90-тонный БЕЛАЗ с новым тяговым электроприводом. Испытание техники будущего
ОАО «БЕЛАЗ», один из крупнейших производителей карьерных самосвалов в мире, поддержал предложение ЗАО «ПТФК «ЗТЭО» о создании модели грузоподъёмностью 90 тонн с одноимённо-полюсным синхронным электроприводом.
Стремясь укрепить позиции продукции автомобильного завода на мировом рынке, специалисты компаний приняли совместное решение о разработке нового типа электропривода, который улучшит тяговые и скоростные характеристики и повысит уровень надёжности карьерного самосвала грузоподъёмностью 90 тонн. По техническому заданию ОАО «БЕЛАЗ» специалисты ЗАО «ПТФК ЗТЭО» разработали новый тяговый электропривод КТЭП Б-90.
Оснащённая им переоборудованная машина проходила опытные испытания на площадке транспортной компании ООО «Регион 42».
В толпе жёлтых карьерных самосвалов мы не сразу находим своего героя. С виду – обычный 90-тонный БЕЛАЗ, однако, как нам объясняют владельцы машины — специалисты транспортной компании «Регион 42», это техника будущего. Самосвал нового века, уверены они, это машина с электроприводом нового типа.
Самосвал, который сегодня работает в «Регионе 42» — это экспериментальная модель.
Команда разработчиков под патронажем давнего партнёра завода «БЕЛАЗ» — ЗАО «ПТФК «ЗТЭО» установила комплект тягового электрооборудования на базе синхронного одноименно-полюсного электродвигателя с независимым возбуждением на уже имеющуюся в парке техники транспортной компании машину.
Сегодня она проходит эксплуатационные испытания — разработчики мониторят изменения эксплуатационных характеристик. Помогают им руководство «Региона 42» и водитель БЕЛАЗа Александр Франкив.
Александр Франкив,оператор БЕЛАЗа ООО «Регион 42»
«Стажировку я проходил на обычном БЕЛАЗе, а придя в «Регион 42», сразу сел за руль машины с новым электроприводом переменного тока. Разница, конечно, ощутима, и на переоборудованном самосвале мне нравится работать намного больше. С разработчиками мы поддерживаем постоянный контакт: они приезжали к нам на предприятие, да и созваниваемся мы регулярно», — рассказывает Александр Франкив, демонстрируя нам своего железного коня.
Глазами оператора БЕЛАЗа
Александр с удовольствием рассказывает нам о работе на необычном самосвале. Первое, что он отмечает, большая мощность и тяга. С полным кузовом машина хорошо идёт в гору.
В карьере на Большой Талде, где работает самосвал, ему даже дали забавное прозвище «Татарсила». Кроме того, Александр на своём самосвале уверенно едет по ямам и кочкам, в то время как другие белазисты стараются их объезжать, а также делать вынужденные остановки и трогания на уклонах.
Для оператора спецтехники это принципиальный момент: в зоне работы экскаватора качество поверхности далеко от идеала, а маневрировать на загруженном БЕЛАЗе не так-то просто.
Кстати, скорость тоже выросла — при езде на большое плечо усовершенствованный самосвал обгоняет своих железных коллег — это возможно, в том числе за счёт большего диапазона регулирования с постоянством мощности.
Заезжать под загрузку Александру на обновлённом самосвале удобно ещё и потому, что на его машине работает интеллектуальная противооткатная система — на площадке загрузки почти всегда есть уклон, и машина скатывается при переводе селектора в положение P.
Для работы в карьере это принципиальный момент: нужно, чтобы, когда машина заезжает на уклон, водитель мог полностью отпустить газ, а самосвал при этом плавно остановился и ни в коем случае не поехал назад.
Ну а при селекторе назад — соответственно, не катился вперёд.
Удерживать гружёную машину — это для водителя тренажёр с элементами акробатики, поэтому разработчики уделили противооткатной системе особое внимание. Созданное разработчиками решение удерживает электродвигатели «под током» и при околонулевых скоростях, и при отпущенной педали хода.
Ещё один важный момент — работа оператора стала безопаснее за счёт улучшенной тормозной системы. Если штатный БЕЛАЗ такой грузоподъёмности имеет мощность торможения 800-1000 кВт, то на данном самосвале разработчикам удалось увеличить этот показатель до 1250 кВт.
