Картинки экструдер, Стоковые Фотографии и Роялти-Фри Изображения экструдер
Картинки экструдер, Стоковые Фотографии и Роялти-Фри Изображения экструдер | Depositphotos®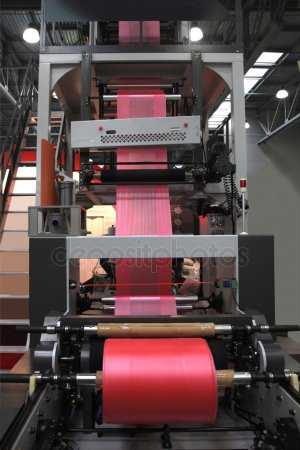
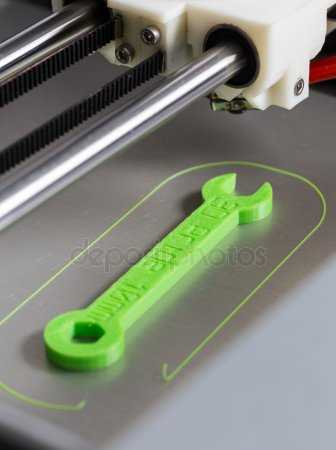
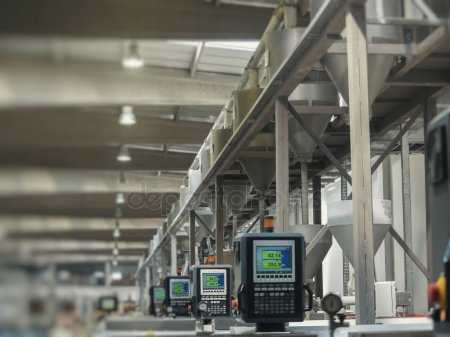
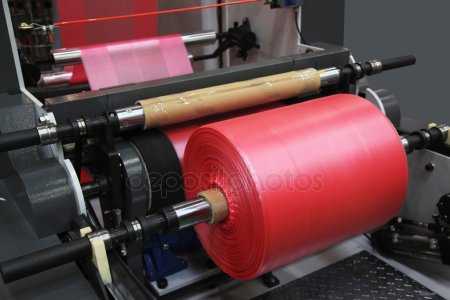
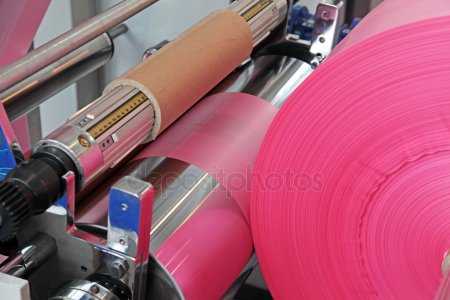
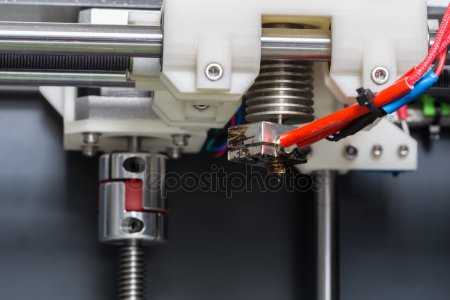
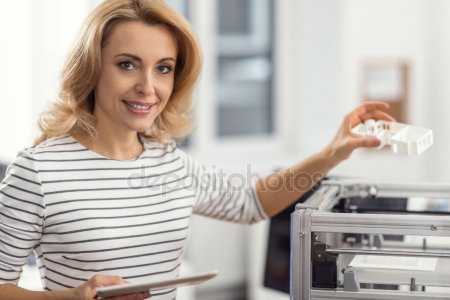
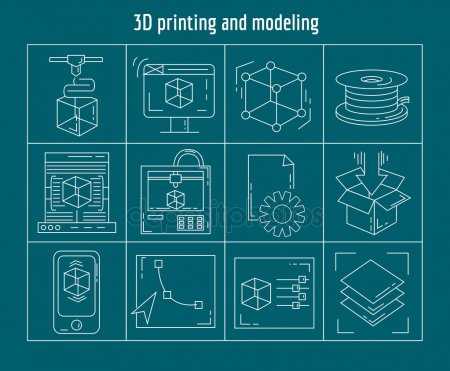
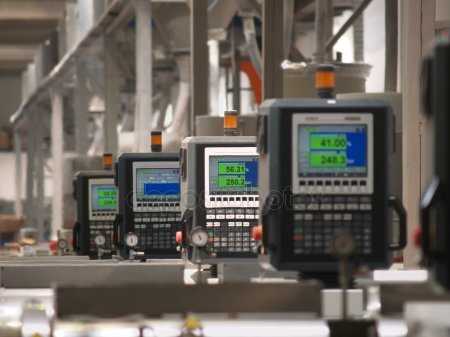
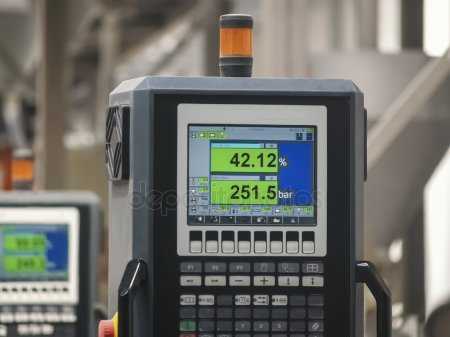
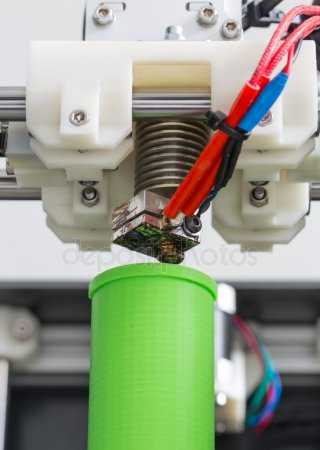
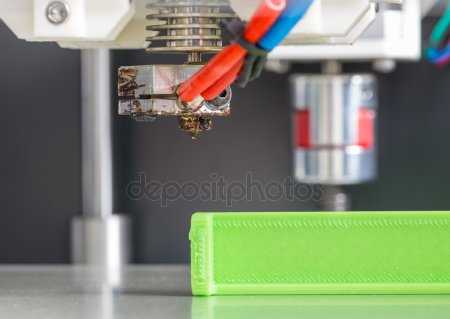
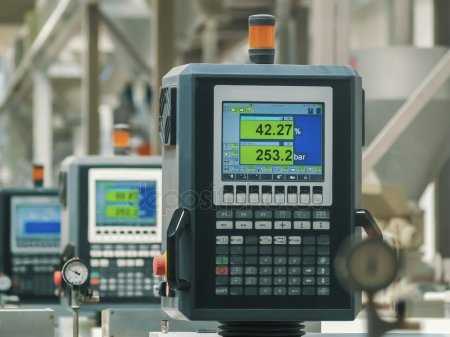
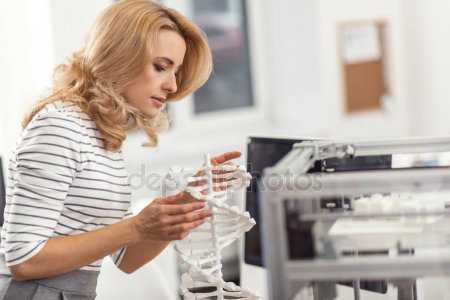

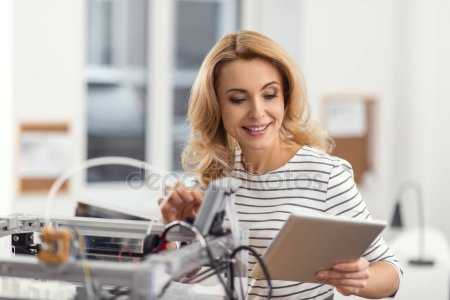
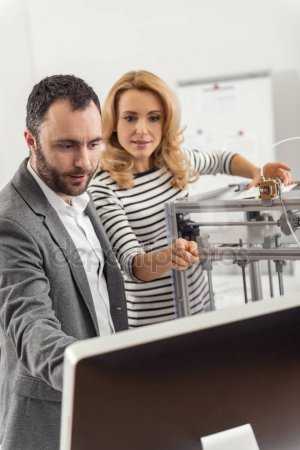
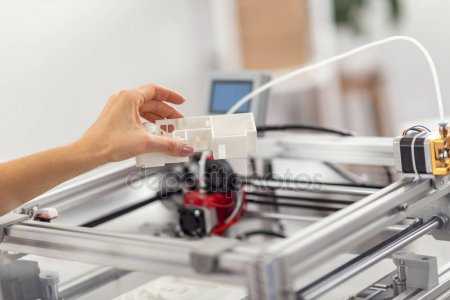
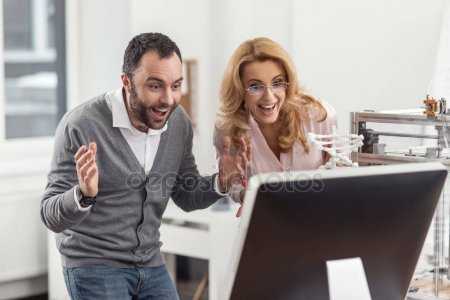
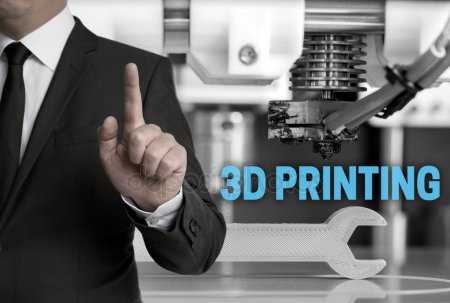
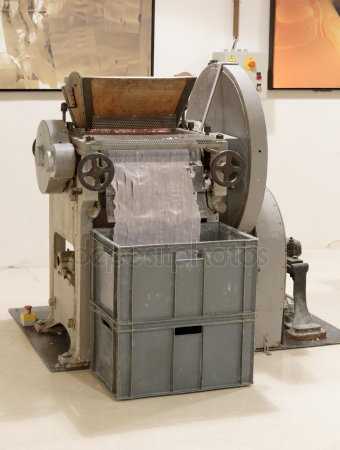
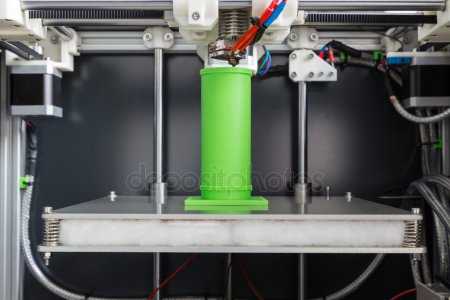
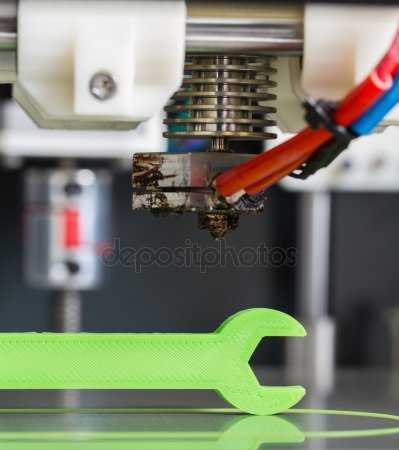
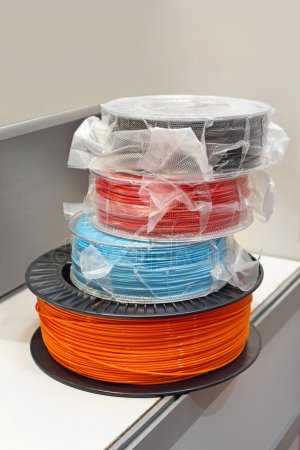
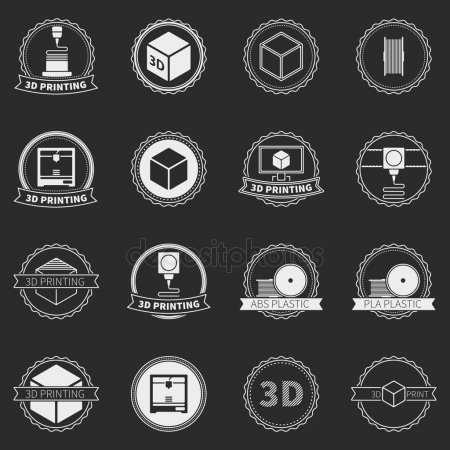
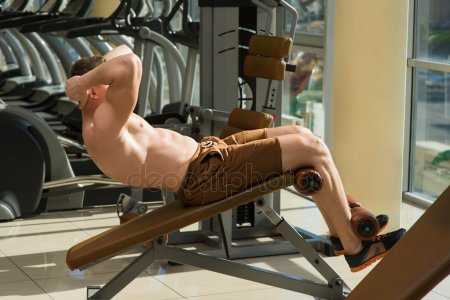
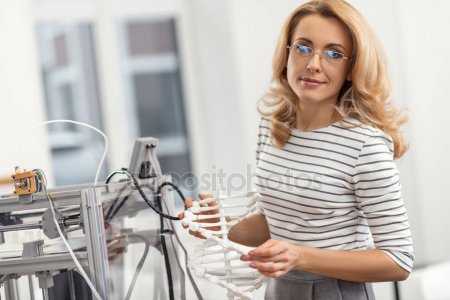
