Экструзионная сварка как вид соединения толстостенных изделий
Экструзионный способ существует для соединения толстостенных элементов. И у него по сравнению со сваркой горячим воздухом с применением прутка есть преимущества: шов получается с первого раза, экструзионная сварка происходит быстрее, человеческий фактор сведен в минимуму, так как нет необходимости следить за параметрами сварки, уметь делать красивые швы. То есть, экструзионная сварка будет самой простой для начинающего. Можно сделать ручной сварочный экструдер своими руками.
Экструзионная сварка может быть двух видов: ручная и автоматическая. Среди ручных экструдеров следует отдельно выделить leister fusion 3c. Leister fusion 3c имеет множество преимуществ: высокая производительность, небольшой вес, простой и удобный корпус, пруток не «закручивается». Хороший выбор сварочного оборудования содержится в интернет-магазине Weldmax. Также для использования в узких местах рекомендуется использовать недорогой ручной сварочный экструдер fusion 2. Ручной сварочный экструдер fusion 2 прост в управлении, компактный, удобный и прочный. Сварочный экструдер leister fusion 2 оснащен системой защиты двигателя от холодного пуска. Ручной сварочный экструдер leister weldplast s6 — самый мощный в линейке данного производителя. Ручной сварочный экструдер leister weldplast s6 шнековый, с небольшим уровнем шума, имеет множество программ.
Содержание статьи
Общие требования
Соединяемые детали из пластика и присадочный материал при экструзионном способе сварки должны быть идентичными по определенным показателям:
- химический состав.
- плотность.
- показатели его текучести.
Если соединяются различные по показателям детали, тогда нужно выбирать присадочный материал, средний между значениями соединяемых поверхностей.
Еще одно правило связано с очищением кромок деталей. Это требование должно выполнятся очень строго. Так как многие виды термопласта на воздухе окисляются, очищать их нужно не раньше, чем за 15-20 минут до соединения. Если будет допущено наличие посторонних предметов или частиц на поверхностях, шов будет некачественный. Если после последнего очищения (не рекомендуется очищать растворителем) прошло более 20 минут, повторите процесс заново.
Принцип работы
Поверхностями для сварки полиэтиленовых труб и иных изделий являются сварочные канавки, углы полипропиленовых листов, поверхности пленки, расположенной внахлест. Сначала поверхности разогреваются до температуры, необходимой для начала процесса пластификации. Для этого используется нагретый воздух, который исходит их сварочного экструдера. Для нагревания также могут быть использованы внешние способы, например тепловое излучение от стационарного экструдера.
Вместе с этим будущий присадочный материал пока что в виде специальных гранул или прутка помещается в специальную камеру экструдера, в которой происходит нагрев содержимого. Содержимое нагревается до текучего состояния и с помощью шнека или диска (в зависимости от вида экструдера) выдавливается через сварочный башмак в область сварки.
Схема работы
Так как соединяемые поверхности должны стать вязкими перед сваркой, нагретый до определенной температуры воздух выходит в зону сварки из специального сопла. Температуру можно регулировать. Нагрев может быть осуществлен встроенными нагревателями в экструдере (термофен), либо может поступать от внешних носителей (компрессор или пневмосеть в организации).
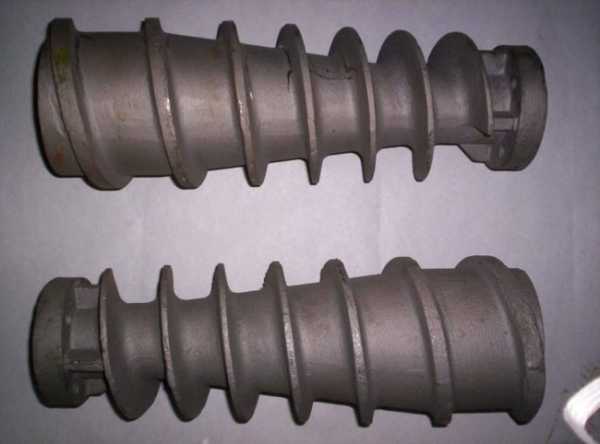
Экструдеры бывают шнековые и безшнековые. Шнековые экструдеры отличаются тем, что присадочный материал расплавляется в шнековой камере и выталкивается наружу с помощью шнека. В безшнековых экструдерах присадочный материал выталкивается с помощью твердой, еще не расплавленной части прутка. Такие экструдеры еще называют плунжерными. Их производительность меньше, чем у шнековых, с ними невозможно использовать гранулы в качестве присадочного материала. Зато его легко можно использовать в малодоступных местах. На окончании сварочного башмака имеется специальное отверстие, которое контролирует поступление присадочного материала в зону сварки.
Экструзионный вид сварки используется чаще для полиэтилена низкого давления, полипропилена, других термопластов 1-й группы. Эта группа отличительна тем, что разница между расплавленным состоянием и состоянием термодеструкции примерно пятьдесят градусов. Таким образом, незначительный перегрев на 30-40 градусов не испортит материал. Термопласты 2-й группы – это ПВДФ и ПВХ. Разница в температурах между вышеуказанными состояниями небольшая, что требует строгого соблюдения температурного режима в зоне нагрева. Шнек для термопластов 2-й группы должен иметь особую форму для более тщательного перемешивания присадочного материала без перегрева.
Таким образом, экструзионный способ сварки полипропиленовых изделий является самым простым для новичков, применяется для соединения толстостенных изделий. Новички могут изготовить ручной сварочный экструдер своими руками. Ручной экструдер для сварки выбрать достаточно легко, так как на рынке существуем множество аппаратов для этого вида соединения, одним из самых популярных является сварочный экструдер leister fusion 2.
[Всего голосов: 0 Средний: 0/5]svarkaed.ru
Сварка экструдером
1. Принцип сварки экструдером
1.1 Назначение
Экструзионная сварка – технологические особенности процесса, устройство оборудования.
Экструзионная сварка – технология, которая применяется для соединения материалов, таких, как:
- Полипропилен;
- Полиэтилен;
- Пластмассы.
- ПВХ
- ПВДФ
Экструзионная сварка не используется для монтажа напорных трубопроводов. Причина – стыковое расположение элементов – труб не дает показатель прочности выше чем 80% от прочности самого изделия в данном случае труб, изготовленных из термопластов.
1.2 Требования
Для достижения высокого показателя прочности стыковых швов при сварке материалов на основе ПВХ, ПВДФ необходимо соблюдать 2 основных требования:
1. Стыковке подлежат только одинаковые по характеристикам материалы, а также химическому составу. Под этим подразумевается следующие показатели:
• Плотность;
• ПТР – показатель текучести расплава.
Применение экструзионной сварки требует использование присадочного материала соответствующего показателям плотности и текучести расплава, стыкующихся пластмассовых поверхностей.
Внимание!
Если соединяемые материалы имеют разные показатели текучести расплава, необходимо подбирать присадку у которой ПТР – это средний показатель текучести.
2. Соединяемые поверхности должны быть тщательно очищены. Экструзионная сварка не терпит наличия даже небольшого количества окислившегося материала на поверхностях материалов. Поэтому для обеспечения прочности стыков, швов очистку полипропилена, полиэтилена, пластмасс, а также других материалов следует проводить за 20 минут до начала сварки. Это требование должно выполняться максимально точно, что обусловлено небольшой текучестью и перешиванием материалов в области формирования шва.
1.3 Экструзионная сварка – спецификация
Экструзионная сварка ориентирована на стыковку толстостенных компонентов, деталей, поверхностей, изготовленных из ПВХ, ПВДФ.
Экструзионная технология обладает такими преимуществами по сравнению с методом сварки материалов горячим воздухом с использованием присадочного материала:
• Уменьшает время сварки;
• Сводит к минимуму влияние человеческого фактора на прочностные показатели швов;
• Формирование сплошного стыка – шва вдоль стыкуемых поверхностей.
1.4 Экструзионная сварка – технологическая организация процесса
Технология экструзионной сварки требует подготовки поверхностей перед стыковкой. Это делается тремя способами:
• Создание сварочной канавки, углубления на стыкуемых поверхностях;
• Формирование скоса, среза под углом на торцах соединяемых поверхностей;
• Укладка материалов внахлест.
Сам сварочный процесс начинается с разогрева материалов с целью доведения их до пластичного состояния. Для этого используется поток разогретого воздуха, подаваемого соплом сварочного экструдера. Стационарные промышленные комплексы разогревают материалы перед сваркой излучением.
Одновременно с пластификацией идет подготовка присадочного материала. Это делается путем подачи в шнек экструдера основы – ПВХ гранул или прутка, который нагревом доводится до вязкотекучего состояния. Перемешивание превращает расплавленный материал в однородную, гомогенную массу.
Полученный материал с помощью сварочного башмака подается к месту стыковки поверхностей, для формирования шва. Сварочным башмаком создается необходимое для этого процесса давление. Стационарные промышленные комплексы может иметь другую схему компрессионного воздействия на присадочный материал, с помощью отдельных узлов, агрегатов.
