Фибролит — Википедия. Что такое Фибролит
Фибролит (от лат. fibra — волокно и греч. Λίθος камень)[источник не указан 140 дней] — строительный плитный материал.
Подобные плиты появились в конце 1920-х годов. Фибролит обычно изготавливается из специальных древесных стружек (волокна) и неорганического вяжущего вещества. Древесное волокно получают на специальных станках в виде тонких и узких лент, то есть получается не щепа, а длинная узкая стружка. В качестве вяжущего используют портландцемент, реже — магнезиальное вяжущее.
Является аналогом арболита.
Технология
Древесное волокно вначале минерализуют раствором хлористого кальция или жидкого стекла или сернистого глинозема. После этого древесное волокно смешивают с цементом и водой. Строительные плиты формуют, используя давление 0,5 МПа. После формовки их помещают для твердения в пропарочные камеры. Затвердевшие плиты сушат до влажности не более 20 %.
По ГОСТу плиты должны иметь длину 240 и 300 см, ширину — 60 и 120 см, толщину — 3—15 см. Иногда делают блоки вместо плит.
Фибролитовые плиты имеет широкую сферу применения, является инновационной заменой традиционных плитных материалов: OSB, ЦСП, СЦП, ГВЛ, ДСП, СМЛ, ППС, фанера и пр.
Свойства
По плотности — делятся на марки Ф-300 (теплоизоляционный фибролит) и Ф-400, Ф-500 (тепло изоляционно-конструктивный фибролит). Теплопроводность — 0,08—0,1 Вт/(мК).
Фибролит не горит открытым пламенем. Легко обрабатывается: его можно пилить, сверлить и вбивать в него гвозди. Водопоглощение цементного фибролита — не более 35—45 %.
При влажности выше 35 % он может поражаться домовым грибом, поэтому его нужно защищать от увлажнения — в частности, путём оштукатуривания. Шероховатая поверхность фибролита способствует хорошему сцеплению со штукатуркой.
Использование
Магнезиальный фибролит
Изготавливают без специальной минерализации, так как каустический магнезит затворяется водными растворами магнезиальных солей, которые связывают содержащиеся в древесине водорастворимые вещества. Прочность его несколько выше, чем цементного. Это связано с тем, что кристаллизующиеся при сушке в клетках древесины соли препятствуют её усушке, а это положительно сказывается на сцеплении магнезиального камня с волокнами. Магнезиальный фибролит обладает, по сравнению с цементным, меньшей водостойкостью и большей гигроскопичностью.
Теплоизоляционно-конструктивный фибролит
Его применяют для утепления стен и покрытий, конструкционный — для перегородок, каркасных стен и перекрытий только в сухих условиях.
В настоящее время основное применение фибролита — установка несъемной опалубки в строительстве. Фибролитовые плиты не удаляются, как некоторые другие виды опалубки, а остаются конструктивной частью или стены, или любого перекрытия.
См. также
Литература
wiki.sc
Фибролит
Здравствуйте, уважаемый читатель блога, вы знаете, что есть такое дерево которое не горит, конечно, оно не натуральное, это фибролит. Новые технологии в строительной области призваны найти универсальный материал. Он должен обладать достойными качествами, быть надежным и, конечно же, экологически чистым.
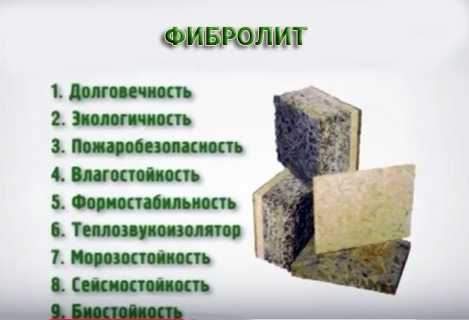
Порою одно противоречит другому. Если свойства строительного материала отвечают всем требованиям: не горюч, инертен к химическим веществам и стоек к биологическим воздействиям, это еще не значит, что он не вредит здоровью людей.
Современные технологии призваны совместить оба требования, так был создан строительный материал под названием фибролит. Еще в 70-х годах, в СССР. Правда, в то время идея не была поддержана на государственном уровне. Зато европейские производители приняли проект и усовершенствовали его качества.
Чем отличается фибролит от других материалов?
Фибролит = волокно + цемент. Вопрос вторичного использования отходов в деревообрабатывающей промышленности всегда был актуален. Одним из применений древесных отходов, стружки и является производство фибролита. С дерева снимают «шерсть» на станках, прессуют и минерализуют.
В стружку добавляют портландцемент марки М400 и наполнители, призванные сохранять древесный материал от горения, влаги, низких и высоких температур, воздействия насекомых и распространения грибка. Такие добавки, как жидкое стекло, известь, хлористый калий и сернокислый алюминий являются составной частью нового материала, фибролита, который был забыт много лет назад.
Где используют фибролит?
Материал производят в форме плит. От ее толщины и наполнения зависит вид фибролита и область применения. При этом он может быть обычным, акустическим, композитным и высокой плотности.
Плита из обычного фибролита имеет толщину до 30 мм. Для минерализации волокна используют серый цемент. Такую разновидность используют в качестве теплоизоляционного материала. Так как фибролит обладает низкой теплопроводностью, им защищают стены, перегородки и кровлю от холода. При этом дом будет дышать, а значит, микроклимат в комнатах будет благоприятным. Материал поглотит излишки влаги и вернет ее при необходимости. Он не даст стенам и кровле промораживаться и защитит их от влаги. Марка фибролита обычного — Ф300.
