ΠΠ»Π΅ΠΊΡΡΠΎΡΡΠΎΠ·ΠΈΠΎΠ½Π½Π°Ρ ΠΎΠ±ΡΠ°Π±ΠΎΡΠΊΠ° β ΠΠΈΠΊΠΈΠΏΠ΅Π΄ΠΈΡ
ΠΠ°ΡΠ΅ΡΠΈΠ°Π» ΠΈΠ· ΠΠΈΠΊΠΈΠΏΠ΅Π΄ΠΈΠΈ β ΡΠ²ΠΎΠ±ΠΎΠ΄Π½ΠΎΠΉ ΡΠ½ΡΠΈΠΊΠ»ΠΎΠΏΠ΅Π΄ΠΈΠΈ
Π’Π΅ΠΊΡΡΠ°Ρ Π²Π΅ΡΡΠΈΡ ΡΡΡΠ°Π½ΠΈΡΡ ΠΏΠΎΠΊΠ° Π½Π΅ ΠΏΡΠΎΠ²Π΅ΡΡΠ»Π°ΡΡ ΠΎΠΏΡΡΠ½ΡΠΌΠΈ ΡΡΠ°ΡΡΠ½ΠΈΠΊΠ°ΠΌΠΈ ΠΈ ΠΌΠΎΠΆΠ΅Ρ Π·Π½Π°ΡΠΈΡΠ΅Π»ΡΠ½ΠΎ ΠΎΡΠ»ΠΈΡΠ°ΡΡΡΡ ΠΎΡ Π²Π΅ΡΡΠΈΠΈ, ΠΏΡΠΎΠ²Π΅ΡΠ΅Π½Π½ΠΎΠΉ 2 ΡΠ΅Π²ΡΠ°Π»Ρ 2014; ΠΏΡΠΎΠ²Π΅ΡΠΊΠΈ ΡΡΠ΅Π±ΡΡΡ 50 ΠΏΡΠ°Π²ΠΎΠΊ. Π’Π΅ΠΊΡΡΠ°Ρ Π²Π΅ΡΡΠΈΡ ΡΡΡΠ°Π½ΠΈΡΡ ΠΏΠΎΠΊΠ° Π½Π΅ ΠΏΡΠΎΠ²Π΅ΡΡΠ»Π°ΡΡ ΠΎΠΏΡΡΠ½ΡΠΌΠΈ ΡΡΠ°ΡΡΠ½ΠΈΠΊΠ°ΠΌΠΈ ΠΈ ΠΌΠΎΠΆΠ΅Ρ Π·Π½Π°ΡΠΈΡΠ΅Π»ΡΠ½ΠΎ ΠΎΡΠ»ΠΈΡΠ°ΡΡΡΡ ΠΎΡ Π²Π΅ΡΡΠΈΠΈ, ΠΏΡΠΎΠ²Π΅ΡΠ΅Π½Π½ΠΎΠΉ 2 ΡΠ΅Π²ΡΠ°Π»Ρ 2014; ΠΏΡΠΎΠ²Π΅ΡΠΊΠΈ ΡΡΠ΅Π±ΡΡΡ 50 ΠΏΡΠ°Π²ΠΎΠΊ. ΠΠΠ ΠΏΡΠΎΡΠΈΠ»ΠΈΡΠΎΠ²Π°Π½Π½ΠΎΠΉ ΠΏΠΎΠ»ΠΎΡΡΠΈ. ΠΠΊΠ»ΡΡΠ΅Π½ΠΈΠ΅ Π½Π° ΠΎΠ±ΡΠ°ΡΠ½ΡΡ ΠΏΠΎΠ»ΡΡΠ½ΠΎΡΡΡ. 1 β ΠΎΠ±ΡΠ°Π±Π°ΡΡΠ²Π°Π΅ΠΌΠ°Ρ Π·Π°Π³ΠΎΡΠΎΠ²ΠΊΠ°, 2 β ΡΠ°Π·ΡΡΠ΄Ρ Π² Π·Π°Π·ΠΎΡΠ΅, 3 β ΡΠ»Π΅ΠΊΡΡΠΎΠ΄-ΠΈΠ½ΡΡΡΡΠΌΠ΅Π½Ρ, 4 β Π³Π΅Π½Π΅ΡΠ°ΡΠΎΡ ΠΈΠΌΠΏΡΠ»ΡΡΠΎΠ² ΡΠ΅Ρ Π½ΠΎΠ»ΠΎΠ³ΠΈΡΠ΅ΡΠΊΠΎΠ³ΠΎ ΡΠΎΠΊΠ°. ΠΠ±ΡΠ°Π±ΠΎΡΠΊΠ° Π·Π°Π³ΠΎΡΠΎΠ²ΠΊΠΈ Π½Π° ΡΠ»Π΅ΠΊΡΡΠΎΡΡΠΎΠ·ΠΈΠΎΠ½Π½ΠΎΠΌ ΠΊΠΎΠΏΠΈΡΠΎΠ²Π°Π»ΡΠ½ΠΎ-ΠΏΡΠΎΡΠΈΠ²ΠΎΡΠ½ΠΎΠΌ ΡΡΠ°Π½ΠΊΠ΅. ΠΠ°Π³ΠΎΡΠΎΠ²ΠΊΠ° Π½Π°Ρ ΠΎΠ΄ΠΈΡΡΡ Π² ΡΠ°Π±ΠΎΡΠ΅ΠΉ Π²Π°Π½Π½Π΅, Π½Π°ΠΏΠΎΠ»Π½Π΅Π½Π½ΠΎΠΉ ΡΠ°Π±ΠΎΡΠ΅ΠΉ ΠΆΠΈΠ΄ΠΊΠΎΡΡΡΡ.ΠΠ»Π΅ΠΊΡΡΠΎΡΡΠΎΠ·ΠΈΠΎΠ½Π½Π°Ρ ΠΎΠ±ΡΠ°Π±ΠΎΡΠΊΠ° (Π°Π±Π±Ρ. ΠΠΠ) β ΠΠ±ΡΠ°Π±ΠΎΡΠΊΠ°, Π·Π°ΠΊΠ»ΡΡΠ°ΡΡΠ°ΡΡΡ Π² ΠΈΠ·ΠΌΠ΅Π½Π΅Π½ΠΈΠΈ ΡΠΎΡΠΌΡ, ΡΠ°Π·ΠΌΠ΅ΡΠΎΠ², ΡΠ΅ΡΠΎΡ ΠΎΠ²Π°ΡΠΎΡΡΠΈ ΠΈ ΡΠ²ΠΎΠΉΡΡΠ² ΠΏΠΎΠ²Π΅ΡΡ Π½ΠΎΡΡΠΈ ΡΠ»Π΅ΠΊΡΡΠΎΠΏΡΠΎΠ²ΠΎΠ΄Π½ΠΎΠΉ Π·Π°Π³ΠΎΡΠΎΠ²ΠΊΠΈ ΠΏΠΎΠ΄ Π΄Π΅ΠΉΡΡΠ²ΠΈΠ΅ΠΌ ΡΠ»Π΅ΠΊΡΡΠΈΡΠ΅ΡΠΊΠΈΡ ΡΠ°Π·ΡΡΠ΄ΠΎΠ² Π²ΠΎΠ·Π½ΠΈΠΊΠ°ΡΡΠΈΡ ΠΌΠ΅ΠΆΠ΄Ρ Π·Π°Π³ΠΎΡΠΎΠ²ΠΊΠΎΠΉ ΠΈ ΡΠ»Π΅ΠΊΡΡΠΎΠ΄ΠΎΠΌ-ΠΈΠ½ΡΡΡΡΠΌΠ΅Π½ΡΠΎΠΌ.
ΠΠ΄ΠΈΠ½ ΠΈΠ· ΡΠ»Π΅ΠΊΡΡΠΎΠ΄ΠΎΠ² ΡΠ²Π»ΡΠ΅ΡΡΡ ΠΎΠ±ΡΠ°Π±Π°ΡΡΠ²Π°Π΅ΠΌΠΎΠΉ Π·Π°Π³ΠΎΡΠΎΠ²ΠΊΠΎΠΉ, Π΄ΡΡΠ³ΠΎΠΉ β ΡΠ»Π΅ΠΊΡΡΠΎΠ΄-ΠΈΠ½ΡΡΡΡΠΌΠ΅Π½ΡΠΎΠΌ. Π Π°Π·ΡΡΠ΄Ρ ΠΏΡΠΎΠΈΠ·Π²ΠΎΠ΄ΡΡΡΡ ΠΏΠ΅ΡΠΈΠΎΠ΄ΠΈΡΠ΅ΡΠΊΠΈ, ΠΈΠΌΠΏΡΠ»ΡΡΠ½ΠΎ, ΡΠ°ΠΊ ΡΡΠΎΠ±Ρ ΡΡΠ΅Π΄Π° ΠΌΠ΅ΠΆΠ΄Ρ ΡΠ»Π΅ΠΊΡΡΠΎΠ΄Π°ΠΌΠΈ Π²ΠΎΡΡΡΠ°Π½ΠΎΠ²ΠΈΠ»Π° ΡΠ²ΠΎΡ ΡΠ»Π΅ΠΊΡΡΠΈΡΠ΅ΡΠΊΡΡ ΠΏΡΠΎΡΠ½ΠΎΡΡΡ. ΠΠ»Ρ ΡΠΌΠ΅Π½ΡΡΠ΅Π½ΠΈΡ ΠΈΠ·Π½ΠΎΡΠ° ΡΠ»Π΅ΠΊΡΡΠΎΠ΄Π°-ΠΈΠ½ΡΡΡΡΠΌΠ΅Π½ΡΠ° ΠΏΠΎΠ΄Π°ΡΡΡΡ ΡΠ½ΠΈΠΏΠΎΠ»ΡΡΠ½ΡΠ΅ ΠΈΠΌΠΏΡΠ»ΡΡΡ ΡΠ΅Ρ Π½ΠΎΠ»ΠΎΠ³ΠΈΡΠ΅ΡΠΊΠΎΠ³ΠΎ ΡΠΎΠΊΠ°. ΠΠΎΠ»ΡΡΠ½ΠΎΡΡΡ Π·Π°Π²ΠΈΡΠΈΡ ΠΎΡ Π΄Π»ΠΈΡΠ΅Π»ΡΠ½ΠΎΡΡΠΈ ΠΈΠΌΠΏΡΠ»ΡΡΠ°, ΠΏΠΎΡΠΊΠΎΠ»ΡΠΊΡ ΠΏΡΠΈ ΠΌΠ°Π»ΠΎΠΉ ΠΏΡΠΎΠ΄ΠΎΠ»ΠΆΠΈΡΠ΅Π»ΡΠ½ΠΎΡΡΠΈ ΠΈΠΌΠΏΡΠ»ΡΡΠ° ΠΏΡΠ΅ΠΎΠ±Π»Π°Π΄Π°Π΅Ρ ΡΡΠΎΠ·ΠΈΡ (ΠΈΠ·Π½ΠΎΡ) Π°Π½ΠΎΠ΄Π°, Π° ΠΏΡΠΈ Π±ΠΎΠ»ΡΡΠΎΠΉ Π΄Π»ΠΈΡΠ΅Π»ΡΠ½ΠΎΡΡΠΈ ΠΈΠΌΠΏΡΠ»ΡΡΠ° ΠΏΡΠ΅ΠΎΠ±Π»Π°Π΄Π°Π΅Ρ ΡΡΠΎΠ·ΠΈΡ (ΠΈΠ·Π½ΠΎΡ) ΠΊΠ°ΡΠΎΠ΄Π°. ΠΠ° ΠΏΡΠ°ΠΊΡΠΈΠΊΠ΅ ΠΈΡΠΏΠΎΠ»ΡΠ·ΡΡΡΡΡ ΠΎΠ±Π° ΡΠΏΠΎΡΠΎΠ±Π° ΠΏΠΎΠ΄Π°ΡΠΈ ΡΠ½ΠΈΠΏΠΎΠ»ΡΡΠ½ΡΡ ΠΈΠΌΠΏΡΠ»ΡΡΠΎΠ²: Ρ ΠΏΠΎΠ΄ΠΊΠ»ΡΡΠ΅Π½ΠΈΠ΅ΠΌ Π·Π°Π³ΠΎΡΠΎΠ²ΠΊΠΈ ΠΊ ΠΏΠΎΠ»ΠΎΠΆΠΈΡΠ΅Π»ΡΠ½ΠΎΠΌΡ ΠΏΠΎΠ»ΡΡΡ Π³Π΅Π½Π΅ΡΠ°ΡΠΎΡΠ° ΠΈΠΌΠΏΡΠ»ΡΡΠΎΠ² (Ρ. Π½. Π²ΠΊΠ»ΡΡΠ΅Π½ΠΈΠ΅ Π½Π° ΠΏΡΡΠΌΡΡ ΠΏΠΎΠ»ΡΡΠ½ΠΎΡΡΡ), ΠΈ Ρ ΠΏΠΎΠ΄ΠΊΠ»ΡΡΠ΅Π½ΠΈΠ΅ΠΌ Π·Π°Π³ΠΎΡΠΎΠ²ΠΊΠΈ ΠΊ ΠΎΡΡΠΈΡΠ°ΡΠ΅Π»ΡΠ½ΠΎΠΌΡ ΠΏΠΎΠ»ΡΡΡ (Ρ. Π½. Π²ΠΊΠ»ΡΡΠ΅Π½ΠΈΠ΅ Π½Π° ΠΎΠ±ΡΠ°ΡΠ½ΡΡ ΠΏΠΎΠ»ΡΡΠ½ΠΎΡΡΡ).
ru.wikipedia.org
ΠΏΡΠΈΠ½ΡΠΈΠΏ ΡΠ°Π±ΠΎΡΡ ΠΈ ΡΠ΅Ρ Π½ΠΎΠ»ΠΎΠ³ΠΈΡ ΠΎΠ±ΡΠ°Π±ΠΎΡΠΊΠΈ
ΠΠ»Π΅ΠΊΡΡΠΎΡΡΠΎΠ·ΠΈΠΎΠ½Π½ΡΡ ΠΎΠ±ΡΠ°Π±ΠΎΡΠΊΡ ΠΌΠ΅ΡΠ°Π»Π»Π° Π΄ΠΎΡΡΠ°ΡΠΎΡΠ½ΠΎ ΡΠΈΡΠΎΠΊΠΎ ΠΏΡΠΈΠΌΠ΅Π½ΡΡΡ Π΄Π»Ρ ΠΈΠ·ΠΌΠ΅Π½Π΅Π½ΠΈΡ ΡΠ°Π·ΠΌΠ΅ΡΠΎΠ² ΠΌΠ΅ΡΠ°Π»Π»ΠΈΡΠ΅ΡΠΊΠΈΡ
Π΄Π΅ΡΠ°Π»Π΅ΠΉ, Π½Π΅ Π½Π°ΡΡΡΠ°Ρ ΠΈΡ
ΡΠΈΠ·ΠΈΡΠ΅ΡΠΊΠΈΡ
ΡΠ²ΠΎΠΉΡΡΠ². Π’Π°ΠΊΠΎΠΉ ΠΏΡΠΎΡΠ΅ΡΡ ΠΎΡΡΡΠ΅ΡΡΠ²Π»ΡΠ΅ΡΡΡ ΠΏΡΠΈ ΠΏΠΎΠΌΠΎΡΠΈ ΡΠΏΠ΅ΡΠΈΠ°Π»ΡΠ½ΠΎΠ³ΠΎ ΠΎΠ±ΠΎΡΡΠ΄ΠΎΠ²Π°Π½ΠΈΡ ΠΈ ΡΡΠ΅Π±ΡΠ΅Ρ Ρ
ΠΎΡΠΎΡΠ΅Π³ΠΎ Π·Π½Π°Π½ΠΈΡ Π½Π΅ΠΎΠ±Ρ
ΠΎΠ΄ΠΈΠΌΡΡ
ΡΠ΅Ρ
Π½ΠΎΠ»ΠΎΠ³ΠΈΠΉ.
ΠΡΠΎΠΌΠ΅ ΡΠΎΠ³ΠΎ, ΡΠ°ΠΊΠ°Ρ ΠΎΠ±ΡΠ°Π±ΠΎΡΠΊΠ° Π΄Π°Π΅Ρ Π²ΠΎΠ·ΠΌΠΎΠΆΠ½ΠΎΡΡΡ ΠΏΠΎΠ»ΡΡΠΈΡΡ ΠΎΡΠ²Π΅ΡΡΡΠΈΡ Π½ΡΠΆΠ½ΠΎΠΉ ΡΠΎΡΠΌΡ ΠΈ ΠΊΠΎΠ½ΡΠΈΠ³ΡΡΠ°ΡΠΈΠΈ, ΠΏΡΠΈ Π½Π΅ΠΎΠ±Ρ ΠΎΠ΄ΠΈΠΌΠΎΡΡΠΈ β ΡΠ΄Π΅Π»Π°ΡΡ ΡΠ°ΡΠΎΠ½Π½ΡΠ΅ ΠΏΠΎΠ»ΠΎΡΡΠΈ, ΠΈ ΠΈΠ·Π³ΠΎΡΠΎΠ²ΠΈΡΡ ΠΏΡΠΎΡΠΈΠ»ΡΠ½ΡΠ΅ ΠΏΠ°Π·Ρ ΠΈ ΠΊΠ°Π½Π°Π²ΠΊΠΈ Π½Π° Π·Π°Π³ΠΎΡΠΎΠ²ΠΊΠ°Ρ , ΡΠΎΠ·Π΄Π°Π½Π½ΡΡ Π½Π° ΠΎΡΠ½ΠΎΠ²Π΅ ΡΠ²Π΅ΡΠ΄ΡΡ ΡΠΏΠ»Π°Π²ΠΎΠ².
Π’Π°ΠΊΠΎΠ΅ ΡΠ»Π΅ΠΊΡΡΠΎΡΡΠΎΠ·ΠΈΠΎΠ½Π½ΠΎΠ΅ Π²ΠΎΠ·Π΄Π΅ΠΉΡΡΠ²ΠΈΠ΅ Π΄Π΅Π»Π°Π΅Ρ ΡΠ°Π·Π»ΠΈΡΠ½ΡΠ΅ ΠΈΠ½ΡΡΡΡΠΌΠ΅Π½ΡΡ Π³ΠΎΡΠ°Π·Π΄ΠΎ ΠΏΡΠΎΡΠ½Π΅Π΅, ΠΎΠ±Π΅ΡΠΏΠ΅ΡΠΈΠ²Π°Π΅Ρ ΠΏΡΠΎΠΈΠ·Π²ΠΎΠ΄ΡΡΠ²ΠΎ ΠΊΠ°ΡΠ΅ΡΡΠ²Π΅Π½Π½ΠΎΠ³ΠΎ ΡΠ»Π΅ΠΊΡΡΠΎΠΏΠ΅ΡΠ°ΡΠ°Π½ΠΈΡ, Π²ΡΡΠΎΠΊΠΎΡΠΎΡΠ½ΠΎΠ³ΠΎ ΡΠ»ΠΈΡΠΎΠ²Π°Π½ΠΈΡ, ΠΎΡΡΡΠ΅ΡΡΠ²Π»ΡΡΡ ΡΠ΅Π·ΠΊΡ Π΄Π΅ΡΠ°Π»Π΅ΠΉ ΠΈ ΠΌΠ½ΠΎΠ³ΠΎΠ΅ Π΄ΡΡΠ³ΠΎΠ΅. ΠΡΠΏΠΎΠ»Π½ΡΠ΅ΡΡΡ ΠΎΠ±ΡΠ°Π±ΠΎΡΠΊΠ° ΠΏΡΠΈ ΠΏΠΎΠ»Π½ΠΎΠΌ ΡΠΎΠ±Π»ΡΠ΄Π΅Π½ΠΈΠΈ Π²ΡΠ΅Ρ Π½Π΅ΠΎΠ±Ρ ΠΎΠ΄ΠΈΠΌΡΡ ΠΏΡΠ°Π²ΠΈΠ» ΡΠ΅Ρ Π½ΠΈΠΊΠΈ Π±Π΅Π·ΠΎΠΏΠ°ΡΠ½ΠΎΡΡΠΈ.
ΠΡΠΈΠ½ΡΠΈΠΏ ΡΠ°Π±ΠΎΡΡ
ΠΡΠΆΠ½ΠΎ ΠΎΡΠΌΠ΅ΡΠΈΡΡ, ΡΡΠΎ Π²Π°ΠΆΠ½Π΅ΠΉΡΠΈΠΌ ΡΠ»Π΅ΠΌΠ΅Π½ΡΠΎΠΌ Π² ΡΡ Π΅ΠΌΠ΅, Π½Π΅ΠΎΠ±Ρ ΠΎΠ΄ΠΈΠΌΠΎΠΉ Π΄Π»Ρ Π²ΡΠΏΠΎΠ»Π½Π΅Π½ΠΈΡ ΡΠ»Π΅ΠΊΡΡΠΎΡΡΠΎΠ·ΠΈΠΎΠ½Π½ΠΎΠΉ ΠΎΠ±ΡΠ°Π±ΠΎΡΠΊΠΈ, ΡΠ²Π»ΡΠ΅ΡΡΡ ΡΠ»Π΅ΠΊΡΡΠΎΠ΄, ΠΊΠΎΡΠΎΡΡΠΉ Π΄ΠΎΠ»ΠΆΠ΅Π½ ΠΈΠΌΠ΅ΡΡ Π΄ΠΎΡΡΠ°ΡΠΎΡΠ½ΡΡ ΡΡΠΎΠ·ΠΈΠΎΠ½Π½ΡΡ ΡΡΠΎΠΉΠΊΠΎΡΡΡ. Π ΡΡΠΎΠΌ ΡΠ»ΡΡΠ°Π΅ Π² ΠΊΠ°ΡΠ΅ΡΡΠ²Π΅ ΡΠ»Π΅ΠΊΡΡΠΎΠ΄Π° ΠΌΠΎΠΆΠ½ΠΎ ΠΈΡΠΏΠΎΠ»ΡΠ·ΠΎΠ²Π°ΡΡ ΡΠ°ΠΊΠΈΠ΅ ΠΌΠ΅ΡΠ°Π»Π»Ρ, ΠΊΠ°ΠΊ:
- Π³ΡΠ°ΡΠΈΡ;
- ΠΌΠ΅Π΄Ρ;
- Π²ΠΎΠ»ΡΡΡΠ°ΠΌ;
- Π°Π»ΡΠΌΠΈΠ½ΠΈΠΉ;
- Π»Π°ΡΡΠ½Ρ.
Π‘ ΡΠΎΡΠΊΠΈ Π·ΡΠ΅Π½ΠΈΡ Ρ
ΠΈΠΌΠΈΠΈ, ΡΠ°ΠΊΠΎΠΉ ΠΌΠ΅ΡΠΎΠ΄ ΡΠ΅ΡΠΌΠΈΡΠ΅ΡΠΊΠΎΠ³ΠΎ Π²ΠΎΠ·Π΄Π΅ΠΉΡΡΠ²ΠΈΡ Π½Π° ΠΌΠ΅ΡΠ°Π»Π» ΡΠΏΠΎΡΠΎΠ±ΡΡΠ²ΡΠ΅Ρ ΡΠ°Π·ΡΡΡΠ΅Π½ΠΈΡ Π΅Π³ΠΎ ΠΊΡΠΈΡΡΠ°Π»Π»ΠΈΡΠ΅ΡΠΊΠΎΠΉ ΡΠ΅ΡΠ΅ΡΠΊΠΈ, Π±Π»Π°Π³ΠΎΠ΄Π°ΡΡ ΡΠ΅ΠΌΡ Π²ΡΡΠ²ΠΎΠ±ΠΎΠΆΠ΄Π°ΡΡΡΡ Π½Π΅ΠΊΠΎΡΠΎΡΡΠ΅ ΠΊΠ°ΡΠ΅Π³ΠΎΡΠΈΠΈ ΠΈΠΎΠ½ΠΎΠ².
ΠΡΠ»ΠΈ Π΄Π»Ρ Π΄Π΅ΡΠ°Π»Π΅ΠΉ ΠΈΠ· ΠΌΠ΅ΡΠ°Π»Π»Π° ΠΏΠΎΡΡΠ΅Π±ΡΠ΅ΡΡΡ ΡΠ΅ΡΠ½ΠΎΠ²Π°Ρ ΠΎΠ±ΡΠ°Π±ΠΎΡΠΊΠ°, ΡΠΎ ΠΎΠ±ΡΡΠ½ΠΎ ΠΏΡΠΈΠΌΠ΅Π½ΡΡΡ ΡΠ»Π΅ΠΊΡΡΠΎΠΈΠΌΠΏΡΠ»ΡΡΠ½ΡΡ ΡΡ Π΅ΠΌΡ. ΠΡΠΈ ΡΡΠΎΠΌ Π²ΠΎ Π²ΡΠ΅ΠΌΡ ΡΠ°Π±ΠΎΡ ΡΠ΅ΠΌΠΏΠ΅ΡΠ°ΡΡΡΠ° Π²ΡΡΠ°Π±Π°ΡΡΠ²Π°Π΅ΠΌΡΡ ΠΈΠΌΠΏΡΠ»ΡΡΠΎΠ² ΠΌΠΎΠΆΠ΅Ρ Π΄ΠΎΡΡΠΈΠ³Π°ΡΡ 5 000 Π³ΡΠ°Π΄ΡΡΠΎΠ². ΠΡΠΎ ΡΠ²Π΅Π»ΠΈΡΠΈΠ²Π°Π΅Ρ ΡΠ°ΠΊΠΎΠΉ ΠΏΠ°ΡΠ°ΠΌΠ΅ΡΡ, ΠΊΠ°ΠΊ ΠΏΡΠΎΠΈΠ·Π²ΠΎΠ΄ΠΈΡΠ΅Π»ΡΠ½ΠΎΡΡΡ.
ΠΡΠ»ΠΈ ΡΡΠ΅Π±ΡΠ΅ΡΡΡ ΠΎΠ±ΡΠ°Π±ΠΎΡΠ°ΡΡ Π·Π°Π³ΠΎΡΠΎΠ²ΠΊΠΈ Ρ Π½Π΅Π±ΠΎΠ»ΡΡΠΈΠΌΠΈ ΡΠ°Π·ΠΌΠ΅ΡΠ°ΠΌΠΈ ΠΈ Π³Π°Π±Π°ΡΠΈΡΠ°ΠΌΠΈ, ΡΠΎ Π² ΠΎΡΠ½ΠΎΠ²Π½ΠΎΠΌ ΠΈΡΠΏΠΎΠ»ΡΠ·ΡΠ΅ΡΡΡ ΡΠ»Π΅ΠΊΡΡΠΎΠΈΡΠΊΡΠΎΠ²ΠΎΠΉ ΡΠΏΠΎΡΠΎΠ±.
ΠΠ»Π΅ΠΊΡΡΠΎΠΊΠΎΠ½ΡΠ°ΠΊΡΠ½Π°Ρ ΠΎΠ±ΡΠ°Π±ΠΎΡΠΊΠ° ΠΏΡΠΈΠΌΠ΅Π½ΡΠ΅ΡΡΡ ΠΏΡΠΈ ΡΠ°Π±ΠΎΡΠ΅ ΡΠΎ ΡΠΏΠ»Π°Π²Π°ΠΌΠΈ, ΠΎΡΡΡΠ΅ΡΡΠ²Π»ΡΠ΅ΠΌΠΎΠΉ Π² ΠΆΠΈΠ΄ΠΊΠΎΠΉ ΡΡΠ΅Π΄Π΅. ΠΠ΅ΠΎΠ±Ρ ΠΎΠ΄ΠΈΠΌΠΎ ΠΎΡΠΌΠ΅ΡΠΈΡΡ, ΡΡΠΎ ΠΏΡΠΈΠΎΠ±ΡΠ΅ΡΠ΅Π½Π½ΡΠ΅ ΡΠ²ΠΎΠΉΡΡΠ²Π° ΠΌΠ΅ΡΠ°Π»Π»Π° ΠΏΠΎΡΠ»Π΅ ΡΠ°ΠΊΠΎΠ³ΠΎ Π²ΠΎΠ·Π΄Π΅ΠΉΡΡΠ²ΠΈΡ ΠΌΠΎΠ³ΡΡ ΠΏΠΎ-ΡΠ°Π·Π½ΠΎΠΌΡ ΠΎΡΡΠ°Π·ΠΈΡΡΡΡ Π½Π° ΡΠΊΡΠΏΠ»ΡΠ°ΡΠ°ΡΠΈΠΎΠ½Π½ΡΡ Ρ Π°ΡΠ°ΠΊΡΠ΅ΡΠΈΡΡΠΈΠΊΠ°Ρ Π΄Π΅ΡΠ°Π»Π΅ΠΉ.
ΠΡΠ°ΠΊΡΠΈΡΠ΅ΡΠΊΠΈ Π²ΡΠ΅Π³Π΄Π° ΠΈΠ·-Π·Π° Π²ΠΎΠ·Π΄Π΅ΠΉΡΡΠ²ΠΈΡ ΡΠΎΠΊΠΎΠ² ΠΈ Π²ΡΡΠΎΠΊΠΈΡ ΡΠ΅ΠΌΠΏΠ΅ΡΠ°ΡΡΡ Ρ ΠΎΠ±ΡΠ°Π±Π°ΡΡΠ²Π°Π΅ΠΌΡΡ Π΄Π΅ΡΠ°Π»Π΅ΠΉ ΠΎΡΠ΅Π½Ρ ΡΠΈΠ»ΡΠ½ΠΎ ΠΏΠΎΠ²ΡΡΠ°Π΅ΡΡΡ ΠΏΡΠΎΡΠ½ΠΎΡΡΡ, Π° Π² ΡΠ°ΠΌΠΎΠΉ ΡΡΡΡΠΊΡΡΡΠ΅ ΡΠΎΡ ΡΠ°Π½ΡΠ΅ΡΡΡ ΠΌΡΠ³ΠΊΠΎΡΡΡ.
ΠΠΈΠ΄Ρ ΠΈΡΠΏΠΎΠ»ΡΠ·ΡΠ΅ΠΌΠΎΠ³ΠΎ ΠΎΠ±ΠΎΡΡΠ΄ΠΎΠ²Π°Π½ΠΈΡ
ΠΠ·Π²Π΅ΡΡΠ½ΠΎ, ΡΡΠΎ ΡΡΡΠ΅ΡΡΠ²ΡΡΡ ΡΠ°Π·Π½ΠΎΠΎΠ±ΡΠ°Π·Π½ΡΠ΅ ΡΠΏΠΎΡΠΎΠ±Ρ ΠΈ ΠΌΠ΅ΡΠΎΠ΄Ρ ΠΎΠ±ΡΠ°Π±ΠΎΡΠΊΠΈ ΠΏΠΎΠ²Π΅ΡΡ
Π½ΠΎΡΡΠ΅ΠΉ ΠΌΠ΅ΡΠ°Π»Π»ΠΎΠ², ΠΈ ΡΠ°ΠΊΠΎΠΉ Π²ΠΈΠ΄ ΡΡΠΈΡΠ°Π΅ΡΡΡ Π±ΠΎΠ»Π΅Π΅ ΡΡΡΠ΅ΠΊΡΠΈΠ²Π½ΡΠΌ, ΡΠ΅ΠΌ ΠΌΠ΅Ρ
Π°Π½ΠΈΡΠ΅ΡΠΊΠΈΠΉ. Π ΠΎΡΠ½ΠΎΠ²Π½ΠΎΠΌ ΡΡΠΎ ΡΠ²ΡΠ·Π°Π½ΠΎ Ρ ΡΠ΅ΠΌ, ΡΡΠΎ ΠΏΡΠΈΠΌΠ΅Π½ΡΠ΅ΠΌΡΠΉ Π΄Π»Ρ ΠΏΡΠΎΠ²Π΅Π΄Π΅Π½ΠΈΡ ΠΌΠ΅Ρ
Π°Π½ΠΈΡΠ΅ΡΠΊΠΎΠΉ ΠΎΠ±ΡΠ°Π±ΠΎΡΠΊΠΈ ΠΈΠ½ΡΡΡΡΠΌΠ΅Π½Ρ ΡΡΠΎΠΈΡ Π·Π½Π°ΡΠΈΡΠ΅Π»ΡΠ½ΠΎ Π΄ΠΎΡΠΎΠΆΠ΅, ΡΠ΅ΠΌ ΠΏΡΠΎΠ²ΠΎΠ»ΠΎΠΊΠ°, ΠΈΡΠΏΠΎΠ»ΡΠ·ΡΠ΅ΠΌΠ°Ρ ΠΏΡΠΈ ΡΠ»Π΅ΠΊΡΡΠΎΡΡΠΎΠ·ΠΈΠΎΠ½Π½ΠΎΠΉ ΠΎΠ±ΡΠ°Π±ΠΎΡΠΊΠ΅.
ΠΡΠΎΠΌΡΡΠ»Π΅Π½Π½ΡΠ΅ ΠΏΡΠ΅Π΄ΠΏΡΠΈΡΡΠΈΡ Π΄Π»Ρ ΡΠ»Π΅ΠΊΡΡΠΎΡΡΠΎΠ·ΠΈΠΎΠ½Π½ΠΎΠΉ ΠΎΠ±ΡΠ°Π±ΠΎΡΠΊΠΈ ΠΌΠ΅ΡΠ°Π»Π»Π° ΠΏΡΠΈΠΌΠ΅Π½ΡΡΡ ΡΠΏΠ΅ΡΠΈΠ°Π»ΡΠ½ΠΎΠ΅ ΠΎΠ±ΠΎΡΡΠ΄ΠΎΠ²Π°Π½ΠΈΠ΅, ΡΠ°ΠΊΠΎΠ΅ ΠΊΠ°ΠΊ:
- ΠΏΡΠΎΠ²ΠΎΠ»ΠΎΡΠ½ΠΎ- ΡΠ»Π΅ΠΊΡΡΠΎΡΡΠΎΠ·ΠΈΠΎΠ½Π½ΠΎΠ΅;
- ΠΊΠΎΠΏΠΈΡΠΎΠ²Π°Π»ΡΠ½ΠΎ-ΠΏΡΠΎΡΠΈΠ²ΠΎΡΠ½ΠΎΠ΅.
ΠΡΠ»ΠΈ Π²ΠΎΠ·Π½ΠΈΠΊΠ°Π΅Ρ Π½Π΅ΠΎΠ±Ρ ΠΎΠ΄ΠΈΠΌΠΎΡΡΡ ΠΈΠ·Π³ΠΎΡΠΎΠ²ΠΈΡΡ Π΄Π΅ΡΠ°Π»ΠΈ ΡΠΎ ΡΠ»ΠΎΠΆΠ½ΠΎΠΉ ΡΠΎΡΠΌΠΎΠΉ ΠΈ ΠΏΡΠ΅ΡΡ-ΡΠΎΡΠΌΡ, Π° ΡΠ°ΠΊΠΆΠ΅ Π΄Π»Ρ ΠΏΡΠΎΠΈΠ·Π²ΠΎΠ΄ΡΡΠ²Π° Π½Π΅ΠΊΠΎΡΠΎΡΡΡ ΠΌΠ°ΡΠ΅ΡΠΈΠ°Π»ΠΎΠ² Ρ Π²ΡΡΠΎΠΊΠΎΠΉ ΡΠΎΡΠ½ΠΎΡΡΡΡ ΠΎΠ±ΡΠ°Π±ΠΎΡΠΊΠΈ, ΠΏΡΠΈΠΌΠ΅Π½ΡΡΡ ΠΏΡΠΎΠ²ΠΎΠ»ΠΎΡΠ½ΠΎ- ΡΠ»Π΅ΠΊΡΡΠΎΡΡΠΎΠ·ΠΈΠΎΠ½Π½ΡΠ΅ Π°Π³ΡΠ΅Π³Π°ΡΡ. Π§Π°ΡΠ΅ Π²ΡΠ΅Π³ΠΎ ΡΠ°ΠΊΠΎΠ΅ ΠΎΠ±ΠΎΡΡΠ΄ΠΎΠ²Π°Π½ΠΈΠ΅ ΠΈΡΠΏΠΎΠ»ΡΠ·ΡΠ΅ΡΡΡ Π΄Π»Ρ ΠΈΠ·Π³ΠΎΡΠΎΠ²Π»Π΅Π½ΠΈΡ ΡΠ°Π·Π»ΠΈΡΠ½ΡΡ Π΄Π΅ΡΠ°Π»Π΅ΠΉ Π΄Π»Ρ ΡΠ»Π΅ΠΊΡΡΠΎΠ½ΠΈΠΊΠΈ, ΡΠ°ΠΌΠΎΠ»Π΅ΡΠΎΠ², ΠΈ Π΄Π°ΠΆΠ΅ ΠΊΠΎΡΠΌΠΈΡΠ΅ΡΠΊΠΎΠΉ ΡΡΠ΅ΡΡ.
ΠΠΎΠΏΠΈΡΠΎΠ²Π°Π»ΡΠ½ΠΎ-ΠΏΡΠΎΡΠΈΠ²ΠΎΡΠ½ΡΠ΅ Π°Π³ΡΠ΅Π³Π°ΡΡ Π² ΠΎΡΠ½ΠΎΠ²Π½ΠΎΠΌ ΠΏΡΠΈΠΌΠ΅Π½ΡΡΡΡΡ Π΄Π»Ρ ΡΠ΅ΡΠΈΠΉΠ½ΠΎΠ³ΠΎ ΠΈ ΠΌΠ°ΡΡΠΎΠ²ΠΎΠ³ΠΎ ΠΏΡΠΎΠΈΠ·Π²ΠΎΠ΄ΡΡΠ²Π° Π΄Π΅ΡΠ°Π»Π΅ΠΉ. ΠΠ»Π°Π³ΠΎΠ΄Π°ΡΡ ΡΠ°ΠΊΠΈΠΌ ΡΡΠ°Π½ΠΊΠ°ΠΌ ΠΏΠΎΠ»ΡΡΠ°ΡΡΡΡ Π΄ΠΎΠ²ΠΎΠ»ΡΠ½ΠΎ ΡΠΎΡΠ½ΡΠ΅ ΡΠΊΠ²ΠΎΠ·Π½ΡΠ΅ ΠΊΠΎΠ½ΡΡΡΡ ΠΈ ΠΌΠ΅Π»ΠΊΠΈΠ΅ ΠΎΡΠ²Π΅ΡΡΡΠΈΡ, ΡΡΠΎ Ρ ΡΡΠΏΠ΅Ρ ΠΎΠΌ ΠΈΡΠΏΠΎΠ»ΡΠ·ΡΠ΅ΡΡΡ ΠΏΡΠΈ ΠΈΠ·Π³ΠΎΡΠΎΠ²Π»Π΅Π½ΠΈΠΈ ΡΠ΅ΡΠΎΠΊ ΠΈ ΡΡΠ°ΠΌΠΏΠΎΠ² Π² ΠΈΠ½ΡΡΡΡΠΌΠ΅Π½ΡΠ°Π»ΡΠ½ΠΎΠΉ ΠΏΡΠΎΠΌΡΡΠ»Π΅Π½Π½ΠΎΠΉ ΡΡΠ΅ΡΠ΅. Π’Π°ΠΊΠΎΠ΅ ΠΎΠ±ΠΎΡΡΠ΄ΠΎΠ²Π°Π½ΠΈΠ΅ ΠΏΠΎΠ΄Π±ΠΈΡΠ°ΡΡ, ΠΎΡΠΈΠ΅Π½ΡΠΈΡΡΡΡΡ Π½Π° ΠΏΠΎΡΡΠ°Π²Π»Π΅Π½Π½ΡΠ΅ ΡΠ΅Π»ΠΈ ΠΈ ΡΠΈΠ½Π°Π½ΡΠΎΠ²ΡΡ ΠΎΠΊΡΠΏΠ°Π΅ΠΌΠΎΡΡΡ. ΠΠ»Π΅ΠΊΡΡΠΎΡΡΠΎΠ·ΠΈΠΎΠ½Π½Π°Ρ ΠΎΠ±ΡΠ°Π±ΠΎΡΠΊΠ° ΠΌΠ΅ΡΠ°Π»Π»Π° ΡΡΠΈΡΠ°Π΅ΡΡΡ ΡΠ»ΠΎΠΆΠ½ΡΠΌ ΠΈ Π΄ΠΎΠ²ΠΎΠ»ΡΠ½ΠΎ ΡΡΡΠ΄ΠΎΠ΅ΠΌΠΊΠΈΠΌ ΡΠ°Π±ΠΎΡΠΈΠΌ ΠΏΡΠΎΡΠ΅ΡΡΠΎΠΌ.
Π’Π°ΠΊΠΈΠ΅ ΡΠ°Π±ΠΎΡΡ Π½Π΅Π²ΠΎΠ·ΠΌΠΎΠΆΠ½ΠΎ Π²ΡΠΏΠΎΠ»Π½ΠΈΡΡ Π² Π΄ΠΎΠΌΠ°ΡΠ½ΠΈΡ
ΡΡΠ»ΠΎΠ²ΠΈΡΡ
. ΠΡΠΏΠΎΠ»Π½ΡΡΡ ΡΠ°Π±ΠΎΡΡ Π½Π° ΡΡΠ°Π½ΠΊΠ°Ρ
Π΄Π»Ρ ΠΎΠ±ΡΠ°Π±ΠΎΡΠΊΠΈ Π΄Π΅ΡΠ°Π»Π΅ΠΉ ΠΈΠΌΠ΅ΡΡ ΠΏΡΠ°Π²ΠΎ ΡΠΎΠ»ΡΠΊΠΎ Π°ΡΡΠ΅ΡΡΠΎΠ²Π°Π½Π½ΡΠ΅ ΠΈ ΠΊΠ²Π°Π»ΠΈΡΠΈΡΠΈΡΠΎΠ²Π°Π½Π½ΡΠ΅ ΡΠΏΠ΅ΡΠΈΠ°Π»ΠΈΡΡΡ, ΠΈΠΌΠ΅ΡΡΠΈΠ΅ Π΄ΠΎΡΡΠ°ΡΠΎΡΠ½ΡΠΉ ΠΎΠΏΡΡ ΡΠ°Π±ΠΎΡΡ Π² ΡΡΠΎΠΉ ΡΡΠ΅ΡΠ΅.
ΠΡΠΏΠΎΠ»Π½ΡΡ ΡΠ»Π΅ΠΊΡΡΠΎΡΡΠΎΠ·ΠΈΠΎΠ½Π½ΡΡ ΠΎΠ±ΡΠ°Π±ΠΎΡΠΊΡ, Π½Π΅ ΡΡΠΎΠΈΡ Π·Π°Π±ΡΠ²Π°ΡΡ ΠΎ ΡΠ΅Ρ Π½ΠΈΠΊΠ΅ Π±Π΅Π·ΠΎΠΏΠ°ΡΠ½ΠΎΡΡΠΈ ΠΈ ΠΈΡΠΏΠΎΠ»ΡΠ·ΠΎΠ²Π°Π½ΠΈΠΈ ΡΠΏΠ΅ΡΠΎΠ΄Π΅ΠΆΠ΄Ρ.
ΠΡΠ΅ΠΈΠΌΡΡΠ΅ΡΡΠ²Π° ΡΠ»Π΅ΠΊΡΡΠΎΡΡΠΎΠ·ΠΈΠΎΠ½Π½ΠΎΠΉ ΠΎΠ±ΡΠ°Π±ΠΎΡΠΊΠΈ
Π’Π°ΠΊΠΈΠ΅ ΡΠ°Π±ΠΎΡΡ Π΄ΠΎΠ»ΠΆΠ½Ρ ΠΎΡΡΡΠ΅ΡΡΠ²Π»ΡΡΡΡΡ ΡΠΎΠ»ΡΠΊΠΎ Π½Π° ΡΠΏΠ΅ΡΠΈΠ°Π»ΡΠ½ΠΎΠΌ ΠΎΠ±ΠΎΡΡΠ΄ΠΎΠ²Π°Π½ΠΈΠΈ ΠΏΠΎΠ΄ ΠΎΠ±ΡΠ·Π°ΡΠ΅Π»ΡΠ½ΡΠΌ ΠΏΡΠΈΡΠΌΠΎΡΡΠΎΠΌ ΠΊΠ²Π°Π»ΠΈΡΠΈΡΠΈΡΠΎΠ²Π°Π½Π½ΠΎΠ³ΠΎ ΡΠΏΠ΅ΡΠΈΠ°Π»ΠΈΡΡΠ°,
ΠΠΎΡΡΠΎΠΌΡ Π½Π΅ΠΎΠ±Ρ ΠΎΠ΄ΠΈΠΌΠΎ ΠΎΡΠΌΠ΅ΡΠΈΡΡ ΠΎΡΠ½ΠΎΠ²Π½ΡΠ΅ Π΄ΠΎΡΡΠΎΠΈΠ½ΡΡΠ²Π° ΡΠ»Π΅ΠΊΡΡΠΎΡΡΠΎΠ·ΠΈΠΎΠ½Π½ΠΎΠ³ΠΎ Π²ΠΎΠ·Π΄Π΅ΠΉΡΡΠ²ΠΈΡ Π½Π° ΡΠ°Π·Π½ΠΎΠΎΠ±ΡΠ°Π·Π½ΡΠ΅ Π²ΠΈΠ΄Ρ Π·Π°Π³ΠΎΡΠΎΠ²ΠΎΠΊ.
ΠΡΠΏΠΎΠ»ΡΠ·ΡΡ ΡΠ°ΠΊΠΎΠΉ ΠΌΠ΅ΡΠΎΠ΄, ΠΏΡΠ°ΠΊΡΠΈΡΠ΅ΡΠΊΠΈ Π²ΡΠ΅Π³Π΄Π° ΡΠ΄Π°Π΅ΡΡΡ Π΄ΠΎΠ±ΠΈΡΡΡΡ ΡΠ°ΠΌΠΎΠ³ΠΎ Π²ΡΡΠΎΠΊΠΎΠ³ΠΎ ΠΊΠ°ΡΠ΅ΡΡΠ²Π° ΠΏΠΎΠ²Π΅ΡΡ Π½ΠΎΡΡΠΈ ΠΌΠ΅ΡΠ°Π»Π»Π°, Π² ΡΠ΅Π·ΡΠ»ΡΡΠ°ΡΠ΅ ΡΠ΅Π³ΠΎ ΠΎΠ½Π° ΡΡΠ°Π½ΠΎΠ²ΠΈΡΡΡ ΠΌΠ°ΠΊΡΠΈΠΌΠ°Π»ΡΠ½ΠΎ ΡΠΎΡΠ½ΠΎΠΉ ΠΈ ΠΎΠ΄Π½ΠΎΡΠΎΠ΄Π½ΠΎΠΉ. ΠΡΠΈ ΡΡΠΎΠΌ ΠΏΠΎΠ»Π½ΠΎΡΡΡΡ ΠΈΡΠΊΠ»ΡΡΠ°Π΅ΡΡΡ Π½Π΅ΠΎΠ±Ρ ΠΎΠ΄ΠΈΠΌΠΎΡΡΡ ΠΏΡΠΎΠ²Π΅Π΄Π΅Π½ΠΈΡ ΡΠΈΠ½ΠΈΡΠ½ΠΎΠΉ ΠΎΠ±ΡΠ°Π±ΠΎΡΠΊΠΈ. Π’Π°ΠΊΠΆΠ΅ ΡΡΠΎΡ ΠΌΠ΅ΡΠΎΠ΄ Π³Π°ΡΠ°Π½ΡΠΈΡΡΠ΅Ρ ΠΏΠΎΠ»ΡΡΠ΅Π½ΠΈΠ΅ Π½Π° Π²ΡΡ ΠΎΠ΄Π΅ ΠΏΠΎΠ²Π΅ΡΡ Π½ΠΎΡΡΠΈ ΡΠ°Π·Π½ΠΎΠΎΠ±ΡΠ°Π·Π½ΠΎΠΉ ΡΡΡΡΠΊΡΡΡΡ.
Π’Π°ΠΊΠΆΠ΅ ΠΊ Π΄ΠΎΡΡΠΎΠΈΠ½ΡΡΠ²Π°ΠΌ ΡΠ»Π΅ΠΊΡΡΠΎΡΡΠΎΠ·ΠΈΠΎΠ½Π½ΠΎΠΉ ΠΎΠ±ΡΠ°Π±ΠΎΡΠΊΠΈ ΠΌΠ΅ΡΠ°Π»Π»Π° ΠΎΡΠ½ΠΎΡΡΡ Π²ΠΎΠ·ΠΌΠΎΠΆΠ½ΠΎΡΡΡ ΠΎΡΡΡΠ΅ΡΡΠ²Π»ΡΡΡ ΡΠ°Π±ΠΎΡΡ Ρ ΠΏΠΎΠ²Π΅ΡΡ Π½ΠΎΡΡΡΡ Π»ΡΠ±ΠΎΠΉ ΡΠ²Π΅ΡΠ΄ΠΎΡΡΠΈ.
ΠΠ»Π΅ΠΊΡΡΠΎΡΡΠΎΠ·ΠΈΠΎΠ½Π½ΠΎΠ΅ Π²ΠΎΠ·Π΄Π΅ΠΉΡΡΠ²ΠΈΠ΅ ΠΏΠΎΠ»Π½ΠΎΡΡΡΡ ΠΈΡΠΊΠ»ΡΡΠ°Π΅Ρ Π²ΠΎΠ·Π½ΠΈΠΊΠ½ΠΎΠ²Π΅Π½ΠΈΠ΅ Π΄Π΅ΡΠΎΡΠΌΠ°ΡΠΈΠΈ ΠΏΠΎΠ²Π΅ΡΡ Π½ΠΎΡΡΠΈ Ρ Π΄Π΅ΡΠ°Π»Π΅ΠΉ, ΠΈΠΌΠ΅ΡΡΠΈΡ Π½Π΅Π±ΠΎΠ»ΡΡΡΡ ΡΠΎΠ»ΡΠΈΠ½Ρ. ΠΡΠΎ Π²ΠΎΠ·ΠΌΠΎΠΆΠ½ΠΎ ΠΈΠ·-Π·Π° ΡΠΎΠ³ΠΎ, ΡΡΠΎ ΠΏΡΠΈ ΡΠ°ΠΊΠΎΠΌ ΠΌΠ΅ΡΠΎΠ΄Π΅ Π½Π΅ Π²ΠΎΠ·Π½ΠΈΠΊΠ°Π΅Ρ Π½ΠΈΠΊΠ°ΠΊΠΎΠΉ ΠΌΠ΅Ρ Π°Π½ΠΈΡΠ΅ΡΠΊΠΎΠΉ Π½Π°Π³ΡΡΠ·ΠΊΠΈ, Π° ΡΠ°Π±ΠΎΡΠΈΠΉ Π°Π½ΠΎΠ΄ ΠΈΠΌΠ΅Π΅Ρ ΠΌΠΈΠ½ΠΈΠΌΠ°Π»ΡΠ½ΡΠΉ ΠΈΠ·Π½ΠΎΡ. ΠΡΠΎΠΌΠ΅ ΡΠΎΠ³ΠΎ, ΡΠ»Π΅ΠΊΡΡΠΎΡΡΠΎΠ·ΠΈΠΎΠ½Π½Π°Ρ ΠΎΠ±ΡΠ°Π±ΠΎΡΠΊΠ° ΡΠΏΠΎΡΠΎΠ±ΡΡΠ²ΡΠ΅Ρ ΠΏΠΎΠ»ΡΡΠ΅Π½ΠΈΡ ΠΏΠΎΠ²Π΅ΡΡ Π½ΠΎΡΡΠΈ ΡΠ°Π·Π½ΠΎΠΎΠ±ΡΠ°Π·Π½ΡΡ Π³Π΅ΠΎΠΌΠ΅ΡΡΠΈΡΠ΅ΡΠΊΠΈΡ ΡΠΎΡΠΌ ΠΈ ΠΊΠΎΠ½ΡΠΈΠ³ΡΡΠ°ΡΠΈΠΉ ΠΏΡΠΈ ΠΌΠΈΠ½ΠΈΠΌΠ°Π»ΡΠ½ΡΡ ΡΡΠΈΠ»ΠΈΡΡ .
Π’Π°ΠΊΠΆΠ΅ ΠΊ ΠΏΡΠ΅ΠΈΠΌΡΡΠ΅ΡΡΠ²Π°ΠΌ ΡΠ°ΠΊΠΎΠ³ΠΎ ΠΏΡΠΎΡΠ΅ΡΡΠ° ΠΎΡΠ½ΠΎΡΡΡ ΠΏΠΎΠ»Π½ΠΎΠ΅ ΠΎΡΡΡΡΡΡΠ²ΠΈΠ΅ ΡΡΠΌΠ° ΠΏΡΠΈ ΡΠ°Π±ΠΎΡΠ΅ Π½Π° ΡΠΏΠ΅ΡΠΈΠ°Π»ΡΠ½ΠΎΠΌ ΠΎΠ±ΠΎΡΡΠ΄ΠΎΠ²Π°Π½ΠΈΠΈ.
ΠΠΎΠ½Π΅ΡΠ½ΠΎ, Π΅ΡΡΡ ΠΈ Π½Π΅Π΄ΠΎΡΡΠ°ΡΠΊΠΈ ΠΏΡΠΈ ΡΠ»Π΅ΠΊΡΡΠΎΡΡΠΎΠ·ΠΈΠΎΠ½Π½ΠΎΠΌ Π²ΠΎΠ·Π΄Π΅ΠΉΡΡΠ²ΠΈΠΈ Π½Π° Π΄Π΅ΡΠ°Π»Ρ ΠΈΠ· ΠΌΠ΅ΡΠ°Π»Π»Π°, Π½ΠΎ Π½Π° Π΅Π΅ ΡΠΊΡΠΏΠ»ΡΠ°ΡΠ°ΡΠΈΠΎΠ½Π½ΡΡ ΡΠ²ΠΎΠΉΡΡΠ²Π°Ρ ΡΠΊΠ°Π·ΡΠ²Π°ΡΡΡΡ ΠΎΠ½ΠΈ Π½Π΅ΡΡΡΠ΅ΡΡΠ²Π΅Π½Π½ΠΎ.
Π’Π΅Ρ Π½ΠΎΠ»ΠΎΠ³ΠΈΡ ΠΎΠ±ΡΠ°Π±ΠΎΡΠΊΠΈ
Π§ΡΠΎΠ±Ρ Π΄ΠΎ ΠΊΠΎΠ½ΡΠ° Π²ΡΡΡΠ½ΠΈΡΡ Π²ΡΠ΅ ΠΏΡΠ΅ΠΈΠΌΡΡΠ΅ΡΡΠ²Π° ΡΠ»Π΅ΠΊΡΡΠΎΡΡΠΎΠ·ΠΈΠΎΠ½Π½ΠΎΠΉ ΠΎΠ±ΡΠ°Π±ΠΎΡΠΊΠΈ ΠΈ ΠΏΠΎΠ½ΡΡΡ ΠΏΡΠΈΠ½ΡΠΈΠΏ Π²ΠΎΠ·Π΄Π΅ΠΉΡΡΠ²ΠΈΡ Π½Π° ΠΌΠ΅ΡΠ°Π»Π»ΠΈΡΠ΅ΡΠΊΡΡ Π·Π°Π³ΠΎΡΠΎΠ²ΠΊΡ, ΡΠ»Π΅Π΄ΡΠ΅Ρ Π±ΠΎΠ»Π΅Π΅ ΠΏΠΎΠ΄ΡΠΎΠ±Π½ΠΎ ΡΠ°ΡΡΠΌΠΎΡΡΠ΅ΡΡ ΡΠ»Π΅Π΄ΡΡΡΠΈΠΉ ΠΏΡΠΈΠΌΠ΅Ρ.
ΠΡΠ°ΠΊ, ΠΏΡΠΎΡΡΠ°Ρ ΡΠ»Π΅ΠΊΡΡΠΎΡΡΠΎΠ·ΠΈΠΎΠ½Π½Π°Ρ ΡΡ Π΅ΠΌΠ° Π΄ΠΎΠ»ΠΆΠ½Π° ΠΎΠ±ΡΠ·Π°ΡΠ΅Π»ΡΠ½ΠΎ ΡΠΎΡΡΠΎΡΡΡ ΠΈΠ· ΡΠ»Π΅Π΄ΡΡΡΠΈΡ ΡΠ»Π΅ΠΌΠ΅Π½ΡΠΎΠ²:
- ΡΠ»Π΅ΠΊΡΡΠΎΠ΄;
- ΠΊΠΎΠ½Π΄Π΅Π½ΡΠ°ΡΠΎΡ;
- Π΅ΠΌΠΊΠΎΡΡΡ Π΄Π»Ρ ΡΠ°Π±ΠΎΡΠ΅ΠΉ ΡΡΠ΅Π΄Ρ;
- ΡΠ΅ΠΎΡΡΠ°Ρ;
- ΠΈΡΡΠΎΡΠ½ΠΈΠΊ, ΠΎΠ±Π΅ΡΠΏΠ΅ΡΠΈΠ²Π°ΡΡΠΈΠΉ ΡΠ»Π΅ΠΊΡΡΠΎΠΏΠΈΡΠ°Π½ΠΈΠ΅.
ΠΠΈΡΠ°Π½ΠΈΠ΅ ΡΡΠΎΠΉ ΡΡ Π΅ΠΌΡ ΠΎΠ±Π΅ΡΠΏΠ΅ΡΠΈΠ²Π°Π΅ΡΡΡ Π½Π°ΠΏΡΡΠΆΠ΅Π½ΠΈΠ΅ΠΌ ΠΈΠΌΠΏΡΠ»ΡΡΠ½ΠΎΠ³ΠΎ ΡΠΈΠΏΠ°, ΠΊΠΎΡΠΎΡΠΎΠ΅ Π΄ΠΎΠ»ΠΆΠ½ΠΎ ΠΈΠΌΠ΅ΡΡ ΡΠ°Π·Π½ΡΡ ΠΏΠΎΠ»ΡΡΠ½ΠΎΡΡΡ. ΠΠ»Π°Π³ΠΎΠ΄Π°ΡΡ ΡΡΠΎΠΌΡ ΠΌΠΎΠΆΠ½ΠΎ ΠΏΠΎΠ»ΡΡΠΈΡΡ ΡΠ»Π΅ΠΊΡΡΠΎΠΈΡΠΊΡΠΎΠ²ΡΠΉ ΠΈ ΡΠ»Π΅ΠΊΡΡΠΎΠΈΠΌΠΏΡΠ»ΡΡΠ½ΡΠΉ ΡΠ΅ΠΆΠΈΠΌΡ, ΠΊΠΎΡΠΎΡΡΠ΅ ΡΡΠ΅Π±ΡΡΡΡΡ Π΄Π»Ρ ΡΠ°Π±ΠΎΡΡ.
ΠΠΎ Π²ΡΠ΅ΠΌΡ ΠΏΠΎΠ΄Π°ΡΠΈ Π½Π°ΠΏΡΡΠΆΠ΅Π½ΠΈΡ ΠΎΡΡΡΠ΅ΡΡΠ²Π»ΡΠ΅ΡΡΡ Π·Π°ΡΡΠ΄ΠΊΠ° ΠΊΠΎΠ½Π΄Π΅Π½ΡΠ°ΡΠ°, ΠΎΡ ΠΊΠΎΡΠΎΡΠΎΠ³ΠΎ Π½Π° ΡΠ»Π΅ΠΊΡΡΠΎΠ΄ ΠΏΠΎΡΡΡΠΏΠ°Π΅Ρ ΡΠ°Π·ΡΡΠ΄Π½ΡΠΉ ΡΠΎΠΊ. ΠΡΠΎΡ ΡΠ»Π΅ΠΊΡΡΠΎΠ΄ Π·Π°ΡΠ°Π½Π΅Π΅ ΠΎΠΏΡΡΠΊΠ°ΡΡ Π² Π΅ΠΌΠΊΠΎΡΡΡ Ρ Π·Π°Π³ΠΎΡΠΎΠ²ΠΊΠΎΠΉ ΠΈ ΡΠ°Π±ΠΎΡΠΈΠΌ ΡΠΎΡΡΠ°Π²ΠΎΠΌ. ΠΠ°ΠΊ ΡΠΎΠ»ΡΠΊΠΎ Π½Π° ΠΊΠΎΠ½Π΄Π΅Π½ΡΠ°ΡΠΎΡΠ΅ Π½Π°ΠΏΡΡΠΆΠ΅Π½ΠΈΠ΅ Π΄ΠΎΡΡΠΈΠ³Π½Π΅Ρ Π½ΡΠΆΠ½ΠΎΠ³ΠΎ ΠΏΠΎΡΠ΅Π½ΡΠΈΠ°Π»Π°, ΠΏΡΠΎΠΈΡΡ
ΠΎΠ΄ΠΈΡ ΠΏΡΠΎΠ±ΠΎΠΉ ΠΆΠΈΠ΄ΠΊΠΎΡΡΠΈ. ΠΠ½Π° Π½Π°ΡΠΈΠ½Π°Π΅Ρ ΠΎΡΠ΅Π½Ρ Π±ΡΡΡΡΠΎ Π½Π°Π³ΡΠ΅Π²Π°ΡΡΡΡ Π΄ΠΎ ΡΠ΅ΠΌΠΏΠ΅ΡΠ°ΡΡΡΡ ΠΊΠΈΠΏΠ΅Π½ΠΈΡ, Π° ΡΠ°ΠΊΠΆΠ΅ Π² Π½Π΅ΠΉ Π²ΠΎΠ·Π½ΠΈΠΊΠ°Π΅Ρ ΠΏΡΠ·ΡΡΡ ΠΈΠ· Π³Π°Π·ΠΎΠ², ΠΊΠΎΡΠΎΡΡΠΉ ΡΠΏΠΎΡΠΎΠ±ΡΡΠ²ΡΠ΅Ρ Π»ΠΎΠΊΠ°Π»ΡΠ½ΠΎΠΌΡ Π½Π°Π³ΡΠ΅Π²Ρ Π·Π°Π³ΠΎΡΠΎΠ²ΠΊΠΈ. Π ΡΠ²ΠΎΡ ΠΎΡΠ΅ΡΠ΅Π΄Ρ, Ρ Π·Π°Π³ΠΎΡΠΎΠ²ΠΊΠΈ ΠΏΡΠΎΠΈΡΡ
ΠΎΠ΄ΠΈΡ ΠΏΠ»Π°Π²Π»Π΅Π½ΠΈΠ΅ ΡΠ°ΠΌΡΡ
Π²Π΅ΡΡ
Π½ΠΈΡ
ΡΠ»ΠΎΠ΅Π², ΡΡΠΎ ΠΎΠ±Π΅ΡΠΏΠ΅ΡΠΈΠ²Π°Π΅Ρ ΠΏΠΎΠ»ΡΡΠ΅Π½ΠΈΠ΅ Π½Π΅ΠΎΠ±Ρ
ΠΎΠ΄ΠΈΠΌΠΎΠΉ ΡΠΎΡΠΌΡ.