1.5. Особенности работы сварочного экструдера
Экструдеры комплектуются нагревателями воздуха для обеспечения пластификации стыкуемых материалов. Это необходимо для подачи присадочного материала. Поток горячего воздуха поступает к месту сварки через сопло предварительного нагрева, за счет чего происходит нагрев стыкуемых материалов. Температурный режим воздушного потока регулируется специальным контроллером.
Существует 2 варианта устройства системы подачи воздуха для нагрева:
- Встроенные узлы подачи воздуха;
- Подача воздуха организуется с применением внешних источников. Это может быть компрессор или пневматическая сеть.
Пластификация присадочного материала в шнеке обеспечивают электрические нагреватели. Они размещаются с внешней стороны шнековой камеры, их температурный режим нагревателей контролируется, устанавливается через специальное регулирующее устройство. Такой системой оснащаются продвинутые модификации экструдеров.
Простые модели аппаратов осуществляют нагрев материала в шнековой камере воздухом, проходящим по внешнему контуру шнековой камеры. Для этого в конструкции экструдера предусмотрена специальная полость. Затем он подается в область сварки для пластификации свариваемых материалов. Такое устройство нагрева присадочного материала предусматривает привязку температуры воздушного потока, проходящего через полость шнековой камеры с температурой воздуха, подаваемого для нагрева материалов перед сваркой. Сама присадка подается в зону сварки через сварочный башмак. Некоторые модели комплектуются упрощенной системой движения присадочного материала через участок термического воздействия.
Сварочный пруток – материал поступает на профильные вальцы, они с силой переводят его в отверстие участка нагрева, имеющее цилиндрическую форму. Тут в дело вступают электрические нагреватели и начинают термическое воздействие на присадку, превращая ее в однородную, разогретую вязкотекучую массу. Такая схема превращает заднюю часть прутка в толкатель для передней.
Плунжерные экструдеры обладают низким показателем производительности. Компенсируют эту особенность компактные размеры, что позволяет работать с аппаратом в труднодоступных местах. Недостатком плунжерных экструдеров является высокая требовательность к диаметру и форме прутка присадочного материала. Она должна быть ровной, без погрешностей. Возможность загрузки гранулированного материала в плунжерных экструдеров отсутствует.
Пластичная присадочная масса поступает к месту формирования шва через сварочный башмак. Это общая технологическая особенность шнековых и плунжерных сварочных аппаратов.
Рабочая поверхность башмака соответствует форме стыкуемых поверхностей. Передняя его часть оснащается специальным носом, который не допускает поступление присадочного материала перед зоной сварки.
Присадка оказывает давление на носовую часть башмака, создает поступательное движение аппарата в заданном направлении, где формируется шов. Скорость движения в этом случае определяется показателем производительности и площадью сечения шва.
1.6 Свариваемые материалы – температурный режим, особенности
Чаще всего экструдером сваривается ПНД и ПП. Это термопласты первой группы, их преимуществом является большой температурный диапазон между достижением состояния пластификации и термодеструкции (разрушению от воздействия температур) составляет 50–186 градусов C. Значительный перегрев таких материалов не оказывает на них критического воздействия.
Во вторую группу термопластов входят ПВХ, ПВДФ наоборот отличаются небольшой температурной разницей между пластификацией и термодеструкцией. Эта особенность требует повышенного внимания к температурному режиму, необходимо его максимально точно соблюдать. Обеспечить ее может только отладка нагревательной системы аппарата.
Сварка ПВХ имеет еще одну особенность – экструдеры, ориентированные на работу с этим материалом оборудуются шнеком специальной формы. Она обеспечивает тщательное перемешивание присадки и контроль на него температурного воздействия. Это позволяет избежать термодеструкции.
Неустойчивость к воздействию температуры второй группы термопластов требует соблюдения еще одного требования при проведении сварки. Аппарат нельзя надолго оставлять в режиме ожидания, его нужно отключать полностью при длительных временных перерывах.
Еще один минус ПВХ – повышенная химическая активность при нагреве, а также абразивность. Из-за этого к шнековой камере предъявляются специализированные технологические требования.
2. Формы сварных экструзионных швов
Основные формы экструзионных швов определены в отраслевом стандарте DVS 2207-4. Также документ содержит правила проведения сварки:
- Швы формируются за один проход;
- Желательно делать двухсторонний шов, он обеспечивает высокие прочностные материалы изделиям из термопластов;
- Двухсторонний шов обеспечивает экономию присадочного материала.
- Двухсторонний шов в меньшей степени влияет на характеристики основы листа или пленки во время остывания.
3. Формы и особенности сварочных башмаков
Готовая к работе присадка поступает в зону формирования шва через сварочный башмак. Также он выполняет следующие функции:
- Оказывает давление на поступающий материал;
- Формирует шов;
- Сглаживает поверхность шва.
Глубина зоны создания давления должна быть не менее 1/5 глубины шва. Глубина разреза должна быть приблизительно 0,5 мм с расширением вперед. Это позволяет опоре не деформировать поверхность корневого слоя. Это сделать легко, так как материал находится в разогретом состоянии. Нос башмака препятствует неконтролируемому распределению присадки. В свою очередь, создаваемой ей давление продвигает аппарат.
Нос башмака не должен соприкасаться со свариваемыми листами, но его форма должна повторять их конфигурацию. Выполнить это требование можно при создании зазора носом башмака и корневым слоем от 1 до 3 мм. Сам он должен иметь скругленный передний и задний край. Такая опора предотвращает утечку присадки. Для этого необходимо создавать прижимное усилие во время сварки.
4. Подготовка к процессу сварки
Подготовка к процессу сварки
Листы, пленка должны проходить подготовку непосредственно перед началом процесса. Это обусловлено быстрым окислением поверхности полимеров. Также причиной такого требования является возможность попадания на поверхность основы загрязнения: пыли, влаги, что значительно снизит прочностные показатели шва.
Проводить подготовку полимеров к сварке необходимо за 20 минут до начала сварки. Если прошло больше указанного временного промежутка, следует повторно провести подготовку и незамедлительно приступить к сварке.
Внимание!
Удаление загрязнения с поверхности полимеров проводится механическим способом, например, с помощью скребков. Обезжиривающие составы неэффективны при подготовке к экструзионной сварке.
4.1 V-образный шов
Шов V-образной формы требует предварительной обработки торцов, кромок стыкующихся материалов. Такая подготовка проводится с использование столярного инструмента:
• Рашпиля;
• Рубанка;
• Ножовки;
• Стамески.
Созданный на кромках скос должен обеспечить раскрытие шва в диапазоне 45–90 градусов. Толстые полимерные листы требуют создания скоса с большим углом тонкие с меньшим. Угол раскрытия должен обеспечивать заполнение присадкой все пространство образуемое торцевыми срезами. Ограниченный угол раскрытия для толстостенных материалов обусловлен показателем общей шириной шва и зон перехлестов на его поверхности. Это показатель не должен превышать 30 мм. Игнорирование этого требования не позволит создать необходимое усилие, которое обеспечит отсутствие выступания присадки за края сварочного башмака.
Корневой слой шва должен содержать миллиметровые нескошенные участки. Их отсутствие приведет к перегреву и оплавлению материала в зоне сварки при неравномерном движении сварочного аппарата. Последствием этого также станет нарушение ширины зазора между листами, он станет заметно шире или уже.
Материал перед началом сварки фиксируется, благодаря чему формируется равномерный зазор. Его оптимальная ширина не должна быть больше 2 мм. Это позволит присадке проникать на внутреннюю часть свариваемых материалов, что гарантирует высокое качество сварки.
Механическая обработка шва должна осуществляться не ближе, чем в 2 мм от кромок скоса. Это делается при условии, что перехлест шляпки стыка в две стороны составляет не более, чем 2 мм.
4.2 X-образный шов
Этот тип шва является двухсторонней версией V-образного стыка. Это позволяет использовать в работе одни и те же требования, правила. Разница заключается только в невозможности контролировать качество проварки корневого слоя X-образным швом. Такая особенность меняет требования к работе с основой:
- На торцах формируются скосы;
- Угол их раскрытия 30–60 градусов;
- Лицевая сторона обрабатывается механически на расстоянии 2 мм от края скоса;
- Корневой слой фиксируется без зазора;
- Предварительно необходимо провести стыковку с помощью термофена с применением специальной насадки;
- Формируется V-образный шов лицевой части;
4.3 Шов типа HV
Для такой формы шва угол раскрытия определяется толщиной корневого слоя и составляет 45–60 градусов. Более значимое влияние на это оказывает вертикальный лист. Здесь необходимо оставить на торце не скошенный участок шириной 1 мм. Листы нужно зафиксировать, чтобы между ними оставался зазор 2 мм. Это даст гарантию качественной проварки.
Внимание!
Расстояние от края горизонтального листа до начала шва, после окончания сварки должно составлять не менее 10 мм.
