ΠΡΠ΅ΡΡΠΎΠ²Π°Π½ΠΈΠ΅ ΠΌΠ°ΠΊΠ°ΡΠΎΠ½Π½ΡΡ ΠΈΠ·Π΄Π΅Π»ΠΈΠΉ
Π’Π΅Ρ Π½ΠΎΠ»ΠΎΠ³ΠΈΡ ΠΏΠΈΡΠ΅Π²ΡΡ ΠΏΡΠΎΠΈΠ·Π²ΠΎΠ΄ΡΡΠ²
ΠΠ·Π²Π΅ΡΡΠ½Ρ Π΄Π²Π° ΡΠΏΠΎΡΠΎΠ±Π° ΡΠΎΡΠΌΠΎΠ²Π°Π½ΠΈΡ ΠΌΠ°ΠΊΠ°ΡΠΎΠ½Π½ΠΎΠ³ΠΎ ΡΠ΅ΡΡΠ°: ΠΏΡΠ΅ΡΒΡΠΎΠ²Π°Π½ΠΈΠ΅ ΠΈ ΡΡΠ°ΠΌΠΏΠΎΠ²Π°Π½ΠΈΠ΅. ΠΡΠΈ ΡΡΠ°ΠΌΠΏΠΎΠ². Π°Π½ΠΈΠΈ ΡΠ½Π°ΡΠ°Π»Π° ΠΏΠΎΠ»ΡΡΠ°ΡΡ Π»Π΅Π½ΡΡ ΡΠ΅ΡΡΠ° ΠΏΡΡΠ΅ΠΌ ΠΏΡΠ΅ΡΡΠΎΠ²Π°Π½ΠΈΡ, Π° Π·Π°ΡΠ΅ΠΌ ΠΈΠ· Π½Π΅Π΅ ΡΡΠ°ΠΌΠΏΡΡΡ ΠΈΠ·Π΄Π΅ΒΠ»ΠΈΡ ΡΠ»ΠΎΠΆΠ½ΠΎΠΉ ΡΠΎΡΠΌΡ.
Π‘ΡΠΎΡΠΌΠΈΡΠΎΠ²Π°Π²ΡΠ΅Π΅ΡΡ Π² ΡΠΏΠ΅ΠΊΠΎΠ²ΠΎΠΉ ΠΊΠ°ΠΌΠ΅ΡΠ΅ ΡΠ΅ΡΡΠΎ Π½Π°Π³Π½Π΅ΡΠ°Π΅ΡΡΡ Π² Π½Π΅Π±ΠΎΠ»ΡΡΠΎΠ΅ ΠΏΡΠ΅Π΄ΠΌΠ°ΡΡΠΈΡΠ½ΠΎΠ΅ ΠΏΡΠΎΡΡΡΠ°Π½ΡΡΠ²ΠΎ, ΠΊΠΎΡΠΎΡΠΎΠ΅ Π·Π°ΠΊΠ°Π½ΡΠΈΠ²Π°ΒΠ΅ΡΡΡ ΠΏΡΠ΅ΡΡΠΎΠ²ΠΎΠΉ ΠΌΠ°ΡΡΠΈΡΠ΅ΠΉ. Π§Π΅ΡΠ΅Π· ΠΎΡΠ²Π΅ΡΡΡΠΈΡ ΠΌΠ°ΡΡΠΈΡΡ ΡΠ΅ΡΡΠΎ Π²Ρ — ΠΏΡΠ΅ΡΡΠΎΠ²ΡΠ²Π°Π΅ΡΡΡ ΠΏΠΎΠ΄ Π΄Π°Π²Π»Π΅Π½ΠΈΠ΅ΠΌ 10.β12 ΠΠΠ°. Π’Π°ΠΊΠΎΠ΅ Π΄Π°Π²Π»Π΅Π½ΠΈΠ΅ Π²ΠΎΠ·Π½ΠΈΠΊΠ°Π΅Ρ Π² ΡΠ΅Π·ΡΠ»ΡΡΠ°ΡΠ΅ ΡΠΎΠΏΡΠΎΡΠΈΠ²Π»Π΅Π½ΠΈΡ ΡΠΎΡΠΌΡΡΡΠΈΡ ΠΎΡΠ²Π΅ΡΡΡΠΈΠΉ ΠΌΠ°ΡΡΠΈΡΡ ΠΈΡΡΠ΅ΡΠ΅Π½ΠΈΡ ΠΊΡΡΡΠΎΠ³ΠΎ ΠΌΠ°ΠΊΠ°ΡΠΎΠ½Π½ΠΎΠ³ΠΎ ΡΠ΅ΡΡΠ°. ΠΠ΅Π»ΠΈΡΠΈΠ½Π° Π΄Π°Π²ΒΠ»Π΅Π½ΠΈΡ Π·Π°Π²ΠΈΡΠΈΡ ΠΎΡ Π²Π»Π°ΠΆΠ½ΠΎΡΡΠΈ ΠΈ ΡΠ΅ΠΌΠΏΠ΅ΡΠ°ΡΡΡΡ ΡΠ΅ΡΡΠ°, ΡΠΊΠΎΡΠΎΡΡΠΈ ΠΏΡΠ΅ΡΡΠΎΠ²Π°Π½ΠΈΡ ΠΈ Π΄ΡΡΠ³ΠΈΡ ΡΠ°ΠΊΡΠΎΡΠΎΠ². ΠΠΊΠΎΠ»ΠΎ 18β20% ΠΏΠΎΠ΄Π°Π²Π°Π΅ΠΌΠΎΠ³ΠΎ ΠΊ ΠΌΠ°ΡΡΠΈΡΠ΅ ΡΠ΅ΡΡΠ° Π²ΡΠΏΡΠ΅ΡΡΠΎΠ²ΡΠ²Π°Π΅ΡΡΡ ΡΠ΅ΡΠ΅Π· Π΅Π΅ ΠΎΡΠ²Π΅ΡΡΡΠΈΡ, Π° ΠΎΡΠ½ΠΎΠ²ΒΠ½Π°Ρ ΠΌΠ°ΡΡΠ° Π·Π° ΡΡΠ΅Ρ ΠΏΡΠΎΡΠΈΠ²ΠΎΠ΄Π°Π²Π»Π΅Π½ΠΈΡ Π·Π°ΠΊΡΡΡΠΈΠ²Π°Π΅ΡΡΡ Π² ΠΌΠ΅ΠΆΠ²ΠΈΡΠΊΠΎ- Π²ΠΎΠΌ ΠΏΡΠΎΡΡΡΠ°Π½ΡΡΠ²Π΅ ΡΠ½Π΅ΠΊΠ° ΠΈ ΠΏΠ΅ΡΠ΅ΠΌΠ΅ΡΠ°Π΅ΡΡΡ Π² ΠΏΡΠΎΡΠΈΠ²ΠΎΠΏΠΎΠ»ΠΎΠΆΠ½ΠΎΠΌ Π½Π°ΠΏΡΠ°Π²Π»Π΅Π½ΠΈΠΈ. ΠΠ΅ΡΠ΅Π΄ ΠΌΠ°ΡΡΠΈΡΠ΅ΠΉ ΠΏΡΠΎΠΈΡΡ ΠΎΠ΄ΠΈΡ ΠΏΠΎΡΠ»ΠΎΠΉΠ½ΠΎΠ΅ ΠΏΠ΅ΡΠ΅ΠΌΠ΅ΡΠ΅ΒΠ½ΠΈΠ΅ ΡΠ΅ΡΡΠ° Π²ΠΏΠ΅ΡΠ΅Π΄ ΠΈ Π½Π°Π·Π°Π΄. ΠΡΠΎ Π²Π΅Π΄Π΅Ρ ΠΊ ΠΏΠ΅ΡΠ΅Ρ ΠΎΠ΄Ρ ΠΌΠ΅Ρ Π°Π½ΠΈΡΠ΅ΡΠΊΠΎΠΉ ΡΠ½Π΅ΡΠ³ΠΈΠΈ Π΄Π²ΠΈΠΆΠ΅Π½ΠΈΡ ΠΎΡΠ΄Π΅Π»ΡΠ½ΡΡ ΡΠ»ΠΎΠ΅Π² Π² ΡΠ΅ΠΏΠ»ΠΎΠ²ΡΡ; Π² ΡΠ΅Π·ΡΠ»ΡΡΠ°ΡΠ΅ ΡΠ΅ΡΡΠΎ ΠΏΡΠΈΠΎΠ±ΡΠ΅ΡΠ°Π΅Ρ Π±ΠΎΠ»ΡΡΡΡ ΠΏΠ»Π°ΡΡΠΈΡΠ½ΠΎΡΡΡ, Π΅Π³ΠΎ ΡΠ΅ΠΌΠΏΠ΅ΡΠ°ΡΡΡΠ° ΠΏΠΎΒΠ²ΡΡΠ°Π΅ΡΡΡ Π½Π° 10β20 Β°Π‘. ΠΠΎ ΠΈΠ·Π±Π΅ΠΆΠ°Π½ΠΈΠ΅ Π΅Π³ΠΎ ΠΏΠ΅ΡΠ΅Π³ΡΠ΅Π²Π° ΡΠ½Π΅ΠΊΠΎΠ²Π°Ρ ΠΈ ΠΌΠ°ΡΡΠΈΡΠ½Π°Ρ ΠΊΠ°ΠΌΠ΅ΡΡ ΡΠ½Π°Π±ΠΆΠ΅Π½Ρ ΡΡΠ±Π°ΡΠΊΠ°ΠΌΠΈ, ΠΏΠΎ ΠΊΠΎΡΠΎΡΡΠΌ ΡΠΈΡΠΊΡΒΠ»ΠΈΡΡΠ΅Ρ Ρ ΠΎΠ»ΠΎΠ΄Π½Π°Ρ Π²ΠΎΠ΄Π° (Π² Π½Π°ΡΠ°Π»ΡΠ½ΡΠΉ ΠΏΠ΅ΡΠΈΠΎΠ΄ ΡΠ°Π±ΠΎΡΡ ΠΏΡΠ΅ΡΡΠ° Π² ΡΡΠ±Π°ΡΠΊΡ ΠΏΠΎΠ΄Π°ΡΡ Π³ΠΎΡΡΡΡΡ Π²ΠΎΠ΄Ρ).
Π£ΠΏΠ»ΠΎΡΠ½Π΅Π½Π½ΠΎΠ΅ ΠΌΠ°ΠΊΠ°ΡΠΎΠ½Π½ΠΎΠ΅ ΡΠ΅ΡΡΠΎ ΡΠ²Π»ΡΠ΅ΡΡΡ ΡΠΏΡΡΠ³ΠΎΠΏΠ»Π°ΡΡΠΈΡΠ½ΠΎΠ²ΡΠ· — ΠΊΠΈΠΌ ΡΠ΅Π»ΠΎΠΌ, ΠΈ Ρ ΡΠ²Π΅Π»ΠΈΡΠ΅Π½ΠΈΠ΅ΠΌ Π΅Π³ΠΎ ΠΏΠ»Π°ΡΡΠΈΡΠ½ΠΎΡΡΠΈ ΡΠ½ΠΈΠΆΠ°Π΅ΡΡΡ ΡΠ°ΡΡ ΠΎΠ΄ ΡΠ½Π΅ΡΠ³ΠΈΠΈ Π½Π° ΡΠΎΡΠΌΠΎΠ²Π°Π½ΠΈΠ΅. ΠΡΠΎΠΌΠ΅ ΡΠΎΠ³ΠΎ, Π²ΡΠ·ΠΊΠΎΠ΅, ΠΏΠ»ΠΎΡΠ½ΠΎΠ΅ ΡΠ΅ΡΡΠΎ ΠΌΠ΅Π½ΡΒΡΠ΅ ΠΏΡΠΈΠ»ΠΈΠΏΠ°Π΅Ρ ΠΊ ΠΏΠΎΠ²Π΅ΡΡ Π½ΠΎΡΡΡΠΌ ΡΠ½Π΅ΠΊΠ°, ΡΠΏΠ΅ΠΊΠΎΠ²ΠΎΠΉ ΠΊΠ°ΠΌΠ΅ΡΡ, ΠΊΠ°Π½Π°-1 Π»ΠΎΠ² ΠΌΠ°ΡΡΠΈΡΡ, Π° ΡΡΠΎΡΠΌΠΎΠ²Π°Π½Π½ΡΠ΅ ΠΈΠ·Π΄Π΅Π»ΠΈΡ Π½Π΅ Π΄Π΅ΡΠΎΡΠΌΠΈΡΡΡΡΡΡ Π½Π° ΠΏΠΎΡΠ»Π΅Π΄ΡΡΡΠΈΡ ΡΡΠ°Π΄ΠΈΡΡ ΠΏΡΠΎΠΈΠ·Π²ΠΎΠ΄ΡΡΠ²Π΅Π½Π½ΠΎΠ³ΠΎ ΠΏΡΠΎΡΠ΅ΡΡΠ°. Π‘ Π΄Π°Π»ΡΠ½Π΅ΠΉΒΡΠΈΠΌ ΡΠ²Π΅Π»ΠΈΡΠ΅Π½ΠΈΠ΅ΠΌ ΡΠ΅ΠΌΠΏΠ΅ΡΠ°ΡΡΡΡ ΠΏΠ»Π°ΡΡΠΈΡΠ½ΠΎΡΡΡ ΠΈΠ·Π΄Π΅Π»ΠΈΠΈ ΡΠ°ΡΡΠ΅Ρ, Π° ΡΠΏΡΡΠ³ΠΎΡΡΡ ΡΠ½ΠΈΠΆΠ°Π΅ΡΡΡ. ΠΠ΄Π½Π°ΠΊΠΎ ΠΏΡΠΈ Π²ΡΡΠΎΠΊΠΎΠΉ ΡΠ΅ΠΌΠΏΠ΅ΡΠ°ΡΡΡΠ΅ Π² ΡΠ²ΡΒΠ·ΠΈ Ρ ΠΊΠ»Π΅ΠΉΡΡΠ΅ΡΠΈΠ·Π°ΡΠΈΠ΅ΠΉ ΠΊΡΠ°Ρ ΠΌΠ°Π»Π° ΠΈ ΠΊΠΎΠ°Π³ΡΠ»ΡΡΠΈΠ΅ΠΉ Π±Π΅Π»ΠΊΠΎΠ² ΡΠ΅ΡΡΠ°, ΠΏΡΠΎΠΈΡΡ ΠΎΠ΄ΡΡ ΠΎΠ±ΡΠ°ΡΠ½ΡΠ΅ ΡΠ²Π»Π΅Π½ΠΈΡ ΠΎΠΏΡΠΈΠΌΠ°Π»ΡΠ½ΠΎΠ΅ ΡΠΎΠΎΡΠ½ΠΎΡΠ΅Π½ΠΈΠ΅ ΡΠΏΡΡ — Π³ΠΎΠ²ΡΠ·ΠΊΠΎΠΏΠ»Π°ΡΡΠΈΡΠ½ΡΡ ΡΠ²ΠΎΠΉΡΡΠ² Π½Π°Π±Π»ΡΠ΄Π°Π΅ΡΡΡ ΠΏΡΠΈ 50β55 Β°Π‘.
ΠΠ°ΠΊ ΠΎΡΠΌΠ΅ΡΠ°Π»ΠΎΡΡ, Π² ΡΠΎΠ²ΡΠ΅ΠΌΠ΅Π½Π½ΡΡ ΠΏΡΠ΅ΡΡΠ°Ρ ΡΠ΅ΡΡΠΎ Π²Π°ΠΊΡΡΠΌΠΈΡΡΡΠ³ ΠΏΠ° ΡΡΠ°Π΄ΠΈΠΈ Π·Π°ΠΌΠ΅ΡΠ°. ΠΠΌΠ΅ΡΡΠ΅ Ρ ΡΠ΅ΠΌ Π² ΠΏΡΠΎΠΌΡΡΠ»Π΅Π½Π½ΠΎΡΡΠΈ ΠΏΡΠΈΠΌΠ΅Π½ΡΠ΅ΡΡΡ ΠΎΠ±ΠΎΡΡΠ΄ΠΎΠ²Π°Π½ΠΈΠ΅ (ΠΏΡΠ΅ΡΡ ΡΠΈΠΏΠ° ΠΠΠ ΠΈ Π΄ΡΡΠ³ΠΈΠ΅), Π³Π΄Π΅ Π²Π°ΠΊΡΡΠΌ ΡΠΎΠ·Π΄Π°Π΅ΡΡΡ Π½Π° ΡΡΠ°Π΄ΠΈΠΈ ΡΠΎΡΠΌΠΎΠ²Π°Π½ΠΈΡ. ΠΠ΄Π½Π°ΠΊΠΎ Π² ΡΡΠΎΠΌ ΡΠ»ΡΡΠ°Π΅ ΡΠ΄Π°Π»ΡΡΡ Π²ΠΎΠ·Π΄ΡΡ ΠΈΠ· ΡΠΏΡΠ΅ΡΡΠΎΠ²Π°Π½Π½ΠΎΠ³ΠΎ ΡΠ΅ΡΡΠ° Π³ΠΎΡΠ°Π·Π΄ΠΎ ΡΡΡΠ΄Π½Π΅^, ΠΈ ΡΡΡΠ΅ΠΊΡ ΠΎΡ ΠΈΡΠΏΠΎΠ»ΡΠ·ΠΎΠ²Π°ΒΠ½ΠΈΡ Π΄Π΅Π°ΡΡΠ°ΡΠΈΠΈ Π½ΠΈΠΆΠ΅.
ΠΠ°ΠΈΠ±ΠΎΠ»Π΅Π΅ Π²Π°ΠΆΠ½ΠΎΠΉ ΡΠ°ΡΡΡΡ ΠΏΡΠ΅ΡΡΠ° ΡΠ²Π»ΡΡΡΡΡ ΠΌΠ°ΡΡΠΈΡΡ. ΠΠ½ΠΈ ΠΌΠΎΠ³ΡΡ Π±ΡΡΡ ΠΊΡΡΠ³Π»ΡΠΌΠΈ Π² ΡΠΎΡΠΌΠ΅ ΠΏΠ»ΠΎΡΠΊΠΎΠ³ΠΎ Π΄ΠΈΡΠΊΠ° ΠΈ ΠΏΡΡΠΌΠΎΡΠ³ΠΎΠ»ΡΠ½ΡΒΠΌΠΈ. ΠΠ°ΡΠ΅ΡΠΈΠ°Π» Π΄Π»Ρ ΠΈΡ ΠΈΠ·Π³ΠΎΡΠΎΠ²Π»Π΅Π½ΠΈΡ Π΄ΠΎΠ»ΠΆΠ΅Π½ Π±ΡΠΏΡ ΠΏΡΠΎΡΠ½ΡΠΌ, Π²ΡΒΠ΄Π΅ΡΠΆΠΈΠ²Π°ΡΡ Π·Π½Π°ΡΠΈΡΠ΅Π»ΡΠ½ΡΠ΅ Π΄Π°Π²Π»Π΅Π½ΠΈΡ ΠΈ Π±ΡΡΡ ΡΡΠΎΠΏ ΠΊΠΈΠΌ ΠΊ ΠΊΠΎΡΡΠΎΠ·ΠΈΠΈ, Π³Π°ΠΊ ΠΊΠ°ΠΊ ΡΠ΅ΡΡΠΎ ΡΠ²Π»ΡΠ΅ΡΡΡ Π°Π³ΡΠ΅ΡΡΠΈΠ²Π½ΠΎΠΉ ΡΡΠ΅Π΄ΠΎΠΉ, ΠΏΠΎΡΠΊΠΎΠ»ΡΠΊΡ ΡΠΎΠ΄Π΅ΡΠΆΠΈΡ Π²Π΅ΡΠ΅ΡΡΠ²Π° Ρ ΠΊΠΈΡΠ»ΠΎΠΉ ΡΠ΅Π°ΠΊΡΠΈΠ΅ΠΉ. ΠΡΡΡΠ΅ Π²ΡΠ΅Π³ΠΎ ΠΌΠ°ΡΡΠΈΡΡ ΠΈΠ·Π³ΠΎΡΠ°Π²Π»ΠΈΒΠ²Π°ΡΡ ΠΈΠ· Π»Π°ΡΡΠ½ΠΈ ΠΈ Π±ΡΠΎΠ½Π·Ρ, Π½ΠΎ Π²ΠΎΠ·ΠΌΠΎΠΆΠ½ΠΎ ΠΈΡΠΏΠΎΠ»ΡΠ·ΠΎΠ²Π°ΡΡ Π½Π΅ΡΠΆΠ°Π²Π΅ΡΒΡΡΡ ΡΡΠ°Π»Ρ.
Π€ΠΎΡΠΌΠ° ΠΈΠ·Π΄Π΅Π»ΠΈΠΉ, ΠΏΠΎΠ»ΡΡΠ°Π΅ΠΌΡΡ ΠΏΡΠΈ ΠΏΡΠ΅ΡΡΠΎΠ²Π°Π½ΠΈΠΈ, Π·Π°Π²ΠΈΡΠΈΡ ΠΎΡ ΠΊΠΎΠ½ΡΠΈΠ³ΡΡΠ°ΡΠΈΠΈ ΡΠΎΡΠΌΡΡΡΠΈΡ ΠΎΡΠ²Π΅ΡΡΡΠΈΠΉ ΠΌΠ°ΡΡΠΈΡΡ. ΠΡΡΡΠ΅ΡΠ°ΡΡΡΡ ΡΡΠΈ Π²ΠΈΠ΄Π° ΠΎΡΠ²Π΅ΡΡΡΠΈΠΉ: ΠΊΠΎΠ»ΡΡΠ΅Π²ΡΠ΅ Ρ Π²ΠΊΠ»Π°Π΄ΡΡΠ°ΠΌΠΈ Π΄Π»Ρ ΠΏΠΎΠ»ΡΡΠ΅Π½ΠΈΡ ΠΌΠ°ΠΊΠ°ΡΠΎΠ½Π½ΠΎΠΉ ΡΡΡΠ±ΠΊΠΈ; Π±Π΅Π· Π²ΠΊΠ»Π°Π΄ΡΡΠ΅ΠΉ Π΄Π»Ρ ΡΠΎΡΠΌΠΎΠ²Π°Π½ΠΈΡ Π½ΠΈΡΠ΅ΠΎΠ±ΒΡΠ°Π·Π½ΡΡ ΠΈΠ·Π΄Π΅Π»ΠΈΠΉ; ΡΠ΅Π»Π΅Π²ΡΠ΅ Π΄Π»Ρ ΠΏΡΠ΅ΡΡΠΎΠ²Π°Π½ΠΈΡ Π»Π°ΠΏΡΠΈ, ΡΠΈΠ³ΡΡΠ½ΡΡ ΠΈΠ·Π΄Π΅Π»ΠΈΠΉ ΠΈ ΡΠΈΡΠΎΠΊΠΈΡ Π»Π΅Π½Ρ ΡΠ΅ΡΡΠ° Π΄Π»Ρ ΠΏΠΎΡΠ»Π΅Π΄ΡΡΡΠ΅Π³ΠΎ ΡΠΎΡΠΌΠΎΠ²Π°Π½ΠΈΡ ΠΈΠ· Π½ΠΈΡ ΡΡΠ°ΠΌΠΏΠΎΠ²Π°Π½Π½ΡΡ ΠΈΠ·Π΄Π΅Π»ΠΈΠΉ.
ΠΠΊΠ»Π°Π΄ΡΡ ΡΠΎΡΡΠΎΠΈΡ ΠΈΠ· ΡΠΈΠ»ΠΈΠ½Π΄ΡΠΈΡΠ΅ΡΠΊΠΎΠΉ Π½ΠΎΠΆΠΊΠΈ ΠΈ Π΄Π²ΡΡ (Π² Π’-ΠΎΠ± — ΡΠ°Π·Π½ΠΎΠΌ Π²ΠΊΠ»Π°Π΄ΡΡΠ΅) ΠΈΠ»ΠΈ ΡΡΠ΅Ρ (Π² ΡΡΠ΅Ρ ΠΎΠΏΠΎΡΠ½ΠΎΠΌ Π²ΠΊΠ»Π°Π΄ΡΡΠ΅) ΠΎΠΏΠΎΡ β Π·Π°ΠΏΠ»Π΅ΡΠΈΠΊΠΎΠ², ΠΊΠΎΡΠΎΡΡΠ΅ ΡΠ°ΡΠΏΠΎΠ»Π°Π³Π°ΡΡΡΡ ΡΠ· Π²Π΅ΡΡ Π½Π΅ΠΉ ΡΠ°ΡΡΠΈ ΠΊΠ°ΠΏΠ°Π»Π° ΠΌΠ°ΡΡΠΈΡΡ ΠΈ ΠΎΠ±Π΅ΡΠΏΠ΅ΡΠΈΠ²Π°ΡΡ ΡΠ΅Π½ΡΡΠΎΠ²ΠΊΡ Π²ΠΊΠ»Π°Π΄ΡΡΠ°. Π’-ΠΎΠ±ΡΠ°Π·ΠΏΡΠ΅ Π²ΠΊΠ»Π°Π΄ΡΡΠΈ ΠΌΠΎΠ³ΡΡ ΡΠΌΠ΅ΡΠ°ΡΡΡΡ, ΠΈ ΠΈΠ·Π΄Π΅Π»ΠΈΡ ΠΏΠΎΠ»ΡΡΠ°ΡΡΡΡ ΡΠΎ ΡΡΠ΅Π½ΠΊΠ°ΒΠΌΠΈ ΡΠ°Π·Π½ΠΎΠΉ ΡΠΎΠ»ΡΠΈΠ½Ρ, ΠΏΠΎΡΡΠΎΠΌΡ ΠΏΡΠ΅ΠΈΠΌΡΡΠ΅ΡΡΠ²ΠΎ ΠΈΠΌΠ΅ΡΡ ΡΡΠ΅Ρ ΠΎΠ³ΡΡΠ½ΡΠ΅ Π²ΠΊΠ»Π°Π΄ΡΡΠΈ. ΠΠΎΠΆΠΊΠ° Π²ΠΊΠ»Π°Π΄ΡΡΠ° Π½Π°Ρ ΠΎΠ΄ΠΈΡΡΡ Π² ΠΎΡΠ½ΠΎΠ²Π½ΠΎΠΉ ΡΠ°ΡΡΠΈ ΠΎΡΒΠ²Π΅ΡΡΡΠΈΡ ΠΌΠ°ΡΡΠΈΡΡ. ΠΠΈΠ°ΠΌΠ΅ΡΡ Π½ΠΎΠΆΠΊΠΈ ΠΌΠ΅Π½ΡΡΠ΅ Π΄ΠΈΠ°ΠΌΠ΅ΡΡΠ° ΡΠΎΡΠΌΡΡΒΡΠ΅ΠΉ ΡΠ΅Π»ΠΈ ΠΌΠ°ΡΡΠΈΡΡ, ΠΏΠΎΡΡΠΎΠΌΡ ΠΎΠ±ΡΠ°Π·ΡΠ΅ΡΡΡ ΠΊΠΎΠ»ΡΡΠ΅Π²ΠΎΠΉ Π·Π°Π·ΠΎΡ. Π’Π΅ΡΡΠΎ ΠΏΠΎΠ΄Π°Π΅ΡΡΡ ΠΊ ΠΌΠ°ΡΡΠΈΡΠ΅, ΡΠ°Π·ΡΠ΅Π·Π°Π΅ΡΡΡ Π·Π°ΠΏΠ»Π΅ΡΠΈΠΊΠ°ΠΌΠΈ ΠΏΠ° Π΄Π²Π΅ ΠΈΠ»ΠΈ ΡΡΠΈ ΡΠ°ΡΡΠΈ, ΠΊΠΎΡΠΎΡΡΠ΅ Π·Π° ΡΡΠ΅Ρ ΠΏΠΎΠ²ΡΡΠ΅Π½Π½ΠΎΠ³ΠΎ Π΄Π°Π²Π»Π΅Π½ΠΈΡ ΠΏΡΠ΅ΡΡΠΎΠ²Π°Π½ΠΈΡ ΠΏΠΎΒΠΏΠ°Π΄Π°ΡΡ Π² ΠΊΠΎΠ»ΡΡΠ΅Π²ΠΎΠΉ Π·Π°Π·ΠΎΡ ΠΈ ΡΠΊΠ»Π΅ΠΈΠ²Π°ΡΡΡΡ Π² ΠΏΡΠΎΡΠ½ΡΡ ΡΠ΅ΡΡΠΎΠ²ΡΡ ΡΡΡΠ±ΠΊΡ. ΠΠ½ΡΡΡΠ΅Π½Π½ΠΈΠΉ Π΄ΠΈΠ°ΠΌΠ΅ΡΡ ΡΠ΅ΡΡΠΎΠ²ΠΎΠΉ ΡΡΡΠ±ΠΊΠΈ ΡΠ°Π²Π΅Π½ Π΄ΠΈΠ°ΠΌΠ΅ΡΡΡ Π½ΠΎΠΆΠΊΠΈ Π²ΠΊΠ»Π°Π΄ΡΡΠ°, Π° Π²Π½Π΅ΡΠ½ΠΈΠΉβΠ΄ΠΈΠ°ΠΌΠ΅ΡΡΡ ΠΎΡΠ²Π΅ΡΡΡΠΈΡ ΠΌΠ°ΡΡΠΈΡΡ.
ΠΡΠΈ ΠΈΡΠΏΠΎΠ»ΡΠ·ΠΎΠ²Π°Π½ΠΈΠΈ ΠΌΠ΅ΡΠ°Π»Π»ΠΈΡΠ΅ΡΠΊΠΈΡ ΠΌΠ°ΡΡΠΈΡ ΠΏΠΎΠ²Π΅ΡΡ Π½ΠΎΡΡΡ ΠΈΠ·ΒΠ΄Π΅Π»ΠΈΠΉ ΠΏΠΎΠ»ΡΡΠ°Π΅ΡΡΡ ΡΠ΅ΡΠΎΡ ΠΎΠ²Π°ΡΠΎΠΉ Π² ΡΠ΅Π·ΡΠ»ΡΡΠ°ΡΠ΅ ΠΏΡΠΈΠ»ΠΈΠΏΠ°Π½ΠΈΡ ΡΠ΅ΡΡΠ° ΠΊ ΠΏΠΎΠ²Π΅ΡΡ Π½ΠΎΡΡΠΈ ΠΌΠ°ΡΡΠΈΡΡ. ΠΡΠΈΠ»ΠΈΠΏΡΠΈΠΉ ΡΠ»Π΅ΠΌΠ΅Π½ΡΠ°ΡΠ½ΡΠΉ ΡΠ»ΠΎΠΉ ΡΠ΅ΡΡΠ° ΠΎΡΡΠ°Π΅ΡΡΡ Π½Π΅ΠΏΠΎΠ΄Π²ΠΈΠΆΠ½ΡΠΌ, Π° ΡΠ»Π΅Π΄ΡΡΡΠΈΠΉ ΡΠ»Π΅ΠΌΠ΅Π½ΡΠ°ΡΠ½ΡΠΉ ΡΠ»ΠΎΠΉ Π΄Π²ΠΈΒΠΆΠ΅ΡΡΡ, ΠΎΡΡΡΠ²Π°ΡΡΡ ΠΎΡ ΠΏΡΠΈΠ»ΠΈΠΏΡΠ΅Π³ΠΎ ΡΠ»ΠΎΡ. ΠΡΠΈ ΡΡΠΎΠΌ ΡΠΊΠΎΡΠΎΡΡΡ Π΄Π²ΠΈΒΠΆΠ΅Π½ΠΈΡ Π²ΡΠΎΡΠΎΠ³ΠΎ ΡΠ»ΠΎΡ ΡΠΌΠ΅Π½ΡΡΠ°Π΅ΡΡΡ, Π½Π° ΠΏΠΎΠ²Π΅ΡΡ Π½ΠΎΡΡΠΈ ΠΎΠ±ΡΠ°Π·ΡΡΡΡΡ «Π°Π΄ΡΡΠ²Ρ, Π·Π°ΡΡΠ΅Π½ΠΈΡΡ.’ Π‘ ΡΠ²Π΅Π»ΠΈΡΠ΅Π½ΠΈΠ΅ΠΌ ΠΏΠ»Π°ΡΡΠΈΡΠ½ΠΎΡΡΠΈ ΡΠ΅ΡΡΠ° ΠΏΠΎ — Π²Π΅ΡΡ ΠΏΠΎΡΡΡ ΠΏΠΎΠ»ΡΡΠ°Π΅ΡΡΡ Π±ΠΎΠ»Π΅Π΅ Π³Π»Π°Π΄ΠΊΠΎΠΉ, ΡΠ°ΠΊ ΠΊΠ°ΠΊ ΠΎΠ±ΡΠ°Π·ΠΎΠ²Π°Π²ΡΠΈΠ΅ΡΡ Π·Π°ΡΡΠ΅Π½ΠΈΡΡ ΠΊΠ°ΠΊ Π±Ρ Π·Π°ΡΡΠ³ΠΈΠ²Π°ΡΡΡΡ.
Π‘ΡΠ΅ΠΏΠ΅Π½Ρ ΠΏΡΠΈΠ»ΠΈΠΏΠ°Π½ΠΈΡ ΡΠ΅ΡΡΠ° Π·Π°Π²ΠΈΡΠΈΡ ΠΎΡ ΠΌΠ°ΡΠ΅ΡΠΈΠ°Π»Π° ΠΌΠ°ΡΡΠΈΡΡ. ΠΠ°ΠΈΠ±ΠΎΠ»Π΅Π΅ ΡΠΈΠ»ΡΠ½ΠΎ ΡΠ΅ΡΡΠΎ ΠΏΡΠΈΠ»ΠΈΠΏΠ°Π΅Ρ ΠΊ ΠΌΠ°ΡΡΠΈΡΠ°ΠΌ, ΠΈΠ·Π³ΠΎΡΠΎΠ²Π»Π΅Π½Π½ΡΠΌ ΠΈΠ· Π½Π΅ΡΠΆΠ°Π²Π΅ΡΡΠ΅ΠΉ ΡΡΠ°Π»ΠΈ, ΠΌΠ΅Π½ΡΡΠ΅ β ΠΊ ΠΌΠ°ΡΡΠΈΡΠ°ΠΌ ΠΈΠ· Π»Π°ΡΡΠ½ΠΈ, Π΅ΡΠ΅ ΡΠ»Π°Π±Π΅Π΅ β ΠΊ ΠΌΠ°ΡΡΠΈΡΠ°ΠΌ ΠΈΠ· Π±ΡΠΎΠ½Π·Ρ. ΠΠ»Ρ ΡΠ½ΠΈΠΆΠ΅Π½ΠΈΡ ΡΡΠ΅ΠΏΠ΅Π½ΠΈ ΠΏΡΠΈΠ»ΠΈΒΠΏΠ°Π½ΠΈΡ Π³Π΅ΡΡΠ° ΠΏΠΎΠ²Π΅ΡΡ Π½ΠΎΡΡΡ ΡΠΎΡΠΌΡΡΡΠ΅ΠΉ ΡΠ΅Π»ΠΈ ΠΌΠ°ΡΡΠΈΡΡ Π΄ΠΎΠ»ΠΆΠ½Π° Π±ΡΡΡ ΡΡΠ°ΡΠ΅Π»ΡΠ½ΠΎ ΠΎΡΡΠ»ΠΈΡΠΎΠ²Π°Π½Π°. Π ΠΏΠΎΡΠ»Π΅Π΄Π½Π΅Π΅ Π²ΡΠ΅ΠΌΡ Π΄Π»Ρ ΠΏΠΎΠ»ΡΡΠ΅ΒΠ½ΠΈΡ ΠΈΠ·Π΄Π΅Π»ΠΈΠΉ Ρ Π³Π»Π°Π΄ΠΊΠΎΠΉ ΠΏΠΎΠ²Π΅ΡΡ Π½ΠΎΡΡΡΡ ΠΈΡΠΏΠΎΠ»ΡΠ·ΡΡΡΡΡ ΠΌΠ°ΡΡΠΈΡΡ ΡΠΎ Π²ΡΡΠ°Π²ΠΊΠ°ΠΌΠΈ ΠΈΠ· ΠΏΠ»Π°ΡΡΠΌΠ°ΡΡ, Π² ΡΠ°ΡΡΠ½ΠΎΡΡΠΈ ΠΈΠ· ΡΡΠΎΡΠΎΠΏΠ»Π°ΡΡΠ°, ΠΊ ΠΊΠΎΡΠΎΡΠΎΒΠΌΡ ΡΠ΅ΡΡΠΎ Π½Π΅ ΠΏΡΠΈΠ»ΠΈΠΏΠ°Π΅Ρ. Π ΡΠ΅Π·ΡΠ»ΡΡΠ°ΡΠ΅ ΡΡΡΠ΅ΡΡΠ²Π΅Π½Π½ΠΎ Π²ΠΎΠ·ΡΠ°ΡΡΠ°Π΅Ρ ΡΠΊΠΎΡΠΎΡΡΡ ΠΏΡΠ΅ΡΡΠΎΠ²Π°Π½ΠΈΡ, Π° Π³ΠΎΡΠΎΠ²ΡΠ΅ ΠΈΠ·Π΄Π΅Π»ΠΈΡ ΠΈΠΌΠ΅ΡΡ Π±ΠΎΠ»Π΅Π΅ ΠΆΠ΅Π»ΡΡΠΉ ΡΠ²Π΅Ρ.
ΠΠΈΠ΄ΡΠΎΠΌΠ΅Π»ΡΠ½ΠΈΡΠ° Π΄Π»Ρ ΠΏΡΠΎΠΈΠ·Π²ΠΎΠ΄ΡΡΠ²Π° ΠΊΠΎΡΠΌΠΎΠ²ΠΎΠΉ ΠΊΠ°ΡΠΈ
ΠΡΠΎΠΈΠ·Π²ΠΎΠ΄ΡΡΠ²ΠΎ ΠΈ ΠΏΡΠΎΠ΄Π°ΠΆΠ° Π³ΠΈΠ΄ΡΠΎΠΌΠ΅Π»ΡΠ½ΠΈΡ Π² ΡΠ±ΠΎΡΠ΅, ΡΠ΅Π½Π° 6500Π³ΡΠ½, Π΄ΠΎΡΡΠ°Π²ΠΊΠ° ΠΏΠΎ Π‘ΠΠ ΠΈ ΠΠ°Π»ΡΠ½Π΅ΠΌΡ ΠΠ°ΡΡΠ±Π΅ΠΆΡΡ, ΠΊΠΎΠ½ΡΠ°ΠΊΡΡ Π΄Π»Ρ Π·Π°ΠΊΠ°Π·ΠΎΠ²: +38 067 2825117 +38 050 4571330 [email protected] Π€ΠΎΡΠΎ Π³ΠΈΠ΄ΡΠΎΠΌΠ΅Π»ΡΠ½ΠΈΡΡ Π² ΡΠ±ΠΎΡΠ΅(ΠΊΠΎΡΠΌΠΎΠΏΡΠΈΠ³ΠΎΡΠΎΠ²ΠΈΡΠ΅Π»Ρ ΠΠΏΠΏΠ΅ΡΠΈΡ): ΠΡΠΎΠΈΠ·Π²ΠΎΠ΄ΡΡΠ²ΠΎΒ β¦
ΠΡΡΠΎΠΊΠΎΡΡΠ½Π°Ρ ΠΌΡΠΊΠ° β ΠΏΡΠΎΠΈΠ·Π²ΠΎΠ΄ΡΡΠ²ΠΎ
ΠΡΠΎΡΠ΅ΠΈΠ½ 30-35% ΠΠΎΡΡΠ°Π²ΠΊΠΈ ΠΌΡΡΠΎΠΊΠΎΡΡΠ½ΠΎΠΉ ΠΌΡΠΊΠΈ ΠΏΠΎ Π£ΠΊΡΠ°ΠΈΠ½Π΅ ΠΈ Π½Π° ΠΠΊΡΠΏΠΎΡΡ Π£ΠΏΠ°ΠΊΠΎΠ²ΠΊΠ°: ΠΌΠ΅ΡΠΎΠΊ ΠΏΠΎΠ»ΠΈΠΏΡΠΎΠΏΠΈΠ»Π΅Π½ΠΎΠ²ΡΠΉ 30ΠΊΠ³, ΡΠ΅Π½Π° 2300Π³ΡΠ½/ΡΠΎΠ½Π½Π° (200Π΄ΠΎΠ»/ΡΠΎΠ½Π½Π°) Π‘ΠΎΡΡΠ°Π²: ΠΊΠΎΡΡΠΈ, ΠΌΡΡΠΎ, ΠΊΠΎΠ»Π±Π°ΡΠ° Π³ΠΎΠ²ΡΠ΄ΠΈΠ½Ρ ΠΈ ΡΠ²ΠΈΠ½ΠΈΠ½Ρ (Π½Π΅Ρ Π΄ΠΎΠ±Π°Π²Π»Π΅Π½ΠΈΡ ΠΏΠ°Π΄Π°Π»ΠΈ) ΠΠ»Π°ΠΆΠ½ΠΎΡΡΡ — 5-8%Β β¦
ΠΠ ΠΠΠΠΠΠΠ‘Π’ΠΠ Π₯ΠΠΠΠΠΠΠΠΠ ΠΠ«Π₯, ΠΠΠΠΠΠ’ΠΠ Π‘ΠΠΠ₯ Π ΠΠ£ΠΠΠΠΠ ΠΠ«Π₯ ΠΠΠ ΠΠ
Π ΡΠΎΡΡΠ°Π² Ρ Π»Π΅Π±ΠΎΠΏΠ΅ΠΊΠ°ΡΠ½ΡΡ , ΠΊΠΎΠ½Π΄ΠΈΡΠ΅ΡΡΠΊΠΈΡ ΠΈ ΠΊΡΠ»ΠΈΠ½Π°ΡΠ½ΡΡ ΠΆΠΈΡΠΎΠ² Π²Ρ ΠΎΠ΄ΡΡ ΡΠ°ΡΡΠΈΡΠ΅Π»ΡΠ½ΡΠ΅ ΠΌΠ°ΡΠ»Π°, ΠΆΠΈΠ²ΠΎΡΠ½ΡΠ΅ ΠΆΠΈΡΡ, Π³ΠΈΠ΄ΡΠΈΡΠΎΠ²Π°Π½Π½ΡΠ΅ ΠΆΠΈΡΡ, Π° ΡΠ°ΠΊΠΆΠ΅ ΡΠΌΡΠ»ΡΠ³Π°ΡΠΎΡΡ, ΠΊΡΠ°ΡΠΈΡΠ΅Π»ΠΈ, Π°ΡΠΎΠΌΠ°ΡΠΈΠ·Π°ΡΠΎΡΡ, Π²ΠΈΡΠ°— ΠΌΠΈΠ½Ρ. Π‘ΠΎΠ΄Π΅ΡΠΆΠ°Π½ΠΈΠ΅ ΠΆΠΈΡΠ° Π² Π±ΠΎΠ»ΡΡΠΈΠ½ΡΡΠ²Π΅ Π²ΠΈΠ΄ΠΎΠ² Ρ Π»Π΅Π±ΠΎΠΏΠ΅ΠΊΠ°ΡΠ½ΡΡ , ΠΊΠΎΠ½Π΄ΠΈΡΠ΅ΡΡΠΊΠΈΡ ΠΈ ΠΊΡΠ»ΠΈΠ½Π°ΡΠ½ΡΡ Β β¦
msd.com.ua
2 ΠΠ±ΠΎΡΡΠ΄ΠΎΠ²Π°Π½ΠΈΠ΅ ΠΌΠ°ΠΊΠ°ΡΠΎΠ½Π½ΠΎΠ³ΠΎ ΠΏΡΠΎΠΈΠ·Π²ΠΎΠ΄ΡΡΠ²Π°
2.1 ΠΠ±ΠΎΡΡΠ΄ΠΎΠ²Π°Π½ΠΈΠ΅ Π΄Π»Ρ Π·Π°ΠΌΠ΅ΡΠ° ΡΠ΅ΡΡΠ°, ΡΠΎΡΠΌΠΎΠ²Π°Π½ΠΈΡ
Π Π ΠΠΠΠΠΠΠ Π‘Π«Π Π«Π₯ ΠΠΠΠΠ ΠΠΠΠ«Π₯ ΠΠΠΠΠΠΠ
ΠΠΎΠ½ΡΡΡΡΠΊΡΠΈΠΈ ΡΠ½Π΅ΠΊΠΎΠ²ΡΡ ΠΏΡΠ΅ΡΡΠΎΠ²
Π¨Π½Π΅ΠΊΠΎΠ²ΡΠ΅ ΠΌΠ°ΠΊΠ°ΡΠΎΠ½Π½ΡΠ΅ ΠΏΡΠ΅ΡΡΡ Π½Π΅ΠΏΡΠ΅ΡΡΠ²Π½ΠΎΠ³ΠΎ Π΄Π΅ΠΉΡΡΠ²ΠΈΡ ΠΏΡΠ΅Π΄Π½Π°ΒΠ·Π½Π°ΡΠ΅Π½Ρ Π΄Π»Ρ ΠΏΡΠΈΠ³ΠΎΡΠΎΠ²Π»Π΅Π½ΠΈΡ ΡΠ΅ΡΡΠ° ΠΈ ΡΠΎΡΠΌΠΎΠ²Π°Π½ΠΈΡ ΠΈΠ· Π½Π΅Π³ΠΎ ΡΡΡΡΡ ΠΌΠ°ΠΊΠ°ΡΠΎΠ½ΒΠ½ΡΡ ΠΈΠ·Π΄Π΅Π»ΠΈΠΉ. ΠΡΠ½ΠΎΠ²Π½ΡΠΌΠΈ ΡΠ·Π»Π°ΠΌΠΈ ΡΠΎΠ²ΡΠ΅ΠΌΠ΅Π½Π½ΡΡ ΠΏΡΠ΅ΡΡΠΎΠ² ΡΠ²Π»ΡΡΡΡΡ Π΄ΠΎΠ·Π°ΒΡΠΎΡ ΠΌΡΠΊΠΈ ΠΈ Π²ΠΎΠ΄Ρ, ΡΠ΅ΡΡΠΎΡΠΌΠ΅ΡΠΈΡΠ΅Π»Ρ, ΠΏΡΠ΅ΡΡΡΡΡΠΈΠΉ ΠΊΠΎΡΠΏΡΡ Ρ Π³ΠΎΠ»ΠΎΠ²ΠΊΠΎΠΉ ΠΈ ΠΌΠ°ΡΡΠΈΡΠ°. ΠΠ°ΠΆΠ΄ΡΠΉ ΠΏΡΠ΅ΡΡ ΠΎΠ±ΠΎΡΡΠ΄ΠΎΠ²Π°Π½ ΡΠΈΡΡΠ΅ΠΌΠΎΠΉ Π²Π°ΠΊΡΡΠΌΠΈΡΠΎΠ²Π°Π½ΠΈΡ.
ΠΡΠ΅ΡΡΡ ΡΠ°Π·Π»ΠΈΡΠ°ΡΡΡΡ ΠΊΠΎΠ½ΡΡΡΡΠΊΡΠΈΠ΅ΠΉ Π΄ΠΎΠ·Π°ΡΠΎΡΠ°, ΡΠΈΡΠ»ΠΎΠΌ ΠΊΠ°ΠΌΠ΅Ρ ΡΠ΅ΡΡΠΎΡΠΌΠ΅ΡΠΈΡΠ΅Π»Ρ ΠΈ ΠΈΡ ΡΠ°ΡΠΏΠΎΠ»ΠΎΠΆΠ΅Π½ΠΈΠ΅ΠΌ, ΠΊΠΎΠ»ΠΈΡΠ΅ΡΡΠ²ΠΎΠΌ ΠΏΡΠ΅ΡΡΡΡΡΠΈΡ ΡΠ½Π΅ΠΊΠΎΠ², ΠΊΠΎΠ½ΡΡΡΡΠΊΡΠΈΠ΅ΠΉ ΠΏΡΠ΅ΡΡΡΡΡΠΈΡ Π³ΠΎΠ»ΠΎΠ²ΠΎΠΊ, ΡΠΎΡΠΌΠΎΠΉ ΠΌΠ°ΡΡΠΈΡ ΠΈ ΠΌΠ΅ΡΡΠΎΠΌ Π²Π°ΠΊΡΒΡΠΌΠΈΡΠΎΠ²Π°Π½ΠΈΡ.
ΠΠ»Π°ΡΡΠΈΡΠΈΠΊΠ°ΡΠΈΡ ΠΌΠ°ΠΊΠ°ΡΠΎΠ½Π½ΡΡ ΠΏΡΠ΅ΡΡΠΎΠ² ΠΏΡΠ΅Π΄ΡΡΠ°Π²Π»Π΅Π½Π° Π½Π° ΡΠΈΡΡΠ½ΠΊΠ΅ 1.
Π ΠΈΡ. 1. ΠΠ»Π°ΡΡΠΈΡΠΈΠΊΠ°ΡΠΈΡ ΡΠ½Π΅ΠΊΠΎΠ²ΡΡ ΠΌΠ°ΠΊΠ°ΡΠΎΠ½Π½ΡΡ ΠΏΡΠ΅ΡΡΠΎΠ²
ΠΠ°ΠΊΠ°ΡΠΎΠ½Π½ΡΠΉ ΠΏΡΠ΅ΡΡ ΠΠΠ-2Π
ΠΠΎΠ½ΡΡΡΡΠΊΡΠΈΡ. Π¨Π½Π΅ΠΊΠΎΠ²ΡΠΉ ΠΌΠ°ΠΊΠ°ΡΠΎΠ½Π½ΡΠΉ ΠΏΡΠ΅ΡΡ ΠΠΠ-2Π (ΡΠΈΡ.2) ΡΠΎΡΡΠΎΠΈΡ ΠΈΠ· ΡΠ»Π΅Π΄ΡΡΡΠΈΡ ΠΎΡΠ½ΠΎΠ²Π½ΡΡ ΡΠ·Π»ΠΎΠ²: Π΄ΠΎΠ·ΠΈΡΠΎΠ²ΠΎΡΠ½ΠΎΠ³ΠΎ ΡΡΡΡΠΎΠΉΡΡΠ²Π°, ΡΠ΅ΡΡΠΎΡΠΌΠ΅ΡΠΈΡΠ΅Π»Ρ, ΠΏΡΠ΅ΡΡΡΡΡΠ΅Π³ΠΎ ΠΊΠΎΡΠΏΡΡΠ°, ΠΏΡΠ΅ΡΡΡΡΒΡΠ΅ΠΉ Π³ΠΎΠ»ΠΎΠ²ΠΊΠΈ, ΠΎΠ±Π΄ΡΠ²ΠΎΡΠ½ΠΎΠ³ΠΎ ΡΡΡΡΠΎΠΉΡΡΠ²Π°, ΠΌΠ΅Ρ Π°Π½ΠΈΠ·ΠΌΠ° ΡΠ΅Π·ΠΊΠΈ.
ΠΠΎΠ·ΠΈΡΠΎΠ²ΠΎΡΠ½ΠΎΠ΅ ΡΡΡΡΠΎΠΉΡΡΠ²ΠΎ ΡΠ°ΡΠΏΠΎΠ»ΠΎΠΆΠ΅Π½ΠΎ Π½Π°Π΄ ΡΠ΅ΡΡΠΎΡΠΌΠ΅ΡΠΈΡΠ΅Π»Π΅ΠΌ ΠΈ ΠΈΠΌΠ΅Π΅Ρ ΡΠ½Π΅ΠΊΠΎΠ²ΡΠΉ Π΄ΠΎΠ·Π°ΡΠΎΡ ΠΌΡΠΊΠΈ, ΡΠΎΡΠΎΡΠ½ΡΠΉ Π΄ΠΎΠ·Π°ΡΠΎΡ Π²ΠΎΠ΄Ρ, ΠΏΡΠΈΠ²ΠΎΠ΄ ΠΈ ΡΠΏΠ΅ΒΡΠΈΠ°Π»ΡΠ½ΡΠΉ ΡΠ΅ΡΠ²ΡΡΠ½ΡΠΉ ΡΠ΅Π΄ΡΠΊΡΠΎΡ.
Π¨Π½Π΅ΠΊΠΎΠ²ΡΠΉ Π΄ΠΎΠ·Π°ΡΠΎΡ Π·Π°ΠΊΠ»ΡΡΡΠ½ Π² ΡΠΈΠ»ΠΈΠ½Π΄ΡΠΈΡΠ΅ΡΠΊΠΈΠΉ ΠΊΠΎΡΠΏΡΡ 1 Ρ Π·Π°Π³ΡΡΠ·ΠΎΡΠ½ΡΠΌ ΠΏΠ°ΡΡΡΠ±ΠΊΠΎΠΌ 4 ΠΈ Π½Π°ΠΏΡΠ°Π²Π»ΡΡΡΠΈΠΌ Π»ΠΎΡΠΊΠΎΠΌ 2 Π΄Π»Ρ ΠΏΠΎΡΡΡΠΏΠ»Π΅Π½ΠΈΡ ΠΌΡΠΊΠΈ Π² ΡΠ΅ΡΡΠΎΡΠΌΠ΅ΡΠΈΡΠ΅Π»Ρ. ΠΠ½ΡΡΡΠΈ ΠΊΠΎΡΠΏΡΡΠ° ΡΡΡΠ°Π½ΠΎΠ²Π»Π΅Π½ ΠΎΠ΄Π½ΠΎΠ·Π°Ρ ΠΎΠ΄Π½ΡΠΉ ΡΠ½Π΅ΠΊ 3.
Π ΠΎΡΠΎΡΠ½ΡΠΉ Π΄ΠΎΠ·Π°ΡΠΎΡ Π²ΠΎΠ΄Ρ ΠΈΠΌΠ΅Π΅Ρ Π±Π°ΡΠΎΠΊ 10, Π²Π½ΡΡΡΠΈ ΠΊΠΎΡΠΎΡΠΎΠ³ΠΎ Π½Π° Π²Π°Π»Ρ Π²ΡΠ°ΡΠ°Π΅ΡΡΡ ΠΊΡΡΠ»ΡΡΠ°ΡΠΊΠ° Ρ ΠΊΠ°ΡΠΌΠ°Π½Π°ΠΌΠΈ 11. ΠΠ°ΡΠΌΠ°Π½ ΠΏΡΠΈ Π²ΡΠ°ΡΠ΅Π½ΠΈΠΈ ΠΊΡΡΠ»ΡΡΠ°ΡΠΊΠΈ Π·Π°Ρ Π²Π°ΡΡΠ²Π°Π΅Ρ ΠΎΠΏΡΠ΅Π΄Π΅Π»ΡΠ½Π½ΠΎΠ΅ ΠΊΠΎΠ»ΠΈΡΠ΅ΡΡΠ²ΠΎ Π²ΠΎΠ΄Ρ, ΠΊΠΎΡΠΎΡΠ°Ρ ΡΠ΅ΡΠ΅Π· ΠΎΡΠ²Π΅ΡΡΡΠΈΡ Π²Π°Π»Π° 12 ΡΠ»ΠΈΠ²Π°Π΅ΡΡΡ Π² ΠΎΡΡΠ΅ΠΊ Π±Π°ΡΠΊΠ° 14.ΠΡΡΡΠ΄Π° ΡΠ΅ΡΠ΅Π· ΠΎΡΠ²ΠΎΠ΄ Π²ΠΎΠ΄Π° ΠΏΠΎ ΡΡΡΠ±Π΅ 13 Π½Π°ΠΏΡΠ°Π²Π»ΡΠ΅ΡΡΡ Π² ΡΠ΅ΡΡΠΎΡΠΌΠ΅ΡΠΈΡΠ΅Π»Ρ ΠΏΡΠ΅ΡΡΠ°.
Π’Π΅ΡΡΠΎΡΠΌΠ΅ΡΠΈΡΠ΅Π»Ρ ΠΈΠΌΠ΅Π΅Ρ ΠΎΠ΄Π½ΠΎΠΊΠ°ΠΌΠ΅ΡΠ½ΡΡ ΡΠΌΠΊΠΎΡΡΡ 15 Π΄Π»ΠΈΠ½Π½ΠΎΠΉ 1500ΠΌΠΌ ΠΈΠ· Π»ΠΈΡΡΠΎΠ²ΠΎΠΉ Π½Π΅ΡΠΆΠ°Π²Π΅ΡΡΠ΅ΠΉ ΡΡΠ°Π»ΠΈ. ΠΠ½ΡΡΡΠΈ ΡΡΡΠ°Π½ΠΎΠ²Π»Π΅Π½Ρ Π²Π°Π» 17 Π΄ΠΈΠ°ΠΌΠ΅ΡΡΠΎΠΌ 60 ΠΌΠΌ Ρ ΡΠΊΡΠ΅ΠΏΠ»ΡΠ½Π½ΡΠΌΠΈ Π½Π° Π½ΡΠΌ ΡΠ°Π±ΠΎΡΠΈΠΌΠΈ ΠΎΡΠ³Π°Π½Π°ΠΌΠΈ; Π½ΠΎΠΆ 22 Π΄Π»Ρ ΠΎΡΠΈΡΡΠΊΠΈ ΡΠΎΡΡΠ΅Π²ΠΎΠΉ ΡΡΠ΅Π½ΠΊΠΈ ΠΊΠ°ΠΌΠ΅ΡΡ ΠΎΡ Π½Π°Π»ΠΈΠΏΠ°ΡΡΠ΅Π³ΠΎ ΡΠ΅ΡΡΠ°; ΠΎΠ΄ΠΈΠ½Π½Π°Π΄ΡΠ°ΡΡ ΠΏΠ°Π»ΡΡΠ΅Π² 18 ΠΈ ΠΏΡΡΡ Π»ΠΎΠΏΠ°ΡΠΎΠΊ 16 Π΄Π»Ρ ΠΎΠ±Π΅ΡΠΏΠ΅ΡΠ΅Π½ΠΈΡ Π½Π΅ΠΎΠ±Ρ ΠΎΠ΄ΠΈΠΌΠΎΠ³ΠΎ ΡΡΠΎΠ²Π½Ρ ΡΠ΅ΡΡΠ° Π² ΠΊΠ°ΠΌΠ΅ΡΠ΅, Π΅Π³ΠΎ ΠΏΠ΅ΡΠ΅ΡΠ°Π±ΠΎΡΠΊΠΈ ΠΈ ΠΏΠ΅ΡΠ΅ΠΌΠ΅ΡΠ΅Π½ΠΈΡ Π²Π½ΡΡΡΠΈ ΠΊΠ°ΠΌΠ΅ΡΡ; ΡΠΎΠ»ΠΊΠ°ΡΠ΅Π»Ρ 21 Π΄Π»Ρ ΠΎΠ±Π΅ΡΠΏΠ΅ΡΠ΅Π½ΠΈΡ ΠΏΠΎΡΡΡΠΏΠ»Π΅Π½ΠΈΡ ΡΠ΅ΡΡΠ° Π² ΠΏΡΠ΅ΡΡΡΡΡΠΈΠΉ ΠΊΠΎΡΠΏΡΡ.
ΠΠΎΠΏΠ°ΡΠΊΠΈ Π½Π° Π²Π°Π»Ρ ΡΠ΅ΡΡΠΎΡΠΌΠ΅ΡΠΈΡΠ΅Π»Ρ ΡΡΡΠ°Π½Π°Π²Π»ΠΈΠ²Π°ΡΡ ΠΏΠΎΠ΄ ΠΎΠΏΡΠ΅Π΄Π΅Π»ΡΠ½Π½ΡΠΌ ΡΠ³Π»ΠΎΠΌ, ΠΊΠΎΡΠΎΡΡΠΉ Π²ΡΠ±ΠΈΡΠ°Π΅ΡΡΡ ΠΏΡΠΈ ΠΏΡΡΠΊΠ΅ ΠΏΡΠ΅ΡΡΠ°. ΠΠΏΡΠΈΠΌΠ°Π»ΡΠ½ΡΠΉ ΡΠ³ΠΎΠ» Π½Π°ΠΊΠ»ΠΎΠ½Π° ΠΏΠ»ΠΎΡΠΊΠΎΡΡΠΈ ΠΏΠ΅ΡΠ²ΡΡ Π΄Π²ΡΡ Π»ΠΎΠΏΠ°ΡΠΎΠΊ (ΠΎΡ ΠΌΠ΅ΡΡΠ° Π·Π°Π³ΡΡΠ·ΠΊΠΈ) ΠΊ ΠΎΡΠΈ Π²Π°Π»Π° 60ΠΎΠ‘, ΡΠ»Π΅Π΄ΡΡΡΠΈΡ ΡΡΡΡ β 40ΠΎΠ‘.