ΠΠ°ΠΊΠ»ΡΡΠ΅Π½ΠΈΠ΅
Π‘ΠΎΠ²ΡΠ΅ΠΌΠ΅Π½Π½ΡΠ΅ ΡΡΠ°Π½ΠΊΠΈ Π΄Π»Ρ ΡΠ»Π΅ΠΊΡΡΠΎΡΡΠΎΠ·ΠΈΠΎΠ½Π½ΠΎΠΉ ΠΎΠ±ΡΠ°Π±ΠΎΡΠΊΠΈ ΠΏΡΠΈΠ·Π²Π°Π½Ρ Π²ΡΠΏΠΎΠ»Π½ΡΡΡ ΠΊΠ°ΠΊ ΠΌΠ°ΡΡΠΎΠ²ΡΠ΅, ΡΠ°ΠΊ ΠΈ Π΅Π΄ΠΈΠ½ΠΈΡΠ½ΡΠ΅ Π·Π°Π΄Π°ΡΠΈ ΡΡΡΠ΅ΡΠΈΡΠ΅ΡΠΊΠΎΠ³ΠΎ (Π΄Π΅ΠΊΠΎΡΠΈΡΠΎΠ²Π°Π½ΠΈΠ΅, ΡΠ»ΠΈΡΠΎΠ²ΠΊΠ° ΠΈ Ρ. ΠΏ.) ΠΈ ΠΏΡΠ°ΠΊΡΠΈΡΠ΅ΡΠΊΠΎΠ³ΠΎ (ΡΠΎΡΠΌΠΈΡΠΎΠ²Π°Π½ΠΈΠ΅ ΠΏΠ°Π·ΠΎΠ², ΠΏΠ΅ΡΡΠΎΡΠ°ΡΠΈΡ ΡΠΊΠ²ΠΎΠ·Π½ΡΡ ΠΈ Π³Π»ΡΡ ΠΈΡ ΠΎΡΠ²Π΅ΡΡΡΠΈΠΉ, Π·Π°ΡΠΎΡΠΊΠ° ΡΠ΅ΠΆΡΡΠ΅Π³ΠΎ ΠΈΠ½ΡΡΡΡΠΌΠ΅Π½ΡΠ°) Ρ Π°ΡΠ°ΠΊΡΠ΅ΡΠ°. Π‘Π΅Π±Π΅ΡΡΠΎΠΈΠΌΠΎΡΡΡ ΠΎΠ±ΡΠ°Π±ΠΎΡΠΊΠΈ Π½Π° ΡΠ°ΠΊΠΎΠΌ ΠΎΠ±ΠΎΡΡΠ΄ΠΎΠ²Π°Π½ΠΈΠΈ Π·Π½Π°ΡΠΈΡΠ΅Π»ΡΠ½ΠΎ Π½ΠΈΠΆΠ΅ Π°Π½Π°Π»ΠΎΠ³ΠΈΡΠ½ΠΎΠ³ΠΎ ΠΏΠΎΠΊΠ°Π·Π°ΡΠ΅Π»Ρ, ΠΊΠΎΡΠΎΡΡΠΉ Ρ Π°ΡΠ°ΠΊΡΠ΅ΡΠ΅Π½ Π΄Π»Ρ ΠΌΠ΅ΡΠ°Π»Π»ΠΎΡΠ΅ΠΆΡΡΠΈΡ ΡΡΠ°Π½ΠΊΠΎΠ².
ΠΡΠ΅Π½ΠΈΡΠ΅ ΡΡΠ°ΡΡΡ: ΠΠΎΠ΄Π΅Π»ΠΈΡΠ΅ΡΡ Ρ Π΄ΡΡΠ·ΡΡΠΌΠΈ!stanok.guru
ΠΠ»Π΅ΠΊΡΡΠΎΡΡΠΎΠ·ΠΈΠΎΠ½Π½Π°Ρ ΠΎΠ±ΡΠ°Π±ΠΎΡΠΊΠ° ΠΌΠ΅ΡΠ°Π»Π»ΠΎΠ²: ΡΠ΅ΠΆΠΈΠΌΡ, ΠΌΠ΅ΡΠΎΠ΄Ρ, ΡΠ΅Ρ Π½ΠΎΠ»ΠΎΠ³ΠΈΡ
Π‘ΡΡΠ΅ΡΡΠ²ΡΠ΅Ρ Π΄ΠΎΠ²ΠΎΠ»ΡΠ½ΠΎ ΠΌΠ½ΠΎΠ³ΠΎ ΡΠ°Π·Π»ΠΈΡΠ½ΡΡ ΡΠΏΠΎΡΠΎΠ±ΠΎΠ², ΠΏΡΠΈΠΌΠ΅Π½ΡΠ΅ΠΌΡΡ Π΄Π»Ρ ΠΈΠ·ΠΌΠ΅Π½Π΅Π½ΠΈΡ ΡΠ°Π·ΠΌΠ΅ΡΠΎΠ², ΡΠΎΡΠΌΡ, ΠΊΠ°ΡΠ΅ΡΡΠ²Π° ΠΌΠ΅ΡΠ°Π»Π»Π°. ΠΠ΅ΠΊΠΎΡΠΎΡΡΠ΅ ΠΏΠΎΠ·Π²ΠΎΠ»ΡΡΡ ΡΡΡΠ΅ΡΡΠ²Π΅Π½Π½ΠΎ ΠΏΠΎΠ²ΡΡΠΈΡΡ ΠΊΠ°ΡΠ΅ΡΡΠ²ΠΎ ΠΏΠΎΠ²Π΅ΡΡ Π½ΠΎΡΡΠΈ ΠΈ ΡΡΠΊΠΎΡΠΈΡΡ ΠΏΡΠΎΡΠ΅ΡΡ ΠΈΠ·ΠΌΠ΅Π½Π΅Π½ΠΈΡ ΡΠ°Π·ΠΌΠ΅ΡΠΎΠ². ΠΠ»Π΅ΠΊΡΡΠΎΡΡΠΎΠ·ΠΈΠΎΠ½Π½Π°Ρ ΠΎΠ±ΡΠ°Π±ΠΎΡΠΊΠ° β ΡΠΏΠΎΡΠΎΠ± ΠΈΠ·ΠΌΠ΅Π½Π΅Π½ΠΈΡ ΡΠΎΡΠΌΡ, ΡΠ°Π·ΠΌΠ΅ΡΠΎΠ², ΠΏΠΎΠΊΠ°Π·Π°ΡΠ΅Π»Ρ ΡΠ΅ΡΠΎΡ ΠΎΠ²Π°ΡΠΎΡΡΠΈ, ΡΠ²ΠΎΠΉΡΡΠ² ΠΏΠΎΠ²Π΅ΡΡ Π½ΠΎΡΡΠΈ, ΠΊΠΎΡΠΎΡΡΠΉ Π·Π°ΠΊΠ»ΡΡΠ°Π΅ΡΡΡ Π² Π²ΠΎΠ·Π΄Π΅ΠΉΡΡΠ²ΠΈΠΈ ΡΠ»Π΅ΠΊΡΡΠΈΡΠ΅ΡΠΊΠΎΠ³ΠΎ ΡΠ°Π·ΡΡΠ΄Π° Π½Π° Π·Π°Π³ΠΎΡΠΎΠ²ΠΊΡ ΠΏΡΠΈ ΠΈΡΠΏΠΎΠ»ΡΠ·ΠΎΠ²Π°Π½ΠΈΠΈ ΡΠ»Π΅ΠΊΡΡΠΎΠ΄Π°-ΠΈΠ½ΡΡΡΡΠΌΠ΅Π½ΡΠ°.
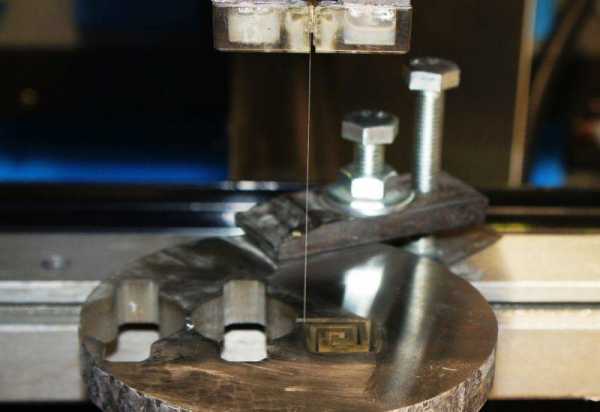
ΠΡΠ½ΠΎΠ²Ρ ΡΠ΅Ρ Π½ΠΎΠ»ΠΎΠ³ΠΈΠΈ
Π ΠΎΡΠΎΠ±Π΅Π½Π½ΠΎΡΡΡΠΌ, ΠΊΠΎΡΠΎΡΡΠΌΠΈ ΠΎΠ±Π»Π°Π΄Π°Π΅Ρ ΡΠ»Π΅ΠΊΡΡΠΎΡΡΠΎΠ·ΠΈΠΎΠ½Π½Π°Ρ ΠΎΠ±ΡΠ°Π±ΠΎΡΠΊΠ°, ΠΌΠΎΠΆΠ½ΠΎ ΠΎΡΠ½Π΅ΡΡΠΈ Π½ΠΈΠΆΠ΅ΠΏΡΠΈΠ²Π΅Π΄Π΅Π½Π½ΡΠ΅ ΠΌΠΎΠΌΠ΅Π½ΡΡ:
- Π ΠΊΠ°ΡΠ΅ΡΡΠ²Π΅ ΠΎΠ΄Π½ΠΎΠ³ΠΎ ΠΈΠ· ΡΠ»Π΅ΠΊΡΡΠΎΠ΄ΠΎΠ² Π²ΡΡΡΡΠΏΠ°Π΅Ρ Π·Π°Π³ΠΎΡΠΎΠ²ΠΊΠ°, Π΄ΡΡΠ³ΠΎΠ³ΠΎ β ΡΠ»Π΅ΠΊΡΡΠΎΠ΄-ΠΈΠ½ΡΡΡΡΠΌΠ΅Π½Ρ.
- ΠΠΎΠ΄Π°ΡΠ° ΡΠ°Π·ΡΡΠ΄Π° ΠΏΡΠΎΠ²ΠΎΠ΄ΠΈΡΡΡ ΠΏΠ΅ΡΠΈΠΎΠ΄ΠΈΡΠ΅ΡΠΊΠΈ, Π² Π²ΠΈΠ΄Π΅ ΠΊΠΎΡΠΎΡΠΊΠΈΡ ΠΈΠΌΠΏΡΠ»ΡΡΠΎΠ², ΡΠ°ΠΊ ΠΊΠ°ΠΊ ΠΏΠΎΠ΄ΠΎΠ±Π½ΠΎΠ΅ Π²Π»ΠΈΡΠ½ΠΈΠ΅ ΠΏΠΎΠ·Π²ΠΎΠ»ΡΠ΅Ρ Π²ΠΎΡΡΡΠ°Π½ΠΎΠ²ΠΈΡΡ ΡΠ»Π΅ΠΊΡΡΠΈΡΠ΅ΡΠΊΡΡ ΠΏΡΠΎΡΠ½ΠΎΡΡΡ ΡΡΠ΅Π΄Ρ ΠΌΠ΅ΠΆΠ΄Ρ ΡΠ»Π΅ΠΊΡΡΠΎΠ΄Π°ΠΌΠΈ.
- Π£Π½ΠΈΠΏΠΎΠ»ΡΡΠ½ΡΠ΅ ΠΈΠΌΠΏΡΠ»ΡΡΡ ΠΏΠΎΠ΄Π°ΡΡΡΡ Π΄Π»Ρ ΡΠΎΠ³ΠΎ, ΡΡΠΎΠ±Ρ ΡΠΌΠ΅Π½ΡΡΠΈΡΡ ΠΈΠ·Π½ΠΎΡ ΠΈΡΠΏΠΎΠ»ΡΠ·ΡΠ΅ΠΌΠΎΠ³ΠΎ ΡΠ»Π΅ΠΊΡΡΠΎΠ΄Π°-ΠΈΠ½ΡΡΡΡΠΌΠ΅Π½ΡΠ°.
- ΠΠ°ΠΆΠ½ΡΠΌ ΠΌΠΎΠΌΠ΅Π½ΡΠΎΠΌ ΠΌΠΎΠΆΠ½ΠΎ Π½Π°Π·Π²Π°ΡΡ ΡΠΎ, ΡΠΊΠΎΠ»ΡΠΊΠΎ Π΄Π»ΠΈΡΡΡ ΠΈΠΌΠΏΡΠ»ΡΡ. ΠΡΠΈ ΠΌΠ°Π»ΠΎΠΉ ΠΏΡΠΎΠ΄ΠΎΠ»ΠΆΠΈΡΠ΅Π»ΡΠ½ΠΎΡΡΠΈ ΠΏΠΎΠ΄Π°Π²Π°Π΅ΠΌΠΎΠ³ΠΎ ΠΈΠΌΠΏΡΠ»ΡΡΠ° ΡΡΡΠ΅ΡΡΠ²Π΅Π½Π½ΠΎ ΠΏΠΎΠ²ΡΡΠ°Π΅ΡΡΡ ΠΈΠ·Π½ΠΎΡ Π°Π½ΠΎΠ΄Π°. ΠΠ΄Π½Π°ΠΊΠΎ ΠΏΡΠΈ Π±ΠΎΠ»ΡΡΠΎΠΉ Π΄Π»ΠΈΡΠ΅Π»ΡΠ½ΠΎΡΡΠΈ ΠΈΠΌΠΏΡΠ»ΡΡΠ° ΡΡΡΠ΅ΡΡΠ²Π΅Π½Π½ΠΎ ΠΏΠΎΠ²ΡΡΠ°Π΅ΡΡΡ ΠΈΠ·Π½ΠΎΡ ΠΊΠ°ΡΠΎΠ΄Π°.
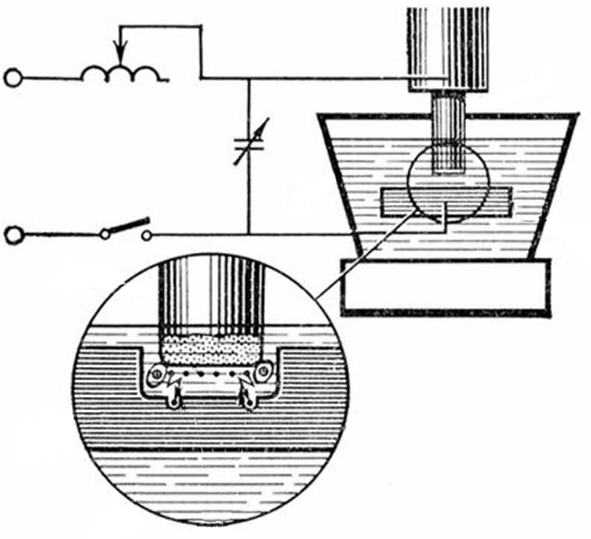
Π‘Ρ Π΅ΠΌΠ° ΡΠ»Π΅ΠΊΡΡΠΎΡΡΠΎΠ·ΠΈΠΎΠ½Π½ΠΎΠ³ΠΎ ΠΌΠ΅ΡΠΎΠ΄Π° ΠΎΠ±ΡΠ°Π±ΠΎΡΠΊΠΈ
ΠΠ°ΡΠ°ΡΡΡΡ Π½Π° ΠΏΡΠ°ΠΊΡΠΈΠΊΠ΅ ΠΈΡΠΏΠΎΠ»ΡΠ·ΡΠ΅ΡΡΡ ΡΠΏΠΎΡΠΎΠ± ΠΏΠΎΠ΄ΠΊΠ»ΡΡΠ΅Π½ΠΈΡ ΠΊ ΠΏΠΎΠ»ΠΎΠΆΠΈΡΠ΅Π»ΡΠ½ΠΎΠΌΡ ΠΈ ΠΎΡΡΠΈΡΠ°ΡΠ΅Π»ΡΠ½ΠΎΠΌΡ ΠΏΠ»ΡΡΡ Π³Π΅Π½Π΅ΡΠ°ΡΠΎΡΠ° ΠΏΠ΅ΡΠ΅ΠΌΠ΅Π½Π½ΠΎΠ³ΠΎ ΡΠΎΠΊΠ°.
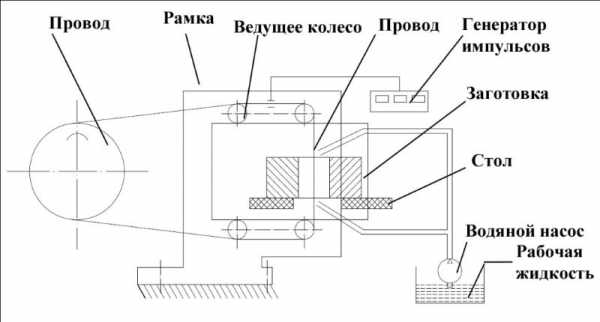
Π‘Ρ Π΅ΠΌΠ° 2
ΠΠ»Π°ΡΡΠΈΡΠΈΠΊΠ°ΡΠΈΡ ΠΌΠ΅ΡΠΎΠ΄ΠΎΠ²
Π‘ΡΡΠ΅ΡΡΠ²ΡΡΡ ΡΠ»Π΅Π΄ΡΡΡΠΈΠ΅ ΡΠΏΠΎΡΠΎΠ±Ρ ΡΠ»Π΅ΠΊΡΡΠΎΡΡΠΎΠ·ΠΈΠΎΠ½Π½ΠΎΠΉ ΠΎΠ±ΡΠ°Π±ΠΎΡΠΊΠΈ Π·Π°Π³ΠΎΡΠΎΠ²ΠΎΠΊ:
- ΠΠΎΠΌΠ±ΠΈΠ½ΠΈΡΠΎΠ²Π°Π½Π½ΡΠΉ ΠΌΠ΅ΡΠΎΠ΄ β ΠΏΡΠ΅Π΄ΡΡΠΌΠ°ΡΡΠΈΠ²Π°Π΅Ρ ΠΈΡΠΏΠΎΠ»ΡΠ·ΠΎΠ²Π°Π½ΠΈΠ΅ ΡΡΠ°Π·Ρ Π½Π΅ΡΠΊΠΎΠ»ΡΠΊΠΈΡ ΠΌΠ΅ΡΠΎΠ΄ΠΎΠ² Π²ΠΎΠ·Π΄Π΅ΠΉΡΡΠ²ΠΈΡ. ΠΠ΅ΠΊΠΎΡΠΎΡΠΎΠ΅ ΠΎΠ±ΠΎΡΡΠ΄ΠΎΠ²Π°Π½ΠΈΠ΅ ΠΏΠΎΠ·Π²ΠΎΠ»ΡΠ΅Ρ ΠΊΠΎΠΌΠ±ΠΈΠ½ΠΈΡΠΎΠ²Π°ΡΡ ΠΌΠ΅Ρ Π°Π½ΠΈΡΠ΅ΡΠΊΡΡ ΠΈ ΡΠ»Π΅ΠΊΡΡΠΎΡΡΠΎΠ·ΠΈΠΎΠ½Π½ΡΡ ΠΎΠ±ΡΠ°Π±ΠΎΡΠΊΡ. ΠΡΠΎΡ ΠΌΠ΅ΡΠΎΠ΄ Π΄ΠΎΠ²ΠΎΠ»ΡΠ½ΠΎ ΠΏΠΎΠΏΡΠ»ΡΡΠ΅Π½ Π² ΠΏΠΎΡΠ»Π΅Π΄Π½Π΅Π΅ Π²ΡΠ΅ΠΌΡ, ΡΠ°ΠΊ ΠΊΠ°ΠΊ Π΄Π°Π΅Ρ Π²ΠΎΠ·ΠΌΠΎΠΆΠ½ΠΎΡΡΡ Π΄ΠΎΡΡΠΈΠ³Π½ΡΡΡ Π²ΡΡΠΎΠΊΠΈΡ ΡΠ΅Π·ΡΠ»ΡΡΠ°ΡΠΎΠ².
- ΠΠΠ₯Π ΠΈΠ»ΠΈ ΡΠ»Π΅ΠΊΡΡΠΎΡΡΠΎΠ·ΠΈΠΎΠ½Π½ΠΎ-Ρ ΠΈΠΌΠΈΡΠ΅ΡΠΊΠΎΠ΅ ΡΠ»ΠΈΡΠΎΠ²Π°Π½ΠΈΠ΅ β ΠΌΠ΅ΡΠΎΠ΄ Π²ΠΎΠ·Π΄Π΅ΠΉΡΡΠ²ΠΈΡ, ΠΊΠΎΡΠΎΡΡΠΉ ΠΏΡΠ΅Π΄ΡΡΠΌΠ°ΡΡΠΈΠ²Π°Π΅Ρ ΠΊΠΎΠΌΠ±ΠΈΠ½ΠΈΡΠΎΠ²Π°Π½ΠΈΠ΅ ΠΌΠ΅ΡΠΎΠ΄Π° ΠΏΠΎΠ΄Π°ΡΠΈ ΡΠΎΠΊΠ° ΠΈ ΡΠ»Π΅ΠΊΡΡΠΎΠ»ΠΈΡΠ°. ΠΠ΅ΡΠΎΠ΄ Π΄ΠΎΠ²ΠΎΠ»ΡΠ½ΠΎ ΠΏΠΎΠΏΡΠ»ΡΡΠ½ΡΠΉ, ΠΏΠΎΠ·Π²ΠΎΠ»ΡΠ΅Ρ ΠΏΠΎΠ²ΡΡΠΈΡΡ ΠΊΠ°ΡΠ΅ΡΡΠ²ΠΎ ΠΏΠΎΠ²Π΅ΡΡ Π½ΠΎΡΡΠΈ ΠΈ ΠΈΠ·ΠΌΠ΅Π½ΠΈΡΡ ΡΠΎΡΠΌΡ Π·Π°Π³ΠΎΡΠΎΠ²ΠΊΠΈ.
- ΠΠ±ΡΠ°Π·ΠΈΠ²Π½Π°Ρ Ρ ΠΏΠΎΠ΄Π°ΡΠ΅ΠΉ ΡΠ»Π΅ΠΊΡΡΠΈΡΠ΅ΡΠΊΠΎΠ³ΠΎ ΡΠΎΠΊΠ° ΠΏΠΎΠ·Π²ΠΎΠ»ΡΠ΅Ρ Π²ΠΎΠ·Π΄Π΅ΠΉΡΡΠ²ΠΎΠ²Π°ΡΡ Π½Π° Π·Π°Π³ΠΎΡΠΎΠ²ΠΊΡ Π΄Π»Ρ ΠΈΠ·ΠΌΠ΅Π½Π΅Π½ΠΈΡ ΡΠ΅ΡΠΎΡ ΠΎΠ²Π°ΡΠΎΡΡΠΈ. Π Π΄Π°Π½Π½ΠΎΠΌ ΡΠ»ΡΡΠ°Π΅ ΠΎΠ±ΠΎΡΡΠ΄ΠΎΠ²Π°Π½ΠΈΠ΅ ΠΏΡΠ΅Π΄Π½Π°Π·Π½Π°ΡΠ΅Π½ΠΎ ΠΈΡΠΊΠ»ΡΡΠΈΡΠ΅Π»ΡΠ½ΠΎ Π΄Π»Ρ ΠΏΠΎΠ»ΡΡΠ΅Π½ΠΈΡ ΠΎΠΏΡΠ΅Π΄Π΅Π»Π΅Π½Π½ΠΎΠΉ ΡΠ΅ΡΠΎΡ ΠΎΠ²Π°ΡΠΎΡΡΠΈ.
- ΠΠ½ΠΎΠ΄Π½ΠΎ-ΠΌΠ΅Ρ Π°Π½ΠΈΡΠ΅ΡΠΊΠΎΠ΅ Π²ΠΎΠ·Π΄Π΅ΠΉΡΡΠ²ΠΈΠ΅ ΠΎΠΏΡΠ΅Π΄Π΅Π»Π΅Π½ΠΎ ΡΠ΅ΠΌ, ΡΡΠΎ ΠΏΡΠΎΡΠ΅ΡΡ ΠΏΡΠΎΠΈΡΡ ΠΎΠ΄ΠΈΡ Π² ΠΆΠΈΠ΄ΠΊΠΎΠΉ ΡΡΠ΅Π΄Π΅. Π Π΄Π°Π½Π½ΠΎΠΌ ΡΠ»ΡΡΠ°Π΅ ΠΏΠΎΡΠ»Π΅ ΠΏΠΎΠ΄Π°ΡΠΈ ΡΠΎΠΊΠ° Π½Π° ΠΏΠΎΠ²Π΅ΡΡ Π½ΠΎΡΡΡ ΠΏΠΎΡΠ²Π»ΡΠ΅ΡΡΡ ΠΏΠ»Π΅Π½ΠΊΠ°, ΠΊΠΎΡΠΎΡΠ°Ρ Π² ΠΏΠΎΡΠ»Π΅Π΄ΡΡΠ²ΠΈΠ΅ ΡΠ΄Π°Π»ΡΠ΅ΡΡΡ ΠΌΠ΅Ρ Π°Π½ΠΈΡΠ΅ΡΠΊΠΈΠΌ ΠΌΠ΅ΡΠΎΠ΄ΠΎΠΌ.
- ΠΠ»Π΅ΠΊΡΡΠΎΡΡΠΎΠ·ΠΈΠΎΠ½Π½ΠΎΠ΅ ΡΠΏΡΠΎΡΠ½Π΅Π½ΠΈΠ΅ ΠΏΡΡΠ΅ΠΌ ΠΎΠ±ΡΠ°Π±ΠΎΡΠΊΠΈ ΡΠ»Π΅ΠΊΡΡΠΈΡΠ΅ΡΡΠ²ΠΎΠΌ Ρ Π°ΡΠ°ΠΊΡΠ΅ΡΠΈΠ·ΡΠ΅ΡΡΡ ΡΠ΅ΠΌ, ΡΡΠΎ ΠΈΡΠΏΠΎΠ»ΡΠ·ΡΠ΅ΠΌΠΎΠ΅ ΠΎΠ±ΠΎΡΡΠ΄ΠΎΠ²Π°Π½ΠΈΠ΅ ΠΏΠΎΠ·Π²ΠΎΠ»ΡΠ΅Ρ ΡΡΡΠ΅ΡΡΠ²Π΅Π½Π½ΠΎ ΠΏΠΎΠ²ΡΡΠΈΡΡ ΠΏΡΠΎΡΠ½ΠΎΡΡΡ ΠΏΠΎΠ²Π΅ΡΡ Π½ΠΎΡΡΠ½ΠΎΠ³ΠΎ ΡΠ»ΠΎΡ. ΠΡΠΎΡΠ΅Π΄ΡΡΠ° Π½Π΅ Π·Π°Π½ΠΈΠΌΠ°Π΅Ρ ΠΌΠ½ΠΎΠ³ΠΎ Π²ΡΠ΅ΠΌΠ΅Π½ΠΈ, ΠΏΡΠΎΡΡΠ° Π² ΠΈΡΠΏΠΎΠ»Π½Π΅Π½ΠΈΠΈ.
- ΠΠ±ΡΠ΅ΠΌΠ½ΠΎΠ΅ ΠΊΠΎΠΏΠΈΡΠΎΠ²Π°Π½ΠΈΠ΅ β ΠΎΠ±ΠΎΡΡΠ΄ΠΎΠ²Π°Π½ΠΈΠ΅ Π² Π΄Π°Π½Π½ΠΎΠΌ ΡΠ»ΡΡΠ°Π΅ ΠΈΠΌΠ΅Π΅Ρ ΠΈΠ½ΡΡΡΡΠΌΠ΅Π½Ρ ΠΎΠΏΡΠ΅Π΄Π΅Π»Π΅Π½Π½ΠΎΠΉ ΡΠΎΡΠΌΡ ΠΈ ΡΠ°Π·ΠΌΠ΅ΡΠΎΠ², ΠΊΠΎΡΠΎΡΡΠ΅ ΠΎΡΡΠ°ΠΆΠ°ΡΡΡΡ Π½Π° Π·Π°Π³ΠΎΡΠΎΠ²ΠΊΠ΅ ΠΏΡΠΈ ΠΏΠΎΠ΄Π°ΡΠ΅ ΡΠΎΠΊΠ°.
- ΠΡΠΎΡΠΈΠ²Π°Π½ΠΈΠ΅ β ΡΠΏΠΎΡΠΎΠ± ΡΠ»Π΅ΠΊΡΡΠΈΡΠ΅ΡΠΊΠΎΠ³ΠΎ Π²ΠΎΠ·Π΄Π΅ΠΉΡΡΠ²ΠΈΡ, ΠΏΡΠΈ ΠΊΠΎΡΠΎΡΠΎΠΌ ΠΎΠ±ΡΠ°Π·ΡΠ΅ΡΡΡ ΠΎΡΠ²Π΅ΡΡΡΠΈΠ΅ ΠΎΠΏΡΠ΅Π΄Π΅Π»Π΅Π½Π½ΠΎΠ³ΠΎ Π΄ΠΈΠ°ΠΌΠ΅ΡΡΠ° ΠΈ ΡΠΎΡΠΌΡ.
- ΠΠ°ΡΠΊΠΈΡΠΎΠ²Π°Π½ΠΈΠ΅ ΠΏΡΠΎΠ²ΠΎΠ΄ΠΈΡΡΡ ΠΏΡΡΠ΅ΠΌ Π½Π°Π½Π΅ΡΠ΅Π½ΠΈΡ ΠΎΠΏΡΠ΅Π΄Π΅Π»Π΅Π½Π½ΠΎΠΉ ΠΈΠ½ΡΠΎΡΠΌΠ°ΡΠΈΠΈ, ΠΊΠΎΡΠΎΡΠ°Ρ ΠΎΡΡΠ°Π΅ΡΡΡ Π½Π° Π΄ΠΎΠ»Π³ΠΎΠ΅ Π²ΡΠ΅ΠΌΡ. ΠΠ°Π½Π½Π°Ρ ΠΌΠ°ΡΠΊΠΈΡΠΎΠ²ΠΊΠ° ΠΏΡΠΎΡΡΠ° Π² ΠΈΡΠΏΠΎΠ»Π½Π΅Π½ΠΈΠΈ, ΠΌΠ΅Π½Π΅Π΅ Π·Π°ΡΡΠ°ΡΠ½Π°Ρ.
- ΠΠ»Π΅ΠΊΡΡΠΎΡΡΠΎΠ·ΠΈΠΎΠ½Π½Π°Ρ ΡΠ΅Π·ΠΊΠ° ΠΏΡΠΎΠ²ΠΎΠ΄ΠΈΡΡΡ Π΄ΠΎΠ²ΠΎΠ»ΡΠ½ΠΎ ΡΠ°ΡΡΠΎ. ΠΠ½Π° ΠΎΡΠ»ΠΈΡΠ°Π΅ΡΡΡ ΡΠ΅ΠΌ, ΡΡΠΎ ΠΌΠΎΠΆΠ½ΠΎ ΠΏΠΎΠ»ΡΡΠΈΡΡ Π²ΡΡΠΎΠΊΠΎΡΠΎΡΠ½ΡΠ΅ ΡΠ°Π·ΠΌΠ΅ΡΡ ΠΏΡΡΠ΅ΠΌ ΡΠ΅Π·Π°Π½ΠΈΡ ΡΡΠΈΠΌ ΠΌΠ΅ΡΠΎΠ΄ΠΎΠΌ.
- Π¨Π»ΠΈΡΠΎΠ²Π°Π½ΠΈΠ΅ ΡΠ°ΠΊΠΆΠ΅ ΠΏΡΠΎΠ²ΠΎΠ΄ΠΈΡΡΡ Π΄ΠΎΠ²ΠΎΠ»ΡΠ½ΠΎ ΡΠ°ΡΡΠΎ.
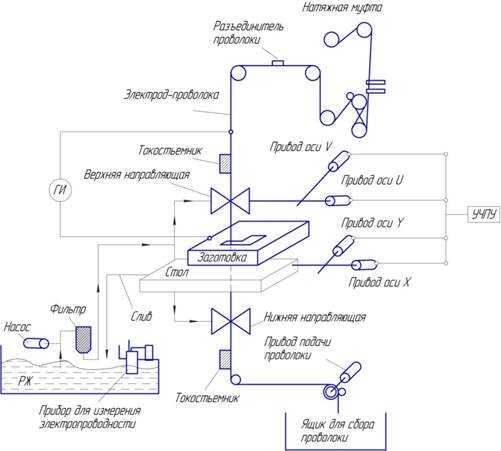
Π‘Ρ Π΅ΠΌΠ° ΠΏΡΠΎΠ²ΠΎΠ»ΠΎΡΠ½ΠΎ-Π²ΡΡΠ΅Π·Π½ΠΎΠ³ΠΎ ΡΠ»Π΅ΠΊΡΡΠΎΡΡΠΎΠ·ΠΈΠΎΠ½Π½ΠΎΠ³ΠΎ ΡΡΠ°Π½ΠΊΠ°
ΠΡΡΠ΅ΠΏΡΠΈΠ²Π΅Π΄Π΅Π½Π½ΡΠ΅ ΠΌΠΎΠΌΠ΅Π½ΡΡ ΠΎΠΏΡΠ΅Π΄Π΅Π»ΡΡΡ ΡΠΎ, ΡΡΠΎ ΡΠ»Π΅ΠΊΡΡΠΎΡΡΠΎΠ·ΠΈΠΎΠ½Π½Π°Ρ ΠΎΠ±ΡΠ°Π±ΠΎΡΠΊΠ° ΠΌΠ΅ΡΠ°Π»Π»ΠΎΠ² ΠΏΠΎΠ·Π²ΠΎΠ»ΡΠ΅Ρ ΠΏΠΎΠ»ΡΡΠΈΡΡ Π·Π°Π³ΠΎΡΠΎΠ²ΠΊΡ Ρ Π½Π°ΠΈΠ±ΠΎΠ»Π΅Π΅ ΠΏΠΎΠ΄Ρ ΠΎΠ΄ΡΡΠΈΠΌΠΈ ΠΏΠΎΠΊΠ°Π·Π°ΡΠ΅Π»ΡΠΌΠΈ.
Π₯Π°ΡΠ°ΠΊΡΠ΅ΡΠΈΡΡΠΈΠΊΠΈ ΡΠ»Π΅ΠΊΡΡΠΈΡΠ΅ΡΠΊΠΎΠ³ΠΎ ΡΠ°Π·ΡΡΠ΄Π°
ΠΡ ΡΠΎΠ³ΠΎ, ΠΊΠ°ΠΊ ΠΏΠΎΠ΄Π°Π΅ΡΡΡ ΡΠ»Π΅ΠΊΡΡΠΈΡΠ΅ΡΠΊΠΈΠΉ ΡΠ°Π·ΡΡΠ΄, Π·Π°Π²ΠΈΡΠΈΡ ΠΌΠ½ΠΎΠ³ΠΎΠ΅. ΠΠ»Π΅ΠΊΡΡΠΎΠΈΡΠΊΡΠΎΠ²Π°Ρ ΠΎΠ±ΡΠ°Π±ΠΎΡΠΊΠ° ΠΌΠΎΠΆΠ΅Ρ Ρ Π°ΡΠ°ΠΊΡΠ΅ΡΠΈΠ·ΠΎΠ²Π°ΡΡΡΡ Π½ΠΈΠΆΠ΅ΠΏΡΠΈΠ²Π΅Π΄Π΅Π½Π½ΡΠΌΠΈ ΠΌΠΎΠΌΠ΅Π½ΡΠ°ΠΌΠΈ:
- ΠΠ΅ΡΠ²ΡΠΉ ΡΡΠ°ΠΏ Π·Π°ΠΊΠ»ΡΡΠ°Π»ΡΡ Π² ΡΠ»Π΅ΠΊΡΡΠΈΡΠ΅ΡΠΊΠΎΠΌ ΠΏΡΠΎΠ±ΠΎΠ΅. ΠΡΠΈ Π½Π΅ΠΌ ΠΏΡΠΎΠΈΡΡ ΠΎΠ΄ΠΈΡ ΠΈΡΠΊΡΠΎΠ²ΠΎΠΉ ΡΠ°Π·ΡΡΠ΄.
- Π‘Π»Π΅Π΄ΡΡΡΠΈΠΌ ΡΡΠ°ΠΏΠΎΠΌ ΡΡΠ°Π½ΠΎΠ²ΠΈΡΡΡ Π²ΠΎΠ·Π½ΠΈΠΊΠ½ΠΎΠ²Π΅Π½ΠΈΠ΅ Π΄ΡΠ³ΠΎΠ²ΠΎΠ³ΠΎ ΡΠ°Π·ΡΡΠ΄, ΠΊΠΎΡΠΎΡΡΠΉ ΠΎΠΊΠ°Π·ΡΠ²Π°Π΅Ρ Π±ΠΎΠ»Π΅Π΅ ΡΠ΅ΡΡΠ΅Π·Π½ΠΎΠ΅ Π²ΠΎΠ·Π΄Π΅ΠΉΡΡΠ²ΠΈΠ΅.
ΠΡΡΠ΅ΠΏΡΠΈΠ²Π΅Π΄Π΅Π½Π½ΡΠ΅ ΠΌΠΎΠΌΠ΅Π½ΡΡ ΠΎΠΏΡΠ΅Π΄Π΅Π»ΡΡΡ ΡΠΎ, ΡΡΠΎ ΠΌΠ½ΠΎΠ³ΠΈΠ΅ Π³Π΅Π½Π΅ΡΠ°ΡΠΎΡΡ ΡΠΏΠΎΡΠΎΠ±Π½Ρ Π²ΡΠ΄Π°Π²Π°ΡΡ ΠΌΠ½ΠΎΠ³ΠΎΡΡΡΠΏΠ΅Π½ΡΠ°ΡΡΠΉ ΡΠ°Π·ΡΡΠ΄. ΠΠΎΠ΄ΠΎΠ±Π½ΡΠΉ ΠΏΠΎΠ΄Ρ ΠΎΠ΄ ΠΏΠΎΠ·Π²ΠΎΠ»ΡΠ΅Ρ ΡΡΡΠ΅ΡΡΠ²Π΅Π½Π½ΠΎ ΠΏΠΎΠ²ΡΡΠΈΡΡ ΠΊΠ°ΡΠ΅ΡΡΠ²ΠΎ ΠΏΠΎΠ»ΡΡΠ°Π΅ΠΌΠΎΠ³ΠΎ ΡΠ΅Π·ΡΠ»ΡΡΠ°ΡΠ°.
ΠΠ»ΠΈΡΠ΅Π»ΡΠ½ΠΎΡΡΡ ΠΈ ΡΠ°ΡΡΠΎΡΠ° ΠΈΠΌΠΏΡΠ»ΡΡΠ° ΠΎΠΏΡΠ΅Π΄Π΅Π»ΡΠ΅ΡΡΡ ΡΠ΅ΠΌ, ΠΊΠ°ΠΊΠΎΠ΅ Π²ΠΎΠ·Π΄Π΅ΠΉΡΡΠ²ΠΈΠ΅ ΡΠ»Π΅Π΄ΡΠ΅Ρ ΠΎΠΊΠ°Π·Π°ΡΡ Π½Π° ΠΏΠΎΠ²Π΅ΡΡ Π½ΠΎΡΡΡ. ΠΠ»ΠΈΡΠ΅Π»ΡΠ½ΠΎΡΡΡ ΠΎΠ΄Π½ΠΎΠ³ΠΎ ΠΈΠΌΠΏΡΠ»ΡΡΠ° ΠΌΠΎΠΆΠ΅Ρ Π½Π°Ρ ΠΎΠ΄ΠΈΡΡΡ Π² ΠΏΡΠ΅Π΄Π΅Π»Π΅ 0,1 β¦ 10β7 ΡΠ΅ΠΊΡΠ½Π΄Ρ. Π’Π°ΠΊΠΆΠ΅ Π²Π°ΠΆΠ½ΡΠΌ ΠΏΠΎΠΊΠ°Π·Π°ΡΠ΅Π»Π΅ΠΌ ΠΌΠΎΠΆΠ½ΠΎ Π½Π°Π·Π²Π°ΡΡ ΡΠ°ΡΡΠΎΡΡ Π² Π΄ΠΈΠ°ΠΏΠ°Π·ΠΎΠ½Π΅ ΠΎΡ 5 ΠΊΠΡ Π΄ΠΎ 0,5 ΠΠΡ. Π‘Π»Π΅Π΄ΡΠ΅Ρ ΠΎΡΠΌΠ΅ΡΠΈΡΡ, ΡΡΠΎ ΡΠ»Π΅ΠΊΡΡΠΎΡΡΠΎΠ·ΠΈΡ ΠΏΠΎΠ·Π²ΠΎΠ»ΡΠ΅Ρ ΠΏΠΎΠ»ΡΡΠ°ΡΡ ΠΊΠ°ΡΠ΅ΡΡΠ²ΠΎ ΠΏΠΎΠ²Π΅ΡΡ Π½ΠΎΡΡΠΈ Ρ Π½Π°ΠΈΠΌΠ΅Π½ΡΡΠ΅ΠΉ ΡΠ΅ΡΠΎΡ ΠΎΠ²Π°ΡΠΎΡΡΡΡ: ΡΠ΅ΠΌ ΠΌΠ΅Π½ΡΡΠ΅ Π΄Π»ΠΈΡΠ΅Π»ΡΠ½ΠΎΡΡΡ ΠΈΠΌΠΏΡΠ»ΡΡΠ°, ΡΠ΅ΠΌ ΠΌΠ΅Π½ΡΡΠ΅ ΠΏΠΎΠΊΠ°Π·Π°ΡΠ΅Π»Ρ. ΠΠΎΠΊΠ°Π·Π°ΡΠ΅Π»Ρ ΠΏΠ»ΠΎΡΠ°Π΄ΠΈ Π·Π°Π³ΠΎΡΠΎΠ²ΠΊΠΈ ΠΎΠΏΡΠ΅Π΄Π΅Π»ΡΠ΅Ρ ΡΠΎ, ΠΊΠ°ΠΊΠ°Ρ ΡΠΈΠ»Π° ΡΠΎΠΊΠ° ΠΈΡΠΏΠΎΠ»ΡΠ·ΡΠ΅ΡΡΡ. Π ΠΏΡΠΈΠΌΠ΅ΡΡ, ΠΏΡΠΈ ΠΏΠ»ΠΎΡΠ°Π΄ΠΈ 3 600 ΠΊΠ²Π°Π΄ΡΠ°ΡΠ½ΡΡ ΠΌΠΈΠ»Π»ΠΈΠΌΠ΅ΡΡΠΎΠ² ΠΏΠΎΠΊΠ°Π·Π°ΡΠ΅Π»Ρ ΡΠΈΠ»Ρ ΡΠΎΠΊΠ° ΡΠΎΡΡΠ°Π²Π»ΡΠ΅Ρ 100 Π.
ΠΡΠ΅ΠΈΠΌΡΡΠ΅ΡΡΠ²Π° ΡΠ°ΡΡΠΌΠ°ΡΡΠΈΠ²Π°Π΅ΠΌΠΎΠ³ΠΎ ΠΌΠ΅ΡΠΎΠ΄Π°
Π Π΄ΠΎΡΡΠΎΠΈΠ½ΡΡΠ²Π°ΠΌ ΡΠ°ΡΡΠΌΠ°ΡΡΠΈΠ²Π°Π΅ΠΌΠΎΠ³ΠΎ ΠΌΠ΅ΡΠΎΠ΄Π° ΠΌΠΎΠΆΠ½ΠΎ ΠΎΡΠ½Π΅ΡΡΠΈ Π½ΠΈΠΆΠ΅ΠΏΡΠΈΠ²Π΅Π΄Π΅Π½Π½ΡΠ΅ ΠΌΠΎΠΌΠ΅Π½ΡΡ:
- ΠΡΠΏΠΎΠ»ΡΠ·ΡΠ΅ΠΌΡΠΉ ΠΈΠ½ΡΡΡΡΠΌΠ΅Π½Ρ, ΠΊΠΎΡΠΎΡΡΠΉ Π²ΡΡΡΡΠΏΠ°Π΅Ρ Π² ΠΊΠ°ΡΠ΅ΡΡΠ²Π΅ ΡΠ»Π΅ΠΊΡΡΠΎΠ΄Π°, ΠΌΠΎΠΆΠ΅Ρ ΠΈΠΌΠ΅ΡΡ ΠΏΡΠΎΠΈΠ·Π²ΠΎΠ»ΡΠ½ΡΡ ΡΠΎΡΠΌΡ. ΠΡΠΎΡ ΠΌΠΎΠΌΠ΅Π½Ρ ΠΎΠΏΡΠ΅Π΄Π΅Π»ΡΠ΅Ρ ΡΠΎ, ΡΡΠΎ ΠΌΠΎΠΆΠ½ΠΎ ΠΏΡΠΎΠ²Π΅ΡΡΠΈ ΠΎΠ±ΡΠ°Π·ΠΎΠ²Π°Π½ΠΈΠ΅ Π·Π°ΠΊΡΡΡΡΡ ΠΊΠ°Π½Π°Π»ΠΎΠ². ΠΠ΅Ρ Π°Π½ΠΈΡΠ΅ΡΠΊΠΎΠ΅ ΡΠ½ΡΡΠΈΠ΅ ΠΌΠ΅ΡΠ°Π»Π»Π° ΠΈΠΌΠ΅Π΅Ρ ΠΌΠ½ΠΎΠ³ΠΎ ΠΎΠ³ΡΠ°Π½ΠΈΡΠ΅Π½ΠΈΠΉ Π² ΠΏΠ»Π°Π½Π΅ ΡΠΎΠ³ΠΎ, ΠΊΠ°ΠΊΠΈΠ΅ ΠΌΠΎΠΆΠ½ΠΎ ΠΏΠΎΠ»ΡΡΠΈΡΡ ΡΠΎΡΠΌΡ.
- ΠΠ°Π³ΠΎΡΠΎΠ²ΠΊΠ° ΠΌΠΎΠΆΠ΅Ρ Π±ΡΡΡ ΠΏΡΠ΅Π΄ΡΡΠ°Π²Π»Π΅Π½Π° Π»ΡΠ±ΡΠΌ ΡΠΎΠΊΠΎΠΏΡΠΎΠ²ΠΎΠ΄ΡΡΠΈΠΌ ΠΌΠ°ΡΠ΅ΡΠΈΠ°Π»ΠΎΠΌ. ΠΠ΄Π½Π°ΠΊΠΎ ΠΎΡΠΌΠ΅ΡΠΈΠΌ, ΡΡΠΎ ΠΈΡΠΏΠΎΠ»ΡΠ·ΠΎΠ²Π°ΡΡ ΠΌΠ°ΡΠ΅ΡΠΈΠ°Π»Ρ Ρ Π²ΡΡΠΎΠΊΠΈΠΌ ΡΠΎΠΏΡΠΎΡΠΈΠ²Π»Π΅Π½ΠΈΠ΅ΠΌ Π½Π΅Π»ΡΠ·Ρ. ΠΡΡΠΎΠΊΠΈΠΉ ΠΏΠΎΠΊΠ°Π·Π°ΡΠ΅Π»Ρ ΡΠΎΠΏΡΠΎΡΠΈΠ²Π»Π΅Π½ΠΈΡ ΠΏΡΠΈΠ²ΠΎΠ΄ΠΈΡ ΠΊ Π½Π°Π³ΡΠ΅Π²Ρ ΠΏΠΎΠ²Π΅ΡΡ Π½ΠΎΡΡΠΈ.
- Π Π°ΡΡΠΌΠ°ΡΡΠΈΠ²Π°Π΅ΠΌΡΠΉ ΠΏΡΠΎΡΠ΅ΡΡ ΠΏΠΎΠ»Π½ΠΎΡΡΡΡ Π°Π²ΡΠΎΠΌΠ°ΡΠΈΠ·ΠΈΡΠΎΠ²Π°Π½Π°. ΠΡΠΎΡ ΠΌΠΎΠΌΠ΅Π½Ρ ΠΎΠΏΡΠ΅Π΄Π΅Π»ΡΠ΅Ρ ΡΠΎ, ΡΡΠΎ Π²Π΅ΡΠΎΡΡΠ½ΠΎΡΡΡ Π²ΠΎΠ·Π½ΠΈΠΊΠ½ΠΎΠ²Π΅Π½ΠΈΡ ΡΠ΅Π»ΠΎΠ²Π΅ΡΠ΅ΡΠΊΠΎΠ³ΠΎ ΡΠ°ΠΊΡΠΎΡΠ°, ΠΏΡΠΈΠ²ΠΎΠ΄ΡΡΠ΅Π³ΠΎ ΠΊ Π±ΡΠ°ΠΊΡ, ΠΈΡΠΊΠ»ΡΡΠ°Π΅ΡΡΡ.
- Π’ΠΎΡΠ½ΠΎΡΡΡ ΠΏΠΎΠ»ΡΡΠ°Π΅ΠΌΡΡ ΡΠ°Π·ΠΌΠ΅ΡΠΎΠ² ΠΈ ΡΡΠ΅ΠΏΠ΅Π½ΠΈ ΡΠ΅ΡΠΎΡ ΠΎΠ²Π°ΡΠΎΡΡΠΈ ΠΎΡΠ΅Π½Ρ Π²Π΅Π»ΠΈΠΊΠ°. ΠΡΠΈ ΡΡΠΎΠΌ Π²Π°ΠΆΠ½ΠΎ ΠΎΡΠΌΠ΅ΡΠΈΡΡ, ΡΡΠΎ ΠΌΠΎΠΆΠ½ΠΎ ΠΏΠΎΠ»ΡΡΠΈΡΡ Π²ΡΡΠΎΠΊΡΡ ΡΠΎΡΠ½ΠΎΡΡΡ ΡΠΎΡΠΌΡ, ΡΠ°Π·ΠΌΠ΅ΡΠΎΠ², ΡΠ΅ΡΠΎΡ ΠΎΠ²Π°ΡΠΎΡΡΠΈ ΠΈ Π΄ΡΡΠ³ΠΈΡ ΠΏΠΎΠΊΠ°Π·Π°ΡΠ΅Π»Π΅ΠΉ.
ΠΠ»Π΅ΠΊΡΡΠΎΡΡΠΎΠ·ΠΈΠΎΠ½Π½Π°Ρ ΠΎΠ±ΡΠ°Π±ΠΎΡΠΊΠ° β ΡΠΎΠ²ΡΠ΅ΠΌΠ΅Π½Π½ΡΠΉ ΠΌΠ΅ΡΠΎΠ΄ ΠΏΡΠΎΠΈΠ·Π²ΠΎΠ΄ΡΡΠ²Π°, ΠΊΠΎΡΠΎΡΡΠΉ Ρ ΠΊΠ°ΠΆΠ΄ΡΠΌ Π³ΠΎΠ΄ΠΎΠΌ ΠΏΠΎΠ»ΡΠ·ΡΠ΅ΡΡΡ Π²ΡΠ΅ Π±ΠΎΠ»ΡΡΠ΅ΠΉ ΠΏΠΎΠΏΡΠ»ΡΡΠ½ΠΎΡΡΡΡ. Π ΠΏΠΎΡΠ»Π΅Π΄Π½Π΅Π΅ Π²ΡΠ΅ΠΌΡ ΡΠΎΠ·Π΄Π°Π΅ΡΡΡ Π΄ΠΎΠ²ΠΎΠ»ΡΠ½ΠΎ ΠΌΠ½ΠΎΠ³ΠΎ ΠΎΠ±ΠΎΡΡΠ΄ΠΎΠ²Π°Π½ΠΈΡ, ΠΊΠΎΡΠΎΡΠΎΠ΅ ΠΌΠΎΠΆΠ΅Ρ ΠΎΠΊΠ°Π·ΡΠ²Π°ΡΡ Π΄Π΅ΠΉΡΡΠ²ΠΈΠ΅ ΡΠ»Π΅ΠΊΡΡΠΈΡΠ΅ΡΠΊΠΎΠ³ΠΎ ΡΠ°Π·ΡΡΠ΄Π°.
ΠΠ΅Π΄ΠΎΡΡΠ°ΡΠΊΠΈ
ΠΡΡΡ ΠΎΠΏΡΠ΅Π΄Π΅Π»Π΅Π½Π½ΡΠ΅ Π½Π΅Π΄ΠΎΡΡΠ°ΡΠΊΠΈ, ΠΊΠΎΡΠΎΡΡΠ΅ ΠΎΠΏΡΠ΅Π΄Π΅Π»ΡΡΡ ΠΎΡΡΡΡΡΡΠ²ΠΈΠ΅ Π²ΠΎΠ·ΠΌΠΎΠΆΠ½ΠΎΡΡΠΈ ΠΏΠΎΠ²ΡΠ΅ΠΌΠ΅ΡΡΠ½ΠΎΠ³ΠΎ ΠΈΡΠΏΠΎΠ»ΡΠ·ΠΎΠ²Π°Π½ΠΈΡ ΡΠ»Π΅ΠΊΡΡΠΎΡΡΠΎΠ·ΠΈΠΎΠ½Π½ΠΎΠΉ ΠΎΠ±ΡΠ°Π±ΠΎΡΠΊΠΈ. Π ΠΎΡΠ½ΠΎΠ²Π½ΡΠΌ Π½Π΅Π΄ΠΎΡΡΠ°ΡΠΊΠ°ΠΌ ΠΌΠΎΠΆΠ½ΠΎ ΠΎΡΠ½Π΅ΡΡΠΈ?
- ΠΠ΅Π²ΡΡΠΎΠΊΠ°Ρ ΠΏΡΠΎΠΈΠ·Π²ΠΎΠ΄ΠΈΡΠ΅Π»ΡΠ½ΠΎΡΡΡ. ΠΠ»Ρ ΠΈΠ·ΠΌΠ΅Π½Π΅Π½ΠΈΡ ΡΠΎΡΠΌΡ ΠΈΠ»ΠΈ ΡΠ°Π·ΠΌΠ΅ΡΠΎΠ², ΠΊΠ°ΡΠ΅ΡΡΠ²Π° ΠΏΠΎΠ²Π΅ΡΡ Π½ΠΎΡΡΠΈ ΡΡΠ΅Π±ΡΠ΅ΡΡΡ Π΄ΠΎΠ²ΠΎΠ»ΡΠ½ΠΎ ΠΏΡΠΎΠ΄ΠΎΠ»ΠΆΠΈΡΠ΅Π»ΡΠ½ΠΎΠ΅ Π²ΠΎΠ·Π΄Π΅ΠΉΡΡΠ²ΠΈΠ΅ ΡΠ»Π΅ΠΊΡΡΠΈΡΠ΅ΡΠΊΠΎΠ³ΠΎ ΡΠ°Π·ΡΡΠ΄Π°. ΠΠΎΠ»ΡΡΠ°Ρ ΡΠ°ΡΡΡ ΠΎΠ±ΠΎΡΡΠ΄ΠΎΠ²Π°Π½ΠΈΡ ΠΈΠΌΠ΅Π΅Ρ ΡΠ»Π΅Π΄ΡΡΡΠΈΠΉ ΠΏΠΎΠΊΠ°Π·Π°ΡΠ΅Π»Ρ ΠΏΡΠΎΠΈΠ·Π²ΠΎΠ΄ΠΈΡΠ΅Π»ΡΠ½ΠΎΡΡΠΈ: 10 ΠΌΠΈΠ»Π»ΠΈΠΌΠ΅ΡΡΠΎΠ² Π·Π° ΠΎΠ΄Π½Ρ ΠΌΠΈΠ½ΡΡΡ.
- ΠΡΡΠΎΠΊΠΎΠ΅ ΡΠ½Π΅ΡΠ³ΠΎΠΏΠΎΡΡΠ΅Π±Π»Π΅Π½ΠΈΠ΅ ΠΎΠΏΡΠ΅Π΄Π΅Π»ΡΠ΅Ρ ΡΠΎ, ΡΡΠΎ ΡΡΠΎΠΈΠΌΠΎΡΡΡ ΠΏΠΎΠ»ΡΡΠ΅Π½ΠΈΡ Π΄Π΅ΡΠ°Π»Π΅ΠΉ ΠΎΡΠ΅Π½Ρ Π²ΡΡΠΎΠΊΠ°. ΠΠ»Π΅ΠΊΡΡΠΈΡΠ΅ΡΡΠ²ΠΎ β ΡΠ°ΠΌΡΠΉ Π΄ΠΎΡΠΎΠ³ΠΎΠΉ ΠΈΡΡΠΎΡΠ½ΠΈΠΊ ΡΠ½Π΅ΡΠ³ΠΈΠΈ, ΠΊΠΎΡΠΎΡΡΠΉ ΠΈΡΠΏΠΎΠ»ΡΠ·ΡΠ΅ΡΡΡ Π²ΠΎ ΠΌΠ½ΠΎΠ³ΠΈΡ ΡΡΠ΅ΡΠ°Ρ ΠΏΡΠΎΠΌΡΡΠ»Π΅Π½Π½ΠΎΡΡΠΈ.
- Π‘Π»ΠΎΠΆΠ½ΠΎΡΡΡ ΠΏΡΠΎΡΠ΅ΡΡΠ° ΠΎΠΏΡΠ΅Π΄Π΅Π»ΡΠ΅Ρ ΡΠΎ, ΡΡΠΎ ΡΠΏΡΠ°Π²Π»ΡΡΡ ΠΎΠ±ΠΎΡΡΠ΄ΠΎΠ²Π°Π½ΠΈΠ΅ΠΌ ΠΌΠΎΠΆΠ΅Ρ ΠΈΡΠΊΠ»ΡΡΠΈΡΠ΅Π»ΡΠ½ΠΎ ΠΏΡΠΎΡΠ΅ΡΡΠΈΠΎΠ½Π°Π».
- ΠΡΡΡ ΠΎΠΏΡΠ΅Π΄Π΅Π»Π΅Π½Π½ΡΠ΅ ΡΡΠ΅Π±ΠΎΠ²Π°Π½ΠΈΡ ΠΊ ΡΠΎΠΌΡ, Π³Π΄Π΅ ΡΡΡΠ°Π½Π°Π²Π»ΠΈΠ²Π°Π΅ΡΡΡ ΡΠ΅Ρ Π½ΠΈΠΊΠ°. Π‘ΡΠΎΠΈΡ ΡΡΠΈΡΡΠ²Π°ΡΡ ΡΠΎ, ΡΡΠΎ ΡΠ΅Ρ Π½ΠΎΠ»ΠΎΠ³ΠΈΡ ΠΏΡΠ΅Π΄ΡΡΠΌΠ°ΡΡΠΈΠ²Π°Π΅Ρ ΠΏΠΎΠ΄Π°ΡΡ ΡΠΎΠΊΠ° Ρ Π²ΡΡΠΎΠΊΠΎΠΉ ΡΠΈΠ»ΠΎΠΉ ΡΠΎΠΊΠ° ΠΈ Π½Π°ΠΏΡΡΠΆΠ΅Π½ΠΈΠ΅ΠΌ.
Π Π·Π°ΠΊΠ»ΡΡΠ΅Π½ΠΈΠ΅ ΠΎΡΠΌΠ΅ΡΠΈΠΌ, ΡΡΠΎ ΡΠ»Π΅ΠΊΡΡΠΎΡΡΠΎΠ·ΠΈΠΎΠ½Π½Π°Ρ ΠΎΠ±ΡΠ°Π±ΠΎΡΠΊΠ° Π² ΠΏΠΎΡΠ»Π΅Π΄Π½Π΅Π΅ Π²ΡΠ΅ΠΌΡ ΠΈΡΠΏΠΎΠ»ΡΠ·ΡΠ΅ΡΡΡ Π² ΡΠ°Π·Π»ΠΈΡΠ½ΡΡ ΠΎΡΡΠ°ΡΠ»ΡΡ ΠΏΡΠΎΠΌΡΡΠ»Π΅Π½Π½ΠΎΡΡΠΈ Π΄Π»Ρ ΠΈΠ·ΠΌΠ΅Π½Π΅Π½ΠΈΡ ΡΠΊΡΠΏΠ»ΡΠ°ΡΠ°ΡΠΈΠΎΠ½Π½ΡΡ ΠΊΠ°ΡΠ΅ΡΡΠ² ΠΌΠ°ΡΠ΅ΡΠΈΠ°Π»Π°. ΠΡΠΈ ΠΎΠΏΡΠ΅Π΄Π΅Π»Π΅Π½Π½ΠΎΠΌ Π²ΠΎΠ·Π΄Π΅ΠΉΡΡΠ²ΠΈΠΈ ΠΌΠΎΠΆΠ½ΠΎ ΠΏΠΎΠ²ΡΡΠΈΡΡ ΡΠΎΠΏΡΠΎΡΠΈΠ²Π»Π΅Π½ΠΈΠ΅ ΠΏΠΎΠ²Π΅ΡΡ Π½ΠΎΡΡΠΈ ΠΊ ΠΎΠ±ΡΠ°Π·ΠΎΠ²Π°Π½ΠΈΡ ΡΠ°ΡΠ°ΠΏΠΈΠ½, ΠΏΠΎΡΠ²Π»Π΅Π½ΠΈΡ ΠΎΡΠΏΠ΅ΡΠ°ΡΠΊΠΎΠ² ΠΏΠ°Π»ΡΡΠ΅Π² ΠΈ ΡΠ°ΠΊ Π΄Π°Π»Π΅Π΅.