Плоскость, находящаяся с левой стороны обрабатывается механически не ближе, чем в 3-х мм от края скоса кромки. Тут необходимо предусмотреть запас. Алгоритм действий при формировании шва формы HV аналогичен созданию X-образного шва.
4.4 K-образный шов
Угловое внутреннее соединение требует предварительной фиксации листов. Это делается с помощью термофена. Для временной сварки подойдет специальная насадка или сопло с присадочным материалом.
Зона временной фиксации обрабатывается с помощью скребка:
- При использовании насадки для сварки это делается заостренным краем скребка;
- Использование присадочного материала требует механической обработки скругленной поверхностью скребка.
Шов с переменным сечением
Представленные выше конфигурации швов являются идеализированными, но зачастую оператор сталкивается с необходимостью формирования шва, у которого сечение будет меняться. Пример такой работы – вваривание патрубка в трубу большего диаметра.
Для качественной реализации такой задачи требуется модернизация башмака. Это параллелепипед со скругленными углами, он соприкасается с верхней частью корневой основы, где угол между листами прямой – 90 градусов и с нижней частью, где угол может достигать 120–140 градусов.
romato.ru
Экструзионная сварка
При помощи данного вида сварки выполняется огромное множество видов соединений в различных изделиях. Наиболее типичным примером, когда без экструзионной сварки не обойтись, можно назвать приваривание днища к стенкам емкости.
Экструзионная сварка обладает рядом неоспоримых преимуществ перед другими видами сварки, например сваркой нагретым воздухом:
- Прочность экструзионного шва достигает 80% прочности основного материала.
- При помощи экструдера можно сваривать детали большой толщины
- Экструзионная сварка обладает высокой производительностью (например, по сравнению, со сваркой феном)
- При правильном подборе режимов сварки значительно снижается влияние человеческого фактора
Однако у экструзионной сварки есть и довольно большой минус – высокие требования к опыту и квалификации сварщиков. Каким минимальным набором знаний должен обладать сварщик, чтобы выполнять качественные сварные соединения при помощи ручного экструдера?
Общие требования
При сварке ручным экструдером необходимо соблюдать общее правило для сварки всех полимерных материалов любыми методами – сваривать следует только изделия из одинаковых материалов, т.е.:
- Которые совпадают по химическому составу (проще говоря, сварить полипропиленовые листы с листами ПВХ у вас вряд ли получится, хотя есть исключения – например сварка ПВХ и ПММА)
- И которые имеют близкие значения ПТР (показателя текучести расплава) — не стоит сваривать детали с разным ПТР, например экструдированные листы с изделиями полученными методом литья. Этого же правила необходимо придерживаться при выборе присадочного материала (сварочного прутка, гранул и т.д.) для сварки конкретных листов.
Еще одним важным требованием является очистка свариваемых поверхностей, причем в случае экструзионной сварки это требование нельзя игнорировать ни при каких обстоятельствах. При экструзионной сварке создается относительно слабое течение и перемешивание материала в зоне сварного шва. Перед началом сварки рекомендуется механически зачистить шов (снять оксидный слой) не более чем за 20 минут до начала процесса сваривания.
Виды сварных соединений
Немецкий стандарт DVS 2207-4 устанавливает 7 основных видов сварных соединений:
V шов
X шов
К шов
НV шов
Double HV шов
Е шов
F шов
Существует так же отечественный стандарт, регламентирующий выполнение сварных швов (ГОСТ 16310-80), выделяющий гораздо больше видов швов.
По возможности, следует изготавливать швы с двусторонней разделкой, это повышает прочность соединения и уменьшает неизбежные деформации изделий при их остывании, особенно при сварке листов большой толщины.
При разнице в толщине свариваемых деталей свыше 1 мм следует делать скос на детали имеющей большую толщину или на обеих деталях как указано на чертежах 1,2 и 3.
Углы разделки сварного шва следует выбирать исходя из толщины свариваемых деталей. Угол должен быть достаточно большим, чтобы обеспечить равномерное закрытие всей зоны шва расплавом прутка, при этом ширина шва не должна превышать 30 мм. В противном случае сварщик не сможет обеспечить равномерный и необходимый прижим расплава сварочным башмаком.
Кроме того проварку швов Х-типа следует проводить в 4 этапа.
- Подготовка зоны сварки
- Проварка верхнего шва
- Разделка корня шва
- Проварка нижнего шва
При изготовлении швов HV типа в корневом слое вертикального листа следует оставлять тонкий (до 1мм) слой нескошенного материала, как показано на рисунке. Также требуется обеспечить расстояние около 2 мм между вертикальным и горизонтальным листами для гарантированной проварки корня. При выполнении шва Double HV очередность действий аналогична очередности при выполнении швов Х-типа.
Режимы сварки
Для получения прочного сварного соединения следует очень внимательно относиться к режимам на которых производится сварка, но прежде чем говорить о том на каких настройках необходимо сваривать детали, давайте разберем принципиальное устройство ручного экструдера.
Экструдер состоит из следующих деталей и узлов:
Все процессы сварки происходят в термопластическом состоянии в зоне сварного шва
Соответственно основной характеристикой влияющей на прочность сварного соединения будет температура и объем подаваемого воздуха для расплавления присадочного и основного материала. Стандарт DVS 2205-1 рекомендует проводить сварку при следующих параметрах:
Температура экструдера, |
Температура воздуха, |
Количество воздуха, литров/мин. |
200-240 |
210-250 |
350-400 |
Современные экструдеры позволяют очень точно настраивать все 3 параметра. При выполнении ответственных швов следует применять экструдер позволяющий раздельно контролировать температуру на выходе из форсунки и температуру подачи воздуха. Такие экструдеры, как правило, стоят дороже чем те, которые отслеживают только температуру воздуха. Однако они гарантируют одинаковую температуру расплава и свариваемых поверхностей.
При экструзионной сварке материалов Vikulen также следует использовать вышеуказанные параметры
Выполнение сварочных работ
- Перед началом сварочных работ следует убедится, что в экструзионной камере не осталось расплава материала. Если какая-то часть материала все же осталась, его необходимо полностью выдавить даже в том случае если планируется проводить сварку таким же прутком
- Тщательно прогрейте сварочный башмак, чаще всего для этого используют специальные экраны установленные на самом экструдере или на подставке для него
- Прогрейте поверхность свариваемых материалов горячим воздухом, поднеся сопло экструдера к началу зоны сварки
- Прижмите сварочный башмак к зоне сварного шва и включите подачу расплава
- При продвижении эктрудера контролируете угол его наклона. Например при сварке швов К угол наклона должен составлять 45°, а при сварке швов V экструдер должен располагаться перпендикулярно к свариваемым поверхностям. Это позволит исключить выдавливание расплава из-под сварочного башмака.
- Контролируйте силу прижима сварочного башмака. Она должна быть такой, чтобы прижим не приводил к выдавливанию расплава из зоны сварного шва.
Эффективная несущая способность сварных соединений
Все сварные соединения имеют разную максимальную прочность при разных нагрузках.
При угловых соединениях следует стремиться к смещению шва как можно дальше от непосредственно угла. Этого можно добиться, если выполнить скругление материала в угле, и выполнить обычный стыковой шов уже за его пределами. Это связано с тем, что угловые соединения плохо переносят изгибающую нагрузку.
Т-образные соединения с двусторонним швом показывают значительно лучшие прочностные характеристики в сравнении с односторонним.
При растягивающей нагрузке разные типы сварных соединений также выдерживают разные напряжения. На иллюстрации ниже представлена схематичная прочность различных соединений при таком типе нагрузки.
Кроме того, для обеспечения максимальной прочности следует избегать скопления швов в одном месте, а также пересечения сварных швов.
Влияние качества материалов на прочность сварных соединений
Последний, и при этом важнейший фактор, влияющий на прочность сварных соединений – качество свариваемых материалов и присадочного прутка. И это вполне логично, ведь если материал низкого качества, то какие бы правила вы не соблюдали и какие методики не применяли, вы все равно не получите прочного сварного соединения.
На качество материала влияют:
— Наличие и объем вторичного сырья в полуфабрикатах
Чем больше вторички в полуфабрикатах, тем большая часть материала уже получила термошок, а следовательно потеряла свою способность образовывать надежное сварное соединение.
— Качественные термостабилизаторы в составе материала
Именно термостабилизаторы позволяют снизить деструктирующее воздействие на материал при экструзии и переработке полипропилена.
— Сырье со стабильными параметрами переработки.
Ни для кого не секрет, что стабильность параметров переработки играет огромную роль как в процессе производства полуфабрикатов, так и в процессе их переработки, данный фактор позволяет не подбирать каждый раз оптимальные параметры сварки, а использовать уже отработанные режимы, обеспечивая максимальные качество и производительность.
— Наличие и объем влаги в полуфабрикатах и исходном сырье
Несмотря на небольшую абсорбцию полипропилена (около 0,01%), даже такое количество влаги может в значительной степени негативно влиять на качество сварного соединения. Данный факт подтвержден многими годами практического опыта переработки полуфабрикатов из полипропилена.