Панели из акустического фибролита имеют пониженную плотность. Толщина — до 100 мм. Размер — 2800х600 мм. Данный материал используют для поглощения шума в производственных цехах, музыкальных студиях, развлекательных комплексах и обычных жилых домах. Акустический фибролит производится с добавлением белого цемента. Его марка — Ф400, Ф500. Панели можно окрашивать.
Композитная разновидность представляет собой сэндвич-панель. Она состоит из обычного фибролита и прослойки утеплителя. В качестве теплоизоляционного материала чаще всего используют минеральную вату, пенополиуретан. Толщина древесного слоя — до 10 мм, утеплителя — до 90 мм. Сэндвич-панелями из композитного фибролита обшивают несущие стены, перегородки, пол и кровлю при каркасном строительстве. При этом дом получит дополнительную изоляцию от холода. В то же время не будут нарушены процессы воздухообмена.
Материал повышенной плотности применяют не только в целях изоляции от шума и от холода. Его используют для установки несъемной опалубки и строительства перегородок в помещении. Эти плиты более устойчивы к нагрузкам. Данный вид фибролита распространен в Японии в сейсмоопасных зонах.
Магнезитовый фибролит сочетает в себе все то, к чему и стремились современные технологии. Обладая высокой прочностью и уникальными качествами, он является экологически чистым материалом, не выделяет неприятного запаха и паров, способных нанести вред здоровью, что очень важно особенно для людей, страдающих бронхиальными заболеваниями.
Эта разновидность материала абсолютно устойчива к огню, имеет категорию стойкости — НГ. Достигается эта способность с помощью использования добавки — каустического магнезита. Он связывает в древесном материале вещества, растворимые в воде. Использования бишофита говорит о том, что материал будет защищен от внешних воздействий.
Прочность материала не такая высокая, как у фибролита с добавлением цемента, но специалисты утверждают, что он имеет целебные качества. Это связано с бишофитом, который является природным компонентом и содержит в себе все компоненты морской соли: йод, бром, калий, натрий, медь, молибден, железо.
Материал используют для несъемной опалубки, устройства перегородок в помещении, в качестве обшивки стен. Магнезитовый фибролит обладает такими же качествами, как и тот, что содержит цемент.
Дом, при строительстве которого использовали фибролитовые плиты, будет теплым, в нем можно наслаждаться тишиной. К тому же бишофит станет вашим невидимым лекарем.
Буду рад вашим комментариям по теме фибролит.
Cтатьи похожей тематики:
Ваша благодарность за мою статью это клик по любой кнопке ниже. Спасибо!
klyshko.ru
📌 Фибролит — это… 🎓 Что такое Фибролит?
Фибролит — строительный плитный материал.
Общие сведения
Подобные плиты появились в конце 20-х годов ХХ века. Фибролит — обычно изготавливается из специальных древесных стружек (древесной шерсти) и неорганического вяжущего вещества (ГОСТ 19222-84).
Древесную шерсть получают на специальных станках в виде тонких и узких лент, то есть получается не щепа, а длинная узкая стружка, похожая на шерсть, отчего и пошло название. В качестве вяжущего используют портландцемент, реже — магнезиальное вяжущее.
Является аналогом арболита.
Технология
Древесную шерсть вначале минерализуют раствором хлористого кальция или жидкого стекла или сернистого глинозема. После этого древесную шерсть смешивают с цементом и водой.
Строительные плиты формуют используя давление 0,5 МПа. После формовки их помещают для твердения в пропарочные камеры. Затвердевшие плиты сушат до влажности не более 20 %.
По ГОСТу плиты должны иметь длину 240 и 300 см, ширину —60 и 120 см, толщину — 3—15 мм. Иногда делают блоки вместо плит.
Свойства
По плотности — делятся на марки Ф-300 (теплоизоляционный фибролит) и Ф-400, Ф-500 (тепло изоляционно-конструктивный фибролит). Теплопроводность — 0,08—0,1 Вт/(мК).
Фибролит не горит открытым пламенем. Легко обрабатывается: его можно пилить, сверлить и вбивать в него гвозди. Водопоглощение цементного фибролита — не более 35—45 %.
При влажности выше 35 % он может поражаться домовым грибом, поэтому его нужно защищать от увлажнения — в частности путем оштукатуривания. Шероховатая поверхность фибролита способствует хорошему сцеплению со штукатуркой.
Использование
Магнезиальный фибролит
Изготавливают без специальной минерализации, так как каустический магнезит затворяется водными растворами магнезиальных солей, которые связывают содержащиеся в древесине водорастворимые вещества. Прочность его несколько выше, чем цементного. Это связано с тем, что кристаллизующиеся при сушке в клетках древесины соли препятствуют ее усушке, а это положительно сказывается на сцеплении магнезиального камня с шерстью. Магнезиальный фибролит обладает, по сравнению с цементным, меньшей водостойкостью и большей гигроскопичностью.
Теплоизоляционно-конструктивный фибролит
Его применяют для утепления стен и покрытий, конструкционный — для перегородок, каркасных стен и перекрытий только в сухих условиях.