ΠΡΠ»ΠΈ Π²Ρ Π½Π°ΡΠ»ΠΈ ΠΎΡΠΈΠ±ΠΊΡ, ΠΏΠΎΠΆΠ°Π»ΡΠΉΡΡΠ°, Π²ΡΠ΄Π΅Π»ΠΈΡΠ΅ ΡΡΠ°Π³ΠΌΠ΅Π½Ρ ΡΠ΅ΠΊΡΡΠ° ΠΈ Π½Π°ΠΆΠΌΠΈΡΠ΅ Ctrl+Enter.
stankiexpert.ru
ΠΠ»Π΅ΠΊΡΡΠΎΡΡΠΎΠ·ΠΈΠΎΠ½Π½Π°Ρ ΠΎΠ±ΡΠ°Π±ΠΎΡΠΊΠ° ΠΌΠ΅ΡΠ°Π»Π»ΠΎΠ²: ΡΠ΅Π·ΠΊΠ°, ΡΡΠ°Π½ΠΎΠΊ
Π§ΡΠΎΠ±Ρ ΠΏΡΠΈΠ΄Π°ΡΡ ΠΌΠ΅ΡΠ°Π»Π»ΠΈΡΠ΅ΡΠΊΠΎΠΌΡ ΠΈΠ·Π΄Π΅Π»ΠΈΡ ΠΎΠΏΡΠ΅Π΄Π΅Π»Π΅Π½Π½ΡΡ ΡΠΎΡΠΌΡ ΠΈ ΡΠ°Π·ΠΌΠ΅Ρ, ΠΌΠΎΠΆΠ½ΠΎ ΠΏΡΠΈΠΌΠ΅Π½ΡΡΡ ΡΠ°Π·Π½ΡΠ΅ ΡΠΏΠΎΡΠΎΠ±Ρ ΡΠΎΠΊΠ°ΡΠ½ΠΎΠΉ ΠΎΠ±ΡΠ°Π±ΠΎΡΠΊΠΈ.
ΠΠΎ ΠΈΠ½ΠΎΠ³Π΄Π° ΡΡΠ΅Π±ΠΎΠ²Π°Π½ΠΈΡ ΠΊ ΠΊΠ°ΡΠ΅ΡΡΠ²Ρ ΡΠ°ΠΊΠΎΠΉ ΠΎΠ±ΡΠ°Π±ΠΎΡΠΊΠΈ ΡΡΠ΅Π±ΡΠ΅Ρ ΠΏΠΎΠ²ΡΡΠ΅Π½Π½ΠΎΠΉ ΠΏΡΠΎΡΠ½ΠΎΡΡΠΈ Π² ΠΎΠ±Π»Π°ΡΡΠΈ Π²ΠΎΠ·Π΄Π΅ΠΉΡΡΠ²ΠΈΡ Π½Π° ΠΌΠ΅ΡΠ°Π»Π». Π‘ ΡΡΠΎΠΉ ΡΠ΅Π»ΡΡ ΠΌΠ΅ΡΠ°Π»Π»ΠΈΡΠ΅ΡΠΊΠΈΠ΅ ΠΈΠ·Π΄Π΅Π»ΠΈΡ ΠΎΠ±ΡΠ°Π±Π°ΡΡΠ²Π°ΡΡ ΡΠ»Π΅ΠΊΡΡΠΎΡΡΠΎΠ·ΠΈΠΎΠ½Π½ΡΠΌ ΡΠΏΠΎΡΠΎΠ±ΠΎΠΌ.
ΠΡΠΎΠΌΠ΅ ΠΏΠΎΠ»ΡΡΠ΅Π½ΠΈΡ Π½ΡΠΆΠ½ΠΎΠΉ ΡΠΎΡΠΌΡ ΠΈ ΠΏΠ°ΡΠ°ΠΌΠ΅ΡΡΠΎΠ² Π΄Π΅ΡΠ°Π»Π΅ΠΉ ΠΎΠ½ ΠΏΠΎΠ·Π²ΠΎΠ»ΡΠ΅Ρ ΠΏΠΎΠ»ΡΡΠ°ΡΡ ΡΠΊΠ²ΠΎΠ·Π½ΡΠ΅ ΠΎΡΠ²Π΅ΡΡΡΠΈΡ, ΡΠ°ΡΠΎΠ½Π½ΡΠ΅ ΠΊΠ°Π½Π°Π²ΠΊΠΈ Π² Π²ΠΈΠ΄Π΅ ΡΠ³Π»ΡΠ±Π»Π΅Π½ΠΈΠΉ ΠΈ ΠΏΠ°Π·Ρ Π² Π·Π°Π³ΠΎΡΠΎΠ²ΠΊΠ°Ρ . Π‘ ΠΏΠΎΠΌΠΎΡΡΡ ΡΠ»Π΅ΠΊΡΡΠΎΡΡΠΎΠ·ΠΈΠΎΠ½Π½ΠΎΠΉ ΠΎΠ±ΡΠ°Π±ΠΎΡΠΊΠΈ ΠΌΠ΅ΡΠ°Π»Π»ΠΎΠ² ΠΌΠΎΠΆΠ½ΠΎ ΠΈΠ·Π³ΠΎΡΠΎΠ²ΠΈΡΡ ΡΠ°Π·Π»ΠΈΡΠ½ΡΠ΅ Π²ΠΈΠ΄Ρ ΠΈΠ½ΡΡΡΡΠΌΠ΅Π½ΡΠΎΠ², ΠΏΡΠΎΡΠ½ΠΎΡΡΠ½ΡΠ΅ ΡΡΠ΅Π±ΠΎΠ²Π°Π½ΠΈΡ ΠΊ ΠΊΠΎΡΠΎΡΡΠΌ ΠΏΠΎΠ²ΡΡΠ΅Π½Ρ.
Π‘ΡΡΡ ΡΠ»Π΅ΠΊΡΡΠΎΡΡΠΎΠ·ΠΈΠΎΠ½Π½ΠΎΠΉ ΠΎΠ±ΡΠ°Π±ΠΎΡΠΊΠΈ
ΠΠ»Π΅ΠΊΡΡΠΎΡΡΠΎΠ·ΠΈΡ ΠΏΡΠ΅Π΄ΡΡΠ°Π²Π»ΡΠ΅Ρ ΡΠΎΠ±ΠΎΠΉ ΠΈΠ·ΠΌΠ΅Π½Π΅Π½ΠΈΠ΅ ΡΡΡΡΠΊΡΡΡΡ ΠΈ ΡΠΎΡΠΌΡ ΠΌΠ΅ΡΠ°Π»Π»Π° ΠΏΡΡΠ΅ΠΌ Π²ΠΎΠ·Π΄Π΅ΠΉΡΡΠ²ΠΈΡ ΡΠ»Π΅ΠΊΡΡΠΈΡΠ΅ΡΠΊΠΎΠ³ΠΎ ΡΠ°Π·ΡΡΠ΄Π°. ΠΠ½Π° Π²ΠΎΠ·Π½ΠΈΠΊΠ°Π΅Ρ ΠΏΡΠΈ ΡΠΎΠ·Π΄Π°Π½ΠΈΠΈ Π½Π°ΠΏΡΡΠΆΠ΅Π½ΠΈΡ ΠΌΠ΅ΠΆΠ΄Ρ ΡΠ»Π΅ΠΊΡΡΠΎΠ΄Π°ΠΌΠΈ. ΠΠ΄Π½ΠΈΠΌ ΠΈΠ· Π½ΠΈΡ ΡΠ»ΡΠΆΠΈΡ ΠΈΠ·Π΄Π΅Π»ΠΈΠ΅ ΠΈΠ· ΠΌΠ΅ΡΠ°Π»Π»Π°, Π° Π²ΡΠΎΡΡΠΌ β ΡΠ°Π±ΠΎΡΠΈΠΉ ΡΠ»Π΅ΠΊΡΡΠΎΠ΄.
ΠΡΠ»ΠΈ ΠΏΠΎ ΡΠ»Π΅ΠΊΡΡΠΎΠ΄Π°ΠΌ ΠΏΡΠΎΠΏΡΡΠΊΠ°ΡΡ ΡΠΎΠΊ, ΡΠΎ Π² ΠΏΡΠΎΡΡΡΠ°Π½ΡΡΠ²Π΅ ΠΌΠ΅ΠΆΠ΄Ρ Π½ΠΈΠΌΠΈ Π²ΠΎΠ·Π½ΠΈΠΊΠ½Π΅Ρ Π½Π°ΠΏΡΡΠΆΠ΅Π½ΠΈΠ΅ Π·Π° ΡΡΠ΅Ρ ΡΠ»Π΅ΠΊΡΡΠΈΡΠ΅ΡΠΊΠΎΠ³ΠΎ ΠΏΠΎΠ»Ρ. ΠΡΠΈ ΡΠ±Π»ΠΈΠΆΠ΅Π½ΠΈΠΈ ΡΠ°ΡΡΡΠΎΡΠ½ΠΈΡ ΠΌΠ΅ΠΆΠ΄Ρ ΡΠ»Π΅ΠΊΡΡΠΎΠ΄Π°ΠΌΠΈ Π΄ΠΎ ΠΊΡΠΈΡΠΈΡΠ΅ΡΠΊΠΎΠ³ΠΎ Π²ΠΎΠ·Π½ΠΈΠΊΠ½Π΅Ρ ΡΠ°Π·ΡΡΠ΄, ΡΠ»ΡΠΆΠ°ΡΠΈΠΉ ΠΏΡΠΎΠ²ΠΎΠ΄ΡΡΠΈΠΌ ΠΊΠ°Π½Π°Π»ΠΎΠΌ ΡΠ»Π΅ΠΊΡΡΠΈΡΠ΅ΡΡΠ²Π°.
Π§ΡΠΎΠ±Ρ ΠΏΠΎΠ²ΡΡΠΈΡΡ ΡΠΈΠ»Ρ ΡΠ°Π·ΡΡΠ΄Π° ΡΠ»Π΅ΠΊΡΡΠΎΠ΄Ρ ΠΏΠΎΠΌΠ΅ΡΠ°ΡΡΡΡ Π² ΠΆΠΈΠ΄ΠΊΠΎΡΡΡ, ΡΠ²Π»ΡΡΡΡΡΡΡ Π΄ΠΈΡΠ»Π΅ΠΊΡΡΠΈΠΊΠΎΠΌ, Π² ΠΊΠ°ΡΠ΅ΡΡΠ²Π΅ ΠΊΠΎΡΠΎΡΠΎΠΉ ΠΈΡΠΏΠΎΠ»ΡΠ·ΡΡΡ ΡΠ°Π·Π»ΠΈΡΠ½ΡΠ΅ ΠΌΠ°ΡΠ»Π° ΠΌΠΈΠ½Π΅ΡΠ°Π»ΡΠ½ΠΎΠ³ΠΎ Ρ Π°ΡΠ°ΠΊΡΠ΅ΡΠ° ΠΈΠ»ΠΈ ΠΊΠ΅ΡΠΎΡΠΈΠ½. ΠΡΠΎΡ ΠΎΠ΄ΡΡΠΈΠΉ ΠΏΠΎ ΠΎΠ±ΡΠ°Π·ΠΎΠ²Π°Π½Π½ΠΎΠΌΡ ΠΊΠ°Π½Π°Π»Ρ ΡΠΎΠΊ, Π½Π°Π³ΡΠ΅Π²Π°Π΅Ρ Π΄ΠΈΡΠ»Π΅ΠΊΡΡΠΈΡΠ΅ΡΠΊΡΡ ΠΆΠΈΠ΄ΠΊΠΎΡΡΡ, Π΄ΠΎΠ²ΠΎΠ΄Ρ Π΅Π΅ Π΄ΠΎ ΠΊΠΈΠΏΠ΅Π½ΠΈΡ ΠΈ ΠΏΠΎΡΠ»Π΅Π΄ΡΡΡΠ΅Π³ΠΎ ΠΈΡΠΏΠ°ΡΠ΅Π½ΠΈΡ Ρ ΠΎΠ±ΡΠ°Π·ΠΎΠ²Π°Π½ΠΈΠ΅ΠΌ Π³Π°Π·ΠΎΠ²ΠΎΠ³ΠΎ ΠΏΡΠ·ΡΡΡ. ΠΠ½ΡΡΡΠΈ ΡΡΠΎΠ³ΠΎ ΠΏΡΠ·ΡΡΡ Π²ΠΎΠ·Π½ΠΈΠΊΠ°Π΅Ρ ΠΌΠΎΡΠ½ΡΠΉ ΡΠ°Π·ΡΡΠ΄, ΡΠΎΠΏΡΠΎΠ²ΠΎΠΆΠ΄Π°ΡΡΠΈΠΉΡΡ ΠΏΠΎΡΠΎΠΊΠΎΠΌ ΡΠ»Π΅ΠΊΡΡΠΎΠ½ΠΎΠ² ΠΈ ΠΈΠΎΠ½ΠΎΠ².
ΠΠΎΠΌΠ±Π°ΡΠ΄ΠΈΡΡΡ ΡΠ»Π΅ΠΊΡΡΠΎΠ΄, ΠΎΠ½ΠΈ ΡΠΎΠ·Π΄Π°ΡΡ ΠΏΠ»Π°Π·ΠΌΠ΅Π½Π½ΡΠΉ ΠΏΠΎΡΠΎΠΊ. Π ΡΠ΅Π·ΡΠ»ΡΡΠ°ΡΠ΅ Π² Π·ΠΎΠ½Π΅ ΡΠ°Π·ΡΡΠ΄Π° ΡΠ΅ΠΌΠΏΠ΅ΡΠ°ΡΡΡΠ° ΠΏΠΎΠ²ΡΡΠ°Π΅ΡΡΡ Π΄ΠΎ 10000β12000Β°C ΠΈ ΠΌΠ³Π½ΠΎΠ²Π΅Π½Π½ΠΎ ΡΠ°ΡΠΏΠ»Π°Π²Π»ΡΠ΅Ρ ΠΌΠ΅ΡΠ°Π»Π» Ρ ΠΎΠ±ΡΠ°Π·ΠΎΠ²Π°Π½ΠΈΠ΅ΠΌ ΡΡΠΎΠ·ΠΈΠΎΠ½Π½ΠΎΠ³ΠΎ ΡΠ³Π»ΡΠ±Π»Π΅Π½ΠΈΡ Π² Π²ΠΈΠ΄Π΅ Π»ΡΠ½ΠΊΠΈ. ΠΠ½Π°ΡΠΈΡΠ΅Π»ΡΠ½Π°Ρ ΡΠ°ΡΡΡ ΡΠ°ΡΠΏΠ»Π°Π²Π° ΠΈΡΠΏΠ°ΡΡΠ΅ΡΡΡ, Π° Π½Π° ΠΏΠΎΠ²Π΅ΡΡ Π½ΠΎΡΡΠΈ ΠΌΠ΅ΡΠ°Π»Π»Π° Π² Π»ΡΠ½ΠΊΠ΅ ΠΏΠΎΡΠ»Π΅ Π΅Π³ΠΎ ΠΎΡΡΡΠ²Π°Π½ΠΈΡ ΠΎΡΡΠ°Π΅ΡΡΡ ΡΠ»ΠΎΠΉ, ΡΠΎΡΡΠ°Π² ΠΊΠΎΡΠΎΡΠΎΠ³ΠΎ ΠΎΡΠ»ΠΈΡΠ°Π΅ΡΡΡ ΠΎΡ ΡΠΎΡΡΠ°Π²Π° ΠΈΡΡ ΠΎΠ΄Π½ΠΎΠ³ΠΎ ΠΌΠ΅ΡΠ°Π»Π»Π°.
ΠΠ° ΡΠΈΡΡΠ½ΠΊΠ΅ (Π½ΠΈΠΆΠ΅) ΠΏΠΎΠΊΠ°Π·Π°Π½Π° Π»ΡΠ½ΠΊΠ°, Π²ΠΎΠ·Π½ΠΈΠΊΡΠ°Ρ ΠΏΡΠΈ Π²ΠΎΠ·Π΄Π΅ΠΉΡΡΠ²ΠΈΠΈ ΡΠ»Π΅ΠΊΡΡΠΈΡΠ΅ΡΠΊΠΎΠ³ΠΎ ΠΈΠΌΠΏΡΠ»ΡΡΠ°, Π³Π΄Π΅: 1β ΠΎΠ±ΡΠ΅ΠΌ Π»ΡΠ½ΠΊΠΈ, 2β Π»Π΅Π³ΠΈΡΠΎΠ²Π°Π½Π½ΡΠΉ ΡΠ»ΠΎΠΉ, 3 β Π»ΡΠ½ΠΎΡΠ½ΡΠΉ Π²Π°Π»ΠΈΠΊ, 4β ΠΌΠ΅ΡΠ°Π»Π»ΠΈΡΠ΅ΡΠΊΠ°Ρ Π΄Π΅ΡΠ°Π»Ρ.
Π ΡΠΎΡΡΠ°Π² ΠΏΠΎΠ²Π΅ΡΡ Π½ΠΎΡΡΠ½ΠΎΠ³ΠΎ ΡΠ»ΠΎΡ Π²Ρ ΠΎΠ΄ΡΡ ΠΊΠΎΠΌΠΏΠΎΠ½Π΅Π½ΡΡ Π½Π΅ ΡΠΎΠ»ΡΠΊΠΎ ΠΈΡΠΏΠ°ΡΠΈΠ²ΡΠ΅ΠΉΡΡ ΠΆΠΈΠ΄ΠΊΠΎΡΡΠΈ, Π½Π°ΡΡΡΠ°ΡΡΠΈΠ΅ ΠΌΠ΅ΡΠ°Π»Π» ΡΠ³Π»Π΅ΡΠΎΠ΄ΠΎΠΌ Ρ ΠΎΠ±ΡΠ°Π·ΠΎΠ²Π°Π½ΠΈΠ΅ΠΌ ΠΊΠ°ΡΠ±ΠΈΠ΄ΠΎΠ² ΠΆΠ΅Π»Π΅Π·Π°, Π½ΠΎ ΠΈ ΡΠ»Π΅ΠΌΠ΅Π½ΡΡ ΡΠ°ΡΠΏΠ»Π°Π²Π° ΠΌΠ΅ΡΠ°Π»Π»Π° ΡΠ°Π±ΠΎΡΠ΅Π³ΠΎ ΡΠ»Π΅ΠΊΡΡΠΎΠ΄Π°.
Π ΡΠ΅Π·ΡΠ»ΡΡΠ°ΡΠ΅ ΡΠ°ΠΊΠΎΠΉ ΡΠ»Π΅ΠΊΡΡΠΎΡΡΠΎΠ·ΠΈΠΎΠ½Π½ΠΎΠΉ ΠΎΠ±ΡΠ°Π±ΠΎΡΠΊΠΈ ΡΡΠ°Π»ΡΠ½ΡΠ΅ Π·Π°Π³ΠΎΡΠΎΠ²ΠΊΠΈ Π² ΠΌΠ΅ΡΡΠ΅ Π²ΠΎΠ·Π΄Π΅ΠΉΡΡΠ²ΠΈΡ ΠΌΠΎΠΆΠ½ΠΎ Π»Π΅Π³ΠΈΡΠΎΠ²Π°ΡΡ ΡΠ°ΠΊΠΈΠΌΠΈ ΡΠ»Π΅ΠΌΠ΅Π½ΡΠ°ΠΌΠΈ, ΠΊΠ°ΠΊ Ρ ΡΠΎΠΌ, ΡΠΈΡΠ°Π½, Π²ΠΎΠ»ΡΡΡΠ°ΠΌ ΠΈ Π΄ΡΡΠ³ΠΈΠΌΠΈ. Π’Π°ΠΊΠΎΠ΅ Π»Π΅Π³ΠΈΡΠΎΠ²Π°Π½ΠΈΠ΅ Π·Π½Π°ΡΠΈΡΠ΅Π»ΡΠ½ΠΎ ΡΠΏΡΠΎΡΠ½ΡΠ΅Ρ ΠΏΠΎΠ²Π΅ΡΡ Π½ΠΎΡΡΡ ΠΌΠ΅ΡΠ°Π»Π»ΠΈΡΠ΅ΡΠΊΠΎΠΉ Π·Π°Π³ΠΎΡΠΎΠ²ΠΊΠΈ Π² ΠΌΠ΅ΡΡΠ΅ ΡΠ»Π΅ΠΊΡΡΠΎΡΡΠΎΠ·ΠΈΠΎΠ½Π½ΠΎΠΉ ΠΎΠ±ΡΠ°Π±ΠΎΡΠΊΠΈ.
ΠΠ»Π΅ΠΊΡΡΠΎΡΡΠΎΠ·ΠΈΠΎΠ½Π½Π°Ρ ΡΠ΅Π·ΠΊΠ°
ΠΠ°ΠΈΠ±ΠΎΠ»Π΅Π΅ Π²ΠΎΡΡΡΠ΅Π±ΠΎΠ²Π°Π½Π½ΠΎΠΉ ΡΠ²Π»ΡΠ΅ΡΡΡ ΡΠ»Π΅ΠΊΡΡΠΎΡΡΠΎΠ·ΠΈΠΎΠ½Π½Π°Ρ ΡΠ΅Π·ΠΊΠ° ΠΌΠ΅ΡΠ°Π»Π»ΠΎΠ². ΠΠ΅ ΡΡΡΠ½ΠΎΡΡΡΡ ΡΠ²Π»ΡΠ΅ΡΡΡ Π΄Π΅ΠΉΡΡΠ²ΠΈΠ΅ Π½Π° ΠΌΠ΅ΡΠ°Π»Π»ΠΈΡΠ΅ΡΠΊΡΡ Π·Π°Π³ΠΎΡΠΎΠ²ΠΊΡ ΠΈΡΠΊΡΠΎΠ²ΡΡ ΡΠ»Π΅ΠΊΡΡΠΈΡΠ΅ΡΠΊΠΈΡ ΡΠ°Π·ΡΡΠ΄ΠΎΠ², ΠΎΠ±ΡΠ°Π·ΠΎΠ²Π°Π½Π½ΡΡ ΠΏΡΠΈ ΠΏΡΠΎΡΠ΅ΠΊΠ°Π½ΠΈΠΈ Π² ΡΠ»Π΅ΠΊΡΡΠΎΠ΄Π°Ρ ΠΈΠΌΠΏΡΠ»ΡΡΠ½ΠΎΠ³ΠΎ ΡΠΎΠΊΠ°, ΠΏΡΠΈ ΠΈΡ ΠΌΠ°ΠΊΡΠΈΠΌΠ°Π»ΡΠ½ΠΎΠΌ ΡΠ±Π»ΠΈΠΆΠ΅Π½ΠΈΠΈ ΠΈ Π½Π°Ρ ΠΎΠΆΠ΄Π΅Π½ΠΈΠΈ Π² ΠΆΠΈΠ΄ΠΊΠΎΠΉ ΡΡΠ΅Π΄Π΅ Π΄ΠΈΡΠ»Π΅ΠΊΡΡΠΈΠΊΠ°.
Π’Π°ΠΊΠΈΠΌ ΠΎΠ±ΡΠ°Π·ΠΎΠΌ, Π΄Π»Ρ ΠΏΡΠΎΠ²Π΅Π΄Π΅Π½ΠΈΡ ΡΠ»Π΅ΠΊΡΡΠΎΡΡΠΎΠ·ΠΈΠΎΠ½Π½ΠΎΠΉ ΡΠ΅Π·ΠΊΠΈ Π½Π° ΠΏΡΠΎΡΡΠΆΠ΅Π½ΠΈΠΈ Π²ΡΠ΅Π³ΠΎ ΠΏΡΠΎΡΠ΅ΡΡΠ° ΡΠ΅Π·Π°Π½ΠΈΡ Π½ΡΠΆΠ½ΠΎ ΠΎΠ±Π΅ΡΠΏΠ΅ΡΠΈΡΡ:
- ΠΏΠΎΠ΄Π°ΡΡ Π½Π°ΠΏΡΡΠΆΠ΅Π½ΠΈΡ ΠΊ ΡΠ»Π΅ΠΊΡΡΠΎΠ΄Π°ΠΌ Π² Π²ΠΈΠ΄Π΅ ΠΈΠΌΠΏΡΠ»ΡΡΠΎΠ²;
- ΠΏΠ΅ΡΠΈΠΎΠ΄ΠΈΡΠ΅ΡΠΊΠΈ ΡΠΎΠΊΡΠ°ΡΠ°ΡΡ ΠΌΠ΅ΠΆΠ΄Ρ ΡΠ»Π΅ΠΊΡΡΠΎΠ΄Π°ΠΌΠΈ ΡΠ°ΡΡΡΠΎΡΠ½ΠΈΠ΅ Π΄ΠΎ ΠΊΡΠΈΡΠΈΡΠ΅ΡΠΊΠΎΠ³ΠΎ ΡΠ°Π·ΠΌΠ΅ΡΠ°;
- ΠΎΠ±Π΅ΡΠΏΠ΅ΡΠΈΡΡ Π½Π°Π»ΠΈΡΠΈΠ΅ ΠΆΠΈΠ΄ΠΊΠΎΠΉ ΡΡΠ΅Π΄Ρ (ΠΊΠ΅ΡΠΎΡΠΈΠ½Π° ΠΈΠ»ΠΈ ΠΌΠ°ΡΠ»Π°).
ΠΡΠΈ ΠΎΠ±Π΅ΡΠΏΠ΅ΡΠ΅Π½ΠΈΠΈ ΡΠ°ΠΊΠΈΡ ΡΡΠ»ΠΎΠ²ΠΈΠΉ ΠΈΠ· ΠΌΠ΅ΡΠ°Π»Π»ΠΈΡΠ΅ΡΠΊΠΎΠΉ Π΄Π΅ΡΠ°Π»ΠΈ ΠΏΠΎΠ΄ Π²Π»ΠΈΡΠ½ΠΈΠ΅ΠΌ Π²ΡΡΠΎΠΊΠΎΠΉ ΡΠ΅ΠΌΠΏΠ΅ΡΠ°ΡΡΡΡ, Π²ΠΎΠ·Π½ΠΈΠΊΠ°ΡΡΠ΅ΠΉ Π·Π° ΡΡΠ΅Ρ Π΄Π΅ΠΉΡΡΠ²ΠΈΡ ΡΠ°Π·ΡΡΠ΄Π½ΠΎΠΉ Π΄ΡΠ³ΠΈ, Π²ΡΠ±ΠΈΠ²Π°ΡΡΡΡ ΡΠ°ΡΡΠΈΡΡ, ΠΊΠΎΡΠΎΡΡΠ΅ Π·Π°ΡΠ΅ΠΌ Π²ΡΠΌΡΠ²Π°ΡΡΡΡ Π΄ΠΈΡΠ»Π΅ΠΊΡΡΠΈΡΠ΅ΡΠΊΠΎΠΉ ΠΆΠΈΠ΄ΠΊΠΎΡΡΡΡ. ΠΠΈΡΠ»Π΅ΠΊΡΡΠΈΠΊ ΡΠ°ΠΊΠΆΠ΅ Π²ΡΠΏΠΎΠ»Π½ΡΠ΅Ρ ΡΡΠ½ΠΊΡΠΈΡ ΠΊΠ°ΡΠ°Π»ΠΈΠ·Π°ΡΠΎΡΠ° ΡΠ°ΡΠΏΠ°Π΄Π° ΡΠ°ΡΡΠΈΡ ΠΌΠ΅ΡΠ°Π»Π»Π°, Ρ. ΠΊ. ΠΏΡΠΈ Π²ΡΡΠΎΠΊΠΈΡ ΡΠ΅ΠΌΠΏΠ΅ΡΠ°ΡΡΡΠ°Ρ ΠΈΡΠΏΠ°ΡΡΠ΅ΡΡΡ.
ΠΠΎΡΠΊΠΎΠ»ΡΠΊΡ Π΅Π΄ΠΈΠ½ΠΈΡΠ½ΡΠΉ ΡΠ°Π·ΡΡΠ΄ Π΄ΠΎΠ»ΠΆΠ΅Π½ ΠΏΡΠΎΠΈΡΡ ΠΎΠ΄ΠΈΡΡ Ρ ΠΏΠ΅ΡΠΈΠΎΠ΄ΠΈΡΠ΅ΡΠΊΠΈΠΌ ΠΏΠΎΡΡΠΎΡΠ½ΡΡΠ²ΠΎΠΌ Π² Π²ΠΈΠ΄Π΅ ΠΊΡΠ°ΡΠΊΠΎΡΡΠΎΡΠ½ΡΡ ΠΈΡΠΊΡ, ΡΡΠΎΠ±Ρ Π΄ΠΎΡΡΠΈΡΡ ΡΠ°Π·ΡΠ΅Π·Π°Π½ΠΈΡ Π·Π°Π³ΠΎΡΠΎΠ²ΠΊΠΈ ΠΏΠΎ Π½Π°ΠΌΠ΅ΡΠ΅Π½Π½ΠΎΠΌΡ ΠΊΠΎΠ½ΡΡΡΡ, Π½ΡΠΆΠ½ΠΎ ΡΠΎΠ±Π»ΡΠ΄Π°ΡΡ ΠΎΠΏΡΠ΅Π΄Π΅Π»Π΅Π½Π½ΡΠΉ ΡΠ΅ΠΆΠΈΠΌ ΡΠ°Π±ΠΎΡΡ. Π Π°Π·Π»ΠΈΡΠ°ΡΡ Π΄Π²Π° ΡΠ΅ΠΆΠΈΠΌΠ° ΠΎΠ±ΡΠ°Π±ΠΎΡΠΊΠΈ: ΡΠ»Π΅ΠΊΡΡΠΎΠΈΡΠΊΡΠΎΠ²ΠΎΠΉ ΠΈ ΡΠ»Π΅ΠΊΡΡΠΎΠΈΠΌΠΏΡΠ»ΡΡΠ½ΡΠΉ Π²ΠΈΠ΄.
ΠΠΈΠ΄Π΅ΠΎ:
ΠΠ»Π΅ΠΊΡΡΠΎΠΈΡΠΊΡΠΎΠ²Π°Ρ ΠΎΠ±ΡΠ°Π±ΠΎΡΠΊΠ°
ΠΡΠΈ ΡΠ΅ΠΆΠΈΠΌΠ΅ ΡΠ»Π΅ΠΊΡΡΠΎΠΈΡΠΊΡΠΎΠ²ΠΎΠΉ ΠΎΠ±ΡΠ°Π±ΠΎΡΠΊΠΈ Π·Π°Π³ΠΎΡΠΎΠ²ΠΎΠΊ ΠΏΡΠΎΠ²ΠΎΠ΄ΠΈΡΡΡ Ρ ΠΈΡΠΏΠΎΠ»ΡΠ·ΠΎΠ²Π°Π½ΠΈΠ΅ΠΌ ΠΊΡΠ°ΡΠΊΠΎΠ²ΡΠ΅ΠΌΠ΅Π½Π½ΡΡ ΡΠ°Π·ΡΡΠ΄ΠΎΠ², ΠΏΡΠΎΠΈΡΡ ΠΎΠ΄ΡΡΠΈΡ Π² ΡΠΎΡΠΌΠ΅ ΠΈΡΠΊΡ ΡΠ΅ΡΠ΅Π· Π΄ΠΈΡΠ»Π΅ΠΊΡΡΠΈΡΠ΅ΡΠΊΡΡ ΠΆΠΈΠ΄ΠΊΠΎΡΡΡ.
ΠΡΠΈ ΡΠ°ΠΊΠΎΠΌ ΡΠ΅ΠΆΠΈΠΌΠ΅ ΡΠΎΠ±Π»ΡΠ΄Π°Π΅ΡΡΡ ΡΠ»Π΅Π΄ΡΡΡΠ°Ρ ΡΡ Π΅ΠΌΠ° ΠΏΠΎΠ΄Π°ΡΠΈ ΠΈΠΌΠΏΡΠ»ΡΡΠΎΠ²:
- ΠΎΠ±ΡΠ°Π±Π°ΡΡΠ²Π°Π΅ΠΌΠ°Ρ Π·Π°Π³ΠΎΡΠΎΠ²ΠΊΠ° ΡΠ»ΡΠΆΠΈΡ Π°Π½ΠΎΠ΄ΠΎΠΌ Ρ ΠΏΠΎΠ»ΠΎΠΆΠΈΡΠ΅Π»ΡΠ½ΡΠΌ Π·Π°ΡΡΠ΄ΠΎΠΌ, ΠΊ ΠΊΠΎΡΠΎΡΠΎΠΉ ΡΡΡΡΠ΅ΠΌΠ»ΡΠ΅ΡΡΡ ΠΏΠΎΡΠΎΠΊ ΡΠ»Π΅ΠΊΡΡΠΎΠ½ΠΎΠ² Ρ ΡΠ°Π±ΠΎΡΠ΅Π³ΠΎ ΡΠ»Π΅ΠΊΡΡΠΎΠ΄Π°.
- ΠΈΠΎΠ½Ρ ΠΌΠ΅ΡΠ°Π»Π»Π° Π΄Π΅ΡΠ°Π»ΠΈ Π²ΠΎΠ·Π΄Π΅ΠΉΡΡΠ²ΡΡΡ Π½Π° ΡΠ°Π±ΠΎΡΠΈΠΉ ΡΠ»Π΅ΠΊΡΡΠΎΠ΄. Π§ΡΠΎΠ±Ρ ΠΎΠ½ Π½Π΅ ΡΠ°Π·ΡΡΡΠΈΠ»ΡΡ, ΠΈΡΠΏΠΎΠ»ΡΠ·ΡΡΡ ΠΈΠΌΠΏΡΠ»ΡΡΠ½ΠΎΠ΅ Π½Π°ΠΏΡΡΠΆΠ΅Π½ΠΈΠ΅ Π½Π° ΠΏΡΠΎΡΡΠΆΠ΅Π½ΠΈΠΈ 10-3 Ρ.
ΠΠΈΠ΄Π΅ΠΎ:
ΠΠ»Π΅ΠΊΡΡΠΎΠΈΠΌΠΏΡΠ»ΡΡΠ½Π°Ρ ΠΎΠ±ΡΠ°Π±ΠΎΡΠΊΠ°
ΠΡΠΈ ΡΠ΅ΠΆΠΈΠΌΠ΅ ΡΠ»Π΅ΠΊΡΡΠΎΠΈΠΌΠΏΡΠ»ΡΡΠ° Π·Π°Π³ΠΎΡΠΎΠ²ΠΊΠ° ΡΠ»ΡΠΆΠΈΡ ΠΊΠ°ΡΠΎΠ΄ΠΎΠΌ Ρ ΠΎΡΡΠΈΡΠ°ΡΠ΅Π»ΡΠ½ΡΠΌ ΠΈΠΌΠΏΡΠ»ΡΡΠΎΠΌ, ΠΊΠΎΡΠΎΡΡΠΉ Π΄Π΅ΠΉΡΡΠ²ΡΠ΅Ρ Π΄ΠΎΠ»ΠΈ ΡΠ΅ΠΊΡΠ½Π΄Ρ. Π‘ΠΎΠ·Π΄Π°Π΅ΡΡΡ Π΄ΡΠ³ΠΎΠ²ΠΎΠΉ ΡΠ°Π·ΡΡΠ΄, Π½Π°ΠΏΡΠ°Π²Π»ΡΡΡΠΈΠΉ ΠΏΠΎΡΠΎΠΊ ΠΈΠΎΠ½ΠΎΠ² Π² ΡΡΠΎΡΠΎΠ½Ρ Π΄Π΅ΡΠ°Π»ΠΈ. Π ΡΠ°ΠΊΠΎΠΌ ΡΠ΅ΠΆΠΈΠΌΠ΅ ΠΎΠ±Π΅ΡΠΏΠ΅ΡΠΈΠ²Π°Π΅ΡΡΡ Π±ΠΎΠ»ΡΡΠ°Ρ ΡΠΊΠΎΡΠΎΡΡΡ ΠΌΠ΅ΡΠ°Π»Π»ΠΈΡΠ΅ΡΠΊΠΎΠ³ΠΎ ΡΡΠ΅ΠΌΠ°, Π½ΠΎ ΡΠΈΡΡΠΎΡΠ° ΠΎΠ±ΡΠ°Π±ΠΎΡΠΊΠΈ ΠΌΠ΅ΡΠ°Π»Π»Π° Ρ ΡΠΆΠ΅, ΡΠ΅ΠΌ ΠΏΡΠΈ ΡΠ»Π΅ΠΊΡΡΠΎΠΈΡΠΊΡΠΎΠ²ΠΎΠΌ ΡΠ΅ΠΆΠΈΠΌΠ΅.
ΠΡΠΈ ΡΠ»Π΅ΠΊΡΡΠΎΡΡΠΎΠ·ΠΈΠΎΠ½Π½ΠΎΠΉ ΡΠ΅Π·ΠΊΠ΅ ΠΈΡΠΏΠΎΠ»ΡΠ·ΡΡΡΡΡ ΠΈΡΠΊΡΠΎΠ²ΡΠ΅ ΡΠ°Π·ΡΡΠ΄Ρ, ΠΊΠΎΡΠΎΡΡΠ΅ ΠΎΠ±Π΅ΡΠΏΠ΅ΡΠΈΠ²Π°ΡΡΡΡ ΠΈΠΌΠΏΡΠ»ΡΡΠ°ΠΌΠΈ ΡΠ»Π΅ΠΊΡΡΠΈΡΠ΅ΡΠΊΠΎΠ³ΠΎ ΡΠΎΠΊΠ°, Π²ΡΡΠ°Π±Π°ΡΡΠ²Π°Π΅ΠΌΠΎΠ³ΠΎ Π³Π΅Π½Π΅ΡΠ°ΡΠΎΡΠΎΠΌ ΡΠΏΠ΅ΡΠΈΠ°Π»ΡΠ½ΠΎΠ³ΠΎ ΡΡΠ°Π½ΠΊΠ°, ΠΏΡΠ΅Π΄Π½Π°Π·Π½Π°ΡΠ΅Π½Π½ΠΎΠ³ΠΎ Π΄Π»Ρ ΡΠ°ΠΊΠΎΠΉ ΠΎΠ±ΡΠ°Π±ΠΎΡΠΊΠΈ.
ΠΠ»Π΅ΠΊΡΡΠΎΡΡΠΎΠ·ΠΈΠΎΠ½Π½ΡΠΉ ΡΡΠ°Π½ΠΎΠΊ
Π£ΠΏΡΠΎΡΠ΅Π½Π½ΠΎ ΡΠ°Π±ΠΎΡΠ° Π½Π° ΡΠ»Π΅ΠΊΡΡΠΎΡΡΠΎΠ·ΠΈΠΎΠ½Π½ΠΎΠΌ ΡΡΠ°Π½ΠΊΠ΅ ΠΏΡΠΎΠΈΡΡ ΠΎΠ΄ΠΈΡ ΡΠ°ΠΊ:
- ΠΠΌΠΏΡΠ»ΡΡΠ½ΡΠΉ ΡΠΎΠΊ ΠΏΠΎΠ΄Π°Π΅ΡΡΡ Π΄Π΅ΡΠ°Π»Ρ ΠΈ ΠΏΡΠΎΠ²ΠΎΠ»ΠΎΡΠ½ΡΠΉ ΡΠ»Π΅ΠΊΡΡΠΎΠ΄ ΠΈΠ· ΠΌΠΎΠ»ΠΈΠ±Π΄Π΅Π½Π°. Π’Π°ΠΊΠΆΠ΅ ΠΌΠΎΠ³ΡΡ Π±ΡΡΡ ΠΈΡΠΏΠΎΠ»ΡΠ·ΠΎΠ²Π°Π½Ρ Π²ΠΎΠ»ΡΡΡΠ°ΠΌ, Π»Π°ΡΡΠ½Ρ, ΠΌΠ΅Π΄Ρ ΠΈ Π΄ΡΡΠ³ΠΈΠ΅ ΠΌΠ΅ΡΠ°Π»Π»Ρ.
- ΠΠ΄Π½ΠΎΠ²ΡΠ΅ΠΌΠ΅Π½Π½ΠΎ Ρ ΠΏΠΎΠ΄Π°ΡΠ΅ΠΉ ΠΈΠΌΠΏΡΠ»ΡΡΠ½ΠΎΠ³ΠΎ ΡΠΎΠΊΠ° Π½Π° ΡΠ»Π΅ΠΊΡΡΠΎΠ΄ ΠΏΡΠΎΠΈΡΡ ΠΎΠ΄ΠΈΡ ΠΏΠ΅ΡΠ΅ΠΌΠ΅ΡΠ΅Π½ΠΈΠ΅ Π΄Π΅ΡΠ°Π»ΠΈ Ρ ΠΏΠΎΠΌΠΎΡΡΡ Π½Π°ΠΏΡΠ°Π²Π»ΡΡΡΠΈΡ ΡΡΠ°Π½ΠΊΠ° Π§ΠΠ£ Π² Π½ΡΠΆΠ½ΠΎΠΌ Π½Π°ΠΏΡΠ°Π²Π»Π΅Π½ΠΈΠΈ.
- ΠΠΎΠ·Π½ΠΈΠΊΠ°ΡΡΠΈΠ΅ ΠΈΡΠΊΡΠΎΠ²ΡΠ΅ ΠΈΠΌΠΏΡΠ»ΡΡΡ ΡΠ°Π·ΡΡΠ΄ΠΎΠ² Π²ΡΠΆΠΈΠ³Π°ΡΡ ΠΎΠ±Π»Π°ΡΡΡ ΠΌΠ΅ΡΠ°Π»Π»Π° Π² ΠΌΠ΅ΡΡΠ΅ ΡΠ°Π·ΡΠ΅Π·Π°.
- Π Π°ΡΠΏΠ»Π°Π²Π»Π΅Π½Π½ΡΠΉ ΠΌΠ΅ΡΠ°Π»Π» ΡΠΌΡΠ²Π°Π΅ΡΡΡ ΠΎΡ Π»Π°ΠΆΠ΄Π°ΡΡΠ΅ΠΉ ΠΆΠΈΠ΄ΠΊΠΎΡΡΡΡ.
- ΠΡΠΈ ΡΠ°Π±ΠΎΡΠ΅ ΠΎΠ±Π΅ΡΠΏΠ΅ΡΠΈΠ²Π°Π΅ΡΡΡ ΠΎΠ΄Π½ΠΎΠ²ΡΠ΅ΠΌΠ΅Π½Π½ΠΎΠ΅ ΠΏΠ΅ΡΠ΅ΠΌΠ΅ΡΠ΅Π½ΠΈΠ΅ ΠΏΡΠΎΠ²ΠΎΠ»ΠΎΠΊΠΈ, Π½Π°ΠΌΠΎΡΠ°Π½Π½ΠΎΠΉ Π½Π° ΡΠΏΠ΅ΡΠΈΠ°Π»ΡΠ½ΡΠΉ Π±Π°ΡΠ°Π±Π°Π½.
ΠΠ»Π΅ΠΊΡΡΠΎΡΡΠΎΠ·ΠΈΠΎΠ½Π½ΠΎΠ΅ ΠΎΠ±ΠΎΡΡΠ΄ΠΎΠ²Π°Π½ΠΈΠ΅ Π²ΠΊΠ»ΡΡΠ°Π΅Ρ:
- ΡΡΠ°Π½ΠΎΠΊ, Π½Π° ΠΊΠΎΡΠΎΡΠΎΠΌ ΠΎΡΡΡΠ΅ΡΡΠ²Π»ΡΠ΅ΡΡΡ ΠΎΠΏΠ΅ΡΠ°ΡΠΈΡ;
- Π³Π΅Π½Π΅ΡΠ°ΡΠΎΡ Π½Π°ΠΏΡΡΠΆΠ΅Π½ΠΈΡ, ΠΎΠ±Π΅ΡΠΏΠ΅ΡΠΈΠ²Π°ΡΡΠΈΠΉ ΠΈΠΌΠΏΡΠ»ΡΡΠ½ΡΠΉ ΡΠ΅ΠΆΠΈΠΌ;
- ΡΡΡΡΠΎΠΉΡΡΠ²ΠΎ ΠΏΠΎΠ΄Π°ΡΠΈ Π΄ΠΈΡΠ»Π΅ΠΊΡΡΠΈΡΠ΅ΡΠΊΠΎΠΉ ΠΆΠΈΠ΄ΠΊΠΎΡΡΠΈ ΠΈ Π΅Π΅ ΠΎΡΠΈΡΡΠΊΠΈ;
- ΡΠΈΡΡΠ΅ΠΌΡ ΠΎΡΠΊΠ°ΡΠΊΠΈ ΠΈΠ· ΡΠ°Π±ΠΎΡΠ΅ΠΉ ΠΎΠ±Π»Π°ΡΡΠΈ ΠΎΠ±ΡΠ°Π·ΠΎΠ²Π°Π½Π½ΡΡ Π³Π°Π·ΠΎΠ².
ΠΠ΅ΠΏΠΎΡΡΠ΅Π΄ΡΡΠ²Π΅Π½Π½ΠΎ ΡΡΠ°Π½ΠΎΠΊ ΡΠΎΡΡΠΎΠΈΡ ΠΈΠ·:
- ΠΎΡΠ½ΠΎΠ²Π°Π½ΠΈΡ Π² Π²ΠΈΠ΄Π΅ ΡΡΠ°Π½ΠΈΠ½Ρ;
- Π²Π°Π½Π½Ρ, ΡΠ°Π·ΠΌΠ΅ΡΠ΅Π½Π½ΠΎΠΉ Π½Π° ΡΡΠΎΠ»Π΅;
- Π³ΠΎΠ»ΠΎΠ²ΠΊΠΈ ΡΠΏΠΈΠ½Π΄Π΅Π»Ρ;
- ΠΏΡΠ»ΡΡΠ° Π΄Π»Ρ ΡΠΏΡΠ°Π²Π»Π΅Π½ΠΈΡ ΠΏΡΠΎΡΠ΅ΡΡΠΎΠΌ;
- ΡΠΈΡΡΠ΅ΠΌΡ ΠΎΠ±Π΅ΡΠΏΠ΅ΡΠ΅Π½ΠΈΡ ΠΏΠΎΠ΄Π°ΡΠΈ ΠΈΠΌΠΏΡΠ»ΡΡΠΎΠ² Π½Π° Π΄Π΅ΡΠ°Π»Ρ;
- ΡΠΈΡΡΠ΅ΠΌΡ Π°Π²ΡΠΎΠΌΠ°ΡΠΈΡΠ΅ΡΠΊΠΎΠΉ ΡΠ΅Π³ΡΠ»ΠΈΡΠΎΠ²ΠΊΠΈ ΠΏΡΠΎΡΠ΅ΡΡΠΎΠ².
ΠΠΈΠ΄Π΅ΠΎ:
ΠΡΡΡΠ΅ΡΠ°ΡΡΡΡ ΡΡΠ°Π½ΠΊΠΈ, ΠΊΠΎΡΠΎΡΡΠ΅ ΠΌΠΎΠ³ΡΡ ΠΈΠΌΠ΅ΡΡ Π½Π΅ΠΊΠΎΡΠΎΡΠΎΠ΅ ΠΎΡΠ»ΠΈΡΠΈΠ΅ Π² ΡΡΡΡΠΎΠΉΡΡΠ²Π΅. ΠΠ°ΠΏΡΠΈΠΌΠ΅Ρ, ΠΌΠΎΠ³ΡΡ ΠΈΠΌΠ΅ΡΡ ΡΠΈΡΡΠ΅ΠΌΡ ΠΎΡΠΈΡΡΠΊΠΈ Π² Π²ΠΈΠ΄Π΅ ΠΎΡΠ΄Π΅Π»ΡΠ½ΠΎΠ³ΠΎ ΡΡΡΡΠΎΠΉΡΡΠ²Π°.
ΠΠΌΠΏΡΠ»ΡΡΠ½ΡΠ΅ Π³Π΅Π½Π΅ΡΠ°ΡΠΎΡΡ ΡΠ²Π»ΡΡΡΡΡ ΠΎΡΠ΄Π΅Π»ΡΠ½ΡΠΌΠΈ Π°Π³ΡΠ΅Π³Π°ΡΠ°ΠΌΠΈ, ΡΠ°Π·ΠΌΠ΅ΡΠ΅Π½Π½ΡΠΌΠΈ ΡΡΠ΄ΠΎΠΌ Ρ ΠΎΡΠ½ΠΎΠ²Π½ΡΠΌ ΡΡΠ°Π½ΠΊΠΎΠΌ. ΠΡΡΡ Π²ΠΈΠ΄Ρ ΡΡΡΡΠΎΠΉΡΡΠ², Π² ΠΊΠΎΡΠΎΡΡΡ Π³Π΅Π½Π΅ΡΠ°ΡΠΎΡ Π²ΡΡΡΠΎΠ΅Π½ Π² ΡΡΠ°Π½ΠΎΠΊ.
Π£ΠΏΡΠΎΡΠ΅Π½Π½ΡΠΉ Π²Π°ΡΠΈΠ°Π½Ρ ΡΠ»Π΅ΠΊΡΡΠΎΠΈΡΠΊΡΠΎΠ²ΠΎΠ³ΠΎ ΡΡΠ°Π½ΠΊΠ° Π½Π΅ Π²ΠΊΠ»ΡΡΠ°Π΅Ρ ΡΠΈΡΡΠ΅ΠΌΡ ΠΏΠΎΠ΄Π°ΡΠΈ ΠΆΠΈΠ΄ΠΊΠΎΡΡΠΈ ΠΈ Π΅Π΅ ΠΎΡΠΈΡΡΠΊΠΈ. ΠΠ±ΡΠ°Π±ΠΎΡΠΊΠ° Π²ΠΊΠ»ΡΡΠ°Π΅Ρ ΠΏΠΎΠ³ΡΡΠΆΠ΅Π½ΠΈΠ΅ ΡΡΠΎΠ»Π° Ρ Π΄Π΅ΡΠ°Π»ΡΡ Π·Π°Π³ΠΎΡΠΎΠ²ΠΊΠΈ Π² Π²ΠΎΠ΄Ρ, Π½Π°Ρ ΠΎΠ΄ΡΡΡΡΡΡ Π² Π²Π°Π½Π½Π΅. ΠΡΠ»ΠΈ ΠΎΠ±ΡΠ°Π±ΠΎΡΠΊΠ° ΠΏΡΠΎΠ²ΠΎΠ΄ΠΈΡΡΡ Ρ ΠΈΡΠΏΠΎΠ»ΡΠ·ΠΎΠ²Π°Π½ΠΈΠ΅ΠΌ ΠΊΠ΅ΡΠΎΡΠΈΠ½Π°, ΡΠΎ ΠΎΠ±ΡΠ°Π·ΡΡΡΠΈΠ΅ΡΡ Π³Π°Π·Ρ ΡΠ΄Π°Π»ΡΡΡΡΡ ΡΠ΅ΡΠ΅Π· ΠΎΠ±ΡΡΡ Π²Π΅Π½ΡΠΈΠ»ΡΡΠΈΡ.
ΠΡΠΈ ΡΠΊΡΠΏΠ»ΡΠ°ΡΠ°ΡΠΈΠΈ ΡΡΠΎΠ³ΠΎ ΠΎΠ±ΠΎΡΡΠ΄ΠΎΠ²Π°Π½ΠΈΡ ΡΡΠ΅Π±ΡΡΡΡΡ ΠΊΠ²Π°Π»ΠΈΡΠΈΠΊΠ°ΡΠΈΡ ΠΈ Π·Π½Π°Π½ΠΈΠ΅ ΡΠ΅Ρ Π½ΠΎΠ»ΠΎΠ³ΠΈΡΠ΅ΡΠΊΠΎΠ³ΠΎ ΠΏΡΠΎΡΠ΅ΡΡΠ°, ΠΊΠΎΡΠΎΡΡΠ΅ ΠΏΠΎΠ·Π²ΠΎΠ»ΡΡ Π²ΡΠΏΠΎΠ»Π½ΡΡΡ ΠΏΡΠΎΡΠ΅ΡΡ Ρ ΡΠΎΠ±Π»ΡΠ΄Π΅Π½ΠΈΠ΅ΠΌ Π²ΡΠ΅Ρ ΡΡΠ΅Π±ΠΎΠ²Π°Π½ΠΈΠΉ, ΠΎΡΡΠ°ΠΆΠ΅Π½Π½ΡΡ Π² Π΄ΠΎΠΊΡΠΌΠ΅Π½ΡΠ°ΡΠΈΠΈ.
ΠΠ°Π³ΡΡΠ·ΠΊΠ°β¦plavitmetall.ru
ΠΠ»Π΅ΠΊΡΡΠΎΡΡΠΎΠ·ΠΈΠΎΠ½Π½Π°Ρ ΠΎΠ±ΡΠ°Π±ΠΎΡΠΊΠ°. ΠΠΏΠΈΡΠ°Π½ΠΈΠ΅ ΠΏΡΠΎΡΠ΅ΡΡΠ°, ΠΏΡΠΈΠ½ΡΠΈΠΏΡ, ΡΡΡΠ°Π½ΠΎΠ²ΠΊΠΈ ΡΠ»Π΅ΠΊΡΡΠΎΡΡΠΎΠ·ΠΈΠΎΠ½Π½ΠΎΠΉ ΠΎΠ±ΡΠ±ΠΎΡΠΊΠΈ.
1. Π‘ΡΡΠ½ΠΎΡΡΡ ΠΈ Π½Π°Π·Π½Π°ΡΠ΅Π½ΠΈΠ΅ ΡΠ»Π΅ΠΊΡΡΠΎΡΡΠΎΠ·ΠΈΠΎΠ½Π½ΠΎΠΉ ΠΎΠ±ΡΠ°Π±ΠΎΡΠΊΠΈ
ΠΠ»Π΅ΠΊΡΡΠΎΡΡΠΎΠ·ΠΈΡ β ΡΡΠΎ ΡΠ°Π·ΡΡΡΠ΅Π½ΠΈΠ΅ ΠΏΠΎΠ²Π΅ΡΡ Π½ΠΎΡΡΠΈ ΠΈΠ·Π΄Π΅Π»ΠΈΡ ΠΏΠΎΠ΄ Π΄Π΅ΠΉΡΡΠ²ΠΈΠ΅ΠΌ ΡΠ»Π΅ΠΊΡΡΠΈΡΠ΅ΡΠΊΠΎΠ³ΠΎ ΡΠ°Π·ΡΡΠ΄Π°. ΠΡΠ½ΠΎΠ²Π°ΡΠ΅Π»ΡΠΌΠΈ ΡΠ΅Ρ Π½ΠΎΠ»ΠΎΠ³ΠΈΠΈ ΡΠ²Π»ΡΡΡΡΡ ΡΠΎΠ²Π΅ΡΡΠΊΠΈΠ΅ ΡΡΠ΅Π½ΡΠ΅-ΡΠ΅Ρ Π½ΠΎΠ»ΠΎΠ³ΠΈ Π.Π . ΠΠ°Π·Π°ΡΠ΅Π½ΠΊΠΎ ΠΈ Π.Π. ΠΠ°Π·Π°ΡΠ΅Π½ΠΊΠΎ.
ΠΠ»Π΅ΠΊΡΡΠΎΡΡΠΎΠ·ΠΈΠΎΠ½Π½Π°Ρ ΠΎΠ±ΡΠ°Π±ΠΎΡΠΊΠ° (ΠΠΠ) ΡΠΈΡΠΎΠΊΠΎ ΠΏΡΠΈΠΌΠ΅Π½ΡΠ΅ΡΡΡ Π΄Π»Ρ ΠΈΠ·ΠΌΠ΅Π½Π΅Π½ΠΈΡ ΡΠ°Π·ΠΌΠ΅ΡΠΎΠ² ΠΌΠ΅ΡΠ°Π»Π»ΠΈΡΠ΅ΡΠΊΠΈΡ ΠΈΠ·Π΄Π΅Π»ΠΈΠΉ β Π΄Π»Ρ ΠΏΠΎΠ»ΡΡΠ΅Π½ΠΈΡ ΠΎΡΠ²Π΅ΡΡΡΠΈΠΉ ΡΠ°Π·Π»ΠΈΡΠ½ΠΎΠΉ ΡΠΎΡΠΌΡ, ΡΠ°ΡΠΎΠ½Π½ΡΡ ΠΏΠΎΠ»ΠΎΡΡΠ΅ΠΉ, ΠΏΡΠΎΡΠΈΠ»ΡΠ½ΡΡ ΠΊΠ°Π½Π°Π²ΠΎΠΊ ΠΈ ΠΏΠ°Π·ΠΎΠ² Π² Π΄Π΅ΡΠ°Π»ΡΡ ΠΈΠ· ΡΠ²Π΅ΡΠ΄ΡΡ ΡΠΏΠ»Π°Π²ΠΎΠ², Π΄Π»Ρ ΡΠΏΡΠΎΡΠ½Π΅Π½ΠΈΡ ΠΈΠ½ΡΡΡΡΠΌΠ΅Π½ΡΠ°, Π΄Π»Ρ ΡΠ»Π΅ΠΊΡΡΠΎΠΏΠ΅ΡΠ°ΡΠ°Π½ΠΈΡ, ΡΠ»ΠΈΡΠΎΠ²Π°Π½ΠΈΡ, ΡΠ΅Π·ΠΊΠΈ ΠΈ Π΄Ρ.