Приобретая полуфабрикаты Vikulen вы гарантировано получаете материал, наилучшим образом отвечающий всем вышеперечисленным требованиям
Экструзионная сварка довольно сложный и трудоемкий процесс, требующий большого опыта и знаний от сварщика. Тем не менее, применяя этот метод вы сможете получать действительно качественные и прочные изделия. Если вы можете дополнить данную статью, то мы будем признательны Вам за Ваши комментарии
vikulen.ru
Сварка труб пнд, как применять ручной сварочный экструдер — Водопровод
Полиэтиленовые трубы не подвержены коррозии, прочны. Это главные условия долговечности таких трубопроводов. Гибкость и относительная эластичность труб пнд позволяет монтировать трубопровод, обходя углы. Полиэтилен — экологичный материал, водопровод из него наиболее желателен для здоровья.
Один из методов монтажа — сварка труб пнд. Сварка встык осуществляется сварочным аппаратом, где нагревательный элемент — зеркало — разогревает трубы до появления грата, затем они стыкуются и фиксируются. При другом способе сварки применяется ручной сварочный экструдер для экструзионной сварки.
Трубы для сварки должны быть из одного вида пластика. Важнейшим требованием при экструзионной сварке является идеальная чистота свариваемых поверхностей, они должны быть очищены от следов окисления не раньше, чем за 20 минут до начала сварки — течение и перемешивание материала в зоне сварки небольшое.
Принцип работы заключается в следующем: поверхности предварительно нагреваются горячим воздухом до начала плавления. Горячий воздух подается из специального сопла экструдера. Для фиксации шва нужен присадочный материал — используется пруток сварочный пнд, который подается в экструдер, где и разогревается до вязкого состояния.
Вязкий материал выдавливается через сварочный башмак, им же создается необходимое давление.
Во время предварительного нагрева поверхностей, температуру горячего воздуха можно контролировать. Сварной шов выполняется сразу, за один проход. Башмак прижимает присадочный материал и одновременно формирует шов. Нос башмака препятствует вытеканию присадочного материла в неправильном направлении, а присадочный материал, давя на нос, способствует продвижению башмака вперед.
Нос башмака повторяет форму соединяемых поверхностей, но не касается их. Чтобы обеспечить это условие, надо соблюдать расстояние 1-3 мм. Зона опоры сварочного башмака не дает присадочному материалу растекаться в разные стороны.
Готовить зону сварки надо непосредственно перед проведением сварочных работ. Загрязнение или пыль снижают прочность шва. Использование растворителя неэффективно, надо применять скребки. Кромки края свариваемых труб должны быть предварительно скошены — для шва V типа. Для толстостенных труб угол поменьше, для тонкостенных — побольше.
Перед началом экструзионной сварки трубы надо прочно зафиксировать относительно друг друга, оставив зазор в 2 мм, тогда присадочный материал сможет немного продавливаться на обратную сторону шва — внутрь трубы.
Сварочный экструдер надо прогреть, настроить производительность. Поднести сопло к началу зоны сварки, прогреть горячим воздухом поверхности, прижать башмак и включить привод.
По окончании работ, экструдер надо поставить на подставку, нагрев выключить, а подачу воздуха не выключать до полного остывания.
arxipedia.ru
Сварка полиэтилена. Основные способы создания шва.
Содержание статьи
Принцип сварки полиэтилена
Сварка полиэтилена — это процесс соединения отдельных участков материала посредством нагрева их до температуры плавления и сжатия слоев с образованием сварочного шва. В момент, когда поверхность пленки плавится, слои скрепляются на молекулярном уровне. После того, как они остывают, образуется прочный шов.
Обратите внимание! В случае, если сварке подвергаются поверхности, которые загрязнены, то прочность стыка становится ниже. Это обусловлено тем, что в расплавленную массу попадают примеси, которые разрушают молекулярную структуру шва.
Для того, чтобы шов получился максимально качественным и надежным, важно соблюдать ряд требования, предъявляемых к процессу сварки:
- необходимо, чтобы куски пленки, которые свариваются, были выполнены из однородного материала,
- следующее условие – это чистота поверхностей полиэтиленовой пленки,
- верно подобранный режим температуры (если будет недостаточная температура, то прочность будет невысокой, если же наоборот температурный режим будет слишком высоким, то стык может деформироваться).
Для создания качественного шва нельзя повторно сваривать куски по тем же кромкам, обычно их обрезают.
Виды сварки полиэтилена
Рассмотрим основные разновидности сварочных работ, при помощи которых можно соединить полиэтилен.
Контактная сварка
Такой метод считается одним из наиболее простых и экономичных, в результате которого образуется качественный шов. Контактная сварка полиэтилена подразумевает нагревание краев пленки или «горячим воздухом», или «горячим клином», до достижения температуры плавления. Для соединения и сжатия краев пленки используется специальное оборудование – зажимные ролики. Таким образом, применяя подобную технологию, вы получите прочный одинарный или двойной шов.
Горячий воздух представляет собой воздушный поток, который нагрет до определенной температуры, именно благодаря ему пленка начинает плавиться. Такой же принцип работы и у горячего клина – нагревательного элемента. В результате его контакта с материалом, с обеих сторон образуется качественный шов, прочностью до 90%.
Ручной аппарат горячего воздуха – это разновидность промышленного фена, который отличается высокой мощностью, небольшой массой, соответствует всем техническим требованиям.
Экструзионная сварка
Данная технология заключается в следующем: расплавленный полимер под давлением подается на участок сварки, в итоге поверхности становятся тягучими. В этот момент они плотно прижимаются друг к другу и свариваются. Прочность такого соединения – примерно 70-80%.
Горячая сварка
Для осуществления соединения полиэтиленовой пленки таким способом необходим специальный аппарат для сварки. При помощи металлического нагревательного элемента этот прибор осуществляет нагрев полиэтилена.
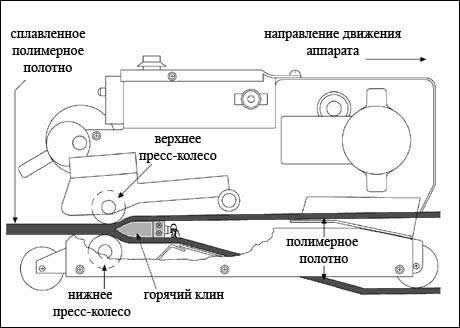
Оборудование, применяемое для горячей сварки функционирует по следующему принципу: через редуктор двигатель заставляет двигаться два колеса. Посредством штатива между листами свариваемого материала вставляется горячий клин. Благодаря терморегулятору поддерживается оптимальный температурный режим горячего клина. Скорость, с которой двигается материал можно регулировать.
Обратите внимание! Горячий клин является разновидностью как горячей сварки, так и контактной.
Благодаря такому способу соединения в итоге образуется двойной шов, прочность которого очень высокая и достигает 90%. Сам процесс сварки осуществляется в автоматическом режиме. Вручную изменяется только температурный режим горячего клина и скорость подачи пленки. Чаще всего такой аппарат применяется в промышленности, но также пригоден и для личного использования.
Выбор оборудования для сварки полиэтилена
Осуществляя выбор аппарата для соединения деталей из полиэтилена, необходимо обращать внимание на ряд факторов. Например, для того, чтобы изготовить большое количество упаковки для товаров подойдет только промышленный аппарат. Если же требуется совсем немного пакетов, то можно воспользоваться и ручным. Если материал достаточно толстый и плотный, то необходимо приобретать дорогой аппарат, потому что иначе шов будет некачественным.
В настоящее время для того, чтобы соединить части полиэтиленовой пленки, выпускаются специальные приборы. Наиболее экономичный вариант — это аппарат ПП-40. Внешне он напоминает паяльник, отличается только наконечник. Благодаря такому прибору можно создать ровный и надежный шов по любому прямому или сложному контуру.
Также для сварки полиэтилена могут применяться специальные насадки, которые крепятся на электрическом утюге. Эта деталь выполнена из листового алюминия. Основание насадки – плоское, снизу находятся ребра, которые являются базисным звеном. Используя этот инструмент, вы получите две спаянные полосы, которые размещены параллельно. Насадка закрепляется на подошве утюга при помощи специальных лепестков, загибающихся под основание прибора. Ребра насадки фиксируются на стыке краев пленки поверх уложенной бумаги, после чего аппарат надо медленно и плавно двигать по предполагаемому участку соединения. В итоге образуется двойной шов.
Схема сварки полиэтиленовой плёнки с помощью электроутюга: 1 – стол (подставка), 2 – рейка, 3, 4 – полотнища плёнки, 5 – подкладка, 6 – утюг.)
Подводя итог вышеизложенного стоит еще раз отметить, что осуществить сварку полиэтилена можно несколькими способами, каждый из которых имеет свои отличительные особенности. Выбирать аппарат для сварки нужно исходя из требований к монтажу и условий, в которых будут проводиться сварочные работы.