В настоящее время основное применение фибролита — установка несъемной опалубки в строительстве. Фибролитовые плиты не удаляются, как некоторые другие виды опалубки, а остаются конструктивной частью или стены, или любого перекрытия.
См. также
Ссылки
dic.academic.ru
Фибролит. Свойства, сырье, производство, применение
Фибролит – это плитный материал из спрессованной древесной шерсти, склеенной затвердевшим минеральным вяжущим. Фирболит характеризуется неоднородным крупнопористым строением с сообщающимися порами. Объемная масса (средняя плотность) – 300…500 кг/м
Теплопроводность сухого фибролита – 0,1…0,15 Вт/(м0С). При равновесной влажности – 6…8% фибролит имеет коэффициент теплопроводности 0,15…0,32 Вт/(м0С). Фибролит – хороший звукопоглощающий материал, благодаря развитой открытой пористой структуре. Коэффициент звукопоглощения при толщине плит 30мм составляет 0,4. Фибролит не горит, но тлеет. В сухом состоянии фибролит биостоек, но при влажности более 35% он подвержен воздействию грызунов и грибков. Фибролит пилится, сверлится, в него можно вбивать гвозди.
Основными сырьевыми компонентами для получения фибролита является древесина в виде древесной шерсти, портландцемент не ниже марки 400. Шерсть – это стружка длинной 200…500мм, шириной 2…5мм, толщиной 0,3…0,5мм.
Древесина представляет собой сложный комплекс веществ органического происхождения: целлюлозы, лигнина, гемицеллюлозы, экстрактивных, а также простейших водорастворимых сахаров и минеральных солей. При попадании в щелочную среду твердеющего цементного камня гемицеллюлоза гидролизуется, переходя в простейшие водорастворимые сахара (сахарозу, фруктозу, глюкозу), являющиеся сильнейшими «цементными ядами». При этом процесс твердения цемента сильно замедляется и может вообще прекратится. Для устранения вредного воздействия «цементных ядов» производят специальную биохимическую, физическую и химическую обработку древесины. Поступающую на завод древесину выдерживают на открытом воздухе не менее 4…6 месяцев в летнее время. Под воздействием солнечных лучей и тепла происходит окисление экстрактивных веществ и перевод простейших водорастворимых сахаров и гемицеллюлозы в менее растворимые формы. После выдержки древесину распиливают на чураки и направляют к древошерстным станкам с возвратно- поступательным движением ножей. Состроганная параллельно волокнам шерсть подсушивают до влажности 20…22% и подвергают минерализации с целью еще более глубокой нейтрализации «цементных ядов». При этом древесную шерсть пропитывают 3…4%-ным водным раствором CaCl2 или растворимым стеклом.
Подготовленная шерсть влажностью 140…160% смешивается с портландцементом в соотношении 1:2,3…2,7 в гравитационных смесителях, обеспечивающих перемешивание шерсти без уплотнения и навивания на вал.
Формирование изделий производят в металлических формах при давлении 0,06…0,4 Мпа. Тепловую обработку фибролита производят в 2 этапа: сначала в формах, а потом без форм. Формы в пакетах поступают в камеру с относительной влажностью 60…70% и температурой 30…350С, время обработки 8…24 часа. Затем плиты распалубливают, обрезают кромки и подают на сушку при температуре 600С относительной влажности 60…70% в течение 1…2 суток.
В СНГ фибролит производится на 40 предприятиях в объеме около 3млн.м3/год (9% общего выпуска теплоизоляционных материалов), 80% фибролита выпускают с объемной массой 300 кг/м3. Эти плиты применяют для утепления ограждающих конструкций щитовых и каркасных деревянных домов, общественных и промышленных зданий. Акустические фибролитовые плиты толщиной 30мм применяют как декоративно-акустический материал.
Фибролит: свойства, сырье, производство, применение – статья на сайте “студент-строитель.ру”
Friend me:
student-stroitel.ru
Фибролит
ТЕХНОЛОГИЯ ТЕПЛОИЗОЛЯЦИИ
Фибролит — плитный материал из опреесованной древесной шсрсти, склеенной затвердевшим вяжущим. Известно довольно большое количество разновидностей фибролита, название которых отражает вид минерального вяжущего: магнезиальный, магнези — ально-доломитовый, известковый, цементно-известковый, извест — ково-трепельный, гипсовый, цементный. В настоящее время в СССР выпускают в основном цементный фибролит, который но назначению разделяют на теплоизоляционный, геплонзоляцноппо- конструкцнонный и акустический.
Свойства, цементного фибролита характеризуют следующие основные показатели.
Пористость фибролита характеризуется неоднородным волокнистым строением с сообщающимися довольно крупными порами. С повышением средней плотности от 300 до 500 кг/мя его пористость уменьшается от 87 до 77″/о-
Плотность и прочность цементного фибролита зависят от средней плотности, его подразделяют на марки: 300, 350, 400 и 500, причем выпуск марки 300 составляет около 80% от общего выпуска фибролитовых плит. Средняя плотность теплоизоляционного фибролита составляет 300 …400 кг/м3, акустического — 350… …400 и теплоизоляционно-конструкционного — 500 кг/м3. Средняя плотность фибролита зависит в основном от расхода вяжущего и усилия прессования. С увеличением средней плотности возрастает сопротивление изгибу и огнестойкость, а теплоизоляционные свойства ухудшаются. Прочность фибролита существенно зависит от размера и качества древесной шерсти и определяется расходом вяжущего, усилием прессования, режимом тепловой обработки и составляет при изгибе 0,4… 1,2 МПа.