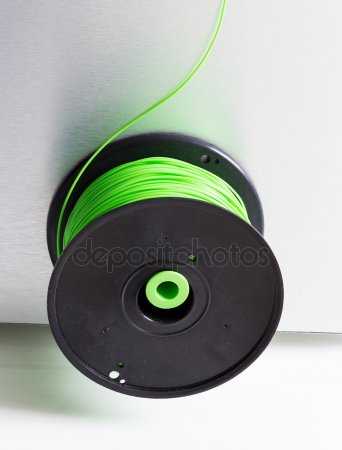
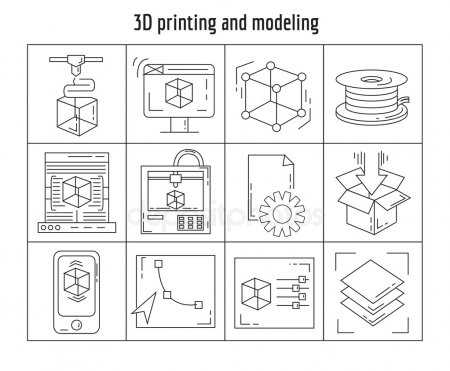
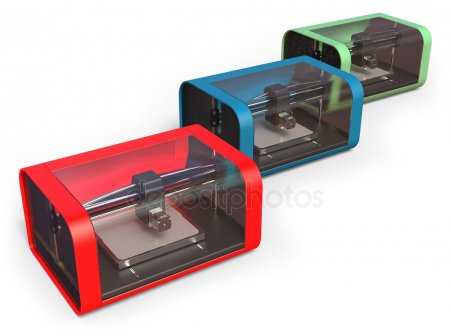

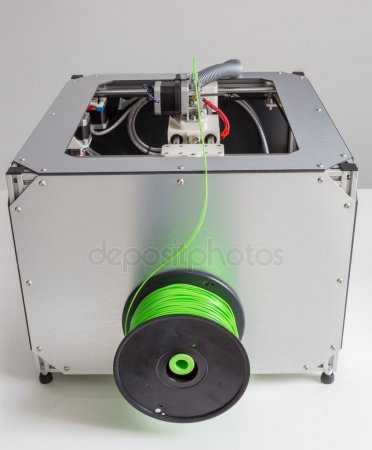
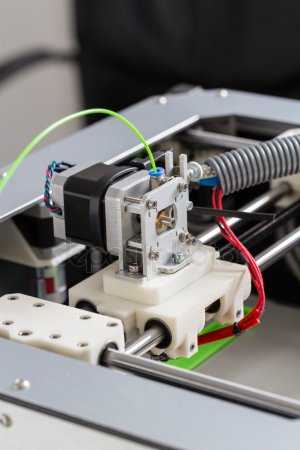
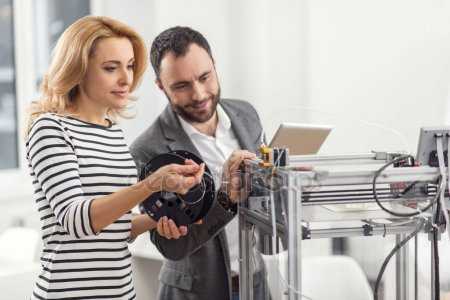
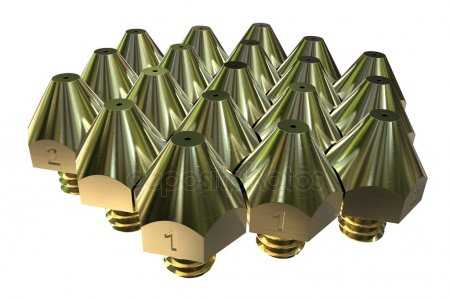
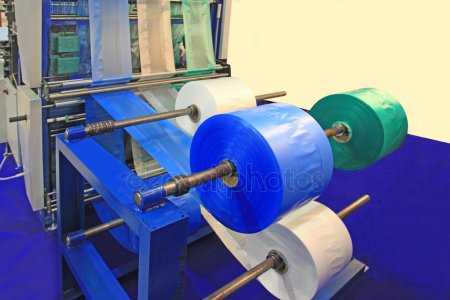
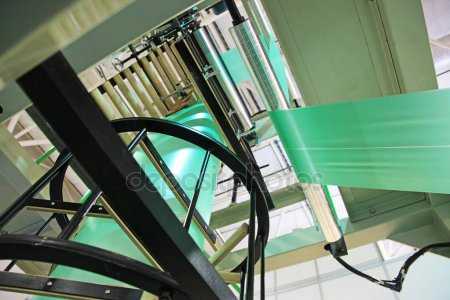
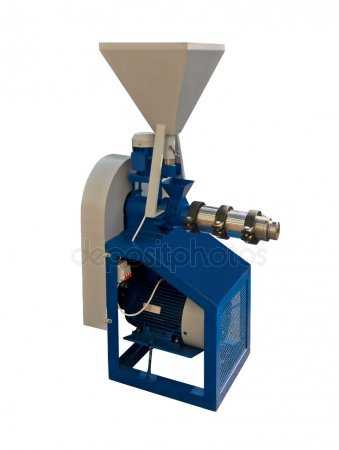
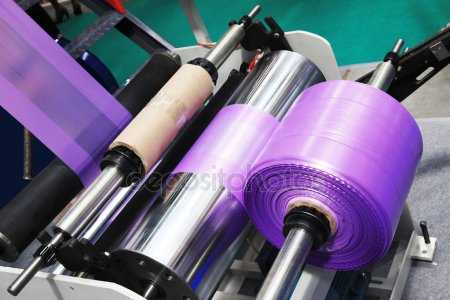
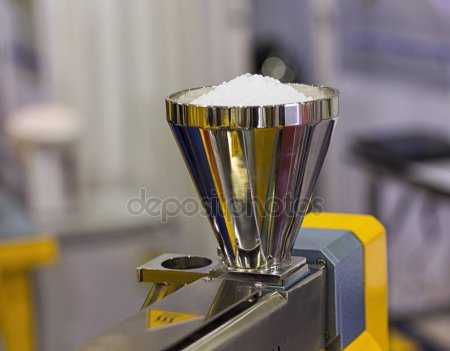
wsintapanon.hotmail.com
4424 x 3456
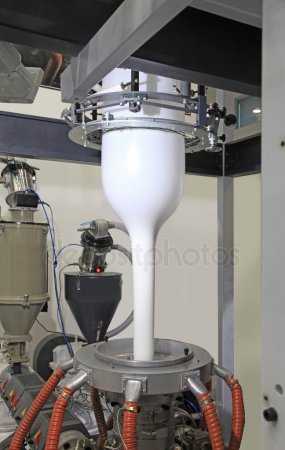
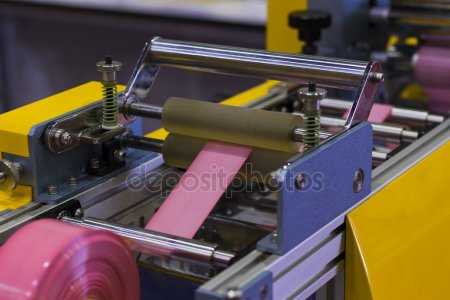
wsintapanon.hotmail.com
5184 x 3456
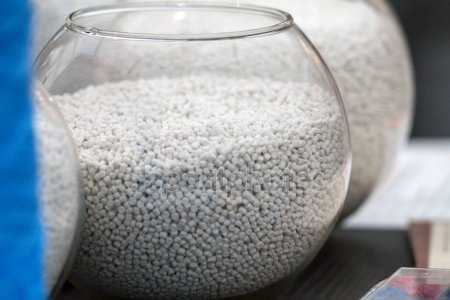
barselona_dreams
5184 x 3456
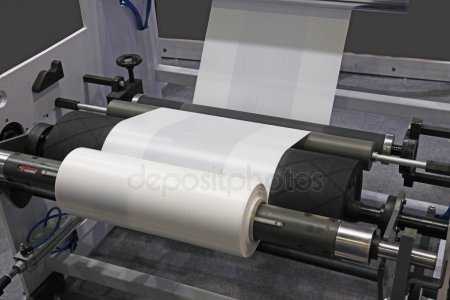
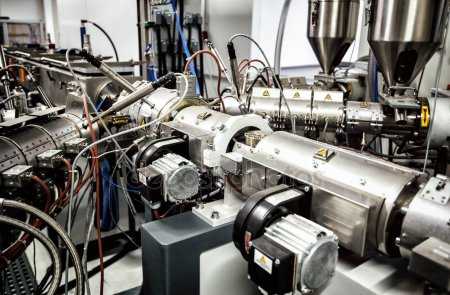
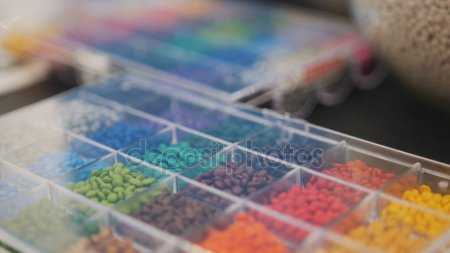
barselona_dreams
3840 x 2160
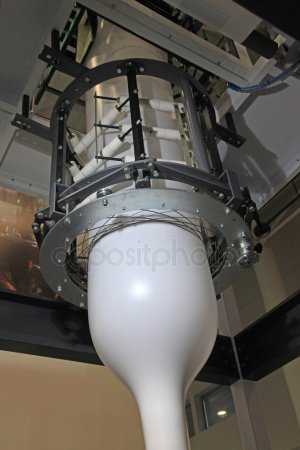
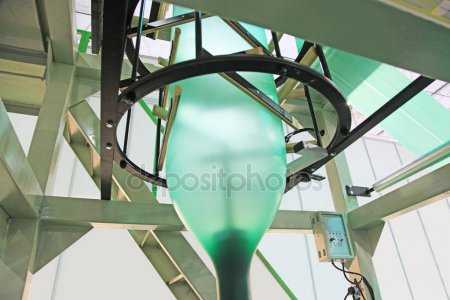
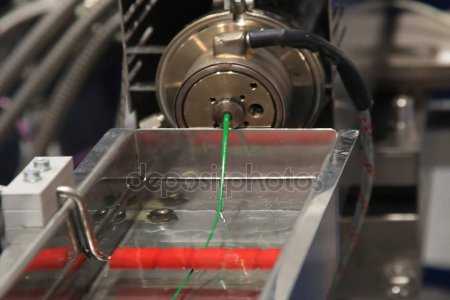
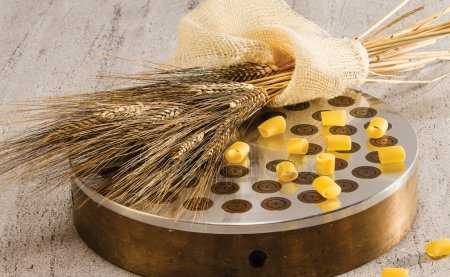
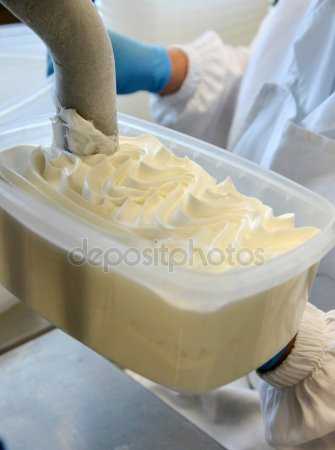
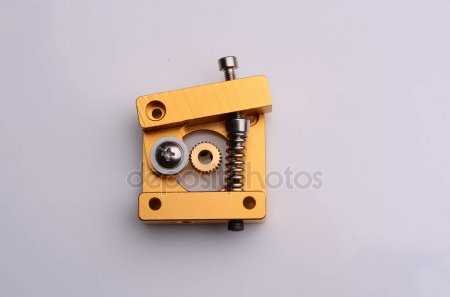
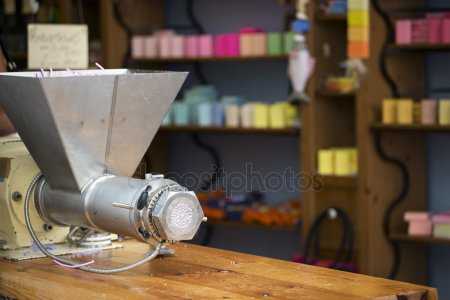
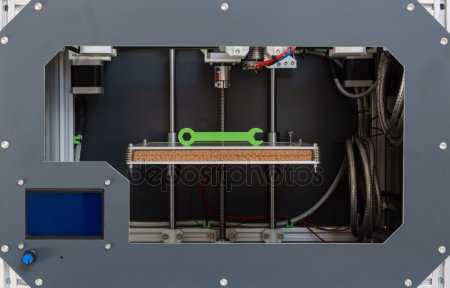
