависят от рецептуры фрикционного материала, которая сегодня представляет собой сложное сочетание многих ингредиентов, количество которых может насчитывать несколько десятков, ведь колодка должна отвечать многим, порой противоречащим друг другу требованиям. Так, колодка должна обеспечивать эффективное торможение в широком диапазоне температур окружающей среды и оставаться стабильной при нагреве без таких сопутствующих явлений, как перегрев, дымление, кипение, прихватывание к тормозному диску, замыливание при длительном торможении. В разумных пределах должно быть пылеобразование, чтобы пыль не забивала подвижные элементы тормозных механизмов и отверстия вентилируемых тормозных дисков, сама пыль не была бы вредной для людей и окружающей среды, а колодки изнашивались бы равномерно с тормозными дисками.
Все материалы фрикционных накладок тормозных колодок можно разделить на 2 большие группы. «Европейские» — материалы группы «low steel» (с низким содержанием стали) и «азиатские» — группы NAO (безасбестовая органика). Есть еще третья группа — фрикционные смеси под общим названием Semi Metallic, которые содержат от 40 до 65% стальных волокон. «Наполовину стальные» колодки отличает эффективное торможение, высокая, даже избыточная теплопроводность, шумность, высокое пылеобразование и не бережное отношение к тормозному диску, поэтому в настоящее время применяются они чаще для легкого коммерческого транспорта.

Тормозные колодки Nisshinbo.

Тормозная колодка Nisshinbo, «выпеченная» из смеси NAO.
Современные рецептуры Low Steel, содержащие от 20 до 30% стальных волокон, распространены на европейском рынке. За счет замещения стали другими ингредиентами, которые производители обычно содержат в секрете, удалось добиться коэффициента трения в диапазоне 0,38–0,5, высокой температурной и скоростной стабильности, информативности педали тормоза, большей прочности и отличного очищения ржавчины с тормозных дисков. Это материалы с высокими характеристиками торможения, отлично подходящие для скоростного движения, которое компенсирует еще достаточно высокое пылеобразование, давая возможность пыли выветриться из тормозных механизмов.