Π ΠΈΡ. 1.9. Π‘Ρ Π΅ΠΌΠ° ΡΠ»Π΅ΠΊΡΡΠΎΡΡΠΎΠ·ΠΈΠΎΠ½Π½ΠΎΠΉ ΠΎΠ±ΡΠ°Π±ΠΎΡΠΊΠΈ ΠΌΠ°ΡΠ΅ΡΠΈΠ°Π»ΠΎΠ²: 1 β ΡΠ»Π΅ΠΊΡΡΠΎΠ΄-ΠΈΠ½ΡΡΡΡΠΌΠ΅Π½Ρ, 2 β ΠΎΠ±ΡΠ°Π±Π°ΡΡΠ²Π°Π΅ΠΌΠ°Ρ Π΄Π΅ΡΠ°Π»Ρ, 3 β ΡΡΠ΅Π΄Π°, Π² ΠΊΠΎΡΠΎΡΠΎΠΉ ΠΏΡΠΎΠΈΠ·Π²ΠΎΠ΄ΠΈΡΡΡ ΡΠ°Π·ΡΡΠ΄, 4 β ΠΊΠΎΠ½Π΄Π΅Π½ΡΠ°ΡΠΎΡ, 5 β ΡΠ΅ΠΎΡΡΠ°Ρ, 6 β ΠΈΡΡΠΎΡΠ½ΠΈΠΊ ΠΏΠΈΡΠ°Π½ΠΈΡ, 1Ρ β ΡΠ΅ΠΆΠΈΠΌ ΡΠ»Π΅ΠΊΡΡΠΎΠΈΡΠΊΡΠΎΠ²ΠΎΠΉ ΠΎΠ±ΡΠ°Π±ΠΎΡΠΊΠΈ, 2Ρ β ΡΠ΅ΠΆΠΈΠΌ ΡΠ»Π΅ΠΊΡΡΠΎΠΈΠΌΠΏΡΠ»ΡΡΠ½ΠΎΠΉ ΠΎΠ±ΡΠ°Π±ΠΎΡΠΊΠΈ
Π‘Ρ Π΅ΠΌΠ° ΡΠ»Π΅ΠΊΡΡΠΎΡΡΠΎΠ·ΠΈΠΎΠ½Π½ΠΎΠΉ ΠΎΠ±ΡΠ°Π±ΠΎΡΠΊΠΈ ΠΌΠ°ΡΠ΅ΡΠΈΠ°Π»ΠΎΠ² ΠΏΡΠΈΠ²Π΅Π΄Π΅Π½Π° Π½Π° ΡΠΈΡ. 1.9. Π‘Ρ Π΅ΠΌΠ° Π·Π°ΠΏΠΈΡΡΠ²Π°Π΅ΡΡΡ ΠΈΠΌΠΏΡΠ»ΡΡΠ½ΡΠΌ Π½Π°ΠΏΡΡΠΆΠ΅Π½ΠΈΠ΅ΠΌ ΡΠ°Π·Π½ΠΎΠΉ ΠΏΠΎΠ»ΡΡΠ½ΠΎΡΡΠΈ, ΡΡΠΎ ΡΠΎΠΎΡΠ²Π΅ΡΡΡΠ²ΡΠ΅Ρ ΡΠ»Π΅ΠΊΡΡΠΎΠΈΡΠΊΡΠΎΠ²ΠΎΠΌΡ ΡΠ΅ΠΆΠΈΠΌΡ (1Ρ) ΠΈ ΡΠ»Π΅ΠΊΡΡΠΎΠΈΠΌΠΏΡΠ»ΡΡΠ½ΠΎΠΌΡ ΡΠ΅ΠΆΠΈΠΌΡ (2Ρ). ΠΠ°ΠΏΡΡΠΆΠ΅Π½ΠΈΠ΅ ΠΏΠΈΡΠ°Π½ΠΈΡ Π·Π°ΡΡΠΆΠ°Π΅Ρ ΠΊΠΎΠ½Π΄Π΅Π½ΡΠ°ΡΠΎΡ (4), ΠΏΠ°ΡΠ°Π»Π»Π΅Π»ΡΠ½ΠΎ ΠΊΠΎΡΠΎΡΠΎΠΌΡ Π²ΠΊΠ»ΡΡΠ΅Π½ ΡΠ°Π·ΡΡΠ΄Π½ΡΠΉ ΠΏΡΠΎΠΌΠ΅ΠΆΡΡΠΎΠΊ ΠΌΠ΅ΠΆΠ΄Ρ ΡΠ»Π΅ΠΊΡΡΠΎΠ΄ΠΎΠΌ-ΠΈΠ½ΡΡΡΡΠΌΠ΅Π½ΡΠΎΠΌ (1) ΠΈ ΠΎΠ±ΡΠ°Π±Π°ΡΡΠ²Π°Π΅ΠΌΠΎΠΉ Π΄Π΅ΡΠ°Π»ΡΡ (2), ΠΊΠΎΡΠΎΡΡΠ΅ ΠΏΠΎΠΌΠ΅ΡΠ΅Π½Ρ Π² ΠΆΠΈΠ΄ΠΊΠΎΡΡΡ Ρ Π½ΠΈΠ·ΠΊΠΎΠΉ Π΄ΠΈΡΠ»Π΅ΠΊΡΡΠΈΡΠ΅ΡΠΊΠΎΠΉ ΠΏΡΠΎΠ½ΠΈΡΠ°Π΅ΠΌΠΎΡΡΡΡ. ΠΠΎΠ³Π΄Π° Π½Π°ΠΏΡΡΠΆΠ΅Π½ΠΈΠ΅ Π½Π° ΠΊΠΎΠ½Π΄Π΅Π½ΡΠ°ΡΠΎΡΠ΅ ΠΏΡΠ΅Π²ΡΡΠΈΡ ΠΏΠΎΡΠ΅Π½ΡΠΈΠ°Π» Π·Π°ΠΆΠΈΠ³Π°Π½ΠΈΡ ΡΠ°Π·ΡΡΠ΄Π°, ΠΏΡΠΎΠΈΡΡ ΠΎΠ΄ΠΈΡ ΠΏΡΠΎΠ±ΠΎΠΉ ΠΆΠΈΠ΄ΠΊΠΎΡΡΠΈ. ΠΠΈΠ΄ΠΊΠΎΡΡΡ Π½Π°Π³ΡΠ΅Π²Π°Π΅ΡΡΡ Π΄ΠΎ ΡΠ΅ΠΌΠΏΠ΅ΡΠ°ΡΡΡΡ ΠΊΠΈΠΏΠ΅Π½ΠΈΡ ΠΈ ΠΎΠ±ΡΠ°Π·ΡΠ΅ΡΡΡ Π³Π°Π·ΠΎΠ²ΡΠΉ ΠΏΡΠ·ΡΡΡ ΠΈΠ· ΠΏΠ°ΡΠΎΠ² ΠΆΠΈΠ΄ΠΊΠΎΡΡΠΈ. ΠΠ°Π»Π΅Π΅ ΡΠ»Π΅ΠΊΡΡΠΈΡΠ΅ΡΠΊΠΈΠΉ ΡΠ°Π·ΡΡΠ΄ ΡΠ°Π·Π²ΠΈΠ²Π°Π΅ΡΡΡ Π² Π³Π°Π·ΠΎΠ²ΠΎΠΉ ΡΡΠ΅Π΄Π΅, ΡΡΠΎ ΠΏΡΠΈΠ²ΠΎΠ΄ΠΈΡ ΠΊ ΠΈΠ½ΡΠ΅Π½ΡΠΈΠ²Π½ΠΎΠΌΡ Π»ΠΎΠΊΠ°Π»ΡΠ½ΠΎΠΌΡ ΡΠ°Π·ΠΎΠ³ΡΠ΅Π²Π°Π½ΠΈΡ Π΄Π΅ΡΠ°Π»ΠΈ, ΠΏΡΠΈΠΏΠΎΠ²Π΅ΡΡ Π½ΠΎΡΡΠ½ΡΠ΅ ΡΠ»ΠΎΠΈ ΠΌΠ°ΡΠ΅ΡΠΈΠ°Π»Π° ΠΏΠ»Π°Π²ΡΡΡΡ ΠΈ ΠΏΡΠΎΠ΄ΡΠΊΡΡ ΡΠ°ΡΠΏΠ»Π°Π²Π° Π² Π²ΠΈΠ΄Π΅ ΡΠ°ΡΠΈΠΊΠΎΠ² Π·Π°ΡΡΡΠ²Π°ΡΡ Π² ΠΏΡΠΎΡΠΎΡΠ½ΠΎΠΉ ΠΆΠΈΠ΄ΠΊΠΎΡΡΠΈ ΠΈ Π²ΡΠ½ΠΎΡΡΡΡΡ ΠΈΠ· Π·ΠΎΠ½Ρ ΠΎΠ±ΡΠ°Π±ΠΎΡΠΊΠΈ.β
2. Π‘ΡΠ°Π΄ΠΈΠΈ ΡΠ»Π΅ΠΊΡΡΠΎΡΡΠΎΠ·ΠΈΠΎΠ½Π½ΠΎΠΉ ΠΎΠ±ΡΠ°Π±ΠΎΡΠΊΠΈ Π Π΅ΠΆΠΈΠΌ ΡΠ»Π΅ΠΊΡΡΠΎΠΈΡΠΊΡΠΎΠ²ΠΎΠΉ ΠΎΠ±ΡΠ°Π±ΠΎΡΠΊΠΈ
ΠΠ±ΡΠ°Π±Π°ΡΡΠ²Π°Π΅ΠΌΠ°Ρ Π΄Π΅ΡΠ°Π»Ρ ΡΠ²Π»ΡΠ΅ΡΡΡ Π°Π½ΠΎΠ΄ΠΎΠΌ (+), ΡΠΎ Π΅ΡΡΡ Π² Π΄Π°Π½Π½ΠΎΠΌ ΡΠ»ΡΡΠ°Π΅ Π΄Π΅ΡΠ°Π»Ρ ΠΎΠ±ΡΠ°Π±Π°ΡΡΠ²Π°Π΅ΡΡΡ ΡΠ»Π΅ΠΊΡΡΠΎΠ½Π½ΡΠΌ ΠΏΠΎΡΠΎΠΊΠΎΠΌ, ΡΠΎ Π΅ΡΡΡ ΡΠ°Π±ΠΎΡΠ°Π΅Ρ ΡΠ»Π΅ΠΊΡΡΠΎΠ½Π½ΡΠΉ ΡΡΡΠΈΠΌΠ΅Ρ, ΡΠ°ΡΠΏΠ»Π°Π²Π»ΡΡ ΠΎΠ±ΡΠ΅ΠΌ Π°Π½ΠΎΠ΄Π°-Π΄Π΅ΡΠ°Π»ΠΈ Π² Π²ΠΈΠ΄Π΅ Π»ΡΠ½ΠΊΠΈ. ΠΠ»Ρ ΡΠΎΠ³ΠΎ ΡΡΠΎΠ±Ρ ΠΈΠΎΠ½Π½ΡΠΉ ΠΏΠΎΡΠΎΠΊ Π½Π΅ ΡΠ°Π·ΡΡΡΠ°Π» ΡΠ»Π΅ΠΊΡΡΠΎΠ΄-ΠΈΠ½ΡΡΡΡΠΌΠ΅Π½Ρ, ΠΈΡΠΏΠΎΠ»ΡΠ·ΡΡΡΡΡ ΠΈΠΌΠΏΡΠ»ΡΡΡ Π½Π°ΠΏΡΡΠΆΠ΅Π½ΠΈΡ Π΄Π»ΠΈΡΠ΅Π»ΡΠ½ΠΎΡΡΡΡ Π½Π΅ Π±ΠΎΠ»Π΅Π΅ 10-3 Ρ. ΠΠ»Π΅ΠΊΡΡΠΎΠΈΡΠΊΡΠΎΠ²ΠΎΠΉ ΡΠ΅ΠΆΠΈΠΌ ΠΈΡΠΏΠΎΠ»ΡΠ·ΡΠ΅ΡΡΡ Π΄Π»Ρ ΡΠΈΡΡΠΎΠ²ΠΎΠΉ, ΡΠΎΡΠ½ΠΎΠΉ ΠΎΠ±ΡΠ°Π±ΠΎΡΠΊΠΈ, ΠΏΠΎΡΠΊΠΎΠ»ΡΠΊΡ ΡΡΠ΅ΠΌ ΠΌΠ΅ΡΠ°Π»Π»Π° Π² Π΄Π°Π½Π½ΠΎΠΌ ΡΠ»ΡΡΠ°Π΅ Π½Π΅Π±ΠΎΠ»ΡΡΠΎΠΉ.
Π Π΅ΠΆΠΈΠΌ ΡΠ»Π΅ΠΊΡΡΠΎΠΈΠΌΠΏΡΠ»ΡΡΠ½ΠΎΠΉ ΠΎΠ±ΡΠ°Π±ΠΎΡΠΊΠΈ
ΠΠ±ΡΠ°Π±Π°ΡΡΠ²Π°Π΅ΠΌΠ°Ρ Π΄Π΅ΡΠ°Π»Ρ ΡΠ²Π»ΡΠ΅ΡΡΡ ΠΊΠ°ΡΠΎΠ΄ΠΎΠΌ, ΡΠΎ Π΅ΡΡΡ Π½Π° Π½Π΅Π΅ ΠΏΠΎΠ΄Π°Π΅ΡΡΡ ΠΎΡΡΠΈΡΠ°ΡΠ΅Π»ΡΠ½ΡΠΉ ΠΈΠΌΠΏΡΠ»ΡΡ Π΄Π»ΠΈΡΠ΅Π»ΡΠ½ΠΎΡΡΡΡ Π±ΠΎΠ»ΡΡΠ΅ 10-3 Ρ. ΠΡΠΈ ΡΠ»Π΅ΠΊΡΡΠΎΠΈΠΌΠΏΡΠ»ΡΡΠ½ΠΎΠΉ ΠΎΠ±ΡΠ°Π±ΠΎΡΠΊΠ΅ ΠΌΠ΅ΠΆΠ΄Ρ ΡΠ»Π΅ΠΊΡΡΠΎΠ΄Π°ΠΌΠΈ Π·Π°ΠΆΠΈΠ³Π°Π΅ΡΡΡ Π΄ΡΠ³ΠΎΠ²ΠΎΠΉ ΡΠ°Π·ΡΡΠ΄ ΠΈ ΠΎΠ±ΡΠ°Π±ΠΎΡΠΊΠ° Π΄Π΅ΡΠ°Π»Π΅ΠΉ Π²Π΅Π΄Π΅ΡΡΡ ΠΈΠΎΠ½Π½ΡΠΌ ΠΏΠΎΡΠΎΠΊΠΎΠΌ. ΠΠ°Π½Π½ΡΠΉ ΡΠ΅ΠΆΠΈΠΌ Ρ Π°ΡΠ°ΠΊΡΠ΅ΡΠΈΠ·ΡΠ΅ΡΡΡ Π±ΠΎΠ»ΡΡΠΎΠΉ ΡΠΊΠΎΡΠΎΡΡΡΡ ΡΡΠ΅ΠΌΠ° ΠΌΠ΅ΡΠ°Π»Π»Π°, ΠΏΡΠ΅Π²ΡΡΠ°ΡΡΠ΅ΠΉ ΠΏΡΠΎΠΈΠ·Π²ΠΎΠ΄ΠΈΡΠ΅Π»ΡΠ½ΠΎΡΡΡ ΡΠ»Π΅ΠΊΡΡΠΎΠΈΡΠΊΡΠΎΠ²ΠΎΠ³ΠΎ ΡΠ΅ΠΆΠΈΠΌΠ° Π² 8-10 ΡΠ°Π·, Π½ΠΎ ΠΏΡΠΈ ΡΡΠΎΠΌ ΡΠΈΡΡΠΎΡΠ° ΠΎΠ±ΡΠ°Π±ΠΎΡΠΊΠΈ ΡΡΡΠ΅ΡΡΠ²Π΅Π½Π½ΠΎ Ρ ΡΠΆΠ΅. ΠΡΠΈ ΠΎΠ±ΠΎΠΈΡ ΡΠ΅ΠΆΠΈΠΌΠ°Ρ Π² ΠΊΠ°ΡΠ΅ΡΡΠ²Π΅ ΡΠ°Π±ΠΎΡΠ΅ΠΉ ΠΆΠΈΠ΄ΠΊΠΎΡΡΠΈ, ΠΊΠ°ΠΊ ΠΏΡΠ°Π²ΠΈΠ»ΠΎ, ΠΈΡΠΏΠΎΠ»ΡΠ·ΡΠ΅ΡΡΡ ΠΊΠ΅ΡΠΎΡΠΈΠ½ ΠΈΠ»ΠΈ ΠΈΠ·ΠΎΠ»ΡΡΠΈΠΎΠ½Π½ΡΠ΅ ΠΌΠ°ΡΠ»Π°.
3. Π€ΠΈΠ·ΠΈΠΊΠ° ΡΠ»Π΅ΠΊΡΡΠΎΡΡΠΎΠ·ΠΈΠΎΠ½Π½ΠΎΠΉ ΠΎΠ±ΡΠ°Π±ΠΎΡΠΊΠΈ
Π―Π²Π»Π΅Π½ΠΈΡ, ΠΏΡΠΎΠΈΡΡ ΠΎΠ΄ΡΡΠΈΠ΅ Π² ΠΌΠ΅ΠΆΡΠ»Π΅ΠΊΡΡΠΎΠ΄Π½ΠΎΠΌ ΠΏΡΠΎΠΌΠ΅ΠΆΡΡΠΊΠ΅, Π²Π΅ΡΡΠΌΠ° ΡΠ»ΠΎΠΆΠ½Ρ ΠΈ ΡΠ²Π»ΡΡΡΡΡ ΠΏΡΠ΅Π΄ΠΌΠ΅ΡΠΎΠΌ ΡΠΏΠ΅ΡΠΈΠ°Π»ΡΠ½ΡΡ ΠΈΡΡΠ»Π΅Π΄ΠΎΠ²Π°Π½ΠΈΠΉ. ΠΠ΄Π΅ΡΡ ΠΆΠ΅ Π±ΡΠ΄Π΅Ρ ΡΠ°ΡΡΠΌΠΎΡΡΠ΅Π½Π° ΠΏΡΠΎΡΡΠ΅ΠΉΡΠ°Ρ ΡΡ Π΅ΠΌΠ° ΡΠ΄Π°Π»Π΅Π½ΠΈΡ ΠΌΠ΅ΡΠ°Π»Π»Π° ΠΈΠ· ΠΎΠ±Π»Π°ΡΡΠΈ ΠΎΠ±ΡΠ°Π±ΠΎΡΠΊΠΈ ΠΏΠΎΡΡΠ΅Π΄ΡΡΠ²ΠΎΠΌ ΡΠ»Π΅ΠΊΡΡΠΈΡΠ΅ΡΠΊΠΎΠΉ ΡΡΠΎΠ·ΠΈΠΈ.
ΠΠ°ΠΊ ΠΏΠΎΠΊΠ°Π·Π°Π½ΠΎ Π½Π° ΡΠΈΡ. 1.10, ΠΊ ΡΠ»Π΅ΠΊΡΡΠΎΠ΄Π°ΠΌ 1 ΠΏΠΎΠ΄Π²Π΅Π΄Π΅Π½ΠΎ Π½Π°ΠΏΡΡΠΆΠ΅Π½ΠΈΠ΅, ΠΊΠΎΡΠΎΡΠΎΠ΅ ΡΠΎΠ·Π΄Π°Π΅Ρ ΡΠ»Π΅ΠΊΡΡΠΈΡΠ΅ΡΠΊΠΎΠ΅ ΠΏΠΎΠ»Π΅ Π² ΠΌΠ΅ΠΆΡΠ»Π΅ΠΊΡΡΠΎΠ΄Π½ΠΎΠΌ ΠΏΡΠΎΠΌΠ΅ΠΆΡΡΠΊΠ΅. ΠΡΠΈ ΡΠ±Π»ΠΈΠΆΠ΅Π½ΠΈΠΈ ΡΠ»Π΅ΠΊΡΡΠΎΠ΄ΠΎΠ² Π½Π° ΠΊΡΠΈΡΠΈΡΠ΅ΡΠΊΠΎΠ΅ ΡΠ°ΡΡΡΠΎΡΠ½ΠΈΠ΅, Π²ΠΎΠ·Π½ΠΈΠΊΠ°Π΅Ρ ΡΠ»Π΅ΠΊΡΡΠΈΡΠ΅ΡΠΊΠΈΠΉ ΡΠ°Π·ΡΡΠ΄ Π² Π²ΠΈΠ΄Π΅ ΠΏΡΠΎΠ²ΠΎΠ΄ΡΡΠ΅Π³ΠΎ ΠΊΠ°Π½Π°Π»Π°. ΠΠ»Ρ ΠΏΠΎΠ²ΡΡΠ΅Π½ΠΈΡ ΠΈΠ½ΡΠ΅Π½ΡΠΈΠ²Π½ΠΎΡΡΠΈ ΡΠ°Π·ΡΡΠ΄Π° ΡΠ»Π΅ΠΊΡΡΠΎΠ΄Ρ ΠΏΠΎΠ³ΡΡΠΆΠ°ΡΡ Π² Π΄ΠΈΡΠ»Π΅ΠΊΡΡΠΈΡΠ΅ΡΠΊΡΡ ΠΆΠΈΠ΄ΠΊΠΎΡΡΡ 2 (ΠΊΠ΅ΡΠΎΡΠΈΠ½, ΠΌΠΈΠ½Π΅ΡΠ°Π»ΡΠ½ΠΎΠ΅ ΠΌΠ°ΡΠ»ΠΎ ΠΈ Π΄Ρ.) ΠΠ° ΠΏΠΎΠ²Π΅ΡΡ Π½ΠΎΡΡΠΈ ΡΠ»Π΅ΠΊΡΡΠΎΠ΄ΠΎΠ² ΠΈΠΌΠ΅ΡΡΡΡ ΠΌΠΈΠΊΡΠΎΠ½Π΅ΡΠΎΠ²Π½ΠΎΡΡΠΈ ΡΠ°Π·Π»ΠΈΡΠ½ΠΎΠΉ Π²Π΅Π»ΠΈΡΠΈΠ½Ρ. ΠΠ°ΠΏΡΡΠΆΠ΅Π½Π½ΠΎΡΡΡ ΡΠ»Π΅ΠΊΡΡΠΈΡΠ΅ΡΠΊΠΎΠ³ΠΎ ΠΏΠΎΠ»Ρ Π±ΡΠ΄Π΅Ρ Π½Π°ΠΈΠ±ΠΎΠ»ΡΡΠ΅ΠΉ ΠΌΠ΅ΠΆΠ΄Ρ Π΄Π²ΡΠΌΡ Π½Π°ΠΈΠ±ΠΎΠ»Π΅Π΅ Π±Π»ΠΈΠ·ΠΊΠΈΠΌΠΈ Π΄ΡΡΠ³ ΠΊ Π΄ΡΡΠ³Ρ Π²ΡΡΡΡΠΏΠ°ΠΌΠΈ Π½Π° ΠΏΠΎΠ²Π΅ΡΡ Π½ΠΎΡΡΠΈ ΡΠ»Π΅ΠΊΡΡΠΎΠ΄ΠΎΠ², ΠΏΠΎΡΡΠΎΠΌΡ ΠΈΠΌΠ΅Π½Π½ΠΎ Π·Π΄Π΅ΡΡ Π²ΠΎΠ·Π½ΠΈΠΊΠ°ΡΡ ΠΏΡΠΎΠ²ΠΎΠ΄ΡΡΠΈΠ΅ ΠΌΠΎΡΡΠΈΠΊΠΈ ΠΈΠ· ΠΏΡΠΈΠΌΠ΅ΡΠ½ΡΡ ΡΠ°ΡΡΠΈΡ ΠΆΠΈΠ΄ΠΊΠΎΡΡΠΈ. Π’ΠΎΠΊ ΠΏΠΎ ΠΌΠΎΡΡΠΈΠΊΠ°ΠΌ Π½Π°Π³ΡΠ΅Π²Π°Π΅Ρ ΠΆΠΈΠ΄ΠΊΠΎΡΡΡ Π΄ΠΎ ΠΈΡΠΏΠ°ΡΠ΅Π½ΠΈΡ ΠΈ ΠΎΠ±ΡΠ°Π·ΡΠ΅ΡΡΡ Π³Π°Π·ΠΎΠ²ΡΠΉ ΠΏΡΠ·ΡΡΡ (4), Π²Π½ΡΡΡΠΈ ΠΊΠΎΡΠΎΡΠΎΠ³ΠΎ ΠΈ ΡΠ°Π·Π²ΠΈΠ²Π°Π΅ΡΡΡ ΠΌΠΎΡΠ½ΡΠΉ ΠΈΡΠΊΡΠΎΠ²ΠΎΠΉ ΠΈΠ»ΠΈ Π΄ΡΠ³ΠΎΠ²ΠΎΠΉ ΡΠ°Π·ΡΡΠ΄, ΡΠΎΠΏΡΠΎΠ²ΠΎΠΆΠ΄Π°ΡΡΠΈΠΉΡΡ ΡΠ΄Π°ΡΠ½ΠΎΠΉ Π²ΠΎΠ»Π½ΠΎΠΉ. ΠΠΎΠ·Π½ΠΈΠΊΠ°ΡΡ ΠΏΠΎΡΠΎΠΊΠΈ ΡΠ»Π΅ΠΊΡΡΠΎΠ½ΠΎΠ² ΠΈ ΠΈΠΎΠ½ΠΎΠ² (ΠΏΠΎΠ»ΠΎΠΆΠΈΡΠ΅Π»ΡΠ½ΡΠ΅ ΠΈ ΠΎΡΡΠΈΡΠ°ΡΠ΅Π»ΡΠ½ΡΠ΅ ΡΡΡΠΈΠΌΠ΅ΡΡ), ΠΊΠΎΡΠΎΡΡΠ΅ Π±ΠΎΠΌΠ±Π°ΡΠ΄ΠΈΡΡΡΡ ΡΠ»Π΅ΠΊΡΡΠΎΠ΄Ρ. ΠΠ±ΡΠ°Π·ΡΠ΅ΡΡΡ ΠΏΠ»Π°Π·ΠΌΠ΅Π½Π½ΡΠΉ ΠΊΠ°Π½Π°Π» ΡΠ°Π·ΡΡΠ΄Π°. ΠΠ»Π°Π³ΠΎΠ΄Π°ΡΡ Π²ΡΡΠΎΠΊΠΎΠΉ ΠΊΠΎΠ½ΡΠ΅Π½ΡΡΠ°ΡΠΈΠΈ ΡΠ½Π΅ΡΠ³ΠΈΠΈ Π² Π·ΠΎΠ½Π΅ ΡΠ°Π·ΡΡΠ΄Π° ΡΠ΅ΠΌΠΏΠ΅ΡΠ°ΡΡΡΠ° Π΄ΠΎΡΡΠΈΠ³Π°Π΅Ρ ΡΡΡΡΡΠΈ ΠΈ Π΄Π΅ΡΡΡΠΊΠΎΠ² ΡΡΡΡΡ Π³ΡΠ°Π΄ΡΡΠΎΠ². ΠΠ΅ΡΠ°Π»Π» Π½Π° ΠΏΠΎΠ²Π΅ΡΡ Π½ΠΎΡΡΠΈ ΡΠ»Π΅ΠΊΡΡΠΎΠ΄ΠΎΠ² ΠΏΠ»Π°Π²ΠΈΡΡΡ ΠΈ ΠΈΡΠΏΠ°ΡΡΠ΅ΡΡΡ. ΠΠ°ΠΏΠ»ΠΈ ΡΠ°ΡΠΏΠ»Π°Π²Π»Π΅Π½Π½ΠΎΠ³ΠΎ ΠΌΠ΅ΡΠ°Π»Π»Π° Π² ΡΠ΅Π·ΡΠ»ΡΡΠ°ΡΠ΅ Π΄Π²ΠΈΠΆΠ΅Π½ΠΈΡ ΠΏΠΎΡΠΎΠΊΠ° ΠΆΠΈΠ΄ΠΊΠΎΡΡΠΈ Π² ΡΠ°Π±ΠΎΡΠ΅ΠΉ Π·ΠΎΠ½Π΅ Π²ΡΠ±ΡΠ°ΡΡΠ²Π°ΡΡΡΡ Π·Π° ΠΏΡΠ΅Π΄Π΅Π»Ρ ΡΠ»Π΅ΠΊΡΡΠΎΠ΄ΠΎΠ² ΠΈ Π·Π°ΡΡΡΠ²Π°ΡΡ Π² ΠΎΠΊΡΡΠΆΠ°ΡΡΠ΅ΠΉ ΡΠ»Π΅ΠΊΡΡΠΎΠ΄Ρ ΠΆΠΈΠ΄ΠΊΠΎΡΡΠΈ Π² Π²ΠΈΠ΄Π΅ ΠΌΠ΅Π»ΠΊΠΈΡ ΡΠ°ΡΡΠΈΡ ΡΡΠ΅ΡΠΈΡΠ΅ΡΠΊΠΎΠΉ ΡΠΎΡΠΌΡ (5).
ΠΡ Π²Π·Π°ΠΈΠΌΠΎΠ΄Π΅ΠΉΡΡΠ²ΠΈΡ ΠΆΠΈΠ΄ΠΊΠΎΡΡΠΈ Ρ ΡΡΠ°ΡΡΠΊΠ°ΠΌΠΈ ΡΠ»Π΅ΠΊΡΡΠΎΠ΄ΠΎΠ², Π½Π°Π³ΡΠ΅ΡΡΡ Π΄ΠΎ ΡΠ΅ΠΌΠΏΠ΅ΡΠ°ΡΡΡΡ 100-400 0Π‘, Π½Π° Π³ΡΠ°Π½ΠΈΡΠ°Ρ ΠΏΠ»Π°Π·ΠΌΠ΅Π½Π½ΠΎΠ³ΠΎ ΠΊΠ°Π½Π°Π»Π° ΡΠ°Π·ΡΡΠ΄Π° ΠΏΡΠΎΠΈΡΡ ΠΎΠ΄ΠΈΡ ΠΏΠΈΡΠΎΠ»ΠΈΠ· Π΄ΠΈΡΠ»Π΅ΠΊΡΡΠΈΡΠ΅ΡΠΊΠΎΠΉ ΠΆΠΈΠ΄ΠΊΠΎΡΡΠΈ. Π ΡΠ΅Π·ΡΠ»ΡΡΠ°ΡΠ΅ Π² ΠΆΠΈΠ΄ΠΊΠΎΡΡΠΈ ΠΎΠ±ΡΠ°Π·ΡΡΡΡΡ Π³Π°Π·Ρ, Π° ΡΠ°ΠΊΠΆΠ΅ Π°ΡΡΠ°Π»ΡΡΠΎΡΠΌΠΎΠ»ΠΈΡΡΡΠ΅ Π²Π΅ΡΠ΅ΡΡΠ²Π°. ΠΠ· Π³Π°Π·ΠΎΠ²ΠΎΠΉ ΡΡΠ΅Π΄Ρ Π²ΡΠ΄Π΅Π»ΡΠ΅ΡΡΡ ΡΠ³Π»Π΅ΡΠΎΠ΄, ΠΎΡΠ»Π°Π³Π°ΡΡΠΈΠΉΡΡ Π½Π° Π½Π°Π³ΡΠ΅ΡΡΡ ΠΏΠΎΠ²Π΅ΡΡ Π½ΠΎΡΡΡΡ ΡΠ»Π΅ΠΊΡΡΠΎΠ΄ΠΎΠ² Π² Π²ΠΈΠ΄Π΅ ΡΠΎΠ½ΠΊΠΎΠΉ ΠΏΠ»Π΅Π½ΠΊΠΈ ΠΊΡΠΈΡΡΠ°Π»Π»ΠΈΡΠ΅ΡΠΊΠΎΠ³ΠΎ Π³ΡΠ°ΡΠΈΡΠ°. Π ΠΌΠ΅ΡΡΠ΅ Π΄Π΅ΠΉΡΡΠ²ΠΈΡ ΠΈΠΌΠΏΡΠ»ΡΡΠ° ΡΠΎΠΊΠ° Π½Π° ΠΏΠΎΠ²Π΅ΡΡ Π½ΠΎΡΡΡΡ ΡΠ»Π΅ΠΊΡΡΠΎΠ΄ΠΎΠ² ΠΎΡΡΠ°ΡΡΡΡ Π½Π΅Π±ΠΎΠ»ΡΡΠΈΠ΅ ΡΠ³Π»ΡΠ±Π»Π΅Π½ΠΈΡ β Π»ΡΠ½ΠΊΠΈ, ΠΎΠ±ΡΠ°Π·ΠΎΠ²Π°Π²ΡΠΈΠ΅ΡΡ Π²ΡΠ»Π΅Π΄ΡΡΠ²ΠΈΠ΅ ΡΠ΄Π°Π»Π΅Π½ΠΈΡ ΡΠ°Π·ΡΡΠ΄ΠΎΠΌ Π½Π΅ΠΊΠΎΡΠΎΡΠΎΠ³ΠΎ ΠΊΠΎΠ»ΠΈΡΠ΅ΡΡΠ²Π° ΠΌΠ΅ΡΠ°Π»Π»Π°.
Π ΡΠ°Π±Π». 1.2 ΠΏΡΠΈΠ²Π΅Π΄Π΅Π½Π° Π·Π°Π²ΠΈΡΠΈΠΌΠΎΡΡΡ Π²Π΅Π»ΠΈΡΠΈΠ½Ρ ΡΡΠΎΠ·ΠΈΠΈ ΡΡΠ°Π»ΡΠ½ΠΎΠ³ΠΎ ΡΠ»Π΅ΠΊΡΡΠΎΠ΄Π° ΠΎΡ ΡΠ½Π΅ΡΠ³ΠΈΠΈ ΠΈ Π΄Π»ΠΈΡΠ΅Π»ΡΠ½ΠΎΡΡΠΈ ΠΎΠ΄ΠΈΠ½ΠΎΡΠ½ΠΎΠ³ΠΎ ΠΈΠΌΠΏΡΠ»ΡΡΠ°.
Π’Π°Π±Π»ΠΈΡΠ° 1.2
ΠΠ°Π²ΠΈΡΠΈΠΌΠΎΡΡΡ Π²Π΅Π»ΠΈΡΠΈΠ½Ρ ΡΡΠΎΠ·ΠΈΠΈ ΡΡΠ°Π»ΡΠ½ΠΎΠ³ΠΎ ΡΠ»Π΅ΠΊΡΡΠΎΠ΄Π° (Π°Π½ΠΎΠ΄Π°) ΠΎΡ ΡΠ½Π΅ΡΠ³ΠΈΠΈ ΠΈ Π΄Π»ΠΈΡΠ΅Π»ΡΠ½ΠΎΡΡΠΈ ΠΎΠ΄ΠΈΠ½ΠΎΡΠ½ΠΎΠ³ΠΎ ΠΈΠΌΠΏΡΠ»ΡΡΠ°
Π₯Π°ΡΠ°ΠΊΡΠ΅ΡΠΈΡΡΠΈΠΊΠ° ΠΈΠΌΠΏΡΠ»ΡΡΠ° | Π Π°Π·ΠΌΠ΅ΡΡ Π»ΡΠ½ΠΊΠΈ | |||
ΠΠ½Π΅ΡΠ³ΠΈΡ, ΠΠΆ | ΠΠ»ΠΈΡΠ΅Π»ΡΠ½ΠΎΡΡΡ, ΠΌΠΊΡ | ΠΠ»ΡΠ±ΠΈΠ½Π°, ΠΌΠΌ | ΠΠΈΠ°ΠΌΠ΅ΡΡ, ΠΌΠΌ | ΠΠ±ΡΠ΅ΠΌ, ΠΌ3 |
0,001 0,1 1,0 2,0 | 9 40 60 1500 | 0,015 0,025 0,042 0,050 | 0,1 0,75 1,65 2,00 | 0,000078 0,0074 0,06 0,10 |
Π ΠΈΡ. 1.10. Π Π΅ΠΆΠΈΠΌ ΡΠ»Π΅ΠΊΡΡΠΎΡΡΠΎΠ·ΠΈΠΎΠ½Π½ΠΎΠΉ ΠΎΠ±ΡΠ°Π±ΠΎΡΠΊΠΈ: 1 β ΡΠ»Π΅ΠΊΡΡΠΎΠ΄Ρ, 2 β ΠΆΠΈΠ΄ΠΊΠΎΡΡΡ, 3 β Π»ΡΠ½ΠΊΠΈ, 4 β Π³Π°Π·ΠΎΠ²ΡΠΉ ΠΏΡΠ·ΡΡΡ, 5 β ΠΏΡΠΎΠ΄ΡΠΊΡΡ ΡΡΠΎΠ·ΠΈΠΈ
ΠΠΎΡΠ»Π΅ ΡΠ°Π·ΡΡΠ΄Π° Π² ΡΠ΅ΡΠ΅Π½ΠΈΠ΅ Π½Π΅ΠΊΠΎΡΠΎΡΠΎΠ³ΠΎ Π²ΡΠ΅ΠΌΠ΅Π½ΠΈ ΠΏΡΠΎΠΈΡΡ ΠΎΠ΄ΠΈΡ ΠΎΡΡΡΠ²Π°Π½ΠΈΠ΅ ΡΡΠΎΠ»Π±Π° ΠΊΠ°Π½Π°Π»Π° ΠΈ Π΄Π΅ΠΈΠΎΠ½ΠΈΠ·Π°ΡΠΈΡ Π²Π΅ΡΠ΅ΡΡΠ²Π° ΠΏΠ»Π°Π·ΠΌΡ Π² ΠΌΠ΅ΠΆΡΠ»Π΅ΠΊΡΡΠΎΠ΄Π½ΠΎΠΌ ΠΏΡΠΎΠΌΠ΅ΠΆΡΡΠΊΠ΅. ΠΠ»Π΅ΠΊΡΡΠΈΡΠ΅ΡΠΊΠ°Ρ ΠΏΡΠΎΡΠ½ΠΎΡΡΡ ΠΌΠ΅ΠΆΡΠ»Π΅ΠΊΡΡΠΎΠ΄Π½ΠΎΠ³ΠΎ ΠΏΡΠΎΠΌΠ΅ΠΆΡΡΠΊΠ° Π²ΠΎΡΡΡΠ°Π½Π°Π²Π»ΠΈΠ²Π°Π΅ΡΡΡ. ΠΡΠ΅ΠΌΡ Π΄Π΅ΠΈΠΎΠ½ΠΈΠ·Π°ΡΠΈΠΈ ΠΆΠΈΠ΄ΠΊΠΎΠ³ΠΎ Π΄ΠΈΡΠ»Π΅ΠΊΡΡΠΈΠΊΠ° ΡΠΎΡΡΠ°Π²Π»ΡΠ΅Ρ 106-10-2 Ρ. Π‘Π»Π΅Π΄ΡΡΡΠΈΠΉ ΡΠ°Π·ΡΡΠ΄ ΠΎΠ±ΡΡΠ½ΠΎ Π²ΠΎΠ·Π½ΠΈΠΊΠ°Π΅Ρ ΡΠΆΠ΅ Π² Π½ΠΎΠ²ΠΎΠΌ ΠΌΠ΅ΡΡΠ΅, ΠΌΠ΅ΠΆΠ΄Ρ Π΄Π²ΡΠΌΡ Π΄ΡΡΠ³ΠΈΠΌΠΈ Π±Π»ΠΈΠΆΠ°ΠΉΡΠΈΠΌΠΈ ΡΠΎΡΠΊΠ°ΠΌΠΈ ΡΠ»Π΅ΠΊΡΡΠΎΠ΄ΠΎΠ².
ΠΠ»ΠΈΡΠ΅Π»ΡΠ½ΠΎΡΡΡ ΠΈΠ½ΡΠ΅ΡΠ²Π°Π»ΠΎΠ² ΠΌΠ΅ΠΆΠ΄Ρ ΠΈΠΌΠΏΡΠ»ΡΡΠ°ΠΌΠΈ Π΄ΠΎΠ»ΠΆΠ½Π° Π±ΡΡΡ Π΄ΠΎΡΡΠ°ΡΠΎΡΠ½ΠΎΠΉ Π΄Π»Ρ ΡΠ΄Π°Π»Π΅Π½ΠΈΡ ΠΈΠ· Π·ΠΎΠ½Ρ ΡΠ°Π·ΡΡΠ΄Π° ΠΏΡΠΎΠ΄ΡΠΊΡΠΎΠ² ΡΡΠΎΠ·ΠΈΠΈ, Π° ΡΠ°ΠΊΠΆΠ΅ Π³Π°Π·ΠΎΠ²ΠΎΠ³ΠΎ ΠΏΡΠ·ΡΡΡ, ΡΠ²Π»ΡΡΡΠ΅Π³ΠΎΡΡ Π³Π»Π°Π²Π½ΡΠΌ ΠΏΡΠ΅ΠΏΡΡΡΡΠ²ΠΈΠ΅ΠΌ Π΄Π»Ρ Π²ΠΎΠ·Π½ΠΈΠΊΠ½ΠΎΠ²Π΅Π½ΠΈΡ ΡΠ»Π΅Π΄ΡΡΡΠ΅Π³ΠΎ ΡΠ°Π·ΡΡΠ΄Π°. Π ΡΠ²ΡΠ·ΠΈ Ρ ΡΡΠΈΠΌ ΡΠ°ΡΡΠΎΡΠ° ΡΠ°Π·ΡΡΠ΄ΠΎΠ² Ρ Π²ΠΎΠ·ΡΠ°ΡΡΠ°Π½ΠΈΠ΅ΠΌ ΠΈΡ ΡΠ½Π΅ΡΠ³ΠΈΠΈ ΡΠ½ΠΈΠΆΠ°Π΅ΡΡΡ.
Π’Π°ΠΊ ΠΏΡΠΎΠΈΡΡ ΠΎΠ΄ΠΈΡ Π΄ΠΎ ΡΠ΅Ρ ΠΏΠΎΡ, ΠΏΠΎΠΊΠ° ΡΠ°Π·ΡΡΠ΄Ρ Π½Π΅ ΡΠ΄Π°Π»ΡΡ Ρ ΠΏΠΎΠ²Π΅ΡΡ Π½ΠΎΡΡΠΈ ΡΠ»Π΅ΠΊΡΡΠΎΠ΄ΠΎΠ² Π²ΡΠ΅ ΡΡΠ°ΡΡΠΊΠΈ ΠΌΠ΅ΡΠ°Π»Π»Π°, ΠΊΠΎΡΠΎΡΡΠ΅ Π½Π°Ρ ΠΎΠ΄ΡΡΡΡ Π½Π° ΡΠ°ΡΡΡΠΎΡΠ½ΠΈΠΈ ΠΏΡΠΎΠ±ΠΎΡ ΠΏΡΠΈ Π²Π΅Π»ΠΈΡΠΈΠ½Π΅ ΠΏΡΠΈΠ»ΠΎΠΆΠ΅Π½Π½ΠΎΠ³ΠΎ Π½Π°ΠΏΡΡΠΆΠ΅Π½ΠΈΡ. ΠΠΎΠ³Π΄Π° ΡΠ°ΡΡΡΠΎΡΠ½ΠΈΠ΅ ΠΌΠ΅ΠΆΠ΄Ρ ΡΠ»Π΅ΠΊΡΡΠΎΠ΄Π°ΠΌΠΈ ΠΏΡΠ΅Π²ΡΡΠΈΡ ΠΏΡΠΎΠ±ΠΈΠ²Π½ΠΎΠ΅, Π΄Π»Ρ Π²ΠΎΠ·ΠΎΠ±Π½ΠΎΠ²Π»Π΅Π½ΠΈΡ ΡΠ°Π·ΡΡΠ΄ΠΎΠ² ΡΠ»Π΅ΠΊΡΡΠΎΠ΄Ρ Π΄ΠΎΠ»ΠΆΠ½Ρ Π±ΡΡΡ ΡΠ±Π»ΠΈΠΆΠ΅Π½Ρ. ΠΠ±ΡΡΠ½ΠΎ ΡΠ»Π΅ΠΊΡΡΠΎΠ΄Ρ ΡΠ±Π»ΠΈΠΆΠ°ΡΡ Π² ΡΠ΅ΡΠ΅Π½ΠΈΠ΅ Π²ΡΠ΅Π³ΠΎ Π²ΡΠ΅ΠΌΠ΅Π½ΠΈ ΠΎΠ±ΡΠ°Π±ΠΎΡΠΊΠΈ ΡΠ°ΠΊ, ΡΡΠΎΠ±Ρ ΡΠ»Π΅ΠΊΡΡΠΈΡΠ΅ΡΠΊΠΈΠ΅ ΡΠ°Π·ΡΡΠ΄Ρ Π½Π΅ ΠΏΡΠ΅ΠΊΡΠ°ΡΠ°Π»ΠΈΡΡ.
ΠΠ°ΡΠ°ΠΌΠ΅ΡΡΡ ΡΠ°Π±ΠΎΡΠΈΡ ΠΈΠΌΠΏΡΠ»ΡΡΠΎΠ². ΠΡΠ½ΠΎΠ²Π½ΡΠΌΠΈ ΠΏΠ°ΡΠ°ΠΌΠ΅ΡΡΠ°ΠΌΠΈ ΡΠ»Π΅ΠΊΡΡΠΈΡΠ΅ΡΠΊΠΈΡ ΠΈΠΌΠΏΡΠ»ΡΡΠΎΠ², ΠΏΠΎΠ΄Π°Π²Π°Π΅ΠΌΡΡ Π½Π° ΠΌΠ΅ΠΆΡΠ»Π΅ΠΊΡΡΠΎΠ΄Π½ΡΠΉ ΠΏΡΠΎΠΌΠ΅ΠΆΡΡΠΎΠΊ, ΡΠ²Π»ΡΡΡΡΡ ΠΈΡ ΡΠ°ΡΡΠΎΡΠ° ΠΏΠΎΠ²ΡΠΎΡΠ΅Π½ΠΈΡ, Π΄Π»ΠΈΡΠ΅Π»ΡΠ½ΠΎΡΡΡ, Π°ΠΌΠΏΠ»ΠΈΡΡΠ΄Π° ΠΈ ΡΠΊΠ²Π°ΠΆΠ½ΠΎΡΡΡ, Π° ΡΠ°ΠΊΠΆΠ΅ ΡΠΎΡΠΌΠ°, ΠΎΠΏΡΠ΅Π΄Π΅Π»ΡΡΡΠΈΠ΅ ΠΌΠ°ΠΊΡΠΈΠΌΠ°Π»ΡΠ½ΡΡ ΠΌΠΎΡΠ½ΠΎΡΡΡ ΠΈ ΡΠ½Π΅ΡΠ³ΠΈΡ. Π€ΠΎΡΠΌΠ° ΠΈ ΠΏΠ°ΡΠ°ΠΌΠ΅ΡΡΡ ΠΈΠΌΠΏΡΠ»ΡΡΠΎΠ² ΠΎΠΊΠ°Π·ΡΠ²Π°ΡΡ ΡΡΡΠ΅ΡΡΠ²Π΅Π½Π½ΠΎΠ΅ Π²Π»ΠΈΡΠ½ΠΈΠ΅ Π½Π° ΠΈΠ·Π½ΠΎΡ ΡΠ»Π΅ΠΊΡΡΠΎΠ΄Π°-ΠΈΠ½ΡΡΡΡΠΌΠ΅Π½ΡΠ°, ΠΏΡΠΎΠΈΠ·Π²ΠΎΠ΄ΠΈΡΠ΅Π»ΡΠ½ΠΎΡΡΡ ΠΈ ΡΠ΅ΡΠΎΡ ΠΎΠ²Π°ΡΠΎΡΡΡ ΠΎΠ±ΡΠ°Π±ΠΎΡΠ°Π½Π½ΠΎΠΉ ΠΏΠΎΠ²Π΅ΡΡ Π½ΠΎΡΡΠΈ.
ΠΠ±ΠΎΠ·Π½Π°ΡΠΈΠΌ ΡΠ°ΡΡΠΎΡΡ ΠΏΠΎΠ²ΡΠΎΡΠ΅Π½ΠΈΡ ΠΈΠΌΠΏΡΠ»ΡΡΠΎΠ², Ρ. Π΅. ΠΈΡ ΡΠΈΡΠ»ΠΎ Π² ΡΠ΅ΠΊΡΠ½Π΄Ρ, ΡΠ΅ΡΠ΅Π· f. Π’ΠΎΠ³Π΄Π° Π’ = 1/f Π±ΡΠ΄Π΅Ρ ΡΠ²Π»ΡΡΡΡΡ ΠΏΠ΅ΡΠΈΠΎΠ΄ΠΎΠΌ. ΠΠ½ ΠΎΠΏΡΠ΅Π΄Π΅Π»ΡΠ΅Ρ ΠΏΡΠΎΠΌΠ΅ΠΆΡΡΠΎΠΊ Π²ΡΠ΅ΠΌΠ΅Π½ΠΈ, ΡΠ΅ΡΠ΅Π· ΠΊΠΎΡΠΎΡΡΠΉ ΡΠ»Π΅Π΄ΡΠ΅Ρ ΠΎΡΠ΅ΡΠ΅Π΄Π½ΠΎΠΉ ΠΈΠΌΠΏΡΠ»ΡΡ.
ΠΠΌΠΏΡΠ»ΡΡ Ρ Π°ΡΠ°ΠΊΡΠ΅ΡΠΈΠ·ΡΠ΅ΡΡΡ Π°ΠΌΠΏΠ»ΠΈΡΡΠ΄Π½ΡΠΌ Π·Π½Π°ΡΠ΅Π½ΠΈΠ΅ΠΌ (ΠΈΠ»ΠΈ Π°ΠΌΠΏΠ»ΠΈΡΡΠ΄ΠΎΠΉ) Π½Π°ΠΏΡΡΠΆΠ΅Π½ΠΈΡ ΠΈ ΡΠΎΠΊΠ° Um ΠΈ Im. ΠΡΠΎ ΠΌΠ°ΠΊΡΠΈΠΌΠ°Π»ΡΠ½ΡΠ΅ Π·Π½Π°ΡΠ΅Π½ΠΈΡ, ΠΊΠΎΡΠΎΡΡΠ΅ ΠΏΡΠΈΠΎΠ±ΡΠ΅ΡΠ°ΡΡ Π½Π°ΠΏΡΡΠΆΠ΅Π½ΠΈΠ΅ ΠΈ ΡΠΎΠΊ Π·Π° Π²ΡΠ΅ΠΌΡ ΠΈΠΌΠΏΡΠ»ΡΡΠ°. ΠΡΠΈ ΡΠ»Π΅ΠΊΡΡΠΎΡΡΠΎΠ·ΠΈΠΎΠ½Π½ΠΎΠΉ ΠΎΠ±ΡΠ°Π±ΠΎΡΠΊΠ΅ Π°ΠΌΠΏΠ»ΠΈΡΡΠ΄Π° Π½Π°ΠΏΡΡΠΆΠ΅Π½ΠΈΡ ΠΈΠ·ΠΌΠ΅Π½ΡΠ΅ΡΡΡ ΠΎΡ Π½Π΅ΡΠΊΠΎΠ»ΡΠΊΠΈΡ Π²ΠΎΠ»ΡΡ Π΄ΠΎ Π½Π΅ΡΠΊΠΎΠ»ΡΠΊΠΈΡ ΡΠΎΡΠ΅Π½ Π²ΠΎΠ»ΡΡ, Π° Π°ΠΌΠΏΠ»ΠΈΡΡΠ΄Π° ΡΠΎΠΊΠ° ΠΎΡ Π΄ΠΎΠ»ΠΈ Π°ΠΌΠΏΠ΅ΡΠ° Π΄ΠΎ Π΄Π΅ΡΡΡΠΊΠΎΠ² ΡΡΡΡΡ Π°ΠΌΠΏΠ΅Ρ. ΠΠΈΠ°ΠΏΠ°Π·ΠΎΠ½ ΡΠΊΠ²Π°ΠΆΠ½ΠΎΡΡΠ΅ΠΉ ΠΈΠΌΠΏΡΠ»ΡΡΠ° ΠΏΡΠΈ ΡΠ»Π΅ΠΊΡΡΠΎΡΡΠΎΠ·ΠΈΠΎΠ½Π½ΠΎΠΉ ΠΎΠ±ΡΠ°Π±ΠΎΡΠΊΠ΅ Π·Π°ΠΊΠ»ΡΡΠ΅Π½ Π² ΠΏΡΠ΅Π΄Π΅Π»Π°Ρ ΠΎΡ 1 Π΄ΠΎ 30.
ΠΠΎΠ»ΡΡΠ½ΡΠΉ ΡΡΡΠ΅ΠΊΡ ΠΈ ΠΏΠΎΠ»ΡΡΠ½ΠΎΡΡΡ ΠΈΠΌΠΏΡΠ»ΡΡΠ°. ΠΡΡΠΎΠΊΠ°Ρ ΡΠ΅ΠΌΠΏΠ΅ΡΠ°ΡΡΡΠ° Π² ΠΊΠ°Π½Π°Π»Π΅ ΡΠ°Π·ΡΡΠ΄Π° ΠΈ ΠΏΡΠΎΠΈΡΡ ΠΎΠ΄ΡΡΠΈΠ΅ Π΄ΠΈΠ½Π°ΠΌΠΈΡΠ΅ΡΠΊΠΈΠ΅ ΠΏΡΠΎΡΠ΅ΡΡΡ Π²ΡΠ·ΡΠ²Π°ΡΡ ΡΡΠΎΠ·ΠΈΡ ΠΎΠ±ΠΎΠΈΡ ΡΠ»Π΅ΠΊΡΡΠΎΠ΄ΠΎΠ². ΠΠΎΠ²ΡΡΠ΅Π½ΠΈΠ΅ ΡΡΠΎΠ·ΠΈΠΈ ΠΎΠ΄Π½ΠΎΠ³ΠΎ ΡΠ»Π΅ΠΊΡΡΠΎΠ΄Π° ΠΏΠΎ ΡΡΠ°Π²Π½Π΅Π½ΠΈΡ Ρ Π΄ΡΡΠ³ΠΈΠΌ ΡΠ»Π΅ΠΊΡΡΠΎΠ΄ΠΎΠΌ Π½Π°Π·ΡΠ²Π°Π΅ΡΡΡ ΠΏΠΎΠ»ΡΡΠ½ΡΠΌ ΡΡΡΠ΅ΠΊΡΠΎΠΌ. ΠΠΎΠ»ΡΡΠ½ΡΠΉ ΡΡΡΠ΅ΠΊΡ ΠΎΠΏΡΠ΅Π΄Π΅Π»ΡΠ΅ΡΡΡ ΠΌΠ°ΡΠ΅ΡΠΈΠ°Π»ΠΎΠΌ ΡΠ»Π΅ΠΊΡΡΠΎΠ΄ΠΎΠ², ΡΠ½Π΅ΡΠ³ΠΈΠ΅ΠΉ ΠΈ Π΄Π»ΠΈΡΠ΅Π»ΡΠ½ΠΎΡΡΡΡ ΠΈΠΌΠΏΡΠ»ΡΡΠΎΠ², Π·Π½Π°ΠΊΠΎΠΌ ΠΏΠΎΠ΄Π²Π΅Π΄Π΅Π½Π½ΠΎΠ³ΠΎ ΠΊ ΡΠ»Π΅ΠΊΡΡΠΎΠ΄Ρ ΠΏΠΎΡΠ΅Π½ΡΠΈΠ°Π»Π°.
ΠΡΠΎΡΠ΅ΡΡΡ ΠΈΠ·ΠΌΠ΅Π½Π΅Π½ΠΈΡ Π½Π°ΠΏΡΡΠΆΠ΅Π½ΠΈΡ ΠΈ ΡΠΎΠΊΠ° ΠΈΠΌΠ΅ΡΡ ΠΊΠΎΠ»Π΅Π±Π°ΡΠ΅Π»ΡΠ½ΡΠΉ Ρ Π°ΡΠ°ΠΊΡΠ΅Ρ ΠΎΡΠ½ΠΎΡΠΈΡΠ΅Π»ΡΠ½ΠΎ ΠΈΡ Π½ΡΠ»Π΅Π²ΠΎΠ³ΠΎ Π·Π½Π°ΡΠ΅Π½ΠΈΡ. ΠΡΠΈ ΡΠ»Π΅ΠΊΡΡΠΎΡΡΠΎΠ·ΠΈΠΎΠ½Π½ΠΎΠΉ ΠΎΠ±ΡΠ°Π±ΠΎΡΠΊΠ΅ ΠΏΡΠΈΠ½ΡΡΠΎ ΡΡΠΈΡΠ°ΡΡ ΡΠ°Π±ΠΎΡΠ΅ΠΉ ΠΈΠ»ΠΈ ΠΏΡΡΠΌΠΎΠΉ ΠΏΠΎΠ»ΡΡΠ½ΠΎΡΡΡΡ ΠΈΠΌΠΏΡΠ»ΡΡΠ° ΡΡ Π΅Π³ΠΎ ΡΠ°ΡΡΡ, ΠΊΠΎΡΠΎΡΠ°Ρ Π²ΡΠ·ΡΠ²Π°Π΅Ρ Π½Π°ΠΈΠ±ΠΎΠ»ΡΡΠΈΠΉ ΡΡΡΠ΅ΠΊΡ ΡΡΠΎΠ·ΠΈΠΈ ΠΎΠ±ΡΠ°Π±Π°ΡΡΠ²Π°Π΅ΠΌΠΎΠΉ Π·Π°Π³ΠΎΡΠΎΠ²ΠΊΠΈ, Π° ΠΎΠ±ΡΠ°ΡΠ½ΠΎΠΉ β ΡΠ°ΡΡΡ ΠΈΠΌΠΏΡΠ»ΡΡΠ°, Π²ΡΠ·ΡΠ²Π°ΡΡΡΡ ΡΡΠΈΠ»Π΅Π½Π½ΡΡ ΡΡΠΎΠ·ΠΈΡ ΡΠ»Π΅ΠΊΡΡΠΎΠ΄Π°-ΠΈΠ½ΡΡΡΡΠΌΠ΅Π½ΡΠ°. ΠΠ±ΡΠ°Π±Π°ΡΡΠ²Π°Π΅ΠΌΡΡ Π·Π°Π³ΠΎΡΠΎΠ²ΠΊΡ ΠΏΡΠΈΡΠΎΠ΅Π΄ΠΈΠ½ΡΡΡ ΠΊ ΡΠΎΠΌΡ ΠΏΠΎΠ»ΡΡΡ, ΡΡΡΠ΅ΠΊΡ ΡΡΠΎΠ·ΠΈΠΈ ΠΊΠΎΡΠΎΡΠΎΠ³ΠΎ Π² Π΄Π°Π½Π½ΡΡ ΡΡΠ»ΠΎΠ²ΠΈΡΡ Π±ΠΎΠ»ΡΡΠ΅. Π ΠΏΡΠΎΡΠΈΠ²ΠΎΠΏΠΎΠ»ΠΎΠΆΠ½ΠΎΠΌΡ ΠΏΠΎΠ»ΡΡΡ ΠΏΡΠΈΡΠΎΠ΅Π΄ΠΈΠ½ΡΡΡ ΡΠ»Π΅ΠΊΡΡΠΎΠ΄- ΠΈΠ½ΡΡΡΡΠΌΠ΅Π½Ρ. ΠΠ°ΠΏΡΠΈΠΌΠ΅Ρ, ΠΏΡΠΈ ΠΊΠΎΡΠΎΡΠΊΠΈΡ ΠΈΠΌΠΏΡΠ»ΡΡΠ°Ρ ΡΠ»Π΅ΠΊΡΡΠΎΠΈΡΠΊΡΠΎΠ²ΠΎΠΉ ΠΎΠ±ΡΠ°Π±ΠΎΡΠΊΠΈ ΡΠ½Π΅ΡΠ³ΠΈΡ ΠΏΡΠ΅ΠΈΠΌΡΡΠ΅ΡΡΠ²Π΅Π½Π½ΠΎ ΠΏΠΎΡΡΡΠΏΠ°Π΅Ρ Π½Π° Π°Π½ΠΎΠ΄, Π² ΠΊΠ°ΡΠ΅ΡΡΠ²Π΅ ΠΊΠΎΡΠΎΡΠΎΠ³ΠΎ Π·Π΄Π΅ΡΡ ΡΠ»Π΅Π΄ΡΠ΅Ρ ΠΈΡΠΏΠΎΠ»ΡΠ·ΠΎΠ²Π°ΡΡ Π·Π°Π³ΠΎΡΠΎΠ²ΠΊΡ (ΠΏΡΡΠΌΠ°Ρ ΠΏΠΎΠ»ΡΡΠ½ΠΎΡΡΡ). ΠΡΠΈ ΡΠ²Π΅Π»ΠΈΡΠ΅Π½ΠΈΠΈ Π΄Π»ΠΈΡΠ΅Π»ΡΠ½ΠΎΡΡΠΈ ΠΈΠΌΠΏΡΠ»ΡΡΠΎΠ² Π½Π°ΡΡΡΠΏΠ°Π΅Ρ ΠΏΠ΅ΡΠ΅ΡΠ°ΡΠΏΡΠ΅Π΄Π΅Π»Π΅Π½ΠΈΠ΅ ΡΠ΅ΠΏΠ»ΠΎΠ²ΠΎΠ³ΠΎ ΠΏΠΎΡΠΎΠΊΠ° Π½Π° ΡΠ»Π΅ΠΊΡΡΠΎΠ΄Π°Ρ . ΠΡΠΎ ΠΏΡΠΈΠ²ΠΎΠ΄ΠΈΡ ΠΊ ΡΠΎΠΌΡ, ΡΡΠΎ ΠΏΡΠΈ ΠΎΠΏΡΠ΅Π΄Π΅Π»Π΅Π½Π½ΡΡ ΡΠ΅ΠΆΠΈΠΌΠ°Ρ ΡΠ»Π΅ΠΊΡΡΠΎΠΈΠΌΠΏΡΠ»ΡΡΠ½ΠΎΠΉ ΠΎΠ±ΡΠ°Π±ΠΎΡΠΊΠΈ ΡΡΠΎΠ·ΠΈΡ Π°Π½ΠΎΠ΄Π° ΡΡΠ°Π½ΠΎΠ²ΠΈΡΡΡ ΠΌΠ΅Π½ΡΡΠ΅, ΡΠ΅ΠΌ ΡΡΠΎΠ·ΠΈΡ ΠΊΠ°ΡΠΎΠ΄Π°. Π ΡΡΠΎΠΌ ΡΠ»ΡΡΠ°Π΅ ΡΠ»Π΅Π΄ΡΠ΅Ρ ΠΏΡΠΈΠΌΠ΅Π½ΡΡΡ ΠΎΠ±ΡΠ°ΡΠ½ΡΡ ΠΏΠΎΠ»ΡΡΠ½ΠΎΡΡΡ, ΠΈΡΠΏΠΎΠ»ΡΠ·ΡΡ Π·Π°Π³ΠΎΡΠΎΠ²ΠΊΡ Π² ΠΊΠ°ΡΠ΅ΡΡΠ²Π΅ ΠΊΠ°ΡΠΎΠ΄Π°.
ΠΠ»Π΅ΠΊΡΡΠΎΡΡΠΎΠ·ΠΈΠΎΠ½Π½Π°Ρ ΠΎΠ±ΡΠ°Π±Π°ΡΡΠ²Π°Π΅ΠΌΠΎΡΡΡ. ΠΡΡΠ΅ΠΊΡ ΡΡΠΎΠ·ΠΈΠΈ ΡΠ°Π·Π»ΠΈΡΠ½ΡΡ ΠΌΠ΅ΡΠ°Π»Π»ΠΎΠ² ΠΈ ΡΠΏΠ»Π°Π²ΠΎΠ², ΠΏΡΠΎΠΈΠ·Π²ΠΎΠ΄ΠΈΠΌΡΠΉ ΠΎΠ΄ΠΈΠ½Π°ΠΊΠΎΠ²ΡΠΌΠΈ ΠΏΠΎ ΡΠ²ΠΎΠΈΠΌ ΠΏΠ°ΡΠ°ΠΌΠ΅ΡΡΠ°ΠΌ ΡΠ»Π΅ΠΊΡΡΠΈΡΠ΅ΡΠΊΠΈΠΌΠΈ ΠΈΠΌΠΏΡΠ»ΡΡΠ°ΠΌΠΈ, ΡΠ°Π·Π»ΠΈΡΠ΅Π½. ΠΠ°Π²ΠΈΡΠΈΠΌΠΎΡΡΡ ΠΈΠ½ΡΠ΅Π½ΡΠΈΠ²Π½ΠΎΡΡΠΈ ΡΡΠΎΠ·ΠΈΠΈ ΠΎΡ ΡΠ²ΠΎΠΉΡΡΠ² ΠΌΠ΅ΡΠ°Π»Π»ΠΎΠ² Π½Π°Π·ΡΠ²Π°ΡΡ ΡΠ»Π΅ΠΊΡΡΠΎΡΡΠΎΠ·ΠΈΠΎΠ½Π½ΠΎΠΉ ΠΎΠ±ΡΠ°Π±Π°ΡΡΠ²Π°Π΅ΠΌΠΎΡΡΡΡ.
Π Π°Π·Π»ΠΈΡΠ½ΠΎΠ΅ Π²Π»ΠΈΡΠ½ΠΈΠ΅ ΠΈΠΌΠΏΡΠ»ΡΡΠ½ΡΡ ΡΠ°Π·ΡΡΠ΄ΠΎΠ² Π½Π° ΠΌΠ΅ΡΠ°Π»Π»Ρ ΠΈ ΡΠΏΠ»Π°Π²Ρ Π·Π°Π²ΠΈΡΠΈΡ ΠΎΡ ΠΈΡ ΡΠ΅ΠΏΠ»ΠΎΡΠΈΠ·ΠΈΡΠ΅ΡΠΊΠΈΡ ΠΊΠΎΠ½ΡΡΠ°Π½Ρ: β ΡΠ΅ΠΌΠΏΠ΅ΡΠ°ΡΡΡ ΠΏΠ»Π°Π²Π»Π΅Π½ΠΈΡ ΠΈ ΠΊΠΈΠΏΠ΅Π½ΠΈΡ, ΡΠ΅ΠΏΠ»ΠΎΠΏΡΠΎΠ²ΠΎΠ΄Π½ΠΎΡΡΠΈ, ΡΠ΅ΠΏΠ»ΠΎΠ΅ΠΌΠΊΠΎΡΡΠΈ. ΠΡΠ»ΠΈ ΠΏΡΠΈΠ½ΡΡΡ ΡΠ»Π΅ΠΊΡΡΠΎΡΡΠΎΠ·ΠΈΠΎΠ½Π½ΡΡ ΠΎΠ±ΡΠ°Π±Π°ΡΡΠ²Π°Π΅ΠΌΠΎΡΡΡ ΡΡΠ°Π»ΠΈ Π·Π° Π΅Π΄ΠΈΠ½ΠΈΡΡ, ΡΠΎ ΡΠ»Π΅ΠΊΡΡΠΎΡΡΠΎΠ·ΠΈΠΎΠ½Π½Π°Ρ ΠΎΠ±ΡΠ°Π±Π°ΡΡΠ²Π°Π΅ΠΌΠΎΡΡΡ Π΄ΡΡΠ³ΠΈΡ ΠΌΠ΅ΡΠ°Π»Π»ΠΎΠ² (ΠΏΡΠΈ ΡΠ΅Ρ ΠΆΠ΅ ΡΡΠ»ΠΎΠ²ΠΈΡΡ ) ΠΌΠΎΠΆΠ΅Ρ Π±ΡΡΡ ΠΏΡΠ΅Π΄ΡΡΠ°Π²Π»Π΅Π½Π° Π² ΡΠ»Π΅Π΄ΡΡΡΠΈΡ ΠΎΡΠ½ΠΎΡΠΈΡΠ΅Π»ΡΠ½ΡΡ Π΅Π΄ΠΈΠ½ΠΈΡΠ°Ρ : Π²ΠΎΠ»ΡΡΡΠ°ΠΌ β 0,3; ΡΠ²Π΅ΡΠ΄ΡΠΉ ΡΠΏΠ»Π°Π² β 0,5; ΡΠΈΡΠ°Π½ β 0,6; Π½ΠΈΠΊΠ΅Π»Ρ β 0,8; ΠΌΠ΅Π΄Ρ β 1,1; Π»Π°ΡΡΠ½Ρ β 1,6; Π°Π»ΡΠΌΠΈΠ½ΠΈΠΉ β 4; ΠΌΠ°Π³Π½ΠΈΠΉ β 6 (ΡΠΊΠ°Π·Π°Π½Π½ΡΠ΅ Π΄Π°Π½Π½ΡΠ΅ ΡΠΏΡΠ°Π²Π΅Π΄Π»ΠΈΠ²Ρ ΡΠΎΠ»ΡΠΊΠΎ ΠΏΡΠΈ ΠΊΠΎΠ½ΠΊΡΠ΅ΡΠ½ΡΡ ΡΡΠ»ΠΎΠ²ΠΈΡΡ : ΡΠ½Π΅ΡΠ³ΠΈΡ ΠΈΠΌΠΏΡΠ»ΡΡΠ° 0,125 ΠΠΆ, Π΄Π»ΠΈΡΠ΅Π»ΡΠ½ΠΎΡΡΡ 1.4-10-5 Ρ, ΡΠ°ΡΡΠΎΡΠ° 1200 1/Ρ, Π°ΠΌΠΏΠ»ΠΈΡΡΠ΄Π° ΡΠΎΠΊΠ° 250 Π).