Водостойкость фибролита недостаточна, поэтому его необходимо защищать от увлажнения. При увлажнении фибролитовых плит до 50% их механическая прочность снижается в 1,5…2 раза. Водопоглощение возрастает с уменьшением средней плотности и расхода вяжущего. Обычно оно колеблется в пределах 35… 60%. К положительным качествам цементно-фибролитовых плит следует отнести их малую гигроскопичность и отсутствие склонности к короблению.
По теплопроводности фибролитовые теплоизоляционные плиты относят к среднему классу. Их теплопроводность колеблется от 0,079 до 0,115 Вт/(м-°С). Однако увлажнение плит в конструкции существенно ухудшает их теплоизоляционные свойства (при увеличении объемной влажности на 1% теплопроводность плит повышается от 5 до 14% в зависимости от средней плотности материала).
По огнестойкости фибролитовые плиты относят к трудносгораемым материалам — фибролит пс горит, но тлеет. Время тления после удаления пламени для плит со средней плотностью 350 кг/м3 составляет 30 с.
В сухом состоянии фибролитовые плиты биостойки, они не подвержены действию грызунов и грибков. Однако при увлажнении свыше 35% плиты поражаются домовым грибом. Если плиты защищены от увлажнения, то их долговечность достаточно велика. Фибролит хорошо обрабатывается пилением, его можно сверлить, вбивать в него гвозди; плиты хорошо окрашиваются и оштукатуриваются.
Сырьевыми материалами для изготовления цементного фибролита являются древесина в виде древесной шерсти, цемент,’минерализующие добавки и вода.
Древесную шерсть получают из неделовой древесины — дровяника, тонкомерного кругляка и отходов лесопиления без гнили с определенными допусками по кривизне и наличию сучков. При выборе древесины большое значение имеет наличие в ней водорастворимых веществ, вредно влияющих на процессы схватывания и твердения портландцемента. Взаимодействие древесины с цементом имеет некоторые особенности. Древесина представляет собой сложный комплекс органических веществ: целлюлозы, лигнина, гемицеллюлозы, экстрактивных и смолистых веществ, а также простейших водорастворимых Сахаров и минеральных солей. При попадании в щелочную среду (которой является твердеющий цементный раствор, покрывающий древесную шерсть) ге — мицеллюлоза гидролизуется и переходит в простейшие водорастворимые сахара (сахарозу, фруктозу, глюкозу), которые являются сильнейшими «цементными ядами». Целлюлоза, лигнин, а также экстрактивные, смолистые вещества и минеральные соли влияния на процесс твердения цемента не оказывают. Продукты гидролиза гемицеллюлозы значительно замедляют твердение цемента, иногда до полного его прекращения, а также сильно (в 5… 10 раз) снижают прочность затвердевшего цемента. Для устранения вредного воздействия «цементных ядов» проводят специальную биохимическую, физическую и химическую обработку древесины.
Содержание водорастворимых веществ в древесине зависит от породы, части дерева, его возраста и времени рубки, а также от продолжительности вылеживания древесины на складе. Наименьшее количество водорастворимых веществ содержится в ели, затем идут пихта, тополь, сосна. Наиболее богаты ими береза, осина, бук. Поэтому древесную шерсть получают преимущественно из хвойных пород. В основании ствола содержится значительно больше водорастворимых веществ, чем в его середине. Древесина летней рубки значительно богаче ими, чем древесина зимней рубки.
Древесная шерсть — длинная тонкая древесная стружка длиной 200… 500 мм, шириной 2… 5 мм и толщиной 0,3… 0,5 мм. Применение древесной шерсти толщиной менее 0,3 мм приводит к сннжению прочности плит, а прн толщине более 0,5 мм шерсть становится ломкой и менее эластичной.
Для изготовления фибролита обычно применяют портландцемент марки не ниже 400, быстротвердеющий портландцемент либо шлакопортландцемент. Наиболее пригодны быстротвердеющие цементы с содержанием C3S более 60% и С3А— не менее 12%), обеспечивающие быстрый рост прочности цементного камня.
Для нейтрализации вредного воздействия на цементный камень выщелачиваемых водорастворимых веществ и улучшения сцепления древесной шерсти с цементом древесную шерсть пропитывают растворами минеральных веществ — минерализаторов. Минерализаторами служат хлористый кальций, жидкое стекло и другие вещества. Вводят минерализатор в строго определенном количестве, так как избыток или недостаток его существенно понижает прочность цементного камня и, следовательно, готовых плит.
При мокром спосибе древесную шерсть окупают в ванну с водным раствором цемента и минерализатора с последующим удалением излишнего раствора на внброгрохоте. Этот способ тре — бует постоянного перемешивания цементного раствора во избежание ею расслоения, введення в формовочную массу большого количества воды, что отрицательно сказывается на качестве плит. Кроме того, цемент часто отверждается в ванне, что приводит к существенным его потерям н требует дополнительных затрат труда по очистке ванны.