[Всего голосов: 0 Средний: 0/5]svarkaed.ru
Экструзионная сварка это
Сварка экструдером
1. Принцип сварки экструдером
1.1 Назначение
Экструзионная сварка – технологические особенности процесса, устройство оборудования.Экструзионная сварка – технология, которая применяется для соединения материалов, таких, как:
- Полипропилен;
- Полиэтилен;
- Пластмассы.
- ПВХ
- ПВДФ
Экструзионная сварка не используется для монтажа напорных трубопроводов. Причина – стыковое расположение элементов – труб не дает показатель прочности выше чем 80% от прочности самого изделия в данном случае труб, изготовленных из термопластов.
1.2 Требования
Для достижения высокого показателя прочности стыковых швов при сварке материалов на основе ПВХ, ПВДФ необходимо соблюдать 2 основных требования:1. Стыковке подлежат только одинаковые по характеристикам материалы, а также химическому составу. Под этим подразумевается следующие показатели:• Плотность;• ПТР – показатель текучести расплава.Применение экструзионной сварки требует использование присадочного материала соответствующего показателям плотности и текучести расплава, стыкующихся пластмассовых поверхностей.Внимание!Если соединяемые материалы имеют разные показатели текучести расплава, необходимо подбирать присадку у которой ПТР – это средний показатель текучести.
2. Соединяемые поверхности должны быть тщательно очищены. Экструзионная сварка не терпит наличия даже небольшого количества окислившегося материала на поверхностях материалов. Поэтому для обеспечения прочности стыков, швов очистку полипропилена, полиэтилена, пластмасс, а также других материалов следует проводить за 20 минут до начала сварки. Это требование должно выполняться максимально точно, что обусловлено небольшой текучестью и перешиванием материалов в области формирования шва.
1.3 Экструзионная сварка – спецификация
Экструзионная сварка ориентирована на стыковку толстостенных компонентов, деталей, поверхностей, изготовленных из ПВХ, ПВДФ.Экструзионная технология обладает такими преимуществами по сравнению с методом сварки материалов горячим воздухом с использованием присадочного материала:• Уменьшает время сварки;• Сводит к минимуму влияние человеческого фактора на прочностные показатели швов;
• Формирование сплошного стыка – шва вдоль стыкуемых поверхностей.
1.4 Экструзионная сварка – технологическая организация процесса
Технология экструзионной сварки требует подготовки поверхностей перед стыковкой. Это делается тремя способами:• Создание сварочной канавки, углубления на стыкуемых поверхностях;• Формирование скоса, среза под углом на торцах соединяемых поверхностей;• Укладка материалов внахлест.Сам сварочный процесс начинается с разогрева материалов с целью доведения их до пластичного состояния. Для этого используется поток разогретого воздуха, подаваемого соплом сварочного экструдера. Стационарные промышленные комплексы разогревают материалы перед сваркой излучением.Одновременно с пластификацией идет подготовка присадочного материала. Это делается путем подачи в шнек экструдера основы – ПВХ гранул или прутка, который нагревом доводится до вязкотекучего состояния. Перемешивание превращает расплавленный материал в однородную, гомогенную массу.
Полученный материал с помощью сварочного башмака подается к месту стыковки поверхностей, для формирования шва. Сварочным башмаком создается необходимое для этого процесса давление. Стационарные промышленные комплексы может иметь другую схему компрессионного воздействия на присадочный материал, с помощью отдельных узлов, агрегатов.
1.5. Особенности работы сварочного экструдера
Экструдеры комплектуются нагревателями воздуха для обеспечения пластификации стыкуемых материалов. Это необходимо для подачи присадочного материала. Поток горячего воздуха поступает к месту сварки через сопло предварительного нагрева, за счет чего происходит нагрев стыкуемых материалов. Температурный режим воздушного потока регулируется специальным контроллером. Существует 2 варианта устройства системы подачи воздуха для нагрева:
- Встроенные узлы подачи воздуха;
- Подача воздуха организуется с применением внешних источников. Это может быть компрессор или пневматическая сеть.
Присадка оказывает давление на носовую часть башмака, создает поступательное движение аппарата в заданном направлении, где формируется шов. Скорость движения в этом случае определяется показателем производительности и площадью сечения шва.
1.6 Свариваемые материалы – температурный режим, особенности
Чаще всего экструдером сваривается ПНД и ПП. Это термопласты первой группы, их преимуществом является большой температурный диапазон между достижением состояния пластификации и термодеструкции (разрушению от воздействия температур) составляет 50–186 градусов C. Значительный перегрев таких материалов не оказывает на них критического воздействия. Во вторую группу термопластов входят ПВХ, ПВДФ наоборот отличаются небольшой температурной разницей между пластификацией и термодеструкцией. Эта особенность требует повышенного внимания к температурному режиму, необходимо его максимально точно соблюдать. Обеспечить ее может только отладка нагревательной системы аппарата. Сварка ПВХ имеет еще одну особенность – экструдеры, ориентированные на работу с этим материалом оборудуются шнеком специальной формы. Она обеспечивает тщательное перемешивание присадки и контроль на него температурного воздействия. Это позволяет избежать термодеструкции.Неустойчивость к воздействию температуры второй группы термопластов требует соблюдения еще одного требования при проведении сварки. Аппарат нельзя надолго оставлять в режиме ожидания, его нужно отключать полностью при длительных временных перерывах.
Еще один минус ПВХ – повышенная химическая активность при нагреве, а также абразивность. Из-за этого к шнековой камере предъявляются специализированные технологические требования.
2. Формы сварных экструзионных швов
Основные формы экструзионных швов определены в отраслевом стандарте DVS 2207-4. Также документ содержит правила проведения сварки:
- Швы формируются за один проход;
- Желательно делать двухсторонний шов, он обеспечивает высокие прочностные материалы изделиям из термопластов;
- Двухсторонний шов обеспечивает экономию присадочного материала.
- Двухсторонний шов в меньшей степени влияет на характеристики основы листа или пленки во время остывания.
3. Формы и особенности сварочных башмаков
Готовая к работе присадка поступает в зону формирования шва через сварочный башмак. Также он выполняет следующие функции:
- Оказывает давление на поступающий материал;
- Формирует шов;
- Сглаживает поверхность шва.
Нос башмака не должен соприкасаться со свариваемыми листами, но его форма должна повторять их конфигурацию. Выполнить это требование можно при создании зазора носом башмака и корневым слоем от 1 до 3 мм. Сам он должен иметь скругленный передний и задний край. Такая опора предотвращает утечку присадки. Для этого необходимо создавать прижимное усилие во время сварки.
4. Подготовка к процессу сварки
Подготовка к процессу сваркиЛисты, пленка должны проходить подготовку непосредственно перед началом процесса. Это обусловлено быстрым окислением поверхности полимеров. Также причиной такого требования является возможность попадания на поверхность основы загрязнения: пыли, влаги, что значительно снизит прочностные показатели шва.Проводить подготовку полимеров к сварке необходимо за 20 минут до начала сварки. Если прошло больше указанного временного промежутка, следует повторно провести подготовку и незамедлительно приступить к сварке. Внимание!
Удаление загрязнения с поверхности полимеров проводится механическим способом, например, с помощью скребков. Обезжиривающие составы неэффективны при подготовке к экструзионной сварке.
4.1 V-образный шов
Шов V-образной формы требует предварительной обработки торцов, кромок стыкующихся материалов. Такая подготовка проводится с использование столярного инструмента:• Рашпиля;• Рубанка;• Ножовки;• Стамески.Созданный на кромках скос должен обеспечить раскрытие шва в диапазоне 45–90 градусов. Толстые полимерные листы требуют создания скоса с большим углом тонкие с меньшим. Угол раскрытия должен обеспечивать заполнение присадкой все пространство образуемое торцевыми срезами. Ограниченный угол раскрытия для толстостенных материалов обусловлен показателем общей шириной шва и зон перехлестов на его поверхности. Это показатель не должен превышать 30 мм. Игнорирование этого требования не позволит создать необходимое усилие, которое обеспечит отсутствие выступания присадки за края сварочного башмака. Корневой слой шва должен содержать миллиметровые нескошенные участки. Их отсутствие приведет к перегреву и оплавлению материала в зоне сварки при неравномерном движении сварочного аппарата. Последствием этого также станет нарушение ширины зазора между листами, он станет заметно шире или уже. Материал перед началом сварки фиксируется, благодаря чему формируется равномерный зазор. Его оптимальная ширина не должна быть больше 2 мм. Это позволит присадке проникать на внутреннюю часть свариваемых материалов, что гарантирует высокое качество сварки.
Механическая обработка шва должна осуществляться не ближе, чем в 2 мм от кромок скоса. Это делается при условии, что перехлест шляпки стыка в две стороны составляет не более, чем 2 мм.