Сравнительные характеристики фрикционных материалов (чем дальше от центра, тем лучше).
Минимальное же пылеобразование достигнуто рецептурами, которые вообще не содержат стали. Гамма рецептур, в которых сталь замещена альтернативными волокнами и керамикой, известных под названием NAO (Non-Asbestos Organic — безасбестовая органика), была разработана в Японии как для внутреннего потребления, так и для рынка США, на котором начали жестко регулировать содержание металлов в тормозных колодках. Рецептуры NAO практически не пылят, не шумят, то есть они обеспечивают комфортное вождение, но имеют меньший коэффициент трения и температурную стабильность и в целом уступают по эффективности торможения рецептурам Low Steel. Поэтому одна и та же модель японского автомобиля на американский рынок поставляется с колодками NAO, а на более требовательный к эффективности тормозов европейский рынок — с колодками Low Steel. Среди производителей тормозных колодок, имеющих статус поставщика на конвейер, можно выделить немецкий бренд Textar — как поставщика колодок группы Low Steel и японский Nisshinbo — как приверженца группы NAO. Как правило, колодки NAO дороже Low Steel. Однако в ассортименте Textar компании TMD Friction есть колодки серии epad, которые не только обладают всеми преимуществами материалов NAO, но и имеют необычайно высокий для этой группы коэффициент трения и температурную стабильность, то есть вписываются в рамки 0,35–0,45 в температурном диапазоне от 100 до 320 °С при пониженном пыле-образовании. Такие свойства обеспечивает уникальная рецептура фрикционной смеси, в которую входят 25 ингредиентов — ноу-хау компании TMD Friction.
Компания проводит интенсивные стендовые испытания и ходовые испытания на собственных треках, на которых в том числе имитируются горные и гоночные условия. На одну колодку приходится до 1000 стендовых часов и до 300 000 километров на треке. В итоге тормозные колодки Textar превосходят требования стандарта ECE R90. Все изделия Textar соответствуют требованиям ведущих европейских автопроизводителей — Audi, BMW, Mercedes-Benz, MINI, Seat, Skoda, Volvo, Volkswagen и других — и уровню качества ОЕМ.
Хочу получать самые интересные статьи
Производители фрикционных материалов | Поставщики фрикционных материалов
Список производителей фрикционных материалов
Применения
Применения включают в себя системы сцепления и тормоза, операционные системы, автомобильное оборудование, системы зубьев зубчатых колес и промышленное оборудование, которые все должны быть в состоянии остановить или замедлить свои процессы. Компоненты, такие как фрикционные колодки и накладки и колодки дискового тормоза, изготовлены из фрикционных материалов.
Отрасли, которые часто используют эти продукты, включают строительство, автомобилестроение, лесное хозяйство, нефтегазовую отрасль и добычу полезных ископаемых.
Тормозные системы
Фрикционные материалы используются в тормозных системах для замедления колес или их остановки, а также для полного предотвращения движения других компонентов. Нажатие на тормоз активирует систему, где фрикционный материал помещается на движущийся диск, тем самым замедляя соединительные колеса.
История фрикционных материалов
Трение — это закон природы, и с незапамятных времен люди пытались им манипулировать.Например, одним из первых способов, которым люди научились разжигать огонь, было создание трения между горючими материалами, такими как дерево.
Некоторые из самых ранних научных заметок, которые мы связали с целью смягчения трения, включают в себя те, которые были написаны древнегреческими и римскими мыслителями. Примеры этих людей включают Плиния Старшего, Аристотеля и Витрувия.
В 1493 году в посмертно опубликованных тетрадях Леонардо да Винчи писал о своем открытии классических законов трения скольжения.Гийом Амонтон заново открыл эти же законы в 1699 году. Он опубликовал свое открытие, и эти законы были названы тремя законами сухого трения Амонтона. После этого другие ученые быстро обнаружили другие вещи о трении, которые были равны классической эмпирической модели трения. Эта модель состоит из статического, кинетического и трения качения. Сначала ученые обнаружили разницу между статическим трением и кинетическим трением. Затем, в 1734 году, Джон Феофил Дезагюльер обнаружил, что трение является достаточно мощной силой, чтобы разрывать прилипшие поверхности.В 1833 году Артур Жюль Мартин опубликовал различие между трением скольжения и трением качения. Законы трения, которые они обнаружили, все еще используются сегодня.
Фрикционные материалы — ProTec Friction Group В 1888 году женщина по имени Берта Бенц изобрела тормозные колодки после того, как она подумала о них, взяв один из первых в мире приводов на дальние расстояния. (Она поехала через Германию.) Ее тормозные колодки и другие ранние тормозные колодки были сделаны с использованием асбестовых фрикционных материалов. Хотя асбест был невероятно эффективным, примерно через 100 лет ученые объявили, что асбест может вызывать рак и заболевания легких.(Национальный институт здравоохранения выпустил официальное объявление в 1989 году.) С тех пор фрикционные материалы из асбеста были отправлены на пыльную книжную полку истории. Его заменили в основном синтетическими арамидными волокнами. Керамика также стала популярным фрикционным материалом благодаря своим термостойким свойствам.
Постоянное развитие отрасли и ее приложений побудило производителей фрикционных материалов и тормозов сохранить свои составы и достижения в секрете.Они делают это, чтобы отличить себя от конкурентов. Например, внедрение керамики в промышленность открыло многочисленные двери для повышения эффективности и долговечности изделий из фрикционных материалов. Снижение шума и более быстрая остановка стали обычными требованиями для тормозов и сцепления. Технологические разработки являются постоянными в этой отрасли, и, таким образом, качество фрикционно-стойких материалов прошло долгий путь и будет продолжать расти.
Design
Материалы
Поскольку тепловая энергия является побочным продуктом процесса создания трения, производители обычно используют материалы, устойчивые к нагреву, для изготовления фрикционных материалов.Самым популярным выбором для фрикционных материалов были волокна из асбеста. Однако из-за растущих проблем со здоровьем, связанных с воздействием асбеста, керамика стала популярным материалом для использования в качестве альтернативы.
Керамика обладает высокой износостойкостью и устойчивостью к нагреванию и поэтому используется в средах с высоким коэффициентом трения. Фрикционные материалы должны выдерживать большие физические нагрузки, поскольку износ материала неизбежно приводит к трению.
Кроме того, производители производили такие изделия, как полуметаллические тормозные материалы, используя латунь, медь и стальную вату, склеенные смолой.Эти элементы похожи на керамику с точки зрения долговечности.
Особенности и настройка
Тип используемого материала в значительной степени зависит от необходимого типа трения. Типы трения включают статическое, кинетическое и трения качения.
Статическое трение , возникает, когда два твердых объекта не движутся относительно друг друга, и движение вообще предотвращается. Важной вещью, которую следует учитывать при реализации этого типа трения, является уклон поверхности.
Кинетическое трение , или динамическое трение, происходит, когда два объекта движутся относительно друг друга. Одна поверхность может двигаться вдоль неподвижного объекта, или обе поверхности могут двигаться.
Трение качения предполагает использование колес или шариков. Во время трения качения грубый материал ловит колесо или шар, предотвращая его скольжение или скольжение. Например, когда автомобильная шина вращается на льду или снегу, трение препятствует ее захвату на земле и позволяет ей продолжать вращаться.
Чтобы определить лучшие фрикционные материалы для работы, производители также думают о том, как быстро трение должно остановить объект или систему (чем выше трение, тем быстрее объект может быть остановлен), как часто будет использоваться фрикционный материал , бюджет, требуемая химическая стойкость, требуемая износостойкость, допустимое выделение тепла, необходимое поглощение энергии и коэффициент трения.
Для обеспечения дополнительного трения и, следовательно, повышения их эффективности фрикционные материалы текстурированы или имеют шероховатую поверхность.Производители используют более гладкие поверхности для более эффективной транспортировки материалов. Кроме того, производители могут добавить резину, чтобы повысить способность тормозной системы производить поверхностное трение. Однако чем больше текстуры добавлено к поверхности, тем больше энергии требуется для ее перемещения. Чтобы обсудить ваши возможности дизайна фрикционных материалов, поговорите с поставщиком сегодня.
Особенности
Вы можете использовать фрикционные материалы несколькими различными способами. В основном они работают как тормоза на автомобилях и других моторизованных транспортных средствах.Чтобы замедлить или остановить обычный автомобиль, фрикционные материалы преобразуют кинетическую энергию в тепло. Однако, чтобы замедлить гибридные и электрические транспортные средства, фрикционные материалы используют регенеративное торможение, процесс, во время которого трение преобразует кинетическую энергию в электрическую энергию.
Типы
Продукция, изготовленная из фрикционных материалов, включает в себя: тормозные колодки, тормозные колодки, фрикционные диски, диски сцепления (дисковые муфты), накладки сцепления, тормозные накладки, комплекты сцепления и тормозные колодки (тормозные ленты).
Тормозные колодки — это блоки из твердого фрикционного материала. Они замедляют колеса при нажатии на обод этих колес, где они обеспечивают трение, необходимое для замедления системы. Они довольно распространены на велосипедах.
Тормозные колодки , также известные как фрикционные колодки, представляют собой металлические пластины, используемые в качестве металлической половины фрикционных тормозных систем.
Фрикционные диски , также известные как фрикционные диски или фрикционные диски, используются в автомобильных тормозных системах.Они состоят из металлической пластины, скрепленной фрикционным материалом. Фрикционные диски обычно изготавливаются из металла. Однако использование металла имеет недостаток, который представляет собой шум шлифования, создаваемый при приложении трения. Поэтому зачастую производители покрывают металлические компоненты торможения другими материалами с высоким коэффициентом трения, такими как резина, чтобы они не были такими громкими.
Диски сцепления , или диски фрикционной муфты, являются подтипом фрикционного диска. Они связывают двигатель автомобиля с входным валом коробки передач, где они облегчают временное разъединение, которое происходит, когда водитель переключает передачи.
Облицовка сцепления — это фрикционный материал, используемый с дисками сцепления. Они помогают сцеплению запускать и останавливать поток энергии между ведомым валом и ведущим валом. Они делают это благодаря низкому коэффициенту трения. Поскольку они работают с более низким коэффициентом трения, чем аналогичные фрикционные материалы, они создают исключительно тихие, стабильные и гладкие системы.
Тормозные накладки представляют собой слои фрикционного материала, связанные с тормозными колодками и накладки на них. Тормозные накладки являются термостойкими, что предотвращает возникновение трения от искр или пожара.
Тормозные колодки , также известные как тормозные ленты, состоят из металлической пластины, прикрепленной к поверхности трения, такой как тормозная накладка. Тормозные колодки доступны в широком диапазоне конфигураций, таких как колодки барабанного тормоза и колодки дискового тормоза.
Правильный уход за фрикционными материалами
Фрикционные материалы используются постоянно, настолько, что они изнашиваются довольно быстро. К сожалению, вы мало что можете сделать, чтобы продлить срок их службы лифта. Вместо этого вам нужно знать, когда их заменить, чтобы не повредить автомобиль или машину.
В тормозной системе характерным признаком износа тормоза является визг. Когда ваш тормоз начинает визжать, проверьте их и посмотрите, нужно ли их заменить. Хотя вам не нужно удалять их при первых признаках износа, вы не хотите ждать, пока они не будут полностью уничтожены. Эксплуатация оборудования без достаточного набивки и трения может привести к повреждению или даже несчастному случаю. Лучше быть в безопасности, чем потом сожалеть. Если вы слышите или чувствуете скрипучий звук при нажатии на тормоза, вы слишком долго ждали, и ваша тормозная система, вероятно, была повреждена.
Еще одна вещь, которую вы должны остерегаться — это повреждение в результате попадания масла или утечки тормозной жидкости. Одним из наиболее распространенных признаков загрязнения тормозов является «тормозная стук» или вибрационный шум, исходящий от тормозов. Если вы слышите или видите стук в тормозе, вам необходимо найти и устранить утечку, а затем заменить тормозные колодки. Вы должны заменить не один, а оба из них. При одновременной замене тормозных колодок убедитесь, что тормозные фрикционные материалы имеют одинаковую толщину. Неровные фрикционные материалы вызывают неравномерное торможение.
Стандарты
Некоторые стандарты, которым должны соответствовать ваши фрикционные материалы, зависят от вашего местоположения. Например, в Соединенных Штатах ваши фрикционные материалы должны соответствовать правилам безопасности, опубликованным EPA (Агентство по защите окружающей среды). Если вы планируете отправлять продукцию за пределы Соединенных Штатов, мы рекомендуем, чтобы ваши фрикционные материалы соответствовали директиве ЕС RoHS (Ограничение использования опасных веществ). Другие стандарты, достойные вашего времени, включают стандарты, разработанные FMSI (Институт стандартов на фрикционные материалы) и SAE International.
Что нужно учитывать
Когда вы рассматриваете фрикционные материалы или изделия из фрикционных материалов, вам необходимо работать с подходящим поставщиком из отрасли. Это ключ к вашему успеху. Чтобы помочь вам на вашем пути, мы составили полный список поставщиков фрикционных материалов высшего качества. Вы найдете их профили по всей этой странице. Прежде чем просматривать их, если вы еще этого не сделали, запишите список своих спецификаций. Не забудьте указать свой бюджет, график, требования к доставке и стандартные требования.Как только вы подготовили свой список, вы можете просмотреть производителей, которые мы перечислили. Часто смотрите свой список, как вы это делаете. Выберите трех или четырех поставщиков, с которыми вы хотели бы поговорить напрямую, а затем обратитесь к своим спецификациям. Не бойтесь задавать вопросы представителям службы поддержки, поэтому они здесь! После того, как вы закончите свои разговоры, сравните и сопоставьте свои заметки и выберите производителя, который, по вашему мнению, лучше всего вам подойдет. Удачи!
Фрикционные материалы Информационное видео
. фрикционные материалы | Тормоза для автомобилей | Продукция | Продукты и технологии
Дисковые и барабанные тормоза оснащены фрикционным материалом, который называется тормозными колодками и тормозными накладками соответственно.

Дисковые и барабанные тормоза оснащены фрикционным материалом, который называется тормозными колодками и тормозными накладками соответственно.
Фрикционные материалы играют важную роль в тормозной системе, поскольку в тормозах используется трение для торможения (замедления и остановки).
Тормозные колодки и тормозные накладки изготавливаются из смеси не менее 10-20 видов сырья. Смешивание подходящих материалов для требуемого состояния и производительности — очень сложная задача, требующая специализированных ноу-хау, которые включают передовой опыт Akebono.
Качество фрикционных материалов также меняется в зависимости от производственного процесса. Благодаря технологиям разработки и производства, усовершенствованным на протяжении многих лет, Akebono предлагает высокопроизводительные и высококачественные фрикционные материалы, которые отвечают потребностям наших клиентов.