В СССР и за рубежом наибольшее распространение получил сухой способ, включающий подготовку сырья, получение древесной шерсти, приготовление формовочной смеси, формование плит прессованием и их тепловую обработку.
Подготовка сырья заключается в следующем. Поступающую на завод древесину окоривают и отправляют на выдержку, чтобы устранить вредное воздействие «цементных ядов». Древесину выдерживают на открытом воздухе не менее 4…6 весенне-летних месяцев В этот период под действием солнечных лучей и тепла происходит окисление экстрактивных веществ и перевод простейших водорастворимых Сахаров и гемицеллюлозы древесины в менее растворимые формы. После выдержки древесину распиливают на чуракн, удаляют гниль и другие пороки, затем чураки подают к древесношерсшым станкам. Используемые для получения древесной шерсти станки имеют рабочий орган, работающий с возвратно-поступательным или вращательным движением ножей. Наибольшее распространение получили древеспошерстпые станки с возвратно-поступателі ным движением ножевой плиты. Строгальные ножи, укрепленные но торнам ножевой или ты, сострагивают шерсц, параллельно волокнам фенееппы. Шерсть с перерезанными волокнами в процессе трапепоршроиапии укорачивается, и качество плит ухудшается. Полученную шерсть подсушивают до влажности 20 …22% для уменьшения отрицательного воздействия водорастворимых веществ на цемент и улучшения условий минерализации шерсти (чем суше древесная шерсть, тем глубже раствор минерализатора проникает в поры и капилляры древесины, тем эффективнее минерализация).
Минерализацию древесной шерсти осуществляют путем ее окунания или обрызгивания 3…4%-ным водным раствором хлористого кальция или жидкого стекла. Для этого применяют различные устройства: шерстетрясы, конвейеры с перфорированной лентой, барабанные смесители. На шерстетрясах из древесной шерсти отсеивается мелочь и стряхивается излишек раствора минерализатора. Влажность минерализованной шерсти составляет 140… … 160%. Если в качестве вяжущего применяют белитовый цемент, содержащий незначительное количество C3S, то обработка древесной шерсти минерализатором не нужна.
При приготовлении формовочной смеси учитывают соотношение между древесной шерстыо и цементом, которое зависит от марки выпускаемых плит и вида древесной шерсти. Для каждого вида древесной шерсти существует рациональный расход цемента, соответствующий оптимальной толщине слоя цементного камня на поверхности ее элементов. Дальнейшее увеличение расхода цемента не приводит к эффективному росту прочности цементного фибролита, а лишь повышает его среднюю плотность. Уменьшение расхода цемента ухудшает скрепление лент древесной шерсти, снижает био — и огнестойкость готовых изделий. Средние значения расхода древесной шерсти, м3, и цемента, кг, следующие: для марки 300 — 0,4 и 190, для марки 400 — 0,55 и 240, для марки 500 — 0,82 и 270. Влажность смеси для получения плит хорошего качества должна поддерживаться в пределах 45… 50%.
Смешивают компоненты формовочной массы в смесителях принудительного действия либо в смесителях свободного падения (гравитационных), обеспечивающих перемешивание шерсти без уплотнения и навивания ее на вал.
При формовании плит приготовленная формовочная масса загрузочным конвейером, оборудованным специальным валковым разделителем и разрыхляющим устройством, распределяется по формам и разравнивается валками или вручную. Формы устанавливают на многополочный пресс в виде пакета, прн этом одновременно прессуют 15… 20 плит. Для прессования применяют механические, пневматические или гидравлические прессы. Удельное давление при прессовании теплоизоляционных плит составляет 0,06… 0,1 МПа; более тяжелые плиты прессуют прн удельном давлении 0,25… 0,4 МПа.
После достижения заданной степени уплотнения массы формы сжимают струбцинами (фиксируют толщину уплотненной массы) с целью исключения упругого последействия лент древесной шерсти. В таком обжатом состоянии формы с уплотненной массой подают на тепловую обработку.
Тепловая обработка фибролитовых плит осуществляется в два этапа. Вначале тепловую обработку плит производят в формах в обжатом состоянии с целью закрепления структуры, полученной при формовании. На этой стадии пакеты форм загружают в камеру твердения, где их выдерживают прн влажности среды 60… …70% и температуре 30…35°С в течение 8 ч при использовании быстротвердеющего цемента и до 24 ч при применении обычного портландцемента. Затем плиты распалубливают, обрезают боковые и торцевые кромки и выдерживают под навесом на открытом воздухе (в летнее время) в течение 5… 7 сут или в специальных сушилках при температуре 50… 60°С и относительной влажности 60… 70% в течение 1… 2 сут. Влажность высушенных плит не должна превышать 20%. Готовые плиты отправляют на склад.
В СССР и за рубежом существуют автоматизированные линии для производства фибролитовых плит. Такая поточная линия работает следующим образом. От станков полученная древесная шерсть пневмотранспортом подается на перфорированный вибростол для минерализации и очистки от мелочи, после чего она поступает в смеситель для приготовления формовочной массы. Из смесителя формовочная масса ленточным транспортером подается к сбрасывающему барабану, который распределяет ее по металлическим формам, установленным на роликовом конвейере. Проходя под подпрессовочным барабаном, масса уплотняется. Установленный на потоке круглопильный станок разрезает образовавшийся ковер по зазору между торцевыми бортами смежных форм, после чего формы с массой подаются к пакетонаборному устройству, являющемуся одновременно прессом. После набора в пакет десяти форм осуществляется процесс прессования путем иагруже — ния пакета плитой. Пакеты плит из пресса электропогрузчиком отправляются в камеры твердения, а набравшие прочность пакеты— из камеры к распределителю, с помощью которого пакеты разбираются на отдельные формы и конвейером подаются к рас — палубочному устройству. Из распалубочного устройства плиты поступают на обрезной станок и после обрезки торцов укладываются в штабеля по 20 шт. и электропогрузчиком отправляются под навес для подсушивания, а формы — на формовочный конвейер.
