Электроды для сварки оцинкованных труб
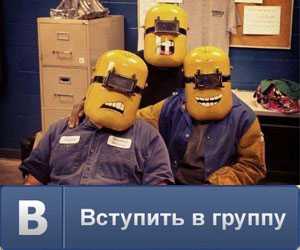
Цинкование является одним из наиболее эффективных способов, защиты стали от коррозии. Широко применяется при изготовлении строительных конструкций, труб, гидротехнических сооружений. Существует несколько способов нанесения цинка на металл- это гальванический метод, горячее цинкование и напыление. Толщина напиленного слоя цинка вольируется от 3 до 150 мкм.
Так как температура кипения цинка составляет 906 С, он имеет свойство интенсивно испариться во время выполнения сварочных работ. Испаряясь, цинк, выделяет вредные пары, которые в свою очередь могут вызвать приступ удушья. При интенсивном испарение в момент сварки цинк попадает в сварочную ванну и из-за этого образуются в сварном шве поры и кристаллизационные трещины. В связи с этим нужно счищать слой цинка с места проведения сварных работ. В некоторых случаях нет возможности для удаления слоя цинка, и тогда приходится применять методы позволяющие получить качественный сварной шов. При выборе способа ручной дуговой сварке большую роль играет правильный выбор электрода. Для выполнения сварки на углеродистых сталях больше всего подходят электроды с рутиловым покрытием, а для выполнения сварных работ на низколегированных сталях нужно отдать предпочтение электродам, имеющим основное покрытие.
Для предотвращения возникновения пор в сварных стыковых и угловых швах оцинкованных труб, нужно увеличить ток и сократить скорость сварки. Цинк не оказывает большого влияния на качество швов только при условии эксплуатации труб при положительной температуре. Для соединения оцинкованных труб без повреждения цинкового слоя производиться, используя метод пайки. Получаемый шов обладает очень высокими характеристиками, время и стоимость монтажа значительно уменьшаются, шов обладает высокой герметичностью и антикоррозийной стойкостью. Для получения швов таким методом нужно пользоваться электродами и припоем покрытых флюсом. Обычные оцинкованные трубы для воды прекрасно свариваются при помощи обычного электрода.
elektrod-3g.ru
Сварка оцинкованных труб – особенности технологии
Трубы с оцинкованным покрытием до недавнего времени были основными для создания водопроводных сетей в домах и производственных зданиях. При прокладке трубных разводок в массовом порядке применялась сварка.
Даже в местах, где по условиям монтажа сварное соединение невозможно, перед установкой элемента сети к нему приваривается резьбовой конец для последующего муфтового соединения.
Для увеличения срока службы для водопроводных и газовых сетей применяются трубы с защитным цинковым покрытием. Это не приводит к сложностям в процессе монтажа, но сама по себе сварка оцинкованных труб имеет ряд особенностей, которые необходимо учитывать в процессе сборки.
Для понимая сущности процесса, рассмотрим, что из себя представляют оцинкованные трубы.
Оцинковка металла как способ защиты от коррозии
Защитное покрытие стальных изделий применялось издавна, поскольку цветные металлы, устойчивые к коррозии слишком дороги для изготовления из них цельных изделий. Да и прочностные свойства таких предметов весьма невысоки. Применялось лужение по поверхности оловом или омеднение для создания защитной пленки.
Оцинкование стало популярным по причине повышенной адгезии цинка к железу. Температура плавления этого металла составляет 900 – 920о. В жидком состоянии он, нанесенный на поверхность стального изделия, образовывает прочную защитную пленку толщиной в несколько микрон, успешно противостоящую коррозии.
На сегодняшний день применяются три основных способа нанесения защитного покрытия:
- Гальванический. При этом ионы цинка осаждаются на поверхности стального изделия, подключенного к противоположному электроду в гальванической ванне. Они прочно закрепляются на поверхности изделия, создавая практически неразрушимую защитную пленку. Толщина защитного слоя регулируется временем обработки, что позволяет рационально использовать дорогостоящий цветной металл, в частности, цинк.
- Способ напыления. Суть его заключается в нанесение на поверхность распыленного металла с использованием специального пистолета, в котором происходит расплавление напыляемого вещества. Затем эта субстанция струйно подается на обрабатываемую поверхность, покрывая ее защитным слоем.
В результате на защищаемой поверхности образуется прочный защитный слой из химически пассивного материала. Способ удобен возможностью применения в полевых условиях на месте выполнения монтажных работ.
- Горячее оцинкование. Применяется на специально созданных технологических линиях. При этом труба полностью окунается в ванну с расплавленным металлом. В конце процесса производится центрифугирования для удаления излишков защитного слоя с поверхности изделий.