«Есть некоторые штатные для колёсной техники опции, которых на БЕЛАЗах изначально предусмотрено не было. Например, ABS.
Нас на стажировке как учили: если ведущие колёса заблокировались, нужно газовать.
А на моей машине такой проблемы вообще не бывает.
А ещё появился полноценный круиз-контроль — мы его называем стабилизатором скорости. Тоже важный момент, потому что технологические дороги — это, чаще всего, либо грязь, либо гололёд, так что без такого решения машина буксует.
А ещё я не сталкиваюсь с такой проблемой, как «выбило коммутатор» — это нередкая для белазистов история. Представьте: едешь на гружёной машине, а тут тебе нужно из кабины быстро вылезать и автоматы включать — совсем не хочется этим заниматься», — рассказывает Александр.
И ещё…
Инженеры компании добавляют от себя: машина ремонтируется реже, чем другие самосвалы. В боксе ей довелось побывать только для ремонта подвески и незначительных неисправностей, выявленных в ходе эксплуатационных испытаний, которые были устранены в последствии (а переоборудованный БЕЛАЗ работает на объектах партнёров «Регион 42» с января 2018 года). К тому же, уменьшилось потребление топлива.
Специалисты «Регион 42» показывает нам установленный на палубе шкаф управления. Преобразовательная техника — ещё одна особенность машины.
Шкаф имеет высокую степень защиты — IP67 и автономное жидкостное охлаждение, и, как нам объясняют, таким образом обеспечивается надёжная защита электроники от пыли, влаги и стабилизация рабочей температуры, что крайне важно для условий эксплуатации карьерных самосвалов.
Мы же отмечаем, что шкаф непривычно маленький — ниже, чем на штатных БЕЛАЗах.
Оказывается, здесь прямая связь — с таким уровнем защиты и способом охлаждения удалось уменьшить габариты изделия. Это важный нюанс: только кажется, что БЕЛАЗ — огромная машина, на самом деле, на палубе не так много места. И более низкий шкаф открывает водителю бОльший обзор справа.
Шкаф управления герметичен, то есть вскрывать его не только не нужно, но и вовсе нельзя. Владельцы самосвала такому повороту только обрадовались: исчез целый пункт в плановом ТО, а ведь работа с электроникой — это не только трудоёмкий, но и небезопасный процесс. Поэтому герметичный шкаф управления — просто то, что доктор прописал.
В общем, владельцы не жалеют, что пошли на эксперимент, и сегодня подтверждают, что он прошёл успешно.
Связь времён
Все эти изменения стали возможны благодаря использованию нового типа электрических машин. Двигатель постоянного тока долго удерживал свои позиции, оставаясь наиболее часто используемым приводом для создания непрерывного движения.
Его слабое место — коллекторный узел, работа с которым накладывает массу ограничений. Этого недостатка лишён двигатель асинхронный, который в последнее время набирает обороты популярности.
Его недостаток — это короткозамкнутая обмотка ротора, которая имеет свойство греться, а, стало быть, возникает задача отведения тепла. Её-то и взялась решить команда разработчиков, которая нашла способ создать синхронный двигатель без обмотки ротора.
Хотя на обновлённом двигателе самосвала стоит маркировка ЗАО «ПТФК «ЗТЭО», в создании системы принял участие целый коллектив.
Синхронный тяговый генератор ГСТ-850 — это действительно разработка ЗАО «ПТФК «ЗТЭО». Одноименно-полюсные синхронные тяговые двигатели ДВИТ-320 разработали в ФГБОУ ВО «НИУ «МЭИ», а оптимизировали конструкцию и произвели в ЗАО «ПТФК «ЗТЭО».
Шкаф управления (ШУ Б-90) — дело рук ООО «НПП «ЦИКЛ ПЛЮС», а над созданием контроллера верхнего уровня поработали специалисты ООО «НПФ Вектор». В результате на свет появился КТЭО, обладающий уникальными характеристиками.
Инженеры «Регион 42» не зря назвали данное тяговое электрооборудование технологией будущего. Сегодня над созданием подобных систем работают сразу несколько производителей — среди них есть представители России, Беларуси, США и Европы, однако, одноименно-полюсный синхронный двигатель и герметичный шкаф управления с таким комплексом интеллектуального управления применены впервые.