ΠΠΎΠ»ΠΈΡΠ΅ΡΡΠ²ΠΎ ΡΠ΅ΡΡΠ°, ΠΏΠΎΡΡΡΠΏΠ°ΡΡΠ΅Π³ΠΎ ΠΈΠ· ΠΌΠ΅ΡΠΈΠ»ΡΠ½ΠΎΠΉ ΠΊΠ°ΠΌΠ΅ΡΡ Π² ΠΏΡΠ΅ΡΡΡΡΡΠΈΠΉ ΠΊΠΎΡΠΏΡΡ, ΡΠ΅Π³ΡΠ»ΠΈΡΡΠ΅ΡΡΡ Ρ ΠΏΠΎΠΌΠΎΡΡΡ Π·Π°ΡΠ»ΠΎΠ½ΠΊΠΈ 20, Π΄Π²ΠΈΠΆΠ΅Π½ΠΈΠ΅ ΠΊΠΎΡΠΎΡΠΎΠΉ ΠΎΡΡΡΠ΅ΡΡΠ²Π»ΡΠ΅ΡΡΡ ΠΏΡΠΈ ΠΏΠΎΠΌΠΎΡΠΈ Π²ΠΈΠ½ΡΠ° Ρ ΠΌΠ°Ρ ΠΎΠ²ΠΈΡΠΊΠΎΠΌ 26.
Π’Π΅ΡΡΠΎΡΠΌΠ΅ΡΠΈΡΠ΅Π»Ρ Π·Π°ΠΊΡΡΠ²Π°Π΅ΡΡΡ ΡΠ΅ΡΡΡΡΠ°ΡΠΎΠΉ ΠΊΡΡΡΠΊΠΎΠΉ 19, ΡΠ±Π»ΠΎΠΊΠΈΡΠΎΠ²Π°Π½Π½ΠΎΠΉ Ρ ΠΊΡΠ»Π°ΡΠΊΠΎΠ²ΠΎΠΉ ΠΌΡΡΡΠΎΠΉ Π²Π°Π»Π° ΡΠ΅ΡΡΠΎΡΠΌΠ΅ΡΠΈΡΠ΅Π»Ρ. ΠΡΠΊΡΡΡΡ ΠΊΡΡΡΠΊΡ ΠΌΠΎΠΆΠ½ΠΎ ΠΏΠΎΡΠ»Π΅ Π²ΡΠΊΠ»ΡΡΠ΅Π½ΠΈΡ ΡΠ»Π΅ΠΊΡΡΠΎΠ΄Π²ΠΈΠ³Π°ΡΠ΅Π»Ρ ΠΏΡΠΈΠ²ΠΎΠ΄Π° ΠΈΠ»ΠΈ ΡΠ°Π·ΡΠ΅Π΄ΠΈΠ½Π΅Π½ΠΈΡ ΠΌΡΡΡΡ.
ΠΡΠ°ΡΠ΅Π½ΠΈΠ΅ Π²Π°Π»Π° ΡΠ΅ΡΡΠΎΡΠΌΠ΅ΡΠΈΡΠ΅Π»Ρ ΠΎΡΡΡΠ΅ΡΡΠ²Π»ΡΠ΅ΡΡΡ ΠΎΡ ΡΠ»Π΅ΠΊΡΡΠΎΠ΄Π²ΠΈΠ³Π°ΡΠ΅Π»Ρ 23 Ρ ΡΠ°ΡΡΠΎΡΠΎΠΉ Π²ΡΠ°ΡΠ΅Π½ΠΈΡ 1450 ΠΎΠ±/ΠΌΠΈΠ½, ΠΊΠ»ΠΈΠ½ΠΎΡΠ΅ΠΌΡΠ½Π½ΠΎΠΉ ΠΏΠ΅ΡΠ΅Π΄Π°ΡΠΈ, ΡΡΡΡ ΡΡΡΠΏΠ΅Π½ΡΠ°ΡΠΎΠ³ΠΎ ΡΠΈΠ»ΠΈΠ½Π΄ΡΠΈΡΠ΅ΡΠΊΠΎΠ³ΠΎ ΡΠ΅Π΄ΡΠΊΡΠΎΡΠ°. ΠΠ°Π» ΡΠ΅ΡΡΠΎΡΠΌΠ΅ΡΠΈΡΠ΅Π»Ρ ΡΠΎΠ΅Π΄ΠΈΠ½ΡΠ½ Ρ Π²Π°Π»ΠΎΠΌ ΡΠ΅Π΄ΡΠΊΡΠΎΡΠ° Π³Π»Π°Π²Π½ΠΎΠ³ΠΎ ΠΏΡΠΈΠ²ΠΎΠ΄Π° ΠΊΡΠ»Π°ΡΠΊΠΎΠ²ΠΎΠΉ ΠΌΡΡΡΠΎΠΉ 24 Ρ Π±Π»ΠΎΠΊΠΈΡΠΎΠ²ΠΊΠΎΠΉ.
ΠΡΠ΅ΡΡΡΡΡΠΈΠΉ ΠΊΠΎΡΠΏΡΡ 27 ΠΏΡΠ΅Π΄ΡΡΠ°Π²Π»ΡΠ΅Ρ ΡΠΎΠ±ΠΎΠΉ ΡΠΈΠ»ΠΈΠ½Π΄ΡΠΈΡΠ΅ΡΠΊΡΡ ΡΡΡΠ±Ρ Ρ Π΄Π²ΡΠΌΡ ΡΠ»Π°Π½ΡΠ°ΠΌΠΈ Π½Π° ΠΊΠΎΠ½ΡΠ°Ρ . ΠΠ΄Π½ΠΈΠΌ ΡΠ»Π°Π½ΡΠ΅ΠΌ ΠΊΠΎΡΠΏΡΡ ΠΊΡΠ΅ΠΏΠΈΡΡΡ ΠΊ ΡΠ΅Π΄ΡΠΊΡΠΎΡΡ Π³Π»Π°Π²Π½ΠΎΠ³ΠΎ ΠΏΡΠΈΠ²ΠΎΠ΄Π°, Π²ΡΠΎΡΡΠΌ β ΠΊ ΠΏΡΠ΅ΡΡΡΡΡΠ΅ΠΉ Π³ΠΎΠ»ΠΎΠ²ΠΊΠ΅. ΠΠ½ΡΡΡΠΈ ΠΊΠΎΡΠΏΡΡΠ° ΡΡΡΠ°Π½ΠΎΠ²Π»Π΅Π½ ΠΎΠ΄Π½ΠΎΠ·Π°Ρ ΠΎΠ΄Π½ΡΠΉ ΠΏΡΠ΅ΡΡΡΡΡΠΈΠΉ ΡΠ½Π΅ΠΊ 28 Π΄Π»ΠΈΠ½Π½ΠΎΠΉ 1400 ΠΌΠΌ, Π΄ΠΈΠ°ΠΌΠ΅ΡΡΠΎΠΌ 120 ΠΌΠΌ, Ρ ΡΠ°Π³ΠΎΠΌ Π²ΠΈΡΠΊΠ° 100 ΠΌΠΌ Ρ ΡΡΡΡ Π·Π°Ρ ΠΎΠ΄Π½ΡΠΌ Π·Π²Π΅Π½ΠΎΠΌ 32 Π½Π° ΠΊΠΎΠ½ΡΠ΅. Π ΡΡΠ΅Π΄Π½Π΅ΠΉ ΡΠ°ΡΡΠΈ ΡΠ½Π΅ΠΊ ΠΈΠΌΠ΅Π΅Ρ ΡΠ°Π·ΡΡΠ² Π²ΠΈΠ½ΡΠΎΠ²ΠΎΠΉ Π»ΠΎΠΏΠ°ΡΡΠΈ, Π² ΠΊΠΎΡΠΎΡΠΎΠΌ Π²ΡΡΡΠΎΠ΅Π½Π° ΡΠ°ΠΉΠ±Π° 29, ΠΎΠ±Π΅ΡΠΏΠ΅ΡΠΈΠ²Π°ΡΡΠ°Ρ Π΄Π²ΠΈΠΆΠ΅Π½ΠΈΠ΅ ΡΠ΅ΡΡΠ° ΠΏΠΎ ΠΏΠ΅ΡΠ΅ΠΏΡΡΠΊΠ½ΠΎΠΌΡ ΠΊΠ°Π½Π°Π»Ρ 30, ΠΈΠ· ΠΊΠΎΡΠΎΡΠΎΠ³ΠΎ ΡΠ΅ΡΠ΅Π· Π²Π°ΠΊΡΡΠΌΠ½ΡΠΉ ΠΊΠ»Π°ΠΏΠ°Π½ Ρ ΠΏΠΎΠΌΠΎΡΡΡ Π²Π°ΠΊΡΡΠΌΠ½ΠΎΠ³ΠΎ Π½Π°ΡΠΎΡΠ° ΠΎΡΡΠ°ΡΡΠ²Π°Π΅ΡΡΡ Π²ΠΎΠ·Π΄ΡΡ ΠΈΠ· ΠΏΡΠΎΡ ΠΎΠ΄ΡΡΠ΅Π³ΠΎ ΡΠ΅ΡΡΠ°. ΠΠ° Π²Π½ΡΡΡΠ΅Π½Π½Π΅ΠΉ ΡΡΠΎΡΠΎΠ½Π΅ ΠΏΡΠ΅ΡΡΡΡΡΠ΅Π³ΠΎ ΠΊΠΎΡΠΏΡΡΠ° ΠΏΠΎ Π²ΡΠ΅ΠΉ Π΅Π³ΠΎ Π΄Π»ΠΈΠ½Π΅ ΡΠ°ΡΠΏΠΎΠ»ΠΎΠΆΠ΅Π½Ρ ΠΊΠ°Π½Π°Π²ΠΊΠΈ 33, ΡΠΌΠ΅Π½ΡΡΠ°ΡΡΠΈΠ΅ ΠΏΡΠΎΠ²ΠΎΡΠ°ΡΠΈΠ²Π°Π½ΠΈΠ΅ ΡΠ΅ΡΡΠ°. Π ΠΊΠΎΠ½ΡΠ΅ ΠΏΡΠ΅ΡΡΡΡΡΠ΅Π³ΠΎ ΠΊΠΎΡΠΏΡΡΠ° ΡΡΡΠ°Π½ΠΎΠ²Π»Π΅Π½Π° ΡΠ²Π°ΡΠ½Π°Ρ Π²ΠΎΠ΄ΡΠ½Π°Ρ ΡΡΠ±Π°ΡΠΊΠ° 31, ΠΏΠΎ ΠΊΠΎΡΠΎΡΠΎΠΉ ΡΠΈΡΠΊΡΠ»ΠΈΡΡΠ΅Ρ Π²ΠΎΠ΄ΠΎΠΏΡΠΎΠ²ΠΎΠ΄Π½Π°Ρ Π²ΠΎΠ΄Π°.
ΠΡΠ΅ΡΡΡΡΡΠ°Ρ Π³ΠΎΠ»ΠΎΠ²ΠΊΠ° 36 ΠΏΡΠ΅Π΄Π½Π°Π·Π½Π°ΡΠ΅Π½Π° Π΄Π»Ρ ΡΡΡΠ°Π½ΠΎΠ²ΠΊΠΈ ΠΊΡΡΠ³Π»ΠΎΠΉ ΠΌΠ°ΡΡΠΈΡΡ 37 ΠΈ ΠΏΡΠ΅Π΄ΡΡΠ°Π²Π»ΡΠ΅Ρ ΡΠΎΠ±ΠΎΠΉ Π»ΠΈΡΡΡ ΠΊΠΎΠ½ΡΡΡΡΠΊΡΠΈΡ ΠΊΡΠΏΠΎΠ»ΠΎΠΎΠ±ΡΠ°Π·Π½ΠΎΠΉ ΡΠΎΡΠΌΡ. ΠΠ° ΡΠΎΡΡΠ΅Π²ΠΎΠΉ Π²Π΅ΡΡ Π½Π΅ΠΉ ΡΠ°ΡΡΠΈ Π³ΠΎΠ»ΠΎΠ²ΠΊΠΈ ΠΈΠΌΠ΅Π΅ΡΡΡ ΠΎΡΠ²Π΅ΡΡΡΠΈΠ΅, Π·Π°ΠΊΡΡΡΠΎΠ΅ ΡΠ»Π°Π½ΡΠ΅ΠΌ 34, ΠΊΠΎΡΠΎΡΠΎΠ΅ ΡΠ»ΡΠΆΠΈΡ Π΄Π»Ρ Π²ΡΠ΅ΠΌΠΊΠΈ ΡΠ½Π΅ΠΊΠ° ΠΈΠ· ΠΏΡΠ΅ΡΡΡΡΡΠ΅Π³ΠΎ ΠΊΠΎΡΠΏΡΡΠ° Π±Π΅Π· ΡΠ½ΡΡΠΈΡ Π³ΠΎΠ»ΠΎΠ²ΠΊΠΈ. ΠΠ° Π³ΠΎΠ»ΠΎΠ²ΠΊΠ΅ ΡΡΡΠ°Π½ΠΎΠ²Π»Π΅Π½ ΠΌΠ°Π½ΠΎΠΌΠ΅ΡΡ 35 Π΄Π»Ρ ΠΊΠΎΠ½ΡΡΠΎΠ»Ρ Π΄Π°Π²Π»Π΅Π½ΠΈΡ ΠΏΡΠ΅ΡΡΠΎΠ²Π°Π½ΠΈΡ.ΠΠ±Π΄ΡΠ²ΠΎΡΠ½ΠΎΠ΅ ΡΡΡΡΠΎΠΉΡΡΠ²ΠΎ 38 ΡΠ»ΡΠΆΠΈΡ Π΄Π»Ρ ΠΏΡΠ΅Π΄Π²Π°ΡΠΈΡΠ΅Π»ΡΠ½ΠΎΠΉ ΠΏΠΎΠ΄ΡΡΡΠΊΠΈ ΠΌΠ°ΠΊΠ°ΡΠΎΠ½Π½ΡΡ ΠΈΠ·Π΄Π΅Π»ΠΈΠΉ, Π²ΡΡ ΠΎΠ΄ΡΡΠΈΡ ΠΈΠ· ΡΠΈΠ»ΡΠ΅Ρ ΠΌΠ°ΡΡΠΈΡΡ. Π£ΡΡΡΠΎΠΉΡΡΠ²ΠΎ ΡΠΎΡΡΠΎΠΈΡ ΠΈΠ· ΡΠ΅Π½ΡΡΠΎΠ±Π΅ΠΆΠ½ΠΎΠ³ΠΎ Π²Π΅Π½ΡΠΈΠ»ΡΡΠΎΡΠ° Ρ ΡΠ»Π΅ΠΊΡΡΠΎΠ΄Π²ΠΈΠ³Π°ΡΠ΅Π»Π΅ΠΌ, ΠΎΠ±Π΄ΡΠ²ΠΎΡΠ½ΠΎΠ³ΠΎ ΠΊΠΎΠ»ΡΡΠ° Ρ ΠΎΡΠ²Π΅ΡΡΡΠΈΡΠΌΠΈ Π΄ΠΈΠ°ΠΌΠ΅ΡΡΠΎΠΌ 8ΠΌΠΌ. Π΄Π»Ρ ΠΏΡΠΎΡ ΠΎΠ΄Π° Π²ΠΎΠ·Π΄ΡΡ Π° ΠΏΠΎ Π΅Π³ΠΎ Π²Π½ΡΡΡΠ΅Π½Π½Π΅ΠΉ ΡΠ°ΡΡΠΈ. ΠΠ±Π΄ΡΠ²ΠΎΡΠ½ΠΎΠ΅ ΠΊΠΎΠ»ΡΡΠΎ ΡΡΡΠ°Π½Π°Π²Π»ΠΈΠ²Π°ΡΡ ΠΏΠΎΠ΄ ΠΌΠ°ΡΡΠΈΡΠ΅ΠΉ. Π Π·Π°Π²ΠΈΡΠΈΠΌΠΎΡΡΠΈ ΠΎΡ ΡΠΊΠΎΡΠΎΡΡΠΈ ΠΏΡΠ΅ΡΡΠΎΠ²Π°Π½ΠΈΡ ΠΏΡΠΎΠ΄ΠΎΠ»ΠΆΠΈΡΠ΅Π»ΡΠ½ΠΎΡΡΡ Π½Π°Ρ ΠΎΠΆΠ΄Π΅Π½ΠΈΡ ΠΈΠ·Π΄Π΅Π»ΠΈΠΉ Π² Π·ΠΎΠ½Π΅ ΠΎΠ±Π΄ΡΠ²ΠΊΠΈ ΠΏΡΠΈ ΠΏΠΎΠ΄Π²Π΅ΡΠ½ΠΎΠΌ ΡΠΏΠΎΡΠΎΠ±Π΅ ΡΠ΅Π·ΠΊΠΈ 5-6 Ρ. ΠΠ° ΡΡΠΎ Π²ΡΠ΅ΠΌΡ Π½Π° ΠΏΠΎΠ²Π΅ΡΡ Π½ΠΎΡΡΠΈ ΠΈΠ·Π΄Π΅Π»ΠΈΠΉ ΡΡΠΏΠ΅Π²Π°Π΅Ρ ΠΎΠ±ΡΠ°Π·ΠΎΠ²ΡΠ²Π°ΡΡΡΡ ΠΏΠΎΠ΄ΡΡΡΠ΅Π½Π½Π°Ρ ΠΊΠΎΡΠΎΡΠΊΠ°, ΠΊΠΎΡΠΎΡΠ°Ρ ΠΏΡΠ΅Π΄ΠΎΡΠ²ΡΠ°ΡΠ°Π΅Ρ ΡΠΊΠ»Π΅ΠΈΠ²Π°Π½ΠΈΠ΅ ΠΌΠ°ΠΊΠ°ΡΠΎΠ½Π½ΡΡ ΠΈΠ·Π΄Π΅Π»ΠΈΠΉ ΠΏΡΠΈ ΠΈΡ Π΄Π°Π»ΡΠ½Π΅ΠΉΡΠ΅ΠΉ ΡΠ΅Π·ΠΊΠ΅ ΠΈΠ»ΠΈ ΡΡΠ°Π½ΡΠΏΠΎΡΡΠΈΡΠΎΠ²ΠΊΠ΅. ΠΠ±Π΄ΡΠ²ΠΊΠ° Π²ΠΎΠ·Π΄ΡΡ ΠΎΠΌ ΠΌΠ°ΠΊΠ°ΡΠΎΠ½Π½ΡΡ ΠΏΡΡΠ΄Π΅ΠΉ ΠΌΠΎΠΆΠ΅Ρ ΠΎΡΡΡΠ΅ΡΡΠ²Π»ΡΡΡΡΡ Π΄Π²ΡΠΌΡ ΡΠΏΠΎΡΠΎΠ±Π°ΠΌΠΈ: Π½Π°Π³Π½Π΅ΡΠ°Π½ΠΈΠ΅ΠΌ ΠΈ Π²ΡΠ°ΡΡΠ²Π°Π½ΠΈΠ΅ΠΌ Π²ΠΎΠ·Π΄ΡΡ Π° ΡΠ΅ΡΠ΅Π· ΠΎΡΠ²Π΅ΡΡΡΠΈΡ Π² ΠΊΠΎΠ»ΡΡΠ΅Π²ΠΎΠΌ ΡΠΎΠΏΠ»Π΅.
Π ΠΈΡ. 2. Π¨Π½Π΅ΠΊΠΎΠ²ΡΠΉ ΠΌΠ°ΠΊΠ°ΡΠΎΠ½Π½ΡΠΉ ΠΏΡΠ΅ΡΡ ΠΠΠ-2Π:
1- ΠΊΠΎΡΠΏΡΡ Π΄ΠΎΠ·Π°ΡΠΎΡΠ°; 2- Π»ΠΎΡΠΎΠΊ; 3,28 — ΡΠ½Π΅ΠΊΠΈ; 4- ΠΏΠ°ΡΡΡΠ±ΠΎΠΊ; 5 — ΡΠ»Π΅ΠΊΡΡΠΎΠ΄Π²ΠΈΠ³Π°ΡΠ΅Π»Ρ; 6-Ρ ΡΠ°ΠΏΠΎΠ²ΠΎΠ΅ ΠΊΠΎΠ»Π΅ΡΠΎ; 7- ΡΡΠΊΠΎΡΡΠΊΠ°; 8- Π΄Π²ΡΠΏΠ»Π΅ΡΠΈΠΉ ΡΡΡΠ°Π³; 9- ΠΏΠΎΠ»ΡΠΊΠΎΠ»ΡΡΠΎ; 10,14 — Π±Π°ΡΠΊΠΈ; 11- ΠΊΠ°ΡΠΌΠ°Π½Ρ ΠΊΡΡΠ»ΡΡΠ°ΡΠΊΠΈ; 12,17 — Π²Π°Π»Ρ; 13 — ΡΡΡΠ±Π°; 15 β ΠΎΠ΄Π½ΠΎΠΊΠ°ΠΌΠ΅ΡΠ½Π°Ρ ΡΠΌΠΊΠΎΡΡΡ; 16 — Π»ΠΎΠΏΠ°ΡΠΊΠ°; 18- ΠΏΠ°Π»Π΅Ρ; 19- ΠΊΡΡΡΠΊΠ°; 20 — Π·Π°ΡΠ»ΠΎΠ½ΠΊΠ°; 21 — ΡΠΎΠ»ΠΊΠ°ΡΠ΅Π»Ρ; 22- Π½ΠΎΠΆ; 23- ΡΠ»Π΅ΠΊΡΡΠΎΠ΄Π²ΠΈΠ³Π°ΡΠ΅Π»Ρ; 24 -ΠΌΡΡΡΠ°; 25- Π·Π²ΡΠ·Π΄ΠΎΡΠΊΠΈ; 26- ΠΌΠ°Ρ ΠΎΠ²ΠΈΡΠΎΠΊ; 27- ΠΏΡΠ΅ΡΡΡΡΡΠΈΠΉ ΠΊΠΎΡΠΏΡΡ; 29- ΡΠ°ΠΉΠ±Π°; 30- ΠΏΠ΅ΡΠ΅ΠΏΡΡΠΊΠ½ΠΎΠΉ ΠΊΠ°Π½Π°Π»; 31- Π²ΠΎΠ΄ΡΠ½Π°Ρ ΡΡΠ±Π°ΡΠΊΠ°;32- ΡΡΡΡ Π·Π°Ρ ΠΎΠ΄Π½ΠΎΠ΅ Π·Π²Π΅Π½ΠΎ;33- ΠΊΠ°Π½Π°Π²ΠΊΠΈ; 34- ΡΠ»Π°Π½Π΅Ρ; 35- ΠΌΠ°Π½ΠΎΠΌΠ΅ΡΡ; 36-ΠΏΡΠ΅ΡΡΡΡΡΠ°Ρ Π³ΠΎΠ»ΠΎΠ²ΠΊΠ°;37- ΠΌΠ°ΡΡΠΈΡΠ°, 38 — ΠΎΠ±Π΄ΡΠ²ΠΎΡΠ½ΠΎΠ΅ ΡΡΡΡΠΎΠΉΡΡΠ²ΠΎ.
ΠΡΠΈΠ½ΡΠΈΠΏ ΡΠ°Π±ΠΎΡΡ. ΠΡΠΊΠ° ΡΠ°ΠΌΠΎΡΠ΅ΠΊΠΎΠΌ Π½Π΅ΠΏΡΠ΅ΡΡΠ²Π½ΠΎ ΠΈΠ· Π±ΡΠ½ΠΊΠ΅ΡΠ° ΠΏΠΎΡΡΡΠΏΠ°Π΅Ρ Π² Π΄ΠΎΠ·Π°ΡΠΎΡ, ΠΈΠ· ΠΊΠΎΡΠΎΡΠΎΠ³ΠΎ Π²ΡΠ°ΡΠ°ΡΡΠΈΠΌΡΡ ΡΠ½Π΅ΠΊΠΎΠΌ ΠΏΠΎΠ΄Π°Π΅ΡΡΡ Π² ΠΊΠΎΡΡΡΠΎ ΡΠ΅ΡΡΠΎΡΠΌΠ΅ΡΠΈΡΠ΅Π»Ρ. ΠΠ΄Π½ΠΎΠ²ΡΠ΅ΠΌΠ΅Π½Π½ΠΎ ΠΏΠΎΠ΄ΠΎΠ³ΡΠ΅ΡΠ°Ρ Π²ΠΎΠ΄Π° ΡΠ΅ΠΌΠΏΠ΅ΡΠ°ΡΡΡΠΎΠΉ 40β60Β°Π‘ ΠΈΠ· Π΄ΠΎΠ·Π°ΡΠΎΡΠ° ΠΏΠΎ ΡΡΡΠ±Π΅ ΠΏΠΎΡΡΡΠΏΠ°Π΅Ρ Π² ΡΠ΅ΡΡΠΎΡΠΌΠ΅ΡΠΈΡΠ΅Π»Ρ ΡΡΠ΄Π°, Π³Π΄Π΅ ΠΏΠΎΠ΄Π°Π΅ΡΡΡ ΠΌΡΠΊΠ°. Π Π·Π°Π²ΠΈΡΠΈΠΌΠΎΡΡΠΈ ΠΎΡ Π²Π»Π°ΠΆΠ½ΠΎΡΡΠΈ ΠΌΡΠΊΠΈ ΡΠ°ΡΡ ΠΎΠ΄ Π²ΠΎΠ΄Ρ ΡΠΎΡΡΠ°Π²Π»ΡΠ΅Ρ 80β90 Π»/Ρ. ΠΡΠΈ Π½ΠΎΡΠΌΠ°Π»ΡΒΠ½ΠΎΠΉ ΡΠ°Π±ΠΎΡΠ΅ ΠΏΡΠ΅ΡΡΠ° ΡΠ΅ΡΡΠΎ Π΄ΠΎΠ»ΠΆΠ½ΠΎ Π·Π°ΠΏΠΎΠ»Π½ΡΡΡ 2/Π· ΠΎΠ±ΡΠ΅ΠΌΠ° ΠΊΠΎΡΡΡΠ° ΠΈ ΠΈΠΌΠ΅ΡΡ Π½Π΅Π±ΠΎΠ»ΡΡΠΎΠΉ ΡΠΊΠ»ΠΎΠ½ ΠΏΠΎ Π½Π°ΠΏΡΠ°Π²Π»Π΅Π½ΠΈΡ ΠΊ Π²ΡΡ ΠΎΠ΄Π½ΠΎΠΌΡ ΠΎΡΠ²Π΅ΡΡΡΠΈΡ.
ΠΠ΅ΠΎΠ±Ρ ΠΎΠ΄ΠΈΠΌΡΠΉ ΡΡΠΎΠ²Π΅Π½Ρ Π·Π°ΠΏΠΎΠ»Π½Π΅Π½ΠΈΡ ΠΊΠΎΡΡΡΠ° ΡΠ΅ΡΡΠΎΠΌ Π΄ΠΎΡΡΠΈΠ³Π°Π΅ΡΡΡ ΡΠ΅Π³ΡΒΠ»ΠΈΡΠΎΠ²Π°Π½ΠΈΠ΅ΠΌ Π½Π°ΠΊΠ»ΠΎΠ½Π° ΠΏΠ»ΠΎΡΠΊΠΎΡΡΠΈ ΠΊΠΎΠ½ΡΠΎΠ² Π»ΠΎΠΏΠ°ΡΠΎΠΊ ΠΊ ΠΎΡΠΈ Π²Π°Π»Π°, ΠΊΠΎΡΠΎΡΡΠ΅ ΠΎΡΒΠ±ΡΠ°ΡΡΠ²Π°ΡΡ ΠΎΠΏΡΠ΅Π΄Π΅Π»Π΅Π½Π½ΡΡ ΡΠ°ΡΡΡ ΠΊΠΎΠΌΠΎΡΠΊΠΎΠ² ΡΠ΅ΡΡΠ° Π² Π½Π°ΠΏΡΠ°Π²Π»Π΅Π½ΠΈΠΈ ΠΎΡ Π²ΡΡ ΠΎΠ΄ΒΠ½ΠΎΠ³ΠΎ ΠΎΡΠ²Π΅ΡΡΡΠΈΡ ΠΊ Π΄ΠΎΠ·Π°ΡΠΎΡΠ°ΠΌ. ΠΡΠ±ΡΠ°ΡΡΠ²Π°Π½ΠΈΠ΅ ΡΠ΅ΡΡΠ° Π² ΠΎΠ±ΡΠ°ΡΠ½ΠΎΠΌ Π½Π°ΠΏΡΠ°Π²Π»Π΅ΒΠ½ΠΈΠΈ Π² ΠΎΠΏΡΠΈΠΌΠ°Π»ΡΠ½ΡΡ ΡΠ°Π·ΠΌΠ΅ΡΠ°Ρ Π½Π΅ΠΎΠ±Ρ ΠΎΠ΄ΠΈΠΌΠΎ Π΄Π»Ρ ΠΎΠ±Π΅ΡΠΏΠ΅ΡΠ΅Π½ΠΈΡ Π½ΠΎΡΠΌΠ°Π»ΡΠ½ΠΎΠΉ ΡΠΈΡΠΊΡΠ»ΡΡΠΈΠΈ ΡΠ΅ΡΡΠ°, ΡΡΠΎ ΡΠΏΠΎΡΠΎΠ±ΡΡΠ²ΡΠ΅Ρ Π½Π°Π±ΡΡ Π°Π½ΠΈΡ ΠΊΠ»Π΅ΠΉΠΊΠΎΠ²ΠΈΠ½Ρ ΠΈ Π»ΡΡΡΠ΅ΠΉ ΠΏΡΠΎΡΠ°Π±ΠΎΡΠΊΠ΅ ΡΠ΅ΡΡΠ° Π»ΠΎΠΏΠ°ΡΠΊΠ°ΠΌΠΈ ΠΈ ΠΏΠ°Π»ΡΡΠ°ΠΌΠΈ.
ΠΠ°ΠΌΠ΅ΡΠ΅Π½Π½Π°Ρ Π² Π²ΠΈΠ΄Π΅ ΠΊΠΎΠΌΠΎΡΠΊΠΎΠ² ΠΈ ΠΊΡΡΠΏΠΈΠ½ΠΎΠΊ ΡΠ΅ΡΡΠΎΠΎΠ±ΡΠ°Π·Π½Π°Ρ ΠΌΠ°ΡΡΠ° ΠΈΠ· ΠΊΠΎΡΡΡΠ° ΡΠΌΠ΅ΡΠΈΡΠ΅Π»Ρ ΡΠ΅ΡΠ΅Π· ΠΎΡΠ²Π΅ΡΡΡΠΈΠ΅ Π² Π½ΠΈΠΆΠ½Π΅ΠΉ ΡΠ°ΡΡΠΈ Π½Π°ΠΏΡΠ°Π²Π»ΡΠ΅ΡΡΡ Π² ΠΏΡΠ΅ΡΒΡΡΡΡΠΈΠΉ ΠΊΠΎΡΠΏΡΡ. ΠΡΠΈ ΡΡΠΎΠΌ, ΡΠ΅Π³ΡΠ»ΠΈΡΡΡ Π·Π°ΡΠ»ΠΎΠ½ΠΊΠΎΠΉ ΡΠ°Π·ΠΌΠ΅Ρ Π²ΡΡ ΠΎΠ΄Π½ΠΎΠ³ΠΎ ΠΎΡΒΠ²Π΅ΡΡΡΠΈΡ, ΠΌΠΎΠΆΠ½ΠΎ ΠΈΠ·ΠΌΠ΅Π½ΡΡΡ ΠΊΠΎΠ»ΠΈΡΠ΅ΡΡΠ²ΠΎ ΡΠ΅ΡΡΠ°, ΠΏΠΎΠ΄Π°Π²Π°Π΅ΠΌΠΎΠ³ΠΎ Π² ΠΏΡΠ΅ΡΡΡΡΡΠΈΠΉ ΠΊΠΎΡΠΏΡΡ, ΠΈ ΡΠ΅ΠΌ ΡΠ°ΠΌΡΠΌ ΠΈΠ·ΠΌΠ΅Π½ΡΡΡ ΠΏΡΠΎΠΈΠ·Π²ΠΎΠ΄ΠΈΡΠ΅Π»ΡΠ½ΠΎΡΡΡ ΠΏΡΠ΅ΡΡΠ°. Π ΠΏΡΠ΅ΡΡΡΡΡΠ΅ΠΌ ΠΊΠΎΡΠΏΡΡΠ΅ ΡΠ΅ΡΡΠΎ ΠΏΠΎΡΡΡΠΏΠ°Π΅Ρ Π² ΠΏΠ΅ΡΠ΅ΠΏΡΡΠΊΠ½ΠΎΠΉ ΠΊΠ°Π½Π°Π», Π³Π΄Π΅ ΠΈΠ· Π½Π΅Π³ΠΎ ΡΠ΅ΡΠ΅Π· Π²Π°ΠΊΡΡΠΌ-ΠΊΠ»Π°ΠΏΠ°Π½ ΡΠ΄Π°Π»ΡΡΡΡΡ Π²ΠΎΠ·Π΄ΡΡ ΠΈ ΠΏΠ°ΡΡ Π²ΠΎΠ΄Ρ. ΠΠ· ΠΏΠ΅ΡΠ΅ΠΏΡΡΠΊΠ½ΠΎΠ³ΠΎ ΠΊΠ°Π½Π°Π»Π° ΡΠ΅ΡΡΠΎ ΠΏΡΠΎΒΡ ΠΎΠ΄ΠΈΡ ΡΠΊΠ²ΠΎΠ·Ρ ΡΠ΅ΡΡΡΠΊΡ Π² ΠΏΡΠ΅ΡΡΡΡΡΠΈΠΉ ΠΊΠΎΡΠΏΡΡ, Π·Π°Ρ Π²Π°ΡΡΠ²Π°Π΅ΡΡΡ Π²ΠΈΡΠΊΠ°ΠΌΠΈ ΡΠ½Π΅ΠΊΠ°, Π½Π°Π³Π½Π΅ΡΠ°Π΅ΡΡΡ Π² Π³ΠΎΠ»ΠΎΠ²ΠΊΡ ΠΈ Π·Π°ΡΠ΅ΠΌ ΠΏΡΠΎΠ΄Π°Π²Π»ΠΈΠ²Π°Π΅ΡΡΡ ΡΠ΅ΡΠ΅Π· ΡΠΎΡΠΌΡΡΡΠΈΠ΅ ΠΎΡΠ²Π΅ΡΡΡΠΈΡ ΠΌΠ°ΡΡΠΈΡΡ. ΠΡΡ ΠΎΠ΄ΡΡΠΈΠ΅ ΠΈΠ· ΠΌΠ°ΡΡΠΈΡΡ ΠΎΡΡΠΎΡΠΌΠΎΠ²Π°Π½Π½ΡΠ΅ ΠΌΠ°ΠΊΠ°ΡΠΎΠ½Π½ΡΠ΅ ΠΈΠ·Π΄Π΅Π»ΠΈΡ ΠΏΡΠΎΡ ΠΎΒΠ΄ΡΡ ΠΎΠ±Π΄ΡΠ²ΠΎΡΠ½ΠΎΠ΅ ΡΡΡΡΠΎΠΉΡΡΠ²ΠΎ, ΠΏΡΠΈ ΡΡΠΎΠΌ ΠΎΠ½ΠΈ ΠΈΠΌΠ΅ΡΡ ΡΠ΅ΠΌΠΏΠ΅ΡΠ°ΡΡΡΡ, ΡΠ°Π²Π½ΡΡ ΡΠ΅ΠΌΠΏΠ΅ΡΠ°ΡΡΡΠ΅ ΠΏΡΠ΅ΡΡΠΎΠ²Π°Π½Π½ΠΎΠ³ΠΎ ΡΠ΅ΡΡΠ° (45β50 Β°Π‘).
Π ΠΏΡΠ΅ΡΡΠΎΠ²ΠΎΠΌ ΠΎΡΠ΄Π΅Π»Π΅Π½ΠΈΠΈ Π·Π½Π°ΡΠΈΡΠ΅Π»ΡΒΠ½ΠΎ ΠΌΠ΅Π½ΡΡΠ°Ρ ΡΠ΅ΠΌΠΏΠ΅ΡΠ°ΡΡΡΠ° ΠΎΠΊΡΡΠΆΠ°ΡΡΠ΅Π³ΠΎ Π²ΠΎΠ·Π΄ΡΡ Π°, Π² ΡΠ΅Π·ΡΠ»ΡΡΠ°ΡΠ΅ Π΄Π»Ρ ΠΈΠ·Π΄Π΅ΒΠ»ΠΈΠΉ, Π²ΡΡ ΠΎΠ΄ΡΡΠΈΡ ΠΈΠ· ΠΌΠ°ΡΡΠΈΡΡ, ΡΠΎΠ·Π΄Π°Π΅ΡΡΡ ΡΠ΅ΠΌΠΏΠ΅ΡΠ°ΡΡΡΠ½ΡΠΉ ΠΏΠ΅ΡΠ΅ΠΏΠ°Π΄, Π²Π΅Π»ΠΈΡΠΈΒΠ½Π° ΠΊΠΎΡΠΎΡΠΎΠ³ΠΎ Π·Π°Π²ΠΈΡΠΈΡ ΠΎΡ ΡΠ°Π·Π½ΠΎΡΡΠΈ ΡΠ΅ΠΌΠΏΠ΅ΡΠ°ΡΡΡ ΠΏΡΠ΅ΡΡΠΎΠ²Π°Π½ΠΈΡ ΠΈ ΠΎΠΊΡΡΠΆΠ°ΡΡΠ΅ΠΉ ΡΡΠ΅Π΄Ρ. Π§Π΅ΠΌ Π±ΠΎΠ»ΡΡΠ΅ ΡΡΠ° ΡΠ°Π·Π½ΠΎΡΡΡ, ΡΠ΅ΠΌ Π²ΡΡΠ΅ ΡΠ΅ΠΌΠΏΠ΅ΡΠ°ΡΡΡΠ½ΡΠΉ ΠΏΠ΅ΡΠ΅ΠΏΠ°Π΄ ΠΈ, ΡΠ»Π΅Π΄ΠΎΠ²Π°ΡΠ΅Π»ΡΠ½ΠΎ, Π±ΠΎΠ»Π΅Π΅ ΠΈΠ½ΡΠ΅Π½ΡΠΈΠ²Π½ΠΎΠ΅ ΠΈΡΠΏΠ°ΡΠ΅Π½ΠΈΠ΅ Π²Π»Π°Π³ΠΈ Ρ ΠΏΠΎΠ²Π΅ΡΡ Π½ΠΎΡΡΠΈ ΠΈΠ·Π΄Π΅Π»ΠΈΡ. ΠΡΠΎΡ ΠΏΡΠΎΡΠ΅ΡΡ ΠΏΡΠΎΠΈΡΡ ΠΎΠ΄ΠΈΡ Π΄ΠΎ ΡΠ΅Ρ ΠΏΠΎΡ, ΠΏΠΎΠΊΠ° ΡΠ΅ΠΌΠΏΠ΅ΡΠ°ΡΡΡΠ° ΠΈΠ·Π΄Π΅ΒΠ»ΠΈΡ ΠΈ ΠΎΠΊΡΡΠΆΠ°ΡΡΠ΅ΠΉ ΡΡΠ΅Π΄Ρ Π½Π΅ Π²ΡΡΠΎΠ²Π½ΡΠ΅ΡΡΡ, ΠΏΠΎΡΠ»Π΅ ΡΠ΅Π³ΠΎ Π½Π° ΠΏΠΎΠ²Π΅ΡΡ Π½ΠΎΡΡΠΈ ΠΈΠ·Π΄Π΅Π»ΠΈΡ Π²ΠΎΠ·Π½ΠΈΠΊΠ°Π΅Ρ Π·Π°ΡΠΈΡΠ½Π°Ρ ΠΊΠΎΡΠΎΡΠΊΠ°, ΠΊΠΎΡΠΎΡΠ°Ρ ΠΏΡΠ΅ΠΏΡΡΡΡΠ²ΡΠ΅Ρ ΡΠ»ΠΈΠΏΠ°Π½ΠΈΡ ΠΈΠ·Π΄Π΅Π»ΠΈΠΉ Π² ΠΏΡΠΎΡΠ΅ΡΡΠ΅ ΠΈΡ Π΄Π°Π»ΡΠ½Π΅ΠΉΡΠ΅ΠΉ ΡΠ°ΡΠΊΠ»Π°Π΄ΠΊΠΈ ΠΈ ΡΡΡΠΊΠΈ.
ΠΡΠΈ ΠΈΠ·Π³ΠΎΡΠΎΠ²Π»Π΅Π½ΠΈΠΈ Π΄Π»ΠΈΠ½Π½ΡΡ ΠΌΠ°ΠΊΠ°ΡΠΎΠ½Π½ΡΡ ΠΈΠ·Π΄Π΅Π»ΠΈΠΉ Π²ΡΡ ΠΎΠ΄ΡΡΠΈΠ΅ ΠΈΠ· ΠΌΠ°ΡΡΠΈΡΡ ΠΏΡΡΠ΄ΠΈ ΠΏΡΠΈΠ½ΠΈΠΌΠ°ΡΡΡΡ Π½Π° ΡΠΏΠ΅ΡΠΈΠ°Π»ΡΠ½ΡΠΉ ΡΡΠΎΠ», ΡΠ°ΡΠΊΠ»Π°Π΄ΡΠ²Π°ΡΡΡΡ Π² ΠΊΠ°ΡΡΠ΅ΡΡ, ΡΠ΅ΠΆΡΡΡΡ ΠΈ Π² ΠΊΠ°ΡΡΠ΅ΡΠ°Ρ ΡΡΠ°Π½ΡΠΏΠΎΡΡΠΈΡΡΡΡΡΡ Π² ΡΡΡΠΈΠ»ΡΠ½ΡΠ΅ ΠΊΠ°ΠΌΠ΅ΡΡ.
ΠΠΎΡΠΎΡΠΊΠΎΡΠ΅Π·Π°Π½ΡΠ΅ ΠΈΠ·Π΄Π΅Π»ΠΈΡ ΠΏΠΎΡΡΡΠΏΠ°ΡΡ Π½Π°ΡΡΠΏΡΡ ΠΊ ΡΡΡΠΈΠ»ΡΠ½ΡΠΌ ΡΡΡΠ°ΒΠ½ΠΎΠ²ΠΊΠ°ΠΌ.
ΠΠ°ΠΊΠ°ΡΠΎΠ½Π½ΡΠΉ ΠΏΡΠ΅ΡΡ Π6-ΠΠΠ¨ -500
ΠΠΎΠ½ΡΡΡΡΠΊΡΠΈΡ. ΠΡΠ½ΠΎΠ²Π½ΡΠΌΠΈ ΡΠ·Π»Π°ΠΌΠΈ ΡΠ½Π΅ΠΊΠΎΠ²ΠΎΠ³ΠΎ ΠΌΠ°ΠΊΠ°ΡΠΎΠ½Π½ΠΎΠ³ΠΎ ΠΏΡΠ΅ΡΒΡΠ° Π6-ΠΠΠ¨-500 ΡΠ²Π»ΡΡΡΡΡ Π΄ΠΎΠ·ΠΈΡΠΎΠ²ΠΎΡΠ½ΠΎΠ΅ ΡΡΡΡΠΎΠΉΡΡΠ²ΠΎ, ΡΡΠ΅Ρ ΠΊΠ°ΠΌΠ΅ΡΠ½ΡΠΉ ΡΠ΅ΡΡΠΎΠΌΠ΅ΡΠΈΡΠ΅Π»Ρ Ρ ΠΏΡΠΈΠ²ΠΎΠ΄ΠΎΠΌ, ΠΏΡΠ΅ΡΡΡΡΡΠΈΠΉ ΠΊΠΎΡΠΏΡΡ Ρ ΠΏΡΠΈΠ²ΠΎΠ΄ΠΎΠΌ, ΠΏΡΠ΅ΡΡΡΡΡΠ°Ρ Π³ΠΎΠ»ΠΎΠ²ΠΊΠ° Π΄Π»Ρ ΠΊΡΡΠ³Π»ΠΎΠΉ ΠΌΠ°ΡΡΠΈΡΡ, ΠΌΠ΅Ρ Π°Π½ΠΈΠ·ΠΌ ΡΠΌΠ΅Π½Ρ ΠΌΠ°ΡΡΠΈΡ, ΠΎΠ±Π΄ΡΠ²ΠΎΡΠ½ΠΎΠ΅ ΡΡΡΡΠΎΠΉΡΡΠ²ΠΎ. ΠΡΠ΅ ΠΏΠ΅ΡΠ΅ΡΠΈΡΠ»Π΅Π½Π½ΡΠ΅ ΡΠ·Π»Ρ Π·Π°ΠΊΡΠ΅ΠΏΠ»Π΅ΒΠ½Ρ Π½Π° ΠΌΠ΅ΡΠ°Π»Π»ΠΈΡΠ΅ΡΠΊΠΎΠΉ ΡΡΠ°Π½ΠΈΠ½Π΅, ΡΡΡΠ°Π½ΠΎΠ²Π»Π΅Π½Π½ΠΎΠΉ Π½Π° ΡΠ΅ΡΡΡΠ΅Ρ ΠΎΠΏΠΎΡΠ°Ρ . Π‘Ρ Π΅ΠΌΠ° ΠΏΡΠ΅ΡΡΠ° Π6-ΠΠΠ¨ ΠΏΡΠ΅Π΄ΡΡΠ°Π²Π»Π΅Π½Π° Π½Π° ΡΠΈΡΡΠ½ΠΊΠ΅ 3.
ΠΠΎΠ·Π°ΡΠΎΡ ΠΌΡΠΊΠΈ Π² Π΅Π³ΠΎ Π²Π΅ΡΡ Π½Π΅ΠΉ ΡΠ°ΡΡΠΈ ΠΈΠΌΠ΅Π΅Ρ ΠΏΡΠΈΠ΅ΠΌΠ½ΡΠΉ ΠΏΠ°ΡΡΡΠ±ΠΎΠΊ 14 Π΄Π»Ρ Π·Π°Π³ΡΡΠ·ΠΊΠΈ ΠΌΡΠΊΠΈ, Π½Π° ΠΏΡΠΎΡΠΈΠ²ΠΎΠΏΠΎΠ»ΠΎΠΆΠ½ΠΎΠΌ ΠΊΠΎΠ½ΡΠ΅ β ΠΎΡΠ²Π΅ΡΡΡΠΈΠ΅ 10 Π΄Π»Ρ Π²ΡΡ ΠΎΠ΄Π° ΠΌΡΠΊΠΈ.
Π ΠΈΡ. 3. Π¨Π½Π΅ΠΊΠΎΠ²ΡΠΉ ΠΌΠ°ΠΊΠ°ΡΠΎΠ½Π½ΡΠΉ ΠΏΡΠ΅ΡΡ Π6-ΠΠΠ¨-500:
1- ΡΠΈΠ»ΡΡΡ; 2 β Π²Π°ΠΊΡΡΠΌΠΌΠ΅ΡΡ;3- ΡΠΎΡΠΎΡΠ½ΡΠΉ ΠΏΠΈΡΠ°ΡΠ΅Π»Ρ; 4- Π²Π°ΠΊΡΡΠΌΠ½ΡΠΉ Π·Π°ΡΠ²ΠΎΡ; 5- ΠΎΠΊΠ½ΠΎ; 6,39 β Π²Π°Π»Ρ ΠΌΠ΅ΡΠΈΠ»ΡΠ½ΡΠ΅; 7,38 β ΠΌΠ΅ΡΠΈΠ»ΡΠ½ΡΠ΅ Π»ΠΎΠΏΠ°ΡΠΊΠΈ; 8,40,44- ΠΌΠ΅ΡΠΈΠ»ΡΠ½ΡΠ΅ ΠΊΠ°ΠΌΠ΅ΡΡ; 9 — ΠΊΡΡΡΠΊΠ°; 10 β ΠΎΡΠ²Π΅ΡΡΡΠΈΠ΅ Π² ΠΊΠΎΡΠΏΡΡΠ΅ Π΄ΠΎΠ·Π°ΡΠΎΡΠ°; 11 β ΠΏΠΎΠ»ΡΠΉ Π²Π°Π»; 12 β ΠΊΠΎΡΠΏΡΡ Π΄ΠΎΠ·Π°ΡΠΎΡΠ°; 13,42- ΡΠ½Π΅ΠΊΠΈ; 14- ΠΏΡΠΈΡΠΌΠ½ΡΠΉ ΠΏΠ°ΡΡΡΠ±ΠΎΠΊ; 15 β ΡΠ΅ΠΏΠ½Π°Ρ ΠΏΠ΅ΡΠ΅Π΄Π°ΡΠ°; 16 — ΠΊΡΡΠ»ΡΡΠ°ΡΠΊΠ°; 17 — Π²Π΅Π½ΡΠΈΠ»Ρ; 18 — ΠΏΡΠΎΡΠ΅Π·Ρ; 19- ΡΡΠΊΠΎΡΡΠΊΠ°; 20 — ΠΌΡΡΡΠ° ΠΊΡΠ»Π°ΡΠΊΠΎΠ²Π°Ρ; 21,33- ΡΠ»Π΅ΠΊΡΡΠΎΠ΄Π²ΠΈΠ³Π°ΡΠ΅Π»ΠΈ; 22- ΠΏΡΠΎΠ±ΠΊΠ°; 23- ΠΌΠ°Π½ΠΎΠΌΠ΅ΡΡ; 24, 43- ΡΠ»Π°Π½ΡΡ; 25 — ΠΏΡΠ΅ΡΡΡΡΡΠ°Ρ Π³ΠΎΠ»ΠΎΠ²ΠΊΠ°; 26 β ΠΏΡΠ΅Π΄ΠΎΡ ΡΠ°Π½ΠΈΡΠ΅Π»ΡΠ½Π°Ρ ΡΠ΅ΡΠΊΠ°; 27 — ΠΌΠ°ΡΡΠΈΡΠ°; 28 — ΠΊΠΎΠ»ΡΡΠΎ; 29 — ΡΡΠ°Π²Π΅ΡΡΠ°; 30- Π½Π°ΠΏΡΠ°Π²Π»ΡΡΡΠ°Ρ; 31 — Π²ΠΈΠ½Ρ;32 ΡΠ΅ΡΠ²ΡΡΠ½ΡΠΉ ΡΠ΅Π΄ΡΠΊΡΠΎΡ;34 β ΠΎΡ Π»Π°ΠΆΠ΄Π°ΡΡΠ°Ρ ΡΡΠ±Π°ΡΠΊΠ°; 35 — Π·Π°ΠΆΠΈΠΌΡ;36, 41 — ΠΎΠΊΠ½Π°;37-ΠΊΡΡΡΠΊΠ° ΠΈΠ· ΠΎΡΠ³Π°Π½ΠΈΡΠ΅ΡΠΊΠΎΠ³ΠΎ ΡΡΠ΅ΠΊΠ»Π°; 45,48 β ΠΏΠ°ΡΡΡΠ±ΠΊΠΈ; 46- ΠΊΠΎΡΠΏΡΡ ΡΠΈΠ»ΡΡΡΠ°; 47 βΡΠΈΠ»ΡΡΡΡΡΡΠ°Ρ ΠΏΠΎΠ²Π΅ΡΡ Π½ΠΎΡΡΡ.
Π ΠΎΡΠΎΡΠ½ΡΠΉ Π΄ΠΎΠ·Π°ΡΠΎΡ ΡΡΡΠ°Π½ΠΎΠ²Π»Π΅Π½ Ρ ΠΏΡΠΎΡΠΈΠ²ΠΎΠΏΠΎΠ»ΠΎΠΆΠ½ΠΎΠΉ ΡΡΠΎΡΠΎΠ½Ρ ΠΏΠΎΠ»ΠΎΠΉ ΡΡΡΠ±Ρ. ΠΠ° ΠΊΠΎΡΠΏΡΡΠ΅ Π΄ΠΎΠ·Π°ΡΠΎΡΠ° ΡΠ°Π·ΠΌΠ΅ΡΠ΅Π½Ρ Π΄Π²Π° Π²Π΅Π½ΡΠΈΠ»Ρ 17 Π΄Π»Ρ ΠΏΠΎΠ΄Π°ΡΠΈ Ρ ΠΎΠ»ΠΎΠ΄Π½ΠΎΠΉ ΠΈ Π³ΠΎΡΡΡΠ΅ΠΉ Π²ΠΎΠ΄Ρ ΠΈ ΠΊΡΡΠ»ΡΡΠ°ΡΠΊΠ° 16 ΡΠΏΠ΅ΡΠΈΠ°Π»ΡΠ½ΠΎΠ³ΠΎ ΠΏΡΠΎΡΠΈΠ»Ρ, ΠΏΠΎΠ΄Π°ΡΡΠ°Ρ ΠΏΡΠΈ Π²ΡΠ°ΡΠ΅Π½ΠΈΠΈ Π²ΠΎΠ΄Ρ Π² ΠΏΠ°Π·Ρ ΠΏΠΎΠ»ΠΎΠ³ΠΎ Π²Π°Π»Π°.
Π’Π΅ΡΡΠΎΡΠΌΠ΅ΡΠΈΡΠ΅Π»Ρ ΠΏΡΠ΅ΡΡΠ° ΡΡΡΡ ΠΊΠ°ΠΌΠ΅ΡΠ½ΡΠΉ. ΠΠ°Π±Π°ΡΠΈΡΠ½ΡΠ΅ ΡΠ°Π·ΠΌΠ΅ΡΡ ΠΊΠ°ΠΌΠ΅Ρ: ΠΏΠ΅ΡΠ²ΠΎΠΉ 1400Ρ 206Ρ 293 ΠΌΠΌ, Π²ΡΠΎΡΠΎΠΉ ΠΈ ΡΡΠ΅ΡΡΠ΅ΠΉ 1400Ρ 328Ρ 424 ΠΌΠΌ. ΠΠ΅ΡΠ²Π°Ρ ΠΌΠ΅ΡΠΈΠ»ΡΠ½Π°Ρ ΠΊΠ°ΠΌΠ΅ΡΠ° 8 ΡΠ°ΡΠΏΠΎΠ»ΠΎΠΆΠ΅Π½Π° Π½Π°Π΄ Π²ΡΠΎΡΠΎΠΉ 44 ΠΈ ΡΡΠ΅ΡΡΠ΅ΠΉ 40 ΠΈ Π·Π°ΠΊΡΡΡΠ° ΡΠ²Π΅ΡΡ Ρ ΡΠ΅ΡΡΡΡΠ°ΡΠΎΠΉ ΠΊΡΡΡΠΊΠΎΠΉ 9 Ρ Π±Π»ΠΎΠΊΠΈΡΠΎΠ²ΠΊΠΎΠΉ. Π ΡΡΠΎΠΉ ΠΊΠ°ΠΌΠ΅ΡΠ΅ Π·Π°ΠΌΠ΅ΡΠΈΠ²Π°Π΅ΡΡΡ ΡΠ΅ΡΡΠΎ Ρ ΠΏΠΎΠΌΠΎΡΡΡ ΠΌΠ΅ΡΠΈΠ»ΡΠ½ΡΡ Π»ΠΎΠΏΠ°ΡΠΎΠΊ 7, ΡΡΡΠ°Π½ΠΎΠ²Π»Π΅Π½Π½ΡΡ Π½Π° ΠΌΠ΅ΡΠΈΠ»ΡΠ½ΠΎΠΌ Π²Π°Π»Ρ 6. Π§Π΅ΡΠ΅Π· ΠΎΠΊΠ½ΠΎ 5 Π² Π±ΠΎΠΊΠΎΠ²ΠΎΠΉ ΡΡΠ΅Π½ΠΊΠ΅ ΠΊΠ°ΠΌΠ΅ΡΡ ΡΠ΅ΡΡΠΎ Π½Π°ΠΏΡΠ°Π²Π»ΡΠ΅ΡΡΡ Π² Π²Π°ΠΊΡΡΠΌΠ½ΡΠΉ Π·Π°ΡΠ²ΠΎΡ 4, ΠΊΠΎΡΠΎΡΡΠΉ ΠΎΠ±Π΅ΡΠΏΠ΅ΡΠΈΠ²Π°Π΅Ρ Π½Π΅ΠΎΠ±Ρ ΠΎΠ΄ΠΈΠΌΠΎΠ΅ ΠΎΡΡΠ°ΡΠΎΡΠ½ΠΎΠ΅ Π΄Π°Π²Π»Π΅Π½ΠΈΠ΅ Π²ΠΎΠ·Π΄ΡΡ Π° ΠΏΡΠΈ ΠΏΠ΅ΡΠ΅Π΄Π°ΡΠ΅ ΡΠ΅ΡΡΠ° Π²ΠΎ Π²ΡΠΎΡΡΡ ΠΈ ΡΡΠ΅ΡΡΡ ΠΌΠ΅ΡΠΈΠ»ΡΠ½ΡΠ΅ ΠΊΠ°ΠΌΠ΅ΡΡ. ΠΠ°ΠΊΡΡΠΌΠ½ΡΠΉ Π·Π°ΡΠ²ΠΎΡ ΠΈΠΌΠ΅Π΅Ρ ΡΠΎΡΠΎΡΠ½ΡΠΉ ΠΏΠΈΡΠ°ΡΠ΅Π»Ρ 3 Ρ Π΄Π²ΡΠΌΡ ΠΊΠ°ΡΠΌΠ°Π½Π°ΠΌΠΈ ΠΎΠ±ΡΡΠΌΠΎΠΌ ΠΏΠΎ 750 ΡΠΌ3 . ΠΡΠΈΠ²ΠΎΠ΄ ΡΠΎΡΠΎΡΠ° ΠΎΡΡΡΠ΅ΡΡΠ²Π»ΡΠ΅ΡΡΡ ΠΎΡ Π²Π°Π»Π° ΠΏΠ΅ΡΠ²ΠΎΠ³ΠΎ ΡΠ΅ΡΡΠΎΡΠΌΠ΅ΡΠΈΡΠ΅Π»Ρ ΡΠ΅ΡΠ΅Π· Π·ΡΠ±ΡΠ°ΡΡΡ ΠΏΠ΅ΡΠ΅Π΄Π°ΡΡ.
ΠΡΠΎΡΠ°Ρ ΠΈ ΡΡΠ΅ΡΡΡ ΠΊΠ°ΠΌΠ΅ΡΡ ΡΠ΅ΡΡΠΎΡΠΌΠ΅ΡΠΈΡΠ΅Π»Ρ ΡΠΎΠ΅Π΄ΠΈΠ½Π΅Π½Ρ ΠΌΠ΅ΠΆΠ΄Ρ ΡΠΎΠ±ΠΎΠΉ ΠΏΠΎ ΠΏΠΎΡΠΎΠΊΡ ΡΠ΅ΡΡΠ° ΠΏΠ΅ΡΠ΅Π³ΡΡΠ·ΠΎΡΠ½ΡΠΌ ΠΎΠΊΠ½ΠΎΠΌ 36. ΠΠ½ΡΡΡΠΈ ΠΊΠ°ΠΌΠ΅Ρ ΡΠ°ΠΊ ΠΆΠ΅, ΠΊΠ°ΠΊ ΠΈ Π² ΠΏΠ΅ΡΠ²ΠΎΠΉ, ΡΠ°ΡΠΏΠΎΠ»ΠΎΠΆΠ΅Π½Ρ ΠΌΠ΅ΡΠΈΠ»ΡΠ½ΡΠ΅ Π²Π°Π»Ρ 39 Ρ ΡΡΡΠ°Π½ΠΎΠ²Π»Π΅Π½Π½ΡΠΌΠΈ Π½Π° Π½ΠΈΡ Π² ΠΎΠΏΡΠ΅Π΄Π΅Π»ΡΠ½Π½ΠΎΠΉ ΠΏΠΎΡΠ»Π΅Π΄ΠΎΠ²Π°ΡΠ΅Π»ΡΠ½ΠΎΡΡΠΈ Π»ΠΎΠΏΠ°ΡΠΊΠ°ΠΌΠΈ ΠΈ ΠΏΠ°Π»ΡΡΠ°ΠΌΠΈ 38. ΠΡΡΡΠΊΠΈ 37 ΠΎΠ±Π΅ΠΈΡ ΠΊΠ°ΠΌΠ΅Ρ Π²ΡΠΏΠΎΠ»Π½Π΅Π½Ρ ΠΈΠ· ΠΏΡΠΎΠ·ΡΠ°ΡΠ½ΠΎΠ³ΠΎ ΠΎΡΠ³Π°Π½ΠΈΡΠ΅ΡΠΊΠΎΠ³ΠΎ ΡΡΠ΅ΠΊΠ»Π°, ΡΡΠΎ Π΄Π°ΡΡ Π²ΠΎΠ·ΠΌΠΎΠΆΠ½ΠΎΡΡΡ Π½Π°Π±Π»ΡΠ΄Π°ΡΡ Π·Π° Ρ ΠΎΠ΄ΠΎΠΌ ΠΏΡΠΎΡΠ΅ΡΡΠ°.