При использовании любого из перечисленных способов нанесения защитного покрытия, поверхность обрабатываемых изделий тщательно обезжиривается.
Толщина слоя составляет от 2-х до 150 микрон.
Соединение сваркой
Такой вид стыковки труб при монтаже отопительных, водопроводных и газовых систем оговаривается рядом регламентирующих документов, одним из которых является СНиП 3.05.01-85 «Внутренние санитарно – технические системы».
Видео
При сварке оцинкованных труб СНиП, упомянутый выше, указывает на необходимость исполнения требований ряда стандартов, определяющих очередность применения материалов и регулирующий процесс производства работ. В частности при сварке оцинкованных труб, ГОСТ 16037-80 регламентирует применение определенных типов сварного соединения, форму и конструктивные особенности швов, а также другие требования к ним.
При газопламенной сварке нужно использовать самозащитную сварочную проволоку марки Св 15ГСТЮЦА, имеющую в своем составе элемент селен. Размер проволоки от 0,8 до 1,2 мм.
Допускается также исполнение соединения электродами для сварки оцинкованных труб марками, содержащими в обмазке фтористо – кальциевые или рутиловые соединения. Их диаметр подбирается в соответствии с толщиной стенок свариваемых деталей, максимальный размер составляет 3 мм в диаметре.
Создание трубопроводной сети предполагает предварительную сборку блоками с выполнением части операции на предприятии, выполняющем ряд действий предварительной сборки монтажных блоков. При этом нормативно предусмотрено применение местных воздухоотсосов для удаления продуктов сгорания цинкового покрытия, опасных для здоровья.
Видео
Технология сварки оцинкованных труб предусматривает также зачистку поверхности от защитного покрытия на расстояние 30 – 40 мм от конца. После обработки сварного шва нужно восстановить защиту от коррозии в месте соединения.
Для этого применяют краску специального состава, состоящую на 95 % из мелкодисперсного цинкового порошка и включающую в состав синтетические связующие вещества в виде эпоксидных смол, каучука синтетического или полистерины.
Стыковка водогазопроводных труб с защитным цинковым покрытием (и без него), имеющих условный проход до 25 мм, следует производить «внахлест», для чего производится предварительная раздача одного конца.
При производстве сварки резьбовые концы труб, как и зеркала фланцев, нуждаются в защите от капель раскаленного металла, образующихся в процессе выполнения сварных работ.
Видео
В сварном шве не допускаются следующие дефекты:
- раковины;
- трещины;
- подрезы;
- поры;
- непроваренные кратеры;
- пережоги и подтеки металла.
Ультразвуковой контроль сварных швов не применяется, их целостность проверяется при опрессовке системы определенным давлением.
Разработан способ соединения оцинкованных заготовок сваркой с
Флюс для сварки оцинкованных труб приводится в жидко – вязкое состояние и наносится на стык соединяемых деталей. В процессе сварки он еще расплавляется, покрывая тонким слоем участок вдоль шва, препятствуя отслоению цинкового слоя и его сгоранию.
При использовании флюса возможно повреждение защитного слоя, когда он наносился способом горячего оцинкования.
Это становится возможным при малейшем отклонении от требований технологического процесса при нанесении покрытия или при производстве сварки.
Попадание флюса во внутреннюю полость трубопровода не опасно, поскольку он легко растворяется в воде и вымывается еще на стадии опрессовки трубопровода.
Существует способ соединения оцинкованных труб, называемый сварко – пайкой. Для этого применяется присадочный пруток, в состав которого входят такие элементы, как цинк, медь, кремний и олово. Технология процесса такова:
- стыкуемые торцы нагревают до температуры плавления присадочного прутка, составляющей 900 – 950о;
- присадочный пруток помещается между фасками свариваемых деталей;
- на место шва насыпается слой флюса таки образом, чтобы он покрывал поверхность на расстояние до 20 мм по сторонам шва;
- присадку нагревают горелкой до полного расплавления, при этом она создает надежное соединение труб без повреждения плакирующего цинкового покрытия.
Диаметр присадочного прутка определяется из соотношения:
- при толщине стенки менее 10 мм D = 0,5S + 1, где
D – диаметр прутка для присадки;
S – толщина стенки трубы;
- для труб с толщиной стенки более 10 мм соотношение принимает вид:
D = 0,5S
Для нарезки фасок на стыкуемых концах труб в полевых условиях применяется специальное оборудование – орбитальные установки. Они могут оснащаться газопламенными резаками для нарезки таких элементов.
Для случая с оцинкованными трубами могут использоваться механические головки, нарезка производится резцом или фрезой. Позиционирование и крепление установки производится непосредственно на трубе.