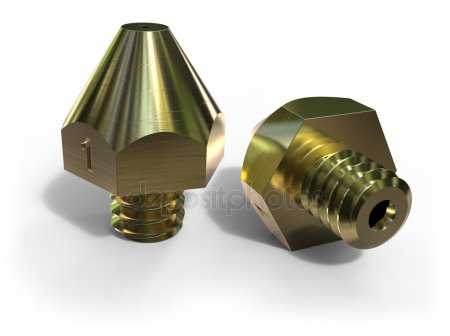
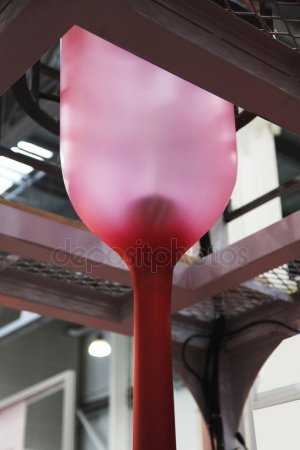
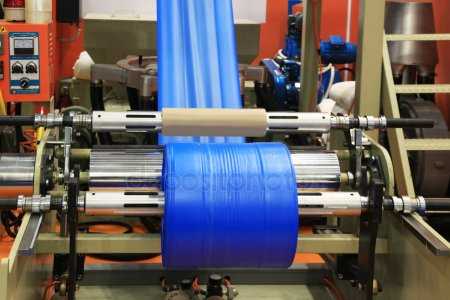
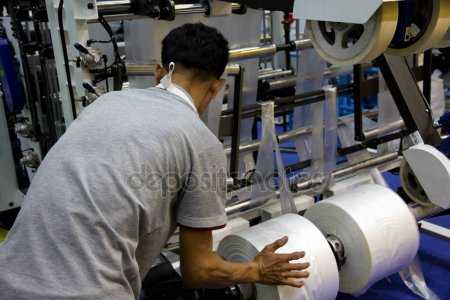
5184 x 3456
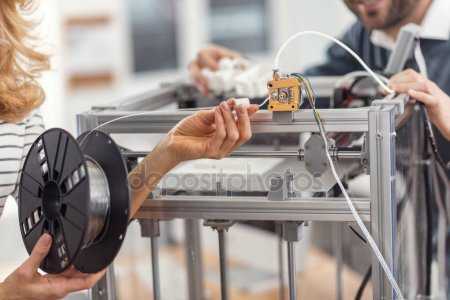
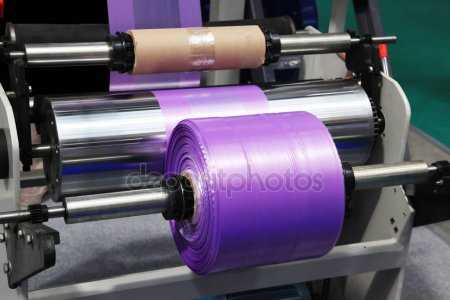
ru.depositphotos.com
Экструдер
По типу основного рабочего органа экструдеры подразделяют на одношнековые, многошнековые, дисковые, поршневые и др. Классификация экструдеров приведена на рисунке 1.
Рисунок 2 — Классификация экструдеров
Поршневые и валковые экструдеры оказывают щадящее воздействие на перерабатываемый продукт, их используют для формования продукта с нежной консистенцией.
Валковые экструдеры применяют в машинах без матриц, шестеренные — для формования однородных и гомогенных материалов в машинах с матрицами.
Производительность шнекового экструдера определяется взаимодействием нагнетателя и формующей головки.
Экструдер состоит из нескольких основных узлов — корпуса, оснащенного нагревательными элементами, рабочего органа (шнека, диска, поршня), размещенного в корпусе, узла загрузки перерабатываемого продукта, привода, системы задания и поддержания температурного режима и других контрольно-измерительных и регулирующих устройств.