В СССР теплоизоляционные фибролитовые плиты выпускают размером 2400X550X75 мм. Плиты марки 300 применяют для утепления ограждающих конструкций щитовых и каркасных деревянных домов, сельскохозяйственных построек различного назначения, а также жилых, общественных и промышленных зданий в виде теплоизоляционного слоя в железобетонных стеновых панелях, облегченных фнбролитоасбестоцемептпых панелей и т. и.
Заканчивая ремонт дома или обнаружив, что большая теплопотеря является следствием прохудившихся стен, мы задумываемся о том, как утеплить дом. Хочется отметить, что это не так сложно, как кажется на первый …
Каждый год в мире строится все больше и больше жилых домов. Новые технологии позволяют сделать нашу жизнь легче и комфортней. Но еще больше существует старых домов, которые нуждаются в ремонте. …
Так же как для теплоизоляционных материалов, вид пористой структуры и характеристика пористости являются определяющими показателями качества для акустических материалов. Их функциональные и строительно-эксплуатационные свойства тесно связаны с видом скелетообразующего материала …
msd.com.ua
Цементный фибролит
Категория: Древесина
Цементный фибролит
Фибролит является плитным строительным материалом и применяется для устройства различных частей зданий: наружных ограждающих стен, перекрытий, утепленных покрытий, перегородок, звукоизоляции для утепления стеновых железобетонных панелей и пр.
В соответствии с ГОСТ 8928—58 фибролитовые плиты на портландцементе в зависимости от назначения и степени прессования изготавливаются объемным весом 300, 350, 400 и 500 кг/м3.
Размеры плит: длина 2000 и 2400 мм, Ширина 500 и 550 мм, толщина 25, 50, 75 и 100 мм. Плиты имеют правильную прямоугольную форму.
Влажность плит не должна превышать 20% (от веса в сухом состоянии). Предел прочности фибролита на изгиб в зависимости от марки (объемного веса) колеблется: для изоляционного фибролита от 4 до 7 кг/см2 и для конструктивного от 10 до 14 кг/см2.
В зависимости от назначения фибролит делится на изоляционный (для тепло- и звукоизоляции) и конструктивный (для устройства стен, перегородок, потолочных и кровельных перекрытий и пр.). Фибролит обладает высокими термоизоляционными свойствами; расчетный коэффициент теплопроводности в ккал/м час град составляет для изоляционного цементного фибролита от 0,085 до 0,105 и для конструктивного от 0,105 до 0,130.
Древесная стружка, обработанная раствором хлористого кальция и покрытая цементом, является основой фибролита. Она обладает биостойкостью по сравнению с цельной древесиной и совершенно не подвержена поражению грызунами и насекомыми. Испытаниями установлено, что изоляционный фибролит хорошо сопротивляется возгоранию, а конструктивный не возгорается вовсе, и тление его прекращается через несколько секунд после удаления факела горелки. Оштукатуривание фибролита значительно повышает его огнестойкость.
Фибролитовые плиты легко пилятся, сверлятся, гвоздятся и хорошо поддаются штукатурке и окраске. Шероховатая, пористая поверхность фибролитовых плит способствует хорошему сцеплению их с бетоном. По этой же причине их можно надежно крепить к вертикальным и горизонтальным плоскостям бетонных и каменных конструкций посредством цементно-известкового раствора или битумной связки.
В конструкциях, где фибролитовые плиты применяются в сочетании с бетоном, их используют в качестве опалубки, что удешевляет строительство и дает экономию в лесоматериалах.
Одними из основных факторов экономичности фибролита являются его транспортабельность и возможность применения в строительных конструкциях в сочетании с другими материалами (кирпичом, бетоном, деревом и др.).
В качестве сырья для изготовления цементного фибролита служат:
а) древесина, из которой изготовляют древесную стружку;
б) портландцемент;
в) минерализаторы —хлористый кальций технический или жидкое стекло;
г) вода.
Древесная стружка может быть изготовлена из древесины любых пород: сосны, ели, пихты, березы, осины, липы и др., при этом древесина должна быть здоровой (без гнили), желательно с большим содержанием заболони, без косослоя и свиловатости. Не допускается древесина с сучками диаметром свыше 30 мм, расположенными на расстоянии менее 200 мм.
Перед строжкой дровяное долготье разделывают на чураки длиной 450—550 мм и при диаметре свыше 18 см раскалывают пополам, а при диаметре свыше 28 см — на четвертины. Древесная стружка имеет форму узких полос длиной 20—50 см, шириной 4—7 мм и толщиной 0,25—1,5 мм. На 1 м3 фибролита расходуется 0,36 м3 древесины или 300 кг древесной стружки.