Необходимые меры безопасности
Особенности сварки оцинкованной трубы предполагают особое внимание к исполнению правил безопасности при производстве работ. Выделяющиеся при выполнении соединения пары цинка являются весьма ядовитыми, поэтому их удаление из помещения обязательно.
Видео
Для этого используются мощные вытяжные устройства для каждого сварочного поста. Остальные требования по безопасности оговариваются соответствующими инструкциями и обязательны для исполнения.
Сварка оцинкованных труб является наиболее распространенным способом их соединения, как по надежности, так и по долговечности. Следует помнить, что шов нуждается специальной защите от коррозии с использованием специальной краски на основе цинкового порошка.
Записи по теме:Опубликовано: Январь 9, 2017 Загрузка…
trubanet.ru
Сварка оцинкованной стали
В целях повышения долговечности эту сталь применяют довольно широко в автомобилестроении и т. п. Цинк предохраняет поверхность стали от электрохимической коррозии на длительное время. Эта сталь достаточно хорошо штампуется, сваривается и окрашивается. Цинковое покрытие считается в условиях эксплуатации автомобиля более долговечным, чем многослойные лакокрасочные покрытия. В целях защиты от коррозии из такой стали изготовляют только наиболее уязвимые детали кузова автомобиля. Например, в США в среднем на один автомобиль расходуется до 90 кг горячеоцинкованной и 9 кг стали с гальваническим покрытием.
Для цинкования часто используют холоднокатаную низкоуглеродистую сталь 08кп, широко применяемую в штампо-сварных конструкциях. Покрытие можно наносить горячим способом (окунанием) или в гальванических ваннах. Первый считается более производительным и дешевым, последний дает более равномерный слой, что благоприятнее для сварки. Горячим цинкованием изготовляют основную массу оцинкованного металла.
Технология цинкования должна исключать образования интерметаллидов железа с цинком, так как эти соединения делают металл менее пластичным и непригодным для штамповки. При сварке металла возможны трещины. На снижение пластичности влияет образование неравновесных структур при отжиге и цинковании, а также возможно появление водородной хрупкости.
В зависимости от назначения применяют легкие, средние и тяжелые покрытия, различающиеся толщиной, задаваемой массой покрытия на единицу площади. В легких покрытиях масса цинка на 1 м2 составляет 120—275 г, средних 245—410 г и тяжелых 390—685 г при средней толщине покрытия соответственно 14,21 и 30 мкм.
В целях снижения расхода цинка и улучшения свариваемости применяют стали с односторонним покрытием или двусторонним, но разной толщины. Например, специально для автомобилестроения разработано дифференцированное покрытие с толщиной слоя цинка на лицевой стороне 2,5—6 мкм, а на стороне, более подверженной коррозии, 20—25 мкм. Толщина покрытия влияет на свариваемость. С увеличением его толщины свариваемость ухудшается, требуются увеличение сварочного тока, изменение цикла сварки, более частая зачистка рабочих поверхностей электродов.
Оцинкованная сталь должна поступать с чистой поверхностью, свободной от масла, грязи и остатков смазки, применяемой при штамповке. Появление на поверхности стали (при ее длительном хранении в условиях повышенной влажности и температуры) окислов цинка (белый налет) препятствует сварке, и их следует удалять.
Сварка оцинкованной стали не требует применения специального оборудования. В связи с более низким контактным сопротивлением, вызванным увеличением площади контакта в месте сварки, необходимо повышение силы сварочного тока. Чем толще цинковое покрытие, тем меньше сопротивление в месте сварки, тем требуется большее повышение силы тока.
Интенсивное увеличение диаметра контактных площадок замедляет повышение температуры центрального столбика металла и вызывает более позднее формирование литого ядра. По мнению исследователей, это приводит при сварке сталей с покрытиями к значительно большему разбросу значений диаметра литого ядра и нагрузки на срез, так как ядро формируется за более короткое время.
В табл. 7 приведены режимы сварки для стали, имеющей среднее гальваническое покрытие. По сравнению с жесткими режимами (см. табл. 3, режим А), для сварки непокрытых сталей в этих режимах увеличены усилие на электродах до 40%, продолжительность импульса сварочного тока до 90% и сила сварочного тока до 20%. Одновременно в этих же соединениях увеличивается и разрушающее усилие частично благодаря дополнительной прочности, полученной за счет сплавления цинка вокруг ядра. Эти же режимы сварки применяют при отношении толщин не более 1:2.