Смесь сырья для наших фрикционных материалов (тормозные колодки, тормозные накладки)
колодки дискового тормоза и накладки барабанного тормоза изготовлены из смеси от 10 до 20 видов сырья. В зависимости от их конкретной роли сырье делится на три категории; «связующий материал», «элемент жесткости» и «материал для регулирования трения».
Связующий материал отверждает сырье и придает материалу его интенсивность.В основном используется фенольная смола.
Элемент жесткости придает фрикционным материалам дополнительную интенсивность. Используются различные виды органических и неорганических волокон, такие как арамидные и металлические волокна.
Материал для регулировки трения в основном регулирует эффективность фрикционных материалов. Он используется для усиления эффективности или стабилизации характеристик фрикционных материалов. При необходимости смешивают различные виды сырья, такие как смазочные материалы, органические наполнители, неорганические наполнители, абразивные материалы и металлический порошок.
Фрикционное сырье
Типы фрикционных материалов

- * 1 Спеченный сплав. Явления, при которых частицы порошкового материала объединяются и превращаются в твердое вещество, создавая давление и создавая порошковый материал и нагревая его при температуре ниже температуры плавления. Материал, который производится не плавлением металла, а спеканием металлических порошков, называется спеченным сплавом.
Композит- * 2 C / C: Углеродный армированный углеродный композит. Углеродный композитный материал был усилен углеродным волокном. Это чрезвычайно термостойкий и легкий. Этот материал часто используется для тормозных роторов и тормозных колодок для самолетов и гоночных автомобилей.
Требования к рабочим характеристикам фрикционных материалов (тормозные колодки, тормозные накладки)
Кроме того, фрикционные материалы необходимы для обеспечения стабильной эффективности (минимальное колебание эффективности) при различных условиях, таких как скорость транспортного средства, масса в груженом состоянии или изменение температуры в результате использования тормоза, а также при различных воздействиях окружающей среды, включая влажность, воду и грязь. ,Прочность, чтобы противостоять тепловым помехам, и механическая прочность также являются важными критериями проектирования.
Долговечность является еще одним важным свойством фрикционных материалов, поскольку они изнашиваются по мере использования. Кроме того, когда применяются тормоза, визг, шум и вибрации должны быть сведены к минимуму. Кроме того, фрикционные материалы не должны вызывать повреждения материала, с которым они контактируют, например, дисковые роторы. Фрикционные материалы также должны иметь низкую теплопроводность для предотвращения повышения температуры самих тормозов или тормозного масла.
Основные эксплуатационные требования к фрикционным материалам:
- — Оптимальная эффективность, то есть соответствующий коэффициент трения (μ)
- — Стабильная эффективность при различных условиях использования и / или условиях окружающей среды
- — прочность против тепловых помех и механическая прочность
- — Высокий уровень прочности
- — Минимизированный визг тормоза, шум и вибрации
- — Низкое повреждение материала контакта, такого как дисковый ротор
- — низкая теплопроводность
Фрикционные материалы Akebono (тормозные колодки, тормозные накладки)
Akebono разрабатывает и производит широкий ассортимент тормозных колодок и тормозных накладок, в том числе для автомобилей, сверхскоростных пассажирских экспрессов и высокопроизводительных автомобилей для автоспорта.Различные типы материалов используются в зависимости от того, где используются тормоза. Когда для торможения требуется высокая интенсивность при высокой температуре и условиях высокой нагрузки, таких как скоростные поезда Shinkansen, движущиеся со скоростью, используются металлические фрикционные материалы. Для автомобилей, используемых в Европе, где торможение на высоких скоростях относительно распространено, используются фрикционные материалы с низким содержанием стали.
Для легковых автомобилей, как правило, используются «не стальные» тормозные колодки из-за их сбалансированных характеристик эффективности, интенсивности и сопротивления визгу тормозов.«Не стальные» тормозные колодки являются основными продуктами Akebono.
Akebono продолжает разрабатывать высокопроизводительные тормоза с целью усовершенствования новейших тормозных технологий. Высокопроизводительные тормоза Akebono поставляются различным командам автоспорта. Опыт, приобретенный в автоспорте, который использует тормоза до предела, применяется для разработки тормозных колодок и тормозных накладок для легковых автомобилей.
-

Тормозные колодки для 24-часовой гонки на выносливость на Нюрбургринге
-

10-цилиндровые тормозные колодки для высокопроизводительных легковых автомобилей
-

6-горшковые тормозные колодки для высокопроизводительных автомобилей
Разработка фрикционных материалов (тормозные колодки, тормозные накладки)
Для разработки фрикционных материалов необходимо учитывать как производительность, так и качество, обеспечивающее длительный срок службы.Это достигается путем нахождения правильной комбинации сырья, а также путем оптимизации условий производства. Есть много шагов, которые необходимо предпринять, прежде чем продукт будет доставлен нашим клиентам. Это может занять несколько месяцев или даже несколько лет. Оценены физико-химические свойства фрикционных материалов. Испытательный инструмент, называемый динамометром, на котором можно установить реальный тормоз, используется для оценки свойств трения. Фактические автомобили используются для оценки совместимости автомобиля и тормоза.Мы также разрабатываем сырье, которое минимизирует воздействие на окружающую среду.
В Akebono мы постоянно стремимся стать экспертами в области фрикционных материалов. У нас есть собственные средства тестирования, с помощью которых мы можем оценить основные свойства от ранних стадий разработки до конечной стадии оценки с использованием реального транспортного средства.
Процесс изготовления фрикционных материалов (тормозные колодки, тормозные накладки)
Фрикционные материалы производятся в процессе производства, контроля и испытаний перед их изготовлением.

При разработке фрикционных материалов, где должны соблюдаться различные требования к рабочим характеристикам, эффективное смешивание различных видов сырья является одним из наиболее важных технологических знаний. То, как производятся материалы, также влияет на качество, поэтому важна и технология производства. Akebono способен обеспечить стабильные рабочие характеристики и качество благодаря своим дисковым тормозным колодкам благодаря своим разработкам и технологиям производства, усовершенствованным за эти годы.
Процессы контроля и испытаний фрикционных материалов (тормозные колодки, тормозные накладки)
Для контроля и испытаний фрикционных материалов используются различные методы для проверки их качества. Процессы включают оценку физических свойств, таких как твердость и интенсивность фрикционных материалов, а также химический анализ органических материалов. Для проверки эффективности, износа и визга тормоза используется динамометр, на котором можно установить и проверить настоящий тормоз.
Для тестирования наших фрикционных материалов с точки зрения клиента мы используем «Ай-Ринг», который является крупнейшим испытательным полигоном в своем роде среди производителей автомобильных запчастей.
На полигоне «Ай-Ринг» могут проводиться различные испытания тормозов, от оценок на испытательном стенде до оценок на реальном автомобиле.
Решение вопросов, связанных с ингредиентами наших фрикционных материалов 