Наибольшее распространение в промышленности получили шнековые экструдеры. Захватывая- исходный продукт, шнек перемещает его от загрузочного устройства вдоль корпуса экструдера. При этом продукт сжимается, разогревается, пластифицируется и гомогенизируется. Давление в экструдере достигает 15… 100 МПа. По частоте вращения шнека экструдеры подразделяют на нормальные и быстроходные с окружной скоростью соответственно до 0,5 и 7 м/мин, а по конструктивному исполнению — на стационарные и с вращающимся корпусом, с горизонтальным и вертикальным расположением шнека.
Существуют экструдеры со шнеками, осуществляющими не только вращательное, но и возвратно-поступательное движение. Для эффективной гомогенизации продукта на шнеках устанавливают дополнительные устройства — зубья, шлицы, диски, кулачки и др. В последнее время получают распространение планетарно-вальцовые экструдеры, у которых вокруг центрального рабочего органа (шпинделя) вращается несколько дополнительных шнеков (от 4 до 12). Принцип действия дискового экструдера основан на использовании возникающих в упруговязком материале напряжений, нормальных к сдвиговым. Основу конструкций такого экструдера составляют два плоскопараллельных диска, один из которых вращается, создавая сдвиговые и нормальные напряжения, а другой неподвижен. В центре неподвижного диска имеется отверстие, через которое выдавливается размеченный материал. Поршневой экструдер из-за низкой производительности используют ограниченно, в основном для изготовления труб и профилей из реактопластов.
Конструкции экструдеров могут быть классифицированы также по геометрической форме, механическим, функциональным или термодинамическим характеристикам. Кроме того, экструдеры рекомендуется классифицировать по их физическим признакам, поскольку они оказывают влияние на химические структурные характеристики экструдированных продуктов. Особое значение имеют такие параметры, как уклон режущей кромки матрицы и количество тепловой энергии, образующейся в процессе экструдирования за счет механического преобразования энергии; температура во время ведения процесса; влажность экструдируемой массы.
При переработке пищевых продуктов наибольшее распространение получили экструдеры со шнеками полного зацепления, вращающимися в одном направлении, когда вершины одного шнека взаимодействуют с впадинами другого.
В двухшнековых самоочищающихся экструдерах обеспечиваются более быстрый пуск шнека и работа на повышенной скорости. В них реже возникают подъемы давления, так как не происходит накопление продукта. В одношнековых экструдерах, вследствие того, что продукт может оставаться в витках и накапливаться, создавая разрывы потока, подъемы давления бывают чаще. В результате продукт из экструдера выпускается неравномерно.
Однако предполагается, что в одношнековом экструдере износ шнека концентрируется по наружной кромке к торцу его витков, и это обеспечивает восстановление шнека.
Двухшнековый экструдер более подвержен износу. Изнашиваются шнеки в местах загрузки и выгрузки продукта. В этой связи свойства конечного продукта и эффективность процесса экструдирования в большой степени зависят от износа рабочих органов машины при обработке в двухшнековом экструдере. При использовании двухшнекового экструдера не требуется предварительной гидротермической обработки продукта, что упрощает производственный процесс. Гидролиз крахмала пшеничной муки протекает гораздо эффективнее в двухшнековом экструдере, чем в одношнековом. В двухшнековом экструдере зоны пластификации и повышения давления отделены друг от друга, что позволяет независимо осуществлять пластификацию и экструдирование продукта. Известно, что затраты, связанные с приобретением одношнековых экструдеров, ниже по сравнению с затратами на приобретение двухшнековых машин. Однако последние компенсируются меньшими эксплуатационными расходами. Высокие расходы по эксплуатации одношнековых машин связаны с длительными простоями при чистке, большими трудозатратами и объемом работ по обслуживанию.
Сравнение конструктивных и технологических достоинств одношнековых и двухшнековых экструдеров показывает значительное преимущество последних.
Материал для матриц должен быть коррозионно-стойким, обладать антиадгезионными свойствами и высокой прочностью. Чтобы снизить прилипаемость формуемого продукта, отверстия полируют и хромируют. Широко применяют в настоящее время матрицы, состоящие из металлической обоймы и сменных вставок. Вставки представляют собой сменные гильзы с формующими отверстиями, изготовляются из пластмасс с сильно выраженными антиадгезионными свойствами.
Форма и размер предматричной камеры зависят от свойств перерабатываемого продукта, типа и размеров нагнетающего механизма и должны способствовать выходу выпрессовываемой массы через каналы матрицы с возможно более равномерной скоростью, а также препятствовать образованию застойных зон. Формование экструзией имеет ряд преимуществ: непрерывность осуществления процесса с высокой скоростью, безотходность технологии и высокая культура производства.
Машина А1-КХП для формования палочек из кукурузной крупы тепловой и механической обработкой
Машина А1-КХП (рисунок 1) предназначена для формования палочек из кукурузной крупы тепловой и механической обработкой.
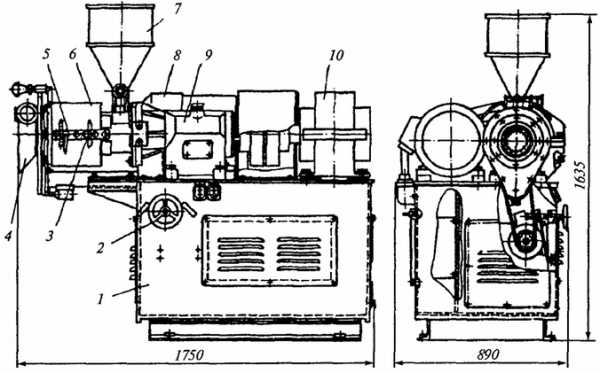
Машина состоит из станины 1, бункера 7, корпуса подшипника 9, цилиндра 3, механизма резки 4, вариатора, щита управления с нагревателями. Машина имеет два индивидуальных привода: для шнека и механизма резки.
На верхней плите сварной станины установлен электродвигатель 8 привода шнека, соединенный через муфту с быстроходным валом редуктора 10. Последний, в свою очередь, с помощью муфты соединяется с валом корпуса подшипника. В литом корпусе подшипника установлен вал, вращающийся в радиальных подшипниках качения. Для восприятия осевой нагрузки от формующего шнека в корпусе установлен упорный шарикоподшипник.
К корпусу подшипника фланцем крепится сварной цилиндр с расположенным внутри него шнеком. С противоположной стороны цилиндр закрыт матрицей. Температура в рабочей зоне контролируется термопарами, введенными в зону через пробку 5. Для нагрева кукурузной массы в передней части цилиндра укреплен блок электронагревателей 6.
У переднего торца матрицы расположен механизм резки с вращающимися ножами, который приводится в движение от отдельного электродвигателя через бесступенчатый вариатор. Электродвигатель и вариатор находятся внутри станины.
Частота вращения вариатора регулируется рукояткой 2, установленной в непосредственной близости от панели управления. Для удобства обслуживания механизм резки отводится в сторону.
Над цилиндром установлен бункер для приема кукурузной крупы. Кукурузная крупа из бункера машины через регулируемую заслонку поступает в приемное отверстие цилиндра, где происходит прессование продукта и нагрев до температуры 145 °С.
В результате воздействия тепла, влаги и давления крупа превращается в пластическую массу, которая выдавливается шнеком через отверстия матрицы. При выходе из отверстий матрицы масса под действием пара, образующегося из перегретой влаги, вспучивается, образуя пористую хрустящую жилу. Механизм резки делит выходящие жилы на палочки, которые уносятся конвейером.
Порция крупы (1,5… 2,0 кг при температуре в цилиндре 80… 145 °С) приготовляется за 30…60 мин до пуска машины.
Режим нагрева цилиндра подбирается для каждой машины индивидуально в зависимости от сорта, помола, влажности крупы и степени износа.
Машина Б8-КХ-ЗП для производства палочек из кукурузной крупы посредством ее тепловой и механической обработки с последующей фасовкой на других автоматах
Машина Б8-КХ-ЗП (рисунок 2) предназначена для производства палочек из кукурузной крупы посредством ее тепловой и механической обработки с последующей фасовкой на других автоматах.
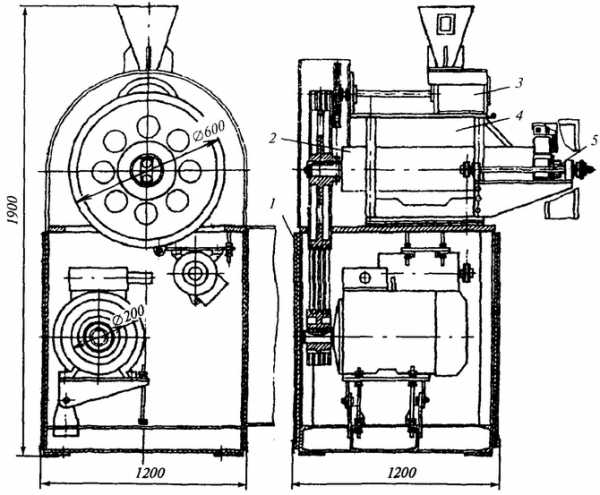
Машина состоит из станины 1, формующего механизма 2, механизма 5 отрезки палочек по длине, ворошителя 3 кукурузной крупы, блока электронагревателей 4.
Формующий механизм состоит из охватываемого шнека с правой нарезкой, шнековой втулки с левой нарезкой, матрицы с двенадцатью отверстиями диаметром 3мм, обоймы с четырьмя отрезными ножами, приводимой во вращение через цепную и клиноременную передачи от электродвигателя.
Ворошитель представляет собой корпус, внутри которого вращается вал с лопастями, перемешивающий поступающую из бункера крупу.
Блок электронагревателей предназначен для нагрева рабочей зоны машины в период пуска и автоматического под держания постоянной температуры от 160 до 180 °С. Во избежание перегрева машины в зоне загрузки предусматривается принудительное водяное циркуляционное охлаждение корпуса формующего механизма с подключением к сети водоснабжения.
Схемой машины предусмотрено ручное управление электроприводами шнека и ножа, а также ручное и автоматическое управление блоком нагревателей.