4.2 X-образный шов
Этот тип шва является двухсторонней версией V-образного стыка. Это позволяет использовать в работе одни и те же требования, правила. Разница заключается только в невозможности контролировать качество проварки корневого слоя X-образным швом. Такая особенность меняет требования к работе с основой:
- На торцах формируются скосы;
- Угол их раскрытия 30–60 градусов;
- Лицевая сторона обрабатывается механически на расстоянии 2 мм от края скоса;
- Корневой слой фиксируется без зазора;
- Предварительно необходимо провести стыковку с помощью термофена с применением специальной насадки;
- Формируется V-образный шов лицевой части;
4.3 Шов типа HV
Для такой формы шва угол раскрытия определяется толщиной корневого слоя и составляет 45–60 градусов. Более значимое влияние на это оказывает вертикальный лист. Здесь необходимо оставить на торце не скошенный участок шириной 1 мм. Листы нужно зафиксировать, чтобы между ними оставался зазор 2 мм. Это даст гарантию качественной проварки.Внимание!Расстояние от края горизонтального листа до начала шва, после окончания сварки должно составлять не менее 10 мм.
Плоскость, находящаяся с левой стороны обрабатывается механически не ближе, чем в 3-х мм от края скоса кромки. Тут необходимо предусмотреть запас. Алгоритм действий при формировании шва формы HV аналогичен созданию X-образного шва.
4.4 K-образный шов
Угловое внутреннее соединение требует предварительной фиксации листов. Это делается с помощью термофена. Для временной сварки подойдет специальная насадка или сопло с присадочным материалом. Зона временной фиксации обрабатывается с помощью скребка:
- При использовании насадки для сварки это делается заостренным краем скребка;
- Использование присадочного материала требует механической обработки скругленной поверхностью скребка.
Для качественной реализации такой задачи требуется модернизация башмака. Это параллелепипед со скругленными углами, он соприкасается с верхней частью корневой основы, где угол между листами прямой – 90 градусов и с нижней частью, где угол может достигать 120–140 градусов.
romato.ru
Экструзионная сварка
Экструзионная сварка – один из наиболее распространенных методов соединения полимерных листовых материалов, в том числе и полипропилена.
При помощи данного вида сварки выполняется огромное множество видов соединений в различных изделиях. Наиболее типичным примером, когда без экструзионной сварки не обойтись, можно назвать приваривание днища к стенкам емкости.
Экструзионная сварка обладает рядом неоспоримых преимуществ перед другими видами сварки, например сваркой нагретым воздухом:
- Прочность экструзионного шва достигает 80% прочности основного материала.
- При помощи экструдера можно сваривать детали большой толщины
- Экструзионная сварка обладает высокой производительностью (например, по сравнению, со сваркой феном)
- При правильном подборе режимов сварки значительно снижается влияние человеческого фактора
Однако у экструзионной сварки есть и довольно большой минус – высокие требования к опыту и квалификации сварщиков. Каким минимальным набором знаний должен обладать сварщик, чтобы выполнять качественные сварные соединения при помощи ручного экструдера?
Общие требования
При сварке ручным экструдером необходимо соблюдать общее правило для сварки всех полимерных материалов любыми методами – сваривать следует только изделия из одинаковых материалов, т.е.:
- Которые совпадают по химическому составу (проще говоря, сварить полипропиленовые листы с листами ПВХ у вас вряд ли получится, хотя есть исключения – например сварка ПВХ и ПММА)
- И которые имеют близкие значения ПТР (показателя текучести расплава) — не стоит сваривать детали с разным ПТР, например экструдированные листы с изделиями полученными методом литья. Этого же правила необходимо придерживаться при выборе присадочного материала (сварочного прутка, гранул и т.д.) для сварки конкретных листов.
Еще одним важным требованием является очистка свариваемых поверхностей, причем в случае экструзионной сварки это требование нельзя игнорировать ни при каких обстоятельствах. При экструзионной сварке создается относительно слабое течение и перемешивание материала в зоне сварного шва. Перед началом сварки рекомендуется механически зачистить шов (снять оксидный слой) не более чем за 20 минут до начала процесса сваривания.
Виды сварных соединений
Немецкий стандарт DVS 2207-4 устанавливает 7 основных видов сварных соединений:
V шов
X шов
К шов
НV шов
Double HV шов
Е шов
F шов
Существует так же отечественный стандарт, регламентирующий выполнение сварных швов (ГОСТ 16310-80), выделяющий гораздо больше видов швов.
По возможности, следует изготавливать швы с двусторонней разделкой, это повышает прочность соединения и уменьшает неизбежные деформации изделий при их остывании, особенно при сварке листов большой толщины.
При разнице в толщине свариваемых деталей свыше 1 мм следует делать скос на детали имеющей большую толщину или на обеих деталях как указано на чертежах 1,2 и 3.
Углы разделки сварного шва следует выбирать исходя из толщины свариваемых деталей. Угол должен быть достаточно большим, чтобы обеспечить равномерное закрытие всей зоны шва расплавом прутка, при этом ширина шва не должна превышать 30 мм. В противном случае сварщик не сможет обеспечить равномерный и необходимый прижим расплава сварочным башмаком.
Кроме того проварку швов Х-типа следует проводить в 4 этапа.
- Подготовка зоны сварки
- Проварка верхнего шва
- Разделка корня шва
- Проварка нижнего шва
При изготовлении швов HV типа в корневом слое вертикального листа следует оставлять тонкий (до 1мм) слой нескошенного материала, как показано на рисунке. Также требуется обеспечить расстояние около 2 мм между вертикальным и горизонтальным листами для гарантированной проварки корня. При выполнении шва Double HV очередность действий аналогична очередности при выполнении швов Х-типа.
Режимы сварки
Для получения прочного сварного соединения следует очень внимательно относиться к режимам на которых производится сварка, но прежде чем говорить о том на каких настройках необходимо сваривать детали, давайте разберем принципиальное устройство ручного экструдера.
Экструдер состоит из следующих деталей и узлов:
Все процессы сварки происходят в термопластическом состоянии в зоне сварного шва
Соответственно основной характеристикой влияющей на прочность сварного соединения будет температура и объем подаваемого воздуха для расплавления присадочного и основного материала. Стандарт DVS 2205-1 рекомендует проводить сварку при следующих параметрах:
Температура экструдера, замеренная на выходе из форсунки, º C |
Температура воздуха, замеренная в форсунке подачи
теплого воздуха, ºC
Количество воздуха, литров/мин.
200-240
210-250
350-400
Современные экструдеры позволяют очень точно настраивать все 3 параметра. При выполнении ответственных швов следует применять экструдер позволяющий раздельно контролировать температуру на выходе из форсунки и температуру подачи воздуха. Такие экструдеры, как правило, стоят дороже чем те, которые отслеживают только температуру воздуха. Однако они гарантируют одинаковую температуру расплава и свариваемых поверхностей.
При экструзионной сварке материалов Vikulen также следует использовать вышеуказанные параметры
Выполнение сварочных работ
- Перед началом сварочных работ следует убедится, что в экструзионной камере не осталось расплава материала. Если какая-то часть материала все же осталась, его необходимо полностью выдавить даже в том случае если планируется проводить сварку таким же прутком
- Тщательно прогрейте сварочный башмак, чаще всего для этого используют специальные экраны установленные на самом экструдере или на подставке для него
- Прогрейте поверхность свариваемых материалов горячим воздухом, поднеся сопло экструдера к началу зоны сварки
- Прижмите сварочный башмак к зоне сварного шва и включите подачу расплава
- При продвижении эктрудера контролируете угол его наклона. Например при сварке швов К угол наклона должен составлять 45°, а при сварке швов V экструдер должен располагаться перпендикулярно к свариваемым поверхностям. Это позволит исключить выдавливание расплава из-под сварочного башмака.
- Контролируйте силу прижима сварочного башмака. Она должна быть такой, чтобы прижим не приводил к выдавливанию расплава из зоны сварного шва.
Эффективная несущая способность сварных соединений
Все сварные соединения имеют разную максимальную прочность при разных нагрузках.
При угловых соединениях следует стремиться к смещению шва как можно дальше от непосредственно угла. Этого можно добиться, если выполнить скругление материала в угле, и выполнить обычный стыковой шов уже за его пределами. Это связано с тем, что угловые соединения плохо переносят изгибающую нагрузку.
Т-образные соединения с двусторонним швом показывают значительно лучшие прочностные характеристики в сравнении с односторонним.
При растягивающей нагрузке разные типы сварных соединений также выдерживают разные напряжения. На иллюстрации ниже представлена схематичная прочность различных соединений при таком типе нагрузки.
Кроме того, для обеспечения максимальной прочности следует избегать скопления швов в одном месте, а также пересечения сварных швов.
Влияние качества материалов на прочность сварных соединений
Последний, и при этом важнейший фактор, влияющий на прочность сварных соединений – качество свариваемых материалов и присадочного прутка. И это вполне логично, ведь если материал низкого качества, то какие бы правила вы не соблюдали и какие методики не применяли, вы все равно не получите прочного сварного соединения.