На протяжении долгой истории разработки и производства фрикционных материалов Akebono последовательно преследовал тему «безопасность и спокойствие».»
Примерно до 2000 года асбест широко использовался в качестве сырья для фрикционных материалов благодаря его благоприятным свойствам для тормозов, таким как превосходная термическая стабильность. В 1970-х годах из-за границы поступали сообщения об опасностях для здоровья асбеста. Сразу после этого Akebono стала одной из первых компаний в Японии, которая приступила к разработке неасбестовой продукции. Мы лидировали в отрасли по выпуску неасбестовой продукции, и в 1992 году вся продукция OEM (для автомобильных заводов) для легковых автомобилей была переведена на неасбестовую.За этим последовал полный переход на не асбестовые OEM-продукты для коммерческих транспортных средств в 1994 году. Начиная с 2000 года, производство асбестовых изделий, включая запасные части, было прекращено.
Принимая во внимание экологические нормы в отношении меди, которая используется для фрикционных материалов из-за ее термической стабильности, мы приступили к разработке и производству фрикционных материалов, не содержащих медь * . С 2007 года мы поставляем запасные части без содержания меди, а с 2014 года — оригинальные фрикционные материалы.Технологии следующего поколения также находятся в стадии разработки. Akebono разрабатывает тормозные колодки, сделанные из растительных ресурсов (биомассы), а также тормозные колодки, которые не генерируют тормозную пыль.
- * Не содержащий меди фрикционный материал: материалы с содержанием меди ниже указанного значения.
, Анализ влияния структуры задней накладки тормозной колодки и материала накладки на трение на шум дискового тормоза
А чем провинилась медь?
Ее тоже объявили вредной. И теперь автопроизводители требуют от поставщиков, чтобы они поставляли на конвейер колодки с нулевым или низким содержанием меди в составе фрикционной смеси. Первым автомобилем в Европе, который стал оснащаться немедесодержащими колодками, стало новое поколение Mercedes-Benz S-класса, анонсированного в 2014 году. А с сентября 2015 года список пополнил Audi A4 — на конвейер по его производству идут колодки с нулевым содержанием меди от Federal-Mogul по технологии Ferodo Eco-Friction. Такие колодки при той же себестоимости лучше тормозят. И у них меньшая степень износа. Немедесодержащая колодка щадящим образом относится к тормозному диску и обеспечивает износ в паре колодка/диск до 60% ниже, чем при использовании медьсодержащей колодки. Сейчас все идет к тому, что вскоре одна замена колодки будет приходиться на одну замену диска, поскольку срок службы тормозной колодки увеличивается.
Кто служит дольше? Колодки или диск?
Сегодня — диск, конечно же. Как правило, 2–3 замены колодки — одна замена диска. Но диск не вечен, у него обычно есть маркировка по минимально допустимой толщине. Допустим она составляет 9 мм, однако человек упрямо может ездить до момента, пока диск не износится, скажем, до 4 мм. В этом случае выделяемое тепло уже не будет эффективно отводиться. Масса диска становится меньше, от перегрева он начинает деформироваться, его может «повести», а в худшем случае рабочая часть может отсоединиться от ступичной. Это — реальность.
Когда надо заменять колодки?
На большинстве современных автомобилей колодки оснащены датчиками износа. Принцип работы простой — электрический контакт интегрируется в структуру фрикционного материала тормозной колодки. Считается, что колодка подлежит замене, когда остаточная толщина фрикционного материала на несущей пластине достигает значения 3 мм. Если он меньше 3 мм, то колодку надо менять, даже если нет датчика износа. При производстве любой тормозной колодки на стальную несущую пластину наносят термоизоляционный слой толщиной 2–3 мм. Когда колодка изнашивается, вы уже тормозите не фрикционным материалом, а именно этим составом. А при полном износе со стальным диском контактирует уже стальная несущая пластина колодки — здесь уже начинается активный износ диска.
Нужно ли притирать новые колодки?
Да, это очень желательно. Общее пожелание понятно: в начальный период хорошо бы не ездить излишне активно, а также не перегружать машину. А рекомендуемый алгоритм притирки такой: торможение со скорости 80 км/ч до 30 км/ч — и так 20 раз с перерывом примерно 30 секунд. Это позволяет сгладить вершины микронеровностей пары колодка/диск.
Часто на форумах советуют применять колодки от другого автомобиля, отпилив от них лишнее «по месту»…
Вообще-то, ни один профессионал такого издевательства не посоветует, поскольку колодка — это критически важный элемент безопасности автомобиля. Но, если исходная колодка взята для премиум-автомобиля похожего класса, и фрикционная смесь обеспечивает требуемую эффективность торможения, скажем, тормозные диски одного размер
что нужно знать о тормозных колодках
Автовладельцы нередко оперируют понятиями «жесткие» и «мягкие» в отношении тормозных колодок, а продавцы автозапчастей уверенно оценивают ассортимент того или иного производителя по этому параметру. В реальности — характеристики торможения зависят совсем от других параметров, а производители тормозных колодок отказываются понимать такую «градацию».
Разработчики тормозных колодок понимают «жесткость» в буквальном смысле — как способность фрикционного материала сжиматься под нагрузкой. Этот параметр регулируется и согласно Европейскому стандарту испытаний тормозных колодок автомобилей ECE-R90 не должен превышать 2% при температуре окружающей среды и 5% при нагреве до 400 °С. Прежде всего, этот параметр нормируется для того, чтобы тормозные колодки обеспечивали адекватное «чувство педали тормоза». Дело в том, что «мягкие» колодки с хорошим коэффициентом трения и параметрами комфорта сделать проще, но тогда может пострадать безопасность.

Комплект тормозных колодок Textar, выполненных по стандарту ECE R90.
Если говорить о свойствах, которые действительно должны интересовать покупателя, то характеристики колодки напрямую зависят от рецептуры фрикционного материала, которая сегодня представляет собой сложное сочетание многих ингредиентов, количество которых может насчитывать несколько десятков, ведь колодка должна отвечать многим, порой противоречащим друг другу требованиям. Так, колодка должна обеспечивать эффективное торможение в широком диапазоне температур окружающей среды и оставаться стабильной при нагреве без таких сопутствующих явлений, как перегрев, дымление, кипение, прихватывание к тормозному диску, замыливание при длительном торможении. В разумных пределах должно быть пылеобразование, чтобы пыль не забивала подвижные элементы тормозных механизмов и отверстия вентилируемых тормозных дисков, сама пыль не была бы вредной для людей и окружающей среды, а колодки изнашивались бы равномерно с тормозными дисками.
Все материалы фрикционных накладок тормозных колодок можно разделить на 2 большие группы. «Европейские» — материалы группы «low steel» (с низким содержанием стали) и «азиатские» — группы NAO (безасбестовая органика). Есть еще третья группа — фрикционные смеси под общим названием Semi Metallic, которые содержат от 40 до 65% стальных волокон. «Наполовину стальные» колодки отличает эффективное торможение, высокая, даже избыточная теплопроводность, шумность, высокое пылеобразование и не бережное отношение к тормозному диску, поэтому в настоящее время применяются они чаще для легкого коммерческого транспорта.

Тормозные колодки Nisshinbo.

Тормозная колодка Nisshinbo, «выпеченная» из смеси NAO.
Современные рецептуры Low Steel, содержащие от 20 до 30% стальных волокон, распространены на европейском рынке. За счет замещения стали другими ингредиентами, которые производители обычно содержат в секрете, удалось добиться коэффициента трения в диапазоне 0,38–0,5, высокой температурной и скоростной стабильности, информативности педали тормоза, большей прочности и отличного очищения ржавчины с тормозных дисков. Это материалы с высокими характеристиками торможения, отлично подходящие для скоростного движения, которое компенсирует еще достаточно высокое пылеобразование, давая возможность пыли выветриться из тормозных механизмов.

Сравнительные характеристики фрикционных материалов (чем дальше от центра, тем лучше).
Минимальное же пылеобразование достигнуто рецептурами, которые вообще не содержат стали. Гамма рецептур, в которых сталь замещена альтернативными волокнами и керамикой, известных под названием NAO (Non-Asbestos Organic — безасбестовая органика), была разработана в Японии как для внутреннего потребления, так и для рынка США, на котором начали жестко регулировать содержание металлов в тормозных колодках. Рецептуры NAO практически не пылят, не шумят, то есть они обеспечивают комфортное вождение, но имеют меньший коэффициент трения и температурную стабильность и в целом уступают по эффективности торможения рецептурам Low Steel. Поэтому одна и та же модель японского автомобиля на американский рынок поставляется с колодками NAO, а на более требовательный к эффективности тормозов европейский рынок — с колодками Low Steel. Среди производителей тормозных колодок, имеющих статус поставщика на конвейер, можно выделить немецкий бренд Textar — как поставщика колодок группы Low Steel и японский Nisshinbo — как приверженца группы NAO. Как правило, колодки NAO дороже Low Steel. Однако в ассортименте Textar компании TMD Friction есть колодки серии epad, которые не только обладают всеми преимуществами материалов NAO, но и имеют необычайно высокий для этой группы коэффициент трения и температурную стабильность, то есть вписываются в рамки 0,35–0,45 в температурном диапазоне от 100 до 320 °С при пониженном пыле-образовании. Такие свойства обеспечивает уникальная рецептура фрикционной смеси, в которую входят 25 ингредиентов — ноу-хау компании TMD Friction.
Компания проводит интенсивные стендовые испытания и ходовые испытания на собственных треках, на которых в том числе имитируются горные и гоночные условия. На одну колодку приходится до 1000 стендовых часов и до 300 000 километров на треке. В итоге тормозные колодки Textar превосходят требования стандарта ECE R90. Все изделия Textar соответствуют требованиям ведущих европейских автопроизводителей — Audi, BMW, Mercedes-Benz, MINI, Seat, Skoda, Volvo, Volkswagen и других — и уровню качества ОЕМ.
Хочу получать самые интересные статьи
Производители фрикционных материалов | Поставщики фрикционных материалов