Π Π°Π±ΠΎΡΠ°Ρ ΡΡΠ΅Π΄Π°. ΠΠΎΠ»ΡΡΠΈΠ½ΡΡΠ²ΠΎ ΠΎΠΏΠ΅ΡΠ°ΡΠΈΠΉ ΠΏΡΠΈ ΡΠ»Π΅ΠΊΡΡΠΎΡΡΠΎΠ·ΠΈΠΎΠ½Π½ΠΎΠΉ ΠΎΠ±ΡΠ°Π±ΠΎΡΠΊΠ΅ ΠΏΡΠΎΠΈΠ·Π²ΠΎΠ΄ΡΡ Π² ΠΆΠΈΠ΄ΠΊΠΎΡΡΠΈ. ΠΠ½Π° ΠΎΠ±Π΅ΡΠΏΠ΅ΡΠΈΠ²Π°Π΅Ρ ΡΡΠ»ΠΎΠ²ΠΈΡ, Π½Π΅ΠΎΠ±Ρ ΠΎΠ΄ΠΈΠΌΡΠ΅ Π΄Π»Ρ ΡΠ΄Π°Π»Π΅Π½ΠΈΡ ΠΏΡΠΎΠ΄ΡΠΊΡΠΎΠ² ΡΡΠΎΠ·ΠΈΠΈ ΠΈΠ· ΠΌΠ΅ΠΆΡΠ»Π΅ΠΊΡΡΠΎΠ΄Π½ΠΎΠ³ΠΎ ΠΏΡΠΎΠΌΠ΅ΠΆΡΡΠΊΠ°, ΡΡΠ°Π±ΠΈΠ»ΠΈΠ·ΠΈΡΡΠ΅Ρ ΠΏΡΠΎΡΠ΅ΡΡ, Π²Π»ΠΈΡΠ΅Ρ Π½Π° ΡΠ»Π΅ΠΊΡΡΠΈΡΠ΅ΡΠΊΡΡ ΠΏΡΠΎΡΠ½ΠΎΡΡΡ ΠΌΠ΅ΠΆΡΠ»Π΅ΠΊΡΡΠΎΠ΄Π½ΠΎΠ³ΠΎ ΠΏΡΠΎΠΌΠ΅ΠΆΡΡΠΊΠ°. ΠΠΈΠ΄ΠΊΠΎΡΡΠΈ, ΠΏΡΠΈΠ³ΠΎΠ΄Π½ΡΠ΅ Π΄Π»Ρ ΡΠ»Π΅ΠΊΡΡΠΎΠΈΡΠΊΡΠΎΠ²ΠΎΠΉ ΠΎΠ±ΡΠ°Π±ΠΎΡΠΊΠΈ, Π΄ΠΎΠ»ΠΆΠ½Ρ ΠΎΠ±Π»Π°Π΄Π°ΡΡ ΡΠΎΠΎΡΠ²Π΅ΡΡΡΠ²ΡΡΡΠ΅ΠΉ Π²ΡΠ·ΠΊΠΎΡΡΡΡ, ΡΠ»Π΅ΠΊΡΡΠΎΠΈΠ·ΠΎΠ»ΡΡΠΈΠΎΠ½Π½ΡΠΌΠΈ ΡΠ²ΠΎΠΉΡΡΠ²Π°ΠΌΠΈ, Ρ ΠΈΠΌΠΈΡΠ΅ΡΠΊΠΎΠΉ ΡΡΡΠΎΠΉΡΠΈΠ²ΠΎΡΡΡΡ ΠΊ Π΄Π΅ΠΉΡΡΠ²ΠΈΡ ΡΠ°Π·ΡΡΠ΄ΠΎΠ².
Π‘ ΠΏΠΎΠ²ΡΡΠ΅Π½ΠΈΠ΅ΠΌ ΡΠ°ΡΡΠΎΡΡ ΠΈΠΌΠΏΡΠ»ΡΡΠΎΠ² ΠΈ ΡΠ½ΠΈΠΆΠ΅Π½ΠΈΠ΅ΠΌ ΡΠ°Π±ΠΎΡΠ΅Π³ΠΎ ΡΠΎΠΊΠ° ΡΡΠ°Π±ΠΈΠ»ΡΠ½ΠΎΡΡΡ ΡΠ°Π±ΠΎΡΠ΅Π³ΠΎ ΠΏΡΠΎΡΠ΅ΡΡΠ° ΡΡ ΡΠ΄ΡΠ°Π΅ΡΡΡ. ΠΡΠΎ Π²ΡΠ·ΡΠ²Π°Π΅Ρ Π½Π΅ΠΎΠ±Ρ ΠΎΠ΄ΠΈΠΌΠΎΡΡΡ ΡΠ²Π΅Π»ΠΈΡΠΈΡΡ ΡΠΊΠ²Π°ΠΆΠ½ΠΎΡΡΡ ΠΈΠΌΠΏΡΠ»ΡΡΠΎΠ². ΠΡΠΈΠΌΠ΅Π½Π΅Π½ΠΈΠ΅ ΠΏΡΡΠΌΠΎΡΠ³ΠΎΠ»ΡΠ½ΡΡ ΠΈΠΌΠΏΡΠ»ΡΡΠΎΠ² ΡΡΡΠ΅ΡΡΠ²Π΅Π½Π½ΠΎ ΠΏΠΎΠ²ΡΡΠ°Π΅Ρ ΠΏΡΠΎΠΈΠ·Π²ΠΎΠ΄ΠΈΡΠ΅Π»ΡΠ½ΠΎΡΡΡ.
ΠΡΠΎΠΈΠ·Π²ΠΎΠ΄ΠΈΡΠ΅Π»ΡΠ½ΠΎΡΡΡ ΠΎΠ±ΡΠ°Π±ΠΎΡΠΊΠΈ ΠΌΠΎΠΆΠ½ΠΎ ΠΏΠΎΠ²ΡΡΠΈΡΡ, Π΅ΡΠ»ΠΈ ΠΏΡΠΈΠΌΠ΅Π½ΡΡΡ ΠΏΡΠΈΠ½ΡΠ΄ΠΈΡΠ΅Π»ΡΠ½ΠΎΠ΅ ΡΠ΄Π°Π»Π΅Π½ΠΈΠ΅ ΠΏΡΠΎΠ΄ΡΠΊΡΠΎΠ² ΡΡΠΎΠ·ΠΈΠΈ ΠΈΠ· ΠΌΠ΅ΠΆΡΠ»Π΅ΠΊΡΡΠΎΠ΄Π½ΠΎΠ³ΠΎ ΠΏΡΠΎΠΌΠ΅ΠΆΡΡΠΊΠ°. ΠΠ»Ρ ΡΡΠΎΠ³ΠΎ Π² ΠΌΠ΅ΠΆΡΠ»Π΅ΠΊΡΡΠΎΠ΄Π½ΡΠΉ ΠΏΡΠΎΠΌΠ΅ΠΆΡΡΠΎΠΊ ΠΏΠΎΠ΄ Π΄Π°Π²Π»Π΅Π½ΠΈΠ΅ΠΌ Π½Π°Π³Π½Π΅ΡΠ°ΡΡ ΠΆΠΈΠ΄ΠΊΠΎΡΡΡ (ΡΠΈΡ. 1.11).
Π ΠΈΡ. 1.11. Π‘Ρ Π΅ΠΌΠ° ΠΏΠΎΠ΄Π²ΠΎΠ΄Π° ΠΆΠΈΠ΄ΠΊΠΎΡΡΠΈ Π² ΠΌΠ΅ΠΆΡΠ»Π΅ΠΊΡΡΠΎΠ΄Π½ΡΠΉ ΠΏΡΠΎΠΌΠ΅ΠΆΡΡΠΎΠΊ ΡΠ΅ΡΠ΅Π· ΠΏΠΎΠ»ΡΠΉ ΡΠ»Π΅ΠΊΡΡΠΎΠ΄ ΠΏΡΠΈ ΠΏΡΠΎΡΠΈΠ²Π°Π½ΠΈΠΈ ΠΎΡΠ²Π΅ΡΡΡΠΈΡ
Π₯ΠΎΡΠΎΡΠΈΠ΅ ΡΠ΅Π·ΡΠ»ΡΡΠ°ΡΡ Π΄Π°Π΅Ρ Π½Π°Π»ΠΎΠΆΠ΅Π½ΠΈΠ΅ Π²ΠΈΠ±ΡΠ°ΡΠΈΠΉ Π½Π° ΡΠ»Π΅ΠΊΡΡΠΎΠ΄-ΠΈΠ½ΡΡΡΡΠΌΠ΅Π½Ρ, Π° ΡΠ°ΠΊΠΆΠ΅ Π²ΡΠ°ΡΠ΅Π½ΠΈΠ΅ ΠΎΠ΄Π½ΠΎΠ³ΠΎ ΠΈΠ»ΠΈ ΠΎΠ±ΠΎΠΈΡ ΡΠ»Π΅ΠΊΡΡΠΎΠ΄ΠΎΠ². ΠΠ°Π²Π»Π΅Π½ΠΈΠ΅ ΠΆΠΈΠ΄ΠΊΠΎΡΡΠΈ Π·Π°Π²ΠΈΡΠΈΡ ΠΎΡ Π³Π»ΡΠ±ΠΈΠ½Ρ ΠΎΡΠ²Π΅ΡΡΡΠΈΡ ΠΈ Π²Π΅Π»ΠΈΡΠΈΠ½Ρ ΠΌΠ΅ΠΆΡΠ»Π΅ΠΊΡΡΠΎΠ΄Π½ΠΎΠ³ΠΎ ΠΏΡΠΎΠΌΠ΅ΠΆΡΡΠΊΠ°. ΠΠΈΠ±ΡΠ°ΡΠΈΠΈ ΠΎΡΠΎΠ±Π΅Π½Π½ΠΎ Π½Π΅ΠΎΠ±Ρ ΠΎΠ΄ΠΈΠΌΡ ΠΏΡΠΈ ΡΠ»Π΅ΠΊΡΡΠΎΠΈΡΠΊΡΠΎΠ²ΠΎΠΉ ΠΎΠ±ΡΠ°Π±ΠΎΡΠΊΠ΅ Π³Π»ΡΠ±ΠΎΠΊΠΈΡ ΠΎΡΠ²Π΅ΡΡΡΠΈΠΉ ΠΌΠ°Π»ΠΎΠ³ΠΎ Π΄ΠΈΠ°ΠΌΠ΅ΡΡΠ° ΠΈ ΡΠ·ΠΊΠΈΡ ΡΠ΅Π»Π΅ΠΉ. ΠΠΎΠ»ΡΡΠΈΠ½ΡΡΠ²ΠΎ ΡΠ»Π΅ΠΊΡΡΠΎΡΡΠΎΠ·ΠΈΠΎΠ½Π½ΡΡ ΡΡΠ°Π½ΠΊΠΎΠ² ΡΠ½Π°Π±ΠΆΠ΅Π½ΠΎ ΡΠΏΠ΅ΡΠΈΠ°Π»ΡΠ½ΠΎΠΉ Π²ΠΈΠ±ΡΠ°ΡΠΈΠΎΠ½Π½ΠΎΠΉ Π³ΠΎΠ»ΠΎΠ²ΠΊΠΎΠΉ.β
ΠΠ°ΡΠ΅ΡΡΠ²ΠΎ ΠΏΠΎΠ²Π΅ΡΡ Π½ΠΎΡΡΠΈ ΠΈ ΡΠΎΡΠ½ΠΎΡΡΡ ΠΎΠ±ΡΠ°Π±ΠΎΡΠΊΠΈ. ΠΠ΅ΡΠ°Π»Π» ΡΠ»Π΅ΠΊΡΡΠΎΠ΄ΠΎΠ² ΠΏΠΎΠ΄Π²Π΅ΡΠ³Π°Π΅ΡΡΡ Ρ ΠΎΡΡ ΠΈ Π»ΠΎΠΊΠ°Π»ΡΠ½ΠΎΠΌΡ, ΠΊΡΠ°ΡΠΊΠΎΠ²ΡΠ΅ΠΌΠ΅Π½Π½ΠΎΠΌΡ, Π½ΠΎ Π²Π΅ΡΡΠΌΠ° ΠΈΠ½ΡΠ΅Π½ΡΠΈΠ²Π½ΠΎΠΌΡ ΡΠ»Π΅ΠΊΡΡΠΎΡΠ΅ΡΠΌΠΈΡΠ΅ΡΠΊΠΎΠΌΡ Π²ΠΎΠ·Π΄Π΅ΠΉΡΡΠ²ΠΈΡ. ΠΠ°ΠΈΠ²ΡΡΡΠ°Ρ ΡΠ΅ΠΌΠΏΠ΅ΡΠ°ΡΡΡΠ° ΡΡΡΠ΅ΡΡΠ²ΡΠ΅Ρ Π½Π° ΠΎΠ±ΡΠ°Π±Π°ΡΡΠ²Π°Π΅ΠΌΠΎΠΉ ΠΏΠΎΠ²Π΅ΡΡ Π½ΠΎΡΡΠΈ ΠΈ Π±ΡΡΡΡΠΎ ΡΠΌΠ΅Π½ΡΡΠ°Π΅ΡΡΡ Π½Π° Π½Π΅ΠΊΠΎΡΠΎΡΠΎΠΌ ΡΠ°ΡΡΡΠΎΡΠ½ΠΈΠΈ ΠΎΡ ΠΏΠΎΠ²Π΅ΡΡ Π½ΠΎΡΡΠΈ. ΠΠΎΠ»ΡΡΠ°Ρ ΡΠ°ΡΡΡ ΡΠ°ΡΠΏΠ»Π°Π²Π»Π΅Π½Π½ΠΎΠ³ΠΎ ΠΌΠ΅ΡΠ°Π»Π»Π° ΠΈ Π΅Π³ΠΎ ΠΏΠ°ΡΠΎΠ² ΡΠ΄Π°Π»ΡΠ΅ΡΡΡ ΠΈΠ· Π·ΠΎΠ½Ρ ΡΠ°Π·ΡΡΠ΄Π°, Π½ΠΎ Π½Π΅ΠΊΠΎΡΠΎΡΠ°Ρ ΡΠ°ΡΡΡ ΠΎΡΡΠ°Π΅ΡΡΡ Π² Π»ΡΠ½ΠΊΠ΅ (ΡΠΈΡ. 1.12). ΠΡΠΈ Π·Π°ΡΡΡΠ²Π°Π½ΠΈΠΈ ΠΌΠ΅ΡΠ°Π»Π»Π° Π½Π° ΠΏΠΎΠ²Π΅ΡΡ Π½ΠΎΡΡΠΈ Π»ΡΠ½ΠΊΠΈ ΠΎΠ±ΡΠ°Π·ΡΠ΅ΡΡΡ ΠΏΠ»Π΅Π½ΠΊΠ°, ΠΏΠΎ ΡΠ²ΠΎΠΈΠΌ ΡΠ²ΠΎΠΉΡΡΠ²Π°ΠΌ ΠΎΡΠ»ΠΈΡΠ°ΡΡΠ°ΡΡΡ ΠΎΡ ΠΎΡΠ½ΠΎΠ²Π½ΠΎΠ³ΠΎ ΠΌΠ΅ΡΠ°Π»Π»Π°.
Π ΠΈΡ. 1.12. ΠΡΠ½ΠΊΠ°, ΠΏΠΎΠ»ΡΡΠ΅Π½Π½Π°Ρ Π² ΡΠ΅Π·ΡΠ»ΡΡΠ°ΡΠ΅ Π²ΠΎΠ·Π΄Π΅ΠΉΡΡΠ²ΠΈΡ Π΅Π΄ΠΈΠ½ΠΈΡΠ½ΠΎΠ³ΠΎ ΠΈΠΌΠΏΡΠ»ΡΡΠ°: 1 β ΠΏΡΠΎΡΡΡΠ°Π½ΡΡΠ²ΠΎ, ΠΎΡΡΠ°Π²ΡΠ΅Π΅ΡΡ ΠΏΠΎΡΠ»Π΅ Π²ΡΠΏΠ»Π°Π²Π»Π΅Π½ΠΈΡ ΠΌΠ΅ΡΠ°Π»Π»Π°; 2 β Π±Π΅Π»ΡΠΉ ΡΠ»ΠΎΠΉ; 3 β Π²Π°Π»ΠΈΠΊ Π²ΠΎΠΊΡΡΠ³ Π»ΡΠ½ΠΊΠΈ; 4 β ΠΎΠ±ΡΠ°Π±Π°ΡΡΠ²Π°Π΅ΠΌΠ°Ρ Π·Π°Π³ΠΎΡΠΎΠ²ΠΊΠ°; ΠΠ, ΠΠ β Π΄ΠΈΠ°ΠΌΠ΅ΡΡ ΠΈ Π³Π»ΡΠ±ΠΈΠ½Π° Π»ΡΠ½ΠΊΠΈ
ΠΠΎΠ²Π΅ΡΡ Π½ΠΎΡΡΠ½ΡΠΉ ΡΠ»ΠΎΠΉ Π² ΡΠ°ΡΠΏΠ»Π°Π²Π»Π΅Π½Π½ΠΎΠΌ ΡΠΎΡΡΠΎΡΠ½ΠΈΠΈ Π°ΠΊΡΠΈΠ²Π½ΠΎ Π²ΡΡΡΠΏΠ°Π΅Ρ Π² Ρ ΠΈΠΌΠΈΡΠ΅ΡΠΊΠΎΠ΅ Π²Π·Π°ΠΈΠΌΠΎΠ΄Π΅ΠΉΡΡΠ²ΠΈΠ΅ Ρ ΠΏΠ°ΡΠ°ΠΌΠΈ ΠΈ ΠΏΡΠΎΠ΄ΡΠΊΡΠ°ΠΌΠΈ ΡΠ°Π·Π»ΠΎΠΆΠ΅Π½ΠΈΡ ΡΠ°Π±ΠΎΡΠ΅ΠΉ ΠΆΠΈΠ΄ΠΊΠΎΡΡΠΈ, ΠΎΠ±ΡΠ°Π·ΡΡΡΠΈΠΌΠΈΡΡ Π² Π·ΠΎΠ½Π΅ Π²ΡΡΠΎΠΊΠΈΡ ΡΠ΅ΠΌΠΏΠ΅ΡΠ°ΡΡΡ. Π Π΅Π·ΡΠ»ΡΡΠ°ΡΠΎΠΌ ΡΡΠΎΠ³ΠΎ Π²Π·Π°ΠΈΠΌΠΎΠ΄Π΅ΠΉΡΡΠ²ΠΈΡ ΡΠ²Π»ΡΠ΅ΡΡΡ ΠΈΠ½ΡΠ΅Π½ΡΠΈΠ²Π½ΠΎΠ΅ Π½Π°ΡΡΡΠ΅Π½ΠΈΠ΅ ΠΌΠ΅ΡΠ°Π»Π»Π° ΠΊΠΎΠΌΠΏΠΎΠ½Π΅Π½ΡΠ°ΠΌΠΈ, ΡΠΎΠ΄Π΅ΡΠΆΠ°ΡΠΈΠΌΠΈΡΡ Π² ΠΆΠΈΠ΄ΠΊΠΎΠΉ ΡΡΠ΅Π΄Π΅, Π° ΡΠ°ΠΊΠΆΠ΅ Π²Π΅ΡΠ΅ΡΡΠ²Π°ΠΌΠΈ, Π²Ρ ΠΎΠ΄ΡΡΠΈΠΌΠΈ Π² ΡΠΎΡΡΠ°Π² ΡΠ»Π΅ΠΊΡΡΠΎΠ΄Π°-ΠΈΠ½ΡΡΡΡΠΌΠ΅Π½ΡΠ°. Π’Π°ΠΊΠΈΠΌ ΠΎΠ±ΡΠ°Π·ΠΎΠΌ, Π² ΠΏΠΎΠ²Π΅ΡΡ Π½ΠΎΡΡΠ½ΡΠΉ ΡΠ»ΠΎΠΉ ΠΌΠΎΠ³ΡΡ Π±ΡΡΡ Π²Π½Π΅ΡΠ΅Π½Ρ ΡΠΈΡΠ°Π½, Ρ ΡΠΎΠΌ, Π²ΠΎΠ»ΡΡΡΠ°ΠΌ ΠΈ Ρ. Π΄. ΠΡΠΈ ΡΠ»Π΅ΠΊΡΡΠΎΡΡΠΎΠ·ΠΈΠΎΠ½Π½ΠΎΠΉ ΠΎΠ±ΡΠ°Π±ΠΎΡΠΊΠ΅ ΡΡΠ°Π»ΡΠ½ΡΡ Π·Π°Π³ΠΎΡΠΎΠ²ΠΎΠΊ Π² ΡΡΠ΅Π΄Π΅, ΡΠΎΡΡΠΎΡΡΠ΅ΠΉ ΠΈΠ· ΠΆΠΈΠ΄ΠΊΠΈΡ ΡΠ³Π»Π΅Π²ΠΎΠ΄ΠΎΡΠΎΠ΄ΠΎΠ² (ΠΊΠ΅ΡΠΎΡΠΈΠ½, ΠΌΠ°ΡΠ»ΠΎ), ΠΏΠΎΠ²Π΅ΡΡ Π½ΠΎΡΡΠ½ΡΠΉ ΡΠ»ΠΎΠΉ Π½Π°ΡΡΡΠ°Π΅ΡΡΡ ΡΠ³Π»Π΅ΡΠΎΠ΄ΠΎΠΌ, Ρ. Π΅. ΠΎΠ±ΡΠ°Π·ΡΡΡΡΡ ΠΊΠ°ΡΠ±ΠΈΠ΄Ρ ΠΆΠ΅Π»Π΅Π·Π°. Π‘Π»Π΅Π΄ΠΎΠ²Π°ΡΠ΅Π»ΡΠ½ΠΎ, ΠΏΡΠΈ ΡΠ»Π΅ΠΊΡΡΠΎΡΡΠΎΠ·ΠΈΠΎΠ½Π½ΠΎΠΉ ΠΎΠ±ΡΠ°Π±ΠΎΡΠΊΠ΅ ΠΏΡΠΎΠΈΡΡ ΠΎΠ΄ΠΈΡ ΡΠΏΡΠΎΡΠ½Π΅Π½ΠΈΠ΅ ΠΏΠΎΠ²Π΅ΡΡ Π½ΠΎΡΡΠΈ Π΄Π΅ΡΠ°Π»ΠΈ.
ΠΠ½ΡΠ΅Π½ΡΠΈΠ²Π½ΡΠΉ ΡΠ΅ΠΏΠ»ΠΎΠΎΡΠ²ΠΎΠ΄ ΠΈΠ· Π·ΠΎΠ½Ρ ΡΠ°Π·ΡΡΠ΄Π° ΡΠ΅ΡΠ΅Π· ΠΏΡΠΈΠ»Π΅Π³Π°ΡΡΠΈΠ΅ ΠΊ Π½Π΅ΠΉ ΠΌΠ°ΡΡΡ Ρ ΠΎΠ»ΠΎΠ΄Π½ΠΎΠ³ΠΎ ΠΌΠ΅ΡΠ°Π»Π»Π° ΠΈ ΡΠ°Π±ΠΎΡΡΡ ΠΆΠΈΠ΄ΠΊΠΎΡΡΡ ΡΠΎΠ·Π΄Π°Π΅Ρ ΡΡΠ»ΠΎΠ²ΠΈΡ Π΄Π»Ρ ΡΠ²Π΅ΡΡ ΡΠΊΠΎΡΠΎΡΡΠ½ΠΎΠΉ Π·Π°ΠΊΠ°Π»ΠΊΠΈ, ΡΡΠΎ ΠΎΠ΄Π½ΠΎΠ²ΡΠ΅ΠΌΠ΅Π½Π½ΠΎ Ρ Π½Π°ΡΠ³Π»Π΅ΡΠΎΠΆΠΈΠ²Π°Π½ΠΈΠ΅ΠΌ ΠΏΡΠΈΠ²ΠΎΠ΄ΠΈΡ ΠΊ ΠΎΠ±ΡΠ°Π·ΠΎΠ²Π°Π½ΠΈΡ ΠΎΡΠ΅Π½Ρ ΡΠ²Π΅ΡΠ΄ΠΎΠ³ΠΎ ΡΠ»ΠΎΡ. ΠΠ°ΠΊΠ°Π»Π΅Π½Π½ΡΠΉ ΠΏΠΎΠ²Π΅ΡΡ Π½ΠΎΡΡΠ½ΡΠΉ ΡΠ»ΠΎΠΉ ΡΡΠ°Π»ΠΈ ΠΎΠ±Π»Π°Π΄Π°Π΅Ρ ΠΏΠΎΠ²ΡΡΠ΅Π½Π½ΠΎΠΉ ΡΡΠΎΠΉΠΊΠΎΡΡΡΡ Π½Π° ΠΈΡΡΠΈΡΠ°Π½ΠΈΠ΅ ΠΈ ΠΌΠ΅Π½ΡΡΠΈΠΌ, ΡΠ΅ΠΌ Ρ Π½Π΅ΡΠ΅ΡΠΌΠΎΠΎΠ±ΡΠ°Π±ΠΎΡΠ°Π½Π½ΠΎΠΉ ΡΡΠ°Π»ΠΈ ΠΊΠΎΡΡΡΠΈΡΠΈΠ΅Π½ΡΠΎΠΌ ΡΡΠ΅Π½ΠΈΡ. Π‘ΡΡΡΠΊΡΡΡΠ° ΠΏΠΎΠ²Π΅ΡΡ Π½ΠΎΡΡΠ½ΠΎΠ³ΠΎ ΡΠ»ΠΎΡ ΡΡΡΠ΅ΡΡΠ²Π΅Π½Π½ΠΎ ΠΎΡΠ»ΠΈΡΠ°Π΅ΡΡΡ ΠΎΡ ΡΡΡΡΠΊΡΡΡΡ ΠΎΡΠ½ΠΎΠ²Π½ΠΎΠ³ΠΎ ΠΌΠ΅ΡΠ°Π»Π»Π° ΠΈ ΡΡ ΠΎΠΆΠ° ΡΠΎ ΡΡΡΡΠΊΡΡΡΠΎΠΉ ΠΎΡΠ±Π΅Π»Π΅Π½Π½ΠΎΠ³ΠΎ ΡΠ»ΠΎΡ, Π²ΠΎΠ·Π½ΠΈΠΊΠ°ΡΡΠ΅Π³ΠΎ Π½Π° ΠΏΠΎΠ²Π΅ΡΡ Π½ΠΎΡΡΠΈ Π½Π΅ΠΊΠΎΡΠΎΡΡΡ ΡΡΠ³ΡΠ½ΠΎΠ². ΠΠΎΡΡΠΎΠΌΡ ΡΡΠΎΡ ΡΠ»ΠΎΠΉ ΠΏΠΎΠ»ΡΡΠΈΠ» Π½Π°Π·Π²Π°Π½ΠΈΠ΅ Β«Π±Π΅Π»ΡΠΉ ΡΠ»ΠΎΠΉΒ». ΠΠ»ΡΠ±ΠΈΠ½Π° Π±Π΅Π»ΠΎΠ³ΠΎ ΡΠ»ΠΎΡ Π·Π°Π²ΠΈΡΠΈΡ ΠΎΡ ΡΠ½Π΅ΡΠ³ΠΈΠΈ ΠΈΠΌΠΏΡΠ»ΡΡΠΎΠ², ΠΈΡ Π΄Π»ΠΈΡΠ΅Π»ΡΠ½ΠΎΡΡΠΈ ΠΈ ΡΠ΅ΠΏΠ»ΠΎΡΠΈΠ·ΠΈΡΠ΅ΡΠΊΠΈΡ ΡΠ²ΠΎΠΉΡΡΠ² ΠΎΠ±ΡΠ°Π±Π°ΡΡΠ²Π°Π΅ΠΌΠΎΠ³ΠΎ ΠΌΠ°ΡΠ΅ΡΠΈΠ°Π»Π°. ΠΡΠΈ Π΄Π»ΠΈΡΠ΅Π»ΡΠ½ΡΡ ΠΈΠΌΠΏΡΠ»ΡΡΠ°Ρ ΡΠΎΠΊΠ° Π±ΠΎΠ»ΡΡΠΎΠΉ ΡΠ½Π΅ΡΠ³ΠΈΠΈ Π³Π»ΡΠ±ΠΈΠ½Π° Π±Π΅Π»ΠΎΠ³ΠΎ ΡΠ»ΠΎΡ ΡΠ°Π²Π½Π° Π΄Π΅ΡΡΡΡΠΌ Π΄ΠΎΠ»ΡΠΌ ΠΌΠΈΠ»Π»ΠΈΠΌΠ΅ΡΡΠ°, Π° ΠΏΡΠΈ ΠΊΠΎΡΠΎΡΠΊΠΈΡ ΠΈΠΌΠΏΡΠ»ΡΡΠ°Ρ β ΡΠΎΡΡΠΌ Π΄ΠΎΠ»ΡΠΌ ΠΌΠΈΠ»Π»ΠΈΠΌΠ΅ΡΡΠ° ΠΈ ΠΌΠΈΠΊΡΠΎΠ½Π°ΠΌ.
Π£ΠΏΡΠΎΡΠ½Π΅Π½ΠΈΠ΅ ΠΏΠΎΠ²Π΅ΡΡ Π½ΠΎΡΡΠ½ΠΎΠ³ΠΎ ΡΠ»ΠΎΡ ΠΌΠ΅ΡΠ°Π»Π»ΠΎΠ² (ΡΠ»Π΅ΠΊΡΡΠΎΡΡΠΎΠ·ΠΈΠΎΠ½Π½ΠΎΠ΅ Π»Π΅Π³ΠΈΡΠΎΠ²Π°Π½ΠΈΠ΅). ΠΠ΄Π½ΠΈΠΌ ΠΈΠ· ΠΏΡΠ΅ΠΈΠΌΡΡΠ΅ΡΡΠ² ΡΠ»Π΅ΠΊΡΡΠΎΠΈΡΠΊΡΠΎΠ²ΠΎΠ³ΠΎ ΠΌΠ΅ΡΠΎΠ΄Π° ΠΎΠ±ΡΠ°Π±ΠΎΡΠΊΠΈ ΠΌΠ°ΡΠ΅ΡΠΈΠ°Π»ΠΎΠ² ΡΠ²Π»ΡΠ΅ΡΡΡ ΡΠΎ, ΡΡΠΎ ΠΏΡΠΈ ΠΎΠΏΡΠ΅Π΄Π΅Π»Π΅Π½Π½ΡΡ ΡΡΠ»ΠΎΠ²ΠΈΡΡ ΡΠ΅Π·ΠΊΠΎ ΠΏΠΎΠ²ΡΡΠ°ΡΡΡΡ ΠΏΡΠΎΡΠ½ΠΎΡΡΠ½ΡΠ΅ ΡΠ²ΠΎΠΉΡΡΠ²Π° ΠΏΠΎΠ²Π΅ΡΡ Π½ΠΎΡΡΠΈ Π·Π°Π³ΠΎΡΠΎΠ²ΠΊΠΈ: ΡΠ²Π΅ΡΠ΄ΠΎΡΡΡ, ΠΈΠ·Π½ΠΎΡΠΎΡΡΠΎΠΉΠΊΠΎΡΡΡ, ΠΆΠ°ΡΠΎΡΡΠΎΠΉΠΊΠΎΡΡΡ ΠΈ ΡΡΠΎΠ·ΠΈΠΎΠ½Π½Π°Ρ ΡΡΠΎΠΉΠΊΠΎΡΡΡ. ΠΡΡ ΠΎΡΠΎΠ±Π΅Π½Π½ΠΎΡΡΡ ΠΈΡΠΏΠΎΠ»ΡΠ·ΡΡΡ Π΄Π»Ρ ΠΏΠΎΠ²ΡΡΠ΅Π½ΠΈΡ ΠΈΠ·Π½ΠΎΡΠΎΡΡΠΎΠΉΠΊΠΎΡΡΠΈ ΡΠ΅ΠΆΡΡΠ΅Π³ΠΎ ΠΈΠ½ΡΡΡΡΠΌΠ΅Π½ΡΠ°, ΡΡΠ°ΠΌΠΏΠΎΠ², ΠΏΡΠ΅ΡΡ-ΡΠΎΡΠΌ ΠΈ Π΄Π΅ΡΠ°Π»Π΅ΠΉ ΠΌΠ°ΡΠΈΠ½, ΡΠΏΡΠΎΡΠ½ΡΡ ΠΌΠ΅ΡΠ°Π»Π»ΠΈΡΠ΅ΡΠΊΠΈΠ΅ ΠΏΠΎΠ²Π΅ΡΡ Π½ΠΎΡΡΠΈ ΡΠ»Π΅ΠΊΡΡΠΎΠΈΡΠΊΡΠΎΠ²ΡΠΌ ΡΠΏΠΎΡΠΎΠ±ΠΎΠΌ.
ΠΡΠΈ ΡΠ»Π΅ΠΊΡΡΠΎΠΈΡΠΊΡΠΎΠ²ΠΎΠΌ Π»Π΅Π³ΠΈΡΠΎΠ²Π°Π½ΠΈΠΈ ΠΏΡΠΈΠΌΠ΅Π½ΡΡΡ ΠΎΠ±ΡΠ°ΡΠ½ΡΡ ΠΏΠΎΠ»ΡΡΠ½ΠΎΡΡΡ (Π·Π°Π³ΠΎΡΠΎΠ²ΠΊΠ° ΡΠ²Π»ΡΠ΅ΡΡΡ ΠΊΠ°ΡΠΎΠ΄ΠΎΠΌ, ΠΈΠ½ΡΡΡΡΠΌΠ΅Π½Ρ β Π°Π½ΠΎΠ΄ΠΎΠΌ) ΠΎΠ±ΡΠ°Π±ΠΎΡΠΊΡ ΠΏΡΠΎΠΈΠ·Π²ΠΎΠ΄ΡΡ ΠΎΠ±ΡΡΠ½ΠΎ Π² Π²ΠΎΠ·Π΄ΡΡΠ½ΠΎΠΉ ΡΡΠ΅Π΄Π΅ ΠΈ, ΠΊΠ°ΠΊ ΠΏΡΠ°Π²ΠΈΠ»ΠΎ, Ρ Π²ΠΈΠ±ΡΠ°ΡΠΈΠ΅ΠΉ ΡΠ»Π΅ΠΊΡΡΠΎΠ΄Π°. ΠΠΏΠΏΠ°ΡΠ°ΡΡΡΠ°, Ρ ΠΏΠΎΠΌΠΎΡΡΡ ΠΊΠΎΡΠΎΡΠΎΠΉ ΠΎΡΡΡΠ΅ΡΡΠ²Π»ΡΠ΅ΡΡΡ ΠΏΡΠΎΡΠ΅ΡΡ ΡΠΏΡΠΎΡΠ½Π΅Π½ΠΈΡ, ΠΌΠ°Π»ΠΎΠ³Π°Π±Π°ΡΠΈΡΠ½Π° ΠΈ ΠΎΡΠ΅Π½Ρ ΠΏΡΠΎΡΡΠ° Π² ΡΠΊΡΠΏΠ»ΡΠ°ΡΠ°ΡΠΈΠΈ. ΠΡΠ½ΠΎΠ²Π½ΡΠ΅ ΠΏΡΠ΅ΠΈΠΌΡΡΠ΅ΡΡΠ²Π° ΡΠ»Π΅ΠΊΡΡΠΎΠΈΡΠΊΡΠΎΠ²ΠΎΠ³ΠΎ ΡΠΏΠΎΡΠΎΠ±Π° Π½Π°Π½Π΅ΡΠ΅Π½ΠΈΡ ΠΏΠΎΠΊΡΡΡΠΈΠΉ Π·Π°ΠΊΠ»ΡΡΠ°ΡΡΡΡ Π² ΡΠ»Π΅Π΄ΡΡΡΠ΅ΠΌ: ΠΏΠΎΠΊΡΡΡΠΈΡ ΠΈΠΌΠ΅ΡΡ Π±ΠΎΠ»ΡΡΡΡ ΠΏΡΠΎΡΠ½ΠΎΡΡΡ ΡΡΠ΅ΠΏΠ»Π΅Π½ΠΈΡ Ρ ΠΌΠ°ΡΠ΅ΡΠΈΠ°Π»ΠΎΠΌ ΠΎΡΠ½ΠΎΠ²Ρ; ΠΏΠΎΠΊΡΡΠ²Π°Π΅ΠΌΡΠ΅ ΠΏΠΎΠ²Π΅ΡΡ Π½ΠΎΡΡΠΈ Π½Π΅ ΡΡΠ΅Π±ΡΡΡ ΠΏΡΠ΅Π΄Π²Π°ΡΠΈΡΠ΅Π»ΡΠ½ΠΎΠΉ ΠΏΠΎΠ΄Π³ΠΎΡΠΎΠ²ΠΊΠΈ; Π²ΠΎΠ·ΠΌΠΎΠΆΠ½ΠΎ Π½Π°Π½Π΅ΡΠ΅Π½ΠΈΠ΅ Π½Π΅ ΡΠΎΠ»ΡΠΊΠΎ ΠΌΠ΅ΡΠ°Π»Π»ΠΎΠ² ΠΈ ΠΈΡ ΡΠΏΠ»Π°Π²ΠΎΠ², Π½ΠΎ ΠΈ ΠΈΡ ΠΊΠΎΠΌΠΏΠΎΠ·ΠΈΡΠΈΠΉ. ΠΡΠΎΡΠ΅ΡΡΡ, ΠΏΡΠΎΠΈΡΡ ΠΎΠ΄ΡΡΠΈΠ΅ ΠΏΡΠΈ ΡΠ»Π΅ΠΊΡΡΠΎΠΈΡΠΊΡΠΎΠ²ΠΎΠΌ ΡΠΏΡΠΎΡΠ½Π΅Π½ΠΈΠΈ, ΡΠ»ΠΎΠΆΠ½Ρ ΠΈ ΡΠ²Π»ΡΡΡΡΡ ΠΏΡΠ΅Π΄ΠΌΠ΅ΡΠΎΠΌ ΡΡΠ°ΡΠ΅Π»ΡΠ½ΡΡ ΠΈΡΡΠ»Π΅Π΄ΠΎΠ²Π°Π½ΠΈΠΉ. Π‘ΡΡΠ½ΠΎΡΡΡ ΡΠΏΡΠΎΡΠ½Π΅Π½ΠΈΡ ΡΠΎΡΡΠΎΠΈΡ Π² ΡΠΎΠΌ, ΡΡΠΎ ΠΏΡΠΈ ΡΠ»Π΅ΠΊΡΡΠΎΠΈΡΠΊΡΠΎΠ²ΠΎΠΌ ΡΠ°Π·ΡΡΠ΄Π΅ Π² Π²ΠΎΠ·Π΄ΡΡΠ½ΠΎΠΉ ΡΡΠ΅Π΄Π΅ ΠΏΡΠΎΠΈΡΡ ΠΎΠ΄ΠΈΡ ΠΏΠΎΠ»ΡΡΠ½ΡΠΉ ΠΏΠ΅ΡΠ΅Π½ΠΎΡ ΠΌΠ°ΡΠ΅ΡΠΈΠ°Π»Π° ΡΠ»Π΅ΠΊΡΡΠΎΠ΄Π° Π½Π° Π·Π°Π³ΠΎΡΠΎΠ²ΠΊΡ. ΠΠ΅ΡΠ΅Π½Π΅ΡΠ΅Π½Π½ΡΠΉ ΠΌΠ°ΡΠ΅ΡΠΈΠ°Π» ΡΠ»Π΅ΠΊΡΡΠΎΠ΄Π° Π»Π΅Π³ΠΈΡΡΠ΅Ρ ΠΌΠ΅ΡΠ°Π»Π» Π·Π°Π³ΠΎΡΠΎΠ²ΠΊΠΈ ΠΈ, Ρ ΠΈΠΌΠΈΡΠ΅ΡΠΊΠΈ ΡΠΎΠ΅Π΄ΠΈΠ½ΡΡΡΡ Ρ Π΄ΠΈΡΡΠΎΡΠΈΠΈΡΠΎΠ²Π°Π½Π½ΡΠΌ Π°ΡΠΎΠΌΠ°ΡΠ½ΡΠΌ Π°Π·ΠΎΡΠΎΠΌ Π²ΠΎΠ·Π΄ΡΡ Π°, ΡΠ³Π»Π΅ΡΠΎΠ΄ΠΎΠΌ ΠΈ ΠΌΠ°ΡΠ΅ΡΠΈΠ°Π»ΠΎΠΌ Π·Π°Π³ΠΎΡΠΎΠ²ΠΊΠΈ, ΠΎΠ±ΡΠ°Π·ΡΠ΅Ρ Π΄ΠΈΡΡΡΠ·ΠΈΠΎΠ½Π½ΡΠΉ ΠΈΠ·Π½ΠΎΡΠΎΡΡΡΠΎΠΉΡΠΈΠ²ΡΠΉ ΡΠΏΡΠΎΡΠ½Π΅Π½Π½ΡΠΉ ΡΠ»ΠΎΠΉ. ΠΡΠΈ ΡΡΠΎΠΌ Π² ΡΠ»ΠΎΠ΅ Π²ΠΎΠ·Π½ΠΈΠΊΠ°ΡΡ ΡΠ»ΠΎΠΆΠ½ΡΠ΅ Ρ ΠΈΠΌΠΈΡΠ΅ΡΠΊΠΈΠ΅ ΡΠΎΠ΅Π΄ΠΈΠ½Π΅Π½ΠΈΡ, Π²ΡΡΠΎΠΊΠΎΡΡΠΎΠΉΠΊΠΈΠ΅ Π½ΠΈΡΡΠΈΠ΄Ρ ΠΈ ΠΊΠ°ΡΠ±ΠΎΠ½ΠΈΡΡΠΈΠ΄Ρ, Π° ΡΠ°ΠΊΠΆΠ΅ Π·Π°ΠΊΠ°Π»ΠΎΡΠ½ΡΠ΅ ΡΡΡΡΠΊΡΡΡΡ. ΠΠΎ ΠΌΠ½Π΅Π½ΠΈΡ ΡΠΏΠ΅ΡΠΈΠ°Π»ΠΈΡΡΠΎΠ², ΠΏΡΠΈ ΡΠ»Π΅ΠΊΡΡΠΎΠΈΡΠΊΡΠΎΠ²ΠΎΠΌ ΡΠΏΡΠΎΡΠ½Π΅Π½ΠΈΠΈ Π² ΠΏΠΎΠ²Π΅ΡΡ Π½ΠΎΡΡΠ½ΠΎΠΌ ΡΠ»ΠΎΠ΅, Π½Π°ΠΏΡΠΈΠΌΠ΅Ρ, ΡΡΠ°Π»ΠΈ ΠΏΡΠΎΠΈΡΡ ΠΎΠ΄ΡΡ ΠΏΡΠΎΡΠ΅ΡΡΡ, ΠΏΡΠΈΠ²Π΅Π΄Π΅Π½Π½ΡΠ΅ Π² ΡΠ°Π±Π». 1.3.β
Π’Π°Π±Π»ΠΈΡΠ° 1.3
Π£ΠΏΡΠΎΡΠ½ΡΠ΅ΠΌΡΠΉ ΠΌΠ°ΡΠ΅ΡΠΈΠ°Π» | ΠΡΠΎΡΠ΅ΡΡ | |
ΠΠΈΠ΄ | ΠΡΠΎΠ±Π΅Π½Π½ΠΎΡΡΠΈ | |
Π£Π³Π»Π΅ΡΠΎΠ΄ΠΈΡΡΠ°Ρ ΡΡΠ°Π»Ρ, ΡΠΎΒΠ΄Π΅ΡΠΆΠ°ΡΠ°Ρ ΡΠ³Π»Π΅ΡΠΎΠ΄ Π² ΠΊΠΎΒΠ»ΠΈΡΠ΅ΡΡΠ²Π΅ ΡΠ²ΡΡΠ΅ 0,6 %, Π° ΡΠ°ΠΊΠΆΠ΅ Π»Π΅Π³ΠΈΡΡΡΡΠΈΠ΅ ΡΠ»Π΅ΒΠΌΠ΅Π½ΡΡ Π² Π±ΠΎΠ»ΡΡΠΎΠΌ ΠΊΠΎΠ»ΠΈΒΡΠ΅ΡΡΠ²Π΅ | Π‘Π²Π΅ΡΡ ΡΠΊΠΎΡΠΎΡΡΒΠ½Π°Ρ Π·Π°ΠΊΠ°Π»ΠΊΠ° | ΠΡΠ°ΡΠΊΠΎΠ²ΡΠ΅ΠΌΠ΅Π½Π½ΡΠΉ Π½Π°Π³ΡΠ΅Π² Π΄ΠΎ Π²ΡΡΠΎΠΊΠΎΠΉ ΡΠ΅ΠΌΠΏΠ΅ΡΠ°ΡΡΡΡ ΠΈ ΠΌΠ³Π½ΠΎΠ²Π΅Π½Π½ΠΎΠ΅ ΠΎΡ Π»Π°ΠΆΠ΄Π΅Π½ΠΈΠ΅ Π½Π°Π³ΡΠ΅ΡΡΡ ΠΈ ΡΠ°ΡΠΏΠ»Π°Π²Π»Π΅Π½Π½ΡΡ ΡΡΠ°ΡΡΠΊΠΎΠ² ΠΌΠ°ΡΒΡΠΎΠΉ Ρ ΠΎΠ»ΠΎΠ΄Π½ΠΎΠ³ΠΎ ΠΌΠ΅ΡΠ°Π»Π»Π° |
ΠΠ½ΡΡΡΡΠΌΠ΅Π½ΡΠ°Π»ΡΠ½Π°Ρ ΡΡΠ°Π»Ρ | ΠΠ·ΠΎΡΠΈΡΠΎΠ²Π°Π½ΠΈΠ΅ | ΠΠΈΡΡΠΎΡΠΈΠ°ΡΠΈΡ Π°ΡΠΌΠΎΡΡΠ΅ΡΠ½ΠΎΠ³ΠΎ Π°Π·ΠΎΡΠ° Π² ΡΠ°Π·ΒΡΡΠ΄Π΅ Ρ ΠΎΠ±ΡΠ°Π·ΠΎΠ²Π°Π½ΠΈΠ΅ΠΌ Π°ΡΠΎΠΌΠ°ΡΠ½ΠΎΠ³ΠΎ Π°Π·ΠΎΡΠ°. Π‘ΠΎΠ΅Π΄ΠΈΠ½Π΅Π½ΠΈΠ΅ Π°Π·ΠΎΡΠ° Ρ ΡΠ»Π΅ΠΌΠ΅Π½ΡΠ°ΠΌΠΈ ΠΏΠΎΠ²Π΅ΡΡ ΒΠ½ΠΎΡΡΠ½ΠΎΠ³ΠΎ ΡΠ»ΠΎΡ ΠΈ ΠΎΠ±ΡΠ°Π·ΠΎΠ²Π°Π½ΠΈΠ΅ Π½ΠΈΡΡΠΈΠ΄ΠΎΠ² ΠΌΠ΅ΡΠ°Π»Π»ΠΎΠ² (ΡΠΈΡΠ°Π½Π°, Ρ ΡΠΎΠΌΠ°, ΠΆΠ΅Π»Π΅Π·Π° ΠΈ Π΄Ρ.) |
ΠΡΠΈ ΡΠ»Π΅ΠΊΡΡΠΎΠΈΡΠΊΡΠΎΠ²ΠΎΠΌ ΡΠΏΡΠΎΡΠ½Π΅Π½ΠΈΠΈ ΠΌΠΈΠΊΡΠΎΡΠ²Π΅ΡΠ΄ΠΎΡΡΡ Π±Π΅Π»ΠΎΠ³ΠΎ ΡΠ»ΠΎΡ Π² ΡΠ³Π»Π΅ΡΠΎΠ΄ΠΈΡΡΡΡ ΡΡΠ°Π»ΡΡ ΠΌΠΎΠΆΠ΅Ρ Π±ΡΡΡ Π΄ΠΎΠ²Π΅Π΄Π΅Π½Π° Π΄ΠΎ 230 ΠΠΠ°, Π²ΡΡΠΎΡΠ° ΠΌΠΈΠΊΡΠΎΠ½Π΅ΡΠΎΠ²Π½ΠΎΡΡΠ΅ΠΉ ΠΎΠ±ΡΠ°Π±ΠΎΡΠ°Π½Π½ΠΎΠΉ ΠΏΠΎΠ²Π΅ΡΡ Π½ΠΎΡΡΠΈ Π΄ΠΎ 2,5 ΠΌΠΊΠΌ. Π’ΠΎΠ»ΡΠΈΠ½Π° ΡΠ»ΠΎΡ ΠΏΠΎΠΊΡΡΡΠΈΡ, ΠΏΠΎΠ»ΡΡΠ°Π΅ΠΌΠΎΠ³ΠΎ Π½Π° Π½Π΅ΠΊΠΎΡΠΎΡΡΡ ΡΡΡΠ°Π½ΠΎΠ²ΠΊΠ°Ρ , ΡΠΎΡΡΠ°Π²Π»ΡΠ΅Ρ 0,003-0,2 ΠΌΠΌ.
4. ΠΡΠ½ΠΎΠ²Π½ΡΠ΅ ΡΠ΅Ρ Π½ΠΎΠ»ΠΎΠ³ΠΈΠΈ ΡΠ»Π΅ΠΊΡΡΠΎΡΡΠΎΠ·ΠΈΠΎΠ½Π½ΠΎΠΉ ΠΎΠ±ΡΠ°Π±ΠΎΡΠΊΠΈ ΠΌΠ΅ΡΠ°Π»Π»ΠΎΠ²
Π’Π΅Ρ Π½ΠΎΠ»ΠΎΠ³ΠΈΠΈ ΡΠ°Π·ΠΌΠ΅ΡΠ½ΠΎΠΉ ΠΎΠ±ΡΠ°Π±ΠΎΡΠΊΠΈ ΠΌΠ΅ΡΠ°Π»Π»ΠΈΡΠ΅ΡΠΊΠΈΡ Π΄Π΅ΡΠ°Π»Π΅ΠΉ.
Π€ΠΎΡΠΌΠΎΠΎΠ±ΡΠ°Π·ΠΎΠ²Π°Π½ΠΈΠ΅ Π΄Π΅ΡΠ°Π»Π΅ΠΉ ΡΠ»Π΅ΠΊΡΡΠΎΡΡΠΎΠ·ΠΈΠΎΠ½Π½ΡΠΌ ΠΌΠ΅ΡΠΎΠ΄ΠΎΠΌ ΠΌΠΎΠΆΠ½ΠΎ ΠΎΡΡΡΠ΅ΡΡΠ²ΠΈΡΡ ΠΏΠΎ ΡΠ»Π΅Π΄ΡΡΡΠΈΠΌ ΡΡ Π΅ΠΌΠ°ΠΌ.
1. ΠΠΎΠΏΠΈΡΠΎΠ²Π°Π½ΠΈΠ΅ ΡΠΎΡΠΌΡ ΡΠ»Π΅ΠΊΡΡΠΎΠ΄Π° ΠΈΠ»ΠΈ Π΅Π³ΠΎ ΡΠ΅ΡΠ΅Π½ΠΈΡ. ΠΡΠΈ ΡΡΠΎΠΌ ΠΎΠ±ΡΠ°Π±Π°ΡΡΠ²Π°Π΅ΠΌΡΠΉ ΡΠ»Π΅ΠΌΠ΅Π½Ρ Π·Π°Π³ΠΎΡΠΎΠ²ΠΊΠΈ ΠΏΠΎ ΡΠΎΡΠΌΠ΅ ΡΠ²Π»ΡΠ΅ΡΡΡ ΠΎΠ±ΡΠ°ΡΠ½ΡΠΌ ΠΎΡΠΎΠ±ΡΠ°ΠΆΠ΅Π½ΠΈΠ΅ΠΌ ΡΠ°Π±ΠΎΡΠ΅ΠΉ ΠΏΠΎΠ²Π΅ΡΡ Π½ΠΎΡΡΠΈ ΠΈΠ½ΡΡΡΡΠΌΠ΅Π½ΡΠ°. ΠΠ°Π½Π½ΡΡ ΠΎΠΏΠ΅ΡΠ°ΡΠΈΡ Π½Π°Π·ΡΠ²Π°ΡΡ ΠΏΡΠΎΡΠΈΠ²Π°Π½ΠΈΠ΅ΠΌ. Π‘ΡΡΠ΅ΡΡΠ²ΡΡΡ ΠΌΠ΅ΡΠΎΠ΄Ρ ΠΏΡΡΠΌΠΎΠ³ΠΎ ΠΈ ΠΎΠ±ΡΠ°ΡΠ½ΠΎΠ³ΠΎ ΠΊΠΎΠΏΠΈΡΠΎΠ²Π°Π½ΠΈΡ. ΠΡΠΈ ΠΏΡΡΠΌΠΎΠΌ ΠΊΠΎΠΏΠΈΡΠΎΠ²Π°Π½ΠΈΠΈ ΠΈΠ½ΡΡΡΡΠΌΠ΅Π½Ρ Π½Π°Ρ ΠΎΠ΄ΠΈΡΡΡ Π½Π°Π΄ Π·Π°Π³ΠΎΡΠΎΠ²ΠΊΠΎΠΉ, Π° ΠΏΡΠΈ ΠΎΠ±ΡΠ°ΡΠ½ΠΎΠΌ β ΠΏΠΎΠ΄ Π½Π΅ΠΉ. ΠΠ΅ΡΠΎΠ΄ ΠΏΡΠΎΡΠΈΠ²Π°Π½ΠΈΡ ΠΏΡΠΎΡΡ Π² ΠΈΡΠΏΠΎΠ»Π½Π΅Π½ΠΈΠΈ, ΠΈ ΠΎΠ½ ΡΠΈΡΠΎΠΊΠΎ ΠΏΡΠΈΠΌΠ΅Π½ΡΠ΅ΡΡΡ Π² ΠΏΡΠΎΠΌΡΡΠ»Π΅Π½Π½ΠΎΡΡΠΈ. ΠΠ° ΡΠΈΡ. 1.13 ΠΏΡΠ΅Π΄ΡΡΠ°Π²Π»Π΅Π½Π° ΡΡ Π΅ΠΌΠ° ΡΠ»Π΅ΠΊΡΡΠΎΡΡΠΎΠ·ΠΈΠΎΠ½Π½ΠΎΠΉ ΠΎΠ±ΡΠ°Π±ΠΎΡΠΊΠΈ ΠΌΠ΅ΡΠΎΠ΄ΠΎΠΌ ΠΊΠΎΠΏΠΈΡΠΎΠ²Π°Π½ΠΈΡ ΡΠΎΡΠΌΡ ΡΠ»Π΅ΠΊΡΡΠΎΠ΄Π°- ΠΈΠ½ΡΡΡΡΠΌΠ΅Π½ΡΠ°. ΠΠΎ ΠΌΠ΅ΡΠ΅ ΡΠ»Π΅ΠΊΡΡΠΎΡΡΠΎΠ·ΠΈΠΎΠ½Π½ΠΎΠΉ ΠΎΠ±ΡΠ°Π±ΠΎΡΠΊΠΈ ΡΠ»Π΅ΠΊΡΡΠΎΠ΄ (1) Π²Π½Π΅Π΄ΡΡΠ΅ΡΡΡ Π² Π΄Π΅ΡΠ°Π»Ρ, ΠΎΠ±Π΅ΡΠΏΠ΅ΡΠΈΠ²Π°Ρ ΠΊΠΎΠΏΠΈΡΠΎΠ²Π°Π½ΠΈΠ΅ ΡΠ»Π΅ΠΊΡΡΠΎΠ΄Π°.
2. ΠΠ·Π°ΠΈΠΌΠ½ΠΎΠ΅ ΠΏΠ΅ΡΠ΅ΠΌΠ΅ΡΠ΅Π½ΠΈΠ΅ ΠΎΠ±ΡΠ°Π±Π°ΡΡΠ²Π°Π΅ΠΌΠΎΠΉ Π·Π°Π³ΠΎΡΠΎΠ²ΠΊΠΈ ΠΈ ΡΠ»Π΅ΠΊΡΡΠΎΠ΄Π°- ΠΈΠ½ΡΡΡΡΠΌΠ΅Π½ΡΠ°. ΠΡΠΈ ΡΡΠΎΠΉ ΡΡ Π΅ΠΌΠ΅ Π²ΠΎΠ·ΠΌΠΎΠΆΠ½Ρ ΠΎΠΏΠ΅ΡΠ°ΡΠΈΠΈ Π²ΡΡΠ΅Π·Π°Π½ΠΈΡ ΡΠ»ΠΎΠΆΠ½ΠΎ- ΠΏΡΠΎΡΠΈΠ»ΡΠ½ΡΡ Π΄Π΅ΡΠ°Π»Π΅ΠΉ ΠΈ ΡΠ°Π·ΡΠ΅Π·Π°Π½ΠΈΠ΅ Π·Π°Π³ΠΎΡΠΎΠ²ΠΎΠΊ ΡΠ»Π΅ΠΊΡΡΠΎΠ΄Π°ΠΌΠΈ, ΡΠ»Π΅ΠΊΡΡΠΎΡΡΠΎΠ·ΠΈΠΎΠ½Π½ΠΎΠ³ΠΎ ΡΠ»ΠΈΡΠΎΠ²Π°Π½ΠΈΡ ΠΈ ΡΠ°ΡΡΠ°ΡΠΈΠ²Π°Π½ΠΈΡ Π΄Π΅ΡΠ°Π»Π΅ΠΉ.
Π ΠΈΡ. 1.13. Π‘Ρ Π΅ΠΌΠ° ΠΊΠΎΠΏΠΈΡΠΎΠ²Π°Π½ΠΈΡ ΡΠΎΡΠΌΡ ΡΠ»Π΅ΠΊΡΡΠΎΠ΄Π°: 1 β ΡΠ»Π΅ΠΊΡΡΠΎΠ΄-ΠΈΠ½ΡΡΡΡΠΌΠ΅Π½Ρ, 2 β ΠΎΠ±ΡΠ°Π±Π°ΡΡΠ²Π°Π΅ΠΌΠ°Ρ Π΄Π΅ΡΠ°Π»Ρ, 3 β ΠΆΠΈΠ΄ΠΊΠΎΡΡΡ, 4 β ΡΠΎΡΡΠ΄
ΠΡΠΎΡΠΈΠ²Π°Π½ΠΈΠ΅ ΠΎΠΊΠΎΠ½, ΡΠ΅Π»Π΅ΠΉ ΠΈ ΠΎΡΠ²Π΅ΡΡΡΠΈΠΉ. ΠΡΠ° ΠΎΠΏΠ΅ΡΠ°ΡΠΈΡ ΠΎΡΡΡΠ΅ΡΡΠ²Π»ΡΠ΅ΡΡΡ Π½Π° ΡΠ½ΠΈΠ²Π΅ΡΡΠ°Π»ΡΠ½ΡΡ ΡΡΠ°Π½ΠΊΠ°Ρ . ΠΠ»Π΅ΠΊΡΡΠΎΡΡΠΎΠ·ΠΈΠΎΠ½Π½ΡΠΌ ΡΠΏΠΎΡΠΎΠ±ΠΎΠΌ ΠΏΡΠΎΡΠΈΠ²Π°ΡΡ ΡΠ΅Π»ΠΈ ΡΠΈΡΠΈΠ½ΠΎΠΉ (2,5-10) ΠΌΠΌ, Π³Π»ΡΠ±ΠΈΠ½ΠΎΠΉ Π΄ΠΎ 100 ΠΌΠΌ. ΠΠ»Ρ ΠΎΠ±Π΅ΡΠΏΠ΅ΡΠ΅Π½ΠΈΡ ΡΠ΄Π°Π»Π΅Π½ΠΈΡ ΠΏΡΠΎΠ΄ΡΠΊΡΠΎΠ² ΡΡΠΎΠ·ΠΈΠΈ ΠΈΠ· ΠΌΠ΅ΠΆΡΠ»Π΅ΠΊΡΡΠΎΠ΄Π½ΠΎΠ³ΠΎ ΠΏΡΠΎΠΌΠ΅ΠΆΡΡΠΊΠ°, ΡΠ»Π΅ΠΊΡΡΠΎΠ΄-ΠΈΠ½ΡΡΡΡΠΌΠ΅Π½Ρ Π΄Π΅Π»Π°ΡΡ Π’-ΠΎΠ±ΡΠ°Π·Π½ΠΎΠΉ ΡΠΎΡΠΌΡ ΠΈΠ»ΠΈ ΡΠΌΠ΅Π½ΡΡΠ°ΡΡ ΡΠΎΠ»ΡΠΈΠ½Ρ Ρ Π²ΠΎΡΡΠΎΠ²ΠΎΠΉ ΡΠ°ΡΡΠΈ ΠΏΠΎ ΡΡΠ°Π²Π½Π΅Π½ΠΈΡ Ρ ΡΠ°Π±ΠΎΡΠ΅ΠΉ ΡΠ°ΡΡΡΡ Π½Π° Π½Π΅ΡΠΊΠΎΠ»ΡΠΊΠΎ Π΄Π΅ΡΡΡΡΡ Π΄ΠΎΠ»Π΅ΠΉ ΠΌΠΈΠ»Π»ΠΈΠΌΠ΅ΡΡΠ°. Π‘ΠΊΠΎΡΠΎΡΡΡ ΠΏΡΠΎΡΠΈΠ²Π°Π½ΠΈΡ ΡΠ΅Π»Π΅ΠΉ ΡΠΎΡΡΠ°Π²Π»ΡΠ΅Ρ (0,5-0,8) ΠΌΠΌ/ΠΌΠΈΠ½, ΡΠ΅ΡΠΎΡ ΠΎΠ²Π°ΡΠΎΡΡΡ ΠΎΠ±ΡΠ°Π±ΠΎΡΠ°Π½Π½ΠΎΠΉ ΠΏΠΎΠ²Π΅ΡΡ Π½ΠΎΡΡΠΈ β Π΄ΠΎ 2,5 ΠΌΠΊΠΌ.