Стружка должна иметь цвет и запах здоровой древесины, она должна быть без коры и посторонних примесей, с влажностью не более 22%. Содержание стружки длиной от 200 до 500 мм в массе должно составлять не менее 88%, длиной от 50 до 200 мм — не более 10% и длиной не менее 50 мм — не более 2%. Портландцемент, расходуемый в количестве 200 кг на 1 м3 фибролита, должен иметь марку не ниже 400.
Технологический процесс механизированного производства фибролита на портландцементе включает в себя следующие основные операции: раскрой долготья на чураки и приготовление древесной шерсти, обработка древесной шерсти минерализатором — раствором хлористого кальция или жидкого стекла; смешивание древесной стружки с цементом; формование и прессование плит; термическая обработка (твердение и сушка плит).
В зимнее время чураки перед строганием оттаивают в специальных камерах.
Выход древесной шерсти из 1 мъ древесины колеблется от 300 до 350 кг при ширине стружки 4—5 мм и толщине 0,25—0,50 мм.
Существует несколько конструкций машин для смешивания стружки с цементом, работающих в основном по сухому способу. Машина для смешивания выполняет операции по просеиванию стружки от мелочи и примесей, равномерной пропитке ее хлористым кальцием и подаче смеси в смесительный барабан для тщательного перемешивания стружки с цементом. Цемент из бункера подается в смесительный барабан при помощи нории. На приводе нории установлена коробка передач. Дозировка цемента производится путем изменения скорости движения нории. Для отсасывания пыли, получающейся при транспортировании стружки, машина закрыта металлическим кожухом и оборудована пылесосом — фильтром. Стекающий после пропитки раствор собирается в резервуар и насосом перекачивается обратно в ванну. Смесительный барабан имеет вал с насаженными на нем спиральными лопастями, который вращается со скоростью 20—22 об/мин.
Наклонное расположение барабана под углом 10—15° и конструкция вала с лопастями обеспечивают хорошее перемешивание смеси из стружек и цемента и регулярное перемещение ее к выходному отверстию. Готовая смесь цемента со стружкой из мешалки поступает в формы и равномерно распределяется по всей ее площади.
Конструкция форм обеспечивает возможность пакетного прессования плит и оставления отпрессованных плит на длительное время в зажатом состоянии.
Формы состоят из поддонов с прикрепленными к «им или свободно лежащими бортовыми элементами. Высота бортовых элементов может равняться требуемой толщине плит либо требуемой толщине слоя засыпки смеси цемента с древесной шерстью в формы. В первом случае верхняя плоскость плиты отформовывается при прессовании поддоном вышележащей плиты, а бортовые элементы формы служат ограничителями; во втором случае формы должны иметь специальные крышки, опускающиеся при прессовании внутрь формы до получения плиты необходимой толщины.
Для прессования плит могут быть применены прессы любой конструкции, обеспечивающие возможность выдержки отпрессованного пакета плит при максимальном давлении в течение срока, необходимого для закрепления плит в зажатом состоянии. Процесс должен обеспечивать давление:
а) 0,1 — 1 кг/см2 при прессовании плит марок 300 и 350;
б) 1,5 — 4 кг/см2 — при прессовании плит марок 400 и 500.
Наилучшими следует считать прессы, обеспечивающие возможность приложения давления не только по плоскостям плит, но и по всем их боковым граням. По достижении необходимой степени уплотнения плит последние закрепляются в формах в зажатом состоянии при помощи специальных приспособлений, после чего давление пресса снимается, а формы убираются из-под пресса.
Плиты, зажатые в формах, подвергаются твердению в естественных или искусственных условиях. Естественное твердение плит производится в закрытом помещении при температуре воздуха 18—20°. Ориентировочно срок твердения при указанной температуре составляет 2 дня.
Искусственное твердение плит производится в специальных камерах при температуре 30—40° и влажности воздуха 60—70%-Ориентировочный срок твердения в указанных условиях составляет 12—24 часа. Отвердевшие плиты расформовываются и сушатся в естественных или искусственных условиях.
Естественная сушка плит производится в проветриваемом помещении при положительной температуре воздуха; в летний период сушка может производиться под навесом. Ориентировочно срок естественной сушки при температуре воздуха 18—20° до остаточной влажности плит 20% составляет 10 дней.
Естественная сушка может сочетаться как с естественным, так и искусственным твердением плит.
Искусственную сушку плит осуществляют в специальных камерах в условиях интенсивного воздухообмена при температуре 60—70° и влажности воздуха 60—70%. Ориентировочно срок искусственной сушки в указанных условиях до остаточной влажности плит 20% составляет 12—24 часа. Искусственную сушку следует сочетать с искусственным твердением плит.
Необходимые сроки твердения и сушки плит уточняются заводской лабораторией в зависимости от применяемого сырья (вид применяемого цемента, влажность древесной шерсти и др.).
В случае применения шерсти иной влажности, чем 22%, расход материалов соответственно меняется; в случае применения цемента марки выше 400 расход материалов устанавливается опытным путем заводской лабораторией.
Плиты должны храниться в условиях, не допускающих их увлажнения, уложенными плашмя и рассортированными по маркам и размерам.