«Мы поставили перед собой задачу сделать новое, более совершенное изделие. ЗАО «ПТФК «ЗТЭО» — это актив холдинга «Татэлектромаш» — предприятия с многолетней историей, и завод специализируется в выпуске электрооборудования именно для карьерных самосвалов большой грузоподъёмности.
Их партнёрство с «БЕЛАЗом» продолжается многие годы.
И сегодня мы собрали целую команду профессионалов, чтобы не просто представить конкурентоспособную иностранным аналогам продукцию, а создать передовое решение», — рассказал ведущий инженер ООО «НПП «ЦИКЛ ПЛЮС» Михаил Котельников.
В основу своей разработки авторы положили синхронную электрическую машину с аксиальным возбуждением, конструкция которой была предложена Павлом Яблочковым для генератора ещё в середине XIX века. И вот сегодня идея создателя «Русского света» обретает второе рождение.
Самосвал 7558С. Первый пошёл!
Конечно же, команда разработчиков хочет пойти дальше. Переоборудованный БЕЛАЗ — это только стартовый вариант: самосвалы с новым КТЭО должны сходить с конвейера белорусского завода. И вот машина номер один уже готова: самосвал модификации 7558С уже выпущен в Жодино и сегодня дожидается своего владельца.
Оптимизация электрических параметров и алгоритмов управления ДВИТ-320 позволила поднять мощность этих двигателей до 370 кВт. После того, как самосвал пройдет эксплуатационные испытания, машины запустят в серию.
Что называется, нет предела совершенству: на первой заводской машине разработчики смогли реализовать ещё несколько полезных опций.
Здесь совершенно необычная адаптивная система управления ДВС.
Штатные системы сознательно недогружают дизель — некоторое количество киловатт отводится для работы гидравлики или иных систем, питающихся от двигателя.
Но, объясняет Михаил Котельников, они не потребляют мощность постоянно, значит, есть незадействованные резервы.
Адаптивная система как раз и позволяет мониторить состояние ДВС и при возможности догружать его до 98%. За счёт этого выросли скоростные характеристики самосвала.
«Благодаря адаптивной системе управления ДВС мы смогли привнести и ещё одно усовершенствование. Когда штатный БЕЛАЗ начинает притормаживать, повышаются обороты двигателя — даже когда едет по прямой или перемещается по боксу.
Мы даже не сразу поняли, зачем нужны такие сложности.
А нужны они для охлаждения двигателя. Но если мы уже создали возможность мониторинга и знаем температуру всех агрегатов, такие «костыли» оказались не нужны.
Мы внедрили систему охлаждения с учётом текущей температуры: двигатель без нужды не увеличивает обороты, мы экономим топливо», — рассказывает Михаил Котельников.
Противооткатная система стала ещё более интеллектуальной: разработчики нашли возможность совместить её работу с рабочим стояночным тормозом. Таким образом удалось снизить нагрев тяговых электродвигателей.
Оригинальное решение — датчик вращения вентилятора тормозных резисторов: если что-то не так, то система сигнализирует или даже останавливает машину. Решение повышает безопасность: при торможении гидравликой могут сгореть колодки, а зачем нужны дополнительные риски?
О своём железном коне разработчики говорят с энтузиазмом, радуясь реализованным идеям. Авторы строят планы на будущее: 90-тонный БЕЛАЗ — это, конечно, одна из самых популярных моделей в российской добыче, однако далеко не самая маленькая (ходят и 55-тонники), и не самая большая (рекорд — 450 тонн). Поэтому работы на перспективу хватит: создатели намерены выпустить норморяд КТЭО, чтобы оснастить всю линейку самосвалов белорусского завода.
«Применение тягового электропривода переменно-переменного тока в конструкции карьерного самосвала дает ряд преимуществ:
- снижение эксплуатационных затрат;
- увеличение производительности при перевозках;
- улучшение тягово-динамических качеств, шире диапазон работы в режиме динамического торможения, которое без ограничения по времени может применяться до нулевых скоростей;
- возможность преодолевать более длительные уклоны, характеристики тяговом режиме и в режиме динамического торможения значительно выше;
- увеличение максимальной скорости до 67 км/ч;
- улучшение эксплуатационных характеристик самосвала;
- уменьшение времени на проведение технического обслуживания и ремонта, количество обслуживаемых узлов меньше, а срок их службы дольше.