ΠΠ±ΡΠ°Π±ΠΎΡΠΊΠ° Π΄Π΅ΡΠ°Π»Π΅ΠΉ ΡΠΈΠΏΠ° ΡΠ΅ΡΠΎΠΊ ΠΈ ΡΠΈΡ. Π‘ΠΎΠ·Π΄Π°Π½Ρ ΡΠ»Π΅ΠΊΡΡΠΎΡΡΠΎΠ·ΠΈΠΎΠ½Π½ΡΠ΅ ΡΡΠ°Π½ΠΊΠΈ, ΠΏΠΎΠ·Π²ΠΎΠ»ΡΡΡΠΈΠ΅ ΠΎΠ±ΡΠ°Π±Π°ΡΡΠ²Π°ΡΡ ΡΠ΅ΡΠΎΡΠ½ΡΠ΅ Π΄Π΅ΡΠ°Π»ΠΈ Ρ ΡΠΈΡΠ»ΠΎΠΌ ΠΎΡΠ²Π΅ΡΡΡΠΈΠΉ Π΄ΠΎ Π½Π΅ΡΠΊΠΎΠ»ΡΠΊΠΈΡ ΡΡΡΡΡ. Π‘ΡΠ°Π½ΠΊΠΈ ΠΌΠΎΠ³ΡΡ ΠΎΠ±ΡΠ°Π±Π°ΡΡΠ²Π°ΡΡ ΠΎΠ΄Π½ΠΎΠ²ΡΠ΅ΠΌΠ΅Π½Π½ΠΎ Π±ΠΎΠ»Π΅Π΅ 800 ΠΎΡΠ²Π΅ΡΡΡΠΈΠΉ Π΄ΠΈΠ°ΠΌΠ΅ΡΡΠΎΠΌ (0,2-2) ΠΌΠΌ Π² Π»ΠΈΡΡΠ°Ρ ΠΈΠ· ΠΊΠΎΡΡΠΎΠ·ΠΈΠΎΠ½Π½ΠΎ- ΡΡΠΎΠΉΠΊΠΈΡ ΡΡΠ°Π»Π΅ΠΉ, Π»Π°ΡΡΠ½ΠΈ ΠΈ Π΄ΡΡΠ³ΠΈΡ ΠΌΠ°ΡΠ΅ΡΠΈΠ°Π»ΠΎΠ² ΡΠΎΠ»ΡΠΈΠ½ΠΎΠΉ Π΄ΠΎ 2 ΠΌΠΌ. ΠΡΠΎΠΈΠ·Π²ΠΎΠ΄ΠΈΡΠ΅Π»ΡΠ½ΠΎΡΡΡ ΠΎΠ±ΡΠ°Π±ΠΎΡΠΊΠΈ Π΄ΠΎ 10000 ΠΎΡΠ²Π΅ΡΡΡΠΈΠΉ Π² ΡΠ°Ρ.
ΠΠ»Π΅ΠΊΡΡΠΎΡΡΠΎΠ·ΠΈΠΎΠ½Π½ΠΎΠ΅ ΡΠ»ΠΈΡΠΎΠ²Π°Π½ΠΈΠ΅. ΠΡΠΎ ΠΎΠ΄Π½Π° ΠΈΠ· ΡΠ°Π·Π½ΠΎΠ²ΠΈΠ΄Π½ΠΎΡΡΠ΅ΠΉ ΡΠ»Π΅ΠΊΡΡΠΎΡΡΠΎΠ·ΠΈΠΎΠ½Π½ΠΎΠΉ ΠΎΠ±ΡΠ°Π±ΠΎΡΠΊΠΈ, ΠΊΠΎΡΠΎΡΠ°Ρ ΠΈΡΠΏΠΎΠ»ΡΠ·ΡΠ΅ΡΡΡ Π΄Π»Ρ ΠΎΠ±ΡΠ°Π±ΠΎΡΠΊΠΈ Π²ΡΡΠΎΠΊΠΎΠΏΡΠΎΡΠ½ΡΡ Π·Π°Π³ΠΎΡΠΎΠ²ΠΎΠΊ ΠΈΠ· ΡΡΠ°Π»Π΅ΠΉ ΠΈ ΡΠ²Π΅ΡΠ΄ΡΡ ΡΠΏΠ»Π°Π²ΠΎΠ². Π£Π΄Π°Π»Π΅Π½ΠΈΠ΅ ΠΌΠ΅ΡΠ°Π»Π»Π° ΠΏΡΠΈ ΡΡΠΎΠΌ ΠΏΡΠΎΠΈΡΡ ΠΎΠ΄ΠΈΡ ΠΏΠΎΠ΄ Π²ΠΎΠ·Π΄Π΅ΠΉΡΡΠ²ΠΈΠ΅ΠΌ ΠΈΠΌΠΏΡΠ»ΡΡΠ½ΡΡ ΡΠ°Π·ΡΡΠ΄ΠΎΠ² ΠΌΠ΅ΠΆΠ΄Ρ Π²ΡΠ°ΡΠ°ΡΡΠΈΠΌΡΡ ΡΠ»Π΅ΠΊΡΡΠΎΠ΄ΠΎΠΌ-ΠΈΠ½ΡΡΡΡΠΌΠ΅Π½ΡΠΎΠΌ ΠΈ ΠΎΠ±ΡΠ°Π±Π°ΡΡΠ²Π°Π΅ΠΌΠΎΠΉ Π·Π°Π³ΠΎΡΠΎΠ²ΠΊΠΎΠΉ, Π° Π½Π΅ Π² ΡΠ΅Π·ΡΠ»ΡΡΠ°ΡΠ΅ ΠΌΠ΅Ρ Π°Π½ΠΈΡΠ΅ΡΠΊΠΎΠ³ΠΎ Π²ΠΎΠ·Π΄Π΅ΠΉΡΡΠ²ΠΈΡ, ΠΊΠ°ΠΊ ΠΏΡΠΈ Π°Π±ΡΠ°Π·ΠΈΠ²Π½ΠΎΠΌ ΡΠ»ΠΈΡΠΎΠ²Π°Π½ΠΈΠΈ.
Π‘Π»ΠΎΠΆΠ½ΠΎΠΊΠΎΠ½ΡΡΡΠ½Π°Ρ ΠΏΡΠΎΠ²ΠΎΠ»ΠΎΡΠ½Π°Ρ Π²ΡΡΠ΅Π·ΠΊΠ°. ΠΠ΅ΡΠΎΠ΄Ρ ΠΏΡΡΠΌΠΎΠ³ΠΎ ΠΈ ΠΎΠ±ΡΠ°ΡΠ½ΠΎΠ³ΠΎ ΠΊΠΎΠΏΠΈΡΠΎΠ²Π°Π½ΠΈΡ ΠΈΠΌΠ΅ΡΡ ΡΡΡΠ΅ΡΡΠ²Π΅Π½Π½ΡΠΉ Π½Π΅Π΄ΠΎΡΡΠ°ΡΠΎΠΊ, Π·Π°ΠΊΠ»ΡΡΠ°ΡΡΠΈΠΉΡΡ Π² Π½Π΅ΠΎΠ±Ρ ΠΎΠ΄ΠΈΠΌΠΎΡΡΠΈ ΠΈΡΠΏΠΎΠ»ΡΠ·ΠΎΠ²Π°Π½ΠΈΡ ΡΠ»ΠΎΠΆΠ½ΡΡ ΡΠ°ΡΠΎΠ½Π½ΡΡ ΡΠ»Π΅ΠΊΡΡΠΎΠ΄ΠΎΠ²- ΠΈΠ½ΡΡΡΡΠΌΠ΅Π½ΡΠΎΠ². ΠΠ·Π½ΠΎΡ ΡΠ»Π΅ΠΊΡΡΠΎΠ΄ΠΎΠ² ΠΎΡΡΠ°ΠΆΠ°Π΅ΡΡΡ Π½Π° ΡΠΎΡΠ½ΠΎΡΡΠΈ ΠΈΠ·Π³ΠΎΡΠΎΠ²Π»Π΅Π½ΠΈΡ Π΄Π΅ΡΠ°Π»Π΅ΠΉ, ΠΏΠΎΡΡΠΎΠΌΡ ΠΎΠ΄Π½ΠΈΠΌ ΡΠ»Π΅ΠΊΡΡΠΎΠ΄ΠΎΠΌ-ΠΈΠ½ΡΡΡΡΠΌΠ΅Π½ΡΠΎΠΌ ΡΠ΄Π°Π΅ΡΡΡ ΠΈΠ·Π³ΠΎΡΠΎΠ²ΠΈΡΡ Π½Π΅ Π±ΠΎΠ»Π΅Π΅ 5-10 Π΄Π΅ΡΠ°Π»Π΅ΠΉ.β
ΠΠ»Π΅ΠΊΡΡΠΎΠΈΡΠΊΡΠΎΠ²ΠΎΠΉ ΠΌΠ΅ΡΠΎΠ΄ ΡΠ»ΠΎΠΆΠ½ΠΎΠΊΠΎΠ½ΡΡΡΠ½ΠΎΠΉ ΠΏΡΠΎΠ²ΠΎΠ»ΠΎΡΠ½ΠΎΠΉ Π²ΡΡΠ΅Π·ΠΊΠΈ Π²ΡΠ³ΠΎΠ΄Π½ΠΎ ΠΎΡΠ»ΠΈΡΠ°Π΅ΡΡΡ ΠΎΡ ΠΌΠ΅ΡΠΎΠ΄ΠΎΠ² ΠΊΠΎΠΏΠΈΡΠΎΠ²Π°Π½ΠΈΡ ΡΠ΅ΠΌ, ΡΡΠΎ Π·Π΄Π΅ΡΡ ΠΈΠ½ΡΡΡΡΠΌΠ΅Π½ΡΠΎΠΌ ΡΠ²Π»ΡΠ΅ΡΡΡ ΡΠΎΠ½ΠΊΠ°Ρ ΠΏΡΠΎΠ²ΠΎΠ»ΠΎΠΊΠ° ΠΈΠ· ΠΌΠ΅Π΄ΠΈ, Π»Π°ΡΡΠ½ΠΈ ΠΈΠ»ΠΈ Π²ΠΎΠ»ΡΡΡΠ°ΠΌΠ° Π΄ΠΈΠ°ΠΌΠ΅ΡΡΠΎΠΌ ΠΎΡ Π½Π΅ΡΠΊΠΎΠ»ΡΠΊΠΈΡ ΠΌΠΈΠΊΡΠΎΠ½ Π΄ΠΎ 0,5 ΠΌΠΌ, Π²ΠΊΠ»ΡΡΠ°Π΅ΠΌΠ°Ρ Π² ΡΠ»Π΅ΠΊΡΡΠΈΡΠ΅ΡΠΊΡΡ ΡΡ Π΅ΠΌΡ ΠΊΠ°ΠΊ ΠΊΠ°ΡΠΎΠ΄ (ΡΠΌ. ΡΠΈΡ. 1.14).
Π ΠΈΡ. 1.14. Π‘Π»ΠΎΠΆΠ½ΠΎΠΊΠΎΠ½ΡΡΡΠ½Π°Ρ ΠΏΡΠΎΠ²ΠΎΠ»ΠΎΡΠ½Π°Ρ Π²ΡΡΠ΅Π·ΠΊΠ°: 1 β ΠΏΡΠΎΠ²ΠΎΠ»ΠΎΠΊΠ°, 2 β ΠΎΠ±ΡΠ°Π±Π°ΡΡΠ²Π°Π΅ΠΌΠ°Ρ Π΄Π΅ΡΠ°Π»Ρ, 3 β Π½Π°ΠΏΡΠ°Π²Π»ΡΡΡΠΈΠ΅ ΡΠΎΠ»ΠΈΠΊΠΈ, 4 β ΡΡΡΡΠΎΠΉΡΡΠ²ΠΎ Π΄Π»Ρ ΡΠ΅Π³ΡΠ»ΠΈΡΠΎΠ²Π°Π½ΠΈΡ ΡΠΊΠΎΡΠΎΡΡΠΈ ΠΏΡΠΎΡΡΠΆΠΊΠΈ ΠΏΡΠΎΠ²ΠΎΠ»ΠΎΠΊΠΈ
ΠΠ»Ρ ΡΡΡΡΠ°Π½Π΅Π½ΠΈΡ Π²Π»ΠΈΡΠ½ΠΈΡ ΠΈΠ·Π½ΠΎΡΠ° ΠΏΡΠΎΠ²ΠΎΠ»ΠΎΠΊΠΈ Π½Π° ΡΠΎΡΠ½ΠΎΡΡΡ ΠΎΠ±ΡΠ°Π±ΠΎΡΠΊΠΈ, ΠΏΡΠΎΠ²ΠΎΠ»ΠΎΠΊΠ° ΠΏΠ΅ΡΠ΅ΠΌΠ°ΡΡΠ²Π°Π΅ΡΡΡ Ρ ΠΎΠ΄Π½ΠΎΠΉ ΠΊΠ°ΡΡΡΠΊΠΈ Π½Π° Π΄ΡΡΠ³ΡΡ, ΡΡΠΎ ΠΏΠΎΠ·Π²ΠΎΠ»ΡΠ΅Ρ Π²ΡΠ΅ Π½ΠΎΠ²ΡΠΌ ΡΠ»Π΅ΠΌΠ΅Π½ΡΠ°ΠΌ ΡΡΠ°ΡΡΠ²ΠΎΠ²Π°ΡΡ Π² ΡΠ°Π±ΠΎΡΠ΅. ΠΡΠΈ ΠΏΠ΅ΡΠ΅ΠΌΠΎΡΠΊΠ΅ ΠΎΡΡΡΠ΅ΡΡΠ²Π»ΡΠ΅ΡΡΡ Π½Π΅Π±ΠΎΠ»ΡΡΠΎΠΉ Π½Π°ΡΡΠ³. ΠΠΎΠ·Π»Π΅ ΠΎΠ±ΡΠ°Π±Π°ΡΡΠ²Π°Π΅ΠΌΠΎΠΉ Π·Π°Π³ΠΎΡΠΎΠ²ΠΊΠΈ ΡΡΡΠ°Π½ΠΎΠ²Π»Π΅Π½Ρ ΡΠΎΠ»ΠΈΠΊΠΈ, ΠΎΡΠΈΠ΅Π½ΡΠΈΡΡΡΡΠΈΠ΅ ΠΏΡΠΎΠ²ΠΎΠ»ΠΎΠΊΡ ΠΎΡΠ½ΠΎΡΠΈΡΠ΅Π»ΡΠ½ΠΎ ΠΎΠ±ΡΠ°Π±Π°ΡΡΠ²Π°Π΅ΠΌΠΎΠΉ Π΄Π΅ΡΠ°Π»ΠΈ. Π‘Π»ΠΎΠΆΠ½ΠΎΠΊΠΎΠ½ΡΡΡΠ½Π°Ρ ΠΏΡΠΎΠ²ΠΎΠ»ΠΎΡΠ½Π°Ρ Π²ΡΡΠ΅Π·ΠΊΠ° ΠΏΡΠΈΠΌΠ΅Π½ΡΠ΅ΡΡΡ ΠΏΡΠΈ ΠΏΡΠ΅ΡΠΈΠ·ΠΈΠΎΠ½Π½ΠΎΠΌ ΡΠ΅Π·Π°Π½ΠΈΠΈ Π·Π°Π³ΠΎΡΠΎΠ²ΠΎΠΊ, ΠΏΡΠΎΡΠ΅Π·Π°Π½ΠΈΠΈ ΡΠΎΡΠ½ΡΡ ΡΠ΅Π»Π΅ΠΉ, ΡΠ΅Π·Π°Π½ΠΈΠΈ ΠΏΠΎΠ»ΡΠΏΡΠΎΠ²ΠΎΠ΄Π½ΠΈΠΊΠΎΠ²ΡΡ ΠΌΠ°ΡΠ΅ΡΠΈΠ°Π»ΠΎΠ², ΠΎΠ±ΡΠ°Π±ΠΎΡΠΊΠ΅ ΡΠΈΠ»ΠΈΠ½Π΄ΡΠΈΡΠ΅ΡΠΊΠΈΡ , ΠΊΠΎΠ½ΠΈΡΠ΅ΡΠΊΠΈΡ Π½Π°ΡΡΠΆΠ½ΡΡ ΠΈ Π²Π½ΡΡΡΠ΅Π½Π½ΠΈΡ ΠΏΠΎΠ²Π΅ΡΡ Π½ΠΎΡΡΠ΅ΠΉ.
Π ΠΎΡΠ½ΠΎΠ²Π½ΡΠΌ Π΄ΠΎΡΡΠΎΠΈΠ½ΡΡΠ²Π°ΠΌ ΡΠ»Π΅ΠΊΡΡΠΎΡΡΠΎΠ·ΠΈΠΎΠ½Π½ΠΎΠΉ ΠΎΠ±ΡΠ°Π±ΠΎΡΠΊΠΈ ΠΏΡΠΎΠ²ΠΎΠ»ΠΎΡΠ½ΡΠΌ ΡΠ»Π΅ΠΊΡΡΠΎΠ΄ΠΎΠΌ-ΠΈΠ½ΡΡΡΡΠΌΠ΅Π½ΡΠΎΠΌ ΠΎΡΠ½ΠΎΡΠΈΡΡΡ Π²ΡΡΠΎΠΊΠ°Ρ ΡΠΎΡΠ½ΠΎΡΡΡ ΠΈ Π²ΠΎΠ·ΠΌΠΎΠΆΠ½ΠΎΡΡΡ ΡΠΈΡΠΎΠΊΠΎΠΉ Π°Π²ΡΠΎΠΌΠ°ΡΠΈΠ·Π°ΡΠΈΠΈ ΠΏΡΠΎΡΠ΅ΡΡΠ°.
ΠΠ»Π΅ΠΊΡΡΠΎΠΊΠΎΠ½ΡΠ°ΠΊΡΠ½ΡΠΉ ΡΠΏΠΎΡΠΎΠ± ΠΎΠ±ΡΠ°Π±ΠΎΡΠΊΠΈ. ΠΠ»Π΅ΠΊΡΡΠΎΠΊΠΎΠ½ΡΠ°ΠΊΡΠ½Π°Ρ ΠΎΠ±ΡΠ°Π±ΠΎΡΠΊΠ° ΠΌΠ°ΡΠ΅ΡΠΈΠ°Π»ΠΎΠ² ΡΠ²Π»ΡΠ΅ΡΡΡ ΡΠ°Π·Π½ΠΎΠ²ΠΈΠ΄Π½ΠΎΡΡΡΡ ΡΠ»Π΅ΠΊΡΡΠΎΡΡΠΎΠ·ΠΈΠΎΠ½Π½ΠΎΠΉ ΠΎΠ±ΡΠ°Π±ΠΎΡΠΊΠΈ. ΠΡΠ»ΠΈΡΠΈΠ΅ Π΅Π΅ ΡΠΎΡΡΠΎΠΈΡ Π² ΡΠΎΠΌ, ΡΡΠΎ ΠΈΠΌΠΏΡΠ»ΡΡΡ ΡΠ»Π΅ΠΊΡΡΠΈΡΠ΅ΡΠΊΠΎΠΉ ΡΠ½Π΅ΡΠ³ΠΈΠΈ Π³Π΅Π½Π΅ΡΠΈΡΡΡΡΡΡ Π² ΡΠ΅Π·ΡΠ»ΡΡΠ°ΡΠ΅ Π²Π·Π°ΠΈΠΌΠ½ΠΎΠ³ΠΎ ΠΏΠ΅ΡΠ΅ΠΌΠ΅ΡΠ΅Π½ΠΈΡ ΡΠ»Π΅ΠΊΡΡΠΎΠ΄ΠΎΠ² ΠΈΠ»ΠΈ ΠΏΡΠ΅ΡΡΠ²Π°Π½ΠΈΡ ΡΠ»Π΅ΠΊΡΡΠΈΡΠ΅ΡΠΊΠΎΠ³ΠΎ ΡΠ°Π·ΡΡΠ΄Π° ΠΏΡΠΈ ΠΏΡΠΎΠΊΠ°ΡΠΊΠ΅ ΠΆΠΈΠ΄ΠΊΠΎΡΡΠΈ ΠΏΠΎΠ΄ Π΄Π°Π²Π»Π΅Π½ΠΈΠ΅ΠΌ. ΠΠ»Π΅ΠΊΡΡΠΎΠΊΠΎΠ½ΡΠ°ΠΊΡΠ½ΡΡ ΠΎΠ±ΡΠ°Π±ΠΎΡΠΊΡ ΠΌΠΎΠΆΠ½ΠΎ ΠΏΡΠΎΠ²ΠΎΠ΄ΠΈΡΡ ΠΏΡΠΈ ΠΏΠΎΡΡΠΎΡΠ½Π½ΠΎΠΌ ΠΈ ΠΏΠ΅ΡΠ΅ΠΌΠ΅Π½Π½ΠΎΠΌ ΡΠΎΠΊΠ΅, Π² Π²ΠΎΠ·Π΄ΡΡ Π΅ ΠΈΠ»ΠΈ ΠΆΠΈΠ΄ΠΊΠΎΡΡΠΈ (Π²ΠΎΠ΄Π° Ρ Π°Π½ΡΠΈΠΊΠΎΡΡΠΎΠ·ΠΈΠΎΠ½Π½ΡΠΌΠΈ Π΄ΠΎΠ±Π°Π²ΠΊΠ°ΠΌΠΈ). ΠΡΠΈ ΠΎΠ±ΡΠ°Π±ΠΎΡΠΊΠ΅ ΡΠ»Π΅ΠΊΡΡΠΎΠ΄-ΠΈΠ½ΡΡΡΡΠΌΠ΅Π½Ρ ΠΈ Π·Π°Π³ΠΎΡΠΎΠ²ΠΊΡ ΠΏΠΎΠ»Π½ΠΎΡΡΡΡ ΠΏΠΎΠ³ΡΡΠΆΠ°ΡΡ Π² ΠΆΠΈΠ΄ΠΊΠΎΡΡΡ Π»ΠΈΠ±ΠΎ ΠΏΠΎΠ΄Π°ΡΡ ΠΆΠΈΠ΄ΠΊΠΎΡΡΡ Π² ΠΌΠ΅ΠΆΡΠ»Π΅ΠΊΡΡΠΎΠ΄Π½ΡΠΉ ΠΏΡΠΎΠΌΠ΅ΠΆΡΡΠΎΠΊ ΡΠ°ΡΠΏΡΠ»Π΅Π½ΠΈΠ΅ΠΌ. ΠΠ±ΡΠ°Π±ΠΎΡΠΊΡ ΠΏΡΠΎΠΈΠ·Π²ΠΎΠ΄ΡΡ ΠΏΡΠΈ Π·Π½Π°ΡΠΈΡΠ΅Π»ΡΠ½ΡΡ ΡΠΎΠΊΠ°Ρ (Π΄ΠΎ 5000 Π) ΠΈ Π½Π°ΠΏΡΡΠΆΠ΅Π½ΠΈΡΡ Ρ ΠΎΠ»ΠΎΡΡΠΎΠ³ΠΎ Ρ ΠΎΠ΄Π° ΠΈΡΡΠΎΡΠ½ΠΈΠΊΠ° ΠΏΠΈΡΠ°Π½ΠΈΡ 18-40 Π. ΠΠ»Π΅ΠΊΡΡΠΎΠΊΠΎΠ½ΡΠ°ΠΊΡΠ½ΡΠΌ ΠΌΠ΅ΡΠΎΠ΄ΠΎΠΌ ΠΏΡΠΎΠΈΠ·Π²ΠΎΠ΄ΡΡ ΠΏΠΎΠ»ΡΡΠΈΡΡΠΎΠ²ΠΎΠ΅ ΡΠΎΡΠ΅Π½ΠΈΠ΅ ΡΠ΅Π» Π²ΡΠ°ΡΠ΅Π½ΠΈΡ, ΡΠΈΡΡΠΎΠ²ΡΡ ΡΠ΅Π·ΠΊΡ, ΠΏΡΠΎΡΠΈΠ²Π°Π½ΠΈΠ΅ ΡΠΈΠ»ΠΈΠ½Π΄ΡΠΈΡΠ΅ΡΠΊΠΈΡ , ΡΠ°ΡΠΎΠ½Π½ΡΡ ΠΎΡΠ²Π΅ΡΡΡΠΈΠΉ ΠΈ ΠΎΠ±ΡΠ΅ΠΌΠ½ΡΡ ΠΏΠΎΠ»ΠΎΡΡΠ΅ΠΉ, ΡΡΠ΅Π·Π΅ΡΠΎΠ²Π°Π½ΠΈΠ΅, ΡΠ»ΠΈΡΠΎΠ²Π°Π½ΠΈΠ΅. ΠΠ»Π΅ΠΊΡΡΠΎΠΊΠΎΠ½ΡΠ°ΠΊΡΠ½ΡΠΉ ΠΌΠ΅ΡΠΎΠ΄ ΠΎΡΠΎΠ±Π΅Π½Π½ΠΎ ΡΡΡΠ΅ΠΊΡΠΈΠ²Π΅Π½ ΠΏΡΠΈ ΠΎΠ±ΡΠ°Π±ΠΎΡΠΊΠ΅ Π·Π°Π³ΠΎΡΠΎΠ²ΠΎΠΊ ΠΈΠ· ΡΡΡΠ΄Π½ΠΎΠΎΠ±ΡΠ°Π±Π°ΡΡΠ²Π°Π΅ΠΌΡΡ ΡΡΠ°Π»Π΅ΠΉ ΠΈ ΡΠΏΠ»Π°Π²ΠΎΠ², Π° ΡΠ°ΠΊΠΆΠ΅ ΡΡΠ³ΡΠ½ΠΎΠ² Π²ΡΡΠΎΠΊΠΎΠΉ ΡΠ²Π΅ΡΠ΄ΠΎΡΡΠΈ, ΠΌΠΎΠ½ΠΎΠΊΡΠΈΡΡΠ°Π»Π»ΠΎΠ², ΠΌΠ°ΡΠ΅ΡΠΈΠ°Π»ΠΎΠ² Ρ Π²ΡΡΠΎΠΊΠΈΠΌΠΈ ΡΠ΅ΠΏΠ»ΠΎΡΠΈΠ·ΠΈΡΠ΅ΡΠΊΠΈΠΌΠΈ ΡΠ²ΠΎΠΉΡΡΠ²Π°ΠΌΠΈ.
ΠΡΠΈΠ½ΡΠΈΠΏΠΈΠ°Π»ΡΠ½Π°Ρ ΡΡ Π΅ΠΌΠ° ΡΡΡΠ°Π½ΠΎΠ²ΠΊΠΈ Π΄Π»Ρ ΡΠ»Π΅ΠΊΡΡΠΎΠΊΠΎΠ½ΡΠ°ΠΊΡΠ½ΠΎΠΉ ΠΎΠ±ΡΠ°Π±ΠΎΡΠΊΠΈ Π²ΡΠ³Π»ΡΠ΄ΠΈΡ ΡΠ»Π΅Π΄ΡΡΡΠΈΠΌ ΠΎΠ±ΡΠ°Π·ΠΎΠΌ. ΠΠ°Π³ΠΎΡΠΎΠ²ΠΊΠ° ΠΈ ΡΠ»Π΅ΠΊΡΡΠΎΠ΄-ΠΈΠ½ΡΡΡΡΠΌΠ΅Π½Ρ, ΠΈΠΌΠ΅ΡΡΠΈΠ΅ ΠΎΡΡ Π²ΡΠ°ΡΠ°ΡΠ΅Π»ΡΠ½ΠΎΠΉ ΡΠΈΠΌΠΌΠ΅ΡΡΠΈΠΈ ΠΈ Π²ΠΊΠ»ΡΡΠ΅Π½Π½ΡΠ΅ Π² ΡΠ΅ΠΏΡ Ρ ΠΈΡΡΠΎΡΠ½ΠΈΠΊΠΎΠΌ ΠΏΠΈΡΠ°Π½ΠΈΡ, ΠΏΠΎΡΠ»Π΅ ΡΠΎΠΏΡΠΈΠΊΠΎΡΠ½ΠΎΠ²Π΅Π½ΠΈΡ ΡΠΎΠ²Π΅ΡΡΠ°ΡΡ Π²ΡΠ°ΡΠ°ΡΠ΅Π»ΡΠ½ΠΎΠ΅ Π΄Π²ΠΈΠΆΠ΅Π½ΠΈΠ΅ Π΄ΡΡΠ³ ΠΎΡΠ½ΠΎΡΠΈΡΠ΅Π»ΡΠ½ΠΎ Π΄ΡΡΠ³Π°.
ΠΡΠΈ ΡΠΎΠ±Π»ΡΠ΄Π΅Π½ΠΈΠΈ ΡΡΠ»ΠΎΠ²ΠΈΠΉ, Π½Π΅ΠΎΠ±Ρ ΠΎΠ΄ΠΈΠΌΡΡ Π΄Π»Ρ ΡΠ΅Π°Π»ΠΈΠ·Π°ΡΠΈΠΈ ΡΠ»Π΅ΠΊΡΡΠΎΡΡΠΎΠ·ΠΈΠΎΠ½Π½ΡΡ ΠΏΡΠΎΡΠ΅ΡΡΠΎΠ², ΠΏΡΠΎΠΈΡΡ ΠΎΠ΄ΠΈΡ ΡΡΠ΅ΠΌ ΠΌΠ΅ΡΠ°Π»Π»Π° Ρ Π·Π°Π³ΠΎΡΠΎΠ²ΠΊΠΈ.
Π£ΠΏΡΠΎΡΠ½Π΅Π½ΠΈΠ΅ ΠΏΠΎΠ²Π΅ΡΡ Π½ΠΎΡΡΠ½ΠΎΠ³ΠΎ ΡΠ»ΠΎΡ ΠΌΠ΅ΡΠ°Π»Π»Π° (ΡΠ»Π΅ΠΊΡΡΠΎΡΡΠΎΠ·ΠΈΠΎΠ½Π½ΠΎΠ΅ Π»Π΅Π³ΠΈΡΠΎΠ²Π°Π½ΠΈΠ΅)
ΠΠ΄Π½ΠΈΠΌ ΠΈΠ· ΠΏΡΠ΅ΠΈΠΌΡΡΠ΅ΡΡΠ² ΡΠ»Π΅ΠΊΡΡΠΎΡΡΠΎΠ·ΠΈΠΎΠ½Π½ΠΎΠΉ ΠΎΠ±ΡΠ°Π±ΠΎΡΠΊΠΈ ΠΌΠ΅ΡΠ°Π»Π»ΠΎΠ² ΡΠ²Π»ΡΠ΅ΡΡΡ ΡΠΎ, ΡΡΠΎ ΠΏΡΠΈ ΠΎΠΏΡΠ΅Π΄Π΅Π»Π΅Π½Π½ΡΡ ΡΡΠ»ΠΎΠ²ΠΈΡΡ ΡΠ΅Π·ΠΊΠΎ ΠΏΠΎΠ²ΡΡΠ°ΡΡΡΡ ΠΏΡΠΎΡΠ½ΠΎΡΡΠ½ΡΠ΅ ΡΠ²ΠΎΠΉΡΡΠ²Π° ΠΏΠΎΠ²Π΅ΡΡ Π½ΠΎΡΡΠΈ Π·Π°Π³ΠΎΡΠΎΠ²ΠΊΠΈ. ΠΡΡ ΠΎΡΠΎΠ±Π΅Π½Π½ΠΎΡΡΡ ΠΈΡΠΏΠΎΠ»ΡΠ·ΡΡΡ Π΄Π»Ρ ΡΠ»ΡΡΡΠ΅Π½ΠΈΡ ΠΈΠ·Π½ΠΎΡΠΎΡΡΠΎΠΉΠΊΠΎΡΡΠΈ ΡΠ΅ΠΆΡΡΠ΅Π³ΠΎ ΠΈΠ½ΡΡΡΡΠΌΠ΅Π½ΡΠ°, ΡΡΠ°ΠΌΠΏΠΎΠ², ΠΏΡΠ΅ΡΡ-ΡΠΎΡΠΌ ΠΈ Ρ.Π΄. ΠΡΠΈ ΡΠ»Π΅ΠΊΡΡΠΎΡΡΠΎΠ·ΠΈΠΎΠ½Π½ΠΎΠΌ Π»Π΅Π³ΠΈΡΠΎΠ²Π°Π½ΠΈΠΈ ΠΏΡΠΈΠΌΠ΅Π½ΡΡΡ ΠΎΠ±ΡΠ°ΡΠ½ΡΡ ΠΏΠΎΠ»ΡΡΠ½ΠΎΡΡΡ (Π·Π°Π³ΠΎΡΠΎΠ²ΠΊΠ° ΡΠ²Π»ΡΠ΅ΡΡΡ ΠΊΠ°ΡΠΎΠ΄ΠΎΠΌ, ΠΈΠ½ΡΡΡΡΠΌΠ΅Π½Ρ β Π°Π½ΠΎΠ΄ΠΎΠΌ) ΠΎΠ±ΡΠ°Π±ΠΎΡΠΊΡ ΠΏΡΠΎΠΈΠ·Π²ΠΎΠ΄ΡΡ ΠΎΠ±ΡΡΠ½ΠΎ Π°ΡΠΎΠΌΠ°ΠΌΠΈ ΠΈΠ½ΡΡΡΡΠΌΠ΅Π½ΡΠ°-ΡΠ»Π΅ΠΊΡΡΠΎΠ΄Π° Π² ΡΠ»Π΅ΠΊΡΡΠΎΠΈΠΌΠΏΡΠ»ΡΡΠ½ΠΎΠΌ ΡΠ΅ΠΆΠΈΠΌΠ΅ (ΡΠΌ. ΡΠΈΡ. 1.15) Π² Π²ΠΎΠ·Π΄ΡΡΠ½ΠΎΠΉ ΡΡΠ΅Π΄Π΅ ΠΈ, ΠΊΠ°ΠΊ ΠΏΡΠ°Π²ΠΈΠ»ΠΎ, Ρ Π²ΠΈΠ±ΡΠ°ΡΠΈΠ΅ΠΉ ΡΠ»Π΅ΠΊΡΡΠΎΠ΄Π°.
Π ΠΈΡ. 1.15 Π‘Ρ Π΅ΠΌΠ° ΡΠ»Π΅ΠΊΡΡΠΎΡΡΠΎΠ·ΠΈΠΎΠ½Π½ΠΎΠ³ΠΎ Π»Π΅Π³ΠΈΡΠΎΠ²Π°Π½ΠΈΡ: 1 β Π»Π΅Π³ΠΈΡΡΡΡΠΈΠΉ ΡΠ»Π΅ΠΊΡΡΠΎΠ΄-ΠΈΠ½ΡΡΡΡΠΌΠ΅Π½Ρ, 2 β Π»Π΅Π³ΠΈΡΡΠ΅ΠΌΠ°Ρ Π΄Π΅ΡΠ°Π»Ρ
ΠΡΠ½ΠΎΠ²Π½ΡΠ΅ ΠΏΡΠ΅ΠΈΠΌΡΡΠ΅ΡΡΠ²Π° ΡΠ»Π΅ΠΊΡΡΠΎΡΡΠΎΠ·ΠΈΠΎΠ½Π½ΠΎΠ³ΠΎ Π»Π΅Π³ΠΈΡΠΎΠ²Π°Π½ΠΈΡ Π·Π°ΠΊΠ»ΡΡΠ°ΡΡΡΡ Π² ΡΠ»Π΅Π΄ΡΡΡΠ΅ΠΌ: ΠΏΠΎΠΊΡΡΡΠΈΡ ΠΈΠΌΠ΅ΡΡ Π±ΠΎΠ»ΡΡΡΡ ΡΡΠ΅ΠΏΠ΅Π½Ρ ΡΡΠ΅ΠΏΠ»Π΅Π½ΠΈΡ Ρ ΠΌΠ°ΡΠ΅ΡΠΈΠ°Π»ΠΎΠΌ ΠΎΡΠ½ΠΎΠ²Ρ; ΠΏΠΎΠΊΡΡΠ²Π°Π΅ΠΌΡΠ΅ ΠΏΠΎΠ²Π΅ΡΡ Π½ΠΎΡΡΠΈ Π½Π΅ ΡΡΠ΅Π±ΡΡΡ ΠΏΡΠ΅Π΄Π²Π°ΡΠΈΡΠ΅Π»ΡΠ½ΠΎΠΉ ΠΏΠΎΠ΄Π³ΠΎΡΠΎΠ²ΠΊΠΈ; Π²ΠΎΠ·ΠΌΠΎΠΆΠ½ΠΎ Π½Π°Π½Π΅ΡΠ΅Π½ΠΈΠ΅ Π½Π΅ ΡΠΎΠ»ΡΠΊΠΎ ΠΌΠ΅ΡΠ°Π»Π»ΠΎΠ² ΠΈ ΡΠΏΠ»Π°Π²ΠΎΠ², Π½ΠΎ ΠΈ ΠΈΡ ΠΊΠΎΠΌΠΏΠΎΠ·ΠΈΡΠΈΠΉ.
ΠΡΠΎΡΠ΅ΡΡΡ, ΠΏΡΠΎΠΈΡΡ ΠΎΠ΄ΡΡΠΈΠ΅ ΠΏΡΠΈ ΡΠ»Π΅ΠΊΡΡΠΎΡΡΠΎΠ·ΠΈΠΎΠ½Π½ΠΎΠΌ ΡΠΏΡΠΎΡΠ½Π΅Π½ΠΈΠΈ, ΡΠ»ΠΎΠΆΠ½Ρ ΠΈ ΡΠ²Π»ΡΡΡΡΡ ΠΏΡΠ΅Π΄ΠΌΠ΅ΡΠΎΠΌ ΡΡΠ°ΡΠ΅Π»ΡΠ½ΡΡ ΠΈΡΡΠ»Π΅Π΄ΠΎΠ²Π°Π½ΠΈΠΉ. ΠΠ΄Π½Π°ΠΊΠΎ, ΡΡΡΠ½ΠΎΡΡΡ ΡΠΏΡΠΎΡΠ½Π΅Π½ΠΈΡ ΡΠΎΡΡΠΎΠΈΡ Π² ΡΠΎΠΌ, ΡΡΠΎ ΠΏΡΠΈ ΡΠ»Π΅ΠΊΡΡΠΎΠΈΡΠΊΡΠΎΠ²ΠΎΠΌ ΡΠ°Π·ΡΡΠ΄Π΅ Π² Π²ΠΎΠ·Π΄ΡΡΠ½ΠΎΠΉ ΡΡΠ΅Π΄Π΅ ΠΏΡΠΎΠΈΡΡ ΠΎΠ΄ΠΈΡ ΠΏΠ΅ΡΠ΅Π½ΠΎΡ ΠΌΠ°ΡΠ΅ΡΠΈΠ°Π»Π° ΡΠ»Π΅ΠΊΡΡΠΎΠ΄Π° Π½Π° Π·Π°Π³ΠΎΡΠΎΠ²ΠΊΡ (ΡΠΌ. ΡΠΈΡ. 1.15). ΠΠ΅ΡΠ΅Π½Π΅ΡΠ΅Π½Π½ΡΠΉ ΠΌΠ°ΡΠ΅ΡΠΈΠ°Π» ΡΠ»Π΅ΠΊΡΡΠΎΠ΄Π° Π»Π΅Π³ΠΈΡΡΠ΅Ρ ΠΌΠ΅ΡΠ°Π»Π» Π·Π°Π³ΠΎΡΠΎΠ²ΠΊΠΈ ΠΈ, Ρ ΠΈΠΌΠΈΡΠ΅ΡΠΊΠΈ ΡΠΎΠ΅Π΄ΠΈΠ½ΡΡΡΡ Ρ ΠΈΠΎΠ½Π°ΠΌΠΈ Π°Π·ΠΎΡΠ° Π²ΠΎΠ·Π΄ΡΡ Π°, ΡΠ³Π»Π΅ΡΠΎΠ΄ΠΎΠΌ ΠΈ ΠΌΠ°ΡΠ΅ΡΠΈΠ°Π»ΠΎΠΌ Π·Π°Π³ΠΎΡΠΎΠ²ΠΊΠΈ, ΠΎΠ±ΡΠ°Π·ΡΠ΅Ρ ΠΈΠ·Π½ΠΎΡΠΎΡΡΡΠΎΠΉΡΠΈΠ²ΡΠΉ ΡΠΏΡΠΎΡΠ½Π΅Π½Π½ΡΠΉ ΡΠ»ΠΎΠΉ, ΡΠΎΡΡΠΎΡΡΠΈΠΉ ΠΈΠ· Π½ΠΈΡΡΠΈΠ΄ΠΎΠ², ΠΊΠ°ΡΠ±ΠΎΠ½ΠΈΡΡΠΈΠ΄ΠΎΠ² ΠΈ Π΄ΡΡΠ³ΠΈΡ Π·Π°ΠΊΠ°Π»ΠΎΡΠ½ΡΡ ΡΡΡΡΠΊΡΡΡ.β
ΠΡΠΈ ΡΠ»Π΅ΠΊΡΡΠΎΠΈΡΠΊΡΠΎΠ²ΠΎΠΌ Π»Π΅Π³ΠΈΡΠΎΠ²Π°Π½ΠΈΠΈ ΠΌΠΈΠΊΡΠΎΡΠ²Π΅ΡΠ΄ΠΎΡΡΡ Π±Π΅Π»ΠΎΠ³ΠΎ ΡΠ»ΠΎΡ Π² ΡΠ³Π»Π΅ΡΠΎΠ΄ΠΈΡΡΡΡ ΡΡΠ°Π»ΡΡ ΠΌΠΎΠΆΠ΅Ρ Π±ΡΡΡ Π΄ΠΎΠ²Π΅Π΄Π΅Π½Π° Π΄ΠΎ 230 ΠΠΠ°. Π’ΠΎΠ»ΡΠΈΠ½Π° ΡΠ»ΠΎΡ ΠΏΠΎΠΊΡΡΡΠΈΡ, ΠΏΠΎΠ»ΡΡΠ°Π΅ΠΌΠΎΠ³ΠΎ Π½Π° Π½Π΅ΠΊΠΎΡΠΎΡΡΡ ΡΡΡΠ°Π½ΠΎΠ²ΠΊΠ°Ρ , ΡΠΎΡΡΠ°Π²Π»ΡΠ΅Ρ 0,003-0,2 ΠΌΠΌ. ΠΡΠΈ ΡΠΏΡΠΎΡΠ½Π΅Π½ΠΈΠΈ ΠΏΠΎΠ²Π΅ΡΡ Π½ΠΎΡΡΠΈ Π΄Π΅ΡΠ°Π»Π΅ΠΉ ΠΌΠ°ΡΠΈΠ½ (Π½Π°ΠΏΡΠΈΠΌΠ΅Ρ, Π½Π° ΡΡΡΠ°Π½ΠΎΠ²ΠΊΠ΅ ΠΠ-2Π) ΠΌΠΎΠΆΠ½ΠΎ ΠΏΠΎΠ»ΡΡΠΈΡΡ Π³Π»ΡΠ±ΠΈΠ½Ρ ΡΠ»ΠΎΡ Π΄ΠΎ 0,5-1,6 ΠΌΠΌ Ρ ΠΌΠΈΠΊΡΠΎΡΠ²Π΅ΡΠ΄ΠΎΡΡΡΡ 50-60 ΠΠΠ° (ΠΏΡΠΈ ΡΠΏΡΠΎΡΠ½Π΅Π½ΠΈΠΈ ΡΠ΅ΡΡΠΎΡ ΡΠΎΠΌΠΎΠΌ).
Π Π°Π·Π»ΠΈΡΠ°ΡΡ ΡΠΈΡΡΡΡ ΠΎΠ±ΡΠ°Π±ΠΎΡΠΊΡ, ΠΊΠΎΡΠΎΡΠ°Ρ ΡΠΎΠΎΡΠ²Π΅ΡΡΡΠ²ΡΠ΅Ρ Π²ΡΡΠΎΠΊΠΈΠΌ Π½Π°ΠΏΡΡΠΆΠ΅Π½ΠΈΡΠΌ ΠΈ Π½Π΅Π±ΠΎΠ»ΡΡΠΈΠΌ Π·Π½Π°ΡΠ΅Π½ΠΈΡΠΌ ΡΠΎΠΊΠΎΠ² ΠΊΠΎΡΠΎΡΠΊΠΎΠ³ΠΎ Π·Π°ΠΌΡΠΊΠ°Π½ΠΈΡ (Π΄ΠΎ 20 Π), ΠΈ Π³ΡΡΠ±ΡΡ (Π³ΡΡΠ±ΠΎΠ΅ Π»Π΅Π³ΠΈΡΠΎΠ²Π°Π½ΠΈΠ΅) ΠΏΡΠΈ Π½ΠΈΠ·ΠΊΠΈΡ Π½Π°ΠΏΡΡΠΆΠ΅Π½ΠΈΡΡ 50-60 Π ΠΈ ΡΠΎΠΊΠ°Ρ ΠΊΠΎΡΠΎΡΠΊΠΎΠ³ΠΎ Π·Π°ΠΌΡΠΊΠ°Π½ΠΈΡ ΡΠ²ΡΡΠ΅ 20 Π.
Π Π°Π±ΠΎΡΠ° Π½Π° ΡΠ»Π΅ΠΊΡΡΠΎΡΡΠΎΠ·ΠΈΠΎΠ½Π½ΡΡ ΡΡΠ°Π½ΠΊΠ°Ρ . ΠΠΎΠ΄Π³ΠΎΡΠΎΠ²ΠΊΠ° ΡΠ»Π΅ΠΊΡΡΠΎΡΡΠΎΠ·ΠΈΠΎΠ½Π½ΡΡ ΡΡΠ°Π½ΠΊΠΎΠ² ΠΊ ΡΠ°Π±ΠΎΡΠ΅ Π·Π°ΠΊΠ»ΡΡΠ°Π΅ΡΡΡ Π² ΡΡΡΠ°Π½ΠΎΠ²ΠΊΠ΅ Π·Π°Π³ΠΎΡΠΎΠ²ΠΊΠΈ ΠΈ ΡΠ»Π΅ΠΊΡΡΠΎΠ΄Π°-ΠΈΠ½ΡΡΡΡΠΌΠ΅Π½ΡΠ° ΠΈ Π²ΡΠ²Π΅ΡΠΊΠ΅ ΠΈΡ Π²Π·Π°ΠΈΠΌΠ½ΠΎΠ³ΠΎ ΡΠ°ΡΠΏΠΎΠ»ΠΎΠΆΠ΅Π½ΠΈΡ, ΠΏΠΎΠ΄Π³ΠΎΡΠΎΠ²ΠΊΠ΅ Π²Π°Π½Π½Ρ ΠΊ ΡΠ°Π±ΠΎΡΠ΅ ΠΈ ΡΠΈΡΡΠ΅ΠΌΡ ΠΏΡΠΎΠΊΠ°ΡΠΊΠΈ ΡΠ°Π±ΠΎΡΠ΅ΠΉ ΠΆΠΈΠ΄ΠΊΠΎΡΡΠΈ, Π²ΡΠ±ΠΎΡΡ ΠΈ Π½Π°ΡΡΡΠΎΠΉΠΊΠ΅ ΡΠ΅ΠΆΠΈΠΌΠΎΠ² Π³Π΅Π½Π΅ΡΠ°ΡΠΎΡΠ°. ΠΠ°Π³ΠΎΡΠΎΠ²ΠΊΡ ΡΡΡΠ°Π½Π°Π²Π»ΠΈΠ²Π°ΡΡ ΠΈ Π·Π°ΠΊΡΠ΅ΠΏΠ»ΡΡΡ Π½Π΅ΠΏΠΎΡΡΠ΅Π΄ΡΡΠ²Π΅Π½Π½ΠΎ Π½Π° ΡΡΠΎΠ»Π΅ ΡΡΠ°Π½ΠΊΠ° ΠΈΠ»ΠΈ Π² ΠΏΡΠΈΡΠΏΠΎΡΠΎΠ±Π»Π΅Π½ΠΈΠΈ. ΠΠ»Π΅ΠΊΡΡΠΎΠ΄-ΠΈΠ½ΡΡΡΡΠΌΠ΅Π½Ρ ΡΡΡΠ°Π½Π°Π²Π»ΠΈΠ²Π°ΡΡ Ρ Π²ΠΎΡΡΠΈΠΊΠΎΠΌ Π² ΡΠΏΠΈΠ½Π΄Π΅Π»Ρ Π³ΠΎΠ»ΠΎΠ²ΠΊΠΈ. ΠΡΠΈ Π²ΡΠ²Π΅ΡΠΊΠ΅ ΠΈΡΠΏΠΎΠ»ΡΠ·ΡΡΡ ΠΈΠ½Π΄ΠΈΠΊΠ°ΡΠΎΡΡ, ΠΎΠΏΡΠΈΡΠ΅ΡΠΊΠΈΠ΅ ΠΏΡΠΈΠ±ΠΎΡΡ, ΠΏΡΠΈΡΠΏΠΎΡΠΎΠ±Π»Π΅Π½ΠΈΡ, ΠΏΠΎΠ·Π²ΠΎΠ»ΡΡΡΠΈΠ΅ ΠΈΠ·ΠΌΠ΅Π½ΡΡΡ ΠΏΠΎΠ»ΠΎΠΆΠ΅Π½ΠΈΠ΅ ΠΈΠ½ΡΡΡΡΠΌΠ΅Π½ΡΠ° ΠΏΠΎ ΠΎΡΠ½ΠΎΡΠ΅Π½ΠΈΡ ΠΊ Π·Π°Π³ΠΎΡΠΎΠ²ΠΊΠ΅ ΠΈ ΡΠ³ΠΎΠ» Π½Π°ΠΊΠ»ΠΎΠ½Π°.
ΠΡΡΡΠ΅ΡΡΠ²ΠΈΠ² Π²ΡΠ²Π΅ΡΠΊΡ ΠΏΠΎΠ»ΠΎΠΆΠ΅Π½ΠΈΡ ΡΠ»Π΅ΠΊΡΡΠΎΠ΄-ΠΈΠ½ΡΡΡΡΠΌΠ΅Π½ΡΠ°, Π·Π°ΠΏΠΎΠ»Π½ΡΡΡ Π²Π°Π½Π½Ρ ΡΠ°Π±ΠΎΡΠ΅ΠΉ ΠΆΠΈΠ΄ΠΊΠΎΡΡΡΡ, ΠΏΡΠΎΠ²Π΅ΡΡΡΡ ΡΠ°Π±ΠΎΡΡ ΡΠΈΡΡΠ΅ΠΌΡ ΠΏΡΠΎΠΊΠ°ΡΠΊΠΈ, ΡΡΡΠ°Π½Π°Π²Π»ΠΈΠ²Π°ΡΡ Π½Π΅ΠΎΠ±Ρ ΠΎΠ΄ΠΈΠΌΠΎΠ΅ Π΄Π°Π²Π»Π΅Π½ΠΈΠ΅ ΠΏΡΠΎΠΊΠ°ΡΠΊΠΈ. ΠΠ°Π΄Π°ΡΡ ΡΠ΅ΠΆΠΈΠΌ Π³Π΅Π½Π΅ΡΠ°ΡΠΎΡΠ° ΠΈΠΌΠΏΡΠ»ΡΡΠΎΠ² (ΠΏΠΎΠ»ΡΡΠ½ΠΎΡΡΡ, ΡΠΎΡΠΌΠ° ΠΈΠΌΠΏΡΠ»ΡΡΠΎΠ², ΡΠΊΠ²Π°ΠΆΠ½ΠΎΡΡΡ, ΡΠ°ΡΡΠΎΡΡ ΡΠ»Π΅Π΄ΠΎΠ²Π°Π½ΠΈΡ ΠΈΠΌΠΏΡΠ»ΡΡΠΎΠ², ΡΡΠ΅Π΄Π½ΠΈΠΉ ΡΠΎΠΊ), ΠΏΠΎΠ»ΡΠ·ΡΡΡΡ ΡΠΎΠΎΡΠ²Π΅ΡΡΡΠ²ΡΡΡΠΈΠΌΠΈ ΡΠ°Π±Π»ΠΈΡΠ°ΠΌΠΈ ΠΈ Π½ΠΎΠΌΠΎΠ³ΡΠ°ΠΌΠΌΠ°ΠΌΠΈ. ΠΠ·ΠΌΠ΅Π½Π΅Π½ΠΈΠ΅ ΠΏΠΎΠ»ΡΡΠ½ΠΎΡΡΠΈ Π½Π°ΠΏΡΡΠΆΠ΅Π½ΠΈΡ Π³Π΅Π½Π΅ΡΠ°ΡΠΎΡΠ° ΠΈΠΌΠΏΡΠ»ΡΡΠΎΠ² ΠΏΡΠΎΠΈΠ·Π²ΠΎΠ΄ΠΈΡΡΡ ΠΏΡΡΠ΅ΠΌ ΠΏΠ΅ΡΠ΅ΠΊΠ»ΡΡΠ΅Π½ΠΈΡ Π½Π° ΡΡΠ΅ΠΏΡΠ΅Π»ΡΠ½ΠΎΠΌ ΡΠ°Π·ΡΠ΅ΠΌΠ΅ ΡΠΎΠΊΠΎΠΏΠΎΠ΄Π²ΠΎΠ΄ΠΎΠ² ΠΊ ΡΡΠ°Π½ΠΊΡ. ΠΡΠΈ ΡΠ°Π±ΠΎΡΠ΅ Ρ ΠΏΡΡΠΌΠΎΠΉ ΠΏΠΎΠ»ΡΡΠ½ΠΎΡΡΡΡ (ΡΠ»Π΅ΠΊΡΡΠΎΠΈΡΠΊΡΠΎΠ²ΠΎΠΉ ΡΠ΅ΠΆΠΈΠΌ) Π½Π° ΡΠ»Π΅ΠΊΡΡΠΎΠ΄ ΠΏΠΎΠ΄Π°Π΅ΡΡΡ ΠΎΡΡΠΈΡΠ°ΡΠ΅Π»ΡΠ½ΡΠΉ ΠΏΠΎΡΠ΅Π½ΡΠΈΠ°Π», Π° Π½Π° Π·Π°Π³ΠΎΡΠΎΠ²ΠΊΡ β ΠΏΠΎΠ»ΠΎΠΆΠΈΡΠ΅Π»ΡΠ½ΡΠΉ. ΠΠ»Ρ ΡΠ°Π±ΠΎΡΡ Ρ ΠΎΠ±ΡΠ°ΡΠ½ΠΎΠΉ ΠΏΠΎΠ»ΡΡΠ½ΠΎΡΡΡΡ (ΡΠ»Π΅ΠΊΡΡΠΎΠΈΠΌΠΏΡΠ»ΡΡΠ½ΡΠΉ ΡΠ΅ΠΆΠΈΠΌ) ΠΏΡΠΎΠΈΠ·Π²ΠΎΠ΄ΡΡ ΠΎΠ±ΡΠ°ΡΠ½ΠΎΠ΅ ΠΏΠ΅ΡΠ΅ΠΊΠ»ΡΡΠ΅Π½ΠΈΠ΅. Π£ΡΡΠ°Π½ΠΎΠ²ΠΊΡ ΡΠ»Π΅ΠΊΡΡΠΈΡΠ΅ΡΠΊΠΈΡ ΠΏΠ°ΡΠ°ΠΌΠ΅ΡΡΠΎΠ² ΠΈ ΡΠ΅ΠΆΠΈΠΌΠΎΠ² ΡΠ°Π±ΠΎΡΡ ΠΎΡΡΡΠ΅ΡΡΠ²Π»ΡΡΡ Ρ ΠΏΠΎΠΌΠΎΡΡΡ ΠΏΠ΅ΡΠ΅ΠΊΠ»ΡΡΠ°ΡΠ΅Π»Π΅ΠΉ, ΡΠ°ΡΠΏΠΎΠ»ΠΎΠΆΠ΅Π½Π½ΡΡ Π½Π° ΠΏΠ°Π½Π΅Π»ΠΈ ΠΏΡΠ»ΡΡΠ° ΡΠΏΡΠ°Π²Π»Π΅Π½ΠΈΡ. ΠΠ°ΡΡΡΠ°ΠΈΠ²Π°ΡΡ ΡΠ΅Π³ΡΠ»ΡΡΠΎΡ ΠΏΠΎΠ΄Π°ΡΠΈ, ΡΡΡΠ°Π½Π°Π²Π»ΠΈΠ²Π°Ρ ΡΠ΅ΠΊΠΎΠΌΠ΅Π½Π΄ΡΠ΅ΠΌΠΎΠ΅ Π½Π°ΠΏΡΡΠΆΠ΅Π½ΠΈΠ΅ ΡΠ΅Π³ΡΠ»ΡΡΠΎΡΠ°.
www.eti.su
ΠΠ»Π΅ΠΊΡΡΠΎΡΡΠΎΠ·ΠΈΠΎΠ½Π½Π°Ρ ΠΎΠ±ΡΠ°Π±ΠΎΡΠΊΠ° ΠΌΠ΅ΡΠ°Π»Π»ΠΎΠ² β ΠΏΡΠ΅ΠΈΠΌΡΡΠ΅ΡΡΠ²Π° ΡΠ΅Ρ Π½ΠΎΠ»ΠΎΠ³ΠΈΠΈ
ΠΠ΅ΡΠ°Π»Π» ΠΌΠΎΠΆΠ½ΠΎ ΠΎΠ±ΡΠ°Π±Π°ΡΡΠ²Π°ΡΡ ΡΠ°Π·Π½ΡΠΌΠΈ ΡΠΏΠΎΡΠΎΠ±Π°ΠΌΠΈ β ΡΠ»ΠΈΡΠΎΠ²ΠΊΠΎΠΉ, ΠΊΠΎΠ²ΠΊΠΎΠΉ, ΡΠΎΠΊΠ°ΡΠ½ΡΠΌΠΈ ΠΎΠΏΠ΅ΡΠ°ΡΠΈΡΠΌΠΈ. ΠΠ°ΠΈΠ±ΠΎΠ»Π΅Π΅ ΡΠΎΡΠ½ΡΠ΅ ΠΈ Π²ΡΡΠΎΠΊΠΎΠΊΠ°ΡΠ΅ΡΡΠ²Π΅Π½Π½ΡΠ΅ ΠΈΠ·Π΄Π΅Π»ΠΈΡ ΠΏΠΎΠΌΠΎΠ³Π°Π΅Ρ ΠΏΠΎΠ»ΡΡΠΈΡΡ ΡΠ»Π΅ΠΊΡΡΠΎΡΡΠΎΠ·ΠΈΠΎΠ½Π½Π°Ρ ΠΎΠ±ΡΠ°Π±ΠΎΡΠΊΠ°.
ΠΡΠ½ΠΎΠ²Π½ΡΠ΅ ΡΡΠ°ΠΏΡ ΡΠ°Π±ΠΎΡΡ
ΠΠ»Π΅ΠΊΡΡΠΎΡΡΠΎΠ·ΠΈΠΎΠ½Π½Π°Ρ ΠΎΠ±ΡΠ°Π±ΠΎΡΠΊΠ° ΠΌΠ΅ΡΠ°Π»Π»ΠΎΠ² ΡΡΠ΅Π±ΡΠ΅Ρ Π΄Π»Ρ ΡΠ°Π±ΠΎΡΡ Π½Π΅ΡΠΊΠΎΠ»ΡΠΊΠΈΡ ΠΊΠΎΠΌΠΏΠΎΠ½Π΅Π½ΡΠΎΠ²:
- ΠΈΡΡΠΎΡΠ½ΠΈΠΊ ΡΠ»Π΅ΠΊΡΡΠΈΡΠ΅ΡΡΠ²Π°;
- ΡΠ΅ΠΎΡΡΠ°Ρ;
- ΡΠ΅Π·Π΅ΡΠ²ΡΠ°Ρ Π΄Π»Ρ Π΄ΠΈΡΠ»Π΅ΠΊΡΡΠΈΡΠ΅ΡΠΊΠΎΠΉ ΠΆΠΈΠ΄ΠΊΠΎΡΡΠΈ;
- ΠΊΠΎΠ½Π΄Π΅Π½ΡΠ°ΡΠΎΡ;
- ΡΠ»Π΅ΠΊΡΡΠΎΠ΄.