Толщина каждой детали, мм | Диаметр контактной поверхности электрода, мм | Усилие на электродах, кгс | Продолжительность импульса сварочного тока, с | Сила сварочного тока, кА | Диаметр литого ядра, мм | Разрушающее усилие при срезе на точку, кгс |
0,8 | 4,0 | 215 | 0,22 | 10,5 | 4,3 | 420 |
0,9 | 4,5 | 250 | 0,24 | 11,0 | 4,6 | 500 |
1.0 | 5,0 | 285 | 0,26 | 12,5 | 5,0 | 635 |
1,3 | 5,5 | 380 | 0,36 | 14,0 | 5,8 | 910 |
1,5 | 6,5 | 487 | 0,46 | 15,0 | 6,6 | 1135 |
1,9 | 8,0 | 635 | 0,56 | 19,5 | 7,9 | 1450 |
2,4 | 9,0 | 820 | 0,64 | 24,0 | 9,0 | 1910 |
2,8 | 10,5 | 1000 | 0,78 | 28,5 | 10,4 | 2315 |
Коррозионная стойкость в месте сварки несколько снижается (до 20%) из-за частичного разрушения покрытия под электродами. Время проковки после выключения сварочного тока необходимо увеличивать, например, до 0,4 с для сварки стали толщиной 1,6 мм. В этот момент слой цинка, расплавленный при сварке, застывает и в меньших количествах переходит на контактную поверхность электродов. В некоторых источниках для металла толщиной свыше 1,5 мм рекомендуется применять повышенное усилие проковки в целях повышения стабильности прочностных показателей и улучшения стойкости электродов (табл. 8).
Толщина каждой детали, мм | Усилие на электродах, кгс | Продолжительность, с | Сила сварочного тока, кА | Диаметр литого ядра точки, мм | Разрушающее усилие при срезе на точку, кгс | ||
при сварке | при проковке | импульса сварочного тока | проковки | ||||
1,65 | 205 | 475 | 0,5 | 0,33 | 11,5 | 7,1 | 1250 |
2,74 | 320 | 900 | 0,8 | 0,51 | 15,5 | 8,9 | 3000 |
3,50 | 680 | 1170 | 1,2 | 0,83 | 19,0 | 12,2 | 4300 |
При сварке оцинкованных сталей применяют электроды из бронзы типа БрХ или сплава БрХЦр, имеющего большую стойкость.
Электроды применяют с рабочей поверхностью в виде усеченного конуса с углом заточки 120—140°. Электроды со сферической заточкой (радиус сферы 75 мм) используют в тех случаях, когда трудно обеспечить перпендикулярность оси электрода к сварочной поверхности. Важно обеспечить интенсивное охлаждение электродов при расходе воды не менее 7 л/мин. Контактную поверхность электродов следует периодически зачищать и заправлять. При сварке стали толщиной до 2,5 мм со средним покрытием эту операцию производят после 1000 точек. С возрастанием толщины свариваемых деталей и толщины покрытия стойкость электродов падает.
Резко ухудшается вид места сварки и снижается стойкость электродов при сварке оцинкованной стали на многоточечных машинах с односторонним токоподводом. Лучшие результаты получаются при сварке непокрытой стали с оцинкованной, если непокрытую сталь расположить со стороны вторичного контура сварочного трансформатора. Плотность тока в контакте электрод — деталь при этом снижается. Для сварки двух оцинкованных листов следует использовать обычную двустороннюю сварку или схему со спаренными трансформаторами, что также облегчает условия работы электродов в результате снижения токов шунтирования.
Статическая прочность на срез сварных соединений из оцинкованной стали несколько выше, чем у непокрытых благодаря дополнительной прочности, полученной за счет сплавления цинка вокруг литого ядра. Прочность при переменных нагрузках также возрастает. Критерием ее оценки обычно является отношение
предела выносливости к максимальной статической прочности на срез, которое для оцинкованных и непокрытых сталей толщиной 1 мм равно соответственно 0,5 и 0,3. Эта разница снижается при увеличении толщины, что объясняется уменьшением эффекта действия соединения, вызванного сплавлением цинка вокруг литого ядра.
www.stroitelstvo-new.ru
Сварка оцинкованного металла
Нанесение слоя цинка на металл — цинкование применяется для защиты металла от коррозии. Толщина слоя цинка составляет 3…150 мкм, и толщина слоя цинка на данном металле указывается в его сертификате.
Температура кипения цинка составляет 906 °С, и при сварке оцинкованного металла цинк испаряется, загрязняя воздух. Поэтому при сварке оцинкованного металла необходимо уделять внимание технике безопасности, так как пары цинка могут привести к удушью.
Рабочее место сварщика должно быть оборудовано местной вентиляцией, а помещение, где производятся сварочные работы — общей вентиляцией.