Перед пуском машины производится нагрев рабочей зоны формующего механизма в течение 30…35 мин до 160… 180 °С с помощью блока электронагревателей. За 25.. .30 мин до пуска машины готовится первая порция крупы влажностью 20.. .21%. Подготовленная крупа по специальному лотку вручную засыпается небольшим потоком в отверстие зоны загрузки при включенной машине. После выхода палочек из формующей матрицы открывается заслонка, и в машину поступает крупа влажностью 13… 14 %.
Нагрев продукта в момент запуска происходит за счет теплопередачи, а в дальнейшем — за счет тепла, образующегося в результате трения между продуктом, шнеком и шнековой втулкой. Выпрессованная полужидкая масса за счет перепада давления при выходе из отверстия формующей матрицы взрывается с диаметра 3 мм до диаметра 8… 1 2 мм.
Экструдер МФБ-1
Экструдер МФБ-1 (рисунок 3) состоит из плиты 15, станины 1 с кронштейном 12, электродвигателя 14, червячного редуктора 13, корпуса 4 со шнеком 3 и формующей матрицей 2, головки 7 с парой конических шестерен 8 и загрузочной воронки 5 со спиралью 11.
Внутри головки 7 находятся горизонтальный вал 9 с конической шестерней и приводной звездочкой 10, вертикальный вал 6 с конической шестерней и спиралью. Спираль 11 подает конфетную массу в корпус 4 и непрерывно перемешивает ее в загрузочной воронке 5. Шнек 3 выпрессовывает массу через формующие каналы матрицы 2 в виде пяти бесконечных жгутов, которые после предварительного охлаждения разрезаются на конфеты.
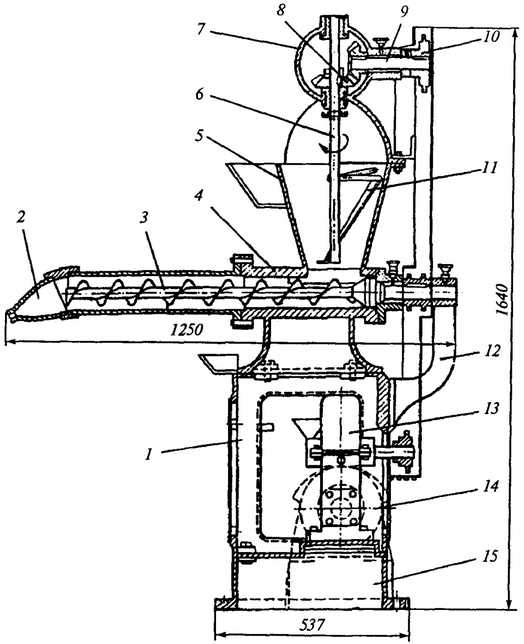
Двухшнековый экструдер поточных линий ШФК
Двухшнековый экструдер поточных линий ШФК (рисунок 4) отличается от экструдера МФБ-1 наличием двух горизонтальных шнеков, находящихся в самостоятельных камерах. Шнеки нагнетают массу в общую предматричную камеру 3. Масса выходит через шесть или восемь формующих каналов. Частота вращения спирали в загрузочной воронке 2 изменяется бесступенчатой рукояткой 1. Нагнетающие шнеки имеют постоянную частоту вращения. При переходе с формования жгутов круглого сечения на прямоугольные шнеки заменяют.
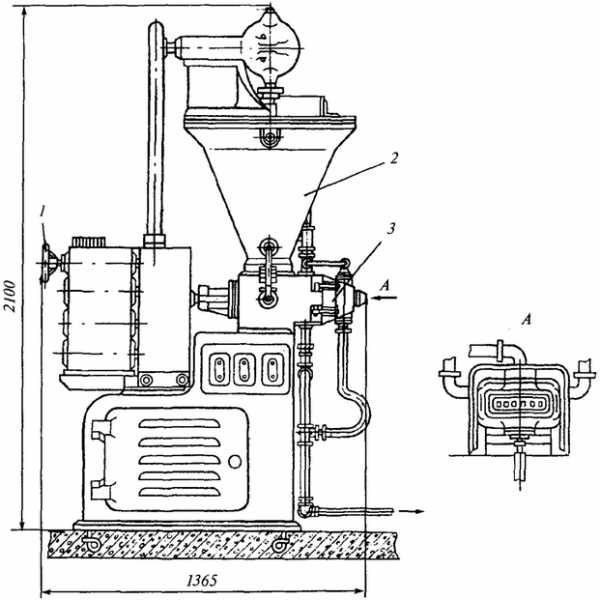
В шнековых экструдерах скорости выхода жгутов через формующие каналы неодинаковы. Для выравнивания скоростей увеличивают длину средних формующих каналов по сравнению с крайними, устанавливают дополнительные сопротивления перед средними каналами или в самих каналах либо устанавливают более высокую температуру стенок крайних формующих каналов. Добиться полного равенства скоростей во всех каналах весьма трудно.
Экструдер ШВФ-22 для выдавливания конфетной массы при производстве пралиновых конфет
Экструдер ШВФ-22 (рисунок 5) предназначен для выдавливания конфетной массы при производстве пралиновых конфет.
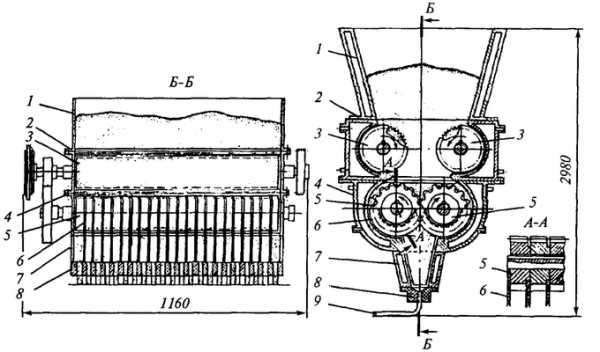
Он имеет в предматричной камере перегородки, образующие секции у каждого выходного отверстия. Это выравнивает скорости у выдавливаемых жгутов. Бункер 1 укреплен на корпусе питателя 2 с расположенными в нем рифлеными валками 3. В корпусе нагнетателя 4 вращаются нагнетающие шестеренные роторы 5, выполненные из набора шестерен. Предматричная камера 7 имеет вертикальные формующие каналы 8. В нижней части корпуса нагнетателя и предматричной камеры имеются вертикальные перегородки 6, которые делят корпус и камеру на отдельные секции.
Бункер, корпус нагнетателя и нагнетатель, а также предматричная камера имеют рубашки для обогрева.
nomnoms.info
Экструдер своими руками
Экструзия является популярным методом получения полуфабрикатов или товаров, произведенных из полимеров любой длины, поэтому сделанный экструдер своими руками в некоторых случаях позволит сэкономить вам деньги. Данный процесс используют в пищевой промышленности или в производстве комбикорма. Процесс происходит так: расплав полимера выдавливается при помощи головки экструдера в формующую головку с необходимым профилем. Данный способ производства наряду с литьем пластмассовых материалов под давлением сейчас один из наиболее популярных. Практически все полимеры могут подвергаться экструзии: термопласты, эластомеры и другие материалы.
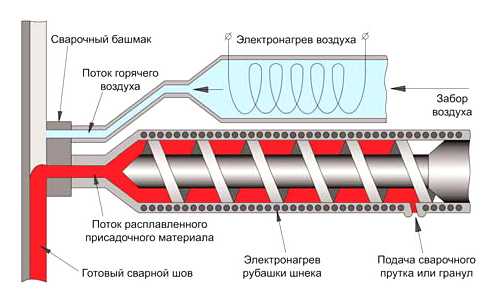
Схема работы сварочного экструдера.
Технология экструдера применяется уже больше шестидесяти лет. За этот длительный период появилось достаточно большое количество машин, которые изготовлены специально для использования данной технологии. Если детально рассмотреть экструдер, то можно понять, что это такое. Процесс экструзии является достаточно сложным, основан он на физических и химических законах. Процесс проходит непосредственно под влиянием механических действий при воздействии высоких температур и наличии влаги.
При обработке экструзионной техникой есть несколько сменных характеристик: состав предоставляемого сырья, процент его влажности и природа. При производстве может меняться давление, температура и т.д.
Применение:
- переработка кормов;
- производство пластика и полиэтилена;
- изготовление труб;
- пищевое производство.
Немного истории
Схема экструдера для пластика.
Экструдер начали применять еще в далеком девятнадцатом столетии. А серийное производство этого оборудования началось в двадцатых годах прошлого века. Сейчас экструдеры значительно отличаются от тех, что были раньше.
В современной промышленности экструдеры пользуются большой популярностью, причем выбрать можно из самых разнообразных видов. Купить новый экструдер — достаточно дорогое удовольствие. Но есть экструдеры, которые можно сделать своими руками.
Наиболее простыми в изготовлении являются экструдеры для глины и кормовые. Чтобы самостоятельно сделать другие виды этого оборудования, необходимо иметь хотя бы какие-нибудь базовые инженерные знания. А для изготовления этих экструдеров требуется не так много времени, и материалы стоят недорого.
Вернуться к оглавлению
Детали экструдеров
Схема экструзии.
- Головка экструдера. Она состоит из корпуса, который обогревается, и инструмента формующего с отверстием. Корпус прикрепляется к экструдеру. Отверстие инструмента может быть сужающимся к центру или в виде круглого канала. Обязательно должен быть раздатчик в виде спирали.
- Корона или активатор улучшает адгезию поверхностей материалов. Активаторы бывают разные, они отличаются по мощности, ширине, бывают с фиксацией односторонней и двусторонней или же с изменяющейся шириной переработки поверхности.
- Горячий нож. Горячий нож достаточно просто устроен, но его нужно правильно направлять относительно рукава, которые движется. Данный элемент увеличивает выход продукции почти в два раза. Горячий нож используется в экономичных целях.
- Шнек может и отсутствовать в оборудовании. Он предназначен для того, чтобы была большая производительность и хорошая гомогенизация расплава обрабатываемого материала полимеров.