Стараясь ускорить эксплуатационные испытания своей разработки, специалисты ПТФК «ЗТЭО» заключили соглашение с «Регион-42», в результате чего и появился описанный модернизированный самосвал.
Привод (КТЭО) создавался с БЕЛАЗом, и первый образец самосвала был бы собран на заводе в любом случае. Основным для начала работ для нас стал ДВИТ-320 (тяговый одноименно-полюсный синхронный электродвигатель).
Сегодня на заводе находится самосвал с КТЭО. В случае, если эксплуатационные испытания будут завершены с положительным результатом и самосвал будет востребован у заказчиков, решение пойдёт в серию», — отмечают специалисты завода «БЕЛАЗ».
e-mail: [email protected]
zteo.ru
Повышение коммутационной устойчивости тяговых электродвигателей ЭДП-800 карьерных самосвалов
Том 329 № 7 (2018)
Актуальность исследования обусловлена необходимостью обеспечения бесперебойной добычи угля открытым способом при работе на угольном карьере. Как свидетельствуют результаты проведенного анализа статистики отказов тяговых электродвигателей ЭДП-800 карьерных самосвалов БелАЗ, основная часть данных отказов непосредственно связана с неудовлетворительным состоянием коммутации. Таким образом, повышение коммутационной устойчивости тяговых электродвигателей ЭДП-800 является неотъемлемой частью задачи повышения надежности карьерных самосвалов БелАЗ и, следовательно, всего процесса добычи угля, обеспечиваемой самосвалами данного типа. Цель исследования: разработка методики настройки коммутации тяговых двигателей карьерных самосвалов, позволяющей повысить их коммутационную устойчивость и снизить износ элементов коллекторно-щеточного узла. Объект исследования — тяговый электродвигатель ЭДП-800 карьерных самосвалов БелАЗ. Методы анализ статистики отказов, математический анализ данных бортовой системы мониторинга самосвала, экспериментальные исследования процесса коммутации тяговых электродвигателей, синтез методики настройки коммутации. Результаты. Анализ данных по эксплуатации тяговых электродвигателей ЭДП-800 карьерных самосвалов БелАЗ выявил высокий процент отказов, связанных с неудовлетворительным состоянием коммутации, обусловивший высокую интенсивность выхода из строя элементов коллекторно-щеточного узла и, в первую очередь, электрических щеток.
Ключевые слова:
карьерный самосвал, методика настройки, износ щеток, режимы работы, коммутационные испытания, бесперебойность, угольные карьеры, карьерные экскаваторы, карьерные машины, тяговые электродвигатели, тяговые двигатели, математический анализ, самосвалы, коммутационная устойчивость, электрические щетки, экспериментальные исследования
Авторы:
Виктор Васильевич Харламов
Евгений Юрьевич Чупрына
Роман Владимирович Сергеев
Павел Константинович Шкодун
Денис Игоревич Попов
Юрий Владимирович Москалев
Скачать bulletin_tpu-2018-v329-i7-13.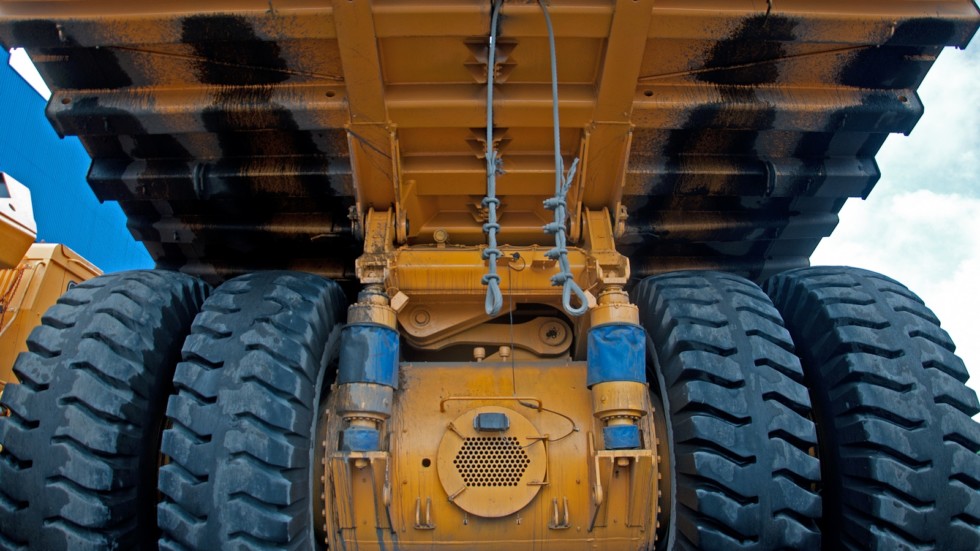
Система электропривода для самого большого в мире грузовика