ΠΡΠΈΠ²ΠΎΠ΄ Π²ΡΠ΅Ρ ΡΡΡΡ Π²Π°Π»ΠΎΠ² ΡΠ΅ΡΡΠΎΡΠΌΠ΅ΡΠΈΡΠ΅Π»Ρ ΠΎΡΡΡΠ΅ΡΡΠ²Π»ΡΠ΅ΡΡΡ ΠΎΡ ΡΠ»Π΅ΠΊΡΡΠΎΠ΄Π²ΠΈΠ³Π°ΡΠ΅Π»Ρ 21 ΡΠ΅ΡΠ΅Π· ΠΊΠ»ΠΈΠ½ΠΎΡΠ΅ΠΌΡΠ½Π½ΡΡ ΠΏΠ΅ΡΠ΅Π΄Π°ΡΡ, ΡΠ΅Π΄ΡΠΊΡΠΎΡ ΠΈ ΡΠΈΡΡΠ΅ΠΌΡ ΡΠ΅ΠΏΠ½ΡΡ ΠΏΠ΅ΡΠ΅Π΄Π°Ρ.
ΠΠ°ΡΠΎΠ²ΠΎΠ·Π΄ΡΡΠ½Π°Ρ ΡΠΌΠ΅ΡΡ, ΠΎΠ±ΡΠ°Π·ΡΡΡΠ°ΡΡΡ ΠΏΡΠΈ Π·Π°ΠΌΠ΅ΡΠ΅ ΡΠ΅ΡΡΠ° Π²ΠΎ Π²ΡΠΎΡΠΎΠΉ 44 ΠΈ ΡΡΠ΅ΡΡΠ΅ΠΉ 40 ΠΊΠ°ΠΌΠ΅ΡΠ°Ρ , ΡΠ΅ΡΠ΅Π· ΡΠΈΠ»ΡΡΡ 1 ΠΎΡΠΊΠ°ΡΠΈΠ²Π°Π΅ΡΡΡ Π²ΠΎΠ΄ΠΎΠΊΠΎΠ»ΡΡΠ΅Π²ΡΠΌ Π²Π°ΠΊΡΡΠΌ-Π½Π°ΡΠΎΡΠΎΠΌ ΠΠΠ-1,5.Π€ΠΈΠ»ΡΡΡ ΡΠΎΡΡΠΎΠΈΡ ΠΈΠ· ΠΊΠΎΡΠΏΡΡΠ° 46 ΡΠΈΠ»ΠΈΠ½Π΄ΡΠΈΡΠ΅ΡΠΊΠΎΠΉ ΡΠΎΡΠΌΡ ΠΈ Π΄Π²ΡΡ ΡΠΈΠ»ΡΡΡΡΡΡΠΈΡ ΠΏΠΎΠ²Π΅ΡΡ Π½ΠΎΡΡΠ΅ΠΉ 47, ΡΠ°Π·ΠΌΠ΅ΡΡΠ½Π½ΡΡ Π²Π½ΡΡΡΠΈ ΠΊΠΎΡΠΏΡΡΠ°. ΠΠ΅ΡΠ²Π°Ρ ΠΏΠΎΠ²Π΅ΡΡ Π½ΠΎΡΡΡ ΠΎΡΡΡΠ΅ΡΡΠ²Π»ΡΠ΅Ρ Π³ΡΡΠ±ΡΡ ΠΎΡΠΈΡΡΠΊΡ ΠΏΠ°ΡΠΎΠ²ΠΎΠ·Π΄ΡΡΠ½ΠΎΠΉ ΡΠΌΠ΅ΡΠΈ ΠΎΡ ΠΌΠ΅Π»ΠΊΠΈΡ ΠΊΡΠΎΡΠ΅ΠΊ ΡΠ΅ΡΡΠ°, Π²ΡΠΎΡΠ°Ρ — ΠΎΡ ΡΠ°ΡΡΠΈΡ ΠΌΡΠΊΠΈ.
ΠΡΠ΅ΡΡΡΡΡΠΈΠΉ ΠΊΠΎΡΠΏΡΡ Π²ΡΠΏΠΎΠ»Π½Π΅Π½ ΡΠ΅Π»ΡΠ½ΡΠΌ ΠΈΠ· ΡΡΡΠ±Ρ Π‘Ρ.20 Π΄Π»ΠΈΠ½ΠΎΠΉ 1989 ΠΈ Π΄ΠΈΠ°ΠΌΠ΅ΡΡΠΎΠΌ 166ΠΌΠΌ, Π² ΠΏΡΠΎΡΠΈΠ²ΠΎΠΏΠΎΠ»ΠΎΠΆΠ½ΠΎΠΉ ΡΠ°ΡΡΠΈ ΠΊΠΎΡΠΎΡΠΎΠ³ΠΎ ΠΈΠΌΠ΅Π΅ΡΡΡ ΠΎΠΊΠ½ΠΎ 41 Π΄Π»Ρ ΠΏΠΎΡΡΡΠΏΠ»Π΅Π½ΠΈΡ ΡΠ΅ΡΡΠ° ΠΈΠ· ΡΡΠ΅ΡΡΠ΅ΠΉ ΠΊΠ°ΠΌΠ΅ΡΡ ΡΠ΅ΡΡΠΎΡΠΌΠ΅ΡΠΈΡΠ΅Π»Ρ. ΠΠ½ΡΡΡΠΈ ΠΊΠΎΡΠΏΡΡΠ° ΡΡΡΠ°Π½ΠΎΠ²Π»Π΅Π½ ΠΎΠ΄Π½ΠΎΠ·Π°Ρ ΠΎΠ΄Π½ΡΠΉ ΠΏΡΠ΅ΡΡΡΡΡΠΈΠΉ ΡΠ½Π΅ΠΊ 42. ΠΡΠ΅ΡΡΡΡΡΠ°Ρ Π³ΠΎΠ»ΠΎΠ²ΠΊΠ° 25 ΠΊΡΠΏΠΎΠ»ΠΎΠΎΠ±ΡΠ°Π·Π½ΠΎΠΉ ΡΠΎΡΠΌΡ Π΄Π»Ρ ΠΎΠ΄Π½ΠΎΠΉ ΠΊΡΡΠ³Π»ΠΎΠΉ ΠΌΠ°ΡΡΠΈΡΡ Π΄ΠΈΠ°ΠΌΠ΅ΡΡΠΎΠΌ 350 ΠΌΠΌ. ΠΠΎΠ»ΠΎΠ²ΠΊΠ° ΡΠ½Π°Π±ΠΆΠ΅Π½Π° ΠΌΠ΅Ρ Π°Π½ΠΈΠ·ΠΌΠΎΠΌ ΡΠΌΠ΅Π½Ρ ΠΌΠ°ΡΡΠΈΡ, ΠΌΠ΅Ρ Π°Π½ΠΈΠ·ΠΌΠΎΠΌ ΡΠ΅Π·ΠΊΠΈ ΠΈ ΠΎΠ±Π΄ΡΠ²ΠΎΡΠ½ΡΠΌ ΡΡΡΡΠΎΠΉΡΡΠ²ΠΎΠΌ.
ΠΠ±Π΄ΡΠ²ΠΎΡΠ½ΠΎΠ΅ ΡΡΡΡΠΎΠΉΡΡΠ²ΠΎ Π°Π½Π°Π»ΠΎΠ³ΠΈΡΠ½ΠΎ ΠΊΠΎΠ½ΡΡΡΡΠΊΡΠΈΠΈ ΠΏΡΠ΅ΡΡΠ° ΠΠΠ-2Π.
ΠΡΠΈΠ½ΡΠΈΠΏ ΡΠ°Π±ΠΎΡΡ. Π Π΄ΠΎΠ·Π°ΡΠΎΡΡ ΠΌΡΡΠ½ΠΎΠΉ ΡΠΈΡΡΠ΅ΠΌΡ ΠΏΠΎΠ΄Π°Π΅ΡΡΡ ΠΌΡΠΊΠ°, Π° ΠΈΠ· Π±Π°ΠΊΠΎΠ² ΠΏΠΎΡΡΠΎΡΠ½Π½ΠΎΠ³ΠΎ ΡΡΠΎΠ²Π½Ρ β Π³ΠΎΡΡΡΠ°Ρ ΠΈ Ρ ΠΎΠ»ΠΎΠ΄Π½Π°Ρ Π²ΠΎΠ΄Π°. Π’Π΅ΠΌΠΏΠ΅ΡΠ°ΡΡΡΠ° Π²ΠΎΠ΄Ρ, ΠΏΠΎΡΡΡΠΏΠ°ΡΡΠ΅ΠΉ Π² ΡΠ΅ΡΡΠΎΡΠΌΠ΅ΡΠΈΡΠ΅Π»Ρ, 55-65ΠΎ Π‘. ΠΠΎΠ½ΡΡΠΎΠ»Ρ ΡΠ΅ΠΌΠΏΠ΅ΒΡΠ°ΡΡΡΡ Π²ΠΎΠ΄Ρ, ΠΏΠΎΡΡΡΠΏΠ°ΡΡΠ΅ΠΉ Π½Π° Π·Π°ΠΌΠ΅Ρ, ΠΎΡΡΡΠ΅ΡΡΠ²Π»ΡΠ΅ΡΡΡ Π½Π° Π²Ρ ΠΎΠ΄Π΅ Π² ΡΠ΅ΡΡΠΎΡΠΌΠ΅ΡΠΈΡΠ΅Π»Ρ ΠΈ ΡΠ΅Π³ΡΠ»ΠΈΡΡΠ΅ΡΡΡ Π΄Π²ΡΠΌΡ Π²Π΅Π½ΡΠΈΠ»ΡΠΌΠΈ Π½Π° Π΄ΠΎΠ·Π°ΡΠΎΡΠ΅ Π²ΡΡΡΠ½ΡΡ, ΠΏΡΡΠ΅ΠΌ ΠΈΠ·ΠΌΠ΅Π½Π΅Π½ΠΈΡ ΡΠΎΠΎΡΠ½ΠΎΡΠ΅Π½ΠΈΡ Ρ ΠΎΠ»ΠΎΠ΄Π½ΠΎΠΉ ΠΈ Π³ΠΎΡΡΡΠ΅ΠΉ Π²ΠΎΠ΄Ρ. Π’Π΅ΡΡΠΎ Π·Π°ΠΌΠ΅ΡΠΈΠ²Π°Π΅ΡΡΡ Π² ΡΡΠ΅Ρ ΠΊΠ°ΠΌΠ΅ΡΠ½ΠΎΠΌ ΡΠΌΠ΅ΡΠΈΡΠ΅Π»Π΅.
Π ΠΏΠ΅ΡΠ²ΠΎΠΉ ΠΊΠ°ΠΌΠ΅ΡΠ΅ ΡΠΌΠ΅ΡΠΈΡΠ΅Π»Ρ ΠΏΡΠΎΠΈΡΡ ΠΎΠ΄ΠΈΡ ΠΈΠ½ΡΠ΅Π½ΡΠΈΠ²Π½ΡΠΉ ΠΏΡΠ΅Π΄Π²Π°ΡΠΈΡΠ΅Π»ΡΠ½ΡΠΉ Π·Π°ΠΌΠ΅Ρ ΡΠ΅ΡΡΠ° Π² ΡΠ΅ΡΠ΅Π½ΠΈΠ΅ 6-8 ΠΌΠΈΠ½ ΠΈ ΠΏΠΎΠ΄Π°ΡΠ° Π΅Π³ΠΎ ΡΠ΅ΡΠ΅Π· Π²Π°ΠΊΡΡΠΌΠ½ΡΠΉ Π·Π°ΡΠ²ΠΎΡ Π²ΠΎ Π²ΡΠΎΡΠΎΠΉ ΠΈ ΡΡΠ΅ΡΠΈΠΉ ΡΠ΅ΡΡΠΎΡΠΌΠ΅ΡΠΈΡΠ΅Π»ΠΈ, ΠΊΠΎΡΠΎΡΡΠ΅ ΡΠ°Π±ΠΎΡΠ°ΡΡ ΠΏΠΎΠ΄ Π²Π°ΠΊΡΡΠΌΠΎΠΌ. ΠΠ±ΡΠ°Ρ ΠΏΡΠΎΠ΄ΠΎΠ»ΠΆΠΈΡΠ΅Π»ΡΠ½ΠΎΡΡΡ ΠΏΡΠΎΡΠ΅ΡΡΠ° Π·Π°ΠΌΠ΅ΡΠ° Π½Π΅ ΠΌΠ΅Π½Π΅Π΅ 20 ΠΌΠΈΠ½, Π·Π° ΡΡΠΎ Π²ΡΠ΅ΠΌΡ ΠΎΠ±Π΅ΡΠΏΠ΅ΡΠΈΠ²Π°Π΅ΡΡΡ Π½Π΅ΠΎΠ±Ρ ΠΎΠ΄ΠΈΠΌΡΠΉ ΠΏΡΠΎΠΌΠ΅Ρ ΡΠ΅ΡΡΠ° Π΄ΠΎ ΠΏΠΎΠ»ΡΡΠ΅Π½ΠΈΡ ΡΡΡ Π»ΠΎΠΉ, ΠΎΠ΄Π½ΠΎΡΠΎΠ΄Π½ΠΎΠ³ΠΎ ΡΠ²Π΅ΡΠ°, Π±Π΅Π· ΡΠ»Π΅Π΄ΠΎΠ² ΠΌΡΠΊΠΈ ΠΌΠ΅Π»ΠΊΠΎΠΊΠΎΠΌΠΊΠΎΠ²Π°ΡΠΎΠΉ ΠΌΠ°ΡΡΡ Ρ ΡΠ°Π·ΠΌΠ΅ΡΠΎΠΌ ΠΊΠΎΠΌΠΊΠ° Π² ΠΏΠΎΠΏΠ΅ΡΠ΅ΡΠ½ΠΈΠΊΠ΅ ΠΎΡ 2 Π΄ΠΎ 10 ΠΌΠΌ.
ΠΠ° ΡΡΠ΅Ρ Π²Π°ΠΊΡΡΠΌΠΈΡΠΎΠ²Π°Π½ΠΈΡ ΡΠ΅ΡΡΠ° Π² ΠΏΡΠΎΡΠ΅ΡΡΠ΅ Π΅Π³ΠΎ ΠΏΡΠΈΠ³ΠΎΡΠΎΠ²Π»Π΅Π½ΠΈΡ ΠΎΠ±ΡΠ°Π·ΡΠ΅ΡΡΡ Π±ΠΎΠ»Π΅Π΅ ΠΏΠ»ΠΎΡΠ½Π°Ρ ΡΡΡΡΠΊΡΡΡΠ° ΠΌΠ°ΠΊΠ°ΡΠΎΠ½Π½ΠΎΠ³ΠΎ ΡΠ΅ΡΡΠ° Ρ Π±ΠΎΠ»ΡΡΠ΅ΠΉ ΠΌΠ΅Ρ Π°Π½ΠΈΡΠ΅ΡΠΊΠΎΠΉ ΠΏΡΠΎΡΠ½ΠΎΡΡΡΡ Π³ΠΎΡΠΎΠ²ΡΡ ΠΈΠ·Π΄Π΅Π»ΠΈΠΉ.
ΠΠ· ΠΏΠΎΡΠ»Π΅Π΄Π½Π΅ΠΉ ΠΊΠ°ΠΌΠ΅ΡΡ ΡΠ΅ΡΡΠΎ ΠΏΠΎΡΡΡΠΏΠ°Π΅Ρ Π² ΡΠ½Π΅ΠΊΠΎΠ²ΡΡ ΠΊΠ°ΠΌΠ΅ΡΡ, ΠΎΡΠΊΡΠ΄Π° ΡΠ½Π΅ΠΊΠΎΠΌ ΠΏΠΎΠ΄Π°Π΅ΡΡΡ Π² ΠΏΡΠ΅ΡΡΡΡΡΡΡ Π³ΠΎΠ»ΠΎΠ²ΠΊΡ ΠΈ Π·Π°ΡΠ΅ΠΌ ΡΠΎΡΠΌΡΠ΅ΡΡΡ ΡΠ΅ΡΠ΅Π· ΠΌΠ°ΡΡΠΈΡΡ.
ΠΠ°Π²Π»Π΅Π½ΠΈΠ΅ ΡΠΎΡΠΌΠΎΠ²Π°Π½ΠΈΡ Π½Π° ΠΏΡΠ΅ΡΡΠ°Ρ Π΄Π°Π½Π½ΠΎΠΉ ΠΊΠΎΠ½ΡΡΡΡΠΊΡΠΈΠΈ ΠΏΠΎΡΡΠΈ Π² 2 ΡΠ°Π·Π° Π²ΡΡΠ΅, ΡΠ΅ΠΌ Π² ΠΏΡΠ΅ΡΡΠ°Ρ ΠΠΠ-2Π, ΠΈ ΡΠΎΡΡΠ°Π²Π»ΡΠ΅Ρ 9β12 ΠΠΠ°.
Π£ΡΡΠ°Π½ΠΎΠ²Π»Π΅Π½ΠΎ, ΡΡΠΎ Π²ΡΡΠΎΠΊΠ°Ρ ΡΠΊΠΎΡΠΎΡΡΡ ΠΏΡΠ΅ΡΡΠΎΠ²Π°Π½ΠΈΡ ΠΏΠΎΒΠ·Π²ΠΎΠ»ΡΠ΅Ρ ΡΠ»ΡΡΡΠΈΡΡ ΠΊΠ°ΡΠ΅ΡΡΠ²ΠΎ Π³ΠΎΡΠΎΠ²ΡΡ ΠΈΠ·Π΄Π΅Π»ΠΈΠΉ, Π² ΡΠ°ΡΡΠ½ΠΎΡΡΠΈ ΠΎΠ΄ΠΈΠ½ ΠΈΠ· ΠΎΡΒΠ½ΠΎΠ²Π½ΡΡ Π΅Π³ΠΎ ΠΏΠΎΠΊΠ°Π·Π°ΡΠ΅Π»Π΅ΠΉ β ΠΏΡΠΎΡΠ½ΠΎΡΡΡ.
ΠΠ°ΠΊΠ°ΡΠΎΠ½Π½ΡΠΉ ΠΏΡΠ΅ΡΡ Π6-ΠΠΠ¨-1000
ΠΠΎΠ½ΡΡΡΡΠΊΡΠΈΡ. ΠΡΠ΅ΡΡ ΡΠΎΡΡΠΎΠΈΡ ΠΈΠ· ΠΎΡΠ½ΠΎΠ²Π½ΡΡ ΡΠ·Π»ΠΎΠ²: Π΄ΠΎΠ·ΠΈΒΡΠΎΠ²ΠΎΡΠ½ΠΎΠ³ΠΎ ΡΡΡΡΠΎΠΉΡΡΠ²Π°, ΡΡΠ΅Ρ ΠΊΠ°ΠΌΠ΅ΡΠ½ΠΎΠ³ΠΎ ΡΠ΅ΡΡΠΎΡΠΌΠ΅ΡΠΈΡΠ΅Π»Ρ Ρ Π΄Π²ΡΠΌΡ ΠΏΡΠΈΠ²ΠΎΠ΄ΒΠ½ΡΠΌΠΈ ΡΠ·Π»Π°ΠΌΠΈ Π΄Π»Ρ ΠΏΠ΅ΡΠ²ΡΡ Π΄Π²ΡΡ ΠΊΠ°ΠΌΠ΅Ρ ΠΈ Π²Π°ΠΊΡΡΠΌΠ½ΠΎΠΉ ΠΊΠ°ΠΌΠ΅ΡΡ, Π΄Π²ΡΡ ΠΏΡΠ΅ΡΡΡΒΡΡΠΈΡ ΠΊΠΎΡΠΏΡΡΠΎΠ² Ρ ΠΈΠ½Π΄ΠΈΠ²ΠΈΠ΄ΡΠ°Π»ΡΠ½ΡΠΌΠΈ ΠΏΡΠΈΠ²ΠΎΠ΄Π°ΠΌΠΈ, ΡΡΡΠ°Π½ΠΎΠ²ΠΊΠΈ Π΄Π»Ρ Π²Π°ΠΊΡΡΠΌΠΈΒΡΠΎΠ²Π°Π½ΠΈΡ. Π‘Ρ Π΅ΠΌΠ° ΠΏΡΠ΅ΡΡΠ° Π6-ΠΠΠ¨- 1000 ΠΏΡΠ΅Π΄ΡΡΠ°Π²Π»Π΅Π½Π° Π½Π° ΡΠΈΡΡΠ½ΠΊΠ΅ 4.
ΠΡΠ΅ΡΡ ΠΌΠΎΠΆΠ΅Ρ ΠΊΠΎΠΌΠΏΠ»Π΅ΠΊΡΠΎΠ²Π°ΡΡΡΡ Π΄Π²ΡΠΌΡ ΠΏΡΠ΅ΡΡΡΡΡΠΈΠΌΠΈ Π³ΠΎΠ»ΠΎΠ²ΠΊΠ°ΠΌΠΈ Π΄Π»Ρ ΠΊΡΡΠ³Π»ΡΡ ΠΌΠ°ΡΡΠΈΡ Ρ ΠΌΠ΅Ρ Π°Π½ΠΈΠ·ΠΌΠ°ΠΌΠΈ ΠΈΡ Π·Π°ΠΌΠ΅Π½Ρ, ΠΎΠ±Π΄ΡΠ²ΠΎΡΠ½ΡΠΌ ΡΡΡΡΠΎΠΉΡΡΠ²ΠΎΠΌ ΠΈ ΠΌΠ΅Ρ Π°Π½ΠΈΠ·ΠΌΠΎΠΌ ΡΠ΅Π·ΠΊΠΈ Π΄Π»Ρ ΠΊΠ°ΠΆΠ΄ΠΎΠΉ Π³ΠΎΠ»ΠΎΠ²ΠΊΠΈ ΠΈΠ»ΠΈ ΡΡΠ±ΡΡΠΎΠΌ Π΄Π»Ρ Π΄Π²ΡΡ ΠΏΡΡΠΌΠΎΡΠ³ΠΎΠ»ΡΠ½ΡΡ ΠΌΠ°ΡΡΠΈΡ Ρ ΠΌΠ΅Ρ Π°Π½ΠΈΠ·ΠΌΠΎΠΌ ΠΈΡ Π·Π°ΠΌΠ΅Π½Ρ ΠΈ ΠΎΠ±Π΄ΡΠ²ΠΎΡΠ½ΡΠΌ ΡΡΡΡΠΎΠΉΡΡΠ²ΠΎΠΌ.
ΠΠΎΠ½ΡΡΡΡΠΊΡΠΈΡ Π΄ΠΎΠ·ΠΈΡΡΡΡΠ΅Π³ΠΎ ΡΡΡΡΠΎΠΉΡΡΠ²Π° 3 Π°Π½Π°Π»ΠΎΠ³ΠΈΡΠ½Π° ΡΠΎΠΎΡΠ²Π΅ΡΡΡΠ²ΡΡΡΠ΅ΠΌΡ ΡΡΡΡΠΎΠΉΡΡΠ²Ρ Π² ΠΏΡΠ΅ΡΡΠ΅ Π6-ΠΠΠ¨-500.Π’Π΅ΡΡΠΎΡΠΌΠ΅ΡΠΈΡΠ΅Π»Ρ ΠΈΠΌΠ΅Π΅Ρ ΡΡΠΈ ΠΊΠ°ΠΌΠ΅ΡΡ 24,19,8.
ΠΡΠ΅ΡΡΡΡΡΠΈΠ΅ Π³ΠΎΠ»ΠΎΠ²ΠΊΠΈ ΠΏΡΠ΅ΡΡΠ° Π΄Π»Ρ ΠΊΡΡΠ³Π»ΡΡ ΠΌΠ°ΡΡΠΈΡ ΠΈΠΌΠ΅ΡΡ ΡΠΈΠ»ΠΈΠ½Π΄ΡΠΈΡΠ΅ΡΠΊΡΡ ΡΠ°ΡΡΡ Ρ ΠΏΡΠΎΠ±ΠΊΠΎΠΉ 15, Π·Π°ΠΊΡΡΠ²Π°Π΅ΠΌΠΎΠΉ ΠΊΡΡΡΠΊΠΎΠΉ 21, ΠΈ ΡΡΠ΅ΡΠΈΡΠ΅ΡΠΊΡΡ 20, Π² ΠΊΠΎΡΠΎΡΠΎΠΉ ΡΡΡΠ°Π½Π°Π²Π»ΠΈΠ²Π°Π΅ΡΡΡ ΠΊΡΡΠ³Π»Π°Ρ ΠΌΠ°ΡΡΠΈΡΠ° 16 Π΄ΠΈΠ°ΠΌΠ΅ΡΡΠΎΠΌ 350 ΠΌΠΌ.
Π ΠΈΡ. 4. Π¨Π½Π΅ΠΊΠΎΠ²ΡΠΉ ΠΌΠ°ΠΊΠ°ΡΠΎΠ½Π½ΡΠΉ ΠΏΡΠ΅ΡΡ Π6- ΠΠΠ¨ -1000:
1,9,18 β ΠΌΠ΅ΡΠΈΠ»ΡΠ½ΡΠ΅ Π²Π°Π»Ρ; 2 — ΠΏΠ°Π»Π΅Ρ; 3 β Π΄ΠΎΠ·ΠΈΡΡΡΡΠ΅Π΅ ΡΡΡΡΠΎΠΉΡΡΠ²ΠΎ; 4,5 — ΠΌΡΡΡΡ; 6 — ΠΊΠ»ΠΈΠ½ΠΎΡΠ΅ΠΌΡΠ½Π½Π°Ρ ΠΏΠ΅ΡΠ΅Π΄Π°ΡΠ°;7,27 — ΡΠ»Π΅ΠΊΡΡΠΎΠ΄Π²ΠΈΠ³Π°ΡΠ΅Π»ΠΈ; 8,19,24 β ΠΌΠ΅ΡΠΈΠ»ΡΠ½ΡΠ΅ ΠΊΠ°ΠΌΠ΅ΡΡ;10- ΠΊΡΡΡΠΊΠ°; 11- ΡΠ½Π΅ΠΊ; 12- Π²ΠΎΠ΄ΡΠ½Π°Ρ ΡΡΠ±Π°ΡΠΊΠ°; 13 β ΡΡΡΡ Π·Π°Ρ ΠΎΠ΄Π½ΠΎΠ΅ Π·Π²Π΅Π½ΠΎ; 14- ΠΊΠ°Π½Π°Π²ΠΊΠΈ; 15 β ΠΏΡΠΎΠ±ΠΊΠ°; 16 — ΠΌΠ°ΡΡΠΈΡΠ°; 17 — Π½ΠΎΠΆ; 20 β ΡΡΠ΅ΡΠΈΡΠ΅ΡΠΊΠ°Ρ ΡΠ°ΡΡΡ ΠΏΡΠ΅ΡΡΡΡΡΠ΅ΠΉ Π³ΠΎΠ»ΠΎΠ²ΠΊΠΈ; 22,25 — ΠΎΠΊΠ½Π°; 21 β ΠΏΡΠ΅ΡΡΡΡΡΠ΅Π΅ ΡΡΡΡΠΎΠΉΡΡΠ²ΠΎ; 26 β ΡΠΎΡΠΎΡΠ½ΡΠΉ ΠΏΠΈΡΠ°ΡΠ΅Π»Ρ
ΠΠ±Π΄ΡΠ²ΠΎΡΠ½ΡΠ΅ ΡΡΡΡΠΎΠΉΡΡΠ²Π° ΠΈ ΠΌΠ΅Ρ Π°Π½ΠΈΠ·ΠΌΡ ΡΠ΅Π·ΠΊΠΈ ΡΠΎΠΎΡΠ²Π΅ΡΡΡΠ²ΡΡΡ Π°Π½Π°Π»ΠΎΠ³ΠΈΡΠ½ΡΠΌ ΡΡΡΡΠΎΠΉΡΡΠ²Π°ΠΌ Π½Π° ΠΏΡΠ΅ΡΡΠ°Ρ Π6-ΠΠΠ¨-500.
ΠΡΠΈΠ½ΡΠΈΠΏ ΡΠ°Π±ΠΎΡΡ. Π’Π΅ΡΡΠΎ Π³ΠΎΡΠΎΠ²ΠΈΡΡΡ Π² ΡΡΠ΅Ρ ΠΊΠ°ΠΌΠ΅ΡΠ½ΠΎΠΌ ΡΠ΅ΡΡΠΎΡΠΌΠ΅ΡΠΈΡΠ΅Π»Π΅ Π² ΡΠ΅ΡΠ΅Π½ΠΈΠ΅ 18-20 ΠΌΠΈΠ½. ΠΡΠΊΠ° ΠΈ Π²ΠΎΠ΄Π° Π² Π½Π΅ΠΎΠ±Ρ ΠΎΠ΄ΠΈΠΌΠΎΠΌ ΡΠΎΠΎΡΠ½ΠΎΡΠ΅Π½ΠΈΠΈ ΠΏΠΎΡΡΡΠΏΠ°ΡΡ Π² ΠΏΠ΅ΡΠ²ΡΡ ΠΊΠ°ΠΌΠ΅ΡΡ 24, Π² ΠΊΠΎΡΠΎΡΠΎΠΉ Ρ ΠΏΠΎΠΌΠΎΡΡΡ Π²ΡΠ°ΡΠ°ΡΡΠ΅Π³ΠΎΡΡ Π²Π°Π»Π° Ρ Π»ΠΎΠΏΠ°ΡΠΊΠ°ΠΌΠΈ ΠΏΡΠ΅Π΄Π²Π°ΒΡΠΈΡΠ΅Π»ΡΠ½ΠΎ ΡΠΌΠ΅ΡΠΈΠ²Π°ΡΡΡΡ ΠΈΠ½Π³ΡΠ΅Π΄ΠΈΠ΅Π½ΡΡ. Π§Π΅ΡΠ΅Π· ΠΎΠΊΠ½ΠΎ 22, ΡΠ°ΡΠΏΠΎΠ»ΠΎΠΆΠ΅Π½Π½ΠΎΠ΅ Π² ΠΊΠΎΠ½ΒΡΠ΅ ΠΏΠ΅ΡΠ²ΠΎΠΉ ΠΊΠ°ΠΌΠ΅ΡΡ, ΡΠ΅ΡΡΠΎ ΠΏΠΎΡΡΡΠΏΠ°Π΅Ρ Π² Π½ΠΈΠΆΠ½ΠΈΠΉ Π΄Π²ΡΡ Π²Π°Π»ΡΠ½ΡΠΉ ΡΠ΅ΡΡΠΎΡΠΌΠ΅ΡΠΈΡΠ΅Π»Ρ 19, Π³Π΄Π΅ Π½Π°Π²ΡΡΡΠ΅ΡΡ Π΄ΡΡΠ³ Π΄ΡΡΠ³Ρ Π²ΡΠ°ΡΠ°ΡΡΡΡ Π΄Π²Π° Π²Π°Π»Π° Ρ Π»ΠΎΠΏΠ°ΡΠΊΠ°ΠΌΠΈ 18. ΠΠΎΠΏΠ°ΡΒΠΊΠΈ ΡΡΡΠ°Π½ΠΎΠ²Π»Π΅Π½Ρ Π² ΠΎΠΏΡΠ΅Π΄Π΅Π»Π΅Π½Π½ΠΎΠΌ ΠΏΠΎΡΡΠ΄ΠΊΠ΅, ΠΎΠ±Π΅ΡΠΏΠ΅ΡΠΈΠ²Π°ΡΡΠ΅ΠΌ ΠΏΠ΅ΡΠ΅ΠΌΠ΅ΡΠΈΠ²Π°ΒΠ½ΠΈΠ΅ ΡΠ΅ΡΡΠ° Π΄ΠΎ Π½Π΅ΠΎΠ±Ρ ΠΎΠ΄ΠΈΠΌΠΎΠΉ ΠΊΠΎΠ½ΡΠΈΡΡΠ΅Π½ΡΠΈΠΈ ΠΈ ΠΏΠ΅ΡΠ΅ΠΌΠ΅ΡΠ΅Π½ΠΈΠ΅ Π΅Π³ΠΎ ΠΊ Π²ΡΠ³ΡΡΠ·ΠΎΡΒΠ½ΠΎΠΌΡ ΠΎΠΊΠ½Ρ 25. ΠΠ°ΠΆΠ΄Π°Ρ ΠΊΠ°ΠΌΠ΅ΡΠ° ΠΈΠΌΠ΅Π΅Ρ ΡΠ΅ΡΠ΅ΡΡΠ°ΡΡΡ ΠΊΡΡΡΠΊΡ, ΠΌΠ΅Ρ Π°Π½ΠΈΡΠ΅ΡΠΊΠΈ ΡΠ±Π»ΠΎΠΊΠΈΒΡΠΎΠ²Π°Π½Π½ΡΡ Ρ ΡΡΡΠ°Π³ΠΎΠΌ Π²ΠΊΠ»ΡΡΠ΅Π½ΠΈΡ ΠΌΡΡΡΡ ΡΡΠ΅ΠΏΠ»Π΅Π½ΠΈΡ ΠΏΡΠΈΠ²ΠΎΠ΄Π° Π²Π°Π»Π° ΡΠ΅ΡΡΠΎΡΠΌΠ΅ΡΠΈΡΠ΅Π»Ρ. Π‘Ρ Π΅ΠΌΠ° Π±Π»ΠΎΠΊΠΈΡΠΎΠ²ΠΊΠΈ ΡΡΡΡΠΎΠ΅Π½Π° ΡΠ°ΠΊ, ΡΡΠΎ Π½Π΅ ΠΏΠΎΠ·Π²ΠΎΠ»ΡΠ΅Ρ ΠΎΡΠΊΡΡΡΡ ΠΊΡΡΡΠΊΡ, Π½Π΅ Π²ΠΊΠ»ΡΡΠΈΠ² ΠΌΡΡΡΡ, ΠΈ ΠΏΡΠΈ ΠΎΡΠΊΡΡΡΠΎΠΉ ΠΊΡΡΡΠΊΠ΅ Π½Π΅Π²ΠΎΠ·ΠΌΠΎΠΆΠ½ΠΎ Π²ΠΊΠ»ΡΡΠΈΡΡ ΠΌΡΡΡΡ. ΠΡΡ ΠΎΠ΄ ΡΠ΅ΡΡΠ° ΠΈΠ· Π²ΡΠΎΡΠΎΠΉ ΠΊΠ°ΠΌΠ΅ΡΡ Π² ΡΡΠ΅ΡΠΈΠΉ Π²Π°ΠΊΡΡΠΌΠ½ΡΠΉ ΡΠΌΠ΅ΡΠΈΡΠ΅Π»Ρ ΠΎΡΡΡΠ΅ΡΡΠ²Π»ΡΠ΅ΡΡΡ ΡΠ΅ΡΠ΅Π· Π²Π°ΠΊΡΡΠΌΠ½ΡΠΉ Π·Π°ΡΠ²ΠΎΡ.
ΠΡΠ½ΠΎΠ²Π½ΡΠ΅ ΠΏΡΠ°Π²ΠΈΠ»Π° Π±Π΅Π·ΠΎΠΏΠ°ΡΠ½ΠΎΠΉ ΡΠ°Π±ΠΎΡΡ ΡΠ½Π΅ΠΊΠΎΠ²ΡΡ ΠΏΡΠ΅ΡΡΠΎΠ²
ΠΠ»Ρ Π±Π΅Π·ΠΎΠΏΠ°ΡΠ½ΠΎΠΉ ΡΠ°Π±ΠΎΡΡ ΡΠ½Π΅ΠΊΠΎΠ²ΡΡ ΠΏΡΠ΅ΡΡΠΎΠ² Π½Π΅ΠΎΠ±Ρ ΠΎΠ΄ΠΈΠΌΠΎ:
— Π΅ΠΆΠ΅Π΄Π½Π΅Π²Π½ΠΎ ΠΏΡΠΎΠ²Π΅ΡΡΡΡ ΠΈΡΠΏΡΠ°Π²Π½ΠΎΡΡΡ ΠΌΠ΅Ρ Π°Π½ΠΈΠ·ΠΌΠΎΠ² Π±Π»ΠΎΠΊΠΈΡΠΎΠ²ΠΊΠΈ ΠΎΡΠΊΡΡΠ²Π°Π½ΠΈΡ ΠΊΡΡΡΠ΅ΠΊ ΠΊΠ°ΠΌΠ΅Ρ;
— Π½Π΅ ΠΏΡΠΎΠΈΠ·Π²ΠΎΠ΄ΠΈΡΡ ΠΏΡΠΈ ΡΠ°Π±ΠΎΡΠ΅ ΠΏΡΠ΅ΡΡΠ° ΠΊΠ°ΠΊΠΎΠΉ Π±Ρ ΡΠΎ Π½ΠΈ Π±ΡΠ»ΠΎ ΡΠ΅ΠΌΠΎΠ½Ρ, ΡΠΌΠ°Π·ΠΊΡ ΠΈΠ»ΠΈ ΠΎΡΠΈΡΡΠΊΡ Π΄Π²ΠΈΠΆΡΡΠΈΡ ΡΡ ΠΌΠ΅Ρ Π°Π½ΠΈΠ·ΠΌΠΎΠ², Π½Π΅ ΡΠ½ΠΈΠΌΠ°ΡΡ ΠΎΠ³ΡΠ°ΠΆΠ΄Π΅Π½ΠΈΡ ΠΈ Π΄Π΅ΡΠ°Π»ΠΈ, Π½Π΅ ΠΊΠ°ΡΠ°ΡΡΡΡ Π΄Π²ΠΈΠΆΡΡΠΈΡ ΡΡ ΡΠ°ΡΡΠ΅ΠΉ;
— ΠΏΡΠ΅ΡΡ Π΄ΠΎΠ»ΠΆΠ΅Π½ Π±ΡΡΡ Π½Π°Π΄Π΅ΠΆΠ½ΠΎ Π·Π°Π·Π΅ΠΌΠ»Π΅Π½, Π²ΡΠ΅ ΠΏΡΡΠΊΠΎΠ²ΡΠ΅ ΡΠ»Π΅ΠΊΡΡΠΎΠΏΡΠΈΠ±ΠΎΡΡ ΠΈ ΠΏΡΠΎΠ²ΠΎΠ΄ΠΊΠ° Π΄ΠΎΠ»ΠΆΠ½Ρ Π½Π°Ρ ΠΎΠ΄ΠΈΡΡΡΡ Π² ΠΈΡΠΏΡΠ°Π²Π½ΠΎΠΌ ΡΠΎΡΡΠΎΡΠ½ΠΈΠΈ;
— ΠΏΡΠΎΠΈΠ·Π²ΠΎΠ΄ΠΈΡΡ ΠΎΡΠΌΠΎΡΡ ΠΈ ΡΠ΅ΠΌΠΎΠ½Ρ ΡΠ»Π΅ΠΊΡΡΠΎΠ΄Π²ΠΈΠ³Π°ΡΠ΅Π»Π΅ΠΉ, ΠΏΡΡΠΊΠΎΠ²ΠΎΠΉ Π°ΠΏΠΏΠ°ΡΠ°ΡΡΡΡ ΠΈ ΡΠ»Π΅ΠΊΡΡΠΎΠΏΡΠΎΠ²ΠΎΠ΄ΠΊΠΈ ΡΠΎΠ»ΡΠΊΠΎ ΠΏΡΠΈ Π²ΡΠΊΠ»ΡΡΠ΅Π½Π½ΠΎΠΌ ΠΏΠΈΡΠ°Π½ΠΈΠΈ;
— Π²ΡΠ΅ Π·Π°ΡΠΈΡΠ½ΡΠ΅ ΠΎΠ³ΡΠ°ΠΆΠ΄Π΅Π½ΠΈΡ ΠΈ ΠΊΠΎΠΆΡΡ ΠΈ ΠΏΡΠ΅ΡΡΠ° Π²ΡΠ΅Π³Π΄Π° Π΄ΠΎΠ»ΠΆΠ½Ρ Π±ΡΡΡ Π½Π° ΡΠ²ΠΎΠΈΡ ΠΌΠ΅ΡΡΠ°Ρ ΠΈ Π² ΠΈΡΠΏΡΠ°Π²Π½ΠΎΠΌ ΡΠΎΡΡΠΎΡΠ½ΠΈΠΈ.
Π ΠΏΡΠΎΡΠ΅ΡΡΠ΅ ΡΠΊΡΠΏΠ»ΡΠ°ΡΠ°ΡΠΈΠΈ ΠΏΡΠ΅ΡΡΠ° Π½Π΅ΠΎΠ±Ρ ΠΎΠ΄ΠΈΠΌΠΎ ΠΏΡΠΎΠ²ΠΎΠ΄ΠΈΡΡ ΡΠ΅ΠΊΡΡΠΈΠΉ ΡΠ΅ΠΌΠΎΠ½Ρ Π½Π΅ ΡΠ΅ΠΆΠ΅ ΠΎΠ΄Π½ΠΎΠ³ΠΎ ΡΠ°Π·Π° Π² 6 ΠΌΠ΅ΡΡΡΠ΅Π², ΠΊΠ°ΠΏΠΈΡΠ°Π»ΡΠ½ΡΠΉ ΡΠ΅ΠΌΠΎΠ½Ρ ΠΎΠ΄ΠΈΠ½ ΡΠ°Π· Π² 3 Π³ΠΎΠ΄Π° ΠΈ ΠΏΠΎΡΡΠΎΡΠ½Π½ΠΎ, ΡΠΎΠ³Π»Π°ΡΠ½ΠΎ ΡΡΡΠ°Π½ΠΎΠ²Π»Π΅Π½Π½ΠΎΠΌΡ Π³ΡΠ°ΡΠΈΠΊΡ, ΠΏΡΠΎΠ²ΠΎΠ΄ΠΈΡΡ ΠΌΠ΅ΠΆΡΠ΅ΠΌΠΎΠ½ΡΠ½ΡΠΉ ΠΎΡΠΌΠΎΡΡ.
studfiles.net
ΠΠ°ΠΊΠ°ΡΠΎΠ½Π½ΡΠ΅ ΠΏΡΠ΅ΡΡΡ
ΠΠ°ΠΌΠ΅Ρ ΠΌΠ°ΠΊΠ°ΡΠΎΠ½Π½ΠΎΠ³ΠΎ ΡΠ΅ΡΡΠ° ΠΈ Π΅Π³ΠΎ ΠΏΠΎΡΠ»Π΅Π΄ΡΡΡΠ΅Π΅ ΡΠΎΡΠΌΠΎΠ²Π°Π½ΠΈΠ΅ ΠΎΡΡΡΠ΅ΡΡΠ²Π»ΡΡΡΡΡ Π² ΡΠ½Π΅ΠΊΠΎΠ²ΡΡ ΠΌΠ°ΠΊΠ°ΡΠΎΠ½Π½ΡΡ ΠΏΡΠ΅ΡΡΠ°Ρ Π½Π΅ΠΏΡΠ΅ΡΡΠ²Π½ΠΎΠ³ΠΎ Π΄Π΅ΠΉΡΡΠ²ΠΈΡ. Π ΠΎΡΠ΅ΡΠ΅ΡΡΠ²Π΅Π½Π½ΡΡ ΡΠ½Π΅ΠΊΠΎΠ²ΡΡ ΠΏΡΠ΅ΡΡΠ°Ρ ΠΏΡΠΈΠ³ΠΎΡΠΎΠ²Π»Π΅Π½ΠΈΠ΅ ΠΌΠ°ΠΊΠ°ΡΠΎΠ½Π½ΠΎΠ³ΠΎ ΡΠ΅ΡΡΠ° ΠΏΡΠΎΠΈΡΡ ΠΎΠ΄ΠΈΡ Π² Π΄Π²Π° ΡΡΠ°ΠΏΠ°.
ΠΠ° ΠΏΠ΅ΡΠ²ΠΎΠΌ ΡΡΠ°ΠΏΠ΅ ΠΌΡΠΊΠ°, Π²ΠΎΠ΄Π° ΠΈ ΠΎΠ±ΠΎΠ³Π°ΡΠΈΡΠ΅Π»ΡΠ½ΡΠ΅ Π΄ΠΎΠ±Π°Π²ΠΊΠΈ (Π΅ΡΠ»ΠΈ ΠΏΠΎΡΠ»Π΅Π΄Π½ΠΈΠ΅ ΠΏΡΠ΅Π΄ΡΡΠΌΠΎΡΡΠ΅Π½Ρ ΡΠ΅ΡΠ΅ΠΏΡΡΡΠΎΠΉ) ΡΠΌΠ΅ΡΠΈΠ²Π°ΡΡΡΡ Π² ΡΠ΅ΡΡΠΎΠΌΠ΅ΡΠΈΡΠ΅Π»Π΅, Π²Ρ ΠΎΠ΄ΡΡΠ΅ΠΌ Π² ΠΊΠΎΠ½ΡΡΡΡΠΊΡΠΈΡ ΠΏΡΠ΅ΡΡΠ°. ΠΡΠΎΡΠ΅ΡΡ ΡΠΌΠ΅ΡΠΈΠ²Π°Π½ΠΈΡ ΠΌΡΠΊΠΈ ΠΈ Π²ΠΎΠ΄Ρ Π² ΡΡΠΈΡ ΠΌΠ°ΡΠΈΠ½Π°Ρ Π½Π΅ΠΏΡΠ΅ΡΡΠ²Π½ΡΠΉ.
ΠΡΠΎΡΠΎΠΉ ΡΡΠ°ΠΏ ΠΎΡΡΡΠ΅ΡΡΠ²Π»ΡΠ΅ΡΡΡ Π² ΠΊΠ°Π½Π°Π»Π΅ ΡΠ½Π΅ΠΊΠΎΠ²ΠΎΠΉ ΠΊΠ°ΠΌΠ΅ΡΡ ΠΏΡΠ΅ΡΡΠ°, Π³Π΄Π΅ ΠΊΡΠΎΡΠΊΠΎΠΎΡΠ°Π·Π½Π°Ρ ΠΌΠ°ΡΡΠ° ΡΠ΅ΡΡΠ° ΠΏΠΎΠ΄ Π²ΠΎΠ·Π΄Π΅ΠΉΡΡΠ²ΠΈΠ΅ΠΌ ΡΠ½Π΅ΠΊΠΎΠ²ΠΎΠΉ Π»ΠΎΠΏΠ°ΡΡΠΈ ΠΏΠΎΡΡΠ΅ΠΏΠ΅Π½Π½ΠΎ ΡΠΏΠ»ΠΎΡΠ½ΡΠ΅ΡΡΡ ΠΈ ΠΏΠ»Π°ΡΡΠΈΡΠΈΡΠΈΡΡΠ΅ΡΡΡ, ΠΏΡΠΈΠΎΠ±ΡΠ΅ΡΠ°Ρ ΡΡΡΡΠΊΡΡΡΡ ΠΈ ΡΠ²ΠΎΠΉΡΡΠ²Π°, Π½Π΅ΠΎΠ±Ρ ΠΎΠ΄ΠΈΠΌΡΠ΅ Π΄Π»Ρ ΠΏΠΎΡΠ»Π΅Π΄ΡΡΡΠ΅Π³ΠΎ ΡΠΎΡΠΌΠΎΠ²Π°Π½ΠΈΡ.
Π’Π°ΠΊΠΈΠΌ ΠΎΠ±ΡΠ°Π·ΠΎΠΌ, ΠΏΡΠΎΠΈΡΡ ΠΎΠ΄ΠΈΡ Π·Π°ΠΊΠ»ΡΡΠΈΡΠ΅Π»ΡΠ½Π°Ρ ΡΡΠ°Π΄ΠΈΡ ΡΠΎΡΠΌΠΈΡΠΎΠ²Π°Π½ΠΈΡ ΡΡΡΡΠΊΡΡΡΡ ΠΌΠ°ΠΊΠ°ΡΠΎΠ½Π½ΠΎΠ³ΠΎ ΡΠ΅ΡΡΠ°, ΡΠ΅Π·ΠΊΠΎ ΠΎΡΠ»ΠΈΡΠ°ΡΡΠ°ΡΡΡ ΠΎΡ ΡΡΡΡΠΊΡΡΡΡ Ρ Π»Π΅Π±Π½ΠΎΠ³ΠΎ ΡΠ΅ΡΡΠ°.
ΠΠ° ΡΡΡΡΠΊΡΡΡΠ½ΠΎ-ΠΌΠ΅Ρ Π°Π½ΠΈΡΠ΅ΡΠΊΠΈΠ΅ ΠΈ ΡΠ΅ΠΎΠ»ΠΎΠ³ΠΈΡΠ΅ΡΠΊΠΈΠ΅ ΡΠ²ΠΎΠΉΡΡΠ²Π° ΡΠ΅ΡΡΠ° ΠΎΠ³ΡΠΎΠΌΠ½ΠΎΠ΅ Π²Π»ΠΈΡΠ½ΠΈΠ΅ ΠΎΠΊΠ°Π·ΡΠ²Π°Π΅Ρ ΡΠ΅ΠΌΠΏΠ΅ΡΠ°ΡΡΡΠ°, Π·Π½Π°ΡΠΈΡΠ΅Π»ΡΠ½ΠΎ ΠΎΠΏΡΠ΅Π΄Π΅Π»ΡΡ Ρ ΠΎΠ΄ ΠΈ ΡΠ΅Π·ΡΠ»ΡΡΠ°Ρ ΠΏΡΠ΅ΡΡΠΎΠ²Π°Π½ΠΈΡ ΡΡΡΡΡ ΠΈΠ·Π΄Π΅Π»ΠΈΠΉ.
Π’Π΅ΠΌΠΏΠ΅ΡΠ°ΡΡΡΠ° ΡΠ΅ΡΡΠ° Π·Π°Π²ΠΈΡΠΈΡ Π½Π΅ ΡΠΎΠ»ΡΠΊΠΎ ΠΎΡ ΡΠ΅ΠΌΠΏΠ΅ΡΠ°ΡΡΡΡ Π΅Π³ΠΎ ΠΊΠΎΠΌΠΏΠΎΠ½Π΅Π½ΡΠΎΠ², Π½ΠΎ ΠΈ ΠΈΠ·ΠΌΠ΅Π½ΡΠ΅ΡΡΡ ΠΏΡΠΈ Π΅Π³ΠΎ ΠΏΡΠΈΠ³ΠΎΡΠΎΠ²Π»Π΅Π½ΠΈΠΈ Π² ΡΠ΅ΡΡΠΎΠΌΠ΅ΡΠΈΡΠ΅Π»Π΅ ΠΈ Π² ΡΠ½Π΅ΠΊΠΎΠ²ΠΎΠΉ ΠΊΠ°ΠΌΠ΅ΡΠ΅, Π³Π΄Π΅ ΠΌΠ΅Ρ Π°Π½ΠΈΡΠ΅ΡΠΊΠ°Ρ ΡΠ½Π΅ΡΠ³ΠΈΡ ΡΠ°Π±ΠΎΡΡ ΡΠ°Π±ΠΎΡΠΈΡ ΠΎΡΠ³Π°Π½ΠΎΠ² ΡΠ΅ΡΡΠΎΠΌΠ΅ΡΠΈΡΠ΅Π»Ρ ΠΈ ΠΏΡΠ΅ΡΡΠ° ΠΏΠΎΡΡΠΈ ΡΠ΅Π»ΠΈΠΊΠΎΠΌ ΠΏΠ΅ΡΠ΅Ρ ΠΎΠ΄ΠΈΡ Π² ΡΠ΅ΠΏΠ»ΠΎΠ²ΡΡ ΡΠ½Π΅ΡΠ³ΠΈΡ, Π·Π° ΡΡΠ΅Ρ ΠΊΠΎΡΠΎΡΠΎΠΉ ΡΠ΅ΡΡΠΎ Π΄ΠΎΠΏΠΎΠ»Π½ΠΈΡΠ΅Π»ΡΠ½ΠΎ ΠΏΡΠΎΠ³ΡΠ΅Π²Π°Π΅ΡΡΡ. ΠΡΠΎΠΌΠ΅ ΡΠΎΠ³ΠΎ, ΡΠ½Π΅ΠΊΠΎΠ²Π°Ρ ΠΊΠ°ΠΌΠ΅ΡΠ° ΠΌΠΎΠΆΠ΅Ρ ΠΈΠΌΠ΅ΡΡ Π³ΡΠ΅ΡΡΠΈΠ΅ ΠΈΠ»ΠΈ ΠΎΡ Π»Π°ΠΆΠ΄Π°ΡΡΠΈΠ΅ ΡΡΡΡΠΎΠΉΡΡΠ²Π°, ΡΠ°ΠΊΠΆΠ΅ ΠΊΠΎΡΡΠ΅ΠΊΡΠΈΡΡΡΡΠΈΠ΅ ΡΠ΅ΠΌΠΏΠ΅ΡΠ°ΡΡΡΡ ΡΠ΅ΡΡΠ°. ΠΠΎΡΡΠΎΠΌΡ Π² Π½Π°ΡΡΠΎΡΡΠ΅Π΅ Π²ΡΠ΅ΠΌΡ Π² ΡΠ΅ΡΡΠΎΠΌΠ΅ΡΠΈΡΠ΅Π»ΡΡ ΡΠ½Π΅ΠΊΠΎΠ²ΠΎΠ³ΠΎ ΡΠΈΠΏΠ° ΡΠ°ΡΠ΅ Π²ΡΠ΅Π³ΠΎ ΠΈΡΠΏΠΎΠ»ΡΠ·ΡΡΡ Π΄Π²Π° ΡΠΈΠΏΠ° Π·Π°ΠΌΠ΅ΡΠΎΠ²: Ρ ΠΎΠ»ΠΎΠ΄Π½ΡΠΉ ΠΈ ΡΠ΅ΠΏΠ»ΡΠΉ.
Π ΡΠ΅ΡΡΠΎΠΌΠ΅ΡΠΈΡΠ΅Π»Π΅ ΠΌΠ°ΠΊΠ°ΡΠΎΠ½Π½ΠΎΠ³ΠΎ ΠΏΡΠ΅ΡΡΠ° ΠΏΡΠΈΠ³ΠΎΡΠΎΠ²Π»ΡΠ΅ΡΡΡ Π²Π΅ΡΡΠΌΠ° Π½Π΅ΠΎΠ΄Π½ΠΎΡΠΎΠ΄Π½Π°Ρ ΠΌΠ°ΡΡΠ°, ΠΊΡΠΎΡΠΊΠΎΠ²Π°ΡΠΎ-ΡΡΡ Π»Π°Ρ ΠΏΠΎ ΡΡΡΡΠΊΡΡΡΠ΅, Π½Π΅ΠΏΡΠΈΠ³ΠΎΠ΄Π½Π°Ρ Π΄Π»Ρ Π½Π΅ΠΏΠΎΡΡΠ΅Π΄ΡΡΠ²Π΅Π½Π½ΠΎΠ³ΠΎ ΠΏΡΠ΅ΡΡΠΎΠ²Π°Π½ΠΈΡ.
ΠΠ΅ΡΠ΅Π΄ ΠΏΡΠ΅ΡΡΠΎΠ²Π°Π½ΠΈΠ΅ΠΌ ΡΠ΅ΡΡΠΎ Π΄ΠΎΠ»ΠΆΠ½ΠΎ ΠΏΡΠΎΠΉΡΠΈ ΠΎΡΠ½ΠΎΠ²Π°ΡΠ΅Π»ΡΠ½ΡΡ ΠΌΠ΅Ρ Π°Π½ΠΈΡΠ΅ΡΠΊΡΡ ΠΎΠ±ΡΠ°Π±ΠΎΡΠΊΡ Ρ ΡΠ΅Π»ΡΡ ΠΏΡΠΈΠ΄Π°Π½ΠΈΡ Π΅ΠΌΡ ΡΠΏΡΡΠ³ΠΈΡ , ΠΏΠ»Π°ΡΡΠΈΡΠ½ΠΎ-Π²ΡΠ·ΠΊΠΈΡ ΡΠ²ΠΎΠΉΡΡΠ². ΠΠ°ΡΠ΅ΠΌ ΠΈΠ· ΡΠΌΠ΅ΡΠΈΡΠ΅Π»Ρ ΡΠ΅ΡΡΠΎ ΠΏΠΎΡΡΡΠΏΠ°Π΅Ρ Π² ΡΠ½Π΅ΠΊΠΎΠ²ΡΡ ΠΊΠ°ΠΌΠ΅ΡΡ, Π³Π΄Π΅ ΠΏΠΎΠ΄ Π΄Π΅ΠΉΡΡΠ²ΠΈΠ΅ΠΌ Π²ΡΠ°ΡΠ°ΡΡΠ΅Π³ΠΎΡΡ ΡΠ½Π΅ΠΊΠ° ΠΏΠΎΡΡΠ΅ΠΏΠ΅Π½Π½ΠΎ ΡΠΏΠ»ΠΎΡΠ½ΡΠ΅ΡΡΡ ΠΈ ΠΏΠ΅ΡΠ΅ΠΌΠ΅ΡΠ°Π΅ΡΡΡ Π² ΠΏΡΠ΅Π΄ΠΌΠ°ΡΡΠΈΡΠ½ΡΡ ΠΊΠ°ΠΌΠ΅ΡΡ, ΠΈΠ· ΠΊΠΎΡΠΎΡΠΎΠΉ ΠΏΠ»Π°ΡΡΠΈΡΠΈΡΠΈΡΠΎΠ²Π°Π½Π½ΠΎΠ΅ ΠΏΠΎΠ΄ Π±ΠΎΠ»ΡΡΠΈΠΌ Π΄Π°Π²Π»Π΅Π½ΠΈΠ΅ΠΌ ΡΠΎΡΠΌΡΠ΅ΡΡΡ ΡΠ΅ΡΠ΅Π· ΡΠΏΠ΅ΡΠΈΠ°Π»ΡΠ½ΡΠ΅ ΠΌΠ°ΡΡΠΈΡΡ.