Π‘ ΠΏΠΎΠΌΠΎΡΡΡ ΠΏΡΠΎΠΏΡΡΠΊΠ°Π½ΠΈΡ ΡΠΎΠΊΠ° ΡΠ΅ΡΠ΅Π· ΡΠ»Π΅ΠΊΡΡΠΎΠ΄Ρ Π²ΡΠΏΠΎΠ»Π½ΡΠ΅ΡΡΡ ΡΠ΅ΡΠΌΠΈΡΠ΅ΡΠΊΠ°Ρ ΠΎΠ±ΡΠ°Π±ΠΎΡΠΊΠ° ΠΏΠΎΠ²Π΅ΡΡ Π½ΠΎΡΡΠ΅ΠΉ. Π ΡΠ΅Π·ΡΠ»ΡΡΠ°ΡΠ΅ ΡΠ΅Π³ΠΎ ΠΏΡΠΎΠΈΡΡ ΠΎΠ΄ΠΈΡ ΡΠ°Π·ΡΡΡΠ΅Π½ΠΈΠ΅ ΠΊΡΠΈΡΡΠ°Π»Π»ΠΈΡΠ΅ΡΠΊΠΎΠΉ ΡΠ΅ΡΡΡΠΊΠΈ ΠΏΠΎΠ²Π΅ΡΡ Π½ΠΎΡΡΠ½ΠΎΠ³ΠΎ ΡΠ»ΠΎΡ ΠΌΠ΅ΡΠ°Π»Π»ΠΈΡΠ΅ΡΠΊΠΈΡ Π΄Π΅ΡΠ°Π»Π΅ΠΉ. ΠΡΠΈ ΡΠΌΠ΅Π½ΡΡΠ΅Π½ΠΈΠΈ ΡΠ°ΡΡΡΠΎΡΠ½ΠΈΡ Π΄ΠΎ ΠΊΡΠΈΡΠΈΡΠ΅ΡΠΊΠΎΠ³ΠΎ ΠΌΠ΅ΠΆΠ΄Ρ ΡΠ»Π΅ΠΊΡΡΠΎΠ΄ΠΎΠΌ ΠΈ ΠΎΠ±ΡΠ°Π±Π°ΡΡΠ²Π°Π΅ΠΌΡΠΌ ΠΌΠ΅ΡΠ°Π»Π»ΠΎΠΌ ΠΏΠΎΡΠ²Π»ΡΠ΅ΡΡΡ ΡΠ°Π·ΡΡΠ΄. Π§ΡΠΎΠ±Ρ ΡΠ²Π΅Π»ΠΈΡΠΈΡΡ Π΅Π³ΠΎ ΡΠΈΠ»Ρ ΡΠ»Π΅ΠΊΡΡΠΎΠ΄Ρ ΠΏΠΎΠ³ΡΡΠΆΠ°ΡΡ Π² ΡΠ°Π±ΠΎΡΡΡ ΡΡΠ΅Π΄Ρ β Π΄ΠΈΡΠ»Π΅ΠΊΡΡΠΈΡΠ΅ΡΠΊΡΡ ΠΆΠΈΠ΄ΠΊΠΎΡΡΡ. ΠΠ»Ρ ΡΡΠΎΠΉ ΡΠ΅Π»ΠΈ Π½Π°ΠΈΠ±ΠΎΠ»Π΅Π΅ ΠΏΠΎΠ΄Ρ ΠΎΠ΄ΡΡ ΠΌΠΈΠ½Π΅ΡΠ°Π»ΡΠ½ΡΠ΅ ΠΌΠ°ΡΠ»Π° ΠΈΠ»ΠΈ ΠΊΠ΅ΡΠΎΡΠΈΠ½.
ΠΠ° ΠΊΠΎΠ½Π΄Π΅Π½ΡΠ°ΡΠΎΡ ΠΏΠΎΠ΄Π°ΡΡΡΡ Π½Π°ΠΏΡΡΠΆΠ΅Π½ΠΈΠ΅ Π΄ΠΎ Π΄ΠΎΡΡΠΈΠΆΠ΅Π½ΠΈΡ ΡΡΠ΅Π±ΡΠ΅ΠΌΠΎΠ³ΠΎ ΠΏΠΎΡΠ΅Π½ΡΠΈΠ°Π»Π°. ΠΠΎΡΠ»Π΅ ΡΡΠΎΠ³ΠΎ ΡΠ»Π΅ΠΊΡΡΠΈΡΠ΅ΡΠΊΠΈΠΉ ΡΠΎΠΊ, ΠΏΠΎΠ΄Π°ΡΡΠΈΠΉΡΡ Π½Π° ΡΠ»Π΅ΠΊΡΡΠΎΠ΄, Π½Π°Π³ΡΠ΅Π²Π°Π΅Ρ ΡΠ°Π±ΠΎΡΡΡ ΠΆΠΈΠ΄ΠΊΠΎΡΡΡ Π΄ΠΎ Π·Π°ΠΊΠΈΠΏΠ°Π½ΠΈΡ. Π ΡΠ΅Π·ΡΠ»ΡΡΠ°ΡΠ΅ ΠΊΠΈΠΏΠ΅Π½ΠΈΡ ΡΠΎΠ·Π΄Π°ΡΡΡΡ Π³Π°Π·ΠΎΠ²ΡΠΉ ΠΏΡΠ·ΡΡΡ, Π² ΠΊΠΎΡΠΎΡΠΎΠΌ ΠΎΠ±ΡΠ°Π·ΡΠ΅ΡΡΡ ΠΏΠΎΡΠΎΠΊ ΠΈΠΎΠ½ΠΎΠ² ΠΈ ΡΠ»Π΅ΠΊΡΡΠΎΠ½ΠΎΠ². Π’Π΅ΠΌΠΏΠ΅ΡΠ°ΡΡΡΠ° ΡΠ°Π±ΠΎΡΠ΅ΠΉ ΡΡΠ΅Π΄Ρ ΠΏΠΎΠ²ΡΡΠ°Π΅ΡΡΡ Π΄ΠΎ 12 ΡΡΡ. Β°C, ΡΡΠΎ ΠΏΠΎΠ·Π²ΠΎΠ»ΡΠ΅Ρ ΡΠ°ΡΠΏΠ»Π°Π²ΠΈΡΡ ΠΌΠ΅ΡΠ°Π»Π». Π’Π°ΠΊΠΈΠΌ ΠΎΠ±ΡΠ°Π·ΠΎΠΌ, Π½Π° ΠΏΠΎΠ²Π΅ΡΡ Π½ΠΎΡΡΠΈ ΠΌΠ΅ΡΠ°Π»Π»ΠΈΡΠ΅ΡΠΊΠΈΡ Π΄Π΅ΡΠ°Π»Π΅ΠΉ ΠΎΠ±ΡΠ°Π·ΡΠ΅ΡΡΡ Π²ΡΠ΅ΠΌΠΊΠ°.
ΠΠ·-Π·Π° ΠΎΠ³ΡΠΎΠΌΠ½ΠΎΠΉ ΡΠ΅ΠΌΠΏΠ΅ΡΠ°ΡΡΡΡ ΡΠ°ΡΡΡ ΠΈΠΎΠ½ΠΎΠ² Π²ΡΠΏΠ°ΡΠΈΠ²Π°Π΅ΡΡΡ, ΠΈ ΠΏΠΎΠ²Π΅ΡΡ Π½ΠΎΡΡΡ ΡΠ»Π΅ΠΌΠ΅Π½ΡΠ° ΠΏΡΠΈΠΎΠ±ΡΠ΅ΡΠ°Π΅Ρ Π΄ΡΡΠ³ΠΈΠ΅ ΡΠ²ΠΎΠΉΡΡΠ²Π°. ΠΡΠ»Π΅Π΄ΡΡΠ²ΠΈΠ΅ ΡΠ°ΠΊΠΎΠΉ ΠΎΠ±ΡΠ°Π±ΠΎΡΠΊΠΈ ΠΌΠ΅ΡΠ°Π»Π»ΠΎΠ² Π΄Π΅ΡΠ°Π»Ρ ΠΏΠΎΠΊΡΡΠ²Π°Π΅Ρ Π»Π΅Π³ΠΈΡΠΎΠ²Π°Π½Π½ΡΠΉ ΡΠ»ΠΎΠΉ ΠΈ ΡΠ°ΡΡΡ ΡΠ»Π΅ΠΌΠ΅Π½ΡΠΎΠ² ΡΠ°Π±ΠΎΡΠ΅Π³ΠΎ ΡΠ»Π΅ΠΊΡΡΠΎΠ΄Π°.
ΠΠ΅ΠΎΠ±Ρ ΠΎΠ΄ΠΈΠΌΠΎΠ΅ ΠΎΠ±ΠΎΡΡΠ΄ΠΎΠ²Π°Π½ΠΈΠ΅
ΠΠ»Π΅ΠΊΡΡΠΎΡΡΠΎΠ·ΠΈΠΎΠ½Π½ΡΠΉ ΡΠΏΠΎΡΠΎΠ± ΡΠΏΠ΅ΡΠΎΠ±ΡΠ°Π±ΠΎΡΠΊΠΈ ΠΏΡΠΈΠΌΠ΅Π½ΡΠ΅ΡΡΡ ΠΊΠΎ Π²ΡΠ΅ΠΌ ΡΠΏΠ»Π°Π²Π°ΠΌ ΠΌΠ΅ΡΠ°Π»Π»ΠΎΠ² Π·Π° ΡΡΡΡ ΠΈΡ ΡΠ»Π΅ΠΊΡΡΠΎΠΏΡΠΎΠ²ΠΎΠ΄ΠΈΠΌΠΎΡΡΠΈ. ΠΠΎΠ΄ Π΄Π΅ΠΉΡΡΠ²ΠΈΠ΅ΠΌ ΡΠ»Π΅ΠΊΡΡΠΈΡΠ΅ΡΠΊΠΎΠ³ΠΎ ΡΠ°Π·ΡΡΠ΄Π° Π²ΡΠΏΠΎΠ»Π½ΡΠ΅ΡΡΡ ΠΌΠ½ΠΎΠΆΠ΅ΡΡΠ²ΠΎ Π²ΠΈΠ΄ΠΎΠ² ΡΠ°Π±ΠΎΡ:
- ΡΠ»Π΅ΠΊΡΡΠΎΡΡΠΎΠ·ΠΈΠΎΠ½Π½Π°Ρ ΡΠ΅Π·ΠΊΠ°;
- ΡΠ²Π΅ΡΠ»Π΅Π½ΠΈΠ΅;
- ΡΠ»ΠΈΡΠΎΠ²Π°Π½ΠΈΠ΅;
- Π³ΡΠ°Π²ΠΈΡΠΎΠ²ΠΊΠ°;
- Π»Π΅Π³ΠΈΡΠΎΠ²Π°Π½ΠΈΠ΅;
- ΡΠΎΠ·Π΄Π°Π½ΠΈΠ΅ ΡΠ°Π±Π»ΠΎΠ½Π½ΡΡ Π΄Π΅ΡΠ°Π»Π΅ΠΉ Ρ Π²ΡΡΠΎΠΊΠΎΠΉ ΡΠΎΡΠ½ΠΎΡΡΡΡ;
- Π²ΠΎΡΡΡΠ°Π½ΠΎΠ²Π»Π΅Π½ΠΈΠ΅ ΡΠΎΡΠΌΡ;
- Π΄ΠΎΠ±Π°Π²Π»Π΅Π½ΠΈΠ΅ ΠΏΠΎΠ²Π΅ΡΡ Π½ΠΎΡΡΠ½ΠΎΠ³ΠΎ ΡΠ»ΠΎΡ.
Π ΡΠΎΠ²ΡΠ΅ΠΌΠ΅Π½Π½ΠΎΠΌ ΠΎΠ±ΠΎΡΡΠ΄ΠΎΠ²Π°Π½ΠΈΠΈ ΠΏΡΠΈΠΌΠ΅Π½ΡΡΡΡΡ ΠΊΡΠ°ΡΠΊΠΎΠ²ΡΠ΅ΠΌΠ΅Π½Π½ΡΠ΅ ΠΈΠΌΠΏΡΠ»ΡΡΡ ΠΈ Π΄Π»ΠΈΡΠ΅Π»ΡΠ½ΡΠ΅. ΠΠ»Ρ ΠΏΠΈΡΠ°Π½ΠΈΡ Π½Π΅ΠΎΠ±Ρ ΠΎΠ΄ΠΈΠΌ ΡΠΎΠ»ΡΠΊΠΎ ΠΏΠΎΡΡΠΎΡΠ½Π½ΡΠΉ ΡΠΎΠΊ. ΠΠ°ΠΏΡΡΠΆΠ΅Π½ΠΈΠ΅ ΠΈ ΡΠΈΠ»Π° ΡΠΎΠΊΠ° ΡΠ΅Π³ΡΠ»ΠΈΡΡΠ΅ΡΡΡ Π² Π·Π°Π²ΠΈΡΠΈΠΌΠΎΡΡΠΈ ΠΎΡ Ρ Π°ΡΠ°ΠΊΡΠ΅ΡΠΈΡΡΠΈΠΊΠΈ ΠΌΠ΅ΡΠ°Π»Π»Π°. Π ΠΏΡΠΎΠΌΡΡΠ»Π΅Π½Π½ΠΎΡΡΠΈ ΡΠ°ΡΠΏΡΠΎΡΡΡΠ°Π½Π΅Π½Ρ Π² ΠΎΡΠ½ΠΎΠ²Π½ΠΎΠΌ Π΄Π²Π° ΡΠΈΠΏΠ° ΡΡΡΡΠΎΠΉΡΡΠ²Π°:
- ΡΠ»Π΅ΠΊΡΡΠΎΡΡΠΎΠ·ΠΈΠΎΠ½Π½ΡΠΉ ΠΏΡΠΎΠ²ΠΎΠ»ΠΎΡΠ½ΡΠΉ ΡΡΠ°Π½ΠΎΠΊ;
- ΡΠ»Π΅ΠΊΡΡΠΎΡΡΠΎΠ·ΠΈΠΎΠ½Π½ΡΠΉ ΠΏΡΠΎΡΠΈΠ²Π½ΠΎΠΉ ΡΡΠ°Π½ΠΎΠΊ.
ΠΡΠΎΠ²ΠΎΠ»ΠΎΡΠ½ΡΠΉ, ΠΎΠ½ ΠΆΠ΅ Π²ΡΡΠ΅Π·Π½ΠΎΠΉ, ΡΡΠ°Π½ΠΎΠΊ ΠΏΡΠΈΠΌΠ΅Π½ΡΡΡ Π΄Π»Ρ ΠΎΠ±ΡΠ°Π±ΠΎΡΠΊΠΈ ΠΌΠ΅ΡΠ°Π»Π»ΠΈΡΠ΅ΡΠΊΠΈΡ Π΄Π΅ΡΠ°Π»Π΅ΠΉ Ρ Π±ΠΎΠ»ΡΡΠΎΠΉ ΡΠΎΠ»ΡΠΈΠ½ΠΎΠΉ. ΠΡΠΎΡΠΈΠ²Π½ΡΠ΅ ΡΡΠ°Π½ΠΊΠΈ Π½Π΅ΠΎΠ±Ρ ΠΎΠ΄ΠΈΠΌΡ Π΄Π»Ρ ΡΠΎΠ·Π΄Π°Π½ΠΈΡ ΠΌΠ½ΠΎΠΆΠ΅ΡΡΠ²Π° ΡΠ»Π΅ΠΌΠ΅Π½ΡΠΎΠ² Ρ ΠΈΠ΄Π΅Π½ΡΠΈΡΠ½ΡΠΌΠΈ ΠΏΠ°ΡΠ°ΠΌΠ΅ΡΡΠ°ΠΌΠΈ.
ΠΡΠΎΠ²ΠΎΠ»ΠΎΡΠ½ΠΎ-Π²ΡΡΠ΅Π·Π½ΠΎΠΉ ΡΡΠ°Π½ΠΎΠΊ
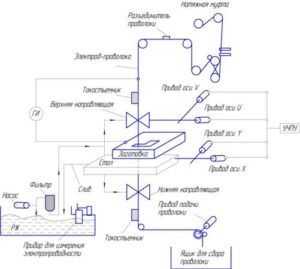
Π‘Ρ Π΅ΠΌΠ° ΠΏΡΠΎΠ²ΠΎΠ»ΠΎΡΠ½ΠΎ-Π²ΡΡΠ΅Π·Π½ΠΎΠ³ΠΎ ΡΡΠ°Π½ΠΊΠ°
ΠΡΠΎΠΌΡΡΠ»Π΅Π½Π½ΡΠΉ ΠΏΡΠΎΠ²ΠΎΠ»ΠΎΡΠ½ΠΎ-Π²ΡΡΠ΅Π·Π½ΠΎΠΉ ΡΡΠ°Π½ΠΎΠΊ ΠΎΠ±ΡΠ°Π±Π°ΡΡΠ²Π°Π΅Ρ Π·Π°Π³ΠΎΡΠΎΠ²ΠΊΠΈ Ρ ΠΏΠΎΠΌΠΎΡΡΡ ΡΠ»Π΅ΠΊΡΡΠΎΠΏΡΠΎΠ²ΠΎΠ΄ΡΡΠ΅ΠΉ ΠΏΡΠΎΠ²ΠΎΠ»ΠΎΠΊΠΈ Π±Π΅Π· Π΅Ρ Π½Π΅ΠΏΠΎΡΡΠ΅Π΄ΡΡΠ²Π΅Π½Π½ΠΎΠ³ΠΎ ΠΊΠΎΠ½ΡΠ°ΠΊΡΠ° Ρ ΠΎΠ±ΡΠ°Π±Π°ΡΡΠ²Π°Π΅ΠΌΠΎΠΉ ΠΏΠΎΠ²Π΅ΡΡ Π½ΠΎΡΡΡΡ. ΠΡΠΎΠ²ΠΎΠ»ΠΎΠΊΠ° ΠΈΠ·Π³ΠΎΡΠ°Π²Π»ΠΈΠ²Π°Π΅ΡΡΡ ΠΈΠ· ΡΡΠ³ΠΎΠΏΠ»Π°Π²ΠΊΠΈΡ ΠΌΠ΅ΡΠ°Π»Π»ΠΎΠ² β Π²ΠΎΠ»ΡΡΡΠ°ΠΌΠ° ΠΈΠ»ΠΈ ΠΌΠΎΠ»ΠΈΠ±Π΄Π΅Π½Π°, Π΄ΠΈΠ°ΠΌΠ΅ΡΡΠΎΠΌ 0,01β0,02 ΡΠΌ.
ΠΠ±ΡΠ°Π±Π°ΡΡΠ²Π°Π΅ΠΌΡΠΉ ΡΠ»Π΅ΠΌΠ΅Π½Ρ Π²ΡΡΡΡΠΏΠ°Π΅Ρ Π² ΠΊΠ°ΡΠ΅ΡΡΠ²Π΅ Π°Π½ΠΎΠ΄Π°, Π° ΠΏΡΠΎΠ²ΠΎΠ»ΠΎΠΊΠ° β ΠΊΠ°ΡΠΎΠ΄Π°. ΠΠ°ΡΠ°Π½ΠΊΠ° ΠΏΠ΅ΡΠ΅ΠΌΠ΅ΡΠ°Π΅ΡΡΡ ΠΎΠ΄Π½ΠΎΠ²ΡΠ΅ΠΌΠ΅Π½Π½ΠΎ ΠΊ Π·Π°Π³ΠΎΡΠΎΠ²ΠΊΠ΅ ΠΈ Π²Π΅ΡΡΠΈΠΊΠ°Π»ΡΠ½ΠΎ. Π ΠΏΡΠΎΡΠ΅ΡΡΠ΅ ΠΏΠ΅ΡΠ΅Π΄Π²ΠΈΠΆΠ΅Π½ΠΈΡ ΠΊΠ°ΡΠΎΠ΄Π° ΡΠΎΠ·Π΄Π°ΡΡΡΡ ΡΠ»Π΅ΠΊΡΡΠΈΡΠ΅ΡΠΊΠΈΠΉ ΡΠ°Π·ΡΡΠ΄, ΠΊΠΎΡΠΎΡΡΠΉ ΡΠ°Π·ΡΠ΅Π·Π°Π΅Ρ ΠΌΠ΅ΡΠ°Π»Π» ΠΏΠΎ Π½Π΅ΠΎΠ±Ρ ΠΎΠ΄ΠΈΠΌΠΎΠΌΡ ΠΊΠΎΠ½ΡΡΡΡ. Π ΠΏΡΠΎΠ²ΠΎΠ»ΠΎΡΠ½ΡΠΉ ΡΡΠ°Π½ΠΎΠΊ Π²ΡΠΏΠΎΠ»Π½ΡΠ΅Ρ ΡΡΠ½ΠΊΡΠΈΡ ΡΡΠ΅Π·Ρ. ΠΠΎ ΠΌΠ΅Ρ Π°Π½ΠΈΡΠ΅ΡΠΊΠ°Ρ ΠΎΠ±ΡΠ°Π±ΠΎΡΠΊΠ° Π½Π΅ ΠΏΠΎΠ·Π²ΠΎΠ»ΡΠ΅Ρ ΠΏΠΎΠ΄Π³ΠΎΡΠΎΠ²ΠΈΡΡ Π·Π°Π³ΠΎΡΠΎΠ²ΠΊΡ Ρ Π²ΡΡΠΎΠΊΠΈΠΌ ΠΊΠ°ΡΠ΅ΡΡΠ²ΠΎΠΌ ΠΏΠΎΠ²Π΅ΡΡ Π½ΠΎΡΡΠΈ.
Π’ΠΎΡΠ½ΠΎΡΡΡ ΠΌΠ΅ΡΠ°Π»Π»ΠΎΠΎΠ±ΡΠ°Π±ΠΎΡΠΊΠΈ ΡΠΎΡΡΠ°Π²Π»ΡΠ΅Ρ ΠΎΡ 12 Π΄ΠΎ 110 ΠΌΠΊΠΌ.
ΠΠΈΠ΄Ρ ΡΠ°Π±ΠΎΡ, Π²ΡΠΏΠΎΠ»Π½ΡΠ΅ΠΌΡΡ Π½Π° Π΄Π°Π½Π½ΠΎΠΌ ΠΎΠ±ΠΎΡΡΠ΄ΠΎΠ²Π°Π½ΠΈΠΈ:
- ΡΠΎΠ·Π΄Π°Π½ΠΈΠ΅ ΡΠ²Π΅ΡΡ ΠΌΠ°Π»ΡΡ ΡΠ³Π»ΠΎΠ²;
- ΠΈΠ·Π³ΠΎΡΠΎΠ²Π»Π΅Π½ΠΈΠ΅ ΡΠ°Π΄ΠΈΡΡΠ½ΡΡ Π²ΡΡΠ΅Π·ΠΎΠ² Ρ ΠΌΠΈΠΊΡΠΎΡΠ°Π·ΠΌΠ΅ΡΠ°ΠΌΠΈ;
- Π²ΡΠΏΠΎΠ»Π½Π΅Π½ΠΈΠ΅ ΡΠΎΡΠ½ΡΡ ΠΏΠ°ΡΠ°Π»Π»Π΅Π»ΡΠ½ΡΡ ΡΠ΅Π·ΠΎΠ²;
- ΡΠΎΡΠΌΠΈΡΠΎΠ²Π°Π½ΠΈΠ΅ Π²ΡΡΠΎΠΊΠΎΡΠΎΡΠ½ΡΡ ΠΊΡΠΎΠΌΠΎΠΊ.
ΠΠ»Π΅ΠΊΡΡΠΎΡΡΠΎΠ·ΠΈΠΎΠ½Π½ΡΠΉ ΠΏΡΠΎΡΠΈΠ²Π½ΠΎΠΉ ΡΡΠ°Π½ΠΎΠΊ
ΠΠ»Π΅ΠΊΡΡΠΎΡΡΠΎΠ·ΠΈΠΎΠ½Π½ΡΠΉ ΠΏΡΠΎΡΠΈΠ²Π½ΠΎΠΉ ΡΡΠ°Π½ΠΎΠΊ Π²ΠΎΠ·Π΄Π΅ΠΉΡΡΠ²ΡΠ΅Ρ Π½Π° Π·Π°Π³ΠΎΡΠΎΠ²ΠΊΡ ΡΠ»Π΅ΠΊΡΡΠΎΠ΄ΠΎΠΌ ΠΈΠ· ΡΠΎΠ½ΠΊΠΎΠΉ ΠΏΡΠΎΠ²ΠΎΠ»ΠΎΠΊΠΈ ΠΊΠΎΠ½ΡΠ°ΠΊΡΠ½ΡΠΌ ΡΠΏΠΎΡΠΎΠ±ΠΎΠΌ. ΠΠΎΠΏΠ΅ΡΠ΅ΡΠ½ΠΎΠ΅ ΡΠ΅ΡΠ΅Π½ΠΈΠ΅ ΡΠ»Π΅ΠΊΡΡΠΎΠ΄Π° ΠΎΠΏΡΠ΅Π΄Π΅Π»ΡΠ΅Ρ ΡΠΎΡΠΌΡ Π²ΡΡΠ΅Π·Π° Π² Π΄Π΅ΡΠ°Π»ΠΈ. ΠΡΠΎΡΠΈΠ²Π½ΡΠ΅ ΡΡΠ°Π½ΠΊΠΈ ΠΈΡΠΏΠΎΠ»ΡΠ·ΡΡΡΡΡ Π΄Π»Ρ ΠΎΠ±ΡΠ°Π±ΠΎΡΠΊΠΈ Π½Π΅ΡΠΊΠΎΠ»ΡΠΊΠΈΡ Π²ΠΈΠ΄ΠΎΠ² ΡΠΏΠ»Π°Π²ΠΎΠ²:
ΠΠ»Π΅ΠΊΡΡΠΎΡΡΠΎΠ·ΠΈΠΎΠ½Π½ΡΠΉ ΠΏΡΠΎΡΠΈΠ²Π½ΠΎΠΉ ΡΡΠ°Π½ΠΎΠΊ
- Π²ΡΡΠΎΠΊΠΎΠΏΡΠΎΡΠ½ΡΠ΅ ΡΠΏΠ»Π°Π²Ρ Π΄Π»Ρ ΠΈΠ·Π³ΠΎΡΠΎΠ²Π»Π΅Π½ΠΈΡ ΠΈΠ½ΡΡΡΡΠΌΠ΅Π½ΡΠΎΠ²;
- ΡΠΈΡΠ°Π½;
- Π·Π°ΠΊΠ°Π»ΡΠ½Π½Π°Ρ ΡΡΠ°Π»Ρ;
- Π½Π΅ΡΠΆΠ°Π²Π΅ΡΡΠ°Ρ ΡΡΠ°Π»Ρ.
ΠΠ° ΠΏΡΠΎΡΠΈΠ²Π½ΡΡ ΡΡΠ°Π½ΠΊΠ°Ρ Π²ΠΎΠ·ΠΌΠΎΠΆΠ½Π° ΠΎΠ±ΡΠ°Π±ΠΎΡΠΊΠ° Π»ΡΠ±ΡΡ ΡΠ»Π΅ΠΊΡΡΠΎΠΏΡΠΎΠ²ΠΎΠ΄ΡΡΠΈΡ ΠΏΠΎΠ²Π΅ΡΡ Π½ΠΎΡΡΠ΅ΠΉ Π΄Π»Ρ Π²ΡΠΏΠΎΠ»Π½Π΅Π½ΠΈΡ Π²ΡΡΠΎΠΊΠΎΡΠΎΡΠ½ΡΡ ΠΎΡΠ²Π΅ΡΡΡΠΈΠΉ, Π²ΡΠ΅ΠΌΠΎΠΊ ΠΎΡΠ΅Π½Ρ ΠΌΠ°Π»Π΅Π½ΡΠΊΠΈΡ Π΄ΠΈΠ°ΠΌΠ΅ΡΡΠΎΠ² Ρ Π±ΠΎΠ»ΡΡΠΎΠΉ Π³Π»ΡΠ±ΠΈΠ½ΠΎΠΉ, ΡΠ³Π»ΡΠ±Π»Π΅Π½ΠΈΠΉ ΡΠΎ ΡΠ»ΠΎΠΆΠ½ΠΎΠΉ ΡΠΎΡΠΌΠΎΠΉ.
ΠΠΎΠ½ΡΠ°ΠΊΡΠ½Π°Ρ ΠΎΠ±ΡΠ°Π±ΠΎΡΠΊΠ° ΠΌΠ΅ΡΠ°Π»Π»ΠΎΠ² ΠΏΠΎΠΌΠΎΠ³Π°Π΅Ρ ΡΠΎΠ·Π΄Π°Π²Π°ΡΡ Π²ΡΡΠΎΠΊΠΎΡΠΎΡΠ½ΡΠ΅ ΠΎΡΡΠΈΡΠΊΠΈ, ΠΏΡΠ΅ΡΡ-ΡΠΎΡΠΌΡ ΠΈ Π΄Π΅ΡΠ°Π»ΠΈ ΠΌΠ°Π»ΡΡ ΡΠ°Π·ΠΌΠ΅ΡΠΎΠ². ΠΠ»Ρ ΡΡΠΎΠΉ ΡΠ΅Π»ΠΈ ΡΠ»Π΅ΠΊΡΡΠΎΠ΄ Π²ΡΠΏΠΎΠ»Π½ΡΡΡ ΠΊΠ°ΠΊ ΠΌΠ°Π»ΠΎΠ³Π°Π±Π°ΡΠΈΡΠ½ΡΡ ΠΊΠΎΠΏΠΈΡ ΠΈΠ·Π΄Π΅Π»ΠΈΡ Π½Π΅ΠΎΠ±Ρ ΠΎΠ΄ΠΈΠΌΠΎΠΉ ΡΠΎΡΠΌΡ ΠΈΠ· Π³ΡΠ°ΡΠΈΡΠ° ΠΈΠ»ΠΈ ΠΌΠ΅Π΄ΠΈ.
ΠΡΠ΅ΠΈΠΌΡΡΠ΅ΡΡΠ²Π° ΠΌΠ΅ΡΠΎΠ΄Π°
ΠΠ°Π½Π½ΡΠΉ ΡΠΏΠΎΡΠΎΠ± Π²ΠΎΠ·Π΄Π΅ΠΉΡΡΠ²ΠΈΡ Π½Π° ΠΌΠ΅ΡΠ°Π»Π» ΠΎΠ±Π»Π°Π΄Π°Π΅Ρ ΡΠ²ΠΎΠΈΠΌΠΈ ΠΏΡΠ΅ΠΈΠΌΡΡΠ΅ΡΡΠ²Π°ΠΌΠΈ:
ΠΡΠΈΠΌΠ΅ΡΡ ΠΎΠ±ΡΠ°Π±ΠΎΡΠΊΠΈ Π½Π° ΡΠ»Π΅ΠΊΡΡΠΎΡΡΠΎΠ·ΠΈΠΎΠ½Π½ΡΡ ΡΡΠ°Π½ΠΊΠ°Ρ
- ΠΡΡΠΎΠΊΠΎΠ΅ ΠΊΠ°ΡΠ΅ΡΡΠ²ΠΎ ΠΎΠ±ΡΠ°Π±ΠΎΡΠ°Π½Π½ΠΎΠ³ΠΎ ΠΌΠ΅ΡΠ°Π»Π»Π°.
- ΠΠ»Π΅ΠΊΡΡΠΎΡΡΠΎΠ·ΠΈΠΎΠ½Π½ΡΠΉ ΠΌΠ΅ΡΠΎΠ΄ ΠΏΠΎΠ·Π²ΠΎΠ»ΡΠ΅Ρ Π΄ΠΎΠ±ΠΈΡΡΡΡ ΠΌΠ°ΠΊΡΠΈΠΌΠ°Π»ΡΠ½ΠΎΠΉ ΡΠΎΡΠ½ΠΎΡΡΠΈ ΡΠ°Π·ΠΌΠ΅ΡΠΎΠ² Π΄Π΅ΡΠ°Π»Π΅ΠΉ β Π΄ΠΎ 12 ΠΌΠΊΠΌ, ΡΡΠΎ Π½Π΅ ΠΎΠ±Π΅ΡΠΏΠ΅ΡΠΈΡ ΠΌΠ΅Ρ Π°Π½ΠΈΡΠ΅ΡΠΊΠ°Ρ ΠΎΠ±ΡΠ°Π±ΠΎΡΠΊΠ°.
- ΠΡΡΡΡΡΡΠ²ΠΈΠ΅ ΡΠΈΠ½ΠΈΡΠ½ΠΎΠΉ ΠΎΠ±ΡΠ°Π±ΠΎΡΠΊΠΈ. ΠΠ°ΠΆΠ΅ ΠΏΠ΅ΡΠΊΠΎΡΡΡΡΠΉΠ½Π°Ρ ΠΎΡΠΈΡΡΠΊΠ° Π½Π΅ ΡΠΎΠ·Π΄Π°ΡΡ ΡΠ°ΠΊΠΎΠ΅ ΡΠ°Π·Π½ΠΎΠΎΠ±ΡΠ°Π·ΠΈΠ΅ ΡΠ΅ΠΊΡΡΡΡ.
- ΠΠ»Π΅ΠΊΡΡΠΎΡΡΠΎΠ·ΠΈΠΎΠ½Π½ΠΎΠ΅ Π²ΠΎΠ·Π΄Π΅ΠΉΡΡΠ²ΠΈΠ΅ ΠΈΡΠΊΠ»ΡΡΠ°Π΅Ρ Π΄Π΅ΡΠΎΡΠΌΠ°ΡΠΈΠΈ ΠΌΠ΅Π»ΠΊΠΈΡ Π·Π°Π³ΠΎΡΠΎΠ²ΠΎΠΊ.
- Π£Π½ΠΈΠ²Π΅ΡΡΠ°Π»ΡΠ½ΠΎΡΡΡ Π² ΠΏΡΠΈΠΌΠ΅Π½Π΅Π½ΠΈΠΈ ΠΊ Π»ΡΠ±ΡΠΌ ΡΠΏΠ»Π°Π²Π°ΠΌ ΠΌΠ΅ΡΠ°Π»Π»ΠΎΠ², Π½Π΅Π·Π°Π²ΠΈΡΠΈΠΌΠΎ ΠΎΡ ΠΈΡ Ρ Π°ΡΠ°ΠΊΡΠ΅ΡΠΈΡΡΠΈΠΊ.
- Π Π°Π·Π½ΠΎΠΎΠ±ΡΠ°Π·ΠΈΠ΅ ΡΠΎΡΠΌ ΠΏΠΎΠ»ΡΡΠ°Π΅ΠΌΡΡ ΡΠ΅Π·ΠΎΠ², ΠΎΡΠ²Π΅ΡΡΡΠΈΠΉ ΠΈ Π²ΡΠ΅ΠΌΠΎΠΊ.
- ΠΠΈΠ·ΠΊΠΈΠΉ ΡΡΠΎΠ²Π΅Π½Ρ ΡΡΠΌΠ° ΠΏΡΠΈ ΡΠ°Π±ΠΎΡΠ΅ ΡΠ»Π΅ΠΊΡΡΠΎΡΡΠΎΠ·ΠΈΠΎΠ½Π½ΡΡ ΡΡΠ°Π½ΠΊΠΎΠ².
- ΠΠ±ΡΠΎΠ»ΡΡΠ½Π°Ρ Π°Π²ΡΠΎΠΌΠ°ΡΠΈΠ·Π°ΡΠΈΡ ΠΏΡΠΎΡΠ΅ΡΡΠ°, ΡΡΠΎ ΡΠΌΠ΅Π½ΡΡΠ°Π΅Ρ ΠΊΠΎΠ»ΠΈΡΠ΅ΡΡΠ²ΠΎ Π±ΡΠ°ΠΊΠ° ΠΈ ΠΏΠΎΠ·Π²ΠΎΠ»ΡΠ΅Ρ ΠΈΠ·Π³ΠΎΡΠ°Π²Π»ΠΈΠ²Π°ΡΡ ΠΌΠ½ΠΎΠΆΠ΅ΡΡΠ²ΠΎ ΠΈΠ΄Π΅Π½ΡΠΈΡΠ½ΡΡ Π΄Π΅ΡΠ°Π»Π΅ΠΉ.
Π’Π΅Ρ Π½ΠΎΠ»ΠΎΠ³ΠΈΡΠ΅ΡΠΊΠΈΠΉ ΠΏΡΠΎΡΠ΅ΡΡ
Π’Π΅Ρ Π½ΠΎΠ»ΠΎΠ³ΠΈΡ ΡΠ»Π΅ΠΊΡΡΠΎΡΡΠΎΠ·ΠΈΠΎΠ½Π½ΠΎΠΉ ΠΎΠ±ΡΠ°Π±ΠΎΡΠΊΠΈ ΠΌΠ΅ΡΠ°Π»Π»ΠΎΠ² Π²ΡΠΏΠΎΠ»Π½ΡΠ΅ΡΡΡ ΡΠ°Π·Π½ΡΠΌΠΈ ΠΌΠ΅ΡΠΎΠ΄Π°ΠΌΠΈ.
ΠΠΎΠΌΠ±ΠΈΠ½ΠΈΡΠΎΠ²Π°Π½Π½ΡΠΉ ΡΠΏΠΎΡΠΎΠ±. Π₯Π°ΡΠ°ΠΊΡΠ΅ΡΠΈΠ·ΡΠ΅ΡΡΡ ΠΎΠ±ΡΠ΅Π΄ΠΈΠ½Π΅Π½ΠΈΠ΅ΠΌ Π½Π΅ΡΠΊΠΎΠ»ΡΠΊΠΈΡ ΠΌΠ΅ΡΠΎΠ΄ΠΎΠ² ΠΎΠ±ΡΠ°Π±ΠΎΡΠΊΠΈ β ΡΠ»Π΅ΠΊΡΡΠΎΡΡΠΎΠ·ΠΈΠΎΠ½Π½ΡΠΉ Ρ ΠΌΠ΅Ρ Π°Π½ΠΈΡΠ΅ΡΠΊΠΈΠΌ. Π’Π°ΠΊΠΎΠ΅ ΠΎΠ±ΡΠ΅Π΄ΠΈΠ½Π΅Π½ΠΈΠ΅ ΠΏΠΎΠ·Π²ΠΎΠ»ΡΠ΅Ρ ΡΠΌΠ΅Π½ΡΡΠΈΡΡ Π²Π»ΠΈΡΠ½ΠΈΠ΅ Π½Π΅Π΄ΠΎΡΡΠ°ΡΠΊΠΎΠ² ΠΎΠ±ΡΠ°Π±ΠΎΡΠΊΠΈ ΠΈ ΠΏΠΎΠ²ΡΡΠΈΡΡ ΡΡΡΠ΅ΠΊΡΠΈΠ²Π½ΠΎΡΡΡ.
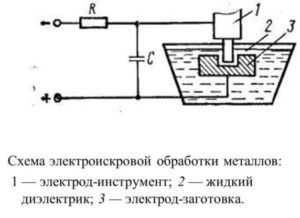
Π‘Ρ Π΅ΠΌΠ° ΡΠ»Π΅ΠΊΡΡΠΎΡΡΠΎΠ·ΠΈΠΎΠ½Π½ΠΎΠΉ ΠΎΠ±ΡΠ°Π±ΠΎΡΠΊΠΈ ΠΌΠ΅ΡΠ°Π»Π»ΠΎΠ²
ΠΠ»Π΅ΠΊΡΡΠΎΡΡΠΎΠ·ΠΈΠΎΠ½Π½ΠΎ-Ρ ΠΈΠΌΠΈΡΠ΅ΡΠΊΠΎΠ΅ ΡΠ»ΠΈΡΠΎΠ²Π°Π½ΠΈΠ΅. Π‘ΡΡΡ ΠΌΠ΅ΡΠΎΠ΄Π° ΡΠΎΡΡΠΎΠΈΡ Π² ΡΠΎΡΠ΅ΡΠ°Π½ΠΈΠΈ ΡΠΏΠΎΡΠΎΠ±Π° ΠΏΠΎΠ΄Π°ΡΠΈ ΡΠ»Π΅ΠΊΡΡΠΈΡΠ΅ΡΡΠ²Π° ΠΈ ΡΠ»Π΅ΠΊΡΡΠΎΠ»ΠΈΡΠ°. Π§ΡΠΎ ΠΏΠΎΠ·Π²ΠΎΠ»ΡΠ΅Ρ ΠΈΠ·ΠΌΠ΅Π½ΡΡΡ ΡΠΎΡΠΌΡ Π΄Π΅ΡΠ°Π»ΠΈ ΠΈ ΡΠ»ΡΡΡΠ°ΡΡ ΠΊΠ°ΡΠ΅ΡΡΠ²Π° ΠΏΠΎΠ²Π΅ΡΡ Π½ΠΎΡΡΠΈ.
ΠΠ±ΡΠ°Π·ΠΈΠ²Π½Π°Ρ ΠΎΠ±ΡΠ°Π±ΠΎΡΠΊΠ° Ρ Π²ΠΎΠ·Π΄Π΅ΠΉΡΡΠ²ΠΈΠ΅ΠΌ ΡΠ»Π΅ΠΊΡΡΠΈΡΠ΅ΡΠΊΠΎΠ³ΠΎ ΡΠ°Π·ΡΡΠ΄Π°. ΠΠ°Π½Π½ΡΠΉ ΠΌΠ΅ΡΠΎΠ΄ ΠΏΠΎΠ·Π²ΠΎΠ»ΡΠ΅Ρ ΠΌΠ΅Π½ΡΡΡ ΡΡΠ΅ΠΏΠ΅Π½Ρ ΡΠ΅ΡΠΎΡ ΠΎΠ²Π°ΡΠΎΡΡΠΈ ΠΌΠ΅ΡΠ°Π»Π»Π°. ΠΡ ΠΏΠ΅ΡΠΊΠΎΡΡΡΡΠΉΠ½ΠΎΠΉ ΠΎΡΠΈΡΡΠΊΠΈ ΠΎΡΠ»ΠΈΡΠ°Π΅ΡΡΡ Π±ΠΎΠ»Π΅Π΅ ΡΠΎΡΠ½ΡΠΌΠΈ ΡΠ΅Π·ΡΠ»ΡΡΠ°ΡΠ°ΠΌΠΈ.
ΠΠ½ΠΎΠ΄Π½ΠΎ-ΠΌΠ΅Ρ Π°Π½ΠΈΡΠ΅ΡΠΊΠΈΠΉ ΡΠΏΠΎΡΠΎΠ± ΠΎΠ±ΡΠ°Π±ΠΎΡΠΊΠΈ ΠΌΠ΅ΡΠ°Π»Π»Π°. ΠΠΏΠ΅ΡΠ°ΡΠΈΡ Π²ΡΠΏΠΎΠ»Π½ΡΠ΅ΡΡΡ Π² ΠΆΠΈΠ΄ΠΊΠΎΡΡΠΈ. ΠΠ±ΡΠ°Π·ΠΎΠ²Π°Π½Π½Π°Ρ Π² ΡΠ΅Π·ΡΠ»ΡΡΠ°ΡΠ΅ ΠΏΠ»ΡΠ½ΠΊΠ° Π½Π° Π΄Π΅ΡΠ°Π»ΠΈ ΡΡΠΈΡΠ°Π΅ΡΡΡ ΠΌΠ΅Ρ Π°Π½ΠΈΡΠ΅ΡΠΊΠΈ.
Π£ΠΏΡΠΎΡΠ½Π΅Π½ΠΈΠ΅. ΠΠ΅ΡΠΎΠ΄ ΠΏΠΎΠ·Π²ΠΎΠ»ΡΠ΅Ρ ΡΠΎΠ·Π΄Π°ΡΡ Π±ΠΎΠ»Π΅Π΅ ΠΏΡΠΎΡΠ½ΡΡ ΠΏΠΎΠ²Π΅ΡΡ Π½ΠΎΡΡΡ ΠΌΠ΅ΡΠ°Π»Π»Π°.
ΠΠ±ΡΡΠΌΠ½ΠΎΠ΅ ΠΊΠΎΠΏΠΈΡΠΎΠ²Π°Π½ΠΈΠ΅. ΠΠ»Π΅ΠΊΡΡΠΎΠ΄ Π²ΡΠΏΠΎΠ»Π½ΡΠ΅ΡΡΡ Π² ΡΠΎΡΠΌΠ΅ ΡΠΌΠ΅Π½ΡΡΠ΅Π½Π½ΠΎΠΉ ΠΊΠΎΠΏΠΈΠΈ ΡΡΠ΅Π±ΡΠ΅ΠΌΠΎΠΉ ΠΊΠΎΠ½ΡΠΈΠ³ΡΡΠ°ΡΠΈΠΈ.
ΠΡΠΎΡΠΈΠ²Π°Π½ΠΈΠ΅ β ΠΌΠ΅ΡΠΎΠ΄ ΡΠΎΠ·Π΄Π°Π½ΠΈΡ ΠΎΡΠ²Π΅ΡΡΡΠΈΠΉ ΡΡΡΠ°Π½ΠΎΠ²Π»Π΅Π½Π½ΠΎΠΉ ΠΊΠΎΠ½ΡΠΈΠ³ΡΡΠ°ΡΠΈΠΈ.
ΠΠ°ΡΠΊΠΈΡΠΎΠ²ΠΊΠ°, ΠΈΠ·Π³ΠΎΡΠΎΠ²Π»Π΅Π½Π½Π°Ρ ΡΠ»Π΅ΠΊΡΡΠΎΡΡΠΎΠ·ΠΈΠΎΠ½Π½ΡΠΌ ΡΠΏΠΎΡΠΎΠ±ΠΎΠΌ Π±ΠΎΠ»Π΅Π΅ Π΄ΠΎΠ»Π³ΠΎΠ²Π΅ΡΠ½Π° ΠΈ Π»Π΅Π³ΠΊΠΎ Π²ΡΠΏΠΎΠ»Π½ΠΈΠΌΠ°.
ΠΠ»Π΅ΠΊΡΡΠΎΡΡΠΎΠ·ΠΈΠΎΠ½Π½Π°Ρ ΡΠ΅Π·ΠΊΠ°. ΠΠ»Π΅ΠΊΡΡΠΎΠ΄ Π±Π΅ΡΠΊΠΎΠ½ΡΠ°ΠΊΡΠ½ΡΠΌ ΡΠΏΠΎΡΠΎΠ±ΠΎΠΌ ΠΏΡΠΎΠΆΠΈΠ³Π°Π΅Ρ ΠΌΠ΅ΡΠ°Π»Π». ΠΠΎΠ½ΡΡΡΡ Π΄Π΅ΡΠ°Π»ΠΈ ΠΎΡΠ»ΠΈΡΠ°ΡΡΡΡ Π²ΡΡΠΎΠΊΠΈΠΌ ΠΊΠ°ΡΠ΅ΡΡΠ²ΠΎΠΌ.
Π¨Π»ΠΈΡΠΎΠ²Π°Π½ΠΈΠ΅ ΠΏΡΠ΅Π΄Π½Π°Π·Π½Π°ΡΠ΅Π½ΠΎ Π΄Π»Ρ ΠΏΡΠΎΠΈΠ·Π²ΠΎΠ΄ΡΡΠ²Π° ΠΌΠ°ΡΡΠΈΡ Π²ΡΡΡΠ±Π½ΡΡ ΡΡΠ°ΠΌΠΏΠΎΠ² ΠΈΠ· ΡΠ²Π΅ΡΠ΄ΠΎΡΠΏΠ»Π°Π²Π½ΡΡ ΠΌΠ΅ΡΠ°Π»Π»ΠΎΠ², ΠΌΠ°Π³Π½ΠΈΡΠΎΠ². ΠΠ΅ΡΠΎΠ΄ ΠΏΠΎΠ·Π²ΠΎΠ»ΡΠ΅Ρ ΡΠ½ΠΈΠΌΠ°ΡΡ Π±ΠΎΠ»ΡΡΠΎΠΉ ΡΠ»ΠΎΠΉ ΠΌΠ΅ΡΠ°Π»Π»Π° Π±Π΅Π· Π΄Π΅ΡΠΎΡΠΌΠ°ΡΠΈΠΈ Π·Π°Π³ΠΎΡΠΎΠ²ΠΎΠΊ, ΠΈΡΠΊΠ»ΡΡΠ°Π΅ΡΡΡ Π²Π΅ΡΠΎΡΡΠ½ΠΎΡΡΡ Π·Π°ΠΌΡΠΊΠ°Π½ΠΈΡ ΠΏΡΠΈ ΠΈΠ·Π³ΠΎΡΠΎΠ²Π»Π΅Π½ΠΈΠΈ ΡΠ»Π΅ΠΊΡΡΠΎΠΌΠ°Π³Π½ΠΈΡΠΎΠ².
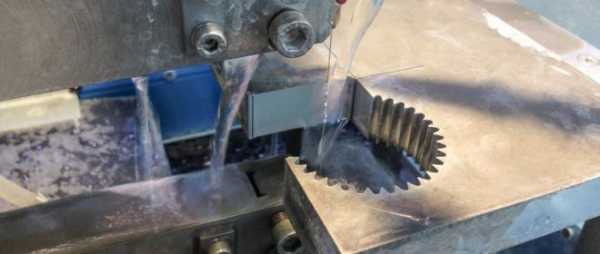
ΠΠ»Π΅ΠΊΡΡΠΎΡΡΠΎΠ·ΠΈΠΎΠ½Π½Π°Ρ ΡΠ΅Π·ΠΊΠ° ΠΌΠ΅ΡΠ°Π»Π»Π°
ΠΡΠ²ΠΎΠ΄Ρ
ΠΠ°ΠΈΠ±ΠΎΠ»Π΅Π΅ ΡΠ°ΡΠΏΡΠΎΡΡΡΠ°Π½Π΅Π½Ρ ΡΠ»Π΅ΠΊΡΡΠΎΠΈΠΌΠΏΡΠ»ΡΡΠ½ΡΠΉ ΠΈ ΡΠ»Π΅ΠΊΡΡΠΎΠΈΡΠΊΡΠΎΠ²ΠΎΠΉ ΠΌΠ΅ΡΠΎΠ΄Ρ. ΠΠ»Ρ ΡΠ΅ΡΠ½ΠΎΠ²ΠΎΠΉ ΠΌΠ΅ΡΠ°Π»Π»ΠΎΠΎΠ±ΡΠ°Π±ΠΎΡΠΊΠΈ Π±ΠΎΠ»ΡΡΠ΅ ΠΏΠΎΠ΄Ρ ΠΎΠ΄ΠΈΡ ΡΠ»Π΅ΠΊΡΡΠΎΠΈΠΌΠΏΡΠ»ΡΡΠ½ΡΠΉ ΡΠΏΠΎΡΠΎΠ±. ΠΡ ΡΠ°Π±ΠΎΡΠ΅Π³ΠΎ ΠΈΠ½ΡΡΡΡΠΌΠ΅Π½ΡΠ° Ρ ΠΎΡΡΠΈΡΠ°ΡΠ΅Π»ΡΠ½ΡΠΌ Π·Π°ΡΡΠ΄ΠΎΠΌ ΠΈΠ΄ΡΡ ΡΠ»Π΅ΠΊΡΡΠΈΡΠ΅ΡΠΊΠΈΠΉ ΡΠ°Π·ΡΡΠ΄, ΠΊΠΎΡΠΎΡΡΠΉ Π½Π°ΠΏΡΠ°Π²Π»ΡΠ΅Ρ ΠΏΠΎΡΠΎΠΊ ΡΠ°ΡΡΠΈΡ Π² Π·Π°Π³ΠΎΡΠΎΠ²ΠΊΡ. Π’Π΅ΠΌΠΏΠ΅ΡΠ°ΡΡΡΠ° ΠΈΠΌΠΏΡΠ»ΡΡΠΎΠ² Π΄ΠΎΡΡΠΈΠ³Π°Π΅Ρ 5 ΡΡΡ. Β°C, ΡΡΠΎ ΠΏΠΎΠΌΠΎΠ³Π°Π΅Ρ ΠΏΠΎΠ²ΡΡΠΈΡΡ ΠΏΡΠΎΠΈΠ·Π²ΠΎΠ΄ΠΈΡΠ΅Π»ΡΠ½ΠΎΡΡΡ.
ΠΠ»Π΅ΠΊΡΡΠΎΠΈΡΠΊΡΠΎΠ²ΠΎΠΉ ΠΌΠ΅ΡΠΎΠ΄ ΡΠ°ΡΠ΅ ΠΈΡΠΏΠΎΠ»ΡΠ·ΡΠ΅ΡΡΡ Π΄Π»Ρ Π΄Π΅ΡΠ°Π»Π΅ΠΉ ΠΌΠ°Π»ΡΡ ΡΠ°Π·ΠΌΠ΅ΡΠΎΠ² ΠΈ Π±ΠΎΠ»Π΅Π΅ ΡΠΎΡΠ½ΠΎΠΉ ΡΠΏΠ΅ΡΠΎΠ±ΡΠ°Π±ΠΎΡΠΊΠΈ. Π‘ΠΊΠ²ΠΎΠ·Ρ ΠΆΠΈΠ΄ΠΊΡΡ ΡΡΠ΅Π΄Ρ Ρ Π΄ΠΈΡΠ»Π΅ΠΊΡΡΠΈΡΠ΅ΡΠΊΠΈΠΌΠΈ ΡΠ²ΠΎΠΉΡΡΠ²Π°ΠΌΠΈ ΠΏΡΠΎΠΈΡΡ ΠΎΠ΄ΠΈΡ ΠΏΡΠΎΠ±ΠΎΠΉ ΠΈΡΠΊΡΠ°ΠΌΠΈ. ΠΠΎ ΡΡΠΎΠΉ ΡΡ Π΅ΠΌΠ΅ ΠΎΠ±ΡΠ°Π±Π°ΡΡΠ²Π°Π΅ΠΌΠ°Ρ Π΄Π΅ΡΠ°Π»Ρ ΡΠ²Π»ΡΠ΅ΡΡΡ Π°Π½ΠΎΠ΄ΠΎΠΌ Ρ ΠΏΠΎΠ»ΠΎΠΆΠΈΡΠ΅Π»ΡΠ½ΡΠΌ Π·Π°ΡΡΠ΄ΠΎΠΌ, ΠΏΡΠΈΡΡΠ³ΠΈΠ²Π°ΡΡΠΈΠΌ ΠΏΠΎΡΠΎΠΊ ΠΈΠΎΠ½ΠΎΠ². ΠΠΎΠ½Ρ Π·Π°Π³ΠΎΡΠΎΠ²ΠΊΠΈ Π΄Π΅ΠΉΡΡΠ²ΡΡΡ Π½Π° ΡΠ°Π±ΠΎΡΠΈΠΉ ΡΠ»Π΅ΠΊΡΡΠΎΠ΄. ΠΠΌΠΏΡΠ»ΡΡΠ½ΠΎΠ΅ Π½Π°ΠΏΡΡΠΆΠ΅Π½ΠΈΠ΅ Π΄Π΅ΠΉΡΡΠ²ΡΠ΅Ρ Π½Π΅ Π±ΠΎΠ»Π΅Π΅ 10 ΡΠ΅ΠΊ., ΡΡΠΎΠ±Ρ ΡΠ»Π΅ΠΊΡΡΠΎΠ΄ ΠΌΠ΅Π½ΡΡΠ΅ ΡΠ°Π·ΡΡΡΠ°Π»ΡΡ.
ΠΠΈΠ΄Π΅ΠΎ: ΠΠ»Π΅ΠΊΡΡΠΎΡΡΠΎΠ·ΠΈΠΎΠ½Π½Π°Ρ ΠΏΡΠΎΡΠΈΠ²ΠΊΠ° ΠΎΡΠ²Π΅ΡΡΡΠΈΡ
promzn.ru
ΠΠ»Π΅ΠΊΡΡΠΎΡΡΠΎΠ·ΠΈΠΎΠ½Π½Π°Ρ ΠΎΠ±ΡΠ°Π±ΠΎΡΠΊΠ° ΠΌΠ΅ΡΠ°Π»Π»ΠΎΠ²: ΠΎΠΏΠΈΡΠ°Π½ΠΈΠ΅, ΡΠ΅Ρ Π½ΠΎΠ»ΠΎΠ³ΠΈΡ, Π²ΠΈΠ΄Π΅ΠΎ
Π§ΡΠΎΠ±Ρ ΠΈΠ·ΠΌΠ΅Π½ΡΡΡ ΡΠ°Π·ΠΌΠ΅ΡΡ ΠΌΠ΅ΡΠ°Π»Π»ΠΈΡΠ΅ΡΠΊΠΈΡ Π΄Π΅ΡΠ°Π»Π΅ΠΉ Π±Π΅Π· ΠΊΠ°ΠΊΠΈΡ -Π»ΠΈΠ±ΠΎ ΠΈΠ·ΠΌΠ΅Π½Π΅Π½ΠΈΠΉ ΠΈΡ ΡΠΈΠ·ΠΈΡΠ΅ΡΠΊΠΈΡ ΡΠ²ΠΎΠΉΡΡΠ², ΠΈΡΠΏΠΎΠ»ΡΠ·ΡΠ΅ΡΡΡ ΡΠ»Π΅ΠΊΡΡΠΎΡΡΠΎΠ·ΠΈΠΎΠ½Π½Π°Ρ ΠΎΠ±ΡΠ°Π±ΠΎΡΠΊΠ°, Π²ΡΠΏΠΎΠ»Π½Π΅Π½ΠΈΠ΅ ΠΊΠΎΡΠΎΡΠΎΠΉ ΡΡΠ΅Π±ΡΠ΅Ρ Π½Π°Π»ΠΈΡΠΈΡ ΡΠΏΠ΅ΡΠΈΠ°Π»ΡΠ½ΠΎΠ³ΠΎ ΠΎΠ±ΠΎΡΡΠ΄ΠΎΠ²Π°Π½ΠΈΡ ΠΈ Ρ ΠΎΡΠΎΡΠ΅Π³ΠΎ Π·Π½Π°Π½ΠΈΡ ΡΠΎΠΎΡΠ²Π΅ΡΡΡΠ²ΡΡΡΠΈΡ ΡΠ΅Ρ Π½ΠΎΠ»ΠΎΠ³ΠΈΠΉ.
ΠΠ»Π΅ΠΊΡΡΠΎΡΡΠΎΠ·ΠΈΠΎΠ½Π½Π°Ρ ΠΎΠ±ΡΠ°Π±ΠΎΡΠΊΠ° ΠΌΠ΅ΡΠ°Π»Π»ΠΎΠ², ΠΏΠΎΠΌΠΈΠΌΠΎ ΠΈΠ·ΠΌΠ΅Π½Π΅Π½ΠΈΡ ΡΠ°Π·ΠΌΠ΅ΡΠΎΠ² ΡΠ°Π·Π»ΠΈΡΠ½ΡΡ Π΄Π΅ΡΠ°Π»Π΅ΠΉ, Π΄Π°Π΅Ρ Π²ΠΎΠ·ΠΌΠΎΠΆΠ½ΠΎΡΡΡ ΡΠ°ΠΊΠΆΠ΅ ΠΏΠΎΠ»ΡΡΠΈΡΡ ΠΎΡΠ²Π΅ΡΡΡΠΈΡ ΡΡΠ΅Π±ΡΠ΅ΠΌΠΎΠΉ ΡΠΎΡΠΌΡ ΠΈ ΠΊΠΎΠ½ΡΠΈΠ³ΡΡΠ°ΡΠΈΠΈ, ΡΠ΄Π΅Π»Π°ΡΡ ΠΏΡΠΈ Π½Π΅ΠΎΠ±Ρ ΠΎΠ΄ΠΈΠΌΠΎΡΡΠΈ ΡΠ°ΡΠΎΠ½Π½ΡΠ΅ ΠΏΠΎΠ»ΠΎΡΡΠΈ, Π° ΡΠ°ΠΊΠΆΠ΅ ΠΈΠ·Π³ΠΎΡΠΎΠ²ΠΈΡΡ ΠΏΡΠΎΡΠΈΠ»ΡΠ½ΡΠ΅ ΠΊΠ°Π½Π°Π²ΠΊΠΈ ΠΈ ΠΏΠ°Π·Ρ Π½Π° ΡΠ΅Ρ Π·Π°Π³ΠΎΡΠΎΠ²ΠΊΠ°Ρ , ΠΊΠΎΡΠΎΡΡΠ΅ ΡΠΎΠ·Π΄Π°Π½Ρ Π½Π° ΠΎΡΠ½ΠΎΠ²Π΅ ΡΠ²Π΅ΡΠ΄ΡΡ ΡΠΏΠ»Π°Π²ΠΎΠ².
ΠΠ° Π²ΠΈΠ΄Π΅ΠΎ Π² ΡΡΠ°ΡΡΠ΅ Π½Π°Π³Π»ΡΠ΄Π½ΠΎ ΠΏΠΎΠΊΠ°Π·Π°Π½ΠΎ, ΠΊΠ°ΠΊ ΠΏΡΠΎΠ²ΠΎΠ΄ΠΈΡΡΡ Π΄Π°Π½Π½ΡΠΉ Π²ΠΈΠ΄ ΠΎΠ±ΡΠ°Π±ΠΎΡΠΊΠΈ ΠΈ ΠΊΠ°ΠΊΠΈΠ΅ ΠΏΡΠΎΠ±Π»Π΅ΠΌΡ ΠΌΠΎΠ³ΡΡ Π²ΠΎΠ·Π½ΠΈΠΊΠ½ΡΡΡ Π² ΠΏΡΠΎΡΠ΅ΡΡΠ΅.