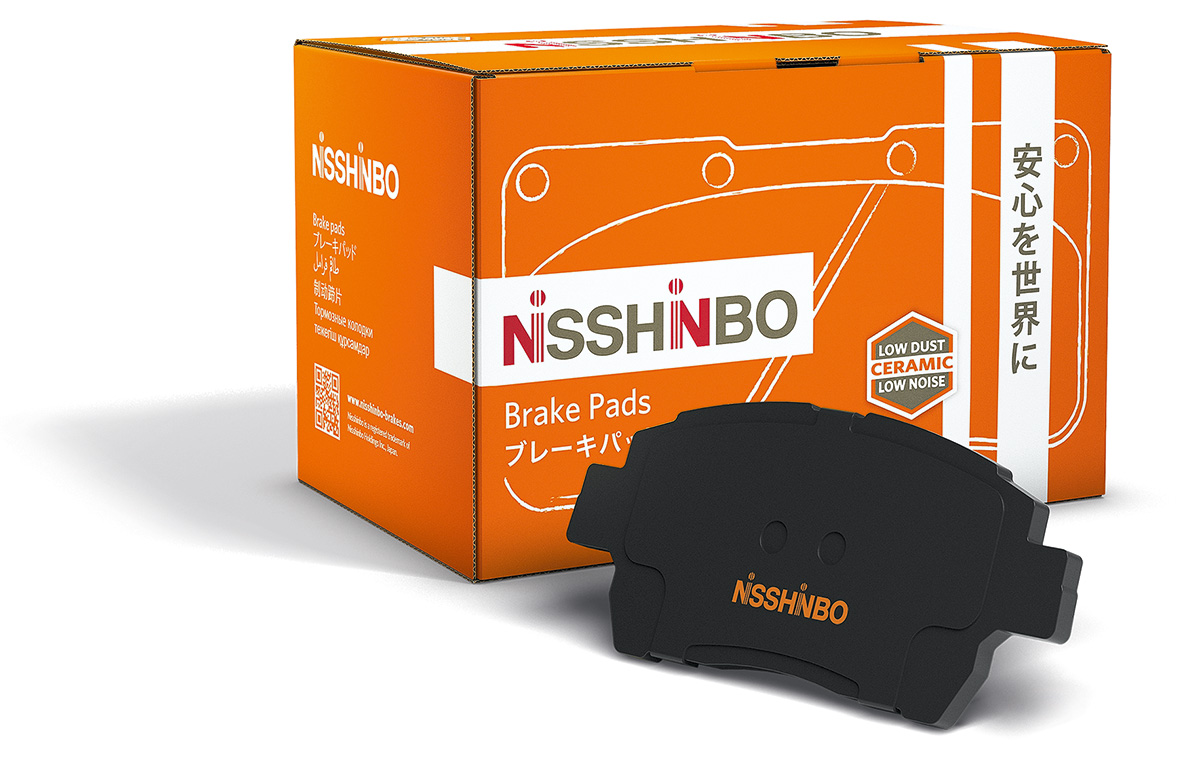
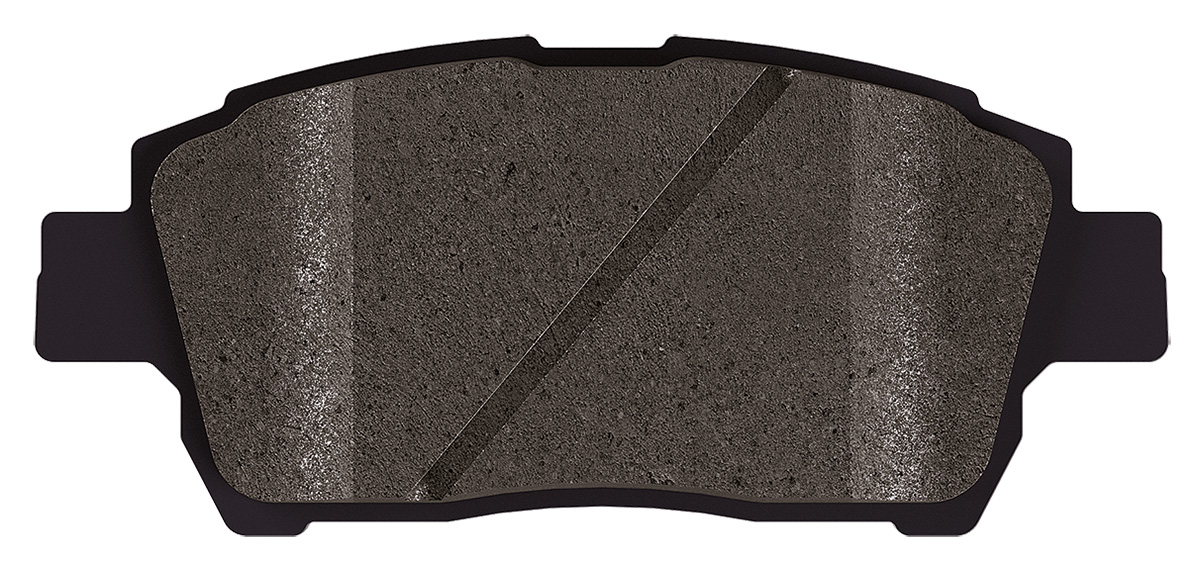
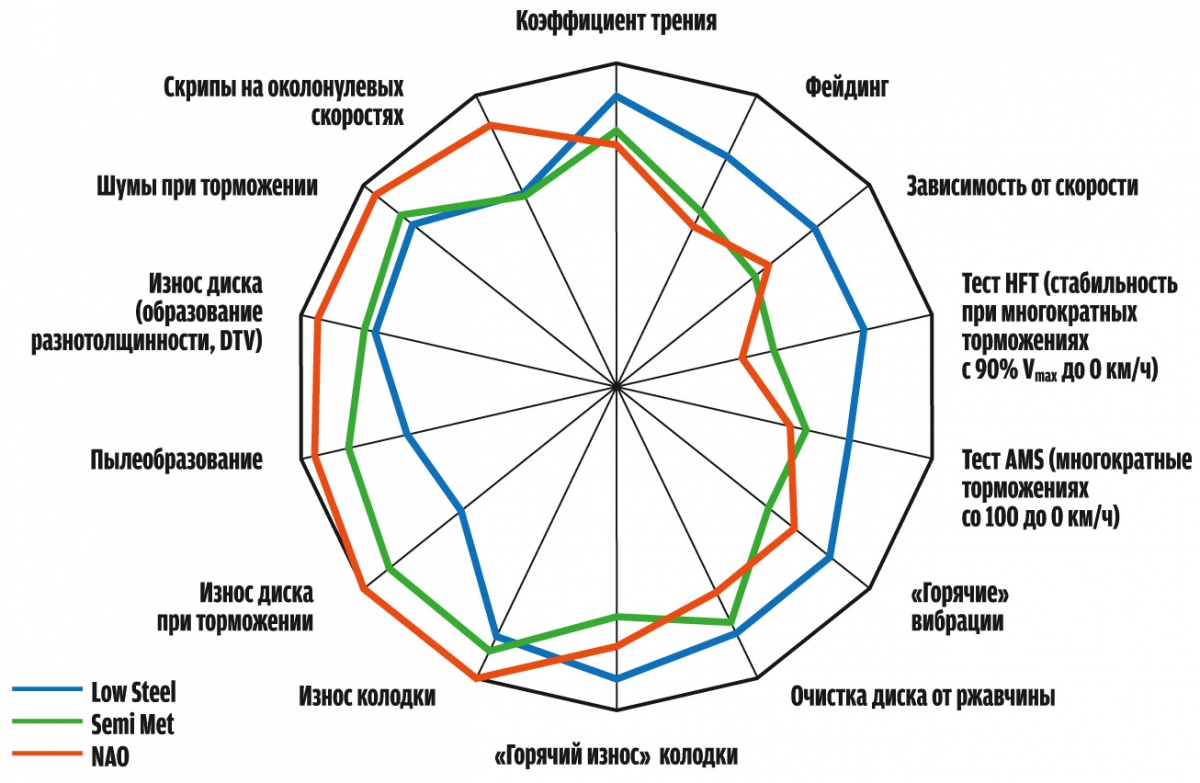
Список производителей фрикционных материалов
Применения
Применения включают в себя системы сцепления и тормоза, операционные системы, автомобильное оборудование, системы зубьев зубчатых колес и промышленное оборудование, которые все должны быть в состоянии остановить или замедлить свои процессы. Компоненты, такие как фрикционные колодки и накладки и колодки дискового тормоза, изготовлены из фрикционных материалов.
Отрасли, которые часто используют эти продукты, включают строительство, автомобилестроение, лесное хозяйство, нефтегазовую отрасль и добычу полезных ископаемых.
Тормозные системы
Фрикционные материалы используются в тормозных системах для замедления колес или их остановки, а также для полного предотвращения движения других компонентов. Нажатие на тормоз активирует систему, где фрикционный материал помещается на движущийся диск, тем самым замедляя соединительные колеса.
История фрикционных материалов
Трение — это закон природы, и с незапамятных времен люди пытались им манипулировать.Например, одним из первых способов, которым люди научились разжигать огонь, было создание трения между горючими материалами, такими как дерево.
Некоторые из самых ранних научных заметок, которые мы связали с целью смягчения трения, включают в себя те, которые были написаны древнегреческими и римскими мыслителями. Примеры этих людей включают Плиния Старшего, Аристотеля и Витрувия.
В 1493 году в посмертно опубликованных тетрадях Леонардо да Винчи писал о своем открытии классических законов трения скольжения.Гийом Амонтон заново открыл эти же законы в 1699 году. Он опубликовал свое открытие, и эти законы были названы тремя законами сухого трения Амонтона. После этого другие ученые быстро обнаружили другие вещи о трении, которые были равны классической эмпирической модели трения. Эта модель состоит из статического, кинетического и трения качения. Сначала ученые обнаружили разницу между статическим трением и кинетическим трением. Затем, в 1734 году, Джон Феофил Дезагюльер обнаружил, что трение является достаточно мощной силой, чтобы разрывать прилипшие поверхности.В 1833 году Артур Жюль Мартин опубликовал различие между трением скольжения и трением качения. Законы трения, которые они обнаружили, все еще используются сегодня.