- Узел тиснения. Он нужен для придания пленке особой жесткости и товарного красивого вида.
- Узел, обеспечивающий вращение головки. Вращение головки экструдера размещает постоянные неровности пленки, при этом качество рулона делается лучше, но качество пленки не повышается.
- Фальцовочное устройство оборудования.
- Тянущее устройство экструдера.
- Намотчик оборудования.
- Обдувочное кольцо экструдера.
Вернуться к оглавлению
Экструдеры для глины своими руками
Для изготовления простейшего экструдера для глины потребуется обычная пластиковая бутылка любой формы.
Такие экструдеры называют экструдеры для лепки. С их помощью можно работать с разнообразными глинами и пластилином. Данные экструдеры позволяют делать различные детали и фигуры. К примеру, можно изготавливать человеческие волосы или отчетливо рисовать траву.
Основой для этого экструдера выступает простая пластиковая бутылка прозрачного цвета. Ее необходимо хорошо вымыть и высушить, и крышку тоже.
Из крышки с внутренней стороны нужно извлечь пластину. Сделать это можно иголкой или булавочкой. Далее в ней необходимо сделать отверстие, из которого будет выдавливаться глина. Его диаметр должен быть таким, как толщина желаемых линий. Это производится с помощью острого ножа. Края отверстия делаются гладенькими.
Дальше необходимо взять диск из металла, к которому нужно прикрепить ручку в форме буквы «Т». Получившийся экструдер должен быть похож на шприц. Пластина должна быть приготовлена из прочного материала, чтобы во время работы она не изменила свою форму под воздействием давления.
Вернуться к оглавлению
Немного об экструдере для сварки
Благодаря ручному сварочному экструдеру можно делать много видов разнообразных работ с полипропиленом и полиэтиленом.
Сначала может показаться, что данные материалы не являются очень распространенными и редко где применяются.
Но в действительности их применяют во многих сферах. Из подобных материалов с помощью данного типа ручного экструдера делают системы для очищения воды, различных типов емкости и т. д. Преимущественно данные материалы пойдут как вспомогательные, но без них в любом случае нельзя обойтись.
Сварочный ручной экструдер имеет ряд преимуществ. Любая выбранная модель экструдера для экструзионной сварки будет гораздо лучше других.
Главным преимуществом такого оборудования считается простота в эксплуатации.
Подобным экструдером работать можно абсолютно в любом помещении и при различных условиях. Проще говоря, для работы не надо подготавливать специально обустроенное пространство или рабочий цех.
Схема бесконтактной и контактно-экструзионной сварки.
Ручным экструдером для сварки можно делать швы на разнообразные формы и конструкции. Это достаточно удобно, ведь при этом можно самостоятельно контролировать всю работу. Нередко случается, что в одном районе шов нужно сделать тонким, а немного дальше — толще. Ни одно оборудование не может такого сделать автоматически.
Помимо всего вышеперечисленного, стоит учесть, что данное устройство не слишком дорого стоит. Его цена будет приемлема практически для любого человека. Экструдер сварочный необязательно применять во время производства. Довольно часто его применяют дома. Дальнейший уход и обслуживание не заберут много денег. Данный экструдер может производить свою работу в течение многих лет, и он всегда остается актуальным и нужным приспособлением.
Ручные сварочные экструдеры бывают таких видов:
- безшнековые;
- шнековые;
- комбинированные.
Комбинированные экструдеры уместно применять при обработке композитного товара. В данных устройствах применяют и дисковую зону, и шнековую часть. Данное оборудование еще называют червячно-дисковым. К тому же у данного типа экструдеров есть прекрасная смесительная особенность.
Экструдеры, которые не имеют шнеков, используют для производства раствора полимеров, имеющих элементы высоко качества.
Обычно, приобретая данную продукцию, в комплекте покупатель получает несколько специальных насадок и подставок, но производители разные, поэтому и комплектация оборудования также различная. Сварочный ручной экструдер может работать при температурах от 180 до 260°С. Чтобы привести в работу устройство, необходимо подключить его к электрической сети. Желательно подключать его к напряжению в 220 В.
Экструзионная сварка — достаточно сложный процесс, поэтому чтобы сделать своими руками экструдер, необходимо иметь определенные знания и навыки. Разумнее будет приобрести оборудование у надежного производителя.
expertsvarki.ru
Экструдер зерновой своими руками чертежи фото – саморобний екструдер
О высокой эффективности дробилки для злаков знают многие собственники животноводческих хозяйств. Используя это устройство без особых усилий и за короткое время можно приготовить смеси для кормления мелких животных и птицы, подробить и перемешать комбикорм для животных, измельчить фрукты и овощи. Найти дешевую дробилку на рынке не просто и нередко фермеры изготавливают экструдер для кормов своими руками.
Чтобы изготовить самодельный экструдер кормов понадобятся отслужившая свой век бытовая техника или ее части и навыки работы со сваркой и на токарном станке.
Устройство экструдера для кормов, изготовленного из ненужного пылесоса
Двигатель старенького пылесоса можно использовать для производства зернодробилки, приготавливающей небольшие объемы кормов. Чтобы изготовить самодельное дробильное устройство к двигателю пылесоса необходимо добавить:
- Десятимиллиметровый фанерный лист;
- Заготовка из стали, которая станет ножом для помола зерна;
- Полоса из металла для изготовления камеры измельчения;
- Штифты из дерева;
- Бункер, закрывающийся задвижкой, для подачи в дробилку измельчаемого материала;
- Крепежный материал и втулка.
Очень поможет в работе чертеж, пусть даже самодельный, изготавливаемого дробильного устройства или фотография действующего.
Основанием устройства служит фанерный квадрат со стороной 300 мм, на который устанавливается снятый с пылесоса электрический двигатель. Двигатель нужно установить таким образом, чтобы вал выступал на 40 мм вниз.
Нож для измельчения
Нож экструдера дробит зерно, работая на очень высоких оборотах, и его изготовление требует особенного внимания. Как заготовку для изготовления ножа экструдера можно применить металлическую пластину полутора миллиметровой толщины размером 200 мм на 15 мм.
Сталь ножа должна быть не ниже марки СТ-3. Отлично подойдут держатели от автомобиля или другие схожие с ними детали.
Затачивается нож в форме лезвия. Передние части затачиваются в направлении оси вращения.
Иногда ножу придают пропеллеровидную форму или изменяют углы кромок. Для доводки размеров лезвия используют наждак.
Для монтажа изготовленного ножа на ось двигателя в средней части ножевой пластины сверлится отверстие с диаметром, подходящим для размеров вала. Крепится нож на резьбе оси двигателя втулкой.
Изготовление рабочей камеры, бункера и сита
Рабочая камера, часть механизма в которой происходит процесс дробления, изготавливается из металлической заготовки с длиной 705-710 мм и шириной не более 60 мм. Полосу изгибают в виде кольца. Торцы полученной конструкции по всей длине ее периметра отгибают наружу, образуя фланцы с шириной не более 10 мм.
Назначение фланцев – фиксация камеры на основании и удерживание сита.
Для надежного крепления механизма равномерно распределяясь на поверхности низа камеры, устанавливаются три деревянных штифта.
Размер ячейки сита экструдера зависит от необходимого результата измельчения. Чем мельче продукт измельчения, тем меньший размер сита используется при его получении. Самое мелкое сито используется при помоле муки, а при приготовлении овощных кормов применяются диски с нанесенной на них перфорацией и просверленными отверстиями.
Зерно поступает в камеру измельчения из бункера, укрепленного на основании. Необходимая деталь бункера, обеспечивающая удобство при работе – заслонка для дозирования подачи измельчаемых продуктов.
Измельченные продукты собирают в любую удобную тару, которую устанавливают под ситом.
Экструдер-мельница
Еще один интересный вариант измельчительного механизма для тех, кто решил сделать кормовой экструдер своими руками — мельница на основе электродвигателя.
В качестве жерновов в этой конструкции дробильного устройства используются металлические ротор и статор.
Электрический двигатель мощностью 1 кВт., рассчитанный на напряжение 220 В., крепится на ящик, служащий основанием изготавливаемого устройства. Важно для изготовления мельницы нужен однофазный двигатель, переделанный из трёхфазного, или оснащенный пусковым конденсатором.
Описание устройства
Корпус – круглая металлическая коробка радиусом 150-170 мм., изготовленная из заготовки толщиной 5 мм. Статор в виде борта, размещается внизу коробки. Верхняя часть емкости накрывается крышкой.
Внутри корпуса располагаются мотор и мельница. Главное условие установки мельницы — она должна быть зафиксирована так, чтобы ее подшипник садился на ось двигателя. При работе вал развивает скорость вращения до трех тысяч оборотов в минуту.
Сверху корпуса устанавливается и закрепляется винтами бункер для загрузки зерна, оснащенный заслонкой, регулирующей поступление зерен для измельчения.
Прошедшая помол мука извлекается из мельницы по специальному рукаву.
Бункер и рукав соединены с корпусом отверстиями, через которые происходит подача зерна и извлечение муки.
Изготовление ротора и статора
Статор – металлическая емкость в форме чаши с дном, покрытая с одного торца алюминием. Изготавливается из двухмиллиметровой металлической заготовки с шириной 50 мм. Пластину размещают в форме для заливки и наносят алюминий на один из торцов.
Ребристую поверхность статора создают, приваривая к его внутренней части металлические уголки 20х20х50 мм. Посредине детали делается отверстие под вал.
Ротор изготавливается из трёхмиллиметрового металлического листа, из которого изготавливается круг с радиусом160 мм. На поверхность внутри круга наносят окружность, располагая ее на расстоянии 20 мм от его края. Окружность делят на 32 одинаковые части.
В намеченных точках сверлят трёхмиллиметровые сквозные отверстия, к которым с внешней стороны детали делают пропилы пилой по металлу.
В центр ротора вваривается втулка диаметром 30 мм и длиной 45 мм.
Последовательность сборки устройства:
- На валу закрепляется статор;
- После ротор на шпонке;
- Все части фиксируются через отверстие втулки шпилькой.