ΠΡΠΎΠΌΠ΅ ΡΡΠΎΠ³ΠΎ, Π΄Π°Π½Π½ΡΠΉ ΠΌΠ΅ΡΠΎΠ΄ Π΄Π°Π΅Ρ Π²ΠΎΠ·ΠΌΠΎΠΆΠ½ΠΎΡΡΡ ΡΠ΄Π΅Π»Π°ΡΡ ΡΠ°Π·Π»ΠΈΡΠ½ΡΠΉ ΠΈΠ½ΡΡΡΡΠΌΠ΅Π½Ρ Π±ΠΎΠ»Π΅Π΅ ΠΏΡΠΎΡΠ½ΡΠΌ, ΠΏΠΎΠ·Π²ΠΎΠ»ΡΠ΅Ρ ΠΏΡΠΎ
>ΠΈΠ·Π²ΠΎΠ΄ΠΈΡΡ ΠΊΠ°ΡΠ΅ΡΡΠ²Π΅Π½Π½ΠΎΠ΅ ΡΠ»Π΅ΠΊΡΡΠΎΠΏΠ΅ΡΠ°ΡΠ°Π½ΠΈΠ΅, Π²ΡΡΠΎΠΊΠΎΡΠΎΡΠ½ΠΎΠ΅ ΡΠ»ΠΈΡΠΎΠ²Π°Π½ΠΈΠ΅, Π²ΡΠΏΠΎΠ»Π½ΡΡΡ ΡΠ΅Π·ΠΊΡ Π΄Π΅ΡΠ°Π»Π΅ΠΉ, Π° ΡΠ°ΠΊΠΆΠ΅ ΠΌΠ½ΠΎΠ³ΠΎΠ΅ Π΄ΡΡΠ³ΠΎΠ΅.
ΠΡΠΎΡΡΠ΅ΠΉΡΠ°Ρ ΡΡ Π΅ΠΌΠ°, ΠΏΡΠΈ ΠΊΠΎΡΠΎΡΠΎΠΉ Π²ΠΎΠ·ΠΌΠΎΠΆΠ½Π° ΠΎΠ±ΡΠ°Π±ΠΎΡΠΊΠ°, Π² ΠΎΠ±ΡΠ·Π°ΡΠ΅Π»ΡΠ½ΠΎΠΌ ΠΏΠΎΡΡΠ΄ΠΊΠ΅ ΡΠΎΠ΄Π΅ΡΠΆΠΈΡ ΠΎΠΏΡΠ΅Π΄Π΅Π»Π΅Π½Π½ΡΠΉ ΡΠ»Π΅ΠΊΡΡΠΎΠ΄, ΡΠΎΡΡΠ°Π², ΠΊΠΎΡΠΎΡΡΠΉ ΠΏΠΎΠ΄Ρ ΠΎΠ΄ΠΈΡ Π΄Π»Ρ Π²ΡΠΏΠΎΠ»Π½Π΅Π½ΠΈΡ ΡΠ»Π΅ΠΊΡΡΠΈΡΠ΅ΡΠΊΠΎΠ³ΠΎ ΡΠ°Π·ΡΡΠ΄Π°, Π° ΡΠ°ΠΊΠΆΠ΅ ΡΠ°ΠΊΠΈΠ΅ ΡΠ»Π΅ΠΌΠ΅Π½ΡΡ, ΠΊΠ°ΠΊ ΠΊΠΎΠ½Π΄Π΅Π½ΡΠ°ΡΠΎΡ, ΡΠ΅ΠΎΡΡΠ°Ρ ΠΈ Π½Π΅ΠΏΠΎΡΡΠ΅Π΄ΡΡΠ²Π΅Π½Π½ΠΎ ΡΠ°ΠΌ ΠΈΡΡΠΎΡΠ½ΠΈΠΊ ΠΏΠΈΡΠ°Π½ΠΈΡ.
ΠΡΠΏΠΎΠ»Π½ΡΡΡ Π΄Π°Π½Π½ΡΠΉ Π²ΠΈΠ΄ ΠΎΠ±ΡΠ°Π±ΠΎΡΠΊΠΈ ΠΌΠ΅ΡΠ°Π»Π»ΠΈΡΠ΅ΡΠΊΠΈΡ Π΄Π΅ΡΠ°Π»Π΅ΠΉ ΡΠ»Π΅Π΄ΡΠ΅Ρ ΠΏΡΠΈ ΠΏΠΎΠ»Π½ΠΎΠΌ ΡΠΎΠ±Π»ΡΠ΄Π΅Π½ΠΈΠΈ ΡΠΎΠΎΡΠ²Π΅ΡΡΡΠ²ΡΡΡΠΈΡ ΠΏΡΠ°Π²ΠΈΠ» ΠΏΠΎ ΡΠ΅Ρ Π½ΠΈΠΊΠ΅ Π±Π΅Π·ΠΎΠΏΠ°ΡΠ½ΠΎΡΡΠΈ.
ΠΡΠ½ΠΎΠ²Π½ΠΎΠΉ ΠΏΡΠΈΠ½ΡΠΈΠΏ ΡΠ°Π±ΠΎΡΡ
ΠΠ»Ρ ΡΠΎΠ³ΠΎ ΡΡΠΎΠ±Ρ Π½Π° ΠΏΡΠ°ΠΊΡΠΈΠΊΠ΅ Π²ΡΠΏΠΎΠ»Π½ΠΈΡΡ Π΄Π°Π½Π½ΡΠΉ Π²ΠΈΠ΄ ΠΎΠ±ΡΠ°Π±ΠΎΡΠΊΠΈ, Π½Π΅ΠΎΠ±Ρ ΠΎΠ΄ΠΈΠΌΠΎ, Π΄Π»Ρ Π½Π°ΡΠ°Π»Π°, ΠΏΡΠ°Π²ΠΈΠ»ΡΠ½ΠΎ ΡΠΎΠ±ΡΠ°ΡΡ Π² Π΅Π΄ΠΈΠ½ΡΡ ΡΠ΅ΠΏΡ Π²ΡΠ΅ Π½Π΅ΠΎΠ±Ρ ΠΎΠ΄ΠΈΠΌΡΠ΅ ΡΠ»Π΅ΠΌΠ΅Π½ΡΡ, Π° ΡΠ°ΠΊΠΆΠ΅ Π²ΡΠΏΠΎΠ»Π½ΠΈΡΡ ΠΏΡΠ΅Π΄Π²Π°ΡΠΈΡΠ΅Π»ΡΠ½ΡΡ ΠΏΠΎΠ΄Π³ΠΎΡΠΎΠ²ΠΊΡ Π΄Π΅ΡΠ°Π»Π΅ΠΉ, Ρ ΠΊΠΎΡΠΎΡΡΠΌΠΈ ΠΏΡΠ΅Π΄ΡΡΠΎΠΈΡ ΡΠ°Π±ΠΎΡΠ°ΡΡ.
Π Π½Π°ΡΡΠΎΡΡΠ΅Π΅ Π²ΡΠ΅ΠΌΡ Π½Π° ΠΏΡΠΎΠΌΡΡΠ»Π΅Π½Π½ΡΡ ΠΏΡΠ΅Π΄ΠΏΡΠΈΡΡΠΈΡΡ ΠΈΡΠΏΠΎΠ»ΡΠ·ΡΡΡ Π½Π΅ΡΠΊΠΎΠ»ΡΠΊΠΎ Π²ΠΈΠ΄ΠΎΠ² ΡΠ»Π΅ΠΊΡΡΠΎΡΡΠΎΠ·ΠΈΠΎΠ½Π½ΠΎΠΉ ΠΎΠ±ΡΠ°Π±ΠΎΡΠΊΠΈ ΠΌΠ΅ΡΠ°Π»Π»ΠΈΡΠ΅ΡΠΊΠΈΡ Π΄Π΅ΡΠ°Π»Π΅ΠΉ.
Π‘Π»Π΅Π΄ΡΠ΅Ρ ΠΎΡΠΌΠ΅ΡΠΈΡΡ, ΡΡΠΎ ΠΎΠ΄Π½ΠΈΠΌ ΠΈΠ· Π³Π»Π°Π²Π½Π΅ΠΉΡΠΈΡ ΡΠ»Π΅ΠΌΠ΅Π½ΡΠΎΠ² Π² ΡΡ Π΅ΠΌΠ΅, ΠΏΠΎ ΠΊΠΎΡΠΎΡΠΎΠΉ Π²ΡΠΏΠΎΠ»Π½ΡΠ΅ΡΡΡ ΡΠ»Π΅ΠΊΡΡΠΎΡΡΠΎΠ·ΠΈΠΎΠ½Π½Π°Ρ ΠΎΠ±ΡΠ°Π±ΠΎΡΠΊΠ°, ΡΠ²Π»ΡΠ΅ΡΡΡ ΡΠ»Π΅ΠΊΡΡΠΎΠ΄, ΠΊΠΎΡΠΎΡΡΠΉ Π΄ΠΎΠ»ΠΆΠ΅Π½ ΠΎΠ±Π»Π°Π΄Π°ΡΡ Π΄ΠΎΡΡΠ°ΡΠΎΡΠ½ΠΎΠΉ ΡΡΠΎΠ·ΠΈΠΎΠ½Π½ΠΎΠΉ ΡΡΠΎΠΉΠΊΠΎΡΡΡΡ.
Π ΡΡΠΎΠΌ ΡΠ»ΡΡΠ°Π΅ ΡΠ΅Π»Π΅ΡΠΎΠΎΠ±ΡΠ°Π·Π½ΠΎ ΠΈΡΠΏΠΎΠ»ΡΠ·ΠΎΠ²Π°ΡΡ Π² ΠΊΠ°ΡΠ΅ΡΡΠ²Π΅ ΡΠ»Π΅ΠΊΡΡΠΎΠ΄Π° ΡΠ°ΠΊΠΈΠ΅ ΠΌΠ΅ΡΠ°Π»Π»Ρ, ΠΊΠ°ΠΊ ΠΌΠ΅Π΄Ρ, Π³ΡΠ°ΡΠΈΡ, Π²ΠΎΠ»ΡΡΡΠ°ΠΌ, Π° ΡΠ°ΠΊΠΆΠ΅ Π»Π°ΡΡΠ½Ρ ΠΈ Π°Π»ΡΠΌΠΈΠ½ΠΈΠΉ.
ΠΡΠ»ΠΈ ΠΏΠΎΡΠΌΠΎΡΡΠ΅ΡΡ ΡΠΎ ΡΡΠΎΡΠΎΠ½Ρ Ρ ΠΈΠΌΠΈΠΈ, ΡΠΎ Π΄Π°Π½Π½ΡΠΉ ΠΌΠ΅ΡΠΎΠ΄ ΡΠ΅ΡΠΌΠΈΡΠ΅ΡΠΊΠΎΠ³ΠΎ Π²ΠΎΠ·Π΄Π΅ΠΉΡΡΠ²ΠΈΡ Π½Π΅ΠΏΠΎΡΡΠ΅Π΄ΡΡΠ²Π΅Π½Π½ΠΎ Π½Π° ΠΌΠ΅ΡΠ°Π»Π» ΠΎΠΏΡΠ΅Π΄Π΅Π»Π΅Π½Π½ΡΠΌ ΠΎΠ±ΡΠ°Π·ΠΎΠΌ ΡΠ°Π·ΡΡΡΠ°Π΅Ρ Π΅Π³ΠΎ ΠΊΡΠΈΡΡΠ°Π»Π»ΠΈΡΠ΅ΡΠΊΡΡ ΡΠ΅ΡΠ΅ΡΠΊΡ, Π·Π° ΡΡΠ΅Ρ ΡΠ΅Π³ΠΎ ΠΏΡΠΎΠΈΡΡ ΠΎΠ΄ΠΈΡ Π²ΡΡΠ²ΠΎΠ±ΠΎΠΆΠ΄Π΅Π½ΠΈΠ΅ Π½Π΅ΠΊΠΎΡΠΎΡΡΡ ΠΊΠ°ΡΠ΅Π³ΠΎΡΠΈΠΉ ΠΈΠΎΠ½ΠΎΠ².
ΠΠΎΡΡΠ°ΡΠΎΡΠ½ΠΎ ΡΠ°ΡΡΠΎ Π΄Π»Ρ ΠΎΠ±ΡΠ°Π±ΠΎΡΠΊΠΈ ΠΌΠ΅ΡΠ°Π»Π»Π° ΠΈΡΠΏΠΎΠ»ΡΠ·ΡΡΡ ΡΠ»Π΅ΠΊΡΡΠΎΠΈΠΌΠΏΡΠ»ΡΡΠ½ΡΠΉ ΠΈ ΡΠ»Π΅ΠΊΡΡΠΎΠΈΡΠΊΡΠΎΠ²ΠΎΠΉ ΠΌΠ΅ΡΠΎΠ΄Ρ. ΠΡΠΎΠΌΠ΅ ΡΡΠΎΠ³ΠΎ, ΠΌΠΎΠΆΠ½ΠΎ Π²ΡΡΡΠ΅ΡΠΈΡΡ ΡΠ°ΠΊ ΠΆΠ΅ ΡΠ»Π΅ΠΊΡΡΠΎΠΊΠΎΠ½ΡΠ°ΠΊΡΠ½ΡΠΉ ΠΈ Π°Π½ΠΎΠ΄Π½ΠΎ-ΠΌΠ΅Ρ Π°Π½ΠΈΡΠ΅ΡΠΊΠΈΠΉ ΡΠΏΠΎΡΠΎΠ±Ρ. ΠΠΎΠ»Π΅Π΅ Π΄Π΅ΡΠ°Π»ΡΠ½ΠΎ ΠΎΠ± ΡΡΠΎΠΌ ΡΠΌΠΎΡΡΠΈΡΠ΅ Π² Π²ΠΈΠ΄Π΅ΠΎ Π² ΡΡΠ°ΡΡΠ΅.
Π ΡΠΎΠΌ ΡΠ»ΡΡΠ°Π΅, ΠΊΠΎΠ³Π΄Π° Π΄Π»Ρ ΠΌΠ΅ΡΠ°Π»Π»ΠΈΡΠ΅ΡΠΊΠΈΡ Π΄Π΅ΡΠ°Π»Π΅ΠΉ ΡΡΠ΅Π±ΡΠ΅ΡΡΡ ΡΠ΅ΡΠ½ΠΎΠ²Π°Ρ ΠΎΠ±ΡΠ°Π±ΠΎΡΠΊΠ°, ΠΊΠ°ΠΊ ΠΏΡΠ°Π²ΠΈΠ»ΠΎ, ΠΈΡΠΏΠΎΠ»ΡΠ·ΡΠ΅ΡΡΡ ΡΠ»Π΅ΠΊΡΡΠΎΠΈΠΌΠΏΡΠ»ΡΡΠ½Π°Ρ ΡΡ Π΅ΠΌΠ° ΠΎΠ±ΡΠ°Π±ΠΎΡΠΊΠΈ.
Π ΡΡΠΎΠΌ ΡΠ»ΡΡΠ°Π΅ ΠΏΡΠΈ ΠΏΡΠΎΠ²Π΅Π΄Π΅Π½ΠΈΠΈ Π½Π΅ΠΎΠ±Ρ ΠΎΠ΄ΠΈΠΌΡΡ ΡΠ°Π±ΠΎΡ ΡΠ΅ΠΌΠΏΠ΅ΡΠ°ΡΡΡΠ° Π²ΡΡΠ°Π±Π°ΡΡΠ²Π°Π΅ΠΌΡΡ ΠΈΠΌΠΏΡΠ»ΡΡΠΎΠ² ΠΌΠΎΠΆΠ΅Ρ ΠΏΠΎΠ΄Π½ΠΈΠΌΠ°ΡΡΡΡ Π΄ΠΎ ΠΏΡΡΠΈ ΡΡΡΡΡ Π³ΡΠ°Π΄ΡΡΠΎΠ² ΠΏΠΎ Π¦Π΅Π»ΡΡΠΈΡ. ΠΡΠΎ ΠΏΠΎΠ·Π²ΠΎΠ»ΡΠ΅Ρ ΡΠ²Π΅Π»ΠΈΡΠΈΡΡ ΡΠ°ΠΊΠΎΠΉ ΠΏΠ°ΡΠ°ΠΌΠ΅ΡΡ, ΠΊΠ°ΠΊ ΠΏΡΠΎΠΈΠ·Π²ΠΎΠ΄ΠΈΡΠ΅Π»ΡΠ½ΠΎΡΡΡ.
ΠΡΠΈ Π½Π΅ΠΎΠ±Ρ ΠΎΠ΄ΠΈΠΌΠΎΡΡΠΈ Π²ΡΠΏΠΎΠ»Π½ΠΈΡΡ Π΄Π°Π½Π½ΡΠΉ ΡΠΈΠΏ ΠΎΠ±ΡΠ°Π±ΠΎΡΠΊΠΈ Π·Π°Π³ΠΎΡΠΎΠ²ΠΎΠΊ Ρ Π½Π΅Π±ΠΎΠ»ΡΡΠΈΠΌΠΈ Π³Π°Π±Π°ΡΠΈΡΠ°ΠΌΠΈ ΠΈ ΡΠ°Π·ΠΌΠ΅ΡΠ°ΠΌΠΈ, ΡΠ΅Π»Π΅ΡΠΎΠΎΠ±ΡΠ°Π·Π½ΠΎ ΠΈΡΠΏΠΎΠ»ΡΠ·ΠΎΠ²Π°ΡΡ ΡΠ»Π΅ΠΊΡΡΠΎΠΈΡΠΊΡΠΎΠ²ΠΎΠΉ ΡΠΏΠΎΡΠΎΠ±.
ΠΠΈΠ΄Π΅ΠΎ:
Π ΡΠ²ΠΎΡ ΠΎΡΠ΅ΡΠ΅Π΄Ρ, ΠΏΡΠΈ ΡΠ°Π±ΠΎΡΠ΅ ΡΠΎ ΡΠΏΠ»Π°Π²Π°ΠΌΠΈ Π² ΠΆΠΈΠ΄ΠΊΠΎΠΉ ΡΡΠ΅Π΄Π΅, Π² Π±ΠΎΠ»ΡΡΠΈΠ½ΡΡΠ²Π΅ ΡΠ»ΡΡΠ°Π΅Π² ΠΏΡΠΈΠΌΠ΅Π½ΡΡΡ ΡΠ»Π΅ΠΊΡΡΠΎΠΊΠΎΠ½ΡΠ°ΠΊΡΠ½ΡΡ ΠΎΠ±ΡΠ°Π±ΠΎΡΠΊΡ.
Π‘Π»Π΅Π΄ΡΠ΅Ρ ΠΎΡΠΌΠ΅ΡΠΈΡΡ, ΡΡΠΎ ΡΠ΅ ΡΠ²ΠΎΠΉΡΡΠ²Π°, ΠΊΠΎΡΠΎΡΡΠ΅ ΠΏΡΠΈΠΎΠ±ΡΠ΅ΡΠ°Π΅Ρ ΠΌΠ΅ΡΠ°Π»Π» ΠΏΠΎΡΠ»Π΅ ΡΠΎΠ³ΠΎ, ΠΊΠ°ΠΊ Π±ΡΠ΄Π΅Ρ ΠΏΡΠΎΠΈΠ·Π²Π΅Π΄Π΅Π½Π° ΡΠ°ΠΊΠ°Ρ ΠΎΠ±ΡΠ°Π±ΠΎΡΠΊΠ°, ΠΌΠΎΠ³ΡΡ ΡΠΎΠ²Π΅ΡΡΠ΅Π½Π½ΠΎ ΠΏΠΎ-ΡΠ°Π·Π½ΠΎΠΌΡ ΡΠΊΠ°Π·Π°ΡΡΡΡ Π½Π° ΡΠΊΡΠΏΠ»ΡΠ°ΡΠ°ΡΠΈΠΎΠ½Π½ΡΡ Ρ Π°ΡΠ°ΠΊΡΠ΅ΡΠΈΡΡΠΈΠΊΠ°Ρ Π΄Π΅ΡΠ°Π»Π΅ΠΉ.
Π Π±ΠΎΠ»ΡΡΠΈΠ½ΡΡΠ²Π΅ ΡΠ»ΡΡΠ°Π΅Π², ΠΏΠΎΠ΄ Π²ΠΎΠ·Π΄Π΅ΠΉΡΡΠ²ΠΈΠ΅ΠΌ Π²ΡΡΠΎΠΊΠΈΡ ΡΠ΅ΠΌΠΏΠ΅ΡΠ°ΡΡΡΡ ΠΈ ΡΠΎΠΊΠΎΠ² Ρ ΠΎΠ±ΡΠ°Π±Π°ΡΡΠ²Π°Π΅ΠΌΡΡ Π΄Π΅ΡΠ°Π»Π΅ΠΉ Π·Π½Π°ΡΠΈΡΠ΅Π»ΡΠ½ΠΎ ΠΏΠΎΠ²ΡΡΠ°Π΅ΡΡΡ ΠΏΡΠΎΡΠ½ΠΎΡΡΡ, ΠΏΡΠΈΡΠΎΠΌ, ΡΡΠΎ Π² ΡΠ°ΠΌΠΎΠΉ ΡΡΡΡΠΊΡΡΡΠ΅ ΡΠΎΡ ΡΠ°Π½ΡΠ΅ΡΡΡ ΠΌΡΠ³ΠΊΠΎΡΡΡ.
Π’ΠΈΠΏΡ ΠΈΡΠΏΠΎΠ»ΡΠ·ΡΠ΅ΠΌΠΎΠ³ΠΎ ΠΎΠ±ΠΎΡΡΠ΄ΠΎΠ²Π°Π½ΠΈΡ
ΠΠ°ΠΊ ΠΈΠ·Π²Π΅ΡΡΠ½ΠΎ, ΡΡΡΠ΅ΡΡΠ²ΡΡΡ ΡΠ°ΠΌΡΠ΅ ΡΠ°Π·Π½ΡΠ΅ ΠΌΠ΅ΡΠΎΠ΄Ρ ΠΈ ΡΠΏΠΎΡΠΎΠ±Ρ ΠΎΠ±ΡΠ°Π±ΠΎΡΠΊΠΈ ΠΏΠΎΠ²Π΅ΡΡ Π½ΠΎΡΡΠ΅ΠΉ ΠΌΠ΅ΡΠ°Π»Π»ΠΎΠ², ΠΏΡΠΈ ΡΡΠΎΠΌ Π΄Π°Π½Π½ΡΠΉ Π²ΠΈΠ΄ ΡΠ²Π»ΡΠ΅ΡΡΡ Π±ΠΎΠ»Π΅Π΅ ΡΡΡΠ΅ΠΊΡΠΈΠ²Π½ΡΠΌ, ΡΠ΅ΠΌ ΠΌΠ΅Ρ Π°Π½ΠΈΡΠ΅ΡΠΊΠΈΠ΅.
Π‘Π²ΡΠ·Π°Π½ΠΎ ΡΡΠΎ Π³Π»Π°Π²Π½ΡΠΌ ΠΎΠ±ΡΠ°Π·ΠΎΠΌ Ρ ΡΠ΅ΠΌ, ΡΡΠΎ ΡΠΎΡ ΠΈΠ½ΡΡΡΡΠΌΠ΅Π½Ρ, ΠΊΠΎΡΠΎΡΡΠΉ ΠΈΡΠΏΠΎΠ»ΡΠ·ΡΠ΅ΡΡΡ Π΄Π»Ρ ΠΏΡΠΎΠ²Π΅Π΄Π΅Π½ΠΈΡ ΠΌΠ΅Ρ Π°Π½ΠΈΡΠ΅ΡΠΊΠΈΡ ΡΠΈΠΏΠΎΠ² ΠΎΠ±ΡΠ°Π±ΠΎΡΠΊΠΈ, ΡΡΠΎΠΈΡ Π³ΠΎΡΠ°Π·Π΄ΠΎ Π΄ΠΎΡΠΎΠΆΠ΅, ΡΠ΅ΠΌ ΠΏΡΠΎΠ²ΠΎΠ»ΠΎΠΊΠ°, ΠΊΠΎΡΠΎΡΠ°Ρ ΠΏΡΠΈΠΌΠ΅Π½ΡΠ΅ΡΡΡ ΠΏΡΠΈ ΡΠ»Π΅ΠΊΡΡΠΎΡΡΠΎΠ·ΠΈΠΎΠ½Π½ΠΎΠΉ ΠΎΠ±ΡΠ°Π±ΠΎΡΠΊΠ΅.
ΠΠ° ΠΏΡΠΎΠΌΡΡΠ»Π΅Π½Π½ΡΡ ΠΏΡΠ΅Π΄ΠΏΡΠΈΡΡΠΈΡΡ Π΄Π»Ρ ΡΠ»Π΅ΠΊΡΡΠΎΡΡΠΎΠ·ΠΈΠΎΠ½Π½ΠΎΠΉ ΠΎΠ±ΡΠ°Π±ΠΎΡΠΊΠΈ ΡΠ°ΠΌΡΡ ΡΠ°Π·Π½ΡΡ Π΄Π΅ΡΠ°Π»Π΅ΠΉ ΠΈΡΠΏΠΎΠ»ΡΠ·ΡΠ΅ΡΡΡ ΡΠΏΠ΅ΡΠΈΠ°Π»ΡΠ½ΠΎΠ΅ ΠΎΠ±ΠΎΡΡΠ΄ΠΎΠ²Π°Π½ΠΈΠ΅.
Π ΡΠΎΠΌ ΡΠ»ΡΡΠ°Π΅, ΠΊΠΎΠ³Π΄Π° Π½Π΅ΠΎΠ±Ρ ΠΎΠ΄ΠΈΠΌΠΎ ΠΈΠ·Π³ΠΎΡΠΎΠ²ΠΈΡΡ ΠΏΡΠ΅ΡΡ-ΡΠΎΡΠΌΡ ΠΈ Π΄Π΅ΡΠ°Π»ΠΈ ΡΠΎ ΡΠ»ΠΎΠΆΠ½ΠΎΠΉ ΡΠΎΡΠΌΠΎΠΉ, Π° ΡΠ°ΠΊΠΆΠ΅ ΠΏΡΠΈ ΠΏΡΠΎΠΈΠ·Π²ΠΎΠ΄ΡΡΠ²Π΅ Π½Π΅ΠΊΠΎΡΠΎΡΡΡ ΠΌΠ°ΡΠ΅ΡΠΈΠ°Π»ΠΎΠ², ΠΊ ΠΊΠΎΡΠΎΡΡΠΌ ΠΏΡΠΈΠΌΠ΅Π½ΡΡΡΡΡ Π²ΡΡΠΎΠΊΠΈΠ΅ ΡΡΠ΅Π±ΠΎΠ²Π°Π½ΠΈΡ ΠΊ ΡΠΎΡΠ½ΠΎΡΡΠΈ ΠΎΠ±ΡΠ°Π±ΠΎΡΠΊΠΈ, ΠΈΡΠΏΠΎΠ»ΡΠ·ΡΡΡ ΠΏΡΠΎΠ²ΠΎΠ»ΠΎΡΠ½ΠΎ-Π²ΡΡΠ΅Π·Π½ΡΠ΅ ΡΠ»Π΅ΠΊΡΡΠΎΡΡΠΎΠ·ΠΈΠΎΠ½Π½ΡΠ΅ Π°Π³ΡΠ΅Π³Π°ΡΡ.
ΠΠ°ΠΊ ΠΏΡΠ°Π²ΠΈΠ»ΠΎ, Π½Π° ΡΠ°ΠΊΠΎΠΌ ΡΠΈΠΏΠ΅ ΠΎΠ±ΠΎΡΡΠ΄ΠΎΠ²Π°Π½ΠΈΡ ΠΈΠ·Π³ΠΎΡΠ°Π²Π»ΠΈΠ²Π°ΡΡ ΡΠ°ΠΌΡΠ΅ ΡΠ°Π·Π½ΡΠ΅ Π΄Π΅ΡΠ°Π»ΠΈ Π΄Π»Ρ ΡΠ°ΠΌΠΎΠ»Π΅ΡΠΎΠ², ΡΠ»Π΅ΠΊΡΡΠΎΠ½ΠΈΠΊΠΈ ΠΈ Π΄Π°ΠΆΠ΅ ΠΊΠΎΡΠΌΠΈΡΠ΅ΡΠΊΠΎΠΉ ΡΡΠ΅ΡΡ.
ΠΠ° Π²ΠΈΠ΄Π΅ΠΎ, ΠΊΠΎΡΠΎΡΠΎΠ΅ ΡΠ°Π·ΠΌΠ΅ΡΠ΅Π½ΠΎ Π½ΠΈΠΆΠ΅, ΠΌΠΎΠΆΠ½ΠΎ ΡΠ²ΠΈΠ΄Π΅ΡΡ, ΠΊΠ°ΠΊ ΠΏΡΠΎΠ²ΠΎΠ΄ΠΈΡΡΡ ΡΠ°ΠΊΠ°Ρ ΠΎΠ±ΡΠ°Π±ΠΎΡΠΊΠ° Ρ ΠΈΡΠΏΠΎΠ»ΡΠ·ΠΎΠ²Π°Π½ΠΈΠ΅ΠΌ ΡΠ»Π΅ΠΊΡΡΠΎΡΡΠΎΠ·ΠΈΠΎΠ½Π½ΠΎΠ³ΠΎ ΠΎΠ±ΠΎΡΡΠ΄ΠΎΠ²Π°Π½ΠΈΡ.
ΠΠ»Ρ ΠΌΠ°ΡΡΠΎΠ²ΠΎΠ³ΠΎ ΠΈ ΡΠ΅ΡΠΈΠΉΠ½ΠΎΠ³ΠΎ ΠΏΡΠΎΠΈΠ·Π²ΠΎΠ΄ΡΡΠ²Π° Π΄Π΅ΡΠ°Π»Π΅ΠΉ ΠΏΠΎ Π΄Π°Π½Π½ΠΎΠΌΡ ΠΌΠ΅ΡΠΎΠ΄Ρ Π² Π±ΠΎΠ»ΡΡΠΈΠ½ΡΡΠ²Π΅ ΡΠ»ΡΡΠ°Π΅Π² ΠΈΡΠΏΠΎΠ»ΡΠ·ΡΡΡ ΠΊΠΎΠΏΠΈΡΠΎΠ²Π°Π»ΡΠ½ΠΎ-ΠΏΡΠΎΡΠΈΠ²ΠΎΡΠ½ΡΠ΅ Π°Π³ΡΠ΅Π³Π°ΡΡ.
Π’Π°ΠΊΠΈΠ΅ ΡΡΠ°Π½ΠΊΠΈ ΠΏΠΎΠ·Π²ΠΎΠ»ΡΡΡ ΠΏΠΎΠ»ΡΡΠΈΡΡ Π΄ΠΎΡΡΠ°ΡΠΎΡΠ½ΠΎ ΡΠΎΡΠ½ΡΠ΅ ΡΠΊΠ²ΠΎΠ·Π½ΡΠ΅ ΠΊΠΎΠ½ΡΡΡΡ, Π° ΡΠ°ΠΊΠΆΠ΅ ΠΌΠ΅Π»ΠΊΠΈΠ΅ ΠΎΡΠ²Π΅ΡΡΡΠΈΡ, ΡΡΠΎ ΡΡΠΏΠ΅ΡΠ½ΠΎ ΠΈΡΠΏΠΎΠ»ΡΠ·ΡΠ΅ΡΡΡ ΠΏΡΠΈ ΠΏΡΠΎΠΈΠ·Π²ΠΎΠ΄ΡΡΠ²Π΅ ΡΠ΅ΡΠΎΠΊ, Π° ΡΠ°ΠΊΠΆΠ΅ ΡΡΠ°ΠΌΠΏΠΎΠ² Π² ΠΈΠ½ΡΡΡΡΠΌΠ΅Π½ΡΠ°Π»ΡΠ½ΠΎΠΉ ΡΡΠ΅ΡΠ΅ ΠΏΡΠΎΠΌΡΡΠ»Π΅Π½Π½ΠΎΡΡΠΈ.
ΠΠ°ΠΊ ΠΏΡΠ°Π²ΠΈΠ»ΠΎ, ΠΎΠ±ΠΎΡΡΠ΄ΠΎΠ²Π°Π½ΠΈΠ΅ Π΄Π°Π½Π½ΠΎΠ³ΠΎ ΡΠΈΠΏΠ° ΠΏΠΎΠ΄Π±ΠΈΡΠ°Π΅ΡΡΡ, ΠΈΡΡ ΠΎΠ΄Ρ ΠΈΠ· ΠΏΠΎΡΡΠ°Π²Π»Π΅Π½Π½ΡΡ Π·Π°Π΄Π°Ρ, Π° ΡΠ°ΠΊΠΆΠ΅ ΡΠΈΠ½Π°Π½ΡΠΎΠ²ΠΎΠΉ ΠΎΠΊΡΠΏΠ°Π΅ΠΌΠΎΡΡΠΈ. Π‘Π»Π΅Π΄ΡΠ΅Ρ ΠΎΡΠΌΠ΅ΡΠΈΡΡ ΠΈ ΡΠΎ, ΡΡΠΎ ΡΠ»Π΅ΠΊΡΡΠΎΡΡΠΎΠ·ΠΈΠΎΠ½Π½ΡΡ ΠΎΠ±ΡΠ°Π±ΠΎΡΠΊΡ ΠΎΡΠ½ΠΎΡΡΡ ΠΊ ΡΠ»ΠΎΠΆΠ½ΡΠΌ ΠΈ Π΄ΠΎΡΡΠ°ΡΠΎΡΠ½ΠΎ ΡΡΡΠ΄ΠΎΠ΅ΠΌΠΊΠΈΠΌ ΡΠ°Π±ΠΎΡΠΈΠΌ ΠΏΡΠΎΡΠ΅ΡΡΠ°ΠΌ.
ΠΠ΅ Π½Π΅Π²ΠΎΠ·ΠΌΠΎΠΆΠ½ΠΎ ΠΏΡΠΎΠ²Π΅ΡΡΠΈ Π² Π΄ΠΎΠΌΠ°ΡΠ½ΠΈΡ ΡΡΠ»ΠΎΠ²ΠΈΡΡ ΡΠ²ΠΎΠΈΠΌΠΈ ΡΡΠΊΠ°ΠΌΠΈ. Π ΡΠ°Π±ΠΎΡΠ΅ Π½Π° ΡΡΠ°Π½ΠΊΠ°Ρ Π΄Π»Ρ Π΄Π°Π½Π½ΠΎΠ³ΠΎ Π²ΠΈΠ΄Π° ΠΎΠ±ΡΠ°Π±ΠΎΡΠΊΠΈ Π΄Π΅ΡΠ°Π»Π΅ΠΉ Π΄ΠΎΠΏΡΡΠΊΠ°ΡΡΡΡ ΡΠΎΠ»ΡΠΊΠΎ ΠΊΠ²Π°Π»ΠΈΡΠΈΡΠΈΡΠΎΠ²Π°Π½Π½ΡΠ΅ ΠΈ Π°ΡΡΠ΅ΡΡΠΎΠ²Π°Π½Π½ΡΠ΅ Π»ΡΠ΄ΠΈ, ΠΊΠΎΡΠΎΡΡΠ΅ ΠΈΠΌΠ΅ΡΡ ΡΠΎΠΎΡΠ²Π΅ΡΡΡΠ²ΡΡΡΠΈΠΉ ΠΎΠΏΡΡ ΡΠ°Π±ΠΎΡΡ Π² Π΄Π°Π½Π½ΠΎΠΉ ΡΡΠ΅ΡΠ΅.
ΠΡΠΈ Π²ΡΠΏΠΎΠ»Π½Π΅Π½ΠΈΠΈ ΡΠ»Π΅ΠΊΡΡΠΎΡΡΠΎΠ·ΠΈΠΎΠ½Π½ΠΎΠΉ ΠΎΠ±ΡΠ°Π±ΠΎΡΠΊΠΈ Π½Π΅ΠΎΠ±Ρ
ΠΎΠ΄ΠΈΠΌΠΎ Π½Π΅ ΡΠΎΠ»ΡΠΊΠΎ ΡΠΎΠ±Π»ΡΠ΄Π°ΡΡ ΡΠ΅Ρ
Π½ΠΈΠΊΡ Π±Π΅Π·ΠΎΠΏΠ°ΡΠ½ΠΎΡΡΠΈ, Π½ΠΎ ΠΈ ΠΎΠ±ΡΠ·Π°ΡΠ΅Π»ΡΠ½ΠΎ Π½Π°Π΄Π΅ΡΡ ΡΠΏΠ΅ΡΠΎΠ΄Π΅ΠΆΠ΄Ρ.
ΠΠΈΠ΄Π΅ΠΎ:
ΠΡΠ΅ΠΈΠΌΡΡΠ΅ΡΡΠ²Π° ΠΎΠ±ΡΠ°Π±ΠΎΡΠΊΠΈ
ΠΠ»Π΅ΠΊΡΡΠΎΡΡΠΎΠ·ΠΈΠΎΠ½Π½ΠΎΠ΅ Π²ΠΎΠ·Π΄Π΅ΠΉΡΡΠ²ΠΈΠ΅ Π½Π° ΠΌΠ΅ΡΠ°Π»Π» Π΄ΠΎΠ»ΠΆΠ½ΠΎ Π²ΡΠΏΠΎΠ»Π½ΡΡΡΡΡ ΡΠΎΠ»ΡΠΊΠΎ Π½Π° ΡΠΏΠ΅ΡΠΈΠ°Π»ΡΠ½ΠΎΠΌ ΠΎΠ±ΠΎΡΡΠ΄ΠΎΠ²Π°Π½ΠΈΠΈ ΠΈ ΠΏΠΎΠ΄ ΠΏΡΠΈΡΠΌΠΎΡΡΠΎΠΌ ΠΊΠ²Π°Π»ΠΈΡΠΈΡΠΈΡΠΎΠ²Π°Π½Π½ΠΎΠ³ΠΎ ΡΠ΅Π»ΠΎΠ²Π΅ΠΊΠ°, ΠΊΠΎΡΠΎΡΡΠΉ ΠΈΠΌΠ΅Π΅Ρ ΡΠΎΠΎΡΠ²Π΅ΡΡΡΠ²ΡΡΡΠΈΠΉ Π΄ΠΎΠΏΡΡΠΊ.
ΠΠ΅ΡΠΌΠΎΡΡΡ Π½Π° ΡΠΎ, ΡΡΠΎ Π΄Π°Π½Π½ΡΠΉ ΡΠΏΠΎΡΠΎΠ± Π΄Π΅Π»Π°Π΅Ρ Π·Π°Π³ΠΎΡΠΎΠ²ΠΊΡ Π±ΠΎΠ»Π΅Π΅ ΠΊΠ°ΡΠ΅ΡΡΠ²Π΅Π½Π½ΠΎΠΉ ΠΈ ΡΠΎΡΠ½ΠΎΠΉ, Π²ΡΠ΅ ΠΆΠ΅ Π½Π° ΠΏΡΠΎΠΌΡΡΠ»Π΅Π½Π½ΡΡ ΠΏΡΠ΅Π΄ΠΏΡΠΈΡΡΠΈΡΡ Π±ΠΎΠ»ΡΡΠ΅ Π²ΡΠ΅Π³ΠΎ ΡΠ°ΡΠΏΡΠΎΡΡΡΠ°Π½Π΅Π½Π° ΠΌΠ΅Ρ Π°Π½ΠΈΡΠ΅ΡΠΊΠ°Ρ ΠΎΠ±ΡΠ°Π±ΠΎΡΠΊΠ° ΠΌΠ΅ΡΠ°Π»Π»ΠΈΡΠ΅ΡΠΊΠΈΡ ΠΏΠΎΠ²Π΅ΡΡ Π½ΠΎΡΡΠ΅ΠΉ.
Π ΡΡΠΎΠΌ ΡΠ»ΡΡΠ°Π΅ ΡΠ»Π΅Π΄ΡΠ΅Ρ ΠΎΡΠΌΠ΅ΡΠΈΡΡ Π²ΡΠ΅ ΠΎΡΠ½ΠΎΠ²Π½ΡΠ΅ ΠΏΡΠ΅ΠΈΠΌΡΡΠ΅ΡΡΠ²Π° ΡΠ»Π΅ΠΊΡΡΠΎΡΡΠΎΠ·ΠΈΠΎΠ½Π½ΠΎΠ³ΠΎ Π²ΠΎΠ·Π΄Π΅ΠΉΡΡΠ²ΠΈΡ Π½Π° ΡΠ°Π·Π»ΠΈΡΠ½ΡΠ΅ ΡΠΈΠΏΡ Π·Π°Π³ΠΎΡΠΎΠ²ΠΎΠΊ.
Π ΠΏΠ΅ΡΠ²ΡΡ ΠΎΡΠ΅ΡΠ΅Π΄Ρ, ΠΏΡΠΈ ΠΈΡΠΏΠΎΠ»ΡΠ·ΠΎΠ²Π°Π½ΠΈΠΈ Π΄Π°Π½Π½ΠΎΠ³ΠΎ ΠΌΠ΅ΡΠΎΠ΄Π° ΡΠ΄Π°Π΅ΡΡΡ Π΄ΠΎΠ±ΠΈΡΡΡΡ Π²ΡΡΠΎΡΠ°ΠΉΡΠ΅Π³ΠΎ ΠΊΠ°ΡΠ΅ΡΡΠ²Π° ΠΏΠΎΠ²Π΅ΡΡ Π½ΠΎΡΡΠΈ ΠΌΠ΅ΡΠ°Π»Π»Π°, ΠΎΠ½Π° ΡΡΠ°Π½ΠΎΠ²ΠΈΡΡΡ ΠΎΠ΄Π½ΠΎΡΠΎΠ΄Π½ΠΎΠΉ ΠΈ ΠΌΠ°ΠΊΡΠΈΠΌΠ°Π»ΡΠ½ΠΎ ΡΠΎΡΠ½ΠΎΠΉ.
Π‘Π»Π΅Π΄ΡΠ΅Ρ ΠΎΡΠΌΠ΅ΡΠΈΡΡ ΠΈ ΡΠΎ, ΡΡΠΎ Π² ΡΡΠΎΠΌ ΡΠ»ΡΡΠ°Π΅ Π½Π΅ΠΎΠ±Ρ ΠΎΠ΄ΠΈΠΌΠΎΡΡΡ Π² ΠΏΡΠΎΠ²Π΅Π΄Π΅Π½ΠΈΠΈ ΡΠΈΠ½ΠΈΡΠ½ΠΎΠΉ ΠΎΠ±ΡΠ°Π±ΠΎΡΠΊΠΈ ΠΏΠΎΠ»Π½ΠΎΡΡΡΡ ΠΈΡΠΊΠ»ΡΡΠ°Π΅ΡΡΡ. ΠΡΠΎΠΌΠ΅ ΡΡΠΎΠ³ΠΎ, Π΄Π°Π½Π½ΡΠΉ ΠΌΠ΅ΡΠΎΠ΄ Π΄Π°Π΅Ρ Π²ΠΎΠ·ΠΌΠΎΠΆΠ½ΠΎΡΡΡ ΠΏΠΎΠ»ΡΡΠ°ΡΡ Π½Π° Π²ΡΡ ΠΎΠ΄Π΅ ΠΏΠΎΠ²Π΅ΡΡ Π½ΠΎΡΡΡ Ρ ΡΠ°ΠΌΠΎΠΉ ΡΠ°Π·Π½ΠΎΠΉ ΡΡΡΡΠΊΡΡΡΠΎΠΉ.
Π Π΄ΠΎΡΡΠΎΠΈΠ½ΡΡΠ²Π°ΠΌ ΡΠ»Π΅ΠΊΡΡΠΎΡΡΠΎΠ·ΠΈΠΎΠ½Π½ΠΎΠ³ΠΎ Π²ΠΎΠ·Π΄Π΅ΠΉΡΡΠ²ΠΈΡ ΡΠ»Π΅Π΄ΡΠ΅Ρ ΠΎΡΠ½Π΅ΡΡΠΈ ΠΈ Π²ΠΎΠ·ΠΌΠΎΠΆΠ½ΠΎΡΡΡ ΡΠ°Π±ΠΎΡΠ°ΡΡ Ρ ΠΏΠΎΠ²Π΅ΡΡ Π½ΠΎΡΡΡΡ ΠΏΡΠ°ΠΊΡΠΈΡΠ΅ΡΠΊΠΈ Π»ΡΠ±ΠΎΠΉ ΡΠ²Π΅ΡΠ΄ΠΎΡΡΠΈ.
Π’Π°ΠΊΠΆΠ΅ ΠΏΡΠΈ Π΄Π°Π½Π½ΠΎΠΌ ΠΌΠ΅ΡΠΎΠ΄Π΅ ΠΏΠΎΠ»Π½ΠΎΡΡΡΡ ΠΈΡΠΊΠ»ΡΡΠ°Π΅ΡΡΡ Π΄Π΅ΡΠΎΡΠΌΠ°ΡΠΈΡ ΠΏΠΎΠ²Π΅ΡΡ Π½ΠΎΡΡΠΈ Ρ Π΄Π΅ΡΠ°Π»Π΅ΠΉ Ρ Π½Π΅Π±ΠΎΠ»ΡΡΠΎΠΉ ΡΠΎΠ»ΡΠΈΠ½ΠΎΠΉ.
ΠΡΠΎ ΠΏΡΠΎΠΈΡΡ ΠΎΠ΄ΠΈΡ ΠΏΠΎ ΠΏΡΠΈΡΠΈΠ½Π΅ ΡΠΎΠ³ΠΎ, ΡΡΠΎ ΠΌΠ΅ΡΠΎΠ΄ Π½Π΅ ΠΏΡΠ΅Π΄ΠΏΠΎΠ»Π°Π³Π°Π΅Ρ ΠΊΠ°ΠΊΠΎΠΉ-Π»ΠΈΠ±ΠΎ ΠΌΠ΅Ρ Π°Π½ΠΈΡΠ΅ΡΠΊΠΎΠΉ Π½Π°Π³ΡΡΠ·ΠΊΠΈ. ΠΡΠΈ Π΄Π°Π½Π½ΠΎΠΌ ΡΠΏΠΎΡΠΎΠ±Π΅ Π²ΠΎΠ·Π΄Π΅ΠΉΡΡΠ²ΠΈΡ Π½Π° ΠΌΠ΅ΡΠ°Π»Π»ΠΈΡΠ΅ΡΠΊΡΡ ΠΏΠΎΠ²Π΅ΡΡ Π½ΠΎΡΡΡ ΡΠ°Π±ΠΎΡΠΈΠΉ Π°Π½ΠΎΠ΄ ΠΈΠΌΠ΅Π΅Ρ ΠΌΠΈΠ½ΠΈΠΌΠ°Π»ΡΠ½ΡΠΉ ΠΈΠ·Π½ΠΎΡ.
Π‘Π»Π΅Π΄ΡΠ΅Ρ ΠΎΡΠΌΠ΅ΡΠΈΡΡ ΠΈ ΡΠΎ, ΡΡΠΎ ΡΠ»Π΅ΠΊΡΡΠΎΡΡΠΎΠ·ΠΈΠΎΠ½Π½ΠΎΠ΅ Π²ΠΎΠ·Π΄Π΅ΠΉΡΡΠ²ΠΈΠ΅ ΠΏΠΎΠ·Π²ΠΎΠ»ΡΠ΅Ρ ΠΏΠΎΠ»ΡΡΠΈΡΡ ΠΏΡΠΈ ΠΌΠΈΠ½ΠΈΠΌΠ°Π»ΡΠ½ΡΡ ΡΡΠΈΠ»ΠΈΡΡ ΠΏΠΎΠ²Π΅ΡΡ Π½ΠΎΡΡΠΈ ΡΠ°ΠΌΡΡ ΡΠ°Π·Π½ΡΡ ΠΊΠΎΠ½ΡΠΈΠ³ΡΡΠ°ΡΠΈΠΉ ΠΈ Π³Π΅ΠΎΠΌΠ΅ΡΡΠΈΡΠ΅ΡΠΊΠΈΡ ΡΠΎΡΠΌ.
ΠΡΠ΅ ΠΎΠ΄Π½ΠΈΠΌ Π΄ΠΎΡΡΠΎΠΈΠ½ΡΡΠ²ΠΎΠΌ Π΄Π°Π½Π½ΠΎΠ³ΠΎ ΠΏΡΠΎΡΠ΅ΡΡΠ° ΡΠ²Π»ΡΠ΅ΡΡΡ ΠΏΠΎΠ»Π½ΠΎΠ΅ ΠΎΡΡΡΡΡΡΠ²ΠΈΠ΅ ΡΡΠΌΠ° Π²ΠΎ Π²ΡΠ΅ΠΌΡ ΡΠ°Π±ΠΎΡΡ Π½Π° ΡΠΏΠ΅ΡΠΈΠ°Π»ΡΠ½ΠΎΠΌ ΠΎΠ±ΠΎΡΡΠ΄ΠΎΠ²Π°Π½ΠΈΠΈ.
ΠΠΎΠ½Π΅ΡΠ½ΠΎ, Π΅ΡΡΡ ΠΈ ΡΠ²ΠΎΠΈ ΠΏΡΠΎΠ±Π»Π΅ΠΌΡ ΡΠ°ΠΊΠΎΠ³ΠΎ Π²ΠΎΠ·Π΄Π΅ΠΉΡΡΠ²ΠΈΡ Π½Π° ΠΌΠ΅ΡΠ°Π»Π»ΠΈΡΠ΅ΡΠΊΡΡ Π΄Π΅ΡΠ°Π»Ρ, ΠΎΠ΄Π½Π°ΠΊΠΎ ΠΎΠ½ΠΈ Π½Π΅ ΡΠΈΠ»ΡΠ½ΠΎ ΡΠΊΠ°Π·ΡΠ²Π°ΡΡΡΡ Π½Π° Π΅Π΅ ΡΠΊΡΠΏΠ»ΡΠ°ΡΠ°ΡΠΈΠΎΠ½Π½ΡΡ ΡΠ²ΠΎΠΉΡΡΠ²Π°Ρ .
ΠΠ»Π΅ΠΊΡΡΠΎΡΡΠΎΠ·ΠΈΠΎΠ½Π½ΡΠΉ ΡΡΠ°Π½ΠΎΠΊ, ΠΈΡΠΏΠΎΠ»ΡΠ·ΡΠ΅ΠΌΡΠΉ Π΄Π»Ρ ΠΎΠ±ΡΠ°Π±ΠΎΡΠΊΠΈ ΡΠ°Π·Π»ΠΈΡΠ½ΡΡ ΠΌΠ΅ΡΠ°Π»Π»ΠΎΠ², ΠΌΠΎΠΆΠ½ΠΎ ΡΠ²ΠΈΠ΄Π΅ΡΡ Π½Π° Π²ΠΈΠ΄Π΅ΠΎ, ΠΊΠΎΡΠΎΡΠΎΠ΅ ΡΠ°Π·ΠΌΠ΅ΡΠ΅Π½ΠΎ Π½ΠΈΠΆΠ΅.
ΠΠΈΠ΄Π΅ΠΎ:
Π’Π΅Ρ Π½ΠΎΠ»ΠΎΠ³ΠΈΡ ΠΎΠ±ΡΠ°Π±ΠΎΡΠΊΠΈ
ΠΠ»Ρ ΡΠΎΠ³ΠΎ ΡΡΠΎΠ±Ρ Π΄ΠΎΡΠΊΠΎΠ½Π°Π»ΡΠ½ΠΎ ΡΠ°Π·ΠΎΠ±ΡΠ°ΡΡΡΡ Π²ΠΎ Π²ΡΠ΅Ρ ΠΏΡΠ΅ΠΈΠΌΡΡΠ΅ΡΡΠ²Π°Ρ ΡΠ»Π΅ΠΊΡΡΠΎΡΡΠΎΠ·ΠΈΠΎΠ½Π½ΠΎΠ³ΠΎ Π²ΠΎΠ·Π΄Π΅ΠΉΡΡΠ²ΠΈΡ Π½Π° ΠΌΠ΅ΡΠ°Π»Π»ΠΈΡΠ΅ΡΠΊΠΈΠ΅ Π·Π°Π³ΠΎΡΠΎΠ²ΠΊΠΈ ΠΈ ΠΏΠΎΠ½ΡΡΡ ΡΠ°ΠΌ ΠΏΡΠΈΠ½ΡΠΈΠΏ, Π½Π΅ΠΎΠ±Ρ ΠΎΠ΄ΠΈΠΌΠΎ ΠΏΠΎΠ΄ΡΠΎΠ±Π½ΠΎ ΡΠ°ΡΡΠΌΠΎΡΡΠ΅ΡΡ ΠΎΠ΄ΠΈΠ½ ΠΈΠ· ΡΠΏΠΎΡΠΎΠ±ΠΎΠ².
Π’Π°ΠΊ, ΠΏΡΠΎΡΡΠ΅ΠΉΡΠ°Ρ ΡΠ»Π΅ΠΊΡΡΠΎΡΡΠΎΠ·ΠΈΠΎΠ½Π½Π°Ρ ΡΡ Π΅ΠΌΠ° Π΄ΠΎΠ»ΠΆΠ½Π° Π² ΠΎΠ±ΡΠ·Π°ΡΠ΅Π»ΡΠ½ΠΎΠΌ ΠΏΠΎΡΡΠ΄ΠΊΠ΅ ΡΠΎΡΡΠΎΡΡΡ ΠΈΠ· ΡΠ°ΠΊΠΈΡ ΡΠ»Π΅ΠΌΠ΅Π½ΡΠΎΠ², ΠΊΠ°ΠΊ ΡΠ»Π΅ΠΊΡΡΠΎΠ΄, Π΅ΠΌΠΊΠΎΡΡΡ Π΄Π»Ρ ΡΠ°Π±ΠΎΡΠ΅ΠΉ ΡΡΠ΅Π΄Ρ, Π° ΡΠ°ΠΊΠΆΠ΅ ΠΊΠΎΠ½Π΄Π΅Π½ΡΠ°ΡΠΎΡΠ°, ΡΠ΅ΠΎΡΡΠ°ΡΠ° ΠΈ Π½Π΅ΠΏΠΎΡΡΠ΅Π΄ΡΡΠ²Π΅Π½Π½ΠΎ ΠΈΡΡΠΎΡΠ½ΠΈΠΊΠ°, ΠΎΠ±Π΅ΡΠΏΠ΅ΡΠΈΠ²Π°ΡΡΠ΅Π³ΠΎ Π½Π΅ΠΎΠ±Ρ ΠΎΠ΄ΠΈΠΌΠΎΠ΅ ΡΠ»Π΅ΠΊΡΡΠΎΠΏΠΈΡΠ°Π½ΠΈΠ΅.
Π Π΄Π°Π½Π½ΡΡ ΡΡ Π΅ΠΌΡ Π΄ΠΎΠ»ΠΆΠ½Ρ Π±ΡΡΡ Π²ΠΊΠ»ΡΡΠ΅Π½Ρ Π²ΡΠ΅ Π½Π΅ΠΎΠ±Ρ ΠΎΠ΄ΠΈΠΌΡΠ΅ ΡΠ»Π΅ΠΌΠ΅Π½ΡΡ Π² ΠΎΠΏΡΠ΅Π΄Π΅Π»Π΅Π½Π½ΠΎΠΉ ΠΏΠΎΡΠ»Π΅Π΄ΠΎΠ²Π°ΡΠ΅Π»ΡΠ½ΠΎΡΡΠΈ. ΠΠΈΡΠ°Π½ΠΈΠ΅ Π΄Π°Π½Π½ΠΎΠΉ ΡΡ Π΅ΠΌΡ ΠΎΡΡΡΠ΅ΡΡΠ²Π»ΡΠ΅ΡΡΡ ΠΎΡ Π½Π°ΠΏΡΡΠΆΠ΅Π½ΠΈΡ ΠΈΠΌΠΏΡΠ»ΡΡΠ½ΠΎΠ³ΠΎ ΡΠΈΠΏΠ°, ΠΏΡΠΈ ΡΡΠΎΠΌ ΠΎΠ½ΠΎ Π΄ΠΎΠ»ΠΆΠ½ΠΎ ΠΈΠΌΠ΅ΡΡ ΡΠ°Π·Π½ΡΡ ΠΏΠΎΠ»ΡΡΠ½ΠΎΡΡΡ.
ΠΡΠΎ Π΄Π°ΡΡ Π²ΠΎΠ·ΠΌΠΎΠΆΠ½ΠΎΡΡΡ ΠΏΠΎΠ»ΡΡΠΈΡΡ Π½Π΅ΠΎΠ±Ρ ΠΎΠ΄ΠΈΠΌΡΠ΅ Π΄Π»Ρ ΡΠ°Π±ΠΎΡΡ ΡΠ»Π΅ΠΊΡΡΠΎΠΈΠΌΠΏΡΠ»ΡΡΠ½ΡΠΉ ΠΈ ΡΠ»Π΅ΠΊΡΡΠΎΠΈΡΠΊΡΠΎΠ²ΡΠΉ ΡΠ΅ΠΆΠΈΠΌΡ.
ΠΡΠΈ ΠΏΠΎΠ΄Π°ΡΠ΅ Π½Π°ΠΏΡΡΠΆΠ΅Π½ΠΈΡ ΠΈΠ΄Π΅Ρ Π·Π°ΡΡΠ΄ΠΊΠ° ΠΊΠΎΠ½Π΄Π΅Π½ΡΠ°ΡΠΎΡΠ°, ΠΎΡ ΠΊΠΎΡΠΎΡΠΎΠ³ΠΎ ΡΠ°Π·ΡΡΠ΄Π½ΡΠΉ ΡΠΎΠΊ ΠΏΠΎΡΡΡΠΏΠ°Π΅Ρ Π½Π° ΡΠ»Π΅ΠΊΡΡΠΎΠ΄, ΠΊΠΎΡΠΎΡΡΠΉ Π΄ΠΎΠ»ΠΆΠ΅Π½ Π±ΡΡΡ ΠΏΡΠ΅Π΄Π²Π°ΡΠΈΡΠ΅Π»ΡΠ½ΠΎ ΠΎΠΏΡΡΠ΅Π½ Π² Π΅ΠΌΠΊΠΎΡΡΡ Ρ ΡΠ°Π±ΠΎΡΠΈΠΌ ΡΠΎΡΡΠ°Π²ΠΎΠΌ ΠΈ Π·Π°Π³ΠΎΡΠΎΠ²ΠΊΠΎΠΉ.
ΠΠΎΡΠ»Π΅ ΡΠΎΠ³ΠΎ, ΠΊΠ°ΠΊ Π½Π° ΠΊΠΎΠ½Π΄Π΅Π½ΡΠ°ΡΠΎΡΠ΅ Π½Π°ΠΏΡΡΠΆΠ΅Π½ΠΈΠ΅ Π΄ΠΎΡΡΠΈΠ³Π½Π΅Ρ Π½Π΅ΠΎΠ±Ρ ΠΎΠ΄ΠΈΠΌΠΎΠ³ΠΎ ΠΏΠΎΡΠ΅Π½ΡΠΈΠ°Π»Π°, ΠΏΡΠΎΠΈΠ·ΠΎΠΉΠ΄Π΅Ρ ΠΏΡΠΎΠ±ΠΎΠΉ ΠΆΠΈΠ΄ΠΊΠΎΡΡΠΈ, ΠΊΠΎΡΠΎΡΠ°Ρ Π±ΡΡΡΡΠΎ Π½Π°Π³ΡΠ΅Π΅ΡΡΡ Π΄ΠΎ ΡΠ΅ΠΌΠΏΠ΅ΡΠ°ΡΡΡΡ ΠΊΠΈΠΏΠ΅Π½ΠΈΡ, Π° ΠΊΡΠΎΠΌΠ΅ ΡΡΠΎΠ³ΠΎ, Π² Π½Π΅ΠΉ Π²ΠΎΠ·Π½ΠΈΠΊΠ½Π΅Ρ ΠΏΡΠ·ΡΡΡ ΠΈΠ· Π³Π°Π·ΠΎΠ².
ΠΡΠΎΡ ΠΏΡΠ·ΡΡΡ Π±ΡΠ΄Π΅Ρ ΡΠΏΠΎΡΠΎΠ±ΡΡΠ²ΠΎΠ²Π°ΡΡ Π»ΠΎΠΊΠ°Π»ΡΠ½ΠΎΠΌΡ Π½Π°Π³ΡΠ΅Π²Ρ Π·Π°Π³ΠΎΡΠΎΠ²ΠΊΠΈ, Ρ ΠΊΠΎΡΠΎΡΠΎΠΉ ΠΏΡΠΎΠΈΠ·ΠΎΠΉΠ΄Π΅Ρ ΠΏΠ»Π°Π²Π»Π΅Π½ΠΈΠ΅ ΡΠ°ΠΌΡΡ Π²Π΅ΡΡ Π½ΠΈΡ ΡΠ»ΠΎΠ΅Π², ΡΡΠΎ ΠΏΠΎΠ·Π²ΠΎΠ»ΠΈΡ ΠΎΠ±Π΅ΡΠΏΠ΅ΡΠΈΡΡ Π·Π°Π΄Π°Π½Π½ΡΡ ΡΠΎΡΠΌΡ.
ΠΠΈΠ΄Π΅ΠΎ:
Π Π΄Π°Π½Π½ΠΎΠΌ ΡΠΏΠΎΡΠΎΠ±Π΅ Π΅ΡΡΡ ΠΎΠΏΡΠ΅Π΄Π΅Π»Π΅Π½Π½ΡΠ΅ ΠΏΡΠΎΠ±Π»Π΅ΠΌΡ, ΠΊΠΎΡΠΎΡΡΠ΅ ΡΡΠ΅Π±ΡΡΡ ΠΏΠΎΡΡΠΎΡΠ½Π½ΠΎΠ³ΠΎ ΠΊΠΎΠ½ΡΡΠΎΠ»Ρ ΡΠ°ΠΌΠΎΠ³ΠΎ ΠΏΡΠΎΡΠ΅ΡΡΠ°, Π° ΠΏΠΎΡΡΠΎΠΌΡ Π»ΡΡΡΠ΅ Π²ΠΎΡΠΏΠΎΠ»ΡΠ·ΠΎΠ²Π°ΡΡΡΡ Π±ΠΎΠ»Π΅Π΅ ΡΠΎΠ²Π΅ΡΡΠ΅Π½Π½ΡΠΌΠΈ ΠΌΠ΅ΡΠΎΠ΄Π°ΠΌΠΈ.
ΠΠ° Π²ΠΈΠ΄Π΅ΠΎ Π²ΡΡΠ΅ ΠΏΠΎΠΊΠ°Π·Π°Π½Π° ΠΎΠ±ΡΠ°Π±ΠΎΡΠΊΠ°, ΠΏΡΠΎΠ²ΠΎΠ΄ΠΈΠΌΠ°Ρ Π½Π° ΠΏΡΠΎΡΠ΅ΡΡΠΈΠΎΠ½Π°Π»ΡΠ½ΠΎΠΌ ΠΎΠ±ΠΎΡΡΠ΄ΠΎΠ²Π°Π½ΠΈΠΈ.
rezhemmetall.ru