Фрикционные материалы — ProTec Friction Group
В 1888 году женщина по имени Берта Бенц изобрела тормозные колодки после того, как она подумала о них, взяв один из первых в мире приводов на дальние расстояния. (Она поехала через Германию.) Ее тормозные колодки и другие ранние тормозные колодки были сделаны с использованием асбестовых фрикционных материалов. Хотя асбест был невероятно эффективным, примерно через 100 лет ученые объявили, что асбест может вызывать рак и заболевания легких.(Национальный институт здравоохранения выпустил официальное объявление в 1989 году.) С тех пор фрикционные материалы из асбеста были отправлены на пыльную книжную полку истории. Его заменили в основном синтетическими арамидными волокнами. Керамика также стала популярным фрикционным материалом благодаря своим термостойким свойствам.
Постоянное развитие отрасли и ее приложений побудило производителей фрикционных материалов и тормозов сохранить свои составы и достижения в секрете.Они делают это, чтобы отличить себя от конкурентов. Например, внедрение керамики в промышленность открыло многочисленные двери для повышения эффективности и долговечности изделий из фрикционных материалов. Снижение шума и более быстрая остановка стали обычными требованиями для тормозов и сцепления. Технологические разработки являются постоянными в этой отрасли, и, таким образом, качество фрикционно-стойких материалов прошло долгий путь и будет продолжать расти.
Design
Материалы
Поскольку тепловая энергия является побочным продуктом процесса создания трения, производители обычно используют материалы, устойчивые к нагреву, для изготовления фрикционных материалов.Самым популярным выбором для фрикционных материалов были волокна из асбеста. Однако из-за растущих проблем со здоровьем, связанных с воздействием асбеста, керамика стала популярным материалом для использования в качестве альтернативы.
Керамика обладает высокой износостойкостью и устойчивостью к нагреванию и поэтому используется в средах с высоким коэффициентом трения. Фрикционные материалы должны выдерживать большие физические нагрузки, поскольку износ материала неизбежно приводит к трению.
Кроме того, производители производили такие изделия, как полуметаллические тормозные материалы, используя латунь, медь и стальную вату, склеенные смолой.Эти элементы похожи на керамику с точки зрения долговечности.
Особенности и настройка
Тип используемого материала в значительной степени зависит от необходимого типа трения. Типы трения включают статическое, кинетическое и трения качения.
Статическое трение , возникает, когда два твердых объекта не движутся относительно друг друга, и движение вообще предотвращается. Важной вещью, которую следует учитывать при реализации этого типа трения, является уклон поверхности.
Кинетическое трение , или динамическое трение, происходит, когда два объекта движутся относительно друг друга. Одна поверхность может двигаться вдоль неподвижного объекта, или обе поверхности могут двигаться.
Трение качения предполагает использование колес или шариков. Во время трения качения грубый материал ловит колесо или шар, предотвращая его скольжение или скольжение. Например, когда автомобильная шина вращается на льду или снегу, трение препятствует ее захвату на земле и позволяет ей продолжать вращаться.
Чтобы определить лучшие фрикционные материалы для работы, производители также думают о том, как быстро трение должно остановить объект или систему (чем выше трение, тем быстрее объект может быть остановлен), как часто будет использоваться фрикционный материал , бюджет, требуемая химическая стойкость, требуемая износостойкость, допустимое выделение тепла, необходимое поглощение энергии и коэффициент трения.
Для обеспечения дополнительного трения и, следовательно, повышения их эффективности фрикционные материалы текстурированы или имеют шероховатую поверхность.Производители используют более гладкие поверхности для более эффективной транспортировки материалов. Кроме того, производители могут добавить резину, чтобы повысить способность тормозной системы производить поверхностное трение. Однако чем больше текстуры добавлено к поверхности, тем больше энергии требуется для ее перемещения. Чтобы обсудить ваши возможности дизайна фрикционных материалов, поговорите с поставщиком сегодня.
Особенности
Вы можете использовать фрикционные материалы несколькими различными способами. В основном они работают как тормоза на автомобилях и других моторизованных транспортных средствах.Чтобы замедлить или остановить обычный автомобиль, фрикционные материалы преобразуют кинетическую энергию в тепло. Однако, чтобы замедлить гибридные и электрические транспортные средства, фрикционные материалы используют регенеративное торможение, процесс, во время которого трение преобразует кинетическую энергию в электрическую энергию.
Типы
Продукция, изготовленная из фрикционных материалов, включает в себя: тормозные колодки, тормозные колодки, фрикционные диски, диски сцепления (дисковые муфты), накладки сцепления, тормозные накладки, комплекты сцепления и тормозные колодки (тормозные ленты).
Тормозные колодки — это блоки из твердого фрикционного материала. Они замедляют колеса при нажатии на обод этих колес, где они обеспечивают трение, необходимое для замедления системы. Они довольно распространены на велосипедах.
Тормозные колодки , также известные как фрикционные колодки, представляют собой металлические пластины, используемые в качестве металлической половины фрикционных тормозных систем.
Фрикционные диски , также известные как фрикционные диски или фрикционные диски, используются в автомобильных тормозных системах.Они состоят из металлической пластины, скрепленной фрикционным материалом. Фрикционные диски обычно изготавливаются из металла. Однако использование металла имеет недостаток, который представляет собой шум шлифования, создаваемый при приложении трения. Поэтому зачастую производители покрывают металлические компоненты торможения другими материалами с высоким коэффициентом трения, такими как резина, чтобы они не были такими громкими.
Диски сцепления , или диски фрикционной муфты, являются подтипом фрикционного диска. Они связывают двигатель автомобиля с входным валом коробки передач, где они облегчают временное разъединение, которое происходит, когда водитель переключает передачи.
Облицовка сцепления — это фрикционный материал, используемый с дисками сцепления. Они помогают сцеплению запускать и останавливать поток энергии между ведомым валом и ведущим валом. Они делают это благодаря низкому коэффициенту трения. Поскольку они работают с более низким коэффициентом трения, чем аналогичные фрикционные материалы, они создают исключительно тихие, стабильные и гладкие системы.
Тормозные накладки представляют собой слои фрикционного материала, связанные с тормозными колодками и накладки на них. Тормозные накладки являются термостойкими, что предотвращает возникновение трения от искр или пожара.
Тормозные колодки , также известные как тормозные ленты, состоят из металлической пластины, прикрепленной к поверхности трения, такой как тормозная накладка. Тормозные колодки доступны в широком диапазоне конфигураций, таких как колодки барабанного тормоза и колодки дискового тормоза.
Правильный уход за фрикционными материалами
Фрикционные материалы используются постоянно, настолько, что они изнашиваются довольно быстро. К сожалению, вы мало что можете сделать, чтобы продлить срок их службы лифта. Вместо этого вам нужно знать, когда их заменить, чтобы не повредить автомобиль или машину.
В тормозной системе характерным признаком износа тормоза является визг. Когда ваш тормоз начинает визжать, проверьте их и посмотрите, нужно ли их заменить. Хотя вам не нужно удалять их при первых признаках износа, вы не хотите ждать, пока они не будут полностью уничтожены. Эксплуатация оборудования без достаточного набивки и трения может привести к повреждению или даже несчастному случаю. Лучше быть в безопасности, чем потом сожалеть. Если вы слышите или чувствуете скрипучий звук при нажатии на тормоза, вы слишком долго ждали, и ваша тормозная система, вероятно, была повреждена.
Еще одна вещь, которую вы должны остерегаться — это повреждение в результате попадания масла или утечки тормозной жидкости. Одним из наиболее распространенных признаков загрязнения тормозов является «тормозная стук» или вибрационный шум, исходящий от тормозов. Если вы слышите или видите стук в тормозе, вам необходимо найти и устранить утечку, а затем заменить тормозные колодки. Вы должны заменить не один, а оба из них. При одновременной замене тормозных колодок убедитесь, что тормозные фрикционные материалы имеют одинаковую толщину. Неровные фрикционные материалы вызывают неравномерное торможение.
Стандарты
Некоторые стандарты, которым должны соответствовать ваши фрикционные материалы, зависят от вашего местоположения. Например, в Соединенных Штатах ваши фрикционные материалы должны соответствовать правилам безопасности, опубликованным EPA (Агентство по защите окружающей среды). Если вы планируете отправлять продукцию за пределы Соединенных Штатов, мы рекомендуем, чтобы ваши фрикционные материалы соответствовали директиве ЕС RoHS (Ограничение использования опасных веществ). Другие стандарты, достойные вашего времени, включают стандарты, разработанные FMSI (Институт стандартов на фрикционные материалы) и SAE International.
Что нужно учитывать