При производстве плит осуществляется постоянный контроль:
а) качества исходного сырья—древесины и древесной шерсти, цемента, гипса, хлористого кальция и жидкого стекла по всем
показателям соответствующих ГОСТов и ТУ;
б) качества выпускаемой продукции по всем показателям в соответствии с ГОСТ 8928—58 «Плиты фибролитовые на портландцементе»;
в) условий ведения технологического процесса — влажности древесной шерсти до и после сушки (или естественного выдерживания), температуры и концентрации рабочих растворов минерализаторов и длительности пропитки ими древесной шерсти; фактических расходов минерализаторов, цемента и гипса; условий вибродомола цемента и его результатов, условий формования и прессования плит, температуры и влажности воздуха при твердении и сушке плит, а также длительности этих процессов и пр.
Результаты испытаний фиксируются в специальных журналах, причем записи в этих журналах должны быть связаны с номерами партий плит, указываемых в паспортах на отгружаемую продукцию.
В настоящее время в СССР цементный фибролит изготавливают в незначительных объемах (100 тыс. м3 в год) на мелких немеханизированных предприятиях.
Планом развития народного хозяйства на 1959—1965 гг. предусматривается широкая организация производства цементного фибролита с доведением объемов производства в 1965 г. свыше 5 млн. м3, для чего намечается построить около 50 цехов. Некоторые из этих цехов (Шарьинский, Павшинский, Васильевский и др.) уже построены и пущены в эксплуатацию в 1960 г.
Фибролит является высокоэффективным плитным строительным материалом. Применение его в строительстве облегчает вес зданий, индустриализирует производство работ, дает значительную экономию качественной древесины.
Для перевозки 400 м3 фибролита, потребного на строительство 1000 м2 жилой площади, требуется 16 вагонов, а для перевозки 500 тыс. шт. кирпича, необходимого для этих же целей, требуется 62 вагона, или в 3,8 раза больше. Капиталовложения на строительство цехов фибролита в 7,8 раза меньше, чем на строительство кирпичных заводов эквивалентной мощности.
При строительстве стандартных деревянных домов с применением фибролита экономия в зависимости от конструкции и типа дома составляет около 0,2 м3 пиломатериалов на 1 м? жилой площади. При применении для этих целей 4 млн. м3 фибролита общая экономия составит 1,6 млн. м3 пиломатериалов или 2,3 млн. м3 круглого леса.
Организация производства фибролита наряду с увеличением объемов плитных строительных материалов создает предпосылки для более рационального использования заготавливаемой древесины и, в частности, древесины лиственных пород.
Древесина — Цементный фибролит
gardenweb.ru
Фибролит (от лат. fibra — волокно и греч. líthos - камень), строительный материал, представляющий собой спрессованную и затвердевшую смесь специально приготовленной древесной стружки (т. н. древесной шерсти), см. фото слева, с портландцементом или (реже) с каустическим магнезитом. В английской литературе используются наименования fibrolite, wood wool cement board, fiber mat, cement fiberboard, cement fibrolite plate Внешний вид некоторых видов фибролита показан на фотографиях ниже
История фибролита
В
СССР фибролит начали производить в конце 30-х годов. Затем в
разные годы было запущено несколько десятков цехов по производству
фибролита, преимущественно в деревообрабатывающей и строительной
промышленностях. Выпуск фибролитовых плит в 1975 году составил
около 3 млн. м3. Отсутствие инвестиций и появление на рынке новых эффективных тепло- звукопоглощающих материалов привели ( в последние 15 лет) к сокращению в России объемов производства фибролитовых плит в десятки раз. За рубежом
производство фибролита увеличивается, как в развитых, так и в
развивающихся странах. Новый стимулом для расширения
производства фибролита стало
его применение для формирования несъемной опалубки в монолитном и
каркаснобетонном строительстве и др. бетонных
работах. Сейчас интерес к
производству
фибролита в нашей стране вновь начинает возрождаться Минерализация позволяет древесному волокну противостоять биологическому воздействию (поражение грибками, плесенью, насекомыми, грызунами), эрозии и гниению. Области применения фибролитаФибролит применяется :
Свойства фибролитовых плитФибролитовые плиты по ГОСТ 8928 — 81 подразделяются на три марки и применяют в качестве теплоизоляционного (марки Ф-300), конструкционно-теплоизоляционного и акустического (марки Ф-400 и Ф-500) материала в строительных конструкциях зданий и сооружений с относительной влажностью воздуха не выше 75% (цифры в марке указывают плотность плит, кг/м3).ГОСТом предусмотрены плиты длиной 2400 и 3000 мм, шириной 600 и 1200 мм и толщиной от 30 до 150 мм. Предел прочности плит при изгибе составляет 0,35… 1,3 МПа. Физико-механические свойства фибролитовых плит
Коэффициент звукопоглощения плит марки Ф-400 и Ф-500 толщиной 30 мм, предназначенных для акустической отделки помещений, должен быть не менее величин, указанных в таблице.
За рубежом выпускаются фибролитовые плиты толщиной от 15 мм различных форматов и свойств, в т.ч. кровельные и отделочные (декорированные). Нормативные документы ГОСТ 8928 — 81 » Плиты фибролитовые. Технические условия « ГОСТ 5244 — 79 » Стружка древесная. Технические условия « составил Абушенко Александр Викторович ноябрь 2005 Почитать об экструзии древесно-полимерных композитов 1 2 3 |
www.c-a-m.narod.ru