Изготовить экструдер для кормов своими руками не сложно. При его изготовлении Вы не только сэкономите средства, но и поспособствуете улучшению экологии, использовав детали бытовых приборов отслуживших свой срок.
aquariumfan.ru
ООО «Полимермаш-сервис» | Экструдер для производства изделий и из пластика
Одна из наиболее сложных экологических проблем мировой экономики – это утилизация химически опасных предметов, в первую очередь, изделий из ПВХ пластика. Многочисленные компании и индивидуальные предприниматели теряют миллионы, которые приходится платить за утилизацию использованной тары, изделий из поливинилхлорида. А затем вновь тратят деньги на покупку сырья!
Принципиальное решение
Есть простой, надежный и действенный способ решения проблемы – купить экструдер для пластика. Это устройство не только позволит выполнить задачу по утилизации пластика, но станет эффективным способом для развития бизнеса. Экструзия – это технология по переработке тары и других изделий из пластика с целью формирования сырья, необходимого для повторного изготовления различных деталей и продукции из ПВХ. Если коротко – суть технологии заключается в формировании расплавленной полимерной массы с дальнейшим формированием небольших гранул, имеющих форму, определенную техническими условиями эксплуатации.
Таким образом, используя технологию экструзии пластмасс можно развивать бизнес, собственное дело, предлагая недорогое сырье, которое получается из отходов производства. В обозримом будущем проблемы с вторсырьем (а именно в эту категорию входит большинство пластиковых отходов) не будет. А ведь именно сырье у производителей составляет большую часть расходов. Очевидно, что в современных условиях возможность переработки и повторного использования полимерных материалов — простое и эффектное решение для бизнеса!
Стоит более подробно изучить вопрос и разобраться, как работает экструдер пластмасс, и какие перспективы есть для ведения такого бизнеса.
Суть процесса
Экструзия представляет собой относительно простой технологический процесс, при котором на специальной линии (в нашем случае – изготовленной инженерами на территории России, на 100% из отечественных комплектующих) происходит процесс переработки сложных композиций, разнородного пластикового сырья. Под воздействием постоянного давления, создаваемого в работе системы, расплавленная масса продавливается через специальные отверстия формующей головки. В зависимости от формы и диаметра этой головки на выходе получают готовые полуфабрикаты, которые впоследствии могут использоваться для производства новых деталей и изделий либо храниться на складе в ожидании отгрузки заказчику.
Общее устройство и принцип работы оборудования
Extruder – это достаточно сложное электромеханическое устройство, предназначенное для переработки использованного поливинилхлорида и изготовления пластмассовых профильных небольших гранул. Такое сырье из полимеров можно в дальнейшем использовать для нового производства разнообразной ПВХ продукции или организации хранения сырья для его последующей продажи.
Специализированная компания «Полимермаш-Сервис» специализируется на изготовлении оборудования и специализированных линий по изготовлению сырья из переработанного пластика. Агрегат российского производства полностью соответствует требованиям качества, надежности и долговечности работы, а использование отечественных комплектующих, узлов и агрегатов, позволяет снизить стоимость оборудования. Наибольшей популярностью и спросом пользуется одношнековое устройство, как наиболее простое, надежное и безотказное в работе, позволяющее с помощью метода экструзии получать полимерное высококачественное сырье.
Конструктивные особенности
Экструдер полимеров состоит из следующих основных узлов и деталей:
- Прочный стальной корпус (цилиндр), оснащенный системой нагрева пластмасс до необходимой температуры. Используются керамические нагревательные элементы.
- Приемный бункер. Экструзионная линия начинается именно с этого элемента. Для переработки сюда насыпается подготовленный полимер в виде гранул, небольших лент или крупнозернистого порошка. Главное назначение бункера – обеспечить равномерную подачу сырья, что обеспечивает высокое качество экструдированного материала на выходе.
- Экструзионная головка. Другое название этой детали – фильера, она и задает необходимую форму полимеров.
- Приводной механизм. Состоит из электродвигателя и системы редукторов, с помощью которых происходит передача необходимого усилия и обеспечение работы одношнековой машины и происходит процесс переработки полимеров.
- Система управления. Стационарный или выносной пульт, с помощью которого управляется процесс экструзионной переработки пластмасс.
Схема работы
Сформированная технологическая линия российского производства отвечает всем необходимым требованиям по надежности и долговечности работы и позволяет осуществлять переработку пластиков на профессиональном уровне. Экструзия заключается в последовательном выполнении следующих операций:
- сырье в виде гранул, порошка или лома пластика поступает в приемный отсек;
- перемешанная масса направляется в рабочую зону одношнекового экструдера, где не нее воздействуют: давление, небольшая сила трения, подаваемая снаружи повышенная температура;
- под воздействием тепла, происходит нагревание пластмасс и их плавление до состояния, позволяющего продолжать экструзию далее;
- в ходе продвижения по направлению к фильере происходит тщательное перемешивание пластиковой массы, в результате чего, к моменту поступления в формирующие головки полихлорвинил имеет единую однородную форму, подготовленную к выдавливанию;
- для повышения качества изделий, перед окончательным формированием гранул, масса проходит под высоким давлением через специальный сетчатый фильтр, где удаляются различные мельчайшие посторонние предметы;
Далее сырье упаковывается и укладывается на хранение либо передается заказчик для переработки и производства новых изделий. Хранить гранулы можно неограниченное время!
Вот так работает экструзионная линия. Ничего сложного в работе экструдера нет. Главное, после принятия решения на покупку данного оборудования, сделать правильный выбор и обратиться к профессионалам.
Отличные перспективы
Метод экструзии используется повсеместно, до 50% термопластов подвергается переработке данным способом. Экструзия позволяет изготавливать из ПВХ следующие материалы:
- пленки;
- листы;
- трубы;
- шланги;
- капилляры;
- прутки;
- сайдинг;
- профильную продукцию независимо от степени сложности и конфигурации;
- нанесение полимерного материала на элементы электропроводов;
- изготовление многослойных элементов и деталей.
При этом количество переработанного термопласта с помощью экструдеров год от года растет. Сейчас на рынке сложилась ситуация, при которой спрос на переработку превышает предложение. А значит, созданы условия для открытия собственного бизнеса!
Выгодное предложение
ООО «Полимермаш-Сервис» предлагает на выгодных условиях приобрести одношнековый экструдер для переработки полимеров, а также ряд другого востребованного на рынке производственного оборудования. Производственные мощности Общества располагаются в Пензенской области, но реализация экструдеров и линий производится в любые города и регионы страны. Каждому клиенту компании мы готовы предложить высококачественное, надежное и недорогое оборудование для переработки полимеров.
Каждая установка, прежде чем поступить в продажу, проходит испытание под нагрузкой, проверку надежности и эффективности работы. В качестве дополнительной услуги выполняем комплекс работ по подготовке экструдеров и производственных линий к вводу в эксплуатацию. Если потребуется – инженеры компании проведут подготовку персонала компании-заказчика.
С нами выгодно сотрудничать. Обращайтесь, господа предприниматели!
polimer-servis.ru
Экструдер
Экструдер в широком понимании (от лат. extrudere=выталкивать, давить, вытягивать) — это машина для придания смеси гомогенной консистенции и выдавливания ее либо ее полимерного расплава через экструзионную фильерную головку. Применяется этот процесс в химической, пищевой, комбикормовой промышленности, производстве профиля, полимеров, пластиковых изделий и мн. др. обласятях. Экструзионная технология как таковая существует более шестидесяти лет, а в стеклопакетной индустрии — и того моложе, но и за это время станки, герметики и технология их нанесения прошли определенную эволюцию.
Применительно к нашей области слово «экструдер» прижилось как подходящее краткое определение станка. Согласитесь, первоначальное название «пресс» для бутилового экструдера не точно, а сегодняшнее немецкое определение «автоматическая дозирующая и смесительная установка высокого давления» для экструдера вторичной герметизации хоть и заметно точнее, но уж черезчур длинно для производственного лексикона. Для стеклопакетной и смежных индустрий мы рассматриваем несколько типов станков по их назначению, подробно описанных на страничке Оборудование новое.
По степени температурного воздействия разделяют два основных метода работы: холодная, теплая и горячая экструзия.
Холодная экструзия — возможны только механические изменения в материале вследствие медленного его перемещения под давлением и формованием этого продукта с образованием заданных форм. Примеры: экструдеры полисульфида, полиуретана, силикона.
Теплая и горячая экструзия — процесс протекает при относительно высоких скоростях и давлениях и подводе тепла. Примеры теплой экструзии: экструдеры бутила или хотмелта.
По количеству смешиваемых компонентов герметика или клея подразделяют однокомпонентые, двухкомпонентные и многокомпонентные герметики или клеевые массы. Пример однокомпонентного использования материала: экструдер силикона, смазки, клея, смолы и пр. Пример двухкомпонентного использования материала: экструдеры двухкомпонентного полисульфида (тиокола), полиуретана, силикона.
По консистенции герметика или клея разделяют жидкие, среднепастообразные или высокопастообразные компоненты герметиков. Пример пастообразного двухкомпонентного материала: полисульфид (тиокол), силикон, полиуретан. Пример жидкого материала: эпоксидные смолы. Пример смешанных компонентов, например, пастообразный базовый компонент и жидкий отвердитель: полиуретан, силикон.
По пропорции смешения компонентов: возможно от 1:1 до 1:100 или по запросу.
По виду работ разделяют внутренние (в цеху) или наружные — на открытой (строй)площадке.
Экструдер бутила или хотмелта состоит из узла загрузки герметика; привода; корпуса с нагревательными элементами; системы управления и узла нанесения расплава однокомпонентного материала. Экструдер двухкомпонентноо полисульфида, полиуретана или силикона состоит из узла загрузки компонентов герметика; привода; системы управления; узла дозировки и узла смешения двухкомпонентного герметика. Экструдер однокомпонентноо материала состоит из узла загрузки материала; привода; системы управления и нанесения материала.