Π ΡΠΎΠ²ΡΠ΅ΠΌΠ΅Π½Π½ΡΡ ΠΊΠΎΠ½ΡΡΡΡΠΊΡΠΈΡΡ ΠΏΡΠ΅ΡΡΠΎΠ² ΠΌΠ°ΠΊΠ°ΡΠΎΠ½Π½ΠΎΠ΅ ΡΠ΅ΡΡΠΎ ΠΏΠ΅ΡΠ΅Π΄ ΠΏΠΎΡΡΡΠΏΠ»Π΅Π½ΠΈΠ΅ΠΌ Π² ΡΠ½Π΅ΠΊΠΎΠ²ΡΡ ΠΊΠ°ΠΌΠ΅ΡΡ ΠΏΠΎΠ΄Π²Π΅ΡΠ³Π°Π΅ΡΡΡ Π²Π°ΠΊΡΡΠΌΠΈΡΠΎΠ²Π°Π½ΠΈΡ, Ρ. Π΅. ΠΈΠ· Π½Π΅Π³ΠΎ ΡΠ΄Π°Π»ΡΠ΅ΡΡΡ Π²ΠΎΠ·Π΄ΡΡ . ΠΡΠΎ ΠΏΠΎΠ·Π²ΠΎΠ»ΡΠ΅Ρ, Π²ΠΎ-ΠΏΠ΅ΡΠ²ΡΡ , ΠΏΠΎΠ»ΡΡΠΈΡΡ ΠΌΠ°ΠΊΠ°ΡΠΎΠ½Π½ΠΎΠ΅ ΡΠ΅ΡΡΠΎ Π±ΠΎΠ»Π΅Π΅ ΠΏΠ»ΠΎΡΠ½ΠΎΠΉ ΡΡΡΡΠΊΡΡΡΡ, ΠΏΠΎΠ²ΡΡΠΈΡΡ ΠΌΠ΅Ρ Π°Π½ΠΈΡΠ΅ΡΠΊΡΡ ΠΏΡΠΎΡΠ½ΠΎΡΡΡ Π²ΡΡΡΡΠ΅Π½Π½ΡΡ ΠΈΠ·Π΄Π΅Π»ΠΈΠΉ ΠΈ, Π²ΠΎ-Π²ΡΠΎΡΡΡ , ΡΠ½ΠΈΠ·ΠΈΡΡ ΡΠΊΠΎΡΠΎΡΡΡ ΡΠ΅Π°ΠΊΡΠΈΠΈ ΠΎΠΊΠΈΡΠ»Π΅Π½ΠΈΡ ΠΊΠΈΡΠ»ΠΎΡΠΎΠ΄ΠΎΠΌ Π²ΠΎΠ·Π΄ΡΡ Π° ΠΏΠΈΠ³ΠΌΠ΅Π½ΡΠ½ΡΡ Π²Π΅ΡΠ΅ΡΡΠ² Π³ΡΡΠΏΠΏΡ ΠΊΠ°ΡΠΎΡΠΈΠ½ΠΎΠΈΠ΄ΠΎΠ², ΠΏΡΠΈΠ΄Π°ΡΡΠΈΡ ΠΈΠ·Π΄Π΅Π»ΠΈΡΠΌ ΠΏΡΠΈΡΡΠ½ΡΠΉ ΠΆΠ΅Π»ΡΠΎ-ΠΊΡΠ΅ΠΌΠΎΠ²ΡΠΉ ΡΠ²Π΅Ρ.
Π¦Π΅Π»Ρ ΡΠΎΡΠΌΠΎΠ²Π°Π½ΠΈΡ β ΠΏΡΠΈΠ΄Π°ΡΡ ΠΌΠ°ΠΊΠ°ΡΠΎΠ½Π½ΠΎΠΌΡ ΡΠ΅ΡΡΡ ΡΠΎΡΠΌΡ, Ρ Π°ΡΠ°ΠΊΡΠ΅ΡΠ½ΡΡ Π΄Π»Ρ Π΄Π°Π½Π½ΠΎΠ³ΠΎ Π²ΠΈΠ΄Π° ΠΈΠ·Π΄Π΅Π»ΠΈΠΉ (ΡΡΡΠ±ΡΠ°ΡΡΠ΅; Π½ΠΈΡΠ΅ΠΎΠ±ΡΠ°Π·Π½ΡΠ΅; Π»Π΅Π½ΡΠΎΡΠ½ΡΠ΅ ΠΈ ΡΠΈΠ³ΡΡΠ½ΡΠ΅), ΠΊΠΎΡΠΎΡΠ°Ρ ΡΠΎΡ ΡΠ°Π½ΡΠ»Π°ΡΡ Π±Ρ Π½Π° ΠΏΠΎΡΠ»Π΅Π΄ΡΡΡΠΈΡ ΡΡΠ°Π΄ΠΈΡΡ ΠΏΡΠΎΠΈΠ·Π²ΠΎΠ΄ΡΡΠ²Π°.
Π¨Π½Π΅ΠΊΠΎΠ²ΡΠ΅ ΠΌΠ°ΠΊΠ°ΡΠΎΠ½Π½ΡΠ΅ ΠΏΡΠ΅ΡΡΡ Π½Π΅ΠΏΡΠ΅ΡΡΠ²Π½ΠΎΠ³ΠΎ Π΄Π΅ΠΉΡΡΠ²ΠΈΡ ΠΏΡΠ΅Π΄Π½Π°Π·Π½Π°ΡΠ΅Π½Ρ Π΄Π»Ρ ΠΏΡΠΈΠ³ΠΎΡΠΎΠ²Π»Π΅Π½ΠΈΡ ΡΠ΅ΡΡΠ° ΠΈ ΡΠΎΡΠΌΠΎΠ²Π°Π½ΠΈΡ ΠΈΠ· Π½Π΅Π³ΠΎ ΡΡΡΡΡ ΠΌΠ°ΠΊΠ°ΡΠΎΠ½Π½ΡΡ ΠΈΠ·Π΄Π΅Π»ΠΈΠΉ. ΠΡΠ½ΠΎΠ²Π½ΡΠΌΠΈ ΡΠ·Π»Π°ΠΌΠΈ ΡΠΎΠ²ΡΠ΅ΠΌΠ΅Π½Π½ΡΡ ΠΏΡΠ΅ΡΡΠΎΠ² ΡΠ²Π»ΡΡΡΡΡ Π΄ΠΎΠ·ΠΈΡΠΎΠ²ΠΎΡΠ½ΠΎΠ΅ ΡΡΡΡΠΎΠΉΡΡΠ²ΠΎ Π΄Π»Ρ ΠΌΡΠΊΠΈ ΠΈ Π²ΠΎΠ΄Ρ, ΡΠ΅ΡΡΠΎΠΌΠ΅ΡΠΈΡΠ΅Π»Ρ, ΠΏΡΠ΅ΡΡΡΡΡΠΈΠΉ ΠΊΠΎΡΠΏΡΡ, ΠΏΡΠ΅ΡΡΡΡΡΠ°Ρ Π³ΠΎΠ»ΠΎΠ²ΠΊΠ° ΠΈ ΠΌΠ°ΡΡΠΈΡΠ°. ΠΠ°ΠΆΠ΄ΡΠΉ ΠΏΡΠ΅ΡΡ ΠΎΠ±ΠΎΡΡΠ΄ΠΎΠ²Π°Π½ ΡΠΈΡΡΠ΅ΠΌΠΎΠΉ Π²Π°ΠΊΡΡΠΌΠΈΡΠΎΠ²Π°Π½ΠΈΡ.
ΠΠ°ΠΊΠ°ΡΠΎΠ½Π½ΡΠ΅ ΠΏΡΠ΅ΡΡΡ (ΡΠΈΡ.) ΡΠ°Π·Π»ΠΈΡΠ°ΡΡΡΡ ΠΊΠΎΠ½ΡΡΡΡΠΊΡΠΈΠ΅ΠΉ Π΄ΠΎΠ·Π°ΡΠΎΡΠΎΠ², ΡΠΈΡΠ»ΠΎΠΌ ΠΊΠ°ΠΌΠ΅Ρ ΡΠ΅ΡΡΠΎΠΌΠ΅ΡΠΈΡΠ΅Π»Ρ ΠΈ ΠΈΡ ΡΠ°ΡΠΏΠΎΠ»ΠΎΠΆΠ΅Π½ΠΈΠ΅ΠΌ, ΠΊΠΎΠ»ΠΈΡΠ΅ΡΡΠ²ΠΎΠΌ ΠΏΡΠ΅ΡΡΡΡΡΠΈΡ ΡΠ½Π΅ΠΊΠΎΠ², ΠΊΠΎΠ½ΡΡΡΡΠΊΡΠΈΠ΅ΠΉ ΠΏΡΠ΅ΡΡΡΡΡΠΈΡ Π³ΠΎΠ»ΠΎΠ²ΠΎΠΊ, ΡΠΎΡΠΌΠΎΠΉ ΠΌΠ°ΡΡΠΈΡ ΠΈ ΠΌΠ΅ΡΡΠΎΠΌ Π²Π°ΠΊΡΡΠΌΠΈΡΠΎΠ²Π°Π½ΠΈΡ. ΠΠ±ΡΡΠ½ΠΎ ΠΌΠ°ΠΊΠ°ΡΠΎΠ½Π½ΡΠ΅ ΠΏΡΠ΅ΡΡΡ ΡΡΠΈΡ ΡΠΈΠΏΠΎΠ² ΡΡΡΠ°Π½Π°Π²Π»ΠΈΠ²Π°ΡΡΡΡ Π² ΠΊΠΎΠΌΠΏΠ»Π΅ΠΊΡΠ½ΠΎ-ΠΌΠ΅Ρ Π°Π½ΠΈΠ·ΠΈΡΠΎΠ²Π°Π½Π½ΡΡ Π»ΠΈΠ½ΠΈΡΡ Π΄Π»Ρ ΠΏΡΠΎΠΈΠ·Π²ΠΎΠ΄ΡΡΠ²Π° Π΄Π»ΠΈΠ½Π½ΡΡ ΠΈ ΠΊΠΎΡΠΎΡΠΊΠΈΡ ΠΌΠ°ΠΊΠ°ΡΠΎΠ½Π½ΡΡ ΠΈΠ·Π΄Π΅Π»ΠΈΠΉ.
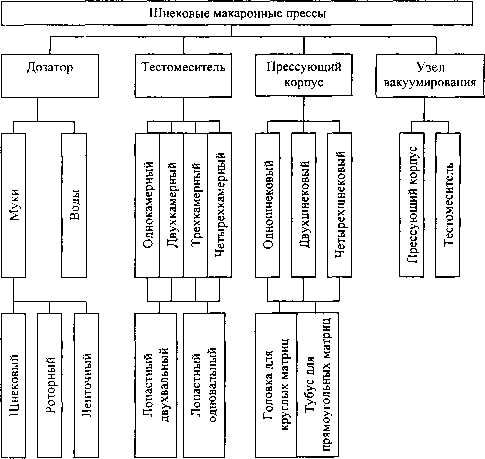
Π ΠΈΡ. ΠΠ»Π°ΡΡΠΈΡΠΈΠΊΠ°ΡΠΈΡ ΠΌΠ°ΠΊΠ°ΡΠΎΠ½Π½ΡΡ ΠΏΡΠ΅ΡΡΠΎΠ²
Π¨Π½Π΅ΠΊΠΎΠ²ΡΠΉ ΠΌΠ°ΠΊΠ°ΡΠΎΠ½Π½ΡΠΉ ΠΏΡΠ΅ΡΡ ΠΠΠ-2Π (ΡΠΈΡ.) ΡΠΎΡΡΠΎΠΈΡ ΠΈΠ· ΠΏΡΠΈΠ²ΠΎΠ΄Π° 1, Π΄ΠΎΠ·ΠΈΡΡΡΡΠ΅Π³ΠΎ ΡΡΡΡΠΎΠΉΡΡΠ²Π° 2, ΡΠ΅ΡΡΠΎΠΌΠ΅ΡΠΈΡΠ΅Π»Ρ 3, ΠΏΡΠ΅ΡΡΡΡΡΠ΅ΠΉ Π³ΠΎΠ»ΠΎΠ²ΠΊΠΈ 4, ΠΎΠ±Π΄ΡΠ²ΠΎΡΠ½ΠΎΠ³ΠΎ ΡΡΡΡΠΎΠΉΡΡΠ²Π° 5, ΡΠΈΡΡΠ΅ΠΌΡ ΡΡΡΠ±ΠΎΠΏΡΠΎΠ²ΠΎΠ΄ΠΎΠ² ΠΈ ΠΏΡΠ΅ΡΡΡΡΡΠ΅Π³ΠΎ ΠΊΠΎΡΠΏΡΡΠ° 8, ΡΡΡΠ°Π½ΠΎΠ²Π»Π΅Π½Π½ΡΡ Π½Π° ΠΎΠ±ΡΠ΅ΠΉ ΡΡΠ°Π½ΠΈΠ½Π΅ 7.
ΠΡΠ΅ΡΡ ΠΊΠΎΠΌΠΏΠ»Π΅ΠΊΡΡΠ΅ΡΡΡ ΠΌΠ΅Ρ Π°Π½ΠΈΠ·ΠΌΠΎΠΌ ΡΠ΅Π·ΠΊΠΈ 6, Π½Π°Π±ΠΎΡΠΎΠΌ ΠΊΡΡΠ³Π»ΡΡ ΠΌΠ°ΡΡΠΈΡ ΠΈ Π²Π°ΠΊΡΡΠΌΠ½ΠΎΠΉ ΡΠΈΡΡΠ΅ΠΌΠΎΠΉ.
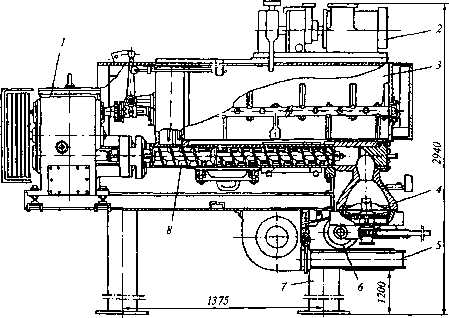
Π ΠΈΡ. Π¨Π½Π΅ΠΊΠΎΠ²ΡΠΉ ΠΌΠ°ΠΊΠ°ΡΠΎΠ½Π½ΡΠΉ ΠΏΡΠ΅ΡΡ ΠΠΠ-2Π
ΠΠ°ΡΡΠΈΡΠ° ΡΠ²Π»ΡΠ΅ΡΡΡ ΠΎΡΠ½ΠΎΠ²Π½ΡΠΌ ΡΠ°Π±ΠΎΡΠΈΠΌ ΠΎΡΠ³Π°Π½ΠΎΠΌ ΠΏΡΠ΅ΡΡΠ° ΠΈ ΠΏΡΠ΅Π΄ΡΡΠ°Π²Π»ΡΠ΅Ρ ΡΠΎΠ±ΠΎΠΉ ΠΌΠ΅ΡΠ°Π»Π»ΠΈΡΠ΅ΡΠΊΠΈΠΉ Π΄ΠΈΡΠΊ (ΠΊΡΡΠ³Π»Π°Ρ ΠΌΠ°ΡΡΠΈΡΠ°) ΠΈΠ»ΠΈ ΠΏΡΡΠΌΠΎΡΠ³ΠΎΠ»ΡΠ½ΡΡ ΠΏΠ»Π°ΡΡΠΈΠ½Ρ (ΡΡΠ±ΡΡΠ½Π°Ρ ΠΌΠ°ΡΡΠΈΡΠ°) ΡΠΎ ΡΠΊΠ²ΠΎΠ·Π½ΡΠΌΠΈ ΠΎΡΠ²Π΅ΡΡΡΠΈΡΠΌΠΈ, ΠΏΡΠΎΡΠΈΠ»Ρ ΠΊΠΎΡΠΎΡΡΡ ΠΎΠΏΡΠ΅Π΄Π΅Π»ΡΠ΅Ρ ΡΠΎΡΠΌΡ ΠΈΠ·Π΄Π΅Π»ΠΈΠΉ.
Π¨Π½Π΅ΠΊΠΎΠ²ΡΠΉ ΠΌΠ°ΠΊΠ°ΡΠΎΠ½Π½ΡΠΉ ΠΏΡΠ΅ΡΡ ΡΠ°Π±ΠΎΡΠ°Π΅Ρ ΡΠ»Π΅Π΄ΡΡΡΠΈΠΌ ΠΎΠ±ΡΠ°Π·ΠΎΠΌ. ΠΡΠΊΠ° ΡΠ°ΠΌΠΎΡΠ΅ΠΊΠΎΠΌ Π½Π΅ΠΏΡΠ΅ΡΡΠ²Π½ΠΎ ΠΈΠ· Π±ΡΠ½ΠΊΠ΅ΡΠ° ΠΏΠΎΡΡΡΠΏΠ°Π΅Ρ Π² Π΄ΠΎΠ·Π°ΡΠΎΡ, ΠΈΠ· ΠΊΠΎΡΠΎΡΠΎΠ³ΠΎ Π²ΡΠ°ΡΠ°ΡΡΠΈΠΌΡΡ ΡΠ½Π΅ΠΊΠΎΠΌ ΠΏΠΎΠ΄Π°Π΅ΡΡΡ Π² ΡΠ΅ΡΡΠΎΠΌΠ΅ΡΠΈΡΠ΅Π»Ρ. ΠΠ΄Π½ΠΎΠ²ΡΠ΅ΠΌΠ΅Π½Π½ΠΎ ΠΏΠΎΠ΄ΠΎΠ³ΡΠ΅ΡΠ°Ρ Π²ΠΎΠ΄Π° Ρ ΡΠ΅ΠΌΠΏΠ΅ΡΠ°ΡΡΡΠΎΠΉ 40…60 Β°Π‘ ΠΈΠ· Π΄ΠΎΠ·Π°ΡΠΎΡΠ° ΠΏΠΎ ΡΡΡΠ±Π΅ ΠΏΠΎΡΡΡΠΏΠ°Π΅Ρ Π² ΡΠ΅ΡΡΠΎΠΌΠ΅ΡΠΈΡΠ΅Π»Ρ. Π Π·Π°Π²ΠΈΡΠΈΠΌΠΎΡΡΠΈ ΠΎΡ Π²Π»Π°ΠΆΠ½ΠΎΡΡΠΈ ΠΌΡΠΊΠΈ ΡΠ°ΡΡ ΠΎΠ΄ Π²ΠΎΠ΄Ρ ΡΠΎΡΡΠ°Π²Π»ΡΠ΅Ρ 80…90 ΠΊΠ³/Ρ. Π Π°ΡΡ ΠΎΠ΄ Π²ΠΎΠ΄Ρ Π½Π° ΠΎΡ Π»Π°ΠΆΠ΄Π΅Π½ΠΈΠ΅ ΠΏΡΠ΅ΡΡΡΡΡΠ΅Π³ΠΎ ΠΊΠΎΡΠΏΡΡΠ° 110 ΠΊΠ³/Ρ. ΠΡΠΈ Π½ΠΎΡΠΌΠ°Π»ΡΠ½ΠΎΠΉ ΡΠ°Π±ΠΎΡΠ΅ ΠΏΡΠ΅ΡΡΠ° ΡΠ΅ΡΡΠΎ Π΄ΠΎΠ»ΠΆΠ½ΠΎ Π·Π°ΠΏΠΎΠ»Π½ΡΡΡ 2/3 ΠΎΠ±ΡΠ΅ΠΌΠ° ΠΊΠΎΡΡΡΠ° ΠΈ ΠΈΠΌΠ΅ΡΡ Π½Π΅Π±ΠΎΠ»ΡΡΠΎΠΉ ΡΠΊΠ»ΠΎΠ½ ΠΏΠΎ Π½Π°ΠΏΡΠ°Π²Π»Π΅Π½ΠΈΡ ΠΊ Π²ΡΡ ΠΎΠ΄Π½ΠΎΠΌΡ ΠΎΡΠ²Π΅ΡΡΡΠΈΡ.
ΠΠ΅ΠΎΠ±Ρ ΠΎΠ΄ΠΈΠΌΡΠΉ ΡΡΠΎΠ²Π΅Π½Ρ Π·Π°ΠΏΠΎΠ»Π½Π΅Π½ΠΈΡ ΠΊΠΎΡΡΡΠ° ΡΠ΅ΡΡΠΎΠΌ Π΄ΠΎΡΡΠΈΠ³Π°Π΅ΡΡΡ ΡΠ΅Π³ΡΠ»ΠΈΡΠΎΠ²Π°Π½ΠΈΠ΅ΠΌ ΠΏΠ»ΠΎΡΠΊΠΎΡΡΠΈ ΠΊΠΎΠ½ΡΠΎΠ² Π»ΠΎΠΏΠ°ΡΠΎΠΊ ΠΊ ΠΎΡΠΈ Π²Π°Π»Π°, ΠΊΠΎΡΠΎΡΡΠ΅ ΠΎΡΠ±ΡΠ°ΡΡΠ²Π°ΡΡ ΠΎΠΏΡΠ΅Π΄Π΅Π»Π΅Π½Π½ΡΡ ΡΠ°ΡΡΡ ΠΊΠΎΠΌΠΎΡΠΊΠΎΠ² ΡΠ΅ΡΡΠ° Π² Π½Π°ΠΏΡΠ°Π²Π»Π΅Π½ΠΈΠΈ ΠΎΡ Π²ΡΡ ΠΎΠ΄Π½ΠΎΠ³ΠΎ ΠΎΡΠ²Π΅ΡΡΡΠΈΡ ΠΊ Π΄ΠΎΠ·Π°ΡΠΎΡΠ°ΠΌ. ΠΡΠ±ΡΠ°ΡΡΠ²Π°Π½ΠΈΠ΅ ΡΠ΅ΡΡΠ° Π² ΠΎΠ±ΡΠ°ΡΠ½ΠΎΠΌ Π½Π°ΠΏΡΠ°Π²Π»Π΅Π½ΠΈΠΈ Π² ΠΎΠΏΡΠΈΠΌΠ°Π»ΡΠ½ΡΡ ΡΠ°Π·ΠΌΠ΅ΡΠ°Ρ Π½Π΅ΠΎΠ±Ρ ΠΎΠ΄ΠΈΠΌΠΎ Π΄Π»Ρ ΠΎΠ±Π΅ΡΠΏΠ΅ΡΠ΅Π½ΠΈΡ Π½ΠΎΡΠΌΠ°Π»ΡΠ½ΠΎΠΉ ΡΠΈΡΠΊΡΠ»ΡΡΠΈΠΈ ΡΠ΅ΡΡΠ°, ΡΡΠΎ ΡΠ΄Π»ΠΈΠ½ΡΠ΅Ρ Π²ΡΠ΅ΠΌΡ Π΅Π³ΠΎ Π½Π°Ρ ΠΎΠΆΠ΄Π΅Π½ΠΈΡ Π² ΠΊΠΎΡΡΡΠ΅ Π΄ΠΎ 10 ΠΌΠΈΠ½ ΠΈ ΡΠΏΠΎΡΠΎΠ±ΡΡΠ²ΡΠ΅Ρ Π½Π°Π±ΡΡ Π°Π½ΠΈΡ ΠΊΠ»Π΅ΠΉΠΊΠΎΠ²ΠΈΠ½Ρ ΠΈ Π»ΡΡΡΠ΅ΠΉ ΠΏΡΠΎΡΠ°Π±ΠΎΡΠΊΠ΅ ΡΠ΅ΡΡΠ° Π»ΠΎΠΏΠ°ΡΠΊΠ°ΠΌΠΈ ΠΈ ΠΏΠ°Π»ΡΡΠ°ΠΌΠΈ.
ΠΠ°ΠΌΠ΅ΡΠ΅Π½Π½Π°Ρ Π² Π²ΠΈΠ΄Π΅ ΠΊΠΎΠΌΠΎΡΠΊΠΎΠ² ΠΈ ΠΊΡΡΠΏΠΈΠ½ΠΎΠΊ ΡΠ΅ΡΡΠΎΠΎΠ±ΡΠ°Π·Π½Π°Ρ ΠΌΠ°ΡΡΠ° ΠΈΠ· ΠΊΠΎΡΡΡΠ° ΡΠΌΠ΅ΡΠΈΡΠ΅Π»Ρ ΡΠ΅ΡΠ΅Π· ΠΎΡΠ²Π΅ΡΡΡΠΈΠ΅ Π² Π½ΠΈΠΆΠ½Π΅ΠΉ ΡΠ°ΡΡΠΈ Π½Π°ΠΏΡΠ°Π²Π»ΡΠ΅ΡΡΡ Π² ΠΏΡΠ΅ΡΡΡΡΡΠΈΠΉ ΠΊΠΎΡΠΏΡΡ. ΠΡΠΈ ΡΡΠΎΠΌ, ΡΠ΅Π³ΡΠ»ΠΈΡΡΡ Π·Π°ΡΠ»ΠΎΠ½ΠΊΠΎΠΉ ΡΠ°Π·ΠΌΠ΅Ρ Π²ΡΡ ΠΎΠ΄Π½ΠΎΠ³ΠΎ ΠΎΡΠ²Π΅ΡΡΡΠΈΡ, ΠΌΠΎΠΆΠ½ΠΎ ΠΈΠ·ΠΌΠ΅Π½ΡΡΡ ΠΊΠΎΠ»ΠΈΡΠ΅ΡΡΠ²ΠΎ ΡΠ΅ΡΡΠ°, ΠΏΠΎΠ΄Π°Π²Π°Π΅ΠΌΠΎΠ³ΠΎ Π² ΠΏΡΠ΅ΡΡΡΡΡΠΈΠΉ ΠΊΠΎΡΠΏΡΡ, ΠΈ ΡΠ΅ΠΌ ΡΠ°ΠΌΡΠΌ ΠΈΠ·ΠΌΠ΅Π½ΡΡΡ ΠΏΡΠΎΠΈΠ·Π²ΠΎΠ΄ΠΈΡΠ΅Π»ΡΠ½ΠΎΡΡΡ ΠΏΡΠ΅ΡΡΠ°.
Π ΠΏΡΠ΅ΡΡΡΡΡΠ΅ΠΌ ΠΊΠΎΡΠΏΡΡΠ΅ ΡΠ΅ΡΡΠΎ, ΠΏΡΠΎΠ΄Π²ΠΈΠ³Π°ΡΡΡ, ΠΎΠ±ΡΠ΅ΠΊΠ°Π΅Ρ ΡΠ°ΠΉΠ±Ρ Π½Π° ΡΠ½Π΅ΠΊΠ΅ ΠΈ ΠΏΠΎΡΡΡΠΏΠ°Π΅Ρ Π² ΠΏΠ΅ΡΠ΅ΠΏΡΡΠΊΠ½ΠΎΠΉ ΠΊΠ°Π½Π°Π», Π³Π΄Π΅ ΠΈΠ· Π½Π΅Π³ΠΎ ΡΠ΅ΡΠ΅Π· Π²Π°ΠΊΡΡΠΌ-ΠΊΠ°Π½Π°Π» ΡΠ΄Π°Π»ΡΡΡΡΡ Π²ΠΎΠ·Π΄ΡΡ ΠΈ ΠΏΠ°ΡΡ Π²ΠΎΠ΄Ρ. ΠΡΡΠ°ΡΠΎΡΠ½ΠΎΠ΅ Π΄Π°Π²Π»Π΅Π½ΠΈΠ΅ Π²ΠΎΠ·Π΄ΡΡ Π° Π² ΠΏΡΠ΅ΡΡΡΡΡΠ΅ΠΌ ΠΊΠΎΡΠΏΡΡΠ΅ ΡΠΎΡΡΠ°Π²Π»ΡΠ΅Ρ 10 ΠΊΠΠ°. ΠΠ· ΠΏΠ΅ΡΠ΅ΠΏΡΡΠΊΠ½ΠΎΠ³ΠΎ ΠΊΠ°Π½Π°Π»Π° ΡΠ΅ΡΡΠΎ ΠΏΡΠΎΡ ΠΎΠ΄ΠΈΡ ΡΠΊΠ²ΠΎΠ·Ρ ΡΠ΅ΡΠ΅ΡΠΊΡ Π² ΠΏΡΠ΅ΡΡΡΡΡΠΈΠΉ ΠΊΠΎΡΠΏΡΡ, Π·Π°Ρ Π²Π°ΡΡΠ²Π°Π΅ΡΡΡ Π²ΠΈΡΠΊΠ°ΠΌΠΈ ΡΠ½Π΅ΠΊΠ°, Π½Π°Π³Π½Π΅ΡΠ°Π΅ΡΡΡ Π² Π³ΠΎΠ»ΠΎΠ²ΠΊΡ ΠΈ Π·Π°ΡΠ΅ΠΌ ΠΏΡΠΎΠ΄Π°Π²Π»ΠΈΠ²Π°Π΅ΡΡΡ ΡΠ΅ΡΠ΅Π· ΡΠΎΡΠΌΡΡΡΠΈΠ΅ ΠΎΡΠ²Π΅ΡΡΡΠΈΡ ΠΌΠ°ΡΡΠΈΡΡ ΠΏΡΠΈ Π΄Π°Π²Π»Π΅Π½ΠΈΠΈ 6,5…7,0 ΠΠΠ°.
ΠΡΡ ΠΎΠ΄ΡΡΠΈΠ΅ ΠΈΠ· ΠΌΠ°ΡΡΠΈΡΡ ΠΌΠ°ΠΊΠ°ΡΠΎΠ½Π½ΡΠ΅ ΠΈΠ·Π΄Π΅Π»ΠΈΡ ΠΏΡΠΎΡ ΠΎΠ΄ΡΡ ΠΎΠ±Π΄ΡΠ²ΠΎΡΠ½ΠΎΠ΅ ΡΡΡΡΠΎΠΉΡΡΠ²ΠΎ, ΠΏΡΠΈ ΡΡΠΎΠΌ ΠΎΠ½ΠΈ ΠΈΠΌΠ΅ΡΡ ΡΠ΅ΠΌΠΏΠ΅ΡΠ°ΡΡΡΡ, ΡΠ°Π²Π½ΡΡ ΡΠ΅ΠΌΠΏΠ΅ΡΠ°ΡΡΡΠ΅ ΠΏΡΠ΅ΡΡΠΎΠ²Π°Π½Π½ΠΎΠ³ΠΎ ΡΠ΅ΡΡΠ°, ΠΊΠΎΡΠΎΡΠ°Ρ ΡΠΎΡΡΠ°Π²Π»ΡΠ΅Ρ 45…50 Β°Π‘.
Π ΠΏΡΠ΅ΡΡΠΎΠ²ΠΎΠΌ ΠΎΡΠ΄Π΅Π»Π΅Π½ΠΈΠΈ Π·Π½Π°ΡΠΈΡΠ΅Π»ΡΠ½ΠΎ ΠΌΠ΅Π½ΡΡΠ°Ρ ΡΠ΅ΠΌΠΏΠ΅ΡΠ°ΡΡΡΠ° ΠΎΠΊΡΡΠΆΠ°ΡΡΠ΅Π³ΠΎ Π²ΠΎΠ·Π΄ΡΡ Π°, Π² ΡΠ΅Π·ΡΠ»ΡΡΠ°ΡΠ΅ Π΄Π»Ρ ΠΈΠ·Π΄Π΅Π»ΠΈΠΉ, Π²ΡΡ ΠΎΠ΄ΡΡΠΈΡ ΠΈΠ· ΠΌΠ°ΡΡΠΈΡΡ, ΡΠΎΠ·Π΄Π°Π΅ΡΡΡ ΡΠ΅ΠΌΠΏΠ΅ΡΠ°ΡΡΡΠ½ΡΠΉ ΠΏΠ΅ΡΠ΅ΠΏΠ°Π΄, Π²Π΅Π»ΠΈΡΠΈΠ½Π° ΠΊΠΎΡΠΎΡΠΎΠ³ΠΎ Π·Π°Π²ΠΈΡΠΈΡ ΠΎΡ ΡΠ°Π·Π½ΠΎΡΡΠΈ ΡΠ΅ΠΌΠΏΠ΅ΡΠ°ΡΡΡ ΠΏΡΠ΅ΡΡΠΎΠ²Π°Π½ΠΈΡ ΠΈ ΠΎΠΊΡΡΠΆΠ°ΡΡΠ΅ΠΉ ΡΡΠ΅Π΄Ρ. Π§Π΅ΠΌ Π±ΠΎΠ»ΡΡΠ΅ ΡΡΠ° ΡΠ°Π·Π½ΠΎΡΡΡ, ΡΠ΅ΠΌ Π²ΡΡΠ΅ ΡΠ΅ΠΌΠΏΠ΅ΡΠ°ΡΡΡΠ½ΡΠΉ ΠΏΠ΅ΡΠ΅ΠΏΠ°Π΄ ΠΈ, ΡΠ»Π΅Π΄ΠΎΠ²Π°ΡΠ΅Π»ΡΠ½ΠΎ, Π±ΠΎΠ»Π΅Π΅ ΠΈΠ½ΡΠ΅Π½ΡΠΈΠ²Π½ΠΎΠ΅ ΠΈΡΠΏΠ°ΡΠ΅Π½ΠΈΠ΅ Π²Π»Π°Π³ΠΈ Ρ ΠΏΠΎΠ²Π΅ΡΡ Π½ΠΎΡΡΠΈ ΠΈΠ·Π΄Π΅Π»ΠΈΡ. ΠΡΠΎΡ ΠΏΡΠΎΡΠ΅ΡΡ ΠΏΡΠΎΠΈΡΡ ΠΎΠ΄ΠΈΡ Π΄ΠΎ ΡΠ΅Ρ ΠΏΠΎΡ, ΠΏΠΎΠΊΠ° ΡΠ΅ΠΌΠΏΠ΅ΡΠ°ΡΡΡΠ° ΠΈΠ·Π΄Π΅Π»ΠΈΡ ΠΈ ΠΎΠΊΡΡΠΆΠ°ΡΡΠ΅ΠΉ ΡΡΠ΅Π΄Ρ Π½Π΅ Π²ΡΡΠΎΠ²Π½ΡΡΡΡΡ, ΠΏΠΎΡΠ»Π΅ ΡΠ΅Π³ΠΎ Π½Π° ΠΏΠΎΠ²Π΅ΡΡ Π½ΠΎΡΡΠΈ ΠΈΠ·Π΄Π΅Π»ΠΈΡ Π²ΠΎΠ·Π½ΠΈΠΊΠ°Π΅Ρ Π·Π°ΡΠΈΡΠ½Π°Ρ ΠΊΠΎΡΠΎΡΠΊΠ°, ΠΊΠΎΡΠΎΡΠ°Ρ ΠΏΡΠ΅ΠΏΡΡΡΡΠ²ΡΠ΅Ρ ΡΠ»ΠΈΠΏΠ°Π½ΠΈΡ ΠΈΠ·Π΄Π΅Π»ΠΈΠΉ Π² ΠΏΡΠΎΡΠ΅ΡΡΠ΅ Π΄Π°Π»ΡΠ½Π΅ΠΉΡΠ΅ΠΉ ΡΠ°ΡΠΊΠ»Π°Π΄ΠΊΠΈ ΠΈ ΡΡΡΠΊΠΈ.
Π’Π΅Ρ Π½ΠΈΡΠ΅ΡΠΊΠ°Ρ Ρ Π°ΡΠ°ΠΊΡΠ΅ΡΠΈΡΡΠΈΠΊΠ° ΡΠ½Π΅ΠΊΠΎΠ²ΠΎΠ³ΠΎ ΠΌΠ°ΠΊΠ°ΡΠΎΠ½Π½ΠΎΠ³ΠΎ ΠΏΡΠ΅ΡΡΠ° ΠΠΠ-2Π
ΠΡΠΎΠΈΠ·Π²ΠΎΠ΄ΠΈΡΠ΅Π»ΡΠ½ΠΎΡΡΡ, ΠΊΠ³/Ρ……..Π΄ΠΎ 375
Π§Π°ΡΡΠΎΡΠ° Π²ΡΠ°ΡΠ΅Π½ΠΈΡ, ΠΌΠΈΠ½»:
ΠΏΡΠ΅ΡΡΡΡΡΠ΅Π³ΠΎ ΡΠ½Π΅ΠΊΠ°……..41
Π²Π°Π»Π° ΡΠ΅ΡΡΠΎΠΌΠ΅ΡΠΈΡΠ΅Π»Ρ……..82
Π§ΠΈΡΠ»ΠΎ ΡΠ΅Π·ΠΎΠ² ΡΠ΅ΠΆΡΡΠ΅Π³ΠΎ ΠΌΠ΅Ρ Π°Π½ΠΈΠ·ΠΌΠ° Π² ΠΌΠΈΠ½.Β 18… 2060
ΠΠΎΠ΄Π°, ΠΈΠ΄ΡΡΠ°Ρ Π½Π° Π·Π°ΠΌΠ΅Ρ ΡΠ΅ΡΡΠ°:
ΡΠ°ΡΡ ΠΎΠ΄, Π»/Ρ………..60…70
ΡΠ΅ΠΌΠΏΠ΅ΡΠ°ΡΡΡΠ°, Β°Π‘………40.. .60
ΠΠ°ΠΊΡΡΠΌ, ΡΠΎΠ·Π΄Π°Π²Π°Π΅ΠΌΡΠΉ Π² ΠΏΡΠ΅ΡΡΡΡΡΠ΅ΠΌ ΠΊΠΎΡΠΏΡΡΠ΅, ΠΠ° ….Β 50…60
ΠΡΠΎΠΈΠ·Π²ΠΎΠ΄ΠΈΡΠ΅Π»ΡΠ½ΠΎΡΡΡ ΠΎΠ±Π΄ΡΠ²Π°ΡΠ΅Π»Ρ, ΠΌ3/Ρ ….Β 500
ΠΠΎΠ³ΡΠ΅Π±Π½Π°Ρ ΠΌΠΎΡΠ½ΠΎΡΡΡ, ΠΊΠΡ……..23
ΠΠ°Π±Π°ΡΠΈΡΠ½ΡΠ΅ ΡΠ°Π·ΠΌΠ΅ΡΡ, ΠΌΠΌ…………….2920x2710x2940
ΠΠ°ΡΡΠ°, ΠΊΠ³……………………..3260
ΠΠΎΡ ΠΎΠΆΠΈΠ΅ ΡΡΠ°ΡΡΠΈ
znaytovar.ru
ΠΡΠ΅ΡΡ ΠΌΠ°ΠΊΠ°ΡΠΎΠ½Π½ΡΠΉ
Β
ΠΠ·ΠΎΠ±ΡΠ΅ΡΠ΅Π½ΠΈΠ΅ ΠΎΡΠ½ΠΎΡΠΈΡΡΡ ΠΊ ΡΡΡΠ°Π½ΠΎΠ²ΠΊΠ°ΠΌ Π΄Π»Ρ ΠΏΡΠ΅ΡΡΠΎΠ²Π°Π½ΠΈΡ ΠΌΠ°ΠΊΠ°ΡΠΎΠ½Π½ΡΡ ΠΈΠ·Π΄Π΅Π»ΠΈΠΉ. ΠΡΠ΅ΡΡ ΠΌΠ°ΠΊΠ°ΡΠΎΠ½Π½ΡΠΉ ΡΠΎΡΡΠΎΠΈΡ ΠΈΠ· Π±Π»ΠΎΠΊΠ° ΡΠ΅ΡΡΠΎΡΠΌΠ΅ΡΠΈΡΠ΅Π»ΡΠ½ΡΡ Π±ΡΠ½ΠΊΠ΅ΡΠΎΠ², ΡΠ½Π΅ΠΊΠ° Π² ΠΊΠΎΡΠΏΡΡΠ΅, ΠΈΠΌΠ΅ΡΡΠ΅Π³ΠΎ ΠΎΠΏΠΎΡΡ, Π° ΡΠ°ΠΊΠΆΠ΅ ΡΠΈΡΡΠ΅ΠΌΡ ΠΎΡ Π»Π°ΠΆΠ΄Π΅Π½ΠΈΡ, ΠΏΡΠ΅Π΄ΠΌΠ°ΡΡΠΈΡΠ½ΠΎΠΉ ΠΊΠ°ΠΌΠ΅ΡΡ, ΠΊΡΡΠ³Π»ΠΎΠΉ ΠΌΠ°ΡΡΠΈΡΡ ΠΈ ΡΠ΅ΠΆΡΡΠ΅Π³ΠΎ ΡΡΡΡΠΎΠΉΡΡΠ²Π°. Π¨Π½Π΅ΠΊ Π½Π° Π²ΡΡ ΠΎΠ΄Π΅ ΠΈΠΌΠ΅Π΅Ρ ΡΡΠ΅Ρ Π·Π°Ρ ΠΎΠ΄Π½ΡΡ Π½Π°ΡΠ°Π΄ΠΊΡ, Π·Π°ΠΊΡΠ΅ΠΏΠ»Π΅Π½Π½ΡΡ Π½Π° Π²Π°Π»Ρ ΡΠ½Π΅ΠΊΠ°. ΠΠ³ΠΎ ΠΎΠΏΠΎΡΠ° Π½Π° Π²ΡΡ ΠΎΠ΄Π΅ ΡΠΎΡΡΠΎΠΈΡ ΠΈΠ· Π΄Π²ΡΡ ΠΎΠ±ΡΠ΅ΠΊΠ°ΡΠ΅Π»Π΅ΠΉ ΠΈ Π²ΡΡΠ»ΠΊΠΈ. ΠΡΠΈΡΠ΅ΠΌ ΠΊΠΎΡΠΏΡΡ ΡΠ½Π΅ΠΊΠ° ΠΆΠ΅ΡΡΠΊΠΎ Π·Π°ΠΊΡΠ΅ΠΏΠ»Π΅Π½ Π² ΠΊΠΎΡΠΏΡΡΠ΅ Π±Π»ΠΎΠΊΠ° ΡΠ΅ΡΡΠΎΡΠΌΠ΅ΡΠΈΡΠ΅Π»ΡΠ½ΡΡ Π±ΡΠ½ΠΊΠ΅ΡΠΎΠ², Π° ΡΠΈΡΡΠ΅ΠΌΠ° ΠΎΡ Π»Π°ΠΆΠ΄Π΅Π½ΠΈΡ ΡΠ½Π΅ΠΊΠ° ΡΠ½Π°Π±ΠΆΠ΅Π½Π° Π΄ΠΎΠΏΠΎΠ»Π½ΠΈΡΠ΅Π»ΡΠ½ΠΎΠΉ ΡΡΠ±Π°ΡΠΊΠΎΠΉ. ΠΠ·ΠΎΠ±ΡΠ΅ΡΠ΅Π½ΠΈΠ΅ ΠΎΠ±Π΅ΡΠΏΠ΅ΡΠΈΠ²Π°Π΅Ρ Π½Π°Π΄Π΅ΠΆΠ½ΠΎΡΡΡ ΠΊΠΎΠ½ΡΡΡΡΠΊΡΠΈΠΈ ΠΈ Π²ΡΡΠΎΠΊΠΎΠ΅ ΠΊΠ°ΡΠ΅ΡΡΠ²ΠΎ Π²ΡΠΏΡΡΠΊΠ°Π΅ΠΌΡΡ ΠΌΠ°ΠΊΠ°ΡΠΎΠ½Π½ΡΡ ΠΈΠ·Π΄Π΅Π»ΠΈΠΉ. 2 Π·.ΠΏ. Ρ-Π»Ρ, 1 ΠΈΠ».
ΠΠ·ΠΎΠ±ΡΠ΅ΡΠ΅Π½ΠΈΠ΅ ΠΎΡΠ½ΠΎΡΠΈΡΡΡ ΠΊ ΠΎΠ±ΠΎΡΡΠ΄ΠΎΠ²Π°Π½ΠΈΡ Π΄Π»Ρ ΠΏΠΈΡΠ΅Π²ΠΎΠΉ ΠΏΡΠΎΠΌΡΡΠ»Π΅Π½Π½ΠΎΡΡΠΈ, Π² ΡΠ°ΡΡΠ½ΠΎΡΡΠΈ ΠΊ ΡΡΡΠ°Π½ΠΎΠ²ΠΊΠ°ΠΌ Π΄Π»Ρ ΠΏΡΠ΅ΡΡΠΎΠ²Π°Π½ΠΈΡ ΠΌΠ°ΠΊΠ°ΡΠΎΠ½Π½ΡΡ ΠΈΠ·Π΄Π΅Π»ΠΈΠΉ.