При сварке цинк попадает в сварочную ванну и способствует образованию пор и трещин в шве. Поэтому должно быть произведено удаление цинка с поверхности металла перед сваркой механически — щетками, абразивными кругами или пламенем газовой горелки. Можно удалять цинк с поверхности металла химическими способами — кислотой с последующей нейтрализацией ее щелочью, промывкой водой и сушкой. При невозможности удаления цинка перед сваркой приходится применять технологические приемы для получения качественного шва. Большое значение имеет выбор электродов для сварки оцинкованных сталей.
Рекомендуется использовать для сварки низкоуглеродистых сталей электроды с рутиловым покрытием — АНО-4, МР-3, ОЭС-4, для сварки низколегированных сталей — электроды с покрытием основного вида — УОНИ-13/45, УОНИ-13/55, ДСК-50 и др.
Для предотвращения появления пор при сварке стыковых и угловых швов ток сварки нужно увеличить на 10…15 А по сравнению с обычным и увеличить зазор между свариваемыми кромками в 2 раза, снизить скорость сварки на 10…20%. Это поможет при слое цинка до 15 мкм. При толщине слоя цинка 15…40 мкм применяется специальная техника сварки, при этом электродом совершается возвратно-поступательное движение для предварительного выгорания цинка. При сварке стали с толщиной слоя цинка более 40 мкм необходимо полное удаление цинка для получения бездефектного шва.
otdelka-profi.narod.ru
Контактная сварка низкоуглеродистых оцинкованных сталей
Контактная сварка низкоуглеродистых оцинкованных сталей как вопрос мало где раскрывается. Мы решили рассмотреть его.
Режимы сварки
Низкоуглеродистые стали имеют хорошую свариваемость всеми видами контактной сварки. При контактной точечной сварке низкоуглеродистой стали можно использовать как мягкий так и жесткий режимы. Мягкий режим характеризуется меньшей силой тока, большей продолжительностью времени его пропускания. Жёсткий режим имеет большое значение сварочного тока и небольшое время его пропускания.
Пример параметров на жестком режиме сварки
Толщина заготовок в мм | Диаметр контактной поверхности электродов в мм | Продолжительность пропускания сварочного тока в сек. | Давление на электродах в КЗ | Сила сварочного тока в А | |
начальный | перед запиливанием | ||||
0,5+0,5 | 5 | 6 | 0,2—0,3 | 30—40 | 4000—5000 |
1+1 | 5 | 6 | 0,2—0,35 | 80—120 | 6000—7000 |
Пример параметров на мягком режиме сварки
Толщина заготовки в мм | Диаметр контактной поверхности электродов в мм | Продолжительность пропускания сварочного тока в сек. | Давление на электродах в кг | Сила сварочного тока в а | |
начальный | перед запиливанием | ||||
0,5+0,5 | 5 | 6 | 0,8 | 30—40 | 3000—4000 |
1+1 | 5 | 6 | 1 | 80—120 | 4500—5000 |
Как и было сказано ранее, режимы отличаются продолжительностью времени пропускания сварочного тока (сек.), и его значения (А).
Жёсткие режимы применяют, когда необходимо получить большее проплавление деталей.
То есть выбор режима осуществляем опираясь на толщину свариваемого изделия, его тепло и температуропроводность. К примеру, при одинаковом времени сварки низкоуглеродистых и оцинкованных сталей, для оцинковки — режим сварки должен быть более жёстким так, как у оцинковки меньшая температуропроводность.
Контактная сварка низкоуглеродистых оцинкованных сталей
При сварке сталей с покрытием, к примеру оцинковки, происходит интенсивное испарения цинка, поскольку его температура кипения составляет 906 °С, поэтому есть большая вероятность его попадания в сварочную ванну. В последствии это способствует образованию пор и кристаллизационных трещин в сварном шве.
Технологическое решение этой проблемы осуществляется двумя способами: механическим (щетками, абразивным кругом) или термическим (газовой горелкой). И возможно удаление слоя цинка химическим способом — за счет обработки металла кислотой с последующей ее нейтрализацией щелочью, промывкой водой и сушкой.
Импульсная контактная сварка
Данный способ сварки производится в две стадии. Вначале деформируют и удаляют цинковое покрытие из зоны сварки путем подачи предварительного импульса тока для нагрева поверхности выше температуры плавления цинка, но ниже температуры образования сварной точки. Затем подают основной импульс тока до образования сварной точки.
На фото показаны примеры контактной сварки оцинковки с применением метода контактной импульсной сварки.