Когда вы рассматриваете фрикционные материалы или изделия из фрикционных материалов, вам необходимо работать с подходящим поставщиком из отрасли. Это ключ к вашему успеху. Чтобы помочь вам на вашем пути, мы составили полный список поставщиков фрикционных материалов высшего качества. Вы найдете их профили по всей этой странице. Прежде чем просматривать их, если вы еще этого не сделали, запишите список своих спецификаций. Не забудьте указать свой бюджет, график, требования к доставке и стандартные требования.Как только вы подготовили свой список, вы можете просмотреть производителей, которые мы перечислили. Часто смотрите свой список, как вы это делаете. Выберите трех или четырех поставщиков, с которыми вы хотели бы поговорить напрямую, а затем обратитесь к своим спецификациям. Не бойтесь задавать вопросы представителям службы поддержки, поэтому они здесь! После того, как вы закончите свои разговоры, сравните и сопоставьте свои заметки и выберите производителя, который, по вашему мнению, лучше всего вам подойдет. Удачи!
Фрикционные материалы Информационное видео
.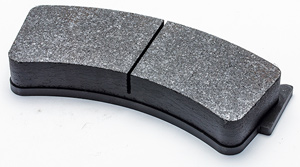
Тормозные колодки для 24-часовой гонки на выносливость на Нюрбургринге
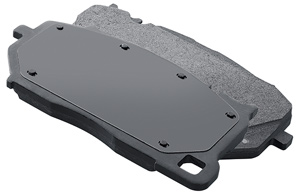
10-цилиндровые тормозные колодки для высокопроизводительных легковых автомобилей
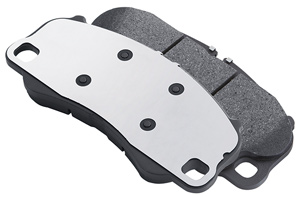
6-горшковые тормозные колодки для высокопроизводительных автомобилей
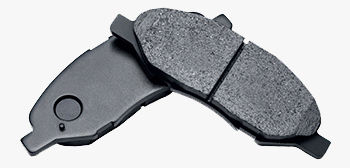
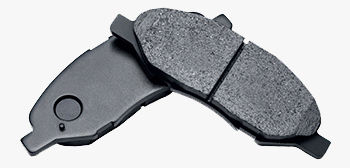
В данном исследовании предлагается трехслойная конструкция тормозной колодки, на которой создана динамическая модель тормозной накладки тормозного диска с шестью степенями свободы, и факторы влияющие на нестабильность системы анализируются. Анализ показывает, что изменение массы и жесткости тормозной колодки будет влиять на устойчивость системы. Из анализа линейных комплексных собственных значений прогнозируются нестабильные режимы вибрации тормозной системы, а эффективность модели анализа комплексного режима подтверждается стендовыми испытаниями тормозной системы.Разработаны тормозные колодки различной конструктивной формы и проанализировано их влияние на устойчивость тормозной системы. Результаты показывают, что конструкция трехслойной структуры и конструкция прорезей тормозной колодки могут эффективно уменьшить возникновение визга тормоза, особенно шума высокочастотного визга.
1. Введение.За последние три десятилетия доля дискового тормоза, используемого в седане, росла год от года. Можно предположить, что дисковые тормоза будут постепенно заменять барабанные тормоза в седане. Однако проблема тормозного шума дисковых тормозов все еще существует, и многие явления тормозного шума до сих пор не были объяснены рационально [1–3]. Процесс автомобильного торможения вызывает вибрацию, а нестабильная вибрация не только приводит к шуму, который одновременно влияет на комфорт вождения и вызывает акустическое загрязнение окружающей среды, но также вызывает усталостный износ автомобильной тормозной системы [4]. Ларс прорезали и обнажили поверхность тормозного диска и экспериментально доказали, что улучшенный тормозной диск может уменьшить появление визга тормоза [5]. Оберст и Лай использовали теорию хаоса для изучения механизма тормозного шума, который имеет большое руководящее значение [6]. Кунг и соавт. вычислил свободный модальный компонент в тормозе и получил компоненты и связанные модальные условия с наибольшей скоростью вклада неустойчивой моды с помощью комплексного анализа собственных значений [7].В дополнение к использованию сложного анализа собственных значений для изучения тормозного шума, динамический анализ переходных процессов впервые используется Nagy et al. Частоты четырех мод, полученные из результатов динамического анализа переходных процессов, совпадают с экспериментальным шумом [8]. Недостатки переходной динамики состоят в том, что она занимает слишком много времени на вычисления и занимает много места на диске, а также затрудняет непосредственное использование данных для внесения изменений в проект. Кроме того, из-за высокой частоты визга тормоза явный шаг интегрального времени очень мал, тогда как неявный интеграл может иметь большой шаг времени, но он ослабит высокочастотный режим.Комплексный анализ собственных значений и переходный динамический анализ используются AbuBakar и Ouyang [9] для изучения визга тормоза при той же модели и граничных условиях. Результаты вышеупомянутых двух анализов идентичны с различным механизмом контакта и интегральным методом. При анализе шума тормозной системы использование комплексного анализа собственных значений в сочетании с разумной комбинацией переходного динамического анализа может быть способом анализа механизма генерации шума.
В эксперименте по скольжению с трением на плоской пластине Чен [3] обнаружил, что мгновенный визг не может быть вызван модальной связью, а переходное возбуждение между диском и блоком может быть ключевым механизмом визга.Тем не менее, этот тип возбуждения с переменной нагрузкой является переходным процессом, который трудно уловить в экспериментах. Динамический анализ переходных процессов может более четко показать процесс и выявить причины этого явления. Для динамической модели тормозного диска и тормозной колодки Zhang et al. Предложили модель фрикционного генератора с четырьмя степенями свободы. [10], чтобы исследовать разницу между линейным анализом и нелинейным анализом шума тормозной системы, и приведены соответствующие меры по улучшению.
В этом контексте на основе теории модального сцепления устанавливается модель движения с шестью степенями свободы тормозного диска и тормозной колодки. В сочетании с конечно-элементным комплексным модальным анализом и стендовыми испытаниями он имеет большое значение для улучшения характеристик NVH за счет улучшения свойств материала тормозной колодки и оптимизации структуры задней панели тормозной колодки, чтобы подавить шум визга тормоза и исследовать шум. Механизм торможения шума, который обеспечивает теоретическую основу для снижения шума визга тормоза.
2. Кинематическая модель Six-DOF тормозной дисковой тормозной колодки
Модель тормозной муфты, созданная Festjens et al. [11] показывает, что структура и демпфирование задней пластины тормозной колодки оказывают важное влияние на тормозной шум. Аналогичным образом, величина демпфирования материала фрикционной накладки также будет оказывать значительное влияние на шум при торможении. Благодаря исследованию, проведенному Ruhai et al. [12], известно, что добавление определенной части вязкоупругого материала к фрикционной накладке может уменьшить резонансную тенденцию между тормозной колодкой и тормозным диском, тем самым, в некоторой степени подавляя визг тормоза.Исходя из важного влияния фрикционной накладки, она разделена на две части, а именно: подложка футеровки и смесь фрикционной накладки. Поскольку состав материала подложки футеровки обладает более сильными демпфирующими характеристиками, чем смесь фрикционной футеровки, он должен рассматриваться по-разному в процессе моделирования и симуляции.
Кинематическая модель с шестью степенями свободы для тормозной дисковой тормозной колодки изображена на рисунке 1. Из-за небольшого демпфирования системы эффект демпфирования игнорируется при анализе кинематики.Тормозная колодка состоит из задней пластины тормозной колодки, подложки накладки и фрикционной накладки. имеет степень свободы z z 1 ; имеет z — степень свободы направления z 2 ; и имеет степень свободы направления z z 3 и степень свободы направления x x 3 ; Тормозной диск имеет две степени свободы, соответственно, x — направление x , d и z — направление z , d ., и — коэффициент трения, сила поршня, действующая на тормозную колодку, и положительная сила, действующая на тормоз
. сверлильных и щелевых дисковых тормозных роторов
Без сомнения, тормоза — самая мощная система в вашем автомобиле. Неважно, сколько у вас лошадиных сил, это бесполезно, если вы не можете сбросить достаточную скорость, чтобы не дать заднему концу машину перед вами. Ваши заводские тормоза обеспечивают достаточную тормозную мощность для случайных поездок на работу или случайного непредвиденного прекращения паники, но для энтузиастов с высокими эксплуатационными характеристиками лучше выбрать модернизированный набор роторов с отверстиями или пазами.Так в чем же разница между сверлильными и щелевыми тормозными роторами? Здесь мы обсудим преимущества и недостатки каждого из них, чтобы вы могли принять собственное обоснованное решение.
Smooth Rotors
Гладкие тормозные роторы
Комплект гладких роторов премиум-класса обеспечивает более чем достаточную тормозную мощность при нормальных условиях вождения. Вот почему 99,9% новых автомобилей все еще идут с ними с завода.Они обеспечивают большую площадь поверхности по сравнению с просверленными или прорезанными роторами и, следовательно, очень эффективны в качестве теплоотвода, а именно для этого предназначен тормозной ротор. Они также не так подвержены растрескиванию при экстремальном использовании, как просверленные роторы. Отсутствие пазов или отверстий позволяет гладким роторам сохранять максимальную структурную целостность, что делает их пригодными для умеренного использования гусениц в сочетании с тормозными колодками с высокими эксплуатационными характеристиками и тормозной жидкостью с высокой температурой кипения. Существует несколько разновидностей, от прямой замены до высококачественных оцинкованных роторов, для борьбы с поверхностной ржавчиной и сохранения их нового облика на многие мили.