ΠΠ·Π²Π΅ΡΡΠ½Π° ΠΌΠ°ΡΠΈΠ½Π° Π΄Π»Ρ ΠΏΡΠΎΠΈΠ·Π²ΠΎΠ΄ΡΡΠ²Π° ΠΌΠ°ΠΊΠ°ΡΠΎΠ½Π½ΡΡ ΠΈΠ·Π΄Π΅Π»ΠΈΠΉ «ΠΠ’ΠΠΠΠ¦Π-1» (ΡΠ°Π·ΡΠ°Π±ΠΎΡΡΠΈΠΊ ΠΈ ΠΈΠ·Π³ΠΎΡΠΎΠ²ΠΈΡΠ΅Π»Ρ ΠΠ «ΠΠΠΠΠ’Π» Π³. Π£Π»ΡΡΠ½ΠΎΠ²ΡΠΊ), ΡΠΎΠ΄Π΅ΡΠΆΠ°ΡΠ°Ρ Π΄Π²Π° ΡΠ΅ΡΡΠΎΡΠΌΠ΅ΡΠΈΡΠ΅Π»ΡΠ½ΡΡ Π±ΡΠ½ΠΊΠ΅ΡΠ°, Π²Π΅ΡΡ Π½Π΅Π³ΠΎ, ΡΡΡΠ°Π½ΠΎΠ²Π»Π΅Π½Π½ΠΎΠ³ΠΎ Ρ Π²ΠΎΠ·ΠΌΠΎΠΆΠ½ΠΎΡΡΡΡ ΠΏΠΎΠ²ΠΎΡΠΎΡΠ°, ΠΈ Π½ΠΈΠΆΠ½Π΅Π³ΠΎ, ΡΠ°ΡΠΏΠΎΠ»ΠΎΠΆΠ΅Π½Π½ΠΎΠ³ΠΎ Π½Π°Π΄ ΡΠ½Π΅ΠΊΠΎΠ²ΠΎΠΉ ΠΏΡΠ΅ΡΡΡΡΡΠ΅ΠΉ ΠΊΠ°ΠΌΠ΅ΡΠΎΠΉ, ΠΊΠΎΡΠΎΡΠ°Ρ ΡΠ½Π°Π±ΠΆΠ΅Π½Π° ΡΠ½Π΅ΠΊΠΎΠΌ, Π° Π½Π° Π²ΡΡ ΠΎΠ΄Π΅ ΠΊΡΡΠ³Π»ΠΎΠΉ ΠΌΠ°ΡΡΠΈΡΠ΅ΠΉ, ΡΠ½Π°ΡΡΠΆΠΈ ΠΊΠΎΡΠΎΡΠΎΠΉ ΡΠ°ΡΠΏΠΎΠ»ΠΎΠΆΠ΅Π½Π° ΠΎΡ Π»Π°ΠΆΠ΄Π°ΡΡΠ°Ρ ΡΡΠ±Π°ΡΠΊΠ° («ΠΠ°ΡΠΈΠ½Ρ, ΠΎΠ±ΠΎΡΡΠ΄ΠΎΠ²Π°Π½ΠΈΠ΅, ΠΏΡΠΈΠ±ΠΎΡΡ ΠΈ ΡΡΠ΅Π΄ΡΡΠ²Π° Π°Π²ΡΠΎΠΌΠ°ΡΠΈΠ·Π°ΡΠΈΠΈ Π΄Π»Ρ ΠΏΠ΅ΡΠ΅ΡΠ°Π±Π°ΡΡΠ²Π°ΡΡΠΈΡ ΠΠΠ», ΠΊΠ°ΡΠ°Π»ΠΎΠ³-Π΄ΠΎΠΏΠΎΠ»Π½Π΅Π½ΠΈΠ΅, Π. : ΠΠ½ΡΠΎΡΠΌ. ΠΠ³ΡΠΎΡΠ΅Ρ , 1993, Ρ. 191-192). ΠΠ΅Π΄ΠΎΡΡΠ°ΡΠΊΠ°ΠΌΠΈ Π΄Π°Π½Π½ΠΎΠ³ΠΎ ΡΡΡΡΠΎΠΉΡΡΠ²Π° ΡΠ²Π»ΡΡΡΡΡ Π½ΠΈΠ·ΠΊΠ°Ρ ΠΏΡΠΎΠΈΠ·Π²ΠΎΠ΄ΠΈΡΠ΅Π»ΡΠ½ΠΎΡΡΡ ΠΈ Π½Π΅Π΄ΠΎΡΡΠ°ΡΠΎΡΠ½ΠΎΠ΅ ΠΊΠ°ΡΠ΅ΡΡΠ²ΠΎ Π²ΡΠΏΡΡΠΊΠ°Π΅ΠΌΡΡ ΠΌΠ°ΠΊΠ°ΡΠΎΠ½Π½ΡΡ ΠΈΠ·Π΄Π΅Π»ΠΈΠΉ ΠΈΠ·-Π·Π° Π½Π΅Π±ΠΎΠ»ΡΡΠΎΠ³ΠΎ Π²ΡΠ΅ΠΌΠ΅Π½ΠΈ Π·Π°ΠΌΠ΅ΡΠ°, Π½ΠΈΠ·ΠΊΠΎΠ³ΠΎ Π΄Π°Π²Π»Π΅Π½ΠΈΡ Π² ΡΠ½Π΅ΠΊΠΎΠ²ΠΎΠΌ ΡΠ°Π±ΠΎΡΠ΅ΠΌ ΠΏΡΠΎΡΡΡΠ°Π½ΡΡΠ²Π΅, ΡΡΠΎ Π²Π΅Π΄Π΅Ρ ΠΊ Π½Π΅Π΄ΠΎΡΡΠ°ΡΠΎΡΠ½ΠΎΠΉ ΠΏΠ»ΠΎΡΠ½ΠΎΡΡΠΈ ΠΏΡΠΎΠ΄ΡΠΊΡΠΈΠΈ ΠΈ Π΄Π΅Π»Π°Π΅Ρ Π΅Π΅ Π½Π΅ΠΏΡΠΈΠ³ΠΎΠ΄Π½ΠΎΠΉ Π΄Π»Ρ Π΄Π»ΠΈΡΠ΅Π»ΡΠ½ΠΎΠ³ΠΎ Ρ ΡΠ°Π½Π΅Π½ΠΈΡ. ΠΠ·Π²Π΅ΡΡΠ΅Π½ ΠΏΡΠ΅ΡΡ ΠΌΠ°ΠΊΠ°ΡΠΎΠ½Π½ΡΠΉ, Π²ΡΠΏΡΡΠΊΠ°Π΅ΠΌΡΠΉ ΠΠ «Π ΠΠ‘Π‘» Π³. Π₯Π°ΡΡΠΊΠΎΠ², ΡΠΎΡΡΠΎΡΡΠΈΠΉ ΠΈΠ· ΡΡΠ°Π½ΠΈΠ½Ρ, ΠΏΡΠ΅Π΄ΡΡΠ°Π²Π»ΡΡΡΠ΅ΠΉ ΡΠΎΠ±ΠΎΠΉ ΡΠ²Π°ΡΠ½ΡΡ ΡΠ°ΠΌΡ, ΠΎΠ±ΡΠΈΡΡΡ Π»ΠΈΡΡΠΎΠ²ΠΎΠΉ ΡΡΠ°Π»ΡΡ, Π΄Π²ΡΡ ΡΠ΅ΡΡΠΎΡΠΌΠ΅ΡΠΈΡΠ΅Π»ΡΠ½ΡΡ Π±ΡΠ½ΠΊΠ΅ΡΠΎΠ², ΡΠ°ΡΠΏΠΎΠ»ΠΎΠΆΠ΅Π½Π½ΡΡ ΠΎΠ΄ΠΈΠ½ Π½Π°Π΄ Π΄ΡΡΠ³ΠΈΠΌ, Π²Π½ΡΡΡΠΈ ΠΊΠΎΡΠΎΡΡΡ ΡΠ°Π·ΠΌΠ΅ΡΠ΅Π½Ρ Π²Π°Π»Ρ Ρ ΡΠ°Π±ΠΎΡΠΈΠΌΠΈ ΠΎΡΠ³Π°Π½Π°ΠΌΠΈ Π² Π²ΠΈΠ΄Π΅ Π»ΠΎΠΏΠ°ΡΠΎΠΊ, Π² ΠΊΠΎΡΠΏΡΡΠ΅ Π½ΠΈΠΆΠ½Π΅Π³ΠΎ ΠΈΠ· ΠΊΠΎΡΠΎΡΡΡ Π²ΡΠΏΠΎΠ»Π½Π΅Π½ΠΎ ΠΎΡΠ²Π΅ΡΡΡΠΈΠ΅ Π΄Π»Ρ ΠΏΠΎΠ΄Π°ΡΠΈ ΡΠ΅ΡΡΠ° Π² ΠΏΡΠ΅ΡΡΡΡΡΡΡ Π³ΠΎΠ»ΠΎΠ²ΠΊΡ, ΡΠΎΡΡΠΎΡΡΡΡ ΠΈΠ· ΠΊΠΎΡΠΏΡΡΠ° Ρ ΡΠ°Π·ΠΌΠ΅ΡΠ΅Π½Π½ΡΠΌΠΈ Π² Π½Π΅ΠΌ ΠΌΠ°ΡΡΠΈΡΠ΅ΠΉ ΠΈ ΡΠΏΠ΅ΡΠΈΠ°Π»ΡΠ½ΠΎΠΉ Π³Π°ΠΉΠΊΠΎΠΉ, ΠΈ ΡΠ½Π°Π±ΠΆΠ΅Π½Π½ΠΎΠ³ΠΎ ΡΡΠ±Π°ΡΠΊΠΎΠΉ ΠΏΡΠΈΠ½ΡΠ΄ΠΈΡΠ΅Π»ΡΠ½ΠΎΠ³ΠΎ ΠΎΡ Π»Π°ΠΆΠ΄Π΅Π½ΠΈΡ (ΠΠ°ΡΠΏΠΎΡΡ, ΡΡΠΊΠΎΠ²ΠΎΠ΄ΡΡΠ²ΠΎ ΠΏΠΎ ΡΠΊΡΠΏΠ»ΡΠ°ΡΠ°ΡΠΈΠΈ Π’Π£ V. 14086152.016-95, «ΠΡΠ΅ΡΡ ΠΌΠ°ΠΊΠ°ΡΠΎΠ½Π½ΡΠΉ /ΡΡΡΠ°Π½ΠΎΠ²ΠΊΠ° Π΄Π»Ρ ΠΈΠ·Π³ΠΎΡΠΎΠ²Π»Π΅Π½ΠΈΡ ΡΠΈΠ³ΡΡΠ½ΡΡ ΠΈΠ·Π΄Π΅Π»ΠΈΠΉ ΠΈΠ· ΡΠ΅ΡΡΠ° Π£ΠΠΠ-5, 2/380-100/). ΠΠ΅Π΄ΠΎΡΡΠ°ΡΠΊΠ°ΠΌΠΈ Π΄Π°Π½Π½ΠΎΠ³ΠΎ ΡΡΡΡΠΎΠΉΡΡΠ²Π° ΡΠ²Π»ΡΡΡΡΡ Π½ΠΈΠ·ΠΊΠ°Ρ Π½Π°Π΄Π΅ΠΆΠ½ΠΎΡΡΡ ΠΈ Π½ΠΈΠ·ΠΊΠΎΠ΅ ΠΊΠ°ΡΠ΅ΡΡΠ²ΠΎ Π²ΡΠΏΡΡΠΊΠ°Π΅ΠΌΡΡ ΠΌΠ°ΠΊΠ°ΡΠΎΠ½Π½ΡΡ ΠΈΠ·Π΄Π΅Π»ΠΈΠΉ ΠΈΠ·-Π·Π° Π½Π΅Π΄ΠΎΡΡΠ°ΡΠΎΡΠ½ΠΎΠ³ΠΎ Π΄Π°Π²Π»Π΅Π½ΠΈΡ Π½Π° ΡΠ΅ΡΡΠΎΠ²ΡΡ ΠΌΠ°ΡΡΡ Π² ΠΏΡΠ΅ΡΡΡΡΡΠ΅ΠΉ Π³ΠΎΠ»ΠΎΠ²ΠΊΠ΅, ΡΡΠΎ ΠΏΡΠΈΠ²ΠΎΠ΄ΠΈΡ ΠΊ Π½ΠΈΠ·ΠΊΠΎΠΉ ΠΏΠ»ΠΎΡΠ½ΠΎΡΡΠΈ ΠΈΠ·Π΄Π΅Π»ΠΈΠΉ ΠΈ Π΄Π΅Π»Π°Π΅Ρ ΠΈΡ Π½Π΅ΠΏΡΠΈΠ³ΠΎΠ΄Π½ΡΠΌΠΈ Π΄Π»Ρ Π΄Π»ΠΈΡΠ΅Π»ΡΠ½ΠΎΠ³ΠΎ Ρ ΡΠ°Π½Π΅Π½ΠΈΡ. ΠΠ°ΠΈΠ±ΠΎΠ»Π΅Π΅ Π±Π»ΠΈΠ·ΠΊΠΎΠΉ ΠΏΠΎ ΡΠ΅Ρ Π½ΠΈΡΠ΅ΡΠΊΠΎΠΉ ΡΡΡΠ½ΠΎΡΡΠΈ ΠΈ ΠΏΠΎΠ»ΡΡΠ°Π΅ΠΌΠΎΠΌΡ ΡΠ΅Π·ΡΠ»ΡΡΠ°ΡΡ ΠΊ Π·Π°ΡΠ²Π»ΡΠ΅ΠΌΠΎΠΌΡ ΠΈΠ·ΠΎΠ±ΡΠ΅ΡΠ΅Π½ΠΈΡ ΡΠ²Π»ΡΠ΅ΡΡΡ ΡΡΡΠ°Π½ΠΎΠ²ΠΊΠ° Π΄Π»Ρ ΠΏΡΠΎΠΈΠ·Π²ΠΎΠ΄ΡΡΠ²Π° ΠΌΠ°ΠΊΠ°ΡΠΎΠ½Π½ΡΡ ΠΈΠ·Π΄Π΅Π»ΠΈΠΉ ΠΌΠ°ΡΠΊΠΈ ΠΠ£-200, ΡΠΎΠ΄Π΅ΡΠΆΠ°ΡΠ°Ρ Π±Π»ΠΎΠΊ ΡΠ΅ΡΡΠΎΡΠΌΠ΅ΡΠΈΡΠ΅Π»ΡΠ½ΡΡ Π±ΡΠ½ΠΊΠ΅ΡΠΎΠ², ΡΠ½Π΅ΠΊΠΎΠ²ΡΠΉ ΠΏΡΠ΅ΡΡ Π² ΠΊΠΎΡΠΏΡΡΠ΅, ΠΈΠΌΠ΅ΡΡΠΈΠΉ ΠΎΠΏΠΎΡΡ, ΡΠΈΡΡΠ΅ΠΌΡ ΠΎΡ Π»Π°ΠΆΠ΄Π΅Π½ΠΈΡ, ΠΏΡΠ΅Π΄ΠΌΠ°ΡΡΠΈΡΠ½ΡΡ ΠΊΠ°ΠΌΠ΅ΡΡ, ΠΊΡΡΠ³Π»ΡΡ ΠΌΠ°ΡΡΠΈΡΡ ΠΈ ΡΠ΅ΠΆΡΡΠ΅Π΅ ΡΡΡΡΠΎΠΉΡΡΠ²ΠΎ (ΠΠ°ΡΠΏΠΎΡΡ «ΠΡΠ΅ΡΡ-Π°Π²ΡΠΎΠΌΠ°Ρ Π΄Π»Ρ ΠΏΡΠΈΠ³ΠΎΡΠΎΠ²Π»Π΅Π½ΠΈΡ ΠΌΠ°ΠΊΠ°ΡΠΎΠ½Π½ΡΡ ΠΈΠ·Π΄Π΅Π»ΠΈΠΉ ΠΠ£-200», Π’Π£ 5.131.001.268876 21.97, Π‘Π°ΡΠ°ΡΠΎΠ², 1997). ΠΠ΅Π΄ΠΎΡΡΠ°ΡΠΊΠ°ΠΌΠΈ Π΄Π°Π½Π½ΠΎΠ³ΠΎ ΡΡΡΡΠΎΠΉΡΡΠ²Π° ΡΠ²Π»ΡΡΡΡΡ Π½Π΅Π΄ΠΎΡΡΠ°ΡΠΎΡΠ½Π°Ρ Π½Π°Π΄Π΅ΠΆΠ½ΠΎΡΡΡ ΠΈ Π½ΠΈΠ·ΠΊΠΎΠ΅ ΠΊΠ°ΡΠ΅ΡΡΠ²ΠΎ Π²ΡΠΏΡΡΠΊΠ°Π΅ΠΌΡΡ ΠΌΠ°ΠΊΠ°ΡΠΎΠ½Π½ΡΡ ΠΈΠ·Π΄Π΅Π»ΠΈΠΉ ΠΈΠ·-Π·Π° Π½ΠΈΠ·ΠΊΠΎΠ³ΠΎ ΡΠ°Π±ΠΎΡΠ΅Π³ΠΎ Π΄Π°Π²Π»Π΅Π½ΠΈΡ, ΡΠΎΠ·Π΄Π°Π²Π°Π΅ΠΌΠΎΠ³ΠΎ Π² ΠΏΡΠ΅Π΄ΠΌΠ°ΡΡΠΈΡΠ½ΠΎΠΉ ΠΊΠ°ΠΌΠ΅ΡΠ΅, ΠΈ ΠΈΠ·-Π·Π° ΠΌΠ°Π»ΠΎΠ³ΠΎ ΡΠ°Π·ΠΌΠ΅ΡΠ° ΠΈ ΠΎΡΠΎΠ±Π΅Π½Π½ΠΎΡΡΠ΅ΠΉ ΠΊΠΎΠ½ΡΠΈΠ³ΡΡΠ°ΡΠΈΠΈ ΠΏΡΠ΅Π΄ΠΌΠ°ΡΡΠΈΡΠ½ΠΎΠΉ ΠΊΠ°ΠΌΠ΅ΡΡ, Π³Π΄Π΅ ΡΠ΅ΡΡΠΎΠ²Π°Ρ ΠΌΠ°ΡΡΠ° Π½Π΅Π΄ΠΎΡΡΠ°ΡΠΎΡΠ½ΠΎ ΡΠΏΠ»ΠΎΡΠ½ΡΠ΅ΡΡΡ, Π° Π΅Π΅ ΡΠΊΠΎΡΠΎΡΡΠΈ Π² ΠΏΠΎΠΏΠ΅ΡΠ΅ΡΠ½ΠΎΠΌ Π½Π°ΠΏΡΠ°Π²Π»Π΅Π½ΠΈΠΈ Π²ΡΡΠ°Π²Π½ΠΈΠ²Π°ΡΡΡΡ ΡΠ»Π°Π±ΠΎ. Π’Π΅Ρ Π½ΠΈΡΠ΅ΡΠΊΠΈΠΌ ΡΠ΅Π·ΡΠ»ΡΡΠ°ΡΠΎΠΌ, Π΄ΠΎΡΡΠΈΠ³Π°Π΅ΠΌΡΠΌ Ρ ΠΏΠΎΠΌΠΎΡΡΡ ΠΏΡΠ΅Π΄Π»ΠΎΠΆΠ΅Π½Π½ΠΎΠ³ΠΎ ΠΈΠ·ΠΎΠ±ΡΠ΅ΡΠ΅Π½ΠΈΡ, ΡΠ²Π»ΡΡΡΡΡ Π±ΠΎΠ»ΡΡΠ°Ρ Π½Π°Π΄Π΅ΠΆΠ½ΠΎΡΡΡ ΠΊΠΎΠ½ΡΡΡΡΠΊΡΠΈΠΈ ΠΈ Π²ΡΡΠΎΠΊΠΎΠ΅ ΠΊΠ°ΡΠ΅ΡΡΠ²ΠΎ Π²ΡΠΏΡΡΠΊΠ°Π΅ΠΌΡΡ ΠΌΠ°ΠΊΠ°ΡΠΎΠ½Π½ΡΡ ΠΈΠ·Π΄Π΅Π»ΠΈΠΉ. ΠΠ°Π½Π½ΡΠΉ ΡΠ΅Ρ Π½ΠΈΡΠ΅ΡΠΊΠΈΠΉ ΡΠ΅Π·ΡΠ»ΡΡΠ°Ρ Π΄ΠΎΡΡΠΈΠ³Π°Π΅ΡΡΡ Π·Π° ΡΡΠ΅Ρ ΡΠΎΠ³ΠΎ, ΡΡΠΎ Π² ΠΏΡΠ΅ΡΡΠ΅ ΠΌΠ°ΠΊΠ°ΡΠΎΠ½Π½ΠΎΠΌ, ΡΠΎΠ΄Π΅ΡΠΆΠ°ΡΠ΅ΠΌ Π±Π»ΠΎΠΊ ΡΠ΅ΡΡΠΎΡΠΌΠ΅ΡΠΈΡΠ΅Π»ΡΠ½ΡΡ Π±ΡΠ½ΠΊΠ΅ΡΠΎΠ², ΡΠ½Π΅ΠΊ Π² ΠΊΠΎΡΠΏΡΡΠ΅, ΠΈΠΌΠ΅ΡΡΠΈΠΉ ΠΎΠΏΠΎΡΡ, Π° ΡΠ°ΠΊΠΆΠ΅ ΡΠΈΡΡΠ΅ΠΌΡ ΠΎΡ Π»Π°ΠΆΠ΄Π΅Π½ΠΈΡ, ΠΏΡΠ΅Π΄ΠΌΠ°ΡΡΠΈΡΠ½ΡΡ ΠΊΠ°ΠΌΠ΅ΡΡ, ΠΊΡΡΠ³Π»ΡΡ ΠΌΠ°ΡΡΠΈΡΡ ΠΈ ΡΠ΅ΠΆΡΡΠ΅Π΅ ΡΡΡΡΠΎΠΉΡΡΠ²ΠΎ, ΡΠ½Π΅ΠΊ Π½Π° Π²ΡΡ ΠΎΠ΄Π΅ ΠΈΠΌΠ΅Π΅Ρ ΡΡΠ΅Ρ Π·Π°Ρ ΠΎΠ΄Π½ΡΡ Π½Π°ΡΠ°Π΄ΠΊΡ, Π·Π°ΠΊΡΠ΅ΠΏΠ»Π΅Π½Π½ΡΡ Π½Π° Π²Π°Π»Ρ ΡΠ½Π΅ΠΊΠ°, Π° Π΅Π³ΠΎ ΠΎΠΏΠΎΡΠ° Π½Π° Π²ΡΡ ΠΎΠ΄Π΅ ΡΠΎΡΡΠΎΠΈΡ ΠΈΠ· Π΄Π²ΡΡ ΠΎΠ±ΡΠ΅ΠΊΠ°ΡΠ΅Π»Π΅ΠΉ ΠΈ Π²ΡΡΠ»ΠΊΠΈ, ΠΏΡΠΈΡΠ΅ΠΌ ΠΊΠΎΡΠΏΡΡ ΡΠ½Π΅ΠΊΠ° ΠΆΠ΅ΡΡΠΊΠΎ Π·Π°ΠΊΡΠ΅ΠΏΠ»Π΅Π½ Π² ΠΊΠΎΡΠΏΡΡΠ΅ Π±Π»ΠΎΠΊΠ° ΡΠ΅ΡΡΠΎΡΠΌΠ΅ΡΠΈΡΠ΅Π»ΡΠ½ΡΡ Π±ΡΠ½ΠΊΠ΅ΡΠΎΠ², Π° ΡΠΈΡΡΠ΅ΠΌΠ° ΠΎΡ Π»Π°ΠΆΠ΄Π΅Π½ΠΈΡ ΡΠ½Π΅ΠΊΠ° ΡΠ½Π°Π±ΠΆΠ΅Π½Π° Π΄ΠΎΠΏΠΎΠ»Π½ΠΈΡΠ΅Π»ΡΠ½ΠΎΠΉ ΡΡΠ±Π°ΡΠΊΠΎΠΉ. ΠΡΡΠΎΠΊΠΎΠ΅ ΠΊΠ°ΡΠ΅ΡΡΠ²ΠΎ ΠΌΠ°ΠΊΠ°ΡΠΎΠ½Π½ΡΡ ΠΈΠ·Π΄Π΅Π»ΠΈΠΉ Π² Π΄Π°Π½Π½ΠΎΠΌ ΠΌΠ°ΠΊΠ°ΡΠΎΠ½Π½ΠΎΠΌ ΠΏΡΠ΅ΡΡΠ΅ ΠΎΠ±Π΅ΡΠΏΠ΅ΡΠΈΠ²Π°Π΅ΡΡΡ Π½Π°Π»ΠΈΡΠΈΠ΅ΠΌ Π½Π° Π²ΡΡ ΠΎΠ΄Π΅ ΡΠ½Π΅ΠΊΠ° ΡΡΠ΅Ρ Π·Π°Ρ ΠΎΠ΄Π½ΠΎΠΉ Π½Π°ΡΠ°Π΄ΠΊΠΈ, ΠΊΠΎΡΠΎΡΠ°Ρ Π·Π°ΠΊΡΠ΅ΠΏΠ»Π΅Π½Π° Π½Π° Π΅Π³ΠΎ Π²Π°Π»Ρ, ΠΊΠΎΠ½ΡΡΡΡΠΊΡΠΈΠ΅ΠΉ ΠΎΠΏΠΎΡΡ Π½Π° Π²ΡΡ ΠΎΠ΄Π΅ ΡΠ½Π΅ΠΊΠ°, ΡΠΎΡΡΠΎΡΡΠ΅ΠΉ ΠΈΠ· Π΄Π²ΡΡ ΠΎΠ±ΡΠ΅ΠΊΠ°ΡΠ΅Π»Π΅ΠΉ ΠΈ Π²ΡΡΠ»ΠΊΠΈ, Π° ΡΠ°ΠΊΠΆΠ΅ ΡΠ΅ΠΌ, ΡΡΠΎ ΡΠΈΡΡΠ΅ΠΌΠ° ΠΎΡ Π»Π°ΠΆΠ΄Π΅Π½ΠΈΡ ΡΠ½Π΅ΠΊΠ° ΡΠ½Π°Π±ΠΆΠ΅Π½Π° Π΄ΠΎΠΏΠΎΠ»Π½ΠΈΡΠ΅Π»ΡΠ½ΠΎΠΉ ΡΡΠ±Π°ΡΠΊΠΎΠΉ, Ρ.Π΅. ΡΠΎΠ²ΠΎΠΊΡΠΏΠ½ΠΎΡΡΡΡ ΠΏΠΎΡΡΠΈ Π²ΡΠ΅Ρ ΠΎΡΠ»ΠΈΡΠΈΡΠ΅Π»ΡΠ½ΡΡ ΡΡΡΠ΅ΡΡΠ²Π΅Π½Π½ΡΡ ΠΏΡΠΈΠ·Π½Π°ΠΊΠΎΠ² ΠΏΠΎΠ»Π΅Π·Π½ΠΎΠΉ ΠΌΠΎΠ΄Π΅Π»ΠΈ. Π¨Π½Π΅ΠΊ ΠΊΠ°ΠΊ ΠΎΡΠ½ΠΎΠ²Π½ΠΎΠΉ ΡΠ°Π±ΠΎΡΠΈΠΉ ΠΎΡΠ³Π°Π½ ΠΌΠ°ΠΊΠ°ΡΠΎΠ½Π½ΠΎΠ³ΠΎ ΠΏΡΠ΅ΡΡΠ° Π²Π»ΠΈΡΠ΅Ρ Π½Π° ΠΊΠ°ΡΠ΅ΡΡΠ²ΠΎ Π²ΡΠΏΡΠ΅ΡΡΠΎΠ²Π°Π½Π½ΡΡ ΠΈΠ·Π΄Π΅Π»ΠΈΠΉ. Π’ΡΠ΅Ρ Π·Π°Ρ ΠΎΠ΄Π½Π°Ρ Π½Π°ΡΠ°Π΄ΠΊΠ°, Π·Π°ΠΊΡΠ΅ΠΏΠ»Π΅Π½Π½Π°Ρ Π½Π° Π²Π°Π»Ρ ΡΠ½Π΅ΠΊΠ°, ΠΏΠΎΠ·Π²ΠΎΠ»ΡΠ΅Ρ ΡΠΎΠ·Π΄Π°Π²Π°ΡΡ Π² ΠΏΡΠ΅Π΄ΠΌΠ°ΡΡΠΈΡΠ½ΠΎΠΉ ΠΊΠ°ΠΌΠ΅ΡΠ΅ ΠΏΠΎΠ²ΡΡΠ΅Π½Π½ΠΎΠ΅ Π΄Π°Π²Π»Π΅Π½ΠΈΠ΅, ΡΡΠΎ ΠΎΠ±Π΅ΡΠΏΠ΅ΡΠΈΠ²Π°Π΅Ρ ΠΏΠ»ΠΎΡΠ½ΠΎΡΡΡ ΠΎΠ±ΡΠ°Π±Π°ΡΡΠ²Π°Π΅ΠΌΠΎΠ³ΠΎ ΡΠ΅ΡΡΠ°, Π½Π΅ΠΎΠ±Ρ ΠΎΠ΄ΠΈΠΌΡΡ Π΄Π»Ρ Π²ΡΡΠΎΠΊΠΎΠ³ΠΎ ΠΊΠ°ΡΠ΅ΡΡΠ²Π° ΠΌΠ°ΠΊΠ°ΡΠΎΠ½Π½ΡΡ ΠΈΠ·Π΄Π΅Π»ΠΈΠΉ. ΠΠΏΠΎΡΠ° ΡΠ½Π΅ΠΊΠ°, ΡΠΎΡΡΠΎΡΡΠ°Ρ Π½Π° Π²ΡΡ ΠΎΠ΄Π΅ ΠΈΠ· Π΄Π²ΡΡ ΠΊΠΎΠ½ΡΡΠ½ΡΡ ΠΎΠ±ΡΠ΅ΠΊΠ°ΡΠ΅Π»Π΅ΠΉ ΠΈ Π²ΡΡΠ»ΠΊΠΈ, ΡΠΎΠ·Π΄Π°Π΅Ρ ΡΠ°ΠΊΡΡ ΠΊΠΎΠ½ΡΠΈΠ³ΡΡΠ°ΡΠΈΡ ΠΏΡΠ΅Π΄ΠΌΠ°ΡΡΠΈΡΠ½ΠΎΠ³ΠΎ ΠΏΡΠΎΡΡΡΠ°Π½ΡΡΠ²Π°, ΠΊΠΎΡΠΎΡΠ°Ρ ΠΎΠ±Π΅ΡΠΏΠ΅ΡΠΈΠ²Π°Π΅Ρ ΡΠ°Π²Π½ΠΎΠΌΠ΅ΡΠ½ΠΎΡΡΡ ΠΏΠΎΠ΄Π°ΡΠΈ ΡΠ΅ΡΡΠ° Π² ΠΏΡΠ΅Π΄ΠΌΠ°ΡΡΠΈΡΠ½ΠΎΠΉ ΠΊΠ°ΠΌΠ΅ΡΠ΅ ΠΊ ΠΌΠ°ΡΡΠΈΡΠ΅, Π² ΡΠ΅Π·ΡΠ»ΡΡΠ°ΡΠ΅ ΡΠ΅Π³ΠΎ ΡΠ΅ΡΡΠΎ Π½Π΅ ΠΌΠ½Π΅ΡΡΡ, Π° ΡΠ°Π²Π½ΠΎΠΌΠ΅ΡΠ½ΠΎ ΡΠΏΠ»ΠΎΡΠ½ΡΠ΅ΡΡΡ, ΡΡΠΎ Π²Π»ΠΈΡΠ΅Ρ Π½Π° ΡΠ°Π²Π½ΠΎΠΌΠ΅ΡΠ½ΠΎΡΡΡ ΡΠΊΠΎΡΠΎΡΡΠΈ ΠΏΡΠ΅ΡΡΠΎΠ²Π°Π½ΠΈΡ, Ρ. Π΅. Π²ΡΡΠ°Π²Π½ΠΈΠ²Π°Π΅Ρ Π°ΠΊΡΠΈΠ°Π»ΡΠ½ΡΠ΅ ΡΠΊΠΎΡΠΎΡΡΠΈ ΠΏΠ΅ΡΠ΅ΠΌΠ΅ΡΠ°ΡΡΠ΅Π³ΠΎΡΡ ΡΠ΅ΡΡΠΎΠ²ΠΎΠ³ΠΎ ΠΏΠΎΡΠΎΠΊΠ° ΠΏΠΎ ΠΏΠΎΠΏΠ΅ΡΠ΅ΡΠ½ΠΎΠΌΡ ΡΠ΅ΡΠ΅Π½ΠΈΡ ΡΠ½Π΅ΠΊΠ°. ΠΡΠ΅ ΡΡΠΎ ΠΏΠΎΠ²ΡΡΠ°Π΅Ρ ΠΊΠ°ΡΠ΅ΡΡΠ²ΠΎ Π²ΡΠΏΡΡΠΊΠ°Π΅ΠΌΡΡ ΠΈΠ·Π΄Π΅Π»ΠΈΠΉ. ΠΠ° ΡΠΊΠΎΡΠΎΡΡΡ Π²ΡΠΏΡΠ΅ΡΡΠΎΠ²ΡΠ²Π°Π½ΠΈΡ ΡΠ°ΠΊΠΆΠ΅ Π²Π»ΠΈΡΠ΅Ρ ΡΠ΅ΠΌΠΏΠ΅ΡΠ°ΡΡΡΠ° Π² Π·ΠΎΠ½Π΅ ΠΏΡΠ΅ΡΡΠΎΠ²Π°Π½ΠΈΡ Π²ΡΠ»Π΅Π΄ΡΡΠ²ΠΈΠ΅ Π·Π°Π²ΠΈΡΠΈΠΌΠΎΡΡΠΈ ΠΏΠ»Π°ΡΡΠΈΡΠ΅ΡΠΊΠΈ-Π²ΡΠ·ΠΊΠΎΡΡΠ½ΡΡ ΡΠ²ΠΎΠΉΡΡΠ² ΡΠ΅ΡΡΠ° ΠΎΡ ΡΠ΅ΠΌΠΏΠ΅ΡΠ°ΡΡΡΡ. ΠΠΎ ΠΌΠ΅ΡΠ΅ Π΄Π²ΠΈΠΆΠ΅Π½ΠΈΡ ΠΏΠΎ ΡΠ½Π΅ΠΊΡ ΡΠ΅ΡΡΠΎ Π½Π°Π³ΡΠ΅Π²Π°Π΅ΡΡΡ Π½Π΅ΠΏΡΠ΅ΡΡΠ²Π½ΠΎ. Π‘Π»ΠΎΠΈ, ΠΏΡΠΈΠ»Π΅Π³Π°ΡΡΠΈΠ΅ ΠΊ ΠΊΠΎΡΠΏΡΡΡ ΡΠ½Π΅ΠΊΠ°, Π½Π°Π³ΡΠ΅Π²Π°ΡΡΡΡ ΠΈΠ½ΡΠ΅Π½ΡΠΈΠ²Π½Π΅Π΅, ΡΠ΅ΠΌ ΡΠ΅Π½ΡΡΠ°Π»ΡΠ½ΡΠ΅, ΡΡΠΎ ΠΏΡΠΈΠ²ΠΎΠ΄ΠΈΡ ΠΊ Π»ΠΎΠΊΠ°Π»ΡΠ½ΠΎΠΌΡ ΡΠ²Π΅Π»ΠΈΡΠ΅Π½ΠΈΡ ΡΠΊΠΎΡΠΎΡΡΠΈ ΠΏΡΠ΅ΡΡΠΎΠ²Π°Π½ΠΈΡ. ΠΠ»Ρ ΠΈΡ Π²ΡΡΠ°Π²Π½ΠΈΠ²Π°Π½ΠΈΡ Π² Π΄Π°Π½Π½ΠΎΠΉ ΠΏΠΎΠ»Π΅Π·Π½ΠΎΠΉ ΠΌΠΎΠ΄Π΅Π»ΠΈ ΠΈΡΠΏΠΎΠ»ΡΠ·ΡΡΡ ΠΊ ΡΠΆΠ΅ ΠΈΠΌΠ΅ΡΡΠ΅ΠΉΡΡ ΡΡΠ±Π°ΡΠΊΠ΅ ΠΎΡ Π»Π°ΠΆΠ΄Π΅Π½ΠΈΡ Π΄ΠΎΠΏΠΎΠ»Π½ΠΈΡΠ΅Π»ΡΠ½ΡΡ, ΠΊΠΎΡΠΎΡΠ°Ρ ΡΠ²Π΅Π»ΠΈΡΠΈΠ²Π°Π΅Ρ Π·ΠΎΠ½Ρ ΠΎΡ Π»Π°ΠΆΠ΄Π΅Π½ΠΈΡ. ΠΡΡΠ°Π²Π½ΠΈΠ²Π°Π½ΠΈΠ΅ ΡΠ΅ΠΌΠΏΠ΅ΡΠ°ΡΡΡ Π² ΠΎΠ±Π»Π°ΡΡΠΈ ΠΏΡΠ΅ΡΡΠΎΠ²Π°Π½ΠΈΡ ΠΎΠ±Π΅ΡΠΏΠ΅ΡΠΈΠ²Π°Π΅Ρ Π²ΡΡΠΎΠΊΠΎΠ΅ ΠΊΠ°ΡΠ΅ΡΡΠ²ΠΎ ΠΌΠ°ΠΊΠ°ΡΠΎΠ½Π½ΡΡ ΠΈΠ·Π΄Π΅Π»ΠΈΠΉ. ΠΠ΅ΡΡΠΊΠΎΠ΅ Π·Π°ΠΊΡΠ΅ΠΏΠ»Π΅Π½ΠΈΠ΅ ΠΊΠΎΡΠΏΡΡΠ° ΡΠ½Π΅ΠΊΠ° Π² ΠΊΠΎΡΠΏΡΡΠ΅ Π±Π»ΠΎΠΊΠ° ΡΠ΅ΡΡΠΎΡΠΌΠ΅ΡΠΈΡΠ΅Π»ΡΠ½ΡΡ Π±ΡΠ½ΠΊΠ΅ΡΠΎΠ² ΠΎΠ±Π΅ΡΠΏΠ΅ΡΠΈΠ²Π°Π΅Ρ Π±ΠΎΠ»ΡΡΡΡ Π½Π°Π΄Π΅ΠΆΠ½ΠΎΡΡΡ ΠΊΠΎΠ½ΡΡΡΡΠΊΡΠΈΠΈ, ΠΈΡΠΊΠ»ΡΡΠ°Ρ ΠΈ ΡΠΌΠ΅Π½ΡΡΠ°Ρ Π½Π΅Π½ΡΠΆΠ½ΡΠ΅ Π²ΠΈΠ±ΡΠ°ΡΠΈΠΈ, ΡΡΠΎ ΠΏΠΎΠ²ΡΡΠ°Π΅Ρ Π½Π°Π΄Π΅ΠΆΠ½ΠΎΡΡΡ Π²ΡΠ΅Ρ Π±Π»ΠΎΠΊΠΎΠ² ΠΈ Π΄Π΅ΡΠ°Π»Π΅ΠΉ Π΄Π°Π½Π½ΠΎΠΉ ΠΊΠΎΠ½ΡΡΡΡΠΊΡΠΈΠΈ, Π° ΡΠ°ΠΊΠΆΠ΅ ΠΈ Π²ΡΡΠΎΠΊΠΎΠ΅ ΠΊΠ°ΡΠ΅ΡΡΠ²ΠΎ Π²ΡΠΏΡΡΠΊΠ°Π΅ΠΌΠΎΠΉ ΠΏΡΠΎΠ΄ΡΠΊΡΠΈΠΈ. ΠΠ° ΡΠ΅ΡΡΠ΅ΠΆΠ΅ ΠΈΠ·ΠΎΠ±ΡΠ°ΠΆΠ΅Π½ ΠΏΡΠ΅ΡΡ ΠΌΠ°ΠΊΠ°ΡΠΎΠ½Π½ΡΠΉ, ΠΎΠ±ΡΠΈΠΉ Π²ΠΈΠ΄ (ΠΏΡΠΎΠ΄ΠΎΠ»ΡΠ½ΡΠΉ ΡΠ°Π·ΡΠ΅Π·). ΠΡΠ΅ΡΡ ΠΌΠ°ΠΊΠ°ΡΠΎΠ½Π½ΡΠΉ ΡΠΎΡΡΠΎΠΈΡ ΠΈΠ· Π±Π»ΠΎΠΊΠ° ΡΠ΅ΡΡΠΎΡΠΌΠ΅ΡΠΈΡΠ΅Π»ΡΠ½ΡΡ Π±ΡΠ½ΠΊΠ΅ΡΠΎΠ² 1 Π² ΠΊΠΎΡΠΏΡΡΠ΅ 2, ΡΠ½Π΅ΠΊΠ° 3, ΠΈΠΌΠ΅ΡΡΠ΅Π³ΠΎ Π²Π°Π» 4 Ρ Π·Π°ΠΊΡΠ΅ΠΏΠ»Π΅Π½Π½ΠΎΠΉ ΡΡΠ΅Ρ Π·Π°Ρ ΠΎΠ΄Π½ΠΎΠΉ Π½Π°ΡΠ°Π΄ΠΊΠΎΠΉ 5, Π² ΠΊΠΎΡΠΏΡΡΠ΅ 6, Π³Π΄Π΅ ΡΠ°ΠΊΠΆΠ΅ ΡΠ°Π·ΠΌΠ΅ΡΠ΅Π½Ρ ΠΏΡΠ΅Π΄ΠΌΠ°ΡΡΠΈΡΠ½Π°Ρ ΠΊΠ°ΠΌΠ΅ΡΠ° 7 ΠΈ ΠΊΡΡΠ³Π»Π°Ρ ΠΌΠ°ΡΡΠΈΡΠ° 8, Π²ΡΡ ΠΎΠ΄Π½Π°Ρ ΠΎΠΏΠΎΡΠ° ΡΠ½Π΅ΠΊΠ° 4 ΡΠΎΡΡΠΎΠΈΡ ΠΈΠ· Π΄Π²ΡΡ ΠΎΠ±ΡΠ΅ΠΊΠ°ΡΠ΅Π»Π΅ΠΉ 9, 10 ΠΈ Π²ΡΡΠ»ΠΊΠΈ 11. Π‘ΠΈΡΡΠ΅ΠΌΠ° ΠΎΡ Π»Π°ΠΆΠ΄Π΅Π½ΠΈΡ 12, ΡΠ°ΡΠΏΠΎΠ»ΠΎΠΆΠ΅Π½Π½Π°Ρ ΡΠ½Π°ΡΡΠΆΠΈ ΠΊΠΎΡΠΏΡΡΠ° 6, ΡΠ½Π°Π±ΠΆΠ΅Π½Π° Π΄ΠΎΠΏΠΎΠ»Π½ΠΈΡΠ΅Π»ΡΠ½ΠΎΠΉ ΡΡΠ±Π°ΡΠΊΠΎΠΉ 13. ΠΡΠ΅ΡΡ ΠΌΠ°ΠΊΠ°ΡΠΎΠ½Π½ΡΠΉ ΡΠ°Π±ΠΎΡΠ°Π΅Ρ ΡΠ»Π΅Π΄ΡΡΡΠΈΠΌ ΠΎΠ±ΡΠ°Π·ΠΎΠΌ. ΠΠΊΠ»ΡΡΠ°ΡΡ ΡΠ»Π΅ΠΊΡΡΠΎΠ΄Π²ΠΈΠ³Π°ΡΠ΅Π»Ρ ΠΈ ΠΏΡΠΈΠ²ΠΎΠ΄ΡΡ Π² Π΄Π²ΠΈΠΆΠ΅Π½ΠΈΠ΅ Π²ΡΠ΅ Π²ΡΠ°ΡΠ°ΡΡΠΈΠ΅ΡΡ ΡΠ·Π»Ρ ΠΏΡΠ΅ΡΡΠ°. Π Π±Π»ΠΎΠΊ ΡΠ΅ΡΡΠΎΡΠΌΠ΅ΡΠΈΡΠ΅Π»ΡΠ½ΡΡ Π±ΡΠ½ΠΊΠ΅ΡΠΎΠ² 1 Π² ΠΊΠΎΡΠΏΡΡΠ΅ 2 ΡΠ°Π²Π½ΠΎΠΌΠ΅ΡΠ½ΠΎ ΠΏΠΎΠ΄Π°Π΅ΡΡΡ ΠΌΡΠΊΠ° ΠΈ ΠΎΡΡΠ°Π»ΡΠ½ΡΠ΅ Π½Π΅ΠΎΠ±Ρ ΠΎΠ΄ΠΈΠΌΡΠ΅ ΠΊΠΎΠΌΠΏΠΎΠ½Π΅Π½ΡΡ Π΄Π»Ρ Π·Π°ΠΌΠ΅ΡΠ° Π² ΡΠΎΠΎΡΠ²Π΅ΡΡΡΠ²ΠΈΠΈ Ρ ΡΠ΅ΡΠ΅ΠΏΡΠΎΠΌ. ΠΠΎΡΠ»Π΅ Π·Π°ΠΌΠ΅ΡΠ° ΠΈ ΠΏΡΠΎΡ ΠΎΠΆΠ΄Π΅Π½ΠΈΡ ΡΠ΅ΡΡΠΎΠ²ΠΎΠΉ ΠΌΠ°ΡΡΡ ΠΏΠΎ Π±Π»ΠΎΠΊΡ ΡΠ΅ΡΡΠΎΡΠΌΠ΅ΡΠΈΡΠ΅Π»ΡΠ½ΡΡ Π±ΡΠ½ΠΊΠ΅ΡΠΎΠ² 1, ΠΏΡΠΈΠΌΠ΅ΡΠ½ΠΎ Π² ΡΠ΅ΡΠ΅Π½ΠΈΠ΅ 12-15 ΠΌΠΈΠ½ΡΡ, ΠΎΠ½Π° ΠΏΠΎΠΏΠ°Π΄Π°Π΅Ρ Π² ΡΠ½Π΅ΠΊ 3 Ρ Π²Π°Π»ΠΎΠΌ 4, Π³Π΄Π΅ ΠΏΡΠΎΡ ΠΎΠ΄ΠΈΡ ΠΏΠΎ Π΅Π³ΠΎ Π²ΠΈΡΠΊΠ°ΠΌ, Π²Ρ ΠΎΠ΄ΠΈΡ Π² ΠΎΠ±Π»Π°ΡΡΡ ΡΡΠ΅Ρ Π·Π°Ρ ΠΎΠ΄Π½ΠΎΠΉ Π½Π°ΡΠ°Π΄ΠΊΠΈ 5, Π³Π΄Π΅ Π²ΡΡΠ°Π²Π½ΠΈΠ²Π°ΡΡΡΡ ΡΠΊΠΎΡΠΎΡΡΠΈ ΡΠ΅ΡΡΠΎΠ²ΠΎΠ³ΠΎ ΠΏΠΎΡΠΎΠΊΠ° Π² ΠΏΠΎΠΏΠ΅ΡΠ΅ΡΠ½ΠΎΠΌ Π½Π°ΠΏΡΠ°Π²Π»Π΅Π½ΠΈΠΈ ΠΈ ΠΏΠΎΠ²ΡΡΠ°Π΅ΡΡΡ Π΄Π°Π²Π»Π΅Π½ΠΈΠ΅, Π·Π°ΡΠ΅ΠΌ ΠΏΠΎΠΏΠ°Π΄Π°Π΅Ρ Π² ΠΏΡΠ΅Π΄ΠΌΠ°ΡΡΠΈΡΠ½ΡΡ ΠΊΠ°ΠΌΠ΅ΡΡ 7, ΠΊΠΎΠ½ΡΠΈΠ³ΡΡΠ°ΡΠΈΡ ΠΊΠΎΡΠΎΡΠΎΠΉ ΠΎΠ±ΡΡΠ»ΠΎΠ²Π»Π΅Π½Π° ΡΠΎΡΠΌΠΎΠΉ Π²ΡΡ ΠΎΠ΄Π½ΠΎΠΉ ΠΎΠΏΠΎΡΡ ΡΠ½Π΅ΠΊΠ°, ΡΠΎΡΡΠΎΡΡΠ΅ΠΉ ΠΈΠ· Π΄Π²ΡΡ ΠΊΠΎΠ½ΠΈΡΠ΅ΡΠΊΠΈΡ ΠΎΠ±ΡΠ΅ΠΊΠ°ΡΠ΅Π»Π΅ΠΉ 9 ΠΈ 10 ΠΈ Π²ΡΡΠ»ΠΊΠΈ 11, ΠΏΡΠΎΡ ΠΎΠ΄Ρ ΡΠ΅ΡΠ΅Π· ΠΊΠΎΡΠΎΡΡΡ, ΡΠΊΠΎΡΠΎΡΡΠΈ ΡΠ΅ΡΡΠΎΠ²ΠΎΠ³ΠΎ ΠΏΠΎΡΠΎΠΊΠ° ΡΠ°ΠΊΠΆΠ΅ Π²ΡΡΠ°Π²Π½ΠΈΠ²Π°ΡΡΡΡ, ΡΡΠΎ ΡΡΡΠ΅ΡΡΠ²Π΅Π½Π½ΠΎ ΡΠΊΠ°Π·ΡΠ²Π°Π΅ΡΡΡ Π½Π° ΠΊΠ°ΡΠ΅ΡΡΠ²Π΅ ΠΌΠ°ΠΊΠ°ΡΠΎΠ½Π½ΡΡ ΠΈΠ·Π΄Π΅Π»ΠΈΠΉ. ΠΠ°ΡΠ΅ΠΌ ΡΠ΅ΡΡΠΎ ΠΏΡΠΎΡ ΠΎΠ΄ΠΈΡ ΡΠ΅ΡΠ΅Π· ΡΠΈΠ»ΡΠ΅ΡΡ ΠΊΡΡΠ³Π»ΠΎΠΉ ΠΌΠ°ΡΡΠΈΡΡ 8, ΠΏΡΠΈΡΠ΅ΠΌ ΡΠ΅ΠΌΠΏΠ΅ΡΠ°ΡΡΡΠ° ΠΏΡΠ΅ΡΡΠΎΠ²Π°Π½ΠΈΡ ΡΠ΅Π³ΡΠ»ΠΈΡΡΠ΅ΡΡΡ Ρ ΠΏΠΎΠΌΠΎΡΡΡ ΡΠΈΡΡΠ΅ΠΌΡ ΠΎΡ Π»Π°ΠΆΠ΄Π΅Π½ΠΈΡ 12 ΠΈ Π΄ΠΎΠΏΠΎΠ»Π½ΠΈΡΠ΅Π»ΡΠ½ΠΎΠΉ ΡΡΠ±Π°ΡΠΊΠΎΠΉ ΠΎΡ Π»Π°ΠΆΠ΄Π΅Π½ΠΈΡ 13, ΠΊΠΎΡΠΎΡΡΠ΅ ΡΠ°ΡΠΏΠΎΠ»ΠΎΠΆΠ΅Π½Ρ ΡΠ½Π°ΡΡΠΆΠΈ ΠΊΠΎΡΠΏΡΡΠ° 6 ΡΠ½Π΅ΠΊΠ° 3. ΠΡΠ΅Π΄ΡΡΠ°Π²Π»Π΅Π½Π½Π°Ρ ΠΊΠΎΠ½ΡΡΡΡΠΊΡΠΈΡ ΠΏΡΠ΅Π΄Π½Π°Π·Π½Π°ΡΠ΅Π½Π° Π΄Π»Ρ ΠΏΡΠΎΠΈΠ·Π²ΠΎΠ΄ΡΡΠ²Π° ΠΌΠ°ΠΊΠ°ΡΠΎΠ½Π½ΡΡ ΠΈΠ·Π΄Π΅Π»ΠΈΠΉ ΠΈΠ· ΠΌΡΠΊΠΈ Π»ΡΠ±ΡΡ ΡΠΎΡΡΠΎΠ² ΠΏΡΠ΅Π½ΠΈΡΡ ΠΈ ΡΡΡΠ°Π½ΠΎΠ²Π»Π΅Π½ΠΈΡ ΠΈΡ Π½Π° ΠΏΡΠ΅Π΄ΠΏΡΠΈΡΡΠΈΡΡ ΠΏΠΈΡΠ΅Π²ΠΎΠΉ ΠΏΡΠΎΠΌΡΡΠ»Π΅Π½Π½ΠΎΡΡΠΈ, ΠΎΠ±ΡΠ΅ΡΡΠ²Π΅Π½Π½ΠΎΠ³ΠΎ ΠΏΠΈΡΠ°Π½ΠΈΡ, Π² ΠΏΠ΅ΠΊΠ°ΡΠ½ΡΡ , Ρ Π»Π΅Π±ΠΎΠ·Π°Π²ΠΎΠ΄Π°Ρ . ΠΡΠΎΠΈΠ·Π²ΠΎΠ΄ΠΈΡΠ΅Π»ΡΠ½ΠΎΡΡΡ ΡΡΡΠ°Π½ΠΎΠ²ΠΊΠΈ ΠΏΡΠΈΠΌΠ΅ΡΠ½ΠΎ 250 ΠΊΠ³/ΡΠ°Ρ.Π€ΠΎΡΠΌΡΠ»Π° ΠΈΠ·ΠΎΠ±ΡΠ΅ΡΠ΅Π½ΠΈΡ
1. ΠΡΠ΅ΡΡ ΠΌΠ°ΠΊΠ°ΡΠΎΠ½Π½ΡΠΉ, ΡΠΎΠ΄Π΅ΡΠΆΠ°ΡΠΈΠΉ Π±Π»ΠΎΠΊ ΡΠ΅ΡΡΠΎΡΠΌΠ΅ΡΠΈΡΠ΅Π»ΡΠ½ΡΡ Π±ΡΠ½ΠΊΠ΅ΡΠΎΠ², ΡΠ½Π΅ΠΊ Π² ΠΊΠΎΡΠΏΡΡΠ΅, ΠΈΠΌΠ΅ΡΡΠΈΠΉ ΠΎΠΏΠΎΡΡ, Π° ΡΠ°ΠΊΠΆΠ΅ ΡΠΈΡΡΠ΅ΠΌΡ ΠΎΡ Π»Π°ΠΆΠ΄Π΅Π½ΠΈΡ, ΠΏΡΠ΅Π΄ΠΌΠ°ΡΡΠΈΡΠ½ΡΡ ΠΊΠ°ΠΌΠ΅ΡΡ, ΠΊΡΡΠ³Π»ΡΡ ΠΌΠ°ΡΡΠΈΡΡ, ΡΠ΅ΠΆΡΡΠ΅Π΅ ΡΡΡΡΠΎΠΉΡΡΠ²ΠΎ, ΠΎΡΠ»ΠΈΡΠ°ΡΡΠΈΠΉΡΡ ΡΠ΅ΠΌ, ΡΡΠΎ ΡΠ½Π΅ΠΊ Π½Π° Π²ΡΡ ΠΎΠ΄Π΅ ΠΈΠΌΠ΅Π΅Ρ ΡΡΠ΅Ρ Π·Π°Ρ ΠΎΠ΄Π½ΡΡ Π½Π°ΡΠ°Π΄ΠΊΡ, Π·Π°ΠΊΡΠ΅ΠΏΠ»Π΅Π½Π½ΡΡ Π½Π° Π²Π°Π»Ρ ΡΠ½Π΅ΠΊΠ°, Π° Π΅Π³ΠΎ ΠΎΠΏΠΎΡΠ° Π½Π° Π²ΡΡ ΠΎΠ΄Π΅ ΡΠΎΡΡΠΎΠΈΡ ΠΈΠ· Π΄Π²ΡΡ ΠΎΠ±ΡΠ΅ΠΊΠ°ΡΠ΅Π»Π΅ΠΉ ΠΈ Π²ΡΡΠ»ΠΊΠΈ. 2. ΠΡΠ΅ΡΡ ΠΌΠ°ΠΊΠ°ΡΠΎΠ½Π½ΡΠΉ ΠΏΠΎ ΠΏ.1, ΠΎΡΠ»ΠΈΡΠ°ΡΡΠΈΠΉΡΡ ΡΠ΅ΠΌ, ΡΡΠΎ ΠΊΠΎΡΠΏΡΡ ΡΠ½Π΅ΠΊΠ° ΠΆΠ΅ΡΡΠΊΠΎ Π·Π°ΠΊΡΠ΅ΠΏΠ»Π΅Π½ Π² ΠΊΠΎΡΠΏΡΡΠ΅ Π±Π»ΠΎΠΊΠ° ΡΠ΅ΡΡΠΎΡΠΌΠ΅ΡΠΈΡΠ΅Π»ΡΠ½ΡΡ Π±ΡΠ½ΠΊΠ΅ΡΠΎΠ². 3. ΠΡΠ΅ΡΡ ΠΌΠ°ΠΊΠ°ΡΠΎΠ½Π½ΡΠΉ ΠΏΠΎ ΠΏ.1, ΠΎΡΠ»ΠΈΡΠ°ΡΡΠΈΠΉΡΡ ΡΠ΅ΠΌ, ΡΡΠΎ ΡΠΈΡΡΠ΅ΠΌΠ° ΠΎΡ Π»Π°ΠΆΠ΄Π΅Π½ΠΈΡ ΡΠ½Π΅ΠΊΠ° ΡΠ½Π°Π±ΠΆΠ΅Π½Π° Π΄ΠΎΠΏΠΎΠ»Π½ΠΈΡΠ΅Π»ΡΠ½ΠΎΠΉ ΡΡΠ±Π°ΡΠΊΠΎΠΉ.Π ΠΠ‘Π£ΠΠΠ
Π ΠΈΡΡΠ½ΠΎΠΊΒ 1www.findpatent.ru
Π’ΠΈΠΏΡ Π·Π°ΠΌΠ΅ΡΠ° ΡΠ΅ΡΡΠ° Π΄Π»Ρ ΠΌΠ°ΠΊΠ°ΡΠΎΠ½Π½ΡΡ ΠΈΠ·Π΄Π΅Π»ΠΈΠΉ
Π Π·Π°Π²ΠΈΡΠΈΠΌΠΎΡΡΠΈ ΠΎΡ Π²Π»Π°ΠΆΠ½ΠΎΡΡΠΈ ΡΠ°Π·Π»ΠΈΡΠ°ΡΡ ΡΡΠΈ ΡΠΈΠΏΠ° Π·Π°ΠΌΠ΅ΡΠ° ΡΠ΅ΡΡΠ°: ΠΌΡΠ³ΠΊΠΈΠΉ β Π²Π»Π°ΠΆΠ½ΠΎΡΡΡ ΡΠ΅ΡΡΠ° 31,1β32,5%, ΡΡΠ΅Π΄Π½ΠΈΠΉ β 29,1β31 ΠΈ ΡΠ²Π΅ΡΠ΄ΡΠΉ β 28β29%. Π’ΠΈΠΏ Π·Π°ΠΌΠ΅ΡΠ° Π²ΡΠ±ΠΈΡΠ°ΡΡ Π² Π·Π°Π²ΠΈΡΠΈΠΌΠΎΡΡΠΈ ΠΎΡ ΡΡΠ΄Π° ΡΠ°ΠΊΡΠΎΡΠΎΠ². ΠΡΠ»ΠΈ ΠΈΡΠΏΠΎΠ»ΡΠ·ΡΠ΅ΡΡΡ ΠΌΡΠΊΠ° Ρ Π½ΠΈΠ·ΠΊΠΈΠΌ ΡΠΎΠ΄Π΅ΡΠΆΠ°Π½ΠΈΠ΅ΠΌ ΠΊΠ»Π΅ΠΉΠΊΠΎΠ²ΠΈΠ½Ρ, ΡΠΎ ΠΆΠ΅Π»Π°ΡΠ΅Π»ΡΠ½ΠΎ ΠΏΡΠΈΠΌΠ΅Π½ΡΡΡ ΠΌΡΠ³ΠΊΠΈΠΉ Π·Π°ΠΌΠ΅Ρ, ΠΏΡΠΈ Π»ΠΈΠΏΠΊΠΎΠΉ, ΡΡΠ½ΡΡΠ΅ΠΉΡΡ ΠΊΠ»Π΅ΠΉΠΊΠΎΠ²ΠΈΠ½Π΅ β ΡΠ²Π΅ΡΠ΄ΡΠΉ Π·Π°ΠΌΠ΅Ρ.
ΠΡΠΈ ΠΏΡΠΎΠΈΠ·Π²ΠΎΠ΄ΡΡΠ²Π΅ ΠΊΠΎΡΠΎΡΠΊΠΎΡΠ΅Π·Π°Π½ΡΡ ΠΈΠ·Π΄Π΅Π»ΠΈΠΉ ΠΈ ΠΌΠ°ΠΊΠ°ΡΠΎΠ½, Π²ΡΡΡΡΠΈΠ²Π°Π΅ΠΌΡΡ Π² Π»ΠΎΡΠΊΠΎΠ²ΡΡ ΠΊΠ°ΡΡΠ΅ΡΠ°Ρ , Π²ΠΎ ΠΈΠ·Π±Π΅ΠΆΠ°Π½ΠΈΠ΅ ΡΠ»ΠΈΠΏΠ°Π½ΠΈΡ ΠΌΠ°ΠΊΠ°ΡΠΎΠ½Π½ΡΡ ΠΈΠ·Π΄Π΅Π»ΠΈΠΉ Π² ΠΏΠ΅ΡΠΈΠΎΠ΄ ΡΡΡΠΊΠΈ, ΠΏΡΠΈΠΌΠ΅Π½ΡΡΡ ΡΠ²Π΅ΡΠ΄ΡΠΉ ΠΈΠ»ΠΈ ΡΡΠ΅Π΄Π½ΠΈΠΉ Π·Π°ΠΌΠ΅Ρ. ΠΡΠΈ ΠΏΡΠΎΠΈΠ·Π²ΠΎΠ΄ΡΡΠ²Π΅ Π΄Π»ΠΈΠ½Π½ΡΡ ΠΈΠ·Π΄Π΅Π»ΠΈΠΉ Ρ ΠΏΠΎΠ΄Π²Π΅ΡΠ½ΠΎΠΉ ΡΡΡΠΊΠΎΠΉ Π΄Π»Ρ Π±ΠΎΠ»ΡΡΠ΅ΠΉ ΠΏΠ»Π°ΡΡΠΈΡΠ½ΠΎΡΡΠΈ ΠΏΡΠΈΠΌΠ΅Π½ΡΡΡ ΡΡΠ΅Π΄Π½ΠΈΠΉ ΠΈΠ»ΠΈ ΠΌΡΠ³ΠΊΠΈΠΉ Π·Π°ΠΌΠ΅Ρ. ΠΡΠ»ΠΈ ΠΈΡΠΏΠΎΠ»ΡΠ·ΡΡΡ ΠΏΠΎΠ»ΡΠΊΡΡΠΏΠΊΡ ΠΈΠ»ΠΈ Ρ Π»Π΅Π±ΠΎΠΏΠ΅ΠΊΠ°ΡΠ½ΡΡ ΠΌΡΠΊΡ, ΡΠΎ Π²Π»Π°ΠΆΠ½ΠΎΡΡΡ ΡΠ΅ΡΡΠ° Π΄ΠΎΠ»ΠΆΠ½Π° Π±ΡΡΡ Π²ΡΡΠ΅ Π½Π° 1β2%, ΡΠ΅ΠΌ ΠΏΡΠΈ ΠΈΡΠΏΠΎΠ»ΡΠ·ΠΎΠ²Π°Π½ΠΈΠΈ ΠΊΡΡΠΏΠΊΠΈ.
ΠΠΎΠ·ΠΈΡΠΎΠ²Π°Π½ΠΈΠ΅ ΠΈ ΡΠΌΠ΅ΡΠΈΠ²Π°Π½ΠΈΠ΅ ΠΈΠ½Π³ΡΠ΅Π΄ΠΈΠ΅Π½ΡΠΎΠ² ΡΠ΅ΡΡΠ° (Π·Π°ΠΌΠ΅Ρ) ΠΎΡΡΡΠ΅ΡΡΠ²Π»ΡΡΡΡΡ Π² ΡΠ΅ΡΡΠΎΡΠΌΠ΅ΡΠΈΡΠ΅Π»ΡΡ Π½Π΅ΠΏΡΠ΅ΡΡΠ²Π½ΠΎΠ³ΠΎ Π΄Π΅ΠΉΡΡΠ²ΠΈΡ, Π²Ρ ΠΎΠ΄ΡΡΠΈΡ Π² ΡΠΎΡΡΠ°Π² ΠΏΡΠΎΠΌΡΡΠ»Π΅Π½Π½ΡΡ ΠΏΡΠ΅ΡΡΠΎΠ². ΠΡΠΊΡ ΠΈ Π²ΠΎΠ΄Ρ ΠΏΠΎΠ΄Π°ΡΡ Π² ΡΠ΅ΡΡΠΎΡΠΌΠ΅ΡΠΈΡΠ΅Π»Ρ ΠΏΡΠΈ ΠΏΠΎΠΌΠΎΡΠΈ Π΄ΠΎΠ·Π°ΡΠΎΡΠΎΠ² Π½Π΅ΠΏΡΠ΅ΡΡΠ²Π½ΠΎΠ³ΠΎ Π΄Π΅ΠΉΡΡΠ²ΠΈΡ.
Π£ΠΏΠ»ΠΎΡΠ½Π΅Π½ΠΈΠ΅ ΠΈ ΡΠΎΡΠΌΠΎΠ²Π°Π½ΠΈΠ΅ ΡΠ΅ΡΡΠ° ΠΏΡΠΎΠΈΠ·Π²ΠΎΠ΄ΡΡΡΡ Π½Π° ΡΠ½Π΅ΠΊΠΎΠ²ΡΡ ΠΏΡΠ΅ΡΡΠ°Ρ . ΠΠ»Π°Π³ΠΎΠ΄Π°ΡΡ ΠΈΠ½ΡΠ΅Π½ΡΠΈΠ²Π½ΠΎΠΌΡ Π²ΠΎΠ·Π΄Π΅ΠΉΡΡΠ²ΠΈΡ Π²ΠΈΠ½ΡΠΎΠ²ΠΎΠΉ Π»ΠΎΠΏΠ°ΡΡΠΈ Π²ΡΠ°ΡΠ°ΡΡΠ΅Π³ΠΎΡΡ ΡΠ½Π΅ΠΊΠ° ΡΠ΅ΡΡΠΎ ΡΡΠ°Π½ΠΎΠ²ΠΈΡΡΡ ΡΠ²ΡΠ·Π½ΡΠΌ, ΠΏΠ»ΠΎΡΠ½ΡΠΌ.
ΠΡΠ½ΠΎΠ²Π½ΡΠΌ ΡΠ°Π±ΠΎΡΠΈΠΌ ΠΎΡΠ³Π°Π½ΠΎΠΌ ΠΌΠ°ΠΊΠ°ΡΠΎΠ½Π½ΠΎΠ³ΠΎ ΠΏΡΠ΅ΡΡΠ° Π½Π°ΡΡΠ΄Ρ Ρ ΠΏΡΠ΅ΡΡΡΡΡΠΈΠΌ ΡΡΡΡΠΎΠΉΡΡΠ²ΠΎΠΌ ΡΠ²Π»ΡΠ΅ΡΡΡ ΠΌΠ°ΡΡΠΈΡΠ°. ΠΠ½Π° ΠΎΠ±ΡΡΠ»ΠΎΠ²Π»ΠΈΠ²Π°Π΅Ρ ΠΏΡΠΎΠΈΠ·Π²ΠΎΠ΄ΠΈΡΠ΅Π»ΡΠ½ΠΎΡΡΡ ΠΏΡΠ΅ΡΡΠ°, Π²ΠΈΠ΄ ΠΈΠ·Π΄Π΅Π»ΠΈΠΉ (ΡΠΎΡΠΌΡ ΠΈ ΡΠ°Π·ΠΌΠ΅ΡΡ ΠΏΠΎΠΏΠ΅ΡΠ΅ΡΠ½ΠΎΠ³ΠΎ ΡΠ΅ΡΠ΅Π½ΠΈΡ), Π² Π±ΠΎΠ»ΡΡΠΎΠΉ ΡΡΠ΅ΠΏΠ΅Π½ΠΈ Π²Π»ΠΈΡΠ΅Ρ Π½Π° ΠΊΠ°ΡΠ΅ΡΡΠ²ΠΎ ΠΏΡΠΎΠ΄ΡΠΊΡΠ° (ΡΡΠ΅ΠΏΠ΅Π½Ρ ΡΠ΅ΡΠΎΡ ΠΎΠ²Π°ΡΠΎΡΡΠΈ ΠΏΠΎΠ²Π΅ΡΡ Π½ΠΎΡΡΠΈ, ΠΏΡΠΎΡΠ½ΠΎΡΡΡ ΡΠΊΠ»Π΅ΠΈΠ²Π°Π½ΠΈΡ ΠΌΠ°ΠΊΠ°ΡΠΎΠ½Π½ΡΡ ΡΡΡΠ±ΠΎΠΊ ΠΈ Π΄Ρ.).
ΠΠΎ ΠΏΡΠΎΡΠΈΠ»Ρ ΠΈ ΠΊΠΎΠ½ΡΡΡΡΠΊΡΠΈΠΈ ΡΠΎΡΠΌΡΡΡΠΈΡ ΠΎΡΠ²Π΅ΡΡΡΠΈΠΉ (ΠΊΠ°Π½Π°Π»ΠΎΠ²) ΠΌΠ°ΡΡΠΈΡΡ ΡΠ°Π·Π΄Π΅Π»ΡΡΡ Π½Π° Π΄Π²Π° ΠΎΡΠ½ΠΎΠ²Π½ΡΡ Π²ΠΈΠ΄Π°:
- Π‘Β Π²ΠΊΠ»Π°Π΄ΡΡΠ°ΠΌΠΈ β Π΄Π»Ρ ΡΠΎΡΠΌΠΎΠ²Π°Π½ΠΈΡ ΡΡΡΠ±ΡΠ°ΡΡΡ ΠΈ Π½Π΅ΠΊΠΎΡΠΎΡΡΡ ΡΠ»ΠΎΠΆΠ½ΡΡ ΠΏΠΎ ΡΠΎΡΠΌΠ΅ ΡΠΈΠ³ΡΡΠ½ΡΡ ΠΈΠ·Π΄Π΅Π»ΠΈΠΉ. ΠΡΠΈ ΠΏΠΎΠΌΠΎΡΠΈ ΠΊΡΡΠ³Π»ΡΡ ΠΌΠ°ΡΡΠΈΡ ΡΠΎΡΠΌΡΡΡ Π²ΡΠ΅ Π²ΠΈΠ΄Ρ Π΄Π»ΠΈΠ½Π½ΡΡ ΠΈ ΠΊΠΎΡΠΎΡΠΊΠΎΡΠ΅Π·Π°Π½ΡΡ ΠΈΠ·Π΄Π΅Π»ΠΈΠΉ. ΠΡΡΠΌΠΎΡΠ³ΠΎΠ»ΡΠ½ΡΠ΅ ΠΌΠ°ΡΡΠΈΡΡ ΠΈΡΠΏΠΎΠ»ΡΠ·ΡΡΡ Π΄Π»Ρ ΡΠΎΡΠΌΠΎΠ²Π°Π½ΠΈΡ Π΄Π»ΠΈΠ½Π½ΡΡ ΠΌΠ°ΠΊΠ°ΡΠΎΠ½Π½ΡΡ ΠΈΠ·Π΄Π΅Π»ΠΈΠΉ (ΠΌΠ°ΠΊΠ°ΡΠΎΠ½Ρ, Π²Π΅ΡΠΌΠΈΡΠ΅Π»Ρ, Π»Π°ΠΏΡΠ°), Π²ΡΡΠ°Π±Π°ΡΡΠ²Π°Π΅ΠΌΡΡ Π½Π° Π°Π²ΡΠΎΠΌΠ°ΡΠΈΠ·ΠΈΡΠΎΠ²Π°Π½Π½ΡΡ Π»ΠΈΠ½ΠΈΡΡ Ρ ΠΏΠΎΠ΄Π²Π΅ΡΠ½ΠΎΠΉ ΡΡΡΠΊΠΎΠΉ ΠΈΠ·Π΄Π΅Π»ΠΈΠΉ;
- ΠΠ΅Π· Π²ΠΊΠ»Π°Π΄ΡΡΠ΅ΠΉ β Π΄Π»Ρ ΡΠΎΡΠΌΠΎΠ²Π°Π½ΠΈΡ Π²ΡΠ΅Ρ Π²ΠΈΠ΄ΠΎΠ² ΠΈΠ·Π΄Π΅Π»ΠΈΠΉ, ΠΊΡΠΎΠΌΠ΅ ΡΡΡΠ±ΡΠ°ΡΡΡ .
ΠΠ»Ρ ΡΠΎΡΠΌΠΎΠ²Π°Π½ΠΈΡ ΡΠΈΠ³ΡΡΠ½ΡΡ ΠΈΠ·Π΄Π΅Π»ΠΈΠΉ ΡΠ°ΠΊΠΆΠ΅ ΠΏΡΠΈΠΌΠ΅Π½ΡΠ΅ΡΡΡ ΠΈ ΡΡΠ°ΠΌΠΏΠΎΠ²Π°Π½ΠΈΠ΅.
proiz-teh.ru
ΠΠ°ΠΊ Π²ΡΠ±ΡΠ°ΡΡ ΠΎΠ±ΠΎΡΡΠ΄ΠΎΠ²Π°Π½ΠΈΠ΅ Π΄Π»Ρ ΠΏΡΠΎΠΈΠ·Π²ΠΎΠ΄ΡΡΠ²Π° ΠΌΠ°ΠΊΠ°ΡΠΎΠ½Π½ΡΡ ΠΈΠ·Π΄Π΅Π»ΠΈΠΉ :: BusinessMan.ru
ΠΠ°ΠΊΠ°ΡΠΎΠ½Π½ΡΠ΅ ΠΈΠ·Π΄Π΅Π»ΠΈΡ ΡΠΎΡΡΠ°Π²Π»ΡΡΡ ΠΎΠ³ΡΠΎΠΌΠ½ΡΡ ΡΠ°ΡΡΡ ΡΠ°ΡΠΈΠΎΠ½Π° ΡΠ΅Π»ΠΎΠ²Π΅ΠΊΠ°. ΠΠΎΡΡΠΎΠΌΡ ΠΈΡ ΠΏΡΠΎΠΈΠ·Π²ΠΎΠ΄ΡΡΠ²ΠΎ ΡΠ²Π»ΡΠ΅ΡΡΡ Π΄ΠΎΡΡΠ°ΡΠΎΡΠ½ΠΎ ΠΏΡΠΈΠ±ΡΠ»ΡΠ½ΡΠΌ, ΠΎΡΠΎΠ±Π΅Π½Π½ΠΎ Π΅ΡΠ»ΠΈ ΠΏΡΠ°Π²ΠΈΠ»ΡΠ½ΠΎ Π΅Π³ΠΎ ΠΎΡΠ³Π°Π½ΠΈΠ·ΠΎΠ²Π°ΡΡ. Π ΠΏΡΠΎΡΠ΅ΡΡΠ΅ ΠΎΡΠ³Π°Π½ΠΈΠ·Π°ΡΠΈΠΈ Π±ΠΈΠ·Π½Π΅ΡΠ° ΠΎΡΠ΅Π½Ρ Π²Π°ΠΆΠ½ΠΎ ΡΠΎΠ±Π»ΡΠ΄Π΅Π½ΠΈΠ΅ ΡΠ°Π½ΠΈΡΠ°ΡΠ½ΠΎ-Π³ΠΈΠ³ΠΈΠ΅Π½ΠΈΡΠ΅ΡΠΊΠΈΡ Π½ΠΎΡΠΌ. Π ΡΠΎΠΌΡ ΠΆΠ΅ Π½Π΅ΠΎΠ±Ρ ΠΎΠ΄ΠΈΠΌΠΎ, ΡΡΠΎΠ±Ρ ΡΡΡΡΠ΅ Π΄Π»Ρ ΠΏΡΠΎΠΈΠ·Π²ΠΎΠ΄ΡΡΠ²Π° ΠΌΠ°ΠΊΠ°ΡΠΎΠ½Π½ΡΡ ΠΈΠ·Π΄Π΅Π»ΠΈΠΉ, Π° ΡΠ°ΠΊΠΆΠ΅ ΠΎΠ±ΠΎΡΡΠ΄ΠΎΠ²Π°Π½ΠΈΠ΅ Π±ΡΠ»ΠΈ Π²ΡΡΠΎΠΊΠΎΠ³ΠΎ ΠΊΠ°ΡΠ΅ΡΡΠ²Π°.