Недостатком этого способа является то, что при деформации покрытия происходит уменьшение толщины покрытия, а основная часть его остается в зоне контактов электрод-деталь и деталь-электрод. Это не обеспечивает надлежащее качество свариваемых деталей и приводит к увеличению времени сварки
blog.svarcom.net
Особенности сварки оцинкованных труб своими руками: ГОСТ на электроды
Не секрет, что оцинкованные стальные изделия используются в различных отраслях промышленности и строительстве довольно часто. И это неудивительно. Ведь материал имеет отличную коррозионную стойкость и стоит недорого. При этом такие трубы имеют более привлекательный внешний вид, в сравнении со стальными. Все это можно увидеть на фото и видео в Сети.
Пример оцинкованных труб
Получение оцинкованного материала
Чтобы нанести на сталь цинк, есть несколько вариантов по ГОСТу. Самый часто используемый способ – напыление. Также часто применяется цинкование и гальванический способ. Цинкование применяется при массовом изготовлении стальных изделий.
Поэтому толщина слоя цинка может быть разной, но находится в пределах от 2 до 150 микрон.
Как соединить оцинкованные трубы
Чтобы соединить трубы, использовать резьбу нецелесообразно, поскольку это нарушает свойства металла (коррозионную стойкость). Поэтому чаще всего используется традиционная сварка. Однако опасность повреждения цинкового покрытия также сохраняется. Поэтому не исключены коррозионные процессы. Если участки поверхности труб окажутся малыми, они все равно будут защищены катодным путем. Если же эти зоны большие, тогда коррозийная защита не может быть обеспечена на все 100 %.
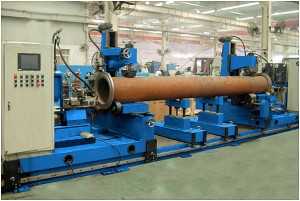
Приваривание фланца к трубе
Особенности
Чтобы соединить оцинкованные трубы своими руками, применяется специальная технология, которая дает возможность избежать нарушения цинкового покрытия. Происходит все таким образом. Флюс наносится на место соединения. Он не выгорает, поскольку находится в расплавленной стадии. Благодаря этому создается высокий уровень коррозионной стойкости.
Такой метод применим и для сварки труб водопровода. Дело в том, что внутри трубы остается флюс, который затем растворяется в воде. При этом он не создает опасности для человека, поскольку безвреден.
И, конечно же, нельзя забывать о безопасности процесса. Поэтому сварка выполняется только в хорошо проветриваемых помещениях. Иначе это чревато ухудшением здоровья. Это особенно важно знать, если планируется выполнять процедуру своими руками. На видео в Сети об этом нюансе не всегда могут сообщить, поэтому его нужно запомнить.
Правила выполнения сварочных работ
Для удачного результата следует соблюсти простые правила, которые можно найти в ГОСТах:
- Кромки не нужно подготавливать (даже если толщина стенок составляет более 4 мм): они должны быть без скосов. При этом необходимо выполнить зачистку до блеска, удалить жир.
- В процессе нужно обеспечить температуру, при которой цинк не перегревается, а иначе о коррозионной стойкости можно забыть. Поэтому нужно наносить слой флюса, которого будет вдвое большое от необходимого количества по расходу.
- Газовое пламя должно поставлять небольшой избыток кислорода.
- Детали предварительно подогреваются.
- Горелка выбирается на номер или два номера меньше, если сравнивать с аналогичной ситуацией при работе со стальными изделиями.
- Прут устанавливается в место стыка, а затем огнем горелки расплавляют его (направление должно быть не на основной металл, а именно на прут).
- Чтобы предотвратить появление пор, следует уменьшить скорость сварки и увеличить ток.
- После процесса флюс следует удалить.
Выбор электрода
Рутиловый электрод
Стандартные оцинкованные трубы для воды можно сваривать обычными электродами. Если выбирается ручной дуговой способ сварки, то выбор электрода – важная составляющая качественности процесса. Если нужно сваривать низколегированные стали, подойдут электроды с основным покрытием, для углеродистых сталей лучше с рутиловым.
В сварке оцинкованных труб есть свои особенности. И если их учесть, тогда процесс пройдет стабильно, а на выходе мы получим качественный шов, который будет служить не один год. Он будет обладать высокой коррозионной стойкостью, герметичностью. А стоимость и время монтажа будут на минимальном уровне.
trubygid.ru
Композиционный материал на основе меди для электродов контактной сварки оцинкованных сталей
Изобретение может быть использовано при контактной сварке оцинкованных сталей. Композиционный материал содержит компоненты в следующем соотношении, мас.%: титан 0,2-1,1, углерод 0,05-0,20, медь — остальное. Изготовленные из указанного материала электроды для контактной сварки обладают высокой сопротивляемостью адгезии к цинковому покрытию при одновременной хорошей жаропрочности, а также стабильностью контактного сопротивления, что обусловливает высокий ресурс их работы. 4 табл.