На качество материала влияют:
— Наличие и объем вторичного сырья в полуфабрикатах
Чем больше вторички в полуфабрикатах, тем большая часть материала уже получила термошок, а следовательно потеряла свою способность образовывать надежное сварное соединение.
— Качественные термостабилизаторы в составе материала
Именно термостабилизаторы позволяют снизить деструктирующее воздействие на материал при экструзии и переработке полипропилена.
— Сырье со стабильными параметрами переработки.
Ни для кого не секрет, что стабильность параметров переработки играет огромную роль как в процессе производства полуфабрикатов, так и в процессе их переработки, данный фактор позволяет не подбирать каждый раз оптимальные параметры сварки, а использовать уже отработанные режимы, обеспечивая максимальные качество и производительность.
— Наличие и объем влаги в полуфабрикатах и исходном сырье
Несмотря на небольшую абсорбцию полипропилена (около 0,01%), даже такое количество влаги может в значительной степени негативно влиять на качество сварного соединения. Данный факт подтвержден многими годами практического опыта переработки полуфабрикатов из полипропилена.
Приобретая полуфабрикаты Vikulen вы гарантировано получаете материал, наилучшим образом отвечающий всем вышеперечисленным требованиям
Экструзионная сварка довольно сложный и трудоемкий процесс, требующий большого опыта и знаний от сварщика. Тем не менее, применяя этот метод вы сможете получать действительно качественные и прочные изделия. Если вы можете дополнить данную статью, то мы будем признательны Вам за Ваши комментарии
vikulen.ru
Экструзионный способ сварки полимеров: особенности и схема работы
Сварка экструзионным способом является одним из видов соединения изделий из полиэтилена, полипропилена, пропилена и иных видов полимера. Экструзионная сварка представляет собой процесс соединения деталей из различных полимеров с использованием специального присадочного материала. Соединение будет прочным и качественным, если присадочный материал по составу аналогичен соединяемым поверхностям. Экструзионный способ используется для сварки полипропиленовых листов, листов из пленки, различных ёмкостей, реже – изделий из ПВХ. Этот вид соединения нельзя применять для сварки полиэтиленовых труб и иных пластиковых труб под напором, так как его прочности в 80% будет недостаточно.
Экструзионный способ существует для соединения толстостенных элементов. И у него по сравнению со сваркой горячим воздухом с применением прутка есть преимущества: шов получается с первого раза, экструзионная сварка происходит быстрее, человеческий фактор сведен в минимуму, так как нет необходимости следить за параметрами сварки, уметь делать красивые швы. То есть, экструзионная сварка будет самой простой для начинающего. Можно сделать ручной сварочный экструдер своими руками.
Экструзионная сварка может быть двух видов: ручная и автоматическая. Среди ручных экструдеров следует отдельно выделить leister fusion 3c. Leister fusion 3c имеет множество преимуществ: высокая производительность, небольшой вес, простой и удобный корпус, пруток не «закручивается». Хороший выбор сварочного оборудования содержится в интернет-магазине Weldmax. Также для использования в узких местах рекомендуется использовать недорогой ручной сварочный экструдер fusion 2. Ручной сварочный экструдер fusion 2 прост в управлении, компактный, удобный и прочный. Сварочный экструдер leister fusion 2 оснащен системой защиты двигателя от холодного пуска. Ручной сварочный экструдер leister weldplast s6 — самый мощный в линейке данного производителя. Ручной сварочный экструдер leister weldplast s6 шнековый, с небольшим уровнем шума, имеет множество программ.
Содержание
- 1 Общие требования
- 2 Принцип работы
- 3 Схема работы
Общие требования
Соединяемые детали из пластика и присадочный материал при экструзионном способе сварки должны быть идентичными по определенным показателям:
- химический состав.
- плотность.
- показатели его текучести.
Если соединяются различные по показателям детали, тогда нужно выбирать присадочный материал, средний между значениями соединяемых поверхностей.
Еще одно правило связано с очищением кромок деталей. Это требование должно выполнятся очень строго. Так как многие виды термопласта на воздухе окисляются, очищать их нужно не раньше, чем за 15-20 минут до соединения. Если будет допущено наличие посторонних предметов или частиц на поверхностях, шов будет некачественный. Если после последнего очищения (не рекомендуется очищать растворителем) прошло более 20 минут, повторите процесс заново.
Принцип работы
Поверхностями для сварки полиэтиленовых труб и иных изделий являются сварочные канавки, углы полипропиленовых листов, поверхности пленки, расположенной внахлест. Сначала поверхности разогреваются до температуры, необходимой для начала процесса пластификации. Для этого используется нагретый воздух, который исходит их сварочного экструдера. Для нагревания также могут быть использованы внешние способы, например тепловое излучение от стационарного экструдера.
Вместе с этим будущий присадочный материал пока что в виде специальных гранул или прутка помещается в специальную камеру экструдера, в которой происходит нагрев содержимого. Содержимое нагревается до текучего состояния и с помощью шнека или диска (в зависимости от вида экструдера) выдавливается через сварочный башмак в область сварки.
Схема работы
Так как соединяемые поверхности должны стать вязкими перед сваркой, нагретый до определенной температуры воздух выходит в зону сварки из специального сопла. Температуру можно регулировать. Нагрев может быть осуществлен встроенными нагревателями в экструдере (термофен), либо может поступать от внешних носителей (компрессор или пневмосеть в организации).
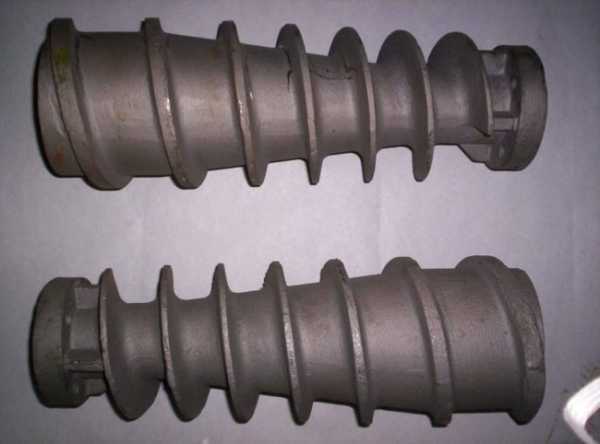
Экструдеры бывают шнековые и безшнековые. Шнековые экструдеры отличаются тем, что присадочный материал расплавляется в шнековой камере и выталкивается наружу с помощью шнека. В безшнековых экструдерах присадочный материал выталкивается с помощью твердой, еще не расплавленной части прутка. Такие экструдеры еще называют плунжерными. Их производительность меньше, чем у шнековых, с ними невозможно использовать гранулы в качестве присадочного материала. Зато его легко можно использовать в малодоступных местах. На окончании сварочного башмака имеется специальное отверстие, которое контролирует поступление присадочного материала в зону сварки.
Экструзионный вид сварки используется чаще для полиэтилена низкого давления, полипропилена, других термопластов 1-й группы. Эта группа отличительна тем, что разница между расплавленным состоянием и состоянием термодеструкции примерно пятьдесят градусов. Таким образом, незначительный перегрев на 30-40 градусов не испортит материал. Термопласты 2-й группы – это ПВДФ и ПВХ. Разница в температурах между вышеуказанными состояниями небольшая, что требует строгого соблюдения температурного режима в зоне нагрева. Шнек для термопластов 2-й группы должен иметь особую форму для более тщательного перемешивания присадочного материала без перегрева.
Таким образом, экструзионный способ сварки полипропиленовых изделий является самым простым для новичков, применяется для соединения толстостенных изделий. Новички могут изготовить ручной сварочный экструдер своими руками. Ручной экструдер для сварки выбрать достаточно легко, так как на рынке существуем множество аппаратов для этого вида соединения, одним из самых популярных является сварочный экструдер leister fusion 2.