Π’Π΅Ρ Π½ΠΎΠ»ΠΎΠ³ΠΈΡ
Π‘ΡΠ΅Π΄ΠΈ ΠΎΠ±ΠΎΡΡΠ΄ΠΎΠ²Π°Π½ΠΈΡ, ΠΊΠΎΡΠΎΡΠΎΠ΅ ΠΈΡΠΏΠΎΠ»ΡΠ·ΡΠ΅ΡΡΡ Π² ΠΏΡΠΎΠΈΠ·Π²ΠΎΠ΄ΡΡΠ²Π΅ ΠΌΠ°ΠΊΠ°ΡΠΎΠ½Π½ΡΡ ΠΈΠ·Π΄Π΅Π»ΠΈΠΉ, ΠΎΠ±ΡΠ·Π°ΡΠ΅Π»ΡΠ½ΡΠΌ ΡΠ²Π»ΡΡΡΡΡ ΠΏΡΠΎΡΠ΅ΠΈΠ²Π°ΡΠ΅Π»ΠΈ ΠΌΡΠΊΠΈ, ΡΡΠ°Π½ΡΠΏΠΎΡΡΠ΅ΡΡ, Π±ΡΠ½ΠΊΠ΅ΡΡ-ΡΡΠ°Π±ΠΈΠ»ΠΈΠ·Π°ΡΠΎΡΡ, Π° ΡΠ°ΠΊΠΆΠ΅ Π°ΠΏΠΏΠ°ΡΠ°ΡΡ, ΠΊΠΎΡΠΎΡΡΠ΅ ΡΠΏΠ°ΠΊΠΎΠ²ΡΠ²Π°ΡΡ ΠΏΡΠΎΠ΄ΡΠΊΡΠΈΡ. Π ΠΊΠ°ΡΠ΅ΡΡΠ²Π΅ ΠΈΡΡ ΠΎΠ΄Π½ΠΎΠ³ΠΎ ΡΡΡΡΡ ΠΈΡΠΏΠΎΠ»ΡΠ·ΡΠ΅ΡΡΡ ΠΌΡΠΊΠ° ΡΠ°Π·Π»ΠΈΡΠ½ΡΡ ΡΠΎΡΡΠΎΠ², ΡΠΈΡΠ½ΡΠΉ Π±Π΅Π»ΠΎΠΊ ΠΈ Π½Π°ΡΡΡΠ°Π»ΡΠ½ΡΠ΅ Π΄ΠΎΠ±Π°Π²ΠΊΠΈ.
Π‘ΡΠ°Π΄ΠΈΠΈ ΠΈΠ·Π³ΠΎΡΠΎΠ²Π»Π΅Π½ΠΈΡ ΠΏΡΠΎΠ΄ΡΠΊΡΠΈΠΈ:
- ΠΠΎΠ΄Π³ΠΎΡΠΎΠ²ΠΊΠ° ΠΈΡΡ ΠΎΠ΄Π½ΠΎΠ³ΠΎ ΡΡΡΡΡ (ΠΏΡΠΎΡΠ΅ΠΈΠ²Π°Π½ΠΈΠ΅ ΠΌΡΠΊΠΈ, ΡΠΌΠ΅ΡΠΈΠ²Π°Π½ΠΈΠ΅ ΡΠ°Π·Π½ΡΡ Π΅Π΅ ΡΠΎΡΡΠΎΠ² ΠΈ ΠΏΠΎΠ΄ΠΎΠ³ΡΠ΅Π²Π°Π½ΠΈΠ΅ Π΄ΠΎ ΠΎΠΏΡΠ΅Π΄Π΅Π»Π΅Π½Π½ΠΎΠΉ ΡΠ΅ΠΌΠΏΠ΅ΡΠ°ΡΡΡΡ).
- ΠΡΠΈΠ³ΠΎΡΠΎΠ²Π»Π΅Π½ΠΈΠ΅ ΡΠ΅ΡΡΠ°.
- ΠΡΠ΅ΡΡΠΎΠ²Π°Π½ΠΈΠ΅ ΡΠ΅ΡΡΠ° ΠΈ ΡΠΎΠ·Π΄Π°Π½ΠΈΠ΅ ΠΈΠ· Π½Π΅Π³ΠΎ ΠΈΠ·Π΄Π΅Π»ΠΈΠΉ ΠΎΠΏΡΠ΅Π΄Π΅Π»Π΅Π½Π½ΠΎΠΉ ΡΠΎΡΠΌΡ.
- Π Π°Π·Π΄Π΅Π»ΠΊΠ° ΠΌΠ°ΠΊΠ°ΡΠΎΠ½Π½ΡΡ ΠΈΠ·Π΄Π΅Π»ΠΈΠΉ Π½Π° ΠΎΡΠ΄Π΅Π»ΡΠ½ΡΠ΅ ΠΊΡΡΠΎΡΠΊΠΈ, ΡΡΠΎΠ±Ρ ΠΎΠ½ΠΈ Π½Π΅ ΡΠ»ΠΈΠΏΠ»ΠΈΡΡ.
- ΠΡΡΡΡΠΈΠ²Π°Π½ΠΈΠ΅ ΠΈΠ·Π΄Π΅Π»ΠΈΠΉ.
- ΠΡ Π»Π°ΠΆΠ΄Π΅Π½ΠΈΠ΅ ΠΌΠ°ΠΊΠ°ΡΠΎΠ½Π½ΠΎΠΉ ΠΏΡΠΎΠ΄ΡΠΊΡΠΈΠΈ Π΄Π»Ρ ΠΏΡΠ΅Π΄ΠΎΡΠ²ΡΠ°ΡΠ΅Π½ΠΈΡ Π·Π°ΠΏΠΎΡΠ΅Π²Π°Π½ΠΈΡ ΡΠΏΠ°ΠΊΠΎΠ²ΠΊΠΈ.
- Π£ΠΏΠ°ΠΊΠΎΠ²ΠΊΠ° ΠΈΠ·Π΄Π΅Π»ΠΈΠΉ Π² ΡΡΠΈΠΊΠΈ, ΠΌΠ΅ΡΠΊΠΈ ΠΈΠ»ΠΈ ΠΏΠ°ΠΊΠ΅ΡΡ.
ΠΠ° Π²ΡΠ΅Ρ ΡΡΠ°ΠΏΠ°Ρ ΠΈΡΠΏΠΎΠ»ΡΠ·ΡΠ΅ΡΡΡ ΡΠΏΠ΅ΡΠΈΠ°Π»ΡΠ½ΠΎΠ΅ ΠΎΠ±ΠΎΡΡΠ΄ΠΎΠ²Π°Π½ΠΈΠ΅ Π΄Π»Ρ ΠΏΡΠΎΠΈΠ·Π²ΠΎΠ΄ΡΡΠ²Π° ΠΌΠ°ΠΊΠ°ΡΠΎΠ½Π½ΡΡ ΠΈΠ·Π΄Π΅Π»ΠΈΠΉ, Π½Π° Π²ΡΠ±ΠΎΡΠ΅ ΠΊΠΎΡΠΎΡΠΎΠ³ΠΎ ΠΌΡ ΠΈ Π·Π°ΠΎΡΡΡΠΈΠΌ Π²Π½ΠΈΠΌΠ°Π½ΠΈΠ΅.
ΠΡΠ±ΠΎΡ ΠΎΠ±ΠΎΡΡΠ΄ΠΎΠ²Π°Π½ΠΈΡ
ΠΠ° Π΄Π°Π½Π½ΡΠΉ ΠΌΠΎΠΌΠ΅Π½Ρ ΠΏΠΎΠΊΡΠΏΠΊΠ° ΠΎΠ±ΠΎΡΡΠ΄ΠΎΠ²Π°Π½ΠΈΡ Π½Π΅ Π²ΡΠ·ΡΠ²Π°Π΅Ρ Π½ΠΈΠΊΠ°ΠΊΠΈΡ ΠΏΡΠΎΠ±Π»Π΅ΠΌ. Π ΡΠΎΠΌΡ ΠΆΠ΅ ΠΊΡΠΎΠΌΠ΅ ΠΈΠΌΠΏΠΎΡΡΠ½ΠΎΠ³ΠΎ ΠΎΠ±ΠΎΡΡΠ΄ΠΎΠ²Π°Π½ΠΈΡ ΠΌΠΎΠΆΠ½ΠΎ ΠΏΡΠΈΠΎΠ±ΡΠ΅ΡΡΠΈ Π²ΠΏΠΎΠ»Π½Π΅ ΠΊΠ°ΡΠ΅ΡΡΠ²Π΅Π½Π½ΡΠ΅ ΠΎΡΠ΅ΡΠ΅ΡΡΠ²Π΅Π½Π½ΡΠ΅ ΡΡΠ°Π½ΠΊΠΈ. Π‘Π°ΠΌΠΎΠ΅ Π³Π»Π°Π²Π½ΠΎΠ΅ β ΡΡΠΎ Π²ΡΠ±ΡΠ°ΡΡ Π΄Π»Ρ ΡΠ΅Π±Ρ ΠΎΠΏΡΠΈΠΌΠ°Π»ΡΠ½ΡΠΉ Π²Π°ΡΠΈΠ°Π½Ρ ΠΏΠΎ ΡΡΠΎΠΈΠΌΠΎΡΡΠΈ, ΠΊΠ°ΡΠ΅ΡΡΠ²Ρ ΠΈ ΠΎΠ±ΡΠ΅ΠΌΠ°ΠΌ Π²ΡΠ΄Π°Π²Π°Π΅ΠΌΠΎΠΉ ΠΏΡΠΎΠ΄ΡΠΊΡΠΈΠΈ.
ΠΠ»Ρ ΠΈΠ·Π³ΠΎΡΠΎΠ²Π»Π΅Π½ΠΈΡ ΠΌΠ°ΠΊΠ°ΡΠΎΠ½Π½ΡΡ ΠΈΠ·Π΄Π΅Π»ΠΈΠΉ Π½Π° Π΄Π°Π½Π½ΡΠΉ ΠΌΠΎΠΌΠ΅Π½Ρ ΠΈΡΠΏΠΎΠ»ΡΠ·ΡΡΡΡΡ ΡΠ°ΠΊΠΈΠ΅ Π»ΠΈΠ½ΠΈΠΈ:
- ΠΠ²ΡΠΎΠΌΠ°ΡΠΈΡΠ΅ΡΠΊΠ°Ρ ΠΊΠΎΠ½Π²Π΅ΠΉΠ΅ΡΠ½Π°Ρ.
- ΠΠΎΠ»ΡΠ°Π²ΡΠΎΠΌΠ°ΡΠΈΡΠ΅ΡΠΊΠ°Ρ.
- Π‘Π±ΠΎΡΠ½Π°Ρ Π»ΠΈΠ½ΠΈΡ.
ΠΠ°ΠΈΠ»ΡΡΡΠΈΠΌ Π²Π°ΡΠΈΠ°Π½ΡΠΎΠΌ Π±ΡΠ΄Π΅Ρ Π°Π²ΡΠΎΠΌΠ°ΡΠΈΡΠ΅ΡΠΊΠ°Ρ Π»ΠΈΠ½ΠΈΡ, ΠΊΠΎΡΠΎΡΠ°Ρ ΡΡΠΊΠΎΡΠΈΡ ΠΈ ΡΠΏΡΠΎΡΡΠΈΡ ΡΠ°Π±ΠΎΡΡ. ΠΠ΄Π½Π°ΠΊΠΎ ΡΠ°ΠΊΠΎΠΉ Π²Π°ΡΠΈΠ°Π½Ρ ΡΠ²Π»ΡΠ΅ΡΡΡ ΠΈ ΡΠ°ΠΌΡΠΌ Π΄ΠΎΡΠΎΠ³ΠΈΠΌ. ΠΡΠ΅ ΠΎΠ΄Π½Π° Π²ΡΠ³ΠΎΠ΄Π° ΡΠ°ΠΊΠΎΠ³ΠΎ ΠΎΠ±ΠΎΡΡΠ΄ΠΎΠ²Π°Π½ΠΈΡ Π·Π°ΠΊΠ»ΡΡΠ°Π΅ΡΡΡ Π² Π²ΠΎΠ·ΠΌΠΎΠΆΠ½ΠΎΡΡΠΈ Π΅Π³ΠΎ ΠΎΠ±ΡΠ»ΡΠΆΠΈΠ²Π°Π½ΠΈΡ Π²ΡΠ΅Π³ΠΎ ΠΎΠ΄Π½ΠΈΠΌ ΡΠ΅Π»ΠΎΠ²Π΅ΠΊΠΎΠΌ. Π’Π°ΠΊ ΡΡΠΎ ΡΠ°ΠΊΠ°Ρ ΠΌΠ°ΡΠΈΠ½Π° Π΄Π»Ρ ΠΏΡΠΎΠΈΠ·Π²ΠΎΠ΄ΡΡΠ²Π° ΠΌΠ°ΠΊΠ°ΡΠΎΠ½Π½ΡΡ ΠΈΠ·Π΄Π΅Π»ΠΈΠΉ ΠΏΠΎΠ·Π²ΠΎΠ»ΠΈΡ ΡΠΎΠΊΡΠ°ΡΠΈΡΡ ΠΏΠ΅ΡΡΠΎΠ½Π°Π» Π·Π°Π²ΠΎΠ΄Π° Π΄ΠΎ ΠΌΠΈΠ½ΠΈΠΌΡΠΌΠ°.
ΠΡΠ΅ΡΡ
ΠΠ»Ρ ΡΠΎΠ·Π΄Π°Π½ΠΈΡ ΠΌΠ°ΠΊΠ°ΡΠΎΠ½Π½ΡΡ ΠΈΠ·Π΄Π΅Π»ΠΈΠΉ Π»ΡΠ±ΠΎΠ³ΠΎ Π²ΠΈΠ΄Π° ΠΈΡΠΏΠΎΠ»ΡΠ·ΡΠ΅ΡΡΡ ΡΠΊΡΡΡΡΠ΄Π΅Ρ, ΠΊΠΎΡΠΎΡΡΠΉ ΡΠ°ΠΊΠΆΠ΅ Π½Π°Π·ΡΠ²Π°Π΅ΡΡΡ ΠΏΡΠ΅ΡΡΠΎΠΌ. ΠΠ½ ΠΏΡΠΈΠΌΠ΅Π½ΡΠ΅ΡΡΡ Π΄Π»Ρ Π°Π²ΡΠΎΠΌΠ°ΡΠΈΡΠ΅ΡΠΊΠΎΠ³ΠΎ ΠΏΡΠΎΠΈΠ·Π²ΠΎΠ΄ΡΡΠ²Π° ΠΏΡΠΎΠ΄ΡΠΊΡΠΈΠΈ ΠΈΠ· ΠΌΡΠΊΠΈ ΡΠ°Π·Π½ΡΡ ΡΠΎΡΡΠΎΠ² ΠΏΡΠ΅Π½ΠΈΡΡ.
ΠΡΠΈ Π²ΡΠ±ΠΎΡΠ΅ ΠΏΡΠ΅ΡΡΠ° ΡΠ»Π΅Π΄ΡΠ΅Ρ ΠΎΡΠ΄Π°Π²Π°ΡΡ ΠΏΡΠ΅Π΄ΠΏΠΎΡΡΠ΅Π½ΠΈΠ΅ ΡΠΎΠΌΡ, ΠΊΠΎΡΠΎΡΡΠΉ Π±ΡΠ΄Π΅Ρ ΠΎΡΠ½Π°ΡΠ΅Π½ Π°Π²ΡΠΎΠΌΠ°ΡΠΈΡΠ΅ΡΠΊΠΎΠΉ Π΄ΠΎΠ·ΠΈΡΠΎΠ²ΠΊΠΎΠΉ ΠΏΠΎΠ΄Π°ΡΠΈ ΡΡΡΡΡ, Π±Π»ΠΎΠΊΠΈΡΠΎΠ²ΠΊΠΎΠΉ ΡΠΈΡΡΠ΅ΠΌΡ ΠΏΡΠΈ ΠΏΠ΅ΡΠ΅Π³ΡΡΠ·ΠΊΠ΅ Π΄Π²ΠΈΠ³Π°ΡΠ΅Π»Ρ ΠΈΠ»ΠΈ ΠΏΠΎΠ²ΡΡΠ΅Π½Π½ΠΎΠΌ Π΄Π°Π²Π»Π΅Π½ΠΈΠΈ, Π° ΡΠ°ΠΊΠΆΠ΅ Π½Π΅ΠΏΡΠ΅ΡΡΠ²Π½ΡΠΌ Π·Π°ΠΌΠ΅ΡΠΎΠΌ ΡΠ΅ΡΡΠ°.
ΠΠ°ΡΠ΅ΡΡΠ²Π΅Π½Π½ΡΠΉ ΠΏΡΠ΅ΡΡ Π΄Π»Ρ ΠΏΡΠΎΠΈΠ·Π²ΠΎΠ΄ΡΡΠ²Π° ΠΌΠ°ΠΊΠ°ΡΠΎΠ½Π½ΡΡ ΠΈΠ·Π΄Π΅Π»ΠΈΠΉ ΡΠ°ΠΊΠΆΠ΅ ΠΏΠΎΠ΄Π°Π΅Ρ ΡΠΈΠ³Π½Π°Π», ΠΊΠΎΠ³Π΄Π° ΠΏΡΠ΅ΠΊΡΠ°ΡΠ°Π΅ΡΡΡ ΠΏΠΎΠ΄Π°ΡΠ° ΡΡΡΡΡ. Π Π²Π°ΠΊΡΡΠΌΠΈΡΠΎΠ²Π°Π½ΠΈΠ΅ Π³ΠΎΡΠΎΠ²ΠΎΠ³ΠΎ ΡΠ΅ΡΡΠ° Π΄ΠΎ ΠΏΡΠΎΡΠ΅ΡΡΠ° ΠΏΡΠ΅ΡΡΠΎΠ²Π°Π½ΠΈΡ Π΄Π°Π΅Ρ Π²ΠΎΠ·ΠΌΠΎΠΆΠ½ΠΎΡΡΡ ΡΠ΄Π°Π»ΠΈΡΡ ΠΈΠ· Π½Π΅Π³ΠΎ Π²ΠΎΠ·Π΄ΡΡ . Π ΡΠ΅Π·ΡΠ»ΡΡΠ°ΡΠ΅ ΡΡΠΎΠ³ΠΎ ΠΌΠ°ΠΊΠ°ΡΠΎΠ½Π½ΡΠ΅ ΠΈΠ·Π΄Π΅Π»ΠΈΡ ΡΡΠ°Π½ΠΎΠ²ΡΡΡΡ Π±ΠΎΠ»Π΅Π΅ ΠΊΡΠ°ΡΠΈΠ²ΡΠΌΠΈ, ΠΏΡΠΎΡΠ½ΡΠΌΠΈ ΠΈ Π²ΠΊΡΡΠ½ΡΠΌΠΈ, ΠΊ ΡΠΎΠΌΡ ΠΆΠ΅ ΠΎΠ½ΠΈ ΠΎΠ±Π»Π°Π΄Π°ΡΡ Π»ΡΡΡΠΈΠΌΠΈ ΠΏΠΈΡΠ°ΡΠ΅Π»ΡΠ½ΡΠΌΠΈ ΡΠ²ΠΎΠΉΡΡΠ²Π°ΠΌΠΈ. Π‘ΠΎΠ²ΡΠ΅ΠΌΠ΅Π½Π½ΡΠΉ ΠΏΡΠ΅ΡΡ ΠΏΠΎΠ·Π²ΠΎΠ»ΡΠ΅Ρ ΡΠΎΠ·Π΄Π°ΡΡ ΠΊΠ°ΡΠ΅ΡΡΠ²Π΅Π½Π½ΡΡ ΠΏΡΠΎΠ΄ΡΠΊΡΠΈΡ Π΄Π°ΠΆΠ΅ ΠΈΠ· ΠΌΡΠΊΠΈ, ΠΊΠΎΡΠΎΡΠ°Ρ ΡΠΎΠ΄Π΅ΡΠΆΠΈΡ Π½Π΅ΠΌΠ½ΠΎΠ³ΠΎ ΠΊΠ»Π΅ΠΉΠΊΠΎΠ²ΠΈΠ½Ρ.
ΠΠ°ΡΡΠΈΡΡ Π΄Π»Ρ ΡΠΎΠ·Π΄Π°Π½ΠΈΡ ΠΌΠ°ΠΊΠ°ΡΠΎΠ½Π½ΡΡ ΠΈΠ·Π΄Π΅Π»ΠΈΠΉ
ΠΠ°ΡΡΠΈΡΠ° ΡΠ²Π»ΡΠ΅ΡΡΡ ΠΎΡΠ½ΠΎΠ²Π½ΡΠΌ ΡΠ°Π±ΠΎΡΠΈΠΌ ΠΌΠ΅Ρ Π°Π½ΠΈΠ·ΠΌΠΎΠΌ ΠΏΡΠ΅ΡΡΠ°. ΠΡ Π΅Π΅ ΡΠΎΡΠΌΡ Π·Π°Π²ΠΈΡΠΈΡ, ΠΊΠ°ΠΊΠΎΠΉ ΠΈΠΌΠ΅Π½Π½ΠΎ Π²ΠΈΠ΄ ΠΈΠ·Π΄Π΅Π»ΠΈΠΉ ΠΏΠΎΠ»ΡΡΠΈΡΡΡ. ΠΡΠΈ Π²ΡΠ±ΠΎΡΠ΅ ΠΌΠ°ΡΡΠΈΡΡ ΡΠ»Π΅Π΄ΡΠ΅Ρ ΠΎΡΠ΄Π°Π²Π°ΡΡ ΠΏΡΠ΅Π΄ΠΏΠΎΡΡΠ΅Π½ΠΈΠ΅ ΡΠΎΠΉ, ΠΊΠΎΡΠΎΡΠ°Ρ ΠΈΠ·Π³ΠΎΡΠΎΠ²Π»Π΅Π½Π° ΠΈΠ· ΠΏΡΠΎΡΠ½ΠΎΠ³ΠΎ ΠΌΠ΅ΡΠ°Π»Π»Π°, ΠΎΠ±Π»Π°Π΄Π°ΡΡΠ΅Π³ΠΎ Π°Π½ΡΠΈΠΊΠΎΡΡΠΎΠ·ΠΈΠΉΠ½ΠΎΠΉ ΡΠΏΠΎΡΠΎΠ±Π½ΠΎΡΡΡΡ. ΠΡΡΡΠ΅ Π²ΡΠ΅Π³ΠΎ, ΡΡΠΎΠ±Ρ ΡΠ°ΠΊΠΎΠ΅ ΠΎΠ±ΠΎΡΡΠ΄ΠΎΠ²Π°Π½ΠΈΠ΅ Π΄Π»Ρ ΠΏΡΠΎΠΈΠ·Π²ΠΎΠ΄ΡΡΠ²Π° ΠΌΠ°ΠΊΠ°ΡΠΎΠ½Π½ΡΡ ΠΈΠ·Π΄Π΅Π»ΠΈΠΉ, ΠΊΠ°ΠΊ ΠΌΠ°ΡΡΠΈΡΠ°, Π±ΡΠ»ΠΎ ΠΈΠ·Π³ΠΎΡΠΎΠ²Π»Π΅Π½ΠΎ ΠΈΠ· Π»Π°ΡΡΠ½ΠΈ, Π±ΡΠΎΠ½Π·Ρ ΠΈΠ»ΠΈ Π½Π΅ΡΠΆΠ°Π²Π΅ΡΡΠ΅ΠΉ ΡΡΠ°Π»ΠΈ.
ΠΠ±ΠΎΡΡΠ΄ΠΎΠ²Π°Π½ΠΈΠ΅ Π΄Π»Ρ ΠΎΡ Π»Π°ΠΆΠ΄Π΅Π½ΠΈΡ ΠΏΡΠΎΠ΄ΡΠΊΡΠΈΠΈ
ΠΠ΅ΡΠ΅Π΄ ΡΠΏΠ°ΠΊΠΎΠ²ΠΊΠΎΠΉ Π³ΠΎΡΠΎΠ²ΠΎΠΉ ΠΏΡΠΎΠ΄ΡΠΊΡΠΈΠΈ Π΅Π΅ Π½Π΅ΠΎΠ±Ρ ΠΎΠ΄ΠΈΠΌΠΎ ΠΎΡ Π»Π°Π΄ΠΈΡΡ. ΠΡΠΈ Π²ΡΠ±ΠΎΡΠ΅ ΡΡΠ°Π±ΠΈΠ»ΠΈΠ·Π°ΡΠΎΡΠΎΠ²-ΠΎΡ Π»Π°Π΄ΠΈΡΠ΅Π»Π΅ΠΉ ΡΡΠΎΠΈΡ ΠΎΡΠΈΠ΅Π½ΡΠΈΡΠΎΠ²Π°ΡΡΡΡ Π½Π° ΡΡΡΠ°Π½Ρ-ΠΈΠ·Π³ΠΎΡΠΎΠ²ΠΈΡΠ΅Π»Ρ, ΡΠ΅Π½Ρ, ΡΡΠ΅ΠΏΠ΅Π½Ρ ΡΠ½Π΅ΡΠ³ΠΎΠΏΠΎΡΡΠ΅Π±Π»Π΅Π½ΠΈΡ, Π° ΡΠ°ΠΊΠΆΠ΅ ΡΡΠΎΠΈΠΌΠΎΡΡΡ ΠΌΠΎΠ½ΡΠ°ΠΆΠ° ΠΈ ΠΎΠ±ΡΠ»ΡΠΆΠΈΠ²Π°Π½ΠΈΡ. ΠΠΌΠΏΠΎΡΡΠ½ΠΎΠ΅ ΠΎΠ±ΠΎΡΡΠ΄ΠΎΠ²Π°Π½ΠΈΠ΅ Π±ΠΎΠ»Π΅Π΅ Π²ΡΠ½ΠΎΡΠ»ΠΈΠ²ΠΎΠ΅ ΠΈ ΠΊΠ°ΡΠ΅ΡΡΠ²Π΅Π½Π½ΠΎΠ΅, ΠΎΠ΄Π½Π°ΠΊΠΎ ΠΈ Π΅Π³ΠΎ ΡΡΠΎΠΈΠΌΠΎΡΡΡ Π½Π°ΠΌΠ½ΠΎΠ³ΠΎ Π²ΡΡΠ΅, ΡΠ΅ΠΌ ΠΎΡΠ΅ΡΠ΅ΡΡΠ²Π΅Π½Π½ΠΎΠ³ΠΎ ΠΈΠ»ΠΈ ΠΊΠΈΡΠ°ΠΉΡΠΊΠΎΠ³ΠΎ.
ΠΡ Π»Π°Π΄ΠΈΡΠ΅Π»ΡΠ½ΠΎΠ΅ ΠΎΠ±ΠΎΡΡΠ΄ΠΎΠ²Π°Π½ΠΈΠ΅ Π΄Π»Ρ ΠΏΡΠΎΠΈΠ·Π²ΠΎΠ΄ΡΡΠ²Π° ΠΌΠ°ΠΊΠ°ΡΠΎΠ½Π½ΡΡ ΠΈΠ·Π΄Π΅Π»ΠΈΠΉ — ΡΡΠΎ ΠΎΡΠ΅Π½Ρ Π²Π°ΠΆΠ½Π°Ρ ΡΠ°ΡΡΡ ΠΏΡΠΎΠΈΠ·Π²ΠΎΠ΄ΡΡΠ²Π΅Π½Π½ΠΎΠΉ Π»ΠΈΠ½ΠΈΠΈ, ΠΏΠΎΡΡΠΎΠΌΡ Π½Π΅ ΡΡΠΎΠΈΡ Π½Π° Π½Π΅ΠΌ ΡΠΊΠΎΠ½ΠΎΠΌΠΈΡΡ, ΠΎΡΠΎΠ±Π΅Π½Π½ΠΎ Π΅ΡΠ»ΠΈ Π²Ρ ΠΏΠ»Π°Π½ΠΈΡΡΠ΅ΡΠ΅ Π²ΡΠ΄Π°Π²Π°ΡΡ ΠΊΡΡΠΏΠ½ΡΠ΅ ΠΎΠ±ΡΠ΅ΠΌΡ ΠΏΡΠΎΠ΄ΡΠΊΡΠΈΠΈ.
Π‘ΡΡΠΊΠ° ΠΏΡΠΎΠ΄ΡΠΊΡΠΈΠΈ
Π‘ΡΡΠΊΠ° ΡΠ²Π»ΡΠ΅ΡΡΡ ΠΎΠ΄Π½ΠΈΠΌ ΠΈΠ· ΡΠ°ΠΌΡΡ Π²Π°ΠΆΠ½ΡΡ ΠΏΡΠΎΡΠ΅ΡΡΠΎΠ² ΠΏΡΠΈ ΠΈΠ·Π³ΠΎΡΠΎΠ²Π»Π΅Π½ΠΈΠΈ ΠΌΠ°ΠΊΠ°ΡΠΎΠ½Π½ΡΡ ΠΈΠ·Π΄Π΅Π»ΠΈΠΉ. ΠΠΌΠ΅Π½Π½ΠΎ Π² ΠΏΡΠΎΡΠ΅ΡΡΠ΅ ΡΡΡΠΊΠΈ ΡΠ΅ΡΡΠΎ ΡΠ΅ΡΡΠ΅Ρ Π²Π»Π°Π³Ρ ΠΈ ΡΡΠ°Π½ΠΎΠ²ΠΈΡΡΡ Ρ ΡΡΠΏΠΊΠΈΠΌ. Π ΡΠ΅Π·ΡΠ»ΡΡΠ°ΡΠ΅ ΡΡΠΎΠ³ΠΎ ΠΏΡΠΎΠ΄ΡΠΊΡ ΡΡΠ°Π½ΠΎΠ²ΠΈΡΡΡ ΡΠ²Π΅ΡΠ΄ΡΠΌ ΠΈ ΠΏΡΠΎΡΠ½ΡΠΌ, Π° ΡΠ°ΠΊΠΆΠ΅ ΡΠΌΠ΅Π½ΡΡΠ°Π΅ΡΡΡ Π² ΡΠ°Π·ΠΌΠ΅ΡΠ΅.
Π‘ΡΠ°Π½ΠΎΠΊ Π΄Π»Ρ ΠΏΡΠΎΠΈΠ·Π²ΠΎΠ΄ΡΡΠ²Π° ΠΌΠ°ΠΊΠ°ΡΠΎΠ½Π½ΡΡ ΠΈΠ·Π΄Π΅Π»ΠΈΠΉ, ΠΊΠΎΡΠΎΡΡΠΉ ΠΏΡΠΎΠΈΠ·Π²ΠΎΠ΄ΠΈΡ ΡΡΡΠΊΡ ΠΈΠ·Π΄Π΅Π»ΠΈΠΉ, ΡΠΎΠ·Π΄Π°Π΅Ρ Π²ΡΡΠΎΠΊΡΡ ΡΠ΅ΠΌΠΏΠ΅ΡΠ°ΡΡΡΡ, Π° ΡΠ°ΠΊΠΆΠ΅ ΡΠΎΠ·Π΄Π°Π΅Ρ Π³ΠΈΠ΄ΡΠΎΡΠ΅ΡΠΌΠΈΡΠ΅ΡΠΊΡΡ ΠΎΠ±ΡΠ°Π±ΠΎΡΠΊΡ. Π§ΡΠΎΠ±Ρ ΠΏΠΎΠ»ΡΡΠΈΡΡ ΠΊΠ°ΡΠ΅ΡΡΠ²Π΅Π½Π½ΡΡ ΠΏΡΠΎΠ΄ΡΠΊΡΠΈΡ, ΠΎΡΠ΅Π½Ρ Π²Π°ΠΆΠ½ΠΎ, ΡΡΠΎΠ±Ρ ΡΡΡΠΈΠ»ΠΊΠ° Π°Π²ΡΠΎΠΌΠ°ΡΠΈΡΠ΅ΡΠΊΠΈ ΠΏΠΎΠ΄Π΄Π΅ΡΠΆΠΈΠ²Π°Π»Π° Π·Π°Π΄Π°Π½Π½ΡΠ΅ ΠΏΠ°ΡΠ°ΠΌΠ΅ΡΡΡ. Π’ΠΎΠ»ΡΠΊΠΎ Π±Π»Π°Π³ΠΎΠ΄Π°ΡΡ ΠΎΠ±ΠΎΡΡΠ΄ΠΎΠ²Π°Π½ΠΈΡ Π²ΡΡΠΎΠΊΠΎΠ³ΠΎ ΠΊΠ°ΡΠ΅ΡΡΠ²Π° ΠΌΠΎΠΆΠ½ΠΎ ΠΏΠΎΠ»ΡΡΠΈΡΡ ΠΌΠ°ΠΊΠ°ΡΠΎΠ½Π½ΡΠ΅ ΠΈΠ·Π΄Π΅Π»ΠΈΡ, ΠΊΠΎΡΠΎΡΡΠ΅ Π±ΡΠ΄ΡΡ ΠΎΡΠ²Π΅ΡΠ°ΡΡ ΡΠΎΠ²ΡΠ΅ΠΌΠ΅Π½Π½ΡΠΌ ΡΡΠ°Π½Π΄Π°ΡΡΠ°ΠΌ. ΠΡΡΡΠ΅ Π²ΡΠ΅Π³ΠΎ ΠΏΠΎΠΊΡΠΏΠ°ΡΡ ΡΠΎ, ΠΊΠΎΡΠΎΡΠΎΠ΅ Π²ΡΠΏΠΎΠ»Π½Π΅Π½ΠΎ ΠΈΠ· Π½Π΅ΡΠΆΠ°Π²Π΅ΡΡΠ΅ΠΉ ΡΡΠ°Π»ΠΈ.
Π€Π°ΡΠΎΠ²ΠΎΡΠ½ΠΎΠ΅ ΠΎΠ±ΠΎΡΡΠ΄ΠΎΠ²Π°Π½ΠΈΠ΅ Π΄Π»Ρ ΠΏΡΠΎΠΈΠ·Π²ΠΎΠ΄ΡΡΠ²Π° ΠΌΠ°ΠΊΠ°ΡΠΎΠ½Π½ΡΡ ΠΈΠ·Π΄Π΅Π»ΠΈΠΉ
ΠΠ΅ΠΌΠ°Π»ΠΎΠ²Π°ΠΆΠ½ΠΎΠΉ ΡΠΎΡΡΠ°Π²Π»ΡΡΡΠ΅ΠΉ ΠΏΡΠΎΡΠ΅ΡΡΠ° ΡΠ²Π»ΡΠ΅ΡΡΡ ΡΠ°ΡΠΎΠ²ΠΎΡΠ½ΠΎΠ΅ ΠΎΠ±ΠΎΡΡΠ΄ΠΎΠ²Π°Π½ΠΈΠ΅. ΠΠ°ΠΊΠ°ΡΠΎΠ½Π½ΡΠ΅ ΠΈΠ·Π΄Π΅Π»ΠΈΡ ΠΏΠΎΡΠ»Π΅ Π²ΡΡΡΡΠΈΠ²Π°Π½ΠΈΡ ΠΏΠΎΡΡΡΠΏΠ°ΡΡ Π² ΡΠ°ΡΠΎΠ²ΠΎΡΠ½ΠΎ-ΡΠΏΠ°ΠΊΠΎΠ²ΠΎΡΠ½ΡΠ΅ ΡΡΠ°Π½ΠΊΠΈ, Π² ΠΊΠΎΡΠΎΡΡΡ ΠΎΠ½ΠΈ Π΄ΠΎΠ·ΠΈΡΡΡΡΡΡ ΠΈ ΡΠΏΠ°ΠΊΠΎΠ²ΡΠ²Π°ΡΡΡΡ Π² ΠΊΠΎΡΠΎΠ±ΠΊΠΈ ΠΈΠ»ΠΈ ΡΠΏΠ΅ΡΠΈΠ°Π»ΡΠ½ΡΠ΅ ΠΏΠ°ΠΊΠ΅ΡΡ.
Π‘Π°ΠΌΡΠΌ ΡΠ΄ΠΎΠ±Π½ΡΠΌ ΡΡΠΈΡΠ°Π΅ΡΡΡ ΠΎΠ±ΠΎΡΡΠ΄ΠΎΠ²Π°Π½ΠΈΠ΅, ΠΊΠΎΡΠΎΡΠΎΠ΅ ΠΈΠΌΠ΅Π΅Ρ ΡΠ»Π΅ΠΊΡΡΠΎΠ½Π½ΡΠΉ Π±Π»ΠΎΠΊ ΡΠΏΡΠ°Π²Π»Π΅Π½ΠΈΡ ΠΈ Π°Π²ΡΠΎΠΌΠ°ΡΠΈΡΠ΅ΡΠΊΠΈ ΠΏΡΠΎΠΈΠ·Π²ΠΎΠ΄ΠΈΡ ΠΌΠ°ΡΠΊΠΈΡΠΎΠ²ΠΊΡ ΡΠΏΠ°ΠΊΠΎΠ²Π°Π½Π½ΠΎΠ³ΠΎ ΠΏΡΠΎΠ΄ΡΠΊΡΠ°. Π ΡΠΎΠΌΡ ΠΆΠ΅ ΡΠ»Π΅Π΄ΡΠ΅Ρ ΠΎΡΠ΄Π°Π²Π°ΡΡ ΠΏΡΠ΅Π΄ΠΏΠΎΡΡΠ΅Π½ΠΈΠ΅ ΠΌΠΎΠ΄Π΅Π»ΡΠΌ, ΠΊΠΎΡΠΎΡΡΠ΅ ΠΈΠΌΠ΅ΡΡ ΠΏΡΠΎΡΡΡΡ ΠΈ Π½Π°Π΄Π΅ΠΆΠ½ΡΡ ΠΊΠΎΠ½ΡΡΡΡΠΊΡΠΈΡ. ΠΠΎΡΠ½ΠΎΡΡΡ ΠΎΠ±ΠΎΡΡΠ΄ΠΎΠ²Π°Π½ΠΈΡ Π½Π΅ΠΎΠ±Ρ ΠΎΠ΄ΠΈΠΌΠΎ Π²ΡΠ±ΠΈΡΠ°ΡΡ Π² Π·Π°Π²ΠΈΡΠΈΠΌΠΎΡΡΠΈ ΠΎΡ ΠΏΠ»Π°Π½ΠΈΡΡΠ΅ΠΌΡΡ ΠΎΠ±ΡΠ΅ΠΌΠΎΠ² ΠΏΡΠΎΠΈΠ·Π²ΠΎΠ΄ΡΡΠ²Π°. ΠΠ°ΠΈΠ»ΡΡΡΠΈΠΌ ΡΡΠΈΡΠ°Π΅ΡΡΡ ΠΈΡΠ°Π»ΡΡΠ½ΡΠΊΠΎΠ΅, ΠΎΠ΄Π½Π°ΠΊΠΎ ΠΈ ΠΎΡΠ΅ΡΠ΅ΡΡΠ²Π΅Π½Π½ΡΠ΅ ΠΌΠΎΠ΄Π΅Π»ΠΈ ΠΌΠΎΠ³ΡΡ ΡΡΠ°ΡΡ Ρ ΠΎΡΠΎΡΠ΅ΠΉ Π½Π΅Π΄ΠΎΡΠΎΠ³ΠΎΠΉ Π°Π»ΡΡΠ΅ΡΠ½Π°ΡΠΈΠ²ΠΎΠΉ.
ΠΠ²ΡΠΎΠΌΠ°ΡΠΈΡΠ΅ΡΠΊΠΎΠ΅ ΡΠΏΡΠ°Π²Π»Π΅Π½ΠΈΠ΅ Π»ΠΈΠ½ΠΈΠ΅ΠΉ
ΠΡΠ»ΠΈ Π²Ρ ΠΏΠ»Π°Π½ΠΈΡΡΠ΅ΡΠ΅ ΠΏΡΠΎΠΈΠ·Π²ΠΎΠ΄ΠΈΡΡ Π±ΠΎΠ»ΡΡΠΈΠ΅ ΠΎΠ±ΡΠ΅ΠΌΡ ΠΏΡΠΎΠ΄ΡΠΊΡΠΈΠΈ, Π»ΡΡΡΠ΅ Π²ΡΠ΅Π³ΠΎ, ΡΡΠΎΠ±Ρ ΠΏΡΠΎΡΠ΅ΡΡΡ Π±ΡΠ»ΠΈ Π°Π²ΡΠΎΠΌΠ°ΡΠΈΠ·ΠΈΡΠΎΠ²Π°Π½Ρ. Π’Π°ΠΊΠΈΠΌ ΠΎΠ±ΡΠ°Π·ΠΎΠΌ, Π²ΡΠ΅ΠΉ Π»ΠΈΠ½ΠΈΠ΅ΠΉ ΠΏΡΠΎΠΈΠ·Π²ΠΎΠ΄ΡΡΠ²Π° ΡΠΌΠΎΠΆΠ΅Ρ ΡΠΏΡΠ°Π²Π»ΡΡΡ ΡΠΎΠ»ΡΠΊΠΎ ΠΎΠ΄ΠΈΠ½ ΡΠ΅Π»ΠΎΠ²Π΅ΠΊ. Π‘ΠΈΡΡΠ΅ΠΌΠ° ΠΏΠΎΠ΄Π΄Π΅ΡΠΆΠΈΠ²Π°Π΅Ρ Π½Π΅ΠΎΠ±Ρ
ΠΎΠ΄ΠΈΠΌΡΠ΅ ΠΏΠ°ΡΠ°ΠΌΠ΅ΡΡΡ, ΡΠ°ΠΊΠΈΠ΅ ΠΊΠ°ΠΊ ΡΠ΅ΠΌΠΏΠ΅ΡΠ°ΡΡΡΠ° ΠΈ Π²Π»Π°ΠΆΠ½ΠΎΡΡΡ. Π ΡΠ»ΡΡΠ°Π΅ Π²ΠΎΠ·Π½ΠΈΠΊΠ½ΠΎΠ²Π΅Π½ΠΈΡ Π½Π΅ΠΏΠΎΠ»Π°Π΄ΠΎΠΊ ΡΠΈΡΡΠ΅ΠΌΠ° Π°Π²ΡΠΎΠΌΠ°ΡΠΈΡΠ΅ΡΠΊΠΈ ΠΎΡΠΊΠ»ΡΡΠ°Π΅ΡΡΡ. Π’Π°ΠΊΠΎΠ΅ ΠΎΠ±ΠΎΡΡΠ΄ΠΎΠ²Π°Π½ΠΈΠ΅ Π΄ΠΎΡΡΠ°ΡΠΎΡΠ½ΠΎ Π΄ΠΎΡΠΎΠ³ΠΎΠ΅, ΠΎΠ΄Π½Π°ΠΊΠΎ ΠΎΠ½ΠΎ Π·Π½Π°ΡΠΈΡΠ΅Π»ΡΠ½ΠΎ ΡΠΏΡΠΎΡΠ°Π΅Ρ ΠΏΡΠΎΡΠ΅ΡΡ ΠΏΡΠΎΠΈΠ·Π²ΠΎΠ΄ΡΡΠ²Π° ΠΈ ΡΠ½ΠΈΠΆΠ°Π΅Ρ Π΄ΠΎ ΠΌΠΈΠ½ΠΈΠΌΡΠΌΠ° Π½Π΅ΠΎΠ±Ρ
ΠΎΠ΄ΠΈΠΌΡΠ΅ ΡΠ°Π±ΠΎΡΠΈΠ΅ ΡΠ΅ΡΡΡΡΡ.
businessman.ru
Π Π΅ΠΆΠΈΠΌΡ Π·Π°ΠΌΠ΅ΡΠ° ΠΌΠ°ΠΊΠ°ΡΠΎΠ½Π½ΠΎΠ³ΠΎ ΡΠ΅ΡΡΠ° — ΠΠΎΠΈ ΡΡΠ°ΡΡΠΈ — ΠΠ°ΡΠ°Π»ΠΎΠ³ ΡΡΠ°ΡΠ΅ΠΉ
ΠΡΡΠΎΠΊΠΎΡΠ΅ΠΌΠΏΠ΅ΡΠ°ΡΡΡΠ½ΡΠΉ ΡΠ΅ΠΆΠΈΠΌ Π·Π°ΠΌΠ΅ΡΠ°.
Π’Π΅Ρ Π½ΠΎΠ»ΠΎΠ³ΠΈΡ ΠΏΡΠΈΠ³ΠΎΡΠΎΠ²Π»Π΅Π½ΠΈΡ ΡΠ΅ΡΡΠ°.
Β Π ΠΌΠ°ΠΊΠ°ΡΠΎΠ½Π½ΠΎΠΌ ΠΏΡΠΎΠΈΠ·Π²ΠΎΠ΄ΡΡΠ²Π΅ Π² Π·Π°Π²ΠΈΡΠΈΠΌΠΎΡΡΠΈ ΠΎΡ ΡΡΠ΄Π° ΡΠ°ΠΊΡΠΎΡΠΎΠ² ΠΈΡΠΏΠΎΠ»ΡΠ·ΡΡΡ Π½Π΅ΡΠΊΠΎΠ»ΡΠΊΠΎ ΡΠΈΠΏΠΎΠ² Π·Π°ΠΌΠ΅ΡΠ° ΡΠ΅ΡΡΠ°.
Π Π·Π°Π²ΠΈΡΠΈΠΌΠΎΡΡΠΈ ΠΎΡ Π²Π»Π°ΠΆΠ½ΠΎΡΡΠΈ Π·Π°ΠΌΠ΅ΡΠΈΠ²Π°Π΅ΠΌΠΎΠ³ΠΎ ΡΠ΅ΡΡΠ° ΡΠ°Π·Π»ΠΈΡΠ°ΡΡ ΡΡΠΈ ΡΠΈΠΏΠ° Π·Π°ΠΌΠ΅ΡΠ°:
—Β Β Β Β Β Β ΡΠ²Π΅ΡΠ΄ΡΠΉ β ΠΏΡΠΈ Π²Π»Π°ΠΆΠ½ΠΎΡΡΠΈ ΡΠ΅ΡΡΠ° ΠΎΡ 28 Π΄ΠΎ 29 %;
—Β Β Β Β Β Β ΡΡΠ΅Π΄Π½ΠΈΠΉ β ΠΏΡΠΈ Π²Π»Π°ΠΆΠ½ΠΎΡΡΠΈ ΡΠ΅ΡΡΠ° ΠΎΡ 29,1 Π΄ΠΎ 31 %;
—Β Β Β Β Β Β ΠΌΡΠ³ΠΊΠΈΠΉ β ΠΏΡΠΈ Π²Π»Π°ΠΆΠ½ΠΎΡΡΠΈ ΡΠ΅ΡΡΠ° ΠΎΡ 31,1 Π΄ΠΎ 32,5 %.
Π’ΠΈΠΏ Π·Π°ΠΌΠ΅ΡΠ° ΠΏΠΎ Π²Π»Π°ΠΆΠ½ΠΎΡΡΠΈ Π·Π°Π²ΠΈΡΠΈΡ ΠΎΡ ΡΠΎΡΡΠ° ΠΌΡΠΊΠΈ, ΠΊΠΎΠ»ΠΈΡΠ΅ΡΡΠ²Π° ΠΈ ΠΊΠ°ΡΠ΅ΡΡΠ²Π° ΠΊΠ»Π΅ΠΉΠΊΠΎΠ²ΠΈΠ½Ρ, ΠΊΡΡΠΏΠ½ΠΎΡΡ ΠΏΠΎΠΌΠΎΠ»Π°, Π²ΠΈΠ΄Π° ΡΡΡΠΈΠ»ΡΠ½ΠΎΠΉ ΠΏΠΎΠ²Π΅ΡΡ Π½ΠΎΡΡΠΈ, ΠΌΠ°ΡΠ΅ΡΠΈΠ°Π»Π° ΠΌΠ°ΡΡΠΈΡΡ, ΡΠΎΡΠΌΡ ΠΈΠ·Π΄Π΅Π»ΠΈΠΉ.
ΠΡΠΈ ΠΈΡΠΏΠΎΠ»ΡΠ·ΠΎΠ²Π°Π½ΠΈΠΈ ΠΌΡΠΊΠΈ Ρ Π½ΠΈΠ·ΠΊΠΈΠΌ ΡΠΎΠ΄Π΅ΡΠΆΠ°Π½ΠΈΠ΅ΠΌ ΠΊΠ»Π΅ΠΉΠΊΠΎΠ²ΠΈΠ½Ρ ΠΆΠ΅Π»Π°ΡΠ΅Π»ΡΠ½ΠΎ ΠΏΡΠΈΠΌΠ΅Π½ΡΡΡ ΠΌΡΠ³ΠΊΠΈΠΉ Π·Π°ΠΌΠ΅Ρ, Π° Π΅ΡΠ»ΠΈ ΠΊΠ»Π΅ΠΉΠΊΠΎΠ²ΠΈΠ½Π° ΠΌΡΠΊΠΈ Π»ΠΈΠΏΠΊΠ°Ρ, ΡΡΠ½ΡΡΠ°ΡΡΡ β ΡΠ²Π΅ΡΠ΄ΡΠΉ.
ΠΡΠΈ ΠΈΠ·Π³ΠΎΡΠΎΠ²Π»Π΅Π½ΠΈΠΈ ΠΊΠΎΡΠΎΡΠΊΠΈΡ ΠΈΠ·Π΄Π΅Π»ΠΈΠΉ ΠΈ ΠΌΠ°ΠΊΠ°ΡΠΎΠ½ Ρ ΠΊΠ°ΡΡΠ΅ΡΠ½ΠΎΠΉ ΡΡΡΠΊΠΎΠΉ Π΄Π»Ρ ΠΏΡΠ΅Π΄ΠΎΡΠ²ΡΠ°ΡΠ΅Π½ΠΈΡ ΡΠ»ΠΈΠΏΠ°Π½ΠΈΡ ΠΈΠ·Π΄Π΅Π»ΠΈΠΉ ΠΌΠ΅ΠΆΠ΄Ρ ΡΠΎΠ±ΠΎΠΉ Π²ΠΎ Π²ΡΠ΅ΠΌΡ ΡΡΡΠΊΠΈ Π»ΡΡΡΠ΅ ΠΏΡΠΈΠΌΠ΅Π½ΡΡΡ ΡΠ²Π΅ΡΠ΄ΡΠΉ ΠΈΠ»ΠΈ ΡΡΠ΅Π΄Π½ΠΈΠΉ Π·Π°ΠΌΠ΅Ρ.
ΠΡΠΈ ΠΏΡΠΎΠΈΠ·Π²ΠΎΠ΄ΡΡΠ²Π΅ Π΄Π»ΠΈΠ½Π½ΡΡ ΠΈΠ·Π΄Π΅Π»ΠΈΠΉ Ρ ΠΏΠΎΠ΄Π²Π΅ΡΠ½ΠΎΠΉ ΡΡΡΠΊΠΎΠΉ (Π½Π° Π±Π°ΡΡΡΠ½Π°Ρ ) Π΄Π»Ρ ΠΏΡΠΈΠ΄Π°Π½ΠΈΡ ΠΈΠ·Π΄Π΅Π»ΠΈΡΠΌ Π±ΠΎΠ»ΡΡΠ΅ΠΉ ΠΏΠ»Π°ΡΡΠΈΡΠ½ΠΎΡΡΠΈ, ΠΈΡΠΊΠ»ΡΡΠ°ΡΡΠ΅ΠΉ ΡΠ°ΡΡΡΠ΅ΡΠΊΠΈΠ²Π°Π½ΠΈΠ΅ ΡΡΡΡΡ ΠΈΠ·Π΄Π΅Π»ΠΈΠΉ Π² ΠΌΠ΅ΡΡΠ°Ρ ΠΏΠ΅ΡΠ΅Π³ΠΈΠ±Π° Π½Π° Π±Π°ΡΡΡΠ½Π°Ρ , ΠΏΡΠΈΠΌΠ΅Π½ΡΡΡ ΡΡΠ΅Π΄Π½ΠΈΠΉ ΠΈΠ»ΠΈ ΠΌΡΠ³ΠΊΠΈΠΉ Π·Π°ΠΌΠ΅Ρ. ΠΡΠΈ ΠΈΡΠΏΠΎΠ»ΡΠ·ΠΎΠ²Π°Π½ΠΈΠΈ ΠΏΠΎΠ»ΡΠΊΡΡΠΏΠΊΠΈ ΠΈΠ»ΠΈ Ρ Π»Π΅Π±ΠΎΠΏΠ΅ΠΊΠ°ΡΠ½ΠΎΠΉ ΠΌΡΠΊΠΈ Π²Π»Π°ΠΆΠ½ΠΎΡΡΡ ΡΠ΅ΡΡΠ° Π΄ΠΎΠ»ΠΆΠ½Π° Π±ΡΡΡ Π½Π° 1-1,5 % Π²ΡΡΠ΅, ΡΠ΅ΠΌ ΠΏΡΠΈ ΠΈΡΠΏΠΎΠ»ΡΠ·ΠΎΠ²Π°Π½ΠΈΠΈ ΠΊΡΡΠΏΠΊΠΈ.
ΠΡΠΈ ΠΈΡΠΏΠΎΠ»ΡΠ·ΠΎΠ²Π°Π½ΠΈΠΈ ΠΌΠ°ΡΡΠΈΡ Ρ ΡΠ΅ΡΠ»ΠΎΠ½ΠΎΠ²ΡΠΌΠΈ Π²ΡΡΠ°Π²ΠΊΠ°ΠΌΠΈ Π²Π»Π°ΠΆΠ½ΠΎΡΡΡ ΡΠ΅ΡΡΠ° ΡΠ½ΠΈΠΆΠ°ΡΡ Π½Π° 1-1,5 %.
ΠΡΠ³ΠΊΠΈΠΉ Π·Π°ΠΌΠ΅Ρ ΠΏΡΠΈΠΌΠ΅Π½ΡΡΡ Π΄Π»Ρ Π³ΠΈΠ±ΠΊΠΈΡ ΠΈΠ·Π΄Π΅Π»ΠΈΠΉ Ρ ΡΠΈΠ³ΡΡΠ½ΠΎΠΉ ΡΠΊΠ»Π°Π΄ΠΊΠΎΠΉ (Π² ΠΌΠΎΡΠΎΠΊ, Π±Π°Π½ΡΠΈΠΊ, Π³Π½Π΅Π·Π΄ΠΎ), Π° ΡΠ²Π΅ΡΠ΄ΡΠΉ β Π΄Π»Ρ ΡΡΠ°ΠΌΠΏΠΎΠ²Π°Π½Π½ΡΡ ΠΈΠ·Π΄Π΅Π»ΠΈΠΉ ΡΠ»ΠΎΠΆΠ½ΠΎΠΉ ΡΠΎΡΠΌΡ.
Π Π·Π°Π²ΠΈΡΠΈΠΌΠΎΡΡΠΈ ΠΎΡ ΡΠ΅ΠΌΠΏΠ΅ΡΠ°ΡΡΡΡ Π²ΠΎΠ΄Ρ, Π΄ΠΎΠ±Π°Π²Π»ΡΠ΅ΠΌΠΎΠΉ ΠΏΡΠΈ Π·Π°ΠΌΠ΅ΡΠ΅ ΠΌΠ°ΠΊΠ°ΡΠΎΠ½Π½ΠΎΠ³ΠΎ ΡΠ΅ΡΡΠ°, ΡΠ°Π·Π»ΠΈΡΠ°ΡΡ ΡΠ°ΠΊΠΆΠ΅ ΡΡΠΈ ΡΠΈΠΏΠ° Π·Π°ΠΌΠ΅ΡΠ°:
—Β Β Β Β Β Β Π³ΠΎΡΡΡΠΈΠΉ β ΠΏΡΠΈ ΡΠ΅ΠΌΠΏΠ΅ΡΠ°ΡΡΡΠ΅ Π²ΠΎΠ΄Ρ 75-85Β°Π‘;
—Β Β Β Β Β Β ΡΠ΅ΠΏΠ»ΡΠΉ β ΠΏΡΠΈ ΡΠ΅ΠΌΠΏΠ΅ΡΠ°ΡΡΡΠ΅ Π²ΠΎΠ΄Ρ 55-65 Β°Π‘;
—Β Β Β Β Β Β Ρ ΠΎΠ»ΠΎΠ΄Π½ΡΠΉ β ΠΏΡΠΈ ΡΠ΅ΠΌΠΏΠ΅ΡΠ°ΡΡΡΠ΅ Π²ΠΎΠ΄Ρ Π½Π΅ Π½ΠΈΠΆΠ΅ 30 Β°Π‘.
Π’ΠΈΠΏ Π·Π°ΠΌΠ΅ΡΠ° ΠΏΠΎ ΡΠ΅ΠΌΠΏΠ΅ΡΠ°ΡΡΡΠ΅ Π²ΡΠ±ΠΈΡΠ°ΡΡ Π² Π·Π°Π²ΠΈΡΠΈΠΌΠΎΡΡΠΈ ΠΎΡ ΠΊΠ°ΡΠ΅ΡΡΠ²Π° ΠΌΡΠΊΠΈ ΠΈ ΡΠΎΡΠΌΡ ΠΈΠ·Π΄Π΅Π»ΠΈΠΉ. Π’Π΅ΠΏΠ»ΡΠΉ ΡΠΈΠΏ Π·Π°ΠΌΠ΅ΡΠ° Π½Π°ΠΈΠ±ΠΎΠ»Π΅Π΅ ΡΠ°ΡΠΏΡΠΎΡΡΡΠ°Π½Π΅Π½ Π² ΠΌΠ°ΠΊΠ°ΡΠΎΠ½Π½ΠΎΠΌ ΠΏΡΠΎΠΈΠ·Π²ΠΎΠ΄ΡΡΠ²Π΅, Π΅Π³ΠΎ ΠΏΡΠΈΠΌΠ΅Π½ΡΡΡ Π΄Π»Ρ ΠΌΡΠΊΠΈ Π½ΠΎΡΠΌΠ°Π»ΡΠ½ΠΎΠ³ΠΎ ΠΊΠ°ΡΠ΅ΡΡΠ²Π° Ρ ΡΠΎΠ΄Π΅ΡΠΆΠ°Π½ΠΈΠ΅ΠΌ ΠΊΠ»Π΅ΠΉΠΊΠΎΠ²ΠΈΠ½Ρ Π½Π΅ ΠΌΠ΅Π½Π΅Π΅ 28 %. ΠΠ° ΡΠ΅ΠΏΠ»ΠΎΠΉ Π²ΠΎΠ΄Π΅ ΠΏΡΠΎΡΠ΅ΡΡ Π·Π°ΠΌΠ΅ΡΠ° ΠΏΡΠΎΠΈΡΡ ΠΎΠ΄ΠΈΡ Π±ΡΡΡΡΠ΅Π΅, ΡΠ΅ΠΌ Π½Π° Ρ ΠΎΠ»ΠΎΠ΄Π½ΠΎΠΉ. ΠΡΠ»ΠΈ Π² ΠΏΡΠΎΠΈΠ·Π²ΠΎΠ΄ΡΡΠ²Π΅ ΠΏΠ΅ΡΠ΅ΡΠ°Π±Π°ΡΡΠ²Π°Π΅ΡΡΡ ΠΌΡΠΊΠ° Ρ ΠΏΠΎΠ½ΠΈΠΆΠ΅Π½Π½ΡΠΌ ΡΠΎΠ΄Π΅ΡΠΆΠ°Π½ΠΈΠ΅ΠΌ ΠΊΠ»Π΅ΠΉΠΊΠΎΠ²ΠΈΠ½Ρ, ΡΠΎ ΡΠ΅ΠΊΠΎΠΌΠ΅Π½Π΄ΡΠ΅ΡΡΡ ΠΈΡΠΏΠΎΠ»ΡΠ·ΠΎΠ²Π°ΡΡ Π²ΠΎΠ΄Ρ ΡΠ΅ΠΌΠΏΠ΅ΡΠ°ΡΡΡΠΎΠΉ 30-45 Β°Π‘.
Π₯ΠΎΠ»ΠΎΠ΄Π½ΡΠΉ Π·Π°ΠΌΠ΅Ρ ΠΏΡΠΈΠΌΠ΅Π½ΡΡΡ ΠΏΡΠΈ Π½ΠΈΠ·ΠΊΠΎΠΌ ΡΠΎΠ΄Π΅ΡΠΆΠ°Π½ΠΈΠΈ ΡΠ»Π°Π±ΠΎΠΉ ΠΊΠ»Π΅ΠΉΠΊΠΎΠ²ΠΈΠ½Ρ, ΠΏΡΠΈ Π½Π°Π»ΠΈΡΠΈΠΈ ΡΠ΅ΠΏΠ»ΠΎΠΉ ΠΌΡΠΊΠΈ (Π² Π»Π΅ΡΠ½Π΅Π΅ Π²ΡΠ΅ΠΌΡ) ΠΈΠ»ΠΈ ΠΏΡΠΈ ΡΠΎΡΠΌΠΎΠ²Π°Π½ΠΈΠΈ ΠΈΠ·Π΄Π΅Π»ΠΈΠΉ ΡΠ»ΠΎΠΆΠ½ΠΎΠΉ ΡΠΎΡΠΌΡ Π΄Π»Ρ ΠΏΠΎΠ»ΡΡΠ΅Π½ΠΈΡ ΠΎΡΠ΅Π½Ρ Π²ΡΠ·ΠΊΠΎΠ³ΠΎ ΠΈ ΡΠΏΡΡΠ³ΠΎΠ³ΠΎ ΡΠ΅ΡΡΠ°.