Щелевые Роторы
щелевых тормозных роторов
Ущелевых роторов, как следует из названия, есть канавки, вырезанные вдоль поверхности ротора, где контактная площадка контактирует. Это связано с тем, что при многократном резком торможении, когда температура вашей тормозной системы увеличивается, между колодкой и ротором образуется слой газа и пыли в результате переноса материала, вызванного трением. Прорези в роторе обеспечивают путь для выхода скопившихся газов. Это позволяет большей площади поверхности тормозной колодки контактировать с ротором, что приводит к лучшему прикусу колодки и более последовательным упорам.Кроме того, этот увеличенный контакт с поверхностью приводит к более высокому коэффициенту трения, поэтому вы фактически используете меньше энергии, чтобы замедлить автомобиль на ту же величину. Вентиляция, обеспечиваемая роторами с прорезями, является одним из основных способов борьбы с затуханием тормозов и поддержания постоянной тормозной способности, круг за кругом. Имейте в виду, однако, что некоторые выделенные «гоночные» роторы с прорезями на самом деле используют острый край на прорезях, чтобы врезать в тормозную колодку небольшое количество для лучшего прикуса, но это может значительно ускорить износ тормоза.

Ротор с перекрестным бурением
Тормозные роторы с перекрестным бурением
перфорированных тормозные диски выглядят неоспоримо охладиться выглянуть из-за множеством кричащих колес, и они держат свои тормоза точно так же — круто. В первые дни гонок просверленные роторы были эффективным способом вентиляции слоя газа и пыли, который неизбежно накапливался между асбестовыми тормозными колодками и ротором при многократном резком торможении. Однако по мере развития технологий и материалов тормозных колодок выделение газа становится все менее серьезной проблемой.В наши дни, несмотря на то, что они по-прежнему выглядят великолепно и хорошо работают, отверстия для сверления больше по эстетическим соображениям, чем что-либо еще. Для эффективной работы роторы с прорезями стали предпочтительным выбором, поскольку роторы с поперечным бурением более подвержены растрескиванию под напряжением при экстремальном использовании. Достаточно взглянуть на спицы на колесе любого современного гоночного автомобиля — в поле зрения не будет просверленного ротора. На улице, однако, температура, с которой сталкиваются ваши тормоза, никогда не приближается к уровням, которые они испытывают на трассе.Таким образом, вентиляционные свойства просверленных роторов обеспечивают дополнительные преимущества, заключающиеся в поддержании температуры при нормальном движении для продления срока службы колодок, а также улучшенные характеристики в сырую погоду, позволяя воде выходить из поверхности ротора, увеличивая первоначальный прикус колодки.

Ротор с отверстиями и прорезями
Сверлильные и прорезные тормозные роторы
Роторы с отверстиями и пазами обеспечивают внешний вид и функциональность как роторов с поперечным бурением, так и роторов с пазами.Хотя они по-прежнему не идеальны для злоупотреблений, они будут страдать на ипподроме (то есть, в отверстиях, подверженных растрескиванию под напряжением), одно из мест, где просверлены и прорезаны роторы, находится на тяжелых транспортных средствах, буксирующих тяжелые грузы. Чем тяжелее транспортное средство, тем больше энергии требуется, чтобы замедлить его до безопасной и надежной остановки. Тормоза преобразуют кинетическую энергию (движение) в тепловую энергию, а более тяжелые транспортные средства неизменно выделяют больше тепла в своих тормозных системах. Таким образом, ротор, который работает более прохладно (с поперечным бурением) в сочетании с ротором, который поддерживает чистую поверхность контакта между собой и тормозной колодкой (с прорезями), когда он не выдвинут за пределы своего теплового порога, может обеспечить дополнительный уровень безопасности и долговечности.Помните, что название игры поддерживает постоянную силу остановки каждый раз, когда вы нажимаете на тормоза. Если вы когда-нибудь буксировали полностью загруженный трейлер по горному перевалу, вы знаете, какое ужасное ощущение затухания тормозов. Набор роторов с поперечными отверстиями и пазами может дать вам дополнительное спокойствие, поддерживая температуру и поверхность ротора в чистоте. Не забывайте сочетать роторы с отверстиями и пазами с высококачественным набором тормозных колодок, разработанных для вашего автомобиля, а также свежей тормозной жидкостью DOT-3 или DOT-4 для достижения наилучших результатов.
Выбор правильного тормозного ротора
Есть несколько вещей, которые следует иметь в виду при выборе тормозных роторов с поперечным бурением или пазами. Что касается уличных транспортных средств, то они одинаково хорошо работают и не испытывают никаких вредных побочных эффектов. Это просто сводится к личным предпочтениям того стиля, который вы предпочитаете. Однако роторы с прорезями или крестовинами не уменьшат исходный тормозной путь вашего автомобиля. Их цель — рассеивать тепло и газы для борьбы с затуханием тормозов и обеспечивать постоянные остановки после продолжительного злоупотребленияДля того, чтобы вытащить значительный кусок из вашего тормозного пути, рекомендуется набор липких шин и специальные тормозные колодки с высокими эксплуатационными характеристиками. Для движения по гусеницам роторы с прорезями являются предпочтительным выбором из-за их способности выпускать газы, не ослабляя их структуру. Для привлекательных, высококлассных стилей, просверленные или просверленные и прорезанные роторы обязательно поворачивают головы. Для ежедневного вождения любое из вышеперечисленного обеспечивает более чем достаточную тормозную способность.
Метки: роторы
,