Изобретение относится к сварочному производству, в частности — к составам материалов на основе меди для электродов контактной сварки оцинкованных сталей.
Известны материалы на основе меди для электродов контактной сварки, например, бронзы, содержащие хром, титан, цирконий и другие элементы, обеспечивающие прочностные характеристики материала за счет дисперсионного упрочнения. Однако эти бронзы имеют низкую температуру рекристаллизации, что приводит к ускоренному разрушению контактной поверхности электродов [1].
Наиболее близким к заявляемому техническому решению является композиционный порошковый материал на основе меди, содержащий ультрадисперсные частицы оксида титана TiO2, полученный методом внутреннего окисления порошка сплава меди с титаном [2], пригодный для сварки оцинкованных сталей. Указанный материал обладает хорошими электрофизическими характеристиками как при комнатной, так и при повышенных температурах и имеет высокую температуру рекристаллизации. Однако недостаточно высокие антифрикционные и противоадгезионные свойства материала, а также нестабильность его контактного сопротивления обусловливают недостаточно высокий ресурс работы изготовленных из него электродов контактной сварки оцинкованных сталей, особенно, электродов для роликовой шовной и стыковой сварки. Кроме этого длительные окислительно-восстановительные отжиги, используемые в технологии получения данного материала, обусловливают высокие цены на него, что не позволяет осуществить его широкое применение в сварочном производстве.
Заявляемое изобретение решает задачу расширения ассортимента материалов, обладающих высокими физико-механическими характеристиками при одновременно высоких показателях антифрикционных, противоадгезионных свойств материала, стабильности его контактного сопротивления и ресурса работы изготовленных из него электродов контактной сварки оцинкованных сталей, а также расширения ассортимента композиционных порошковых материалов на основе меди, обладающих высокими физико-механическими характеристиками.
Эта задача решается тем, что композиционный материал на основе меди, содержащий титан, дополнительно содержит углерод при следующем соотношении компонентов, масс. %:
Титан | 0,2-1,1 |
Углерод | 0,05-0,20 |
Медь | остальное |
Из уровня технически не известны аналоги, обладающие тождественной совокупностью признаков.
Заявляемый материал изготавливают из шихты, приготовленной смешиванием порошков титана (ТУ 48-0501-385-94), углерода (ГОСТ 4404-78) и меди (ГОСТ 4960-75), путем обработки шихты в шаровой мельнице, последующего холодного компактирования полученных гранул в брикеты и их горячей экструзии в пруток или профиль при температуре 750-850°С. При этом компоненты шихты вступают в твердофазные реакции, в результате которых образуется структура материала, представляющая собой практически чистую матрицу с равномерно распределенными в ней ультрадисперсными (10-50 нм) частицами оксида и карбида титана, а также свободного углерода. Наличие в материале равномерно распределенного ультрадисперсного углерода придает материалу высокие антифрикционные и противоадгезионные свойства, обеспечивая тем самым высокий ресурс изготовленных из него электродов контактной сварки и токоподводящих наконечников дуговой сварки.
В соответствии с описанной технологией были изготовлены прутки заявленного материала с вышеуказанным содержанием компонентов, а также материала-прототипа (табл.1).
Таблица 1 | ||||
Компоненты | Составы, масс.% | |||
№1 | №2 | №3 | Прототип | |
Титан | 0,20 | 0,50 | 1,10 | 0,50 |
Углерод | 0,20 | 0,15 | 0,05 | — |
Медь | 99,60 | 99,35 | 98,85 | 99,5 |
Все полученные прутки были подвергнуты испытаниям с целью определения их физико-механических характеристик, которые приведены в табл.2.
Твердость определялась по ГОСТ 9012-59, электропроводность — по ГОСТ 7229-76, а испытания на растяжение проводились по ГОСТ 1497-84.
Таблица 2 | |||||
Составы | Физико-механические характеристики | ||||
Твердость НВ | Электропроводность, % от электропроводности меди | Временное сопротивление растяжению, МПа | Относительное удлинение, % | Относительное сужение, % | |
Прототип | 143 | 83 | 420 | 18 | 32 |
Состав №1 | 145 | 87 | 425 | 18 | 33 |
Состав №2 | 155 | 85 | 510 | 16 | 28 |
Состав №3 | 185 | 72 | 560 | 12 | 22 |
Из табл.2 видно, что прочностные свойства заявляемого материала превосходят прочностные свойства материала-прототипа. При этом заявляемый материал составов №1 и №2 по сравнению с материалом-прототипом имеет и более высокую электропроводность.