svarkaed.ru
Большая Энциклопедия Нефти и Газа
Cтраница 2
Схемы сварки термопластов экструдируемой присадкой. [16] |
Основными технологическими параметрами экструзионной сварки являются: температура присадочного материала, сварочное давление и скорость сварки. [17]
Различают две разновидности техники экструзионной сварки: бесконтактно-экструзионную и контактно-экструзионную. [18]
При производстве защитной футеровки химического обору дования в основном применяют экструзионную сварку, сварку нагретым газом и термоконтактную сварку. Выбор способа зависит от наличия оборудования, размеров и геометрической формы свариваемых деталей, физико-химических свойств и толщины материала. [19]
Сварочный аппарат установки ПЭСУ-2000. [20] |
Установка ПЭСУ-2000 ( табл. 2.25, рис. 2.31) предназначена для экструзионной сварки в полуавтоматическом режиме протяженных стыков полиэтиленовых пленок и листов на горизонтальных поверхностях в различных условиях работы с применением гранулированного присадочного материала. В комплект установки входят пульт управления и сварочный аппарат. [21]
Способ по первой схеме получил название бесконтактной экстру з и он но и сварки, либо просто экструзионной; по второй схеме — контактной экструзионной сварки. [22]
Экструзионная сварка успешно заменяет сварку нагретым газом с присадочным материалом, когда необходимо значительно повысить скорость процесса, особенно при сборке толстостенных изделий. Экструзионная сварка наплавкой, при которой расплав присадочного материала подается по кромке детали, уложенной сверху на другую деталь с перекрытием, применяется при сборке крупногабаритных полотнищ из листовых эластичных ПМ типа геомембран. [23]
Сварка нагретым присадочным материалом основана на использовании теплоты расплавленного присадочного материала, подаваемого между соединяемыми поверхностями, который, попадая в разделку шва, часть своей теплоты передает материалу соединяемых поверхностей, он плавится и образуется сварной шов. Этот способ подразделяется на сварку экструдируе-мой присадкой ( экструзионная сварка) и сварку нагревом прутка в контактном нагревателе, которые могут выполняться как с подогревом ( нагретым газом или контактным способом), так и без подогрева соединяемых поверхностей. При экструзионной сварке расплав получается с помощью микроэкструдера, обеспечивающего непрерывную подачу расплава, а в качестве исходного сырья используется гранулированный материал. При сварке нагревом прутка в контактном нагревателе-расплав получается из присадочного прутка путем. Для сварки труб чаще применяют сварку экструдируемой присадкой. [24]
Существуют различные способы сварки пластмасс. При производстве защитной футеровки химического оборудования в основном применяют экструзионную сварку, сварку нагретым газом с присадочным прутком и термоконтактную сварку. Выбор способа диктуется наличием оборудования, размерами и геометрической формой свариваемых деталей, физико-химическими свойствами и толщиной материала. [25]
Сварка нагретым присадочным материалом основана на использовании теплоты расплавленного присадочного материала, подаваемого между соединяемыми поверхностями, который, попадая в разделку шва, часть своей теплоты передает материалу соединяемых поверхностей, он плавится и образуется сварной шов. Этот способ подразделяется на сварку экструдируе-мой присадкой ( экструзионная сварка) и сварку нагревом прутка в контактном нагревателе, которые могут выполняться как с подогревом ( нагретым газом или контактным способом), так и без подогрева соединяемых поверхностей. При экструзионной сварке расплав получается с помощью микроэкструдера, обеспечивающего непрерывную подачу расплава, а в качестве исходного сырья используется гранулированный материал. При сварке нагревом прутка в контактном нагревателе-расплав получается из присадочного прутка путем. Для сварки труб чаще применяют сварку экструдируемой присадкой. [26]
Сварка нагретым присадочным материалом основана на использовании теплоты расплавленного присадочного материала, подаваемого между соединяемыми поверхностями, который, попадая в разделку шва, часть своей теплоты передает материалу соединяемых поверхностей. Он плавится и образуется сварной шов. Этот способ подразделяется на сварку экструдируемой присадкой ( экструзионная сварка) и сварку нагревом прутка в контактном нагревателе, которые могут выполняться как с подогревом ( нагретым газом или контактным способом), так и без подогрева соединяемых поверхностей. При экструзионной сварке расплав получается с помощью микроэкструдера, обеспечивающего непрерывную подачу расплава, а в качестве исходного сырья используется гранулированный материал. [27]
Сварка нагретым присадочным материалом основана на использовании теплоты расплавленного присадочного материала, подаваемого между соединяемыми поверхностями, который, попадая в разделку шва, часть своей теплоты передает материалу соединяемых поверхностей. Он плавится и образуется сварной шов. Этот способ подразделяется на сварку экструдируемой присадкой ( экструзионная сварка) и сварку нагревом прутка в контактном нагревателе, которые могут выполняться как с подогревом ( нагретым газом или контактным способом), так и без подогрева соединяемых поверхностей. При экструзионной сварке расплав получается с помощью микроэкструдера, обеспечивающего непрерывную подачу расплава, а в качестве исходного сырья используется гранулированный материал. [28]
Страницы: 1 2
www.ngpedia.ru
www.samsvar.ru
Экструзионная сварка — Большая Энциклопедия Нефти и Газа, статья, страница 2
Экструзионная сварка
Cтраница 2
Основными технологическими параметрами экструзионной сварки являются: температура присадочного материала, сварочное давление и скорость сварки. [17]
Различают две разновидности техники экструзионной сварки: бесконтактно-экструзионную и контактно-экструзионную. [18]
При производстве защитной футеровки химического обору дования в основном применяют экструзионную сварку, сварку нагретым газом и термоконтактную сварку. Выбор способа зависит от наличия оборудования, размеров и геометрической формы свариваемых деталей, физико-химических свойств и толщины материала. [19]
Установка ПЭСУ-2000 ( табл. 2.25, рис. 2.31) предназначена для экструзионной сварки в полуавтоматическом режиме протяженных стыков полиэтиленовых пленок и листов на горизонтальных поверхностях в различных условиях работы с применением гранулированного присадочного материала. В комплект установки входят пульт управления и сварочный аппарат. [21]
Способ по первой схеме получил название бесконтактной экстру з и он но и сварки, либо просто экструзионной; по второй схеме — контактной экструзионной сварки. [22]
Экструзионная сварка успешно заменяет сварку нагретым газом с присадочным материалом, когда необходимо значительно повысить скорость процесса, особенно при сборке толстостенных изделий. Экструзионная сварка наплавкой, при которой расплав присадочного материала подается по кромке детали, уложенной сверху на другую деталь с перекрытием, применяется при сборке крупногабаритных полотнищ из листовых эластичных ПМ типа геомембран. [23]
Сварка нагретым присадочным материалом основана на использовании теплоты расплавленного присадочного материала, подаваемого между соединяемыми поверхностями, который, попадая в разделку шва, часть своей теплоты передает материалу соединяемых поверхностей, он плавится и образуется сварной шов. Этот способ подразделяется на сварку экструдируе-мой присадкой ( экструзионная сварка) и сварку нагревом прутка в контактном нагревателе, которые могут выполняться как с подогревом ( нагретым газом или контактным способом), так и без подогрева соединяемых поверхностей. При экструзионной сварке расплав получается с помощью микроэкструдера, обеспечивающего непрерывную подачу расплава, а в качестве исходного сырья используется гранулированный материал. При сварке нагревом прутка в контактном нагревателе-расплав получается из присадочного прутка путем. Для сварки труб чаще применяют сварку экструдируемой присадкой. [24]
Существуют различные способы сварки пластмасс. При производстве защитной футеровки химического оборудования в основном применяют экструзионную сварку, сварку нагретым газом с присадочным прутком и термоконтактную сварку. Выбор способа диктуется наличием оборудования, размерами и геометрической формой свариваемых деталей, физико-химическими свойствами и толщиной материала. [25]
Сварка нагретым присадочным материалом основана на использовании теплоты расплавленного присадочного материала, подаваемого между соединяемыми поверхностями, который, попадая в разделку шва, часть своей теплоты передает материалу соединяемых поверхностей, он плавится и образуется сварной шов. Этот способ подразделяется на сварку экструдируе-мой присадкой ( экструзионная сварка) и сварку нагревом прутка в контактном нагревателе, которые могут выполняться как с подогревом ( нагретым газом или контактным способом), так и без подогрева соединяемых поверхностей. При экструзионной сварке расплав получается с помощью микроэкструдера, обеспечивающего непрерывную подачу расплава, а в качестве исходного сырья используется гранулированный материал. При сварке нагревом прутка в контактном нагревателе-расплав получается из присадочного прутка путем. Для сварки труб чаще применяют сварку экструдируемой присадкой. [26]
Сварка нагретым присадочным материалом основана на использовании теплоты расплавленного присадочного материала, подаваемого между соединяемыми поверхностями, который, попадая в разделку шва, часть своей теплоты передает материалу соединяемых поверхностей. Он плавится и образуется сварной шов. Этот способ подразделяется на сварку экструдируемой присадкой ( экструзионная сварка) и сварку нагревом прутка в контактном нагревателе, которые могут выполняться как с подогревом ( нагретым газом или контактным способом), так и без подогрева соединяемых поверхностей. При экструзионной сварке расплав получается с помощью микроэкструдера, обеспечивающего непрерывную подачу расплава, а в качестве исходного сырья используется гранулированный материал. [27]
Сварка нагретым присадочным материалом основана на использовании теплоты расплавленного присадочного материала, подаваемого между соединяемыми поверхностями, который, попадая в разделку шва, часть своей теплоты передает материалу соединяемых поверхностей. Он плавится и образуется сварной шов. Этот способ подразделяется на сварку экструдируемой присадкой ( экструзионная сварка) и сварку нагревом прутка в контактном нагревателе, которые могут выполняться как с подогревом ( нагретым газом или контактным способом), так и без подогрева соединяемых поверхностей. При экструзионной сварке расплав получается с помощью микроэкструдера, обеспечивающего непрерывную подачу расплава, а в качестве исходного сырья используется гранулированный материал. [28]
Страницы: 1 2
www.ngpedia.ru