Самый большой в мире грузовик оснащен системой электропривода. Передвигать 800-тонный гигант помогают четыре электромашины по 1200 киловатт каждая от Siemens. Недавно первый грузовик серии БелАЗ 75710 заработал на сибирском руднике в Кузбассе. Грузовик имеет длину более 20 метров, ширину 10 метров и высоту 8 метров. Он весит 360 тонн без груза и может перевозить 450 тонн материала. Это количество равно весу полностью загруженного Airbus A380. Самый большой в мире грузовик приводится в действие системой электропривода, состоящей из четырех электродвигателей Siemens, каждый мощностью 1200 киловатт (примерно 1800 л.с.), которые обеспечивают движение автомобиля полной массой более 800 тонн по дороге. Первая модель БелАЗ 75710 недавно начала работать на Сибирском руднике в Кузбассе. Грузовик имеет длину более 20 метров, ширину почти десять метров и высоту восемь метров.
Инженеры Siemens, разработавшие систему привода, столкнулись с серьезной проблемой, поскольку белорусский производитель грузовиков БелАЗ хотел, чтобы этот грузовик был не только самым большим в мире, но и имел на 25 % большую полезную нагрузку, чем самый большой самосвал в мире. время. В планах также предусматривалось значительное снижение себестоимости тонны транспортируемого материала. Грузовик развивает максимальную скорость 64 километра в час в пустом состоянии.
Подземные и открытые горнодобывающие компании сталкиваются со все более строгими правилами защиты окружающей среды. Эти компании также хотят, чтобы их транспортные средства были доступны круглосуточно, чтобы они могли работать максимально продуктивно. Имея это в виду, специалисты Siemens по тяговому приводу в Нюрнберге разработали надежную и мощную систему полного привода, в которой используются четыре электродвигателя.
В отличие от предыдущих моделей, новый грузовик должен был быть оснащен восемью шинами, поскольку каждая шина рассчитана на нагрузку всего около 100 тонн. В качестве основы привода нового грузовика была использована проверенная система привода, инженеры также разработали новый тип системы управления. Все компоненты системы электропривода были произведены Siemens. Это гарантировало, что все элементы будут совместимы и будут отлично работать вместе.
Полноприводная конфигурация предоставила инженерам новые возможности, такие как динамическое распределение тяги на обе оси грузовика. Кроме того, в случае отказа одного из электродвигателей грузовик по-прежнему имел бы аварийный привод, то есть его можно было бы доставить в сервисный центр своим ходом, т. е. его не нужно было бы буксировать, и он не будет мешать другим автомобилям.
«Сименс» разрабатывает приводные системы для самосвалов уже около 20 лет, всегда стремясь найти способы сделать этих гигантов шахт более эффективными. Среди примеров — «троллейбусы», которые получают электричество от воздушных линий электропередач. Эта инновация позволяет этим грузовикам почти удвоить скорость даже на крутых пандусах.
Предоставлено Сименс
Цитата : Система электропривода для самого большого в мире грузовика (2014, 14 ноября) получено 7 февраля 2023 г. с https://phys.org/news/2014-11-electric-world-largest-truck.html
Этот документ защищен авторским правом. Помимо любой добросовестной сделки с целью частного изучения или исследования, никакие
часть может быть воспроизведена без письменного разрешения. Контент предоставляется только в ознакомительных целях.