Оптимальный дизайн дозирующих и смесительных систем требует большого объема знаний о материалах, подлежащих обработке. Вязкость, абразивность, тиксотропия, температура обработки, жизнеспособность смеси, реакционная способность и скорость реакции: все эти факторы определяют конструкцию оптимальной технологической разработки и ее оснащения, от индивидуального уплотнения в насосных системах до конфигурации комплектного оборудования для склеивания или герметизации. Cообщите нам Ваш запрос на [email protected] и мы подготовим Вам коммерческое предложение для Вашего проекта.
Схема работы экструдера
- Пневматический или гидравлический привод
- А-компонент
- В-компонент
- Устройство дозировки
- А-дозирующий насос
- В-дозирующий насос
- Контроль дозировки
- Смесительная часть
extruder.ru
Портативные экструдеры прутка | Энциклопедия 3D-печати
Описание
Одним из сдерживающих факторов развития FDM-печати является относительно высокая стоимость расходных материалов. Хотя большинство пластиков вполне по карману обыденному пользователю, разница между сырьем и готовой нитью весьма значительна – зачастую стоимость прутка превышает стоимость гранул аналогичного веса в десятки раз. Таким образом, нет ничего удивительного, что на свет появились портативные, настольные устройства для домашнего производства нити из гранул и пластиковых отходов. Устройство экструдера
Такие установки позволяют значительно снизить себестоимость печати и, конечно же, улучшить экологию. В этом разделе мы рассмотрим наиболее известные наработки по домашнему производству прутка, включая экструдеры нити и шредеры пластиковых отходов.
Filabot Original
Наиболее известная разработка, отличающаяся высокой производительностью. Устройство предназначено для работы с ABS, PLA и HIPS. В качестве расходного материала используется гранулированный пластик, но возможно и использование пластиковых отходов при том условии, что размер частиц не превышает 5мм. Filabot Original — наиболее известное устройство для домашнего производства прутка
Компания предлагает выбор из семи цветов гранулированных красителей для ABS-пластика, позволяющих придавать готовому материалу необходимый оттенок. Красители поставляются в упаковках по 25гр. Для окраски одного килограмма ABS потребуются одна-две упаковки. Для лучших результатов рекомендуется использование красителей с гранулами ABS-пластика белого цвета.
Кроме того, возможно смешивание ABS, PLA и HIPS с углеволокном для получения более прочных и износоустойчивых материалов. Для получения подобного композита требуется лишь смешать пластик с гранулами углеволокна и, если требуется, красителя, а затем загрузить готовую смесь в бункер.
Filabot Original обладает наиболее высокой производительностью среди аналогичных устройств. На экструзию одного килограмма прутка уходит около пяти часов. Температурный диапазон при нагревании составляет 40°С-400°С, что позволяет экспериментировать с широким спектром материалов, включая композиты с древесным наполнителем, электропроводящими добавками и др.
Диаметр прутка может составлять 1,75мм или 3мм в зависимости от насадки. Скорость экструзии составляет 250-750мм в минуту в зависимости от диаметра изготовляемого прутка.
Скорость вращения шнека составляет 35 оборотов в минуту. Потребляемая мощность устройства достигает 300Вт в зависимости от температуры экструзии. Экструдер оснащен фильтром для удаления загрязняющих частиц непосредственно перед экструзией.
Устройство оснащено прочным металлическим корпусом и имеет достаточно компактные габариты, сравнимые с системным блоком компьютера: 431х178×203мм.
Отпускная цена производителя: $899.
Filabot Wee
Filabot Wee — более доступный вариант, мало чем уступающий Filabot OriginalВерсия оригинального экструдера Filabot, оснащенная деревянным корпусом. Данный вариант позиционируется в качестве бюджетной версии и доступен как в собранном виде, так и в качестве комплекта для самостоятельной сборки.
Бюджетная версия слегка уступает своему более дорогому собрату в плане производительности: скорость экструзии варьируется от 125мм до 500мм в минуту. Температура экструзии варьируется от 40°С до 350°С.
Устройство предназначено в первую очередь для производства прутка из HIPS, ABS и PLA, хотя возможно и использование других материалов, подходящих в плане температуры экструзии.
Благодаря использованию гранулированных красителей возможно достижение широкой цветовой гаммы – при применении красителей рекомендуется использование белого ABS-пластика, либо материала с легкими цветовыми оттенками.
Добавление гранулированного углеволокна позволяет добиваться более высокой прочности готового прутка. Углеволокно может использоваться в комбинации с любым из расчетных пластиков.
Максимальная потребляемая мощность составляет 300Вт. Устройство поставляется со сменными насадками, позволяющими производить пруток двух наиболее популярных диаметров: 1,75мм и 3мм.
Габариты Filabot Wee аналогичны Filabot Original: 431х178×203мм.
Компания Filabot выложила чертежи Filabot Wee в открытый доступ. Желающие построить экструдер собственными руками могут скачать необходимые файлы здесь и здесь.
Отпускная цена производителя: $749 за экструдер в собранном виде, либо $649 за комплект для самостоятельной сборки.
Filastruder
Относительно недорогой экструдер, разработанный двумя студентами из Университета Флориды: Тимом Элмором и Алленом Хэйнсом. Filastruder — относительно недорогой, но весьма эффективный экструдер
Filastruder позволяет производить один килограмм нити за 12 часов работы устройства или от 150мм до 600мм в минуту в зависимости от диаметра сопла, температуры экструзии и используемого материала. Разработчики протестировали экструдер с ABS-пластиком, но допускают возможность использования PLA, HIPS, нейлона, полиэтилена и других пластиков. Максимальная температура экструзии достигает 225°С.
Экструдер достаточно экономичен – максимальная потребляемая мощность составляет 60Вт при среднем показателе в 50Вт.
Filastruder поставляется с соплами диаметром 1,75 или 3мм.
Отпускная цена экструдера Filastruder составляет $300 без бункера или $310 с напечатанным бункером.
Экструдер Лаймана
Экструдер Лаймана – пионер настольных фабрик по производству пластиковой нитиУстройство получило название в честь разработчика – Хью Лаймана. Оригинальная разработка является, вероятно, первым домашним экструдером для производства прутка. Именно этот дизайн выиграл главный приз на конкурсе Desktop Factory Competition в 2013 году.
Конструкция экструдера максимально упрощена, что стало следствием главного условия конкурса: общая стоимость компонентов, использованных в конструкции, не должна была превышать $250.
Экструдер Лаймана не является коммерческой разработкой и недоступен в розничной торговле. Разработчик выложил инструкции по созданию экструдера в открытый доступ. Необходимые файлы можно скачать здесь.
OmniDynamics Struder
OmniDynamics Struder рассчитан на безопасность и удобство эксплуатацииКомпактное устройство, анонсированное на площадке Kickstarter в мае 2014 года. Целью разработчиков является создание портативного, удобного и безопасного в использовании устройства.
Поставки первых партий экструдера намечены на сентябрь 2014 года. Розничная цена устройства еще не анонсирована, но стоимость предварительного заказа на Kickstarter составляет £149.
Дизайн экструдера рассчитан на работу с любыми термопластиками, используемыми в 3D-печати, включая ABS, PLA, PET, HDPE, HIPS и т.д. Устройство оснащается полноценным контрольным модулем с цветным LCD-дисплеем.
STRUdittle
STRUdittle – перспективный экструдер с компактными габаритами и высокой производительностьюЕще одна интересная разработка, получившая необходимое финансирование на Kickstarter.
Дизайн устройства нацелен на высокую компактность и хорошую ценовую доступность с сохранением высокой производительности.
По заявлениям разработчиков, устройство способно вырабатывать до 600мм прутка в минуту. Экструдер рассчитан на работу с ABS-пластиком. Отклонения по диаметру нити не превышают 0,03мм при использовании наматывающего устройства или 0,05мм, если пруток просто экструдируется на пол. Заказчики могут указать требуемый диаметр сопла: 1,75мм или 3мм.
Стоимость предварительного заказа на Kickstarter составляет $385 за экструдер в комплекте с наматывающим устройством.
Filabot Reclaimer
Ручная дробилка Filabot Reclaimer позволяет перерабатывать всевозможные пластиковые отходыПеречисленные экструдеры рассчитаны на работу с гранулированными пластиками. В то же время, FDM-принтеры в комбинации с настольными экструдерами обладают прекрасным потенциалом по переработке пластикового мусора в новые изделия. Таким образом, для использования пластиковых отходов в качестве расходных материалов требуется устройство, способное дробить пластик до получения мелких частиц – как правило, не более 5мм. Компания Filabot разработала простой, но эффективный шредер, предназначенный именно для этой цели. Приспособление получило название Filabot Reclaimer.
Filabot Reclaimer оснащен прочной сварной металлической рамой и зазубренными валиками из закаленной стали. Устройство не оснащено электроприводом – валики приводятся в движение вручную с помощью рычага.
В качестве сырья может использоваться практический любой термопластик, применяемый в 3D-печати.
Filabot Reclaimer позволяет перерабатывать неудачные модели, отходы 3D-печати и просто ненужные пластиковые изделия. Размеры горловины и, соответственно, перерабатываемых кусков пластика достигают 50х90мм. Ввиду прочной металлической конструкции приспособления, вес Filabot Reclaimer составляет внушительные 11кг. Габариты установки достаточно скромны, достигая 255х255х380мм.
Отпускная цена Filabot Reclaimer составляет $439. Несмотря на относительно высокую стоимость, устройство достаточно быстро окупается, позволяя вкупе с экструдером экономить до 90% от стоимости прутка.
FilaMaker
FilaMaker сочетает функциональность дробилки и экструдераFilaMaker сочетает функции дробилки и экструдера в одном устройстве. Установка была продемонстрирована на ярмарке Maker Faire Rome в 2013 году и завоевала внимание благодаря высокой функциональности, аккуратному дизайну и высокой производительности.
FilaMaker способен производить до одного метра нити диаметром 3мм в минуту. Отклонение заданного диаметра не превышает 0,05мм. К сожалению, отпускная цена устройства весьма высока, достигая €1 200.
Перейти на главную страницу Энциклопедии 3D-печати
3dtoday.ru