ΠΠΎΡΡΡΠΈΠΉ Π·Π°ΠΌΠ΅Ρ ΠΏΡΠΈΠΌΠ΅Π½ΡΡΡ Π΄Π»Ρ ΠΌΡΠΊΠΈ ΠΈΠ· ΡΠ²Π΅ΡΠ΄ΡΡ ΠΏΡΠ΅Π½ΠΈΡ Ρ ΡΠΎΠ΄Π΅ΡΠΆΠ°Π½ΠΈΠ΅ΠΌ ΠΊΠ»Π΅ΠΉΠΊΠΎΠ²ΠΈΠ½Ρ Π±ΠΎΠ»Π΅Π΅ 38 % ΠΈ ΡΡΠ΅Π·ΠΌΠ΅ΡΠ½ΠΎ ΡΠΏΡΡΠ³ΠΎΠΉ ΠΏΠΎ ΠΊΠ°ΡΠ΅ΡΡΠ²Ρ.
ΠΠ°Π³ΡΠ΅Π² ΠΌΠ°ΠΊΠ°ΡΠΎΠ½Π½ΠΎΠ³ΠΎ ΡΠ΅ΡΡΠ° ΠΏΡΠΈ Π·Π°ΠΌΠ΅ΡΠ΅ Π΄ΠΎ ΡΠ΅ΠΌΠΏΠ΅ΡΠ°ΡΡΡ 60… 65Β°Π‘ (Π²ΡΡΠΎΠΊΠΎΡΠ΅ΠΌΠΏΠ΅ΡΠ°ΡΡΡΠ½ΡΠΉ ΡΠ΅ΠΆΠΈΠΌ Π·Π°ΠΌΠ΅ΡΠ°), Π½Π΅ ΠΏΡΠΈΠ²ΠΎΠ΄Ρ ΠΊ Π±ΠΎΠ»Π΅Π΅ Π³Π»ΡΠ±ΠΎΠΊΠΎΠΌΡ ΠΈΠ·ΠΌΠ΅Π½Π΅Π½ΠΈΠΈ ΡΠ²ΠΎΠΉΡΡΠ² Π±Π΅Π»ΠΊΠ° ΠΈ ΠΊΡΠ°Ρ ΠΌΠ°Π»Π° Π² ΠΏΡΠΎΡΠ΅ΡΡΠ΅ ΠΏΡΠ΅ΡΡΠΎΠ²Π°Π½ΠΈΡ ΡΠ΅ΡΡΠ° Π½Π° ΡΠ½Π΅ΠΊΠΎΠ²ΠΎΠΌ ΠΏΡΠ΅ΡΡΠ΅, ΡΠ΅ΠΌ ΠΏΡΠΈ ΡΡΠ°Π΄ΠΈΡΠΈΠΎΠ½Π½ΡΡ ΡΠ΅ΠΆΠΈΠΌΠ°Ρ Π·Π°ΠΌΠ΅ΡΠ°, ΠΏΠΎΠ²ΡΡΠ°Π΅Ρ ΠΏΠ»Π°ΡΡΠΈΡΠ½ΠΎΡΡΡ ΡΠΊΡΡΡΡΠ΄ΠΈΡΡΠ΅ΠΌΠΎΠ³ΠΎ ΡΠ΅ΡΡΠ°. ΠΡΠ»Π΅Π΄ΡΡΠ²ΠΈΠ΅ ΡΡΠΎΠ³ΠΎ, Π²ΡΡΠΎΠΊΠΎΡΠ΅ΠΌΠΏΠ΅ΡΠ°ΡΡΡΠ½ΡΠΉ ΡΠ΅ΠΆΠΈΠΌ Π·Π°ΠΌΠ΅ΡΠ° Π½Π°ΡΡΠ΄Ρ Ρ ΡΠΎΡ ΡΠ°Π½Π΅Π½ΠΈΠ΅ΠΌ Π½ΠΎΡΠΌΠ°Π»ΡΠ½ΠΎΠ³ΠΎ ΠΊΠ°ΡΠ΅ΡΡΠ²Π° ΠΌΠ°ΠΊΠ°ΡΠΎΠ½Π½ΡΡ ΠΈΠ·Π΄Π΅Π»ΠΈΠΉ ΡΠ²Π΅Π»ΠΈΡΠΈΠ²Π°Π΅Ρ ΠΏΡΠΎΠΈΠ·Π²ΠΎΠ΄ΠΈΡΠ΅Π»ΡΠ½ΠΎΡΡΡ ΠΏΡΠ΅ΡΡΠ° Π² ΡΡΠ΅Π΄Π½Π΅ΠΌ Π½Π° 15%, ΡΠΌΠ΅Π½ΡΡΠ°Π΅Ρ ΡΠ°ΡΡ ΠΎΠ΄ ΡΠ½Π΅ΡΠ³ΠΈΠΈ Π½Π° ΠΏΡΠ΅ΡΡΠΎΠ²Π°Π½ΠΈΠ΅ Π½Π΅ ΠΌΠ΅Π½Π΅Π΅, ΡΠ΅ΠΌ Π½Π° 10%, ΠΏΡΠ΅Π΄ΠΎΡΠ²ΡΠ°ΡΠ°Π΅Ρ Π²ΡΠΏΡΠ΅ΡΡΠΎΠ²ΡΠ²Π°Π½ΠΈΠ΅ Π±Π΅Π»Π΅ΡΡΡ ΠΈΠ·Π΄Π΅Π»ΠΈΠΉ; ΠΊΡΠΎΠΌΠ΅ ΡΡΠΎΠ³ΠΎ, Π»ΠΈΠΊΠ²ΠΈΠ΄ΠΈΡΡΠ΅ΡΡΡ ΡΠ°ΡΡ ΠΎΠ΄ Π²ΠΎΠ΄Ρ Π½Π° ΠΎΡ Π»Π°ΠΆΠ΄Π΅Π½ΠΈΠ΅ ΡΠ½Π΅ΠΊΠΎΠ²ΠΎΠΉ ΠΊΠ°ΠΌΠ΅ΡΡ, ΡΠΎΠΊΡΠ°ΡΠ°Π΅ΡΡΡ ΠΏΡΠΎΠ΄ΠΎΠ»ΠΆΠΈΡΠ΅Π»ΡΠ½ΠΎΡΡΡ ΡΡΡΠΊΠΈ ΠΈ ΠΏΡΠ΅Π΄ΠΎΡΠ²ΡΠ°ΡΠ°Π΅ΡΡΡ ΠΎΠ±ΡΠ°Π·ΠΎΠ²Π°Π½ΠΈΠ΅ Π²ΠΎ Π²ΡΠ΅ΠΌΡ ΡΡΡΠΊΠΈ ΡΠ»ΠΈΠΏΡΠΈΡ ΡΡ ΠΈΠ·Π΄Π΅Π»ΠΈΠΉ.
ΠΠ°Π³ΡΠ΅Π² ΠΌΠ°ΡΡΠΈΡ Ρ ΡΡΠΎΡΠΎΠΏΠ»Π°ΡΡΠΎΠ²ΡΠΌΠΈ ΡΠΈΠ»ΡΠ΅ΡΠ°ΠΌΠΈ Π΄ΠΎ ΡΠ΅ΠΌΠΏΠ΅ΡΠ°ΡΡΡ 75…85Β°Π‘ ΠΏΡΠΈΠ²ΠΎΠ΄ΠΈΡ ΠΊ ΡΠΈΠΊΡΠΈΡΠΎΠ²Π°Π½ΠΈΡ ΡΡΡΡΠΊΡΡΡΡ Π½Π°ΡΡΠΆΠ½ΠΎΠ³ΠΎ ΡΠ»ΠΎΡ Π²ΡΠΏΡΠ΅ΡΠΎΠ²ΡΠ²Π°Π΅ΠΌΡΡ ΠΈΠ·Π΄Π΅Π»ΠΈΠΉ, ΠΊ ΡΠ²Π΅Π»ΠΈΡΠ΅Π½ΠΈΡ ΠΏΠ»Π°ΡΡΠΈΡΠ½ΠΎΡΡΠΈ ΠΈΡ Π²Π½ΡΡΡΠ΅Π½Π½ΠΈΡ ΡΠ»ΠΎΠ΅Π² ΠΈ ΠΊ ΡΡΡΡΠ°Π½Π΅Π½ΠΈΡ Π°Π΄Π³Π΅Π·ΠΈΠΈ ΡΠ΅ΡΡΠ° ΠΊ ΠΌΠ΅ΡΠ°Π»Π»ΠΈΡΠ΅ΡΠΊΠΎΠΉ ΠΏΠΎΠ²Π°ΡΡ Π½ΠΎΡΡΠΈ ΡΠΎΡΠΌΡΡΡΠ΅Π³ΠΎ ΠΊΠ°Π½Π°Π»Π°. ΠΡΠ»Π΅Π΄ΡΡΠ²ΠΈΠ΅ ΡΡΠΎΠ³ΠΎ, Π²ΡΡΠΎΠΊΠΎΡΠ΅ΠΌΠΏΠ΅ΡΠ°ΡΡΡΠ½ΡΠΉ ΡΠ΅ΠΆΠΈΠΌ ΡΠΎΡΠΌΠΎΠ²Π°Π½ΠΈΡ ΡΠ»ΡΡΡΠ°Π΅Ρ ΡΠ°Π²Π½ΠΎΠΌΠ΅ΡΠ½ΡΠΉ Π²ΡΡ ΠΎΠ΄ ΠΌΠ°ΠΊΠ°ΡΠΎΠ½Π½ΡΡ ΠΈΠ·Π΄Π΅Π»ΠΈΠΉ, Π° ΠΏΠΎ ΡΡΠ°Π²Π½Π΅Π½ΠΈΡ Ρ ΡΡΠ°Π΄ΠΈΡΠΈΠΎΠ½Π½ΡΠΌ ΡΠ΅ΠΆΠΈΠΌΠΎΠΌ ΡΠΎΡΠΌΠΎΠ²Π°Π½ΠΈΡ ΡΠ²Π΅Π»ΠΈΡΠΈΠ²Π°Π΅Ρ ΠΏΡΠΎΠΈΠ·Π²ΠΎΠ΄ΠΈΡΠ΅Π»ΡΠ½ΠΎΡΡΡ ΠΏΡΠ΅ΡΡΠ° Π² ΡΡΠ΅Π΄Π½Π΅ΠΌ Π½Π° 10% ΠΈ ΠΏΠΎΠ·Π²ΠΎΠ»ΡΠ΅Ρ Π΄ΠΎΡΡΠΈΡΡ Π΄ΡΡΠ³ΠΈΠ΅ ΠΏΡΠ΅ΠΈΠΌΡΡΠ΅ΡΡΠ²Π°, ΠΏΠΎΠ΄ΠΎΠ±Π½ΡΠ΅ Π²ΡΡΠΎΠΊΠΎ-ΡΠ΅ΠΌΠΏΠ΅ΡΠ°ΡΡΡΠ½ΠΎΠΌΡ ΡΠ΅ΠΆΠΈΠΌΡ Π·Π°ΠΌΠ΅ΡΠ°.
Β
Π‘ΡΠ°Π΄ΠΈΠΈ ΠΏΡΠΈΠ³ΠΎΡΠΎΠ²Π»Π΅Π½ΠΈΡ ΡΠ΅ΡΡΠ°
ΠΡΠΈΠ³ΠΎΡΠΎΠ²Π»Π΅Π½ΠΈΠ΅ ΠΌΠ°ΠΊΠ°ΡΠΎΠ½Π½ΠΎΠ³ΠΎ ΡΠ΅ΡΡΠ° ΠΎΡΡΡΠ΅ΡΡΠ²Π»ΡΠ΅ΡΡΡ Π½Π΅ΠΏΡΠ΅ΡΡΠ²Π½ΠΎ Π² Π΄Π²Π° ΡΡΠ°ΠΏΠ° Π² ΠΌΠ°ΠΊΠ°ΡΠΎΠ½Π½ΡΡ ΠΏΡΠ΅ΡΡΠ°Ρ Π½Π΅ΠΏΡΠ΅ΡΡΠ²Π½ΠΎΠ³ΠΎ Π΄Π΅ΠΉΡΡΠ²ΠΈΡ.
ΠΠ° ΠΏΠ΅ΡΠ²ΠΎΠΌ ΡΡΠ°ΠΏΠ΅ ΠΏΡΠΎΠ²ΠΎΠ΄ΠΈΡΡΡ ΡΠΌΠ΅ΡΠΈΠ²Π°Π½ΠΈΠ΅ ΠΌΡΠΊΠΈ, ΠΆΠΈΠ΄ΠΊΠΈΡ ΠΊΠΎΠΌΠΏΠΎΠ½Π΅Π½ΡΠΎΠ² Π² ΡΠ΅ΡΡΠΎΡΠΌΠ΅ΡΠΈΡΠ΅Π»ΡΡ , Π½Π° Π²ΡΠΎΡΠΎΠΌ β ΡΠΏΠ»ΠΎΡΠ½Π΅Π½ΠΈΠ΅ Π² ΡΠ½Π΅ΠΊΠΎΠ²ΠΎΠΉ ΠΊΠ°ΠΌΠ΅ΡΠ΅ ΠΏΡΠ΅ΡΡΠ°.
ΠΠΎΠ·ΠΈΡΠΎΠ²Π°Π½ΠΈΠ΅ ΠΈΠ½Π³ΡΠ΅Π΄ΠΈΠ΅Π½ΡΠΎΠ² Ρ.Π΅. ΠΏΠΎΠ΄Π°ΡΠ° ΠΌΡΠΊΠΈ ΠΈ Π²ΠΎΠ΄Ρ Π² ΡΠ΅ΡΡΠΎΡΠΌΠ΅ΡΠΈΡΠ΅Π»Ρ Π² Π½Π΅ΠΎΠ±Ρ ΠΎΠ΄ΠΈΠΌΠΎΠΌ ΡΠΎΠΎΡΠ½ΠΎΡΠ΅Π½ΠΈΠΈ, ΡΠΎΠΎΡΠ²Π΅ΡΡΡΠ²ΡΡΡΠ΅ΠΌ ΡΠ΅ΡΠ΅ΠΏΡΡΡΠ΅, ΠΎΡΡΡΠ΅ΡΡΠ²Π»ΡΠ΅ΡΡΡ ΠΏΡΠΈ ΠΏΠΎΠΌΠΎΡΠΈ Π΄ΠΎΠ·Π°ΡΠΎΡΠΎΠ² ΠΌΡΠΊΠΈ ΠΈ Π²ΠΎΠ΄Ρ, ΠΊΠΎΡΠΎΡΡΠ΅, ΡΠ²Π»ΡΡΡΡ ΡΠΎΡΡΠ°Π²Π½ΡΠΌΠΈ ΡΠ°ΡΡΡΠΌΠΈ ΠΌΠ°ΠΊΠ°ΡΠΎΠ½Π½ΠΎΠ³ΠΎ ΠΏΡΠ΅ΡΡΠ°, ΡΠ°Π±ΠΎΡΠ°ΡΡ ΡΠΈΠ½Ρ ΡΠΎΠ½Π½ΠΎ.
ΠΠΎΠ±Π°Π²ΠΊΠΈ ΠΏΠΎΡΠ»Π΅ ΡΠ°ΡΡΠ²ΠΎΡΠ΅Π½ΠΈΡ Π² Π²ΠΎΠ΄Π΅ ΠΈΠ»ΠΈ ΠΏΡΠΈΠ³ΠΎΡΠΎΠ²Π»Π΅Π½ΠΈΡ Π²ΠΎΠ΄Π½ΠΎΠΉ ΡΠΌΡΠ»ΡΡΠΈΠΈ ΠΏΠΎΡΡΡΠΏΠ°ΡΡ Π² ΡΠ΅ΡΡΠΎΡΠΌΠ΅ΡΠΈΡΠ΅Π»Ρ ΡΠ΅ΡΠ΅Π· Π΄ΠΎΠ·Π°ΡΠΎΡ Π²ΠΎΠ΄Ρ.
ΠΠ°ΠΌΠ΅Ρ ΡΠ΅ΡΡΠ°. ΠΠΎΡΠ»Π΅ ΡΠ΅Π³ΡΠ»ΠΈΡΠΎΠ²ΠΊΠΈ Π΄ΠΎΠ·Π°ΡΠΎΡΠΎΠ² Π²ΠΊΠ»ΡΡΠ°ΡΡ ΡΠ΅ΡΡΠΎΡΠΌΠ΅ΡΠΈΡΠ΅Π»Ρ. ΠΠ»Ρ Ρ ΠΎΡΠΎΡΠ΅Π³ΠΎ ΠΏΡΠΎΠΌΠ΅ΡΠ° ΠΊΠΎΡΡΡΠΎ ΡΠ΅ΡΡΠΎΡΠΌΠ΅ΡΠΈΡΠ΅Π»Ρ Π΄ΠΎΠ»ΠΆΠ½ΠΎ Π±ΡΡΡ Π·Π°ΠΏΠΎΠ»Π½Π΅Π½ΠΎ ΡΠ΅ΡΡΠΎΠΌ ΠΏΡΠΈΠΌΠ΅ΡΠ½ΠΎ Π½Π° 2/3 ΠΎΠ±ΡΠ΅ΠΌΠ°. ΠΠΎΡΠ»Π΅ ΡΠ΅ΡΡΠΎ ΠΏΠΎΡΡΡΠΏΠ°Π΅Ρ Π² ΡΠ»Π΅Π΄ΡΡΡΠ΅Π΅ ΠΊΠΎΡΡΡΠΎ (Π² ΠΌΠ½ΠΎΠ³ΠΎΠΊΠΎΡΡΡΠ½ΡΡ ΠΏΡΠ΅ΡΡΠ°Ρ ), Π³Π΄Π΅ ΠΎΡΡΡΠ΅ΡΡΠ²Π»ΡΠ΅ΡΡΡ Π΄Π°Π»ΡΠ½Π΅ΠΉΡΠΈΠΉ ΠΏΡΠΎΠΌΠ΅Ρ ΡΠ΅ΡΡΠ°, Π»ΠΈΠ±ΠΎ Π² ΡΠ½Π΅ΠΊΠΎΠ²ΡΡ ΠΊΠ°ΠΌΠ΅ΡΡ (Π² ΠΎΠ΄Π½ΠΎΠΊΠΎΡΡΡΠ½ΡΡ ΠΏΡΠ΅ΡΡΠ°Ρ ).
ΠΠΎ Π²ΡΠ΅ΠΌΡ Π·Π°ΠΌΠ΅ΡΠ° ΡΠ΅ΡΡΠ° ΠΏΡΠΎΠΈΡΡ ΠΎΠ΄ΠΈΡ ΠΏΠΎΡΡΠ΅ΠΏΠ΅Π½Π½ΠΎΠ΅ Π½Π°Π±ΡΡ Π°Π½ΠΈΠ΅ ΠΊΡΠ°Ρ ΠΌΠ°Π»ΡΠ½ΡΡ Π·Π΅ΡΠ΅Π½ ΠΈ Π±Π΅Π»ΠΊΠΎΠ²ΡΡ ΠΊΠΎΠΌΠΎΡΠΊΠΎΠ² ΠΌΡΠΊΠΈ, Π° ΡΠ°ΠΊΠΆΠ΅ ΡΠ°Π²Π½ΠΎΠΌΠ΅ΡΠ½ΠΎΠ΅ ΡΠ°ΡΠΏΡΠ΅Π΄Π΅Π»Π΅Π½ΠΈΠ΅ Π²Π»Π°Π³ΠΈ ΠΏΠΎ Π²ΡΠ΅ΠΉ ΠΌΠ°ΡΡΠ΅ ΡΠ΅ΡΡΠ°.
ΠΡΠΎΡΠ΅ΡΡΡ, ΠΏΡΠΎΠΈΡΡ ΠΎΠ΄ΡΡΠΈΠ΅ ΠΏΡΠΈ Π·Π°ΠΌΠ΅ΡΠ΅ ΠΌΠ°ΠΊΠ°ΡΠΎΠ½Π½ΠΎΠ³ΠΎ ΡΠ΅ΡΡΠ°. ΠΠ°ΠΌΠ΅Ρ ΡΠ΅ΡΡΠ° β ΡΡΠΎ ΡΠ»ΠΎΠΆΠ½ΡΠΉ ΠΏΡΠΎΡΠ΅ΡΡ ΡΠΌΠ΅ΡΠΈΠ²Π°Π½ΠΈΡ ΠΊΠΎΠΌΠΏΠΎΠ½Π΅Π½ΡΠΎΠ² ΠΌΡΠΊΠΈ Ρ Π²ΠΎΠ΄ΠΎΠΉ. Π ΡΠ΅Π·ΡΠ»ΡΡΠ°ΡΠ΅ ΡΡΠΎΠ³ΠΎ ΡΠΌΠ΅ΡΠΈΠ²Π°Π½ΠΈΡ ΠΏΡΠΎΠΈΡΡ ΠΎΠ΄ΡΡ Π³Π»ΡΠ±ΠΎΠΊΠΈΠ΅ ΡΠΈΠ·ΠΈΠΊΠΎ-Ρ ΠΈΠΌΠΈΡΠ΅ΡΠΊΠΈΠ΅ ΠΈΠ·ΠΌΠ΅Π½Π΅Π½ΠΈΡ Π³Π»Π°Π²Π½ΡΡ ΠΊΠΎΠΌΠΏΠΎΠ½Π΅Π½ΡΠΎΠ² ΠΌΡΠΊΠΈ: ΠΊΡΠ°Ρ ΠΌΠ°Π»Π° ΠΈ Π±Π΅Π»ΠΊΠΎΠ².
ΠΡΠΈ ΠΏΡΠΈΠ³ΠΎΡΠΎΠ²Π»Π΅Π½ΠΈΠΈ ΠΌΠ°ΠΊΠ°ΡΠΎΠ½Π½ΠΎΠ³ΠΎ ΡΠ΅ΡΡΠ° ΠΏΡΠΎΠΈΡΡ ΠΎΠ΄ΡΡ ΡΠ»ΠΎΠΆΠ½ΡΠ΅ Π±ΠΈΠΎΡ ΠΈΠΌΠΈΡΠ΅ΡΠΊΠΈΠ΅, ΠΊΠΎΠ»Π»ΠΎΠΈΠ΄Π½ΡΠ΅, ΡΠ΅ΡΠΌΠ΅Π½ΡΠ°ΡΠΈΠ²Π½ΡΠ΅ ΠΈ ΡΠΈΠ·ΠΈΡΠ΅ΡΠΊΠΈΠ΅ ΠΏΡΠΎΡΠ΅ΡΡΡ. ΠΡΠ½ΠΎΠ²Π½ΡΡ ΡΠΎΠ»Ρ ΠΏΡΠΈ ΠΏΡΠΈΠ³ΠΎΡΠΎΠ²Π»Π΅Π½ΠΈΠΈ ΠΌΠ°ΠΊΠ°ΡΠΎΠ½Π½ΠΎΠ³ΠΎ ΡΠ΅ΡΡΠ° ΠΈΠ³ΡΠ°ΡΡ ΠΊΠΎΠ»Π»ΠΎΠΈΠ΄Π½ΡΠ΅ ΠΏΡΠΎΡΠ΅ΡΡΡ.
ΠΡΠ½ΠΎΠ²Π½ΡΠ΅ ΠΊΠΎΠΌΠΏΠΎΠ½Π΅Π½ΡΡ ΠΌΡΠΊΠΈ Π±Π΅Π»ΠΎΠΊ ΠΈ ΠΊΡΠ°Ρ ΠΌΠ°Π» ΠΎΠ±Π»Π°Π΄Π°ΡΡ ΡΠ°Π·Π»ΠΈΡΠ½ΠΎΠΉ Π²ΠΎΠ΄ΠΎΠΏΠΎΠ³Π»ΠΎΡΠΈΡΠ΅Π»ΡΠ½ΠΎΠΉ ΡΠΏΠΎΡΠΎΠ±Π½ΠΎΡΡΡΡ. ΠΠ·Π°ΠΈΠΌΠΎΠ΄Π΅ΠΉΡΡΠ²ΠΈΠ΅ Π²ΠΎΠ΄Ρ Ρ ΠΊΡΠ°Ρ ΠΌΠ°Π»ΠΎΠΌ ΠΈ Π±Π΅Π»ΠΊΠΎΠΌ ΠΏΡΠΎΡΠ΅ΠΊΠ°Π΅Ρ Π² Π΄Π²Π° ΡΡΠ°ΠΏΠ°. ΠΠ° ΠΏΠ΅ΡΠ²ΠΎΠΌ ΡΡΠ°ΠΏΠ΅ ΠΏΡΠΎΠΈΡΡ ΠΎΠ΄ΠΈΡ Π°Π΄ΡΠΎΡΠ±ΡΠΈΠΎΠ½Π½ΠΎΠ΅ ΡΠ²ΡΠ·ΡΠ²Π°Π½ΠΈΠ΅ Π²ΠΎΠ΄Ρ Π² ΡΠ΅Π·ΡΠ»ΡΡΠ°ΡΠ΅ Π½Π° ΠΏΠΎΠ²Π΅ΡΡ Π½ΠΎΡΡΠΈ ΠΌΡΡΠ½ΡΡ ΡΠ°ΡΡΠΈΡ ΠΎΠ±ΡΠ°Π·ΡΡΡΡΡ ΡΠΎΠ½ΡΠ°ΠΉΡΠΈΠ΅ Π²ΠΎΠ΄ΡΠ½ΡΠ΅ ΠΏΠ»Π΅Π½ΠΊΠΈ. ΠΠΎΠ»ΠΈΡΠ΅ΡΡΠ²ΠΎ Π²ΠΎΠ΄Ρ, ΡΠ²ΡΠ·ΡΠ²Π°Π΅ΠΌΠΎΠΉ Π°Π΄ΡΠΎΡΠ±ΡΠΈΠΎΠ½Π½ΠΎ Π½Π΅Π²Π΅Π»ΠΈΠΊΠΎ. ΠΡΠΎΡΠ΅ΡΡ ΡΠΌΠ°ΡΠΈΠ²Π°Π½ΠΈΡ ΡΠΎΠΏΡΠΎΠ²ΠΎΠΆΠ΄Π°Π΅ΡΡΡ Π²ΡΠ΄Π΅Π»Π΅Π½ΠΈΠ΅ΠΌ ΡΠ΅ΠΏΠ»Π°.Β ΠΠ° Π²ΡΠΎΡΠΎΠΌ ΡΡΠ°ΠΏΠ΅ ΠΏΡΠΎΠΈΡΡ ΠΎΠ΄ΠΈΡ Π²ΠΏΠΈΡΡΠ²Π°Π½ΠΈΠ΅ Π²ΠΎΠ΄Ρ ΡΠ°ΡΡΠΈΡΠ°ΠΌΠΈ ΠΌΡΠΊΠΈ. ΠΠ½ΠΎ ΠΎΠ±ΡΡΠ»ΠΎΠ²Π»Π΅Π½ΠΎ Π½Π°Π»ΠΈΡΠΈΠ΅ΠΌ Π²Π½ΡΡΡΠΈ Π±Π΅Π»ΠΊΠ° ΠΈ ΠΊΡΠ°Ρ ΠΌΠ°Π»Π° Π²ΠΎΠ΄ΠΎΡΠ°ΡΡΠ²ΠΎΡΠΈΠΌΡΡ ΡΡΠ°ΠΊΡΠΈΠΉ. ΠΠ° ΡΡΠΎΠΌ ΡΡΠ°ΠΏΠ΅ ΠΈΠΌΠ΅Π΅Ρ ΠΌΠ΅ΡΡΠΎ ΠΏΠΎΠ³Π»ΠΎΡΠ΅Π½ΠΈΠ΅ Π²ΠΎΠ΄Ρ ΠΏΠΎΠ΄ Π΄Π΅ΠΉΡΡΠ²ΠΈΠ΅ΠΌ ΠΎΡΠΌΠΎΡΠΈΡΠ΅ΡΠΊΠΎΠ³ΠΎ Π΄Π°Π²Π»Π΅Π½ΠΈΡ (ΠΎΡΠΌΠΎΡΠΈΡΠ΅ΡΠΊΠΎΠ΅ ΡΠ²ΡΠ·ΡΠ²Π°Π½ΠΈΠ΅ Π²Π»Π°Π³ΠΈ).
ΠΡΠΈ ΡΠ΅ΠΌΠΏΠ΅ΡΠ°ΡΡΡΠ½ΡΡ ΡΡΠ»ΠΎΠ²ΠΈΡΡ ΠΏΠΎΠ»ΡΡΠ΅Π½ΠΈΡ ΠΌΠ°ΠΊΠ°ΡΠΎΠ½Π½ΠΎΠ³ΠΎ ΡΠ΅ΡΡΠ° Π΅Π³ΠΎ ΠΊΡΠ°Ρ ΠΌΠ°Π»ΡΠ½Π°Ρ ΡΠ°ΡΡΡ ΠΎΠ±Π»Π°Π΄Π°Π΅Ρ ΡΠ»Π°Π±ΠΎΠΉ ΡΠΏΠΎΡΠΎΠ±Π½ΠΎΡΡΡΡ ΠΊ Π½Π°Π±ΡΡ Π°Π½ΠΈΡ.
ΠΡΠ°Ρ ΠΌΠ°Π»ΡΠ½ΡΠ΅ Π·Π΅ΡΠ½Π° ΡΠ΄Π΅ΡΠΆΠΈΠ²Π°ΡΡ Π²Π»Π°Π³Ρ Π² ΠΎΡΠ½ΠΎΠ²Π½ΠΎΠΌ ΡΠ²ΠΎΠ΅ΠΉ ΠΏΠΎΠ²Π΅ΡΡ Π½ΠΎΡΡΡΡ, Ρ.Π΅. Π°Π΄ΡΠΎΡΠ±ΡΠΈΠΎΠ½Π½ΠΎ. ΠΡΠΌΠΎΡΠΈΡΠ΅ΡΠΊΠΎΠ΅ Π½Π°Π±ΡΡ Π°Π½ΠΈΠ΅ ΠΊΡΠ°Ρ ΠΌΠ°Π»ΡΠ½ΡΡ Π·Π΅ΡΠ΅Π½ Π½Π°ΡΠΈΠ½Π°Π΅ΡΡΡ ΠΏΡΠΈ ΡΠ΅ΠΌΠΏΠ΅ΡΠ°ΡΡΡΠ΅ 70Β°Π‘ ΠΈ Π²ΡΡΠ΅, Ρ.Π΅. ΠΏΡΠΈ ΡΠ΅ΠΌΠΏΠ΅ΡΠ°ΡΡΡΠ΅ ΠΊΠΎΡΠΎΡΠΎΠΉ ΠΏΡΠΈ Π½ΠΎΡΠΌΠ°Π»ΡΠ½ΡΡ ΡΡΠ»ΠΎΠ²ΠΈΡΡ Π² ΠΌΠ°ΠΊΠ°ΡΠΎΠ½Π½ΠΎΠΌ ΡΠ΅ΡΡΠ΅ Π½Π΅ Π½Π°Π±Π»ΡΠ΄Π°Π΅ΡΡΡ.
ΠΠ»Π΅ΠΉΠΊΠΎΠ²ΠΈΠ½Π° (Π±Π΅Π»ΠΎΠΊ) Π΄ΠΎΡΡΠΈΠ³Π°Π΅Ρ ΠΌΠ°ΠΊΡΠΈΠΌΡΠΌΠ° Π½Π°Π±ΡΡ Π°Π½ΠΈΡ Π² ΠΈΠ½ΡΠ΅ΡΠ²Π°Π»Π΅ ΡΠ΅ΠΌΠΏΠ΅ΡΠ°ΡΡΡΡ ΠΎΡ 20 Π΄ΠΎ 30Β°Π‘, ΠΏΡΠΈ Π±ΠΎΠ»Π΅Π΅ Π²ΡΡΠΎΠΊΠΈΡ ΡΠ΅ΠΌΠΏΠ΅ΡΠ°ΡΡΡΠ°Ρ Π΅Π΅ Π½Π°Π±ΡΡ Π°Π΅ΠΌΠΎΡΡΡ ΡΠ½ΠΈΠΆΠ°Π΅ΡΡΡ. ΠΠ°Π±ΡΡ Π°Π½ΠΈΠ΅ ΠΌΡΠΊΠΈ ΠΏΡΠΈ Π·Π°ΠΌΠ΅ΡΠ΅ ΠΌΠ°ΠΊΠ°ΡΠΎΠ½Π½ΠΎΠ³ΠΎ ΡΠ΅ΡΡΠ° ΠΎΠ±ΡΡΠ»ΠΎΠ²Π»Π΅Π½ΠΎ Π² ΠΎΡΠ½ΠΎΠ²Π½ΠΎΠΌ Π³ΠΈΠ΄ΡΠ°ΡΠΈΠΎΠ½Π½ΠΎΠΉ ΡΠΏΠΎΡΠΎΠ±Π½ΠΎΡΡΡΡ ΠΊΠ»Π΅ΠΉΠΊΠΎΠ²ΠΈΠ½Ρ.
ΠΠ»Π΅ΠΉΠΊΠΎΠ²ΠΈΠ½Π° ΠΌΡΠΊΠΈ ΠΌΡΠ³ΠΊΠΎΠΉ ΠΏΡΠ΅Π½ΠΈΡΡ Π½Π°Π±ΡΡ Π°Π΅Ρ Π±ΡΡΡΡΠΎ, Π½ΠΎ ΠΏΠΎΠ³Π»ΠΎΡΠ°Π΅Ρ ΠΌΠ΅Π½ΡΡΠ΅ Π²ΠΎΠ΄Ρ. Π ΠΊΠ»Π΅ΠΉΠΊΠΎΠ²ΠΈΠ½Π° ΠΌΡΠΊΠΈ ΠΈΡ ΡΠ²Π΅ΡΠ΄ΠΎΠΉ ΠΏΡΠ΅Π½ΠΈΡΡ, Π½Π°ΠΎΠ±ΠΎΡΠΎΡ, Π½Π°Π±ΡΡ Π°Π΅Ρ ΠΌΠ΅Π΄Π»Π΅Π½Π½ΠΎ, Π½ΠΎ ΠΏΠΎΠ³Π»ΠΎΡΠ°Π΅Ρ Π±ΠΎΠ»ΡΡΠ΅ Π²ΠΎΠ΄Ρ.
ΠΠ»Π΅ΠΉΠΊΠΎΠ²ΠΈΠ½Π° Π² ΠΌΠ°ΠΊΠ°ΡΠΎΠ½Π½ΠΎΠΌ ΡΠ΅ΡΡΠ΅ ΡΠ²Π»ΡΠ΅ΡΡΡ ΠΎΡΠ½ΠΎΠ²Π½ΡΠΌ ΡΠ²ΡΠ·ΡΡΡΠΈΠΌ Π²Π΅ΡΠ΅ΡΡΠ²ΠΎΠΌ. ΠΠ½Π° ΡΠ²ΡΠ·ΡΠ²Π°Π΅Ρ ΡΠ²Π»Π°ΠΆΠ½Π΅Π½Π½ΡΠ΅ ΠΊΡΠ°Ρ ΠΌΠ°Π»ΡΠ½ΡΠ΅ Π·Π΅ΡΠ½Π° ΠΈ ΠΎΡΡΠ°ΡΠΊΠΈ ΠΌΡΡΠ½ΡΡ ΠΊΡΡΠΏΠΎΠΊ.
ΠΠ°ΠΊΠ°ΡΠΎΠ½Π½ΠΎΠ΅ ΡΠ΅ΡΡΠΎ ΠΏΠΎΡΠ»Π΅ Π·Π°ΠΌΠ΅ΡΠ° ΠΏΡΠ΅Π΄ΡΡΠ°Π²Π»ΡΠ΅Ρ ΡΠΎΠ±ΠΎΠΉ ΡΡΠ΅Ρ ΡΠ°Π·Π½ΡΡ Π΄ΠΈΡΠΏΠ΅ΡΡΠ½ΡΡ ΡΠΈΡΡΠ΅ΠΌΡ. Π’Π²Π΅ΡΠ΄ΠΎΠΉ Π΄ΠΈΡΠΏΠ΅ΡΡΠ½ΠΎΠΉ ΡΠ°Π·ΠΎΠΉ ΡΠ²Π»ΡΡΡΡΡ ΡΠ²Π»Π°ΠΆΠ½Π΅Π½Π½ΡΠ΅ ΠΊΡΠ°Ρ ΠΌΠ°Π»ΡΠ½ΡΠ΅ Π·Π΅ΡΠ½Π° ΠΈ ΠΎΡΡΠ°ΡΠΊΠΈ ΠΌΡΡΠ½ΡΡ ΠΊΡΡΠΏΠΎΠΊ. ΠΠΈΡΠΏΠ΅ΡΡΠΈΠΎΠ½Π½ΠΎΠΉ ΡΡΠ΅Π΄ΠΎΠΉ ΡΠ²Π»ΡΠ΅ΡΡΡ ΠΏΠ»Π°ΡΡΠΈΡΠΈΡΠΈΡΠΎΠ²Π°Π½Π½Π°Ρ ΠΊΠ»Π΅ΠΉΠΊΠΎΠ²ΠΈΠ½Π°. Π’ΡΠ΅ΡΡΠ΅ΠΉ Π³Π°Π·ΠΎΠΎΠ±ΡΠ°Π·Π½ΠΎΠΉ ΡΠ°Π·ΠΎΠΉ ΡΠ²Π»ΡΡΡΡΡ Π²ΠΊΠ»ΡΡΠ΅Π½ΠΈΡ Π²ΠΎΠ·Π΄ΡΡ Π°, Π·Π°Ρ Π²Π°ΡΠ΅Π½Π½ΡΠ΅ ΠΏΡΠΈ Π·Π°ΠΌΠ΅ΡΠ΅.
ΠΡΠ° ΡΡΠ΅Ρ ΡΠ°Π·Π½Π°Ρ Π³Π΅ΡΠ΅ΡΠΎΠ³Π΅Π½Π½Π°Ρ ΡΠΈΡΡΠ΅ΠΌΠ° ΠΎΠ±Π»Π°Π΄Π°Π΅Ρ ΡΠΏΠΎΡΠΎΠ±Π½ΠΎΡΡΡΡ ΡΠΏΠ»ΠΎΡΠ½ΡΡΡΡΡ ΠΈ ΡΠΏΡΠΎΡΠ½ΡΡΡΡΡ. Π‘ΡΠ΅ΠΏΠ΅Π½Ρ ΡΡΠΎΠ³ΠΎ ΡΠΏΠ»ΠΎΡΠ½Π΅Π½ΠΈΡ Π·Π°Π²ΠΈΡΠΈΡ ΠΎΡ ΡΠ΅ΠΆΠΈΠΌΠ° Π·Π°ΠΌΠ΅ΡΠ°.
Π Π΅ΠΆΠΈΠΌ Π·Π°ΠΌΠ΅ΡΠ° ΠΌΠ°ΠΊΠ°ΡΠΎΠ½Π½ΠΎΠ³ΠΎ ΡΠ΅ΡΡΠ°. Π Π΅ΠΆΠΈΠΌ Π·Π°ΠΌΠ΅ΡΠ° ΠΌΠ°ΠΊΠ°ΡΠΎΠ½Π½ΠΎΠ³ΠΎ ΡΠ΅ΡΡΠ° Ρ Π°ΡΠ°ΠΊΡΠ΅ΡΠΈΠ·ΡΠ΅ΡΡΡ Π΄Π²ΡΠΌΡ ΠΏΠ°ΡΠ°ΠΌΠ΅ΡΡΠ°ΠΌΠΈ: ΠΏΡΠΎΠ΄ΠΎΠ»ΠΆΠΈΡΠ΅Π»ΡΠ½ΠΎΡΡΡΡ ΠΈ ΠΈΠ½ΡΠ΅Π½ΡΠΈΠ²Π½ΠΎΡΡΡΡ Π·Π°ΠΌΠ΅ΡΠ° (ΡΠ°ΡΡΠΎΡΠΎΠΉ Π²ΡΠ°ΡΠ΅Π½ΠΈΡ ΠΌΠ΅ΡΠΈΠ»ΡΠ½ΠΎΠ³ΠΎ ΠΎΡΠ³Π°Π½Π°).
ΠΠ½ΡΠ΅Π½ΡΠΈΠ²Π½ΡΠΉ Π·Π°ΠΌΠ΅Ρ ΠΏΡΠΈΠ²ΠΎΠ΄ΠΈΡ ΠΊ ΡΠΏΡΠΎΡΠ½Π΅Π½ΠΈΡ ΡΡΡΡΠΊΡΡΡΡ ΠΌΠ°ΠΊΠ°ΡΠΎΠ½Π½ΠΎΠ³ΠΎ ΡΠ΅ΡΡΠ° Π·Π° ΡΡΠ΅Ρ Π±ΠΎΠ»Π΅Π΅ ΠΏΠ»ΠΎΡΠ½ΠΎΠΉ ΡΠΏΠ°ΠΊΠΎΠ²ΠΊΠΈ ΡΠ°ΡΡΠΈΡ ΡΠ²Π΅ΡΠ΄ΠΎΠΉ ΡΠ°Π·Ρ Π² Π΄ΠΈΡΠΏΠ΅ΡΡΠΈΠΎΠ½Π½ΠΎΠΉ ΡΡΠ΅Π΄Π΅ ΠΈ ΠΏΠΎΠ²ΡΡΠ΅Π½ΠΈΡ Π°Π΄Π³Π΅Π·ΠΈΠΎΠ½Π½ΠΎΠΉ ΡΠΏΠΎΡΠΎΠ±Π½ΠΎΡΡΠΈ ΠΊΠ»Π΅ΠΉΠΊΠΎΠ²ΠΈΠ½Ρ, ΠΊΠΎΡΠΎΡΠ°Ρ ΠΏΡΠΎΡΠ½Π΅Π΅ ΡΠΊΠ»Π΅ΠΈΠ²Π°Π΅Ρ ΡΠ°ΡΡΠΈΡΡ ΡΠ²Π΅ΡΠ΄ΠΎΠΉ ΡΠ°Π·Ρ.
Π£ΡΠΈΠ»Π΅Π½ΠΈΠ΅ ΠΌΠ΅Ρ Π°Π½ΠΈΡΠ΅ΡΠΊΠΎΠ³ΠΎ Π²ΠΎΠ·Π΄Π΅ΠΉΡΡΠ²ΠΈΡ Π½Π° ΡΠ΅ΡΡΠΎ ΠΏΡΠΈΠ²ΠΎΠ΄ΠΈΡ ΠΊ ΡΠ²Π΅Π»ΠΈΡΠ΅Π½ΠΈΡ Π²ΠΎΠ΄ΠΎΠΏΠΎΠ³Π»ΠΎΡΠΈΡΠ΅Π»ΡΠ½ΠΎΠΉ ΡΠΏΠΎΡΠΎΠ±Π½ΠΎΡΡΠΈ ΠΊΠ»Π΅ΠΉΠΊΠΎΠ²ΠΈΠ½Ρ. Π ΡΠ΅Π·ΡΠ»ΡΡΠ°ΡΠ΅ Π²ΠΎΠ·ΡΠ°ΡΡΠ°Π΅Ρ ΠΊΠΎΠ»ΠΈΡΠ΅ΡΡΠ²ΠΎ ΡΡΡΠΎΠΉ ΠΊΠ»Π΅ΠΉΠΊΠΎΠ²ΠΈΠ½Ρ, ΠΊΠΎΠ»ΠΈΡΠ΅ΡΡΠ²ΠΎ ΡΠ΅Π΄ΡΡΠΈΡΡΡΡΠΈΡ ΡΠ°Ρ Π°ΡΠΎΠ² ΠΈ Π²ΠΎΠ΄ΠΎΡΠ°ΡΡΠ²ΠΎΡΠΈΠΌΠΎΠ³ΠΎ Π°Π·ΠΎΡΠ°, Ρ.Π΅. ΠΏΡΠΎΡΠ΅ΡΡ ΡΠΎΠ·ΡΠ΅Π²Π°Π½ΠΈΡ ΠΌΠ°ΠΊΠ°ΡΠΎΠ½Π½ΠΎΠ³ΠΎ ΡΠ΅ΡΡΠ° ΡΡΠΊΠΎΡΡΠ΅ΡΡΡ.
Π§ΡΠ΅Π·ΠΌΠ΅ΡΠ½Π°Ρ ΠΌΠ΅Ρ Π°Π½ΠΈΡΠ΅ΡΠΊΠ°Ρ ΠΎΠ±ΡΠ°Π±ΠΎΡΠΊΠ° Π²ΡΠ·ΡΠ²Π°Π΅Ρ ΠΎΡΠ»Π°Π±Π»Π΅Π½ΠΈΠ΅ ΡΠΏΡΡΠ³ΠΎ-Π²ΡΠ·ΠΊΠΈΡ ΡΠ²ΠΎΠΉΡΡΠ² ΠΌΠ°ΠΊΠ°ΡΠΎΠ½Π½ΠΎΠ³ΠΎ ΡΠ΅ΡΡΠ° ΠΈΠ·-Π·Π° ΡΠ°ΡΡΠΈΡΠ½ΠΎΠ³ΠΎ ΡΠ°Π·ΡΡΡΠ΅Π½ΠΈΡ Π±Π΅Π»ΠΊΠΎΠ²ΠΎΠΉ ΡΡΡΡΠΊΡΡΡΡ, Ρ.Π΅. ΠΌΠ΅Ρ Π°Π½ΠΈΡΠ΅ΡΠΊΠΎΠΉ Π΄Π΅Π½Π°ΡΡΡΠ°ΡΠΈΠΈ ΠΊΠ»Π΅ΠΉΠΊΠΎΠ²ΠΈΠ½Ρ.
Π’Π΅ΡΡΠΎ, ΠΈΠ· ΠΌΠ°ΠΊΠ°ΡΠΎΠ½Π½ΠΎΠΉ ΠΌΡΠΊΠΈ (ΠΊΡΡΠΏΠΊΠΈ ΠΈΠ»ΠΈ ΠΏΠΎΠ»ΡΠΊΡΡΠΏΠΊΠΈ), ΡΡΠ΅Π±ΡΠ΅Ρ
Π±ΠΎΠ»ΡΡΠ΅ΠΉ ΠΏΡΠΎΠ΄ΠΎΠ»ΠΆΠΈΡΠ΅Π»ΡΠ½ΠΎΡΡΠΈ Π·Π°ΠΌΠ΅ΡΠ°, ΡΠ΅ΠΌ ΡΠ΅ΡΡΠΎ ΠΈΠ· Ρ
Π»Π΅Π±ΠΎΠΏΠ΅ΠΊΠ°ΡΠ½ΠΎΠΉ ΠΌΡΠΊΠΈ, ΡΠ°ΠΊ ΠΊΠ°ΠΊ
ΠΏΡΠΎΠ½ΠΈΠΊΠ½ΠΎΠ²Π΅Π½ΠΈΠ΅ Π²Π»Π°Π³ΠΈ Π²Π½ΡΡΡΡ ΠΏΠ»ΠΎΡΠ½ΡΡ
ΠΊΡΡΠΏΠΈΡΡΠ°ΡΡΡ
ΡΠ°ΡΡΠΈΡ ΠΏΡΠΎΠΈΡΡ
ΠΎΠ΄ΠΈΡ Π·Π½Π°ΡΠΈΡΠ΅Π»ΡΠ½ΠΎ
ΠΌΠ΅Π΄Π»Π΅Π½Π½Π΅Π΅, ΡΠ΅ΠΌ Π²Π½ΡΡΡΡ ΠΌΠ΅Π»ΠΊΠΈΡ
ΡΠ°ΡΡΠΈΡ Ρ
Π»Π΅Π±ΠΎΠΏΠ΅ΠΊΠ°ΡΠ½ΠΎΠΉ ΠΌΡΠΊΠΈ. ΠΡΠΎΠ΄ΠΎΠ»ΠΆΠΈΡΠ΅Π»ΡΠ½ΠΎΡΡΡ
Π·Π°ΠΌΠ΅ΡΠ° ΡΠ΅ΡΡΠ° ΠΈΠ· ΠΌΠ°ΠΊΠ°ΡΠΎΠ½Π½ΠΎΠΉ ΠΌΡΠΊΠΈ ΡΠΎΡΡΠ°Π²Π»ΡΠ΅Ρ 20 ΠΌΠΈΠ½.
Π£ΠΏΠ»ΠΎΡΠ½Π΅Π½ΠΈΠ΅ ΡΠ΅ΡΡΠ°. Π ΡΠ½Π΅ΠΊΠΎΠ²ΠΎΠΌ ΡΠΈΠ»ΠΈΠ½Π΄ΡΠ΅ ΠΌΠ°ΡΡΠ° ΡΠ²Π»Π°ΠΆΠ½Π΅Π½Π½ΡΡ ΡΠ΅ΡΡΠΎΠ²ΡΡ ΠΊΠΎΠΌΠΊΠΎΠ² ΠΈ ΠΊΡΠΎΡΠ΅ΠΊ ΠΏΠΎΠ΄Ρ Π²Π°ΡΡΠ²Π°Π΅ΡΡΡ Π»ΠΎΠΏΠ°ΡΡΡΠΌΠΈ Π²ΡΠ°ΡΠ°ΡΡΠ΅Π³ΠΎΡΡ ΡΠ½Π΅ΠΊΠ° ΠΈ ΠΏΠ΅ΡΠ΅ΠΌΠ΅ΡΠ°Π΅ΡΡΡ Π²Π΄ΠΎΠ»Ρ ΡΠΈΠ»ΠΈΠ½Π΄ΡΠ° ΠΊ ΠΌΠ°ΡΡΠΈΡΠ΅. Π¨Π½Π΅ΠΊ Π² ΡΡΠΎΠΉ ΡΠ°ΡΡΠΈ Π²ΡΠΏΠΎΠ»Π½ΡΠ΅Ρ ΡΠ°Π±ΠΎΡΡ ΡΡΠ°Π½ΡΠΏΠΎΡΡΠΈΡΡΡΡΠ΅Π³ΠΎ ΠΌΠ΅Ρ Π°Π½ΠΈΠ·ΠΌΠ°, ΠΏΠ΅ΡΠ΅ΠΌΠ΅ΡΠ°ΡΡΠ΅Π³ΠΎ ΡΡΠΏΡΡΠΈΠΉ ΠΏΡΠΎΠ΄ΡΠΊΡ.
Π§Π°ΡΡΠΈΡΡ ΡΠ΅ΡΡΠ°, ΡΠ΅ΡΠ½ΠΎ ΡΠΎΠΏΡΠΈΠΊΠ°ΡΠ°ΡΡΡ Π΄ΡΡΠ³ Ρ Π΄ΡΡΠ³ΠΎΠΌ, ΠΏΠΎΡΡΠ΅ΠΏΠ΅Π½Π½ΠΎ ΡΠΆΠΈΠΌΠ°ΡΡΡΡ. ΠΡΠΎΠΈΡΡ ΠΎΠ΄ΠΈΡ ΡΠΏΠ»ΠΎΡΠ½Π΅Π½ΠΈΠ΅ ΠΌΠ°ΡΡΡ, ΠΏΡΠ΅Π²ΡΠ°ΡΠ΅Π½ΠΈΠ΅ Π΅Π΅ Π² ΠΊΡΡΡΠΎΠ΅ ΠΏΠ»Π°ΡΡΠΈΡΠ½ΠΎΠ΅ ΡΠ΅ΡΡΠΎ. ΠΠΎΠ·Π΄ΡΡ , Π·Π°ΠΏΠΎΠ»Π½ΡΡΡΠΈΠΉ ΠΏΠΎΡΡ ΠΈ ΠΏΡΠΎΠΌΠ΅ΠΆΡΡΠΊΠΈ ΠΌΠ΅ΠΆΠ΄Ρ ΡΠ°ΡΡΠΈΡΠ°ΠΌΠΈ ΡΠ΅ΡΡΠ°, Π²ΡΡΠ΅ΡΠ½ΡΠ΅ΡΡΡ Π² ΡΡΠΎΡΠΎΠ½Ρ Π·Π°Π³ΡΡΠ·ΠΎΡΠ½ΠΎΠ³ΠΎ ΠΎΡΠ²Π΅ΡΡΡΠΈΡ ΡΠ½Π΅ΠΊΠΎΠ²ΠΎΠΉ ΠΊΠ°ΠΌΠ΅ΡΡ. ΠΠ°Π²Π»Π΅Π½ΠΈΠ΅ ΠΎΡ Π½ΡΠ»Ρ ΠΏΠΎΠ²ΡΡΠ°Π΅ΡΡΡ 5-12 ΠΠΠ°.
ΠΠ°Π»Π΅Π΅ ΠΏΠ»ΠΎΡΠ½Π°Ρ ΡΠ²ΡΠ·Π°Π½Π½Π°Ρ ΠΌΠ°ΡΡΠ° ΡΠ΅ΡΡΠ° Π½Π°Π³Π½Π΅ΡΠ°Π΅ΡΡΡ Π² ΠΏΡΠ΅Π΄ΠΌΠ°ΡΡΠΈΡΠ½ΡΡ ΠΊΠ°ΠΌΠ΅ΡΡ (ΠΏΡΠ΅ΡΡΠΎΠ²ΡΡ Π³ΠΎΠ»ΠΎΠ²ΠΊΡ) ΠΈ, ΠΏΡΠ΅ΠΎΠ΄ΠΎΠ»Π΅Π²Π°Ρ ΡΠΎΠΏΡΠΎΡΠΈΠ²Π»Π΅Π½ΠΈΠ΅ ΠΌΠ°ΡΡΠΈΡΡ, ΠΏΡΠΎΠ΄Π°Π²Π»ΠΈΠ²Π°Π΅ΡΡΡ ΡΠ΅ΡΠ΅Π· ΡΠΎΡΠΌΡΡΡΠΈΠ΅ ΠΎΡΠ²Π΅ΡΡΡΠΈΡ.
ΠΡΠΈ ΠΏΠ΅ΡΠ΅ΠΌΠ΅ΡΠ΅Π½ΠΈΠΈ ΡΠΏΡΠ΅ΡΡΠΎΠ²Π°Π½Π½ΠΎΠ³ΠΎ ΡΠ΅ΡΡΠ° ΠΊ ΠΌΠ°ΡΡΠΈΡΠ΅ ΠΏΡΠΎΠΈΡΡ ΠΎΠ΄ΠΈΡ ΡΡΠ΅Π½ΠΈΠ΅ ΡΠ΅ΡΡΠ° ΠΎ Π²Π½ΡΡΡΠ΅Π½Π½ΡΡ ΠΏΠΎΠ²Π΅ΡΡ Π½ΠΎΡΡΡ ΡΠ½Π΅ΠΊΠΎΠ²ΠΎΠΉ ΠΊΠ°ΠΌΠ΅ΡΡ ΠΈ ΠΎ Π»ΠΎΠΏΠ°ΡΡΠΈ ΡΠΏΠ΅ΠΊΠ°, Π° ΡΠ°ΠΊΠΆΠ΅ ΠΈΠ½ΡΠ΅Π½ΡΠΈΠ²Π½ΠΎΠ΅ ΠΏΠ΅ΡΠ΅ΡΠΈΡΠ°Π½ΠΈΠ΅ ΡΠ»ΠΎΠ΅Π² ΡΠ΅ΡΡΠ° Π΄ΡΡΠ³ ΠΎ Π΄ΡΡΠ³Π°. ΠΡΠΎ ΠΎΠ±ΡΡΡΠ½ΡΠ΅ΡΡΡ ΡΠ΅ΠΌ, ΡΡΠΎ ΡΠ΅ΡΠ΅Π· Π΅Π΅ ΠΎΡΠ²Π΅ΡΡΡΠΈΡ ΠΏΡΠΎΠ΄Π°Π²Π»ΠΈΠ²Π°Π΅ΡΡΡ ΠΎΠΊΠΎΠ»ΠΎ 20 % ΡΠ΅ΡΡΠ°, Π½Π°Π³Π½Π΅ΡΠ°Π΅ΠΌΠΎΠ³ΠΎ ΡΠ½Π΅ΠΊΠΎΠΌ ΠΊ ΠΌΠ°ΡΡΠΈΡΠ΅. ΠΡΡΠ°Π»ΡΠ½Π°Ρ ΠΌΠ°ΡΡΠ° ΡΠ΅ΡΡΠ° Π·Π°ΠΊΡΡΡΠΈΠ²Π°Π΅ΡΡΡ Π² ΠΏΡΠ΅Π΄ΠΌΠ°ΡΡΠΈΡΠ½ΠΎΠΉ ΠΊΠ°ΠΌΠ΅ΡΠ΅, ΡΡΡΠ΅ΠΌΡΡΡ Π²ΠΎΠ·Π²ΡΠ°ΡΠΈΡΡΡΡ Π² ΠΌΠ΅ΠΆΠ²ΠΈΡΠΊΠΎΠ²ΠΎΠ΅ ΠΏΡΠΎΡΡΡΠ°Π½ΡΡΠ²ΠΎ ΡΠ½Π΅ΠΊΠ°. Π ΡΠ΅Π·ΡΠ»ΡΡΠ°ΡΠ΅ ΡΡΠΎΠ³ΠΎ ΠΏΠ΅ΡΠ΅ΡΠΈΡΠ°Π½ΠΈΡ ΡΠ΅ΠΌΠΏΠ΅ΡΠ°ΡΡΡΠ° ΡΠ΅ΡΡΠ° ΠΏΠΎΠ²ΡΡΠ°Π΅ΡΡΡ Π½Π° 10-20 Β°Π‘. Π’Π΅ΠΌΠΏΠ΅ΡΠ°ΡΡΡΠ° ΡΠ΅ΡΡΠ° ΠΏΠ΅ΡΠ΅Π΄ ΠΌΠ°ΡΡΠΈΡΠ΅ΠΉ 55-60 Β°Π‘. Π’Π΅ΡΡΠΎ ΠΏΡΠΈ ΡΠ°ΠΊΠΎΠΉ ΡΠ΅ΠΌΠΏΠ΅ΡΠ°ΡΡΡΠ΅ ΠΏΠ»Π°ΡΡΠΈΡΠ½ΠΎΠ΅, Π»Π΅Π³ΠΊΠΎ ΡΠΊΠΎΠ»ΡΠ·ΠΈΡ ΡΠ΅ΡΠ΅Π· ΠΎΡΠ²Π΅ΡΡΡΠΈΡ ΠΌΠ°ΡΡΠΈΡΡ. Π’Π΅Ρ Π½ΠΎΠ»ΠΎΠ³ΠΈΡΠ΅ΡΠΊΠΈΠ΅ ΠΈΠ½ΡΡΡΡΠΊΡΠΈΠΈ ΠΏΡΠ΅Π΄ΡΡΠΌΠ°ΡΡΠΈΠ²Π°ΡΡ ΠΎΡ Π»Π°ΠΆΠ΄Π΅Π½ΠΈΠ΅ ΡΠ΅ΡΡΠ° ΠΏΡΡΠ΅ΠΌ ΠΏΠΎΠ΄Π°ΡΠΈ Π² Π²ΠΎΠ΄ΡΠ½ΡΡ ΡΡΠ±Π°ΡΠΊΡ ΡΠ½Π΅ΠΊΠΎΠ²ΠΎΠΉ ΠΊΠ°ΠΌΠ΅ΡΡ Ρ ΠΎΠ»ΠΎΠ΄Π½ΠΎΠΉ Π²ΠΎΠ΄Ρ.