Антифрикционные свойства материалов определялись на машине СМЦ-2 по схеме «ролик-колодка» при давлении на контактную поверхность пары трения 2 МПа и скорости скольжения 0,4 м/с. В качестве материала колодки использовались заявляемый материал указанных выше составов и материал-прототип. Для изготовления контртела (ролика) использовалась качественная углеродистая сталь 20, часто применяемая в конструкциях ответственного назначения, получаемых из листовых заготовок роликовой шовной сваркой.
Результаты испытаний приведены в табл.3.
Для оценки противоадгезионных свойств, а также стабильности контактного сопротивления заявляемого материала и материала-прототипа были отштампованы колпачковые электроды типа F диаметром 16 мм по ISO 5821. Испытания проводили при сварке оцинкованной стали толщиной 0,8±0,8 мм при сварочном токе силой 10-11 кА, усилии сжатия электродов — 230 кГс и темпе сварки — 7 пер.
Критерием оценки противоадгезионных свойств материалов, а также стабильности их контактного сопротивления было принято относительное изменение контактного сопротивления электродов, обусловленное в основном диффузией жидкого цинка в материал электродов, а также зашлаковыванием их контактных поверхностей. Измерялось контактное сопротивление между двумя электродами до (RO) и после (R) испытаний и определялось относительное его изменение по формуле:
ΔR=RO/R.
Результаты измерений приведены в табл.3.
Таблица 3 | ||||
Составы | Антифрикционные свойства | Относительное изменение контактного сопротивления | ||
Коэффициент трения | Удельный износ, мг/км | Удельная нагрузка заедания, кгс/см2 | ||
Прототип | 0,030 | 0,403 | 163 | 1,34 |
Состав №1 | 0,028 | 0,365 | 181 | 1,24 |
Состав №2 | 0,024 | 0,347 | 287 | 1,29 |
Состав №3 | 0,022 | 0,326 | 363 | 1,32 |
Из табл.3 видно, что заявляемый материал обладает значительно более высокими антифрикционными и противоадгезионными свойствами, а также более стабильным контактным сопротивлением, чем материал-прототип.
Для определения ресурса электродов контактной сварки были проведены сравнительные испытания холодноштампованных колпачковых электродов типа F диаметром 16 мм по ISO 5821, изготовленных из заявляемого материала указанных выше составов и материала-прототипа. Испытания проводили при сварке оцинкованной стали толщиной 0,8±0,8 мм при сварочном токе силой 10-11 кА, усилии сжатия электродов — 230 кГс и темпе сварки -7 пер.
Критерием оценки ресурса работы электрода служило количество сваренных точек до его перезаточки, необходимость в которой наступала в том случае, когда диаметр контактной поверхности электрода увеличивался на 20% по сравнению с его исходным диаметром. Измерение диаметра контактной поверхности электрода производилось через каждые 100 циклов сварки. Если измеренный диаметр превосходил исходный диаметр на 20%, то за значение ресурса электрода принималось количество сваренных им точек, которое было зафиксировано при проведении предыдущего измерения контактной поверхности электрода.
Результаты ресурсных испытаний приведены в табл.4.
Таблица 4 | ||||||
Составы | Количество сваренных точек до переточки электрода, шт. | |||||
№ испытания | ||||||
1 | 2 | 3 | 4 | 5 | Среднее значение | |
Прототип | 2300 | 2500 | 2100 | 2700 | 2400 | 2400 |
Состав №1 | 2400 | 2900 | 2800 | 3000 | 2500 | 2720 |
Состав №2 | 2600 | 2300 | 2900 | 3100 | 3200 | 2820 |
Состав №3 | 2800 | 3300 | 3100 | 3400 | 2900 | 3100 |
Из табл.4 видно, что электроды из заявляемого материала имеют ресурс, превосходящий ресурс электродов из материала-прототипа.
Источники информации, принятые во внимание при составлении описания и формулы изобретения
1. Справочник по обработке цветных металлов и сплавов / А.П. Смирягин, Н.З. Днестровский, А.Д. Ландиков и др. / Под ред. Л.Е. Миллера — М.: Металлургиздат, 1961. 872 с.
2. Данелия Е.П., Розенберг В.М. Внутреннеокисленные сплавы. — М.: Металлургия, 1978. 232 с.
Композиционный материал на основе меди для электродов контактной сварки оцинкованных сталей, содержащий титан, отличающийся тем, что он дополнительно содержит углерод при следующем соотношении компонентов, мас.%:
Титан | 0,2-1,1 |
Углерод | 0,05-0,20 |
Медь | остальное |
www.findpatent.ru