Β
Π‘ΡΡΡΠΊΡΡΡΠ½ΠΎ-ΠΌΠ΅Ρ Π°Π½ΠΈΡΠ΅ΡΠΊΠΈΠ΅ ΡΠ²ΠΎΠΉΡΡΠ²Π° ΡΠ΅ΡΡΠ°
Π£ΠΏΠ»ΠΎΡΠ½Π΅Π½Π½ΠΎΠ΅ ΠΌΠ°ΠΊΠ°ΡΠΎΠ½Π½ΠΎΠ΅ ΡΠ΅ΡΡΠΎ, ΠΏΠΎΡΡΡΠΏΠ°ΡΡΠ΅Π΅ ΠΊ ΠΌΠ°ΡΡΠΈΡΠ΅, ΡΠ²Π»ΡΠ΅ΡΡΡ ΡΠΏΡΡΠ³ΠΎ-ΠΏΠ»Π°ΡΡΠΈΡΠ½ΠΎΠ²ΡΠ·ΠΊΠΈΠΌ ΠΌΠ°ΡΠ΅ΡΠΈΠ°Π»ΠΎΠΌ.
Π£ΠΏΡΡΠ³ΠΎΡΡΡ ΡΠ΅ΡΡΠ° β ΡΡΠΎ ΡΠΏΠΎΡΠΎΠ±Π½ΠΎΡΡΡ ΡΠ΅ΡΡΠ° Π²ΠΎΡΡΡΠ°Π½Π°Π²Π»ΠΈΠ²Π°ΡΡ ΠΏΠ΅ΡΠ²ΠΎΠ½Π°ΡΠ°Π»ΡΠ½ΡΡ ΡΠΎΡΠΌΡ ΠΏΠΎΡΠ»Π΅ Π±ΡΡΡΡΠΎΠ³ΠΎ ΡΠ½ΡΡΠΈΡ Π½Π°Π³ΡΡΠ·ΠΊΠΈ, ΠΏΡΠΎΡΠ²Π»ΡΠ΅ΡΡΡ ΠΏΡΠΈ ΠΌΠ°Π»ΡΡ ΠΈ ΠΊΡΠ°ΡΠΊΠΎΠ²ΡΠ΅ΠΌΠ΅Π½Π½ΡΡ Π½Π°Π³ΡΡΠ·ΠΊΠ°Ρ .
ΠΠ»Π°ΡΡΠΈΡΠ½ΠΎΡΡΡ β ΡΡΠΎ ΡΠΏΠΎΡΠΎΠ±Π½ΠΎΡΡΡ ΡΠ΅ΡΡΠ° Π΄Π΅ΡΠΎΡΠΌΠΈΡΠΎΠ²Π°ΡΡΡΡ. ΠΡΠΈ Π΄Π»ΠΈΡΠ΅Π»ΡΠ½ΡΡ ΠΈ Π·Π½Π°ΡΠΈΡΠ΅Π»ΡΠ½ΡΡ ΠΏΠΎ Π²Π΅Π»ΠΈΡΠΈΠ½Π΅ Π½Π°Π³ΡΡΠ·ΠΊΠ°Ρ (Π²ΡΡΠ΅ ΡΠ°ΠΊ Π½Π°Π·ΡΠ²Π°Π΅ΠΌΠΎΠ³ΠΎ ΠΏΡΠ΅Π΄Π΅Π»Π° ΡΠΏΡΡΠ³ΠΎΡΡΠΈ) ΠΌΠ°ΠΊΠ°ΡΠΎΠ½Π½ΠΎΠ΅ ΡΠ΅ΡΡΠΎ Π²Π΅Π΄Π΅Ρ ΡΠ΅Π±Ρ ΠΊΠ°ΠΊ ΠΏΠ»Π°ΡΡΠΈΡΠ½ΡΠΉ ΠΌΠ°ΡΠ΅ΡΠΈΠ°Π», Ρ.Π΅. ΠΏΠΎΡΠ»Π΅ ΡΠ½ΡΡΠΈΡ Π½Π°Π³ΡΡΠ·ΠΊΠΈ ΡΠΎΡ ΡΠ°Π½ΡΠ΅Ρ ΠΏΡΠΈΠ΄Π°Π½Π½ΡΡ Π΅ΠΌΡ ΡΠΎΡΠΌΡ, Π΄Π΅ΡΠΎΡΠΌΠΈΡΡΠ΅ΡΡΡ. ΠΠΌΠ΅Π½Π½ΠΎ ΡΡΠΎ ΡΠ²ΠΎΠΉΡΡΠ²ΠΎ ΠΏΠΎΠ·Π²ΠΎΠ»ΡΠ΅Ρ ΡΠΎΡΠΌΠΎΠ²Π°ΡΡ ΠΈΠ· ΡΠ΅ΡΡΠ° ΡΡΡΡΠ΅ ΠΌΠ°ΠΊΠ°ΡΠΎΠ½Π½ΡΠ΅ ΠΈΠ·Π΄Π΅Π»ΠΈΡ ΠΎΠΏΡΠ΅Π΄Π΅Π»Π΅Π½Π½ΠΎΠ³ΠΎ Π²ΠΈΠ΄Π°.
ΠΡΠ·ΠΊΠΎΡΡΡ β Ρ Π°ΡΠ°ΠΊΡΠ΅ΡΠΈΠ·ΡΠ΅ΡΡΡ Π²Π΅Π»ΠΈΡΠΈΠ½ΠΎΠΉ ΡΠΈΠ» ΡΡΠ΅ΠΏΠ»Π΅Π½ΠΈΡ ΡΠ°ΡΡΠΈΡ ΠΌΠ΅ΠΆΠ΄Ρ ΡΠΎΠ±ΠΎΠΉ (ΡΠΈΠ» ΠΊΠΎΠ³Π΅Π·ΠΈΠΈ). Π§Π΅ΠΌ Π±ΠΎΠ»ΡΡΠ΅ Π²Π΅Π»ΠΈΡΠΈΠ½Π° ΡΠΈΠ» ΠΊΠΎΠ³Π΅Π·ΠΈΠΈ ΡΠ΅ΡΡΠ°, ΡΠ΅ΠΌ ΠΎΠ½ΠΎ Π±ΠΎΠ»Π΅Π΅ Π²ΡΠ·ΠΊΠΎΠ΅ (ΠΏΡΠΎΡΠ½ΠΎΠ΅), ΠΌΠ΅Π½Π΅Π΅ ΠΏΠ»Π°ΡΡΠΈΡΠ½ΠΎΠ΅.
ΠΠ»Π°ΡΡΠΈΡΠ½ΠΎΠ΅ ΡΠ΅ΡΡΠΎ ΡΡΠ΅Π±ΡΠ΅Ρ ΠΌΠ΅Π½ΡΡΠ΅ ΡΠ½Π΅ΡΠ³ΠΈΠΈ Π½Π° ΡΠΎΡΠΌΠΎΠ²Π°Π½ΠΈΠ΅, Π»Π΅Π³ΡΠ΅ ΠΏΠΎΠ΄Π΄Π°Π΅ΡΡΡ ΡΠΎΡΠΌΠΎΠ²Π°Π½ΠΈΡ. ΠΡΠΈ ΠΈΡΠΏΠΎΠ»ΡΠ·ΠΎΠ²Π°Π½ΠΈΠΈ ΠΌΠ΅ΡΠ°Π»Π»ΠΈΡΠ΅ΡΠΊΠΈΡ ΠΌΠ°ΡΡΠΈΡ ΠΈΠ· Π±ΠΎΠ»Π΅Π΅ ΠΏΠ»Π°ΡΡΠΈΡΠ½ΠΎΠ³ΠΎ ΡΠ΅ΡΡΠ° ΠΏΠΎΠ»ΡΡΠ°ΡΡΡΡ ΠΈΠ·Π΄Π΅Π»ΠΈΡ Ρ Π±ΠΎΠ»Π΅Π΅ Π³Π»Π°Π΄ΠΊΠΎΠΉ ΠΏΠΎΠ²Π΅ΡΡ Π½ΠΎΡΡΡΡ. Π‘ ΠΏΠΎΠ²ΡΡΠ΅Π½ΠΈΠ΅ΠΌ ΠΏΠ»Π°ΡΡΠΈΡΠ½ΠΎΡΡΠΈ ΡΠ΅ΡΡΠΎ ΡΡΠ°Π½ΠΎΠ²ΠΈΡΡΡ ΠΌΠ΅Π½Π΅Π΅ ΡΠΏΡΡΠ³ΠΈΠΌ, ΠΌΠ΅Π½Π΅Π΅ ΠΏΡΠΎΡΠ½ΡΠΌ, Π±ΠΎΠ»Π΅Π΅ Π»ΠΈΠΏΠΊΠΈΠΌ, ΡΠΈΠ»ΡΠ½Π΅Π΅ ΠΏΡΠΈΠ»ΠΈΠΏΠ°Π΅Ρ ΠΊ ΡΠ°Π±ΠΎΡΠΈΠΌ ΠΏΠΎΠ²Π΅ΡΡ Π½ΠΎΡΡΡΠΌ ΡΠ½Π΅ΠΊΠΎΠ²ΠΎΠΉ ΠΊΠ°ΠΌΠ΅ΡΡ ΠΈ ΡΠ½Π΅ΠΊΠ°, Π° ΡΡΡΡΠ΅ ΠΈΠ·Π΄Π΅Π»ΠΈΡ ΠΈΠ· ΡΠ°ΠΊΠΎΠ³ΠΎ ΡΠ΅ΡΡΠ° ΡΠΈΠ»ΡΠ½Π΅Π΅ ΡΠ»ΠΈΠΏΠ°ΡΡΡΡ ΠΌΠ΅ΠΆΠ΄Ρ ΡΠΎΠ±ΠΎΠΉ, ΠΏΠ»ΠΎΡ ΠΎ ΡΠΎΡ ΡΠ°Π½ΡΡΡ ΡΠΎΡΠΌΡ.
Π Π΅ΠΎΠ»ΠΎΠ³ΠΈΡΠ΅ΡΠΊΠΈΠ΅ ΡΠ²ΠΎΠΉΡΡΠ²Π° ΡΠΏΠ»ΠΎΡΠ½Π΅Π½Π½ΠΎΠ³ΠΎ ΡΠ΅ΡΡΠ°, Ρ.Π΅. ΡΠΎΠΎΡΠ½ΠΎΡΠ΅Π½ΠΈΠ΅ Π΅Π³ΠΎ ΡΠΏΡΡΠ³ΠΈΡ , ΠΏΠ»Π°ΡΡΠΈΡΠ΅ΡΠΊΠΈΡ ΠΈ ΠΏΡΠΎΡΠ½ΠΎΡΡΠ½ΡΡ ΡΠ²ΠΎΠΉΡΡΠ², ΠΎΠΏΡΠ΅Π΄Π΅Π»ΡΡΡΡΡ ΡΠ»Π΅Π΄ΡΡΡΠΈΠΌΠΈ ΡΠ°ΠΊΡΠΎΡΠ°ΠΌΠΈ.
Π‘ ΡΠ²Π΅Π»ΠΈΡΠ΅Π½ΠΈΠ΅ΠΌ Π²Π»Π°ΠΆΠ½ΠΎΡΡΠΈ ΡΠ΅ΡΡΠ° ΡΠ²Π΅Π»ΠΈΡΠΈΠ²Π°Π΅ΡΡΡ Π΅Π³ΠΎ ΠΏΠ»Π°ΡΡΠΈΡΠ½ΠΎΡΡΡ ΠΈ ΡΠΌΠ΅Π½ΡΡΠ°ΡΡΡΡ ΠΏΡΠΎΡΠ½ΠΎΡΡΡ ΠΈ ΡΠΏΡΡΠ³ΠΎΡΡΡ.
Π‘ ΡΠΎΡΡΠΎΠΌ ΡΠ΅ΠΌΠΏΠ΅ΡΠ°ΡΡΡΡ ΡΠ΅ΡΡΠ° ΡΠ°ΠΊΠΆΠ΅ Π½Π°Π±Π»ΡΠ΄Π°Π΅ΡΡΡ ΡΠ²Π΅Π»ΠΈΡΠ΅Π½ΠΈΠ΅ Π΅Π³ΠΎ ΠΏΠ»Π°ΡΡΠΈΡΠ½ΠΎΡΡΠΈ ΠΈ ΡΠ½ΠΈΠΆΠ΅Π½ΠΈΠ΅ ΠΏΡΠΎΡΠ½ΠΎΡΡΠΈ ΠΈ ΡΠΏΡΡΠ³ΠΎΡΡΠΈ. Π’Π°ΠΊΠ°Ρ Π·Π°Π²ΠΈΡΠΈΠΌΠΎΡΡΡ Π½Π°Π±Π»ΡΠ΄Π°Π΅ΡΡΡ ΠΈ ΠΏΡΠΈ ΡΠ΅ΠΌΠΏΠ΅ΡΠ°ΡΡΡΠ΅ Π±ΠΎΠ»ΡΡΠ΅ΠΉ 62,5 Β°Π‘, Ρ.Π΅. ΠΏΡΠ΅Π²ΡΡΠ°ΡΡΠ΅ΠΉ ΡΠ΅ΠΌΠΏΠ΅ΡΠ°ΡΡΡΡ ΠΊΠ»Π΅ΠΉΡΡΠ΅ΡΠΈΠ·Π°ΡΠΈΠΈ ΠΏΡΠ΅Π½ΠΈΡΠ½ΠΎΠ³ΠΎ ΠΊΡΠ°Ρ ΠΌΠ°Π»Π°. ΠΡΠΎ ΠΎΠ±ΡΡΡΠ½ΡΠ΅ΡΡΡ ΡΠ΅ΠΌ, ΡΡΠΎ ΠΌΠ°ΠΊΠ°ΡΠΎΠ½Π½ΠΎΠ΅ ΡΠ΅ΡΡΠΎ ΠΈΠΌΠ΅Π΅Ρ Π½Π΅Π΄ΠΎΡΡΠ°ΡΠΎΡΠ½ΠΎΠ΅ ΠΊΠΎΠ»ΠΈΡΠ΅ΡΡΠ²ΠΎ Π²Π»Π°Π³ΠΈ, Π½Π΅ΠΎΠ±Ρ ΠΎΠ΄ΠΈΠΌΠΎΠΉ Π΄Π»Ρ ΠΏΠΎΠ»Π½ΠΎΠΉ ΠΊΠ»Π΅ΠΉΡΡΠ΅ΡΠΈΠ·Π°ΡΠΈΠΈ ΠΊΡΠ°Ρ ΠΌΠ°Π»Π° ΠΏΡΠΈ ΡΠΊΠ°Π·Π°Π½Π½ΠΎΠΉ ΡΠ΅ΠΌΠΏΠ΅ΡΠ°ΡΡΡΠ΅.
Π‘ ΡΠ²Π΅Π»ΠΈΡΠ΅Π½ΠΈΠ΅ΠΌ ΡΠΎΠ΄Π΅ΡΠΆΠ°Π½ΠΈΡ ΠΊΠ»Π΅ΠΉΠΊΠΎΠ²ΠΈΠ½Ρ ΡΠΌΠ΅Π½ΡΡΠ°ΡΡΡΡ ΠΏΡΠΎΡΠ½ΠΎΡΡΠ½ΡΠ΅ ΡΠ²ΠΎΠΉΡΡΠ²Π° ΡΠ΅ΡΡΠ° ΠΈ Π²ΠΎΠ·ΡΠ°ΡΡΠ°Π΅Ρ Π΅Π³ΠΎ ΠΏΠ»Π°ΡΡΠΈΡΠ½ΠΎΡΡΡ. ΠΠ°ΠΈΠ±ΠΎΠ»ΡΡΠ΅ΠΉ Π²ΡΠ·ΠΊΠΎΡΡΡΡ (ΠΏΡΠΎΡΠ½ΠΎΡΡΡΡ) ΡΠ΅ΡΡΠΎ ΠΎΠ±Π»Π°Π΄Π°Π΅Ρ ΠΏΡΠΈ ΡΠΎΠ΄Π΅ΡΠΆΠ°Π½ΠΈΠΈ Π² ΠΌΡΠΊΠ΅ ΠΎΠΊΠΎΠ»ΠΎ 25 % ΡΡΡΠΎΠΉ ΠΊΠ»Π΅ΠΉΠΊΠΎΠ²ΠΈΠ½Ρ. ΠΡΠΈ ΡΠΎΠ΄Π΅ΡΠΆΠ°Π½ΠΈΠΈ ΡΡΡΠΎΠΉ ΠΊΠ»Π΅ΠΉΠΊΠΎΠ²ΠΈΠ½Ρ Π½ΠΈΠΆΠ΅ 25 % Ρ ΡΠΌΠ΅Π½ΡΡΠ΅Π½ΠΈΠ΅ΠΌ ΠΏΠ»Π°ΡΡΠΈΡΠ΅ΡΠΊΠΈΡ ΡΠ²ΠΎΠΉΡΡΠ² ΡΠ΅ΡΡΠ° ΡΠΌΠ΅Π½ΡΡΠ°Π΅ΡΡΡ ΠΈ Π΅Π³ΠΎ ΠΏΡΠΎΡΠ½ΠΎΡΡΡ. ΠΠΈΠΏΠΊΠ°Ρ, ΡΠΈΠ»ΡΠ½ΠΎ ΡΡΠ½ΡΡΠ°ΡΡΡ ΡΡΡΠ°Ρ ΠΊΠ»Π΅ΠΉΠΊΠΎΠ²ΠΈΠ½Π° ΡΠ²Π΅Π»ΠΈΡΠΈΠ²Π°Π΅Ρ ΠΏΠ»Π°ΡΡΠΈΡΠ½ΠΎΡΡΡ ΡΠ΅ΡΡΠ° ΠΈ Π·Π½Π°ΡΠΈΡΠ΅Π»ΡΠ½ΠΎ ΡΠ½ΠΈΠΆΠ°Π΅Ρ Π΅Π³ΠΎ ΡΠΏΡΡΠ³ΠΎΡΡΡ ΠΈ ΠΏΡΠΎΡΠ½ΠΎΡΡΡ.
Π‘ ΡΠΌΠ΅Π½ΡΡΠ΅Π½ΠΈΠ΅ΠΌ ΡΠ°Π·ΠΌΠ΅ΡΠ° ΡΠ°ΡΡΠΈΡ ΠΌΡΠΊΠΈ ΡΠ²Π΅Π»ΠΈΡΠΈΠ²Π°Π΅ΡΡΡ ΠΏΡΠΎΡΠ½ΠΎΡΡΡ ΠΈ ΡΠΌΠ΅Π½ΡΡΠ°Π΅ΡΡΡ ΠΏΠ»Π°ΡΡΠΈΡΠ½ΠΎΡΡΡ ΡΠ΅ΡΡΠ° ΠΈΠ· Π½Π΅Π΅: ΡΠ΅ΡΡΠΎ ΠΈΠ· Ρ Π»Π΅Π±ΠΎΠΏΠ΅ΠΊΠ°ΡΠ½ΠΎΠΉ ΠΌΡΠΊΠΈ Π±ΠΎΠ»Π΅Π΅ ΠΏΡΠΎΡΠ½ΠΎΠ΅, ΡΠ΅ΠΌ ΠΈΠ· ΠΏΠΎΠ»ΡΠΊΡΡΠΏΠΊΠΈ, Π° ΠΈΠ· ΠΏΠΎΠ»ΡΠΊΡΡΠΏΠΊΠΈ Π±ΠΎΠ»Π΅Π΅ ΠΏΡΠΎΡΠ½ΠΎΠ΅, ΡΠ΅ΠΌ ΠΈΠ· ΠΊΡΡΠΏΠΊΠΈ. ΠΠΏΡΠΈΠΌΠ°Π»ΡΠ½ΠΎΠ΅ ΡΠΎΠΎΡΠ½ΠΎΡΠ΅Π½ΠΈΠ΅ ΠΏΡΠΎΡΠ½ΠΎΡΡΠ½ΡΡ ΠΈ ΠΏΠ»Π°ΡΡΠΈΡΠ΅ΡΠΊΠΈΡ ΡΠ²ΠΎΠΉΡΡΠ² Ρ Π°ΡΠ°ΠΊΡΠ΅ΡΠ½ΠΎ Π΄Π»Ρ ΡΠ°ΡΡΠΈΡ ΠΈΡΡ ΠΎΠ΄Π½ΠΎΠΉ ΠΌΡΠΊΠΈ ΡΠ°Π·ΠΌΠ΅ΡΠΎΠΌ ΠΎΡ 250 Π΄ΠΎ 350 ΠΌΠΊΠΌ.
Π‘ ΡΠ²Π΅Π»ΠΈΡΠ΅Π½ΠΈΠ΅ΠΌ Π΄Π°Π²Π»Π΅Π½ΠΈΡ ΠΏΡΠ΅ΡΡΠΎΠ²Π°Π½ΠΈΡ ΡΠ²Π΅Π»ΠΈΡΠΈΠ²Π°Π΅ΡΡΡ ΠΏΠ»ΠΎΡΠ½ΠΎΡΡΡ ΠΈ ΠΏΡΠΎΡΠ½ΠΎΡΡΡ ΡΠ΅ΡΡΠ° ΠΈ ΡΠΌΠ΅Π½ΡΡΠ°Π΅ΡΡΡ Π΅Π³ΠΎ ΠΏΠ»Π°ΡΡΠΈΡΠ½ΠΎΡΡΡ.
Π‘ΠΏΠΎΡΠΎΠ±Ρ ΡΠΎΡΠΌΠΎΠ²Π°Π½ΠΈΡ ΡΠ΅ΡΡΠ°
ΠΠ°Π·Π½Π°ΡΠ΅Π½ΠΈΠ΅ ΡΠΎΡΠΌΠΎΠ²Π°Π½ΠΈΡ Π·Π°ΠΊΠ»ΡΡΠ°Π΅ΡΡΡ Π² ΠΏΡΠΈΠ΄Π°Π½ΠΈΠΈ ΠΌΠ°ΠΊΠ°ΡΠΎΠ½Π½ΠΎΠΌΡ ΡΠ΅ΡΡΡ ΠΎΠΏΡΠ΅Π΄Π΅Π»Π΅Π½Π½ΠΎΠΉ ΡΠΎΡΠΌΡ.
Π€ΠΎΡΠΌΠΎΠ²Π°Π½ΠΈΠ΅ ΠΌΠ°ΠΊΠ°ΡΠΎΠ½Π½ΡΡ ΠΈΠ·Π΄Π΅Π»ΠΈΠΉ ΠΏΡΠ΅ΡΡΠΎΠ²Π°Π½ΠΈΠ΅ΠΌ ΠΎΡΡΡΠ΅ΡΡΠ²Π»ΡΠ΅ΡΡΡ Π²ΡΠΏΡΠ΅ΡΡΠΎΠ²ΡΠ²Π°Π½ΠΈΠ΅ΠΌ ΡΠΏΠ»ΠΎΡΠ½Π΅Π½Π½ΠΎΠ³ΠΎ ΠΏΠ»Π°ΡΡΠΈΡΠ½ΠΎΠ³ΠΎ ΡΠ΅ΡΡΠ° ΡΠ΅ΡΠ΅Π· ΠΎΡΠ²Π΅ΡΡΡΠΈΡ ΠΌΠ°ΡΡΠΈΡΡ. Π£ΡΠ»ΠΎΠ²ΠΈΡ ΠΏΡΠΎΠ²Π΅Π΄Π΅Π½ΠΈΡ ΠΏΡΠΎΡΠ΅ΡΡΠ° ΡΠΎΡΠΌΠΎΠ²Π°Π½ΠΈΡ ΠΈΠ· ΡΠ΅ΡΡΠ° ΡΡΡΡΡ ΠΌΠ°ΠΊΠ°ΡΠΎΠ½Π½ΡΡ ΠΈΠ·Π΄Π΅Π»ΠΈΠΉ ΠΎΠΏΡΠ΅Π΄Π΅Π»ΡΡΡ ΠΏΡΠΎΠΈΠ·Π²ΠΎΠ΄ΠΈΡΠ΅Π»ΡΠ½ΠΎΡΡΡ ΠΏΡΠ΅ΡΡΠ°, Π° ΡΠ°ΠΊΠΆΠ΅ ΠΊΠ°ΡΠ΅ΡΡΠ²ΠΎ Π³ΠΎΡΠΎΠ²ΡΡ ΠΈΠ·Π΄Π΅Π»ΠΈΠΉ (ΡΠ²Π΅Ρ, ΡΡΠ΅ΠΏΠ΅Π½Ρ ΡΠ΅ΡΠΎΡ ΠΎΠ²Π°ΡΠΎΡΡΠΈ ΠΏΠΎΠ²Π΅ΡΡ Π½ΠΎΡΡΠΈ, ΠΏΠ»ΠΎΡΠ½ΠΎΡΡΡ ΠΈ ΠΏΡΠΎΡΠ½ΠΎΡΡΡ, Π²Π°ΡΠΎΡΠ½ΡΠ΅ ΡΠ²ΠΎΠΉΡΡΠ²Π°).
ΠΠ°ΡΡΠΈΡΡ ΠΈΠ·Π³ΠΎΡΠ°Π²Π»ΠΈΠ²Π°ΡΡ ΠΈΠ· ΡΠΏΠ»Π°Π²ΠΎΠ² ΡΡΡΠΎΠΉΡΠΈΠ²ΡΡ ΠΊ ΠΊΠΎΡΡΠΎΠ·ΠΈΠΈ, ΠΎΠ±Π»Π°Π΄Π°ΡΡΠΈΡ Π΄ΠΎΡΡΠ°ΡΠΎΡΠ½ΠΎΠΉ ΠΏΡΠΎΡΠ½ΠΎΡΡΡΡ, ΠΈΠ·Π½ΠΎΡΠΎΡΡΠΎΠΉΠΊΠΎΡΡΡΡ ΠΈ ΠΌΠ°Π»ΠΎΠΉ Π°Π΄Π³Π΅Π·ΠΈΠΎΠ½Π½ΠΎΠΉ ΡΠΏΠΎΡΠΎΠ±Π½ΠΎΡΡΡΡ. ΠΡΠΈΠΌ ΡΡΠ΅Π±ΠΎΠ²Π°Π½ΠΈΡΠΌ ΡΠ΄ΠΎΠ²Π»Π΅ΡΠ²ΠΎΡΡΡΡ ΡΠΎΡΡΠΎΡΠΈΡΡΠ°Ρ Π»Π°ΡΡΠ½Ρ, Π±ΡΠΎΠ½Π·Π°, Π½Π΅ΡΠΆΠ°Π²Π΅ΡΡΠ°Ρ ΡΡΠ°Π»Ρ. ΠΠ»Ρ ΠΏΠΎΠ²ΡΡΠ΅Π½ΠΈΡ Π°Π½ΡΠΈΠ°Π΄Π³Π΅Π·ΠΈΠΎΠ½Π½ΠΎΠΉ ΡΠΏΠΎΡΠΎΠ±Π½ΠΎΡΡΠΈ ΡΠΎΡΠΌΡΡΡΠΈΠ΅ ΠΊΠ°Π½Π°Π»Ρ ΠΌΠ°ΡΡΠΈΡ ΠΏΠΎΠΊΡΡΠ²Π°ΡΡ ΡΡΠΎΡΠΎΠΏΠ»Π°ΡΡΠΎΠΌ (ΡΠ΅ΡΠ»ΠΎΠ½ΠΎΠΌ).
ΠΠΎ ΡΠΎΡΠΌΠ΅ ΠΌΠ°ΡΡΠΈΡΡ Π΄Π΅Π»ΡΡ Π½Π° ΠΊΡΡΠ³Π»ΡΠ΅ (Π΄ΠΈΡΠΊΠΎΠ²ΡΠ΅) ΠΈ ΠΏΡΡΠΌΠΎΡΠ³ΠΎΠ»ΡΠ½ΡΠ΅. ΠΡΡΠΌΠΎΡΠ³ΠΎΠ»ΡΠ½ΡΠ΅ ΠΌΠ°ΡΡΠΈΡΡ ΡΡΡΠ°Π½Π°Π²Π»ΠΈΠ²Π°ΡΡ Π΄Π»Ρ ΡΠΎΡΠΌΠΎΠ²Π°Π½ΠΈΡ Π΄Π»ΠΈΠ½Π½ΡΡ ΠΈΠ·Π΄Π΅Π»ΠΈΠΉ (ΡΠΏΠ°Π³Π΅ΡΡΠΈ) Π½Π° Π°Π²ΡΠΎΠΌΠ°ΡΠΈΠ·ΠΈΡΠΎΠ²Π°Π½Π½ΡΡ Π»ΠΈΠ½ΠΈΡΡ Ρ ΠΏΠΎΠ΄Π²Π΅ΡΠ½ΠΎΠΉ ΡΡΡΠΊΠΎΠΉ, Π° Π΄ΠΈΡΠΊΠΎΠ²ΡΠ΅ β Π΄Π»Ρ ΡΠΎΡΠΌΠΎΠ²Π°Π½ΠΈΡ ΠΎΡΡΠ°Π»ΡΠ½ΡΡ Π²ΠΈΠ΄ΠΎΠ² Π΄Π»ΠΈΠ½Π½ΡΡ ΠΈ ΠΊΠΎΡΠΎΡΠΊΠΈΡ ΠΈΠ·Π΄Π΅Π»ΠΈΠΉ.
ΠΡΠΎΠΈΠ·Π²ΠΎΠ΄ΠΈΡΠ΅Π»ΡΠ½ΠΎΡΡΡ ΠΏΡΠ΅ΡΡΠΎΠ²ΡΡ ΠΌΠ°ΡΡΠΈΡ. ΠΡΠΎΠΈΠ·Π²ΠΎΠ΄ΠΈΡΠ΅Π»ΡΠ½ΠΎΡΡΡ ΠΌΠ°ΡΡΠΈΡ Ρ Π°ΡΠ°ΠΊΡΠ΅ΡΠΈΠ·ΡΠ΅ΡΡΡ ΠΊΠΎΠ»ΠΈΡΠ΅ΡΡΠ²ΠΎΠΌ ΡΡΡΡΡ ΠΈΠ·Π΄Π΅Π»ΠΈΠΉ, ΠΊΠΎΡΠΎΡΡΠ΅ Π²ΡΠΏΡΠ΅ΡΡΠΎΠ²ΡΠ²Π°ΡΡΡΡ ΡΠ΅ΡΠ΅Π· Π΅Π΅ ΠΎΡΠ²Π΅ΡΡΡΠΈΡ Π² Π΅Π΄ΠΈΠ½ΠΈΡΡ Π²ΡΠ΅ΠΌΠ΅Π½ΠΈ. ΠΡΠΎΠΈΠ·Π²ΠΎΠ΄ΠΈΡΠ΅Π»ΡΠ½ΠΎΡΡΡ ΠΏΡΠ΅ΡΡΠΎΠ²ΠΎΠΉ ΠΌΠ°ΡΡΠΈΡΡ Π·Π°Π²ΠΈΡΠΈΡ ΠΎΡ ΡΠΊΠΎΡΠΎΡΡΠΈ Π²ΡΠΏΡΠ΅ΡΡΠΎΠ²ΡΠ²Π°Π½ΠΈΡ, ΠΏΠ»ΠΎΡΠ°Π΄ΠΈ ΠΆΠΈΠ²ΠΎΠ³ΠΎ ΡΠ΅ΡΠ΅Π½ΠΈΡ ΠΌΠ°ΡΡΠΈΡΡ.
Π‘ΠΊΠΎΡΠΎΡΡΡ Π²ΡΠΏΡΠ΅ΡΡΠΎΠ²ΡΠ²Π°Π½ΠΈΡ ΠΌΠ°ΠΊΠ°ΡΠΎΠ½Π½ΠΎΠ³ΠΎ ΡΠ΅ΡΡΠ° ΡΠ΅ΡΠ΅Π· ΡΠΎΡΠΌΡΡΡΠΈΠ΅ ΠΎΡΠ²Π΅ΡΡΡΠΈΡ ΠΌΠ°ΡΡΠΈΡΡ ΠΎΠΏΡΠ΅Π΄Π΅Π»ΡΡΡΡΡ ΠΏΠ»Π°ΡΡΠΈΡΠ½ΠΎΡΡΡΡ ΡΠ΅ΡΡΠ° ΠΈ Π²Π΅Π»ΠΈΡΠΈΠ½ΠΎΠΉ Π΄Π°Π²Π»Π΅Π½ΠΈΡ ΠΏΡΠ΅ΡΡΠΎΠ²Π°Π½ΠΈΡ. ΠΠ»Π°ΡΡΠΈΡΠ½ΠΎΡΡΡ ΡΠ΅ΡΡΠ° Π·Π°Π²ΠΈΡΠΈΡ Π² ΠΎΡΠ½ΠΎΠ²Π½ΠΎΠΌ ΠΎΡ Π΅Π³ΠΎ Π²Π»Π°ΠΆΠ½ΠΎΡΡΠΈ ΠΈ ΡΠ΅ΠΌΠΏΠ΅ΡΠ°ΡΡΡΡ. Π‘ ΡΠ²Π΅Π»ΠΈΡΠ΅Π½ΠΈΠ΅ΠΌ Π²Π»Π°ΠΆΠ½ΠΎΡΡΠΈ ΡΠ΅ΡΡΠ° Π΄ΠΎ 33 % Π²ΠΎΠ·ΡΠ°ΡΡΠ°Π΅Ρ ΠΏΠ»Π°ΡΡΠΈΡΠ½ΠΎΡΡΡ ΠΈ ΡΠΊΠΎΡΠΎΡΡΡ Π²ΡΠΏΡΠ΅ΡΡΠΎΠ²ΡΠ²Π°Π½ΠΈΡ. ΠΠ°Π»ΡΠ½Π΅ΠΉΡΠ΅Π΅ ΡΠ²Π΅Π»ΠΈΡΠ΅Π½ΠΈΠ΅ Π²Π»Π°ΠΆΠ½ΠΎΡΡΠΈ ΡΠΏΠΎΡΠΎΠ±ΡΡΠ²ΡΠ΅Ρ ΠΏΠΎΠ»ΡΡΠ΅Π½ΠΈΡ ΠΏΠΎΡΠ»Π΅ Π·Π°ΠΌΠ΅ΡΠ° ΠΊΡΡΠΏΠ½ΠΎΠΊΠΎΠΌΠΊΠΎΠ²Π°ΡΠΎΠ³ΠΎ ΡΠ΅ΡΡΠ°, ΠΏΠ»ΠΎΡ ΠΎ Π·Π°ΠΏΠΎΠ»Π½ΡΡΡΠ΅Π³ΠΎ ΡΠ½Π΅ΠΊΠΎΠ²ΡΡ ΠΊΠ°ΠΌΠ΅ΡΡ, ΠΏΡΠΈΠ»ΠΈΠΏΠ°Π½ΠΈΡ ΡΠ΅ΡΡΠ° ΠΊ ΡΠ½Π΅ΠΊΡ ΠΈ ΡΡΠ΅Π½ΠΊΠ°ΠΌ ΠΊΠ°ΠΌΠ΅ΡΡ β ΠΏΠ°Π΄Π°Π΅Ρ Π΄Π°Π²Π»Π΅Π½ΠΈΠ΅ ΠΏΡΠ΅ΡΡΠΎΠ²Π°Π½ΠΈΡ. ΠΡΠ΅ ΡΡΠΎ ΠΏΡΠΈΠ²ΠΎΠ΄ΠΈΡ ΠΊ ΡΠ½ΠΈΠΆΠ΅Π½ΠΈΡ ΡΠΊΠΎΡΠΎΡΡΠΈ ΠΏΡΠ΅ΡΡΠΎΠ²Π°Π½ΠΈΡ.
Π‘ ΡΠΎΡΡΠΎΠΌ ΡΠ΅ΠΌΠΏΠ΅ΡΠ°ΡΡΡΡ ΡΠ΅ΡΡΠ° ΠΏΡΠΈΠΌΠ΅ΡΠ½ΠΎ Π΄ΠΎ 70Β°Π‘ ΡΠΊΠΎΡΠΎΡΡΡ Π²ΡΠΏΡΠ΅ΡΡΠΎΠ²ΡΠ²Π°Π½ΠΈΡ Π±ΡΠ΄Π΅Ρ ΡΠ²Π΅Π»ΠΈΡΠΈΠ²Π°ΡΡΡΡ. ΠΠ°Π»ΡΠ½Π΅ΠΉΡΠ΅Π΅ ΡΠ²Π΅Π»ΠΈΡΠ΅Π½ΠΈΠ΅ ΡΠ΅ΠΌΠΏΠ΅ΡΠ°ΡΡΡΡ ΠΏΡΠΈΠ²ΠΎΠ΄ΠΈΡ ΠΊ ΡΠΎΡΡΡ ΡΠΊΠΎΡΠΎΡΡΠΈ ΠΏΡΠ΅ΡΡΠΎΠ²Π°Π½ΠΈΡ: ΡΠΌΠ΅Π½ΡΡΠ΅Π½ΠΈΠ΅ ΡΠΎΠΏΡΠΎΡΠΈΠ²Π»Π΅Π½ΠΈΡ ΠΌΠ°ΡΡΠΈΡΡ ΠΏΡΠΎΠ΄Π°Π²Π»ΠΈΠ²Π°Π½ΠΈΡ ΠΎΡΠ΅Π½Ρ ΠΏΠ»Π°ΡΡΠΈΡΠ½ΠΎΠ³ΠΎ ΡΠ΅ΡΡΠ° ΠΏΡΠΈΠ²ΠΎΠ΄ΠΈΡ ΠΊ ΠΏΠ°Π΄Π΅Π½ΠΈΡ Π΄Π°Π²Π»Π΅Π½ΠΈΡ ΠΏΡΠ΅ΡΡΠΎΠ²Π°Π½ΠΈΡ.
ΠΠ»ΠΎΡΠ°Π΄Ρ ΠΆΠΈΠ²ΠΎΠ³ΠΎ ΡΠ΅ΡΠ΅Π½ΠΈΡ ΠΌΠ°ΡΡΠΈΡΡ ΠΈΠ»ΠΈ ΠΏΠ»ΠΎΡΠ°Π΄Ρ ΠΌΠ°ΡΡΠΈΡΡ Π½Π° ΡΠ²Π΅ΡΡ Π·Π°Π²ΠΈΡΠΈΡ ΠΎΡ ΡΠΎΡΠΌΡ ΠΎΡΠ²Π΅ΡΡΡΠΈΠΉ ΠΈ ΠΎΡ ΠΊΠΎΠ»ΠΈΡΠ΅ΡΡΠ²Π° ΠΎΡΠ²Π΅ΡΡΡΠΈΠΉ Π² ΠΌΠ°ΡΡΠΈΡΠ΅. ΠΡΠΈ ΡΠΊΡΠΏΠ»ΡΠ°ΡΠ°ΡΠΈΠΈ Π·Π°ΡΠΎΡΠ΅Π½Π½ΡΡ ΠΌΠ°ΡΡΠΈΡ ΠΏΠ»ΠΎΡΠ°Π΄Ρ ΠΆΠΈΠ²ΠΎΠ³ΠΎ ΡΠ΅ΡΠ΅Π½ΠΈΡ ΠΌΠ°ΡΡΠΈΡΡ ΡΠΌΠ΅Π½ΡΡΠ°Π΅ΡΡΡ, ΡΡΠΎ ΠΏΡΠΈΠ²ΠΎΠ΄ΠΈΡ ΠΊ ΡΠ½ΠΈΠΆΠ΅Π½ΠΈΡ ΠΏΡΠΎΠΈΠ·Π²ΠΎΠ΄ΠΈΡΠ΅Π»ΡΠ½ΠΎΡΡΠΈ ΠΌΠ°ΡΡΠΈΡ. ΠΠ·Π΄Π΅Π»ΠΈΡ, ΠΈΠ·Π³ΠΎΡΠΎΠ²Π»Π΅Π½Π½ΡΠ΅ ΠΈΠ· ΡΠ΅ΡΡΠ°, Π½Π°Π³ΡΠ΅ΡΠΎΠ³ΠΎ Π΄ΠΎ ΡΠ΅ΠΌΠΏΠ΅ΡΠ°ΡΡΡΡ Π²ΡΡΠ΅ 70Β°Π‘, ΠΈΠΌΠ΅ΡΡ ΠΏΠ»ΠΎΡ ΠΈΠ΅ Π²Π°ΡΠΎΡΠ½ΡΠ΅ ΡΠ²ΠΎΠΉΡΡΠ²Π° Π²ΡΠ»Π΅Π΄ΡΡΠ²ΠΈΠ΅ Π³Π»ΡΠ±ΠΎΠΊΠΈΡ ΠΈΠ·ΠΌΠ΅Π½Π΅Π½ΠΈΠΉ ΡΠ²ΠΎΠΉΡΡΠ² Π±Π΅Π»ΠΊΠΎΠ²ΡΡ Π²Π΅ΡΠ΅ΡΡΠ². ΠΠΏΡΠΈΠΌΠ°Π»ΡΠ½ΡΠΌΠΈ ΡΠ΅ΠΌΠΏΠ΅ΡΠ°ΡΡΡΠ°ΠΌΠΈ ΡΠ΅ΡΡΠ° ΠΏΠ΅ΡΠ΅Π΄ ΠΌΠ°ΡΡΠΈΡΠ΅ΠΉ ΡΠ»Π΅Π΄ΡΠ΅Ρ ΡΡΠΈΡΠ°ΡΡ: ΠΏΡΠΈ ΠΏΡΠΎΠΈΠ·Π²ΠΎΠ΄ΡΡΠ²Π΅ Π΄Π»ΠΈΠ½Π½ΡΡ ΠΈΠ·Π΄Π΅Π»ΠΈΠΉ β 60Β°Π‘, ΠΏΡΠΈ ΠΏΡΠΎΠΈΠ·Π²ΠΎΠ΄ΡΡΠ²Π΅ ΠΊΠΎΡΠΎΡΠΊΠΈΡ β 70Β°Π‘. ΠΠ΄Π½Π°ΠΊΠΎ ΡΠΎΠ²ΡΠ΅ΠΌΠ΅Π½Π½ΡΠ΅ ΠΏΡΠ΅ΡΡΡ ΠΏΡΠΈ ΠΎΡΡΡΡΡΡΠ²ΠΈΠΈ ΡΠΏΠ΅ΡΠΈΠ°Π»ΡΠ½ΠΎΠ³ΠΎ ΠΏΠΎΠ΄ΠΎΠ³ΡΠ΅Π²Π° ΡΠ΅ΡΡΠ° ΡΠ΅Π΄ΠΊΠΎ ΠΌΠΎΠ³ΡΡ ΠΎΠ±Π΅ΡΠΏΠ΅ΡΠΈΡΡ ΡΠ°ΠΊΠΈΠ΅ ΡΠ΅ΠΌΠΏΠ΅ΡΠ°ΡΡΡΡ.
Β
Π Π°Π·Π΄Π΅Π»ΠΊΠ° ΡΡΡΡΡ ΠΌΠ°ΠΊΠ°ΡΠΎΠ½Π½ΡΡ ΠΈΠ·Π΄Π΅Π»ΠΈΠΉ
Π Π°Π·Π΄Π΅Π»ΠΊΡ ΡΡΡΡΡ ΠΌΠ°ΠΊΠ°ΡΠΎΠ½Π½ΡΡ ΠΈΠ·Π΄Π΅Π»ΠΈΠΉ ΠΎΡΡΡΠ΅ΡΡΠ²Π»ΡΡΡ Π½Π΅ΠΏΠΎΡΡΠ΅Π΄ΡΡΠ²Π΅Π½Π½ΠΎ ΠΏΠΎΡΠ»Π΅ Π²ΡΠΏΡΠ΅ΡΡΠΎΠ²ΡΠ²Π°Π½ΠΈΡ; Π΅Π΅ ΡΠ΅Π»ΡΡ ΡΠ²Π»ΡΠ΅ΡΡΡ ΠΏΠΎΠ΄Π³ΠΎΡΠΎΠ²ΠΊΠ° ΠΈΠ·Π΄Π΅Π»ΠΈΠΉ ΠΊ ΡΡΡΠΊΠ΅.
Π Π°Π·Π΄Π΅Π»ΠΊΠ° Π·Π°ΠΊΠ»ΡΡΠ°Π΅ΡΡΡ Π² ΠΎΠ±Π΄ΡΠ²ΠΊΠ΅, ΡΠ΅Π·ΠΊΠ΅ ΠΈ ΡΠ°ΡΠΊΠ»Π°Π΄ΠΊΠ΅ (ΠΈΠ»ΠΈ ΡΠ°Π·Π²Π΅ΡΠΈΠ²Π°Π½ΠΈΠΈ) ΠΎΡΡΠΎΡΠΌΠΎΠ²Π°Π½Π½ΡΡ ΡΡΡΡΡ ΠΌΠ°ΠΊΠ°ΡΠΎΠ½Π½ΡΡ ΠΈΠ·Π΄Π΅Π»ΠΈΠΉ. ΠΡ ΠΏΡΠ°Π²ΠΈΠ»ΡΠ½ΠΎΡΡΠΈ ΡΠ°Π·Π΄Π΅Π»ΠΊΠΈ Π·Π°Π²ΠΈΡΡΡ ΡΠ°ΠΊΠΈΠ΅ ΠΏΠΎΠΊΠ°Π·Π°ΡΠ΅Π»ΠΈ, ΠΊΠ°ΠΊ ΠΏΡΠΎΠΈΠ·Π²ΠΎΠ΄ΠΈΡΠ΅Π»ΡΠ½ΠΎΡΡΡ ΡΡΡΠΈΠ»ΡΠ½ΠΎΠ³ΠΎ ΠΎΠ±ΠΎΡΡΠ΄ΠΎΠ²Π°Π½ΠΈΡ, ΡΠ°ΡΡ ΠΎΠ΄ ΡΡΡΡΡ ΠΈ ΠΊΠ°ΡΠ΅ΡΡΠ²ΠΎ Π³ΠΎΡΠΎΠ²ΡΡ ΠΌΠ°ΠΊΠ°ΡΠΎΠ½Π½ΡΡ ΠΈΠ·Π΄Π΅Π»ΠΈΠΉ.
ΠΠ±Π΄ΡΠ²ΠΊΠ° ΡΡΡΡΡ ΠΈΠ·Π΄Π΅Π»ΠΈΠΉ. ΠΡΠΏΡΠ΅ΡΡΠΎΠ²ΡΠ²Π°Π΅ΠΌΡΠ΅ ΡΡΡΡΠ΅ ΠΌΠ°ΠΊΠ°ΡΠΎΠ½Π½ΡΠ΅ ΠΈΠ·Π΄Π΅Π»ΠΈΡ Π½Π° Π²ΡΡ ΠΎΠ΄Π΅ ΠΈΠ· ΠΌΠ°ΡΡΠΈΡΡ ΡΠ²Π»ΡΡΡΡΡ ΠΏΠ»Π°ΡΡΠΈΡΠ½ΡΠΌ, Π΄ΠΎΠ²ΠΎΠ»ΡΠ½ΠΎ Π»Π΅Π³ΠΊΠΎ Π΄Π΅ΡΠΎΡΠΌΠΈΡΡΠ΅ΠΌΡΠΌ ΠΌΠ°ΡΠ΅ΡΠΈΠ°Π»ΠΎΠΌ. ΠΠ»Ρ ΠΎΠ±Π»Π΅Π³ΡΠ΅Π½ΠΈΡ ΡΠ΅Π·ΠΊΠΈ ΠΈ ΠΏΡΠ΅Π΄ΠΎΡΠ²ΡΠ°ΡΠ΅Π½ΠΈΡ ΡΠ»ΠΈΠΏΠ°Π½ΠΈΡ ΡΡΡΡΠ΅ ΠΈΠ·Π΄Π΅Π»ΠΈΡ ΠΏΡΠΈ Π²ΡΡ ΠΎΠ΄Π΅ ΠΈΠ· ΡΠΎΡΠΌΡΡΡΠΈΡ ΠΎΡΠ²Π΅ΡΡΡΠΈΠΉ ΠΌΠ°ΡΡΠΈΡΡ ΠΈΠ½ΡΠ΅Π½ΡΠΈΠ²Π½ΠΎ ΠΎΠ±Π΄ΡΠ²Π°ΡΡΡΡ Π²ΠΎΠ·Π΄ΡΡ ΠΎΠΌ. ΠΡΠΎ ΠΏΡΠΈΠ²ΠΎΠ΄ΠΈΡ ΠΊ ΠΎΠ±ΡΠ°Π·ΠΎΠ²Π°Π½ΠΈΡ Π½Π° ΠΈΡ ΠΏΠΎΠ²Π΅ΡΡ Π½ΠΎΡΡΠΈ ΠΏΠΎΠ΄ΡΡΡΠ΅Π½Π½ΠΎΠ³ΠΎ ΡΠ»ΠΎΡ, ΠΊΠΎΡΠΎΡΡΠΉ ΠΏΡΠ΅ΠΏΡΡΡΡΠ²ΡΠ΅Ρ ΡΠ»ΠΈΠΏΠ°Π½ΠΈΡ ΠΈΠ·Π΄Π΅Π»ΠΈΠΉ ΠΏΡΠΈ ΡΡΡΠΊΠ΅ ΠΈΡ Π½Π° ΡΡΠ°Π½ΡΠΏΠΎΡΡΠ΅ΡΠ°Ρ (ΠΊΠΎΡΠΎΡΠΊΠΈΡ ΠΈΠ·Π΄Π΅Π»ΠΈΡ) ΠΈΠ»ΠΈ Π² Π»ΠΎΡΠΊΠΎΠ²ΡΡ ΠΊΠ°ΡΡΠ΅ΡΠ°Ρ (ΠΌΠ°ΠΊΠ°ΡΠΎΠ½Ρ), Π° ΡΠ°ΠΊΠΆΠ΅ ΠΏΡΠΈΠ»ΠΈΠΏΠ°Π½ΠΈΡ ΠΈΡ ΠΊ Π±Π°ΡΡΡΠ½Π°ΠΌ (ΠΏΠΎΠ΄Π²Π΅ΡΠ½Π°Ρ ΡΡΡΠΊΠ° Π΄Π»ΠΈΠ½Π½ΡΡ ΠΈΠ·Π΄Π΅Π»ΠΈΠΉ).
ΠΠ±Π΄ΡΠ²ΠΊΡ ΠΎΡΡΡΠ΅ΡΡΠ²Π»ΡΡΡ Π²ΠΎΠ·Π΄ΡΡ ΠΎΠΌ ΡΠΎΡΠΌΠΎΠ²ΠΎΡΠ½ΠΎΠ³ΠΎ ΠΎΡΠ΄Π΅Π»Π΅Π½ΠΈΡ ΡΠ΅ΠΌΠΏΠ΅ΡΠ°ΡΡΡΠΎΠΉ ΠΎΠΊΠΎΠ»ΠΎ 25Β°Π‘ ΠΈ ΠΎΡΠ½ΠΎΡΠΈΡΠ΅Π»ΡΠ½ΠΎΠΉ Π²Π»Π°ΠΆΠ½ΠΎΡΡΡΡ 60-70%. ΠΡΠΈ ΡΡΠΎΠΌ ΠΎΡΠ½ΠΎΡΠΈΡΠ΅Π»ΡΠ½Π°Ρ Π²Π»Π°ΠΆΠ½ΠΎΡΡΡ ΡΡΡΡΡ ΠΈΠ·Π΄Π΅Π»ΠΈΠΉ ΡΠ½ΠΈΠΆΠ°Π΅ΡΡΡ Π½Π° 1-2 % ΠΏΡΠΈ ΡΡΠ°Π΄ΠΈΡΠΈΠΎΠ½Π½ΡΡ ΡΠ΅ΠΆΠΈΠΌΠ°Ρ Π·Π°ΠΌΠ΅ΡΠ° ΠΈ ΡΠΎΡΠΌΠΎΠ²Π°Π½ΠΈΡ, Π½Π° 3-4 % ΠΏΡΠΈ Π²ΡΡΠΎΠΊΠΎΡΠ΅ΠΌΠΏΠ΅ΡΠ°ΡΡΡΠ½ΡΡ ΡΠ΅ΠΆΠΈΠΌΠ°Ρ .
ΠΡΠΈ ΠΈΡΠΏΠΎΠ»ΡΠ·ΠΎΠ²Π°Π½ΠΈΠΈ ΠΏΠΎΠ΄Π²Π΅ΡΠ½ΠΎΠΉ ΡΡΡΠΊΠΈ Π΄Π»ΠΈΠ½Π½ΡΡ ΠΈΠ·Π΄Π΅Π»ΠΈΠΉ (Π½Π° Π±Π°ΡΡΡΠ½Π°Ρ ) ΠΎΠ±Π΄ΡΠ²ΠΊΡ Π½Π΅ΠΎΠ±Ρ ΠΎΠ΄ΠΈΠΌΠΎ ΠΏΡΠΎΠ²ΠΎΠ΄ΠΈΡΡ ΡΡΠ°ΡΠ΅Π»ΡΠ½ΠΎ, ΠΈΠ·Π±Π΅Π³Π°Ρ ΡΡΠ΅Π·ΠΌΠ΅ΡΠ½ΠΎΠΉ ΠΏΠΎΠ΄ΡΡΡΠΊΠΈ ΠΏΠΎΠ²Π΅ΡΡ Π½ΠΎΡΡΠΈ ΠΈΠ·Π΄Π΅Π»ΠΈΠΉ, ΡΠ°ΠΊ ΠΊΠ°ΠΊ Π²ΠΎΠ·ΠΌΠΎΠΆΠ½ΠΎ ΡΠ°Π·ΡΡΡΠ΅Π½ΠΈΠ΅ ΠΏΠΎΠ²Π΅ΡΡ Π½ΠΎΡΡΠ½ΠΎΠ³ΠΎ ΡΠ»ΠΎΡ ΠΈΠ·Π΄Π΅Π»ΠΈΠΉ Π² ΠΌΠ΅ΡΡΠ°Ρ ΠΏΠ΅ΡΠ΅Π³ΠΈΠ±Π° ΠΈ ΠΏΠ°Π΄Π΅Π½ΠΈΠ΅ ΠΈΡ Ρ Π±Π°ΡΡΡΠ½ΠΎΠ² ΠΏΡΠΈ ΡΠ°Π·Π²Π΅ΡΠΈΠ²Π°Π½ΠΈΠΈ ΠΈΠ»ΠΈ Π² ΠΏΡΠΎΡΠ΅ΡΡΠ΅ Π²ΡΡΡΡΠΈΠ²Π°Π½ΠΈΡ.
Π Π°ΡΠΊΠ»Π°Π΄ΠΊΠ°. ΠΠ°Π·Π½Π°ΡΠ΅Π½ΠΈΠ΅
ΡΠ°ΡΠΊΠ»Π°Π΄ΠΊΠΈ Π·Π°ΠΊΠ»ΡΡΠ°Π΅ΡΡΡ Π² ΡΠ°Π·ΠΌΠ΅ΡΠ΅Π½ΠΈΠΈ ΡΠ°Π·ΡΠ΅Π·Π°Π½Π½ΠΎΠ³ΠΎ ΠΏΠΎΠ»ΡΡΠ°Π±ΡΠΈΠΊΠ°ΡΠ° Π½Π° ΡΡΡΠΈΠ»ΡΠ½ΡΡ
ΠΏΠΎΠ²Π΅ΡΡ
Π½ΠΎΡΡΡΡ
. ΠΠΎΠ΄Π°ΡΠ° ΡΡΡΠΎΠ³ΠΎ ΠΏΡΠΎΠ΄ΡΠΊΡΠ° Π² ΡΡΡΠΈΠ»ΠΊΡ ΠΎΡΡΡΠ΅ΡΡΠ²Π»ΡΠ΅ΡΡΡ Ρ ΠΏΠΎΠΌΠΎΡΡΡ
ΠΌΠ΅Ρ
Π°Π½ΠΈΡΠ΅ΡΠΊΠΎΠ³ΠΎ ΡΠ°ΡΠΊΠ»Π°Π΄ΡΠΈΠΊΠ° (ΡΠ°ΡΡΡΡΡΡΠΈΠΊΠ°). Π’ΡΡΠ±Π° ΠΈΠ»ΠΈ ΡΡΠ°Π½ΡΠΏΠΎΡΡΠ΅Ρ ΡΠ°ΡΠΊΠ»Π°Π΄ΡΠΈΠΊΠ°
ΡΠΎΠ²Π΅ΡΡΠ°Π΅Ρ ΠΊΠ°ΡΠ°ΡΠ΅Π»ΡΠ½ΡΠ΅ Π΄Π²ΠΈΠΆΠ΅Π½ΠΈΡ Π½Π°Π΄ Π΄Π²ΠΈΠΆΡΡΠ΅ΠΉΡΡ Π»Π΅Π½ΡΠΎΠΉ Π²Π΅ΡΡ
Π½Π΅Π³ΠΎ ΡΡΠ°Π½ΡΠΏΠΎΡΡΠ΅ΡΠ° ΡΡΡΠΈΠ»ΠΊΠΈ,
ΡΠ°ΡΠΏΡΠ΅Π΄Π΅Π»ΡΡ Π½Π° Π½Π΅ΠΉ ΠΏΡΠΎΠ΄ΡΠΊΡ ΡΠ°Π²Π½ΠΎΠΌΠ΅ΡΠ½ΡΠΌ ΡΠ»ΠΎΠ΅ΠΌ. Π’ΠΎΠ»ΡΠΈΠ½Π° ΡΠ»ΠΎΡ ΠΏΡΠΎΠ΄ΡΠΊΡΠ°
ΡΠ΅Π³ΡΠ»ΠΈΡΡΠ΅ΡΡΡ ΠΈΠ·ΠΌΠ΅Π½Π΅Π½ΠΈΠ΅ΠΌ ΡΠΊΠΎΡΠΎΡΡΠΈ Π΄Π²ΠΈΠΆΠ΅Π½ΠΈΡ Π»Π΅Π½ΡΡ. Π’ΠΎΠ»ΡΠΈΠ½Π° ΡΠ»ΠΎΡ ΡΠΎΡΡΠ°Π²Π»ΡΠ΅Ρ ΠΎΡ 2
Π΄ΠΎ 5 ΡΠΌ Π² Π·Π°Π²ΠΈΡΠΈΠΌΠΎΡΡΠΈ ΠΎΡ Π°ΡΡΠΎΡΡΠΈΠΌΠ΅Π½ΡΠ° ΠΈΠ·Π΄Π΅Π»ΠΈΠΉ. ΠΠ»Ρ ΠΏΡΠ΅Π΄ΠΎΡΠ²ΡΠ°ΡΠ΅Π½ΠΈΡ ΠΎΠ±ΡΠ°Π·ΠΎΠ²Π°Π½ΠΈΡ
ΡΠ»ΠΈΡΠΊΠΎΠ² ΠΈΠ·Π΄Π΅Π»ΠΈΠΉ Π½Π΅ΠΎΠ±Ρ
ΠΎΠ΄ΠΈΠΌΠΎ ΠΏΠΎΠ΄Π΄Π΅ΡΠΆΠΈΠ²Π°ΡΡ Π½Π° Π²Π΅ΡΡ
Π½ΠΈΡ
Π»Π΅Π½ΡΠ°Ρ
ΡΡΡΠΈΠ»ΠΎΠΊ (ΠΏΠΎΠΊΠ° ΠΈΠ·Π΄Π΅Π»ΠΈΡ
Π΅ΡΠ΅ ΠΏΠ»Π°ΡΡΠΈΡΠ½Ρ ΠΈ ΠΌΠΎΠ³ΡΡ ΡΠ»ΠΈΠΏΠ°ΡΡΡΡ ΠΌΠ΅ΠΆΠ΄Ρ ΡΠΎΠ±ΠΎΠΉ) ΠΌΠΈΠ½ΠΈΠΌΠ°Π»ΡΠ½ΡΡ ΡΠΎΠ»ΡΠΈΠ½Ρ ΡΠ»ΠΎΡ.
ΠΡΡΠΎΡΠ½ΠΈΠΊ: http://ΠΏΠΎ ΠΌΠ°ΡΠ΅ΡΠΈΠ°Π»Π°ΠΌ ΠΈΠ½ΡΠ΅ΡΠ½Π΅Ρ ΠΈΠ·Π΄Π°Π½ΠΈΠΉ ΠΈ ΡΠΎΠ±ΡΡΠ²Π΅Π½Π½ΡΡ Π½Π°Π±Π»ΡΠ΄Π΅Π½ΠΈΠΉ
filerkin.at.ua